Algorytmy projektowania operacji technologicznych
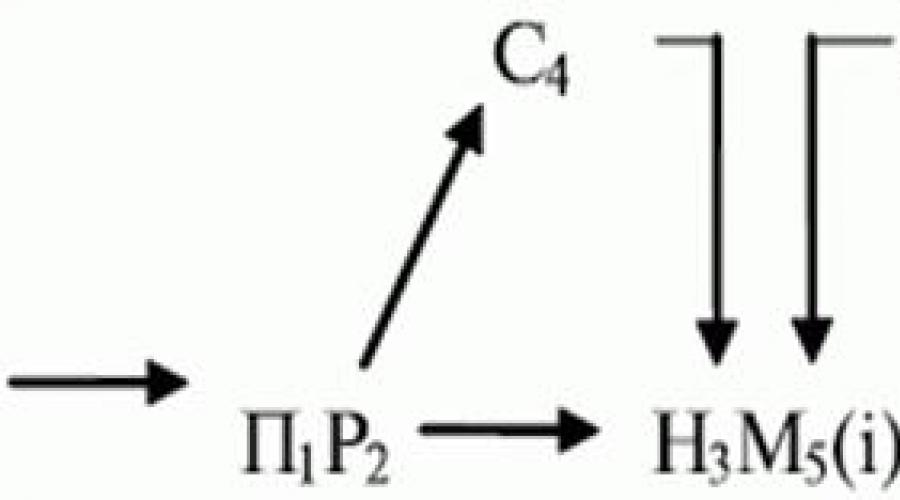
Przeczytaj także
Zagadnienia automatyzacji syntezy procesy technologiczne długie lata pozostają w centrum uwagi badaczy i twórców komponentów SAPRTP. Jest to w pełni uzasadnione, gdyż to właśnie synteza struktury jest procesem najtrudniejszym do sformalizowania przy tworzeniu systemów projektowych.
Należy zauważyć, że w zakresie opracowania metodologii automatyzacji syntezy technologii routingu istnieją znaczące wyniki, które umożliwiają stworzenie w pełni operacyjnych komponentów CAD TP. Obecnie stosowana jest głównie synteza tras technologie ogólne budowane w oparciu o podstawowe trasy, listy produkcyjne czy sieci semantyczne. Zastosowanie sztucznych sieci neuronowych umożliwia stworzenie ogólnego procesu opartego na zasadach samouczącego się CAD TP, co upraszcza i obniża koszty dostosowania systemu do specyficznych warunków produkcyjnych.
W opracowywaniu metod automatyzacji syntezy technologii operacyjnych sukcesy nie są już tak oczywiste. W procesie syntezy technologii operacyjnej bierze się pod uwagę zbyt wiele parametrów, w tym parametry dokładnościowe i wymiarowe - wymiary części i przedmiotu obrabianego, wymiary technologiczne i regulacyjne, odchyłki kształtu i położenia powierzchni, naddatki itp.
Liczba możliwych opcji schematów wymiarowania, zarówno na rysunkach części i przedmiotu obrabianego, jak i na szkicach operacyjnych, jest tak duża, że bardzo trudno jest je uwzględnić na wszystkich etapach szkolenia systemu.
To znacznie komplikuje pracę specjalisty dostosowującego system do tradycji i możliwości środowiska produkcyjnego konkretnego przedsiębiorstwa. Zatem techniki stosowane w syntezie tras i działaniu z ograniczoną liczbą parametrów nie są tutaj zbyt skuteczne, a w niektórych przypadkach po prostu nie mają zastosowania.
Jak wiadomo, kryterium jakości powiązanych łańcuchów wymiarowych syntetyzowanej technologii operacyjnej jest analiza wymiarowa. Metody analizy wymiarowej zostały obecnie rozwinięte w stopniu wystarczającym do praktycznego zastosowania, chociaż niektóre aspekty wymagają wyjaśnienia lub rozwinięcia.
Z doświadczenia analizy wymiarowej technologii wynika, że przy pierwszej próbie stworzenie struktury procesu spełniającej wszystkie wymagania dokumentu projektowego i zapewniającej pozytywne wyniki analizy wymiarowej jest dość trudne, wręcz niemożliwe.
W procesie syntezy technologii eksploatacji niezbędna jest możliwość nie tylko stworzenia pojedynczej wersji struktury eksploatacyjnej, ale także modyfikacji konstrukcji w oparciu o wyniki analizy wymiarowej. Mechanizm modyfikacji (resyntezy) struktury nie został dotychczas praktycznie opracowany.
Kolejny problem syntezy strukturalnej operacji technologicznej pojawia się podczas przygotowywania informacji wstępnej. Oczywiście wskazane jest uzyskanie większości danych związanych z geometrią części i jej parametrami z systemu projektowania. Eliminuje to błędy subiektywne typowe dla wprowadzania dużych wolumenów danych i nie wymaga włączania wsparcia językowego do technologicznego systemu CAD w celu opisania części i sposobu jej interpretacji, co zwykle komplikuje i zwiększa koszty oprogramowanie. Jednak większość edytorów graficznych podczas tworzenia rysunku dwuwymiarowego operuje prymitywami, takimi jak odcinek, okrąg, łuk itp., których prawie nie da się skorelować z elementami konstrukcyjnymi operacji i trasy. Nawet w przypadku modelu trójwymiarowego pojawiają się znaczne trudności.
Prawie wszystkie systemy graficzne przedstawiają model części, model przedmiotu obrabianego oraz szkice operacyjne w postaci odrębnych, niepowiązanych ze sobą obiektów graficznych (rysunki, fragmenty lub modele trójwymiarowe). W związku z tym pojawiają się trudności nie do pokonania w automatycznej identyfikacji relacji wymiarowych, na podstawie których
synteza struktury procesu technologicznego i jego analiza wymiarowa.
Zatem, aby stworzyć metodologię syntezy technologii operacyjnej obróbki części, konieczne jest rozwiązanie co najmniej następujących problemów:
- opracować model obiektu projektowego spełniający wymagania syntezy technologii i analizy wymiarowej;
- opracowywać procedury syntezy struktury procesu technologicznego z wykorzystaniem wyników analizy wymiarowej;
- doprecyzować i uzupełnić metodologię analizy wymiarowej procesu technologicznego.
Edytor procesów technologicznych RTP2000 umożliwia tworzenie technologii eksploatacyjnej metodami konwencjonalnymi w oparciu o doświadczenie technologa lub w oparciu o wykorzystanie technologii analogowych. Jednak to nie jest najwięcej skuteczna metoda, ponieważ jakość otrzymanego rozwiązania projektowe tutaj w dużej mierze zależą od kwalifikacji wykonawcy projektu.
Najlepsze wyniki uzyskuje się metodą wykorzystania operacji ogólnych, która pozwala na syntezę technologii operacyjnych w trybie automatycznym na podstawie wcześniej opracowanego wsparcia informacyjnego, co pozwala uzyskać rozwiązania projektowe bliskie optymalnym.
Podstawą informacyjną automatycznej syntezy technologii jest:
- biblioteka elementów formularzy;
- biblioteka standardowych operacji technologicznych.
Przykładowo geometria części utworzona przy użyciu biblioteki elementów formy pozwala na jednoznaczną zgodność geometrii części z przejściami technologicznymi oraz zapewnia automatyczne generowanie szkiców eksploatacyjnych i analiz wymiarowych. System umożliwia przekształcenie rysunku części wykonanego przy użyciu konwencjonalnego edytora graficznego, takiego jak Compass, w wewnętrzną reprezentację opartą na bibliotece elementów formularzy.
Biblioteka standardowych operacji technologicznych (TTO) opracowywana jest w odniesieniu do warunków konkretnego przedsiębiorstwa, z uwzględnieniem tradycji projektowania operacji. Operacje TTO mogą być stosowane w ramach ogólnych procesów technologicznych lub indywidualnie.
Operacja biblioteczna zawiera uporządkowany zestaw przejść, z których każde jest powiązane z jednym lub zespołem elementów kształtu części.
W procesie stosowania TTO system sprawdza obecność odpowiedniego elementu formy w części. Jeśli go nie ma, przejście nie jest uwzględnione w jednej technologii. W przeciwnym razie generowana jest jedno lub określona liczba przejść (w zależności od liczby elementów formularza).
Zatem kompozycja przejść dla każdej operacji jest automatycznie tworzona na podstawie ogólnego procesu technologicznego. W kolejnym etapie przeprowadzany jest proces syntezy technologii w oparciu o podejście ewolucyjne, która polega na sekwencyjnym stosowaniu etapów trasy z analizą zależności wymiarowych w celu oceny możliwości osiągnięcia określonej dokładności i innych parametrów części na każdym etapie. Proces ewolucji kończy się w momencie osiągnięcia wymaganych parametrów części.
Na tym etapie zasadniczą rolę odgrywa mechanizm analizy wymiarowej. Ze względu na to, że różnorodność możliwych kształtów geometrycznych części nie pozwala z góry zapewnić wszystkich schematów ustalania wymiarów technologicznych, schematy wymiarowe generowane są za pomocą algorytmu genetycznego. Pozwala szybko znaleźć akceptowalne schematy wymiarowania operacyjnego dla każdej operacji, które spełniają wymagania analizy wymiarowej.
NA Ostatni etap Szkice operacyjne operacji i rysunek obrabianego przedmiotu są generowane automatycznie.
Opis obiektów projektowych
1. Model konstrukcyjny
Model części opracowywany jest w oparciu o wymagania zadania:
- model powinien umożliwiać wygodny i prosty opis charakterystyk charakterystycznych części mechanicznych figury geometryczne;
- model musi umożliwiać wygodny import i eksport obrazów przy użyciu najpopularniejszych standardów wymiany danych graficznych, takich jak DXF czy KSF;
- elementy modelu muszą zapewniać jednoznaczne powiązanie z operacjami i przejściami procesu technologicznego;
- model musi zapewniać jednoznaczne połączenie wymiarów części, przedmiotu obrabianego i wymiarów operacyjnych;
- model powinien umożliwiać automatyczną identyfikację zależności wymiarowych, analizę wymiarową i resyntezę procesu technologicznego.
