Виды термической обработки металлов. Термическая обработка сплавов. Виды термообработки
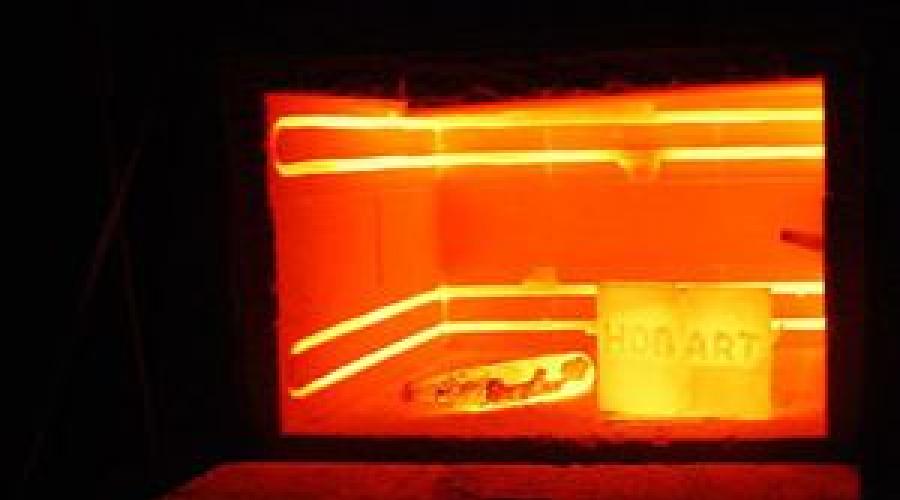
Читайте также
Термическая обработка металлов
Но для дальнейшей эксплуатации деталей и узлов оборудования зачастую требуются совсем иные характеристики – прочность, твёрдость, жёсткость и т.д. Именно для этих целей и предназначена термическая обработка металлов.
Сущность процессов термообработки
Задачами различных технологий термической обработки является:
- Обеспечение наиболее благоприятной микроструктуры сталей и сплавов;
- Получение нужного уровня твёрдости: либо в тонкой поверхностной (или подповерхностной) зоне, либо по всему поперечному сечению заготовки;
- Коррекция химического состава в зёрнах макроструктур различных сплавов.
В первом случае необходимо обеспечить максимальную степень однородности свойств металлов, что важно, например, для последующей механической или – особенно – деформирующей их обработки. В результате условия формоизменения заготовки по всем трём координатным осям оказываются одинаковыми, а брак конечной детали исключается.
Кроме того, выравнивание микро и макроструктуры для процессов обработки металлов давлением необходимо для того, чтобы повысить степень деформации полуфабрикатов, приближая в итоге форму заготовки к форме готового изделия. Причём за наименьшее количество переходов, и используя минимально необходимое для этого усилие оборудования.
Изменение твёрдости (как следствие термической обработки) имеет своей целью улучшение эксплуатационных показателей деталей. Поскольку условия эксплуатации могут быть самыми разными, то и комплекс физико-механических свойств подбирается строго индивидуально: универсальных процессов термообработки сплавов с различным составом не существует.
Изменение химического состава в зёрнах микроструктуры, вследствие образования новых соединений в большинстве случаев не только поднимает показатели твёрдости, но и повышает износостойкость деталей, которые должны эксплуатироваться при повышенном трении, температуре или увеличенных против обычного удельных нагрузках.
Закалка-отпуск
В первую группу технологий термообработки различных сплавов, включая сталь, входят отжиг и отпуск. Во вторую — закалка, нормализация, улучшение, старение, обработка холодом. В третью – все виды термохимической обработки.
Отжиг
Суть процессов, протекающих в структуре большинства сплавов, подвергаемых отжигу – обеспечить наиболее равновесную структуру заготовки, в которой или отсутствуют внутренние напряжения, или их уровень достаточно низок, а потому не влияет на последующую обрабатываемость металлов/сплавов.
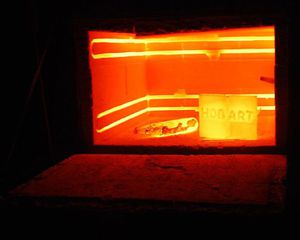
Исходная структура практически всех сплавов и сталей представляет собой достаточно крупные зёрна, между которыми располагаются включения и примеси, преимущественно сера и фосфор. Это увеличивает хрупкость металла, что может быть важно при формообразовании из слитка (или катанки) изделий сложной конфигурации. Поэтому необходимо снизить размер зерна и придать ему оптимальную форму эллипсоида, при которой механические свойства будут примерно одинаковы по всем трём координатным осям.
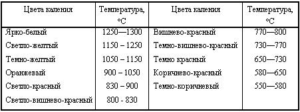
С этой целью исходную заготовку необходимо нагреть до температуры на 50…70 0 С выше температуры начала аустенитного превращения. Именно его итогом является образование мелких и хорошо ориентированных зёрен аустенита между зёрнами основных структурных составляющих стали – феррита и цементита. Аустенит образуется из перлита – структуры, имеющей наиболее крупные зёрна, которая способствует повышенной хрупкости любого слитка. Аустенитное превращение для большинства сплавов протекает достаточно медленно, поэтому отжиг – длительная процедура, которая должна продолжаться не менее часа.
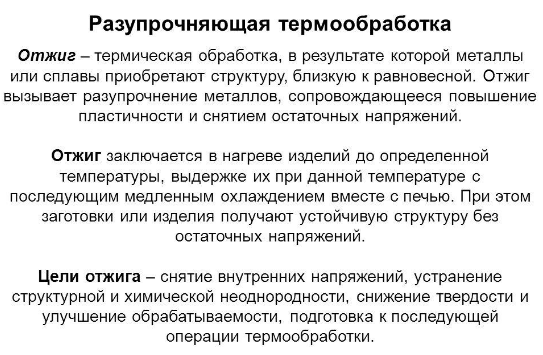
Вторая важная задача отжига – снять внутренние напряжения, которые формируются в заготовке при её обработке давлением в холодном состоянии. Дело в том, что любая деформация сопровождается дроблением зёрен исходной структуры сталей и сплавов. В итоге зёрен становится больше, сопротивление деформации возрастает, что не только требует повышенного усилия деформирования, но и становится причиной разрушения полуфабриката, степень деформации которого превысила критический для данного металла показатель.
Соответственно, для реализации первой задачи применяется технология высокотемпературного отжига (для сталей, в зависимости от содержания углерода, она колеблется в пределах 550…750 0 С), а во втором – низкотемпературного отжига (180…220 0 С).
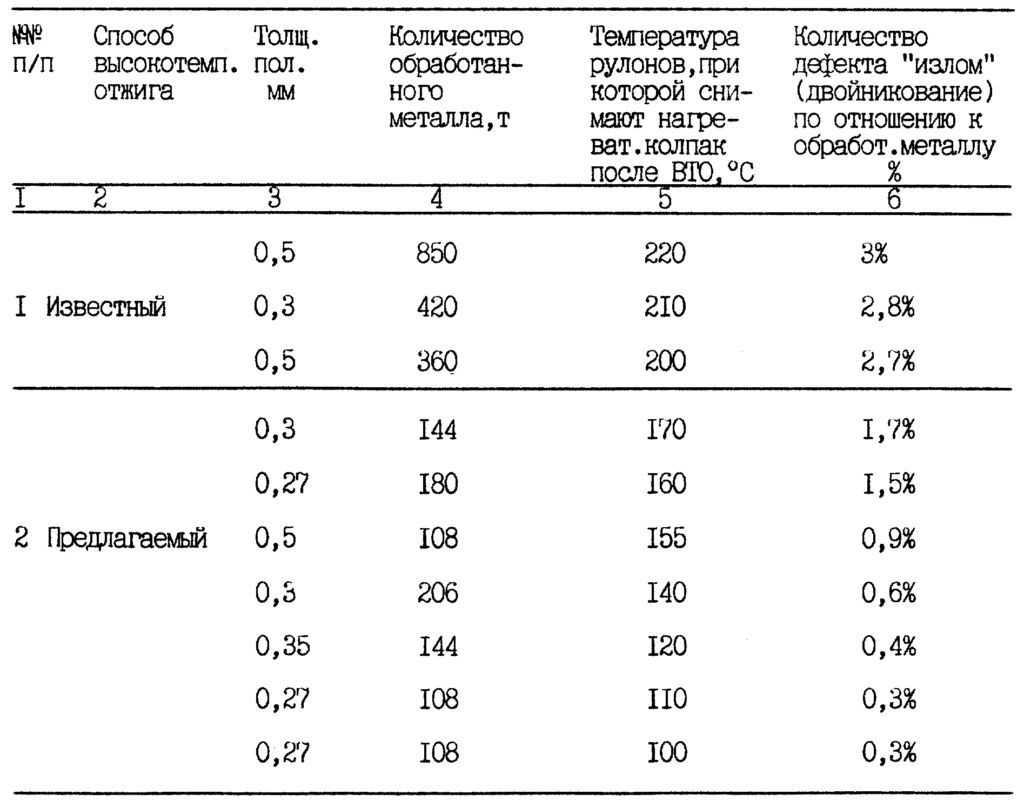
Нагрев происходит медленно, с последующей выдержкой изделия при заданной температуре, после чего следует медленное же охлаждение. Для легированных сталей и сплавов такое охлаждение ведут с особо низкой скоростью, в самой печи, где происходил отжиг.
Отпуск
Отпуск по технологии напоминает отжиг, но производится не с заготовкой, а с готовым изделием, а потому преследует иные задачи – снять внутренние напряжения после термической обработки, которая проводилась на повышенную твёрдость детали.
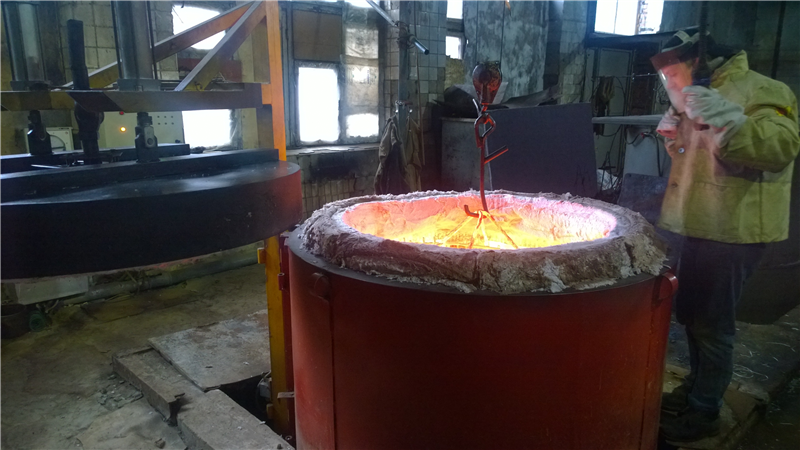
Самостоятельным процессом термической обработки отпуск не является. В отличие от отжига, отпуск иногда выполняется в несколько приёмов: в большинстве случаев это касается изделий, для производства которых использовались различные виды высоколегированной стали.
Закалка
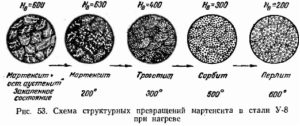
Закалка заключается в быстром нагреве заготовки до температуры окончания аустенитного превращения (900…1100 0 С – для низкоуглеродистых сталей, 750…850 0 С – для высокоуглеродистых) и последующем быстром охлаждении в специальных закалочных средах. В качестве последних используется вода (для изделий малоответственного назначения) или масло.
Режимы закалки отличаются наибольшим разнообразием. Основным фактором, определяющим эффективность закалки, является интенсивность образования в структуре мартенсита – высокотемпературной составляющей, которая придаёт металлу или сплаву повышенную твёрдость.
