System sterowania chłodnictwem. Cele automatyzacji agregatów chłodniczych. Zasady automatyzacji chłodnictwa
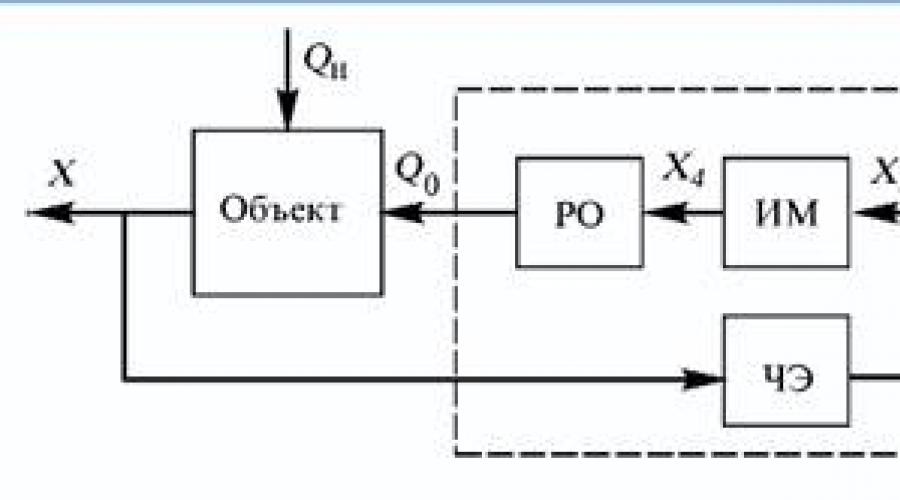
Przeczytaj także
WYKŁAD 9
Temat „Oprzyrządowanie i automatyka maszyna chłodnicza»
Cel: Poznanie budowy i zasady działania oprzyrządowania i urządzeń automatyki chłodni wagonowych
1. Maszyny chłodnicze i urządzenia klimatyzacyjne. Pigarev V.E., Arkhipov P.E. M., Trasa, 2003.
2. Program kontroli edukacyjnej „Klimatyzacja w samochodzie osobowym”.
Zarys wykładu:
1. Zasady automatyzacji agregaty chłodnicze.
2. Podstawowe pojęcia dotyczące automatyki
urządzenia automatyki.
4. Regulatory napełnienia parownika czynnikiem chłodniczym.
Zasady automatyzacji chłodnictwa
Opcje środowisko- temperatura, wilgotność, kierunek i siła wiatru, opady, Promieniowanie słoneczne zmieniają się stale w ciągu dnia, a także z powodu szybkiego ruchu samochodu. Odpowiednio zmienia się również obciążenie termiczne samochodu. Aby w tych warunkach utrzymać stabilne parametry powietrza we wnętrzu samochodu, konieczna jest ciągła zmiana wydajności układu chłodzenia (latem) lub ogrzewania (zimą) oraz, w razie potrzeby, wydajności układu wentylacji. W rezultacie niezależnie od tego, jak doskonałe będą same systemy wentylacji, ogrzewania, chłodzenia i zasilania, niezależnie od tego, jak dobrze ich parametry będą skoordynowane ze sobą i z obciążeniami cieplnymi samochodu, instalacja klimatyzacji nie będzie w stanie zapewnić komfortowe warunki w wagonie, jeżeli jego sterowanie nie jest zautomatyzowane, a maszyna chłodnicza zapewnia wymagane obróbka cieplnaładunek łatwo psujący się i utrzymywać określone warunki temperaturowe panujące w chłodni. W taborze chłodni stosowane są agregaty chłodnicze, w pełni lub częściowo zautomatyzowane. Stopień automatyzacji agregatu chłodniczego dobiera się w zależności od jego konstrukcji, wielkości i warunków pracy. W instalacjach w pełni zautomatyzowanych uruchomienie, wyłączenie maszyn oraz regulacja wydajności chłodniczej odbywa się automatycznie, bez ingerencji personelu obsługującego. ARV i sekcje są wyposażone w takie instalacje ZB-5. Pełna automatyzacja wymaga dużych kosztów początkowych i późniejszych kosztów utrzymania skomplikowanych maszyn i urządzeń. Jednakże pełna automatyzacja agregatów chłodniczych ARV umożliwiła rezygnację z obsługi wagonów na trasie przez obsługę i przejście na okresową Konserwacja w wyspecjalizowanych punktach (PTO ARV).
Podczas eksploatacji częściowo zautomatyzowanych agregatów chłodniczych wymagana jest stała praca personelu konserwacyjnego. Obecność personelu pozwala na rezygnację z automatyzacji włączania i wyłączania agregatu chłodniczego, procesu rozmrażania chłodnicy powietrza itp. W rezultacie osiąga się znaczną redukcję kosztów początkowych. Automatyka bezpieczeństwa w takich maszynach musi być zapewniona w pełni, jak w przypadku w pełni zautomatyzowanej instalacji.
Od częściowo instalacje automatyczne Konwencjonalnie wyróżnia się instalacje półautomatyczne, w których sprzęt jest włączany i wyłączany ręcznie przez mechanika, a utrzymanie ustalonego trybu pracy odbywa się za pomocą urządzeń automatyki. Do półautomatycznych agregatów chłodniczych zaliczają się instalacje 5-wagonowego odcinka BMZ.
Zautomatyzowane agregaty chłodnicze zawsze działają w trybie optymalnym. Pozwala to na skrócenie czasu osiągnięcia wymaganej temperatury w pomieszczeniu ładunkowym, zwiększając tym samym czas pomiędzy naprawami sprzętu i zmniejszając zużycie energii. Automatyczna jednostka chłodnicza dokładniej utrzymuje zadaną temperaturę w chłodzonym pomieszczeniu, czego nie można osiągnąć przy sterowaniu ręcznym. Pozwala to zachować jakość przewożonego towaru i ograniczyć jego straty podczas transportu. Układ automatyki niezawodnie chroni agregat chłodniczy przed niebezpiecznymi warunkami pracy, zwiększając jego żywotność i zapewniając bezpieczeństwo obsługującemu personelowi. Automatyzacja poprawia kulturę produkcji, poprawia i ułatwia warunki pracy personelu serwisowego. W praktyce obowiązki obsługi pociągu sprowadzają się do okresowych przeglądów i kontroli stanu pracy urządzeń oraz usuwania stwierdzonych usterek. Naturalnie systemy automatyki są różne. W odniesieniu do systemów automatyki instalacje klimatyzacyjne można sklasyfikować według trzech kryteriów: według parametrów powietrza kontrolowanego: temperatury lub wilgotności, lub obu tych parametrów, tj. według zawartości ciepła; w zależności od charakteru procesu obróbki powietrza: komory mokrego nawilżania i suszenia z bezpośrednim natryskiwaniem i filtracją189 mieszaniny parowo-powietrznej, lub komory ze zwilżaniem powierzchniowym, a także bezpośrednim przekazywaniem ciepła i masy, lub komory wykorzystujące wymianę ciepła poprzez zimno (lub gorąca) ściana, chłodzona zimną wodą lub solanką (ogrzewana gorąca woda lub solanką), albo komory z chłodnicami powietrza chłodzącego bezpośrednio, albo komory z pochłaniaczami wilgoci w postaci stałej lub ciekłej – adsorbenty; według schematu uzdatniania powietrza: komory z przepływem bezpośrednim (bez stosowania recyrkulacji) lub komory ze stałym lub zmienny recyrkulacja pierwotna lub komory z podwójną recyrkulacją, stałą lub zmienną. Specjalne urządzenie do regulacji wilgotności (specjalne suszenie powietrza odbywa się poprzez schładzanie go głębiej niż jest to konieczne do utrzymania). reżim temperaturowy z późniejszym ogrzewaniem) nie jest stosowany w klimatyzatorach wagonów. Latem, gdy wymagane jest osuszanie powietrza, odbywa się ono jednocześnie z procesem chłodzenia w chłodnicy powietrza. Zimą, gdy konieczne jest nawilżanie powietrza, odbywa się to dzięki wilgoci wydzielanej przez pasażerów. Zatem zgodnie z pierwszym znakiem proces automatyczna regulacja Obsługa urządzeń klimatyzacyjnych wagonu jest najprostsza i sprowadza się do utrzymania temperatury w pomieszczeniu wagonu w określonych granicach. W samochodach osobowych nie stosuje się komór mokrych, adsorbentów stałych i ciekłych oraz wymiany ciepła przy wykorzystaniu chłodzenia wodą lub solanką. Wynika z tego, że pod względem drugiej cechy systemy automatyczne klimatyzatorów wagonowych są dość proste. W samochodach nie stosuje się zmiennej, ani nawet podwójnej recyrkulacji, zarówno stałej, jak i zmiennej. Obecność recyrkulacji ze stałym stosunkiem powietrza zewnętrznego i recyrkulowanego tylko komplikuje system wentylacji bez wprowadzania jakichkolwiek zmian w systemie automatyczna kontrola. Zatem zgodnie z trzecią cechą, a więc w ogóle, systemy automatyki klimatyzatorów w samochodach osobowych, w porównaniu z systemami automatyki innych klimatyzatorów, zarówno komfortowymi, jak i technologicznymi, są stosunkowo proste. Aby utrzymać temperaturę w pomieszczeniu chłodniczym w zadanym zakresie, należy regulować wydajność chłodniczą instalacji, dostosowaną do maksymalnego zapotrzebowania na chłód. Regulacja może być płynna lub pozycyjna (stopniowa).
Płynna regulacja można to zrobić: poprzez płynną zmianę prędkości obrotowej wału sprężarki; omijanie (równoważenie) pary z przewodu tłocznego do przewodu ssawnego; zmiana objętości roboczej sprężarki (w sprężarkach śrubowych); poprzez otwarcie zaworu ssącego na część skoku tłoka itp. Wiele z powyższych metod jest rzadko stosowanych ze względu na złożoność ich realizacji konstrukcyjnej lub ze względu na znaczne straty energii.
