Estructura organizativa y productiva de las centrales nucleares. El principio de funcionamiento de TPP. Breve descripción. Rasgos característicos de las centrales eléctricas de condensación.
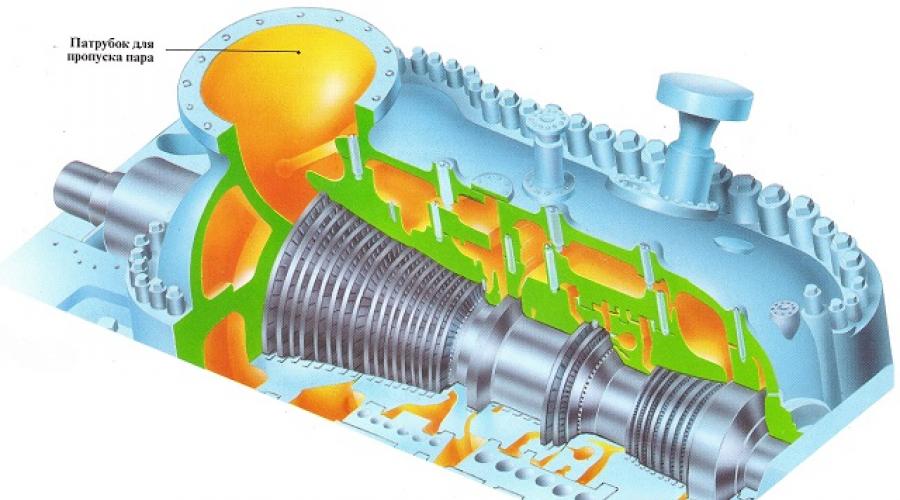
Leer también
gilev alexander
Ventajas de TPP:
Desventajas de TPP:
por ejemplo :
Descargar:
Avance:
CARACTERÍSTICAS COMPARATIVAS DE TPP Y NPP DESDE EL PUNTO DE VISTA DEL PROBLEMA AMBIENTAL.
Terminado: Gilev Alexander, 11 clase "D", Liceo FGBOU VPO "Dalrybvtuz"
Supervisor:Kurnosenko Marina Vladimirovna, profesora de física de la categoría de calificación más alta, liceoFGBOU VPO "Dalrybvtuz"
Central térmica (TPP), una central eléctrica que genera energía eléctrica como resultado de la conversión de la energía térmica liberada durante la combustión de combustibles fósiles.
¿Con qué combustible funcionan los TPP?
- Carbón: En promedio, quemar un kilogramo de este tipo de combustible libera 2,93 kg de CO2 y produce 6,67 kWh de energía o, con una eficiencia del 30 %, 2,0 kWh de electricidad. Contiene 75-97% de carbono,
1,5-5,7 % hidrógeno, 1,5-15 % oxígeno, 0,5-4 % azufre, hasta 1,5 % nitrógeno, 2-45 %
sustancias volátiles, la cantidad de humedad varía de 4 a 14%.La composición de los productos gaseosos (gas de horno de coque) incluye benceno,
tolueno, xioles, fenol, amoníaco y otras sustancias. De gas de horno de coque
purificación a partir de amoníaco, sulfuro de hidrógeno y compuestos de cianuro extracto crudo
benceno, del que se extraen hidrocarburos individuales y una serie de otros
sustancias
- Gasolina: Fuel oil (posiblemente del árabe mazkhulat - desecho), un producto líquido de color marrón oscuro, el residuo después de la separación de las fracciones de gasolina, queroseno y gasóleo del petróleo o sus productos de procesamiento secundario, que hierve hasta 350-360 ° C. El fuel oil es una mezcla de hidrocarburos (con peso molecular de 400 a 1000 g/mol), resinas de petróleo (con un peso molecular de 500-3000 g/mol o más), asfaltenos, carbenos, carboide y compuestos orgánicos que contienen metales (V, Ni, Fe, Mg, Na, Ca)
- Gas: La parte principal del gas natural es el metano (CH4), del 92 al 98%. La composición del gas natural también puede incluir hidrocarburos más pesados: homólogos del metano.
Ventajas y desventajas de TPP:
Ventajas de TPP:
- La ventaja más importante es la baja tasa de accidentes y la resistencia del equipo.
- El combustible utilizado es bastante barato.
- Requiere menos inversión en comparación con otras centrales eléctricas.
- Se puede construir en cualquier lugar independientemente de la disponibilidad de combustible. El combustible se puede transportar a la ubicación de la central eléctrica por ferrocarril o por carretera.
- El uso de gas natural como combustible reduce virtualmente las emisiones sustancias nocivas a la atmósfera, lo cual es una gran ventaja sobre las plantas de energía nuclear.
- Un grave problema para las centrales nucleares es su liquidación una vez agotado el recurso, según estimaciones puede suponer hasta el 20% del coste de su construcción.
Desventajas de TPP:
- Aún así, las centrales térmicas que utilizan como combustible el fuel oil, el carbón están muy contaminadas medioambiente. En las TPP, las emisiones anuales totales de sustancias nocivas, que incluyen dióxido de azufre, óxidos de nitrógeno, óxidos de carbono, hidrocarburos, aldehídos y cenizas volantes, por 1000 MW Capacidad instalada oscilan entre unas 13.000 toneladas por año para las centrales eléctricas alimentadas con gas y 165.000 para las centrales eléctricas alimentadas con carbón.
