Mapa procesu technologicznego przygotowania mieszanek betonowych. TTK. Przygotowanie mieszanki betonowej na budowie. Harmonogram procesu produkcyjnego
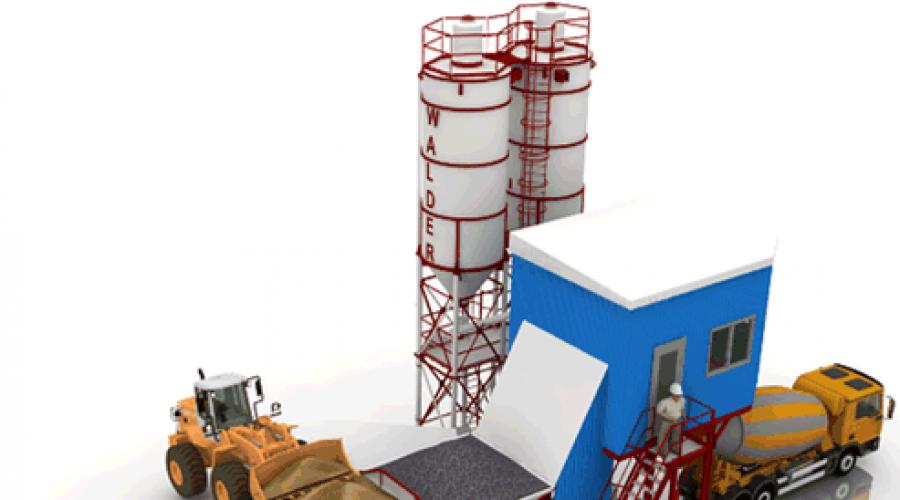
Przeczytaj także
TYPOWA WYKRES TECHNOLOGICZNY (TTK)
PRZYGOTOWANIE MIESZANKI BETONOWEJ NA PLACU BUDOWY
I. ZAKRES
1.1. Typowa mapa technologiczna (zwana dalej TTK) to kompleksowy dokument regulacyjny, który ustala, zgodnie z konkretną technologią, organizację procesów pracy przy budowie konstrukcji przy użyciu najnowocześniejszych środków mechanizacji, postępowych projektów i metod wykonywania praca. Są przeznaczone do przeciętnych warunków pracy. SIWZ jest przeznaczona do wykorzystania przy opracowywaniu Projektów na wykonanie robót (PPR), innej dokumentacji organizacyjnej i technologicznej, a także w celu zapoznania (przeszkolenia) pracowników oraz pracowników inżynieryjno-technicznych z zasadami wytwarzania prace nad przygotowaniem mieszanki betonowej w mieszalni do przygotowania mieszanek cementowo-betonowych na placu budowy.
1.2. W prawdziwa mapa podano instrukcje dotyczące przygotowania mieszanki betonowej za pomocą racjonalnych środków mechanizacji, podano dane dotyczące kontroli jakości i odbioru pracy, podano wymagania dotyczące bezpieczeństwa przemysłowego i ochrony pracy w produkcji pracy.
1.3. Ramy regulacyjne dla opracowania map technologicznych to: SNiP, SN, SP, GESN-2001 ENiR, normy produkcyjne dotyczące zużycia materiałów, lokalne progresywne normy i ceny, normy dotyczące kosztów pracy, normy zużycia materiałów i zasobów technicznych .
1.4. Celem stworzenia KT jest opisanie rozwiązań w zakresie organizacji i technologii przygotowania mieszanki betonowej w celu zapewnienia jej wysokiej jakości, a także:
Obniżenie kosztów pracy;
Skrócenie czasu budowy;
Zapewnienie bezpieczeństwa wykonywanych prac;
Organizacja pracy rytmicznej;
Unifikacja rozwiązań technologicznych.
1.5. Na podstawie TTC, w ramach PPR (jako obowiązkowych elementów Projektu Realizacji Pracy), opracowywane są schematy przepływu pracy (RTC) do wykonywania określonych rodzajów prac związanych z przygotowaniem mieszanki betonowej. Robocze mapy technologiczne opracowywane są na podstawie standardowe mapy na specyficzne warunki danej organizacji budowlanej, z uwzględnieniem jej materiałów projektowych, warunków naturalnych, dostępnego parku maszynowego i materiałów budowlanych, związanych z warunkami lokalnymi. Robocze mapy technologiczne regulują środki wsparcia technologicznego oraz zasady realizacji procesów technologicznych w produkcji pracy. Cechy technologiczne, w zależności od marki przygotowywanej mieszanki, każdorazowo określa Projekt Roboczy. Skład i szczegółowość materiałów opracowanych w RTK ustala właściwa organizacja wykonawcza wykonawstwa, na podstawie specyfiki i zakresu wykonywanych prac. We wszystkich przypadkach zastosowania TTK konieczne jest powiązanie go z warunkami lokalnymi, w zależności od składu, marki i ilości produkowanej mieszanki betonowej.
Schematy pracy są przeglądane i zatwierdzane w ramach PPR przez kierownika Generalnego Wykonawcy w porozumieniu z organizacją Zamawiającego, Dozorem Technicznym Zamawiającego.
1.6. Mapa technologiczna przeznaczona jest dla majstrów, majstrów i majstrów wykonujących prace przy przygotowaniu mieszanki betonowej, a także pracowników dozoru technicznego Zamawiającego i przeznaczona jest do specyficznych warunków pracy w III strefie temperaturowej.
^ II. POSTANOWIENIA OGÓLNE
2.1. Opracowano mapę technologiczną zestawu prac związanych z przygotowaniem mieszanki betonowej.
2.2. Prace nad przygotowaniem mieszanki betonowej odbywają się na jednej zmianie, czas pracy podczas zmiany wynosi:
gdzie 0,828 to współczynnik wykorzystania mechanizmów przez czas podczas zmiany (czas związany z przygotowaniem do pracy i przeprowadzeniem ETO - 15 minut, przerwy związane z organizacją i technologią procesu produkcyjnego oraz odpoczynkiem kierowcy - 10 minut co godzinę pracy).
2.3. Mapa technologiczna przewiduje wykonanie pracy przez zintegrowane łącze z mobilna betoniarnia BSU-30TZ, gabaryty agregatu 42500x5850x8400 m, o wydajności 30 m3/h wyposażony w betoniarka SB-138, bunkry materiały obojętne m, pojemność silosu na cement wynosi 60 ton, całkowite zużycie energii elektrycznej wynosi 75 kW (patrz rys. 1).
Rys.1. Betoniarnia BSU-30TZ
2.4. Betoniarnia wyposażona jest w zautomatyzowany system sterowania oparty na komputerze przemysłowym, który zapewnia:
Zautomatyzowana kontrola wszystkich procesów technologicznych produkcji;
Technologia wielu receptur do przygotowywania mieszanek (do 50 receptur);
Rozliczanie zużycia materiałów i produkcji betonu według gatunku;
Rozliczanie realizacji wniosków z zachowaniem informacji o Kliencie, czasu wejścia i realizacji wniosku, numeru receptury oraz objętości mieszanki;
Wyświetlanie informacji księgowych na wyświetlaczu i drukarce.
2.5. Prace należy wykonywać zgodnie z wymaganiami następujących dokumentów regulacyjnych:
SP 48.13330.2011. Organizacja budowy;
SNiP 3.03.01-87. Konstrukcje nośne i zamykające;
GOST 27006-86. Beton. Zasady doboru kompozycji;
GOST 30515-97. cementy. Ogólne warunki techniczne;
GOST 8736-93. piasek dla Roboty budowlane;
GOST 8267-93. Kruszywo i żwir z gęstych skał do prac budowlanych;
SNiP 12-03-2001. Bezpieczeństwo pracy w budownictwie. Część 1. Wymagania ogólne;
SNiP 12-04-2002. Bezpieczeństwo pracy w budownictwie. Część 2. Produkcja budowlana.
^ III. ORGANIZACJA I TECHNOLOGIA WYKONYWANIA PRACY
3.1. Zautomatyzowana wytwórnia betonu (BSU) wraz z urządzeniem SB-138 przeznaczona jest do przygotowywania mieszanek betonowych sztywnych i plastycznych z kruszywem do 40 mm. Wydajność instalacji do 30 m/h; pojemności lejów zasypowych na cement, kruszywo, zbiornik na wodę są zaprojektowane na pół godziny pracy przy maksymalnej wydajności i najwyższym stosunku wodno-cementowym 0,5. Mobilna wytwórnia betonu składa się z działów mieszania i dozowania, magazynu kruszywa oraz magazynu cementu (patrz rys. 2). Instalacja sterowana jest z kabiny maszynisty, a osprzęt elektryczny znajduje się w specjalnym pomieszczeniu. Kabina maszynisty wyposażona jest w przyrządy rejestrujące przebieg procesu technologicznego.
Rys.2. Schemat betoniarni
1 - eksploatacyjne wypełniacze bunkrów; 2 - przenośnik-dozownik; 3 - przenośnik przeładunkowy; 4 - betoniarka; 5 - rama betoniarki; 6 - dozownik cementu; 7 - dozownik dodatków chemicznych; 8 - dozownik wody; 9 - jednostka dodatków chemicznych (na życzenie klienta); 10 - silos cementu eksploatacyjnego z filtrem; 11 - przenośnik ślimakowy
3.2. Magazyn materiałów eksploatacyjnych piasku i tłucznia frakcyjnego Typ otwarty ze ściankami działowymi, zlokalizowanymi bezpośrednio przy betoniarni. Piasek i tłuczeń frakcyjny dostarczany jest do magazynu materiałów eksploatacyjnych wagonami kolejowymi. W przypadku dostaw niefrakcyjnych lub zanieczyszczonych tłucznia odbywa się tu również sortowanie materiału na frakcje (przesiewanie) oraz mycie materiału. Piasek i tłuczeń są podawane do podajników porcjowni i rozładowywane ładowacz czołowy TO-49 bezpośrednio nad lejami tac wibracyjnych przenośnika chodnikowego. Jednostka dozująca SBU składa się z lejów serwisowych-napełniaczy z dozowniki wahadłowe ciągłego działania С-633. Dozowniki są instalowane nad przenośnikiem poziomym, który dostarcza materiały do przenośnika pochyłego. Na przenośniku pochyłym wpadają do wanny załadowczej wydziału mieszania.
3.3. Materiały eksploatacyjne automatyczny magazyn cementu S-753 o pojemności 300 ton przeznaczony jest do krótkotrwałego składowania cementu. Cement z wagonów kolejowych jest rozładowywany bezpośrednio do magazynu cementu za pomocą wyładunek pneumatyczny С-577 lub cementowozy.
Wieża silosowa o pojemności 60 ton wyposażona jest w dwa wskaźniki poziomu cementu typu UKM. Lej podający cement to cylinder ze stożkową częścią na dole. Cement podawany jest bezpośrednio do dozownik S-781 z podajnikiem bębnowym. Wewnątrz bunkra są dwa wskaźnik poziomu cementu С-609А uwzględnione w systemie gospodarki magazynowej. Włączenie lub wyłączenie mechanizmu dostarczającego cement z magazynu odbywa się za pomocą tych samych wskaźników.
3.4. ^ Betoniarnia SB-138 Ciągłe wymuszone mieszanie jest głównym wyposażeniem węzła betoniarskiego. Korpus roboczy mieszarki to dwa wały o przekroju kwadratowym 80x80 mm z zamontowanymi na nich łopatkami. Ostrza zakończone są ostrzami o wymiarach 100x100 mm. Korpus mieszadła zakończony jest lejem magazynowym z zasuwą szczękową.
^ Betoniarnia SB-138 jest połączona z magazynami kruszyw cementowych i dozownikiem systemem podajników taśmowych i kubełkowych.
3.5. W zależności od zmieniających się potrzeb mieszanki betonowo-cementowej, wytwórnię można dostosować do dowolnej wydajności w zakresie od 15 do 30 m/h zmieniając wydajność jego dozowników: cement z 5 na 10 t/h, piasek i tłuczeń od 12,5 do 25 t/h i wody do 6 m.
Czyli na przykład przy zużyciu materiałów na 1 m3 betonu określonym przez laboratorium zakładu (cement - 340 kg, piasek - 547 kg, kamień łamany frakcji 5-20 mm - 560 kg, kamień łamany ułamek 20-40 mm - 840 kg, woda - 170 kg) wydajność roślin wyniesie:
Tabela 1
Dozownik na | Wydajność dozowników, t/h przy wydajności zakładu, m/h |
|||
15 | 20 | 25 | 30 |
|
cement | | 6,8 | 8,5 | 10,2 |
Piasek | ![]() | 10,9 | 13,7 | 16,4 |
Kruszywo frakcja 5-20 mm | | 11,2 | 14,0 | 16,8 |
Frakcja kamienia łamanego 20-40 mm | ![]() | 16,8 | 21,0 | 25,2 |
Woda | | 3,4 | 4,3 | 5,1 |
3.6. Przed rozpoczęciem pracy cementowni z instalacją SB-138 cały sprzęt jest sprawdzany i w razie potrzeby kalibrowane są dozowniki kruszywa, cementu i wody. Kalibracja dozowników odbywa się ze zmianą wydajności zakładu, marki i składu mieszanki betonowej, masy objętościowej i rozkładu granulometrycznego kruszyw. Przy określonej wydajności zakładu i odpowiednio składzie i marce mieszanki konieczna jest również okresowa kalibracja dozowników.
3.7. Dozowniki kruszywa są kalibrowane przez pobieranie próbek. Do tego potrzebujesz:
Zbiorniki serwisowe napełniać piaskiem, małym i dużym żwirem w ilości co najmniej 5 m3 każdego materiału;
Ustaw dozowniki poziomu w pozycji poziomej (z materiałem) przesuwając dźwignię obciążenia lub zmieniając ładunek w skrzyni balastowej (w pobliżu wariatora). W takim przypadku klapy ruchome powinny być ustawione na wysokość 100 mm dla tłucznia i 80 mm dla piasku. Klapy stałe są montowane o 10 mm wyżej niż klapy ruchome. Sprawdzenie braku zakleszczeń lub zakleszczeń w systemie ważenia dozowników odbywa się poprzez lekkie dociśnięcie krawędzi platformy wagowej lub poprzez umieszczenie odważnika 0,5 kg. W takim przypadku platformę należy opuścić do przystanku;
Przygotować do kalibracji wagi towarowe o nośności co najmniej 0,5, pudełko o pojemności 200 m3 oraz stoper.
3.7.1. Do pobierania próbek konieczne jest włączenie poziomego przenośnika zbiorczego na ruch w przeciwnym kierunku poprzez zmianę kierunku silnika elektrycznego (wsteczny). Podczas testowania jednego dozownika, resztę należy wyłączyć. Poziomy przenośnik odbiorczy powinien być włączony na czas testu. Na polecenie asystenta laboratoryjnego trzymającego stoper operator włącza dozownik. Piasek lub tłuczeń wylewany jest na blachę przez 4-5 sekund, aż do uzyskania stabilnego płynięcia wsypywanego materiału. Następnie włącza się stoper, a pudełko umieszcza się pod strumieniem dozowanego materiału.
3.7.2. Pudełko jest ładowane w ciągu 60 sekund na 1, 2, 3 pozycje strzałki wariatora, aw ciągu 30 sekund - na 4 i 5 pozycji strzałki. Po upływie czasu pobierania próbek, na sygnał asystenta laboratorium, przenośnik odbiorczy i dozownik zostają wyłączone. Pobrana próbka jest ważona na wadze. Dla jednej pozycji wariatora wykonywane są trzy ważenia.
3.7.3. Wydajność godzinową dozownika określa średnia arytmetyczna masy trzech próbek według wzoru:
gdzie jest średnią arytmetyczną masy trzech próbek w kg bez tary;
Czas próbkowania w sek.
3.7.4. Jeżeli masa próbek nie przekracza ±2% obliczonej wartości, uważa się, że w tej pozycji wskazówki wariatora dozownik pracuje stabilnie. Podobnie wykonuje się kalibrację innych dozowników kruszyw.
3.8. Aby skalibrować dozownik cementu, musisz:
Poluzuj śruby mocujące rurę zasypu cementu i obróć rurę o 90°;
Upewnij się, że zasobnik na cement jest całkowicie wypełniony cementem. Sprawdź poziom cementu w leju zasypowym za pomocą wskaźników poziomu na panelu sterowania mieszalni;
Przygotować do tarowania wag handlowych o nośności co najmniej 0,5, dwóch pudełek o pojemności 200 litrów, stopera, łopaty, blaszanej rurki o średnicy 130-150 mm, długości 3-3,5 m.
3.8.1. Próbkowanie jest przeprowadzane dla każdej z pięciu pozycji strzałki wariatora. Aby to zrobić, pod dyszą instalowana jest skrzynka, na polecenie asystenta laboratorium kierowca włącza dozownik cementu. Cement z dozownika wchodzi do rury, a z niej do pudełka, aż do ustalenia stabilnego trybu podawania cementu i normalnej liczby obrotów silnika elektrycznego. Czas wymagany do uzyskania stabilnego przepływu materiału wynosi zwykle 50-60 sekund. Po tym czasie stoper jest jednocześnie włączany, a rura jest przenoszona do załadunku pudełka.
3.8.2. Pudełko jest ładowane w ciągu 90 sekund na 1, 2, 3 pozycje strzałki wariatora, aw ciągu 60 sekund - na 4, 5 pozycji strzałki. Po upływie określonego czasu pobrana próbka jest ważona na wadze. Dla każdej pozycji igły wariatora pobierane są trzy próbki. Dokładność dozowania cementu ±2% obliczonej wagi.
3.8.3. W celu kontroli poprawności kalibracji sprawdza się działanie dozownika przy wybranej pojemności i przy ciągłej pracy dozownika przez - 10 minut poprzez pobranie trzech próbek w pudełku, zwracając szczególną uwagę na działanie wszystkich mechanizmów i nieprzerwany przepływ materiał do dozownika.
3.9. Aby skalibrować dystrybutor wody, musisz:
Rurkę spustową, przez którą woda wpływa do mieszalnika, obrócić o 180° na kołnierzu i przedłużyć dodatkową rurą o długości do 4 m;
Wyłącz wszystkie urządzenia niezwiązane z dozowaniem wody.
3.9.1. Urządzenie dozujące jest kalibrowane przez próbkowanie, dla którego konieczne jest włączenie pompy dozującej, gdy rura spustowa. W tym samym czasie woda ze zbiornika przez pompę dozującą i zawór trójdrożny wraca do zbiornika przez pierścień. Na polecenie asystenta laboratoryjnego trzymającego stoper, operator przełącza zawór trójdrożny w położenie podawania wody do mieszalnika, a do beczki podawana jest woda do momentu ustalenia stałego stałego przepływu wody.
3.9.2. Następnie stoper jest jednocześnie włączany, a zawór trójdrożny jest natychmiast przełączany na dostarczanie wody do zbiornika wodomierza. Pojemnik jest napełniany w ciągu 60 sekund dla pozycji 1, 2 i 3 strzałki wariatora oraz w ciągu 30 sekund dla pozycji 4 i 5 strzałki. Po upływie określonego czasu, na polecenie asystenta laboratoryjnego, zawór trójdrożny zostaje przełączony na spust i stoper zostaje wyłączony. Operator przełącza zawór trójdrożny w położenie do dostarczania wody przez pierścień. Pobrana próbka jest mierzona.
3.9.3. Aby zachować główny wskaźnik jakości mieszanki betonowej (stosunek wodno-cementowy) konieczne jest kalibrowanie dozownika wody z dokładnością ±1%.
3.10. Po skalibrowaniu wszystkich dozowników instalacji budowany jest wykres wydajności betoniarni w zależności od położenia strzałki wariatora każdego dozownika (rys. 3).
Rys.3. Wykres zależności wydajności dozowników od pozycji strzałek wariatorów:
1 - woda; 2 - frakcja kruszonego kamienia 5-20 mm; 3 - frakcja kruszonego kamienia 20-40 mm; 4 - piasek; 5 - cement
3.11. Ten wykres jest ważny, gdy zakład pracuje na trwałych materiałach, które składają się na mieszankę betonową. Aby zmienić wydajność dozowników, konieczna jest zmiana przełożenia za pomocą wariatora. Aby to zrobić, ustaw strzałki wariatora (tylko w ruchu) na odpowiedni podział wzdłuż przybliżonej krzywej, a następnie, kalibrując, dokonaj niezbędnej korekty ich położenia.
3.12. Przed uwolnieniem mieszanki betonu cementowego wykonywane są następujące operacje:
Sprawdź obecność cementu, kruszyw, wody i dodatków w zbiornikach zasilających;
Włącz zasilanie;
Sprawdź poprawność działania dozowników;
Podaj operatorowi maszyny skład mieszanki cementowo-betonowej, dobrany przez laboratorium zgodnie z wilgotnością materiałów;
Zamontować dozowniki urządzeń ważących zgodnie ze składem mieszanki.
3.12.1. Przed włączeniem jednostek instalacji kierowca wydaje dwa ostrzegawcze sygnały dźwiękowe w odstępie 1 minuty (pierwszy sygnał jest długi, drugi krótki).
