Opis i właściwości techniczne cementu budowlanego, jego skład chemiczny. Skład cementu: zastosowanie właściwości i przeznaczenie w budownictwie Gdzie jest cement
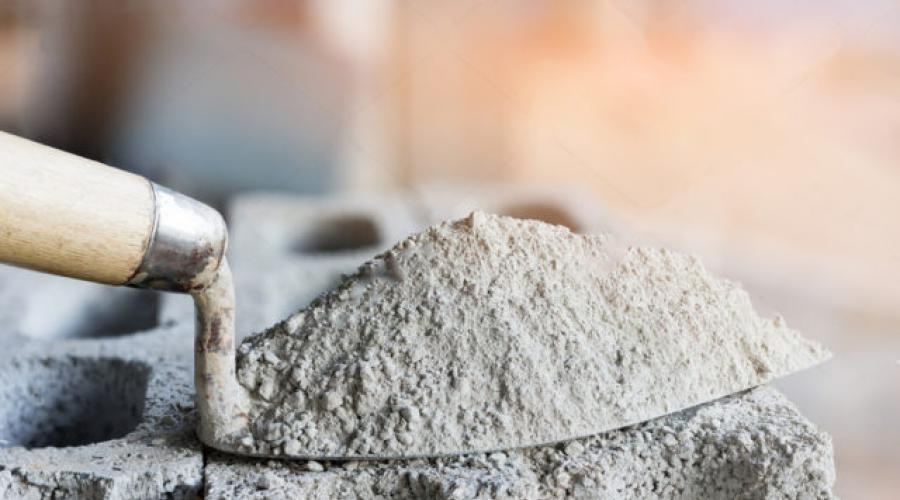
Przeczytaj także
Pełni funkcję spoiwa. Ostateczna wytrzymałość produktu betonowego zależy od jego jakości. Wielu początkujących budowniczych interesuje pytanie o cement - z czego jest wykonany i co decyduje o jego właściwościach? Materiał uzyskuje się poprzez zniszczenie klinkieru, gipsu i dodatków. Klinkier jest główną substancją cementu, otrzymywaną po spiekaniu surowców, których podstawą jest glina i wapień. Kompozycja może zawierać margiel, żużel z wielkich pieców, osad nefelinowy.
Skład cementu
W kwestii tego, z czego wykonany jest cement, od dawna nie zaszły żadne zasadnicze zmiany; Podstawą zawsze był klinkier; w składzie znajdują się również dodatki mineralne o optymalnej zawartości 15-20%. Przy tym stężeniu minerały mają niewielki wpływ na działanie i specyfikacje. Jeśli stężenie dodatków przekracza 20%, właściwości znacznie się zmienią; skład nazywa się cementem pucolanowym.
Skład chemiczny cementu:
- alit (Ca3SiO5) – zwiększa szybkość interakcji z wodą. Składnik jest ważny na etapie nabywania siły. Zawartość krzemitu trójwapniowego w klinkierze wynosi 50–70%;
- Belit (Ca2SiO4) – zapewnia przyrost wytrzymałości w późniejszych etapach hartowania. Początkowo słabo reaguje na wodę; początkowo wzrost wytrzymałości pod wpływem krzemianu dwuwapniowego praktycznie nie występuje. Klinkier zawiera 15–30%;
- faza glinianowa (Ca3Al2O6) – zmieszana z wodą powoduje szybką reakcję i zapewnia wstępne wiązanie. Aby kontrolować proces utwardzania, do kompozycji dodaje się gips i podobne substancje. Glinian trójwapniowy zawiera 5–10%;
- faza ferrytowa (Ca3Al2O6). Wchodzi w aktywną fazę reakcji pomiędzy cyklami alitu i belitu. Ilość glinoferrytu tetrawapniowego wynosi 5–15%;
- pozostałe składniki to alkaliczne siarczany, tlenek wapnia - do 3%.
Proporcje substancji chemicznych w zaprawie cementowej mogą się różnić, ale zwykle mieszczą się w określonych wartościach.
Główne cechy cementu
Technologia produkcji wymaga zgodności z normami GOST 10178-76. Kompozycja może zawierać dodatki.