Kontrola pozycji można tego dokonać poprzez zmianę współczynnika czasu pracy, tj. zmiana czasu pracy agregatu chłodniczego na cykl. Metoda ta jest szeroko stosowana w układach o dużej pojemności magazynowania ciepła. Sterowanie położeniem odbywa się również poprzez stopniową zmianę prędkości obrotowej wału korbowego sprężarki za pomocą wielobiegowych silników elektrycznych. Zmiana prędkości obrotowej wału silnika elektrycznego następuje poprzez zamianę biegunów stojana. W taborze chłodni wydajność chłodniczą reguluje się poprzez zmianę współczynnika czasu pracy. Cykliczną pracę agregatu chłodniczego osiąga się poprzez jego okresowe włączanie i wyłączanie. Stosunek czasu pracy agregatu chłodniczego p do całkowitego czasu trwania cyklu nazywa się współczynnikiem czasu pracy: b =р / .
Współczynnik czasu pracy można również zdefiniować jako stosunek dopływu ciepła do chłodni Q t do wydajności chłodniczej instalacji Q 0, tj. b = Qt/Q 0.
Temperaturę w chłodni samochodów chłodni reguluje się zazwyczaj poprzez okresowe włączanie i wyłączanie agregatu chłodniczego za pomocą dwupołożeniowego automatu - termostatu (przełącznika temperatury). Podczas pracy cyklicznej temperatura w chłodni nie pozostaje stała, ale waha się w pewnych granicach, które zależą od ustawienia różnicy termostatu. Wraz ze wzrostem różnicy zwiększa się czas trwania cyklu i limity wahań temperatury. Gdy temperatura w chłodni osiągnie górną ustawioną granicę, termostat włączy agregat chłodniczy. Po osiągnięciu temperatury w chłodni dolna granica termostat wysyła impuls elektryczny wyłączający instalację. Wraz ze wzrostem dopływu ciepła do samochodu wydłuża się czas pracy instalacji.
2. Podstawowe pojęcia
o automatycznej regulacji
Automatyczny system sterowania to połączenie obiektu sterującego i urządzenia sterującego, które realizuje proces w całości lub w części bez udziału personelu serwisowego. Obiekt kontrolny to zespół elementów technicznych, które wykonują główne zadanie problemem technologicznym- charakteryzuje się wartościami pewnych wielkości na wejściu i wyjściu. Jeśli za obiekt kontrolny uznamy samochód chłodnię, wówczas wartością wyjściową będzie temperatura w pomieszczeniu ładunkowym T waga , a wartością wejściową jest wydajność chłodnicza maszyny chłodniczej Q 0. Nazywa się wartość wyjściową, która musi zostać utrzymana w określonym przedziale regulowany parametr i oznaczać X 0. Wartość na wejściu obiektu jest parametrem, za pomocą którego kontrolowana jest wartość wartości wyjściowej. Zewnętrzny wpływ na obiekt regulacji, powodujący odchylenie kontrolowanego parametru od wartości początkowej X 0, zwane obciążeniem. W tym przypadku będą to napływy ciepła do samochodu Q N. Rzeczywista wartość kontrolowanego parametru X pod obciążeniem Q n odbiega od określonej wartości X 0. To odchylenie nazywa się niedopasowaniem: X=X – X 0. Uderzenie w obiekt, które zmniejsza niedopasowanie X, jest wpływem regulacyjnym. W naszym przykładzie będzie to wydajność chłodzenia maszyny Q 0. Jeśli Q 0 = Qn, następnie X = 0, a regulowany parametr nie zmienia się: X 0 - konst .
Urządzenie, które wykrywa niedopasowanie AX i działa na obiekt w celu zmniejszenia niedopasowania, nazywa się automatycznym regulatorem lub po prostu regulatorem.
Obiekt i sterownik tworzą automatyczny układ sterowania (rys. 1).
Ryż. 1. Automatyczny system sterowania
Regulację można przeprowadzić w oparciu o obciążenie i niedopasowanie. W pierwszym przypadku regulator
dostrzega zmianę obciążenia i zmienia wpływ regulacji o tę samą kwotę, zachowując równość Q 0 = Qn. Łatwiej jest jednak monitorować odchylenie regulowanego parametru X 0, te. zmienić wpływ regulacyjny Q 0 w zależności od wartości X.
Systemy automatyki różnią się przeznaczeniem: sterowaniem, alarmem, zabezpieczeniem, regulacją i kombinowanym. Różnią się one między sobą składem elementów i połączeniami między nimi. Schemat strukturalny System automatyczny określa, z jakich części się składa. Na przykład automatyczny system sterowania obejmuje obiekt sterujący i automatyczny sterownik składający się z kilku elementów - elementu wrażliwego, urządzenia nadrzędnego, elementu porównawczego, regulatora itp. Na ryc. Rysunek 2 przedstawia prosty jednoobwodowy układ automatycznego sterowania, szeroko stosowany w automatyzacji agregatów chłodniczych. Działanie obiektu charakteryzuje się parametrem X na wyjściu, przez które realizowana jest regulacja. Na obiekt przykładane jest zewnętrzne obciążenie Q N. Zarządzanie odbywa się poprzez wpływ regulacyjny Q 0. Automat powinien zmienić tę wartość w ten sposób Q 0 do wartości X. odpowiadał podanemu X 0. System zawiera bezpośrednie i informacja zwrotna. Obwód komunikacji bezpośredniej służy do generowania i przekazywania wpływu regulacyjnego na obiekt Q 0; Obwód sprzężenia zwrotnego dostarcza informacji o postępie procesu. Obwód komunikacji bezpośredniej obejmuje wzmacniacz (A), element wykonawczy (AM) ) oraz organ regulacyjny (RO). W obwodzie sprzężenia zwrotnego znajduje się element czuły (SE). ).
Ryż. 2. Schemat blokowy automatyki
Obydwa obwody są zamykane elementem porównawczym (EC). W regulatorze nie można stosować pojedynczych elementów (wzmacniacz, siłownik). Niektóre części mogą pełnić funkcje kilku elementów.
System działa w następujący sposób. Regulator odbiera kontrolowany parametr za pomocą czułego elementu X i konwertuje go na wartość X 1, wygodne do dalszego transferu.
Ta przeliczona wartość wchodzi do elementu porównawczego, którego drugie wejście otrzymuje sygnał X 2, reprezentujących zadanie kontrolerowi z urządzenia 3. W elemencie porównania wykonywana jest operacja odejmowania, w wyniku której powstaje niedopasowanie X= X– X 0.
Sygnał X sprawia, że pozostałe elementy obwodu działają. We wzmacniaczu jego moc wzrasta do X 3 i oddziałuje na element wykonawczy, który przetwarza ten sygnał na dogodną formę energii. X 4 i zmienia stanowisko organu regulacyjnego. W efekcie zmienia się przepływ energii lub materii dostarczanej do obiektu, tj. zmienia się wpływ regulacji.
Na przykładzie samochodu chłodni można prześledzić interakcję elementów schematu konstrukcyjnego (ryc. 1 i 2).
Temperatura w wagonie X wykrywa wrażliwy na temperaturę układ termostatu i przetwarza go na ciśnienie X 1 i działa na sprężynę termostatu ES, dostosowany do określonej siły ściskającej za pomocą śruby urządzenia ustalającego 3. Gdy temperatura w samochodzie wzrasta T vag w wyniku napływu ciepła Q n niedopasowanie wzrasta X.
Przy określonej wartości T vag zamknij styki termostatu, w tym Układ elektryczny sterowanie maszyną chłodniczą Uch, który otrzymuje energię mi ze źródła zewnętrznego. Siłowniki ICH systemy elektryczne obejmują agregat chłodniczy RO, co wpływa na wielkość Q n do obiektu. Z rozważanego schematu można uzyskać schematy blokowe innych urządzeń automatyki. Układ sygnalizacji różni się od układu sterowania tym, że nie posiada elementu wykonawczego. Obwód komunikacji bezpośredniej jest uszkodzony i sygnał X3 dostarczany jest serwisantowi (dzwonek, włączenie lampki sygnalizacyjnej), który musi dokonać regulacji. W systemie automatyczna ochrona Zamiast siłownika i regulatora znajduje się urządzenie sterujące wyłączające agregat chłodniczy. W systemach alarmowych i ochronnych sygnał X3 zmienia się gwałtownie, gdy wartość X osiągnie ustawioną wartość. Automatyczne regulatory są klasyfikowane według przeznaczenia: regulatory ciśnienia, temperatury, poziomu itp. Różnią się konstrukcją elementu czujnikowego. Organy regulacyjne przychodzą bezpośrednio i działanie pośrednie. Jeżeli moc sygnału niedopasowania jest wystarczająca, aby wpłynąć na regulator, uważa się, że regulator jest bezpośredni. Regulatory działania pośredniego wykorzystują zewnętrzne źródło energii do napędzania regulatora mi(elektryczne, pneumatyczne, hydrauliczne, kombinowane), zasilane przez wzmacniacz mocy U.
W zależności od sposobu oddziaływania na obiekt rozróżnia się regulatory działania płynnego i pozycyjnego (przekaźnikowego). W regulatorach płynnie działających regulator może przyjmować dowolne położenie pomiędzy maksimum a minimum. W przypadku regulatorów pozycyjnych organ regulacyjny może zajmować dwa lub więcej określonych stanowisk. W zależności od rodzaju elementu nastawczego regulatory mogą pełnić funkcję stabilizującą, programującą, śledzącą lub optymalizującą. Regulatory stabilizujące utrzymują wielkość sterowaną na stałym, zadanym poziomie. Sterowniki programowe zmieniają wielkość sterowaną zgodnie z zadanym programem, sterowniki monitorujące – w zależności od zmian jakiegoś parametru zewnętrznego, sterowniki optymalizujące, analizujące parametry zewnętrzne, zapewniają optymalny przebieg procesu. W agregatach chłodniczych częściej stosuje się regulatory stabilizujące.
Układ sterowania koordynuje charakterystykę poszczególnych elementów maszyny w przypadku zmiany ich wydajności chłodniczej.
Charakterystyki przedstawiają zależność wydajności chłodniczej, zużycia energii na pracę sprężarki i chłodzenia skraplacza od warunków zewnętrznych tj. na temperaturę otoczenia. Pozwalają ustalić wzajemną zależność pomiędzy parametrami sprężarki, parownika i skraplacza. Charakterystyki konstruuje się wykorzystując równania bilansu cieplnego układu „maszyna chłodnicza – chłodnia” oraz zależności energetyczne opisujące pracę głównych elementów maszyny, biorąc pod uwagę zmiany parametrów czynnika chłodniczego i otoczenia w czasie. W tym przypadku przedstawiono zależności bilansowo-energetyczne w funkcji temperatury chłodzonego obiektu (temperatury wrzenia czynnika chłodniczego) i temperatury otoczenia (temperatury skraplania czynnika chłodniczego).
