Budowa domu z betonu drzewnego (bloczki arbolitowe) - technologia budowy, od fundamentu po dach. Prefabrykowane podłogi monolityczne z betonu drzewnego: montaż, zalety, wady Żelbetowe płyty podłogowe w domu z betonu drzewnego
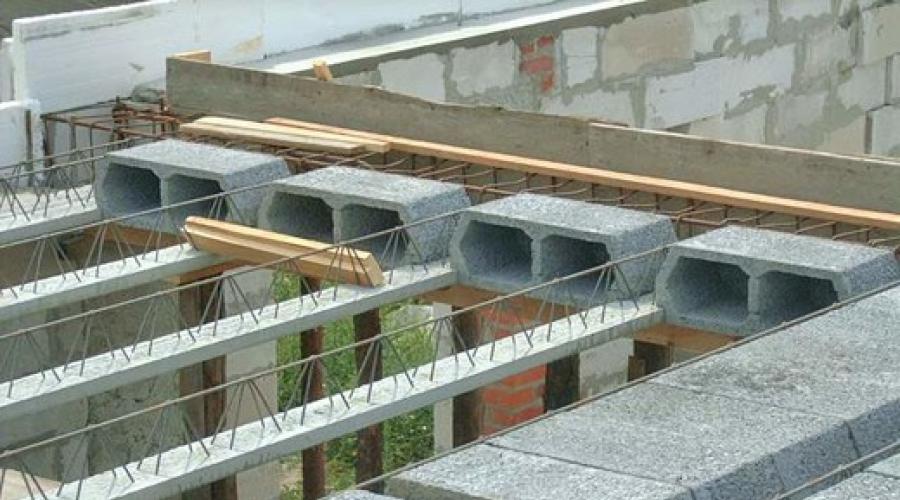
Prefabrykowany monolit (sufit)
Pomimo rozwoju technologii budowlanych we wszystkich kierunkach, konstrukcja podłóg nadal pozostaje konserwatywna, tam gdzie są one najczęściej stosowane tradycyjne metody, uparcie ignorując postępowe rozwiązania.
Montaż podłóg jest pracochłonnym i kosztownym zadaniem. W kosztorysy budowlane do udziału posadzki betonowe redukcja kosztów nawet o 20%.
Technologia prefabrykatów monolitycznych jest sprawdzona w praktyce w krajach europejskich od 20 lat. Ta sama zasada montażu tę technologię może wymagać użycia różnych materiałów.
1. Drewniana deska szalunkowa
2. Pionowy wspornik drewniany
3. Ściana nośna budynku
4,5. Blok ścienny do budowy
6. Warstwa betonu (300-500 mm)
7. Płaska konstrukcja wzmacniająca łączona w formie „siatki” (zbrojenie D-6, komórka 200x200 mm.)
8. Kaseta blokowa / materiał wypełniający
9. Wolumetryczna konstrukcja wzmacniająca łączona na zasadzie „kwadratu” (zbrojenie D-12)
10. Betonowe wypełnienie przestrzeni wzmocnionej międzyblokami
Prefabrykowane stropy monolityczne z betonu drzewnego opierają się na ogólnie przyjętych zasadach technologii prefabrykatów monolitycznych,
jednocześnie posiadają elementy udoskonaleń mających na celu uproszczenie montażu i poprawę jakości efektu końcowego.
1. Zastosowanie gotowych specjalistycznych konstrukcji metalowych wykonanych w formie „kratownic” z dodatkowymi usztywnieniami, jest wielokrotnie lepszy od objętościowych konstrukcji wzmacniających łączonych przez pracowników na budowie, zarówno pod względem szybkości i łatwości montażu, jak i pod względem właściwości wytrzymałościowych. Tak więc jedna taka konstrukcja, o maksymalnej długości 11,7 m, była podparta tylko w dwóch miejscach skrajne punkty, z łatwością utrzymuje ciężar osoby dorosłej bez widocznych oznak ugięcia.
Zalety konstrukcji metalowych SPAIT w porównaniu z powszechnymi analogami europejskimi:
- lekka waga - metalowa konstrukcja ma 11,7 m długości i waży zaledwie 44 kg.
(dla porównania 6 belka metrowa dla prefabrykowanego monolitu Teriva (Polska) waży 72 kg., 8-metrowa belka SerboCeramika (Serbia) - 68 kg.)
- łatwość instalacji , transport i użytkowanie - Każdemu projektowi można łatwo nadać wymaganą długość zarówno podczas transportu, jak i już na miejscu
(cięcie, spawanie, wiązanie)
- prędkość instalacji - montaż podłóg z wykorzystaniem gotowych konstrukcji metalowych znacznie oszczędza czas i koszty pracy podczas instalacji
- niezawodność - konstrukcje metalowe, dzięki ich cechy konstrukcyjne(w formie „farmy”), są lżejsze(ze względu na użycie mniejszej ilości
ilość metalu), a jednocześnie bardziej trwałe niż powszechnie stosowane metody dziania wolumetrycznej struktury wzmacniającej (w kształcie „kwadratu”)
- efektywność
2. Zastosowanie wkładek blokowych z arbolitu jako materiału wypełniającego pozwala stworzyć nie tylko niesamowicie lekką i mocną podłogę, ale także o najwyższych właściwościach dźwiękochłonnych i termoizolacyjnych, przewyższających swoimi właściwościami znane zagraniczne analogi.
Charakterystyka często żebrowanej prefabrykowanej podłogi monolitycznej
Jest to często żebrowany sufit składający się z konstrukcje żelbetowe(według rodzaju kratownic) i bloczków z betonu drzewnego umieszczonych pomiędzy nimi. Długość konstrukcji może osiągnąć 11,7 m, a waga metr liniowy konstrukcja wynosi 3,8 kg. Konstrukcje podłogowe mają szerokość 100 mm. i są instalowane w odległości 650 mm. od siebie i w tej przestrzeni pasują bloki arbolitu, ważący około 7 kg. Zaleca się ułożyć pod konstrukcjami dwie płyty pokryte polietylenem (nieobrzynane), które będą służyć jako szalunek dla konstrukcji metalowych, a także punkty podparcia do ułożenia wykładzin z bloczków drewniano-betonowych. Aby deski szalunkowe nie osunęły się podczas betonowania posadzki, zaleca się montaż ich pod nimi w kilku miejscach. posty wsparcia(podpory drewniane montuje się w odległości od 1 m do 2 m, w zależności od grubości deski szalunkowej). Umieszczane na konstrukcjach i blokach siatka metalowa, stopień 200x200 mm. (pręt D 6 mm) i przeprowadza się betonowanie, a mieszaninę betonową zagęszcza się za pomocą wibracji, dzięki czemu konstrukcja stropu jest zwarta i pozbawiona porów. Przyjmuje się, że klasa betonu jest nie niższa niż B-25. Grubość beton monolityczny nad powierzchnią bloczków wynosi 30 mm, a całkowita wysokość sufitu wynosi 200 mm. Po osiągnięciu przez beton 100% wytrzymałości posadzka będzie w stanie wytrzymać obciążenie do 670 kg/m2. bez ciężaru własnego, dla porównania: płyty żelbetowe mają podobny wskaźnik 400 - 430 kg/m2, monolit 200 - 250 kg/m2.
