Struktura organizacyjna i produkcyjna elektrowni jądrowych. Zasada działania TPP. Krótki opis. Cechy charakterystyczne elektrowni kondensacyjnych
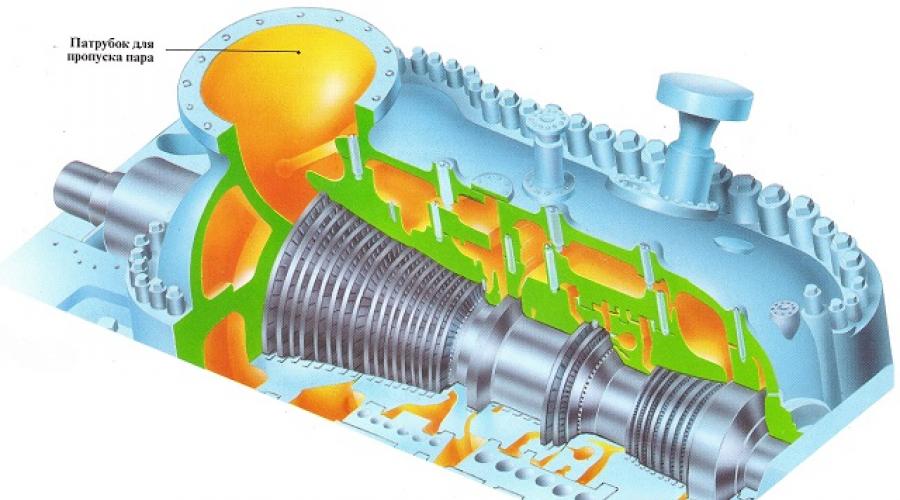
Gilew Aleksander
Zalety TPP:
Wady TPP:
na przykład :
Pobierać:
Zapowiedź:
CHARAKTERYSTYKA PORÓWNAWCZA TPP I EJ Z PUNKTU WIDZENIA PROBLEMU ŚRODOWISKOWEGO.
Zakończony: Gilev Alexander, klasa 11 „D”, Liceum FGBOU VPO „Dalrybvtuz”
Kierownik:Kurnosenko Marina Vladimirovna, nauczycielka fizyki najwyższej kategorii kwalifikacji, liceumFGBOU VPO „Dalrybvtuz”
Elektrownia cieplna (TPP), elektrownia wytwarzająca energię elektryczną w wyniku konwersji energii cieplnej uwalnianej podczas spalania paliw kopalnych.
Na jakim paliwie jeżdżą TPP?
- Węgiel: Spalanie jednego kilograma tego rodzaju paliwa uwalnia średnio 2,93 kg CO2 i wytwarza 6,67 kWh energii lub przy 30% wydajności 2,0 kWh energii elektrycznej. Zawiera 75-97% węgla,
1,5-5,7% wodór, 1,5-15% tlen, 0,5-4% siarka, do 1,5% azot, 2-45%
substancje lotne, ilość wilgoci waha się od 4 do 14%.Skład produktów gazowych (gaz koksowniczy) zawiera benzen,
toluen, ksyole, fenol, amoniak i inne substancje. Z gazu koksowniczego
oczyszczanie z surowego ekstraktu amoniaku, siarkowodoru i związków cyjankowych
benzen, z którego poszczególne węglowodory i szereg innych cennych
Substancje.
- Olej opałowy: Olej opałowy (ewentualnie z arabskiego mazkhulatu - odpady), ciemnobrązowy produkt płynny, pozostałość po oddzieleniu benzyny, nafty i frakcji oleju napędowego z ropy lub jej wtórnych produktów przeróbki, wrząca do 350-360 ° C. Olej opałowy jest mieszaniną węglowodorów (z waga molekularna od 400 do 1000 g/mol), żywice naftowe (o masie cząsteczkowej 500-3000 g/mol lub większej), asfalteny, karbeny, karboidy i związki organiczne zawierające metale (V, Ni, Fe, Mg, Na, Ca)
- Gaz: Główną część gazu ziemnego stanowi metan (CH4) – od 92 do 98%. W skład gazu ziemnego mogą również wchodzić cięższe węglowodory – homologi metanowe.
Zalety i wady TPP:
Zalety TPP:
- Najważniejszą zaletą jest niska wypadkowość i wytrzymałość sprzętu.
- Używane paliwo jest dość tanie.
- Wymaga mniej inwestycji w porównaniu do innych elektrowni.
- Może być budowany w dowolnym miejscu, niezależnie od dostępności paliwa. Paliwo można transportować do lokalizacji elektrowni koleją lub drogą.
- Wykorzystanie gazu ziemnego jako paliwa praktycznie zmniejsza emisje szkodliwe substancje do atmosfery, co jest ogromną przewagą nad elektrowniami jądrowymi.
- Poważnym problemem dla elektrowni jądrowych jest ich likwidacja po wyczerpaniu zasobu, według szacunków może to być nawet do 20% kosztów ich budowy.
Wady TPP:
- Mimo to elektrociepłownie wykorzystujące jako paliwo olej opałowy, węgiel są bardzo zanieczyszczone środowisko. W TPP łączna roczna emisja szkodliwych substancji, do których zalicza się dwutlenek siarki, tlenki azotu, tlenki węgla, węglowodory, aldehydy i popiół lotny na 1000 MW moc zainstalowana wahają się od około 13.000 ton rocznie dla elektrowni gazowych do 165.000 dla elektrowni węglowych.
- Elektrownia cieplna o mocy 1000 MW zużywa 8 mln ton tlenu rocznie
Na przykład : CHP-2 spala dziennie połowę składu węgla. Prawdopodobnie ta wada jest najważniejsza.
Co jeśli?!
- A co, jeśli dojdzie do wypadku w elektrowni jądrowej wybudowanej w Primorye?