- Una central térmica de 1000 MW consume 8 millones de toneladas de oxígeno al año
Por ejemplo : CHP-2 quema la mitad de la composición de carbón por día. Probablemente esta carencia sea la principal.
¡¿Y si?!
- ¿Y si ocurre un accidente en la central nuclear construida en Primorye?
- ¿Cuántos años se recuperará el planeta después de eso?
- ¡Después de todo, el CHPP-2, que está cambiando gradualmente a gas, prácticamente detiene las emisiones de hollín, amoníaco, nitrógeno y otras sustancias a la atmósfera!
- A la fecha, las emisiones de CHPP-2 han disminuido en un 20%.
- Y, por supuesto, se eliminará un problema más: el basurero.
Un poco sobre los peligros de las centrales nucleares:
- Basta recordar simplemente el accidente de la central nuclear de Chernóbil el 26 de abril de 1986. En apenas 20 años, aproximadamente 5.000 liquidadores de este grupo murieron por todas las causas, y esto sin contar a los civiles... Y claro, estos son todos datos oficiales.
Planta "MAYAK":
- 15/03/1953 - comenzó una reacción en cadena autosostenida. Sobreexposición del personal de la planta;
- 13/10/1955 - brecha Equipo tecnológico y destrucción de partes del edificio.
- 21/04/1957 - SCR (reacción en cadena espontánea) en la planta N° 20 en la captación de decantados de oxalato tras la filtración del sedimento de oxalato de uranio enriquecido. Seis personas recibieron dosis de radiación de 300 a 1000 rems (cuatro mujeres y dos hombres), una mujer murió.
- 02/10/1958 - SCR en la planta. Se llevaron a cabo experimentos para determinar la masa crítica de uranio enriquecido en un recipiente cilíndrico a diversas concentraciones de uranio en solución. El personal violó las reglas e instrucciones para trabajar con material fisionable nuclear (material fisionable nuclear). En el momento de la SCR, el personal recibió dosis de radiación de 7600 a 13000 rem. Tres personas murieron, una persona se enfermó por radiación y se quedó ciega. En el mismo año, I. V. Kurchatov habló en nivel más alto y demostró la necesidad del establecimiento de un división estatal sobre seguridad LYAB se convirtió en una organización de este tipo.
- 28/07/1959 - ruptura de equipo tecnológico.
- 05/12/1960 - SCR en la planta. Cinco personas estaban sobreexpuestas.
- 26/02/1962 - explosión en una columna de sorción, destrucción del equipo.
- 07/09/1962 - RCS.
- 16/12/1965 - SCR en la planta número 20 duró 14 horas.
- 10 de diciembre de 1968 - SCR. La solución de plutonio se llenó en un recipiente cilíndrico con una geometría peligrosa. Una persona murió, otra recibió una alta dosis de radiación y enfermedad por radiación, después de lo cual le amputaron dos piernas y su brazo derecho.
- El 11 de febrero de 1976, como resultado de acciones no calificadas del personal, se desarrolló en la planta radioquímica una reacción autocatalítica de ácido nítrico concentrado con un líquido orgánico de composición compleja. El artefacto explotó, se produjo la contaminación radiactiva de la zona de reparación y el área adyacente de la planta. Índice en la escala INEC-3.
- 02/10/1984 - Explosión en el equipo de vacío del reactor.
- 16/11/1990 - reacción explosiva en contenedores de reactivos. Dos personas recibieron quemaduras químicas, una murió.
- 17/07/1993 - Accidente en la planta de radioisótopos de la Asociación de Producción de Mayak con destrucción de la columna de sorción y liberación de una cantidad insignificante de α-aerosoles al medio ambiente. La liberación de radiación se localizó dentro locales industriales Talleres de trabajo.
- 08.02.1993 - Ocurrió accidente en la línea de emisión de pulpa de una planta de tratamiento de residuos radiactivos líquidos, incidente ocurrido por la despresurización de la tubería y el ingreso de 2 m3 de pulpa radiactiva a la superficie terrestre (unos 100 m2 de la superficie estaba contaminada). La despresurización de la tubería condujo a la salida de pulpa radiactiva a la superficie de la tierra con una actividad de alrededor de 0,3 Ci. Se localizó el rastro radiactivo, se eliminó el suelo contaminado.
- El 27 de diciembre de 1993 ocurrió un incidente en una planta de radioisótopos, donde se liberaron aerosoles radiactivos a la atmósfera durante un cambio de filtro. La liberación fue de 0,033 Ci para la actividad α y de 0,36 mCi para la actividad β.
- El 4 de febrero de 1994 se registró una mayor liberación de aerosoles radiactivos: según la actividad β de los niveles de 2 días, según los niveles diarios de 137Cs, la actividad total fue de 15,7 mCi.
- El 30 de marzo de 1994, durante la transición, se registró un exceso de la liberación diaria de 137Cs por 3, actividad β - 1,7, actividad α - 1,9 veces.