Model opiera się na pomysłach przedstawionych w pracy. Opis geometrii odbywa się za pomocą biblioteki elementów formy (EF), tworzących zewnętrzny - główny kontur części oraz elementów pomocniczych (EA), nałożonych na EF, z uwzględnieniem rodzaju części.
Rodzaj części określa się na podstawie podejścia kinematycznego i określa się metodą uzyskania powierzchni tworzącej główny kontur części:
- część obrotowa (wał, tuleja, tarcza itp.) jest utworzona poprzez obrót tworzącej względem głównej osi części;
- część rysunkowa (pręt, korpus, płyta itp.) jest tworzona poprzez przesuwanie tworzącej względem kierunku współrzędnych.
Struktura geometrii zależy od rodzaju części (ze względu na ograniczoną objętość, w przyszłości będziemy rozważać tylko części obrotowe) i obejmuje:
- obiekt (część, przedmiot obrabiany, szkic operacyjny);
- kierunek współrzędnych określony dla każdego obiektu przez płaszczyznę wizualizacji (liczba kierunków jest dowolna, wystarczająca do opisania części).
Każdy kierunek współrzędnych zawiera opis:
- główny obwód;
- dodatkowe obwody (liczba dodatkowych obwodów nie jest ograniczona).
Znakiem początku opisu konturu jest układ współrzędnych (CS).
W obrębie każdego obwodu konstrukcja jest podzielona na sekcje:
- Sekcja EF (zaczyna się od SK);
- sekcja EV;
- sekcja rozmiarów koordynujących.
Każdy EF zawiera listę parametrów niezbędnych do syntezy procesu technologicznego:
- jakość;
- parametr chropowatości;
- wartość parametru chropowatości;
- rodzaj parametru odchyłki kształtu;
- wartość parametru odchyłki kształtu;
- rodzaj parametru odchylenia położenia powierzchni;
- wartość parametru odchylenia położenia powierzchni;
- rodzaj obróbki cieplnej;
- grubość warstwy obróbki cieplnej;
- skala twardości;
- wartość twardości;
- rodzaj powłoki;
- grubość powłoki;
- rodzaj środka chemicznego obróbka cieplna;
- grubość warstwy obróbki chemiczno-termicznej;
- rodzaj dodatkowego przetwarzania.
Całość (wraz z układami współrzędnych konturów dodatkowych) opisana jest w układzie współrzędnych konturu głównego.
EF w przekroju są uporządkowane (sortowane) według wartości współrzędnej kotwicy do początku konturu (do początku układu współrzędnych). Podczas sortowania określany jest wskaźnik pozycji (lewy, środkowy, prawy). Znak jest zapisany w EF.
HF nie są sortowane (ułożone w kolejności, w jakiej zostały zapisane), ale są powiązane z EF, na podstawie których zostały utworzone, dwukierunkowa komunikacja. Wiązanie VF odbywa się z uwzględnieniem znaku jego położenia - najbliższego lub odległego względem początku SC. Znak pozycji umożliwia zorientowanie pojazdu EV. Odległa pozycja wiąże EV z prawą stroną EF z obrotem o 180. Dla każdego EF ustalana jest lista akceptowalnych EV.
EF i EV nazywane są swoimi oryginalnymi nazwami – identyfikatorami, które są przypisywane każdemu nowemu EF automatycznie za pomocą generatora identyfikatorów. Identyfikator jest reprezentowany jako liczba całkowita i służy do identyfikacji powierzchni objętych analizą wymiarową.
Niektóre EF mają charakter systemowy. Są one określane automatycznie przez system podczas tworzenia głównych EF. Przykładem elementu systemu jest koniec kroku.
Pierwszym etapem projektowania TP jest opracowanie projektu wstępnego, drugim etapem jest opracowanie roboczej dokumentacji technologicznej prototyp(partia), seria instalacyjna, ustalona produkcja seryjna lub masowa.
Projekt wstępny przeznaczony jest do testowania i testowania wykonalności projektu produktu na etapach projektów wstępnych i technicznych w celu opracowania dokumentacji projektowej, w celu przygotowania i opracowania dokumentacji roboczej.
Robocza dokumentacja technologiczna oznacza zbiór dokumentów technologicznych (mapy, instrukcje, zestawienia), które zawierają wszystkie dane niezbędne do wytworzenia i kontroli wyrobu.
Procesy technologiczne dzielą się na następujące typy:
· Projekt TP wykonano według wstępnego projektu dokumentacji technologicznej.
· Pracownik TP wykonane zgodnie z obowiązującą dokumentacją technologiczną i projektową.
· Jednostka TP dotyczy produktów o tej samej nazwie, standardowym rozmiarze i wykonaniu, niezależnie od rodzaju produkcji.
· Typowy TP, który charakteryzuje się jednolitością treści i kolejności większości operacji i przejść technologicznych dla grupy produktów o wspólnych cechach konstrukcyjnych.
· Standard TP to proces technologiczny ustalony normą.
· Tymczasowy TP użytkowana w przedsiębiorstwie przez ograniczony okres czasu ze względu na brak odpowiedniego sprzętu lub w wyniku wypadku, do czasu wymiany na nowszy.
· Perspektywiczny TP odpowiada współczesnym osiągnięciom nauki i techniki, których metody i środki realizacji muszą być w pełni lub częściowo opanowane w przedsiębiorstwie.
· Trasa
· Operacyjny TP wykonywana jest zgodnie z dokumentacją, w której podana jest treść operacji, ze wskazaniem przejść i trybów przetwarzania.
· Trasa i działanie TP wykonywana jest według dokumentacji, w której podana jest treść operacji bez wskazania przejść i trybów przetwarzania.
· Grupa TP, który został opracowany nie dla jednej części, ale dla grupy części o podobnych właściwościach technologicznych.
Kompleks prac nad projektowaniem procesów technologicznych
Procesy technologiczne opracowywane są dla wyrobów, których projekt został przebadany pod kątem wykonalności i obejmuje zestaw powiązanych ze sobą prac, do których zalicza się:
· wybór półfabrykatów;
· wybór baz technologicznych;
· wybór standardowego procesu technologicznego;
· określenie kolejności i treści operacji technologicznych;
· identyfikacja, selekcja i zamawianie nowego wyposażenia technologicznego (w tym narzędzi kontrolnych i testujących);
· cel i obliczanie sposobów przetwarzania;
· standaryzacja procesu;
· dobór środków mechanizacji i automatyzacji elementów procesów technologicznych i wewnątrzzakładowych środków transportu i innych.
Przy opracowywaniu procesów technologicznych klasyfikatory operacji technologicznych, systemy oznaczeń, standardowe procesy technologiczne, normy, katalogi, podręczniki i „ jeden system dokumentacja technologiczna (ESTD)”.
Opracowując standardowe procesy technologiczne, należy wziąć pod uwagę specyficzne warunki produkcji typowego przedstawiciela grupy produktów, które mają wspólne cechy konstrukcyjne i technologiczne.
Do typowego przedstawiciela grupy wyrobów zalicza się zazwyczaj wyrób, którego wytworzenie wymaga największej liczby operacji głównych i pomocniczych charakterystycznych dla wyrobów zaliczanych do tej grupy.
O konieczności opracowania standardowych procesów technologicznych decyduje wykonalność ekonomiczna związana z częstotliwością stosowania danej grupy wyrobów.
Pisanie odbywa się w dwóch kierunkach:
· typizacja złożonych procesów technologicznych wytwarzania podobnych wyrobów;
· typizacja i standaryzacja poszczególnych operacji przetwórczych różnych produktów.
Typowe procesy technologiczne mogą być operacyjne i obiecujące.
Standardowe procesy technologiczne i standardy operacji technologicznych stanowią podstawę informacyjną do opracowania działającego procesu technologicznego.
Rodzaje dokumentów technologicznych
Opracowane procesy technologiczne sporządzane są w formie dokumentów technologicznych określonych typów Norma państwowa ESTD.
1. Mapa trasy(MK) zawiera opis procesu technologicznego wytworzenia lub naprawy wyrobu (w tym kontrolę i ruch) dla wszystkich operacji różnego rodzaju i sekwencji technologicznej, ze wskazaniem danych dotyczących wyposażenia, oprzyrządowania, standardów materiałowych i robocizny zgodnie z ustalone formy. Mapa trasy jest dokumentem obowiązkowym. Mapę tę można opracować dla określonych rodzajów prac.
2. Szkicowana Mapa(FE) zawiera szkice, schematy i tabele niezbędne do wykonania procesu technologicznego, operacji lub przejścia w procesie wytwarzania lub naprawy produktu.
3. Instrukcje technologiczne(TI) zawiera opis metod pracy lub procesów technologicznych przy wytwarzaniu lub naprawie wyrobu, zasady obsługi urządzeń technologicznych, opisy zjawisk fizykochemicznych powstających podczas poszczególnych operacji.
4. Wybieranie karty(QC) zawiera dane dotyczące części, zespołów montażowych i materiałów wchodzących w skład zestawu zmontowanego produktu.
5. Arkusz do cięcia(VR) zawiera dane dotyczące drogi przejścia wyprodukowanego (naprawionego) produktu przez usługi przedsiębiorstwa.
6. Lista wyposażenia(VO) zawiera wykaz urządzeń technologicznych niezbędnych do wykonania danego procesu technologicznego lub operacji.
