Strategie utrzymania ruchu i sposoby poprawy efektywności prac naprawczych. Poprawa obsługi produkcyjnej
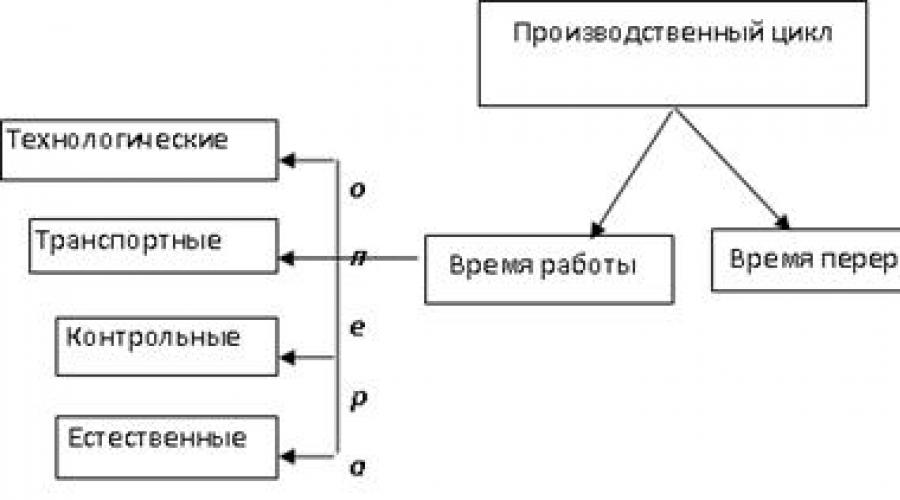
100 r bonus za pierwsze zamówienie
Wybierz rodzaj pracy Praca dyplomowa Zajęcia Streszczenie Praca magisterska Sprawozdanie z praktyki Artykuł Sprawozdanie Recenzja Test Monografia Rozwiązywanie problemów Biznesplan Odpowiedzi na pytania kreatywna praca Esej Rysunek Eseje Tłumaczenia Prezentacje Pisanie Inne Zwiększanie wyjątkowości tekstu praca doktorska Praca laboratoryjna Pomoc online
Zapytaj o cenę
Z przeprowadzonych badań wynika, że po remoncie urządzeń kolejne cykle remontowe ulegają znacznemu skróceniu. Na przykład sprzęt w wieku 20 lat ma o 20% krótszy czas realizacji niż sprzęt w wieku 10 lat. Koszty rutynowej konserwacji i napraw sprzętu podczas drugiego cyklu remontowego wzrastają średnio o 9-15% w porównaniu z pierwszym. W związku z tym niezwykle ważne jest znalezienie sposobów rozwiązania tych dwóch problemów. krytyczne problemy Gospodarka remontowa kraju, jako specjalizacja i koncentracja naprawy sprzętu, jego przeniesienie na szyny przemysłowe i zaopatrzenie serwis naprawczy części zamienne.
W przemyśle zalety specjalizacji produkcji naprawczej nie są dostatecznie wykorzystywane. Naprawa prawie wszystkich rodzajów sprzętu odbywa się w warsztatach naprawczych lub warsztatach przedsiębiorstw, w których jest eksploatowana. Jeden rodzaj produkcji naprawczej prowadzi do ogromnych kosztów pracy przy naprawie sprzętu. Wysokie koszty praca jest wyjaśniona niski poziom mechanizacja pracy robotników remontowych, tylko 20-30% nawet w dużych gospodarstwach remontowych.
Reorganizacja działalności remontowej w oparciu o jej specjalizację pozwoli na przejście na przemysłowe metody wykonywania operacji naprawczych i tym samym podniesienie poziomu technicznego gospodarki remontowej, uwolnienie części sprzętu i pracy skoncentrowanej w serwisie naprawczym na potrzeby produkcji głównej. Specjalizacja naprawy poprawia jakość naprawy, skraca czas jej realizacji, zmniejsza zużycie materiałów. Na tej podstawie zmniejsza się koszt naprawy jednej jednostki naprawczej.
Badania i praktyka zaawansowanych wyspecjalizowanych fabryk pokazują, że wraz ze wzrostem liczby jednomodelowych maszyn, które są jednocześnie remontowane, pracochłonność wszystkich prace naprawcze zmniejszona w porównaniu z pracochłonnością pojedynczej naprawy. Tak więc przy sprowadzeniu partii jednocześnie naprawianych maszyn do 10 jednostek pracochłonność jednostki złożoności naprawy zmniejsza się o 20%; przy partii 20 jednostek – o 25%, przy 50 jednostkach – o 38%, a przy partii 100 jednostek – o 45%. Zwiększenie partii jednocześnie naprawianych jednomodelowych obrabiarek wpływa również na zmniejszenie pracochłonności pracy maszyn zarówno przy produkcji nowych, jak i renowacji starych części.
Pierwszym etapem specjalizacji produkcji naprawczej jest tworzenie warsztatów naprawczych, które naprawiają określone rodzaje sprzętu. Drugi to tworzenie zakładów naprawczych, ich specjalizacja w naprawie i modernizacji niektórych typów maszyn i zespołów oraz w produkcji części zamiennych do urządzeń określonego typu. Takie fabryki mogą być wyposażone w zaawansowaną technologię, wykorzystywać wysokowydajne procesy technologiczne, zarówno w operacjach montażowych, jak i produkcji części zamiennych i zespołów.
ważna impreza racjonalna organizacja prace naprawcze polegają na zapewnieniu im części zamiennych. Badania pokazują, że żywotność sprzętu wynosi 15-25 lat, a zmiana wzorców produkcji sprzętu następuje po 6-8 latach. Tak więc sprzęt pracuje w przedsiębiorstwie przez około 3-4 cykle napraw, a jego naprawa wymaga ogromnej ilości części zamiennych.
