Korozja w kotle. Korozja i erozja w kotłach średnio- i niskociśnieniowych od strony paleniska. Zjawiska korozyjne w kotłach pojawiają się najczęściej na wewnętrznej powierzchni naprężonej cieplnie, a stosunkowo rzadziej na zewnętrznej.
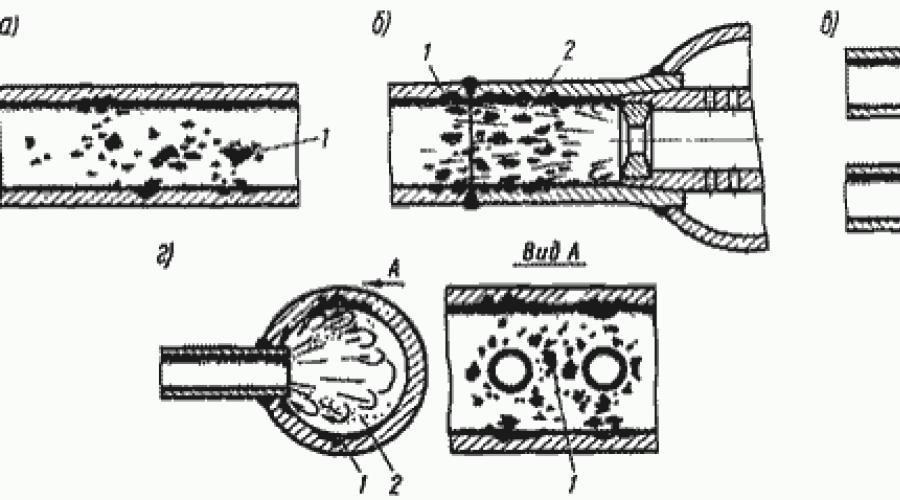
Przeczytaj także
Ta korozja pod względem wielkości i intensywności jest często bardziej znacząca i niebezpieczna niż korozja kotłów podczas ich eksploatacji.
Podczas pozostawiania wody w systemach, w zależności od jej temperatury i dostępu powietrza, może wystąpić wiele różnych przypadków korozji parkingowej. Przede wszystkim należy zauważyć skrajną niepożądaną obecność wody w rurach jednostek, gdy znajdują się one w rezerwie.
Jeśli woda pozostaje w układzie z tego czy innego powodu, może wystąpić poważna korozja parkingowa w parze, a zwłaszcza w przestrzeni wodnej zbiornika (głównie wzdłuż linii wodnej) o temperaturze wody 60-70 ° C. Dlatego w praktyce dość często obserwuje się korozję parkingową o różnej intensywności, pomimo tych samych trybów wyłączania systemu i jakości zawartej w nich wody; urządzenia o znacznej akumulacji cieplnej podlegają silniejszej korozji niż urządzenia o wymiarach paleniska i powierzchni grzewczej, ponieważ woda kotłowa w nich stygnie szybciej; jego temperatura spada poniżej 60-70°C.
Przy temperaturze wody powyżej 85-90°C (na przykład podczas krótkotrwałych przestojów aparatu) ogólna korozja maleje, a korozja metalu przestrzeni parowej, w której obserwuje się w tym przypadku zwiększoną kondensację pary , może przekroczyć korozję metalu przestrzeni wodnej. Korozja parkingowa w przestrzeni parowej jest we wszystkich przypadkach bardziej równomierna niż w przestrzeni wodnej kotła.
Rozwój korozji postojowej jest znacznie ułatwiony przez szlam gromadzący się na powierzchniach kotła, który zwykle zatrzymuje wilgoć. W związku z tym znaczne dziury korozyjne często znajdują się w agregatach i rurach wzdłuż dolnej tworzącej i na ich końcach, tj. w miejscach największego nagromadzenia szlamu.
Metody konserwacji sprzętu w rezerwie
Do konserwacji sprzętu można zastosować następujące metody:
a) suszenie - usuwanie wody i wilgoci z kruszyw;
b) napełnianie ich roztworami sody kaustycznej, fosforanu, krzemianu, azotynu sodu, hydrazyny;
c) napełnienie układu technologicznego azotem.
Sposób konserwacji należy dobrać w zależności od charakteru i czasu przestoju, a także rodzaju i cech konstrukcyjnych sprzętu.
Przestoje sprzętu można podzielić na dwie grupy ze względu na czas trwania: krótkoterminowy – nie dłuższy niż 3 dni i długoterminowy – dłuższy niż 3 dni.
Istnieją dwa rodzaje krótkotrwałych przestojów:
a) planowane, związane z wycofaniem do rezerwy w weekendy z powodu spadku obciążenia lub wycofaniem do rezerwy w nocy;
b) wymuszone – spowodowane awarią rur lub uszkodzeniem innych elementów wyposażenia, których usunięcie nie wymaga dłuższego postoju.
W zależności od przeznaczenia długotrwałe przestoje można podzielić na następujące grupy: a) oddanie sprzętu do rezerwy; b) bieżące naprawy; c) remonty kapitalne.
W przypadku krótkotrwałego przestoju urządzenia należy zastosować konserwację poprzez napełnianie wodą odgazowaną z zachowaniem nadciśnienia lub metodą gazową (azotową). Jeśli wymagane jest awaryjne wyłączenie, jedyną akceptowalną metodą jest konserwacja azotem.
W przypadku odstawienia systemu do rezerwy lub długotrwałego przestoju bez prac naprawczych, wskazane jest przeprowadzenie konserwacji poprzez napełnienie go roztworem azotynu lub krzemianu sodu. W takich przypadkach można również zastosować konserwację azotu, koniecznie podejmując działania w celu stworzenia szczelności systemu, aby zapobiec nadmiernemu zużyciu gazu i bezproduktywnej pracy instalacji azotowej, a także stworzyć bezpieczne warunki konserwacji urządzeń.
Metody konserwacji poprzez wytworzenie nadciśnienia, napełnianie azotem można stosować niezależnie od cech konstrukcyjnych powierzchni grzewczych urządzenia.
Aby zapobiec korozji parkingowej metalu podczas remontów głównych i bieżących, stosuje się wyłącznie metody konserwacji, które pozwalają na wytworzenie na powierzchni metalu warstwy ochronnej, która zachowuje swoje właściwości przez co najmniej 1–2 miesiące po spuszczeniu roztworu konserwującego, od momentu opróżnienia i rozhermetyzowania system są nieuniknione. Czas trwania filmu ochronnego na powierzchni metalu po obróbce azotynem sodu może osiągnąć 3 miesiące.
Metody konserwacji z użyciem roztworów wody i odczynników są praktycznie niedopuszczalne do ochrony przed korozją postojową przegrzewaczy pośrednich kotłów ze względu na trudności związane z ich napełnieniem i późniejszym czyszczeniem.
Metody konserwacji kotłów gorącej wody i kotłów parowych niskociśnieniowych oraz innych urządzeń zamkniętych obiegów technologicznych zaopatrzenia w ciepło i wodę różnią się pod wieloma względami od obecnie stosowanych metod zapobiegania korozji parkingowej w elektrociepłowniach. Poniżej opisano główne metody zapobiegania korozji w trybie jałowym wyposażenia aparatów takich układów obiegowych, biorąc pod uwagę specyfikę ich działania.
Uproszczone metody konserwacji
Te metody są przydatne w przypadku małych kotłów. Polegają na całkowitym usunięciu wody z kotłów i umieszczeniu w nich środka osuszającego: prażony chlorek wapnia, wapno palone, żel krzemionkowy w ilości 1-2 kg na 1 m3 objętości.
Ta metoda konserwacji jest odpowiednia w temperaturach pokojowych poniżej i powyżej zera. W pomieszczeniach ogrzewanych zimą można zastosować jeden z kontaktowych sposobów konserwacji. Sprowadza się to do wypełnienia całej wewnętrznej objętości urządzenia roztworem alkalicznym (NaOH, Na 3 P0 4 itp.), co zapewnia pełną stabilność warstwy ochronnej na powierzchni metalu nawet w przypadku nasycenia cieczy tlenem.
