Projekty instalacji napowietrznych sieci ciepłowniczych. Metody układania rurociągów sieci ciepłowniczych Układanie sieci ciepłowniczych jedna nad drugą
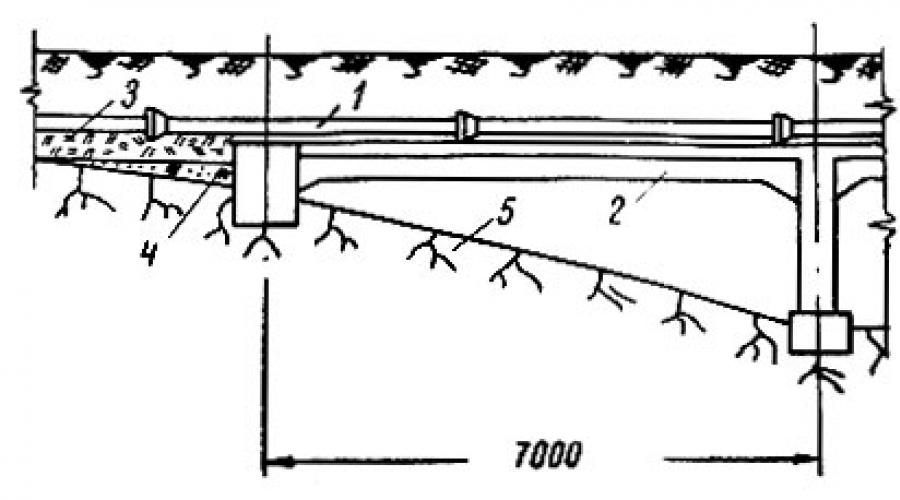
Przeczytaj także
Zawartość sekcji
Ze względu na sposób montażu sieci ciepłownicze dzielą się na podziemne i naziemne (powietrzne). Instalacja podziemna rurociągi sieci ciepłowniczych wykonywane są: w kanałach o przekrojach nieprzelotowych i półprzelotowych, w tunelach (kanałach przelotowych) o wysokości 2 m lub większej, we wspólnych kolektorach do wspólnego układania rurociągów i kabli do różnych celów , w kolektorach wewnątrzblokowych oraz w podziemiach i korytarzach technicznych, bezkanałowe.
Układanie rurociągów pod głową odbywa się na masztach wolnostojących lub niskich podporach, na wiaduktach o ciągłej rozpiętości, na masztach z rurami podwieszonymi na prętach (konstrukcja podwieszona) oraz na wspornikach.
Do szczególnej grupy obiektów zaliczają się konstrukcje specjalne: przeprawy mostowe, przejścia podwodne, przejścia tunelowe oraz przejścia w skrzyniach. Konstrukcje te z reguły są projektowane i budowane według odrębnych projektów przy zaangażowaniu wyspecjalizowanych organizacji.
O wyborze metody i projektu układania rurociągów decyduje wiele czynników, z których główne to: średnica rurociągów, wymagania dotyczące niezawodności eksploatacyjnej rurociągów ciepłowniczych, opłacalność konstrukcji i sposób budowy.
Przy lokalizacji tras sieci ciepłowniczych na obszarach istniejącej lub przyszłej zabudowy miejskiej, ze względów architektonicznych, przyjmuje się najczęściej podziemną instalację rurociągów. Przy budowie podziemnych sieci ciepłowniczych najczęściej stosowanym jest układanie rurociągów w kanałach nieprzelotowych i półprzelotowych.
Konstrukcja kanału ma wiele pozytywnych właściwości, które spełniają specyficzne warunki pracy gorących rurociągów. Kanały to konstrukcja budowlana chroniąca rurociągi i izolację termiczną przed bezpośrednim kontaktem z gruntem, co oddziałuje na nie zarówno mechanicznie, jak i elektrochemicznie. Konstrukcja kanału całkowicie odciąża rurociągi od działania masy gruntu i tymczasowych obciążeń transportowych, dlatego przy obliczaniu ich wytrzymałości uwzględniane są jedynie naprężenia wynikające z wewnętrznego ciśnienia chłodziwa, ciężaru własnego i wydłużeń temperaturowych rurociągu, które można wyznaczyć z wystarczającą dokładnością.
Układanie w kanałach zapewnia swobodny ruch temperatur rurociągów zarówno w kierunku wzdłużnym (osiowym), jak i poprzecznym, co pozwala na wykorzystanie ich zdolności samokompensacyjnych na narożnych odcinkach trasy sieci ciepłowniczej.
Wykorzystanie naturalnej elastyczności rurociągów do samokompensacji podczas montażu kanałów pozwala na zmniejszenie lub całkowite wyeliminowanie montażu kompensatorów osiowych (dławnicowych), wymagających budowy i konserwacji studni, a także kompensatorów zagiętych , którego stosowanie jest niepożądane w warunkach miejskich i prowadzi do wzrostu kosztów rur o 8-15%.
Projekt ułożenia kanału jest uniwersalny, ponieważ można go stosować w różnych hydrogeologicznych warunkach gruntowych.
Przy wystarczającej szczelności konstrukcji budynku kanału i prawidłowym działaniu urządzenia odwadniające Stwarza to warunki uniemożliwiające przedostawanie się wód powierzchniowych i gruntowych do kanału, co zapewnia, że izolacja termiczna nie zostanie zamoczona oraz chroni zewnętrzną powierzchnię rur stalowych przed korozją. Trasę sieci ciepłowniczych układanych kanałowo (w odróżnieniu od bezkanałowych) można bez większych trudności wybierać wzdłuż obszarów drogowych i pozadrogowych miasta wraz z pozostałą komunikacją, omijając lub z lekkim podejściem do istniejących obiektów, a także biorąc pod uwagę uwzględnić różne wymagania planistyczne (potencjalne zmiany terenu, przeznaczenie terytorium itp.).
Jeden z pozytywne właściwości układanie kanałów to możliwość stosowania lekkich materiałów (wełna mineralna, włókno szklane itp.) o niskim współczynniku przewodzenia ciepła jako podwieszanej izolacji termicznej rurociągów, co pozwala na zmniejszenie straty ciepła w sieciach.
Pod względem wydajności instalacja sieci grzewczych w kanałach nieprzelotowych i półprzelotowych różni się znacznie. Nieprzejezdne kanały, niedostępne do oględzin bez rozebrania nawierzchni drogowej, wykopania gruntu i demontażu konstrukcji budynku, nie pozwalają na wykrycie uszkodzeń izolacji termicznej i rurociągów, a także zapobiegawczą ich eliminację, co prowadzi do konieczności produkcji prace naprawcze w momencie wystąpienia awaryjnego uszkodzenia.
Pomimo wad, instalacja w kanałach nieprzejściowych jest powszechnym rodzajem podziemnej instalacji sieci ciepłowniczych.
W kanałach półprzelotowych dostępnych dla przejścia personelu obsługującego (przy odłączonych rurkach cieplnych) inspekcja i wykrywanie uszkodzeń izolacji termicznej, rur i konstrukcji budowlanych, a także ich bieżące naprawy mogą w większości przypadków odbywać się bez rozkopanie i demontaż kanału, co znacznie zwiększa niezawodność i żywotność sieci ciepłowniczych. Jednakże wymiary wewnętrzne kanałów półprzelotowych przewyższają wymiary kanałów nieprzelotowych, co w naturalny sposób je zwiększa koszt budowy i zużycie materiału. Dlatego kanały półprzelotowe stosuje się głównie przy układaniu rurociągów o dużych średnicach lub na niektórych odcinkach sieci ciepłowniczych, gdy trasa przebiega przez teren uniemożliwiający kopanie, a także gdy kanały układane są na dużej głębokości, gdy zasypka nad stropem przekracza 2,5 m.
Jak pokazuje doświadczenie eksploatacyjne, rurociągi o dużej średnicy ułożone w nieprzejezdnych kanałach niedostępnych dla kontroli i konserwacji są najbardziej podatne na awaryjne uszkodzenia spowodowane korozją zewnętrzną. Uszkodzenia te prowadzą do długotrwałego wstrzymania dostaw ciepła do całych obszarów mieszkalnych i przedsiębiorstw przemysłowych, awaryjnych prac remontowych, zakłóceń w ruchu, zakłóceń w udogodnieniach, co wiąże się z wysokimi kosztami materiałowymi i zagrożeniem dla personelu obsługującego i ludności. Szkodeń powstałych na skutek uszkodzenia rurociągów o dużych średnicach nie można porównywać z uszkodzeniami rurociągów o średnich i małych średnicach.
Biorąc pod uwagę, że wzrost kosztów budowy jednokomorowych kanałów półprzelotowych w porównaniu do kanałów nieprzelotowych o średnicy sieci ciepłowniczej 800 - 1200 mm jest niewielki, należy zalecać ich stosowanie we wszystkich przypadkach i na całej długości sieć grzewcza określone średnice. Polecając układanie rurociągów o dużych średnicach w kanałach półprzelotowych, nie można nie zauważyć ich zalet w porównaniu z kanałami nieprzelotowymi pod względem stopnia łatwości konserwacji, a mianowicie możliwości wymiany w nich zużytych rurociągów na znaczną odległość bez kopania montaż i demontaż konstrukcji budynku przy użyciu metoda zamknięta produkcja prac instalacyjnych.
Istotą zamkniętej metody wymiany zużytych rurociągów jest usunięcie ich z kanału poprzez ruch poziomy z jednoczesnym montażem nowych izolowane rurociągi za pomocą instalacji przeciskowej.
Konieczność budowy tuneli (kanałów przejściowych) powstaje z reguły na czołowych odcinkach głównych sieci ciepłowniczych rozciągających się od dużych elektrowni cieplnych, gdy konieczne jest ułożenie dużej liczby rurociągów gorąca woda i para. W takich tunelach grzewczych nie zaleca się układania kabli wysoko- i niskoprądowych ze względu na praktyczną niemożność stworzenia w nich wymaganego reżimu stałej temperatury.
Tunele ciepłownicze budowane są głównie na odcinkach tranzytowych rurociągów duża średnica, ułożonych z elektrowni cieplnych zlokalizowanych na obrzeżach miasta, w przypadku gdy ze względów architektonicznych i planistycznych nie można dopuścić do napowietrznego układania rurociągów.
Tunele należy lokalizować w najkorzystniejszych warunkach hydrogeologicznych, aby uniknąć instalowania głębokich towarzyszących im przepompowni odwadniających i odwadniających.
Z reguły należy zapewnić kolektory ogólne następujące przypadki: w razie potrzeby jednoczesne ułożenie dwururowych sieci ciepłowniczych o średnicy od 500 do 900 mm, wodociąg o średnicy do 500 mm, kable komunikacyjne 10 szt. i więcej, kable elektryczne napięcie do 10 kV w ilości 10 szt. i więcej; podczas przebudowy autostrad miejskich z rozwiniętą infrastrukturą podziemną; w przypadku niedoboru wolne miejsca w profilu poprzecznym ulic do ułożenia sieci w rowach; na skrzyżowaniach z głównymi ulicami.
W wyjątkowych przypadkach, w porozumieniu z klientem i organizacjami operacyjnymi, w kolektorze dopuszcza się układanie rurociągów o średnicy 1000 mm i wodociągów do 900 mm, kanałów powietrznych, rurociągów chłodniczych, rurociągów wody recyklingowej i innych sieci użyteczności publicznej . Zabrania się układania wszelkiego rodzaju gazociągów w miejskich kanałach ściekowych [1].