3.12.2. Następnie uruchamiane są zespoły instalacji w następującej kolejności: betoniarka, pompa dozująca (zgodnie z wzór pierścienia), przenośnik skośny, przenośnik prefabrykowany, dozowniki kruszywa, dozownik cementu, zawór trójdrogowy z doprowadzeniem wody do mieszalnika. Po 1-2 minutach od rozpoczęcia bezczynnej pracy zaczynają uwalniać mieszaninę.
3.12.3. Najpierw partie testowe wykonywane są w trybie półautomatycznym. W tym momencie kierowca i asystent laboratorium określają ruchliwość mieszaniny (ciąg stożka) poprzez pobranie próbki. Jeżeli ciąg stożka różni się od podanego, zmienia się dozowanie wody. Po osiągnięciu określonego ciągu stożka i upewnieniu się, że dozowanie materiałów składowych jest prawidłowe, sterownik przełącza urządzenie w tryb pracy automatycznej.
3.13. Instalacja działa według następującego schematu, przedstawionego na rys. 4
Rys.4. System technologii eksploatacja wytwórni betonu BSU-30TZ
1 - podajniki wibracyjne; 2 - przenośniki; 3 - bunkry kruszywa; 4 - dozowniki kruszyw; 5 - dozownik cementu; 6 - bunkier cementowy; 7 - przenośnik taśmowy; 8 - mikser; 9 - napęd do betonu; 10 - zbiornik na wodę; 11 - dozownik wody; 12 - zawór trójdrożny; 13 - kosz przyjęciowy; 14 - silos bankowy; 15 - filtry
3.13.1. Spychacz naprzemiennie wpycha kruszywo na tace wibracyjne 1, skąd przenośniki 2 podają je do zasobników 3. W przypadku braku kruszywa piasek i tłuczeń są podawane przez ładowacz czołowy do zasobników. Gdy bunkry są w pełni załadowane, włącza się wskaźnik górnego poziomu, a taca wibracyjna i przenośniki są wyłączane po przejściu materiału pozostałego na taśmie i włącza się sygnał świetlny końca załadunku. W momencie wyczerpania się materiału w leju zasypowym do wskaźnika poziomu dolnego włącza się przenośnik, taca wibracyjna, sygnały świetlne i dźwiękowe rozpoczęcia załadunku.
3.13.2. Cement z puszki silosu 15 jest podawany do zasobnika 6 za pomocą pneumatycznego systemu wtrysku. Z leja zasypowego cement wchodzi do dozownika wahadłowego 5. Wskaźniki górnego i dolnego poziomu cementu mają sygnały świetlne i dźwiękowe do panelu sterowania magazynu cementu.
3.13.3. Woda w zbiorniku 10 komory mieszania jest pompowana ze specjalnego zbiornika. Kruszywo o frakcji 5-20, 20-40 mm oraz piasek dozowane są w sposób ciągły taśmowymi dozownikami wahadłowymi 4, do których materiał trafia z zasobników.
Najpierw na taśmę dozowany jest tłuczeń o frakcji 20-40 mm, następnie tłuczeń o frakcji 5-20 mm i piasek, a na wierzch tych materiałów cement. Ta kolejność podawania eliminuje gromadzenie się małych cząstek materiału na taśmie. Dozowane materiały są podawane przez lejek podający do mieszalnika. Woda ze zbiornika dozowana jest za pomocą pompy dozującej i podawana rurociągiem bezpośrednio do mieszalnika roboczego.
3.13.4. Bard siarczynowo-alkoholowy przygotowywany jest w specjalnej instalacji i wprowadzany do wody w ilości 0,2-0,3% wagi cementu na 1 m betonu (0,68-1,0 kg/m). W mieszarce elementy betonowe są intensywnie mieszane i transportowane wały łopatkowe do gniazdka. Z mieszalnika gotowa mieszanka trafia do leja magazynowego, a następnie przez bramę szczękową jest rozładowywana do wywrotek.
3.14. Na koniec dnia, po zakończeniu wydawania mieszanki betonowej, cała ekipa przystępuje do czyszczenia bloków betoniarni. Szczególnie dokładnie wyczyść mikser.
Pokruszony kamień jest najpierw podawany do mieszalnika i jest czyszczony na sucho, następnie mieszalnik jest myty wodą, a także czyszczona jest brama szczękowa leja magazynowego.
Pozostała część instalacji czyszczona jest sprężonym powietrzem.
Opis pracy
Ten schemat technologiczny dotyczy mieszanki betonowej do przygotowania ciężki beton o średniej gęstości 2,4-2,5 kg/cm³ i Lekki beton o średniej gęstości 1,7-1,9 kg/cm³ stosowany jako surowiec do produkcji wyrobów żelbetowych i betonowych.
Organizacja i technologia przygotowania mieszanki betonowej
Cement M 400 dostarczany jest do magazynów cementu koleją w wagonach samowyładowczych. Z wagonów cement jest wyładowywany grawitacyjnie przez włazy do urządzenia odbiorczego-magazynu. Wagony samowyładowcze są rozładowywane za pomocą sprężonego powietrza. Z urządzenia odbiorczego cement jest pompowany pneumatyczną pompą śrubową typu NPV 36-2 do silosów żelbetowych nr silosów lub może być podawany bezpośrednio rurociągami cementu z rozładunku wagonów cementowych do silosów betonu zakład.
Dostawa cementu z silosów do mieszalnika odbywa się za pomocą ślimaków. Aby wyeliminować zawieszanie się cementu w silosach (sklepieniach), na stożkowej części silosów zainstalowane są wibratory.
Dostarczanie materiałów obojętnych do mieszalnika odbywa się za pomocą przenośnika z dozowników odpowiednich materiałów obojętnych. Leje odbiorcze są zainstalowane przed dystrybutorami. Przyjmowanie bunkrów dla obojętnych 3 jednostek. 12 m³ każdy. Załadunek materiałów obojętnych do lejów odbiorczych odbywa się za pomocą ładowarki łyżkowej. Przenośnik montowany jest w ogrzewanej galerii, aby zapobiec przyklejaniu się materiałów obojętnych do nieczynnej gałęzi przenośnika i tworzeniu się pod nią zatorów.
W celu poprawy jakości mieszanek betonowych zakład posiada wydział przygotowania dodatków: plastyfikatorów i dodatków do betonu zimowego.
Mieszanki betonowe przygotowywane są według zatwierdzonych receptur. Przygotowanie mieszanki betonowej ogranicza się do dozowania i mieszania materiałów składowych. Dozowanie materiałów obojętnych i cementu odbywa się na dozownikach wagowych. Do przygotowania mieszanki betonowej stosuje się dodatki uplastyczniające. Dokładność dozowania cementu, wody, dodatków może odbiegać od obliczonej nie więcej niż 1%, kruszywa - 2%.
Aby uzyskać jednorodną mieszankę, miesza się ją w betoniarce o objętości 1,5 m³ (objętość wyjściowa mieszarki). Optymalny czas mieszania w mieszalnikach cyklicznych jest określony przez empirycznie w laboratorium. Czas mieszania dla mieszanin o ruchliwości 4-5 cm wynosi 75-100 sekund.
Materiały wyjściowe są ładowane z reguły jednocześnie, roztwór roboczy dodatków wprowadzany jest z wodą zarobową. Podczas pracy z ciepłą wodą kolejność ładowania jest następująca: kruszywo, gorąca woda i dodatki chemiczne, cement. Kruszywa zimne szybko obniżają temperaturę mieszanki, zapobiegając szybkiemu wiązaniu cementu pod wpływem kontaktu z gorącą wodą. Mieszanie betonu w zimie zwiększa się o 25%. Pod koniec mieszania mieszanka betonowa jest rozładowywana do leja dozującego lub samochodu.
Kuczmin
Krótka instrukcja:
- Wyszukaj odpowiednią pracę w pasku wyszukiwania na środku strony u góry lub w bocznym pasku nawigacyjnym po lewej stronie.
- Oceń jakość pracy, korzystając z treści i zrzutów ekranu rysunków znajdujących się w archiwum. Aby wyświetlić zrzuty ekranu, pobierz archiwum na dole strony.
- Jeśli jesteś zadowolony z pracy, wybierz metodę płatności (Yandex-Money, WebMoney lub Interkassa) lub skorzystaj z konta osobistego i konta osobistego.
- Oczekuj, że hasło do archiwum zostanie wysłane na Twój e-mail. Aby przyspieszyć otrzymanie hasła, musisz poprawnie wypełnić formularz płatności - podaj swój adres e-mail.
- W przypadku wszystkich pytań prosimy o kontakt
KARTA TECHNOLOGICZNA Nr
do prac betonowych
1 Zakres... 3
2 organizacja i technologia pracy .. 3
3 WYMAGANIA DOTYCZĄCE JAKOŚCI I ODBIORU PRAC. 4
4 ZDROWIE I BEZPIECZEŃSTWO.. 5
5 OCHRONA ŚRODOWISKA… 6
6 WYKAZ DOKUMENTACJI PRAWNO-technicznej i referencyjnej. 7
6 Arkusz zapoznawczy.. 8
- Obszar zastosowań
Mapa technologiczna przewiduje organizację i technologię robót betonowych
Rozważane prace obejmują:
- przygotowanie mieszanki betonowej;
- prace wzmacniające;
- układanie betonu;
- metody kontroli.
- organizacja i technologia wykonywania pracy
Podczas wykonywania pracy konieczne jest przestrzeganie wymagań dokumentów regulacyjnych podanych w sekcji 6.
Surowce używane do produkcji fundamentów monolitycznych muszą być zgodne z aktualną dokumentacją regulacyjną i techniczną, której towarzyszą dokumenty od przedsiębiorstw dostawców poświadczających ich jakość.
Projekt fundament monolityczny musi spełniać wymagania dokumentacja normatywna.
Przygotowanie mieszanki betonowej.
Mieszankę betonową przygotowuje się w betoniarce o działaniu wymuszonym.
Wybór cementów do przygotowania mieszanek betonowych powinien być dokonany zgodnie z GOST 30515-97. Przyjmowanie cementów powinno odbywać się zgodnie z GOST 30515-97, transport i przechowywanie cementów - zgodnie z GOST 30515-97 i SNiP 3.09.01-85.
Kruszywa do betonu są używane do frakcjonowania i płukania. Zabronione jest używanie naturalna mieszanka piasek i żwir bez przesiewania na frakcje.
Dozowanie składników mieszanek betonowych powinno odbywać się na wagę. Dozwolone jest objętościowe dozowanie wody dodatków wprowadzanych do mieszanki betonowej w postaci roztworów wodnych. Stosunek składników określa się dla każdej partii cementu i kruszyw podczas przygotowywania betonu o wymaganej wytrzymałości i ruchliwości. Dawkowanie składników powinno być dostosowane podczas przygotowywania mieszanki betonowej, biorąc pod uwagę dane z monitorowania wskaźników właściwości cementu, wilgotności, granulometrii kruszyw oraz kontroli wytrzymałości.
Przygotowując mieszankę betonową przy użyciu oddzielnej technologii, należy przestrzegać następującej procedury:
- woda, część piasku, drobno zmielony wypełniacz mineralny (jeśli jest stosowany) i cement są dozowane do działającego mieszalnika szybkoobrotowego, gdzie wszystko jest mieszane;
- powstałą mieszaninę podaje się do betoniarki, wstępnie załadowanej resztą kruszywa i wody, i ponownie wszystko jest mieszane.
- przerwa między etapami betonowania (lub układania warstw mieszanki betonowej) powinna wynosić co najmniej 40 minut, ale nie więcej niż 2 godziny.
- dozwolone jest stosowanie dodatków (przeciwmrozowych, napowietrzających, przyspieszających i opóźniających twardnienie betonu itp.).
Grubość warstwy ochronnej betonu należy uwzględnić rolę zbrojenia w konstrukcjach (robocze lub konstrukcyjne), rodzaj konstrukcji (słupy betonowe, płyty, belki, elementy fundamentowe, ściany itp.), średnicę i rodzaj wzmocnienie.
Działa armatura.
Prace zbrojarskie należy prowadzić zgodnie z mapą technologiczną P
Układanie i zagęszczanie mieszanek betonowych
Układanie mieszanki betonowej powinno być wykonywane przez betoniarki, które mają urządzenia dozujące i rozprowadzające mieszankę w ograniczających urządzeniach bocznych, z reguły bez użycia pracy ręcznej.
Podczas układania mieszanek betonowych na otwartym składowisku należy podjąć środki (specjalne schrony, szopy, powłoki foliowe) w celu ochrony mieszanek betonowych i świeżo formowanych produktów przed szkodliwym działaniem wpływów atmosferycznych.
Tryby formowania powinny zapewniać współczynnik zagęszczenia mieszanki betonowej (stosunek jej rzeczywistej gęstości do obliczonej teoretycznej): dla ciężkiego betonu - nie mniej niż 0,98; przy stosowaniu sztywnych mieszanek i odpowiednim uzasadnieniu, a także w przypadku betonu drobnoziarnistego - nie mniej niż 0,96. Objętość międzykrystalicznych pustek w zagęszczonej lekkiej mieszance betonowej musi być zgodna z wymaganiami GOST 25820-83.
Zdejmowanie produktów po obróbce cieplnej należy przeprowadzić po osiągnięciu przez beton wytrzymałości na zdzieranie.
WYMAGANIA DOTYCZĄCE JAKOŚCI I ODBIORU ROBÓT
Kontrola jakości pracy powinna być przeprowadzana zgodnie z wymaganiami dokumentów regulacyjnych podanych w sekcji 6:
Przyjmując gotowy beton i żelazo konstrukcje betonowe lub części konstrukcji należy sprawdzić:
- zgodność konstrukcji z rysunkami roboczymi;
- jakość betonu pod względem wytrzymałości i, jeśli to konieczne, mrozoodporności, wodoodporności i innych wskaźników określonych w projekcie;
- jakość materiałów użytych do budowy, półproduktów i wyrobów.
Odbiór gotowych konstrukcji betonowych i żelbetowych lub części konstrukcji powinien być sformalizowany zgodnie z ustaloną procedurą wraz z protokołem kontroli ukryte prace lub akt akceptacji struktur krytycznych.
Skład operacji i środków kontroli podczas betonowania
Czołowi pracownicy i specjaliści organizacji, zgodnie z listą stanowisk zatwierdzonych przez kierownika organizacji, przed przyjęciem do pracy, a następnie okresowo w ustalonych terminach, są sprawdzani pod kątem znajomości zasad ochrony i bezpieczeństwa pracy , biorąc pod uwagę ich obowiązki służbowe i charakter wykonywanej pracy. Procedura przeprowadzania szkoleń i testowania wiedzy została ustalona zgodnie z GOST 12.0.004-90 SSBT „Organizacja szkoleń z zakresu bezpieczeństwa pracy. Postanowienia ogólne” oraz zgodnie z Rozporządzeniem Ministerstwa Pracy Federacji Rosyjskiej z dnia 13.01.2003 nr. „Procedura szkolenia w zakresie ochrony pracy i testowania znajomości wymagań pracy pracowników organizacji”. Przybliżone rozporządzenie w sprawie trybu szkolenia i testowania wiedzy z zakresu ochrony pracy dla kierowników i specjalistów organizacji, przedsiębiorstw i instytucji oraz instytucji budownictwa, przemysłu materiały budowlane oraz mieszkalnictwo i usługi komunalne.ZDROWIE I BEZPIECZEŃSTWO
Pracownicy wykonujący pracę muszą zdać test wiedzy i posiadać certyfikaty sprawdzające wiedzę z zakresu ochrony pracy.
Pracownicy nie przeszkoleni wcześniej bezpieczne metody pracy według zawodu, w ciągu miesiąca od dnia przyjęcia do pracy, muszą zostać przeszkoleni zgodnie z GOST 12.0.004-90 SSBT w zakresie instrukcji ochrony pracy dla odpowiednich zawodów, sporządzonych na podstawie branżowych instrukcje ochrony pracy i otrzymać świadectwo ochrony pracy.
Stanowiska pracy powinny być wyposażone w apteczki z lekami.
Lista dokumentów, które muszą znajdować się w miejscu pracy:
- Nakazy spotkania Odpowiedzialne osoby w sprawie ochrony pracy, bezpieczeństwa przemysłowego;
- Nakazy powołania osób odpowiedzialnych za dobry stan i bezpieczną eksploatację maszyn i mechanizmów;
- Zamówienia na sprzęt zabezpieczający;
- dziennik odpraw w miejscu pracy;
- dziennik komentarzy i sugestii;
- dziennik kontroli wejścia.
OCHRONA ŚRODOWISKA
W celu ochrony środowiska przy wykonywaniu powyższych prac zabrania się:
- naruszać granice terytoriów przeznaczonych do budowy;
- zanieczyszczać środowisko odpadami budowlanymi, dla których na etapie projektowania należy przewidzieć sposoby przetwarzania i unieszkodliwiania odpadów;
- zakłócać naturalną sieć odwadniającą;
- przejazd maszyn i pojazdów w miejscach nieprzewidzianych projektem do produkcji robót;
- planować i wycinać strome zbocza na stanowiskach ze względu na możliwość erozji gleby;
- nie spełniają wymagań lokalnych władz ochrony środowiska.
Za wyrządzanie szkód w środowisku (niszczenie pokrywy glebowej i roślinnej, zanieczyszczenie zbiorników wodnych, pożary lasów, torfowisk itp.) poza pasem drogowym, kierownicy robót, a także pracownicy bezpośrednio wyrządzający szkody środowisko.
- WYKAZ DOKUMENTACJI PRAWNO-technicznej i referencyjnej
- SNiP III-42-80*. Główne rurociągi;
- - SNiP 3.02.01-87. Roboty ziemne, fundamenty i fundamenty;
- SNiP 3.03.01-87. Konstrukcje nośne i zamykające;
- VSN 004-88. Budowa głównych rurociągów. Technologia i organizacja;
- VSN 014-89. Budowa rurociągów głównych i polowych. ochrona środowiska;
- GOST R 51285-99. Siatki skręcone z sześciokątnymi komórkami do konstrukcji gabionowych. Specyfikacje;
- GOST 7502-98. Ruletki mierzące metal. Wymagania techniczne.
- GOST 12-03-01. SSBT. Fundusze ochrona osobista narządy oddechowe. Klasyfikacja i oznakowanie;
- GOST 12.3.003-86*. SSBT. Roboty elektryczne. Wymagania bezpieczeństwa;
- GOST 123.016-87. SSBT. Budowa. Prace antykorozyjne. Wymagania bezpieczeństwa;
- SNiP 12-03-2001. Bezpieczeństwo pracy w budownictwie. Część 1. Wymagania ogólne;
- SNiP 12-04-2002. Bezpieczeństwo pracy w budownictwie. Część 2. Produkcja budowlana;
- SP 12-136-2002. Rozwiązania z zakresu ochrony pracy i bezpieczeństwa pracy w projektach organizacji budowy i projektach produkcji robót
- POT R M-016-2001. Międzysektorowe zasady ochrony pracy (zasady bezpieczeństwa) podczas eksploatacji instalacji elektrycznych;
- PB 10-382-00. Zasady budowy i bezpiecznej eksploatacji dźwigów;
- Zasady eksploatacji technicznej konsumenckich instalacji elektrycznych”;
- POT R M-027-2003. Międzysektorowe przepisy dotyczące ochrony pracy w transporcie drogowym;
- Zasady bezpieczeństwa eksploatacji głównych rurociągów naftowych.
6 Arkusz zapoznawczy
Liczba stron | Pełne imię i nazwisko | Stanowisko pracownika | data | Podpis |
1. | ||||
2. | ||||
3. | ||||
4. | ||||
5. | ||||
6. | ||||
7. | ||||
8. | ||||
9. | ||||
10. | ||||
11. | ||||
12. | ||||
13. | ||||
14. | ||||
15. | ||||
16. | ||||
17. | ||||
18. | ||||
19. | ||||
20. | ||||
21. | ||||
22. |
Popieram:
______________________
______________________
______________________
„____” __________ 200 g.
WYTYCZANIE
KARTA TECHNOLOGICZNA DO BETONOWANIA KONSTRUKCJI
PRACE ZBROJENIOWE, SZALUNKOWE I BETONOWE
Numer strony |
||
Postanowienia ogólne | ||
Wymagania dotyczące betonu i mieszanki betonowej | ||
Oprzyrządowanie i wyposażenie technologiczne | ||
Prace przygotowawcze, szalunkowe i zbrojarskie | ||
betonowanie | ||
utwardzanie betonu | ||
Kontrola jakości robót | ||
Ochrona pracy w produkcji pracy | ||
ochrona środowiska | ||
Bibliografia | ||
Załącznik 1. Lista inżynierów i pracowników zaznajomionych z mapą technologiczną. |
1. Postanowienia ogólne
1.1. Mapa technologiczna dotyczy wykonywania prac szalunkowych, zbrojeniowych i betoniarskich.
1.2. Mapa technologiczna to część integralna projekt wykonania robót, opracowany w odniesieniu do konkretnego obiektu budowlanego, oraz określa wymagania dotyczące cech organizacji i technologii produkcji szalunków przygotowawczych, robót zbrojarskich i betoniarskich, mających na celu zapewnienie wysokiej jakości wykonywanych konstrukcji wybudowany.