- Ile lat po tym odbuduje się planeta?
- W końcu CHPP-2, który stopniowo przechodzi na gaz, praktycznie zatrzymuje emisję sadzy, amoniaku, azotu i innych substancji do atmosfery!
- Do tej pory emisje CHPP-2 spadły o 20%.
- I oczywiście zostanie wyeliminowany jeszcze jeden problem - wysypisko popiołu.
Trochę o niebezpieczeństwach elektrowni jądrowych:
- Wystarczy przypomnieć sobie wypadek w elektrowni jądrowej w Czarnobylu 26 kwietnia 1986 roku. W ciągu zaledwie 20 lat około 5000 likwidatorów w tej grupie zginęło ze wszystkich przyczyn, nie licząc cywilów… I oczywiście to wszystko są oficjalne dane.
Zakład "MAYAK":
- 15.03.1953 - rozpoczęła się samopodtrzymująca się reakcja łańcuchowa. Nadmierna ekspozycja personelu zakładu;
- 10.10.1955 - przerwa sprzęt technologiczny i zniszczenie części budynku.
- 21.04.1957 - SCR (spontaniczna reakcja łańcuchowa) w zakładzie nr 20 w kolekcji dekantacji szczawianu po przefiltrowaniu osadu wzbogaconego szczawianu uranu. Sześć osób otrzymało dawki promieniowania od 300 do 1000 rem (cztery kobiety i dwóch mężczyzn), jedna kobieta zmarła.
- 10.02.1958 - SCR w zakładzie. Przeprowadzono eksperymenty w celu określenia masy krytycznej wzbogaconego uranu w cylindrycznym pojemniku przy różnych stężeniach uranu w roztworze. Personel naruszył zasady i instrukcje dotyczące pracy z jądrowym materiałem rozszczepialnym (jądrowym materiałem rozszczepialnym). W czasie SCR personel otrzymał dawki promieniowania od 7600 do 13000 rem. Trzy osoby zmarły, jedna zachorowała na chorobę popromienną i straciła wzrok. W tym samym roku I. V. Kurczatow przemawiał w najwyższy poziom i udowodnił potrzebę powołania specjalnego podział stanowy w sprawie bezpieczeństwa. LYAB stała się taką organizacją.
- 28.07.1959 - zerwanie urządzeń technologicznych.
- 12.05.1960 - SCR w zakładzie. Pięć osób było prześwietlonych.
- 26.02.1962 - wybuch w kolumnie sorpcyjnej, zniszczenie sprzętu.
- 09.07.1962 - SCR.
- 16.12.1965 - SCR w zakładzie nr 20 trwał 14 godzin.
- 10 grudnia 1968 - SCR. Roztwór plutonu wlano do cylindrycznego pojemnika o niebezpiecznej geometrii. Jedna osoba zmarła, inna otrzymała wysoką dawkę promieniowania i chorobę popromienną, po czym amputowano mu dwie nogi i prawą rękę.
- 11 lutego 1976 r. w wyniku niewykwalifikowanych pracowników w zakładzie radiochemicznym doszło do autokatalitycznej reakcji stężonego kwasu azotowego z cieczą organiczną o złożonym składzie. Urządzenie eksplodowało, nastąpiło skażenie radioaktywne strefy naprawy i przyległego terenu zakładu. Indeks w skali INEC-3.
- 10.02.1984 - wybuch na wyposażeniu próżniowym reaktora.
- 16.11.1990 - reakcja wybuchowa w pojemnikach z odczynnikami. Dwie osoby doznały oparzeń chemicznych, jedna zmarła.
- 17.07.1993 - Awaria zakładu radioizotopowego Towarzystwa Produkcyjnego Majak z zniszczeniem kolumny sorpcyjnej i uwolnieniem nieznacznej ilości α-aerozoli do środowiska. Uwalnianie promieniowania było zlokalizowane w obrębie pomieszczenia przemysłowe warsztaty.
- 02.08.1993 - doszło do wypadku na linii wydającej miazgę z oczyszczalni ciekłych odpadów promieniotwórczych, doszło do wypadku na skutek rozszczelnienia rurociągu i przedostania się 2 m3 miazgi promieniotwórczej na powierzchnię ziemi (ok. 100 m2 powierzchnia była zanieczyszczona). Rozprężanie rurociągu doprowadziło do wypływu radioaktywnej pulpy na powierzchnię ziemi o aktywności około 0,3 Ci. Ślad radioaktywny został zlokalizowany, zanieczyszczona gleba została usunięta.
- 27 grudnia 1993 r. w fabryce radioizotopów doszło do incydentu, w którym podczas wymiany filtra do atmosfery przedostały się radioaktywne aerozole. Uwalnianie wynosiło 0,033 Ci dla aktywności α i 0,36 mCi dla aktywności β.
- 4 lutego 1994 r. odnotowano zwiększone uwalnianie aerozoli promieniotwórczych: zgodnie z β-aktywnością poziomów 2-dniowych, zgodnie z dziennymi poziomami 137Cs, całkowita aktywność wynosiła 15,7 mCi.
- 30 marca 1994 r. w okresie przejściowym zanotowano przekroczenie dziennego uwalniania 137Cs o 3, β-aktywność – 1,7, α-aktywność – 1,9 razy.
- W maju 1994 roku przez system wentylacyjny budynku fabryki zostały uwolnione β-aerozole o aktywności 10,4 mCi. Uwalnianie 137Cs stanowiło 83% poziomu kontrolnego.
- 7 lipca 1994 r. radioaktywna plama o powierzchni kilku decymetry kwadratowe. Szybkość dawki ekspozycji wynosiła 500 µR/s. Plama powstała w wyniku wycieku z zatkanego kanału.