Kanały zwykłe należy układać wzdłuż ulic i dróg miejskich w linii prostej, równolegle do osi jezdni lub linii czerwonej. Zaleca się umieszczanie kolektorów na pasach technicznych i pod pasami zieleni. Profil podłużny kolektora musi zapewniać grawitacyjne odprowadzanie wód awaryjnych i gruntowych. Nachylenie tacy zbiorczej powinno wynosić co najmniej 0,005. Głębokość kolektora należy określić biorąc pod uwagę głębokość przecinających się komunikacji i innych konstrukcji, nośność konstrukcji i warunków temperaturowych panujących wewnątrz kolektora.
Podejmując decyzję o ułożeniu rurociągu w tunelu lub w kanale, należy wziąć pod uwagę możliwość zapewnienia drenażu i wody awaryjne od kolekcjonera do istniejącego Burza deszczowa i naturalne zbiorniki wodne. Umiejscowienie kolektora na rzucie i profilu w stosunku do budynków, budowli i komunikacji równoległej powinno zapewniać możliwość prowadzenia prac budowlanych bez pogorszenia wytrzymałości, stabilności i warunków pracy tych konstrukcji i komunikacji.
Tunele i kanały kanalizacyjne zlokalizowane wzdłuż ulic i dróg miejskich budowane są zwykle w sposób otwarty, przy użyciu standardowych prefabrykowanych konstrukcji żelbetowych, których niezawodność należy sprawdzić, biorąc pod uwagę specyficzne warunki lokalne trasy (charakterystyka warunków hydrogeologicznych, obciążenia ruchem itp. .).
W zależności od ilości i rodzaju sieci elektroenergetycznych połączonych z rurociągami, kolektor wspólny może być jedno- lub dwusekcyjny. Wyboru projektu i wymiarów wewnętrznych kolektora należy również dokonać w zależności od obecności ułożonej komunikacji.
Projekt kanałów ogólnych należy wykonać zgodnie ze schematem ich budowy na przyszłość, sporządzonym z uwzględnieniem głównych postanowień planu generalnego rozwoju miasta na przewidywany okres. Przy budowie nowych terenów z zielonymi ulicami i zabudową mieszkaniową o planie wolnostojącym sieci ciepłownicze wraz z innymi sieciami podziemnymi układa się poza jezdnią – pod pasami technicznymi, pasami terenów zielonych, a w wyjątkowych przypadkach – pod chodnikami. Zaleca się lokalizowanie sieci podziemnych na terenach niezabudowanych w pobliżu pasów ruchu ulic i dróg.
Układanie sieci ciepłowniczych na terenie nowo wybudowanych obszarów może odbywać się w kolektorach budowanych na obszarach mieszkalnych i mikrodzielnicach, aby pomieścić komunikacja inżynierska obsługujących tę zabudowę [2], a także w podziemiach technicznych i korytarzach technicznych budynków.
Układanie sieci ciepłowniczych o średnicy do D Dopuszcza się 300 mm w korytarzach technicznych lub piwnicach budynków o wysokości w świetle co najmniej 2 m, pod warunkiem że możliwa jest ich normalna eksploatacja (łatwość konserwacji i naprawy urządzeń). Rurociągi należy układać na podporach lub wspornikach betonowych, a kompensację wydłużeń cieplnych należy wykonać za pomocą dylatacji giętych w kształcie litery U oraz odcinków narożnych rur. Podziemne pomieszczenia techniczne muszą posiadać dwa wejścia, które nie komunikują się z wejściami do lokali mieszkalnych. Okablowanie elektryczne należy przeprowadzić w rurach stalowych, a konstrukcja lamp musi wykluczać dostęp do lamp bez nich specjalne urządzenia. Zabrania się organizowania magazynów lub innych obiektów w obszarach, przez które przebiega rurociąg. Układanie sieci ciepłowniczych w mikrookręgach wzdłuż tras pokrywających się z inną komunikacją inżynieryjną należy łączyć we wspólnych wykopach z układaniem rurociągów w kanałach lub bez kanałów.
Metoda napowietrznej (napowietrznej) instalacji sieci ciepłowniczych ma ograniczone zastosowanie w warunkach istniejącej i przyszłej zabudowy miasta ze względu na wymagania architektoniczne i planistyczne stawiane tego typu obiektom.
Instalacja naziemna rurociągów ma szerokie zastosowanie w strefach przemysłowych i zakładach indywidualnych, gdzie umieszcza się je na wiaduktach i masztach wraz z rurociągami pary produkcyjnej i rurociągami technologicznymi, a także na wspornikach montowanych na ścianach budynków.
Instalacja naziemna ma znaczną przewagę nad metodą podziemną przy budowie sieci ciepłowniczych na obszarach o wysokim poziomie wód gruntowych, a także na gruntach osiadających i na obszarach wiecznej zmarzliny.
Należy wziąć pod uwagę, że konstrukcja izolacji termicznej oraz same rurociągi ułożone drogą powietrzną nie podlegają destrukcyjnemu działaniu wilgoci gruntowej, przez co znacznie zwiększa się ich trwałość i zmniejszają się straty ciepła. Ważna jest także opłacalność układanie nad głową sieci ciepłownicze. Nawet przy sprzyjających warunkach gruntowych, pod względem kosztów kapitałowych i zużycia materiałów budowlanych, układanie rurociągów o średniej średnicy w powietrzu jest o 20–30% bardziej ekonomiczne niż układanie pod ziemią w kanałach, a dla dużych średnic – o 30–40% .
W związku ze zwiększonym projektowaniem i budową podmiejskich elektrowni cieplnych i ciepłowni jądrowych (AST) do scentralizowanego zaopatrzenia w ciepło dużych miast bardzo ważne pojawiają się problemy zwiększenia niezawodności działania i trwałości tranzytowych sieci ciepłowniczych o dużych średnicach (1000 - 1400 mm) i długości przy jednoczesnym zmniejszeniu w nich zużycia metalu i zużycia zasobów materiałowych. Dotychczasowe doświadczenia w projektowaniu, budowie i eksploatacji napowietrznych sieci ciepłowniczych o dużej średnicy (1200-1400 mm) i długości 5-10 km dały pozytywne rezultaty, co wskazuje na potrzebę ich dalszej budowy. Szczególnie wskazane jest układanie rurociągów ciepłowniczych nad ziemią w niesprzyjających warunkach hydrogeologicznych, a także na odcinkach trasy zlokalizowanych na terenach niezabudowanych, wzdłuż autostrad oraz na skrzyżowaniach małych barier wodnych i wąwozów.
Wybierając metody i projekty układania sieci ciepłowniczych, należy wziąć pod uwagę specjalne warunki konstrukcyjne na obszarach: z sejsmicznością 8 punktów lub większą, rozkładem wiecznej zmarzliny i osiadaniem z nasiąkających gleb, a także w obecności gleb torfowych i mulistych . Dodatkowe wymagania dla sieci ciepłowniczych w specjalne warunki konstrukcja jest określona w SNiP 2.04.07-86*.
Metodę układania sieci grzewczych podczas przebudowy wybiera się zgodnie z instrukcjami SNiP 2.04.07-86 „Sieci grzewcze”. Obecnie w naszym kraju około 84% sieci ciepłowniczych układa się kanałowo, około 6% – bezkanałowo, pozostałe 10% – naziemnie. O wyborze tej czy innej metody decydują warunki lokalne, takie jak rodzaj gruntu, obecność i poziom wód gruntowych, wymagana niezawodność, opłacalność budowy, a także koszty operacyjne utrzymania. Metody układania dzielą się na naziemne i podziemne.
Naziemne układanie sieci ciepłowniczych
Naziemne instalacje sieci ciepłowniczych są rzadko stosowane, gdyż zaburzają zespół architektoniczny terenu, przy wszystkich innych czynnikach powodują większe straty ciepła w porównaniu z instalacją podziemną, nie gwarantują zamarznięcia chłodziwa w przypadku awarii i wypadków i ogranicza przejścia. Podczas rekonstrukcji sieci zaleca się jego użycie wysoki poziom wód gruntowych, w warunkach wiecznej zmarzliny, na niesprzyjającym terenie, na terenach przedsiębiorstw przemysłowych, na terenach niezabudowanych, poza miastem lub w miejscach, gdzie nie wpływa to na projekt architektoniczny i nie zakłóca ruchu.
Zalety instalacji naziemnej: dostępność inspekcji i łatwość obsługi; okazja w tak szybko, jak to możliwe wykrywać i eliminować awarie rurociągów ciepłowniczych; brak elektrokorozji spowodowanej prądami błądzącymi i korozji spowodowanej agresywnymi wodami gruntowymi; niższy koszt budowy w porównaniu do kosztu podziemnej instalacji sieci ciepłowniczych. Instalacja naziemna sieci ciepłowniczych odbywa się: na osobnych podporach (masztach); na wiaduktach o przęśle w postaci płatwi, kratownic lub konstrukcji podwieszanych; wzdłuż ścian budynków. Maszty lub podpory wolnostojące mogą być wykonane ze stali lub żelbetu. Do małych kubatur konstrukcji naziemnych sieci ciepłowniczych stosuje się maszty stalowe wykonane ze stali profilowanej, są one jednak drogie i pracochłonne i dlatego są zastępowane masztami żelbetowymi. Maszty żelbetowe są szczególnie wskazane przy budowie masowej na terenach przemysłowych, gdzie opłacalne jest zorganizowanie ich produkcji w fabryce.
Do wspólnego układania sieci ciepłowniczych z innymi rurociągami do różnych celów stosuje się wiadukty wykonane z metalu lub żelbetu. W zależności od liczby jednocześnie ułożonych rurociągów rozpiętości wiadukty mogą być jednopoziomowe lub wielopoziomowe. Rurociągi ciepłownicze układane są najczęściej na dolnej kondygnacji wiaduktu, natomiast rurociągi na większej wysoka temperatura chłodziwo jest umieszczone bliżej krawędzi, zapewniając w ten sposób najlepsza lokalizacja Kompensatory w kształcie litery U o różnych rozmiarach. Podczas układania sieci ciepłowniczych na terenie przedsiębiorstw przemysłowych stosuje się również metodę montażu naziemnego na wspornikach zamocowanych w ścianach budynków. Rozpiętość rurek cieplnych, tj. odległości między wspornikami dobiera się z uwzględnieniem nośności konstrukcji budowlanych.
Podziemne układanie sieci ciepłowniczych
W miastach i miasteczkach przewody ciepłownicze prowadzone są głównie pod ziemią, co nie psuje wyglądu architektonicznego, nie zakłóca ruchu i ogranicza straty ciepła, wykorzystując właściwości termoizolacyjne gruntu. Zamarzanie gruntu nie stanowi zagrożenia dla rurociągów grzewczych, dlatego można je układać w strefie sezonowego zamarzania gruntu. Im płytsza głębokość sieci ciepłowniczej, tym mniejszy jest zakres robót ziemnych i niższy koszt budowy. Sieci podziemne układa się najczęściej na głębokości od 0,5 do 2 m i pod powierzchnią ziemi.
Wadami podziemnych rurociągów ciepłowniczych są: niebezpieczeństwo zawilgocenia i zniszczenia izolacji w wyniku narażenia na działanie wód gruntowych lub powierzchniowych, co prowadzi do gwałtownego wzrostu strat ciepła, a także niebezpieczeństwo korozji zewnętrznej rur pod wpływem błądzące prądy elektryczne, wilgoć i agresywne substancje zawarte w glebie. Podziemna instalacja ciepłociągów wiąże się z koniecznością udrożnienia ulic, podjazdów i podwórek.
Strukturalnie podziemne sieci ciepłownicze dzielą się zasadniczo na dwie części różne rodzaje: kanałowe i bezkanałowe.
Konstrukcja kanału całkowicie odciąża rurociągi ciepłownicze od mechanicznych oddziaływań masy gruntowej i tymczasowych obciążeń transportowych oraz zabezpiecza rurociągi i izolację termiczną przed korozyjnym wpływem gruntu. Układanie w kanałach zapewnia swobodny ruch rurociągów podczas odkształceń temperaturowych zarówno w kierunku wzdłużnym (osiowym), jak i poprzecznym, co pozwala na wykorzystanie ich zdolności samokompensacyjnych na narożnych odcinkach trasy.
