Biblioteca científica electrónica. Implementación del concepto de "producción ajustada" en JSC "Nizhnekamskshina"
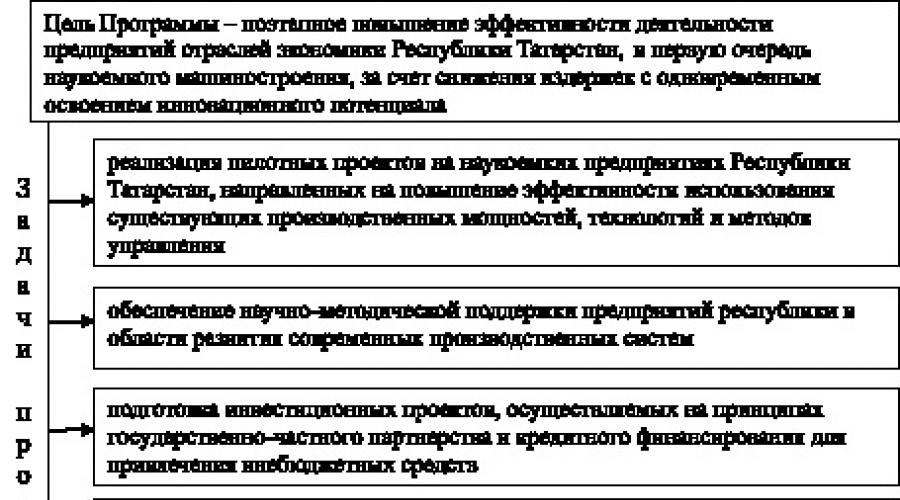
El efecto económico de la manufactura esbelta de una sola unidad de negocio de TechnoNICOL es comparable al presupuesto promedio de un programa objetivo regional
/junio, 2014/ Más de 200 millones de rublos al año: este es el efecto económico de implementar los principios de producción ajustada en las plantas de fabricación lana de roca Corporación TechnoNIKOL.
TechnoNIKOL Corporation es uno de los líderes en Rusia en términos de productividad laboral. La productividad promedio en la empresa es de 12 millones de rublos de ingresos por persona por año, mientras que las empresas en Rusia se consideran altamente productivas en las que este indicador comienza con 3 millones de rublos. Uno de los secretos del éxito en la lucha por aumentar el nivel de productividad laboral es el uso activo de los principios de producción ajustada en las empresas de la empresa.
Según el director de desarrollo sistema de producción Tatiana Bertova, Inclinarse desde 2010, se ha introducido, entre otras cosas, en seis unidades de producción de la dirección de Aislamiento de minerales, que se encuentran en Ucrania, el Distrito Federal Central, la región del Volga, Siberia, así como en los Urales y el Lejano Oriente. En todas las plantas se presta gran atención a la formación en sistemas y herramientas de producción ajustada, que abarca a todos, tanto al personal operativo como a la alta dirección.
Una parte integral de la producción ajustada de la dirección "Aislamiento Mineral" es el trabajo con mejoras, en el que participan todos los empleados de la SBU. Anualmente se implementan más de dos mil propuestas de racionalización de trabajadores y especialistas técnicos e ingenieros. Estos pueden ser tanto pequeñas mejoras como proyectos innovadores con un gran efecto económico. Por ejemplo, la mejora de los procesos de cambio de línea de producción permitió reducir el tiempo de cambio de un tipo de producto a otro en un 60% durante tres años con un efecto económico de 150 millones de rublos por año, así como reducir el tiempo para la sustitución prevista de elementos de equipamiento en un 25% con un efecto económico de 50 millones de rublos al año. Al construir un sistema TRM (operación y mantenimiento de equipos) en las plantas, se redujo en un 25% el tiempo de inactividad no programado de los equipos.
La eliminación de las pérdidas por sobreproducción salvó a las empresas del uso irracional de los recursos energéticos y redujo el costo de mantenimiento de los almacenes. La logística del almacén, calculada en segundos, eliminó las pérdidas por transporte innecesario y, en general, se volvió un 90 % más eficiente. La adquisición de materias primas justo a tiempo minimizó las pérdidas que ocurrían anteriormente cuando se acumulaban excesos de existencias. Rendimiento del almacén productos terminados aumentó en un 61%.
La reducción de pérdidas en la producción de lana de roca también se ve facilitada por la mejora de los procesos comerciales, incluida su automatización utilizando sistemas de información nivel mundial. Se han realizado mejoras en procesos como la planificación de ventas y operaciones, la gestión mantenimiento y reparar Equipo de producción, planificación de la producción en fábricas, gestión de pedidos de clientes. Debido a las innovaciones, el servicio al cliente mejoró en un 71%.
El uso anual de herramientas de calidad integradas permite que SBE "Mineral Isolation" aumente la producción de productos de aislamiento térmico de alta calidad.
El efecto económico general de la introducción de los principios de fabricación ajustada en las plantas de producción de lana de roca de TechnoNIKOL Corporation ascendió a más de 200 millones de rublos por año, lo que es comparable al presupuesto promedio del programa objetivo regional. Según los expertos de TechnoNICOL Corporation, la difusión activa de las prácticas de fabricación ajustada en las empresas rusas permitirá acercarse a la implementación del decreto del Presidente de la Federación Rusa "Sobre la política económica estatal a largo plazo" en términos de aumento productividad laboral para 2018 en un 50% (en comparación con el nivel de 2011).
TechnoNIKOL Corporation es uno de los mayores fabricantes y proveedores de materiales para techos, impermeabilizantes y materiales de aislamiento térmico. Trabajando en el mercado de materiales de construcción desde 1992, la empresa ha acumulado una experiencia significativa en la producción de materiales de aislamiento hidráulico, acústico y térmico, y hoy ofrece al mercado últimos materiales y tecnologías que combinan experiencia mundial y desarrollos propios Centro de ciencia. La cooperación con institutos de diseño y talleres de arquitectura permite a la Corporación responder con flexibilidad y rapidez a los cambios en las demandas de los consumidores. Hoy, TechnoNIKOL Corporation tiene 38 sitios de producción en Rusia, Ucrania, Bielorrusia, Lituania, República Checa e Italia, su propia red de ventas de 180 sucursales y oficinas de representación en 36 países. Los clientes de la Corporación son más de 500 socios comerciales y más de 50.000 organizaciones y individuos en Rusia, los países de la CEI, los Estados Bálticos, Europa Oriental y Central.
Enviar su buen trabajo en la base de conocimiento es simple. Utilice el siguiente formulario
Los estudiantes, estudiantes de posgrado, jóvenes científicos que utilizan la base de conocimientos en sus estudios y trabajos le estarán muy agradecidos.
Alojado en http://www.allbest.ru/
Introducción
La manufactura esbelta es un sistema para organizar y administrar el desarrollo de productos, operaciones, relaciones con proveedores y clientes, en el que los productos se fabrican en estricta conformidad con los requisitos del cliente y con menos defectos en comparación con los productos fabricados con tecnología de producción en masa. Esto reduce el costo de mano de obra, espacio, capital y tiempo.
Filosofía de la Manufactura Esbelta:
Determinar el valor de cada familia de productos desde el punto de vista del cliente;
Identificar todas las etapas del flujo de valor para cada familia de productos y eliminar, en la medida de lo posible, las actividades que no crean valor;
Alinear las operaciones de creación de valor en una secuencia estricta que asegure el movimiento fluido del producto en el flujo dirigido al cliente;
Al final de la formación del flujo, creando una oportunidad para que los clientes "saquen" valor de la etapa anterior;
Una vez que se ha identificado el valor, se han identificado los flujos de valor, se han eliminado las etapas que causan desperdicio y se ha establecido el sistema de flujo y extracción, repita todo el proceso tantas veces como sea necesario para lograr un estado de perfección donde absoluto se crea valor y no hay desperdicio.
El punto de partida del Pensamiento Lean es el valor. El valor solo puede ser determinado por el usuario final, quien, por un precio determinado y en un momento determinado, es capaz de satisfacer las necesidades de los compradores. El valor lo crea el fabricante. Desde el punto de vista del consumidor, para eso existe el fabricante.
"Lean Manufacturing" es un componente del vasto sistema de gestión japonés Kaizen (mejora continua) basado en las ideas de Deming, Juran, Feigenbaum y sus homólogos japoneses Ishikawa, Taguchi y Shingu. Estudio cuidadoso de otros conceptos, presentados como una nueva última palabra en la construcción de una gestión eficaz, expuestos en muchos libros que llenaron los estantes domésticos, como BSC (Balanced Scorecard), ABC (Contabilidad basada en el enfoque de procesos), BPR (Business Process Reengineering). ) ), Agile Manufacturing System (sistema de fabricación de respuesta rápida), Synchronous Manufacturing System (sistema de fabricación sincrónica), son encarnaciones menos efectivas de las mismas ideas. Es decir, se trata simplemente de sistemas que facilitan el paso de una gestión empresarial estricta y centralizada a un negocio basado en la implicación de los empleados y el predominio de los enfoques de gestión horizontales sobre los verticales. Desde este punto de vista, varias variantes clásicas de MRP y ERP también brindan soporte para conceptos comerciales ineficientes que se están convirtiendo en cosa del pasado. Están siendo reemplazados por varias versiones de la presentación Kaizen, uno de cuyos componentes más importantes es Lean Production.
El tema de este trabajo es "Lean production" en la empresa.
El propósito del proyecto de graduación es determinar la efectividad de la implementación del concepto de "Producción ajustada" en la empresa. Para lograr el objetivo, es necesario resolver las siguientes tareas:
Estudiar el concepto de "producción ajustada", aspectos teóricos y metodológicos del concepto;
Historia del origen, principios y herramientas;
Considere los tipos de pérdidas y métodos para evaluar la efectividad de la implementación de "Producción ajustada";
Analizar el proceso de implementación de "Lean production" en el ejemplo de JSC "Nizhnekamskshina";
Dé una evaluación del aumento de la eficiencia a partir de la introducción de la "producción ajustada" en la industria nacional.
El objeto del proyecto de graduación es OAO Nizhnekamskshina. La industria de los neumáticos es una de las ramas de desarrollo dinámico de la industria petroquímica. El suministro estable de materias primas y las ventas oportunas de productos terminados permitieron a OAO Nizhnekamskshina mantener su posición de liderazgo frente a la feroz competencia entre las fábricas de neumáticos rusas.
JSC "Nizhnekamskshina" es la empresa más grande en la industria de neumáticos, ocupa una posición de liderazgo entre los fabricantes de neumáticos en Federación Rusa y países de la CEI. La empresa produce neumáticos para automóviles de las marcas KAMA, KAMA EURO. El surtido incluye más de 120 tamaños y modelos de neumáticos, incluidos los desarrollados por los especialistas del Centro Científico y Técnico "Kama".
El 22 de julio de 2007, el neumático número 300 millones salió de la línea de montaje de OAO Nizhnekamskshina. Era el modelo KAMA EURO 228, medida 205/75 R15, diseñado para autos Chevrolet Niva.
La empresa es el primer proveedor en el mercado ruso,
recibió el estatus de "homologador" de neumáticos en las plantas de automóviles Fiat, Volkswagen, Skoda.
