Rodzaje obróbki cieplnej metali. Obróbka cieplna stopów. Rodzaje obróbki cieplnej
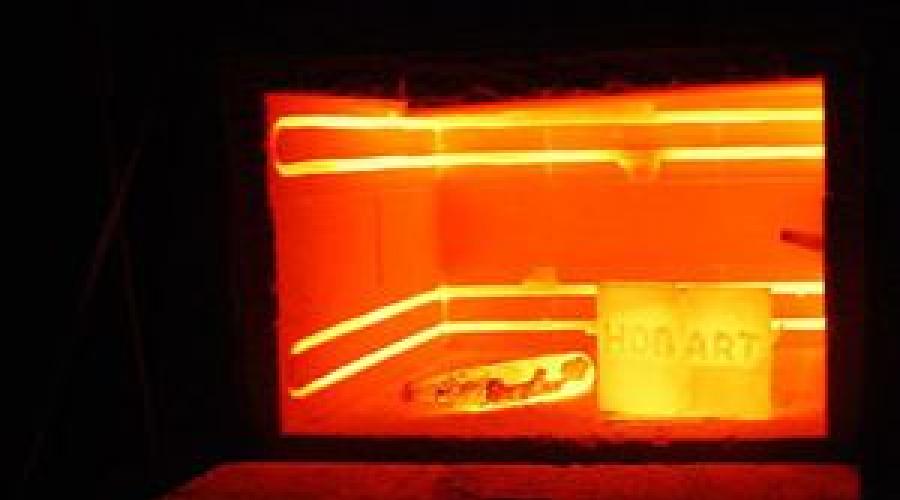
Obróbka cieplna metali
Ale dla dalsza eksploatacja części i elementy wyposażenia często wymagają zupełnie innych właściwości – wytrzymałości, twardości, sztywności itp. Do tych celów przeznaczona jest obróbka cieplna metali.
Istota procesów obróbki cieplnej
zadania różne technologie obróbka cieplna to:
- Zapewnienie najkorzystniejszej mikrostruktury stali i stopów;
- Uzyskanie pożądanego poziomu twardości: w strefie cienkiej powierzchni (lub podpowierzchniowej) lub w całym Przekrój puste miejsca;
- Korekta skład chemiczny w ziarnach makrostruktur różne stopy.
W pierwszym przypadku konieczne jest zapewnienie maksymalnego stopnia jednorodności właściwości metali, co ma znaczenie np. dla późniejszej obróbki mechanicznej, a zwłaszcza odkształcającej. W rezultacie warunki zmiany kształtu przedmiotu obrabianego we wszystkich trzech osie współrzędnych są takie same, a małżeństwo ostatniej części jest wykluczone.
Ponadto niezbędne jest wyrównanie mikro i makrostruktury dla procesów obróbki plastycznej metali w celu zwiększenia stopnia odkształcenia półfabrykatów, co docelowo zbliży kształt detalu do kształtu gotowego wyrobu. Co więcej, dla jak najmniejszej liczby przejść i przy minimalnym nakładzie pracy wymaganego do tego sprzętu.
Zmiana twardości (w wyniku obróbki cieplnej) ma na celu poprawę wydajności części. Ponieważ warunki pracy mogą być bardzo różne, kompleks fizycznych i właściwości mechaniczne dobierany jest ściśle indywidualnie: nie ma uniwersalnych procesów obróbki cieplnej dla stopów o różnych składach.
Zmiana składu chemicznego w ziarnach o mikrostrukturze, spowodowana powstawaniem nowych związków, w większości przypadków nie tylko podnosi wskaźniki twardości, ale także zwiększa odporność na zużycie części, które muszą być eksploatowane przy zwiększonym tarciu, temperaturze lub zwiększone w stosunku do normalnych określonych obciążeń.
hartowanie-odpuszczanie
Pierwsza grupa technologii obróbki cieplnej różnych stopów, w tym stali, obejmuje wyżarzanie i odpuszczanie. W drugim - hartowanie, normalizacja, poprawa, starzenie, leczenie na zimno. W trzecim - wszystkie rodzaje obróbki termochemicznej.
Wyżarzanie
Istotą procesów zachodzących w strukturze większości stopów poddawanych wyżarzaniu jest zapewnienie najbardziej zrównoważonej struktury przedmiotu obrabianego, w której albo nie występują naprężenia wewnętrzne, albo ich poziom jest wystarczająco niski, a tym samym nie wpływa na późniejszą skrawalność metale/stopy.
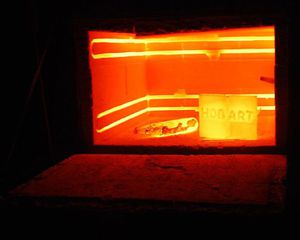
Początkowa struktura prawie wszystkich stopów i stali to dość duże ziarna, pomiędzy którymi znajdują się wtrącenia i zanieczyszczenia, głównie siarka i fosfor. Zwiększa to kruchość metalu, co może być ważne przy formowaniu wyrobów o złożonej konfiguracji z wlewka (lub walcówki). Dlatego konieczne jest zmniejszenie wielkości ziarna i nadanie mu optymalnego kształtu elipsoidy, w której właściwości mechaniczne będą w przybliżeniu takie same we wszystkich trzech osiach współrzędnych.
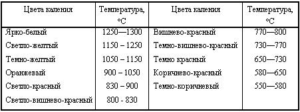
W tym celu oryginalny przedmiot musi zostać podgrzany do temperatury o 50 ... 70 0 C wyższej od temperatury początku przemiany austenitu. Jej efektem jest powstawanie drobnych i dobrze zorientowanych ziaren austenitu pomiędzy ziarnami głównych składników konstrukcyjnych stali - ferrytu i cementytu. Austenit powstaje z perlitu, struktury o największych ziarnach, co przyczynia się do zwiększonej kruchości każdego wlewka. Przemiana austenityczna dla większości stopów przebiega dość wolno, więc wyżarzanie jest procesem długotrwałym, który powinien trwać co najmniej godzinę.
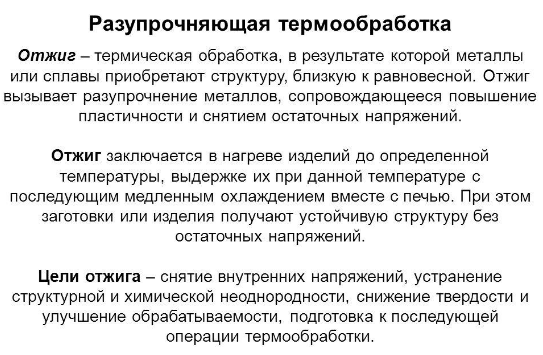
druga ważne zadanie wyżarzanie - usuń naprężenia wewnętrzne, które powstają w przedmiocie obrabianym podczas jego obróbki pod wpływem ciśnienia w stanie zimnym. Faktem jest, że każdej deformacji towarzyszy kruszenie ziarna pierwotnej struktury stali i stopów. W efekcie pojawia się więcej ziaren, wzrasta odporność na odkształcenia, co wymaga nie tylko zwiększenia siły odkształcania, ale także powoduje zniszczenie półfabrykatu, którego stopień odkształcenia przekroczył krytyczny wskaźnik dla tego metalu.
W związku z tym do realizacji pierwszego zadania stosuje się technologię wyżarzania w wysokiej temperaturze (dla stali, w zależności od zawartości węgla, waha się ona od 550 ... 750 0 С), aw drugim - wyżarzanie w niskiej temperaturze (180 .. 220 0 C).
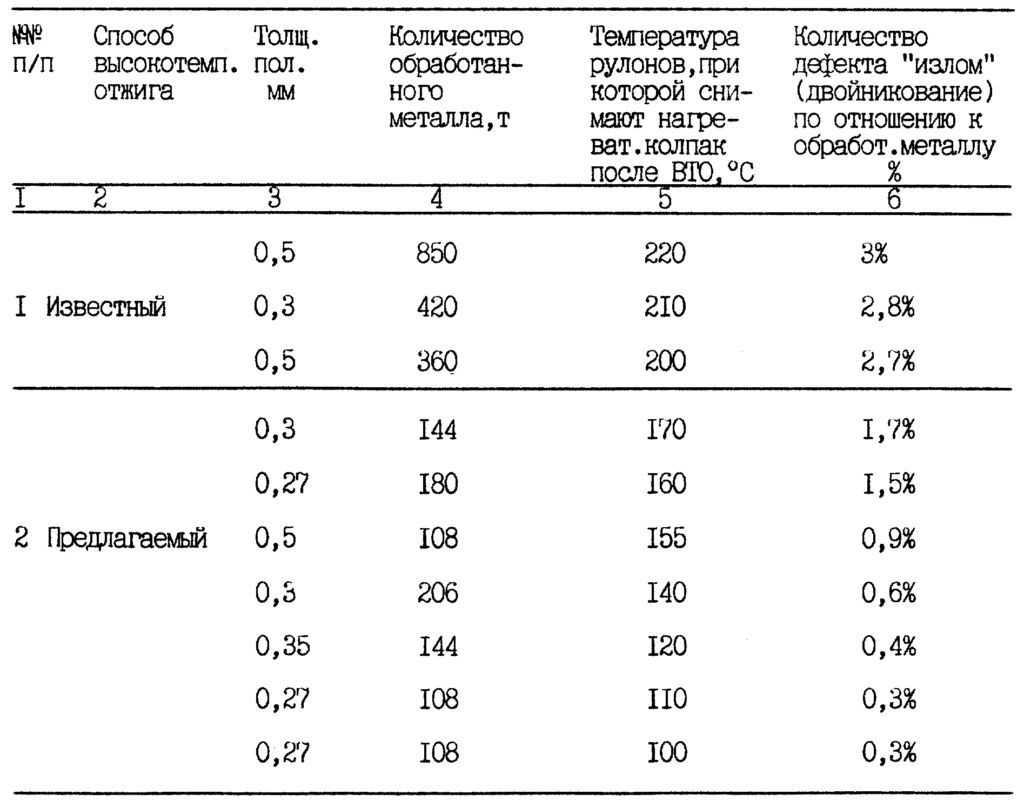
Ogrzewanie następuje powoli, po czym następuje utrzymywanie produktu w danej temperaturze, a następnie powolne chłodzenie. W przypadku stali stopowych i stopów takie chłodzenie odbywa się ze szczególnie małą szybkością w samym piecu, w którym miało miejsce wyżarzanie.
Wakacje
Odpuszczanie według technologii przypomina wyżarzanie, ale odbywa się nie z przedmiotem obrabianym, ale z gotowym produktem, a zatem realizuje inne zadania - odciążenie naprężeń wewnętrznych po obróbce cieplnej, którą przeprowadzono w celu zwiększenia twardości części.
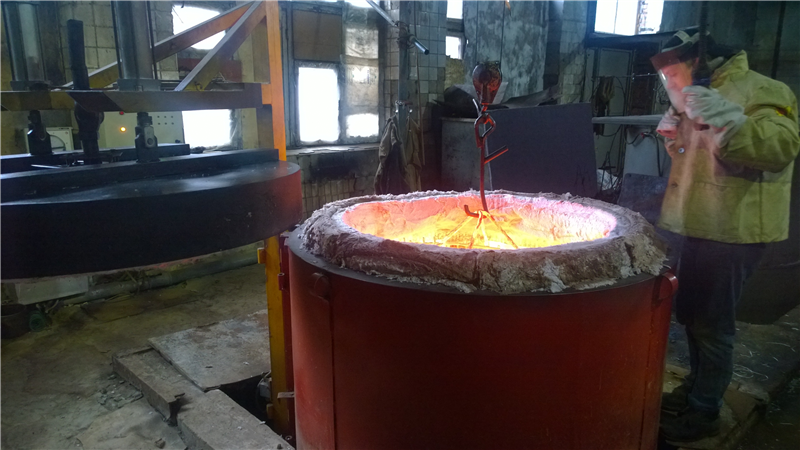
Proces własny urlop na obróbkę cieplną nie jest. W przeciwieństwie do wyżarzania, odpuszczanie czasami odbywa się w kilku etapach: w większości przypadków dotyczy to produktów, do produkcji których zastosowano Różne rodzaje stal wysokostopowa.
hartowanie
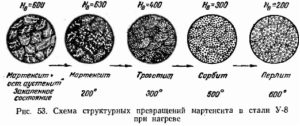
Hartowanie polega na szybkim nagrzaniu przedmiotu obrabianego do temperatury końca przemiany austenitycznej (900...1100 0 C - dla stali niskowęglowych, 750...850 0 C - dla stali wysokowęglowych) a następnie szybkie chłodzenie w specjalnych mediach hartowniczych. Jako te ostatnie stosuje się wodę (w przypadku produktów o niskiej odpowiedzialności) lub olej.
Tryby hartowania są najbardziej zróżnicowane. Głównym czynnikiem decydującym o skuteczności hartowania jest intensywność tworzenia się w strukturze martenzytu - składnika wysokotemperaturowego, który nadaje metalowi lub stopowi zwiększoną twardość.
Warunki powstawania martenzytu określają następujące okoliczności:
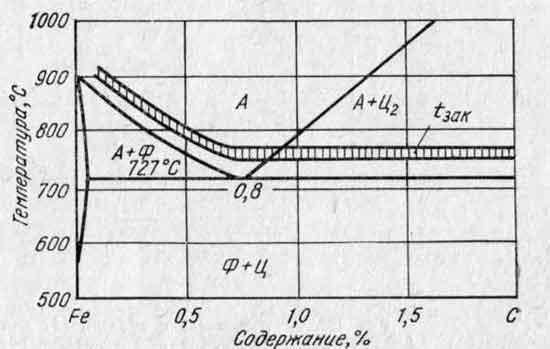
W związku z tym dla każdego gatunku stali lub stopu opracowano indywidualne tryby hartowania, które różnią się:
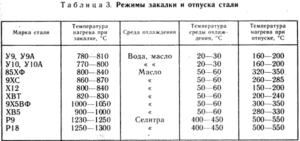
Ze szczególną starannością przeprowadza się hartowanie stali i stopów o złożonym składzie, zawierających kilka pierwiastków stopowych (w szczególności kobalt, molibden). Metale te w procesie tworzą związki międzymetaliczne wzdłuż granic ziaren struktury głównej, które znacznie zwiększają twardość i wytrzymałość stali (w szczególności stali narzędziowych). Kształt i stężenie związków międzymetalicznych zależą tylko i wyłącznie od dokładności technologii hartowania.