1.3. Mapa technologiczna nakreśla środki organizacyjne, techniczne i konstrukcyjno-technologiczne, jakie należy podjąć, aby zapewnić techniczne bezpieczeństwo jakości betonu w całości, uzyskanie wymaganej wytrzymałości do czasu odspajania oraz zmniejszenie prawdopodobieństwa pęknięcia termiczne w konstrukcjach na etapach dojrzewania i usuwania betonu.
1.4. Mapa technologiczna przewiduje prace przygotowawcze, szalunkowe, zbrojarskie i betoniarskie podczas całorocznej budowy z uwzględnieniem wykonywania prac betoniarskich w warunki zimowe w cieplarniach.
1.5. Przy opracowywaniu Mapy technologicznej zakłada się, że mieszanka betonowa będzie dostarczana z betoniarni znajdującej się w odległości, w której podczas transportu nie nastąpi utrata ruchliwości poniżej zadanej wartości urabialności betonu podanej w tej mapie technologicznej .
1.6. Przy opracowywaniu „Mapy technologicznej” zakłada się, że betonowanie rusztów, stelaży i głowic podpór odbywa się w metalowym szalunku składanym.
1.7. Spełnienie wymagań przepisów gwarantuje otrzymanie betonu o wymaganych klasach wytrzymałości, wodoodporności, mrozoodporności, a docelowo zapewnienia wymaganej jakości i trwałości konstrukcji.
1.8. Przy opracowywaniu „Mapy technologicznej” wzięto pod uwagę, że zapobieganie pękaniu betonu pod wpływem temperatury lub jego znaczne zmniejszenie osiąga się tylko dzięki odpowiedniej kombinacji środków konstrukcyjnych i technologicznych do produkcji robót betonowych.
1.9. Działalność budowlana obejmuje:
dobór rozwiązań projektowych dla konstrukcji jako całości i jej poszczególnych elementów, zapewniających odporność konstrukcji na działanie temperatury, z uwzględnieniem lokalnych warunków klimatycznych;
Minimalizacja w projektowaniu stref-koncentratorów naprężeń termicznych;
Zastosowanie obniżonych gatunków betonu, zapewniające minimalne zużycie cementu;
Zbrojenie betonu z uwzględnieniem prawdopodobieństwa pęknięć termicznych.
1.10. Środki technologiczne obejmują środki określone poniżej w niniejszym „Regulaminie technologicznym”.
1.11. Produkcja robót betonowych musi odbywać się zgodnie z projektem, PPR, niniejszym „Przepisem technologicznym”, z aktualnymi numerami technicznymi i przepisami, w tym SNiP 3.06.04-91 „Mosty i rury”, SNiP 3.03.01-87 „Konstrukcje nośne i zamykające”; SNiP 12-03.2001 „Bezpieczeństwo pracy w budownictwie” część 1. Postanowienia ogólne. SNiP 12-04.2002 "Bezpieczeństwo pracy w budownictwie" część 2. Produkcja budowlana. VSN 150-93 „Instrukcja poprawy mrozoodporności betonowych konstrukcji transportowych”, M., 1993; Podręcznik „Kontrola jakości budowy mostów”, M., „Nedra”, 1994.
1.12. Opracowując „Mapę technologiczną” wzięto pod uwagę, że wszystkie operacje dla procesów wiodących i większość procesów pomocniczych wykonuje się za pomocą maszyn i mechanizmów, a prace ręczne - za pomocą zmechanizowanego narzędzia.
1.13. Odpowiedzialność za jakość prac wykonywanych przy budowie konstrukcji betonowych spoczywa na głównym inżynierze, który musi zapewnić organizację ich bezawaryjnego wykonania zgodnie z PPR, dokumentami regulacyjnymi oraz niniejszym „Przepisem Technologicznym”.
1.14. Prace przy betonowaniu i wznoszeniu konstrukcji betonowych prowadzone są pod kierunkiem brygadzisty, a na każdej zmianie - brygadzista zmianowy.
1.15. Podczas wykonywania prac betoniarskich na budowie niezbędna jest stała obecność przedstawicieli laboratorium budowlanego, którzy muszą monitorować parametry mieszanki betonowej, przestrzeganie zasad układania betonu, reżim temperaturowy utwardzania betonu i temperatury zewnętrznej, a także jakości wszystkich przychodzących materiałów.
1.16. Przy wykonywaniu prac betoniarskich na budowie niezbędne jest posiadanie odpowiedniego sprzętu laboratoryjnego (standardowy stożek do określania ruchliwości mieszanki betonowej, urządzenia do określania ilości powietrza napowietrzonego w mieszance betonowej, termometry, komplety form do doboru kostki kontrolne i inne niezbędne instrumenty i sprzęt).
2. Wymagania dotyczące betonu i mieszanki betonowej
2.1. Zgodnie z wymaganiami określonymi na rysunkach roboczych skład materiałowy mieszanki betonowej musi zapewniać uzyskanie przez beton określonych w projekcie wskaźników wytrzymałości, mrozoodporności i wodoodporności, a mianowicie:
Wskaźniki wytrzymałości, mrozoodporności i wodoodporności są określone zgodnie z rysunkami roboczymi projektu.
Dla każdej partii mieszanki betonowej umieszczonej w oddzielnej konstrukcji wystawiany jest dokument o jakości mieszanki betonowej. Firma dostawcy ponosi zobowiązania gwarancyjne za jakość dostarczanej na plac budowy mieszanki betonowej.
Wniosek o dostawę mieszanki betonowej sporządza WYKONAWCA-WYKONAWCA ROBÓT na papierze firmowym zakładu z obowiązkowym wskazaniem odbiorcy mieszanki betonowej (WYKONAWCA-WYKONAWCA ROBÓT), klasa betonu (B25, B30 . ..), ruchliwość mieszanki betonowej w miejscu ułożenia (P3, P4), mrozoodporność (F300...), wodoodporność (W6, W8...), wymagania techniczne dotyczące materiałów - spoiwo, kruszywa i dodatki . Czas rozpoczęcia dostawy mieszanki betonowej, adres dostawy, wymagana ilość mieszanki betonowej, wymagana ilość betonomieszarek.
3. Oprzyrządowanie i wyposażenie technologiczne
3.1. Miejsce budowy konstrukcji betonowej musi posiadać niezbędny sprzęt i wyposażenie technologiczne, a także materiały i osprzęt (patrz tabela 1).
3.2. Bez względu na porę roku należy zwrócić uwagę na zintegrowane urządzenia przeciwwilgociowo-temperaturowe, które powinny zapewniać przyspieszenie twardnienia betonu w warunkach dojrzewania w szalunku lub pod powłoką chroniącą przed ciepłem i wilgocią oraz na etapie nagrzewania i chłodzenie betonu, wyklucza możliwość pęknięć termicznych.
3.3 Zintegrowane urządzenia chroniące przed wilgocią i ciepłem składają się z:
Inwentarzowe szalunki metalowe z powierzchnią formującą;
Powłoki inwentaryzacyjne chroniące przed wilgocią i ciepłem - do ochrony nieuformowanych powierzchni świeżo ułożonego betonu przed wilgocią i wymianą ciepła z otoczeniem;
Markiza chroniąca betonową powierzchnię przed deszczem podczas pracy w deszczową pogodę;
Zamykanie szklarni-muszli z rama nośna oraz wymaganą liczbę generatorów ciepła (przy wykonywaniu prac w sezonie zimowym).
3.4. Folie polimerowe (polietylen, polichlorek winylu itp.) o grubości co najmniej 100 mikronów lub gumowana tkanina mogą być stosowane jako panele przeciwwilgociowe z inwentaryzacyjnej powłoki chroniącej przed wilgocią i ciepłem.
3.5. Jako materiały termoizolacyjne można zastosować geowłókninę, dornit, len lub inne panele termoizolacyjne. materiały rolkowe.
3.6. Oprócz skomplikowanych urządzeń technologicznych chroniących przed wilgocią i ciepłem, miejsce betonowania musi być wyposażone w:
Pompa do betonu zdolna do ciągłego dostarczania mieszanki betonowej z wymaganą mobilnością do szalunku;
Żuraw o wystarczającym wysięgu do dostarczania materiałów podczas budowy podpór;
Wibratory ręczne do zagęszczania mieszanki betonowej;
Bunkier (wiadro) do dostarczania w razie potrzeby betonu;
Zestaw narzędzi ręcznych do wyrównywania mieszanki betonowej;
Zestaw „lamp nośnych” do wizualnej kontroli, w razie potrzeby, jakości robót zbrojeniowych i szalunkowych, układania i zagęszczania mieszanki betonowej;
3.7. Ciepłownie powinny być wykonane z materiałów, które mają niską dmuchalność (tkanina gumowana, folie polimerowe itp.) i nie stają się kruche na zimno.
3.8. Przy montażu szklarni należy zapewnić hermetyczne przyleganie powłok do podłoża oraz wcześniej zabetonowanych elementów betonowych i żelbetowych.
3.9. Aby zmniejszyć ryzyko pękania w strefie styku stwardniałego betonu z stwardniałym, szklarnie powinny zapewniać ogrzewanie wcześniej zabetonowanych konstrukcji.
3.10. Aby zapewnić normalne warunki wymiany ciepła, w szklarni nie powinno być zbyt wąskich zagłębień. Odległość między ogrodzeniem szklarni a ogrzewaną konstrukcją musi wynosić co najmniej 1,0 ... 1,5 m.
3.11. W szklarniach o wysokości powyżej 4,0 m temperaturę należy kontrolować na wysokości 0,4 m od podłogi i przy suficie. Jeżeli różnica temperatur na wysokości szklarni jest większa niż 5 - 7 °C, konieczne jest wyrównanie temperatury powietrza za pomocą wentylatorów, dostarczających ogrzane powietrze od góry szklarni do dołu.
3.12. W przypadku korzystania z generatorów ciepła na paliwo płynne, jeśli to konieczne, należy zapewnić wentylację szklarni.
3.13. Teplyaki są wyposażone w generatory ciepła na paliwo ciekłe lub grzejniki elektryczne. Liczbę generatorów ciepła należy określić obliczeniowo, w zależności od temperatury zewnętrznej, wymaganej temperatury powietrza wewnątrz szklarni, warunków wymiany ciepła między szklarnią a otoczeniem oraz konstrukcji obudowy szklarni.
3.14. Szklarnia powinna być wyposażona w generatory ciepła lub grzejniki elektryczne z regulowana moc, co następnie pozwoli im płynnie regulować temperaturę powietrza w szklarni poprzez ich włączanie i wyłączanie.
3.15. Szklarnia musi mieć sztywną konstrukcję, która wytrzyma ciężar własny ogrodzeń, napór wiatru, opady śniegu itp.
3.16. Szklarnia musi być odpowiednio oświetlona, aby zapewnić normalne warunki pracy podczas układania betonu i wykańczania wierzchniej warstwy betonu.
3.17. W szklarniach do pielęgnacji betonu niezbędna jest wystarczająca liczba powłok chroniących przed ciepłem i wilgocią.
3.18. Ogrzewanie szklarni jest zatrzymywane tylko wtedy, gdy istnieje dopuszczalna różnica temperatur między twardniejącym betonem na powierzchni konstrukcji a powietrzem w szklarni (różnica nie przekracza 20 ° C). Generatory ciepła należy wyłączać sekwencyjnie, zapewniając płynny spadek temperatury powietrza w szklarni.
3.19. Szklarnię należy zdemontować po ostygnięciu betonu na powierzchni rusztu do temperatury nieprzekraczającej temperatury powietrza zewnętrznego o więcej niż 20 °C.
Przewidywaną minimalną temperaturę na następne 24 godziny należy przyjąć jako projektowaną temperaturę powietrza zewnętrznego.
Tabela 1
Cel sprzętu lub wyposażenia | Sprzęt lub oprzyrządowanie | Opis, marka. | Ilość (szt.) | Uwagi |
|
Dostawa betonu | ciężarówka z pompą do betonu | "SZCZELNY" Lstr = 42 m | |||
Zagęszczanie betonu | Wibrator głęboki, d = 50 mm, l = 35 cm. | ||||
Roboty instalacyjne | Udźwig dźwigu 16 t | ||||
Zagęszczanie betonu | Wibrator terenowy | 2800 obr/min |
|||
Wyrównywanie i przesuwanie betonu | łopata łopata | ||||
Wygładzanie powierzchni betonu | drewniana reguła |
4. Prace przygotowawcze, szalunkowe i zbrojarskie
4.1. Przed przystąpieniem do prac szalunkowych i zbrojarskich przy wznoszeniu konstrukcji betonowych należy w całości zakończyć prace związane z oznakowaniem geodezyjnym, ustalając osie konstrukcji betonowych. Szczególna uwaga na zachowanie prace geodezyjne należy podać podczas konstruowania szalunków i instalowania klatek wzmacniających.
4.2. W trakcie prac należy zwrócić szczególną uwagę na zapewnienie sztywności ułożonego szalunku oraz niedopuszczalność jego odkształcenia i oddzielenia pod naciskiem słupa ułożonej mieszanki betonowej, a także na określenie szybkości wznoszenia wszystkie elementy nośne z uwzględnieniem czasu wiązania mieszanki betonowej.
4.3. Przed rozpoczęciem prac zbrojarskich podłoże należy oczyścić z gruzu i brudu.
4.4. Podczas przygotowywania podłoży betonowych i spoin roboczych do usunięcia warstwy cementu, obróbka powierzchni odbywa się za pomocą strumienia wody i powietrza, szczotek metalowych lub urządzeń do piaskowania.
4.5. Przed zabetonowaniem konstrukcji konieczne jest wykonanie i zamontowanie koszy zbrojeniowych oraz zamontowanie szalunku w strefie betonowania i elementów zatopionych wymaganych przez projekt.
4.6. Prace zbrojarskie prowadzone są zgodnie z rysunkami roboczymi zbrojenia konstrukcji.
Do zbrojenia zbrojenie o średnicy 32 mm, 22 mm, 20 mm, 16 mm, 14 mm, 12 mm kl. AIII, stal zbrojeniowa gat. 25G2S, zbrojenie o średnicy 10 mm, 8 mm kl. AI stal gat. St5 sp. GOST 5781-82.
Kolejność przechowywania zbrojenia i kąta.
Zbrojenie stalowe jest składowane w specjalnie do tego celu wydzielonym miejscu. Pakiety zbrojenia układane są na okładzinach drewnianych i pokryte materiałem wodoodpornym. Ze zbrojeniem nie należy obchodzić się w sposób nieostrożny, zrzucany z wysokości, poddawany obciążeniom udarowym, uszkodzenie mechaniczne.
Kontrola.
Pręty zbrojeniowe należy sprawdzić pod kątem wad takich jak pęknięcia, miejscowe ścieńczenia, pory, łuszczenie, wgniecenia, wygięcia, rdza, lokalne lub ogólne zniekształcenia, odchylenia od określonej długości odcięcia pręta.
Czystość armatury.
Do czasu montażu klatki wzmacniającej wzmocnienie musi być czyste, wolne od brudu, oleju, smaru, farby, rdzy, zgorzeliny walcowniczej i podobnych materiałów.
Okucia łączone są w ramy przestrzenne drutem dziewiarskim D = 1,6 mm. Zbrojenie na zakładkę wykonuje się drutem dziewiarskim, zakładka prętów zbrojeniowych wynosi co najmniej 30 średnic zbrojenia. W jednej sekcji nie powinno znajdować się więcej niż 50% połączeń prętów.
4.7. Przed rozpoczęciem prac przy konstrukcjach betonowych konieczne jest wyprodukowanie wymaganej liczby przekładek – „krakerów”, które zapewnią wymaganą grubość warstwy ochronnej i położenie konstrukcyjne koszy zbrojeniowych we wszystkich odcinkach betonowanych elementów konstrukcyjnych. Jakość podkładek betonowych – „krakerów” do projektowania warstwy ochronnej betonu nie powinna być niższa niż jakość konstrukcji betonowych.
Dopuszcza się stosowanie przekładek plastikowych - "krakersów" produkowanych fabrycznie.
4.8. Podkładki dystansowe powinny być wykonane z betonu drobnoziarnistego z uwzględnieniem skratek z tłucznia kamiennego. Wymiary i konfiguracja podkładek betonowych - „krakerów” muszą odpowiadać konstrukcji klatki zbrojeniowej i wartościom konstrukcyjnym betonowej warstwy ochronnej, zapewniać ich stabilne położenie w szalunku i na prętach zbrojeniowych klatki.
Aby wykluczyć możliwość zaplamienia i późniejszego zniszczenia wierzchniej warstwy betonu w miejscach uszczelek „krakersów”, zewnętrzna (nośna) powierzchnia uszczelki z betonu drobnoziarnistego stykająca się z szalunkiem powinna mieć zarys krzywoliniowy (promień krzywizny 30 - 50 m).
4.9. Podczas wykonywania prac zbrojarskich konieczne jest zamontowanie elementów zatopionych zgodnie z projektem.
4.10. Przygotowanie klatek zbrojeniowych (oddzielnych elementów) i części zatopionych, ich montaż i montaż w szalunku oraz inne prace związane z cechy konstrukcyjne zbrojenie zabetonowanych elementów wykonuje się zgodnie z rysunkami roboczymi.
4.11. Pręty zbrojeniowe ułożone w szalunku elementów ramy są mocowane za pomocą wymaganej liczby przekładek - „krakerów”, niezawodnie zapewniając projektowe położenie klatki zbrojeniowej w szalunku i wielkość warstwy ochronnej betonu na wszystkich odcinkach.
4.12. Zbrojenie montowane na miejscu ze wszystkimi osadzonymi elementami (częściami) musi być sztywną ramą, która nie może ulec zniszczeniu podczas betonowania.
4.13. Do koszy zbrojeniowych w warstwie wierzchniej oraz w strefach środkowych należy przymocować rury plastikowe lub metalowe w celu utworzenia studzienek do pomiaru temperatury betonu podczas jego utwardzania.
4.14. Płyty szalunkowe montuje się zgodnie z projektem. Do betonowania stosuje się szalunek inwentarzowy wykonany zgodnie z TU. Dodatkowe sekcje szalunku wykonywane są na miejscu. Do dodatkowego szalunku stosuje się drewnianą ramę. Niezbędne jest zapewnienie dobrej szczelności wzajemnego styku krawędzi płyt szalunkowych. W przypadku stwierdzenia nieszczelności mogących prowadzić do wycieku zaprawy cementowej podczas betonowania, wszystkie wykryte miejsca przed nałożeniem smaru należy dokładnie uszczelnić poprzez przyklejenie taśmą klejącą (tynk budowlany) o szerokości 30 - 40 mm lub posmarowanie masą uszczelniającą. Połączenia płyt szalunkowych są uszczelniane silikonem lub innymi uszczelniaczami. Płyty szalunkowe należy mocować i mocować (podpory, ograniczniki, zastrzały, ściągi itp.) w taki sposób, aby tworzyły sztywną, niezmienną geometrycznie konstrukcję.
4.15. Przed montażem powierzchnie formujące płyt szalunkowych należy przetrzeć płótnem impregnowanym smarem lub innym smarem. Smar należy nakładać bardzo cienką warstwą, co wyklucza wnikanie smaru na zbrojenie podczas montażu płyt szalunkowych.
4.16. Po oględzinach instrumentalnych położenia koszy zbrojeniowych następuje oględziny zamontowanych płyt szalunkowych, koszy zbrojeniowych i zamontowanego szalunku oraz sporządzona zostaje ustawa o pracy niejawnej przy udziale przedstawicieli Zamawiającego, generalnego wykonawcy i służb nadzorczych.
5. Betonowanie
5.1 Przed przystąpieniem do prac przy układaniu betonu należy przygotować do eksploatacji sprzęt do podawania betonu oraz sprawdzić jego sprawność użytkową.
5.2 Przed rozpoczęciem prac kierownik budowy musi wyjaśnić: czas dostawy betonu z zakładu do obiektu, dostępność dokumentacji potwierdzającej zgodność wskaźników mieszanki betonowej i betonu z wymaganiami niniejszego „Technologicznego mapa". Przedstawiciel laboratorium budowlanego musi sprawdzić dostępność standardowego stożka do określania ruchliwości mieszanki betonowej, termometrów do pomiaru temperatury mieszanki betonowej i powietrza zewnętrznego, urządzenia do określania ilości powietrza napowietrzonego w mieszance betonowej oraz wystarczalność form do wykonywania kontrolnych kostek betonowych.
5.3 Należy stworzyć skuteczne połączenie eksploatacyjne pomiędzy betoniarnią a budowanym obiektem, zapewniające dostawę mieszanki betonowej w pełnej zgodności z wymaganiami projektu i niniejszą „Mapą technologiczną”.
5.4 Dostawa mieszanki betonowej na plac budowy musi odbywać się za pomocą betonomieszarek. Liczba betonomieszarek musi być przypisana z warunków objętości betonowanej elementy konstrukcyjne, intensywność układania mieszanki betonowej, odległość jej dostawy, czas wiązania betonu. Całkowity czas dostarczenia mieszanki betonowej na plac budowy, jej układania w elementach konstrukcyjnych nie powinien przekraczać czasu jej wiązania.
