Jak zrobić własny blok betonowy. Jak zarabiać pieniądze robiąc klocki. Jak wymieszać rozwiązanie, aby utworzyć blok żużlowy
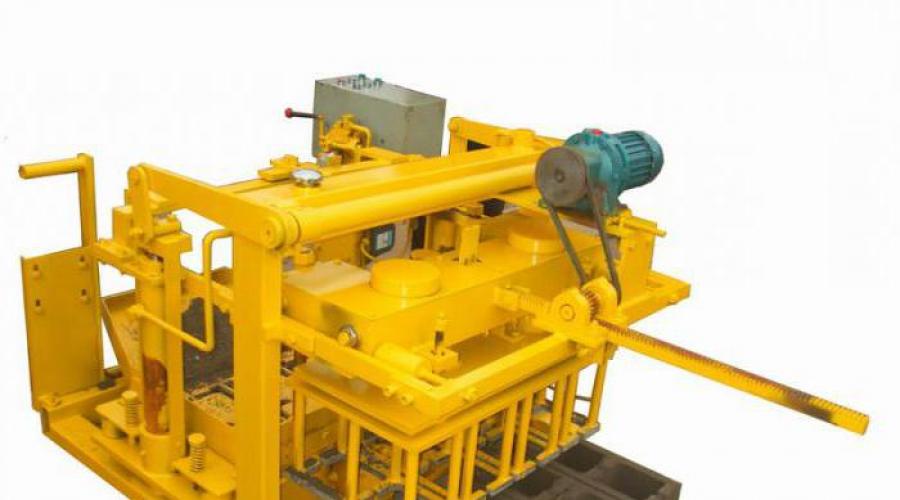
Przeczytaj także
Bloki budowlane są powszechnym materiałem do budowy konstrukcji o różnym przeznaczeniu. Różnią się rozmiarem, komponentami, metodą produkcji, ale wszystkie są popularnymi ścianami materiał konstrukcyjny. Bloki konstrukcyjne produkowane są w warunkach przemysłowych, m.in gospodarstwo domowe Produkują także wyroby betonowe i bloki żużlowe, co wymaga samodzielnego producenta klocków budowlanych. W zależności od użytego materiału produkty te dzielą się na następujące typy:
- beton żużlowy;
- Beton;
- gazobeton;
- Pianobeton włóknisty;
- styropian.
Bloki żużlowe jako materiał budowlany
Blok żużlowy jest standardem wyroby betonowe, jedynie zamiast ciężkiego żwiru i tłucznia kamiennego stosuje się wypełniacz w postaci żużla odpadowego. To zastąpienie nadaje materiałowi lekkość w porównaniu z betonem i dodatkowe właściwości termoizolacyjne, ponieważ żużel wypada korzystnie w porównaniu z ciężkim i gęstym kruszonym kamieniem pod względem przewodności cieplnej.
Produkcja bloków żużlowych wymaga precyzyjnego dozowania składników roztworu, a mianowicie:
- cement gatunku nie niższego niż 400 lub 500, weź jedną część (wiadro);
- piasek z kamieniołomu, wymieszaj 3 części (wiadra);
- żużel, cegła wypalona, glina ekspandowana, materiał ten dodaje się w ilości 5 części (wiadra);
- woda.
Aby uzyskać bloki żużlowe o tej samej jakości jak w fabryce, użyj roztworu o średnio lepkiej konsystencji. Płynny roztwór zmniejszy wytrzymałość bloków, a gęsty roztwór po stwardnieniu utworzy wewnątrz niekontrolowane puste przestrzenie.
Bloki betonowe
Do budowy ścian i innych konstrukcji, jeśli wymagana jest zwiększona wytrzymałość, stosuje się bloczki budowlane z cementu, piasku i tłucznia kamiennego. Stosunek składników do standardowego betonu przyjmuje się w stosunku 1: 3: 6, inne opcje mieszanka betonowa są opisane w podręcznikach budowniczych i zależą od marki użytego cementu, wielkości kruszywa i rodzaju piasku.
Bloki z trocin budowlanych
Do budowy budynki mieszkalne, dacze, domki korzystają z światła i ciepła materiał ścienny z trocin, piasku i wody. Składnikiem wiążącym roztworu jest wapno. Ilość materiału dodanego do roztworu zmienia właściwości produktu końcowego. Wzrost masy trocin prowadzi do wzrostu właściwości termoizolacyjne, ale przyczynia się do spadku siły. Wraz ze wzrostem ilości piasku w roztworze wzrasta wytrzymałość, a jednocześnie zwiększa się granica mrozoodporności, co zwiększa właściwości użytkowe materiału. Bloki są szeroko stosowane w budownictwie mieszkaniowym jako okładziny konstrukcji izolacyjnych.
Głównymi zaletami bloków są dostępność materiałów i niska cena, długa żywotność bez zniszczenia, przyjazność dla środowiska materiału i łatwość produkcji. Instalacja do produkcji klocków budowlanych własnymi rękami jest dostępna w produkcji i jest popularna wśród rzemieślników domowych. Beton trocinowy jest inny zwiększony czas suszenia, dlatego wewnątrz produktu wykonano kilka otworów przelotowych poprawiających przepływ powietrza.
Wymiary bloków trocin nie są ściśle regulowane, ich szerokość przyjmuje się jako wielokrotność grubości ścianki. Jeśli mówimy o standardowych rozmiarach, bloki są wykonane zgodnie z podwójną grubością cegły (140 mm - 65 x 2 + 10 cm). Przy wytwarzaniu trocin najpierw miesza się suche składniki, następnie dodaje się wodę i do pracy wykorzystuje się mieszalniki zapraw.
Bloczki budowlane z betonu komórkowego
Ich przygotowanie wiąże się ze złożonym procesem nasycania roztworu gazami, który jest trudny do odtworzenia w domu. Pustaki z betonu komórkowego wyróżniają się lekkością, wysokimi właściwościami dźwiękochłonnymi i termoizolacyjnymi.
Produkty z pianki włóknistej do murów
Pianobeton włóknisty jest z natury przyjaznym dla środowiska materiałem ściennym zawierającym piasek, pianę i cement. Zaawansowane technologicznie maszyny do budowy klocków natryskują piankę w masę roztworu, która tworzy jednolite, zamknięte cząstki przestrzeni. Aby zwiększyć wytrzymałość bloków, producenci stosują wzmocnienie włóknem poliamidowym w całej masie. Ten materiał ścienny jest bardzo trwały, nie gnije, jest lekki i trwały.
Produkowane są bloki z betonu piankowego z włóknami różne rozmiary. Dla ściany nośne użyj 20x30x60 cm, który waży 22 kg. Aby zbudować ceglany mur tego samego rozmiaru, będziesz potrzebować 18 kamieni, będą one ważyć 72 kg. Bloczki o mniejszej grubości (10 cm) stosowane są do budowy ścian wewnątrz budynków, przegród, a także służą do izolacji podłóg i ścian. Przewodność cieplna betonu piankowego jest 2,7 razy mniejsza niż cegły i 2 razy mniejsza niż betonu żużlowego i skał łupkowych.