- En mayo de 1994, se liberaron aerosoles β con una actividad de 10,4 mCi a través del sistema de ventilación del edificio de la fábrica. La liberación de 137Cs fue del 83% del nivel de control.
- El 7 de julio de 1994, una mancha radiactiva con un área de varios decímetros cuadrados. La tasa de dosis de exposición fue de 500 µR/s. La mancha se formó como resultado de fugas de una alcantarilla bloqueada.
- 31.08. En 1994 se registró un aumento de la emisión de radionucleidos en la chimenea atmosférica del edificio de la planta radioquímica (238,8 mCi, incluida la proporción de 137Cs que representaba el 4,36% de la emisión máxima anual permisible de este radionucleido). El motivo de la liberación de radionucleidos fue la despresurización de la barra de combustible VVER-440 durante la operación de corte de los extremos inactivos de los SFA (conjuntos de combustible gastado) como resultado de un arco eléctrico no controlado.
- El 24 de marzo de 1995 se registró un exceso del 19% de la norma para cargar el aparato con plutonio, lo que puede ser considerado como un incidente nuclear peligroso.
- El 15 de septiembre de 1995 se detectó una fuga de agua de refrigeración en el horno de vitrificación de LRW (residuos radiactivos líquidos) de alto nivel. Se suspendió la operación del horno en el modo programado.
- El 21 de diciembre de 1995, al cortar el canal termométrico, cuatro trabajadores fueron irradiados (1,69, 0,59, 0,45, 0,34 rem). La causa del incidente es una violación de las normas tecnológicas por parte de los empleados de la empresa.
- El 24 de julio de 1995 se liberaron aerosoles de 137Cs, cuyo valor ascendió al 0,27% del MPE anual de la empresa. La razón es el encendido de la tela del filtro.
- El 14 de septiembre de 1995, al reemplazar las cubiertas y lubricar los manipuladores paso a paso, se registró un fuerte aumento de la contaminación del aire con α-núclidos.
- El 22 de octubre de 1996 falló el serpentín de agua de enfriamiento de uno de los tanques de almacenamiento de desechos de alto nivel. Como resultado, las tuberías del sistema de refrigeración del almacenamiento se contaminaron. Como resultado de este incidente, 10 empleados del departamento recibieron una exposición radiactiva de 2,23×10-3 a 4,8×10-2 Sv.
- El 20 de noviembre de 1996, en la planta químico-metalúrgica, durante los trabajos en el equipo eléctrico del extractor de aire, se produjo una emisión de aerosoles de radionucleidos a la atmósfera, que ascendió al 10% de la emisión anual permitida de la planta.
- El 27 de agosto de 1997 en el edificio de la planta RT-1, en uno de los cuartos se encontró contaminación del piso con un área de 1 a 2 m2, la tasa de dosis de radiación gamma del punto fue de 40 a 200 µR/s.
- El 06/10/97 se registró un aumento del fondo radiactivo en el edificio de montaje de la planta RT-1. La medición de la tasa de dosis de exposición mostró un valor de hasta 300 μR/s.
- 23/09/98 al aumentar la potencia del reactor LF-2 (Lyudmila) después de que se activó la protección automática nivel permitido la potencia se superó en un 10%. Como resultado, se produjo la despresurización de parte de las barras de combustible en tres canales, lo que provocó la contaminación de los equipos y tuberías del circuito primario. El contenido de 133Xe en la descarga del reactor superó el nivel permitido anual durante 10 días.
- El 09/09/2000, se cortó el suministro eléctrico en Mayak durante 1,5 horas, lo que podría provocar un accidente.
- En el curso de una auditoría en 2005, la oficina del fiscal estableció una violación de las reglas para el manejo ambiental residuos peligrosos producción en el período 2001-2004, lo que provocó el vertido en la cuenca del río Techa de varias decenas de millones de metros cúbicos de residuos radiactivos líquidos producidos por Mayak. Según el jefe adjunto del departamento de la Fiscalía General de la Federación Rusa en los Urales Distrito Federal Andrey Potapov, “se ha establecido que la represa de la fábrica, que hace mucho tiempo que necesita reconstrucción, permite que los desechos radiactivos líquidos pasen al reservorio, lo que representa una grave amenaza para el medio ambiente no solo en Región de Cheliábinsk sino también en las regiones vecinas. Según la fiscalía, debido a las actividades de la planta Mayak en la planicie de inundación del río Techa, el nivel de radionucleidos se ha multiplicado varias veces en estos cuatro años. Como mostró el examen, el territorio de infección era de 200 kilómetros. Cerca de 12 mil personas viven en la zona de peligro. Al mismo tiempo, los investigadores declararon que estaban bajo presión en relación con la investigación. al director general La Asociación de Producción Mayak Vitaly Sadovnikov fue acusada en virtud del artículo 246 del Código Penal de la Federación Rusa “Violación de las normas de protección ambiental en el curso del trabajo” y las partes 1 y 2 del artículo 247 del Código Penal de la Federación Rusa “Violación de las normas para el manejo ambiental sustancias peligrosas y desperdicio". En 2006, el caso penal contra Sadovnikov terminó debido a una amnistía por el centenario de la Duma del Estado.
