Technologia wykonywania napraw dziur z użyciem mieszanki asfaltobetonowej. Czy zimą można naprawiać asfalt? Nowy trend w renowacji dróg
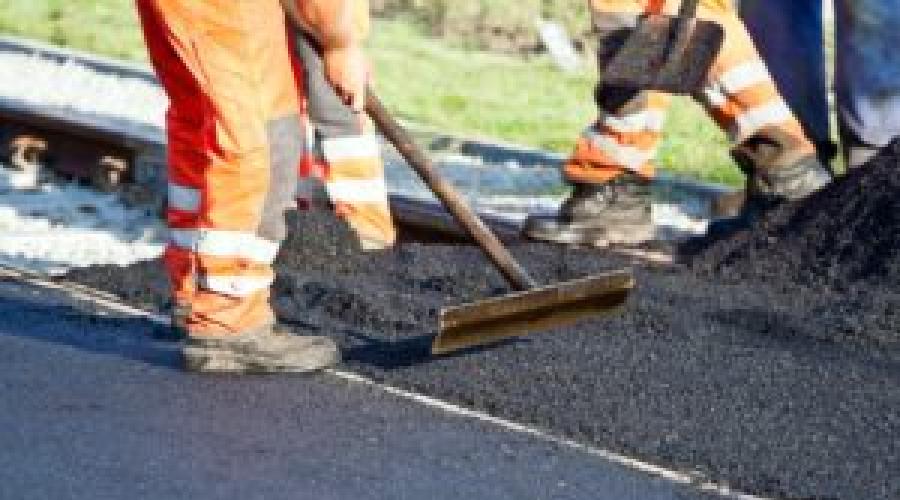
Przeczytaj także
ODM 218.3.060-2015
DOKUMENT METODOLOGICZNY PRZEMYSŁU DROGOWEGO
Przedmowa
1 OPRACOWANE przez Federalny Budżet Państwa instytucja edukacyjna wyższe wykształcenie zawodowe „Moskiewskie Państwo Samochodowe i Autostradowe Uniwersytet Techniczny(MADI)”
2 WPROWADZONE przez Departament Badań Naukowo-Technicznych i Wsparcia Informacyjnego Federalnej Agencji Drogowej
5 WPROWADZONE PO RAZ PIERWSZY
1 obszar zastosowania
1 obszar zastosowania
2 Odniesienia normatywne
Pęknięcia temperaturowe powstają na skutek chłodzenia i odporności powłoki na skurcz termiczny. Pionowo pęknięcia te rozwijają się od góry do dołu, od powierzchni powłoki do podstawy.
Pęknięcia zmęczeniowe powstające podczas uginania się warstwy monolitycznej pod powtarzającymi się obciążeniami transportowymi rozwijają się od dołu do góry, od podstawy do powierzchni powłoki.
Odbite pęknięcia imitują szwy lub pęknięcia nawierzchni z betonu cementowego i są najbardziej charakterystyczne dla warstw betonu asfaltowego układanych na nawierzchni z betonu cementowego. Wraz ze spadkiem temperatury dochodzi do deformacji powłoki betonu cementowego w postaci skrócenia płyt. W rezultacie szwy lub pęknięcia w nawierzchni z betonu cementowego rozszerzają się, powodując rozciąganie i pękanie leżących nad nimi warstw betonu asfaltowego, tworząc odbite pęknięcia. Do tych naprężeń rozciągających dodaje się własne naprężenia rozciągające powstałe w wyniku spadku temperatury betonu asfaltowego. Jest to proces cykliczny w czasie, który prowadzi do zniszczenia nawierzchni asfaltobetonowej.
W zależności od szerokości pęknięcia dzielimy na wąskie (do 5 mm), średnie (5-10 mm) i szerokie (10-30 mm). Klasyfikacja ta jest typowa dla pęknięć temperaturowych i zmęczeniowych. W przypadku pęknięć odbitych podejście to jest nieprawidłowe, ze względu na obecność odkształceń temperaturowych podłoża cementowobetonowego, powodujących przemieszczanie się krawędzi pęknięcia w zależności od temperatury, długości płyty cementowo-betonowej, grubości nawierzchni asfaltobetonowej i innych czynników. czynniki.
W zależności od szerokości i rodzaju pęknięć dobiera się technologię ich naprawy oraz skład użytego sprzętu. Głównym zadaniem naprawy pęknięć jest niedopuszczenie do przedostawania się przez nie wody do leżących poniżej warstw nawierzchni. Hydroizolację pęknięć uzyskuje się poprzez uszczelnienie ich specjalnymi mastyksami i mieszankami naprawczymi.
6.1.3 Wybierając masy uszczelniające, należy skupić się na ich podstawowych właściwościach fizycznych i mechanicznych. Jeden z najważniejsze wskaźniki przy wyborze mas uszczelniających jest siła przyczepności, której wymagania muszą być zgodne z GOST 32870-2014.
6.1.4 Uszczelnianie wąskich pęknięć temperaturowych lub zmęczeniowych na powierzchni warstw asfaltobetonów ułożonych na nawierzchni z betonu cementowego nie wymaga skomplikowanych operacji technologicznych. Pęknięcia są czyszczone przez przedmuchanie skompresowane powietrze, suszone, podgrzewane i wypełnione emulsją bitumiczną lub mastyksem o dużej zdolności penetracji.
6.1.5 Na cienkie pęknięcia temperaturowe lub zmęczeniowe (2-5 mm) można nałożyć podgrzany kit polimerowo-bitumiczny w postaci taśmy zapobiegającej odpryskiwaniu powłoki na krawędziach pęknięcia. Wygładza się go specjalnym żelazkiem grzewczym (butem) i posypuje piaskiem frakcjonowanym. Powłokę w strefie pęknięć poddaje się wstępnemu suszeniu podgrzanym strumieniem sprężonego powietrza.
6.1.6 Jeżeli pęknięcie ma zniszczone krawędzie, technologię naprawy należy rozpocząć od operacji jej rozcięcia, czyli sztucznego rozszerzenia górnej części pęknięcia do komory, w której zapewniona jest optymalna wytrzymałość materiału uszczelniającego na rozciąganie podczas okres otwierania się pęknięć.
6.1.7 Szerokość komory nie może być mniejsza niż strefa zniszczenia krawędzi pęknięć. Aby stworzyć jak najlepsze warunki pracy szczeliwa w komorze, stosunek szerokości i głębokości komory przyjmuje się zwykle jako 1:1. Dodatkowo przy określaniu wymiarów geometrycznych komory należy uwzględnić maksymalne możliwe otwarcie pęknięcia oraz wydłużenie względne użytego materiału uszczelniającego. Typowo szerokość komory mieści się w zakresie 12-20 mm.
6.1.8 Jeżeli pęknięcie temperaturowe lub zmęczeniowe nie zostanie wycięte na pełną głębokość (grubość pękniętej powłoki przekracza 10 cm), to przed uszczelnieniem należy zastosować specjalny sznur uszczelniający wykonany z elastycznego materiału odpornego termicznie i chemicznie na szczeliwo a środowisko umieszcza się w szczelinie na dnie komory. Kiedy jest używany do prasowania sznur uszczelniający należy wziąć pod uwagę, że jego średnica powinna być 1,2-1,3 razy większa niż szerokość komory wyciętego pęknięcia.
Głębokość rowka po wciśnięciu sznura uszczelniającego (górna wolna część komory) jest przyjmowana w zależności od właściwości uszczelniacza.
Zamiast sznura uszczelniającego można również zastosować warstwę piasku bitumicznego lub warstwę okruchów gumy ułożoną na dnie komory o grubości równej średnio 1/3 jej głębokości, po czym komorę wypełniony uszczelniaczem.
Przy stosowaniu piasku bitumicznego stosuje się piasek gruby i średni, który spełnia wymagania GOST 8736-2014 i GOST 11508-74 *.
Gumowy okruszek musi mieć wielkość cząstek w przedziale 0,3-0,5 mm i spełniać wymagania*.
________________
*Patrz sekcja. - Uwaga producenta bazy danych.
W zależności od temperatury lepkości i odporności szczeliwa na zużycie pod wpływem kół samochodowych, należy go wypełnić podsypką, równo lub z utworzeniem plamy na powierzchni powłoki.
6.1.9 W przypadku, gdy krawędzie pęknięcia temperaturowego lub zmęczeniowego nie uległy zniszczeniu i możliwe jest jakościowe uszczelnienie pęknięcia bez jego przecinania, operację tę można wyłączyć z procesu technologicznego.
6.1.10 Najważniejszy warunek zapewnieniem jakości uszczelnienia pęknięć jest obecność dobrej przyczepności szczeliwa do ścianek nienaciętej szczeliny lub wyfrezowanej komory. W związku z tym wiele uwagi poświęca się pracom przygotowawczym dotyczącym czyszczenia i suszenia pęknięcia. Aby poprawić przyczepność, ściany frezowanej komory zagruntowuje się podkładem - cieczą błonotwórczą (klejącą) o niskiej lepkości.
6.1.11 Główną operacją technologiczną przy naprawie pęknięć temperaturowych lub zmęczeniowych jest wypełnienie ich gorącą masą uszczelniającą. Mastyk jest wstępnie podgrzewany do temperatury 150-180°C, po czym jest podawany do wbudowanej komory lub bezpośrednio do szczeliny. W tym przypadku, w zależności od użytego sprzętu, można uszczelnić samo pęknięcie lub jednocześnie z wypełnieniem masą uszczelniającą, nałożyć tynk na powierzchnię powłoki w miejscu pęknięcia. Łata ta o szerokości 6-10 cm i grubości 1 mm pozwala wzmocnić krawędzie pęknięcia i zapobiec ich zniszczeniu.