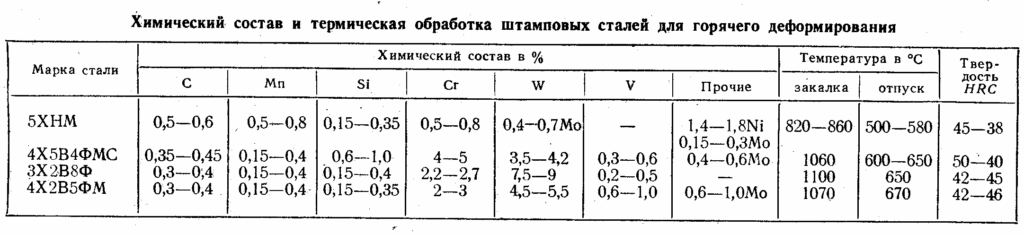
Rodzaje hartowania są określone przez sprzęt, na którym jest wykonywane. Na przykład w przypadku produktów takich jak koła zębate, wały, prowadnice kolumnowe, tam gdzie jest to wymagane optymalna kombinacja wysoka twardość powierzchni i stosunkowo wytrzymały rdzeń, stosuje się utwardzanie powierzchni prądami o wysokiej częstotliwości.
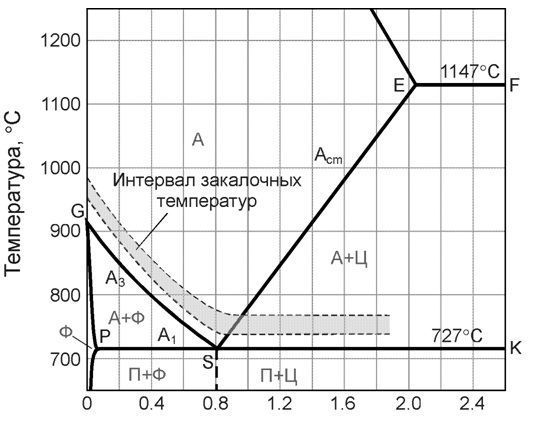
W tym celu produkt umieszcza się w cewce indukcyjnej, przez którą przepływa prąd o wysokiej częstotliwości (do 15 000 ... 25 000 Hz). Przenikając do ograniczonej głębokości, prąd ten przyczynia się do wzrostu wytrzymałości powierzchniowej stali lub stopów. W efekcie znacznie wzrasta wytrzymałość zmęczeniowa części, które pracują w cyklicznie zmieniających się naprężeniach rozciągająco-ściskających.
Bardziej intensywną zmianę twardości powierzchni części można uzyskać stosując do hartowania wysokoenergetyczne źródła ciepła – iskra lub wyładowanie łukowe. Wyładowania muszą być podekscytowane w płynne medium, gdzie umieszczany jest obrabiany przedmiot lub część.
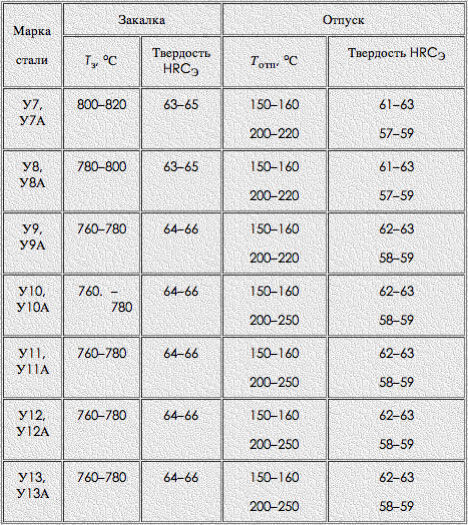
Po hartowaniu w zdecydowanej większości przypadków konieczne jest odpuszczanie, w przeciwnym razie nadmierna twardość końcowa części staje się przyczyną zwiększonej kruchości pod obciążeniami udarowymi.
Poprawa i normalizacja
Jako rodzaj obróbki cieplnej procesy te są zbliżone do wyżarzania, chociaż mają inne przeznaczenie - zwiększenie trwałości eksploatacyjnej krytycznych części maszyn i narzędzi.
Podczas normalizacji część poddawana jest powolnemu nagrzewaniu, utrzymywanemu w określonej temperaturze, po czym koniecznie jest chłodzona wraz z piecem. W rezultacie struktura części staje się bardziej zrównoważona, a poziom naprężenia wewnętrzne idzie w dół.
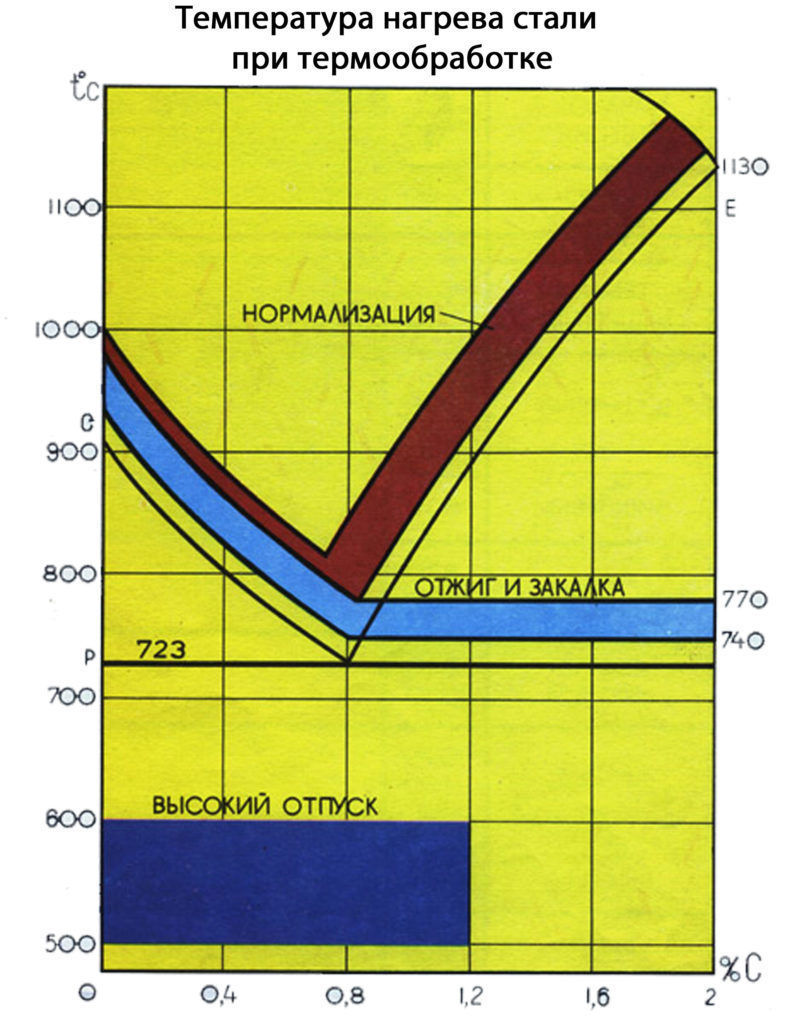
Istotną różnicą jest skład atmosfery, pieca, w którym wykonywane są te operacje obróbki cieplnej. Musi być nieutleniający, ponieważ intensywne tworzenie się tlenku na powierzchni produktu nie tylko pogarsza jego prezentację, ale także zmienia jego wymiary. Wypalenie węgla, które towarzyszy również obróbce cieplnej w konwencjonalnym piecu, pogarsza skład chemiczny stali i zmniejsza jej wytrzymałość.
Zmniejszenie dostępu tlenu do powierzchni części podczas normalizacji odbywa się na kilka sposobów:
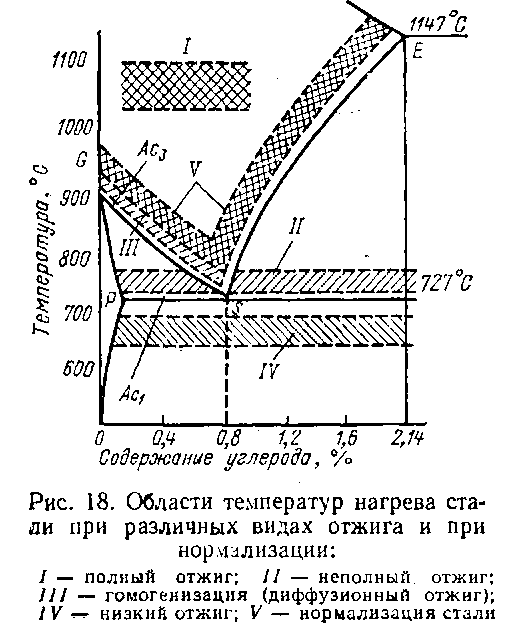
- Ogrzewanie z planowanym brakiem tlenu. W tym przypadku stabilność palniki gazowe piece do obróbki cieplnej są kompensowane przez zwiększenie szybkości dopływu powietrza do strefy spalania;
- Obróbka cieplna w środowisku gazu ochronnego. W przypadku części krytycznych stosuje się pary litu, argon lub inne gazy szlachetne, w innych przypadkach - dwutlenek węgla;
- Poprzez nakładanie powłok ochronnych na powierzchnię produktu, który ma zostać znormalizowany.
Po normalizacji część jest chłodzona w nieruchomym powietrzu, zapobiegając jej przedmuchiwaniu: może to spowodować niejednorodną, „plamistą” mikrostrukturę produktu.
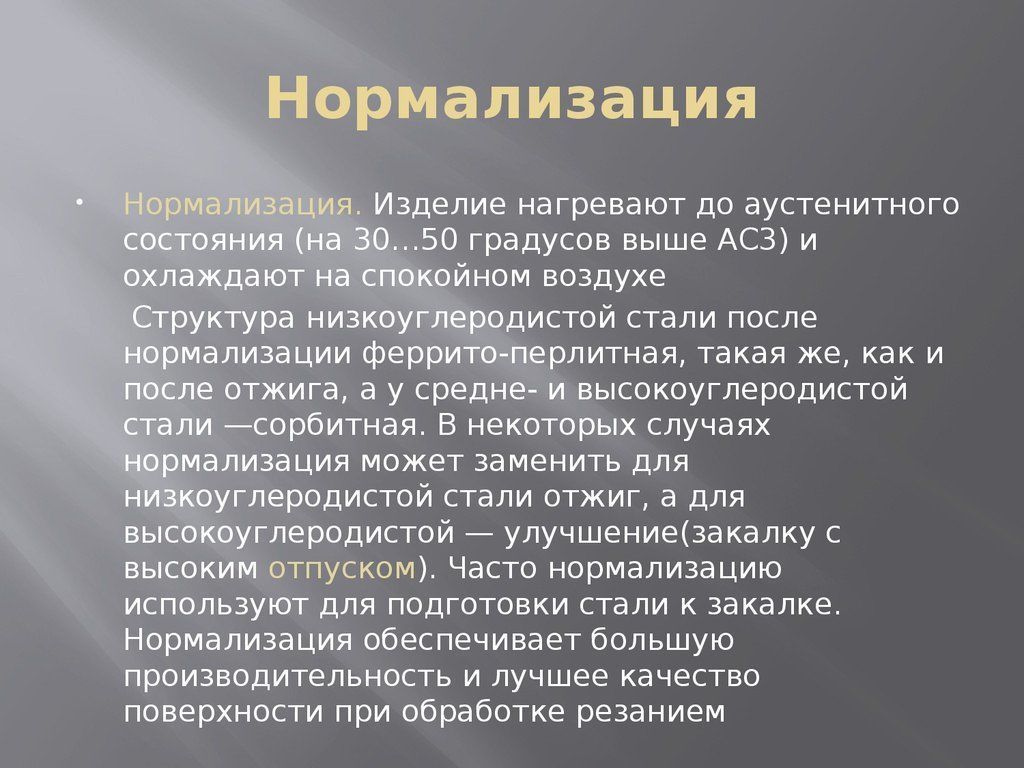
Ulepszenie jest operacją obróbki cieplnej, w wyniku której zwiększa się skrawalność stali i stopów, a poziom naprężeń szczątkowych w nich ulega zmniejszeniu. Towarzyszy temu pewien spadek twardości.
Składnik martenzytyczny w strukturze większości stali i stopów może występować nie tylko przy podwyższonym, ale również przy niska temperatura. Technologia obróbki na zimno wypada korzystnie w porównaniu z tradycyjne technologie obróbka cieplna w następujący sposób:
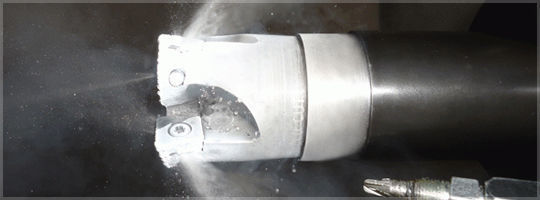
Sposoby obróbki kriogenicznej zależą od gatunku stali/stopów i wahają się w zakresie -60…-1400 С. niskie temperatury. Dzięki połączeniu cykli ogrzewania i chłodzenia całkowity rozkład austenitu szczątkowego osiąga się w ciągu 4 ... 7 godzin (wyższe wartości dla stali wysokostopowych).
Szczególnym rodzajem obróbki cieplnej są procesy obróbki chemiczno-termicznej. Ich zadaniem jest formowanie w mikrostrukturze powierzchni węglików i azotków - związków, które znacznie zwiększają mikrotwardość części i tworzą w nich szczątkowe naprężenia ściskające. Takie produkty wykazują szczególnie wysoką odporność na obciążenia zmienne.
Wideo: Jak hartować dowolny gatunek stali
Obróbka metalu termicznie to zmiana Struktura wewnętrzna(struktura) metalu pod wpływem zmian warunki temperaturowe i uzyskanie w rezultacie niezbędnych mechanicznych i właściwości fizyczne metal. Ogromna część obróbki cieplnej odbywa się w temperaturach krytycznych, w których zachodzi przemiana strukturalna stopów.
W związku z tym zmniejsza się obróbka cieplna metalu o trzy kolejne operacje i rodzaje:
- podgrzewanie metalu z określoną szybkością do określonej temperatury;
- ekspozycja metalu przez pewien czas w tej temperaturze;
- chłodzenie z szybkością określoną przez proces.
