Elementos del proceso tecnológico de mecanizado. Proceso tecnológico de mecanizado de una pieza.
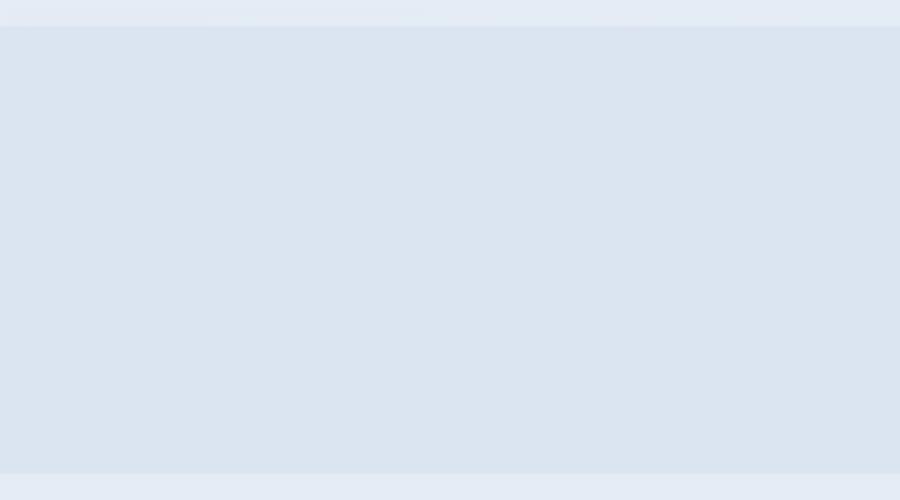
Leer también
PROCESOS PRODUCTIVOS Y TECNOLÓGICOS
El proceso de producción se entiende como un conjunto de procesos individuales llevados a cabo para obtener máquinas (productos) terminados a partir de materiales y productos semielaborados.
El proceso de producción incluye no solo los principales, es decir, los procesos directamente relacionados con la fabricación de piezas y el montaje de máquinas a partir de ellas, sino también todos los procesos auxiliares que garantizan la posibilidad de fabricar productos (por ejemplo, transporte de materiales y piezas, control de piezas, fabricación de útiles y utillajes, etc.).
Un proceso tecnológico es un cambio secuencial en la forma, dimensiones, propiedades de un material y un producto semielaborado para obtener una pieza o producto de acuerdo con los requisitos técnicos especificados.
Proceso tecnológico mecanizado partes es parte del proceso de fabricación general para la fabricación de la máquina completa.
El proceso de producción se divide en las siguientes etapas:
1) producción de piezas en blanco: fundición, forja, estampado;
2) procesamiento de piezas en bruto en máquinas de corte de metales para obtener piezas con dimensiones y formas finales;
3) ensamblaje de componentes y ensamblajes (o mecanismos), es decir, la conexión de partes individuales en unidades de ensamblaje y ensamblajes; en la producción de una sola pieza, se utiliza el procesamiento de cerrajería y el ajuste de piezas al lugar de instalación durante el ensamblaje; en la producción en serie, estos trabajos se realizan en un volumen pequeño, y en la producción en masa y a gran escala no se utilizan, ya que debido al uso de calibres limitadores durante el procesamiento en máquinas para corte de metales, se logra la intercambiabilidad de las piezas;
4) montaje final toda la máquina;
5) regulación y prueba de la máquina;
6) pintura y acabado de la máquina (producto). La coloración consiste en varias operaciones realizadas en etapas diferentes proceso, por ejemplo, masilla, imprimación y primera pintura de piezas fundidas, pintura de piezas mecanizadas, pintura final de toda la máquina).
En cada etapa del proceso de producción, para operaciones individuales del proceso tecnológico, el control sobre la fabricación de piezas se lleva a cabo de acuerdo con las especificaciones de la pieza para garantizar la calidad adecuada de la máquina terminada (producto). El proceso tecnológico de elaboración mecánica de las piezas debe diseñarse y realizarse de forma que, a través de los medios más racionales y formas economicas procesamiento, se cumplieron los requisitos de detalles (precisión de procesamiento y rugosidad de la superficie, disposición mutua de ejes y superficies, corrección de contornos, etc.), proporcionando trabajo correcto coche ensamblado.
Según GOST 3.1109-73, el proceso tecnológico puede ser de diseño, de trabajo, único, típico, estándar, temporal, prospectivo, de ruta, operativo, de ruta-operacional.
COMPOSICIÓN DE LA PRODUCCIÓN DE LA PLANTA DE FABRICACIÓN DE MAQUINARIA
Las fábricas de construcción de maquinaria consisten en unidades de producción separadas llamadas talleres y varios dispositivos.
La composición de los talleres, dispositivos e instalaciones de la planta está determinada por el volumen de producción, la naturaleza de los procesos tecnológicos, los requisitos de calidad de los productos y otros factores de producción, así como en gran medida por el grado de especialización de producción y cooperación de la planta con otras empresas e industrias relacionadas.
La especialización implica la concentración de un gran volumen de producción de tipos de productos estrictamente definidos en cada empresa.
La cooperación prevé el suministro de piezas brutas (fundidas, forjadas, estampadas), componentes, diversos instrumentos y dispositivos fabricados en otras empresas especializadas.
Si la planta proyectada recibirá piezas fundidas en orden de cooperación, entonces no incluirá talleres de fundición. Por ejemplo, algunas fábricas de máquinas-herramienta reciben piezas fundidas de una fundición especializada que suministra piezas fundidas a los clientes de forma centralizada.
La composición de las instalaciones energéticas y sanitarias de la planta también puede ser diferente dependiendo de la posibilidad de cooperación con otros industriales y utilidades para el suministro de electricidad, gas, vapor, aire comprimido, en cuanto a transporte, abastecimiento de agua, alcantarillado, etc.
El mayor desarrollo de la especialización y, en relación con esto, la amplia cooperación de las empresas afectará significativamente la estructura de producción de las fábricas. En muchos casos, la composición de las plantas de construcción de maquinaria no incluye fundiciones y talleres de forja y estampación, talleres para la fabricación de elementos de fijación, etc., ya que las plantas especializadas suministran piezas brutas, herrajes y otras piezas. Muchas plantas de producción en masa, en cooperación con plantas especializadas, también pueden suministrarse con componentes y conjuntos (mecanismos) listos para fabricar para máquinas fabricadas; por ejemplo, fábricas de automóviles y tractores - motores terminados, etc.
La composición de la planta de construcción de maquinaria se puede dividir en los siguientes grupos:
1. Talleres de aprovisionamiento (fundiciones de hierro, fundiciones de acero, fundiciones de metales no ferrosos, forja, forja y prensado, prensado, forja y estampación, etc.);
2. Talleres de transformación (mecánica, térmica, estampación en frío, carpintería, revestimiento de metales, montaje, pintura, etc.);
3. Talleres auxiliares (herramienta, reparación mecánica, eléctrica, maqueta, experimental, ensayo, etc.);
4. Dispositivos de almacenamiento (para metal, herramientas, materiales de moldeo y carga, etc.);
5. Dispositivos de energía (central eléctrica, central combinada de calor y electricidad, instalaciones de compresores y generadores de gas);
6. Dispositivos de transporte;
7. Equipamiento sanitario (calefacción, ventilación, abastecimiento de agua, alcantarillado);
8. Instituciones y dispositivos de toda la planta (laboratorio central, laboratorio tecnológico, laboratorio central de medición, oficina central, oficina de control, centro médico, ambulatorio, dispositivos de comunicación, comedor, etc.).
ESTRUCTURA DEL PROCESO TECNOLÓGICO
Para garantizar el proceso más racional de mecanizado de la pieza de trabajo, se elabora un plan de procesamiento que indica qué superficies deben procesarse, en qué orden y de qué manera.
En este sentido, todo el proceso de mecanizado se divide en componentes separados: operaciones tecnológicas, instalaciones, posiciones, transiciones, movimientos, técnicas.
Una operación tecnológica es una parte de un proceso tecnológico que se realiza en un lugar de trabajo y cubre todas las acciones secuenciales de un trabajador (o un grupo de trabajadores) y una máquina para procesar una pieza de trabajo (uno o más al mismo tiempo).
Por ejemplo, girar un eje, realizado secuencialmente primero en un extremo y luego después del giro, es decir, reorganizar el eje en los centros, sin quitarlo de la máquina, y en el otro extremo, es una sola operación.
Si todos los espacios en blanco (ejes) de un lote dado se tornean primero en un extremo y luego en el otro, entonces esto equivaldrá a dos operaciones.
La parte de instalación de la operación se denomina parte de la operación realizada con una fijación de la pieza de trabajo (o varias procesadas simultáneamente) en la máquina o en el accesorio, o la unidad de ensamblaje ensamblada.
Entonces, por ejemplo, girar el eje cuando se fija en los centros es el primer ajuste, girar el eje después de girarlo y fijarlo en los centros para procesar el otro extremo es el segundo ajuste. Cada vez que la pieza se gira en cualquier ángulo, se crea una nueva configuración (cuando gira la pieza, debe especificar el ángulo de rotación).
La instalación instalada y fija puede cambiar su posición en la máquina con respecto a sus cuerpos de trabajo bajo la influencia de dispositivos móviles o giratorios, tomando una nueva posición.
Cada uno se llama una posición. disposición separada pieza de trabajo, ocupada por ella en relación con la máquina con su fijación sin cambios.
Por ejemplo, cuando se mecaniza en máquinas semiautomáticas y automáticas de varios husillos, la pieza, con una fijación, ocupa diferentes posiciones con respecto a la máquina al girar la mesa (o el tambor), que lleva secuencialmente la pieza a diferentes herramientas.
La operación se divide en transiciones: tecnológica y auxiliar.
Transición tecnológica: una parte completa de una operación tecnológica, caracterizada por la constancia de la herramienta utilizada, las superficies formadas por el procesamiento o el modo de operación de la máquina.
Transición auxiliar: una parte completa de una operación tecnológica, que consiste en acciones humanas y (o) de equipo que no van acompañadas de un cambio en la forma, el tamaño y la rugosidad de la superficie, pero que son necesarias para realizar una transición tecnológica. Ejemplos de transiciones auxiliares son la configuración de la pieza, el cambio de herramienta, etc.
Cambiar solo uno de los elementos enumerados (superficie trabajada, herramienta o modo de corte) define una nueva transición.
La transición consiste en movimientos de trabajo y auxiliares.
El golpe de trabajo se entiende como parte de la transición tecnológica, abarcando todas las acciones asociadas a la eliminación de una capa de material con la misma herramienta, superficie de procesamiento y modo de funcionamiento de la máquina.
En las máquinas que procesan cuerpos de revolución, la carrera de trabajo se entiende como trabajo continuo instrumento, por ejemplo torno eliminación de una capa de virutas con un cortador de forma continua, en cepilladora- eliminación de una capa de metal sobre toda la superficie.
Si la capa de material no se elimina, pero se somete a deformación plástica (por ejemplo, durante la formación de ondulaciones y cuando la superficie se enrolla con un rodillo liso para compactarla), también se utiliza el concepto de carrera de trabajo. , como en el caso de la eliminación de virutas.
Carrera auxiliar: una parte completa de la transición tecnológica, que consiste en un solo movimiento de la herramienta en relación con la pieza de trabajo, no acompañada de un cambio en la forma, las dimensiones, la rugosidad de la superficie o las propiedades de la pieza de trabajo, pero necesario para completar la carrera de trabajo .
Todas las acciones del trabajador, realizadas por él durante la realización de la operación tecnológica, se dividen en métodos separados. Bajo la recepción se entiende la acción cumplida del trabajador. Por lo general, las recepciones son acciones auxiliares, por ejemplo, colocar o quitar una pieza, poner en marcha una máquina, cambiar la velocidad o el avance, etc. El concepto de “recepción” se utiliza en el reglamento técnico de una operación.
El plan de mecanizado también incluye trabajos intermedios: control, cerrajería, etc., necesarios para el procesamiento posterior, por ejemplo, soldadura, ensamblaje de dos partes, tratamiento térmico, etc.; las operaciones finales para otros tipos de trabajos realizados después del mecanizado se incluyen en el plan para los tipos de procesamiento correspondientes.
PROGRAMA DE FABRICACIÓN
El programa de producción de una planta de construcción de maquinaria contiene una gama de productos manufacturados (indicando sus tipos y tamaños), las cantidades de productos de cada artículo que se producirán durante el año, una lista y cantidad de repuestos para productos manufacturados.