- El Techa es un río contaminado con desechos radiactivos descargados por la Combinación Química Mayak, ubicada en la región de Chelyabinsk. En las orillas del río, el fondo radiactivo se supera muchas veces. De 1946 a 1956 se realizaron descargas de residuos líquidos de media y alta actividad de la Asociación de Producción Mayak al sistema fluvial abierto Techa-Iset-Tobol, a 6 km del nacimiento del río Techa. En total, durante estos años, se descargaron 76 millones de m3 de aguas residuales con una actividad de radiación β total de más de 2,75 millones de Ci. Los residentes de las aldeas costeras estuvieron expuestos a la radiación tanto externa como interna. En total, 124 mil personas que viven en asentamientos a orillas de los ríos de este sistema hídrico estuvieron expuestas a la radiación. Los residentes de la costa del río Techa (28,1 mil personas) fueron los que tuvieron mayor exposición. Cerca de 7,5 mil personas fueron reasentadas de 20 asentamientos, recibieron dosis equivalentes efectivas promedio en el rango de 3 - 170 cSv. Posteriormente, se construyó una cascada de embalses en la parte alta del río. La mayor parte de los desechos radiactivos líquidos (en términos de actividad) se vertieron en el lago. Karachay (embalse 9) y el "Cengal Viejo". La planicie de inundación del río y los sedimentos del fondo están contaminados, los depósitos de limo en la parte superior del río se consideran desechos radiactivos sólidos. el agua subterránea en la región del lago Karachay y la cascada de embalses Techensky están contaminados.
- El accidente de Mayak en 1957, también conocido como la "tragedia de Kyshtym", es el tercer mayor desastre en la historia de la energía nuclear después del accidente de Chernobyl y el Accidente en la central nuclear de Fukushima I (según la escala INES).
- El tema de la contaminación radiactiva de la región de Chelyabinsk se planteó repetidamente, pero debido a la importancia estratégica de la planta química, cada vez se ignoró.
FUKUSHIMA-1
- El accidente de la central nuclear de Fukushima-1 es un gran accidente de radiación (según los japoneses funcionarios- Nivel 7 en la escala INES), ocurrido el 11 de marzo de 2011 como consecuencia del terremoto más fuerte de Japón y del tsunami que le siguió
Las palas de los impulsores son claramente visibles en esta turbina de vapor.
La planta de energía térmica (CHP) utiliza la energía liberada por la quema de combustibles fósiles (carbón, petróleo y gas natural) para convertir el agua en vapor. presión alta. Este vapor, que tiene una presión de unos 240 kilogramos por centímetro cuadrado y una temperatura de 524°C (1000°F), impulsa una turbina. La turbina hace girar un imán gigante dentro de un generador que genera electricidad.
Moderno las centrales térmicas alrededor del 40 por ciento del calor liberado durante la combustión del combustible se convierte en electricidad, el resto se descarga al medio ambiente. En Europa, muchas centrales térmicas utilizan el calor residual para calentar los hogares y negocios cercanos. La generación combinada de calor y electricidad aumenta la eficiencia energética de la planta de energía hasta en un 80 por ciento.
Planta de turbina de vapor con generador eléctrico
Una turbina de vapor típica contiene dos juegos de álabes. El vapor a alta presión que proviene directamente de la caldera ingresa a la ruta de flujo de la turbina y hace girar los impulsores con el primer grupo de álabes. Luego, el vapor se calienta en el sobrecalentador y nuevamente ingresa a la ruta de flujo de la turbina para hacer girar los impulsores con el segundo grupo de álabes, que operan a una presión de vapor más baja.
Vista seccionada
Un generador típico en una planta de energía térmica (CHP) es accionado directamente por una turbina de vapor que gira a 3000 revoluciones por minuto. En generadores de este tipo, el imán, también llamado rotor, gira y los devanados (estator) están estacionarios. El sistema de refrigeración evita que el generador se sobrecaliente.
Generación de energía de vapor
En una central térmica, el combustible se quema en una caldera para formar una llama de alta temperatura. El agua pasa a través de los tubos a través de la llama, se calienta y se convierte en vapor a alta presión. El vapor impulsa la turbina, produciendo energía mecánica que el generador convierte en electricidad. Después de salir de la turbina, el vapor ingresa al condensador, donde lava los tubos con agua fría. agua corriendo, y como resultado vuelve a convertirse en líquido.
Caldera de gasóleo, carbón o gas
Dentro de la caldera
La caldera está llena de tubos intrincadamente curvados a través de los cuales pasa agua calentada. La compleja configuración de los tubos le permite aumentar significativamente la cantidad de calor transferido al agua y, por lo tanto, producir mucho más vapor.
1 - generador eléctrico; 2 - turbina de vapor; 3 - panel de control; 4 - desaireador; 5 y 6 - búnkeres; 7 - separador; 8 - ciclón; 9 - caldera; 10 – superficie de calentamiento (intercambiador de calor); once - Chimenea; 12 - sala de trituración; 13 - almacén combustible de reserva; 14 - vagón; 15 - dispositivo de descarga; 16 - transportador; 17 - extractor de humo; 18 - canal; 19 - recogedor de cenizas; 20 - ventilador; 21 - caja de fuego; 22 - molino; 23- gasolinera; 24 - fuente de agua; 25- bomba de circulación; 26 – calentador regenerativo de alta presión; 27 - bomba de alimentación; 28 - condensador; 29 - instalación limpieza quimica agua; 30 - transformador elevador; 31 - calentador regenerativo baja presión; 32 - bomba de condensado.
