Ogólne informacje na temat montażu suwnic. Platformy, ogrodzenia i galerie do obsługi suwnic bramowych Wymiary belek suwnicy pomostowej
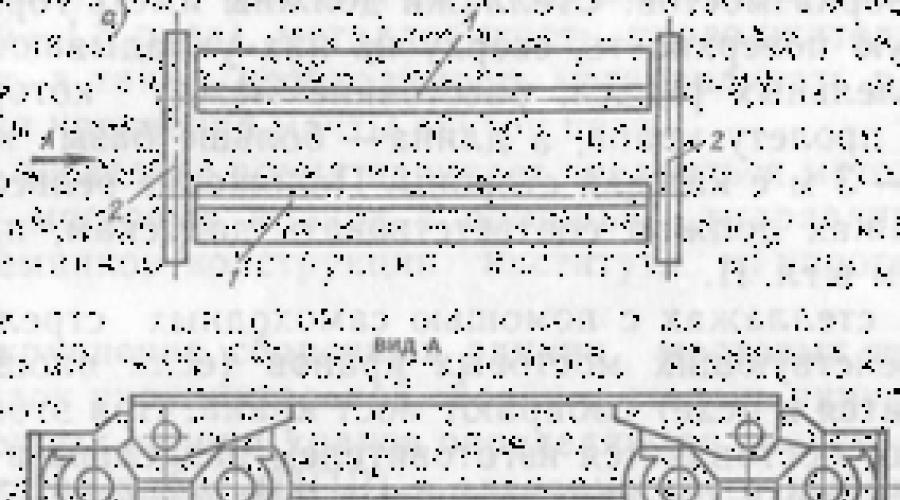
Przepisy dotyczące dźwigów regulują budowę schodów przeznaczonych do dostępu z piętra warsztatu na podesty i podesty remontowe oraz galerie zlokalizowane wzdłuż torów dźwigu, a także schodów znajdujących się na samym dźwigu.
Wymagania dla drabin umieszczonych na zewnątrz dźwigu i dla drabin umieszczonych na dźwigu są różne.
Schody umożliwiające dostęp z podłogi warsztatu do platform i galerii znajdujących się na zewnątrz żurawia muszą być nachylone pod kątem nachylenia do horyzontu nie większym niż 60° i szerokości co najmniej 600 mm. Za szerokość schodów przyjmuje się wolną odległość pomiędzy wewnętrznymi krawędziami balustrad. Stopnie tych schodów wykonane są z blachy stalowej falistej lub gładkiej o szerokości co najmniej 120 mm z topionym reliefem. W przypadku schodów nowo instalowanych nie dopuszcza się stosowania stopni wykonanych z prętów.
Umiejscowienie drabin musi zapobiegać możliwości przytrzaśnięcia na nich osób przez poruszający się dźwig lub jego kabinę. Na już wykończonych schodach w niebezpieczne miejsca Należy zapewnić ogrodzenie pełne lub siatkowe. Schody na samym dźwigu wykonujemy pionowo lub z dowolnym wymaganym kątem nachylenia; przyjmuje się, że szerokość tych schodów wynosi co najmniej 500 mm.
W przypadku drabin o wysokości mniejszej niż 1,5 m, znajdujących się na dźwigu, a także drabin przeznaczonych do wyjścia z kabiny na galerię żurawi pomostowych lub przejezdnych, szerokość może zostać zmniejszona do 350 mm. Dla wygody i bezpieczeństwa użytkowania stopnie schodów pionowych muszą być oddzielone od metalowej konstrukcji dźwigu na odległość co najmniej 150 mm, gdyż w przeciwnym razie trudno będzie postawić stopę na stopniu i ryzyko upadku z schodów nie można wykluczyć.
Ogrodzenie schodów pionowych wykonane jest z łuków umieszczonych w odległości nie większej niż 800 mm od siebie i połączonych co najmniej trzema podłużnymi pasami. Odległość schodów od łuku nie może być mniejsza niż 700 i nie większa niż 800 mm przy promieniu łuku 400 mm.
Takie ogrodzenie wykonuje się dla schodów o wysokości większej niż 5 m, zaczynając od wysokości 3 m. Jeżeli klatka schodowa na dźwigu jest ustawiona pod kątem do horyzontu większym niż 75°, wówczas wymagania dotyczące ogrodzenia pionowego. schody w pełni go dotyczą. Odgromniki łukowe nie są wymagane, jeśli klatka schodowa przebiega wewnątrz słupa kratowego o przekroju nie większym niż 900 x 900 mm lub wieży rurowej o średnicy nie większej niż 1000 mm.
Jeżeli wysokość schodów przekracza 10 m, podesty należy rozmieszczać co 6-8 m. W przypadku schodów umiejscowionych wewnątrz wieży rurowej, podestów takich nie można stosować.
Popularne artykuły
|
Zespół ekspertów firmy Crane-Expert zajmuje się montażem, konserwacją i wsparciem księgowym podczas uruchomień suwnic warsztatowych,
jak również inne mniejsze mechanizmy podnoszenia ładunków, mające wpływ na cały cykl prac specjalistycznych – od projektu po serwis gotowego sprzętu.
Obszary usług dźwigowych
Dźwigi to obszar sprzętu skutecznego, ale bardzo niebezpiecznego w obsłudze. Wymagają stałej i starannej obsługi oraz generalny remont, co zajmuje niezwykle dużo czasu. Firma Crane-Expert zajmuje się tworzeniem projektów, produkcją i montażem podestów obsługowych dźwigów, drabin wspinających się na tor podsuwnicowy oraz paneli do chodników dla suwnic. Proces ten dzieli się na kilka etapów.
Projekt
Pracownicy firmy tworzą dla nich projekty podestów serwisowych do obsługi pracy dźwigów oraz chodników. Ich kształt i wytrzymałość zależą od warunków montażu i zadań stojących przed pracownikami. Wszystkie konstrukcje przechodzą cyfrowe uzasadnienie wytrzymałości.
Budowa
Projekty obliczone w teorii są niezawodnie montowane trwałe materiały na bazie wyrobów metalowych. Konsumenci w drodze do nich otrzymują podesty usługowe i schody, teoretycznie uzasadnione i wielokrotnie sprawdzone w produkcji.
Niezawodność i trwałość
Firma Crane-Expert posiada wspaniałe doświadczenie konserwacja pracujących dźwigów w utworzonych serwisach, ich obsługa i naprawy. Jest to jeden z ważnych i niezbędne wskazówki utrzymanie funkcjonalności dźwigów. Jeśli posiadasz w swojej organizacji dźwig, a nie ma podestu do jego konserwacji, skontaktuj się z firmą Crane-Expert, a Twoje dźwigi zostaną serwisowane z nowych, zaprojektowanych i zamontowanych przez nas podestów dźwigowych w ramach jednego kontraktu.
Most wsparcia kran elektryczny posiada most dźwigowy, który rozciąga się przez przęsło budynku i opiera się na kołach jezdnych na szynach toru suwnicy. Najczęściej stosuje się mosty dwubelkowe, które stanowią konstrukcję ramową składającą się z dwóch przestrzennie sztywnych belek głównych z ułożonymi na nich szynami do przemieszczania wózka towarowego oraz dwóch belek końcowych przylegających do belek głównych na końcach przęsła.
Na belkach głównych znajdują się stałe podesty, w których mieszczą się mechanizmy ruchu dźwigu, szafy z osprzętem elektrycznym oraz przejście kierowcy i pracowników serwisu. Wszystkie podesty posiadają poręcze. Belki końcowe są również wyposażone w poręcze i służą do mocowania maźnic z kołami jezdnymi, za pomocą których żuraw opiera się na szynach toru suwnicy. Na końcach tych belek znajdują się zderzaki i wyłączniki krańcowe, które ograniczają ruch żurawia po torze kolejowym.
Dla łatwości obsługi konstrukcje metaloweżurawie wyposażone są w galerie, podesty i schody. Szerokość swobodnego przejścia przez chodnik przeznaczony do obsługi mechanizmów i urządzeń elektrycznych wynosi zwykle co najmniej 500 mm dla żurawi z napędem centralnym i 400 mm dla żurawi z napędem oddzielnym. Na galerii przeznaczonej do montażu przewodów jezdnych szerokość przejścia pomiędzy poręczami a urządzeniami podtrzymującymi wózki i odbierakami prądu ustala się na co najmniej 400 mm. Podłogi galerii, obszarów napraw i podestów wykonane są z metalu lub drewna na całej długości galerii lub obszaru. Podłogi metalowe wykonane są ze stalowych blach falistych lub perforowanych z otworami o średnicy nie większej niż 20 mm.
Platformy, galerie, belki końcowe, a także kabina do obsługi przewodów jezdnych suwnic ogrodzona jest poręczami o wysokości co najmniej 1 m, a w dolnej części ogrodzeniem ciągłym o wysokości co najmniej 100 mm. Ta ostatnia pozwala wyeliminować mimowolne spadanie narzędzi i części zamiennych z pomostu dźwigu podczas serwisowania dźwigu. Poręcze i płoty montuje się także po bokach końcowych wózków towarowych, a w przypadku braku galerii - wzdłuż mostu po bokach wzdłużnych. Włazy podłóg galerii i pomieszczeń remontowych wyposażone są w wygodnie otwierane pokrywy. Jeżeli pokrywa jest uchylna, to kąt pomiędzy pokrywą włazu w pozycji otwartej a pokładem nie przekracza 75°. Wymiary włazu wynoszą co najmniej 500 x 500 mm.
Schody umożliwiające dostęp z podłogi na perony i galerie wykonuje się o szerokości co najmniej 600 mm, a odległość między stopniami nie przekracza 300 mm. Jeżeli wysokość drabiny na dźwigu jest mniejsza niż 1,5 m, dopuszczalna jest szerokość drabiny 500 mm. Schody prowadzące do wyjścia z kabiny na galerię mostu dźwigowego mogą mieć szerokość co najmniej 350 mm. Schody pochyłe o kącie nachylenia do poziomu 75° lub mniejszym wyposażone są w poręcze i stopnie płaskie z blachy falistej lub gładkiej z wtopionym reliefem; Szerokość stopni musi wynosić co najmniej 120 mm. Na schodach pionowych, a także na schodach o kącie nachylenia do horyzontu większym niż 75°, na wysokości 3 m montuje się ogrodzenia łukowe. Ogrodzenia te znajdują się w odległości nie większej niż 800 mm od siebie i są połączone co najmniej trzema podłużnymi stalowymi pasami.
Ogólne informacje na temat montażu suwnic
Podczas montażu suwnic zespoły montażowe są powiększane, dostarczane na miejsce montażu i rozkładane w obszarze pracy urządzeń dźwigowych, zawieszane, powiększone elementy wciągane na tory dźwigowe, montowane i kalibrowane zamontowane suwnice.
Wybór sposobu montażu podpór mostowych zależy od ich konstrukcji i ciężaru, miejsca montażu: wewnątrz lub na zewnątrz budynku, czasu dostawy przez producentów, gotowości obiektu do budowy, konstrukcji szkieletu budynku, a także rodzaju i charakterystyki dostępnych maszyn dźwigowych do organizacji instalacyjnej.
Do najczęściej stosowanych metod montażu suwnic zalicza się: – wykorzystanie suwnic wieżowych lub szynowych przeznaczonych do montażu konstrukcje budowlane Budynki; – przy użyciu żurawi samojezdnych; przy użyciu konstrukcji szkieletowych budynków, w tym kół pasowych, mocowanych do słupów lub belek montażowych wspartych na dwóch sąsiednich kratownicach, rzadziej - bezpośrednio do kratownic.
Ostatnio rozpowszechniona stała się opracowana przez Instytut Giprometallurgmontazh metoda instalowania dźwigów, całkowicie zmontowanych w dolnym położeniu, z wykorzystaniem urządzeń linii przenośnikowych do montażu i instalowania bloków pokryciowych budynków.
Powszechną dotychczas metodę montażu dźwigów za pomocą masztów stosuje się obecnie jedynie w przypadkach, gdy nie ma innych urządzeń lub mechanizmów podnoszących lub nie można ich zastosować, np. warunki warsztatowe nie pozwalają na zastosowanie dźwigu samojezdnego, a konstrukcja jego ramy nie pozwala na montaż belki montażowej.
Głównymi wadami tej metody są większa pracochłonność w porównaniu do innych (1,5-1,8 razy), zużycie metalu, czas pracy, a także konieczność instalowania stężeń w celu zabezpieczenia masztu wewnątrz warsztatu.
Ostatnio zaczęto wprowadzać metodę montażu suwnic za pomocą podnośników hydraulicznych zaprojektowanych przez Instytut Giprotechmontazh.
Konsolidacja jednostek montażowych suwnic.