La base teórica del estudio fueron los trabajos de autores que estudian la gestión de calidad, el concepto de producción ajustada, no solo como un sistema en su conjunto, sino también en relación con la industria de neumáticos, como Boronenkova S.A., Melnik L.A., Loganina VI y etc.
La base de información consta de materiales reglamentarios y legales, literatura especial y materiales de base práctica.
La importancia práctica del trabajo radica en el hecho de que los resultados del estudio se pueden utilizar tanto en una comprensión general del concepto de "producción ajustada" como en su aplicación práctica.
El trabajo utilizó métodos de investigación como comparativo, dinámico, tabular, gráfico, de red, así como el método de análisis y otros métodos estadísticos de gestión de la calidad.
Este trabajo consta de tres capítulos: el primero contiene los aspectos teóricos y metodológicos del concepto de "Lean production", el segundo caracteriza las actividades generales, el sistema de gestión de calidad, el proceso de implementación de "Lean production" en OAO Nizhnekamskshina, el tercero incluye formas de aumentar la eficiencia a partir de la introducción de “Lean production” en la industria nacional.
Por lo tanto, el concepto de manufactura esbelta está ganando cada vez más popularidad en Rusia. A menudo, la introducción de nuevos sistemas de producción encuentra serias resistencias por parte del personal de la empresa. Muchas empresas manufactureras están interesadas en reducir costos, aumentar la productividad y mejorar los indicadores de calidad.
1. Aspectos teóricos y metodológicos del concepto de “Lean production”
1.1 La historia del origen del “Lean Manufacturing”
El término "producción ajustada" (producción "lean"), que más tarde comenzó a traducirse como "producción ajustada", fue introducido en la circulación científica por John Krafchik en el libro "La máquina que cambió el mundo", que se publicó en 1990. . Sin embargo, los orígenes de la filosofía de la manufactura esbelta se remontan a principios del siglo XX.
Las ideas de "fabricación ajustada" fueron formuladas e implementadas por primera vez por Henry Ford. Pero estas ideas tenían la naturaleza de eventos dispares y no afectaron la perspectiva misma de los trabajadores. En 1913 (algunas fuentes dicen que en 1908), Henry Ford creó el primer modelo de flujo de trabajo del mundo, que se basaba en el movimiento de una pieza de trabajo entre procesos mediante un transportador. Se creó una producción fluida y de bajo costo, y el automóvil de la marca Ford-T no tuvo competidores en el mundo en términos de precio, calidad y nivel de servicio. Pero las ideas de Henry Ford no se generalizaron, ya que la economía del país se desarrolló dinámicamente, el mercado se cerró a otros estados y hubo oportunidades para un desarrollo extenso. Japón no tuvo tales oportunidades y, por lo tanto, tomó de inmediato el camino del uso racional de los recursos, eliminando todo tipo de pérdidas, aumentando la iniciativa y la responsabilidad de los trabajadores y mejorando constantemente y sistemáticamente la calidad y los procedimientos.
La compañía de automóviles Toyota se ha convertido en el centro para el desarrollo y la implementación de los principios y métodos de "fabricación ajustada", tomando prestado todo lo mejor de los sistemas de producción de empresas de todo el mundo. Toyota Toyota (Toyota Motor Corporation, Toyota Jidosha KK) es una empresa automovilística japonesa que forma parte del grupo financiero e industrial Toyota. Una de las empresas automotrices más grandes del mundo. Lanza sus productos bajo varias marcas, incluyendo Daihatsu. La sede se encuentra en Toyota (Toyota).
El comienzo de la historia de Toyota se puede considerar en 1933, cuando Toyoda Automatic Loom Works, que originalmente no estaba relacionado con los automóviles y se dedicaba a la industria textil, abrió un departamento de automóviles. Fue inaugurado por el hijo mayor del propietario de la empresa Sakichi Toyoda (Sakichi Toyoda) Kiichiro Toyoda (Kiichiro Toyoda), quien más tarde llevó a la marca de automóviles Toyota a la fama mundial. El capital inicial para el desarrollo de los primeros coches fue el dinero recibido por la venta de los derechos de patente de las máquinas de hilar a la empresa inglesa Platt Brothers.
En 1935, se completó el trabajo en el primer automóvil de pasajeros, llamado Modelo A1 (más tarde AA), y el primer camión, el Modelo G1, y en 1936 se puso en producción el Modelo AA. Al mismo tiempo, se realizó la primera entrega de exportación: cuatro camiones G1 fueron al norte de China. Un año más tarde, en 1937, el departamento de automóviles se convirtió en una empresa separada, llamada Toyota Motor Co., Ltd.
La noción de trabajo que no agrega valor, más tarde incorporada en el término MUDA, fue introducida por Frank Gilbert (1868-1924), quien una vez observó que un albañil que erigía un muro tenía el efecto secundario de agacharse para recoger el siguiente ladrillo. . Después de estudiar los pasos necesarios para que un albañil complete un trabajo determinado, Frank Gilbert sugirió apilar ladrillos en un pedestal al lado del trabajador. Tal, a primera vista, una solución elemental al problema condujo a un aumento de casi tres veces en la velocidad de trabajo y una reducción significativa en el esfuerzo dedicado a ello.
En 1934, Toyoda se reorganizó en Japón. En adelante, la empresa pasó a ser conocida como Toyota, y los principales productos que se fabricaban en sus fábricas no eran textiles, sino automóviles. Kiichiro Toyoda, el fundador de Toyota Motor Corp., estaba a cargo de la producción de motores y constantemente descubría más y más problemas asociados con su producción. La dirección principal para mejorar la calidad, reconoció, fue el estudio intensivo de cada etapa del proceso de producción. En aquellos tiempos de la posguerra, Japón estaba en ruinas y el país necesitaba autos nuevos. Pero el problema era que la demanda no era lo suficientemente fuerte como para justificar la compra de una poderosa línea de producción, al estilo de Ford. Se necesitaban muchos tipos diferentes de vehículos (turismos, camiones pequeños y medianos, etc.), pero la demanda de vista específica el coche era pequeño. Los japoneses tuvieron que aprender a trabajar con eficacia creando una multitud de diferentes modelos en condiciones de baja demanda para cada modelo. Nadie había resuelto tal problema antes que ellos, ya que la eficiencia se entendía exclusivamente en términos de producción en masa.
En 1936, Toyota ganó su primera licitación para la producción de camiones, durante la ejecución de este pedido, se identificaron nuevos problemas en el proceso tecnológico de fabricación de automóviles. La necesidad de solucionarlos impulsó a Kiichiro Toyoda a crear los grupos “KAIZEN”, cuya tarea principal era el estudio continuo de todas las etapas del proceso productivo con el posterior desarrollo e implementación de métodos para su mejora.
En el Japón de la posguerra, el nivel de demanda en la economía estaba en un nivel bajo, por lo que no era posible reducir el costo de los productos fabricados en las fábricas japonesas a través de economías de escala.
El padre de la manufactura esbelta es Taiichi Ohno (1912-1990), quien comenzó a trabajar en Toyota Motor Corporation en 1943, integrando las mejores prácticas mundiales. Taiichi Ohno era un empleado de Toyota Corporation y poco a poco fue ascendiendo hasta llegar a la cabeza de la empresa. Como ingeniero, Taiichi Ohno desarrolló el Sistema de Gestión de Costos Kanban, la Manufactura Esbelta y el Justo a Tiempo. La empresa todavía se adhiere a este sistema. En 1949 fue nombrado jefe del taller de máquinas. A principios de la década de 1950, cuando murió Kiichiro Toyoda, Taiichi Ono concibió y luego fabricó un revolucionario sistema de gestión de la producción ("kanban") para esos años, con la ayuda de los japoneses pudieron eliminar cualquier tipo de desperdicio del proceso de producción. Desarrollos científicos tanto en la gestión como reequipamiento tecnico, siempre han sido muy valorados en esta empresa. A mediados de la década de 1950, comenzó a construir un sistema de organización de producción especial llamado Sistema de producción de Toyota o Sistema de producción de Toyota (TPS). El sistema Toyota se hizo conocido en la interpretación occidental como Lean production, Lean manufacturing, Lean. El término lean fue propuesto por John Krafcik, uno de los consultores estadounidenses. En la década de 1950, Toyota fue más activa en esta área. Gracias a la política científica e industrial avanzada, la empresa logró crear los vehículos todoterreno Land Cruiser y Crown. En 1954, Taiichi Ohno asumió como director de la planta de Toyota. Habiendo pasado algunos pasos más de la compleja escalera jerárquica japonesa, en 1975 se convirtió en el vicepresidente ejecutivo de toda la compañía, desde 1978, presidente de la junta directiva de Toyota Spinning and Weaving.
En los Estados Unidos, Taiichi Ohno escribió varios libros sobre el sistema, el más famoso de los cuales es The Toyota Production System.
Dejando la producción en masa. Taiichi Ohno presenta los pensamientos e ideas de tres gerentes del siglo XX: Henry Ford, Sakichi Toyoda y Kiichiro Toyoda.
Una contribución significativa al desarrollo de la teoría de la producción ajustada fue realizada por un asociado y asistente de Taiichi Ono, Shigeo Shingo, quien creó, entre otras cosas, el método SMED. Después de visitar los Estados Unidos y familiarizarse con el sistema de supermercados, Taiichi Ohno llegó a la conclusión de que la producción no debe basarse en volúmenes de ventas planeados (estrategia push), sino en demanda real (estrategia pull).
Fue Taiichi Ohno quien reunió todos los métodos avanzados para aumentar la eficiencia de la producción dentro de las paredes de la planta de Toyota.
Posteriormente, se le preguntó a Taiichi Ohno qué lo inspiró a crear el Sistema de Producción Toyota, a lo que respondió: Todo lo aprendí del libro de Henry Ford. Sin embargo, es la escala, la precisión y la mejora continua del Sistema de Producción de Toyota lo que lo ha convertido en un elemento fundamental de Lean Manufacturing, cuya principal ventaja radica en seguir su propia regla de oro: el máximo impacto proviene de la mejora continua.
En un principio, el concepto de manufactura esbelta se aplicó en industrias con manufactura discreta, principalmente en la industria automotriz. Luego se adaptó el concepto a las condiciones de producción continua, y luego en comercio, servicios, utilidades Publicas, el cuidado de la salud, el ejército y el sector público.
Gradualmente, la producción ajustada fue más allá de la empresa. Ahora, con la ayuda de la manufactura esbelta, optimizan el sector de servicios y el proceso de comunicación entre el consumidor y el proveedor, el proceso de entrega y servicio de productos. Las ideas de Lean son promovidas por conferencias internacionales y regionales periódicas, muchas de las cuales son iniciadas por el Lean Enterprise Institute (EE. UU.) y la Lean Enterprise Academy (Inglaterra). En muchos países, la expansión de la manufactura esbelta es apoyo gubernamental. En el período de máxima competencia y crisis creciente, las empresas de todo el mundo no tienen otro camino que utilizar las mejores tecnologías de gestión mundial para crear productos y servicios que maximicen la satisfacción del cliente en términos de calidad y precio.