- 31.08. W 1994 r. zarejestrowano zwiększone uwalnianie radionuklidów do komina atmosferycznego budynku zakładu radiochemicznego (238,8 mCi, w tym udział 137Cs stanowił 4,36% rocznego maksymalnego dopuszczalnego uwolnienia tego radionuklidu). Przyczyną uwolnienia radionuklidów było rozprężenie pręta paliwowego WWER-440 podczas operacji odcinania jałowych końców SFA (zespołów zużytego paliwa) w wyniku niekontrolowanego łuku elektrycznego.
- 24 marca 1995 r. odnotowano przekroczenie 19% normy obciążenia aparatu plutonem, co można uznać za incydent z zagrożeniem nuklearnym.
- 15 września 1995 r. wykryto wyciek wody chłodzącej w piecu witryfikacyjnym dla wysokoaktywnych odpadów promieniotwórczych LRW (płynne odpady promieniotwórcze). Praca pieca w trybie planowym została przerwana.
- 21 grudnia 1995 r. podczas cięcia kanału termometrycznego napromieniowano czterech robotników (1,69, 0,59, 0,45, 0,34 rem). Przyczyną incydentu jest naruszenie przepisów technologicznych przez pracowników przedsiębiorstwa.
- 24 lipca 1995 roku wypuszczono aerozole 137Cs, których wartość wyniosła 0,27% rocznego MPE dla przedsiębiorstwa. Powodem jest zapłon tkaniny filtracyjnej.
- 14 września 1995 r. podczas wymiany osłon i smarowania manipulatorów krokowych zarejestrowano gwałtowny wzrost zanieczyszczenia powietrza α-nuklidami.
- 22 października 1996 roku awaria wężownicy wody chłodzącej jednego ze zbiorników wysokiego składowania odpadów. W wyniku tego doszło do zanieczyszczenia rurociągów układu chłodzenia magazynu. W wyniku tego zdarzenia 10 pracowników oddziału zostało napromieniowanych promieniotwórczo od 2,23×10-3 do 4,8×10-2 Sv.
- W dniu 20.11.1996 r. w zakładzie chemiczno-hutniczym podczas prac na osprzęcie elektrycznym wentylatora wyciągowego nastąpiło uwolnienie aerozolu radionuklidów do atmosfery, które wyniosło 10% dopuszczalnego rocznego uwolnienia zakładu.
- 27 sierpnia 1997 r. w budynku RT-1 w jednym z pomieszczeń stwierdzono zanieczyszczenie posadzki o powierzchni od 1 do 2 m2, moc dawki promieniowania gamma z miejsca wynosiła od 40 do 200 μR/s.
- W dniu 10.06.97 w budynku montażowym zakładu RT-1 odnotowano wzrost tła promieniotwórczego. Pomiar mocy dawki ekspozycji wykazał wartość do 300 μR/s.
- 23.09.98 podczas podnoszenia mocy reaktora LF-2 (Ludmiła) po uruchomieniu automatycznej ochrony dopuszczalny poziom moc została przekroczona o 10%. W efekcie w trzech kanałach nastąpiło rozprężenie części prętów paliwowych, co doprowadziło do zanieczyszczenia urządzeń i rurociągów obiegu pierwotnego. Zawartość 133Xe w wylocie z reaktora przez 10 dni przekraczała dopuszczalny poziom roczny.
- 09.09.2000 r. w Majaku odcięto zasilanie na 1,5 godziny, co mogło doprowadzić do wypadku.
- W trakcie kontroli w 2005 roku prokuratura stwierdziła naruszenie zasad postępowania ze środowiskiem niebezpieczne odpady produkcji w latach 2001-2004, co doprowadziło do zrzutu do dorzecza rzeki Techa kilkudziesięciu milionów metrów sześciennych płynnych odpadów promieniotwórczych wytwarzanych przez firmę Mayak. Według zastępcy szefa wydziału Prokuratury Generalnej Federacji Rosyjskiej na Uralu okręg federalny Andrey Potapov, „ustalono, że zapora fabryczna, która od dawna wymaga odbudowy, umożliwia przedostawanie się ciekłych odpadów radioaktywnych do zbiornika, co stanowi poważne zagrożenie dla środowiska nie tylko w Obwód czelabiński ale także w sąsiednich regionach. Według prokuratury, w związku z działalnością zakładu Majak na równinie zalewowej rzeki Techa poziom radionuklidów w ciągu tych czterech lat wzrósł kilkukrotnie. Jak wykazały badania, obszar infekcji wynosił 200 kilometrów. W strefie zagrożenia mieszka około 12 tys. osób. Jednocześnie śledczy stwierdzili, że byli pod presją w związku z śledztwem. do CEO Stowarzyszenie Producentów Majaków Witalij Sadownikow został oskarżony na podstawie artykułu 246 Kodeksu karnego Federacji Rosyjskiej „Naruszenie zasad ochrony środowiska w trakcie pracy” oraz części 1 i 2 artykułu 247 Kodeksu karnego Federacji Rosyjskiej „Naruszenie zasad postępowania ekologicznego niebezpieczne substancje i odpady." W 2006 roku sprawa karna przeciwko Sadovnikowowi została umorzona w związku z amnestią z okazji 100-lecia Dumy Państwowej.