Zalety prefabrykowanych podłóg monolitycznych:
Lekka(czyli 1 m2 podłogi (łącznie z wierzchnią warstwą betonu) waży około 260 kg, zaś 1 m2 żelbetowej płyty podłogowej waży około 380 kg. W efekcie pokrywając powierzchnię 200 m2) m2 z podłogą, oszczędzasz na wadze - 24 tony!).
Nie ma potrzeby stosowania dźwigu samochodowego(sufit składany jest z pojedynczych, drobnogabarytowych elementów. Charakterystyczną cechą jest to, że są na tyle lekkie, że do ich montażu nie jest potrzebny dźwig – montuje się je ręcznie. Zmontowane w ten sposób elementy sufitu można zamontować od razu po dostarczeniu na plac budowy , mocując je do ścian i tworząc niezbędny sufit).
Do wyrównania podłoża nie jest wymagana wylewka(przy montażu podgrzewanej podłogi jest to szczególnie ważne, ponieważ można ją układać bezpośrednio na suficie).
Podłogi z łatwością zastąpią drewniane i osłabione podłogi w istniejących domach(niewielkie wymiary elementów kompozytowych podłogi umożliwiają pracę z nią w trudno dostępne miejsca).
Łatwa konstrukcja podłóg w pomieszczeniach z złożone kształty- wykusze, gzymsy, otwory (na schody) itp.
Zapewnienie nośności podłóg do 1000 kg/m2. (biorąc pod uwagę własną wagę).
Najwyższy poziom ochrony termicznej i izolacji akustycznej w budynku(podłogi składają się prawie w całości z bloczków drewniano-betonowych, co oznacza, że nie wymagają izolacji ani izolacji akustycznej).
Możliwość modyfikacji konstrukcji podłóg na placu budowy: przyciąć, skrócić, nadać wymagany kształt.
Zastosowanie konstrukcji kratownicowych do montażu potężnych zworek nośnych(pod przegrody nośne Zainstalowane są 2 konstrukcje, które zapewniają niezbędne nośność sufity).
Oszczędność o 20-25% kosztów w porównaniu do podłóg wykonanych z płyty żelbetowe i o 35-40% - w porównaniu z monolitem.
Znaczące oszczędności przy dostawie(ze względu na mały całkowite wymiary sekcje belek, istnieje możliwość dostawy budowa do 250 mkw. SMP z jedną maszyną).
Biorąc zatem pod uwagę wszystkie materiały, robociznę i koszty użytkowania ciężkiego sprzętu
Prefabrykowane podłogi monolityczne z arbolitu w jeden i pół razy tańsze od podłóg z płyt żelbetowych
i prawie w dwa razy tańsze niż podłogi monolityczne.
Prefabrykowany monolit (fundament)
Warunkowe połączenie zasad montażu często żebrowanej prefabrykowanej podłogi monolitycznej i zasady izolowanej szwedzkiej płyty fundamentowej
umożliwiło opracowanie ciepłej prefabrykowanej monolitycznej płyty fundamentowej (FSMP).
Podobieństwa i zalety FSMP w porównaniu z USP:
1. Niezawodny - podstawą FSMP są bloki arbolitu, których właściwości wytrzymałościowe znacznie przewyższają wytrzymałość styropianu.
Grubość FSMP wynosi 30 cm. Może służyć jako pełnoprawny fundament dla budynków o wysokości do 3 pięter, doskonały fundament dla domów wykonanych z dowolnych materiałów od światła.
rama do cegły.
2. Doskonałe właściwości oszczędzania ciepła - zapewnia materiał o doskonałych właściwościach termoizolacyjnych - beton drzewny, równomiernie rozprowadzony na całej powierzchni
lokale mieszkalne przyszłego budynku.
3. Najwyższe właściwości dźwiękochłonne (dobrze tłumi wibracje).
4. Zintegrowana komunikacja - możliwość podłączenia wszystkich systemów komunikacyjnych za pośrednictwem FSMP, w tym kanalizacji, wody, prądu, układania rur wodociągowych
instalacja grzewcza (pozostaje tylko podłączyć instalację wodno-kanalizacyjną i wykonać okablowanie).
5. Całkowicie przyjazne dla środowiska - beton drzewny (w przeciwieństwie do EPPS, który jest tradycyjnie stosowany w ramach USP) jest wykonany z całkowicie bezpiecznego dla
surowce ludzkie (drewno, cement, siarczan glinu – stosowane do oczyszczania wody pitnej)
5. Nieobecność szwy montażowe - po zakończeniu instalacji powierzchnia FSMP jest absolutnie gładka powierzchnia, nadaje się do stosowania jako baza do
wykończeniowy posadzka(nie jest wymagana wylewka wykończeniowa).
6. Absolutna biostabilność - FSMP zawiera materiały, które nie są podatne na gnicie ani działanie pleśni.
7. Bezpieczeństwo przeciwpożarowe - beton drzewny nie jest palny.
8. Prostota i wysoka prędkość instalacja - koszty robocizny potrzebnej do montażu i wylania 200 m2. powierzchniowy FSMP to 3 osoby; okres montażu i napełniania FSMP
wynosi 2-3 dni.
9. Brak szeroko zakrojonych prac wykopaliskowych.
10. Nie trzeba używać ciężkich specjalny sprzęt (z wyjątkiem pompy do betonu).
11. Ekonomiczny - najdroższym składnikiem każdego fundamentu jest beton, którego zawartość w FSMP jest ograniczona do minimum (oszczędności betonu w FSMP będą
około 20-30% w stosunku do objętości betonu potrzebnego do wylania podkład listwowy; jednocześnie FSMP jest nie tylko podstawą, ale jednocześnie
pełne pokrycie podłogi).