Zwykle stosuje się roztwory zawierające od 1,5-2 do 10 kg/m 3 NaOH lub 5-20 kg/m 3 Na 3 P0 4 w zależności od zawartości soli obojętnych w wodzie źródłowej. Mniejsze wartości odnoszą się do kondensatu, większe do wody zawierającej do 3000 mg/l soli obojętnych.
Korozji można również zapobiegać metodą nadciśnieniową, w której ciśnienie pary w zatrzymanej jednostce jest stale utrzymywane na poziomie powyżej ciśnienia atmosferycznego, a temperatura wody utrzymuje się powyżej 100°C, co uniemożliwia dostęp głównego czynnika korozyjnego, tlenu .
Ważnym warunkiem skuteczności i ekonomiczności każdej metody ochrony jest maksymalna możliwa szczelność armatury parowo-wodnej w celu uniknięcia zbyt szybkiego spadku ciśnienia, utraty roztworu ochronnego (lub gazu) lub wnikania wilgoci. Ponadto w wielu przypadkach przydatne jest wstępne oczyszczenie powierzchni z różnych osadów (soli, szlamu, kamienia).
Przy wdrażaniu różnych metod ochrony przed korozją parkingową należy pamiętać o następujących kwestiach.
1. W przypadku wszystkich rodzajów konserwacji konieczne jest wstępne usunięcie (przemycie) osadów łatwo rozpuszczalnych soli (patrz wyżej) w celu uniknięcia zwiększonej korozji parkingowej w niektórych obszarach zabezpieczanej jednostki. Wykonanie tego środka jest obowiązkowe podczas konserwacji stykowej, w przeciwnym razie możliwa jest intensywna miejscowa korozja.
2. Z podobnych powodów przed długotrwałą konserwacją pożądane jest usunięcie wszelkiego rodzaju osadów nierozpuszczalnych (szlam, kamień, tlenki żelaza).
3. W przypadku zawodności osprzętu konieczne jest odłączenie urządzenia rezerwowego od jednostek operacyjnych za pomocą wtyczek.
Wyciek pary i wody jest mniej niebezpieczny przy zachowaniu kontaktu, ale jest niedopuszczalny w przypadku suchych i gazowych metod ochrony.
Wybór desykantów jest determinowany względną dostępnością odczynnika i celowością uzyskania najwyższej możliwej wilgotności właściwej. Najlepszym środkiem osuszającym jest granulowany chlorek wapnia. Wapno palone jest znacznie gorsze od chlorku wapnia, nie tylko ze względu na niższą pojemność wilgoci, ale również ze względu na szybką utratę jego aktywności. Wapno absorbuje nie tylko wilgoć z powietrza, ale również dwutlenek węgla, dzięki czemu pokryta jest warstwą węglanu wapnia, co zapobiega dalszemu wchłanianiu wilgoci.
Strona morska Rosja nr 05.10.2016 Utworzono: 05.10.2016 Zaktualizowano: 05.10.2016 Wyświetleń: 5363Rodzaje korozji. Podczas eksploatacji elementy kotła parowego narażone są na działanie agresywnych mediów - wody, pary i spalin. Rozróżnij korozję chemiczną i elektrochemiczną.
Korozja chemiczna, wywołany parą wodną lub wodą, niszczy metal równomiernie na całej powierzchni. Szybkość takiej korozji w nowoczesnych kotłach morskich jest niska. Bardziej niebezpieczna jest miejscowa korozja chemiczna wywołana agresywnymi związkami chemicznymi zawartymi w osadach popiołu (tlenki siarki, wanadu itp.).
Najczęstszym i najbardziej niebezpiecznym jest korozja elektrochemiczna, płynący w wodnych roztworach elektrolitów w momencie wystąpienia prądu elektrycznego, spowodowany różnicą potencjałów pomiędzy poszczególnymi odcinkami metalu, różniącymi się niejednorodnością chemiczną, temperaturą lub jakością obróbki.
Rolę elektrolitu pełni woda (z korozją wewnętrzną) lub skondensowana para wodna w osadach (z korozją zewnętrzną).
Występowanie takich par mikrogalwanicznych na powierzchni rur powoduje, że jon-atomy metalu przechodzą do wody w postaci jonów naładowanych dodatnio, a powierzchnia rury w tym miejscu uzyskuje ładunek ujemny. Jeżeli różnica potencjałów takich par mikrogalwanicznych jest nieznaczna, to na granicy metal-woda stopniowo tworzy się podwójna warstwa elektryczna, co spowalnia dalszy przebieg procesu.
Jednak w większości przypadków potencjały poszczególnych sekcji są różne, co powoduje pojawienie się pola elektromagnetycznego skierowanego z większego potencjału (anody) na mniejszy (katoda).
W tym przypadku jony metali - atomy przechodzą z anody do wody, a nadmiar elektronów gromadzi się na katodzie. W rezultacie znacznie zmniejsza się pole elektromagnetyczne, a w konsekwencji intensywność procesu niszczenia metalu.
Zjawisko to nazywamy polaryzacją. Jeżeli potencjał anodowy zmniejszy się w wyniku powstania ochronnej warstwy tlenkowej lub wzrostu stężenia jonów metali w obszarze anodowym, a potencjał katodowy pozostaje praktycznie niezmieniony, wówczas polaryzację nazywamy anodową.
Przy polaryzacji katodowej w roztworze w pobliżu katody stężenie jonów i cząsteczek zdolnych do usuwania nadmiaru elektronów z powierzchni metalu gwałtownie spada. Z tego wynika, że głównym celem w walce z korozją elektrochemiczną jest stworzenie takich warunków, w których zachowane zostaną oba typy polaryzacji.
Osiągnięcie tego jest praktycznie niemożliwe, ponieważ woda kotłowa zawsze zawiera depolaryzatory - substancje powodujące zakłócenie procesów polaryzacyjnych.
Depolaryzatory zawierają cząsteczki O 2 i CO 2, jony H+, Cl- i SO-4, a także tlenki żelaza i miedzi. Rozpuszczone w wodzie CO 2 , Cl - i SO - 4 hamują tworzenie gęstej ochronnej warstwy tlenkowej na anodzie i tym samym przyczyniają się do intensywnego przebiegu procesów anodowych. Jony wodorowe H+ redukują ujemny ładunek katody.
Wpływ tlenu na szybkość korozji zaczął przejawiać się w dwóch przeciwnych kierunkach. Z jednej strony tlen przyspiesza proces korozji, gdyż jest silnym depolaryzatorem sekcji katodowych, z drugiej zaś działa pasywnie na powierzchnię.
Zazwyczaj części kotłów wykonane ze stali mają wystarczająco mocną początkową warstwę tlenku, która chroni materiał przed działaniem tlenu do czasu jego zniszczenia przez czynniki chemiczne lub mechaniczne.
Szybkość reakcji heterogenicznych (w tym korozji) regulowana jest intensywnością następujących procesów: doprowadzanie odczynników (przede wszystkim depolaryzatorów) na powierzchnię materiału; zniszczenie ochronnej warstwy tlenku; usuwanie produktów reakcji z miejsca jej wystąpienia.
Intensywność tych procesów jest w dużej mierze zdeterminowana czynnikami hydrodynamicznymi, mechanicznymi i termicznymi. Dlatego też działania mające na celu zmniejszenie stężenia agresywnych chemikaliów przy dużej intensywności pozostałych dwóch procesów, jak pokazują doświadczenia z eksploatacji kotłów, są zwykle nieskuteczne.
Wynika z tego, że rozwiązanie problemu zapobiegania uszkodzeniom korozyjnym powinno być złożone, gdy uwzględni się wszystkie czynniki wpływające na pierwotne przyczyny niszczenia materiałów.
Korozja elektrochemiczna
W zależności od miejsca przepływu i substancji biorących udział w reakcjach rozróżnia się następujące rodzaje korozji elektrochemicznej:
- tlen (i jego odmiana - parking),
- osad (czasami nazywany „skorupą”),
- międzykrystaliczny (kruchość alkaliczna stali kotłowych),
- gniazdo i
- siarkowy.