Basado en los generales programa de producción la planta elabora un programa de producción detallado para los talleres, indicando el nombre, cantidad, peso negro y neto (masa) de las piezas a fabricar y procesar en cada taller determinado (fundición, forja, mecánica, etc.) y en proceso en varios Talleres de trabajo; Se elabora un programa para cada taller y un resumen, indicando qué partes y cuántos pasan por cada taller. Al compilar programas detallados para talleres, al número total de piezas determinado por el programa de producción, se agregan repuestos, se adjuntan a las máquinas fabricadas y se suministran como repuestos para garantizar el buen funcionamiento de las máquinas en funcionamiento. El número de piezas de repuesto se toma como un porcentaje del número de piezas principales.
Los dibujos se adjuntan al programa de producción. tipos generales máquinas, planos de montaje y piezas individuales, especificaciones de las piezas, así como una descripción de los diseños de máquinas y especificaciones para su fabricación y entrega.
producción tecnológica de la planta de construcción de maquinaria
TIPOS (TIPOS) DE PRODUCCIÓN Y CARACTERÍSTICAS DE SUS PROCESOS TECNOLÓGICOS. FORMAS DE ORGANIZACIÓN DEL TRABAJO
Según el tamaño del programa de producción, la naturaleza del producto y las condiciones técnicas y Condiciones económicas la implementación del proceso de producción, todas las diversas producciones se dividen condicionalmente en tres tipos principales (o tipos): individual (o individual), en serie y en masa. Cada uno de estos tipos de procesos productivos y tecnológicos tienen sus propias características, y cada uno de ellos se caracteriza por una determinada forma de organización del trabajo.
Cabe señalar que en la misma empresa e incluso en el mismo taller pueden existir diferentes tipos de producción, es decir, en una fábrica o en un taller se pueden fabricar productos o piezas individuales de acuerdo con diferentes principios tecnológicos: la tecnología de fabricación de algunos las partes corresponden a una sola producción, y otras - en masa, o algunas - en masa, otras - en serie. Así, por ejemplo, en la ingeniería pesada, que tiene el carácter de una sola producción, las piezas pequeñas que se requieren en grandes cantidades pueden fabricarse según el principio de producción en serie e incluso en masa.
Por lo tanto, es posible caracterizar la producción de toda la planta o taller como un todo solo sobre la base de la naturaleza predominante de los procesos tecnológicos y de producción.
Una producción única es una producción en la que los productos se fabrican en copias únicas, de diseño o tamaño diversos, y la repetición de estos productos es rara o está completamente ausente.
La producción única es universal, es decir, abarca diversos tipos de productos, por lo que debe ser muy flexible, adaptada al desempeño de diversas tareas. Para ello, la planta debe contar con un conjunto de equipos universales que aseguren la fabricación de productos de una gama relativamente amplia. Este conjunto de equipos debe seleccionarse de tal manera que, por un lado, se puedan aplicar diferentes tipos de procesamiento y, por otro lado, de modo que la relación cuantitativa de los tipos individuales de equipos garantice un cierto rendimiento de la planta. .
El proceso tecnológico de fabricación de piezas en este tipo de producción tiene un carácter compacto: se realizan varias operaciones en una máquina y, a menudo, se realiza un procesamiento completo de piezas de varios diseños y de varios materiales. En vista de la diversidad de trabajos realizados en una máquina, y la inevitabilidad como resultado de esto, en cada caso, la preparación y ajuste de la máquina para nuevo trabajo el tiempo principal (tecnológico) en la estructura general de la norma del tiempo es pequeño.
Los dispositivos para el procesamiento de piezas en máquinas herramienta son aquí de carácter universal, es decir, pueden usarse en una variedad de casos (por ejemplo, un tornillo de banco para sujetar piezas, escuadras, abrazaderas, etc.). Accesorios especiales no se usan o se usan raramente, ya que los costos significativos para su fabricación no están económicamente justificados.
La herramienta de corte requerida para este tipo de producción también debe ser universal (brocas estándar, escariadores, fresas, etc.), ya que debido a la variedad de piezas, el uso de herramientas especiales no es económicamente posible.
Así mismo y herramienta de medición, utilizado en el procesamiento de piezas, debe ser universal, es decir, medir piezas de varios tamaños. En este caso, se utilizan ampliamente calibradores vernier, micrómetros, calibradores, shtihmas, indicadores y otros instrumentos de medición universales.
La diversidad de productos fabricados, la desigualdad en el tiempo de entrada en producción de diseños más o menos similares, la diferencia en los requisitos del producto en cuanto a la precisión de procesamiento de las piezas y la calidad de los materiales utilizados, la necesidad, debido a la variedad de detalles, para realizar diversas operaciones en equipos universales, todo esto crea condiciones especiales trabajo exitoso talleres y toda la planta, característica de una sola producción.
Estas características de este tipo de producción determinan el costo relativamente alto de los productos manufacturados. Un aumento en la demanda de este producto con una disminución simultánea de su rango y la estabilización de los diseños de productos crea la posibilidad de pasar de la producción de una sola pieza a la producción en serie.
La producción en serie ocupa una posición intermedia entre la producción individual y la producción en masa.
En la producción en serie, los productos se fabrican en lotes o series, que consisten en productos del mismo nombre, del mismo tipo en diseño y del mismo tamaño, lanzados a la producción al mismo tiempo. El principio básico de este tipo de producción es la producción de todo el lote como un todo, tanto en el procesamiento de piezas como en el ensamblaje.
El concepto de "lote" se refiere al número de piezas y el concepto de "serie" al número de máquinas puestas en producción al mismo tiempo.
En la producción en serie, según el número de productos en la serie, su naturaleza e intensidad de mano de obra, la frecuencia de repetición de la serie durante el año, se distinguen la producción a pequeña escala, la producción a mediana y gran escala. Tal división es condicional para varias ramas de la ingeniería.
En la producción en serie, el proceso tecnológico está predominantemente diferenciado, es decir, se divide en operaciones separadas que se asignan a máquinas individuales.
Aquí se utilizan máquinas herramienta de diferentes tipos: universales, especializadas, especiales, automatizadas, modulares. El parque de máquinas debe estar especializado hasta tal punto que sea posible pasar de la producción de una serie de máquinas a la producción de otra, algo diferente de la primera en un sentido constructivo.
La producción en serie es mucho más económica que la producción individual, ya que mejor uso equipo, especialización de los trabajadores, un aumento en la productividad del trabajo asegura una reducción en el costo de producción.
La producción en serie es el tipo de producción más común en la ingeniería general y media.
La producción en masa se denomina producción, en la que, con una cantidad suficientemente grande de productos idénticos, su fabricación se lleva a cabo realizando continuamente las mismas operaciones que se repiten constantemente en los lugares de trabajo.
La producción en masa es de los siguientes tipos:
Producción en flujo-masa, en la que se lleva a cabo la continuidad del movimiento de piezas en puestos de trabajo dispuestos en secuencia operaciones tecnológicas asignados a ciertos trabajos y realizados aproximadamente en el mismo intervalo de tiempo;
· producción masiva de flujo directo. Aquí, las operaciones tecnológicas también se realizan en ciertos lugares de trabajo, dispuestos en el orden de las operaciones, pero el tiempo para realizar operaciones individuales no siempre es el mismo.
La producción en masa es posible y económicamente rentable cuando se produce una cantidad suficientemente grande de productos, cuando todos los costos de organizar la producción en masa compensan y el costo por unidad de producción es menor que en la producción en masa.
La rentabilidad de producir un número suficientemente grande de productos se puede expresar mediante la siguiente fórmula
donde n es el número de unidades de productos; C - el monto de los costos en la transición de la producción en serie a la producción en masa; - el costo de una unidad de productos en producción en masa; - el costo de una unidad de productos en producción en masa.
Las condiciones que determinan la efectividad de la producción en masa incluyen, en primer lugar, el volumen del programa de producción y la especialización de la planta en ciertos tipos de productos, con los más condición favorable La producción en masa es un tipo, un diseño de producto.
En la producción en masa ya gran escala, el proceso tecnológico se basa en el principio de diferenciación o en el principio de concentración de operaciones.
Según el primer principio, el proceso tecnológico se diferencia en operaciones elementales con aproximadamente el mismo tiempo de ejecución; cada máquina realiza una operación específica. En este sentido, aquí se utilizan máquinas especiales y altamente especializadas; los dispositivos de procesamiento también deben ser especiales, diseñados para realizar una sola operación. A menudo, dicho dispositivo es una parte integral de la máquina.
De acuerdo con el segundo principio, el proceso tecnológico prevé la concentración de operaciones realizadas en máquinas automáticas de varios husillos, máquinas semiautomáticas, máquinas de corte múltiple, por separado en cada máquina o en máquinas automáticas conectadas en una línea, realizando varias operaciones simultáneamente. con bajo costo tiempo principal. Este tipo de máquinas se están introduciendo cada vez más en la producción.
La organización técnica de la producción en masa debe ser muy perfecta. Como ya se mencionó, el proceso tecnológico debe desarrollarse con detalle y precisión tanto en los métodos de procesamiento como en los cálculos de tiempos principales y auxiliares.
El equipo debe estar definido con precisión y dispuesto de tal manera que su cantidad, tipos, integridad y productividad correspondan a la producción dada.
De particular importancia en la producción en masa es la organización del control tecnológico, ya que la verificación insuficientemente cuidadosa de las piezas y el rechazo intempestivo de las piezas inadecuadas pueden provocar un retraso y una interrupción de todo el proceso de producción. Los mejores resultados se logran utilizando el control automático durante el procesamiento.
A pesar de los pequeños costes de capital iniciales necesarios para la organización de la producción en masa, su efecto técnico y económico no es correcto. empresa organizada suele ser alto y mucho mayor que en la producción en serie.
El costo del mismo tipo de producto en la producción en masa es mucho menor, la rotación de fondos es mayor, el costo del transporte es menor, la producción es mayor que en la producción en masa.
Cada una de las producciones descritas anteriormente (única, en serie, en masa) se caracteriza por las correspondientes formas de organización del trabajo y métodos de ubicación de equipos, que están determinados por la naturaleza del producto y el proceso de producción, el volumen de producción y una serie de otros factores
Existen las siguientes formas principales de organización del trabajo.
o Por tipo de equipo, característico principalmente de producción de una sola pieza; para piezas individuales utilizadas en la producción en masa.
Las máquinas herramienta se ubican sobre la base de la uniformidad del procesamiento, es decir, crean secciones de máquinas diseñadas para un tipo de procesamiento: torneado, cepillado, fresado, etc.
o Sujeto, característico principalmente de la producción en serie, para piezas individuales se utiliza en la producción en masa.
Las máquinas se colocan en una secuencia de operaciones tecnológicas para una o más partes que requieren el mismo orden de procesamiento. En la misma secuencia, se forma el movimiento de las piezas. Las piezas se mecanizan en lotes; al mismo tiempo, la ejecución de operaciones en máquinas individuales no puede coordinarse con otras máquinas. Las piezas fabricadas se almacenan en las máquinas y luego se transportan como un lote completo.
o Las máquinas de flujo en serie, o de flujo variable, características de la producción en masa, se ubican en la secuencia de operaciones tecnológicas establecidas para las piezas procesadas en esta línea de máquinas. La producción se lleva a cabo en lotes, y los detalles de cada lote pueden diferir ligeramente entre sí en tamaño o diseño. El proceso de producción se lleva a cabo de tal manera que el tiempo de una operación en una máquina es consistente con el tiempo de trabajo en la siguiente máquina.
o De flujo directo, característico de la producción en masa y, en menor medida, a gran escala; las máquinas están dispuestas en una secuencia de operaciones tecnológicas asignadas a ciertas máquinas; las piezas se transfieren de una máquina a otra pieza por pieza. El transporte de piezas de un lugar de trabajo a otro se realiza mediante mesas de rodillos, bandejas inclinadas, a veces también se utilizan transportadores, que sirven aquí solo como transportadores.
o Flujo continuo, característico únicamente de la producción en masa. Con esta forma de organización del trabajo, las máquinas se ubican en la secuencia de operaciones del proceso tecnológico asignado a ciertas máquinas, el tiempo para realizar operaciones individuales en todos los lugares de trabajo es aproximadamente igual o múltiplo de un ciclo.