- Techa to rzeka skażona odpadami radioaktywnymi odprowadzanymi przez Kombinat Chemiczny Majów, znajdujący się w obwodzie czelabińskim. Na brzegach rzeki tło promieniotwórcze jest wielokrotnie przekraczane. W latach 1946-1956 zrzuty średnio- i wysokoaktywnych odpadów płynnych ze Stowarzyszenia Produkcyjnego Majak prowadzono do otwartego systemu rzecznego Techa-Iset-Tobol, 6 km od źródła rzeki Techa. Łącznie w tych latach odprowadzono 76 mln m3 ścieków o łącznej aktywności promieniowania β ponad 2,75 mln Ci. Mieszkańcy nadmorskich wiosek byli narażeni zarówno na promieniowanie zewnętrzne, jak i wewnętrzne. W sumie 124 tys. osób mieszkających w osadach nad brzegami rzek tego systemu wodnego było narażonych na promieniowanie. Na największą ekspozycję narażeni byli mieszkańcy wybrzeża rzeki Techa (28,1 tys. osób). Około 7,5 tys. osób przesiedlonych od 20 rozliczenia, otrzymali średnie skuteczne dawki równoważne w zakresie 3 – 170 cSv. Następnie w górnej części rzeki zbudowano kaskadę zbiorników. Większość (pod względem aktywności) ciekłych odpadów promieniotwórczych trafiła do jeziora. Karaczaj (zbiornik 9) i „Stare bagno”. Równina zalewowa rzeki i osady denne są zanieczyszczone, osady mułu w górnej części rzeki są uważane za stałe odpady promieniotwórcze. Wody gruntowe w rejonie jeziora Karaczaj i kaskada zbiorników Techensky są zanieczyszczone.
- Awaria pod Majakiem w 1957 r., zwana także „tragedią kisztyńską”, jest trzecią co do wielkości katastrofą w historii energetyki jądrowej po awarii w Czarnobylu i wypadku w elektrowni jądrowej Fukushima I (według skali INES).
- Kwestia skażenia radioaktywnego obwodu czelabińskiego była wielokrotnie podnoszona, ale ze względu na strategiczne znaczenie zakładu chemicznego za każdym razem była ignorowana.
FUKUSHIMA-1
- Wypadek w elektrowni jądrowej Fukushima-1 to poważna awaria radiacyjna (według Japończyków urzędnicy- Poziom 7 w skali INES), który miał miejsce 11 marca 2011 r. w wyniku najsilniejszego trzęsienia ziemi w Japonii i następującego po nim tsunami
Łopatki wirników są wyraźnie widoczne w tej turbinie parowej.
Elektrownia cieplna (CHP) wykorzystuje energię uwalnianą przez spalanie paliw kopalnych – węgla, ropy naftowej i gazu ziemnego – do przekształcenia wody w parę wysokie ciśnienie. Ta para, która ma ciśnienie około 240 kilogramów na centymetr kwadratowy i temperaturę 524°C (1000°F), napędza turbinę. Turbina obraca gigantyczny magnes wewnątrz generatora, który wytwarza energię elektryczną.
Nowoczesny elektrownie cieplne około 40 procent ciepła uwalnianego podczas spalania paliwa zamienia się w energię elektryczną, reszta jest odprowadzana do środowiska. W Europie wiele elektrowni cieplnych wykorzystuje ciepło odpadowe do ogrzewania pobliskich domów i firm. Skojarzone wytwarzanie ciepła i energii elektrycznej zwiększa efektywność energetyczną elektrowni nawet o 80 procent.
Elektrownia z turbiną parową z generatorem elektrycznym
Typowa turbina parowa zawiera dwa zestawy łopatek. Para pod wysokim ciśnieniem pochodząca bezpośrednio z kotła wchodzi w tor przepływu turbiny i obraca wirniki wraz z pierwszą grupą łopatek. Następnie para jest podgrzewana w przegrzewaczu i ponownie wchodzi na ścieżkę przepływu turbiny, aby obracać wirniki z drugą grupą łopatek, które pracują przy niższym ciśnieniu pary.
Przekrój
Typowy generator w elektrociepłowni (CHP) jest napędzany bezpośrednio przez turbinę parową, która obraca się z prędkością 3000 obrotów na minutę. W tego typu generatorach magnes, zwany również wirnikiem, obraca się, a uzwojenia (stojan) są nieruchome. Układ chłodzenia zapobiega przegrzaniu generatora.
Wytwarzanie energii parowej
W elektrociepłowni paliwo spalane jest w kotle, tworząc płomień o wysokiej temperaturze. Woda przepływa przez rurki przez płomień, nagrzewa się i zamienia w parę pod wysokim ciśnieniem. Para napędza turbinę, wytwarzając energia mechanicznaże generator zamienia się w energię elektryczną. Para po opuszczeniu turbiny wchodzi do skraplacza, gdzie myje rurki zimnem bieżąca woda, w wyniku czego zamienia się z powrotem w ciecz.
Kocioł olejowy, węglowy lub gazowy
Wewnątrz kotła
Kocioł wypełniony jest misternie wygiętymi rurkami, przez które przepływa podgrzana woda. Złożona konfiguracja rurek pozwala znacznie zwiększyć ilość ciepła przekazywanego do wody i dzięki temu wytwarzać znacznie więcej pary.
1 - generator elektryczny; 2 - turbina parowa; 3 - panel sterowania; 4 - odpowietrznik; 5 i 6 - bunkry; 7 - separator; 8 - cyklon; 9 - kocioł; 10 – powierzchnia grzewcza (wymiennik ciepła); jedenaście - komin; 12 - pokój kruszenia; 13 - magazyn rezerwa paliwa; 14 - wagon; 15 - urządzenie rozładowujące; 16 - przenośnik; 17 - oddymiacz; 18 - kanał; 19 - łapacz popiołu; 20 - wentylator; 21 - palenisko; 22 - młyn; 23- przepompownia; 24 - źródło wody; 25- pompa obiegowa; 26 – wysokociśnieniowa nagrzewnica regeneracyjna; 27 - pompa zasilająca; 28 - kondensator; 29 - instalacja czyszczenie chemiczne woda; 30 - transformator podwyższający; 31 - grzałka regeneracyjna niskie ciśnienie; 32 - pompa kondensatu.
