Corrosión en la caldera. Corrosión y erosión en calderas de media y baja presión desde el lado del horno. Los fenómenos de corrosión en las calderas aparecen con mayor frecuencia en la superficie interna sometida a esfuerzos térmicos y con relativa menor frecuencia en la exterior.
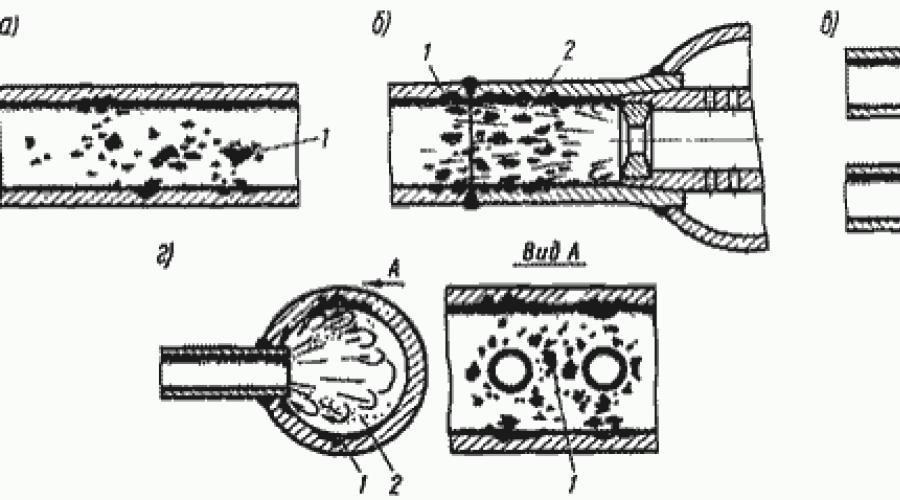
Leer también
Esta corrosión en tamaño e intensidad suele ser más importante y peligrosa que la corrosión de las calderas durante su funcionamiento.
Al dejar agua en los sistemas, dependiendo de su temperatura y acceso de aire, pueden ocurrir una amplia variedad de casos de corrosión por estacionamiento. En primer lugar, cabe señalar la extrema indeseabilidad de la presencia de agua en las tuberías de las unidades cuando se encuentran en reserva.
Si el agua permanece en el sistema por una razón u otra, entonces puede ocurrir una severa corrosión por estacionamiento en el vapor y especialmente en el espacio de agua del tanque (principalmente a lo largo de la línea de flotación) a una temperatura del agua de 60-70 ° C. Por lo tanto, en la práctica, a menudo se observa corrosión de estacionamiento de diferente intensidad, a pesar de los mismos modos de apagado del sistema y la calidad del agua contenida en ellos; los dispositivos con una acumulación térmica significativa están sujetos a una corrosión más severa que los dispositivos que tienen las dimensiones de un horno y una superficie de calentamiento, ya que el agua de la caldera se enfría más rápido; su temperatura cae por debajo de 60-70°C.
A una temperatura del agua superior a 85–90°C (por ejemplo, durante paradas breves del aparato), la corrosión general disminuye y la corrosión del metal del espacio de vapor, en el que se observa una mayor condensación de vapor en este caso , puede superar la corrosión del metal del espacio de agua. La corrosión de estacionamiento en el espacio de vapor es en todos los casos más uniforme que en el espacio de agua de la caldera.
El desarrollo de la corrosión por estacionamiento se ve facilitado en gran medida por los lodos que se acumulan en las superficies de la caldera, que normalmente retienen la humedad. En este sentido, a menudo se encuentran agujeros de corrosión importantes en los áridos y tuberías a lo largo de la generatriz inferior y en sus extremos, es decir, en las zonas de mayor acumulación de lodos.
Métodos de conservación de equipos en reserva
Se pueden utilizar los siguientes métodos para conservar el equipo:
a) secado: eliminación de agua y humedad de los agregados;
b) llenarlos con soluciones de soda cáustica, fosfato, silicato, nitrito de sodio, hidracina;
c) llenar el sistema tecnológico con nitrógeno.
El método de conservación debe elegirse en función de la naturaleza y la duración del tiempo de inactividad, así como del tipo y las características de diseño del equipo.
El tiempo de inactividad del equipo se puede dividir en dos grupos por duración: a corto plazo: no más de 3 días y a largo plazo: más de 3 días.
Hay dos tipos de tiempo de inactividad a corto plazo:
a) programada, asociada al retiro a la reserva los fines de semana por baja de carga o retiro a la reserva por la noche;
b) forzado: debido a fallas en las tuberías o daños a otros componentes del equipo, cuya eliminación no requiere una parada más prolongada.
Dependiendo del propósito, el tiempo de inactividad a largo plazo se puede dividir en los siguientes grupos: a) poner equipos en reserva; b) reparaciones actuales; c) reparaciones capitales.
En caso de tiempo de inactividad breve del equipo, es necesario utilizar la conservación mediante el llenado con agua desaireada manteniendo una sobrepresión o el método de gas (nitrógeno). Si se requiere una parada de emergencia, el único método aceptable es la conservación con nitrógeno.
Cuando el sistema se pone en reserva o parada prolongada sin trabajos de reparación, se aconseja realizar la conservación llenándolo con una solución de nitrito o silicato de sodio. En estos casos, también se puede utilizar la conservación de nitrógeno, tomando necesariamente medidas para crear una estanqueidad del sistema para evitar el consumo excesivo de gas y la operación improductiva de la planta de nitrógeno, así como para crear condiciones seguras para el mantenimiento del equipo.
Los métodos de conservación mediante la creación de un exceso de presión, el llenado con nitrógeno se pueden utilizar independientemente de las características de diseño de las superficies de calentamiento del equipo.
Para evitar la corrosión por estacionamiento del metal durante las reparaciones mayores y actuales, solo son aplicables los métodos de conservación que permitan crear una película protectora sobre la superficie del metal que conserve sus propiedades durante al menos 1 o 2 meses después de drenar la solución conservante, desde el vaciado y la despresurización del sistema son inevitables. La duración de la película protectora sobre la superficie metálica después del tratamiento con nitrito de sodio puede alcanzar los 3 meses.
Los métodos de conservación que utilizan agua y soluciones de reactivos son prácticamente inaceptables para la protección contra la corrosión de estacionamiento de los sobrecalentadores intermedios de las calderas debido a las dificultades asociadas con su llenado y posterior limpieza.
Los métodos para la conservación de agua caliente y calderas de vapor de baja presión, así como otros equipos de circuitos cerrados tecnológicos de suministro de calor y agua, difieren en muchos aspectos de los métodos utilizados actualmente para prevenir la corrosión por estacionamiento en las centrales térmicas. A continuación se describen los principales métodos para prevenir la corrosión en el modo inactivo de equipos de aparatos de dichos sistemas de circulación, teniendo en cuenta las características específicas de su funcionamiento.
Métodos de conservación simplificados
Estos métodos son útiles para calderas pequeñas. Consisten en la eliminación completa del agua de las calderas y la colocación de desecante en ellas: cloruro de calcio calcinado, cal viva, gel de sílice a razón de 1-2 kg por 1 m 3 de volumen.
Este método de conservación es adecuado para temperaturas ambiente por debajo y por encima de cero. En habitaciones calentadas en invierno, se puede implementar uno de los métodos de conservación por contacto. Se trata de llenar todo el volumen interno de la unidad con una solución alcalina (NaOH, Na 3 P0 4, etc.), lo que garantiza la total estabilidad de la película protectora sobre la superficie metálica incluso cuando el líquido está saturado de oxígeno.