Условия образования мартенсита определяются следующими обстоятельствами:
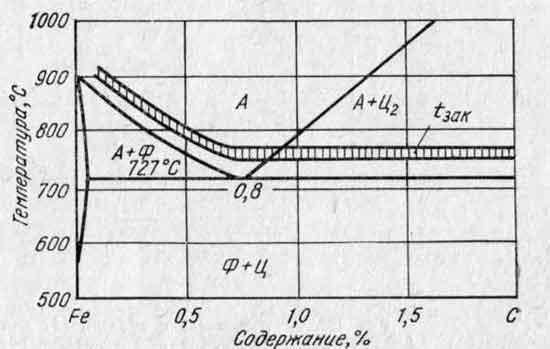
Соответственно для каждой марки стали или сплава разработаны индивидуальные режимы закалки, которые различаются:
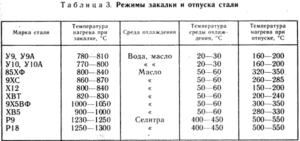
Особенно тщательно ведут закалку сталей и сплавов со сложным составом, включающим несколько легирующих элементов (в частности, кобальта, молибдена). Указанные металлы в процессе образуют по границам зёрен основной структуры интерметаллидные соединения, которые существенно увеличивают твёрдость и прочность сталей (в частности, инструментальных). Форма и концентрация интерметаллидов зависят только от точности соблюдения технологии закалки.
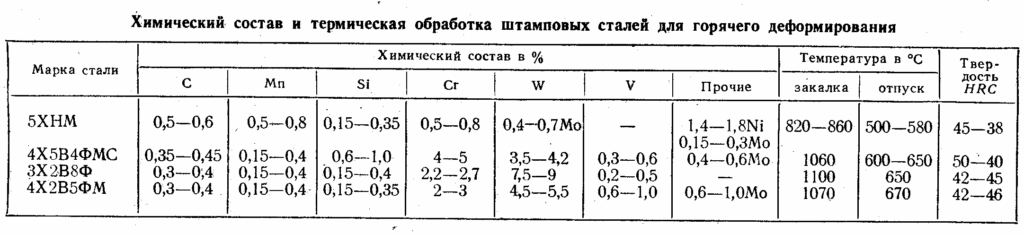
Виды закалки определяются оборудованием, на котором она выполняется. Например, для таких изделий, как шестерни, валы, направляющие колонки, где требуется оптимальное сочетание высокой поверхностной твёрдости и относительно вязкой сердцевины, используется поверхностная закалка токами высокой частоты.
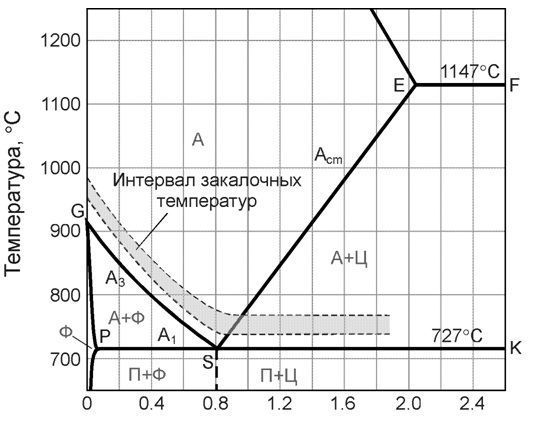
Для этого изделие помещают в индукционную катушку, по которой пропускается высокочастотный (до 15000…25000 Гц) ток. Проникая на ограниченную глубину, этот ток способствует увеличению поверхностной прочности сталей или сплавов. В результате усталостная прочность деталей, которые работают при циклически изменяющихся напряжениях растяжения-сжатия, заметно возрастает.
Более интенсивное изменение твёрдости поверхности детали можно получить, используя для закалки высокоэнергетические источники тепла – искровой или дуговой разряд. Разряды должны возбуждаться в жидкой среде, куда помещают обрабатываемую заготовку или деталь.
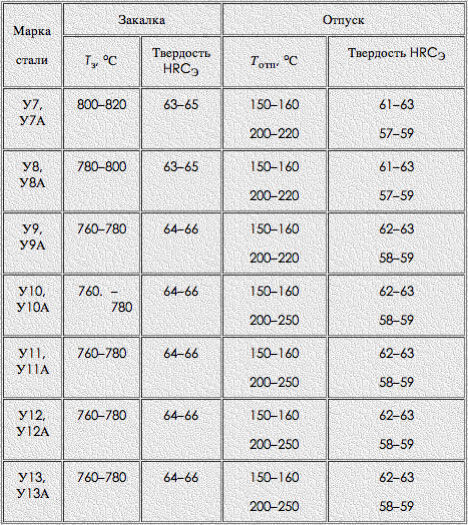
После закалки в подавляющем большинстве случаев необходим отпуск, иначе чрезмерная конечная твёрдость детали становится причиной повышенной хрупкости при ударных нагрузках.
Улучшение и нормализация
Как виды термообработки, эти процессы схожи с отжигом, хотя и предназначены для иных целей – повышения эксплуатационной долговечности ответственных деталей машин и инструмента.
При нормализации деталь подвергается медленному нагреву, выдерживается при заданной температуре, после чего обязательно охлаждается вместе с печью. В результате структура детали становится более равновесной, а уровень внутренних напряжений понижается.
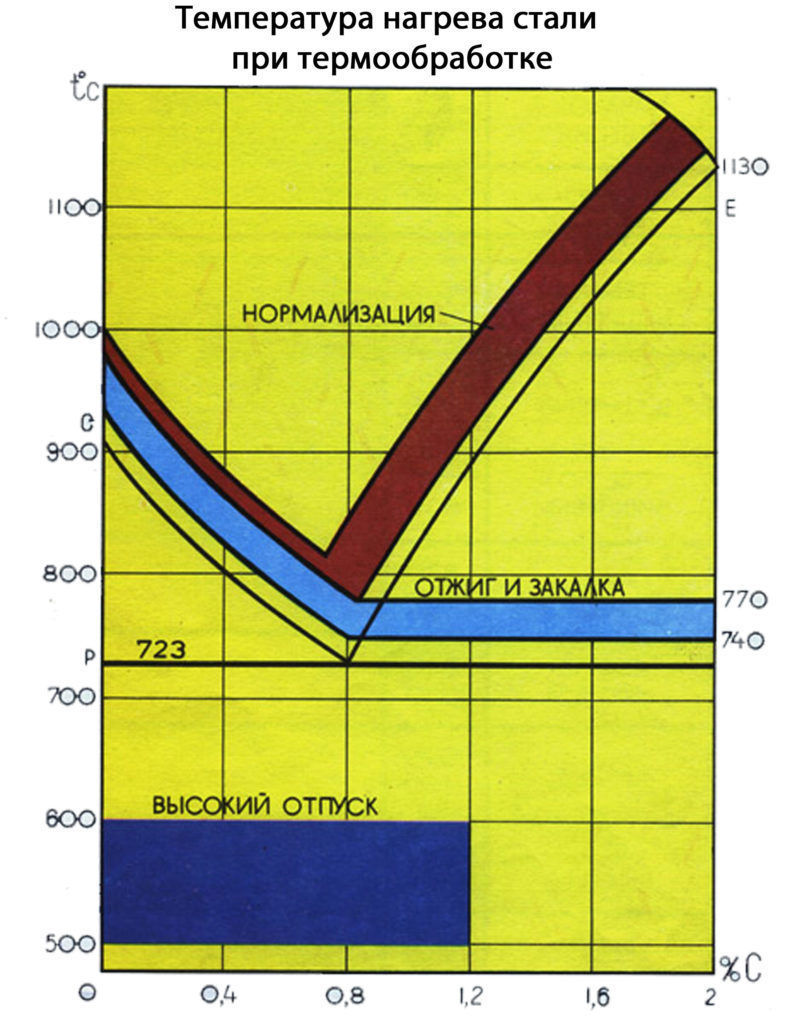
Существенным отличием считается состав атмосферы, печи, в которой выполняются данные операции термической обработки. Она должна быть безокислительной, поскольку интенсивное оксидообразование на поверхности изделия не только ухудшает его товарный вид, но и изменяет размеры. Выгорание углерода, которым также сопровождается термообработка в обычной печи, ухудшает химический состав стали и снижает её прочность.
Уменьшение доступа кислорода к поверхности детали при нормализации выполняют несколькими путями:
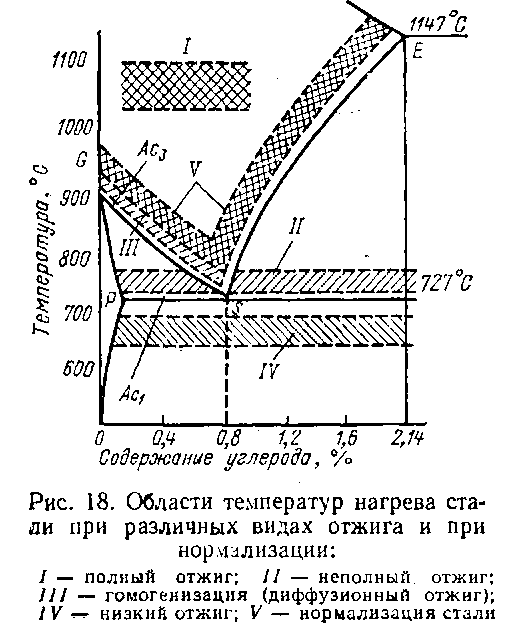
- Нагревом при плановом недостатке кислорода. В этом случае стабильность работы газовых горелок печей для термообработки компенсируют увеличением скорости подачи воздуха в зону горения;
- Термической обработкой в среде защитных газов. Для ответственных деталей применяются пары лития, аргон или другие благородные газы, в остальных случаях – двуокись углерода;
- Нанесением защитных обмазок на поверхность изделия, подлежащего нормализации.
После нормализации деталь охлаждают на спокойном воздухе, не допуская её обдув: это может вызвать неоднородную, «пятнистую» микроструктуру изделия.
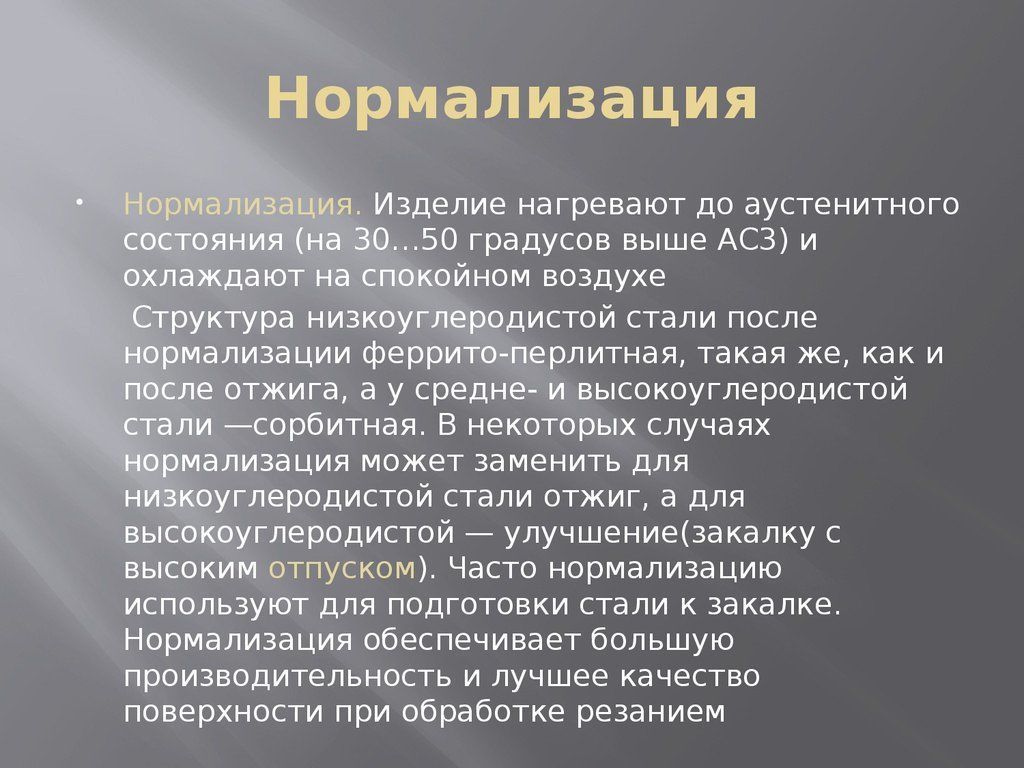
Улучшение — операция термообработки, в результате которой повышается механическая обрабатываемость сталей и сплавов, снижается уровень остаточных напряжений в них. Это сопровождается некоторым уменьшением твёрдости.