Poniższy schemat przedstawia skład głównego wyposażenia elektrociepłowni i połączenia jej systemów. Zgodnie z tym schematem możliwe jest prześledzenie ogólnej sekwencji procesów technologicznych zachodzących w TPP.
Oznaczenia na schemacie TPP:
- Oszczędność paliwa;
- przygotowanie paliwa;
- przegrzewacz pośredni;
- część wysokiego ciśnienia (CHVD lub CVP);
- część niskociśnieniowa (LPH lub LPC);
- generator elektryczny;
- transformator pomocniczy;
- transformator komunikacyjny;
- główna rzecz Rozdzielnica;
- pompa kondensatu;
- pompa obiegowa;
- źródło zaopatrzenia w wodę (na przykład rzeka);
- (PND);
- stacja uzdatniania wody (VPU);
- konsument energii cieplnej;
- odwrócona pompa kondensatu;
- odgazowywacz;
- pompa zasilająca;
- (PVD);
- usuwanie żużla i popiołu;
- wysypisko popiołu;
- wyciąg dymu (DS);
- komin;
- wentylatory dmuchawy (DV);
- łapacz popiołu.
Opis schematu technologicznego TPP:
Podsumowując wszystkie powyższe, otrzymujemy skład elektrociepłowni:
- oszczędność paliwa i układ przygotowania paliwa;
- kotłownia: połączenie samego kotła i sprzęt pomocniczy;
- zakład turbin: turbina parowa i jej urządzenia pomocnicze;
- stacja uzdatniania wody i uzdatniania kondensatu;
- system zaopatrzenie w wodę techniczną,;
- system usuwania popiołu i żużla (dla elektrociepłowni na paliwo stałe);
- urządzenia elektryczne i układ sterowania urządzeniami elektrycznymi.
Oszczędność paliwa, w zależności od rodzaju paliwa stosowanego na stacji, obejmuje urządzenie odbiorcze i rozładowcze, mechanizmy transportowe, magazyny paliw stałych i płynne paliwo, urządzenia do wstępnego przygotowania paliwa (tłucznie do węgla). W skład ekonomii oleju opałowego wchodzą również pompy do pompowania oleju opałowego, podgrzewacze oleju opałowego, filtry.
Przygotowanie paliwa stałego do spalania polega na rozdrobnieniu i wysuszeniu go w instalacji proszkowej, a przygotowanie oleju opałowego na jego podgrzaniu, oczyszczeniu z zanieczyszczeń mechanicznych, a czasem obróbce specjalnymi dodatkami. Z paliwem gazowym wszystko jest łatwiejsze. Szkolenie paliwo gazowe sprowadza się głównie do regulacji ciśnienia gazu przed palnikami kotła.
Powietrze niezbędne do spalania paliwa dostarczane jest do przestrzeni spalania kotła za pomocą wentylatorów nadmuchowych (DV). Produkty spalania paliw - spaliny - są odsysane przez oddymiacze (DS) i odprowadzane przez kominy do atmosfery. Połączenie kanałów (powietrznych i gazowych) oraz różnych elementów wyposażenia, przez które przepływa powietrze i spaliny, tworzy ścieżkę gazowo-powietrzną elektrociepłowni (ciepłowni). Zawarte w jej składzie oddymiacze, komin i wentylatory nadmuchowe tworzą instalację ciągową. W strefie spalania paliwa zawarte w jego składzie zanieczyszczenia niepalne (mineralne) ulegają przemianom chemicznym i fizycznym i są częściowo usuwane z kotła w postaci żużla, a znaczna ich część jest usuwana spaliny w postaci drobnych cząstek popiołu. Dla strażnika powietrze atmosferyczne przed emisją popiołu przed oddymiaczami montowane są odpylacze (aby zapobiec ich zużyciu popiołu).
Żużel i uwięziony popiół są zwykle usuwane hydraulicznie do kopalni złota.
Podczas spalania oleju opałowego i gazu nie montuje się kolektorów popiołu.
Kiedy paliwo jest spalane, chemicznie związana energia zamienia się w ciepło. W efekcie powstają produkty spalania, które w powierzchniach grzewczych kotła oddają ciepło wodzie i powstającej z niej parze.
Zespół urządzeń, jego poszczególne elementy, rurociągi, którymi przemieszcza się woda i para, tworzą ścieżkę parowo-wodną stacji.
W kotle woda jest podgrzewana do temperatury nasycenia, odparowuje, a para nasycona powstająca z wrzącej wody kotłowej ulega przegrzaniu. Z kotła para przegrzana przesyłana jest rurociągami do turbiny, gdzie jej energia cieplna zamieniana jest na energię mechaniczną przekazywaną na wał turbiny. Para wyrzucana w turbinie trafia do skraplacza, oddaje ciepło do wody chłodzącej i skrapla się.
W nowoczesnych elektrociepłowniach i elektrociepłowniach z blokami o mocy bloku 200 MW i więcej stosuje się dogrzewanie pary. W tym przypadku turbina ma dwie części: część wysokociśnieniową i część niskociśnieniową. Para odprowadzana w wysokociśnieniowej części turbiny kierowana jest do przegrzewacza pośredniego, gdzie dodatkowo dostarczane jest do niej ciepło. Następnie para wraca do turbiny (do części niskociśnieniowej) i stamtąd wchodzi do skraplacza. Przegrzanie pośrednie pary zwiększa sprawność turbiny i zwiększa niezawodność jej pracy.
Kondensat jest wypompowywany ze skraplacza przez pompę kondensatu i po przejściu przez grzałki niskociśnieniowe (LPH) trafia do odgazowywacza. Tutaj jest podgrzewany parą do temperatury nasycenia, podczas gdy tlen i dwutlenek węgla są z niego uwalniane i usuwane do atmosfery, aby zapobiec korozji sprzętu. Woda odgazowana, zwana wodą zasilającą, pompowana jest przez podgrzewacze wysokociśnieniowe (HPH) do kotła.