Korozja tlenowa obserwowane w ekonomizerach, armaturze, rurach zasilających i spustowych, kolektorach wodno-parowych oraz urządzeniach wewnątrzkolektorowych (osłony, rury, schładzacze itp.). Cewki obiegu wtórnego kotłów dwuobwodowych, wykorzystujących kotły i parowe nagrzewnice powietrza są szczególnie podatne na korozję tlenową. Korozja tlenowa zachodzi podczas pracy kotłów i zależy od stężenia tlenu rozpuszczonego w wodzie kotłowej.
Szybkość korozji tlenowej w głównych kotłach jest niska ze względu na wydajną pracę odgazowywaczy i reżim wody fosforanowo-azotanowej. W pomocniczych kotłach wodnorurowych często dochodzi do 0,5 – 1 mm/rok, choć średnio mieści się w przedziale 0,05 – 0,2 mm/rok. Charakter uszkodzeń stali kotłowych to małe wżery.
Bardziej niebezpiecznym rodzajem korozji tlenowej jest korozja parkingowa płynący w okresie bezczynności kotła. Ze względu na specyfikę działania wszystkie kotły okrętowe (zwłaszcza kotły pomocnicze) podlegają intensywnej korozji postojowej. Z reguły korozja postojowa nie prowadzi do awarii kotła, jednak metal skorodowany podczas postojów, ceteris paribus, jest intensywniej niszczony podczas pracy kotła.
Główną przyczyną korozji parkingowej jest wnikanie tlenu do wody, gdy kocioł jest pełny, lub do warstewki wilgoci na powierzchni metalu, gdy kocioł jest suchy. Ważną rolę odgrywają zawarte w wodzie chlorki i NaOH oraz rozpuszczalne w wodzie złoża soli.
W przypadku obecności chlorków w wodzie nasila się równomierna korozja metalu, a jeśli zawiera ona niewielką ilość zasad (poniżej 100 mg/l) korozja lokalizowana. Aby uniknąć korozji parkingowej w temperaturze 20 - 25 °C, woda powinna zawierać do 200 mg/l NaOH.
Zewnętrzne oznaki korozji z udziałem tlenu: małe miejscowe owrzodzenia (ryc. 1, a), wypełnione brązowymi produktami korozji, które tworzą guzki nad wrzodami.
Usuwanie tlenu z wody zasilającej jest jednym z ważnych środków ograniczania korozji tlenowej. Od 1986 r. zawartość tlenu w wodzie zasilającej kotły okrętowe pomocnicze i ściekowe została ograniczona do 0,1 mg/l.
Jednak nawet przy takiej zawartości tlenu w wodzie zasilającej obserwuje się uszkodzenia korozyjne elementów kotła podczas eksploatacji, co wskazuje na dominujący wpływ procesów niszczenia warstewki tlenkowej i wymywania produktów reakcji z ognisk korozji. Najbardziej obrazowym przykładem ilustrującym wpływ tych procesów na uszkodzenia korozyjne jest zniszczenie wężownic eksploatacji kotłów z obiegiem wymuszonym.
Ryż. 1. Uszkodzenia spowodowane korozją tlenową
Uszkodzenia korozyjne w przypadku korozji tlenowej są one zwykle ściśle zlokalizowane: na wewnętrznej powierzchni sekcji wlotowych (patrz ryc. 1, a), w obszarze zakrętów (ryc. 1, b), na sekcjach wylotowych oraz w kolano wężownicy (patrz ryc. 1, c), a także w kolektorach parowo-wodnych kotłów utylizacyjnych (patrz ryc. 1, d). To właśnie w tych obszarach (2 - obszar kawitacji przyściennej) hydrodynamiczne właściwości przepływu stwarzają warunki do zniszczenia filmu tlenkowego i intensywnego wymywania produktów korozji.
Rzeczywiście, wszelkim deformacjom przepływu wody i mieszanki parowo-wodnej towarzyszy pojawienie się kawitacja w warstwach przyściennych rozszerzający się przepływ 2, gdzie powstające i natychmiast zapadające się pęcherzyki pary powodują zniszczenie warstewki tlenkowej pod wpływem energii mikrowstrząsów hydraulicznych.
Jest to również ułatwione dzięki naprzemiennym naprężeniom w folii, spowodowanym drganiami cewek oraz wahaniami temperatury i ciśnienia. Zwiększona lokalna turbulencja przepływu w tych obszarach powoduje aktywne wymywanie produktów korozji.
Na bezpośrednich odcinkach wylotowych wężownic warstewka tlenkowa ulega zniszczeniu w wyniku uderzeń o powierzchnię kropel wody podczas turbulentnych pulsacji przepływu mieszaniny para-woda, której rozproszony-pierścieniowy tryb ruchu przechodzi tutaj w rozproszony przy prędkość przepływu do 20-25 m/s.
W tych warunkach nawet niska zawartość tlenu (~0,1 mg/l) powoduje intensywne niszczenie metalu, co prowadzi do pojawienia się przetok na odcinkach wlotowych wężownic kotłów odzysknicowych typu La Mont po 2- 4 lata eksploatacji, aw pozostałych obszarach - po 6-12 latach.
Ryż. Rys. 2. Uszkodzenia korozyjne cewek ekonomizera kotłów utylizacyjnych KUP1500R statku motorowego „Indira Gandhi”.
Jako ilustrację powyższego rozważmy przyczyny uszkodzenia cewek ekonomizera dwóch kotłów utylizacyjnych typu KUP1500R zainstalowanych na nośniku zapalniczki Indira Gandhi (typu Alexey Kosygin), który wszedł do służby w październiku 1985 r. Już w lutym 1987 r. z powodu uszkodzenia wymieniono ekonomizery obu kotłów. Po 3 latach uszkodzenia wężownic pojawiają się również w tych ekonomizerach, zlokalizowanych w obszarach do 1-1,5 m od kolektora dolotowego. Charakter uszkodzenia wskazuje (rys. 2, a, b) typową korozję tlenową, po której następuje uszkodzenie zmęczeniowe (pęknięcia poprzeczne).
Jednak charakter zmęczenia w poszczególnych obszarach jest inny. Pojawienie się pęknięcia (i wcześniejsze pękanie warstwy tlenkowej) w obszarze spoiny (patrz ryc. 2, a) jest konsekwencją naprężeń przemiennych spowodowanych drganiami wiązki rur i cechą konstrukcyjną połączenie cewek z głowicą (koniec cewki o średnicy 22x3 jest przyspawany do zakrzywionej złączki o średnicy 22x2).
Zniszczenie warstwy tlenkowej i powstawanie pęknięć zmęczeniowych na wewnętrznej powierzchni prostych odcinków cewek, oddalonych od wlotu o 700-1000 mm (patrz ryc. 2, b), są spowodowane naprzemiennymi naprężeniami termicznymi, które występują podczas rozruchu kotła, gdy dostarczana jest zimna woda grzewcza. W tym przypadku działanie naprężeń termicznych jest wzmocnione przez fakt, że użebrowanie cewek utrudnia swobodne rozszerzanie się metalu rury, powodując dodatkowe naprężenia w metalu.
Korozja podszlamowa obserwowane zwykle w głównych kotłach wodnorurowych na wewnętrznych powierzchniach sita i rurach parowych wiązek dopływowych zwróconych w stronę pochodni. Istotą korozji podszlamowej są owalne wgłębienia o wielkości wzdłuż głównej osi (równolegle do osi rury) do 30-100 mm.
Na owrzodzeniach znajduje się gęsta warstwa tlenków w postaci „muszli” 3. Korozja podszlamowa zachodzi w obecności stałych depolaryzatorów – tlenków żelaza i miedzi 2, które osadzają się na najbardziej obciążonej cieplnie rurze przekroje w miejscach aktywnych ognisk korozji, które powstają podczas niszczenia filmów tlenkowych.
Na wierzchu tworzy się luźna warstwa kamienia i produktów korozji.