Produkcja części zamiennych na własne potrzeby przez każde przedsiębiorstwo z osobna wymaga dodatkowe wyposażenie oraz dodatkowe obszary produkcyjne, których nie można efektywnie wykorzystać. Na przykład stopień wykorzystania mocy produkcyjnych obrabiarek w warsztacie mechanicznym jest różny dla poszczególnych typów obrabiarek i wynosi 0,2-0,5. Dlatego koszt produkcji części zamiennych w zakładach budowy maszyn jest 3-5 razy wyższy niż w wyspecjalizowanych przedsiębiorstwach.
Jednym ze sposobów na zaspokojenie zapotrzebowania na części zamienne jest odtworzenie zużytych części i ponowne ich użycie. Badania pokazują, że w ten sposób można zaspokoić 20-25% istniejącego zapotrzebowania na części zamienne. W rzeczywistości niewielka część z nich jest odnawiana i ponownie wykorzystywana, co potwierdzają wyniki ankiety w zakładach budowy maszyn na Uralu. Pomimo różnorodności metod odzyskiwania, dla ponowne użycie w zakładach budowy maszyn odnawia się średnio około 6% zużytych części. Według naukowców ekonomicznie opłacalne jest przywrócenie 25-30% podczas napraw. W najlepszych warsztatach samochodowych liczba regenerowanych części sięga 60-70%.
Niski odsetek ponownie używanych części tłumaczy się przede wszystkim zdecentralizowanym systemem naprawy sprzętu i produkcji części zamiennych istniejącym w przedsiębiorstwach. W tych warunkach nie zawsze jest możliwe zorganizowanie opłacalnej renowacji zużytych części, ponieważ wymaga to specjalnej wiedzy, odpowiedniego sprzętu i znacznego poziomu koncentracji prac naprawczych.
Wraz ze wzrostem poziomu koncentracji produkcji rośnie udział ponownie wykorzystywanych zasobów materiałowych. Przesądza o tym lepsze wyposażenie techniczne służb naprawczych dużych przedsiębiorstw. Dlatego wskazane jest tworzenie specjalnych miejsc i usług restauracyjnych w dużych przedsiębiorstwach. Potrzebujemy wyspecjalizowanych fabryk, które odrestaurują i wzmocnią zużyte części. Można je umieszczać w małych miasteczkach i osiedlach robotniczych, które straciły już na znaczeniu i mają bezrobotną populację. Opłata będzie mały, a wiele części odrestaurowanych w nowoczesny sposób, taniej o 70-80%. Wskazane jest łączenie takich wyspecjalizowanych przedsiębiorstw w firmy produkcyjne. Odbiorem części zużytych i wydawaniem części regenerowanych mogą zajmować się małe hurtownie podległe bezpośrednio firmom produkcyjnym. W ten sposób można zaoszczędzić setki tysięcy ton metalu rocznie.
Analizując problemy organizacji i ekonomiki gospodarki naprawczej w kraju, nie należy dopuszczać do ich rozwiązania stereotypowego podejścia. Dla dużych przedsiębiorstw stowarzyszenia produkcyjne w jeden sposób rozwiązywane są problemy gospodarki naprawczej, a dla małych i średnich w inny sposób. Podejmowane decyzje powinny zapewnić wzrost wydajności głównej produkcji, do której obsługi powołana jest służba remontowa przedsiębiorstwa.
Analiza obiektów utrzymania ruchu UE „Polymerprom” ma na celu zidentyfikowanie osiągnięć i niedociągnięć w tym zakresie, nakreślenie sposobów eliminacji niedociągnięć oraz działań usprawniających system PPR w zakładzie.
Główne kierunki usprawnienia zaplecza remontowego UE „Polymerprom” to:
1. Organizacja scentralizowanej specjalistycznej naprawy sprzętu. Ten warunek jest możliwy, jeśli istnieje centrum serwisowe dostawcy sprzętu, ponieważ ponad 70% sprzętu jest wyprodukowane za granicą.
2. Organizacja specjalistycznej produkcji części zamiennych do urządzeń. Wydaje się możliwe, w celu obniżenia kosztów wytwarzania części zamiennych do urządzeń i poprawy ich jakości, przeprowadzenie poszukiwania w drodze przetargu wytwórcy (producentów) spośród zakładów obrabiarek i remontów, które są w stanie wyprodukować asortyment części niezbędnych do naprawy.
3. Dalsze doskonalenie w przedsiębiorstwie systemu konserwacji prewencyjnej sprzętu, który zapewni jasny nadzór i terminową konserwację prewencyjną sprzętu, co z kolei zwiększy jego wydajność, wydłuży okresy remontów.
4. Poprawa technicznego przygotowania napraw, w tym opracowanie standardu procesy technologiczne a także wsparcie materialne.
Ze względu na niewielkie rozmiary przedsiębiorstwa, serwis naprawczy UE „Polymerprom” ma również ograniczone rozmiary. Dlatego słuszne wydaje się posiadanie w przedsiębiorstwie działającego scentralizowanego serwisu naprawczego, który wykonuje wszystkie funkcje serwisowania i naprawy sprzętu.
W stosunku do pracowników serwisu stosowany jest czasowo-premiowy system wynagradzania. Ta forma wynagrodzenia nie jest wystarczająco skuteczna. Bardzo efektywna forma wynagrodzenie jest umowną formą wynagrodzenia z ustaleniem wysokości dodatków i premii, uzależnionych od występowania awarii sprzętu z winy pracownika serwisu naprawczego, a także od wystąpienia reklamacji na działanie sprzętu z szefowie sekcji.
W celu podniesienia efektywności serwisu naprawczego celowe wydaje się zastosowanie w przedsiębiorstwie zautomatyzowanego systemu zarządzania serwisem naprawczym.
Niezbędne jest także szerokie wykorzystanie wytycznych i zaleceń o charakterze krajowym, opracowań i propozycji organizacji badawczych i projektowych.
Zautomatyzowany system zarządzania serwisem naprawczym jest funkcjonalnym podsystemem zarządzania, gdzie przy odpowiednim podziale organizacyjno-administracyjnym, głównym ośrodkiem koordynującym i niezbędnym ogniwem w zintegrowany system zarządzanie przedsiębiorstwem. Wprowadzenie tego podsystemu umożliwia, poprzez wykorzystanie komputerów i metody matematyczne określić optymalną strategię konserwacji i napraw sprzętu, optymalną koncentrację prac i koncentrację sprzętu dla warunków specjalistycznych prac naprawczych.