Normalmente se utilizan soluciones que contienen de 1,5-2 a 10 kg/m 3 NaOH o 5-20 kg/m 3 Na 3 P0 4 dependiendo del contenido de sales neutras en la fuente de agua. Los valores más pequeños se refieren al condensado, los más grandes al agua que contiene hasta 3000 mg/l de sales neutras.
La corrosión también se puede prevenir mediante el método de sobrepresión, en el que la presión del vapor en la unidad parada se mantiene constantemente a un nivel superior a la presión atmosférica, y la temperatura del agua se mantiene por encima de los 100 °C, lo que impide el acceso del principal agente corrosivo, el oxígeno. .
Una condición importante para la eficacia y economía de cualquier método de protección es la estanqueidad máxima posible de los accesorios de vapor-agua para evitar una disminución demasiado rápida de la presión, la pérdida de una solución protectora (o gas) o la entrada de humedad. Además, en muchos casos, es útil la limpieza preliminar de las superficies de varios depósitos (sales, lodos, incrustaciones).
Al implementar varios métodos de protección contra la corrosión de estacionamiento, se debe tener en cuenta lo siguiente.
1. Para todos los tipos de conservación, es necesario eliminar (lavar) previamente los depósitos de sales fácilmente solubles (ver arriba) para evitar una mayor corrosión por estacionamiento en ciertas áreas de la unidad protegida. Es obligatorio realizar esta medida durante la conservación del contacto, de lo contrario es posible una corrosión local intensa.
2. Por razones similares, es deseable eliminar todo tipo de depósitos insolubles (lodos, incrustaciones, óxidos de hierro) antes de la conservación a largo plazo.
3. Si los accesorios no son confiables, es necesario desconectar el equipo de reserva de las unidades operativas mediante enchufes.
Las fugas de vapor y agua son menos peligrosas con la preservación por contacto, pero son inaceptables con los métodos de protección secos y de gas.
La elección de los desecantes está determinada por la disponibilidad relativa del reactivo y el deseo de obtener el contenido de humedad específico más alto posible. El mejor desecante es el cloruro de calcio granular. La cal viva es mucho peor que el cloruro de calcio, no sólo por su menor capacidad de humedad, sino también por la rápida pérdida de su actividad. La cal absorbe no solo la humedad del aire, sino también el dióxido de carbono, por lo que se cubre con una capa de carbonato de calcio que evita una mayor absorción de la humedad.
Sitio marino Rusia no 05 de octubre de 2016 Creado: 05 de octubre de 2016 Actualizado: 05 de octubre de 2016 Vistas: 5363Tipos de corrosión. Durante el funcionamiento, los elementos de una caldera de vapor están expuestos a medios agresivos: agua, vapor y gases de combustión. Distinguir entre corrosión química y electroquímica.
corrosión química, provocado por el vapor o el agua, destruye el metal uniformemente en toda la superficie. La tasa de tal corrosión en las calderas marinas modernas es baja. Más peligrosa es la corrosión química local provocada por compuestos químicos agresivos contenidos en los depósitos de cenizas (azufre, óxidos de vanadio, etc.).
La más común y peligrosa es corrosión electroquímica, que fluye en soluciones acuosas de electrolitos cuando se produce una corriente eléctrica, provocada por una diferencia de potencial entre secciones individuales del metal, que difieren en heterogeneidad química, temperatura o calidad de procesamiento.
El papel del electrolito lo realiza el agua (con corrosión interna) o el vapor de agua condensado en depósitos (con corrosión externa).
La aparición de tales pares microgalvánicos en la superficie de la tubería conduce al hecho de que los átomos de iones metálicos pasan al agua en forma de iones cargados positivamente, y la superficie de la tubería en este lugar adquiere una carga negativa. Si la diferencia en los potenciales de tales pares microgalvánicos es insignificante, entonces se crea gradualmente una doble capa eléctrica en la interfaz metal-agua, lo que ralentiza el curso posterior del proceso.
Sin embargo, en la mayoría de los casos, los potenciales de las secciones individuales son diferentes, lo que provoca la aparición de un EMF dirigido desde un potencial más grande (ánodo) a uno más pequeño (cátodo).
En este caso, los átomos de iones metálicos pasan del ánodo al agua y el exceso de electrones se acumula en el cátodo. Como resultado, la EMF y, en consecuencia, la intensidad del proceso de destrucción del metal se reducen drásticamente.
Este fenómeno se llama polarización. Si el potencial del ánodo disminuye como resultado de la formación de una película protectora de óxido o un aumento en la concentración de iones metálicos en la región del ánodo, y el potencial del cátodo permanece prácticamente sin cambios, entonces la polarización se llama anódica.
Con la polarización catódica en solución cerca del cátodo, la concentración de iones y moléculas capaces de eliminar el exceso de electrones de la superficie del metal cae bruscamente. De esto se deduce que el punto principal en la lucha contra la corrosión electroquímica es la creación de tales condiciones en las que se mantendrán ambos tipos de polarización.
Es prácticamente imposible lograr esto, ya que el agua de la caldera siempre contiene despolarizantes, sustancias que causan la interrupción de los procesos de polarización.
Los despolarizadores incluyen moléculas de O 2 y CO 2, iones H +, Cl - y SO - 4, así como óxidos de hierro y cobre. Disueltos en agua, el CO 2 , el Cl - y el SO - 4 inhiben la formación de una densa película protectora de óxido sobre el ánodo y contribuyen así al curso intensivo de los procesos anódicos. Los iones de hidrógeno H+ reducen la carga negativa del cátodo.
La influencia del oxígeno sobre la velocidad de corrosión comenzó a manifestarse en dos direcciones opuestas. Por un lado, el oxígeno aumenta la velocidad del proceso de corrosión, ya que es un fuerte despolarizador de las secciones catódicas, por otro lado, tiene un efecto pasivante sobre la superficie.
Por lo general, las partes de la caldera hechas de acero tienen una película de óxido inicial lo suficientemente fuerte que protege el material de la exposición al oxígeno hasta que se destruye por factores químicos o mecánicos.
La velocidad de las reacciones heterogéneas (incluida la corrosión) está regulada por la intensidad de los siguientes procesos: suministro de reactivos (principalmente despolarizantes) a la superficie del material; destrucción de la película protectora de óxido; eliminación de los productos de reacción del lugar de su ocurrencia.
La intensidad de estos procesos está determinada en gran medida por factores hidrodinámicos, mecánicos y térmicos. Por lo tanto, las medidas para reducir la concentración de productos químicos agresivos a alta intensidad de los otros dos procesos, como muestra la experiencia de funcionamiento de calderas, suelen ser ineficaces.
De ello se deduce que la solución al problema de la prevención del daño por corrosión debe ser compleja, cuando se tienen en cuenta todos los factores que influyen en las causas iniciales de la destrucción de los materiales.
Corrosión electroquímica
Según el lugar del flujo y las sustancias involucradas en las reacciones, se distinguen los siguientes tipos de corrosión electroquímica:
- oxígeno (y su variedad - estacionamiento),
- sublodo (a veces llamado "capa"),
- intergranular (fragilidad alcalina de los aceros para calderas),
- ranura y
- sulfuroso.
corrosión por oxígeno observado en economizadores, accesorios, bajantes y alimentadores, colectores de vapor-agua y dispositivos intra-colectores (protecciones, tuberías, atemperadores, etc.). Los serpentines del circuito secundario de las calderas de doble circuito, que utilizan calderas y calentadores de aire a vapor, son especialmente susceptibles a la corrosión por oxígeno. La corrosión por oxígeno se produce durante el funcionamiento de las calderas y depende de la concentración de oxígeno disuelto en el agua de la caldera.