Duże rozmiary bloków ograniczają zastosowanie zaprawa cementowo-piaskowa na mur 20 razy w porównaniu do budowania ściany z małych kamieni. Pianobeton włóknisty nie pali się, nie zmienia kształtu pod wpływem wysokich temperatur i nie wydziela szkodliwych zanieczyszczeń po podgrzaniu.
Bloki styropianowe
Materiał zaliczany jest do innego rodzaju lekkich bloczków betonowych. Różni się od betonu standardowego lepszymi parametrami użytkowymi i niższymi kosztami produkcji. Innowacyjny materiał ścienny przewyższa wagą wszystkie znane lekkie betony, nawet piankowy jest półtora razy cięższy. Dzięki temu wskaźnikowi domy budowane są bez zwykłego masywnego fundamentu, a koszt transportu materiału jest zmniejszony.
Produkcja bloków styropianowych polega na starannym połączeniu cementu, piasku, cząstek styropianu i specjalnych dodatków zatrzymujących powietrze w całej masie. Inny Charakterystyka fizyczna materiał stawia go o krok wyżej niż materiały konwencjonalne. Niska nasiąkliwość i paroprzepuszczalność sprawiają, że styropian jest odporny na wielokrotne zamrażanie i rozmrażanie, co wpływa na trwałość budowanych konstrukcji. Po wzniesieniu ścian standardowe materiały niewielki skurcz występuje przez cały rok. W przypadku bloczków styropianowych nie trzeba czekać tak długo.
Instalacja do produkcji klocków budowlanych własnymi rękami
Do produkcji konstrukcje budowlane stosować specjalne urządzenie, działający na zasadzie procesora wibracyjnego.
Taka maszyna wibracyjna lub stół wibracyjny jest projektowany niezależnie. Własnoręcznie wykonana instalacja do produkcji bloków konstrukcyjnych znacznie obniża koszt bloków i, odpowiednio, ścian domu.
Przygotowanie roztworu
Roztwór przygotowuje się z piasku, cementu, wody i wypełniacza, który stosuje się jako różne materiały, jak napisano powyżej. Aby sprawdzić konsystencję roztworu pod kątem płynności, niewielką ilość wysypać na ziemię. Wysokiej jakości mieszanka nie rozprowadza się wodnistymi strumieniami, zaciśnięta w pięść skleja się w grudkę.
Produkcja bloków żużlowych polega na dokładnym oczyszczeniu żużla z obcych cząstek, a niespalone części węgla nie mogą przedostać się do roztworu. Czasami do roztworu dodaje się gips. W tym przypadku miesza się trzy części żużla i jedną część gipsu, jednocześnie wprowadzając wodę. Rozwiązanie to jest szybkie w użyciu, ponieważ tynk twardnieje w ciągu kilku minut. Przed zmieszaniem żużel nasącza się wodą. Aby poprawić jakość produktów wyjściowych, do roztworu dodaje się nowoczesne dodatki plastyfikatorów. Ich działanie zwiększa mrozoodporność, wodoodporność i wytrzymałość mechaniczną bloczków.
W zależności od przeznaczenia wykonuje się dwa rodzaje bloczków betonowych – pełne i puste. Te pierwsze służą do budowy trwałe konstrukcje, ściany nośne, fundamenty. Drugi rodzaj bloków służy jako materiał przegrodowy, dobrze izoluje od zimnych i obcych dźwięków.
Wykonywanie bloczków betonowych bez stołu wibracyjnego
Spośród tych dwóch technologii zastosowanie drewnianej formy, która została zaprojektowana tak, aby umożliwić naturalny przepływ rozwiązania bez wibracji, cieszy się niesłabnącym zainteresowaniem. Umieszczenie roztworu w przygotowanej formie odbywa się w kilku etapach. Najpierw pojemnik napełnia się jedną trzecią roztworu, po czym ściany formy są ostrożnie pukane młotkiem na obwodzie, aby uzyskać wysokiej jakości skurcz. zaprawa betonowa. W kolejnych dwóch etapach dodawany jest roztwór według oryginalnej technologii, aż do wypełnienia formy. Produkcja bloczków z pustkami polega na włożeniu dwóch plastikowe butelki wodą, którą należy usunąć po zastygnięciu.
Formy pozostawia się do wyschnięcia na 2-5 dni. Następnie ostrożnie usuń bloki z składana konstrukcja i układane na paletach do całkowicie suchy. Dzięki tej metodzie produkcji nie ma potrzeby zakupu.
Potrzebne będą następujące narzędzia i sprzęt: sito do przesiewania piasku, formy do zaprawy, koryto do mieszania lub betoniarka, młotek do gwintowania, wiadro, łopata, kielnia i tace do suszenia.
Sposób wytwarzania bloków za pomocą maszyny wibracyjnej
Aby to zrobić, kup lub wykonaj własną maszynę wibracyjną do bloków żużlowych. Na płaszczyźnie maszyny instalowana jest specjalna metalowa forma i wlewa się do niej mieszankę betonową z wypełniaczem żużlowym do jednej trzeciej. Następnie do akcji podłącza się stół wibracyjny na maksymalnie 20 sekund, co pozwala usunąć wszystkie niepotrzebne pęcherzyki powietrza z roztworu, a cement uzyska dobry skurcz. Roztwór wlewa się do formy trzykrotnie. Bloki są wyjmowane z formy w taki sam sposób, jak w przypadku produkcji bezwibracyjnej.
Blok żużlowy nie toleruje wysychania gorąca pogoda w otwartych promieniach słońca, dlatego w upalne dni spryskuje się go wodą i przykrywa ceratą lub celofanem, aby wilgoć nie odparowywała tak aktywnie. Uformowane, całkowicie wyschnięte bloczki betonowe uzyskują 100% wytrzymałości w 28 dniu i po tym czasie są gotowe do użycia w budownictwie.
Funkcje wytwarzania bloków żużlowych
Formy wykonuje się niezależnie, przy użyciu metalu lub drewna, szerokość desek wynosi co najmniej 190-200 mm. Są one połączone w prefabrykowaną konstrukcję, której boczne części są odłączane w celu usunięcia gotowego bloku. W projekt ogólny w celu ułożenia betonu łączy się nie więcej niż 6 komórek. Gotowy projekt instalowany na gęstym, wodoodpornym materiale, takim jak cerata, tworzącym dno formy.
Jeśli jako materiał na formę wybrano drewno, jest ono wstępnie impregnowane lub podkładowane w celu zwiększenia odporności na wilgoć. Formy wykonane są z suchego drewna. Warunki te są spełnione, w przeciwnym razie podczas pracy drzewo odsunie się od wody i zmieni rozmiar geometryczny blok. Standardowe wymiary kamieni to 400x200x200 mm, ale każdy prywatny producent wykonuje bloki do własnej konstrukcji.
