Sprzęt do produkcji betonu komórkowego. Sprzęt niezbędny do produkcji bloczków z betonu komórkowego. Sprzęt do produkcji
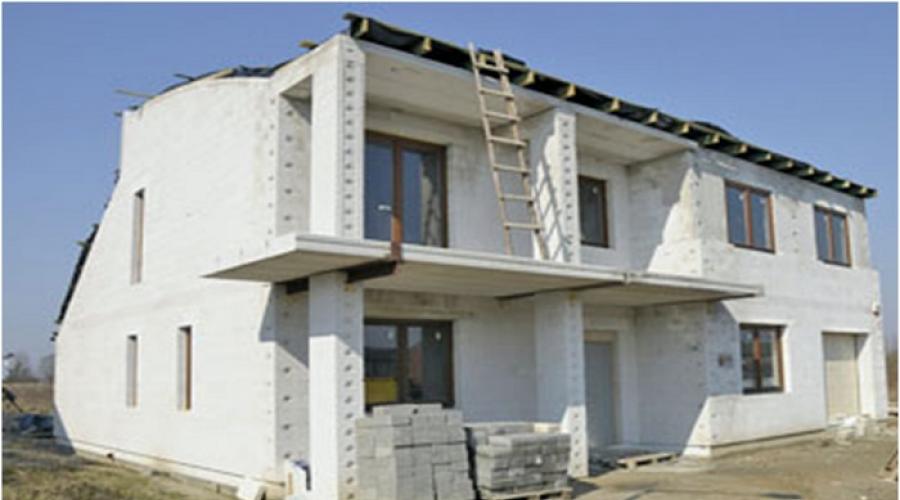
Przeczytaj także
Współczesne budownictwo wyróżnia połączenie tradycyjnych metod budowlanych z najnowszymi technologiami budownictwa kubaturowego. Zastosowanie betonu komórkowego znacząco podniosło efektywność budownictwa i poprawiło jakość prac budowlanych. Powszechna produkcja betonu komórkowego na potrzeby budownictwa prywatnego podkreśla zwiększoną popularność wśród deweloperów opcji budżetowych na materiały ścienne o wystarczająco wysokiej wytrzymałości i właściwościach termoizolacyjnych.
Jednym z takich popularnych materiałów budowlanych na ściany jest gazobeton stosowany w budowie niskich budynków mieszkalnych i gospodarczych. Ze względu na swoją porowatą strukturę jest betonem komórkowym i jest sztuczną porowatą formacją przypominającą kamień.
Producenci betonu komórkowego produkują wyroby z betonu komórkowego w postaci bloków o różnych konfiguracjach, które spełniają wymagania następujących norm:
- GOST 31359-2007, ustanawiające wymagania dla betonu komórkowego przeznaczonego do produkcji bloczków i paneli ściennych, płyt, nadproży i innych elementów budowlanych;
- GOST 31360-2007, regulujący wymagania dotyczące wyrobów ściennych wykonanych z betonu komórkowego.
GOST 31359-2007 definiuje materiały z betonu komórkowego jako rodzaj betonu komórkowego, który różni się od innych materiałów komórkowych sposobem tworzenia porów (punkt 4.2). Pod względem struktury wyrób z betonu komórkowego przypomina rodzaj betonowej „gąbki”, składającej się z małych pęcherzyków-komórek o średnicy nie większej niż 3 mm.
Ze względu na drobno porowatą strukturę produkty blokowe, które są w stanie wyprodukować nowoczesny sprzęt do produkcji bloków gazowych, mają właściwości fizyczne i mechaniczne, które korzystnie odróżniają je od podobnych produktów wykonanych z innych materiałów betonowych:
- niski ciężar właściwy;
- niska przewodność cieplna;
- odporność na ogień;
- odporność na grzyby i pleśń;
- łatwość obróbki;
- produkcja i zastosowanie.
Zalety
Jako zalety techniczne i ekonomiczne materiałów z betonu komórkowego wymienia się następujące aspekty:
- Ciężar budowy bloczków z betonu komórkowego jest kilkakrotnie mniejszy niż ciężar podobnych produktów wykonanych z cegły lub betonu. Blok gazowy o standardowych wymiarach 300x250x600 mm waży tylko 30 kg, czyli ponad 3 razy mniej niż waga tej samej objętości cegieł o wymiarach 60x125x250 mm.
- Łatwość obróbki produktów konwencjonalnymi narzędziami mechanicznymi pozwala na dopasowanie bloczków podczas budowy budynków w celu poprawy jakości montażu.
- Wysoka izolacyjność cieplna i akustyczna ścian z bloczków gazobetonowych zapewnia komfort mieszkania w budynkach mieszkalnych.
- Niezawodna odporność ogniowa w stosunku do otwartego płomienia zapewnia bezpieczeństwo przeciwpożarowe budynku.
- Wysoka produkcyjność konstrukcji przy zastosowaniu bloków gazowych zwiększa wydajność i jakość pracy.
- Przystępny koszt bloków gazowych zapewnia im odpowiednią konkurencyjność na rynku materiałów budowlanych.
- Możliwość zorganizowania produkcji wyrobów z bloków gazowych jako firmy prywatnej, ponieważ rzeczywista cena produkcji betonu komórkowego, mini-fabryki lub wyposażenia linii typu przenośnik jest stosunkowo przystępna. Możliwość produkcyjna produkcji materiałów z betonu komórkowego stwarza warunki do prowadzenia działalności gospodarczej o wysokiej rentowności.
Technologia produkcji betonu komórkowego
Pierwotnymi składnikami stosowanymi przez producentów bloczków z betonu komórkowego do produkcji materiału z betonu komórkowego są:
- Cement portlandzki w proporcjach 50 - 70% objętości przygotowanej mieszanki;
- Wapno - nie więcej niż 5% objętości mieszaniny;
- piasek kwarcowy o frakcji nieprzekraczającej 2,1 mm, proporcje w mieszance - 20-40%;
- woda - 0,8-1,0%;
- złożone dodatki gazotwórcze w zakresie od 0,04 do 0,09%.