5.5 Zejście Doprowadzanie mieszanki betonowej na miejsce układania może odbywać się poprzez łącznik, łatwo zmontowane demontowane pnie, rurociągi betonowe oraz wąż końcowy pompy do betonu.
5.6 Przed doprowadzeniem mieszanki betonowej bezpośrednio do korpusu konstrukcji, pompę do betonu należy przetestować próbnym ciśnieniem hydraulicznym, którego wartość wynosi
Przypisany skład i mobilność mieszanki betonowej należy sprawdzić, doprecyzować na podstawie próbnego pompowania mieszanki betonowej.
Powierzchnie wewnętrzne rurociągu betonowego przed betonowaniem należy zwilżyć i posmarować wapnem lub zaprawa cementowa.
5.7 Podczas wykonywania prac betonowych należy wziąć pod uwagę, że w przypadku przerw w pompowaniu mieszanki od 20 do 60 minut konieczne jest pompowanie mieszanki betonowej przez system co 10 minut przez 10-15 sekund. przy niskich trybach pracy pompy do betonu. W przypadku przerw przekraczających określony czas rurociąg betonowy należy opróżnić i przepłukać.
5.8 Intensywność betonowania powinna być określona przez laboratorium budowlane, biorąc pod uwagę właściwości mieszanki betonowej, odległość dostawy betonu.
5.9 Przy wykonywaniu prac w okresie zimowym, przed betonowaniem każdego elementu należy podgrzać dolną i górną strefę wcześniej betonowanych elementów do temperatury co najmniej plus 5°C na głębokość co najmniej 0,5 m.
5.10 Aby zapobiec powstawaniu pęknięć termicznych w konstrukcjach, wartość temperatur nagrzewania wcześniej betonowanych elementów jest powiązana z temperaturą dopływającej mieszanki betonowej zgodnie z Tabelą 1.
Tabela 1
Uwaga:*) Jeżeli średnia dobowa temperatura otoczenia jest wyższa od plus 25 °C, grubość betonowanych konstrukcji jest większa lub równa 1 m, maksymalna wartość temperatury układanej mieszanki betonowej jest ograniczona do plus 20 °C
5.11 Przed zabetonowaniem oczyszczone powierzchnie, przygotowane zgodnie z wymaganiami pkt. 4.5 - 4.6, należy obficie zwilżyć wodą lub potraktować 2...5% roztworem polimeru Acryl 100.
5.12 Zejście i dostarczenie mieszanki betonowej na miejsce układania można przeprowadzić przez wąż końcowy pompy do betonu.
5.13 Mieszankę betonową należy układać w betonowaną konstrukcję warstwami o jednakowej grubości 25 - 30 cm (ale nie większej niż 40 cm), bez szczelin, z jednakowym kierunkiem układania w jednym kierunku we wszystkich warstwach.
5.14 Grubość kolejno układanych warstw poziomych dobierana jest na podstawie rzeczywistej szybkości podawania mieszanki betonowej do układania, z zastrzeżeniem, że przerwa przed ułożeniem kolejnej warstwy mieszanki betonowej w każdym konkretnym miejscu nie przekracza czasu dla utraty ruchliwości wcześniej ułożonej mieszanki w poprzedniej warstwie do 1 - 1,5 obserwuje się wytrącanie standardowego stożka (w ciągu 40 - 50 minut) w zależności od właściwości cementu i rzeczywistej temperatury mieszanki betonowej. Wskaźnikiem zgodności z tą zasadą jest brak wgłębienia w betonie, gdy końcówka wibratora z wałem giętkim jest powoli usuwana.
5.15 Podczas układania betonu warstwami w każdej warstwie należy utworzyć wiodący odcinek poziomy o długości 1–1,5 m, kąt nachylenia do poziomu powierzchni mieszanki betonowej przed zagęszczeniem nie powinien przekraczać 30 °.
5.16 Doprowadzanie, rozprowadzanie i zagęszczanie mieszanki betonowej w każdej warstwie należy wykonywać wyłącznie od dołu do góry.
5.17 Przed zagęszczeniem każdej ułożonej warstwy, mieszankę betonową należy równomiernie rozprowadzić na jej powierzchni. Wysokość poszczególnych występów i zagłębień powyżej ogólnego poziomu powierzchni rozprowadzania mieszanki betonowej nie powinna przekraczać 10 cm Rozprowadzanie mieszanki betonowej powinno odbywać się rurociągiem betonowym. Stosowanie wibratorów do redystrybucji i wyrównywania mieszanki betonowej jest zabronione.
5.18 Wibracje mieszanki betonowej w każdej warstwie iw każdym położeniu permutacji końcówki wibratora wgłębnego są prowadzone do momentu, gdy mieszanka betonowa przestanie osadzać się, a zaczyn cementowy będzie świecił na powierzchni.
5.19 Podczas wykonywania betonowania należy wykluczyć możliwość rozwarstwienia mieszanki betonowej na końcu każdego pasa zabetonowanej warstwy i nieuniknionego przecieku, zanurzenie w mieszance betonowej w odległości 50 - 70 cm od krawędź paska. Po ułożeniu kolejnej dawki mieszanki betonowej przeprowadza się dokładne badanie spoinowe strefy pozostającej na krawędzi pasa.
5.20 Po ułożeniu mieszanki betonowej w pierwszej warstwie konstrukcji przeznaczonej do betonowania, pompa do betonu zostaje wyłączona, rurociągi betonowe przenoszone są na jej powierzchnię końcową, a mieszankę betonową rozprowadza się w drugiej warstwie. Zagęszczanie wibracyjne mieszanki betonowej odbywa się również z opóźnieniem 1,0 - 1,5 m od miejsca podawania za pomocą pompy do betonu. Wibracje należy przeprowadzać z obowiązkowym „wejściem” wibratora do warstwy leżącej poniżej.
W podobny sposób odbywa się układanie i zagęszczanie mieszanki betonowej w kolejnych warstwach. Ściśle równomierne rozłożenie mieszanki betonowej w warstwach poziomych, z wykluczeniem możliwości jej rozdzielenia podczas obróbki wibracyjnej, jest najważniejszym czynnikiem zapewniającym jakość i jednolitość betonu w konstrukcji.
5.21 Po ułożeniu i zagęszczeniu betonu w warstwie wierzchniej na całej otwartej powierzchni konstrukcji betonowej konieczne jest jej wykończenie i wykończenie w celu zapewnienia parametrów projektowych dotyczących spadków, równości i jakości powierzchni.
5.22 Po związaniu betonu (po 1,5 - 2 godzinach od ułożenia) należy na odsłoniętych powierzchniach betonu nałożyć powłokę chroniącą przed wilgocią i wysoką temperaturą, składającą się z folia polietylenowa, dwie warstwy dornitu i górna warstwa folii polietylenowej.
6. Utwardzanie betonu
6.1 Podczas wznoszenia konstrukcji betonowych, biorąc pod uwagę zwiększone wymagania Ze względu na jakość betonu wznoszonych konstrukcji szczególną uwagę należy zwrócić na warunki i czas dojrzewania betonu.
6.2 Po okresie maksymalnego nagrzewania betonu, na etapie spadku temperatury, można usunąć dodatkowe okrycie plandekowe szalunku.
6.3 Zatrzymaj ogrzewanie szklarni, usuń izolacja cieplna od konstrukcji (powłoka chroniąca przed ciepłem i wilgocią na wierzchu rusztu) dopuszcza się demontaż szklarni, szalunku, z zastrzeżeniem ograniczeń określonych w paragrafie 3.18 i paragrafie 3.19 niniejszej „Mapy technologicznej”.
Jednocześnie jako projektowaną temperaturę otoczenia należy przyjąć minimalną przewidywaną temperaturę powietrza na zewnątrz na następne 24 godziny.
6.4 Podczas pielęgnacji betonu przewidywaną wytrzymałość betonu należy potwierdzić badaniami kontrolnymi próbek umieszczonych pod termo-wilgociową powłoką ochronną.
6.5 Pomiary temperatur twardnienia betonu konstrukcji w pierwszych trzech dniach po zabetonowaniu wykonywane są przez pierwszy dzień - co 4 godziny, następnie co 8 godzin i bezbłędnie przed zdjęciem termo-wilgociowych powłok ochronnych i szalunków .
7. Kontrola jakości pracy
7.1. Główny inżynier jest bezpośrednio odpowiedzialny za jakość prac zgodnie z systemem zarządzania jakością robót budowlano-montażowych.
Do przeprowadzenia pomiarów i testów zaangażowane jest laboratorium.
Technicy laboratoryjni są odpowiedzialni za pobieranie próbek na miejscu.
7.2. Kontrola jakości robót betoniarskich prowadzona jest zgodnie z planem zapewnienia jakości w celu zapewnienia pełnej zgodności z zatwierdzonym projektem, rysunkami roboczymi i wymaganiami tego schematu, a także zgodności z przepisami i regulacjami budowlanymi, normami i specyfikacjami.
7.3. Kontrola jakości prac podczas betonowania przeprowadzana jest:
Szczególną uwagę należy zwrócić na kontrolę produkcji, która obejmuje:
Kontrola wejściowa przychodzących struktur, produktów i materiałów;
kontrola operacyjna;
Kontrola odbioru;
Kontrola inspekcyjna.
Kontrola przychodząca konstrukcji, wyrobów i materiałów prowadzona jest przez komisję składającą się z przedstawicieli wykonawcy, generalnego wykonawcy oraz nadzoru technicznego zamawiającego z wykonaniem ustawy przepisana forma.
Sprawdzana jest zgodność materiałów z wymaganiami projektu, specyfikacjami technicznymi, SNiP, GOST;
7.4. Okucia i części wbudowane
Zgodność otrzymanej armatury z danymi podanymi w atestach i dokumentach przewozowych. Pręty zbrojeniowe należy sprawdzić pod kątem wad takich jak pęknięcia, miejscowe ścieńczenia, pory, łuszczenie, wgniecenia, wygięcia, rdza, lokalne lub ogólne zniekształcenia, odchylenia od określonej długości odcięcia pręta.
W razie potrzeby próbki są testowane.
7.5. Mieszanka betonowa.
W miejscu układania wykonuje się:
Kontrola plastyczności mieszanki betonowej (ciąg stożka) co najmniej 2 razy na zmianę, z rytmicznym dostarczaniem mieszanki betonowej; przy nierytmicznej dostawie mieszanki betonowej - plastyczność określana jest w każdej betonomieszarce;
Pomiar temperatury mieszanki betonowej - w każdej mieszarce;
Określanie naciągu powietrza - raz na zmianę;
Doboru próbek betonu (kostek) do kolejnych badań dokonuje asystent laboratoryjny w momencie rozładunku mieszanki betonowej do pompy do betonu.
W trakcie pracy jest to ustalane następująca informacja dla betonu:
Data betonowania każdego bloku, klasa betonu, czas układania mieszanki, położenie konstrukcji do betonowania.
Szczegóły mieszanki betonowej, w tym rodzaj i źródło każdego z materiałów składowych, źródło produkcji betonu; sugerowane proporcje (zgodnie z tabelą mieszanki betonowej) lub ilość każdego składnika na metr sześcienny całkowicie zagęszczonego betonu i szczegółowe dodatki.
Dzienna maksymalna i minimalna temperatura powietrza;
Pochodzenie próbek i daty pobrania próbek, w tym znaki identyfikacyjne.
Wyniki badań na wybranych próbkach oraz opis bloczka betonowego reprezentowanego przez próbki.
Sprawozdania z badań próbek kontrolnych betonu z wynikami badań wytrzymałości próbek w wieku 7 i 28 dni.
Ewidencja powinna być prowadzona w formie uzgodnionej przez klienta, aktualizowana i dostępna do wglądu przez klienta.
Aby zapewnić identyczność sposobu twardnienia betonu wybranych próbek oraz sposobu twardnienia betonu betonowanej konstrukcji, próbki pozostają na bloczku betonowym przez czas wiązania i twardnienia. Po zaniku charakterystycznego „połysku” testu cementowego na wykończonym obszarze powierzchni betonowanej konstrukcji, w tym obszarze układane są próbki kontrolne - kostki i pokryte panelami z wodoodpornej powłoki z folii polimerowej , układane są maty termoizolacyjne, a następnie układana jest druga warstwa powłoki (folii) odpornej na wilgoć. Próbki kontrolne przechowuje się pod pokrywą do momentu jej wyjęcia, następnie próbki przechowuje się w normalnej komorze magazynowej (temperatura 20 °C ± 2 °C, wilgotność 95%).
7.6. Materiały szalunkowe.
Materiały szalunkowe, sklejka, tarcica sprawdzane są pod kątem zgodności z atestami i dokumentami przewozowymi, przeprowadzana jest kontrola zewnętrzna w celu wykrycia widocznych wad, uszkodzeń itp. Materiały nienadające się do użytku są odrzucane wraz ze sporządzeniem ustawy o nieprzydatności tych materiałów. Odrzuconego materiału nie wolno używać do deskowania.
Materiały na urządzenie szklarni.
Przeprowadzana jest kontrola zgodności z certyfikatami i dokumentami przewozowymi, przeprowadzana jest inspekcja zewnętrzna w celu zidentyfikowania widocznych uszkodzeń i naruszeń.
Zabrania się wprowadzania do produkcji wzorów, materiałów i produktów, które przychodzą bez towarzyszących dokumentów!!!
7.8. Kontrolę operacyjną przeprowadza wykonawca.
Kontrola jakości operacyjnej prowadzona jest podczas następujących prac budowlanych:
Montaż i demontaż szalunków;
Montaż okuć i części osadzonych;
Układanie mieszanki betonowej;
Odnalezienie.
Kontrola operacyjna powinna zapewnić terminowe wykrywanie defektów oraz podejmowanie środków w celu ich eliminacji i zapobiegania.
Główne dokumenty dotyczące kontroli operacyjnej to:
Rysunki robocze;
Schematy technologiczne,
Ta regulacja i standardowe schematy blokowe;
SNiP, GOST;
Schematy kontroli jakości;
Wyniki kontroli operacyjnej należy odnotować w Ogólnym Dzienniku Prac, a także w specjalnych dziennikach prac, w tym w Dzienniku Prac Betonowych.
W przypadku pracy ukrytej sporządzaj akty o ustalonej formie.
7.9. Kontrola odbioru;
Podczas kontroli odbiorowej wykonywane są:
Akceptacja konstrukcji pośrednich;
Sprawdzenie jakości wykonanych elementów konstrukcyjnych.
Podczas kontroli odbioru Wykonawca przedłoży następującą dokumentację:
Rysunki wykonawcze z wprowadzonymi zmianami (jeśli występują) oraz dokumenty potwierdzające ich zatwierdzenie;
Fabryka karty danych technicznych, certyfikaty;
Świadectwa badania ukrytych prac;
Akty pośredniego odbioru konstrukcji;
Wykonawcze schematy geodezyjne położenia konstrukcji i szalunków;
Dzienniki pracy;
Wyniki badań laboratoryjnych betonu na zgodność z wymaganiami projektowymi;
7.10. Kontrola inspekcyjna;
Kontrola inspekcyjna przeprowadzana jest w celu sprawdzenia skuteczności wcześniej przeprowadzonej kontroli produkcji. Kontrola ta realizowana jest przez specjalnie utworzone komisje.
7.11. Po odbiorze zamontowanego szalunku i jego zamocowań należy sprawdzić:
Zgodność z tą mapą technologiczną;
Niezawodność mocowania szalunków;
Prawidłowa instalacja wtyczek i osadzonych części;
Tabela 2
Parametr | ||
1. Odchylenie linii płaszczyzn przecięcia od pionu lub nachylenia projektowego do całej wysokości konstrukcji dla: | ||
podwaliny | Pomiar, każdy element konstrukcyjny, dziennik pracy |
|
ściany i słupy podtrzymujące monolityczne stropy i stropy | ||
ściany i słupy podtrzymujące prefabrykowane konstrukcje belkowe, | ||
ściany budynków i budowli wznoszonych w szalunku przesuwnym, w przypadku braku stropów pośrednich, | 1/500 wysokości konstrukcji, ale nie więcej niż 100 mm | Pomiar, wszystkie ściany i linie ich przecięcia, dziennik pracy |
ściany budynków i budowli posadowionych w szalunku przesuwnym, w obecności stropów pośrednich, | 1/1000 wysokości konstrukcji, ale nie więcej niż 50 mm | |
2. Odchylenie płaszczyzn poziomych na całej długości odcinka podlegającego weryfikacji | Pomiar, co najmniej 5 pomiarów na każde 50 - 100 m, dziennik pracy |
|
3. Lokalne nierówności powierzchni betonu przy sprawdzaniu za pomocą dwumetrowej szyny, z wyjątkiem powierzchni nośnych | ||
4. Długość lub rozpiętość elementów | Pomiar, każdy element, dziennik pracy |
|
5. Rozmiar Przekrój elementy | 6 mm; -3mm | |
6. Ślady powierzchni i zatopionych wyrobów służących jako podpory dla stalowych lub prefabrykowanych słupów betonowych oraz innych prefabrykatów | Pomiar, każdy element odniesienia, obwód wykonawczy |
|
7. Nachylenie powierzchni nośnych fundamentów przy podpieraniu stalowych słupów bez zaprawy | To samo, każda fundacja, schemat wykonawczy |
|
8. Lokalizacja śrub kotwiących: | To samo, każda śruba fundamentowa, schemat wykonawczy |
|
w planie wewnątrz obrysu podpory | ||
w planie poza obrysem podpory | ||
wzrost | ||
9. Różnica znaków wysokości na styku dwóch sąsiednich powierzchni | Ten sam, każdy wspólny, wykonawczy schemat |
Deskowanie panelowe
Tabela 3
Produkcja płyt szalunkowych | Montaż szalunków |
|
Skład kontroli | Wymiary szalunku | Wymiary wewnętrzne, oznaczenia, pionowość, położenie osi szalunku |
Metoda i środki kontroli | Wizualne, pomiarowe; taśma miernicza ze stali, | Wizualne, pomiarowe; teodolit, poziom, pion, szyna, stalowa taśma miernicza |
Tryb i zakres kontroli | Każda tarcza | Wszystkie zmontowane szalunki |
Osoba kontrolująca operację | Mistrz, geodeta |
|
Pomiary geodezyjne |
||
Miejsce rejestracji wyników kontroli | Świadectwo przeglądu i odbioru zamontowanego szalunku |
Szalunek przygotowany do betonowania musi być przyjęty zgodnie z ustawą o pracy ukrytej.
7.12. Kontrola jakości robót zbrojarskich polega na sprawdzeniu zgodności z projektem i normami wyrobów oraz elementów osadzonych, dzianiu i spawaniu zbrojenia. Wymiana stali zbrojeniowej przewidziana w projekcie musi być uzgodniona z organizacją projektującą (nadzór projektowy).
Przychodząca stal zbrojeniowa musi być zarejestrowana w „Dzienniku kontroli przychodzących”.
Na kontrola wejścia wszystkie przychodzące elementy ze stali zbrojeniowej i osadzone muszą podlegać obowiązkowi egzamin zewnętrzny i zmierzyć.
Kontrola produktów wzmacniających i osadzonych musi być przeprowadzona zgodnie z wymaganiami Tabeli 4.
Kontrola zbrojenia
Tabela 4
Parametr | Wartość parametru, mm | Kontrola (metoda, zakres, rodzaj rejestracji) |
1. Odchyłka odległości pomiędzy oddzielnie zamontowanymi prętami roboczymi dla: | Przegląd techniczny wszystkich elementów, dziennik pracy |
|
kolumny i belki | ||
płyty i ściany fundamentowe, | ||
masywne konstrukcje | ||
2. Odchylenie odległości między rzędami zbrojenia dla: | ||
płyty i belki o grubości do 1 m | ||
konstrukcje o grubości powyżej 1 m | ||
3. Odchylenie od projektowej grubości warstwy ochronnej betonu nie powinno przekraczać: | ||
o grubości warstwy ochronnej do 15 mm i liniowych wymiarach przekroju konstrukcji, mm: | ||
od 101 do 200 | ||
o grubości warstwy ochronnej od 16 do 20 mm włącznie. i liniowe wymiary przekroju konstrukcji, mm: | ||
od 101 do 200 | ||
od 201 do 300 | ||
o grubości warstwy ochronnej większej niż 20 mm i liniowych wymiarach przekroju konstrukcji, mm: | ||
od 101 do 200 | ||
od 201 do 300 | ||
Całe zbrojenie zainstalowane w szalunku należy wykonać przed betonowaniem; wyniki ankiety i akceptacji powinny być udokumentowane w akcie o pracę ukrytą.
Główne operacje podlegające kontroli w produkcji robót zbrojarskich, metody kontroli i operacje kontrolowane przedstawiono w tabeli 5.
