System konserwacji i napraw urządzeń energetycznych: Podręcznik. Zasady bezpiecznej eksploatacji urządzeń technologicznych i urządzeń produkcyjnych
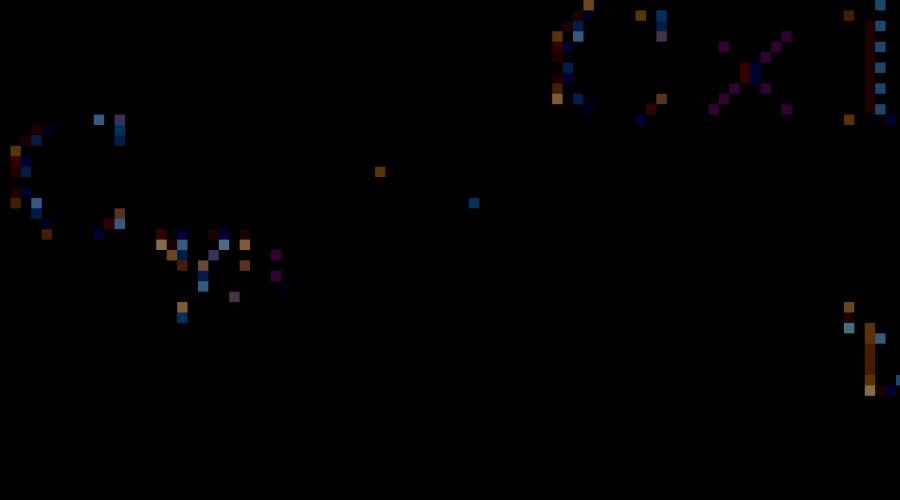
DANIA MIĘSNE
Rodzaje sprzęt technologiczny, sprzęt produkcyjny i jego bezpieczne zastosowanie w przygotowaniu dań mięsnych. zasady bezpieczna operacja wyposażenie technologiczne i inwentaryzacja produkcji.
2. Charakterystyka towarowa surowców. Kulinarne zastosowanie głównych surowców (mięso), przypraw, przypraw, mieszanek aromatyzujących i spożywczych, sosów przemysłowych, octów, dodatków do żywności, win, serów do przygotowania złożonych gorących kulinarnych produktów mięsnych i możliwości ich wykorzystania.
Dział sosów gorącego sklepu. Dział sosów przeznaczony jest do przygotowywania drugich dań, dodatków i sosów. Do wykonywania różnych procesów obróbki cieplnej i mechanicznej wyrobów stanowiska pracy wyposażane są w odpowiedni sprzęt oraz różnorodne sprzęty, narzędzia i inwentaryzacje.
Dobierają urządzenia cieplne i mechaniczne zgodnie ze standardami wyposażenia przedsiębiorstw w sprzęt Żywnościowy.
Głównym wyposażeniem działu sosów są kuchenki, piekarniki, patelnie elektryczne, frytownice, a także garnki, napęd uniwersalny. Warniki stacjonarne są wykorzystywane w dziale sosów w dużych warsztatach do gotowania przystawek warzywnych i zbożowych.
Domy grillowe są instalowane w gorących sklepach wyspecjalizowanych przedsiębiorstw i restauracji. Przedsiębiorstwa używają kuchenek do kiełbasek, kuchenek do jajek itp.
Przyspieszenie gotowania potraw można osiągnąć za pomocą urządzeń mikrofalowych. W urządzeniach mikrofalowych półprodukty nagrzewane są w całej objętości produktu dzięki właściwościom fal elektromagnetycznych, które wnikają w produkt na znaczną głębokość.
Wyposażenie działu sosów można pogrupować w dwie lub trzy linie technologiczne.
Pierwsza linia przeznaczony jest do obróbki cieplnej i przyrządzania potraw z półproduktów z mięsa, ryb, warzyw oraz do przyrządzania przystawek i sosów w naczyniach blaszanych. Linia składa się z sekcyjnego urządzenia modulowanego i obejmuje piekarnik, kuchenki, patelnie elektryczne, frytownice. W restauracjach w tej linii instalowane są również podgrzewacze żywności, przeznaczone do krótkotrwałego przechowywania drugich dań w stanie gorącym.
Miejsce pracy kucharza działu sosów:
Marmite do sosów;
Piec czteropalnikowy;
Wkładki termiczne;
frytownica;
Patelnia;
Szafa piekarnika dwukomorowego;
Stół z wbudowaną wanną myjącą;
Stół przemysłowy;
Wagi tarczowe lub elektroniczne;
Stół do instalacji mechanizacji na małą skalę;
Stół z szafką chłodniczą i zjeżdżalnią;
Tablet ścienny do mapy technologicznej
Druga linia przeznaczony do wykonywania czynności pomocniczych i zawiera segmentowe stoły modulowane: stół z wbudowaną wanną myjącą, stół do montażu drobnego sprzętu mechanizacji, stół z chłodzoną zjeżdżalnią oraz szafę (w restauracjach).
Półprodukty mięsne, rybne, warzywne przygotowywane są do obróbki cieplnej na stołach produkcyjnych. Stół produkcyjny ze zjeżdżalnią chłodniczą i szafką wykorzystywany jest w restauracjach do porcjowania i dekorowania potraw.
trzecia linia- do gotowania przystawek. Praca kucharzy działu sosów rozpoczyna się od zapoznania się z programem produkcji (planem menu), doborem map technologicznych, określeniem ilości produktów potrzebnych do gotowania. Następnie kucharze otrzymują produkty, półprodukty i wybierają dania. W restauracji dania smażone i pieczone przygotowywane są wyłącznie na zamówienie zwiedzających; pracochłonne dania, które wymagają dużo czasu na gotowanie (gulasze, sosy) przygotowywane są w małych partiach.
Zabrania się wychodzenia następnego dnia w dziale sosów gorącego sklepu:
Naleśniki z mięsem i twarogiem, siekane produkty z mięsa, drobiu, ryb;
Puree ziemniaczane, gotowany makaron.
W surowcach i produktach spożywczych używanych do gotowania zawartość potencjalnie niebezpiecznych substancji chemicznych i pochodzenie biologiczne(elementy toksyczne, antybiotyki, pestycydy, drobnoustroje chorobotwórcze itp.) nie powinny przekraczać norm ustalonych przez wymagania biomedyczne i normy sanitarne jakość jedzenia. To wymaganie jest określone w GOST R 50763-95 „Catering publiczny. Produkty kulinarne sprzedawane publicznie. Ogólne warunki techniczne".
Dział sosów wykorzystuje:
Kotły piecowe o pojemności 20, 30,40,50 litrów do gotowania i duszenia potraw z mięsa, warzyw; bojlery (skrzynki) do gotowania i gotowania całych ryb i ogniw;
- kotły do gotowania dietetycznych potraw dla pary z wkładką do rusztu;
- patelnie o pojemności 1,5,2,4,5,8 i 10 litrów do przygotowania niewielkiej ilości porcji gotowanych, duszonych drugich dań, sosów;
- rondle o pojemności 2, 4, 6, 8 i 10 litrów do smażenia warzyw, przecieru pomidorowego. W przeciwieństwie do kotłów, garnki mają pogrubione dno;
Tace metalowe i duże patelnie żeliwne do smażenia półproduktów z mięsa, ryb, warzyw, drobiu;
- małe i średnie patelnie żeliwne z uchwytem do smażenia naleśników, naleśników, gotowania omletów;
- patelnie z 5, 7 i 9 komorami do gotowania jajek sadzonych luzem;
- patelnie żeliwne z prasą do smażenia kurczaków tytoniowych itp.
Spis:
Corollas, veselka, widelce szefa kuchni (duże i małe);
- ryk;
Ostrza do naleśników, klopsików, ryb;
Urządzenie do przecedzania bulionu, różne sita, miarki,
umovki, szaszłyki do smażenia szaszłyków.
W dziale sosów miejsca pracy są zorganizowane głównie według rodzaju obróbki cieplnej. Na przykład stanowisko do smażenia i przyrumieniania produktów i półproduktów; drugi - do gotowania, duszenia i kłusowania produktów; trzeci - do przygotowania przystawek i płatków zbożowych.
W miejscu pracy kucharze używają kuchenek, piekarników, stołów produkcyjnych i ruchomych stojaków do smażenia i smażenia produktów. W restauracjach, w których asortyment dań jest bardziej zróżnicowany, a dania smażone w głębokim tłuszczu przyrządzane są na otwartym ogniu (grillowany jesiotr, grillowany drób itp.) w linię grzewczą wchodzą grille elektryczne. Przygotowane półprodukty w siatce zanurza się we frytownicy z rozgrzanym tłuszczem, następnie gotowe produkty wraz z siatką lub łyżką cedzakową przenosi się do durszlaka zamontowanego na rondlu w celu odsączenia nadmiaru tłuszczu. Jeśli w asortymencie potraw znajdują się kebaby, organizowane jest specjalistyczne miejsce pracy, składające się ze stołu produkcyjnego i pieca do kebabu.
Stanowiska do gotowania, duszenia, kłusownictwa i pieczenia produktów są zorganizowane z uwzględnieniem wykonywania przez kucharzy kilku czynności jednocześnie. W tym celu urządzenia termiczne (piece, piekarniki, patelnie elektryczne) są pogrupowane z obliczeniem wygody przejścia kucharzy z jednej operacji do drugiej. Operacje pomocnicze prowadzone są na stołach produkcyjnych zainstalowanych równolegle do linii grzewczej. Urządzenia termiczne mogą być instalowane nie tylko liniowo, ale również wyspowo.
Zasady bezpiecznej eksploatacji urządzeń technologicznych i urządzeń produkcyjnych.
Demontaż, smarowanie, czyszczenie sprzętu możliwy jest dopiero po zatrzymaniu maszyny i odłączeniu jej od źródeł prądu, pary, gazu;
Otwieranie pokryw kotłów i wylewanie ich zawartości jest dozwolone nie wcześniej niż 5 minut po ustaniu dopływu pary lub energii elektrycznej;
Przed ułożeniem produktów w gorącym tłuszczu należy usunąć z nich płyn i odłożyć je od siebie;
Otworzyć pokrywy kotłów z wrzącą cieczą w taki sposób, aby para wydobywała się z przeciwnej strony;
Kotły z gorącą cieczą lub ważące powyżej 15 kg mogą być usuwane tylko przez dwie osoby.
Kucharze i inni pracownicy hotshopu zobowiązani są do zapoznania się z zasadami obsługi sprzętu oraz poinstruowania ich przez brygadzistę.
Charakterystyka towarowa surowców - mięso
Mięso to produkt spożywczy uzyskiwany po uboju bydła i poddany obróbce poubojowej: wykrwawianiu, cięciu rzeźniczym (usuwanie nieszczątków, wnętrzności, skórek itp.), dojrzewaniu, chłodzeniu i znakowaniu. Składa się z tkanki mięśniowej, łącznej, kostnej i tłuszczowej.
W zależności od rodzaju i wieku zwierząt rozróżnia się wołowinę i cielęcinę, wieprzowinę i prosięta, mięso jagnięce, kozie i inne.
W zależności od stanu termicznego mięso można schłodzić, zamrozić, schłodzić. W przetwórstwie rzeźniczym uzysk mięsa wynosi od 50 do 60% żywej wagi.
Według otłuszczenia mięso dzieli się na: wołowinę, jagnięcinę i mięso kozie kategorii 1 i 2, wieprzowinę - tłustą, boczek, mięso i mięso krojone.
Właściwości surowców determinują sposób ich kulinarnego wykorzystania, schemat obróbki mechanicznej oraz ilość odpadów. Tak więc mrożone mięso wymaga wcześniejszego rozmrożenia. Liczba kości przy rozbiorze tusz wołowych I kategorii otłuszczenia wynosi 26,4%, II kategorii 29,5% itd.
Mięso dostarczane jest do zakładów żywienia zbiorowego w całych tuszach, półtuszach, mniejszych częściach tusz lub w postaci półproduktów przygotowanych do celów kulinarnych.
Mięso to jeden z najcenniejszych produktów spożywczych. Przede wszystkim zawiera znaczną ilość białek (w%): wołowina - 18,6-20, jagnięcina - 15,6 - 19,8, tłusta wieprzowina - 11-12 itd. większość tych białek jest kompletna. Zawierają wszystkie niezbędne aminokwasy, które również są w zbliżonych do optymalnych proporcjach. Ilość tłuszczu waha się w zależności od rodzaju mięsa i jego otłuszczenia w bardzo szerokim zakresie: od 1-2% w cielęcinie do 49% w tłustej wieprzowinie.
Przez eksploatację środków technicznych rozumie się zespół działań organizacyjnych pracowników inżynieryjno-technicznych i pracowników w celu doprowadzenia sprzętu do wymaganego stanu, jego efektywnego wykorzystania oraz utrzymania parametrów eksploatacyjnych i technicznych w określonych granicach.
Generalnie na cały okres eksploatacji składają się następujące etapy: transport sprzętu na miejsce eksploatacji, składowanie przedinstalacyjne, montaż sprzętu, przygotowanie do użytkowania, przeznaczenie (eksploatacja), konserwacja i naprawa.
Transport sprzętu dotyczy dostawy sprzętu i jego instalacji w przedsiębiorstwie handlowym. Okres ten ma charakter epizodyczny i występuje, gdy instalowany jest nowy sprzęt lub wymieniany jest stary sprzęt ze względu na koniec jego żywotności. Transport sprzętu musi odbywać się w pełnej zgodności z „Instrukcją transportu” opracowaną przez producenta.
Przechowywanie to zestaw środków zapewniających bezpieczeństwo sprzętu w stanie niepracującym w odstępach czasu niezwiązanych z użytkowaniem sprzętu zgodnie z jego przeznaczeniem (eksploatacją). Podczas przechowywania sprzęt może znajdować się w magazynach, na terenach otwartych lub zamkniętych, w pomieszczeniach roboczych przedsiębiorstw handlowych i gastronomicznych. Podczas przechowywania bezpieczeństwo sprzętu zapewnia się poprzez zachowanie warunków ograniczających wpływ środowiska zewnętrznego na jego działanie, poprzez konserwację i odpowiednią konserwację.
Instalacja sprzętu ma na celu instalację sprzętu w pomieszczeniach roboczych przedsiębiorstwa, jego debugowanie i uruchomienie. Montaż urządzeń odbywa się w pełnej zgodności z dokumentacją projektową i projektową.
Przygotowanie sprzętu do użytkowania obejmuje zestaw czynności, w wyniku których sprzęt zostaje doprowadzony ze stanu spoczynku do stanu gotowości do użytkowania zgodnie z przeznaczeniem. Przygotowanie sprzętu do eksploatacji można przeprowadzić zarówno po jego zainstalowaniu, jak i po jego zgodnym z przeznaczeniem użytkowaniu. W tym drugim przypadku nazywa się to przygotowaniem operacyjnym do pracy. Typowe czynności, które są wykonywane w ramach przygotowania sprzętu do użytku to; ponowne otwarcie, oględziny, sprawdzanie funkcjonowania (operacyjności) wszystkich systemów i testowanie w różne tryby. Podczas przygotowania operacyjnego do użytku przeprowadzana jest inspekcja zewnętrzna, diagnostyka techniczna działania wszystkich systemów urządzeń, ich testowanie w różnych trybach, testowanie urządzeń zapewniających bezpieczną pracę i inne środki ochrony pracy.
Wykorzystanie sprzętu zgodnie z jego przeznaczeniem to bezpośrednie wykorzystanie sprzętu do realizacji procesów technologicznych. Użytkowanie sprzętu zgodnie z jego przeznaczeniem jest najbardziej krytycznym etapem eksploatacji, którego prawidłowa realizacja zależy od niezawodności i bezpieczeństwa jego działania. Praca operatorów w tym okresie regulowana jest przez pewien zestaw technologiczno-operacyjny dokumentacja techniczna. Jednocześnie w tym okresie kadra inżynieryjno-techniczna przedsiębiorstwa prowadzi prace nad uogólnieniem doświadczeń eksploatacyjnych, docelowo mającymi na celu poprawę niezawodności działania i bezpieczeństwa eksploatacji.
Konserwacja to faza eksploatacji, której celem jest utrzymanie operacyjności oraz innych parametrów operacyjnych i technicznych w ustalonych granicach. Istotą konserwacji jest kontrola i zapobieganie wszystkim systemom urządzeń.
Naprawa to etap eksploatacji, podczas którego przeprowadzane są operacje mające na celu doprowadzenie sprzętu do określonego stanu roboczego plan zapobiegawczy, oraz na odbudowę sprzętu z powodu awarii.
Na ryc. 11.1 przedstawia schemat blokowy działania sprzętu.