En los últimos años, en Rusia, al igual que en los países de la antigua Unión Soviética, se ha producido un aumento significativo del interés por la dirección, la gestión empresarial y la transformación de las estructuras organizativas de las empresas. Desafortunadamente, este interés se ha manifestado recientemente. Recientemente, se han creado muchos conceptos y métodos de gestión nuevos en la práctica mundial: reingeniería de procesos comerciales (BPR), Gestión de calidad total (TQM), cuadro de mando integral (BSC), control estadístico de procesos (SPC), coaching, modelos de normas internacionales ISO 9000 , ISO 14000, HACCP, Five S's, Six Sigma y más. Desafortunadamente, los países del espacio postsoviético no tienen desarrollos propios en esta industria. No hay tradiciones, escuelas, experiencia de predecesores, ni sistemas de gestión bien establecidos. Por lo tanto, los gerentes rusos tienen que aprender mucho de los métodos extranjeros para sobrevivir y seguir siendo competitivos.
El concepto de “Lean Thinking and Manufacturing” (Lean Thinking and Manufacturing) ocupa uno de los lugares más destacados entre propuestas modernas sobre la gestión. Sin embargo, la cultura de nuestro país en su conjunto dista mucho del concepto de “frugalidad”. Esto puede evidenciarse por el hecho de que tenemos virutas almacenadas en talleres y espacios en blanco de metal, al aire libre; las cercas se construyen con madera natural y los muebles con aserrín; un taller se encuentra a pocos kilómetros de otro. Francamente, es imposible encontrar una explicación razonable para esto. Ventaja competitiva empresas rusas sólo puede garantizarse con alta calidad y bajo costo.
Así, hoy es necesario revisar toda la organización de la producción para eliminar todo tipo de pérdidas. Esto requiere la necesidad de un enfoque integrado, que incluya la calidad y el concepto, los métodos y las herramientas de la manufactura esbelta. Sobre la base de los problemas del funcionamiento de las empresas rusas, los expertos en el campo de la gestión de la calidad creen que el desarrollo del concepto de "Producción ajustada" y la aplicación de sus métodos es un factor extremadamente importante para mejorar el rendimiento de todas las partes del sistema de producción.
1.2 Principios y herramientas de "Lean production"
pérdida de producción ajustada
La manufactura esbelta es un concepto moderno de organización de la producción, destinado a reducir varios tipos pérdidas a través de la introducción de nuevas tecnologías de producción y gestión, acelerando la producción y asegurando la competitividad a largo plazo de la organización sin inversiones de capital significativas.
Principios de manufactura esbelta.
El principio de comprensión del valor implica la necesidad de comprender cuál es el valor para el usuario final. El valor es considerado como un concepto fuera de la producción. El valor es el punto de partida del Pensamiento Lean. El valor (de un producto, servicio) solo puede ser determinado por el usuario final. Sólo tiene sentido hablar de ella si quiere decir producto específico(bien o servicio o todo junto), que por un precio determinado y en un tiempo determinado es capaz de satisfacer las necesidades de los compradores. El valor lo crea el fabricante. Desde el punto de vista del consumidor, para eso existe el fabricante. Sin embargo, por varias razones, es muy difícil para un fabricante determinar exactamente cuál es el valor de un producto o servicio. Por regla general, los gerentes dedicaron la mayor parte de su atención a los sistemas de gestión: procesos, departamentos, empresas enteras, que incluían muchos productos a la vez. Lo que realmente necesita hacer es administrar todos los flujos de valor para cada producto o servicio.
El principio de control de pérdidas: prevé una reducción significativa o la eliminación completa de siete tipos principales de pérdidas:
1 - pérdida de sobreproducción;
2 - pérdidas por defectos y necesidad de reelaboración;
3 - pérdidas durante el movimiento;
4 - pérdidas durante el transporte;
5 - pérdidas por exceso de existencias;
6 - pérdidas por procesamiento excesivo;
7 - pérdida de tiempo de espera.
El principio del flujo de productos: se prevé que en lugar de mover el producto de un centro de trabajo a otro en lotes, es necesario crear un flujo en el que haya un movimiento continuo desde las materias primas hasta los productos terminados a través de células de producción especializadas.
El principio de atracción, que implica que en lugar de trabajar para un almacén, se le debe dar al consumidor la oportunidad de "sacar" productos terminados del sistema de producción. No se realiza ningún trabajo si sus resultados no pueden utilizarse inmediatamente en operaciones posteriores.
El principio de mejora continua: cuando se eliminen todas las pérdidas de los procesos tecnológicos y los productos se muevan sin problemas y de manera continua a medida que se entregan al consumidor, quedará claro que no habrá fin para el proceso de mejora continua, por ejemplo, reduciendo el tiempo de las operaciones, el costo, el área, los defectos y el alcance del trabajo.
Herramientas ajustadas
Para la implementación práctica de la manufactura esbelta, herramientas como:
5S - cinco pasos para mantener el orden. 5S se forma a partir de cinco palabras japonesas que forman la base para mantener las cosas limpias y ordenadas. La ausencia de 5S en una celda de trabajo indica:
Para baja eficiencia;
La presencia de pérdidas;
Débil autodisciplina y moralidad;
Mala calidad;
Altos precios;
Falta de disciplina en la entrega, tanto a consumidores internos como externos.
Los clientes potenciales no tomarán en serio a los proveedores que no practican las 5S. Estos cinco puntos de limpieza son el punto de partida para cualquier empresa que aspire a ser un fabricante responsable de clase mundial.
Hay cinco formas de evaluar el nivel de 5S en cada etapa:
Autoestima;
Evaluación de un consultor experto;
Evaluación de la gestión;
Una combinación de los primeros tres métodos;
Competiciones entre células de trabajo.
Kaizen: La idea central de kaizen es que no debe pasar un día sin que se mejore en una empresa. Kaizen no es una técnica única, es el paraguas bajo el cual viven la mayoría de las prácticas "exclusivas de Japón".
La comprensión japonesa de la gestión se reduce a lo siguiente: cumplir con los estándares y mejorarlos. El objetivo de la gestión dentro del mantenimiento es garantizar que todos los empleados de la empresa puedan seguir el procedimiento operativo estándar. Si los empleados no pueden seguir un procedimiento estándar, la gerencia debe educarlos o revisar y enmendar el estándar para que sea posible actuar de acuerdo con él. Cuanto más alto es el nivel de gestión, más tiempo se dedica a la mejora. El punto de partida para la mejora es reconocer que hay un problema. La complacencia y la complacencia son los enemigos jurados de kaizen. Por eso, la queja de un cliente debe tratarse como un regalo. Reconociendo que la denuncia
relacionado con el problema, tienes la oportunidad de mejorar la calidad del producto o
servicios. Al ignorar la queja, pierde esta oportunidad.
Kanban: método justo a tiempo. La especificación correcta de piezas y el producto terminado - con la cantidad correcta de ellos - en tiempo correcto- sin matrimonio. Un sistema justo a tiempo es un sistema de extracción: es una organización del proceso de este tipo cuando cada etapa posterior de producción consume todo lo necesario de la etapa anterior en el momento adecuado. El resultado de la etapa final de producción en este caso se basa en las solicitudes del consumidor o corresponde al programa de producción. Just-in-time proporciona al fabricante los siguientes beneficios:
Reducir el nivel de inventarios, materiales comprados y productos terminados en stock;
Reducción de las áreas ocupadas;
Crecimiento de la calidad del producto, reducción del matrimonio y procesamiento;
Mayor flexibilidad en la oferta de producción;
Crecimiento en productividad y factor de carga de equipos;
Participación del trabajador en la solución de problemas;
Buena relación con el consumidor.
Cambio rápido (SMED): producción flexible en minutos. Gracias a esta herramienta, la empresa ahorra recursos materiales y laborales, aumenta la productividad y agiliza el cumplimiento de pedidos.
Poka-yoke: “a prueba de tontos”: consiste en estructurar el proceso de tal manera que se elimine la posibilidad misma de error. Más ampliamente formulado por programadores: si el usuario puede cometer un error, definitivamente lo cometerá. De hecho, cualquier elemento importante no funcionará con la suficiente eficacia si no se tiene en cuenta previamente el factor humano.
Hay 10 tipos de errores humanos que conducen a defectos:
Olvido;
Incomprensión de las razones (ocurrencia de algo);
Subestimación de cualquier situación (o incapacidad para identificar cualquier objeto);
Inexperiencia;
Falta de voluntad (para seguir procedimientos y reglas);
inatención;
Lentitud (en tomar una decisión);
Falta de estándares;
Sorpresa;
Cometer deliberadamente un error (o sabotaje).
Las fuentes de defectos son los siguientes hechos:
operación perdida;
errores de procesamiento;
errores de posicionamiento de piezas;
Falta detalle;
Artículo incorrecto;
Procesamiento de la parte incorrecta;
Operación incorrecta en la parte correcta;
errores de configuración;
Instalación incorrecta de equipos y uso de herramienta o herramienta incorrecta.
Es necesario distinguir tres fases principales de la implementación de los principios de manufactura esbelta: estudiar la demanda, asegurar la continuidad de los flujos de valor y suavizarlos. Solo un estudio profundo de la demanda, los flujos de valor y cómo suavizarlos, junto con el uso de recomendaciones para administrar los flujos de valor, puede dar confiabilidad no solo al proceso de transformación en sí, sino también garantizar su sostenibilidad.
Fase de estudio de la demanda del consumidor. Es necesario, en primer lugar,
identificar quiénes son los consumidores de los resultados de algún trabajo, cuáles son
sus requisitos, solo después de eso podrá satisfacer al consumidor
demanda de señales para sus resultados. Se pueden utilizar varias herramientas y métodos para identificar y satisfacer la demanda de los consumidores, por ejemplo:
Cálculos de tiempo takt;
Cálculos de tono;
Cálculos de existencias de reserva y de reserva;
Aplicación del sistema 5S;
Uso de técnicas de resolución de problemas.
Fase de continuidad del flujo de valor. En esta etapa, tome Medidas necesarias para asegurar que los resultados del trabajo en cuestión lleguen a todos los clientes internos y externos de manera oportuna y en las cantidades adecuadas. Por ejemplo:
Creación de supermercados dentro de los procesos;
sistema Kanban;
Aplicación del principio FIFO (“first in, first out”);
Asegurar un equilibrio en la carga de las líneas de producción;
Estandarización del trabajo;
Diseño adecuado de las áreas de producción.
fase de suavizado. Finalmente, una vez que se ha identificado la demanda del cliente de resultados de trabajo y se ha establecido un proceso continuo para entregarlos, pasan a suavizarlo para garantizar una distribución uniforme y eficiente de los volúmenes de trabajo a lo largo de días, semanas y meses. Para ello, se utilizan las siguientes herramientas de suavizado de flujo:
Uso de un tablero para propuestas y discusión de ideas (pitch board visible);
Cajas niveladoras de carga (heijunka);
El uso de la logística.
Por lo tanto, la promoción de un sistema en particular es imposible sin comprenderlo. Por lo tanto, los empleados responsables de la eficacia de las principales actividades de la empresa deben estar provistos
oportunidad de aprender el concepto de manufactura esbelta.