Proces regulacji maszyny do wymaganego trybu chłodzenia lub do zadanego trybu temperatury teoretycznie może być realizowany ilościowo lub w sposób jakościowy. Pierwsza polega na zmianie przepływu czynnika chłodniczego przez parownik, druga na zmianie jego parametrów. Jednakże temperatura chłodzonego obiektu zależy od temperatury wrzenia czynnika chłodniczego, która ustala się automatycznie w zależności od wydajności chłodniczej sprężarki, parownika i skraplacza. Dlatego od procesu sterowania zależy nie tylko bilans wydajności chłodniczej sprężarki Q ok i parownik Q oj , ale także poziom temperatury odprowadzania lub dostarczania ciepła. W związku z tym regulacja sprężarki pary jest procesem złożonym, łączącym metody ilościowe i jakościowe.
Organ wykonawczy Układem sterowania (regulatorem wydajności chłodzenia) jest przepustnica. Tryb pracy maszyny, który odpowiada punktowi, w którym przecinają się charakterystyki sprężarki i parownika Q ok = Q oj , zapewnione poprzez zmianę obszaru przepływu zaworu. Schemat dopasowywania charakterystyk głównych elementów maszyny przy określonej stałej wartości temperatury otoczenia pokazano na ryc. 3.
Charakterystyka parownika Q ok = F(T 0) (T 0 - temperatura wrzenia czynnika chłodniczego) odpowiada zmianie dopływów ciepła do chłodni, charakterystyki sprężarki Q ok = F(T 0) - regulacja jego wydajności, charakterystyki przepływu przepustnicy Q dw = f(T 0) ustawia stopień jego zamknięcia lub otwarcia. Charakterystyki wymienionych elementów maszyny przy zmianie trybu pracy pokazano liniami przerywanymi. Kropka A określa punkt pracy układu „maszyna – chłodnia” jako przedmiot regulacji przy przejściu z jednego trybu pracy do drugiego. Jednocześnie rzecz A′odpowiada trybowi pracy podczas procesu sterowania sprężarką oraz punktowi A′′ - gdy zmienia się charakterystyka parownika. Regulacja wydajności chłodniczej maszyny ze sprężarką tłokową odbywa się poprzez płynną lub skokową (pozycyjną) regulację jej wydajności. W maszynach małej i średniej mocy rozpowszechniły się następujące metody płynnego sterowania za pomocą zewnętrznych lub wbudowanych urządzeń konstrukcyjnych: obejście czynnika chłodniczego od strony tłocznej do strony ssącej (równoważenie), które realizowane jest za pomocą zaworów regulacyjnych sterowanych z czujnik ciśnienia lub temperatury; dławienie ssania polegające na włączeniu sprężarki do pracy przy obniżonym ciśnieniu ssania; zmiana objętości martwej przestrzeni poprzez podłączenie do niej dodatkowej objętości zewnętrznej; zmiana prędkości obrotowej wału sprężarki.
Ryż. 3. Charakterystyka głównych elementów maszyny chłodniczej
Sterowanie krokowe w maszynach o małej i średniej wydajności chłodniczej odbywa się głównie metodą „start-stop” z maksymalną częstotliwością cykli do 5-6 na godzinę; w przypadku sprężarek wielostopniowych efektywnie wykorzystują wyłączenie poszczególnych cylindrów poprzez wciśnięcie zaworów ssących za pomocą popychaczy mechanicznych. Ruch popychaczy sterowany jest za pomocą napędów hydraulicznych, pneumatycznych lub elektromagnetycznych. Wprowadzany jest elektroniczny system kontroli wydajności, który oddziałuje na zawory ssące za pomocą pola elektromagnetycznego.
Przykładem krokowego sterowania proporcjonalnego jest regulacja temperatury powietrza w samochodzie w okresie letnim, gdy wraz ze wzrostem dopływu ciepła do samochodu wzrasta wydajność chłodnicza agregatu chłodniczego (zwiększa się prędkość obrotowa wału sprężarki lub duża ilość jego cylindry). Impulsem sygnalizującym potrzebę zwiększenia wydajności chłodniczej jest w tym przypadku dalszy wzrost temperatury powietrza w samochodzie.
Przykładem płynnej regulacji proporcjonalnej jest regulacja temperatury powietrza w samochodzie w okresie zimowym, kiedy wraz ze wzrostem strat ciepła z samochodu stopniowo wzrasta temperatura wody w bojlerze. Impulsem sygnalizującym konieczność podwyższenia temperatury wody w kotle jest w tym przypadku zmiana temperatury powietrza zewnętrznego. Najbardziej zaawansowanym, ale jednocześnie najbardziej złożonym typem sterowania proporcjonalnego jest sterowanie izodromiczne, polegające na zastosowaniu czułego i elastycznego sprzężenia zwrotnego, dzięki któremu kontrolowany parametr zmienia się w bardzo wąskich granicach lub nawet utrzymuje się na niemal stałym poziomie. Początkowo regulację izodromiczną stosowano w celu zapewnienia stałej prędkości obrotowej części maszyn, stąd wzięła się jej nazwa (po grecku iso – stała, równa; dromos – bieg, prędkość). Obecnie jest on używany najczęściej różne procesy np. do jazdy automatycznej statki morskie w danym tempie.
Ze względu na złożoność urządzeń, trudne warunki pracy podczas wibracji i drgań, a co najważniejsze ze względu na brak praktycznej potrzeby niezwykle precyzyjnej kontroli temperatury powietrza, w klimatyzatorach samochodowych nie stosuje się sterowania izodromicznego.
Wybierając metodę sterowania, należy wziąć pod uwagę koszty początkowe i operacyjne, produktywność i niezawodność projektu. Do oceny efektywności energetycznej układu sterowania wykorzystuje się stosunek wydajności chłodniczej sprężarki przy danym stopniu regulacji do nominalnej: =qop/qon = f(T 0). Wskaźniki porównawczej efektywności głównych metod regulacji wydajności sprężarek tłokowych pokazano na ryc. 4. Dla metod start-stop (linia 1) i ściskania zaworów dolotowych (linia 2 ) charakteryzują się niskimi stratami energii i praktyczną niezależnością od trybu pracy. Podczas dławienia na ssaniu (linia 3 ) następuje gwałtowny spadek wydajności wraz ze wzrostem temperatury wrzenia czynnika chłodniczego, dlatego metodę tę stosuje się w sprężarkach pracujących w wąskim zakresie ciśnień wrzenia. Równowaga (linia 4 ) jest najmniej skuteczną opcją sterowania, ponieważ wiąże się ze stratami energii sprężonej pary podczas jej obejścia, wzrostem temperatury zasysania czynnika chłodniczego, a w konsekwencji temperatury tłoczenia; Straty energii w tej metodzie odpowiadają stopniowi zmniejszenia wydajności chłodniczej maszyny.
W agregatach chłodniczych ze sprężarkami śrubowymi stosuje się następujące metody regulacji wydajności chłodniczej: dławienie ssania, wyważanie, zmiana prędkości obrotowej wału, zastosowanie układu suwakowego.
Dławienie realizowane jest poprzez automatyczne zamykanie przepustnicy zamontowanej na wlocie sprężarki. Skuteczność tej metody jest ograniczona przez zmniejszenie wydajności do 70% wartości nominalnej; Przy głębszym dławieniu wydajność znacznie spada.
Ryż. 4. Efektywność energetyczna głównych metod regulacji wydajności sprężarek tłokowych
Równoważenie odbywa się poprzez ominięcie części czynnika chłodniczego przez zawór bezpieczeństwa od strony tłocznej do strony ssawnej.
Stosowanie tej metody ogranicza się zwykle do sprężarek suchych.
Najbardziej ekonomiczną regulację polegającą na odcięciu części objętości wnęk roboczych podczas procesu sprężania zapewnia system szpuli. Pomimo złożoności konstrukcji sprężarki, taki system otwiera dodatkowe możliwości obwodów w celu ulepszenia parowych maszyn chłodniczych.
Pozwala na automatyzację pracy maszyny chłodniczej wysoka celność utrzymać wymagany poziom parametrów procesu chłodzenia, odpowiadający optymalnemu reżimowi technologicznemu, a także częściowo lub całkowicie wyeliminować udział personelu serwisowego w eksploatacji urządzeń chłodniczych.
W maszynach parowych przedmiotem automatyki są wymienniki ciepła, w szczególności stopień napełnienia parownika ciekłym czynnikiem chłodniczym oraz ciśnienie procesu skraplania. Obiektywnym i najdogodniejszym technicznie wskaźnikiem odzwierciedlającym stopień napełnienia parownika jest przegrzanie pary
przy wyjściu z niego. Rzeczywiście, gdy część powierzchni wymiany ciepła parownika zapewnia przegrzanie par czynnika chłodniczego, zmniejszenie jego dopływu prowadzi do zmniejszenia stopnia napełnienia, a w konsekwencji do wzrostu przegrzania. Jednocześnie wzrost temperatury przegrzania powyżej obliczonego poziomu pogarsza charakterystykę energetyczną maszyny i niezawodność jej pracy. Dostarczenie do parownika większej ilości czynnika chłodniczego, niż jest w stanie obsłużyć proces wymiany ciepła, wiąże się z przepełnieniem parownika i zmniejszeniem przegrzania. To ostatnie prowadzi do zmniejszenia wydajności chłodniczej maszyny, a w niektórych przypadkach do pracy sprężarki na mokrej parze, co może prowadzić do uderzenia wodnego.
Układy automatycznej kontroli stopnia napełnienia parownika na podstawie przegrzania par czynnika chłodniczego są płynne i pozycyjne (najczęściej dwustopniowe). Jako automatyczną regulację w układach płynnych powszechnie stosuje się zawory termostatyczne (TRV), w których wielkość przegrzania pary czynnika chłodniczego uzyskiwana jest w postaci różnicy pomiędzy temperaturą pary opuszczającej parownik a temperaturą wrzenia czynnika chłodniczego. . Zawory termostatyczne, które zapewniają proces dławienia czynnika chłodniczego od ciśnienia skraplania do ciśnienia parowania, instalowane są na linii pomiędzy skraplaczem a parownikiem.