Przy pomocy zautomatyzowanego systemu zarządzania usługami naprawczymi konieczne jest stworzenie takiej organizacji naprawy i utrzymania parku maszynowego przedsiębiorstw, w której wykorzystanie zasobów pracy, zasobów materialnych i finansowych byłoby optymalne, a przestoje sprzętu byłyby być minimalne.
Na podstawie danych ankietowych pracy jednostek naprawczych opracowywany jest model ekonomiczny i organizacyjny zarządzania produkcją naprawczą, opracowywane są ujednolicone formularze dokumentów, budowany jest schemat przepływu pracy i opracowywany jest model relacji informacyjnych, metody ekonomiczne i matematyczne oraz dobierane i opracowywane są modele mechanizacji i automatyzacji obliczeń ekonomicznych, wymaganej liczby i składu środków technicznych. Model ekonomiczno-organizacyjny jest podstawą tworzonego remontowego podsystemu produkcji, określa zasady jego funkcjonowania i organizacyjne podstawy systemu zarządzania, a także uwzględnia potrzebę szerokiego rozwoju samonośnych relacji, więcej pełne wykorzystanie zasady zachęt finansowych.
Projektując zautomatyzowany system sterowania dla serwisu naprawczego, konieczne jest opracowanie połączonego zestawu prac w celu rozwiązania głównych problemów produkcji naprawczej. Ten zespół prac koncentruje się na tworzeniu podsystemów sterowania funkcjonalnego oraz podsystemów wspomagających niezbędnych do ich funkcjonowania.
Podsystemy funkcjonalne realizują funkcje zarządcze w zakresie organizacyjno-technicznego przygotowania produkcji remontowej, prognozowania i planowania długoterminowego, planowania technicznego, ekonomicznego i operacyjnego, rozliczania, raportowania i analizy działalności gospodarczej oraz monitorowania i regulowania pracy jednostek remontowych.
Podsystemy wspomagające to: ekonomiczno-organizacyjny, informacyjny, podsystem wsparcia matematyczno-technicznego. Główną funkcją podsystemów wspomagających jest przekształcenie wszystkich informacji krążących pomiędzy podsystemami funkcjonalnymi a wydziałami produkcyjnymi w celu opracowania akcji kontrolnej na wydziałach produkcyjnych głównego serwisu mechanicznego.
Opracowanie zautomatyzowanego systemu kontroli usług naprawczych UE „Polymerprom” powinno być prowadzone przez wyspecjalizowane organizacje z udziałem przedsiębiorstwa klienta lub przez przedsiębiorstwa, jeśli istnieje wystarczająca liczba specjalistów.
Przy projektowaniu podsystemu zautomatyzowanego systemu sterowania dla serwisu naprawczego konieczne jest Specjalna uwaga przejdź do następującej pracy:
1. Stworzenie zautomatyzowanego rozliczania dostępnej floty sprzętowej według sekcji i przedsiębiorstwa jako całości; wykorzystanie sprzętu produkcyjnego pod względem czasu i mocy; przestoje sprzętu rejestrującego w celu naprawy; awarie i awarie każdego elementu wyposażenia oraz poszczególnych jednostek, bloków, części; potrzeb, dostępności i przemieszczania części zamiennych dla istniejącego parku maszynowego.
Automatyzacja planowanych obliczeń w warunkach pracy nad systemem prewencyjnym opartym na wykorzystaniu nowoczesnej techniki komputerowej, zastosowanych metodach matematycznych oraz postępujących standardach kosztów materiałowych i robocizny.
Organizacja smarowania urządzeń regulowanych.
Ustalenie optymalnego terminu wymiany zużytego sprzętu w zależności od stopnia jego amortyzacji oraz niezbędnych kosztów utrzymania napraw.
Sukces zautomatyzowanego systemu zarządzania usługami naprawczymi zależy od tego, jak dokładnie i dokładnie zostaną wykonane następujące etapy prac: Postanowienia ogólne; przedprojektowa (diagnostyczna) kontrola pracy jednostek naprawczych; projekt techniczny; projekt roboczy; wdrożenie podsystemu.
Produkcja naprawcza charakteryzuje się szeregiem specyficznych cech, które utrudniają proces zarządzania i racjonalną organizację elementów konstrukcyjnych (jednostek naprawczych). Cechy te obejmują przede wszystkim niejednorodność prac naprawczych.
Ekonomicznemu uzasadnieniu możliwości wprowadzenia zautomatyzowanego systemu zarządzania usługami utrzymania ruchu powinna towarzyszyć kalkulacja efektywności ekonomicznej.
Warsztaty mechaniczne i warsztatowe usługi naprawcze powinny być jak najbardziej wyspecjalizowane, wyposażone w nowoczesny sprzęt, który pozwala na zastosowanie postępowej technologii, zaawansowanych form organizacji produkcji, środków mechanizacji i automatyzacji procesów produkcyjnych.
Funkcjonowanie ekip remontowych zapewnia prawidłowy podział pracy pomiędzy członków zespołu, efektywna organizacja stanowisk pracy, stosowanie postępowych metod organizacji napraw oraz przejrzysta organizacja utrzymania stanowisk pracy.
Istotną rezerwą na zmniejszenie kosztów napraw i przestojów sprzętu w naprawie jest wielokrotne używanie części.
Renowacja części pozwala osiągnąć zmniejszenie zużycia środków materialnych i finansowych podczas naprawy części nawet o 60-90%. Koszt części odnowionych to często 10-25% kosztu części nowej.
Wniosek
Wykonując prace naprawcze w przedsiębiorstwach przemysłowych, należy dążyć do maksymalnej koncentracji tego samego rodzaju pracy w niektórych obszarach produkcyjnych usług naprawczych. Muszą być tworzone i wyposażone w pełnej zgodności z przydzielonymi im zadaniami i zakresem pracy do wykonania.
