Características de los productos de combustión emitidos por las calderas a la atmósfera. Combustión completa e incompleta de gas Combustión completa e incompleta de gas
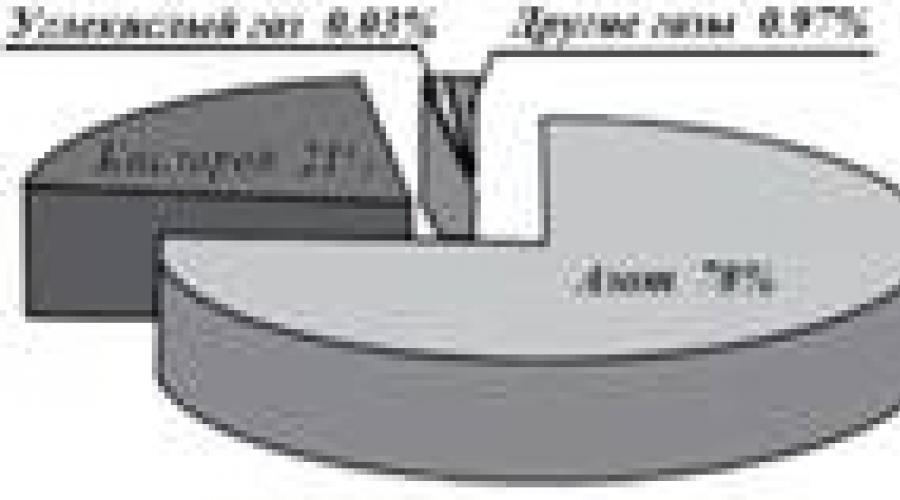
Leer también
Contenido de la sección
Al quemar combustibles orgánicos en hornos de calderas, se forman varios productos de combustión, como óxidos de carbono CO x \u003d CO + CO 2, vapor de agua H 2 O, óxidos de azufre SO x \u003d SO 2 + SO 3, óxidos de nitrógeno NO x \ u003d NO + NO 2 , hidrocarburos aromáticos policíclicos (HAP), fluoruros, compuestos de vanadio V 2 O 5 , material particulado, etc. (ver Tabla 7.1.1). En el caso de la combustión incompleta del combustible en los hornos, los gases de escape también pueden contener hidrocarburos CH4, C2H4, etc. Todos los productos de la combustión incompleta son dañinos, pero su formación se puede minimizar con la tecnología moderna de combustión de combustible [1].
Tabla 7.1.1. Emisiones específicas de la quema de combustibles orgánicos en calderas de potencia [3]
Símbolos: A p, S p – respectivamente, el contenido de ceniza y azufre por masa de trabajo de combustible, %.
El criterio para la evaluación sanitaria del medio ambiente es la concentración máxima permisible (MAC) de una sustancia nociva en el aire atmosférico a nivel del suelo. MPC debe entenderse como una concentración tal de diversas sustancias y compuestos químicos que, con la exposición diaria durante mucho tiempo al cuerpo humano, no causa ningún cambio patológico o enfermedad.
Las concentraciones máximas permitidas (MPC) de sustancias nocivas en el aire atmosférico de las áreas pobladas se dan en la Tabla. 7.1.2 [4]. La concentración máxima de una sola vez de sustancias nocivas se determina mediante muestras tomadas dentro de los 20 minutos, el promedio diario, por día.
Tabla 7.1.2. Concentraciones máximas permisibles de sustancias nocivas en el aire atmosférico de áreas pobladas
Contaminante | Concentración máxima admisible, mg/m 3 | |
Máximo una vez | Promedio diario | |
Polvo no tóxico | 0,5 | 0,15 |
dióxido de azufre | 0,5 | 0,05 |
monóxido de carbono | 3,0 | 1,0 |
monóxido de carbono | 3,0 | 1,0 |
dioxido de nitrogeno | 0,085 | 0,04 |
Oxido de nitrógeno | 0,6 | 0,06 |
hollín (hollín) | 0,15 | 0,05 |
sulfuro de hidrógeno | 0,008 | 0,008 |
Benz(a)pireno | - | 0,1 µg / 100 m 3 |
pentóxido de vanadio | - | 0,002 |
Compuestos de flúor (para flúor) | 0,02 | 0,005 |
Cloro | 0,1 | 0,03 |
Los cálculos se realizan para cada sustancia nociva por separado, de modo que la concentración de cada uno de ellos no supere los valores indicados en la Tabla. 7.1.2. Para las salas de calderas, estas condiciones se endurecen mediante la introducción de requisitos adicionales sobre la necesidad de sumar los efectos de los óxidos de azufre y nitrógeno, que se determina mediante la expresión
Al mismo tiempo, debido a deficiencias locales de aire o condiciones térmicas y aerodinámicas desfavorables, se forman productos de combustión incompletos en los hornos y cámaras de combustión, que consisten principalmente en monóxido de carbono CO (monóxido de carbono), hidrógeno H 2 y varios hidrocarburos, que caracterizan el calor. pérdidas en la unidad de caldera debido a una combustión química incompleta (quemado químico inferior).