W przypadku pęknięć ze znacznym zniszczeniem krawędzi (10-50% długości pęknięcia) zaleca się uszczelnianie klejem, ponieważ w tym przypadku następuje zagojenie defektów na powierzchni powłoki w strefie pęknięć.
Metodę naprawy pęknięć średnio- i szerokotemperaturowych lub zmęczeniowych warstw betonu asfaltowego ułożonych na betonie cementowym dzieli się na pięć etapów:
1. Cięcie pęknięć. W tym przypadku stosuje się specjalne separatory pęknięć. Aby uniknąć uszkodzenia krawędzi podczas wycinania pęknięcia w nawierzchni z betonu asfaltowego, jest to konieczne przy wyborze narzędzie tnące wziąć pod uwagę skład betonu asfaltowego. W przypadku, gdy wielkość ziaren kruszywa wynosi 20 mm i więcej, zaleca się użycie narzędzia diamentowego, a gdy wielkość kruszywa do 20 mm, można zastosować frezy z napawaniem węglikowym.
2. Usunięcie zniszczonego betonu asfaltowego. W tym celu stosuje się wysokowydajny kompresor. Do dokładnego oczyszczenia zarówno z pyłu powstającego przy cięciu, jak i do usunięcia osadów zalegających głęboko w szczelinie.
3. Suszenie i podgrzewanie. Wyciętą wnękę pęknięcia suszy się i podgrzewa tzw. lancą cieplną.
Parametrem zatrzymania ogrzewania jest pojawienie się stopionego bitumu na ścianach pęknięć. W żadnym wypadku nie należy przegrzewać pęknięcia; wypalenie bitumu spowoduje gwałtowny spadek przyczepności i dalsze zniszczenie powłoki wokół pęknięcia.
W związku z tym ogrzewanie pęknięcia za pomocą palników otwarty ogień gorszący.
4. Wypełnienie szczeliny szczeliny uszczelniaczem. Natychmiast wprowadzany do oczyszczonej, osuszonej i podgrzanej jamy wyciętego pęknięcia mastyks bitumiczny z maszyny do topienia i odlewania.
Nowoczesne nalewaki to na ogół podgrzewany zbiornik zamontowany na ramie wyposażonej w koła. Ogrzewanie można przeprowadzić za pomocą oleju chłodzącego, gazu lub palnika na olej napędowy. Materiał uszczelniający ładowany jest do zbiornika, gdzie jest podgrzewany do temperatury roboczej, a następnie za pomocą pompy poprzez węże żaroodporne wprowadzany jest do przygotowanej szczeliny.
Pęknięcia uszczelniane są bezpośrednio za pomocą różnych dysz, których wielkość zależy od szerokości wypełnianej szczeliny. W razie potrzeby dyszę napełniającą można wyposażyć w stopki umożliwiające montaż masy uszczelniającej na powierzchni powłoki w strefie pęknięcia.
Aby zmniejszyć obciążenie dynamiczne szwu i zmniejszyć przyczepność szczeliwa do koła przejeżdżającego samochodu, konieczne jest wypełnienie tylko wewnętrznej wnęki pęknięcia bez rozlewania się na krawędzie.
5. Proszek. Natychmiast po wypełnieniu pęknięcia szczeliwem miejsce naprawy pokrywa się piaskiem lub mieszanką drobnego kruszonego kamienia i proszku mineralnego.
6.1.12 Do proszkowania stosuje się specjalny sprzęt - dystrybutor. Sprzęt stanowi bunkier osadzony na trzech kołach. Ponadto przednie koło fortepianowe pozwala na ruch dokładnie w kierunku pęknięcia, a rolka dozująca zamontowana jest na osi tylnych kół wewnątrz leja zasypowego. Dystrybutor przesuwany jest ręcznie wzdłuż uszczelnionej szczeliny, bezpośrednio za wylewką, natomiast koła obracają wał, dozując kruszony piasek lub drobny tłuczeń kamienny na powierzchnię wsypanej do szczeliny masy uszczelniającej.
Proszek służy do przywrócenia ogólnej tekstury i chropowatości powłoki, zapobiega przyklejaniu się masy uszczelniającej do kół samochodu i zmniejsza płynność szczeliwa natychmiast po wypełnieniu pęknięcia.
6.1.13 Podczas wykonywania prac związanych z renowacją pęknięć należy zapewnić ciągłość procesu technologicznego. Dopuszczalne odstępy czasowe pomiędzy poszczególnymi osobami operacji technologicznych nie powinna przekraczać następujących wartości: 1 - wycinanie pęknięć - do 3 godzin; 2 - czyszczenie pęknięć - do 1 godziny; 3 - nagrzewanie bocznych ścian pęknięcia - do 0,5 min; 4 - uszczelnienie pęknięć - do 10 minut; 5 - posypać powierzchnię szczeliwa piaskiem lub drobnym kruszonym kamieniem proszkiem mineralnym.
6.1.14 Technologia renowacji pęknięć realizowana jest za pomocą zestawu urządzeń składającego się z:
Separator pęknięć z narzędziem diamentowym do wielkości kruszywa nawierzchnia drogi powyżej 20 mm, przy uziarnieniu kruszywa do 20 mm stosuje się frezy z napawaniem węglikowym;
Szczotka mechaniczna lub traktor kołowy z zamontowaną szczotką (w przypadkach, gdy zachodzi konieczność renowacji dość szerokich i silnie zanieczyszczonych pęknięć, można je czyścić szczotkami tarczowymi z metalowym włosiem, szczotkami z tarczą o średnicy 300 mm i grubość 6, 8, 10 lub 12 mm, grubość powinna być o 2-4 mm mniejsza niż szerokość czyszczonej szczeliny);
Kompresor;
Generator gazu lub lanca grzewcza. Zasada działania lancy grzewczej polega na tym, że sprężone powietrze pochodzące ze sprężarki o wydajności 2,5-5,0 m/min i ciśnieniu 3,5-12 kg/cm jest mieszane z gazu ziemnego i wchodzi do komory spalania w postaci mieszanki gazowo-powietrznej, gdzie ulega zapaleniu. Powietrze ogrzane do temperatury 200-1300°C dostarczane jest poprzez dyszę z prędkością 400-600 m/s do strefy leczonego pęknięcia. Zużycie gazu w tym przypadku wynosi 3-6 kg/godz. Przepływ sprężonego powietrza o dużej prędkości, oprócz ogrzewania, skutecznie oczyszcza wnękę samego pęknięcia, a ponadto wyciąga pojedyncze zniszczone cząsteczki powłoki z obszaru sąsiadującego z pęknięciem;
Maszyna do topienia i odlewania zamontowana na podwoziu pojazdu;
Sprzęt do wypełniania uszczelnionych pęknięć.
6.1.15 Podczas naprawy pęknięć odbitych należy przede wszystkim ustalić, czy naprawiane pęknięcie jest typu odbitego. Wizualnie odbite pęknięcia można łatwo odróżnić od pęknięć temperaturowych i zmęczeniowych, ponieważ przechodzą przez szwy znajdującej się pod spodem powłoki z betonu cementowego, jakby je „kopiowały”.
Jeżeli w samym betonie cementowym występują pęknięcia, to takie odbite pęknięcia można zidentyfikować na powierzchni warstwy asfaltobetonu za pomocą badania georadarowego.
6.1.16 Jednym ze sposobów naprawy pęknięć odbitych jest sztuczne rozszerzenie ich górnej części w celu utworzenia komory, której szerokość uwzględnia maksymalne możliwe rozwarcie pęknięcia (zwykle co najmniej 1 cm) i względne wydłużenie pęknięcia zastosowany materiał uszczelniający.
Technologia wykonywania tego typu prac naprawczych omówiono w punktach 6.1.6-6.1.8.
6.1.17 Inną metodą jest naprawa pęknięć odbitych za pomocą geosiatek wzmacniających w połączeniu z ciągłymi geowłókninami. W tym przypadku geosiatka uczestniczy w pracy naprężenia podczas zginania, zapobiegając otwarciu się pęknięcia, a geowłóknina pełni rolę warstwy tłumiącej, która pochłania naprężenia powstające w strefie pęknięcia podczas ruchów temperaturowych płyt z betonu cementowego.
Geosiatce stawiane są następujące wymagania: musi ona charakteryzować się dużą wytrzymałością cieplną, niskim pełzaniem w odpowiednio wysokich temperaturach układania mieszanki asfaltobetonowej (120-160°C) oraz dobrą przyczepnością do bitumu. Rozmiary komórek przyjmuje się w zależności od składu mieszanki asfaltobetonowej i zapewnienia dobrej przyczepności pomiędzy warstwami powłoki (około 30-40 mm przy stosowaniu gorących mieszanek asfaltobetonowych na lepkim bitumie).
Przedstawiono warstwę geowłókniny z włókniny następujące wymagania: gęstość międzywarstwy nie powinna przekraczać 150-200 g/m, wytrzymałość na rozciąganie 8-9 kN/m, wydłużenie przy zerwaniu 50-60%.