7. Zestawienie materiałów(VM) zawiera dane dotyczące detali, wskaźników zużycia materiału, trasy wytworzonego produktu i jego komponentów.
8. Lista jednostek montażowych dla standardowego procesu technologicznego(VTP) zawiera listę jednostek montażowych. Jednostki te produkowane są według standardowego procesu technologicznego (operacji) ze wskazaniem odpowiednich danych dotyczących kosztów pracy oraz, w razie potrzeby, materiałów, urządzeń technologicznych i trybów.
9. Mapa procesu(KTP) zawiera opis procesu technologicznego wytworzenia lub naprawy wyrobu (w tym kontrolę i ruch) dla wszystkich operacji wykonywanych w jednym warsztacie w ciągu technologicznym, ze wskazaniem danych o wyposażeniu technologicznym, standardach materiałowych i robocizny.
Dla niektórych rodzajów prac połączonych drogą technologiczną wytwarzania wyrobów z innymi rodzajami prac dopuszcza się opracowanie dokumentu projektu opakowania wskazującego wszystkie rodzaje prac wykonywanych w różnych warsztatach. Co więcej, jeśli KTP obejmuje całą drogę produkcyjną danego produktu, to zastępuje MK, a ten drugi nie jest rozwijany.
10. Typowa mapa procesu(KTTP) zawiera opis typowego procesu technologicznego wytwarzania i naprawy zespołu zespołów montażowych w ciągu technologicznym, ze wskazaniem operacji i przejść oraz odpowiednich danych dotyczących urządzeń technologicznych i standardów materiałowych.
11. Karta operacji(OK) zawiera opis operacji technologicznej ze wskazaniem przejść, trybów przetwarzania oraz danych o urządzeniach technologicznych.
12. Standardowa karta operacyjna(OCT) zawiera opis typowej operacji technologicznej ze wskazaniem przejść, danych o wyposażeniu technologicznym oraz, w razie potrzeby, wyposażeniu technologicznym i sposobach przetwarzania.
13. Oświadczenie o transakcji(VOP) zawiera wykaz i opis wszystkich operacji kontroli technologicznej wykonywanych w jednym warsztacie, ze wskazaniem danych o sprzęcie, osprzęcie i wymaganiach dotyczących kontrolowanych parametrów.
Podstawowe dokumenty ACPP
Główne dokumenty to:
· MK – mapa trasy;
· KTP – mapa procesu technologicznego;
· VTP - lista jednostek montażowych dla standardowego procesu technologicznego.
Dokument główny, samodzielnie lub w połączeniu z innymi zapisanymi w nim dokumentami, całkowicie i jednoznacznie określa proces technologiczny wytwarzania wyrobu dla całości lub pewne gatunki Pracuje Formy ogólne i specjalny cel Zainstalowano ESTD.
Budowa diagramu procesu technologicznego
Na tym etapie formułowane są zadania, etapy i wstępne dane do projektu schemat proces technologiczny. Przeprowadzono klasyfikację metod projektowanie wspomagane komputerowo Trwają prace nad TP oraz modelem wielopoziomowego procesu projektowania z możliwością wyboru racjonalne decyzje. Rozważono iteracyjny algorytm procesu projektowania na każdym poziomie oraz algorytm tworzenia schematycznego diagramu procesu technologicznego.
Celem projektowania procesu jest dawanie szczegółowy opis operacji wytwarzania wyrobów wraz z niezbędnymi obliczeniami techniczno-ekonomicznymi oraz uzasadnieniami przyjętej opcji. Dopełnieniem tego głównego problemu projektanta jest późniejsze zadanie wdrożenia zaprojektowanego TP w przedsiębiorstwie. W wyniku sporządzenia dokumentacji technologicznej kadra inżynieryjno-techniczna oraz pracownicy wykonawczy otrzymują niezbędne dane i instrukcje do realizacji zaprojektowanego procesu technologicznego w określonych warunkach produkcyjnych.
Projektowanie TP rozpoczyna się od analizy specyfikacji technicznych (TOR) projektu, która obejmuje następujące elementy: rysunek roboczy produktu z Specyfikacja techniczna Lub rysunek montażowy węzeł z warunkami akceptacji, programem wydania i innymi wymaganiami.
Generowane są opcje struktury TP, które następnie oceniane są z punktu widzenia warunków wykonania (np. zapewnienia określonych parametrów, jakości produktu). Dla każdej opcji konstrukcji przewidziana jest optymalizacja parametrów, ponieważ ocenę należy przeprowadzić na poziomie optymalnym lub zbliżonym wartości optymalne parametry. Jeżeli dla jakiegoś wariantu struktury, przebiegu lub przejścia procesu technologicznego zostaną osiągnięte określone parametry jakościowe produktu, wówczas proces syntezy uważa się za zakończony.
Wyniki projektowania są sformalizowane w postaci niezbędnej dokumentacji technologicznej wraz z utworzeniem specyfikacji technicznych dla kolejnego etapu projektowania. Dla każdego wariantu konstrukcji tworzony jest model TP lub jego elementów. W projektowaniu komputerowym model ten ma charakter matematyczny; musi być adekwatny do obiektu pod względem jego podstawowych właściwości. Analiza modelu weryfikuje spełnienie warunków wykonawczych (np. uzyskanie maksymalnej produktywności przy zapewnieniu parametrów jakościowych produktu) i podejmowanie decyzji. Na podstawie wyników badań przeprowadzana jest optymalizacja parametryczna.
Jeżeli warunki eksploatacyjne nie są spełnione, kontrolowane parametry są ponownie zmieniane, a model matematyczny jest analizowany pod kątem ich nowych wartości. W przypadku powtarzającego się niespełnienia warunków wykonawczych przystępują do wygenerowania nowej wersji konstrukcji lub przeglądu specyfikacji technicznych.
Generalnie strukturę funkcjonalną koncepcji procesu charakteryzuje sekwencja przekształceń wytwarzanego produktu od stanu początkowego na etapie zaopatrzenia do stanów C 1, Z 2 , z n na etapach pośrednich i końcowych. Transformacja ta odbywa się etapami. Proces projektowania na każdym poziomie jest procedurą wieloczynnikową. W oparciu o jedną opcję projektu ( k-1)-ty poziom, powstaje wiele bardziej szczegółowych opcji k- poziom.
W wyniku projektowania na wszystkich poziomach powstaje drzewo akceptowalnych opcji procesu technologicznego, które spełniają określone ograniczenia techniczne. Wierzchołki drzewa odpowiadają operacji syntezy rozwiązań projektowych, a łuki odpowiadają wynikowym wersjom tych rozwiązań. Łuki drzewa ostatniego poziomu charakteryzują opcje projektowe o danym poziomie szczegółowości. Aby rozwiązać problemy optymalizacji wielopoziomowej na I-poziom projektudlatego otrzymują nie jedną optymalną opcję, ale grupę opcji bliskich optymalnej. Spośród tych parametrów wybierz rozwiązanie dla ( I+1)-ty poziom projektowania.
Rysunek przedstawia model wielopoziomowego procesu projektowania z wyborem najbardziej racjonalnego rozwiązania na ostatnim poziomie: TZ- zadanie techniczne; C ii- operacje syntezy rozwiązań projektowych; Rq(k)- opcje projektowania
Generując strukturę procesu technologicznego, posługujemy się różne metody: projektowanie oparte na typizacji i technologii grupowej; transformacja procesów analogowych; wielopoziomowa metoda iteracyjna; metoda aksjomatyczna itp.
Projektowanie konkretnych procesów technologicznych poprzez parametryczne dopasowanie procesu standardowego obejmuje dwie grupy operacji projektowych: wyszukiwanie w banku danych technologicznych wymaganego procesu standardowego oraz obliczanie parametrów każdej operacji (ustalanie norm czasowych, materiałowych i robocizny). Metodę tę stosuje się w przypadku produktów standardowych. Algorytmy przekształcania procesu analogowego nie zawierają gotowych warunków logicznych wyboru operacji i przejść. Warunki te ustalane są w wyniku analizy produktu i analogu TP. Po znalezieniu produktów i analogów TP w banku danych technologicznych (I, TN) projektowanie opiera się na modelu informacyjnym C k konkretnego produktu, określić racjonalną strukturę i parametry procesu produkcyjnego:
W: ( C k(I, TN)an),
Gdzie W - operacje transformacji procesów analogowych.
Transformację przeprowadza się metodami wykluczania i dodawania elementy konstrukcyjne na analogiczne procesy, polegające na identyfikacji różnic pomiędzy konkretnymi produktami a produktami analogicznymi.
Metoda eliminacji elementów konstrukcyjnych opiera się na tym, że z wykresu Sa(C, A)
, opisującego strukturę procesu analogowego, niektóre ścieżki lub łuki są wyłączone
{Cq -1,q,Cq}
, odpowiadające operacjom lub przejściom w obróbce powierzchni, których brakuje w danym produkcie lub powierzchni o większej precyzji.
Struktura konkretnego procesu powstaje w wyniku zastosowania wykresów różnicowych
Sk ( C 1 ,A 1) = Sa(C,A)\ {Cq-1,q,Cq},
Gdzie C 1 =C\{Cq} - wiele stanów pośrednich niezbędnych do wytworzenia konkretnego produktu; A 1 =A\{woda) - wiele operacji technologicznych niezbędnych do wytworzenia konkretnego produktu.
W wyniku zastosowania takiej operacji struktura konkretnego procesu jest prostsza niż jego odpowiednik. Transformacja procesu analogicznego poprzez eliminację elementów konstrukcyjnych odbywa się poprzez ustalenie technologicznego podobieństwa stanów produktu analogowego do struktury i parametrów konkretnego produktu. W tym celu na wykresie struktury funkcjonalnej analogowego procesu technologicznego identyfikuje się wierzchołki wiszące, które odpowiadają stanom końcowym grup obrabianych powierzchni. Jeśli C a~ C k , potem operacja A zawarte w drodze przetwarzania konkretnego produktu; w przeciwnym razie jest wykluczony z trasy analogowej.