Podstawowa technologia wytwarzania betonu komórkowego składa się z kilku etapów:
- Etap 1 - dozowanie głównych składników - cementu, piasku, wapna - zgodnie z proporcjami danej receptury na materiał z betonu komórkowego.
- Etap 2 - dostawa głównych składników i wody do specjalnej betoniarki gazobetonu. Dokładne wymieszanie składników aż do uzyskania wysoce jednorodnej mieszanki.
- Etap 3 - dodanie poroforu do przygotowanej mieszaniny (najczęściej poroforem jest wodna zawiesina proszku aluminiowego). proces porowatości mieszaniny. To jest ważne! W procesie chemicznego oddziaływania metalicznego aluminium, które stanowi podstawę proszku, z zaprawami wapiennymi i cementowymi uwalniany jest wolny wodór w postaci pęcherzyków gazu, które „pęcznieją” zaczyn cementowy. Urządzenia do betonu komórkowego powinny zapewniać równomierną emisję gazów w całej objętości mieszanki w celu uzyskania jednolitej porowatej struktury.
- Utwardzanie mieszanki gazobetonowej w specjalnych formach, cięcie bloków o wymaganej konfiguracji. Kształt gotowych produktów można nadać najbardziej zróżnicowany - od tradycyjnych równoległościanów po bloki w kształcie litery U lub łukowe.
W zależności od rodzaju obróbki twardniejącej masy z betonu komórkowego Istnieją dwa sposoby wytwarzania bloków gazowych:
- metoda nieautoklawowa, w której dojrzewanie półproduktów do zestawu o regulowanej wytrzymałości przebiega w sposób naturalny bez wymuszonej ekspozycji na czynniki zewnętrzne;
- metoda autoklawowa lub autoklawowanie, w której produkty poddawane są działaniu ciśnienia w podwyższonych temperaturach w komorach autoklawowych.
Cechy produktów z bloczków z betonu komórkowego do autoklawowania
Jeżeli komora autoklawowa wchodzi w skład wyposażenia bloku gazowniczego, to produkty utwardzania autoklawowego znacznie przewyższają jakością produkty wykonane metodą nieautoklawową. Skurcz bloczków autoklawowych podczas pracy nie przekracza 0,5 mm/m, podczas gdy ten sam wskaźnik dla bloczków ściennych nieautoklawowych osiąga 5 mm/m. Ostateczna wytrzymałość na ściskanie materiałów z autoklawizowanego betonu komórkowego sięga 3,2 MPa, dla materiałów nie autoklawowanych - nie więcej niż 1,0 MPa. Autoklawowane bloki gazowe mają stabilną jednorodną strukturę, która z góry determinowała ich właściwości użytkowe jako uniwersalny materiał budowlany. Budynki ścienne o grubości 375-400 mm, zbudowane z wyrobów z betonu komórkowego, sprawdziły się dobrze w rosyjskich warunkach pogodowych bez dodatkowej izolacji.
Zasadą autoklawowania komórkowego materiału budowlanego jest umieszczenie już uformowanych wyrobów w autoklawie, w którym bloczki będą przez długi czas pod wpływem wysokiego ciśnienia (do 1,2 MPa) i poddane obróbce parą wodną w temperaturze 190-191 stopnie. Z. Takie warunki inicjują reakcje, które wzmacniają gęstość strukturalną materiału i zwiększają jego wytrzymałość.
Wyposażenie techniczne produkcji betonu komórkowego
Aby rozpocząć działalność produkcyjną w zakresie wytwarzania wyrobów z betonu komórkowego, kompletowana jest linia technologiczna do produkcji betonu komórkowego, w skład której wchodzą następujące elementy funkcjonalne:
- dozowniki składników mieszanki z betonu komórkowego;
- mieszalnik do betonu komórkowego (mikser-aktywator) do przygotowania mieszanki pianki z betonu komórkowego;
- formy do wylewania mieszanki spienionego betonu komórkowego i późniejszego utwardzania;
- urządzenia do cięcia bloków gazowych;
- wózki do przewożenia gotowych produktów do magazynu.
Do pracy w technologii autoklawowej linia wyposażona jest w komorę autoklawową oraz automatyczny system kontroli i regulacji trybów pracy autoklawu.
Przed zorganizowaniem mini-fabryki do produkcji bloków gazowych lub innych wyrobów z betonu komórkowego konieczne jest określenie wydajności linii produkcyjnej. Od tego zależy wyposażenie techniczne miejsca produkcji lub zakładu oraz stopień automatyzacji regulowanych operacji technologicznych. Do produkcji wyrobów budowlanych na skalę przemysłową wymagany będzie zupełnie inny sprzęt niż do produkcji na małą skalę lub do produkcji bloków gazowych w warunkach rzemieślniczych. Linie produkcyjne i technologiczne do produkcji wyrobów z betonu komórkowego dzielą się na trzy kategorie.
mini linie
1.mini linie, które są mini-fabrykami o zdolności produkcyjnej 15-25 metrów sześciennych. m/dzień wyrobów z betonu komórkowego. Mają niski stopień automatyzacji procesów. Siłowniki obsługiwane są przez 2-3 pracowników. Powierzchnia produkcyjna minifabryk nie przekracza 140-160 m2. metrów. W skład wyposażenia głównego wchodzą:
- mikser do betonu komórkowego;
- urządzenia do cięcia mieszanki utwardzającej;
- formy, tace do dojrzewania bloków gazowych;
- tory kolejowe i wózki do transportu gotowych produktów.
W minifabrykach stosuje się mieszalniki typu mobilnego, które po wymieszaniu mieszanki gazobetonowej zwijają się do stacjonarnych form stacjonarnych, aby wypełnić je przygotowaną mieszanką.