6.1.18 Naprawa pęknięć odbitych za pomocą geosiatek zbrojeniowych w połączeniu z geowłókninami wykonywana jest w następującej technologii:
Organizacja ruch drogowy na miejscu pracy montaż ogrodzenia;
Oczyszczenie powłoki z kurzu i brudu;
Frezowanie istniejącej nawierzchni asfaltobetonowej w strefie spękań na szerokość 30-50 cm i do głębokości naprawianej warstwy (ale nie mniejszej niż 5 cm);
Podgruntowanie zmielonej powierzchni asfaltobetonowej kationową emulsją bitumiczną w ilości co najmniej 1 l/m2 w przeliczeniu na bitum;
Ułożenie warstwy geowłókniny na szerokość 30 cm ściśle symetrycznie do osi naprawianego pęknięcia (przy układaniu paska geowłókniny należy zapewnić jej wstępne naprężenie co najmniej 3%. Tkaninę rozciąga się o 30 cm długość paska 10 m);
Na warstwę geowłókniny należy ułożyć warstwę gruboziarnistej mieszanki asfaltobetonowej na szerokość wyfrezowanego pęknięcia, a następnie zagęszczać warstwa po warstwie grubością 5-6 cm. Jeżeli występują warstwy niższe, przeprowadza się zagęszczanie przez ubicie górnej warstwy - wałkami lub płytami wibracyjnymi, tak aby zagęszczona powierzchnia asfaltobetonu zrównała się z istniejącą powłoką;
Zagruntowanie powierzchni ułożonej warstwy betonu asfaltowego emulsją bitumiczną w ilości co najmniej 0,6 l/m w przeliczeniu na bitum dla szerokości ułożenia geosiatki 150-170 cm;
Ułożenie arkusza geosiatki ściśle symetrycznie do osi naprawianego pęknięcia;
Wielokrotne wylewanie spoiwa na całą szerokość powierzchni powłoki;
Ułożenie i zagęszczenie wierzchniej warstwy nawierzchni z gęstej, drobnoziarnistej mieszanki asfaltobetonowej w warstwie co najmniej 5-6 cm na całej szerokości naprawianej nawierzchni.
6.1.19 Jednym ze sposobów naprawy pęknięć odbitych jest ich renowacja za pomocą gorącego, drobnoziarnistego uszczelniania pęknięć mieszanka asfaltobetonowa ze spoiwem bitumiczno-gumowym. Dzięki temu możliwe jest znaczne tłumienie naprężeń powstających nad szwami nawierzchni z betonu cementowego oraz pochłanianie wewnętrznych odkształceń plastycznych. Okruchy gumy zawarte w spoiwie pełnią rolę cząstek składnika polimerowego, które zapewniają rozproszone elastyczne wzmocnienie betonu asfaltowego.
Mieszanki asfaltobetonowe na bazie spoiwa bitumiczno-gumowego należy projektować w zależności od rodzaju i przeznaczenia betonu asfaltowego, zgodnie z GOST 9128.
Wymagania techniczne dla kompozytowych lepiszczy bitumiczno-gumowych muszą spełniać ustalone wymagania.
W przypadku kompozytowych lepiszczy bitumiczno-gumowych jako materiały wyjściowe stosuje się lepkie asfalty drogowe naftowe gatunków BN, BND zgodnie z GOST 22245 oraz asfalty ciekłe gatunków MG i MGO zgodnie z GOST 11955.
Wykorzystuje się drobnoziarnistą gumę, czyli okruchy gumy ogólnego przeznaczenia, w tym gumy otrzymywanej w wyniku kruszenia zużytych opon samochodowych lub innych gumowych wyrobów technicznych. Miąższ musi mieć wielkość cząstek w przedziale 0,3-0,5 mm i spełniać wymagania.
6.1.20 Technologia naprawy pęknięć odbitych przy użyciu gorącej drobnoziarnistej mieszanki asfaltobetonowej ze spoiwem bitumiczno-gumowym obejmuje następujące operacje technologiczne:
Cięcie pęknięć;
Mechaniczne czyszczenie pęknięcia;
Wydmuchanie pęknięcia sprężonym powietrzem;
Ocieplenie bocznych ścian pęknięcia, zagruntowanie dna i ścian pęknięcia;
Uszczelnienie pęknięcia gorącą drobnoziarnistą mieszanką asfaltobetonową ze spoiwem bitumiczno-gumowym;
Zagęszczanie mieszanki asfaltobetonowej.
Do zagęszczania stosuje się małogabarytowy wał lub płytę wibracyjną.
Temperatura mieszanki asfaltobetonowej na asfaltach BND 40/60, BND 60/90, BND 90/130, BND 130/200, BND 200/300 ze spoiwem bitumiczno-gumowym na początku zagęszczania nie powinna być niższa niż 130- 160°C dla gęstych asfaltobetonów typu A i B oraz asfaltobetonów o dużej gęstości.
6.1.21 Sekwencja technologiczna prac przy naprawie dziur składa się z następujących operacji: oczyszczenie powierzchni asfaltobetonowej z wilgoci, brudu i kurzu w miejscu pracy; wyznaczenie granic prac remontowych liniami prostymi wzdłuż i w poprzek osi drogi, uwzględniając 3-5 cm nieuszkodzonej powierzchni (w przypadku naprawy kilku sąsiadujących ze sobą dziur łączy się je w jeden kontur lub mapę); cięcie - cięcie lub frezowanie na zimno naprawionego betonu asfaltowego wzdłuż zarysowanego konturu na całą głębokość ubytku, nie mniej jednak niż grubość warstwy asfaltobetonu. W której boczne ściany musi być pionowy; czyszczenie dna i ścian miejsca naprawy z małych kawałków okruchów, kurzu, brudu i wilgoci; obróbka dna i ścian cienką warstwą płynnego (gorącego) lub upłynnionego bitumu lub emulsji bitumicznej, ułożenie mieszanki asfaltobetonowej; wyrównywanie i zagęszczanie warstwy powłokowej.
6.1.22 W przypadku odprysków w płytach chodnikowych z betonu cementowego, powstałe wyboje w leżącej nad nimi warstwie asfaltobetonowej mogą mieć znaczną głębokość (ponad 20-25 cm). Naprawę takich miejsc należy przeprowadzić poprzez usunięcie całej grubości zniszczonej warstwy asfaltobetonowej, szerokości odłupanej powierzchni płyty cementobetonowej. Naprawę odprysków powierzchni płyty cementowo-betonowej należy przeprowadzić zgodnie z. Następnie układa się i zagęszcza mieszankę asfaltobetonową.
6.1.23 Do napraw łatających warstwy betonu asfaltowego ułożonego na nawierzchni z betonu cementowego zaleca się stosowanie głównie asfaltobetonu mieszanego na gorąco lub lanego asfaltobetonu typu I i II zgodnie z wymaganiami GOST 9128-2013 i GOST R Odpowiednio 54401-2011.
Zaleca się stosowanie mieszanek asfaltobetonowych odpowiadających wytrzymałością, odkształcalnością i chropowatością betonowi asfaltowemu istniejącej nawierzchni. Należy stosować gorące mieszanki drobnoziarniste typu B i C, gdyż są one bardziej zaawansowane technologicznie do pracy łopatami, grabiami i kielniami w operacjach pomocniczych niż mieszanki wielokruszeniowe typu A.
Do przygotowania gorących drobnoziarnistych mieszanek asfaltobetonowych stosuje się lepkie bitumy drogowe BND 40/60, BND 60/90, BND 90/130, BND 130/200, BND 200/300 zgodnie z GOST 22245, a także modyfikowany polimer -spoiwa bitumiczne zgodnie z OST 218.010-98.
6.1.24 Do prac związanych z obróbką krawędzi wykorzystuje się małe frezarki, piły tarczowe i wiertarki udarowe.
W zależności od obszaru naprawianego obszaru cięcie powłoki odbywa się na różne sposoby. Niewielkie powierzchnie (do 2-3 m) konturuje się za pomocą frezu do szwów wyposażonego w specjalne cienkie (2-3 mm) tarcze diamentowe o średnicy 300-400 mm. Następnie powłokę wewnątrz obwodu demontuje się za pomocą młotów pneumatycznych. Usunięto okruszki betonu asfaltowego i przygotowano teren do ułożenia mieszanki asfaltobetonowej.
6.1.25 Przygotowując się do naprawy wąskich, długich dziur lub obszarów o powierzchni większej niż 2-3 m, zaleca się użycie zamontowanych na stałe, ciągnionych lub zamontowanych frezów, które odcinają wadliwy materiał powłokowy o szerokości 200-500 mm do głębokość 50-150 mm.
Jeśli powierzchnia jest duża, stosuje się specjalne wysokowydajne frezarki drogowe o dużej szerokości ciętego materiału (500-1000 mm) i maksymalnej głębokości do 200-250 mm.
6.1.26 Zagruntowanie dna i ścian konturowego otworu oczyszczonego z drobnych kawałków i pyłu cienką warstwą płynnego (gorącego) lub ciekłego bitumu lub emulsji bitumicznej (zużycie asfaltu 0═3-0═5 l/m) można to zrobić za pomocą: mobilnej nagrzewnicy bitumicznej ═ dystrybutora asfaltu ═ mechanika drogowego itp.
Skuteczny do smarowania naprawianych dziur małe instalacje(5 KM) ═ pompowanie emulsji bitumicznej do dyszy natryskowej wędki ręcznej z wężem o długości 3-4 m, instalacje z podawaniem emulsji z beczki za pomocą pompy ręcznej.
W przypadku małych nakładów pracy i małych dziur gruntowanie emulsją można wykonać z przenośnych pojemników (10-20 l) metodą natrysku sprężonym powietrzem na zasadzie natrysku.
6.1.27 Układanie mieszanki asfaltobetonowej odbywa się ręcznie lub przy użyciu drobnogabarytowych układarek asfaltowych. Podczas ręcznego układania mieszanki wyrównywanie mieszanki asfaltobetonowej odbywa się za pomocą improwizowanych środków (grabie i kielnie).
Dziurę wypełnia się mieszanką asfaltobetonową w warstwach o grubości 5-6 cm, biorąc pod uwagę współczynnik bezpieczeństwa zagęszczenia. Wśród środków mechanizacji do zagęszczania stosuje się mały wałek lub płytę wibracyjną. Powierzchnia naprawianego miejsca po zagęszczeniu powinna znajdować się na poziomie istniejącej powłoki.
