Elementy procesu technologicznego obróbki skrawaniem. Proces technologiczny obróbki części
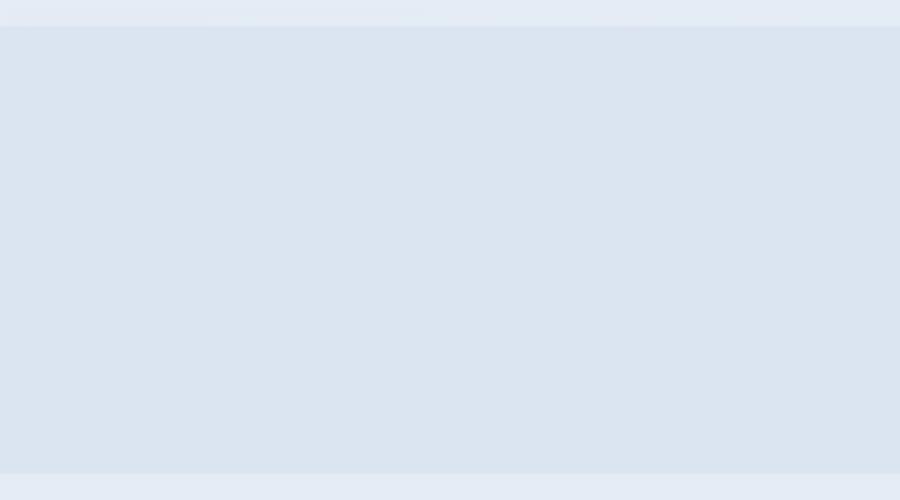
PROCESY PRODUKCYJNE I TECHNOLOGICZNE
Proces produkcyjny rozumiany jest jako zespół poszczególnych procesów realizowanych w celu uzyskania gotowych maszyn (produktów) z materiałów i półproduktów.
Proces produkcyjny obejmuje nie tylko główne, tj. procesy bezpośrednio związane z wytwarzaniem części i montażem z nich maszyn, ale także wszelkie procesy pomocnicze, które zapewniają możliwość wytwarzania produktów (np. transport materiałów i części, kontrola części, produkcja osprzętu i narzędzi itp.).
Proces technologiczny to sekwencyjna zmiana kształtu, wymiarów, właściwości materiału i półproduktu w celu uzyskania części lub wyrobu zgodnie z określonymi wymaganiami technicznymi.
Proces technologiczny obróbka skrawaniem części są częścią ogólnego procesu produkcyjnego całej maszyny.
Proces produkcji podzielony jest na następujące etapy:
1) produkcja półfabrykatów - odlewanie, kucie, tłoczenie;
2) obróbka wykrojów na maszynach do cięcia metalu w celu uzyskania części o ostatecznych wymiarach i kształtach;
3) montaż komponentów i zespołów (lub mechanizmów), tj. łączenie poszczególnych części w zespoły montażowe i zespoły; w produkcji jednostkowej stosuje się obróbkę ślusarską i dopasowanie części do miejsca montażu podczas montażu; w produkcji seryjnej prace te są wykonywane w małej objętości, aw produkcji masowej i na dużą skalę nie są używane, ponieważ dzięki zastosowaniu kalibrów ograniczających podczas obróbki na maszynach do cięcia metalu uzyskuje się wymienność części;
4) montaż końcowy cała maszyna;
5) regulacja i testowanie maszyny;
6) malowanie i wykończenie maszyny (produktu). Kolorowanie składa się z kilku operacji wykonywanych na różne etapy proces, np. szpachlowanie, gruntowanie i pierwsze malowanie odlewów, malowanie elementów obrabianych, lakierowanie końcowe całej maszyny.)
Na każdym etapie procesu produkcyjnego, dla poszczególnych operacji procesu technologicznego, przeprowadzana jest kontrola wytwarzania części zgodnie ze specyfikacją części w celu zapewnienia odpowiedniej jakości gotowej maszyny (wyrobu). Proces technologiczny mechanicznej obróbki części musi być zaprojektowany i przeprowadzony w taki sposób, aby poprzez najbardziej racjonalny i ekonomiczne sposoby obróbki, spełnione zostały wymagania dotyczące detali (dokładność obróbki i chropowatość powierzchni, wzajemne ułożenie osi i powierzchni, poprawność konturów itp.), zapewniając poprawna praca zmontowany samochód.
Według GOST 3.1109-73 proces technologiczny może być projektowy, roboczy, pojedynczy, typowy, standardowy, tymczasowy, perspektywiczny, trasowy, operacyjny, trasowo-operacyjny.
SKŁAD PRODUKCYJNY ZAKŁADU MASZYNOWEGO
Fabryki budowy maszyn składają się z odrębnych jednostek produkcyjnych zwanych warsztatami oraz różnych urządzeń.
Skład warsztatów, urządzeń i obiektów zakładu determinowany jest wielkością produkcji, charakterem procesów technologicznych, wymaganiami dotyczącymi jakości produktów i innych czynników produkcji, a także w dużej mierze stopniem specjalizacji produkcja i współpraca zakładu z innymi przedsiębiorstwami i branżami pokrewnymi.
Specjalizacja polega na koncentracji dużej ilości produkcji ściśle określonych rodzajów produktów w każdym przedsiębiorstwie.
Współpraca przewiduje dostarczanie wykrojów (odlewy, odkuwki, wytłoczki), części składowych, różnych przyrządów i urządzeń produkowanych w innych wyspecjalizowanych przedsiębiorstwach.
Jeżeli projektowany zakład otrzyma odlewy w kolejności współpracy, to nie będzie obejmował odlewni. Na przykład niektóre fabryki obrabiarek otrzymują odlewy z wyspecjalizowanej odlewni, która w sposób scentralizowany dostarcza klientom odlewy.
Skład zaplecza energetyczno-sanitarnego zakładu może być również różny w zależności od możliwości współpracy z innymi obiektami przemysłowymi i narzędzia do dostaw energii elektrycznej, gazu, pary, sprężonego powietrza w zakresie transportu, wodociągów, kanalizacji itp.
Dalszy rozwój specjalizacji, aw związku z tym szeroka kooperacja przedsiębiorstw w istotny sposób wpłynie na strukturę produkcyjną fabryk. W wielu przypadkach skład zakładów budowy maszyn nie przewiduje odlewni i kuźni, warsztatów do produkcji elementów złącznych itp., ponieważ półfabrykaty, okucia i inne części są dostarczane przez wyspecjalizowane zakłady. Wiele zakładów produkcji masowej, we współpracy z wyspecjalizowanymi zakładami, może być również zaopatrywanych w gotowe komponenty i zespoły (mechanizmy) do produkowanych maszyn; na przykład fabryki samochodów i ciągników - gotowe silniki itp.
Skład zakładu budowy maszyn można podzielić na następujące grupy:
1. Zaopatrzenie (odlewnie żelaza, odlewnie stali, odlewnie metali nieżelaznych, kucie, kucie i prasowanie, prasowanie, kucie i tłoczenie itp.);
2. Zakłady przetwórcze (mechaniczne, termiczne, tłoczenie na zimno, obróbka drewna, powlekanie metali, montaż, malowanie itp.);
3. Warsztaty pomocnicze (narzędziowe, mechaniczne, elektryczne, modelowe, eksperymentalne, testujące itp.);
4. Urządzenia do przechowywania (na metal, narzędzia, materiały formierskie i wsadowe itp.);
5. Urządzenia energetyczne (elektrownie, elektrociepłownie, instalacje sprężarkowe i generatory gazu);
6. Urządzenia transportowe;
7. Urządzenia sanitarne (ogrzewanie, wentylacja, zaopatrzenie w wodę, kanalizacja);
8. Ogólne instytucje i urządzenia fabryczne (laboratorium centralne, laboratorium technologiczne, centralne laboratorium pomiarowe, centrala, punkt kontrolny, centrum medyczne, przychodnia lekarska, urządzenia komunikacyjne, stołówka itp.).
STRUKTURA PROCESU TECHNOLOGICZNEGO
Aby zapewnić najbardziej racjonalny przebieg obróbki przedmiotu, sporządzany jest plan obróbki wskazujący, które powierzchnie wymagają obróbki, w jakiej kolejności i w jaki sposób.
W związku z tym cały proces obróbki podzielony jest na odrębne elementy: operacje technologiczne, instalacje, pozycje, przejścia, ruchy, techniki.
Operacja technologiczna to część procesu technologicznego, która odbywa się na jednym stanowisku pracy i obejmuje wszystkie sekwencyjne czynności pracownika (lub grupy pracowników) oraz maszyny do obróbki przedmiotu (jednego lub więcej jednocześnie).
Np. obracanie wału, wykonywane kolejno najpierw na jednym końcu, a potem po skręceniu, czyli przestawieniu wału w kłach, bez wyjmowania go z maszyny, a na drugim końcu, to jedna operacja.
Jeśli wszystkie półfabrykaty (wały) danej partii zostaną obrócone najpierw z jednej strony, a potem z drugiej, będzie to oznaczać dwie operacje.
Część instalacyjna operacji nazywana jest częścią operacji wykonywanej z jednym zamocowaniem przedmiotu obrabianego (lub kilku jednocześnie przetwarzanych) na maszynie lub w uchwycie lub zmontowanym zespole montażowym.
Tak więc np. obracanie wałka przy mocowaniu w kłach jest pierwszym ustawieniem, obracanie wałka po skręceniu i mocowanie go w kłach w celu obróbki drugiego końca to drugie ustawienie. Za każdym razem, gdy część jest obracana o dowolny kąt, tworzone jest nowe ustawienie (podczas obracania części należy określić kąt obrotu).
Zainstalowana i nieruchoma instalacja może zmieniać swoje położenie na maszynie względem jej ciał roboczych pod wpływem urządzeń ruchomych lub obrotowych, przyjmując nowe położenie.
Każda nazywana jest pozycją. odrębny przepis zajmowanego przez niego przedmiotu względem maszyny z niezmienionym mocowaniem.
Na przykład podczas obróbki na wielowrzecionowych maszynach półautomatycznych i automatycznych część z jednym mocowaniem zajmuje różne pozycje względem maszyny poprzez obrót stołu (lub bębna), który sekwencyjnie przenosi część do różnych narzędzi.
Operacja podzielona jest na przejścia - technologiczne i pomocnicze.
Przejście technologiczne - ukończona część operacji technologicznej, charakteryzująca się niezmiennością użytego narzędzia, powierzchni powstałych w wyniku obróbki lub trybu pracy maszyny.
Przejście pomocnicze - zakończona część operacji technologicznej, składająca się z czynności ludzkich i (lub) sprzętowych, którym nie towarzyszy zmiana kształtu, wielkości i chropowatości powierzchni, ale są niezbędne do wykonania przejścia technologicznego. Przykładami przejść pomocniczych są ustawianie przedmiotu obrabianego, zmiana narzędzia itp.
Zmiana tylko jednego z wymienionych elementów (obrobionej powierzchni, narzędzia lub trybu cięcia) definiuje nowe przejście.
Przejście składa się z ruchów roboczych i pomocniczych.
Skok roboczy rozumiany jest jako część przejścia technologicznego, obejmującego wszystkie czynności związane z usuwaniem jednej warstwy materiału tym samym narzędziem, powierzchnią obróbkową i trybem pracy maszyny.
W maszynach przetwarzających korpusy obrotowe skok roboczy rozumiany jest jako: ciągła praca na przykład instrument tokarka usuwanie jednej warstwy wiórów frezem w sposób ciągły, wł strugarka- usunięcie jednej warstwy metalu z całej powierzchni.
Jeżeli warstwa materiału nie jest usuwana, ale poddawana jest odkształceniom plastycznym (np. podczas formowania pofałdowań i walcowania powierzchni wałkiem gładkim w celu jej zagęszczenia), stosuje się również pojęcie suwu roboczego , jak w przypadku usuwania wiórów.
Suw pomocniczy - zakończona część przejścia technologicznego, polegająca na pojedynczym ruchu narzędzia względem przedmiotu obrabianego, nie towarzyszy mu zmiana kształtu, wymiarów, chropowatości powierzchni lub właściwości przedmiotu obrabianego, ale niezbędny do wykonania suwu roboczego .
Wszystkie czynności pracownika, wykonywane przez niego podczas wykonywania operacji technologicznej, są podzielone na odrębne metody. Pod recepcją rozumie się zrealizowaną czynność pracownika. Zazwyczaj odbiory są czynnościami pomocniczymi, na przykład ustawianie lub usuwanie części, uruchamianie maszyny, przełączanie prędkości lub posuwu itp. Pojęcie „odbioru” jest używane w technicznej regulacji operacji.
Plan obróbki obejmuje również prace pośrednie - kontrolne, ślusarskie itp., niezbędne do dalszej obróbki np. lutowanie, składanie dwóch części, obróbka cieplna itp.; operacje końcowe dla innych rodzajów prac wykonywanych po obróbce są zawarte w planie dla odpowiednich rodzajów obróbki.
PROGRAM PRODUKCJI
Program produkcyjny zakładu budowy maszyn zawiera asortyment produkowanych wyrobów (ze wskazaniem ich rodzajów i rozmiarów), ilości wyrobów z poszczególnych pozycji do wyprodukowania w ciągu roku, wykaz i ilość części zamiennych do produkowanych wyrobów.