W przypadku matryc metalowych pobiera się arkusze o grubości nie większej niż 3-4 mm. Podczas spawania konstrukcji wszystkie spoiny wykonuje się od zewnątrz, aby nie zaokrąglać narożników bloku. Pustki wewnątrz bloku żużlowego wykonane są za pomocą segmentów metalowe rury odpowiednią średnicę, na przykład 80 mm. Kontrolowana jest odległość między rurami i odległość od ścian, kompozycja jest spawana w paski w celu zapewnienia sztywności i mocowania.
Jeśli wytwarzany jest sprzęt do produkcji bloków konstrukcyjnych, to podczas mocowania wibratora do stołu, po dokręceniu nakrętek, są one nadal lekko zespawane. Silnik musi się zamknąć obudowa ochronna z dowolnego materiału przed rozpryskami roztworu, wodą, kurzem.
Technologia produkcji bloczków trocinowych
Dostępne materiały nie są wstępnie przetworzone i można je kupić w dowolnym miejscu sklep z narzędziami dlatego produkcja bloków z piasku, wapna i trocin rozpoczyna się natychmiast po zakupie. Do mieszania roztworu należy używać betoniarki lub mieszarki do zapraw, mieszając ręcznie odpady drzewne trudny.
Suche trociny, przesiane przez grube sito, miesza się z piaskiem i cementem. Do roztworu dodaje się wapno lub przygotowane ciasto gliniane. Powstałą mieszaninę dobrze miesza się i dopiero potem dodaje wodę, stopniowo wlewając ją małymi porcjami. Aby określić gotowość roztworu, należy go wycisnąć w dłoni, po czym na grudce powinny pozostać odciski palców, co wskazuje prawidłowe proporcje.
Przed wypełnieniem formularzy roztworem są one wyłożone cienka warstwa trociny Wewnętrzne otwory w blokach wykonuje się za pomocą drewnianych kołków o wielkości około 70-80 mm, które wbija się w matrycę przed wylaniem roztworu. Materiał bloków konstrukcyjnych jest szczelnie umieszczany w formie za pomocą specjalnego ubijaka. Pojemnik napełnia się do góry i pozostawia do wyschnięcia na trzy dni. Po tym okresie roztwór zyskuje około 40% wymaganej wytrzymałości.
Formy są demontowane, a bloki suszone przez kolejne cztery dni, po czym wytrzymałość osiąga 70% wymaganego limitu. Gotowe produkty przenoszone są na palety i zabezpieczane bezpośrednio promienie słoneczne. Suszenie bloków jest szybsze, jeśli podczas przechowywania pozostawisz szczeliny między produktami. Zaleca się ustawienie tac w miejscu przeciągu lub zastosowanie wentylatora w celu wymuszonej wentylacji.
Opilko bloki betonowe zyskują 100% wytrzymałości po wyschnięciu przez 3 miesiące, ale można je stosować po miesiącu wietrzenia. W tej chwili ich siła wynosi 90%.
Maszyny i urządzenia
Aby uzyskać wymaganą do budowy liczbę bloków, kupuje się gotową maszynę do wibroformowania. Marka TL-105 ma dobrą wydajność. I choć jego moc wynosi zaledwie 0,55 kW, to w ciągu godziny pracy produkuje około 150 bloczków betonowych o różnym kruszywa. Jego przybliżony koszt na rynku wynosi około 42 800 rubli. Współcześni producenci oprzyrządowania obrabiarkowego produkują wiele typów maszyn do produkcji bloków o dodatkowych funkcjach. Ceny maszyn są różne, a koszt klocków zależy bezpośrednio od tego.
W przypadku małych konstrukcji prywatnych odpowiednia jest maszyna wibracyjna 1IKS, która kosztuje około 17 000 rubli, moc wynosi tylko 0,15 kW, taki sprzęt wytwarza 30 bloków na godzinę. Kupując maszynę, należy wziąć pod uwagę poziom produkcji bloków na potrzeby konstrukcyjne.
Podsumowując, należy zauważyć, że tworzenie klocków własnymi rękami znacznie zaoszczędzi pieniądze na produkcji produktów. Koszt nie jest brany pod uwagę wynagrodzenie, który jest wypłacany pracownikowi. Koszt bloku nie obejmuje kosztów ogólnych i produkcyjnych, podatków i innych odliczeń, dzięki czemu materiał budowlany jest tańszy niż dom.
Blok żużlowy jest dziś jednym z najpopularniejszych materiałów. Służy do budowy obiektów o różnym przeznaczeniu i różnej wielkości. Może być mały budynki gospodarcze lub budynki przemysłowe.
Do wykonania bloków żużlowych stosuje się specjalne urządzenie, którego zasada polega na wibrowaniu mieszanki betonowej. Aby znacznie zaoszczędzić na materiałach budowlanych, możesz to zrobić cegiełki własnymi rękami. Aby to zrobić, musisz kupić lub samodzielnie zaprojektować maszynę wibroprasującą.
Aby rozpocząć produkcję bloczków betonowych własnymi rękami, musisz przygotować wszystkie narzędzia i materiały, które mogą być potrzebne w tym procesie. Standardowy rozmiar blok żużlowy ma wymiary 390x188x190 mm. Wnętrze produktu pozostaje puste. Dwa lub trzy otwory działają jak puste przestrzenie, których kształt i rozmiar zależą bezpośrednio od konfiguracji maszyny.
Dzięki takim pustkom blok żużlowy zapewnia wystarczające pochłanianie dźwięku i izolację termiczną domu. Ale pomimo tak pustej struktury materiał jest bardzo trwały i przetrwa wiele lat. Gdy zaczniesz robić, możesz znacznie zaoszczędzić na materiałach budowlanych.
Początkowo bloki betonowe wytwarzano z żużla. Aby przygotować klasyczną wersję bloku żużlowego, należy zachować pewne proporcje:
- 7 części żużla węglowego z wielkiego pieca;
- 2 części ekspandowanego piasku gliniastego (lepiej jest preferować dużą frakcję);
- 2 części żwiru, frakcja nie może być mniejsza niż 5 i nie większa niż 215 mm;
- 1,5 części cementu klasy 500;
- 3 części wody.
Jako wypełniacz można zastosować inne materiały, tyle że w wersji klasycznej użyto żużla. Dziś jest on trudno dostępny, dlatego zamiast niego można wykorzystać odpady ceglane, keramzyt, popiół, żwir, przesiewacze, tłuczeń kamienny, gips czy przetworzone trociny. Ilość wody może się nieznacznie różnić w zależności od wypełniacza. Jego ilość należy dostosować w trakcie przygotowywania roztworu. Najważniejsze jest to, że nie jest zbyt suchy, ale rozprzestrzenianie się roztworu jest również uważane za niedopuszczalne.
Aby sprawdzić konsystencję roztworu, należy wyrzucić niewielką ilość na ziemię. Uważa się za normalne, że mieszanka rozprowadza się gładko i bez smug wody, jednak jeśli mieszanina zostanie ściśnięta w pięść, powinna się skleić.