La tasa de corrosión por oxígeno en las calderas principales es baja, debido a la operación eficiente de los desaireadores y al régimen de agua de fosfato-nitrato. En calderas acuotubulares auxiliares suele alcanzar 0,5 - 1 mm/año, aunque de media se sitúa en el rango de 0,05 - 0,2 mm/año. La naturaleza del daño a los aceros de las calderas son pequeños hoyos.
Un tipo más peligroso de corrosión por oxígeno es corrosión de estacionamiento fluyendo durante el período de inactividad de la caldera. Debido a las características específicas de la operación, todas las calderas de los barcos (especialmente las calderas auxiliares) están sujetas a una intensa corrosión por estacionamiento. Como regla general, la corrosión de estacionamiento no provoca fallas en la caldera, sin embargo, el metal corroído durante las paradas, ceteris paribus, se destruye más intensamente durante el funcionamiento de la caldera.
La causa principal de la corrosión por estacionamiento es la entrada de oxígeno en el agua si la caldera está llena, o en la película de humedad de la superficie metálica si la caldera está seca. Los cloruros y el NaOH contenidos en el agua y los depósitos de sal solubles en agua juegan un papel importante.
Si hay cloruros en el agua, se intensifica la corrosión uniforme del metal, y si contiene una pequeña cantidad de álcalis (menos de 100 mg/l), la corrosión es localizada. Para evitar la corrosión por estacionamiento a una temperatura de 20 - 25 °C, el agua debe contener hasta 200 mg/l de NaOH.
Signos externos de corrosión con la participación de oxígeno: pequeñas úlceras locales (Fig. 1, a), llenas de productos de corrosión marrones, que forman tubérculos sobre las úlceras.
La eliminación de oxígeno del agua de alimentación es una de las medidas importantes para reducir la corrosión por oxígeno. Desde 1986, el contenido de oxígeno en el agua de alimentación de las calderas auxiliares y residuales marinas se ha limitado a 0,1 mg/l.
Sin embargo, incluso con tal contenido de oxígeno en el agua de alimentación, se observan daños por corrosión en los elementos de la caldera durante la operación, lo que indica la influencia predominante de los procesos de destrucción de la película de óxido y la lixiviación de los productos de reacción de los centros de corrosión. El ejemplo más ilustrativo que ilustra el efecto de estos procesos sobre el daño por corrosión es la destrucción de los serpentines de utilizar calderas con circulación forzada.
Arroz. 1. Daños debido a la corrosión por oxígeno
daños por corrosión en caso de corrosión por oxígeno, generalmente se localizan estrictamente: en la superficie interna de las secciones de entrada (ver Fig. 1, a), en el área de las curvas (Fig. 1, b), en las secciones de salida y en el codo de la bobina (ver Fig. 1, c), así como en colectores de vapor y agua de calderas de utilización (ver Fig. 1, d). Es en estas áreas (2 - el área de cavitación cerca de la pared) donde las características hidrodinámicas del flujo crean condiciones para la destrucción de la película de óxido y el lavado intensivo de los productos de corrosión.
De hecho, toda deformación del flujo de agua y de la mezcla vapor-agua se acompaña de la aparición cavitación en capas cercanas a la pared flujo de expansión 2, donde las burbujas de vapor formadas y que colapsan inmediatamente provocan la destrucción de la película de óxido debido a la energía de los microshocks hidráulicos.
Esto también se ve facilitado por tensiones alternas en la película, causadas por la vibración de las bobinas y las fluctuaciones de temperatura y presión. El aumento de la turbulencia del flujo local en estas áreas provoca un lavado activo de los productos de corrosión.
En las secciones de salida directa de las bobinas, la película de óxido se destruye debido a los impactos en la superficie de las gotas de agua durante las pulsaciones turbulentas del flujo de la mezcla de vapor y agua, cuyo modo de movimiento anular disperso pasa aquí a uno disperso en una velocidad de flujo de hasta 20-25 m/s.
En estas condiciones, incluso un bajo contenido de oxígeno (~ 0,1 mg/l) provoca una intensa destrucción del metal, lo que conduce a la aparición de fístulas en las secciones de entrada de los serpentines de las calderas de calor residual del tipo La Mont después de 2- 4 años de operación, y en otras áreas, después de 6-12 años.
Arroz. Fig. 2. Daño por corrosión en los serpentines del economizador de las calderas de utilización KUP1500R de la motonave "Indira Gandhi".
Como ilustración de lo anterior, consideremos las causas de daño en los serpentines economizadores de dos calderas de aprovechamiento del tipo KUP1500R instaladas en el portamechero Indira Gandhi (tipo Alexey Kosygin), que entró en servicio en octubre de 1985. Ya en febrero de 1987 por avería se cambiaron economizadores de ambas calderas. Después de 3 años, también aparecen daños en las bobinas de estos economizadores, ubicados en áreas de hasta 1-1,5 m del colector de admisión. La naturaleza del daño indica (Fig. 2, a, b) corrosión típica por oxígeno seguida de falla por fatiga (fisuras transversales).
Sin embargo, la naturaleza de la fatiga en áreas individuales es diferente. La aparición de una grieta (y antes, el agrietamiento de la película de óxido) en el área de la soldadura (ver Fig. 2, a) es consecuencia de tensiones alternas causadas por la vibración del haz de tubos y la característica de diseño de la unión de las bobinas con el cabezal (el extremo de la bobina de 22x3 de diámetro se suelda a un accesorio curvo de 22x2 de diámetro).
La destrucción de la película de óxido y la formación de grietas por fatiga en la superficie interna de las secciones rectas de las bobinas, alejadas de la entrada por 700-1000 mm (ver Fig. 2, b), se deben a tensiones térmicas alternas que ocurren durante la puesta en marcha de la caldera, cuando se suministra agua fría a la superficie caliente. En este caso, la acción de las tensiones térmicas se ve reforzada por el hecho de que el aleteo de las bobinas dificulta que el metal de la tubería se expanda libremente, creando tensiones adicionales en el metal.
Corrosión bajo lodo generalmente se observa en las calderas acuotubulares principales en las superficies internas de la pantalla y en las tuberías de vapor de los haces de entrada que miran hacia la antorcha. La naturaleza de la corrosión por debajo del lodo son picaduras ovaladas con un tamaño a lo largo del eje principal (paralelas al eje de la tubería) de hasta 30-100 mm.
Hay una capa densa de óxidos en forma de "cáscaras" 3 en las úlceras (Fig. 3). La corrosión por suspensión se produce en presencia de despolarizadores sólidos: óxidos de hierro y cobre 2, que se depositan en la tubería más sometida a estrés térmico. secciones en lugares de centros de corrosión activos que ocurren durante la destrucción de películas de óxido.
En la parte superior se forma una capa suelta de incrustaciones y productos de corrosión.
Para las calderas auxiliares, este tipo de corrosión no es típico, pero bajo altas cargas térmicas y modos de tratamiento de agua apropiados, no se excluye la aparición de corrosión debajo del lodo en estas calderas.