Rysunek 11.1 - Schemat strukturalny eksploatacja urządzeń komercyjnych
Jak wynika z powyższego wykresu, w proces eksploatacji zaangażowana jest znaczna liczba przedsiębiorstw, pracowników inżynieryjno-technicznych oraz robotników (operatorów). W związku z tym eksploatacja sprzętu wymaga celowych działań inżynierów, operatorów, mechaników, pracowników - mechaników i innego personelu konserwacyjnego.
Problem ten można rozwiązać, jeśli wszyscy uczestnicy procesu operacyjnego działają według jednej technologii.
Jak wiadomo, technologia jest rozumiana jako udokumentowane naukowe uogólnienie metod pracy.
Na cały proces eksploatacji składa się zespół określonych procesów technologicznych, które opierają się na operacjach technologicznych wykonywanych przez operatora (pracownika) na jednym stanowisku pracy.
W tym samym czasie każdy oddzielna akcja operator reprezentuje przemianę technologiczną.
Spójny opis operacji technologicznych wraz z niezbędnymi ilustracjami i schematami jest wyświetlany w głównym dokumencie inżynieryjno-technologicznym - operacyjnej mapie technologicznej.
Dla każdego operatora uczestniczącego w tym opracowaniu sporządzana jest mapa operacyjna i technologiczna proces technologiczny. Mapa operacyjno-technologiczna powinna zawierać: następująca informacja:
nazwa przejścia technologicznego;
Czas przejścia;
tempo produkcji;
Szkic wykonania przejść lub operacji jako całości.
Ostateczny cel przeprowadzenie procesów operacyjnych i technologicznych ma zapewnić: maksymalna wydajność użytkowanie sprzętu.
Niewłaściwe działanie sprzętu może spowodować awarie i wypadki. Przez awarię rozumie się niewielkie uszkodzenie części maszyn, które nie zakłóca procesu produkcyjnego na budowie, w warsztacie. Przez wypadek rozumie się awarię maszyny lub kilku maszyn, której towarzyszy zakłócenie procesu produkcyjnego lub uszkodzenie krytycznych mechanizmów i poszczególnych części. Sytuacja wypadku lub awarii nie powinna zostać zakłócona do czasu przybycia komisji śledczej.
Ogólne wymagania bezpieczeństwa dotyczące projektowania urządzeń technologicznych
Ogólne wymagania wymagania bezpieczeństwa dotyczące projektowania urządzeń procesowych są określone przez GOST 12.2.003-91 „SSBT. Sprzęt produkcyjny. Ogólne wymagania bezpieczeństwa”. Elementy konstrukcji maszyn nie powinny mieć ostre rogi, krawędzie itp., stanowiące źródło zagrożenia podczas konserwacji. Konstrukcja powinna wykluczać możliwość przypadkowego kontaktu z gorącymi lub przechłodzonymi częściami. Wszystkie jego elementy, w tym komunikacja wlotowa i wylotowa, muszą zapobiegać możliwości przypadkowego uszkodzenia, które powoduje zagrożenie podczas konserwacji. Systemy zaopatrzenia w sprężone powietrze, parę, wodę muszą odpowiadać aktualnym wymaganiom i normom.
Uwalnianie ciepła, wilgoci i pyłu do pomieszczenia produkcyjnego nie powinno przekraczać dopuszczalnych poziomów (stężeń) ustalonych dla obszarów roboczych. W tym celu należy zainstalować wbudowane urządzenia do usuwania substancji wybuchowych i łatwopalnych z miejsc ich powstawania. W pomieszczeniach przemysłowych należy zapewnić wentylację i klimatyzację oraz odsysanie sprzętu.
Zespoły i części maszyn muszą być wykonane z bezpiecznych i nieszkodliwych materiałów. Co do zasady nowe materiały przechodzą kontrole sanitarno-higieniczne i przeciwpożarowe. Stanowiska pracy powinny być bezpieczne i wygodne do wykonywania prac konserwacyjnych. Wszystkie zespoły maszyn wymagające smarowania wyposażone są w automatyczne smarownice lub olejarki ze zbiornikami o wystarczającej pojemności do napełniania podczas postojów maszyny.
Konstrukcja maszyn musi zapewniać ochronę przed porażeniem elektrycznym, w tym w przypadku błędnych działań personelu obsługującego. Ponadto należy wykluczyć możliwość akumulacji ładunków elektryczności statycznej w niebezpiecznych ilościach. W tym celu wszystkie maszyny, aparaty, odcinki rur grawitacyjnych i inne urządzenia generujące ładunek elektrostatyczny są wyposażone w niezawodny system uziemiający. Konstrukcja urządzenia powinna również przewidywać systemy alarmowe, automatyczne wyłączanie i odłączanie od źródeł energii w przypadku awarii, wypadków i niebezpiecznych trybów pracy.
Chronione są ruchome części sprzętu stanowiące źródło zagrożenia. Jeżeli sprzęt jest obsługiwany bez ogrodzenia, wówczas w tym przypadku zainstalowany jest sygnał ostrzegawczy, aby uruchomić maszyny oraz środki do zatrzymania i odłączenia od źródła zasilania. W obecności maszyn transportowych o znacznej długości, środki postoju znajdują się co najmniej co 10 m. Sprzęt produkcyjny, których obsługa związana jest z przemieszczaniem się ludzi, musi posiadać wygodne i bezpieczne przejścia oraz urządzenia do prowadzenia prac (schody, cokoły, podesty robocze).
Na sterowanie urządzeniami nakładane są następujące podstawowe wymagania:
- pod względem kształtu, wymiarów powierzchni muszą być bezpieczne i łatwe w użyciu;
- ich lokalizacja (dostępność) nie powinna utrudniać wykonywania poszczególnych operacji;
- wysiłek związany z uruchomieniem elementów sterujących nie powinien być zbyt duży (nie do zniesienia) ani mały (przypadkowe dotknięcie powoduje uruchomienie lub zatrzymanie maszyn);
- konstrukcja powinna wykluczać spontaniczne uruchomienie lub zatrzymanie sprzętu;
- kontrole tego samego typu sprzętu powinny być ujednolicone.
Środki ochrony niebezpiecznych obszarów sprzętu. Aby zapobiec urazom zawodowym podczas konserwacji sprzętu, konieczne jest zainstalowanie specjalnych urządzeń, które zamykają obszary niebezpieczne. Te ostatnie reprezentują przestrzeń, w której stale lub okresowo działają niebezpieczne czynniki, stwarzając możliwość kontuzji. Na przykład niebezpieczne obszary to pas, przekładnia, łańcuch i inne przekładnie; strefy podawania i mielenia młynów walcowych itp.
Aby chronić przed działaniem niebezpieczne czynniki stosuje się następujące podstawowe środki ochrony: urządzenia ochronne, zabezpieczające i sygnalizacyjne oraz zdalne sterowanie.
Urządzenia ochronne. Ze względów bezpieczeństwa obowiązkowa jest ochrona:
- ruchome części maszyn (koła pasowe, pasy, łańcuchy, koła zębate, sprzęgła, wystające końcówki wałów itp.);
- otwarte przewodzące prąd części sprzętu elektrycznego;
- strefy latających cząstek;
- strefy wysokich temperatur i ciśnień;
- strefy wybuchowe;
- włazy, otwory;
- wysokie obszary robocze.
Z założenia urządzenia ochronne są podzielone na stacjonarne, zdejmowane i przenośne (ryc. 10.1).
Osłony stacjonarne trwale zamykają strefę niebezpieczną, ale można je zdjąć w celu kontroli, smarowania lub naprawy części roboczych. Takie ogrodzenia muszą być mocno przymocowane do stałych części wyposażenia lub do konstrukcji budowlanych co najmniej w trzech punktach.
Ryż. 10.1. Rodzaje ogrodzeń: a - stacjonarne; b - telefon komórkowy
Zdejmowane osłony są instalowane w obszarach wymagających okresowego dostępu, takich jak zmiana narzędzi, ustawienie przedmiotu obrabianego, regulacja itp. w maszynach wsadowych. Zdejmowane osłony muszą posiadać zamek, który wyklucza możliwość obsługi maszyn bez osłony.
Urządzenia blokujące są różnego rodzaju: elektromechaniczne, mechaniczne, elektryczne, fotoelektryczne itp. W przypadku zdjęcia lub nieprawidłowego zamontowania osłon następuje przerwanie obwodu zasilania silnika maszyny.
Przenośne ogrodzenia obszarów niebezpiecznych są instalowane na ograniczony czas, na przykład w celu zakrycia włazów instalacyjnych, rowów i innych otworów.
Do projektu różnego rodzaju bariery stref niebezpiecznych mają następujące podstawowe wymagania:
- ogrodzenia zdejmowane, składane, przesuwane, a także drzwi, osłony, osłony tych ogrodzeń lub korpusy maszyn muszą posiadać urządzenia zapobiegające ich przypadkowemu usunięciu lub otwarciu (niezawodne zamocowanie, zablokowanie);
- osłony kratowe (siatkowe) do napędów pasowych powinny znajdować się nie bliżej niż 50 mm od części ruchomych, wielkość szczelin, szerokość szczelin w kratach, żaluzje nie powinny być większe niż 10 mm, rozmiary oczek w kratach kratki nie powinny mieć więcej niż 20 x 20 mm;
- ogrodzenia muszą wytrzymać przypadkowe obciążenia personelu obsługi (skoncentrowane) co najmniej 70 kg;
- metalowe konstrukcje osłaniające (solidne) o powierzchni ponad 0,75 m 2 i grubości mniejszej niż 3 mm wyposażone są w powłoki tłumiące drgania;
- Ogrodzenia stref niebezpiecznych na zewnątrz powinny być pomalowane na żółto, a od wewnątrz na czerwono.
Urządzenia bezpieczeństwa. Służą zapobieganiu wypadkom i awariom poszczególnych jednostek sprzętu, komunikacji transportowej i związanemu z nimi ryzyku obrażeń. W przypadku naruszenia ustawionych parametrów urządzenia zabezpieczające działają automatycznie, wyłączając odpowiednie urządzenia.
Urządzenia sygnalizacyjne. Przeznaczone są do informowania personelu konserwacyjnego o działaniu sprzętu lub naruszeniu ustalonych trybów, w których mogą wystąpić niebezpieczne sytuacje.
W sytuacjach produkcyjnych stosowany jest system alarmów operacyjnych i ostrzegawczych. Zgodnie z metodą powiadamiania system alarmowy może być świetlny, dźwiękowy, sygnalizacyjny i łączony. Alarm informuje o osiągnięciu granicznego poziomu temperatury, ciśnienia, obecności i braku produktu, wody, powietrza i innych parametrów. Alarmy ostrzegawcze zawierają również znaki typu: „Nie włączaj – naprawiaj!”, „Ludzie pracują!”, „Uwaga, trucizna!” itp.
Zdalne sterowanie. Pomaga poprawić warunki pracy, zmniejszyć wpływ na organizm człowieka wibracji, hałasu oraz innych szkodliwych i niebezpiecznych czynników. Wprowadzenie wysoce zmechanizowanego i zautomatyzowanego procesu produkcyjnego, sterowanego zdalnie z konsoli, pozwala na skrócenie czasu spędzanego przez personel serwisowy bezpośrednio na hali produkcyjnej.
Urządzenia technologiczne, transportowe i inne, kanały materiałowe i powietrzne muszą być zlokalizowane tak, aby ich montaż, naprawa i konserwacja zapewniały bezpieczeństwo i wygodę oraz możliwość utrzymania niezbędnego stanu sanitarnego pomieszczeń przemysłowych.
Przemysłowe przepisy dotyczące bezpieczeństwa i warunków sanitarnych przewidują pewne przejścia i szczeliny, które są minimalnymi odległościami między obiektami, z których jeden lub oba stwarzają potencjalne ryzyko obrażeń, jeśli odległość między nimi zostanie zmniejszona.
Umieszczając sprzęt stacjonarny w pomieszczeniach produkcyjnych przedsiębiorstw, należy zapewnić przejścia poprzeczne i wzdłużne bezpośrednio połączone z wyjściami do klatek schodowych lub sąsiednich pomieszczeń, szczeliny między grupami maszyn o szerokości co najmniej 1 m oraz między oddzielne maszyny- nie mniej niż 0,8 m (z wyjątkiem odrębnie przewidzianych przypadków).
Urządzenia, które nie posiadają żadnych części ruchomych ani z jednej strony i nie wymagają konserwacji z tej strony (rurociąg grawitacyjny, materiałowy, kanał powietrzny itp.) mogą być instalowane w odległości co najmniej 0,25 m od ściany .
Podczas montażu sprzętu należy dokładnie ustawić jego położenie w pionie i poziomie oraz zamocować go na podstawach, fundamentach i sufitach przepływowych.
Do obsługi sprzętu upoważnione są osoby, które znają zasadę działania, urządzenie, zasady obsługi i konserwacji sprzętu, które przeszły odpowiednią odprawę i badania lekarskie.
Sprzęt musi być w dobrym stanie technicznym, a parametry jego pracy muszą być zgodne karty danych technicznych. Wirujące elementy maszyny (wały, wirniki itp.) muszą być wyważone zarówno jako zespół, jak i jako oddzielne części. Nie można dopuścić do nietypowego hałasu, stukania, wibracji i zakleszczania się ciał roboczych, a także przeciążania maszyn.
Zabrania się uruchamiania i obsługi maszyn z uszkodzonymi lub usuniętymi osłonami, urządzeniami blokującymi, zabezpieczającymi i sygnalizacyjnymi. W trakcie pracy maszyny zabrania się również zdejmowania i zakładania pasów napędowych, regulacji napięcia ciał trakcyjnych i roboczych (ostrza biczów, ślimaków, szczotek, wałków itp.), wykonywania drobnych napraw, smarowania, dokręcania śrub itp. Prace te można wykonywać tylko po całkowitym zatrzymaniu sprzętu.
Zgodnie z art. 209 Kodeks pracy Federacji Rosyjskiej (ustawodawstwo zebrane Federacji Rosyjskiej, 2002, nr 1, art. 3; 2006, nr 27, art. 2878; 2009, nr 30, art. 3732; 2011, nr 30, art. 4586; 2013, nr 52, art. 6986) i podpunkt 5.2.28 Rozporządzenia w sprawie Ministerstwa Pracy i Ochrony Socjalnej Federacji Rosyjskiej, zatwierdzonego dekretem rządu Federacji Rosyjskiej z dnia 19 czerwca 2012 r. Nr 610 (Ustawodawstwo zebrane Federacji Rosyjskiej, 2012, nr 26, art. 3528), zamawiam:
1. Zatwierdź Zasady ochrony pracy, konserwacji i naprawy urządzeń technologicznych zgodnie z załącznikiem.
2. Niniejsze rozporządzenie wchodzi w życie trzy miesiące po jego oficjalnej publikacji.
Załącznik
na zlecenie Ministerstwa Pracy
i ochrona socjalna Federacji Rosyjskiej
z dnia 23 czerwca 2016 r. nr 310n
Zasady ochrony pracy
podczas ustawiania, instalacji, konserwacji i naprawy urządzeń technologicznych
I. Postanowienia ogólne
1. Zasady ochrony pracy podczas umieszczania, instalacji, konserwacji i naprawy urządzeń technologicznych (zwane dalej Zasadami) są ustalane przez państwo wymogi regulacyjne ochrona pracy podczas głównych operacji technologicznych i prac związanych z umieszczaniem, instalacją, konserwacją i naprawą stacjonarnych maszyn, mechanizmów, urządzeń, instrumentów i innego sprzętu wykorzystywanego do produkcji wyrobów przemysłowych (zwanych dalej urządzeniami technologicznymi).
2. Wymagania Regulaminu obowiązują pracodawców – osoby prawne, niezależnie od ich formy organizacyjno-prawnej oraz osób fizycznych (z wyłączeniem pracodawców – osób fizycznych nie będących indywidualnymi przedsiębiorcami) przy organizowaniu i wykonywaniu prac związanych ze stażem, instalacją , konserwacja i naprawa urządzeń technologicznych.
3. Odpowiedzialność za realizację Regulaminu spoczywa na pracodawcy.
Na podstawie Przepisów i wymagań dokumentacji technicznej producenta urządzeń technologicznych pracodawca opracowuje instrukcje dotyczące ochrony pracy, które są zatwierdzone przez lokalny akt prawny pracodawcy, biorąc pod uwagę opinię odpowiedniego organu związkowego lub inny upoważniony przez pracowników wykonujących prace związane z rozmieszczeniem, instalacją, konserwacją i naprawą urządzeń technologicznych (zwani dalej pracownikami), organ przedstawicielski (jeśli istnieje).
4. W przypadku stosowania materiałów, urządzeń i sprzętu technologicznego, do wykonywania prac, wymagań bezpiecznego użytkowania i wykonywania których nie reguluje Regulamin, należy kierować się wymaganiami odpowiednich przepisów prawnych akty zawierające państwowe wymagania regulacyjne dotyczące ochrony pracy * (1) oraz wymagania dokumentacji technicznej (operacyjnej) ) producenta.