Najbardziej zaawansowaną metodą jest układanie kanałów przelotowych (tuneli), gdyż zapewnia to stały dostęp personelu konserwacyjnego do rurociągów w celu monitorowania ich pracy i przeprowadzania napraw, co jest najlepszym sposobem zapewnienia ich niezawodności i trwałości. Jednak koszt układania w kanałach przejściowych jest bardzo wysoki, a same kanały mają duże wymiary (wysokość w świetle - co najmniej 1,8 m i przejście - 0,7 m). Kanały przelotowe instaluje się zwykle podczas układania dużej liczby rur ułożonych w jednym kierunku, na przykład na wylotach z elektrociepłowni.
Wraz z układaniem w nieprzejezdnych kanałach coraz popularniejsze staje się układanie rurek cieplnych bezkanałowo. Odmowa korzystania z kanałów przy układaniu sieci ciepłowniczych jest bardzo obiecująca i jest jednym ze sposobów obniżenia ich kosztów. Jednakże w przypadku układania bezkanałowego izolowany termicznie rurociąg, ze względu na bezpośredni kontakt z gruntem, podlega bardziej aktywnym wpływom fizycznym i mechanicznym (wilgotność gleby, ciśnienie gruntu i obciążenia zewnętrzne itp.) niż w przypadku układania kanałowego. Możliwy jest montaż bezkanałowy przy zastosowaniu wytrzymałej mechanicznie powłoki termoizolacyjnej i hydroizolacyjnej, która chroni rurociągi przed utratą ciepła i wytrzymuje obciążenia przenoszone przez grunt. Sieci ciepłownicze o średnicach rur do 400 mm włącznie zaleca się układać przede wszystkim metodą bezkanałową.
Wśród uszczelek bezkanałowych najbardziej rozpowszechnione są ostatnie lata otrzymała zaawansowane uszczelki wykorzystujące żelbeton, perlit bitumiczny, beton asfaltowo-keramzytowy, piankę fenolową, piankę poliuretanową, piankę poliuretanową i inne materiały termoizolacyjne jako monolityczną izolację termiczną. Bezkanałowe instalacje sieci ciepłowniczych są stale udoskonalane i stają się coraz bardziej powszechne w praktyce budowlanej i rekonstrukcyjnej. Przy rekonstrukcji wewnątrzblokowych sieci ciepłowniczych jest ich więcej szerokie możliwości układanie sieci w piwnicach niż podczas nowej budowy, ponieważ budowa nowych obiektów często poprzedza budowę budynków.
Montaż sieci ciepłowniczych, układanie rur
Montaż rurociągów i montaż na nich izolacji termicznej odbywa się przy użyciu rur preizolowanych z pianki poliuretanowej, wyrobów kształtowych w izolacji z pianki poliuretanowej (podpory stałe, trójniki i trójniki, przejścia, elementy końcowe i pośrednie itp.), a także jako skorupy z pianki poliuretanowej. Wykonuje się izolacje termiczne odcinków prostych, odgałęzień, elementów rurociągów, podpór ślizgowych, zaworów kulowych oraz złączy doczołowych przy użyciu złączek termokurczliwych, taśmy termokurczliwej, elementów z pianki poliuretanowej, osłon ocynkowanych i poliuretanu termoizolacyjnego skorupy piankowe.
Układanie sieci grzewczych i montaż izolacji z pianki poliuretanowej odbywa się w kilku etapach - etap przygotowawczy ( wykop, dostawa rur i elementów z pianki poliuretanowej na trasę, inspekcja wyrobów), układanie rurociągów (montaż rur i elementów), montaż urządzeń systemu UEC oraz montaż złączy doczołowych.
Głębokość ułożenia rur z pianki poliuretanowej przy układaniu sieci ciepłowniczych należy uwzględnić różnicę gęstości pomiędzy rurą stalową z pianki poliuretanowej a warstwą termoizolacyjną z pianki poliuretanowej, a także standardy przenikania ciepła i normatywnie dopuszczalne straty ciepła.
Należy przeprowadzić zabudowę rowów do instalacji bezkanałowej mechanicznie zgodnie z wymaganiami SNiP 3.02.01 - 87 „Konstrukcje ziemne”.
Minimalna głębokość układania rur z pianki poliuretanowej w osłonie polietylenowej przy układaniu sieci ciepłowniczej w gruncie powinna wynosić co najmniej 0,5 m poza jezdnią i 0,7 m w obrębie jezdni, licząc do szczytu izolacji termicznej.
Maksymalną głębokość układania rur izolowanych termicznie przy układaniu rurociągów w izolacji z pianki poliuretanowej przy układaniu sieci ciepłowniczych należy określić na podstawie obliczeń uwzględniających stabilność warstwy pianki poliuretanowej pod działaniem obciążenia statycznego.
Montaż rur z pianki poliuretanowej odbywa się zwykle na dnie wykopu. Dopuszcza się spawanie odcinków prostych na odcinku przy krawędzi wykopu. Montaż rur z pianki poliuretanowej w osłonie polietylenowej odbywa się przy temperaturach zewnętrznych do -15... -18°C.
Rury stalowe tnie się (w razie potrzeby) za pomocą maszyny do cięcia gazowego, a izolację termiczną usuwa się za pomocą maszyny zmechanizowanej. narzędzia ręczne na odcinku o długości 300 mm, a końce izolacji termicznej podczas cięcia rur stalowych przykrywa się zwilżoną szmatką lub sztywną siatką w celu zabezpieczenia warstwy termoizolacyjnej pianki poliuretanowej.
Spawanie połączeń rurowych i kontrola połączeń spawanych rurociągów podczas montażu rur z pianki poliuretanowej należy wykonywać zgodnie z wymaganiami SNiP 3.05.03-85 „Sieci ciepłownicze”, VSN 29-95 i VSN 11-94.
Podczas wykonywania prac spawalniczych należy chronić izolację z pianki poliuretanowej i osłonę polietylenową oraz końcówki przewodów wychodzących z izolacji przed iskrami.
W przypadku stosowania opaski termokurczliwej jako zabezpieczenia złącza spawanego, zakłada się ją na rurociąg przed rozpoczęciem prac spawalniczych. W przypadku uszczelniania złącza za pomocą złącza wypełniającego lub złącza płaszczowego z pianki poliuretanowej, gdzie jako warstwę ochronną zastosowano osłonę ocynkowaną i taśmę termokurczliwą, zgrzewanie rur przeprowadza się niezależnie od dostępności materiałów do uszczelniania połączeń.
Przed rozpoczęciem budowy magistrali grzewczej przy układaniu rur bez kanałów, rur z pianki poliuretanowej, produkty w kształcie w izolacji PPU zawory kulowe oraz elementy instalacji rurociągów izolowane termicznie pianką poliuretanową poddawane są dokładnej kontroli w celu wykrycia pęknięć, odprysków, głębokich nacięć, przebić i innych uszkodzeń mechanicznych polietylenowego płaszcza izolacji termicznej. W przypadku wykrycia pęknięć, głębokich nacięć i innych uszkodzeń powłoki rur z pianki poliuretanowej w powłoce polietylenowej lub ocynkowanej, naprawia się je poprzez zgrzewanie ekstruzyjne, stosując mankiety termokurczliwe (złączki) lub bandaże ocynkowane.
Przed montażem bezkanałowej magistrali grzewczej rurociągi w izolacji z pianki poliuretanowej i kształtki z pianki poliuretanowej układa się na krawędzi lub dnie wykopu za pomocą dźwigu lub układacza rur, miękkich „ręczników” lub elastycznych zawiesi.
Opuszczanie izolowanych rur z pianki poliuretanowej do rowu powinno odbywać się płynnie, bez szarpnięć i uderzania o ściany oraz dno kanałów i rowów. Przed zamontowaniem rur z pianki poliuretanowej w wykopach lub kanałach należy koniecznie sprawdzić integralność przewodów sygnałowych systemu zdalnego sterowania operacyjnego (systemu SODC) oraz ich izolację od rury stalowej.
Aby zapobiec uszkodzeniu powłoki, rury z pianki poliuretanowej układane na podłożu piaszczystym podczas montażu bezkanałowego nie powinny opierać się na kamieniach, cegłach i innych wtrąceniach stałych, które należy usunąć, a powstałe wgłębienia wypełnić piaskiem.
W razie potrzeby obliczenia kontrolne głębokości ułożenia rurociągów ciepłowniczych z izolacją z pianki poliuretanowej w płaszczu polietylenowym dla określonych warunków montażu odporność projektowa piankę poliuretanową należy przyjmować przy 0,1 MPa, skorupę polietylenową - 1,6 MPa.
W przypadku konieczności układania podziemnych sieci ciepłowniczych z izolacją termiczną z pianki poliuretanowej w płaszczu polietylenowym na głębokości większej niż dopuszczalna, należy je układać w kanałach (tunelach). Przy układaniu tras pod jezdnią, torami kolejowymi i innymi obiektami znajdującymi się nad rurą PPU, rury w izolacji PPU wykonane są ze wzmocnieniem (polietylenowe pierścienie nakładkowe na całej długości płaszcza) i układane są w osłonie stalowej zabezpieczającej przed czynnikami zewnętrznymi. wpływy mechaniczne.
Uszczelka kanałowa spełnia większość wymagań, ale jego koszt, w zależności od średnicy, jest o 10-50% wyższy niż bezkanałowy. Kanały chronią rurociągi przed działaniem wód gruntowych, atmosferycznych i powodziowych. Rurociągi w nich układane są na ruchomych i stałych podporach, zapewniając jednocześnie zorganizowane wydłużenie termiczne.
Wymiary technologiczne kanału przyjmuje się na podstawie minimalnej wolnej odległości rur od elementów konstrukcyjnych, którą w zależności od średnicy rur 25-1400 mm przyjmuje się odpowiednio jako: do ściany 70-120 mm; zachodzić na siebie 50-100 mm; do powierzchni izolacji sąsiedniego rurociągu 100-250 mm. Głębokość kanału
przyjęte na podstawie minimalnej objętości robót ziemnych i równomiernego rozkładu skupionych obciążeń pojazdów na podłożu. W większości przypadków grubość warstwy gleby nad stropem wynosi 0,8-1,2 m, ale nie mniej niż 0,5 m.
Na centralne ogrzewanie Do układania sieci grzewczych stosuje się kanały nieprzelotowe, półprzelotowe lub przelotowe. Jeżeli głębokość układania przekracza 3 m, wówczas budowane są kanały półprzelotowe lub przelotowe, aby umożliwić wymianę rur.
Nieprzejezdne kanały służy do układania rurociągów o średnicy do 700 mm, niezależnie od liczby rur. Konstrukcja kanału zależy od wilgotności gleby. Na suchych glebach zablokuj kanały betonem lub ceglane ściany lub żelbetowe jedno- i wielokomórkowe. Na miękkich glebach najpierw wykonaj betonowa podstawa, na którym zainstalowana jest płyta żelbetowa. Gdy poziom wód gruntowych jest wysoki, u podstawy kanału układa się rurociąg drenażowy w celu jego osuszenia. Sieć ciepłownicza w nieprzejezdnych kanałach, jeśli to możliwe, umieszczaj je wzdłuż trawników.
Obecnie kanały budowane są głównie z prefabrykowanych żelbetowych elementów korytowych (niezależnie od średnicy układanych rurociągów) typu KL, KLS lub płyt ściennych typu KS itp. Kanały pokryte są blachą płaską płyty żelbetowe. Z tego wykonane są podstawy kanałów wszystkich typów płyty betonowe, przygotowanie chudego betonu lub piasku.