Algorytm pracy podczas instalacji FSMP:
1) Wykopy- górny jest usunięty żyzna warstwa glebę, a dno wykopu musi być zrównane z horyzontem.
2) Podłogi z geowłókniny- dobrze radzi sobie z funkcją warstwy oddzielającej. Podczas pracy nie gnije i nie zapada się.
3) Budowa poduszki z piasku- polega na wypełnieniu poduszki piaskowej i jej zagęszczeniu. Zaleca się prasowanie mokrego piasku warstwami, aby uzyskać maksymalną gęstość poduszki. Grubość warstwy piasku wynosi około 15 cm.
4) Instalacja system drenażowy i układanie komunikacji(woda, kanalizacja, prąd) - przy układaniu sieci kanalizacyjnej należy przestrzegać następującej kolejności: zagęszczenie poduszki piaskowej, wykopanie piasku pod ułożenie kanalizacji, zasypanie piasku, rozsypanie go, ponowne ogólne zagęszczenie.
5) Podłoże żwirowe- podobnie jak poduszka z piasku, jej grubość również wynosi około 15 cm. Kruszony kamień jest dokładnie wyrównywany na całej powierzchni przyszłego fundamentu, wyrównywany na wysokość (pręty wzmacniające ze znakami umieszczonymi wcześniej w grubości piasku i poduszka żwirowa może służyć jako latarnie morskie) i staranowana.
6) Montaż organu FSMP polega na ułożeniu konstrukcji metalowych i bloczków drewniano-betonowych zgodnie z projektem - najlepiej zacząć od bloczków szalunkowych (po obwodzie), ułożonych na końcu (wysokość 300 mm) i skręconych ze sobą (żwir/bloczek, bloczek/bloczek) za pomocą zaprawa murarska; wszystkie konstrukcje metalowe muszą być bezpiecznie ze sobą połączone (wiązanie i spawanie nie ma znaczenia).
7) Rozmieszczenie wyjść systemów łączności(woda, kanalizacja, prąd) - pustak z betonu drzewnego jest łatwy w obróbce (przetarty, cięty), dzięki czemu aranżacja wyjść nie wymaga dużo czasu i wysiłku.
8) Układ siatki murarskiej
9) Instalacja ogrzewania ciepłej wody- wykonane zgodnie z projektem.
10) Układ siatki murarskiej(200x200mm., D6) - siatkę należy ułożyć z lekkim zakładem (wystarczy jedna komórka), a także w niektórych miejscach przywiązać drutem do konstrukcji metalowych (upewniając się, że siatka nie przemieszcza się).
11) Wypełnienie betonem (gatunek nie mniejszy niż M25)- zastosowanie pompy do betonu i listwy wibracyjnej przyspieszy i uprości proces, a także poprawi jakość wykonania FSMP.
Po całkowicie suchy FSMP może rozpocząć układanie ścian przyszłego budynku!
Prefabrykowany strop monolityczny ma za zadanie podzielić budynek na kondygnacje i wygłuszyć pomieszczenia pomiędzy sobą. Jako materiały wypełniające stosuje się beton drzewny, beton piankowy i beton komórkowy. Ale teraz porozmawiamy o podłogach z betonu drzewnego.
Opis
Innowacja w technologie budowlane uprościć proces budowy. Ale układ sufitów międzywarstwowych nie uległ wielu zmianom. Podłogi Arbolite nie są dziś nowym produktem stosowanym przy budowie budynków. Montaż podłóg można wykonać bez specjalistycznego sprzętu. Technologie instalacyjne we wszystkich krajach nie różnią się od siebie. Prefabrykowane podłogi monolityczne (arbolit jako materiał wypełniający) mają szereg zalet.
Schemat montażu podłóg betonowych drewnopodobnych: na szalunkach drewniane tablice, które są instalowane równolegle do siebie, układane są bloczki z betonu drzewnego. Siatka wzmacniająca jest układana na blokach. Ostatnim etapem montażu jest betonowanie całej konstrukcji.
Płyty podłogowe Arbolite składają się ze zbrojenia sprężonego, warstwy arbolitu i warstw betonu. W ten sposób postanowiliśmy ograniczyć konsumpcję mieszanka betonowa i zwiększyć nośność płyt z betonu drzewnego. Roztwór mieszanki betonowej przygotowuje się z cementu klasy M400 i wyższej, a beton drzewny przyjmuje się nie niżej niż klasa B 3,5.
Instalacja
Wiele firmy budowlane oferta gotowe ramki, w które wkładane są bloczki z betonu drzewnego. Często są to stropy żebrowe składające się z konstrukcji żelbetowych. Długość takich produktów może osiągnąć 12 m, a szerokość - 100 mm. Krok między tymi konstrukcjami sięga 650 mm. Wolna przestrzeń wypełnione bloczkami z betonu drzewnego. Pod ramami układane są drewniane deski, które służą jako punkt odniesienia do umieszczania produktów blokowych. Aby zapewnić sztywność konstrukcji, co 2 m montuje się podpory. Następnie płyty stropowe z betonu drzewnego wzmacnia się siatką wzmacniającą wykonaną z drutu metalowego o średnicy 5 mm. Na całą konstrukcję układana jest mieszanka betonowa, którą zagęszcza się zagęszczarką wibracyjną. Grubość tej warstwy jest nie mniejsza niż 30 mm, ale nie większa niż 50 mm.
Zamiast belki żelbetowe czasami używa się drewnianych Dwuteowniki. Są wykonane z Płyty OSB. Jeśli kupisz gotowe belki, nie wymagają one dalszej obróbki. Podłoga z betonu drzewnego drewniane belki jest najtańszą opcją. Jest lżejszy od żelbetu i ma lepszą przewodność cieplną.
Belki drewniane charakteryzują się wytrzymałością na zginanie i skręcanie. Parametry belki można łatwo obliczyć samodzielnie. Aby to zrobić, musisz przyjąć stosunek wysokości i szerokości w proporcji 7:5. Zapobiegnie to ugięciom i deformacjom. Aby całkowicie wyeliminować osiadanie belki od spodu drewnianej belki, użyj strugarki elektrycznej, aby usunąć ilość równą maksymalnej dopuszczalna wartość ugięcie.
Montaż sufitów na drewnianych belkach nie różni się od innych opcji.