Kolejność powiększonego montażu oraz stopień powiększenia zespołów montażowych żurawia określa plan wykonania robót (WPP), w zależności od wybranego sposobu montażu i warunków dostawy dźwigów.
Celem powiększonego montażu konstrukcji, mechanizmów i wyposażenia elektrycznego suwnic jest wykonanie maksymalnej objętości prac montażowych w dolnym położeniu i, w związku z tym, ograniczenie do minimum liczby operacji wykonywanych na wysokości. Dlatego najlepsza opcja to taki, w którym most podnoszony jest na tory suwnicy, całkowicie zmontowany w pozycji dolnej wraz z zamontowanym na nim wózkiem, lub most podnoszony jest osobno, a następnie wózek. Często jednak nie ma możliwości podniesienia i zainstalowania w pełni zmontowanego mostu suwnicowego na torach podsuwnicowych ze względu na niewystarczający udźwig istniejących mechanizmów i urządzeń, ograniczoną przestrzeń pod wysięgnikiem stosowanych żurawi samobieżnych oraz niemożność (ze względu na brak miejsca) rozłożyć zmontowany most dźwigowy w płaszczyźnie poziomej nad torami suwnicy. Ponadto nie zawsze ekonomicznie opłaca się wytwarzać stojaki i organizować miejsca do montażu mostów dźwigowych.
Najczęściej pomosty suwnicowe montowane są w dwóch lub czterech zespołach montażowych, w jednym powiększonym zespole montowany jest wózek, a w drugim kabina sterownicza.
Powiększony montaż mostów. Konstrukcje metalowe mostów powiększa się w dolnym położeniu w przypadku, gdy most jest podnoszony na tory dźwigowe w jednym bloku. W tym celu na powiększonym miejscu montażu (jeśli pozwala na to miejsce) lub w miejscu specjalnie do tego wyznaczonym, jak najbliżej miejsca montażu, instalowane są stojaki do montażu mostów. Regały muszą mieć poziomą powierzchnię, na nich ułożone są dwie równoległe szyny, których odległość jest równa rozpiętości dźwigu, a długość jest o 2,5-3 m większa niż podstawa dźwigu z każdej strony.
Most dźwigowy montowany jest na stojakach za pomocą wysięgnika samobieżnego lub działających suwnic (jeśli budowa znajduje się w warsztacie). W takim przypadku, jeśli most jest dostarczany przez producenta osobno w postaci dwóch belek głównych i dwóch belek końcowych (ryc. 74, a), montowane są cztery złącza montażowe belek głównych z belkami końcowymi. Jeżeli most dostarczany jest w postaci dwóch belek głównych wraz z częściami belek końcowych (półmostami), należy zamontować złącza łączące części belek końcowych: dwa - jeżeli belki główne dostarczane są do montażu z połówkami belek czołowych belki końcowe (ryc. 74, b) i cztery, jeśli Zewnętrzne części belek końcowych są przymocowane do belek głównych, a ich części środkowe (wkładki) 3 są dostarczane osobno (ryc. 74, c).
Montaż złączy montażowych odbywa się w dwóch etapach: w pierwszej kolejności za pomocą śrub montażowych (montażowych), a po wyrównaniu i wyeliminowaniu zniekształceń, na koniec za pomocą spawania, oczyszczenia śrub lub nitów zgodnie z instrukcją na rysunkach wykonawczych.
Podczas montażu mostu instalowanego zgodnie ze schematem pokazanym na ryc. 74, a w pierwszej kolejności na szynach ułożonych na stojakach montuje się belki końcowe z kołami lub wyważarkami i mocuje (tymczasowo zabezpiecza) w we właściwej pozycji. Następnie jedną z belek głównych wkłada się pomiędzy belki końcowe, aż otwory na śruby mocujące w złączach zrównają się i zostaną połączone śrubami. Następnie instalowana jest również druga belka główna i łączona z belkami końcowymi.
Montaż mostów suwnicowych dostarczonych według schematów pokazanych na rys. 74, b, c, zacznij od zainstalowania półmostów z kołami lub wyważarkami na stojakach. Jeżeli mosty są dostarczane zgodnie ze schematem pokazanym na ryc. 74, c, następnie środkowe części belek końcowych - wkładki - są instalowane pomiędzy półmostami. Następnie półmostki łączy się i wyrównuje otwory pod śruby montażowe w stopkach zgodnie ze wzorem oznakowania, po czym łączy się je śrubami.
74. Schematy dostawy suwnicy IOSG a - oddzielne belki główne i końcowe: b - belki główne z połówkami belek końcowych; c - belki główne z zewnętrznymi częściami belek końcowych i wkładkami; 1 - belka główna; 2 - belka końcowa; 3 - wstaw
Przed montażem powierzchnie dolników są dokładnie oczyszczane z zaschniętego brudu, farby i rdzy, a powierzchnie zespawanych elementów doczołowych są czyszczone do metalicznego połysku. Podczas montażu połączeń należy osiągnąć maksymalną zbieżność otworów i nie dopuścić do ich regulacji poprzez rozciąganie za pomocą stożkowych trzpieni, ponieważ powoduje to dodatkowe naprężenia w metalu. Szczelność doczołówek sprawdza się szczelinomierzem: płytka sondy o grubości 0,1 mm nie powinna przechodzić pomiędzy nakładkę a korpus belki końcowej.
Połączenia nitowane montuje się poprzez wbicie trzpieni (zaślepek) w otwory (na nity), którymi należy równomiernie wypełnić 10-15% otworów z każdej strony złącza montażowego. Jednocześnie instalowane są śruby mocujące, które służą do równomiernego wypełnienia 20-25% otworów. Nakrętki na śrubach nie są całkowicie dokręcone.
Do montażu złączy montażowych oprócz dźwigów stosuje się wciągarki dźwigniowe, podnośniki, a także proste urządzenia do tymczasowego mocowania elementów mostu w żądanym położeniu: podpory, okładziny, wsporniki, podstawki itp.
Po zmontowaniu mostu do zewnętrznych ścian belek głównych mocowane są podesty, montowane są schody i płoty.
Zebrane o godz śruby montażowe Most dźwigowy sprawdza się poprzez sprawdzenie i porównanie z tymi wskazanymi na rysunkach lub w paszporcie: prostopadłość mostu, rozpiętość dźwigu, tor wózka ładunkowego, winda konstrukcyjna mostu, montaż szyn jezdnych i kół jezdnych dźwigu.
Prostokątność mostu sprawdza się na dwa sposoby: poprzez różnicę przekątnych lub metodą wyrównania (za pomocą teodolitu). Przekątne mierzy się w symetrycznych punktach mostu, które mogą być punktami przecięcia osi wzdłużnej i poprzecznej kół jezdnych; praktycznie wykonuje się je na belkach końcowych lub szynach wózków (rys. 75), ale w tym przypadku wymiary a i a’, b i b’ muszą być odpowiednio sobie równe. Pomiary przekątnych często przeprowadza się w punktach przeniesionych na belki końcowe ze stycznych pionowych na obwody obrzeży kół jezdnych. Jeżeli u producenta sprawdzono prostopadłość mostu (o czym dokonano odpowiedniego wpisu w paszporcie dźwigu), to podczas montażu dokonuje się pomiarów przekątnych zgodnie ze znakami kontrolnymi zaznaczonymi na belkach końcowych lub szynach wózków. Różnica między przekątnymi mostu prostokątnego nie powinna przekraczać 5 mm.
75. Schemat wyrównywania mostu suwnicowego za pomocą taśmy mierniczej
76. Schemat ustawienia mostu suwnicowego z wykorzystaniem teodolitu
1 - teodolit; 2-5 - koła; 6 - siatka
W przypadku dużych rozpiętości dźwigów ta metoda sprawdzania nie jest wystarczająco dokładna, ponieważ pomiar dużych długości za pomocą miarki wymaga stałego naprężenia taśmy stalowej; Ponadto prawie nie zawsze można zmierzyć przekątne na moście dźwigowym. W takich przypadkach częściej stosuje się drugą metodę, która jest następująca.
W punkcie A, w odległościach wskazanych na ryc. 76, zainstaluj teodolit, a w punkcie B - znak celowniczy 6. Wyrównaj oś celowania teodolitu ze środkiem znaku celowniczego, a następnie obróć luneta teodolit pod kątem 90° w płaszczyźnie poziomej (wzdłuż kończyny) i zabezpieczyć. Następnie zmierzyć odległości X\, Xr, X3 i X4 od pionu zainstalowanego wzdłuż osi celowania teodolitu do powierzchni czołowej kół wzdłuż cięciwy przechodzącej przez punkty oddalone od osi o co najmniej 300 mm. Zakłada się, że długość cięciwy jest taka sama na wszystkich kołach. Następnie teodolit przenosi się do punktu A’, a znacznik celu do punktu B’ i dokonuje się podobnych pomiarów na kołach.
Warunkiem prostokątności mostu jest zgodność wymiarów xx i x4, Xg i x3 oraz xb, przyjętych pomiędzy kołami 3 i 4, 2 i 5. Dopuszczalne odchylenie tych wymiarów od siebie wynosi 3 dla kołnierzowych koła i 4 mm dla kół kołnierzowych.
Druga metoda pozwala również na jednoczesne sprawdzenie niewspółosiowości kół jezdnych w płaszczyźnie poziomej i pionowej, ponieważ różnica wymiarów xx i X2, Xb określa niewspółosiowość w płaszczyźnie poziomej, a różnica odległości od płaszczyzny pionowej do podobne punkty znajdujące się na końcach cięciwy pionowej charakteryzują niewspółosiowość w płaszczyźnie pionowej.
W pierwszej metodzie sprawdzania prostopadłości mostu w ten sam sposób określa się niewspółosiowość kół, z tym że zamiast linii celowniczej teodolitu stosuje się sznurek i pion. Odchylenia powierzchni czołowych kół od płaszczyzny poziomej i pionowej nie powinny przekraczać i mm na 1000 mm średnicy koła. Tę samą tolerancję ustala się dla odchylenia końców kół od płaszczyzny ogólnej.
Jeżeli odchylenia od prostopadłości mostu przekraczają podane wartości, należy wyeliminować niewspółosiowość.
Najczęstsza poprawka kształt geometryczny mosty dźwigowe jest następująca. W jednym z narożników mostu o większej przekątnej umieszczony jest ogranicznik zapobiegający jego ruchowi wzdłużnemu i poprzecznemu, a w drugim narożniku - podnośnik. Po poluzowaniu śrub mocujących skierować siłę podnośnika wzdłuż osi belki głównej, która jest przesuwana, aż różnica przekątnych osiągnie zero lub będzie mieściła się w tolerancji. Innym sposobem skorygowania kształtu mostu jest zamocowanie jednej belki końcowej i przesunięcie drugiej w kierunku osi toru suwnicy.
Dopuszczalne odchylenie rozpiętości żurawia LK, mierzone w środku powierzchni nośnych kół jezdnych, dla żurawi z LK do 40 m wynosi ±6 mm, dla żurawi z LK powyżej 40 m – ±7,5 mm.
Odchylenie połączeń szyn wózka 2 w rzucie i wysokości nie powinno przekraczać 1 mm, a szczelina na stykach nie powinna być większa niż 2 mm.
Dopuszczalny odstęp podstawy szyny wózka od podkładki lub pasa górnego belki zależy od rodzaju szyny i może wynosić na krawędziach podstawy (patrz wielkość g na rys. 77) od 0,75 mm dla P4 szynę na 2,5 mm dla szyny SKR140. W środkowej części podeszwy szczelina ta nie powinna przekraczać 0,3 mm (P4) do 1 mm (skr140).
Odkształcenia kół jezdnych przekraczające powyższe tolerancje eliminujemy stosując przekładki montowane pomiędzy płytami i maźnicami kół w belce końcowej lub wyważarce, zapewniając, że położenie kół odpowiada wymiarom uzyskanym podczas montażu u producenta i zapisanym w specjalny formularz dołączany do paszportu dźwigu.
Ostateczne połączenie złączy montażowych podczas spawania wykonują spawacze certyfikowani zgodnie z przepisami Gosgortekhnadzor w temperaturze nie niższej niż minus 10 ° C zgodnie z wymagania techniczne producent.
Czyste śruby stosowane do łączenia złączy montażowych muszą mieć długość niegwintowanej części o 8-10 mm mniejszą niż grubość pakietu łączonych elementów. Włóż je ciasno w otwory za pomocą młotka. Dokręcenie śrub podczas końcowego montażu złączy powinno zapewnić szczelne dopasowanie łączonych części. W przypadku szczelnego połączenia, pomiędzy częściami można włożyć sondę o grubości 0,1 mm na głębokość nie większą niż 20 mm w dowolnym miejscu połączenia.
