Mapa del proceso tecnológico para la preparación de mezclas de concreto. TTK. Preparación de la mezcla de hormigón en el sitio de construcción. Cronograma del proceso de producción
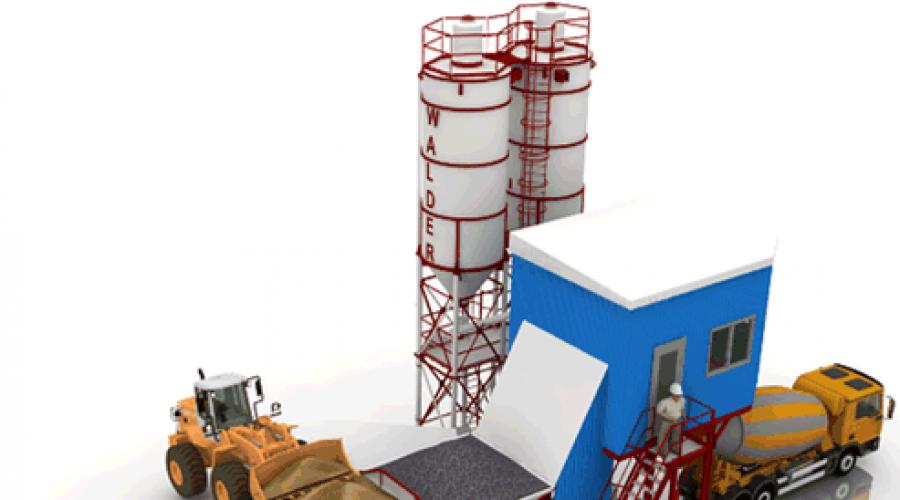
GRÁFICO TECNOLÓGICO TÍPICO (TTK)
PREPARACIÓN DE LA MEZCLA DE CONCRETO EN EL SITIO DE LA CONSTRUCCIÓN
I. ALCANCE
1.1. Un mapa tecnológico típico (en adelante, TTK) es un documento normativo completo que establece, de acuerdo con una tecnología específica, la organización de los procesos de trabajo para la construcción de una estructura utilizando los más modernos medios de mecanización, diseños progresivos y métodos de ejecución. trabajar. Están diseñados para algunas condiciones de trabajo promedio. El TTC está destinado a ser utilizado en el desarrollo de Proyectos para la producción de obras (PPR), otra documentación organizativa y tecnológica, así como con el fin de familiarizar (capacitar) a los trabajadores y trabajadores técnicos y de ingeniería con las reglas para la producción de trabajo en la preparación de una mezcla de hormigón en una planta mezcladora para la preparación de mezclas de hormigón de cemento en un sitio de construcción.
1.2. EN mapa real se dan instrucciones para la preparación de mezclas de concreto por medios racionales de mecanización, se dan datos sobre el control de calidad y aceptación del trabajo, requisitos de seguridad industrial y protección laboral en la producción del trabajo.
1.3. El marco normativo para la elaboración de mapas tecnológicos son: SNiP, SN, SP, GESN-2001 ENiR, normas de producción para el consumo de materiales, normas y precios locales progresivos, normas de costos laborales, normas de consumo de recursos materiales y técnicos .
1.4. El propósito de crear el TC es describir soluciones para la organización y tecnología de preparación de mezclas de concreto para asegurar su alta calidad, así como:
Reducir el costo del trabajo;
Reducir la duración de la construcción;
Garantizar la seguridad del trabajo realizado;
Organización del trabajo rítmico;
Unificación de soluciones tecnológicas.
1.5. Sobre la base de los TTC, como parte de los PPR (como componentes obligatorios del Proyecto de Ejecución de Obra), se desarrollan Diagramas de Flujo de Trabajo (RTC) para la ejecución de ciertos tipos de trabajo en la preparación de la mezcla de concreto. Los mapas tecnológicos de trabajo se desarrollan sobre la base de mapas estándar para las condiciones específicas de una organización de construcción determinada, teniendo en cuenta sus materiales de diseño, las condiciones naturales, la flota disponible de máquinas y materiales de construcción, vinculados a las condiciones locales. Los mapas tecnológicos de trabajo regulan los medios de soporte tecnológico y las reglas para la implementación de procesos tecnológicos en la producción de trabajo. Características tecnológicas, en función de la marca de la mezcla preparada, se deciden en cada caso por el Proyecto de Trabajo. La composición y el nivel de detalle de los materiales desarrollados en el RTC los establece la organización de construcción contratante pertinente, en función de las especificaciones y el alcance del trabajo realizado. En todos los casos de aplicación del TTK, es necesario sujetarlo a las condiciones locales, dependiendo de la composición, grado y cantidad de la mezcla de concreto producida.
Los diagramas de flujo de trabajo son revisados y aprobados como parte del PPR por el jefe del Contratista General de Construcción, de acuerdo con la organización del Cliente, la Supervisión Técnica del Cliente.
1.6. El mapa tecnológico está destinado a capataces, capataces y capataces que realizan trabajos de preparación de mezcla de concreto, así como a empleados de la supervisión técnica del Cliente y está diseñado para condiciones específicas de trabajo en la zona de temperatura III.
^ II. PROVISIONES GENERALES
2.1. Se ha desarrollado el mapa tecnológico para un conjunto de obras de preparación de mezclas de hormigón.
2.2. Los trabajos de preparación de la mezcla de concreto se llevan a cabo en un turno, la duración de las horas de trabajo durante el turno es:
donde 0.828 es el coeficiente de uso de mecanismos por tiempo durante el turno (el tiempo asociado con la preparación para el trabajo y la realización de ETO - 15 minutos, descansos asociados con la organización y tecnología del proceso de producción y descanso del conductor - 10 minutos cada hora de trabajo).
2.3. El mapa tecnológico prevé la realización del trabajo mediante un enlace integrado con planta mezcladora de hormigón móvil BSU-30TZ, dimensiones totales de la unidad 42500x5850x8400 m, con una capacidad de 30 m3/hora equipada con hormigonera SB-138, búnkeres materiales inertes m, la capacidad del silo de suministro de cemento es de 60 toneladas, el consumo total de energía eléctrica es de 75 kW (ver Fig. 1).
Figura 1. Planta mezcladora de hormigón BSU-30TZ
2.4. La planta mezcladora de concreto está equipada con un sistema de control automatizado basado en una computadora industrial, que proporciona:
Control automatizado de todos los procesos tecnológicos de producción;
Tecnología multireceta para la preparación de mezclas (hasta 50 recetas);
Contabilización del consumo de materiales y la producción de hormigón por grado;
Contabilización de la ejecución de aplicaciones con la conservación de información sobre el Cliente, el momento de entrada y ejecución de la aplicación, el número de receta y el volumen de la mezcla;
Salida de información contable a la pantalla e impresora.
2.5. El trabajo debe llevarse a cabo de acuerdo con los requisitos de los siguientes documentos reglamentarios:
SP 48.13330.2011. Organización de la construcción;
SNiP 3.03.01-87. Estructuras portantes y envolventes;
GOST 27006-86. Concreto. Reglas para la selección de la composición;
GOST 30515-97. cementos. Condiciones técnicas generales;
GOST 8736-93. arena para trabajos de construcción;
GOST 8267-93. Piedra triturada y grava de rocas densas para trabajos de construcción;
SNiP 12-03-2001. Seguridad laboral en la construcción. Parte 1. Requisitos generales;
SNiP 12-04-2002. Seguridad laboral en la construcción. Parte 2. Producción de la construcción.
^ tercero ORGANIZACIÓN Y TECNOLOGÍA DEL DESEMPEÑO DEL TRABAJO
3.1. La planta mezcladora de concreto automatizada (BSU) con la planta SB-138 está diseñada para la preparación de mezclas de concreto rígido y plástico con agregados de hasta 40 mm. Capacidad de instalación hasta 30 m/h; Las capacidades de las tolvas de suministro de cemento, agregados, tanque de agua están diseñadas para media hora de funcionamiento a la máxima productividad y la mayor relación agua-cemento de 0,5. La planta mezcladora de hormigón móvil consta de departamentos de mezcla y dosificación, depósito de áridos y depósito de cemento (ver fig. 2). La instalación se controla desde la cabina del conductor y el equipo eléctrico se encuentra en una sala especial. La cabina del conductor está equipada con instrumentos que registran el progreso del proceso tecnológico.
Figura 2. Diagrama de una planta mezcladora de concreto.
1 - rellenos de búnker consumibles; 2 - transportador-dispensador; 3 - transportador de recarga; 4 - hormigonera; 5 - marco de la hormigonera; 6 - dispensador de cemento; 7 - dispensador de aditivos químicos; 8 - dispensador de agua; 9 - unidad de aditivos químicos (a pedido del cliente); 10 - silo de cemento consumible con filtro; 11 - transportador de tornillo
3.2. Almacén de consumibles de arena y piedra triturada fraccionada de tipo abierto con paredes medianeras, ubicada directamente al lado de la planta mezcladora de concreto. La arena y la piedra triturada fraccionada se entregan al almacén de consumibles en vagones de ferrocarril. En el caso de la entrega de piedra triturada no fraccionada o contaminada, también se organiza aquí la clasificación del material en fracciones (cribado) y el lavado del material. La arena y la piedra triturada se introducen en los alimentadores del departamento de procesamiento por lotes y se descargan cargador frontal TO-49 directamente sobre los embudos de las bandejas vibratorias del transportador de galería. El dosificador SBU está formado por tolvas-llenadoras de servicio con dispensadores de péndulo de acción continua С-633. Los dispensadores se instalan sobre el transportador horizontal, que suministra materiales al transportador inclinado. En el transportador inclinado caen en la bandeja de carga del departamento de mezcla.
3.3. Consumible almacén automático de cemento S-753 con una capacidad de 300 toneladas está diseñado para el almacenamiento a corto plazo de cemento. El cemento de los vagones de ferrocarril se descarga directamente en el depósito de cemento utilizando descargador neumático S-577 o camiones de cemento.
La torre del silo con una capacidad de 60 toneladas está equipada con dos indicadores de nivel de cemento del tipo UKM. La tolva de suministro de cemento es un cilindro con una parte cónica en la parte inferior. El cemento se introduce directamente en dispensador S-781 con alimentador de bidones. Dentro del búnker hay dos indicador de nivel de cemento С-609А incluidos en el esquema de gestión de almacenes. El encendido o apagado del mecanismo que suministra cemento desde el almacén se realiza mediante los mismos indicadores.
3.4. ^ Planta mezcladora de hormigón SB-138 La mezcla forzada de acción continua es el equipo principal de la planta dosificadora de concreto. El cuerpo de trabajo de la batidora son dos ejes de sección cuadrada de 80x80 mm con cuchillas montadas en ellos. Las palas terminan con palas de 100x100 mm. El cuerpo del agitador termina en una tolva de almacenamiento con compuerta de mordaza.
^ Planta mezcladora de hormigón SB-138 está conectado a los almacenes de áridos de cemento ya la unidad de dosificación mediante un sistema de alimentadores de cinta y cangilones.
3.5. Dependiendo de las necesidades cambiantes de la mezcla de cemento y hormigón, la planta se puede ajustar a cualquier capacidad que va desde 15 a 30 m/h cambiando la capacidad de sus dosificadores: cemento de 5 a 10 t/h, arena y piedra triturada de 12,5 hasta 25 t/h y agua hasta 6 m.
Entonces, por ejemplo, al consumo de materiales por 1 m3 de concreto especificado por el laboratorio de la planta (cemento - 340 kg, arena - 547 kg, piedra triturada de una fracción de 5-20 mm - 560 kg, piedra triturada de una fracción de 20-40 mm - 840 kg, agua - 170 kg) la productividad de la planta será:
tabla 1
Dispensador para | Productividad de dosificadores, t/h en productividad de planta, m/h |
|||
15 | 20 | 25 | 30 |
|
cemento | | 6,8 | 8,5 | 10,2 |
arena | ![]() | 10,9 | 13,7 | 16,4 |
Fracción de piedra triturada 5-20 mm | | 11,2 | 14,0 | 16,8 |
Fracción de piedra triturada 20-40 mm | ![]() | 16,8 | 21,0 | 25,2 |
Agua | | 3,4 | 4,3 | 5,1 |
3.6. Previo al inicio de los trabajos de la planta de cemento cemento con instalación SB-138, se inspeccionan todos los equipos y, en caso de ser necesario, se calibran los dosificadores de áridos, cemento y agua. La calibración de los dosificadores se realiza con un cambio en la productividad de la planta, la marca y composición de la mezcla de concreto, el peso volumétrico y la distribución granulométrica de los agregados. Con una determinada productividad de la planta y, en consecuencia, la composición y marca de la mezcla, también es necesario calibrar periódicamente los dosificadores.
3.7. Los dosificadores de agregados se calibran mediante muestreo. Para esto necesitas:
Llenar los silos de servicio con arena, gravilla pequeña y grande en una cantidad de al menos 5 m3 de cada material;
Coloque los dosificadores de nivel en posición horizontal (con material) moviendo la palanca de carga o cambiando la carga en la caja de lastre (cerca del variador). En este caso, los amortiguadores móviles deben ajustarse a una altura de 100 mm para piedra triturada y 80 mm para arena. Los amortiguadores fijos se instalan 10 mm más altos que los amortiguadores móviles. La verificación de la ausencia de atascos o atascos en el sistema de pesaje de los dispensadores se realiza presionando ligeramente en el borde de la plataforma de pesaje o colocando un peso de 0,5 kg. En este caso, la plataforma debe bajarse hasta el tope;
Prepárese para la calibración de básculas de mercancías con una capacidad de carga de al menos 0,5, una caja con una capacidad de 200 m3 y un cronómetro.
3.7.1. Para el muestreo, es necesario encender el transportador de recolección horizontal para el movimiento en la dirección opuesta al cambiar la dirección del motor eléctrico (inversa). Al probar un dispensador, el resto debe estar apagado. El transportador colector horizontal se encenderá durante el período de prueba. A las órdenes de un asistente de laboratorio que sostiene un cronómetro, el operador enciende el dispensador. Se vierte arena o piedra triturada sobre una lámina de metal durante 4-5 segundos hasta que se obtiene un flujo estable de material vertido. Después de eso, se enciende el cronómetro y se coloca la caja bajo el flujo del material dosificado.
3.7.2. La caja se carga en 60 segundos para 1, 2, 3 posiciones de la flecha del variador y en 30 segundos para 4 y 5 posiciones de la flecha. Transcurrido el tiempo de muestreo, a la señal del ayudante de laboratorio, se apaga la cinta colectora y el dosificador. La muestra tomada se pesa en una balanza. Se realizan tres pesajes para una posición del variador.
3.7.3. La productividad horaria del dispensador está determinada por la media aritmética del peso de tres muestras según la fórmula:
donde es la media aritmética del peso de tres muestras en kg sin tara;
Tiempo de muestreo en seg.
3.7.4. Si el peso de las muestras no supera el ±2% del valor calculado, se considera que en esta posición de la aguja del variador el dosificador funciona de forma estable. De igual manera, se realiza la calibración de otros dosificadores de áridos.
3.8. Para calibrar el dispensador de cemento, debe:
Afloje los tornillos que sujetan el tubo de la tolva de cemento y gire el tubo 90°;
Asegúrese de que la tolva de suministro de cemento esté completamente llena de cemento. Verifique el nivel de cemento en la tolva de suministro usando los indicadores de nivel en el panel de control de la planta mezcladora;
Prepárese para tarar balanzas comerciales con una capacidad de carga de al menos 0,5, dos cajas con una capacidad de 200 litros, un cronómetro, una pala, un tubo de estaño con un diámetro de 130-150 mm, una longitud de 3-3,5 m.
3.8.1. El muestreo se lleva a cabo para cada una de las cinco posiciones de la flecha del variador. Para hacer esto, se instala una caja debajo de la boquilla, a las órdenes del asistente de laboratorio, el conductor enciende el dispensador de cemento. El cemento del dispensador ingresa a la tubería y de allí a la caja hasta que se establece a simple vista un modo estable de suministro de cemento y un número normal de revoluciones del motor eléctrico. El tiempo necesario para obtener un flujo estable de material suele ser de 50 a 60 segundos. Después de este tiempo, el cronómetro se enciende simultáneamente y la tubería se transfiere a la carga de la caja.
3.8.2. La caja se carga durante 90 segundos para 1, 2, 3 posiciones de la flecha del variador, y durante 60 segundos - para 4, 5 posiciones de la flecha. Una vez transcurrido el tiempo especificado, la muestra tomada se pesa en la balanza. Se realizan tres muestreos para cada posición de la aguja del variador. Precisión de dosificación de cemento ±2% del peso calculado.
3.8.3. Para controlar la correcta calibración se comprueba el funcionamiento del dosificador a la capacidad seleccionada y con funcionamiento continuo del dosificador durante - 10 minutos tomando tres muestras en una caja, prestando especial atención al funcionamiento de todos los mecanismos y al flujo ininterrumpido de material en el dispensador.
3.9. Para calibrar el dispensador de agua, debe:
Girar 180° sobre la brida el tubo de desagüe por el que entra el agua en el mezclador y extenderlo con un tubo adicional de hasta 4 m de largo;
Apague todos los equipos no relacionados con la dosificación de agua.
3.9.1. El dispositivo dosificador se calibra por muestreo, para lo cual es necesario encender la bomba dosificadora cuando el Tubo de desagüe. Al mismo tiempo, el agua del tanque a través de la bomba dosificadora y la válvula de tres vías regresa al tanque a través del anillo. A las órdenes de un ayudante de laboratorio que sostiene un cronómetro, el operador cambia la válvula de tres vías a la posición de suministro de agua al mezclador, y se suministra agua al barril hasta que se establece un flujo de agua continuo y estable.
3.9.2. Después de eso, el cronómetro se enciende simultáneamente y la válvula de tres vías se cambia instantáneamente para suministrar agua al tanque del medidor de agua. El contenedor se llena en 60 segundos para las posiciones 1, 2 y 3 de la flecha del variador, y en 30 segundos para las posiciones 4 y 5 de la flecha. Una vez transcurrido el tiempo especificado, a la orden del asistente de laboratorio, la válvula de tres vías se cambia a drenaje y el cronómetro se apaga. El operador cambia la válvula de tres vías a la posición de suministro de agua a través del anillo. Se mide la muestra tomada.
3.9.3. Para mantener el principal indicador de calidad de la mezcla de concreto (relación agua-cemento), es necesario calibrar el dispensador de agua con una precisión de ±1%.
3.10. Tras calibrar todos los dosificadores de la instalación, se construye un gráfico de la productividad de una planta de hormigón en función de la posición de la flecha del variador de cada dosificador (Fig. 3).
Fig. 3. El gráfico de la dependencia de la productividad de los dispensadores de las posiciones de la flecha de los variadores:
1 - agua; 2 - fracción de piedra triturada 5-20 mm; 3 - fracción de piedra triturada 20-40 mm; 4 - arena; 5 - cemento
3.11. Este gráfico es válido cuando la planta está funcionando con materiales permanentes que componen la mezcla de hormigón. Para cambiar la productividad de los dosificadores, es necesario cambiar la relación de transmisión del variador. Para ello, coloque las flechas del variador (solo en movimiento) en la división adecuada a lo largo de la curva aproximada y, mediante la calibración posterior, realice la corrección necesaria en su posición.