6.1.28 Aby zwiększyć skuteczność naprawy dziur gorącą mieszanką asfaltobetonową, stosuje się specjalne maszyny naprawcze. Na maszynie podstawowej umieszczony jest zbiornik termiczny na gorącą mieszankę asfaltobetonową z izolacją termiczną i ogrzewaniem; zbiornik, pompa i opryskiwacz emulsji bitumicznej; kompresor do czyszczenia i odkurzania map naprawczych, napęd młota pneumatycznego do odcinania krawędzi map naprawczych, płyta wibracyjna do zagęszczania mieszanki asfaltobetonowej.
6.1.29 Podczas prac w warunkach zwiększonej wilgotności, przed gruntowaniem ubytki są osuszane sprężonym powietrzem (gorącym lub zimnym).
6.1.30 Naprawę dziur metodą wtrysku strumieniowego z użyciem kationowej emulsji bitumicznej wykonuje się przy użyciu specjalnego sprzętu ciągnionego. Ubytek do naprawy oczyszcza się strumieniem sprężonego powietrza lub metodą odsysania, zagruntowuje emulsją podgrzaną do temperatury 60-75°C i wypełnia kruszonym kamieniem poczerniałym w procesie wtrysku. W przypadku tej metody naprawy nie ma potrzeby odcinania krawędzi (ryc. 6.1).
Rysunek 6.1 – Kolejność operacji w przypadku metody wtrysku strumieniowego przy wypełnianiu dziury: 1 – czyszczenie dziury strumieniem powietrza o dużej prędkości; 2 - pokrycie powierzchni dziury; 3 - wypełnianie i zagęszczanie; 4 - sucha polewa
Rysunek 6.1 – Kolejność operacji w przypadku metody wtrysku strumieniowego przy wypełnianiu dziury: 1 – czyszczenie dziury strumieniem powietrza o dużej prędkości; 2 - pokrycie powierzchni dziury; 3 - wypełnianie i zagęszczanie; 4 - sucha polewa
6.1.31 Jako materiały naprawcze stosuje się kruszony kamień o frakcji 5-10 mm oraz emulsję typu EBK-2. Stosować skoncentrowaną emulsję (60-70%) na bazie bitumu BND 90/130 lub BND 60/90 przy przybliżonym zużyciu 10% wagowych kruszonego kamienia. Powierzchnię „pieczęci” posypuje się białym kruszonym kamieniem w warstwie jednego kruszonego kamienia. Ruch zostanie otwarty za 10-15 minut. Prace wykonujemy w temperaturze powietrza co najmniej +5°C, zarówno na suchych, jak i mokrych powierzchniach.
6.1.32 Na drogach kategorii III-IV oraz w przypadku „awaryjnych” napraw dróg wyższych kategorii, naprawa dziur w warstwie asfaltobetonowej na nawierzchni z betonu cementowego może być wykonywana przy użyciu mokrych mieszanek organicznych i mineralnych (MOMS) . Metoda naprawy za pomocą VOMS polega na oczyszczeniu dziury, wypełnieniu jej zwilżoną mieszanką materiał mineralny wybrany skład i ciekłe spoiwo organiczne (smoła lub bitum ciekły) oraz zagęszczenie mieszanki. Grubość ułożonej warstwy materiału musi wynosić co najmniej 3 cm.
W skład VOMS wchodzi kamień wapienny lub tłuczeń dolomitowy o frakcji 5...20 mm (do 40%)═ piasek o module uziarnienia co najmniej 1═0═ mączka mineralna (6...12% )═ spoiwo (smoła, bitum płynny lub ciekły lepki) w ilości 6...7% oraz woda. Zamiast kruszywa kamiennego dopuszcza się stosowanie pokruszonych przesiewów pokruszonego żużla. Mieszankę można przygotować do przyszłego zastosowania w konwencjonalnych wytwórniach betonu asfaltowego, wyposażonych w system doprowadzania i dozowania wody.
VOMS można stosować w temperaturach powietrza do -10°C i układać na wilgotnej powierzchni dziury.
6.1.33 Inną metodą „awaryjnej naprawy” dziur jest naprawa za pomocą zimnych mieszanek asfaltobetonowych (naprawczych).
Ten typ naprawy stosuje się w przypadku dziur o średnicy do 1 m. Dziury są naprawiane natychmiast po ich wykryciu; w niektórych przypadkach prace można przeprowadzić bez wycinania dziury lub jej frezowania.
Naprawcza mieszanka na zimno składa się z wypełniacza mineralnego, spoiwa organicznego z dodatkiem specjalnych dodatków. Mieszanie mieszaniny odbywa się w instalacjach o działaniu wymuszonym.
Jako spoiwo organiczne stosuje się asfalty marki BND 60/90 i BND 90/130, spełniające wymagania GOST 33133-2014. Właściwości asfaltów poprawia się poprzez wprowadzenie różnych dodatków z rozpuszczalnikiem organicznym (rozcieńczalnikiem).
Rozcieńczalniki stosowane w celu nadania określonej lepkości oryginalnemu bitumowi MG 130/200 (GOST 11955-82) muszą spełniać wymagania GOST R 52368-2005 i GOST 10585-99. Ilość rozcieńczalnika wynosi 20-40% wagowych lepiszcza bitumicznego i jest określana przez laboratorium.
W procesie sporządzania mieszanek naprawczych stosuje się środki powierzchniowo czynne w celu zwiększenia siły przyczepności spoiwa do powierzchni materiałów mineralnych i zapewnienia określonych właściwości.
Temperatura mieszaniny nie powinna być niższa niż -10°C. Dopuszcza się układanie mieszanki naprawczej na zamarzniętym i mokrym podłożu, ale pod warunkiem braku kałuż, lodu i śniegu w naprawionym obszarze.
Podczas naprawy dziur w nawierzchni, w zależności od głębokości zniszczenia mieszanina naprawcza układać w jednej lub dwóch warstwach o grubości nie większej niż 5-6 cm, przy dokładnym zagęszczeniu każdej warstwy.
Podczas eliminacji dziur na powierzchni należy obserwować ciąg technologiczny, który obejmuje oczyszczenie uszkodzonego obszaru, wyrównanie i zagęszczenie mieszanki naprawczej.
Gruntowanie naprawianej powierzchni bitumem lub emulsją bitumiczną nie jest konieczne.
Mieszankę naprawczą układa się biorąc pod uwagę zmniejszenie grubości warstwy podczas zagęszczania, dla którego grubość nałożonej warstwy powinna być o 25-30% większa niż głębokość dziury.
Podczas naprawy dziur, w zależności od powierzchni naprawianego obszaru, mieszaninę zagęszcza się za pomocą płyty wibracyjnej, ręcznego walca wibracyjnego, mechanicznego, a przy małych nakładach pracy - ręcznego ubijaka. Jeżeli wielkość dziury przekracza 0,5 m, mieszaninę zagęszcza się za pomocą płyty wibracyjnej. Ruch środków zagęszczających kierowany jest od krawędzi obszaru do środka. Zagęszczenie uważa się za zakończone, jeśli nie ma śladów szczeliwa.
Mieszanka najczęściej pakowana jest w worki foliowe o wadze 20, 25, 30 kg lub w innej ilości uzgodnionej z konsumentem. Nieopakowaną mieszaninę można przechowywać pod daszkiem w otwartych stosach betonowa podłoga w ciągu 1 roku. Mieszanka zapakowana w szczelne worki zachowuje swoje właściwości przez dwa lata.
6.1.34 Jedną z metod naprawy dziur jest ich uszczelnienie laną mieszanką asfaltobetonową. Mieszanka ta różni się od zwykłej mieszanki asfaltobetonowej zwiększoną zawartością mączki mineralnej (20-24%) i bitumu (9-10%) gatunku BND 40/60. Zawartość kruszonego kamienia - 40-45%. Przy temperaturze układania 200-220°C masa ma konsystencję odlewu, co eliminuje konieczność zagęszczania. Mieszankę dowożą na plac budowy specjalnymi pojazdami z podgrzewanym kontenerem i wypełniają nią przygotowaną kartę do naprawy dziur.
Po ochłodzeniu mieszaniny do 50-60°C ruch w naprawianym obszarze zostaje otwarty.
Przy układaniu nowych warstw nawierzchni asfaltobetonowej niedopuszczalne jest stosowanie lanych mieszanek asfaltobetonowych do naprawy dziur. Podczas układania nowych warstw asfaltobetonów należy usunąć wylane płyty naprawcze z warstw leżących poniżej.
6.1.35 Pojedyncze wady na powierzchni nawierzchni asfaltobetonowej w postaci odprysków i łuszczenia eliminujemy metodą wtrysku strumieniowego, podobnie jak w przypadku naprawy wybojów.
6.2 Urządzenie do obróbki powierzchni na nawierzchni drogi
6.2.1 Urządzenie do obróbki powierzchni nawierzchni drogi pozwala zwiększyć jej właściwości przyczepne, a także chronić przed zużyciem i działaniem czynników atmosferycznych. Podczas stosowania obróbki powierzchniowej zwiększa się szczelność powłoki i wydłuża się jej żywotność. Ponadto eliminowane są drobne nieprawidłowości i wady.
6.2.2 Jednorazową obróbkę powierzchniową przeprowadza się na powierzchni nawierzchni asfaltobetonowej, jeżeli posiada ona wady w postaci: łuszczenia, odprysków, pęknięć i małych dziur.
Podwójną obróbkę powierzchni przeprowadza się w przypadku znacznego zniszczenia nawierzchni asfaltobetonowej (ponad 15%. Całkowita powierzchnia powłoki). W takim przypadku można podjąć decyzję o frezowaniu wierzchniej warstwy nawierzchni asfaltobetonowej.
6.2.3 Montaż pojedynczej obróbki powierzchniowej przeprowadza się zgodnie z Zaleceniami Metodologicznymi dotyczącymi instalacji pojedynczej obróbki powierzchni szorstkiej przy użyciu sprzętu z synchronicznym rozprowadzaniem bitumu i kruszonego kamienia.