La aplicación de los principios y el uso hábil de las herramientas de manufactura esbelta asegurará la competitividad en cualquier área de negocios. La conveniencia de introducir "Lean production" en la organización:
Alto costo de producción;
Productos de baja calidad;
Tecnologías obsoletas;
equipo obsoleto;
Alta intensidad energética;
Alto costo de producción;
Violación de los términos de las entregas;
Falta de personal calificado;
Alta competencia en el mercado.
Son las herramientas de la manufactura esbelta las que nos permiten resolver estos y otros problemas.
La organización se impone una tarea global: mejorar cada día, progresar día a día. Avanzar depende de los propios líderes, porque no basta con introducir herramientas, hay que cambiar la cultura de gestión, el comportamiento de los directivos.
1.3 Tipos de pérdidas y métodos para evaluar la efectividad de la implementación del concepto de "producción ajustada"
Lean manufacturing es un concepto de gestión que se centra en optimizar los procesos de negocio con la máxima orientación al mercado y teniendo en cuenta la motivación de cada empleado. La producción ajustada constituye la base de una nueva filosofía de gestión. El objetivo es: minimización de los costos laborales y términos de creación de nuevos productos; garantía de entrega de productos al cliente; máxima calidad en
costo mínimo. La idea principal es eliminar las pérdidas.
cualquier actividad que consume recursos pero no crea valor.
Taiichi Ohno, el fundador de este sistema, identificó siete tipos de desperdicio: por sobreproducción; tiempo debido a la espera; en caso de transporte innecesario; debido a pasos de procesamiento innecesarios; por exceso de stock; por movimientos innecesarios; por productos defectuosos. También hay otras dos fuentes de desperdicio: "carga que excede la capacidad" y "carga desigual", que en última instancia conduce a la liberación de productos defectuosos.
Superproducción. La sobreproducción generalmente se denomina producción de una cantidad excesiva de productos o su producción prematura antes de que surja la demanda real. En las tiendas, la sobreproducción conduce a la producción de productos en exceso, y en las oficinas, a la creación de documentos innecesarios o información redundante. La producción de cantidades excesivas de productos o su producción prematura no contribuye a aumentar la eficiencia, ya que están asociadas con el consumo de material adicional y recursos laborales, la necesidad de almacenar productos excedentes. Esto obliga a los empleados a trabajar más rápido de lo necesario, lo que va acompañado de otras pérdidas.
Para eliminar las pérdidas causadas por la sobreproducción, se requiere:
Desarrollar procesos tecnológicos de tal manera que las operaciones anteriores proporcionen confiablemente las posteriores;
Establecer normas y estándares de producción para cada puesto de trabajo del proceso;
Proporcionar señales para evitar el inicio prematuro de la producción.
Expectativa. Cualquier expectativa -personas, documentos, equipos o información- es siempre una pérdida. Esperar significa trabajo ocioso, y esto hace que todo el proceso se detenga. Esperar no crea valor agregado y, naturalmente, el consumidor no está dispuesto a pagar por el tiempo de inactividad. Las pérdidas de este tipo son las más fáciles de detectar. Son especialmente molestos para los trabajadores. En cualquier oficina, no es raro que los empleados esperen mucho tiempo por las firmas de los superiores, la oportunidad de utilizar el equipo ocupado, las llamadas telefónicas, la recepción de materiales de los proveedores, etc.
Analice qué firmas en los documentos son realmente necesarias, elimine todas las innecesarias y estandarice el nuevo procedimiento;
Capacitar a los empleados en profesiones afines para que puedan reemplazarse entre sí;
Distribuya uniformemente las cargas de trabajo a lo largo del día para utilizar de manera óptima los recursos laborales disponibles;
Garantizar la producción para todos equipo necesario y la entrega oportuna de los productos y materiales comprados.
Exceso de procesamiento. Aquellas operaciones que no son necesarias para los consumidores que no quieren pagar de más por su implementación se consideran superfluas. A menudo, tales operaciones resultan ser acciones innecesarias (por ejemplo, controles mutuos del trabajo realizado por diferentes empleados), obtención de un número excesivo de firmas, consideración innecesaria de documentos y resultados del trabajo.
Para eliminar este tipo de pérdida, necesita:
Analice todo el trabajo que crea valor agregado, optimice o elimine todas las operaciones innecesarias;
Determine qué firmas de coordinación en los documentos son realmente necesarias y elimine todas las innecesarias.
Inventario excesivo. Cualquier excedente de inventario en poder de una empresa es un desperdicio. El almacenamiento de dichas existencias requiere espacio adicional, pueden afectar negativamente la seguridad al bloquear pasillos y áreas de producción. Es posible que estos inventarios no se necesiten en absoluto y se vuelvan obsoletos cuando cambie la demanda de productos. La manufactura esbelta requiere un cambio radical en la forma en que vemos el inventario. La presencia de exceso de inventario significa la necesidad de esfuerzos adicionales para gestionarlo, puede ralentizar el flujo de otros procesos de producción, ya que es necesario voltear montones de papeles y materiales en busca de lo necesario.
Para eliminar este tipo de pérdida, necesita:
Producir en cada sitio o lugar de trabajo solo la cantidad de productos requeridos por los consumidores aguas abajo del flujo de producción;
Estandarizar el diseño de los sitios de producción y su carga;
Asegúrese de que todo lo necesario se entregue a las partes posteriores del proceso de producción exactamente en el momento designado y que no haya demoras en el movimiento posterior de materiales a través del proceso de producción.
Movimientos adicionales. Cualquier movimiento que no sea necesario para completar con éxito la operación en cuestión es un desperdicio. Dichos movimientos se consideran una forma de desperdicio, ya que cada movimiento realizado debe incrementar el valor agregado del producto o servicio. A menudo, la organización ineficiente del proceso de trabajo y el diseño incorrecto de los lugares de trabajo provocan movimientos innecesarios de los artistas: caminar, estirarse, agacharse, etc.
Para eliminar este tipo de pérdida, necesita:
Estandarizar carpetas de documentos, cajones y gabinetes en toda la oficina, aplique códigos de colores lo más ampliamente posible;
Organizar los archivos (con documentos en escritorios o archivos electrónicos en computadoras) de tal manera que facilite el acceso a ellos;
Ubique el equipo de oficina común en
la parte central de la oficina, compre equipo adicional para reducir la cantidad de movimiento de los empleados alrededor de la oficina.
Pérdidas por defectos o alteraciones. Costos de reelaboración, o re-
La ejecución repetida de un trabajo ya hecho, en el que se encontraron defectos, pertenece ciertamente a la categoría de pérdidas, ya que cualquier trabajo en exceso del necesario es superfluo, aumentando las pérdidas de la empresa. Las pérdidas por defectos también incluyen la pérdida de productividad debido a la interrupción del flujo normal del flujo de trabajo para corregir defectos o reprocesar productos. Este tipo de gastos generales es mucho más fácil de identificar que otros tipos de desperdicio.
Para eliminar pérdidas por defectos, se requiere:
Introducir métodos de trabajo estandarizados y formas de documentos de oficina;
Desarrollar e implementar herramientas para facilitar el trabajo.
Transportación. El transporte en distancias mayores a las necesarias, o la creación de alojamiento temporal, almacenamiento y depósito, el movimiento innecesario de un lugar a otro de materiales, personas, información o documentos, todo esto conduce a la pérdida de tiempo y energía. Los materiales y artículos comprados a menudo se mueven de un lugar a otro dentro de una instalación varias veces hasta que llegan a su destino final. Naturalmente, todos estos movimientos conducen a pérdidas. Además, colocar productos en lugares de almacenamiento temporal aumenta la probabilidad de daño, pérdida y robo, e interfiere con el movimiento normal dentro de la empresa.
Para eliminar las pérdidas causadas por el exceso de transporte,
requerido:
Minimizar la distancia de cualquier transporte;
Eliminar todos los lugares de almacenamiento temporal o depósito
materiales
El problema de determinar la eficiencia económica predetermina
la necesidad de considerar y analizar adecuadamente el nivel y el alcance de
implementación de medidas de manufactura esbelta. Esto significa que la definición de efectividad requiere el uso de métodos de medición y análisis cuantitativos, lo que implica establecer una relación entre el aumento en la escala de implementación del concepto de manufactura esbelta y el aumento en la utilidad de la empresa.
El análisis de la eficiencia económica de la implementación del concepto de producción ajustada se inicia con el cálculo del volumen total de producción anual por parte de las unidades estructurales en las que se introdujo la producción ajustada V?, según la fórmula:
j - índice de la unidad estructural;
J es el número de unidades estructurales donde se implementa la producción ajustada;
Vj - volumen de salida unidad estructural donde se introdujo la manufactura esbelta.
Por lo tanto, la participación está determinada por la fórmula:
Para determinar aún más la eficiencia económica, se realizan los siguientes pasos:
El volumen de inversiones para la implementación de actividades de manufactura esbelta se prevé para cada actividad implementada en
unidad estructural;
Dependiendo del volumen proyectado de inversiones y la cobertura de divisiones estructurales con actividades de manufactura esbelta, se determina la participación del volumen de producción (g);
Una forma experta determina el valor umbral r*, en el cual el efecto económico de la introducción de medidas para la producción ajustada comenzará a manifestarse en forma de un aumento en la ganancia de la empresa (?P).
El valor umbral r* también puede depender de la eficacia con la que se implemente la medida. Cuanto mayor sea la eficacia de la implementación de la medida, menor será el valor umbral r*.
La relación entre el aumento de la participación r por encima del valor umbral r * (? r = r - r *) y el aumento de la ganancia de la empresa se puede expresar como:
K: un indicador que caracteriza el aumento en la ganancia de la empresa por unidad de aumento en la escala de implementación de medidas para la producción ajustada. En el paso al límite, este indicador se expresa como una derivada:
El efecto económico de cualquier actividad, incluidas las actividades de manufactura esbelta, radica en la ganancia adicional recibida. La ganancia adicional, a su vez, está determinada por cuánto cambiarán los ingresos y los costos de producción de la empresa en relación con la implementación de estas medidas de manufactura esbelta. Por lo tanto, el enfoque clave para calcular el efecto de cualquier actividad (incluidas las actividades lean) es determinar cuánto más recibirá la empresa y cuánto más pagará en relación con la implementación del concepto.
manufactura esbelta.
Como criterios de eficiencia económica de la implementación de medidas para organizar la producción ajustada, se propone utilizar los indicadores de desempeño tradicionales del Programa, tales como: valor presente neto (VAN), tasa interna de retorno (TIR) y período de recuperación descontado .
Valor actual neto (VAN).
En la práctica internacional, un indicador ampliamente utilizado para evaluar la efectividad de los proyectos es el valor actual neto o valor actual neto (VPN), que se determina mediante la fórmula:
It - la cantidad de inversión (costos) en período t-ésimo para actividades de manufactura esbelta;
T es el número total de años, donde t = 0, 1, 2,…, n;
r - tasa de descuento (tasa);
Pt: aumento de la ganancia de la empresa a partir de la implementación del concepto de producción ajustada.
Si el valor del VPN calculado es positivo, esto indica que la suma de todas las pérdidas que se supone que se eliminarán es mayor que la inversión en la actividad de LP, lo que significa que la actividad en cuestión debe aceptarse para su implementación. Si el VAN es menor que cero, entonces esta actividad debe abandonarse.