Kondensat w HDPE i odgazowywaczu oraz woda zasilająca w HPH ogrzewane są parą pobieraną z turbiny. Ta metoda ogrzewania oznacza zwrot (regenerację) ciepła do obiegu i nazywana jest ogrzewaniem regeneracyjnym. Dzięki temu zmniejsza się dopływ pary do skraplacza, a co za tym idzie ilość ciepła przekazywanego do wody chłodzącej, co prowadzi do wzrost wydajności elektrownia parowa.
Zestaw elementów zaopatrujących skraplacze w wodę chłodzącą nazywany jest systemem zaopatrzenia w wodę użytkową. W jego skład wchodzą: źródło zaopatrzenia w wodę (rzeka, zbiornik, chłodnia kominowa – chłodnia kominowa), pompa obiegowa, przewody wlotowe i wylotowe. W skraplaczu około 55% ciepła pary wchodzącej do turbiny jest przenoszone do schłodzonej wody; ta część ciepła nie jest wykorzystywana do wytwarzania energii elektrycznej i jest marnowana.
Straty te ulegają znacznemu zmniejszeniu, gdy częściowo wydmuchana para jest odbierana z turbiny, a jej ciepło wykorzystywane na potrzeby technologiczne. przedsiębiorstwa przemysłowe lub ogrzewanie wody do ogrzewania i zaopatrzenia w ciepłą wodę. Tym samym stacja staje się elektrociepłownią (CHP), która zapewnia skojarzone wytwarzanie energii elektrycznej i cieplnej. W elektrociepłowniach instalowane są specjalne turbiny z odciągiem pary – tzw. turbiny kogeneracyjne. Podano kondensat pary konsument ciepła, jest zawracany do elektrociepłowni przez pompę powrotną kondensatu.
W TPP występują straty wewnętrzne pary i kondensatu wynikające z niepełnej szczelności toru parowo-wodnego oraz bezzwrotnego zużycia pary i kondensatu na potrzeby techniczne stacji. Stanowią one około 1 - 1,5% całkowitego przepływu pary do turbin.
W elektrociepłowniach mogą wystąpić zewnętrzne straty pary i kondensatu związane z dostarczaniem ciepła do odbiorców przemysłowych. Średnio wynoszą 35 - 50%. Wewnętrzne i zewnętrzne straty pary i kondensatu uzupełniane są wodą uzupełniającą wstępnie uzdatnioną w stacji uzdatniania wody.
Zatem woda zasilająca kocioł jest mieszaniną kondensatu turbiny i wody uzupełniającej.
Zaplecze elektryczne stacji obejmuje prądnicę, transformator komunikacyjny, rozdzielnicę główną, układ zasilania mechanizmów własnych elektrowni poprzez transformator pomocniczy.
System sterowania zbiera i przetwarza informacje o przebiegu procesu technologicznego i stanie urządzeń, automatycznym i zdalne sterowanie mechanizmy i regulacja głównych procesów, automatyczna ochrona sprzętu.
STRUKTURA ORGANIZACYJNO-PRODUKCYJNA ELEKTROWNI CIEPŁOWYCH (TPP)
W zależności od mocy urządzeń i obwodów łącza technologiczne pomiędzy etapami produkcji w nowoczesnych TPP wyróżnia się struktury organizacyjne i produkcyjne sklepowe, bezsklepowe i blokowe.
Struktura organizacyjna i produkcyjna warsztatu przewiduje podział urządzeń technologicznych i terenu elektrociepłowni na odrębne sekcje i przypisanie ich do wyspecjalizowanych jednostek - warsztatów, laboratoriów. W tym przypadku główny jednostka strukturalna to warsztat. Sklepy w zależności od udziału w produkcji dzielą się na główne i pomocnicze. Ponadto TPP mogą obejmować gospodarstwa nieprzemysłowe (gospodarstwa mieszkalne i zależne, przedszkola, domy opieki, sanatoria itp.).
Warsztaty główne są bezpośrednio zaangażowane w produkcję energii. Należą do nich magazyny paliwowo-transportowe, kotłowe, turbinowe, elektryczne i chemiczne.
W skład składu paliwowo-transportowego wchodzą sekcje obiektów kolejowych oraz zaopatrzenie w paliwo wraz z magazynem paliw. Warsztaty organizowane w płonących elektrowniach paliwo stałe lub olej opałowy, gdy jest dostarczany koleją.
W skład kotłowni wchodzą obszary do dostarczania paliw płynnych lub gazowych, odpylania, odpopielania.
W skład turbinowni wchodzą: wydział ciepłowniczy, centralna pompownia oraz gospodarka wodna.
Z dwoma sklepami struktura produkcji, a także w dużych TPP, kotłownie i turbiny są łączone w jedną kotłownię-turbinę (KTC).
Warsztat elektryczny zajmuje się: całym wyposażeniem elektrociepłowni, laboratorium elektrycznym, gospodarką olejową, warsztatem elektrycznym.
Warsztat chemiczny obejmuje laboratorium chemiczne i chemiczne uzdatnianie wody.
Sklepy pomocnicze służyć głównej produkcji. Należą do nich: sklep dla scentralizowanych napraw, remontów i konstrukcji, automatyki cieplnej i łączności.
Gospodarstwa nieprzemysłowe nie są bezpośrednio związane z produkcją energii i służą potrzebom domowym pracowników TPP.