Cena sprzętu do produkcji bloczków z betonu komórkowego na takich liniach może znacznie wzrosnąć, gdy zostanie wyposażony w dodatkowe opcje, np. kompresor powietrza do lepszego mieszania mieszanki betonowej lub automatyczne dozowniki.
Linie stacjonarne
2. Linie stacjonarne moce produkcyjne od 30 do 60 metrów sześciennych. metrów/dzień. Wytwórnia betonu komórkowego tego typu wyposażona jest w stacjonarną mieszarkę do betonu komórkowego, do której podjeżdżają mobilne wózki w celu wypełnienia masą pianobetonową. Poziom automatyzacji produkcji jest dość wysoki, co pozwala na zaangażowanie jednego lub dwóch pracowników. Powierzchnia produkcyjna linii stacjonarnych nie przekracza 500 m2. metrów.
Linie typu przenośnika
3. Linie typu przenośnika moce produkcyjne od 75 do 150 metrów sześciennych. metrów/dzień. Pomimo wysokiego stopnia automatyzacji sterowania procesami, do utrzymania kompleksu wymagane jest minimum 8 pracowników serwisu. Powierzchnia zajmowana przez zakład przenośników do produkcji bloczków z betonu komórkowego przekracza 600 metrów kwadratowych. metrów.
Problemy organizacyjne podczas otwierania produkcji betonu komórkowego
Otwarcie zakładu produkującego gazobeton będzie wymagało sporządzenia szeregu dokumentów związanych ze specyfiką produkcji i sprzedaży bloczków z betonu komórkowego. Jeśli sprzęt jest używany do produkcji betonu komórkowego w rzemieślniczych warunkach domowych bez użycia autoklawu, wówczas nie będą wymagane żadne zezwolenia na taką pracę. W dekretach Rządu Federacji Rosyjskiej z dnia 13.08.97 nr 1013 i Państwowej Normie Federacji Rosyjskiej z 08.10.2001, które określają wykazy wyrobów podlegających obowiązkowej certyfikacji, nie ma bloków z betonu komórkowego i wyposażenia do ich produkcji. Jednak w przypadku zastosowania technologii autoklawowej producent musi uzyskać zgodę władz Gosgortekhnadzor, sprzęt pracuje pod podwyższonym ciśnieniem. Oddzielnie konieczne jest uzyskanie pozwolenia od straży pożarnej, ponieważ moc elektryczna autoklawu wynosi 5-10 kW. Swoje uwagi może zgłosić miejska SES, gdyż zastosowanie pyłu aluminiowego powinno zapewnić możliwość wykorzystania opartej na nim zawiesiny gazotwórczej.
Jeszcze nie tak dawno tylko duże wyspecjalizowane przedsiębiorstwa dysponujące drogim sprzętem mogły produkować gazobeton i inne betony komórkowe.
Wprowadzenie nowych procesów technicznych znacznie uprościło produkcję tak poszukiwanych materiałów, co dało impuls do rozwoju produkcji wyrobów z betonu komórkowego przez małe i średnie przedsiębiorstwa.
Wcześniej możliwe było wyprodukowanie tak popularnego materiału budowlanego w dużych przedsiębiorstwach ze specjalnym sprzętem do produkcji bloczków z betonu komórkowego. Dziś ulepszony proces technologiczny umożliwił rozpoczęcie produkcji betonu komórkowego w przedsiębiorstwie lub w domu, w oparciu o wymaganą ilość, cechy technologiczne i dostępność środków. W zależności od organizacji procesu nabywają stacjonarne urządzenia, minifabryki lub małe mobilne zakłady, za pomocą których wykonuje się bloczki z betonu komórkowego o różnym stopniu gęstości.
Technologia
Proces produkcji bloczków z betonu komórkowego nie sprawia trudności.
Grupa wyrobów betonowych charakteryzuje się budową komórkową. Pęcherzyki gazu zajmują do osiemdziesięciu pięciu procent objętości, dzięki czemu gotowe bloki są lekkie.
Surowiec ugniata się w betoniarce przez pięć minut, po czym do masy dodaje się wodną zawiesinę proszku aluminiowego, który reaguje z wapnem. W procesie tym wytwarzany jest wodór, który tworzy liczne pory, które równomiernie przenikają przez materiał.
Po dodaniu proszku aluminiowego masę przelewa się do specjalnych metalowych pojemników i już tam następuje pęcznienie. Aby przyspieszyć proces reakcji, wiązania i twardnienia, półprodukt poddawany jest obciążeniu wibracyjnemu. Z masy, która zaczyna twardnieć drucianym sznurkiem, usuwa się nierówne miejsca, pozostałe w formie surowce tnie się na kawałki o pożądanej wielkości. Produkcja bloków gazowych jest kontynuowana w autoklawie, po czym produkty są kalibrowane na frezarkach.
Zastosowanie urządzeń autoklawowych w technologii produkcji betonu komórkowego zajmuje szczególne miejsce, gdyż poprawiają się właściwości materiału. Uformowany i podzielony na osobne bloki gazobeton trafia do autoklawów i poddawany jest dwunastogodzinnej obróbce parą wodną.
Ten sposób wytwarzania pozwala na uzyskanie materiału, który praktycznie nie kurczy się, charakteryzuje się jednolitą strukturą oraz dobrymi parametrami w zakresie izolacyjności akustycznej i zatrzymywania ciepła.
Drugą opcją do produkcji betonu komórkowego jest metoda bez autoklawowania. Pełne utwardzenie następuje w normalnych warunkach, nie jest wymagany nowoczesny sprzęt do produkcji. W takim przypadku możliwe staje się samodzielne wykonanie bloków gazowych.
Materiał nie będzie trwały.