Jeśli wykonujesz własne bloki betonowe przy użyciu żużla, bardzo ważne jest, aby upewnić się, że nie ma w nich żadnych ciał obcych. Żużel należy oczyścić z różnych wiórów i ziemi. Niedopuszczalne jest, aby w roztworze znajdował się węgiel niespalony. W celu usunięcia zanieczyszczeń materiał należy przesiać przez sito.
Jeśli do bloku żużlowego zostanie dodatkowo dodany gips, proporcje materiałów ulegną niewielkiej zmianie. Gips (1 część) miesza się z trzema częściami mieszaniny żużla, podczas mieszania dodaje się wodę. Roztwór ten należy zastosować natychmiast po przygotowaniu, ponieważ tynk zacznie szybko schnąć. Przed przygotowaniem takiego roztworu zaleca się namoczenie żużla w wodzie.
Nowoczesny rynek materiałów budowlanych oferuje różnorodne dodatki, które znacząco poprawiają jakość zaprawy. Do roztworu można dodać plastyfikator; potrzeba około 5 g na blok żużlowy. Takie dodatki zwiększają mrozoodporność, wodoodporność i wytrzymałość.
Istnieją dwa rodzaje bloczków betonowych. Mogą być puste lub pełne. Te pierwsze są znacznie lżejsze, służą do budowy ścian, ponieważ nie powodują zbyt dużego obciążenia fundamentu; ponadto takie bloki mają dobrą izolację akustyczną i cieplną. Do budowy fundamentów najczęściej wykorzystuje się bloki lite.
Aby wykonać blok żużlowy, możesz zastosować dwie technologie. Jeden opiera się na zastosowaniu drewnianej formy, w której wysycha zaprawa betonowa. W przypadku drugiej metody musisz samodzielnie kupić lub wykonać specjalną maszynę.
Wróć do treści
Metoda wytwarzania przy użyciu form
Jako materiał, z którego wykonuje się takie formy, można zastosować zarówno drewno, jak i metal. Jeśli do wykonania formy używane jest drewno, musi ono być bardzo dobrze wysuszone. Należy dodatkowo zabezpieczyć środkiem zwiększającym odporność na wilgoć. W przeciwnym razie po krótkim czasie formy mogą ulec deformacji, co wpłynie na geometrię bloczków betonowych. Wewnętrzny rozmiar formy powinien wynosić 400x200x200 mm. Ale to nie jest ograniczenie; kształt może mieć różne rozmiary.
Forma ta składa się z dna i ścian bocznych. Aby przyspieszyć proces produkcji, zaleca się wykonanie kilku form. Aby wszystkie rogi formy były dobrze wypełnione, należy przygotować roztwór bardziej płynny. Aby zrobić puste bloki za pomocą formy w domu, możesz użyć pustych szklanych butelek.
Po wlaniu roztworu do formy szyjkę butelki opuszcza się do mieszanki, wyrównuje się powierzchnię i wykonuje się wymaganą wysokość bloku betonowego. Po 5-6 godzinach butelki należy wyjąć, a kostki pozostawić do dalszego wyschnięcia. Suszenie bloków trwa co najmniej jeden dzień, po czym można je wyjąć z form i ułożyć w stosy. Przed budową takie bloki muszą odpocząć przez co najmniej 1 miesiąc.
Wróć do treści
Bloki betonowe przy użyciu zagęszczarki wibracyjnej
Dzięki specjalnemu sprzętowi bloczki betonowe stają się trwalsze i wyższej jakości. Czy można wykonać prasę wibracyjną własnymi rękami? Całkiem.
Narzędzia potrzebne do stworzenia specjalnego wyposażenia:
- szlifierka do cięcia blach;
- spawarka;
- metr i kreda (ołówek) do znakowania;
- szczypce;
- młotek.
Aby wykonać matryce, w które zostanie wylana mieszanka betonowa, należy wziąć blachę o grubości nie większej niż 3 mm. Maszyna musi być wyposażona w silnik o mocy 100 W, dodatkowo należy przygotować obciążenie, które będzie powodować niewyważenie i wibracje.
Aby wykonać taką maszynę, konieczne jest użycie blachy stalowej. Wycinane są z niego puste miejsca:
- 2 sztuki o wymiarach 400x250 mm;
- 2 sztuki o wymiarach 200x250 mm;
- daszek 400x150 mm;
- żebra – 4 sztuki o wymiarach 40x40 mm;
- rozmiar zacisku 39,5x19,5 mm.
Po wykonaniu wszystkich półfabrykatów możesz rozpocząć montaż głównej matrycy. W tym celu stosuje się części o wymiarach 400x200 mm i 200x250 mm. Bardzo ważne jest, aby wszyscy szwy spawalnicze byli na zewnątrz. W przeciwnym razie gotowe bloki betonowe będą miały zaokrąglone rogi. Rezultatem będzie matryca o wymiarach 400x200x250. Aby wykonać puste przestrzenie wewnątrz bloku żużlowego, należy użyć rury o średnicy 80 mm. Długość detali nie powinna przekraczać 250 mm.
Po przygotowaniu głównej matrycy konieczne jest zainstalowanie w niej półfabrykatów rurowych. Bardzo ważne jest kontrolowanie ich odległości od siebie i od ścian. Wszystkie rozmiary muszą być identyczne. W celu połączenia rur ze sobą i nadania im dodatkowej wytrzymałości należy zastosować przygotowane żebra usztywniające o wymiarach 40x40 mm. Ta konstrukcja jest przyspawana do matrycy.
DO Ostatni etap Obejmuje to instalację wibratora; jest on przymocowany do najdłuższego boku matrycy. Do jego zabezpieczenia służą śruby. Po dokręceniu śrub są one przyspawane w celu zwiększenia wytrzymałości. Aby chronić silnik przed wodą i zanieczyszczeniami moździerz, na górze przyspawany jest daszek ochronny. Do krawędzi wizjera przyspawana jest nogawka, co doda dodatkowej wytrzymałości. Dla wygody uchwyty przyspawane są do matryc.
W zależności od pożądanego rezultatu kształt bloku będzie się różnić. Rynek budowlany jest pełna zagranicznych/krajowych producentów bloczków betonowych. Produkują materiał o dowolnej kategorii złożoności. Gdy samonaprawa, możliwość stworzenia bloku w domu jest całkiem realna.
Uwaga: montaż bloków zajmie znacznie mniej czasu w porównaniu do innych materiałów ze względu na ich rozmiar.
Szereg zastosowań
Coraz częściej bloczki betonowe wykorzystuje się jako podstawowy element budynków: garaży, wielokondygnacyjnych budynków mieszkalnych, biur, domów prywatnych, domki letnie I tak dalej. Zakres zastosowania nie ogranicza się do dużej skali projektów budowlanych. Istnieje możliwość samodzielnej produkcji/użytkowania bloczków betonowych w domu. Jedyna trudność: konieczne jest użycie dodatkowego sprzętu budowlanego (suszarka, betoniarka). Zamknięte pomieszczenie (gospodarstwo) z grzejnikiem może pełnić funkcję suszarki. Wymagana temperatura dla suszarki zrób to sam - 70 stopni. Formy betonowe stosowane są do następujących wyrobów:
- materiał budowlany z betonu;
- dekoracyjny elementy architektoniczne(wazony, );
- płyty chodnikowe(typ może się różnić);
- ogrodzenia (w tym dekoracyjne);
- żelbetowe płyty budowlane.