Hay varios tipos de trabajo en un flujo continuo: a) con transferencia de partes (productos) por simple dispositivos de transporte- sin elemento de tracción; b) con suministro periódico de piezas por medio de un dispositivo de transporte con elemento de tracción. El movimiento de piezas de un lugar de trabajo a otro se lleva a cabo con la ayuda de transportadores mecánicos, que se mueven periódicamente, en sacudidas. El transportador mueve la pieza después de un período de tiempo correspondiente al valor del ciclo de trabajo, durante el cual el transportador se detiene y se realiza la operación de trabajo; la duración de la operación es aproximadamente igual al valor del ciclo de trabajo; c) con suministro continuo de piezas (productos) mediante dispositivos de transporte con elemento de tracción; en este caso, el transportador mecánico se mueve continuamente, moviendo las piezas ubicadas en él de un lugar de trabajo a otro. La operación se realiza mientras el transportador está en movimiento; en este caso, la pieza se retira del transportador para realizar la operación o permanece en el transportador, en cuyo caso la operación se realiza mientras la pieza se mueve junto con el transportador. La velocidad del transportador debe corresponder al tiempo requerido para completar la operación. El ciclo de trabajo está soportado mecánicamente por el transportador.
Para todos los casos considerados de trabajo con flujo continuo, se puede establecer que el factor decisivo que determina la observancia del principio de flujo continuo no es el transporte mecánico de piezas, sino el ciclo de trabajo.
CARACTERÍSTICAS GENERALES DEL COMPLEJO MAQUINARIO
En Ucrania, la participación de los productos del complejo en el volumen total de la producción industrial es del 20%; planta de tractores, la planta de Jarkov "Electrotyazhmash", las plantas de aviación de Jarkov y Kyiv, la planta de transformadores en Zaporozhye, la planta de microscopios electrónicos en Sumy y muchos otros. Los nuevos centros de ingeniería mecánica desarrollados eran medianos y grandes ciudades regiones occidentales de Ucrania.
El complejo de construcción de maquinaria de Ucrania es una producción diversificada compleja e interconectada que se especializa en la producción de maquinaria y equipos, dispositivos y equipos informáticos, repuestos para ellos, equipos tecnológicos, etc. Un lugar especial pertenece a la producción de equipos para industrias. . Las principales son química y petroquímica, minería y minería, ingeniería metalúrgica, aviación, ingeniería de máquina-herramienta para industrias ligeras y alimentarias y electrodomésticos, maquinaria agrícola.
La producción de equipos para trabajar metales, especialmente máquinas herramienta, ocupa un lugar importante en la ingeniería mecánica, proporcionándole los activos fijos de producción necesarios. Las capacidades de producción de la propia industria de construcción de maquinaria, su cumplimiento de requisitos modernos y la capacidad para el reequipamiento tecnológico de toda la producción y, sobre todo, de la ingeniería mecánica. El estado y el nivel técnico y tecnológico de la construcción de máquinas herramienta, la estructura del dispositivo metalúrgico del país es uno de los principales indicadores del desarrollo de la ingeniería mecánica, sus capacidades de producción.
Los centros para la producción de equipos para trabajar metales, en particular máquinas herramienta, así como herramientas, son predominantemente las ciudades más grandes y confiables: Odessa, Kharkov, Kyiv, Zhitomir, Kramatorsk, Lvov, Berdichev; la producción de máquinas de forja y prensado se encuentra en Odessa, Khmelnitsk, Dnepropetrovsk, Striya; industria para la producción de diamantes artificiales y materiales abrasivos - en Poltava, Lvov, Zaporozhye, Kiev; producción de herramientas para trabajar el metal y la madera - en Zaporozhye, Khmelnitsk, Vinnitsa, Kharkov, Kamyanets-Podolsky, Luhansk. Los centros de fabricación de aeronaves son Kyiv y Kharkov.
la maquina se llama Dispositivo mecánico con partes coordinadas que realizan ciertos y oportunos movimientos para la transformación de energía, materiales o información.
El objetivo principal de la máquina es reemplazar las funciones de producción de una persona para facilitar el trabajo y aumentar la productividad.
Las máquinas se dividen en energía (es decir, aquellas que convierten la energía de una forma a otra): motores eléctricos, generadores eléctricos, motores de combustión interna, turbinas (vapor, gas, agua, etc.).
Máquinas de trabajo: máquinas herramienta, construcción, textil, máquinas de computación, máquinas automáticas.
La ingeniería mecánica es una rama para la producción de máquinas. La ingeniería mecánica es la ciencia de las máquinas (TMM, ciencia de los metales, resistencia, materiales, partes de máquinas, etc.).
Cualquier máquina consta de componentes y partes separados. Al mismo tiempo, una parte significativa de las piezas está estandarizada y es común a muchos tipos de máquinas: pernos, tornillos, ejes, escalas, etc. Se pueden producir en empresas de producción en masa especializadas separadas, lo que hace posible automatizar y mecanizar todo línea técnica su fabricación.
A veces, las unidades también se fabrican en masa a partir de piezas individuales. propósito general- cajas de cambios, bombas, frenos, etc. Las conexiones más grandes de piezas y conjuntos pueden considerarse como unidades o conjuntos.
Por ejemplo, los motores son componentes de automóviles, cosechadoras, aeronaves y también se fabrican en fábricas separadas.
Es decir, todas las empresas de construcción de maquinaria están muy estrechamente interconectadas por indicadores técnicos y económicos. el trabajo de todos empresa de construcción de maquinaria depende en gran medida de los proveedores de productos metálicos, piezas, conjuntos.
Además de las conexiones de las ramas internas, la ingeniería mecánica está conectada con otras ramas que suministran a la ingeniería mecánica polímeros, caucho, tejidos, madera, etc., que se utilizan en la ingeniería mecánica como materiales estructurales y adicionales.
Documentos similares
Estructura y características de la industria. Procesos productivos y tecnológicos. Tipos de producción, sus características técnicas y económicas. Elementos del proceso tecnológico y los fundamentos de su construcción. Formas de organización de la producción industrial.
tutorial, añadido el 11/04/2010
Etapas de procesos tecnológicos para la fabricación de piezas de máquinas y operaciones. Características del engranaje utilizado para la transmisión. movimiento rotatorio. El proceso de producción de la pieza "Eje" para un tipo de producción a gran escala. Elección de equipos, materiales.
documento final, agregado el 14/07/2012
Determinación de los principales indicadores técnicos y económicos del proceso de producción de la sección para el mecanizado de piezas en las condiciones del tipo de producción seleccionado. Cálculo de la cantidad de equipo del sitio y su carga, el número de personal del sitio.
documento final, agregado el 12/12/2010
Tipos de producción, formas de organización y tipos de procesos tecnológicos. Precisión de mecanizado. Bases de base y base de preparación. Calidad de la superficie de las piezas de la máquina y los espacios en blanco. Etapas del diseño de procesos tecnológicos de procesamiento.
curso de conferencias, añadido el 29/11/2010
El concepto de producción y procesos tecnológicos, su clasificación. Tamaño del trabajo del programa. Características del proceso tecnológico. Característica tecnológica varios tipos producción. Fabricación de productos, control de calidad.
presentación, añadido el 26/10/2013
Desarrollo de una propuesta tecnológica para la creación de un complejo tecnológico robótico para la fabricación de piezas específicas por mecanizado, estampación o fundición. Diseñar tareas de automatización de la producción de maquinaria.
trabajo final, agregado el 25/10/2014
La esencia del proceso de producción. Estructura y procedimiento tecnológico para la ejecución de las operaciones. El cumplimiento de los principios de organización de la producción como condición fundamental para su eficacia. La conveniencia de sus tipos individuales y seriales en la economía.
presentación, añadido el 24/03/2014
Esquema del proceso tecnológico en la fábrica de lino. Especificaciones técnicas equipo. El equilibrio de la jornada laboral y el modo de funcionamiento de la planta. Cálculo de la capacidad de producción de la planta para productos terminados. Cálculo de la carga de trabajo de la unidad de preparación de la estopa.
documento final, agregado el 09/12/2014
Tipo de producción, número de piezas en el lote. Tipo de pieza de trabajo y tolerancias de procesamiento. La estructura del proceso tecnológico, la elección de equipos y accesorios. Racionamiento de tiempo, determinación del precio y costo del procesamiento mecánico de piezas.
documento de término, agregado el 08/03/2016
La estructura del proceso tecnológico según los bocetos del procesamiento del eje: el número de operaciones, configuraciones, posiciones, transiciones y movimientos de trabajo. Cálculos para producción individual y en gran escala. Lograr la precisión del procesamiento. El número de configuraciones de piezas de trabajo en la operación.
La esencia del proceso de producción, sus tipos y estructura, las principales operaciones y su propósito, características distintivas del proceso tecnológico. El procedimiento para determinar la intensidad de trabajo de una operación tecnológica y la norma de tiempo requerida para su implementación.
INTRODUCCIÓN
La totalidad de métodos y técnicas para la fabricación de máquinas, desarrollados durante un largo período de tiempo y utilizados en un área particular de producción, constituye la tecnología de esta área. En este sentido, surgieron conceptos: tecnología de fundición, tecnología de soldadura, tecnología de mecanizado, etc. Todas estas áreas de producción pertenecen a la tecnología de la ingeniería mecánica, cubriendo todas las etapas del proceso de fabricación de productos de ingeniería.
La disciplina "Tecnología de ingeniería mecánica" estudia exhaustivamente la interacción de la máquina herramienta, el accesorio, la herramienta de corte y la pieza de trabajo, formas de construir los procesos tecnológicos más racionales para procesar piezas de máquinas, incluida la elección de equipos y herramientas, métodos para la construcción racional de tecnología Procesos de montaje de máquinas.
La doctrina de la tecnología de la ingeniería mecánica en su desarrollo a lo largo de algunos años ha pasado de una simple sistematización de la experiencia de producción en el mecanizado de piezas y máquinas de ensamblaje a la creación de disposiciones con base científica desarrolladas sobre la base de investigaciones teóricas, científicamente realizadas. experimentos y generalización de la experiencia avanzada de plantas de construcción de maquinaria. El desarrollo de la tecnología de mecanizado y ensamblaje y su dirección están determinados por las tareas que enfrenta la industria de construcción de maquinaria para mejorar los procesos tecnológicos, la investigación y el estudio de nuevos métodos de producción, un mayor desarrollo e implementación de la mecanización integrada y la automatización de los procesos de producción basados en los logros. de la ciencia y la tecnología, asegurando la mayor productividad laboral con la calidad adecuada y el menor costo de los productos.
1. Procesos productivos y tecnológicos
Bajo el proceso de producción se entiende la totalidad de todas las acciones de personas y herramientas realizadas en la empresa para obtener productos terminados a partir de materiales y productos semielaborados.
El proceso de producción incluye no solo los procesos principales directamente relacionados con la fabricación de piezas y el montaje de máquinas a partir de ellas, sino también todos los procesos auxiliares que aseguran la posibilidad de fabricar productos (por ejemplo, transporte de materiales y piezas, control de piezas, fabricación de útiles y útiles, etc.).
Un proceso tecnológico es un cambio secuencial en la forma, dimensiones, propiedades de un material o producto semielaborado con el fin de obtener una pieza o producto de acuerdo con los requisitos técnicos especificados.
El proceso tecnológico de mecanizado de piezas debe diseñarse y realizarse de forma que, mediante los métodos de procesamiento más racionales y económicos, se cumplan los requisitos de las piezas (precisión de mecanizado, rugosidad superficial, posición relativa de ejes y superficies, regularidad de contornos, etc.) están satisfechos, asegurando el correcto funcionamiento de los coches montados.
2. Estructura del proceso
Para garantizar el proceso más racional de mecanizado de la pieza de trabajo, se elabora un plan de procesamiento que indica qué superficies deben procesarse, en qué orden y de qué manera.
En este sentido, todo el proceso de mecanizado se divide en componentes separados: operaciones tecnológicas, posiciones, transiciones, movimientos, técnicas.
Una operación tecnológica es una parte de un proceso tecnológico que se realiza en un lugar de trabajo y cubre todas las acciones secuenciales de un trabajador (o un grupo de trabajadores) y una máquina para procesar una pieza de trabajo (uno o más al mismo tiempo).
Por ejemplo, girar un eje, realizado secuencialmente primero en un extremo y luego después del giro, es decir. la permutación del eje en los centros, sin sacarlo de la máquina, - en el otro extremo, es una sola operación.
Si todas las piezas de trabajo de un lote dado se tornean primero en un extremo y luego en el otro, esto equivaldrá a dos operaciones.
La parte de instalación de la operación se denomina parte de la operación realizada con una fijación de la pieza de trabajo (o varias procesadas simultáneamente) en la máquina o en el accesorio, o la unidad de ensamblaje ensamblada.
Por ejemplo, girar el eje mientras se fija en los centros es el primer ajuste; girando el eje después de girarlo y fijándolo en los centros para procesar el otro extremo: la segunda configuración. Cada vez que la pieza se gira en un ángulo, se crea una nueva configuración.