Surowce do betonu komórkowego
Aby uzyskać blok komórkowy, stosuje się mieszaninę składającą się z następujących składników:
- piasek o uziarnieniu nieprzekraczającym 2,1 mm i nie zawierający dużo gliny. Ten materiał stanowi 20-40% masy ugniecionej;
- wapno (1 - 5%);
- skład cementu - od 50 do 70% (gatunek M 40 lub M 500);
- czysta woda - 0,25 - 0,8%;
- proszek aluminiowy do tworzenia gazów - 0,04 - 0,09%.
Przegląd wymaganego sprzętu
Rozważ cechy linii do produkcji betonu komórkowego.
Przenośnik
Ten rodzaj sprzętu to:
- najbardziej zautomatyzowany proces;
- minimalny udział pracowników w produkcji bloków;
- znaczny koszt;
- znaczne wielkości produkcji;
- z całą niezbędną kompletnością;
- wysoki poziom rentowności.
Standardowy pakiet zawiera:
- kontenery i bunkry na surowce;
- przenośniki taśmowe, przez które podawane są komponenty;
- jednostka do mieszania roztworu;
- instalacje autoklawowe;
- formularze;
- kompleks do krojenia surowej masy na bloki;
- przenośnik mieszający;
- zakład kruszenia;
- wózki;
- zdalne sterowanie do sterowania procesem w trybie automatycznym;
- Wózek widłowy.
Cena takiego sprzętu jest wysoka, sięga 55 000 000 rubli. Kwota jest poważna, ale wydajność linii pozwala wyprodukować co najmniej trzysta tysięcy metrów sześciennych materiału w ciągu roku.
Aby pomieścić cały sprzęt, konieczne będzie przygotowanie terenu o powierzchni około czterech tysięcy metrów kwadratowych.
Jeśli porównamy, który producent bloków gazowych jest lepszy, to jako alternatywę zaleca się zwrócenie uwagi na używany sprzęt. Istnieją szczególne zagrożenia, ale koszt linii będzie znacznie niższy.
Kontynuując porównywanie bloków gazowych różnych producentów, eksperci zalecają zakup przenośnika Inntech-100. Koszt wynosi do 3 000 000 rubli, a wydajność jest znacznie niższa.
Cechą takiej linii jest bezruch mieszalnika. Formularze są przenoszone i wypełniane automatycznie. Kompleks do cięcia - mechanicznego.
Dużą popularnością cieszą się niemieckie linie do produkcji bloków. Są bardzo wydajne i działają przez długi czas. Okazuje się, że materiał na takim sprzęcie jest wysokiej jakości.
Stacjonarny
Jego koszt jest znacznie niższy niż w przypadku pierwszej opcji. Ale pod względem wydajności linia będzie produkować nie więcej niż pięćdziesiąt metrów sześciennych materiału dziennie.
W skład zestawu montażowego wchodzą dozowniki surowca oraz przenośniki taśmowe, które dostarczają komponenty do mieszalnika.
Niestety ten zestaw nie jest uważany za w pełni zautomatyzowany. Aby mógł on w pełni funkcjonować, będzie musiało być zaangażowanych kilku pracowników.
Do instalacji linii wymagane będzie pomieszczenie o powierzchni od pięciuset metrów kwadratowych.
mobilny
Tego typu sprzęt jest świetny dla początkujących, którzy chcą wykonać klocki na własny użytek. Nawiasem mówiąc, niektórzy eksperci wykonują taki sprzęt do betonu komórkowego własnymi rękami.
Linia zasilana jest mocą 220 watów, podczas gdy inne typy maszyn wymagają 360 watów. Wielkość produkcji jest niewielka - od dwóch do dziesięciu metrów sześciennych dziennie.
Własna produkcja
Aby rozpocząć produkcję materiałów budowlanych w domu, będziesz potrzebować pewnych narzędzi do bloku gazowego i sprzętu. Ich minimalny zestaw składa się z:
- Betoniarka;
- formularze blokowe;
- metalowe struny przeznaczone do odcinania nadmiaru masy.
Postępując zgodnie z instrukcjami, całkiem możliwe jest wykonanie bloku gazowego własnymi rękami przy użyciu takiego zestawu sprzętu. Pozytywną cechą tej metody jest możliwość ustalenia procesu produkcyjnego bezpośrednio na placu budowy poprzez zainstalowanie tam maszyny do produkcji bloków gazowych.
Domowe bloki gazowe są gorszej jakości niż materiał wyprodukowany fabrycznie.
Autoklawowanie
Przyjrzymy się temu procesowi produkcji bardziej szczegółowo, zrozumiemy jego różnice i zalety.
Za pomocą takiego przetwarzania poprawia się właściwości jakościowe gotowego produktu. Proces przebiega tak:
- bloczki pocięte zgodnie z wymaganymi parametrami trafiają do komór autoklawowych. Wewnątrz powstaje wysoka temperatura i ciśnienie;
- czas przetwarzania wynosi dwanaście godzin;
- po zakończeniu ekspozycji w autoklawie bloki prawie natychmiast mogą być używane w budownictwie, ponieważ osiągnęły w pełni wymagany wskaźnik wytrzymałości;
- metoda wytwarzania bez użycia autoklawów zakłada czterotygodniową ekspozycję, podczas której bloki ostatecznie twardnieją.
Analiza porównawcza produkcji autoklawowanej i nieautoklawowanej
Porównajmy dwa rodzaje materiałów:

Instrukcje dotyczące produkcji materiału blokowego
Zaczynają od tego, że z desek strącono piórnik. Prefabrykowane zworki są wkładane do niego na całej długości, dzieląc wspólną ramę na komórki. Aby to zrobić, użyj wodoodpornej sklejki. Aby było dobrze zamocowane, w deskach ułożone są nacięcia.
Rozmiary komórek powinny odpowiadać wymaganym rozmiarom bloków. Aby przyspieszyć proces produkcyjny, konieczne jest wykonanie kilku form w różnych rozmiarach.