Мартенситная составляющая в структуре большинства сталей и сплавов может появиться не только при повышенной, но и при пониженной температуре. Технология обработки холодом выгодно отличается от традиционных технологий термической обработки следующим:
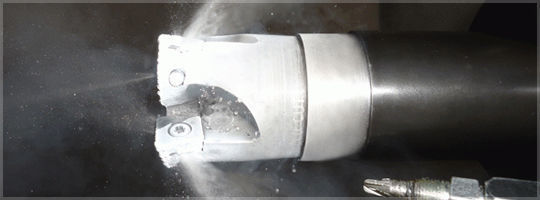
Режимы криогенной обработки зависят от марки сталей/сплавов, и колеблются в диапазоне -60…-140 0 С. Обычно криогенную обработку ведут при циклическом сочетании периодов глубокого охлаждения с периодами старения – выдержки при менее низких температурах. При сочетании циклов нагрева и охлаждения полный распад остаточного аустенита достигается за 4…7 часов (большие значения – для высоколегированных сталей).
Особый вид термообработки представляют процессы химико-термической обработки. Их задачей является формирование в поверхностной микроструктуре карбидов и нитридов – соединений, существенно увеличивающих микротвёрдость деталей, и создающих в них остаточные напряжения сжатия. Такие изделия показывают особо высокую стойкость при знакопеременных нагрузках.
Видео: Как закалить любую марку стали
Обработка металла термическим способом - это изменение внутреннего строения (структуры) металла под воздействием изменения температурных условий и получение вследствие этого необходимых механических и физических свойств металла. Огромная часть термической обработки происходит при критических температурах, при которых происходит структурное превращение в сплавах.
Поэтому термическая обработка металла сводится к трём последовательным операциям и видам:
- нагрев металла с определённой скоростью до заданной температуры;
- выдержка металла в течение некоторого времени при этой температуре;
- охлаждение с заданной по процессу скоростью.
Зависит от того как надо изменить свойства определённого стального изделия и применяют различные виды термической обработки, которые отличаются максимальной температурой нагрева, временем выдержки и скоростью охлаждения. В машиностроении термическая обработка нашла самое широкое применение.
Термическая обработка металла, сплава, стали
Все свойства любого сплава зависят от его структуры. Основной способ, который позволяет изменять эту структуру и является термическая обработка. Её основы разработал Чернов Д.К., а в дальнейшем его работы поддержали Бочвара А.А., Курдюмова Г.В., Гуляева А.П.
Термическая обработка металла и сплава - это последовательность операций таких как: нагрев, выдержка и охлаждение , которые выполняются в определённой последовательности и при определённом режиме, чтобы изменить внутреннее строение сплава и получения нужных свойств, при этом химический состав металла не изменяется.
В чём заключается термическая обработка металла и сплава?
- В отжиге
- Закалке
- Отпуске
- Нормализации
Отжиг . Это нагрев металла до высокой температуры, а потом происходит медленное охлаждение. Отжиг бывает разного вида - все зависит от температурного режима нагрева и скорости охлаждения.
Закалка . Термообработка стали, сплавов, металла, которая основана на перекристаллизации стали при нагреве выше критической температуры. После выдержки стали при такой температуре следует очень быстрое охлаждение. Такая сталь бывает неравновесной структуры и поэтому после закалки следует - отпуск.
Отпуск . Проводится после закалки, чтобы уменьшить или снять остаточное напряжение в стали и сплавах, повысить вязкость, уменьшить твёрдость и хрупкость металла.
Нормализация . Она похожа на отжиг, различие только в том, что нормализация металла происходит на воздухе, а отжиг - в печи.
Нагрев заготовки
Эта операция очень ответственная. От её правильного проведения зависит, во-первых - качество изделия, а во-вторых - производительность труда. Необходимо знать, что при нагреве металл меняет структуру, свойства и все характеристики поверхностного слоя. Так как при взаимодействии стали или сплава с воздухом происходит окисление железа и на поверхности образуется окалина. Толщина окалины зависит от того - какой химический состав металла, какая была температура и время его нагрева.
Сталь начинает интенсивно окисляться при нагреве больше 900 градусов , потом окисляемость увеличивается в два раза - при нагреве 1000 градусов С, а при температуре 1200 градусов С - в 5 раз.
Какое бывает окисление у разных сталей?
Хромоникелевая сталь - её называют жаростойкой потому, что она практически не поддаётся окислению.
Легированная сталь - у неё образуется плотный, но тонкий слой окалины, который защищает от дальнейшего окисления и не даёт растрескиваться при ковке.
Углеродистая сталь - она теряет около 2–4 мм углерода с поверхности при нагреве. Это для металла очень плохо, так как он теряет прочность, твёрдость и сталь ухудшается в закаливании. А особенно очень пагубным является обезуглероживание для ковки небольших деталей с последующей закалкой. Чтобы не было трещин на высоколегированной и высокоуглеродистой стали, их надо нагревать медленно.
Обязательно нужно обращаться к диаграмме «железо-углерод», где определена температура для начала и конца ковки. Делать это надо для того, чтобы металл при нагреве не приобретал крупнозернистую структуру и не снижалась его пластичность.
Но перегрев заготовки можно исправить методом термообработки, но для этого нужно дополнительная энергия и время. Если металл нагреть до ещё большей температуры, то это приведёт к пережогу, что дойдёт до того, что в металле нарушится связь между зёрнами и он полностью разрушится при ковке.
Пережог
Это самый неисправимый брак
. При нагреве металла или сплава обязательно нужно следить за температурой, временем и конца нагрева. Окалина растёт, если увеличено время нагрева, а при быстром или интенсивном нагреве могут появиться трещины.
Пережог сплава происходит вследствие диффузии кислорода на границах зёрен, где сразу образуются окислы, которые разъединяют зёрна при высокой температуре сплава и при этом сразу резко падает прочность. А пластичность в это время приходит к нулю. Этот брак сразу отправляется на переплавку.
Какой бывает термообработка металла и сплавов
Термическая обработка подразделяется на:
- термическую;
- термомеханическую;
- химикотермическую
В термическую обработку входят основные виды - отжиг 1-го рода, отжиг 2-го рода, закалка и отпуск. Нормализация применяется не ко всем видам стали, все зависит от её степени легированности.
У всех видов термической обработки разная температура нагрева, продолжительность выдержки при этой температуре и скорость охлаждения после окончания выдержки.
1-ый род отжига - это диффузионный отжиг, отжиг для снятия напряжений.
2-ой род отжига подразделяется на неполный, полный, изотермический отжиг, сфероидезацию, нормализацию.
Закалка применяется для того, чтобы изделия были твёрдые, прочные и износостойкие .
Химикотермическая обработка
Это такая термообработка стали, которая совокупляется с насыщением поверхности изделия - углеродом, азотом, алюминием, кремнием, хромом и др., которые образуют с железом твёрдые растворы замещения. Они более длительные и энергоёмкие, чем сталь насыщенная железом и углеродом, образующая с железом твёрдые растворы внедрения.
Химико - термическая обработка при создании на поверхности изделий благоприятных остаточных напряжений сжатия увеличивает долговечность и надёжность изделия. Также она повышает коррозионную стойкость, твёрдость .
Такая обработка предназначена для изменения в определённом слое состава стали. К таким методам относятся:
- цементация - при таком методе верхний слой стали обогащается углеродом. При этом получаются изделия с комбинированными свойствами - мягкая сердцевина и твёрдый поверхностный слой;
- азотирование - э то обогащение поверхностного слоя азотом, чтобы была повышена коррозионная стойкость и усталостная прочность изделия;
- борирование - это насыщение поверхностных слоёв стали бором, при таком методе у изделия повышается износостойкость, особенно при трении и сухом скольжении. Кроме того при борировании исключается схватываемость или сваривание деталей в холодном состоянии. Детали после борирования делаются очень стойкими к кислоте и щелочи;
- алитирование - это насыщение стали алюминием. Делается это для того, чтобы придать стали стойкость к агрессивным газам - серному ангидриду, сероводороду;
- хромирование -
насыщение хромом поверхностного слоя стали. Хромирование малоуглеродистых сталей почти совсем не влияет на их прочностные характеристики . Хромирование стали с более высоким содержанием хрома называется твёрдым хромированием, так как на поверхности деталей образуется карбид хрома, который имеет:
- высокую твёрдость
- окалиностойкость
- коррозионную стойкость
- повышенную износостойкость
Это упрочняющая термическая обработка металла и сплавов при криогенных, очень низких температурах - ниже -153 градусов С
. Ранее такая термическая обработка называлась «обработка холодом» или «термическая обработка металла при температуре ниже нуля». Но эти названия не совсем отображали всю суть криогенной обработки.
Её суть заключается в следующем: обрабатываемые детали помещают в криогенный процессор, где происходит их медленное охлаждение, а потом выдерживают детали при температуре -196 градусов С определённое время. Затем они постепенно возвращаются опять к комнатной температуре. Когда идёт этот процесс, то в металле происходят структурные изменения. За счёт этого повышается износостойкость, циклическая прочность, коррозионная и эрозионная стойкости.
Основные свойства, полученные при обработке, как холодное охлаждение, сохраняются на весь срок службы обрабатываемой детали и поэтому не требует повторной обработки.
Конечно, криогенная технология не заменит методы термического упрочнения, а при обработке холодом придаст материалу новые свойства.
Инструменты обработанные сверхнизкими температурами позволяют предприятиям сократить расходы потому, что:
- увеличивается износостойкость инструмента, деталей и механизмов;
- снижается количество брака;
- сокращаются затраты на ремонт и замену технологического оснащения и инструмента.
Именно советские учёные позволили полноценно оценить эффект влияния обработки холодом на металл и сплав и положили начало для использования этого метода.
В данное время метод криогенной обработки изделий широко применяется во всех отраслях промышленности.
Машиностроение и металлообработка:
- увеличивает ресурс оборудования и инструмента до 300%;
- увеличивает износостойкость материала;
- увеличивает циклическую прочность;
- увеличивает коррозионную и эрозионную стойкость;
- снимает остаточное напряжение.
Спецтехника и транспорт:
- увеличивает ресурс тормозных дисков на 250%;
- повышает эффективность работы тормозной системы;
- увеличивает циклическую прочность пружин подвески и других упругих элементов на 125%;
- увеличивает ресурс и мощность двигателя;
- снижает расходы на эксплуатацию транспортных средств.
Оборонная промышленность:
- увеличивает живучесть стволов до 200%;
- уменьшает влияние нагрева стволов на результаты стрельбы;
- увеличивает ресурс узлов и механизмов.
Добывающая и обрабатывающая промышленность:
- увеличивает стойкость породоразрушающего инструмента до 200%;
- уменьшает абразивный износ узлов и механизмов;
- увеличивает коррозионную и эрозийную стойкость оборудования;
- увеличивает ресурс промышленного и горнодобывающего оборудования.
Аудиотехника и музыкальные инструменты:
- уменьшает искажение сигнала в проводниках;
- улучшает музыкальную деятельность, ясность и прозрачность звучания;
- расширяет диапазон звучания музыкальных инструментов.
Криогенная обработка применяется практически во всех отраслях, где необходимо повысить ресурс, увеличить прочность и износостойкость, а также поднять производительность.