Metoda dodawania elementów konstrukcyjnych polega na dodaniu procesu analogowego do wykresu konstrukcji Sa(S,A) zestaw łuków {C r -1,A r,C r} , odpowiadające nowo wprowadzonym operacjom i przejściom do obróbki powierzchni danego produktu, których nie ma w analogicznych wyrobach lub mają mniejszą dokładność. Struktura konkretnego procesu jest bardziej złożona i powstaje w wyniku operacji łączenia grafów
Sk ( C 1 ,A 1) = Sa(C,A)Ty ( Cr-1,A r,C r} ,
Gdzie C 1 = C U C r; A 1 =A U A R.
W wielu przypadkach problemy projektowe pojawiają się, gdy transformacja procesów analogowych odbywa się przy użyciu tej lub innej metody
Sk ( C 1 ,A 1) = Sa(C,A) \ {Cq-1,q,Cq) Ty ( Cr-1,A r,C r}
Transformacja procesu analogicznego poprzez dodanie elementów strukturalnych (operacji, przejść) polega na ustaleniu rodzaju i ilości tych elementów oraz ich racjonalnym rozmieszczeniu.
Zasada rozkładu wielopoziomowego
Jeden z najbardziej wspólne metody Pokonywanie początkowej niepewności problemu projektowania technologicznego jest wielopoziomową metodą iteracyjną. Jej istotę ujawnia zbiór zasad i stwierdzeń, które określają naturę i strukturę procesów projektowych.
Projektowanie dyskretnych procesów technologicznych i złożonych obiektów podzielone jest na kilka wzajemnie powiązanych poziomów, charakteryzujących się sukcesywnie rosnącym stopniem szczegółowości rozwiązań projektowych z poziomu na poziom.
Podstawą zasady rozkładu wielopoziomowego są następujące stwierdzenia:
1. Projektowanie procesów technologicznych wytwarzania wyrobów można podzielić na 4 poziomy:
· schematyczny diagram procesu;
· technologia tras;
· technologia obsługi;
· programy sterujące.
Poziom pierwszy charakteryzuje się najwyższym stopniem abstrakcji i określeniem jedynie podstawowych cech struktury i funkcji procesu technologicznego. Z poziomu na poziom wzrasta stopień szczegółowości rozwiązań projektowych. Na ostatnim poziomie doprowadzono do instrukcji i poleceń sterujących sprzętem.
2 . Wielopoziomowy proces projektowania rozwija się od góry do dołu, tj. od syntezy ogólnych modeli podstawowych na pierwszym poziomie do projektowania rozwiązań o wymaganym poziomie szczegółowości na kolejnych poziomach. Ponadto rozwiązania otrzymane w poprzednim ( k-1), służą jako dodatkowe dane wyjściowe do obliczeń na poziomie k- poziom. Zatem informacje o schemacie TP uzyskane na pierwszym poziomie służą syntezie trasy na drugim poziomie. Opracowywanie technologii eksploatacyjnych na poziomie trzecim odbywa się w oparciu o informacje o trasie technologicznej, a informacje o technologii eksploatacyjnej służą do syntezy programów sterujących.
3 . Na wszystkich poziomach z wyjątkiem ostatniego, ze względu na niewystarczającą szczegółowość rozwiązań projektowych, kryteria wyboru opcji mają charakter uogólniony, heurystyczny. Są one stopniowo udoskonalane w miarę przechodzenia z poziomu na poziom, osiągając wymaganą dokładność na ostatnim poziomie projektowania
Zatem na pierwszym poziomie nie da się stworzyć kryterium pozwalającego wybrać jedną optymalną opcję dla schematu TP. Dzieje się tak dlatego, że idea projektowanego procesu ma charakter czysto zasadniczy i z reguły jest doprecyzowywana na kolejnych poziomach.
4 . Na początkowym i pośrednim poziomie projektowania, ze względu na heurystyczny charakter kryteriów, spośród wielu zsyntetyzowanych opcji wybiera się nie jedno, ale kilka (dwa lub trzy) najbardziej racjonalne rozwiązania. Ostateczna wersja TP, odpowiadająca skrajnym wartościom dokładnego kryterium, jest ustalana dopiero na ostatnim poziomie.
5 . Projektowanie na każdym poziomie dzieli się na zestaw następujących operacji projektowych, wzajemnie powiązanych iteracyjnie:
Iteracyjny algorytm procesu projektowania można przedstawić w następujący sposób
Tutaj P jest poszukiwaniem rozwiązań analogicznych, H jest przekształceniem procesów analogicznych, C jest syntezą różne opcje technologia, M – modelowanie symulacyjne procesu przetwarzania, A – analiza wyników symulacji, E – ocena wyników symulacji, Q – optymalizacja, W – wybór najbardziej racjonalnych opcji.
Proces projektowy rozpoczyna się od poszukiwania produktów i analogów technologicznych w szeregu banków danych technologicznych. Jeśli takie procesy zostaną znalezione, blok logiczny R 2 sterowanie zostaje przeniesione do operacji konwersji procesu analogowego N 3, jeżeli nie znaleziono – operacje syntezy Z 4. W tym bloku w sposób scentralizowany syntetyzuje się szereg opcji TP spełniających określone wymagania techniczne i ograniczenia. Działanie symulacji pozwala m.in. przewidzieć charakter obróbki powierzchni, wynikające z niej błędy oraz wartości parametrów techniczno-ekonomicznych. Za pomocą operacji „analizy” ustalane są przyczyny wystąpienia określonych odchyleń i niedoszacowanych wartości poszczególnych kryteriów lokalnych. Analizę przeprowadza się na wszystkich wskaźnikach technicznych i ekonomicznych.
Operacja „oceny” sprawdza stopień spełnienia określonych wymagań wymagania techniczne. Na podstawie zidentyfikowanych kryteriów lokalnych ustala się integralne kryterium jakości danej opcji i ustala potrzebę uzyskania określonych jej wskaźników. Operacja „optymalizacja” wybiera kierunek doskonalenia wariantu projektowego zgodnie z modelem charakteryzującym relację kryteriów lokalnych. W wyniku przekształceń dokonanych w wersji oryginalnej pojawia się nowa, ulepszona wersja. Informacje na ten temat ponownie trafiają do bloków modelowania, analizy, oceny i optymalizacji. Połączenie tych operacji tworzy iteracyjny cykl procesu projektowania.
W ciągu kilku iteracji jakość oryginalnej wersji poprawia się. Proces kończy się, gdy opcja spełnia określone wymagania we wszystkich głównych wskaźnikach, a jej dalsze doskonalenie nie prowadzi do istotnej poprawy kryterium integralnego. Korzystanie z bloku R 8, operacje modelowania, oceny, analizy i optymalizacji powtarzane są cyklicznie dla wszystkich opcji uzyskanych w operacjach wyszukiwania i syntezy. W rezultacie do operacji „wyboru” przygotowywanych jest wiele odpowiednich opcji, z których następnie wybierane są te najbardziej racjonalne.
W powyższym modelu zbiór operacji projektowych i bloków sterujących definiuje dwie metody projektowania: transformację obiektów analogowych i syntezę.
Metody różnią się operacjami generowania wariantów projektu. W pierwszej metodzie jest to poszukiwanie obiektów analogowych i ich transformacja, w drugiej ukierunkowana synteza rozwiązań projektowych. Pozostałe operacje cyklu iteracyjnego i wybór opcji są wspólne dla obu metod projektowania.
Jak pokazuje doświadczenie rozwojowe i wdrożeniowe, metody te są szeroko stosowane w CAD TP. Pod względem możliwości nie zaprzeczają, lecz się uzupełniają.
Programy zbudowane w oparciu o metody typowania charakteryzują się mniejszą (30-40%) objętością i czasochłonnością komputera w porównaniu do wielopoziomowej metody iteracyjnej. W tym zakresie wskazana jest automatyzacja projektowania procesów technologicznych dla wyrobów standardowych w oparciu o metody typizacji, a dla pozostałych wyrobów – poprzez transformację procesów analogowych i wielopoziomową metodę iteracyjną.
Zatem cały proces wytwarzania urządzenia traktuje się jako sekwencję wzajemnie powiązanych operacji technologicznych. Na przykład przy produkcji tranzystora p-n-p z podstawą epitaksjalną głównymi operacjami są dyfuzja i utlenianie, tworzenie bazy i emitera. Każda operacja charakteryzuje się zestawem parametrów wejściowych i wyjściowych, które z kolei stanowią dane wyjściowe do obliczeń komputerowych z wykorzystaniem wybranych modeli matematycznych.
Tym samym w zespole dyfuzji i utleniania znajduje się panel sterowania procesem dyfuzji, za pomocą którego ustawia się parametry procesu obróbki płyt, wybiera się tryb pracy pieca, czas trwania cyklu technologicznego i charakterystykę procesu są korygowane, jeśli odbiegają od podanych wartości. Na wyjściu z piekarnika specjalne urządzenie mierzy parametry płyt, dane przekazywane są do centrali, która porównuje zmierzone parametry z zadanymi i odpowiednio dostosowuje parametry procesu dyfuzji, z których głównym jest np. grubość tlenku .
miejsca obróbki cieplnej w procesie technologicznym, zaczynają formułować optymalne operacje obróbcze na obrabiarkach, uwzględniając ograniczenia.Problem tworzenia operacji optymalnych ma charakter wielowymiarowy, a zakres rozwiązań można ograniczyć do dwóch przypadków granicznych: każdemu przejściu odpowiada operacja jednego przejścia; wszystkie przejścia wykonywane są w jednej operacji.