Tasa interna de retorno (TIR).
La TIR de un proyecto es la tasa de rendimiento (tasa de barrera, tasa de descuento) a la que el valor presente neto de una inversión es cero, o es la tasa de descuento a la que los rendimientos descontados del proyecto igualan los costos de inversión. Tasa interna de retorno
determina la tasa de descuento máxima aceptable a la que
invertir fondos sin ninguna pérdida para el propietario.
TIR = r, donde VAN = f(r) = 0.
El valor de la TIR se encuentra usando la siguiente fórmula:
El significado económico de este indicador es que muestra la tasa de retorno esperada (ROI) o la tasa máxima nivel permitido costos de inversión en el proyecto evaluado.
Período de recuperación descontado.
El período de recuperación de una inversión es el tiempo que tarda una inversión en generar suficientes flujos de efectivo para recuperar los costos de inversión.
La fórmula general para calcular el período de recuperación:
Actual - período de recuperación de las inversiones;
Io - el valor de la inversión inicial en el período cero.
Por lo tanto, es posible no solo obtener una imagen operativa del estado de los procesos comerciales en la organización, sino también mejorar el estado de cosas existente.
La eficiencia resultante de la implementación de medidas de producción ajustada se puede utilizar tanto para analizar los resultados de la implementación de medidas como para determinar aquellos departamentos en los que es más rentable implementar la producción ajustada. Por lo tanto, este enfoque permitirá (especialmente en condiciones de recursos limitados) distribuir racionalmente las inversiones de capital entre los departamentos destinados a implementar el concepto de producción ajustada.
2. Análisis y evaluación de actividadesJSC« Nizhnekamskshina" en el campo de la "producción ajustada"
2.1 Características generales de la actividad,indicadores técnicos y económicos de la empresa
Hasta la fecha, OAO Nizhnekamskshina es el mayor fabricante de neumáticos de Rusia y los países de la CEI. Casi uno de cada tres neumáticos producidos en Rusia se fabrica en la ciudad de Nizhnekamsk.
OAO Nizhnekamskshina se estableció de conformidad con el Decreto del Presidente de la República de Tatarstán "Sobre medidas para transformar empresas estatales, organizaciones y asociaciones en sociedades anónimas" de fecha 26 de septiembre de 1992 No. UP-466, la Ley de la República de Tatarstán "Sobre la transformación de la propiedad estatal y comunal en la República de Tatarstán (sobre desnacionalización y privatización)".
OAO Nizhnekamskshina se estableció el 2 de marzo de 1994 mediante la transformación de la asociación de producción Nizhnekamskshina. La transformación se llevó a cabo sobre la base de un plan de privatización aprobado por el Decreto del Comité de Propiedad Estatal de la República de Tatarstán No. 64 del 15 de febrero de 1994, y se inscribió en el registro de sociedades anónimas con el número 700. El empresa se constituyó por tiempo indefinido.
La empresa como entidad legal independiente existe desde 1971. La empresa tiene dos plantas: una planta de neumáticos en masa y una planta de neumáticos para camiones. En 1994 Asociación de producción Nizhnekamskshina se transformó en sociedad Anónima de tipo abierto; en 1997 - en OAO Nizhnekamskshina.
La planta de neumáticos en masa fue diseñada para proporcionar neumáticos a la planta de automóviles Volga, la planta de automóviles Ulyanovsk y la flota de vehículos en las regiones adyacentes a la planta. La gama principal: neumáticos para automóviles y camiones.
La planta de neumáticos para camiones fue diseñada para proporcionar neumáticos para KamAZ y la flota de vehículos en las regiones adyacentes a la planta. El surtido principal son neumáticos para camiones.
La estructura de la Planta de Neumáticos Masivo y la Planta de Neumáticos para Camiones incluye al director de la planta, quien está subordinado directamente a Ingeniero jefe, subdirector de producción, tecnólogo jefe, subdirector de análisis económico, así como la producción principal de la planta y talleres auxiliares de las plantas.
La producción principal de la planta incluye:
Preparación de producción de materias primas y envío de productos terminados;
Producción preparatoria, que se dedica a la preparación;
materias primas para la futura producción de neumáticos;
Producción de calandrias, que recoge el marco para los talleres de montaje;
Planta de Montaje No. 1;
Producción de montaje No. 2;
Fabricación de vulcanización de neumáticos de automóviles;
Producción de neumáticos para camiones;
Producción automotriz.
Los talleres auxiliares de la planta incluyen un taller eléctrico, un taller de calefacción, un taller de reparación mecánica, transporte eléctrico en la planta, sistemas de flujo de proceso, sistemas de control automatizado y talleres de servicios públicos.
Los órganos de gobierno de OAO Nizhnekamskshina de acuerdo con la Carta de la Compañía son:
- Reunion general de accionistas;
- Junta Directiva;
- órgano ejecutivo único;
- El órgano ejecutivo colegiado es la Junta.
JSC Nizhnekamskshina es el más grande entre los neumáticos rusos
fábricas, la empresa en términos de capacidad de producción, volumen y gama de productos. La participación de OAO Nizhnekamskshina en la producción total de neumáticos de las plantas rusas fue del 30%. Casi un tercio de la producción se destina al montaje de las fábricas de automóviles rusas.
En 2009, los líderes de producción son: Nizhnekamskshina OJSC ocupa el primer lugar, produciendo el 27 % de la producción total de neumáticos de Rusia, seguido por Yaroslavl Tire Plant OJSC - 16 % y Omskshina OJSC - 14 %. La capacidad total de las empresas nacionales de neumáticos es de 38,7 millones de neumáticos al año.
La versatilidad de la producción de la empresa está garantizada por la producción de neumáticos de la más diversa gama. La empresa fabrica llantas para varias condiciones: carretera, universal (todo tiempo), invierno, todoterreno, cantera. Los neumáticos producidos están diseñados para diferentes tipos de equipos automotrices y, dependiendo de esto, se dividen en tipos. Los neumáticos de la empresa están equipados con muchas plantas de automóviles no solo en Rusia, sino también en Ucrania.
Los principales consumidores de productos OAO Nizhnekamskshina se presentan en la Tabla 2.1.1.
Tabla 2.1.1. Principales consumidores de productos OAO Nizhnekamskshina
Se puede ver en los datos de la tabla que la mayor parte del consumo de productos recae en JSC AVTOVAZ - 61%; El 11% de los productos de neumáticos se distribuyen a las plantas de Volkswagen Group Rus LLC, Kaluga, SHKODA, UAZ OJSC, Ulyanovsk; 6,0% para OAG LLC, Izhevsk, el consumo insignificante de productos lo contabiliza JSC AK Bogdan Motors, Ucrania.
Más visual porcentaje puedes ver la fig. 2.1.3.
Arroz. 2.1.3. Los principales consumidores de productos en OAO Nizhnekamskshina
JSC "Nizhnekamskshina" ha acumulado una vasta experiencia en el desarrollo y mejora de neumáticos fabricados, pruebas de productos terminados. El desarrollo de diseños de neumáticos de nueva generación y la última tecnología han permitido ofrecer alta calidad y el nivel de indicadores de productos terminados en el mercado mundial. Hasta la fecha, la empresa produce más de 120 tamaños para todo tipo de neumáticos y maquinaria agrícola. Teniendo en cuenta las mayores exigencias de los fabricantes de automóviles a la calidad de los neumáticos, se reconstruyó el flujo de pasajeros de Mass Tire Plant y se dominó la tecnología para la fabricación de neumáticos radiales para pasajeros en el equipo y se obtuvo la licencia de Pirelli (Italia).
En 2001, se continuó con la reconstrucción del tráfico de pasajeros de la Planta Mass Tire. De acuerdo con el plan de desarrollo a largo plazo de OAO Nizhnekamskshina, se compró una licencia para una nueva tecnología y en 2004 se organizó y puso en funcionamiento la producción de neumáticos radiales para automóviles. El proyecto fue financiado a expensas de OAO TATNEFT.
Desde el 1 de julio de 2004, se encargó la capacidad de los neumáticos radiales de pasajeros de alto rendimiento "KAMA-EURO": 500 mil piezas.
Al 1 de enero de 2006, la capacidad de diseño para la producción de llantas de la empresa ascendía a 11.900 mil llantas por año, incluyendo 8.940 mil llantas para la Planta de Llantas Masivas, 2.960 mil llantas para la Planta de Llantas para Camión y 2.960 mil llantas para la producción de neumáticos radiales para automóviles - 500 mil neumáticos.
Entre los factores internos de OAO Nizhnekamskshina se encuentran la asociación estratégica con OAO Tatneft, porque la empresa opera como parte de ella. OOO Tatneft-Neftehimsnab realiza la función de suministro de materias primas en la cantidad de la demanda, OOO Trading House Kama realiza la función de comercialización de productos terminados. Por decisión de la extraordinaria reunión general accionistas de OAO Nizhnekamskshina, actas de fecha 27.06.2002, los poderes del único órgano ejecutivo se transfirieron a la sociedad de gestión OOO Tatneft-Neftekhim.
La planta ha implementado y opera efectivamente el sistema de calidad ISO -
9001:2000, certificado por el organismo de certificación internacional TUV CERT, que prevé un control exhaustivo de las materias primas, componentes, componentes que ingresan a la planta, cumplimiento estricto de las normas de proceso durante todo el ciclo de producción y prueba de productos terminados.
Dominar la producción de neumáticos radiales para pasajeros de alto rendimiento "KAMA-EURO" según una nueva tecnología en equipos importados utilizando materias primas importadas y homologadas. Por decisión de la Junta Directiva, se tomó un conjunto de medidas para retirar servicios, estructuras no esenciales y actividades de servicio del OJSC
Nizhnekamskshina.
En una economía de mercado, OAO Nizhnekamskshina presta considerable atención a los problemas de optimización del proceso de promoción de bienes del productor al consumidor.
La dinámica de la producción de productos de OAO Nizhnekamskshina se presenta en la Tabla 2.1.2.
Tabla 2.1.2. Dinámica de producción de OAO Nizhnekamskshina
Volumen de producción, |
Tasa de crecimiento, % |
|||
Básico |
||||
La tabla muestra que el volumen de producción en 2011 disminuyó en 1096,3 mil unidades. (10%) en comparación con 2010; En comparación con 2009, la producción de neumáticos en 2011 es menor en 4939,2 mil unidades. (33,4%). Una disminución significativa en la producción se debe al cese de la producción de la gama principal de neumáticos para camiones en la segunda mitad de 2011. Una representación visual de esta dinámica se muestra en la fig. 2.1.4.
