Wentylator nadmuchowy do podbierania kotła TPP 210 a. Opracowanie projektowe JSC TKZ „Krasny Kotelshchik” w celu wprowadzenia nowych technologii spalania paliw stałych w piecach kotłów parowych. Spalanie etapowe paliw stałych
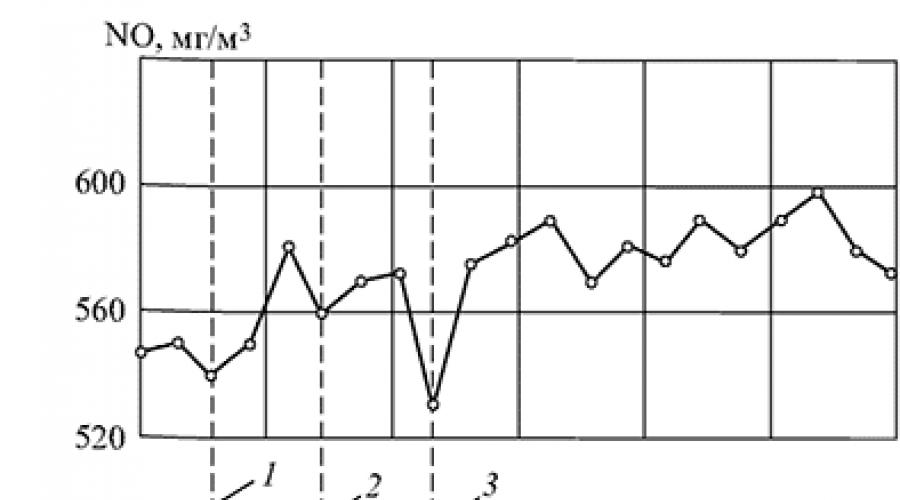
Kocioł parowy jednoprzelotowy TPP-210A jest traktowany jako przedmiot regulacji, analizowane są istniejące układy sterowania, zwraca się uwagę na jego zalety i wady, proponuje się schemat konstrukcyjny regulatora obciążenia termicznego kotła TPP-210A na paliwo gazowe za pomocą regulacyjnego sterownika mikroprocesorowego Remikont R-130
Obliczanie parametrów nastawczych i modelowanie procesu regulacji obciążenia cieplnego kotła TPP-210A na paliwo gazowe, w tym aproksymacja danych eksperymentalnych i modelowanie obiektu regulacji dla dwuobwodowego układu regulacji, obliczenia nastawy dwupętlowych układów regulacji, a także symulacja procesu przejściowego w regulacji układów dwupętlowych. Przeprowadzana jest analiza porównawcza otrzymanych charakterystyk przejściowych.
Wyciąg z tekstu
Pod względem poziomu automatyzacji energetyka cieplna zajmuje jedno z czołowych miejsc wśród innych branż. Elektrownie cieplne charakteryzują się ciągłością zachodzących w nich procesów. Prawie wszystkie operacje w elektrowniach cieplnych są zmechanizowane i zautomatyzowane.
Automatyzacja parametrów zapewnia znaczące korzyści
Lista wykorzystanej literatury
Bibliografia
1. Grigoriev V.A., Zorin V.M. „Elektrownie cieplne i jądrowe”. Informator. — M.: Energoatomizdat, 1989.
2. Pletnev G. P. Zautomatyzowane systemy sterowania elektrowniami cieplnymi: Podręcznik dla uniwersytetów / G. P. Pletnev. - 3. ed., poprawione. i dodatkowe — M.: Wyd. MPEI, 2005, - 355 s
3. Pletnev T.P. Automatyzacja procesów technologicznych i produkcji w energetyce cieplnej. /MPEI. M, 2007. 320 s.
4. Małokanałowy wielofunkcyjny regulator mikroprocesorowy regulacyjny Remikont R-130″ Zestaw dokumentacji YALBI.421 457.001TO 1−4
5. Pletnev G.P. Zaichenko Yu.P. „Projektowanie, montaż i eksploatacja automatycznych systemów sterowania procesami elektroenergetycznymi” MPEI 1995 316 s.-il.
6. Rotach V.Ya. Teoria automatycznego sterowania procesami cieplnymi i energetycznymi, - M.: MPEI, 2007. - 400s.
7. Kozlov OS i inne Kompleks oprogramowania „Modelowanie w urządzeniach technicznych” (PK „MVTU”, wersja 3.7).
Instrukcja obsługi. - M .: MSTU im. Bauman, 2008.
Fil S.A., Golyshev L.V., inżynierowie, Mysak I.S., doktor inżynier. Sci., Dovgoteles G. A., Kotelnikov I. I., Sidenko A. P., inżynierowie JSC LvovORGRES - Uniwersytet Narodowy "Politechnika Lwowska" - Trypilska TPP
Spalanie węgla kamiennego o niskiej reaktywności (Vdaf< 10%) в камерных топках котельных установок сопровождается повышенным механическим недожогом, который характеризуется двумя показателями: содержанием горючих в уносе Гун и потерей тепла от механического недожога q4.
Goon jest zwykle oznaczany metodą laboratoryjną przy użyciu pojedynczych próbek popiołu pobranych z kanałów gazowych ostatniej powierzchni konwekcyjnej kotła przy użyciu zwykłych instalacji przedmuchowych. Główną wadą metody laboratoryjnej jest zbyt duże opóźnienie w uzyskaniu wyniku Gong (powyżej 4 – 6 godzin), na które składa się czas powolnego gromadzenia się próbki popiołu w urządzeniu do wydmuchiwania oraz czas trwania laboratorium analiza. Tak więc w jednej próbce popiołu wszystkie możliwe zmiany w gongu są sumowane przez długi czas, co utrudnia szybkie i efektywne dostosowanie i optymalizację reżimu spalania.
Według danych w trybie zmiennym i niestacjonarnym kotła współczynnik zbierania popiołu (stopień oczyszczenia) cyklonu nastawy prowadzenia zmienia się w zakresie 70 - 95%, co prowadzi do dodatkowych błędów w określenie gongu.
Wady instalacji popiołów lotnych są przezwyciężane przez wprowadzenie systemów ciągłego pomiaru gongami, takich jak analizatory zawartości węgla w popiele lotnym.