La corrosión más activa de las tuberías de pantalla se manifiesta en lugares donde se concentran las impurezas del refrigerante. Esto incluye secciones de tubos de pared con altas cargas térmicas, donde se produce una evaporación profunda del agua de la caldera (especialmente si hay depósitos porosos de baja conductividad térmica en la superficie de evaporación). Por lo tanto, en relación con la prevención de daños a las tuberías de pantalla asociados con la corrosión interna del metal, es necesario tener en cuenta la necesidad de un enfoque integrado, es decir, impacto tanto en los regímenes de agua y productos químicos como en los hornos.
El daño del tubo de pared es principalmente de naturaleza mixta, se pueden dividir condicionalmente en dos grupos:
1) Daños con signos de sobrecalentamiento del acero (deformación y adelgazamiento de las paredes de la tubería en el punto de destrucción; presencia de granos de grafito, etc.).
2) Fracturas frágiles sin signos característicos de sobrecalentamiento del metal.
Se observaron depósitos significativos de un carácter de dos capas en la superficie interna de muchas tuberías: la superior está débilmente adherida, la inferior está descascarada, fuertemente adherida al metal. El grosor de la capa de escala inferior es de 0,4-0,75 mm. En la zona de daño, la escala en la superficie interior se destruye. Cerca de los sitios de destrucción ya cierta distancia de ellos, la superficie interna de las tuberías se ve afectada por hoyos de corrosión y microdaños por fragilidad.
La apariencia general del daño indica la naturaleza térmica de la destrucción. Los cambios estructurales en el lado frontal de los tubos - esferidización profunda y descomposición de perlita, formación de grafito (transición de carbono a grafito 45-85%) - indican que no solo se superó la temperatura de funcionamiento de las pantallas, sino también la permitida para el acero 20.500 ºC La presencia de FeO también confirma el alto nivel de temperaturas del metal durante el funcionamiento (por encima de 845 oK, es decir, 572 oC).
El daño por fragilidad causado por el hidrógeno generalmente ocurre en áreas con altos flujos de calor, bajo capas gruesas de depósitos y tuberías inclinadas u horizontales, así como en áreas de transferencia de calor cerca de anillos de respaldo de soldadura u otros dispositivos que impiden el libre movimiento de los flujos. .Experiencia ha demostrado que el daño por hidrógeno ocurre en calderas que operan a presiones inferiores a 1000 psi. pulgada (6,9 MPa).
El daño por hidrógeno generalmente resulta en rupturas con bordes gruesos. Otros mecanismos que contribuyen a la formación de grietas con bordes gruesos son el agrietamiento por corrosión bajo tensión, la fatiga por corrosión, las fracturas por tensión y (en algunos casos raros) el sobrecalentamiento severo. Puede ser difícil distinguir visualmente el daño causado por el hidrógeno de otros tipos de daño, pero algunas de sus características pueden ayudar aquí.
Por ejemplo, el daño por hidrógeno casi siempre está asociado con la formación de agujeros en el metal (ver las precauciones dadas en los Capítulos 4 y 6). Otros tipos de daños (con la posible excepción de la fatiga por corrosión, que a menudo comienza en capas individuales) no suelen estar asociados con una corrosión severa.
Las fallas en las tuberías como resultado del daño por hidrógeno metálico a menudo se manifiestan como la formación de una "ventana" rectangular en la pared de la tubería, lo cual no es típico de otros tipos de destrucción.
Para evaluar la capacidad de daño de las tuberías de pantalla, debe tenerse en cuenta que el contenido metalúrgico (inicial) de hidrógeno gaseoso en el acero perlítico (incluido el acero 20) no supera los 0,5–1 cm3/100 g. Cuando el contenido de hidrógeno es superior a 4-5 cm3/100g, las propiedades mecánicas del acero se deterioran significativamente. En este caso, es necesario centrarse principalmente en el contenido local de hidrógeno residual, ya que en el caso de fracturas frágiles de las tuberías de pantalla, se observa un fuerte deterioro de las propiedades del metal solo en una zona estrecha a lo largo de la sección transversal de la tubería. con una estructura y propiedades mecánicas invariablemente satisfactorias del metal adyacente a una distancia de solo 0,2-2 mm.
Los valores obtenidos de las concentraciones medias de hidrógeno en el borde de la destrucción son 5-10 veces superiores a su contenido inicial para la estación 20, lo que no podría sino tener un efecto significativo en el daño de las tuberías.
Los resultados presentados indican que la fragilización por hidrógeno resultó ser el factor decisivo en el daño de los tubos de pared de las calderas KrCHPP.
Se requirió un estudio adicional de cuál de los factores tiene una influencia decisiva en este proceso: a) ciclos térmicos debido a la desestabilización del régimen normal de ebullición en áreas de aumento de los flujos de calor en presencia de depósitos en la superficie evaporativa, y, como resultado , daño a las películas protectoras de óxido que lo recubren; b) la presencia en el medio de trabajo de impurezas corrosivas, concentrándose en depósitos cerca de la superficie de evaporación; c) la acción combinada de los factores "a" y "b".
La cuestión del papel del régimen de hornos es de particular interés. La naturaleza de las curvas indica la acumulación de hidrógeno en varios casos cerca de la superficie exterior de los tubos de pantalla. Esto es posible, en primer lugar, si hay una capa densa de sulfuros en la superficie indicada, que son en gran medida impermeables al hidrógeno que se difunde desde la superficie interior hacia la exterior. La formación de sulfuros se debe a: alto contenido de azufre del combustible quemado; lanzando una antorcha en los paneles de la pantalla. Otra razón para la hidrogenación del metal en la superficie exterior es la aparición de procesos de corrosión cuando el metal entra en contacto con los gases de combustión. Como mostró el análisis de los depósitos externos de las tuberías de la caldera, por lo general se produjeron ambas causas.
El papel del modo de combustión también se manifiesta en la corrosión de las tuberías de pantalla bajo la acción del agua pura, que se observa con mayor frecuencia en los generadores de vapor de alta presión. Los focos de corrosión suelen estar ubicados en la zona de máximas cargas térmicas locales y solo en la superficie calentada de la tubería. Este fenómeno conduce a la formación de depresiones redondas o elípticas con un diámetro superior a 1 cm.
El sobrecalentamiento del metal ocurre con mayor frecuencia en presencia de depósitos debido al hecho de que la cantidad de calor percibido será casi la misma tanto para una tubería limpia como para una tubería que contiene incrustaciones, la temperatura de la tubería será diferente.
Los fenómenos de corrosión en las calderas aparecen con mayor frecuencia en la superficie interna sometida a esfuerzos térmicos y con relativa menor frecuencia en la exterior.
En este último caso, la destrucción del metal se debe, en la mayoría de los casos, a la acción combinada de la corrosión y la erosión, que en ocasiones tiene un significado predominante.
Un signo externo de destrucción por erosión es una superficie metálica limpia. Bajo acción corrosiva, los productos de corrosión generalmente permanecen en su superficie.
Los procesos de corrosión e incrustaciones internas (en el ambiente del agua) pueden agravar la corrosión externa (en el ambiente del gas) debido a la resistencia térmica de la capa de incrustaciones y depósitos de corrosión y, en consecuencia, al aumento de la temperatura en la superficie del metal.
La corrosión externa del metal (del lado del horno de la caldera) depende de varios factores, pero, sobre todo, del tipo y composición del combustible que se quema.