Zależy to od tego, jak zmienić właściwości danego wyrobu stalowego i stosuje się różne rodzaje obróbki cieplnej, które różnią się maksymalną temperaturą nagrzewania, czasem utrzymywania i szybkością chłodzenia. W inżynierii mechanicznej obróbka cieplna znalazła najszersze zastosowanie.
Obróbka cieplna metalu, stopu, stali
Wszystkie właściwości dowolnego stopu zależą od jego struktury. Głównym sposobem pozwalającym na zmianę tej struktury jest obróbka cieplna. Jego fundamenty zostały opracowane przez D.K. Chernova, a później jego pracę wspierali A.A. Bochvar, G.V. Kurdyumov, A.P.
Obróbka cieplna metalu i stopu to ciąg operacji takich jak: grzanie, podtrzymywanie i chłodzenie, które są wykonywane w określonej kolejności i w określonym trybie, w celu zmiany wewnętrznej struktury stopu i uzyskania pożądanych właściwości, podczas gdy skład chemiczny metalu nie ulega zmianie.
Jaka jest obróbka cieplna metalu i stopu?
- w wyżarzaniu
- hartowanie
- Wakacje
- Normalizacja
Wyżarzanie. Jest to podgrzanie metalu do wysokiej temperatury, a następnie powolne chłodzenie. Wyżarzanie się dzieje różnego rodzaju- wszystko zależy od reżim temperaturowy szybkość ogrzewania i chłodzenia.
hartowanie. Obróbka cieplna stali, stopów, metali polegająca na rekrystalizacji stali po nagrzaniu powyżej krytyczna temperatura. Po utrzymywaniu stali w tej temperaturze następuje bardzo szybkie schłodzenie. Taka stal ma strukturę nierównowagową i dlatego po hartowaniu następuje odpuszczanie.
Wakacje. Przeprowadza się go po hartowaniu w celu zmniejszenia lub usunięcia naprężeń szczątkowych w stali i stopach, zwiększenia wiązkości, zmniejszenia twardości i kruchości metalu.
Normalizacja. Jest to podobne do wyżarzania, jedyną różnicą jest to, że normalizacja metalu zachodzi w powietrzu, a wyżarzanie odbywa się w piecu.
Ogrzewanie przedmiotu obrabianego
Ta operacja jest bardzo odpowiedzialna. Od niej prawidłowy przebieg zależy po pierwsze od jakości produktu, a po drugie od wydajności pracy. Trzeba wiedzieć, że metal po podgrzaniu zmienia strukturę, właściwości i wszystkie cechy warstwy wierzchniej. Ponieważ stal lub stop wchodzi w interakcję z powietrzem, żelazo utlenia się, a na powierzchni tworzy się kamień. Grubość zgorzeliny zależy od składu chemicznego metalu, temperatury i czasu jego nagrzewania.
Stal zaczyna się szybko utleniać po podgrzaniu powyżej 900 stopni, wtedy utlenialność podwaja się - po podgrzaniu do 1000 stopni C, a w temperaturze 1200 stopni C - 5 razy.
Na czym polega utlenianie różnych stali?
Stal chromowo-niklowa- nazywa się to odpornym na ciepło, ponieważ praktycznie nie podlega utlenianiu.
Stali stopowej- tworzy gęsty, ale cienka warstwa zgorzelina, która zabezpiecza przed dalszym utlenianiem i zapobiega pękaniu podczas kucia.
Stal węglowa- po podgrzaniu traci około 2–4 mm węgla z powierzchni. Jest to bardzo niekorzystne dla metalu, ponieważ traci on swoją wytrzymałość, twardość, a stal pogarsza się podczas hartowania. A szczególnie bardzo szkodliwe jest odwęglenie przy kuciu małych części, a następnie hartowanie. Aby uniknąć pęknięć w stali wysokostopowej i wysokowęglowej, należy je powoli podgrzewać.
Pamiętaj, aby zapoznać się z wykresem „żelazo-węgiel”, gdzie określana jest temperatura początku i końca kucia. Należy to zrobić, aby metal po podgrzaniu nie nabrał gruboziarnistej struktury, a jego plastyczność nie zmniejszyła się.
Ale przegrzanie przedmiotu obrabianego można skorygować poprzez obróbkę cieplną, ale wymaga to dodatkowej energii i czasu. Jeśli metal zostanie podgrzany do podwyższona temperatura, to doprowadzi to do przepalenia, które doprowadzi do zerwania wiązania między ziarnami w metalu i całkowitego zapadnięcia się podczas kucia.
Wypalić się
To jest najbardziej niepoprawne małżeństwo. Podczas ogrzewania metalu lub stopu konieczne jest monitorowanie temperatury, czasu i końca ogrzewania. W przypadku wydłużenia czasu ogrzewania żużel rośnie, a przy szybkim lub intensywnym ogrzewaniu mogą pojawić się pęknięcia.
Przegrzanie stopu następuje w wyniku dyfuzji tlenu na granicach ziaren, gdzie natychmiast tworzą się tlenki, które rozdzielają ziarna w wysokiej temperaturze stopu, a jednocześnie wytrzymałość natychmiast gwałtownie spada. A plastyczność w tym czasie dochodzi do zera. To małżeństwo jest natychmiast wysyłane do stopienia.
Jaka jest obróbka cieplna metali i stopów
Obróbka cieplna podzielony na:
- termiczny;
- termomechaniczny;
- chemiotermiczny
W termiczny obróbka obejmuje główne rodzaje - wyżarzanie I rodzaju, wyżarzanie II rodzaju, hartowanie i odpuszczanie. Normalizacja nie dotyczy wszystkich rodzajów stali, wszystko zależy od jej stopnia stopowania.
Wszystkie rodzaje obróbki cieplnej mają różne temperatury ogrzewania, czas utrzymywania w tej temperaturze i szybkość chłodzenia po zakończeniu utrzymywania.
Pierwszym rodzajem wyżarzania jest wyżarzanie dyfuzyjne, wyżarzanie odprężające.
Drugi rodzaj wyżarzania dzieli się na wyżarzanie niepełne, całkowite, izotermiczne, sferoidyzację i normalizację.
Hartowanie służy do zapewnienia, że produkty są twardy, mocny i odporny na zużycie.
Obróbka termiczna chemiczna
Jest to taka obróbka cieplna stali, która połączona jest z nasycaniem powierzchni produktu – węgla, azotu, aluminium, krzemu, chromu itp., które tworzą substytucyjne roztwory stałe z żelazem. Są dłuższe i bardziej energochłonne niż stal nasycona żelazem i węglem, która z żelazem tworzy międzywęzłowe roztwory stałe.
Obróbka chemiczno-termiczna, tworząc korzystne szczątkowe naprężenia ściskające na powierzchni produktów, zwiększa trwałość i niezawodność produktu. Ona też podnosi odporność na korozję, twardość.
Taka obróbka ma na celu zmianę składu stali w określonej warstwie. Metody te obejmują:
- cementowanie - tą metodą Górna warstwa stal jest wzbogacona w węgiel. W tym przypadku uzyskuje się produkty o połączonych właściwościach - miękki rdzeń i twardy rdzeń. warstwa powierzchniowa;
- azotowanie - e wzbogacenie warstwy wierzchniej azotem w celu zwiększenia odporności na korozję i zmęczenia produktu;
- nudne - to nasycenie warstwy powierzchniowe stal z borem, dzięki tej metodzie wzrasta odporność na zużycie produktu, zwłaszcza podczas tarcia i poślizgu na sucho. Ponadto w przypadku borowania wykluczone jest zatarcie na zimno lub spawanie części. Detale po borowaniu są bardzo odporne na kwasy i zasady;
- aluminiowanie - to jest nasycenie stali aluminium. Odbywa się to w celu nadania stali odporności na agresywne gazy - bezwodnik siarkowy, siarkowodór;
- chromowanie - nasycenie chromem warstwy wierzchniej stali. Chromowanie stali miękkich nie ma prawie żadnego wpływu na ich właściwości wytrzymałościowe. Chromowanie stali o wyższej zawartości chromu nazywane jest chromowaniem twardym, ponieważ na powierzchni części tworzy się węglik chromu, który posiada:
- wysoka twardość
- odporność na skalę
- odporność na korozję
- zwiększona odporność na zużycie
Jest to utwardzająca obróbka cieplna metali i stopów w kriogenicznych, bardzo niskich temperaturach - poniżej -153 stopni C. Wcześniej taka obróbka cieplna była nazywana „obróbką na zimno” lub „obróbką cieplną metalu w temperaturze poniżej zera”. Ale te nazwy nie do końca oddawały całą istotę przetwarzania kriogenicznego.
Jego istota jest następująca: detale przeznaczone do obróbki umieszczane są w procesorze kriogenicznym, gdzie są powoli schładzane, a następnie detale przetrzymywane przez pewien czas w temperaturze -196 stopni C. Następnie stopniowo wracają do temperatury pokojowej. Kiedy ten proces ma miejsce, w metalu zachodzą zmiany strukturalne. Dzięki temu wzrasta odporność na zużycie, wytrzymałość cykliczna, odporność na korozję i erozję.
Główne właściwości uzyskane podczas obróbki, takie jak chłodzenie na zimno, są zachowywane przez cały okres użytkowania przedmiotu obrabianego i dlatego nie wymagają ponownej obróbki.
Na pewno, technologia kriogeniczna nie zastąpi metod hartowania termicznego, ale obrobiony na zimno nada materiałowi nowe właściwości.
Narzędzia poddane obróbce w ultraniskiej temperaturze pozwalają firmom obniżyć koszty, ponieważ:
- zwiększa odporność na zużycie narzędzi, części i mechanizmów;
- maleje liczba małżeństw;
- obniżony zostaje koszt naprawy i wymiany wyposażenia technologicznego i narzędzi.
To sowieccy naukowcy umożliwili pełną ocenę wpływu obróbki na zimno na metal i stop oraz położyli podwaliny pod zastosowanie tej metody.
W dany czas metoda kriogenicznej obróbki produktów znajduje szerokie zastosowanie we wszystkich gałęziach przemysłu.
Inżynieria mechaniczna i obróbka metali:
- zwiększa zasoby sprzętu i narzędzi do 300%;
- zwiększa odporność materiału na zużycie;
- zwiększa siłę cykliczną;
- zwiększa odporność na korozję i erozję;
- łagodzi naprężenia szczątkowe.
Wyposażenie specjalne i transport:
- zwiększa zasoby tarcz hamulcowych o 250%;
- poprawia sprawność układu hamulcowego;
- zwiększa cykliczną wytrzymałość sprężyn zawieszenia i innych elementów elastycznych o 125%;
- zwiększa zasoby i moc silnika;
- obniża koszty eksploatacji pojazdu.
Przemysł obronny:
- zwiększa przeżywalność lufy do 200%;
- zmniejsza wpływ nagrzewania się lufy na wyniki strzelania;
- zwiększa zasoby węzłów i mechanizmów.
Przemysł wydobywczy i produkcyjny:
- zwiększa trwałość narzędzia do cięcia skał do 200%;
- zmniejsza zużycie ścierne jednostek i mechanizmów;
- zwiększa odporność sprzętu na korozję i erozję;
- zwiększa zasoby sprzętu przemysłowego i górniczego.
Sprzęt audio i instrumenty muzyczne:
- zmniejsza zniekształcenia sygnału w przewodnikach;
- poprawia aktywność muzyczną, czystość i przejrzystość dźwięku;
- poszerza zakres brzmieniowy instrumentów muzycznych.
Przetwarzanie kriogeniczne jest stosowane w prawie wszystkich gałęziach przemysłu, w których konieczne jest zwiększenie zasobów, zwiększenie wytrzymałości i odporności na zużycie, a także zwiększenie produktywności.
Niezawodność i trwałość konstrukcje metalowe, wyposażenia, rurociągów zależy od jakości jednostek produkcyjnych, części, elementów, z których się składają. Podczas eksploatacji poddawane są obciążeniom statycznym, dynamicznym i cyklicznym oraz wpływowi agresywnych środowisk. Muszą pracować na niskim poziomie i wysokie temperatury i jest w warunkach szybkiego zużycia.
A zatem działanie dowolnych produktów metalowych zależy bezpośrednio od odporności na zużycie, wytrzymałości, odporności termicznej i korozyjnej elementów, z których się składają.
Aby poprawić wszystkie te cechy, konieczne jest dobranie odpowiedniego materiału na części, udoskonalenie ich konstrukcji, wyeliminowanie niedokładności montażowych oraz udoskonalenie metod pracy na gorąco i na zimno.
Tak wysokie wymagania rzadko spełniają materiały w stanie dostawy. Główna część dostarczonej elementy konstrukcyjne potrzebuje stabilizacji właściwości użytkowe więc nie zmieniają się w czasie. I w celu wzmocnienia mechanicznego i właściwości fizykochemiczne materiały metalowe, zastosować obróbkę cieplną. Jest to sekwencja operacji ogrzewania, utrzymywania i chłodzenia metali i stopów.
Ma na celu zmianę struktury i właściwości metali i stopów w wyznaczonym kierunku. Obróbka cieplna służy do zmiany struktury składu fazowego i redystrybucji składników, wielkości i kształtu ziaren krystalicznych, rodzajów defektów, ich liczby i rozmieszczenia. A wszystko to sprawia, że uzyskanie wymaganej właściwości materiału jest dość łatwe.
Należy pamiętać, że właściwości metali i stopów zależą nie tylko od struktury, ale także od składu chemicznego, jaki powstaje w procesie metalurgicznym i odlewniczym.
Zadaniem obróbki cieplnej jest eliminacja naprężeń wewnętrznych w metalu i stopie, poprawa właściwości mechanicznych i eksploatacyjnych i nie tylko.
poddany obróbce cieplnej stal, żeliwo, stop metali nieżelaznych.
Musisz wiedzieć, że materiały o tym samym składzie chemicznym podczas różne tryby obróbka cieplna, można uzyskać kilka zupełnie różnych struktur, które będą miały zupełnie inne właściwości. Poprzez poprawę właściwości mechanicznych poprzez obróbkę cieplną, stopy o wyższej prosta kompozycja. Dopuszczalne naprężenia, zmniejszające masę części i mechanizmów, zwiększające ich niezawodność i trwałość, można również osiągnąć stosując obróbkę cieplną.