Metody kontroli i elementów kontrolowanych w produkcji robót zbrojarskich
Tabela 5
Główne operacje, które mają być kontrolowane | Pręty zbrojeniowe | Wzmacniający zespół siatki |
Skład kontroli | Czystość, jakość zbrojenia, wymiary prętów, gatunek stali | Spoiny, wymiary, rozmieszczenie siatek, otulina, jakość |
Metoda i środki kontroli | Pomiar wizualny, miernik | Pomiar wizualny, miernik stali |
Tryb i zakres kontroli | Solidny | Wszystkie siatki |
Osoba pod kontrolą | Mistrz, asystent laboratorium |
|
Osoba odpowiedzialna za organizację i sprawowanie kontroli | ||
Usługi zajmujące się monitoringiem | Laboratorium |
|
Kreator rejestracji wyników kontroli | Czasopismo prace ogólne. Dziennik spawania |
7.13. Wymagania technologiczne, które muszą być przestrzegane podczas wykonywania robót betonowych, a sprawdzane podczas kontroli operacyjnej, a także zakres, metody lub metody kontroli podano w tabeli 6.
Produkcja robót betoniarskich.
Tabela 6
Wymagania techniczne | Kontrola | Metoda lub metoda kontroli |
1. W miejscu układania mobilność mieszanki betonowej powinna mieścić się w zakresie 10-15 cm dla elementów konstrukcyjnych | Co najmniej dwa razy na zmianę z rytmicznym układaniem masy betonowej, wizualnie inne betonomieszarki. | Sprawdzanie zgodnie z GOST 10181.1-81 z rejestracją w dzienniku prac betonowych, pielęgnacji betonu, ustawą o próbkach kontrolnych produkcji, dziennikiem przybycia mieszanki betonowej. |
2. Temperatura mieszanki betonowej w miejscu ułożenia nie powinna różnić się od regulowanej o więcej niż ±2°C (od 5 do 25°) | W każdej betoniarce na budowie | Rejestracja, pomiar |
3. Grubość ułożonej warstwy betonu nie powinna przekraczać 40 cm | Trwałe, podczas betonowania | Pomiarowy, wizualny |
4. Objętość powietrza napowietrzonego w mieszance betonowej wynosi od 3 do 5% dla betonu o klasie mrozoodporności F 200 | Raz na zmianę (ze stałym: składem betonu, jakością materiałów, trybami przygotowania mieszanki betonowej) | Sprawdzanie zgodnie z GOST 10181.3-81 |
5. Normy próbek podczas betonowania konstrukcji | Dla każdego elementu konstrukcyjnego monolitycznych konstrukcji betonowych co najmniej jedna seria na zmianę. | Zobacz GOST 18105-86 |
6. Liczba serii próbek wykonanych z jednej próbki mieszanki betonowej na obiekcie | Zgodnie z klauzulą 2.3 GOST 18105-86 | Rejestracja |
7. Odbiór konstrukcji na wodoszczelność i mrozoodporność przeprowadza się w oparciu o wymagania dokumentacji projektowej | Zgodnie z ustawami zakładu dostawcy wyniki określenia mrozoodporności betonu ułożonego w konstrukcji. | Zgodnie z dokumentem jakości zgodnie z GOST 7473-94, punkt 4.1 - 5.2 z zastosowaniem fabrycznego certyfikatu badania zgodnie z GOST 10060-95 i zgodnie z GOST 12730.5-84 |
7.14. Formy z próbkami do określenia wytrzymałości betonu w wieku 28 dni bezpośrednio po wyprodukowaniu należy montować w miejscach o najniższych temperaturach iw kontakcie z powierzchnią betonu dla każdego elementu konstrukcyjnego.
Formy ze świeżo uformowanymi próbkami należy przed montażem owinąć folią i umieścić pod powłoką termoizolacyjną.
Formy z próbkami należy przechowywać pod powłoką przeciwwilgociową do czasu badania. Po usunięciu z konstrukcji powłoki chroniącej przed wilgocią i ciepłem pozostałe próbki kontrolne (które uzyskały co najmniej 70% wytrzymałości) są usuwane i przechowywane do wymaganych testów w normalnych warunkach zgodnie z GOST 10180-90.
8. Ochrona pracy w trakcie pracy
Ochrona pracy odbywa się zgodnie z planem BHP (zgodnie z SNiP 12-03-2001, SNiP 12-4-2002, PB 10-382-00).
8.1. Ogólne wymagania
Osoby, które ukończyły 18 lat, zostały uznane przez komisję lekarską za zdolne do wykonywania tej pracy, zostały przeszkolone w zakresie bezpiecznych metod i technik wykonywania pracy oraz instruktaży dotyczących bezpieczeństwa pracy i posiadają zaświadczenie o prawie do wykonywania pracy betoniarz może pracować samodzielnie jako betoniarz.
Konkretny pracownik rozpoczynający pracę musi przejść odprawę wprowadzającą w zakresie bezpieczeństwa pracy, warunków sanitarnych, pierwszej pomocy, bezpieczeństwa przeciwpożarowego, wymagań środowiskowych, warunków pracy, odprawę wstępną w miejscu pracy, którą należy odnotować w odpowiednich dziennikach z obowiązkowym podpisem pouczonego i instruowanie. Powtarzana odprawa odbywa się co najmniej 1 raz na 3 miesiące. Nieplanowane odprawy są przeprowadzane w przypadku wejścia w życie nowych lub zmienionych norm lub innych dokumentów regulacyjnych dotyczących ochrony pracy, zmiany procesu technologicznego, wymiany lub modernizacji sprzętu i narzędzi, wymiany materiałów, naruszenia przez pracowników wymogów bezpieczeństwa pracy, na żądanie organów nadzoru, w czasie przerw w pracy dłuższych niż 30 dni kalendarzowych. Odprawa tarczowa przeprowadzana jest przy wykonywaniu jednorazowej pracy.
Przed rozpoczęciem pracy należy oczyścić miejsca pracy i przejścia do nich obce obiekty, gruzu, brudu, a zimą - ze śniegu i lodu i posyp je piaskiem.
Zabrania się przebywania w strefie niebezpiecznej mechanizmów podnoszących, a także przebywania pod podniesionym ładunkiem.
Maszyny, elektronarzędzia i lampy oświetleniowe można włączać tylko za pomocą rozruszników nożowych. Nie dopuszczaj do obecności słabo izolowanych przewodów elektrycznych, niezabudowanych urządzeń elektrycznych na miejscu. Podczas pracy z elektronarzędziami betoniarz musi być przeszkolony i posiadać I grupa kwalifikacyjna na bezpieczeństwo.
Przed uruchomieniem urządzenia należy sprawdzić zabezpieczenie osłon we wszystkich odsłoniętych częściach obrotowych i ruchomych.
W przypadku wykrycia awarii mechanizmów i narzędzi, z którymi pracuje pracownik betonu, a także ogrodzeń, konieczne jest przerwanie pracy i natychmiastowe poinformowanie brygadzisty.
Po otrzymaniu narzędzia należy upewnić się, że jest ono w dobrym stanie, wadliwe narzędzie należy przekazać do naprawy.
Podczas pracy z narzędziami ręcznymi (skrobaki, młotki, łopaty, ubijaki) należy monitorować sprawność uchwytów, szczelność na nich dysz, a także upewnić się, że powierzchnie robocze narzędzia nie zostaną powalone , tępe itp.
Naelektryzowane narzędzie, jak również zasilający je przewód elektryczny, muszą mieć niezawodną izolację. Po otrzymaniu elektronarzędzia należy sprawdzić stan izolacji przewodu poprzez kontrolę zewnętrzną. Podczas pracy z narzędziem upewnij się, że przewód zasilający nie jest uszkodzony.
8.2. Wymagania przed i w trakcie pracy
Przystępując do pracy, betoniarz powinien nosić kombinezon określony przez normy, a włosy należy usunąć pod nakryciem głowy, mankiety zapiąć lub zacisnąć elastyczną opaską.
Przy układaniu mieszanki betonowej pompą do betonu należy sprawdzić działanie sygnalizacji dwukierunkowej (dźwiękowej, świetlnej) pomiędzy sterownikiem pompy do betonu a pracownikami odbierającymi beton. Oczyścić i szczelnie zablokować wszystkie blokady rurociągu betonowego. Nie akceptuj mieszanki betonowej z uszkodzoną pompą do betonu. Kierowca zamontowanej na ciężarówce pompy do betonu przed uruchomieniem musi dać sygnał ostrzegawczy i uruchomić pompę do testów na biegu jałowym na 2-3 minuty.
Podczas dostarczania betonu w betonomieszarce należy przestrzegać następujących zasad:
Podczas rozładowywania pompy do betonu do bunkra należy najpierw zaciągnąć betoniarkę na hamulec ręczny i dać sygnał dźwiękowy;
W momencie zbliżania się betonomieszarki wszyscy pracownicy powinni znajdować się po stronie drogi dojazdowej, przeciwnej do tej, po której odbywa się ruch;
Zabronione jest zbliżanie się do betoniarki aż do jej całkowitego zatrzymania.
Przed przystąpieniem do układania mieszanki betonowej w szalunku należy sprawdzić:
Mocowanie szalunków, rusztowań podpierających i pomostów roboczych;
Mocowanie do wsporników lejów załadunkowych, tac i pni w celu obniżenia mieszanki betonowej do konstrukcji, a także niezawodność mocowania poszczególnych ogniw metalowych pni do siebie;
Stan osłon ochronnych lub podłogi wokół lejów paszowych.
Betoniści pracujący z wibratorami są zobowiązani do poddawania się badaniom lekarskim co 6 miesięcy.
Kobietom nie wolno pracować z wibratorem ręcznym.
Betoniści pracujący z narzędziami elektrycznymi muszą znać środki ochrony przed porażeniem prądem i być w stanie udzielić pierwszej pomocy poszkodowanemu.
Przed rozpoczęciem pracy należy dokładnie sprawdzić przydatność wibratora i upewnić się, że:
Wąż jest dobrze przymocowany, a jeśli zostanie przypadkowo pociągnięty, końce uzwojenia nie pękną;
Kabel zasilający nie ma przerw i gołych plam;
Kontakt z ziemią nie jest uszkodzony;
Przełącznik działa prawidłowo;
Śruby zapewniające szczelność obudowy są dobrze dokręcone;
Połączenia części wibratora są dość szczelne, a uzwojenie silnika jest dobrze chronione przed wilgocią;
Amortyzator na uchwycie wibratora jest w dobrym stanie i wyregulowany tak, aby amplituda drgań uchwytu nie przekraczała norm dla tego narzędzia.
Przed rozpoczęciem pracy należy uziemić korpus wibratora elektrycznego. Ogólny stan techniczny wibratora elektrycznego sprawdzany jest przez praca próbna zawieszony przez 1 minutę, bez opierania końcówki o solidną podstawę.
Do zasilania wibratorów elektrycznych (z rozdzielnicy) należy użyć czterożyłowych przewodów wężowych lub przewodów zamkniętych w gumowej rurce; czwarty rdzeń jest niezbędny do uziemienia obudowy wibratora, działającego przy napięciu 127 V lub 220 V.
Wibrator elektryczny można włączyć tylko wyłącznikiem nożowym chronionym obudową lub umieszczonym w pudełku. Jeśli skrzynka jest metalowa, musi być uziemiona.
Przewody wężowe muszą być zawieszone i nie mogą przebiegać po ułożonym betonie.
Nie ciągnij wibratora za przewód węża lub kabel podczas jego przemieszczania.
W przypadku przerwy w przewodach pod napięciem, iskrzenia styków i awarii wibratora elektrycznego należy przerwać pracę i niezwłocznie poinformować kapitana.
Praca z wibratorami na drabinach, a także na niestabilnych rusztowaniach, pokładach, szalunkach itp. zabroniony.
Podczas pracy z wibratorami elektrycznymi zasilanymi napięciem sieciowym do 220 V i wyższym konieczne jest noszenie gumowych rękawic dielektrycznych i butów.
Podczas ciągłej pracy wibrator musi być wyłączany co pół godziny na pięć minut w celu ostygnięcia.
Kiedy pada deszcz, wibratory należy przykryć plandeką lub trzymać w pomieszczeniu.
W czasie przerw w pracy, a także podczas przemieszczania się betoniarzy z miejsca na miejsce, wibratory muszą być wyłączone.
Betonista pracujący z wibratorem nie może dopuścić do kontaktu wody z wibratorem.
8.3. Środki ostrożności podczas pracy na wysokości.
Wszystkie prace wykonywać zgodnie z SNiP 12-03-2001 „Bezpieczeństwo pracy w budownictwie” cz.1 „Bezpieczeństwo pracy w budownictwie” cz.2.
Miejsca pracy i przejścia do nich na wysokości 1,3 m lub większej oraz w odległości mniejszej niż 2 m od granicy różnicy wysokości są chronione tymczasowymi ogrodzeniami inwentaryzacyjnymi zgodnie z GOST 12.4.059-89. W przypadku braku możliwości zastosowania ogrodzeń ochronnych lub w przypadku krótkiego okresu przebywania pracowników na wysokości dopuszcza się wykonywanie prac przy użyciu pasa bezpieczeństwa.
Rusztowania wyposażone są w drabiny lub drabiny do podnoszenia i opuszczania osób w ilości co najmniej dwóch.
Drabiny i drabiny wyposażone są w urządzenie zapobiegające możliwości ich przesunięcia i przewrócenia podczas pracy.
Pracownicy zajmujący się montażem i demontażem rusztowań muszą zostać poinstruowani o metodach i kolejności wykonywania pracy oraz środków bezpieczeństwa.
Rusztowania metalowe nie mogą być instalowane bliżej niż 5 m od masztów sieci elektrycznej i urządzeń operacyjnych. Przewody elektryczne znajdujące się w odległości mniejszej niż 5 m od rusztowania muszą być odłączone od napięcia i uziemione lub zamknięte w puszkach lub zdemontowane podczas ich montażu lub demontażu. Rusztowania muszą być uziemione.
Dostęp osób nieuprawnionych (nie bezpośrednio zaangażowanych w te prace) do terenu, na którym są montowane lub demontowane rusztowania, musi być zamknięty.
Podczas prac na wysokości przejście pod miejscem pracy musi być zamknięte, a strefa niebezpieczna ogrodzona i oznaczona znakami bezpieczeństwa. Do przechowywania materiałów nie należy używać rusztowania.
Na rusztowanie trafiają tylko te materiały, które są bezpośrednio wykorzystywane (recykling).
9. Ochrona środowiska!
9.1. WYKONAWCA-WYKONAWCA ROBÓT powinien utrzymywać teren budowy w czystości oraz zapewnić odpowiednie urządzenia do czasowego składowania wszelkiego rodzaju odpadów do czasu ich usunięcia. Odpady budowlane składowane są wyłącznie w specjalnie wyznaczonych miejscach wskazanych na planie budowy.
WYKONAWCA-WYKONAWCA jest odpowiedzialny za zapewnienie bezpiecznego transportu i unieszkodliwiania wszystkich rodzajów odpadów w taki sposób, aby nie powodowały one zanieczyszczenia środowiska lub szkody dla zdrowia ludzi lub zwierząt.
Wszystkie miejsca i budynki są utrzymywane w czystości i porządku. Cały personel pracujący został poinstruowany przed podpisem, wpisany do odpowiedniego dziennika i poinformowany o wymaganiach dotyczących utrzymania miejsca pracy i odpowiedzialności każdego za porządek w miejscu pracy i odpoczynku.
Utylizacja odpadów powinna obejmować:
Oddzielne pojemniki na różne rodzaje odpadów (metale, odpady żywnościowe, materiały niebezpieczne, śmieci itp.) ze szczelnymi pokrywami;
Miejsca na kontenery;
Odpady złomowe są czasowo składowane na wyznaczonych składowiskach odpadów uzgodnionych z Komisją Ochrony Środowiska, Komisją ds. Gruntów, władzami lokalnymi;
Odpady betonowe są tymczasowo składowane na tymczasowych składowiskach odpadów w specjalnie wyposażonych obszarach o lepszym pokryciu. Odpady konstrukcji żelbetowych będą wywożone specjalnymi pojazdami do składowania na składowisku;
Mycie betonomieszarek i pomp do betonu powinno odbywać się wyłącznie w miejscach wskazanych przez Generalnego Wykonawcę.
Zbrylone odpady drzewne, nienadające się do wykorzystania na składowisku, są tymczasowo składowane na składowisku czasowym i będą transportowane transportem drogowym w celu umieszczenia na składowisku;
Odpady z gospodarstw domowych będą wywożone specjalnymi samochodami do utylizacji i przerobu na składowisko zgodnie z umową o wywóz odpadów z wyspecjalizowanym przedsiębiorstwem.
Wszystkie odpady niebezpieczne dla zdrowia podlegają ostatecznemu unieszkodliwieniu w odpowiednich przedsiębiorstwach lub składowiskach odpadów uzgodnionych z lokalną administracją i organami regulacyjnymi, na podstawie umów, których kopie zostaną przekazane Klientowi.
Tankowanie sprzętu budowlanego w trakcie pracy odbywa się na atestowanych cysternach „z kół”. Wszystkie oleje i smary przechowywane są w magazynach w hermetycznie zamkniętych pojemnikach z wyraźnym oznaczeniem w języku rosyjskim. Jeśli paliwo i smary dostaną się na glebę lub powierzchnię betonu, natychmiast podejmuje się działania w celu odcięcia i usunięcia zanieczyszczonej gleby, paliwo i smary usuwa się z powierzchni betonu za pomocą piasku lub trocin, a następnie usuwa.
9.2. Ochrona flory, fauny i siedlisk.
Planowane działanie stawia sobie za cel minimalną i czasową alienację gruntów, naruszenie szaty roślinnej.
W celu zminimalizowania negatywnego wpływu na zwierzę i świat warzyw, w trakcie budowy obiektu WYKONAWCA-WYKONAWCA ROBÓT musi przeprowadzić środki organizacyjne i techniczne:
Wyposażenie obiektu w indywidualny, bierny i czynny sprzęt przeciwpożarowy, ścisła kontrola przestrzegania przepisów bezpieczeństwo przeciwpożarowe;
Utrzymanie pokrywy glebowej poprzez utrzymanie sprzętu w dobrym stanie, eliminowanie rozlewania się produktów ropopochodnych na glebę;
Eksploatacja maszyn tylko w granicach działki budowy przy wykorzystaniu istniejących dróg dojazdowych;
W okresie budowy ochrona przyrody polegać będzie przede wszystkim na przestrzeganiu przepisów środowiskowych, minimalizujących wpływ na powietrze atmosferyczne, powierzchnia wody, co pośrednio zmniejszy oddziaływanie obiektu na środowisko.
9.3. Minimalizacja zanieczyszczenia powietrza i zanieczyszczenia hałasem środowiska.
Zmniejszenie zapylenia powietrza występującego podczas budowy uzyskuje się dzięki:
Wykorzystanie nawierzchni z tłucznia tłuczonego, zarówno na placu budowy, jak i pomiędzy placem budowy a osiedlem dla robotników budowlanych, a także w obrębie osiedla;
Regularne czyszczenie dróg i zwilżanie ich, aby zapobiec pyleniu w powietrzu.
W celu ograniczenia ewentualnych negatywnych oddziaływań na powietrze atmosferyczne podczas budowy WYKONAWCA-WYKONAWCA ROBÓT powinien używać wyłącznie sprawny sprzęt budowlany z dostosowanym wyposażeniem paliwowym zapewniającym jak najmniejszą emisję zanieczyszczeń do środowiska, w tym skutecznymi tłumikami hałasu;
Obsługuje i konserwuje maszyny zgodnie z instrukcjami i instrukcjami producentów, ze szczególnym uwzględnieniem kontroli emisji hałasu i zanieczyszczeń;
Zapewnia stały monitoring przestrzegania obowiązujących zasad eksploatacji;
Sprzęt używany do budowy podlega regularnej konserwacji i kontrolom pod kątem ewentualnych usterek;
Nie wolno spalać odpadów produkcyjnych;
Zabrania się stosowania środków zubożających warstwę ozonową i freonów w instalacjach chłodniczych i gaśniczych;
W okres letni budowlane, w celu zmniejszenia zapylenia dróg dojazdowych lub roboczych konieczne jest stałe podlewanie powierzchni koryta wodą za pomocą zraszaczy.
9.4. Zaplanuj WYKONAWCĘ-WYKONAWCĘ ROBÓT dla organizacji prac przy odbiorze, magazynowaniu i unieszkodliwianiu odpadów
Podczas produkcji prac na obiekcie powstają 2 rodzaje odpadów:
Przemysłowe (odpady budowlane);
Odpady z gospodarstw domowych.
Kiedy mamy do czynienia z odpady niebezpieczne sporządzić odpowiedni akt na podstawie wyników doprowadzenia wyrobów do bezpiecznego stanu, który zatwierdza kierownik przedsiębiorstwa – właściciel wyrobu.
W procesie zbierania i gromadzenia odpadów identyfikuje się je poprzez określenie przynależności do określonego rodzaju odpadów, dla każdego rodzaju odpadów znajdują się osobne zamykane pojemniki (metale, odpady spożywcze, materiały niebezpieczne, śmieci itp.), oznakowane ze znakami ostrzegawczymi.