Główne kierunki doskonalenia obsługi remontowej przedsiębiorstwa to:
Organizacja scentralizowanej specjalistycznej naprawy sprzętu;
Organizacja specjalistycznej produkcji części zamiennych do urządzeń;
Dalsze doskonalenie systemu konserwacji prewencyjnej sprzętu;
Usprawnienie przygotowania technicznego napraw, w tym opracowanie standardowych procesów technologicznych, a także wsparcie materiałowe prac naprawczych;
Poprawa planowania, w tym harmonogramowanie prac naprawczych.
Usprawnianiu organizacji zaplecza remontowego w przedsiębiorstwach dokonuje się w następujących obszarach.
Usługi remontowe przedsiębiorstwa powinny być jak najbardziej wyspecjalizowane, wyposażone w nowoczesne lub pozwalające na zastosowanie postępowej technologii, zaawansowane formy organizacji produkcji, środki mechanizacji i automatyzacji procesów produkcyjnych.
Najskuteczniejsze wykorzystanie wyspecjalizowanych ekip naprawczych. Jednocześnie wskazane jest tworzenie zintegrowanych zespołów, które wykonują całą konserwację i naprawy sprzętu w przydzielonym zespołowi miejscu produkcji.
Wśród postępowych metod naprawy na pierwszym miejscu znajdują się węzły. Istota metody polega na tym, że komponenty i mechanizmy wymagające naprawy są usuwane i zastępowane nowymi lub wstępnie naprawianymi. Zastosowanie tej metody pozwala zminimalizować przestoje sprzętu podczas napraw, poprawić jakość napraw oraz obniżyć koszty napraw dzięki możliwości najbardziej racjonalnej organizacji naprawy podzespołów i mechanizmów.
Istotną rezerwą na zmniejszenie kosztów napraw i przestojów sprzętu w naprawie jest również wielokrotne używanie części.
Lista wykorzystanej literatury:
1. Bakanov MI, Sherimet A.D. Teoria analizy ekonomicznej. – M.: Finanse i statystyka, 2011.
2. Latfullin, G.R. Teoria organizacji: podręcznik dla uniwersytetów / G. R. Latfullin, A. V. Raichenko - St. Petersburg: Peter, 2007.
3. Milner, B.Z. Teoria organizacji: podręcznik / B. Z. Milner- M .: INFRA-M, 2008.
4. Tertyshnik, Michaił Iwanowicz Ekonomia przedsiębiorstwa: instruktaż dla studentów uczelni instytucje edukacyjne studenci specjalności 080101 „Teoria ekonomii” (nr rej. 404 z 3 lipca 2009 r., Moskiewskie Państwowe Przedsiębiorstwo Unitarne) / M. I. Tertysznik; Stan Bajkał. Uniwersytet Ekonomii i Prawa. - wyd. 2 - Moskwa: INFRA-M, 2010.
5. Siergiejew I.V. Gospodarka przedsiębiorstwa. – M.: Finanse i statystyka, 2013.
6. Analiza działalności gospodarczej organizacji: podręcznik / pod sumą. wyd. D. A. Pankova, E. A. Golovkova. - wyd. 2, poprawione. - M.: Nowa wiedza, 2013.
7. Organizacja produkcji w przedsiębiorstwie (firmie): podręcznik. dodatek / red.: O. I. Volkov, O. V. Devyatkina - M .: INFRA-M, 2010.
8. Ekonomia przedsiębiorstwa: podręcznik. dla uczelni ekonomicznych. specjalista. / [W. Ya Gorfinkel i inni]; wyd. V. Ya Gorfinkel, V. A. Shvandar. - wyd. 4 - Moskwa: UNITY-DANA, 2014.
9. Ekonomia przedsiębiorstwa (w diagramach, tabelach, obliczeniach): podręcznik dla studentów studiujących na kierunku 521600 „Ekonomia” / V. K. Sklyarenko [i inni]; wyd. V.K. Sklyarenko, V.M. Prudnikova. - Moskwa: INFRA-M, 2010.
10. Ekonomia przedsiębiorstwa (firmy): podręcznik dla studentów wyższych uczelni studiujących ekonomię. specjalności / [O. I. Wołkow i inni]; wyd. O. I. Volkova, O. V. Devyatkina; Ros. gospodarka Acad. ich. G. W. Plechanow. - 3. ed., poprawione. i dodatkowe - Moskwa: INFRA-M, 2009.
3. Główne kierunki usprawnienia serwisu naprawczego i międzynaprawczego
3.1 Reorganizacja struktury zarządzania brygadami remontowymi sprzęt technologiczny
W celu jak najskuteczniejszego i najbardziej ekonomicznego wykonania zadań powierzonych służbie naprawczej przedsiębiorstwa konieczne jest opracowanie racjonalnej struktury i schematu zarządzania. Opracowując schemat zarządzania zakładami naprawczymi przedsiębiorstwa, należy wziąć pod uwagę istniejące nowoczesna technologia kierownictwo, ogólny styl pracy, a także szereg innych czynników, od których zależy organizacja zarządzania naprawami.
1. Ponieważ inicjatorami większości bieżących nieplanowych konserwacji sprzętu są pracownicy utrzymania ruchu, ich praca z góry determinuje określony sposób zarządzania zespołami, to znaczy nie wymaga bezpośredniego kierowania, a jedynie wymaga administracji (rozwiązanie ogólnego kwestie organizacyjne, rejestracja wykonanych czynności i wykonanych prac) oraz organizacja dostaw (części zamienne, podzespoły i materiały eksploatacyjne), co przesądza o nieskuteczności posiadania w strukturze trzech kierowników, których obowiązki są zasadniczo identyczne.
2. Niepełne obciążenie sprzętu podczas pracy na drugiej zmianie (średni współczynnik zmianowy sprzętu wynosi 1,45), sprowadza pracę personelu konserwacyjnego do trybu czuwania i wykonywanie nieistotnej części planowanych czynności konserwacyjnych sprzętu, co wynika z pracy większości usług pomocniczych (magazyny, część mechaniczna RMC ) przedsiębiorstw w trybie jednozmianowym, wszystko to sprawia, że obecność kierownika kontrolującego pracę drugiej zmiany zespołów jest nieracjonalna.