Na podstawie ogólnego program produkcyjny zakład opracowuje szczegółowy program produkcji dla warsztatów ze wskazaniem nazwy, ilości, czerni i wagi netto (masy) części, które mają być wyprodukowane i przetworzone w danym warsztacie (odlewniczym, kuźniczym, mechanicznym itp.) i poddawanych obróbce w kilku warsztaty; dla każdego warsztatu opracowywany jest program i jedno podsumowanie, wskazujące, które części i ile przechodzą przez każdy warsztat. Przy opracowywaniu szczegółowych programów dla warsztatów do całkowitej liczby części określonej programem produkcyjnym doliczane są części zamienne, dołączane do produkowanych maszyn, jak również dostarczane jako części zamienne, aby zapewnić płynną pracę maszyn w eksploatacji. Liczba części zamiennych jest traktowana jako procent liczby części głównych.
Rysunki są dołączone do programu produkcyjnego typy ogólne maszyn, rysunki montażowe i poszczególne części, specyfikacje części, a także opis projektów maszyn oraz specyfikacje ich wykonania i dostawy.
produkcja technologiczna zakładu budowy maszyn
RODZAJE (TYPY) PRODUKCJI I CHARAKTERYSTYKA ICH PROCESÓW TECHNOLOGICZNYCH. ORGANIZACYJNE FORMY PRACY
W zależności od wielkości programu produkcyjnego, charakteru produktu oraz technicznych i warunki ekonomiczne realizacji procesu produkcyjnego wszystkie różne produkcje są warunkowo podzielone na trzy główne typy (lub typy): pojedyncze (lub indywidualne), seryjne i masowe. Każdy z tych rodzajów procesów produkcyjnych i technologicznych ma swoje własne cechy charakterystyczne, a każdy z nich charakteryzuje się pewną formą organizacji pracy.
Należy zauważyć, że w tym samym przedsiębiorstwie, a nawet w tym samym warsztacie mogą występować różne rodzaje produkcji, tj. poszczególne produkty lub części mogą być wytwarzane w fabryce lub w warsztacie według różnych zasad technologicznych: technologia wytwarzania niektórych części odpowiadają jednej produkcji, a inne - masowej, lub jedne - masowej, inne - seryjnej. I tak np. w ciężkiej inżynierii, która ma charakter pojedynczej produkcji, małe części, które są potrzebne w dużych ilościach, mogą być wytwarzane na zasadzie produkcji seryjnej, a nawet masowej.
Tym samym można scharakteryzować produkcję całego zakładu lub warsztatu jako całości tylko na podstawie dominującego charakteru procesów produkcyjnych i technologicznych.
Pojedyncza produkcja to taka produkcja, w której produkty powstają w pojedynczych egzemplarzach, zróżnicowane pod względem wzornictwa lub wielkości, a powtarzalność tych produktów jest rzadka lub całkowicie nieobecna.
Pojedyncza produkcja jest uniwersalna, czyli obejmuje różne rodzaje produktów, dlatego musi być bardzo elastyczna, dostosowana do wykonywania różnych zadań. Aby to zrobić, zakład musi posiadać zestaw uniwersalnego sprzętu, który zapewnia wytwarzanie produktów o stosunkowo szerokim asortymencie. Taki zestaw urządzeń musi być dobrany w taki sposób, aby z jednej strony można było zastosować różne rodzaje przerobu, a z drugiej, aby stosunek ilościowy poszczególnych typów urządzeń gwarantował określoną przepustowość zakładu .
Proces technologiczny wytwarzania części w tego typu produkcji ma charakter zwarty: na jednej maszynie wykonywanych jest kilka operacji i często wykonywana jest kompletna obróbka części o różnych konstrukcjach iz różnych materiałów. Ze względu na różnorodność prac wykonywanych na jednej maszynie i wynikającą z tego nieuchronność przygotowania i regulacji maszyny w każdym przypadku Nowa praca główny (technologiczny) czas w ogólnej strukturze normy czasu jest niewielki.
Urządzenia do obróbki części na obrabiarkach mają tu charakter uniwersalny, tzn. mogą być stosowane w różnych przypadkach (np. imadło do mocowania części, kątowniki, zaciski itp.). Oprawy specjalne nie są używane lub są rzadko używane, ponieważ znaczne koszty ich produkcji nie są ekonomicznie uzasadnione.
Potrzebne do tego typu produkcji narzędzie skrawające musi być również uniwersalne (standardowe wiertła, rozwiertaki, frezy itp.), ponieważ ze względu na różnorodność obrabianych przedmiotów stosowanie narzędzi specjalnych nie jest ekonomicznie możliwe.
Podobnie i Urządzenie pomiarowe, stosowany w obróbce części, musi być uniwersalny, czyli mierzyć części o różnych rozmiarach. W tym przypadku szeroko stosowane są suwmiarki noniuszowe, mikrometry, suwmiarki, sztihmy, wskaźniki i inne uniwersalne przyrządy pomiarowe.
Różnorodność wytwarzanych produktów, nierównomierność w momencie wejścia do produkcji mniej lub bardziej podobnych wzorów, różnica wymagań dla produktu w zakresie dokładności obróbki części i jakości użytych materiałów, konieczność, należytego do różnorodności detali, wykonywania różnych operacji na uniwersalnym sprzęcie – wszystko to stwarza specjalne warunki udana praca warsztaty i cały zakład, charakterystyczne dla jednej produkcji.
Te cechy tego rodzaju produkcji decydują o stosunkowo wysokim koszcie wytwarzanych produktów. Wzrost popytu na ten produkt przy jednoczesnym zmniejszeniu jego asortymentu i stabilizacji wzorów wyrobów stwarza możliwość przejścia z produkcji jednostkowej do produkcji seryjnej.
Produkcja seryjna zajmuje pozycję pośrednią między produkcją jednostkową a masową.
W produkcji seryjnej produkty wytwarzane są w partiach lub seriach, składających się z produktów o tej samej nazwie, tego samego typu konstrukcji i tej samej wielkości, wprowadzonych do produkcji w tym samym czasie. Podstawową zasadą tego typu produkcji jest produkcja całej partii jako całości, zarówno w obróbce części, jak i montażu.
Pojęcie „partia” odnosi się do liczby części, a pojęcie „serii” do liczby maszyn wprowadzanych do produkcji w tym samym czasie.
W produkcji seryjnej, w zależności od liczby produktów w serii, ich charakteru i pracochłonności, wyróżnia się częstotliwość powtarzania serii w ciągu roku, produkcję małoseryjną, średnioseryjną i wielkoseryjną. Taki podział jest warunkowy dla różnych gałęzi inżynierii.
W produkcji seryjnej proces technologiczny jest przede wszystkim zróżnicowany, to znaczy podzielony na odrębne operacje, które są przypisane do poszczególnych maszyn.
Stosowane są tu obrabiarki różnego typu: uniwersalne, specjalistyczne, specjalne, zautomatyzowane, modułowe. Park maszynowy musi być do tego stopnia wyspecjalizowany, aby możliwe było przejście z produkcji jednej serii maszyn na produkcję innej, nieco odmiennej od pierwszej w sensie konstruktywnym.
Produkcja seryjna jest znacznie bardziej ekonomiczna niż produkcja jednostkowa, ponieważ najlepszy użytek sprzęt, specjalizacja pracowników, wzrost wydajności pracy zapewnia obniżenie kosztów produkcji.
Produkcja seryjna jest najczęstszym rodzajem produkcji w inżynierii ogólnej i średniej.
Produkcja masowa nazywana jest produkcją, w której przy wystarczająco dużej liczbie identycznych wyjść produktów ich wytwarzanie odbywa się poprzez ciągłe wykonywanie tych samych, stale powtarzających się operacji w miejscach pracy.
Produkcja masowa obejmuje następujące rodzaje:
Produkcja przepływowo-masowa, w której wykonywana jest ciągłość ruchu części na stanowiskach pracy ułożonych sekwencyjnie operacje technologiczne przypisane do określonych zadań i wykonywane mniej więcej w tym samym przedziale czasowym;
· masowa produkcja w przepływie bezpośrednim. Tutaj również operacje technologiczne wykonywane są na określonych stanowiskach pracy, ułożonych w kolejności operacji, ale czas wykonywania poszczególnych operacji nie zawsze jest taki sam.
Produkcja masowa jest możliwa i opłacalna ekonomicznie, gdy wytwarzana jest odpowiednio duża liczba produktów, gdy wszystkie koszty organizacji produkcji masowej się opłacają, a koszt jednostkowy produkcji jest niższy niż przy produkcji masowej.
Opłacalność wytwarzania wystarczająco dużej liczby produktów można wyrazić następującym wzorem:
gdzie n to liczba jednostek produktów; C - wysokość kosztów w przejściu z produkcji seryjnej na masową; - koszt jednostki produktów w produkcji masowej; - koszt jednostki produktów w produkcji masowej.
Warunkami decydującymi o efektywności produkcji masowej są przede wszystkim wielkość programu produkcyjnego oraz specjalizacja zakładu w określonych rodzajach produktów, przy czym najwięcej korzystny stan Produkcja masowa to jeden rodzaj, jeden projekt produktu.
W produkcji masowej i wielkoseryjnej proces technologiczny opiera się na zasadzie zróżnicowania lub na zasadzie koncentracji operacji.
Zgodnie z pierwszą zasadą proces technologiczny dzieli się na operacje elementarne o mniej więcej tym samym czasie realizacji; każda maszyna wykonuje jedną określoną operację. W tym celu stosuje się tutaj specjalne i wysokospecjalistyczne maszyny; urządzenia przetwarzające muszą być również specjalne, zaprojektowane do wykonywania tylko jednej operacji. Często takie urządzenie jest integralną częścią maszyny.
Zgodnie z drugą zasadą, proces technologiczny przewiduje koncentrację operacji wykonywanych na automatach wielowrzecionowych, półautomatach, maszynach wielostrzałkowych, osobno na każdej maszynie lub na automatach połączonych w jedną linię, wykonujących kilka operacji jednocześnie z niska cena główny czas. Takie maszyny są coraz częściej wprowadzane do produkcji.
Organizacja techniczna produkcji masowej musi być bardzo doskonała. Jak już wspomniano, proces technologiczny musi być szczegółowo i dokładnie opracowany zarówno pod względem metod obróbki, jak i obliczeń czasów głównych i pomocniczych.
Sprzęt musi być precyzyjnie zdefiniowany i rozplanowany w taki sposób, aby jego ilość, rodzaj, kompletność i wydajność odpowiadały danej wydajności.
Szczególne znaczenie w produkcji masowej ma organizacja kontroli technologicznej, ponieważ niewystarczająco dokładna kontrola części i przedwczesne odrzucenie nieodpowiednich części może prowadzić do opóźnienia i zakłócenia całego procesu produkcyjnego. Najlepsze rezultaty osiąga się stosując automatyczną kontrolę podczas przetwarzania.
Pomimo niewielkich początkowych nakładów kapitałowych wymaganych do organizacji produkcji masowej, jej efekt techniczny i ekonomiczny nie jest prawidłowy. zorganizowane przedsiębiorstwo jest zwykle wysoka i znacznie większa niż w produkcji seryjnej.
Koszt tego samego rodzaju produktu w produkcji masowej jest znacznie niższy, obrót środków jest wyższy, koszt transportu jest mniejszy, wydajność jest większa niż w produkcji masowej.
Każda z opisanych powyżej produkcji (pojedyncza, seryjna, masowa) charakteryzuje się odpowiednimi formami organizacji pracy oraz sposobami lokalizacji sprzętu, które determinowane są charakterem produktu i procesem produkcyjnym, wielkością produkcji oraz szeregiem innych czynniki.
Wyróżniamy następujące główne formy organizacji pracy.
o Według rodzaju wyposażenia, charakterystycznego głównie dla produkcji jednostkowej; na poszczególne części używane w produkcji seryjnej.
Obrabiarki są lokalizowane na zasadzie równomierności obróbki, czyli tworzą sekcje maszyn przeznaczone do jednego rodzaju obróbki - toczenia, strugania, frezowania itp.
o Przedmiot, charakterystyczny głównie dla produkcji seryjnej, na poszczególne części wykorzystywany jest w produkcji masowej.
Maszyny są umieszczane w sekwencji operacji technologicznych dla jednej lub więcej części, które wymagają tej samej kolejności obróbki. W tej samej kolejności powstaje ruch części. Części są obrabiane partiami; jednocześnie wykonywanie operacji na poszczególnych maszynach może nie być skoordynowane z innymi maszynami. Wyprodukowane części składowane są na maszynach, a następnie transportowane w całości.
o Maszyny przepływowo-seryjne lub zmienne, charakterystyczne dla produkcji masowej, znajdują się w sekwencji operacji technologicznych ustalonych dla części obrabianych na tej linii maszynowej. Produkcja odbywa się partiami, a szczegóły każdej partii mogą nieznacznie różnić się od siebie wielkością lub konstrukcją. Proces produkcyjny realizowany jest w taki sposób, aby czas pracy na jednej maszynie był zgodny z czasem pracy na kolejnej maszynie.
o Przepływ bezpośredni, charakterystyczny dla produkcji masowej iw mniejszym stopniu wielkoseryjnej; maszyny są ułożone w sekwencji operacji technologicznych przypisanych do określonych maszyn; części są przenoszone z maszyny na maszynę kawałek po kawałku. Transport części z jednego miejsca pracy do drugiego odbywa się za pomocą stołów rolkowych, pochylonych tac, czasami stosuje się również przenośniki, które służą tutaj tylko jako przenośniki.
o Ciągły przepływ, charakterystyczny tylko dla produkcji masowej. Przy tej formie organizacji pracy maszyny są umieszczane w sekwencji operacji procesu technologicznego przypisanej do poszczególnych maszyn, czas wykonywania poszczególnych operacji na wszystkich stanowiskach pracy jest w przybliżeniu taki sam lub wielokrotność cyklu.