Corrosión de calderas de gas-oil
El fuel oil contiene compuestos orgánicos de vanadio y sodio. Si se acumulan depósitos fundidos de escoria que contienen compuestos de vanadio (V) en la pared de la tubería frente al horno, entonces con un gran exceso de aire y / o una temperatura de la superficie del metal de 520-880 ° C, ocurren las siguientes reacciones:
4Fe + 3V2O5 = 2Fe2O3 + 3V2O3 (1)
V2O3 + O2 = V2O5 (2)
Fe2O3 + V2O5 = 2FeVO4 (3)
7Fe + 8FeVO4 = 5Fe3O4 + 4V2O3 (4)
(Compuestos de sodio) + O2 = Na2O (5)
También es posible otro mecanismo de corrosión que involucra al vanadio (mezcla eutéctica líquida):
2Na2O. V2O4. 5V2O5 + O2 = 2Na2O. 6V2O5 (6)
Na2O. 6V2O5 + M = Na2O. V2O4. 5V2O5 + MO (7)
(M - metálico)
Los compuestos de vanadio y sodio se oxidan a V2O5 y Na2O durante la combustión del combustible. En los depósitos que se adhieren a la superficie del metal, el Na2O es un aglomerante. El líquido formado como resultado de las reacciones (1)-(7) derrite la película protectora de magnetita (Fe3O4), lo que conduce a la oxidación del metal debajo de los depósitos (la temperatura de fusión de los depósitos (escoria) es 590-880 ° C).
Como resultado de estos procesos, las paredes de los tubos de pantalla que miran hacia el horno se adelgazan uniformemente.
El aumento de la temperatura del metal, en el que los compuestos de vanadio se vuelven líquidos, se ve facilitado por los depósitos internos de incrustaciones en las tuberías. Y así, cuando se alcanza la temperatura límite de fluencia del metal, se produce una rotura de la tubería, como consecuencia de la acción combinada de los depósitos externos e internos.
Las partes de sujeción de las pantallas de las tuberías, así como las protuberancias de las soldaduras de las tuberías, también se corroen; el aumento de temperatura en su superficie se acelera: la mezcla de vapor y agua no las enfría, como las tuberías.
El fuel oil puede contener azufre (2,0-3,5%) en forma de compuestos orgánicos, azufre elemental, sulfato de sodio (Na2SO4), que ingresa al petróleo desde las aguas de formación. En la superficie del metal en tales condiciones, la corrosión por vanadio va acompañada de corrosión por óxido de sulfuro. Su efecto combinado es más pronunciado cuando los depósitos contienen 87% V2O5 y 13% Na2SO4, lo que corresponde al contenido de vanadio y sodio en el fuel oil en una proporción de 13/1.
En invierno, cuando se calienta fuel oil con vapor en tanques (para facilitar el drenaje), ingresa agua adicional en una cantidad de 0.5-5.0%. Consecuencia: aumenta la cantidad de depósitos en las superficies de baja temperatura de la caldera y, obviamente, aumenta la corrosión de las tuberías de combustible y los tanques de combustible.
Además del esquema descrito anteriormente para la destrucción de los tubos de pantalla de la caldera, la corrosión de sobrecalentadores, tubos de festón, conjuntos de calderas, economizadores tiene algunas características debido al aumento, en algunas secciones, de las velocidades del gas, especialmente aquellos que contienen partículas de fuel oil sin quemar y exfoliado. partículas de escoria.
Identificación de la corrosión
La superficie exterior de las tuberías está cubierta con una densa capa similar al esmalte de depósitos grises y grises oscuros. En el lado que mira hacia el horno, hay un adelgazamiento de la tubería: las secciones planas y las grietas poco profundas en forma de "marcas" son claramente visibles si la superficie se limpia de depósitos y películas de óxido.
Si la tubería se destruye en una emergencia, entonces se ve una grieta longitudinal estrecha.
Corrosión de calderas de carbón pulverizado
En la corrosión formada por la acción de los productos de la combustión del carbón, el azufre y sus compuestos tienen una importancia decisiva. Además, los cloruros (principalmente NaCl) y los compuestos de metales alcalinos influyen en el curso de los procesos de corrosión. La corrosión es más probable cuando el carbón contiene más de un 3,5 % de azufre y un 0,25 % de cloro.
Las cenizas volantes que contienen compuestos alcalinos y óxidos de azufre se depositan sobre la superficie del metal a una temperatura de 560-730 °C. En este caso, como resultado de las reacciones en curso, se forman sulfatos alcalinos, por ejemplo, K3Fe(SO4)3 y Na3Fe(SO4)3. Esta escoria fundida, a su vez, destruye (derrite) la capa protectora de óxido sobre el metal: magnetita (Fe3O4).
La tasa de corrosión es máxima a una temperatura del metal de 680-730 °C, con su aumento, la tasa disminuye debido a la descomposición térmica de las sustancias corrosivas.
La mayor corrosión se encuentra en las tuberías de salida del sobrecalentador, donde la temperatura del vapor es más alta.
Identificación de la corrosión
En las tuberías de pantalla, se pueden observar áreas planas a ambos lados de la tubería, que están sujetas a la destrucción por corrosión. Estas áreas están ubicadas en un ángulo de 30-45 °C entre sí y están cubiertas por una capa de sedimentos. Entre ellos hay un área relativamente "limpia", sujeta al impacto "frontal" del flujo de gas.
Los depósitos constan de tres capas: la capa exterior es ceniza volante porosa, la capa intermedia son sulfatos alcalinos solubles en agua blanquecinos y la capa interior es óxidos de hierro negro brillante (Fe3O4) y sulfuros (FeS).
En las partes de baja temperatura de las calderas (economizador, calentador de aire, extractor de aire), la temperatura del metal cae por debajo del "punto de rocío" del ácido sulfúrico.
Cuando se quema combustible sólido, la temperatura del gas disminuye de 1650 °C en la antorcha a 120 °C o menos en la chimenea.
Debido al enfriamiento de los gases, se forma ácido sulfúrico en la fase de vapor y, al entrar en contacto con una superficie metálica más fría, los vapores se condensan para formar ácido sulfúrico líquido. El "punto de rocío" del ácido sulfúrico es de 115-170 °C (tal vez más; depende del contenido de vapor de agua y óxido de azufre (SO3) en la corriente de gas).
El proceso se describe mediante las reacciones:
S + O2 = SO2 (8)
SO3 + H2O = H2SO4 (9)
H2SO4 + Fe = FeSO4 + H2 (10)
En presencia de óxidos de hierro y vanadio, es posible la oxidación catalítica de SO3:
2SO2 + O2 = 2SO3 (11)
En algunos casos, la corrosión por ácido sulfúrico cuando se quema carbón es menos significativa que cuando se quema marrón, esquisto, turba e incluso gas natural, debido a la liberación relativamente mayor de vapor de agua de ellos.
Identificación de la corrosión
Este tipo de corrosión provoca una destrucción uniforme del metal. Por lo general, la superficie es rugosa, con una ligera capa de óxido y es similar a una superficie sin fenómenos corrosivos. Con una exposición prolongada, el metal puede cubrirse con depósitos de productos de corrosión, que deben eliminarse con cuidado durante el examen.
Corrosión durante las interrupciones del servicio
Este tipo de corrosión aparece en el economizador y en aquellos lugares de la caldera donde las superficies exteriores están cubiertas con compuestos de azufre. A medida que la caldera se enfría, la temperatura del metal cae por debajo del "punto de rocío" y, como se describió anteriormente, si hay depósitos de azufre, se forma ácido sulfúrico. Quizás un compuesto intermedio sea el ácido sulfúrico (H2SO3), pero es muy inestable e inmediatamente se convierte en ácido sulfúrico.