W przypadku kotłów pomocniczych ten rodzaj korozji nie jest typowy, ale przy dużych obciążeniach cieplnych i odpowiednich trybach uzdatniania wody nie wyklucza się pojawienia się korozji podszlamowej w tych kotłach.
Najbardziej aktywna korozja rur ekranowych objawia się w miejscach, w których gromadzą się zanieczyszczenia chłodziwa. Obejmuje to odcinki rur ściennych o dużym obciążeniu termicznym, w których następuje głębokie parowanie wody kotłowej (zwłaszcza jeśli na powierzchni parowania znajdują się porowate osady o niskiej przewodności cieplnej). Dlatego w związku z zapobieganiem uszkodzeniom rur osłonowych związanych z wewnętrzną korozją metalu należy uwzględnić potrzebę zintegrowanego podejścia, tj. wpływ zarówno na reżimy wodno-chemiczne, jak i piecowe.
Uszkodzenia rur ściennych mają głównie charakter mieszany, można je warunkowo podzielić na dwie grupy:
1) Uszkodzenia ze śladami przegrzania stali (odkształcenie i ścieńczenie ścianek rury w miejscu zniszczenia; obecność ziaren grafitu itp.).
2) Kruche pęknięcia bez charakterystycznych oznak przegrzania metalu.
Na wewnętrznej powierzchni wielu rur odnotowano znaczne osady o charakterze dwuwarstwowym: górna jest słabo związana, dolna jest łuszcząca się, ściśle związana z metalem. Grubość dolnej warstwy zgorzeliny wynosi 0,4-0,75 mm. W strefie uszkodzenia łuska na wewnętrznej powierzchni ulega zniszczeniu. W pobliżu miejsc zniszczenia i w pewnej odległości od nich na wewnętrzną powierzchnię rur wpływają wżery korozyjne i kruche mikrouszkodzenia.
Ogólny wygląd uszkodzeń wskazuje na termiczny charakter zniszczenia. Zmiany strukturalne na przedniej stronie rur - głęboka sferydyzacja i rozkład perlitu, powstawanie grafitu (przemiana węgla w grafit 45-85%) - wskazuje na przekroczenie nie tylko temperatury pracy sit, ale również dopuszczalnej dla stali 20500 °C. Obecność FeO potwierdza również wysoki poziom temperatur metalu podczas eksploatacji (powyżej 845 oK - tj. 572 oC).
Kruche uszkodzenia spowodowane przez wodór zwykle występują w obszarach o dużym przepływie ciepła, pod grubymi warstwami osadów oraz nachylonych lub poziomych rurach, a także w obszarach wymiany ciepła w pobliżu podkładek spawalniczych lub innych urządzeń, które uniemożliwiają swobodny przepływ przepływów. wykazali, że uszkodzenia wodorowe występują w kotłach pracujących pod ciśnieniem poniżej 1000 psi. cal (6,9 MPa).
Uszkodzenia wodorowe zwykle powodują pęknięcia o grubych krawędziach. Inne mechanizmy, które przyczyniają się do powstawania pęknięć o grubych krawędziach, to pękanie korozyjne naprężeniowe, zmęczenie korozyjne, pęknięcia naprężeniowe i (w niektórych rzadkich przypadkach) poważne przegrzanie. Wizualne odróżnienie uszkodzeń spowodowanych przez uszkodzenia wodorowe od innych rodzajów uszkodzeń może być trudne, ale niektóre ich cechy mogą w tym pomóc.
Na przykład uszkodzenie wodorowe prawie zawsze wiąże się z powstawaniem dziur w metalu (patrz środki ostrożności podane w rozdziałach 4 i 6). Inne rodzaje uszkodzeń (może z wyjątkiem zmęczenia korozyjnego, które często zaczyna się w poszczególnych powłokach) zwykle nie są związane z poważną korozją.
Awarie rur w wyniku uszkodzenia metalu wodorem często objawiają się powstaniem prostokątnego „okna” w ściance rury, co nie jest typowe dla innych rodzajów zniszczeń.
Przy ocenie podatności na uszkodzenia rur ekranowych należy wziąć pod uwagę, że metalurgiczna (początkowa) zawartość wodoru gazowego w stali perlitycznej (w tym st. 20) nie przekracza 0,5–1 cm3/100g. Gdy zawartość wodoru jest wyższa niż 4-5 cm3/100g, właściwości mechaniczne stali znacznie się pogarszają. W tym przypadku należy skupić się głównie na lokalnej zawartości wodoru resztkowego, ponieważ w przypadku kruchych pęknięć rur ekranowych gwałtowne pogorszenie właściwości metalu obserwuje się tylko w wąskiej strefie wzdłuż przekroju rury o niezmiennie zadowalającej strukturze i właściwościach mechanicznych sąsiedniego metalu w odległości zaledwie 0,2-2 mm.
Uzyskane wartości średnich stężeń wodoru na krawędzi zniszczenia są 5-10 razy wyższe od jego początkowej zawartości dla stacji 20, co nie mogło nie mieć istotnego wpływu na uszkodzenia rur.
Przedstawione wyniki wskazują, że kruchość wodorowa okazała się decydującym czynnikiem w uszkodzeniu rur ściennych kotłów KrCHPP.
Wymagane było dodatkowe badanie, który z czynników ma decydujący wpływ na ten proces: a) cykl termiczny na skutek destabilizacji normalnego reżimu wrzenia w obszarach wzmożonych przepływów ciepła w obecności osadów na powierzchni parowania, a w rezultacie , uszkodzenie pokrywających go ochronnych warstw tlenkowych; b) obecność w medium roboczym zanieczyszczeń korozyjnych, skoncentrowanych w osadach w pobliżu powierzchni parowania; c) połączone działanie czynników „a” i „b”.
Szczególnie interesująca jest kwestia roli reżimu piecowego. Charakter krzywych wskazuje na akumulację wodoru w wielu przypadkach w pobliżu zewnętrznej powierzchni rur ekranowych. Jest to możliwe przede wszystkim wtedy, gdy na wskazanej powierzchni znajduje się gęsta warstwa siarczków, które są w dużej mierze nieprzepuszczalne dla wodoru dyfundującego z powierzchni wewnętrznej na zewnętrzną. Powstawanie siarczków spowodowane jest: wysoką zawartością siarki w spalanym paliwie; rzucanie pochodnią na panele ekranu. Innym powodem uwodornienia metalu na powierzchni zewnętrznej jest występowanie procesów korozyjnych, gdy metal wchodzi w kontakt ze spalinami. Jak wykazała analiza osadów zewnętrznych rur kotłowych, zwykle miały miejsce obie te przyczyny.
Rola trybu spalania przejawia się również w korozji rur ekranowych pod działaniem czystej wody, co najczęściej obserwuje się na wytwornicach pary o wysokim ciśnieniu. Ośrodki korozji znajdują się zwykle w strefie maksymalnych lokalnych obciążeń termicznych i tylko na nagrzanej powierzchni rury. Zjawisko to prowadzi do powstawania okrągłych lub eliptycznych zagłębień o średnicy większej niż 1 cm.
Przegrzanie metalu występuje najczęściej w obecności osadów, ponieważ ilość odbieranego ciepła będzie prawie taka sama zarówno dla czystej rury, jak i rury zawierającej kamień, temperatura rury będzie inna.
Zjawiska korozyjne w kotłach pojawiają się najczęściej na wewnętrznej powierzchni naprężonej cieplnie, a stosunkowo rzadziej na zewnętrznej.
W tym ostatnim przypadku zniszczenie metalu jest w większości przypadków wynikiem połączonego działania korozji i erozji, co czasami ma dominujące znaczenie.
Zewnętrzną oznaką zniszczenia erozyjnego jest czysta metalowa powierzchnia. Pod wpływem korozji produkty korozji zwykle pozostają na jego powierzchni.
Procesy korozji wewnętrznej (w środowisku wodnym) i zgorzeliny mogą nasilać korozję zewnętrzną (w środowisku gazowym) ze względu na odporność termiczną warstwy zgorzeliny i osadów korozyjnych, a w konsekwencji wzrost temperatury na powierzchni metalu.