Надёжность и долговечность металлических конструкций, оборудования, трубопроводов зависит от качества изготовления узлов, деталей, элементов из которых они состоят. Во время эксплуатации они подвергаются статистическим, динамическим и циклическим нагрузкам и влиянию агрессивных сред. Им приходится работать при низких и высоких температурах и находится в условиях быстрого износа
.
И поэтому эксплуатация любых металлоизделий напрямую зависит от износостойкости, прочности, термо- и коррозионной стойкости элементов из которых они состоят.
Для того чтобы повысить все эти характеристики необходимо правильно подобрать материал для деталей, усовершенствовать их конструкцию, устранить неточности сборки, улучшить методы горячей и холодной обработки.
Таким высоким требованиям редко отвечают материалы в состоянии поставки. Основная часть доставляемых конструкционных элементов нуждается в стабилизации эксплуатационных свойств, чтобы они не изменялись с течением времени. И чтобы повысить механические и физико-химические свойства металлических материалов, применяют термическую обработку . Это последовательность операций нагрева, выдержки и охлаждения металлов и сплавов.
Её проводят для изменения структуры и свойств металлов и сплавов в направлении, которое было задано. Термообработка применяется для изменения структуры фазового состава и перераспределения компонентов, размера и формы кристаллических зёрен, видов дефектов, их количества и распределения. И это все позволяет достаточно легко получить требуемое свойство материала.
Обязательно надо помнить, что свойства металла и сплавов зависит не только от не только от структуры, но и от химического состава, который образуется во время металлургического и литейного процесса.
Задачей термической обработки является ликвидация внутреннего напряжения в металле и сплаве, улучшение механических и эксплуатационных свойств и другое.
Термической обработке подвергается сталь, чугун, сплав на основе цветных металлов .
Нужно знать, что материалам с одним химическим составом при проведении различных режимов термообработки можно получить несколько совершенно разных структур, которые будут обладать абсолютно разными свойствами. При улучшении механических свойств с помощью термической обработки можно использовать сплавы более простого состава. Допускаемые напряжения, уменьшение массы деталей и механизмов, повышение их надёжности и долговечности также можно достичь с помощью термической обработки.
Тема 1.2 Термическая и химико-термическая обработка металлов и сплавов
Термической обработкой называются процессы, сущность которых заключается в нагреве и охлаждении изделий по определенным режимам, в результате которых происходит изменение структуры, фазового состава, механических и физических свойств. Применяют также различные виды химико-термической обработки, сущность которой заключается в легировании поверхностного слоя изделий азотом, углеродом, или некоторыми металлами (алюминием, хромом. Бериллием) с последующей термической обработкой.
В зависимости от целей термической обработки существуют различные ее виды, отличающиеся температурой нагревания, продолжительностью выдержки и скоростью охлаждения.
Основными видами термической обработки стали являются отжиг, нормализация, закалка, отпуск.
Отжиг применяется для снижения твердости, измельчения зерна, улучшения обрабатываемости, снятия напряжений. Для отжига сталь нагревают до определенной температуры, выдерживают и охлаждают с малой скоростью в печи с отключением источника тепла.
Нормализация – представляет нагрев стали до температуры выше критической точки, выдержке при этой температуре, охлаждении на спокойном воздухе со скоростью, большей, чем при отжиге. Назначение – придание стали мелкозернистой структуры. Нормализация дает более заметное повышение прочности, но меньшую пластичность. Преимущество перед отжигом – более низкая стоимость.
Закалка – заключается в нагреве стали, выдержке при данной температуре в течение определенного времени и последующем резком охлаждении. Цель – повышение твердости и прочности. При закалке возникают внутренние напряжения в материале, резко снижается пластичность и ударная вязкость. Это может привести к хрупкому разрушению детали при эксплуатации.
Для уменьшения внутренних напряжений и повышения пластичности и ударной вязкости после закалки применяют отпуск , который заключается в нагревании закаленной стали до температуры, не превышающей нижнюю критическую точку, выдержке при этой температуре и последующем охлаждении.
В зависимости от температуры различают три вида отпуска: низкий, средний, высокий.
Низкий отпуск производится при температуре 150...250°С. Твердость стали снижается незначительно. Струк-туру, образующуюся в результате низкого отпуска, называют мар- тенситом отпуска или отпущенным мартенситом. Низкому отпус-ку подвергается режущий и измерительный инструмент, штампы для холодной штамповки, а также детали, которые должны обла-дать высокой износостойкостью.
Средний отпуск производится при температуре 350...450°С. При среднем отпуске цементит образуется не в виде пластинок, а в виде мельчайших зерен, что способствует повыше-нию вязкости стали. Среднему отпуску подвергаются изделия, ко-торые должны обладать высокой упругостью и достаточным запа-сом вязкости (рессоры, пружины и др.).
Высокий отпуск производится при температуре 500...650°С. В результате проис-ходит полное устранение остаточных напряжений, сталь приоб-ретает хорошие пластичность и вязкость при достаточно высокой прочности. Такой отпуск предназначен для деталей ответственно-го назначения, которые испытывают в процессе эксплуатации удар-ные и знакопеременные нагрузки.
Двойную термическую обработку, включающую в себя закалку и последующий высокий отпуск называют термическим улучшением, поскольку улучшается весь комплекс механических свойств стали.
Химико-термическая обработка. Химико-термическая обработ-ка заключается в химическом и термическом воздействии с целью изменения химического состава, структуры и свойств поверхност-ного слоя металла. В процессе химико-термической обработки про-исходит поверхностное насыщение металла соответствующим элементом в процессе его диффузии в атомарном виде из жидкой, твер-дой или газовой среды при высокой температуре. Основные виды химико-термической обработки классифицируют по названиям элементов, которыми насыщается поверхностный слой. Например, насыщение углеродом называется цементацией, азотом - азотиро-ванием, хромом - хромированием.
Широкое применение химико-термической обработки в различ-ных областях техники объясняется тем, что она, повышая твердость, износостойкость, коррозионную стойкость поверхности, увеличи-вает надежность и долговечность работы деталей машин и меха-низмов.
Химико-термическая обработка складывается из:
диссоциации, которая происходит на контактной поверхности «металл - газовая среда» и приводит к выделению диффундирую-щего элемента в атомарном состоянии;
абсорбции - поглощения поверхностью свободных атомов;
диффузии - проникновения насыщающего элемента вглубь по-верхностного слоя.
Основным физическим процессом является диффузия, скорость которой увеличивается при повышении температуры, диффунди-рующий элемент проникает на большую глубину.
Цементация заключается в диффузионном насыщении по-верхностного слоя стали углеродом при нагревании в соответству-ющей среде - карбюризаторе. Процесс цементации проходит при температурах (900...950°С), когда устойчив аустенит, растворяющий углерод в больших количествах. Цементацию проводят в твердых, жидких и газовых карбюризаторах. Газовая цементация является наиболее производительным процессом. Ос-новной реакцией, обеспечивающей науглероживание, является дис-социация метана:
СН→ 2Н 2 +С ат.
Цементации подвергают низкоуглеродистые и легированные стали, содержащие от 0,1 до 0,35% углерода. Поверхностный слой стали после цементации имеет переменную концентрацию углеро-да по толщине, убывающую от поверхности к сердцевине детали. В связи с этим после медленного охлаждения в структуре цементо-ванного слоя можно различить (начиная от поверхности) три зоны: заэвтектоидную, эвтектоидную, доэвтектоидную. Общая толщина цементованного слоя составляет 0,8...3,0 мм.
После цементации для получения необходимых свойств прово-дят термическую обработку – закалку с низким отпуском. В резуль-тате термической обработки поверхностный слой приобретает из-носостойкую структуру, а низ-коуглеродистая сердцевина детали оказывается достаточно вязкой. Чаще всего цементации подвергают шестерни различных механизмов с целью повышения их долговечности.
Азотирование заключается в диффузионном насыщении по-верхностного слоя азотом в соответствующей среде. Перед азоти-рованием стали подвергают термической обработке – закалке и вы-сокому отпуску.
Азотированию подвергаются легированные стали, содержащие хром, молибден, ванадий и другие элементы, способные образо-вывать с азотом очень твердые и термостойкие нитриды. Азотиро-вание проводят при температуре 500...600°С. Основная реакция, происходящая на поверхности детали – реакция диссоциации ам-миака.
После азотирования сталь приобретает высокую твердость, из-носостойкость и коррозионную стойкость. По этим свойствам азо-тированные стали превосходят цементованные. Однако азотиро-ванный слой хуже противостоит ударным нагрузкам и имеет более низкую контактную выносливость. Из-за большой длительности процесса (до 70 ч) применение азотирования экономически целе-сообразно для обработки ответственных изделий, например колен-чатых валов автомобилей, гильз цилиндров двигателей внутрен-него сгорания, различных деталей арматуры и др.
Хромирование заключается в диффузионном насыщении поверхностного слоя стали хромом при температуре 900...1300°С в соответствующей среде. Хромирование обеспечивает повышен-ную жаростойкость стали до температуры 800 °С, высокие корро-зионную и эрозионную стойкость. Хромированию подвергаются детали паросиловых установок, паропроводной арматуры, венти-ли, клапаны, патрубки. Для увеличения сопротивляемости корро-зии хромированию подвергают трансформаторную сталь. При этом сталь дополнительно приобретает высокую жаропрочность.
Контрольные вопросы
Чем характеризуется кристаллическое строение металлов?
Какие типы кристаллических решеток Вам известны?
Каковы основные дефекты кристаллического строения?
Что такое аллотропия металлов?
Какие механические свойства характеризуют прочность и пластичность материалов при растяжении?
Что такое диаграмма состояния сплавов и что позволяет она установить?
Каковы основные виды термической обработки?
В чем заключается цементация стали?
Раздел 2 ПОЛУПРОВОДНИКОВЫЕ МАТЕРИАЛЫ
Тема 2.1 Классификация полупроводниковых материалов
Вещества различают по их способности проводить электрический ток. Эта способность характеризуется величиной удельного электрического сопротивления – ρ или удельной электрической проводимостью – γ. Значение γ при нормальной температуре составляет для диэлектриков менее 10 -10 См/м, а для проводников – более 10 4 См/м.
Рассмотрим характер изменения удельной проводимости твердых тел при температуре, стремящейся к абсолютному нулю.
Удельная проводимость проводников при этом увеличивается, а многие металлы переходят в сверхпроводящее состояние, характеризующееся бесконечно большим значением γ.
Совершенно иначе ведут себя полупроводники. При уменьшении температуры их удельная проводимость уменьшается, а при Т → 0 К полупроводники вообще не проводят электрический ток, т.е. становятся диэлектриками. Зато при возрастании температуры γ полупроводников резко увеличивается.
Для появления у полупроводников свободных носителей заряда не обязательно подводить к ним тепловую энергию. Это можно достигать в них освещением, механическими нагрузками, электрическим полем и т.д. Сильное влияние на электропроводность оказывает внутренняя структура полупроводников. Кроме того, введение в полупроводник даже незначительного количества атомов постороннего элемента обычно резко изменяет его электропроводность. Все это открывает широкие возможности для управления электрофизическими свойствами полупроводниковых материалов.
Итак, полупроводник – это вещество, основным свойством которого является сильная зависимость его электропроводности от воздействия внешних факторов.
Все полупроводники можно разделить на простые и сложные.
Простым называют такой полупроводник, основной состав которого образован атомами одного химического элемента (кремний, германий, селен, теллур, бор, углерод, фосфор, серу, мышьяк, сурьму, йод, серое олово).
Структура сложных полупроводников образована атомами различных химических элементов. К этой группе относятся твердые растворы (кремния и германия) и химические соединения, обозначаемые АB. В этой формуле верхние индексы (m и n) означают номер группы периодической системы, в которую входит соответствующий элемент, а нижние (x и y) – число атомов этого элемента в соединении. Например, полупроводник арсенид галлия GaAr относят к соединениям типа А III В V , а оксид меди Cu 2 O – к соединения типа A 2 I B VI .