La pieza de trabajo instalada y fija puede cambiar su posición en la máquina en relación con sus cuerpos de trabajo bajo la influencia de dispositivos móviles o giratorios, tomando una nueva posición.
La posición se denomina cada posición individual de la pieza de trabajo, ocupada por ella en relación con la máquina con su fijación sin cambios.
Por ejemplo, cuando se mecaniza en máquinas semiautomáticas y automáticas de varios husillos, la pieza, con una fijación, ocupa diferentes posiciones con respecto a la máquina al girar la mesa (o el tambor), que lleva secuencialmente la pieza a diferentes herramientas.
La operación se divide en transiciones: tecnológica y auxiliar.
Transición tecnológica: una parte completa de una operación tecnológica, caracterizada por la constancia de la herramienta utilizada, las superficies formadas por el procesamiento o el modo de operación de la máquina.
Transición auxiliar - una parte completa de la operación tecnológica, que consiste en la acción de una persona y/o un equipo, que no van acompañadas de un cambio en la forma, tamaño y rugosidad de la superficie, pero que son necesarias para completar la transición tecnológica. Ejemplos de transiciones auxiliares son la configuración de la pieza, el cambio de herramienta, etc.
Cambiar solo uno de los elementos enumerados (superficie trabajada, herramienta o modo de corte) define una nueva transición.
La transición consiste en movimientos de trabajo y auxiliares.
El golpe de trabajo se entiende como parte de la transición tecnológica, abarcando todas las acciones asociadas a la eliminación de una capa de material con la misma herramienta, superficie de procesamiento y modo de funcionamiento de la máquina.
En máquinas que procesan cuerpos de revolución, la carrera de trabajo se entiende como la operación continua de la herramienta, por ejemplo, en un torno, la eliminación de una capa de virutas por un cortador es continua, en una cepilladora, la eliminación de una capa de metal en toda la superficie. Si la capa de material no se elimina, sino que se somete a una deformación plástica (por ejemplo, cuando se forman ondulaciones o cuando se pasa un rodillo liso por la superficie para compactarla), también se utiliza el concepto de carrera de trabajo, como en la eliminación de virutas.
Carrera auxiliar: una parte completa de la transición tecnológica, que consiste en un solo movimiento de la herramienta en relación con la pieza de trabajo, no acompañada de un cambio en la forma, las dimensiones, la rugosidad de la superficie o las propiedades de la pieza de trabajo, pero necesario para completar la carrera de trabajo .
Todas las acciones del trabajador, realizadas por él durante la realización de la operación tecnológica, se dividen en métodos separados.
Por recepción se entiende la acción completada del trabajador, normalmente las recepciones son acciones auxiliares, por ejemplo, poner o quitar una pieza, poner en marcha la máquina, cambiar de velocidad o de avance, etc. El concepto de recepción se utiliza en el reglamento técnico de la operación.
El plan de mecanizado también incluye trabajos intermedios: control, cerrajería, etc., necesarios para el procesamiento posterior, por ejemplo, soldadura, ensamblaje de dos partes, prensado de partes acopladas, tratamiento térmico, etc. Las operaciones finales para otros tipos de trabajos realizados después del mecanizado se incluyen en el plan para los tipos de procesamiento correspondientes.
Estructura productiva de una empresa con especialización tecnológica
3. La complejidad de la operación tecnológica.
El tiempo y los costos de realizar operaciones son los criterios más importantes que caracterizan su efectividad en las condiciones de un programa dado para la producción de productos. El programa de lanzamiento de productos es una lista de productos fabricados establecida para una empresa determinada, que indica el volumen de producción de cada artículo durante el período de tiempo planificado.
El volumen de producción es el número de productos de ciertos nombres, tipos, tamaños y diseños, fabricados durante el período de tiempo planificado. El volumen de producción está determinado en gran medida por los principios de construcción del proceso tecnológico. El estimado, máximo posible bajo ciertas condiciones, el volumen de producción de productos por unidad de tiempo se llama capacidad de producción.
Con un volumen dado de producción, los productos se fabrican en lotes. Este es el número de piezas o un conjunto de productos que se ponen en producción simultáneamente. Un lote de producción o parte del mismo que llega al lugar de trabajo para realizar una operación tecnológica se denomina lote operativo.
la serie es total productos a fabricar según planos fijos.
Para realizar cada operación, el trabajador gasta una determinada cantidad de trabajo. La intensidad de mano de obra de una operación es la cantidad de tiempo empleado por un trabajador de la calificación requerida bajo intensidad de mano de obra y condiciones normales para la realización de este trabajo. Unidades de medida - hombre/hora.
4. Normatiempo
El racionamiento correcto del gasto de tiempo de trabajo para el procesamiento de piezas, montaje y fabricación de toda la máquina es de gran importancia para la producción.
Norma de tiempo - el tiempo asignado para la producción de una unidad de producción o la ejecución cierto trabajo(en horas, minutos, segundos).
La norma del tiempo se determina sobre la base del cálculo y análisis técnico, según las condiciones, quizás más uso completo habilidades técnicas equipos y herramientas de acuerdo con los requisitos para el procesamiento de una determinada pieza o conjunto de un producto.
En la producción de maquinaria, cuando se procesan piezas en máquinas para corte de metales, la norma de tiempo para operaciones individuales (un conjunto de operaciones) o la norma para la producción de piezas (productos) en piezas por unidad de tiempo (hora, turno) está determinado.
La norma técnica del tiempo, que determina el tiempo dedicado al procesamiento (ensamblaje u otro trabajo), sirve como base para pagar el trabajo, calculando el costo de las piezas y productos. Basado estándares técnicos se calcula la duración del ciclo de producción, se calcula el número requerido de máquinas, herramientas y trabajadores, se determina la capacidad de producción de los talleres (o secciones individuales), se lleva a cabo toda la planificación de la producción.
Clasificación de las normas laborales
Conclusión
El desarrollo de la tecnología de mecanizado y ensamblaje y su dirección están determinados por las tareas que enfrenta la industria de construcción de maquinaria para mejorar los procesos tecnológicos, la investigación y el estudio de nuevos métodos de producción, un mayor desarrollo e implementación de la mecanización integrada y la automatización de los procesos de producción basados en los logros. de la ciencia y la tecnología, asegurando la mayor productividad laboral con la calidad adecuada y el menor costo de los productos. Para mejorar el proceso tecnológico en cualquier producción, es necesario utilizar el potencial gerencial, de investigación, de desarrollo y humano.
Referencias
1. Egorov M. E. etc. Tecnología de la ingeniería. Libro de texto para escuelas secundarias. Edición 2, añadir. M., "Más alto. escuela", 1976.
2. Gusev A.A., Kovalchuk E.R., Komsov I.M. y otros libros de texto de ingeniería mecánica. especialista. universidades 1986.
3. Skhirtladze A.G. Procesos tecnológicos en ingeniería mecánica. Para estudiantes de especialidades de ingeniería de universidades, “Escuela Superior”, 2007.
Para descargar trabajo libre de unirse a nuestro grupo En contacto con. Simplemente haga clic en el botón de abajo. Por cierto, en nuestro grupo ayudamos a escribir trabajos académicos de forma gratuita. Unos segundos después de que se verifique la suscripción, aparecerá un enlace para continuar con la descarga de la obra. ![]() |
|
Estimación gratuíta | |
Aumentar originalidad este trabajo. Bypass antiplagio. | |
REF-Master- un programa único para autoescribir ensayos, trabajos finales, control y tesis. Con la ayuda de REF-Master, puede hacer fácil y rápidamente un resumen original, control o trabajo final basado en el trabajo terminado - La estructura del proceso tecnológico. |
|
como escribir correctamente ¿Introducción?
Los secretos de la introducción ideal de trabajos finales (así como resúmenes y diplomas) de autores profesionales de las agencias de resúmenes más grandes de Rusia. Aprenda a formular correctamente la relevancia del tema de trabajo, determine las metas y objetivos, indique el tema, el objeto y los métodos de investigación, así como las bases teóricas, legales y prácticas de su trabajo. |
|
|
El proceso tecnológico es una parte del proceso de producción que contiene un cambio constante en tamaño, forma, apariencia el sujeto de la producción, y su control.
Elementos del proceso tecnológico: operación, instalación, posición, procesamiento, transición, paso, método de trabajo, movimiento.
El proceso tecnológico suele dividirse en partes llamadas operaciones.
Operación representa una parte completa del proceso tecnológico. O. está diseñado para cambiar la forma geométrica y parámetros físicos productos para 1 puesto de trabajo con 1 trabajador.
Operación realizado continuamente en un lugar de trabajo.
Una operación es la unidad básica de planificación y contabilidad de la producción. Sobre la base de las operaciones, se determina la complejidad de la fabricación de piezas, se establecen estándares de tiempo y precios, se establece la cantidad requerida de equipos, accesorios y herramientas, y se determina el procesamiento de s / s.
Composición O.: AYUDAS: máquina herramienta, utillaje, herramienta, detalle.
Instalación- Esta es la determinación de la posición de la pieza de trabajo en la máquina utilizando máquinas herramienta.
Para poder presentar la estructura de la operación y tener en cuenta el tiempo empleado en su ejecución, fue necesario dividir la operación en partes separadas, llamadas transiciones.
Posición- esta es una posición fija ocupada por una pieza de trabajo fija junto con un accesorio relativo a la herramienta. (tornos de torreta con eje de giro horizontal y vertical del cabezal.)
Tratamiento. Los objetivos del procesamiento de pieles son un cambio en las propiedades, características geométricas y dimensiones de la pieza de trabajo.
Transición tecnológica- este es el procesamiento mecánico de una o más repeticiones de la pieza de trabajo, con una o más herramientas, en condiciones tecnológicas y de instalación constantes.
De acuerdo con esto, la transición directamente relacionada con la implementación del impacto tecnológico se denomina principal (perforación). La transición, constituida por las acciones del trabajador o los mecanismos necesarios para realizar la transición principal, se denomina auxiliar (instalación y fijación de la pieza).
Pase: procesamiento de giros individuales con la misma configuración de la pieza de trabajo.
trazo de trabajo llamado movimiento relativo único de la herramienta y la pieza de trabajo, como resultado del cual se elimina una capa de material de su superficie. Para poder procesar la pieza de trabajo, debe instalarse y fijarse en el accesorio, en la mesa de la máquina. Cada nueva posición fija del objeto de producción, junto con el dispositivo en el que se instala y fija el objeto, se denomina la posición de trabajo. posición.
Movimiento - estas son acciones individuales de la máquina (encender, apagar).
Una técnica de trabajo es un conjunto completo de acciones humanas al realizar una determinada parte de una operación, utilizada al realizar una transición o parte de ella. Por ejemplo, encienda la máquina, cambie la alimentación, etc.
La recepción es parte de una transición auxiliar.
Tipos de producción
Hay tres tipos de producción: I/masa, 2/serie, S/sencillo.
Único: la producción única se denomina producción, caracterizada por un pequeño volumen de producción de productos idénticos, reproducción de productos que, por regla general, no se proporciona. No hay una producción cíclica inherente a la producción en masa.
La falta de repetibilidad en la fabricación conduce a la búsqueda de formas más simplificadas de fabricar productos. La mayoría de las veces, los talleres experimentales, de reparación, etc. funcionan de esta manera. A los trabajadores aquí les gusta
generalmente altamente calificado. Equipo y equipo - universal. El costo de producción es alto.