Jeśli są obecne, zmieniają się właściwości cementu:
- Wytrzymałość to zdolność materiału do wytrzymywania określonych obciążeń przed zniszczeniem. Wskaźniki wytrzymałości i zdolność do twardnienia podczas hydratacji to powiązane ze sobą pojęcia; aby uzyskać siłę, jest to wymagane długi czas, od 28 dni. Cement dzieli się na gatunki oznaczone literą M i indeksem: 300, 400, 500, rzadziej spotykane są kompozycje o wysokiej wytrzymałości - M600, M700, M800;

- czas utwardzania. Na proces hydratacji i ostatecznego utwardzenia materiału wpływa stopień rozdrobnienia klinkieru. W miarę zmniejszania się ziarna wzrasta wytrzymałość. Przy określaniu twardnienia zapraw i betonu bierze się pod uwagę normalną gęstość kompozycji. Czas wiązania zależy od zapotrzebowania na wodę i ilości minerałów. Przy normalnej gęstości wiązanie trwa od 45 minut do 10 godzin. Gdy temperatura wzrasta, okres czasu maleje, w przypadku zimnej pogody wzrasta;
- Zapotrzebowanie na wodę to zużycie wody w celu uwodnienia substancji i uzyskania wystarczającej plastyczności. Zwykle zaleca się stosowanie preparatu zawierającego 15–17% płynu. Aby zwiększyć mobilność roztworu, można dodać wodę w proporcji 30–35%;
- gęstość nasypu. Prawdziwa gęstość materiału wynosi 3000–3100 kg/cm3. Gęstość po wylaniu wynosi 900–1100 kg/cm3, po zagęszczeniu 1400–1700 kg/cm3;
- odporność na korozję. Ma to wpływ na wskaźnik skład mineralny I . W miarę zmniejszania się wielkości ziaren klinkieru i wzrostu porowatości zmniejsza się odporność na korozję;
- usuwanie ciepła. Podczas utwardzania ciepło jest nieuchronnie uwalniane z cementu. Jeśli prędkość procesu jest stosunkowo niska, ryzyko pęknięć występujących podczas pracy jest zmniejszone. Szybkie wydzielanie ciepła jest procesem niepożądanym przy budowie budynków wielokondygnacyjnych i mocno obciążonych. Aby regulować wytwarzanie ciepła, do kompozycji dodaje się aktywne i obojętne dodatki;
- mrozoodporność. Wskaźnik odzwierciedla odporność na zamarzanie i rozmrażanie zarówno w wodzie słodkiej, jak i słonej.
Rodzaje cementu
W zależności od tego, z czego wykonany jest cement, materiał różni się w grupach. Każdy typ ma specjalne właściwości techniczne.

W zależności od materiału produkcyjnego wyróżnia się następujące grupy:
- Limonka;
- marglowaty;
- gliniasty. W celu zapewnienia odporności ogniowej i mrozowej zaleca się dodatek składników pomocniczych: cementu, boksytu i żużla.
Większość produkcji cementu obejmuje związki węgla i gliny, ale pewne rodzaje wprowadza się substancje sztuczne (żużel, odpady z hutnictwa i produkcji chemicznej) oraz składniki naturalne (tlenek glinu).
Cement dzieli się na następujące typy:
- Cement portlandzki. Jest inny wysoka prędkość hartowanie, zawiera 10–15% minerały. Cement portlandzki powstaje na bazie gipsu i klinkieru, które wypala się w temperaturze 1500°C. Jest aktywnie wykorzystywany nowoczesna konstrukcja dzięki umiejętności tworzenia konstrukcje monolityczne po zmieszaniu z wodą;
- Cement żużlowy portlandzki. Kompozycja zawiera te same składniki, a także żużel wielkopiecowy;
- hydrauliczny;
- napinanie – szybko wiąże i twardnieje;
- fugowanie. Używany do tworzenia konstrukcje betonowe w zakresie wydobycia gazu i ropy;
- dekoracyjny, wyróżniający się białym kolorem;
- odporny na siarczany. Główne różnice sprowadzają się do niskiej szybkości utwardzania i dużej odporności na ujemne temperatury.

Obszary zastosowań
Beton jest stosowany wszędzie w budownictwie, jego zakres jest praktycznie nieograniczony. Używając zaprawa cementowa tworzyć konstrukcje żelbetowe wylewane są fundamenty, belki, fundamenty i inne części konstrukcji. Ostatnio popularne stało się wykonywanie budynków monolitycznych, w których ściany, podstawa i dach wykonane są w całości z betonu, nie licząc pokrycia dachowego i materiałów wykończeniowych.
Co powstaje z cementu:
- ściany nośne, kolumny, ścianki działowe;
- płyty podłogowe;
- fundament, jastrych, ;
- różne talerze, bloki ścienne itp.
Mieszanina
W praktyce procedura wytwarzania materiału nie jest zbyt skomplikowana, ale substancje chemiczne są prezentowane w formie wspólnej zasoby naturalne. Zasady wytwarzania cementu są w przybliżeniu takie same dla wszystkich marek; podstawą jest zawsze wapień i glina.
