Naukowa biblioteka elektroniczna. Wdrożenie koncepcji „odchudzonej produkcji” w JSC „Nizhnekamskshina”
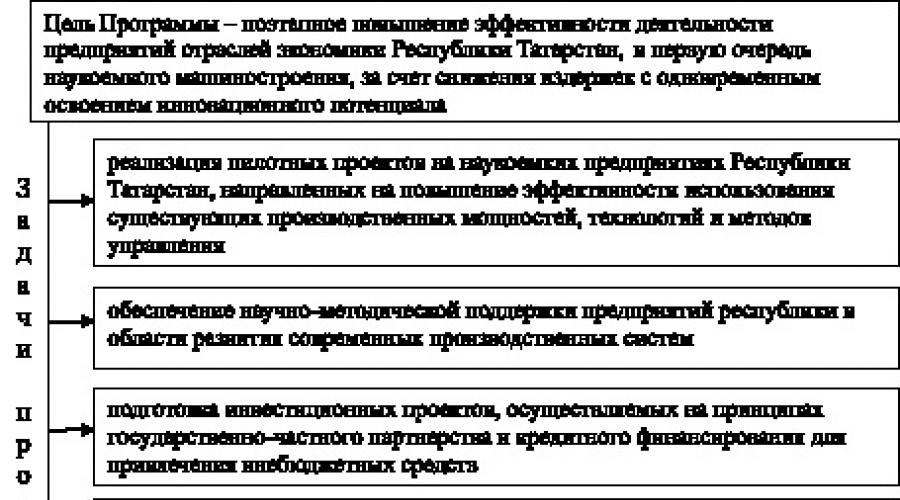
Efekt ekonomiczny szczupłej produkcji tylko jednej jednostki biznesowej TechnoNICOL jest porównywalny ze średnim budżetem regionalnego programu docelowego
/czerwiec 2014/ Ponad 200 mln rubli rocznie – to efekt ekonomiczny wdrożenia zasad lean manufacturing w zakładach produkcyjnych wełna kamienna Korporacja TechnoNIKOL.
Korporacja TechnoNIKOL jest jednym z liderów w Rosji pod względem wydajności pracy. Średnia produktywność w firmie wynosi 12 milionów rubli przychodu na osobę rocznie, podczas gdy przedsiębiorstwa w Rosji są uważane za wysoce produktywne, w których wskaźnik ten zaczyna się od 3 milionów rubli. Jedną z tajemnic sukcesu w walce o podniesienie poziomu wydajności pracy jest aktywne wykorzystywanie zasad lean manufacturing w przedsiębiorstwach firmy.
Według dyrektora ds. rozwoju system produkcji Tatiana Bertowa, Pochylać się od 2010 roku wprowadzono go m.in. w sześciu oddziałach produkcyjnych kierunku Izolacja Mineralna, które znajdują się na Ukrainie, Centralnym Okręgu Federalnym, Wołdze, Syberii, a także na Uralu i Dalekim Wschodzie. We wszystkich zakładach dużą wagę przywiązuje się do szkoleń w zakresie systemów i narzędzi szczupłej produkcji, które obejmują wszystkich – zarówno personel pracujący, jak i najwyższe kierownictwo.
Integralną częścią lean production w kierunku „Mineral Isolation” jest praca z ulepszeniami, w którą zaangażowani są wszyscy pracownicy SBU. Rocznie realizowanych jest ponad dwa tysiące propozycji racjonalizacji od pracowników oraz specjalistów inżynieryjno-technicznych. Mogą to być zarówno drobne usprawnienia, jak i przełomowe projekty o dużym efekcie ekonomicznym. I tak np. usprawnienie procesów zmiany linii produkcyjnej pozwoliło na skrócenie czasu przejścia z jednego rodzaju produktu na inny o 60% w ciągu trzech lat z efektem ekonomicznym 150 mln rubli rocznie, a także skrócenie czas planowanej wymiany elementów wyposażenia o 25% z efektem ekonomicznym 50 mln rubli rocznie. Dzięki zbudowaniu systemu TRM (obsługa i konserwacja sprzętu) w zakładach, nieplanowane przestoje sprzętu zostały zredukowane o 25%.
Wyeliminowanie strat z nadprodukcji uratowało przedsiębiorstwa przed nieracjonalnym wykorzystaniem zasobów energetycznych i obniżyło koszty utrzymania magazynów. Logistyka magazynowa, liczona w kilka sekund, wyeliminowała straty spowodowane niepotrzebnym transportem i ogólnie stała się o 90% bardziej efektywna. Zaopatrzenie w surowce w systemie just-in-time zminimalizowało straty, które wcześniej występowały przy akumulacji nadmiernych zapasów. Wydajność magazynu produkt końcowy wzrosła o 61%.
Ograniczeniu strat w produkcji wełny skalnej sprzyja także usprawnienie procesów biznesowych, w tym ich automatyzacja za pomocą systemy informacyjneświatowym poziomie. Wprowadzono usprawnienia w procesach, takich jak planowanie sprzedaży i operacji, zarządzanie utrzymanie i naprawy sprzęt produkcyjny, planowanie produkcji w fabrykach, zarządzanie zamówieniami klientów. Dzięki innowacjom obsługa klienta poprawiła się o 71%.
Stosowanie wbudowanych narzędzi wysokiej jakości corocznie pozwala firmie SBE „Mineral Isolation” na zwiększenie wydajności wysokiej jakości produktów termoizolacyjnych.
Ogólny efekt ekonomiczny wprowadzenia zasad lean manufacturing w zakładach produkcji wełny skalnej korporacji TechnoNIKOL wyniósł ponad 200 milionów rubli rocznie, co jest porównywalne ze średnim budżetem regionalnego programu docelowego. Według ekspertów TechnoNIKOL Corporation, aktywne rozpowszechnianie praktyk Lean Production w rosyjskich przedsiębiorstwach umożliwi podejście do realizacji dekretu Prezydenta Federacji Rosyjskiej „O długoterminowej polityce gospodarczej państwa” w zakresie zwiększenia wydajności pracy do 2018 r. o 50% (w stosunku do poziomu z 2011 r.).
Korporacja TechnoNIKOL jest jednym z największych producentów i dostawców pokryć dachowych, hydroizolacji i materiały termoizolacyjne. Działając na rynku materiałów budowlanych od 1992 roku, firma zgromadziła duże doświadczenie w produkcji materiałów hydroizolacyjnych, dźwiękowych i termoizolacyjnych, a dziś oferuje na rynku najnowsze materiały i technologie, które łączą światowe doświadczenie i własne osiągnięcia Centrum naukowe. Współpraca z instytutami projektowymi i pracowniami architektonicznymi pozwala Korporacji elastycznie i szybko reagować na zmiany wymagań konsumentów. Dziś TechnoNIKOL Corporation posiada 38 zakładów produkcyjnych w Rosji, Ukrainie, Białorusi, Litwie, Czechach i Włoszech, własną sieć sprzedaży 180 oddziałów i przedstawicielstwa w 36 krajach. Klientami Korporacji jest ponad 500 partnerów handlowych i ponad 50 000 organizacji oraz osoby fizyczne w Rosji, krajach WNP, krajach bałtyckich, Europie Wschodniej i Środkowej.
Wysyłanie dobrej pracy do bazy wiedzy jest proste. Skorzystaj z poniższego formularza
Studenci, doktoranci, młodzi naukowcy korzystający z bazy wiedzy w swoich studiach i pracy będą Ci bardzo wdzięczni.
Hostowane na http://www.allbest.ru/
Wstęp
Lean Manufacturing to system organizowania i zarządzania rozwojem produktu, operacjami, relacjami z dostawcami i klientami, w którym produkty wytwarzane są ściśle według wymagań klienta i z mniejszą liczbą wad w porównaniu z produktami wytwarzanymi przy użyciu technologii produkcji masowej. Zmniejsza to koszty pracy, przestrzeni, kapitału i czasu.
Filozofia Lean Manufacturing:
Ustalenie wartości każdej rodziny produktów z punktu widzenia klienta;
Zidentyfikuj wszystkie etapy strumienia wartości dla każdej rodziny produktów i wyeliminuj, w miarę możliwości, działania, które nie tworzą wartości;
Zestawianie operacji tworzących wartość w ścisłej kolejności, która zapewnia płynny ruch produktu w strumieniu skierowanym do klienta;
Pod koniec formowania się przepływu – stwarzając klientom możliwość „wyciągnięcia” wartości z poprzedniego etapu;
Po zidentyfikowaniu wartości, zidentyfikowaniu strumieni wartości, wyeliminowaniu etapów powodujących marnotrawstwo oraz ustanowieniu systemu przepływu i ciągnięcia, powtórz cały proces tyle razy, ile jest to konieczne, aby osiągnąć stan doskonałości, w którym powstaje wartość i nie ma marnotrawstwa.
Punktem wyjścia Lean Thinking jest wartość. Wartość może określić jedynie odbiorca końcowy, który za określoną cenę i w określonym czasie jest w stanie zaspokoić potrzeby nabywców. Wartość tworzy producent. Z punktu widzenia konsumenta po to istnieje producent.
„Lean Manufacturing” jest elementem rozległego japońskiego systemu zarządzania Kaizen (ciągłe doskonalenie) opartego na pomysłach Deminga, Jurana, Feigenbauma i ich japońskich odpowiedników Ishikawy, Taguchi i Shingu. Uważne studium innych koncepcji, przedstawionych jako nowe ostatnie słowo w budowaniu efektywnego zarządzania, zawartych w wielu książkach, które zapełniły półki krajowe, takich jak BSC (zrównoważona karta wyników), ABC (rachunkowość oparta na podejściu procesowym), BPR (reengineering procesów biznesowych ) ), Agile Manufacturing System (szybko reagujący system produkcyjny), Synchronous Manufacturing System (synchroniczny system produkcyjny), są mniej efektywnym ucieleśnieniem tych samych pomysłów. Oznacza to, że są to tylko systemy, które ułatwiają przejście od scentralizowanego, ścisłego zarządzania biznesowego do biznesu opartego na zaangażowaniu pracowników i przewadze horyzontalnych podejść do zarządzania nad wertykalnymi. Z tego punktu widzenia różne klasyczne warianty MRP i ERP wspierają również nieefektywne koncepcje biznesowe, które odchodzą w przeszłość. Zastępują je różne wersje prezentacji Kaizen, których jednym z najważniejszych elementów jest Lean Production.
Tematem tej pracy jest „Lean production” w przedsiębiorstwie.
Celem projektu dyplomowego jest określenie skuteczności wdrożenia koncepcji „Lean production” w przedsiębiorstwie. Aby osiągnąć cel, konieczne jest rozwiązanie następujących zadań:
Zbadanie pojęcia „odchudzonej produkcji”, teoretycznych i metodologicznych aspektów koncepcji;
Historia pochodzenia, zasady i narzędzia;
Rozważ rodzaje strat i metody oceny skuteczności wdrożenia „Lean production”;
Analiza procesu wdrażania „Lean production” na przykładzie JSC „Nizhnekamskshina”;
Oceń wzrost wydajności po wprowadzeniu „Lean production” w krajowym przemyśle.
Przedmiotem projektu dyplomowego jest OAO Nizhnekamskshina. Przemysł oponiarski to jedna z dynamicznie rozwijających się gałęzi przemysłu petrochemicznego. Stabilne dostawy surowców i terminowa sprzedaż gotowych produktów pozwoliły OAO Nizhnekamskshina utrzymać wiodącą pozycję w obliczu ostrej konkurencji między fabrykami opon w Rosji.
UAB „Nizhnekamskshina” jest największym przedsiębiorstwem w branży oponiarskiej, zajmuje wiodącą pozycję wśród producentów opon w Federacja Rosyjska i krajów WNP. Przedsiębiorstwo produkuje opony samochodowe marek KAMA, KAMA EURO. Asortyment obejmuje ponad 120 rozmiarów i modeli opon, w tym opracowane przez specjalistów Centrum Naukowo-Technicznego „Kama”.
22 lipca 2007 roku 300-milionowa opona zjechała z linii montażowej OAO Nizhnekamskshina. Był to model KAMA EURO 228, rozmiar 205/75 R15, przeznaczony do samochodów Chevrolet Niva.
Przedsiębiorstwo jest pierwszym dostawcą na rynku rosyjskim,
uzyskał status „homologatora” opon w zakładach samochodowych Fiat, Volkswagen, Skoda.