W 2000 roku osiem zestawów (po dwa na każdy zbiornik) stacjonarnych analizatorów pracujących w trybie ciągłym RCA-2000 wyprodukowanych przez Mark and Wedell (Dania).
Zasada działania analizatora RCA-2000 opiera się na metodzie fotoabsorpcyjnej analizy w zakresie podczerwieni widma.
Zakres pomiarowy 0 - 20% bezwzględnych wartości Gong, względny błąd pomiaru w zakresie 2 - 7% - nie więcej niż ± 5%.
Pobieranie popiołu do układu pomiarowego analizatora odbywa się z kanałów gazowych przed elektrofiltrami.
Ciągłą rejestrację gongów prowadzono na samorejestrującym urządzeniu sterowni z częstotliwością pełnego cyklu pomiarowego w ciągu 3 minut.
Przy spalaniu popiołu o różnym składzie i jakości rzeczywiste bezwzględne wartości gongów z reguły przekraczały 20%. Dlatego obecnie analizatory są wykorzystywane jako wskaźniki zmian względnych wartości zawartości materiałów palnych w porywaniu Gv ° w skali rejestratora 0 - 100%.
W celu zgrubnego oszacowania rzeczywistego poziomu Gong opracowano charakterystykę kalibracji analizatora, która jest relacją między bezwzględnymi wartościami Gong wyznaczonymi metodą laboratoryjną a względnymi wartościami analizatora G°Gong. W zakresie zmian gongu od 20 do 45% charakterystykę w postaci analitycznej wyraża równanie
Podczas badań doświadczalnych i normalnej eksploatacji kotła analizatory mogą być wykorzystywane do wykonywania następujących prac:
optymalizacja trybu spalania;
ocena zmiany gongu podczas planowanych przełączeń technologicznych układów i zespołów kotłowni;
określenie dynamiki i poziomu spadku sprawności w trybie niestacjonarnym i porozruchowym kotła oraz w przypadku przemiennego spalania popiołów i gazu ziemnego.
W okresie prób cieplnych kotła analizatory służyły do optymalizacji trybu spalania oraz oceny wpływu załączania planowanych urządzeń na stabilność procesu spalania pyłu węglowego.
Eksperymenty prowadzono przy obciążeniach stacjonarnych kotła w zakresie 0,8-1,0 nominalnym i spalaniu SA o następujących charakterystykach: dolna właściwa wartość opałowa Qi = 23,06 - 24,05 MJ/kg (5508 - 5745 kcal/kg), popiół zawartość na ciężar roboczy Ad = 17,2 - 21,8%, wilgotność na ciężarze roboczym W = 8,4 - 11,1%; udział gazu ziemnego do rozświetlenia płomienia pyłu węglowego wynosił 5-10% całkowitego wydzielanego ciepła.
Wyniki i analizę eksperymentów dotyczących optymalizacji trybu spalania za pomocą analizatorów podano w. Podczas ustawiania kotła zoptymalizowano:
prędkości wyjściowe powietrza wtórnego poprzez zmianę otwarcia bramek peryferyjnych w palnikach;
prędkości wyjściowe powietrza pierwotnego poprzez zmianę obciążenia wentylatora gorącego nadmuchu;
proporcja rozświetlenia płomienia gazem ziemnym poprzez dobranie (zgodnie z warunkami zapewnienia stabilności spalania) minimalnej możliwej liczby pracujących palników gazowych.
Główne cechy procesu optymalizacji trybu spalania podano w tabeli. jeden.
Podano w tabeli. 1, dane wskazują na ważną rolę analizatorów w procesie optymalizacji, polegającym na ciągłym pomiarze i rejestracji bieżących informacji o zmianie H°h, co umożliwia terminowe i
wyraźnie ustalić optymalny tryb, zakończenie procesu stabilizacji i uruchomienie kotła w trybie optymalnym.
Przy optymalizacji trybu spalania główny nacisk położono na znalezienie możliwie najniższego poziomu względnych wartości H°un. W tym przypadku wartości bezwzględne gongu zostały określone przez charakterystykę kalibracji analizatora.
Zatem efektywność wykorzystania analizatorów do optymalizacji trybu spalania kotła można z grubsza oszacować zmniejszając zawartość materiałów palnych w porwaniu średnio o 4% i straty ciepła z dopalania mechanicznego o 2%.
W stacjonarnych trybach kotła regularne przełączanie technologiczne np. w układach pyłowych lub palnikach zakłóca proces stabilnego spalania pyłu węglowego.
Tabela 1
Charakterystyka procesu optymalizacji trybu spalania
Kocioł TPP-210A wyposażony jest w trzy układy odpylania z młynami kulowymi typu ShBM 370/850 (Sh-50A) oraz wspólny pojemnik na pył.
Z instalacji pyłowej zużyty środek suszący jest odprowadzany do komory spalania (przedpaleniska) za pomocą wentylatora młynowego typu MB 100/1200 przez specjalne dysze wylotowe umieszczone nad głównymi palnikami pyłowo-gazowymi.
Przedpalnik każdego korpusu kotła otrzymuje pełny wyrzut z odpowiedniego zewnętrznego układu pyłowego i połowę zrzutu ze środkowego układu pyłowego.
Zużytym środkiem suszącym jest niskotemperaturowe, wilgotne i zapylone powietrze, którego główne parametry mieszczą się w granicach:
udział powietrza odpadowego wynosi 20 - 30% całkowitego zużycia powietrza przez organizm (kocioł); temperatura 120 - 130°C; udział miału węglowego, który nie został wychwycony przez cyklon układu pyłowego, 10 - 15% wydajności młyna;
wilgotność odpowiada ilości wilgoci uwalnianej podczas procesu suszenia zmielonego paliwa roboczego.
Zużyty środek suszący odprowadzany jest w strefę maksymalnych temperatur płomienia i tym samym znacząco wpływa na kompletność wypalenia miału węglowego.
Podczas pracy kotła najczęściej zatrzymywany i ponownie uruchamiany jest układ środkowego pyłu, za pomocą którego w bunkrze przemysłowym utrzymywany jest wymagany poziom zapylenia.
Przedstawiono dynamikę zmian głównych wskaźników reżimu spalania korpusu kotła - zawartości materiałów palnych w porwaniu oraz stężenia masowego tlenków azotu w spalinach (NO) - podczas planowanego wyłączenia instalacji pyłu średniego na ryc. jeden.