Bezwarsztatowa struktura organizacyjna i produkcyjna przewiduje specjalizację jednostek w realizacji głównego funkcje produkcyjne: działanie sprzętu, jego serwis naprawczy, kontrola technologiczna. Powoduje to powstanie usług produkcyjnych zamiast warsztatów: obsługi, napraw, kontroli i ulepszania urządzeń. Z kolei usługi produkcyjne podzielone są na działy specjalistyczne.
kreacja struktura organizacyjna i produkcyjna blokowiska, z powodu pojawienia się skomplikowanych bloków energetycznych. Urządzenie blokowe realizuje kilka faz procesu energetycznego – spalanie paliwa w wytwornicy pary, wytwarzanie energii elektrycznej w turbogeneratorze, a czasem jego przekształcenie w transformatorze. W przeciwieństwie do warsztatu o konstrukcji blokowej, główną jednostką produkcyjną elektrowni są bloki. Są one zawarte w CTC, które zajmują się scentralizowaną pracą głównych i pomocniczych urządzeń kotłowych i turbinowych. Konstrukcja blokowa zapewnia zachowanie składów głównych i pomocniczych, które występują w strukturze sklepu, np. skład paliwowo-transportowy (TTTS), chemiczny itp.
Wszystkie typy struktur organizacyjnych i produkcyjnych przewidują wdrożenie zarządzania produkcją w oparciu o jedność dowodzenia. W każdym TPP znajduje się dział administracyjny, ekonomiczny, produkcyjno-techniczno-operacyjny.
Kierownikiem administracyjno-gospodarczym TPP jest dyrektor, kierownikiem technicznym jest Główny inżynier. Kontrolę operacyjną i dyspozytorską sprawuje inżynier dyżurny elektrowni. Podlega operacyjnie dyspozytorowi EPS dyżurnemu.
Nazwa i ilość podziały strukturalne, a konieczność wprowadzenia odrębnych stanowisk ustalana jest w zależności od standardowej liczby personelu przemysłowego i produkcyjnego elektrowni.
Określone cechy technologiczno-organizacyjne i ekonomiczne wytwarzania energii elektrycznej wpływają na treść i zadania kierowania działalnością przedsiębiorstw i stowarzyszeń energetycznych.
Głównym wymaganiem dla branży elektroenergetycznej jest niezawodne i nieprzerwane zasilanie odbiorców w wymaganym harmonogramie obciążenia. Wymóg ten przekształcany jest w konkretne wskaźniki oceniające udział elektrowni i przedsiębiorstw sieciowych w realizacji programu produkcyjnego stowarzyszeń energetycznych.
Dla elektrowni ustalana jest gotowość do przeniesienia obciążenia, którą określa harmonogram wysyłek. W przypadku przedsiębiorstw sieciowych ustalany jest harmonogram napraw sprzętu i obiektów. W planie przewidziano również inne wskaźniki techniczne i ekonomiczne: koszt jednostki paliwo w elektrowniach, ograniczenie strat energii w sieciach, wskaźniki finansowe. Program produkcyjny przedsiębiorstw energetycznych nie może być jednak sztywno określony wielkością produkcji lub podaży. energia elektryczna i ciepło. Jest to niepraktyczne ze względu na wyjątkową dynamikę zużycia energii, a tym samym produkcję energii.
Jednak wielkość produkcji energii jest ważnym wskaźnikiem obliczeniowym, który determinuje poziom wielu innych wskaźników (np. koszt) oraz wyniki działalności gospodarczej.
Na ryc. 1 przedstawia klasyfikację elektrociepłowni zasilanych paliwami kopalnymi.
Ryż. jeden.
Elektrociepłownia to zespół urządzeń i urządzeń, które przekształcają energię paliwową w energię elektryczną i (w ogólnym przypadku) energia cieplna.
Elektrociepłownie charakteryzują się dużą różnorodnością i mogą być klasyfikowane według różnych kryteriów.
W zależności od przeznaczenia i rodzaju dostarczanej energii elektrownie dzielą się na regionalne i przemysłowe.
Elektrownie okręgowe to niezależne elektrownie publiczne, które obsługują wszystkie rodzaje odbiorców na danym obszarze (przedsiębiorstwa przemysłowe, transport, ludność itp.). Powiatowe elektrownie kondensacyjne, które wytwarzają głównie energię elektryczną, często zatrzymują historyczna nazwa- GRES (państwowe elektrownie okręgowe). Elektrownie okręgowe wytwarzające energię elektryczną i cieplną (w postaci pary lub gorąca woda) nazywane są elektrociepłowniami (CHP). Z reguły państwowe elektrownie okręgowe i regionalne elektrociepłownie mają moc ponad 1 mln kW.
Elektrownie przemysłowe to elektrownie, które dostarczają ciepło i energię elektryczną do określonych przedsiębiorstwa produkcyjne lub ich kompleks, na przykład zakład do produkcji produktów chemicznych. Elektrownie przemysłowe są częścią obsługiwanych przedsiębiorstw przemysłowych. Ich moc jest zdeterminowana zapotrzebowaniem przedsiębiorstw przemysłowych na ciepło i energię elektryczną iz reguły jest znacznie mniejsza niż w ciepłowniach okręgowych. Często elektrownie przemysłowe działają na wspólnym sieć elektryczna, ale nie podlegają dyspozytorowi systemu elektroenergetycznego.
W zależności od rodzaju stosowanego paliwa elektrownie cieplne dzielą się na elektrownie pracujące na paliwie organicznym i paliwie jądrowym.
Za elektrowniami kondensacyjnymi działającymi na paliwa kopalne, w czasach, gdy nie było elektrowni jądrowych (NPP), historycznie wykształciła się nazwa termiczna (TPP - elektrociepłownia). W tym sensie termin ten będzie używany poniżej, chociaż zarówno CHP, NPP, jak i elektrownie z turbinami gazowymi(GTPP) i elektrociepłownie (PGPP) to także elektrownie cieplne działające na zasadzie zamiany energii cieplnej na energię elektryczną.
