Potężny silnik Stirlinga zrób to sam. Zrób to sam Silnik Stirlinga, schemat i rysunek Zrób to sam Rysunki Stirlinga
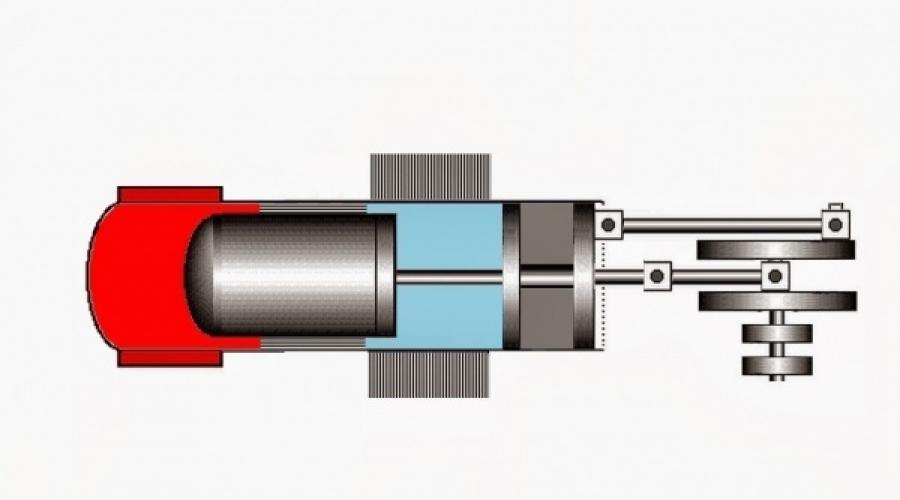
Przeczytaj także
Współczesny przemysł motoryzacyjny osiągnął poziom rozwoju, w którym bez fundamentalnych badania naukowe osiągnięcie radykalnych ulepszeń w konstrukcji tradycyjnych silników jest prawie niemożliwe wewnętrzne spalanie. Ta sytuacja zmusza projektantów do zwrócenia uwagi alternatywne projekty elektrowni. Niektóre ośrodki inżynierskie skupiły swoje wysiłki na stworzeniu i przystosowaniu do seryjnej produkcji hybryd i modele elektryczne inni producenci samochodów inwestują w rozwój silników zasilanych ze źródeł odnawialnych (np. biodiesel z olejem rzepakowym). Istnieją inne projekty jednostek napędowych, które w przyszłości mogą stać się nowym standardowym napędem Pojazd.
Wśród możliwych źródeł energia mechaniczna dla samochodów przyszłości powinniśmy nazwać silnik spalinowy, który został wynaleziony w połowie XIX wieku przez Szkota Roberta Stirlinga jako maszyna do rozszerzalności cieplnej.
Schemat pracy
Silnik Stirlinga konwertuje energia cieplna, zasilany z zewnątrz, w użytkowe Praca mechaniczna kosztem zmiany temperatury płynu roboczego(gaz lub ciecz) krążące w zamkniętej objętości.
W ogólny widok schemat działania urządzenia jest następujący: w dolnej części silnika substancja robocza (na przykład powietrze) nagrzewa się i, zwiększając swoją objętość, popycha tłok do góry. Gorące powietrze przenika do górnej części silnika, gdzie jest chłodzony przez chłodnicę. Ciśnienie płynu roboczego jest zmniejszone, tłok jest opuszczany do następnego cyklu. W tym przypadku system jest uszczelniony, a substancja robocza nie jest zużywana, a jedynie przemieszcza się wewnątrz cylindra.
Istnieje kilka opcji projektowania jednostek napędowych wykorzystujących zasadę Stirlinga.
Modyfikacja Stirlinga „Alfa”
Silnik składa się z dwóch oddzielnych tłoków zasilających (gorącego i zimnego), z których każdy znajduje się we własnym cylindrze. Ciepło dostarczane jest do cylindra za pomocą gorącego tłoka, a zimny cylinder znajduje się w chłodzącym wymienniku ciepła.