Na powyższych i wszystkich kolejnych rysunkach przy konstruowaniu zależności graficznych akceptowane są następujące warunki:
zawartość materiałów palnych w porywaniu odpowiada wartościom skal dwóch pionowych osi współrzędnych: uśrednionym pomiarom Gong i danym przeliczenia zgodnie z charakterystyką kalibracji Gong;
stężenie masowe NO z nadmiarem powietrza w spalinach (bez redukcji do NO2) zaczerpnięto z ciągłych pomiarów stacjonarnego analizatora gazów Mars-5 MP „Ekomak” (Kijów);
dynamika zmian H°un i NO jest ustalona na
przez cały okres operacji technologicznej i trybu stabilizacji; początek operacji technologicznej przyjmuje się w pobliżu zerowego czasu odniesienia.
Kompletność spalania pyłu węglowego oszacowano na podstawie jakości trybu spalania (KTR), który analizowano dwoma wskaźnikami Gong i NO, które z reguły zmieniały się w przeciwnych kierunkach.
Ryż. 1. Zmiany wskaźników trybu spalania po zatrzymaniu środkowego układu zapylenia
Przeanalizowano wpływ planowanego wyłączenia instalacji średniego pyłu na wskaźniki KTP (rys. 1) w zależności od kolejności następujących operacji technologicznych:
operacja 1 - wyłączenie podajnika węgla surowego (CFC) i wstrzymanie dopływu węgla do młyna zmniejszyło obciążenie bębna SBM, zmniejszyło miałkość miału węglowego oraz podwyższyło temperaturę powietrza wylotowego, co powodowało terminowa poprawa CTE: spadek Hn° i wzrost NO; proces dalszej emaskulacji młyna przyczynił się do usunięcia pyłu z powietrza odlotowego i wzrostu nadmiaru powietrza w przedpaleniu, co negatywnie wpłynęło na WRC;
operacja 2 - zatrzymanie SHM i zmniejszenie wentylacji układu pyłowego najpierw nieznacznie poprawiło WRC, a następnie z opóźnieniem z wyłączeniem wentylatora młyna (MF) WRC uległo pogorszeniu;
operacja 3 - zatrzymanie MW i zatrzymanie zrzutu zużytego osuszacza do komory spalania znacznie poprawiło WRC.
W ten sposób, przy wszystkich innych rzeczach, zatrzymanie systemu pyłowego poprawiło proces spalania paliwa, zmniejszając mechaniczne niedopalanie i zwiększając stężenie masowe NO.
Typowym naruszeniem stabilności układu pyłowego jest przeciążenie bębna młyna paliwem lub „zasmarowanie” kulek mielących mokrym materiałem gliniastym.
Wpływ długotrwałej emaskulacji bębna freza palcowego na WRC korpusu kotła przedstawiono na ryc. 2.
Wyłączenie zasilacza (operacja 1) z powodów podobnych do rozważanych podczas postoju instalacji proszkowej, w pierwszym etapie emaskulacji młyna poprawiło na krótki czas WRC. W późniejszej kastracji młyna, aż do włączenia zasilacza (operacja 2), pojawiła się tendencja do pogorszenia WRC i wzrostu G°un.
Ryż. Rys. 2. Zmiany wskaźników reżimu spalania podczas emaskulacji bębna ostatniego młyna
Ryż. 3. Zmiany wskaźników trybu spalania przy uruchamianiu ostatniego układu pyłowego i wyłączaniu palników gazowych
W mniejszym stopniu automatyczna praca zasilacza okresowo destabilizuje tryb paleniska, który reguluje niezbędne obciążenie młyna węglem poprzez wyłączenie, a następnie włączenie napędu zasilacza.
Wpływ trybu rozruchu układu ekstremalnego pyłu na KTP przedstawiono na ryc. 3.
Stwierdzono następujący wpływ rozruchu instalacji pyłowej na tryb spalania:
operacja 1 - uruchomienie MW i przewietrzenie (rozgrzanie) ścieżki instalacji pyłowej z wyprowadzeniem stosunkowo zimnego powietrza do przedpalenia zwiększyło nadmiar powietrza w strefie spalania i obniżyło temperaturę pochodni, co doprowadziło do pogorszenia w CTE;
operacja 2 – uruchomienie SHBM i kontynuowanie wentylacji ciągu miało negatywny wpływ na CTE;
operacja 3 - uruchomienie zasilacza i załadowanie młyna paliwem przy wzroście do nominalnego zużycia środka suszącego znacznie pogorszyło WRC.
Można stwierdzić, że włączenie układu pyłowego do pracy wpływa negatywnie na WRC, zwiększając podpalenie mechaniczne i zmniejszając stężenie masowe NO.
Przedpiec korpusu kotła TPP-210A wyposażony jest w sześć palników gazowo-ślimakowych pyłowo-gazowych o mocy cieplnej 70 MW, zabudowanych w jednej kondygnacji na ścianie przedniej i tylnej oraz dwa palniki gazowo-olejowe nad paleniskiem zapewnienie stabilnego odżużlania płynnego w całym zakresie obciążeń roboczych kotła.
Podczas spalania pyłu węglowego ASh gaz ziemny był dostarczany ze stałym natężeniem przepływu (ok. 5% całkowitego wydzielanego ciepła) do palników nad paleniskowych oraz zmiennym natężeniem przepływu przez główne palniki pyłowo-gazowe w celu stabilizacji procesu spalania pyłu węglowego. Doprowadzanie gazu do każdego głównego palnika odbywało się przy najniższym możliwym natężeniu przepływu, odpowiadającym 1,0-1,5% całkowitego wydzielanego ciepła. Dlatego też zmianę udziału gazu ziemnego do rozpalania pochodni przeprowadzono poprzez włączenie lub wyłączenie określonej liczby głównych palników gazowych.
Wpływ wyłączenia palników gazowych (zmniejszenie udziału gazu ziemnego) na WRC korpusu kotła przedstawiono na ryc. 3.
Sekwencyjne wyłączanie pierwszego palnika gazowego (operacja 4), a następnie trzech palników gazowych (operacja 5) wpłynęło pozytywnie na WRC i doprowadziło do znacznego zmniejszenia podpalenia mechanicznego.