Nitowanie odbywa się za pomocą ręcznych młotków pneumatycznych. Jest to bardzo pracochłonna i trudna operacja, dlatego starają się wykonać maksymalną ilość prac nitujących w dolnym położeniu, przed podniesieniem jednostek montażowych na tory dźwigu.
Przed rozpoczęciem nitowania dokręć czyste śruby mocujące okładziny na złączach.
Następnie sprawdza się otwory pod nity miernikiem o średnicy o 1,5 mm mniejszej od średnicy nominalnej otworu i usuwa się zadziory na krawędziach otworów, przy czym głębokość i szerokość pogłębienia otworów nie powinna przekraczać 1,5 mm.
Rozbudowa półmostów suwnic polega na zamontowaniu podwozia i napędu mechanizmu ruchu (jeśli są dostarczane osobno) oraz platform. Czasami podczas powiększonego montażu półmostów suwnicy instalowanych według schematu pokazanego na ryc. 74, c, pośrodku, na jednym z półmostów umieszcza się części belek końcowych, aby zmniejszyć ilość prac montażowych na wysokości. Ten schemat powiększenia stosuje się, gdy podczas podnoszenia można obracać powiększony półmostek w płaszczyźnie poziomej.
Układ jezdny mechanizmu ruchu żurawia, w którym belki główne opierają się bezpośrednio na wyważarkach z kołami jezdnymi, montuje się poprzez przetaczanie ich po szynach pod belką główną, a po wyrównaniu otworów łączy się je osią (wałem łączącym). .
Montaż układu jezdnego żurawi, w którym belki główne opierają się na wyważarkach głównych (ryc. 78), rozpoczyna się od przymocowania do nich małych wyważarek z kołami jezdnymi. W tym celu najpierw montuje się małe wyważarki, które tymczasowo mocuje się na szynach, do których na haku mechanizmu podnoszącego podawana jest wyważarka główna. Osie wkłada się w dopasowane otwory w wyważarkach głównych i małych. Następnie wyważarka główna złożona z małych jest podawana tym samym mechanizmem podnoszącym na koniec belki głównej, układany na okładzinach z podkładów i po wyrównaniu otworów łączy się je osią.
Położenie wyważarek z kołami reguluje się za pomocą pierścieni dystansowych montowanych na osi po obu stronach wyważarki, zgodnie z oznaczeniami fabrycznymi. Nieprawidłowy montaż pierścieni dystansowych lub ich brak może spowodować zmianę rozpiętości żurawia, co jest niedopuszczalne. Zainstalowane wyważarki sprawdza się pod kątem zakleszczenia poprzez kołysanie nimi na osiach.
Napęd mechanizmu jezdnego dźwigu montuje się po zamontowaniu i wyosiowaniu podwozia, a wyosiowaniu i połączeniu wału wyjściowego skrzyni biegów z osią koła napędowego w belce końcowej lub wyważarce – po ostatecznym połączeniu mocowania połączenia metalowych konstrukcji mostu. Najtrudniejszą operacją przy montażu napędu jest osiowanie sprzęgieł zębatych typu MZ i MZP (z wałem pośrednim). Stan prawidłowe połączenie wałów jest ich ustawienie i brak odkształceń (w granicach tolerancji).
78. Schemat zawieszenia wyważarek na belkach głównych
1 - hak mechanizmu podnoszącego; 2 - belka główna; 3 - otwory; 4 - główny balanser; b - mały balanser
79. Schemat określania niewspółosiowości i przemieszczeń promieniowych sprzęgieł
a - typ MZ; b - typ MZP
Podczas montażu sprzęgieł typu MZ (ryc. 79, a) określa się przemieszczenie promieniowe a, które charakteryzuje niewspółosiowość połączonych wałów i niewspółosiowość ilość liniowa s - tn-n lub kąt с. Wielkości a, m i n wyznaczane są w czterech punktach (w dwóch wzajemnie prostopadłych płaszczyznach). Największy dopuszczalna wartość co = 0°30.
Przy montażu sprzęgieł typu MZP (Rys. 79.6) kontrolowane jest przemieszczenie promieniowe a i odkształcenia e-b-c.
Dopuszczalne wartości a, s, b, c i e zależą od rozmiarów (liczb) sprzęgieł, w których są wskazane; dokumentacja techniczna producent.
W procesie osiowania łączone wały są osiowane, czyli osiągane jest ich współosiowość i eliminowane są zniekształcenia, po czym następuje ostateczny montaż sprzęgieł.
Na koniec instalowane są silniki elektryczne i hamulce, sprawdzane jest położenie silników elektrycznych, ich wały są ustawiane w jednej linii z wałkami skrzyni biegów i mocowane do płyty lub ramy pod silnikiem.
Hamulec należy zamontować tak, aby jego środek pokrywał się ze środkiem koła pasowego hamulca. Nierównoległość i niewspółosiowość powierzchni klocków względem siebie powierzchnia robocza koła pasowe nie powinny przekraczać 0,1 mm na 100 mm szerokości koła pasowego, a bicie promieniowe - 0,05 mm na 100 mm średnicy koła pasowego.
Zintegrowany montaż wózków. Wózki dźwigowe o udźwigu do 50 ton włącznie dostarczane są przez producentów w stanie całkowicie zmontowanym i gotowym do montażu na pomoście dźwigowym.
Wózki dźwigowe o udźwigu 80 ton i większym dostarczane są jako oddzielne zespoły montażowe według następujących schematów: – rama wózka zmontowana z mechanizmem ruchu, głównym i pomocniczym mechanizmem podnoszącym – zespoły montażowe; – połowa ramy z mechanizmem jezdnym (bez układu jezdnego) i mechanizmem podnoszenia głównego, połowa ramy z mechanizmem podnoszenia pomocniczego i z podwoziem mechanizmu jezdnego; – cała rama wózka, mechanizmy ruchu, podnośniki główne i pomocnicze – jako jednostki montażowe; – rama wózka jest w częściach, mechanizmy ruchu, podnośnik główny i pomocniczy znajdują się w oddzielnych zespołach montażowych.
Oczywiście najwięcej pracy przy powiększonym montażu trzeba wykonać przy dostawie wózków według ostatniego z powyższych schematów (w ten sposób dostarczane są wózki dźwigowe o udźwigu 200/32 ton i więcej). Większy montaż wózka odbywa się na specjalnym stojaku z szynami lub na pomoście dźwigowym. Można zamontować wózek na klatce podkładowej, a następnie przeprowadzić ostateczne ustawienie układu jezdnego mechanizmu jego ruchu na pomoście suwnicy. W pierwszej kolejności należy zamontować ramę wózka (jeśli producent dostarcza ją w osobnych częściach) na śruby mocujące i zamontować układ jezdny mechanizmu jezdnego: koła lub wyważarki.
Podczas montażu ramy należy sprawdzić jej prostopadłość mierząc przekątne w punktach oznaczonych jako zagrożenia u producenta podczas montażu kontrolnego wózka lub bezpośrednio w miejscu montażu. Różnica między przekątnymi nie powinna przekraczać 3 mm.
Następnie sprawdź poprawność montażu kół jezdnych lub wyważaczy w taki sam sposób, jak podwozia mechanizmu ruchu żurawia. W tym przypadku oprócz skosu kół jezdnych sprawdza się przesunięcie pionowej płaszczyzny symetrii koła jezdnego od tej samej płaszczyzny szyny, które jest dopuszczalne nie więcej niż 2 mm, a także oparcie wózka na szynach wózka ze wszystkimi kołami (środki kół jezdnych muszą znajdować się w tej samej płaszczyźnie poziomej) i podstawa wózka mierzona z jednej i drugiej strony, której tolerancja wynosi ±2 mm . Po wyrównaniu i wyeliminowaniu zniekształceń ramy i podwozia wykonuje się żelowanie montaż końcowy ramy są nitowane lub spawane zgodnie z wytycznymi na rysunkach producenta. Czasami układ jezdny mechanizmu ruchu wózka jest montowany na odwróconej ramie, która następnie jest przechylana do pozycji konstrukcyjnej.
Po zanitowaniu lub zespawaniu ramy wózka następuje ostateczny montaż mechanizmu ruchu: montowana jest (wstępnie) skrzynia biegów, składane i ustawiane są sprzęgła i wały przekładni, a także łączone z kołami, po czym zabezpieczana jest skrzynia biegów. Następnie zamontować hamulec i silnik elektryczny z połówką sprzęgła wykonaną w postaci koła pasowego hamulca, wycentrować wały silnika elektrycznego i skrzyni biegów, hamulca i zabezpieczyć je śrubami. Jeżeli zajdzie potrzeba nałożenia połówki sprzęgła na wał silnika elektrycznego, należy to zrobić lekkimi uderzeniami młotka drewnianego lub miedzianego, przy czym przeciwny koniec wału zostaje zatrzymany; połówkę sprzęgła nagrzewa się wstępnie do temperatury 60–80°C.
Zespoły montażowe mechanizmów podnoszących spoczywają na obrobionych płytach, dzięki czemu nie ma konieczności regulacji ich wysokości za pomocą podkładek.
Główny mechanizm podnoszenia montuje się w następującej kolejności: montuje się bęben z łożyskami blokowymi i stojakiem (po ustawieniu i zamocowaniu kliny zabezpieczające są wbijane i zabezpieczane przez spawanie elektryczne), małe koła zębate otwartej przekładni i skrzynia biegów, a następnie silnik elektryczny i hamulec.
Montaż pomocniczego mechanizmu podnoszenia rozpoczyna się od skrzyni biegów, a następnie instaluje się bęben, silnik elektryczny i hamulec.
Podczas instalowania bębnów głównych i pomocniczych mechanizmów podnoszących Specjalna uwaga należy podać prawidłowy montaż i ustawienie otwartych kół zębatych.
Zęby przekładni wału wyjściowego skrzyni biegów muszą być równomiernie zagłębione pomiędzy zębami napędzanego koła zębatego bębna. Podczas wyrównywania należy zapewnić odległość międzyosiową określoną na rysunkach i brak przesunięcia osi.
O poprawności montażu decydują maksymalne odchylenia luzu bocznego i odległości środkowej, a także wielkość powierzchni styku zębów, która jest sprawdzana pod kątem farby.
Silniki elektryczne i hamulce są instalowane po całkowitym montażu i wyrównaniu mechanizmów. Jednocześnie sprzęgła zębate i wały są montowane i wyrównywane. Niewspółosiowość i wzajemne przemieszczenie wałów silników elektrycznych i skrzyń biegów musi mieścić się w tolerancjach określonych na rysunkach producenta i w żadnym przypadku nie może przekraczać wartości dopuszczalnej dla sprzęgła zębatego o odpowiednim numerze.
Po zmontowaniu mostu dźwigowego lub powiększeniu półmostu, a także po złożeniu wózka, przed podniesieniem jednostek montażowych na tory suwnicy, montuje się osprzęt elektryczny. Prace te wykonywane są przez ekipę elektryków, którzy zgodnie z rysunkami instalacji elektrycznej montują skrzynki zaciskowe i adaptery, co oznacza aparatura elektryczna, ułożyć wiązki przewodów elektrycznych w skrzynkach i metalowych tulejach.
Następnie należy zamontować urządzenia elektryczne (transformatory, rozruszniki, skrzynki oporowe itp.), upewniając się, że szerokość przejść pomiędzy nimi a poręczami ogrodzenia placu budowy mostu wynosi co najmniej 400 mm. Następnie podłącz końce przewodów elektrycznych do zacisków sprzętu elektrycznego i zainstaluj uziemienie sprzętu elektrycznego i przewodów elektrycznych.
Kabiny sterujące dla suwnic są zwykle instalowane z wysoki stopień gotowość instalacji elektrycznej. Czasami jednak instalacja elektryczna kabiny musi zostać wykonana w miejscu instalacji, obejmująca montaż panelu ochronnego, sterowników, lamp, wyłączników krańcowych i awaryjnych, przycisków, skrzynek zaciskowych i przyłączowych.
Ponadto przed podniesieniem mostu (lub półmostu) dźwigu instaluje się i podłącza oprawy oświetleniowe dźwigu.
Jeżeli jednostki montażowe powiększone są w pozycji projektowej od miejsca ustawienia suwnic, to po powiększeniu transportowane są na miejsce montażu po torach kolejowych na peronach, specjalnych wózkach lub pojazdami na przyczepach. Jeżeli miejsce montażu konsolidacji zlokalizowane jest w pobliżu miejsca montażu suwnic, zespoły montażowe dostarczane są na miejsce montażu za pomocą układaczy rur.
W obszarze montażu jednostki montażowe są rozmieszczane zgodnie z wybranym sposobem montażu i w zależności od dostępności wolna przestrzeń na stronie.