Przed przystąpieniem do rozwiązywania problemu cały zbiór przejść rozkłada się na podzbiory przy spełnieniu ograniczeń (patrz tabela 12.1). Każda kolumna odpowiada sposobowi obróbki powierzchni produktu. Jeśli nie ma przejścia, komórki tablicy nie są wypełnione (ustawione na 0).
Podwójne linie w tabeli pokazują możliwy podział całkowitego zbioru przejść na podzbiory. Całkowity zbiór przejść wchodzących w skład zbioru i umieszczonych w jakiejś ustalonej kolejności oznacza się liczbami odpowiadającymi (z wyjątkiem) pośrednim numerom przejść; - numer ostatniego przejścia, równy Łączna Jest wiele przejść.
Konieczne jest takie rozłożenie dostępnych przejść pomiędzy operacjami, aby wartość funkcji celu (na przykład koszt wykonania operacji) danej opcji była minimalna.
Tworzenie opcji operacji rozpoczyna się od połączenia w operację maksymalna ilość przejścia. Takie podejście pozwala znacznie zmniejszyć liczbę analizowanych opcji.
Aby zawęzić obszar poszukiwań optymalnej kombinacji, należy skorzystać z kryterium wyboru, które pozwala wykluczyć niektóre opcje z rozważań.
Na pierwszym etapie selekcji technologicznej możliwe opcje biorąc pod uwagę ograniczenia nałożone na kolejność przetwarzania, minimalną liczbę ponownych instalacji i możliwości technologiczne sprzętu.
Na kolejnym etapie projektowania, gdy generowana jest opcja dla konkretnego modelu maszyny, sprawdzane jest, czy zostały spełnione ograniczenia dotyczące dokładności obróbki i chropowatości powierzchni.
Jeżeli opcja jest realizowana, obliczana jest odpowiadająca jej wartość funkcji celu. Obliczenia są kontynuowane do momentu rozłożenia wszystkich przejść pomiędzy operacjami i znalezienia wartości funkcji celu. Po otrzymaniu wyników obliczeń dla dwóch etapów (iteracji) należy je porównać i wybrać najlepszy. Jeśli ostatnia opcja gorszy od przedostatniego, wówczas w oparciu o regułę dominacji obliczenia zostają zatrzymane.
Ilość obrobionej powierzchni produktu | |||||||||||
---|---|---|---|---|---|---|---|---|---|---|---|
1 | 2 | … | 1 | … | N | … | … | … | … | … | … |
11 | 12 | … | I | … | 1n | 1 | 1 | … | 0 | … | 1 |
21 | 22 | … | 2i | … | 2n | … | … | … | … | … | … |
… | … | … | … | … | … | M | 0 | … | M | … | M |
K1 | k2 | … | ki | … | kn | P | 0 | … | Liczba Pi | … | Pn |
Jeżeli opcja zostanie poprawiona, obliczenia są kontynuowane aż do uzyskania optymalnej. Następnie w miejscu najgorszych tworzą się nowa opcja. Zasada dominacji polega na tym, że dalsze zmniejszanie liczby przejść operacji prowadzi do wzrostu liczby operacji oraz wzrostu czasu i kosztów technologicznych przetwarzania. W oparciu o podane koszty oceniane są możliwości kształtowania operacji przerobowych według opisanej metodyki. Zatem, jeśli wiadomo trasę technologiczną obróbki części, istnieje możliwość jej dostosowania w zależności od składu i treści poszczególnych operacji, a także w zależności od rodzaju użytego sprzętu.
12.3. Ogólny algorytm projektowania technologii eksploatacji
Rozważmy ogólny algorytm projektowania technologia obsługi .
Zgodnie z charakterem rozwiązywanych problemów i strukturą kryterium optymalnego projektowania syntezę operacji technologicznych dzieli się na cztery składowe (rys. 12.1). W pierwszym określa się najbardziej racjonalny kształt, naddatki, tolerancje i wymiary międzyoperacyjne produktu przyjętego do zabiegu, czyli stan.
Druga część algorytmów związana jest z doborem elementów systemu obróbki powierzchni produktu (modele urządzeń, osprzętu, głównych, pomocniczych i urządzenia pomiarowe) i układ przestrzenny instrumentalnego wyposażenia sprzętu.
Ryż. 12.1.
Algorytmy części trzeciej dokonują syntezy struktury czasowej operacji, tj. wyjaśniają skład przejść, określają kolejność ich wykonywania i charakter ich połączenia w czasie.
Część czwarta zawiera algorytmy wyznaczania parametrów oraz charakterystyk techniczno-ekonomicznych operacji.
W przypadku prostych operacji może brakować wielu algorytmów. Przykładowo w operacji pojedynczego przejścia pomijany jest algorytm ustalania kolejności przejść, a w niektórych operacjach nie są potrzebne algorytmy generowania ustawień narzędzi i rozdzielania przejść pomiędzy pozycjami. Cechy te są brane pod uwagę przy ustalaniu składu strukturalnego algorytmów projektowania konkretnych operacji. Algorytm sterowania z ogólny schemat niektóre algorytmy są wykluczane lub dodawane w zależności od celu i celów osiągniętych w każdym konkretnym przypadku.
Wynikiem projektowania wspomaganego komputerowo jest indywidualny proces technologiczny, zaprojektowany w formie mapy trasy, która zawiera informacje o kolejności operacji i przejść, o sprzęcie i akcesoriach, o trybach poszczególnych operacji technologicznych oraz szereg innych informacje wykorzystywane do organizacji produkcji sprzętu elektronicznego.
Rozważaliśmy zatem trzy poziomy systemów projektowania TP wspomaganych komputerowo:
- projekt schematu;
- projektowanie tras technologicznych;
- projekt technologia obsługi.
Proces projektowania przebiega z poziomu na poziom i na każdym poziomie jest iteracyjny z gromadzeniem doświadczeń, uogólnianiem i dostosowywaniem na każdym poziomie (ryc. 12.2).
Wyniki te można wykorzystać do opracowania algorytmów standardowych, grupowych i analogów technologicznych.
Poprzez operację „uogólnienia” zgromadzonego doświadczenia z szeregu wcześniej zaprojektowanych procesów technologicznych powstają standardowe rozwiązania projektowe, algorytmy standardowe i grupowe. Poprawia się wartość heurystycznych kryteriów samoselekcji, poprawia się strukturę i parametry algorytmów syntezy, analizy i optymalizacji. Uogólnienie zgromadzonego doświadczenia odbywa się w trybie projektowania człowiek-maszyna z operacyjnym wyświetlaniem procesów analogowych na ekranach wyświetlaczy.
W wyniku szkolenia i samokształcenia coraz skuteczniejsze stają się algorytmy syntezy rozwiązań projektowych oraz kryteria heurystyczne pośredniego samodzielnego wyboru. Zamiast generować dużą liczbę możliwych opcji, celowo syntetyzuje się mniejszą liczbę najbardziej obiecujących rozwiązań projektowych (opcji), biorąc pod uwagę pozytywne doświadczenia z przeszłości. Poprawiając wartości kryteriów heurystycznych w procesie samouczenia, na każdym etapie pośrednim wybierana jest do dalszego projektowania mniejsza niż dotychczas liczba najbardziej racjonalnych opcji, poprawiając opcję wyjściową do wymaganego stopnia doskonałości.
Na podstawie analizy dokumentacji projektowej i technologicznej w procesie opracowywania algorytmów projektowych tworzony jest fundusz informacji służący do zautomatyzowanego projektowania procesów technologicznych do produkcji elementów OZE; fundusz ten uzupełniany jest w procesie funkcjonowania CAD.
Pytania testowe i ćwiczenia
- Co obejmuje technologia obsługi?
- Co musisz wiedzieć, aby zbudować operację?
- Co obejmuje trasa zaprojektowana komputerowo?
- Jakie czynniki wpływają na projekt operacji?
- Co obejmuje zadanie stworzenia optymalnego działania?
- Jakie dane początkowe wykorzystuje się przy projektowaniu TP przy pomocy komputera?
- To jest ograniczenia technologiczne, określenie akceptowalnych opcji produkcji TP w przedsiębiorstwie?
- Co decyduje o strukturze operacji technologicznej?
- Jak określa się liczbę przejść w operacji?
- Nazwij ograniczenia technologiczne, które determinują dopuszczalne możliwości wytwarzania procesów technologicznych w przedsiębiorstwie.
Wyślij swoją dobrą pracę do bazy wiedzy jest prosta. Skorzystaj z poniższego formularza
Studenci, doktoranci, młodzi naukowcy, którzy wykorzystują bazę wiedzy w swoich studiach i pracy, będą Państwu bardzo wdzięczni.
Wysłany dnia http://www.allbest.ru/
Algorytmy projektowania operacji technologicznych
1. Dane wyjściowe do projektowania operacji technologicznych
2. Kształtowanie optymalnego działania
3. Algorytm ogólny projekt technologii operacyjnej
1 . Dane wyjściowe do projektowania operacji technologicznych
Projektowanie operacji to zadanie wielowymiarowe. Aby skonstruować operację, należy znać trasę obróbki przedmiotu, układ jego instalacji, jakie powierzchnie i z jaką dokładnością zostały przetworzone w poprzednich operacjach. Trasa zaprojektowana przy pomocy komputera zawiera treść operacji, model sprzętu, nazwę urządzenia i narzędzia.
Na strukturę działalności wpływa wiele czynników:
Projekt produktu (rozmiar, waga, konfiguracja);
Wymagania techniczne dotyczące jego produkcji (tolerancje wymiarów i wzajemne porozumienie elementy);
Rodzaj przedmiotu obrabianego;
Wydanie programu;
Model wyposażenia;
Projekt urządzenia.