3.12. Previo al desmoldeo de la mezcla de cemento y hormigón, se realizan las siguientes operaciones:
Comprobar la presencia de cemento, áridos, agua y aditivos en los depósitos de abastecimiento;
Encienda la fuente de alimentación;
Verificar el correcto funcionamiento de los dispensadores;
Dar al operador de la máquina la composición de la mezcla de cemento y hormigón, seleccionada por el laboratorio de acuerdo con el contenido de humedad de los materiales;
Instalar dosificadores de dispositivos de pesaje de acuerdo con la composición de la mezcla.
3.12.1. Antes de encender las unidades de la instalación, el conductor emite dos señales sonoras de advertencia con un intervalo de 1 minuto (la primera señal es larga, la segunda es corta).
3.12.2. A continuación, se ponen en funcionamiento las unidades de la instalación en el siguiente orden: hormigonera, bomba dosificadora (según patrón de anillo), transportador inclinado, transportador prefabricado, dosificadores de áridos, dosificador de cemento, válvula de tres vías con alimentación de agua a la mezcladora. Después de 1-2 minutos después del inicio del trabajo inactivo, comienzan a liberar la mezcla.
3.12.3. Primero, los lotes de prueba se hacen en modo semiautomático. En este punto, el conductor y el ayudante de laboratorio determinan la movilidad de la mezcla (tiro de cono) mediante muestreo. Si el calado del cono difiere del especificado, entonces se cambia la dosificación de agua. Habiendo logrado el tiro especificado del cono y asegurándose de que la dosificación de los materiales constituyentes es correcta, el conductor cambia la planta al modo de operación automático.
3.13. La planta opera de acuerdo con el siguiente esquema, dado en la Fig. 4
Figura 4. sistema de tecnología funcionamiento de la planta mezcladora de hormigón BSU-30TZ
1 - alimentadores de vibración; 2 - transportadores; 3 - búnkeres agregados; 4 - dosificadores de agregados; 5 - dispensador de cemento; 6 - búnker de cemento; 7 - cinta transportadora; 8 - batidora; 9 - accionamiento para hormigón; 10 - tanque de agua; 11 - dispensador de agua; 12 - válvula de tres vías; 13 - tolva receptora; 14 - banco de silos; 15 - filtros
3.13.1. La excavadora empuja alternativamente los agregados sobre las bandejas vibratorias 1, desde donde los transportadores 2 los alimentan a los contenedores de suministro 3. En ausencia de agregados, un cargador frontal alimenta arena y piedra triturada a los contenedores de suministro. Cuando los bunkers están completamente cargados, se activa el indicador de nivel superior, y la bandeja vibratoria y los transportadores se apagan después de que haya pasado el material restante en la cinta, y se enciende la señal luminosa de fin de carga. Cuando el material se agota en la tolva de suministro hasta el indicador de nivel inferior, se encienden el transportador, la bandeja vibratoria, las señales de luz y sonido para el inicio de la carga.
3.13.2. El cemento de la lata de silo 15 se alimenta al depósito de alimentación 6 mediante un sistema de inyección neumática. Desde la tolva de suministro, el cemento ingresa al dosificador de péndulo de pesaje 5. Los indicadores de los niveles superior e inferior de cemento tienen señales de luz y sonido al panel de control del almacén de cemento.
3.13.3. El agua del depósito 10 del compartimento de mezcla se bombea desde un depósito especial. La piedra triturada de la fracción 5-20, 20-40 mm y la arena se dosifican continuamente mediante dosificadores pendulares de cinta 4, a los que llega el material procedente de tolvas de suministro.
Primero, se dosifica piedra triturada de una fracción de 20-40 mm sobre la cinta, luego piedra triturada de una fracción de 5-20 mm y arena, y encima de estos materiales, cemento. Este orden de alimentación elimina la acumulación de pequeñas partículas de material en la banda. Los materiales dosificados se alimentan a través del embudo de alimentación al mezclador. El agua del tanque se dosifica por medio de una bomba dosificadora y se alimenta a través de la tubería directamente al mezclador de trabajo.
3.13.4. La barda de sulfito-alcohol se prepara en una instalación especial y se introduce en el agua en una cantidad de 0,2-0,3% del peso del cemento por 1 m de hormigón (0,68-1,0 kg/m). En la hormigonera, los componentes de hormigón se mezclan y transportan intensamente ejes de paleta a la salida. Desde el mezclador, la mezcla terminada ingresa a la tolva de almacenamiento y luego, a través de la compuerta de mordaza, se descarga en camiones de volteo.
3.14. Al final del día, luego de finalizada la liberación de la mezcla de concreto, todo el equipo inicia la limpieza de las unidades de la planta mezcladora de concreto. Especialmente limpie a fondo la batidora.
La piedra triturada se alimenta primero a la mezcladora y se limpia en seco, luego la mezcladora se lava con agua y también se limpia la compuerta de mordaza de la tolva de almacenamiento.
El resto de la planta se limpia con aire comprimido.
Descripción del trabajo
Este diagrama de flujo se aplica a la mezcla de concreto para la preparación hormigón pesado con una densidad media de 2,4-2,5 kg/cm³, y concreto ligero con una densidad media de 1,7-1,9 kg/cm³ utilizada como materia prima para la fabricación de hormigón armado y productos de hormigón.
Organización y tecnología de preparación de mezclas de hormigón.
La Cement M 400 se entrega a los almacenes de cemento por ferrocarril en vagones tolva. De los vagones, el cemento se descarga por gravedad a través de escotillas hacia el depósito-dispositivo receptor. Los vagones tolva se descargan con aire comprimido. Desde el dispositivo receptor, el cemento se bombea mediante una bomba neumática de tornillo del tipo NPV 36-2 a los silos de hormigón armado Nº silos, o se puede alimentar directamente a través de tuberías de cemento desde el descargador de vagones de cemento hasta los silos de hormigón. planta.
El suministro de cemento desde los silos hasta la mezcladora se realiza mediante sinfines. Para eliminar el cemento colgado en los silos (bóvedas), se instalan vibradores en la parte cónica de los silos.
El suministro de inertes al mezclador se realiza mediante un transportador desde dosificadores de los correspondientes inertes. Las tolvas de recepción están instaladas frente a los dispensadores. Recepción de bunkers para inertes 3 unidades. 12 m³ cada uno. La carga de materiales inertes en las tolvas receptoras se realiza mediante una pala cargadora. El transportador está instalado en una galería calentada para evitar la adherencia de materiales inertes en el ramal inactivo del transportador y la formación de bloqueos debajo de este.
Para mejorar la calidad de las mezclas de concreto, la planta cuenta con un departamento de preparación de aditivos: plastificantes y aditivos para concreto de invierno.
Las mezclas de hormigón se preparan según recetas aprobadas. La preparación de una mezcla de hormigón se reduce a la dosificación y mezclado de los materiales constituyentes. La dosificación de inertes y cemento se realiza en dosificadores por peso. Los aditivos plastificantes se utilizan para preparar la mezcla de hormigón. La precisión de dosificación de cemento, agua, aditivos puede desviarse de la calculada en no más del 1%, agregados - 2%.
Para obtener una mezcla homogénea, se mezcla en una hormigonera con un volumen de 1,5 m³ (volumen de salida de la mezcladora). La duración óptima de la mezcla en mezcladores cíclicos está determinada por empíricamente en el laboratorio. La duración de la mezcla para mezclas con una movilidad de 4-5 cm es de 75-100 segundos.
Los materiales iniciales se cargan, por regla general, simultáneamente, la solución de trabajo de aditivos se introduce con agua de mezcla. Cuando se trabaja con agua caliente, la secuencia de carga es la siguiente: árido, agua caliente y aditivos químicos, cemento. Los áridos fríos bajan rápidamente la temperatura de la mezcla, evitando un fraguado rápido del cemento por contacto con agua caliente. La mezcla de hormigón en invierno se incrementa en un 25%. Al final de la mezcla, la mezcla de hormigón se descarga en una tolva o carro dosificador.
Kuchmin
Breve instrucción:
- Busque un trabajo adecuado en la barra de búsqueda en el centro de la página en la parte superior o en la barra de navegación lateral a la izquierda.
- Evalúe la calidad del trabajo utilizando el contenido y las capturas de pantalla de los dibujos que se encuentran en el archivo. Para ver capturas de pantalla, descargue el archivo en la parte inferior de la página.
- Si está satisfecho con el trabajo, elija un método de pago (Yandex-Money, WebMoney o Interkassa) o use su cuenta personal y su cuenta personal.
- Espere que la contraseña para el archivo se envíe a su correo electrónico. Para acelerar la recepción de la contraseña, debe completar correctamente el formulario de pago: indique su dirección de correo electrónico.
- Para todas las preguntas, póngase en contacto con
Nº TARJETA TECNOLÓGICA
para trabajos de hormigón
1 Alcance.. 3
2 organización y tecnología del trabajo .. 3
3 REQUISITOS DE CALIDAD Y ACEPTACIÓN DEL TRABAJO.. 4
4 SALUD Y SEGURIDAD.. 5
5 PROTECCIÓN DEL MEDIO AMBIENTE… 6
6 LISTA DE DOCUMENTACIÓN REGLAMENTARIA-técnica y de referencia.. 7
6 Hoja de familiarización.. 8
- Área de aplicación
El mapa tecnológico prevé la organización y tecnología del trabajo concreto.
El trabajo en consideración incluye:
- preparación de mezcla de hormigón;
- trabajo de refuerzo;
- colocación de hormigón;
- métodos de control.
- organización y tecnología del desempeño del trabajo
Al realizar el trabajo, es necesario cumplir con los requisitos de los documentos reglamentarios que figuran en la Sección 6.
Las materias primas utilizadas en la fabricación de cimientos monolíticos deben cumplir con la documentación técnica y reglamentaria vigente, acompañada de documentos de las empresas proveedoras que certifiquen su calidad.
Diseño fundación monolítica debe cumplir con los requisitos de documentación normativa.
Preparación de mezcla de hormigón.
La mezcla de hormigón se prepara en una hormigonera de acción forzada.
La elección de los cementos para la preparación de mezclas de hormigón debe realizarse de acuerdo con GOST 30515-97. La aceptación de cementos debe realizarse de acuerdo con GOST 30515-97, transporte y almacenamiento de cementos, de acuerdo con GOST 30515-97 y SNiP 3.09.01-85.
Los áridos para hormigón se utilizan fraccionados y lavados. Está prohibido usar mezcla natural arena y grava sin tamizar en fracciones.
La dosificación de los componentes de las mezclas de concreto debe hacerse por peso. Se permite la dosificación por volumen de agua de los aditivos introducidos en la mezcla de hormigón en forma de soluciones acuosas. La relación de componentes se determina para cada lote de cemento y agregados, al preparar concreto de la resistencia y movilidad requeridas. La dosificación de los componentes debe ajustarse durante la preparación de la mezcla de concreto, teniendo en cuenta los datos de seguimiento de los indicadores de propiedades del cemento, contenido de humedad, granulometría de los agregados y control de resistencia.
Al preparar una mezcla de concreto utilizando una tecnología separada, se debe observar el siguiente procedimiento:
- el agua, parte de la arena, el relleno mineral finamente molido (si se usa) y el cemento se dosifican en un mezclador de alta velocidad en funcionamiento, donde se mezcla todo;
- la mezcla resultante se introduce en una hormigonera, precargada con el resto de áridos y agua, y una vez más se mezcla todo.
- el descanso entre las etapas de hormigonado (o colocación de capas de mezcla de hormigón) debe ser de al menos 40 minutos, pero no más de 2 horas.
- se permite el uso de aditivos (anticongelantes, inclusores de aire, aceleradores y retardadores del endurecimiento del hormigón, etc.).
El espesor de la capa protectora de hormigón debe tenerse en cuenta el papel del refuerzo en las estructuras (de trabajo o estructurales), el tipo de estructuras (columnas de hormigón, losas, vigas, elementos de cimentación, muros, etc.), diámetro y tipo de reforzamiento.
La armadura funciona.
El trabajo de refuerzo debe llevarse a cabo de acuerdo con el mapa tecnológico P
Colocación y compactación de mezclas de hormigón.
La colocación de la mezcla de hormigón debe ser realizada por adoquines que dispongan de dispositivos que dosifiquen y distribuyan la mezcla en los equipos laterales limitadores, por regla general, sin el uso de mano de obra.
Al colocar mezclas de hormigón en un vertedero abierto, es necesario tomar medidas (refugios especiales, cobertizos, revestimientos de película) para proteger las mezclas de hormigón y los productos recién moldeados de los efectos nocivos de las influencias atmosféricas.
Los modos de moldeo deben garantizar el coeficiente de compactación de la mezcla de hormigón (la relación entre su densidad real y la teórica calculada): para hormigón pesado, no menos de 0,98; cuando se usan mezclas rígidas y justificación adecuada, así como para concreto de grano fino, no menos de 0.96. El volumen de vacíos intergranulares en la mezcla de concreto liviano compactado debe cumplir con los requisitos de GOST 25820-83.
El decapado de los productos después del tratamiento térmico debe realizarse después de que el hormigón haya alcanzado la resistencia al decapado.
REQUISITOS DE CALIDAD Y ACEPTACIÓN DE LAS OBRAS
El control de calidad del trabajo debe llevarse a cabo de acuerdo con los requisitos de los documentos reglamentarios que figuran en la Sección 6:
Al aceptar concreto terminado y hierro estructuras de concreto o partes de las estructuras deben comprobarse:
- conformidad de las estructuras con los planos de trabajo;
- la calidad del concreto en términos de resistencia y, si es necesario, resistencia a las heladas, resistencia al agua y otros indicadores especificados en el proyecto;
- la calidad de los materiales utilizados en la construcción, productos semiacabados y productos.
La recepción de estructuras o partes de estructuras de hormigón armado y acabados debe formalizarse de acuerdo con el procedimiento establecido con un informe de inspección. obras ocultas o un acto de aceptación de estructuras críticas.
Composición de operaciones y medios de control durante el hormigonado.
Los empleados líderes y especialistas de la organización, de acuerdo con la lista de puestos aprobada por el jefe de la organización, antes de ser admitidos a trabajar, y posteriormente periódicamente dentro de los límites de tiempo establecidos, son evaluados por su conocimiento de las normas de protección y seguridad laboral. , teniendo en cuenta sus funciones laborales y la naturaleza del trabajo realizado. El procedimiento para realizar capacitación y probar conocimientos se establece de acuerdo con GOST 12.0.004-90 SSBT "Organización de capacitación en seguridad laboral". Disposiciones generales” y de conformidad con el Decreto del Ministerio de Trabajo de la Federación Rusa del 13.01.2003 No. "El procedimiento para la capacitación en protección laboral y prueba de conocimiento de los requisitos laborales de los empleados de las organizaciones". Reglamento aproximado sobre el procedimiento de capacitación y prueba de conocimientos sobre protección laboral para gerentes y especialistas de organizaciones, empresas e instituciones e instituciones de construcción, industria. materiales de construcción y vivienda y servicios comunales.SALUD Y SEGURIDAD
Los empleados que realicen el trabajo deben aprobar una prueba de conocimiento y tener certificados de prueba de conocimiento sobre protección laboral.
Trabajadores no formados previamente métodos seguros trabajo por profesión, dentro de un mes a partir de la fecha de admisión al trabajo, deben estar capacitados de acuerdo con GOST 12.0.004-90 SSBT en el alcance de las instrucciones de protección laboral para las profesiones relevantes, elaborado sobre la base de industrias específicas instrucciones de protección laboral, y recibir un certificado de protección laboral.
Los lugares de trabajo deben contar con botiquines de primeros auxilios con medicamentos.
La lista de documentos que deben ubicarse en el lugar de trabajo:
- Órdenes de cita personas responsables en protección laboral, seguridad industrial;
- Órdenes sobre la designación de personas responsables del buen estado y funcionamiento seguro de máquinas y mecanismos;
- Pedidos para asegurar equipos;
- bitácora de información en el lugar de trabajo;
- diario de comentarios y sugerencias;
- registro de control de entrada.
PROTECCIÓN DEL MEDIO AMBIENTE
Con el fin de proteger el medio ambiente, al realizar los trabajos anteriores, está prohibido:
- violar los límites de los territorios asignados para la construcción;
- contaminar el medio ambiente con desechos de construcción, para lo cual es necesario en la etapa de diseño prever métodos de procesamiento y eliminación de desechos;
- perturbar la red de drenaje natural;
- paso de maquinaria y vehículos en lugares no previstos por el proyecto para la producción de obras;
- planificar y cortar pendientes pronunciadas en los sitios debido a la posibilidad de erosión del suelo;
- no cumplan con los requisitos de las autoridades ambientales locales.
Por causar daños al medio ambiente (destrucción del suelo y cobertura vegetal, contaminación de cuerpos de agua, incendios en bosques, turberas, etc.) fuera del derecho de vía, los encargados de las obras, así como los trabajadores que causen directamente daños al medio ambiente. ambiente.
- LISTA DE DOCUMENTACIÓN REGLAMENTARIA-técnica y de referencia
- SNiP III-42-80*. Tuberías principales;
- - SNiP 3.02.01-87. Movimientos de tierra, fundaciones y cimientos;
- SNiP 3.03.01-87. Estructuras portantes y envolventes;
- VSN 004-88. Construcción de oleoductos principales. Tecnología y organización;
- VSN 014-89. Construcción de tuberías principales y de campo. protección del medio ambiente;
- GOST R 51285-99. Mallas de alambre trenzado con celdas hexagonales para diseños de gaviones. Especificaciones;
- GOST 7502-98. Ruletas midiendo metal. Requerimientos técnicos.
- GOST 12-03-01. SSBT. Fondos protección personalórganos respiratorios. Clasificación y etiquetado;
- GOST 12.3.003-86*. SSBT. Trabajos eléctricos. Requerimientos de seguridad;
- GOST 123.016-87. SSBT. Construcción. Trabajos anticorrosión. Requerimientos de seguridad;
- SNiP 12-03-2001. Seguridad laboral en la construcción. Parte 1. Requisitos generales;
- SNiP 12-04-2002. Seguridad laboral en la construcción. Parte 2. Producción de la construcción;
- SP 12-136-2002. Soluciones para la protección laboral y seguridad industrial en proyectos para la organización de la construcción y proyectos para la producción de obras
- POT R M-016-2001. Normas intersectoriales sobre protección laboral (normas de seguridad) durante la operación de instalaciones eléctricas;
- PB 10-382-00. Reglas para la construcción y operación segura de grúas;
- Normas para el funcionamiento técnico de las instalaciones eléctricas de consumo”;
- POT R M-027-2003. Normas intersectoriales sobre protección laboral en el transporte por carretera;
- Normas de seguridad para la operación de los principales oleoductos.
6 Hoja de familiarización
No p. p. | Nombre completo | puesto de empleado | la fecha | Firma |
1. | ||||
2. | ||||
3. | ||||
4. | ||||
5. | ||||
6. | ||||
7. | ||||
8. | ||||
9. | ||||
10. | ||||
11. | ||||
12. | ||||
13. | ||||
14. | ||||
15. | ||||
16. | ||||
17. | ||||
18. | ||||
19. | ||||
20. | ||||
21. | ||||
22. |
Lo apruebo:
______________________
______________________
______________________
"____" __________ 200 g.