Aby masa zaprawy nie przywierała do desek, poddaje się je obróbce specjalnymi związkami lub olejem silnikowym rozcieńczonym w wodzie.
Aby wymieszać roztwór, będziesz musiał kupić mikser, kompresor i rękawy. Nawiasem mówiąc, taka instalacja służy nie tylko do jednorazowej produkcji bloków, ale także do organizacji produkcji na małą skalę.
Oprócz powyższego będziesz potrzebować drutu do odcięcia nadmiaru zaprawy.
Jeśli nie ma dozownika, będziesz musiał sam zważyć surową masę. Tutaj należy przestrzegać dokładności proporcji, aby nie naruszać jakości produktów.
Wszystkie komponenty są ładowane w odpowiednich proporcjach. Przyspieszy to hartowanie, zwiększy właściwości techniczne bloków. Nawiasem mówiąc, takie proporcje obserwuje się nie tylko w domu, ale także w produkcji fabrycznej materiału.
Przygotowaną masę przelewa się do foremek, nie są one wypełnione po brzegi, ponieważ mieszanina nadal pęcznieje. Z reguły napełnianie odbywa się do połowy objętości.
Powstaje gaz. Następnie konieczne jest usunięcie nadmiaru mieszanki. Ta praca jest wykonywana od pięciu do sześciu godzin po wylaniu.
Po czternastu godzinach wykonuje się striptiz. Aby klocki się odsunęły, zaleca się delikatne pukanie w ściany form. Aby uzyskać wytrzymałość techniczną, materiał pozostaje na otwartej przestrzeni lub jest przechowywany w pomieszczeniach.
Pamiętaj, że idealny materiał może nie zadziałać za pierwszym razem.
Wniosek
Jak zrobić blok gazowy, odkryliśmy to. Pozostaje tylko ustalić ilość materiału, zakupić wszystko, czego potrzebujesz i rozpocząć proces produkcyjny.
Ten sztuczny kamień od dawna cieszy się popularnością, zwłaszcza w dziedzinie budownictwa niskiego. Poszczególni deweloperzy potrafili docenić wszystkie jego zalety, w tym niski koszt produkcji. A szybkość budowy budynków jest taka, że według tego wskaźnika ten przedstawiciel klasy betonu komórkowego znajduje się na jednym z pierwszych miejsc wśród wszystkich użytych materiałów budowlanych.
Jest to również atrakcyjne, ponieważ w razie potrzeby produkcję betonu komórkowego można zorganizować w dowolnym miejscu, a nie tylko w wyspecjalizowanym przedsiębiorstwie. Technologia jest na tyle prosta, że bloki można wykonać samodzielnie, na konkretne potrzeby, o różnych kształtach i rozmiarach, co stwarza dodatkowe udogodnienie dla prywatnego dewelopera.
Jaka jest zaleta produkcji betonu komórkowego w domu?
W procesie przygotowania do budowy zwykle niemożliwe jest obliczenie dokładnej liczby niektórych półfabrykatów (rozmiaru). I nie chodzi tylko o błędy pomiarowe. Osobliwością muru jest to, że w każdym kolejnym rzędzie „cegły” są instalowane z przesunięciem, aby uniknąć zbieżności połączeń wzdłuż pionu. W konsekwencji musisz poświęcić czas na cięcie produktów, co ostatecznie prowadzi do przekroczenia materiału. Dlatego z reguły bloki kupowane są z marżą, a są to dodatkowe koszty.
Wszystkie obliczenia elementów konstrukcyjnych są „dołączone” do określonych standardowych rozmiarów produktów. Ale w praktyce życzenia właściciela i wymiary zakupionych bloków nie zawsze się pokrywają. Na przykład grubość ścian wewnętrznych. Organizacja produkcji betonu komórkowego w domu pozwala na produkcję sztucznego kamienia o dowolnej niezbędnej geometrii, w tym o skomplikowanych konfiguracjach (łukowych lub innych).
Bloki z tego materiału są przygotowywane na dwa sposoby - w autoklawie lub bez użycia specjalnego sprzętu. Rozważmy ostatnią opcję, ponieważ przy budowie jednego lub dwóch budynków na miejscu nie ma sensu wydawać pieniędzy na zakup komór cieplnych, które nie będą potrzebne później, ale są dość drogie. Ta metoda ma pewne cechy i należy je wziąć pod uwagę.
„Plusy”– minimalne koszty, prostota technologii. Kupowanie gotowych bloków, z uwzględnieniem ich dostawy na miejsce, będzie kosztować znacznie więcej.
„Minusy”- jakość produktów jest gorsza od tych, które zostały poddane obróbce cieplnej, dlatego nie zaleca się budowania budynków o więcej niż 2 piętrach z takich bloków. Plus - utwardzanie następuje naturalnie. Dlatego produkcja betonu komórkowego nie autoklawowanego może odbywać się tylko w temperaturze powyżej + 5 0C, aby zapewnić normalne odparowanie wody.
Wideo - Produkcja betonu komórkowego w domu
Ekwipunek
Betoniarka. Osiągnięcie wysokiej jakości jednorodnej kompozycji mieszanki przy ręcznym mieszaniu nie zadziała, a to zależy od kilku czynników. A jakość gotowych bloków jest bezpośrednio związana z surowcami. Na przykład wiele cech (hałas, izolacja cieplna i wiele innych) zależy od równomiernego rozmieszczenia pęcherzyków powietrza w całej objętości materiału.
Formularze.
Cienki drut stalowy (do odcinania nadmiaru masy po wylaniu).
Składniki mieszanki do produkcji betonu komórkowego
Cement
Doświadczeni rzemieślnicy twierdzą, że nikt nie nadaje się do samodzielnej produkcji bloków. Zaleca się używanie marki „400” D20.
Kwarc piaskowy
Najlepiej przesiać przez sito, dokładnie wypłukać (w celu usunięcia zanieczyszczeń) i wysuszyć.