1. amplitud de la gama de productos manufacturados 2. pequeño volumen de su producción, decenas de piezas por año. 3. Cobertura universal de varios tipos de productos. 4. flexibilidad en cuanto al uso de equipos universales (p. ej., torno de corte de tornillos, herramienta estándar de corte o medición)5. El proceso tecnológico de fabricación de una pieza tiene un carácter compactado, es decir en una maquina se realizan varias operaciones o se completa el procesamiento 6.C/s del producto fabricado es relativamente alta 7. cualificacion del trabajador - 5 - 6 categoria, alta. 8 máquina - equipo universal y preciso. 9. Coeficiente fijo de operaciones mayor de 40. 10. Se aplica sistema de documentación simplificado. 11. estas normas están ausentes, se utiliza el racionamiento laboral experimental-estadístico. 12. Espacios en blanco: laminados en caliente, fundición en tierra, piezas forjadas
Serie: (serie pequeña, mediana, grande - depende del lote V)
pequeño-: 1. calificación esclavo 5-6 categoría, 2. satnki - dispositivos semiautomáticos 3. coeficiente de fijación de la operación 20 - 40
medio-: 1. calificación esclavo 4 categoría, 2. satnki - dispositivos semiautomáticos 3. coeficiente de fijación de la operación 10-20
a gran escala: 1. calificación esclavo 3 categoría, 2. automático. satnki, módulos de producción 3. coeficiente de operación de sujeción de 1-10
1. se fabrica una gama limitada de productos en lotes que se repiten periódicamente 2. el volumen de producción es mayor que en una sola producción, periódicamente, en lotes que se repiten 3. piezas brutas: laminación en caliente y en frío, colada en el suelo bajo presión, colada, estampado 4. El proceso tecnológico se diferencia principalmente, es decir. dividido en secciones operaciones realizadas en el máquinas herramientas 5. Al elegir equipos tecnológicos (usando dispositivos auxiliares, especiales), es necesario calcular los costos y los períodos de recuperación, así como el eq licuado. Efecto. 6. c/c es menor que en una sola producción
Bulto:
Producción en masa, caracterizada por un gran volumen de salida de productos de forma continua.
fabricado o reparado durante mucho tiempo, durante el cual la mayoría de los lugares de trabajo realizan una operación de trabajo. En producción en masa para cada operación
se selecciona el equipo más productivo y costoso /máquinas automáticas, máquinas semiautomáticas/, el lugar de trabajo está equipado con dispositivos y dispositivos complejos y de alto rendimiento, en
Como resultado, con un gran volumen de producción, se logra el costo de producción más bajo.
1. coeficiente fijo =1. 2. calificación 3-4 (se realiza 1 operación repetitiva en cada puesto de trabajo) 3. automática. satnki, módulos de producción. 4 producción en línea 5. La precisión requerida se logra mediante métodos de dimensionamiento automático en máquinas sintonizadas.
gama 1.narrow de productos. 2. gran volumen de productos, continuamente fabricados en tecnología. largo período de tiempo 3. El proceso tecnológico se desarrolla en detalle, que se caracteriza por una baja intensidad de mano de obra y baja en comparación con la producción en serie de productos s / c. 4. el uso de la mecanización y automatización de los procesos productivos. 5. uso de tecnología. proceso con operaciones elementales. 6. el uso de especiales de alta velocidad. accesorios, así como herramientas de corte y medición. 7. Usar plantilla
Calidad de la superficie
La calidad de la superficie es una combinación de todas sus propiedades de servicio y, en primer lugar, la resistencia al desgaste, la resistencia a la corrosión, la resistencia a la fatiga, así como algunas otras propiedades. La calidad de la superficie se evalúa mediante dos parámetros:
características físicas;
Características geométricas
Las características geométricas son los parámetros de la desviación de la superficie del ideal, dado. La superficie puede ser no plana, ovalada, facetada, etc. La superficie se puede ampliar como una línea ondulada.
Geom. las características de la calidad de la superficie mecanizada están determinadas por la desviación de la superficie real de la nominal. Estas desviaciones se pueden dividir en 3 variedades: rugosidad, ondulación y desviación de derechos. geom. formularios..
La rugosidad es un conjunto de irregularidades, overhnosti mecanizado con pasos relativamente pequeños. La rugosidad de la superficie está determinada por su perfil, que se forma en la sección transversal de esta superficie.
La rugosidad y la ondulación son características de la calidad de la superficie que tienen una gran influencia en muchas propiedades de rendimiento de las piezas de la máquina.
Las microrrugosidades consideradas se forman en el proceso de mecanizado copiando la forma de las herramientas de corte, deformación plástica de la capa superficial de las piezas bajo la influencia de la herramienta de procesamiento, su fricción contra la pieza, vibraciones, etc.
La rugosidad de la superficie de las piezas tiene un impacto significativo en la resistencia al desgaste, la resistencia a la fatiga, la estanqueidad y otras propiedades de rendimiento.
La ondulación ocupa una posición intermedia entre las desviaciones de forma y la rugosidad de la superficie. La ocurrencia de ondulaciones está asociada a procesos dinámicos provocados por la pérdida de estabilidad del sistema máquina-herramienta-herramienta-pieza y se expresa en la ocurrencia de vibraciones.
La ondulación de la superficie es un conjunto de irregularidades que se repiten periódicamente, en las que las distancias entre colinas o depresiones adyacentes superan la longitud base de la rugosidad de la superficie existente.
Desviación de forma es la desviación de la forma de la superficie real o perfil real de la forma de la superficie nominal o perfil nominal.
La precisión es el grado de cumplimiento de los valores reales de los parámetros geométricos con sus valores dados (calculados).
Las propiedades físicas y mecánicas incluyen dureza y tensión.
La tensión residual se produce después del mecanizado, las operaciones de recolección, durante la molienda (el material de la capa superficial experimenta endurecimiento, debilitamiento, su estructura y cambio de microdureza, se forman tensiones residuales). Después de las operaciones de recolección, las piezas obtenidas en la prensa se someten a un tratamiento térmico. Procesando.
Tipos tratamiento térmico y tensión residual:
Normalización- calentar la pieza y luego enfriarla al aire. En este caso, se elimina la tensión residual y se forma una dureza mayor que durante la cocción. Incendio- caracterizado por el hecho de que la pieza de trabajo se libera de la tensión residual como resultado del calentamiento del horno, seguido de un enfriamiento en su interior a la velocidad del enfriamiento del horno. endurecimiento se puede producir en soluciones salinas, en agua, en aceite. La tensión residual se determina mediante cálculos y métodos experimentales.
Cuando experimento. métodos de descanso. las tensiones se determinan mediante cálculos sobre la deformación de la muestra después de quitarle la capa estresada. Este método es yavl. destructivo.
11. Mecanizado de precisión. Error absoluto. sistema de SIDA. Tipos de errores.
Por debajo precisión de procesamiento se debe comprender el grado de correspondencia entre el valor real del indicador y el valor nominal.
La precisión de los parámetros geométricos es un concepto complejo que incluye:
La precisión de las dimensiones de los elementos de las partes;
Exactitud formas geométricas superficies de elementos de piezas;
Exactitud posición relativa elementos de detalle;
rugosidad superficial de las piezas (microgeometría);
Ondulación de superficies (macrogeometría).
El aumento de la precisión de las piezas de trabajo originales reduce la complejidad y el procesamiento s / c del procesamiento mecánico, reduce los valores de las asignaciones y genera ahorros de metal.
La precisión de una pieza depende de una serie de factores:
Desviación de geom. la forma de la pieza o su otd. elementos.
Desviación de las dimensiones reales de la pieza de las nominales
Desviación de superficies y ejes de piezas de la posición relativa exacta (de paralelismo, perpendicularidad, concentricidad)
Porque la precisión del procesamiento en condiciones industriales depende de muchos factores; el procesamiento en máquinas herramienta no se lleva a cabo con una precisión alcanzable, sino con una precisión económica.
Mec. de precisión Ek. Procesando– tal exactitud, a la gata. min s / s el procesamiento se logra en condiciones normales de producción (el trabajo se realiza en máquinas reparables utilizando los accesorios y herramientas necesarios en el tiempo normal y la operación normal de los trabajadores) Precisión alcanzable- precisión, cat. se puede lograr cuando se procesa en naib especial. condiciones favorables requeridas para esta producción por trabajadores altamente calificados con un aumento significativo en los costos de tiempo, sin contar el procesamiento s / c.
AYUDAS: máquina herramienta, utillaje, herramienta, detalle.
El error de medición total es un conjunto de errores que surgen bajo la influencia de una gran cantidad de factores.
Errores: teóricos, errores causados por la acción de la fuerza elástica AIDS, errores causados por la deformación de la pieza bajo la acción de fuerzas desequilibradas, debido a la acción del calor, debido al desgaste de la herramienta de corte, error de base
Estructura del proceso
PROCESO TECNOLOGICO Y SU ESTRUCTURA (CONCEPTOS BASICOS Y DEFINICIONES)
Procesos productivos y tecnológicos
proceso de producción en fábrica(sitio, taller) denominan a todo el complejo de procesos de organización, planificación, suministro, fabricación, control, contabilidad, etc., necesarios para la transformación de materiales y productos semielaborados que ingresan a la planta en productos terminados fábrica (taller). Por lo tanto, proceso de manufactura- este es un conjunto de todas las acciones de personas y herramientas de producción realizadas para la fabricación de productos manufacturados en una empresa determinada.
El proceso de fabricación es complejo y variado. Incluye: procesamiento de espacios en blanco para obtener piezas de ellos; montaje de componentes y motores y sus pruebas; movimiento en todas las etapas de producción; organización del mantenimiento de lugares de trabajo y sitios; gestión de todas las etapas de la producción, así como todo el trabajo en entrenamiento tecnico producción.
Por supuesto, en cualquier proceso de producción, el lugar más importante lo ocupan los procesos directamente relacionados con el logro de los parámetros específicos del producto. Tales procesos se llaman tecnológicos. Proceso tecnológico- esta es una parte del proceso de producción, que contiene acciones para cambiar constantemente el tamaño, la forma o el estado del objeto de trabajo y su control (GOST 3.1109-82).
En producción motores de avión utilizan una variedad de procesos: fundición, presión y corte, procesamiento térmico y físico-químico, soldadura, soldadura blanda, ensamblaje, prueba. Así, según el tipo de proceso y tipo de producto, se distingue el proceso tecnológico de fundición, por ejemplo, álabes de turbina; proceso tecnológico de tratamiento térmico, por ejemplo, un eje de turbina; proceso tecnológico de mecanizado, etc. En relación con los procesos de conformado, se puede formular que un proceso tecnológico es un sistema de operaciones mutuamente acordadas que prevén la transformación secuencial de un producto semiacabado en un producto (parte, pieza de trabajo...) mediante el conformado por medios mecánicos. , métodos físico-mecánicos, electrofísicos-químicos y otros.
Estructura del proceso
El elemento principal del proceso tecnológico es la operación. .
Operación- esta es una parte del proceso tecnológico realizado en un lugar de trabajo por uno o más trabajadores, uno o más equipos antes de pasar al procesamiento de la pieza de trabajo de la siguiente parte.
Al menos una de las dos condiciones especificadas es suficiente para que exista la operación. Si, por ejemplo, el proceso consiste en rectificar una pieza en bruto en máquina de molienda y la aleación por electrochispa de esta superficie sobre otra, entonces, independientemente del número de partes (al menos una parte), habrá dos operaciones en el proceso tecnológico, ya que el lugar de trabajo cambia (Fig. 2.1).
|
Arroz. 2.1. Operaciones del proceso tecnológico (fragmento)
Sin embargo, el procesamiento en un lugar de trabajo también puede consistir en varias operaciones. Si, por ejemplo, se realiza el taladrado y escariado de piezas en la misma máquina taladradora, de forma que primero se taladre todo el lote de piezas, y luego, según las circunstancias, cambiando el equipo (reemplazo de herramientas, fijaciones, modos de procesamiento, medio enfriado por lubricación, herramientas de medición, etc.), para implementar, obtiene dos operaciones: "perforación", la segunda "implementación", aunque el lugar de trabajo es uno.
El lugar de trabajo es una parte del área (volumen) del taller, destinada a la realización de una operación por uno o un grupo de trabajadores, en la que Equipo tecnológico, herramientas, accesorios, etc.
El concepto de "operación" se refiere no sólo al proceso tecnológico (TP), que prevé la conformación. Las hay de control, de ensayo, de lavado, de endurecimiento, térmicas, etc. operaciones.
La operación se caracteriza por:
Inmutabilidad del objeto de procesamiento;
Inmutabilidad del equipo (lugar de trabajo);
La constancia de los artistas que trabajan;
Continuidad de ejecución.
El diseño del proceso tecnológico consiste en establecer:
Composición (nomenclatura) de operaciones;
Secuencias de operaciones en TP;
Una operación es una parte indivisible del PT en términos de planificación y organización. Es la unidad básica de planificación de la producción. Todo el proceso de producción se basa en un conjunto de operaciones:
Intensidad laboral;
Logística (máquinas, herramientas, etc.);
Calificación y número de trabajadores;
Áreas de producción requeridas;
La cantidad de electricidad, etc. está determinada por las operaciones.
La operación está cuidadosamente documentada.
La operación puede consistir en varios transiciones. Una transición es una parte de una operación durante la cual se mecaniza la misma superficie de la pieza con la misma herramienta, sin cambiar el modo de funcionamiento de la máquina.