Operacje technologiczne tworzą złożoną strukturę, której elementami są przejścia technologiczne. Te elementy procesu technologicznego (TP) są ze sobą powiązane różnymi relacjami, z których najważniejsze to: czasowa, przestrzenna, logiczna i matematyczna.
Podczas optymalizacji przejść określa się ich liczbę i kolejność wykonania, tryby, naddatki na wymiary pośrednie, standardy czasowe, tolerancje pośrednie (technologiczne), liczbę korekt, wymiary dostosowawcze i technologiczne.
Zadanie stworzenia optymalnego działania obejmuje organizowanie i rozbijanie całkowity zestaw przejść (zestaw) na podzbiory biorąc pod uwagę obecność obróbki cieplnej, minimalizując liczbę instalacji przedmiotu obrabianego i jałowych ruchów narzędzia. Na etapie operacji formowania obliczane są standardy czasowe i doprecyzowywany jest dobór sprzętu, urządzeń i narzędzi.
Baza informacyjna proces projektowania obejmuje dane referencyjne i normatywne I wskaźniki techniczne i ekonomiczne.
Zbiór możliwych opcji tworzy obszar możliwych rozwiązań, w którym konieczne jest znalezienie najlepszego ze wszystkich konkretnych warunków. Ponieważ rozpatrywany problem poprzedzony jest wyborem opcji i rodzaju sprzętu, możliwe rozwiązania zawierają wszystkie możliwe kombinacje parametrów w ich różnych sekwencjach, biorąc pod uwagę dokładność produktu, charakterystykę sprzętu i narzędzia.
Rozważmy budowę modelu TP na przykładzie wytwarzania elementów sprzętu radioelektronicznego (REA).
Wiadomo, że procesy technologiczne wytwarzania elementów elektronicznych w wielu przypadkach opierają się na obróbce mechanicznej, termicznej, mechanotermicznej i chemicznej.
Na przykład, rozważając hierarchiczne systemy automatycznego sterowania operacjami obróbki cieplnej (metalizacja, lutowanie, wyżarzanie) Specjalna uwaga poddaje się kształtowaniu elementy pierwotnegliniarze projekty REA. Te pierwiastki pierwotne można otrzymać poprzez różne operacje obróbki powierzchni, a mianowicie:
Odlewanie do form metalowych;
Tłoczenie na zimno i na gorąco;
Spęczanie, odlewanie i prasowanie materiałów polimerowych;
Prasowanie i spiekanie materiałów proszkowych;
Toczenie, wiercenie, frezowanie, szlifowanie i inne metody przetwarzania.
Jednocześnie wskazano, że dowolny podstawowy element konstrukcyjny REA można uzyskać nie na jeden, ale na kilka sposobów (na przykład odlewanie, ciśnienie, obróbka mechaniczna). Preferowana jest metoda, która w warunkach konkretnej produkcji zapewnia wyższą produktywność i wydajność, wymaganą dokładność technologiczną oraz stwarza warunki dla mechanizacji i automatyzacji procesów technologicznych.
Inną cechą technologii kształtowania jest to, że wytwarzanie podstawowych elementów konstrukcyjnych REA można przeprowadzić przy użyciu jednego lub drugiego opcja strukturalna technologii, urządzeń o różnych parametrach technicznych i ekonomicznych.
Niech liczba przejść będzie równa p, a liczba pozycji na maszynie równa. Aby wykonać przejście
w dowolnej pozycji wymagany jest czas ti oraz do zakończenia przejścia j-ta pozycja gdzie potrzeba czasu
Dodatkowo przed wykonaniem -tego przejścia muszą zostać wykonane przejścia (zestaw złożony z indeksów tych przejść, które muszą zostać wykonane przed -tym przejściem).
wtedy równość
wskazuje, że przejście zostanie wykonane w co najmniej jednej pozycji.
Liczba przejść wykonanych na tej pozycji nie przekracza if
Rozkład wszystkich przejść pomiędzy stanowiskami maszynowymi z kombinacją kilku przejść w jednym położeniu odbywa się również z uwzględnieniem zasad technologicznych i doświadczenia eksploatacyjnego takiego sprzętu. Istnieje zatem kilka grup ograniczeń. Pierwszy z nich związany jest z wymaganiami dotyczącymi określonej kolejności przejść.
Kolejna grupa ograniczeń dotyczy możliwości łączenia kilku przejść w jednej operacji
; (tutaj - liczba całkowita). (5)
Można podać grupę ograniczeń całkowitego czasu przetwarzania na każdej pozycji, biorąc pod uwagę skoki robocze i jałowe narzędzia
gdzie R jest regulowanym czasem przetwarzania na każdej pozycji. Wszystkie ograniczenia można zapisać w ogólnej formie:
gdzie jest zbiorem indeksów pozycji, przy których - można wykonać przejście.
Optymalna ilość przejść do każdej powierzchni oraz optymalna kolejność ich wykonania ustalana jest na poprzednich poziomach konstrukcji eksploatacyjnej. Tworząc optymalną operację, konieczne jest połączenie wykonania przejść określonej liczby powierzchni na jednej maszynie. W tym celu należy uporządkować cały zestaw przejść i podzielić je na zestawy, biorąc pod uwagę ograniczenia podobne do ograniczeń przy rozdzielaniu przejść pomiędzy stanowiskami maszyny wielopozycyjnej.
2. Fotkształtowanie optymalnego działania
Aby sformułować optymalne działanie, stosuje się metodę sekwencyjnej analizy opcji. Zgodnie ze schematem analizy sekwencyjnej w wyniku porównania ustala się dominację niektórych opcji nad innymi. Następnie tworzona jest reguła filtrowania opcji. Znając możliwości technologiczne sprzętu, optymalna ilość i kolejność przejść, a także miejsce obróbki cieplnej w procesie technologicznym, zaczynają formułować optymalne operacje obróbcze na obrabiarkach, biorąc pod uwagę ograniczenia.
Problem tworzenia operacji optymalnych ma charakter wielowymiarowy, a zakres rozwiązań można ograniczyć do dwóch przypadków granicznych: każdemu przejściu odpowiada operacja jednego przejścia; wszystkie przejścia wykonywane są w jednej operacji.
Przed przystąpieniem do rozwiązywania problemu cały zbiór przejść rozkłada się na podzbiory przy spełnieniu ograniczeń (tabela 1). Każda kolumna odpowiada sposobowi obróbki powierzchni produktu. Jeśli nie ma przejścia, komórki tablicy nie są wypełnione (ustawione na 0).
Podwójne linie w tabeli pokazują możliwy podział całkowitego zbioru przejść na podzbiory. Całkowity zbiór przejść zawartych w zbiorze i umieszczonych w jakiejś ustalonej kolejności jest oznaczony liczbami, które odpowiadają (z wyjątkiem) pośrednim numerom przejść; - numer ostatniego przejścia, równy całkowitej liczbie przejść w zbiorze. Należy rozdzielić dostępne przejścia pomiędzy operacje tak, aby wartość funkcji celu (np. koszt wykonania operacji C_(o)n) danej opcji była minimalna.
Tabela 1. Liczba obrobionej powierzchni produktu
Ilość obrobionej powierzchni produktu |
||||||
Tworzenie wariantów operacji rozpoczyna się od połączenia maksymalnej liczby przejść w operację. Takie podejście pozwala znacznie zmniejszyć liczbę analizowanych opcji.
Aby zawęzić obszar poszukiwań optymalnej kombinacji, stosuje się kryterium wyboru, które pozwala wykluczyć niektóre opcje z rozważań.
Na pierwszym etapie selekcji identyfikowane są możliwe opcje technologiczne, biorąc pod uwagę ograniczenia nałożone na kolejność przetwarzania, minimalną liczbę ponownych instalacji i możliwości technologiczne sprzętu.
Na kolejnym etapie projektowania, gdy generowana jest opcja dla konkretnego modelu maszyny, sprawdzane jest, czy zostały spełnione ograniczenia dotyczące dokładności obróbki i chropowatości powierzchni.
Jeżeli opcja jest realizowana, obliczana jest odpowiadająca jej wartość funkcji celu. Obliczenia są kontynuowane do momentu rozłożenia wszystkich przejść pomiędzy operacjami i znalezienia wartości funkcji celu. Po otrzymaniu wyników obliczeń dla dwóch etapów (iteracji) należy je porównać i wybrać najlepszy. Jeżeli ostatnia opcja jest gorsza od przedostatniej, wówczas na podstawie reguły dominacji obliczenia zostają zatrzymane.
Jeżeli opcja zostanie poprawiona, obliczenia są kontynuowane aż do uzyskania optymalnej. Wtedy w miejsce najgorszego powstaje nowa opcja. Zasadą dominacji jest to, że dalsze zmniejszanie liczby przejść w operacji prowadzi do wzrostu liczby operacji oraz wzrostu czasu i kosztów technologicznych przetwarzania. W oparciu o podane koszty oceniane są możliwości kształtowania operacji przerobowych według opisanej metodyki. Zatem, jeśli znana jest droga technologiczna obróbki części, można ją dostosować w zależności od składu i zakresu poszczególnych operacji, a także rodzaju użytego sprzętu.
3. Ogólny algorytm projektowania technologii eksploatacji
Pierwsza część algorytmów projektowania technologii operacyjnej określa tryby przetwarzania i dobór urządzeń technologicznych. Każda technologia operacyjna, w tym produkcja podzespołów elektronicznych, budowana jest według następującego algorytmu.
Ryż. 1. Ogólny algorytm projektowania technologii eksploatacji
Druga część algorytmów związana jest z doborem elementów systemu obróbki powierzchni produktu (modele sprzętu, osprzęt, narzędzia główne, pomocnicze i pomiarowe) oraz rozmieszczeniem przestrzennym układu wyposażenia instrumentalnego.