ENRUTAMIENTO
CARTA TECNOLOGICA PARA ESTRUCTURAS DE HORMIGON
OBRAS DE ARMADURA, ENCOFRADO Y HORMIGÓN
Número de página |
||
Provisiones generales | ||
Requisitos para el hormigón y la mezcla de hormigón. | ||
Herramientas y equipos tecnológicos. | ||
Trabajos preparatorios, de encofrado y de refuerzo | ||
hormigonado | ||
curado de concreto | ||
Control de calidad de las obras. | ||
Protección laboral en la producción de obras | ||
protección del medio ambiente | ||
Bibliografía | ||
Anexo 1. Relación de ingenieros y trabajadores familiarizados con el mapa tecnológico. |
1. Disposiciones generales
1.1. El mapa tecnológico se aplica a la ejecución de encofrados, armaduras y trabajos de hormigón.
1.2. El mapa tecnológico es parte integral el proyecto para la producción de obras, desarrollado en relación con un objeto de construcción específico, y establece requisitos para las características de la organización y tecnología para la producción de encofrados preparatorios, refuerzos y trabajos de hormigón, destinados a garantizar la alta calidad de las estructuras que se están construyendo construido.
1.3. El Mapa Tecnológico describe las medidas organizativas, técnicas y estructural-tecnológicas que deben tomarse para garantizar la seguridad técnica de la calidad del hormigón en su totalidad, para que el hormigón adquiera la resistencia requerida en el momento del desencofrado, y para reducir la probabilidad de fisuras térmicas en estructuras en las etapas de curado y desencofrado del hormigón.
1.4. El Mapa Tecnológico contempla los trabajos de preparación, encofrado, refuerzo y hormigonado durante todo el año de construcción, teniendo en cuenta el desempeño de los trabajos de hormigonado en condiciones de invierno en casas de calor.
1.5. Al desarrollar el mapa Tecnológico, se asume que la mezcla de concreto será suministrada desde una planta de concreto ubicada a una distancia a la cual durante el transporte no habrá pérdida de movilidad por debajo del valor establecido de trabajabilidad del concreto, los cuales se dan en este mapa tecnológico. .
1.6. Durante el desarrollo del “Mapa tecnológico” se supone que el hormigonado de rejas, cremalleras y cabezas de apoyos se realiza en encofrado desmontable metálico.
1.7. El cumplimiento de los requisitos de la normativa garantiza la recepción de hormigón de las calidades exigidas en cuanto a resistencia, resistencia al agua, resistencia a las heladas y, en definitiva, asegura la calidad y durabilidad requeridas de las estructuras.
1.8. Al desarrollar el "Mapa tecnológico", se tuvo en cuenta que la prevención del agrietamiento en el concreto por efectos de la temperatura o su reducción significativa se logra solo con la combinación adecuada de medidas estructurales y tecnológicas para la producción de trabajos de concreto.
1.9. Las actividades de construcción incluyen:
selección de soluciones de diseño para la estructura en su conjunto y sus elementos individuales, asegurando la resistencia de las estructuras a los efectos de la temperatura, teniendo en cuenta las condiciones climáticas locales;
Minimización en el diseño de zonas-concentradores de tensiones térmicas;
El uso de grados reducidos de hormigón, proporcionando un consumo mínimo de cemento;
Refuerzo del hormigón, teniendo en cuenta la probabilidad de fisuras térmicas.
1.10. Las medidas tecnológicas incluyen las medidas que se establecen a continuación en este "Reglamento Tecnológico".
1.11. La producción de trabajos de hormigón debe llevarse a cabo de acuerdo con el proyecto, PPR, este "Reglamento Tecnológico", con los números y reglas técnicas actuales, incluido SNiP 3.06.04-91 "Puentes y tuberías", SNiP 3.03.01-87 "Estructuras portantes y de cerramiento"; SNiP 12-03.2001 "Seguridad laboral en la construcción" parte 1. Disposiciones generales. SNiP 12-04.2002 "Seguridad laboral en la construcción" parte 2. Producción de la construcción. VSN 150-93 "Instrucciones para mejorar la resistencia a las heladas de las estructuras de transporte de hormigón", M., 1993; Manual "Control de calidad de la construcción de puentes", M., "Nedra", 1994.
1.12. Al desarrollar el "Mapa tecnológico", se tuvo en cuenta que todas las operaciones para los procesos principales y la mayoría de los auxiliares se realizan utilizando máquinas y mecanismos, y trabajo manual, utilizando una herramienta mecanizada.
1.13. La responsabilidad por la calidad del trabajo realizado en la construcción de estructuras de hormigón recae en el ingeniero jefe, quien debe garantizar la organización de su desempeño sin defectos de acuerdo con el PPR, los documentos reglamentarios y este "Reglamento tecnológico".
1.14. Los trabajos de hormigonado y montaje de estructuras de hormigón se llevan a cabo bajo la dirección del capataz y en cada turno, un capataz de turno.
1.15. Durante la realización de trabajos de hormigón en el sitio de construcción, es necesario ser constantemente representantes del laboratorio de construcción, quienes deben monitorear los parámetros de la mezcla de concreto, el cumplimiento de las reglas para la colocación de concreto, régimen de temperatura el endurecimiento del hormigón y la temperatura exterior, así como la calidad de todos los materiales entrantes.
1.16. Al realizar trabajos de hormigonado en el sitio de construcción, es necesario contar con el equipo de laboratorio adecuado (cono estándar para determinar la movilidad de la mezcla de concreto, dispositivos para determinar la cantidad de aire incorporado en la mezcla de concreto, termómetros, juegos de moldes para seleccionar cubos de control y otros instrumentos y equipos necesarios).
2. Requisitos para el hormigón y la mezcla de hormigón
2.1. De acuerdo con los requisitos especificados en los planos de trabajo, la composición del material de la mezcla de concreto debe garantizar que el concreto adquiera los indicadores de resistencia, resistencia a las heladas y resistencia al agua establecidos por el proyecto, a saber:
Los indicadores de resistencia, resistencia a las heladas y resistencia al agua se especifican de acuerdo con los planos de trabajo del proyecto.
Para cada lote de mezcla de concreto colocado en una construcción separada, se emite un documento sobre la calidad de la mezcla de concreto. La empresa proveedora tiene obligaciones de garantía por la calidad de la mezcla de hormigón suministrada al sitio de construcción.
Una solicitud para el suministro de mezcla de concreto es redactada por el CONTRATISTA-EJECUTOR DE OBRAS en el membrete de la planta con la indicación obligatoria del consumidor de la mezcla de concreto (CONTRATISTA-EJECUTOR DE OBRAS), clase de concreto (B25, B30 . ..), movilidad de la mezcla de hormigón en el lugar de colocación (P3, P4), resistencia a las heladas (F300 ...), resistencia al agua (W6, W8 ...), requisitos técnicos para materiales - aglutinante, agregados y aditivos . Hora de inicio de la entrega de la mezcla de concreto, dirección de entrega, volumen requerido de mezcla de concreto, número requerido de camiones mezcladores.
3. Herramientas y equipos tecnológicos
3.1. El sitio para la construcción de una estructura de hormigón debe contar con los equipos y equipos tecnológicos necesarios, así como con los materiales y accesorios (ver tabla 1).
3.2. Independientemente de la época del año, se debe prestar la debida atención al equipo integrado de protección contra la humedad y el calor, que debe garantizar la aceleración del endurecimiento del concreto en condiciones de curado en el encofrado o bajo un revestimiento protector contra el calor y la humedad, y en la etapa de calentamiento. y enfriamiento del concreto, excluyen la posibilidad de grietas térmicas.
3.3 El equipo integrado de protección contra la humedad y el calor consta de:
Encofrado de metal de inventario con una superficie de formación;
Recubrimientos de inventario de protección contra la humedad y el calor: para proteger las superficies sin encofrar de concreto recién colocado de la humedad y el intercambio de calor con el medio ambiente;
Toldo para proteger la superficie de hormigón de la lluvia durante el trabajo en tiempo lluvioso;
Invernaderos envolventes-cáscaras con marco de carga y la cantidad requerida de generadores de calor (al realizar trabajos en la temporada de invierno).
3.4. Las películas de polímero (polietileno, cloruro de polivinilo, etc.) con un espesor de al menos 100 micrones o tela recubierta de goma se pueden usar como paneles a prueba de humedad de un revestimiento protector contra la humedad y el calor de inventario.
3.5. Como materiales de protección térmica se pueden utilizar geotextil, dornita, lino u otros paneles termoaislantes. rollo de materiales.
3.6. Además del complejo equipo tecnológico de protección contra la humedad y el calor, el sitio de hormigonado debe contar con:
Una bomba de hormigón capaz de suministrar continuamente la mezcla de hormigón con la movilidad requerida en el encofrado;
Grúa con alcance suficiente para suministro de materiales durante la construcción de soportes;
Vibradores manuales para compactación de mezclas de concreto;
Bunker (balde) para suministrar, si es necesario, hormigón;
Un conjunto de herramientas manuales para nivelar la mezcla de hormigón;
Un conjunto de "lámparas portadoras" para el control visual, si es necesario, de la calidad del trabajo de refuerzo y encofrado, colocación y compactación de la mezcla de hormigón;
3.7. Los invernaderos deben estar hechos de materiales que tengan baja capacidad de soplado (tela de goma, películas de polímero, etc.) y que no se vuelvan quebradizos con el frío.
3.8. Al instalar invernaderos, es necesario garantizar una unión hermética de los revestimientos a la base y elementos de hormigón y hormigón armado previamente hormigonados.
3.9. Para reducir el riesgo de fisuración en la zona de contacto del hormigón endurecido con el endurecido, los invernaderos deben proporcionar calefacción a las estructuras previamente hormigonadas.
3.10. Para asegurar condiciones normales para el intercambio de calor, no debe haber cavidades muy estrechas en el invernadero. La distancia entre la cerca del invernadero y la estructura calentada debe ser de al menos 1,0 ... 1,5 m.
3.11. En invernaderos con una altura de más de 4,0 m, la temperatura debe controlarse a una altura de 0,4 m desde el suelo y hasta el techo. Si hay una diferencia de temperatura a lo largo de la altura del invernadero de más de 5 - 7 °C, es necesario igualar la temperatura del aire con la ayuda de ventiladores, suministrando aire caliente desde la parte superior del invernadero hasta la parte inferior.
3.12. Cuando se utilicen generadores de calor con combustible líquido, si es necesario, se debe disponer la ventilación de los invernaderos.
3.13. Los Teplyaks están equipados con generadores de calor de combustible líquido o calentadores eléctricos. El número de generadores de calor debe determinarse por cálculo, dependiendo de la temperatura exterior, la temperatura del aire requerida dentro del invernadero, las condiciones para el intercambio de calor entre el invernadero y el medio ambiente, y el diseño de los recintos del invernadero.
3.14. El invernadero debe estar equipado con generadores de calor o calentadores eléctricos con potencia ajustable, que posteriormente les permitirá regular suavemente la temperatura del aire en el invernadero encendiéndolos o apagándolos.
3.15. El invernadero debe tener una estructura rígida que pueda soportar el peso propio de las vallas, la presión del viento, las nevadas, etc.
3.16. El invernadero debe estar adecuadamente iluminado para garantizar condiciones de trabajo normales al colocar el hormigón y terminar la capa superficial de hormigón.
3.17. En los invernaderos, es necesario tener una cantidad suficiente de recubrimientos protectores contra el calor y la humedad para el cuidado del concreto.
3.18. El calentamiento de los invernaderos se detiene solo si hay una diferencia de temperatura aceptable entre el concreto que se endurece en la superficie de la estructura y el aire en el invernadero (la diferencia no es más de 20 ° C). Los generadores de calor deben apagarse secuencialmente, asegurando una disminución suave de la temperatura del aire en el invernadero.
3.19. El invernadero debe desmontarse después de que el hormigón de la superficie de la rejilla se haya enfriado a una temperatura que no supere la temperatura del aire exterior en más de 20 °C.
La temperatura mínima prevista para las próximas 24 horas debe tomarse como la temperatura de diseño del aire exterior.
tabla 1
Propósito del equipo o equipo | Equipo o herramientas | Descripción, marca. | Cantidad (pieza) | notas |
|
Suministro de hormigón | camión bomba de hormigón | "SHCVING" Lstr = 42 m | |||
Compactación de hormigón | Vibrador profundo, d = 50 mm, l = 35 cm. | ||||
Trabajo de instalación | Capacidad de grúa 16 t | ||||
Compactación de hormigón | vibrador de sitio | 2800rpm |
|||
Nivelación y movimiento de hormigón. | pala pala | ||||
Alisado de la superficie de hormigón | regla de madera |
4. Trabajos preparatorios, de encofrado y de refuerzo
4.1. Antes del inicio del trabajo de encofrado y refuerzo en la construcción de estructuras de hormigón, el trabajo de marcado geodésico debe completarse por completo con la fijación de los ejes de las estructuras de hormigón en su lugar. Atención especial a la conducta trabajos geodésicos se debe dar al construir encofrados e instalar jaulas de refuerzo.
4.2. En el curso del trabajo, se debe prestar especial atención para garantizar la rigidez del encofrado instalado y la inadmisibilidad de su deformación y separación bajo la presión de la columna de la mezcla de hormigón colocada, así como para determinar la tasa de erección de todos los elementos de apoyo, teniendo en cuenta el tiempo de fraguado de la mezcla de hormigón.
4.3. Antes del inicio del trabajo de refuerzo, la base debe limpiarse de escombros y suciedad.
4.4. En la preparación de bases de hormigón y juntas de trabajo para eliminar la película de cemento, el tratamiento superficial se realiza con chorro de agua y aire, cepillos metálicos o instalaciones de chorro de arena.
4.5. Antes del hormigonado de la estructura, es necesario fabricar y montar jaulas de armadura e instalar el encofrado en la zona de hormigonado y los embutidos que requiera el proyecto.
4.6. Los trabajos de refuerzo se llevan a cabo de acuerdo con los planos de trabajo del refuerzo de la estructura.
Para refuerzo, refuerzo con un diámetro de 32 mm, 22 mm, 20 mm, 16 mm, 14 mm, 12 mm clase AIII, acero de refuerzo grado 25G2S, refuerzo con un diámetro de 10 mm, acero de 8 mm clase AI grado St5 sp. GOST 5781-82.
El orden de almacenamiento de refuerzo y ángulo.
El refuerzo de acero se almacena en un área especialmente designada. Los paquetes de refuerzo se colocan sobre revestimientos de madera y se cubren con material impermeable. El refuerzo no debe manipularse bruscamente, dejarse caer desde una altura, someterse a cargas de choque, daños mecanicos.
Inspección.
Las barras de refuerzo deben revisarse en busca de defectos, como grietas, adelgazamiento local, poros, descamación, abolladuras, dobleces, oxidación, distorsiones locales o generales, desviaciones de la longitud de corte especificada de la barra.
Limpieza de armaduras.
Al momento de armar la jaula de refuerzo, el refuerzo debe estar limpio, libre de suciedad, aceite, grasa, pintura, óxido, cascarilla de laminación y materiales similares.
Los accesorios se conectan en marcos espaciales utilizando un alambre de tejer D = 1,6 mm. El refuerzo de refuerzo se superpone utilizando un alambre de tejido, la superposición de las barras de refuerzo es de al menos 30 diámetros del refuerzo. No más del 50% de las juntas de barra deben estar ubicadas en una sección.
4.7. Antes de comenzar a trabajar en estructuras de hormigonado, es necesario producir la cantidad requerida de espaciadores-"crackers" que proporcionen el espesor requerido de la capa protectora y la posición de diseño de las jaulas de refuerzo en todas las secciones de los elementos estructurales hormigonados. La calidad de los espaciadores de hormigón - "crackers" para el diseño de la capa protectora de hormigón no debe ser inferior a la calidad de las estructuras de hormigón.
Está permitido usar espaciadores de plástico: "galletas" hechas en la fábrica.
4.8. Las almohadillas de distancia deben estar hechas de hormigón de grano fino con la inclusión de cribas de piedra triturada. Las dimensiones y la configuración de los espaciadores de hormigón-"crackers" deben corresponder al diseño de la jaula de refuerzo y los valores de diseño de la capa protectora de hormigón, garantizar su posición estable en el encofrado y en las barras de refuerzo de la jaula.
Para excluir la posibilidad de manchado y posterior destrucción de la capa superficial de hormigón en las ubicaciones de las juntas "crackers", la superficie exterior (de apoyo) de la junta hecha de hormigón de grano fino en contacto con el encofrado debe tener un contorno curvilíneo. (radio de curvatura 30 - 50 m).
4.9. Durante la ejecución del trabajo de refuerzo, es necesario instalar partes incrustadas de acuerdo con el proyecto.
4.10. Preparación de jaulas de refuerzo (artículos separados) y piezas incrustadas, su instalación e instalación en el encofrado y otros trabajos relacionados con caracteristicas de diseño el refuerzo de los elementos hormigonados se realiza de acuerdo con los planos de trabajo.
4.11. Las barras de refuerzo colocadas en el encofrado de los elementos del marco se fijan con la cantidad requerida de espaciadores - "grietas", asegurando de manera confiable la ubicación del diseño de la jaula de refuerzo en el encofrado y el tamaño de la capa protectora de concreto en todas las secciones.
4.12. El refuerzo instalado en el lugar con todos los elementos (partes) incrustados debe ser un marco rígido que no pueda alterarse durante el hormigonado.
4.13. Se deben fijar tubos de plástico o metal a las jaulas de refuerzo en la capa superficial y en las zonas centrales para formar pozos para medir la temperatura del concreto durante su curado.
4.14. Los paneles de encofrado se instalan de acuerdo con el proyecto. Para el hormigonado, se utiliza un encofrado de inventario hecho de acuerdo con TU. Las secciones adicionales del encofrado se hacen en el sitio. Para encofrado adicional, se utiliza un marco de madera. Es necesario garantizar una buena estanqueidad de la unión mutua de los bordes de los paneles de encofrado. Si se encuentran fugas que pueden provocar fugas de mortero de cemento durante el hormigonado, todos los lugares detectados deben sellarse de forma segura antes de aplicar el lubricante pegando con cinta adhesiva (yeso de construcción) de 30 - 40 mm de ancho o untando con sellador. Las juntas de los paneles de encofrado se sellan con silicona u otros selladores. Los paneles de encofrado deben sujetarse y fijarse (montantes, topes, puntales, tirantes, etc.) de forma que se cree una estructura rígida y geométricamente invariable.
4.15. Antes de la instalación, las superficies de formación de los paneles de encofrado deben limpiarse con arpillera impregnada con grasa u otra grasa. El lubricante debe aplicarse en una capa extremadamente delgada, lo que excluye la entrada de lubricante en el refuerzo durante la instalación de los paneles de encofrado.
4.16. Después de una verificación instrumental de la posición de las jaulas de refuerzo, se examinan los paneles de encofrado instalados, las jaulas de refuerzo y el encofrado instalado y se redacta un acta para el trabajo encubierto con la participación de representantes del Cliente, el contratista general y los servicios de supervisión.
5. Hormigonado
5.1 Antes de comenzar a trabajar en la colocación de hormigón, el equipo para el suministro de hormigón debe estar preparado para funcionar y debe verificarse su capacidad de servicio.
5.2 Previo al inicio de los trabajos, el jefe de obra deberá aclarar: el tiempo de entrega del concreto de la planta a la instalación, la disponibilidad de documentación que acredite el cumplimiento de los indicadores de la mezcla de concreto y concreto con los requisitos de este “Tecnológico mapa". Un representante del laboratorio de construcción debe verificar la disponibilidad de un cono estándar para determinar la movilidad de la mezcla de concreto, termómetros para medir la temperatura de la mezcla de concreto y del aire exterior, un dispositivo para determinar la cantidad de aire incorporado en la mezcla de concreto y la suficiencia de moldes para la fabricación de cubos de hormigón de control.
5.3 Debe establecerse una conexión operativa efectiva entre la planta de hormigón y la instalación en construcción, asegurando la entrega de la mezcla de hormigón en pleno cumplimiento de los requisitos del proyecto y de este “Mapa Tecnológico”.