Jeśli konieczna jest wymiana uszkodzonych rur lub naprawa sieci grzewczej w nieprzejezdnych kanałach, konieczne jest rozerwanie gleby i demontaż kanału. W niektórych przypadkach towarzyszy temu otwarcie mostu lub nawierzchni asfaltowej.
Kanały półotworowe. W trudne warunki W przypadku, gdy rurociągi sieci ciepłowniczej krzyżują się z istniejącą komunikacją podziemną, pod jezdnią, przy wysokim poziomie wód gruntowych, zamiast nieprzejezdnych instaluje się kanały półprzejezdne. Stosuje się je również przy układaniu niewielkiej ilości rur w miejscach, gdzie ze względu na warunki eksploatacyjne wykluczone jest otwarcie jezdni, a także przy układaniu rurociągów o dużych średnicach (800-1400 mm). Przyjmuje się, że wysokość kanału półotworowego wynosi co najmniej 1400 mm. Kanały wykonane są z prefabrykowanych elementów żelbetowych – płyt dennych, blok ścienny i płyty podłogowe.
Kanały przelotowe. W przeciwnym razie nazywa się ich kolekcjonerami; są budowane w obecności dużej liczby rurociągów. Znajdują się one pod chodnikami dużych autostrad, na terenie dużych przedsiębiorstw przemysłowych, na terenach sąsiadujących z budynkami elektrociepłowni. Wraz z rurociągami ciepłowniczymi w tych kanałach umieszczana jest również inna komunikacja podziemna: elektryczna i kable telefoniczne, wodociągowe, gazociągi niskociśnieniowe itp. W celu przeglądu i naprawy kolektorów zapewnia się swobodny dostęp personelu konserwacyjnego do rurociągów i urządzeń.
Kolektory wykonane są z żelbetowych płyt żebrowych, ogniw konstrukcji ramowych, dużych bloków i elementów objętościowych. Są wyposażone w oświetlenie i naturalne wentylacja nawiewno-wywiewna z potrójną wymianą powietrza, zapewniającą temperaturę powietrza nie wyższą niż 30°C, oraz urządzeniem do usuwania wody. Wejścia do kolektorów są zapewnione co 100-300 m. Do montażu kompensacji i urządzenia blokujące Na sieci ciepłowniczej należy wykonać specjalne nisze i dodatkowe studzienki.
Instalacja bezkanałowa. Aby chronić rurociągi przed wpływami mechanicznymi za pomocą tej metody montażu, instalowana jest wzmocniona izolacja termiczna - powłoka. Zaletami bezkanałowego montażu ciepłociągów są stosunkowo niskie koszty prac budowlano-montażowych, niewielki nakład prac ziemnych oraz skrócenie czasu budowy. Do jego wad należy zwiększona podatność rur stalowych na działanie gleby zewnętrznej, korozję chemiczną i elektrochemiczną.
W przypadku tego typu uszczelki nie stosuje się ruchomych podpór; rury z izolacją termiczną układa się bezpośrednio na poduszce piaskowej wylanej na wstępnie wypoziomowane dno wykopu. Podpory stałe do układania rur bezkanałowych oraz rur kanałowych to żelbetowe ściany osłonowe instalowane prostopadle do rur grzewczych. W przypadku rurek cieplnych o małych średnicach wsporniki te są zwykle stosowane na zewnątrz komór lub w komorach o dużej średnicy poddawanych dużym siłom osiowym. Aby skompensować wydłużenia termiczne rur, stosuje się kompensatory gięte lub dławnicowe, umieszczone w specjalnych wnękach lub komorach. Na zakrętach trasy, aby uniknąć wbijania rur w ziemię i zapewnić ich możliwy ruch, budowane są nieprzejezdne kanały.
W przypadku montażu bezkanałowego stosuje się zasypkę, prefabrykowane i monolityczne rodzaje izolacji. Monolityczne skorupy wykonane z autoklawizowanego betonu zbrojonego stały się powszechne.
Układanie nad głową. Ten typ uszczelki jest najwygodniejszy w obsłudze i naprawie, charakteryzuje się minimalnymi stratami ciepła i łatwością wykrywania miejsc wypadków. Konstrukcje wsporcze dla rur to wolnostojące podpory lub maszty, które zapewniają umiejscowienie rur w wymaganej odległości od podłoża. W przypadku niskich podpór odległość w świetle (pomiędzy powierzchnią izolacji a gruntem) dla grupy rur o szerokości do 1,5 m przyjmuje się 0,35 m i co najmniej 0,5 m dla większych szerokości. Podpory wykonywane są najczęściej z bloczków żelbetowych, maszty i wiadukty ze stali i żelbetu. Odległość między podporami lub masztami przy układaniu rur o średnicy 25-800 mm nad ziemią przyjmuje się jako równą 2-20 m. Czasami instaluje się jedną lub dwie pośrednie podpory podwieszane za pomocą odciągów, aby zmniejszyć liczbę masztów i zmniejszyć inwestycje kapitałowe w sieć ciepłowniczą.
Do obsługi armatury i innych urządzeń zainstalowanych na rurociągach sieci ciepłowniczej stosuje się specjalne podesty z płotami i drabinami: stacjonarne na wysokości 2,5 m i więcej oraz mobilne na niższej wysokości. W miejscach, w których zainstalowane są zawory główne, zawory spustowe i urządzenia powietrzne dostarczają izolowane skrzynki, a także urządzenia do podnoszenia ludzi i osprzętu.
5.2. Odwodnienie sieci ciepłowniczych
Podczas układania rur grzewczych pod ziemią, aby zapobiec przedostawaniu się wody do izolacji termicznej, przewiduje się sztuczne obniżenie poziomu wód gruntowych. W tym celu wraz z rurami grzewczymi układa się rurociągi drenażowe 200 mm poniżej podstawy kanału. Urządzenie odwadniające składa się z rury drenażowej i materiału filtracyjnego z piasku i żwiru. W zależności od warunków pracy stosuje się różne rury drenażowe: do drenażu bezciśnieniowego - kielichowe ceramiczne, betonowe i azbestowo-cementowe, do drenażu ciśnieniowego - stalowe i żeliwne o średnicy co najmniej 150 mm.
Na zmianę i gdy występują różnice w układaniu rur, układają się studnie inspekcyjne w zależności od rodzaju kanalizacji. Na prostych odcinkach studnie takie wykonuje się w odległości co najmniej 50 m od siebie, jeżeli grawitacyjne odprowadzanie wód drenażowych do zbiorników, wąwozów lub kanałów ściekowych nie jest możliwe, buduje się przepompownie, które umieszcza się w pobliżu studni na głębokości zależnej od wysokości. rury drenażowe. Przepompownie budowane są najczęściej z kręgów żelbetowych o średnicy 3 m. Stacja posiada dwa przedziały – maszynownię i zbiornik do odbioru wody drenażowej.
5.3. Konstrukcje na sieciach ciepłowniczych
Komory grzewcze przeznaczone są do obsługi urządzeń zainstalowanych w sieciach ciepłowniczych z instalacją podziemną. O wymiarach komory decyduje średnica rurociągów sieci ciepłowniczej oraz wymiary urządzeń. W komorach zainstalowane są zawory odcinające, dławnice i urządzenia drenażowe itp. Szerokość kanałów wynosi co najmniej 600 mm, a wysokość co najmniej 2 m.
Komory grzewcze są skomplikowanymi i kosztownymi konstrukcjami podziemnymi, dlatego wykonuje się je tylko w miejscach, w których instalowane są zawory odcinające i kompensatory dławnic. Przyjmuje się, że minimalna odległość powierzchni gruntu od szczytu stropu komory wynosi 300 mm.
Obecnie komory grzewcze wykonane z Prefabrykaty betonowe. W niektórych miejscach komory wykonane są z cegły lub monolitycznego żelbetu.
Na rurociągach ciepłowniczych o średnicy 500 mm i większej stosuje się zawory napędzane elektrycznie z wysokim wrzecionem, dzięki czemu nad zagłębioną częścią komory zabudowany jest pawilon naziemny o wysokości około 3 m.
Obsługuje. Aby zapewnić zorganizowany ruch złącza rury i izolacji podczas rozszerzalności cieplnej, stosuje się podpory ruchome i stałe.
Stałe podpory, przeznaczone do zabezpieczania rurociągów sieci ciepłowniczych w charakterystycznych punktach, stosowane są do wszystkich sposobów montażu. Za charakterystyczne punkty na trasie sieci ciepłowniczej uważa się miejsca odgałęzień, miejsca montażu zaworów, kompensatorów dławnicowych, odmulaczy oraz miejsca montażu podpór stałych. Najbardziej rozpowszechnione są wsporniki panelowe, które służą zarówno do montażu bezkanałowego, jak i do układania rurociągów sieci ciepłowniczej w nieprzejezdnych kanałach.
Odległości pomiędzy podporami stałymi określa się zazwyczaj poprzez obliczenie wytrzymałości rur na podporze stałej i w zależności od wielkości zdolności kompensacyjnej przyjętych kompensatorów.
Ruchome podpory przeznaczone do montażu kanałowego i bezkanałowego rurociągów sieci ciepłowniczej. Istnieć następujące typy różne konstrukcje podpór ruchomych: przesuwnych, rolkowych i podwieszanych. Podpory przesuwne używany do wszystkich metod instalacji, z wyjątkiem bezkanałowej. Rolki służą do układania pod sufitem wzdłuż ścian budynków, a także w kolektorach i na wspornikach. Podpory podwieszane instaluje się podczas układania nad ziemią. W miejscach, w których możliwy jest pionowy ruch rurociągu, stosuje się podpory sprężynowe.
Odległość pomiędzy ruchomymi podporami przyjmuje się na podstawie ugięcia rurociągów, które zależy od średnicy i grubości ścianek rur: im mniejsza średnica rury, tym mniejsza odległość między podporami. Podczas układania rurociągów o średnicy 25–900 mm w kanałach odległość między ruchomymi podporami przyjmuje się 1,7–15 m. W przypadku układania nad ziemią, gdzie dopuszczalne jest nieco większe ugięcie rur, odległość między podporami jest taka sama średnica rur zwiększa się do 2-20 m.
Kompensatory stosowany do łagodzenia naprężeń temperaturowych powstających w rurociągach podczas wydłużania. Mogą być elastyczne w kształcie litery U lub w kształcie omegi, zawiasowe lub dławnicowe (osiowe). Dodatkowo stosowane są dostępne na trasie zakręty rurociągu pod kątem 90-120°, które pełnią funkcję kompensatorów (samokompensacja). Montaż kompensatorów wiąże się z dodatkowymi kosztami kapitałowymi i operacyjnymi. Minimalne koszty uzyskuje się w obecności sekcji samokompensacyjnych i zastosowaniu elastycznych kompensatorów. Przy opracowywaniu projektów sieci ciepłowniczych stosuje się minimalną liczbę kompensatorów osiowych, maksymalnie wykorzystując naturalną kompensację rurek cieplnych. Wybór rodzaju kompensatora zależy od specyficznych warunków układania rurociągów sieci ciepłowniczych, ich średnicy i parametrów chłodziwa.
Powłoka antykorozyjna rurociągów. W celu zabezpieczenia rurociągów ciepłowniczych przed korozją zewnętrzną, wywołaną procesami elektrochemicznymi i chemicznymi pod wpływem środowiska, stosuje się powłoki antykorozyjne. Fabrycznie wykonane powłoki charakteryzują się wysoką jakością. Rodzaj powłoki antykorozyjnej zależy od temperatury chłodziwa: podkład bitumiczny, kilka warstw izolacji na mastyksie izolacyjnym, papier pakowy lub szpachlówka i emalia epoksydowa.