Schemat ideowy automatycznej kontroli poziomu czynnika w parowniku za pomocą zaworu rozprężnego, stosowanego w maszynach chłodniczych RPS, przedstawiono na rys. 5. Element czujnikowy głowica pomiarowa 1 zawór termostatyczny wykonany w formie membrany 2 lub mieszek, znajduje się pod wpływem różnicy ciśnień pomiędzy parą przegrzaną, odpowiadającą temperaturze przegrzania, a czynnikiem chłodniczym na wylocie parownika 7 odpowiadający temperaturze wrzenia. Para przegrzana powstająca w systemie cieplnym składającym się z cylindra termicznego 6 i kapilarne 3 , wchodzi w przestrzeń nad membraną; przestrzeń pod membraną połączona jest rurką wyrównawczą 4 z przewodem ssawnym sprężarki 5 . W tym przypadku rurkę wyrównawczą podłącza się do przewodu ssawnego w miejscu montażu zasobnika termicznego. W niektórych konstrukcjach do cylindra termicznego wprowadza się absorber stały i cały układ cieplny wypełnia się gazem.
Ruch pręta 12 w wyniku odkształcenia elementu czujnikowego przy zmianie temperatury przegrzania zapewnia otwarcie lub zamknięcie zaworu odcinającego 11 regulujący przepływ ciekłego czynnika chłodniczego ze skraplacza do parownika przez przewód 10 . Ze śrubą regulacyjną 8 zmienić napięcie sprężyny 9 a tym samym wymaganą wartość temperatury przegrzania. W procesie automatycznej regulacji zawór rozprężny musi zapewniać optymalny poziom napełnienia parownika oraz stabilność układu w całym wymaganym zakresie zmian wydajności chłodniczej, co jest szczególnie istotne w przypadku maszyn chłodniczych taboru chłodni. Prawie stabilna praca układu zaworu rozprężnego rozpoczyna się w momencie jego przegrzania (3 6) K. Aby rozszerzyć zakres regulacji i zwiększyć jego stabilność, w systemie można zastosować kilka zaworów rozprężnych.
Ryż. 5. Schemat automatycznej kontroli poziomu czynnika chłodniczego w parowniku za pomocą zaworów rozprężnych
Proces automatycznej regulacji ciśnienia skraplania czynnika chłodniczego w maszynach ze skraplaczami chłodzonymi powietrzem odbywa się poprzez zmianę prędkości lub przepływu powietrza chłodzącego.
Technicznie zapewnia to system żaluzji lub przepustnic obrotowych, zastosowanie wentylatorów o zmiennym kącie montażu łopatek kierujących, zastosowanie dwubiegowych silników elektrycznych, a także okresowe wyłączanie wentylatorów. Zmiana prędkości lub przepływu powietrza chłodzącego prowadzi do zmiany współczynnika przenikania ciepła skraplacza, a co za tym idzie do
zmiany temperatury i ciśnienia procesu kondensacji.
W niektórych przypadkach wzrost temperatury skraplania osiąga się poprzez częściowe zalanie powierzchni skraplacza cieczą
chłodziwo.
Automatyka sterująca, oprócz monitorowania parametrów parownika i skraplacza, utrzymuje zadaną temperaturę powietrza w chłodni, zapewnia terminowe usuwanie szronu („płaszcza śnieżnego”) z powierzchni parownika, reguluje poziom oleju w oleju separatory itp. Działanie układu regulacji połączone jest z automatyczną ochroną, która zawiera zestaw środków mających na celu bezpieczna operacja maszyn chłodniczych i zapobiega trybom awaryjnym poprzez wyłączenie maszyny.
W skład automatyki zabezpieczeniowej wchodzą odpowiednie czujniki (przekaźniki zabezpieczeniowe oraz urządzenia przetwarzające impulsy z tych przekaźników na sygnał stopu). W niektórych przypadkach układ zabezpieczeń uzupełniany jest o blokadę, która uniemożliwia ponowne uruchomienie maszyny bez usunięcia przyczyny, która spowodowała zadziałanie zabezpieczenia.
W chłodniach kompresorowych czujniki układu zabezpieczającego monitorują poziom maksymalnego ciśnienia i temperatury czynnika chłodniczego na tłoczeniu sprężarki, minimalne ciśnienie na ssaniu, ciśnienie i temperaturę oleju w układzie smarowania oraz pracę silnika elektrycznego, zapobiegając jego przeciążeniu lub zwarciu. Do automatycznego systemu zabezpieczeń można wprowadzić alarm świetlny lub dźwiękowy, informujący o osiągnięciu wartości granicznej kontrolowanej wartości lub o wejściu maszyny w niebezpieczny tryb pracy.
3. Klasyfikacja i główne elementy
urządzenia automatyki
Ze względu na przeznaczenie urządzenia automatyki można podzielić na cztery główne grupy: regulacja, ochrona, sterowanie, alarm.
Automatyczne urządzenia sterujące zapewniają włączenie i wyłączenie agregatu chłodniczego i jego poszczególnych urządzeń, a także kontrolują procesy pracy. W agregatach chłodniczych taboru urządzenia sterujące spełniają następujące funkcje: prawidłowe napełnienie parownika czynnikiem chłodniczym (zawory termostatyczne itp.); utrzymywać temperaturę w pomieszczeniach chłodniczych w określonych odstępach czasu (termostaty, duostaty); regulować ciśnienie w skraplaczu w zadanym zakresie (przełączniki ciśnieniowe); zapewnić terminowe rozmrożenie szronu z parownika (przełączniki ciśnienia, przekaźniki programowe, termostaty); otworzyć lub zatrzymać dopływ ciekłego lub parowego czynnika chłodniczego (zawory elektromagnetyczne, Sprawdź zawory); ograniczyć przepływ czynnika chłodniczego do sprężarki z parownika (regulatory ciśnienia ssania).
Automatyczne urządzenia zabezpieczające wyłączają cały agregat chłodniczy lub poszczególne urządzenia w przypadku wystąpienia niebezpiecznych warunków pracy: po osiągnięciu maksymalnego dopuszczalnego ciśnienia tłoczenia (przełączniki ciśnieniowe); z podciśnieniem po stronie ssawnej (presostaty); gdy spada ciśnienie oleju w układzie smarowania sprężarki (różnica ciśnień); przy niskiej temperaturze oleju w skrzyni korbowej sprężarki (termostaty); przy wysokich temperaturach par czynnika chłodniczego sprężonych w sprężarce (przełącznik temperaturowy); gdy silnik elektryczny jest przeciążony lub zwarty (przekaźniki termiczne, wyłączniki automatyczne, bezpieczniki).
Automatyczne urządzenia sterujące mierzą, a w niektórych przypadkach rejestrują określone parametry pracy agregatu chłodniczego, np. temperaturę w chłodni (termograf), zużycie energii elektrycznej (licznik elektryczny), czas pracy urządzeń (liczniki godzin pracy silnika) itp. Automatyczne urządzenia alarmowe obejmują sygnały świetlne lub dźwiękowe w przypadku osiągnięcia określonej wartości kontrolowanej lub zbliżania się niebezpiecznego stanu pracy maszyny.
Urządzenia automatyki składają się z następujących głównych części: elementu czułego (czujnika), mechanizmu przekładniowego, elementu regulacyjnego (roboczego) i urządzenia nastawczego (ustawiającego). Element czujnikowy rejestruje kontrolowaną wartość (temperaturę, ciśnienie, poziom cieczy itp.) i przekształca ją w wygodną formę energii do zdalnej transmisji. Mechanizm nadawczy łączy element czujnikowy z korpusem regulacyjnym (roboczym).
Organ regulacyjny działa na sygnał z elementu czujnikowego. W urządzeniach dwupozycyjnych (przekaźnikach) element roboczy może zajmować tylko dwie pozycje. Na przykład styki elektryczne wyłącznika ciśnieniowego (presostatu) lub wyłącznika temperatury (termostatu) mogą być zamknięte lub otwarte, zawór elektromagnetyczny może być zamknięty lub otwarty. W urządzeniach o działaniu płynnym (proporcjonalnym) każda zmiana wielkości regulowanej odpowiada ruchowi elementu regulacyjnego (na przykład płynnemu ruchowi zaworu sterującego, gdy zmienia się obciążenie termiczne parownika). Urządzenie do ustawiania urządzenia ustawia określoną wartość kontrolowanej lub kontrolowanej wielkości. Odchylenie wielkości kontrolowanej, które nie powoduje ruchu elementu sterującego, nazywane jest martwą strefą lub różnicą urządzenia. Wrażliwe elementy urządzeń ciśnieniowych wykonane są w postaci mieszków i membran. Mieszek jest cienkościenną rurą falistą. Mieszki wykonane są z mosiądzu, brązu i stali nierdzewnej. Kiedy zmienia się ciśnienie w miechu, jego długość może znacznie się zmienić. Membrany wykonane są w postaci okrągłych elastycznych płytek mocowanych na obwodzie. Membrany mogą być elastyczne (metalowe) i miękkie (guma, tworzywa sztuczne, tkaniny gumowane).
204 Elementy wrażliwe na temperaturę wykonywane są w postaci płyt bimetalicznych oraz układów wrażliwych na temperaturę z różnymi wypełniaczami. W elementach opartych na rozszerzeniach ciała stałe po podgrzaniu temperatura przekształca się w ruch mechaniczny (elementy dylatometryczne). Ruch następuje z powodu nierównych współczynników rozszerzalności liniowej dla różnych metali. Na ryc. 3.6 a, b pokazane są elementy z dwiema metalowymi częściami 1 I 2 z różnych materiałów, na rys. 3.6 płyta CD - czuły element wykonany z bimetalu, tj. wykonany z dwóch zespawanych ze sobą warstw metali.
W elementach z rozszerzalnością cieplną cieczy wykorzystuje się zależność zmiany objętości cieczy od temperatury. Czujniki wypełnione rtęcią (ryc. 3.7, a, b), służą do przetwarzania temperatury na sygnał elektryczny bez pośredniego układu mechanicznego. Czujnik na rys. 3,7, A ma charakterystykę przekaźnikową, jak na rys. 3,7, B - gładki. Rtęciowe czujniki temperatury stosowane wcześniej w pociągach chłodniach okazały się niewystarczająco niezawodne, gdyż pojawiały się pęknięcia na skutek wibracji i wstrząsów podczas jazdy. rtęć i został naruszony obwód elektryczny. Ponadto rtęciowe czujniki kontaktowe są zaprojektowane z myślą o niskiej mocy sygnału elektrycznego.