Полупроводниковыми свойствами обладают многие тройные и боле сложные химические соединения, например ZnSiAs 2 . Полупроводниковыми является целый ряд органических соединений: антрацен, нафталин, фталоцианин и др.
Замечательным свойством полупроводников является также то, что они допускают обратное преобразование электрической энергии в световую, тепловую или механическую.
Полупроводники используют для усиления и генерации электрических сигналов (транзисторы, диоды, интегральные схемы), в качестве первичных преобразователей температуры и источников тепловой энергии (терморезисторы и нагревательные элементы), в качестве первичных преобразователей и источников оптических сигналов (фоторезисторы, светодиоды, лазеры), для преобразования механических колебаний (тензорезисторы и пьезодатчики) и т.д.
Энергетические уровни и зоны
Атом состоит из ядра и движущихся по определенным орбитам электронов.
Полная энергия электронов, равная сумме его кинетической (движения по орбите) и потенциальной (притяжения к ядру) энергий, называется энергетическим состоянием атома. Каждой разрешенной орбите соответствует свое энергетическое состояние, которое на диаграмме представляют в виде энергетического уровня. Так как орбиты и их энергии делятся на разрешенные и запрещенные, то и энер гетические уровни могут быть также разрешенными и запрещенными.
Энергия электрона Е выражена в электрон-вольтах. Электрон-вольт - это энергия, которую приобретает электрон, разгоняясь в электрическом поле с разно стью потенциалов в 1 В.
Взаимодействие атомов в решетке приводит к тому, что их энергетические уровни расщепляются на большое количество почти сливающихся подуровней, образующих энер гетические зоны .
Энергетическая зона, заполненная подуровнями, тем шире, чем ближе расположены атомы и чем выше энергетический уровень. Вероятность «пребывания» электрона в запрещенной зоне равна нулю.
Классификация материалов по электрическим свойствам (зонная теория)
Классификация электроматериалов по электрическим свойствам основана на представлениях зонной теории электропроводности твердых тел, сущность которой состоит в следующем.
В изолированном атоме электроны вращаются вокруг ядра на определенных орбитах. Согласно принципу Паули на каждой ор- бите может находиться не более двух электронов. Каждой орбите соответствует строго определенное значение энергии, которой может обладать электрон, т.е. каждая орбита представляет собой определенный энергетический уровень. Под воздействием притя-жения положительно заряженного атомного ядра электроны стре-мятся занять ближайшие к ядру уровни с минимальным значени-ем энергии. Поэтому нижние энергетические уровни оказываются заполненными электронами, а верхние уровни - свободными. Электрон может скачкообразно перейти с нижнего энергетиче-ского уровня W x на другой свободный уровень W 2 (рис. 1). Для этого электрону необходимо сообщить дополнительную энергию ∆ W = W 2 - W 1 . Если свободных уровней в атоме нет, то электрон не может изменить свою энергию, поэтому не участвует в созда-нии электропроводности.
W - энергия электрона; W 1 - нижний энергетический уровень; W 2 - свобод-ный энергетический уровень; ∆ W C - зона проводимости (свободная зона); ∆ W - запрещенная зона; ∆ W в , - валентная зона
Рисунок 2.1 – Диаграмма энергетических уровней изолированного атома (1) и твердого тела (2).
В кристаллической решетке, состоящей из нескольких атомов, отдельные энергетические уровни расщепляются на подуровни, которые образуют энергетические зоны (см. рис. 2.1). При этом расщепляются свободные и заполненные энергетические уровни. Зона, заполненная электронами, называется валентной. Верхний уровень валентной зоны обозначается W в . Свободная зона называ-ется зоной проводимости. Нижний уровень зоны проводимости (свободной зоны) обозначается W a . Промежуток между валентной зоной и зоной проводимости называется запрещенной зоной ∆ W . Значение запрещенной зоны существенно влияет на свойства ма-териалов.
Если ∆ W равна или близка к нулю, то электроны могут перей-ти на свободные уровни благодаря собственной тепловой энергии и увеличить проводимость вещества. Вещества с такой структурой энергетических зон относятся к проводникам. Проводнико-вые материалы служат для проведения электрического тока. Обычно к проводникам относятся вещества с удельным электрическим сопротивлением р < 10 Ом*м. Типичными проводниками явля-ются металлы.
Если значение запрещенной зоны превышает несколько элект-ронвольт, то для перехода электронов из валентной зоны в зону проводимости требуется значительная энергия. Такие ве-щества относятся к диэлектрикам. Диэлектрики имеют высо-кое удельное электрическое сопротивление и обладают способно-стью препятствовать прохождению тока. К диэлектрическим мате-риалам относятся вещества с удельным электрическим сопротив-лением р > 10 7 Ом* м. Благодаря высокому удельному электриче-скому сопротивлению их используют в качестве электроизоляци-онных материалов.
Если значение запрещенной зоны составляет 0,1...0,3 эВ, то электроны легко переходят из валентной зоны в зону проводимо-сти благодаря внешней энергии. Вещества с управляемой прово-димостью относятся к полупроводникам. Удельное электри-ческое сопротивление полупроводников составляет р 10 9 Ом * м.
Полупроводниковые материалы обладают проводимостью, с помощью которой можно управлять напряжением, температурой, освещенностью и т.д.
В зависимости от структуры и внешних условий материалы мо-гут переходить из одного класса в другой. Например, твердые и жидкие металлы - проводники, а пары металлов - диэлектрики; типичные при нормальных условиях полупроводники германий и кремний при воздействии высоких гидростатических давлений становятся проводниками; углерод в модификации алмаза - диэ-лектрик, а в модификации графита - проводник.
Основным свойством вещества по отношению к электрическо-му полю является электропроводность, характеризующая способ-ность материала проводить электрический ток под воздействием постоянного электрического поля, т.е. поля, напряжение которо-го не меняется во времени.
Электропроводность характеризуется удельной электрической проводимостью и удельным электрическим сопротивлением:
Значения удельной электрической проводимости и удельного электрического сопротивления у разных материалов существенно различаются. В сверхпроводящем состоянии удельное электричес-кое сопротивление материалов равно нулю, а у разреженных га-зов стремится к бесконечности.
Легко понять, что проводящие свойства кристалла зависят от ширины запрещенной зоны, разделяю-щей валентную зону и зону проводимости. Чем шире запрещенная зона, тем меньше (при заданной темпе-ратуре) количество электронов, которые проникнут в зону проводимости, тем меньше проводимость кри-сталла.
Кристаллы могут быть хорошими проводниками даже в том случае, когда валентная зона заполнена целиком, если она непосредственно примыкает к зоне проводимости или пересекается с ней (в результате размытия зон при образовании решетки). С увели- чением ширины запрещенной зоны кристаллы приоб- ретают свойства изоляторов. Средним значениям ширины запрещенной зоны соответствуют полупро- водниковые кристаллы.
Так как валентная зона и зона проводимости у кристаллических проводни-ков не разделены, электроны свободно переходят с одного разрешенного подуровня на другой, приобретая упорядо-ченную скорость под дейст-вием приложенного напря-жения. При этом с увеличением темпера-туры сопротивление провод-ника увеличивается вследст-вие уменьшения длины сво-бодного пробега электронов в кристалле.
У полупроводниковых кристаллов проводимость определяется прежде всего количеством электронов, преодолевших запрещенную зону и проникших в зону проводимости.
Полупроводниковые материалы
Химическая связь между атомами полупроводника осуществляется за счет взаимодействия валентных электронов, при этом каждый атом получает от соседа в совместное владение и отдает ему свои валентные электроны, недостающие до образования устойчивой восьмиэлектроннои зоны. Таким образом, в идеальном полупроводнике все валентные элект- роны участвуют в образовании химической связи и свободных электронов нет. Такой тип химической связи называется кова лентной.
На рис. 2.2 показана схема образования химической связи в кристаллической решетке кремния, у атома которого в свободном изолированном состоянии имеется четыре валентных электрона, а в кристаллической решетке внешний электронный уровень каж-дого атома заполняется до восьми электронов, за счет совместно-го владения электронами четырех ближайших атомов-соседей.
Рисунок 2.2 – Схема образования химической связи в кристаллической решетке кремния. Вследствие малой ширины (1 эВ) запрещенной зоны полупроводника тепловые колебания атомов способны сообщить валентным электронам энергию, достаточную для перехода из заполненной валентной зоны в свободную зону проводимости. Каждый такой переход приводит к возникновению пары носителей заряда: свободного электрона в зоне проводимости и свободного энергетического состояния – дырки – в валентной зоне. Под действием приложенного к кристаллу напряжения электрон проводимости дви-жется «навстречу» электрическому полю, а электрон в валентной зоне занимает свободный уровень, осво-бождая свой уровень для другого электрона. Это мож-но рассматривать как движение положительного за-ряда (дырки) в направлении электрического поля.
Генерация пар свободных, т. е. способных пере- мещаться под действием приложенного напряжения, зарядов делает кристалл способным проводить элект- рический ток, а электропроводность такого кристалла называется собственной.
Полупроводник, в котором электропроводность осуществляется за счет возбуждения электронов химической связи, называется собственным полупроводником.
Носителями тока в таких полу-проводниках являются собственные электроны и дырки.
На рис. 2.3 приведена схема кристаллической решетки собст-венного полупроводника. При возбуждении собственного валентного электрона образуется n -тип носитель тока - свободный электрон и р- тип носитель тока – дырка – незанятая химическая связь.
Одновременно с образованием пар носителей часть электронов из зоны проводимости спонтанно перехо-дит обратно в валентную зону, излучая кванты энергии. Этот процесс называется рекомбинацией пар. При постоянной температуре устанавливается динамическое равновесие, определяющее концентра-цию свободных электронов и дырок (при данной температуре).
Чем выше температура, тем выше концентрация свободных носителей заряда, тем больше собственная электропроводность кристалла.
При температуре 0К пары носителей не образуются, и кристалл полностью теряет собственную элект-ропроводность. При этом электроны внутри кристалла хаотически движутся с большими скоростями (поряд-ка 10 6 м/с), но на приложенное внешнее напряже-ние не реагируют.
Рисунок 2.3 – Схема кристаллической решетки собст-венного полупроводника.
Реальные кристаллы содержат многочис-ленные дефекты кристаллической решетки: точечные, линейные, объемные и поверхностные. В местах нару-шения периодической структуры кристалла (внедре-ния атомов в междоузлия) энергия связи электронов с ядрами изменяется, в результате чего возникают новые энергетические уровни, которые могут выхо-дить за пределы валентной зоны и размещаться в запрещенной зоне вблизи зоны проводимости. Это облегчает переход электронов в зону проводимости.
Учебно-методический комплекс... – дать основы материаловедения , принципы выбора необходимых материалов, привить навыки практического определения физико -механических... группу химических соединений. 6.3.1. Классификация полимеров и свойства полимеров По происхождению полимеры разделяют ...
Евгений петрович прокопьев (rus)(eng) общий список публикаций антиматерия и позитроника позитроника и нанотехнологии позитроника позитронная аннигиляция физика сложных систем синергетика материаловедение нанотехнологии другие смежные проблемы
ДокументПрокопьев Е.П. О поверхностных состояниях на границе раздела полупроводник-металл. М., 1985. 5 с. - Деп. в... процессах. Третья Российская конференция по материаловедению и физико -химическим основам технологий получения легированных кристаллов кремния...
Свойства сплава зависят от его структуры. Основным способом, позволяющим изменять структуру, а, следовательно, и свойства является термическая обработка.
Основы термической обработки разработал Чернов Д.К.. В дальнейшем они развивались в работах Бочвара А.А., Курдюмова Г.В., Гуляева А.П.