Dodatki
Wapno (wapno palone), siarczan sodu, soda kaustyczna, porofor (proszek aluminiowy).
Oczywiście będziesz potrzebować czystej wody.
Technologia pracy
Tworzenie form. Możesz je kupić (prefabrykowane) lub zrobić własne. Potrzebne będą deski, w których jedna ze stron musi być dokładnie strugana. Zbija się z nich „piórnik”, do którego wkłada się zworki, dzieląc je na całej długości na przegródki. Takie „wkładki” można wyciąć ze sklejki odpornej na wilgoć. Wcześniej na planszach, zgodnie z wcześniej przygotowanym znacznikiem, pod „wstawkami” wykonywane są nacięcia.
Wymiary komórek określają wymiary przyszłych bloków, dlatego dobiera się je w zależności od tego, jakie parametry powinien mieć sztuczny kamień. Aby przyspieszyć proces produkcji betonu komórkowego, należy przygotować kilka różnych form, dla wszystkich wymaganych rozmiarów.
Aby mieszanina nie przywierała do desek, wewnętrzne powierzchnie ogniw smaruje się obficie olejem zużytym rozcieńczonym w wodzie (3 części) (olej maszynowy - 1 część). Nawiasem mówiąc, robi się to za każdym razem przed nowym napełnieniem roztworu.
Przygotowanie mieszanki do betonu komórkowego
Ten krok jest zawsze najtrudniejszy. I nie chodzi o jakość mieszania, ale o proporcje składników. Należy od razu zauważyć, że tylko dzięki doświadczeniu można osiągnąć wymaganą jakość gotowych produktów. Wiele zależy od marki cementu, piasku i właściwości innych składników. Nawet jakość użytej wody wpływa na przebieg reakcji chemicznej zachodzącej po wprowadzeniu gazogeneratora. Dlatego nie ma jednoznacznej rekomendacji do produkcji betonu komórkowego w domu.
Na przykład należy podać taką proporcję (zostało to już sprawdzone w praktyce). Pobiera się cement (100 kg) i piasek (180 kg). Do tej ilości potrzebujesz około 60 litrów wody. Aby uzyskać wysokiej jakości partię, składniki należy wlewać porcjami, w małych partiach, do których wlewa się kilka litrów płynu. Każde mieszanie - 5 minut Stopniowo do roztworu dodaje się inne składniki - siarczan sodu i ług (odpowiednio 0,5 kg i 1,5 kg). Na sam koniec – proszek (0,4 kg). Powstałą mieszaninę miesza się przez kolejną 1 minutę.
Uwaga: związek sodu może, ale nie musi być używany. Służy tylko do przyspieszenia procesu produkcyjnego.
Rozwiązanie powinno wypełnić każdą komórkę o około połowę. Rozpocznie się reakcja i zwiększy się objętość (wzrost). Zajmuje to około 5 do 8 minut (w zależności od temperatury zewnętrznej). Po chwili rozpocznie się proces odwrotny (obniżenie masy).
Kiedy się „uspokaja”, górną (grudkowatą) część odcina się drucianym sznurkiem. Następnie roztwór jest trzymany w formach, aż stwardnieje (około 20-24 godzin). Następnie bloki są usuwane z komórek i przenoszone do wyznaczonego obszaru, aż do ostatecznego zestalenia się masy.
Praktyczne wskazówki
Nie ma sensu kupować betoniarki do jednorazowej budowy. Na przykład koszt najtańszej betoniarki napowietrzonej wynosi około 40-45 tysięcy rubli. Lepiej wypożyczyć sprzęt. Ale tutaj należy zauważyć, że opłata naliczana jest za każdy dzień użytkowania. Dlatego najpierw trzeba wszystko przygotować, dokonać dokładnych obliczeń liczby bloków tego samego typu, a dopiero potem zawrzeć umowę najmu.
Aby wszystkie produkty miały tę samą wysokość, formę należy podgrzać na całej długości do tej samej temperatury. W przeciwnym razie masa w skrajnych komórkach zmniejszy się bardziej niż w środku.
Należy uważać, aby uniknąć przeciągów. Na przykład do prowadzenia prac w pomieszczeniu gospodarczym lub do ogrodzenia terenu ze wszystkich stron.
Wykonując w formie różne wkładki drewniane, można uzyskać bloki o różnych konfiguracjach powierzchni bocznych. Na przykład wgłębienia na czop, uchwyty do przenoszenia ręcznego.
Dziś technologia produkcji bloczków z betonu komórkowego jest interesująca dla wszystkich, którzy planują budowę domu wiejskiego lub otwarcie firmy zajmującej się produkcją betonu komórkowego. W końcu ten materiał budowlany jest bardzo dobrym wyborem pod względem wytrzymałości i właściwości termoizolacyjnych, a poza tym produkcja betonu komórkowego może być dość opłacalnym projektem biznesowym.
Co musisz wiedzieć o betonie komórkowym?
Beton komórkowy to sztuczny kamień z mikroskopijnymi porami powietrza. Inną nazwą jest autoklawowany beton komórkowy, a sam w sobie mówi o technologii jego produkcji. Bloki gazowe mają doskonałe właściwości energooszczędne właśnie ze względu na ich porowatą strukturę. Ponadto wyróżnia je stosunkowo niska waga, w tym w porównaniu z cegłami i innymi rodzajami ceramiki budowlanej.
Bloczki z betonu komórkowego to materiał budowlany, który można wykorzystać zarówno do budowy przegród wewnętrznych, jak i konstrukcji nośnych. Nie nadaje się do budynków wysokościowych ani obiektów przemysłowych, ale sprawdził się w budownictwie indywidualnym. Stosunkowo lekkie bloki gazowe nie wywierają dużego obciążenia na fundament, co zmniejsza koszty budowy fundamentu. Ponadto mają duże rozmiary, co pozwala przyspieszyć proces budowy.