Podstawą teoretyczną badania były prace takich autorów, którzy badają zarządzanie jakością, koncepcję produkcji szczupłej, nie tylko jako systemu jako całości, ale także w odniesieniu do przemysłu oponiarskiego, takich jak Boronenkova S.A., Melnik L.A., Loganina V.I. itd.
Baza informacyjna składa się z materiałów regulacyjnych i prawnych, literatury specjalistycznej oraz materiałów z zakresu praktyki.
Praktyczne znaczenie pracy polega na tym, że wyniki badania mogą być wykorzystane zarówno w ogólnym zrozumieniu pojęcia „Lean production”, jak i w jego praktycznym zastosowaniu.
W pracy wykorzystano takie metody badawcze jak: porównawcze, dynamiczne, tabelaryczne, graficzne, sieciowe, a także metodę analizy i inne statystyczne metody zarządzania jakością.
Niniejsza praca składa się z trzech rozdziałów: pierwszy zawiera teoretyczne i metodologiczne aspekty koncepcji „Odchudzonej produkcji”, drugi charakteryzuje ogólne działania, system zarządzania jakością, proces wdrażania „Odchudzonej produkcji” w OAO Nizhnekamskshina, trzeci obejmuje sposoby zwiększenia wydajności od wprowadzenia „Lean production” w krajowym przemyśle.
Tym samym koncepcja Lean Manufacturing zyskuje w Rosji coraz większą popularność. Często wprowadzanie nowych systemów produkcyjnych spotyka się z poważnym oporem ze strony personelu firmy. Wiele firm produkcyjnych jest zainteresowanych obniżeniem kosztów, zwiększeniem produktywności i poprawą wskaźników jakości.
1. Teoretyczne i metodologiczne aspekty koncepcji „Lean production”
1.1 Historia powstania „Lean Manufacturing”
Termin „szczupła produkcja” („szczupła produkcja”), który później zaczęto tłumaczyć jako „szczupła produkcja”, wprowadził do obiegu naukowego John Krafchik w książce „Maszyna, która zmieniła świat”, która ukazała się w 1990 roku . Jednak początki filozofii lean manufacturing sięgają początku XX wieku.
Idee „odchudzonej produkcji” po raz pierwszy sformułował i wdrożył Henry Ford. Ale te idee miały charakter odmiennych wydarzeń i nie wpływały na same poglądy pracowników. W 1913 (niektóre źródła podają 1908), Henry Ford stworzył pierwszy na świecie model przepływu pracy, który opierał się na ruchu elementu obrabianego pomiędzy procesami za pomocą przenośnika. Powstała płynna, tania produkcja, a samochód marki Ford-T nie miał konkurencji na świecie pod względem ceny, jakości i poziomu obsługi. Ale idee Henry'ego Forda nie rozpowszechniły się, ponieważ gospodarka kraju rozwijała się dynamicznie, rynek był zamknięty dla innych państw i istniały możliwości szerokiego rozwoju. Japonia nie miała takich możliwości, dlatego od razu obrała drogę racjonalnego wykorzystania zasobów, eliminowania wszelkiego rodzaju strat, zwiększania inicjatywy i odpowiedzialności pracowników oraz stałego systematycznego podnoszenia jakości i procedur.
Centrum rozwoju i wdrażania zasad i metod „odchudzonej produkcji” była firma motoryzacyjna Toyota, która zapożyczyła wszystko, co najlepsze z systemów produkcyjnych firm na całym świecie. Toyota Toyota (Toyota Motor Corporation, Toyota Jidosha KK) to japońska firma motoryzacyjna, która jest częścią finansowej i przemysłowej grupy Toyota. Jedna z największych firm motoryzacyjnych na świecie. Wypuszcza swoje produkty pod różne marki, w tym Daihatsu. Siedziba znajduje się w Toyota (Toyota).
Początek historii Toyoty można uznać za rok 1933, kiedy to Zakłady Automatyczne Krosna Toyoda, które początkowo nie miały nic wspólnego z samochodami i zajmowały się przemysłem tekstylnym, otworzyły dział motoryzacyjny. Otworzył ją najstarszy syn właściciela firmy Sakichi Toyoda (Sakichi Toyoda) Kiichiro Toyoda (Kiichiro Toyoda), który później doprowadził markę samochodów Toyota do światowej sławy. Kapitałem początkowym na rozwój pierwszych samochodów były pieniądze otrzymane ze sprzedaży praw patentowych na maszyny przędzalnicze angielskiej firmie Platt Brothers.
W 1935 roku zakończono prace nad pierwszym samochodem osobowym, nazwanym Model A1 (później AA), oraz pierwszą ciężarówką, Modelem G1, a w 1936 wprowadzono do produkcji Model AA. W tym samym czasie zrealizowano pierwszą dostawę eksportową - cztery ciężarówki G1 trafiły do północnych Chin. Rok później, w 1937 roku, dział motoryzacyjny stał się odrębną firmą o nazwie Toyota Motor Co., Ltd.
Pojęcie pracy, która nie dodaje wartości, którą później ucieleśnił termin MUDA, wprowadził Frank Gilbert (1868-1924), który zauważył kiedyś, że murarz wznoszący ścianę miał efekt uboczny schylania się, by podnieść następną cegłę. . Po przestudiowaniu kroków wymaganych przez murarza do wykonania danej pracy, Frank Gilbert zasugerował ułożenie cegieł na piedestale obok robotnika. Takie, na pierwszy rzut oka, elementarne rozwiązanie problemu doprowadziło do prawie trzykrotnego zwiększenia szybkości pracy i znacznego zmniejszenia wkładanego na nią wysiłku.
W 1934 Toyoda została zreorganizowana w Japonii. Odtąd firma stała się znana jako Toyota, a głównymi produktami wytwarzanymi w jej fabrykach nie były tekstylia, ale samochody. Kiichiro Toyoda, założyciel Toyota Motor Corp., odpowiadał za produkcję silników i stale odkrywał coraz więcej problemów związanych z ich produkcją. Uznał, że głównym kierunkiem poprawy jakości jest intensywne badanie każdego etapu procesu produkcyjnego. W tych powojennych czasach Japonia legła w gruzach, a kraj potrzebował nowych samochodów. Problem polegał jednak na tym, że popyt nie był wystarczająco silny, aby uzasadnić zakup potężnej linii produkcyjnej, na modłę Forda. Potrzebnych było wiele różnych typów pojazdów (samochody osobowe, małe i średnie ciężarówki itp.), ale zapotrzebowanie na konkretny widok samochód był mały. Japończycy musieli nauczyć się efektywnie pracować, tworząc mnóstwo różne modele w warunkach małego zapotrzebowania na każdy model. Nikt przed nimi nie rozwiązał takiego problemu, ponieważ wydajność rozumiana była wyłącznie w kategoriach produkcji masowej.
W 1936 roku Toyota wygrała swój pierwszy przetarg na produkcję samochodów ciężarowych, podczas realizacji tego zamówienia zidentyfikowano nowe problemy w procesie technologicznym produkcji samochodów. Potrzeba ich rozwiązania skłoniła Kiichiro Toyoda do stworzenia grup „KAIZEN”, których głównym zadaniem było ciągłe badanie wszystkich etapów procesu produkcyjnego, a następnie opracowywanie i wdrażanie metod jego doskonalenia.
W powojennej Japonii poziom popytu w gospodarce był na niskim poziomie, więc obniżenie kosztów produktów wytwarzanych w japońskich fabrykach poprzez efekt skali nie było możliwe.
Ojcem lean manufacturing jest Taiichi Ohno (1912-1990), który rozpoczął pracę w Toyota Motor Corporation w 1943, integrując najlepsze światowe praktyki. Taiichi Ohno był pracownikiem Toyota Corporation i stopniowo piął się po szczeblach kariery do szefa firmy. Jako inżynier, Taiichi Ohno opracował system zarządzania kosztami Kanban, Lean Manufacturing i Just-in-Time. Firma nadal trzyma się tego systemu. W 1949 został kierownikiem warsztatu mechanicznego. Na początku lat pięćdziesiątych, kiedy zmarł Kiichiro Toyoda, Taiichi Ono wymyślił, a następnie stworzył na tamte lata rewolucyjny system zarządzania produkcją („kanban”), za pomocą którego Japończykom udało się wyeliminować wszelkiego rodzaju odpady z procesu produkcyjnego. Rozwój naukowy zarówno w zarządzaniu, jak i ponowne wyposażenie techniczne, zawsze były wysoko cenione w tym przedsiębiorstwie. W połowie lat pięćdziesiątych zaczął budować specjalny system organizacji produkcji zwany Toyota Production System lub Toyota Production System (TPS). System Toyoty stał się znany w zachodniej interpretacji jako szczupła produkcja, szczupła produkcja, szczupła produkcja. Termin lean został zaproponowany przez Johna Krafcika, jednego z amerykańskich konsultantów. W latach 50-tych Toyota była najbardziej aktywna w tym obszarze. Dzięki zaawansowanej polityce naukowej i przemysłowej przedsiębiorstwu udało się stworzyć pojazdy terenowe Land Cruiser i Crown. W 1954 Taiichi Ohno objął stanowisko dyrektora fabryki Toyoty. Po przejściu kilku kolejnych stopni skomplikowanej japońskiej drabiny hierarchicznej, w 1975 roku został wiceprezesem wykonawczym całej firmy, od 1978 - prezesem zarządu Toyota Spinning and Weaving.
W USA Taiichi Ohno napisał kilka książek na temat tego systemu, z których najsłynniejszą jest The Toyota Production System.
Wyjście z masowej produkcji. Taiichi Ohno przedstawia myśli i idee trzech menedżerów XX wieku - Henry'ego Forda, Sakichiego Toyody i Kiichiro Toyody.
Znaczący wkład w rozwój teorii Lean Production wniósł współpracownik i asystent Taiichi Ono – Shigeo Shingo, który stworzył m.in. metodę SMED. Po wizycie w Stanach Zjednoczonych i zapoznaniu się z systemem supermarketów Taiichi Ohno doszedł do wniosku, że produkcja nie powinna opierać się na planowanych wielkościach sprzedaży (strategia push), ale na realnym popycie (strategia pull).
To właśnie Taiichi Ohno połączył w murach fabryki Toyoty wszystkie zaawansowane metody zwiększania wydajności produkcji.
Następnie zapytano Taiichi Ohno, co zainspirowało go do stworzenia Toyota Production System, na co odpowiedział: Wszystkiego nauczyłem się z książki Henry'ego Forda. Jednak to skala, precyzja i ciągłe doskonalenie Systemu Produkcyjnego Toyoty uczyniły z niego fundamentalny element Lean Manufacturing, którego główną korzyścią jest przestrzeganie własnej złotej zasady: Maksymalny wpływ pochodzi z ciągłego doskonalenia.
Początkowo koncepcja Lean Manufacturing była stosowana w branżach z produkcją dyskretną, przede wszystkim w branży motoryzacyjnej. Następnie koncepcja została dostosowana do warunków ciągłej produkcji, a następnie w handlu, usługach, użyteczności publicznej, służba zdrowia, wojsko i sektor publiczny.
Stopniowo szczupła produkcja wychodziła poza przedsiębiorstwo. Teraz przy pomocy lean manufacturing optymalizują sektor usług i proces komunikacji między konsumentem a dostawcą, proces dostawy i obsługi produktów. Idee Lean są promowane przez regularne międzynarodowe i regionalne konferencje, z których wiele jest inicjowanych przez Lean Enterprise Institute (USA) i Lean Enterprise Academy (Anglia). W wielu krajach rozprzestrzenianie się lean manufacturing: wsparcie rządowe. W okresie największej konkurencji i nasilającego się kryzysu przedsiębiorstwa na całym świecie nie mają innego wyjścia, jak wykorzystanie najlepszych światowych technologii zarządzania do tworzenia produktów i usług maksymalizujących zadowolenie klientów pod względem jakości i ceny.
W ostatnich latach w Rosji, podobnie jak w krajach byłego Związku Radzieckiego, nastąpił znaczny wzrost zainteresowania zarządzaniem, zarządzaniem przedsiębiorstwem oraz przekształceniami struktur organizacyjnych przedsiębiorstw. Niestety zainteresowanie to ujawniło się dopiero od niedawna. W ostatnim czasie w praktyce światowej powstało wiele nowych koncepcji i metod zarządzania: reengineering procesów biznesowych (BPR), Total Quality Management (TQM), zrównoważona karta wyników (BSC), statystyczna kontrola procesów (SPC), coaching, modele międzynarodowych norm ISO 9000 , ISO 14000, HACCP, Five S's, Six Sigma i więcej. Niestety kraje przestrzeni postsowieckiej nie mają własnych rozwiązań w tej branży. Nie ma tradycji, szkół, doświadczeń poprzedników, ugruntowanych systemów zarządzania. Dlatego rosyjscy menedżerowie muszą wiele nauczyć się od zagranicznych metod, aby przetrwać i pozostać konkurencyjnymi.