3. Wydzielenie odrębnych zintegrowanych zespołów na terenie przedsiębiorstwa powoduje, że nieoperacyjna komunikacja z menedżerami, których lokalizacja (w związku z wykonywaniem obowiązków służbowych) nie może być stała. Gdy konieczne staje się szybkie rozwiązanie problemów produkcyjnych, dochodzi do nieuzasadnionego przestoju sprzętu, co wynika z nieracjonalności podziału obowiązków pomiędzy szefa, brygadzistę i mechanika.
Powyższe niedociągnięcia w strukturalnej organizacji zarządzania centrum handlowym powodują konieczność reorganizacji i rewizji struktury zarządzania opisy stanowisk pracy niektórzy członkowie centrum handlowego. Zgodnie z tym, w celu zapewnienia bardziej racjonalnej organizacji zarządzania personelem naprawczym, konieczna jest reorganizacja struktury zarządzania:
1. Zlikwidować w strukturze zarządzania stanowisko mechanika i energetyka ośrodków technicznych wchodzących w skład CRiOK, których obowiązki są dublowane przez obowiązki zawodowe mechanika CRiOK i energetyka CRiOK.
2. Określ główny zakres odpowiedzialności mechanika sprzętu - bezpośredni nadzór mechaników i elektryków w zakresie konserwacji sprzętu elektrycznego, organizacji produkcji części zamiennych i produkcji mechanicznych prac naprawczych.
Szereg realizowanych działań pozwala na racjonalne rozłożenie odpowiedzialności pomiędzy uczestników struktury zarządzania produkcją remontową, co pozwala na:
1. Uprość strukturę podporządkowania niektórych kategorii personelu naprawczego, poprawiając w ten sposób psychologiczny mikroklimat personelu centrum handlowego;
2. Skrócenie czasu nieplanowanych przestojów sprzętu poprzez przyspieszenie poszczególnych operacji naprawczych produkcji – produkcja części zamiennych, produkcja mechanicznych prac naprawczych.
3.2 Postępujące formy i metody naprawy
Stały wzrost kosztów napraw wymaga poszukiwania coraz bardziej postępowych form i metod naprawy sprzętu. Te formy i metody obejmują:
specjalizacja i centralizacja naprawy sprzętu;
ekspansja zaawansowanych metod naprawy;
wprowadzenie postępowej technologii prac naprawczych i ich mechanizacji;
poprawa organizacji pracy personelu naprawczego itp.
Najważniejszy kierunek należy uznać za wszechstronne rozszerzenie scentralizowanej formy organizowania napraw w oparciu o specjalizację prac naprawczych, czyli rozwój wyspecjalizowanych przedsiębiorstw naprawczych i scentralizowaną produkcję części zamiennych. Organizacja wyspecjalizowanych przedsiębiorstw stwarza warunki do: skuteczna aplikacja w produkcji naprawczej wysokowydajnych urządzeń i oprzyrządowania, zaawansowanych procesów technologicznych i metod pracy związanych z produkcją seryjną i in-line.
Centralizacja napraw może odbywać się w skali poszczególnych przedsiębiorstw, branż i Gospodarka narodowa ogólnie. W skali zakładu mogą powstać duże warsztaty naprawcze produkujące części zamienne i sprzęt remontowy.
W dużych warsztatach wskazane jest tworzenie wyspecjalizowanych zespołów do naprawy sprzętu jednomodelowego, standardowych jednostek różnego sprzętu.
W obecności duża liczba fabryk określonej branży w jednym regionie gospodarczym, wskazane jest utworzenie dużego zakładu naprawczego lub warsztatu o znaczeniu branżowym dla produkcji części zamiennych i pewne rodzaje naprawa. Centralizacja międzysektorowa jest wskazana w przypadku naprawy najbardziej masywnych modeli sprzętu przy użyciu floty wymiany sprzętu w branży obrabiarek. W takim przypadku naprawy powinny być przeprowadzane albo przez fabryki, które produkują ten sprzęt, albo przez specjalne fabryki.
Metody wykonywania prac naprawczych są różnorodne: węzłowe, sekwencyjno-węzłowe, „pod prąd”, standardowe itp.
Metoda węzłowa polega na wymianie zużytych jednostek jednostki na zapasowe, wcześniej wyprodukowane lub naprawione. Jednocześnie czas przestoju sprzętu jest znacznie skrócony, ponieważ większość prac naprawczych jest wykonywana przed oddaniem maszyny do naprawy.
Metodą sekwencyjno-węzłową zużytych jednostek nie naprawia się jednocześnie, ale sekwencyjnie, wykorzystując przerwy w pracy jednostek. Ta metoda służy do naprawy sprzętu, który ma konstrukcyjnie oddzielne jednostki (maszyny agregujące).
Metoda „pod prąd” służy do naprawy zautomatyzowanych linii przepływowych i wymaga poważnych Praca przygotowawcza.
Najczęściej sprzęt tych linii jest naprawiany jednocześnie z wyłączeniem linii lub w oddzielnych odcinkach przy powszechnym stosowaniu metod węzłowych.
Niezbędnym warunkiem specjalizacji remontowej jest doskonalenie struktury parku maszynowego poprzez zmniejszenie liczby standardowych rozmiarów i modeli podstawowych maszyn i zespołów produkowanych w przemyśle obrabiarkowym i zakładach budowy maszyn.
Szerokie zastosowanie standardowe komponenty i części w branży obrabiarek pozwalają na kilkukrotne zmniejszenie zapotrzebowania na części zamienne i czas trwania prac naprawczych.
Nowy sprzęt musi spełniać wszystkie wymagania dotyczące łatwości konserwacji i wysokiej niezawodności działania (łatwość demontażu i montażu, przegląd i regulacja, trwałość współpracujących części itp.). Cała dokumentacja techniczna dotycząca naprawy nowego sprzętu jest dostarczana przez producentów.
Wyposażanie zakładów budowy maszyn w obrabiarki produkowane seryjnie, w połączeniu z powszechną standaryzacją zarówno w budowie maszyn, jak iw produkcji naprawczej, pozwoli na wyodrębnienie naprawy jako samodzielnej, wyspecjalizowanej gałęzi produkcji maszynowej.