5.4 La entrega de la mezcla de hormigón a la obra debe realizarse mediante camiones hormigoneras. El número de camiones hormigonera debe asignarse a partir de las condiciones del volumen de hormigón hormigonado. elementos estructurales, la intensidad de colocación de la mezcla de hormigón, la distancia de su entrega, el tiempo de fraguado del hormigón. El tiempo total de entrega de la mezcla de concreto al sitio de construcción, su colocación en elementos estructurales no debe exceder su tiempo de fraguado.
5.5 Descenso El abastecimiento de la mezcla de hormigón al lugar de colocación se puede realizar a través de enlaces, troncos de fácil montaje y desmontaje, tuberías de hormigón y la manguera final de la bomba de hormigón.
5.6 Antes de suministrar la mezcla de concreto directamente al cuerpo de la estructura, la bomba de concreto debe ser probada con una presión hidráulica de prueba, cuyo valor es
La composición asignada y la movilidad de la mezcla de concreto deben verificarse, refinarse sobre la base del bombeo de prueba de la mezcla de concreto.
Las superficies internas de la tubería de hormigón antes del hormigonado deben humedecerse y lubricarse con cal o mortero de cemento.
5.7 Al realizar trabajos de concreto, se debe tener en cuenta que en casos de interrupciones en el bombeo de la mezcla de 20 a 60 minutos, es necesario bombear la mezcla de concreto a través del sistema cada 10 minutos durante 10 a 15 segundos. en modos de funcionamiento bajos de la bomba de hormigón. Para interrupciones que excedan el tiempo especificado, la tubería de concreto debe vaciarse y enjuagarse.
5.8 La intensidad del hormigonado debe ser determinada por el laboratorio de construcción, teniendo en cuenta las propiedades de la mezcla de hormigón, la distancia de entrega del hormigón.
5.9 Cuando se realicen trabajos en el período invernal, antes de hormigonar cada elemento, se deberá calentar la base y la zona superior de los elementos previamente hormigonados a una temperatura de al menos más 5 °C hasta una profundidad de al menos 0,5 m.
5.10 Para evitar la aparición de fisuras térmicas en las estructuras, el valor de las temperaturas de calentamiento de los elementos previamente hormigonados está vinculado a la temperatura de la mezcla de hormigón entrante de acuerdo con la Tabla 1.
tabla 1
Nota:*) Si la temperatura ambiente media diaria es superior a +25 °C, el espesor de las estructuras hormigonadas es superior o igual a 1 m, el valor máximo de la temperatura de la mezcla de hormigón colocada se limita a +20 °C
5.11 Antes de hormigonar, las superficies limpias, preparadas de acuerdo con los requisitos de los párrafos 4.5 - 4.6, deben humedecerse abundantemente con agua o tratarse con una solución al 2 ... 5% del polímero Acryl 100.
5.12 El descenso y suministro de la mezcla de hormigón al lugar de colocación se puede realizar a través de la manguera final de la bomba de hormigón.
5.13 La mezcla de concreto debe colocarse en la estructura a hormigonar en capas del mismo espesor de 25 a 30 cm (pero no más de 40 cm), sin espacios, con una dirección uniforme de colocación en una dirección en todas las capas.
5.14 El espesor de las capas horizontales colocadas secuencialmente se selecciona en función de la tasa real de suministro de la mezcla de concreto a la colocación, sujeto a la condición de que el descanso antes de colocar la siguiente capa de la mezcla de concreto en cada lugar en particular no exceda el tiempo por la pérdida de movilidad de la mezcla previamente colocada en la capa anterior hasta 1 - 1.5 vea la precipitación de un cono estándar (dentro de 40 - 50 minutos) dependiendo de las características del cemento y la temperatura real de la mezcla de hormigón. Un indicador del cumplimiento de esta regla es la ausencia de un rebaje en el concreto cuando se retira lentamente la punta del vibrador de eje flexible.
5.15 Durante la colocación de hormigón capa por capa en cada capa, se debe formar una sección horizontal delantera de 1-1,5 m de largo, el ángulo de inclinación hacia el horizonte de la superficie de la mezcla de hormigón antes de su compactación no debe exceder los 30 °.
5.16 El suministro, distribución y compactación de la mezcla de concreto en cada capa debe hacerse únicamente de abajo hacia arriba.
5.17 Antes de la compactación de cada capa colocada, la mezcla de concreto debe distribuirse uniformemente sobre su superficie. La altura de las protuberancias y depresiones individuales por encima del nivel general de la superficie de distribución de la mezcla de hormigón no debe exceder los 10 cm.La distribución de la mezcla de hormigón debe realizarse mediante una tubería de hormigón. Se prohíbe el uso de vibradores para redistribuir y nivelar la mezcla de concreto.
5.18 La vibración de la mezcla de concreto en cada capa y en cada posición de la permutación de la punta del vibrador profundo se realiza hasta que la mezcla de concreto deja de asentarse y la pasta de cemento brilla en la superficie.
5.19 Al realizar el hormigonado, es necesario excluir la posibilidad de delaminación de la mezcla de hormigón al final de cada tira de la capa hormigonada y la inevitable fuga, sumergir en la mezcla de hormigón a una distancia de 50 - 70 cm desde el borde de la tira. Tras la colocación de la siguiente dosis de mezcla de hormigón, se realiza un estudio minucioso de las juntas de la zona remanente en el borde de la franja.
5.20 Después de colocar la mezcla de hormigón en la primera capa de la estructura a hormigonar, se apaga la bomba de hormigón, las tuberías de hormigón se trasladan a su superficie final y la mezcla de hormigón se distribuye en la segunda capa. La vibrocompactación de la mezcla de hormigón también se lleva a cabo con un retraso de 1,0 a 1,5 m desde el lugar de suministro de la bomba de hormigón. La vibración debe llevarse a cabo con la "entrada" obligatoria del vibrador en la capa subyacente.
De manera similar, se lleva a cabo la colocación y compactación de la mezcla de hormigón en capas posteriores. La distribución estrictamente consistente de la mezcla de concreto en capas horizontales, excluyendo la posibilidad de su separación durante el tratamiento de vibración, es el factor más importante que asegura la calidad y uniformidad del concreto en la estructura.
5.21 Después de colocar y compactar el concreto en la capa superior sobre toda la superficie abierta de la estructura de concreto, es necesario terminarlo y terminarlo para garantizar los parámetros de diseño de pendientes, uniformidad y calidad de la superficie.
5.22 Después de que el concreto haya fraguado (en 1.5 - 2 horas después de la colocación), es necesario colocar una capa protectora contra la humedad y el calor en las superficies expuestas del concreto, que consiste en película de polietileno, dos capas de dornite y una capa superior de film de polietileno.
6. Curado del hormigón
6.1 Al erigir estructuras de hormigón, teniendo en cuenta mayores requisitos a la calidad del hormigón de las estructuras erigidas, se debe prestar especial atención a las condiciones y la duración del curado del hormigón.
6.2 Después del período con el máximo calentamiento del hormigón, en la etapa de disminución de la temperatura, se puede quitar la cubierta de lona adicional del encofrado.
6.3 Dejar de calentar invernaderos, eliminar aislamiento térmico de la estructura (revestimiento protector térmico y de humedad en la parte superior del enrejado), se permite desmontar el invernadero, el encofrado, sujeto a las restricciones establecidas en el párrafo 3.18 y el párrafo 3.19 de este "Mapa tecnológico".
Al mismo tiempo, la temperatura del aire exterior mínima prevista para las próximas 24 horas debe tomarse como la temperatura ambiente de diseño.
6.4 Al curar el concreto, la resistencia prevista del concreto debe confirmarse mediante pruebas de control de muestras colocadas bajo una capa protectora contra el calor y la humedad.
6.5 Las mediciones de la temperatura del hormigón de endurecimiento de la estructura en los primeros tres días después del hormigonado se llevan a cabo durante el primer día: cada 4 horas, luego cada 8 horas y, sin falta, antes de retirar los revestimientos y encofrados protectores contra el calor y la humedad. .
7. Control de calidad del trabajo
7.1. El ingeniero jefe es directamente responsable de la calidad del trabajo de acuerdo con el sistema de gestión de calidad de los trabajos de construcción e instalación.
Un laboratorio está involucrado para llevar a cabo mediciones y pruebas.
Los técnicos de laboratorio son responsables del muestreo in situ.
7.2. El control de calidad de los trabajos de hormigonado se lleva a cabo de acuerdo con el plan de garantía de calidad para garantizar el pleno cumplimiento del proyecto aprobado, los planos de trabajo y los requisitos de este diagrama de flujo, así como el cumplimiento de los códigos y reglamentos de construcción, normas y especificaciones.
7.3. El control de calidad del trabajo durante el hormigonado se lleva a cabo:
Debe prestarse especial atención al control de la producción, que incluye:
Control de entrada de estructuras, productos y materiales entrantes;
control operacional;
control de aceptación;
Control de inspección.
El control de entrada de estructuras, productos y materiales entrantes lo realiza una comisión integrada por representantes del contratista, el contratista general y la supervisión técnica del cliente con la ejecución de la Ley. forma prescrita.
Se verifica el cumplimiento de los materiales con los requisitos del proyecto, especificaciones técnicas, SNiP, GOST;
7.4. Accesorios y piezas incrustadas
Cumplimiento de los accesorios recibidos con los datos proporcionados en los certificados y documentos de envío. Las barras de refuerzo deben revisarse en busca de defectos, como grietas, adelgazamiento local, poros, descamación, abolladuras, dobleces, oxidación, distorsiones locales o generales, desviaciones de la longitud de corte especificada de la barra.
Si es necesario, se analizan muestras.
7.5. Mezcla de hormigón.
En el lugar de colocación se hacen:
Control de la plasticidad de la mezcla de hormigón (tiro de cono) al menos 2 veces por turno, con el suministro rítmico de la mezcla de hormigón; en el suministro no rítmico de la mezcla de hormigón, la plasticidad se determina en cada camión hormigonera;
Medición de la temperatura de la mezcla de concreto - en cada camión hormigonera;
Determinación del arrastre de aire - una vez por turno;
La selección de las muestras de concreto (cubos) para los ensayos posteriores la realiza un ayudante de laboratorio al momento de descargar la mezcla de concreto al camión bomba de concreto.
En el curso del trabajo, se fija. la siguiente información para hormigón:
Fecha de hormigonado de cada bloque, clase de hormigón, duración de la colocación de la mezcla, posición de la estructura a hormigonar.
Detalles de la mezcla de concreto, incluyendo la naturaleza y fuente de cada uno de los materiales constituyentes, la fuente de producción de concreto; proporciones sugeridas (según la tabla de mezclas de concreto) o la cantidad de cada componente por metro cúbico de concreto completamente compactado y aditivos detallados.
Temperatura del aire máxima y mínima diaria;
Origen de las muestras y fechas de muestreo, incluidas las marcas de identificación.
Resultados de los ensayos sobre muestras seleccionadas y descripción del bloque de hormigón representado por las muestras.
Informes de prueba de muestras de control de concreto con los resultados de las pruebas de resistencia de las muestras a la edad de 7 y 28 días.
Los registros se mantendrán en la forma acordada por el cliente, se mantendrán actualizados y estarán disponibles para su inspección por parte del cliente.
Para garantizar la identidad del modo de endurecimiento del hormigón de las muestras seleccionadas y el modo de endurecimiento del hormigón de la estructura hormigonada, las muestras permanecen en el bloque de hormigón durante el tiempo de fraguado y endurecimiento. Después de la desaparición del "brillo" característico de la prueba de cemento en el área terminada de la superficie de la estructura de hormigón, se colocan muestras de control en esta área: cubos y se cubren con paneles de un revestimiento a prueba de humedad de una película de polímero. , se colocan esteras protectoras contra el calor y luego se coloca una segunda capa de un revestimiento (película) a prueba de humedad. Las muestras de control se almacenan bajo la cubierta hasta que se retira, luego las muestras se almacenan en una cámara de almacenamiento normal (temperatura 20 °C ± 2 °C, humedad 95%).
7.6. Materiales de encofrado.
Los materiales de encofrado, la madera contrachapada, la madera se verifican para verificar el cumplimiento de los certificados y documentos de envío, se lleva a cabo una inspección externa para identificar defectos visibles, daños, etc. Los materiales inservibles se rechazan con la elaboración de una Ley sobre la inadecuación de estos materiales. El material desechado no debe utilizarse para encofrado.
Materiales para el dispositivo del invernadero.
Se lleva a cabo una verificación del cumplimiento de los certificados y documentos de envío, se lleva a cabo una inspección externa para identificar daños y violaciones visibles.
¡¡¡Prohibido poner en producción los diseños, materiales y productos que lleguen sin los documentos de acompañamiento!!!
7.8. El control operativo es realizado por el contratista.
El control de calidad operacional se lleva a cabo durante las siguientes obras de construcción:
montaje y desmontaje de encofrados;
Instalación de accesorios y piezas incrustadas;
Colocación de mezcla de hormigón;
Curación.
El control operativo debe asegurar la detección oportuna de defectos y la adopción de medidas para eliminarlos y prevenirlos.
Los principales documentos para el control operativo son:
Dibujos de trabajo;
esquemas tecnológicos,
Este reglamento y diagramas de flujo estándar;
SNiP, GOST;
esquemas de control de calidad;
Los resultados del control operativo deben ser registrados en la Bitácora General de Trabajo, así como en bitácoras especiales de trabajo, incluyendo la Bitácora de Trabajo de Hormigón.
Para el trabajo oculto, levantar actas de la forma establecida.
7.9. control de aceptación;
Durante el control de aceptación, se realiza lo siguiente:
Aceptación de construcciones intermedias;
Comprobación de la calidad de los elementos estructurales construidos.
Durante el control de aceptación, el Contratista deberá presentar la siguiente documentación:
Planos ejecutivos con cambios realizados (si los hubiere) y documentos sobre su aprobación;
Fábrica Hojas de datos técnicos, certificados;
Certificados de examen de obras ocultas;
Actos de aceptación intermedia de estructuras;
Esquemas geodésicos ejecutivos de posición de estructuras y encofrados;
registros de trabajo;
Resultados de las pruebas de laboratorio del hormigón para el cumplimiento de los requisitos de diseño;
7.10. control de inspección;
El control de inspección se lleva a cabo con el fin de verificar la eficacia del control de producción realizado previamente. Este control es realizado por comisiones especialmente creadas.
7.11. Una vez aceptado el encofrado instalado y sus fijaciones, se comprobará lo siguiente:
Cumplimiento de este mapa tecnológico;
Fiabilidad de la fijación del encofrado;
Correcta instalación de enchufes y piezas empotradas;
Tabla 2
Parámetro | ||
1. Desviación de las líneas de los planos de intersección de la vertical o la pendiente de diseño a toda la altura de las estructuras para: | ||
cimientos | Medición, cada elemento estructural, bitácora de trabajo |
|
paredes y columnas que soportan techos y pisos monolíticos | ||
muros y columnas que soportan estructuras de vigas prefabricadas | ||
muros de edificios y estructuras levantadas en encofrado deslizante, en ausencia de pisos intermedios | 1/500 de la altura de la estructura, pero no más de 100 mm | Medición, todas las paredes y líneas de su intersección, registro de trabajo |
paredes de edificios y estructuras levantadas en encofrado deslizante, en presencia de pisos intermedios | 1/1000 de la altura de la estructura, pero no más de 50 mm | |
2. Desviación de los planos horizontales en toda la longitud de la sección a verificar | Medición, al menos 5 mediciones por cada 50 - 100 m, registro de trabajo |
|
3. Desniveles locales de la superficie del hormigón al verificar con un carril de dos metros, excepto las superficies de apoyo | ||
4. Longitud o vano de los elementos | Medición, cada elemento, registro de trabajo. |
|
5. Tamaño sección transversal elementos | 6 mm; -3mm | |
6. Marcas de superficies y productos empotrados que sirvan de soporte para columnas de acero o de hormigón prefabricado y otros elementos prefabricados | Medición, cada elemento de referencia, circuito ejecutivo |
|
7. La pendiente de las superficies de apoyo de los cimientos cuando se apoyan columnas de acero sin lechada | Lo mismo, cada fundación, esquema ejecutivo |
|
8. Ubicación de los pernos de anclaje: | Lo mismo, cada perno de cimentación, diagrama ejecutivo |
|
en planta dentro del contorno del soporte | ||
en planta fuera del contorno del apoyo | ||
altura | ||
9. Marcas de diferencia de altura en la unión de dos superficies adyacentes | El mismo, cada esquema ejecutivo conjunto |
Encofrado de paneles
Tabla 3
Fabricación de paneles de encofrado | Instalación de encofrado |
|
Composición de control | Dimensiones del encofrado | Dimensiones internas, marcas, verticalidad, posición de los ejes de encofrado |
Método y medios de control | visual, de medición; cinta métrica de acero | visual, de medición; teodolito, nivel, plomada, riel, cinta métrica de acero |
Modo y ámbito de control | cada escudo | Todo el encofrado ensamblado |
Persona a cargo de la operación. | Maestro, geodesta |
|
Levantamiento geodésico |
||
Lugar de registro de los resultados del control | Certificado de reconocimiento y aceptación del encofrado instalado |
El encofrado preparado para el hormigonado debe aceptarse según la ley de obra oculta.
7.12. El control de calidad de los trabajos de refuerzo consiste en verificar el cumplimiento del proyecto y los estándares de los productos y las piezas empotradas, el tejido y la soldadura del refuerzo. La sustitución del acero de refuerzo previsto por el proyecto debe acordarse con la organización de diseño (supervisión de diseño).
El acero de refuerzo entrante debe registrarse en el "Registro de control entrante".
A control de entrada todo el acero de refuerzo entrante y las partes incrustadas deben estar sujetas a examen externo y medir
El control de los productos de refuerzo y embebidos debe realizarse de acuerdo con los requisitos de la Tabla 4.
control de refuerzo
Tabla 4
Parámetro | Valor del parámetro, mm | Control (método, alcance, tipo de registro) |
1. Desviación en la distancia entre barras de trabajo instaladas por separado para: | Inspección técnica de todos los elementos, bitácora de trabajo |
|
columnas y vigas | ||
losas y muros de cimentacion | ||
estructuras masivas | ||
2. Desviación en la distancia entre las filas de refuerzo para: | ||
losas y vigas de hasta 1 m de espesor | ||
estructuras con un espesor de más de 1 m | ||
3. La desviación del espesor de diseño de la capa protectora de hormigón no debe exceder: | ||
con un espesor de capa protectora de hasta 15 mm y dimensiones lineales de la sección transversal de la estructura, mm: | ||
del 101 al 200 | ||
con un espesor de capa protectora de 16 a 20 mm incl. y dimensiones lineales de la sección transversal de las estructuras, mm: | ||
del 101 al 200 | ||
del 201 al 300 | ||
con un espesor de capa protectora de más de 20 mm y dimensiones lineales de la sección transversal de estructuras, mm: | ||
del 101 al 200 | ||
del 201 al 300 | ||
Todo el refuerzo instalado en el encofrado debe tomarse antes del hormigonado; los resultados del reconocimiento y la aceptación deben documentarse en un acta de trabajo oculto.
Las principales operaciones sujetas a control en la producción de armaduras, métodos de control y operaciones controladas se muestran en la Tabla 5.
Métodos de control y elementos controlados en la producción de armaduras.