Ryż. 3.6. Czujniki dylatometryczne
Ryż. 3.7. Płyn
wrażliwy na ciepło
Zimno wykorzystuje się w technologiach wielu procesów przetwarzania produktów rolnych. Dzięki lodówkom straty podczas przechowywania produktów są znacznie zmniejszone. Produkty schłodzone można transportować na duże odległości.
Mleko przeznaczone do przetworzenia lub sprzedaży jest zazwyczaj wstępnie schłodzone. Mleko przed wysłaniem do przedsiębiorstwa przemysłu mleczarskiego można przechowywać nie dłużej niż 20 godzin w temperaturze nieprzekraczającej 10°C.
W rolnictwie mięso schładza się głównie w gospodarstwach rolnych i fermach drobiu. Stosuje się następujące metody chłodzenia: w powietrzu, zimna woda, w wodzie z topniejącym lodem i nawadnianiu zimną wodą. Zamrażanie mięsa drobiowego odbywa się za pomocą zimnego powietrza lub poprzez zanurzenie w zimnej solance. Zamrażanie powietrzem odbywa się przy temperaturze powietrza w komorach chłodniczych od -23 do -25°C i prędkości powietrza 3...4 m/s. Do zamrażania poprzez zanurzenie w solance stosuje się roztwory chlorku wapnia lub glikolu propylenowego o temperaturze -10°C i niższej.
Mięso przeznaczone do długoterminowe przechowywanie, zamrożone w taki sam sposób jak zamrażanie. Zamrażanie
z powietrzem przeprowadza się w temperaturze schłodzonego powietrza od -30 do -40°C; przy zamrażaniu w solance temperatura roztworu wynosi -25...-28°C.
Jajka przechowuje się w lodówkach w temperaturze -1...-2°C i wilgotność względna 85...88%. Po ochłodzeniu do temperatury 2...3°C umieszcza się je w komorze magazynowej.
Owoce i warzywa chłodzone są w stacjonarnych magazynach. Przetwory owocowo-warzywne przechowywane są w komorach chłodniczych z bateriami chłodniczymi, w których krąży czynnik chłodniczy lub solanka.
W systemach z chłodzony powietrzem Najpierw powietrze jest schładzane, a następnie za pomocą wentylatorów pompowane do komór magazynujących. W systemach mieszanych produkty chłodzone są zimnym powietrzem i akumulatorem.
W rolnictwie chłód uzyskuje się zarówno bez maszyn (lodowce, chłodzenie solne lodem), jak i przy użyciu specjalnych maszyn chłodniczych. W chłodnictwie maszynowym ciepło ze schłodzonego czynnika jest odprowadzane do środowiska zewnętrznego za pomocą niskowrzących czynników chłodniczych (freon lub amoniak).
W rolnictwie szeroko stosowane są sprężarki parowe i absorpcyjne maszyny chłodnicze.
Najprostszym sposobem uzyskania temperatury płynu roboczego poniżej temperatury otoczenia jest sprężenie płynu roboczego (czynnika chłodniczego) w sprężarce, następnie schłodzenie go do temperatury otoczenia, a następnie poddanie go rozprężaniu adiabatycznemu. W tym przypadku ciało robocze działa dzięki swojemu energia wewnętrzna a jego temperatura maleje w porównaniu z temperaturą otoczenia. W ten sposób płyn roboczy staje się źródłem zimna.
W zasadzie jako czynniki chłodnicze można zastosować dowolną parę lub gaz. W pierwszych maszynach chłodniczych napędzanych mechanicznie jako czynnik chłodniczy stosowano powietrze, ale z koniec XIX V. zastąpiono go amoniakiem i dwutlenkiem węgla, ponieważ maszyna chłodnicza powietrzna jest mniej ekonomiczna i bardziej uciążliwa niż maszyna parowa, ze względu na duży przepływ powietrza wynikający z jej małej pojemności cieplnej.
W nowoczesnych agregatach chłodniczych czynnikiem roboczym jest para cieczy, która pod ciśnieniem zbliżonym do atmosferycznego wrze w niskich temperaturach. Przykładami takich czynników chłodniczych są amoniak NH3, dwutlenek siarki SO2, dwutlenek węgla CO2 i freony – pochodne chlorofluorowęglowe typu CmHxFyCl2. Temperatura wrzenia amoniaku przy ciśnienie atmosferyczne wynosi 33,5°C, „Freona-12” -30°C, „Freona-22” -42°C.
Jako czynniki chłodnicze szeroko stosowane są freony - halogenowe pochodne węglowodorów nasyconych (CmHn), otrzymywane przez zastąpienie atomów wodoru atomami chloru i fluoru. W technologii, ze względu na dużą różnorodność freonów i ich stosunkowo złożone nazwy, ustalono konwencjonalny system oznaczeń numerycznych, zgodnie z którym każdy taki związek ma swój własny numer, w zależności od jego wzoru chemicznego. Pierwsze cyfry tej liczby umownie wskazują węglowodór, którego pochodną jest ten freon: metan - 1, etan - 11, propan - 21. Jeżeli związek zawiera niepodstawione atomy wodoru, to ich liczbę dodaje się do tych liczb. Następnie dodaj do otrzymanej sumy lub do pierwotnej liczby (jeśli w związku zastąpiono wszystkie atomy wodoru) w formularzu następny znak liczba wyrażająca liczbę atomów fluoru. W ten sposób uzyskuje się oznaczenia: R11 zamiast monofluorotrichlorometanu CFCI2, R12 zamiast difluorodichlorometanu CF 2 C1 2 itd.
W agregatach chłodniczych jako czynnik chłodniczy zwykle stosuje się R12, a w przyszłości powszechnie stosowane będą R22 i R142. Zaletami freonów są względna nieszkodliwość, obojętność chemiczna, niepalność i bezpieczeństwo wybuchowe; Wady - niska lepkość, która sprzyja wyciekom i zdolność rozpuszczania się w oleju.
Rysunek 8.15 przedstawia schemat obwodu agregat chłodniczy ze sprężarką parową i jej idealny cykl na diagramie 75. W kompresorze 1 mokre pary czynnika chłodniczego są sprężane, co powoduje (sekcja a-b) efektem jest sucha para nasycona lub przegrzana. Zwykle stopień przegrzania nie przekracza
130... 140 „C, aby nie komplikować pracy sprężarki na skutek zwiększonych naprężeń mechanicznych i nie stosować olejów
Ryż. 8.15.
/ - sprężarka; 2 - chłodnia; 3- zawór dławiący; 4 - kondensator specjalnej klasy. Para przegrzana ze sprężarki o parametrach Liczba Pi i 02 wchodzi do chłodnicy (skraplacz 2). W skraplaczu pod stałym ciśnieniem przegrzana para oddaje ciepło przegrzania wodzie chłodzącej (proces pne) i jego temperatura staje się jednakowa temperatura nasycenie 0 n2. Następnie uwalniane jest ciepło parowania (proces płyta CD), para nasycona zamienia się we wrzącą ciecz (pkt D). Płyn ten przepływa do przepustnicy 3, po przejściu przez którą zamienia się w parę nasyconą o niewielkim stopniu suchości (x 5 = 0,1...0,2).
Wiadomo, że entalpia płynu roboczego przed i po dławieniu jest taka sama, a ciśnienie i temperatura spadają. Wykres 7s przedstawia linię przerywaną stałej entalpii d-e, kropka mi który charakteryzuje stan pary po dławieniu.
Następnie mokra para wchodzi do schłodzonego pojemnika zwanego lodówką 4. Tutaj, przy stałym ciśnieniu i temperaturze, para rozszerza się (proces e-a), odbierając pewną ilość ciepła. Zwiększa się stopień suchości pary (x| = 0,9...0,95). Para z parametrami stanu charakteryzującymi się punktem 1, zostaje zassany do sprężarki, a praca instalacji zostaje powtórzona.
W praktyce para za przepustnicą nie dostaje się do lodówki, lecz do parownika, gdzie odbiera ciepło z solanki, która z kolei odbiera ciepło z lodówki. Wyjaśnia to fakt, że w większości przypadków agregat chłodniczy obsługuje wielu zimnych odbiorców, a następnie niezamarzająca solanka służy jako pośredni czynnik chłodzący, stale krążący pomiędzy parownikiem, gdzie jest chłodzony, a specjalnymi chłodnicami powietrza w lodówkach . Jako solanki stosuje się wodne roztwory chlorku sodu i chlorku wapnia, które mają dość niskie temperatury zamarzania. Roztwory nadają się do stosowania jedynie w temperaturach powyżej tych, w których zamarzają jako jednorodna mieszanina, tworząc solny lód (tzw. temperatura kriohydratowa). Temperatura kriohydratu dla roztworu NaCl o stężeniu masowym 22,4% odpowiada temperaturze -21,2°C, a dla roztworu CaCl2 o stężeniu 29,9 - temperaturze -55°C.
Wskaźnikiem efektywności energetycznej agregatów chłodniczych jest współczynnik chłodniczy e, będący stosunkiem właściwej wydajności chłodniczej do zużytej energii.
Rzeczywisty cykl agregatu chłodniczego ze sprężarką parową różni się od teoretycznego tym, że ze względu na obecność strat tarcia wewnętrznego sprężanie w sprężarce nie zachodzi wzdłuż ścieżki adiabatycznej, ale wzdłuż politropu. W rezultacie zmniejsza się zużycie energii w sprężarce i zmniejsza się współczynnik chłodzenia.
W niektórych przypadkach wymagane jest uzyskanie niskich temperatur (-40...70°C). procesy technologiczne Jednostopniowe agregaty sprężarkowe okazują się albo nieekonomiczne, albo zupełnie nieprzydatne ze względu na spadek wydajności sprężarki spowodowany wysoką temperaturą cieczy roboczej pod koniec procesu sprężania. W takich przypadkach stosuje się specjalne cykle chłodnicze lub w większości przypadków sprężanie dwustopniowe lub wielostopniowe. Na przykład dwustopniowe sprężanie par amoniaku daje temperaturę do -50°C, a trzystopniowe sprężanie - do -70°C.