Термической обработкой называют тепловое воздействие на металл с целью придания металлу необходимых механических и физических свойств в результате изменения внутреннего строения (структуры) металла.
Термической обработке подвергают большинство заготовок (полуфабрикатов) и изделий из стали и цветных сплавов. Именно термическая обработка позволяет изменять структуру металла в нужном направлении и позволяет получать необходимый уровень твердости, прочности, пластичности и других свойств.
Режим термической обработки характеризуют следующие основные параметры: скорость и режим нагрева, максимальная температура нагрева, время выдержки в печи при температуре нагрева, и скорость и режим охлаждения.
Термическая обработка является одним из наиболее распространенных в современной технике способов получения заданных свойств металла. Термическую обработку используют либо в качестве промежуточной операции для улучшения обрабатываемости полуфабриката давлением, резанием и др., либо как окончательную операцию технологического процесса, обеспечивающую заданный уровень физико-механических свойств детали.
Термическая обработка включает в себя нагрев, выдержку и охлаждение металла, выполняемые в определенной последовательности при определенных режимах, с целью изменения внутреннего строения сплава и получения нужных свойств. Обычно ее схематично можно представить в виде графика в осях температура – время, (рис. 21).
Термическая обработка подразделяется на собственно термическую, химико-термическую и термомеханическую (или деформационно-термическую).
Собственно термическая обработка заключается только в термическом воздействии на металл или сплав, химико-термическая - в сочетании термического и химического воздействия, термомеханическая - в сочетании термического воздействия и пластической деформации.
Рис.21. График термообработки
Собственно термическая обработка включает следующие основные виды:
Отжиг 1-го рода
Отжиг 2-го рода
Закалку с полиморфным превращением
Закалку без полиморфного превращения
Старение
Эти виды термической обработки относятся и к сталям, и к цветным металлам.
Отжиг
Отжиг – термическая обработка, заключающаяся в нагреве металла до определенной температуры, выдержки и охлаждении с отключенной печью (т.е. с минимально возможной скоростью, порядка 50-100 град/час).
Отжиг 1 рода – применяется для любых металлов и сплавов. Его проведение не обусловлено фазовыми превращениями в твердом состоянии. Нагрев, при отжиге первого рода, повышая подвижность атомов, частично или полностью устраняет химическую неоднородность, уменьшает внутренние напряжения. Основное значение имеет температура нагрева и время выдержки. Характерным является медленное охлаждение
Разновидностями отжига первого рода являются:
· гомогенизационный (диффузионный)
· рекристаллизационный;
· отжиг для снятия внутреннего напряжения после ковки, сварки, литья.
Гомогенизационный (диффузионный) отжиг - это термическая обработка, при которой главным процессом является устранение последствий дендритной ликвации (химической неоднородности) в отливках и слитках. Он представляет собой длительную выдержку при высоких температурах, при которых протекают диффузионные процессы, не успевшие завершиться при кристаллизации. Ориентировочная температура для сталей -1100-1300 о С в течение 20-50 ч, для алюминиевых сплавов 420-450 о С.
Рекристаллизационный отжиг - это термическая обработка деформированного металла, при которой главным процессом является рекристаллизация металла. Этот вид отжига устраняет отклонения в структуре от равновесного состояния, возникающие при пластической деформации. При обработке давлением, особенно холодной, металл наклёпывается, его прочность возрастает, а пластичность снижается из-за повышения плотности дислокаций в кристаллитах. При нагреве наклёпанного металла выше некоторой температуры развивается первичная, и затем собирательная рекристаллизация, при которой плотность дислокаций резко снижается. В результате металл разупрочняется и становится пластичнее. Такой отжиг используют для улучшения обрабатываемости давлением и придания металлу необходимого сочетания твёрдости, прочности и пластичности. Как правило, при рекристаллизационном отжиге стремятся получить без текстурный материал, в котором отсутствует анизотропия свойств. В производстве листов из трансформаторной стали рекристаллизационный отжиг применяют для получения желательной текстуры металла, возникающей при рекристаллизации.
Отжиг для снятия внутренних напряжений - это термическая обработка, при которой главным процессом является полная или частичная релаксация остаточных напряжений при нагреве и охлаждении. Отжиг, уменьшающий напряжения, применяют к изделиям, в которых при обработке давлением, литье, сварке, термообработке и др. технологических процессах возникли недопустимо большие остаточные напряжения, взаимно уравновешивающиеся внутри тела без участия внешних нагрузок. Остаточные напряжения могут вызвать искажение формы и размеров изделия во время его обработки, эксплуатации или хранении на складе. При нагревании изделия предел текучести снижается и, когда он становится меньше остаточных напряжений, происходит быстрая их разрядка путём пластического течения в разных слоях металла.
Отжиг II рода – отжиг металлов и сплавов, испытывающих фазовые превращения в твердом состоянии. Этот вид отжига проводится для сплавов, в которых имеются полиморфные или эвтектоидные превращения, а также переменная растворимость компонентов в твердом состоянии.
Рис.22.Изменение структуры при отжиге II рода
Отжиг второго рода проводят с целью получения равновесной структуры и подготовки ее к дальнейшей обработке. В результате отжига измельчается зерно, повышаются пластичность и вязкость, снижаются прочность и твердость, улучшается обрабатываемость резанием. Он характеризуется нагревом до температур выше критических и очень медленным охлаждением, как правило, вместе с печью или на воздухе. В последнем случае процесс называется нормализацией. Отжиг 2-го рода применяют чаще всего для общего измельчения структуры, смягчения и улучшения обрабатываемости резанием.
Термическая обработка металлов и сплавов
Курсовая работа
на тему: «Термическая обработка металлов и сплавов»
Введение
Термическую обработку применяют на различных стадиях производства деталей машин и металлоизделий. В одних случаях она может быть промежуточной операцией, служащей для улучшения обрабатываемости сплавов давлением, резанием, в других – является окончательной операцией, обеспечивающей необходимый комплекс показателей механических, физических и эксплуатационных свойств изделий или полуфабрикатов. Полуфабрикаты подвергают термической обработке для улучшения структуры, снижения твердости (улучшения обрабатываемости), а детали – для придания им определенных, требуемых свойств (твердости, износостойкости, прочности и других).
В результате термической обработки свойства сплавов могут быть изменены в широких пределах. Возможность значительного повышения механических свойств после термической обработки по сравнению с исходным состоянием позволяет увеличить допускаемые напряжения, уменьшить размеры и массу машин и механизмов, повысить надежность и срок службы изделий. Улучшение свойств в результате термической обработки позволяет применять сплавы более простых составов, а поэтому более дешевые. Сплавы приобретают также некоторые новые свойства, в связи с чем расширяется область их применения.
Назначение и виды термической обработки
Термической (тепловой) обработкой называются процессы, сущность которых заключается в нагреве и охлаждении изделий по определенным режимам, в результате чего происходят изменения структуры, фазового состава, механических и физических свойств материала, без изменения химического состава.
Назначение термической обработки металлов – получение требуемой твердости, улучшение прочностных характеристик металлов и сплавов. Термическая обработка подразделяется на термическую, термомеханическую и химико-термическую. Термическая обработка – только термическое воздействие, термомеханическая – сочетание термического воздействия и пластической деформации, химико-термическая – сочетание термического и химического воздействия. Термическая обработка, в зависимости от структурного состояния, получаемого в результате ее применения, подразделяется на отжиг (первого и второго рода), закалку и отпуск.
Отжиг
Отжиг – термическая обработка заключающаяся в нагреве металла до определенных температур, выдержка и последующего очень медленного охлаждения вместе с печью. Применяют для улучшения обработки металлов резанием, снижения твердости, получения зернистой структуры, а также для снятия напряжений, устраняет частично (или полностью) всякого рода неоднородности, которые были внесены в металл при предшествующих операциях (механическая обработка, обработка давлением, литье, сварка), улучшает структуру стали.
Отжиг первого рода. Это отжиг при котором не происходит фазовых превращений, а если они имеют место, то не оказывают влияния на конечные результаты, предусмотренные его целевым назначением. Различают следующие разновидности отжига первого рода: гомогенизационный и рекристаллизационный.
Гомогенизационный – это отжиг с длительной выдержкой при температуре выше 950єС (обычно 1100–1200єС) с целью выравнивания химического состава.
Рекристаллизационный – это отжиг наклепанной стали при температуре, превышающей температуру начала рекристаллизации, с целью устранения наклепаи получение определенной величины зерна.
Отжиг второго рода. Это отжиг, при котором фазовые превращения определяют его целевое назначение. Различают следующие виды: полный, неполный, диффузионный, изотермический, светлый, нормализованный (нормализация), сфероидизирующий (на зернистый перлит).
Полный отжиг производят путем нагрева стали на 30–50 °С выше критической точки, выдержкой при этой температуре и медленным охлаждением до 400–500 °С со скоростью 200 °С в час углеродистых сталей, 100 °С в час для низколегированных сталей и 50 °С в час для высоколегированных сталей. Структура стали после отжига равновесная, устойчивая.
Неполный отжиг производится путем нагрева стали до одной из температур, находящейся в интервале превращений, выдержкой и медленным охлаждением. Неполный отжиг применяют для снижения внутренних напряжений, понижения твердости и улучшения обрабатываемости резанием
Диффузионный отжиг. Металл нагревают до температур 1100–1200єС, так как при этом более полно протекают диффузионные процессы, необходимые для выравнивания химического состава.
Изотермический отжиг заключается в следующем: сталь нагревают, а затем быстро охлаждают (чаще переносом в другую печь) до температуры, находящейся ниже критической на 50–100єС. В основном применяется для легированных сталей. Экономически выгоден, так как длительность обычного отжига (13 – 15) ч, а изотермического отжига (4 – 6) ч
Сфероидизирующий отжиг (на зернистый перлит) заключается в нагреве стали выше критической температуры на 20 – 30 °С, выдержке при этой температуре и медленном охлаждении.
Светлый отжиг осуществляется по режимам полного или неполного отжига с применением защитных атмосфер ил в печах с частичным вакуумом. Применяется с целью защиты поверхности металла от окисления и обезуглероживания.
Нормализация – заключается в нагреве металла до температуры на (30–50) єС выше критической точки и последующего охлаждения на воздухе. Назначение нормализации различно в зависимости от состава стали. Вместо отжига низкоуглеродистые стали подвергают нормализации. Для среднеуглеродистых сталей нормализацию применяют вместо закалки и высокого отпуска. Высокоуглеродистые стали подвергают нормализации с целью устранения цементитной сетки. Нормализацию с последующим высоким отпуском применяют вместо отжига для исправления структуры легированных сталей. Нормализация по сравнению с отжигом – более экономичная операция, так как не требует охлаждения вместе с печью.
Закалка
Закалка – это нагрев до оптимальной температуры, выдержка и последующее быстрое охлаждение с целью получения неравновесной структуры.
В результате закалки повышается прочность и твердость и понжается пластичность стали. Основные параметры при закалке – температура нагрева и скорость охлаждения. Критической скоростью закалки называется скорость охлаждения, обеспечивающая получение структуры – мартенсит или мартенсит и остаточный аустенит.
В зависимости от формы детали, марки стали и требуемого комплекса свойств применяют различные способы закалки.
Закалка в одном охладителе. Деталь нагревают до температуры закалки и охлаждают в одном охладителе (вода, масло).
Закалка в двух средах (прерывистая закалка) – это закалка при которой деталь охлаждают последовательно в двух средах: первая среда – охлаждающая жидкость (вода), вторая – воздух или масло.
Ступенчатая закалка. Нагретую до температуры закалки деталь охлаждают в расплавленных солях, после выдержки в течении времени необходимого для выравнивания температуры по всему сечению, деталь охлаждают на воздухе, что способствует снижению закалочных напряжений.