Skład bloczków z betonu komórkowego
Wszystkie te zalety tego materiału budowlanego wynikają z jego składu. Wszystko, z czego składa się gazobeton, to cement, piasek kwarcowy i porofor, którym jest proszek aluminiowy. Niektórzy producenci dodają do kompozycji gips, wapno, popiół i inne składniki.
Tak więc beton komórkowy powstaje na bazie suchych składników, które miesza się z wodą. Do tych celów odpowiednia jest każda techniczna czysta woda, która spełnia wymagania GOST 23732-79. W tym przypadku ważna jest temperatura wody. Pożądane jest, aby nie był on niższy niż 45 ° C, ponieważ przyspieszy to twardnienie bloków, zwiększy ich wytrzymałość, a dla przedsiębiorstwa jest to korzystne, ponieważ wzrośnie wydajność linii jako całości. Dlatego wielu producentów podgrzewa wodę, gdyż wyższa temperatura oznacza lepszą jakość materiału. Przyczynia się również do zmniejszenia ilości zużywanego cementu, ponieważ podgrzewanie wody stymuluje aktywność suchych składników mieszanki.
Produkcja betonu komórkowego wymaga dość poważnego podejścia do wyboru piasku. Teoretycznie zarówno piasek kamieniołomowy, jak i rzeczny nadają się do tych celów, ale ważne jest, aby zawierał jak najmniej cząstek mułu lub gliny. Ważne jest również, aby wybrać wielkość ziarna - nie więcej niż 2 mm. Technologia produkcji betonu komórkowego metodą autoklawową umożliwia zastąpienie piasku żużlem lub popiołem pozyskiwanym z przemysłu metalurgicznego. Popioły z elektrociepłowni pozwalają uzyskać gazobeton o mniejszej gęstości. Pomaga to dodatkowo obniżyć koszty produkcji materiałów.
Do produkcji bloczków z betonu komórkowego wymagane są gatunki cementu portlandzkiego M400 i M500. Najlepiej, aby cement portlandzki spełniał wymagania GOST 10178-85. Ale proszek aluminiowy powinien być gatunku PAP-1 lub PAP-2 – pełni on rolę poroforu. Czasami do tego samego celu używa się specjalnej pasty. Może to być również zawiesina, ponieważ sproszkowane aluminium nie jest tak wygodne podczas mieszania roztworu. Można również zastosować oparte na nim zawieszenia.
Jaki jest efekt proszku aluminiowego? Reaguje z zaprawą cementową lub wapienną o właściwościach alkalicznych, a podczas tego procesu chemicznego powstają sole wapnia (gliniany) i gazowy wodór, co zapewnia powstawanie porów.
Przy produkcji betonu komórkowego bardzo ważne jest prawidłowe obliczenie zużycia dla każdego składnika wsadu. Istnieją standardowe zalecenia dotyczące autoklawowanych bloków gazowych. W oparciu o ten przepis na całą objętość mieszanki pobiera się 50-70% cementu, 0,04-0,09% proszku aluminiowego i do 20-40% piasku. Ponadto będziesz potrzebować wody (0,25-0,8%) i wapna (1-5%). Tak więc, aby uzyskać 1 metr sześcienny betonu komórkowego, trzeba zabrać do 90 kg cementu, do 300 litrów wody, wapna - 35 kg, piasku - 375 kg, proszku aluminiowego - 0,5 kg. Ale tę ilość można regulować już w warunkach konkretnej produkcji, w zależności od cech jakościowych samego surowca.
Jaki sprzęt będzie potrzebny?
Technologia produkcji betonu komórkowego jest stosunkowo prosta. Niemniej jednak metody rzemieślnicze nie zadziałają tutaj. Musisz kupić specjalny sprzęt, który zwykle zamawia się w kompleksie od producenta lub jego oficjalnego przedstawiciela - jest to najbardziej opłacalna opcja. To nie jest tylko jedna instalacja, to cała zautomatyzowana mini-fabryka. Niekiedy producent zapewnia nawet usługi specjalisty, który doradzi w zakresie instalacji takiej linii, pomoże w jej ustawieniu i dobierze optymalny skład mieszanki stosowanej do takiego sprzętu.
Mini-wytwórnia do produkcji betonu komórkowego nie autoklawowanego
W skład linii wchodzą różne urządzenia i teoretycznie każde z nich można dokupić osobno, jeśli z jakiegoś powodu któreś ulegnie awarii. Mowa o takich rzeczach jak formy i mobilne palety przeznaczone do ich transportu, urządzenia do cięcia gotowych bloków, mieszalniki do betonu komórkowego, dozowniki materiałów sypkich itp. Ale najważniejsze jest autoklaw, ponieważ mówimy o produkcji autoklawowanych bloków gazowych, które wyróżniają się najwyższą jakością.
Sprzęt do produkcji betonu komórkowego dzieli się na kilka rodzajów. Wybór konkretnej opcji zależy od wymaganej dziennej produktywności, od tego, ilu pracowników przedsiębiorca planuje zatrudnić oraz jak zostaną zorganizowane zmiany. Możliwe są następujące opcje:
- Linie stacjonarne mają dobową przepustowość do 60 metrów sześciennych wyrobów gotowych. Z reguły wymagają pomieszczeń magazynowych i produkcyjnych o powierzchni co najmniej 500 m². Główną cechą takich linii jest to, że formy podjeżdżają do zainstalowanego na stałe mieszalnika i tam są napełniane roztworem, po czym wykonywane są wszystkie pozostałe etapy technologiczne. Jest to bardzo prosta technologia, do obsługi takiej linii wystarczy zatrudnić jednego dodatkowego pracownika.