6.2.4 Obróbkę pojedynczej powierzchni przeprowadza się z reguły w ciepłych, letnich porach roku, na suchej i odpowiednio ciepłej powierzchni przy temperaturze powietrza co najmniej +15°C.
Sekwencja pojedynczego urządzenia do obróbki powierzchni:
Praca przygotowawcza;
Pojedyncze urządzenie do obróbki powierzchni;
Pielęgnacja warstwy wierzchniej.
6.2.5 Prace przygotowawcze obejmują:
Eliminacja wad powłoki;
Selekcja i przygotowanie kruszonego kamienia i bitumu;
Wybór początkowego zużycia kruszonego kamienia i bitumu;
Dobór i dostosowanie sprzętu i maszyn wchodzących w skład specjalistycznego oddziału;
Kształcenie i szkolenie personelu obsługującego maszyny i mechanizmy.
6.2.6 Na obszarach wybranych do obróbki pojedynczej powierzchni likwidacja usterek na jezdni odbywa się zgodnie z wymaganiami. Wypełnianie ubytków i pęknięć należy zakończyć co najmniej 7 dni przed rozpoczęciem obróbki powierzchni.
6.2.7 Dobór przybliżonego zużycia kruszonego kamienia i bitumu na jedno urządzenie do obróbki powierzchni odbywa się zgodnie z tabelą 6.1.
Tabela 6.1 - Wybór przybliżonego zużycia kruszonego kamienia i bitumu dla pojedynczego urządzenia do obróbki powierzchni
Frakcja kruszonego kamienia, mm |
Konsumpcja |
|
kruszony kamień, m/100 m |
bitum, kg/m |
|
6.2.8 Do obróbki powierzchni zaleca się stosowanie maszyn z synchronicznym rozkładem lepiszcza i kruszonego kamienia (synchroniczny sposób rozkładu lepiszcza i kruszonego kamienia, rys. 6.2).
6.2.9 Urządzenie do obróbki powierzchni przeprowadza się w następującej kolejności:
Oczyszczenie powierzchni z kurzu i brudu;
Wyjaśnienie standardów zużycia materiałów;
Synchroniczne rozmieszczenie bitumu i kruszonego kamienia na powierzchni jezdni;
Zagęszczenie świeżo ułożonej szorstkiej warstwy;
Pielęgnacja powierzchni.
6.2.10 Oczyszczenie powierzchni powłoki z kurzu i brudu przeprowadza się za pomocą specjalistycznych maszyn ze szczotką nylonową, a w przypadku silnego zanieczyszczenia powierzchni - szczotką metalową i urządzeniami do podlewania. Powłokę czyści się w dwóch do pięciu przejściach wzdłuż toru.
Rysunek 6.2 - Synchroniczne rozmieszczenie spoiwa i kruszonego kamienia podczas obróbki powierzchni
Rysunek 6.2 - Synchroniczne rozmieszczenie spoiwa i kruszonego kamienia podczas obróbki powierzchni
6.2.11 Zagęszczanie świeżo ułożonej warstwy przeprowadza się bezpośrednio po przejeździe maszyny z synchronicznym rozprowadzaniem spoiwa i kruszonego kamienia. Wykonać 5-6 przejazdów walcem samobieżnym na kołach pneumatycznych po powierzchni o nacisku koła co najmniej 1,5 tony i ciśnieniu w oponach 0,7-0,8 MPa lub walcem z rolkami metalowymi pokrytymi gumą. Ostateczne uformowanie się warstwy następuje pod wpływem przejeżdżającego transportu samochodowego z dopuszczalną prędkością do 40 km/h. Okres tworzenia świeżo ułożonej warstwy powinien wynosić co najmniej 10 dni.
6.2.12 Konserwacja świeżo ułożonej powłoki powierzchniowej obejmuje następujące operacje:
Ograniczenie prędkości do 40 km/h;
Regulacja ruchu na całej szerokości jezdni za pomocą płotów prowadzących;
Oczyszczenie nieukorzenionego pokruszonego kamienia szczotką podlewacza nie później niż jeden dzień po zakończeniu zagęszczania;
Dodatkowe zagęszczenie walcem.
6.2.13 W przypadku stosowania pojedynczej obróbki powierzchni w sposób synchroniczny, odstęp czasu pomiędzy wylaniem asfaltu a rozłożeniem kruszywa jest krótszy niż 1 s. Zapewnia to znaczną poprawę przyczepności spoiwa poprzez wnikanie go w mikropory kruszonego kamienia. W tym przypadku pokruszony kamień dobrze przylega do powierzchni powłoki. Dzięki synchronicznemu rozprowadzaniu lepiszcza i kruszonego kamienia jakość obróbki powierzchni ulega znacznej poprawie, zarówno przy zastosowaniu gorącego bitumu, jak i emulsji bitumicznej jako spoiwa.
6.2.14 Prace przy montażu podwójnej obróbki powierzchniowej prowadzi się na czystej, odpylonej powierzchni powłoki, suchej w przypadku stosowania bitumu i zwilżonej w przypadku stosowania emulsji bitumicznych. Temperatura powietrza przy stosowaniu asfaltu jako spoiwa nie powinna być niższa niż +15°C, a przy stosowaniu emulsji asfaltowej nie niższa niż +5°C. W niektórych przypadkach, gdy nie jest możliwe zapewnienie wymaganej czystości zmielonej powłoki, zaleca się jej zagruntowanie poprzez wylanie ciekłego bitumu w ilości 0,3-0,5 l/m.
6.2.15 Proces technologiczny urządzenia do podwójnej obróbki powierzchni obejmuje:
Frezowanie nawierzchni asfaltobetonowej;
Oczyszczenie frezowanej powierzchni z kurzu i resztek asfaltu;
Zagruntować powierzchnię powłoki (jeśli to konieczne);
Pierwsze wylanie spoiwa bitumicznego wynosi 1,0...1,2 l/m i rozprowadzenie obrobionego kruszywa kamiennego frakcji 20...25 mm w ilości 20...25 kg/m, a następnie walcowanie warstwy dwoma lub trzy przejazdy lekkiego walca (5...8 t);
Drugie wypełnienie spoiwem w ilości 0,8...0,9 l/m;
Rozprowadzenie przetworzonej frakcji kruszywa kamiennego 10…15 mm (13…17 kg/m), a następnie zagęszczenie czterema do pięciu przejściami lekkiego walca.
6.2.16 Przybliżone koszty spoiwa i kruszonego kamienia w rozłożeniu na powłokę podano w tabeli 6.2.
Tabela 6.2 - Zużycie spoiwa i kruszonego kamienia (z wyłączeniem obróbki wstępnej)
Rozmiar kruszonego kamienia, mm |
Wskaźnik zużycia |
|||
kruszony kamień, m/100 m |
bitum, l/m |
emulsja, l/m, przy stężeniu bitumu, % |
||
Obróbka pojedynczej powierzchni |
||||
Podwójna obróbka powierzchni |
||||
Pierwszy lokator |
Pierwsze butelkowanie |
|||
Drugie miejsce |
Drugie butelkowanie |
|||
Uwaga - Przy zastosowaniu czarnego kruszonego kamienia zużycie spoiwa zmniejsza się o 20-25%. |
6.2.17 Decyzję o wstępnej obróbce kruszywa spoiwem w instalacji (czernienie kruszywa) podejmuje się na podstawie wyników badania laboratoryjne przyczepność kruszonego kamienia do spoiwa zgodnie z GOST 12801-98 *. Do czernienia zaleca się stosowanie asfaltów w klasach BND 60/90, BND 90/130, BND 130/200, MG 130/200, MG 70/130.
6.2.18 Zasadnicze wylewanie lepiszcza odbywa się na połowie jezdni za jednym razem, bez szczelin i przerw. Jeśli istnieje możliwość wykonania obejścia, spoiwo wylewa się na całą szerokość jezdni.
6.2.19 Temperatura asfaltu podczas jego rozprowadzania powinna mieścić się w następujących granicach: dla asfaltów lepkich BND 60/90, BND 90/130 – 150-160°C; dla gatunków BND 130/200 - 100130°C; dla spoiw polimerowo-bitumicznych - 140-160°C.
6.2.20 Przy obróbce powierzchni emulsjami bitumicznym stosuje się emulsje kationowe EBK-1, EBK-2 i emulsje anionowe EBA-1, EBA-2. Do obróbki powierzchni przy użyciu kationowych emulsji bitumicznych stosuje się kruszony kamień, który nie został poddany wstępnej obróbce spoiwami organicznymi. W przypadku stosowania emulsji anionowych - głównie czarny kruszony kamień.
6.2.21 Temperaturę i stężenie emulsji ustala się w zależności od warunków atmosferycznych:
Przy temperaturze powietrza poniżej 20°C emulsja powinna mieć temperaturę 4050°C (przy stężeniu asfaltu w emulsji 55-60%). Emulsję podgrzewa się do tej temperatury bezpośrednio w dystrybutorze asfaltu;
Przy temperaturze powietrza powyżej 20°C emulsja nie wymaga podgrzewania (przy stężeniu bitumu w emulsji 50%).
6.2.22 Natychmiast po rozsypaniu pokruszony kamień zagęszcza się go gładkimi walcami o masie 6-8 ton (4-5 przejazdów po jednym torze). Następnie ciężkimi gładkimi walcami o masie 10-12 ton (2-4 przejazdy po jednym torze). Dla lepszego uwidocznienia chropowatej struktury zaleca się wykonanie końcowego etapu zagęszczania za pomocą walców gładkich z wałkami gumowanymi.