Istnieje kilka rodzajów pracy w ciągłym przepływie: a) z przenoszeniem części (produktów) przez proste urządzenia transportowe- bez elementu trakcyjnego; b) przy okresowym zasilaniu części przez urządzenie transportowe z elementem trakcyjnym. Przemieszczanie części z jednego miejsca pracy do drugiego odbywa się za pomocą przenośników mechanicznych, które poruszają się okresowo - wstrząsami. Przenośnik przesuwa detal po czasie odpowiadającym wartości cyklu pracy, podczas którego przenośnik zatrzymuje się i wykonywana jest operacja pracy; czas trwania operacji jest w przybliżeniu równy wartości cyklu pracy; c) przy ciągłej dostawie części (produktów) urządzeniami transportowymi z elementem trakcyjnym; w tym przypadku przenośnik mechaniczny porusza się w sposób ciągły, przenosząc znajdujące się na nim części z jednego miejsca pracy do drugiego. Operacja jest wykonywana podczas ruchu przenośnika; w tym przypadku część jest albo usuwana z przenośnika w celu wykonania operacji, albo pozostaje na przenośniku, w którym to przypadku operacja jest wykonywana, gdy część porusza się wraz z przenośnikiem. Prędkość przenośnika musi odpowiadać czasowi wymaganemu do zakończenia operacji. Cykl pracy jest mechanicznie wspomagany przez przenośnik.
Dla wszystkich rozważanych przypadków pracy z przepływem ciągłym można stwierdzić, że czynnikiem decydującym o przestrzeganiu zasady przepływu ciągłego nie jest transport mechaniczny części, ale cykl pracy.
OGÓLNA CHARAKTERYSTYKA ZESPOŁU BUDOWY MASZYN
Na Ukrainie udział produktów kompleksu w całkowitej wielkości produkcji przemysłowej wynosi 20%; fabryka ciągników, zakład Charkowski „Elektrotyazmasz”, zakłady lotnicze w Charkowie i Kijowie, zakład transformatorów w Zaporożu, zakład mikroskopów elektronowych w Sumach i wiele innych. Nowe ośrodki rozwiniętej inżynierii mechanicznej były średnie i duże miasta zachodnie regiony Ukrainy.
Kompleks maszynowy Ukrainy to złożona, połączona zróżnicowana produkcja, która specjalizuje się w produkcji maszyn i urządzeń, urządzeń i sprzętu komputerowego, części zamiennych do nich, urządzeń technologicznych itp. Szczególne miejsce zajmuje produkcja sprzętu dla przemysłu . Wiodące z nich to chemia i petrochemia, górnictwo i górnictwo, hutnictwo, lotnictwo, budowa maszyn dla przemysłu lekkiego i spożywczego oraz AGD, maszyny rolnicze.
Produkcja sprzętu do obróbki metali, zwłaszcza obrabiarek, zajmuje w inżynierii mechanicznej ważne miejsce, zapewniając jej niezbędny trwały majątek produkcyjny. Możliwości produkcyjne samego przemysłu maszynowego, jego zgodność z nowoczesne wymagania oraz zdolność do technologicznego ponownego wyposażenia całej produkcji, a przede wszystkim inżynierii mechanicznej. Stan i techniczny i technologiczny poziom budowy obrabiarek, konstrukcja krajowego urządzenia do obróbki metali jest jednym z głównych wskaźników rozwoju inżynierii mechanicznej, jej możliwości produkcyjnych.
Ośrodki produkcji sprzętu do obróbki metali, w szczególności obrabiarek, a także narzędzi, to przede wszystkim największe i najbardziej niezawodne miasta – Odessa, Charków, Kijów, Żytomierz, Kramatorsk, Lwów, Berdyczów; produkcja maszyn kuźniczych i prasujących znajduje się w Odessie, Chmielnicku, Dniepropietrowsku, Strii; przemysł do produkcji sztucznych diamentów i materiałów ściernych - w Połtawie, Lwowie, Zaporożu, Kijowie; produkcja narzędzi do obróbki metali i drewna - w Zaporożu, Chmielnicku, Winnicy, Charkowie, Kamieniec-Podolskim, Ługańsku. Centra produkcji samolotów to Kijów i Charków.
Maszyna nazywa się urządzenie mechaniczne ze skoordynowanymi częściami, które wykonują określone i celowe ruchy w celu transformacji energii, materiałów lub informacji.
Głównym celem maszyny jest zastąpienie funkcji produkcyjnych osoby w celu ułatwienia pracy i zwiększenia wydajności.
Maszyny dzielą się na energię (tj. te, które przetwarzają energię z jednej postaci w drugą) - silniki elektryczne, generatory elektryczne, silniki spalinowe, turbiny (parowe, gazowe, wodne itp.).
Maszyny robocze - obrabiarki, budowlane, tekstylne, maszyny liczące, automaty.
Inżynieria mechaniczna to gałąź produkcji maszyn. Inżynieria mechaniczna to nauka o maszynach (TMM, metaloznawstwo, odporność, materiały, części maszyn itp.).
Każda maszyna składa się z oddzielnych komponentów i części. Jednocześnie znaczna część części jest znormalizowana i wspólna dla wielu typów maszyn - sworznie, śruby, osie, wagi itp. Mogą być produkowane w oddzielnych wyspecjalizowanych zakładach produkcji masowej, co pozwala na pełną automatyzację i zmechanizować całość linia techniczna ich produkcja.
Jednostki są również czasami masowo produkowane z pojedynczych części. ogólny cel- skrzynie biegów, pompy, hamulce itp. Większe połączenia części i zespołów można traktować jako zespoły lub zespoły.
Na przykład silniki są komponentami samochodów, kombajnów, samolotów, a także są produkowane w osobnych fabrykach.
Oznacza to, że wszystkie przedsiębiorstwa budowy maszyn są bardzo ściśle powiązane wskaźnikami technicznymi i ekonomicznymi. Wszyscy pracują przedsiębiorstwo budowy maszyn w dużej mierze zależy od dostawców wyrobów metalowych, części, zespołów.
Oprócz wewnętrznych połączeń odgałęzionych, inżynieria mechaniczna jest połączona z innymi gałęziami, które zaopatrują inżynierię mechaniczną w polimery, gumę, tkaniny, drewno itp., które są wykorzystywane w inżynierii mechanicznej jako materiały konstrukcyjne i dodatkowe.
Podobne dokumenty
Struktura i charakterystyka przemysłu. Produkcja i procesy technologiczne. Rodzaje produkcji, ich charakterystyka techniczna i ekonomiczna. Elementy procesu technologicznego i podstawy jego budowy. Formy organizacji produkcji przemysłowej.
samouczek, dodany 11.04.2010
Etapy procesów technologicznych wytwarzania części maszyn i operacji. Charakterystyka przekładni używanej do skrzyni biegów ruch obrotowy. Proces produkcji części „Wał” dla wielkoseryjnej produkcji. Dobór sprzętu, materiałów.
praca semestralna, dodana 14.07.2012
Wyznaczenie głównych wskaźników techniczno-ekonomicznych procesu produkcyjnego sekcji do obróbki części w warunkach wybranego rodzaju produkcji. Obliczanie ilości sprzętu na placu budowy i jego obciążenia, liczby personelu na placu budowy.
praca semestralna, dodana 12.12.2010
Rodzaje produkcji, formy organizacji i rodzaje procesów technologicznych. Precyzja obróbki. Podstawy bazowania i podstawy przygotowania. Jakość powierzchni części maszyn i półfabrykatów. Etapy projektowania procesów technologicznych przetwórstwa.
przebieg wykładów, dodany 29.11.2010
Pojęcie procesów produkcyjnych i technologicznych, ich klasyfikacja. Zaprogramuj wielkość zadania. Charakterystyka procesu technologicznego. Charakterystyka technologiczna różne rodzaje produkcja. Produkcja wyrobów, kontrola jakości.
prezentacja, dodano 26.10.2013
Opracowanie propozycji technologicznej stworzenia zrobotyzowanego kompleksu technologicznego do wytwarzania określonych części metodą obróbki skrawaniem, tłoczenia lub odlewania. Zadania projektowe automatyzacji produkcji maszynowej.
praca semestralna, dodana 25.10.2014
Istota procesu produkcyjnego. Struktura i procedura technologiczna realizacji operacji. Przestrzeganie zasad organizacji produkcji jako podstawowy warunek jej efektywności. Celowość jego pojedynczych i seryjnych typów w gospodarce.
prezentacja, dodano 24.03.2014
Schemat procesu technologicznego w przędzalni. Specyfikacja techniczna ekwipunek. Bilans godzin pracy i tryb pracy zakładu. Kalkulacja zdolności produkcyjnych zakładu dla wyrobów gotowych. Obliczanie obciążenia pracą zespołu przygotowania do holowania.
praca semestralna, dodana 12.09.2014
Rodzaj produkcji, ilość części w partii. Rodzaj obrabianego przedmiotu i naddatki obróbkowe. Struktura procesu technologicznego, dobór urządzeń i osprzętu. Racjonowanie czasu, określenie ceny i kosztu obróbki mechanicznej części.
praca semestralna, dodana 03.08.2016
Struktura procesu technologicznego według szkiców obróbki wałów: ilość operacji, ustawień, pozycji, przejść i ruchów roboczych. Obliczenia dla produkcji jednostkowej i wielkoseryjnej. Osiągnięcie dokładności przetwarzania. Liczba ustawień przedmiotu obrabianego w operacji.
Istota procesu produkcyjnego, jego rodzaje i struktura, główne operacje i ich przeznaczenie, cechy charakterystyczne z procesu technologicznego. Procedura określania pracochłonności operacji technologicznej i normy czasu potrzebnego na jej wykonanie.
WPROWADZENIE
Całość metod i technik wytwarzania maszyn, wypracowanych przez długi czas i wykorzystywanych w określonym obszarze produkcji, stanowi technologię tego obszaru. W tym zakresie powstały koncepcje: technologia odlewania, technologia spawania, technologia obróbki itp. Wszystkie te obszary produkcji należą do technologii budowy maszyn, obejmującej wszystkie etapy procesu wytwarzania wyrobów inżynierskich.
Dyscyplina „Technologia Inżynierii Mechanicznej” kompleksowo bada interakcję obrabiarki, osprzętu, narzędzia skrawającego i przedmiotu obrabianego, sposoby budowania najbardziej racjonalnych procesów technologicznych obróbki części maszyn, w tym dobór wyposażenia i oprzyrządowania, metody racjonalnej konstrukcji technologicznej procesy montażu maszyn.
Doktryna technologii inżynierii mechanicznej w swoim rozwoju na przestrzeni kilku lat przeszła od prostej systematyzacji doświadczeń produkcyjnych w zakresie obróbki części i montażu maszyn do tworzenia przepisów naukowych opartych na badaniach teoretycznych, prowadzonych naukowo eksperymenty i uogólnienie zaawansowanych doświadczeń zakładów budowy maszyn. Rozwój technologii obróbki skrawaniem i montażu oraz jej kierunek wyznaczają zadania stojące przed przemysłem budowy maszyn w zakresie doskonalenia procesów technologicznych, badań i studiów nad nowymi metodami produkcji, dalszego rozwoju i wdrażania zintegrowanej mechanizacji i automatyzacji procesów produkcyjnych w oparciu o osiągnięcia nauki i techniki, zapewniając najwyższą wydajność pracy przy odpowiedniej jakości i najniższych kosztach produktów.
1. Produkcja i procesy technologiczne
Przez proces produkcyjny rozumie się ogół wszystkich działań ludzi i narzędzi wykonywanych w przedsiębiorstwie w celu uzyskania gotowych produktów z materiałów i półproduktów.
Proces produkcyjny obejmuje nie tylko główne procesy bezpośrednio związane z wytwarzaniem części i montażem z nich maszyn, ale także wszelkie procesy pomocnicze, które zapewniają możliwość wytwarzania produktów (np. transport materiałów i części, kontrola części, produkcja osprzętu i narzędzi itp.).
Proces technologiczny to sekwencyjna zmiana kształtu, wymiarów, właściwości materiału lub półfabrykatu w celu uzyskania części lub produktu zgodnie z określonymi wymaganiami technicznymi.
Proces technologiczny obróbki części musi być zaprojektowany i przeprowadzony w taki sposób, aby poprzez najbardziej racjonalne i ekonomiczne metody obróbki, wymagania stawiane częściom (dokładność obróbki, chropowatość powierzchni, względne położenie osi i powierzchni, regularność konturów, itp.) są spełnione, zapewniając prawidłowe działanie zmontowanych samochodów.
2. Struktura procesu
Aby zapewnić najbardziej racjonalny przebieg obróbki przedmiotu, sporządzany jest plan obróbki wskazujący, które powierzchnie wymagają obróbki, w jakiej kolejności i w jaki sposób.
W związku z tym cały proces obróbki podzielony jest na odrębne elementy: operacje technologiczne, pozycje, przejścia, ruchy, techniki.
Operacja technologiczna to część procesu technologicznego, która odbywa się na jednym stanowisku pracy i obejmuje wszystkie sekwencyjne czynności pracownika (lub grupy pracowników) oraz maszyny do obróbki przedmiotu (jednego lub więcej jednocześnie).
Np. obracanie wałka, wykonywane kolejno najpierw na jednym końcu, a następnie po skręceniu, tj. permutacja wału w kłach, bez wyjmowania go z maszyny, - na drugim końcu to jedna operacja.
Jeżeli wszystkie detale z danej partii zostaną obrócone najpierw na jednym końcu, a potem na drugim, będzie to oznaczać dwie operacje.
Część instalacyjna operacji nazywana jest częścią operacji wykonywanej z jednym zamocowaniem przedmiotu obrabianego (lub kilku jednocześnie przetwarzanych) na maszynie lub w uchwycie lub zmontowanym zespole montażowym.