El siguiente diagrama muestra la composición de los equipos principales de una central térmica y la interconexión de sus sistemas. De acuerdo con este esquema, es posible rastrear la secuencia general de procesos tecnológicos que ocurren en las TPP.
Designaciones en el diagrama TPP:
- Economía de combustible;
- preparación de combustible;
- sobrecalentador intermedio;
- parte de la alta presión (CHVD o CVP);
- parte de baja presión (LPH o LPC);
- generador eléctrico;
- transformador auxiliar;
- transformador de comunicación;
- lo principal Subestación de control;
- bomba de condensado;
- bomba de circulación;
- fuente de suministro de agua (por ejemplo, un río);
- (PND);
- planta de tratamiento de agua (VPU);
- consumidor de energía térmica;
- bomba de condensado inversa;
- desaireador;
- Bomba de alimentación;
- (PVD);
- eliminación de escorias y cenizas;
- vertedero de cenizas;
- extractor de humo (DS);
- Chimenea;
- ventiladores (DV);
- recogedor de cenizas.
Descripción del esquema tecnológico de TPP:
Resumiendo todo lo anterior, obtenemos la composición de una central térmica:
- economía de combustible y sistema de preparación de combustible;
- planta de calderas: la combinación de la propia caldera y equipo auxiliar;
- planta de turbinas: turbina de vapor y sus equipos auxiliares;
- planta de tratamiento de agua y condensados;
- sistema abastecimiento tecnico de agua;
- sistema de eliminación de cenizas y escorias (para centrales térmicas que funcionan con combustible sólido);
- equipo eléctrico y sistema de control de equipo eléctrico.
El ahorro de combustible, dependiendo del tipo de combustible utilizado en la estación, incluye un dispositivo de recepción y descarga, mecanismos de transporte, instalaciones de almacenamiento de combustible sólido y combustible líquido, dispositivos para la preparación preliminar de combustible (plantas trituradoras de carbón). La composición de la economía de fuel oil también incluye bombas para bombear fuel oil, calentadores de fuel oil, filtros.
La preparación de combustible sólido para combustión consiste en molerlo y secarlo en una planta pulverizadora, y la preparación de fuel oil consiste en calentarlo, limpiarlo de impurezas mecánicas y, en ocasiones, tratarlo con aditivos especiales. Todo es más fácil con combustible de gas. Capacitación combustible gaseoso se reduce principalmente a la regulación de la presión del gas frente a los quemadores de la caldera.
El aire necesario para la combustión del combustible se suministra al espacio de combustión de la caldera mediante ventiladores (DV). Los productos de la combustión del combustible, los gases de combustión, son aspirados por extractores de humo (DS) y descargados a través de chimeneas a la atmósfera. La combinación de canales (conductos de aire y conductos de gas) y varios elementos del equipo a través de los cuales pasan el aire y los gases de combustión forma la ruta gas-aire de una central térmica (central térmica). Los extractores de humos, una chimenea y los ventiladores incluidos en su composición conforman un proyecto de instalación. En la zona de combustión del combustible, las impurezas no combustibles (minerales) incluidas en su composición sufren transformaciones químicas y físicas y se eliminan parcialmente de la caldera en forma de escoria, y una parte importante de ellas se elimina gases de combustión en forma de finas partículas de ceniza. para guardia aire atmosférico de las emisiones de cenizas, se instalan colectores de cenizas frente a los extractores de humos (para evitar el desgaste de las cenizas).
La escoria y la ceniza atrapada generalmente se eliminan hidráulicamente a las minas de oro.
Cuando se quema fuel oil y gas, no se instalan colectores de cenizas.
Cuando se quema el combustible, la energía ligada químicamente se convierte en calor. Como resultado, se forman productos de combustión, que en las superficies de calentamiento de la caldera emiten calor al agua y al vapor que se forma a partir de ella.
El conjunto de equipos, sus elementos individuales, tuberías a través de las cuales se mueven el agua y el vapor, forman el trayecto vapor-agua de la estación.
En la caldera, el agua se calienta a la temperatura de saturación, se evapora y el vapor saturado formado a partir del agua de la caldera en ebullición se sobrecalienta. Desde la caldera, el vapor sobrecalentado se envía a través de tuberías a la turbina, donde su energía térmica se convierte en energía mecánica que se transmite al eje de la turbina. El vapor que sale de la turbina entra en el condensador, cede calor al agua de refrigeración y se condensa.
En centrales térmicas modernas y centrales térmicas con unidades con una capacidad unitaria de 200 MW y más, se utiliza el recalentamiento del vapor. En este caso, la turbina tiene dos partes: una parte de alta presión y una parte de baja presión. El vapor que sale en la sección de alta presión de la turbina se envía a un sobrecalentador intermedio, donde se le suministra calor adicional. A continuación, el vapor vuelve a la turbina (a la parte de baja presión) y de esta entra al condensador. El sobrecalentamiento de vapor intermedio aumenta la eficiencia de la planta de turbinas y aumenta la confiabilidad de su operación.