Modyfikacja Stirlinga „Beta”
Cylinder zawierający tłok jest ogrzewany z jednej strony i chłodzony z przeciwnej strony. W cylindrze porusza się tłok napędowy i wypornik, których zadaniem jest zmiana objętości gazu roboczego. Ruch powrotny schłodzonej substancji roboczej do gorącej wnęki silnika jest wykonywany przez regenerator.
Modyfikacja Stirlinga „Gamma”
Konstrukcja składa się z dwóch cylindrów. Pierwszy jest całkowicie zimny, w którym porusza się tłok napędowy, a drugi, gorący z jednej strony i zimny z drugiej, służy do poruszania wypornika. Regenerator do cyrkulacji zimnego gazu może być wspólny dla obu cylindrów lub może być zawarty w konstrukcji wypornika.
Zalety silnika Stirlinga
Podobnie jak większość silników spalinowych, Stirling jest nieodłączny wielopaliwowy: silnik pracuje przy różnicy temperatur, niezależnie od przyczyn, które ją spowodowały.
Interesujący fakt! Kiedyś zademonstrowano instalację, która działała na dwudziestu opcjach paliwowych. Bez zatrzymywania silnika kamera zewnętrzna spalanie, dostarczano benzynę, olej napędowy, metan, surowy olej oraz olej roślinny- jednostka napędowa nadal pracowała stabilnie.
Silnik ma prostota konstrukcji i nie wymaga dodatkowe systemy oraz załączniki(rozrząd, rozrusznik, skrzynia biegów).
Cechy urządzenia gwarantują długą żywotność: ponad sto tysięcy godzin ciągła praca.
Silnik Stirlinga jest cichy, ponieważ w cylindrach nie dochodzi do detonacji i nie ma potrzeby usuwania spalin. Modyfikacja „Beta”, wyposażona w rombowy mechanizm korbowy, to doskonale wyważony system, który nie ma wibracji podczas pracy.
W cylindrach silnika nie ma procesów, które mogą mieć negatywny wpływ na środowisko. Przy wyborze odpowiedniego źródła ciepła (np. energia słoneczna) Stirling może być absolutnie przyjazny dla środowiska jednostka mocy.
Wady projektu Stirlinga
Z całym zestawem pozytywne właściwości natychmiastowe masowe użycie silników Stirlinga jest niemożliwe z następujących powodów:
Główny problem tkwi w materiałochłonności konstrukcji. Chłodzenie czynnika roboczego wymaga obecności radiatorów o dużej pojemności, co znacznie zwiększa gabaryty i zużycie metalu instalacji.
Obecny poziom technologiczny pozwoli silnikowi Stirlinga porównać osiągi z nowoczesnymi silnikami benzynowymi tylko dzięki zastosowaniu typy złożone płyn roboczy (hel lub wodór) pod ciśnieniem ponad stu atmosfer. Fakt ten rodzi poważne pytania zarówno w dziedzinie materiałoznawstwa, jak i bezpieczeństwa użytkowników.
Ważny problem eksploatacyjny związany jest z zagadnieniami przewodnictwa cieplnego i odporności temperaturowej metali. Ciepło dostarczane jest do objętości roboczej przez wymienniki ciepła, co prowadzi do nieuniknionych strat. Ponadto wymiennik ciepła musi być wykonany z metali żaroodpornych odpornych na działanie wysokie ciśnienie. Odpowiednie materiały bardzo drogie i trudne w obróbce.
Zasady zmiany trybów pracy silnika Stirlinga również zasadniczo różnią się od tradycyjnych, co wymaga opracowania specjalnych urządzeń sterujących. Aby więc zmienić moc, konieczna jest zmiana ciśnienia w cylindrach, kąta fazowego między wypornikiem a tłokiem napędowym lub oddziaływanie na pojemność wnęki cieczą roboczą.