Główne składniki kompozycji:
- klinkier. Najczęściej stężenie wapienia w klinkierze jest 3 razy większe niż ilość gliny, która decyduje o wskaźnikach wytrzymałościowych. Nakłada się go w postaci granulatu o wielkości do 60 mm. Element poddawany jest obróbce cieplnej w temperaturze 1500°C. Podczas procesu topienia pojawia się masa duża ilość krzemionka i dwutlenek wapnia;

- gips wpływa na szybkość hydratacji cementu. Standardowo do kompozycji dodaje się do 6% składnika;
- różne dodatki pomocnicze. Dodatki służą zwiększeniu plastyczności kompozycji, zwiększeniu odporności na zimno i przyspieszeniu utwardzania. Dzięki obecności dodatków cement może mieć szersze zastosowanie w pracach.
Proces produkcji
Ważne jest, aby dokładnie wiedzieć, jak powstaje cement i z czego, pomoże to poprawnie zrozumieć właściwości materiału i zapewnić wysoka jakość projekty.
Przyjrzyjmy się, jak krok po kroku powstaje cement:
- Mieszanie wszystkich składników do uzyskania klinkieru. Zawiera 75% wapienia i 25% gliny.
- Wypalanie w wysokiej temperaturze pozwala uzyskać klinkier. Glinkę i wapno łączy się po podgrzaniu do temperatury 1450°C i wyższej.
- Zniszczenie materiału w celu wytworzenia frakcji przypominającej pył. Mielenie odbywa się za pomocą młynów kulowych - są to bębny umieszczone poziomo, wewnątrz nich znajdują się metalowe kulki, które niszczą stałe, duże cząstki klinkieru. Wraz ze spadkiem frakcji wzrastają właściwości techniczne i stopień kompozycji.
Wniosek
Charakterystycznymi cechami cementu są trwałość, stosunkowo szybki proces utwardzania, odporność na otoczenie zewnętrzne, łatwość przygotowania i użycia. Po utwardzeniu otrzymuje się materiał o wysokiej wytrzymałości, który jest w stanie utrzymać budynki wielokondygnacyjne przy minimalnym zużyciu i niskim ryzyku odkształcenia.
Cement jest substancją ściągającą, która ma tendencję do twardnienia w wodzie i na świeżym powietrzu. Zastanówmy się, z czego wykonany jest cement, jednak wszystko tutaj jest nadal zależne. Powstaje poprzez zmielenie klinkieru, gipsu i specjalnych dodatków. Klinkier powstaje w wyniku wypalenia mieszanki surowców, w skład której wchodzą wapień, glina i inne materiały (żużel wielkopiecowy, muł nefelinowy, margiel). Składniki są przyjmowane w określonym stosunku, który zapewnia tworzenie faz krzemianów wapnia, glinoferrytu i glinianu.
Pierwszy patent na cement zarejestrował w 1824 roku w Anglii D. Aspind. Następnie autor patentu zmieszał pył wapienny z gliną i poddał mieszaninę działaniu wysokiej temperatury. Rezultatem był szary klinkier. Następnie materiał rozdrobniono i zalano wodą.
Z czego dzisiaj produkuje się cement? Podobnie jak poprzednio, głównym składnikiem cementu jest klinkier. Od tego zależą właściwości i wytrzymałość materiału budowlanego. Dodatkowo w składzie znajdują się aktywne dodatki mineralne (15%) zgodnie ze standardami produkcyjnymi. Mają niewielki wpływ na podstawowe właściwości i właściwości techniczne materiału budowlanego. Jeśli zwiększymy ilość dodatków do 20%, właściwości cementu ulegną niewielkiej zmianie i będzie on nazywany cementem pucolanowym.
W stanie rozproszonym wynosi 900-1300 kg/m3, po zagęszczeniu do 2000 kg/m3. m. Obliczając pojemność magazynów, waga cementu wynosi 1200 kg/m3. m. Produkcja cementu bez dodatków jest regulowana przez GOST 10178-76, z dodatkami - przez GOST 21-9-74.
Główne cechy cementu
W zależności od tego, z czego wykonany jest cement, materiał ma różne właściwości. Do najważniejszych z nich należą:
1. Wytrzymałość. Jest to parametr odpowiedzialny za zniszczenie materiału pod wpływem określonych warunków. W zależności od wytrzymałości mechanicznej wyróżnia się cztery rodzaje cementu: 400, 500, 550 i 600.
2. . Określa się poprzez nałożenie zaczynu cementowego o normalnej grubości płaska powierzchnia– cement powinien podczas wysychania zmieniać swoją objętość równomiernie. W przeciwnym razie nie można go stosować w budownictwie ze względu na możliwość zniszczenia powłoki w wyniku nadmiernych naprężeń. Zmiany objętości bada się poprzez gotowanie stwardniałych placków cementu.