Koncepcja „Lean Thinking and Manufacturing” (Lean Thinking and Manufacturing) zajmuje jedno z najważniejszych miejsc wśród nowoczesne propozycje na zarządzanie. Jednak kultura naszego kraju jako całości jest bardzo daleka od pojęcia „oszczędności”. Świadczyć o tym może fakt, że mamy wióry przechowywane w warsztatach, a metalowe półfabrykaty - na świeżym powietrzu; ogrodzenia buduje się z naturalnego drewna, a meble z trocin; jeden warsztat znajduje się kilka kilometrów od drugiego. Szczerze mówiąc, nie sposób znaleźć rozsądnego wytłumaczenia tego. Przewaga konkurencyjna Rosyjskie przedsiębiorstwa zapewnić tylko wysoka jakość i niskie koszty.
Dlatego dzisiaj konieczna jest rewizja całej organizacji produkcji w celu wyeliminowania wszelkiego rodzaju strat. Wymaga to zintegrowanego podejścia, obejmującego jakość i koncepcję, metody i narzędzia szczupłego wytwarzania. Opierając się na problemach funkcjonowania rosyjskich przedsiębiorstw, eksperci w dziedzinie zarządzania jakością uważają, że opracowanie koncepcji „Lean Production” i zastosowanie jej metod jest niezwykle ważnym czynnikiem poprawy wydajności wszystkich części system produkcji.
1.2 Zasady i narzędzia „Lean production”
straty w produkcji szczupłej
Lean Manufacturing to nowoczesna koncepcja organizacji produkcji, której celem jest ograniczenie różnego rodzaju straty poprzez wprowadzenie nowych technologii produkcji i zarządzania, przyspieszenie produkcji i zapewnienie długoterminowej konkurencyjności organizacji bez znaczących inwestycji kapitałowych.
Zasady produkcji szczupłej.
Zasada rozumienia wartości – implikuje potrzebę zrozumienia, jaka jest wartość dla końcowego użytkownika. Wartość jest uważana za pojęcie poza produkcją. Wartość jest punktem wyjścia Lean Thinking. Wartość (produktu, usługi) może określić tylko użytkownik końcowy. Rozmowa o niej ma sens tylko wtedy, gdy ma na myśli… konkretny produkt(towar lub usługa lub wszystko razem), które za określoną cenę i w określonym czasie jest w stanie zaspokoić potrzeby nabywców. Wartość tworzy producent. Z punktu widzenia konsumenta po to istnieje producent. Jednak z wielu powodów producentowi bardzo trudno jest określić dokładną wartość produktu lub usługi. Z reguły menedżerowie najwięcej uwagi poświęcali systemom zarządzania: procesami, działami, całymi firmami, które obejmowały jednocześnie wiele produktów. To, co naprawdę musisz zrobić, to zarządzać wszystkimi strumieniami wartości dla każdego produktu lub usługi.
Zasada kontroli strat – przewiduje znaczne ograniczenie lub całkowitą eliminację siedmiu głównych rodzajów strat:
1 - utrata nadprodukcji;
2 - straty z powodu wad i konieczności przeróbek;
3 - straty podczas ruchu;
4 - straty podczas transportu;
5 - straty z nadmiernych zapasów;
6 - straty z nadmiernego przetwarzania;
7 - strata czasu oczekiwania.
Zasada przepływu produktu - przewiduje się, że zamiast przemieszczania produktu z jednego stanowiska do drugiego partiami, konieczne jest stworzenie przepływu, w którym następuje ciągły ruch od surowców do wyrobów gotowych poprzez wyspecjalizowane gniazda produkcyjne.
Zasada pull, która zakłada, że zamiast pracy w magazynie konsument powinien mieć możliwość „wyciągnięcia” gotowych produktów z systemu produkcyjnego. Nie wykonuje się żadnej pracy, jeśli jej wyników nie można od razu wykorzystać w kolejnych operacjach.
Zasada ciągłego doskonalenia – gdy wszystkie straty z procesów technologicznych zostaną wyeliminowane, a produkty poruszają się płynnie i nieprzerwanie w miarę ich dostarczania do konsumenta, stanie się jasne, że procesowi ciągłego doskonalenia nie będzie końca, na przykład zmniejszenie czas operacji, koszt, powierzchnia, wady i zakres prac.
Narzędzia odchudzone
Do praktycznego wdrożenia lean manufacturing narzędzia takie jak:
5S - pięć kroków do utrzymania porządku. 5S składa się z pięciu japońskich słów, które stanowią podstawę do utrzymywania porządku i czystości. Brak 5S w działającej komórce wskazuje:
Dla niskiej wydajności;
Obecność strat;
Słaba samodyscyplina i moralność;
Słaba jakość;
Wysokie koszty;
Brak dyscypliny dostaw, zarówno do odbiorców wewnętrznych, jak i zewnętrznych.
Potencjalni klienci nie będą traktować poważnie dostawców, którzy nie praktykują 5S. Te pięć punktów czystości to punkt wyjścia dla każdej firmy, która aspiruje do miana odpowiedzialnego, światowej klasy producenta.
Istnieje pięć sposobów oceny poziomu 5S na każdym etapie:
Poczucie własnej wartości;
Ocena konsultanta-eksperta;
Ocena zarządzania;
Połączenie pierwszych trzech metod;
Rywalizacja między komórkami roboczymi.
Kaizen: Główną ideą kaizen jest to, że nie ma dnia bez poprawy w firmie. Kaizen nie jest pojedynczą techniką, jest parasolem, pod którym żyje większość praktyk „unikalnych dla Japonii”.
Japońskie rozumienie zarządzania sprowadza się do: spełniania standardów i doskonalenia ich. Celem zarządzania w zakresie utrzymania ruchu jest zapewnienie, aby każdy pracownik w firmie był w stanie postępować zgodnie ze standardową procedurą operacyjną. Jeśli pracownicy nie mogą postępować zgodnie ze standardową procedurą, kierownictwo musi albo ich przeszkolić, albo zrewidować i zmienić standard tak, aby możliwe było działanie zgodnie z nim. Im wyższy poziom zarządzania, tym więcej czasu poświęca na doskonalenie. Punktem wyjścia do poprawy jest rozpoznanie problemu. Samozadowolenie i samozadowolenie to zaprzysięgli wrogowie kaizen. Dlatego reklamację klienta należy traktować jako prezent. Uznając, że skarga
związanego z problemem masz szansę na poprawę jakości produktu lub
usługi. Odrzucając skargę, tracisz tę szansę.
Kanban: metoda just-in-time. Prawidłowa specyfikacja części i gotowego produktu - z odpowiednią ich ilością - w odpowiedni czas- nie ma małżeństwa. System just-in-time to system pull – jest to taka organizacja procesu, w której każdy kolejny etap produkcji zużywa w odpowiednim czasie wszystko, co potrzebne z poprzedniego etapu. Wynik końcowego etapu produkcji w tym przypadku opiera się na żądaniach konsumenta lub odpowiada harmonogramowi produkcji. Just-in-time zapewnia producentowi następujące korzyści:
Zmniejszenie poziomu zapasów, zakupionych materiałów i wyrobów gotowych na magazynie;
Zmniejszenie zajmowanych obszarów;
Wzrost jakości produktów, redukcja małżeństw i przetwórstwa;
Większa elastyczność w dostarczaniu produkcji;
Wzrost produktywności i współczynnika obciążenia sprzętu;
Udział pracownika w rozwiązywaniu problemów;
Dobre relacje z konsumentem.
Szybka zmiana (SMED): elastyczna produkcja w kilka minut. Dzięki temu narzędziu firma oszczędza zasoby materiałowe i robocze, zwiększa produktywność i przyspiesza realizację zamówień.
Poka-yoke: „niezawodny”: polega na zorganizowaniu procesu w taki sposób, aby wyeliminować samą możliwość błędu. Szerzej sformułowane przez programistów: jeśli użytkownik może popełnić błąd, to na pewno go popełni. W rzeczywistości żaden ważny element nie będzie działał wystarczająco skutecznie, jeśli z góry nie zostanie uwzględniony czynnik ludzki.
Istnieje 10 rodzajów błędów ludzkich, które prowadzą do defektów:
Zapomnienie;
Niezrozumienie przyczyn (wystąpienie czegoś);
Niedocenianie jakiejkolwiek sytuacji (lub niemożność zidentyfikowania jakiegokolwiek obiektu);
Brak doświadczenia;
niechęć (do przestrzegania procedur i zasad);
nieuwaga;
Powolność (w podejmowaniu decyzji);
Brak standardów;
Niespodzianka;
Celowe popełnienie błędu (lub sabotażu).
Źródłami wad są następujące fakty:
Przeoczona operacja;
Błędy przetwarzania;
Błędy pozycjonowania części;
Brakujący szczegół;
Zły przedmiot;
Przetwarzanie niewłaściwej części;
Nieprawidłowa operacja na prawidłowej części;
Błędy konfiguracji;
Nieprawidłowa instalacja sprzętu i użycie niewłaściwego narzędzia lub narzędzia.
Należy wyróżnić trzy główne fazy wdrażania zasad lean manufacturing: badanie popytu, zapewnienie ciągłości przepływów wartości oraz ich wygładzanie. Tylko dogłębne badanie popytu, strumieni wartości i sposobów ich wygładzania, wraz z wykorzystaniem rekomendacji zarządzania strumieniami wartości, może uwiarygodnić nie tylko sam proces transformacji, ale także zapewnić jego trwałość.
Faza badania popytu konsumenckiego. Konieczne jest przede wszystkim
określić, kim są konsumenci wyników niektórych prac, jakie są
ich wymagania, dopiero po tym będziesz mógł zadowolić konsumenta
wskazywać zapotrzebowanie na jego wyniki. Do identyfikacji i zaspokojenia zapotrzebowania konsumentów można wykorzystać różne narzędzia i metody, na przykład:
Obliczenia czasu taktu;
Obliczenia skoku;
Obliczanie zapasów buforowych i ubezpieczeniowych;
Zastosowanie systemu 5S;
Korzystanie z technik rozwiązywania problemów.
Faza ciągłości strumienia wartości. Na tym etapie weź niezbędne środki zapewnić, aby wyniki prac, o których mowa, dotarły do wszystkich klientów wewnętrznych i zewnętrznych w odpowiednim czasie i w odpowiedniej ilości. Na przykład:
Tworzenie supermarketów w ramach procesów;
system kanban;
Stosowanie zasady FIFO („pierwsze weszło, pierwsze wyszło”);
Zapewnienie równowagi w obciążeniu linii produkcyjnych;
Standaryzacja pracy;
Właściwe rozplanowanie obszarów produkcyjnych.
faza wygładzająca. Wreszcie, po zidentyfikowaniu zapotrzebowania klientów na wyniki pracy i ustaleniu ciągłego procesu ich dostarczania, przechodzą do wygładzania go, aby zapewnić równomierny i wydajny rozkład ilości pracy na dni, tygodnie i miesiące. W tym celu wykorzystywane są następujące narzędzia do wygładzania przepływu:
Wykorzystanie tablicy do propozycji i dyskusji nad pomysłami (widoczna tablica);
Skrzynie do poziomowania ładunku (heijunka);
Wykorzystanie logistyki.
Tak więc promocja konkretnego systemu jest niemożliwa bez jego zrozumienia. Dlatego należy zapewnić pracowników odpowiedzialnych za efektywność głównych działań przedsiębiorstwa
możliwość poznania koncepcji lean manufacturing.
Stosowanie zasad i umiejętne wykorzystanie narzędzi lean manufacturing zapewni konkurencyjność w każdym obszarze biznesowym. Celowość wprowadzenia „Lean production” w organizacji:
Wysoki koszt produkcji;
Produkty niskiej jakości;
przestarzałe technologie;
przestarzały sprzęt;
Wysoka energochłonność;
Wysoki koszt produkcji;
Naruszenie warunków dostaw;
Brak wykwalifikowanego personelu;
Wysoka konkurencja na rynku.
To właśnie narzędzia lean manufacturing pozwalają nam rozwiązywać te i inne problemy.
Organizacja stawia sobie globalne zadanie - ulepszać się każdego dnia, robić postępy z dnia na dzień. Posuwanie się naprzód zależy od samych liderów, bo nie wystarczy wprowadzić narzędzia, trzeba zmienić kulturę zarządzania, zachowania menedżerów.