Tabla 5
Principales operaciones a controlar | Material de barras de refuerzo | Montaje de malla de refuerzo |
Composición de control | Limpieza, calidad del refuerzo, dimensiones de la barra, grado del acero | Soldaduras, dimensiones, colocación de mallas, cobertura, calidad. |
Método y medios de control | Medición visual, metro | Medición visual, medidor de acero |
Modo y ámbito de control | Sólido | Todas las cuadrículas |
La persona en control | Maestro, asistente de laboratorio |
|
La persona responsable de organizar y ejercer el control. | ||
Servicios implicados en el seguimiento | Laboratorio |
|
Asistente de registro de resultados de control | Revista trabajos generales. Registro de soldadura |
7.13. Los requisitos tecnológicos que deben ser observados durante la producción de la obra de hormigón, y verificados durante el control operativo, así como el alcance, métodos o métodos de control, se dan en la Tabla 6.
Producción de obras de hormigón.
Tabla 6
Requerimientos técnicos | Control | Método o método de control |
1. En el lugar de colocación, la movilidad de la mezcla de hormigón debe estar en el rango de 10 - 15 cm para elementos estructurales. | Al menos dos veces por turno con colocación de hormigón en masa rítmica, otros camiones hormigonera visualmente. | Comprobación de acuerdo con GOST 10181.1-81 con registro en el diario de trabajo concreto, cuidado concreto, el Certificado de producción de muestras de control, el diario de la llegada de la mezcla de hormigón. |
2. La temperatura de la mezcla de hormigón en el lugar de colocación no debe diferir de la regulada en más de ± 2 ° C (de 5 a 25 °) | En cada hormigonera de la obra | registro, medición |
3. El espesor de la capa de hormigón colocado no debe exceder los 40 cm. | Permanente, durante la colocación del hormigón | de medición, visual |
4. El volumen de aire incorporado en la mezcla de concreto es de 3 a 5% para concreto con grado de resistencia a las heladas F 200 | Una vez por turno (con constante: composición del concreto, calidad de los materiales, modos de preparación de la mezcla de concreto) | Comprobación de acuerdo con GOST 10181.3-81 |
5. Normas de muestras al hormigonar estructuras. | Para cada elemento estructural de estructuras monolíticas de hormigón, al menos una serie por turno. | Ver GOST 18105-86 |
6. Número de series de muestras hechas de una muestra de mezcla de concreto en la instalación | Según la cláusula 2.3 GOST 18105-86 | Registro |
7. La aceptación de estructuras para estanqueidad al agua y resistencia a las heladas se lleva a cabo en función de los requisitos de la documentación del proyecto. | De acuerdo con los actos de la planta proveedora, los resultados de determinar la resistencia a las heladas del hormigón colocado en la construcción. | De acuerdo con el documento de calidad de acuerdo con GOST 7473-94 cláusula 4.1 - 5.2 con la aplicación del certificado de prueba de fábrica de acuerdo con GOST 10060-95 y de acuerdo con GOST 12730.5-84 |
7.14. Los moldes con muestras para determinar la resistencia del concreto a la edad de 28 días inmediatamente después de la producción deben instalarse en los lugares de las temperaturas más bajas y en contacto con la superficie del concreto para cada elemento estructural.
Los formularios con muestras recién moldeadas deben envolverse en papel de aluminio y colocarse bajo una capa de protección contra el calor antes de la instalación.
Los formularios con muestras deben almacenarse bajo una capa a prueba de humedad hasta el momento de la prueba. Después de quitar el revestimiento de protección contra la humedad y el calor de la estructura, las muestras de control restantes (que han ganado al menos un 70 % de resistencia) se decapan y almacenan hasta las pruebas requeridas en condiciones normales de acuerdo con GOST 10180-90.
8. Protección laboral en el curso del trabajo
La protección laboral se lleva a cabo de acuerdo con el plan de salud y seguridad (de acuerdo con SNiP 12-03-2001, SNiP 12-4-2002, PB 10-382-00).
8.1. Requerimientos generales
Las personas que hayan cumplido los 18 años de edad, sean reconocidas como aptas para este trabajo por una comisión médica, hayan sido capacitadas en métodos y técnicas seguras para la producción del trabajo e instrucciones sobre seguridad laboral y tengan un certificado para el derecho al trabajo como a los trabajadores del hormigón se les permite trabajar de forma independiente como trabajadores del hormigón.
Un trabajador de concreto que ingrese a laborar deberá someterse a una charla introductoria sobre seguridad laboral, saneamiento industrial, primeros auxilios, seguridad contra incendios, requisitos ambientales, condiciones de trabajo, charla inicial en el lugar de trabajo, la cual deberá ser registrada en los diarios correspondientes con la firma obligatoria del instruido. e instruyendo. La sesión informativa repetida se lleva a cabo al menos 1 vez en 3 meses. Las sesiones informativas no programadas se llevan a cabo cuando se ponen en vigencia normas nuevas o revisadas u otros documentos reglamentarios sobre protección laboral, cuando se cambia un proceso tecnológico, cuando se reemplazan o modernizan equipos y herramientas, cuando se reemplazan materiales, cuando los empleados violan los requisitos de seguridad laboral, a solicitud de las autoridades de control, durante las pausas en el trabajo superiores a 30 días naturales. El informe de destino se lleva a cabo cuando se realiza un trabajo de una sola vez.
Antes de comenzar a trabajar, los lugares de trabajo y los pasajes a ellos deben estar libres de objetos extraños, escombros, suciedad y, en invierno, de la nieve y el hielo y espolvoréelos con arena.
Está prohibido estar en la zona de peligro de los mecanismos de elevación, así como permanecer debajo de la carga levantada.
Las máquinas, las herramientas eléctricas y las lámparas de iluminación solo se pueden encender con la ayuda de arrancadores de interruptor de cuchilla. No permita la presencia de cables eléctricos mal aislados, dispositivos eléctricos no cerrados en el sitio. Al trabajar con herramientas eléctricas, el trabajador del concreto debe estar capacitado y tener I grupo de calificación sobre seguridad
Antes de poner en marcha el equipo, verifique la seguridad de las protecciones en todas las partes rotatorias y móviles expuestas.
Si se detecta un mal funcionamiento de los mecanismos y herramientas con las que trabaja el trabajador del concreto, así como las cercas, es necesario detener el trabajo e informar de inmediato al capataz.
Al recibir la herramienta, debe asegurarse de que esté en buenas condiciones; la herramienta defectuosa debe entregarse para su reparación.
Cuando se trabaja con herramientas manuales (raspadores, martillos de arbustos, palas, apisonadores), es necesario controlar la capacidad de servicio de los mangos, el ajuste de las boquillas en ellos y también asegurarse de que las superficies de trabajo de la herramienta no se derriben. , contundente, etc
Una herramienta electrificada, así como el cable eléctrico que la alimenta, debe tener un aislamiento confiable. Al recibir la herramienta eléctrica, es necesario verificar el estado del aislamiento del cable mediante una inspección externa. Cuando trabaje con la herramienta, asegúrese de que el cable de alimentación no esté dañado.
8.2. Requisitos antes y durante el trabajo.
Al comenzar a trabajar, el trabajador del hormigón debe ponerse el mono prescrito por las normas, mientras que el cabello debe quitarse debajo del tocado, los puños deben sujetarse o apretarse con una banda elástica.
Al colocar la mezcla de hormigón con una autobomba de hormigón, es necesario comprobar el funcionamiento de una señalización bidireccional (sonora, luminosa) entre el conductor de la autobomba de hormigón y los trabajadores que reciben el hormigón. Limpie y cierre herméticamente todos los enclavamientos de la tubería de concreto. No acepte mezcla de concreto con una bomba de concreto defectuosa. El conductor de la bomba de hormigón montada en camión antes de arrancar debe dar una señal de advertencia y poner en marcha la bomba de hormigón para probarla al ralentí durante 2-3 minutos.
Al entregar concreto en un camión hormigonera, se deben observar las siguientes reglas:
Al descargar la bomba de hormigón en el búnker, primero debe poner el camión hormigonera en el freno de mano y dar una señal sonora;
En el momento de la aproximación del camión hormigonera, todos los trabajadores deberán estar del lado de la vía de acceso, opuesto a aquel por el que se realiza el movimiento;
Está prohibido acercarse al camión hormigonera hasta que se haya detenido por completo.
Antes de comenzar a colocar la mezcla de hormigón en el encofrado, es necesario comprobar:
Fijación de encofrados, andamios de apoyo y plataformas de trabajo;
Fijación a los soportes de los embudos de carga, bandejas y baúles para bajar la mezcla de hormigón a la estructura, así como la fiabilidad de sujetar los enlaces individuales de los baúles metálicos entre sí;
El estado de las cubiertas o pisos protectores alrededor de los embudos de alimentación.
Los trabajadores de hormigón que trabajan con vibradores deben someterse a un examen médico cada 6 meses.
Las mujeres no pueden trabajar con un vibrador manual.
Los trabajadores del hormigón que trabajen con herramientas electrificadas deben conocer las medidas de protección contra descargas eléctricas y ser capaces de prestar primeros auxilios a la víctima.
Antes de comenzar a trabajar, es necesario verificar cuidadosamente la capacidad de servicio del vibrador y asegurarse de que:
La manguera está bien unida y, si se tira accidentalmente, los extremos del devanado no se romperán;
El cable de alimentación no tiene roturas ni puntos desnudos;
El contacto con el suelo no está dañado;
El interruptor funciona correctamente;
Los tornillos que aseguran la estanqueidad de la carcasa están bien apretados;
Las conexiones de las partes del vibrador son bastante apretadas y el devanado del motor está bien protegido de la humedad;
El amortiguador en el mango del vibrador está en buenas condiciones y ajustado para que la amplitud de vibración del mango no exceda los estándares para esta herramienta.
Antes de comenzar a trabajar, el cuerpo del vibrador eléctrico debe estar conectado a tierra. El estado general del vibrador eléctrico se comprueba mediante trabajo de prueba suspendido durante 1 minuto, sin apoyar la punta contra una base sólida.
Para alimentar los vibradores eléctricos (desde el tablero) se deben utilizar cables de manguera de cuatro hilos o cables encerrados en un tubo de goma; el cuarto núcleo es necesario para conectar a tierra la caja del vibrador, operando a un voltaje de 127 V o 220 V.
Puede encender el vibrador eléctrico solo con un interruptor de cuchillo protegido por una carcasa o colocado en una caja. Si la caja es de metal, debe estar conectada a tierra.
Los cables de las mangueras deben estar suspendidos y no pasar sobre el hormigón colocado.
No arrastre el vibrador por el alambre de la manguera o el cable cuando lo mueva.
En caso de rotura de cables vivos, chispas de contactos y mal funcionamiento del vibrador eléctrico, detenga el trabajo e informe inmediatamente al maestro.
Trabajo con vibradores en escaleras, así como en andamios inestables, cubiertas, encofrados, etc. prohibido.
Cuando se trabaja con vibradores eléctricos que funcionan con una tensión de red de hasta 220 V y superior, es necesario llevar guantes y botas dieléctricos de goma.
Durante el funcionamiento continuo, el vibrador debe apagarse cada media hora durante cinco minutos para que se enfríe.
Cuando llueve, los vibradores deben cubrirse con una lona o mantenerse bajo techo.
Durante las pausas en el trabajo, así como cuando los trabajadores del hormigón se mueven de un lugar a otro, los vibradores deben estar apagados.
El hormigonero que trabaje con el vibrador no debe permitir que el agua entre en contacto con el vibrador.
8.3. Precauciones de seguridad al trabajar en altura.
Realice todo el trabajo de acuerdo con SNiP 12-03-2001 "Seguridad laboral en la construcción" parte 1, "Seguridad laboral en la construcción" parte 2.
Los lugares de trabajo y los pasajes a ellos a una altura de 1,3 m o más, y a una distancia de menos de 2 m del límite de la diferencia de altura, están protegidos por cercas de inventario temporales de acuerdo con GOST 12.4.059-89. Si es imposible el uso de vallas de seguridad o en el caso de que los trabajadores estén en altura por un período corto, se permite realizar el trabajo utilizando el cinturón de seguridad.
Los andamios están equipados con escaleras o escaleras para levantar y bajar personas en la cantidad de al menos dos.
Las escaleras y escaleras están equipadas con un dispositivo que evita la posibilidad de que se muevan y vuelquen durante la operación.
Los empleados involucrados en el montaje y desmontaje de andamios deben ser instruidos sobre los métodos y la secuencia de trabajo y las medidas de seguridad.
No se permite la instalación de andamios metálicos a menos de 5 m de los mástiles de la red eléctrica y de los equipos de operación. Los cables eléctricos ubicados a menos de 5 m de los andamios deben estar desenergizados y conectados a tierra, o encerrados en cajas, o desmantelados durante su instalación o desmontaje. Los andamios deben estar conectados a tierra.
Se deberá cerrar el acceso de personas no autorizadas (que no participen directamente en estos trabajos) a la zona de instalación o desmontaje de los andamios.
Durante los trabajos en altura, el paso por debajo del lugar de trabajo debe estar cerrado, y la zona de peligro está vallada y señalizada con señales de seguridad. Los andamios no deben utilizarse para almacenar materiales.
Solo aquellos materiales que se utilizan directamente (reciclados) se alimentan al andamio.
9. Protección del medio ambiente
9.1. El CONTRATISTA-EJECUTOR DE OBRAS deberá mantener limpio el sitio de construcción y proveer las instalaciones adecuadas para el almacenamiento temporal de todo tipo de residuos hasta que sean retirados. Los residuos de construcción se almacenan solo en áreas especialmente designadas indicadas en el plan de construcción.
El CONTRATISTA-EJECUTOR es responsable de garantizar el transporte y la eliminación seguros de todo tipo de residuos de tal manera que no conlleven a la contaminación ambiental o daños a la salud humana o animal.
Todos los sitios y edificios se mantienen limpios y ordenados. Todo el personal de trabajo fue instruido contra firma, anotado en el diario correspondiente e informado sobre los requisitos para el mantenimiento del lugar de trabajo y la responsabilidad de cada uno por el orden en su lugar de trabajo y descanso.
La eliminación de desechos debe incluir lo siguiente:
Contenedores separados para diferentes tipos de residuos (metales, residuos de alimentos, materiales peligrosos, basura, etc.) con tapas herméticas;
Ubicaciones para contenedores;
La chatarra de desecho se almacena temporalmente en vertederos designados acordados con el Comité de Protección Ambiental, el Comité de Tierras, las autoridades locales;
Los residuos de hormigón se almacenan temporalmente en sitios de almacenamiento temporal de residuos en áreas especialmente equipadas con cobertura mejorada. Los residuos de estructuras de hormigón armado serán retirados por vehículos especiales para su disposición en el vertedero;
El lavado de camiones hormigoneras y bombas de hormigón deberá realizarse únicamente en los lugares indicados por el Contratista General.
Los residuos de madera en terrones, no aptos para su uso en el sitio, se almacenan temporalmente en el sitio de almacenamiento temporal y se transportarán por carretera para ser depositados en el vertedero;
Desechos domésticos serán retirados por vehículos especiales para su eliminación y procesamiento en el vertedero de acuerdo con el acuerdo de eliminación de residuos con una empresa especializada.
Todos los residuos peligrosos para la salud se someten a disposición final en las empresas o vertederos correspondientes acordados con la administración local y las autoridades reguladoras, en virtud de contratos, de los cuales se proporcionarán copias al Cliente.
El reabastecimiento de combustible de los equipos de construcción en el proceso de trabajo se lleva a cabo mediante camiones cisterna certificados "desde las ruedas". Todos los aceites y lubricantes se almacenan en depósitos en contenedores herméticamente sellados con marcas claras en ruso. Si el combustible y los lubricantes entran en contacto con el suelo o una superficie de hormigón, se toman medidas inmediatas para cortar y eliminar el suelo contaminado, el combustible y los lubricantes se eliminan de la superficie de hormigón con arena o con aserrín y su posterior eliminación.
9.2. Protección de la flora, la fauna y el hábitat.
La actividad prevista establece el objetivo de enajenación mínima y temporal de la tierra, perturbación de la cubierta vegetal.
Con el fin de minimizar el impacto negativo sobre el animal y mundo vegetal, durante la construcción de la instalación, el CONTRATISTA-EJECUTOR DE OBRAS deberá llevar a cabo medidas organizativas y técnicas:
Dotación de la instalación con equipos de extinción de incendios individuales, pasivos y activos, estricto control del cumplimiento de la normativa seguridad contra incendios;
Preservación de la cobertura del suelo manteniendo los equipos en buen estado, eliminando el derrame de productos petrolíferos en el suelo;
Operación de maquinaria solo dentro de los límites de la asignación del sitio de construcción usando caminos de acceso existentes;
Durante el período de construcción, la protección de la vida silvestre consistirá, en primer lugar, en el cumplimiento de la legislación ambiental, minimizando el impacto en el aire atmosférico, Superficie del agua, lo que reducirá indirectamente el impacto de la instalación en el medio ambiente.
9.3. Minimización de la contaminación atmosférica y la contaminación acústica del medio ambiente.
La reducción del contenido de polvo del aire que se produce durante la construcción se logra gracias a lo siguiente:
El uso de pavimento de piedra triturada en las carreteras, tanto en el sitio de construcción como entre el sitio de construcción y el asentamiento para los trabajadores de la construcción, así como dentro del asentamiento;
Limpieza periódica de las carreteras y humectación de las mismas para evitar el polvo en el aire.
Para reducir los posibles impactos negativos en el aire atmosférico durante la construcción, el CONTRATISTA-EJECUTOR DE OBRAS deberá utilizar únicamente equipo de construcción reparable con equipo de combustible ajustado que asegure la menor emisión posible de contaminantes al medio ambiente, incluyendo supresores de ruido efectivos;
Opera y mantiene la maquinaria de acuerdo con las instrucciones e instrucciones de los fabricantes, con especial atención al control del ruido y las emisiones contaminantes;
Brinda monitoreo constante del cumplimiento de las normas de operación aplicables;
El equipo utilizado para la construcción está sujeto a mantenimiento regular y controles por posibles fallas;
No está permitido quemar residuos de producción;
Está prohibido el uso de agentes que agotan la capa de ozono y freones en los sistemas de enfriamiento y extinción de incendios;
EN período de verano construcción, para reducir el polvo en los caminos de acceso o de trabajo, es necesario regar constantemente la superficie del firme con agua usando máquinas de riego.
9.4. Plan CONTRATISTA-EJECUTOR DE OBRAS para la organización de los trabajos de recogida, almacenamiento y eliminación de residuos
Durante la producción de obras en la instalación se generan 2 tipos de residuos:
Industrial (residuos de la construcción);
Desechos domésticos.
al tratar con residuos peligrosos redactar un acto apropiado basado en los resultados de llevar los productos a un estado seguro, que sea aprobado por el jefe de la empresa, el propietario del producto.
En el proceso de recolección y acumulación de residuos, se identifican con la determinación de pertenecer a un determinado tipo de residuo, para cada tipo de residuo existen contenedores cerrados separados (metales, residuos de alimentos, materiales peligrosos, basura, etc.), marcados con señales de advertencia.
El CONTRATISTA-EJECUTOR desarrolla medidas para minimizar la cantidad de residuos generados:
Uso de equipos y repuestos durante todo el período previsto de su funcionamiento;
Aprovechamiento de residuos como materia prima en nuevos ciclo tecnológico;
Los capataces de turno son responsables del cumplimiento de los requisitos de protección ambiental.