Na przykład obracanie wału podczas mocowania w środkach jest pierwszym ustawieniem; obracanie wału po obróceniu go i zamocowanie w środkach do obróbki drugiego końca - drugie ustawienie. Za każdym razem, gdy część jest obracana o kąt, tworzona jest nowa konfiguracja.
Zainstalowany i nieruchomy przedmiot obrabiany może zmieniać swoje położenie na maszynie względem jego ciał roboczych pod wpływem ruchu lub obracających się urządzeń, przyjmując nową pozycję.
Pozycja nazywana jest każdą pojedynczą pozycją przedmiotu obrabianego, którą zajmuje w stosunku do maszyny z jej niezmienionym mocowaniem.
Na przykład podczas obróbki na wielowrzecionowych maszynach półautomatycznych i automatycznych część z jednym mocowaniem zajmuje różne pozycje względem maszyny poprzez obrót stołu (lub bębna), który sekwencyjnie przenosi część do różnych narzędzi.
Operacja podzielona jest na przejścia - technologiczne i pomocnicze.
Przejście technologiczne - ukończona część operacji technologicznej, charakteryzująca się niezmiennością użytego narzędzia, powierzchni powstałych w wyniku obróbki lub trybu pracy maszyny.
Przejście pomocnicze - zakończona część operacji technologicznej, składająca się z działania osoby i/lub sprzętu, której nie towarzyszy zmiana kształtu, wielkości i chropowatości powierzchni, ale jest niezbędna do zakończenia przejścia technologicznego. Przykładami przejść pomocniczych są ustawianie przedmiotu obrabianego, zmiana narzędzia itp.
Zmiana tylko jednego z wymienionych elementów (obrobionej powierzchni, narzędzia lub trybu cięcia) definiuje nowe przejście.
Przejście składa się z ruchów roboczych i pomocniczych.
Skok roboczy rozumiany jest jako część przejścia technologicznego, obejmującego wszystkie czynności związane z usuwaniem jednej warstwy materiału tym samym narzędziem, powierzchnią obróbkową i trybem pracy maszyny.
Na maszynach przetwarzających korpusy obrotowe skok roboczy rozumiany jest jako ciągła praca narzędzia, na przykład na tokarce usuwanie jednej warstwy wiórów przez frez jest ciągłe, na strugarce usuwanie jednej warstwy metalu na całej powierzchni. Jeżeli warstwa materiału nie jest usuwana, ale poddawana jest odkształceniom plastycznym (np. podczas formowania się pofałdowań lub walcowania powierzchni wałkiem gładkim w celu jej zagęszczenia), stosuje się również pojęcie suwu roboczego, jak przy usuwaniu wiórów.
Suw pomocniczy - zakończona część przejścia technologicznego, polegająca na pojedynczym ruchu narzędzia względem przedmiotu obrabianego, nie towarzyszy mu zmiana kształtu, wymiarów, chropowatości powierzchni lub właściwości przedmiotu obrabianego, ale niezbędny do wykonania suwu roboczego .
Wszystkie czynności pracownika, wykonywane przez niego podczas wykonywania operacji technologicznej, są podzielone na odrębne metody.
Pod recepcją rozumie się zakończoną czynność pracownika, zwykle recepcje są czynnościami pomocniczymi, na przykład ustawianie lub wyjmowanie części, uruchamianie maszyny, przełączanie prędkości lub posuwu itp. Pojęcie odbioru jest stosowane w technicznej regulacji operacji.
Plan obróbki obejmuje również prace pośrednie - kontrolne, ślusarskie itp., niezbędne do dalszej obróbki np. lutowanie, składanie dwóch części, prasowanie części współpracujących, obróbka cieplna itp. Operacje końcowe dla innych rodzajów prac wykonywanych po obróbce są zawarte w planie dla odpowiednich rodzajów obróbki.
Struktura produkcyjna przedsiębiorstwa o specjalizacji technologicznej
3. Złożoność operacji technologicznej
Czas i koszt wykonania operacji są najważniejszymi kryteriami charakteryzującymi jego skuteczność w warunkach danego programu wytwarzania wyrobów. Program wydawania wyrobów to utworzona dla danego przedsiębiorstwa lista wyprodukowanych wyrobów, wskazująca wielkość produkcji dla każdej pozycji w planowanym okresie czasu.
Wielkość produkcji to liczba produktów o określonych nazwach, rodzajach, rozmiarach i wzorach, wytworzonych w planowanym okresie. Wielkość produkcji jest w dużej mierze zdeterminowana zasadami budowy procesu technologicznego. Szacunkową, maksymalną możliwą pod pewnymi warunkami wielkość produkcji produktów na jednostkę czasu nazywamy zdolnością produkcyjną.
Przy danej wielkości produkcji produkty wytwarzane są partiami. Jest to liczba sztuk części lub zestawu produktów jednocześnie wprowadzanych do produkcji. Partia produkcyjna lub jej część, która dotarła na miejsce pracy w celu wykonania operacji technologicznej, nazywana jest partią operacyjną.
Seria jest całkowity produkty, które mają być wytwarzane zgodnie z ustalonymi rysunkami.
Aby wykonać każdą operację, pracownik poświęca określoną ilość pracy. Pracochłonność operacji to czas spędzony przez pracownika o wymaganych kwalifikacjach przy normalnej pracochłonności i warunkach wykonywania tej pracy. Jednostki miary - osob./godz.
4. Normaczas
Duże znaczenie dla produkcji ma prawidłowe racjonowanie nakładów czasu pracy na obróbkę części, montaż i wykonanie całej maszyny.
Norma czasu - czas przeznaczony na wyprodukowanie jednostki produkcji lub wykonanie pewna praca(w godzinach, minutach, sekundach).
Normę czasu określa się na podstawie obliczeń i analiz technicznych, w oparciu o warunki, być może więcej pełne wykorzystanie możliwości techniczne sprzęt i narzędzia zgodnie z wymaganiami dotyczącymi obróbki danej części lub montażu produktu.
W produkcji maszynowej, przy obróbce części na maszynach do cięcia metalu, norma czasu dla poszczególnych operacji (zestaw operacji) lub norma produkcji części (produktów) w sztukach na jednostkę czasu (godzina, zmiana) jest zdeterminowany.
Techniczna norma czasu, która określa czas poświęcony na przetwarzanie (montaż lub inną pracę), służy jako podstawa do zapłaty za pracę, obliczenia kosztów części i produktów. Na podstawie normy techniczne czas trwania cyklu produkcyjnego, obliczana jest wymagana liczba maszyn, narzędzi i pracowników, określana jest zdolność produkcyjna warsztatów (lub poszczególnych sekcji), przeprowadzane jest całe planowanie produkcji.
Klasyfikacja standardów pracy
Wniosek
Rozwój technologii obróbki skrawaniem i montażu oraz jej kierunek wyznaczają zadania stojące przed przemysłem budowy maszyn w zakresie doskonalenia procesów technologicznych, badań i studiów nad nowymi metodami produkcji, dalszego rozwoju i wdrażania zintegrowanej mechanizacji i automatyzacji procesów produkcyjnych w oparciu o osiągnięcia nauki i techniki, zapewniając najwyższą wydajność pracy przy odpowiedniej jakości i najniższych kosztach produktów. Aby usprawnić proces technologiczny w dowolnej produkcji, konieczne jest wykorzystanie potencjału menedżerskiego, badawczego, rozwojowego i ludzkiego.
Bibliografia
1. Egorov M.E. itp. Technologia inżynieryjna. Podręcznik dla szkół średnich. Wydanie 2, dodatek. M., „Wyżej. szkoła”, 1976.
2. Gusiew A.A., Kowalczuk E.R., Komsow I.M. oraz inny podręcznik do inżynierii mechanicznej. specjalista. uniwersytety. 1986.
3. Skhirtladze A.G. Procesy technologiczne w inżynierii mechanicznej. Dla studentów kierunków inżynierskich uczelni wyższych, „Szkoła Wyższa”, 2007.
W celu pobierz pracę za darmo dołączyć do naszej grupy W kontakcie z. Wystarczy kliknąć poniższy przycisk. Przy okazji w naszej grupie pomagamy bezpłatnie w pisaniu prac naukowych. Kilka sekund po zweryfikowaniu subskrypcji pojawi się link do dalszego pobierania pracy. ![]() |
|
Bezpłatna wycena | |
Zwiększyć oryginalność ta praca. Obejście antyplagiatowe. | |
REF-Master- unikalny program do samodzielnego pisania esejów, prac semestralnych, kontroli i tezy. Za pomocą REF-Mastera można w łatwy i szybki sposób wykonać oryginalny abstrakt, kontrolną lub semestralną pracę na podstawie gotowej pracy - Struktura procesu technologicznego. |
|
Jak pisać poprawnie wprowadzenie?
Sekrety idealnego wprowadzenia prac semestralnych (a także abstraktów i dyplomów) od profesjonalnych autorów największych agencji abstrakcyjnych w Rosji. Dowiedz się, jak poprawnie sformułować trafność tematu pracy, określić cele i zadania, wskazać przedmiot, przedmiot i metody badań, a także teoretyczne, regulacyjne i praktyczne podstawy swojej pracy. |
|
|
Proces technologiczny jest częścią procesu produkcyjnego, która zawiera konsekwentną zmianę wielkości, kształtu, wygląd zewnętrzny przedmiot produkcji i ich kontrola.
Elementy procesu technologicznego: obsługa, instalacja, pozycja, obróbka, przejście, przejście, metoda pracy, ruch.
Proces technologiczny zwykle dzieli się na części zwane operacjami.
Operacja stanowi kompletną część procesu technologicznego. O. ma na celu zmianę geometrii i parametry fizyczne produkty dla 1 miejsca pracy z 1 pracownikiem.
Operacja wykonywane w sposób ciągły na jednym stanowisku pracy.
Operacja jest podstawową jednostką planowania i rozliczania produkcji. Na podstawie operacji określa się złożoność produkcji części, ustala się normy czasowe i ceny, ustala się wymaganą liczbę sprzętu, osprzętu i narzędzi oraz określa się obróbkę s/s.
Skład O.: AIDS: obrabiarka, osprzęt, narzędzie, detal.
Instalacja- Jest to określenie położenia przedmiotu obrabianego na maszynie za pomocą obrabiarek.
Aby móc przedstawić strukturę operacji i uwzględnić czas poświęcony na jej wykonanie, konieczne było podzielenie operacji na odrębne części, zwane przejściami.
Pozycja- jest to stała pozycja zajmowana przez nieruchomy przedmiot wraz z uchwytem względem narzędzia. (tokarki rewolwerowe z poziomą i pionową osią obrotu głowicy.)
Leczenie. Celem obróbki futra jest zmiana właściwości, cech geometrycznych i wymiarów przedmiotu obrabianego.
Przemiana technologiczna- jest to obróbka mechaniczna jednego lub więcej powtórzeń przedmiotu, jednym lub kilkoma narzędziami, w stałych warunkach technologicznych i instalacji.
Zgodnie z tym przejście bezpośrednio związane z realizacją wpływu technologicznego nazywa się głównym (wierceniem). Przejście, składające się z działań pracownika lub mechanizmów niezbędnych do wykonania głównego przejścia, nazywa się pomocniczym (instalacja i mocowanie części).
Pass - obróbka poszczególnych zwojów przy tym samym ustawieniu przedmiotu obrabianego.
skok roboczy zwany pojedynczym ruchem względnym narzędzia i przedmiotu obrabianego, w wyniku którego jedna warstwa materiału zostaje usunięta z jego powierzchni. Aby móc obrabiać przedmiot, musi być zainstalowany i zamocowany w uchwycie, na stole maszyny. Każda nowa ustalona pozycja obiektu produkcyjnego wraz z urządzeniem, w którym obiekt jest instalowany i mocowany, nazywana jest pracą pozycja.
Ruch - są to indywidualne czynności maszyny (włączanie, wyłączanie).
Technika pracy to pełny zestaw ludzkich działań podczas wykonywania określonej części operacji, używany podczas wykonywania przejścia lub jego części. Na przykład - włącz maszynę, przełącz posuwy itp.
Odbiór jest częścią przejścia pomocniczego.
Rodzaje produkcji
Istnieją trzy rodzaje produkcji: I/masowa, 2/seryjna, S/pojedyncza.
Pojedynczy: Pojedyncza produkcja nazywana jest produkcją, charakteryzującą się niewielką ilością produkcji identycznych produktów, reprodukcją produktów, która z reguły nie jest zapewniona. W produkcji masowej nie ma produkcji cyklicznej.
Brak powtarzalności wytwarzania skłania do poszukiwania jak najbardziej uproszczonych sposobów wytwarzania produktów. Najczęściej w ten sposób działają warsztaty eksperymentalne, naprawcze itp. Pracownicy tutaj lubią
zwykle wysoko wykwalifikowani. Sprzęt i wyposażenie - uniwersalne. Koszt produkcji jest wysoki.