Jeden ze sposobów kontrolowania prędkości wału w modelu silnika Stirlinga można zobaczyć w następny film:
Efektywność
W obliczeniach teoretycznych sprawność silnika Stirlinga zależy od różnicy temperatur płynu roboczego i może osiągnąć 70% lub więcej zgodnie z cyklem Carnota.
Jednak pierwsze próbki wykonane z metalu miały wyjątkowo niską wydajność z następujących powodów:
- nieefektywne opcje chłodziwa (płynu roboczego), ograniczające maksymalna temperatura ogrzewanie;
- straty energii spowodowane tarciem części i przewodnością cieplną obudowy silnika;
- brak materiały budowlane odporny na wysokie ciśnienie.
Rozwiązania inżynieryjne stale ulepszały konstrukcję jednostki napędowej. Tak więc w drugiej połowie XX wieku czterocylindrowy samochód Silnik Stirlinga z napędem rombowym wykazał w testach sprawność równą 35%. na chłodziwie wodnym o temperaturze 55 ° C. Dokładne przestudiowanie projektu, zastosowanie nowych materiałów i precyzyjne dostrojenie jednostek roboczych zapewniło wydajność próbek eksperymentalnych na poziomie 39%.
Uwaga! Nowoczesne silniki benzynowe o podobnej mocy mają współczynnik pożyteczna akcja na poziomie 28-30%, a silniki diesla z turbodoładowaniem w granicach 32-35%.
Współczesne egzemplarze silnika Stirlinga, takie jak zbudowany przez amerykańską firmę Mechanical Technology Inc, wykazują sprawność dochodzącą do 43,5%. A wraz z rozwojem produkcji ceramiki żaroodpornej i podobnych innowacyjnych materiałów możliwe będzie znaczne podniesienie temperatury środowiska pracy i osiągnięcie wydajności na poziomie 60%.
Przykłady udanych wdrożeń motoryzacyjnych Stirlingów
Pomimo wszystkich trudności istnieje wiele wykonalnych modeli silnika Stirlinga mających zastosowanie w przemyśle motoryzacyjnym.
Zainteresowanie Stirlingiem, nadającym się do montażu w samochodzie, pojawiło się w latach 50. XX wieku. Prace w tym kierunku prowadziły takie koncerny jak Ford Motor Company, Volkswagen Group i inne.
UNITED STIRLING (Szwecja) opracował Stirling, który maksymalnie wykorzystał seryjne komponenty i zespoły produkowane przez producentów samochodów (wał korbowy, korbowody). Powstały czterocylindrowy silnik w kształcie litery V miał ciężar właściwy 2,4 kg / kW, co jest porównywalne z charakterystyką kompaktowego silnika wysokoprężnego. Ta jednostka została pomyślnie przetestowana jako elektrownia dla siedmiotonowego samochodu dostawczego.
Jednym z udanych przykładów jest czterocylindrowy silnik Stirlinga holenderskiego modelu produkcyjnego „Philips 4-125DA”, przeznaczony do montażu na samochód. Silnik miał moc roboczą 173 litrów. Z. w wymiarach zbliżonych do klasycznej jednostki benzynowej.
Inżynierowie General Motors osiągnęli znaczące wyniki, budując w latach 70-tych ośmiocylindrowy (4 cylindry robocze i 4 cylindry sprężające) silnik Stirlinga w kształcie litery V ze standardowym mechanizmem korbowym.
podobny elektrownia w 1972 roku wyposażony w limitowaną serię samochodów Ford Torino, którego zużycie paliwa spadło o 25% w porównaniu z klasyczną ósemką benzynową w kształcie litery V.
Obecnie ponad pięćdziesiąt firm zagranicznych pracuje nad udoskonaleniem konstrukcji silnika Stirlinga w celu przystosowania go do masowej produkcji na potrzeby przemysłu motoryzacyjnego. A jeśli uda ci się wyeliminować niedociągnięcia tego typu silników, zachowując przy tym swoje zalety, to właśnie Stirling, a nie turbiny i silniki elektryczne, zastąpi benzynowy silnik spalinowy.