Korozja zewnętrzna metalu (od strony paleniska kotła) zależy od różnych czynników, ale przede wszystkim od rodzaju i składu spalanego paliwa.
Korozja kotłów gazowo-olejowych
Olej opałowy zawiera organiczne związki wanadu i sodu. Jeżeli stopione osady żużla zawierające związki wanadu (V) gromadzą się na ścianie rury skierowanej do pieca, to przy dużym nadmiarze powietrza i/lub temperaturze powierzchni metalu wynoszącej 520-880 ° C zachodzą następujące reakcje:
4Fe + 3V2O5 = 2Fe2O3 + 3V2O3 (1)
V2O3 + O2 = V2O5 (2)
Fe2O3 + V2O5 = 2FeVO4 (3)
7Fe + 8FeVO4 = 5Fe3O4 + 4V2O3 (4)
(Związki sodu) + O2 = Na2O (5)
Możliwy jest również inny mechanizm korozji z udziałem wanadu (ciekła mieszanina eutektyczna):
2Na2O. V2O4 . 5V2O5 + O2 = 2Na2O. 6V2O5 (6)
Na2O. 6V2O5 + M = Na2O. V2O4 . 5V2O5 + MO (7)
(M - metal)
Związki wanadu i sodu podczas spalania paliwa utleniają się do V2O5 i Na2O. W osadach przylegających do powierzchni metalu spoiwem jest Na2O. Ciecz powstająca w wyniku reakcji (1)-(7) topi warstwę ochronną magnetytu (Fe3O4), co prowadzi do utleniania metalu pod osadami (temperatura topnienia osadów (żużla) wynosi 590-880 ° C).
W wyniku tych procesów ścianki rur sitowych zwrócone do pieca są równomiernie pocienione.
Wzrost temperatury metalu, przy której związki wanadu stają się płynne, ułatwiają osadzanie się kamienia wewnętrznego w rurach. I tak, po osiągnięciu granicy plastyczności metalu, następuje pęknięcie rury - konsekwencja połączonego działania osadów zewnętrznych i wewnętrznych.
Części mocujące osłony rur, a także występy spoin rur również ulegają korozji – wzrost temperatury na ich powierzchni przyspiesza: nie są one chłodzone mieszaniną parowo-wodną, jak rury.
Olej opałowy może zawierać siarkę (2,0-3,5%) w postaci związków organicznych, siarkę elementarną, siarczan sodu (Na2SO4), która przedostaje się do oleju z wód złożowych. Na powierzchni metalu w takich warunkach korozji wanadu towarzyszy korozja tlenków siarczków. Ich łączny efekt jest najbardziej wyraźny, gdy złoża zawierają 87% V2O5 i 13% Na2SO4, co odpowiada zawartości wanadu i sodu w oleju opałowym w stosunku 13/1.
Zimą przy podgrzewaniu oleju opałowego parą w zbiornikach (w celu ułatwienia spuszczania) wpływa do niego dodatkowa woda w ilości 0,5-5,0%. Konsekwencja: zwiększa się ilość osadów na niskotemperaturowych powierzchniach kotła i oczywiście wzrasta korozja rurociągów oleju opałowego i zbiorników oleju opałowego.
Oprócz opisanego powyżej schematu niszczenia rur ekranów kotłowych korozja przegrzewaczy, girland, wiązek kotłowych, ekonomizerów ma pewne cechy wynikające ze zwiększonych - w niektórych odcinkach - prędkości gazu, zwłaszcza zawierających cząstki niespalonego oleju opałowego i złuszczany cząstki żużla.
Identyfikacja korozji
Zewnętrzna powierzchnia rur pokryta jest gęstą, podobną do emalii warstwą szarych i ciemnoszarych osadów. Od strony paleniska następuje pocienienie rury: płaskie odcinki i płytkie pęknięcia w postaci „śladów” są wyraźnie widoczne po oczyszczeniu powierzchni z osadów i warstw tlenków.
W przypadku awaryjnego zniszczenia rury, widoczne jest podłużne wąskie pęknięcie.
Korozja kotłów pyłowych
W korozji powstałej w wyniku działania produktów spalania węgla decydujące znaczenie ma siarka i jej związki. Ponadto na przebieg procesów korozyjnych wpływają chlorki (głównie NaCl) oraz związki metali alkalicznych. Korozja jest najbardziej prawdopodobna, gdy węgiel zawiera więcej niż 3,5% siarki i 0,25% chloru.
Popiół lotny zawierający związki alkaliczne i tlenki siarki osadza się na powierzchni metalu w temperaturze 560-730 °C. W tym przypadku w wyniku zachodzących reakcji powstają siarczany metali alkalicznych, np. K3Fe(SO4)3 i Na3Fe(SO4)3. Ten stopiony żużel z kolei niszczy (topi) ochronną warstwę tlenku na metalu - magnetyt (Fe3O4).
Szybkość korozji jest maksymalna przy temperaturze metalu 680-730 °C, przy jej wzroście szybkość maleje na skutek termicznego rozkładu substancji korozyjnych.
Największa korozja występuje w rurach wylotowych przegrzewacza, gdzie temperatura pary jest najwyższa.
Identyfikacja korozji
Na rurach ekranowych po obu stronach rury widoczne są płaskie obszary, które ulegają zniszczeniu korozyjnemu. Obszary te położone są względem siebie pod kątem 30-45°C i pokryte są warstwą osadów. Pomiędzy nimi znajduje się stosunkowo „czysty” obszar, poddany „czołowemu” oddziaływaniu przepływu gazu.
Osady składają się z trzech warstw: warstwa zewnętrzna to porowaty popiół lotny, warstwa pośrednia to białawe rozpuszczalne w wodzie siarczany alkaliczne, a warstwa wewnętrzna to błyszczące czarne tlenki żelaza (Fe3O4) i siarczki (FeS).
Na niskotemperaturowych częściach kotłów - ekonomizer, nagrzewnica powietrza, wentylator wyciągowy - temperatura metalu spada poniżej „punktu rosy” kwasu siarkowego.
Podczas spalania paliw stałych temperatura gazu spada od 1650 °C w pochodni do 120 °C lub mniej w kominie.
W wyniku chłodzenia gazów w fazie gazowej powstaje kwas siarkowy, który w kontakcie z zimniejszą powierzchnią metalu kondensuje, tworząc ciekły kwas siarkowy. „Punkt rosy” kwasu siarkowego wynosi 115-170 °C (może więcej – zależy to od zawartości pary wodnej i tlenku siarki (SO3) w strumieniu gazu).
Proces opisują reakcje:
S + O2 = SO2 (8)
SO3 + H2O = H2SO4 (9)
H2SO4 + Fe = FeSO4 + H2 (10)
W obecności tlenków żelaza i wanadu możliwe jest katalityczne utlenianie SO3:
2SO2 + O2 = 2SO3 (11)
W niektórych przypadkach korozja kwasu siarkowego przy spalaniu węgla jest mniej znacząca niż przy spalaniu brązu, łupków, torfu, a nawet gazu ziemnego - ze względu na stosunkowo większe wydzielanie się z nich pary wodnej.
Identyfikacja korozji
Ten rodzaj korozji powoduje równomierne niszczenie metalu. Zwykle powierzchnia jest szorstka, z lekką powłoką rdzy i jest podobna do powierzchni bez zjawisk korozyjnych. Przy dłuższej ekspozycji metal może pokryć się osadami produktów korozji, które należy ostrożnie usunąć podczas badania.
Korozja podczas przerw w działaniu
Ten rodzaj korozji pojawia się na ekonomizerze oraz w tych miejscach kotła, gdzie powierzchnie zewnętrzne są pokryte związkami siarki. W miarę ochładzania kotła temperatura metalu spada poniżej „punktu rosy” i, jak opisano powyżej, w przypadku osadów siarki powstaje kwas siarkowy. Być może związkiem pośrednim jest kwas siarkowy (H2SO3), ale jest on bardzo niestabilny i natychmiast zamienia się w kwas siarkowy.