5. Pracodawca zapewnia:
2) szkolenie pracowników w zakresie ochrony pracy i sprawdzanie znajomości wymogów ochrony pracy;
3) kontrola przestrzegania przez pracowników wymagań instrukcji ochrony pracy.
6. Podczas wykonywania prac związanych z rozmieszczeniem, instalacją, konserwacją i naprawą urządzeń technologicznych (zwanych dalej pracami) pracownicy mogą być narażeni na działanie szkodliwych i (lub) niebezpiecznych czynników produkcyjnych, w tym:
1) poruszające się pojazdy, maszyny i mechanizmy podnoszące, ruchome materiały;
2) ruchome części wyposażenia technologicznego;
3) ostre krawędzie, zadziory i nierówności na powierzchni urządzeń technologicznych;
4) spadające przedmioty (elementy wyposażenia technologicznego);
5) podwyższona zawartość pyłów i gazów w powietrzu obszaru roboczego;
6) podwyższona lub obniżona temperatura powierzchni urządzeń technologicznych;
7) podwyższona lub obniżona temperatura powietrza w miejscu pracy;
8) podwyższony poziom hałasu na stanowisku pracy;
9) podwyższony poziom wibracji;
10) wysoka lub niska wilgotność powietrza;
11) zwiększona lub zmniejszona ruchliwość powietrza;
12) podwyższona wartość napięcia w obwód elektryczny, którego zamknięcie może nastąpić poprzez ciało pracownika;
13) podwyższony poziom elektryczności statycznej;
14) podwyższony poziom promieniowanie elektromagnetyczne;
15) zwiększone natężenie pola elektrycznego;
16) zwiększone natężenie pola magnetycznego;
17) brak lub niedostatek naturalnego światła;
18) niedostateczne oświetlenie miejsca pracy;
20) usytuowanie stanowisk pracy na znacznej wysokości w stosunku do powierzchni ziemi (podłogi);
21) chemiczne czynniki produkcji;
22) psychofizjologiczne czynniki produkcji.
7. Pracodawca, organizując wykonywanie prac związanych z narażeniem pracowników na szkodliwe i (lub) niebezpieczne czynniki produkcji, jest obowiązany podjąć działania w celu ich wyeliminowania lub ograniczenia do poziomów dopuszczalnego narażenia, ustalone wymagania odpowiednich regulacyjnych aktów prawnych.
Jeżeli ze względu na charakter i warunki procesu produkcyjnego niemożliwe jest wykluczenie lub obniżenie poziomów szkodliwych i (lub) niebezpiecznych czynników produkcji do poziomów dopuszczalnych oddziaływań, zabrania się wykonywania prac bez zapewnienia pracownikom odpowiednich środków i zbiorowy sprzęt ochronny.
8. Pracodawca ma prawo ustalić dodatkowe wymagania bezpieczeństwa przy wykonywaniu pracy, które poprawiają warunki pracy pracowników.
II. Wymagania BHP dotyczące organizacji pracy
9. Pracownicy, którzy zostali przeszkoleni w zakresie ochrony pracy i sprawdzili swoją znajomość wymagań ochrony pracy w określony sposób * (2), mogą wykonywać pracę.
Pracodawca organizując wykonywanie prac, dla których nakładane są dodatkowe (podwyższone) wymogi ochrony pracy, zapewnia sprawdzanie wiedzy pracowników na temat wymogów ochrony pracy nie rzadziej niż raz na dwanaście miesięcy, a także powtarzanie szkoleń z zakresu ochrony pracy, co najmniej raz na trzy miesiące. Lista zawodów, stanowisk pracowników i rodzajów pracy, które podlegają dodatkowym (podwyższonym) wymogom ochrony pracy, jest zatwierdzana przez lokalny akt prawny pracodawcy.
Pracodawca zapewnia, że pracownicy przechodzą obowiązkowe wstępne (po zatrudnieniu) i okresowe (w trakcie aktywność zawodowa) badania lekarskie we wskazany sposób*(3).
Na oddzielne prace ze szkodliwym i (lub) niebezpieczne warunki praca ogranicza wykorzystanie pracy kobiet. Wykazy prac o szkodliwych i (lub) niebezpiecznych warunkach pracy, w których korzystanie z pracy kobiet jest ograniczone, są zatwierdzane w określony sposób * (7).
Zabrania się wykorzystywania pracy osób poniżej osiemnastego roku życia przy pracach o szkodliwych i (lub) niebezpiecznych warunkach pracy. Wykazy zawodów, w których zabrania się korzystania z pracy osób poniżej osiemnastego roku życia, zatwierdza się zgodnie z ustaloną procedurą * (5).
10. Pracownikom należy zapewnić specjalną odzież, specjalne obuwie i inne środki; ochrona osobista(dalej - ŚOI) w określony sposób * (6).
Na zakończenie umowa o pracę pracodawca ma obowiązek zapewnić, aby pracownicy zostali poinformowani o przysługujących im ŚOI, a pracownicy są zobowiązani do prawidłowego stosowania wydanych im ŚOI w określony sposób.
11. Reżimy pracy i odpoczynku pracowników określają wewnętrzne przepisy pracy i inne lokalne przepisy pracodawcy zgodnie z przepisami prawa pracy.
12. Pracodawca musi być wyposażony zgodnie z ustalonymi standardami w zaplecze sanitarne, pomieszczenia do jedzenia, pomieszczenia opieki medycznej, pomieszczenia do odpoczynku w czas pracy i rozładunku psychologicznego, zorganizowano punkty pierwszej pomocy, wyposażone w apteczki * (7), zainstalowano aparaty (urządzenia) do zaopatrywania pracowników w gorących warsztatach i rejonach ze słoną wodą gazowaną.
13. Pracodawca zapewnia badanie, rejestrację, rejestrację i ewidencję wypadków, które miały miejsce z pracownikami w określony sposób * (8).
III. Wymagania dotyczące ochrony pracy na terenie organizacji, dla budynków produkcyjnych (konstrukcji), pomieszczeń produkcyjnych (zakładów produkcyjnych) i organizacji miejsc pracy
Wymagania dotyczące ochrony pracy na terytorium organizacji, dla budynków przemysłowych (konstrukcji) i obiektów przemysłowych (miejsca produkcyjne)
14. Pracodawca musi opracować schemat ruchu pojazdów i pieszych na terenie organizacji.
Schemat ruchu pojazdów i pieszych powinien być umieszczony przed wejściem i wejściem na terytorium organizacji.
15. Terytorium organizacji w ciemny czas dni powinny być oświetlone.
16. Na terenie organizacji w miejscach, w których znajdują się przemysły wybuchowe i pożarowe, których opary i gazy są cięższe od powietrza, zabrania się budowania kanałów, niewypełnionych rowów, które mogą służyć jako miejsce gromadzenia się oparów i gazy.
Dozwolone jest instalowanie dołów przykrytych wyjmowanymi kratami o głębokości nie większej niż 0,8 m oraz tac o głębokości nie większej niż 0,4 m do zbierania i odprowadzania wody deszczowej.
17. Okopy, komunikacja podziemna na terenie organizacji muszą być zamknięte lub ogrodzone. Na ogrodzeniach należy umieścić napisy i znaki ostrzegawcze, a w nocy oświetlenie sygnalizacyjne.
W miejscach przejść przez wykopy, doły, rowy należy zamontować mosty przejściowe o szerokości co najmniej 1 m, ogrodzone obustronnie balustradami o wysokości co najmniej 1,1 m, z solidnym poszyciem wzdłuż dna do wysokości 0,15 m oraz z dodatkową belką ogrodzeniową na wysokość 0,5 m od posadzki.
18. Studnie i zbiorniki technologiczne znajdujące się na terenie organizacji muszą być zamknięte. Tymczasowo otwarte studnie i zbiorniki technologiczne muszą mieć ogrodzenia o wysokości co najmniej 1,1 m.
19. Budynki produkcyjne (konstrukcje) i pomieszczenia produkcyjne (miejsca produkcji) muszą spełniać wymagania prawo federalne z dnia 30 grudnia 2009 nr 384-FZ” Przepisy techniczne w sprawie bezpieczeństwa budynków i budowli „* (9).
20. Wejścia i wyjścia, przejścia i podjazdy zarówno wewnątrz budynków przemysłowych (konstrukcji), jak i pomieszczeń przemysłowych (miejsca produkcyjne), a także na zewnątrz na przylegającym do nich terytorium, muszą być wolne i wyposażone w oświetlenie dla bezpiecznego przemieszczania się pracowników i przejazdu pojazdów .
Zabrania się blokowania przejść i podjazdów oraz wykorzystywania ich do umieszczania towarów.
21. Wyjścia zewnętrzne budynków (konstrukcji) przemysłowych muszą być wyposażone w wiatrołapy lub kurtyny powietrzno-termiczne.
22. Przejścia, schody, podesty i balustrady do nich muszą być utrzymywane w dobrym stanie.
Na czas remontu zamiast zdemontowanych balustrad należy zamontować tymczasowe ogrodzenie. Balustrady i posadzki, usunięte w trakcie naprawy, po jej zakończeniu należy montować na miejscu.
Przejścia, schody i posadzki peronów znajdujących się na wolnym powietrzu, in zimowy czas należy oczyścić ze śniegu i lodu oraz posypać środkami antypoślizgowymi.
23. W pomieszczeniach przemysłowych wysokość od podłogi do dna wystających konstrukcji podłogi (pokrywa) musi wynosić co najmniej 2,2 m, wysokość od podłogi do dna wystających części komunikacji i urządzeń w miejscach regularnego przejścia pracowników i na drogach ewakuacyjnych - co najmniej 2 m, aw miejscach nieregularnego przejścia pracowników - co najmniej 1,8 m.
24. Granice przejść transportowych wewnątrz pomieszczeń produkcyjnych (jeżeli jest to integralna część procesu produkcyjnego) muszą być oznaczone na posadzce liniami o szerokości co najmniej 50 mm, wykonanymi nieścieralną bielą lub żółty kolor, lub za pomocą metalowych kratek wpuszczanych lub w inny sposób zapewniający bezpieczeństwo linii granicznych podczas procesu produkcyjnego.
Linie graniczne nie powinny być prowadzone bliżej niż 0,5 m od urządzeń technologicznych i ścian zakładów produkcyjnych.
25. Szerokość przejść wewnątrz pomieszczeń produkcyjnych musi odpowiadać wymiarom pojazdów lub przewożonych towarów.
Odległość od granic jezdni do elementów konstrukcyjnych budynku i wyposażenia musi wynosić co najmniej 0,5 m, a podczas przemieszczania się pracowników co najmniej 0,8 m.
26. Tory wewnątrzzakładowe powinny być ułożone równo z posadzką.
27. Kanały, doły i inne wnęki w posadzce pomieszczeń przemysłowych należy przykryć mocnymi stropami (płytami), a otwarte wnęki i podesty wystające ponad 0,3 m ponad poziom posadzki należy zabezpieczyć balustradami o wysokości co najmniej 1,1 m .
28. Otwory w podłodze do przejścia pasów napędowych, przenośniki muszą mieć minimalne wymiary i być chronione deskami o wysokości co najmniej 0,2 m, niezależnie od obecności wspólnego ogrodzenia. W przypadkach, gdy ze względu na warunki procesu technologicznego nie można zamknąć kanałów, rynien i wykopów, zabezpiecza się je balustradą o wysokości min. 1,1 mz poszyciem wzdłuż dna na wysokość min. 0,15 m od dna piętro.
29. W zakładach produkcyjnych muszą znajdować się pojazdy podnoszące i transportowe (dźwigi, suwnice, wciągniki, wciągarki) do wykonywania prac związanych z naprawą urządzeń technologicznych.
Aby podnieść ładunek na wysokość większą niż 6 m, a także na długość toru startowego większą niż 18 m, konieczne jest użycie sprzętu dźwigu elektrycznego.
Do podnoszenia i przenoszenia urządzeń technologicznych o masie do 0,3 tony dopuszcza się stosowanie narzędzi i urządzeń olinowania (podnośniki, metalowe stojaki, rolki, łączniki, karabińczyki, łańcuchy, linki).
30. W pomieszczeniach przemysłowych z urządzeniami dźwigowymi należy wyznaczyć miejsca na miejsca instalacji. Wymiary miejsc montażowych powinny zapewniać przejścia o szerokości co najmniej 0,7 m wokół osprzętu żurawia zainstalowanego na miejscach montażowych w obszarze obsługi.
31. W pomieszczeniach przemysłowych, w których w wyniku warunków pracy gromadzą się płyny, posadzki muszą być wykonane z materiałów wodoodpornych, nieprzepuszczalnych dla płynów oraz posiadać niezbędne spadki i kanały odwadniające. Kanały w posadzkach do odprowadzania cieczy lub układania rurociągów są blokowane pokrywami stałymi lub kratowymi na tym samym poziomie co podłoga.
32. Sztuczne oświetlenie pomieszczeń przemysłowych powinno składać się z dwóch systemów: ogólnego (jednolitego lub zlokalizowanego) i kombinowanego (do oświetlenie ogólne lokalny jest dodany). Zabronione jest używanie tylko lokalnego oświetlenia.
33. Aby otworzyć, zamontować w wymaganej pozycji i zamknąć skrzydła osłon okien i latarni lub innych urządzeń otwierających w pomieszczeniach przemysłowych, należy zapewnić urządzenia, które można łatwo obsługiwać z podłogi lub z podestów roboczych.
Wymagania ochrony pracy dotyczące organizacji miejsc pracy
34. Przy organizacji miejsc pracy ochronę pracowników zapewniają:
1) ochrona pracowników przed narażeniem na szkodliwe i (lub) niebezpieczne czynniki produkcji;
2) racjonalne rozmieszczenie urządzeń technologicznych w pomieszczeniach produkcyjnych i poza nimi: zapewnienie bezpiecznej odległości między urządzeniami, urządzeniami i ścianami, kolumnami, bezpieczną szerokość przejść i podjazdów;
3) wygodna i bezpieczna obsługa materiałów, półfabrykatów, półproduktów;
4) regularna konserwacja i naprawa
sprzęt technologiczny, narzędzia i osprzęt;
5) ochronę pracowników przed niekorzystnymi czynnikami meteorologicznymi.
35. Miejsca pracy powinny być zlokalizowane:
1) w maksymalnej odległości od urządzeń technologicznych generujących szkodliwe i (lub) niebezpieczne czynniki produkcji;
2) poza linią ruchu towarów przewożonych za pomocą urządzeń dźwigowych.
Stanowiska pracy znajdujące się na świeżym powietrzu na zewnątrz pomieszczeń produkcyjnych muszą być wyposażone w zadaszenia lub wiaty chroniące pracowników przed opadami atmosferycznymi.
36. Rozplanowanie stanowiska pracy powinno zapewniać swobodne przejście i dostęp pracowników do pulpitów i sterowań urządzeń technologicznych, wygodę i bezpieczeństwo wykonywania czynności produkcyjnych, a także możliwość szybkiej ewakuacji pracowników w przypadku zagrożenia .
37. Sprzęt technologiczny obsługiwany przez kilku pracowników lub mający znaczną długość musi mieć urządzenie startowe tylko w jednym miejscu na panelu sterowania. Urządzenia do zatrzymywania sprzętu powinny znajdować się na wszystkich stanowiskach pracy.
38. Pulpity sterownicze urządzeń i oprzyrządowania technologicznego powinny znajdować się w łatwo dostępnym miejscu.
39. Do konserwacji okuć i mechanizmów urządzeń technologicznych, które nie posiadają zdalne sterowanie, a także urządzenia oprzyrządowania i sterowania umieszczone nad podłogą na wysokości powyżej 1,8 m, stacjonarne platformy metalowe z balustradami o wysokości nie mniejszej niż 0,9 m z solidnym poszyciem wzdłuż dna o wysokości nie mniejszej niż 0,1 m.
Szerokość swobodnego przejścia peronów powinna wynosić co najmniej 0,8 m.
Schody na perony muszą być wyposażone w poręcze i mieć kąt nachylenia:
eksploatowane na stałe - nie więcej niż 45 °;
używane okresowo - nie więcej niż 60 °.
Drabiny i podesty muszą być wykonane z blachy falistej.
Zabronione jest stosowanie gładkich podestów i stopni schodów oraz ich wykonanie ze stali prętowej (okrągłej).
40. Podesty przeznaczone do konserwacji urządzeń technologicznych muszą mieć wysokość od posadzki do elementów konstrukcyjnych obiektu produkcyjnego co najmniej 2,0 m. W galeriach, tunelach i wiaduktach podana wysokość może być zmniejszona do 1,8 m.
Wymagania niniejszego paragrafu dotyczą również miejsc przeznaczonych do przejścia przez urządzenia lub łączność.