El condensado es bombeado fuera del condensador por una bomba de condensado y, después de pasar por calentadores de baja presión (LPH), ingresa al desaireador. Aquí se calienta con vapor hasta la temperatura de saturación, mientras que el oxígeno y el dióxido de carbono se liberan y se eliminan a la atmósfera para evitar la corrosión del equipo. El agua desaireada, llamada agua de alimentación, se bombea a través de calentadores de alta presión (HPH) a la caldera.
El condensado en el HDPE y el desaireador, así como el agua de alimentación en el HPH, son calentados por el vapor tomado de la turbina. Este método de calefacción supone el retorno (regeneración) de calor al ciclo y se denomina calefacción regenerativa. Gracias a él, se reduce el flujo de vapor hacia el condensador y, en consecuencia, la cantidad de calor transferido al agua de enfriamiento, lo que conduce a aumento de la eficiencia planta de turbinas de vapor.
El conjunto de elementos que abastecen de agua de refrigeración a los condensadores se denomina sistema de abastecimiento de agua de servicio. Incluye: una fuente de suministro de agua (un río, un embalse, una torre de enfriamiento - una torre de enfriamiento), una bomba de circulación, conductos de entrada y salida. En el condensador, alrededor del 55% del calor del vapor que ingresa a la turbina se transfiere al agua enfriada; esta parte del calor no se utiliza para generar electricidad y se desperdicia.
Estas pérdidas se reducen significativamente si se toma vapor parcialmente agotado de la turbina y su calor se utiliza para necesidades tecnológicas. empresas industriales o Calentamiento de agua para calefacción y suministro de agua caliente. Así, la central se convierte en una planta combinada de calor y electricidad (CHP), que proporciona generación combinada de energía eléctrica y térmica. En CHPP, se instalan turbinas especiales con extracción de vapor, las llamadas turbinas de cogeneración. Condensado de vapor dado consumidor de calor, se devuelve a la planta CHP mediante una bomba de retorno de condensado.
En la TPP existen pérdidas internas de vapor y condensado por estanqueidad incompleta del trayecto vapor-agua, así como consumos no retornables de vapor y condensado para las necesidades técnicas de la central. Constituyen aproximadamente del 1 al 1,5% del flujo de vapor total a las turbinas.
En CHPP, puede haber pérdidas externas de vapor y condensado asociadas con el suministro de calor a los consumidores industriales. En promedio, son 35 - 50%. Las pérdidas internas y externas de vapor y condensado se reponen con agua de reposición pretratada en la planta de tratamiento de agua.
Por lo tanto, el agua de alimentación de la caldera es una mezcla de condensado de turbina y agua de reposición.
Las instalaciones eléctricas de la central incluyen un generador eléctrico, un transformador de comunicaciones, una aparamenta principal, un sistema de alimentación de los mecanismos propios de la central a través de un transformador auxiliar.
El sistema de control recopila y procesa información sobre el progreso del proceso tecnológico y el estado del equipo, automático y control remoto mecanismos y regulación de los principales procesos, protección automática de equipos.
ESTRUCTURA ORGANIZATIVA Y PRODUCTIVA DE LAS CENTRALES TÉRMICAS (TPP)
Según la potencia de los equipos y circuitos enlaces tecnológicos Entre las etapas de producción en los TPP modernos, se distinguen estructuras organizativas y de producción de taller, sin taller y de taller en bloque.
Estructura organizativa y productiva del taller. prevé la división de equipos tecnológicos y el territorio de la central térmica en secciones separadas y su asignación a unidades especializadas: talleres, laboratorios. En este caso, el principal unidad estructural es un taller Las tiendas, según su participación en la producción, se dividen en principales y auxiliares. Además, los TPP también pueden incluir hogares no industriales (viviendas y granjas subsidiarias, jardines de infancia, casas de reposo, sanatorios, etc.).
Talleres principales participan directamente en la producción de energía. Estos incluyen los talleres de combustible y transporte, calderas, turbinas, electricidad y productos químicos.
La composición del taller de combustible y transporte incluye secciones de las instalaciones ferroviarias y suministro de combustible con un almacén de combustible. Este taller se organiza en centrales eléctricas que queman combustible sólido o fueloil cuando se entrega por ferrocarril.
La composición de la sala de calderas incluye áreas para el suministro de combustibles líquidos o gaseosos, preparación de polvo, eliminación de cenizas.
El taller de turbinas incluye: departamento de calefacción, estación central de bombeo y gestión del agua.
Con dos tiendas estructura productiva, así como en las grandes TPP, los talleres de calderas y turbinas se combinan en un solo taller de calderas y turbinas (KTC).
El taller eléctrico tiene a su cargo: todo el equipo eléctrico de la central térmica, un laboratorio eléctrico, una economía petrolera, un taller de reparación eléctrica.
El taller químico incluye laboratorio químico y tratamiento químico de aguas.
Tiendas auxiliares servir a la producción principal. Estos incluyen: un taller para reparación centralizada, reparación y construcción, automatización térmica y comunicaciones.
Las granjas no industriales no están directamente relacionadas con la producción de energía y atienden las necesidades domésticas de los trabajadores de TPP.