Silnik Stirlinga. Dla prawie każdego majsterkowicza ta cudowna rzecz może stać się prawdziwym narkotykiem. Wystarczy zrobić to raz i zobaczyć w akcji, bo chce się to robić wielokrotnie. Względna prostota tych silników pozwala zrobić je dosłownie ze śmieci. nie będę się rozwodzić ogólne zasady i urządzenie. W internecie jest dużo informacji na ten temat. Na przykład: Wikipedia. Przejdźmy od razu do budowy najprostszej niskotemperaturowej gamma-Stirlinga.
Aby zbudować silnik własnymi rękami, potrzebujemy dwóch osłon szklane słoiki. Będą działać jako część zimna i gorąca. Krawędź jest odcinana od tych okładek nożyczkami
Otwór jest wykonany w środku jednej pokrywy. Rozmiar otworu powinien być nieco mniejszy niż średnica przyszłego cylindra.
Wycięta obudowa silnika Stirlinga plastikowa butelka spod mleka. Te butelki są po prostu podzielone na pierścienie. Będziemy potrzebować jednego. Należy zaznaczyć, że o godz różne odmiany butelki mleka mogą się nieznacznie różnić.
Obudowa jest przyklejona do pokrywy plastikową masą epoksydową lub uszczelniaczem.
Korpus markera idealnie sprawdza się jako cylinder. W tym modelu nasadka ma mniejszą średnicę niż sam znacznik i może stać się tłokiem.
Mała część jest odcięta od znacznika. Przy skuwce część jest odcięta od góry.
To jest wypieracz. Podczas pracy silnika Stirlinga przemieszcza powietrze wewnątrz obudowy z części gorącej do części zimnej i odwrotnie. Wykonane z gąbki do mycia naczyń. W środku wklejony magnes.
Ponieważ górna pokrywa jest wykonana z blachy, może być przyciągana przez magnes. Przenośnik może utknąć. Aby temu zapobiec, magnes należy dodatkowo przymocować kartonowym kółkiem.
Czapka jest wypełniona żywicą epoksydową. Na obu końcach wywiercone są otwory do zamocowania magnesu i uchwytu korbowodu. Gwinty w otworach są nacinane bezpośrednio przez śrubę. Te śruby są potrzebne do precyzyjnego dostrojenia silnika. Magnes w tłoku jest przyklejony do śruby i ustawiony w taki sposób, że będąc w dolnej części cylindra przyciąga pływak. Będziesz także musiał przykleić gumowy ogranicznik do tego magnesu. Wystarczy kawałek dętki rowerowej lub gumka. Ogranicznik jest potrzebny, aby magnesy tłoka i wypornika nie przyciągały zbyt mocno. W przeciwnym razie ciśnienie może nie być wystarczające do zerwania wiązania magnetycznego.
Gumowa uszczelka jest przyklejona do górnej części tłoka. Jest potrzebny do szczelności i zabezpieczenia obudowy przed rozerwaniem.
Obudowa tłoka wykonana jest z gumowej rękawicy. Musisz odciąć mały palec.
Po sklejeniu obudowy na wierzch przyklejana jest kolejna gumowa uszczelka. Otwór przebija się przez uszczelki gumowe i obudowę za pomocą szydła. W ten otwór wkręca się uchwyt korbowodu. Uchwyt ten wykonany jest ze śruby i lutowanej podkładki.
Jako uchwyt wału korbowego opakowanie epoksydowe było idealne. Dokładnie ten sam słoik można wyjąć spod musujących witamin lub aspiryny.
Dno tego słoika jest odcięte i wykonane są otwory. W górnej części - do trzymania wału korbowego. Na dole - dostęp do mocowania korbowodu.