6.2.23 W przypadku stosowania emulsji bitumicznych prace wykonuje się w następującej kolejności:
Zwilżenie poddanej obróbce powłoki wodą (0,5 l/m);
Zalanie powłoki emulsją w ilości 30% zużycia;
Podział 70% kruszonego kamienia z całkowitego zużycia (odstęp nie większy niż 20 m w odstępie czasu nie większym niż 5 minut od momentu wylania emulsji);
Wylewanie pozostałej emulsji;
Dystrybucja pozostałego kruszonego kamienia;
Zagęszczanie walcami o masie 6-8 ton, 3-4 przejazdy po jednym torze (początek zagęszczania powinien pokrywać się z początkiem rozpadu emulsji);
Konserwacja wykonanej nawierzchni.
6.2.24 W przypadku stosowania kationowych emulsji bitumicznych ruch pojazdów zostaje otwarty natychmiast po zagęszczeniu. Utrzymanie podwójnego wykończenia nawierzchni odbywa się przez 10...15 dni, regulując ruch na szerokości nawierzchni i ograniczając prędkość do 40 km/h.
W przypadku stosowania emulsji anionowej ruch należy otworzyć nie wcześniej niż dzień po wykonaniu urządzenia do obróbki powierzchni.
6.3 Montaż cienkich, odpornych na zużycie warstw ochronnych na powierzchni nawierzchni drogi
6.3.1 Budowa cienkich warstw ochronnych lanych mieszanek emulsyjno-mineralnych
6.3.1.1 Cienkie, odporne na zużycie warstwy ochronne z lanych mieszanek emulsyjno-mineralnych (LEMS) stosowane są jako warstwy ścierne cierne i hydroizolacyjne w celu zwiększenia trwałości nawierzchni drogowych i poprawy warunków jazdy. Warstwy użytkowe są przede wszystkim niezbędne do przywrócenia właściwości użytkowych powłok.
6.3.1.2 Podczas naprawy warstw asfaltobetonowych ułożonych na nawierzchni z betonu cementowego możliwe są następujące opcje stosowania lanych mieszanek emulsyjno-mineralnych:
1) ułożenie LEMS-ów na wierzchniej warstwie nawierzchni asfaltobetonowej;
2) ułożenie LEMS-ów na zmielonej nawierzchni asfaltobetonowej.
6.3.1.3 Przed położeniem warstwy LEMS powłokę zagruntować emulsją lub asfaltem BND 200/300 w ilości 0,3-0,4 l/m (w przeliczeniu na bitum).
6.3.1.4 Przygotowanie i montaż LEMS odbywa się za pomocą specjalnych maszyn jednoprzebiegowych, które mieszają materiały i rozprowadzają mieszaninę po powierzchni powłoki.
Zaleca się stosowanie kruszonego kamienia różnych frakcji do 15 mm ze skał magmowych i metamorficznych o wytrzymałości co najmniej 1200. Frakcja piasku 0,1 (0,071)-5 mm składa się z piasku kruszonego lub mieszaniny piasku naturalnego i kruszonego w równych częściach. W przypadku proszku mineralnego (najlepiej aktywowanego) ze skał węglanowych przyjmuje się, że całkowity cząstek mniejszych niż 0,071 mm zawartych w mieszaninie wynosi 5-15%. Spoiwo stosowane jest w postaci kationowych emulsji bitumicznych klasy EBK-2 i EBK-3, zawierających 50-55% asfaltu. Składy LEMS podano w tabeli 6.3.
Tabela 6.3 - Składy odlewanych mieszanin emulsyjno-mineralnych
Typ mieszanki |
Liczba składników,% wag |
|||||||
kruszony granit, mm |
kopalnia- |
Portland- |
woda do wstępnego |
emulsja bitumiczna (w przeliczeniu na bitum) |
||||
zgnieciony |
Natura |
|||||||
Skruszony kamień |
||||||||
Piaszczysty |
||||||||
[e-mail chroniony], rozwiążemy to. |
MINISTERSTWO TRANSPORTU FEDERACJI ROSYJSKIEJ
PAŃSTWOWA SŁUŻBA DROGOWA
(ROSAWTODOR)
CENTRUM
ORGANIZACJA PRACY I GOSPODARCZA
METODY ZARZĄDZANIA
(TSENTRORGTRUD)
KOLEKCJA KART
PROCESY PRACY PRZY NAPRAWIE I
UTRZYMANIE AUTOSTRAD
Mapa procesu pracy
Naprawa dziury nawierzchnie asfaltobetonowe
z dziurami o głębokości do 50 mm
przy użyciu maszyn ED-105
KTP-1.01-2001
Wydanie drugie, poprawione i rozszerzone.
(Problem 1)
Moskwa, 2001
Mapy procesów pracy mają na celu poprawę organizacji pracy pracowników zajmujących się naprawą i utrzymaniem autostrad.
Mapy wyznaczają postępową technologię pracy, racjonalne wykorzystanie czas pracy, ciąg technologiczny wykonywania pracy w oparciu o zaawansowane techniki i metody pracy.
Mapy można wykorzystać przy opracowywaniu dokumentacji organizacyjno-technologicznej przy remontach i utrzymaniu autostrad (PPR i innych), planowaniu pracy, a także w celach edukacyjnych w kształceniu wysoko wykwalifikowanych pracowników.
Zbiór map procesów pracy przygotowanych przez inżynierów A.I. Anashko, E.V. Kupcowa,
TELEWIZJA. Ubezpieczenie.Odpowiedzialny za wydanie A.A. Morozow.
. Zasięg i skuteczność mapy
Notatka: Koszty pracy na mapie obejmują czas na prace przygotowawcze i końcowe - 5% oraz odpoczynek - 10%.
Stosowanie metod i technik zalecanych przez mapę zwiększy wydajność o 8%.
. Przygotowanie i warunki prowadzenia procesów
3.3 . Odzież robocza i obuwie ochronne.
1 . Kombinezony bawełniane 4
2 . Botki skórzane 4 pary
3 . Rękawiczki płócienne 3 pary
4 . Rękawiczki łączone 1 para
5 . Płócienne nakolanniki 3 pary
6 . Kamizelka sygnalizacyjna 3 szt.
3.4 . Zapotrzebowanie na materiały na 10 m 2 naprawianej powierzchni przy głębokości dziur do 50 mm: gorąca drobnoziarnista mieszanka asfaltobetonowa ( GOST 9128-84 ) - 1,19 t; płynny bitum - 5 l; olej napędowy.
4. Technologia procesu i organizacja pracy
4.1 . Prace przy naprawie dziur w nawierzchniach asfaltobetonowych maszynami ED-105 do naprawy nawierzchni asfaltobetonowych prowadzone są w następującej kolejności technologicznej:
Montaż i demontaż ogrodzeń i przejść dla pracowników w odległości do 50 m;
Łamanie i odcinanie krawędzi osłony naprawianego otworu młotkiem pneumatycznym;
Oczyszczanie dołów z kurzu, brudu i gruzu;
Smarowanie krawędzi powłoki i podłoża bitumem;
Układanie i wyrównywanie mieszanki asfaltobetonowej;
Wałkowanie mieszanki za pomocą ręcznego wałka wibracyjnego;
Rozgrzewanie asfaltu przy konserwacji kotła bitumicznego;
Konserwacja sprężarek i generatorów.
4.3 . Schemat organizacji miejsca pracy
M 1, A 1, A 2, A 3 - lokalizacje pracowników; 1 - bariera inwentarzowa; 2 - znak drogowy; 3- stożki prowadzące; 4 - dziury na powierzchni; 5 - znak drogowy; 6 - znak drogowy; 7 - maszyna do naprawy czarnych powłok; 8 - mapa rozkroju wypełniona mieszanką asfaltobetonową. Strzałka wskazuje kierunek ruchu łącza.
Schemat umieszczenia znaków drogowych podczas prac remontowych (objazd wzdłuż jezdni).
Łamanie i odcinanie krawędzi pokryć naprawianego otworu za pomocą młota pneumatycznego
Podczas eksploatacji dróg utwardzonych po pewnym okresie eksploatacji zaczynają one ulegać awariom z wielu powodów:
- Wpływ czynników pogodowych i klimatycznych;
- Intensywne obciążenie od poruszających się pojazdów;
- Naturalne starzenie się i zużycie;
- Naruszenia technologii budowlanej;
- Stosowanie materiałów o nieodpowiedniej jakości;
- Niewykonanie w terminie profilaktycznego utrzymania dróg.
Standardy
Wszystkie rodzaje prac naprawczych, w tym naprawa dziur w nawierzchni asfaltowej, są regulowane wystarczająco szczegółowo przez GOST i SNiP. Główne standardy to:
- norma krajowa 50597. Tekst tego GOST R został zatwierdzony przez Państwową Normę Federacji Rosyjskiej 11 października 1993 r. uchwałą nr 221;
- „Zalecenia metodologiczne”, obowiązujące od 17 marca 2004 r., przyjęte przez Rosavtodora (patrz pismo OS-28/1270-is);
- VSN 24-88. Ministerstwo Transportu Drogowego Federacji Rosyjskiej zatwierdziło wymienione standardy 29 czerwca 1988 roku.
Opcje technologiczne
Jednym z typów jest łatanie dróg naprawy bieżące i odbywa się wg różne technologie za pomocą różne materiały i specjalny sprzęt drogowy.
Konkretną technologię dobiera się biorąc pod uwagę:
- główne zadania, które należy rozwiązać wykonując wspomnianą pracę:
- Bezpieczeństwo eliminacja jakościowa zidentyfikowana wada. Naprawiany obszar musi spełniać swoje podstawowe parametry (wytrzymałość, gęstość, chropowatość i równość powierzchni) zbliżone do wartości charakterystycznych dla powłoki zasadniczej;
- Znaczące wydłużenie żywotności leczonego obszaru;
- Stopień złożoności opcji naprawy dróg, biorąc pod uwagę istniejące warunki pogodowe;
- Dostępność wymaganej ilości i asortymentu Zaopatrzenie i sprzęt specjalny;
- Zapewnienie minimalnych terminów wykonania prac;
- Oceny komponentów ekonomicznych.