Paliwa gazowe, płynne i stałe są wykorzystywane jako paliwa kopalne w elektrowniach cieplnych. Większość elektrowni cieplnych w Rosji, zwłaszcza w części europejskiej, zużywa gazu ziemnego, a jako paliwo zapasowe - olej opałowy, wykorzystując ten ostatni ze względu na jego wysoki koszt tylko w skrajnych przypadkach; takie elektrownie cieplne nazywane są opalanymi olejem. W wielu regionach, głównie w azjatyckiej części Rosji, głównym paliwem jest węgiel energetyczny – węgiel niskokaloryczny lub odpady z wydobycia węgla wysokokalorycznego (szlam antracytowy – ASh). Ponieważ takie węgle są mielone w specjalnych młynach do stanu sproszkowanego przed spaleniem, takie elektrownie cieplne nazywane są sproszkowanym węglem.
W zależności od rodzaju elektrociepłowni stosowanych w elektrociepłowniach do zamiany energii cieplnej na energię mechaniczną obrotów wirników zespołów turbinowych wyróżnia się turbinę parową, turbinę gazową oraz elektrownie o cyklu kombinowanym.
Podstawą elektrowni z turbinami parowymi są: instalacje turbin parowych(PTU), które do zamiany energii cieplnej na energię mechaniczną wykorzystują najbardziej złożoną, najpotężniejszą i niezwykle zaawansowaną maszynę energetyczną – turbinę parową. PTU jest głównym elementem elektrowni cieplnych, elektrociepłowni i elektrowni jądrowych.
PTU, które mają turbiny kondensacyjne jako napęd generatorów elektrycznych i nie wykorzystują ciepła pary odlotowej do dostarczania energii cieplnej do odbiorców zewnętrznych, nazywane są elektrowniami kondensacyjnymi. PTU wyposażone w turbiny ciepłownicze i oddające ciepło pary odlotowej do odbiorców przemysłowych lub domowych nazywane są elektrociepłowniami (CHP).
Elektrociepłownie z turbiną gazową (GTPP) są wyposażone w zespoły turbin gazowych (GTU) pracujące na paliwie gazowym lub w skrajnych przypadkach na paliwie płynnym (diesel). Ponieważ temperatura gazów za turbiną gazową jest dość wysoka, można je wykorzystać do dostarczania energii cieplnej do zewnętrznego odbiorcy. Takie elektrownie nazywają się GTU-CHP. Obecnie w Rosji działa jeden GTPP (GRES-3 od Klasson, Elektrogorsk, obwód moskiewski) o mocy 600 MW oraz jeden GTU-CHPP (w Elektrostal, obwód moskiewski).
Tradycyjna nowoczesna elektrownia gazowa (GTU) to zespół kompresor powietrza, komorę spalania i turbinę gazową oraz układy pomocnicze zapewniające jej działanie. Kombinacja turbiny gazowej i generatora elektrycznego nazywana jest jednostką turbiny gazowej.
Zakończono budowę elektrociepłowni w cyklu skojarzonym instalacje cyklu łączonego(CCP), które są połączeniem turbin gazowych i parowych, co pozwala na uzyskanie wysokiej wydajności. CCGT-TPP mogą być kondensacyjne (CCGT-CES) oraz z mocą grzewczą (CCGT-CHP). Obecnie w Rosji działają cztery nowe elektrociepłownie CCGT (EC Severo-Zapadnaya St. Petersburg, Kaliningradskaya, CHPP-27 OAO Mosenergo i Sochinskaya), a także zbudowano elektrociepłownię w Tiumenskaya. W 2007 roku oddano do użytku Iwanowskaja CCGT-IES.
TPP blokowe składają się z oddzielnych, zwykle tego samego typu elektrownie- jednostki napędowe. W bloku energetycznym każdy kocioł dostarcza parę tylko do własnej turbiny, z której po skropleniu powraca tylko do własnego kotła. Zgodnie ze schematem blokowym budowane są wszystkie potężne elektrownie państwowe i elektrociepłownie, które mają tak zwane pośrednie przegrzanie pary. Eksploatacja kotłów i turbin w elektrociepłowniach z usieciowaniem jest zapewniona inaczej: wszystkie kotły elektrociepłowni dostarczają parę do jednego wspólnego rurociągu parowego (kolektora) i wszystkie turbiny parowe TPP. Zgodnie z tym schematem, elektrociepłownie budowane są bez pośredniego przegrzewania, a prawie wszystkie elektrociepłownie budowane są dla podkrytycznych początkowych parametrów pary.
W zależności od poziomu ciśnienia początkowego rozróżnia się TPP ciśnienia podkrytycznego, ciśnienia nadkrytycznego (SKP) i parametrów nadkrytycznych (SSCP).
Ciśnienie krytyczne wynosi 22,1 MPa (225,6 atm). W rosyjskiej energetyce cieplnej parametry początkowe są standaryzowane: elektrownie cieplne i elektrociepłownie budowane są na podkrytyczne ciśnienie 8,8 i 12,8 MPa (90 i 130 atm), a dla SKD - 23,5 MPa (240 atm). TPP na parametry nadkrytyczne ze względów technicznych przeprowadza się z dogrzewaniem i według schematu blokowego. Do parametrów nadkrytycznych warunkowo zalicza się ciśnienie powyżej 24 MPa (do 35 MPa) i temperaturę powyżej 5600C (do 6200C), których zastosowanie wymaga nowych materiałów i nowych konstrukcji urządzeń. Często elektrociepłownie lub elektrociepłownie o różnych poziomach parametrów budowane są w kilku etapach – w kolejkach, których parametry zwiększają się wraz z wprowadzeniem każdej nowej kolejki.