W przypadku wystarczającej ilości miejsca zespoły montażowe ramy wnoszone są w całości na miejsce montażu i układane w taki sposób, aby najcięższe z nich znajdowały się w zasięgu działania urządzeń podnoszących i nie było konieczności ich przeciągania je, aby unieść je do pozycji projektowej.
Jeżeli ze względu na brak miejsca na rozmieszczenie wszystkie zespoły montażowe dźwigu nie mogą zostać dostarczone na miejsce montażu, są one dostarczane zgodnie z ustalonym harmonogramem, określonym przed dostawą każdego powiększonego zespołu. Najskuteczniejszy jest „montaż z kół”, czyli podnoszenie zespołów montażowych dźwigu bezpośrednio z Pojazd.
Zawieszenie. Ta operacja jest bardzo krytyczna w produkcji prace montażowe i musi być wykonywane ściśle według G1PR, która wskazuje schematy zawiesi jednostek montażowych i średnicę liny użytej do produkcji zawiesi. Zmiana wzoru zawiesia lub wymiana liny jest możliwa wyłącznie za zgodą organizacji, która opracowała PPR.
Zestawy dźwigów muszą być montowane przez doświadczonych dźwigarzy.
Wybierając zespół zawiesia i liczbę nitek liny w zawiesiu, zwykle stosuje się zawiesia z jak najmniejszą liczbą nitek, zwiększając średnicę liny, ale nie więcej niż 39 mm, ponieważ lina duża średnica trudno jest wiązać węzły, szczególnie przy noszeniu z węzłem „martwej pętli”, a końce liny splatać węzłem prostym („ósemka”).
Przy podnoszeniu jednostek montażowych o małej masie zawiesie wykonuje się za pomocą zawiesia uniwersalnego lub lekkiego.
Przy podnoszeniu ciężkich jednostek montażowych stosuje się linę stalową o takiej długości, która jest niezbędna do zawieszenia zgodnie z przyjętym schematem.
Końce lin w tych przypadkach łączy się za pomocą węzłów prostych lub bagnetowych, a także za pomocą różnych zacisków.
Belki mostów skrzynkowych są ryflowane różnymi zespołami (ryc. 80). Prosty węzeł pierścieniowy (ryc. 80, a) wykonuje się za pomocą uniwersalnych zawiesi lub kawałków liny.
Najczęściej belki są strzyżone jednym lub dwoma węzłami „martwej pętli” (pętli) (ryc. 80, b, c). Ponieważ belki podnoszone są razem z platformami i elementami mechanizmów ruchu, środek ciężkości podnoszonego zespołu montażowego jest przesunięty od osi symetrii przekroju belki o wielkość K. Dlatego też podczas zawieszania powstaje „martwa pętla” ” jednostka jest przesuwana (patrz rys. 80.6) o tę wielkość, którą można ustalić na podstawie obliczeń lub, jak to ma miejsce w praktyce, poprzez próbne podniesienie na wysokość 100 mm z późniejszym ponownym zawieszeniem, jeśli zajdzie taka potrzeba. Czasami w tym samym celu stosuje się zawiesie pomocnicze z przekładką (patrz ryc. 80, c), które pochłania moment wywracający spowodowany przesunięciem środka ciężkości.
80. Belki zawieszające mostów skrzynkowych
a - prosty węzeł pierścieniowy „w popręgu”; b - przesunięty węzeł „martwej pętli”; c - węzeł „martwej pętli” z zawiesiem pomocniczym; g - węzeł z zachodzącą na siebie nitką; 1 - belka mostowa; 2 - wspornik; 3 - proca; 4 - okładzina - 5 - platforma: 6 - hak lub wspornik mechanizmu podnoszącego; 7 - element dystansowy; 8 - zawiesie pomocnicze; 9 - nakładająca się nić; 10 - kompresja
Belki dźwigów ciężkich są często zawieszane za pomocą węzła z zachodzącą na siebie nitką 9 (ryc. 80, d), co zapewnia niezawodne mocowanie nici zawiesia głównego i którym węzeł ten różni się od prostego węzła pierścieniowego. W takich przypadkach stosuje się również zawiesie pomocnicze. Aby zapewnić stabilność podnoszonej belki, odległość L pomiędzy zawiesiami lub rozstaw gałęzi jednego zawiesia nie może być mniejsza niż połowa wysokości belki I, tj. L> >0,5 R.
Aby zabezpieczyć linę przed uszkodzeniem przez ostre krawędzie podnoszonego ładunku, pod nią umieszcza się podkładki metalowe lub drewniane.
W niektórych przypadkach producent dźwigu lub instalatorzy (w porozumieniu z nim) przyspawają oczka (z elementami wzmacniającymi) do górnych pasów belek w celu zamocowania ruchomego bloku mechanizmu podnoszącego (ryc. 81). W takich przypadkach nie ma potrzeby stosowania zawiesi linowych, a ruchomy blok wielokrążka mocuje się do belki 1 za pomocą sworznia 5, mocowanego w otworach ucha i ucha bloku.
Zmontowany most dźwigowy jest zawieszony za pomocą zespołów pierścieniowych, jak pokazano na ryc. 82. Aby zapobiec deformacji mostu podczas podnoszenia, pomiędzy belkami głównymi montuje się rozpórki rurowe o regulowanej długości.
Wózki dźwigowe zawiesza się za belkami ramy tak, aby odgałęzienia zawiesia okrążające części urządzeń nie uszkodziły ich (ryc. 83).
Wózki o małej nośności zawieszane są na zawiesiach uniwersalnych lub przywiązywane liną pod ramą (ryc. 83, a, b). Jeżeli na ramie wózka znajdują się specjalne urządzenia zawiesiowe - piasty, osie, zszywki itp., wówczas zawiesia są mocowane do tych urządzeń. Za belką ramy głównej, która łączy belki boczne, zawieszone są wózki dźwigowe o dużej wytrzymałości. Na ryc. 83, c pokazuje, że wózek jest zawieszony za pomocą dwóch zawiesi: głównego, przewiązującego belkę główną ramy i pośredniego, przywiązanego do zawiesia głównego i prowadzącego do haka lub wspornika ruchomego koła pasowego mechanizmu podnoszącego . Stosowane są również inne schematy zawieszania ciężkich wózków - bez zawiesi pośrednich.
81 Mocowanie wciągnika łańcuchowego do ucha
1 – belka mostowa; 2 - wzmocnienie: 3 - oko; 4 - kolczyk z klipsem blokowym; 5 - palec
82. Schemat zawiesia mostu dźwigowego 1 - belka końcowa; 2 - proca; 3 - podszewka; 4 - belka główna; 5 - element dystansowy
83. Schematy zawiesia wózków suwnicowych
A. b - zawiesie uniwersalne lub linowe pod ramą; c - zawiesia główne i pośrednie; 1 - zawiesie pośrednie; 2 - zawiesie główne
Podnoszenie zespołów montażowych dźwigu na tory dźwigu. Operacja ta jest najbardziej krytyczną operacją podczas montażu suwnic i musi być przeprowadzona w ścisłej zgodności z PPR (ze schematami instalacji i instrukcjami zapewniającymi bezpieczne warunki produkcja pracy). Schemat instalacji można zmienić w przypadkach, gdy niemożliwe jest (z różnych powodów) użycie mechanizmów podnoszących pierwotnie przewidzianych w projekcie lub gdy zmienia się sytuacja w miejscu instalacji.
Najtrudniejszą operacją podnoszenia zespołów dźwigów jest podnoszenie belek głównych, półmostów i całkowicie zmontowanych mostów.
Istnieją dwa główne sposoby ich montażu na torach podsuwnicowych: – podniesienie półmostu (belki głównej lub całego mostu) nad tory podsuwnicy w położeniu, w którym jest on zorientowany wzdłuż przęsła lub pod pewnym kątem do swojej osi wzdłużnej , a następnie obrócić go w płaszczyźnie poziomej i opuścić na tory dźwigu .
O możliwości zamontowania w ten sposób półmostu decyduje odległość osi szyny dźwigu od ściany budynku oraz szerokość półmostu; – podnoszenie półmostu w pozycji ukośnej – „ryba”, gdy jedna strona wyprzedza drugą. Po przejściu jednej strony przez belkę podsuwnicy, półmost jest cofany lub przeciągany w tę samą stronę, a drugi bok półmostu przechodzi obok drugiej belki podsuwnicy, po czym półmost jest opuszczany na tory podsuwnicy.
Kolejność podnoszenia zespołów dźwigowych zależy od stopnia ich powiększenia i praktycznie nie zależy od zastosowanych w tym celu mechanizmów podnoszących.
Tak więc, jeśli żuraw jest montowany z dwoma półmostami (belki główne z częściami końcowymi), to najpierw jeden półmost jest podnoszony na tory suwnicy, następnie drugi, łączone są złącza montażowe, po czym podnosi się wózek suwnicy i zainstalowany na mostku, a następnie w kabinie sterowniczej.
Często stosowana jest inna wersja tego schematu, gdy półmosty podnoszone i instalowane na torach suwnicy rozsuwa się na odległość przekraczającą szerokość wózka o 400-600 mm, następnie podnosi się je pomiędzy rozłożonymi półmostami nad torami szyny wózka, po czym następuje połączenie półmostów, połączenie złączy montażowych i opuszczenie wózka na most.
Jeśli most dźwigowy jest złożony z dwóch belek głównych i dwóch końcowych, najpierw podnoszą się na tory dźwigu i tymczasowo mocują na nich jedną belkę końcową, następnie drugą, a następnie z kolei podnoszą belki główne i łączą je z końcem belki, po czym podnoszą i instalują wózek na pomoście, a następnie montują kabinę.
W przypadku, gdy półmost dźwigu, w którym belki główne spoczywają na wyważarkach, nie może zostać razem z nimi podniesiony (udźwig istniejących mechanizmów jest niewystarczający), w pierwszej kolejności podnoszone są stabilizatory wraz z wózkami wyrównoważającymi i tymczasowo zabezpieczane na tory dźwigu. Następnie podnosi się jedną belkę główną i łączy jej końce z wyważarkami, podnosi się również drugą belkę i montuje ją na wyważarkach, po czym naprzemiennie podnosi się belki końcowe i łączy z belkami głównymi. Kolejność montażu wózka i kabiny sterowniczej jest taka sama jak w pierwszym z omówionych powyżej schematów, obejmująca podniesienie wózka pomiędzy rozsuniętymi półmostami, zbliżenie ich do siebie, połączenie przegubów i opuszczenie wózka na most.
Najmniej dźwigów występuje w przypadkach, gdy suwnice montowane są w pozycji projektowej za pomocą dwóch lub jednego bloku montażowego: w pierwszym przypadku pomostu i wózka, w drugim przypadku, gdy suwnica jest całkowicie zmontowana (wraz z zamontowanym wózkiem) do mostu) jest zainstalowany na torach dźwigowych.
Niezależnie od kolejności montażu suwnicy na torach podsuwnicowych, ostateczne połączenie złączy montażowych na moście suwnicy należy wykonać dopiero po jego wyosiowaniu, co odbywa się analogicznie jak przy montażu mostu w dolna pozycja.
Podczas montażu półmosty przesuwane są po torach podsuwnicowych za pomocą wciągarek ręcznych dźwigniowych (montaż mechanizmów trakcyjnych). Sterowanie odciągami odbywa się ręcznie podczas procesu podnoszenia, obracania i montażu półmostów na torach suwnicy (za pomocą liny konopnej). Wyjątkiem są liny odciągowe, za pomocą których półmostek przesuwa się na bok podczas podnoszenia w pozycji pochyłej - „ryba”. Te liny odciągowe są wykonane z liny stalowej i są obsługiwane za pomocą wciągarek z dźwignią ręczną.
84. Schemat podnoszenia półmostu za pomocą dwóch dźwigów
1 - żuraw wieżowy BK-1000; 2- półmostek zamontowanego dźwigu; 3 - dźwig SKR-1500
Najbardziej efektywne do podnoszenia zespołów montażowych suwnic są suwnice wieżowe lub z wysięgnikiem (typ SKR), które służą do montażu konstrukcji szkieletowych budynków. Metoda ta jest możliwa w przypadku zasilania suwnic przed lub w trakcie budowy szkieletu budynku. W takich przypadkach montaż zespołów montażowych lub dźwigów całkowicie zmontowanych w dolnym położeniu przeprowadza się jednocześnie z montażem konstrukcji budynku przed jego stropem lub w suficie pozostawia się otwór wystarczający do wprowadzenia półmostów i wózków przez go do miejsca instalacji; następnie otwór zostaje zamknięty.