...La esencia del concepto de "producción ajustada", la historia de su origen, aspectos teóricos y metodológicos. Evaluación de la efectividad de su implementación en la empresa. Análisis de la competitividad de LLC "Energoshinservis" en el marco del concepto de producción ajustada.
tesis, agregada el 24/06/2014
La historia del desarrollo del pensamiento gerencial. Desventajas y ventajas de la teoría de la gestión para la implementación de actividades de gestión competentes. Disposiciones básicas, principios e ideas de las tendencias de la gestión moderna. El concepto de "producción ajustada".
resumen, añadido el 04/01/2016
La tecnología de producción ajustada en la teoría y la práctica de la gestión. Una descripción general de las herramientas de manufactura esbelta. Análisis de las oportunidades para la implementación y operación de manufactura esbelta en Rusia y en el extranjero. Características del modelo de gestión japonés.
trabajo final, agregado el 28/01/2014
El enfoque de Toyota en la producción basada en pedidos mientras minimiza el inventario de productos terminados. La manufactura esbelta como un enfoque progresivo para la gestión y la gestión de la calidad. La necesidad de utilizar solo tecnología fiable y probada.
prueba, agregada el 22/03/2014
Las principales actividades de OAO EVRAZ Kachkanar Mining and Processing Plant. El proceso tecnológico de obtención de productos. Estructura organizativa de la gestión laboral. Política y objetivos en el ámbito de la calidad. Principios de manufactura esbelta.
informe de práctica, añadido el 12/03/2015
La producción ajustada como concepto de gestión logística, sus metas y objetivos, ventajas y desventajas. Características de las herramientas Lean: método Kaizen, sistema 5S, sistema de mantenimiento general de equipos productivos, sistema Kanban.
trabajo de control, añadido el 03/12/2013
La esencia y el contenido principal del enfoque de procesos, las etapas y principios de su implementación en una empresa moderna. Trilogía de Jurán. Información general sobre JSC "Planta empacadora de carne tártara", implementación del enfoque de proceso y evaluación de la efectividad de este concepto.
documento final, agregado el 09/09/2012
El concepto de gestión de la calidad total, sus objetivos, elementos y características. El problema de introducir el concepto de "Gestión de la Calidad Total" en las actividades de la organización. Propiedades del producto que determinan sus principales funciones. Evaluación de la calidad de los productos terminados.
Al implementar métodos y herramientas de manufactura esbelta, a menudo surge la pregunta: ¿cómo evaluar el efecto de los cambios realizados? Por encima de todo, por supuesto, a los gerentes les interesa el efecto económico, es decir, el efecto expresado en rublos o dólares de ganancia adicional (que es mejor) o reducción de costos (que es peor, pero, en principio, también se acepta) .
Muy a menudo, en los primeros meses de la introducción de la manufactura esbelta, uno tiene que hablar de la imposibilidad de calcular el efecto económico, y he aquí por qué...
Fundamentalmente, hay dos enfoques para evaluar el efecto económico.
El primero implica la revisión por pares basada en una cantidad limitada de datos numéricos, cuando se calcula un cierto "efecto potencial". Por ejemplo, estamos hablando que una de las propuestas para mejorar el trabajo del maquinista le permite reducir el tiempo salir adelante por sí mismo al cargar y descargar piezas de la máquina durante 15 minutos por turno. Saber el costo de una hora de mano de obra operador dado, por ejemplo, 100 rublos, puede calcular que el ahorro potencial por turno es de 25 rublos, por mes - 500 rublos, por año - 6000 rublos.
Este método tiene muchas desventajas. La desventaja obvia es la inexactitud revisión por pares ahorro de tiempo: no es un hecho que este operador realmente ahorre 15 minutos por turno. Como dice el refrán, si evitas que una persona tenga que hacer un trabajo inútil, inmediatamente encontrará diez cosas más en las que gastar todo el tiempo ahorrado. Por lo tanto, estos 15 minutos no se convertirán automáticamente en un trabajo que realmente genere ganancias.
El segundo enfoque implica una evaluación basada en los resultados del trabajo durante un cierto período de tiempo, por ejemplo, durante un mes o un trimestre. El departamento de contabilidad resume todas las cifras e informes: el beneficio se ha convertido en tal y tal. (por ejemplo, en nuestro caso, la ganancia de la empresa para el mismo mes aumentó en 2 millones 127 mil rublos, pero no es un hecho que todo esto se deba solo al ahorro de 15 minutos del trabajo del operador de la máquina). En este caso, las cifras de ahorro o ganancia adicional son mucho más creíbles, pero si espera que los contadores puedan darle una respuesta a la pregunta "¿cuánto dinero obtuvimos (ahorramos) después de implementar esta propuesta?", entonces usted están equivocados no dará:
- la oferta implementada es solo uno de los factores que afectan los beneficios entre todo tipo de fluctuaciones en el nivel de demanda de los clientes, retrasos en los proveedores, retrasos en los pagos de los clientes, averías en los equipos de otras áreas de producción, etc. etc. Es prácticamente imposible aislar la influencia de este factor en particular: evaluar el resultado obtenido SOLAMENTE gracias a la propuesta implementada, en la gran mayoría de los casos.
- muchos costos generales que se tienen en cuenta al calcular la rentabilidad de productos u obras individuales se distribuyen de acuerdo con proporciones especificadas condicionalmente (por ejemplo, sucede que el costo de mantenimiento de edificios y estructuras se traslada al costo de producción, dependiendo de la área del local ocupada por los correspondientes medios de producción) y cuando tal proporción deja de corresponder a nuestro entendimiento de una justa valoración de los costos, la exactitud del efecto económico comienza a plantear preguntas obvias.
En términos simples, un economista que mira las cifras del efecto económico las creerá en un solo caso:
- cuando la estructura del efecto económico es totalmente consistente con la estructura del costo de los productos/servicios adoptados en su empresa
- cuando los datos son confirmados por documentos contables
- cuando hay datos históricos sobre qué resultados económicos estaban disponibles ANTES de la implementación de esta propuesta
Ahora veamos qué encuentran con más frecuencia los recién llegados a la producción ajustada:
- muchas empresas no tienen métodos aprobados para calcular los costos de los productos (calcular el costo de producir un tipo particular de producto o el costo de proporcionar un tipo particular de servicio) con una estructura de costos establecida
- no todas las transacciones internas van acompañadas de documentos contables y, por lo tanto, es poco probable que todos los datos sobre gastos estén disponibles en el departamento de contabilidad
- Muy a menudo no es posible restaurar los datos históricos, incluso debido al hecho de que el estado realiza cambios y ajustes en el sistema contable de las empresas rusas con bastante frecuencia, por lo que los datos de producción de diferentes años no siempre son comparables.
Si estos argumentos no le convencen, le contaré un hecho más notable.
Normas Internacionales de Información Financiera NIIF y Normas rusas La contabilidad RAS tiene una característica que impide su uso directo para la contabilidad en una empresa esbelta: ambos estándares se desarrollaron en la era de la producción en masa y postulan el alto valor de tener recursos de producción y grandes existencias de materias primas, productos semielaborados y productos terminados. .
Desde el punto de vista de la contabilidad clásica, el exceso de inventario en los almacenes es "bueno" y "bueno" en muchos sentidos. Desde el punto de vista de la manufactura esbelta, cualquier exceso de existencias es "malvado". Parecería que estas son solo palabras generales, pero al final, al compilar el balance, el estado de pérdidas y ganancias, esto lleva a que los hechos que, desde el punto de vista de la producción ajustada, deben evaluarse como logros. y un efecto positivo, desde el punto de vista de la contabilidad clásica percibido como un resultado negativo.
No quiero convencer a nadie de que al implementar manufactura esbelta, no se puede calcular el efecto económico. Necesita ser calculado. Pero a la hora de evaluar los ahorros hay que tener en cuenta que las cifras obtenidas serán percibidas con bastante escepticismo. Y este escepticismo tiene razones bastante objetivas.
Quién podría estar interesado
En el contexto de la implementación práctica de la "producción ajustada", los problemas de evaluación del estado actual y las perspectivas futuras para el uso de las herramientas de la "producción ajustada" son de particular importancia. Dado que, en primer lugar, puede aparecer la ilusión de que ya se ha hecho mucho en la empresa y es posible reducir la actividad en la implementación de herramientas y métodos de producción ajustada y, en segundo lugar, cada paso siguiente para reducir las pérdidas y aumentar la la eficiencia de la empresa requerirá esfuerzos más significativos.
La mayoría metodos efectivos organizaciones "Lean production" en la empresa son la definición de objetivos, la implementación proyecto de piloto y cálculo del efecto económico.
Los objetivos Lean son necesarios para el desarrollo de la estrategia y la política por parte de la alta dirección de la empresa, en la que los recursos se dirigen a aquellos objetivos que son críticos para el negocio. Es necesario unificar recursos y desarrollar indicadores medibles específicos que monitoreen periódicamente el logro de metas clave. Función clave El modelo es un bloque para evaluar la eficacia y desarrollar nuevos objetivos, que es totalmente coherente con la filosofía de "producción ajustada" y está orientado a la mejora continua. El modelo incluye una evaluación experta de la efectividad de la implementación del sistema Lean Production, presentado en la Tabla. 9.
Los resultados de una evaluación de expertos sobre la efectividad de la implementación de la producción ajustada en KAMAZ OJSC demuestran lo siguiente:
1. El subsistema “personal” ha recibido más desarrollo en KAMAZ OJSC en comparación con otros subsistemas (5,5 puntos de 10 máximo), el subsistema “procesos” tiene el menor desarrollo en la empresa (4,6 puntos).
2. Todos los subsistemas "procesos", "personal", "gestión estratégica" fueron calificados por expertos en KAMAZ OJSC en un nivel promedio (puntaje máximo - 10 puntos), lo que indica que todavía hay reservas significativas para la implementación de herramientas y métodos. de producción ajustada.
3. Indicadores como (4,0 puntos), (3,2 puntos), (3,7 puntos), trabajo con proveedores en manufactura esbelta (3,7 puntos), (3,8 puntos), trabajo con distribuidores en manufactura esbelta (3,9 puntos), recibidos por KAMAZ OJSC, tienen la calificación más baja y son puntos de referencia para intensificar el trabajo.
Tabla 9
Evaluación de la efectividad de la organización de "Lean production" en OJSC "KAMAZ"
Indicadores medidos |
Proporción de evaluaciones de expertos, % |
|||||||||||
Subsistema "dirección estratégica" |
||||||||||||
Tener una filosofía de BP |
||||||||||||
Declaración y principios de BP |
||||||||||||
KPI - indicadores clave de rendimiento |
||||||||||||
Estudio de requerimientos del consumidor |
||||||||||||
Evaluación de la satisfacción del cliente |
||||||||||||
subsistema "personal" |
Formación de los empleados |
|||||||||||
Cohesión de los empleados |
||||||||||||
Subsistema "procesos" |
Disponibilidad de 5C |
|||||||||||
Usando el sistema de tracción |
||||||||||||
reducción de pérdidas |
||||||||||||
Mejora de la calidad del producto |
||||||||||||
Trabajar con proveedores de BP |
||||||||||||
Trabajar con distribuidores de BP |
A pesar de que KAMAZ OJSC es líder entre las empresas rusas de construcción de maquinaria en términos de implementación de herramientas y métodos de producción ajustada, las evaluaciones de los expertos sobre la situación en KAMAZ OJSC no difieren fundamentalmente de las evaluaciones de las empresas de construcción de maquinaria de la Federación Rusa. Todo esto indica que los expertos internos son propensos a la autocrítica, ven las deficiencias existentes y las perspectivas para el desarrollo de la empresa en la implementación de herramientas y métodos de producción ajustada.
En la práctica, esto significa la necesidad de intensificar el trabajo en la implementación de las herramientas del sistema de producción KAMAZ: estas son soluciones que le permiten ver oportunidades de mejora y reducir significativamente las pérdidas.