Deski montuje się w odstępach nie większych niż 600 mm; po opuszczeniu ściany końce belek są owinięte hydroizolacją. Następnie układane są bloczki z betonu drzewnego lub płyta z betonu litego. W pierwszym przypadku konstrukcja jest wzmocniona i wypełniona mieszanką betonową. Płyta arbolitowa tego nie potrzebuje.
Zalety
- Umiejętność planowania złożonego Konstruktywne decyzje Budynki. Prefabrykowane płyty monolityczne umożliwiają optymalne pokrycie konstrukcji o skomplikowanych konfiguracjach. Nie ma potrzeby zaczynać od ogólnie przyjętych rozmiarów płyt, układać je i układać obszary monolityczne.
- Podłogi monolityczne wytrzymują duże obciążenia. Możesz to obliczyć sam. Na podłogę stosuje się bloczki drewnobetonowe klasy B 3,5 o gęstości 800 kg/m3. Wylewka cementowa przejmuje siły ściskające, a zbrojenie siły rozciągające. Razem mają gęstość ponad 200 kg/m3.
- Prefabrykowana podłoga monolityczna nie wymaga montażu osobnego pasa pancernego. Betonowanie konstrukcji z belkami, zbrojeniem i drewnem betonowym samo w sobie stanowi pas pancerny. Wylewka betonowa spełnia te same funkcje, co powinna spełniać podłoga zbrojona: chroni konstrukcję przed pęknięciami w wyniku pęcznienia gleby.
- Waga i gabaryty konstrukcji pozwalają na przewiezienie jednym pojazdem do 200 m2 podłóg.
- Montaż i aranżację podłóg można wykonać bez użycia dodatkowego sprzętu. Ciężar konstrukcji pozwala na ręczne wykonanie wszelkich prac budowlanych.
- W przeciwieństwie do płyt żelbetowych, monolityczna podłoga arbolitowa wymaga mniejszego zużycia betonu i zbrojenia.
- Beton drzewny ma wysokie właściwości termoizolacyjne i dźwiękochłonne.
- Prefabrykowane podłogi monolityczne są tańsze niż inne rodzaje podłóg. I nie tylko sam materiał, ale także możliwość montażu bez drogiego sprzętu, również zmniejsza koszty budowy.
- Możliwość wykonania podłóg betonowych z drewna własnymi rękami.
Wady
Każdy materiał ma swoje wady. Arbolit bardzo boi się wilgoci. Jednorazowa wilgoć mu nie zagraża, ale ciągłe narażenie na opady atmosferyczne niszczy materiał.
Palność betonu drzewnego
Wielu producentów twierdzi, że materiał nie pali się, ale kiedy wysokie temperatury zrębki zaczynają się tlić.
Po pożarze sufitu nie da się odnowić. Wielu producentów nie przestrzega sumiennie wszystkich wymagań technologii podczas produkcji. Niedostateczna ilość wapna w drewnie betonowym prowadzi do gnicia trociny. Niestandardowe rozmiary bloków można również uznać za wadę. Występują odchylenia w wysokości i szerokości do 2 cm.
Prefabrykowaną monolityczną podłogę arbolitową należy wykonać zgodnie ze wszystkimi zasadami technologii montażu. Wewnątrz takiego sufitu bloki arbolitu mogą zacząć gnić. A wylewanie betonu ukrywa drewniany beton, utrudniając zaobserwowanie tego procesu, dopóki podłoga nie zacznie się zapadać.
Domy z betonu drzewnego
Jeśli projekt budynku zakłada konstrukcję z betonu drzewnego, pojawia się pytanie: jakiego rodzaju podłogę zastosować?
Drewniany sufity międzykondygnacyjne w domu wykonanym z drewna beton można stosować tylko wtedy, gdy drewno jest traktowane specjalnymi środkami.
Dzięki temu belki nie będą gnić ani zapadać się. Warto zadbać także o bezpieczeństwo przeciwpożarowe.
Dom z drewna betonowego: jak pokryć pierwsze piętro? Lepiej jest używać lekkich materiałów, które są lekkie, ale wytrzymują znaczne obciążenia. Istnieją żebrowane płyty stropowe z betonu drzewnego z nośnymi krawędziami bocznymi. Nadają konstrukcji dodatkową sztywność i stabilność.
Niezawodna i trwała podłoga do domu z betonu komórkowego spełniająca ogólnie przyjęte standardy, możesz zrobić trzy rodzaje- jest to płyta wykonana z metalu lub belek, a także monolityczny rodzaj podłogi.
Co to jest podłoga monolityczna?
Najpierw zrozumiemy właściwości betonu komórkowego i zasady budowy domów z tego materiału.
Bloczki z betonu komórkowego produkowane są z mieszaniny wapna, cementu i piasku, do której dodaje się substancję chemiczną na bazie aluminium, czyli kompozycję pieniącą. Beton komórkowy wytwarzany jest zarówno metodą autoklawową poprzez aktywne oddziaływanie na roztwór wlewany do form blokowych za pomocą pary i ciśnienia, jak i metodą bezautoklawową. Od tego zależy stopniowanie jego jakości i ceny.
Taka bryła waży stosunkowo niewiele, dobrze zatrzymuje ciepło, jest także ognioodporna i przyjazna dla środowiska, co pozwala na budowę domu w możliwie najkrótszym czasie.
Beton komórkowy wymaga specjalnego podejścia, ponieważ struktura komórkowa bloczków minimalizuje właściwości wytrzymałościowe, a strop jest konstruowany z uwzględnieniem tej okoliczności.
Konieczne jest, aby ciężar konstrukcji dociskającej do podpór nośnych był kompensowany poprzez zapewnienie sztywności ścian nośnych. Okucia umieszczone są na dole, na górze i pośrodku, zapewniając ochronę bloczki z betonu komórkowego przed efektem wypychania z sufitu. Sam sufit jest również uzupełniony wzmocnieniem.
Sekcje ścian nośnych należy dokładnie zmierzyć pod kątem odchyleń od ściśle poziomej linii, ale jeśli taki problem wystąpi, wówczas gazobeton ułatwia skorygowanie sytuacji poprzez spiłowanie materiału.
Płyta monolityczna
Monolityczny strop w domu z betonu komórkowego jest układany na belkach różne rozmiary sekcje na całej powierzchni. Najważniejszą jego częścią jest rama pełniąca funkcję wzmacniającą. Pręty metalowe o małym przekroju mocowane są drutem w jeden system wzmacniający. To właśnie wytrzyma największe obciążenie, nadając betonowi dosłownie „żelazną wytrzymałość”.