W zależności od lokalizacji żurawi wieżowych budowa Gdy udźwig jednego dźwigu przy wymaganym wysięgu haka nie jest wystarczający, zespoły montażowe suwnic podnoszone są za pomocą dwóch suwnic wieżowych (ryc. 84).
Zaletami tej metody jest to, że po pierwsze nie ma potrzeby stosowania innych maszyn dźwigowych, a po drugie można połączyć montaż ramy budynku i suwnic, co pozwala na ich wcześniejsze uruchomienie, a następnie użytkowanie nie tylko podczas instalacji sprzętu, przed i przed - podczas budowy fundamentów pod niego. Zastosowanie żurawi wieżowych umożliwia ponadto montaż suwnic na dużych wysokościach, np. w części wysokościowej konwertorów tlenu, w „półkach” szybów górniczych itp.
Głównym czynnikiem utrudniającym jak najszersze zastosowanie tej metody jest późna dostawa suwnic, czyli po wykonaniu szkieletu budynku, kiedy suwnice wieżowe zostały już zdemontowane.
Ponadto Fie można zawsze zamontować na dowolnym zespole suwnicy ze względu na niewystarczający udźwig dźwig wieżowy w wymaganym zasięgu haka.
Stosowanie żurawi samobieżnych z wysięgnikiem montażowym do podnoszenia zespołów mostów mostowych na tory podsuwnicowe jest jedną z najpowszechniejszych metod instalowania tych żurawi.
Warunki stosowania w tym celu dźwigów samojezdnych wewnątrz budynku są następujące: – otwory w budynku umożliwiające przejście dźwigu do obszaru instalacji; – wypoziomowane i zagęszczone platformy do montażu na nich dźwigów; - wystarczający nośność stropy piwnic i kanałów w rejonie przejazdu dźwigu; – obecność dźwigów samobieżnych o charakterystyce wysokości ładunku, które zapewniają podnoszenie i montaż elementów zamontowanego dźwigu do pozycji projektowej; Do cech tych zalicza się udźwig, który przy danym wysięgu haka musi odpowiadać masie podnoszonego ładunku, a także przestrzeń pod wysięgnikiem (wymiar a na rys. 85), która musi zapewnić podniesienie elementów zamontowanego dźwigu bez opierania ich na wysięgniku i wynosić co najmniej 200 mm.
Ponadto żuraw instalacyjny musi pasować swoim wysięgnikiem do wymiarów budynku, w którym suwnica jest zainstalowana: odległość h (patrz rys. 85) od szczytu wysięgnika w jego najwyższym położeniu do dachu musi wynosić co najmniej co najmniej 200 mm.
85. Schemat montażu półmostów suwnicy na torach podsuwnicowych przy użyciu jednej suwnicy montażowej
86. Schemat podnoszenia wózka suwnicy za pomocą dwóch suwnic samobieżnych
1 - dotknij; 2 - trawers; 3 - proca; 4 - przekładka pomiędzy głównymi belkami mostu; 5 - most dźwigowy; 6 - belka dźwigu; 7 - strzałka
87. Schemat podnoszenia mostu suwnicowego za pomocą dźwigu samobieżnego ze specjalnym wyposażeniem wysięgnika
Często ograniczona przestrzeń pod spodem i udźwig przy wymaganym zasięgu haka to główne przeszkody w podnoszeniu całkowicie zmontowanego mostu lub wózka za pomocą jednego dźwigu montażowego. W takich przypadkach duże elementy podnoszone są za pomocą dwóch dźwigów (ryc. 86). Czasami wykorzystuje się do tego celu specjalnie wyprodukowany osprzęt wysięgnika (ryc. 87), jakim jest wysięgnik rurowy z trawersą, którego wysięg umożliwia umieszczenie w przestrzeni wysięgnika całkowicie zmontowanego pomostu dźwigowego, a gdy pozycja pionowaŻuraw do montażu wysięgnika ma maksymalny udźwig.
Na ryc. Na rys. 85 przedstawiono schemat montażu dwóch półmostów 2 i 3 suwnicy na torach podsuwnicowych za pomocą dźwigu montażowego. Linią przerywaną zaznaczono położenie dźwigu montażowego podczas podnoszenia półmostu I oraz położenie początkowe obu półmostów. Most mostowy według tego schematu jest montowany w następujący sposób. W pierwszej kolejności półmost podnosi się z pierwotnego położenia, rozkłada w płaszczyźnie poziomej nad torami suwnicy i opuszcza na nie, a następnie za pomocą zamontowanych mechanizmów trakcyjnych wjeżdża do położenia pokazanego na rysunku. Następnie dźwig montażowy przesuwa się w prawo, do pozycji oznaczonej pozycją i za jego pomocą półmost zostaje podniesiony i zamontowany na torach dźwigu w taki sam sposób jak półmost.
Montaż mostu odbywa się w zależności od przyjętego schematu montażu wózka: jeżeli jest on doprowadzany do mostu z boku, wówczas półmosty łączone są bezpośrednio po wciągnięciu ich na tory suwnicy; jeżeli wózek podnoszony jest pomiędzy rozsuniętymi półmostkami, to łączenie następuje po podniesieniu wózka nad tory jezdne i przed opuszczeniem na nie wózka. W tym przypadku dźwig montażowy do podnoszenia wózka instaluje się pod rozłożonymi półmostami pośrodku tak, aby jego wysięgnik skierowany był wzdłuż półmostów, a krążek ładunkowy znajdował się powyżej środka masy wózka. Po zamontowaniu wózka na pomoście dźwigowym następuje jego zwolnienie z zawiesi i odjazd dźwigu montażowego z jednoczesnym opuszczeniem jego wysięgnika pomiędzy półmostami.
Gdy udźwig jednego dźwigu nie jest wystarczający, półmosty są następnie odwracane i instalowane na torach dźwigowych za pomocą dwóch dźwigów montażowych. W tym przypadku półmostek jest podwieszany z obu stron, podnoszony nad torami suwnicy i na przemian pomiędzy manewrowaniem wysięgnikami i zmianą pozycji dźwigu, półmost rozkłada się w płaszczyźnie poziomej, po czym jest opuszczany na dźwig utwory.
Dwa dźwigi montażowe podnoszą półmosty w pozycji ukośnej – „rybę” (ryc. 88). Po podniesieniu jednej strony półmostu ponad tory dźwigu, poprzez obrót wysięgników dźwigu, półmost przesuwa się na tę stronę, a drugi bok półmostu podnosi się ponad tory suwnicy. Następnie obróć ramiona dźwigu Odwrotna strona a zmieniając wysokość ich podnoszenia, na torach suwnicy instaluje się półmostek.
88. Schemat podnoszenia półmostu za pomocą dwóch dźwigów montażowych
Według tych pokazanych na ryc. Schematy 85 i 88 podnoszą belki główne mostów na tory podsuwnicowe, z tą różnicą, że według drugiego z tych schematów końce belki głównej należy podnieść ponad belkę końcową lub wyważarkę (a nie tory podsuwnicowe), co instalowane są przed belkami głównymi.
89. Schemat montażu belki końcowej na torach podsuwnicowych
1 - belka końcowa; 2 - róg; 3 - zacisk; 4 - dwuteownik; 5 - kolumna; 6 - szyna dźwigu
Przy montażu dźwigów montażowych od strony pomostów półmostowych w razie potrzeby nie montuje się tych podestów lub w miejscach przechodzenia wysięgników dźwigów wycina się pomosty i balustrady ogrodzeń.
Na ryc. 89 przedstawiono schemat montażu belki końcowej lub wyważarki na torach podsuwnicowych, gdy pomost podsuwnicowy składa się z czterech belek (w tym dwie razem z podwoziem) lub z czterech belek i wyważarek podnoszonych oddzielnie.
Do tymczasowego mocowania belek końcowych lub wyważaczy na torach dźwigowych należy zastosować różne urządzenia, z których jeden pokazano na ryc. 89. Zawiera dwuteownik oraz wspornik składający się z kątownika i elementu ustalającego wykonanego w postaci płytki z wycięciem w kształcie litery T. Zacisk jest przyspawany do kątownika, a kątownik do górnego pasa belki końcowej. Dwuteownik jest również przyspawany do kolumny warsztatowej. Zacisk utrzymując belkę końcową lub wyważarkę na torze dźwigu nie uniemożliwia ich przemieszczania się po szynie dźwigu, co jest niezbędne do wykonania operacji łączenia belki głównej z belką końcową lub mocowania do niej wyważarki.
Belkę końcową (lub stabilizator) montuje się na torze suwnicy zgodnie z poniższym schematem. Najpierw do kolumn warsztatowych nad torami suwnicy mocuje się dwuteownik wraz ze wspornikami. Następnie belka końcowa jest podnoszona za pomocą dźwigu montażowego i instalowana na torze suwnicy. Bez zdejmowania zawiesia przyspawaj róg wspornika do jego górnego pasa (lub korpusu wyważarki), po czym belkę odłącza się od zawiesia. Montowana jest także druga belka końcowa mostu (lub równoważnia), po czym jednym z opisanych powyżej sposobów podnosi się jedną belkę główną i łączy z belkami końcowymi, a następnie drugą. Jeżeli belki główne opierają się na wyważarkach, to podnosząc je jedna po drugiej, łączymy ich końce z wyważarkami, a następnie podnosimy belki końcowe i łączymy je z belkami głównymi.
Bardzo w prosty sposób montaż wózków dźwigowych oznacza montaż wózka całkowicie zmontowanego w dolnym położeniu bezpośrednio na pomoście dźwigowym za pomocą jednego lub dwóch dźwigów montażowych zainstalowanych z boku mostu. Jeżeli charakterystyka istniejących dźwigów samobieżnych na to nie pozwala, montaż wózka odbywa się poprzez podniesienie go pomiędzy rozłożonymi półmostami, jak opisano powyżej.
Gdy udźwig dźwigów samojezdnych nie jest wystarczający do podniesienia wózka w ten sposób, montowany jest on w oddzielnych zespołach montażowych: w pierwszej kolejności na pomoście suwnicy montowana jest rama wózka wraz z mechanizmem ruchu i pomocniczym mechanizmem podnoszącym, a następnie podnoszone są zespoły montażowe głównego mechanizmu podnoszącego i montowane na jego ramie.
90. Schematy montażu belek montażowych
91. Belka montażowa
1 - stal nośna gładka; 2 - nakładka; 3 - dwuteownik; 4 - rura; 5 - żebro; 6 - gospodarstwo; 7 - blok kranowy; 8 -
wciągnik łańcuchowy
Po wózku instalowana jest kabina dźwigu. W tym celu w posadzce platformy roboczej mostu dźwigowego wytnij otwór w środku mocowania kabiny, w którym będzie przechodził hak dźwigu montażowego, i zainstaluj go na parkingu wskazanym na schemacie montażu. Następnie po zabezpieczeniu kabiny podnoszą ją do pozycji projektowej i mocują do mostu dźwigu.
W przypadku, gdy z różnych powodów nie jest możliwe zastosowanie suwnic wieżowych lub wysięgników samobieżnych, zespoły suwnic, zwłaszcza ciężkich, podnoszone są za pomocą krążków linowych podwieszonych do konstrukcji szkieletowych budynku lub do belek montażowych spoczywających na tych konstrukcjach. Ta metoda montażu wymaga obowiązkowego wstępnego wzmocnienia konstrukcji budynku, z wyjątkiem przypadków, gdy wzmocnienie to zostało przewidziane wcześniej podczas projektowania szkieletu budynku.
Jednym ze sposobów podnoszenia zespołów dźwigów mostowych za pomocą konstrukcji szkieletowych budynków jest podwieszenie odpowiednio dwóch lub czterech krążków linowych u szczytów dwóch lub czterech słupów budynku, za pomocą których półmosty lub całkowicie zmontowany most dźwigowy, podnoszone są w niektórych przypadkach „ryby” – wraz z wózkiem przymocowanym do mostu tak, aby nie przesuwał się podczas podnoszenia. W tym schemacie instalacji nitki kół pasowych są skierowane w dół wzdłuż kolumn, gdzie połączone są bloki odgałęzień, a przez nie do wciągarek znajdujących się za warsztatem lub wewnątrz warsztatu w pewnej odległości od miejsca instalacji. Wadami tej metody są konieczność duże ilości olinowanie i wciągarki, a także zapewnienie stabilności kolumn przed siłami, dla których nie są one zaprojektowane. Dlatego ta metoda jest rzadko stosowana. Czasami koła pasowe są zawieszone na dwóch sąsiadujących ze sobą kratownicach, a pomiędzy nimi umieszczone są przekładki.