Identificación de la corrosión
Las superficies metálicas suelen estar recubiertas con revestimientos. Si se eliminan, se encontrarán áreas de destrucción de metal, donde hubo depósitos de azufre y áreas de metal no corroído. Esta apariencia distingue la corrosión en una caldera parada de la corrosión descrita anteriormente del metal del economizador y otras partes "frías" de la caldera en funcionamiento.
Al lavar la caldera, los fenómenos de corrosión se distribuyen más o menos uniformemente sobre la superficie metálica debido a la erosión de los depósitos de azufre y al secado insuficiente de las superficies. Con un lavado insuficiente, la corrosión se localiza donde había compuestos de azufre.
erosión de metales
Bajo ciertas condiciones, varios sistemas de calderas están expuestos a la destrucción por erosión del metal, tanto desde el interior como desde el exterior del metal calentado, y donde se producen flujos turbulentos a alta velocidad.
A continuación sólo se considera la erosión de la turbina.
Las turbinas están sujetas a la erosión por el impacto de partículas sólidas y gotas de condensado de vapor. Las partículas sólidas (óxidos) se exfolian desde la superficie interna de los sobrecalentadores y las tuberías de vapor, especialmente en condiciones de procesos térmicos transitorios.
Las gotas de condensado de vapor destruyen principalmente las superficies de los álabes de la última etapa de la turbina y las tuberías de drenaje. Los efectos erosivos y corrosivos del condensado de vapor son posibles si el condensado es "agrio": el pH está por debajo de cinco unidades. La corrosión también es peligrosa en presencia de vapor de cloruro (hasta un 12 % del peso de los depósitos) y soda cáustica en gotas de agua.
Identificación de la erosión
La destrucción del metal por los impactos de las gotas de condensado es más notable en los bordes de ataque de las palas de las turbinas. Los bordes están cubiertos con dientes transversales delgados y ranuras (ranuras), puede haber protuberancias cónicas inclinadas dirigidas hacia los impactos. Hay protuberancias en los bordes de ataque de las palas y están casi ausentes en sus planos posteriores.
Los daños causados por partículas sólidas se presentan en forma de espacios, microabolladuras y muescas en los bordes delanteros de las palas. Las ranuras y los conos inclinados están ausentes.
La identificación de los tipos de corrosión es difícil y, por lo tanto, no son infrecuentes los errores al determinar las medidas tecnológica y económicamente óptimas para contrarrestar la corrosión. Las principales medidas necesarias se toman de acuerdo con la normativa, que establece los límites de los principales iniciadores de la corrosión.
GOST 20995-75 “Calderas de vapor estacionarias con presión de hasta 3,9 MPa. Indicadores de calidad del agua de alimentación y del vapor” estandariza los indicadores en el agua de alimentación: transparencia, es decir, la cantidad de impurezas en suspensión; dureza general, contenido de compuestos de hierro y cobre - prevención de la formación de incrustaciones y depósitos de óxido de hierro y cobre; Valor de pH: prevención de la corrosión alcalina y ácida y también formación de espuma en el tambor de la caldera; contenido de oxígeno - prevención de la corrosión por oxígeno; contenido de nitrito - prevención de la corrosión por nitrito; contenido de aceite - prevención de la formación de espuma en el tambor de la caldera.
GOST determina los valores de las normas según la presión en la caldera (por lo tanto, la temperatura del agua), la potencia del flujo de calor local y la tecnología de tratamiento del agua.
Al investigar las causas de la corrosión, en primer lugar, es necesario inspeccionar (cuando estén disponibles) los lugares de destrucción de metales, analizar las condiciones de funcionamiento de la caldera en el período previo al accidente, analizar la calidad del agua de alimentación, vapor y depósitos , y analizar las características de diseño de la caldera.
En un examen externo, se pueden sospechar los siguientes tipos de corrosión.
corrosión por oxígeno
: secciones de tubería de entrada de economizadores de acero; tuberías de suministro cuando se encuentran con agua insuficientemente desoxigenada (por encima de lo normal): "avances" de oxígeno en caso de desaireación deficiente; calentadores de agua de alimentación; todas las áreas húmedas de la caldera durante su parada y la falta de medidas para evitar que entre aire en la caldera, especialmente en áreas estancadas, al drenar el agua, donde es difícil eliminar el condensado de vapor o llenarlo completamente con agua, por ejemplo, tubos verticales de sobrecalentadores. Durante el tiempo de inactividad, la corrosión aumenta (se localiza) en presencia de álcali (menos de 100 mg/l).
La corrosión por oxígeno rara vez (cuando el contenido de oxígeno en el agua es significativamente más alto que la norma - 0,3 mg / l) se manifiesta en los dispositivos de separación de vapor de los tambores de la caldera y en la pared de los tambores en el límite del nivel del agua; en bajantes. En las tuberías ascendentes, no se produce corrosión debido al efecto desaireador de las burbujas de vapor.
Tipo y naturaleza del daño.. Úlceras de varias profundidades y diámetros, a menudo cubiertas de tubérculos, cuya corteza superior son óxidos de hierro rojizos (probablemente hematita Fe 2 O 3). Evidencia de corrosión activa: debajo de la corteza de los tubérculos: un precipitado líquido negro, probablemente magnetita (Fe 3 O 4) mezclada con sulfatos y cloruros. Con la corrosión amortiguada, hay un vacío debajo de la costra y el fondo de la úlcera está cubierto con depósitos de escamas y lodo.
A pH > 8,5: las úlceras son raras, pero más grandes y profundas, a pH< 8,5 - встречаются чаще, но меньших размеров. Только вскрытие бугорков помогает интерпретировать бугорки не как поверхностные отложения, а как следствие коррозии.
A una velocidad del agua superior a 2 m/s, los tubérculos pueden adoptar una forma oblonga en la dirección del chorro.
. Las costras de magnetita son lo suficientemente densas y podrían servir como una barrera confiable para la penetración de oxígeno en los tubérculos. Pero a menudo se destruyen como resultado de la fatiga por corrosión, cuando la temperatura del agua y el metal cambia cíclicamente: paradas y arranques frecuentes de la caldera, movimiento pulsante de la mezcla de vapor y agua, estratificación de la mezcla de vapor y agua en vapor y agua separados. tapones de agua que siguen uno tras otro.
La corrosión se intensifica con un aumento de la temperatura (hasta 350 °C) y un aumento del contenido de cloruro en el agua de la caldera. A veces, la corrosión se ve reforzada por los productos de descomposición térmica de ciertas sustancias orgánicas en el agua de alimentación.
Arroz. 1. La aparición de corrosión por oxígeno.
Corrosión alcalina (en un sentido más estricto, intergranular)
Lugares de daños por corrosión en el metal.. Tuberías en zonas de flujo de calor de alta potencia (área del quemador y frente al soplete alargado) - 300-400 kW / m 2 y donde la temperatura del metal es 5-10 ° C superior al punto de ebullición del agua a una presión dada; tuberías inclinadas y horizontales, donde hay poca circulación de agua; lugares bajo depósitos gruesos; zonas cerca de los anillos de respaldo y en las propias soldaduras, por ejemplo, en los lugares de soldadura de dispositivos separadores de vapor intratambor; lugares cerca de los remaches.