Wpływ włączenia palników gazowych (zwiększenie udziału gazu ziemnego) na WRC przedstawiono na ryc. 4. Sekwencyjne włączanie jednego palnika gazowego (operacja 1), dwóch palników (operacja 2) i jednego palnika (operacja 3) negatywnie wpłynęło na WRC i znacznie zwiększyło podpalenie mechaniczne.
Ryż. 4. Zmiana wskaźników trybu spalania przy włączonych palnikach gazowych
Tabela 2
Zmiany zawartości materiałów palnych w pozostałościach podczas przełączania technologicznego urządzeń
Ekwipunek | Tryb | ||
zmniejszać | zwiększać |
||
System ekstremalnego/średniego pyłu | |||
wykastrowanie | Nagły wypadek | ||
podajnik surowca | |||
Główny palnik gazowy | Zamknąć | ||
Włączenie |
Przybliżoną ocenę wpływu sprawdzonego przełączania technologicznego urządzeń kotłowych na zmianę WRC (Kun) zestawiono w tabeli. 2.
Z analizy przedstawionych danych wynika, że największy spadek sprawności kotłowni w trybach stacjonarnych następuje w wyniku rozruchu instalacji pyłowej oraz przy zawyżonym zużyciu gazu ziemnego do rozświetlania płomienia.
Należy zauważyć, że o konieczności przeprowadzenia operacji rozruchowych instalacji pyłowej decydują wyłącznie względy technologiczne, a zawyżone zużycie gazu ziemnego do rozpalania płomienia z reguły jest ustalane przez obsługę w celu zapobieżenia ewentualnym naruszenia stabilności procesu spalania w przypadku nagłego pogorszenia jakości SZR.
Zastosowanie analizatorów RCA-2000 pozwala na ciągłe zmiany, terminowe
oceniać wszelkie zmiany jakości paliwa i stale utrzymywać wartość natężenia oświetlenia płomienia na odpowiednim optymalnym poziomie przy minimalnym niezbędnym zużyciu gazu ziemnego, co pozwala zmniejszyć zużycie deficytowego paliwa gazowego i zwiększyć sprawność kotła.
wnioski
- System ciągłego pomiaru zawartości materiałów palnych w pozostałościach pozwala na szybką i sprawną ocenę przebiegu procesów spalania podczas spalania AS w kotle TPP-210A, który jest rekomendowany do stosowania w pracach rozruchowych i badawczych, jako oraz do systematycznego monitorowania sprawności urządzeń kotłowych.
- Efektywność wykorzystania analizatorów RCA-2000 do optymalizacji trybu spalania wstępnie szacuje się zmniejszając wskaźniki niedopalenia mechanicznego - zawartość materiałów palnych w porywaniu średnio o 4% i odpowiednio straty ciepła z niedopalania mechanicznego o 2% .
- W stacjonarnych trybach kotła regularne przełączanie technologiczne urządzeń wpływa na jakość procesu spalania. Rozruch instalacji pyłowej oraz zawyżone zużycie gazu ziemnego do rozpalenia pochodni pyłowej znacznie obniżają sprawność kotłowni.
Bibliografia
- Madoyan A. A., Baltyan V. N., Grechany A. N. Efektywne spalanie węgli niskogatunkowych w kotłach energetycznych. Moskwa: Energoatomizdat, 1991.
- Wykorzystanie analizatora zawartości substancji palnych RCA-2000 w pozostałościach oraz analizatora gazu Mars-5 do optymalizacji trybu spalania kotła pyłowego TPP-210A firmy Tripolskaya TPP / Golyshev L.V., Kotelnikov N.I., Sidenko A.P. i inni - Tr. Kijowski Instytut Politechniczny. Energia: ekonomia, technologia, ekologia, 2001, nr 1.
- Zusin S.I. Zmiana strat ciepła z podpaleniem mechanicznym w zależności od trybu pracy kotła. - Energetyka cieplna, 1958, nr 10.
Krótki opis zespołu kotłowego „Kocioł przepływowy typ TPP-210”
Krótki opis zespołu kotłowego Kocioł przelotowy typu TPP-210 (p/p 950-235 GOST 3619-59 model TKZ TPP-210) o wydajności pary 950 ton/h dla pary o parametrach nadkrytycznych został zaprojektowany i wykonany przez Zakład Taganrog „Krasny Kotelshchik”. Zespół kotłowy przeznaczony jest do pracy w bloku z turbiną kondensacyjną K-300-240 o mocy 300 MW produkcji KhTGZ. Kocioł przeznaczony jest do spalania osadów antracytowych z płynnym odpopielaniem i gazem ziemnym ze złoża Szebelinskiego. Zespół kotłowy jest dwupłaszczowy z układem każdej obudowy w kształcie litery U oraz regeneracyjnymi nagrzewnicami powietrza wyjętymi spod kotła, znajdującymi się na zewnątrz budynku kotłowni. Płaszcze kotłów tej samej konstrukcji o wydajności 475 t/h pary każdy. Kadłuby mogą pracować niezależnie od siebie. Ogólne dane kotła: Wydajność 475 t/h Temperatura pary przegrzanej: pierwotna 565 °C Wtórna 565°C Zużycie pary wtórnej 400 t/h Ciśnienie pary pierwotnej za kotłem 255 kg/cm² Ciśnienie pary wtórnej na wlocie do kotła 39,5 kg/ cm² Ciśnienie pary wtórnej na wylocie z kotła 37 kg/cm² Temperatura pary wtórnej na wlocie 307 °C Temperatura wody zasilającej 260 °C Temperatura gorącego powietrza 364 °C Całkowity ciężar metalu kotła 3438 t Szerokość kotła wzdłuż osi kolumn 12 m Kocioł głębokość w osiach kolumn 19 m Wysokość kotła 47 m Objętość wodna zespołu kotłowego w stanie zimnym 243 m³ Wymiary paleniska w rzucie (wzdłuż osi rur): para pierwotna i wtórna na wylocie zredukowana do 545 °C) Kocioł jest obsługiwany przez dwa osiowe oddymiacze, dwie dmuchawy z silnikami dwubiegowymi i dwa wentylatory gorącego nadmuchu. Schemat przygotowania pyłu z bunkrem i transportu pyłu do palników gorącym powietrzem. Kocioł wyposażony jest w trzy młyny bębnowo-kulowe ShBM-50 o wydajności 50 ton pyłu na godzinę. Powierzchnie grzewcze: Ekrany pieca 1317 m² W tym: NRCh 737 m² THR 747 m² Ekrany komory nawrotnej i sufit 1674 m² Przegrzewacz SVD: w tym: Parowy wymiennik ciepła 800 m² Pośredni pakiet konwekcyjny 1994 m² Nagrzewnica powietrza 78730 m² Wylotowy pakiet konwekcyjny 1205 m² Ekonomizer konwekcyjny 1994 m²