Izolacja cieplna. Do izolacji termicznej rurociągów sieci ciepłowniczych stosuje się różne materiały: wełnę mineralną, piankowy beton, żelbeton piankowy, gazobeton, perlit, cement azbestowy, sovelit, keramzyt itp. Do montażu kanałów izolacja podwieszana z wełny mineralnej jest szeroko stosowany do instalacji bezkanałowych - z autoklawizowanego żelbetonu, asfaltu -toizolu, perlitu bitumicznego i szkła piankowego, a czasem także izolacji zasypki.
Izolacja termiczna składa się zazwyczaj z trzech warstw: termoizolacji, osłony i wykończenia. Warstwa wierzchnia ma za zadanie chronić izolację przed uszkodzeniami mechanicznymi i wilgocią, czyli zachować jej właściwości termiczne. Do budowy warstwy wierzchniej stosuje się materiały posiadające niezbędną wytrzymałość i przepuszczalność wilgoci: papę, szkło, włókno szklane, folię izolacyjną, blachę stalową i duraluminium.
Jako warstwa wierzchnia do bezkanałowej instalacji rur grzewczych w warunkach umiarkowanie wilgotnych gleby piaszczyste nałóż wzmocnioną hydroizolację i tynk azbestowo-cementowy na ramę z siatki drucianej; do montażu kanałów - tynk azbestowo-cementowy na ramie wykonanej z siatka druciana; do montażu naziemnego - półcylindry azbestowo-cementowe, obudowa z blachy stalowej, farba aluminiowa ocynkowana lub malowana.
Izolacja podwieszana to cylindryczny płaszcz na powierzchni rury wykonany z wełny mineralnej, wyrobów formowanych (płyt, płaszczy i segmentów) oraz autoklawizowanego betonu piankowego.
Grubość warstwy termoizolacyjnej przyjmuje się zgodnie z obliczeniami. Maksymalną temperaturę płynu chłodzącego przyjmuje się jako obliczoną temperaturę płynu chłodzącego, jeśli nie zmienia się ona w okresie eksploatacji sieci (na przykład w sieciach parowych i kondensatu oraz rurach doprowadzających ciepłą wodę), a średnią za rok, jeśli zmienia się temperatura płynu chłodzącego (na przykład w sieciach wodociągowych). Za temperaturę otoczenia w kolektorach przyjmuje się +40°C, grunt na osi rury to średnia roczna, temperatura powietrza zewnętrznego dla instalacji naziemnej to średnia roczna. Zgodnie z normami projektowymi dla sieci ciepłowniczych maksymalną grubość izolacji termicznej przyjmuje się w oparciu o sposób montażu:
Do montażu napowietrznego oraz w kolektorach o średnicach rur 25-1400
mm grubość izolacji 70-200 mm;
W kanałach sieci parowych - 70-200 mm;
Do sieci wodociągowych - 60-120 mm.
Kształtki, połączenia kołnierzowe i inne kształtki sieci ciepłowniczych, a także rurociągi pokrywane są warstwą izolacji o grubości równej 80% grubości izolacji rury.
Podczas układania rur grzewczych bez kanałów w glebach o zwiększonej aktywności korozyjnej istnieje niebezpieczeństwo korozji rur na skutek prądów błądzących. Aby zabezpieczyć się przed korozją elektryczną, podejmuje się środki zapobiegające przedostawaniu się prądów błądzących do metalowych rur lub instaluje się tzw. Drenaż elektryczny lub ochronę katodową (stacje ochrony katodowej).
Zakład technologii informatycznych LIT w Pereslavl-Zalessky produkuje elastyczne wyroby termoizolacyjne ze spienionego polietylenu o zamkniętej strukturze porów „Energoflex”. Są przyjazne dla środowiska, ponieważ są produkowane bez użycia chlorofluorowęglowodorów (freonów). Podczas eksploatacji i obróbki materiał nie przedostaje się do środowiska substancje toksyczne i nie zapewnia Szkodliwe efekty na organizm ludzki poprzez bezpośredni kontakt. Praca z nim nie wymaga specjalne narzędzia oraz zwiększone środki bezpieczeństwa.
„Energoflex” przeznaczony jest do izolacji termicznej komunikacji inżynierskiej przy temperaturze płynu chłodzącego od minus 40 do plus 100 ° C.
Produkty Energoflex produkowane są w następujących postaciach:
Rury w 73 standardowych rozmiarach o średnicach wewnętrznych od 6 do 160 mm i
grubość ścianki od 6 do 20 mm;
Rolki mają szerokość 1 m i grubość 10, 13 i 20 mm.
Współczynnik przewodności cieplnej materiału w temperaturze 0°C wynosi 0,032 W/(m-°C).
Produkty do izolacji termicznej z wełny mineralnej produkowane są przez przedsiębiorstwa Termosteps JSC (Twer, Omsk, Perm, Samara, Salavat, Jarosław), AKSI (Czelabińsk), Tizol JSC, Nazarovsky ZTI, zakład Komat (Rostów nad Donem), CJSC „ Wełna mineralna” (Zheleznodorożny, obwód moskiewski) itp.
Wykorzystywane są także materiały importowane firm ROCKWOLL, Ragos, Izomat i innych.
Właściwości użytkowe włóknistych materiałów termoizolacyjnych zależą od składu użytego materiału. różni producenci surowców i urządzeń technologicznych i różnią się w dość szerokim zakresie.
Techniczną izolację termiczną wykonaną z wełny mineralnej dzielimy na dwa rodzaje: wysokotemperaturową i niskotemperaturową. Firma SA "Mineral Wool" produkuje izolacje termiczne "ROCKWOLL" w postaci płyt i mat z wełny mineralnej z włókna szklanego. Ponad 27% wszystkich włóknistych materiałów termoizolacyjnych produkowanych w Rosji to izolacja termiczna URSA produkowana przez JSC Flyderer-Chudovo. Produkty te wykonane są z ciętego włókna szklanego i charakteryzują się wysokimi właściwościami termicznymi i akustycznymi. W zależności od marki produktu współczynnik przewodności cieplnej
taka izolacja waha się od 0,035 do 0,041 W/(m-°C) w temperaturze 10°C. Produkty charakteryzują się wysoką efektywnością ekologiczną; można je stosować, jeśli temperatura płynu chłodzącego mieści się w zakresie od minus 60 do plus 180°C.
CJSC „Zakład Izolacyjny” (St. Petersburg) produkuje izolowane rury do sieci ciepłowniczych. Jako izolację stosuje się tutaj żelbeton, którego zalety obejmują:
Wysoka maksymalna temperatura aplikacji (do 300°C);
Wysoka wytrzymałość na ściskanie (nie mniej niż 0,5 MPa);
Może być stosowany do montażu bezkanałowego na dowolnej głębokości
bez układania rurociągów ciepłowniczych i we wszystkich warunkach glebowych;
Obecność pasywującej warstwy ochronnej na izolowanej powierzchni
folia powstająca w wyniku kontaktu betonu piankowego z metalem rury;
Izolacja jest niepalna, co pozwala na jej zastosowanie w każdym przypadku
rodzaje instalacji (naziemna, podziemna, kanałowa lub bezkanałowa).
Współczynnik przewodzenia ciepła takiej izolacji wynosi 0,05-0,06 W/(m-°C).
Jedną z najbardziej obiecujących obecnie metod jest zastosowanie preizolowanych rurociągów bezkanałowych z izolacją z pianki poliuretanowej (PPU) w płaszczu polietylenowym. Najbardziej postępowym sposobem oszczędzania energii przy budowie sieci ciepłowniczych jest zastosowanie rurociągów typu „rura w rurze”. W USA i Europie Zachodniej, zwłaszcza w regionach północnych, konstrukcje te stosowane są od połowy lat 60-tych. W Rosji – dopiero od lat 90.
Główne zalety takich projektów:
Zwiększenie trwałości konstrukcji do 25-30 lat i więcej, tj.
2-3 razy;
Redukcja strat ciepła nawet o 2-3% w stosunku do istniejących
20^40% (lub więcej) w zależności od regionu;
Obniżenie kosztów operacyjnych 9-10 razy;
Obniżenie kosztów naprawy sieci ciepłowniczych co najmniej 3-krotnie;
Obniżenie kosztów inwestycyjnych podczas budowy nowych sieci ciepłowniczych w
1,2-1,3 razy i znaczne (2-3 razy) skrócenie czasu budowy;
Znaczące zwiększenie niezawodności sieci ciepłowniczych zbudowanych wg
Nowa technologia;
Możliwość zastosowania działającego systemu zdalnego sterowania
kontrola zawilgocenia izolacji, co pozwala na szybką reakcję
uszkodzić integralność rury stalowej lub prowadnicy polietylenowej
powłokę izolacyjną i zapobiegać wyciekom i wypadkom z wyprzedzeniem.
Z inicjatywy Rządu Moskwy, Gosstroya z Rosji, RAO JES z Rosji, CJSC MosFlowline, TVEL Corporation (St. Petersburg) i szeregu innych organizacji, w 1999 roku powstało Stowarzyszenie Producentów i Konsumentów Rurociągów z Przemysłową Izolacją Polimerową .
ROZDZIAŁ 6. KRYTERIA WYBORU OPCJI OPTYMALNEJ
Układanie rurociągu naziemnego
Instalacja naziemna rurociągów przez drogi wewnętrzne zakładowe i drogi dojazdowe kolejowe wykonywana jest z zachowaniem poniższych wymagań podstawowych. Dopuszcza się przecięcie dróg sieciami rurociągów pod kątem 90° do osi drogi, a w przypadkach, w których nie jest możliwe spełnienie tego wymagania, dopuszcza się zmniejszenie kąta przecięcia do 45°C.
Sieci ciepłownicze układane są metodami naziemnymi lub podziemnymi (niezwykle rzadkimi). Podczas układania naziemnego rurociągi układa się na wiaduktach lub na wolnostojących podporach. Metodą podziemną rurociągi układa się w nieprzejezdnych kanałach.
Proste podpory podwieszane służą do napowietrznego układania rurociągów na wiaduktach z odciągami w obszarach samokompensacji lub przy montażu kompensatorów w kształcie litery U. Maksymalne rozpiętości pomiędzy podwieszonymi podporami sprawdza się dodatkowo obliczając maksymalne dopuszczalne obciążenie podpory.
W budynkach i konstrukcjach przemysłowych konieczne jest zapewnienie naziemnego układania rurociągów (wzdłuż ścian, kolumn i innych konstrukcji budowlanych), a jeśli takie umieszczenie nie jest możliwe, dopuszcza się układanie rurociągów pod ziemią kanały. układanie rurociągów napowietrznych
Podczas układania rurociągów nad ziemią, aby uniknąć zamarzania transportowanego medium przy ujemnych temperaturach zewnętrznych, należy zapewnić ciągły dopływ pary i kondensatu (szczególnie w przypadku rurociągów o małych średnicach) lub towarzyszące ogrzewanie rurociągów kondensatu.
Linie pary wylotowej i wtórnej oraz linie kondensatu należy, jeśli to możliwe, układać razem z istniejącymi liniami pary świeżej, liniami wody i rurociągami technologicznymi. W przypadku wysokiego poziomu wód gruntowych preferuje się naziemną instalację rurociągów pary i kondensatu.
Układanie rurociągów naziemnych prowadzono głównie na wiaduktach i wysokich podporach. Niektóre krajowe fabryki stosowały również układanie obniżone (2-2,5 m od poziomu gruntu).
Z reguły naziemny montaż rurociągów powinien odbywać się na wiaduktach lub podporach wolnostojących.
Nadziemne układanie rurociągów do transportu podgrzanych produktów należy prowadzić na wolnostojących podporach i wiaduktach o wysokości eliminującej termiczne oddziaływanie rurociągów na grunty fundamentowe wiecznej zmarzliny.