- Linie przenośnikowe są potrzebne tam, gdzie wymagana jest wysoka wydajność - do 75-150 m³ dziennie. Tutaj produkcja odbywa się w szybszym tempie (oczywiście czas dojrzewania produktu się nie zmienia, nie jest zależny od linii). Linie przenośnikowe wymagają jednak dużego zaplecza produkcyjnego, a do ich obsługi potrzeba co najmniej 8 osób, choć większość procesów technologicznych odbywa się tu automatycznie.
- Mini-linie nie mogą pochwalić się wysoką wydajnością, do 15 metrów sześciennych gotowych bloków dziennie. Różnica w stosunku do linii stacjonarnych polega na tym, że mieszadło porusza się w nich, a formy są zamontowane na stałe. Główną zaletą jest to, że nie potrzebują dużych powierzchni produkcyjnych, wystarczy 140-160 m², więc są popularne jako opcja startowa.
W budownictwie prywatnym często stosuje się instalacje mobilne, które są potrzebne do samodzielnej produkcji bloków gazowych. To się opłaca, a według ekspertów koszty budowy zmniejszają się o około 30%. Jednostki mobilne dostarczane są w komplecie ze sprężarką. Pracują nawet przy zasilaniu domowym.
Etapy produkcji
Istnieją dwa rodzaje betonu komórkowego - autoklawowany lub nieautoklawowany. Ta druga opcja jest tańsza, chociaż uzyskany materiał ma niższą wytrzymałość. Jednak ze względu na niższy koszt produkcji (nie trzeba kupować autoklawu, konserwować go, dopłacać za energię) jest to dość popularna opcja, dlatego warto ją bardziej szczegółowo rozważyć. Jeśli przedsiębiorca zamierza produkować gazobeton nieautoklawowany, technologia jego produkcji powinna zostać zredukowana do następujących głównych kroków:
- Dokładne dozowanie wszystkich opisanych powyżej składników, a następnie ich dokładne wymieszanie. Przy odpowiednim sprzęcie ten krok zajmuje nie więcej niż 10 minut.
- Przygotowana masa za pomocą specjalnego sprzętu jest rozładowywana do specjalnych form (są tylko do połowy wypełnione, ponieważ mieszanina zwiększy swoją objętość podczas procesu tworzenia gazu). Ten proces zajmie 4 godziny. W tym czasie mikstura wypełnia przydzieloną jej w formie objętość, a czasem nawet jej to nie wystarcza. Następnie po 2 godzinach nadmiar można usunąć.
- Proces utwardzania produktów trwa około 16 godzin, a po tym czasie są one rozbierane i przeładowywane na palety, gdzie zyskują tzw. wytrzymałość odpuszczania. Ten etap zajmuje kolejne 2-3 dni. Następnie produkty mogą zostać wysłane do magazynu, ale jest jeszcze za wcześnie na ich sprzedaż, ponieważ zyskają na sile marki dopiero 28 dnia.
Produkcja bloczków z betonu komórkowego przy użyciu autoklawu na pierwszych etapach praktycznie nie różni się od technologii opisanej powyżej. Najpierw musisz zmierzyć wymaganą ilość wszystkich składników (pożądane jest, aby zrobić to za pomocą dozowników, pomoże to zwiększyć dokładność). Następnie cała ta masa jest ładowana do miksera i dokładnie mieszana. Czasami eksperci sugerują użycie betoniarki do tych celów. Następnie wprowadza się porofor – dzieje się to po 10-15 minutach mieszania początkowych składników. W każdym przypadku proszek aluminiowy reaguje z roztworem, nie trzeba go w tym celu sterylizować w autoklawie.
Półprodukt wlewa się do form, przechowuje przez 4-6 godzin, po czym tnie się bloki gazowe. Zanim nabiorą sił, powinny leżeć przez kolejne 10-18 godzin.
Ale najważniejszą rzeczą jest wiedzieć, jak odbywa się autoklawowanie po wszystkich opisanych powyżej procedurach. Uformowane bloki są ładowane do specjalnego pieca, w szczelnej komorze, gdzie każdy blok jest poddawany działaniu pary nasyconej o wysokiej temperaturze. Ciśnienie również musi być wysokie – do 12 kg/cm².
Beton nieautoklawowany jest naturalnie suszony, ale nie jest to konieczne w przypadku produktów autoklawowanych. Niemniej jednak trzeba je również przechowywać przez około 28-30 dni w magazynie, gdzie zyskają siłę marki.
Nie wystarczy wiedzieć, jak zrobić gazobeton, nadal trzeba być w stanie dostarczyć go konsumentowi. W tym celu bloki gazowe pakowane są w specjalną folię termokurczliwą i transportowane na paletach drewnianych.
Budowa domów z betonu komórkowegobardzo popularny, ze względu na to, że ten rodzaj materiału budowlanego ma dobre właściwości i stosunkowo niskie ceny, a w ciągu długiej historii stosowania betonu komórkowego otrzymał wiele och recenzje.
Składa się z kilku kluczowych kroków. Opiszemy technologię produkcji bloczków z betonu komórkowego, opowiemy o niezbędnym sprzęcie, który jest używany w technologii do produkcji betonu komórkowego.
Suszenie blokowe
Po około 1,5-2 godzinach produkty uzyskają pożądane
siły, należy je wyciągnąć z form i wysłać do ciepłego magazynu lub komór parowych, aby zakończyć procesy hartowania.
Wykorzystywane są również opcje wylewania nie pojedynczych bloków, ale całej masy, która po wyschnięciu jest cięta na bloki.
Różnica między autoklawizowanym gazobetonem a nieautoklawizowanym gazobetonem
- autoklawowany gazobeton , nabiera wytrzymałości pod wysokim ciśnieniem i w wysokiej temperaturze w specjalnych piecach (komorach suszących), zwanych autoklawami
- gazobeton nieautoklawowany twardnieje w środowisku naturalnym, pod ciśnieniem atmosferycznym lub stosuje się obróbkę cieplno-wilgotnościową z wykorzystaniem ekspozycji termicznej