Rozwiązaniem tego problemu jest sprowadzenie naprawy głównej do operacji wymiany części, podzespołów i zespołów, co w istocie jest specjalizacją naprawy na poziomie indywidualnym.
Uprzemysłowienie naprawy urządzeń zapewnia zbliżenie poziomu organizacyjnego, technicznego i ekonomicznego remontu do poziomu wytwarzania nowych obrabiarek w przemyśle obrabiarkowym.
WNIOSEK
Gospodarka remontowa jest jednym z najważniejszych ogniw w konstrukcji przedsiębiorstwo produkcyjne, ponieważ efektywność jego pracy w dużej mierze determinuje koszt produktów, ich jakość i wydajność pracy w przedsiębiorstwie.
Aby rozwiązać problemy związane z organizacją zakładu naprawczego, przedsiębiorstwa opracowują i stosują systemy konserwacji i naprawy urządzeń technologicznych, które opierają się na zasadzie aktualnej Utrzymanie i planowana konserwacja zapobiegawcza sprzętu. Jednak specyfika eksploatacji sprzętu i struktura obiektów naprawczych przedsiębiorstwa często wymagają rewizji przyjętych systemów obsługi urządzeń technologicznych w celu ich racjonalizacji i uwzględnienia warunków ekonomicznych, które rozwinęły się w przedsiębiorstwie.
Rozpatrzenie zagadnień leżących u podstaw budowy systemu utrzymania ruchu urządzeń w przedsiębiorstwie inżynierii mechanicznej oraz analiza organizacji i działalności zakładu remontowego, a także znalezienie sposobów jego doskonalenia. W związku z tym pojawiają się następujące pytania:
Organizacja planowych napraw i rutynowej konserwacji sprzętu dla przedsiębiorstwo budowy maszyn, analizę ich skuteczności, a także usprawnienie organizacji planowych napraw prewencyjnych z wykorzystaniem zgromadzonych informacji statystycznych o liczbie i charakterze przestojów serwisowanych urządzeń;
Badanie cech zarządzania personelem naprawczym, analizowanie i znajdowanie sposobów na zwiększenie efektywności przyjętej struktury zarządzania naprawami;
Organizacja warsztatów naprawczych w Remservis LLC ma szereg cech, które obejmują:
Organizacja produkcji naprawczej realizowana jest w oparciu o ulepszone ujednolicony system PPR, zapisane w Regulaminie PPR.
Konserwacja sprzętu odbywa się zgodnie z STP przyjętym w przedsiębiorstwie zgodnie z miesięcznymi planami-harmonogramami PPR wydawanymi przez PGM.
Konserwacja i naprawy planowe sprzętu high-tech są wykonywane przez kilka zintegrowanych zespołów naprawczych, a duża złożoność sprzętu wymaga wysoko wykwalifikowanego personelu naprawczego.
Inicjatorami większości bieżących nieplanowanych prac utrzymaniowych są pracownicy utrzymania ruchu, więc ich praca z góry determinuje określony sposób zarządzania zespołami i wymaga jedynie administracji.
Produkcja operacyjna części zamiennych przez siły warsztatu mechanicznego odbywa się na miejscu obróbka skrawaniem lub na zamówienie międzysklepowe sił głównych warsztatów mechanicznych.
W wyniku przeprowadzonej analizy systemu organizacji gospodarki remontowej w Remservice LLC zaproponowano przeprowadzenie szeregu działań usprawniających i racjonalizujących działalność służby remontowej:
zniesienia w strukturze zarządczej centrum handlowego stanowiska mechanika naprawy urządzeń, którego obowiązki są powielane przez obowiązki brygadzisty ds. napraw urządzeń centrum handlowego oraz mechanika Centralnego Ośrodka Krytycznego i Ochrony Środowiska,
Głównymi czynnikami oszczędności z realizacji działań na rzecz poprawy technologii i organizacji napraw jest zmniejszenie pracochłonności prac remontowych, skrócenie przestojów sprzętu w naprawach, a także poprawa jakości naprawy sprzętu. Dlatego głównymi wskaźnikami oceny wykonania usługi naprawczej są: środek ciężkości prace planowe w łącznym wolumenie wykonanych i ilości przestojów sprzętu w nieplanowanych naprawach.
Obliczenie wskaźników oceny działań serwisu naprawczego pokazuje, że:
Wprowadzenie środków usprawniających organizację utrzymania, pozwala na zwiększenie proporcji planowanych prac.
Wraz z poprawą wykonania usługi naprawczej wdrożenie proponowanych środków doprowadzi do efektu poprawy jakości napraw, co można określić poprzez warunkową ilość wydanego sprzętu, co również wskazuje na racjonalność propozycji.
Stosowanie coraz bardziej postępowych form organizacji i systemów utrzymania sprzętu pozwala nie tylko usprawnić pracę złożonych ekip remontowych, ale także zracjonalizować wycofywanie sprzętu do napraw planowych, a tym samym:
Skróć przestoje sprzętu;
Ze względu na terminowe planowanie indywidualnych środków naprawy i konserwacji sprzętu, zmniejsz pracochłonność prac naprawczych;
Eliminując nieracjonalne i nieterminowo zaplanowane naprawy, zmniejsz koszty konserwacji;
Dzięki szybkiemu wprowadzaniu poprawek i zmian w harmonogramach PPR, a tym samym planowaniu nadchodzących kosztów materiałowych i robocizny na prace naprawcze, skracamy czas realizacji i podnoszą jakość napraw.