Wał korbowy i korbowód są wykonane z drutu. Białe figury są ogranicznikiem. Wykonane z tubki typu Lollipop. Małe kawałki są wycinane z tej rury, a powstałe części są cięte wzdłużnie. Dzięki temu łatwiej je założyć. Wysokość kolana jest określona przez połowę odległości, jaką cylinder musi pokonać od najniższego punktu do najwyższego punktu, w którym połączenie magnetyczne przestaje działać.
Tak więc wszyscy jesteśmy gotowi na pierwszy test. Najpierw musisz sprawdzić szczelność. Musisz dmuchnąć w cylinder. Wszystkie spoiny można przemyć płynem do mycia naczyń. Najmniejszy wyciek powietrza i silnik nie będzie działał. Jeśli wszystko jest w porządku ze szczelnością można włożyć tłok i zabezpieczyć obudowę gumką recepturką.
W dolnym położeniu cylindra pływak powinien być przyciągany do góry. Następnie całą konstrukcję umieszcza się na kubku z gorąca woda. Po chwili powietrze wewnątrz silnika zacznie się nagrzewać i wypchnąć tłok. W pewnym momencie połączenie magnetyczne zostanie przerwane i pływak opadnie na dno. W ten sposób powietrze w silniku nie będzie już stykać się z nagrzaną częścią i zacznie się ochładzać. Tłok zacznie się cofać. W idealnym przypadku tłok powinien zacząć poruszać się w górę iw dół. Ale to może się nie zdarzyć. Albo ciśnienie nie będzie wystarczające do poruszenia tłoka, albo powietrze za bardzo się nagrzeje i tłok nie będzie się całkowicie cofał. W związku z tym ten silnik może mieć martwe strefy. To nie jest szczególnie przerażające. Najważniejsze, że martwe strefy nie są zbyt duże. Koło zamachowe jest potrzebne do kompensacji martwych stref.
Kolejną bardzo ważną częścią tego etapu jest to, że tutaj możesz poczuć zasadę działania silnika Stirlinga. Pamiętam mój pierwszy stirling, który nie zadziałał tylko dlatego, że nie mogłem rozgryźć, jak i dlaczego to coś działa. Tutaj, pomagając dłonią tłokowi poruszać się w górę iw dół, możesz poczuć, jak ciśnienie rośnie i spada.
Ten projekt można nieco poprawić, dodając strzykawkę do górnej pokrywy. Tę strzykawkę należy również nałożyć na żywicę epoksydową, uchwyt igły należy nieco przyciąć. Pozycja tłoka w strzykawce powinna znajdować się w pozycji środkowej. Ta strzykawka może regulować objętość powietrza wewnątrz silnika. Uruchamianie i regulacja będą znacznie łatwiejsze.
Więc możesz dopasować uchwyt wału korbowego. Wysokość korbowodu do cylindra jest regulowana za pomocą śruby.
Koło zamachowe jest wykonane z płyty CD. Otwór jest uszczelniony plastikową żywicą epoksydową. Następnie musisz wywiercić otwór dokładnie w środku. Znalezienie centrum jest bardzo łatwe. Korzystanie z właściwości trójkąt prostokątny wpisany w okrąg. Jego przeciwprostokątna przechodzi przez środek. Konieczne jest przymocowanie kartki papieru pod kątem prostym do obrzeży dysku. Orientacja nie jest ważna. W miejscach, w których boki arkusza przecinają się z krawędzią dysku, umieszczamy znaczniki. Linia poprowadzona przez te znaki przejdzie przez środek. Jeśli drugą linię narysujemy w innym miejscu, to na przecięciu otrzymamy dokładny środek.
Cały silnik jest gotowy.
Umieściliśmy silnik Stirlinga na filiżance wrzącej wody. Poczekamy trochę i powinien sobie zapracować. Jeśli tak się nie stanie, musisz mu trochę pomóc ręką.
Proces produkcji wideo.