Przy układaniu rurociągów naziemnych, w zależności od ich charakterystyki i warunków pracy, stosuje się następujące rodzaje podpór: stałe i ruchome (przesuwne, rolkowe i podwieszane). Ruchome podpory umożliwiają przemieszczanie się rurociągu podczas odkształceń temperaturowych.
Układanie rurociągów naziemnych wzdłuż stojaków jest wygodne w użyciu, ponieważ rurociągi są dostępne do naprawy i monitorowania, jednak metoda ta jest kosztowna i dlatego nie jest powszechnie stosowana.
Dla trybu turbulentnego (średnica rury 200-300 mm, g 80°C) Besh zaleca przyjęcie następujących wartości dla k w W/m stopnia sucha gleba, piasek – 5,8 wilgotna wilgotna gleba – 5,8 + 11,6 gleba, zawierająca wody gruntowe, ruchome piaski, - 17,4 87,0. Do układania rurociągów pod głową w nieruchomym powietrzu = 12-14 W/m st. oraz podczas deszczu i wiatru A = 14-23 W/m st.
Uwaga Masę śniegu i lodu należy uwzględniać w obliczeniach tylko w przypadku układania rurociągów nad ziemią na zewnątrz.
Podczas układania rurociągów nad ziemią przez jezdnie i ulice, wysokość rurociągów (w widocznym miejscu) od poziomu gruntu do zewnętrznej powierzchni izolacji musi wynosić co najmniej 4,5 m, z wyjątkiem układania przez tory kolejowe, gdy odległość od odległość główki szyny od zewnętrznej powierzchni izolacji nie powinna być mniejsza niż 6 m (dla toru normalnego). Jeżeli odległość od dolnego punktu izolacji rurociągu do poziomu gruntu jest mniejsza niż 2 m, należy zastosować schody przejściowe umożliwiające przejście ludzi. Przy układaniu rurociągów na wiadukcie krawędzie tego ostatniego muszą znajdować się w odległości co najmniej 5 m od budynków palnych i pomieszczeń produkcyjnych materiałów wybuchowych, od magazynu amoniaku – 10 m od osi toru kolejowego – 3 m oraz od dróg dojazdowych i pieszych.
Zagraniczna praktyka w funkcjonowaniu rafinerii chemicznych i ropy naftowej potwierdza również możliwość naziemnej instalacji rurociągów.
Każdy z trzy typy naziemne układanie rurociągów (wysokie, niskie i niskie) ma swoje własne wskaźniki techniczne i ekonomiczne, które służą jako kryterium wyboru optymalnego rodzaju układania w określonych warunkach, w tym w połączeniu wysokiego z niskim, niskiego z niskim itp.
Przy układaniu rurociągu naziemnego, w celu utrzymania temperatury solanki nie niższej niż 2-3°C, w zależności od lokalnych warunków warunki klimatyczne rurociąg powinien być izolowany termicznie lub dodatkowo podgrzewany. Podczas układania rurociągu solanki nad ziemią w regionach południowych nie zapewnia się jego izolacji termicznej.
Układanie rurociągów pod głową odbywa się na wiaduktach, podporach pali, wzdłuż ścian budynków oraz podczas przechodzenia przez drogi i wąwozy, na terenach fabrycznych. Rury układane są w izolacji pierścieniowej lub w izolowanych puszkach. Układanie rurociągu naziemnego odbywa się na podsypce z nasypem. Podczas układania nad ziemią zapewnione jest ogrzewanie i hydroizolacja rurociągów.
Wadą naziemnej instalacji rurociągu jest konieczność przeznaczenia do stałego użytkowania pasa gruntów nawodnionych lub gruntów ornych o szerokości co najmniej 4 m.
Na skrzyżowaniach wiaduktów, na których układane są rurociągi z gazami palnymi, torów kolejowych i wewnętrznych zakładów, zaworów, kolektorów wodnych, kompensatorów dławnicowych, połączeń kołnierzowych i innych elementów montażowych, w których podczas eksploatacji mogą wystąpić nieszczelności, nie należy montować na rurociągach. W takich przypadkach rurociągi są instalowane wyłącznie przez spawanie. Zabronione jest układanie pod ziemią lub na ziemi rurociągów z gazami palnymi wraz z kablami telefonicznymi, energetycznymi i oświetleniowymi.
Podczas układania rurociągów naziemnych na estakadach lub wolnostojących podporach dopuszczalne jest łączenie rurociągów wszystkich kategorii z rurociągami technologicznymi różnego przeznaczenia, z wyjątkiem układania w chodnikach typu estakady, a także przypadków, gdy takie układanie jest sprzeczne z wymaganiami innych zasad bezpieczeństwa.
Usterki są eliminowane po obniżeniu nadciśnienia do zera i wyłączeniu sprężarki. Podczas pneumatycznych testów wytrzymałościowych należy wyznaczyć chroniony (bezpieczny) obszar zarówno wewnątrz, jak i na zewnątrz. Minimalna odległość między strefami musi wynosić co najmniej 25 m w przypadku instalacji rurociągów napowietrznych i co najmniej 10 m w przypadku instalacji podziemnej. Granice strefy są ogrodzone.
Odchylenia od projektowego położenia podpór przy układaniu rurociągów nad ziemią nie powinny przekraczać 5 mm dla przemieszczenia fundamentów względem osi wyrównania, 10 mm dla odchylenia osi podpór od pionu i +5 mm dla elewacji górnej części podpór.
Układanie rurociągów naziemnych na wysokich podporach jest pracą niebezpieczną, dlatego należy ściśle przestrzegać wszystkich przepisów bezpieczeństwa i wymagań projektu pracy.
Podczas układania rurociągów nad ziemią przez przejścia wysokość rurociągów (w świetle) od poziomu gruntu do zewnętrznej powierzchni izolacji musi wynosić co najmniej 5 m, z wyjątkiem przypadków układania przez tor kolejowy, gdy odległość (w czysta) od główki szyny do zewnętrznej powierzchni izolacji rurociągu musi wynosić co najmniej 6 m (dla normalnej szerokości toru).
Przy układaniu rurociągów napowietrznych o dużych i małych średnicach w celu zwiększenia odległości pomiędzy konstrukcjami wsporczymi (masztami wiaduktów) zaleca się a) zastosowanie rur o dużej średnicy Vu = 500 mn lub więcej) jako konstrukcji nośnych w celu utworzenia podpór lub zawiesić na nich rury o małych średnicach. b) zastosować miejscowe usztywnienie rur o małych i średnich średnicach poprzez spawanie usztywnień.
Armatura i przyrządy do układania rurociągów naziemnych i naziemnych umieszczane są w komorach-studniach, komorach-kabinach, komorach-centrach termicznych.
Podczas układania rurociągów naziemnych stosuje się powłoki malarskie i lakiernicze, z których najczęstsze są następujące.
Układanie rurociągów naziemnych na niskich podporach zapewnia się tylko w przypadkach, gdy nie przewiduje się przemieszczania ruchu, mechanizmów podnoszących i sprzętu na obszarze terytorium, przez które układane są rurociągi.
Schemat układania rurociągów naziemnych realizowany jest w taki sposób, aby maksymalnie wykorzystać teren zakładu przeznaczony do tworzenia szczelin przeciwpożarowych pomiędzy obiektami.
Kompensatory w kształcie litery U charakteryzują się dużą zdolnością kompensacyjną (do 700 mm) i stosowane są przede wszystkim do nadziemnego układania rurociągów, niezależnie od ich średnicy.
Układanie rurociągów naziemnych odbywa się na wiaduktach, podporach pali, wzdłuż ścian budynków i jest stosowane podczas przekraczania dróg i wąwozów na terenach fabrycznych. Rury układane są w izolacji pierścieniowej lub w izolowanych puszkach.
Zamówienie na opracowanie rysunków kanałów i wiaduktów sporządzane jest na podstawie przebiegu głównych linii technologicznych i wytycznych prawnych dotyczących układania rurociągów pod ziemią i naziemną. Z reguły przewody wodne i kanalizacyjne układane są w kanałach wewnątrzzakładowych. Wymiary przekroju kanału powinny zapewniać łatwość montażu i naprawy rur, rozmieszczenie wydzielonych odgałęzień do urządzeń technologicznych, rozmieszczenie podstawowych elementów aparatury pomiarowej i sterującej (przesłony, wodomierze itp.) oraz montaż armatury odcinającej. zawory.
Układanie rurociągów może odbywać się pod ziemią (w kanałach przelotowych - tunelach, kanałach nieprzelotowych i bez kabli - bezpośrednio w ziemi), naziemnie na podporach i naziemnie - na wiaduktach. Preferowane jest układanie rurociągów naziemnie i naziemnie, ponieważ zapewnia możliwość wizualnego monitorowania stanu rurociągów oraz ułatwia ich montaż i naprawę. Układanie rurociągów w ziemi, szczególnie gazociągów, jest niebezpieczne, ponieważ nieszczelności mogą przemieszczać się na znaczne odległości od miejsca uszkodzenia rurociągu, a określenie miejsca wycieku jest trudne i powszechne.
Przed napełnieniem rurociągów chłodziwem są one dokładnie myte i sprawdzane jest dokręcenie śrub na połączeniach kołnierzowych, działanie zaworów odcinających, odpowietrzających, urządzeń odwadniających, uszczelnienie uszczelek olejowych na kompensatorach, zasuwach i zawory, obecność niezbędne miejsca tuleje do termometrów i armatura do manometrów, dostępność i uporządkowanie pomieszczeń wejść abonenckich. Podczas układania rurociągów naziemnych sprawdzany jest również stan konstrukcji wsporczych i prawidłowy montaż podpór ruchomych.
Zabrania się układania pod ziemią lub naziemną rurociągów z gazami palnymi wraz z kablami telefonicznymi, energetycznymi i oświetleniowymi.
Hydranty przeciwpożarowe instalowane są na głównych odcinkach sieci. Zaleca się układanie rurociągów naziemnych w grzbietach ziemnych, kanałach zakopanych przy użyciu ciągłej zasypki, a także w kanałach częściowo zakopanych. Montaż rurociągów naziemnych odbywa się na niskich podporach, masztach, wiaduktach lub w wentylowanych podziemiach budynków, w ogrzewanych pomieszczeniach i izolowanych kanałach.
§ 2. Metody układania podziemnego, naziemnego i naziemnego oraz ich wskaźniki techniczno-ekonomiczne
Instalacja komunikacji sanitarnej i technicznej na obszarach wiecznej zmarzliny może spowodować rozmrożenie gleby na skutek ciepła wytwarzanego przez rurociągi. W rezultacie stabilność zarówno samych rurociągów, jak i budynków może zostać zagrożona. Metody układania komunikacji sanitarnej i technicznej muszą być powiązane ze sposobami wznoszenia budynków i budowli oraz zależeć od właściwości gruntów fundamentowych i innych czynników, z których najważniejszym jest położenie trasy sieci w stosunku do zabudowanej up area oraz jego rozwiązania architektoniczne i planistyczne.
Istnieć następujące typy układanie komunikacji sanitarnej i technicznej: podziemnej, naziemnej i naziemnej. Z kolei tego typu uszczelki mogą być pojedyncze lub łączone.
Układanie naziemne i nad głową Ze względu na brak kontaktu rur z gruntem i ograniczone oddawanie ciepła do gruntu, fundamenty w najmniejszym stopniu zakłócają naturalny reżim termiczny gruntów wiecznej zmarzliny. Takie uszczelki zaśmiecają terytorium obszarów zaludnionych, komplikują budowę przejść, organizację ochrony przed śniegiem i odśnieżanie.