Temat 1.2 Obróbka cieplna i chemiczno-termiczna metali i stopów
Obróbka cieplna to proces, którego istotą jest ogrzewanie i chłodzenie produktów według określonych trybów, w wyniku którego następuje zmiana struktury, składu fazowego, właściwości mechanicznych i fizycznych. Stosuje się również różne rodzaje obróbki chemiczno-termicznej, której istotą jest stapianie warstwy wierzchniej wyrobów azotem, węglem lub niektórymi metalami (aluminium, chrom, beryl) z późniejszą obróbką cieplną.
W zależności od celu obróbki cieplnej wyróżnia się jej różne rodzaje, różniące się temperaturą grzania, czasem utrzymywania i szybkością chłodzenia.
Główne rodzaje obróbki cieplnej stali to wyżarzanie, normalizowanie, hartowanie i odpuszczanie.
Wyżarzanie stosowany w celu zmniejszenia twardości, rozdrobnienia ziarna, poprawy skrawalności, odprężenia. W celu wyżarzania stal jest podgrzewana do określonej temperatury, utrzymywana i chłodzona z małą prędkością w piecu z wyłączonym źródłem ciepła.
Normalizacja - przedstawia ogrzewanie stali do temperatury powyżej punktu krytycznego, utrzymywanie w tej temperaturze, chłodzenie w nieruchomym powietrzu z szybkością większą niż podczas wyżarzania. Cel - nadanie stali drobnoziarnistej struktury. Normalizacja daje bardziej zauważalny wzrost wytrzymałości, ale mniejszą ciągliwość. Przewaga nad wyżarzaniem to niższy koszt.
Hartowanie - Polega na podgrzaniu stali, utrzymywaniu jej w określonej temperaturze przez określony czas, a następnie gwałtownym schłodzeniu. Celem jest zwiększenie twardości i siły. Podczas hartowania w materiale powstają naprężenia wewnętrzne, gwałtownie spada ciągliwość i udarność. Może to prowadzić do kruchego pęknięcia części podczas pracy.
Aby zmniejszyć naprężenia wewnętrzne i zwiększyć ciągliwość i udarność po hartowaniu, wakacje, który polega na nagrzaniu utwardzonej stali do temperatury nieprzekraczającej dolnego punktu krytycznego, utrzymywaniu tej temperatury i późniejszym schłodzeniu.
W zależności od temperatury rozróżniamy trzy rodzaje wakacji: niskie, średnie, wysokie.
Niskie odpuszczanie odbywa się w temperaturze 150...250°C. Twardość stali nieznacznie spada. Strukturę powstałą w wyniku niskiego odpuszczania nazywamy zniszczyć-uwalnianie napięcia lub hartowany martenzyt. Cięcie i Urządzenie pomiarowe, matryce do formowania na zimno, a także części, które muszą mieć wysoką odporność na zużycie.
Przeciętny urlop odbywa się w temperaturze 350...450 °C. Podczas odpuszczania średniego cementyt powstaje nie w postaci płyt, ale w postaci drobnych ziaren, co przyczynia się do wzrostu twardości stali. Produkty, które muszą charakteryzować się wysoką elastycznością i wystarczającym marginesem lepkości (sprężyny, sprężyny itp.) poddawane są średniemu odpuszczaniu.
Odpuszczanie wysokie odbywa się w temperaturze 500...650°C. W efekcie naprężenia szczątkowe zostają całkowicie wyeliminowane, stal uzyskuje dobrą ciągliwość i wiązkość przy odpowiednio wysokiej wytrzymałości. Takie wakacje są przeznaczone dla krytycznych części, które podczas pracy doświadczają wstrząsów i przemiennych obciążeń.
Nazywa się podwójną obróbką cieplną, która obejmuje hartowanie, a następnie wysokie odpuszczanie termomodernizacja, ponieważ cały kompleks właściwości mechanicznych stali ulega poprawie.
Obróbka chemiczno-termiczna. Obróbka chemiczno-termiczna polega na ekspozycji chemicznej i termicznej w celu zmiany składu chemicznego, struktury i właściwości warstwy wierzchniej metalu. W procesie obróbki chemiczno-termicznej nasycenie powierzchni metalu odpowiednim pierwiastkiem następuje w procesie jego dyfuzji w postaci atomowej z ośrodka ciekłego, stałego lub gazowego w wysokiej temperaturze. Główne rodzaje obróbki chemiczno-termicznej są klasyfikowane według nazw pierwiastków, którymi nasycona jest warstwa wierzchnia. Na przykład nasycenie węglem nazywa się cementacją, azotowanie azotem, chromowanie - chromowanie.
Powszechne stosowanie obróbki chemiczno-termicznej w różnych dziedzinach techniki tłumaczy się tym, że zwiększając twardość, odporność na zużycie i odporność na korozję powierzchni, zwiększa niezawodność i trwałość działania części maszyn i mechanizmów.
Obróbka chemiczno-termiczna polega na:
dysocjacja, który występuje na powierzchni styku "metal - środowisko gazowe„i prowadzi do uwolnienia pierwiastka dyfundującego w stanie atomowym;
wchłanianie - absorpcja powierzchniowa wolnych atomów;
dyfuzja - wnikanie elementu nasycającego w głąb warstwy wierzchniej.
Głównym procesem fizycznym jest dyfuzja, której szybkość wzrasta wraz ze wzrostem temperatury, element dyfuzyjny wnika na większą głębokość.
Nawęglanie polega na dyfuzyjnym nasycaniu węglem warstwy wierzchniej stali po nagrzaniu w odpowiednim medium - nawęglaczu. Proces nawęglania odbywa się w temperaturach (900...950 °C), kiedy austenit jest stabilny, rozpuszczając węgiel w duże ilości. Nawęglanie odbywa się w gaźnikach stałych, ciekłych i gazowych. Nawęglanie gazowe jest najbardziej produktywnym procesem. Główną reakcją zapewniającą nawęglanie jest dysocjacja metanu:
CH → 2H 2 + C w.
Nawęglanie prowadzi się na stalach niskowęglowych i stopowych zawierających od 0,1 do 0,35% węgla. Warstwa wierzchnia stali po nawęglaniu ma zmienną koncentrację węgla na grubości, zmniejszającą się od powierzchni do rdzenia części. W związku z tym, po powolnym schłodzeniu w strukturze warstwy kąpieli cementowej, można wyróżnić trzy strefy (zaczynając od powierzchni): nadeutektoidalne, eutektoidalne, podeutektoidalne. Całkowita grubość zacementowanej warstwy wynosi 0,8...3,0 mm.
Po zacementowaniu w celu uzyskania wymaganych właściwości przeprowadza się obróbkę cieplną – hartowanie z niskim odpuszczaniem. W wyniku obróbki cieplnej warstwa powierzchniowa zyskuje strukturę odporną na zużycie, a niskowęglowy rdzeń części okazuje się dość lepki. Najczęściej nawęglaniu poddawane są koła zębate różnych mechanizmów w celu zwiększenia ich trwałości.
Azotowanie polega na dyfuzyjnym nasycaniu warstwy powierzchniowej azotem w odpowiednim medium. Stale przed azotowaniem poddawane są obróbce cieplnej – hartowaniu i wysokiemu odpuszczaniu.
Azotowane to stale stopowe zawierające chrom, molibden, wanad i inne pierwiastki zdolne do tworzenia z azotem bardzo twardych i żaroodpornych azotków. Azotowanie prowadzi się w temperaturze 500...600°C. Główną reakcją zachodzącą na powierzchni części jest reakcja dysocjacji amoniaku.
Stal po azotowaniu uzyskuje wysoką twardość, odporność na zużycie i korozję. Pod względem tych właściwości stale azotowane przewyższają stal nawęglaną. Jednak azotowana warstwa jest bardziej odporna na obciążenia udarowe i ma mniejszą wytrzymałość na kontakt. Ze względu na długi czas trwania procesu (do 70 godzin) zastosowanie azotowania jest ekonomicznie opłacalne do przetwarzania krytycznych produktów, takich jak wały korbowe samochodów, tuleje cylindrowe silników spalinowych, różnego rodzaju armatura itp.
Chromowanie polega na dyfuzyjnym nasycaniu warstwy wierzchniej stali chromem w temperaturze 900…1300°C w odpowiednim medium. Chromowanie zapewnia podwyższoną odporność cieplną stali do temperatury 800°C, wysoką odporność na korozję i erozję. Części elektrowni parowych, armatura rurociągów parowych, zawory, zawory, odgałęzienia są poddawane chromowaniu. W celu zwiększenia odporności na korozję stal transformatorową poddaje się chromowaniu. W tym przypadku stal dodatkowo uzyskuje wysoką odporność na ciepło.
pytania testowe
Co charakteryzuje strukturę krystaliczną metali?
Jakie znasz rodzaje sieci krystalicznych?
Jakie są główne wady struktury krystalicznej?
Co to jest alotropia metali?
Jakie właściwości mechaniczne charakteryzują wytrzymałość i ciągliwość rozciąganych materiałów?
Co to jest diagram stanu stopu i co pozwala na ustalenie?
Jakie są główne rodzaje obróbki cieplnej?
Co to jest nawęglanie stali?
Sekcja 2 MATERIAŁY PÓŁPRZEWODNIKOWE
Temat 2.1 Klasyfikacja materiałów półprzewodnikowych
Substancje wyróżniają się zdolnością przewodzenia Elektryczność. Umiejętność ta charakteryzuje się wartością specyficzną opór elektryczny– ρ lub przewodnictwo elektryczne – γ. Wartość γ w normalna temperatura wynosi mniej niż 10 -10 S/m dla dielektryków i ponad 104 S/m dla przewodników.
Rozważmy naturę zmiany przewodnictwa właściwego ciał stałych w temperaturze zmierzającej do zera absolutnego.
W tym przypadku wzrasta przewodność właściwa przewodników, a wiele metali przechodzi w stan nadprzewodnictwa, który charakteryzuje się nieskończoną liczbą Świetna cena γ.
Półprzewodniki zachowują się zupełnie inaczej. Wraz ze spadkiem temperatury zmniejsza się ich przewodność właściwa, a przy T → 0 K półprzewodniki w ogóle nie przewodzą prądu elektrycznego, tj. stać się dielektrykiem. Z drugiej strony wraz ze wzrostem temperatury γ półprzewodników gwałtownie wzrasta.
Aby pojawiły się nośniki bezpłatnych ładunków w półprzewodnikach, nie jest konieczne doprowadzenie ich do energia cieplna. Można to w nich osiągnąć poprzez oświetlenie, obciążenia mechaniczne, pole elektryczne itp. Struktura wewnętrzna półprzewodników ma silny wpływ na przewodnictwo elektryczne. Ponadto wprowadzenie nawet niewielkiej ilości atomów obcego pierwiastka do półprzewodnika zwykle drastycznie zmienia jego przewodność elektryczną. Wszystko to się otwiera szerokie możliwości do kontrolowania właściwości elektrofizycznych materiałów półprzewodnikowych.
Więc, Półprzewodnik to substancja, której główną właściwością jest silna zależność jego przewodnictwa elektrycznego od wpływu czynników zewnętrznych.
Wszystkie półprzewodniki można podzielić na proste i złożone.
Jedyny nazywa się taki półprzewodnik, którego główny skład tworzą atomy jednego pierwiastka chemicznego (krzem, german, selen, tellur, bor, węgiel, fosfor, siarka, arsen, antymon, jod, szara cyna).
Struktura złożony półprzewodniki składają się z atomów o różnej pierwiastki chemiczne. Do tej grupy należą roztwory stałe (krzem i german) oraz związki chemiczne, oznaczone AB. W tym wzorze indeksy górne (m i n) wskazują numer grupy układ okresowy, który zawiera odpowiedni pierwiastek, a dolne (x i y) to liczba atomów tego pierwiastka w związku. Na przykład półprzewodnikowy arsenek galu GaAr jest klasyfikowany jako związek typu A III B V, a tlenek miedzi Cu 2 O jest klasyfikowany jako związek typu A 2 I B VI.
Wiele trójskładnikowych i bardziej złożonych związków chemicznych ma właściwości półprzewodnikowe, takie jak ZnSiAs 2 . Półprzewodnik to cała linia związki organiczne: antracen, naftalen, ftalocyjanina itp.
Niezwykłą właściwością półprzewodników jest również to, że umożliwiają odwrotną transformację energia elektryczna na lekkie, termiczne lub mechaniczne.
Półprzewodniki służą do wzmacniania i generowania sygnałów elektrycznych (tranzystory, diody, układy scalone), jako pierwotne przetworniki temperatury i źródła energii cieplnej (termistory i elementy grzejne), jako podstawowe przetworniki i źródła sygnałów optycznych (fotorezystory, diody LED, lasery), do przetwarzania wibracje mechaniczne(rezystory naprężeń i czujniki piezoelektryczne) itp.
Poziomy energii i strefy
Atom składa się z jądra i elektronów poruszających się po określonych orbitach.
Całkowita energia elektronów, równa sumie ich energii kinetycznej (ruch orbitalny) i potencjalnej (przyciąganie do jądra), nazywana jest stanem energetycznym atomu. Każda dozwolona orbita ma swój własny stan energetyczny, który jest przedstawiony na schemacie jako poziom energii. Ponieważ orbity i ich energie są podzielone na dozwolone i zabronione, to enerpoziomy getic również mogą być dozwolonei zabronione.
Energia elektronowa mi wyrażona w elektronowoltach. Elektrowolt- jest energia, któraelektron przyspiesza do pole elektryczne z innympotencjały w 1 V.
Interakcja atomów w sieci prowadzi do tego, że ich poziomy energetyczne są podzielone na dużą liczbę prawie łączących się podpoziomów, tworząc energeticstrefy.
Pasmo energii wypełnione podpoziomami jest tym szersze, im bliżej znajdują się atomy i tym wyższy poziom energii. Prawdopodobieństwo "pozostania" elektronu w przerwie energetycznej wynosi zero.
Klasyfikacja materiałów według elektrykiwłaściwości (teoria pasmowa)
Klasyfikacja materiałów elektrycznych według ich właściwości elektrycznych opiera się na ideach teorii pasmowej przewodności elektrycznej ciał stałych, której istota jest następująca.