41. Stanowiska pracy, w zależności od rodzaju pracy, wyposażone są w stoły warsztatowe, stojaki, stoły, szafki, szafki narzędziowe umożliwiające wygodne rozmieszczenie materiałów, wyposażenia, przedmiotów obrabianych, wyrobów gotowych, przechowywanie narzędzi i osprzętu oraz bezpieczne wykonywanie pracy.
Lokalizacja stołów warsztatowych, stojaków, stołów, szafek, szafek narzędziowych w miejscu pracy nie powinna utrudniać działań pracowników i uniemożliwiać przemieszczania się pracowników podczas obsługi, konserwacji i naprawy urządzeń technologicznych.
42. Minimalna szerokość pojedynczych przejść na stanowiska pracy i na stanowiska pracy z uwzględnieniem wystających części urządzeń technologicznych musi wynosić co najmniej 0,6 m.
Wszystkie ruchome, obracające się i wystające części wyposażenia procesowego i mechanizmów pomocniczych muszą być bezpiecznie osłonięte lub umieszczone tak, aby wykluczyć możliwość zranienia pracowników.
43. Przy wykonywaniu pracy w pozycji „siedzącej” na każdym stanowisku pracy powinny znajdować się wygodne krzesła i taborety.
Podczas wykonywania pracy w pozycji „stojącej” stanowiska pracy muszą być wyposażone w krzesła, aby pracownicy mogli odpocząć podczas przerw.
44. Materiały i półfabrykaty należy dostarczać do obróbki w specjalnym pojemniku i umieszczać na stanowisku pracy oddzielnie od narzędzia.
Uwolnione pojemniki i materiały opakowaniowe należy niezwłocznie usunąć z miejsc pracy do specjalnie do tego wyznaczonych magazynów.
Zabrania się zaśmiecania miejsc pracy, a także przejść i podjazdów materiałami, sprzętem, wykrojami, wyrobami gotowymi, odpadami produkcyjnymi i opakowaniami.
45. Materiały, wyposażenie, półfabrykaty, wyroby gotowe, ułożone na stojakach lub na stołach, nie powinny wystawać poza swoje wymiary. W przypadku małych części i półfabrykatów należy zapewnić specjalne pojemniki.
Dla wygody i bezpiecznego użytkowania mechanizmów wyciągowych w procesie produkcyjnym, przy układaniu materiałów, długich elementów i produktów należy stosować uszczelki.
46. Przy organizacji miejsc pracy i wykonywaniu pracy przy użyciu narzędzi i osprzętu konieczne jest przestrzeganie wymagań Przepisów Ochrony Pracy podczas pracy z narzędziami i osprzętem * (10).
47. Aby poruszać się w miejscu pracy ciężkie materiały, sprzęt, półfabrykaty i gotowe produkty powinny być wyposażone w urządzenia i mechanizmy podnoszące.
48. Organizacja miejsc pracy powinna zapewniać możliwość ich codziennego sprzątania.
Czyszczenie miejsc pracy z kurzu, trocin, wiórów powinno odbywać się za pomocą szczotek lub przy pomocy instalacji próżniowych (odsysających).
Zabronione jest stosowanie sprężonego powietrza do czyszczenia stanowisk pracy, do przedmuchiwania części (produktów), urządzeń technologicznych i odzieży.
49. Miejsca pracy związane z rozmieszczeniem, instalacją, konserwacją i naprawą urządzeń technologicznych muszą być wyposażone w sprzęt i sprzęt przeciwpożarowy do ochrony obiektów produkcyjnych zgodnie z wymogami przepisów przeciwpożarowych Federacji Rosyjskiej * (11).
IV. Wymagania ochrony pracy przy wykonywaniu pracy (wdrażanie procesów produkcyjnych)
Ogólne wymagania
50. Prace muszą być wykonywane zgodnie z wymogami aktów prawnych zawierających przepisy państwowe dotyczące ochrony pracy oraz dokumentację techniczną (operacyjną) producenta.
51. Przy wykonywaniu prac przy użyciu maszyn wyciągowych należy przestrzegać wymagań Przepisów Bezpieczeństwa dla niebezpiecznych obiektów produkcyjnych wykorzystujących konstrukcje dźwigowe * (12).
W przypadkach, gdy praca fizyczna jest wykonywana przez kobiety i pracowników poniżej osiemnastego roku życia, należy przestrzegać ustalonych norm dotyczących maksymalnych dopuszczalnych obciążeń podczas ręcznego podnoszenia i przenoszenia ciężkich ładunków * (13).
52. Prace związane z rozmieszczeniem, instalacją, konserwacją i naprawą urządzeń procesowych wytwarzających ciepło i zużywających ciepło muszą być wykonywane zgodnie z wymaganiami określonymi przez upoważnione federalne organy wykonawcze * (14).
53. Podczas wykonywania spawania elektrycznego i spawania gazowego należy przestrzegać wymagań Zasad ochrony pracy podczas wykonywania spawania elektrycznego i spawania gazowego * (15).
54. Prace przy częściach pod napięciem urządzeń technologicznych, a także prace w istniejących instalacjach elektrycznych muszą być wykonywane zgodnie z wymaganiami określonymi przez upoważnione federalne organy wykonawcze * (16).
55. Przy wykonywaniu prac związanych z rozmieszczeniem, instalacją, konserwacją i naprawą urządzeń technologicznych stosowanych w obróbce drewna należy spełnić wymagania Przepisów ochrony pracy przy wyrębie, przemyśle drzewnym i podczas prac leśnych * (17).
56. Prace wykonywane przy użyciu rusztowań, rusztowań, rusztowań ruchomych, drabin i drabin muszą być wykonywane zgodnie z wymogami Przepisów ochrony pracy podczas pracy na wysokości * (18).
57. Podczas wykonywania prac na wysokości używane narzędzia i urządzenia muszą być umieszczone w przenośnych skrzynkach narzędziowych lub torbach.
Zjazd materiałów i wszelkich przedmiotów musi odbywać się po specjalnie ułożonych rynnach, zjazdach lub za pomocą liny.
Zabrania się zrzucania materiałów i jakichkolwiek przedmiotów.
58. Prace o podwyższonym niebezpieczeństwie w procesie umieszczania, instalacji, konserwacji i naprawy urządzeń technologicznych muszą być wykonywane zgodnie z zezwoleniem na pracę przy wykonywaniu prac o podwyższonym niebezpieczeństwie (zwanym dalej zezwoleniem na pracę), wydanym przez urzędnicy upoważnieni przez pracodawcę zgodnie z zalecanym wzorem, przewidzianym w Załączniku nr 1 do Regulaminu.
Zezwolenie na pracę określa treść, miejsce, czas i warunki wykonywania prac o podwyższonym niebezpieczeństwie, niezbędne środki bezpieczeństwa, skład zespołu oraz pracowników odpowiedzialnych za organizację i bezpieczną produkcję pracy.
Procedurę wykonywania pracy o podwyższonym niebezpieczeństwie, wydawanie zezwolenia na pracę oraz obowiązki urzędników upoważnionych przez pracodawcę odpowiedzialnego za organizację i bezpieczne wykonywanie pracy określa lokalny akt prawny pracodawcy.
59. Do prac o podwyższonym zagrożeniu, na których wykonanie wydawane jest zezwolenie na pracę zalicza się:
1) roboty ziemne w rejonie podziemnych sieci energetycznych, gazociągów, ropociągów oraz innych podziemnych mediów i obiektów;
2) prace związane z demontażem (zawaleniem) budynków i budowli, a także wzmacnianiem i odbudową awaryjnych części i elementów budynków i budowli;
3) montaż i demontaż urządzeń technologicznych;
4) produkcja montażu i prace naprawcze w pobliżu otwartych ruchomych części sprzętu operacyjnego, a także w pobliżu przewodów elektrycznych pod napięciem;
5) prace instalacyjno-remontowe wykonywane w warunkach istniejących zakładów produkcyjnych jednego oddziału organizacji siłami innego oddziału (praca łączona);
6) prace instalacyjno-remontowe na wysokości powyżej 1,8 m od poziomu posadzki bez użycia rusztowań inwentarzowych i rusztowań;
7) naprawa rurociągów parowych oraz gorąca woda wyposażenie technologiczne;
8) pracy w pomieszczeniach zamkniętych, w pomieszczeniach zamkniętych;
9) spawanie elektryczne i spawanie gazowe w zbiornikach zamkniętych, w zbiornikach, w dołach, w studniach, w tunelach;
10) prace przy badaniu zbiorników ciśnieniowych;
11) czyszczenie i naprawa kanałów powietrznych, filtrów i wentylatorów układ wydechowy wentylacja pomieszczeń, w których przechowywane są silne substancje chemiczne i inne niebezpieczne substancje;
12) prace przy konserwacji i naprawie instalacji elektrycznych na kablowych lub napowietrznych liniach elektroenergetycznych, prace instalacyjne dźwigami w pobliżu napowietrznych linii elektroenergetycznych;
13) wykonywanie prac niebezpiecznych gazowo;
14) wykonywanie prac gorących w pomieszczeniach zagrożonych pożarem i wybuchem;
15) naprawa maszyn do podnoszenia ładunków (z wyjątkiem kołowych i gąsienicowych z własnym napędem), wózków suwnicowych, torów jezdnych suwnic;
16) naprawa mechanizmów obrotowych;
17) pracy w miejscach niebezpiecznych ze względu na zanieczyszczenie gazem, niebezpieczeństwo wybuchu, porażenie prądem oraz o ograniczonym dostępie do widzeń;
18) prace termoizolacyjne, nakładanie powłok antykorozyjnych;
19) wykonywanie prac remontowych instalacji ciepłowniczych i energochłonnych, sieci ciepłowniczych i innych urządzeń ciepłowniczych.
60. Wykaz prac wykonywanych na podstawie zezwolenia na pracę jest zatwierdzany przez pracodawcę i może być przez niego uzupełniany.
61. Wydane i wydane zezwolenia na pracę są uwzględniane w czasopiśmie, w którym zaleca się odzwierciedlenie następujących informacji:
1) nazwę pododdziału;
2) numer zezwolenia na pracę;
3) datę wydania zezwolenia na pracę;
4) krótki opis prac nad zezwoleniem;
5) okres, na jaki zostało wydane zezwolenie na pracę;
6) nazwiska i inicjały urzędników, którzy wydali i otrzymali zezwolenie na pracę, poświadczone ich podpisami z datą podpisania;
7) nazwisko i inicjały urzędnika, który otrzymał zezwolenie na pracę zamknięte do wykonywania pracy, poświadczone jego podpisem z datą otrzymania.
62. Prace o tej samej nazwie o podwyższonym niebezpieczeństwie, wykonywane na stałe i wykonywane przez stały personel w podobnych warunkach, mogą być wykonywane bez wydawania pozwolenia na pracę zgodnie z instrukcjami ochrony pracy zatwierdzonymi dla każdego rodzaju pracy ze zwiększonym niebezpieczeństwem.
63. W przypadku pracy w instalacjach elektrycznych zezwolenie na pracę jest sporządzane w formie określonej w Zasadach ochrony pracy podczas eksploatacji instalacji elektrycznych * (19).
64. W zależności od cech organizacji i charakteru pracy wykonywanej ze zwiększonym niebezpieczeństwem, pozwolenie na pracę może być wydane zgodnie z federalnymi normami i zasadami w tej dziedzinie bezpieczeństwo przemysłowe„Regulamin stosowania zezwoleń na pracę przy wykonywaniu pracy” podwyższone niebezpieczeństwo w niebezpiecznych zakładach produkcyjnych przemysłu wydobywczego i hutniczego „*(20).
65. Wykonywanie prac spawalniczych elektrycznych i gazowych poza stałymi stanowiskami spawalniczymi w miejscach tymczasowych (z wyjątkiem place budowy) pracodawca lub osoba odpowiedzialna za bezpieczeństwo przeciwpożarowe wydaje zezwolenie na pracę na wykonywanie prac gorących w formie określonej w przepisach reżimu przeciwpożarowego w Federacji Rosyjskiej * (21).
66. Gdy praca jest wykonywana przez organizacje strony trzeciej (wykonawcy), odpowiedzialni przedstawiciele klienta i wykonawcy muszą wydać na cały okres wykonywania pracy akt dopuszczenia do wykonywania pracy na terytorium organizacji zgodnie zgodnie z zalecanym wzorem określonym w Załączniku nr 2 do Regulaminu, opracować i wdrożyć środki organizacyjne i techniczne mające na celu zapewnienie bezpieczeństwa tych prac, a także bezpiecznej eksploatacji urządzeń technologicznych.
67. Za zgodność z wymaganiami Regulaminu i dokumentacji technicznej (operacyjnej) producenta odpowiada kierownik organizacji (wykonawcy) wykonującej pracę.
Wymagania ochrony pracy dotyczące rozmieszczenia urządzeń technologicznych i zapewnienia zbiorowej ochrony pracowników
68. Podczas projektowania procesy produkcji i podejmując decyzję o umieszczeniu określonego wyposażenia technologicznego dla każdego zakładu produkcyjnego, pracodawca musi zidentyfikować i uwzględnić szkodliwe i (lub) niebezpieczne czynniki produkcyjne, które mogą być generowane przez urządzenia procesowe podczas procesów produkcyjnych oraz w sytuacjach awaryjnych.
69. Przy rozmieszczaniu urządzeń technologicznych należy zapewnić zgrupowanie urządzeń o podobnych wytwarzanych szkodliwych i (lub) niebezpiecznych czynnikach produkcyjnych.
Urządzenia technologiczne, w trakcie których eksploatacji wydzielają się substancje szkodliwe, palne i wybuchowe (pyły, gazy, opary), należy instalować w izolowanych pomieszczeniach wyposażonych w ogólną wymianę nawiewno-wywiewną oraz lokalną wentylację wywiewną.
Jeżeli zakłady produkcyjne o różnych warunkach sanitarno-higienicznych znajdują się w tym samym pomieszczeniu produkcyjnym, należy podjąć środki zapobiegające rozprzestrzenianiu się szkodliwych i (lub) niebezpiecznych czynników produkcyjnych w całym pomieszczeniu produkcyjnym.
70. Sprzęt technologiczny musi być zlokalizowany w pomieszczeniach produkcyjnych zgodnie z ogólny kierunek główny przepływ ładunków. Umieszczenie urządzeń technologicznych powinno zapewniać bezpieczeństwo i wygodę jego instalacji (demontażu), konserwacji i naprawy.
71. Niedopuszczalne jest umieszczanie urządzeń technologicznych nad i pod budynkami pomocniczymi i socjalnymi oraz pomieszczeniami.
72. Stacjonarne urządzenia technologiczne muszą być instalowane na solidnych fundamentach lub fundamentach.
Wykonując fundamenty, umieszczając na nich sprzęt, przygotowując śruby fundamentowe, należy kierować się dokumentacją projektową, a także wymaganiami dokumentacji technicznej (eksploatacyjnej) producenta.
Dopuszcza się stosowanie bezfundamentowego montażu sprzętu na podporach tłumiących drgania.
73. Rozmieszczenie urządzeń technologicznych musi odbywać się zgodnie z planem technologicznym zatwierdzonym przez pracodawcę lub innego upoważnionego przez pracodawcę urzędnika, z zastrzeżeniem norm projektowania technologicznego.
74. Układ technologiczny wyświetla:
1) kontury i wymiary zakładów produkcyjnych, elementów budowlanych (kolumny, ścianki działowe, otwory drzwiowe i okienne, bramy, kanały, włazy, studnie, drabiny);
2) ogólne kontury i wymiary wyposażenia technologicznego znajdującego się na powierzchniach produkcyjnych, podestów do jego konserwacji (stoły, szafy narzędziowe, regały), urządzeń dźwigowych i transportowych;
3) miejsca do przechowywania materiałów, wykrojów, sprzętu, produkt końcowy i odpady produkcyjne;
4) kontury i wymiary przejść i podjazdów.
75. Ewentualne przearanżowanie istniejącego wyposażenia technologicznego powinno być uwidocznione na planach technologicznych.
76. Odległości między urządzeniami technologicznymi, między urządzeniami a ścianami, kolumnami pomieszczeń przemysłowych powinny być ustalane w zależności od specyficznych warunków procesu produkcyjnego i powinny być:
1) nie mniej niż 0,6 m - dla małego sprzętu (o wymiarach rzutu do 1,5 x 1,0 m);
2) nie mniej niż 0,7 m - dla sprzętu średniej wielkości (o wymiarach planu do 4,0 x 3,5 m);
3) dla dużych urządzeń (o wymiarach rzutu do 8,0 x 6,0 m): od ścian - co najmniej 1,0 m, od słupów - co najmniej 0,9 m;
4) dla pieców technologicznych: od ścian - nie mniej niż 1,2 m, od kolumn - nie mniej niż 1,0 m.
77. Podczas instalowania urządzeń technologicznych na fundacja indywidualna odległości od urządzeń do ścian i kolumn należy uwzględnić konfigurację sąsiednich fundamentów.