Identyfikacja korozji
Powierzchnie metalowe są zwykle pokrywane powłokami. Jeśli zostaną usunięte, zostaną znalezione obszary zniszczenia metalu, w których znajdowały się osady siarki i obszary nieskorodowanego metalu. Ten wygląd odróżnia korozję na zatrzymanym kotle od opisanej powyżej korozji metalu ekonomizera i innych „zimnych” części pracującego kotła.
Podczas mycia kotła zjawiska korozji rozkładają się mniej więcej równomiernie na powierzchni metalu z powodu erozji osadów siarki i niedostatecznego wysuszenia powierzchni. Przy niewystarczającym myciu korozja lokalizuje się tam, gdzie znajdowały się związki siarki.
erozja metalu
W określonych warunkach różne układy kotłowe narażone są na erozyjną destrukcję metalu, zarówno od wewnątrz, jak i na zewnątrz nagrzanego metalu oraz tam, gdzie przepływy turbulentne występują z dużą prędkością.
Poniżej omówiono tylko erozję turbiny.
Turbiny ulegają erozji w wyniku uderzenia cząstek stałych i kropel kondensatu pary. Cząstki stałe (tlenki) złuszczają się z wewnętrznej powierzchni przegrzewaczy i rurociągów parowych, zwłaszcza w warunkach nieustalonych procesów termicznych.
Krople kondensatu pary niszczą głównie powierzchnie łopatek ostatniego stopnia turbiny oraz rurociągi drenażowe. Erozyjne i korozyjne działanie kondensatu pary jest możliwe, jeśli kondensat jest „kwaśny” - pH jest poniżej pięciu jednostek. Korozja jest również niebezpieczna w obecności oparów chlorków (do 12% wagowo osadów) oraz sody kaustycznej w kropelkach wody.
Identyfikacja erozji
Zniszczenie metalu w wyniku uderzeń kropel kondensatu jest najbardziej widoczne na krawędziach natarcia łopatek turbiny. Krawędzie pokryte są cienkimi poprzecznymi zębami i rowkami (rowkami), mogą występować skośne stożkowe występy skierowane w stronę uderzeń. Na krawędziach natarcia ostrzy znajdują się występy i prawie nie ma ich na ich tylnych płaszczyznach.
Uszkodzenia spowodowane cząstkami stałymi mają postać szczelin, mikrowgnieceń i nacięć na krawędziach natarcia ostrzy. Brak rowków i nachylonych stożków.
Identyfikacja rodzajów korozji jest trudna, dlatego też nierzadko zdarzają się błędy przy określaniu optymalnych technologicznie i ekonomicznie środków przeciwdziałania korozji. Główne niezbędne środki podejmowane są zgodnie z przepisami, które określają granice głównych inicjatorów korozji.
GOST 20995-75 „Stacjonarne kotły parowe o ciśnieniu do 3,9 MPa. Wskaźniki jakości wody zasilającej i pary” standaryzuje wskaźniki w wodzie zasilającej: przezroczystość, czyli ilość zawieszonych zanieczyszczeń; twardość ogólna, zawartość związków żelaza i miedzi - zapobieganie tworzeniu się kamienia kotłowego i osadów tlenku żelaza i miedzi; wartość pH - zapobiega korozji zasadowej i kwasowej oraz pienieniu w walczaku kotła; zawartość tlenu - zapobieganie korozji tlenowej; zawartość azotynów - zapobieganie korozji azotynowej; zawartość oleju - zapobieganie pienieniu w walczaku kotła.
Wartości norm są określane przez GOST w zależności od ciśnienia w kotle (a więc od temperatury wody), od mocy lokalnego przepływu ciepła i technologii uzdatniania wody.
Badając przyczyny powstawania korozji należy przede wszystkim zbadać (jeśli są dostępne) miejsca destrukcji metali, przeanalizować stan pracy kotła w okresie przedawaryjnym, przeanalizować jakość wody zasilającej, pary i osadów i przeanalizuj cechy konstrukcyjne kotła.
Podczas oględzin zewnętrznych można podejrzewać następujące rodzaje korozji.
Korozja tlenowa
: odcinki rur wlotowych ekonomizerów stalowych; rurociągi zasilające w przypadku spotkania z niewystarczająco odtlenioną (powyżej normalnej) wodą - „przełomy” tlenu w przypadku słabego odpowietrzenia; podgrzewacze wody zasilającej; wszystkie mokre obszary kotła podczas jego wyłączania i niepodjęcia działań zapobiegających przedostawaniu się powietrza do kotła, szczególnie w miejscach stagnacji, podczas spuszczania wody, skąd trudno jest usunąć kondensat pary lub całkowicie napełnić go wodą, na przykład, pionowe rury przegrzewaczy. W czasie przestoju korozja nasila się (lokalizuje) w obecności zasad (poniżej 100 mg/l).
Korozja tlenowa rzadko (gdy zawartość tlenu w wodzie jest znacznie wyższa niż norma - 0,3 mg/l) objawia się w urządzeniach do oddzielania pary bębnów kotłów i na ściankach bębnów na granicy poziomu wody; w rurach spustowych. W rurach wznoszących się nie dochodzi do korozji ze względu na odpowietrzające działanie pęcherzyków pary.
Rodzaj i charakter uszkodzeń. Wrzody o różnej głębokości i średnicy, często pokryte guzkami, których górna skorupa to czerwonawe tlenki żelaza (prawdopodobnie hematyt Fe 2 O 3). Ślady aktywnej korozji: pod skorupą guzków - czarny płynny osad, prawdopodobnie magnetyt (Fe 3 O 4) zmieszany z siarczanami i chlorkami. Przy tłumionej korozji pod skorupą powstaje pustka, a dno wrzodu pokryte jest osadami kamienia i szlamu.
Przy pH > 8,5 - wrzody są rzadkie, ale przy pH większe i głębsze< 8,5 - встречаются чаще, но меньших размеров. Только вскрытие бугорков помогает интерпретировать бугорки не как поверхностные отложения, а как следствие коррозии.
Przy prędkości wody większej niż 2 m/s guzki mogą przybierać podłużny kształt w kierunku strumienia.
. Skorupy magnetytu są wystarczająco gęste i mogą służyć jako niezawodna bariera dla przenikania tlenu do guzków. Często jednak ulegają zniszczeniu w wyniku zmęczenia korozyjnego, gdy temperatura wody i metalu zmienia się cyklicznie: częste wyłączanie i uruchamianie kotła, ruch pulsacyjny mieszanki parowo-wodnej, rozwarstwienie mieszanki parowo-wodnej na osobną parę i korki wodne następujące po sobie.
Korozja nasila się wraz ze wzrostem temperatury (do 350°C) i wzrostem zawartości chlorków w wodzie kotłowej. Czasami korozja jest wzmacniana przez produkty rozkładu termicznego niektórych substancji organicznych w wodzie zasilającej.
Ryż. 1. Pojawienie się korozji tlenowej
Korozja alkaliczna (w węższym znaczeniu - międzykrystaliczna)
Miejsca uszkodzeń korozyjnych metalu. Rury w strefach przepływu ciepła o dużej mocy (obszar palnika i naprzeciwko wydłużonego palnika) - 300-400 kW/m2 i gdzie temperatura metalu jest o 5-10 °C wyższa niż temperatura wrzenia wody pod danym ciśnieniem; rury pochyłe i poziome, w których występuje słaba cyrkulacja wody; miejsca pod grubymi osadami; strefy w pobliżu pierścieni podkładowych i w samych spoinach, na przykład w miejscach spawania urządzeń do oddzielania pary wewnątrzbębnowej; miejsca w pobliżu nitów.
Rodzaj i charakter uszkodzeń. Zagłębienia półkuliste lub eliptyczne wypełnione produktami korozji, często zawierającymi błyszczące kryształy magnetytu (Fe 3 O 4). Większość zagłębień pokryta jest twardą skórką. Od strony rur zwróconej do pieca można połączyć wnęki, tworząc tzw. ścieżkę korozji o szerokości 20-40 mm i długości do 2-3 m.