![]()
|
![]() |
Arroz. 2.2. Transiciones tecnológicas
un– dos transiciones simples (Ι y ΙΙ); b- un complejo (explicaciones en el texto)
En la fig. 2.2 muestra el funcionamiento de los agujeros de tapajuntas por el método electroquímico. Como puede verse en la fig. 2.2, un los agujeros se obtienen secuencialmente durante la implementación de las transiciones Ι y ΙΙ. Para mejorar el rendimiento, a menudo combinan varias transiciones simples en una transición compleja (Fig. 2.2, b); esto le permite procesar varias superficies al mismo tiempo.
Una transición tecnológica puede contener varias pasajes Una pasada es una parte de una transición durante la cual se quita (aplica) una capa de metal. La división en pasadas es necesaria en aquellos casos en los que no es posible eliminar (aplicar) toda la capa de metal de una sola vez (según las condiciones de resistencia de la herramienta, rigidez de la máquina, requisitos de precisión, etc.).
La operación se puede realizar en una o más configuraciones de piezas de trabajo. configuración es una parte de una operación tecnológica realizada con una sujeción de la pieza de trabajo.
En muchos casos, las operaciones se dividen en posiciones. Posición- una posición fija ocupada por una pieza de trabajo invariablemente fija, junto con un accesorio, en relación con una herramienta o una parte fija del equipo para realizar una determinada parte de la operación. Así, una posición es cada una de las diversas posiciones de la pieza con respecto a la herramienta, o la herramienta con respecto a la pieza en una de sus fijaciones, por ejemplo, fresar cada una de las cuatro caras de la cabeza del tornillo en una de sus fijaciones en un dispositivo divisorio.
La diferencia entre posición y configuración es que en cada nueva configuración, se logra una nueva posición relativa de la pieza de trabajo y la herramienta volviendo a fijar la pieza de trabajo, y en cada nueva posición, sin separar la pieza de trabajo, moviendo o rotando la pieza de trabajo o la herramienta. a una nueva posición. Reemplazar configuraciones con posiciones siempre da como resultado una reducción en el tiempo de mecanizado, ya que girar un accesorio con una pieza de trabajo o un cabezal con una herramienta lleva menos tiempo que desatar, reposicionar y sujetar la pieza de trabajo.
Enviar su buen trabajo en la base de conocimiento es simple. Utilice el siguiente formulario
Los estudiantes, estudiantes de posgrado, jóvenes científicos que utilizan la base de conocimientos en sus estudios y trabajos le estarán muy agradecidos.
Publicado enhttp:// www. todo lo mejor. es/
Introducción
1. Datos iniciales de la tarea
2. Tipo de producción, número de piezas en un lote
3. Tipo de pieza de trabajo y tolerancias de procesamiento
4. Estructura del proceso tecnológico
5. Selección de equipos y accesorios
6. Selección de herramientas
7. Cálculo de las condiciones de corte
8. Racionamiento del tiempo, determinación del precio y coste del mecanizado de la pieza
9. Información básica sobre seguridad al trabajar en máquinas herramienta
10. Diseño de accesorios
11. Registro de documentación técnica
Literatura
Introducción
La ingeniería mecánica moderna impone requisitos muy altos en cuanto a la precisión y el estado de las superficies de las piezas de la máquina, que principalmente solo pueden proporcionarse mediante procesamiento mecánico.
El corte de metales es un conjunto de acciones destinadas a cambiar la forma de la pieza de trabajo eliminando el margen con herramientas de corte en máquinas para cortar metales, proporcionando la precisión y rugosidad especificadas de la superficie mecanizada.
Dependiendo de la forma de las piezas, la naturaleza de las superficies procesadas y los requisitos para ellas, su procesamiento puede llevarse a cabo de varias maneras: mecánica: torneado, cepillado, fresado, brochado, rectificado, etc.; eléctrico - electrochispa, electropulso o ánodo-mecánico, así como ultrasónico, electroquímico, haz y otros métodos de procesamiento.
El proceso de corte de metales juega un papel principal en la ingeniería mecánica, ya que la precisión de las formas y tamaños y la alta frecuencia de las superficies de las partes metálicas de las máquinas en la mayoría de los casos solo se garantizan mediante dicho procesamiento.
Este proceso se utiliza con éxito en todas las industrias sin excepción.
El mecanizado de metales por corte es un proceso costoso y que consume mucho tiempo. Entonces, por ejemplo, en promedio en ingeniería mecánica, el costo de procesar piezas de trabajo por corte es de 50 a 60 veces el costo de los productos terminados.
El mecanizado de metales por corte, por regla general, se lleva a cabo en máquinas para cortar metales. Solo ciertos tipos de corte relacionados con la metalurgia se realizan manualmente o con la ayuda de herramientas mecanizadas.
En los métodos modernos de procesamiento mecánico de metales, se notan las siguientes tendencias:
procesamiento de piezas de trabajo con pequeñas tolerancias, lo que genera ahorros en metales y un aumento en la participación de las operaciones de acabado;
uso generalizado de métodos de endurecimiento sin arranque de viruta mediante laminación con rodillos y bolas, soplado con granalla, mandrilado, cincelado, etc.;
el uso de procesamiento de herramientas múltiples en lugar de una herramienta de corte de una sola herramienta y de cuchillas múltiples en lugar de una de cuchilla única;
aumentar las velocidades de corte y los avances;
aumento de la parte del trabajo realizado en máquinas automáticas y semiautomáticas, complejos robóticos que utilizan sistemas de control de programas;
amplia modernización de los equipos de corte de metales;
el uso de dispositivos de alta velocidad y de múltiples lugares para fijar piezas y mecanismos en la automatización de máquinas universales para corte de metales;
producción de piezas a partir de aleaciones especiales y resistentes al calor, cuya maquinabilidad es mucho peor que la de los metales ordinarios;
participación de tecnólogos en el desarrollo del diseño de máquinas para garantizar su alta capacidad de fabricación.
Más racional para recibir inmediatamente pieza terminada pasando por alto la etapa de preparación. Esto se logra mediante el uso de técnicas precisas de fundición y formación, metalurgia de polvos. Estos procesos son más progresivos y se introducirán cada vez más en la tecnología.
1. Inicialdatossobretarea
detalle de procesamiento de corte de metal mecánico
Título profesional:
Proceso tecnológico de mecanizado de una pieza.
Los datos iniciales para la tarea se dan en la tabla 1:
tabla 1
La composición química del acero (GOST 1050-88) en la tabla 2:
Tabla 2
Propiedades mecánicas del acero 30 GOST 1050-88 en la tabla 3:
Tabla 3
Propiedades tecnológicas del acero 30 GOST 1050-88 en la tabla 4:
Tabla 4
2 . Tipoproducción,Montodetallesenfiestas
El número de partes en un lote se puede determinar mediante la fórmula:
donde N es el programa anual de producción de piezas, uds.
t es el número de días para los que es necesario tener un stock de detalles anuales.
F es el número de días laborables en un año.
241 (uds.) De la tabla 1, seleccione el tipo de producción:
tabla 1
Tipo de producción - en serie.
Producción en serie: los productos se fabrican o procesan en lotes (series), que consisten en partes del mismo tipo y del mismo tamaño, que se lanzan a la producción al mismo tiempo.
Ahora de la tabla 2 seleccionamos el tipo de producción:
Tabla 2
La producción es de mediana escala y produce piezas pequeñas (ligeras), la cantidad en un lote es de 51 a 300 artículos.
3. Vistaespacios en blancoyasignacionessobre elProcesando
Una pieza de trabajo es un objeto de producción, a partir del cual se fabrica la pieza requerida cambiando la forma, el tamaño, la calidad de la superficie y las propiedades del material. La elección del tipo de pieza de trabajo depende del material, la forma y el tamaño, su propósito, las condiciones de trabajo y la carga experimentada, en el tipo de producción.
Para la fabricación de piezas se pueden utilizar los siguientes tipos espacios en blanco:
a) fundición de hierro fundido, acero, metales no ferrosos, aleaciones y plásticos para piezas moldeadas y de cuerpo en forma de marcos, cajas, cajas de grasa, mordazas, etc.;
b) forjados - para piezas que trabajan en flexión, torsión, tensión. En la producción en serie y en masa, los estampados se utilizan principalmente, en la producción a pequeña escala y de una sola pieza, así como para piezas de gran tamaño - forjas;
c) acero laminado en caliente y en frío: para piezas como ejes, varillas, discos y otras formas que tienen dimensiones de sección transversal ligeramente modificadas.
En nuestro caso, es recomendable hacer una tapa de metal laminado, ya que el círculo encaja bien con las dimensiones de la pieza.
Los márgenes de mecanizado se muestran en la Tabla 1:
Tabla 1 - Asignaciones y tolerancias para el procesamiento
EN este caso lo mejor es elegir una fundición de acero.
La fundición es una rama de la ingeniería dedicada a la fabricación de piezas o piezas en bruto moldeadas mediante el vertido de metal fundido en un molde especial que tiene la forma de una pieza en bruto. Cuando se enfría, el metal vertido se solidifica y en estado sólido conserva la configuración de la cavidad en la que se vertió. El producto final se llama fundición. En el proceso de cristalización del metal fundido, se forman las propiedades mecánicas y operativas de las piezas fundidas.
Casting produce varios diseños de piezas fundidas que pesan desde unos pocos gramos hasta 300 toneladas, desde unos pocos centímetros hasta 20 metros de largo, con paredes de 0,5 a 500 mm de espesor. Para la fabricación de piezas de fundición se utilizan muchos métodos de fundición: en moldes de arena, en moldes de concha, según modelos de inversión, en molde frío, bajo presión, fundición centrífuga, etc. El alcance de un determinado método de fundición está determinado por el volumen de producción, los requisitos de precisión geométrica y rugosidad de la superficie de las piezas fundidas, la viabilidad económica y otros factores.
4. Estructuratecnológicoproceso
Ruta de fabricación de piezas
1. Perforación (marca de la máquina 2H135):
a) Taladro 35
b) avellanado 38,85
c) (máquina T15K6) - escaneo 40
(Mandril normalizado de 3 mordazas)
2. Cerrajería
3. (marca de la máquina 16K20F3) torno CNC
a) cortar el extremo al tamaño 163 (-0.3)
b) afilar la esfera R150
(mandril de expansión (pinza))
4. (marca de máquina 16K20F3) torno CNC
a) cortar el extremo, manteniendo el tamaño 161 (-0,3)
b) afilar la esfera R292
(mandril de expansión)
5. Fresadora horizontal marca 6M82G con end mill de 8 mm., 10,5 mm de profundidad. (dispositivo especial)
6. Cerrajería.
7. Cementación.
8. Endurecimiento
9.Vacaciones
10. Limpieza y control de dureza
11. Limpieza (tratamiento térmico y calibración)
12. (marca de la máquina 2H135) escariador 40.
13. (marca de la máquina 3E710A) rectificado de superficies. Restablezca el lijado al tamaño 160.
14. Lavado.
15. Controlar.
5. Elecciónequipoyaccesorios
A la hora de elegir el tipo de máquina y su grado de automatización hay que tener en cuenta los siguientes factores:
1. Dimensiones generales y forma de la pieza;
2. La forma de las superficies tratadas, su ubicación;
3. Requisitos técnicos de precisión dimensional, forma y rugosidad de las superficies maquinadas;
4. El tamaño del programa de producción, que caracteriza el tipo de producción de esta pieza.
En la producción única a pequeña escala, se utilizan máquinas universales; en la producción en serie, junto con las máquinas universales, las máquinas semiautomáticas y las máquinas automáticas son ampliamente utilizadas; en la producción a gran escala y en masa, máquinas especiales, máquinas automáticas, máquinas modulares y máquinas automáticas Se utilizan líneas.
Actualmente se está utilizando cada vez más en la producción en serie máquinas automáticas con control numérico, que permiten pasar rápidamente del procesamiento de una pieza a otra reemplazando un programa fijado, por ejemplo, en cinta perforada de papel o en cinta magnética.