1. szerokość asortymentu wytwarzanych wyrobów 2. niewielka wielkość ich produkcji, kilkadziesiąt sztuk rocznie. 3. uniwersalne pokrycie różnego rodzaju produktów. 4. elastyczność w zakresie stosowania uniwersalnego osprzętu (np. tokarki śrubowej, standardowego narzędzia tnącego lub pomiarowego)5. Proces technologiczny wytwarzania części ma charakter zagęszczony tj. na jednej maszynie wykonywanych jest kilka operacji lub całkowite przetworzenie 6.C/s wytworzonego produktu jest stosunkowo wysokie 7. kwalifikacja pracownika - kategoria 5 - 6, wysokie. 8 maszyna - uniwersalny, precyzyjny sprzęt. 9. Współczynnik transakcji stałych powyżej 40. 10. Stosowany jest uproszczony system dokumentacji. 11. Brak tych norm, stosuje się eksperymentalno-statystyczną reglamentację pracy. 12. półfabrykaty: gorącowalcowane, odlewane, odkuwki
Serial: (mały, średni, duży serial - w zależności od partii V)
małe-: 1. kwalifikacja slave kategoria 5-6, 2. satnki - urządzenia półautomatyczne 3. współczynnik mocowania operacji 20 - 40
średni-: 1. kwalifikacja slave 4 kategoria, 2. satnki - urządzenia półautomatyczne 3. współczynnik mocowania działania 10-20
duża skala: 1. kwalifikacja slave 3 kategoria, 2. automatyczna. satnki, moduły produkcyjne 3. współczynnik operacji mocowania od 1-10
1. ograniczona gama wyrobów wytwarzana w cyklicznie powtarzających się partiach 2. wielkość produkcji większa niż w pojedynczej produkcji, okresowo w powtarzalnych partiach 3. półfabrykaty - walcowanie na gorąco i na zimno, odlewanie pod ciśnieniem w gruncie, odlewanie, tłoczenie 4. Proces technologiczny jest głównie zróżnicowany tj. podzielone na sekcje operacje wykonywane na obrabiarki 5. Przy doborze oprzyrządowania technologicznego (z wykorzystaniem urządzeń pomocniczych, specjalnych) należy obliczyć koszty i okresy zwrotu, a także skroplone równ. Efekt. 6. c/c jest niższe niż w pojedynczej produkcji
Cielsko:
Masowe - produkcja, charakteryzująca się dużą wielkością produkcji wyrobów w sposób ciągły
produkowane lub naprawiane przez długi czas, podczas którego większość stanowisk pracy wykonuje jedną operację roboczą. W masowej produkcji dla każdej operacji
wybierany jest najbardziej produktywny, kosztowny sprzęt /automaty, półautomaty/, stanowisko pracy wyposażone jest w złożone, wysokowydajne urządzenia i urządzenia, w
W rezultacie przy dużej wielkości produkcji osiągany jest najniższy koszt produkcji.
1. współczynnik stały =1. 2. kwalifikacja 3-4 (1 powtarzalna operacja wykonywana na każdym stanowisku pracy) 3. automatyczna. satnki, moduły produkcyjne. 4 produkcja w linii 5. Wymaganą dokładność osiąga się metodami automatycznego wymiarowania na dostrojonych maszynach.
1. wąska gama produktów. 2. duża ilość produktów, stale wytwarzanych w technologii. długi okres czasu 3. Szczegółowo opracowany jest proces technologiczny, który charakteryzuje się niską pracochłonnością i niską w porównaniu z seryjną produkcją wyrobów s/c. 4. zastosowanie mechanizacji i automatyzacji procesów produkcyjnych. 5. wykorzystanie technologii. proces z podstawowymi operacjami. 6. korzystanie z szybkich ofert specjalnych. osprzęt, a także narzędzia tnące i pomiarowe. 7. Użyj szablonu
Jakość powierzchni
Jakość powierzchni to połączenie wszystkich jej właściwości użytkowych, a przede wszystkim odporności na zużycie, odporności na korozję, wytrzymałości zmęczeniowej oraz kilku innych właściwości. Jakość powierzchni ocenia się na podstawie dwóch parametrów:
Charakterystyka fizyczna;
Charakterystyka geometryczna
Charakterystyki geometryczne to parametry odchylenia powierzchni od idealnej, danej. Powierzchnia może być niepłaska, owalna, fasetowana itp. Powierzchnię można powiększyć w postaci falistej linii.
Geom. Charakterystyki jakości obrabianej powierzchni są określone przez odchylenie powierzchni rzeczywistej od nominalnej. Odchylenia te można podzielić na 3 odmiany: szorstkość, falistość i odstępstwo od praw. geom. formularze...
Chropowatość to zestaw nieregularności, obrobionych maszynowo ze stosunkowo małymi krokami. Chropowatość powierzchni określa jej profil, który tworzy się w przekroju tej powierzchni.
Chropowatość i falistość to cechy jakości powierzchni, które mają ogromny wpływ na wiele właściwości użytkowych części maszyn.
Rozważane mikronierówności powstają w procesie obróbki skrawaniem poprzez kopiowanie kształtu narzędzi skrawających, odkształcenie plastyczne warstwy wierzchniej części pod wpływem narzędzia obróbczego, jego tarcie o część, drgania itp.
Chropowatość powierzchni części ma znaczący wpływ na odporność na zużycie, wytrzymałość zmęczeniową, szczelność i inne właściwości użytkowe.
Falistość zajmuje pozycję pośrednią między odchyleniami kształtu a chropowatością powierzchni. Występowanie falistości jest związane z procesami dynamicznymi wywołanymi utratą stabilności układu maszyna-narzędzie-część i wyraża się występowaniem drgań.
Falistość powierzchni to zespół powtarzających się okresowo nierówności, w których odległości pomiędzy sąsiednimi wzniesieniami lub zagłębieniami przekraczają długość podstawy dla istniejącej chropowatości powierzchni.
Odchylenie kształtu to odchylenie kształtu powierzchni rzeczywistej lub profilu rzeczywistego od kształtu powierzchni nominalnej lub profilu nominalnego.
Dokładność to stopień zgodności rzeczywistych wartości parametrów geometrycznych z ich podanymi (obliczonymi) wartościami.
Właściwości fizyczne i mechaniczne obejmują twardość i napięcie.
Naprężenia szczątkowe występują po obróbce skrawaniem, operacjach żniwnych, podczas szlifowania (materiał warstwy wierzchniej ulega stwardnieniu, osłabieniu, zmianie jego struktury i mikrotwardości, powstają naprężenia szczątkowe). Po operacjach zbioru, detale uzyskane na prasie poddawane są obróbce termicznej. przetwarzanie.
Rodzaje obróbka cieplna i naprężenia szczątkowe:
Normalizacja- podgrzanie części a następnie schłodzenie w powietrzu. W takim przypadku naprężenia szczątkowe są usuwane i powstaje twardość wyższa niż podczas wypalania. Palenie- charakteryzuje się tym, że przedmiot obrabiany jest odciążany od naprężeń szczątkowych w wyniku nagrzewania pieca, a następnie chłodzenia w jego wnętrzu z szybkością stygnięcia pieca. hartowanie można wytwarzać w roztworach soli, wodzie, oleju. Naprężenie szczątkowe określa się metodami obliczeniowymi i eksperymentalnymi.
Kiedy eksperyment. metody odpoczynku. naprężenia są określane na podstawie obliczeń odkształcenia próbki po usunięciu z niej naprężonej warstwy. Ta metoda to yavl. destrukcyjny.
11. Precyzyjna obróbka. Całkowity błąd. System AIDS. Rodzaje błędów.
Pod dokładność przetwarzania należy rozumieć stopień zgodności między rzeczywistą wartością wskaźnika a wartością nominalną.
Dokładność parametrów geometrycznych to złożona koncepcja, która obejmuje:
Dokładność wymiarów elementów części;
Dokładność figury geometryczne powierzchnie elementów części;
Dokładność względne położenie elementy detali;
Chropowatość powierzchni części (mikrogeometria);
Falistość powierzchni (makrogeometria).
Zwiększenie dokładności oryginalnych detali zmniejsza złożoność i obróbkę mechaniczną obróbki mechanicznej, zmniejsza wartości naddatków i prowadzi do oszczędności metalu.
Dokładność części zależy od wielu czynników:
Odchylenie od geometrii. kształt części lub jej otd. elementy.
Odchylenie rzeczywistych wymiarów części od nominalnych
Odchylenie powierzchni i osi części od dokładnego położenia względnego (od równoległości, prostopadłości, współśrodkowości)
Ponieważ dokładność obróbki w warunkach przemysłowych zależy od wielu czynników, obróbka na obrabiarkach odbywa się nie z osiągalną, ale ekonomiczną dokładnością.
Ek.accuracy mech. przetwarzanie– taka dokładność, u kota. przetwarzanie min s/s odbywa się w normalnych warunkach produkcyjnych (praca wykonywana jest na sprawnych maszynach przy użyciu niezbędnego osprzętu i narzędzi w normalnym czasie i normalnej pracy pracowników) Osiągalna dokładność- celność, kat. można osiągnąć podczas obróbki w specjalnym naib. dogodne warunki wymagane do tej produkcji przez wysoko wykwalifikowanych pracowników przy znacznym wzroście kosztów czasu, nie licząc obróbki s/c.
AIDS: obrabiarka, uchwyt, narzędzie, detal.
Całkowity błąd pomiaru to zbiór błędów powstających pod wpływem dużej liczby czynników.
Błędy: teoretyczne, błędy spowodowane działaniem siły sprężystej AIDS, błędy spowodowane odkształceniem przedmiotu obrabianego pod działaniem sił niezrównoważonych, spowodowane działaniem ciepła, spowodowane zużyciem narzędzia skrawającego, błąd bazowania
Struktura procesu
PROCES TECHNOLOGICZNY I JEGO STRUKTURA (PODSTAWOWE POJĘCIA I DEFINICJE)
Produkcja i procesy technologiczne
Fabryczny proces produkcji(sekcja, sklep) wzywają cały kompleks procesów organizacji, planowania, zaopatrzenia, wytwarzania, kontroli, księgowości itp., niezbędnych do przetwarzania materiałów i półproduktów wprowadzanych do zakładu w produkt końcowy fabryka (warsztat). Zatem, proces produkcji- jest to zbiór wszystkich działań ludzi i narzędzi produkcji wykonywanych w celu wytworzenia wytwarzanych produktów w danym przedsiębiorstwie.
Proces produkcyjny jest złożony i zróżnicowany. Obejmuje: przetwarzanie półfabrykatów w celu uzyskania z nich części; montaż podzespołów i silników oraz ich testowanie; ruch na wszystkich etapach produkcji; organizacja utrzymania miejsc pracy i placów; zarządzanie wszystkimi etapami produkcji, a także wszystkimi pracami nad trening techniczny produkcja.
Oczywiście w każdym procesie produkcyjnym najważniejsze miejsce zajmują procesy bezpośrednio związane z osiągnięciem określonych parametrów produktu. Takie procesy nazywane są technologicznymi. Proces technologiczny- jest to część procesu produkcyjnego, zawierająca działania mające na celu konsekwentną zmianę wielkości, kształtu lub stanu przedmiotu pracy i ich kontrolę (GOST 3.1109-82).
W produkcji Silniki lotnicze stosować różnorodne procesy: odlewanie, ciśnieniowo-cięcie, obróbkę cieplną i fizyko-chemiczną, spawanie, lutowanie, montaż, testowanie. Tak więc, w zależności od rodzaju procesu i rodzaju produktu, rozróżnia się proces technologiczny odlewania, na przykład łopatek turbin; proces technologiczny obróbki cieplnej np. wał turbiny; proces technologiczny obróbki skrawaniem itp. W odniesieniu do procesów kształtowania można sformułować, że proces technologiczny jest układem wzajemnie uzgodnionych operacji, które zapewniają sekwencyjną przemianę półfabrykatu w wyrób (część, przedmiot...) poprzez kształtowanie mechaniczne , fizyko-mechaniczne, elektrofizyczno-chemiczne i inne.
Struktura procesu
Głównym elementem procesu technologicznego jest operacja .
Operacja- jest to część procesu technologicznego wykonywanego na jednym stanowisku pracy przez jednego lub więcej pracowników, jeden lub więcej urządzeń przed przejściem do obróbki części następnej części.
Co najmniej jeden z dwóch określonych warunków jest wystarczający, aby operacja zaistniała. Jeśli na przykład proces polega na szlifowaniu półwyrobu na maszyna do mielenia i stopienie elektroiskrowe tej powierzchni na innej, to niezależnie od liczby części (co najmniej jednej części), w procesie technologicznym będą dwie operacje, ponieważ zmienia się miejsce pracy (ryc. 2.1).
|
Ryż. 2.1. Operacje procesu technologicznego (fragment)
Jednak przetwarzanie w jednym miejscu pracy może również składać się z kilku operacji. Jeżeli np. wiercenie i rozwiercanie detali wykonuje się na tej samej wiertarce, w taki sposób, że najpierw wierci się całą partię detali, a następnie, w zależności od okoliczności, poprzez zmianę wyposażenia (wymiana narzędzi, osprzętu, tryby przetwarzania, środek smarujący chłodzony, narzędzia pomiarowe itp.), Aby wdrożyć, otrzymujesz dwie operacje - „wiercenie”, drugie „rozmieszczenie”, chociaż miejsce pracy jest jedno.
Stanowisko pracy to część powierzchni (kubatura) warsztatu przeznaczona do wykonywania czynności przez jednego lub grupę pracowników, w której sprzęt technologiczny, narzędzia, osprzęt itp.
Pojęcie „eksploatacja” odnosi się nie tylko do procesu technologicznego (TP), który przewiduje kształtowanie. Istnieje kontrola, test, mycie, hartowanie, termiczne itp. operacje.
Operacja charakteryzuje się:
Niezmienność przedmiotu przetwarzania;
Niezmienność wyposażenia (miejsca pracy);
Stałość pracujących wykonawców;
Ciągłość wykonania.
Projektowanie procesu technologicznego polega na ustaleniu:
Skład (nomenklatura) operacji;
Sekwencje operacji w TP;
Operacja jest niepodzielną pod względem planistycznym i organizacyjnym częścią TP. Jest to podstawowa jednostka planowania produkcji. Cały proces produkcyjny opiera się na zestawie operacji:
Intensywność pracy;
Logistyka (maszyny, narzędzia itp.);
Kwalifikacje i liczba pracowników;
Wymagane obszary produkcyjne;
Ilość energii elektrycznej itp. zależy od operacji.