W izolowanym atomie elektrony krążą wokół jądra po określonych orbitach. Zgodnie z zasadą Pauliego na każdymBit może mieć co najwyżej dwa elektrony. Każda orbita odpowiada ściśle określonej wartości energii, jaką może posiadać elektron, tj. każda orbita reprezentuje określony poziom energii. Pod wpływem przyciągania dodatnio naładowanego jądro atomowe elektrony mają tendencję do zajmowania poziomów najbliżej jądra o minimalnej wartości energetycznej. Dlatego dolne poziomy energetyczne są wypełnione elektronami, a górne poziomy są wolne. Elektron może skakać z niższego poziomu energii W x na inny wolny poziom W 2 (rys. 1). Aby to zrobić, elektron musi otrzymać dodatkową energię ∆ W = W 2 - W 1 . Jeśli w atomie nie ma wolnych poziomów, elektron nie może zmienić swojej energii, dlatego nie uczestniczy w tworzeniu przewodnictwa elektrycznego.
W - energia elektronów; W 1 - niższy poziom energii; W 2 - poziom energii swobodnej; ∆ W C - pasmo przewodzenia (wolna strefa); ∆ W - strefa zakazana; ∆ Ww, - pasmo walencyjne
Rysunek 2.1 - Schemat poziomów energii izolowanego atomu (1) i ciało stałe (2).
W sieci krystalicznej składającej się z kilku atomów poszczególne poziomy energii są podzielone na podpoziomy, które tworzą strefy energetyczne (patrz ryc. 2.1). W tym przypadku poziomy energii wolnej i napełnionej są dzielone. Obszar wypełniony elektronami nazywa się wartościowość. Oznaczono górny poziom pasma walencyjnego W w . Wolna strefa nazywana jest strefą przewodność. Oznaczono dolny poziom pasma przewodnictwa (pasmo wolne) W a . Przerwa między pasmem walencyjnym a pasmem przewodnictwa nazywa się zakazana strefa ∆ W. Wartość przerwy energetycznej znacząco wpływa na właściwości materiałów.
Jeśli ∆ W jest równy lub bliski zeru, to elektrony mogą przejść do wolnych poziomów dzięki własnej energii cieplnej i zwiększyć przewodność substancji. Substancje o takiej budowie pasm energetycznych nazywane są przewodnikami. Materiały przewodzące służą do przewodzenia prądu elektrycznego. Zazwyczaj przewodniki zawierają substancje o oporności elektrycznej p< 10 Ом*м. Типичными проводниками явля-ются металлы.
Jeśli pasmo zabronione przekracza kilka elektronowoltów, to do przeniesienia elektronów z pasma walencyjnego do pasma przewodnictwa potrzebna jest znaczna energia. Takie substancje nazywane są dielektrykami. Dielektryki mają wysoką oporność elektryczną i mają zdolność zapobiegania przepływowi prądu. Materiały dielektryczne obejmują substancje o oporności elektrycznej p > 10 7 Ohm * m. Ze względu na wysoką oporność elektryczną są stosowane jako materiały elektroizolacyjne.
Jeśli pasmo zabronione wynosi 0,1...0,3 eV, elektrony łatwo przechodzą z pasma walencyjnego do pasma przewodnictwa dzięki energii zewnętrznej. Substancje o kontrolowanej przewodności to półprzewodniki. Właściwa rezystancja elektryczna półprzewodników wynosi p 10 9 omów * m.
Materiały półprzewodnikowe mają przewodnictwo, które można wykorzystać do kontrolowania napięcia, temperatury, oświetlenia itp.
W zależności od konstrukcji i warunków zewnętrznych materiały mogą przechodzić z jednej klasy do drugiej. Na przykład twardy i metale płynne- przewodniki i pary metalowe - dielektryki; półprzewodniki german i krzem, które są typowe w normalnych warunkach, stają się przewodnikami pod wpływem wysokiego ciśnienia hydrostatycznego; węgiel w modyfikacji diamentowej jest dielektrykiem, aw modyfikacji grafitowej jest przewodnikiem.
Główną właściwością materii w odniesieniu do pola elektrycznego jest przewodnictwo elektryczne, charakteryzujący zdolność materiału do przewodzenia prądu elektrycznego pod wpływem stałego pola elektrycznego, tj. pole, którego napięcie nie zmienia się w czasie.
Przewodność elektryczna charakteryzuje się określoną przewodnością elektryczną i określoną opornością elektryczną:
Wartości przewodności elektrycznej i oporności elektrycznej y różne materiały różnią się znacznie. W stanie nadprzewodzącym specyficzny opór elektryczny materiałów wynosi zero, podczas gdy dla gazów rozrzedzonych dąży do nieskończoności.
Łatwo zrozumieć, że właściwości przewodzące kryształu zależą od przerwy energetycznej oddzielającej pasma walencyjne i przewodnictwa. Im szersza przerwa wzbroniona, tym mniejsza (w danej temperaturze) liczba elektronów przenikających przez pasmo przewodnictwa, tym mniejsza przewodność kryształu.
Kryształy mogą być dobrymi przewodnikaminawet jeśli pasmo walencyjne jest wypełnionecałkowicie, jeśli sąsiaduje bezpośrednio ze strefąprzewodnictwo lub przecina się z nim (w rezultacierozmycie stref podczas tworzenia kraty). Z powiększonymzwiększając przerwę wzbronioną, nabyte kryształyprzywrócić właściwości izolatorów. Wartości średnieprzerwy w pasmach odpowiadająpółprofesjonalny-woda kryształy.
Ponieważ pasma walencyjne i przewodnictwa przewodników krystalicznych nie są rozdzielone, elektrony swobodnie przemieszczają się z jednego dozwolonego podpoziomu do drugiego, uzyskując uporządkowaną prędkość pod działaniem przyłożonego napięcia. Jednocześnie wraz ze wzrostem temperatury opór przewodnika wzrasta z powodu zmniejszenia swobodnej drogi elektronów w krysztale.
W kryształach półprzewodnikowych przewodnictwo zależy przede wszystkim od liczby elektronów, które pokonały przerwę wzbronioną i przeniknęły do pasma przewodnictwa.
materiały półprzewodnikowe
Wiązanie chemiczne między atomami półprzewodnika odbywa się dzięki wzajemnemu oddziaływaniu elektronów walencyjnych, podczas gdy każdy atom otrzymuje od współwłaściciela sąsiada i oddaje mu swoje elektrony walencyjne, których brakuje przed powstaniem stabilnego pasma ośmioelektronowego . Zatem, w idealnym półprzewodniku wszystkie elektrony walencyjne rons uczestniczą w edukacji wiązanie chemiczne i wolne nie ma elektronów. Ten rodzaj wiązania chemicznego nazywa się cova. taśma.
Na ryc. 2.2 pokazuje schemat powstawania wiązania chemicznego w sieci krystalicznej krzemu, którego atom ma cztery elektrony walencyjne w swobodnym stanie izolowanym, oraz zewnętrzny poziom elektroniczny każdy atom jest wypełniony maksymalnie ośmioma elektronami, ze względu na wspólną własność elektronów czterech najbliższych sąsiednich atomów.
Rysunek 2.2 - Schemat powstawania wiązania chemicznego w sieci krystalicznej krzemu. Ze względu na małą szerokość (1 eV) przerwy wzbronionej półprzewodnika, drgania termiczne atomów są w stanie przekazać elektronom walencyjnym energię wystarczającą do przejścia z pełnego pasma walencyjnego do pasma swobodnej przewodności. Każde takie przejście prowadzi do pojawienia się pary nośników ładunku: wolny elektron w paśmie przewodzenia i stanie energii swobodnej - otwory- w paśmie walencyjnym. Pod działaniem napięcia przyłożonego do kryształu elektron przewodzący porusza się „w kierunku” pole elektryczne, a elektron w paśmie walencyjnym zajmuje wolny poziom, uwalniając swój poziom dla innego elektronu. Można to uznać za ruch ładunku dodatniego (dziury) w kierunku pola elektrycznego.
Generowanie par wolnych, tj. zdolnych do przenoszeniaporuszać się pod wpływem przyłożonego napięcia,ładunki sprawiają, że kryształ jest w stanie przewodzić prądprąd ric, a przewodność elektryczna takiego kryształunazywaposiadać.
Nazywa się półprzewodnik, w którym przewodność elektryczna jest prowadzona w wyniku wzbudzenia elektronów z wiązaniami chemicznymiwłasny półprzewodnik.
Nośnikami prądu w takich półprzewodnikach są ich własne elektrony i dziury.
Na ryc. 2.3 przedstawia schemat sieci krystalicznej własnego półprzewodnika. Po wzbudzeniu własnego elektronu walencyjnego, n-rodzaj nośnika prądu - swobodny elektron i R- rodzaj nośnik prądu - dziura - niezajęte wiązanie chemiczne.
Równolegle z formowaniem się par nośników część elektronów z pasma przewodnictwa samorzutnie przechodzi z powrotem do pasma walencyjnego, emitując kwanty energii. Ten proces nazywa się rekombinacja parowy. W stałej temperaturze ustala się dynamiczna równowaga, która określa stężenie wolne elektrony i dziury (w danej temperaturze).
Im wyższa temperatura, tym wyższe stężenie nośników wolnych ładunków, tym większa wewnętrzna przewodność elektryczna kryształu.
W temperaturze 0K nie tworzą się pary nośników, a kryształ całkowicie traci własną przewodność elektryczną. W tym przypadku elektrony wewnątrz kryształu poruszają się losowo z dużymi prędkościami (rzędu 106 m/s), ale nie reagują na przyłożone napięcie zewnętrzne.
Rysunek 2.3 - Schemat sieci krystalicznej własnego półprzewodnika.
Prawdziwe kryształy zawierają liczne defekty sieci krystalicznej: punktowe, liniowe, objętościowe i powierzchniowe. W miejscach naruszenia okresowej struktury kryształu (implantacja atomów w szczeliny) zmienia się energia wiązania elektronów z jądrami, w wyniku czego powstają nowe poziomy energetyczne, które mogą wykraczać poza pasmo walencyjne i znajdować się w pasmo wzbronione w pobliżu pasma przewodnictwa. Ułatwia to przejście elektronów do pasma przewodnictwa.
Kompleks szkoleniowo-metodologiczny... - dawać podstawyInżynieria materiałowa, zasady selekcji niezbędne materiały, zaszczepić umiejętności praktycznego definiowania fizyczny-mechaniczna... grupa chemiczny znajomości. 6.3.1. Klasyfikacja polimerów i właściwości polimerów Polimery według pochodzenia udział ...
Evgeny Petrovich Prokopyev (ros.) (pol.) ogólna lista publikacji antymateria i pozytonika pozytonika i nanotechnologia pozytonika anihilacja pozytonów fizyka układów złożonych synergetyka materiałoznawstwo nanotechnologia inne zagadnienia pokrewne
DokumentProkopiew E.P. Na stanach powierzchniowych na granicy Sekcja półprzewodnik-metal. M., 1985. 5 s. - Dep. w... procesach. Trzecia rosyjska konferencja w sprawie Inżynieria materiałowa oraz fizyczny-chemicznypodstawy technologie otrzymywania domieszkowanych kryształów krzemu...
Właściwości stopu zależą od jego struktury. Głównym sposobem zmiany struktury, a co za tym idzie właściwości, jest obróbka cieplna.
Podstawy obróbki cieplnej zostały opracowane przez DK Chernova, a później zostały opracowane w pracach A.A. Bochvara, G.V. Kurdyumova, A.P. Gulyaeva.
obróbka cieplna nazywany efektem termicznym metalu w celu nadania mu niezbędnych właściwości mechanicznych i fizycznych w wyniku zmiany wewnętrznej struktury (struktury) metalu.
Większość półfabrykatów (półfabrykatów) oraz wyrobów ze stali i stopów metali nieżelaznych poddawana jest obróbce cieplnej. To obróbka cieplna, która pozwala na zmianę struktury metalu we właściwym kierunku i pozwala uzyskać wymagany poziom twardość, wytrzymałość, plastyczność i inne właściwości.
Tryb obróbki cieplnej charakteryzują następujące główne parametry: prędkość i tryb grzania, Maksymalna temperatura grzanie, czas utrzymywania w piekarniku w temperaturze grzania oraz szybkość i tryb chłodzenia.
Obróbka cieplna jest jedną z najczęstszych nowoczesna technologia sposoby uzyskania określonych właściwości metalu. Obróbka cieplna jest stosowana albo jako operacja pośrednia w celu poprawy skrawalności półproduktu przez nacisk, cięcie itp., albo jako operacja końcowa. proces technologiczny, zapewniając określony poziom właściwości fizycznych i mechanicznych części.
Obróbka cieplna obejmuje podgrzewanie, trzymanie i chłodzenie metalu, wykonywane w określonej kolejności w określonych trybach, w celu zmiany wewnętrznej struktury stopu i uzyskania pożądanych właściwości. Zwykle można to schematycznie przedstawić jako wykres w osiach temperatury i czasu (rys. 21).
Obróbka cieplna dzieli się na rzeczywistą cieplną, chemiczno-termiczną i termomechaniczną (lub deformacyjno-termiczną).
Właściwa obróbka cieplna polega jedynie na oddziaływaniu termicznym na metal lub stop, obróbce chemiczno-termicznej - w połączeniu efektu cieplnego i chemicznego, termomechanicznej - w połączeniu efektu cieplnego i odkształcenia plastycznego.
Rys.21. Harmonogram obróbki cieplnej
W rzeczywistości obróbka cieplna obejmuje następujące główne typy:
Wyżarzanie I rodzaju
Wyżarzanie II rodzaju
Hartowanie z transformacją polimorficzną
Hartowanie bez transformacji polimorficznej
Starzenie się
Te rodzaje obróbki cieplnej dotyczą zarówno stali, jak i metali nieżelaznych.
Wyżarzanie
Wyżarzanie- obróbka cieplna, która polega na podgrzaniu metalu do określonej temperatury, trzymaniu i chłodzeniu przy wyłączonym piecu (tj. z minimum możliwa prędkość około 50-100 st./godz.).