Jeśli skorupa nie jest wystarczająco stabilna i gęsta, to korozja może prowadzić - w warunkach naprężeń mechanicznych - do pojawienia się pęknięć w metalu, zwłaszcza w pobliżu pęknięć: nity, połączenia toczne, punkty spawania urządzeń oddzielających parę.
Przyczyny uszkodzeń korozyjnych. W wysokich temperaturach - powyżej 200 ° C - i wysokim stężeniu sody kaustycznej (NaOH) - 10% lub więcej - folia ochronna (skorupa) na metalu ulega zniszczeniu:
4NaOH + Fe 3 O 4 \u003d 2NaFeO 2 + Na 2 FeO 2 + 2H 2 O (1)
Produkt pośredni NaFeO 2 ulega hydrolizie:
4NaFeО 2 + 2Н 2 О = 4NaОН + 2Fe 2 О 3 + 2Н 2 (2)
Oznacza to, że w tej reakcji (2) wodorotlenek sodu jest redukowany, w reakcjach (1), (2) nie jest zużywany, ale działa jako katalizator.
Po usunięciu magnetytu wodorotlenek sodu i woda mogą bezpośrednio reagować z żelazem, uwalniając wodór atomowy:
2NaOH + Fe \u003d Na 2 FeO 2 + 2H (3)
4H2O + 3Fe \u003d Fe3O4 + 8H (4)
Uwolniony wodór może dyfundować do metalu i tworzyć metan (CH 4) z węglikiem żelaza:
4H + Fe 3 C \u003d CH 4 + 3Fe (5)
Możliwe jest również połączenie wodoru atomowego w wodór cząsteczkowy (H + H = H 2).
Metan i wodór cząsteczkowy nie mogą wnikać w metal, gromadzą się na granicach ziaren iw przypadku pęknięć rozszerzają się i pogłębiają. Ponadto gazy te zapobiegają tworzeniu się i zagęszczaniu folii ochronnych.
W miejscach głębokiego parowania wody kotłowej powstaje stężony roztwór sody kaustycznej: gęste osady soli (rodzaj korozji osadowej); kryzys wrzenia pęcherzyków, gdy na metalu tworzy się stabilna warstwa pary - tam metal prawie nie jest uszkodzony, ale soda kaustyczna koncentruje się wzdłuż krawędzi folii, gdzie zachodzi aktywne parowanie; obecność pęknięć, w których następuje parowanie, co różni się od parowania w całej objętości wody: soda kaustyczna paruje gorzej niż woda, nie jest wypłukiwana przez wodę i gromadzi się. Działając na metal, soda kaustyczna tworzy pęknięcia na granicach ziaren skierowanych do wnętrza metalu (rodzajem korozji międzykrystalicznej jest korozja szczelinowa).
Korozja międzykrystaliczna pod wpływem alkalicznej wody kotłowej najczęściej koncentruje się w walczaku kotła.
Ryż. Rys. 3. Korozja międzykrystaliczna: a – mikrostruktura metalu przed korozją, b – mikrostruktura na etapie korozji, powstawanie pęknięć wzdłuż granicy ziaren metalu
Taki korozyjny wpływ na metal jest możliwy tylko przy jednoczesnej obecności trzech czynników:
- lokalne naprężenia mechaniczne rozciągające bliskie lub nieznacznie przekraczające granicę plastyczności, tj. 2,5 MN/mm 2 ;
- luźne połączenia części bębna (wspomniane powyżej), gdzie może wystąpić głębokie parowanie wody kotłowej i gdzie nagromadzona soda kaustyczna rozpuszcza warstwę ochronną tlenków żelaza (stężenie NaOH powyżej 10%, temperatura wody powyżej 200°C oraz - szczególnie - bliżej 300°C). Jeżeli kocioł pracuje przy ciśnieniu niższym niż paszportowe (na przykład 0,6-0,7 MPa zamiast 1,4 MPa), wówczas zmniejsza się prawdopodobieństwo tego rodzaju korozji;
- niekorzystna kombinacja substancji w wodzie kotłowej, w której nie ma koniecznych ochronnych stężeń inhibitorów tego typu korozji. Sole sodu mogą działać jako inhibitory: siarczany, węglany, fosforany, azotany, siarczynowy płyn celulozowy.
Ryż. 4. Pojawienie się korozji międzykrystalicznej
Pęknięcia korozyjne nie rozwijają się, jeśli zachowany jest stosunek:
(Na 2 SO 4 + Na 2 CO 3 + Na 3 PO 4 + NaNO 3) / (NaOH) ≥ 5, 3 (6)
gdzie Na 2 SO 4, Na 2 CO 3, Na 3 PO 4, NaNO 3, NaOH - zawartość odpowiednio siarczanu sodu, węglanu sodu, fosforanu sodu, azotanu sodu i wodorotlenku sodu, odpowiednio, mg / kg.
Obecnie produkowane kotły nie mają co najmniej jednego z tych warunków korozyjnych.
Obecność związków krzemu w wodzie kotłowej może również nasilać korozję międzykrystaliczną.
NaCl w tych warunkach nie jest inhibitorem korozji. Pokazano powyżej: jony chloru (Сl -) są przyspieszaczami korozji, ze względu na swoją dużą ruchliwość i małe rozmiary, łatwo przenikają ochronne warstwy tlenków i tworzą z żelazem wysokorozpuszczalne sole (FeCl 2, FeCl 3) zamiast słabo rozpuszczalnych tlenków żelaza .
W wodzie kotłowni tradycyjnie kontroluje się wartości całkowitej mineralizacji, a nie zawartość poszczególnych soli. Prawdopodobnie z tego powodu racjonowanie wprowadzono nie według wskazanego stosunku (6), ale według wartości względnej zasadowości wody kotłowej:
SH kv rel = SH ov rel = SH ov 40 100/S ov ≤ 20, (7)
gdzie U q rel - względna zasadowość wody kotłowej,%; Shchov rel - względna alkaliczność uzdatnionej (dodatkowej) wody, %; Shchov - całkowita alkaliczność uzdatnionej (dodatkowej) wody, mmol/l; S ov - mineralizacja wody uzdatnionej (dodatkowej) (w tym zawartość chlorków), mg/l.
Całkowita zasadowość uzdatnionej (dodatkowej) wody może być równa, mmol/l:
- po kationizacji sodowej - całkowita alkaliczność wody źródłowej;
- po kationizacji wodorowo-sodowej równolegle - (0,3-0,4) lub sekwencyjnie z "głodną" regeneracją filtra wodoro-kationitowego - (0,5-0,7);
- po kationizacji sodu z zakwaszeniem i jonizacją chlorkiem sodu - (0,5-1,0);
- po kationizacji amonowo-sodowej - (0,5-0,7);
- po wapnowaniu w 30-40 ° C - (0,35-1,0);
- po koagulacji - (W około ref - D do), gdzie W około ref - całkowita zasadowość wody źródłowej, mmol/l; D do - dawka koagulantu, mmol/l;
- po wapnie sodowanym w 30-40 °C - (1,0-1,5), a w 60-70 °C - (1,0-1,2).
Przyjmuje się wartości względnej alkaliczności wody kotłowej zgodnie z normami Rostekhnadzor,%, nie więcej niż:
- dla kotłów z nitowanymi bębnami - 20;
- dla kotłów ze spawanymi bębnami i zwiniętymi w nie rurami - 50;
- dla kotłów ze spawanymi bębnami i przyspawanymi do nich rurami - wartość dowolna, niestandaryzowana.
Ryż. 4. Wynik korozji międzykrystalicznej
Zgodnie z normami Rostekhnadzora U kv rel jest jednym z kryteriów bezpiecznej eksploatacji kotłów. Bardziej słuszne jest sprawdzenie kryterium potencjalnej agresywności alkalicznej wody kotłowej, które nie uwzględnia zawartości jonów chloru:
K u = (S ov - [Сl - ]) / 40 u ov, (8)
gdzie K u - kryterium potencjalnej agresywności alkalicznej wody kotłowej; S s - zasolenie wody uzdatnionej (dodatkowej) (w tym zawartość chlorków), mg/l; Cl - - zawartość chlorków w uzdatnionej (dodatkowej) wodzie, mg/l; Szczow - całkowita alkaliczność uzdatnionej (dodatkowej) wody, mmol/l.