Operacja jest dokładnie udokumentowana.
Operacja może składać się z kilku przejścia. Przejście to część operacji, podczas której ta sama powierzchnia części jest obrabiana tym samym narzędziem, przy niezmienionym trybie pracy maszyny.
![]()
|
![]() |
Ryż. 2.2. Przejścia technologiczne
a– dwa proste przejścia (Ι i ΙΙ); b- jeden kompleks (wyjaśnienia w tekście)
Na ryc. 2.2 pokazuje działanie otworów migających metodą elektrochemiczną. Jak widać na ryc. 2.2, a dziury są sekwencyjnie uzyskiwane podczas realizacji przejść Ι i ΙΙ. Aby poprawić wydajność, często łączą kilka prostych przejść w jedno złożone przejście (ryc. 2.2, b); pozwala to na obróbkę kilku powierzchni jednocześnie.
Przejście technologiczne może zawierać kilka intymny stosunek dwojga ludzi. Przejście to część przejścia, podczas której jedna warstwa metalu jest usuwana (nakładana). Podział na przejścia jest konieczny w tych przypadkach, gdy nie ma możliwości usunięcia (nałożenia) całej warstwy metalu za jednym razem (zgodnie z warunkami wytrzymałości narzędzia, sztywności maszyny, wymagań dokładności itp.).
Operację można wykonać w jednym lub kilku konfiguracjach przedmiotu obrabianego. organizować coś jest częścią operacji technologicznej wykonywanej przy jednym zamocowaniu przedmiotu obrabianego.
W wielu przypadkach operacje są podzielone na stanowiska. Pozycja- ustalone położenie zajmowane przez niezmiennie nieruchomy przedmiot obrabiany, wraz z uchwytem, względem narzędzia lub nieruchomej części wyposażenia w celu wykonania określonej części operacji. Tak więc pozycja jest każdą z różnych pozycji obrabianego przedmiotu względem narzędzia lub narzędzia względem przedmiotu obrabianego w jednym z jego mocowań, na przykład frezowaniem każdej z czterech powierzchni łba śruby w jednym z jego mocowań w urządzenie dzielące.
Różnica między pozycją a ustawieniem polega na tym, że w każdym nowym ustawieniu nowe względne położenie przedmiotu obrabianego i narzędzia jest osiągane przez ponowne zamocowanie przedmiotu obrabianego, a w każdej nowej pozycji bez odłączania przedmiotu obrabianego przez przesuwanie lub obracanie przedmiotu obrabianego lub narzędzia na nową pozycję. Zastąpienie konfiguracji pozycjami zawsze skutkuje skróceniem czasu obróbki, ponieważ toczenie uchwytu z przedmiotem obrabianym lub głowicy z narzędziem zajmuje mniej czasu niż odkręcanie, przestawianie i mocowanie przedmiotu obrabianego.
Wysyłanie dobrej pracy do bazy wiedzy jest proste. Skorzystaj z poniższego formularza
Studenci, doktoranci, młodzi naukowcy korzystający z bazy wiedzy w swoich studiach i pracy będą Ci bardzo wdzięczni.
Wysłany dniahttp:// www. wszystkiego najlepszego. en/
Wstęp
1. Dane wyjściowe do zadania
2. Rodzaj produkcji, ilość części w partii
3. Rodzaj obrabianego przedmiotu i naddatki obróbkowe
4. Struktura procesu technologicznego
5. Dobór sprzętu i osprzętu
6. Wybór narzędzia
7. Obliczanie warunków skrawania
8. Racjonowanie czasu, określenie ceny i kosztu obróbki części
9. Podstawowe informacje o bezpieczeństwie podczas pracy na obrabiarkach
10. Projekt oprawy
11. Rejestracja dokumentacji technicznej
Literatura
Wstęp
Współczesna inżynieria mechaniczna stawia bardzo wysokie wymagania dotyczące dokładności i stanu powierzchni części maszyn, które można zapewnić głównie poprzez obróbkę mechaniczną.
Obróbka metali to zespół czynności mających na celu zmianę kształtu przedmiotu obrabianego poprzez usunięcie naddatku narzędziami skrawającymi na obrabiarkach do metalu, zapewniających określoną dokładność i chropowatość obrabianej powierzchni.
W zależności od kształtu części, charakteru obrabianych powierzchni i wymagań wobec nich, ich obróbka może odbywać się na różne sposoby: mechaniczne - toczenie, struganie, frezowanie, przeciąganie, szlifowanie itp.; elektryczne - elektroiskrowe, elektropulsowe lub anodowo-mechaniczne, a także ultradźwiękowe, elektrochemiczne, wiązkowe i inne metody przetwarzania.
Proces cięcia metalu odgrywa wiodącą rolę w inżynierii mechanicznej, ponieważ dokładność kształtów i rozmiarów oraz wysoka częstotliwość powierzchni metalowych części maszyn w większości przypadków jest zapewniona tylko przez taką obróbkę.
Proces ten jest z powodzeniem stosowany we wszystkich bez wyjątku branżach.
Obróbka metali metodą cięcia to bardzo czasochłonny i kosztowny proces. Tak więc, na przykład, średnio w inżynierii mechanicznej koszt obróbki przedmiotów przez cięcie jest od 50 do 60 razy większy niż koszt gotowych produktów.
Obróbka metali przez cięcie z reguły odbywa się na maszynach do cięcia metalu. Tylko niektóre rodzaje cięcia związane z obróbką metali wykonywane są ręcznie lub za pomocą narzędzi zmechanizowanych.
W nowoczesnych metodach obróbki mechanicznej metali zauważalne są następujące trendy:
obróbka detali z małymi naddatkami, co prowadzi do oszczędności metali i wzrostu udziału operacji wykończeniowych;
powszechne stosowanie metod hartowania bez usuwania wiórów poprzez walcowanie wałkami i kulkami, przedmuchiwanie śrutem, wbijanie, struganie itp.;
zastosowanie obróbki wielonarzędziowej zamiast jednonarzędziowej oraz wieloostrzowego narzędzia skrawającego zamiast jednoostrzowego;
zwiększenie prędkości skrawania i posuwów;
wzrost części prac wykonywanych na automatach i półautomatach, kompleksach robotycznych z wykorzystaniem systemów sterowania programami;
szeroko zakrojona modernizacja sprzętu do obróbki metali;
zastosowanie szybkich i wielomiejscowych urządzeń do mocowania obrabianych przedmiotów i mechanizmów w automatyzacji uniwersalnych maszyn do cięcia metalu;
produkcja części ze specjalnych i żaroodpornych stopów, których obrabialność jest znacznie gorsza niż w przypadku zwykłych metali;
udział technologów w opracowywaniu konstrukcji maszyn w celu zapewnienia ich wysokiej produkcyjności.
Bardziej racjonalne, aby otrzymać natychmiast gotowa część z pominięciem etapu przygotowania. Osiąga się to dzięki zastosowaniu precyzyjnych technik odlewania i formowania, Metalurgia proszków. Procesy te są bardziej postępowe i będą coraz częściej wprowadzane do technologii.
1. Wstępnydanenazadanie
szczegóły obróbki mechanicznej metalu,
Stanowisko:
Proces technologiczny obróbki części.
Wstępne dane do zadania podano w tabeli 1:
Tabela 1
Skład chemiczny stali (GOST 1050-88) w tabeli 2:
Tabela 2
Właściwości mechaniczne stali 30 GOST 1050-88 w tabeli 3:
Tabela 3
Właściwości technologiczne stali 30 GOST 1050-88 w tabeli 4:
Tabela 4
2 . Rodzajprodukcja,ilośćDetalewimprezy
Liczbę części w partii można określić za pomocą wzoru:
gdzie N to roczny program produkcji części, szt.
t to liczba dni, dla których konieczne jest posiadanie zapasu danych rocznych.
F to liczba dni roboczych w roku.
241 (szt.) Z tabeli 1 wybierz rodzaj produkcji:
Tabela 1
Rodzaj produkcji - seryjny.
Produkcja seryjna - produkty są wytwarzane lub przetwarzane w partiach (serii), składających się z części tego samego typu o tej samej wielkości, wprowadzanych do produkcji w tym samym czasie.
Teraz z tabeli 2 wybieramy rodzaj produkcji:
Tabela 2
Produkcja jest na średnią skalę i wytwarza małe (lekkie) części, ilość w partii od 51 do 300 sztuk.
3. Poglądpuste miejscaorazdodatkinaprzetwarzanie
Obrabiany przedmiot to przedmiot produkcji, z którego poprzez zmianę kształtu, wielkości, jakości powierzchni i właściwości materiału powstaje wymagana część. Wybór rodzaju przedmiotu obrabianego zależy od materiału, kształtu i rozmiaru, jego przeznaczenia, warunków pracy i doświadczanego obciążenia, od rodzaju produkcji.
Do produkcji części mogą być używane następujące typy puste miejsca:
a) odlewanie z żeliwa, stali, metali kolorowych, stopów i tworzyw sztucznych części kształtowych i karoserii w postaci ram, maźnic, maźnic, szczęk itp.;
b) odkuwki - na części pracujące w zginaniu, skręcaniu, rozciąganiu. W produkcji seryjnej i masowej stosowane są głównie wytłoczki, w produkcji małoseryjnej i jednostkowej, a także dla części o dużych gabarytach - odkuwki;
c) stal gorącowalcowana i zimnowalcowana – na części takie jak wały, pręty, tarcze i inne kształty, które nieznacznie zmieniły wymiary przekroju.
W naszym przypadku wskazane jest wykonanie okładki z walcowanego metalu, ponieważ okrąg dobrze pasuje do wymiarów części.
Naddatki na obróbkę przedstawiono w tabeli 1:
Tabela 1 - naddatki i tolerancje dla przetwarzania
W ta sprawa najlepiej wybrać odlew wykonany ze stali.
Odlewnia jest gałęzią inżynierii zajmującą się wytwarzaniem półfabrykatów kształtowych lub części poprzez wlewanie stopionego metalu do specjalnej formy, która ma kształt półfabrykatu. Po schłodzeniu wlany metal krzepnie i w stanie stałym zachowuje konfigurację wnęki, do której został wlany. Produkt końcowy nazywa się odlewaniem. W procesie krystalizacji roztopionego metalu kształtują się właściwości mechaniczne i eksploatacyjne odlewów.
Odlewnia produkuje różne konstrukcje odlewów o wadze od kilku gramów do 300 ton, o długości od kilku centymetrów do 20 metrów, o grubości ścianek 0,5-500 mm. Do produkcji odlewów stosuje się wiele metod odlewania: w formach piaskowych, w formach skorupowych, według modeli inwestycyjnych, w formie chłodzącej, pod ciśnieniem, odlewaniu odśrodkowym itp. Zakres poszczególnej metody odlewania determinowany jest objętością produkcji, wymagania dotyczące dokładności geometrycznej i chropowatości powierzchni odlewów, wykonalności ekonomicznej i innych czynników.
4. Strukturatechnicznyproces
Ścieżka produkcji części
1. Wiercenie (marka maszyny 2H135):
a) Wywierć otwór 35
b) pogłębiacz 38,85
c) (maszyna T15K6) - skan 40
(Znormalizowany uchwyt 3-szczękowy)
2. Ślusarz
3. (marka maszyny 16K20F3) tokarka CNC
a) przyciąć końcówkę do rozmiaru 163 (-0,3)
b) naostrzyć kulę R150
(Trzpień rozprężny (tulejka))
4. (marka maszyny 16K20F3) tokarka CNC
a) odciąć koniec, zachowując rozmiar 161 (-0,3)
b) naostrzyć kulę R292
(trzpień rozprężny)
5. Frezarka pozioma marki 6M82G z frezem walcowo-czołowym 8 mm, głębokość 10,5 mm. (urządzenie specjalne)
6. Ślusarz.
7. Cementowanie.
8. Hartowanie
9. Wakacje
10. Czyszczenie i kontrola twardości
11. Czyszczenie (obróbka cieplna i kalibracja)
12. (marka maszyny 2H135) rozwiertak 40.
13. (marka maszyny 3E710A) szlifowanie powierzchni. Przywróć szlifowanie do rozmiaru 160.
14. Pranie.
15. Kontrola.
5. Wybórekwipunekorazarmatura
Przy wyborze typu maszyny i jej stopnia automatyzacji należy wziąć pod uwagę następujące czynniki:
1. Wymiary gabarytowe i kształt części;
2. Kształt obrabianych powierzchni, ich lokalizacja;
3. Wymagania techniczne dotyczące dokładności wymiarowej, kształtu i chropowatości obrabianych powierzchni;
4. Wielkość programu produkcyjnego, która charakteryzuje rodzaj produkcji tej części.
W jednostkowej produkcji małoseryjnej stosuje się maszyny uniwersalne, w produkcji seryjnej obok maszyn uniwersalnych szeroko stosowane są półautomaty i automaty, w produkcji wielkoseryjnej i masowej maszyny specjalne, automaty, maszyny modułowe i automaty używane są linie.
Coraz powszechniejsze jest obecnie zastosowanie w produkcji seryjnej automatów sterowanych numerycznie, które umożliwiają szybkie przechodzenie z obróbki jednej części na drugą poprzez wymianę programu umocowanego np. na taśmie dziurkowanej lub na taśmie magnetycznej.