Silnik Stirlinga w pracy
Wyjaśnienie działania silnika Stirlinga.
|
Zaczynamy od zaznaczenia koła zamachowego.
|
Sześć dołków nie powiodło się. Okazuje się, że nie jest piękny, dziury są małe, a ciało między nimi cienkie.
|
Po pierwsze ostrzymy przeciwwagi do wału korbowego. Łożyska są wciskane. Następnie łożyska są wciskane, aw ich miejsce nacinany jest gwint M3.
|
Frezowałem ale można też złożyć.
|
To jest część pręta. Reszta jest lutowana przez PSR.
|
Praca rozwiertaka na podkładce uszczelniającej.
|
Wiercenie w złożu Stirlinga. Otwór łączący pływak z cylindrem roboczym. Wiertło do gwintu 4,8 na M6. Wtedy trzeba to uciszyć.
|
Wiercenie tulei cylindra roboczego, w trakcie opracowywania.
|
Wiercenie pod gwint na M4.
|
Jak to zostało zrobione.
|
Wymiary podane z uwzględnieniem przerobionego Wykonano dwie pary cylinder-tłok 10mm. i 15 mm. Obydwa były testowane.Jeśli założysz cylinder na 15mm. wtedy skok tłoka wyniesie 11-12 mm. i nie działa. A tutaj 10mm. ze skokiem 24mm. dokładnie.
|
Wymiary korbowodów Do nich przylutowany jest drut mosiężny Ф3mm.
|
Zespół mocowania korbowodu Awaria opcji łożyska. Podczas dokręcania korbowodu łożysko odkształca się i wytwarza dodatkowe tarcie. Zamiast łożyska zrobiłem Al. tuleja ze śrubą.
|
Wymiary niektórych części.
|
Niektóre rozmiary kół zamachowych.
|
Niektóre wymiary dotyczą sposobu montażu na wale i przegubach.
|
Pomiędzy chłodnicą a komorą płomieniową umieszczamy uszczelkę azbestową na 2-3 mm. Pod śruby mocujące obie części warto podłożyć uszczelki paronitowe lub coś mniej przewodzącego ciepło.
|
Wypornik jest sercem stirlinga, powinien być lekki i przewodzić mało ciepła. Zapas jest pobierany z tego samego starego dysku twardego. Jest to jedna z liniowych prowadnic silnikowych.Bardzo odpowiednia, hartowana, chromowana. Aby przeciąć nitkę, środek owinęłam namoczoną szmatką, a końce podgrzałam do czerwoności.
|
Korbowód z cylindrem roboczym. Długość całkowita 108mm. Spośród nich 32mm to tłok o średnicy 10mm.Tłok powinien wchodzić do cylindra swobodnie, bez zauważalnego zarysowania.W celu sprawdzenia zamknij go mocno palcem od dołu i włóż tłok od góry, powinien być bardzo powoli zwalniane.
|
Planowałem to zrobić, ale w trakcie wprowadziłem zmiany. Aby poznać skok cylindra roboczego, przesuń pływak do komora chłodziarki, Wydłużamy cylinder roboczy o 25mm Podgrzewamy komorę płomienia Ostrożnie podkładamy linijkę pod korbowód roboczy i zapamiętujemy dane. Mocno wciskamy wypornik, a o ile przesunie się cylinder roboczy to jego skok.Ta wielkość odgrywa bardzo ważną rolę.
|
Widok cylindra roboczego. Długość korbowodu 83mm. Skok 24mm Koło ręczne mocowane jest do wału za pomocą śruby M4. Na zdjęciu jego głowa. W ten sposób mocowana jest również przeciwwaga korbowodu wypornika.
|
Widok korbowodu pływaka Długość całkowita z pływakiem 214mm. Długość korbowodu 75mm. Skok 24mm. Zwróć uwagę na rowek w kształcie litery U na kole zamachowym. Został on wykonany do przystawki odbioru mocy. Pomysł dotyczył albo generatora, albo paska na wentylatorze chłodnicy. Górna część frezowana jest z jednej strony na głębokość 7mm i długość 32mm.Środek łożyska od dołu to 55mm. Mocowana jest od dołu dwoma śrubami na M4.Odległość między środkami pylonów wynosi 126mm.