3. Mielenie wielkości ziarna. Parametr wpływa na szybkość i wytrzymałość suszenia. Im drobniejsze zmielenie, tym lepszy i mocniejszy cement, szczególnie w pierwszej fazie twardnienia. Ziarnistość mielenia zależy od powierzchni właściwej cząstek wchodzących w skład 1 kg cementu i waha się w granicach 3000-3200 kg/m3. M.
4. Gęstość. Zużycie wody do wytworzenia mieszanki. Jest to ilość wody zarobowej potrzebna do normalnego układania i suszenia materiału. Aby zmniejszyć jego zużycie i zwiększyć plastyczność cementu, plastyfikatorów organicznych i substancje nieorganiczne. Na przykład zacier drożdżowo-siarczkowy.
5. Mrozoodporność. Parametr pozwala określić odporność na chwilowe zamarznięcie wody, w wyniku czego jej objętość wzrasta o 8-9%. Woda wywiera nacisk na ścianki powłoki cementowej (betonowej), a to z kolei zakłóca strukturę zaprawy, stopniowo ją niszcząc.
6. Połączenie ze wzmocnieniem.
7. Rozpraszanie ciepła– Podczas procesu utwardzania cementu wydziela się ciepło. Jeśli dzieje się to powoli i stopniowo, powłoka twardnieje równomiernie, bez pęknięć. Ilość i szybkość wydzielania ciepła można zmniejszyć, stosując specjalną kompozycję mineralogiczną dodawaną do roztworu.
Obecnie produkuje się wiele rodzajów cementu. To, z czego wykonany jest cement, ma ogromny wpływ na jego właściwości. W zależności od bazy surowcowej wyróżnia się następujące rodzaje cementu:
- Limonka;
- marglowaty;
- cement ilasty z dodatkami żużla i boksytu. Jego właściwości są wodoodporne, mrozoodporne i ognioodporne.
Do produkcji cementu wykorzystuje się głównie związki gliny i węglanu. Czasami - surowce sztuczne (odpady, żużel) lub inne naturalne materiały(pozostałości tlenku glinu).
Wyróżnić. Cement portlandzki szybko twardnieje i może zawierać dodatki mineralne w ilości od 10 do 15%. Klinkier i gips (główne składniki) zawarte w jego składzie wypalane są w temperaturze 1500 stopni Celsjusza. Cement portlandzki jest aktywnie wykorzystywany w nowoczesnych Roboty budowlane. Jego główną właściwością jest zdolność do przemiany w ciało stałe blok kamienia nawet podczas kontaktu z wodą.
Oprócz cementu portlandzkiego i cementu żużlowego portlandzkiego wyróżnia się następujące rodzaje cementu:
- hydrauliczny;
- napinający – ma tendencję do szybkiego wiązania i wysychania;
- iniekcja – przeznaczona do betonowania odwiertów gazowych i naftowych;
- dekoracyjny (biały);
- odporny na siarczany - jego osobliwość – niska prędkość twardnienie i podwyższona mrozoodporność.
Obszary zastosowań
Bardzo często cement wykorzystuje się w budownictwie do tworzenia konstrukcji betonowych i żelbetowych. Gatunek 400 służy do wylewania fundamentów i wykonywania belek stropowych w budynkach wysokościowych.
Cement to sztucznie wytworzony materiał, bez którego nie obejdzie się żadna konstrukcja. Ponadto, w zależności od metody produkcji i rodzaju cementu, materiały do jego produkcji mogą być różne substancje naturalne, nadając każdemu rodzajowi cementu specjalne właściwości.
Z jakich substancji składa się cement?
Głównymi surowcami do produkcji cementu są skały ilaste i węglanowe – klinkier, a w niektórych przypadkach odpady przemysłowe – żużel hutniczy wielkopiecowy.
Przez „skały węglanowe” rozumie się i wykorzystuje się do produkcji cementu: wapień, skałę muszlową, kredę, margiel, dolomit i inne skały osadowe posiadające amorficzną strukturę węglanowo-gliniastą, kredową lub wapienną.
Faktem jest, że kreda i wapień to substancje łatwo kruszące się, co jest bardzo ważne przy produkcji cementu – drobnego proszku o unikalnych właściwościach.
Przez „skały ilaste” rozumiemy: gliny, iły, lessy i łupki. Rasy te składają się z różne rodzaje minerały (skalenie, kwarc, krzemiany itp.), które mają zdolność zwiększania objętości, a także nabywania plastyczności w kontakcie z wodą.