78. Podczas serwisowania sprzętu z konstrukcjami podnoszących (suwnice) jego umieszczenie (odległość od ścian i kolumn) należy przeprowadzić z uwzględnieniem przepisu bezpieczna konserwacja konstrukcje podnoszące.
79. Odległość między sterowaniem sąsiedniego sprzętu technologicznego, którym steruje jeden operator, musi wykluczać możliwość błędnego włączenia sterowania sąsiedniego sprzętu.
80. Szerokość głównych naw wzdłuż frontu obsługi oraz między rzędami urządzeń technologicznych w obecności stałych prac powinna wynosić co najmniej 1,5m.
Główne przejścia wzdłuż frontu obsługowego central muszą mieć co najmniej 2,0 m szerokości.
81. Podczas konserwacji wielu maszyn, urządzenia technologiczne powinny być rozmieszczane z uwzględnieniem maksymalnego możliwego zmniejszenia odległości między stanowiskami pracy.
82. Przy rozmieszczaniu urządzeń technologicznych należy uwzględnić szerokość przejazdów, gabaryty używanych pojazdów lub przewożonych towarów.
83. Umieszczenie urządzeń technologicznych w pomieszczeniach przemysłowych powinno zapewniać możliwość bezpiecznej ewakuacji pracowników w sytuacjach awaryjnych.
84. W celu ochrony pracowników przed narażeniem na szkodliwe i (lub) niebezpieczne czynniki produkcyjne, oprócz ŚOI, należy stosować środki ochrony zbiorowej do ochrony każdego pracownika (grupy pracowników), który znajduje się (znajduje się) w obszarze pracy.
Środki ochrony zbiorowej obejmują środki, które są konstrukcyjnie lub funkcjonalnie związane z procesem produkcyjnym lub urządzeniami technologicznymi.
85. Zbiorowy sprzęt ochronny zapewnia ochronę pracownikom:
1) od wpływu czynników mechanicznych (urządzenia zabezpieczające, zabezpieczające i hamujące; urządzenia zdalnego sterowania, automatycznego sterowania i sygnalizacji);
2) przed porażeniem prądem (urządzenia ochronne; urządzenia automatyki i sygnalizacji; urządzenia i powłoki izolacyjne; urządzenia) uziemienie ochronne i zerowanie; urządzenia automatyczne wyłączanie; urządzenia do wyrównania potencjałów i redukcji napięcia; urządzenia do zdalnego sterowania; urządzenia bezpieczeństwa; piorunochrony i odgromniki);
3) przed upadkiem z wysokości (ogrodzenia, siatki ochronne);
4) od podwyższonego poziomu hałasu (wygłuszenia, urządzenia dźwiękochłonne; tłumiki hałasu; piloty, automatyka i urządzenia sygnalizacyjne);
5) od podwyższonego poziomu wibracji (urządzenia ochronne; urządzenia izolujące wibracje, tłumiące i pochłaniające wibracje; urządzenia zdalnego sterowania do automatycznego sterowania i sygnalizacji);
6) od podwyższonego poziomu elektryczności statycznej (urządzenia uziemiające, ekranujące, nawilżające; neutralizatory, substancje antyelektrostatyczne);
7) od niskiego lub podwyższonych temperaturach powierzchnie urządzeń, materiałów i półfabrykatów (urządzenia ochronne, termoizolacyjne i ekranujące; urządzenia zdalnego sterowania, automatycznego sterowania i sygnalizacji);
8) od wysokich lub niskich temperatur powietrza i wahań temperatury (urządzenia ochronne i termoizolacyjne; urządzenia do ogrzewania i chłodzenia; urządzenia do zdalnego sterowania, automatycznego sterowania i sygnalizacji);
9) od podwyższonego poziomu ultradźwięków (urządzenia ochronne, dźwiękoszczelne i dźwiękochłonne; urządzenia do zdalnego sterowania, automatycznego sterowania i sygnalizacji);
10) przed podwyższonym poziomem promieniowania jonizującego (urządzenia ochronne, uszczelnienia i powłoki ochronne; urządzenia do wychwytywania i oczyszczania powietrza i cieczy; urządzenia do dekontaminacji; automatyczne urządzenia sterujące; urządzenia do zdalnego sterowania; środki ochrony podczas transportu i czasowego przechowywania substancji promieniotwórczych; pojemniki na odpady promieniotwórcze) ;
11) przed podwyższonym poziomem promieniowania podczerwonego (urządzenia ochronne, uszczelniające, termoizolacyjne i wentylacyjne; urządzenia zdalnego sterowania, automatycznego sterowania i sygnalizacji);
12) przed podwyższonym poziomem promieniowania elektromagnetycznego (urządzenia ochronne, uszczelnienia i powłoki ochronne; urządzenia do zdalnego sterowania, automatycznego sterowania i sygnalizacji);
13) od zwiększonego natężenia pól elektromagnetycznych (urządzenia ochronne, powłoki izolacyjne i ochronne; ochronne urządzenia uziemiające);
14) z poziomu podwyższonego promieniowanie laserowe(urządzenia ochronne i zabezpieczające; urządzenia do zdalnego sterowania, automatycznego sterowania i sygnalizacji);
15) od uderzenia czynniki chemiczne(urządzenia ochronne, uszczelniające; urządzenia do wentylacji i oczyszczania powietrza, do usuwania substancji toksycznych; urządzenia do zdalnego sterowania, automatycznego sterowania i sygnalizacji);
16) przed wpływem czynników biologicznych (urządzenia ochronne i uszczelniające; sprzęt i preparaty do dezynfekcji, dezynsekcji, sterylizacji, deratyzacji; urządzenia do wentylacji i oczyszczania powietrza; urządzenia do zdalnego sterowania, automatycznego sterowania i sygnalizacji).
86. Montaż (zastosowanie) środków zbiorowej ochrony pracowników wykonuje pracodawca w zależności od określonych szkodliwych i (lub) niebezpiecznych czynników produkcji na podstawie decyzji projektowych przyjętych zgodnie z przepisami akty prawne oraz dokumentacja techniczna (eksploatacyjna) producenta.
87. Zbiorowy sprzęt ochronny obejmuje również kolory sygnałowe, znaki bezpieczeństwa i oznaczenia sygnałowe zgodnie z GOST R 12.4.026-2001 „SSBT. Kolory sygnałowe, znaki bezpieczeństwa i oznaczenia sygnałowe „* (22) (opublikowane w IUS „Normy krajowe”, nr 10, 2005).
88. Znaki bezpieczeństwa muszą być wyraźnie widoczne i rozpoznawalne, nie mogą odwracać uwagi pracowników i nie zakłócać wykonywania operacji produkcyjnych.
Barwy sygnalizacyjne służą do oznaczania powierzchni, konstrukcji, osprzętu, zespołów i elementów urządzeń technologicznych stanowiących źródło zagrożenia dla pracowników, do oznaczania urządzeń ochronnych, ogrodzeń i blokad, a także do znaków bezpieczeństwa, oznaczeń sygnalizacyjnych, oznakowania dróg ewakuacyjnych i innych wizualne środki zapewnienia bezpieczeństwa pracownicy.
Znakowanie sygnałowe wykonywane jest na powierzchni konstrukcji budowlanych, elementach budynków, konstrukcji, pojazdów, urządzeń i jest stosowane w miejscach, w których występują zagrożenia i przeszkody.
Wymagania ochrony pracy podczas montażu urządzeń technologicznych
89. Przed rozpoczęciem prac przy instalacji urządzeń technologicznych należy określić miejsca przejazdu pojazdów, ruch sprzętu instalacyjnego i przejście pracowników, należy ustalić granice stref niebezpiecznych i niezbędne ogrodzenia, znaki bezpieczeństwa i umieszczone znaki ostrzegawcze.
W nocy podjazdy, chodniki i miejsca pracy w obszarze prac instalacyjnych muszą być oświetlone.
90. Otwory montażowe dla zamontowanych urządzeń technologicznych, kanały, wykopy, rowy, studnie fundamentowe muszą być zamknięte (zakryte) wymiennymi drewniane tarcze. W razie potrzeby należy zainstalować balustrady lub barierki.
91. W celu zabezpieczenia pracowników przed upadkiem, otwory montażowe w piwnicach technologicznych i głębokie doły w fundamentach muszą być ogrodzone barierami ochronnymi inwentaryzacyjnymi lub pokryte solidną posadzką.
92. Zespoły i części wyposażenia technologicznego podczas instalacji muszą być bezpiecznie zamocowane za pomocą odpowiednich uchwytów, zacisków, przekładek.
Jednostki i części tymczasowo umieszczone w obszarze instalacji muszą być przechowywane na stojakach o wysokości co najmniej 0,1 m lub na specjalnych stojakach.
93. Montaż ciężkiego sprzętu technologicznego w pozycji projektowej za pomocą jednego lub dwóch żurawi musi odbywać się pod bezpośrednim nadzorem kierownika instalacji.
94. Zabrania się wykonywania jakichkolwiek prac na (lub pod) sprzęcie technologicznym, jeśli znajduje się on w pozycji podniesionej i jest podparty przez wciągarki, podnośniki i inne mechanizmy podnoszące.
95. Podczas wykonywania operacji montażu i montażu na dużych wysokościach te części wyposażenia technologicznego, które będą montowane na wysokości, muszą zostać oczyszczone z brudu, śniegu lub lodu oraz ciał obcych przed podniesieniem. Połączenia montażowe i elementy stykowe należy oczyścić z rdzy, olejów, zadziorów.
Systemy mocowania poszczególnych podzespołów i części muszą być sprawdzone, aby zapobiec upadkowi podzespołów i części.
96. Jeżeli instalacja urządzeń technologicznych odbywa się na terenie działającej jednostki produkcyjnej, kierownik prac instalacyjnych musi opracować i skoordynować z kierownictwem jednostki produkcyjnej środki w celu bezpiecznego wykonywania prac instalacyjnych.
97. Montaż urządzeń technologicznych w jednostkach produkcyjnych, w których istnieje możliwość uwolnienia gazów wybuchowych, należy wykonywać przy użyciu narzędzia wykonanego z metali kolorowych lub pokrytego miedzią. Podczas instalowania urządzeń technologicznych w takich warunkach zabrania się:
1) używać otwartego ognia do podgrzewania różnych elementów i części w zimnych porach roku (dopuszcza się podgrzewanie elementów i części w zimnych porach roku tylko ciepłą wodą lub parą);
2) używać narzędzi, mechanizmów i osprzętu mogącego powodować iskrzenie, a także rzucać narzędziami, częściami metalowymi i innymi przedmiotami wytwarzającymi iskry na powierzchnię zamontowanego urządzenia technologicznego;
3) po zakończeniu pracy pozostawić na miejscu pracy zaolejone szmaty i inne środki czyszczące (należy je wyczyścić w metalowej skrzynce zainstalowanej w specjalnie wyznaczonym miejscu);
4) używać specjalnych butów z metalowymi wyściółkami iskrzącymi, wyłożonymi metalowymi podkowami lub metalowymi gwoździami.
98. Zabrania się używania naoliwionych szmat i uszczelek podczas wykonywania instalacji instalacji tlenowych. Narzędzie stosowane przy montażu instalacji tlenowych musi być dokładnie odtłuszczone.
99. Na wibroizolatorach lub podporach tłumiących drgania należy montować urządzenia technologiczne będące źródłem podwyższonych drgań osobny pokój, na podkładach tłumiących drgania (podkładki wibroizolacyjne) lub na oddzielnych masywnych fundamentach odizolowanych od sąsiednich konstrukcji budowlanych.
100. Przy montażu urządzeń technologicznych będących źródłem zwiększonego poziomu hałasu należy przewidzieć montaż tłumików na kanałach powietrznych i komorach wlotowych powietrza, rurę ssącą sprężarki, izolację rur ssących i kanałów powietrznych oraz miękkie wkładki i miękkie uszczelki na kanałach powietrznych.
Najbardziej hałaśliwe urządzenia (sprężarki, dmuchawy, pompy, wentylatory) powinny znajdować się w odizolowanych pomieszczeniach.
101. Wyposażenie pomocnicze sprężarek gazu i pomp próżniowych musi być zainstalowane nie niżej niż znak zerowy. Sprężarki gazu muszą być ustawione w jednym rzędzie.
Usytuowanie kompresorów powinno zapewniać swobodny dostęp do czyszczenia i wymiany rur chłodnic końcowych i pośrednich.
102. Pompy muszą być zainstalowane w taki sposób, aby zapewnić minimalną długość przewodów ssących.
Usytuowanie pomp powinno zapewniać możliwość zbierania i spuszczania płynu z dławnic podczas pracy, jak również podczas napraw i płukania pomp.
W przypadkach, w których uszczelnienia dławnic są chłodzone wodą, należy zapewnić odprowadzenie wody ze wszystkich typów urządzeń technologicznych.
Orurowanie pomp podczas ich montażu powinno być wykonane w taki sposób, aby zapewnić swobodny dostęp do pakowania dławnic i prowadzenia prac naprawczych.
103. Pompy do pompowania cieczy palnych i palnych podczas obsługi strumienia produkcyjnego mogą znajdować się we wspólnym pomieszczeniu produkcyjnym, a przy pompowaniu cieczy z magazynu do hali produkcyjnej lub do wysyłki z magazynu - w osobnych, wydzielonych pomieszczeniach.
104. Rurociągi przylegające do urządzeń technologicznych nie powinny być sztywno przymocowane do konstrukcji budowlanych lub powinny być wyposażone w odpowiednie urządzenia kompensacyjne.
Przy montażu urządzeń technologicznych rurociągi technologiczne przechodzące przez ściany i stropy należy prowadzić w tulejach stalowych z rur, których średnica wewnętrzna jest o 10–20 mm większa od średnicy zewnętrznej rurociągu (uwzględniając jego izolację termiczną).
Szczelinę pomiędzy rurociągiem a tuleją na obu końcach należy wypełnić niepalnym materiałem, który umożliwi ruch rurociągu wzdłuż jego osi podłużnej.
105. Konstrukcje wsporcze do mocowania kanałów powietrznych instalacji wentylacyjnych muszą być niezawodne, wykonane z materiałów niepalnych, nie powodujące i nie przenoszące drgań.
Ssaki miejscowe muszą być przymocowane do niewibrujących lub najmniej drgających elementów wyposażenia technologicznego.
106. Sprzęt technologiczny obsługiwany za pomocą mechanizmów podnoszących powinien być zainstalowany w strefie najazdu haka mechanizmu. Na tym samym obszarze należy zapewnić miejsca do montażu transportowanych części sprzętu.
107. Podczas instalowania stacjonarnych przenośników w budynkach produkcyjnych i magazynowych, po obu stronach należy przewidzieć galerie, tunele, na wiaduktach wzdłuż ich trasy, przejścia do bezpiecznej konserwacji i naprawy, a także miejsca do zmechanizowanego czyszczenia wycieków lub upadłego ładunku.
108. Piece grzewcze powinny być instalowane w taki sposób, aby obsługujący je pracownicy nie byli narażeni na dopływ ciepła z okien załadowczych jednocześnie z dwóch lub więcej pieców oraz aby nie było potrzeby przekazywania nagrzanego metalu do odkształcających się urządzeń technologicznych wzdłuż przejściach i podjazdach.
Piekarniki-wanny nie powinny być umieszczane pod świetlikami, aby krople wody kondensującej się na lampach nie dostały się do produktu.
109. Urządzenia technologiczne, rurociągi, kanały powietrzne i armatura, które nie są wykorzystywane przy realizacji procesów produkcyjnych w wyniku zmiany schematu technologicznego lub z innych przyczyn, muszą zostać zdemontowane.
110. Po zakończeniu prac instalacyjnych należy sprawdzić obecność i sprawność wszystkich zabezpieczeń i urządzenia bezpieczeństwa i systemy alarmowe.
Wymagania BHP dotyczące konserwacji i naprawy urządzeń technologicznych
111. Konserwację i naprawę urządzeń technologicznych należy przeprowadzać zgodnie z opracowanym przepisy technologiczne(instrukcje obsługi, mapy technologiczne, projekty organizacji i produkcji prac naprawczych), które ustalają kolejność i kolejność prac, niezbędne osprzęt i narzędzia, a także określają urzędnicy odpowiedzialny za ich realizację.
112. Pracodawca musi zapewnić pracownikom zajmującym się konserwacją i naprawą urządzeń technologicznych niezbędny zestaw narzędzi serwisowych, odpowiednich osprzętów i materiałów.
113. Urządzenia procesowe i łączność zatrzymane w celu konserwacji lub naprawy muszą być odłączone od pary, wody i rurociągi technologiczne, przewody gazowe. Wtyczki muszą być instalowane na rurociągach; sprzęt technologiczny i komunikacja muszą być wolne od materiałów technologicznych.