WYKONAWCA-WYKONAWCA opracowuje środki minimalizujące ilość wytwarzanych odpadów:
Użytkowanie sprzętu i części zamiennych przez cały przewidywany okres ich eksploatacji;
Wykorzystanie odpadów jako surowca w nowych cykl technologiczny;
Za przestrzeganie wymogów ochrony środowiska odpowiedzialni są brygadziści zmianowi.
Bibliografia
GOST 2379-85 | ||
GOST 7473-85* | Mieszanki betonowe. Specyfikacje |
|
GOST 8267-93 | Kruszywo i żwir z gęstego wydobycia do prac budowlanych. Specyfikacje. |
|
GOST 8478-81 | ||
GOST 10060,0-95 | Metody określania mrozoodporności. Beton. Ogólne wymagania |
|
GOST 10178-95 | Cement portlandzki i cement portlandzki żużlowy. Specyfikacje |
|
GOST 10180-90 | Beton. Metody określania siły przez próbki kontrolne |
|
GOST 10181,1-81 | ||
GOST 10181-2000 | Mieszanki betonowe. Metody testowe |
|
GOST 10922-90 | Produkty wzmacniające i osadzone połączenia spawane spawane produkty wzmacniające i osadzone w konstrukcjach żelbetowych. Ogólne specyfikacje. produkty wzmacniające i wbudowane, |
|
GOST 12730,5-84 | Beton. Metody określania wodoodporności |
|
GOST 14098-91 | Spawane produkty wzmacniające i osadzane konstrukcji żelbetowych. Rodzaje, konstrukcja i wymiary. |
|
GOST 18105-86* | Beton. Zasady kontroli siły |
|
GOST 18242-72* | Statystyczna kontrola akceptacji według funkcji alternatywnej. Plany kontroli. |
|
GOST 23732-79 | Woda do betonu i roztworów. Specyfikacje. |
|
GOST 24211-91 | ||
GOST 25346-89 | EPBiO. Postanowienia ogólne, serie tolerancji i podstawowe odchylenia 7.16 |
|
GOST 25347-82* | ||
GOST 26633-91 | Beton jest ciężki i drobnoziarnisty. Specyfikacje. |
|
SNiP 2.05.03-84* | Mosty i rury |
|
SNiP 3.03.01-87 | Konstrukcje nośne i zamykające |
|
SNiP 3.06.04-91 | Mosty i rury |
Załącznik 1
snipov.net
WETERYNARZ
KARTA TECHNOLOGICZNA Nr
do prac betonowych
1 Zakres... 3
2 organizacja i technologia pracy .. 3
3 WYMAGANIA DOTYCZĄCE JAKOŚCI I ODBIORU PRAC. 4
4 ZDROWIE I BEZPIECZEŃSTWO.. 5
5 OCHRONA ŚRODOWISKA… 6
6 WYKAZ DOKUMENTACJI PRAWNO-technicznej i referencyjnej. 7
6 Arkusz zapoznawczy.. 8
Mapa technologiczna przewiduje organizację i technologię robót betonowych
Rozważane prace obejmują:
- przygotowanie mieszanki betonowej;
- prace wzmacniające;
- układanie betonu;
- metody kontroli.
- organizacja i technologia wykonywania pracy
Podczas wykonywania pracy konieczne jest przestrzeganie wymagań dokumentów regulacyjnych podanych w sekcji 6.
Surowce używane do produkcji fundamentów monolitycznych muszą być zgodne z aktualną dokumentacją regulacyjną i techniczną, której towarzyszą dokumenty od przedsiębiorstw dostawców poświadczających ich jakość.
Projekt fundamentu monolitycznego musi spełniać wymagania istniejącej dokumentacji regulacyjnej.
Przygotowanie mieszanki betonowej.
Mieszankę betonową przygotowuje się w betoniarce o działaniu wymuszonym.
Wybór cementów do przygotowania mieszanek betonowych powinien być dokonany zgodnie z GOST 30515-97. Przyjmowanie cementów powinno odbywać się zgodnie z GOST 30515-97, transport i przechowywanie cementów - zgodnie z GOST 30515-97 i SNiP 3.09.01-85.
Kruszywa do betonu są używane do frakcjonowania i płukania. Zabronione jest stosowanie naturalnej mieszanki piasku i żwiru bez przesiewania na frakcje.
Dozowanie składników mieszanek betonowych powinno odbywać się na wagę. Dozwolone jest objętościowe dozowanie wody dodatków wprowadzanych do mieszanki betonowej w postaci roztworów wodnych. Stosunek składników określa się dla każdej partii cementu i kruszyw podczas przygotowywania betonu o wymaganej wytrzymałości i ruchliwości. Dawkowanie składników powinno być dostosowane podczas przygotowywania mieszanki betonowej, biorąc pod uwagę dane z monitorowania wskaźników właściwości cementu, wilgotności, granulometrii kruszyw oraz kontroli wytrzymałości.
Przygotowując mieszankę betonową przy użyciu oddzielnej technologii, należy przestrzegać następującej procedury:
- woda, część piasku, drobno zmielony wypełniacz mineralny (jeśli jest stosowany) i cement są dozowane do działającego mieszalnika szybkoobrotowego, gdzie wszystko jest mieszane;
- powstałą mieszaninę podaje się do betoniarki, wstępnie załadowanej resztą kruszywa i wody, i ponownie wszystko jest mieszane.
- przerwa między etapami betonowania (lub układania warstw mieszanki betonowej) powinna wynosić co najmniej 40 minut, ale nie więcej niż 2 godziny.
- dozwolone jest stosowanie dodatków (przeciwmrozowych, napowietrzających, przyspieszających i opóźniających twardnienie betonu itp.).
Działa armatura.
Prace zbrojarskie należy prowadzić zgodnie z mapą technologiczną P
Układanie i zagęszczanie mieszanek betonowych
Układanie mieszanki betonowej powinno być wykonywane przez betoniarki, które mają urządzenia dozujące i rozprowadzające mieszankę w ograniczających urządzeniach bocznych, z reguły bez użycia pracy ręcznej.
Podczas układania mieszanek betonowych na otwartym składowisku należy podjąć środki (specjalne schrony, szopy, powłoki foliowe) w celu ochrony mieszanek betonowych i świeżo formowanych produktów przed szkodliwym działaniem wpływów atmosferycznych.
Tryby formowania powinny zapewniać współczynnik zagęszczenia mieszanki betonowej (stosunek jej rzeczywistej gęstości do obliczonej teoretycznej): dla ciężkiego betonu - nie mniej niż 0,98; przy stosowaniu sztywnych mieszanek i odpowiednim uzasadnieniu, a także w przypadku betonu drobnoziarnistego - nie mniej niż 0,96. Objętość międzykrystalicznych pustek w zagęszczonej lekkiej mieszance betonowej musi być zgodna z wymaganiami GOST 25820-83.
Zdejmowanie produktów po obróbce cieplnej należy przeprowadzić po osiągnięciu przez beton wytrzymałości na zdzieranie.
Kontrola jakości pracy powinna być przeprowadzana zgodnie z wymaganiami dokumentów regulacyjnych podanych w sekcji 6:
Przy odbiorze gotowych konstrukcji betonowych i żelbetowych lub części konstrukcji należy sprawdzić:
- zgodność konstrukcji z rysunkami roboczymi;
- jakość betonu pod względem wytrzymałości i, jeśli to konieczne, mrozoodporności, wodoodporności i innych wskaźników określonych w projekcie;
- jakość materiałów użytych do budowy, półproduktów i wyrobów.
Akceptacja gotowych konstrukcji betonowych i żelbetowych lub części konstrukcji powinna być sformalizowana zgodnie z ustaloną procedurą przez akt kontroli ukrytych robót lub akt akceptacji krytycznych konstrukcji.
Skład operacji i środków kontroli podczas betonowania
pobierz KARTĘ TECHNOLOGICZNĄ dla robót betonowych
Czołowi pracownicy i specjaliści organizacji, zgodnie z listą stanowisk zatwierdzonych przez kierownika organizacji, przed przyjęciem do pracy, a następnie okresowo w ustalonych terminach, są sprawdzani pod kątem znajomości zasad ochrony i bezpieczeństwa pracy , biorąc pod uwagę ich obowiązki służbowe i charakter wykonywanej pracy. Procedura przeprowadzania szkoleń i testowania wiedzy została ustalona zgodnie z GOST 12.0.004-90 SSBT „Organizacja szkoleń z zakresu bezpieczeństwa pracy. Postanowienia ogólne” oraz zgodnie z Rozporządzeniem Ministerstwa Pracy Federacji Rosyjskiej z dnia 13.01.2003 nr. „Procedura szkolenia w zakresie ochrony pracy i testowania znajomości wymagań pracy pracowników organizacji”. Przybliżone rozporządzenie w sprawie trybu szkolenia i sprawdzania wiedzy z zakresu ochrony pracy dla kierowników i specjalistów organizacji, przedsiębiorstw i instytucji oraz instytucji budowlanych, przemysłu materiałów budowlanych oraz usług mieszkaniowych i komunalnych BEZPIECZEŃSTWO PRACY I PRZEMYSŁOWE
Pracownicy wykonujący pracę muszą zdać test wiedzy i posiadać certyfikaty sprawdzające wiedzę z zakresu ochrony pracy.
Pracownicy, którzy wcześniej nie zostali przeszkoleni zawodowo w zakresie bezpiecznych praktyk pracy, w ciągu miesiąca od dnia dopuszczenia do pracy, muszą zostać przeszkoleni zgodnie z GOST 12.0.004-90 SSBT w zakresie instrukcji ochrony pracy dla odpowiednich zawodów, sporządzony na podstawie branżowych instrukcji ochrony pracy i uzyskaj certyfikat bezpieczeństwa.
Stanowiska pracy powinny być wyposażone w apteczki z lekami.
Lista dokumentów, które muszą znajdować się w miejscu pracy:
- Rozkazy w sprawie powołania osób odpowiedzialnych za ochronę pracy, bezpieczeństwo przemysłowe;
- Nakazy powołania osób odpowiedzialnych za dobry stan i bezpieczną eksploatację maszyn i mechanizmów;
- Zamówienia na sprzęt zabezpieczający;
- dziennik odpraw w miejscu pracy;
- dziennik komentarzy i sugestii;
- dziennik kontroli wejścia.
W celu ochrony środowiska przy wykonywaniu powyższych prac zabrania się:
- naruszać granice terytoriów przeznaczonych do budowy;
- zanieczyszczać środowisko odpadami budowlanymi, dla których na etapie projektowania należy przewidzieć sposoby przetwarzania i unieszkodliwiania odpadów;
- zakłócać naturalną sieć odwadniającą;
- przejazd maszyn i pojazdów w miejscach nieprzewidzianych projektem do produkcji robót;
- planować i wycinać strome zbocza na stanowiskach ze względu na możliwość erozji gleby;
- nie spełniają wymagań lokalnych władz ochrony środowiska.
Za wyrządzanie szkód w środowisku (niszczenie pokrywy glebowej i roślinnej, zanieczyszczenie zbiorników wodnych, pożary lasów, torfowisk itp.) poza pasem drogowym, kierownicy robót, a także pracownicy bezpośrednio wyrządzający szkody środowisko.
- WYKAZ DOKUMENTACJI PRAWNO-technicznej i referencyjnej
- SNiP III-42-80*. Główne rurociągi;
- - SNiP 3.02.01-87. Roboty ziemne, fundamenty i fundamenty;
- SNiP 3.03.01-87. Konstrukcje nośne i zamykające;
- VSN 004-88. Budowa głównych rurociągów. Technologia i organizacja;
- VSN 014-89. Budowa rurociągów głównych i polowych. ochrona środowiska;
- GOST R 51285-99. Siatki skręcone z sześciokątnymi komórkami do konstrukcji gabionowych. Specyfikacje;
- GOST 7502-98. Ruletki mierzące metal. Wymagania techniczne.
- GOST 12-03-01. SSBT. Osobista ochrona dróg oddechowych. Klasyfikacja i oznakowanie;
- GOST 12.3.003-86*. SSBT. Roboty elektryczne. Wymagania bezpieczeństwa;
- GOST 123.016-87. SSBT. Budowa. Prace antykorozyjne. Wymagania bezpieczeństwa;
- SNiP 12-03-2001. Bezpieczeństwo pracy w budownictwie. Część 1. Wymagania ogólne;
- SNiP 12-04-2002. Bezpieczeństwo pracy w budownictwie. Część 2. Produkcja budowlana;
- SP 12-136-2002. Rozwiązania z zakresu ochrony pracy i bezpieczeństwa pracy w projektach organizacji budowy i projektach produkcji robót
- POT R M-016-2001. Międzysektorowe zasady ochrony pracy (zasady bezpieczeństwa) podczas eksploatacji instalacji elektrycznych;
- PB 10-382-00. Zasady budowy i bezpiecznej eksploatacji dźwigów;
- Zasady eksploatacji technicznej konsumenckich instalacji elektrycznych”;
- POT R M-027-2003. Międzysektorowe przepisy dotyczące ochrony pracy w transporcie drogowym;
- Zasady bezpieczeństwa eksploatacji głównych rurociągów naftowych.
Liczba stron | Pełne imię i nazwisko | Stanowisko pracownika | data | Podpis |
1. | ||||
2. | ||||
3. | ||||
4. | ||||
5. | ||||
6. | ||||
7. | ||||
8. | ||||
9. | ||||
10. | ||||
11. | ||||
12. | ||||
13. | ||||
14. | ||||
15. | ||||
16. | ||||
17. | ||||
18. | ||||
19. | ||||
20. | ||||
21. | ||||
22. |
otdel-pto.ru
Ogólne instrukcje
Prawdziwy wytyczne przeznaczone są dla studentów kierunku przygotowania 270800.62 „Budownictwo” i mają na celu pomoc w realizacji zajęć i tezy w dziale „Technologia i organizacja produkcji budowlanej”
Mapy technologiczne są jednym z głównych dokumentów projektu do produkcji robót, zawierającym zestaw wytycznych dotyczących racjonalnej organizacji i technologii produkcji budowlanej, które przyczyniają się do zwiększenia wydajności pracy, poprawy jakości i obniżenia kosztów robót budowlano-montażowych .
Mapy technologiczne są obowiązkowe do wykorzystania przez brygadzistów pracy, brygadzistów i brygadzistów jako przewodnik w organizacji produkcji i pracy pracowników przy wykonywaniu prac budowlano-montażowych na określonym obiekcie.
Instrukcja zawiera ogólną metodologię i kolejność opracowywania map technologicznych, podano przykłady realizacji map technologicznych dla następujących procesów budowlanych:
Wykop;
Prace betonowe;
Roboty instalacyjne;
prace z kamienia;
prace palowe;
Zasypywanie i zagęszczanie gleby.
Mapy technologiczne, które są częścią projektu do produkcji prac, są zwykle opracowywane dla złożonych rodzajów prac i prac wykonywanych nowymi metodami. Głównym celem tych map jest pomoc budowniczym i projektantom w opracowaniu dokumentacji technologicznej.
Na podstawie map technologicznych ustalana jest kolejność technologiczna procesów budowlanych, opracowywane są tygodniowe harmonogramy dzienne i zlecenia prac. Wykorzystywane są zarówno przy wykonywaniu prac budowlano-montażowych, jak i przy uzasadnianiu czasu budowy obiektów w planach kalendarzowych oraz wykresy sieciowe projekty produkcyjne pracy.
Wykorzystanie map technologicznych, w tym standardowych, pomaga poprawić organizację produkcji, zwiększyć wydajność pracy i jej organizację naukową, obniżyć koszty, poprawić jakość i skrócić czas budowy, bezpieczne wykonywanie pracy, organizację pracy rytmicznej, racjonalne użytkowanie zasobów pracy i maszyn, a także skrócenie czasu kompilacji WEP i ujednolicenie rozwiązań technologicznych.
Mapy technologiczne (TC) są opracowywane w celu realizacji procesów budowlano-montażowych i specjalnych procesów budowlanych, których produktami są gotowe elementy konstrukcyjne budynku lub konstrukcji, urządzenia technologiczne, rurociągi i ich elementy, a także do produkcji niektórych typów robót - roboty ziemne, dekarskie, malarskie, antykorozyjne, termoizolacyjne itp. W niektórych przypadkach opracowywane są mapy technologiczne dla kompleksowych prac budowlano-montażowych (dla ułożenia 100 m rurociągu, kolektora, 1 km elektrycznego kabel itp.). Mapy technologiczne muszą być opracowane i powiązane wcześniej opracowane (standardowe) z obowiązkowym uwzględnieniem rzeczywistych warunków budowy – przyjętej organizacji pracy, określonego zestawu dostępnych maszyn budowlanych, mechanizmów, urządzeń, pojazdów, a także warunków klimatycznych i innych. Jednocześnie należy postawić na zaawansowaną technologię inżynieryjną i budowlaną.
Do opracowania KT, jako dane i dokumenty wyjściowe, wymagane są: rysunki robocze, kodeksy budowlane i regulaminów (SNiP), instrukcje, normy, instrukcje fabryczne i specyfikacje dotyczące instalacji, uruchomienia i uruchomienia sprzętu, paszporty sprzętu, jednolite normy i ceny robót budowlano-montażowych (ENiR), lokalne progresywne normy i ceny, organizacja pracy i procesy pracy .
Typowe mapy technologiczne (TTK) są opracowywane w celu zapewnienia budowy standardowych i powtarzalnych budynków, konstrukcji i ich części racjonalne decyzje w sprawie organizacji i technologii produkcji budowlanej, które przyczyniają się do zwiększenia wydajności pracy, poprawy jakości i obniżenia kosztów prac budowlano-montażowych. TTC są przeznaczone do użytku przez organizacje opracowujące projekty dotyczące produkcji prac przy budowie nowych lub przebudowie i rozbudowie istniejących obiektów.
TTK jest opracowywany na podstawie rysunków roboczych typowych i wielokrotnego użytku budynków i konstrukcji w oparciu o badanie i uogólnienie najlepszych praktyk, z uwzględnieniem: wykorzystania procesów technologicznych zapewniających wymagany poziom jakości pracy; kompleksowe dostawy konstrukcji, wyrobów, półfabrykatów i materiałów; maksymalne wykorzystanie zakresu prac i kombinacji procesów budowlanych; wprowadzenie zintegrowanej mechanizacji z maksymalnym wykorzystaniem maszyn na dwie lub więcej zmian, a także zastosowanie mechanizacji na małą skalę; dostawa konstrukcji i urządzeń technologicznych w powiększonych blokach; przestrzeganie zasad higieny przemysłowej, ochrony i bezpieczeństwa pracy. Przyjęte w TTK rozwiązania organizacyjne i technologiczne powinny zapewniać wysokie wskaźniki techniczno-ekonomiczne, jakość i bezpieczeństwo pracy zgodnie z wymaganiami obowiązujących norm i zasad produkcji budowlanej.
Skład mapy technologicznej
Mapa technologiczna powinna zawierać następujące sekcje:
Tu są:
charakterystyka budynku, elementów konstrukcyjnych i ich części lub części budynków i budowli (wskazując standardowe projekty, podstawowe parametry i schematy);
nomenklatura rodzajów prac objętych mapą;
charakterystyka warunków i cech produkcji utworów przyjętych na mapie;
instrukcja powiązania mapy z konkretnym obiektem i warunkami budowy.
II. Organizacja i technologia proces konstruowania. Ta sekcja zawiera:
instrukcje przygotowania obiektu i wymagania dotyczące gotowości do wcześniejszych prac i konstrukcji budowlanych, które zapewniają niezbędny i wystarczający front prac do zakończenia procesu budowlanego przewidzianego przez mapę;
plan i sekcje części konstrukcyjnej budynku lub konstrukcji, na której będą wykonywane prace przewidziane mapą technologiczną, a także schematy organizacji placu budowy (obszaru roboczego) w okresie tego rodzaju prac ( plany, przekroje i schematy muszą wskazywać wszystkie główne wymiary i rozmieszczenie jednostek, maszyn, urządzeń do załadunku i rozładunku, magazynów materiałów podstawowych, półproduktów, produktów, dróg);
instrukcje dotyczące czasu przechowywania oraz zapasów konstrukcji, wyrobów i materiałów na placu budowy (obszar roboczy);
metody i kolejność prac, podział budynku (konstrukcji) na uchwyty i kondygnacje, sposoby transportu materiałów i konstrukcji na stanowiska pracy, rodzaje rusztowań, osprzętu, stosowane urządzenia montażowe;
skład liczebny i kwalifikacyjny brygad i powiązań pracowników z uwzględnieniem kombinacji zawodów;
harmonogram pracy i kalkulacja kosztów pracy;
instrukcja łączenia map procesów pracy w produkcji budowlanej, zapewniająca racjonalną organizację, metody i techniki pracy pracowników do wykonywania poszczególnych operacji zawartych w procesie budowlanym przewidzianym przez mapę technologiczną;
instrukcje dotyczące monitorowania i oceny jakości pracy zgodnie z wymaganiami rozdziałów SNiP dotyczących produkcji i odbioru pracy oraz wykaz wymaganych certyfikatów badania pracy ukrytej;
rozwiązania z zakresu ochrony pracy i bezpieczeństwa przy wykonywaniu prac wymagających opracowania projektowego.