Tipo y naturaleza del daño.. Depresiones semiesféricas o elípticas llenas de productos de corrosión, que a menudo incluyen cristales brillantes de magnetita (Fe 3 O 4). La mayoría de los huecos están cubiertos con una costra dura. En el lado de las tuberías que miran hacia el horno, los huecos se pueden conectar, formando el llamado camino de corrosión de 20-40 mm de ancho y hasta 2-3 m de largo.
Si la costra no es lo suficientemente estable y densa, la corrosión puede conducir, en condiciones de estrés mecánico, a la aparición de grietas en el metal, especialmente cerca de las grietas: remaches, juntas rodantes, puntos de soldadura de dispositivos de separación de vapor.
Causas del daño por corrosión. A altas temperaturas - más de 200 ° C - y una alta concentración de sosa cáustica (NaOH) - 10% o más - la película protectora (corteza) sobre el metal se destruye:
4NaOH + Fe 3 O 4 \u003d 2NaFeO 2 + Na 2 FeO 2 + 2H 2 O (1)
El producto intermedio NaFeO 2 sufre hidrólisis:
4NAFeО 2 + 2Н 2 О = 4NAОН + 2Fe 2 О 3 + 2Н 2 (2)
Es decir, en esta reacción (2) se reduce el hidróxido de sodio, en las reacciones (1), (2) no se consume, sino que actúa como catalizador.
Cuando se elimina la magnetita, el hidróxido de sodio y el agua pueden reaccionar directamente con el hierro para liberar hidrógeno atómico:
2NaOH + Fe \u003d Na 2 FeO 2 + 2H (3)
4H 2 O + 3Fe \u003d Fe 3 O 4 + 8H (4)
El hidrógeno liberado puede difundirse en el metal y formar metano (CH 4) con carburo de hierro:
4H + Fe 3 C \u003d CH 4 + 3Fe (5)
También es posible combinar hidrógeno atómico en hidrógeno molecular (H + H = H 2).
El metano y el hidrógeno molecular no pueden penetrar en el metal, se acumulan en los límites de grano y, en presencia de grietas, las expanden y profundizan. Además, estos gases evitan la formación y compactación de películas protectoras.
Una solución concentrada de soda cáustica se forma en lugares de evaporación profunda del agua de la caldera: depósitos de sales densos (un tipo de corrosión por lodo); crisis de ebullición de burbujas, cuando se forma una película de vapor estable sobre el metal; allí, el metal casi no se daña, pero la soda cáustica se concentra a lo largo de los bordes de la película, donde tiene lugar la evaporación activa; la presencia de grietas donde se produce la evaporación, que es diferente de la evaporación en todo el volumen de agua: la sosa cáustica se evapora peor que el agua, no es arrastrada por el agua y se acumula. Al actuar sobre el metal, la soda cáustica forma grietas en los límites de los granos dirigidos hacia el interior del metal (un tipo de corrosión intergranular es la corrosión por grietas).
La corrosión intergranular bajo la influencia del agua alcalina de la caldera se concentra con mayor frecuencia en el tambor de la caldera.
Arroz. Fig. 3. Corrosión intergranular: a - microestructura del metal antes de la corrosión, b - microestructura en la etapa de corrosión, formación de grietas a lo largo del límite de grano del metal
Tal efecto corrosivo sobre el metal solo es posible con la presencia simultánea de tres factores:
- tensiones mecánicas de tracción locales próximas o ligeramente superiores al límite elástico, es decir, 2,5 MN/mm2;
- juntas sueltas de partes del tambor (mencionadas anteriormente), donde puede ocurrir una evaporación profunda del agua de la caldera y donde la sosa cáustica acumulada disuelve la película protectora de óxidos de hierro (la concentración de NaOH es superior al 10%, la temperatura del agua es superior a 200 ° C y, especialmente - más cerca de 300 ° C). Si la caldera funciona con una presión inferior a la del pasaporte (por ejemplo, 0,6-0,7 MPa en lugar de 1,4 MPa), la probabilidad de este tipo de corrosión disminuye;
- una combinación desfavorable de sustancias en el agua de la caldera, en la que no hay concentraciones protectoras necesarias de inhibidores de este tipo de corrosión. Las sales de sodio pueden actuar como inhibidores: sulfatos, carbonatos, fosfatos, nitratos, licor de sulfito de celulosa.
Arroz. 4. Aparición de corrosión intergranular
Las grietas por corrosión no se desarrollan si se observa la relación:
(Na 2 SO 4 + Na 2 CO 3 + Na 3 PO 4 + NaNO 3) / (NaOH) ≥ 5, 3 (6)
donde Na 2 SO 4, Na 2 CO 3, Na 3 PO 4, NaNO 3, NaOH - el contenido de sulfato de sodio, carbonato de sodio, fosfato de sodio, nitrato de sodio e hidróxido de sodio, respectivamente, mg / kg.
Las calderas fabricadas actualmente no tienen al menos una de estas condiciones de corrosión.
La presencia de compuestos de silicio en el agua de la caldera también puede aumentar la corrosión intergranular.
El NaCl en estas condiciones no es un inhibidor de la corrosión. Se mostró arriba: los iones de cloro (Сl -) son aceleradores de la corrosión, debido a su alta movilidad y pequeño tamaño, penetran fácilmente en las películas protectoras de óxido y forman sales altamente solubles con hierro (FeCl 2, FeCl 3) en lugar de óxidos de hierro poco solubles .
En el agua de las salas de calderas, tradicionalmente se controlan los valores de la mineralización total y no el contenido de sales individuales. Probablemente, por esta razón, el racionamiento no se introdujo según la relación indicada (6), sino según el valor de la alcalinidad relativa del agua de la caldera:
SH kv rel = SH ov rel = SH ov 40 100/S ov ≤ 20, (7)
donde U q rel - alcalinidad relativa del agua de la caldera,%; Shch ov rel - alcalinidad relativa del agua tratada (adicional), %; Shch ov - Alcalinidad total del agua tratada (adicional), mmol/l; S ov - mineralización del agua tratada (adicional) (incluido el contenido de cloruros), mg / l.
La alcalinidad total del agua tratada (adicional) puede tomarse igual, mmol/l:
- después de la cationización de sodio - alcalinidad total del agua de origen;
- después de la cationización hidrógeno-sodio paralela - (0,3-0,4), o secuencial con regeneración "hambrienta" del filtro de hidrógeno-cationito - (0,5-0,7);
- después de cationización de sodio con acidificación e ionización de cloro de sodio - (0.5-1.0);
- después de la cationización de amonio-sodio - (0.5-0.7);
- después del encalado a 30-40°C - (0,35-1,0);
- después de la coagulación - (W sobre ref - Dto), donde W sobre ref - alcalinidad total de la fuente de agua, mmol/l; D a - dosis de coagulante, mmol/l;
- después de cal sodada a 30-40 °C - (1,0-1,5), ya 60-70 °C - (1,0-1,2).
Se aceptan los valores de la alcalinidad relativa del agua de la caldera según las normas de Rostekhnadzor,%, no más de:
- para calderas con tambores remachados - 20;
- para calderas con tambores soldados y tubos enrollados en ellos - 50;
- para calderas con tambores soldados y tuberías soldadas a ellos: cualquier valor, no estandarizado.