Cecha: W zależności od potrzebnego produktu jakość, części i odlewy będą różne. Aby stworzyć kształt, a następnie wykonać produkt własnymi rękami, powinieneś dokładne obliczenia, uważnie monitoruj proces, przestrzegaj zasad tworzenia, poznaj cechy materiału/przyszłego produktu.
Materiał do produkcji
Różnorodność bloczków betonowych i cechy ich zastosowania wprowadziły na rynek wiele nowych materiałów. Surowiec co nada formie cechy jakościowe mogą się różnić w zależności od wymagań dotyczących produktu końcowego. Każdy materiał jest przeznaczony kategoria cenowa, jakość, metody przetwarzania, wskaźniki techniczne.

Produkcja wyrobów z Małe szczegóły, tworzenie jak najwięcej dokładne kopie, wymaga zastosowania form elastomerowych. Obszar zastosowań:
- złożone produkty wolumetryczne;
- płaskorzeźby o wysokiej precyzji;
- konstrukcje architektoniczne.
Produkcja tych produktów nie jest możliwa bez następujących komponentów:
- guma (kauczuk syntetyczny);
- formoplast;
- związki (poliuretan/silikon).
Przybliżone zużycie materiału: 10-40 kg/m2.
Wada: wykonanie takiego produktu w domu jest niezwykle trudne. Należy używać specjalistycznego sprzętu do gotowania i kruszenia. Ponadto przed rozpoczęciem pracy z substancją należy skonsultować się ze specjalistą. Ze względu na zawiłości pracy z materiałem taka konsultacja jest obowiązkowa.
Plastikowy
Z nich najlepiej wykonywać konstrukcje wielkogabarytowe, które nie wymagają precyzyjnych obliczeń geometrycznych formy plastikowe. Podstawowe materiały:
- włókno szklane (niska kompatybilność z matrycą cementową, dlatego możliwe są pęknięcia i pęknięcia);
- twardy plastik (podatny na wypaczenia, dlatego głównym obszarem zastosowania są płyty chodnikowe, krawężniki, kostka betonowa);
- arkusz Plastik ABS(podatny na rozwarstwianie, należy zastosować dodatkowy smar silikonowy. Można z niego wykonać materiał małogabarytowy);
- styropian arkuszowy (dobrze oddaje fakturę i kontury przedmiotów, jest materiałem delikatnym);
- Tworzywo PCV (najtrwalsze, wysokiej jakości. Przyczepność jest na jak najniższym poziomie, nie wymaga czyszczenia i smarowania).
Jeśli zdecydujesz się użyć plastiku do wykonania bloku, upewnij się, że masz sztywny szalunek. To szalunek zapewni materiałowi niezbędną ulgę, sztywność i zapewni łatwy demontaż. W przypadku niezgodności tej zasady, produkty albo rozpadną się podczas suszenia, albo wynik będzie niskiej jakości i krótkotrwały.
Samodzielne utworzenie formularza
Proszę to zanotować obróbka końcowa Wyrób należy wykonywać po całkowitym stwardnieniu. Jeśli produkt jest surowy, dalsze działania(na przykład cięcie) są nielogiczne, nieskuteczne. Tworzenie formularza:
- Rozpocznij produkcję z dostępnymi materiałami. Można na przykład użyć styropianu. Wytnij stempel, wypełnij go wcześniej przygotowaną mieszanką (piasek i cement). Otrzymasz jeden egzemplarz formy do dekoracji betonu. Możesz użyć plastikowych pojemników różne rozmiary zamiast znaczków.
- Złóż produkt z resztek płyty wiórowej i drewna. Podstawową zasadą jest to, że powierzchnia powinna być gładka. Jeżeli będzie szorstka, pomiędzy bloczkami a podłożem utworzą się pęknięcia lub beton będzie nierównomiernie rozłożony, co utrudni usunięcie produktu.
- Wypełnij formę mieszanką betonową i pozostaw ją na kilka dni do całkowitego wyschnięcia (w zależności od rodzaju mieszanki i materiału, z którego wykonany jest produkt). Wymagane wskaźniki zobacz instrukcje dotyczące materiału).
- Po całkowitym wyschnięciu ostrożnie usuń (na przykład szpatułką lub podobnym przedmiotem) gotowy produkt.
- Wykonaj (jeśli to konieczne) wymagane prace dekoracyjne.
Jeśli nie masz czasu/chęci na samodzielne przeprowadzenie procesu, skorzystaj z usług firmy budowlane. Kontaktując się z firmą, której potrzebujesz, możesz złożyć zamówienie na potrzebny formularz. Wyjaśnij cel budowy, pożądany materiał i określ czas. Za ustaloną cenę (do ustalenia osobiście, telefonicznie) zostaniesz poinformowany i Twoje zamówienie zostanie przyjęte. Dzięki temu możesz mieć pewność co do jakości powstałego produktu, jego trwałości i poprawności jego wykonania.
Po co robić bloki?
Co trzeba do tego mieć?
Z czego wykonane są bloki?
Jak je wyprodukować?
Dlaczego opłaca się samodzielnie tworzyć klocki?
Jaki jest z tego zysk?
Od czego zacząć i jak rozwijać ten biznes?
W tym artykule otrzymasz odpowiedzi na wszystkie postawione pytania i będziesz mógł „włączyć” dla siebie wiarygodne źródło dochodu, które zależy tylko od Ciebie.
A więc rozwiążmy to po kolei.
Po co robić klocki?
Zapewne zauważyłeś, że budownictwo przeżywa boom przez ostatnie 4-5 lat. Budują od małych i średnich budynków prywatnych: garaży, daczy, osiedli, warsztatów, warsztatów, budynków rolniczych, po duże budynki przemysłowe i mieszkalne, magazyny, centra. Specjaliści specjalności budowlane popyt jak nigdy dotąd.
Pojawiają się nowe technologie i materiały budowlane. Ale czy zawsze są dostępne pod względem ceny i technologii dla szerokiego grona programistów?
Dlatego rzadko stosuje się je w budownictwie małej i średniej wielkości, jak np główne miasta i w małych wioskach.
Najbardziej przystępnymi cenowo materiałami budowlanymi pozostają tzw. blok żużlowy i cegła.
Co więcej, cegła jest często gorsza od bloku żużlowego pod względem ceny, przewodności cieplnej i łatwości układania.
Jednak puste w środku elementy konstrukcyjne są wygodne i niedrogie dla większości prywatnych deweloperów.