Bibliografía
GOST 2379-85 | ||
GOST 7473-85* | Mezclas de concreto. Especificaciones |
|
GOST 8267-93 | Piedra triturada y grava de minería densa para trabajos de construcción. Especificaciones. |
|
GOST 8478-81 | ||
GOST 10060.0-95 | Métodos para determinar la resistencia a las heladas. Concreto. Requerimientos generales |
|
GOST 10178-95 | Cemento portland y cemento portlant de escoria. Especificaciones |
|
GOST 10180-90 | Concreto. Métodos para determinar la fuerza por muestras de control |
|
GOST 10181.1-81 | ||
GOST 10181-2000 | Mezclas de concreto. Métodos de prueba |
|
GOST 10922-90 | Productos de refuerzo y embebidos uniones soldadas refuerzos soldados y productos embebidos de estructuras de hormigón armado. Especificaciones generales. productos de refuerzo y embebidos |
|
GOST 12730.5-84 | Concreto. Métodos para determinar la resistencia al agua. |
|
GOST 14098-91 | Productos de refuerzo soldados y embebidos de estructuras de hormigón armado. Tipos, diseño y dimensiones. |
|
GOST 18105-86* | Concreto. Reglas de control de fuerza |
|
GOST 18242-72* | Control estadístico de aceptación por característica alternativa. Planes de control. |
|
GOST 23732-79 | Agua para hormigones y soluciones. Especificaciones. |
|
GOST 24211-91 | ||
GOST 25346-89 | PESD. Disposiciones generales, series de tolerancias y desviaciones básicas 7.16 |
|
GOST 25347-82* | ||
GOST 26633-91 | El concreto es pesado y de grano fino. Especificaciones. |
|
SNiP 2.05.03-84* | Puentes y tuberías |
|
SNiP 3.03.01-87 | Estructuras portantes y envolventes |
|
SNiP 3.06.04-91 | Puentes y tuberías |
Anexo 1
snipov.net
VETERINARIO
Nº TARJETA TECNOLÓGICA
para trabajos de hormigón
1 Alcance.. 3
2 organización y tecnología del trabajo .. 3
3 REQUISITOS DE CALIDAD Y ACEPTACIÓN DEL TRABAJO.. 4
4 SALUD Y SEGURIDAD.. 5
5 PROTECCIÓN DEL MEDIO AMBIENTE… 6
6 LISTA DE DOCUMENTACIÓN REGLAMENTARIA-técnica y de referencia.. 7
6 Hoja de familiarización.. 8
El mapa tecnológico prevé la organización y tecnología del trabajo concreto.
El trabajo en consideración incluye:
- preparación de mezcla de hormigón;
- trabajo de refuerzo;
- colocación de hormigón;
- métodos de control.
- organización y tecnología del desempeño del trabajo
Al realizar el trabajo, es necesario cumplir con los requisitos de los documentos reglamentarios que figuran en la Sección 6.
Las materias primas utilizadas en la fabricación de cimientos monolíticos deben cumplir con la documentación técnica y reglamentaria vigente, acompañada de documentos de las empresas proveedoras que certifiquen su calidad.
El diseño de una base monolítica debe cumplir con los requisitos de la documentación reglamentaria existente.
Preparación de mezcla de hormigón.
La mezcla de hormigón se prepara en una hormigonera de acción forzada.
La elección de los cementos para la preparación de mezclas de hormigón debe realizarse de acuerdo con GOST 30515-97. La aceptación de cementos debe realizarse de acuerdo con GOST 30515-97, transporte y almacenamiento de cementos, de acuerdo con GOST 30515-97 y SNiP 3.09.01-85.
Los áridos para hormigón se utilizan fraccionados y lavados. Está prohibido utilizar una mezcla natural de arena y grava sin tamizar en fracciones.
La dosificación de los componentes de las mezclas de concreto debe hacerse por peso. Se permite la dosificación por volumen de agua de los aditivos introducidos en la mezcla de hormigón en forma de soluciones acuosas. La relación de componentes se determina para cada lote de cemento y agregados, al preparar concreto de la resistencia y movilidad requeridas. La dosificación de los componentes debe ajustarse durante la preparación de la mezcla de concreto, teniendo en cuenta los datos de seguimiento de los indicadores de propiedades del cemento, contenido de humedad, granulometría de los agregados y control de resistencia.
Al preparar una mezcla de concreto utilizando una tecnología separada, se debe observar el siguiente procedimiento:
- el agua, parte de la arena, el relleno mineral finamente molido (si se usa) y el cemento se dosifican en un mezclador de alta velocidad en funcionamiento, donde se mezcla todo;
- la mezcla resultante se introduce en una hormigonera, precargada con el resto de áridos y agua, y una vez más se mezcla todo.
- el descanso entre las etapas de hormigonado (o colocación de capas de mezcla de hormigón) debe ser de al menos 40 minutos, pero no más de 2 horas.
- se permite el uso de aditivos (anticongelantes, inclusores de aire, aceleradores y retardadores del endurecimiento del hormigón, etc.).
La armadura funciona.
El trabajo de refuerzo debe llevarse a cabo de acuerdo con el mapa tecnológico P
Colocación y compactación de mezclas de hormigón.
La colocación de la mezcla de hormigón debe ser realizada por adoquines que dispongan de dispositivos que dosifiquen y distribuyan la mezcla en los equipos laterales limitadores, por regla general, sin el uso de mano de obra.
Al colocar mezclas de hormigón en un vertedero abierto, es necesario tomar medidas (refugios especiales, cobertizos, revestimientos de película) para proteger las mezclas de hormigón y los productos recién moldeados de los efectos nocivos de las influencias atmosféricas.
Los modos de moldeo deben garantizar el coeficiente de compactación de la mezcla de hormigón (la relación entre su densidad real y la teórica calculada): para hormigón pesado, no menos de 0,98; cuando se usan mezclas rígidas y justificación adecuada, así como para concreto de grano fino, no menos de 0.96. El volumen de vacíos intergranulares en la mezcla de concreto liviano compactado debe cumplir con los requisitos de GOST 25820-83.
El decapado de los productos después del tratamiento térmico debe realizarse después de que el hormigón haya alcanzado la resistencia al decapado.
El control de calidad del trabajo debe llevarse a cabo de acuerdo con los requisitos de los documentos reglamentarios que figuran en la Sección 6:
Al aceptar estructuras o partes de estructuras de concreto armado y terminado, se debe verificar lo siguiente:
- conformidad de las estructuras con los planos de trabajo;
- la calidad del concreto en términos de resistencia y, si es necesario, resistencia a las heladas, resistencia al agua y otros indicadores especificados en el proyecto;
- la calidad de los materiales utilizados en la construcción, productos semiacabados y productos.
La recepción de estructuras o partes de estructuras de hormigón acabado y hormigón armado deberá formalizarse de acuerdo con el procedimiento establecido mediante un acto de inspección de obras ocultas o un acto de recepción de estructuras críticas.
Composición de operaciones y medios de control durante el hormigonado.
descargar CARTA TECNOLOGICA para Obras de Hormigón
Los empleados líderes y especialistas de la organización, de acuerdo con la lista de puestos aprobada por el jefe de la organización, antes de ser admitidos a trabajar, y posteriormente periódicamente dentro de los límites de tiempo establecidos, son evaluados por su conocimiento de las normas de protección y seguridad laboral. , teniendo en cuenta sus funciones laborales y la naturaleza del trabajo realizado. El procedimiento para realizar capacitación y probar conocimientos se establece de acuerdo con GOST 12.0.004-90 SSBT "Organización de capacitación en seguridad laboral". Disposiciones generales” y de conformidad con el Decreto del Ministerio de Trabajo de la Federación Rusa del 13.01.2003 No. "El procedimiento para la capacitación en protección laboral y prueba de conocimiento de los requisitos laborales de los empleados de las organizaciones". Reglamento aproximado sobre el procedimiento de capacitación y prueba de conocimientos en materia de protección laboral para directivos y especialistas de organismos, empresas e instituciones e instituciones de la construcción, de la industria de materiales de construcción y de la vivienda y los servicios comunales.
Los empleados que realicen el trabajo deben aprobar una prueba de conocimiento y tener certificados de prueba de conocimiento sobre protección laboral.
Los empleados que no hayan sido capacitados previamente en prácticas laborales seguras por profesión, dentro de un mes a partir de la fecha de admisión al trabajo, deben recibir capacitación de acuerdo con GOST 12.0.004-90 SSBT en el alcance de las instrucciones de protección laboral para las profesiones relevantes, elaborado sobre la base de las instrucciones de protección laboral específicas de la industria, y obtener un certificado de seguridad.
Los lugares de trabajo deben contar con botiquines de primeros auxilios con medicamentos.
La lista de documentos que deben ubicarse en el lugar de trabajo:
- Órdenes sobre designación de responsables de protección laboral, seguridad industrial;
- Órdenes sobre la designación de personas responsables del buen estado y funcionamiento seguro de máquinas y mecanismos;
- Pedidos para asegurar equipos;
- bitácora de información en el lugar de trabajo;
- diario de comentarios y sugerencias;
- registro de control de entrada.
Con el fin de proteger el medio ambiente, al realizar los trabajos anteriores, está prohibido:
- violar los límites de los territorios asignados para la construcción;
- contaminar el medio ambiente con desechos de construcción, para lo cual es necesario en la etapa de diseño prever métodos de procesamiento y eliminación de desechos;
- perturbar la red de drenaje natural;
- paso de maquinaria y vehículos en lugares no previstos por el proyecto para la producción de obras;
- planificar y cortar pendientes pronunciadas en los sitios debido a la posibilidad de erosión del suelo;
- no cumplan con los requisitos de las autoridades ambientales locales.
Por causar daños al medio ambiente (destrucción del suelo y cobertura vegetal, contaminación de cuerpos de agua, incendios en bosques, turberas, etc.) fuera del derecho de vía, los encargados de las obras, así como los trabajadores que causen directamente daños al medio ambiente. ambiente.
- LISTA DE DOCUMENTACIÓN REGLAMENTARIA-técnica y de referencia
- SNiP III-42-80*. Tuberías principales;
- - SNiP 3.02.01-87. Movimientos de tierra, fundaciones y cimientos;
- SNiP 3.03.01-87. Estructuras portantes y envolventes;
- VSN 004-88. Construcción de oleoductos principales. Tecnología y organización;
- VSN 014-89. Construcción de tuberías principales y de campo. protección del medio ambiente;
- GOST R 51285-99. Mallas de alambre trenzado con celdas hexagonales para diseños de gaviones. Especificaciones;
- GOST 7502-98. Ruletas midiendo metal. Requerimientos técnicos.
- GOST 12-03-01. SSBT. Protección respiratoria personal. Clasificación y etiquetado;
- GOST 12.3.003-86*. SSBT. Trabajos eléctricos. Requerimientos de seguridad;
- GOST 123.016-87. SSBT. Construcción. Trabajos anticorrosión. Requerimientos de seguridad;
- SNiP 12-03-2001. Seguridad laboral en la construcción. Parte 1. Requisitos generales;
- SNiP 12-04-2002. Seguridad laboral en la construcción. Parte 2. Producción de la construcción;
- SP 12-136-2002. Soluciones para la protección laboral y seguridad industrial en proyectos para la organización de la construcción y proyectos para la producción de obras
- POT R M-016-2001. Normas intersectoriales sobre protección laboral (normas de seguridad) durante la operación de instalaciones eléctricas;
- PB 10-382-00. Reglas para la construcción y operación segura de grúas;
- Normas para el funcionamiento técnico de las instalaciones eléctricas de consumo”;
- POT R M-027-2003. Normas intersectoriales sobre protección laboral en el transporte por carretera;
- Normas de seguridad para la operación de los principales oleoductos.
No p. p. | Nombre completo | puesto de empleado | la fecha | Firma |
1. | ||||
2. | ||||
3. | ||||
4. | ||||
5. | ||||
6. | ||||
7. | ||||
8. | ||||
9. | ||||
10. | ||||
11. | ||||
12. | ||||
13. | ||||
14. | ||||
15. | ||||
16. | ||||
17. | ||||
18. | ||||
19. | ||||
20. | ||||
21. | ||||
22. |
otdel-pto.ru
Instrucciones generales
real pautas están destinados a estudiantes de la dirección de preparación 270800.62 "Construcción" y están destinados a ayudar en la implementación del trabajo del curso y tesis en la sección "Tecnología y organización de la producción de la construcción"
Los mapas tecnológicos son uno de los documentos principales del proyecto para la producción de obras, que contiene un conjunto de pautas para la organización racional y la tecnología de la producción de la construcción, que contribuyen a aumentar la productividad laboral, mejorar la calidad y reducir el costo de los trabajos de construcción e instalación. .
Los mapas tecnológicos son de uso obligatorio por parte de los capataces de obra, capataces y capataces como guía para organizar la producción y la mano de obra de los trabajadores al momento de realizar trabajos de construcción e instalación en una instalación específica.
La instrucción contiene una metodología general y una secuencia para el desarrollo de mapas tecnológicos, se dan ejemplos de la implementación de mapas tecnológicos para los siguientes procesos de construcción:
Excavación;
Trabajos concretos;
Trabajo de instalación;
trabajo de piedra;
Obras apiladas;
Relleno y compactación de suelos.
Los mapas tecnológicos que forman parte del proyecto para la producción de obras generalmente se desarrollan para tipos de trabajo complejos y trabajos realizados con nuevos métodos. El objetivo principal de estos mapas es ayudar a los constructores y diseñadores en el desarrollo de la documentación tecnológica.
De acuerdo a los mapas tecnológicos se establece la secuencia tecnológica de los procesos constructivos, se elaboran cronogramas semanales-diarios y órdenes de trabajo. Se utilizan tanto a la hora de realizar obras de construcción e instalación, como a la hora de justificar la duración de la construcción de las instalaciones en planos calendario y gráficos de red proyectos de producción de trabajo.
El uso de mapas tecnológicos, incluidos los estándar, ayuda a mejorar la organización de la producción, aumentar la productividad laboral y su organización científica, reducir costos, mejorar la calidad y reducir la duración de la construcción, la realización segura del trabajo, la organización del trabajo rítmico, el uso racional. de recursos laborales y máquinas, así como reducir el tiempo de compilación de WEPs y unificar soluciones tecnológicas.
Los mapas tecnológicos (TC) se desarrollan para la implementación de procesos de construcción e instalación y construcción especiales, cuyos productos son elementos estructurales terminados de un edificio o estructura, equipos de proceso, tuberías y sus componentes, así como para la producción de ciertos tipos. de trabajo: movimiento de tierras, techado, pintura, anticorrosión, aislamiento térmico, etc. En algunos casos, se desarrollan mapas tecnológicos para trabajos complejos de construcción e instalación (para colocar 100 m de una tubería, un colector, 1 km de un eléctrico cables, etc.). Los mapas tecnológicos deben desarrollarse y vincularse previamente desarrollados (estándar) con la consideración obligatoria de las condiciones de construcción reales: la organización de trabajo aceptada, un conjunto específico de máquinas de construcción disponibles, mecanismos, dispositivos, vehículos, así como condiciones climáticas y otras. Al mismo tiempo, uno debe centrarse en la ingeniería avanzada y la tecnología de la construcción.
Para el desarrollo del TC, como datos y documentos iniciales, se requiere lo siguiente: planos de trabajo, construyendo códigos y reglas (SNiP), instrucciones, estándares, instrucciones de fábrica y especificaciones para la instalación, puesta en marcha y puesta en marcha de equipos, pasaportes de equipos, normas y precios uniformes para trabajos de construcción e instalación (ENiR), estándares y precios progresivos locales, organización laboral y procesos laborales .
Los mapas tecnológicos típicos (TTK) se desarrollan para garantizar la construcción de edificios, estructuras y sus partes estándar y repetitivas. decisiones racionales en la organización y tecnología de la producción de la construcción, que contribuyen a aumentar la productividad laboral, mejorar la calidad y reducir el costo de los trabajos de construcción e instalación. Los TTC están destinados a ser utilizados por organizaciones que desarrollan proyectos para la producción de obras para la construcción de instalaciones nuevas o la reconstrucción y expansión de instalaciones existentes.
TTK se desarrolla según planos de trabajo de estructuras y edificios típicos y reutilizables basados en el estudio y generalización de las mejores prácticas, teniendo en cuenta: el uso de procesos tecnológicos que aseguren el nivel requerido de calidad de trabajo; suministro complejo de estructuras, productos, productos semiacabados y materiales; aprovechamiento máximo del alcance del trabajo y la combinación de procesos de construcción; la introducción de la mecanización integrada con el máximo aprovechamiento de las máquinas en dos o más turnos, así como el uso de la mecanización a pequeña escala; suministro de estructuras y equipos tecnológicos en bloques ampliados; cumplimiento de las normas de saneamiento industrial, protección y seguridad laboral. Las soluciones organizativas y tecnológicas adoptadas en el TTK deben garantizar altos indicadores técnicos y económicos, calidad y seguridad del trabajo de acuerdo con los requisitos de las normas y reglas vigentes de producción de la construcción.
La composición del mapa tecnológico
El mapa tecnológico debe contener las siguientes secciones:
Aquí están:
características del edificio, elementos estructurales y sus partes o partes de edificios y estructuras (indicando proyectos estándar, parámetros básicos y esquemas);
nomenclatura de tipos de trabajo cubiertos por el mapa;
características de las condiciones y características de la producción de obras adoptadas en el mapa;
instrucciones sobre cómo vincular el mapa a un objeto específico y las condiciones de construcción.
II. Organización y tecnología proceso de construcción. Esta sección contiene:
instrucciones para la preparación de la instalación y requisitos para la preparación de obras y estructuras de construcción previas, que proporcionen el frente de trabajo necesario y suficiente para completar el proceso de construcción previsto en el plano;
el plano y las secciones de la parte estructural del edificio o estructura en la que se realizará el trabajo previsto en el mapa tecnológico, así como los esquemas para organizar el sitio de construcción (área de trabajo) durante el período de este tipo de trabajo ( los planos, secciones y diagramas deben indicar todas las dimensiones principales y la ubicación de las unidades, máquinas, dispositivos de carga y descarga, almacenes de materiales básicos, productos semielaborados, productos, caminos);
instrucciones sobre la duración del almacenamiento y el stock de estructuras, productos y materiales en el sitio de construcción (área de trabajo);
métodos y secuencia de trabajo, desglose del edificio (estructura) en agarres y niveles, métodos de transporte de materiales y estructuras a los lugares de trabajo, tipos de andamios, accesorios, equipo de montaje utilizado;
la composición numérica y de calificación de las brigadas y eslabones de trabajadores, teniendo en cuenta la combinación de profesiones;
cálculo de horarios de trabajo y costos de mano de obra;
instrucciones para vincular mapas de procesos laborales en la producción de la construcción, que prevén la organización racional, los métodos y las técnicas de trabajo de los trabajadores para realizar operaciones individuales incluidas en el proceso de construcción previsto por el mapa tecnológico;
instrucciones para monitorear y evaluar la calidad del trabajo de acuerdo con los requisitos de los capítulos de SNiP para la producción y aceptación del trabajo y una lista de certificados requeridos de examen de trabajo oculto;
soluciones para la protección laboral y la seguridad en el desempeño de los trabajos que requieran desarrollo de diseño.
Los mapas tecnológicos para el trabajo realizado en invierno también deben contener instrucciones sobre el modo de mantener estructuras, lugares para medir la temperatura y la humedad, métodos para aislar y sellar juntas en estructuras, esquemas para realizar trabajos en invierno.
tercero Indicadores técnicos y económicos. Esta sección proporciona:
1. Costos laborales para todo el ámbito de trabajo, días-hombre.
Los costos laborales para todo el alcance del trabajo se determinan mediante el cálculo de los costos laborales como la suma de las líneas de la columna 8 (consulte la tabla 1.1)
2. El costo de los turnos de máquina para todo el alcance del trabajo.
La necesidad total de máquinas está determinada por el cálculo de los costos laborales como la suma de la columna 9 (ver tabla 1.1).