La elección de las máquinas se realiza de acuerdo con las siguientes tablas:
Tabla 1. Tornos de corte de tornillos
Indicador |
Modelos de máquinas |
||||
El diámetro más grande de la pieza de trabajo, mm. |
|||||
Distancia entre centros, mm |
|||||
Velocidad del husillo, rpm |
|||||
Número de pasos de alimentación del calibrador |
|||||
Suministro de apoyo. Mm. Transversal longitudinal |
0,08-1,9 0,04-0,95 |
0,065-0.091 0,065-0,091 |
0,074,16 0,035-2,08 |
0,05- 4,16 0,035-2,08 |
|
Potencia del motor eléctrico principal, kW |
|||||
Eficiencia de la máquina |
|||||
La mayor fuerza admisible de dar por el mecanismo, n |
Tabla 2. Fresadoras horizontales y verticales
Indicador |
Modelos de máquinas |
||||
Horizontal |
vertical |
||||
Superficie de trabajo de la mesa, mm. |
|||||
Número de pasos de velocidad del husillo |
|||||
Velocidad del husillo, rpm |
|||||
Número de pasos de alimentación |
|||||
Avance de mesa, mm/min: Longitudinal Transversal |
25-1250 15,6-785 |
||||
Fuerza de avance máxima permitida, kN |
|||||
Potencia del motor principal |
|||||
Eficiencia de la máquina |
Tabla 3. Vertical - máquinas de perforación
Indicador |
Modelos de máquinas |
|||
2H118 |
2H125 |
2Н135 |
||
Diámetro nominal máximo de perforación.mm |
18 |
25 |
35 |
|
Movimiento vertical del cabezal de perforación, mm |
150 |
200 |
250 |
|
Número de pasos de velocidad del husillo |
9 |
12 |
12 |
|
RPM de la velocidad del husillo |
180-2800 |
45-2000 |
31,5-1400 |
|
Número de pies de servicio |
6 |
9 |
9 |
|
Avance del husillo.rpm |
0,1-0,56 |
0,1-1,6 |
0,1-1,6 |
|
Par de husillo, N |
88 |
250 |
400 |
|
La mayor fuerza admisible de dar, N |
5,6 |
9 |
15 |
|
Potencia del motor eléctrico, kW |
1,5 |
2.2 |
4 |
|
Eficiencia de la máquina |
0,85 |
0,8 |
0,8 |
De las tablas seleccionamos las siguientes máquinas: 2N135 16K20F3 6M82G 3E10A
6 . Elecciónherramienta
1 Al elegir una herramienta de corte, es necesario proceder del método de procesamiento y el tipo de máquina, la forma y ubicación de las superficies a mecanizar, el material de la pieza de trabajo y su propiedades mecánicas.
La herramienta debe proporcionar una precisión dada de forma y tamaño, la rugosidad requerida de las superficies maquinadas, alto rendimiento y durabilidad, debe ser lo suficientemente fuerte, resistente a las vibraciones, económica.
Publicado enhttp:// www. todo lo mejor. es/
Figura 2 - Fresa de extremo
El material de la parte cortante de la herramienta tiene básico para lograr un alto rendimiento de procesamiento.
Para el fresado de superficies, elijo un fresado a tope con fijación mecánica de insertos de carburo de cinco lados (GOST 22085-76).
Diámetro del cortador, mm D = 100
Número de dientes de corte z = 12
Parámetros geométricos de la parte de corte del cortador.
El ángulo principal en el plan c = 67є
Ángulo auxiliar en planta ц1 = 5є
Ángulo de ataque principal r = 5є
El ángulo trasero principal b \u003d 10º
Ángulo de inclinación del filo principal l = 10є
Ángulo de inclinación de los dientes oblicuos o helicoidales u = 10є
El material de la parte de corte del cortador es acero de alta velocidad T15K6 en forma de placa de cinco lados.
Para fresar una ranura, elijo un cortador ranurado (GOST 8543-71).
cortador de ranuras
Diámetro de fresa D = 100
Número de dientes de corte z = 16
Diámetro del agujero d = 32
Ancho de fresa B = 10
El material de la parte de corte del cortador es aleación dura VK6M según GOST (3882-88)
Para perforar un agujero, elijo un taladro helicoidal estándar equipado con placas de aleación dura, un vástago cónico (GOST 2092-88)
broca helicoidal
Diámetro del taladro en mm d = 35
Longitud total del taladro en mm L = 395
La longitud de la parte de trabajo del taladro Lo = 275
Parámetros de nitidez geométrica
ángulo en la parte superior 2c = 120º
ángulo de ataque principal r = 7є
ángulo trasero principal b \u003d 19º
ángulo de inclinación del borde transversal w = 55є
ángulo de inclinación de la ranura helicoidal w = 18º
ángulo en la parte superior 2ц0 = 73є
El material de la parte de corte del taladro es acero de alta velocidad T15K6 en forma de placas.
Para rectificar la ranura, elijo una muela abrasiva cilíndrica de perfil recto GOST 8692-82
Publicado enhttp:// www. todo lo mejor. es/
Figura 7 - Muela abrasiva
Diámetro exterior máximo, mm D = 100
Altura del círculo H = 10
Diámetro interior d = 16
Dureza (GOST 18118-78) - círculo medio duro.
Grano - 50.
Gavilla de cerámica quinta.
2 La elección de la herramienta de medición depende de la forma de las superficies a medir, la precisión de mecanizado requerida y el tipo de producción.
Para controlar la precisión requerida de las superficies maquinadas, elijo la siguiente herramienta de medición.
Calibre (GOST 166-63).
Calibre micrométrico (GOST 10-58).
Para controlar la rugosidad de la superficie tratada, elijo un perfilómetro tipo 240 (GOST 9504-60).
7 . Cálculomodoscorte
1 La profundidad de corte t, mm, depende del margen de mecanizado y de la clase de rugosidad requerida de la superficie mecanizada inferior a 5 mm, luego el fresado se realizará en una sola pasada.
2 La velocidad de avance se selecciona de acuerdo con la literatura de referencia, dependiendo de las propiedades mecánicas del material que se está procesando, la herramienta de corte y la clase de rugosidad superficial requerida.
Sobre el fresadoras se establece el avance de minutos Sm, mm / min, es decir. la velocidad de movimiento de la mesa con una parte fija en relación con el cortador. Los elementos de la capa de corte y, por tanto, los parámetros físicos y mecánicos del proceso de fresado, dependen del avance por diente Sz, es decir, movimiento de la mesa con la pieza (en mm) durante la rotación de la fresa en 1 diente. La rugosidad de la superficie mecanizada depende del avance por revolución de la fresa S0, mm/rev.
Entre estos tres valores existe la siguiente relación:
donde n y z son, respectivamente, la velocidad de rotación y el número de dientes de corte.
Tomamos el valor del avance Sz de la literatura de referencia
Luego, usando la fórmula (2), calculamos SM
3 La velocidad de corte calculada está determinada por la fórmula empírica
donde Cv es el coeficiente de velocidad de corte, dependiendo de los materiales de la parte de corte de la herramienta y la pieza y de las condiciones de procesamiento;
T - resistencia calculada del cortador, min;
m - indicador de estabilidad relativa;
Xv, Yv, Uv, pv, qv, respectivamente, indicadores del grado de influencia de la profundidad de corte, avance, ancho de fresado, número de dientes y diámetro de la fresa en la velocidad de corte;
Kv - factor de corrección para condiciones modificadas.
El valor del coeficiente y los exponentes en la fórmula para la velocidad de corte durante el fresado.
cv = 445; qv = 0,2;pv; xv = 0,15; Yv = 0,35, nv = 0,2; pv=0; metro = 0,32
El factor de corrección Kv se define como el producto de una serie de factores
donde Kmv es un coeficiente que tiene en cuenta la influencia de las propiedades mecánicas del material que se procesa en la velocidad de corte;
Kpv: coeficiente que tiene en cuenta el estado de la superficie de la pieza de trabajo;
Kv - coeficiente teniendo en cuenta el material de la herramienta.
Kpv = 0,8; Kv = 1.
De la fórmula (4) encontramos el factor de corrección:
Entonces, según la fórmula (3), encontramos la velocidad de corte calculada
Velocidad del husillo, rpm, calculada por la fórmula
donde Vp - velocidad de corte de diseño, m/min;
D - diámetro del cortador, mm.
Usando la fórmula (5), encontramos la velocidad del husillo calculada
Ahora calculemos la velocidad de rotación real nf, el más cercano de los datos de pasaporte de la máquina. Para hacer esto, encuentre n y defina la serie completa n
donde nz y n1 son el máximo y valor mínimo velocidad de rotación;
n es el número de pasos de velocidad.
Ahora determinamos a partir de la serie geométrica
n2 \u003d n1 cn \u003d 31 1.261 \u003d 39.091;
n3 \u003d n1 c2n \u003d 31 1.2612 \u003d 49.294;
n4 \u003d n1 c3n \u003d 31 1.2613 \u003d 62.159
n5 \u003d n1 c4n \u003d 31 1.2614 \u003d 78.383
n6 \u003d n1 c5n \u003d 31 1.2615 \u003d 98.841
n4 \u003d n1 c3n \u003d 31 1.2613 \u003d 124.638
n4 \u003d n1 c3n \u003d 31 1.2613 \u003d 157.169
n4 \u003d n1 c3n \u003d 31 1.2613 \u003d 198.19
n4 \u003d n1 c3n \u003d 31 1.2613 \u003d 249.918
n4 \u003d n1 c3n \u003d 31 1.2613 \u003d 315.147
n4 \u003d n1 c3n \u003d 31 1.2613 \u003d 397.4
Así nf = 315,147 rpm.
Ahora podemos determinar Vph por la fórmula (7)
donde D - diámetro del cortador, mm;
nf - frecuencia de rotación, rpm.
4 Calcule el avance por minuto utilizando la fórmula
Sustituimos los valores en la fórmula (8) y obtenemos
Determinemos el valor de Sm el más pequeño más cercano a partir de los datos de pasaporte de la máquina Sm = 249,65 mm / min
Determinar el avance real por diente
Sustituyendo los valores en la fórmula (9), obtenemos
5 La fuerza de corte durante el fresado está determinada por la fórmula empírica
donde t es la profundidad de fresado;
Sz - avance real, mm/diente;
z es el número de dientes de corte;
D - diámetro del cortador, mm
nf - frecuencia real de rotación del cortador rpm.
Los valores del coeficiente Cp y los exponentes Xp, Yp, Up, qp tienen los siguientes significados
cp=545; XP = 0,9; Yp = 0,74; Arriba = 1; qp = 1.
El valor del factor de corrección Kp para fresado depende de la calidad del material a mecanizar.
Entonces obtenemos
El factor de utilización de potencia de la máquina está determinado por la fórmula
donde Ned es la potencia del motor de accionamiento, kW;
Npot: la potencia requerida en el husillo, que está determinada por la fórmula
donde Ne - potencia de corte efectiva, kW, está determinada por la fórmula
Sustituyendo el valor en la fórmula (13) obtenemos
Sustituyendo los valores en la fórmula (12) obtenemos
Ahora calculamos el factor de utilización de energía de la máquina.
La vida real de la herramienta Тf se calcula mediante la fórmula
Sustituimos los valores en la fórmula (14) y obtenemos
6 El tiempo empleado en el proceso de molienda está determinado por la fórmula
donde L es la longitud de procesamiento estimada, mm;
i - número de pasadas;
Sm - avance real, mm / min;
La duración estimada del procesamiento está determinada por la fórmula (16)
donde l - longitud de procesamiento, mm;
l1 - valor de entrada, mm;
l2 - sobrepaso del cortador, mm.
El valor de penetración l1 se calcula mediante la fórmula (17)
donde t es la profundidad de corte, mm;
D - diámetro del cortador, mm.
Obtenemos
El valor de rebasamiento l2 se toma como 4 mm.
Encuentre la longitud de procesamiento estimada L:
Usando la fórmula (15), calculamos el tiempo principal
8 . Racionamientotiempodefinicióntarifasycosto de producciónmecánicoProcesandodetalles
1 El tiempo de pieza para mecanizar una pieza se calcula mediante la fórmula
donde t0 es el tiempo tecnológico principal, min;
tv - tiempo auxiliar, min;
tob - tiempo de mantenimiento organizativo y técnico del lugar de trabajo, min;
tf - tiempo de pausas para descanso y necesidades físicas, min.
El tiempo tecnológico principal es igual a la suma de los valores de tiempo de la máquina para todas las transiciones de esta operación.
Así obtenemos
donde t01, t02, t03 es el tiempo principal para procesar cada superficie, que calcularemos a partir de la proporción
De la proporción (20) obtenemos
encontrar t0i
t01 = 0,00456 100 = 0,456 minutos
t02 = 0,00456 100 = 0,456 minutos
t03 = 0,00456 100 = 0,456 minutos
Usando la fórmula (19), calculamos Уt0:
Tiempo auxiliar: tiempo de instalación, fijación y extracción de la pieza, acercamiento y retiro de la herramienta, encendido de la máquina, verificación de dimensiones.
Usando la literatura, obtenemos
Tiempo de organización y Mantenimiento tb lugar de trabajo incluye: tiempo de reajuste, limpieza y engrase de la maquina, de recepcion y replanteo de la herramienta, cambio de herramienta desafilada, etc.
El tiempo para el servicio del lugar de trabajo tb, así como para el descanso y las necesidades físicas tf se asignan a la operación y se calculan mediante la fórmula
donde b es el porcentaje por atender el lugar de trabajo;
c - porcentaje para descanso y necesidades físicas.