Konserwacja i naprawa urządzeń technologicznych musi być wykonywana, gdy zespół napędowy (siłowy) nie pracuje, z wyjątkiem czynności, które nie mogą być wykonywane, gdy zespół napędowy (energetyczny) nie pracuje. Podczas wykonywania prac naprawczych dozwolone jest dostarczanie energii elektrycznej zgodnie z projektem organizacji i produkcji pracy, zatwierdzonym przez pracodawcę.
Obwody elektryczne napędów zatrzymanych urządzeń technologicznych muszą zostać zdemontowane, na urządzeniach rozruchowych umieszczone są znaki zakazu: „Nie włączaj! Ludzie pracują” i podjęto działania mające na celu zapobieżenie błędnej lub spontanicznej aktywacji urządzeń rozruchowych.
114. Jeśli w sprzęcie procesowym znajdują się toksyczne lub wybuchowe gazy, opary lub pyły, należy je oczyścić, a następnie przeprowadzić analizę środowiska powietrza pod kątem pozostałości szkodliwych i (lub) niebezpiecznych substancji.
Analizy kontrolne środowiska powietrza należy przeprowadzać okresowo podczas konserwacji lub naprawy.
115. Zabrania się przeprowadzania konserwacji w bezpośrednim sąsiedztwie niezabezpieczonych ruchomych i wirujących części oraz części związanych z nimi urządzeń technologicznych, przewodów elektrycznych i części pod napięciem.
116. Podczas wykonywania prac związanych z naprawą urządzeń technologicznych, ich montażem i demontażem miejsce prac naprawczych (miejsce naprawy) musi być ogrodzone. Na ogrodzeniach należy umieścić znaki bezpieczeństwa, plakaty i urządzenia sygnalizacyjne.
Wymiary miejsc napraw muszą odpowiadać wymiarom jednostek i części wyposażenia, materiałów, osprzętu i narzędzi na nich umieszczonych, a także zapewniać rozmieszczenie bezpiecznych przejść i podjazdów.
Zabronione jest zaśmiecanie miejsca naprawy, przejść i podjazdów.
117. Podczas wykonywania prac naprawczych na obszarach o temperaturze powietrza powyżej 32 ° C należy zapewnić mobilne instalacje odpylania powietrza.
118. Do podnoszenia i przenoszenia wyposażenia procesowego, zespołów i części należy zapewnić sprzęt i urządzenia do podnoszenia.
119. Odłączone okrągłe lub długie części naprawianego sprzętu należy umieszczać na specjalnych stojakach lub stojakach.
120. Podczas rąbania, cięcia metalu, tankowania i ostrzenia narzędzi należy pracować z użyciem odpowiednich ŚOI.
121. Wióry, trociny i ścinki metalu podczas prac naprawczych należy usuwać za pomocą szczotek, skrobaków, haczyków.
Zabrania się zdmuchiwania wiórów, trocin i skrawków metalu sprężonym powietrzem.
122. Wyciskanie i wciskanie tulei, łożysk i innych części o ciasnym pasowaniu powinno odbywać się za pomocą pras i specjalnych urządzeń.
123. Aby sprawdzić wyrównanie otworów części, należy użyć specjalnych trzpieni.
Zabronione jest sprawdzanie palcami wyrównania otworów części.
124. Konserwacja instalacji elektrycznych, w tym tych, które są częścią wyposażenia procesowego, musi być przeprowadzana zgodnie z wymaganiami ustanowionymi przez upoważnione federalne organy wykonawcze * (23).
Pracownicy dopuszczeni do konserwacji sprzętu elektrycznego muszą mieć odpowiednią grupę bezpieczeństwa elektrycznego.
125. Przy naprawie sprzętu w pomieszczeniach zagrożonych wybuchem zabrania się używania otwartego ognia oraz używania mechanizmów i urządzeń powodujących iskrzenie.
126. Prace przy naprawie urządzeń technologicznych, w których znajdowały się substancje toksyczne lub toksyczne należy prowadzić przy użyciu odpowiednich ŚOI po usunięciu (neutralizacji) substancji toksycznych lub toksycznych.
127. Drabiny i rusztowania używane do prac remontowych muszą być w dobrym stanie, bez pęknięć, pęknięć i odkształceń.
Drabiny montowane na gładkich powierzchniach muszą mieć podstawy obite gumą, a te montowane na ziemi muszą mieć ostre metalowe końcówki.
Drabiny muszą być bezpiecznie podparte górnymi końcami na solidnej podstawie.
Podczas instalowania drabin na wysokości na elementach konstrukcji metalowych konieczne jest bezpieczne przymocowanie góry i dołu drabiny do konstrukcji metalowych. Drabiny muszą być odpowiednio przetestowane i oznaczone.
Podczas konserwacji i naprawy instalacji elektrycznych zabronione jest używanie drabin metalowych.
128. Podczas wykonywania prac naprawczych na wysokości dwóch lub więcej poziomów, między poziomami należy umieścić mocne sufity lub należy zawiesić siatki, aby zapobiec spadaniu materiałów, części lub narzędzi na pracowników.
129. Po zakończeniu naprawy urządzeń technologicznych i łączności należy upewnić się, że żadne materiały, narzędzia i inne ciała obce nie pozostają wewnątrz urządzeń technologicznych i łączności.
130. Eksploatacja próbna urządzeń technologicznych po naprawie musi być przeprowadzona przez pracowników uprawnionych do obsługi tego urządzenia w obecności kierownika prac naprawczych oraz urzędnika wyznaczonego na zlecenie pracodawcy odpowiedzialnego za bezpieczną eksploatację wyposażenie.
V. Wymagania ochrony pracy podczas transportu (przemieszczenia) i przechowywania urządzeń technologicznych, komponentów i materiałów eksploatacyjnych
Wymagania ochrony pracy podczas transportu (przemieszczenia) urządzeń technologicznych, komponentów i materiałów eksploatacyjnych
131. Podczas transportu (przemieszczania) urządzeń technologicznych, komponentów i materiałów eksploatacyjnych należy kierować się dokumentacją techniczną (operacyjną) producenta oraz wymaganiami określonymi przez upoważnione federalne organy wykonawcze * (24).
132. Aby zapewnić przepływ ładunków w organizacji, drogi dojazdowe i podjazdy muszą być dostosowane do wymiarów używanych pojazdów i przewożonych towarów, wyposażone w niezbędny sprzęt przeładunkowy zapewniający operacje załadunku i rozładunku.
133. Podczas transportu urządzeń technologicznych, komponentów i materiałów eksploatacyjnych konieczne jest zapewnienie bezpieczeństwa komunikacji transportowej.
134. Bezpieczeństwo komunikacji transportowej zapewniają:
1) rozwój schematów transportowych i technologicznych;
2) organizację ruchu na terenie zgodnie ze schematem ruchu pojazdów i pieszych;
3) montaż znaków i znaków drogowych.
135. Aby uniknąć przesuwania się lub spadania ładunku, gdy pojazd jest w ruchu, ładunek musi być umieszczony i zabezpieczony zgodnie z specyfikacje do załadunku i zabezpieczenia tego typu ładunków.
Manewrowanie pojazdami z ładunkami po usunięciu mocowań z ładunków jest zabronione.
136. Do transportu małych elementów tego samego typu i materiałów eksploatacyjnych należy stosować odpowiednie opakowania.
137. Podczas transportu towarów w szklanych pojemnikach należy podjąć środki zapobiegające wstrząsom i uderzeniom.
138. Dostawa transportu samochodowego rewersem w rejonie wykonywania czynności załadunku i rozładunku musi być wykonywana przez kierowcę wyłącznie na polecenie jednego z pracowników zatrudnionych przy tych pracach.
139. W pomieszczeniach przemysłowych z podwyższony poziom hałas, powinno być możliwe określenie przez pracowników na czas sygnałów dźwiękowych lub świetlnych emitowanych przez poruszające się pojazdy.
140. Transport drogowy wielkogabarytowych i ciężkich urządzeń technologicznych po drogach otwartych do użytku publicznego musi odbywać się zgodnie z wymogami określonymi przez upoważnione federalne organy wykonawcze * (25).
141. Cysterny przewożące ciecze palne i palne muszą być wyposażone w uziemienie, sprzęt gaśniczy, oznakowany zgodnie ze stopniem niebezpieczeństwa ładunku, a rury wydechowe muszą być prowadzone pod chłodnicą i wyposażone w łapacze iskier.
142. Podczas obsługi wózków widłowych i elektrycznych wózków widłowych wymagania ustanowione przez upoważniony organ federalny władza wykonawcza * (26).
143. W obiektach przemysłowych o dużym natężeniu ruchu preferowane powinny być środki transportu ciągłego (przenośniki, przenośniki).
144. Ruchome i obracające się części przenośników i przenośników, do których pracownicy mają dostęp, muszą być zabezpieczone.
145. W przypadku stosowania przenośników montowanych do transportu towarów na wysokości większej niż 2 m, pod przenośnikiem należy zainstalować urządzenia ochronne, aby zapewnić bezpieczeństwo pracowników w przypadku przypadkowego upadku ładunku.
Wymagania bezpieczeństwa pracy dotyczące przechowywania wyposażenia procesowego, komponentów i materiałów eksploatacyjnych
146. Przechowywanie wyposażenia procesowego, komponentów i materiałów eksploatacyjnych powinno obejmować:
1) stosowanie metod przechowywania wykluczających występowanie szkodliwych i (lub) niebezpiecznych czynników produkcji;
2) korzystanie z bezpiecznych urządzeń magazynujących; mechanizacja i automatyzacja operacji załadunku i rozładunku.
147. Przechowywanie komponentów i materiałów eksploatacyjnych należy przeprowadzać z uwzględnieniem ich palnych właściwości fizykochemicznych, oznak zgodności i jednorodności środków gaśniczych.
148. Przy umieszczaniu urządzeń technologicznych, komponentów, materiałów eksploatacyjnych, półfabrykatów, półproduktów, wyrobów gotowych i odpadów produkcyjnych należy przestrzegać wymagań Zasad ochrony pracy podczas operacji załadunku i rozładunku oraz umieszczania towarów * (27 ).
149. Przechowywanie łatwopalnych i palnych cieczy, materiałów palnych i wybuchowych musi odbywać się zgodnie z zasadami reżimu przeciwpożarowego w Federacji Rosyjskiej * (28).
150. Materiały palne mieszanek egzotermicznych należy przechowywać w specjalnie do tego celu przeznaczonych magazynach spełniających wymagania bezpieczeństwa przeciwpożarowego i przeciwwybuchowego.
151. W pomieszczeniach, w których przechowywane są chemikalia i roztwory, instrukcje dotyczące bezpieczna obsługa z nimi.
152. Materiały i wyroby ogniotrwałe należy przechowywać w magazynach zamkniętych. Na otwartych przestrzeniach materiały ogniotrwałe można przechowywać wyłącznie w pojemnikach.
153. Proszki, materiały proszkowe należy przechowywać w zamkniętych pojemnikach (pudełka, tuby, worki).
154. Materiały sypkie należy przechowywać w pojemnikach o kącie spoczynku.
155. Matryce, formy, kolby, formy, wlewki, odkuwki należy przechowywać w stosach zgodnie z ustalonymi wymiarami stosów, w zależności od charakteru przechowywanych produktów, ich rzędów i przerw między stosami.
Stemple duże i średnie należy umieszczać w specjalnie wyznaczonych miejscach na okładzinach drewnianych, zapewniających wystarczający prześwit do usunięcia urządzenia podnoszące lub wózek widłowy.
156. Detale i produkty podczas przechowywania muszą być zainstalowane w stabilnej pozycji.
157. Miejsce składowania odpadów musi być ogrodzone solidnym ogrodzeniem o wysokości co najmniej 0,5 m.
158. Komponenty i drobne części należy umieszczać w specjalnych pojemnikach na regałach obsługiwanych przez układnicę.
159. Chemikalia należy przechowywać w szczelnie zamkniętych pojemnikach w specjalnie wyznaczonych i wyposażonych miejscach.
160. Przechowywanie czystego i zużytego środka czyszczącego w zakładach produkcyjnych powinno odbywać się oddzielnie w metalowych skrzyniach zamykanych pokrywkami.
Pudełka ze zużytym środkiem czyszczącym należy opróżniać w miarę ich napełniania, ale przynajmniej raz na zmianę.
W pomieszczeniach przemysłu wybuchowego zabronione jest stosowanie materiałów czyszczących wykonanych z włókien syntetycznych i sztucznych.
VI. Postanowienia końcowe
161. Nadzór państwa federalnego nad przestrzeganiem wymogów Regulaminu sprawują urzędnicy Federalnej Służby Pracy i Zatrudnienia oraz jej organów terytorialnych ( inspekcje państwowe pracy w podmiotach wchodzących w skład Federacji Rosyjskiej) * (29).
162. Szefowie i inni urzędnicy organizacji, a także pracodawcy - osoby fizyczne winni naruszenia wymagań Regulaminu ponoszą odpowiedzialność w sposób określony przez ustawodawstwo Federacji Rosyjskiej * (30).
_____________________________
*(1) Artykuł 211 Kodeksu pracy Federacji Rosyjskiej (Sobraniye Zakonodatelstva Rossiyskoy Federatsii, 2002, nr 1, art. 3; 2006, nr 27, art. 2878; 2009, nr 30, art. 3732) .
*(2) Dekret Ministerstwa Pracy Rosji i Ministerstwa Edukacji Rosji z dnia 13 stycznia 2003 r. Nr 1/29 „W sprawie zatwierdzenia Procedury szkolenia w zakresie ochrony pracy i sprawdzania znajomości wymagań ochrony pracy dla pracowników organizacje” (zarejestrowana przez Ministerstwo Sprawiedliwości Rosji w dniu 12 lutego 2003 r., nr rejestracyjny 4209 ).
*(3) Rozporządzenie Ministerstwa Zdrowia i Rozwoju Społecznego Rosji z dnia 12 kwietnia 2011 r. Nr 302n „O zatwierdzeniu wykazów szkodliwych i (lub) niebezpiecznych czynników produkcji i prac, podczas których obowiązkowo wstępne i okresowe Przeprowadzane są badania lekarskie (egzaminy) oraz procedura przeprowadzania obowiązkowych wstępnych i okresowych badań lekarskich (badań) pracowników wykonujących ciężką pracę i pracę w szkodliwych i (lub) niebezpiecznych warunkach pracy ”(zarejestrowane przez Ministerstwo Sprawiedliwości Rosji w dniu 21 października 2011 r., nr rejestracyjny 22111) zmieniony rozporządzeniami Ministerstwa Zdrowia Rosji z dnia 15 maja 2013 r. nr 296n (zarejestrowany przez Ministerstwo Sprawiedliwości Rosji w dniu 3 lipca 2013 r., nr rejestracyjny 28970) oraz z dnia 5 grudnia 2014 r. nr 801n (zarejestrowany przez Ministerstwo Sprawiedliwości Rosji w dniu 3 lutego 2015 r., nr rejestracyjny 35848).
*(4) Dekret Rządu Federacji Rosyjskiej z dnia 25 lutego 2000 r. nr 162 „O zatwierdzeniu wykazu ciężkiej pracy i pracy w szkodliwych lub niebezpiecznych warunkach pracy, przy wykonywaniu których zabronione jest korzystanie z pracy kobiet ” (Prawodawstwo zebrane Federacji Rosyjskiej, 2000, nr 10, artykuł 1130).
*(8) Dekret Rządu Federacji Rosyjskiej z dnia 25 lutego 2000 r. Nr 163 „O zatwierdzeniu wykazu prac ciężkich i pracy w szkodliwych lub niebezpiecznych warunkach pracy, przy wykonywaniu których korzysta się z pracy osób pod osiemnaście lat jest zabronione” (Ustawy Zbiorowe Federacji Rosyjskiej, 2000, Nr 10, poz. 1131; 2001, Nr 26, poz. 2685; 2011, Nr 26, poz. 3803).
*(6) Rozporządzenie Ministerstwa Zdrowia i Rozwoju Społecznego Rosji z dnia 1 czerwca 2009 r. Nr 290n „W sprawie zatwierdzenia międzysektorowych zasad zapewniania pracownikom specjalnej odzieży, obuwia specjalnego i innego sprzętu ochrony osobistej” (zarejestrowane przez Ministerstwo Sprawiedliwości Rosji z dnia 10 września 2009 r., nr rejestracyjny 14742), z późniejszymi zmianami, wprowadzony rozporządzeniem Ministerstwa Zdrowia i Rozwoju Społecznego Rosji z dnia 27 stycznia 2010 r. nr 28n (zarejestrowany przez Ministerstwo Sprawiedliwości Rosji z dnia 1 marca 2010 r. nr rejestracyjny 16530), zarządzenia Ministerstwa Pracy Rosji z dnia 20 lutego 2014 r. nr 103n (zarejestrowane przez Ministerstwo Sprawiedliwości Rosji w dniu 15 maja 2014 r., nr rejestracyjny 32284) i datowane 12 stycznia 2015 r. nr 2n (zarejestrowany przez Ministerstwo Sprawiedliwości Rosji 11 lutego 2015 r., nr rejestracyjny 35962).