1.3 Rodzaje strat i metody oceny skuteczności realizacji koncepcji „Lean production”
Lean Manufacturing to koncepcja zarządzania, która koncentruje się na optymalizacji procesów biznesowych przy maksymalnym ukierunkowaniu na rynek i uwzględnieniu motywacji każdego pracownika. Produkcja odchudzona stanowi podstawę nowej filozofii zarządzania. Celem jest: minimalizacja kosztów pracy i warunków tworzenia nowych produktów; gwarancja dostawy produktów do klienta; maksymalna jakość w
minimalny koszt. Główną ideą jest wyeliminowanie strat
wszelkie działania, które zużywają zasoby, ale nie tworzą wartości.
Taiichi Ohno, twórca tego systemu, zidentyfikował siedem rodzajów marnotrawstwa: z powodu nadprodukcji; czas z powodu oczekiwania; w przypadku niepotrzebnego transportu; z powodu zbędnych etapów przetwarzania; z powodu nadmiaru zapasów; z powodu niepotrzebnych ruchów; z powodu wadliwych produktów. Istnieją również dwa inne źródła marnotrawstwa – „obciążenie przekraczające udźwig” i „nierówny ładunek”, co ostatecznie prowadzi do uwolnienia wadliwych produktów.
Nadprodukcja. Nadprodukcję zwyczajowo nazywa się wytwarzaniem nadmiernej ilości produktów lub jej przedwczesną produkcją, zanim pojawi się rzeczywisty popyt. W sklepach nadprodukcja prowadzi do wytwarzania nadmiaru produktów, a w biurach do tworzenia zbędnych dokumentów lub zbędnych informacji. Produkcja nadmiernych ilości produktów lub ich przedwczesna produkcja nie przyczyniają się do zwiększenia wydajności, ponieważ wiążą się ze zużyciem dodatkowego materiału i zasoby pracy, konieczność przechowywania nadwyżek produktów. Zmusza to pracowników do pracy szybciej niż to konieczne, czemu towarzyszą inne straty.
Aby wyeliminować straty spowodowane nadprodukcją, wymagane jest:
Rozwijać procesy technologiczne w taki sposób, aby poprzednie operacje niezawodnie zapewniały kolejne;
Ustal normy i standardy produkcyjne dla każdego miejsca pracy procesu;
Dostarczaj sygnały, aby zapobiec przedwczesnemu rozpoczęciu produkcji.
Oczekiwanie. Każde oczekiwanie – ludzie, dokumenty, sprzęt czy informacje – jest zawsze stratą. Czekanie oznacza bezczynną pracę, a to powoduje zatrzymanie całego procesu. Czekanie nie tworzy wartości dodanej, a konsument naturalnie nie chce płacić za przestoje. Straty tego typu są najłatwiejsze do wykrycia. Szczególnie denerwują pracowników. W każdym biurze nierzadko zdarza się, że pracownicy długo czekają na podpisy przełożonych, możliwość skorzystania z zajmowanego sprzętu, rozmowy telefoniczne, odbiór materiałów od dostawców itp.
Przeanalizuj, które podpisy na dokumentach są naprawdę potrzebne, wyeliminuj wszystkie niepotrzebne i ustandaryzuj nową procedurę;
Szkolenie pracowników w zawodach pokrewnych, aby mogli się nawzajem zastępować;
Równomiernie rozkładaj obciążenia w ciągu dnia, aby optymalnie wykorzystać dostępne zasoby pracy;
Zapewnij produkcję dla wszystkich niezbędny sprzęt oraz terminową dostawę zakupionych produktów i materiałów.
Nadmierne przetwarzanie. Te operacje, które nie są potrzebne konsumentom, którzy nie chcą przepłacać za ich wdrożenie, są uważane za zbędne. Często takie operacje okazują się niepotrzebnymi czynnościami (np. wzajemne sprawdzanie pracy wykonywanej przez różnych pracowników), uzyskiwaniem nadmiernej liczby podpisów, niepotrzebnym rozpatrywaniem dokumentów i wyników pracy.
Aby wyeliminować tego typu straty, potrzebujesz:
Analizuj wszystkie prace, które tworzą wartość dodaną, optymalizuj lub eliminuj wszystkie niepotrzebne operacje;
Określ, które podpisy koordynujące na dokumentach są naprawdę potrzebne i wyeliminuj wszystkie niepotrzebne.
Nadmiar zapasów. Wszelkie nadwyżki magazynowe posiadane przez przedsiębiorstwo są odpadem. Przechowywanie takich zapasów wymaga dodatkowej przestrzeni, mogą one niekorzystnie wpływać na bezpieczeństwo poprzez blokowanie przejść i obszarów produkcyjnych. Te zapasy mogą wcale nie być potrzebne i stają się przestarzałe, gdy zmienia się popyt na produkty. Produkcja odchudzona wymaga radykalnej zmiany sposobu, w jaki patrzymy na zapasy. Obecność nadmiaru zapasów oznacza konieczność dodatkowych wysiłków, aby nimi zarządzać, może spowolnić przepływ innych procesów produkcyjnych, ponieważ konieczne jest obracanie stosów papierów i materiałów w poszukiwaniu niezbędnych.
Aby wyeliminować tego typu straty, potrzebujesz:
Wytwarzać w każdym miejscu lub miejscu pracy tylko taką ilość produktów, jakiej potrzebują konsumenci w toku procesu produkcyjnego;
Ujednolicić układ miejsc produkcyjnych i ich załadunek;
Zadbaj o to, aby wszystko, co potrzebne, trafiało na kolejne etapy procesu produkcyjnego dokładnie w wyznaczonym czasie i nie było opóźnień w dalszym przepływie materiałów przez proces produkcyjny.
Dodatkowe ruchy. Każdy ruch, który nie jest wymagany do pomyślnego zakończenia danej operacji, jest marnotrawstwem. Takie ruchy są uważane za formę marnotrawstwa, ponieważ każdy wykonany ruch musi zwiększać wartość dodaną produktu lub usługi. Często nieefektywna organizacja procesu pracy oraz nieprawidłowe rozplanowanie stanowisk pracy powodują niepotrzebne ruchy wykonawców – chodzenie, rozciąganie, schylanie się itp.
Aby wyeliminować tego typu straty, potrzebujesz:
Standaryzuj foldery dokumentów, szuflady i szafki w całym biurze, stosuj kodowanie kolorami tak szeroko, jak to możliwe;
Uporządkuj akta (z dokumentami na biurkach lub aktami elektronicznymi w komputerach) w taki sposób, aby ułatwić do nich dostęp;
Zlokalizuj wspólny sprzęt biurowy w
centralna część biura, zakup dodatkowego wyposażenia w celu zmniejszenia ilości przemieszczania się pracowników po biurze.
Straty z powodu wad lub przeróbek. Koszty przeróbek lub ponowne
Wielokrotne wykonywanie już wykonanej pracy, w której wykryto wady, z pewnością należy do kategorii strat, ponieważ każda praca przekraczająca niezbędne jest zbędna, zwiększając straty przedsiębiorstwa. Straty spowodowane defektami obejmują również utratę produktywności spowodowaną przerwaniem normalnego przepływu pracy w celu naprawienia defektów lub przerobienia produktów. Ten rodzaj kosztów ogólnych jest znacznie łatwiejszy do zidentyfikowania niż inne rodzaje odpadów.
Aby wyeliminować straty z wad, wymagane jest:
Wprowadzenie ustandaryzowanych metod pracy i form dokumentów biurowych;
Opracowuj i wdrażaj narzędzia ułatwiające pracę.
Transport. Transport na odległości większe niż to konieczne, czy tworzenie tymczasowych pomieszczeń, składowanie i magazynowanie, niepotrzebne przemieszczanie się z miejsca na miejsce materiałów, ludzi, informacji czy dokumentów – to wszystko prowadzi do straty czasu i energii. Materiały i zakupione przedmioty są często wielokrotnie przenoszone z miejsca na miejsce w obiekcie, aż dotrą do miejsca docelowego. Oczywiście wszystkie te ruchy prowadzą do strat. Ponadto umieszczanie produktów w miejscach tymczasowego przechowywania zwiększa prawdopodobieństwo uszkodzenia, utraty i kradzieży oraz zakłóca normalne przemieszczanie się w przedsiębiorstwie.
Aby wyeliminować straty spowodowane nadmiernym transportem,
wymagany:
Zminimalizuj odległość każdego transportu;
Wyeliminuj wszystkie miejsca tymczasowego składowania lub magazynowania
materiały.
Problem określania efektywności ekonomicznej z góry determinuje
konieczność właściwego rozważenia i przeanalizowania poziomu i zakresu
wdrożenie środków szczupłej produkcji. Oznacza to, że definicja efektywności wymaga zastosowania ilościowych metod analizy i pomiaru, co wiąże się z ustaleniem zależności pomiędzy wzrostem skali realizacji koncepcji lean manufacturing a wzrostem zysku przedsiębiorstwa.
Analiza efektywności ekonomicznej wdrożenia koncepcji Lean Production rozpoczyna się od obliczenia całkowitego rocznego wolumenu produkcji przez jednostki strukturalne, w których wprowadzono Lean Production V?, zgodnie ze wzorem:
j - indeks jednostki strukturalnej;
J to liczba jednostek strukturalnych, w których wdrażana jest szczupła produkcja;
Vj - objętość wyjściowa jednostka strukturalna gdzie wprowadzono odchudzoną produkcję.
Zatem udział określa wzór:
W celu dalszego określenia efektywności ekonomicznej wykonuje się następujące kroki:
Wielkość inwestycji na wdrożenie działań lean manufacturing jest przewidziana dla każdej działalności realizowanej w
jednostka strukturalna;
W zależności od przewidywanej wielkości inwestycji i pokrycia działów strukturalnych działaniami lean manufacturing określany jest udział wielkości produkcji (g);
Ekspercki sposób określa wartość progową r*, przy której efekt ekonomiczny z wprowadzenia środków na szczupłą produkcję zacznie przejawiać się w postaci wzrostu zysku przedsiębiorstwa (?P).
Wartość progowa r* może również zależeć od tego, jak skutecznie wdrażany jest środek. Im wyższa skuteczność realizacji działania, tym niższa będzie wartość progowa r*.
Zależność między wzrostem udziału r powyżej wartości progowej r * (? r = r - r *) a wzrostem zysku przedsiębiorstwa można wyrazić jako:
K - wskaźnik charakteryzujący wzrost zysku przedsiębiorstwa na jednostkę wzrostu skali realizacji działań na rzecz szczupłej produkcji. W przejściu do limitu wskaźnik ten jest wyrażony jako pochodna:
Efekt ekonomiczny każdej działalności, w tym działalności lean manufacturing, polega na dodatkowym otrzymywanym zysku. Z kolei dodatkowy zysk jest determinowany tym, jak bardzo zmienią się przychody i koszty produkcji firmy w związku z wdrożeniem tych środków szczupłej produkcji. Kluczowym zatem podejściem do kalkulacji efektu dowolnej działalności (w tym działań lean) jest ustalenie, o ile więcej firma otrzyma, a ile więcej zapłaci w związku z wdrożeniem koncepcji.
odchudzona produkcja.
Jako kryteria efektywności ekonomicznej realizacji działań na rzecz organizacji szczupłej produkcji proponuje się wykorzystanie tradycyjnych wskaźników efektywności Programu, takich jak: wartość bieżąca netto (NPV), wewnętrzna stopa zwrotu (IRR) oraz zdyskontowany okres zwrotu .
Wartość bieżąca netto (NPV).
W praktyce międzynarodowej szeroko stosowanym wskaźnikiem oceny efektywności projektów jest wartość zaktualizowana netto lub zaktualizowana wartość netto (NPV), którą określa wzór:
It - wielkość inwestycji (kosztów) w okres t dla działań związanych z odchudzoną produkcją;
T to całkowita liczba lat, gdzie t = 0, 1, 2,…, n;
r - stopa dyskontowa (stopa);
Pt - wzrost zysku przedsiębiorstwa z wdrożenia koncepcji szczupłej produkcji.
Jeżeli obliczona wartość NPV jest dodatnia, oznacza to, że suma wszystkich strat, które mają zostać wyeliminowane, jest większa niż inwestycja w działalność LP, co oznacza, że należy tę działalność przyjąć do realizacji. Jeśli NPV jest mniejsze od zera, należy z tej działalności zrezygnować.
Wewnętrzna stopa zwrotu (IRR).