|
Widok komory płomieniowej i chłodnicy.Obudowa silnika wciśnięta w pylon.Wymiary pylonu to 47x25x15,wgłębienie na podest 12mm.Mocowany jest od spodu deski dwoma śrubami M4.
|
Lampada 40mm. w średnicy wysokość 35mm. Pogłębiony w trzonie o 8mm. Na dole nakrętka M4 jest przylutowana pośrodku i zabezpieczona śrubą od dołu.
|
Gotowy wygląd. Podstawa dąb 300x150x15mm.
|
Tabliczka z nazwiskiem.
|
Długo poszukiwany schemat pracy. Znalazłem, ale zawsze było to związane z tym, że były problemy albo ze sprzętem, albo z materiałami.Postanowiłem zrobić z niej kuszę. Po przejrzeniu wielu opcji i zastanowieniu się, co mam do dyspozycji i co mogę zrobić sam na własnym sprzęcie, nie podobały mi się wymiary, które ustaliłem od razu po złożeniu urządzenia.Okazało się, że jest za szerokie. Musiałem skrócić łoże cylindra. I założyć koło zamachowe na jedno łożysko (na jeden pylon).Materiały koła zamachowego, korbowody, przeciwwaga, podkładka uszczelniająca, lampa i cylinder roboczy to brąz.Pylony, tłok roboczy, łoże cylindra, chłodnica i podkładka z gwintem z komory płomieniowej aluminium stal komora płomienia ze stali nierdzewnej wypornik grafitowy A to, co się stało, pokazałem, ty będziesz sędzią.
Silnik Stirlinga to silnik, który może pracować na energię cieplną. W tym przypadku źródło ciepła jest absolutnie nieistotne. Najważniejsze jest to, że istnieje różnica temperatur, w którym to przypadku ten silnik będzie działał. Autor wymyślił, jak to zrobić Model taki silnik z puszki coca-coli.
Materiały i narzędzia
- jeden balon;
- 3 puszki coli;
- zaciski elektryczne, pięć sztuk (dla 5A);
- nyple do mocowania szprych rowerowych (2 sztuki);
- wełna metalowa;
- kawałek drutu stalowego o długości 30 cm i przekroju 1 mm;
- kawałek grubego drutu ze stali lub miedzi o średnicy od 1,6 do 2 mm;
- szpilka wykonana z drewna o średnicy 20 mm (długość 1 cm);
- zakrętka do butelki (plastikowa);
- okablowanie elektryczne (30cm);
- Super klej;
- wulkanizowana guma (około 2 centymetry kwadratowe);
- żyłka wędkarska (długość ok. 30 cm);
- para ciężarków do wyważania (na przykład nikiel);
- płyty CD (3 sztuki);
- Pinezki;
- kolejna puszka do zrobienia paleniska;
- żaroodporny silikon i cyna stworzyć chłodzenie wodne.
Krok pierwszy. Przygotowanie słoików
Przede wszystkim musisz wziąć dwa słoiki i odciąć ich wierzchołki. Jeśli wierzchołki są cięte nożyczkami, powstałe nacięcia będą musiały zostać zeszlifowane pilnikiem.
Następnie musisz wyciąć dno słoika. Można to zrobić nożem.
Krok drugi. Tworzenie przysłony
Jako przepony autor użył balonu, który został wzmocniony wulkanizowaną gumą. Kulę należy przeciąć i przeciągnąć po słoiku, jak pokazano na rysunku. Następnie kawałek wulkanizowanej gumy przykleja się do środka membrany. Po stwardnieniu kleju w środku membrany wybija się otwór do zainstalowania drutu. Najprościej zrobić to za pomocą pinezki, którą można pozostawić w otworze do czasu montażu.
Krok trzeci. Cięcie i tworzenie otworów w pokrywie
W ścianach pokrywy należy wywiercić dwa otwory o średnicy 2 mm każdy, są one potrzebne do zainstalowania osi obrotu dźwigni. W dnie pokrywy należy wywiercić kolejny otwór, przez który przejdzie drut, który zostanie podłączony do wypornika.