3. Costos laborales por unidad de medida aceptada, horas-hombre. (días-hombre).
Se calcula dividiendo la suma de los costos laborales (intensidad laboral) por el volumen físico de trabajo.
4. Producción por trabajador por turno en términos físicos;
La producción se calcula dividiendo el costo del trabajo de construcción e instalación a realizar por la intensidad de mano de obra de su implementación, y luego el indicador tiene un valor monetario (rublos / persona-día), o dividiendo el volumen físico de trabajo por la intensidad de mano de obra, y luego la producción se obtiene en términos de (1 m2 de área, 1 m3 de construcción, 1 m3 de edificio por 1 hombre-día o 1 hombre-hora, etc.).
5. La duración de la obra en días. La duración del trabajo en días se determina de acuerdo con el cronograma del calendario para la producción del trabajo (columna 15, tabla 1.5).
IV. Recursos materiales y técnicos. Esta sección enumera los requisitos de recursos necesarios para completar el proceso de construcción descrito en el mapa, según lo determinado por los planos de taller, las especificaciones o las cantidades físicas y las tasas de uso de recursos. El número y tipos de máquinas, herramientas, inventario y accesorios se determinan de acuerdo con el esquema de organización del trabajo adoptado en el mapa de acuerdo con el alcance del trabajo, el momento de su implementación y el número de trabajadores. La necesidad de materiales operativos se determina de acuerdo con sus tasas de consumo.
Registro de un mapa tecnológico
El texto del mapa se redacta en forma de nota explicativa en hojas A4, las páginas deben estar numeradas. Las secciones deben estar numeradas. números arábigos dentro de todo el mapa tecnológico. Dentro de las secciones, el texto se subdivide en párrafos, que están numerados con números arábigos dentro de cada sección. El número de artículo debe constar de números de sección y de artículo separados por puntos.
El cálculo de los costos laborales se realiza en la forma de la tabla 1.1.
Tabla 2.1. Costo de mano de obra
La lista de obras (columna 2) se rellena secuencia tecnológica realización del trabajo.
El alcance del trabajo (columnas Z, 4) se determina de acuerdo con los planos y estimaciones de trabajo. La selección de volúmenes a partir de estimaciones requiere menos tiempo, pero dado que no hay división de volúmenes en capturas en estimaciones, para aclarar los volúmenes de trabajo individual, utilizan directamente dibujos y especificaciones de trabajo para ellos, controlando la exactitud de los cálculos de acuerdo con estimados. El volumen de trabajo debe expresarse en las unidades adoptadas para calcular la intensidad del trabajo y la intensidad de la máquina.
Razón fundamental. En gr. 5 indica la justificación (número de párrafo, cuadro, columnas y posiciones de la norma adoptada según ENiR, GESN u otras).
La norma de tiempo por unidad de medida (columnas 6, 7) se completa según la justificación aceptada.
La base de los cálculos en el cálculo de los costos laborales (LLC) puede basarse en datos de diversos grados de objetividad, cuya adecuación condiciones reales no es el mísmo.
El propósito de calcular los costos de mano de obra y la intensidad de la máquina en KTZ es determinar la necesidad de estos recursos. Pero en presencia de datos confiables de experiencia, la intensidad del trabajo y la intensidad de la máquina deben tomarse de acuerdo con las que realmente se logran en una instalación similar. En este caso, se conocen simultáneamente datos sobre la composición del equipo, costes laborales y otros parámetros.
Por lo tanto, la mayor precisión está garantizada por el uso de información sobre el rendimiento logrado por un equipo determinado en el mismo tipo de objeto (por ejemplo, casas de la misma serie). Los cálculos son menos precisos, que se basan en la producción de la misma brigada a corta distancia. soluciones constructivas instalación u otro equipo de la misma organización en una instalación similar.
Los cálculos basados en normas estimadas, ENiR, etc. son menos precisos, ya que no tienen en cuenta una serie de factores diferentes que se pueden agrupar en los siguientes grupos:
influencia de las condiciones naturales-climáticas y estacionales del desempeño del trabajo;
soluciones específicas para la mecanización del trabajo, promediadas en las normas de costos laborales;
la forma de realizar el trabajo y el nivel de organización de la producción y la productividad del trabajo alcanzado por este equipo.
La intensidad laboral del trabajo (columnas 8, 9) y el costo del tiempo de la máquina están determinados por las siguientes fórmulas:
donde 8 horas es la duración del turno.
La composición del enlace (columna 10) se acepta según la justificación aceptada sin cambios.
Al final de la KTZ, los resultados se anotan en las columnas 8 y 9.
El esquema de control de calidad operativo del trabajo se lleva a cabo en forma de tabla.
Tabla 2.2. Control de calidad operacional
El nombre de las operaciones (columnas 2, 3) sujetas a control se completan en la secuencia tecnológica de su implementación.
Control de calidad de las operaciones (columnas 4, 5, 6, 7). Describe la composición de operaciones controladas, métodos y métodos de control, una lista de herramientas de metrología, el tiempo de control (generalmente el control operativo se realiza después de la finalización de las operaciones de producción) y, si es necesario, los servicios involucrados: laboratorios de construcción, geodésico, servicios geológicos y otros.
La necesidad de recursos materiales y técnicos en la producción de obras consideradas por el mapa se da en las tablas 2.3 y 2.4.
La necesidad de una herramienta, el inventario se da para un enlace o equipo por separado.
Tabla 2.3. La necesidad de herramientas, inventario.
Tabla 2.4. La necesidad de materiales, productos semiacabados.
La parte gráfica de los mapas tecnológicos incluye planos y secciones, diagramas, gráficos, dibujos previstos en el párrafo II del párrafo 2.2, mientras que los materiales gráficos deben ser extremadamente claros para la comprensión y no deben contener dimensiones, designaciones innecesarias.
El cronograma de trabajo se elabora en la forma de la tabla 2.5.
Tabla 2.5. Horario de trabajo
Las columnas 1 ÷ 9 del horario de trabajo corresponden completamente a las columnas 1 ÷ 9 del cálculo del costo laboral (tabla 2.1).
El número requerido de máquinas y mecanismos (columna l0) depende del volumen y la naturaleza de los trabajos de construcción e instalación y el momento de su implementación.
El número de trabajadores por turno (columna 12) y la composición del equipo se determinan de acuerdo con la complejidad y duración del trabajo. Al calcular la composición de la brigada, se asume que la transición de una captura a otra no debe causar cambios en la composición numérica y de calificación de la brigada. Teniendo en cuenta esta circunstancia, se establece la estructura más racional para la combinación de profesiones en la brigada. Por lo general, los equipos tienen una composición establecida, que se tiene en cuenta al elaborar un programa de trabajo.
El cálculo de la composición de la brigada se lleva a cabo en una secuencia determinada:
esbozar un conjunto de trabajos asignados a la brigada (según columna 2);
calcule la intensidad laboral estándar de las obras incluidas en el complejo (columna 6), a partir del cálculo, seleccione los costos laborales por profesión y categoría de trabajadores;
establecer recomendaciones para la combinación racional de profesiones; sobre la base de los datos sobre el rendimiento de los principales mecanismos de elevación para la implementación del complejo previsto, se establece la duración del proceso líder;
calcular el número de unidades (columna 11) y la brigada;
determinar la composición profesional y de calificación de la brigada;
calcular la complejidad del diseño (columna 8).
Para determinar la composición cuantitativa y de calificación de una brigada, puede usar ENiR.
El rango de trabajo asignado al equipo incluye todo el trabajo necesario para el buen funcionamiento de la máquina líder, todo el trabajo tecnológicamente relacionado o dependiente. Así, al levantar la parte sobre rasante de las casas de grandes paneles, que se realiza en dos ciclos, el primer ciclo, junto con la instalación, incluye todos los trabajos asociados a la instalación (carpintería, trabajos especiales, etc.), proporcionando preparación de la casa para Trabajos de pintura). Durante la construcción de edificios de ladrillo en tres ciclos, en el primer ciclo, se encomienda el equipo de construcción, junto con la construcción e instalación, y relacionados Obras civiles Proporcionar preparación para trabajos de enlucido. En el segundo y tercer ciclo se realizan trabajos de enlucido y pintura respectivamente.
Para que la fuerza de la brigada corresponda a la productividad de la máquina líder, es necesario tomar como base para el cálculo el período de trabajo determinado sobre la base del tiempo estimado de operación de la máquina o datos de experiencia de producción. .
La composición cuantitativa de cada eslabón nw se determina en base a los costos laborales por el trabajo asignado al eslabón, Qp (días-hombre) y la duración del proceso conductor T mech (días) según la fórmula:
donde: m es el número de turnos de trabajo por día (columna 9).
La composición cuantitativa de la brigada se determina sumando el número de trabajadores de todas las unidades que componen la brigada.
Los costos laborales por profesión y categoría se establecen por muestreo a partir del cálculo de los costos laborales. El número de trabajadores por profesión y categoría se determina mediante la fórmula:
donde Nbr es el número total de la brigada;
d- Gravedad específica costos laborales por profesión y categoría en la intensidad laboral total del trabajo.
Con una pequeña cantidad de trabajo para cualquier profesión que no proporciona una carga completa en período de facturación, plan para compaginar profesiones. La intensidad laboral normativa del trabajo realizado en el orden de combinación no debe exceder el 15% de la intensidad laboral total del trabajo. Suelen combinar las profesiones de instalador y carpintero, carpintero y hormigonero, soldador eléctrico e instalador, aislador y techador, etc. lista indicativa los trabajos combinados se dan en la tabla 2.6.
Tabla 2.6. Lista aproximada de obras combinadas
Instalador estructuras | Instalación de estructuras prefabricadas de hormigón armado; instalación en lugar de carpintería; soldadura y trabajo de levantamiento; la colocación de la mezcla de hormigón a zamonolichivaniya de las construcciones. |
Aparejador | trabajos de aparejo; cocción de betún, colocación de mezcla de hormigón en construcciones monolíticas; calafateo de juntas |
soldador electrico | Montaje de estructuras prefabricadas; trabajos de soldadura eléctrica; instalación cercas de metal; trabajo de levantamiento |
Masón | trabajos de albañilería; instalación de estructuras prefabricadas de hormigón armado junto con un instalador calificado; andamio; colocación de mezcla de hormigón al incrustar estructuras; trabajos de elevación; enlucido de lugares individuales |
Yesero | trabajo de yeso; revestimiento de hormigón armado Vuelos de escaleras placas de mosaico; junto con un carpintero calificado, rellenando las aberturas de ventanas y puertas y ensamblando el equipo incorporado. |
Aberturas de llenado; montaje e instalación de armarios empotrados; acristalamiento; colocar la mezcla de hormigón en el dispositivo de preparación debajo de los pisos; impermeabilización de baños. |
|
Transporte | Calafateo de juntas de estructuras y bloques de ventanas junto con trabajadores calificados; enlucido de superficies; Enladrillado |
Número de turnos (columna 13). Cuando se utilizan las máquinas principales (grúas de montaje, etc.), el número de turnos de trabajo se toma como mínimo dos. El turno de trabajo realizado manualmente y con la ayuda de una herramienta mecanizada depende del alcance del trabajo disponible y la disponibilidad de los trabajadores. Además, algunos trabajos donde se requiere alta precisión (alineación de columnas) deben realizarse solo durante el turno de día. La realización de una serie de trabajos en el segundo turno, especialmente en el período otoño-invierno, requiere medidas adicionales de protección laboral, iluminación de los lugares de trabajo, pasillos, etc. Sin embargo, la implementación de estas medidas no elimina por completo las molestias de trabajar. en el segundo turno. El trabajo realizado manualmente se asigna al segundo turno solo en los casos excepcionales en que el alcance del trabajo está muy limitado y el equipo (enlace) se ve obligado a dividirse para el trabajo por turnos.
Duración del trabajo (columna 14). Primero, se determina la duración del trabajo mecanizado, cuyo ritmo determina toda la programación, y luego se calcula la duración del trabajo manual.
La duración del trabajo mecanizado Tmeh (días) está determinada por la fórmula:
donde: Nmach.-cambio. - el número requerido de turnos de máquina (columna 9);
nmash - número de coches;
m es el número de turnos de trabajo por día (columna 13).
El número requerido de máquinas depende del volumen y la naturaleza de los trabajos de construcción e instalación y el momento de su implementación.
La duración del trabajo manual Tr (días) se calcula dividiendo la intensidad laboral del trabajo Qp (días-hombre) por el número de trabajadores nh que pueden ocupar el frente de trabajo y por el número de turnos por día:
El número límite de trabajadores que pueden trabajar en la garra se puede determinar dividiendo el frente de trabajo en parcelas, cuyo tamaño debe ser igual a la productividad del turno de un eslabón o de un trabajador individual, así como el número y la productividad de mecanismos de elevación. El producto del número de parcelas y la composición de las unidades da el número máximo de la brigada en esta zona.
La minimización de la duración tiene un límite en forma de tres restricciones: el tamaño del frente de trabajo, la disponibilidad de trabajadores y la tecnología de trabajo.
El cronograma para la producción de obras (columna 15) se da en forma de gráfico lineal. Los plazos del calendario para la ejecución de las obras individuales se fijan a partir de la condición de observar una estricta secuencia tecnológica, teniendo en cuenta la necesidad de prever la ejecución de las obras posteriores en el menor tiempo posible.
El período de preparación del frente de trabajo en algunos casos aumenta debido a la necesidad de observar pausas tecnológicas entre dos obras sucesivas. Por ejemplo, la instalación de estructuras de hormigón armado superpuestas solo se puede llevar a cabo después de que las juntas monolíticas de las estructuras de soporte hayan adquirido la resistencia requerida (al menos el 70% de R28). Las pausas tecnológicas no son fijas, dependen de una serie de factores.
Entonces, el tiempo de secado del yeso depende del período del año, la temperatura y los métodos utilizados: ventilación natural o artificial. Si es necesario, las pausas tecnológicas pueden reducirse utilizando métodos más intensivos. Por lo tanto, al construir una junta monolítica, se pueden usar diferentes tipos y marcas de cemento, calefacción eléctrica y otros métodos para acelerar el endurecimiento del concreto.
INSTITUTO CENTRAL DE ESTUDIOS REGULATORIOS E INFORMACIÓN CIENTÍFICA Y TÉCNICA "ORGTRANSSTROY"
MINISTERIOS DE TRANSPORTE CONSTRUCCIÓN
PREPARACIÓN DE MEZCLA DE HORMIGÓN DE CEMENTO EN LA INSTALACIÓN C-780
1 ÁREA DE USO
El mapa tecnológico se desarrolló sobre la base de la aplicación de métodos de organización científica del trabajo y está destinado a ser utilizado en el desarrollo de un proyecto para la producción de trabajo y organización del trabajo en plantas mezcladoras para la preparación de mezclas de cemento y concreto.
La planta automatizada de hormigón de cemento (CBZ) con la planta S-780 está diseñada para la preparación de mezclas de hormigón rígido y plástico con áridos de hasta 40 mm.
La capacidad de la planta es de hasta 30 m 3 /h Las capacidades de los silos de suministro de cemento, áridos, tanque de agua están diseñadas para media hora de funcionamiento a máxima productividad y la mayor relación agua-cemento = 0,5.
La planta consta de departamentos de mezcla y dosificación, almacén de áridos y almacén de cemento.
El almacén de consumibles de agregados está abierto, ubicado directamente cerca de la planta mezcladora de concreto S-780. Aquí también se organiza el cribado y lavado del material. La arena y la piedra triturada se entregan en vagones de ferrocarril, descargados por un descargador de pórtico de múltiples cangilones S-492 directamente sobre los embudos de las tolvas vibratorias del transportador de galería.
El almacén automático de cemento S-753 está destinado al almacenamiento de cemento a corto plazo. La torre del silo con una capacidad de 25 g está equipada con dos indicadores de nivel de cemento del tipo UKM. El cemento de los vagones de ferrocarril se descarga directamente al depósito de cemento mediante un descargador neumático S-577.
La unidad de dosificación de la planta consta de tolvas de alimentación con dosificadores pendulares continuos S-633. Los dispensadores se instalan sobre el transportador horizontal, que suministra materiales al transportador inclinado. En el transportador inclinado caen en la bandeja de carga del departamento de mezcla.
La tolva de suministro de cemento es un cilindro con una parte cónica en la parte inferior. El cemento se alimenta directamente al dispensador S-781 con un alimentador de tambor. En el interior del búnker se encuentran instalados dos indicadores de nivel de cemento C-609A, incluidos en el esquema de control del almacén. El encendido o apagado del mecanismo que suministra cemento desde el almacén se realiza mediante los mismos indicadores.
La planta de mezcla forzada continua S-780 es el equipo principal de la planta de hormigón. El cuerpo de trabajo del mezclador son dos ejes de sección cuadrada de 80 × 80 mm con cuchillas montadas en ellos. Las palas terminan con palas de 100×100 mm. El cuerpo del agitador termina en una tolva de almacenamiento con compuerta de mordaza.
La planta mezcladora de hormigón S-780 está conectada con los almacenes: áridos de cemento y unidad de dosificación mediante un sistema de alimentadores de cinta y cangilones.
En todos los casos de aplicación del mapa tecnológico, es necesario vincularlo a las condiciones locales, dependiendo de la composición, marca y cantidad de la mezcla producida.
Dependiendo de las necesidades cambiantes de la mezcla de cemento y hormigón, la planta se puede ajustar a cualquier capacidad que va desde 15 a 30 m h y agua hasta 6 m 3.
Entonces, por ejemplo, según lo especificado por el laboratorio de la planta, el consumo de materiales por 1 m 3 de hormigón (cemento - 340 kg, arena - 547 kg, fracción de piedra triturada 5-20 mm - 560 kg, fracción de piedra triturada 20-40 mm - 840 kg, agua - 170 kg ) la productividad de la planta será:
Dispensador de día |
Productividad de dosificadores, t/h a productividad de planta m 3 /h |
|||
Fracción de piedra triturada 15-20 mm |
||||
Fracción de piedra triturada 20-40 mm |
||||
2. INSTRUCCIONES SOBRE LA TECNOLOGÍA DEL PROCESO DE PRODUCCIÓN
Previo al inicio de los trabajos de la planta de hormigón cemento con la instalación S-780, se inspeccionan todos los equipos y, en su caso, se calibran los dosificadores de áridos, cemento y agua.
La calibración de los dosificadores se realiza con un cambio en la productividad de la planta, la marca y composición de la mezcla de concreto, el peso volumétrico y la distribución granulométrica de los agregados.
Con una determinada productividad de la planta y, en consecuencia, la composición y marca de la mezcla, también es necesario calibrar periódicamente los dosificadores.
Calibración del dosificador de agregados
Los dosificadores de agregados se calibran mediante muestreo. Para esto necesitas:
a) llenar los contenedores de suministro con arena, grava pequeña y grande en una cantidad de al menos 5 m 3 de cada material;
b) colocar los dosificadores por nivel en posición horizontal (con material) moviendo la palanca de carga o cambiando la carga en la caja de lastre (cerca del variador).
En este caso, los amortiguadores móviles deben ajustarse a una altura de 100 mm para piedra triturada y 80 mm para arena. Los amortiguadores fijos se instalan 10 mm más altos que los amortiguadores móviles. La verificación de la ausencia de atascos o atascos en el sistema de pesaje de los dispensadores se realiza presionando ligeramente en el borde de la plataforma de pesaje o colocando un peso de 0,5 kg. En este caso, la plataforma debe bajarse hasta el tope;
c) prepararse para la calibración de básculas para mercancías con una capacidad de carga de al menos 0,5 T, una caja de 200 m de capacidad y un cronómetro.