W każdym korpusie kotła znajdują się dwa strumienie (w opisie kotła iw instrukcji strumień nazywany jest wątkiem). Ponieważ konstrukcja kadłuba jest podobna, schemat i konstrukcja jednego kadłuba zostaną opisane w przyszłości. Woda zasilająca o temperaturze 260°C przepływa przez jednostkę napędową i wchodzi do komór wlotowych ekonomizera wody Sh325*50, które są jednocześnie skrajnymi belkami nośnymi pakietu. Po przejściu przez wężownice ekonomizera wody woda o temperaturze 302°C wpływa do komór wylotowych Ш235*50, które są środkowymi belkami nośnymi tej powierzchni. Za ekonomizerem woda jest kierowana rurami obejściowymi 159*16 do środkowych belek nośnych tej powierzchni rurami Ш133*15 do części dolnej (НРЧ). Ekrany NRC składają się z oddzielnych paneli, ponadto powierzchnie grzewcze paleniska tworzą jednoczęściowe wieloprzebiegowe taśmy z przodu iz tyłu. Dopływ wody do paneli odbywa się przez dolną komorę, a odpływ z górnej. Takie rozmieszczenie komór wlotowych i wylotowych poprawia wydajność hydrauliczną panelu. Schemat przepływu medium przez ekrany NRC jest następujący: Najpierw medium wchodzi na tylne panele przesiewacza i tylne panele przesiewacza bocznego, następnie kierowane jest na przednią szybę i przednie panele przesiewaczy bocznych z obejściem rury Ш 135*15. Podkładki Ш30 mm są instalowane na rurach obejściowych w celu poprawy hydrodynamiki. Po LFC medium o temperaturze 393 °C przesyłane jest rurami 133*15 do kolektora pionowego Ш273*45, a stamtąd rurami obejściowymi 133* wchodzi na ekrany boczne i przednie górnej części radiacyjnej (RTC) 15. Względne położenie komór wlotowych i wylotowych paneli TRC jest podobne do położenia paneli RRC. Po przejściu przez wielociągowe panele przesiewacza przedniego i bocznego TCG, para kierowana jest rurami obejściowymi 133*15 do pionowego kolektora mieszającego Ш325*45, a stamtąd trafia do paneli w kształcie litery N przesiewacza tylnego TRC przez rury Ш159*16.
Po przejściu wielociągowych paneli przednich i bocznych ekranów TRC para kierowana jest rurami obejściowymi Sh133*15 do pionowego kolektora mieszającego Sh325*45, a po podgrzaniu do 440°C w promieniujących powierzchniach pieca, para kierowana jest na panele osłon bocznych i tylnych ścian kamer obrotowych. Para po przejściu przez sita komory nawrotnej przechodzi rurkami do 1 schładzacza wtryskowego Ш279*36. W schładzaczu 1 wtryskowym przepływy są przenoszone przez całą szerokość komina. Za schładzaczem para doprowadzana jest do przegrzewacza stropowego rurami Ш159*16. W przegrzewaczu stropowym para przemieszcza się z tylnej ściany czopuchu na przód kotła i wchodzi do komór wylotowych stropu Ш273*45 o temperaturze 463°C. Na rurociągach parowych Ш273*39, które są kontynuacją komór wylotowych przegrzewacza stropowego, montuje się zawory (VZ) DU-225 wbudowane w trakt. Za przegrzewaczem stropowym przepływy przepływają na całej szerokości przewodu gazowego, a para przewodami 159*18 kierowana jest do sit wlotowych pierwszego stopnia przegrzewacza ekranowego, znajdujących się w środkowej części przewodu gazowego. Para po przejściu przez sita wlotowe o temperaturze 502°C trafia do drugiego schładzacza wtryskowego Ш325*50, po czym kierowana jest na sita wylotowe pierwszego stopnia usytuowane wzdłuż krawędzi czopuchu. Komora odbiorcza pary sit wlotowych oraz przewód parowy drugiego schładzacza realizują przenoszenie przepływów po szerokości czopuchu. Przed drugim zatłaczaniem znajduje się rurociąg parowy Ш194*30 do odprowadzania części pary WPN do wymiennika ciepła gazowo-parowego, a po zatłaczaniu rurociąg parowy zawracania tej pary. Drugi schładzacz wtryskowy posiada podkładkę oporową. Za kratami wylotowymi pierwszego stopnia znajduje się trzeci schładzacz wtryskowy Ш325*50, którego rurociąg parowy przepływa wzdłuż szerokości kanału gazowego. Para kierowana jest następnie do środkowych części kanału gazowego i po przejściu przez nie jest przekazywana rurociągiem parowym Ш325*60 o temperaturze 514 °C wzdłuż szerokości kanału gazowego na ekrany wylotowe drugiego scena, znajdująca się wzdłuż krawędzi kanału gazowego. Za sitami wylotowymi drugiego stopnia para o temperaturze 523°C wchodzi do czwartego schładzacza wtryskowego Ш325*60. Zarówno ekrany wlotowy jak i wylotowy obu stopni przegrzewacza sitowego posiadają współprądowy schemat wzajemnego ruchu pary i gazów. Za schładzaczem para o temperaturze 537 °C rurociągiem parowym Ш237*50 wchodzi do pakietu konwekcyjnego, który jest wykonany według schematu współprądowego, przepuszcza go o temperaturze 545°C i jest podawana do turbiny . Począwszy od komór wlotowych ekonomizera wody, wszystkie rury obejściowe i komory traktu SVD wykonane są ze stali 12Kh1MF. Po HPC turbiny para o ciśnieniu 39,5 atm. Temperatura 307°C przesyłana jest do przegrzewacza pośredniego w dwóch strumieniach. Jedna „zimna” linia pary niskociśnieniowej zbliża się do korpusu, rozdzielają się na dwie przed nagrzewnicą. W nagrzewnicy każdej obudowy znajdują się dwa niskociśnieniowe strumienie pary z niezależną regulacją temperatury wzdłuż gwintów. Konstrukcja kotła Ściany komory spalania są całkowicie osłonięte rurami promiennikowych powierzchni grzewczych. Komora spalania każdego korpusu jest podzielona na komorę spalania (przedpalnik) i komorę dopalania za pomocą wypustek utworzonych przez występy przedniego i tylnego ekranu. Ekrany w strefie przedpiecowej do el. 15.00 w pełni nabijane i pokryte masą chromitową. Izolacja komory spalania i zacisku w palenisku ogranicza przenoszenie ciepła promieniowania z rdzenia palnika, co podnosi poziom temperatury w przedpaleniu, a tym samym poprawia warunki zapłonu i spalania paliwa, a także przyczynia się do lepszego tworzenia płynnego żużla. Proces spalania AS zachodzi głównie w przedpaleniu, jednak spalanie trwa nadal w dopalaczu, gdzie dopalanie mechaniczne spada z 7,5-10% do 2,5%. W tym samym miejscu temperatura gazów spada do 1210°C, co zapewnia pracę powierzchni grzewczych przegrzewacza SVD bez żużla. Naprężenie cieplne całej objętości pieca wynosi Vt=142*103 kcal m3/godz., a przedpiecowego Vtp=491*103 kcal m3/godz.