Jeśli zajdzie potrzeba naprawy dziury, można ją wykonać przy użyciu jednej z powyższych technologii.

Etap przygotowawczy
Niezależnie od wybranej technologii naprawy, wspomniane prace rozpoczynają się od przygotowania terenu, na którym znajduje się stwierdzona usterka nawierzchni drogi.
Algorytm jest następujący:
- Powierzchnię uszkodzonego obszaru oraz przyległą nawierzchnię drogi oczyszcza się z wilgoci, brudu i kurzu;
- Obszar, na którym planowana jest naprawa dróg, jest oznaczony liniami prostymi (wzdłuż i w poprzek osi podłużnej nawierzchni drogi). W tym przypadku cała powłoka jest chwytana o 50 mm z każdej strony. Jeśli w pobliżu znajduje się kilka obszarów wymagających naprawy, są one łączone w jeden. Wybrana powierzchnia nazywana jest mapą naprawy;
- Na całej głębokości uszkodzenia, zgodnie z naniesionymi oznaczeniami, wybiera się starą powłokę za pomocą jednego z nich dostępne sposoby(frezowanie na zimno, wykrawanie lub nacinanie). Jednocześnie kontroluje się, czy materiał został usunięty na pełną grubość istniejącej powłoki, a ściany są ściśle pionowe. Technologia i kolejność operacji, zgodnie z którymi należy przeprowadzać naprawy dziur, są wystarczająco szczegółowo regulowane przez GOST;
- Usunięto kawałki starej powłoki, nagromadzony brud, kurz i nagromadzoną wodę;
- Ściany próbki i jej dno traktuje się emulsją zawierającą bitum lub ciekłym roztworem bitumu.
Scena główna
W zależności od wielkości uszkodzonego obszaru stosuje się go Różne rodzaje naprawa dziur, sprzęt i narzędzia.
- Jeżeli dziura ma powierzchnię ≤ 3 m², jej kontur wycina się za pomocą ręcznych przecinarek wyposażonych w wiertła diamentowe. tarcze tnące d= (300-400) mm. Pocięty materiał rozbija się i usuwa za pomocą młota pneumatycznego, który działa z przenośnej stacji hydraulicznej posiadającej własny silnik lub z napędu hydraulicznego specjalnego sprzętu służącego do napraw. Młot może być pneumatyczny. W takim przypadku wymagana będzie sprężarka.
- Jeżeli wyboje o tej samej powierzchni mają odpowiednią długość i małą szerokość, naprawę ubytków powłok wykonujemy przy użyciu frezarek na zimno w dowolnym wariancie (ciągnionych, samojezdnych, zawieszanych), które umożliwiają jednoprzejazdowe zdjęcie powłoki do głębokość do 150 mm przy szerokości usuwanego obszaru od 200 mm do 500 mm. Zastosowanie tej techniki zapewnia penetrację godzinową do 300 metry liniowe. Jeśli obrażenia zostaną odniesione Duża powierzchnia, a następnie użyj bardziej wydajnych noży.
Technologia łatania polega na smarowaniu dna i ścian ciekłym bitumem lub emulsją. Można to przeprowadzić przy użyciu specjalistycznego sprzętu lub urządzenia przenośne(dystrybutorzy asfaltu, podgrzewacze bitumu, naprawcy dróg itp.).
Następnie przygotowany obszar wypełnia się masą naprawczą. Idealnie powinien całkowicie odpowiadać swoim składem i właściwościami materiałowi powłoki głównej. Ale jest to niezwykle trudne do osiągnięcia. Dlatego stosuje się różne mieszanki asfaltobetonów: gorące średnioziarniste i drobnoziarniste (typy G, V, B).
Mieszanki „A”, mocne, twarde, o dużych ziarnach i znaczne odsetek Firmy wykonujące naprawy łatające powłok znacznie rzadziej korzystają z kruszonego kamienia, gdyż trudno jest go dołożyć i wypoziomować ręcznie.
Najpopularniejszym obecnie rozwiązaniem do naprawy dziur jest mieszanka z wypełniaczem do betonu asfaltowego (ABC). Używany jest podgrzewany.
Asfalt dostarczamy na miejsce użytkowania specjalny sprzęt wyposażone w zasobniki termosowe. Zastosowanie termosów podyktowane jest technologicznym sposobem wykorzystania materiału. Jeżeli masa szpachlowa ma temperaturę niższą niż 110°C, prace przy jej montażu zostają odpisane jako wadliwe. Najczęściej rosyjscy drogowcy, którzy naprawiają dziury w drogach, wykorzystują do powyższych celów amerykańską maszynę uniwersalną model TR-4.
Technika podobny projekt nazywa się warsztatem, ponieważ jest wyposażony we wszystko, co niezbędne do naprawy dziur pod klucz, bez angażowania dodatkowych sił i zasobów:
- Zdolność do magazynowania i transportu mieszanek bitumicznych;
- Pojemnik z emulsją do gruntowania;
- Kosz na śmieci;
- Płyta wibracyjna;
- Młot hydrauliczny itp.
Podczas transportu wymaganą temperaturę mieszanki, której zastosowanie zapewnia technologia łatania, utrzymuje się za pomocą grzejnika elektrycznego lub palnika propanowego.
Drugim pod względem częstotliwości użytkowania jest specjalny sprzęt SSG25 produkcji niemieckiej, którego zasada działania różni się od produktu TR-4.
Jeśli prace prowadzone są w zimnych porach roku lub odległość, na którą trzeba przewieźć asfaltownię, jest znaczna, drogowcy powszechnie korzystają z innych metod naprawy dziur, na przykład recyklingu.
Jego istota: beton asfaltowy z recyklingu (okruchy lub kawałki) podgrzewany jest w specjalnym pojemniku, przy stałym mieszaniu grawitacyjnym bezpośrednio na miejscu pracy. Asfalt przygotowywany jest w recyklerach, specjalnych kontenerach na przyczepach lub na podwoziach samobieżnych. Technika ta najlepiej sprawdza się w przypadku okruchów, czyli odpadów z mielenia na zimno. Aby poprawić jakość gotowego kruszywa, dodaje się do niego bitum po stopieniu w objętości 2% w stosunku do masy załadowanego surowca wtórnego.
Gotową szpachlówkę dostarczamy na naprawiane miejsce dyskretnie, dzięki czemu wypełnienie następuje warstwowo. Grubość każdego z nich nie powinna przekraczać 60 mm.
Naprawa dziur w powłokach z wadami o mniejszej głębokości i powierzchni zostanie przeprowadzona poprzez ręczne ułożenie, a następnie wyrównanie mieszanki. Jeśli mapy są duże (S ≥ 20 m²), stosuje się małą kostkę asfaltową (chodnik).
Jeśli asfalt zostanie ułożony zgodnie ze wszystkimi zasadami, powinien wytrzymać dłużej niż rok. Ale to teoretycznie. W naszym życiu wszystko jest inne. Z reguły pierwsze dziury na drogach pojawiają się już po kilku miesiącach od odnowienia nawierzchni.
Dlaczego to się dzieje? Głównymi przyczynami są oczywiście zaniedbania i naruszenie technologii układania asfaltu. Aby zaoszczędzić pieniądze (chcą mieć więcej pieniędzy i wydać mniej), drogowcy dodają do mieszanki mniej emulsji bitumicznej i oszczędzają na piasku i kruszonym kamieniu. Z tego powodu asfalt staje się kruchy, w wyniku czego pojawiają się załamania, pęknięcia i dziury.Obecne przepisy nie pozwalają służbom drogowym czekać na dobrą i komfortową pogodę z naprawami. Oceń sam, istniejący GOST R 50597–93 „Drogi i ulice. Wymagania dotyczące warunków eksploatacyjnych dopuszczalnych w warunkach zapewnienia bezpieczeństwa ruchu drogowego” określa maksymalne dopuszczalne wymiary dziur w drogach: szerokość jezdni – nie więcej niż 60 cm, długość – 15, głębokość – 5.
Jeśli zostaną zidentyfikowane obszary problematyczne, należy natychmiast powiadomić pracowników drogowych. Oni z kolei są zobowiązani do niezwłocznego naprawienia jezdni. W końcu, jeśli samochód wpadnie do takiej dziury, organizacja obsługująca ten odcinek drogi będzie musiała odpowiedzieć.
Dlatego pomimo deszczu i śniegu asfalt roluje się w dziury. Przecież zgodnie ze standardami okres eliminacji wynosi maksymalnie 10 dni. Czy to jest poprawne?Prace drogowe przy układaniu asfaltu (w tym podczas łatania) prowadzone są zgodnie z SNIP i GOST. Podczas naprawy dziur zwykle stosuje się metodę układania na zimno. W tym przypadku mieszanka asfaltowa wiąże się bardzo szybko i niemal natychmiast można jechać po naprawionym terenie.
Czy jest jeszcze coś? gorący sposób. Stosowany jest głównie przy budowie nowych dróg i rekonstrukcji starych. Tutaj używają gorącej mieszanki bitumicznej i zwijają ją, aż całkowicie ostygnie. Czasami podczas naprawy dziur stosuje się również układanie na gorąco. Częściej w ciepłe dni, gdy temperatura na zewnątrz nie jest niższa niż 10 ° C. Istnieją jednak tak zwane mieszanki odlewane, które umożliwiają stylizację na gorąco nawet w temperatury poniżej zera. Mieszankę tę przywozi się na miejsce naprawy w specjalnej przyczepie termosowej. Skład jest stan ciekły jak gęsty klej. Temperatura mieszaniny wynosi poniżej 200°С. Dzięki zastosowaniu technologii można go układać nawet w trudnych warunkach. warunki zimowe. Wysoka temperatura po prostu odparowuje wilgoć z dołu. Po stwardnieniu mieszanki odcinek drogi można użytkować. Ta przyjemność jest dość kosztowna. Dlatego tego typu naprawę stosuje się w przypadku poważnych uszkodzeń nawierzchni drogi, gdy konieczne jest szybkie przywrócenie ruchu w rejonie awaryjnym.