Tak, ponieważ dzięki swoim właściwościom:
Z łatwością można z nich zbudować niską (2-3 piętra) konstrukcję (garaż, dom, domek, budynek gospodarczy, warsztat itp.), Nawet bez uciekania się do usług murarza. (1 blok = 3-4 cegły);
Ściany z pustaków żużlowych są dźwiękoszczelne i nieprzepuszczalne dla ciepła;
Cena bloku żużlowego jest niższa niż cena cegły, bloku piankowego i innych materiałów budowlanych ze względu na niski koszt i dostępność jego składników (patrz poniżej);
Tylko bloki żużlowe można wykonać samodzielnie. Możesz także samodzielnie wykonać adobe (cegłę ze słomy glinianej).
Jak więc samodzielnie wykonać bloki żużlowe?
Co jest potrzebne do produkcji klocków?
Wiadomo, że bloki żużlowe wytwarzano ze zbrojonego betonu specjalny sprzęt za pomocą komory parowej. Dlatego produkcja wysokiej jakości bloku w domu nie była dostępna.
Ale jeśli jest popyt, podaż jest nieunikniona. I to jest!
Od 1994 roku doświadczenie w produkcji elementów konstrukcyjnych w produkcji indywidualnej i małoseryjnej daje odpowiedź na postawione pytanie.
Czego to wymaga?
Maszyna wibracyjna
- Surowy materiał
- Technologia
- Stosunkowo płaski teren
- Sieć domowa na 220V (bez komentarza).
Wyjaśnijmy każdy punkt bardziej szczegółowo.
Maszyna wibracyjna
Jeść różne projekty maszyny wibracyjne. W krajowych warunkach produkcji i małych przedsiębiorstwach ręczna, elektryczna, małogabarytowa wibrator bloków żużlowych MZ30 (14 rok produkcji) z pewnością sprawdziła się w krajach WNP. Popularnie znany jako „Sen dewelopera”
Surowy materiał
Do produkcji klocków potrzebne są następujące komponenty:
Cement- Cement portlandzki gatunek 400. Dopuszczalny jest inny. Ale dobór proporcji jest konieczny. Na przykład przy stosowaniu cementu klasy 300 jego zużycie należy zwiększyć o 10-15%.
Wypełniacze do betonu może być najbardziej różne materiały: piasek, tłuczeń kamienny, żużel, żużel granulowany, popiół, trociny, wióry, przesiewy, keramzyt, gips, złom ceglany i inne materiały naturalne i przemysłowe.
W zależności od lokalnych warunków, wymagań dotyczących produkowanych bloków i kosztu można wybrać odpowiedni wypełniacz. Wymienię kilka popularnych kompozycji betonów oraz główne grupy betonów
1). Żużel z zakładów hutniczych (szary lub ciemnoszary o dużej zawartości cementu, przesiana drobna frakcja) – 9 części
Cement – 1 część
Woda 0,5 objętości cementu
2). Żużel ziarnisty z zakładów hutniczych (kolor żółto-zielonkawy o dużej zawartości cementu, przesiana drobna frakcja) – 4 części
Małe pokazy – 4 części
Cement – 1 część
Woda 0,5 objętości cementu
3). Inny beton żużlowy
4). Beton na piasku i kruszonym kamieniu
5). Beton na odpadach ceglanych
6). Beton ekspandowany
7). Beton popiołowy
8). Beton trocinowy
9). Beton perlitowy
10). Beton styropianowy
i inne betony z inna kombinacja katalogowany.
Teraz jest jasne, że obecna nazwa „blok żużlowy” nie jest najodpowiedniejsza precyzyjna definicja możliwe elementy konstrukcyjne.
Dodatek plastyfikujący- Nie jest to istotny składnik betonu. Ale jego obecność zapewnia: wczesną wytrzymałość bloczków (jest to bardzo ważne przy ograniczonej przestrzeni produkcyjnej), poprawia jakość bloczków (zmniejsza się pękanie i ścieranie bloczków), poprawia wodoodporność i mrozoodporność betonu.
Ilość dodatku jest bardzo mała - około 5g w kostce.
Technologia produkcji elementów konstrukcyjnych:
- Przygotowanie betonu
- Produkcja blokowa
- Suszenie i przechowywanie gotowych bloków.
Przygotowanie betonu(na przykładzie podanej wcześniej drugiej receptury betonu)
1). Wsyp 4 łopaty drobnego przesiewu + 4 łopaty granulowanego żużla
2). Napełnij 1 łyżkę cementu
3). Dokładnie wymieszać
4). Dodaje rozpuszczony UPD do 7-9 litrów wody + 250 ml (pół półlitrowego słoika). Roztwór dodatku przygotowuje się w następujący sposób: do 40-litrowego pojemnika wsypać 0,5 kg UPD i dokładnie wymieszać aż do całkowitego rozpuszczenia.
5). Zamieszać. W tym przypadku beton jest jakościowo impregnowany roztworem UPD.
Produkcja blokowa
1). Zasypiasz w wibrującej maszynie gotowy beton Z mała zjeżdżalnia. Krótko, przez 1-2 sekundy. włącza wibrator - beton zagęszcza się, za pomocą pacy jednym ruchem wyrównujesz powierzchnię lekko osiadłego betonu.
2). Zamontuj zacisk i bez większego wysiłku dociśnij go, włączając wibrator.
Bloki z okrągłymi i prostokątnymi pustkami wibrują przez 4-5 sekund. aż zacisk opuści się na ograniczniki.
Wąskie pełne bloki (2 szt.) wibrują przez 5-7 sekund.
3). Maszynę podnosisz za pomocą wibracji - blok pozostaje na platformie.
Suszenie i przechowywanie gotowych bloków
W przypadku stosowania UPD gotowe bloki można usunąć z placu budowy i przechowywać w ciągu 5-6 godzin. Bez UPD - za dwa dni.
Po tym czasie bloczki nie kruszą się pod warunkiem zachowania proporcji betonu i technologii ich wytwarzania.
Gotowe bloki zalecam przechowywać w piramidalnych stosach w jednym bloku z niewielką (2-3 cm) szczeliną między blokami - w celu dalszego wysuszenia krawędzi bocznych.
W każdej takiej piramidzie znajduje się 100 elementów. Łatwo policzyć. Przydatne jest oznaczenie każdej piramidy datą i godziną produkcji ostatniego bloku. Przyda się to podczas wdrażania. Możesz wysłać 4 lub 5 dnia.
Miejsce produkcji
- Pokój z gładką betonową podłogą.
Można produkować bloki cały rok. Pożądany dobra wentylacja i ogrzewanie w zimne dni.
- Otwarta płaska powierzchnia.
Może być betonowy lub ziemny, kryty folia z tworzywa sztucznego aby zachować prezentację klocków (tylna krawędź nie ulega zabrudzeniu).
- Otwarty, stosunkowo płaski teren bez wstępnego przygotowania.
Na takiej platformie można układać gotowe bloki na paletach.
Od czego zacząć produkcję klocków konstrukcyjnych?