Na Ostatni etap Osłonę należy przyciąć tak, jak pokazano na rysunku. Odbywa się to tak, aby drut wypierający nie przylegał do krawędzi pokrywy. Do takiej pracy odpowiednie są nożyczki użytkowe.
Krok czwarty. Wiercenie
W słoiku musisz wywiercić dwa otwory na łożyska. W ta sprawa zrobiono to wiertłem 3,5 mm.
Krok piąty. Tworzenie okna podglądu
W obudowie silnika należy wyciąć okienko kontrolne. Teraz będzie można obserwować, jak działają wszystkie węzły urządzenia.
Krok szósty. Modyfikacja terminala
Musisz wziąć terminale i usunąć z nich izolacja z tworzywa sztucznego. Następnie wykonuje się wiertło i wykonuje otwory przelotowe na krawędziach zacisków. W sumie musisz wywiercić 3 zaciski, podczas gdy dwa powinny pozostać niewywiercone.
Krok siódmy. Tworzenie dźwigni
Jako materiał do tworzenia dźwigni stosuje się drut miedziany, którego średnica wynosi 1,88 mm. Jak dokładnie zginać druty pokazano na zdjęciach. Możesz także użyć drutu stalowego, po prostu przyjemniej jest pracować z drutem miedzianym.
Krok ósmy. Tworzenie łożysk
Do wykonania łożysk potrzebujesz dwóch smoczków rowerowych. Należy sprawdzić średnicę otworu. Autor przewiercił je wiertłem 2 mm.
Krok dziewiąty. Montaż dźwigni i łożysk
Dźwignie można montować bezpośrednio przez wziernik. Jeden koniec drutu powinien być długi, będzie miał koło zamachowe. Łożyska muszą być mocno osadzone. Jeśli występuje luz, można je skleić.
Krok dziesiąty. Tworzenie wypieracza
Pływak wykonany jest z wełny stalowej do polerowania. Aby utworzyć wypornik, bierze się drut stalowy, wykonuje się na nim haczyk, a następnie wokół drutu nawija się wymaganą ilość waty. Wypornik musi być wystarczająco duży, aby mógł się swobodnie poruszać w puszce. Całkowita wysokość wypornika nie powinna przekraczać 5 cm.
W efekcie z jednej strony waty konieczne jest uformowanie spirali z drutu, aby nie wychodziła ona z waty, az drugiej strony wykonana jest pętla z drutu. Następnie do tej pętli przywiązuje się żyłkę, którą następnie przeciąga się przez środek przepony. Wulkanizowana guma powinna znajdować się na środku pojemnika.
Krok 11 Utwórz zbiornik ciśnieniowy
Konieczne jest przecięcie dna słoika, aby od jego podstawy pozostało około 2,5 cm. Pływak wraz z membraną należy umieścić w zbiorniku. Następnie cały ten mechanizm jest instalowany na końcu puszki. Membranę należy trochę dokręcić, aby się nie zwisała.
Następnie musisz wziąć terminal, który nie został wywiercony i przeciągnąć przez niego żyłkę. Węzeł musi być przyklejony, aby się nie poruszał. Drut musi być dobrze nasmarowany olejem, a jednocześnie upewnić się, że pływak łatwo ciągnie linkę.
Krok 12 Utwórz popychacze
Popychacze łączą membranę i dźwignie. Jest zrobiony z kawałka. miedziany przewód 15 cm długości.
Krok 13 Utwórz i zainstaluj koło zamachowe
Do stworzenia koła zamachowego używane są 3 stare płyty CD. Używany jako część środkowa drewniany pręt. Po zamontowaniu koła zamachowego drążek wału korbowego jest wygięty, dzięki czemu koło zamachowe nie spadnie.
Na ostatnim etapie cały mechanizm jest montowany razem.