Cement otrzymuje się przez drobno zmielony klinkier i gips. Klinkier jest produktem równomiernego wypalenia przed spiekaniem jednorodnej mieszaniny surowców składającej się z wapienia i gliny o określonym składzie, zapewniającym przewagę krzemianów wapnia.
Oprócz głównych rodzajów surowców, do produkcji cementu stosuje się różne dodatki, aby nadać „spoiwu” specjalne właściwości: dodatki glinowe i krzemionkowe, fluoryt, gips, apatyty, fluoryty, fluorek sodu, chlorek sodu i inne.
Główne etapy technologii produkcji cementu, wyraźnie pokazujące, z czego składa się cement/
- Wydobywanie i wzbogacanie podstawowych surowców (wapienia, gliny i kamień gipsowy);
- Kruszenie, suszenie, mielenie, mieszanie i dostosowywanie surowców w jasno określonych warunkach dokumenty regulacyjne proporcje;
- Pozyskiwanie osadów w zależności od przyjętych metod produkcji: mokrych, suchych lub kombinowanych;
- Wypalanie mieszanki surowców w temperaturze 1450 stopni Celsjusza – otrzymanie klinkieru;
- Szlifowanie klinkieru do stanu drobnego;
- Mieszanie składników: kruszony klinkier, gips i dodatki mineralne.
Powstały drobny szaro-zielony proszek jest najczęściej stosowanym rodzajem spoiwa - cementem portlandzkim tej czy innej marki.
Rodzaje cementu - przeznaczenie i cechy
- Biały cement. Stosowany jest do produkcji suchych mieszanek budowlanych w opakowaniach oraz do budowy dekoracyjnych konstrukcji kolorowych. Charakteryzuje się przyspieszonym przyrostem siły, wyjątkowy właściwości dekoracyjne, podwyższona odporność na czynniki atmosferyczne i wysoki koszt w stosunku do standardowego cementu portlandzkiego;
- Cementy szybkotwardniejące. Są to cementy portlandzkie ze specjalnymi dodatkami przyspieszającymi proces wiązania i hydratacji;
- Ekspandowanie cementów. Ten rodzaj cementu wytwarzany jest z cementu glinowego i gipsu. W przeciwieństwie do wszystkich innych typów „spoiw”, które kurczą się po zestaleniu, cement ekspandujący, zgodnie ze swoją nazwą, zwiększa swoją objętość;
- Wodoodporny, nieskurczący się cement. Stosowany do uszczelniania szwów, konstrukcji konstrukcje hydrauliczne, podziemne zbiorniki betonowe, tunele i inne konstrukcje funkcjonujące w wysoka wilgotność;
- Cement hydrofobowy. Jest to cement ze specjalnymi dodatkami wydłużającymi okres gwarantowanego przechowywania i transportu w warunkach dużej wilgotności powietrza. Służy do przygotowania betonu mrozoodpornego i odpornego na wilgoć;
- Cement glinowy. Charakteryzuje się bardzo szybkie wybieranie wytrzymałość – do 50% siła marki w ciągu 24 godzin. Proces hydratacji przebiega ze znacznym wydzielaniem ciepła, co jest pozytywną właściwością przy betonowaniu w niskich temperaturach;
- Cement rozciągający. Ten rodzaj betonu na bazie cementu ma atrybut pozytywny rozszerzać się w miarę nabierania sił. Dodatkowo tego typu betony przodują pod względem współczynnika wodoodporności – aż do W20, co jest bardzo istotne przy budowie zbiorników, basenów, dachy monolityczne i konstrukcje hydrauliczne bez dodatkowej hydroizolacji;
- Cement pucolanowy to cement portlandzki z dodatkiem drobnej krzemionki. Charakteryzuje się wydłużonym czasem wiązania i niskim wydzielaniem ciepła podczas hydratacji. Służy do budowy potężnych wolumetrycznych konstrukcji betonowych;
- Cement odporny na siarczany. Charakteryzuje się dużą odpornością na agresywne sole. Służy do budowy konstrukcji hydraulicznych działających pod wpływem wody morskiej;
- Cement żużlowy portlandzki. Produkowany z kruszonego żużla hutniczego z dodatkiem substancje czynne: wapno, gips itp.
Cement jest jednym z głównych materiałów budowlanych. Wykorzystuje się go do tworzenia spoiw moździerze, cement jest używany do produkcji betonu i żelaza wyroby betonowe. Od jakości tego materiału Zależy to od tego, jak mocny i trwały będzie budynek lub konstrukcja żelbetowa.
Historia cementu rozpoczęła się w Anglii, gdzie w 1824 roku zarejestrowano patent na jego wynalazek. Do produkcji cementu używano wówczas pyłu wapiennego zmieszanego z gliną. Powstałą mieszaninę poddano działaniu wysokich temperatur, w których uległa spiekaniu.