1. Wybierz najlepszy lokalny materiał betonowy na podstawie kosztów i dostawy.
2. Oblicz koszt 1 bloku, biorąc pod uwagę składniki betonu.
3. Zdecyduj o miejscu produkcji.
4. Kup maszynę wibracyjną.
5. Opanuj podane technologie.
Na początku beton można przygotować ręcznie. Następnie jest to bardziej wydajne i łatwiejsze - na elektrycznej betoniarce o pojemności 0,2-0,5 metra sześciennego (najlepiej 0,5, biorąc pod uwagę przyszłość).
Dlaczego warto samodzielnie tworzyć elementy konstrukcyjne?
Podam realne koszty kruszywa z dostawą i cementem, kalkulację kosztów wytworzenia bloczków i zwrotu maszyny wibracyjnej „Marzenie Dewelopera” do produkcji bloków żużlowych w Zaporożu (Ukraina) w 2004 roku na przykładzie betonu wykonanego z granulowanego żużla (szarego) i cementu.
Wstępne dane:
8 metrów sześciennych żużla– 30 dolarów/samochód z dostawą na terenie miasta (KRAZ lub duży MAZ)
Cement:
Proporcja 1:9 - 0,88 metra sześciennego lub 18 worków po 3 dolary = 54 dolary
Cena maszyny wibracyjnej- 200 dolarów
Całkowita objętość roztworu:
Proporcja 1:9 – 8 + 0,88 = 8,88 (metrów sześciennych)
Objętość roztworu na 1 blok żużlowy GOST:
Całkowita objętość: 39 cm x 19 cm x 19 cm = 0,014 (m3)
objętość pustek:
Przy d = 9,5 cm: 3 x 3,14 x 4,75**2 x 15 = 3188 cm3 = 0,003188 m3
Objętość roztworu na 1 blok przy d = 9,5 cm: 0,011 metra sześciennego
Tabela wyników obliczeń:
Notatka:
1. W przypadku bloku żużlowego z 2 prostokątnymi pustkami potrzeba mniej zaprawy (ale wytrzymałość takiego bloku jest mniejsza)
2. Zastępując granulowany żużel lokalnym kruszywem do betonu, które jest dla Ciebie akceptowalne, ceny w Twoim regionie (w Rosji cena detaliczna bloku żużlowego są wyższe) i korzystając z wymiarów bloku żużlowego, możesz łatwo obliczyć koszt 1 szt./blok i zwrot pieniędzy za maszynę dla siebie.
Obliczanie rentowności i zysku:
Przyjmujemy wstępne założenia: |
||
Nazwa |
Zakres wartości |
Wartość referencyjna |
Czas na utworzenie 1 bloku (sek.) bez UPD | ||
Liczba bloków na 1 godzinę, biorąc pod uwagę czas obciążania betonu w 30 sekund. (rzeczy) | ||
Liczba bloków w 1 dzień (8 godzin) sztuk | ||
Cena detaliczna 1 bloku żużlowego (w 2005 r.): na Ukrainie |
2,0 UAH (0,4 USD) 15 rub. (0,5 USD) |
|
Rentowność(Z poprzedniej tabeli wynika, że koszt 1 bloku to 1/3 jego ceny detalicznej) |
||
Produkuj bloki dziennie w ilości: na Ukrainie | ||
Wyprodukuj bloki w ilości: na Ukrainie | ||
Koszt będzie wynosić: na Ukrainie | ||
Zyskiem będzie: na Ukrainie |
Notatka :
- Jeśli zastosujesz UPD, produktywność znacznie wzrośnie.
- Rekord należy do Wiktora Romanowa i Siergieja Rachmaninowa, którzy w lipcu 1998 r. w ciągu jednego dnia wyprodukowali 700 bloków 390*138*188
Rozwój i ekspansja biznesu
1. Zatrudniaj odpowiedzialnych pracowników, godnych ich zainteresowania. (W naszym mieście - 20 kopiejek (0,04 centa) za blok, w regionie - 0,02 centa.)
2. Rozpoczynając sprzedaż, obniż cenę detaliczną, tworząc w ten sposób godną konkurencję i otrzymując wdzięcznych klientów i ich rekomendacje. (Ważne! Jakość musi być godna).
3. W sezonie ciepłym lub w ogrzewanym pomieszczeniu (niezależnie od pory roku) pracę można zorganizować na 2 zmiany.
4. W tym przypadku przedsiębiorca zależy tylko od: obecności napięcia w sieci i zdrowia siły roboczej (na pierwszym etapie, przed zwrotem kosztów, możesz samodzielnie pracować z maszyną).
5. Jeśli to konieczne, wynajmij maszynę „programistom”.
6. Realizuj zamówienia od „programistów” bezpośrednio na ich stronie, oszczędzając im pieniądze na załadunku, transporcie i rozładunku bloków.
7. Ponadto – nie będziesz potrzebować pozwolenia od Państwowego Elektronadzoru, ponieważ cały sprzęt jest przeznaczony do zwykłej sieci domowej!
Dekrety Rządu Federacji Rosyjskiej z dnia 13.08.97 nr 1013, Gosstandart Federacji Rosyjskiej nr 86 z dnia 10.08.2001 i Gosstroy Federacji Rosyjskiej nr 128 z dnia 24.12.2001, wykaz do wyrobów wymagających obowiązkowej certyfikacji nie zalicza się bloczków betonowych budowlanych z różnymi wypełniaczami (żużel, keramzyt, trociny itp.) oraz urządzeń wibracyjnych do ich produkcji.
W ten sposób działalność związaną z produkcją bloków konstrukcyjnych można rozwijać etapami:
- Zaczynać się minimalne koszty na zakup maszyny wibracyjnej, 1 maszyny lokalnego surowca jako wypełniacza do betonu, 15-20 worków cementu.
Udostępnij bezpłatne ogłoszenia sprzedaży wysokiej jakości bloków żużlowych.
Wyprodukuj 800-1000 bloków. Sprzedaj szybko, obniżając cenę detaliczną.
- Zakup betoniarki oraz kolejną partię surowców + UPD.
Wyrównaj cenę do poziomu detalicznego (opcjonalnie).
Publikuj ogłoszenia darmowe + płatne.
- Produktywnie, dzięki zgromadzonemu doświadczeniu produkcyjnemu, produkujemy bloki wysokiej jakości, realizując zamówienia.
Nie ma już potrzeby reklamowania: wysoka jakość bloki + reklama szeptana załatwią sprawę.
Zorganizuj dwuzmianową produkcję klocków konstrukcyjnych.
Poszerzyć asortyment produkowanych bloków.
Zakup dodatkowych maszyn wibracyjnych i ewentualnie betoniarki.
Rekrutuj twardych pracowników
Miej czas na przekazywanie swoich zysków lub inwestowanie ich nowy biznes, tak samo opłacalne.
Czego Ci szczerze życzę!
Sukces i dobrobyt!!