Wyżarzanie I rodzaju - stosuje się do dowolnych metali i stopów. Jego realizacja nie wynika z przemian fazowych w stanie stałym. Ogrzewanie podczas wyżarzania pierwszego rodzaju, zwiększające ruchliwość atomów, częściowo lub całkowicie eliminuje niejednorodność chemiczną, zmniejsza naprężenia wewnętrzne. Najważniejsza jest temperatura grzania i czas utrzymywania. Charakteryzuje się powolnym chłodzeniem
Odmiany wyżarzania pierwszego rodzaju to:
homogenizacja (dyfuzja)
· rekrystalizacja;
· wyżarzanie w celu odciążenia naprężeń wewnętrznych po kuciu, spawaniu, odlewaniu.
Wyżarzanie homogenizujące (dyfuzyjne) to obróbka cieplna, w której głównym procesem jest eliminacja skutków segregacji dendrytycznej (niejednorodności chemicznej) w odlewach i wlewkach. Jest to długa ekspozycja w wysokich temperaturach, w których zachodzą procesy dyfuzyjne, które nie zdążyły się zakończyć podczas krystalizacji. Przybliżona temperatura dla stali wynosi -1100-1300 ° C przez 20-50 godzin, dla stopów aluminium 420-450 ° C.
Wyżarzanie rekrystalizacyjne to obróbka cieplna odkształconego metalu, w której głównym procesem jest rekrystalizacja metalu. Ten rodzaj wyżarzania eliminuje odchylenia konstrukcji od stanu równowagi, które występują podczas odkształcenia plastycznego. Podczas obróbki ciśnieniowej, zwłaszcza na zimno, metal jest nitowany, jego wytrzymałość wzrasta, a plastyczność maleje na skutek wzrostu gęstości dyslokacji w krystalitach. Gdy metal obrobiony na zimno zostanie podgrzany powyżej pewnej temperatury, następuje pierwotna, a następnie zbiorowa rekrystalizacja, przy której gęstość dyslokacji gwałtownie spada. W rezultacie metal mięknie i staje się bardziej plastyczny. Takie wyżarzanie stosuje się w celu poprawy podatności na obróbkę pod ciśnieniem i nadania metalowi niezbędnej kombinacji twardości, wytrzymałości i ciągliwości. Z reguły podczas wyżarzania rekrystalizującego dąży się do uzyskania materiału bezteksturowego, w którym nie występuje anizotropia właściwości. W produkcji blach transformatorowych stosuje się wyżarzanie rekrystalizacyjne w celu uzyskania pożądanej tekstury metalu powstałej w wyniku rekrystalizacji.
Wyżarzanie odprężające to obróbka cieplna, w której głównym procesem jest całkowite lub częściowe rozluźnienie naprężeń szczątkowych podczas ogrzewania i chłodzenia. Wyżarzanie redukujące naprężenia stosuje się do wyrobów, w których podczas obróbki ciśnieniowej, odlewania, spawania, obróbki cieplnej i innych procesów technologicznych powstały niedopuszczalnie duże naprężenia szczątkowe, które są wzajemnie równoważone wewnątrz korpusu bez udziału obciążeń zewnętrznych. Naprężenia szczątkowe mogą powodować zniekształcenie kształtu i wymiarów produktu podczas jego przetwarzania, eksploatacji lub przechowywania w magazynie. Gdy produkt jest podgrzewany, granica plastyczności spada, a gdy staje się mniejsza niż naprężenia szczątkowe, są one szybko rozładowywane przez płynięcie plastyczne w różnych warstwach metalu.
Wyżarzanie Drugim rodzajem jest wyżarzanie metali i stopów przechodzących przemiany fazowe w stanie stałym. Ten rodzaj wyżarzania przeprowadza się dla stopów, w których występują przemiany polimorficzne lub eutektoidalne, a także zmienna rozpuszczalność składników w stanie stałym.
Rys. 22. Zmiana struktury podczas wyżarzania drugiego rodzaju
Wyżarzanie drugiego rodzaju prowadzi się w celu uzyskania struktury równowagowej i przygotowania jej do dalszej obróbki. W wyniku wyżarzania ziarno jest kruszone, wzrasta ciągliwość i wiązkość, spada wytrzymałość i twardość oraz poprawia się skrawalność. Charakteryzuje się nagrzewaniem do temperatur powyżej krytycznej i bardzo powolnym chłodzeniem z reguły razem z piecem lub w powietrzu. W tym drugim przypadku proces ten nazywa się normalizacją. Wyżarzanie II rodzaju stosuje się najczęściej do ogólnego udoskonalenia struktury, zmiękczenia i poprawy skrawalności.
Obróbka cieplna metali i stopów
Kurs pracy
na temat: „Obróbka cieplna metali i stopów”
Wstęp
Obróbka cieplna stosowana jest na różnych etapach produkcji części maszyn i wyrobów metalowych. W niektórych przypadkach może to być operacja pośrednia służąca poprawie skrawalności stopów metodą ciśnieniową, skrawaniem, w innych operacja końcowa dostarczająca niezbędny zestaw wskaźników właściwości mechanicznych, fizycznych i eksploatacyjnych wyrobów lub pół- produkt końcowy. Półfabrykaty poddawane są obróbce cieplnej w celu poprawy struktury, zmniejszenia twardości (poprawy skrawalności), a części - w celu nadania im określonych wymaganych właściwości (twardość, odporność na ścieranie, wytrzymałość i inne).
W wyniku obróbki cieplnej właściwości stopów mogą być zmieniane w szerokim zakresie. Możliwość znacznego wzrostu właściwości mechanicznych po obróbce cieplnej w porównaniu ze stanem wyjściowym pozwala na zwiększenie dopuszczalnych naprężeń, zmniejszenie gabarytów i masy maszyn i mechanizmów oraz zwiększenie niezawodności i żywotności wyrobów. Poprawa właściwości w wyniku obróbki cieplnej pozwala na stosowanie stopów o prostszych składach, a więc i tańszych. Stopy zyskują również nowe właściwości, w związku z czym rozszerza się zakres ich zastosowania.
Cel i rodzaje obróbki cieplnej
Obróbka termiczna (ciepła) to proces, którego istotą jest ogrzewanie i chłodzenie produktów w określonych trybach, powodujące zmiany w strukturze, składzie fazowym, właściwościach mechanicznych i fizycznych materiału, bez zmiany składu chemicznego.
Celem obróbki cieplnej metali jest uzyskanie wymaganej twardości, poprawa właściwości wytrzymałościowych metali i stopów. Obróbka cieplna dzieli się na cieplną, termomechaniczną i chemiczno-termiczną. Obróbka cieplna - tylko oddziaływanie termiczne, termomechaniczna - połączenie oddziaływania termicznego i odkształcenia plastycznego, chemiczno-termiczna - połączenie efektów termicznych i chemicznych. Obróbka cieplna, w zależności od stanu strukturalnego uzyskanego w wyniku jej zastosowania, dzieli się na wyżarzanie (pierwszy i drugi rodzaj), hartowanie i odpuszczanie.
Wyżarzanie
Wyżarzanie to obróbka cieplna polegająca na podgrzaniu metalu do określonych temperatur, utrzymywaniu, a następnie bardzo powolnym chłodzeniu wraz z piecem. Służą do usprawnienia obróbki metali poprzez cięcie, zmniejszenia twardości, uzyskania struktury ziarnistej, a także do odciążenia naprężeń, częściowo (lub całkowicie) niwelują wszelkiego rodzaju niejednorodności, które zostały wprowadzone do metalu podczas poprzednich operacji (obróbka , obróbka ciśnieniowa, odlewanie, spawanie), poprawia konstrukcję stalową.
Wyżarzanie pierwszego rodzaju. Jest to wyżarzanie, podczas którego przemiany fazowe nie zachodzą, a jeśli już zachodzą, to nie wpływają na przewidziany jej przeznaczeniem efekt końcowy. Wyróżnia się następujące rodzaje wyżarzania pierwszego rodzaju: homogenizacja i rekrystalizacja.
Homogenizacja to wyżarzanie z długą ekspozycją w temperaturze powyżej 950ºC (zwykle 1100–1200ºC) w celu wyrównania składu chemicznego.
Rekrystalizacja to wyżarzanie stali utwardzonej przez zgniot w temperaturze przekraczającej temperaturę początku rekrystalizacji w celu wyeliminowania zgniotu i uzyskania określonej wielkości ziarna.
Wyżarzanie drugiego rodzaju. Jest to wyżarzanie, w którym przemiany fazowe determinują jego przeznaczenie. Wyróżnia się następujące typy: kompletne, niekompletne, dyfuzyjne, izotermiczne, lekkie, znormalizowane (normalizacja), sferoidyzujące (dla perlitu ziarnistego).
Całkowite wyżarzanie odbywa się poprzez ogrzewanie stali o 30–50°C powyżej punktu krytycznego, utrzymywanie w tej temperaturze i powolne chłodzenie do 400–500°C z szybkością 200°C na godzinę dla stali węglowych, 100°C na godzinę dla stali niskostopowych i 50°C na godzinę dla stali wysokostopowych. Konstrukcja stalowa po wyżarzaniu jest wyważona i stabilna.
Wyżarzanie niepełne odbywa się poprzez nagrzanie stali do jednej z temperatur w zakresie przemiany, utrzymywanie i powolne chłodzenie. Wyżarzanie niepełne służy do zmniejszenia naprężeń wewnętrznych, obniżenia twardości i poprawy skrawalności.
Wyżarzanie dyfuzyjne. Metal jest podgrzewany do temperatur 1100–1200°C, ponieważ w tym przypadku procesy dyfuzyjne niezbędne do wyrównania składu chemicznego przebiegają pełniej.
Wyżarzanie izotermiczne przebiega następująco: stal jest podgrzewana, a następnie szybko schładzana (często przez przeniesienie do innego pieca) do temperatury o 50–100 °C niższej od temperatury krytycznej. Stosowany głównie do stali stopowych. Ekonomiczny, ponieważ czas trwania wyżarzania konwencjonalnego (13 - 15) h oraz wyżarzania izotermicznego (4 - 6) h
Wyżarzanie sferoidyzujące (dla perlitu ziarnistego) polega na podgrzaniu stali powyżej temperatury krytycznej o 20–30 °C, utrzymywaniu tej temperatury i powolnym chłodzeniu.
Wyżarzanie jasne odbywa się według trybów pełnego lub niepełnego wyżarzania w atmosferach ochronnych lub w piecach z częściową próżnią. Służy do ochrony powierzchni metalu przed utlenianiem i odwęgleniem.
Normalizacja - polega na podgrzaniu metalu do temperatury (30-50) ºС powyżej punktu krytycznego, a następnie schłodzeniu w powietrzu. Cel normalizacji jest różny w zależności od składu stali. Zamiast wyżarzania normalizuje się stale niskowęglowe. W przypadku stali średniowęglowych zamiast hartowania i wysokiego odpuszczania stosuje się normalizację. Stale wysokowęglowe poddawane są normalizacji w celu wyeliminowania sieci cementytowej. Normalizacja, po której następuje wysokie odpuszczanie, jest stosowana zamiast wyżarzania w celu poprawienia struktury stali stopowych. Normalizacja jest operacją bardziej ekonomiczną niż wyżarzanie, gdyż nie wymaga chłodzenia wraz z piecem.
hartowanie
Hartowanie to podgrzewanie do optymalnej temperatury, utrzymywanie, a następnie szybkie chłodzenie w celu uzyskania struktury nierównowagi.
W wyniku hartowania wzrasta wytrzymałość i twardość oraz maleje ciągliwość stali. Głównymi parametrami podczas hartowania są temperatura nagrzewania i szybkość chłodzenia. Krytyczną szybkością hartowania jest szybkość chłodzenia, która zapewnia powstawanie struktury - martenzytu lub martenzytu i austenitu szczątkowego.
W zależności od kształtu części, gatunku stali i wymaganego zestawu właściwości stosuje się różne metody hartowania.
Hartowanie w jednej chłodnicy. Część jest podgrzewana do temperatury hartowania i chłodzona w jednym chłodziwie (woda, olej).
Hartowanie w dwóch środowiskach (hartowanie przerywane) to hartowanie, w którym część jest chłodzona sukcesywnie w dwóch środowiskach: pierwszym medium jest chłodziwo (woda), drugim powietrzem lub olejem.
Hartowanie stopniowe. Część nagrzana do temperatury hartowania jest chłodzona w stopionych solach, po przetrzymaniu przez czas niezbędny do wyrównania temperatury na całym odcinku, część jest chłodzona powietrzem, co pomaga zredukować naprężenia hartownicze.
Utwardzanie izotermiczne, podobnie jak utwardzanie stopniowe, odbywa się w dwóch czynnikach chłodzących. Temperatura gorącego medium (kąpiele solne, azotanowe lub alkaliczne) jest różna: zależy od składu chemicznego stali, ale jest zawsze o 20–100 °C wyższa od punktu przemiany martenzytycznej dla danej stali. Ostateczne chłodzenie do temperatury pokojowej odbywa się na powietrzu. Hartowanie izotermiczne jest szeroko stosowane w przypadku części wykonanych ze stali wysokostopowych. Stal po hartowaniu izotermicznym uzyskuje wysokie właściwości wytrzymałościowe, czyli połączenie wysokiej ciągliwości z wytrzymałością.
Hartowanie z samoodpuszczaniem jest szeroko stosowane w produkcji narzędzi. Proces polega na tym, że detale utrzymywane są w medium chłodzącym dopiero po całkowitym schłodzeniu, ale w pewnym momencie są z niego usuwane w celu zaoszczędzenia pewnej ilości ciepła w rdzeniu detalu, dzięki czemu następuje późniejsze odpuszczanie.
Wakacje
Odpuszczanie stali to ostatnia operacja obróbki cieplnej, która kształtuje strukturę, a co za tym idzie właściwości stali. Odpuszczanie polega na nagrzewaniu stali do różnych temperatur (w zależności od rodzaju odpuszczania, ale zawsze poniżej punktu krytycznego), utrzymywaniu tej temperatury i chłodzeniu z różnymi szybkościami. Celem odpuszczania jest złagodzenie naprężeń wewnętrznych powstających podczas procesu hartowania i uzyskanie niezbędnej struktury.
W zależności od temperatury nagrzewania części hartowanej rozróżnia się trzy rodzaje odpuszczania: wysokie, średnie i niskie.
Wysokie odpuszczanie przeprowadza się w temperaturach ogrzewania powyżej 350–600 °C, ale poniżej punktu krytycznego; takie odpuszczanie stosuje się do stali konstrukcyjnych.