IRR projektu to stopa zwrotu (stopa barierowa, stopa dyskontowa), przy której wartość bieżąca netto inwestycji wynosi zero, lub jest to stopa dyskontowa, przy której zdyskontowane zwroty z projektu są równe kosztom inwestycji. Wewnętrzna stopa zwrotu
określa maksymalną dopuszczalną stopę dyskontową, przy której
inwestować środki bez strat dla właściciela.
IRR = r, gdzie NPV = f(r) = 0.
Wartość IRR oblicza się za pomocą następującego wzoru:
Ekonomiczne znaczenie tego wskaźnika polega na tym, że pokazuje on oczekiwaną stopę zwrotu (ROI) lub maksymalną dopuszczalny poziom koszty inwestycji w ocenianym projekcie.
Zdyskontowany okres zwrotu.
Okres zwrotu inwestycji to czas potrzebny na wygenerowanie przez inwestycję przepływów pieniężnych wystarczających do odzyskania kosztów inwestycji.
Ogólna formuła obliczania okresu zwrotu:
Bieżący - okres zwrotu inwestycji;
Io - wartość początkowej inwestycji w okresie zerowym.
Dzięki temu możliwe staje się nie tylko uzyskanie operacyjnego obrazu stanu procesów biznesowych w organizacji, ale także poprawa istniejącego stanu rzeczy.
Uzyskana efektywność wdrożenia mierników szczupłej produkcji może być wykorzystana zarówno do analizy rezultatów wdrożenia mierników, jak i do określenia tych działów, w których bardziej opłacalne jest wdrożenie szczupłej produkcji. Dlatego takie podejście pozwoli (zwłaszcza w warunkach ograniczonych zasobów) racjonalnie rozłożyć inwestycje kapitałowe pomiędzy działy mające na celu wdrożenie koncepcji szczupłej produkcji.
2. Analiza i ocena działańUAB« Nizhnekamskshina” w zakresie „Lean production”
2.1 Ogólna charakterystyka działalności,wskaźniki techniczno-ekonomiczne przedsiębiorstwa,
Do tej pory OAO Nizhnekamskshina jest największym przedsiębiorstwem produkującym opony w Rosji i krajach WNP. Prawie co trzecia opona produkowana w Rosji jest produkowana w mieście Niżniekamsk.
OAO Nizhnekamskshina została utworzona zgodnie z dekretem Prezydenta Republiki Tatarstanu „O środkach przekształcenia przedsiębiorstwa państwowe, organizacje i stowarzyszenia w spółki akcyjne” z dnia 26 września 1992 r. Nr UP-466, Ustawa Republiki Tatarstanu „O przekształceniach własności państwowej i komunalnej w Republice Tatarstanu (o wynarodowieniu i prywatyzacji)”.
OAO Nizhnekamskshina została założona 2 marca 1994 roku poprzez przekształcenie ze stowarzyszenia produkcyjnego Nizhnekamskshina. Przekształcenia dokonano na podstawie planu prywatyzacji zatwierdzonego Dekretem Komisji Majątku Państwowego Republiki Tadżykistanu nr 64 z dnia 15 lutego 1994 r. i wpisanej do rejestru spółek akcyjnych pod numerem 700. przedsiębiorstwo zostało utworzone na czas nieoznaczony.
Przedsiębiorstwo jako samodzielny podmiot prawny istnieje od 1971 roku. Firma posiada dwa zakłady - fabrykę opon masowych i fabrykę opon do samochodów ciężarowych. W 1994 Stowarzyszenie Produkcyjne Nizhnekamskshina została przekształcona w spółka akcyjna Typ otwarty; w 1997 r. - w OAO Nizhnekamskshina.
Fabryka opon masowych została zaprojektowana, aby zaopatrywać w opony Wołga Automobile Plant, Ulyanovsk Automobile Plant oraz flotę pojazdów w regionach sąsiadujących z fabryką. Główny asortyment - opony do samochodów osobowych i ciężarowych.
Fabryka opon do samochodów ciężarowych została zaprojektowana, aby dostarczać opony dla KamAZ i floty pojazdów w regionach sąsiadujących z fabryką. Głównym asortymentem są opony do samochodów ciężarowych.
W strukturze Fabryki Opon Masowych i Fabryki Opon Ciężarowych znajduje się dyrektor zakładu, który podlega bezpośrednio Główny inżynier, zastępca dyrektora ds. produkcji, główny technolog, zastępca dyrektora ds. analiz ekonomicznych, a także produkcji głównej zakładu i warsztatów pomocniczych zakładów.
Główna produkcja zakładu obejmuje:
Przygotowanie produkcji surowców i wysyłka gotowych produktów;
Produkcja przygotowawcza, która zajmuje się przygotowaniem;
surowce do przyszłej produkcji opon;
Produkcja kalandra, który zbiera ramę dla warsztatów montażowych;
Zakład montażowy nr 1;
Produkcja montażowa nr 2;
Produkcja wulkanizacji opon samochodowych;
Produkcja opon do ciężarówek;
Produkcja motoryzacyjna.
Warsztaty pomocnicze zakładu obejmują warsztat elektryczny, warsztat grzewczy, warsztat naprawy mechanicznej, wewnątrzzakładowy transport elektryczny, systemy przepływu procesów, automatyczne systemy sterowania i warsztaty użytkowe.
Organami zarządzającymi OAO Nizhnekamskshina zgodnie ze Statutem Spółki są:
- Walne Zgromadzenie Akcjonariuszy;
- Rada Dyrektorów;
- Jedyny organ wykonawczy;
- Kolegialnym organem wykonawczym jest Zarząd.
UAB Nizhnekamskshina jest największą wśród rosyjskich opon
fabryki, przedsiębiorstwo pod względem zdolności produkcyjnych, wielkości i asortymentu produktów. Udział OAO Nizhnekamskshina w całkowitej produkcji opon rosyjskich zakładów wyniósł 30%. Prawie jedna trzecia produkcji trafia do montażu w rosyjskich fabrykach samochodów.
W 2009 roku liderami produkcji są - na pierwszym miejscu Nizhnekamskshina OJSC, produkująca 27% całkowitej rosyjskiej produkcji opon, a następnie Yaroslavl Tyre Plant OJSC - 16% i Omskshina OJSC - 14%. Łączna zdolność produkcyjna krajowych przedsiębiorstw oponiarskich wynosi 38,7 mln opon rocznie.
Wszechstronność produkcji przedsiębiorstwa zapewnia produkcja opon o najróżniejszym asortymencie. Firma produkuje opony do różne warunki: szosa, uniwersalna (na każdą pogodę), zimowa, terenowa, kamieniołom. Produkowane opony przeznaczone są do różnego rodzaju wyposażenia samochodowego i w zależności od tego dzielą się na typy. Opony firmy są wyposażone w wiele fabryk samochodów nie tylko w Rosji, ale także na Ukrainie.
Główni konsumenci produktów OAO Nizhnekamskshina przedstawiono w tabeli 2.1.1.
Tabela 2.1.1. Główni konsumenci produktów OAO Nizhnekamskshina
Z danych w tabeli widać, że główny udział konsumpcji produktu przypada na JSC AVTOWAZ - 61%; 11% produktów oponiarskich jest dystrybuowanych do zakładów Volkswagen Group Rus LLC, Kaługa, SHKODA, UAZ OJSC, Uljanowsk; 6,0% dla OAG LLC, Iżewsk, znikome zużycie produktów odpowiada JSC AK Bogdan Motors, Ukraina.
Więcej wizualnych odsetek widać na ryc. 2.1.3.
Ryż. 2.1.3. Główni konsumenci produktów w OAO Nizhnekamskshina
JSC „Nizhnekamskshina” zgromadziła ogromne doświadczenie w opracowywaniu i ulepszaniu produkowanych opon, testowaniu gotowych produktów. Rozwój konstrukcji opon nowej generacji oraz najnowsza technologia umożliwiły świadczenie wysoka jakość oraz poziom wskaźników wyrobów gotowych na rynku światowym. Do chwili obecnej firma produkuje ponad 120 rozmiarów do wszystkich typów opon i maszyn rolniczych. Mając na uwadze zwiększone wymagania producentów samochodów co do jakości opon, zrekonstruowano przepływ pasażerski w Wytwórni Opon Masowych oraz opanowano na sprzęcie i na licencji Pirelli (Włochy) technologię wytwarzania pasażerskich opon radialnych.
W 2001 roku kontynuowano odbudowę ruchu pasażerskiego Fabryki Opon Masowych. Zgodnie z długoterminowym planem rozwoju OAO Nizhnekamskshina zakupiono licencję na nową technologię, aw 2004 roku zorganizowano i uruchomiono produkcję samochodowych opon radialnych. Projekt został sfinansowany kosztem OAO TATNEFT.
Od 1 lipca 2004 r. oddano do eksploatacji pojemność wysokowydajnych pasażerskich opon radialnych "KAMA-EURO" - 500 tys. sztuk.
Na dzień 1 stycznia 2006 roku zdolność projektowa do produkcji opon przedsiębiorstwa wynosiła 11 900 tys. opon rocznie, w tym dla Fabryki Opon Masowych 8 940 tys., dla Fabryki Opon Ciężarowych 2 960 tys., dla 2960 tys. produkcja samochodowych opon radialnych - 500 tys. opon.
Wśród wewnętrznych czynników OAO Nizhnekamskshina są takie, jak strategiczne partnerstwo z OAO Tatnieft', ponieważ firma działa w jego ramach. Funkcję zaopatrzenia w surowce w ilości zapotrzebowania pełni OOO Tatneft-Neftehimsnab, funkcję marketingu gotowych produktów pełni OOO Trading House Kama. Decyzją nadzwyczajnego walne zgromadzenie udziałowcy OAO Nizhnekamskshina, protokół z dnia 27.06.2012 r., uprawnienia jedynego organu wykonawczego zostały przeniesione na spółkę zarządzającą OOO Tatneft-Neftekhim.
Zakład wdrożył i skutecznie funkcjonuje system jakości ISO -
9001:2000, certyfikowany przez międzynarodową jednostkę certyfikującą TUV CERT, który zapewnia dokładną kontrolę surowców, komponentów, komponentów wprowadzanych do zakładu, ścisłe przestrzeganie przepisów procesowych w całym cyklu produkcyjnym i testowaniu wyrobów gotowych.
Opanowanie produkcji wysokowydajnych opon radialnych do samochodów osobowych „KAMA-EURO” według nowej technologii na importowanym sprzęcie przy użyciu importowanych i homologowanych surowców. Decyzją Rady Dyrektorów podjęto szereg środków w celu wycofania usług, struktur niezwiązanych z podstawową działalnością i działalności usługowej z OJSC
Niżniekamskszyna.
W gospodarce rynkowej OAO Nizhnekamskshina przywiązuje dużą wagę do problemów optymalizacji procesu promocji towarów od producenta do konsumenta.
Dynamikę produkcji wyrobów OAO Nizhnekamskshina przedstawiono w tabeli 2.1.2.
Tabela 2.1.2. Dynamika produkcji OAO Nizhnekamskshina
Wielkość produkcji, |
Tempo wzrostu, % |
|||
Podstawowy |
||||
Z tabeli wynika, że wielkość produkcji w 2011 roku zmniejszyła się o 1096,3 tys. sztuk. (10%) w porównaniu do 2010 r.; W porównaniu do 2009 roku produkcja opon w 2011 roku jest mniejsza o 4939,2 tys. sztuk. (33,4%). Znaczący spadek wolumenu produkcji związany jest z zaprzestaniem produkcji głównego asortymentu opon do samochodów ciężarowych w II półroczu 2011 roku. Wizualne przedstawienie tej dynamiki pokazano na ryc. 2.1.4.