Beton zamówiony gotowa wersja w firmach specjalizujących się w sprzedaży materiałów budowlanych lub zrób to sam. Na produkcja własna stosowane są mieszalniki o małych wymiarach, co obniża jakość projektu, ponieważ istnieje duże ryzyko mieszania objętości betonu o różnych proporcjach składu, co spowoduje niejednorodność wylewania i zmniejszy wytrzymałość.
Uwaga!
Dlatego przy tak odpowiedzialnym zadaniu wypełnienie niskiej jakości naraża życie ludzi nie eksperymentuj ręcznie przygotowanie rozwiązania.
Prefabrykowana podłoga monolityczna
Można zastosować zarówno metodę krycia monolitycznego, jak i metodę krycia betonu komórkowego na zasadzie prefabrykatu. Jest to podtyp metody monolitycznej. Nadaje się do budynku składającego się z jednego lub dwóch pięter. Przestrzeń międzykondygnacyjna jest „zszyta belkami” w odstępach co 60 cm. Układa się na nich styropian lub bloczki keramzytowe, które pełnią zarówno funkcję szalunku, jak i części podłogi. wylać na wierzch zaprawa betonowa, wzmocniony zbrojeniem i pozostawiony do całkowitego wyschnięcia.

Gotowe płyty
Odpowiedni, jeśli chcesz wydać dużo pieniędzy, ponieważ Zarówno same płyty, jak i ich montaż są droższe, wymagają wypożyczenia sprzętu do podnoszenia. Pod względem ceny sytuacja staje się mniej uciążliwa, jeśli w pobliżu znajduje się fabryka produkująca takie płyty, ponieważ można zamówić bezpośrednio u producenta, a budżet na dostawę będzie całkiem do zaakceptowania. W takim przypadku projekt będzie kosztować nawet mniej niż monolityczny.
W jakich przypadkach łączone są metody monolityczne i prefabrykowane-monolityczne?
Zachodzić na siebie prefabrykowany typ monolityczny określa określone przepisy dotyczące parametrów samego budynku w zakresie długości i szerokości oraz umiejscowienia ścian nośnych.
To jest podyktowane standardowe rozmiary płyt oraz fakt, że płyty wymagają podparcia na konstrukcjach wsporczych. Oznacza to, że konieczne jest dostosowanie planu domu i układu pomieszczeń do standardowych wymiarów płyt kanałowych.
Podparcie stanowią przeciwległe strony płyt na ścianach nośnych. Niedopuszczalne jest układanie płyt na trzech ścianach, ponieważ ta okoliczność nieprawidłowo rozłoży obciążenie na fundament domu, co w przypadku betonu komórkowego jest kategorycznie niedopuszczalne.
W obszarach zakładkowych, gdzie nie ma możliwości ułożenia płyt, budowane są fragmenty monolityczne. Zwykle dzieje się tak ze względu na zmniejszoną powierzchnię domu lub w miejscach, w których znajdują się przejścia kopalniane system wentylacji z łazienki lub kuchni.

Monolityczny sposób tworzenia przegrody międzykondygnacyjnej jest wygodniejszy i wielofunkcyjny, nie ogranicza planowania pomieszczeń i stosunku długości do szerokości budynku.
Sufit zrób to sam
Materiał, narzędzia i technika
- Do pracy należy zamówić mieszarki z betonem, pompę do betonu (w przypadku konieczności podniesienia zaprawy na wysokość) oraz wibrator budowlany do zaprawy. Ponadto, jeśli mieszanka betonowa nie zostanie zakupiona, ale zostanie wykonana samodzielnie, użyj betoniarki.
- Do zbrojenia należy kupić specjalne metalowe pręty i drut wiążący, a do szalunków - drewniana belka, desek i sklejki odpornej na wilgoć.
- Do napełniania będziesz potrzebować gotowy beton lub jego zwykłe składniki w postaci cementu, wody, oczyszczonego piasku i drobnego kruszonego kamienia 5-20 mm.
Przejście od procesu wznoszenia ścian do wykonania płyty podłogowej następuje na etapie całkowitego doprowadzenia ich do zamierzonej wysokości. Zaczynają od szalunków.
Jak wykonać szalunki?
Najpierw wykonują szalunki, które wyglądają ogromna forma wanny do późniejszego napełniania zaprawa cementowa . Jest zbudowany z odpornych na wilgoć arkuszy sklejki i pionowo zamontowanych elementów nośnych.

Jak elementy wspierające Zamiast drewnianych belek można zastosować specjalne teleskopowe metalowe stojaki rurowe. Zamiast arkuszy sklejki można wziąć deski, układając je według tej samej zasady.
Podpory szalunku rozmieszczane są w oparciu o wytrzymałość, która utrzyma nie tylko jego ciężar, ale także wylany tam beton w połączeniu z ciężarem elementu zbrojeniowego.

Tak więc sekwencja prac nad szalunkiem dla monolitu:
- Budowa podpór. Tutaj musisz bardzo dokładnie sprawdzić poziom, ponieważ nawet niewielkie odchylenie wysokości będzie miało szkodliwy wpływ na siłę. Każdy regał przyjmuje obciążenie od minimum 300 kg do optymalnie pół tony.
- Ze ścian wykonano wcięcie 20-25 cm, między stojakami zachowano metrową odległość.
- Układanie belek w poprzek proponowanej płyty podłogowej są mocowane do ścian i wszyte w miejscach styku ze stojakami, aby zapewnić maksymalną stabilność i stabilność podczas zalewania i suszenia.
- Rozmiar belki dobiera się tak, aby masa betonowa nie powodowała ugięcia w dnie szalunku powyżej dopuszczalnej miary 1/150 rozpiętości.
- Na stworzonej podstawie ułożyć deski lub arkusze sklejki, które są dodatkowo izolowane folią. Szczeliny między deskami można również spienić, aby zapewnić większą niezawodność.
- Na tym samym etapie układane są rury do instalacji elektrycznej i wentylacji.
- Szalunek jest gotowy i można przystąpić do budowy siatki wzmacniającej.
Wymagania dotyczące armatury
- Weź metalowe pręty o przekroju od 8 mm do 10 mm.
- Tworzą siatkę, mocując je drutem o przekroju nie większym niż półtora milimetra i nie mniejszym niż 1,2 mm.