Główna zaleta absorpcyjne agregaty chłodnicze W porównaniu do silników sprężarkowych do wytworzenia chłodu wykorzystują one nie energię elektryczną, lecz energię cieplną o niskim i średnim potencjale. Ten ostatni można uzyskać z pary wodnej pobieranej np. z turbiny w elektrowniach cieplnych.
Absorpcja to zjawisko wchłaniania pary wodnej przez substancję ciekłą (absorbent). W takim przypadku temperatura pary może być niższa od temperatury absorbenta, który pochłania parę. Dla procesu absorpcji konieczne jest, aby stężenie zaabsorbowanej pary było równe lub większe od stężenia równowagowego tej pary nad absorbentem. Naturalnie w absorpcyjnych agregatach chłodniczych absorbenty cieczy muszą absorbować czynnik chłodniczy z odpowiednią prędkością i przy tych samych ciśnieniach, a ich temperatura wrzenia musi być znacznie wyższa niż temperatura wrzenia czynnika chłodniczego.
Najczęściej spotykane są instalacje absorpcji wodno-amoniakalnej, w których amoniak pełni rolę czynnika chłodniczego, a woda jako absorbenta. Amoniak jest dobrze rozpuszczalny w wodzie. Na przykład w temperaturze 0°C w jednej objętości wody rozpuszcza się do 1148 objętości pary amoniaku i wydziela się ciepło o wartości około 1220 kJ/kg.
Chłód w jednostce absorpcyjnej wytwarzany jest według schematu pokazanego na rysunku 8.16. Wykres ten przedstawia przybliżone wartości parametrów cieczy roboczej w instalacji bez uwzględnienia strat ciśnienia w rurociągach i strat ciśnienia temperaturowego w skraplaczu.
W generatorze 1 odparowanie nasyconego roztworu amoniaku następuje podczas ogrzewania go parą wodną. W efekcie oddestylowuje się niskowrzący składnik – parę amoniakalną z niewielką domieszką pary wodnej. Jeśli utrzyma się temperaturę roztworu około 20°C, wówczas ciśnienie nasycenia par amoniaku wyniesie w przybliżeniu 0,88 MPa. Aby zapobiec spadkowi zawartości NH3 w roztworze, należy zastosować pompę transferową 10 od absorbera do generatora silnie skoncentrowany

Ryż. 8.16.
/-generator; 2- kondensator; 3 - zawór dławiący; 4- parownik; 5 pomp; b-zawór obejściowy; 7- kontener chłodniczy; absorber; 9-cewka; 10- pompa
roztwór amoniaku do kąpieli. Nasycona para amoniakalna (x = 1), powstająca w generatorze, kierowana jest do skraplacza 2, gdzie amoniak zamienia się w ciecz (x = 0). Po przepustnicy 3 amoniak dostaje się do parownika 4, w tym przypadku jego ciśnienie spada do 0,3 MPa (/n = -10°C), a stopień suchości wynosi w przybliżeniu 0,2–0,3. W parowniku roztwór amoniaku odparowuje pod wpływem ciepła dostarczonego przez solankę z ochłodzonego zbiornika 7. W tym przypadku temperatura solanki spada z -5 do -8°C. Z pompą 5 jest on destylowany z powrotem do pojemnika 7, gdzie ponownie jest podgrzewany do -5°C, pobierając ciepło z pomieszczenia i utrzymując w nim stałą temperaturę, około -2°C. Amoniak odparowany w parowniku o stopniu suchości x = 1 trafia do absorbera 8, gdzie jest absorbowany przez słaby roztwór dostarczany przez zawór obejściowy 6 z generatora. Ponieważ absorpcja jest reakcją egzotermiczną, aby zapewnić ciągłość procesu wymiany ciepła, absorbent usuwa się wodą chłodzącą. Silny roztwór amoniaku uzyskany w pompie absorbera 10 pompowany do generatora.
Zatem w rozważanej instalacji występują dwa urządzenia (generator i parownik), w których ciepło dostarczane jest do płynu roboczego z zewnątrz, oraz dwa urządzenia (skraplacz i absorber), w których ciepło jest odbierane z płynu roboczego. Porównując schematy ideowe sprężarki pary i instalacji absorpcyjnej można zauważyć, że generator w instalacji absorpcyjnej zastępuje część tłoczną, a absorber zastępuje część ssącą sprężarki tłokowej. Sprężanie czynnika chłodniczego odbywa się bez nakładu energii mechanicznej, za wyjątkiem niewielkich kosztów przepompowania mocnego roztworu z absorbera do generatora.
W praktycznych obliczeniach współczynnik chłodzenia e, który jest stosunkiem ilości ciepła q 2 odbieranej przez ciecz roboczą w parowniku na ilość ciepła q ty spędził w generatorze. Obliczony w ten sposób współczynnik chłodniczy jest zawsze mniejszy od współczynnika chłodniczego agregatu parowego. Jednakże ocena porównawcza Efektywność energetyczna rozważanych metod wytwarzania chłodu w wyniku bezpośredniego porównania metod samych chłodniczych współczynników absorpcji i agregatów sprężarkowych jest błędna, ponieważ determinuje ją nie tylko ilość, ale także rodzaj wydatkowana energia. Obydwa sposoby pozyskiwania chłodu należy porównać w oparciu o wartość zredukowanego współczynnika wydajności, czyli stosunku wydajności chłodniczej q 2 na zużycie ciepła paliwa q to tj. ? pr = Yag Ya- Okazuje się, że przy temperaturach parowania od -15 do -20°C (stosowanych przez większość konsumentów) sprawność e jednostek absorpcyjnych jest wyższa niż jednostek sprężarkowych, w wyniku czego w niektórych przypadkach Jednostki absorpcyjne są bardziej opłacalne nie tylko przy zasilaniu ich parą pobieraną z turbin, ale także przy zasilaniu parą bezpośrednio z kotłów parowych.
Systemy automatyki. Automatyka pracy maszyn chłodniczych, w zależności od pełnionych funkcji, dzieli się na systemy:
– rozporządzenie , utrzymanie określonej wartości kontrolowanej wielkości (temperatura, ciśnienie, ilość czynnika chłodniczego itp.);
–ochrona, to znaczy wyłączyć instalację, jeśli występuje nadmierne odchylenie parametrów jej trybu pracy;
– alarm , tj. włączenie sygnału wizualnego i/lub dźwiękowego w przypadku naruszenia trybu pracy agregatu chłodniczego;
– kontrola , gdy zachodzi konieczność kontrolowania jakichkolwiek parametrów pracy maszyny chłodniczej.
W zależności od napędu systemy automatyki są elektryczny, pneumatyczny I łączny i zgodnie z zasadą działania - pozycyjny I ciągły.
System automatycznego sterowania agregatem chłodniczym pozwala zapewnić określony reżim temperaturowy dla przewożonego ładunku bez udziału personelu konserwacyjnego.
System automatyki to połączenie obiektu automatyki i urządzeń automatyki, które umożliwiają sterowanie pracą tego obiektu bez udziału personelu. Przedmiotem automatyki może być agregat chłodniczy jako całość lub jego poszczególne zespoły, podzespoły, urządzenia itp. Układy automatyki mogą być zamknięte lub otwarte.
Ryż. 4,26 - Zamknięty system automatyzacja
System zamknięty składa się z obiektu ( O) i urządzenie automatyczne ( A), które są połączone ze sobą linią prostą ( PS) i odwrotność ( system operacyjny) połączenia, które pokazano na ryc. 4.26. Wpływ wejściowy jest dostarczany do obiektu poprzez bezpośrednie połączenie X , odwrotnością jest wartość wyjściowa Na , które wpływają A. System system operacyjny działa zgodnie z odchyleniem od wartości rzeczywistej Na od ustawionej wartości Na H.
Jeśli celem systemu jest utrzymanie wartości Na wokół ustawionej wartości, gdy zmienia się wpływ zewnętrzny F vn, wówczas taki system nazywa się automatycznym systemem sterowania ( SAR), a urządzeniem automatycznym jest regulator automatyczny ( AR). System funkcjonalny SAR pokazany na ryc. 4,27.
Ryż. 4,27 - Schemat funkcjonalny automatyczny
rozporządzenie ( SAR)
Na schemacie funkcjonalnym SARŁańcuch komunikacji bezpośredniej obejmuje: wzmacniacz, mechanizm uruchamiający ( ICH) i organ regulacyjny ( RO). Zawarte w obwodzie sprzężenia zwrotnego czujnik, z którym regulator AR postrzega kontrolowaną zmienną U i konwertuje go na wartość U n, wygodny do dalszego przeniesienia. Do jednego z wejść elementu porównawczego ( ES) dostarczana jest przeliczona wartość U p, a na drugie wejście - sygnał U z gospodarz.
Ten sygnał w przetworzonej formie to ćwiczenia regulator. Dopasowana wartość d = U H - U n jest sygnałem motywacyjnym. Jego moc jest zwiększana we wzmacniaczu poprzez dostarczenie energii zewnętrznej mi VN i jako sygnał D ma wpływ ICH, który przekształca sygnał w dogodną formę energii Dx i układa się w RO. W rezultacie wejście do O przepływ energii, co odpowiada zmianie wpływu regulacyjnego X .
Jeżeli normalne działanie obiektu następuje przy wartościach Na , różny od Na h, a gdy zostanie osiągnięta równość między nimi, do obiektu wysyłany jest sygnał X wyłączyć, wówczas taki system nazywa się automatycznym systemem ochrony ( SAZ), a automat jest urządzeniem zabezpieczającym ( AZ). Taki układ funkcjonalny pokazany na ryc. 4,28.
Schemat SAZ różni się od schematu SAR to w urządzeniu automatycznym AZ nic ICH I RO. Sygnał ze wzmacniacza działa bezpośrednio na O, wyłączając całość lub poszczególne części.
Ryż. 4.28 - Schemat funkcjonalny automatycznego układu zabezpieczającego ( SAZ)
Ryż. 4.29 - System automatyki w pętli otwartej
System z otwartą pętlą to system, w którym brakuje jednego z połączeń (odwrotnego lub bezpośredniego) (ryc. 4.29). Parametr Z powiązane z wielkością wyjściową Na i jest odbierany przez urządzenie automatyczne A. Odchylenie od ustawionej wartości Z 3 powoduje zmiany ekspozycji X .