Algorytmy części trzeciej dokonują syntezy struktury czasowej operacji, czyli wyjaśniają kompozycję przejść, określają kolejność ich wykonywania i charakter ich połączenia w czasie.
Część czwarta zawiera algorytmy wyznaczania parametrów oraz charakterystyk techniczno-ekonomicznych operacji.
W przypadku prostych operacji może brakować wielu algorytmów. Na przykład w operacji pojedynczego przejścia pomijany jest algorytm ustalania kolejności przejść, a w niektórych operacjach nie są potrzebne algorytmy generowania ustawień narzędzi i rozdzielania przejść według pozycji. Cechy te są brane pod uwagę przy ustalaniu składu strukturalnego algorytmów projektowania konkretnych operacji. Algorytm sterujący wyklucza lub dodaje pewne algorytmy z ogólnego schematu, w zależności od celu i celów osiąganych w każdym konkretnym przypadku.
Wynikiem projektowania wspomaganego komputerowo jest indywidualny proces technologiczny, zaprojektowany w formie mapy trasy, która zawiera informacje o kolejności operacji i przejść, o sprzęcie i akcesoriach, o trybach poszczególnych operacji technologicznych oraz szereg innych informacje wykorzystywane do organizacji produkcji sprzętu elektronicznego.
Rozważaliśmy zatem trzy poziomy systemów projektowania TP wspomaganych komputerowo:
· projekt schematu;
· projekt trasy technologicznej;
· projekt technologia obsługi.
Proces projektowania przebiega z poziomu na poziom i na każdym poziomie jest iteracyjny z gromadzeniem doświadczeń, uogólnianiem i dostosowywaniem na każdym poziomie (ryc. 2).
Wyniki te można wykorzystać do opracowania algorytmów standardowych, grupowych i analogów technologicznych.
Poprzez operację „uogólnienia” zgromadzonego doświadczenia z szeregu wcześniej zaprojektowanych procesów technologicznych powstają standardowe rozwiązania projektowe, algorytmy standardowe i grupowe. Poprawia się wartość heurystycznych kryteriów samoselekcji, poprawia się strukturę i parametry algorytmów syntezy, analizy i optymalizacji. Uogólnienie zgromadzonego doświadczenia odbywa się w trybie projektowania człowiek-maszyna z operacyjnym wyświetlaniem analogicznych procesów na ekranach wyświetlaczy.
W wyniku szkolenia i samokształcenia coraz skuteczniejsze stają się algorytmy syntezy rozwiązań projektowych oraz kryteria heurystyczne pośredniego samodzielnego wyboru. Zamiast generować dużą liczbę możliwych opcji, celowo syntetyzuje się mniejszą liczbę najbardziej obiecujących rozwiązań projektowych (opcji), biorąc pod uwagę pozytywne doświadczenia z przeszłości. Poprawiając wartości kryteriów heurystycznych w procesie samouczenia, na każdym etapie pośrednim do dalszego projektowania wybierana jest mniejsza liczba najbardziej racjonalnych niż dotychczas opcji.
W konsekwencji pętla samoucząca się, oparta na wykorzystaniu doświadczeń projektowych, może poprawić jakość rozwiązań projektowych i radykalnie obniżyć koszt czasu pracy komputera.
W wyniku ukierunkowanej syntezy i selekcji pośredniej na każdym poziomie powstają nie wszystkie możliwe opcje, a jedynie te najbardziej obiecujące. Mogą posiadać wady, które są identyfikowane poprzez operacje analityczne i ewaluacyjne, a następnie eliminowane przez algorytmy optymalizacyjne. Podobną sytuację obserwuje się przy automatyzacji projektowania analogów TP.
W rezultacie dochodzimy do konieczności zorganizowania iteracyjnego modelu procesu projektowego, którego główną cechą jest konsekwentne doskonalenie wersji oryginalnej do wymaganego stopnia doskonałości. Na podstawie analizy dokumentacji projektowej i technologicznej w procesie opracowywania algorytmów projektowych tworzony jest zasób informacji do komputerowego wspomagania projektowania procesów technologicznych do produkcji elementów OZE.
zaprojektować operację technologiczną
Ryż. 2. Model zautomatyzowanego systemu projektowania z przechowywaniem i uogólnianiem doświadczeń projektowych na każdym poziomie.
W rezultacie dochodzimy do konieczności zorganizowania iteracyjnego modelu procesu projektowego, którego główną cechą jest konsekwentne doskonalenie wersji oryginalnej do wymaganego stopnia doskonałości.
Na podstawie analizy dokumentacji projektowej i technologicznej w procesie opracowywania algorytmów projektowych tworzony jest fundusz informacji służący do zautomatyzowanego projektowania procesów technologicznych do produkcji elementów OZE; fundusz ten uzupełniany jest w procesie funkcjonowania CAD.
1. Co obejmuje technologia obsługi?
2. Co musisz wiedzieć, aby zbudować operację?
3. Co obejmuje trasa zaprojektowana komputerowo?
4. Jakie czynniki wpływają na projekt operacji?
5. Co obejmuje zadanie stworzenia optymalnego działania?
6. Jakie dane początkowe wykorzystuje się przy projektowaniu TP przy pomocy komputera?
7. Co to jest ograniczenia technologiczne, określenie akceptowalnych opcji produkcji TP w przedsiębiorstwie?
8. Co decyduje o strukturze operacji technologicznej?
9. Jak określa się liczbę przejść w operacji?
Nazwa ograniczenia technologiczne, które określają dopuszczalne opcje produkcji TP w przedsiębiorstwie.
Opublikowano na Allbest.ru
Podobne dokumenty
Podstawowe pojęcia projektowania optymalnego. Etapy rozwiązywania problemu projektowego urządzenie radioelektroniczne Z optymalne właściwości z wykorzystaniem parametrycznych metod optymalizacji. Optymalizacja wielokryterialna w problemach z ograniczeniami.
streszczenie, dodano 03.04.2009
Metody i etapy projektowania sprzętu elektronicznego. Rola języka programowania w systemach projektowania wspomaganego komputerowo. krótki opis komputery stosowane w rozwiązywaniu problemów automatyzacji projektowania sprzętu elektronicznego.
streszczenie, dodano 25.09.2010
Charakterystyka etapów projektowania systemy elektroniczne. Zastosowanie wysokiego poziomu grafiki i redaktorzy tekstu podczas procesu projektowania. Opcje konfiguracji sprzętu. Kolejność zabiegów projektowych etapu architektonicznego.
test, dodano 11.11.2010
Proces projektowania wspomagany komputerowo w systemie projektowym P-CAD płytka drukowana wzmacniacz mocy. Pakowanie obwodu na płytkę. Automatyczna procedura trasowania PCB. Opis tekstowy schematu obwodu elektrycznego.
praca na kursie, dodano 18.01.2014
Analiza stan aktulany projektowanie nadawczo-odbiorczych urządzeń radiowych. Opis systemów wspomagania decyzji, perspektywy wykorzystania takich systemów w projektowaniu. Obliczanie szerokości pasma ścieżki wysokiej częstotliwości odbiornika.
teza, dodano 30.12.2015
Algorytmy projektowania układów sterowania urządzeń radioelektronicznych: główne zadania, kryteria konstrukcyjne. Algorytmy układu wykorzystujące techniki programowania liczb całkowitych. Iteracyjne algorytmy ulepszania układu.
test, dodano 23.11.2013
Zapoznanie z możliwościami pracy w środowisku komputerowego systemu projektowania „Max+Plus II”. Analiza etapów rozwoju specjalistycznych urządzeń cyfrowych. Charakterystyka obwodu po zmianie adresów. Rozważenie sposobów konfiguracji dodatków.
test, dodano 01.03.2014
Badanie metod projektowania, obliczania i modelowania wzmacniaczy z wykorzystaniem ARPA. Obliczanie wzmocnienia napięciowego wzmacniacza w pętli otwartej. Stopień wyjściowy, stopień wejściowy i obliczanie elementów pojemnościowych. Obwód wzmocnienia i sprzężenia zwrotnego.
praca na kursie, dodano 05.03.2011
Nauka podstawowych zasad konstruowania baz danych - nazwanego zbioru danych odzwierciedlających stan obiektów i ich relacje w rozpatrywanym obszarze tematycznym. System zarządzania bazą danych. Koncepcje ich budowy i etapy projektowania.
test, dodano 14.12.2010
Typowy schemat proces komputerowego wspomagania projektowania OZE. Klasyfikacja problemów projektowych rozwiązywanych w procesie projektowania OZE. Struktura CAD, wsparcie matematyczne, wsparcie językowe. Języki dialogu, ich odmiany i typy.
Proces produkcji młyna końcowego
Uzasadnienie wykorzystania narzędzia.
Przykładowo konieczne jest opracowanie konstrukcji frezu palcowego do obróbki rowka, który wykonuje jednocześnie dwie operacje: wycinanie rowka na zadaną głębokość oraz fazowanie pod kątem 45.
Główne parametry noża, które należy wziąć pod uwagę:
Kierunek zęba
Konstrukcja zębów: zaostrzona / cofnięta
Materiał zębów Liczba i wielkość zębów (np surowy frezowanie - frezy o dużej podziałce obwodowej i małej liczbie dużych zębów. Dla wykończeniowy frezowanie i frezowanie materiałów kruchych - frezy o małej podziałce obwodowej i duża ilość małe zęby)
· Konstrukcja frezów: litych, kompozytowych (z lutowanymi elementami tnącymi) i prefabrykowanych (z mocowanie mechaniczne nieostrzące się wymienne wielościenne wkładki)
Sposób montażu na wrzecionie maszyny: mocowanie (z otworem) / zakończenie (z trzpieniem)
Projekt. Pomimo tego, że projektanci oferują setki różne rodzaje i odmiany noży, wszystkie mają szeroki asortyment Pospolite elementy(widzieć zdjęcie).