Najbardziej rozpowszechniona metoda podnoszenia zespołów montażowych suwnic za pomocą kół pasowych zawieszonych na belkach montażowych spoczywających na dwóch sąsiednich kratownicach 5 (ryc. 90, a) lub na dwóch belkach pomocniczych b (ryc. 90.6), które opierają się na sąsiednich gospodarstwach. Za pomocą belek montażowych, zwanych także belkami naprawczo-montażowymi (ponieważ służą do opuszczania i podnoszenia zespołów montażowych dźwigów podczas ich napraw w istniejących warsztatach), montuje się do 60% wszystkich suwnic w warsztatach hutniczych. Znacznie częściej stosuje się pierwszą wersję tej metody, gdy belka opiera się bezpośrednio na więźbach dachowych warsztatu wzdłuż osi podłużnej przęsła.
92. Schemat koła pasowego belki montażowej
1 - ruchomy uchwyt bloku; 2 - gałąź poli, spasta; 3 - stały uchwyt bloku; 4 - belka montażowa; 5 - blok odpływowy; 6 - kolumna
93. Schemat podnoszenia półmostu za pomocą krążka zawieszonego na belce montażowej
1 - więźba dachowa; 2 - stały uchwyt bloku; 3 - liny; 4 - ruchomy uchwyt bloku; 5 - proca; 6 - podszewka; 7 - pół mostu
Aktualnie dostępne duża liczba belki o różnych konstrukcjach, w tym największa dystrybucja otrzymano belki dwuteowe (z jednej lub dwóch belek teowych), przekroje skrzynkowe (z blachy), a także belki o konstrukcji kratowej: dwie boczne ściany takiej belki to kratownice kratowe.
Na ryc. 91 przedstawia widok ogólny i schemat montażu belki montażowej wykonanej z dwóch dwuteowników połączonych nakładkami listwowymi i wzmocnionych żebrami. Koło pasowe zawieszone jest na rurze przymocowanej do górnych kołnierzy belek dwuteowych i wewnątrz której włożony jest okrągły kawałek drewna. Belkę montuje się na grzbietach kratownic za pomocą stołów wsporczych.
Nośność belek montażowych wynosi od 30 do 160 ton, długość (najczęściej stosowana) to 6 i 12 m.
Zunifikowane belki do naprawy i montażu suwnic w warsztatach przedsiębiorstw metalurgii żelaza mają konstrukcję podobną do podanej powyżej. Ich nośność wynosi 50, 70 i 100 ton, schemat ich kół pasowych i kierunek gwintu pokazano na ryc. 92.
Krążek zawieszony na belce montażowej służy do rozładunku jednostek montażowych z pojazdów, którymi są one dostarczane na miejsce montażu.
W zależności od nośności belki montażowej i masy zespołów montażowych dźwigu, belki główne, półmosty, mosty w pełni zmontowane (z późniejszym ich obrotem w płaszczyźnie poziomej nad torami suwnicy), a także podwieszone wózki dźwigowe podnoszone są za pomocą wciągników wielokrążkowych (ryc. 93).
Ponieważ belki montażowe montowane są wzdłuż osi przęsła, belki końcowe lub wyważarki podnoszone są na tory dźwigu za pomocą dwóch krążków linowych zawieszonych na szczytach przeciwległych słupów budynku warsztatu.
94. Schemat montażu mostu mostowego za pomocą belki montażowej
1 - belka montażowa; 2 - projektowe położenie półmostu; 3, 7 - montaż mechanizmów trakcyjnych; 4, 13 - wciągniki łańcuchowe; 5 - położenie projektowe belek końcowych; B - pozycja początkowa belka końcowa: 8 - położenie początkowe półmostu; 9 - początkowa pozycja wózka; 10 - tymczasowe urządzenie mocujące; 11 - blok kranowy; 12 - podłoga podkładowa; 14 - odciąg z liny konopnej; 15 - pozycja pośrednia pół mostu
Najpierw za pomocą wciągników wielokrążkowych podnoszone są urządzenia 10 i mocowane do kolumn w celu tymczasowego zabezpieczenia belek końcowych na torach dźwigowych (patrz wyżej). Następnie belki końcowe są podnoszone i instalowane, wykorzystując jedno z kół pasowych jako obciążenie, a drugie jako odciąg. Następnie półmosty podnosi się za pomocą wciągnika wielokrążkowego, obracając je w płaszczyźnie poziomej i łącząc z belkami końcowymi (jeden z półmostów nie jest pokazany na rysunku).
Po złożeniu mostu przesuwa się go na bok za pomocą dwóch zamontowanych mechanizmów trakcyjnych, po czym wózek podnosi się za pomocą układu krążków ponad poziom szyn wózka i za pomocą mechanizmów trakcyjnych most podjeżdża pod wózek i opuszcza na szyny. Następnie montowana jest kabina i pozostałe elementy żurawia. Schemat wciągnika łańcuchowego pokazano na ryc. 92, nieruchomy zblocze jest przywiązany do górnej części kolumny, biegnąca nić jest skierowana w dół wzdłuż kolumny, przez blok wylotowy i na wciągarkę.
Kompletnie zmontowany montaż suwnic metodą przenośnikową. Metoda ta, w której suwnice są całkowicie składane w dolnym położeniu, a następnie podnoszone i instalowane na torach podsuwnicowych za pomocą urządzeń przenośnikowych do montażu i montażu bloczków budowlanych, jest najbardziej postępowa i daje największy efekt przy dużej objętości prac związanych z montażem dźwigu na miejscu. Metoda przenośnikowa umożliwia organizację montażu liniowego dźwigów o wysokim stopniu gotowości montażowej, w tym wykonanie maksymalnej ilości prac elektroinstalacyjnych i uruchomieniowych w dolnym położeniu, a tym samym ograniczenie do minimum objętości i czasu trwania prac prace wykonywane na wysokości po zamontowaniu żurawia na torach podsuwnicowych.
Warunkiem zastosowania tej metody jest montaż suwnic podczas budowy budynku warsztatu, ponieważ do przemieszczania, podnoszenia i instalowania w pełni zmontowanych suwnic na torach dźwigowych potrzebny jest sprzęt używany do wykonywania podobnych operacji z blokami powłokowymi tj. windy, żurawie szynowe, portale itp.
Na ryc. 95 przedstawia schemat organizacji montażu suwnic metodą przenośnikową z wykorzystaniem dźwigu szynowego 1 (przeznaczonego do montażu bloczków dachowych budynku warsztatowego) do przemieszczania całkowicie zmontowanej suwnicy 2 z powiększonego miejsca montażu do rozpiętość, w jakiej ma być zamontowany, a także podniesienie dźwigu i ustawienie go na torach dźwigu jodowego.
Dostarczone do montażu jednostki montażowe dźwigów są rozładowywane z pojazdów i układane na miejscu składowania za pomocą jednej lub dwóch układarek rur, które następnie w zasięgu dźwigu gąsienicowego przenoszą elementy żurawia na plac budowy w celu montażu. Żuraw ten służy do montażu belek końcowych i głównych na stanowisku montażowym oraz wózka dźwigowego na moście po jego montażu. Kolejność czynności związanych z montażem i wyrównywaniem mostu opisano powyżej. Zmontowaną suwnicę przetacza się na drugi koniec stojaka w zasięg suwnicy kolejowej za pomocą wciągarki elektrycznej. Tutaj występują prace związane z instalacją elektryczną, po czym suwnica jest przenoszona suwnicą kolejową na stanowisko i w celu montażu kabiny. Za pomocą dźwigu samochodowego za pomocą belki poprzecznej montuje się kabinę operatora dźwigu i kabinę do obsługi wózków oraz zawiesza się kołyski i drabinki montażowe.
Na tym samym stanowisku testowane są mechanizmy ruchu dźwigu i wózka, a także przechowywane są koła pasowe mechanizmów podnoszących.
95. Schemat organizacji montażu suwnic metodą przenośnikową z wykorzystaniem dźwigu szynowego 1 - dźwig szynowy SKU-1500R; 2 - w pełni zmontowany mostek krawędziowy; 3 - dźwig samochodowy; 4 - dźwig gąsienicowy; 5 - platforma do montażu dźwigu; 6 - platforma instalacji elektrycznej; 7 - warstwa rur; 8 - platforma do przechowywania elementów dźwigu; 9 - montaż mechanizmu trakcyjnego; 10 - lina zabezpieczająca; 11, 12 - stoiska
96. Schemat organizacji sposobu montażu suwnic przenośnikowych
korzystanie z portalu t - miejsce do powiększonego montażu; 2 - żurawie gąsienicowe; 3 - suwnica całkowicie zmontowana; 4 - portal; 5 - stanowisko testowe do warsztatowego montażu bloków powłokowych
Następnie za pomocą suwnicy kolejowej ostatecznie zmontowaną suwnicę przesuwa się na przęsło budynku warsztatu i instaluje na torach dźwigu, następuje rozczesywanie, po czym dwa trakcyjne mechanizmy montażowe 9 wożą suwnicę wewnątrz warsztatu.
Stosowane są również inne warianty opisanego sposobu montażu suwnic, które zależą głównie od sprzętu do podnoszenia i przenoszenia bloków powlekających i który jest stosowany podczas montażu suwnic. Na ryc. 96 przedstawiono schemat organizacji przenośnikowego sposobu montażu suwnic z wykorzystaniem portalu, po którym przemieszczane są bloki pokryć budowlanych z miejsca 5 w celu montażu tych bloków na zadaną rozpiętość warsztatową.
W tym przypadku po drugiej stronie torów portalowych ze składowiska utworzono miejsce montażu konsolidacji, na którym przy pomocy dwóch dźwigów gąsienicowych i mechanizmów trakcyjnych instalacji wszystko odbywa się Prace montażowełącznie z montażem całkowicie zmontowanego wózka na pomoście dźwigowym. Tutaj wykonywane są prace związane z instalacją elektryczną, testowaniem mechanizmów, składowaniem kół pasowych, po czym zmontowany dźwig jest podnoszony za pomocą dźwigów gąsienicowych i instalowany na portalu, który przemieszczany jest do danego stanowiska warsztatowego. Po połączeniu szyn portalu z szynami suwnicy warsztatu żuraw wsuwa się w przęsło za pomocą montażowych mechanizmów trakcyjnych.
Montaż układów smarowania mechanizmów dźwigowych. Układy smarowania montuje się zgodnie z rysunkami, schematami oznaczeń i instrukcjami producentów.
Montaż poszczególnych układów smarowania polega na sprawdzeniu czystości wewnętrznej powierzchni osłon łożysk, sprawności smarownic, zamontowaniu ich na miejscu i napełnieniu smarem.
Instalację instalacji centralnego smarowania wykonuje się w następującej kolejności: – ręczną pompę smarującą (stacja smarowania) oraz podajniki montuje się i mocuje do powierzchni nośnych; – zamontować i podłączyć główne zespoły rurociągów, odgałęzienia od nich do podajników i odgałęzienia od podajników do punktów smarowanych; – napełnić rurociągi smarem; - skonfiguruj i przetestuj system.
Przed montażem systemu należy upewnić się, że pompa i podajniki działają prawidłowo oraz że wewnętrzna powierzchnia wszystkich elementów rurociągu jest czysta (bez brudu, rdzy). Producenci w większości przypadków dostarczają wszystkie elementy układów smarowania całkowicie gotowe do montażu na miejscu.
Jeżeli jednak po przyjęciu do montażu na wewnętrznej powierzchni zespołów rurociągów i kolanek stwierdzone zostaną zabrudzenia lub rdza, należy je umyć i wytrawić w kąpielach. Trawienie jest również obowiązkowe po spawaniu, aby usunąć zgorzelinę powstałą na wewnętrznej powierzchni rurociągu w strefie spawania.
Trawienie przeprowadza się w roztworach kwasu siarkowego, solnego lub fosforowego. Trawienie w roztworach kwasu siarkowego lub solnego polega na następujących operacjach: samo wytrawianie, przemywanie, neutralizowanie pozostałości roztworu trawiącego, mycie, suszenie i smarowanie wytrawionych powierzchni. Do trawienia należy stosować 20% roztwory kwasu siarkowego w temperaturze 50-80°C lub kwasu solnego w temperaturze nieprzekraczającej 40 °C, ponieważ w wyższych temperaturach wzrasta wydzielanie par chlorowodoru z kąpieli z kwasem solnym. Czas trawienia zależy od stanu wewnętrznej powierzchni odcinków rurociągów i kolanek, od temperatury roztworów i może wynosić od 2 do 24 godzin. Czasami trawienie prowadzi się w mieszaninie roztworów kwasów o składzie: kwas siarkowy - 60 g na 1 litr roztworu, kwas solny - 40 g/l, urotropina - 6 g/l, sól kuchenna- 25 g/l w temperaturze 40-50°C.