Es necesario mejorar constantemente toda la gama de procesos comerciales, aumentar la transparencia y la capacidad de gestión de la organización, utilizar el potencial de cada empleado de la empresa, aumentar la competitividad, obtener un efecto económico significativo sin incurrir en grandes costos financieros (Fig. 22) .
Tabla 10
Evaluación de la efectividad de la implementación del sistema "Lean production" en OJSC "KAMAZ" y en las empresas de ingeniería mecánica de la Federación Rusa
Indicadores medidos |
Casarse partitura para KAMAZ OJSC |
Casarse Puntuación de ingeniería mecánica rusa |
|
Subsistema "dirección estratégica" |
Disponibilidad de gestión estratégica |
||
Tener una filosofía de BP |
|||
Declaración y principios de BP |
|||
Participación de la alta dirección, implementación proyectos personales |
|||
KPI - indicadores clave de rendimiento |
|||
Estudio de requerimientos del consumidor |
|||
Evaluación de la satisfacción del cliente |
|||
Subsistema "personal" |
Formación de los empleados |
||
Cohesión de los empleados |
|||
Disponibilidad y calidad de las ofertas kaizen |
|||
Nutriendo líderes con la filosofía de BP |
|||
Construyendo una organización de aprendizaje |
|||
Subsistema "procesos" |
Disponibilidad de 5C |
||
Usando el sistema de tracción |
|||
Igual distribución del trabajo. |
|||
Usando el control visual |
|||
reducción de pérdidas |
|||
Mejora de la calidad del producto |
|||
Mejorando la calidad del servicio |
|||
Trabajar con proveedores de BP |
|||
Trabajar con distribuidores de BP |
Cada una de las herramientas del Sistema de Producción KAMAZ resuelve alguna parte específica de los problemas, y solo su aplicación conjunta resolverá el problema por completo, o lo minimizará a valores aceptables.
Arroz. 22. Aplicación de las herramientas del Sistema de Producción KAMAZ
Convencionalmente, las herramientas del Sistema de Producción KAMAZ se pueden dividir en tres grandes grupos: herramientas de análisis y detección de pérdidas, herramientas de mejora, herramientas de gestión e implicación (Tabla 11).
Tabla 11
Herramientas del Sistema de Producción KAMAZ
Dado que los expertos evaluaron los indicadores de desempeño de la implementación de herramientas y métodos de manufactura esbelta en un nivel promedio, es necesario intensificar el trabajo en la empresa en áreas como KPI: indicadores clave de desempeño, el uso de un sistema de extracción, estudio del cliente requisitos, evaluación de la satisfacción del cliente, distribución uniforme del trabajo, mejora del mantenimiento de la calidad, trabajo con proveedores en producción ajustada, trabajo con distribuidores en producción ajustada.
Arroz. 23. Metas y objetivos del Programa de la República de Tartaristán "Implementación del proyecto Lean Production en la República de Tartaristán para 2011-2013"
La implementación del Programa de la República de Tatarstán "Implementación del Proyecto de Producción Lean en la República de Tatarstán para 2011-2013" contribuye a la intensificación de este trabajo, que prevé la financiación de proyectos para introducir herramientas y métodos de producción ajustada, incluyendo proyectos para capacitar al personal en producción ajustada.
Como resultado de la implementación de las actividades del Programa de la República de Tatarstán "Implementación del proyecto Lean Production en la República de Tatarstán para 2011-2013", se planea alcanzar los indicadores presentados en la Tabla. 12
Tabla 12
Indicadores del Programa de la República de Tatarstán "Implementación del Proyecto de Producción Esbelta para 2011-2013"
Nombre del indicador |
||
Índice de producción industrial de las empresas participantes del programa, en % |
||
Tasa de crecimiento de la productividad laboral (contra el período correspondiente del último año) de las empresas participantes del programa, en % |
||
La proporción de empresas industriales que implementan programas de desarrollo de producción ajustada en el número total de empresas industriales que emplean a más de 500 personas, en % |
||
El nivel de rentabilidad de la producción de las empresas participantes en el programa, en % |
||
Número de empresas cuyo personal realizó desarrollo profesional en el marco del Programa |
Tal enfoque para un aumento gradual en la eficiencia de las empresas de la economía de la República de Tatarstán, incluido OJSC KAMAZ, al reducir las pérdidas y capacitar al personal, contribuye al crecimiento del potencial de producción de la economía regional y al crecimiento de la competitividad. .
Hasta la fecha, se ha acumulado y probado un extenso arsenal de métodos, con la ayuda de los cuales una empresa puede implementar herramientas de "producción ajustada". Los métodos más efectivos para implementar el sistema Lean Production en una empresa son el establecimiento de objetivos, la implementación de proyectos piloto y el cálculo del efecto económico. Los indicadores objetivo de producción ajustada y el logro de los objetivos del Sistema de producción KAMAZ se presentan en la Tabla. 13
Tabla 13
Dinámica de indicadores de cumplimiento de las metas del sistema productivo KAMAZ
Indicadores |
|||||||
Formado en los principios y métodos de BP |
|||||||
proyectos abiertos |
|||||||
proyectos implementados |
|||||||
propuestas kaizen presentadas |
|||||||
ofertas kaizen implementadas |
|||||||
Estandarización |
|||||||
visualización |
|||||||
superficie liberada m2 |
|||||||
unidades de equipo liberadas. |
|||||||
efecto económico obtenido (millones de rublos) |
|||||||
incluido kaizen |
|||||||
los costos para el desarrollo de PSK ascendieron a |
|||||||
% de efecto económico |
Objetivos del sistema de producción KAMAZ para 2012:
1. Aumentar la eficiencia operativa de OJSC KAMAZ al reducir el tiempo de inactividad de emergencia de los equipos en un 50 %, aumentando la productividad laboral en un 16 %. reducción de los costes energéticos específicos en un 5 % por vehículo, reducción de los costes de adquisición en 1500 millones de rublos, alineando el número de configuraciones de vehículos actuales con el plan de negocio para 2012, proporcionando a la producción una reserva de personal para operación estable durante el periodo de verano.
2. Para aumentar la eficiencia del sistema de gestión de KAMAZ OJSC mediante la introducción del estándar "SFM - gestión de procesos desde el lugar de creación de valor", introduciendo el principio "la logística entrega, el ensamblaje ensambla" mediante el desarrollo e implementación de estándares en el proceso principal: montaje, logística, implementación de la quinta y sexta fase del proyecto “Calendario”, desarrollo e implementación del mapa de desarrollo del personal del proceso principal, implementación de un sistema de reporte gerencial basado en los KPI del proceso principal.
3. Mejorar la calidad y confiabilidad de los productos KAMAZ OJSC mediante la introducción de un sistema de calidad incorporado en los procesos principales en un 100 %, reduciendo las pérdidas por chatarra en un 10 % y reduciendo el PPM en un 25 %.
4. Involucrar al 100% del personal en la mejora del sistema productivo KAMAZ capacitando a todo el personal de nuevo ingreso en los principios, métodos y herramientas de PSK, presentando 4 propuestas kaizen por empleado por año, abriendo 4200 proyectos kaizen, implementando al menos 3800 , implementando el 80 % de las propuestas kaizen y proyectos kaizen presentados, apertura de un proyecto personal por cada jefe de KAMAZ OJSC.
5. Garantizar el desarrollo sostenible de proveedores, filiales, empresas conjuntas sobre la base de los principios del sistema de producción KAMAZ a través de la formación. tasa básica PSK para jefes de todos los centros automotrices y proveedores clave, realizando un seminario de 3 días para los jefes de distribuidores de KAMAZ OJSC sobre el curso básico de PSK, introduciendo PSK en todos subsidiarias con capital 100% de KAMAZ OJSC, creación de secciones de referencia sobre los principios PSK en 3 proveedores clave y en una de las plantas -
representante del cliente, apertura por parte de los líderes de la empresa conjunta de proyectos personales sobre la integración de los sistemas de producción de la empresa conjunta y PSK.
6. Asegurar la lealtad del personal de la empresa, los clientes, los residentes de la ciudad y la República de Tatarstán a OJSC KAMAZ a través de la transmisión sistémica de experiencias exitosas en el desarrollo del sistema de producción KAMAZ.
7. Obtener un efecto económico al reducir las pérdidas por un monto de 1,418 millones de rublos.
Un elemento importante que aumenta la efectividad de la implementación de la "producción ajustada" es la implementación de proyectos piloto. Por ejemplo, el proyecto Mayak en la planta de automóviles de KAMAZ OJSC se inauguró el 8 de septiembre de 2010 con el objetivo de la implementación intensiva de estándares, métodos y tecnologías de gestión modernos del sistema operativo TOS (Daimler AG) para optimizar los procesos del Automóvil Planta de KAMAZ OJSC. En el transcurso del proyecto Mayak, la carga de trabajo de los operadores se igualó a un ciclo de 240 s, un nuevo estructura organizativa. Las metas, resultados y herramientas utilizadas en el proyecto Mayak se presentan en la Tabla. catorce.
Además, en el transcurso del proyecto Mayak, se cambió la norma de controlabilidad del maestro: era 1:35, se convirtió en 1:10 (el maestro es el líder del equipo y su ideólogo, para apoyar la nueva estructura de tubería). Trabajo operativo organizado de gerentes y Retroalimentación a través de centros de información de 3 niveles: brigada, taller, fábrica. Más del 60% de las reuniones se han trasladado a centros de información para garantizar el flujo de información y el procedimiento de escalamiento. Los lugares de trabajo se organizaron de acuerdo con 15 principios de ensamblaje de Daimler (del 19% al 69% de cumplimiento). Desde el comienzo del proyecto, los empleados han presentado unas 1.300 propuestas kaizen con un efecto económico por valor de más de 17 millones de rublos. El trabajo del servicio de logística se organiza sobre la base de 14 principios de la logística de Daimler. Durante el proyecto se llevó a cabo una formación continua del personal en los principios y herramientas y métodos de Lean (se formaron unos 1.400 trabajadores y 350 ingenieros). Un elemento integral de la introducción del sistema de "producción ajustada" en la empresa es el cálculo del efecto económico de la introducción de herramientas y métodos de "producción ajustada".
Tabla 14
Objetivos, resultados y herramientas utilizadas en el proyecto Mayak
Objetivos del proyecto |
resultados del proyecto |
Principios, herramientas y métodos de Lean Manufacturing utilizados en el proyecto |
Reducir el número de modificaciones (ensamblaje) de automóviles ensamblados en un 50% |
Objetivo alcanzado |
Mapeo detallado de todos los procesos en el área de cobertura del proyecto. Planificación del trabajo en cascada en el formato de planes tácticos estándar. eliminación |
Implementando la calidad integrada |
Bucles de calidad implementados 1, 2, puertas de calidad, publicaciones de calidad |
|
Implementación del sistema Andón |
Objetivo alcanzado |
|
Implementación de estándares TOS en montaje y logística |
Objetivo alcanzado |
|
Aumentar la productividad laboral |
La productividad laboral aumentó un 49%. |
|
Asegurar la posibilidad de ensamblar 48.100 vehículos en GSK 1 en 2012 (24.000 vehículos fueron ensamblados en GSK 1 en 2010) |
Capacidad para ensamblar 48,100 vehículos en GSK 1 proporcionada en 2011 |
|
Implementar el estándar de gestión de planta para la gestión empresarial |
Estándar de gestión de planta implementado en el área del proyecto |
|
El costo del proyecto debe pagarse dentro del período de su implementación. |
El efecto económico del proyecto ascendió a 629 millones de rublos. y superó los costos |
El cálculo del efecto económico se realiza sobre la base de indicadores clave de rendimiento (reducción de stocks, reducción de la ruta de transporte, reducción de tiempo de inactividad no planificado de los equipos, etc.) y se expresa en el ahorro resultante de recursos o producción adicional en el sitio. , taller, organización, se tienen en cuenta como un efecto condicional.