- Zbrojenie umieszcza się na dwóch poziomach - na górnym poziomie, tworząc efekt rozciągania, i na dolnym, działając na ściskanie.
- Pomiędzy siatką zbrojeniową a szalunkiem wykonuje się wgłębienia o wielkości 20-25 mm w celu utrzymania optymalna grubość warstwę betonu w tych obszarach nakładania się.
- Górna warstwa zbrojenia powinna znajdować się w odległości 100 mm od dolnej.
- Powstałą szczelinę wyposaża się w obejmy typu dystansowego z nóżkami podporowymi.
- Pręt o przekroju 10 mm można w razie potrzeby zwiększyć o nie więcej niż 480 mm.
- Pręty wzmacniające w poziomach mocuje się zgodnie z zasadą szachownicy.

Jak wzmocnić
- Dolna część zbrojenia jest ułożona wzdłużnie, a na niej zamontowany jest poprzeczny rząd prętów o rozstawie dwóch metrów.
- Trzeci rząd jest ponownie układany wzdłużnie, przylegając do stopnia metrowego.
- Weź drut o wystarczającej miękkości i przejdź przez wszystkie przecięcia prętów, ostrożnie łącząc je ze sobą.
- Plastikowe obejmy mocuje się do dolnej warstwy zbrojenia pod kątem 15° w odległości metrowej od siebie.
- Wypełnij więc dolną warstwę siatką wzmacniającą i rozpocznij tworzenie górny poziom dokładnie ta sama zasada.
- Co 40 cm krawędzie obu poziomów mocowane są specjalnymi łącznikami.
Wylewanie betonu
Wymagania dotyczące wytrzymałości, jakości, grubości:
- Dopuszczalne jest stosowanie wyłącznie betonu wysokiej jakości, zwykle przyjmuje się M200 lub więcej wysokiej jakości materiały. Jakość betonu jest kluczem do wymaganej wytrzymałości podłogi.
- Grubość płyty oblicza się od minimum 15 cm do maksymalnie 30 cm.
- Nie należy wypełniać w temperaturze poniżej +5°C. Jeśli sytuacja nie pozostawia wyboru, kompozycję uzupełnia się specjalnymi dodatkami, a roztwór podgrzewa się przed użyciem.

- Zaznacz wysokość napełnienia.
- Sam zabieg odbywa się za jednym razem. Pełną objętość betonu wlewa się w sposób ciągły do formy za pomocą pompy do betonu. W przeciwnym razie, jeśli zostanie wylany w kilku etapach, sufit straci wytrzymałość.
- Beton wyrównuje się do kształtu szalunku.
- Koniecznie użyj wibratora budowlanego, aby usunąć pęcherzyki powietrza ze składu. Nie obejdzie się bez pracy wibracyjnej. Ciężar samego betonu nie jest wystarczający do wymaganego zagęszczenia; konieczne jest poddanie kompozycji wibracjom, ponieważ tylko w tym przypadku zostanie ona ściśnięta do wymaganego standardu i przylega do siatki wzmacniającej.
Aby w pełni stwardnieć i osiągnąć maksymalną wytrzymałość, beton suszy się przez 27-28 dni.
Po całkowitym stwardnieniu prace budowlane zostają wznowione.
Zalety i wady tego rodzaju nakładania się
Plusy:
- Funkcja nośna jest wielokrotnie wyższa pod względem jakości niż w przypadku stosowania belek.
- Swoboda w planowaniu budynku, zarówno pod względem proporcji, jak i kształtu budynku.
- Trwały rodzaj posadzki jest dobrze dostosowany do specyfiki betonu komórkowego.
Z minusów:
- Zarówno sama praca, jak i proces suszenia zajmują dużo czasu.
- Potrzebujesz specjalnego sprzętu i wyposażenia technicznego.
- Do określenia parametrów płyty monolitycznej wymagane jest dokładne obliczenie obciążenia.
- Koszt projektu będzie znacznie wyższy niż przy użyciu drewna.
- Aby wzmocnić górną część ścian, aby zrekompensować obciążenie płyty, ułożony jest pas wzmacniający, ciągła konstrukcja wzdłuż całego obrysu budynku.
- Aby sprawdzić wyschnięcie betonu, należy na wierzch położyć kawałek papy i sprawdzić po kilku godzinach. Jeśli materiał z wewnętrznej części zostanie zwilżony i ulegnie kondensacji, monolit nie jest jeszcze gotowy, ale jeśli jest suchy, utwardzanie jest zakończone i pomyślne.
Po zapoznaniu się ze wszystkimi niuansami budowy monolitycznej płyty podłogowej dla domu z betonu komórkowego, możesz wybrać zrównoważone podejście do wyboru metody pokrycia dachowego, rozważając zalety i wady, szacując swoje możliwości pod względem czasu i budżetu.
Przydatne wideo
Zobacz jak działa ten proces. Specjalista powie Ci, na co powinieneś zwrócić uwagę:
ARBOLIT- jest materiałem budowlanym, jest rodzajem Lekki beton. Skład betonu drzewnego obejmuje cement M500; woda; zrębki drzewne o określonej wielkości, impregnowane wapnem, siarczanem tlenku glinu lub po prostu leżakowane przez co najmniej miesiąc na dworze(wióry powinny stanowić co najmniej 80-90% całkowitej objętości bloku). Arbolit wytwarzany jest bez użycia piasku. Arbolit jest szeroko stosowany w Rosji do budowy domów, daczy, łaźni, garaży, ale głównie w tych regionach, gdzie jest dużo lasów. W końcu, aby wyprodukować 1 m3 betonu drzewnego, potrzeba 1,3 m3 suchych zrębków drzewnych o rozmiarach określonych przez GOST. Dlatego cała główna produkcja betonu drzewnego w Rosji zlokalizowana jest w regionach bogatych w lasy.