Automatyka parowników. Jednym z ważnych procesów sterowania maszyną chłodniczą jest automatyczne zasilanie parowników w oparciu o przegrzanie pary i poziom cieczy w parowniku. Jak automatyczny regulator stosowane jest głównie przegrzanie zawory termostatyczne (TRV).
Zawór rozprężny montowany jest przed parownikiem. Rurka kapilarna jest przylutowana u góry zaworu (ryc. 4.30) 7 , łączący wewnętrzną część roboczą 6 zawór z cylindrem termicznym 8 . Górna część zasilająca zaworu jest uszczelniona. Cylinder termiczny jest szczelnie połączony z rurą ssącą łączącą parownik ze sprężarką. Podczas produkcji zaworu cylinder termiczny, kapilara i przestrzeń nad membraną napełniane są ściśle odmierzoną ilością czynnika chłodniczego. Od spodu membrany 5 pręt opada 4 Z zawór odcinający 3 , który jest dociskany do siedziska za pomocą sprężyny 2 ze śrubą regulacyjną 1 .
Ryż. 4.30 - Schemat zaworu termostatycznego z wyrównaniem wewnętrznym
Zasada działania zaworu rozprężnego opiera się na porównaniu temperatury wrzenia czynnika chłodniczego w parowniku z temperaturą opuszczających go par. Porównanie przeprowadza się poprzez przeliczenie temperatury pary odbieranej przez cylinder termiczny T w odpowiednim ciśnieniu R s w części zasilającej urządzenia (patrz ryc. 4.30). Ciśnienie działa na membranę od góry i ma tendencję do otwierania zaworu przez trzpień 3 do większego obszaru przepływu. Ten ruch zaworu jest zapobiegany przez ciśnienie wrzenia freonu w parowniku R o działanie na membranę od dołu, a także siła sprężyny F i ciśnienie R do zaworu.
Przy prawidłowym napełnieniu parownika temperatura pary na wylocie nie powinna przekraczać 4,7°C. W tym celu cały czynnik chłodniczy dostarczany przez zawór rozprężny do parownika musi wyparować w obszarze od zaworu 3 do punktu A. Tutaj temperatura freonu nie zmienia się i jest T O. W ostatnich zwojach parownika od punktu A do cylindra termicznego czynnik chłodniczy, kontynuując odbieranie ciepła z chłodzonego pomieszczenia, przegrzewa się do temperatury T w > T O. Temperatura T Wykrywany jest cylinder termiczny i ustalane jest ciśnienie w systemie zasilania R Z. W równowadze R c = R o + F +R Gdy parownik jest całkowicie wypełniony czynnikiem chłodniczym, maszyna chłodnicza działa w trybie optymalnym.
Wraz ze spadkiem temperatury w chłodni zmniejsza się przepływ ciepła do parownika. Wrzenie czynnika chłodniczego w punkcie A nie kończy się, ale trwa dalej do punktu B. Droga czynnika chłodniczego w postaci pary do cylindra termicznego ulega skróceniu, a przegrzanie pary zmniejsza się. Zasobnik termiczny odbiera niższą temperaturę, a w systemie zasilania ustawiana jest niższa wartość R Z. Pod działaniem sprężyny zawór przesuwa się w górę, zmniejszając powierzchnię przepływu zaworu, a tym samym dopływ czynnika chłodniczego do parownika.
Przy mniejszej ilości czynnika chłodniczego jego wrzenie w parowniku kończy się wcześniej, a przegrzanie przyjmuje wartość zbliżoną do pierwotnej. Zawór porusza się w górę, aż do ustalenia się nowej równowagi pomiędzy zmniejszonym ciśnieniem i zmniejszonym naprężeniem sprężyny, tj. R c = R o + F +R j. Przegrzanie par w parowniku jest kontrolowane przez napięcie wstępne sprężyny 2 za pomocą śruby regulacyjnej 1 .
Balon termiczny 8 , kapilarny 7 i membrana 5 (patrz ryc. 4.30) są głównymi elementami przyrządów manometrycznych - termostaty , które służą do automatycznej regulacji pracy generatorów diesla i agregaty chłodnicze w taborze chłodni.
Automatyczna kontrola temperatury w przestrzeni ładunkowej. Aby ustalić wymagany reżim temperaturowy w pomieszczeniu ładunkowym modułu transportu chłodniczego lub magazynu i automatycznie utrzymać go w określonych granicach, stosuje się wyłącznik ciśnieniowy-termostat , którego urządzenie pokazano na ryc. 4.31.
Ryż. 4.31 - Urządzenie presostatyczne
Przełącznik ciśnienia instaluje się na rurociągu ssawnym pomiędzy parownikiem a sprężarką. Składa się z tłoka 1 , pręt sztywno z nim połączony 2 , sprężyny 4 , uchwyty 5 , dwa styki elektryczne: ruchomy 6 i nieruchomy 7 .
Tłok jest w kolanie 3 podłączony do rury ssącej 8 . Pod presją R o, większa niż siła skręcenia sprężyny 4 , tłok znajduje się w najwyższym położeniu. Jednocześnie kontakty 6 I 7 Zamknięte. Sprężarka zostaje włączona i wysysa pary czynnika chłodniczego z parownika. Podczas ekstrakcji pary ciśnienie R o maleje, staje się mniejsza niż siła skręcenia sprężyny. Tłok z ruchomym stykiem przesuwa się do najniższego położenia, a sprężarka wyłącza się.
Z powodu ciągłego wrzenia czynnika chłodniczego w parowniku wzrasta jego objętość właściwa, czyli ciśnienie R o zacznie ponownie rosnąć. Styki 6 i 7 zamkną się, sprężarka zacznie zasysać pary czynnika chłodniczego z parownika. Cykl się powtarza.
Skok tłoka jest ograniczony specjalnymi ogranicznikami, które można regulować. Siłę sprężyny na tłoku reguluje się za pomocą rączki 5 . Po ustawieniu klamki w pozycji „zimnej” moment obrotowy sprężyny maleje. W rezultacie w strefie parownika powstanie niższe ciśnienie R och, co oznacza niską temperaturę wrzenia freonu.
W ten sposób presostat-termostat utrzymuje ciśnienie wrzenia w parowniku na wymaganym poziomie, kontrolując ilość czynnika chłodniczego wpływającego do parownika.
Automatyzacja agregatów chłodniczych polega na wyposażeniu ich w urządzenia automatyczne (przyrządy i urządzenia automatyki), za pomocą których zapewnione są bezpieczną pracę i dyrygowanie proces produkcji lub pojedyncze operacje bez bezpośredniego udziału personelu serwisowego lub z jego częściowym udziałem.
Obiekty automatyki wraz z urządzeniami automatyki tworzą systemy automatyki o różnych funkcjach: sterowania, alarmowania, zabezpieczeń, regulacji i zarządzania. Automatyzacja zwiększa efektywność ekonomiczną agregatów chłodniczych, ponieważ zmniejsza się liczba personelu obsługującego, zmniejsza się zużycie energii elektrycznej, wody i innych materiałów, a żywotność agregatów wzrasta dzięki utrzymywaniu optymalnego trybu pracy urządzeń automatycznych. Automatyzacja wymaga nakładów kapitałowych, dlatego należy ją przeprowadzić w oparciu o wyniki analizy techniczno-ekonomicznej.
Agregat chłodniczy może być zautomatyzowany częściowo, całkowicie lub kompleksowo.
Częściowa automatyzacja zapewnia obowiązkową automatyczną ochronę wszystkich agregatów chłodniczych, a także monitorowanie, alarmowanie i często kontrolę. Personel obsługujący reguluje podstawowe parametry (temperaturę i wilgotność w komorach, temperatury wrzenia i skraplania czynnika chłodniczego itp.) w przypadku ich odchyleń od zadanych wartości oraz nieprawidłowe działanie urządzeń, zgłaszane przez systemy sterujące i alarmowe, oraz niektóre pomocnicze procesy okresowe (rozmrażanie szronu z powierzchni urządzeń chłodniczych, usuwanie oleju z układu) wykonywane są ręcznie.
Pełna automatyzacja obejmuje wszystkie procesy związane z utrzymaniem wymaganych parametrów w pomieszczeniach chłodniczych i elementach agregatu chłodniczego. Personel konserwacyjny może być obecny tylko okresowo. W pełni automatyzują małe agregaty chłodnicze, są bezawaryjne i trwałe.
W przypadku dużych przemysłowych agregatów chłodniczych jest to bardziej typowe złożoną automatykę(automatyka, alarm, ochrona).
Sterowanie automatyczne zapewnia zdalny pomiar, a czasami rejestrację parametrów decydujących o trybie pracy sprzętu.
Automatyczny alarm - powiadomienie za pomocą dźwięku lub sygnał świetlny o osiągnięciu zadanych wartości, określonych parametrów, włączeniu lub wyłączeniu elementów agregatu chłodniczego. Automatyczny alarm dzielą się na technologiczne, zapobiegawcze i awaryjne.
Alarm procesowy - świeci, informuje o pracy sprężarek, pomp, wentylatorów oraz obecności napięcia w obwodach elektrycznych.
Alarm ostrzegawczy w odbiornikach obiegu ochronnego informuje, że wartość monitorowanego parametru zbliża się do maksymalnej dopuszczalnej wartości.
System alarmowy powiadamia sygnałami świetlnymi i dźwiękowymi o zadziałaniu automatycznej ochrony.
Automatyczne zabezpieczenia zapewniające bezpieczeństwo personelu obsługującego są obowiązkowe w przypadku każdej produkcji. Zapobiega wystąpieniu sytuacji awaryjnych poprzez wyłączenie poszczególnych elementów lub całej instalacji, gdy kontrolowany parametr osiągnie maksymalną dopuszczalną wartość.
Niezawodna ochrona w przypadku wystąpienia niebezpieczna sytuacja powinien być zapewniany przez automatyczny system ochrony (APS). W najprostszej wersji SAZ składa się z czujnika-przekaźnika (przekaźnika zabezpieczeniowego), który kontroluje wartość parametru i generuje sygnał po osiągnięciu jego wartości granicznej oraz urządzenia przetwarzającego sygnał przekaźnika zabezpieczeniowego na sygnał stopu, który jest przesłane do systemu sterującego.