Doboru maszyn dokonujemy według poniższych tabel:
Tabela 1. Tokarki do wkrętów
Wskaźnik |
Modele maszyn |
||||
Największa średnica przedmiotu obrabianego, mm |
|||||
Odległość między środkami, mm |
|||||
Prędkość obrotowa wrzeciona, obr/min |
|||||
Liczba kroków posuwu suwmiarki |
|||||
Wsparcie dostaw. Mm. Poprzeczny wzdłużny |
0,08-1,9 0,04-0,95 |
0,065-0.091 0,065-0,091 |
0,074,16 0,035-2,08 |
0,05- 4,16 0,035-2,08 |
|
Moc głównego silnika elektrycznego, kW |
|||||
Wydajność maszyny |
|||||
Największa dopuszczalna siła dawania przez mechanizm, n |
Tabela 2. Frezarki poziome i pionowe
Wskaźnik |
Modele maszyn |
||||
Poziomy |
pionowy |
||||
Powierzchnia robocza stołu, mm |
|||||
Liczba kroków prędkości wrzeciona |
|||||
Prędkość obrotowa wrzeciona, obr/min |
|||||
Liczba kroków podawania |
|||||
Posuw stołu, mm/min: wzdłużnie w poprzek |
25-1250 15,6-785 |
||||
Maksymalna dopuszczalna siła posuwu, kN |
|||||
Moc silnika głównego |
|||||
Wydajność maszyny |
Tabela 3. Pionowe - wiertarki
Wskaźnik |
Modele maszyn |
|||
2H118 |
2H125 |
2Н135 |
||
Maksymalna nominalna średnica wiercenia.mm |
18 |
25 |
35 |
|
Ruch pionowy głowicy wiercącej, mm |
150 |
200 |
250 |
|
Liczba kroków prędkości wrzeciona |
9 |
12 |
12 |
|
Prędkość obrotowa wrzeciona obr/min |
180-2800 |
45-2000 |
31,5-1400 |
|
Liczba nóżek do serwowania |
6 |
9 |
9 |
|
Posuw wrzeciona.rpm |
0,1-0,56 |
0,1-1,6 |
0,1-1,6 |
|
Moment obrotowy wrzeciona, N |
88 |
250 |
400 |
|
Największa dopuszczalna siła dawania, N |
5,6 |
9 |
15 |
|
Moc silnika elektrycznego, kW |
1,5 |
2.2 |
4 |
|
Wydajność maszyny |
0,85 |
0,8 |
0,8 |
Z tabel wybieramy następujące maszyny: 2N135 16K20F3 6M82G 3E10A
6 . Wybórnarzędzie
1 Przy doborze narzędzia skrawającego należy kierować się sposobem obróbki i rodzajem maszyny, kształtem i położeniem obrabianych powierzchni, materiałem obrabianego przedmiotu i jego właściwości mechaniczne.
Narzędzie musi zapewniać określoną dokładność kształtu i rozmiaru, wymaganą chropowatość obrabianych powierzchni, wysoką wydajność i trwałość, musi być wystarczająco mocne, odporne na wibracje, ekonomiczne.
Wysłany dniahttp:// www. wszystkiego najlepszego. en/
Rysunek 2 - Frez palcowy
Materiał części tnącej narzędzia ma kluczowy w osiąganiu wysokiej wydajności przetwarzania.
Do frezowania powierzchni wybieram frezowanie doczołowe z mechanicznym mocowaniem pięciostronnych wkładek z węglików spiekanych (GOST 22085-76).
Średnica noża, mm D = 100
Liczba zębów frezu z = 12
Parametry geometryczne części tnącej frezu
Kąt główny w planie c = 67є
Kąt pomocniczy w planie ц1 = 5є
Główny kąt natarcia r = 5є
Główny tylny kąt b \u003d 10º
Kąt nachylenia głównej krawędzi skrawającej l = 10є
Kąt pochylenia zębów skośnych lub śrubowych u = 10є
Materiałem części tnącej noża jest stal szybkotnąca T15K6 w postaci pięciobocznej płyty.
Do frezowania rowka wybieram frez do rowków (GOST 8543-71).
frez do rowków
Średnica noża D = 100
Liczba zębów frezu z = 16
Średnica otworu d = 32
Szerokość noża B = 10
Materiałem części tnącej noża jest twardy stop VK6M według GOST (3882-88)
Do wywiercenia otworu wybieram standardowe wiertło kręte wyposażone w płyty z twardego stopu, chwyt stożkowy (GOST 2092-88)
wiertło kręte
Średnica wiertła w mm d = 35
Całkowita długość wiertła w mm L = 395
Długość części roboczej wiertła Lo = 275
Geometryczne parametry ostrzenia
kąt u góry 2c = 120º
główny kąt natarcia r = 7є
główny tylny kąt b \u003d 19º
kąt nachylenia krawędzi poprzecznej w = 55є
kąt nachylenia rowka śrubowego w = 18º
kąt u góry 2ц0 = 73є
Materiałem części tnącej wiertła jest stal szybkotnąca gatunku T15K6 w postaci płyt.
Do szlifowania rowka wybieram ściernicę cylindryczną o prostym profilu GOST 8692-82
Wysłany dniahttp:// www. wszystkiego najlepszego. en/
Rysunek 7 - Tarcza szlifierska
Maksymalna średnica zewnętrzna, mm D = 100
Wysokość koła H = 10
Średnica otworu d = 16
Twardość (GOST 18118-78) - średnio twardy okrąg.
Ziarno - 50.
Snop ceramiczny piąty.
2 Wybór narzędzia pomiarowego zależy od kształtu mierzonych powierzchni, wymaganej dokładności obróbki oraz rodzaju produkcji.
Aby kontrolować wymaganą dokładność obrabianych powierzchni, wybieram następujące narzędzie pomiarowe.
Suwmiarka (GOST 166-63).
Suwmiarka mikrometryczna (GOST 10-58).
Aby kontrolować chropowatość obrabianej powierzchni, wybieram profilometr typu 240 (GOST 9504-60).
7 . Obliczenietrybyciąć
1 Głębokość skrawania t, mm, zależy od naddatku na obróbkę i wymaganej klasy chropowatości obrabianej powierzchni mniejszej niż 5 mm, wówczas frezowanie zostanie wykonane w jednym przejściu.
2 Prędkość posuwu dobiera się zgodnie z literaturą referencyjną, w zależności od właściwości mechanicznych obrabianego materiału, narzędzia skrawającego i wymaganej klasy chropowatości powierzchni.
Na frezarki ustawiony jest posuw minutowy Sm, mm / min, tj. prędkość ruchu stołu ze stałą częścią względem noża. Elementy warstwy ciętej, a co za tym idzie parametry fizyko-mechaniczne procesu frezowania, zależą od posuwu na ząb Sz, tj. ruch stołu z częścią (w mm) podczas obrotu frezu o 1 ząb. Chropowatość obrabianej powierzchni zależy od posuwu na obrót frezu S0, mm/obr.
Pomiędzy tymi trzema wartościami istnieje następująca zależność:
gdzie n i z to odpowiednio prędkość obrotowa i liczba zębów frezu.
Wartość paszy Sz pobieramy z literatury referencyjnej
Następnie korzystając ze wzoru (2) obliczamy SM
3 Obliczoną prędkość skrawania określa wzór empiryczny
gdzie Cv jest współczynnikiem prędkości skrawania, zależnym od materiałów części skrawającej narzędzia i przedmiotu obrabianego oraz od warunków obróbki;
T - obliczony opór noża, min;
m - wskaźnik względnej stabilności;
odpowiednio Xv, Yv, Uv, pv, qv, wskaźniki stopnia wpływu głębokości skrawania, posuwu, szerokości frezowania, liczby zębów i średnicy frezu na prędkość skrawania;
Kv - współczynnik korygujący dla zmienionych warunków.
Wartość współczynnika i wykładników we wzorze na prędkość skrawania podczas frezowania
cv = 445; qv = 0,2; pv; Xv = 0,15; Yv = 0,35, nv = 0,2; pv=0; m = 0,32
Współczynnik korekcji Kv jest zdefiniowany jako iloczyn szeregu czynników
gdzie Kmv jest współczynnikiem uwzględniającym wpływ właściwości mechanicznych obrabianego materiału na prędkość skrawania;
Kpv - współczynnik uwzględniający stan powierzchni przedmiotu obrabianego;
Kv - współczynnik uwzględniający materiał narzędzia.
Kpv = 0,8; Kv = 1.
Ze wzoru (4) znajdujemy współczynnik korekcji:
Następnie zgodnie ze wzorem (3) znajdujemy obliczoną prędkość skrawania
Prędkość obrotowa wrzeciona, obr./min, obliczona ze wzoru
gdzie Vp - projektowa prędkość skrawania, m/min;
D - średnica frezu, mm.
Korzystając ze wzoru (5), znajdujemy obliczoną prędkość wrzeciona
Teraz obliczmy rzeczywistą prędkość obrotową nf, najbardziej zbliżoną do danych paszportowych maszyny. Aby to zrobić, znajdź n i zdefiniuj cały szereg n
gdzie nz i n1 są maksimum i minimalna wartość prędkość obrotowa;
n to liczba kroków prędkości.
Teraz wyznaczamy z szeregu geometrycznego
n2 \u003d n1 cn \u003d 31 1,261 \u003d 39,091;
n3 \u003d n1 c2n \u003d 31 1,2612 \u003d 49,294;
n4 \u003d n1 c3n \u003d 31 1,2613 \u003d 62,159
n5 \u003d n1 c4n \u003d 31 1,2614 \u003d 78,383
n6 \u003d n1 c5n \u003d 31 1,2615 \u003d 98,841
n4 \u003d n1 c3n \u003d 31 1,2613 \u003d 124,638
n4 \u003d n1 c3n \u003d 31 1,2613 \u003d 157,169
n4 \u003d n1 c3n \u003d 31 1,2613 \u003d 198,19
n4 \u003d n1 c3n \u003d 31 1,2613 \u003d 249,918
n4 \u003d n1 c3n \u003d 31 1,2613 \u003d 315,147
n4 \u003d n1 c3n \u003d 31 1,2613 \u003d 397,4
Zatem nf = 315,147 obr/min.
Teraz możemy wyznaczyć Vph ze wzoru (7)
gdzie D - średnica frezu, mm;
nf - częstotliwość obrotów, obr./min.
4 Oblicz minimalny posuw za pomocą wzoru
Podstawiamy wartości do wzoru (8) i otrzymujemy
Określmy wartość Sm najbliższą mniejszą z danych paszportowych maszyny Sm = 249,65 mm/min
Określ rzeczywisty posuw na ząb
Podstawiając wartości do wzoru (9) otrzymujemy
5 Siła skrawania podczas frezowania jest określona wzorem empirycznym
gdzie t jest głębokością frezowania;
Sz - rzeczywisty posuw, mm/ząb;
z to liczba zębów frezu;
D - średnica frezu, mm
nf - rzeczywista częstotliwość obrotów frezu na minutę.
Wartości współczynnika Cp i wykładników Xp, Yp, Up, qp mają następujące znaczenia
cp=545; Xp = 0,9; Yp = 0,74; w górę = 1; qp = 1.
Wartość współczynnika korekcji Kp dla frezowania zależy od jakości obrabianego materiału.
Wtedy dostajemy
Współczynnik wykorzystania mocy maszyny określa wzór
gdzie Ned jest mocą silnika napędowego, kW;
Npot - wymagana moc na wrzecionie, która jest określona wzorem
gdzie Ne - efektywna moc cięcia, kW, jest określona wzorem
Podstawiając wartość do wzoru (13) otrzymujemy
Podstawiając wartości do wzoru (12) otrzymujemy
Teraz obliczamy współczynnik wykorzystania mocy maszyny
Rzeczywistą trwałość narzędzia Тf oblicza się ze wzoru
Podstawiamy wartości do wzoru (14) i otrzymujemy
6 Czas spędzony w procesie mielenia określa wzór
gdzie L jest szacowaną długością przetwarzania, mm;
i - liczba przejść;
Sm - rzeczywisty posuw, mm / min;
Szacunkową długość przetwarzania określa wzór (16)
gdzie l - długość przetwarzania, mm;
l1 - wartość dosuwu, mm;
l2 - przekroczenie noża, mm.
Wartość dosuwu l1 oblicza się ze wzoru (17)
gdzie t jest głębokością cięcia, mm;
D - średnica frezu, mm.
dostajemy
Przyjmuje się, że wartość przekroczenia l2 wynosi 4 mm.
Znajdź szacowaną długość przetwarzania L:
Korzystając ze wzoru (15) obliczamy czas główny
8 . Racjonowanieczasdefinicjastawkiorazpodstawowa cenamechanicznyprzetwarzanieDetale
1 Sztuka Czas obróbki jednej części jest obliczany ze wzoru
gdzie t0 jest głównym czasem technologicznym, min;
tv - czas pomocniczy, min;
tob - czas utrzymania organizacyjno-technicznego stanowiska pracy, min;
tf - czas przerw na odpoczynek i potrzeby fizyczne, min.
Główny czas technologiczny jest równy sumie wartości czasu maszyny dla wszystkich przejść tej operacji.
W ten sposób otrzymujemy
gdzie t01, t02, t03 to główny czas obróbki każdej powierzchni, który obliczymy z proporcji
Z proporcji (20) otrzymujemy
Znalezienie t0i
t01 = 0,00456 100 = 0,456 min
t02 = 0,00456 100 = 0,456 min
t03 = 0,00456 100 = 0,456 min
Korzystając ze wzoru (19) obliczamy Уt0:
Czas pomocniczy - czas na montaż, mocowanie i demontaż części, podejście i wycofanie narzędzia, włączenie maszyny, sprawdzenie wymiarów.
Korzystając z literatury, otrzymujemy
Czas na organizację i Utrzymanie miejsce pracy tb obejmuje: czas na ponowną regulację, czyszczenie i smarowanie maszyny, przyjęcie i rozłożenie narzędzia, wymianę tępego narzędzia itp.