Beton drzewny to materiał wielkoporowaty, który zapewnia doskonałą wymianę powietrza w pomieszczeniach, dzięki czemu mikroklimat w domu jest bardzo komfortowy do zamieszkania;
gęstość betonu drzewnego wynosi 500-600 kg/m3, co pozwala zaoszczędzić na fundamencie;
beton drzewny ma niską przewodność cieplną;
wytrzymałość betonu drzewnego B2 i doskonałe właściwości pod względem wytrzymałości na rozciąganie i zginanie umożliwiają bezproblemowe budowanie domów o wysokości 2-3 pięter i grubości ścian 30-40 cm. W tym przypadku można stosować zarówno podłogi drewniane, jak i żelbetowe;
duży i wygodne rozmiary bloki przyspieszają proces budowy i oszczędzają pieniądze na płacących pracownikach;
pomimo tego, że beton drzewny składa się prawie wyłącznie z wiórów drzewnych, nie gnije i nie jest podatny na infekcje mikroorganizmami i grzybami. Drewno uzyskuje takie właściwości po obróbce, jeśli znajduje się w roztworze wysokiej jakości cementu i dodatków mineralnych.
beton drzewny należy do klasy materiałów ognioodpornych i jest w stanie wytrzymać otwarty ogień w temperaturze co najmniej 1000°C przez 45-90 minut.
Beton drzewny jest odporny na uderzenia i naprężenia mechaniczne, a jednocześnie łatwo się go wierci i piłuje oraz dobrze trzyma elementy złączne.
Ciepło właściwe drewna betonowego jest kilkakrotnie większe niż cegły, dlatego w domach wykonanych z drewna betonowego letni upał Jest chłodno, a w mroźną zimę ściany z betonu drzewnego mogą długo zatrzymywać ciepło.
Beton drzewny jest produkowany zgodnie z aktualnym GOST 19222-84 oraz Instrukcją projektowania, produkcji i użytkowania konstrukcji i wyrobów wykonanych z betonu drzewnego (Zatwierdzone uchwałą Komitet Państwowy ZSRR do Spraw Budowlanych z dnia 4 maja 1982 r. nr 116).
Historia betonu drzewnego
Opracowane i ujednolicone w latach 60-tych. W latach ZSRR zbudowano ponad 100 betoniarni.
Technologia produkcji betonu drzewnego
Do produkcji betonu drzewnego i wyrobów z niego wykonanych stosuje się go następujące materiały:
* spoiwo mineralne (cement portlandzki, cement portlandzki z dodatkami mineralnymi, cement odporny na siarczany - z wyjątkiem pucolanu - zgodnie z GOST 10178 i GOST 22266 w klasach co najmniej 300 - dla termoizolacyjnego betonu drewnianego i 400 - dla konstrukcyjnego betonu drewnianego);
* wypełniacze organiczne (posiekane drewno z odpadów pochodzących z wyrębu, tartaku i obróbki drewna gatunków iglastych (świerk, sosna, jodła) i liściastych (brzoza, osika, buk, topola), ogniska konopne i lniane, posiekane łodygi bawełny i posiekana słoma ryżowa);
* substancje dodatkowe (przyspieszacze utwardzania, wytwornice pary, plastyfikatory, inhibitory korozji stali itp.) zgodnie z GOST 24211;
* woda zgodnie z GOST 23723.
Rodzaje betonu drzewnego
Wyróżnia się następujące rodzaje betonu drzewnego – termoizolacyjny (gęstość od 400 do 500 kg/m3) i konstrukcyjny (gęstość od 500 do 850 kg/m3). Stosowany jest w postaci gotowych pustaków lub płyt budowlanych ściany samonośne lub wewnętrzne przegrody budynków, a także materiał termoizolacyjny i dźwiękochłonny.
Charakterystyka
Przewodność cieplna betonu drzewnego wynosi 0,07-0,17 W/(m·K). Najważniejsza cecha betonu drzewnego, jak każda inna materiał budowlany, to wytrzymałość na ściskanie. Wytrzymałość na ściskanie betonu drzewnego waha się od M5-M10 dla izolacji termicznej do M25-M50, a nawet do M100 dla konstrukcji.
Beton drzewny ma zwiększoną wytrzymałość na zginanie i dość dobrze pochłania fale dźwiękowe.
Beton drzewny nie wspomaga spalania i jest wygodny w obróbce. Typy strukturalne mają wysoką wytrzymałość na zginanie i potrafią przywrócić swój kształt po chwilowym przekroczeniu maksymalnego obciążenia.
Wady betonu drzewnego obejmują zmniejszoną odporność na wilgoć. Zewnętrzna powierzchnia konstrukcji drewniano-betonowych stykająca się z wilgocią atmosferyczną musi posiadać ochronną warstwę wykończeniową. W pomieszczeniach o ścianach z betonu drewniano-betonowego zaleca się utrzymywanie wilgotności powietrza na poziomie nie wyższym niż 75%.
Zastosowanie betonu drzewnego
Arbolit jest używany do konstrukcja monolityczna niska zabudowa mieszkalnych, handlowych i celów przemysłowych, a także w formie bloków.
Pytania i odpowiedzi
Ile bloków potrzeba na łaźnię o wymiarach 2 x 4 metry?
Przybliżone obliczenia dla wanny o wymiarach 2x4 metry (wg wymiarów zewnętrznych)
Obwód budynku (2+4)x2= 12 metrów, grubość muru 20 cm (blok układany na krawędzi)
Przy wysokości ściany 2,4 m od podstawy 12x0,2x2,4 = 5,76 metra sześciennego. minus okna i drzwi.
Przy wysokości ściany 2,1 m od podstawy 12x0,2x2,1 = 5,04 metra sześciennego. minus okna i drzwi.
Jakie rozwiązanie stosuje się do układania bloków arbolitowych?
Układanie bloków arbolitowych odbywa się dalej mieszanka cementowo-piaskowa(CPS). Aby uzyskać większą plastyczność, do mieszaniny można dodać pewną ilość wapna puszystego. Aby uniknąć mostków termicznych, podczas układania można dodać perlit do CPS. W ten sam sposób zamiast perlitu można zastosować trociny, ale będą one wymagały mineralizacji w celu zneutralizowania cukrów.
Czy można użyć bloczków z betonu drzewnego jako fundamentu lub do budowy piwnicy?
Nie zaleca się stosowania betonu drzewnego w fundamencie nie dlatego, że nie wytrzyma obciążeń, ale dlatego, że naturalna wilgotność ziemi jest znacznie wyższa naturalna wilgotność po pierwsze, nawet w czasie deszczu, po drugie, wilgotność ta jest stała, a jeśli występuje również dopływ wody w postaci wody stojącej lub wody gruntowe, wtedy wszystko się pogorszy. Arbolit to materiał o dużej absorpcji wody, czyli tzw. zacznie wchłaniać wodę z gleby i stale odpowiednio materiał będzie miał wysoka wilgotność. Kiedy jednak wilgotność zaczyna znacznie odbiegać od normy, przewodność cieplna drewna betonowego natychmiast wzrasta, a niektóre inne właściwości ściany ulegają pogorszeniu. Dlatego nie jest zalecany do podkładu. W ścianie takie wartości krytyczne Wilgotności nie da się osiągnąć, nawet jeśli podlejesz ją z bransboya w ciągu dnia; wyschnie w ciągu nocy i uwolni nadmiar wody do atmosfery.