Tak więc, jeśli w ciepłym sezonie (+10°С i więcej) stosuje się stylizację na gorąco, stylizacja na zimno ogranicza się do lekkich mrozów (nie niższych niż -5°С), a mieszanki odlewane nadają się na poważniejsze zimne dni, już przy -10°С, dla przykład. Wiadomo, że jeśli zajdzie taka potrzeba, drogowcy będą jeszcze bardziej łatać drogę niskie temperatury. Jeśli na autostradzie nagle pojawi się dziura (awaria itp.), ruch jest zablokowany, a na zewnątrz jest minus 30, nie będziesz czekać na wiosenne ocieplenie. Ogólnie rzecz biorąc, wszelkie zimowe naprawy związane z układaniem asfaltu są zasadniczo awaryjne. Ich zadaniem jest dopilnowanie, aby naprawiony teren przetrwał do czasu, aż zrobi się cieplej, kiedy prace renowacyjne będą mogły ruszyć na dobre.Jak widać drogi można naprawiać nawet zimą. Najważniejsze jest podążanie za technologią. To tylko w naszych realiach naprawy jakościowe Niewiele osób myśli o drogach. Przecież dla większości usług drogowych ważniejsze jest dobre i stałe dochody z napraw i utrzymania dróg. Jeśli zrobisz wszystko sprawnie, nie dostaniesz pieniędzy z budżetu. Problem w tym, że nie ustaliliśmy jeszcze gwarancji na żywotność nawierzchni drogowej. Gdyby był taki termin, drogowcy naprawiliby wszystkie dziury na własny koszt. Zbudowali więc drogę i otrzymali pieniądze. Pojawiły się dziury, załatali je i znów dostali pieniądze. W rezultacie jesteśmy po prostu skazani na jazdę przez dziury i wyboje.
Cóż, na przykład kilka liczb. W zeszłym roku na naprawę sieci dróg i ulic wydano: w Kazaniu – 2,87 miliarda rubli, we Władywostoku – 2 miliardy, w obwodzie moskiewskim – 12 miliardów, w stolicy – 22,4 miliarda. A teraz wyobraźcie sobie, ile można by zaoszczędzić, gdyby drogi po budowie (przebudowie i kapitalnym remoncie) nie wymagały napraw przez co najmniej cztery lata.
Według oficjalnych dokumentów regulacyjnych (SNiP) regulujących standardy układania asfaltu, drogi można asfaltować tylko w temperaturze +5 C. Jak przeprowadzić pilne naprawy dróg w okres zimowy? Na ratunek służbom drogowym przychodzą nowe technologie.
Asfalt jest droższy w chłodne dni
W zimnym rosyjskim klimacie reżim temperaturowy układanie asfaltu ulega ciągłym zakłóceniom, co prowadzi do znacznego pogorszenia jakości tworzonej nawierzchni drogowej i wzrostu kosztów sezonowych i generalny remont. Starając się terminowo zakończyć prace, firmy wykonawcze realizują budowa dróg w ujemnych temperaturach i wysoka wilgotność. Po stwardnieniu mieszanki wilgoć, która przedostaje się do najmniejszych porów i pęknięć nowej powłoki, pod wpływem niskich temperatur szybko zamienia się w lód. Objętość zamarzniętej wody zwiększa się o około 8-9%, dlatego w okresach silnych mrozów można zaobserwować pękanie rury wodne I różne pojemniki z płynem. Ten sam efekt rozszerzania powoduje, że wypełnione lodem pęknięcia w betonie asfaltowym powiększają się i niszczą nawierzchnię od wewnątrz.
Dodatkowym problemem jest także przyczepność pomiędzy poszczególnymi warstwami powłoki układanej w niskich temperaturach lub podczas deszczu. Jak zauważają eksperci, nawet ciągłe podgrzewanie i suszenie podłoża gruntowego za pomocą specjalnych urządzeń nie pozwala w 100% pozbyć się wilgoci, która uniemożliwia wysokiej jakości przyczepność warstw nawierzchni drogowej. Zgodnie ze współczesnymi standardami jedyny rodzaj nawierzchni asfaltowej, który można wykonać niemal w każdym warunki pogodowe(z wyjątkiem silnych mrozów), pozostaje tylko naprawa dziur za pomocą specjalnych mieszanek.
„Zimne technologie”: czy jakość odpowiada cenie?
Stosowanie zimnych mieszanek asfaltowych jest dziś jednym z najczęstszych nowoczesne technologie awaryjna naprawa dziur w zimnych porach roku. W przeciwieństwie do tradycyjnego gorącego asfaltu, zimny asfalt zawiera elastyczne bitumy, których lepkość wzrasta wraz ze spadkiem temperatury. środowisko. Formuły marek dostępnych na rynku są stale udoskonalane, włączając w to specjalne dodatki kompozytowe, które poprawiają przyczepność mieszanki do podłoża oraz gwarantują zwiększoną łatwość montażu i trwałość. Pod ciśnieniem podczas walcowania i dalsza eksploatacja Na drogach zimny asfalt ostatecznie polimeryzuje i uzyskuje znaczną twardość.
Przyjrzyjmy się zaletom i wadom zimnych mieszanek w porównaniu ze zwykłym gorącym asfaltem.
plusy
- Gotowe mieszanki na zimno można przechowywać bez utraty swoich właściwości przez okres do 1 roku, co pozwala na ciągłe ich przechowywanie gotowy materiał do pilnej pracy;
- Według różnych dostawców minimalna temperatura podczas układania zimnego betonu asfaltowego wynosi od -20 C° do -25 C°;
- Naprawiony na zimno tor można udostępnić do ruchu natychmiast po ułożeniu. Pod ciężarem transportu zimna mieszanka zostaje ostatecznie zagęszczona i staje się trwalsza;
- Układanie zimnego asfaltu nie wymaga kosztownych usług specjalnego sprzętu i specjalnych pojazdy do transportu materiału.
Minusy
- "Zimna stylizacja„można go używać tylko do małych dziur i dołów;
- „Łatka” wykonana z zimnej mieszanki łatwo się przecina i szybciej ulega zniszczeniu w miejscach hamowania - skrzyżowaniach, przejściach dla pieszych itp.;
- Powierzchnie świeżego asfaltu przylegające do nieużywanych fragmentów drogi (pasy przy krawędzi krawężnika, wokół włazów i innych obiektów technicznych) nie są wystarczająco ugniatane przez koła samochodów i szybciej ulegają zniszczeniu;
- Cena zimnych mieszanek jest wielokrotnie wyższa niż cena zwykłego gorącego asfaltu (koszt 1 tony importowanego zimnego betonu asfaltowego to około 60 tysięcy rubli, 1 tona standardu to około 2,5 tysiąca rubli).
Odlewanie na gorąco: droga alternatywa
Asfalt lany różni się od asfaltu standardowego obecnością twardego bitumu o dużej lepkości i wtrąceń mineralnych (piasek, drobny kruszywo). Praca z gorącymi mieszankami odbywa się w temperaturach od +200 C°, dzięki czemu naprawy dziur w autostradach można przeprowadzać przy dużej wilgotności i niskich temperaturach. Koszt materiału jest nieco niższy niż cena zimnych mieszanek, jednak wymaga ułożenia lanego asfaltu dodatkowe wydatki za wypożyczenie specjalistycznego sprzętu. Ze względu na nadmierną plastyczność na gorąco sezon letni Odlewanie na gorąco jest uważane za tymczasową metodę naprawy awaryjnej.
W porównaniu do konwencjonalnego gorącego asfaltu, asfalt lany ma następujące zalety i wady:
plusy
- Po wylaniu gorąca mieszanka w procesie utwardzania zagęszcza się, dzięki czemu nie jest wymagana obsługa walca asfaltowego;
- Asfalt lany ma wyjątkowe właściwości adhezyjne i tworzy silną przyczepność do podłoża nawet przy niskich temperaturach i dużej wilgotności;
- Możliwość przeprowadzenia pilnych napraw w ujemnych temperaturach i podczas opadów atmosferycznych.
Minusy
- Transport gorącej mieszanki wymaga drogiego sprzętu drogowego (kotły i chłodnie), co pozwala na utrzymanie stabilności wysoka temperatura materiał i stale go mieszaj;
- Wymagana jest naprawa dróg za pomocą lanego asfaltu Wysokie koszty energia ( wymagana temperatura podczas układania wynosi około +200 C°);
- W ciepłym sezonie „plastry” mogą nagrzewać się na słońcu do +60°C i wciskać się pod koła samochodów.
Podsumowując można zauważyć, że obecnie najnowocześniejszą i uniwersalną metodą naprawy dziur w każdych warunkach atmosferycznych jest zastosowanie zimnych mieszanek asfaltowych. Zdaniem części ekspertów, w nadchodzących latach dalsze udoskonalanie formuły zimnego asfaltu umożliwi skuteczne przeprowadzanie awaryjnych napraw dróg nawet w bardzo niskich temperaturach. I tu jakość konstrukcji autostrady w zimnych porach roku to wciąż kwestia przyszłości - dalej ten moment Na rynku nie ma materiałów i technologii, które pozwoliłyby na stworzenie trwałej nawierzchni asfaltowej spełniającej wszystkie niezbędne normy przy dużej wilgotności powietrza i ujemnych temperaturach.