Estructura organizativa y productiva sin talleres prevé la especialización de las unidades en la ejecución de los principales funciones de producción: funcionamiento del equipo, su servicio de reparación, control tecnológico. Esto provoca la creación de servicios de producción en lugar de talleres: operación, reparación, control y mejora de equipos. A su vez, los servicios de producción se dividen en secciones especializadas.
Creación estructura organizativa y productiva de la tienda de bloques debido a la aparición de complejos bloques de unidades de energía. El equipo del bloque realiza varias fases del proceso energético: combustión de combustible en un generador de vapor, generación de electricidad en un turbogenerador y, en ocasiones, su transformación en un transformador. A diferencia del taller, con estructura de block-shop, la principal unidad productiva de la central son los block. Están incluidos en los CTC, que se dedican a la operación centralizada de los equipos principales y auxiliares de las unidades de caldera y turbina. La estructura de la tienda en bloque prevé la preservación de las tiendas principales y auxiliares que tienen lugar en la estructura de la tienda, por ejemplo, la tienda de combustible y transporte (TTTS), química, etc.
Todos los tipos de estructuras organizativas y de producción prevén la implementación de la gestión de la producción sobre la base de la unidad de mando. En cada TPP existe un departamento administrativo, económico, productivo y de despacho técnico y operativo.
El responsable administrativo y económico del TPP es el director, el responsable técnico es Ingeniero jefe. El control operativo y de despacho es realizado por el ingeniero de turno de la central. Operacionalmente está subordinado al despachador de turno de la EPS.
Nombre y cantidad divisiones estructurales, y la necesidad de introducir puestos separados se determina según el número estándar de personal industrial y de producción de la central eléctrica.
Las características tecnológicas, organizativas y económicas especificadas de la producción de energía eléctrica afectan el contenido y las tareas de gestión de las actividades de las empresas y asociaciones de energía.
El principal requisito para la industria de la energía eléctrica es un suministro de energía confiable e ininterrumpido para los consumidores, que cubra el horario de carga requerido. Este requisito se transforma en indicadores específicos que evalúan la participación de las empresas de la central y de la red en la implementación del programa de producción de las asociaciones de energía.
Para la planta de energía, se establece la disponibilidad para transportar la carga, que se establece mediante el programa de despacho. Para las empresas de red, se establece un cronograma de reparaciones de equipos e instalaciones. En el plan también se establecen otros indicadores técnicos y económicos: costo unitario combustible en centrales, reducción de pérdidas de energía en redes, indicadores financieros. Sin embargo, el programa de producción de las empresas energéticas no puede estar estrictamente determinado por el volumen de producción o suministro. energía eléctrica y calidez Esto es poco práctico debido al excepcional dinamismo del consumo de energía y, en consecuencia, de la producción de energía.
Sin embargo, el volumen de producción de energía es un indicador de cálculo importante que determina el nivel de muchos otros indicadores (por ejemplo, el costo) y los resultados de la actividad económica.
En la fig. 1 muestra la clasificación de las centrales térmicas que funcionan con combustibles fósiles.
Arroz. uno.
Una central térmica es un conjunto de equipos y dispositivos que convierten la energía del combustible en energía eléctrica y (en el caso general) energía térmica.
Las centrales térmicas se caracterizan por una gran diversidad y pueden clasificarse según varios criterios.
Según el propósito y el tipo de energía suministrada, las centrales eléctricas se dividen en regionales e industriales.
Las centrales eléctricas de distrito son centrales eléctricas públicas independientes que dan servicio a todo tipo de consumidores de la zona (empresas industriales, transporte, población, etc.). Las plantas de energía de condensación de distrito, que generan principalmente electricidad, a menudo retienen nombre histórico- GRES (centrales distritales estatales). Centrales eléctricas de distrito que generan electricidad y calor (en forma de vapor o agua caliente) se denominan plantas combinadas de calor y electricidad (CHP). Como regla general, las centrales eléctricas de distrito estatales y las centrales térmicas regionales tienen una capacidad de más de 1 millón de kW.
Las centrales eléctricas industriales son centrales eléctricas que suministran calor y electricidad a empresas manufactureras o su complejo, por ejemplo, una planta para la producción de productos químicos. Las centrales eléctricas industriales son parte de las empresas industriales a las que sirven. Su capacidad está determinada por las necesidades de calor y electricidad de las empresas industriales y, por regla general, es significativamente menor que la de las centrales térmicas regionales. A menudo, las centrales eléctricas industriales funcionan con un sistema común red eléctrica, pero no están subordinados al despachador del sistema eléctrico.
Según el tipo de combustible utilizado, las centrales térmicas se dividen en centrales que funcionan con combustible orgánico y con combustible nuclear.
Detrás de las centrales de condensación que funcionan con combustibles fósiles, en una época en la que no había centrales nucleares (NPP), se ha desarrollado históricamente el nombre térmico (TPP - planta de energía térmica). Es en este sentido que se utilizará este término a continuación, aunque tanto CHP, NPP y centrales eléctricas de turbinas de gas(GTPP), y las centrales eléctricas de ciclo combinado (PGPP) también son centrales térmicas que funcionan según el principio de convertir la energía térmica en energía eléctrica.