Economía efecto = [Costos antes - Costos después] - -Costos para la realización del evento. (una)
El efecto económico es el efecto cuyo cálculo tiene en cuenta en términos de valor todo tipo de resultados y costos debidos a la implementación de la medida.
Costos = ¿Consumo de recursos físicos? Costo de los recursos. (2)
Costos previos a la implementación: calculados en función de los resultados del mapeo estado actual proceso o datos de contabilidad, contabilidad de gestión.
Z a \u003d P p a? St res, frotar. (3)
Costos posteriores: calculados según lo planificado (en la etapa de evaluación preliminar) o gasto real de recursos después de la implementación de la actividad
Z después de = P p después de St res, frotar, (4)
donde P p antes, P p después - el consumo de recursos antes y después de la implementación del evento, St res - el costo de los recursos
Los costos para la implementación del evento son costos únicos para la implementación del evento (costos de energía, materiales, mano de obra, etc.)
El uso de la metodología propuesta para evaluar la eficacia permitirá a la empresa evaluar con mayor precisión el efecto de la introducción de herramientas y métodos de producción ajustada, sobre la base de los cuales es posible tomar una decisión de gestión sobre la eficacia de la empresa. trabajar en la producción ajustada y la necesidad de intensificar este trabajo.
Realizó análisis de correlación-regresión series de tiempo nos permitió evaluar el grado de influencia de los factores sobre la variable dependiente y entre sí. Los resultados del análisis indican la presencia de una relación particularmente estrecha entre la capacidad de producción de la empresa y el volumen de productos enviados, los ingresos por ventas de productos, los salarios mensuales medios, el costo total de producción, la productividad del capital y la productividad laboral. Con un aumento en estos indicadores, aumenta el indicador de capacidad de producción (conexión directa).
El análisis de regresión de series de tiempo muestra lo siguiente. En primer lugar, el índice de rendimiento de los activos tiene una estrecha relación directa con la capacidad de producción, la producción en términos físicos, la tasa de utilización de la capacidad de producción, el volumen de productos enviados, los ingresos por ventas de productos, los salarios mensuales promedio y el costo total de ventas. Al mismo tiempo, existe una relación inversa con el costo de los activos fijos de producción. En segundo lugar, la rentabilidad de los productos ha nivel alto estanqueidad de la conexión con el beneficio de la venta de productos y el número de personal. En este caso, existe una relación directa entre los indicadores. El valor negativo del coeficiente de correlación (-0.716) con el indicador de costos por 1 rublo de productos vendidos indica una retroalimentación cercana.
Sin embargo, cabe señalar que los coeficientes de correlación de pares se obtuvieron bajo la condición de que otros factores influyeran en el resultado. Para abstraerse de su influencia y obtener una característica cuantitativa de la conexión entre los indicadores efectivos y factoriales en su forma pura, se calculan los coeficientes de correlación parcial.
Como resultado de la construcción de una matriz de coeficientes de correlación parcial para los datos de desarrollo de KAMAZ OJSC, fue posible identificar una relación positiva bastante estrecha entre los costos de desarrollo del PSC con indicadores tales como el número de propuestas kaizen enviadas e implementadas y el cantidad de área liberada (los coeficientes de correlación fueron 0,888; 0,894 y 0,891, respectivamente). El número de proyectos abiertos se correlaciona positivamente con el número de proyectos implementados, así como con el número de propuestas kaizen enviadas e implementadas. El número de áreas desocupadas está estrechamente relacionado con el número de proyectos abiertos e implementados, así como con las propuestas kaizen presentadas e implementadas. Los altos coeficientes de correlación indican un nivel significativo de dependencia de los indicadores.
Parece apropiado determinar el impacto del desarrollo de PSK en los principales indicadores económicos de la empresa. El mejor efecto positivo se observa cuando las variables se rezagan 3 años (Cuadro 15). En particular, existe una estrecha relación positiva entre la capacidad de producción de la empresa y los costos de desarrollo de PSK, así como indicadores de proyectos abiertos e implementados y propuestas kaizen. Además, estos indicadores tienen un impacto positivo en el volumen de productos enviados, los ingresos por ventas y el retorno del capital.
Parece inapropiado cambiar más los indicadores debido a los datos iniciales limitados sobre la empresa.
La siguiente etapa del análisis de correlación es el cálculo de la ecuación de relación (regresión). Los coeficientes de la ecuación muestran el impacto cuantitativo de cada factor en el indicador de desempeño, mientras que los demás permanecen sin cambios. Parece apropiado construir un modelo de regresión lineal múltiple con los mejores coeficientes de correlación para el modelo, es decir cuando se rezagan las variables durante tres años.
En nuestro caso, las ecuaciones de regresión se verán así:
y = 0.582x16 + 0.04x19 + 86.04x27 + 63692.33, (5)
En este caso, podemos dar la siguiente interpretación de la ecuación resultante: la rentabilidad aumenta en 0,582 unidades. con un aumento en el número de proyectos abiertos; por 0,04 uds. - con un aumento en el número de propuestas kaizen implementadas; para 86,04 uds. - con un aumento en el costo de introducir PSK en 1 millón de rublos.
Tabla 15
Matriz de coeficientes de correlación de pares (sesgo - 3 años)
Capacitado en los principios y métodos de seguridad del personal. |
proyectos abiertos |
Proyectos implementados |
Propuestas Kaizen enviadas |
Ofertas kaizen implementadas |
Superficie liberada m2 |
Unidades de equipo liberadas. |
Efecto económico obtenido (millones de rublos) |
Incluyendo kaizen |
Porcentaje de efecto económico |
Los costos para el desarrollo de PSK ascendieron a (millones de rublos) |
|
Capacidad de producción, uds. |
|||||||||||
Salida de producción en términos físicos, uds. |
|||||||||||
Factor de utilización de la capacidad |
|||||||||||
El volumen de productos enviados, |
|||||||||||
Ingresos por ventas de productos, millones de rublos. |
|||||||||||
Salario medio mensual, frotar. |
|||||||||||
Costo total de bienes vendidos, millones de rublos |
|||||||||||
El costo de los activos fijos de producción, millones de rublos. |
|||||||||||
Beneficio (pérdida) de las ventas, millones de rublos |
|||||||||||
Número de personal de producción industrial, pers. |
|||||||||||
Productividad del capital, frotar. |
|||||||||||
Productividad laboral, millones de rublos. |
A su vez, el valor de R2 = 0,995 indica que la variación de la productividad laboral en un 99,5% se debe a la influencia lineal de los factores anteriores.
La aplicación de los métodos propuestos para organizar la producción ajustada en una empresa implica la creación de un entorno adaptativo y sistema flexible gestión y producción, capaz de mejora continua, y ayudará a reducir las pérdidas en la empresa, aumentar la competitividad y aumentar la productividad laboral.
Traemos a su atención las revistas publicadas por la editorial "Academia de Historia Natural"
Efecto económico: la esencia del concepto, la necesidad de cálculo y análisis.
Definición 1
En el contexto del concepto de "manufactura ajustada", efecto economico representa la diferencia entre los resultados de las actividades de una entidad comercial y los costos incurridos para obtenerlos; en otras palabras, se trata de ingresos adicionales recibidos debido a que, al aplicar ciertos enfoques y métodos, la empresa funciona de manera más eficiente.
Debe comprender la diferencia entre reducción de costos (minimización de costos) y eliminación/reducción de desperdicios. De hecho, estas son cosas algo diferentes (aunque, por otro lado, reducir las pérdidas conduce a costos más bajos).
El efecto económico de la implementación de tal o cual mejora es la diferencia entre los estados "antes" y "después" (menos los costos asociados con la implementación de la medida). A veces, la diferencia entre los costos unitarios por unidad de producción, "antes" y "después" y otros indicadores se toma como un efecto económico.
Muy a menudo, el efecto económico se calcula en una escala de 1 año. Entonces, por ejemplo, si los movimientos diarios del operador se reducen en 5 minutos, entonces el ahorro para 1 semana será de 50 minutos (con una jornada de cinco días y dos turnos). semana de trabajo); durante un año ya son unos 2400 minutos (o 5 días hábiles). Así, el cálculo del efecto económico a escala anual permite ver con mayor claridad todo el potencial de la mejora implantada.
Los cálculos preliminares del potencial efecto económico permiten priorizar correctamente, así como centrar la atención y los esfuerzos en aquellas obras y proyectos que pueden traer el mayor beneficio y deben pagar más rápido. Al principio, se debe dar preferencia a la implementación simple, no costosa y proyectos a corto plazo. Si tiene que elegir entre dos proyectos que son similares en costo y complejidad, debe elegir el que tenga el mayor efecto económico potencial.
Indicadores de desempeño de las actividades
Es necesario analizar la implementación de medidas del concepto de producción ajustada (lean) solo con base en datos confiables de los resultados de los estudios de la dinámica de los indicadores de producción. Además, asegúrese de centrarse en el costo unitario de producción.
En general, la implementación de un proyecto de manufactura esbelta se considera exitosa si se cumplen las siguientes condiciones:
- aumento de la productividad laboral y aumento de los volúmenes de producción
- disminución de las tasas de matrimonio
- el indicador de entrega oportuna de productos manufacturados ha mejorado
- costo reducido por unidad.
Observación 1
Si al menos un indicador mostró una dinámica positiva y el resto permaneció en el mismo nivel, entonces se debe aceptar el proyecto. Si la mayoría de los indicadores calculados muestran la dinámica adecuada, pero uno de los indicadores muestra lo contrario, entonces se necesita un análisis adicional más profundo de las razones de esto.
Entre otras cosas, se pueden lograr ahorros significativos en los costos de producción en una empresa manufacturera mediante la implementación de las siguientes medidas:
- introducción de tecnologías de ahorro de energía
- optimización de costos de mantenimiento y reparaciones corrientes de activos fijos liberados
- cambio en la depreciación debido a la liberación de equipo y espacio (principalmente almacenamiento)
- optimización de impuestos, leasing, alquiler, pagos de seguros, costos de seguridad, etc.
- disminución de la tasa de matrimonio
- eliminación de exceso de existencias
- pérdida de tiempo de trabajo asociada a la espera del suministro de recursos materiales y técnicos
- respuesta más rápida al minimizar o eliminar el inventario, el tiempo de inactividad, etc.
- eliminación de desperdicio de materiales, etc.
Así, la esencia es que es necesario eliminar o minimizar todo lo que no crea valor para el consumidor.