Mapy technologiczne do prac wykonywanych zimą powinny dodatkowo zawierać instrukcje dotyczące sposobu konserwacji konstrukcji, miejsc pomiaru temperatury i wilgotności, sposobów izolowania i uszczelniania połączeń w konstrukcjach, schematów wykonywania prac zimą.
III. Wskaźniki techniczne i ekonomiczne. Ta sekcja zawiera:
1. Koszty pracy dla całego zakresu pracy, osobodni.
Koszty pracy dla całego zakresu prac są określane przez obliczenie kosztów pracy jako sumę wierszy kolumny 8 (patrz tabela 1.1)
2. Koszt zmian maszyny za cały zakres prac.
Całkowite zapotrzebowanie na maszyny jest określane przez obliczenie kosztów pracy jako sumę z kolumny 9 (patrz tabela 1.1).
3. Koszty pracy na przyjętą jednostkę miary, roboczogodziny. (osobodni).
Oblicza się ją, dzieląc sumę kosztów pracy (pracochłonność) przez fizyczną wielkość pracy.
4. Wydajność na pracownika na zmianę w ujęciu fizycznym;
Wydajność oblicza się albo dzieląc koszt prac budowlanych i instalacyjnych do wykonania przez pracochłonność ich realizacji, a następnie wskaźnik ma wartość pieniężną (ruble / osobodnia) lub dzieląc fizyczną objętość pracy przez pracochłonność, a następnie uzyskuje się produkcję w naturze w przeliczeniu na (1 m2 powierzchni, 1 m3 konstrukcji, 1 m3 budynku na 1 osobodzień lub 1 roboczogodzinę itp.).
5. Czas trwania pracy w dniach. Czas trwania pracy w dniach ustalany jest zgodnie z kalendarzowym harmonogramem produkcji pracy (kolumna 15, tabela 1.5).
IV. Zasoby materiałowe i techniczne. Ta sekcja zawiera listę wymagań dotyczących zasobów wymaganych do ukończenia procesu budowlanego przedstawionego na mapie, zgodnie z rysunkami warsztatowymi, specyfikacjami lub ilościami fizycznymi i wskaźnikami wykorzystania zasobów. Liczbę i rodzaje maszyn, narzędzi, zapasów i osprzętu ustala się według przyjętego na mapie schematu organizacji pracy zgodnie z zakresem prac, terminem ich wykonania oraz liczbą pracowników. Zapotrzebowanie na materiały eksploatacyjne określa się na podstawie ich wskaźników zużycia.
Rejestracja mapy technologicznej
Tekst mapy sporządzony jest w formie noty wyjaśniającej na arkuszach A4, strony muszą być ponumerowane. Sekcje muszą być ponumerowane cyfry arabskie w obrębie całej mapy technologicznej. W sekcjach tekst jest podzielony na akapity, które są ponumerowane cyframi arabskimi w każdej sekcji. Numer pozycji musi składać się z numerów sekcji i pozycji oddzielonych kropkami.
Kalkulacja kosztów pracy dokonywana jest w formie tabeli 1.1.
Tabela 2.1. Koszty pracy
Lista prac (kolumna 2) jest wypełniona sekwencja technologiczna wykonywanie pracy.
Zakres prac (kolumny Z, 4) ustala się na podstawie rysunków roboczych i kosztorysów. Wybór tomów z kosztorysów jest mniej czasochłonny, ale ponieważ w kosztorysach nie ma podziału tomów na ujęcia, w celu wyjaśnienia tomów poszczególnych prac wykorzystują oni bezpośrednio dla nich rysunki robocze i specyfikacje, kontrolując poprawność obliczeń zgodnie z szacunki. Wielkość pracy powinna być wyrażona w jednostkach przyjętych do obliczania pracochłonności i maszynochłonności.
Racjonalne uzasadnienie. W gr. 5 wskazuje uzasadnienie (numer paragrafu, tabela, kolumny i pozycje normy przyjętej według ENiR, GESN lub innych).
Normę czasu na jednostkę miary (kolumny 6, 7) wypełnia się zgodnie z przyjętym uzasadnieniem.
Podstawą obliczeń w kalkulacji kosztów pracy (LLC) mogą być dane o różnym stopniu obiektywności, których adekwatność prawdziwe warunki nie ten sam.
Celem obliczenia kosztów pracy i maszynochłonności w KTZ jest określenie zapotrzebowania na te zasoby. Ale w obecności wiarygodnych danych z doświadczenia, pracochłonność i intensywność maszyn należy przyjąć zgodnie z tymi faktycznie osiągniętymi na podobnym obiekcie. W tym przypadku znane są jednocześnie dane dotyczące składu zespołu, kosztów pracy i innych parametrów.
Tym samym największą dokładność zapewnia wykorzystanie informacji o osiągniętych wynikach danego zespołu na tym samym typie obiektu (np. domy z tej samej serii). Obliczenia są mniej dokładne, które opierają się na produkcji tej samej brygady z bliskiej odległości. konstruktywne rozwiązania obiekt lub inny zespół tej samej organizacji w podobnym obiekcie.
Obliczenia oparte na normach szacunkowych, ENiR itp. są mniej dokładne, ponieważ nie uwzględniają szeregu różnych czynników, które można pogrupować w następujące grupy:
wpływ warunków przyrodniczo-klimatycznych i sezonowych wykonywania pracy;
specyficzne rozwiązania mechanizacji pracy, uśrednione w normach kosztów pracy;
sposób prowadzenia pracy oraz poziom organizacji produkcji i osiągnięta przez ten zespół produktywność pracy.
Pracochłonność pracy (kolumny 8, 9) oraz koszt czasu maszynowego określają następujące wzory:
gdzie 8 godzin to czas trwania zmiany.
Kompozycja linku (kolumna 10) jest akceptowana zgodnie z przyjętym uzasadnieniem bez zmian.
Na końcu KTZ wyniki umieszczane są w kolumnach 8 i 9.
Schemat operacyjnej kontroli jakości pracy odbywa się w formie tabeli.
Tabela 2.2. Kontrola jakości operacyjnej
Nazwy operacji (kolumny 2, 3) podlegające kontroli są wypełniane w ciągu technologicznym ich realizacji.
Kontrola jakości operacji (kolumny 4, 5, 6, 7). Opisuje skład kontrolowanych operacji, metody i metody kontroli, wykaz narzędzi metrologicznych, czas kontroli (zwykle kontrola operacyjna jest wykonywana po zakończeniu operacji produkcyjnych) oraz w razie potrzeby zaangażowane usługi - laboratoria konstrukcyjne, geodezyjne, usługi geologiczne i inne.
Zapotrzebowanie na zasoby materiałowe i techniczne do wykonania robót uwzględnionych w mapie podano w tabelach 2.3 i 2.4.
Potrzeba narzędzia, inwentaryzacja jest podana dla osobnego łącza lub zespołu.
Tabela 2.3. Potrzeba narzędzi, inwentaryzacji
Tabela 2.4. Zapotrzebowanie na materiały, półprodukty
Część graficzna map technologicznych obejmuje plany i przekroje, schematy, wykresy, rysunki przewidziane w paragrafie II paragrafu 2.2, natomiast materiały graficzne muszą być niezwykle czytelne dla zrozumienia i nie powinny zawierać zbędnych wymiarów, oznaczeń.
Harmonogram prac sporządzany jest w formie tabeli 2.5.
Tabela 2.5. Plan pracy
Kolumny 1 ÷ 9 harmonogramu prac w pełni odpowiadają kolumnom 1 ÷ 9 rachunku kosztów pracy (tabela 2.1).
Wymagana ilość maszyn i mechanizmów (kolumna l0) uzależniona jest od wielkości i charakteru prac budowlano-montażowych oraz terminów ich realizacji.
Liczba pracowników na zmianę (kolumna 12) i skład zespołu są określane zgodnie ze złożonością i czasem pracy. Przy obliczaniu składu brygady zakłada się, że przejście od jednego schwytania do drugiego nie powinno powodować zmian w składzie liczebnym i kwalifikacyjnym brygady. Biorąc pod uwagę tę okoliczność, ustala się najbardziej racjonalną strukturę łączenia zawodów w brygadzie. Zazwyczaj zespoły mają ustalony skład, który jest brany pod uwagę przy sporządzaniu harmonogramu pracy.
Obliczenie składu brygady odbywa się w określonej kolejności:
zarysować zestaw prac przypisanych do brygady (wg kolumny 2);
obliczyć standardową pracochłonność prac wchodzących w skład kompleksu (kolumna 6), z obliczeń wybrać koszty pracy według zawodu i kategorii pracowników;
ustalić zalecenia dotyczące racjonalnego łączenia zawodów; na podstawie danych dotyczących wydajności głównych mechanizmów podnoszących do realizacji zamierzonego kompleksu ustala się czas trwania procesu wiodącego;
obliczyć liczbę jednostek (kolumna 11) i brygady;
określić skład zawodowy i kwalifikacyjny brygady;
obliczyć złożoność projektu (kolumna 8).
Do określenia składu ilościowego i kwalifikacyjnego jednej brygady można wykorzystać ENiR.
Zakres prac powierzonych zespołowi obejmuje wszystkie prace niezbędne do sprawnej pracy maszyny wiodącej, wszelkie prace związane technologicznie lub zależne. Tak więc przy wznoszeniu nadziemnej części domów wielkopłytowych, która odbywa się w dwóch cyklach, pierwszy cykl wraz z instalacją obejmuje wszystkie prace związane z instalacją (stolarstwo, prace specjalne itp., zapewniające przygotowanie domu na Prace malarskie). Podczas budowy budynków murowanych w trzech cyklach, w pierwszym cyklu powierza się ekipie budowlanej wraz z budową i montażem oraz związanymi z tym prace budowlane przygotowanie do prac tynkarskich. W drugim i trzecim cyklu wykonywane są odpowiednio prace tynkarskie i malarskie.
Aby siła brygady odpowiadała wydajności maszyny prowadzącej, za podstawę obliczeń należy przyjąć okres pracy ustalony na podstawie szacunkowego czasu pracy maszyny lub danych z doświadczenia produkcyjnego .
Skład ilościowy każdego łącza nw określany jest na podstawie kosztów pracy za pracę przypisaną do łącza, Qp (osobodni) oraz czasu trwania procesu wiodącego T mech (dni) według wzoru:
gdzie: m to liczba zmian roboczych w ciągu dnia (kolumna 9).
Skład ilościowy brygady określa się sumując liczbę pracowników wszystkich jednostek wchodzących w skład brygady.
Koszty pracy według zawodu i kategorii ustala się na podstawie doboru próby z kalkulacji kosztów pracy. Liczbę pracowników według zawodu i kategorii określa wzór:
gdzie Nbr jest całkowitą liczbą brygady;
d- środek ciężkości koszty pracy według zawodów i kategorii w całkowitej pracochłonności pracy.
Przy niewielkim nakładzie pracy dla każdego zawodu, który nie zapewnia pełnego obciążenia w okres rozliczeniowy, planuję łączyć zawody. Normatywna pracochłonność pracy wykonywanej w kolejności kombinacji nie powinna przekraczać 15% całkowitej pracochłonności pracy. Zwykle łączą zawody montera i cieśli, cieśli i betoniarza, spawacza elektrycznego i montera, izolatora i dekarza itp. Lista orientacyjna połączone prace podano w tabeli 2.6.
Tabela 2.6. Przybliżona lista połączonych prac
Instalator Struktury | Montaż prefabrykowanych konstrukcji żelbetowych; montaż w miejscu stolarki; spawanie i prace dźwigowe; układanie mieszanki betonowej w zamonolichivaniye wzorów. |
Pasowy | Prace olinowania; gotowanie bitumu, układanie mieszanki betonowej w konstrukcje monolityczne; uszczelnianie stawów |
spawacz elektryczny | Montaż konstrukcji prefabrykowanych; prace spawalnicze elektryczne; instalacja ogrodzenia metalowe; prace dźwigowe |
Mason | prace murarskie; montaż prefabrykowanych konstrukcji żelbetowych wraz z wykwalifikowanym instalatorem; rusztowanie; układanie mieszanki betonowej podczas osadzania konstrukcji; prace dźwigowe; tynkowanie poszczególnych miejsc |
Tynkarz | Prace tynkarskie; okładzina żelbetowa biegi schodów płytki mozaikowe; wraz z wykwalifikowanym stolarzem, wypełnianie otworów okiennych i drzwiowych oraz montaż osprzętu do zabudowy. |
Otwory do napełniania; montaż i instalacja szaf wnękowych; przeszklenie; układanie mieszanki betonowej na urządzeniu do przygotowania pod posadzką; hydroizolacja łazienek. |
|
Transport | Uszczelnianie połączeń konstrukcji i bloków okiennych wraz z wykwalifikowanymi pracownikami; tynkowanie powierzchni; murarstwo |
Liczba zmian (kolumna 13). Podczas korzystania z głównych maszyn (dźwigi montażowe itp.) Liczba zmian roboczych wynosi co najmniej dwie. Przesunięcie pracy wykonywanej ręcznie oraz za pomocą zmechanizowanego narzędzia uzależnione jest od dostępnego zakresu pracy i dyspozycyjności pracowników. Ponadto niektóre prace wymagające dużej dokładności (wyrównanie kolumn) powinny być wykonywane tylko podczas dziennej zmiany. Wykonanie szeregu prac na drugiej zmianie, zwłaszcza w okresie jesienno-zimowym, wymaga dodatkowych środków ochrony pracy, oświetlenia miejsc pracy, przejść itp. Jednak wdrożenie tych środków nie eliminuje całkowicie niedogodności pracy na drugiej zmianie. Praca wykonywana ręcznie jest przypisywana do drugiej zmiany tylko w tych rzadkich przypadkach, gdy zakres prac jest mocno ograniczony i zespół (link) jest zmuszony rozdzielić się na pracę zmianową.
Czas trwania pracy (kolumna 14). Najpierw określany jest czas pracy zmechanizowanej, którego rytm determinuje cały harmonogram, a następnie obliczany jest czas pracy ręcznej.
Czas trwania zmechanizowanej pracy Tmeh (dni) określa wzór:
gdzie: Nmach.-zmiana. - wymagana liczba zmian maszyny (kolumna 9);
nmash - liczba samochodów;
m to liczba zmian roboczych w ciągu dnia (kolumna 13).
Wymagana ilość maszyn uzależniona jest od wielkości i charakteru prac budowlano-montażowych oraz terminów ich realizacji.
Czas trwania pracy fizycznej Tr (dni) oblicza się dzieląc pracochłonność pracy Qp (osobodni) przez liczbę pracowników nh, którzy mogą zajmować front pracy oraz liczbę zmian w ciągu dnia:
Ograniczenie liczby robotników mogących pracować na uchwycie można określić dzieląc front pracy na poletka, których wielkość powinna być równa produktywności zmianowej ogniwa lub pojedynczego pracownika, a także liczby i produktywności mechanizmy podnoszące. Iloczyn liczby działek i składu jednostek daje maksymalną liczebność brygady na tym terenie.
Minimalizacja czasu trwania ma limit w postaci trzech ograniczeń: wielkości frontu pracy, dostępności pracowników i technologii pracy.
Harmonogram wykonania prac (kolumna 15) podany jest w postaci wykresu liniowego. Terminy kalendarzowe wykonania poszczególnych prac ustalane są pod warunkiem zachowania ścisłej sekwencji technologicznej, z uwzględnieniem konieczności zapewnienia frontu do realizacji kolejnych prac w możliwie najkrótszym czasie.
Okres gotowości frontu pracy w niektórych przypadkach wydłuża się ze względu na konieczność obserwacji przerw technologicznych między dwoma kolejne prace. Na przykład montaż leżących powyżej konstrukcji żelbetowych można przeprowadzić dopiero po uzyskaniu przez monolityczne połączenia konstrukcji wsporczych wymaganej wytrzymałości (co najmniej 70% R28). Przerwy technologiczne nie są stałe, zależą od wielu czynników.
Tak więc czas schnięcia tynku zależy od pory roku, temperatury i zastosowanych metod - wentylacji naturalnej lub sztucznej. W razie potrzeby przerwy technologiczne można skrócić, stosując bardziej intensywne metody. Tak więc przy konstruowaniu złącza monolitycznego można zastosować inny rodzaj i markę cementu, ogrzewanie elektryczne i inne metody przyspieszania utwardzania betonu.
CENTRALNY INSTYTUT STUDIUM REGULACJI I INFORMACJI NAUKOWO-TECHNICZNEJ „ORGTRANSTROY”
MINISTERSTWA BUDOWNICTWA TRANSPORTOWEGO
PRZYGOTOWANIE MIESZANKI BETONU CEMENTOWEGO W INSTALACJI C-780
1 OBSZAR ZASTOSOWANIA
Mapa technologiczna została opracowana na podstawie zastosowania metod naukowej organizacji pracy i jest przeznaczona do wykorzystania przy opracowywaniu projektu produkcji pracy i organizacji pracy w mieszalniach do przygotowania mieszanek cementowo-betonowych.
Zautomatyzowana betoniarnia cementowa (CBZ) wraz z instalacją S-780 przeznaczona jest do przygotowania mieszanek betonowych sztywnych i plastycznych z kruszywem do 40 mm.
Wydajność zakładu do 30 m 3 /h.Pojemności zbiorników na cement, kruszywa, zbiornik na wodę są zaprojektowane na pół godziny pracy przy maksymalnej wydajności i najwyższym stosunku wodno-cementowym = 0,5.
Zakład składa się z wydziału mieszania i dozowania, magazynu kruszywa oraz magazynu cementu.
Magazyn materiałów eksploatacyjnych kruszyw czynny, zlokalizowany bezpośrednio przy betoniarni S-780. Organizowane jest tu również przesiewanie i mycie materiału. Piasek i tłuczeń dostarczany jest w wagonach kolejowych, rozładowywany przez wielokubełkowy rozładunkowy portal S-492 bezpośrednio nad lejami zsuwni wibracyjnych przenośnika chodnikowego.
Zautomatyzowany magazyn cementu S-753 przeznaczony jest do krótkotrwałego składowania cementu. Wieża silosowa o pojemności 25 g wyposażona jest w dwa wskaźniki poziomu cementu typu UKM. Cement z wagonów rozładowywany jest bezpośrednio do magazynu cementu za pomocą rozładunku pneumatycznego S-577.
Jednostka dozująca zakładu składa się z lejów zasypowych z ciągłymi dozownikami wahadłowymi S-633. Dozowniki są instalowane nad przenośnikiem poziomym, który dostarcza materiały do przenośnika pochyłego. Na przenośniku pochyłym wpadają do wanny załadowczej wydziału mieszania.
Lej podający cement to cylinder ze stożkową częścią na dole. Cement podawany jest bezpośrednio do dozownika S-781 z podajnikiem bębnowym. Wewnątrz bunkra zainstalowane są dwa wskaźniki poziomu cementu C-609A, objęte schematem kontroli magazynu. Włączenie lub wyłączenie mechanizmu dostarczającego cement z magazynu odbywa się za pomocą tych samych wskaźników.
Podstawowym wyposażeniem betoniarni jest ciągła wymuszona wytwórnia mieszania S-780. Korpus roboczy mieszarki to dwa wały o przekroju kwadratowym 80×80 mm z zamontowanymi na nich łopatkami. Ostrza zakończone są ostrzami o wymiarach 100×100 mm. Korpus mieszadła zakończony jest lejem magazynowym z zasuwą szczękową.
Betoniarnia S-780 połączona jest z magazynami: kruszywa cementowego oraz dozownikiem systemem podajników taśmowych i kubełkowych.
We wszystkich przypadkach wykorzystania mapy technologicznej konieczne jest powiązanie jej z warunkami lokalnymi, w zależności od składu, marki i ilości produkowanej mieszanki.
W zależności od zmieniających się potrzeb mieszanki cementowo-betonowej urządzenie można dostosować do dowolnej wydajności w zakresie od 15 do 30 mh i wody do 6 m3.
Czyli np. przy określonym przez laboratorium zakładu zużycie materiałów na 1 m3 betonu (cement - 340 kg, piasek - 547 kg, frakcja tłucznia 5-20 mm - 560 kg, frakcja tłucznia 20-40 mm - 840 kg, woda - 170 kg) wydajność zakładu będzie wynosić:
Dozownik dzienny |
Wydajność dozowników, t/h przy wydajności zakładu m 3 /h |
|||
Frakcja kamienia łamanego 15-20 mm |
||||
Frakcja kamienia łamanego 20-40 mm |
||||
2. INSTRUKCJE DOTYCZĄCE TECHNOLOGII PROCESU PRODUKCJI
Przed rozpoczęciem pracy cementowni z instalacją S-780 cały sprzęt jest sprawdzany i w razie potrzeby kalibrowane są dozowniki kruszywa, cementu i wody.
Kalibracja dozowników odbywa się ze zmianą wydajności zakładu, marki i składu mieszanki betonowej, masy objętościowej i rozkładu granulometrycznego kruszyw.
Przy określonej wydajności zakładu i odpowiednio składzie i marce mieszanki konieczna jest również okresowa kalibracja dozowników.