Urządzenie frezów palcowych.
(na przykładzie frezu okrągłego i wycinaka prostego)
Krawędzie tnące. Frez może mieć jedną, dwie lub więcej krawędzi tnących. Frezy jednoostrzowe znajdują zastosowanie w zastosowaniach, gdzie wymagana jest duża produktywność, w związku z czym czystość powierzchni ma drugorzędne znaczenie. Większość frezów ma dwie lub więcej krawędzi tnących, co zapewnia równowagę między jakością cięcia a produktywnością.
Krawędzie tnące frezu mogą być wykonane ze stali szybkotnącej (w skrócie HSS) lub węglika (TCT). Te ostatnie z reguły są nieco droższe.
Aby frez mógł być zanurzony w materiale w dowolnym miejscu przedmiotu obrabianego, frez musi posiadać końcowe krawędzie tnące (jak pokazano na rysunku).
Cholewka noże charakteryzują się średnicą i długością. Oczywiście średnica trzpienia musi odpowiadać średnicy tulei frezarskiej. Frezy sprzedawane w Rosji z reguły dostarczane są z tulejami zaciskowymi o średnicy 8 i 12 mm lub tylko 8 mm (typowe dla modeli o małej mocy). Tuleje zaciskowe o podanych wymiarach są standardem w krajach europejskich. Narzędzia przeznaczone na rynek amerykański są przystosowane do stosowania frezów z chwytem ¼” (6,35 mm) i ½” (12,7 mm) cala. Jednak wielu producentów, zarówno europejskich, jak i amerykańskich, oferuje do swoich frezów dodatkowe tuleje zaciskowe w rozmiarach calowych lub odwrotnie, metrycznych.
Trzon może być również stożkowy, jak nazywają się stożkiem Morse'a. We wrzecionie lub koniku maszyny znajduje się stożkowy otwór o odpowiedniej wielkości (gniazdo). Zaprojektowane do szybkiej wymiany narzędzi z dużą dokładnością centrowania i niezawodnością.
Przy opracowywaniu nowych konstrukcji frezów spełnione są następujące podstawowe wymagania.
Liczba zębów powinna być jak największa, ponieważ od niej proporcjonalnie zależy posuw minutowy, czyli wydajność obróbki.
Jednocześnie zęby muszą być odpowiednio mocne, a odstępy między nimi, kształt i chropowatość powierzchni rowków wiórowych muszą zapewniać pewne osadzanie i odprowadzanie wiórów (to ostatnie jest szczególnie ważne w przypadku frezów walcowo-czołowych wykonujących głębokie rowki). W niektórych przypadkach, na przykład, gdy tworzą się ciągłe, ciągłe wióry, przednia powierzchnia zębów frezów walcowo-czołowych jest stopniowana w celu kruszenia wiórów.
Wybór sprzętu
Zadaniem tej sekcji jest dobranie dla każdej operacji technologicznej takiego sprzętu i urządzeń, które zapewnią wytworzenie części o zadanej jakości i ilości przy minimalnych kosztach.
Przy wyborze rodzaju i modelu maszyn do cięcia metalu będziemy kierować się następującymi zasadami:
1) Wydajność, dokładność, wymiary i moc maszyny muszą być minimalne i wystarczające, aby zapewnić spełnienie wymagań dotyczących operacji.
2) Maszyna musi zapewniać maksymalną koncentrację przejść do operacji, aby zmniejszyć liczbę operacji, ilość sprzętu, zwiększyć produktywność i dokładność poprzez zmniejszenie liczby przestawień przedmiotu obrabianego.
3) Sprzęt musi spełniać wymagania bezpieczeństwa, ergonomii i ochrony środowiska.
Jeżeli dla jakiejś operacji kilka modeli maszyn spełnia te wymagania, to w celu ostatecznego wyboru przeprowadzimy porównanie analiza ekonomiczna. Wybieramy sprzęt w następującej kolejności:
1) Na podstawie kształtu obrabianej powierzchni i sposobu obróbki dobieramy grupę maszyn.
2) W zależności od położenia obrabianej powierzchni wybierz typ maszyny.
3) Na podstawie całkowite wymiary obrabianego przedmiotu, wymiarów obrabianych powierzchni i dokładności obróbki, dobieramy standardowy rozmiar (model) maszyny. Dane dotyczące wyboru sprzętu wprowadzono do tabeli 5.1.
Tabela 5.1
Wybór wyposażenie technologiczne
Nie. op. | Nazwa operacji | Typ, model sprzętu | Mocowanie maszyny |
Nabywanie | Pozioma piła taśmowa UE-330A | Imadło samocentrujące ze szczękami pryzmatycznymi zgodnie z GOST 12195-66 | |
Obrócenie | |||
Spawalniczy | Spawarka zgrzewanie doczołowe metoda rozpływowa MSMU-150 | Specjalista. Pryzmaty przewodzące | |
Wyżarzanie | |||
Test | - | - | |
Obrócenie | Tokarka do gwintowania 1K62 | Uchwyt 3-szczękowy GOST 2675-63 | |
Obrócenie | Uchwyt 3-szczękowy GOST 2675-63 | ||
Obrócenie | Tokarka rewolwerowa 1N365BP | Uchwyt 3-szczękowy GOST 2675-63 | |
Obrócenie | Tokarka do gwintowania 1K62 | Uchwyt 3-szczękowy GOST 2675-63 | |
Przemiał | Frezarka pionowa 6T104 | Uchwyt 3-szczękowy GOST 2675-63 | |
Przemiał | Frezarka CNC MANO-700 | Specjalny uchwyt zaciskowy | |
Test | |||
Termiczny | |||
Foliowanie cylindryczne | Uchwyt napędowy | ||
Foliowanie cylindryczne | Szlifierka cylindryczna 3131 | Uchwyt napędowy | |
Szlifowanie | Specjalista. Szlifierka CNC 55С CNC6 | Specjalny uchwyt zaciskowy | |
Test | |||
Cechowanie |
Przykład frezowania rury skrzyni korbowej nowym frezem
Czas przetwarzania
Aby określić czas obróbki, konieczne jest określenie warunków skrawania. Tryby skrawania przypiszemy tak, jak dla podstawowej wersji obróbki rury skrzyni korbowej dwoma rodzajami narzędzi, a mianowicie:
Posuw przy cięciu do noża:
Sв= 100 mm/min
Posuw przy frezowaniu wzdłużnym rowka rurowego:
Sp = 200 mm/min
Przyspieszony posuw przy dosuwaniu/odsuwaniu frezu:
Sу= 5000 mm/min
Następnie znajdujemy czas obróbki maszyny korzystając ze wzoru:
ТМ = Lв / Sв + Lп / Sв + Lу / Sу, gdzie:
Lв – długość skoku przy cięciu noża, 10 mm
Lп – długość skoku frezu podczas ruchu poprzecznego 205 mm (wg rysunku)
Lу – długość skoku podczas przyspieszonych ruchów frezu podczas zbliżania się do przedmiotu obrabianego i usuwania, 400 mm.
Czas maszynowy jest równy:
TM= 10/100 + 205/200 + 400/5000 = 1,185 min
Czas jednostkowy tej operacji znajdujemy korzystając ze wzoru:
Tsht=Tv+Tm
TV – czas pomocniczy, traktujmy go jak w wersji podstawowej (na podstawie wyników ćwiczeń),
Telewizja=0,57 min
Zatem czas jednostkowy operacji będzie wynosić:
Tsht=0,57+1,185=1,755 min
Ponieważ w jednej operacji obrabiane są jednocześnie 2 przedmioty, czas wykonania w przeliczeniu na 1 przedmiot będzie wynosić:
Tszt1 = Tszt/2
Tsht1 = 1,755/2 = 0,878 min
Kolejność opracowania (algorytm projektowania) procesu technologicznego.
1. Badanie specyfikacji technicznych i wybór typu oraz formę organizacyjną proces produkcji.
2. Dobór metod obróbki wykańczającej, które ostatecznie kształtują jakość narzędzia dla każdej powierzchni.
3. Dobór przedmiotu obrabianego, który w pełni zapewnia ekonomiczną produkcję narzędzi w zadanych lub wybranych warunkach produkcyjnych.
4. Porównanie kształtu, wielkości i jakości przedmiotu obrabianego z gotowym narzędziem oraz określenie charakteru pośrednich rodzajów obróbki: toczenie, frezowanie, wiercenie itp.
5. Opracowanie ścieżki technologicznej tj. sekwencje wszystkich rodzajów przetwarzania poprzez przejścia.
6. Dobór podstaw technologicznych. Wymagania dla nich są takie same jak w ogólnej inżynierii mechanicznej: dążenie do jedności podstaw projektowych, technologicznych i pomiarowych, a także ich stałości, tj. niezmienność podczas wykonywania różnych operacji technologicznych. Dobór podstawowych podstaw obróbki zgrubnej, które pozwalają na prawidłowe zorientowanie przedmiotu do obróbki z wymaganą dokładnością głównych baz technologicznych.
7. Dobór urządzeń technologicznych i akcesoriów.
8. Rozwój technologii szlaków.
9. Opracowanie technologii eksploatacji dla warunków produkcji seryjnej i masowej:
§ a) obliczanie naddatków i tolerancji eksploatacyjnych;
§ b) określenie wielkości i kształtu przedmiotu obrabianego;
§ c) standaryzacja operacji technologicznych.
10. Porównanie efektywności ekonomicznej kilku wariantów procesu technologicznego i wybór optymalnego.
11. Ostateczna rewizja wybranej opcji technologicznej. Opracowanie szczegółowych kart eksploatacyjnych obróbki mechanicznej, cieplnej, chemiczno-termicznej, spawania, lutowania itp. oraz kart kontroli technicznej.