Jakość czyszczenia jest monitorowana wizualnie. Jeżeli powierzchnia nie została dostatecznie oczyszczona, widoczne są na niej plamy i pojedyncze obszary nierozpuszczonych tlenków; dobrze oczyszczona powierzchnia ma stalowoszary kolor, natomiast powierzchnia nadmiernie trawiona ma kolor czarny.
Po wytrawieniu węzły i zagięcia są usuwane z roztworu i trzymane nad wanną w celu odsączenia roztworu, a następnie przenoszone do kąpieli wodnej, w której są myte, a następnie przenoszone do kąpieli z 3-5% sodą lub wapnem roztwór neutralizujący pozostały roztwór trawiący przez 1 godzinę.
Po neutralizacji produkty myje się w kąpieli gorąca woda, podgrzano do 80-90°C i wysuszono na powietrzu.
Wysuszoną, wytrawioną powierzchnię należy nasmarować olejem, ponieważ ponownie bardzo szybko koroduje. W tym celu zespoły rurociągów i łuki zanurza się w kąpieli olejowej, a po wyjęciu z niej umieszcza się je na stojakach w pozycji pochylonej w celu spuszczenia oleju na 2-3 godziny.
Wszystkie powyższe operacje są wykonywane bez przerwy, po zakończeniu końce węzłów i zakrętów zamyka się zatyczkami.
Trawienie w roztworach kwasu ortofosforowego różni się od opisanego powyżej brakiem takich operacji jak mycie, neutralizowanie i smarowanie wytrawionych powierzchni olejem.
Elementy rurociągów i łuki, które zostały wcześniej oczyszczone z zanieczyszczeń, trawione są najpierw w 15-20% roztworze kwasu ortofosforowego w temperaturze 50-60°C przez 6-12 godzin (w zależności od stanu wewnętrznej powierzchni wyrobów ), sprawdzając jakość czyszczenia analogicznie jak i przy trawieniu w roztworach kwasu siarkowego lub solnego, a następnie przenosi do kąpieli z 2% roztworem tego samego kwasu, po spuszczeniu pozostałego roztworu trawiącego do kąpieli z 15-20% roztwór. W 2% roztworze kwasu ortofosforowego po trawieniu na powierzchni wyrobów stalowych tworzy się cienki film fosforanowy, który pasywuje (pokrywa) powierzchnię metalu i chroni ją przed korozją przez kilka miesięcy. W kąpieli z takim roztworem zespoły rurociągów i kolana utrzymuje się przez 1-2 godziny w temperaturze 50 ° C, po czym usuwa się je z roztworu, pozostałość pozostawia do spuszczenia z powrotem do wanny, umieszczonej na stojak i suszy skompresowane powietrze, uprzednio oczyszczone z wilgoci i oleju oraz w miarę możliwości podgrzane (w celu przyspieszenia suszenia). Następnie końce produktów zamykane są zatyczkami, aby zapobiec przedostawaniu się zanieczyszczeń do środka, a także wody, która niszczy folia ochronna. Powierzchnia wytrawiona i pokryta folią pasywującą ma kolor ciemnoszary z ledwo zauważalnym zielonkawym odcieniem.
Dozowniki smaru z okres gwarancji nie upłynął termin ważności i podczas oględzin zewnętrznych nie stwierdzono żadnych usterek, montuje się je na miejscu i mocuje do konstrukcji żurawia za pomocą wkrętów, które szczelnie dociągają podajnik do podpory.
Jeżeli okres gwarancyjny minął, ale nie stwierdzono żadnych usterek, podajniki poddawane są badaniu pod kątem szczelności olej mineralny przy ciśnieniu próbnym określonym w paszporcie przez 2 minuty w każdym z skrajnych położeń tłoków.
W takim przypadku olej nie powinien wyciekać przez uszczelki korbowodów i zaślepione otwory łączące w obudowach, a jego wyciek przez którykolwiek z wylotów do smarowanych punktów nie powinien przekraczać trzech kropli na minutę. Dozowniki muszą pracować i dozować wymaganą ilość smaru, gdy różnica ciśnień w przewodach głównych nie jest większa niż 1 MPa, a liczba skoków tłoka jest nie mniejsza niż 6. Ruch tłoków i szpul musi być płynny, bez zakleszczania się wzdłuż całą długość skoku. Testowanie i sprawdzanie działania odbywa się poprzez pompowanie smar na przemian w każdym wierszu. Podajniki, które nie przejdą testów, są wysyłane do naprawy i zamiast nich instalowane są nowe.
Rurociągi instalacji montowane są z zespołów i kolanek wyprodukowanych u producenta. Jeśli producent dostarcza rury oddzielnie w postaci prostych odcinków i części rur, instalatorzy konstruują główne zespoły rur i ginają je z rur wstępnie trawionych.
Połączenia rurociągów wykonywane są głównie na stożku gwint rury przy użyciu nakrętek i kształtek złączkowych (kątowniki, trójniki, złączki). Niedopuszczalne jest stosowanie w tych złączach środków uszczelniających w postaci wybielacza, ołowiu czerwonego i pakułów; Montowane są na lakierze nitro marki NTs lub lakierze bakelitowym marki LBS. Często zamiast kątowników stosuje się gięcie rur, a zamiast trójników stosuje się wkładki wykonane metodą spawania; W ten sposób zagięcia od przewodów do podajników i od podajników do punktów smarowania są w wielu przypadkach zakrzywione, a odgałęzienia są połączone z przewodami za pomocą przyspawanych do nich złączek gwintowanych.
Rurociągi są również łączone poprzez spawanie, ale konieczne jest, aby złącze spawane znajdowało się pomiędzy dwoma złączami gwintowanymi. Pozwala to po zmontowaniu rurociągu na demontaż odcinka ze złączem spawanym i jego wytrawienie. Jeśli złącze spawane wykonane w kielichu lub ze złączem przyspawanym na zewnątrz złącza, wówczas nie ma konieczności trawienia po spawaniu.
Po zainstalowaniu systemu rurociągi przedmuchuje się sprężonym powietrzem w celu usunięcia cząstek stałych, które dostały się do środka podczas montażu połączeń, a następnie za pomocą pompy napełnia się je smarem, podając smar najpierw jednym rurociągiem głównym, a następnie drugim. Jednym z głównych wymagań podczas wykonywania tej operacji jest usunięcie powietrza z rurociągów. Powietrze dostające się do systemu zakłóca normalna praca. Aby to zrobić, podczas napełniania otwiera się przeciwny koniec rurociągu i dopiero po wypłynięciu z niego 0,5 kg smaru zamyka się.
W miarę napełniania rurociągu wyloty do podajników i podajniki napełniane są smarem, w tym celu przed przepłukaniem po kolei usuwane są korki zamontowane na tych wylotach. Krany podłącza się do podajników dopiero po wypłynięciu z każdego kranu 50-100 g smaru. Podajnik uznaje się za naładowany, gdy wypłynie z niego 10-20 g smaru. Następnie podajnik zamyka się zatyczkami. Napełnianie kranów od podajników do punktów smarowania odbywa się w następujący sposób. Odłączyć krany od podajników i punktów smarowania, przedmuchać je sprężonym powietrzem i napełnić smarem za pomocą pompa ręczna aż 50-100 g zanieczyszczonego smaru wypłynie z wolnego końca każdego wylotu, który zostanie usunięty. Następnie wylot jest instalowany na miejscu.
Po napełnieniu układu przystępują do jego ustawiania, które polega na sprawdzeniu pracy podajników i ustaleniu ciśnienia wymaganego do ich pracy. Działanie podajników sprawdza się poprzez naprzemienne wtryskiwanie smaru do obu przewodów.
Podczas pompowania do pierwszej linii wszystkie pręty muszą znajdować się w górnym położeniu, podczas pompowania do drugiej linii w dolnym położeniu. W przypadku rozbieżności w położeniu prętów, odgałęzienia od głównych rurociągów do części podajników zamieniane są w taki sposób, aby pręty wszystkich podajników znajdowały się w pozycji podniesionej lub opuszczonej podczas pompowania smaru do jednego z dwóch rurociągów.
Ciśnienie, pod jakim powinna pracować instalacja, określane jest za pomocą manometru w momencie załączenia najdalszego podajnika plus 0,5 MPa. Po sprawdzeniu pracy podajników i ustaleniu ciśnienia roboczego rurociągi poddaje się próba hydrauliczna ciśnienie próbne. Wykorzystuje się do tego pompę wysokie ciśnienie, który służy do naprzemiennego wtryskiwania smaru do pierwszego i drugiego rurociągu głównego. Ciśnienie próbne w każdym rurociągu jest 1,2 razy większe od ciśnienia roboczego i utrzymuje się przez 20-30 minut. W tym czasie spadek ciśnienia nie powinien przekraczać 10%.
Montaż lin dźwigowych. Krytyczną operacją podczas montażu dźwigów jest przeplatanie lin na mechanizmach podnoszących, podczas którego muszą zostać spełnione następujące wymagania: zapewnienie bezpieczeństwa liny podczas jej montażu; zapobieganie niepotrzebnemu naprężenia wewnętrzne, spowodowane warunkami rezerwowymi; prawidłowe wstępne ułożenie liny na bębnie mechanizmu podnoszącego.
W przypadku nieprawidłowego odwijania liny ze zwojów lub bębnów może dojść do uszkodzenia i powstania dodatkowych naprężeń w linie. Rezerwując należy zachować kolejność okablowania liny, której jeden koniec należy kolejno okrążyć wszystkie rolki w klatkach blokowych, a następnie przymocować do bębna. Drugi koniec jest również mocowany do bębna lub do górnego uchwytu bloku. Linę można układać ręcznie lub metodą zastępczą.
Na ryc. 97 przedstawia olinowanie mechanizmu koła pasowego głównego mechanizmu podnoszącego suwnicy metodą wymiany. Bęben lub bęben z liną 1 instaluje się pod suwnicą na podporach, w których mogą się swobodnie obracać. Ruchoma klatka wielokrążka 5 z zawieszeniem hakowym jest zamocowana w dolnym położeniu wzdłuż osi żurawia. Montowany również pod kranem wciągarka elektryczna 6, na bęben, na który nawinięta jest cienka lina.
Lina ta jest ręcznie przepuszczana przez wszystkie rolki krążka i łączy się z końcem liny konstrukcyjnej nawiniętej na bęben 1. Następnie włączając wciągarkę elektryczną, przez wszystkie rolki przepuszcza się cienką linę w przeciwnym kierunku, ale zgodnie z konstrukcją lina, która w ten sposób zastępuje cienką linę w linie bloczka.
97. Schemat przeciągnięcia wciągnika łańcuchowego metodą wymiany
a - schemat organizacji pracy; b - schemat przeciągnięcia; 1 - bęben z liną; 2 - stały uchwyt bloku; 3 - bęben mechanizmu podnoszącego; 4 - wózek suwnicy; 5 - ruchomy uchwyt bloku; 6 - wciągarka elektryczna
Podczas rezerwacji bardzo ważne To ma precyzyjna definicja długości liny, w przeciwnym razie hak nie podniesie się na wymaganą wysokość lub nie osiągnie dolnego położenia.
Jeżeli hak zgodnie z projektem spadnie poniżej poziomu podłogi warsztatu (w obecności zagłębionych pomieszczeń), długość liny należy zwiększyć o odległość od podłogi do dolnego położenia osi ruchomej klatki, pomnożoną przez wielość koła pasowego dźwigu.
Rezerwując nowe liny, krążek często ulega przekręceniu. Skręcanie można wyeliminować na dwa sposoby: najpierw podczas nawijania liny rozwinąć ją na całej długości w jedną linię prostą, albo odwinąć bloczek.
W drugiej metodzie podnieś ładunek, którego masa stanowi 30% masy największego ładunku, o 150-200 mm i pozwól, aby koło pasowe swobodnie się obracało, zapobiegając jedynie przyspieszaniu ładunku. W takim przypadku liczba obrotów dolnej klatki bloku jest zliczana do momentu, aż koło pasowe przestanie się obracać.
Po przymocowaniu liny do bębna hak jest kilkakrotnie podnoszony i opuszczany, równomiernie rozkładając skręt na całej długości liny.
Cechy instalacji dźwigów metalurgicznych są określone przez cechy konstrukcyjne mosty, wózki i mechanizmy do wykonywania specjalnych operacji technologicznych. Kolejność i zasady wykonywania wszystkich czynności montażowych podczas montażu dźwigów hutniczych są szczegółowo określone w instrukcjach producentów, dlatego omówiono tutaj procedurę montażu powiększonych zespołów montażowych tych dźwigów.