Los combustibles gaseosos, líquidos y sólidos se utilizan como combustibles fósiles para centrales térmicas. La mayoría de las centrales térmicas en Rusia, especialmente en la parte europea, consumen gas natural, y como combustible de respaldo el fuel oil, utilizando este último por su Alto costo solo en casos extremos; tales plantas de energía térmica se llaman de petróleo. En muchas regiones, principalmente en la parte asiática de Rusia, el combustible principal es el carbón térmico: carbón bajo en calorías o desechos de la extracción de carbón con alto contenido calórico (lodo de antracita - ASH). Dado que tales carbones se muelen en molinos especiales hasta un estado pulverizado antes de quemarse, estas centrales térmicas se denominan carbón pulverizado.
Según el tipo de centrales térmicas utilizadas en las centrales térmicas para convertir la energía térmica en energía mecánica de rotación de los rotores de las unidades de turbina, se distinguen las centrales eléctricas de turbina de vapor, turbina de gas y ciclo combinado.
La base de las centrales eléctricas de turbina de vapor son plantas de turbinas de vapor(PTU), que, para convertir la energía térmica en energía mecánica, utiliza la máquina de energía más compleja, potente y extremadamente avanzada: una turbina de vapor. La PTU es el elemento principal de las centrales térmicas, centrales térmicas y centrales nucleares.
Las STP que tienen turbinas de condensación como accionamiento de los generadores eléctricos y no utilizan el calor del vapor de escape para suministrar energía térmica a los consumidores externos se denominan centrales eléctricas de condensación. Las PTU equipadas con turbinas de calefacción y que emiten el calor del vapor de escape a los consumidores industriales o domésticos se denominan plantas combinadas de calor y electricidad (CHP).
Las centrales térmicas de turbina de gas (GTPP) están equipadas con unidades de turbina de gas (GTU) que funcionan con combustible gaseoso o, en casos extremos, líquido (diésel). Dado que la temperatura de los gases detrás de la turbina de gas es bastante alta, se pueden utilizar para suministrar energía térmica a un consumidor externo. Tales plantas de energía se llaman GTU-CHP. Actualmente, hay un GTPP operando en Rusia (GRES-3 llamado así por Klasson, Elektrogorsk, Región de Moscú) con una capacidad de 600 MW y un GTU-CHPP (en Elektrostal, Región de Moscú).
La planta de turbina de gas moderna tradicional (GTU) es un conjunto de compresor de aire, cámara de combustión y turbina de gas, así como sistemas auxiliares que aseguran su funcionamiento. La combinación de una turbina de gas y un generador eléctrico se llama unidad de turbina de gas.
Finalizadas las centrales térmicas de ciclo combinado centrales de ciclo combinado(CCP), que son una combinación de turbinas de gas y turbinas de vapor, lo que permite una alta eficiencia. Los CCGT-TPP pueden ser de condensación (CCGT-CES) y con salida de calor (CCGT-CHP). En la actualidad, cuatro nuevos CCGT-CHPP están operando en Rusia (Severo-Zapadnaya CHPP de San Petersburgo, Kaliningradskaya, CHPP-27 de OAO Mosenergo y Sochinskaya), y también se ha construido una planta combinada de calor y electricidad en Tyumenskaya CHPP. En 2007 se puso en funcionamiento Ivanovskaya CCGT-IES.
Los TPP en bloque consisten en bloques separados, generalmente del mismo tipo plantas de energía- unidades de potencia. En la unidad de potencia, cada caldera suministra vapor solo para su propia turbina, desde la cual regresa después de la condensación solo a su propia caldera. De acuerdo con el esquema de bloque, se construyen todas las poderosas centrales eléctricas de distrito estatal y centrales térmicas, que tienen el llamado sobrecalentamiento intermedio de vapor. La operación de calderas y turbinas en centrales térmicas con enlaces cruzados se proporciona de manera diferente: todas las calderas de centrales térmicas suministran vapor a una tubería de vapor común (colector) y todas turbinas de vapor TPP. De acuerdo con este esquema, los CPP se construyen sin sobrecalentamiento intermedio y casi todos los CHPP se construyen para parámetros de vapor iniciales subcríticos.
Según el nivel de presión inicial, se distinguen TPP de presión subcrítica, presión supercrítica (SKP) y parámetros supersupercríticos (SSCP).
La presión crítica es de 22,1 MPa (225,6 atm). En la industria de energía térmica rusa, los parámetros iniciales están estandarizados: las centrales térmicas y las centrales térmicas se construyen para una presión subcrítica de 8,8 y 12,8 MPa (90 y 130 atm), y para SKD - 23,5 MPa (240 atm). El TPP para parámetros supercríticos por razones técnicas se realiza con sobrecalentamiento intermedio y según el esquema de bloques. Los parámetros supersupercríticos incluyen condicionalmente una presión superior a 24 MPa (hasta 35 MPa) y una temperatura superior a 5600C (hasta 6200C), cuyo uso requiere nuevos materiales y nuevos diseños de equipos. A menudo, las centrales térmicas o las centrales térmicas para diferentes niveles de parámetros se construyen en varias etapas, en colas, cuyos parámetros aumentan con la introducción de cada nueva cola.