...Istota pojęcia „odchudzonej produkcji”, historia jej powstania, aspekty teoretyczne i metodologiczne. Ocena skuteczności jego wdrożenia w przedsiębiorstwie. Analiza konkurencyjności LLC „Energoshinservis” w ramach koncepcji szczupłej produkcji.
praca dyplomowa, dodana 24.06.2014
Historia rozwoju myśli menedżerskiej. Wady i zalety teorii zarządzania dla realizacji kompetentnych działań zarządczych. Podstawowe przepisy, zasady i idee współczesnych trendów zarządzania. Pojęcie „Odchudzonej produkcji”.
streszczenie, dodane 01.04.2016
Technologia Lean Production w teorii i praktyce zarządzania. Przegląd narzędzi Lean Manufacturing. Analiza możliwości wdrożenia i funkcjonowania lean manufacturing w Rosji i za granicą. Charakterystyka japońskiego modelu zarządzania.
praca semestralna, dodano 28.01.2014
Koncentracja Toyoty na produkcji opartej na zamówieniach przy jednoczesnej minimalizacji zapasów gotowych produktów. Produkcja szczupła jako postępowe podejście do zarządzania i zarządzania jakością. Konieczność korzystania tylko z niezawodnej, sprawdzonej technologii.
test, dodano 22.03.2014
Główna działalność Zakładu Górniczo-Przetwórczego OAO EVRAZ Kachkanar. Proces technologiczny otrzymywania produktów. Struktura organizacyjna zarządzania pracą. Polityka i cele w zakresie jakości. Zasady produkcji szczupłej.
raport z praktyki, dodany 03.12.2015
Lean production jako koncepcja zarządzania logistyką, jej cele i zadania, zalety i wady. Charakterystyka narzędzi Lean: metoda Kaizen, system 5S, system ogólnego utrzymania urządzeń produkcyjnych, system Kanban.
praca kontrolna, dodano 12.03.2013
Istota i główna treść podejścia procesowego, etapy i zasady jego realizacji w nowoczesnym przedsiębiorstwie. Trylogia Jurana. Ogólne informacje o JSC "Tatarsko-zakład mięsny", wdrożenie podejścia procesowego do niego i ocena skuteczności tej koncepcji.
praca semestralna, dodano 09.09.2012
Pojęcie całościowego zarządzania jakością, jego cele, elementy i cechy. Problem wprowadzenia pojęcia „Kompletnego Zarządzania Jakością” w działaniach organizacji. Właściwości produktu, które determinują jego główne funkcje. Ocena jakości gotowych produktów.
Przy wdrażaniu metod i narzędzi lean manufacturing często pojawia się pytanie: jak ocenić efekt wprowadzonych zmian? Przede wszystkim oczywiście menedżerów interesuje efekt ekonomiczny, czyli wyrażony w rublach lub dolarach dodatkowego zysku (co jest najlepsze) lub redukcji kosztów (co jest gorsze, ale w zasadzie też jest akceptowane). .
Bardzo często w pierwszych miesiącach wprowadzenia lean manufacturing trzeba mówić o niemożności wyliczenia efektu ekonomicznego, a oto dlaczego…
Zasadniczo istnieją dwa podejścia do oceny efektu ekonomicznego.
Pierwsza dotyczy wzajemnej oceny opartej na ograniczonej ilości danych liczbowych, podczas której obliczany jest pewien „potencjalny efekt”. Na przykład, rozmawiamyże jedna z propozycji usprawnienia pracy operatora maszyny pozwala mu na skrócenie czasu Wykonany ręcznie podczas załadunku i rozładunku części z maszyny przez 15 minut na zmianę. Znając koszt godziny pracy podany operator, na przykład 100 rubli, możesz obliczyć, że potencjalne oszczędności na zmianę wynoszą 25 rubli miesięcznie - 500 rubli, rocznie - 6000 rubli.
Ta metoda ma wiele wad. Oczywistą wadą jest niedokładność wzajemna recenzja oszczędność czasu - nie jest faktem, że ten operator faktycznie zaoszczędzi 15 minut na zmianę. Jak mówi przysłowie, jeśli uratujesz osobę przed wykonaniem jednej bezużytecznej pracy, natychmiast znajdzie dziesięć dodatkowych rzeczy, na które może poświęcić cały zaoszczędzony czas. Dlatego te 15 minut nie zamieni się automatycznie w pracę, która naprawdę przynosi zysk.
Drugie podejście polega na ocenie na podstawie wyników pracy za pewien okres czasu, na przykład za miesiąc lub kwartał. Dział księgowości podsumowuje wszystkie liczby i raporty: zysk stał się taki a taki. (na przykład w naszym przypadku zysk przedsiębiorstwa za ten sam miesiąc wzrósł o 2 miliony 127 tysięcy rubli, ale nie jest faktem, że wszystko to wynika tylko z zaoszczędzenia 15 minut pracy operatora maszyny). W tym przypadku dane dotyczące oszczędności lub dodatkowego zysku są znacznie bardziej wiarygodne, ale jeśli oczekujesz od księgowych, że będą w stanie udzielić Ci odpowiedzi na pytanie „ile pieniędzy otrzymaliśmy (zaoszczędziliśmy) po wdrożeniu tej propozycji”, to Ty są w błędzie. Nie da:
- wdrożona oferta jest tylko jednym z czynników wpływających na zyski wśród wszelkiego rodzaju wahań poziomu zapotrzebowania klientów, opóźnień dostawców, opóźnień w płatnościach klientów, awarii sprzętu w innych obszarach produkcyjnych itp. itp. Wyizolowanie wpływu tego konkretnego czynnika jest praktycznie niemożliwe – ocena uzyskanego wyniku TYLKO dzięki wdrożonej propozycji, w zdecydowanej większości przypadków.
- wiele kosztów ogólnych, które są brane pod uwagę przy obliczaniu opłacalności poszczególnych produktów lub robót, rozkłada się według warunkowo określonych proporcji (np. zdarza się, że koszt utrzymania budynków i budowli przesuwany jest na koszt wytworzenia, w zależności od powierzchnia pomieszczeń zajmowanych przez odpowiednie zasoby produkcyjne) i gdy taka proporcja przestaje odpowiadać naszemu zrozumieniu uczciwej oceny kosztów, dokładność efektu ekonomicznego zaczyna budzić oczywiste pytania.
Mówiąc prościej, ekonomista, który przygląda się wynikom gospodarczym, uwierzy im tylko w jednym przypadku:
- gdy struktura efektu ekonomicznego jest w pełni zgodna ze strukturą kosztów produktów/usług przyjętą w Państwa przedsiębiorstwie
- gdy dane są potwierdzone dowodami księgowymi
- gdy istnieją dane historyczne o tym, jakie wyniki ekonomiczne były dostępne PRZED wdrożeniem tej propozycji
Zobaczmy teraz, z czym najczęściej spotykają się nowicjusze w zakresie Lean Production:
- wiele przedsiębiorstw nie posiada zatwierdzonych metod kalkulacji kosztów produktu (obliczenia kosztu wytworzenia określonego rodzaju produktu lub kosztu świadczenia określonego rodzaju usługi) o ustalonej strukturze kosztów
- nie wszystkim transakcjom wewnętrznym towarzyszą dokumenty księgowe, dlatego jest mało prawdopodobne, aby wszystkie dane o wydatkach były dostępne w dziale księgowości
- Dość często nie jest możliwe odtworzenie danych historycznych, m.in. ze względu na to, że państwo dość często dokonuje zmian i korekt w systemie rachunkowości rosyjskich przedsiębiorstw, przez co dane produkcyjne za różne lata nie zawsze pozostają porównywalne.
Jeśli nie przekonują Cię te argumenty, opowiem Ci o jeszcze jednym niezwykłym fakcie.
Międzynarodowe Standardy Sprawozdawczości Finansowej MSSF i rosyjskie standardy Księgowość RAS ma jedną cechę, która uniemożliwia ich bezpośrednie wykorzystanie do księgowości w przedsiębiorstwie lean: oba standardy powstały w dobie produkcji masowej i postulują wysoką wartość posiadania zasobów produkcyjnych i dużych zapasów surowców, półproduktów i wyrobów gotowych .
Z punktu widzenia klasycznej księgowości nadmiar zapasów w magazynach jest „dobry” i „dobry” pod wieloma względami. Z punktu widzenia lean manufacturing każdy nadmiar zapasów jest „złem”. Wydawałoby się, że to tylko ogólne słowa, ale w końcu przy sporządzaniu bilansu, rachunku zysków i strat prowadzi to do tego, że fakty, które z punktu widzenia lean production należy oceniać jako osiągnięcia oraz efekt pozytywny, z punktu widzenia klasycznej rachunkowości postrzegany jako wynik negatywny.
Nie chcę nikogo przekonywać, że wdrażając lean manufacturing, nie da się obliczyć efektu ekonomicznego. Trzeba to obliczyć. Jednak oceniając oszczędności, należy pamiętać, że uzyskane liczby będą postrzegane z dużym sceptycyzmem. A ten sceptycyzm ma dość obiektywne powody.
Kto może być zainteresowany
W kontekście praktycznego wdrażania „odchudzonej produkcji” szczególne znaczenie mają kwestie oceny stanu faktycznego i dalszych perspektyw wykorzystania narzędzi „odchudzonej produkcji”. Po pierwsze bowiem może pojawić się złudzenie, że w przedsiębiorstwie już wiele zrobiono i można ograniczyć aktywność we wdrażaniu narzędzi i metod szczupłej produkcji, a po drugie, każdy kolejny krok w celu zmniejszenia strat i zwiększenia wydajność przedsiębiorstwa będzie wymagała większych wysiłków.
Bardzo skuteczne metody organizacje „Lean production” w przedsiębiorstwie to określenie celów, realizacja projekty pilotażowe i obliczenie efektu ekonomicznego.
Cele lean są niezbędne do opracowania strategii i polityki przez najwyższe kierownictwo przedsiębiorstwa, w którym zasoby są kierowane na te cele, które są krytyczne dla biznesu. Niezbędne jest ujednolicenie zasobów i wypracowanie konkretnych mierzalnych wskaźników, które na bieżąco monitorują realizację kluczowych celów. Kluczowa cecha Model jest blokiem do oceny efektywności i wypracowywania nowych celów, co jest w pełni zgodne z filozofią „szczupłej produkcji” i ma na celu ciągłe doskonalenie. Model zawiera ekspercką ocenę skuteczności wdrożenia systemu Lean Production, przedstawioną w tabeli. dziewięć.
Wyniki eksperckiej oceny skuteczności wdrożenia lean production w KAMAZ OJSC pokazują, co następuje:
1. Podsystem „personel” został bardziej rozwinięty w KAMAZ OJSC w porównaniu z innymi podsystemami (5,5 punktu na 10 maksimum), podsystem „procesy” ma najmniej rozwinięty w przedsiębiorstwie (4,6 punktu).
2. Wszystkie podsystemy „procesy”, „personel”, „zarządzanie strategiczne” zostały ocenione przez ekspertów KAMAZ SA na poziomie średnim (maksymalna ocena – 10 pkt), co wskazuje, że nadal istnieją znaczne rezerwy na wdrożenie narzędzi i metod szczupłej produkcji.
3. Wskaźniki takie jak (4,0 pkt), (3,2 pkt), (3,7 pkt), praca z dostawcami nad lean manufacturing (3,7 pkt), (3,8 pkt), praca z dealerami nad lean manufacturing (3,9 pkt), otrzymane przez KAMAZ OJSC, mają najniższą ocenę i są punktem odniesienia dla intensyfikacji pracy.
Tabela 9
Ocena efektywności organizacji „Lean production” w OJSC „KAMAZ”
Mierzone wskaźniki |
Udział ocen ekspertów, % |
|||||||||||
Podsystem „Zarządzanie strategiczne” |
||||||||||||
Posiadanie filozofii BP |
||||||||||||
Deklaracja i zasady BP |
||||||||||||
KPI - kluczowe wskaźniki wydajności |
||||||||||||
Badanie wymagań konsumentów |
||||||||||||
Ocena satysfakcji klienta |
||||||||||||
podsystem „personel” |
Szkolenie personelu |
|||||||||||
Spójność pracowników |
||||||||||||
Podsystem „procesy” |
Dostępność 5C |
|||||||||||
Korzystanie z systemu ciągnięcia |
||||||||||||
Redukcja strat |
||||||||||||
Poprawa jakości produktów |
||||||||||||
Współpraca z dostawcami BP |
||||||||||||
Współpraca z dealerami BP |
Pomimo tego, że KAMAZ SA jest liderem wśród rosyjskich przedsiębiorstw budowy maszyn pod względem wdrażania narzędzi i metod lean production, oceny ekspertów sytuacji w KAMAZ SA nie różnią się zasadniczo od ocen przedsiębiorstw budowy maszyn Federacji Rosyjskiej. Wszystko to wskazuje, że eksperci wewnętrzni są skłonni do samokrytyki, widzą istniejące niedociągnięcia i perspektywy rozwoju przedsiębiorstwa we wdrażaniu narzędzi i metod lean production.
W praktyce oznacza to konieczność zintensyfikowania prac nad wdrożeniem narzędzi systemu produkcyjnego KAMAZ – są to rozwiązania, które pozwalają dostrzec możliwości usprawnień i znacząco ograniczyć straty.