Por la fórmula (21) obtenemos
Así, ahora según la fórmula (18) podemos calcular tpcs
2 El tiempo de cálculo de piezas para la operación se calcula mediante la fórmula (22)
donde tpz - tiempo preparatorio y final para todo el lote de piezas, min;
n es el número de partes en el lote.
3 Este tiempo se define como un todo para la operación e incluye el tiempo empleado por el trabajador para familiarizarse con mapa tecnológico procesar la pieza, estudiar el dibujo, configurar la máquina, recibir, preparar, instalar y quitar accesorios para realizar esta operación.
De acuerdo con la literatura, el tiempo preparatorio-final se toma igual a 30 minutos.
4 La tarifa por el trabajo realizado, es decir, el costo de la mano de obra P está determinada por la fórmula (23)
donde Ct es la tasa arancelaria de la categoría correspondiente;
K - coeficiente.
Se toma el valor de la tasa arancelaria correspondiente a la 4ª categoría igual a
St = 247,64 rublos/h
El coeficiente K se toma igual a 2,15.
Así, por la fórmula (23), obtenemos
5 El costo de mecanizar las piezas C incluye el costo de la mano de obra P y el costo de los gastos generales H y está determinado por la fórmula (24)
donde H es el costo de los gastos generales, rublos;
P - el costo de la mano de obra, frotar.
El costo de los gastos generales se toma igual al 1000% del costo de la mano de obra
Por la fórmula (25) encontramos Н
Por lo tanto, calculamos el costo del mecanizado.
9 . Construcciónaccesorios
La tarea del trabajo del curso es desarrollar el diseño de un dispositivo, que se incluye en el equipo tecnológico del proceso de mecanizado diseñado.
Los accesorios de la máquina están diseñados para instalar y reparar la pieza de trabajo y se dividen: según el grado de especialización, en piezas y ensamblajes universales, reconfigurables, prefabricados a partir de normalizados; según el grado de mecanización - manual, mecanizado, automático; con cita previa - para accesorios para torneado, taladrado, fresado, rectificado y otras máquinas; por diseño, en uno y varios asientos, una y varias posiciones.
La elección del tipo de accesorio depende del tipo de producción, el programa de producción de piezas, la forma, las dimensiones de la pieza de trabajo y la precisión de procesamiento requerida.
Al diseñar un accesorio de máquina, se resuelven las siguientes tareas principales:
1) la abolición de una operación intensiva en mano de obra: marcar partes antes del procesamiento;
2) reducción del tiempo auxiliar de instalación, fijación y reinstalación de la pieza relativa a la herramienta;
3) mejorar la precisión del procesamiento;
reducción del tiempo de máquina y auxiliar debido al procesamiento simultáneo de varias piezas o procesamiento combinado con varias herramientas;
facilitando el trabajo del trabajador y reduciendo la complejidad de la tramitación;
aumentar las capacidades tecnológicas y la especialización de la máquina
Como resultado del uso del accesorio, la productividad debería aumentar significativamente y el costo de procesamiento disminuirá.
Como dispositivo para fresado, elegimos un tornillo de banco GOST 18684-73, en el que se han modernizado las mordazas de sujeción. Esta modernización ayuda a facilitar el trabajo de los trabajadores.
10. Registrotécnicodocumentación
Como principal documento de documentación técnica, se presenta un mapa de ruta, en el que se indican todas las operaciones y transiciones, así como los equipos, útiles, herramientas de corte y medición, y el número de trabajadores.
Se indican el perfil y las dimensiones.
El segundo documento tecnológico es la tarjeta de funcionamiento. Indica las transiciones a una operación, su número y material de la pieza de trabajo, su masa y dureza de la pieza. Para todas las transiciones, se indica la herramienta de corte y medición.
Además, las dimensiones calculadas, la profundidad de corte, el número de pasadas, la velocidad del eje y la velocidad de los modos de procesamiento. Tiempo calculado de máquina y auxiliar.
11 . Principalinteligenciaacerca detécnicaseguridadentrabajasobre elCorte de metalesHerramientas de máquina
Las medidas de seguridad cubren un complejo de dispositivos técnicos y reglas que aseguran el funcionamiento normal de una persona en el proceso de trabajo y excluyen las lesiones laborales. Al trabajar en máquinas para corte de metales, el trabajador debe estar protegido de la acción de la corriente eléctrica, de los impactos de las partes móviles de la máquina, así como de las piezas o piezas de trabajo. herramienta para cortar por su débil fijación o rotura, por separación de virutas, por exposición al polvo y refrigerante.
Normas generales de seguridad para trabajar en máquinas para corte de metales
1. Las personas que hayan pasado un examen médico, hayan pasado una sesión informativa introductoria, una sesión informativa inicial en el lugar de trabajo y que tengan un certificado de protección laboral pueden trabajar de forma independiente.
2. Realizar únicamente trabajos que formen parte del ámbito de sus funciones.
3. Trabajar únicamente con overol servible, bien abrochado y calzado especial, previsto en el instructivo de protección del trabajo.
4. Utilice únicamente accesorios, equipos y herramientas reparables, utilícelos para el fin previsto.
5. No deje máquinas y mecanismos encendidos (en funcionamiento), equipos desatendidos.
Al salir, aunque sea por poco tiempo, desconéctelo de la red eléctrica con el interruptor de introducción.
6. No pase por debajo de una carga levantada.
7. No lave los overoles en queroseno, gasolina, solventes, emulsiones y no se lave las manos en ellos.
8. No toque las partes conductoras de corriente del equipo eléctrico de máquinas y mecanismos, piezas de trabajo procesadas y partes durante su rotación.
9. No sople aire comprimido sobre las piezas, no utilice aire comprimido para eliminar las virutas.
10. Uso en el trabajo cubierta de madera y mantenerlo en buenas condiciones y limpio.
11. Los principales factores de producción peligrosos y nocivos:
la posibilidad de descarga eléctrica;
posibilidad de quemaduras y daños mecanicos virutas;
aumento del nivel de ruido;
la posibilidad de caída de piezas instaladas y mecanizadas, piezas de trabajo.
12. Al trabajar en máquinas, no se permite el uso de guantes o manoplas.
Requisitos de seguridad al final del trabajo.
1. Apague la máquina, desconecte el equipo eléctrico.
2. Poner en orden el lugar de trabajo.
3. Limpie y lubrique las partes de fricción de la máquina.
4. Retire el aceite y la emulsión derramados rociando arena en las áreas contaminadas.
5. Limpie las virutas y el polvo con un cepillo de barrido.
6. Trapos utilizados durante la limpieza y durante el trabajo, sacar los trapos fuera del taller a los lugares designados para tal fin.
7. Al entregar el turno, informar al capataz y al turno sobre las deficiencias observadas y las medidas tomadas para subsanarlas.
8. Lávese la cara y las manos con agua tibia y jabón o tome una ducha.
Técnica seguridad en trabaja sobre el corte de tornillos máquina.
1. Antes de encender la máquina, asegúrese de que su puesta en marcha no sea peligrosa para las personas que se encuentran en la máquina.
3. Proporcionar sujeción segura detalles.
4. Al mecanizar una pieza en centros, está prohibido utilizar centros con conos desgastados.
7. Está prohibido tocar las partes giratorias de la máquina, así como la pieza de trabajo con las manos.
8. Para evitar que la ropa quede atrapada por las piezas giratorias, es necesario meter con cuidado el mono y quitarse el pelo debajo del casco.
9. Está prohibido limpiar, limpiar, lubricar, instalar y quitar piezas mientras la máquina está funcionando.
10. Los accesos al armario eléctrico y al lugar de trabajo no deben estar abarrotados.
11. En caso de lesión, es necesario avisar al capataz de obra o al jefe de taller.
12. ¡Atención!
Para evitar el sobrecalentamiento del motor, no se permite hacer más de 60 arranques por hora a revoluciones por minuto del husillo hasta 250, no más de 30 arranques por hora a revoluciones superiores a 250 por minuto y no más de 6 arranques por hora a revoluciones del husillo de 750 por minuto.
Bibliografía
1. Referencia tecnólogo-fabricante de máquinas: En 2 vols.T./Ed. Kosilova A.G. y Meshcheryakova R.K. M., 1972.-694 pág. T. 2 / Ed. Malova A. N. - M.: 1972. - 568 págs.
2. Fedin AP Ciencia de materiales y tecnología de materiales: (Directrices y asignaciones para papeles de prueba). - Gomel: BelGUT.-1992.-83s.
3. Parque Nacional Zobnin etc. Procesamiento de metales por corte. - M.: Asociación de publicaciones e imprentas de toda la Unión del Ministerio de Ferrocarriles, 1962. - 299 p.
Lakhtin Yu.M., Leontieva V.P. Ciencia de los Materiales.-M., 1990.-528 p.
Manual del trabajador metalúrgico. T. 5/. / Ed. LICENCIADO EN DERECHO. Boguslavsky. -M.: Mashinostroenie, 1997. -673s.
Masterov V. A., Berkovsky V. S. Teoría de la deformación plástica y tratamiento a presión de metales. -M.: Metalurgia, 1989.400 p.
Kazachenko V.P., Savenko A.N., Tereshko Yu.D. Ciencia de materiales y tecnología de materiales. Parte III. Procesamiento de metales por corte: una guía para el diseño de cursos.-Gomel: BelGUT.1997.-47p.
Alojado en Allbest.ru
...Documentos similares
Desarrollo de un dispositivo para el fresado de un chavetero. La estructura del proceso tecnológico de mecanizado de una pieza. Elección de equipos, herramientas; cálculo de las condiciones de corte; racionamiento, determinación del costo de una parte; equipo de seguridad.
trabajo final, agregado el 26/07/2013
El proceso de corte de metales, su papel en la ingeniería mecánica. Los principales requisitos para la pieza diseñada. La elección de equipos, accesorios, herramientas para el procesamiento de piezas. Cálculo de modos de corte. Tipo de pieza de trabajo y tolerancias de procesamiento.
trabajo final, agregado el 26/03/2013
Desarrollo de un proceso tecnológico para el procesamiento mecánico de un eje para un cargador de granos multicangilones TO-18A. Determinación del tipo de producción. Cálculo de tolerancias de procesamiento, condiciones de corte, estándares de tiempo, precisión de operaciones. Proyecto de Máquina Herramienta.
documento final, añadido el 07/12/2010
Tipo de producción, número de piezas en el lote. Tipo de pieza de trabajo y tolerancias de procesamiento. La estructura del proceso tecnológico, la elección de equipos y accesorios. Racionamiento de tiempo, determinación del precio y costo del procesamiento mecánico de piezas.
documento de término, agregado el 08/03/2016
Desarrollo de un proceso tecnológico para el mecanizado de una pieza, método para la obtención de un cuerpo de válvula en bruto. esquemas de funcionamiento y sistema de tecnología ensamblaje, un proyecto para arreglar e instalar una pieza, asignaciones para su procesamiento.
trabajo final, agregado el 27/01/2012
Determinación de la secuencia de operaciones tecnológicas para el mecanizado de la pieza "Shaft". Justificación de la elección de máquinas, la designación de asignaciones para el procesamiento. Cálculo de condiciones de corte, estándares de tiempo y factores de carga de máquinas herramienta, su número requerido.
trabajo final, agregado el 29/01/2015
El método de obtención de espacios en blanco para la parte "carcasa de cojinete inferior". Tipo de producción, finalidad de servicio de la pieza. Ruta tecnológica proceso de montaje y mecanizado del casco. Cálculo de tolerancias para el procesamiento de las dimensiones de la pieza de trabajo; modos de corte.
documento final, agregado el 22/12/2014
Proceso tecnológico de procesamiento mecánico de la parte "portadora", elección del material, propósito de la producción. Métodos de evaluación, procesamiento y ensamblaje de la complejidad. Determinación de las condiciones de corte, regulación detallada de una operación y preparación de un dibujo de la pieza.
documento final, agregado el 26/04/2012
Descripción y análisis tecnológico de la pieza "Carcasa de freno auxiliar". Características de un determinado tipo de producción. La elección de la pieza de trabajo, su diseño. Desarrollo y justificación del proceso tecnológico de elaboración mecánica. Cálculo de modos de corte.
trabajo final, agregado el 10/02/2016
Finalidad y diseño de la pieza "tornillo", vía tecnológica de mecanizado. Determinar el tipo de producción y el método de obtención de la pieza. Cálculo de provisiones, selección de equipos, herramientas de corte y medición; selección de modos de corte.