„Katalog kompletnych pakietów biznesowych” masterdela.info
napisz na adres: [e-mail chroniony],
Ukraina, Zaporoże, sierpień 2005
Jeden z najczęstszych materiałów do budowy ścian nośnych i przegród budynków mieszkalnych, a także małych budynki przemysłowe są bloki betonowe. Ich popularność wynika z niskiego kosztu, doskonałego Charakterystyka wydajności I duża ilość odmiany, co pozwala wybrać odpowiedni blok do niemal każdego zadania.
Instrukcje podane w tym artykule pomogą Ci nauczyć się samodzielnie wykonywać bloczki betonowe, a także zapoznają Cię z ich istniejącymi rodzajami.
Bloki betonowe na ściany
Rodzaje sztucznych kamieni wykonanych z betonu
Przyjrzyjmy się głównym rodzajom + cechom betonowych elementów konstrukcyjnych, które są najczęściej spotykane w nowoczesnym budownictwie.
blok żużlowy
Te kamienie ścienne produkowane są metodą wibrokompresji zaprawy betonowej na specjalnych platformach.
Skład mieszanki, z której wykonany jest blok żużlowy, może obejmować:
- kruszony kamień do wyrobów betonowych;
- walka na cegły;
- trociny;
- ekspandowana glina
Dane techniczne Bloczki betonowe z żużlem pozostawiają wiele do życzenia, jednak ze względu na to, że ich cena jest jedną z najniższych na rynku, bloczki żużlowe znajdują szerokie zastosowanie w budownictwie prywatnym.
Ale koszt jest prawie jedyną zaletą, ponieważ pozostają daleko w tyle za innymi materiałami pod względem następujących parametrów:
- trwałość;
- parametry oszczędzania ciepła;
- wytrzymałość.
Głównym zakresem zastosowania bloków jest małe budynki, które nie będą poddawane dużym obciążeniom:
- szopy;
- garaże;
- kuchnie letnie;
- warsztaty i tak dalej.
Zdjęcie bloku żużlowego
Mniej powszechny materiał wykonany z następujących elementów:
- materia organiczna (głównie drewno);
- element wiążący (proszek);
- utwardzacz.
Zasadniczo ten sztuczny kamień składa się z trocin zamkniętych w betonowej skorupie.
Zalety materiału są oczywiste:
- niewielka waga bloku betonowego;
- wysokie właściwości termoizolacyjne;
- dobra izolacja akustyczna;
- wydajna wymiana powietrza.
Aby chronić bloki przed negatywny wpływ środowisko, kamienie są traktowane specjalnym roztworem. Zapobiegnie to tworzeniu się pleśni i gniciu.
Arbolit doskonale nadaje się do budowy małych domów, które nadają się do rezydencja całoroczna bez stosowania dodatkowej izolacji termicznej.
Blok Arbolitowy
Bloki gazowe i bloki piankowe
Bloczki z betonu komórkowego, według GOST, który określa ich właściwości techniczne, muszą składać się w 70-85% ze sztucznie utworzonych porów (komórek) wypełnionych powietrzem. Najpopularniejsze są bloki piankowe i gazowe.
Materiały te mają następujące zalety:
- Są lekkie, dzięki czemu transport bloczków betonowych i ich montaż w budownictwie prywatnym nie wymaga użycia specjalnego sprzętu;
- łatwe w obróbce – nadają pożądany kształt blok komórkowy Do drewna możesz użyć zwykłej piły do metalu;
- ściany z bloczków z betonu komórkowego dobrze zatrzymują ciepło i mają doskonałe właściwości dźwiękochłonne.
Bloczki z betonu komórkowego produkowane są z roztworu zawierającego piasek, cement i kruszywo. Aby utworzyć pianę, dodaje się do niej wapno, proszek aluminiowy lub inny środek spieniający.
Notatka!
W przeciwieństwie do piankowego betonu, gazobeton jest poddawany dodatkowe przetwarzanie w autoklawie, gdzie jest poddawany działaniu wysoka temperatura pod wysokim ciśnieniem (10-12 MPa).
W rezultacie materiał ten zyskuje zwiększoną wytrzymałość: prawie niemożliwe jest jego rozdrobnienie lub złamanie.
Bloczek z betonu komórkowego
Samodzielna produkcja bloków
Technologia produkcji Sztuczny kamień z zaprawa cementowa z wypełniaczem jest stosunkowo proste, co pozwala na samodzielne wykonanie bloczków betonowych.
Praca przygotowawcza
NA etap początkowy należy określić wymiary przyszłego bloku. Gdy własnej roboty parametry każdego element indywidualny podejmowane w oparciu o wymaganą szerokość ściany.
Grubość dna bloczka nie powinna być mniejsza niż 2 cm, a ścianki pustek nie mniejsze niż 4 cm W tym przypadku standardowy kamień o wymiarach 20x20x40 cm z pustymi przestrzeniami w środku waży około 40 kg, co daje. jest wygodny do układania ścian.
Do produkcji potrzebny będzie dowolny płaski obszar pokryty folią z tworzywa sztucznego i specjalne formy bez dna.
Materiałami do formularzy będą:
- deski;
- sklejka.
Aby chronić drzewo przed uszkodzeniem, wewnętrzna część formy są osłonięte metalowa blacha. Wstawki wykonane są w podobny sposób, dzięki czemu gotowy blok tworzą się puste przestrzenie. Poprawiają właściwości termoizolacyjne materiału i sprawiają, że jest on lżejszy.
Formy do produkcji bloczków betonowych
Możesz szybciej produkować bloki betonowe własnymi rękami, jeśli wykonasz kilka form w jednym bloku na raz. Aby to zrobić, potrzebujesz sklejki lub deski o szerokości równej wysokości przyszłego bloku. Materiał jest cięty na kawałki i mocowany za pomocą wkrętów samogwintujących. Następnie wykonywane są przegrody wewnętrzne.
Rada!
Aby zamrożony blok można było łatwo oddzielić od formy, wszystkie jego części należy nasmarować naftą, olejem maszynowym lub środkiem niezamarzającym.
Proces produkcji
Do odlewania bloków betonowych potrzebne będą następujące materiały:
- drobny żwir;
- cement;
- piasek;
- woda;
- Limonka;
- drut do wzmocnienia.
Ilość każdego składnika ustalana jest na podstawie zapotrzebowania na sztuczny kamień. Proporcje cementu, piasku i żwiru przyjmuje się w stosunku 1:3:5.
Do mieszania roztworu betonowego lepiej jest użyć betoniarki.
Dla ułatwienia prezentacji cały kolejny proces podzielimy na kilka etapów.
Blok betonowy własnej roboty
Opisana powyżej technologia pozwala na wykonanie bloczków betonowych własnymi rękami bez większego wysiłku. Dane techniczne produkt końcowy Praktycznie w niczym nie ustąpią analogom sprzedawanym w supermarketach budowlanych, a rozmiarem idealnie dopasują się do Twoich potrzeb. Ponadto może to znacznie obniżyć koszty zakupu materiałów budowlanych i ich dostawy.
Film w tym artykule pomoże Ci bardziej szczegółowo zapoznać się z materiałem.