Bibliografia
1. Fatkhutdinov R.A. Organizacja produkcji. Moskwa: Infra-M 2000
2. Organizacja i planowanie produkcji inżynierskiej, wyd. MI. Ipatowa. M.: Szkoła podyplomowa 1998
3. www.retail.ru - elektroniczny tygodnik „DETAIL”
4. Wasiliew W.N. „Organizacja produkcji w warunkach rynkowych” Mashinostroenie, 99
5. Makarenko M.V., Makhalin O.M., "Zarządzanie produkcją": Proc. Korzyść. Dla uczelni - M.: Wydawnictwo "PRIOR", 1998
6. Fatkhudinov R.A. „Organizacja produkcji”: podręcznik INFRA-M. 2001
Złożona lub lokalna; strategiczne, taktyczne (z reguły roczne) lub operacyjne. Powszechnymi metodami organizacji prac planistycznych są metody sieciowe i konstrukcja operogramów. Rozważmy krótko te metody. Planowanie i zarządzanie siecią (SPU) to graficzno-analityczna metoda zarządzania procesami tworzenia (projektowania) dowolnych systemów. Schemat sieci - ...
otrzymane podczas praktyka przemysłowa, nabycie umiejętności samodzielnego opracowywania zagadnień organizacji i planowania obiektów elektrycznych przedsiębiorstwo przemysłowe. Zadanie Praca semestralna– zapewnienie organizacji, planowania i zarządzania obiektami elektrycznymi przedsiębiorstwa przemysłowego. Jako obiekt do zajęć kursowych dowolny warsztatowy sprzęt elektryczny przemysłowego ...
Nadając im właściwości elektroizolacyjne. Jak widać, asortyment produkowanych przez firmę produktów jest dość szeroki. Prowadzi to do niezmiennie wysokiej sprzedaży wytwarzanych produktów. 2.2 Analiza organizacji zarządzania naprawami urządzeń technologicznych w UE „Polymerprom” Głównym zadaniem serwisu naprawczego UE „Polymerprom” jest zapewnienie stałej sprawności sprzętu i ...
Zapobieganie niepotrzebnym kosztom. W efekcie wzmacnia się ekonomia przedsiębiorstwa, zwiększa się efektywność jego działań. 2. Analiza działalności przedsiębiorstwa transportu samochodowego na przykładzie NPATP LLC 2.1 ogólna charakterystyka działalność przedsiębiorstwa W trakcie zapoznania się z głównymi dokumentami organizacyjnymi uzyskano następujące informacje o przedsiębiorstwie. Forma organizacyjno-prawna...
Zakłady naprawcze - zespół ogólnozakładowych i sklepowych działów, które wykonują zestaw środków do pielęgnacji i nadzoru stanu sprzętu, a także jego naprawy.
W skład zakładu naprawczego wchodzą warsztaty naprawcze, warsztatowe biura naprawcze oraz specjalistyczne magazyny do przechowywania części zamiennych itp. Ponadto w zapleczu remontowym znajduje się biuro konstrukcyjno-technologiczne wykonujące prace związane z naprawą, modernizacją i konserwacją urządzeń, biuro projektowo-produkcyjne zajmujące się planowaniem i ekspedycją prac oraz biuro utrzymania ruchu prewencyjnego.
Zadaniem ekonomii napraw jest zapobieganie przedwczesnemu zużyciu sprzętu i utrzymywanie go w stanie ciągłej gotowości eksploatacyjnej, minimalizacja przestojów sprzętu podczas remontów minimalny koszt, pod opieką i nadzorem jego pozycji.
Naprawa urządzeń technologicznych organizowana jest zgodnie z postanowieniami Zunifikowanego Systemu Planowej Obsługi Prewencyjnej (ESPR).
System PPR to zestaw planowanych środków technicznych i organizacyjnych dotyczących pielęgnacji, nadzoru i naprawy sprzętu. Jest to opieka i nadzór nad sprzętem podczas jego eksploatacji, tj. konserwacja remontowa, przeglądy okresowe i mycie, testy dokładności sprzętu; naprawy okresowe urządzeń (małe, średnie, duże). Kuchariew, ON. Organizacja i zarządzanie produkcją / O.N. Kukharev - Penza: RIO PGSKhA, 2007, - 82s.
Należy podkreślić, że szczególną uwagę w systemie PPR przywiązuje się do: środki zapobiegawcze. Pozwala to wydłużyć żywotność sprzętu, skrócić przestoje związane z awarią sprzętu oraz koszty związane z eksploatacją sprzętu. Ponadto znaczna część prac związanych z utrzymaniem remontowym jest przekazywana bezpośrednio pracownikom produkcyjnym, co zwiększa ich odpowiedzialność za stan sprzętu.
System PPR przewiduje ścisłą kolejność zmian czynności i ich realizację w ustalonych terminach. W harmonogramie napraw urządzeń, zgodnie z naukowymi normami, dla każdego urządzenia ustalane są terminy i skład kolejnych napraw. W przerwach między naprawami środki zapobiegawcze są przeprowadzane w tej samej ścisłej kolejności.
System PPR zapewnia kompleksowe przygotowanie do naprawy; przygotowywanie dokumentacji technicznej, materiałów, wykrojów, części zamiennych i zespołów; szkolenie baza naprawcza itp. Pozwala to zminimalizować przestoje sprzętu na naprawy i ogólne koszty naprawy.
Opracowanie harmonogramów i organizacji obsługi technicznej i nadzoru stanu urządzeń, które stanowią podstawę systemu PPR, przewidują zastosowanie ujednolicona klasyfikacja wszystkie organizacyjne i środki techniczne i specjalne przepisy.
Aby określić harmonogram prac naprawczych i czynności naprawczych, stosuje się podstawę regulacyjną PPR: normy dotyczące czasu trwania cykli remontowych, ich struktury, czasu trwania planowanych przestojów naprawianych urządzeń.
Czas trwania cyklu remontu (przedział czasu między uruchomieniem nowego sprzętu a pierwszym remontem generalnym lub odstęp czasu między dwoma kolejnymi remonty) określa się na podstawie żywotności głównych części, zespołów i mechanizmów. Kolejność naprzemiennych prac naprawczych i przeglądów podczas cyklu remontowego jest ustalana w zależności od żywotności głównych części, które mają zostać wymienione podczas danej naprawy.