W agregatach chłodniczych duża moc SAZ jest zaprojektowany w taki sposób, że po zadziałaniu przekaźnika zabezpieczeniowego nie jest możliwe automatyczne uruchomienie uszkodzonego elementu bez usunięcia przyczyny, która spowodowała zatrzymanie. W małych agregatach chłodniczych, np. w placówkach handlowych, gdzie awaria nie może mieć poważnych konsekwencji, nie ma ciągłej konserwacji, instalacja załącza się automatycznie, gdy wartość parametru sterującego powróci do akceptowalnego zakresu.
Sprężarki mają największą liczbę rodzajów zabezpieczeń, ponieważ zgodnie z doświadczeniem eksploatacyjnym zdarza się z nimi 75% wszystkich wypadków w urządzeniach chłodniczych.
Liczba parametrów kontrolowanych przez BAS zależy od rodzaju, mocy sprężarki i rodzaju czynnika chłodniczego.
Rodzaje zabezpieczeń sprężarki:
przed niedopuszczalnym wzrostem ciśnienia tłoczenia - zapobiega naruszeniu szczelności połączeń lub zniszczeniu elementów;
niedopuszczalny spadek ciśnienia ssania - zapobiega zwiększonemu obciążeniu uszczelki sprężarki, spienianiu oleju w skrzyni korbowej, zamarzaniu płynu chłodzącego w parowniku (prawie wszystkie sprężarki wyposażone są w presostat wysokiego i niskiego ciśnienia);
zmniejszenie różnicy ciśnień (przed i za pompą) w układzie olejowym - zapobiega awaryjnemu zużyciu części trących i zakleszczeniu mechanizmu ruchu sprężarki, przekaźnik różnicy ciśnień kontroluje różnicę ciśnień po stronie tłocznej i ssawnej pompy olejowej;
niedopuszczalny wzrost temperatury tłoczenia - zapobiega zakłóceniu reżimu smarowania cylindra i awaryjnemu zużyciu części trących;
podwyższenie temperatury uzwojeń wbudowanego silnika elektrycznego sprężarek chłodniczych uszczelnionych i bezuszczelnionych – zapobiega przegrzaniu uzwojeń, zakleszczeniu wirnika i pracy w dwóch fazach;
uderzenie wodne (wejście ciekłego czynnika chłodniczego do komory sprężania) - zapobiega poważnej awarii sprężarki tłokowej: utracie gęstości, a czasem zniszczeniu.
Rodzaje zabezpieczeń pozostałych elementów agregatu chłodniczego:
przed zamarznięciem płynu chłodzącego - zapobiega pękaniu rurek parownika;
przepełnienie odbiornika liniowego - zabezpiecza przed spadkiem wydajności skraplacza w wyniku zapełnienia części jego objętości ciekłym czynnikiem chłodniczym;
opróżnienie odbiornika linii - zapobiega przedostawaniu się gazu wysokie ciśnienie V układ odparowywania i niebezpieczeństwo uderzenia wodnego.
Zapobieganie sytuacja awaryjna zapewnia ochronę przed niedopuszczalnym stężeniem amoniaku w pomieszczeniu, które może spowodować pożar i eksplozję. Stężenie amoniaku (maksymalnie 1,5 g/m3, czyli 0,021% objętościowo) w powietrzu monitoruje się za pomocą analizatora gazów.
2. Kontrola temperatury w chłodzonym obiekcie
3. Regulacja ciśnienia czynnika chłodniczego
4. Przekaźnik kontroli smarowania
5. Regulacja wydajności chłodniczej
6.Regulacja ciśnienia skraplania
7. Regulatory ciśnienia parowania.
8. Regulatory wydajności.
9. Regulatory rozruchu.
10. Zawory elektromagnetyczne i zawory odwracające cykl
11. Automatyczne odszranianie parowników.
12. Mikroprocesorowe urządzenia sterujące agregatami chłodniczymi.
13. Schematy automatyki komercyjnych urządzeń chłodniczych.
1. Automatyczne systemy sterowania
Aby zapewnić normalną pracę agregatu chłodniczego, należy utrzymywać w określonych granicach lub regulować zgodnie z danym programem wartości szeregu wielkości fizycznych lub parametrów, z których główne to:
1. Temperatura w schłodzonej objętości.
2. Optymalne napełnienie parownika czynnikiem chłodniczym.
3. Ciśnienie wrzenia i kondensacji czynnika chłodniczego.
4. Wydajność sprężarki.
Automatyczne sterowanie agregatem chłodniczym zapewnia dokładne utrzymanie zadanych parametrów. W wyniku utrzymania tryb optymalny eksploatację urządzeń chłodniczych, zmniejszenie strat produktów spożywczych w komorze chłodniczej, utrzymanie ich jakości, zmniejszenie kosztów eksploatacji i wydłużenie żywotności agregatów chłodniczych.
Automatyzacja procesów regulacji, zabezpieczeń i sygnalizacji. Automatyka instalacji chłodniczej obejmuje automatyzację procesów alarmowych, zabezpieczających i regulacyjnych.
Rozporządzenie- jest to proces utrzymywania wartości parametru (temperatury, ciśnienia itp.), zwanej nastawialną, stałą lub w określonych granicach. Proces utrzymywania stałej temperatury w chłodni nazywa się kontrolą temperatury. W związku z tym sama temperatura będzie parametrem regulowanym. Automatyczny system kontroli zapewnia utrzymanie kontrolowanego parametru (temperatury, ciśnienia lub poziomu) w określonych granicach.
Obejmuje przedmiot regulacji, automatyczny regulator, organ regulacyjny, a także połączenia między nimi (ryc. 12.1).
Ryż . 12.1. Schemat blokowy układu automatyki
Przedmiot regulacji- jest to pomieszczenie, pojemnik, system lub mechanizm, w którym reguluje się zachodzący proces, tj. utrzymywana jest stała wartość kontrolowanego parametru. Zatem regulując temperaturę w pomieszczeniu chłodniczym, przedmiotem regulacji będzie samo pomieszczenie.
Automatyczny regulator- kontroluje dany proces w przedmiocie regulacji i kieruje pracą organu regulacyjnego zgodnie z zadaniem regulacji.
Organ regulacyjny(zawór, mechanizm) służy do zmiany natężenia przepływu substancji (czynnika chłodniczego, powietrza, solanki) dostarczanej do kontrolowanego obiektu.
Automatyczny system sterowania działa w następujący sposób. Automatyka na bieżąco mierzy wartość kontrolowanego parametru i porównuje ją z wartością zadaną. Jeżeli regulowany parametr odbiega od wartości zadanej, automatyka poprzez regulator zmienia natężenie przepływu podawanej substancji tak, aby regulowany parametr powrócił do stanu pierwotnego. Na przykład wzrost obciążenia cieplnego w chłodzonym pomieszczeniu spowoduje wzrost jego temperatury. Automatyczny regulator po ustaleniu wartości i znaku odchyłki temperatury kontrolowanej od zadanej podaje sygnał sterujący do regulatora. Zwiększa odbiór ciepła z pomieszczenia, a jego temperatura powróci do zadanej wartości.
Automatyczne systemy zabezpieczające - wyeliminować możliwość wypadków w przypadku nagłej zmiany trybu pracy urządzenia. Po osiągnięciu wartości granicznej kontrolowanego parametru automatyka poprzez element regulacyjny albo wyłącza sterowaną jednostkę, albo ogranicza wzrost parametru, aby uniknąć zniszczenia mechanizmu.
Systemyautomatycznyalarm W zależności od przeznaczenia dzieli się je na dwie grupy:
1. Systemy ostrzegania awaryjnego.
2. Systemy alarmowe mechanizmów napędowych.
System alarmowy- gdy kontrolowany parametr osiągnie wartość graniczną, emitowany jest sygnał świetlny lub dźwiękowy. Personel obsługujący zmienia niebezpieczny tryb pracy mechanizmu, wpływając na organ regulacyjny.
System alarmowy mechanizmów wykonawczych- daje świetlną sygnalizację na panelu sterowania o uruchomieniu najważniejszych mechanizmów.
Urządzenia do automatycznej regulacji i monitorowania procesów zachodzących podczas pracy agregatu chłodniczego mają na celu zapewnienie bezpiecznej pracy agregatu i zwiększenie jego efektywności operacyjnej. Efektywność operacyjną zwiększa się głównie poprzez zmniejszenie kosztów pracy związanych z obsługą agregatu chłodniczego oraz zwiększenie produktywności personelu. Stosowanie urządzenia automatyki I ochrona pozwala ci podjąć decyzję główne zadanie- utrzymanie zadanej temperatury chłodzonego obiektu. Do zadań automatyzacji procesów instalacyjnych należy także utrzymanie określonego poziomu ciekłego czynnika chłodniczego w urządzeniach oraz stałej temperatury skraplania; zapewniając ochronę przed uderzeniem wodnym, przegrzaniem poszczególnych części instalacji, eksplozją urządzeń, zamarznięciem chłodziwa i awarią pompy.
Zadaniem personelu konserwacyjnego jest fachowa konserwacja urządzeń wchodzących w skład obwodu i okresowa kontrola ich przydatności do użytku: przekaźniki poziomu ochronnego – raz na 10 dni, pozostałe urządzenia automatyki – raz w miesiącu. Wśród urządzeń automatyki najczęściej stosowane są przełączniki temperatury, ciśnienia i różnicy ciśnień, regulatory poziomu oraz przełączniki poziomu z siłownikami, zawory termostatyczne, przełączniki przepływu i przepływu. Urządzenia te są zwykle konfigurowane podczas uruchamiania. Nowoczesne komercyjne maszyny chłodnicze freonowe wyposażone są w szereg urządzeń, które w pełni lub częściowo automatyzują procesy pracy. Stosowane są różne schematy automatyzacji. Przy pełnej automatyzacji nie ma potrzeby systematycznego monitorowania pracy maszyny chłodniczej, a personel konserwacyjny wykonuje jedynie okresowe obserwacje, sprawdzając przydatność urządzeń i eliminując pojawiające się problemy techniczne.
Powszechnie stosowane w handlu freonowe maszyny chłodnicze z bezpośrednim systemem chłodzenia są z reguły w pełni zautomatyzowane.
Zastosowanie automatyzacji sprawia, że praca maszyn chłodniczych jest bardziej produktywna, ekonomiczna i bezpieczna.