Średnie odpuszczanie odbywa się w temperaturach ogrzewania 350 - 500 °C; takie odpuszczanie jest szeroko stosowane w przypadku stali sprężynowych i sprężynowych.
Niskie odpuszczanie odbywa się w temperaturach 150–250 °C. Twardość części po hartowaniu prawie się nie zmienia; Niskie odpuszczanie jest stosowane do stali narzędziowych węglowych i stopowych, gdzie wymagana jest wysoka twardość i odporność na zużycie.
Kontrola temperowania jest realizowana przez kolory temperowania, które pojawiają się na powierzchni części.
Starzenie się
Starzenie to proces zmiany właściwości stopów bez zauważalnej zmiany w mikrostrukturze. Istnieją dwa rodzaje starzenia: termiczne i deformacyjne.
Starzenie termiczne następuje w wyniku zmian rozpuszczalności węgla w żelazie w zależności od temperatury.
Jeśli zmiana twardości, plastyczności i wytrzymałości następuje w temperaturze pokojowej, to takie starzenie nazywa się naturalnym.
Jeśli proces przebiega w podwyższonej temperaturze, starzenie nazywa się sztucznym.
Starzenie odkształceniowe (mechaniczne) następuje po odkształceniu plastycznym na zimno.
Leczenie na zimno
Nowy rodzaj obróbki cieplnej w celu zwiększenia twardości stali poprzez przekształcenie austenitu szczątkowego z utwardzonej stali w martenzyt. Odbywa się to poprzez schłodzenie stali do temperatury dolnego punktu martenzytycznego.
Metody utwardzania powierzchni
Utwardzanie powierzchniowe to proces obróbki cieplnej, polegający na nagrzaniu warstwy wierzchniej stali do temperatury powyżej temperatury krytycznej, a następnie schłodzeniu w celu uzyskania w warstwie wierzchniej struktury martenzytu.
Istnieją następujące typy: hartowanie indukcyjne; hartowanie w elektrolicie, hartowanie przez nagrzewanie prądami wysokiej częstotliwości (HFC), hartowanie z nagrzewaniem płomieniowym.
Hartowanie indukcyjne opiera się na zjawisku fizycznym, którego istotą jest to, że przepływający przez przewodnik prąd elektryczny o wysokiej częstotliwości wytwarza wokół niego pole elektromagnetyczne. Na powierzchni części umieszczonej w tym polu indukowane są prądy wirowe, powodując nagrzewanie się metalu do wysokich temperatur. Umożliwia to zachodzenie przemian fazowych.
W zależności od metody nagrzewania hartowanie indukcyjne dzieli się na trzy rodzaje:
jednoczesne nagrzewanie i utwardzanie całej powierzchni (stosowane do małych części);
sekwencyjne nagrzewanie i hartowanie poszczególnych sekcji (stosowane do wałów korbowych i podobnych części);
ciągłe sekwencyjne nagrzewanie i utwardzanie ruchem (stosowane do długich części).
Utwardzanie w płomieniu gazowym. Proces hartowania płomieniowego polega na szybkim podgrzaniu powierzchni części płomieniem tlenowo-acetylenowym, tlenowo-paliwowym lub tlenowo-naftowym do temperatury hartowania, a następnie schłodzeniu wodą lub emulsją.
Hartowanie w elektrolicie. Proces utwardzania w elektrolicie przebiega następująco: część do hartowania zanurza się w kąpieli z elektrolitem (5–10% roztwór soli kalcynowanej) i przepływa przez nią prąd 220–250 V. W rezultacie część jest podgrzewana do wysokich temperatur. Część jest chłodzona albo w tym samym elektrolicie (po wyłączeniu prądu) albo w specjalnym zbiorniku hartowniczym.
Obróbka termomechaniczna
Obróbka termomechaniczna (T.M.O.) to nowa metoda wzmacniania metali i stopów przy zachowaniu odpowiedniej plastyczności, łącząca odkształcenie plastyczne i hartującą obróbkę cieplną (hartowanie i odpuszczanie). Istnieją trzy główne metody obróbki termomechanicznej.
Obróbka termomechaniczna w niskich temperaturach (L.T.M.O.) polega na stopniowym hartowaniu, czyli odkształcaniu plastycznym stali w temperaturach względnej stabilności austenitu, a następnie hartowaniu i odpuszczaniu.
Obróbka termomechaniczna w wysokiej temperaturze (H.T.M.O.) w tym przypadku odkształcenie plastyczne odbywa się w temperaturach stabilności austenitu, a następnie hartowanie i odpuszczanie.
Odkształcenie wstępne obróbki termomechanicznej (P.T.M.O) w tym przypadku można przeprowadzić w temperaturach N.T.M.O i V.T.M.O lub w temperaturze 20ºC. Ponadto przeprowadza się zwykłą obróbkę cieplną: hartowanie i odpuszczanie.
Cel i rodzaje obróbki chemiczno-termicznej
Obróbka chemiczno-termiczna to proces będący połączeniem efektów cieplnych i chemicznych w celu zmiany składu, struktury i właściwości warstwy wierzchniej stali.
Celem obróbki chemiczno-termicznej jest zwiększenie twardości powierzchni, odporności na zużycie, wytrzymałości granicznej, odporności na korozję, odporności na ciepło (odporność na zgorzelinę), odporności na kwasy.
Największe zastosowanie w przemyśle mają następujące rodzaje obróbki chemiczno-termicznej: nawęglanie; azotonawęglanie; azotowanie; cyjanizacja; metalizacja dyfuzyjna.
Cementowanie to proces nawęglania powierzchni wytworzony w celu utwardzenia powierzchni części.
W zależności od zastosowanego nawęglacza nawęglanie dzieli się na trzy typy: nawęglanie z nawęglaniem pełnym; nawęglanie gazowe (metan, propan, gaz ziemny).
Nawęglanie gazowe. Części są podgrzewane do temperatury 900-950ºC w specjalnych hermetycznie zamkniętych piecach, do których w ciągłym strumieniu doprowadzany jest gaz zawierający węgiel cementujący [naturalny (naturalny) lub sztuczny].
Proces nawęglania w gaźniku stałym przebiega następująco. Części zapakowane w pudełko wraz z gaźnikiem (mieszaniną węgla drzewnego z aktywatorem) są podgrzewane do określonej temperatury i utrzymywane w tej temperaturze przez długi czas, a następnie schładzane i poddawane obróbce cieplnej.
Części wykonane ze stali węglowej i stopowej o zawartości węgla nie większej niż 0,2% są nawęglane dowolną z omówionych powyżej metod. Szczególnie dobre wyniki daje nawęglanie stali stopowych zawierających pierwiastki węglikotwórcze Cr, W, V: oprócz zwiększenia twardości powierzchni i odporności na zużycie, zwiększają one również granicę zmęczeniową.
Azotowanie- jest to proces nasycania azotem warstwy wierzchniej różnych metali i stopów, wyrobów stalowych lub części po podgrzaniu w odpowiednim środowisku. Zwiększa twardość powierzchni produktu, wytrzymałość, odporność na zużycie, zwiększa odporność na korozję.
Cyjanizacja– nasycenie warstwy powierzchniowej wyrobów jednocześnie węglem i azotem.
W zależności od użytego medium rozróżnia się cyjanizację: w mediach stałych; w mediach płynnych; w środowiskach gazowych.
W zależności od temperatury ogrzewania cyjanizację dzieli się na cyjanizację niskotemperaturową i wysokotemperaturową.
Cyjanizacja w ciekłych mediach odbywa się w kąpieli ze stopionej soli.
Cyjanizacja w mediach gazowych (azotonawęglanie). Proces jednoczesnego nasycania powierzchni części węglem i azotem. W tym celu części są nagrzewane w środowisku składającym się z gazu nawęglającego i amoniaku, czyli wazotonawęglanie łączy procesy nawęglania gazowego i azotowania.
Nasycenie dyfuzyjne metalami i niemetalami
Istnieją i są stosowane w przemyśle metody nasycania powierzchni części różnymi metalami (aluminium, chrom itp.) oraz metaloidami (krzem, bor itp.) Celem takiego nasycenia jest zwiększenie odporności na zgorzelinę, odporność na korozję, kwasoodporność, twardość i odporność na zużycie części. W rezultacie warstwa wierzchnia nabiera specjalnych właściwości, co pozwala na zaoszczędzenie pierwiastków stopowych.
Aluminiowanie– proces nasycania warstwy wierzchniej stali aluminium w celu zwiększenia żaroodporności (odporności na zgorzelinę) oraz odporności na korozję atmosferyczną.
Aluminiowanie odbywa się w mieszaninach proszkowych, w kąpielach z roztopionym aluminium, w środowisku gazowym oraz przez natryskiwanie ciekłego aluminium.
Chromowanie- proces nasycania warstwy wierzchniej stali chromem w celu zwiększenia odporności na korozję i żaroodporności, a w przypadku chromowania stali wysokowęglowych – w celu zwiększenia twardości i odporności na zużycie.
Silikonizacja– proces nasycania warstwy wierzchniej detalu krzemem w celu zwiększenia odporności na korozję i kwasoodporność. Silikonowaniu poddawane są części wykonane ze stali nisko- i średniowęglowych oraz żeliwa ciągliwego i wysokowytrzymałego.
Wytaczanie- proces nasycania borem warstwy powierzchniowej detalu. Celem borowania jest zwiększenie twardości, odporności na zużycie ścierne i korozję w agresywnych środowiskach, żaroodporności i żaroodporności części stalowych. Istnieją dwie metody borowania: elektroliza cieczowa i borowanie gazowe.
siarczkowanie– proces nasycania siarką warstwy wierzchniej części stalowych w celu polepszenia właściwości ekstremalnych ciśnieniowych oraz zwiększenia odporności na zużycie części.
Sulfocyjanian– proces nasycania powierzchni części stalowych siarką, węglem i azotem. Połączone działanie siarki i azotu w warstwie powierzchniowej metalu zapewnia wyższe właściwości ekstremalnego ciśnienia i odporność na zużycie w porównaniu do nasycenia samą siarką.
Obróbka cieplna żeliwa
Obróbkę cieplną żeliwa przeprowadza się w celu złagodzenia naprężeń wewnętrznych powstających podczas odlewania i powodujących zmiany wielkości i kształtu odlewu w czasie, zmniejszenia twardości i poprawy skrawalności oraz poprawy właściwości mechanicznych. Żeliwo poddawane jest wyżarzaniu, normalizacji, hartowaniu i odpuszczaniu, a także niektórym rodzajom obróbki chemiczno-termicznej (azotowanie, aluminiowanie, chromowanie).
Wyżarzanie odprężające. Wyżarzaniu temu poddawane są żeliwa w następujących temperaturach: żeliwo szare z grafitem płytkowym 500 - 570ºС; żeliwo sferoidalne z grafitem sferoidalnym 550 - 650ºС; żeliwo niskostopowe 570 - 600ºС; żeliwo wysokostopowe 620 - 650ºС. Podczas tego wyżarzania przemiany fazowe nie występują, ale naprężenia wewnętrzne są usuwane, wzrost lepkości, wypaczanie i pękanie podczas pracy są wykluczone.
Wyżarzanie zmiękczające (niskotemperaturowe wyżarzanie grafityzujące). Wykonywany w celu poprawy skrawalności i zwiększenia ciągliwości. Przeprowadza się go przez przedłużoną ekspozycję w temperaturze 680 - 700ºС lub powolne chłodzenie odlewów w temperaturze 760 - 700ºС. W przypadku detali o złożonej konfiguracji chłodzenie jest powolne, a w przypadku części o prostym kształcie jest przyspieszane.
Wyżarzanie grafityzacji, w wyniku czego z żeliwa białego otrzymuje się żeliwo ciągliwe.
Normalizacja stosowany do zwiększenia ilości związanego węgla, zwiększenia twardości, wytrzymałości i odporności na zużycie żeliwa szarego, sferoidalnego i o wysokiej wytrzymałości. Podczas normalizacji żeliwo (odlewy) jest podgrzewane powyżej temperatur z zakresu transformacji 850 - 950ºС i po przetrzymaniu jest chłodzone na powietrzu.
hartowanie poddać szare, ciągliwe i sferoidalne żelazo w celu zwiększenia twardości, wytrzymałości i odporności na zużycie. Zgodnie z metodą wykonania hartowanie żeliwa może być ciągłe wolumetryczne, izotermiczne i powierzchniowe.
Podczas ciągłego wolumetrycznego hartowania żeliwo nagrzewa się do temperatury 850 - 950ºС. Następnie odstaw na podgrzanie i całkowite rozpuszczenie węgla. Chłodzenie odbywa się w wodzie lub oleju. Po hartowaniu odpuszczanie odbywa się w temperaturze 200 - 600ºС. W rezultacie wzrasta twardość, wytrzymałość i odporność na zużycie żeliwa.
Podczas hartowania izotermicznego żeliwa są podgrzewane w taki sam sposób jak podczas ciągłego hartowania wolumetrycznego, przetrzymywane przez 10 do 90 minut i chłodzone w stopionej soli o temperaturze 200 - 400 ° C, a po przetrzymaniu chłodzone są na powietrzu.
Utwardzanie powierzchniowe z nagrzewaniem warstwy wierzchniej płomieniem tlenowo-acetylenowym, prądami o wysokiej częstotliwości lub w elektrolicie. Temperatura ogrzewania 900 - 1000ºС. Chłodzenie w wodzie, oleju lub emulsji olejowej.
Starzenie się służy do stabilizacji wymiarów części żeliwnych, zapobiegania wypaczaniu i łagodzenia naprężeń wewnętrznych. Zazwyczaj starzenie odbywa się po obróbce zgrubnej. Istnieją dwa rodzaje starzenia: naturalne i sztuczne.
Naturalne starzenie odbywa się na zewnątrz lub w pomieszczeniach. Produkty po odlaniu leżakują 6-15 miesięcy.
Sztuczne starzenie odbywa się w podwyższonych temperaturach; czas trwania - kilka godzin. Przy sztucznym starzeniu odlewy żeliwne ładowane są do pieca nagrzanego do 100 - 200ºC, nagrzanego do temperatury 550 - 570ºC z szybkością 30 - 60ºC na godzinę, utrzymywane przez 3 - 5 godzin i schładzane wraz z piec z prędkością 20 – 40ºC na godzinę do temperatury 150 – 200ºC, a następnie chłodzony powietrzem.