Piec każdego z dwóch budynków wyposażony jest w 12 pyłowo-gazowych palników turbulentnych umieszczonych w dwóch kondygnacjach (po trzy palniki w każdej kondygnacji przedniej i tylnej ściany pieca). Dopływ gazu do palników jest obwodowy, wydajność palnika na pyle wynosi 0,5 t/h. Każdy palnik turbulentny ma wbudowaną dyszę olejową do mechanicznego rozpylania z chłodzeniem i zorganizowanym dopływem powietrza. Aby usunąć płynny żużel, przedpalnik posiada dwa chłodzone otwory spustowe, przedpiec jest wykonany ze spadkiem 80 do otworów spustowych i jest zamknięty cegłami szamotowymi. Każdy piec wyposażony jest w dwa (w zależności od ilości karbów) zmechanizowane zespoły odżużlania. Ciekły żużel jest granulowany w łaźniach wodnych i odprowadzany do kanałów płukania żużla. Środek suszący wyprowadzany jest przez prostokątne palniki, które znajdują się na bocznych ścianach przedpalenia w dwóch kondygnacjach: w dolnej znajdują się 4 palniki, w górnej 2. W piecu znajdują się włazy do prac remontowych . Palenisko osłonięte jest w dolnej części do 23,00 m rurami dolnej części radiacyjnej (LRC), aw górnej części rurami górnej części radiacyjnej (RTC) od sufitu. Rury tylnych i przednich sit NRCH posiadają zagięcia, które tworzą zacisk paleniska. Tylny ekran TRC w górnej części posiada występ, który poprawia aerodynamikę przepływu gazu na wylocie pieca oraz częściowo chroni powierzchnie ekranu przed bezpośrednim promieniowaniem z pieca. Przednie i tylne ekrany NRCH są strukturalnie identyczne, każdy ekran składa się z sześciu identycznych taśm, z rurami połączonymi równolegle Sh42*6 z materiału 12X1MF. Rury taśmowe są najpierw przesiewane pod i dolną częścią przedpieca, a następnie przechodzą do pionowego panelu NRCH, gdzie wykonują pięć przejść podnoszących i opuszczających oraz wychodzą do komory górnej. Rury NRCH są okablowane do otworów strzelniczych palników, włazów, peperów. Ekrany boczne NRC składają się z czterech paneli, które są wykonane w następujący sposób.
Opuszczając dolną komorę, taśma składająca się z 17 równolegle połączonych zwojów Ш42*5, materiał 12Х1МФ, najpierw osłania dolną część ściany bocznej, następnie przesuwa się do części pionowej, gdzie wykonuje również pięć ruchów podnoszenia i opuszczania oraz następnie wychodzi do górnej komory. Przedni i tylny ekran NRCH mają dwa poziomy mocowań stałych na poziomie 22,00 i 14,5 m. Kompensacja rozszerzalności temperaturowej następuje na skutek zginania rur na zacisku. Ekrany boczne są zawieszone na stałych uchwytach na wysokości 21,9 m i można je swobodnie opuszczać. Aby zapobiec wychodzeniu poszczególnych rur do pieca, ekrany posiadają pięć pasów ruchomych łączników. Przedni i tylny ekran TCG również składają się z paneli wieloprzebiegowych z ruchami podnoszenia i opuszczania pary. Do dolnej komory paneli doprowadzana jest para, zdejmowana z górnych. Panele środkowe ekranu przedniego i wszystkie panele ekranów bocznych składają się z ośmiu, a panele skrajne ekranu przedniego z dziewięciu rur połączonych równolegle, tworzących taśmę. Panel w kształcie litery N tylnej szyby TCG składa się z dwudziestu rur połączonych równolegle. Wszystkie powierzchnie grzewcze VRC wykonane są z rur Ш42*5, materiał 12Х1МФ. Szyby przednie i boczne TCG są nieruchomo zawieszone na wysokości 39,975 m i swobodnie rozszerzają się w dół. Tylny ekran TCG ma dwa stałe mocowania na 8,2 i 32,6. Kompensacja rozszerzalności cieplnej rur następuje w wyniku wygięcia rur w górnej części tylnej szyby TCG. Przednia i boczna osłona posiadają siedem rzędów ruchomych mocowań, tylna - trzy. Wszystkie ekrany NRC i TRC mają odstęp między rurami wynoszący 45 mm. Strop paleniska i szczyt poziomego kanału dymowego są osłonięte rurami przegrzewacza stropowego. W sumie są połączone równolegle 304 rury (154 na gwint) Ш32*4, materiał 12Х1МФ. Wzdłuż długości rur przegrzewacza stropowego znajduje się 8 rzędów łączników, które mocowane są do ramy za pomocą prętów.