Spalony półprodukt cementowy nazywany jest klinkierem. Staje się cementem po zmieleniu klinkieru na proszek.
W budownictwie wykorzystuje się główną właściwość cementu - po zmieszaniu z wodą stopniowo twardnieje, a następnie zamienia się w trwały kamień. Charakterystyczne dla ukończony produkt materiał może nabrać siły nawet w środowisko powietrzne jeśli występuje nadmiar wilgoci.
Surowce do produkcji cementu, z czego jest wytwarzany, technologia wytwarzania
Obecnie proces wytwarzania cementu uległ zmianie. Wykonany jest na kilka sposobów, a zawarte w nim podzespoły również różnią się od tych stosowanych dwieście lat temu.
Aby zrozumieć, z czego i jak powstaje cement, należy wiedzieć, jakich surowców używają dziś producenci tego ważnego materiału budowlanego.
Ponieważ surowcem do produkcji cementu są skały naturalne, przedsiębiorstwa zajmujące się jego produkcją zlokalizowane są najczęściej w pobliżu miejsc wydobywania tych skał.
Wszystkie skamieniałości, z których wytwarzany jest cement, dzielą się na dwa typy:
- Minerały węglanowe różniące się właściwościami i cechami strukturalnymi. To właśnie budowa skały zapewnia jej efektywną interakcję z pozostałymi składnikami produktu.
- Gliny i skały pochodzenia osadowego. Mający baza mineralna po zwilżeniu nabierają plastyczności i zwiększają objętość. Ponieważ ten rodzaj surowca charakteryzuje się lepkością, można go stosować do produkcji cementu metodą suchą.
Teraz należy konkretnie wymienić, które minerały należą do każdego z rodzajów surowców stosowanych w produkcji cementu.
Do skał węglanowych zalicza się następujące rodzaje surowców naturalnych:
- kreda, która jest rodzajem wapienia. Ma zdolność łatwego zmiażdżenia;
- wapień marglisty, występujący w przyrodzie zarówno luzem, jak i w stan stały. Skała może zawierać domieszki ilaste, dlatego ten rodzaj wapienia uważany jest za surowiec przejściowy, posiadający właściwości charakterystyczne zarówno dla wapienia, jak i gliny;
- wapienie to skały muszlowe, które nie zawierają wtrąceń krzemu. Skała ma porowatą strukturę, która łatwo ulega zniszczeniu przez ściskanie;
Wapienie - skały muszlowe
- skały dolomitowe i inne skamieniałości pochodzenia osadowego. Zawierają węglany, które nadają skale cenne właściwości.
Do skał gliniastych zalicza się następujące rodzaje skamieniałości:
- glina z wtrąceniami mineralnymi, które pęcznieją w kontakcie z wodą;
- iły zawierające duże stężenie cząstek;
- łupki posiadające podłoże gliniaste. Surowiec ten zaliczany jest do tzw skały, zwiększona siła. Pod wpływem naprężeń mechanicznych dzieli się na płytki lamelarne. Charakteryzuje się stabilnym składem i niską zawartością wilgoci;
- lessowa, porowata skała z wtrąceniami cząstek i krzemianów.
Oprócz tego typu surowców, co produkować mieszanina cementu Zakład wykorzystuje niektóre rodzaje odpadów przemysłowych. Aby poprawić jakość, do jego składu dodaje się odpowiednie dodatki proces technologiczny: tlenek glinu i krzemionka, fluoryt i apatyty.
Użycie piasku jest po prostu konieczne podczas wykonywania różnych prac naprawczych i budowlanych. wszystko na temat wykorzystania piasku z kamieniołomów.
Podczas dyrygowania prace wykończeniowe W kuchni, łazience czy innym pomieszczeniu trzeba znać czas schnięcia kleju do płytek. Możesz dowiedzieć się, jak długo schnie klej do płytek.
Obecnie tynk dekoracyjny jest słusznie najpopularniejszą i najbardziej postępową metodą wykańczania. Klikając w link dowiesz się jak samodzielnie go przygotować.
Wszystkie dodatki zwane plastyfikatorami również są pochodzenia naturalnego. Wpływają lepsza strona dla następujących jakości cementu:
- zwiększyć odporność na zmiany temperatury;
- zwiększyć siłę;
- mobilność i elastyczność produktu;
- ogranicza przenikanie wody do gotowego produktu.
W zależności od właściwości plastyfikatorów dodanych do cementu, jego roztwór będzie twardniał szybciej lub wolniej.
Skład, z którego wytwarzany jest cement
Część osób pracujących w branży budowlanej nie wie, z czego składa się cement.