Jak wysokie można budować domy z betonu drzewnego?
Arbolit dzieli się na izolację strukturalną i termiczną. Jak sama nazwa wskazuje, buduj budynki za pomocą ściany nośne stojaki z drewna betonowego z betonu konstrukcyjnego drewna. Wytrzymałość bloczków z betonu drzewnego M25 jest wystarczająca do wzniesienia budynku o 2,5 kondygnacji ze stropami wykonanymi z płyt kanałowych.
Czy przy budowie domu można zastosować beton drzewny jako podłogę? płyty kanałowe?
Może być użyte Różne rodzaje wykładziny podłogowe, takie jak płyty kanałowe, sufity międzykondygnacyjne z betonu ekspandowanego, podłóg na drewnianych belkach itp. Aby równomiernie rozłożyć obciążenie na ściany, zaleca się wykonanie pasa pancernego między piętrami.
Czy zamiast stacji mieszania można zastosować zwykłą betoniarkę?
Nie, betoniarki nie są w stanie wyprodukować wysokiej jakości mieszanka drewna i betonu. Przykład tego co dzieje się z betoniarką podczas mieszania betonu drzewnego można zobaczyć w naszej produkcji. Jednocześnie stanowisko mieszania nie tylko miesza mieszaninę, ale dodatkowo rozdrabniając zrębki ślimakiem, doprowadza ją do rozmiaru wymaganego przez GOST.
Beton drzewny jest droższy niż beton piankowy, dlaczego jest lepszy?
Oprócz najlepszych właściwości termoizolacyjne(średnio o 70%), co pozwala na odmowę dodatkowa praca Pod względem izolacyjnym bloczki arbolitowe po przekroczeniu obciążenia, pod wpływem obciążeń udarowych, nie pękają jak pianka, lecz kurczą się, łatwo przywracając swój pierwotny kształt po zdjęciu obciążenia. Ta plastyczność nie tylko oszczędza pieniądze podczas transportu i budowy, ale także chroni dom przed pęknięciami podczas pracy spowodowanymi skurczem, zmianami temperatury i innymi czynnikami. Pod względem odporności na trzęsienia ziemi domy z betonu drzewnego prawie nie mają konkurentów. Budując dom z betonu drzewnego, w przeciwieństwie do piankowego betonu, nie jest wymagane żadne zbrojenie, co również znacznie obniża koszty pracy i materiałów. Sumując wszystkie koszty budowy, dom z betonu drzewnego jest tańszy niż dom z betonu komórkowego. Beton drzewny ma lepszą mrozoodporność (zdolność wytrzymywania wielokrotnego zamrażania i rozmrażania w stanie nasyconym wodą bez oznak zniszczenia lub utraty wytrzymałości), jest bardziej przyjazny dla środowiska itp.
Czy można wyprodukować beton drzewny nie z zrębków, ale z trocin?
Jest to możliwe, beton drzewny wykonany z trocin jest często nazywany betonem trocinowym. Właściwości betonu trocinowego są pod wieloma względami lepsze od innych podobnych materiałów, chociaż są gorsze od betonu drzewnego wykonanego z zrębków drzewnych.
Mówimy o montażu podłóg monolitycznych w domu z drewna betonowego.
Sufit monolityczny jest Podstawowa struktura, który dzieli budynek na piętra. Tak naprawdę jest to podłoga, więc musi spełniać wymagania dotyczące wytrzymałości i sztywności oraz wytrzymać ciężar własny i ciężar wszystkiego, co się na niej znajduje. Sufit musi także posiadać niezbędne właściwości termoizolacyjne i dźwiękochłonne oraz być ognioodporny. Budowę podłogi monolitycznej można podzielić na etapy:
1. Montaż szalunków
Szalunek składa się z pomostu i stojaków teleskopowych, bezpiecznie zamocowanych na statywach. Regały instaluje się w tej samej odległości od siebie, co zależy od grubości płyty: im jest ona grubsza, tym bliżej znajdują się stojaki. Umieścić na stojakach teleskopowych belki podłużne, następnie prostopadle do nich - poprzeczne. Równość konstrukcji szalunkowej sprawdzamy za pomocą poziomnicy i poziomnicy. Od tego zależy jakość powierzchni przyszłej monolitycznej podłogi. Następnie wykonujemy podłogę z laminowanych arkuszy sklejki o grubości 18 mm. Pełni funkcję pokładu, który jest jednym z głównych elementy konstrukcyjne płyta szalunkowa. Do korzyści użytkowania sklejka laminowana wysoka odporność na wilgoć – dzięki laminowanej powierzchni arkusze wytrzymują wielokrotne cykle zalewania bez odkształceń arkusz sklejki podłogi monolityczne są gładkie i równe. Połączenia pomiędzy sklejkami uszczelniamy folią, aby zapobiec przedostawaniu się do nich betonu podczas wylewania.
2. Wzmocnienie podłogi
Zbrojenie nadaje konstrukcji sztywność, zapobiegając pękaniu lub wyginaniu się płyty monolitycznej. Zbrojenie montujemy w odległości 25-30 mm od końca, aby wyeliminować interakcję metalu z powietrzem i zapobiec korozji. Specjalne plastikowe ograniczniki i zaciski podnoszą zbrojenie i tworzą pod nim ochronną warstwę betonu. Rozmiar tej warstwy zależy od grubości podłogi, długości przęsła i innych czynników.
3. Wylewanie mieszanki betonowej
Po zbrojeniu wykonujemy fugowanie za pomocą pompy do betonu. Aby zagęścić mieszankę betonową, musimy użyć wibratora wewnętrznego.
W pierwszych dniach beton należy chronić przed opadami atmosferycznymi i utratą wilgoci, dlatego w przypadku opadów przykrywamy go specjalną folią, w chłodne dni podgrzewamy go i stosujemy dodatki przeciw zamarzaniu, a w czasie upałów zwilżamy go do zapobiegać pęknięciom.
4. Demontaż szalunków
Demontaż szalunków, Ostatni etap do montażu płyty monolitycznej następuje po 4 tygodniach od betonowania.