Czas na obsługę miejsca pracy tb, a także na odpoczynek i potrzeby fizyczne tf są przypisane do operacji i obliczane według wzoru
gdzie b jest wartością procentową obsługi miejsca pracy;
c - procent na odpoczynek i potrzeby fizyczne.
Ze wzoru (21) otrzymujemy
Zatem teraz zgodnie ze wzorem (18) możemy obliczyć tszt
2 Czas naliczania sztuk dla operacji obliczany jest ze wzoru (22)
gdzie tpz - czas przygotowawczy i końcowy dla całej partii części, min;
n to liczba części w partii.
3 Czas ten jest określany jako całość operacji i obejmuje czas poświęcony przez pracownika na zapoznanie się z mapa technologiczna przetwarzanie części, studiowanie rysunku, konfigurowanie maszyny, odbieranie, przygotowywanie, instalowanie i usuwanie osprzętu w celu wykonania tej operacji.
Zgodnie z literaturą czas przygotowawczo-końcowy wynosi 30 minut.
4 Stawka za wykonaną pracę, czyli koszt robocizny P jest określony wzorem (23)
gdzie Ct jest stawką taryfową odpowiedniej kategorii;
K - współczynnik.
Wartość stawki taryfowej odpowiadającej IV kategorii przyjmuje się jako
St = 247,64 rub./h
Przyjmuje się współczynnik K równy 2,15.
Zatem ze wzoru (23) otrzymujemy
5 Koszt obróbki części C obejmuje koszt robocizny P oraz koszt kosztów ogólnych H i jest określony wzorem (24)
gdzie H to koszt kosztów ogólnych, ruble;
P - koszt robocizny, pocierać.
Koszt kosztów ogólnych jest równy 1000% kosztów pracy
Ze wzoru (25) znajdujemy H
W ten sposób obliczamy koszt obróbki
9 . Budowaarmatura
Zadaniem zajęć jest opracowanie projektu jednego urządzenia, które wchodzi w skład wyposażenia technologicznego projektowanego procesu obróbki.
Mocowania maszyn przeznaczone są do montażu i mocowania przedmiotu obrabianego i są podzielone: według stopnia specjalizacji - na uniwersalne, rekonfigurowalne, prefabrykowane ze znormalizowanych części i zespołów; w zależności od stopnia mechanizacji - ręczny, zmechanizowany, automatyczny; po uzgodnieniu - na osprzęt do tokarek, wiertarek, frezarek, szlifierek i innych; z założenia - jedno i wielomiejscowe, jedno i wielostanowiskowe.
Wybór rodzaju mocowania uzależniony jest od rodzaju produkcji, programu produkcyjnego części, kształtu, wymiarów przedmiotu obrabianego oraz wymaganej dokładności obróbki.
Podczas projektowania osprzętu maszyny rozwiązywane są następujące główne zadania:
1) zniesienie pracochłonnej operacji - znakowanie części przed przetwarzaniem;
2) skrócenie czasu pomocniczego na montaż, mocowanie i ponowny montaż części względem narzędzia;
3) poprawić dokładność przetwarzania;
skrócenie czasu maszynowego i pomocniczego dzięki jednoczesnej obróbce kilku części lub obróbce łączonej kilkoma narzędziami;
ułatwienie pracy pracownika i zmniejszenie złożoności przetwarzania;
zwiększenie możliwości technologicznych i specjalizacji maszyny
W wyniku zastosowania osprzętu wydajność powinna znacząco wzrosnąć, a koszt obróbki zmniejszy się.
Jako urządzenie do frezowania wybieramy imadło maszynowe GOST 18684-73, w którym zmodernizowano szczęki zaciskowe. Ta modernizacja pomaga usprawnić pracę pracowników.
10. Rejestracjatechnicznydokumentacja
Jako główny dokument dokumentacji technicznej prezentowana jest mapa tras, która wskazuje wszystkie operacje i przejścia, a także sprzęt, osprzęt, narzędzia tnące i pomiarowe oraz liczbę pracowników.
Podano profil i wymiary.
Drugim dokumentem technologicznym jest karta operacyjna. Wskazuje przejścia do jednej operacji, jej ilość i materiał obrabianego przedmiotu, jego masę i twardość części. Dla wszystkich przejść wskazane jest narzędzie tnące i pomiarowe.
Dodatkowo obliczone wymiary, głębokość skrawania, ilość przejść, prędkość wrzeciona oraz prędkość trybów obróbki. Obliczony czas maszynowy i pomocniczy.
11 . Głównyinteligencjaotechnikabezpieczeństwowpracanacięcie metalunarzędzia maszynowe
Środki bezpieczeństwa obejmują kompleks urządzeń technicznych i zasad, które zapewniają normalne funkcjonowanie osoby w trakcie pracy i wykluczają urazy zawodowe. Podczas pracy na maszynach do cięcia metalu pracownik musi być chroniony przed działaniem prądu elektrycznego, przed uderzeniami ruchomych części maszyny, a także przedmiotów obrabianych lub przedmiotów obrabianych. narzędzie tnące ze względu na ich słabe mocowanie lub pękanie, oddzielanie wiórów, kontakt z kurzem i chłodziwem.
Ogólne zasady bezpieczeństwa pracy na maszynach do cięcia metalu
1. Do samodzielnej pracy mogą pracować osoby, które przeszły badania lekarskie, przeszły odprawę wprowadzającą, odprawę wstępną w miejscu pracy oraz posiadają świadectwo ochrony pracy.
2. Wykonuj tylko prace, które wchodzą w zakres obowiązków.
3. Pracować tylko w sprawnych, starannie schowanych kombinezonach i specjalnym obuwiu, przewidzianych w instrukcjach ochrony pracy.
4. Używaj tylko sprawnych urządzeń, sprzętu, narzędzi, używaj ich zgodnie z ich przeznaczeniem.
5. Nie pozostawiaj włączonych (działających) maszyn i mechanizmów, sprzętu bez nadzoru.
Wychodząc, nawet na krótki czas, odłącz go od sieci za pomocą przełącznika wstępnego.
6. Nie przechodź pod podniesionym ładunkiem.
7. Nie prać kombinezonów w nafcie, benzynie, rozpuszczalnikach, emulsjach i nie myć w nich rąk.
8. Nie dotykaj przewodzących prąd części wyposażenia elektrycznego maszyn i mechanizmów, obrabianych przedmiotów i części podczas ich obrotu.
9. Nie dmuchaj sprężonym powietrzem na części, nie używaj sprężonego powietrza do usuwania wiórów.
10. Używaj w pracy drewniany pokład i utrzymuj go w dobrym stanie i czystości.
11. Główne niebezpieczne i szkodliwe czynniki produkcji:
możliwość porażenia prądem;
możliwość poparzeń i uszkodzenie mechaniczne wióry;
zwiększony poziom hałasu;
możliwość spadania zainstalowanych i obrobionych części, detali.
12. Podczas pracy na maszynach nie wolno używać rękawiczek ani rękawiczek.
Wymagania bezpieczeństwa na końcu pracy.
1. Wyłącz maszynę, odłącz zasilanie urządzeń elektrycznych.
2. Uporządkuj miejsce pracy.
3. Wytrzyj i nasmaruj trące części maszyny.
4. Usunąć rozlany olej i emulsję przez posypanie piaskiem na zanieczyszczonych miejscach.
5. Usuń wióry i kurz za pomocą szczotki do zamiatania.
6. Ścierki używane podczas sprzątania i podczas pracy wynieść poza warsztat do miejsc do tego wyznaczonych.
7. Przy przekazywaniu zmiany należy poinformować brygadzistę i zmiennokształtnego o zauważonych uchybieniach i podjętych działaniach w celu ich usunięcia.
8. Umyj twarz i dłonie ciepłą wodą z mydłem lub weź prysznic.
Technika bezpieczeństwo w praca na wycinanie śrub maszyna.
1. Przed włączeniem maszyny należy upewnić się, że jej uruchomienie nie jest niebezpieczne dla osób przy maszynie.
3. Zapewnij bezpieczne mocowanie Detale.
4. Przy obróbce części w kłach zabrania się używania kła ze zużytymi stożkami.
7. Zabrania się dotykania rękoma obracających się części maszyny oraz przedmiotu obrabianego.
8. Aby odzież nie została wciągnięta przez obracające się części, należy ostrożnie założyć kombinezon, usunąć włosy pod nakryciem głowy.
9. Zabrania się czyszczenia, czyszczenia, smarowania, montażu i demontażu części podczas pracy maszyny.
10. Podejścia do szafki elektrycznej i miejsca pracy nie powinny być zagracone.
11. W przypadku kontuzji należy powiadomić brygadzistę budowy lub kierownika warsztatu.
12. Uwaga!
W celu uniknięcia przegrzania silnika nie wolno wykonywać więcej niż 60 uruchomień na godzinę przy obrotach wrzeciona do 250 na minutę, nie więcej niż 30 uruchomień na godzinę przy obrotach powyżej 250 na minutę i nie więcej niż 6 uruchomień na minutę godzinę przy obrotach wrzeciona 750 na minutę.
Bibliografia
1. Referencyjny technolog-konstruktor maszyn: W 2 tomach T. / Ed. Kosiłowa A.G. i Meshcheryakova R.K. M., 1972.-694 s. T. 2 / Wyd. Malova A.N. - M.: 1972. - 568 s.
2. Fedin A.P. Materiałoznawstwo i technologia materiałów: (Wytyczne i zadania dla papiery testowe). - Homel: BelGUT.-1992.-83s.
3. Zobnin N.P. itp. Obróbka metali przez cięcie. - M.: Ogólnounijne stowarzyszenie wydawniczo-drukarskie Ministerstwa Kolei, 1962. - 299 s.
Lakhtin Yu.M., Leontieva V.P. Materiałoznawstwo.-M., 1990.-528 s.
Podręcznik metalowca. T.5/. / Wyd. B.L. Bogusławski. -M.: Mashinostroenie, 1997. -673s.
Masterov V.A., Berkovsky V.S. Teoria odkształcenia plastycznego i obróbki ciśnieniowej metali. -M.: Metalurgia, 1989.400 s.
Kazachenko V.P., Savenko A.N., Tereshko Yu.D. Materiałoznawstwo i technologia materiałów. Część III. Obróbka metali przez cięcie: Przewodnik po projektowaniu kursu.-Homel: BelGUT.1997.-47p.
Hostowane na Allbest.ru
...Podobne dokumenty
Opracowanie urządzenia do frezowania rowka wpustowego. Struktura procesu technologicznego obróbki części. Wybór sprzętu, narzędzi; obliczanie warunków skrawania; racjonowanie, określenie kosztu części; sprzęt bezpieczeństwa.
praca semestralna, dodano 26.07.2013 r.
Proces skrawania metalu, jego rola w budowie maszyn. Główne wymagania dotyczące projektowanej części. Dobór sprzętu, osprzętu, narzędzi do obróbki części. Obliczanie trybów cięcia. Rodzaj obrabianego przedmiotu i naddatki obróbkowe.
praca semestralna, dodana 26.03.2013
Opracowanie procesu technologicznego obróbki mechanicznej szybu wielokubełkowej ładowarki zbożowej TO-18A. Ustalenie rodzaju produkcji. Obliczanie naddatków obróbkowych, warunków cięcia, norm czasowych, dokładności operacji. Projekt obrabiarki.
praca semestralna, dodana 12.07.2010
Rodzaj produkcji, ilość części w partii. Rodzaj obrabianego przedmiotu i naddatki obróbkowe. Struktura procesu technologicznego, dobór urządzeń i osprzętu. Racjonowanie czasu, określenie ceny i kosztu obróbki mechanicznej części.
praca semestralna, dodana 03.08.2016
Opracowanie procesu technologicznego obróbki części, sposobu otrzymywania półfabrykatu sterownika hydraulicznego. Szkice operacyjne i system technologii montaż, projekt mocowania i instalacji części, dodatki do jej obróbki.
praca semestralna, dodana 27.01.2012
Określenie kolejności operacji technologicznych obróbki części „Wał”. Uzasadnienie wyboru maszyn, wyznaczenie uprawnień do przerobu. Obliczanie warunków skrawania, norm czasowych i współczynników obciążenia obrabiarek, ich wymaganej liczby.
praca semestralna, dodano 29.01.2015
Sposób otrzymywania półfabrykatów na część „obudowa łożyska dolnego”. Rodzaj produkcji, cel serwisowy części. Droga technologiczna procesu montażu i obróbki kadłuba. Obliczanie naddatków na obróbkę wymiarów przedmiotu obrabianego; tryby cięcia.
praca semestralna, dodano 22.12.2014
Proces technologiczny obróbki mechanicznej części „nośnej”, dobór materiału, cel produkcji. Ocena złożoności, metody obróbki i montażu. Wyznaczenie warunków skrawania, szczegółowa regulacja jednej operacji oraz sporządzenie rysunku detalu.
praca semestralna, dodano 26.04.2012
Opis i analiza technologiczna części „Obudowa hamulca pomocniczego”. Charakterystyka danego rodzaju produkcji. Wybór przedmiotu obrabianego, jego konstrukcja. Opracowanie i uzasadnienie procesu technologicznego obróbki mechanicznej. Obliczanie trybów cięcia.
praca semestralna, dodana 2.10.2016
Przeznaczenie i konstrukcja części „śrubowej”, technologiczna droga obróbki. Ustalenie rodzaju produkcji i sposobu pozyskania przedmiotu obrabianego. Obliczanie naddatków, dobór sprzętu, narzędzi tnących i pomiarowych; wybór trybów cięcia.