Obróbka chemiczno-termiczna żeliwa
Aby zwiększyć twardość powierzchni i odporność na zużycie, żeliwo szare poddaje się azotowaniu. Częściej azotowane są żeliwa szare perlityczne stopowe z chromem, molibdenem i aluminium. Temperatura azotowania 550 - 580ºС, czas ekspozycji 30 - 70 godzin. Oprócz azotowania, zwiększenie twardości powierzchniowej i odporności na zużycie stopowego szarego żeliwa perlitycznego można osiągnąć poprzez cyjanizację gazową i cieczową w temperaturze 570ºC. W celu zwiększenia odporności cieplnej odlewy żeliwne można poddać aluminiowaniu, a w celu uzyskania wysokiej odporności na korozję w kwasach - silikonowaniu.
Obróbka cieplna stopów metali nieżelaznych
Stopy aluminium
Stopy aluminium poddawane są trzem rodzajom obróbki cieplnej: wyżarzaniu, hartowaniu i starzeniu. Główne rodzaje wyżarzanie są to: stopy dyfuzyjne, rekrystalizacji i utwardzane termicznie.
Homogenizacja służy do wyrównania chemicznej mikroheterogeniczności ziaren roztworu stałego. W celu przeprowadzenia homogenizacji stopy aluminium są podgrzewane do 450 - 520ºС i utrzymywane w tych temperaturach od 4 do 40 godzin; po ekspozycji - chłodzenie razem z piecem lub do powietrza. W efekcie struktura staje się bardziej jednorodna, a plastyczność wzrasta.
Wyżarzanie rekrystalizujące aluminium i opartych na nim stopów jest stosowane znacznie szerzej niż stali. Tłumaczy się to tym, że metale, takie jak aluminium i miedź, a także wiele stopów na ich bazie, nie są utwardzane przez hartowanie, a wzrost właściwości mechanicznych można osiągnąć tylko przez obróbkę na zimno, a operacja pośrednia w takiej obróbce jest wyżarzanie rekrystalizacyjne. Temperatura wyżarzania rekrystalizacyjnego stopów aluminium 300 - 500ºC ekspozycja 0,5 - 2 godziny.
Wyżarzanie stopów hartowanych termicznie służy do całkowitego usunięcia utwardzenia, przeprowadza się je w temperaturze 350 - 450 ° C z czasem przetrzymywania 1 - 2 godzin, a następnie dość powolnym chłodzeniem.
Po hartowanie wytrzymałość stopu nieznacznie wzrasta, ale ciągliwość się nie zmienia. Po hartowaniu stopy aluminium poddawane są starzenie się, w którym następuje rozkład przesyconego roztworu stałego.
Obrabiane plastycznie stopy aluminium
W stanie utwardzonym duraluminium jest ciągliwe i łatwo odkształca się. Po utwardzeniu i naturalnym lub sztucznym starzeniu siła duraluminium dramatycznie wzrasta.
Odlewane stopy aluminium
W przypadku odlewanych stopów aluminium stosuje się różne rodzaje obróbki cieplnej w zależności od składu chemicznego. W celu hartowania odlewane stopy aluminium poddaje się hartowaniu w celu uzyskania przesyconego roztworu stałego i sztucznemu starzeniu, a także hartowaniu bez starzenia w celu uzyskania stabilnego roztworu stałego w stanie zahartowanym.
stopy magnezu
Stopy magnezu, podobnie jak aluminium, poddawane są wyżarzaniu, hartowaniu i starzeniu. W celu wyrównania chemicznej mikroheterogeniczności ziaren roztworu stałego przez dyfuzję wlewki ze stopu magnezu poddaje się homogenizacji w temperaturze 350–400°C z ekspozycją 18–24 godzin. Półwyroby z kutych plastycznie stopów magnezu poddawane są wyżarzaniu rekrystalizującemu w temperaturze ≈ 350ºC, a także w niższych temperaturach 150 - 250ºC w celu zmniejszenia naprężeń szczątkowych.
Stopy magnezu są utwardzone lub utwardzone i sztucznie starzone. W temperaturze 20°C w utwardzonych stopach magnezu nie zachodzą żadne zmiany, to znaczy nie podlegają one naturalnemu starzeniu.
Miedź i stopy miedzi
Obróbka cieplna miedzi. Odkształceniu miedzi towarzyszy wzrost jej wytrzymałości i spadek ciągliwości. W celu zwiększenia plastyczności miedź poddawana jest wyżarzaniu rekrystalizującemu w temperaturze 500 - 600ºC, w wyniku czego plastyczność gwałtownie wzrasta, a wytrzymałość spada.
Obróbka cieplna mosiądzu. Poddaje się je tylko wyżarzaniu rekrystalizacyjnemu w temperaturze 600 - 700ºC (w celu usunięcia stwardnienia). Mosiądz jest chłodzony podczas wyżarzania w powietrzu lub w celu przyspieszenia chłodzenia i lepszego oddzielenia kamienia w wodzie. Dla części mosiężnych, które po odkształceniu wykazują naprężenia szczątkowe, w wilgotnej atmosferze, charakterystyczne jest zjawisko pękania samoistnego. Aby tego uniknąć, elementy mosiężne poddaje się wyżarzaniu w niskiej temperaturze w zakresie 200 - 300 C, w wyniku którego usuwane są naprężenia szczątkowe, a twardnienie pozostaje. Wyżarzanie niskotemperaturowe jest szczególnie konieczne w przypadku mosiądzów aluminiowych, które są podatne na samoistne pękanie.
Obróbka cieplna brązów. W celu wyrównania składu chemicznego brąz poddawany jest homogenizacji w temperaturze 700 - 750ºC, a następnie szybkiemu schłodzeniu. Aby zmniejszyć naprężenia wewnętrzne, odlewy są wyżarzane w temperaturze 550°C. Aby przywrócić plastyczność między operacjami obróbki na zimno pod ciśnieniem, poddaje się je wyżarzaniu rekrystalizacyjnemu w temperaturze 600 - 700ºС.
Brązy aluminiowe o zawartości glinu od 8 do 11%, które ulegają rekrystalizacji fazowej podczas ogrzewania i chłodzenia, mogą być utwardzane. W wyniku hartowania wzrasta wytrzymałość i twardość, ale maleje ciągliwość. Po hartowaniu następuje odpuszczanie w temperaturze 400 - 650º C, w zależności od wymaganych właściwości. Poddawane również homogenizacji, a półprodukty odkształcalne - wyżarzanie rekrystalizacyjne w temperaturze 650 - 800ºC.
Brąz berylowy utwardza się w wodzie o temperaturze 760 - 780ºС; w tym przypadku nadmiar fazy nie ma czasu na wytrącenie, a po hartowaniu stop składa się z przesyconego roztworu stałego i ma niską twardość i wytrzymałość oraz wysoką ciągliwość. Po hartowaniu odpuszczanie (starzenie) odbywa się w temperaturze 300 - 350ºС przez 2 godziny. W celu zwiększenia stabilności przesyconego roztworu stałego i ułatwienia utwardzania brązy berylowe są dodatkowo stapiane z niklem.
stopy tytanu
Stopy tytanu poddawane są wyżarzaniu rekrystalizującemu i wyżarzaniu z rekrystalizacją fazową oraz hartowaniu poprzez obróbkę cieplną – hartowanie i starzenie. Aby poprawić odporność na zużycie i ścieranie, stopy tytanu poddaje się azotowaniu, nawęglaniu lub utlenianiu.
Wyżarzanie rekrystalizujące stosuje się do tytanu i stopów w celu usunięcia umocnienia przez zgniot po obróbce na zimno. Temperatura wyżarzania rekrystalizacyjnego wynosi 520 - 850ºC w zależności od składu chemicznego stopu i rodzaju półfabrykatu.
Wyżarzanie z rekrystalizacją fazową stosuje się w celu zmniejszenia twardości, zwiększenia ciągliwości, rozdrobnienia ziarna i wyeliminowania niejednorodności strukturalnej. Zastosuj proste, izotermiczne i podwójne wyżarzanie; temperatura nagrzewania podczas wyżarzania 750 - 950ºС w zależności od stopu.
Podczas wyżarzania izotermicznego, po utrzymywaniu w temperaturze wyżarzania, części są chłodzone do 500 - 650 ° C (w zależności od stopu) w tym samym piecu lub przenoszone do innego pieca i utrzymywane przez pewien czas i chłodzone w powietrzu. Przy wyżarzaniu izotermicznym skraca się czas wyżarzania, a ciągliwość jest wyższa.
W podwójnym wyżarzaniu części są podgrzewane do temperatury wyżarzania, utrzymywane i chłodzone na powietrzu. Następnie ponownie podgrzewam do 500 - 650ºС, trzymam i schładzam na powietrzu. Wyżarzanie podwójne w porównaniu do wyżarzania izotermicznego zwiększa wytrzymałość na rozciąganie przy niewielkim spadku ciągliwości oraz skraca czas obróbki.
Spośród wszystkich rodzajów obróbki chemiczno-termicznej stopów tytanu najszerzej stosowane jest azotowanie prowadzone w środowisku azotu lub w mieszaninie azotu i argonu w temperaturze 850–950 C przez 10–50 godzin. Części wykonane ze stopów tytanu po azotowaniu mają dobre właściwości przeciwcierne.
Wniosek
Obróbka cieplna jest jedną z głównych, najważniejszych operacji ogólnego cyklu technologicznego obróbki, od prawidłowego wykonania zależy jakość (właściwości mechaniczne i fizykochemiczne) wytwarzanych części maszyn i mechanizmów, narzędzi i innych wyrobów. Opracowano i zracjonalizowano technologiczne procesy obróbki cieplnej żeliwa szarego i białego, stopów metali nieżelaznych
Obiecującym kierunkiem doskonalenia technologii obróbki cieplnej jest instalowanie jednostek obróbki cieplnej w warsztatach mechanicznych, tworzenie linii automatycznych z włączeniem w nie procesów obróbki cieplnej, a także opracowywanie metod poprawiających właściwości wytrzymałościowe części, ich niezawodność i trwałość.
Literatura
B.V. Zacharow. V.N. Berseneva „Postępowe procesy technologiczne i urządzenia do obróbki cieplnej metali” M. ” Szkoła podyplomowa» 1988
W.M. Zuev „Obróbka cieplna metali” M. Szkoła wyższa 1986
licencjat Kuźmina „Technologia metali i materiałów konstrukcyjnych” M. „Inżynieria” 1981
W.M. Nikiforov „Technologia metali i materiałów konstrukcyjnych” M. „Wyższa Szkoła” 1968
AI Samohotsky N.G. Parfenovskaya „Technologia obróbki cieplnej metali” M. Engineering 1976
Dobór materiału i opracowanie procesu technologicznego obróbki cieplnej matrycy
Stan roboczy matrycy, narzędzie do gwintowania do cięcia gwint zewnętrzny ręcznie lub na obrabiarce. Charakterystyka stali, jej właściwości chemiczne, mechaniczne i inne. Metody monitorowania trybów obróbki cieplnej i jakości produktu.
Gatunek stali 18KhGT: stal chromowo-manganowa zawiera 0,18% węgla, do 1% chromu, mangan. Kolejność operacji wstępnej i końcowej obróbki cieplnej części. Sposób działania wstępnej i końcowej obróbki cieplnej detali.
Podstawy teoretyczne obróbka cieplna stali. Wyżarzanie dyfuzyjne i rekrystalizacyjne. Hartowanie to obróbka cieplna, w której stal uzyskuje strukturę nierównowagową i wzrasta twardość stali. Zastosowanie obróbki cieplnej w praktyce.
Istota celu noża i jego zastosowanie. Analiza właściwości technologicznych i składu chemicznego stali szybkotnących. Etapy procesu technologicznego obróbki cieplnej wstępnej i hartowniczej, dobór osprzętu, wady i ich eliminacja.
Podstawy technologii obróbki cieplnej metali i stopów. Obróbka cieplna to etap procesu technologicznego wytwarzania części. Poprawa skrawalności materiałów przez docisk lub cięcie. Kształtowanie właściwości technicznych i elektrycznych.
Opis procedury stosowania hartowania stali węglowych i wyznaczania temperatury hartowania zgodnie z zadaniem. Obliczanie wymaganego czasu utwardzania. Powołanie wyżarzania i określenie jego czasu zgodnie z zadaniem. Zasady protokołu.
Kształtowanie właściwości materiałowych części. Uderzenie obróbka skrawaniem na właściwościach materiałowych przedmiotów obrabianych. Wpływ chłodziwa (chłodziwa).
Rozszyfrowanie gatunku stali. Charakter wpływu pierwiastków stopowych i węglowych danej stali na położenie punktów krytycznych. Dobór i uzasadnienie kolejności operacji wstępnej i końcowej obróbki cieplnej części. Tryb obróbki cieplnej części.
Teoria obróbki cieplnej. Przemiany w stali podczas ogrzewania i chłodzenia. Wyżarzanie i normalizacja. Wady obróbki cieplnej. Wady podczas wyżarzania i normalizacji. Wady hartowania. Obróbka chemiczno-termiczna i hartowanie powierzchni stali.
Teoria i technologia obróbki cieplnej. Rodzaje obróbki cieplnej. Wyżarzanie, normalizacja, hartowanie, starzenie, poprawa. Obróbka chemiczno-termiczna. Jej typy. Materiały kompozytowe.
Zasady obróbki części przez cięcie - usuwanie z obrabianego przedmiotu za pomocą narzędzie tnące naddatek, konsekwentnie dostosowując jego kształt i wymiary do wymaganych, zmieniając go w gotowy produkt. Kontrola jakości powierzchni poprzez obróbkę chemiczno-termiczną.
Zapoznanie z metodyką opracowywania procesu technologicznego obróbki cieplnej części: samochodów, ciągników i maszyn rolniczych. Rozszyfrowanie gatunku danej stali, opis jej mikrostruktury, właściwości mechanicznych przed obróbką cieplną.
Gatunek stali 20HNR - stal chromowo-niklowa o zawartości węgla 0,20%, do 1% chromu, niklu i boru. Sposobem działania wstępnej i końcowej obróbki cieplnej detali jest temperatura nagrzewania oraz mikrostruktura w stanie nagrzanym czynnika chłodzącego.