Kalibracja dozownika kruszywa
Dozowniki kruszywa są kalibrowane przez pobieranie próbek. Do tego potrzebujesz:
a) napełnić zasobniki piaskiem, małym i dużym żwirem w ilości co najmniej 5 m 3 każdego materiału;
b) ustawić dozowniki poziomo w pozycji poziomej (z materiałem) przesuwając dźwignię ładowania lub zmieniając ładunek w skrzyni balastowej (w pobliżu wariatora).
W takim przypadku klapy ruchome powinny być ustawione na wysokość 100 mm dla tłucznia i 80 mm dla piasku. Klapy stałe są montowane o 10 mm wyżej niż klapy ruchome. Sprawdzenie braku zakleszczeń lub zakleszczeń w systemie ważenia dozowników odbywa się poprzez lekkie dociśnięcie krawędzi platformy wagowej lub poprzez umieszczenie odważnika 0,5 kg. W takim przypadku platformę należy opuścić do przystanku;
c) przygotować do kalibracji wagi towarowe o nośności co najmniej 0,5 T, skrzynia o pojemności 200 m oraz stoper.
Do pobierania próbek konieczne jest włączenie poziomego przenośnika zbiorczego na ruch w przeciwnym kierunku poprzez zmianę kierunku silnika elektrycznego (wsteczny). Podczas testowania jednego dozownika, resztę należy wyłączyć.
Poziomy przenośnik odbiorczy powinien być włączony na czas testu.
Na polecenie asystenta laboratoryjnego trzymającego stoper operator włącza dozownik. Piasek lub tłuczeń wylewany jest na blachę przez 4-5 sekund, aż do uzyskania stabilnego płynięcia wsypywanego materiału. Następnie włącza się stoper, a pudełko umieszcza się pod strumieniem dozowanego materiału.
Po upływie czasu pobierania próbek, na sygnał asystenta laboratorium, przenośnik odbiorczy i dozownik zostają wyłączone. Pobrana próbka jest ważona na wadze.
Dla jednej pozycji wariatora wykonywane są trzy ważenia.
Wydajność godzinową dozownika określa średnia arytmetyczna masy trzech próbek według wzoru:
gdzie α - średnia arytmetyczna masy trzech próbek w kg bez tary;
t- czas pobierania próbek w sek. Jeżeli masa próbek nie przekracza ±2% obliczonej wartości, uważa się, że w danym położeniu wskazówki wariatora dozownik pracuje stabilnie.
Podobnie wykonuje się kalibrację innych dozowników kruszyw.
Aby skalibrować dozownik cementu, musisz:
a) odkręcić śruby mocujące rurę rozgałęzioną leja cementowego i obrócić rurę rozgałęzioną o 90 °;
b) upewnić się, że zasobnik cementu jest całkowicie wypełniony cementem. Sprawdź poziom cementu w leju zasypowym za pomocą wskaźników poziomu na panelu sterowania mieszalni;
c) przygotować do tary wag handlowych o nośności co najmniej 0,5 T, dwie skrzynie o pojemności 200 l, stoper, łopata, rura rozgałęźna wykonana z cyny o średnicy 130-150 mm, długość 3-3,5m.
Próbkowanie jest przeprowadzane dla każdej z pięciu pozycji strzałki wariatora.
Aby to zrobić, pod dyszą instalowana jest skrzynka, na polecenie asystenta laboratorium kierowca włącza dozownik cementu. Cement z dozownika wchodzi do rury, a z niej do skrzynki, aż naocznie ustali się stabilny, tryb podawania cementu i normalna prędkość silnika elektrycznego. Czas wymagany do uzyskania stabilnego przepływu materiału wynosi zwykle 50-60 sekund. Po tym czasie stoper jest jednocześnie włączany, a rura jest przenoszona do załadunku pudełka. Pudełko jest ładowane w ciągu 90 sekund na 1, 2, 3 pozycje strzałki wariatora, aw ciągu 60 sekund - na 4, 5 pozycji strzałki. Po upływie określonego czasu pobrana próbka jest ważona na wadze. Dla każdej pozycji igły wariatora pobierane są trzy próbki. Dokładność dozowania cementu ± 2% obliczonej wagi.
Aby kontrolować prawidłową kalibrację sprawdzane jest działanie dozownika przy wybranej pojemności i ciągłej pracy dozownika przez 10 minut poprzez pobranie trzech próbek w pudełku, zwracając szczególną uwagę na działanie wszystkich mechanizmów i nieprzerwany przepływ materiału do dozownika.
Aby skalibrować dystrybutor wody, musisz:
a) obrócić rurę spustową, przez którą woda wpływa do mieszalnika o 180° na kołnierz i przedłużyć ją dodatkową rurą o długości do 4 m;
b) wyłączyć wszystkie urządzenia niezwiązane z dozowaniem wody.
Dozownik jest kalibrowany przez pobranie próbki, dla której konieczne jest włączenie pompy dozującej z zatkaną rurą spustową. W tym samym czasie woda ze zbiornika przez pompę dozującą i zawór trójdrożny wraca do zbiornika przez pierścień. Na polecenie asystenta laboratoryjnego trzymającego stoper, operator przełącza zawór trójdrożny w położenie podawania wody do mieszalnika, a do beczki podawana jest woda do momentu ustalenia stałego stałego przepływu wody. Następnie stoper jest jednocześnie włączany, a zawór trójdrożny jest natychmiast przełączany na dostarczanie wody do zbiornika wodomierza. Pojemnik jest napełniany w ciągu 60 sekund dla pozycji 1, 2 i 3 strzałki wariatora oraz w ciągu 30 sekund dla pozycji 4 i 5 strzałki. Po upływie określonego czasu, na polecenie asystenta laboratoryjnego, zawór trójdrożny zostaje przełączony na spust i stoper zostaje wyłączony. Operator przełącza zawór trójdrożny w położenie do dostarczania wody przez pierścień. Pobrana próbka jest mierzona.
Aby zachować główny wskaźnik jakości mieszanki betonowej (stosunek wodno-cementowy), konieczne jest kalibrowanie dozownika wody z dokładnością ± 1%.
Po skalibrowaniu wszystkich dozowników instalacja buduje wykres wydajności betoniarni w zależności od położenia strzałki wariatora każdego dozownika (rys. 1).
Ryż. 1. Wykres zależności wydajności dozowników od pozycji strzałek wariatorów:
1 - woda; 2 - frakcja kruszonego kamienia 5-20 mm; 3 - frakcja kruszonego kamienia 20-40 mm; 4 - piasek; 5 - cement
Ten wykres jest ważny, gdy zakład pracuje na trwałych materiałach, które składają się na mieszankę betonową.
Aby zmienić wydajność dozowników, konieczna jest zmiana przełożenia za pomocą wariatora. Aby to zrobić, ustaw strzałki wariatora (tylko w ruchu) na odpowiedni podział wzdłuż przybliżonej krzywej, a następnie, kalibrując, dokonaj niezbędnej korekty ich położenia.
Prawidłowe działanie dystrybutorów jest sprawdzane codziennie na początku zmiany przez przedstawiciela laboratorium CBZ. Urządzenie ważące montuje się zgodnie ze składem mieszanki betonowej zatwierdzonym przez głównego inżyniera wydziału budowlanego iz uwzględnieniem wilgotności kruszywa. Dostęp do szafek wagowych i urządzeń dozujących oraz zmiany ilości materiałów jest dozwolony tylko dla pracowników laboratorium.
Składniki mieszanki betonowej bezpośrednio po wejściu do betoniarni podlegają kontroli laboratorium Centralnego Zakładu Biomedycznego oraz Centralnego Laboratorium Zarządzania Budową. Jakość materiałów sprawdzana jest przez kontrolę zewnętrzną i pobieranie próbek.
Instalacja działa według schematu podanego na ryc. 2.
Ryż. 2. Schemat technologiczny betonowni cementowej z wytwornicą S-780 do przygotowania mieszanki betonowej:
1 - podajniki wibracyjne; 2 - przenośniki; 3 - bunkry kruszywa; 4-dozowniki kruszyw; 5 - dozownik cementu; 6 - bunkier cementowy; 7 - przenośnik taśmowy; 8 - mikser; 9 - napęd do betonu; 10 - zbiornik na wodę; 11 - dozownik wody; 12 - zawór trójdrożny; 13 - kosz przyjęciowy; 14 - silos bankowy; 15 - filtry
Spychacz naprzemiennie wpycha kruszywo na 1 tace wibracyjne, skąd 2 przenośniki podają je do 3 pojemników paszowych.
Gdy bunkry są w pełni załadowane, po przejściu materiału pozostałego na taśmie włącza się wskaźnik górnego poziomu i wyłącza się tacę wibracyjną i przenośniki oraz włącza się sygnał świetlny końca załadunku. W momencie wyczerpania się materiału w leju zasypowym do wskaźnika poziomu dolnego włącza się przenośnik, taca wibracyjna, sygnały świetlne i dźwiękowe rozpoczęcia załadunku.
Cement z puszki silosu 15 jest podawany do zasobnika 6 za pomocą pneumatycznego systemu wtrysku. Z leja zasypowego cement wchodzi do dozownika wahadłowego 5. Wskaźniki górnego i dolnego poziomu cementu mają sygnały świetlne i dźwiękowe do panelu sterowania magazynu cementu.
Woda w zbiorniku 10 komory mieszania jest pompowana ze specjalnego zbiornika.
Kruszywo o frakcji 5-20, 20-40 mm oraz piasek dozowane są w sposób ciągły taśmowymi dozownikami wahadłowymi 4, do których materiał trafia z zasobników.
Najpierw na taśmę dozowany jest tłuczeń o frakcji 20-40 mm, następnie tłuczeń o frakcji 5-20 mm i piasek, a na wierzch tych materiałów cement. Ta kolejność podawania eliminuje gromadzenie się małych cząstek materiału na taśmie.
Dozowane materiały są podawane przez lejek podający do mieszalnika. Woda ze zbiornika dozowana jest za pomocą pompy dozującej i podawana rurociągiem bezpośrednio do mieszalnika roboczego.
Wywar siarczynowo-alkoholowy przygotowywany jest w specjalnej instalacji i wprowadzany do wody w ilości 0,2-0,3% masy cementu na 1 m 3 betonu (0,68-1,0 kg/m 3).
W mieszalniku elementy betonowe są intensywnie mieszane i transportowane za pomocą wałów łopatkowych do wylotu. Z mieszalnika gotowa mieszanka trafia do zbieracza i jest rozładowywana przez bramę szczękową do wywrotki.
Jakość mieszanki cementowo-betonowej uzyskanej w mieszarni C-780 zależy przede wszystkim od ciągłości jej pracy, gdyż na każdym postoju zmienia się wyliczony stosunek składników mieszanki betonowej, zwłaszcza cementu i wody.
Kontrola jakości mieszanki cementowo-betonowej przeprowadzana jest przez laboratorium zakładowe 2-3 razy na zmianę.
Przy takim samym składzie i prawidłowym dozowaniu mobilność, urabialność, gęstość nasypowa i wydajność betonu muszą być stałe.
Wydajność betonu określa się co najmniej raz w miesiącu ze zmianą składu betonu.
Codziennie należy sprawdzać ilość betonu wydanego z fabryki i umieszczonego w walizce.
Podczas wykonywania pracy należy przestrzegać następujących zasad bezpieczeństwa:
Osoby zaznajomione z konstrukcją tego urządzenia i przepisami bezpieczeństwa mogą obsługiwać urządzenia betoniarni;
Przed uruchomieniem sprzętu należy sprawdzić niezawodność osłon na wszystkich otwartych, obrotowych i ruchomych; Części;
Należy zadbać o dobry stan nie tylko systemu automatyki, ale również lokalnych mechanizmów rozruchowych. W przypadku awarii lokalnego rozruchu eksploatacja zautomatyzowanej instalacji jest niedozwolona;
Dozwolone jest włączanie maszyn, narzędzi i lamp oświetleniowych tylko za pomocą rozruszników lub przełączników nożowych;
Naprawy sprzętu elektrycznego i okablowania mogą być wykonywane wyłącznie przez elektryka;
Naprawa rurociągów instalacji pneumatycznych pod ciśnieniem jest zabroniona;
Pod koniec pracy wytwórni należy wyłączyć wyłącznik główny i zamknąć skrzynkę, w której się znajduje;
W przypadku braku transportu przez ponad 1,5 godziny należy oczyścić łopatki i korytko z mieszanki betonowej i wypłukać mieszadło wodą oraz wyczyścić zasuwę szczękową leja magazynowego;
Aby zapobiec przedostawaniu się ciał obcych do leja, nad otworem załadunkowym należy zainstalować ruszt. Podczas przygotowywania mieszanki z dodatkami chemicznymi pracownik musi używać gumowych rękawic i okularów ochronnych.
3. INSTRUKCJE ORGANIZACJI PRACY
Prace nad przygotowaniem mieszanki cementowo-betonowej prowadzone są na dwie zmiany.
Mieszalnię obsługuje zespół składający się z 8 osób, w tym przygotowujący mieszanki cementowo-betonowe, maszyniści: 5 razr.-1; 4 bity-1; Dozownik składników mieszanki cementowo-betonowej 3 rozm.-1; monter elektryczny 5 kat.-1; konstrukcja ślusarska 4 razr.-1; kierowca spychacza 5 lat - 1; transport (pracownicy pomocni) 2 razr.-2.
Przed rozpoczęciem pracy przygotowujący mieszankę cementową i dozownik muszą sprawdzić kompletność wyposażenia instalacji, brak ciał obcych w pobliżu części wirujących lub na przenośnikach taśmowych.
Operator mieszalni 5 lat zarządza pracą betoniarni jako całości: monitoruje dojazd, załadunek i wysyłkę pojazdów, daje sygnał dźwiękowy kierowcom do załadunku, w przypadku braku pojazdów wyłącza zakład i zapewnia, że po wyłączeniu zakładu , w mieszalniku nie pozostała żadna mieszanka betonowa.
Operator mieszalni IV klasa. sprawdza obecność wody w zbiorniku i zbiorniku dozującym, cement w leju zasypowym, sprawdza mieszadło, sprawdza pustą pracę zamka szczęki i mieszadła bez materiałów, sprawdza działanie wariatora, włącza pompę wody, która dostarcza wodę do zbiornika dozującego wodę o stałym poziomie, włącza mieszadło, następnie przenośnik podający kruszywo otwiera zawór odcinający wodę, włącza dozownik cementu i steruje przygotowaniem mieszanki cementowo-betonowej. Monitoruje działanie mechanizmów instalacyjnych, zapewnia sprawne działanie wszystkich jednostek oraz przeprowadza rutynowe naprawy.
Dozownik składników mieszanki betonowo-cementowej 3 razr. sprawdza obecność kruszywa w zasobnikach wydziału dozowania, wysokość montażu żaluzji stałych i ruchomych, łatwość kołysania przenośnika wagowego oraz jego poziomą pozycję. Sprawdza pustą pracę przenośników prefabrykowanych i skośnych oraz podczas ich normalnej pracy włącza w określonej kolejności przenośniki prefabrykowane, zsypy wibracyjne i dozowniki.
Ślusarz budowlany 4 razy. sprawdza obecność cementu w magazynie, położenie zasuw przesuwnych oraz obecność wymaganej ilości cementu w wykopie lub wannie transferowej. Na polecenie kierowcy konsoli środkowej sprawdza on na biegu jałowym pracę układu pneumatycznego.
Elektryk 5 kategorii sprawdza uziemienie silników elektrycznych, podłącza urządzenie do sieci, wraz ze sterownikami sprawdza pracę silników elektrycznych na biegu jałowym, monitoruje poprawność działania automatyki. Podczas pracy silników elektrycznych okresowo monitoruje tryb ich pracy, nagrzewanie oraz stan styków.
Kierowca spychacza 5 lat podaje kruszywa do zsypów galerii podziemnej.
Pracownicy transportu (pomocniczy) 2 sek. są zajęci pracami przygotowawczymi i końcowymi: przygotowują wywar siarczynowo-alkoholowy, usuwają rozsypany materiał z przenośników i dozowników, usuwają ciała obce z przenośników.
4. HARMONOGRAM PROCESU PRODUKCYJNEGO
Nazwa prac |
jednostka miary |
Zakres prac |
Skład linku (zespołu) |
|||||||||||||||||
Praca przygotowawcza |
0,05 |
4 " - 1
elektryk Ślusarz budowlany Kierowca spychacza
|
||||||||||||||||||
14,27 |
||||||||||||||||||||
Przekazanie zmiany |
0,03 |
|||||||||||||||||||
Prace końcowe |
0,05 |
|||||||||||||||||||
kontynuacja
Nazwa prac |
jednostka miary |
Zakres prac |
Pracochłonność dla całego zakresu pracy, osobodni |
Skład linku (zespołu) |
Czas procesu produkcyjnego |
|||||||||||||||
Praca przygotowawcza |
0,05 |
Przygotowacze mieszanki betonowo-cementowej, maszyniści: 4 " - 1 Jednostka dozująca składniki mieszanki betonowo-cementowej: elektryk Ślusarz budowlany Kierowca spychacza Transport (pracownicy pomocni) |
||||||||||||||||||
Przygotowanie mieszanki cementowo-betonowej (dostawa kruszyw, cementu, wody, ich dozowanie, mieszanie, przygotowanie dodatków) |
14,27 |
|||||||||||||||||||
Przekazanie zmiany |
0,03 |
|||||||||||||||||||
Prace końcowe |
0,05 |
|||||||||||||||||||
Notatki.
1. Harmonogram nie przewiduje conocnej konserwacji zapobiegawczej.
2. W okresie rozruchu i regulacji instalacji skład zespołu może ulec zmianie według uznania głównego inżyniera działu konstrukcyjnego.
5. OBLICZANIE KOSZTÓW PRACY PRZY PRZYGOTOWANIU 210 m²
Kod stawek i cen |
Skład linku |
Opis prac |
jednostka miary |
Zakres prac |
Norma czasu, roboczogodzina |
Cena, rub.-kop. |
Standardowy czas na pełny zakres prac |
Koszt kosztów pracy dla pełnego zakresu pracy, rub.-kop. |
TNR, § T-1-38, tab. 2a |
Przygotowujący mieszankę cementowo-betonową: Dozownik składników mieszanka betonu cementowego: elektryk Ślusarz budowlany |
Przygotowanie mieszanki cementowo-betonowej (doprowadzenie cementu do leja zasypowego, dozowanie kruszywa w cemencie przy doprowadzeniu do mieszarki), doprowadzenie wody do mieszarki i wprowadzenie (w razie potrzeby) roztworu dodatków; mieszanie materiałów z uwolnieniem mieszanki do leja magazynowego; uwolnienie gotowej mieszanki do wywrotek; przygotowanie dokumentów do mieszanki |
100 m 3 |
12-84 |
26-96 |
|||
Do czasu |
Kierowca spychacza Pracownicy transportu (pomocniczy) |
Dostawa materiałów mineralnych (przepychanie materiałów na chodnik przenośnika spychaczem; konserwacja punktów podających przenośnika taśmowego i przenośnika magazynu materiałów eksploatacyjnych oraz przygotowanie wywaru siarczynowo-alkoholowego) |
1 zmiana |
13-50 |
13-50 |
|||
Razem za 210 m 3 |
6. GŁÓWNE WSKAŹNIKI TECHNICZNE I EKONOMICZNE
Nazwa wskaźników |
jednostka miary |
Według wyceny |
W rozkładzie |
O ile mniej więcej wskaźniki według harmonogramu niż według obliczeń, %. |
Złożoność pracy na 100 m 3 mieszanki |
||||
Średnia ranga pracowników |
||||
Średnia dzienna płaca na pracownika |
||||
Stopień wykorzystania instalacji S-780 |
7. ZASOBY MATERIAŁOWE I TECHNICZNE
a) Podstawowe materiały
Zużycie materiałów określa się zgodnie z recepturą mieszanki betonowo-cementowej. Ta tabela pokazuje średnie zużycie materiałów.
Nazwa |
Marek, GOST |
jednostka miary |
Ilość |
|
na jednostkę produkcji (100 m 3 mieszanki) |
na zmianę (210 m 3 mix) |
|||
Klasa cementu 500 |
GOST 10178-62* |
|||
Średni piasek |
GOST 10268-62 |
|||
Kruszywo frakcja 5-20 mm |
GOST 8267-64 |
|||
Frakcja kamienia łamanego 20-40 mm |
GOST 8267-64 |
|||
Wywar siarczynowo-alkoholowy |
b) Maszyny, sprzęt, narzędzia, inwentarz
Nazwa |
jednostka miary |
Ilość |
|
mieszalnia z automatycznym |
|||
Dozowniki ciągłe |
|||
Automatyczne ładowanie cementu |
|||
Spychacz |
|||
wyładunek cementu |
|||
Przenośniki taśmowe |
T-144 i RTU-30 |
||
Instalacja do przygotowania dodatków SSB |
|||
Klucze |
ustawić |
||
Mapa technologiczna została opracowana przez wydział wdrażania najlepszych praktyk i przepisów technicznych w zakresie budowy dróg i lotnisk (wykonał inżynier T.P. Bagirova) na podstawie materiałów z dozorowych stacji badawczych Instytutu Orgtransstroy w Rostowie i Czelabińsku