Konieczne jest ciągłe doskonalenie całego zakresu procesów biznesowych, zwiększenie przejrzystości i zarządzania organizacją, wykorzystanie potencjału każdego pracownika firmy, zwiększenie konkurencyjności, uzyskanie znaczącego efektu ekonomicznego bez ponoszenia dużych kosztów finansowych (rys. 22) .
Tabela 10
Ocena skuteczności wdrożenia systemu „Lean production” w OJSC „KAMAZ” oraz w przedsiębiorstwach inżynierii mechanicznej Federacji Rosyjskiej
Mierzone wskaźniki |
Poślubić ocena dla KAMAZ OJSC |
Poślubić Rosyjski wynik inżynierii mechanicznej |
|
Podsystem „Zarządzanie strategiczne” |
Dostępność zarządzania strategicznego |
||
Posiadanie filozofii BP |
|||
Deklaracja i zasady BP |
|||
Zaangażowanie najwyższego kierownictwa, wdrożenie projekty osobiste |
|||
KPI - kluczowe wskaźniki wydajności |
|||
Badanie wymagań konsumentów |
|||
Ocena satysfakcji klienta |
|||
Podsystem „personel” |
Szkolenie personelu |
||
Spójność pracowników |
|||
Dostępność i jakość ofert kaizen |
|||
Liderzy Wychowania z Filozofią BP |
|||
Budowanie organizacji uczącej się |
|||
Podsystem „procesy” |
Dostępność 5C |
||
Korzystanie z systemu ciągnięcia |
|||
Równomierny rozkład pracy |
|||
Korzystanie z kontroli wizualnej |
|||
Redukcja strat |
|||
Poprawa jakości produktów |
|||
Poprawa jakości usług |
|||
Współpraca z dostawcami BP |
|||
Współpraca z dealerami BP |
Każde z narzędzi Systemu Produkcyjnego KAMAZ rozwiązuje jakąś konkretną część problemów i dopiero ich wspólne zastosowanie rozwiąże problem całkowicie lub zminimalizuje go do akceptowalnych wartości.
Ryż. 22. Zastosowanie narzędzi KAMAZ Production System
Konwencjonalnie narzędzia Systemu Produkcyjnego KAMAZ można podzielić na trzy główne grupy: narzędzia analizy i wykrywania strat, narzędzia doskonalenia, narzędzia zarządzania i zaangażowania (tab. 11).
Tabela 11
Narzędzia Systemu Produkcyjnego KAMAZ
Ponieważ eksperci ocenili wskaźniki efektywności wdrażania narzędzi i metod lean manufacturing na poziomie przeciętnym, konieczne jest zintensyfikowanie pracy w przedsiębiorstwie w takich obszarach jak KPI – kluczowe wskaźniki efektywności, wykorzystanie systemu pull, badanie klienta wymagania, ocena satysfakcji klienta, równomierny rozkład pracy, poprawa utrzymania jakości, praca z dostawcami nad szczupłą produkcją, współpraca z dealerami nad szczupłą produkcją.
Ryż. 23. Cele i zadania Programu Republiki Tatarstanu „Wdrożenie projektu Lean Production w Republice Tatarstanu na lata 2011-2013”
Do intensyfikacji tych prac przyczynia się realizacja Programu Republiki Tatarstanu „Wdrożenie Projektu Lean Production w Republice Tatarstanu na lata 2011-2013”, który przewiduje finansowanie projektów wprowadzenia narzędzi i metod lean production, w tym projekty szkolenia personelu w zakresie szczupłej produkcji.
W wyniku realizacji działań Programu Republiki Tatarstanu „Wdrożenie projektu Lean Production w Republice Tatarstanu na lata 2011-2013” planowane jest osiągnięcie wskaźników przedstawionych w tabeli. 12.
Tabela 12
Wskaźniki Programu Republiki Tatarstanu „Wdrożenie Projektu Lean Production na lata 2011-2013”
Nazwa wskaźnika |
||
Wskaźnik produkcji przemysłowej przedsiębiorstw uczestniczących w programie, w % |
||
Tempo wzrostu wydajności pracy (w stosunku do analogicznego okresu ubiegłego roku) przedsiębiorstw uczestniczących w programie, w % |
||
Udział przedsiębiorstw przemysłowych realizujących programy rozwoju szczupłej produkcji w ogólnej liczbie przedsiębiorstw przemysłowych zatrudniających powyżej 500 osób, w % |
||
Poziom opłacalności produkcji przedsiębiorstw uczestniczących w programie, w % |
||
Liczba przedsiębiorstw, których kadra przeszła doskonalenie zawodowe w ramach Programu |
Takie podejście do stopniowego wzrostu efektywności przedsiębiorstw gospodarki Republiki Tatarstanu, w tym OJSC KAMAZ, poprzez redukcję strat i szkolenie personelu, przyczynia się do wzrostu potencjału produkcyjnego gospodarki regionalnej i wzrostu konkurencyjności .
Do tej pory zgromadzono i przetestowano obszerny arsenał metod, za pomocą których przedsiębiorstwo może wdrożyć narzędzia „odchudzonej produkcji”. Najskuteczniejszymi metodami wdrożenia systemu Lean Production w przedsiębiorstwie są wyznaczanie celów, realizacja projektów pilotażowych oraz obliczanie efektu ekonomicznego. Docelowe wskaźniki szczupłej produkcji oraz realizacji celów Systemu Produkcyjnego KAMAZ przedstawia tabela. trzynaście.
Tabela 13
Dynamika wskaźników realizacji celów systemu produkcyjnego KAMAZ
Wskaźniki |
|||||||
Przeszkolony w zakresie zasad i metod BP |
|||||||
otwarte projekty |
|||||||
zrealizowane projekty |
|||||||
zgłoszone propozycje kaizen |
|||||||
wdrożone oferty kaizen |
|||||||
normalizacja |
|||||||
wyobrażanie sobie |
|||||||
uwolniona powierzchnia mkw |
|||||||
zwolnione jednostki wyposażenia. |
|||||||
uzyskany efekt ekonomiczny (mln rubli) |
|||||||
łącznie z kaizen |
|||||||
koszty rozwoju PSK wyniosły |
|||||||
% efektu ekonomicznego |
Cele systemu produkcyjnego KAMAZ na 2012 rok:
1. Zwiększenie efektywności operacyjnej OJSC KAMAZ poprzez zmniejszenie awaryjnych przestojów sprzętu o 50%, zwiększenie wydajności pracy o 16%. zmniejszenie jednostkowych kosztów energii o 5% na pojazd, zmniejszenie kosztów zakupu o 1500 mln rubli, dostosowanie liczby obecnych konfiguracji pojazdów do biznesplanu na 2012 r., zapewnienie produkcji z rezerwą personelu na stabilna praca w okresie letnim.
2. Zwiększenie efektywności systemu zarządzania KAMAZ SA poprzez wprowadzenie standardu „SFM – zarządzanie procesem od miejsca tworzenia wartości”, wprowadzenie zasady „logistyka dostarcza, montaż montuje” poprzez opracowanie i wdrożenie standardów w procesie głównym: montaż, logistyka, realizacja piątej i szóstej fazy projektu „Kalendarz”, opracowanie i wdrożenie mapy rozwoju kadr procesu głównego, wdrożenie systemu raportowania dla menedżerów w oparciu o KPI procesu głównego.
3. Poprawa jakości i niezawodności produktów KAMAZ OJSC poprzez wprowadzenie wbudowanego systemu jakości do głównych procesów o 100%, zmniejszenie strat ze złomu o 10% i zmniejszenie PPM o 25%.
4. Zaangażuj 100% personelu w doskonalenie systemu produkcyjnego KAMAZ poprzez przeszkolenie wszystkich nowozatrudnionych pracowników z zasad, metod i narzędzi PSK, złożenie 4 propozycji kaizen na pracownika rocznie, otwarcie 4200 projektów kaizen, wdrożenie co najmniej 3800 , realizacja 80% zgłoszonych propozycji kaizen i projektów kaizen, otwarcie własnego projektu przez każdego szefa KAMAZ OJSC.
5. Zapewnienie zrównoważonego rozwoju dostawców, spółek zależnych, wspólnych przedsięwzięć w oparciu o zasady systemu produkcyjnego KAMAZ poprzez szkolenia Stopa bazowa PSK dla szefów wszystkich centrów samochodowych i kluczowych dostawców, zorganizowanie 3-dniowego seminarium dla szefów dealerów KAMAZ OJSC na podstawowym kursie PSK, wprowadzenie PSK we wszystkich spółki zależne ze 100% kapitałem KAMAZ SA, stworzenie sekcji referencyjnych na zasadach PSK u 3 kluczowych dostawców oraz w jednym z zakładów -
przedstawiciel klienta, otwierający przez liderów joint venture personalnych projektów na integrację systemów produkcyjnych joint venture i PSK.
6. Zapewnienie lojalności personelu firmy, klientów, mieszkańców miasta i Republiki Tatarstanu wobec OJSC KAMAZ poprzez systemowe przekazywanie udanych doświadczeń w rozwoju systemu produkcyjnego KAMAZ.
7. Uzyskaj efekt ekonomiczny, zmniejszając straty w wysokości 1418 mln rubli.
Ważnym elementem zwiększającym efektywność wdrożenia „odchudzonej produkcji” jest realizacja projektów pilotażowych. Na przykład projekt Mayak w Fabryce Samochodów KAMAZ OJSC został otwarty 8 września 2010 r. w celu intensywnego wdrażania nowoczesnych standardów, metod i technologii zarządzania systemem operacyjnym TOS (Daimler AG) w celu optymalizacji procesów Zakład KAMAZ SA. W trakcie realizacji projektu Mayak obciążenie operatorów zostało wyrównane do cyklu 240 s, nowy struktura organizacyjna. Cele, wyniki i narzędzia wykorzystane w projekcie Mayak przedstawiono w tabeli. czternaście.
Ponadto w trakcie projektu Mayak zmieniono normę sterowności kapitana: było 1:35, stało się 1:10 (mistrz jest liderem zespołu i jego ideologiem, wspierającym nową strukturę rurociągu). Zorganizowana praca operacyjna menedżerów i Informacja zwrotna przez centra informacyjne na 3 poziomach: brygada, warsztat, fabryka. Ponad 60% spotkań zostało przeniesionych do centrów informacyjnych, aby zapewnić przepływ informacji i procedurę eskalacji. Stanowiska pracy zostały zorganizowane zgodnie z 15 zasadami montażu Daimlera (zgodność od 19% do 69%). Od początku projektu pracownicy złożyli około 1300 propozycji kaizen z efektem ekonomicznym na kwotę ponad 17 mln rubli. Praca serwisu logistycznego zorganizowana jest w oparciu o 14 zasad logistyki Daimlera. W trakcie projektu odbywało się ciągłe szkolenie personelu w zakresie zasad i narzędzi oraz metod Lean (przeszkolono około 1400 pracowników i 350 inżynierów). Integralnym elementem wprowadzenia systemu „odchudzonej produkcji” w przedsiębiorstwie jest wyliczenie efektu ekonomicznego z wprowadzenia narzędzi i metod „odchudzonej produkcji”.
Tabela 14
Cele, wyniki i narzędzia wykorzystane w projekcie Mayak
Cele projektu |
Wyniki projektu |
Zasady, narzędzia i metody Lean Manufacturing zastosowane w projekcie |
Zmniejszenie liczby modyfikacji (montażu) zmontowanych samochodów o 50% |
Cel osiągnięty |
Szczegółowe mapowanie wszystkich procesów w obszarze objętym projektem. Kaskadowe planowanie pracy w formacie standardowych planów taktycznych. eliminacja |
Wdrażanie wbudowanej jakości |
Wdrożone pętle jakości 1, 2, bramki jakości, stanowiska jakości |
|
Wdrożenie systemu Andon |
Cel osiągnięty |
|
Wdrażanie standardów TOS w montażu i logistyce |
Cel osiągnięty |
|
Zwiększ wydajność pracy |
Wydajność pracy wzrosła o 49%. |
|
Zapewnienie możliwości montażu 48 100 pojazdów na GSK 1 w 2012 roku (24 000 pojazdów zostało zmontowanych na GSK 1 w 2010 roku) |
Możliwość montażu 48 100 pojazdów na GSK 1 dostarczona w 2011 r. |
|
Wdrożenie standardu Shop floor Management do zarządzania przedsiębiorstwem |
Standard zarządzania warsztatem wdrożony w obszarze projektu |
|
Koszt projektu musi zwrócić się w okresie jego realizacji. |
Efekt ekonomiczny projektu wyniósł 629 milionów rubli. i przekroczyły koszty |
Kalkulacja efektu ekonomicznego dokonywana jest w oparciu o kluczowe wskaźniki efektywności (redukcja zapasów, skrócenie trasy transportu, skrócenie nieplanowanych przestojów sprzętu itp.) i wyrażona w uzyskanych oszczędnościach w zasobach lub dodatkowej produkcji na miejscu , warsztat, organizacja, są brane pod uwagę jako efekt warunkowy.