Układanie pod ziemią wskazane jest przeprowadzenie w granicach zabudowy osada w celu osiągnięcia maksymalnej poprawy terytorium. Sieci wodociągowe i kanalizacyjne można układać bezpośrednio w gruncie, a sieci ciepłownicze i rurociągi parowe można układać w specjalnych kanałach. Jeśli istnieją takie kanały, zaleca się ułożenie w nich kabli wodociągowych, kanalizacyjnych i elektrycznych.
Podziemna instalacja sieci ciepłowniczych jest bardzo kosztowna i wymaga specjalnych środków w celu utrzymania reżimu termicznego gleb wiecznej zmarzliny u podstawy sieci. A więc na przykład koszt 1 liniowy M kanał dla sieci ciepłowniczej w warunkach Norylska wynosi średnio 300 rubli. Koszt dwupoziomowego kanału do połączonej instalacji sieci grzewczej, wodociągowej, kanalizacyjnej i kabli elektrycznych na tych samych warunkach wynosi średnio około 450 rubli. za 1 liniowy M. Dlatego podziemna instalacja sieci grzewczych jest wskazana tylko w zwartych budynkach z budynkami wielopiętrowymi (4-5 pięter) oraz w połączeniu z inną komunikacją.
Jeśli zabudowa prowadzona jest w budynkach dwu- i trzypiętrowych ze szczelinami, wówczas podziemna instalacja sieci ciepłowniczych zwykle okazuje się nieopłacalna ekonomicznie. W takich przypadkach układanie naziemne najczęściej stosuje się wzdłuż elewacji i poddaszy budynków oraz pomiędzy budynkami - wzdłuż wiaduktów, ogrodzeń i płotów. W takim przypadku wodociągi i kanalizację można układać w ziemi bez kanałów. Jeżeli grunty u podstawy rur są osiadane, wówczas dla zapewnienia ich stabilności należy zastąpić grunty gruntami nieosiadającymi na głębokość określoną na podstawie obliczeń termotechnicznych.
W przypadku małych wsi, jeśli istnieje możliwość poprowadzenia sieci w obrębie bloków bez przecinania ulic lub przy minimalnej liczbie skrzyżowań, najbardziej ekonomiczną opcją jest ułożenie sieci ciepłowniczych naziemnie w izolacji pierścieniowej lub w izolowanych kanałach wraz z instalacją wodną. W takim przypadku sieć kanalizacyjną należy ułożyć w ziemi bez kanałów.
W glebach osiadających podczas rozmrażania, zwłaszcza w glebach, które podczas rozmrażania przekształcają się w stan płynno-plastyczny lub płynny, podczas układania podziemnych rurociągów konieczne jest sztuczne podłoże. Koszt takiego fundamentu zależy bezpośrednio od głębokości rozmrożenia gleby pod rurami.
Układając rurociągi w gruntach nieosiadających i nie tracących nośności po rozmrożeniu, decydującym warunkiem jest zabezpieczenie ich przed zamarzaniem poprzez ograniczenie strat ciepła. W takim przypadku głębokość umieszczenia zwiększa się do 1,5-2,0 m; większa głębokość jest niepożądana, gdyż utrudnia wykrycie miejsc awarii rurociągów i ich naprawę, zarówno latem, jak i szczególnie zimą.
W celu ograniczenia strat ciepła i wielkości talików pod rurami, w izolacji termicznej stosuje się podziemne układanie sieci wodociągowych i kanalizacyjnych: w skrzynkach drewnianych lub żelbetowych wypełnionych trocinami lub wełną mineralną, w skrzynce pierścieniowej wykonanej z betonu komórkowego, wełny mineralnej, filcu impregnowanego żywicą. Wszystkie te rodzaje izolacji termicznej nie osiągają swojego celu, gdy materiał izolacyjny jest wilgotny. Lokalne wady hydroizolacji (a tym samym izolacji termicznej) prowadzą do rozmrożenia podłoża i nierównego osiadania rurociągów, co jest najbardziej niepożądane. Przywrócenie termoizolacji i hydroizolacji podczas napraw jest procesem złożonym i pracochłonnym. Stosowanie skrzynek stwarza dodatkowe trudności w wykrywaniu i eliminowaniu nieszczelności. Każdy wyciek oznacza naruszenie izolacji termicznej. Koszt izolacji termicznej zwykle przewyższa koszt sztucznego fundamentu pod wodociąg i kanalizację. Dlatego szerokie zastosowanie izolacja termiczna rurociągów wodno-kanalizacyjnych przy układaniu ich w ziemi jest niepraktyczna.
Rozważmy niektóre projekty fundamentów rurociągów układanych w ziemi.
Podstawa gruntowa(Rysunek IV-1). Lokalne gleby nasycone lodem u podstawy rurociągu paliwowego zastępowane są gruntami nieosiadającymi, o niskim współczynniku filtracji do obliczonej głębokości rozmrożenia. Gleby piaszczyste, żwirowo-piaszczyste w niektórych przypadkach są zagęszczane przez wstępne rozmrożenie. Do wymiany stosuje się lekkie gliny piaszczyste i drobnoziarniste piaski pylaste w stanie rozmrożonym; w tym przypadku pożądana jest domieszka otoczaków, żwiru, tłucznia kamiennego w ilości do 40.....-45% lub lokalnie odwodniona i zagęszczona gleba. Warstwa hydroizolacyjna z betonu komórkowego lub gliny o grubości 25-30cm.
Przyjmuje się, że szerokość sztucznego fundamentu jest równa szerokości wykopu, a wysokość określa się na podstawie obliczeń.
W przypadku braku wycieku promień rozmrażania w wyniku uwolnienia ciepła z rurociągów wodociągowych lub kanalizacyjnych średnio nie przekracza 1,2 m. Jeśli weźmiemy pod uwagę zwiększoną intensywność rozmrażania gleb zastępujących gleby nasycone lodem, wówczas głębokość wymiany nie przekroczy 1,5 m. Należy założyć, że w wielu przypadkach podłoże gruntowe będzie opłacalne ekonomicznie i technicznie wykonalne.
Płaska podstawa Służy do zmniejszenia nierówności osiadania podczas rozmrażania gruntów osiadających i wykonywany jest w formie podłużnych kłód w dwóch kłodach. Aby zapobiec wypaczeniu torów podczas osiadania, w wyniku czego rurociąg zostanie zniszczony, należy je bezpiecznie zamocować.
Pływająca podstawa stosowany na glebach nasyconych lodem i stanowi ciągłą podłogę z płyt ułożonych w poprzek rowu; ten rodzaj fundamentu jest dość niezawodny, ale nie może być powszechnie zalecany ze względu na wysoki koszt i zużycie duża ilość drewno.
>
Ryż. IV-2. Rurociąg na fundamencie palowym. 1 - rurociąg; 2 - kłoda (drewno) ∅30cm na kołkach (połączenia schodkowe); 3 - stosy ∅30cm Poprzez 3 m z włączoną przerwą 3 m poniżej warstwy aktywnej; 4 - uszczelki przelotowe 10 cm; 5 - zasypywanie lokalną ziemią
Podstawa palowa(Rys. IV-2) stosowany jest na glebach silnie osiadających. Wbijanie pali w wieczną zmarzlinę wymaga pracochłonnych i kosztownych prac związanych z parowaniem gleby lub wierceniem studni. Pale muszą być układane często, ponieważ w rurach przenoszących duże obciążenie z gruntu na podporach występują znaczne momenty zginające. Takie podstawy charakteryzują się wysokimi kosztami.
Podziemne wiadukty(Rys. IV-3) ze względu na wysoki koszt, stosuje się je w wyjątkowych przypadkach, np. do kanalizacji w gruntach osiadających rozmrażających się na duże głębokości, gdy trasa przebiega w pobliżu budynku o dużych wydzielaniach ciepła, budowanego według metod I lub IV i położone wyżej w reliefie.
Kwestię zastosowania tego lub innego rodzaju podstawy rozwiązuje się poprzez porównanie wskaźników technicznych i ekonomicznych.
Aby wyeliminować możliwość intensywnego przemieszczania się wody ponadwiecznej zmarzliną wzdłuż podziemnych rurociągów, w poprzek rowów stosuje się mosty z betonu gliniastego. Nadproża wcinają się w zamarzniętą podstawę i ściany rowów 0,6-1,0 m. Odległość pomiędzy nadprożami ustala się w zależności od nachylenia podłużnego, tak aby nacisk na nadproże nie przekraczał 0,4-0,5 m; Zazwyczaj odległość ta waha się od 50 do 200 m.
Na glebach żwirowych, żwirowych i innych dobrze filtrujących nie zaleca się instalowania zapór, ponieważ przepływ wody ponadwiecznej zmarzliny z łatwością je omija.
Układanie w glinianych koralikach
>
Ryż. IV-4. Układanie rur w glinianych koralikach. 1 - rurociąg; 2 - gruba warstwa gliniastego betonu 20 cm; 3 - lokalna gleba; 4 - warstwa piasku i żwiru; 5 - lokalnie odwodniona i zagęszczona gleba
Ten sposób montażu (rys. IV-4) stosuje się w dość korzystnych warunkach wiecznej zmarzliny i gruntu, przy braku na miejscu materiałów termoizolacyjnych, a trasa rurociągu musi przebiegać przez teren niezabudowany. Ten typ uszczelki ma kilka zalet:
- nie ma potrzeby wykonywania pracochłonnych robót ziemnych polegających na kopaniu rowów;
- nieszczelności rur są łatwiejsze do wykrycia i naprawienia;
- wyeliminowane jest filtrowanie wody ponadwiecznej zmarzliny wzdłuż rur;
- obecność talika wokół rur pozwala na dłuższe przerwy w przepływie wody przez nie niż w przypadku instalacji naziemnych i naziemnych;
- nie ma potrzeby termoizolacji i hydroizolacji rur.
Główne wady Ta metoda jest nadmierne zagracenie terytorium i złożoność przejść. Dodatkowo stwarza to warunki do większej pokrywy śnieżnej na tym terenie.
Podziemne układanie rurociągów w kanałach
Układanie rurociągów w kanałach podziemnych jest stosunkowo kosztownym rodzajem budowy sieci; niemniej jednak w wielu przypadkach wskazane jest układanie kanałów, jeśli weźmiemy pod uwagę nie tylko jednorazowe inwestycje kapitałowe, ale także koszty operacyjne. Możliwość łączonego układania komunikacji w kanałach podziemnych w porównaniu z jednym podziemnym powinna potwierdzić koszt budowy przypisany 1 m2 przestrzeń życiową i niezawodność działania sieci użyteczności publicznej. Układanie kombinowane jest zwykle uzasadnione w niesprzyjających warunkach klimatycznych i zamarzniętych glebach.
Kanały mogą być przelotowe (półprzejściowe) i nieprzejściowe, jednopoziomowe i dwupoziomowe. W kanałach dwupoziomowych, których dolny poziom jest przejezdny, górny poziom może być półprzejezdny lub nieprzejezdny. Konstrukcja kanałowa z półotworem Górna warstwa nieporęczne i wysokie koszty. Jednopoziomowa konstrukcja kanału jest najbardziej ekonomiczna i wygodna w użyciu.
W przypadku instalowania różnych typów kanałów na terenie zaludnionym (co należy uzasadnić) konieczne jest, biorąc pod uwagę warunki uprzemysłowienia budownictwa, osiągnięcie minimalna ilość standardowe rozmiary elementów.
Nieprzejezdne do 0,9 m kanały (rys. IV-5) można stosować na krótkich odcinkach (wloty i wloty domów, skrzyżowania dróg itp.) przy zapewnieniu warunków stateczności i wymagań eksploatacyjnych. Kanały nieprzejezdne należy budować z minimalną penetracją gruntu (nie więcej niż 0,5-0,7 m z podłogi na powierzchnię ziemi). Muszą mieć zdejmowaną pokrywę do czyszczenia kanałów, kontroli i naprawy rurociągów. Nachylenie podłużne nieprzejezdnych kanałów zapewniających odprowadzanie wody wzdłuż dna musi wynosić co najmniej 0,007.