Przegrzewacze sitowe Na wylocie pieca znajduje się przegrzewacz sitowy, który składa się z dwóch rzędów sit. W rzędzie 16 ekranów o rastrze 630 mm, zawieszonych w pionie. W trakcie pary sita każdego stopnia dzielą się na wlot i wylot, które znajdują się bliżej ścian bocznych kanału gazowego. Strukturalnie ekrany wlotowe i wylotowe pierwszego etapu są identyczne (z wyjątkiem usytuowania kształtek i rur obejściowych na komorach). Ekran pierwszego stopnia kotła 20 składa się z 42 wężownic 32*6, materiał rury to głównie 12Х1МФ, ale dla 11 skrajnych wężownic część wylotową stanowią rury 32*6, materiał 1Х18Н12Т. Na kotle 19 ekranów pierwszego stopnia składa się z 37 wężownic, materiał 1X18H12T. Aby nadać konstrukcji sztywność, ekran jest połączony 5 zwojami, które posiadają listwy mocujące wykonane ze stali X20H14S2. Sita drugiego stopnia składają się z 45 cewek Ш32*6. Materiał ekranów wejściowych to 12Kh1MF, a reszta cewek wykonana jest ze stali 1Kh18N12T. Ekran połączony jest sześcioma cewkami. Komory wlotowa i wylotowa, z wyjątkiem komór sit wylotowych drugiego stopnia, są połączone w pojedyncze kolektory oddzielone przegrodą. Komory na prętach zawieszone są na belkach ramy. Ściany komory obrotowej są osłonięte czterema blokami. Klocki wykonane są w formie dwupętelkowych taśm. W każdym bloku znajduje się 38 równolegle połączonych cewek Ш32*6 z materiału 12Х1МФ, które są umieszczone poziomo. Bloki posiadają paski usztywniające. Zawieszenie bloków odbywa się za pomocą trzech rzędów (na blok) łączników. W gazowym przewodzie opadowym znajdują się następujące powierzchnie grzewcze: konwekcyjny komin SVD, przegrzewacz niskiego ciśnienia z wymiennikiem gazowo-parowym oraz ekonomizer wody. Dla wszystkich powierzchni konwekcyjnych przyjęto naprzemienny układ cewek. Wszystkie powierzchnie wykonane są z wężownic równoległych do czoła kotła.
Przegrzewacz konwekcyjny SVD
Pakiet przegrzewacza konwekcyjnego SVD każdej linii składa się ze 129 wężownic 32*6, materiał 1Х18Н12Т, które wsparte są na stojakach wykonanych z materiału Х23Н13 oraz na belkach nośnych chłodzonych wodą zasilającą. Istnieją trzy rzędy listew dystansowych wykonanych ze stali 1X18H12T, aby wytrzymać stopnie i usztywnić konstrukcję, opakowanie ma wysokość 557 mm. Przegrzewacz niskiego ciśnienia Przegrzewacz niskiego ciśnienia znajduje się za pakietem konwekcyjnym SVD. Pakiety każdego strumienia znajdują się w odpowiednich połówkach rury opadowej, przenoszenie strumieni przez szerokość komina nie jest realizowane. Przegrzewacz LP składa się z pakietu wyjściowego, pakietu pośredniego i stopnia regulacyjnego. Część wyjściowa przegrzewacza LP składa się ze 108 zawieszonych wężownic Sh42*3,5, z materiału połączonej stali: Kh2MFSR i 12Kh1MF. Wężownice są montowane w pakietach ze stojakami z materiału X17H2, które są zawieszone na kolektorach wsporczych pakietu wysokociśnieniowego. Wysokość opakowania 880 mm. Pakiet pośredni składa się również ze 108 podwójnych cewek Ш42 * 3,5 podwójnych cewek Ш42 * 3,5 materiału 12Х1МФ. Wysokość opakowania 1560 mm. Cewki oparte są na zębatkach, materiał Kh17N2, a te na komorach wlotowych pakietu pośredniego Sh325*50, materiał 12Kh1MF. W ten sposób komory wlotowe pakietu przemysłowego są również belkami nośnymi dla tej powierzchni grzewczej. Komory oprócz izolacji posiadają dodatkowe chłodzenie powietrzem wymagane w trybach rozruchu i po wyłączeniu turbiny. Za pakietem przemysłowym wzdłuż przepływu gazu, na obu korpusach kotłów TPP-210, zamiast GPP TO zainstalowano stopień kontrolny, który jest pierwszym stopniem przegrzewacza wzdłuż przepływu pary, wykonany jest ze stali perlitowej i , zgodnie z warunkami niezawodnej pracy rur o znacznym odparowaniu, znajduje się w strefie, w której temperatura gazów na wlocie nie może przekraczać 600°C. Jej działanie polega całkowicie na zmianie pochłaniania ciepła pary wtórnej poprzez zmianę jej dystrybucji przez obejściowe rurociągi parowe. Według obliczeń, przy znamionowym obciążeniu bloku, przez stopień kontrolny przechodzi 20% całkowitego przepływu pary. Przy zmniejszeniu obciążenia bloku do 70% zużycie pary wynosi 88% Wzrost sprawności bloku uzyskuje się poprzez rozszerzenie zakresu obciążeń, przy którym zapewniona jest projektowa temperatura przegrzania wtórnego z optymalnym nadmiarem powietrze. Powierzchnia sterująca jest zamontowana w gabarytach zdemontowanego GPP TO, kolektory wejściowe są opuszczone 300 mm niżej. Powierzchnia sterowa składa się z części lewej i prawej o łącznej powierzchni grzewczej 2020 m² na korpus. Obie części są złożone z pakietów podwójnych cewek i mają 4 pętle wzdłuż przepływu gazu z przeciwprądowym wzorcem przepływu pary. Wężownice są wykonane z rur Ш32*4, stali 12Х1МФ i są ułożone w szachownicę z krokiem 110 i 30 mm. Cewki są składane w paczki za pomocą tłoczonych stojaków wykonanych ze stali 12X13. Na długości każdego pakietu zainstalowano 5 stojaków. Dwa z nich montowane są na kolektorach chłodzonych wodą znajdujących się w kanale gazowym, które podczas naprawy są obniżane o 290 mm. Para z HPC wchodzi do komór wlotowych powierzchni