Изотермическая закалка так же, как и ступенчатая, производится в двух охлаждающих средах. Температура горячей среды (соляные, селитровые или щелочные ванны) различна: она зависит от химического состава стали, но всегда на 20–100 °С выше точки мартенситного превращения для данной стали. Окончательное охлаждение до комнатной температуры производится на воздухе. Изотермическая закалка широко применяется для деталей из высоколегированных сталей. После изотермической закалки сталь приобретает высокие прочностные свойства, то есть сочетание высокой вязкости с прочностью.
Закалка с самоотпуском имеет широкое применение в инструментальном производстве. Процесс состоит в том, что детали выдерживаются в охлаждающей среде не до полного охлаждения, а в определенный момент извлекаются из нее с целью сохранения в сердцевине детали некоторого количества тепла, за счет которого производится последующий отпуск.
Отпуск
Отпуск стали является завершающей операцией термической обработки, формирующей структуру, а следовательно, и свойства стали. Отпуск заключается в нагреве стали до различных температур (в зависимости от вида отпуска, но всегда ниже критической точки), выдержке при этой температуре и охлаждении с разными скоростями. Назначение отпуска – снять внутренние напряжения, возникающие в процессе закалки, и получить необходимую структуру.
В зависимости от температуры нагрева закаленной детали различают три вида отпуска: высокий, средний и низкий.
Высокий отпуск производится при температурах нагрева выше 350–600 °С, но ниже критической точки; такой отпуск применяется для конструкционных сталей.
Средний отпуск производится при температурах нагрева 350 – 500 °С; такой отпуск широко применяется для пружинной и рессорной сталей.
Низкий отпуск производится при температурах 150–250 °С. Твердость детали после закалки почти не изменяется; низкий отпуск применяется для углеродистых и легированных инструментальных сталей, для которых необходимы высокая твердость и износостойкость.
Контроль отпуска осуществляется по цветам побежалости, появляющимся на поверхности детали.
Старение
Старение –это процесс изменения свойств сплавов без заметного изменения микроструктуры. Известны два вида старения: термическое и деформационное.
Термическое старение протекает в результате изменения растворимости углерода в железе в зависимости от температуры.
Если изменение твердости, пластичности и прочности протекает при комнатной температуре, то такое старение называется естественным.
Если же процесс протекает при повышенной температуре, то старение называется искусственным.
Деформационное (механическое) старение протекает после холодной пластической деформации.
Обработка холодом
Новый вид термической обработки, для повышения твердости стали путем перевода остаточного аустенита закаленной стали в мартенсит. Это выполняется при охлаждении стали до температуры нижней мартенситной точки.
Методы поверхностного упрочнения
Поверхностной закалкой называют процесс термической обработки, представляющий собой нагрев поверхностного слоя стали до температуры выше критической и последующее охлаждение с целью получения в поверхностном слое структуры мартенсита.
Различают следующие виды: индукционная закалка; закалка в электролите, закалка при нагреве токами высокой частоты(ТВЧ), закалка с газопламенным нагревом.
Индукционная закалка основана на физическом явлении, сущность которого заключается в том, что электрический ток высокой частоты, проходя по проводнику, создает вокруг него электромагнитное поле. На поверхности детали, помещенной в этом поле, индуцируются вихревые токи, вызывая нагрев металла до высоких температур. Это обеспечивает возможность протекания фазовых превращений.
В зависимости от способа нагрева индукционная закалка подразделяется на три вида:
одновременный нагрев и закалка всей поверхности (используется для мелких деталей);
последовательный нагрев и закалка отдельных участков (используется для коленчатых валов и подобных им деталей);
непрерывно-последовательный нагрев и закалка перемещением (используется для длинных деталей).
Газопламенная закалка. Процесс газопламенной закалки заключается в быстром нагреве поверхности детали ацетилено-кислородным, газокислородным или кислородно-керосиновым пламенем до температуры закалки с последующим охлаждением водой или эмульсией.
Закалка в электролите. Процесс закалки в электролите заключается в следующем: в ванну с электролитом (5–10% раствор кальцинированной соли) опускают закаливаемую деталь и пропускают ток напряжением 220–250 В. В результате чего происходит нагрев детали до высоких температур. Охлаждение детали производят или в том же электролите (после выключения тока) или в специальном закалочном баке.
Термомеханическая обработка
Термомеханическая обработка (Т.М.О.) – новый метод упрочнения металлов и сплавов при сохранении достаточной пластичности, совмещающий пластическую деформацию и упрочняющую термическую обработку (закалку и отпуск). Различают три основных способа термомеханической обработки.
Низкотемпературная термомеханическая обработка (Н.Т.М.О) основана на ступенчатой закалке, то есть пластическая деформация стали осуществляется при температурах относительной устойчивости аустенита с последующей закалкой и отпуском.
Высокотемпературная термомеханическая обработка (В.Т.М.О) при этом пластическую деформацию проводят при температурах устойчивости аустенита с последующей закалкой и отпуском.
Предварительная термомеханическая обработка (П.Т.М.О) деформация при этом может осуществляться при температурах Н.Т.М.О и В.Т.М.О или при температуре 20єС. Далее осуществляется обычная термическая обработка: закалка и отпуск.
Назначение и виды химико-термической обработки
Химико-термической обработкой называют процесс, представляющий собой сочетание термического и химического воздействия с целью изменения состава, структуры и свойств поверхностного слоя стали.
Цель химико-термической обработки: повышение поверхностной твердости, износостойкости, предела выносливости, коррозионной стойкости, жаростойкости (окалиностойкости), кислотоустойчивости.
Наибольшее применение в промышленности получили следующие виды химико-термической обработки: цементация; нитроцементация; азотирование; цианирование; диффузионная металлизация.
Цементация – это процесс поверхностного насыщения углеродом, произведенный с целью поверхностного упрочнения деталей.
В зависимости от применяемого карбюризатора цементация подразделяется на три вида: цементация твердым карбюризатором; газовая цементация (метан, пропан, природный газ).
Газовая цементация. Детали нагревают до 900–950єС в специальных герметически закрытых печах, в которые непрерывным потоком подают цементующий углеродосодержащий газ [естественный (природный) или искусственный].
Процесс цементации в твердом карбюризаторе заключается в следующем. Детали, упакованные в ящик вместе с карбюризатором (смесь древесного угля с активизатором), нагревают до определенной температуры и в течении длительного времени выдерживают при этой температуре, затем охлаждают и подвергают термической обработке.
Цементации любым из рассмотренных выше способов подвергаются детали из углеродистой и легированной стали с содержанием углерода не более 0,2%. Цементация легированных сталей, содержащих карбидообразующие элементы Cr, W, V, дает особо хорошие результаты: у них, кроме повышения поверхностной твердости и износостойкости, увеличивается также предел усталости.
Азотирование – это процесс насыщения поверхностного слоя различных металлов и сплавов, стальных изделий или деталей азотом при нагреве в соответствующей среде. Повышается твердость поверхности изделия, выносливости, износостойкости, повышение коррозионной стойкости.
Цианирование – .насыщение поверхностного слоя изделий одновременно углеродом и азотом.
В зависимости от используемой среды различают цианирование: в твердых средах; в жидких средах; в газовых средах.
В зависимости от температуры нагрева цианирование подразделяется на низкотемпературное и высокотемпературное.
Цианирование в жидких средах производят в ваннах с расплавленными солями.
Цианирование в газовых средах (нитроцементация). Процесс одновременного насыщения поверхности детали углеродом и азотом. Для этого детали нагревают в среде, состоящей из цементующего газа и аммиака, то есть нитроцементация совмещает в себе процессы газовой цементации и азотирования.
Диффузионное насыщение металлами и металлоидами
Существуют и применяются в промышленности способы насыщения поверхности деталей различными металлами (алюминием, хромом и др.) и металлоидами (кремнием, бором и др.) Назначение такого насыщения – повышение окалиностойкости, коррозионностойкости, кислотостойкости, твердости и износостойкости деталей. В результате поверхностный слой приобретает особые свойства, что позволяет экономить легирующие элементы.
Алитирование – процесс насыщения поверхностного слоя стали алюминием для повышения жаростойкости (окалиностойкости) и сопротивления атмосферной коррозии.
Алитирование проводят в порошкообразных смесях, в ваннах с расплавленным алюминием, в газовой среде и распыливанием жидкого алюминия.
Хромирование – процесс насыщения поверхностного слоя стали хромом для повышении коррозионной стойкости и жаростойкости, а при хромировании высокоуглеродистых сталей – для повышения твердости и износостойкости.
Силицирование – процесс насыщения поверхностного слоя детали кремнием для повышения коррозионной стойкости и кислотостойкости. Силицированию подвергают детали из низко- и среднеуглеродистых сталей, а также из ковкого и высокопрочного чугунов.
Борирование – процесс насыщения поверхностного слоя детали бором. Назначение борирования – повысить твердость, сопротивление абразивному износу и коррозии в агрессивных средах, теплостойкость и жаростойкость стальных деталей. Существует два метода борирования: жидкостное электролизное и газовое борирование.
Сульфидирование – процесс насыщения поверхностного слоя стальных деталей серой для улучшения противозадирных свойств и повышения износостойкости деталей.
Сульфоцианирование – процесс поверхностного насыщения стальных деталей серой, углеродом и азотом. Совместное влияние серы и азота в поверхностном слое металла обеспечивает более высокие противозадирные свойства и износостойкость по сравнению насыщение только серой.
Термическая обработка чугуна
Термическую обработку чугунов проводят с целью снятия внутренних напряжений, возникающих при литье и вызывающих с течением времени изменения размеров и формы отливки, снижения твердости и улучшения обрабатываемости резанием, повышения механических свойств. Чугун подвергают отжигу, нормализации, закалке и отпуску, а также некоторым видам химико-термической обработки (азотированию, алитированию, хромированию).
Отжиг для снятия внутренних напряжений . Этому отжигу подвергают чугуны при следующих температурах: серый чугун с пластинчатым графитом 500 – 570єС; высокопрочный чугун с шаровидным графитом 550 – 650єС; низколегированный чугун 570 – 600єС; высоколегированный чугун 620 – 650єС. При этом отжиге фазовых превращении не происходит, а снимаются внутренне напряжения, повышается вязкость, исключается коробление и образование трещин в процессе эксплуатации.
Смягчающий отжиг (отжиг графитизирующий низкотемпературный). Проводят для улучшения обрабатываемости резанием и повышения пластичности. Его осуществляют продолжительной выдержкой при 680 – 700єС или медленным охлаждением отливок при 760 – 700єС. Для деталей сложной конфигурации охлаждение медленное, а для деталей простой формы – ускоренное.
Отжиг графитизирующий , в результате которого из белого чугуна получают ковкий чугун.
Нормализацию применяют для увеличения связанного углерода, повышения твердости, прочности и износостойкости серого, ковкого и высокопрочного чугунов. При нормализации чугун (отливки) нагревают выше температур интервала превращения 850 – 950єС и после выдержки, охлаждают на воздухе.
Закалке подвергают серый, ковкий и высокопрочный чугун для повышения твердости, прочности и износостойкости. По способу выполнения закалка чугуна может быть объемной непрерывной, изотермической и поверхностной.
При объемной непрерывной закалке чугун нагревают до температуры 850 – 950єС. Затем выдерживают для прогрева и полного растворения углерода. Охлаждение осуществляют в воде или масле. После закалки проводят отпуск при температуре 200 – 600єС. В результате повышается твердость, прочность и износостойкость чугуна.
При изотермической закалке чугуны нагревают так же, как и при объемной непрерывной закалке, выдерживают от 10 до 90 минут и охлаждают в расплавленной соли при 200 – 400єС, и после выдержки охлаждают на воздухе.
Поверхностная закалка с нагревом поверхностного слоя кислородно – ацетиленовым пламенем, токами высокой частоты или в электролите. Температура нагрева 900 – 1000єС. Охлаждение в воде, масле или масляной эмульсии.