Kanały przelotowe o wysokości min 1,8 m(Rys. IV-6) muszą mieć wymiary zapewniające swobodne przejście przez nie w celu kontroli i naprawy rur, kształtek i kabli elektrycznych.
>
Ryż. IV-7. Żelbetowy dwupoziomowy kanał przejściowy. 1 - kanalizacja; 2 - sieć ciepłownicza: 3 - wodociąg; 4 - półki na kable elektryczne i komunikacyjne; 5 - piasek, δ = 10 cm; 6 - beton gliniasty, δ = 20 cm; 7 - zastąpiony grunt (obliczona grubość)
Przy znacznych głębokościach kanałów i dużych wydzielaniach ciepła z komunikacji, taliki utworzone pod kanałami mogą osiągnąć znaczne rozmiary. W takich przypadkach, aby zmniejszyć przenikanie ciepła do podstawy, w oparciu o porównanie techniczne i ekonomiczne z innymi opcjami, ujawnia się możliwość zainstalowania kanałów dwupoziomowych (ryc. IV-7). W dolnym poziomie przejścia takiego kanału układa się rurociąg kanalizacyjny i kable elektryczne, w górnym - nieprzejezdne lub półprzepuszczalne - rury sieci ciepłowniczej i wodociągowej.
Podczas układania ogólnospławnej sieci kanalizacyjnej i wodociągowej zawory wodne należy umieścić w specjalnych komorach lub sekcjach odizolowanych od rurociągu kanalizacyjnego.
Aby zapobiec zniszczeniu zarówno samych kanałów, jak i pobliskich budynków i konstrukcji w wyniku rozmrożenia gleby u podstawy, konieczne jest:
- zaizolować termicznie rurociągi, minimalizując w jak największym stopniu wytwarzanie przez nie ciepła;
- wentyluj kanały zimą, aby usunąć ciepło, aby gleby u ich podstawy, które rozmroziły się latem, zostały całkowicie zamarznięte;
- ułóż hydroizolację wzdłuż dna kanału, zapobiegając przedostawaniu się wody do gruntów fundamentowych. Fundamenty pod kanałami należy wykonać z gruntów nieosiadających lub słabo osiadających.
Oprócz wymiany gruntów osiadających możliwe jest zastosowanie wstępnego rozmrożenia i zagęszczenia gruntów fundamentowych. Kanały muszą być wykonane ze zbrojonego betonu, zbrojonego cementu lub innego skutecznego materiału. Budowa kanałów z drewna lub betonu może być dopuszczona ze szczególnym uzasadnieniem, gdyż kanały betonowe drogi i nie spełniają wymagań wytrzymałościowych na nierównomierne osiadanie podłoża, a drewniane są podatne na gnicie, wymagają rozległych prac hydroizolacyjnych i zamulają się najmniejszymi cząstkami gleby; Jeśli mają kanalizację, stwarzają niehigieniczne warunki zaopatrzenia w wodę.
Wentylacja kanałów jest naturalna i sztuczna (wymuszona). Naturalne odbywa się za pomocą urządzenia otwory wentylacyjne wzdłuż górnej części kanału w pewnej odległości 20-25 m w zależności od wymiarów kanału i ułożonej w nim komunikacji (ryc. IV-8). Skuteczność wentylacji naturalnej można zwiększyć instalując szyby wyciągowe w budynkach położonych w pobliżu kanału; w tym przypadku można zwiększyć odległość pomiędzy otworami w kanale przepływu powietrza 100-150 m.
Odprowadzanie wody awaryjnej lub ściekowej z kanału należy prowadzić od jego końcowej części, wykorzystując skardę podłużną, lub z pośrednich kolektorów wody (doły wodoszczelne) poprzez wypompowanie wody za pomocą pomp.
Rurociągi cieplne i parowe umieszczone w kanałach należy odsunąć jak najdalej od dna kanału; muszą być w pierścieniowej izolacji termicznej (na przykład piankobeton z tynkiem azbestowo-cementowym i hydroizolacją). Zastosowanie do tych celów tworzyw sztucznych o podwyższonych właściwościach cieplnych i wodoodpornych (pianki, polietylen itp.) ma ogromne perspektywy.
Techniczną i ekonomiczną wykonalność układania sieci kanalizacyjnych w kanałach wraz z sieciami o różnym przeznaczeniu w porównaniu z pojedynczym układaniem pod ziemią stwierdza się na podstawie porównania kosztów budowy i eksploatacji, przypisanych 1 m2 przestrzeni życiowej, a także ocenę stabilności sieci, ich trwałości i wpływu termicznego na pobliskie budynki i budowle.
Układanie rurociągów naziemnych
Instalacja naziemna obejmuje zazwyczaj rurociągi układane na niskich podporach. W takim przypadku pomiędzy rurą a powierzchnią gruntu musi znajdować się wentylowana przestrzeń o powierzchni min 30cm, co jest konieczne, aby ograniczyć uwalnianie ciepła do gruntów fundamentowych i zapobiec zaspom śniegu.
Układanie rurociągów w terenie należy stosować poza obszarami zabudowanymi obszarów zaludnionych (jest to najtańsze rozwiązanie), na nisko położonych i podmokłych odcinkach trasy, w miejscach o silnie przesiąkniętych lodem glebach wiecznej zmarzliny.
Na terenie zabudowanym dopuszcza się montaż naziemny w przypadku niewielkiej liczby skrzyżowań rurociągów z podjazdami i chodnikami. Rurociągi są izolowane termicznie i wodoodporne. Przepisy przeciwpożarowe nie zalecają stosowania materiałów palnych zarówno do produkcji kanałów, jak i zasypek termoizolacyjnych rurociągów parowych i sieci ciepłowniczych, przy temperaturze chłodziwa wynoszącej 90°C i wyższej. Zasypka żużlowa nie powinna być również szeroko stosowana ze względu na możliwość zniszczenia rur metalowych przez korozję pod wpływem zwilżenia żużla.
Skrzynki drewniane znajdujące się w warunkach zmiennej wilgotności ulegają deformacji, wypełnienie zostaje wydmuchane, rozsypuje się i łatwo ulega zawilgoceniu. Hydroizolacja skrzynek materiałami w rolkach nie osiąga celu, ponieważ pokrycia rolek łatwo ulegają uszkodzeniu. Dlatego skrzynki wykonane ze zbrojonego betonu są bardziej niezawodne, ale ich koszt z zasypką jest wyższy niż koszt ogrzewania pierścieniowego i hydroizolacji rur.
W przypadku instalacji kombinowanej, głównie ze względu na wygodę użytkowania, izolację termiczną wykonuje się niezależnie dla rurociągów o różnym przeznaczeniu.
Podłożem pod rurociągi naziemne może być żwir sypki lub inny grunt nieosiadający lub słabo osiadający, ułożony w sposób nienaruszający w trakcie prac naturalnej pokrywy mchów i roślinności. W przypadku osiadania naturalnych gruntów fundamentowych należy je zastąpić gruntami nieosiadającymi do głębokości określonej obliczeniowo.
Specjalne podpory instalowane są na sztucznym fundamencie gruntowym pod rurociągami.
Podpórki na nogi belek poprzecznych mają niewielką wysokość, w wyniku czego po osiadaniu podpór izolacja termiczna rur spada na ziemię, łatwo ulega zawilgoceniu i ulega zniszczeniu. Nie zaleca się instalowania wspólnych podpór dla kilku rurociągów, ponieważ przy nierównym obciążeniu tory powodują nierównomierne osiadanie.
Podpory miejskie(Rys. IV-9) są bardziej zaawansowanym rodzajem podpór drewnianych; ułatwiają prostowanie profilu rurociągów w przypadku niewielkich osiadań fundamentów poprzez zaklinowanie elementów miast.
Podpory pośrednie żelbetowe przesuwne i rolkowe (ryc. IV-10) są bardziej ekonomiczne i trwałe niż drewniane. Ich wadą jest trudność prostowania rurociągów w przypadku osiadania nasypów; Aby wypoziomować podstawę, należy podnieść rurociąg i usunąć podpory.
Naprawił(kotwica) obsługuje(Rys. IV-11) wykonane są z drewna, betonu i żelbetu. W przypadku podpór drewnianych rury mocuje się do belek nośnych za pomocą śrub lub kołków.
Stałe wsporniki ramy wymagają dużego nakładu pracy przy zagospodarowaniu i wydobyciu gleby z dołów. Można je zatem polecić w przypadkach, gdy zastosowanie podpór palowych jest niepraktyczne (warstwa aktywna duża moc, gleby zamarznięte wysokotemperaturowo, charakteryzujące się niskimi siłami zamarzania, gleby rozdrobnione głazami itp.).
Masywne betonowe podpory są rozmieszczone dla rurociągów o dużych średnicach i podczas budowy rurociągów w 2 etapach. Do mocowania części metalowych w masie betonowej pozostawia się gniazda, które należy wypełnić betonem najniższych klas aż do budowy rurociągu drugiego etapu. W przeciwnym razie gromadzi się w nich woda, która po zamrożeniu może rozerwać masę betonową. Aby uniknąć rozmrożenia gruntu fundamentowego w wyniku egzotermii podczas utwardzania betonu, a także przepływu ciepła przez korpus wsporczy, na dnie studzienki kładzie się poduszkę z piasku o grubości 20-30 cm.
Ogólnie rzecz biorąc, układanie gruntu w warunkach Dalekiej Północy jest najbardziej ekonomicznym rodzajem układania komunikacji sanitarnej i technicznej (z wyjątkiem kanalizacji).
Układanie rurociągu naziemnego
Układanie rurociągów naziemnych odbywa się na wiaduktach, na podporach palowych wznoszących się nad terenem (ryc. IV-12), wzdłuż ścian budynków, strychów i ogrodzeń. Układanie rurociągów naziemnych stosuje się przy przekraczaniu dróg, zagłębień, wąwozów i strumieni, na terenach fabrycznych oraz w miejscach o silnie przesiąkniętych lodem glebach wiecznej zmarzliny.
Podobnie jak w przypadku instalacji naziemnej, rury układa się w izolacji termicznej pierścieniowej lub w izolowanych puszkach.
Wiadukty mogą być wykonane z drewna, żelbetu i metalu. W obszarach łatwopalnych stosuje się kozły metalowe. Produkcja wiaduktów żelbetowych jest trudna, a ich koszt wysoki. Dlatego stosuje się głównie drewniane kozły palowe i ramowe.
Zalety instalacji naziemnej:
- rury i kanały nie powodują osadzania się śniegu i nie utrudniają jego odśnieżania;
- pomyślnie rozwiązano kwestię skrzyżowań z podjazdami i chodnikami;
- rury i ich izolacja nie są odsłonięte uszkodzenie mechaniczne od transportu i pieszych;
- rurociągi nie są narażone na zaspy śniegu i są łatwo dostępne w celu kontroli i naprawy.
Wady instalacji naziemnej:
- wysoki koszt w porównaniu z instalacją lądową;
- niedogodności związane z instalacją armatury, zwłaszcza hydrantów przeciwpożarowych;
- większe straty ciepła niż podczas instalacji naziemnej ze względu na duże prędkości wiatru i brak osadów śniegu na rurach;
- rury ułożone wzdłuż fasad budynków, wiaduktów i ogrodzeń psują wygląd zaludnionego obszaru;
- Podczas układania rur wzdłuż ścian budynków naruszana jest zasada pierwszeństwa w budowie komunikacji sanitarnej.
Wskaźniki techniczne i ekonomiczne dla niektórych rodzajów uszczelek podano w załącznikach 1 i 2.