*(7) Rozporządzenie Ministerstwa Zdrowia i Rozwoju Społecznego Rosji z dnia 5 marca 2011 r. Nr 169n „W sprawie zatwierdzenia wymagań dotyczących kompletowania apteczek pierwszej pomocy wraz z wyrobami medycznymi do udzielania pierwszej pomocy pracownikom” (zarejestrowane przez Ministerstwo Sprawiedliwość Rosji w dniu 11 kwietnia 2011 r., nr rejestracji 20452).
*(8) Art. 227-231 Kodeksu pracy Federacji Rosyjskiej (ustawodawstwo zebrane Federacji Rosyjskiej, 2002, nr 1, art. 3; 2006, nr 27, art. 2878; 2008, nr 30, Art. 3616; 2009, nr 19, 2270; 2011, nr 30, art. 4590; 2013, nr 27, art. 3477; 2015, nr 14, art. 2022).
*(9) Zbiór ustawodawstwa Federacji Rosyjskiej, 2010, nr 1, art. 5; 2013, nr 27, art. 3477.
*(10) Rozporządzenie Ministerstwa Pracy Rosji z dnia 17 sierpnia 2015 r. Nr 552n „W sprawie zatwierdzenia zasad ochrony pracy podczas pracy z narzędziami i urządzeniami” (zarejestrowane przez Ministerstwo Sprawiedliwości Rosji w dniu 2 października 2015 r. , nr rej. 39125).
*(11) Dekret Rządu Federacji Rosyjskiej z dnia 25 kwietnia 2012 r. nr 390 „On tryb ognia» (Ustawodawstwo zebrane Federacji Rosyjskiej, 2012, nr 19, art. 2415; 2014, nr 9, art. 906, nr 26, art. 3577; 2015, nr 11, art. 1607; nr 46 , Art. 6397; 2016, Nr 15, poz. 2105).
*(12) Rozkaz Rostekhnadzor z dnia 12 listopada 2013 r. nr 533 „Po zatwierdzeniu przepisy federalne oraz przepisy z zakresu bezpieczeństwa przemysłowego „Zasady bezpieczeństwa dla niebezpiecznych obiektów produkcyjnych z wykorzystaniem konstrukcji podnoszących” (zarejestrowane przez Ministerstwo Sprawiedliwości Rosji w dniu 31 grudnia 2013 r., nr rejestracyjny 30992), zmienione rozporządzeniem Rostekhnadzor nr 146 z dnia 12 kwietnia , 2016 (zarejestrowany przez Ministerstwo Sprawiedliwości Rosji w dniu 20 maja 2016 r., numer rejestracyjny 42197);
*(13) Dekret Rady Ministrów – Rządu Federacji Rosyjskiej z dnia 6 lutego 1993 r. nr 105 „O nowych normach dotyczących maksymalnych dopuszczalnych obciążeń dla kobiet przy ręcznym podnoszeniu i przenoszeniu ciężarów” (Zbiór aktów Prezydenta i Rządu Federacji Rosyjskiej, 1993, Nr 7, Art. 566);
Dekret Ministerstwa Pracy Rosji z dnia 7 kwietnia 1999 r. Nr 7 „O zatwierdzeniu norm maksymalnych dopuszczalnych obciążeń dla osób poniżej osiemnastego roku życia przy ręcznym podnoszeniu i przenoszeniu ciężarów” (zarejestrowany przez Ministerstwo Sprawiedliwości Rosji w dniu 1 lipca 1999, nr rej. 1817).
*(14) Zarządzenie Rostekhnadzor z dnia 25 marca 2014 r. Nr 116 „W sprawie zatwierdzania federalnych norm i zasad w dziedzinie bezpieczeństwa przemysłowego” Zasady bezpieczeństwa przemysłowego w niebezpiecznych obiektach produkcyjnych wykorzystujących urządzenia działające pod nadciśnienie” (zarejestrowany przez Ministerstwo Sprawiedliwości Rosji w dniu 19 maja 2014 r., numer rejestracyjny 32326);
rozporządzenie Ministerstwa Energetyki Rosji z dnia 24 marca 2003 r. Nr 115 „W sprawie zatwierdzenia regulaminu eksploatacji technicznej elektrociepłowni” (zarejestrowane przez Ministerstwo Sprawiedliwości Rosji w dniu 2 kwietnia 2003 r., nr rejestracyjny 4358 );
zarządzenie Ministerstwa Pracy Rosji z dnia 17 sierpnia 2015 r. Nr 551n „W sprawie zatwierdzenia zasad ochrony pracy podczas eksploatacji elektrowni cieplnych” (zarejestrowane przez Ministerstwo Sprawiedliwości Rosji w dniu 5 października 2015 r., nr rejestracyjny 39138)).
*(15) Zarządzenie Ministerstwa Pracy Rosji z dnia 23 grudnia 2014 r. Nr 1101n „W sprawie zatwierdzenia zasad ochrony pracy przy wykonywaniu prac spawalniczych elektrycznych i gazowych” (zarejestrowane przez Ministerstwo Sprawiedliwości Rosji w dniu 20 lutego, 2015, nr rej. 36155).
*(16) Rozporządzenie Ministerstwa Pracy Rosji z dnia 24 lipca 2013 r. Nr 328n „W sprawie zatwierdzenia zasad ochrony pracy podczas eksploatacji instalacji elektrycznych” (zarejestrowane przez Ministerstwo Sprawiedliwości Rosji w dniu 12 grudnia 2013 r. , nr rejestracyjny 30593) zmieniony rozporządzeniem Ministerstwa Pracy Rosji z dnia 19 lutego 2016 r. nr 74n (zarejestrowany przez Ministerstwo Sprawiedliwości Rosji w dniu 13 kwietnia 2016 r., nr rejestracyjny 41781);
rozporządzenie Ministerstwa Energetyki Rosji z dnia 13 stycznia 2003 r. Nr 6 „W sprawie zatwierdzenia zasad eksploatacji technicznej instalacji elektrycznych odbiorców” (zarejestrowane przez Ministerstwo Sprawiedliwości Rosji w dniu 22 stycznia 2003 r., nr rej. 4145).
*(17) Zarządzenie Ministerstwa Pracy Rosji z dnia 2 listopada 2015 r. Nr 835n „W sprawie zatwierdzenia zasad ochrony pracy przy wyrębie, obróbce drewna i leśnictwie” (zarejestrowane przez Ministerstwo Sprawiedliwości Rosji w dniu 9 lutego, 2016, nr rejestracji 41009).
*(18) Zarządzenie Ministerstwa Pracy Rosji z dnia 28 marca 2014 r. Nr 155n „W sprawie zatwierdzenia zasad ochrony pracy podczas pracy na wysokości” (zarejestrowane przez Ministerstwo Sprawiedliwości Rosji w dniu 5 września 2014 r., rejestracja nr 33990, zmienione rozporządzeniem Ministerstwa Pracy Rosji z dnia 17 czerwca 2015 r. nr 383n (zarejestrowany przez Ministerstwo Sprawiedliwości Rosji w dniu 22 lipca 2015 r., nr rejestracyjny 38119).
*(19) Zarządzenie Ministerstwa Pracy Rosji z dnia 24 lipca 2013 r. Nr 328n „W sprawie zatwierdzenia Zasad ochrony pracy podczas eksploatacji instalacji elektrycznych”.
*(20) Zarządzenie Rostekhnadzor z dnia 18 stycznia 2012 r. Nr 44 „W sprawie zatwierdzenia federalnych norm i zasad w dziedzinie bezpieczeństwa przemysłowego” Przepisy dotyczące stosowania pozwoleń na pracę podczas wykonywania wysoce niebezpiecznych prac w niebezpiecznych obiektach przemysłowych górnictwa i przemysłu metalurgicznego” (zarejestrowana przez Ministerstwo Sprawiedliwości Rosji 6 marca 2012 r., numer rejestracyjny 23411).
*(21) Dekret Rządu Federacji Rosyjskiej z dnia 25 kwietnia 2012 r. nr 390 „O reżimie przeciwpożarowym”.
*(22) Regulamin Techniczny Unii Celnej „W sprawie bezpieczeństwa maszyn i urządzeń” (TP CU 010/2011) (zatwierdzony decyzją Komisji Unii Celnej z dnia 18 października 2011 nr 823) z późniejszymi zmianami Decyzje Kolegium Euroazjatyckiej Komisji Gospodarczej z dnia 4 grudnia 2012 r. nr 248 oraz z dnia 19 maja 2015 r. nr 55.
* (23) Rozporządzenie Ministerstwa Pracy Rosji z dnia 24 lipca 2013 r. Nr 328n „W sprawie zatwierdzenia Zasad ochrony pracy podczas eksploatacji instalacji elektrycznych”;
zarządzenie Ministerstwa Energii Rosji z dnia 13 stycznia 2003 r. Nr 6 „W sprawie zatwierdzenia zasad eksploatacji technicznej konsumenckich instalacji elektrycznych”.
*(24) Dekret Rządu Federacji Rosyjskiej z dnia 15 kwietnia 2011 r. Nr 272 „O zatwierdzeniu Regulaminu przewozu drogowego towarów” (Ustawodawstwo zebrane Federacji Rosyjskiej, 2011, nr 17, Art. 2407; 2012 r. Nr 10, Art. 1223; 2014 r. Nr 3, poz. 281; 2015 r. Nr 50, poz. 7162);
zarządzenie Ministerstwa Transportu Rosji z dnia 8 sierpnia 1995 nr 73 „O zatwierdzeniu Regulaminu przewozu” towary niebezpieczne transport drogowy” (zarejestrowany w Ministerstwie Sprawiedliwości Rosji w dniu 18 grudnia 1995 r., nr rejestracyjny 997) zmieniony rozporządzeniami Ministerstwa Transportu Rosji z dnia 11 czerwca 1999 r. Nr 37 (zarejestrowany w Ministerstwie Sprawiedliwości Rosji Rosja 8 lipca 1999 r., nr rejestracyjny 1826) i datowana 14 października 1999 r. nr 77 (zarejestrowana przez Ministerstwo Sprawiedliwości Rosji 28 października 1999 r., nr rejestracyjny 1960);
zarządzenie Ministerstwa Pracy Rosji z dnia 17 września 2014 r. Nr 642n „W sprawie zatwierdzenia zasad ochrony pracy podczas załadunku i rozładunku oraz umieszczania towarów” (zarejestrowane przez Ministerstwo Sprawiedliwości Rosji w dniu 5 listopada 2014 r., nr rejestracyjny 34558).
*(25) Rozporządzenie Ministerstwa Transportu Rosji z dnia 24 lipca 2012 r. Nr 258 „W sprawie zatwierdzenia procedury wydawania specjalnego zezwolenia na prowadzenie pojazdu po drogach samochodowych wykonującego przewóz ciężkich i (lub) wielkogabarytowych Towary” (zarejestrowany przez Ministerstwo Sprawiedliwości Rosji w dniu 11 października 2012 r., nr rejestracyjny 25656) zmieniony rozporządzeniem Ministerstwa Transportu Rosji z dnia 15 stycznia 2014 r. Nr 7 (zarejestrowany przez Ministerstwo Sprawiedliwości Rosji w dniu 5 czerwca 2014 r. nr ewidencyjny 32585).
* (26) Dekret Ministerstwa Pracy Rosji z dnia 12 maja 2003 r. Nr 28 „W sprawie zatwierdzenia Międzysektorowych zasad ochrony pracy w transport drogowy” (zarejestrowany przez Ministerstwo Sprawiedliwości Rosji w dniu 19 czerwca 2003 r., numer rejestracyjny 4734).
*(27) Zarządzenie Ministerstwa Pracy Rosji z dnia 17 września 2014 r. Nr 642n „W sprawie zatwierdzenia zasad ochrony pracy podczas operacji załadunku i rozładunku oraz umieszczania towarów” (zarejestrowane przez Ministerstwo Sprawiedliwości Rosji w listopadzie 5, 2014, nr rej. 34558).
*(28) Dekret Rządu Federacji Rosyjskiej z dnia 25 kwietnia 2012 r. nr 390 „O reżimie przeciwpożarowym”.
*(29) Dekret rządu Federacji Rosyjskiej z dnia 30 czerwca 2004 r. Nr 324 „W sprawie zatwierdzenia regulaminu Federalnej Służby Pracy i Zatrudnienia” (ustawodawstwo zebrane Federacji Rosyjskiej, 2004, nr 28, art. 2901; 2007, nr 37, art. 4455; 2008, nr 46, art. 5337; 2009, nr 1, art. 146; nr 6, art. 738; nr 33, art. 4081; 2010, nr 26, art. 3350; 2011 nr 14, art. 1935; 2012 nr 1, poz. 171; nr 15, poz. 1790; nr 26, poz. 3529; 2013, nr 33, poz. 4385; nr 45, poz. 5822 ; 2014 Nr 26, poz. 3577; Nr 32, art. 4499; 2015, Nr 2, art. 491; Nr 16, art. 2384; 2016, Nr 2, art. 325);
zarządzenie Ministerstwa Pracy Rosji z dnia 26 maja 2015 r. Nr 318n „W sprawie zatwierdzenia regulaminu modelowego w sprawie organu terytorialnego Federalnej Służby Pracy i Zatrudnienia” (zarejestrowane przez Ministerstwo Sprawiedliwości Rosji w dniu 30 czerwca 2015 r. , nr rej. 37852).
*(30) Rozdział 62 Kodeksu pracy Federacji Rosyjskiej (Sobraniye Zakonodatelstva Rossiyskoy Federatsii, 2002, nr 1, art. 3; 2006, nr 27, art. 2878).
Wniosek nr 1
do Zasad Ochrony Pracy
podczas montażu, instalacji, technicznych
konserwacja i naprawa
wyposażenie technologiczne,
zatwierdzone zamówienie
Ministerstwo Pracy i
ochrona socjalna Federacji Rosyjskiej
z dnia 23 czerwca 2016 r. nr 310n
ZEZWOLENIE N_____
DO WYKONYWANIA PRAC O PODWYŻSZONYM ZAGROŻENIU
(Nazwa firmy)
1.1. Do brygadzisty robót ________________________________________________
(stanowisko, nazwa jednostki, nazwisko i inicjały) z drużyną w
składający się z ________ osób jest poinstruowany, aby wykonać następujące prace: _______
________________________________________________________________________
________________________________________________________________________
_______________________________________________________________________.
1.2. Podczas przygotowywania i wykonywania pracy należy zapewnić następujące środki:
bezpieczeństwo:
________________________________________________________________________
_______________________________________________________________________,
1.3. Rozpocznij pracę: o godzinie ____. ____ min. „_____” ___________ 20____
1.4. Zakończ pracę: o godzinie ____. ____ min. „_____” ___________ 20____
1.5. Zamówienie zostało wydane przez kierownika pracy ____________________________________
________________________________________________________________________
(tytuł stanowiska, nazwisko i inicjały, podpis)
1.6. Zaznajomiony z warunkami pracy
Brygadzista _________ "___" _______ 20___ _____
Zezwolenie _________ "___" _______ 20___ _____
(podpis) (nazwisko i inicjały)
2.1. Odprawa na temat ochrony pracy w zakresie instrukcji ____________________
________________________________________________________________________
________________________________________________________________________
________________________________________________________________________
(wskazać nazwy lub numery instrukcji, na których
odprawa)
realizowane przez zespół ____________ osób, w tym:
2.2. Zakończono działania mające na celu zapewnienie bezpieczeństwa pracy.
Brygadzista i członkowie zespołu znają cechy pracy.
Obiekt gotowy do pracy.
Zezwolenie na pracę ________________ "_____" ____________ 20_____
(podpis)
2.3. Zapoznałem się z warunkami pracy i otrzymałem pozwolenie na pracę.
(podpis)
2.4. Sprawdziłem przygotowanie miejsca pracy. pozwalam ci zacząć
produkcja dzieł.
(podpis)
3. Dekoracja dzienny wstęp do produkcji dzieł
3.2. Praca zakończona, prace usunięte, pracownicy odeszli
prace produkcyjne są wycofywane.
Zezwolenie na pracę jest zamykane o ______ godz. _______ min. „_____” _________ 20____
Brygadzista robót ________________ „_____” ____________ 20_____
(podpis)
Kierownik Pracy ________________ "_____" ____________ 20_____
(podpis)
Notatka.
Zezwolenie na pracę wydawane jest w dwóch egzemplarzach: pierwszy przechowuje
pracownik, który wydał zezwolenie na pracę, drugi - od kierownika pracy.