Gospodarka effect = [Koszty przed - Koszty po] - -Koszty realizacji wydarzenia. (jeden)
Efekt ekonomiczny to efekt, którego kalkulacja uwzględnia wartościowo wszystkie rodzaje rezultatów i kosztów wynikających z realizacji działania.
Koszty = Zużycie zasobów fizycznych?Koszt zasobów. (2)
Koszty przedwdrożeniowe - kalkulowane na podstawie wyników mapowania stan obecny proces lub dane księgowe, rachunkowość zarządcza.
Z do \u003d P p do? St res, pocierać. (3)
Koszty po - obliczone zgodnie z planem (na etapie oceny wstępnej) lub rzeczywiste wydatkowanie zasobów po realizacji działania
Z po = P p po? St res, pocierać, (4)
gdzie P p przed, P p po – zużycie zasobów przed i po realizacji wydarzenia, St res – koszt zasobów
Koszty realizacji imprezy to jednorazowe koszty realizacji imprezy (koszty energii, materiałów, koszty robocizny itp.)
Zastosowanie zaproponowanej metodyki oceny efektywności pozwoli przedsiębiorstwu dokładniej ocenić efekt wprowadzenia narzędzi i metod szczupłej produkcji, na podstawie których możliwe jest podjęcie decyzji zarządczej o efektywności przedsiębiorstwa. pracy nad szczupłą produkcją i koniecznością zintensyfikowania tej pracy.
Przeprowadzono analizę korelacji i regresji szereg czasowy pozwoliło ocenić stopień wpływu czynników na zmienną zależną i na siebie nawzajem. Wyniki analizy wskazują na występowanie szczególnie ścisłego związku między zdolnościami produkcyjnymi przedsiębiorstwa a wielkością wysyłanych wyrobów, przychodami ze sprzedaży wyrobów, przeciętnym miesięcznym wynagrodzeniem, pełnym kosztem produkcji, wydajnością kapitału i wydajnością pracy. Wraz ze wzrostem tych wskaźników wzrasta wskaźnik zdolności produkcyjnych (połączenie bezpośrednie).
Analiza regresji szeregów czasowych pokazuje, co następuje. Po pierwsze, wskaźnik zwrotu z aktywów ma ścisły bezpośredni związek ze zdolnościami produkcyjnymi, wielkością produkcji w ujęciu fizycznym, stopniem wykorzystania mocy produkcyjnych, wolumenem wysyłanych produktów, przychodami ze sprzedaży produktów, średnimi miesięcznymi zarobkami oraz całkowitym kosztem sprzedaży. Jednocześnie istnieje odwrotna zależność z kosztem środków trwałych produkcji. Po drugie, rentowność produktów ma wysoki poziomścisłe powiązanie z zyskiem ze sprzedaży produktów i liczbą personelu. W tym przypadku istnieje bezpośredni związek między wskaźnikami. Ujemna wartość współczynnika korelacji (-0,716) ze wskaźnikiem kosztów na 1 rubel sprzedanych produktów wskazuje na ścisłą informację zwrotną.
Należy jednak zauważyć, że współczynniki korelacji parami uzyskano pod warunkiem wpływu na wynik innych czynników. W celu wyabstrahowania z ich wpływu i uzyskania ilościowej charakterystyki związku między wskaźnikami efektywnymi i czynnikowymi w czystej postaci obliczane są współczynniki korelacji cząstkowej.
W wyniku skonstruowania macierzy współczynników korelacji cząstkowych dla danych rozwojowych KAMAZ SA, udało się zidentyfikować dość bliską pozytywną zależność między kosztami rozwoju PSC a takimi wskaźnikami, jak liczba zgłoszonych i zrealizowanych wniosków kaizen oraz ilość uwolnionego obszaru (współczynniki korelacji wynosiły odpowiednio 0,888; 0,894 i 0,891). Liczba projektów otwartych jest pozytywnie skorelowana z liczbą projektów realizowanych, a także liczbą złożonych i wdrożonych wniosków kaizen. Liczba zwalnianych powierzchni jest ściśle powiązana z liczbą otwartych i realizowanych projektów oraz składanych i realizowanych wniosków kaizen. Wysokie współczynniki korelacji wskazują na znaczny poziom zależności wskaźników.
Właściwe wydaje się określenie wpływu rozwoju PSK na główne wskaźniki ekonomiczne przedsiębiorstwa. Najlepszy pozytywny efekt obserwuje się, gdy zmienne są opóźnione o 3 lata (tab. 15). W szczególności istnieje ścisły pozytywny związek między zdolnościami produkcyjnymi przedsiębiorstwa a kosztami rozwoju PSK, a także wskaźnikami otwartych i realizowanych projektów oraz propozycji kaizen. Ponadto wskaźniki te mają pozytywny wpływ na wolumen wysyłanych produktów, przychody ze sprzedaży oraz zwrot z kapitału.
Dalsze przesuwanie wskaźników ze względu na ograniczone dane wyjściowe o przedsiębiorstwie wydaje się niewłaściwe.
Kolejnym etapem analizy korelacji jest obliczenie równania relacji (regresja). Współczynniki równania pokazują ilościowy wpływ każdego czynnika na wskaźnik efektywności, podczas gdy inne pozostają niezmienione. Właściwe wydaje się zbudowanie modelu regresji liniowej wielokrotnej z najlepszymi współczynnikami korelacji dla modelu, tj. przy zmiennych opóźnieniach przez trzy lata.
W naszym przypadku równania regresji będą wyglądać tak:
y = 0,582x16 + 0,04x19 + 86,04x27 + 63692,33, (5)
W tym przypadku możemy podać następującą interpretację otrzymanego równania: rentowność wzrasta o 0,582 jednostki. wraz ze wzrostem liczby otwartych projektów; o 0,04 szt. - wraz ze wzrostem liczby wdrożonych propozycji kaizen; za 86,04 szt. - przy wzroście kosztów wprowadzenia PSK o 1 mln rubli.
Tabela 15
Macierz współczynników korelacji par (obciążenie - 3 lata)
Przeszkoleni w zakresie zasad i metod bezpieczeństwa personelu |
Otwarte projekty |
Zrealizowane projekty |
Złożone propozycje Kaizen |
Wdrożone oferty kaizen |
Zwolniona powierzchnia mkw |
Wydane jednostki wyposażenia. |
Uzyskany efekt ekonomiczny (mln rubli) |
W tym kaizeny |
Procent efektu ekonomicznego |
Koszty rozwoju PSK wyniosły (mln rubli) |
|
Zdolność produkcyjna, szt. |
|||||||||||
Produkcja w ujęciu fizycznym, szt. |
|||||||||||
Współczynnik wykorzystania mocy produkcyjnych |
|||||||||||
ilość wysyłanych produktów, |
|||||||||||
Wpływy ze sprzedaży produktów, mln rubli |
|||||||||||
Średnia miesięczna pensja, rub. |
|||||||||||
Całkowity koszt sprzedanych towarów, mln rubli |
|||||||||||
Koszt trwałych aktywów produkcyjnych, mln rubli |
|||||||||||
Zysk (strata) ze sprzedaży, mln rubli |
|||||||||||
Liczba pracowników produkcji przemysłowej, os. |
|||||||||||
Produktywność kapitału, pocierać. |
|||||||||||
Wydajność pracy, miliony rubli |
Jednocześnie wartość R2 = 0,995 wskazuje, że zmienność wydajności pracy o 99,5% wynika z liniowego wpływu powyższych czynników.
Zastosowanie proponowanych metod organizacji lean production w przedsiębiorstwie polega na stworzeniu adaptacyjnej i elastyczny system zarządzania i produkcji, zdolnych do ciągłego doskonalenia i przyczyni się do zmniejszenia strat w przedsiębiorstwie, zwiększenia konkurencyjności i zwiększenia wydajności pracy.
Zwracamy uwagę na czasopisma wydawane przez wydawnictwo „Akademia Historii Naturalnej”
Efekt ekonomiczny: istota koncepcji, potrzeba obliczeń i analiz
Definicja 1
W kontekście koncepcji „odchudzonej produkcji” efekt ekonomiczny stanowi różnicę między wynikami działalności podmiotu gospodarczego a kosztami poniesionymi na ich uzyskanie; innymi słowy są to dodatkowe dochody uzyskiwane dzięki temu, że stosując określone podejścia i metody, przedsiębiorstwo działa wydajniej.
Musisz zrozumieć różnicę między redukcją kosztów (minimalizacją kosztów) a eliminacją/redukcją marnotrawstwa. W rzeczywistości są to nieco inne rzeczy (chociaż z drugiej strony zmniejszenie strat prowadzi do niższych kosztów).
Efektem ekonomicznym wdrożenia tego czy innego usprawnienia jest różnica między stanami „przed” i „po” (pomniejszona o koszty związane z wdrożeniem działania). Czasami różnica między kosztami jednostkowymi na jednostkę produktu, „przed” i „po” a innymi wskaźnikami jest traktowana jako efekt ekonomiczny.
Najczęściej efekt ekonomiczny liczony jest w skali 1 roku. Tak więc, na przykład, jeśli dzienne ruchy operatora zostaną skrócone o 5 minut, to oszczędność za 1 tydzień wyniesie 50 minut (przy pięciodniowej i dwuzmianowej tydzień pracy); na rok to już około 2400 minut (czyli 5 dni roboczych). Tym samym kalkulacja efektu ekonomicznego w skali roku pozwala wyraźniej dostrzec pełny potencjał wprowadzonej poprawy.
Wstępne wyliczenia potencjalnego efektu ekonomicznego pozwalają na prawidłowe ustalenie priorytetów, a także skoncentrowanie uwagi i wysiłków na tych pracach i projektach, które przyniosą najwięcej korzyści i powinny najszybciej się zwrócić. W pierwszej kolejności należy preferować proste w realizacji, niedrogie i projekty krótkoterminowe. Jeśli musisz wybierać między dwoma projektami, które są podobne pod względem kosztów i złożoności, powinieneś wybrać ten, który ma większy potencjalny efekt ekonomiczny.
Wskaźniki efektywności działań
Konieczna jest analiza realizacji mierników koncepcji szczupłej produkcji (lean) wyłącznie w oparciu o rzetelne dane z wyników badań dynamiki wskaźników produkcji. Pamiętaj też, aby skupić się na jednostkowym koszcie produkcji.
Ogólnie rzecz biorąc, wdrożenie projektu Lean Manufacturing jest uważane za udane, jeśli spełnione są następujące warunki:
- wzrost wydajności pracy i wzrost wielkości produkcji
- spadek wskaźnika małżeństw
- poprawił się wskaźnik terminowości dostaw wytwarzanych produktów
- zmniejszony koszt na jednostkę.
Uwaga 1
Jeśli choć jeden wskaźnik wykazywał dodatnią dynamikę, a reszta pozostała na tym samym poziomie, to projekt powinien zostać zaakceptowany. Jeśli większość obliczonych wskaźników wykazuje odpowiednią dynamikę, ale jeden ze wskaźników wykazuje coś przeciwnego, to potrzebna jest dodatkowa, głębsza analiza przyczyn tego stanu rzeczy.
Znaczące oszczędności kosztów produkcji w przedsiębiorstwie produkcyjnym można osiągnąć m.in. poprzez wdrożenie następujących działań:
- wprowadzenie energooszczędnych technologii
- optymalizacja kosztów utrzymania i napraw bieżących zwolnionych środków trwałych
- zmiana amortyzacji w związku z uwolnieniem sprzętu i przestrzeni (przede wszystkim magazynowanie)
- optymalizacja podatków, leasingu, najmu, opłat ubezpieczeniowych, kosztów ochrony itp.
- spadek wskaźnika małżeństw
- eliminacja nadmiernych zapasów
- strata czasu pracy związana z oczekiwaniem na dostawę zasobów materiałowych i technicznych
- szybsza realizacja dzięki zminimalizowaniu lub wyeliminowaniu zapasów, przestojów itp.
- eliminacja marnotrawstwa materiałów itp.
Istotą jest więc konieczność wyeliminowania lub zminimalizowania wszystkiego, co nie tworzy wartości dla konsumenta.