Старение применяют для стабилизации размеров литых чугунных деталей, предотвращения коробления и снятия внутренних напряжений. Обычно старении проводят после грубой механической обработки. Различают два вида старения: естественное и искусственное.
Естественное старении осуществляется на открытом воздухе или в помещении. Изделия после литья выдерживаются в течении 6 – 15 месяцев.
Искусственное старение осуществляется при повышенных температурах; длительность – несколько часов. При искусственном старении отливки чугуна загружают в печь, нагретую до 100 – 200є С, нагревают до температуры 550 – 570єС со скоростью 30 – 60єС в час, выдерживаю 3 – 5 часов и охлаждают вместе с печью со скоростью 20 – 40єС в час до температуры 150 – 200єС, а затем охлаждают на воздухе.
Химико-термическая обработка чугуна
Для повышения поверхностной твердости и износостойкости серые чугуны подвергают азотированию. Чаще азотируют серые перлитные чугуны, легированные хромом, молибденом, алюминием. Температура азотирования 550 – 580єС, время выдержки 30 – 70 часов. Кроме азотирования, повышения поверхностной твердости и износостойкости легированного серого перлитного чугуна можно достигнуть газовым и жидкостным цианированием при температуре 570єС. Для повышения жаростойкости чугунные отливки можно подвергать алитированию, а для получения высокой коррозионной стойкости в кислотах – силицированию.
Термическая обработка сплавов цветных металлов
Алюминиевые сплавы
Алюминиевые сплавы подвергаются трем видам термической обработки: отжигу, закалке и старению. Основными видами отжига являются: диффузионный, рекристаллизационный и термически упрочненных сплавов.
Гомогенизацию применяют для выравнивания химической микронеоднородности зерен твердого раствора. Для выполнения гомогенизации алюминиевые сплавы нагревают до 450 – 520єС и выдерживают при этих температурах от 4 до 40 часов; после выдержки – охлаждение вместе с печью или на воздух. В результате этого структура становится более однородной и повышается пластичность.
Рекристаллизационный отжиг для алюминия и сплавов на ег основе применяют гораздо шире, чем для стали. Это объясняется тем, что такие металлы, как алюминий и медь, а так же многие сплавы на их основе, не упрочняются закалкой и повышение механических свойств может быть достигнуто только холодной обработкой давлением, а промежуточной операцией при такой обработке является рекристаллизационный отжиг. Температура рекристаллизационного отжига алюминиевых сплавов 300 – 500єС выдержка 0,5 – 2 часа.
Отжиг термически упрочненных сплавов применяют для полного снятия упрочнения, он проводится при температурах 350 – 450єС с выдержкой 1 – 2 часа и последующим достаточно медленным охлаждением.
После закалки прочность сплава несколько повышается, а пластичность не изменяется. После закалки алюминиевые сплавы подвергают старению , при котором происходит распад пересыщенного твердого раствора.
Деформируемые алюминиевые сплавы
В закаленном состоянии дуралюмины пластичны и легко деформируются. После закалки и естественного или искусственного старения прочность дуралюмина резко повышается.
Литейные алюминиевые сплавы
Для литейных алюминиевых сплавов используют различные виды термической обработки в зависимости от химического состава. Для упрочнения литейные алюминиевые сплавы подвергают закалке с получением пересыщенного твердого раствора и искусственному старению, а также только закалке без старения с получением в закаленном состоянии устойчивого твердого раствора.
Магниевые сплавы
Магниевые сплавы, так же как и алюминиевые, подвергают отжигу, закалке и старению. Для выравнивания химической микронеоднородности зерен твердого раствора путем диффузии слитки магниевых сплавов подвергают гомогенизации при температурах 350 – 400єС с выдержкой 18 – 24 часа. Полуфабрикаты деформируемых магниевых сплавов подвергают рекристаллизационному отжигу при температуре ≈ 350єС, а также при боле низких температурах 150 – 250єС отжигу для снятия остаточных напряжений.
Магниевые сплавы подвергают закалке, или закалке и искусственному старению. При температуре 20С в закаленных магниевых сплавах никаких изменений не происходит, то есть они не подвержены естественному старению.
Медь и медные сплавы
Термическая обработка меди. Деформирование меди сопровождается повышением ее прочности и понижением пластичности. Для повышения пластичности медь подвергают рекристаллизационному отжигу при 500 – 600єС, в результате которого пластичность резко повышается, а прочность снижается.
Термическая обработка латуней. Они подвергаются только рекристаллизационному отжигу при 600 – 700єС (для снятия наклепа). Охлаждают латуни при отжиге на воздухе или для ускорения охлаждения и лучшего отделения окалины в воде. Для латунных деталей, имеющих после деформации остаточные напряжения, в условиях влажной атмосферы характерно явление самопроизвольного растрескивания. Чтобы этого избежать латунные детали подвергают низкотемпературному отжигу при 200 – 300 С, в результате чего остаточные напряжения снимаются, а наклеп остается. Низкотемпературному отжигу особенно необходимо подвергать алюминиевые латуни, которые склонны к самопроизвольному растрескиванию.
Термическая обработка бронз. Для выравнивания химического состава бронзы подвергают гомогенизации при 700 – 750єС с последующим быстрым охлаждением. Для снятия внутренних напряжений отливки отжигают при 550єС. Для восстановления пластичности между операциями холодной обработки давлением подвергают рекристаллизационному отжигу при 600 – 700єС.
Алюминиевые бронзы с содержанием алюминия от 8 до 11%, испытывающие при нагреве и охлаждении фазовую перекристаллизацию, могут подвергаться закалке. В результате закалки повышается прочность и твердость, но снижается пластичность. После закалки следует отпуск при 400 – 650є С в зависимости о требуемых свойств. Также подвергают гомогенизации, а деформируемые полуфабрикаты – рекристаллизационному отжигу при 650 – 800єС.
Бериллиевую бронзу закаливают в воде от температуры 760 – 780єС; при это избыточная фаза выделиться не успевает, и после закалки сплав состоит из пересыщенного твердого раствора и обладает небольшой твердостью и прочностью и большой пластичностью. После закалки проводится отпуск (старение) при 300 – 350єС выдержкой 2 часа. Для повышения устойчивости пересыщенного твердого раствора и облегчения закалки бериллиевые бронзы дополнительно легируют никелем.
Титановые сплавы
Титановые сплавы подвергают рекристаллизационному отжигу и отжигу с фазовой перекристаллизацией, атак же упрочнению термической обработкой – закалкой и старением. Для повышения износостойкости и задиростойкости титановые сплавы подвергают азотированию, цементации или окислению.
Рекристаллизационный отжиг применяют для титана и сплавов для снятия наклепа после холодной обработки давлением. Температура рекристаллизационного отжига 520 – 850єС в зависимости от химического состава сплава и вида полуфабриката.
Отжиг с фазовой перекристаллизацией применяют с целью снижения твердости, повышения пластичности, измельчения зерна, устранения структурной неоднородности. Применяют простой, изотермический и двойной отжиг; температура нагрева при отжиге 750 – 950єС в зависимости от сплава.
При изотермическом отжиге после выдержки при температуре отжига детали охлаждают до 500 – 650єС (в зависимости от сплава) в той же печи иди переносят в другую печь и выдерживают определенное время, и охлаждают на воздухе. При изотермическом отжиге сокращается продолжительность отжига, а пластичность получается более высокой.
При двойном отжиге детали нагревают до температуры отжига, выдерживают и охлаждают на воздухе. Затем повторно нагреваю до 500 – 650єС, выдерживают и охлаждают на воздухе. Двойной отжиг по сравнению с изотермическим повышает предел прочности при незначительном снижении пластичности и сокращает длительность обработки.
Из всех видов химико-термической обработки титановых сплавов наибольшее распространение получило азотирование, осуществляемое в среде азота или в смеси азота и аргона при температурах 850 – 950 С в течении 10 – 50 часов. Детали из титановых сплавов после азотирования обладают хорошими антифрикционными свойствами.
Заключение
Термическая обработка является одной из основных, наиболее важных операций общего технологического цикла обработки, от правильного выполнения которой зависит качество (механические и физико-химические свойства) изготовляемых деталей машин и механизмов, инструмента и другой продукции. Разработаны и рационализированы технологические процессы термической обработки серых и белых чугунов, сплавов цветных металлов
Перспективным направлением совершенствования технологии термической обработки является установка агрегатов для термической обработки в механических цехах, создание автоматических линий с включением в них процессов термической обработки, а также и разработка методов, обеспечивающих повышение прочностных свойств деталей, их надежности и долговечности.
Литература
Б.В. Захаров. В.Н. Берсенева «Прогрессивные технологические процессы и оборудование при термической обработке металлов» М. «Высшая школа» 1988 г.
В.М. Зуев «Термическая обработка металлов» М. Высшая школа 1986 г.
Б.А. Кузьмин «Технология металлов и конструкционные материалы» М. «Машиностроение» 1981 г.
В.М. Никифоров «Технология металлов и конструкционные материалы» М. «Высшая школа» 1968 г.
А.И. Самохоцкий Н.Г. Парфеновская «Технология термической обработки металлов» М. Машиностроение 1976 г.
Выбор материала и разработка технологического процесса термической обработки плашки
Условие работы плашка, резьбонарезного инструмента для нарезания наружной резьбы вручную или на металлорежущем станке. Характеристика стали, ее химические, механические и других свойства. Методы контроля режимов термической обработки и качества изделия.
Сталь марки 18ХГТ: хромомарганцевая сталь содержит 0,18% углерода, до 1% хрома, марганца. Последовательность операции предварительной и окончательной термообработки деталей. Режим операций предварительной и окончательной термообработки деталей.
Теоретические основы термической обработки стали. Диффузионный и рекристаллизационный отжиг. Закалка как термообработка, при которой сталь приобретает неравновесную структуру и повышенаяеться твердость стали. Применение термической обработки на практике.
Сущность назначения резца и его применение. Анализ технологических свойств и химического состава быстрорежущих сталей. Этапы технологического процесса предварительной и упрочняющей термической обработки, выбор приспособлений, дефекты и их устранение.
Основы технологии термической обработки металлов и сплавов. Термическая обработка - этап технологического процесса изготовления деталей. Улучшение обрабатываемости материалов давлением или резанием. Формирования технических и электрических свойств.
Описание порядка применения закалки углеродистых сталей и определение температуры закалки согласно заданию. Вычисление необходимой продолжительности закалки. Назначение отжига и определение его времени согласно заданию. Правила составления протокола.
Формирование свойств материала детали. Воздействие механической обработки на свойства материала заготовок. Влияние смазочно-охлаждающей жидкости (СОЖ).
Расшифровка марки стали. Характер влияния углерода и легирующих элементов заданной стали на положение критических точек. Выбор и обоснование последовательности операции предварительной и окончательной термообработки деталей. Режим термообработки деталей.
Теория термической обработки. Превращения в стали при нагреве и охлаждении. Отжиг и нормализация. Дефекты термической обработки. Дефекты при отжиге и нормализации. Дефекты при закалке. Химико-термическая обработка и поверхностное упрочнение стали.
Теория и технология термической обработки. Виды термической обработки. Отжиг, нормализация, закалка, старение, улучшение. Химико – термическая обработка. Её виды. Композиционные материалы.
Правила обработки деталей резанием – удаление с заготовки с помощью режущего инструмента припуска, последовательно приближая ее форму и размеры к требуемым, превращая ее в готовое изделие. Управление качеством поверхности химико-термической обработкой.
Ознакомление с методикой разработки технологического процесса термической обработки деталей: автомобилей, тракторов и сельскохозяйственных машин. Расшифровка марки заданной стали, описание ее микростуктуры, механических свойств до термической обработки.
Сталь марки 20ХНР - хромоникелевая сталь с содержанием углерода 0,20%, до 1% хрома, никеля и бора. Режим операций предварительной и окончательной термообработки деталей - температура нагрева и микроструктура в нагретом состоянии, охлаждающая среда.