Wniosek nr 2
do Zasad Ochrony Pracy
podczas montażu, instalacji, technicznych
konserwacja i naprawa
wyposażenie technologiczne,
zatwierdzone zamówienie
Ministerstwo Pracy i
ochrona socjalna Federacji Rosyjskiej
z dnia 23 czerwca 2016 r. nr 310n
ACT-ZEZWOLENIE
DO WYKONANIA PRAC NA TERYTORIUM ORGANIZACJI
„______” ______________ 20____
________________________________________________________________________
(Nazwa firmy)
1. My niżej podpisani:
przedstawiciel organizacji ________________________________________________,
przedstawiciel wykonawcy ________________________________________________,
(nazwisko i inicjały, stanowisko)
sporządziły niniejsze świadectwo dopuszczenia w następujący sposób.
Organizacja zapewnia działkę (terytorium) ograniczoną
współrzędne ________________________________________________________________,
(nazwa osi, znaki i numer rysunku)
do produkcji na nim ________________________________________________
________________________________________________________________________
(Nazwa dzieła)
pod kierunkiem personelu technicznego – przedstawiciela wykonawcy
data następna: początek „____” ____________________ 20___, koniec
„____” ____________________ 20____
2. Przed rozpoczęciem pracy należy wykonać następujące czynności
środki zapewniające bezpieczeństwo pracy:
3. Po zakończeniu pracy musisz wykonać następujące czynności
Wydarzenia:
Przedstawiciel organizacji _________________________________
(podpis)
Przedstawiciel Wykonawcy _________________________________
(podpis)
Przegląd dokumentów
Państwowe wymagania regulacyjne dotyczące ochrony pracy zostały zatwierdzone podczas wykonywania podstawowych operacji technologicznych i prac związanych z umieszczaniem, instalacją, konserwacją i naprawą stacjonarnych maszyn, mechanizmów, urządzeń, instrumentów i innego sprzętu stosowanego do produkcji produktów przemysłowych.
Odpowiedzialność za wdrożenie ustalone zasady ponosi pracodawca. Zapewnia utrzymanie w dobrym stanie urządzeń technologicznych, narzędzi i urządzeń oraz ich eksploatację zgodnie z zatwierdzonymi wymaganiami i dokumentacją techniczną (eksploatacyjną) producenta.
Do wykonywania pracy mogą być dopuszczone osoby, które zostały przeszkolone w zakresie ochrony pracy i sprawdzania wiedzy.
Podczas wykonywania pracy, która podlega dodatkowym (podwyższonym) wymogom ochrony pracy, testowanie wiedzy przeprowadza się co najmniej raz na 12 miesięcy, a powtarzane odprawy przeprowadza się co najmniej raz na 3 miesiące. Lista odpowiednich zawodów, stanowisk i rodzajów pracy jest zatwierdzana przez lokalny akt prawny pracodawcy.
Wymagania dotyczące ochrony pracy na terytorium organizacji, dla budynki przemysłowe(budowle), pomieszczenia (miejsca produkcji), do miejsc pracy, w celu zapewnienia zbiorowej ochrony pracowników.
Pracodawca ma prawo ustalić dodatkowe wymagania bezpieczeństwa przy wykonywaniu pracy poprawiające warunki pracy.
Zamówienie wchodzi w życie 3 miesiące po jego oficjalnej publikacji.
Podstawowe pojęcia niezawodności sprzętu
Zadania postęp naukowy i technologiczny a poprawa efektywności handlu nie może sprowadzać się jedynie do zwiększenia technicznego wyposażenia przedsiębiorstwa. Integralną częścią tego procesu jest możliwość efektywnego wykorzystania sprzętu z największym zwrotem. Aby utrzymać go w sprawności, konieczne jest zorganizowanie konserwacji i naprawy sprzętu.
Racjonalna organizacja eksploatacja i wysoka jakość serwisu technologicznego podnoszą niezawodność urządzeń.
Pod niezawodnością odnosi się do właściwości systemu technicznego do wykonania funkcje produkcyjne, utrzymując wskaźniki techniczne i operacyjne w ustalonych granicach w danym okresie eksploatacji.
Niezawodność jest złożoną właściwością systemu, która zależy od całości wpływu takich cech jak trwałość, niezawodność i łatwość konserwacji. Czym są te cechy i jak są mierzone?
trwałość nazywana jest właściwością, która ma pozostawać operacyjna aż do pojawienia się stanu granicznego w zainstalowany system konserwacja i naprawa.
Każde urządzenie techniczne, gdy jest tworzone, jest przeznaczone do pewnego dożywotni, tj. okres kalendarzowy odpowiadający zasobowi technicznemu, w którym eksploatacja tego produktu jest ekonomicznie i technicznie wykonalna. Żywotność obejmuje czas trwania wszelkiego rodzaju napraw. W przypadku większości systemów technicznych żywotność T leży w ciągu 5 - 15 lat.
Krótszy okres użytkowania nie uzasadnia kosztów, które zostały poniesione na rozwój i stworzenie produktu, a dłuższy prowadzi do tego, że albo Specyfikacja techniczna produkty nie odpowiadają już poziomowi nauki i technologii lub ze względu na wzrost liczby usterek działanie „starego” produktu staje się ekonomicznie niecelowe.
Ponieważ eksploatacja składa się z kilku faz (transport, magazynowanie, instalacja, przeznaczenie itp.), czas trwania okresu pracy jest szczególnie wyróżniany w okresie użytkowania, tj. w głównej fazie eksploatacji - przeznaczenie. Ta opcja nazywa się ratunek systemy. Jest uważany za ilościową miarę trwałości maszyny.
ratunek urządzenie techniczne to rozsądna wartość czasu pracy urządzenia (w godzinach, cyklach, kilometrach itp.), przy której z pewnym prawdopodobieństwem zostanie zachowana sprawność bez nieprzewidzianego zatrzymania.
Jak wiadomo, każdy sprzęt (urządzenie) składa się z pewnej liczby części maszyn. Ze względu na szereg uwarunkowań technicznych i ekonomicznych nie jest obecnie możliwe doprowadzenie wszystkich części do jednakowej wytrzymałości, tj. o tej samej trwałości. Dlatego zasób, jako miara trwałości, jest indywidualną właściwością pojedynczej części. Jednocześnie trwałość jest fizycznie determinowana przez stosunek rzeczywistej zdolności materiału o danej konfiguracji do przeciwstawiania się zniszczeniu do działania pewnych czynników zewnętrznych (siła, chemiczna, termiczna itp.), którym poddawana jest część podczas operacja.
Utrzymanie. W celu utrzymania działania i niezawodności sprzętu na ustalonym poziomie przewidziana jest konserwacja i planowe naprawy sprzętu. Konserwacja w swej istocie to zestaw środków zapobiegawczych, których wdrożenie powinno utrzymać sprawność lub wydajność sprzętu przez cały okres jego eksploatacji. Jednocześnie przez stan zdatności maszyny rozumie się stan, w którym maszyna spełnia wszystkie wymagania dokumentacji regulacyjnej, technicznej i projektowej, a stan zdatności to stan, w którym maszyna jest zdolna do wykonywania funkcji, które spełniają wymagania niniejszej dokumentacji. Osiąga się to poprzez szybkie wykrywanie uszkodzeń (diagnostyka), wykluczanie nadmiernego zużycia (ze względu na terminowe czyszczenie brudu i smaru), drobne naprawy itp.
Pewne zasoby materiałowe i robocizny są wydawane na konserwację i naprawy.
Konserwacja może obejmować kontrolę stanu technicznego, czyszczenie, smarowanie, naprawę połączeń, wymianę niektórych elementów produktu, regulację itp.
Niezawodność jest właściwością obiektu polegającą na ciągłym utrzymywaniu zdrowego stanu przez pewien czas.
Jak wynika z definicji, taka właściwość maszyn jak niezawodność determinuje cykliczność procesu eksploatacji, w którym stan zdatności jest okresowo naruszany i maszyna przechodzi w stan niesprawności, w którym nie jest w stanie wykonywać określonych funkcji.
Odmowa- jest to zdarzenie polegające na naruszeniu dokładności odmierzonych porcji produktu. Awarie mogą być spowodowane czynnikami projektowymi, operacyjnymi i innymi.
Dla większości typów urządzeń handel i gastronomia nie posiadają obecnie kompletnego systemu do analizy wskaźników niezawodności, z których najważniejsze to: prawdopodobieństwo bezawaryjnej pracy, czas pracy do stanu granicznego, parametr awaryjności, wykorzystanie techniczne i koszty operacyjne.
Prawdopodobieństwo bezawaryjnej pracy Р(τ) jest funkcją malejącą w czasie od 1 do 0, która charakteryzuje prawdopodobieństwo, że w danym czasie eksploatacji nie wystąpią awarie produktu. Funkcja jest określana z wyrażenia
gdzie n 0 to liczba wadliwych elementów wyposażenia w początkowym czasie (τ=0); n(τ) to liczba elementów wyposażenia, które uległy awarii w czasie τ.
Na przykład, jeśli Р(τ)= 0,86, oznacza to, że jeszcze maszyny tego modelu średnio 86% maszyn będzie działać przez dany czas, a 14% nie będzie działać.
Funkcjonować F(t)=1-P(t) nazywa prawdopodobieństwo awarii.
Czas pracy do stanu granicznego zależy od wielu czynników, znajduje się w różnych kategoriach. Często za podstawę obliczeń przyjmuje się wskaźniki ekonomiczne, których istota jest następująca. Wraz ze wzrostem czasu pracy maleje jednostkowy koszt sprzętu w przeliczeniu na 1000 godzin jego pracy, co jest wskaźnikiem
gdzie C to koszt sprzętu; τ to jego żywotność w godzinach.
Uderzenie wartości C. nie pozostaje stałą wartością, podczas pracy zmniejsza się, ponieważ wraz ze wzrostem żywotności zmniejsza się amortyzacja sprzętu. Koszt konserwacji i napraw od pewnego momentu zaczyna gwałtownie rosnąć. W związku z tym rosną konkretne koszty (w rublach za 1000 godzin pracy) utrzymania sprzętu w stanie roboczym. Czas pracy, gdy suma jednostkowych kosztów sprzętu i jednostkowych kosztów utrzymania go w stanie roboczym jest najmniejszy i jest uważany za czas pracy do stanu granicznego.
Błąd parametru przepływu to funkcja zależna od czasu, która dla określonej liczby elementów wyposażenia N tego samego typu oblicza się według wzoru
gdzie m jest całkowitą liczbą awarii w grupie; τ to czas obserwacji, h.
Współczynnik wykorzystania technicznego reprezentuje relację
gdzie sumy τ to całkowity czas pracy urządzenia w okresie eksploatacji, h; τ czas + τ obs to całkowity czas przestoju spowodowany naprawami i konserwacją dla tego samego okresu eksploatacji, h.
Im bliżej Km jest jeden, tym bardziej niezawodna maszyna.
Współczynnik kosztów eksploatacji charakteryzuje ekonomiczną stronę oceny maszyny i jest wyznaczany z wyrażenia
gdzie Сizg to koszt wytworzenia maszyny; C o - Całkowity koszt jego eksploatacji, naprawy i konserwacji.
Przez eksploatację środków technicznych rozumie się zespół działań organizacyjnych pracowników inżynieryjno-technicznych i pracowników w celu doprowadzenia sprzętu do wymaganego stanu, jego efektywnego wykorzystania oraz utrzymania parametrów eksploatacyjnych i technicznych w określonych granicach.
Generalnie na cały okres eksploatacji składają się następujące etapy: transport sprzętu na miejsce eksploatacji, składowanie przedinstalacyjne, montaż sprzętu, przygotowanie do użytkowania, przeznaczenie (eksploatacja), konserwacja i naprawa.
Pod transport sprzęt rozumiany jest jako dostawa sprzętu i jego montaż w przedsiębiorstwie handlowym. Okres ten ma charakter epizodyczny i występuje, gdy instalowany jest nowy sprzęt lub wymieniany jest stary sprzęt ze względu na koniec jego żywotności. Transport sprzętu musi odbywać się w pełnej zgodności z „Instrukcją transportu” opracowaną przez producenta.
Składowanie to zestaw środków zapewniających bezpieczeństwo sprzętu w stanie spoczynku w odstępach czasu niezwiązanych z użytkowaniem sprzętu zgodnie z jego przeznaczeniem (eksploatacją). Podczas przechowywania sprzęt może znajdować się w magazynach, na terenach otwartych lub zamkniętych, w pomieszczeniach roboczych przedsiębiorstw handlowych i gastronomicznych. Podczas przechowywania bezpieczeństwo sprzętu zapewnia się poprzez zachowanie warunków ograniczających wpływ środowiska zewnętrznego na jego działanie, poprzez konserwację i odpowiednią konserwację.
Montowanie sprzęt przeznaczony jest do instalowania sprzętu w pomieszczeniu roboczym przedsiębiorstwa, jego debugowania i uruchamiania. Montaż urządzeń odbywa się w pełnej zgodności z dokumentacją projektową i projektową.
Przygotowanie sprzętu do użytku obejmuje zestaw środków, w wyniku których sprzęt zostaje doprowadzony z niesprawności do stanu gotowości do użytkowania zgodnie z przeznaczeniem. Przygotowanie sprzętu do eksploatacji można przeprowadzić zarówno po jego zainstalowaniu, jak i po jego zgodnym z przeznaczeniem użytkowaniu. W tym drugim przypadku nazywa się to przygotowaniem operacyjnym do pracy. Typowe czynności, które są wykonywane w ramach przygotowania sprzętu do użytku to; konserwacja, inspekcja zewnętrzna, sprawdzanie funkcjonowania (operacyjności) wszystkich systemów oraz testowanie w różnych trybach. Podczas przygotowania operacyjnego do użytku przeprowadzana jest inspekcja zewnętrzna, diagnostyka techniczna działania wszystkich systemów urządzeń, ich testowanie w różnych trybach, testowanie urządzeń zapewniających bezpieczną pracę i inne środki ochrony pracy.
Używanie sprzętu zgodnie z jego przeznaczeniem oznacza bezpośrednie wykorzystanie sprzętu do realizacji procesów technologicznych. Użytkowanie sprzętu zgodnie z jego przeznaczeniem jest najbardziej krytycznym etapem eksploatacji, którego prawidłowa realizacja zależy od niezawodności i bezpieczeństwa jego działania. Praca operatorów w tym okresie regulowana jest pewnym zestawem dokumentacji technologicznej i operacyjnej. Jednocześnie w tym okresie kadra inżynieryjno-techniczna przedsiębiorstwa prowadzi prace nad uogólnieniem doświadczeń eksploatacyjnych, docelowo mającymi na celu poprawę niezawodności działania i bezpieczeństwa eksploatacji.
Utrzymanie jest fazą eksploatacji, której celem jest utrzymanie operacyjności oraz innych parametrów operacyjnych i technicznych w ustalonych granicach. Istotą konserwacji jest kontrola i zapobieganie wszystkim systemom urządzeń.
Naprawa- jest to etap eksploatacji, podczas którego przeprowadzane są operacje mające na celu doprowadzenie sprzętu do stanu roboczego zarówno zgodnie z określonym planem zapobiegawczym, jak i odtworzenie sprzętu z powodu awarii.
Na ryc. 10.1 przedstawia schemat blokowy działania sprzętu.
Jak wynika z powyższego wykresu, w proces eksploatacji zaangażowana jest znaczna liczba przedsiębiorstw, pracowników inżynieryjno-technicznych oraz robotników (operatorów). W związku z tym eksploatacja sprzętu wymaga celowych działań inżynierów, operatorów, mechaników, pracowników - mechaników i innego personelu konserwacyjnego.
Problem ten można rozwiązać, jeśli wszyscy uczestnicy procesu operacyjnego działają według jednej technologii.
Jak wiadomo, technologia jest rozumiana jako udokumentowane naukowe uogólnienie metod pracy.
Na cały proces eksploatacji składa się zespół określonych procesów technologicznych, które opierają się na operacjach technologicznych wykonywanych przez operatora (pracownika) na jednym stanowisku pracy. W tym przypadku każde pojedyncze działanie operatora jest przejściem technologicznym.
![]() |
Ryż. 10.1. Schemat blokowy eksploatacji urządzeń komercyjnych.
Spójny opis operacji technologicznych wraz z niezbędnymi ilustracjami i schematami jest wyświetlany w głównym dokumencie inżynieryjno-technologicznym - operacyjnej mapie technologicznej.
Dla każdego operatora uczestniczącego w tym procesie technologicznym sporządzana jest mapa operacyjno-technologiczna. Mapa operacyjno-technologiczna powinna zawierać następujące informacje:
nazwa przejścia technologicznego;
Czas przejścia;
tempo produkcji;
Szkic wykonania przejść lub operacji jako całości.
Nadrzędnym celem realizacji procesów operacyjnych i technologicznych jest zapewnienie maksymalnej efektywności w użytkowaniu sprzętu.