Wartość K u można przyjąć:
- dla kotłów z nitowanymi bębnami o ciśnieniu większym niż 0,8 MPa ≥ 5;
- dla kotłów ze spawanymi bębnami i rurami walcowanymi w nich pod ciśnieniem większym niż 1,4 MPa ≥ 2;
- dla kotłów ze spawanymi bębnami i przyspawanymi do nich rurami, a także dla kotłów ze spawanymi bębnami i wkręcanymi w nie rurami o ciśnieniu do 1,4 MPa oraz kotłów z nitowanymi bębnami o ciśnieniu do 0,8 MPa - nie standaryzować.
Korozja podszlamowa
Ta nazwa łączy w sobie kilka różnych rodzajów korozji (alkaliczna, tlenowa itp.). Nagromadzenie luźnych i porowatych osadów i szlamu w różnych strefach kotła powoduje korozję metalu pod szlamem. Główny powód: zanieczyszczenie wody zasilającej tlenkami żelaza.
Korozja azotynowa
. Rury sitowe i kotłowe kotła od strony paleniska.
Rodzaj i charakter uszkodzeń. Rzadkie, mocno ograniczone duże owrzodzenia.
. W obecności jonów azotynowych (NO - 2) w wodzie zasilającej powyżej 20 μg / l, temperatura wody przekracza 200 ° C, azotyny służą jako katodowe depolaryzatory korozji elektrochemicznej, odzyskując do HNO 2, NO, N 2 (patrz wyżej).
Korozja parowo-wodna
Miejsca uszkodzeń korozyjnych metalu. Część wylotowa wężownic przegrzewaczy, rurociągi pary przegrzanej, poziome i lekko nachylone rury wytwarzające parę w obszarach słabej cyrkulacji wody, czasami wzdłuż górnej generacji wężownic wylotowych ekonomizerów wody wrzącej.
Rodzaj i charakter uszkodzeń. Płytki gęstych czarnych tlenków żelaza (Fe 3 O 4), mocno związanych z metalem. Przy wahaniach temperatury ciągłość płytki (skorupy) zostaje przerwana, łuski odpadają. Równomierne pocienienie metalu z wybrzuszeniami, pęknięciami podłużnymi, pęknięciami.
Można ją zidentyfikować jako korozję podszlamową: w postaci głębokich wżerów o niewyraźnie odgraniczonych krawędziach, częściej w pobliżu spoin wystających wewnątrz rury, gdzie gromadzi się szlam.
Przyczyny uszkodzeń korozyjnych:
- medium myjące - para w przegrzewaczach, rurociągach parowych, „poduszkach” parowych pod warstwą szlamu;
- temperatura metalu (stal 20) przekracza 450 ° C, strumień ciepła do sekcji metalowej wynosi 450 kW / m 2;
- naruszenie trybu spalania: żużel palników, zwiększone zanieczyszczenie rur wewnątrz i na zewnątrz, niestabilne (wibracyjne) spalanie, wydłużenie palnika w kierunku rur ekranów.
W rezultacie: bezpośrednie oddziaływanie chemiczne żelaza z parą wodną (patrz wyżej).
Korozja mikrobiologiczna
Wywołany przez bakterie tlenowe i beztlenowe, pojawia się w temperaturze 20-80 °C.
Miejsca uszkodzeń metalu. Rury i zbiorniki do kotła z wodą o określonej temperaturze.
Rodzaj i charakter uszkodzeń. Guzki o różnych rozmiarach: średnica od kilku milimetrów do kilku centymetrów, rzadko - kilkadziesiąt centymetrów. Guzki pokryte są gęstymi tlenkami żelaza - produktem odpadowym bakterii tlenowych. Wewnątrz - czarny proszek i zawiesina (siarczek żelaza FeS) - produkt bakterii beztlenowych redukujących siarczany, pod czarną formacją - okrągłe wrzody.
Przyczyny uszkodzeń. Siarczany żelaza, tlen i różne bakterie są zawsze obecne w wodzie naturalnej.
Bakterie żelaza w obecności tlenu tworzą film tlenków żelaza, pod którym bakterie beztlenowe redukują siarczany do siarczku żelaza (FeS) i siarkowodoru (H 2 S). Z kolei siarkowodór powoduje powstawanie kwasu siarkowego (bardzo nietrwałego) i siarkowego, a metal koroduje.
Ten rodzaj korozji ma pośredni wpływ na korozję kotła: przepływ wody z prędkością 2-3 m/s odrywa guzki, przenosi ich zawartość do kotła, zwiększając gromadzenie się szlamu.
W rzadkich przypadkach korozja ta może wystąpić w samym kotle, jeśli podczas długiego postoju kotła w rezerwie zostanie on napełniony wodą o temperaturze 50-60 ° C, a temperatura jest utrzymywana na skutek przypadkowych przebić pary z sąsiednie kotły.
Korozja „chelatowana”
Miejsca uszkodzeń korozyjnych. Urządzenia, w których oddzielana jest para od wody: walczaki, separatory pary do iz walczaka, rzadziej także w rurociągach wody zasilającej i ekonomizerze.
Rodzaj i charakter uszkodzeń. Powierzchnia metalu jest gładka, ale jeśli medium porusza się z dużą prędkością, to skorodowana powierzchnia nie jest gładka, ma zagłębienia w kształcie podkowy i „ogony” zorientowane w kierunku ruchu. Powierzchnia pokryta jest cienką matową lub czarną błyszczącą folią. Nie ma widocznych osadów, nie ma też produktów korozji, ponieważ „chelat” (organiczne związki poliamin wprowadzone specjalnie do kotła) już przereagował.
W obecności tlenu, co rzadko zdarza się w normalnie pracującym kotle, skorodowana powierzchnia jest „ożywiona”: szorstkość, metalowe wysepki.
Przyczyny uszkodzeń korozyjnych. Mechanizm działania „chelatu” został opisany wcześniej („Kotłownie przemysłowe i ciepłownicze oraz mini-CHP”, 1 (6) ΄ 2011, s. 40).
Korozja „chelatowa” występuje, gdy przedawkowanie „chelatu” jest możliwe, ale nawet przy normalnej dawce jest możliwe, ponieważ „chelat” koncentruje się w obszarach, w których następuje intensywne parowanie wody: wrzenie pęcherzykowe zostaje zastąpione przez warstewkę. W urządzeniach do oddzielania pary występują przypadki szczególnie niszczącego działania korozji „chelatowej” na skutek dużych turbulentnych prędkości mieszaniny wody i wody z parą wodną.
Wszystkie opisane uszkodzenia korozyjne mogą mieć efekt synergiczny, tak że łączne uszkodzenia wynikające z łącznego działania różnych czynników korozyjnych mogą przekroczyć wielkość uszkodzeń od poszczególnych rodzajów korozji.
Z reguły działanie czynników korozyjnych potęguje niestabilny reżim cieplny kotła, co powoduje zmęczenie korozyjne i wzmaga korozję zmęczeniową cieplną: liczba rozruchów ze stanu zimnego przekracza 100, łączna liczba rozruchów ponad 200 Ponieważ tego typu zniszczenia metalu są rzadkie, pęknięcia, pęknięcia rur mają wygląd identyczny jak uszkodzenia metalu z różnego rodzaju korozji.
Zwykle, aby zidentyfikować przyczynę zniszczenia metalu, wymagane są dodatkowe badania metalograficzne: radiografia, ultradźwięki, defektoskopia barwna i magnetyczna.
Różni badacze proponowali programy do diagnozowania rodzajów uszkodzeń korozyjnych stali kotłowych. Znany jest program VTI (A.F. Bogachev i współpracownicy) - głównie dla kotłów energetycznych wysokoprężnych, oraz rozwój stowarzyszenia Energochermet - głównie dla kotłów energetycznych nisko i średniociśnieniowych oraz kotłów na ciepło odpadowe.