Podczas montażu suwnic słupowych po zmontowaniu mostu na torach podsuwnicowych (lub podniesieniu zmontowanego mostu) na most podnoszona jest główna rama wózka wraz z układem jezdnym oraz mechanizmami do przesuwania, obracania i podnoszenia kolumny. Jednocześnie montowana jest dolna część wózka głównego, zaczynając od kabiny sterującej. Kabina montowana jest na platformie roboczej na podporach. Przed montażem i zamocowaniem na platformie sterującej kolumnę oczyszcza się z powłoki konserwującej i sprawdza pod kątem prostości i braku wyszczerbień; krzywizna czoła kolumny nie powinna przekraczać 1 mm na długości 1 m. Po przymocowaniu kolumny do miejsca montażu wsuwa się w nią ramę z mechanizmami i montuje się ją wzdłuż osi obrotu. Następnie składa się tułów z ustnikiem.
Po zmontowaniu dolnej części wózka głównego, wał zakłada się na kolumnę za pomocą dźwigu samojezdnego lub krążków przywiązanych do ramy wózka głównego. Wał z kolumną zabezpieczono w pozycji pionowej (dla stabilności) za pomocą zastrzałów lub stojaków. Następnie na głowicę kolumny zakłada się trawersę z zawieszeniem mechanizmu podnoszącego kolumnę i zabezpiecza.
Następnie zespół wału z kolumną i kabiną jest podnoszony i mocowany do ramy wózka głównego.
Podnoszenie wału odbywa się za pomocą wciągników wielokrążkowych zawieszonych na ramie wózka lub belce montażowej lub za pomocą mechanizmu podnoszącego kolumnę.
Montaż dźwigów odlewniczych różni się od montażu dźwigów ogólnego przeznaczenia tym, że najpierw na torach suwnicy montuje się most główny, następnie most pomocniczy, po czym montuje się wózki. Mosty ciężkich dźwigów odlewniczych montowane są na torach dźwigowych z półmostów lub poszczególne elementy, gdy masa elementów (wózki wyrównawcze, belki mostu) oraz nośność istniejących mechanizmów montażowych nie pozwalają na ich rozbudowę w półmosty. Dźwigi tego typu montuje się najczęściej za pomocą wciągników wielokrążkowych zawieszonych na belkach montażowych. Z tego samego powodu wózki główne ciężkich dźwigów odlewniczych montowane są na pomoście suwnicy z powiększonych jednostek montażowych, a wózki pomocnicze są montowane w całości, w takiej formie, w jakiej pochodzą od producenta. Do zawieszania głównych wózków dźwigów odlewniczych często wykorzystuje się urządzenie z Instytutu Giprometallurgmontazh, składające się z trawersu, który za pomocą czterech drążków ślizgowych jest połączony przegubowo z dwoma płozami umieszczonymi pod środkową belką ramy wózka.
Przy montażu dźwigów do rozbierania wlewków, po zmontowaniu pomostu i osadzeniu na nim wózka, podwiesza się i mocuje do niego wał, złożony wcześniej z kabiną, platformami i drabinami w jeden powiększony element montażowy.
Specyficzne dla tych żurawi jest mocowanie mechanizmu wyrzucania wlewków za pomocą szczypiec, który z reguły pochodzi od producenta i jest montowany. Mechanizm ten, ułożony w pozycji poziomej w pobliżu specjalnego wykopu naprawczego o głębokości 4,6 m, opuszczany jest do dołu za pomocą krążka zawieszonego na belce na ramie wózka lub głównego mechanizmu podnoszącego.
Jeśli mechanizm wyrzutowy zostanie dostarczony zdemontowany, jest on montowany w pozycji poziomej obok dołu naprawczego i opuszczany do niego. Następnie nad wykopem naprawczym instaluje się pomost dźwigowy i wózek, tak aby można było podnieść mechanizm wyrzutowy i włożyć go do wału bezpośrednio ze studzienki, bez przesuwania go w kierunku poziomym.
Jeżeli do tego czasu montaż głównego mechanizmu podnoszącego wózka dźwigowego nie został jeszcze ukończony, wówczas mechanizm wyrzutowy jest podnoszony za pomocą tego samego koła pasowego, za pomocą którego został opuszczony do dołu naprawczego. Po podniesieniu mechanizmu wzdłuż prowadnic wału, tymczasowo zabezpiecz go i dalsza praca należy wykonać po zakończeniu montażu mechanizmu podnośnika głównego i prac związanych z instalacją elektryczną.
Gdy działa główny mechanizm podnoszący, mechanizm wyrzucający jest montowany w następujący sposób.
Liny podnoszące mocowane są do bębna, zaginają się wokół bloków mechanizmu wyrzutowego i w pierwszej kolejności mocowane są do jego wyważarki. Liny mechanizmu sterującego szczypcami przechodzą przez bloki i mocowane są do dźwigni tego mechanizmu oraz do bębna. Następnie mechanizm wyrzutowy podnosi się z zagłębienia do dolnego położenia konstrukcyjnego (przy maksymalnym rozwarciu szczypiec) i tymczasowo mocuje w wale na dwóch belkach umieszczonych pod wystającymi częściami naboju. Następnie uwolnione liny naciąga się i ponownie mocuje do równoważni i dźwigni (bez odcinania ich końcówek). Po podniesieniu mechanizmu wyrzutowego do górnego konstrukcyjnego położenia (przy minimalnym rozwarciu szczypiec) liny mocuje się do przeciwwagi w celu zrównoważenia mechanizmu sterującego szczypcami.
Technologia montażu kranów studniowych (zaciskowych) jest podobna do technologii montażu kurków do wlewków.
Demontaż suwnic odbywa się najczęściej za pomocą suwnic samojezdnych lub krążków linowych zawieszonych na belkach montażowych. Znacznie rzadziej wykorzystuje się do tego celu maszty montażowe (z tych samych powodów, dla których rzadko wykorzystuje się je przy montażu dźwigów).
Obiecujące jest wykorzystanie podnośników hydraulicznych firmy Giprotechmontazh do demontażu suwnic.
Dźwigi można demontować tylko wtedy, gdy istnieje specjalnie opracowany PPR.
Przed rozpoczęciem prac demontażowych wykonywane są czynności przygotowawcze obejmujące: – przygotowanie niezbędnych mechanizmów i urządzeń dźwigowych, w tym montaż wciągarek, krążków łączących i wielokrążków, montaż urządzeń do tymczasowego mocowania belek końcowych lub wyważarek na torach podsuwnicowych, itp.; – przygotowanie i montaż rusztowania niezbędnego do demontażu dźwigu; – ogrodzenie niebezpiecznego obszaru prac i przygotowanie miejsca do umieszczenia zdemontowanych zespołów montażowych dźwigu.
Instalując buty pod kołami dźwigu i wózka, aby zapobiec ich spontanicznemu przemieszczaniu się,
i po odłączeniu zasilania mechanizmów dźwigu zaczynają go demontować.
Najpierw wózek jest zawieszany i zdejmowany z pomostu dźwigowego. Jeżeli nośność istniejących mechanizmów i wyposażenia jest mniejsza niż masa zmontowanego wózka, wówczas jest on rozbierany na minimalną wymaganą liczbę elementów i usuwany jeden po drugim.
Z tych samych powodów most dźwigowy jest demontowany w całości lub rozbierany na dwa półmosty lub inną liczbę elementów zgodnie z PPR.
Czynności związane z demontażem mostu wykonuje się w odwrotnej kolejności do jego montażu.
Podkładki montażowe usuwa się metodą cięcia gazowego, po uprzednim zabezpieczeniu belki głównej (lub półmostu), którą należy zdemontować w pierwszej kolejności i tymczasowym przymocowaniu belek końcowych lub wyważarek do torów dźwigu.
Opuszczanie półmostów, pojedynczych belek lub zmontowanego mostu odbywa się według schematów odwrotnych do przyjętych podczas montażu dźwigu.
DO kategoria: - Montaż dźwigów załadunkowych
Konieczność instalowania specjalnych platform do kontroli i konserwacji mechanizmów znajdujących się na zewnątrz dźwigu, Przepisy Dźwigowe (art. 229) przewidują tylko dla suwnic podwieszonych jednodźwigarowych (podparcie i zawieszenie) i dwudźwigarowych podwieszanych, jeżeli są one instalowane w budynku i nie mają platform i galerii znajdujących się na rzeczywistym kranie. W innych przypadkach o wykonalności budowy platform decyduje organizacja projektująca instalację dźwigów lub przedsiębiorstwo je obsługujące.
Platformy mogą być stacjonarne lub mobilne. W obiektach stacjonarnych odległość podłogi od dolnego wymiaru serwisowanego żurawia musi wynosić co najmniej 1800 mm, jednakże przy tej odległości dostęp do mechanizmów jest bardzo utrudniony. Aby stworzyć normalne warunki pracy, odległość tę można zmniejszyć, instalując na schodach drzwi blokujące z automatycznym ryglowaniem elektrycznym, które odłącza napięcie od głównych przewodów wózka w obszarze naprawy.
Klatka schodowa musi posiadać drzwi, po otwarciu sekcja wózka w obszarze podestu zostaje automatycznie odłączona od zasilania. Trolle włącza się po naprawie dźwigu za pomocą przełącznika w obszarze naprawy. Schemat elektryczny blokowania wejścia do miejsca naprawy, patrz 7.13.
Przybliżone rozwiązania dla stacjonarnych miejsc naprawy pokazano na ryc. 4. 16-4. 22.
Wymagania dotyczące drzwi platformy naprawczej suwnic podwieszanych jednodźwigarowych i dwudźwigarowych, gdy odległość od podłogi platformy naprawczej do dolne części dźwig jest mniejszy niż 1800 mm i gdy zasilanie żurawia odbywa się nie za pomocą przewodów jezdnych, ale za pomocą giętkiego kabla. W związku z tym istnieje w tym przypadku zapotrzebowanie na urządzenie blokujące, które automatycznie zwalnia napięcie z giętkiego kabla
Rysunek 4.18 Pomost naprawczy na końcu przęsła suwnic elektrycznych jednodźwigarowych ze sterowaniem z kabiny o udźwigu 1-5 tf i rozpiętości od 4,5 do 10,5 m: 1 - podest; 2 - łańcuch; 3 - nacisk; 4 - kabina
należy ustalać biorąc pod uwagę liczbę dźwigów pracujących w jednym przęśle, sposób obsługi dźwigów (z kabiny lub z podłogi) oraz możliwość podjęcia innych działań zapobiegających przedostawaniu się ludzi na teren remontu w czasie pracy dźwigów i wbiegając na nie. Miejsce naprawy zaprojektowane jest na równomiernie rozłożone obciążenie dźwigiem wynoszące 20U kgf/cm2, a powierzchnia placu budowy jest wyznaczona
Rysunek 4.19. Miejsce naprawy na końcu przęsła napowietrznych suwnic jednodźwigarowych sterowanych z kabiny o udźwigu 1-5 tf i rozpiętości od 13,5 do 23,5 m (1-4, patrz rys. 4. 18):
do naprawy wciągników elektrycznych, na skoncentrowany ciężar stali elektrycznej o odpowiedniej nośności. W przypadku dźwigów podporowych z dwoma belkami zaleca się zapewnienie w samochodzie naprawczym (patrz 7.5) stanowisk do kontroli i wymiany kół jezdnych dźwigu, jeżeli odległość od końcowej części dźwigu do ścianę budynku. Dostęp do takich miejsc zapewnia się z pomostu dźwigowego lub przez właz w pokładzie, który jest zamykany na czas pracy dźwigów. Dostęp do takiego miejsca naprawy wymaga zezwolenia.
Suwnice pomostowe sterowane z kabiny (z wyjątkiem jednodźwigarowych i podwieszanych) muszą być wyposażone w kabiny do obsługi głównych przewodów jezdnych i pantografów, jeżeli znajdują się one poniżej pomostu pomostu (art. 230 Przepisów Dźwigowych). Właz umożliwiający wejście do tej kabiny z pomostu musi być wyposażony w pokrywę z zamkiem.
Wymiary kabiny do obsługi wózków głównych i ich pantografów nie są regulowane i zwykle przyjmuje się je jako 1000X1400 przy wysokości co najmniej 1800 mm. Powierzchnia kabiny nie powinna być mniejsza niż 800 x 800 mm. Chata musi być ogrodzona balustradami o wysokości co najmniej 1 m z ciągłym rąbkiem wzdłuż dna i wysokości 100 mm. Zawieszony jest w odległości 1000-1100 od osi szyny dźwigu. Gdy zasilanie odbywa się kablem, kabiny nie są rozmieszczone. Podłoga kabiny pokryta jest matą dielektryczną.
Rysunek 4.20. Miejsce naprawy elektrycznych suwnic podwieszanych dwu- i trzyprzęsłowych o udźwigu 1-5 t (1-3 - patrz rys. 4.18)