Skład cementu może się różnić w zależności od marki i przeznaczenia.
Niezależnie jednak od rodzaju cementu, czyli receptury zastosowanej przy jego produkcji, podstawą jego powstania są dwa składniki – kamień wapienny z dodatkiem gliny.
Ilość wapienia jest trzykrotnie większa od ilości gliny. Są one niezbędne do uzyskania wysokiej jakości klinkieru, będącego półproduktem do produkcji cementu.
Teraz możemy nazwać główne składniki kompozycji, aby każdy mógł zrozumieć, z czego wykonany jest cement:
- klinkier, będący podstawą produktu końcowego, określający jego cechy wytrzymałościowe. Stosowany w postaci granulatu o średnicy do 60 mm. Obróbkę cieplną prowadzi się w temperaturach dochodzących do 1500°. Po stopieniu klinkieru powstaje masa charakteryzująca się dużą zawartością krzemionki i dwutlenku wapnia;
- te składniki wpływają Charakterystyka wydajności produkt finalny. Przed wypaleniem granulki klinkieru rozdrabnia się do stanu pylącego;
- gips, który określa szybkość twardnienia cementu. W podstawowe przepisy do kompozycji można dodać do 6% czystego gipsu Łączna składniki;
- dodatki specjalne (plastyfikatory, dodatki mrozoodporne, mydło w płynie itp.), wzmacniając właściwości już istniejące w wyrobie lub nadając mu specjalne właściwości, które mogą rozszerzyć zakres zastosowań cementu.
Produkcja - jak powstaje cement, proces jego otrzymywania w zakładzie
Produkcja materiału odbywa się w określonej kolejności, etapami. Technologia produkcji obejmuje następujące operacje:
- Składniki przeznaczone do produkcji klinkieru są wstępnie wymieszane. Konieczne jest ścisłe przestrzeganie proporcji kompozycji - 25% gliny i 75% wapienia.
- Powstałą kompozycję wypala się wysoka temperatura. Po wypaleniu w wysokich temperaturach glina i wapno łączą się, tworząc klinkier.
- Gotowy produkt kruszy się w młynach kulowych, składających się z bębnów umieszczonych w pozycji poziomej, wewnątrz których się znajdują stalowe kule. Umieszczony w nich klinkier zostaje rozdrobniony do stanu proszku.
- Im drobniejsze frakcje cementu, tym lepsze będzie jego właściwości użytkowe.
Istnieje kilka metod wytwarzania tego materiału budowlanego. O ich wyborze decyduje wiele czynników, z których głównymi są specyfika sprzętu dostępnego w przedsiębiorstwie oraz zapotrzebowanie na określone marki cementu.
Opracowane technologie różnią się sposobami przygotowania surowców wykorzystywanych do produkcji kompozycji. Kolejność jego wytwarzania pozostaje taka sama.
Opracowano następujące metody:
- Technologia mokra, która polega na zastąpieniu wapna kredą. W procesie mieszania składników kompozycji są one mielone w młynie kulowym. Proces ten przeprowadza się z dodatkiem wody. W rezultacie powstaje mieszanina o stężeniu wilgoci do 50%.
- Powstały materiał jest następnie wypalany w piecu. Po wypaleniu staje się klinkierem. Następnie jest kruszone.
- Technologia sucha znacznie obniża koszty produkcji, ponieważ łączy w sobie kilka operacji technologicznych w jeden proces. Przy zastosowaniu tej technologii składniki wchodzące do młyna kulowego są jednocześnie mielone i suszone.
- Do suszenia wykorzystuje się działanie gorących gazów. Gotowa masa wsadowa ma konsystencję proszku.
- Technologia kombinowana łączy w sobie cechy opisanych powyżej metod produkcji. W zależności od sprzętu stosowanego w przedsiębiorstwie można uzyskać półsuchą kompozycję o zawartości wilgoci do 18%.
- W drugiej opcji początkowo przygotowuje się susz, a następnie zwilża do 14%. W obu wariantach przygotowaną kompozycję następnie poddaje się wyżarzaniu i mieleniu.
Więcej informacji na temat produkcji cementu można znaleźć w filmie:
Klasyfikacja mieszanek cementowych
Istnieje wiele odmian i różnych rodzajów tego materiału budowlanego. Wyróżniają się podstawowym składem i dodatkami, które nadają każdemu rodzajowi szczególne właściwości.