Para el muestreo, es necesario encender el transportador de recolección horizontal para el movimiento en la dirección opuesta al cambiar la dirección del motor eléctrico (inversa). Al probar un dispensador, el resto debe estar apagado.
El transportador colector horizontal se encenderá durante el período de prueba.
A las órdenes de un asistente de laboratorio que sostiene un cronómetro, el operador enciende el dispensador. Se vierte arena o piedra triturada sobre una lámina de metal durante 4-5 segundos hasta que se obtiene un flujo estable de material vertido. Después de eso, se enciende el cronómetro y se coloca la caja bajo el flujo del material dosificado.
Transcurrido el tiempo de muestreo, a la señal del ayudante de laboratorio, se apaga la cinta colectora y el dosificador. La muestra tomada se pesa en una balanza.
Se realizan tres pesajes para una posición del variador.
La productividad horaria del dispensador está determinada por la media aritmética del peso de tres muestras según la fórmula:
dónde α - valor medio aritmético del peso de tres muestras en kg sin tara;
t- tiempo de muestreo en seg. Si el peso de las muestras no supera el ± 2% del valor calculado, se considera que en la posición dada de la aguja del variador el dispensador funciona de forma estable.
De igual manera, se realiza la calibración de otros dosificadores de áridos.
Para calibrar el dispensador de cemento, debe:
a) destornillar los pernos que sujetan el ramal de la tolva de cemento y girar el ramal 90°;
b) asegúrese de que la tolva de suministro de cemento esté completamente llena de cemento. Verifique el nivel de cemento en la tolva de suministro usando los indicadores de nivel en el panel de control de la planta mezcladora;
c) preparar para la tara balanzas comerciales con una capacidad de carga de al menos 0,5 T, dos cajas con una capacidad de 200 l, un cronómetro, una pala, una tubería de derivación de hojalata con un diámetro de 130-150 mm, una longitud de 3-3,5 m.
El muestreo se lleva a cabo para cada una de las cinco posiciones de la flecha del variador.
Para hacer esto, se instala una caja debajo de la boquilla, a las órdenes del asistente de laboratorio, el conductor enciende el dispensador de cemento. El cemento del dispensador ingresa a la tubería y de esta a la caja hasta que se establece a simple vista un modo de suministro de cemento estable y la velocidad normal del motor eléctrico. El tiempo necesario para obtener un flujo estable de material suele ser de 50 a 60 segundos. Después de este tiempo, el cronómetro se enciende simultáneamente y la tubería se transfiere a la carga de la caja. La caja se carga durante 90 segundos para 1, 2, 3 posiciones de la flecha del variador, y durante 60 segundos - para 4, 5 posiciones de la flecha. Una vez transcurrido el tiempo especificado, la muestra tomada se pesa en la balanza. Se realizan tres muestreos para cada posición de la aguja del variador. Precisión de dosificación de cemento ± 2% del peso calculado.
Para controlar la correcta calibración se comprueba el funcionamiento del dosificador a la capacidad seleccionada y con funcionamiento continuo del dosificador durante 10 minutos tomando tres muestras en una caja, prestando especial atención al funcionamiento de todos los mecanismos y al flujo ininterrumpido de material. en el dispensador.
Para calibrar el dispensador de agua, debe:
a) gire la tubería de drenaje a través de la cual ingresa el agua al mezclador 180 ° en la brida y alargue con una tubería adicional de hasta 4 m de largo;
b) apagar todos los equipos no relacionados con la dosificación de agua.
El dosificador se calibra por toma de muestras, para lo cual es necesario encender la bomba dosificadora con el tubo de desagüe bloqueado. Al mismo tiempo, el agua del tanque a través de la bomba dosificadora y la válvula de tres vías regresa al tanque a través del anillo. A las órdenes de un ayudante de laboratorio que sostiene un cronómetro, el operador cambia la válvula de tres vías a la posición de suministro de agua al mezclador, y se suministra agua al barril hasta que se establece un flujo de agua continuo y estable. Después de eso, el cronómetro se enciende simultáneamente y la válvula de tres vías se cambia instantáneamente para suministrar agua al tanque del medidor de agua. El contenedor se llena en 60 segundos para las posiciones 1, 2 y 3 de la flecha del variador, y en 30 segundos para las posiciones 4 y 5 de la flecha. Una vez transcurrido el tiempo especificado, a la orden del asistente de laboratorio, la válvula de tres vías se cambia a drenaje y el cronómetro se apaga. El operador cambia la válvula de tres vías a la posición de suministro de agua a través del anillo. Se mide la muestra tomada.
Para mantener el principal indicador de calidad de la mezcla de concreto (relación agua-cemento), es necesario calibrar el dispensador de agua con una precisión de ± 1%.
Tras calibrar todos los dosificadores, la instalación construye un gráfico de la productividad de una planta de hormigón, en función de la posición de la flecha del variador de cada dosificador (Fig. 1).
Arroz. 1. Gráfico de la dependencia de la productividad de los dosificadores de las posiciones de la flecha de los variadores:
1 - agua; 2 - fracción de piedra triturada 5-20 mm; 3 - fracción de piedra triturada 20-40 mm; 4 - arena; 5 - cemento
Este gráfico es válido cuando la planta está funcionando con materiales permanentes que componen la mezcla de hormigón.
Para cambiar la productividad de los dosificadores, es necesario cambiar la relación de transmisión del variador. Para ello, coloque las flechas del variador (solo en movimiento) en la división adecuada a lo largo de la curva aproximada y, mediante la calibración posterior, realice la corrección necesaria en su posición.
El correcto funcionamiento de los dosificadores es controlado diariamente al inicio del turno por un representante del laboratorio CBZ. El dispositivo de pesaje se instala de acuerdo con la composición de la mezcla de concreto aprobada por el ingeniero jefe del departamento de construcción y teniendo en cuenta el contenido de humedad de los agregados. El acceso a las cabinas de pesaje y dispositivos de dosificación, así como los cambios en la cantidad de materiales, está permitido solo para los empleados del laboratorio.
Los componentes de la mezcla de concreto inmediatamente después de ingresar a la planta de concreto están sujetos a control por parte del laboratorio de la Planta Biomédica Central y del Laboratorio Central de Gerencia de Construcción. La calidad de los materiales se comprueba mediante inspección externa y mediante muestreo.
La planta opera de acuerdo con el esquema dado en la Fig. 2.
Arroz. 2. Esquema tecnológico de la planta de hormigón de cemento con la planta S-780 para la preparación de mezcla de hormigón:
1 - alimentadores de vibración; 2 - transportadores; 3 - búnkeres agregados; 4-dispensadores de áridos; 5 - dispensador de cemento; 6 - búnker de cemento; 7 - cinta transportadora; 8 - batidora; 9 - accionamiento para hormigón; 10 - tanque de agua; 11 - dispensador de agua; 12 - válvula de tres vías; 13 - tolva receptora; 14 - banco de silos; 15 - filtros
La excavadora empuja alternativamente los agregados hacia las 1 bandejas vibratorias, desde donde los 2 transportadores los alimentan a los 3 silos de alimentación.
Cuando los bunkers están completamente cargados, se activa el indicador de nivel superior y se apagan la bandeja vibratoria y los transportadores después de que haya pasado el material que queda en la cinta, y se enciende la señal luminosa de fin de carga. Cuando el material se agota en la tolva de suministro hasta el indicador de nivel inferior, se encienden el transportador, la bandeja vibratoria, las señales de luz y sonido para el inicio de la carga.
El cemento de la lata de silo 15 se alimenta al depósito de alimentación 6 mediante un sistema de inyección neumática. Desde la tolva de suministro, el cemento ingresa al dosificador de péndulo de pesaje 5. Los indicadores de los niveles superior e inferior de cemento tienen señales de luz y sonido al panel de control del almacén de cemento.
El agua del depósito 10 del compartimento de mezcla se bombea desde un depósito especial.
La piedra triturada de la fracción 5-20, 20-40 mm y la arena se dosifican continuamente mediante dosificadores pendulares de cinta 4, a los que llega el material procedente de tolvas de suministro.
Primero, se dosifica piedra triturada de una fracción de 20-40 mm sobre la cinta, luego piedra triturada de una fracción de 5-20 mm y arena, y encima de estos materiales, cemento. Este orden de alimentación elimina la acumulación de pequeñas partículas de material en la banda.
Los materiales dosificados se alimentan a través del embudo de alimentación al mezclador. El agua del tanque se dosifica por medio de una bomba dosificadora y se alimenta a través de la tubería directamente al mezclador de trabajo.
La vinaza de sulfito-alcohol se prepara en una instalación especial y se introduce en el agua en una cantidad de 0,2-0,3% del peso del cemento por 1 m 3 de hormigón (0,68-1,0 kg / m 3).
En la mezcladora, los componentes de hormigón se mezclan intensamente y se transportan mediante ejes de paletas hasta la salida. Desde el mezclador, la mezcla terminada ingresa al acumulador y se descarga a través de la compuerta de mordaza en un camión volquete.
La calidad de la mezcla de cemento y hormigón obtenida en la planta mezcladora C-780 depende principalmente de la continuidad de su funcionamiento, ya que en cada parada cambia la relación calculada de los componentes de la mezcla de hormigón, especialmente cemento y agua.
El laboratorio de la fábrica lleva a cabo el control de calidad de la mezcla de cemento y hormigón 2-3 veces por turno.
Con la misma composición y correcta dosificación, la movilidad, trabajabilidad, densidad aparente y rendimiento del hormigón deben ser constantes.
La salida de hormigón se determina al menos una vez al mes con un cambio en la composición del hormigón.
La cantidad de hormigón liberado de la fábrica y colocado en la caja debe controlarse diariamente.
Al realizar el trabajo, se deben observar las siguientes reglas de seguridad:
Las personas familiarizadas con el diseño de este equipo y las normas de seguridad pueden operar el equipo de las plantas de concreto;
Antes de poner en marcha el equipo, es necesario verificar la confiabilidad de las protecciones en todos los abiertos, giratorios y móviles; partes;
Es necesario asegurar el buen estado no solo del sistema de automatización, sino también de los mecanismos locales de puesta en marcha. En caso de mal funcionamiento de la puesta en marcha local, no se permite la operación de la planta automatizada;
Está permitido encender máquinas, herramientas y lámparas de iluminación solo con la ayuda de arrancadores o interruptores de cuchilla;
Las reparaciones de equipos y cableados eléctricos solo pueden ser realizadas por un electricista;
Está prohibida la reparación de tuberías de sistemas neumáticos bajo presión;
Al final de la operación de la planta mezcladora, es necesario apagar el interruptor general y cerrar la caja en la que se encuentra;
En ausencia de transporte durante más de 1,5 horas, es necesario limpiar las cuchillas y el canal de la mezcla de hormigón y enjuagar la mezcladora con agua, así como limpiar la compuerta de mordaza de la tolva de almacenamiento;
Para evitar que entren objetos extraños en la tolva, se debe instalar una rejilla encima de la abertura de carga. Al preparar una mezcla con aditivos químicos, el trabajador debe utilizar guantes de goma y gafas de seguridad.
3. INSTRUCCIONES PARA LA ORGANIZACIÓN DEL TRABAJO
Los trabajos de preparación de la mezcla de cemento y hormigón se realizan en dos turnos.
La planta mezcladora es atendida por un equipo compuesto por 8 personas, incluidos los preparadores de mezcla de cemento y concreto, maquinistas: 5 razr.-1; 4 bits-1; dosificador de componentes de mezcla de cemento y hormigón 3 tamaño-1; instalador eléctrico 5 categoría-1; construcción de cerrajería 4 razr.-1; conductor de excavadora 5 años - 1; transporte (trabajadores auxiliares) 2 razr.-2.
Antes de iniciar los trabajos, los preparadores de la mezcla de cemento y hormigón y el dosificador deben comprobar la integridad del equipamiento de la instalación, la ausencia de objetos extraños cerca de las partes giratorias o en las cintas transportadoras.
Operador de planta mezcladora 5 años gestiona el funcionamiento de la planta mezcladora de hormigón en su conjunto: supervisa la aproximación, la carga y el envío de vehículos, da una señal audible a los conductores para que carguen, en ausencia de vehículos, apaga la planta y se asegura de que después de que se apague la planta , no queda mezcla de hormigón en la mezcladora.
Operador de planta mezcladora 4° grado. comprueba la presencia de agua en el depósito y el depósito dosificador, cemento en la tolva de alimentación, inspecciona el agitador, comprueba el funcionamiento vacío de la mordaza y el agitador sin materiales, comprueba el funcionamiento del variador, enciende la bomba de agua que suministra agua al tanque de dosificación de agua de un nivel constante, enciende el mezclador, luego el transportador de suministro de agregados abre la válvula de cierre de agua, enciende el dispensador de cemento y controla la preparación de la mezcla de cemento y concreto. Supervisa el funcionamiento de los mecanismos de instalación, asegura el buen funcionamiento de todas las unidades y realiza reparaciones de rutina.
El dosificador de los componentes de cemento concrete mix 3 razr. comprueba la presencia de áridos en los silos de alimentación del departamento de dosificación, la altura de instalación de las compuertas fijas y móviles, la facilidad de basculación del transportador de peso y su posición horizontal. Comprueba el funcionamiento en vacío de los transportadores prefabricados e inclinados y, durante su funcionamiento normal, enciende los transportadores prefabricados, los conductos vibratorios y los dispensadores en una secuencia determinada.
Cerrajería de obra 4 tiempos. verifica la presencia de cemento en el depósito, la posición de las compuertas correderas y la presencia de la cantidad requerida de cemento en el foso o bandeja de transferencia. Bajo la dirección del conductor de la consola central, verifica el funcionamiento inactivo del sistema de neumopresión.
Electricista 5ta categoria verifica la conexión a tierra de los motores eléctricos, conecta la unidad a la red eléctrica, junto con los conductores verifica el funcionamiento de los motores eléctricos en ralentí, supervisa el funcionamiento preciso del sistema de control automático. Durante el funcionamiento de los motores eléctricos, supervisa periódicamente el modo de funcionamiento, el calentamiento y el estado de los contactos.
Conductor de excavadora 5 años alimenta agregados a los conductos de la galería subterránea.
Trabajadores de transporte (auxiliares) 2 seg. están ocupados con el trabajo preparatorio y final: preparan la vinaza de alcohol al sulfito, eliminan el material derramado de los transportadores y las unidades de dosificación, eliminan los objetos extraños de los transportadores.
4. CALENDARIO DEL PROCESO DE PRODUCCIÓN
nombre de las obras |
unidad de medida |
Alcance del trabajo |
La composición del enlace (equipo) |
|||||||||||||||||
Trabajo de preparatoria |
0,05 |
4 " - 1
electricista cerrajero de construccion conductor de excavadora
|
||||||||||||||||||
14,27 |
||||||||||||||||||||
traspaso de turno |
0,03 |
|||||||||||||||||||
trabajos finales |
0,05 |
|||||||||||||||||||
continuación
nombre de las obras |
unidad de medida |
Alcance del trabajo |
Intensidad laboral para todo el ámbito de trabajo, días-hombre |
La composición del enlace (equipo) |
tiempo del proceso de producción |
|||||||||||||||
Trabajo de preparatoria |
0,05 |
Preparadores de mezcla de cemento y concreto, maquinistas: 4 " - 1 Unidad de dosificación para componentes de mezcla de cemento y hormigón: electricista cerrajero de construccion conductor de excavadora Transporte (trabajadores auxiliares) |
||||||||||||||||||
Preparación de mezcla cemento-hormigón (suministro de áridos, cemento, agua, su dosificación, mezclado, preparación de aditivos) |
14,27 |
|||||||||||||||||||
traspaso de turno |
0,03 |
|||||||||||||||||||
trabajos finales |
0,05 |
|||||||||||||||||||
notas
1. El programa no contempla el mantenimiento preventivo nocturno.
2. Durante el período de puesta en marcha y ajuste de la planta, la composición del equipo podrá ser modificada a discreción del ingeniero jefe del departamento de construcción.
5. CÁLCULO DE COSTES DE MANO DE OBRA PARA LA ELABORACIÓN DE 210 m
Código de tarifas y precios |
La composición del enlace. |
Descripción de obras |
unidad de medida |
Alcance del trabajo |
Norma de tiempo, hora-hombre |
Precio, rub.-kop. |
Tiempo estándar para el alcance completo del trabajo |
El costo de los costos laborales para el alcance total del trabajo, rub.-kop. |
TNR, § T-1-38, tab. 2a |
Preparadores de mezcla de hormigón de cemento: Dispensador de componentes mezcla de cemento y concreto: electricista cerrajero de construccion |
Preparación de la mezcla cemento-hormigón (alimentación de cemento a la tolva de alimentación, dosificación de áridos en cemento cuando se alimenta a la mezcladora), alimentación de agua a la mezcladora e introducción (si es necesario) de una solución de aditivos; mezcla de materiales con la liberación de la mezcla en la tolva de almacenamiento; liberación de la mezcla terminada en camiones de volteo; preparación de documentos para la mezcla |
100m3 |
12-84 |
26-96 |
|||
Para el momento |
conductor de excavadora Trabajadores del transporte (auxiliares) |
Suministro de materiales minerales (empuje de materiales a la galería de transportadores con bulldozer; mantenimiento de los puntos de alimentación de la cinta transportadora y del transportador de almacén de consumibles y preparación de vinazas al sulfito-alcohol) |
1 turno |
13-50 |
13-50 |
|||
Total para 210 m 3 |
6. PRINCIPALES INDICADORES TÉCNICOS Y ECONÓMICOS
El nombre de los indicadores. |
unidad de medida |
Según el costo |
En la fecha prevista |
Cuánto más o menos son los indicadores según el cronograma que según el cálculo, %. |
La complejidad del trabajo por 100 m 3 de la mezcla. |
||||
Rango promedio de trabajadores |
||||
Promedio diario salario por trabajador |
||||
La tasa de utilización de la instalación S-780 |
7. RECURSOS MATERIALES Y TÉCNICOS
a) Materiales básicos
El consumo de materiales se determina de acuerdo con la receta de la mezcla de cemento y concreto. En esta tabla se muestra el consumo medio de materiales.
Nombre |
Marcos, GOST |
unidad de medida |
Cantidad |
|
por unidad de producción (100 m 3 de mezcla) |
por turno (210 m 3 mixtos) |
|||
Cemento grado 500 |
GOST 10178-62* |
|||
Arena media |
GOST 10268-62 |
|||
Fracción de piedra triturada 5-20 mm |
GOST 8267-64 |
|||
Fracción de piedra triturada 20-40 mm |
GOST 8267-64 |
|||
vinaza de alcohol al sulfito |
b) Maquinaria, equipo, herramientas, inventario
Nombre |
unidad de medida |
Cantidad |
|
planta mezcladora con automático |
|||
Dispensadores continuos |
|||
Carga de cemento automatizada |
|||
Excavadora |
|||
descargador de cemento |
|||
Transportadores de correa |
T-144 y RTU-30 |
||
Planta para la preparación de aditivos SSB |
|||
llaves inglesas |
establecer |
||
El mapa tecnológico fue desarrollado por el departamento para la implementación de mejores prácticas y regulaciones técnicas en la construcción de carreteras y aeródromos (realizado por el ingeniero T.P. Bagirova) basado en los materiales de las estaciones de investigación regulatoria de Rostov y Chelyabinsk del Instituto Orgtransstroy