sterowej Sh425*20 stal 20. Po przejściu przez wężownice para wchodzi do komór wylotowych o średnicy 426*20 stal 12Kh1MF, gdzie miesza się z parą pochodzącą z obejścia rurociąg parowy. Stare zawory RKT wycięto wzdłuż linii „B” i „C” ze starego RKT, wyjęto części wewnętrzne, a korpusy RKT wyparzono i wykorzystano jako trójniki. Na linii obejściowej pomiędzy rozdzielaczem wlotowym i wylotowym instalowane są nowe zasuwy RKT. Gdy zawór jest otwarty do 100%, para w ilości 80% przechodzi obok powierzchni sterującej i p/p maleje. Gdy zawór jest zamknięty, para przepływa przez powierzchnię sterującą i temperatura ponownego podgrzewania wzrasta. Klawisze KDU i klawisze sterujące nowego RKT pozostały takie same. Wymieniono wężownice ekonomizera wody na obu kadłubach (100%). Podkładki ustalające zostały zdemontowane na kolektorach drugiego wtrysku, a wyloty do GPP TO zostały wyłączone. Ekonomizer konwekcyjny to ostatnia powierzchnia grzewcza w strumieniu gazu, znajdująca się w rurze opadowej. Składa się z rur Ш32*6, materiał st20. Komory wylotowa i wlotowa ekonomizera są również belkami nośnymi - ciężar tej powierzchni grzewczej przenoszony jest na nie poprzez zębatki. Rama kotła wykonana jest w postaci identycznych ram obu budynków, połączonych połączeniami międzykadłubowymi i rusztowaniami przejściowymi. Ciężar powierzchni grzewczej, okładziny i izolacji przenoszony jest za pomocą poziomych belek i wiązarów na trzy rzędy słupów pionowych, jeden wzdłuż czoła kotła, drugi między paleniskiem a rurami spustowymi i trzeci przy tył kotła. Aby usztywnić ramę, zastosowano szereg nachylonych belek. Okładziny pieca, kanały gazowe kotłów wykonane są w postaci oddzielnych osłon. Piec i czopy osłonięte są blachami o grubości 3 mm, co zapewnia wysoką gęstość paleniska i czopuchu.
Zmiana z 1,12 na 1,26 prowadzi do spadku z 2,5 do 1,5% dla drugiej grupy paliw. Dlatego, aby zwiększyć niezawodność komory spalania, konieczne jest utrzymanie nadmiaru powietrza na wylocie pieca powyżej 1,2.
Na stole. 1-3 w zakresie zmian naprężeń cieplnych objętości pieca i stopnia rozdrobnienia /? 90 (rys. 6-9, c, d) nie stwierdzono ich wpływu na wartość. Nie udało się również wykazać wpływu stosunku prędkości powietrza wtórnego i mieszaniny pyłowo-powietrznej w badanym zakresie ich zmiany na sprawność pracy pieca. Jednak wraz ze spadkiem przepływu powietrza przez kanał zewnętrzny (przy zmniejszonych obciążeniach) i odpowiednim wzrostem powietrza przez kanał wewnętrzny (przy stałym natężeniu przepływu przez palnik) wydajność żużla poprawia się. Strumienie żużla stają się cieńsze, a ich liczba wzrasta.
Z równomiernym rozprowadzeniem kurzu i powietrza. nie ma dopalania chemicznego na wylocie paleniska przy palnikach i przy > 1,15.
Sprawność brutto wytwornicy pary przy spalaniu węgla (1/g "14%), przy obciążeniu znamionowym sięga 90,6%.
Podobne wyniki uzyskano w pracy, potwierdzając, że wytwornica pary TPP-210A pracuje ekonomicznie i niezawodnie również przy spalaniu AS (1/g = 3,5%; 0 szt. = 22,2 MJ/kg;
Przy nadmiarze powietrza w palenisku przy = 1,26h-1,28, stopień zmielenia /?9o = ----6-^8%, w zakresie obciążenia D< = 0,7-^ 1,0£)н величина потери тепла с механическим недожогом достигает 3%. Максимальный к. п. д. брутто парогенератора при номинальной нагрузке составляет 89,5%.
W pracy przedstawiono dane stwierdzające, że podczas spalania antracytu w komorze spalania wytwornicy pary TPP-210A wartość podpalenia mechanicznego<74 в условиях эксплуатации примерно в 1,5 ниже, чем при работе котлов ТПП-110 и ТПП-210 с двухъярусным расположением вихревых горелок мощностью 35 МВт.
Przeprowadzone badania, jak również wieloletnia eksploatacja pilotażowa wytwornicy pary TPP-210A wykazały, że w zakresie zmian obciążenia od 0,65 do wartości nominalnej komora spalania pracuje ekonomicznie i stabilnie, bez odpylania i bez naruszania płynny reżim usuwania żużla.
Czas trwania akcji (przed remontem) wytwornicy pary z palnikami pyłowo-gazowymi bez ich naprawy wynosił 14545 godzin. Jednocześnie stan palników był zadowalający; spalenie ceglanych strzelnic, wypaczenie rur gazowych i dysz jest nieistotne.
Podczas oględzin komory spalania podczas postojów nie stwierdzono gromadzenia się żużla na palenisku oraz żużla ścian komory dopalania. Cały pas z ćwiekami pokryty był gładką, błyszczącą warstwą żużlu. Nie zaobserwowano również dryfu konwekcyjnych powierzchni grzewczych.
Wyłączenie jednego lub dwóch średnich palników nie zmniejsza stabilności zapłonu, nie wpływa na tryb usuwania popiołu ciekłego i nie prowadzi do naruszenia reżimu temperaturowego LRC i TRC.
Miot JAKO ZASOBY ENERGETYCZNE. Zróbmy od razu zastrzeżenie, że wykorzystanie rodzimej (bez ściółki) ściółki do zaspokojenia potrzeb energetycznych jest znacznie droższe niż ściółka pod względem zarówno kapitałowym, jak i operacyjnym...
KOMPLEKSOWA SPOSÓB ZAGOSPODAROWANIA OBORNIKA Z KURCZAKA Z POZYSKIWANIEM NAWOZÓW ORGANOMINERALNYCH ORAZ GAZÓW PALNYCH, ENERGII CIEPLNEJ I ELEKTRYCZNEJ Obornik jest silnym zanieczyszczeniem zbiorników glebowych, wodnych i powietrznych. W tym samym czasie śmieci…