Do głównych typów należą:
- Cement portlandzki, od którego rozpoczęła się produkcja popularnego produktu budowlanego. Nie stosuje się go do wytwarzania roztworów wiążących. Służy do tworzenia wyrobów betonowych i zapraw o dużej wytrzymałości;
- cement glinowy, charakteryzujący się odpornością na wilgoć i szybkim twardnieniem;
- cement kwasoodporny, w którym wykorzystuje się kwarc i fluorek sodu. Materiał jest odporny na kwasy, ale jest krótkotrwały.
Kupując jakikolwiek rodzaj cementu, powinieneś wiedzieć, że jego skład aktywnie oddziałuje środowisko, tracąc swoją wytrzymałość podczas długotrwałego przechowywania.
Nawet jeśli będzie przechowywany w suchym miejscu, po kilku miesiącach jego stopień ulegnie obniżeniu. Dlatego przy zakupie należy zwrócić uwagę na datę produkcji. Możesz także przeczytać nasz artykuł na temat specyfikacji technicznych.
Dziś nie sposób sobie wyobrazić budowy jakiegokolwiek obiektu bez użycia cementu. Stosuje się go na wszystkich etapach proces konstruowania. Bez tego nie da się ukończyć fundamentów, ułożyć ścian, a także wewnętrznych i wykończenie zewnętrzne. Do chwili obecnej nie wynaleziono żadnych analogów tego materiału budowlanego, co wskazuje unikalne właściwości cement. Czy wiesz z czego składa się cement?
Co to jest cement
Cement jest materiał konstrukcyjny, który występuje w postaci rozdrobnionego proszku otrzymywanego z klinkieru. W swoim składzie może zawierać składniki modyfikujące i wypełniacze.
Według GOST
Proces otrzymywania cementów ogólnobudowlanych należy prowadzić z uwzględnieniem wymagań GOST 31108-2003. Jest to norma, która jest w stanie regulować proporcje niezbędnych składników wchodzących w skład suchej masy oraz technologię produkcji materiału. Ale ta norma nie obejmuje materiałów specjalnego przeznaczenia.
O czym środek ciężkości W tym dokumencie opisano gatunek cementu M 500
Definicja gatunku
Obecnie definicja najpopularniejszych materiałów obejmuje:
- glinowy;
- wapno-popiół;
- wodoodporny.
Glinowy
Proces otrzymywania takiego materiału odbywa się metodą topienia pod wpływem temperatur 1380 - 1600 stopni. W takim przypadku nie ma potrzeby stosowania drobnego mielenia wsadu. Proces otrzymywania tego typu materiału odbywa się w piecach różne rodzaje. Najczęściej stosowane są metody wybuchowe i elektryczne.
Skład tego materiału obejmuje następujące składniki:
- Tlenek glinu.
- Tlenek wapnia.
- Tlenek krzemu.
- Tlenek żelaza.
Jak używać suchego cementu mieszanina piasku Opisano M 150
Ponadto skład cementu glinowego jest bogaty w krzemian dwuwapniowy. Pozwala na opóźnione utwardzanie. Aby zwiększyć określone właściwości, kompozycję można uzupełnić glinianami i domieszkami balastowymi. Ta mieszanka pozwoli uzyskać niezawodną i trwałą konstrukcję.
Hermetyczny
Cement ten zawiera drobno zmielony żużel wielkopiecowy i kamień gipsowy w stosunku 2:1. Konstrukcja ułożona na bazie takiego materiału uzyskuje niezbędną twardość w wodzie i powietrzu. Jeżeli utwardzanie przeprowadzono w wodzie, wówczas procent skurczu jest minimalny.
Proces wiązania następuje po 10 minutach i przez całkowicie suchy musisz odczekać 3 dni. Powstałe rozwiązania oparte na materiale hermetycznym charakteryzują się takimi właściwościami jak wodoodporność, ognioodporność, trwałość i stabilność. W porównaniu z cementem portlandzkim materiał ten ma dowolną klasę odporności ogniowej. Ponadto proces utwardzania zachodzi szybciej niż w przypadku aluminium.
Jaka jest opisana gęstość nasypowa cementu M 500
Wapno-popiół
Aby uzyskać taki skład, stosuje się takie składniki, jak popiół paliwowy i żużel z wapnem. Po wymieszaniu tych elementów są one drobno mielone. Aby poprawić właściwości cementu wapienno-popiołowego, należy dodać 5 g gipsu. Pozwala na szybkie utwardzanie i zwiększa wytrzymałość konstrukcji.
Budując konstrukcję do określonego celu, konieczne jest zakupienie wymaganej marki cementu, która zawierałaby wszystkie niezbędne komponenty. Jeśli producent będzie ściśle przestrzegał wszystkich proporcji, powstały produkt będzie miał doskonałą wytrzymałość, trwałość i odporność na różne agresywne środowiska. O tym, co to jest, przeczytasz w naszym artykule.