System PPR przewiduje użycie określonej jednostki do pomiaru złożoności naprawy sprzętu - jednostki naprawczej. Każdemu modelowi sprzętu przypisana jest pewna kategoria złożoności naprawy, jest ona określana w zależności od projektu i cechy technologiczne ten sprzęt. Normy dotyczące ilości prac naprawczych, przestojów, zużycia materiałów itp. są ustalane na jednostkę złożoności naprawy, co znacznie upraszcza planowane obliczenia. Mosiądz AA Podstawy zarządzania. - M.: Ekoperspektiva, 2006. - 239 s.
Normy pracochłonności napraw ustalane są dla urządzeń technologicznych i przeładunkowych, urządzeń elektrycznych i elektroenergetycznych. Rozróżnia się je ze względu na rodzaje czynności naprawczych, naprawy oraz charakter pracy (ślusarz, obrabiarka i inne).
Normy przestojów są ustalane dla określonych warunków (skład ekipy remontowej, technologia naprawy, warunki organizacyjno-techniczne itp.) i są zróżnicowane dla urządzeń produkcyjnych niezautomatyzowanych i wycofania urządzeń do naprawy według sekcji. Są instalowane dla różnego rodzaju remonty i czynności naprawcze oraz różne prace zmianowe ekip remontowych.
Wskaźniki zużycia materiałów podczas naprawy sprzętu są określane metodą obliczeniową. Dla stali węglowych i stopowych, odlewów staliwnych, kształtowników konstrukcyjnych, metali nieżelaznych itp. ustalane są jednolite normy zużycia materiałów do naprawy sprzętu.
Dla surowych i unikalny sprzęt oraz specjalny sprzęt fabryki zegarków i instrumentów. Baza normatywna PPR podlega systematycznemu monitorowaniu i dostosowaniu w kierunku redukcji aktualne przepisy poprzez wprowadzenie środków organizacyjnych i technicznych. System PPR ustanowił również standardy konserwacji remontowej. Zakres prac związanych z utrzymaniem remontowym nie może być dokładnie uregulowany i określony. W związku z tym liczbę pracowników naprawczych (operatorów maszyn, mechaników, olejarzy) określa się zgodnie ze standardami obsługi ustalonymi empirycznie.
Techniczne przygotowanie naprawy obejmuje opracowanie technologii naprawy różne modele sprzęt, procesy technologiczne wytwarzania części wymiennych, naprawa i renowacja części i zespołów, projektowanie urządzeń technologicznych.
Podstawowy dokumentacja techniczna wykorzystywane w organizacji napraw to: albumy rysunków części zamiennych, zespołów i mechanizmów, projekty modernizacji sprzętu, a także paszporty i instrukcje konserwacji i eksploatacji sprzętu.
Zeszyty rysunków do części zamiennych są używane na przykład w planowaniu wymagań i produkcji części zamiennych; opracowanie technologii wytwarzania, naprawa i renowacja części zamiennych; prowadzenie prac nad normalizacją i unifikacją; tworzenie floty części zamiennych; wprowadzenie zamienników itp.
Prawie cała dokumentacja zwykle pochodzi od producentów sprzętu. Zakłady obsługujące sprzęt uzupełniają archiwum techniczne tylko w przypadku braku takiej lub innej dokumentacji lub korekty oryginalnej dokumentacji.
Doświadczenie pokazuje, że około 80% wszystkich prac naprawczych jest stałych i takich samych dla sprzętu tego samego modelu, tego samego typu naprawy. W tych warunkach standardowy proces technologiczny naprawy sprzętu jednomodelowego może stać się głównym dokumentem technologicznym.
W przypadkach, gdy operacje naprawcze są podobne pod względem treści do odpowiednich operacji wykonywanych przy produkcji nowego sprzętu, zadaniem jest maksymalne wykorzystanie postępowej technologii produkcji głównej w naprawie sprzętu. Im wyższy stopień koncentracji tego samego rodzaju prac naprawczych, tym wyższa skuteczność wprowadzenia zaawansowanej technologii. Jeśli chodzi o konkretne prace naprawcze, doskonalenie technologii ich realizacji następuje ścieżką maksymalnej mechanizacji procesów, wielokrotnego użytkowania części (metalizacja, spawanie, zastosowanie metody napraw gabarytów itp.), powszechne stosowanie zamienniki metali, wysokowydajny sprzęt, zwiększenie wyposażenia procesów technologicznych, wprowadzenie operacji zwiększających odporność na zużycie części itp.
Wsparcie materialne naprawy polega na terminowym przygotowaniu wszystkich niezbędne materiały, części zamienne, zespoły i mechanizmy oraz tworzenie floty części zamiennych. Zapotrzebowanie na materiały, półprodukty, zakupione produkty, zakupione części zamienne i zespoły oblicza się na podstawie wskaźników zużycia i zapasów, w oparciu o ilość prac naprawczych.
Terminowe dostawy materiałów, półproduktów, produkt końcowy a części zamienne są dostarczane przez dział zaopatrzenia, biorąc pod uwagę termin wycofania sprzętu do naprawy, określony w harmonogramie.
Ważną kwestią w organizacji naprawy sprzętu jest tworzenie i regulacja floty części zamiennych. Części zamienne to części zamienne, które są ekonomicznie opłacalne w magazynie, utrzymywane na ściśle określonym poziomie.
Zakres floty części zamiennych z reguły obejmuje: części zużywające się o żywotności krótszej niż okres remontu; części o żywotności przekraczającej okres remontu, ale wymagane w duże ilości(identyczne części wchodzące w skład wyposażenia jednego lub różne modele); duże, skomplikowane i pracochłonne części wykonane z odkuwek (odlewów) pozyskiwanych z zewnątrz; części zamienne do wysoce precyzyjnych, unikalnych i limitujących urządzeń produkcyjnych; wymienne części linii automatycznych; części ulegające nagłym awariom (części bezpieczników itp.).
Monitorowanie stanu floty części zamiennych można przeprowadzić wykorzystując wskaźnik rotacji floty części zamiennych.
Spadek wskaźnika rotacji do 0,3 i poniżej to sygnał o konieczności zrewidowania struktury floty części zamiennych. Maksymalna ilość zapasów z reguły nie powinna przekraczać trzytygodniowego wymogu. . Vikhansky OS Zarządzanie strategiczne. - M.: Gardariki, 2002r. - 292 s.