Arroz. 4. El resultado de la corrosión intergranular
Según las normas de Rostekhnadzor, U kv rel es uno de los criterios para el funcionamiento seguro de las calderas. Es más correcto verificar el criterio de potencial agresividad alcalina del agua de caldera, que no tiene en cuenta el contenido de iones de cloro:
K tu = (S ov - [Сl - ]) / 40 u ov, (8)
donde K u - criterio de potencial agresividad alcalina del agua de caldera; S s - salinidad del agua tratada (adicional) (incluido el contenido de cloruros), mg/l; Cl - - el contenido de cloruros en el agua tratada (adicional), mg/l; Shch ov - Alcalinidad total del agua tratada (adicional), mmol/l.
El valor de K u se puede tomar:
- para calderas con tambores remachados con una presión de más de 0,8 MPa ≥ 5;
- para calderas con tambores soldados y tuberías enrolladas con una presión de más de 1,4 MPa ≥ 2;
- para calderas con tambores soldados y tuberías soldadas, así como para calderas con tambores soldados y tuberías enrolladas con una presión de hasta 1,4 MPa y calderas con tambores remachados con una presión de hasta 0,8 MPa, no estandarizar.
Corrosión bajo lodo
Este nombre combina varios tipos diferentes de corrosión (alcalina, oxígeno, etc.). La acumulación de depósitos y lodos sueltos y porosos en diferentes zonas de la caldera provoca la corrosión del metal debajo del lodo. La razón principal: contaminación del agua de alimentación con óxidos de hierro.
Corrosión por nitrito
. Tubos de pantalla y caldera de la caldera en el lado que da al horno.
Tipo y naturaleza del daño.. Grandes úlceras raras, marcadamente limitadas.
. En presencia de iones de nitrito (NO - 2) en el agua de alimentación de más de 20 μg / l, la temperatura del agua es superior a 200 ° C, los nitritos sirven como despolarizadores catódicos de la corrosión electroquímica, recuperando HNO 2, NO, N 2 (ver arriba).
Corrosión vapor-agua
Lugares de daños por corrosión en el metal.. Parte de salida de serpentines de sobrecalentadores, tuberías de vapor sobrecalentado, tuberías generadoras de vapor horizontales y ligeramente inclinadas en áreas de mala circulación de agua, a veces a lo largo de la generatriz superior de los serpentines de salida de economizadores de agua en ebullición.
Tipo y naturaleza del daño.. Placas de óxidos negros densos de hierro (Fe 3 O 4), firmemente adheridos al metal. Con fluctuaciones de temperatura, la continuidad de la placa (corteza) se rompe, las escamas se caen. Adelgazamiento uniforme del metal con protuberancias, grietas longitudinales, roturas.
Puede identificarse como corrosión subslurry: en forma de hoyos profundos con bordes indistintamente delimitados, más a menudo cerca de soldaduras que sobresalen en el interior de la tubería, donde se acumula el lodo.
Causas del daño por corrosión:
- medio de lavado: vapor en sobrecalentadores, tuberías de vapor, "almohadas" de vapor debajo de una capa de lodo;
- la temperatura del metal (acero 20) es superior a 450 ° C, el flujo de calor a la sección de metal es de 450 kW / m 2;
- violación del modo de combustión: escoria de los quemadores, aumento de la contaminación de las tuberías por dentro y por fuera, combustión inestable (vibratoria), alargamiento de la antorcha hacia las tuberías de las pantallas.
Como resultado: interacción química directa del hierro con el vapor de agua (ver arriba).
Corrosión microbiológica
Causada por bacterias aerobias y anaerobias, aparece a temperaturas de 20-80 °C.
Lugares de daño de metal.. Tuberías y recipientes a la caldera con agua de la temperatura especificada.
Tipo y naturaleza del daño.. Tubérculos de diferentes tamaños: diámetro de varios milímetros a varios centímetros, rara vez, varias decenas de centímetros. Los tubérculos están cubiertos con óxidos de hierro densos, un producto de desecho de las bacterias aeróbicas. En el interior, polvo negro y suspensión (sulfuro de hierro FeS), un producto de bacterias anaeróbicas reductoras de sulfato, debajo de la formación negra, úlceras redondas.
Causas del daño. Los sulfatos de hierro, el oxígeno y varias bacterias están siempre presentes en el agua natural.
En presencia de oxígeno, las bacterias del hierro forman una película de óxidos de hierro, bajo la cual las bacterias anaerobias reducen los sulfatos a sulfuro de hierro (FeS) y sulfuro de hidrógeno (H 2 S). A su vez, el sulfuro de hidrógeno da lugar a la formación de ácidos sulfuroso (muy inestable) y sulfúrico, y el metal se corroe.
Este tipo de corrosión tiene un efecto indirecto sobre la corrosión de la caldera: el flujo de agua a una velocidad de 2-3 m / s arranca los tubérculos, lleva su contenido a la caldera, aumentando la acumulación de lodos.
En casos raros, esta corrosión puede ocurrir en la propia caldera, si durante un apagado prolongado de la caldera en la reserva se llena con agua a una temperatura de 50-60 ° C, y la temperatura se mantiene debido a la penetración accidental de vapor de calderas vecinas.
Corrosión "quelada"
Ubicaciones de daños por corrosión. Equipos donde se separa el vapor del agua: tambor de caldera, separadores de vapor dentro y fuera del tambor, también - raramente - en tubería de agua de alimentación y economizador.
Tipo y naturaleza del daño.. La superficie del metal es lisa, pero si el medio se mueve a alta velocidad, entonces la superficie corroída no es lisa, tiene depresiones en forma de herradura y "colas" orientadas en la dirección del movimiento. La superficie está cubierta con una fina película mate o negra brillante. No hay depósitos evidentes y no hay productos de corrosión, porque el "quelato" (compuestos orgánicos de poliaminas especialmente introducidos en la caldera) ya ha reaccionado.
En presencia de oxígeno, lo que rara vez ocurre en una caldera que funciona normalmente, la superficie corroída se “anima”: asperezas, islas de metal.
Causas del daño por corrosión. El mecanismo de acción del "quelato" se describió anteriormente ("Salas de calderas industriales y de calefacción y mini-CHP", 1 (6) ΄ 2011, p. 40).
La corrosión del "quelato" ocurre cuando una sobredosis de "quelato", pero incluso en una dosis normal es posible, ya que el "quelato" se concentra en áreas donde hay una evaporación intensa de agua: la ebullición nucleada se reemplaza por una película. En los dispositivos de separación de vapor, hay casos de efecto especialmente destructivo de corrosión "quelada" debido a las altas velocidades turbulentas del agua y la mezcla de vapor y agua.
Todos los daños por corrosión descritos pueden tener un efecto sinérgico, de modo que el daño total por la acción combinada de varios factores de corrosión puede exceder la cantidad de daño por tipos individuales de corrosión.
Como regla general, la acción de los agentes corrosivos mejora el régimen térmico inestable de la caldera, lo que provoca fatiga por corrosión y excita la corrosión por fatiga térmica: el número de arranques desde un estado frío es más de 100, el número total de arranques es más de 200 Dado que estos tipos de destrucción de metales son raros, las grietas y las tuberías rotas tienen una apariencia idéntica a las lesiones metálicas de varios tipos de corrosión.
Por lo general, para identificar la causa de la destrucción del metal, se requieren estudios metalográficos adicionales: radiografía, ultrasonido, color y detección de defectos por partículas magnéticas.
Varios investigadores han propuesto programas para diagnosticar tipos de daños por corrosión en aceros para calderas. El programa VTI (A.F. Bogachev y colaboradores) es conocido, principalmente para calderas de potencia de alta presión, y el desarrollo de la asociación Energochermet, principalmente para calderas de potencia de baja y media presión y calderas de calor residual.