Además, durante el proceso de combustión, se obtienen una serie de compuestos químicos, que se forman como resultado de la oxidación de varios componentes del combustible y nitrógeno en el aire N 2. La parte más significativa de ellos son los óxidos de nitrógeno NO x y el azufre SO x .
Los óxidos de nitrógeno se forman debido a la oxidación tanto del nitrógeno molecular del aire como del nitrógeno contenido en el combustible. Los estudios experimentales han demostrado que la mayor parte del NO x formado en los hornos de las calderas, a saber, el 96 ÷ 100 %, recae sobre el monóxido de nitrógeno (óxido) NO. El dióxido de nitrógeno NO 2 y el hemióxido N 2 O se forman en cantidades mucho más pequeñas, y su participación es aproximadamente: para NO 2 - hasta 4%, y para N 2 O - centésimas de porcentaje de la emisión total de NO x. En condiciones típicas de quema de combustible en calderas, las concentraciones de dióxido de nitrógeno NO 2 son, por regla general, insignificantes en comparación con el contenido de NO y normalmente oscilan entre 0 y 7 ppm hasta 20÷30 ppm. Al mismo tiempo, la rápida mezcla de regiones frías y calientes en una llama turbulenta puede provocar la aparición de concentraciones relativamente grandes de dióxido de nitrógeno en las zonas frías del flujo. Además, se produce una emisión parcial de NO 2 en la parte superior del horno y en la chimenea horizontal (en T> 900÷1000 K) y bajo ciertas condiciones también puede alcanzar tamaños apreciables.
El hemóxido de nitrógeno N 2 O, formado durante la combustión de combustibles, es, aparentemente, un intermedio de corta duración. El N 2 O está prácticamente ausente en los productos de combustión detrás de las calderas.
El azufre contenido en el combustible es fuente de formación de óxidos de azufre SOx: SO 2 sulfuroso (dióxido de azufre) y SO 3 sulfúrico (trióxido de azufre) anhídridos. La emisión másica total de SO x depende únicamente del contenido de azufre en el combustible S p , y su concentración en los gases de combustión también depende del coeficiente de flujo de aire α. Por regla general, la proporción de SO 2 es del 97 ÷ 99 % y la proporción de SO 3 es del 1 ÷ 3 % de la producción total de SO x . El contenido real de SO 2 en los gases que salen de las calderas varía de 0,08 a 0,6%, y la concentración de SO 3, de 0,0001 a 0,008%.
Entre los componentes nocivos de los gases de combustión, un nutrido grupo de hidrocarburos aromáticos policíclicos (HAP) ocupa un lugar especial. Muchos HAP tienen alta actividad cancerígena y (o) mutagénica, activan el smog fotoquímico en las ciudades, lo que requiere un estricto control y limitación de sus emisiones. Al mismo tiempo, algunos HAP, como el fenantreno, el fluoranteno, el pireno y otros, son casi fisiológicamente inertes y no cancerígenos.
Los PAH se forman como resultado de la combustión incompleta de cualquier combustible de hidrocarburo. Esto último ocurre debido a la inhibición de las reacciones de oxidación de los hidrocarburos combustibles por las paredes frías de los dispositivos de combustión, y también puede ser causado por una mezcla insatisfactoria de combustible y aire. Esto conduce a la formación en los hornos (cámaras de combustión) de zonas oxidantes locales con baja temperatura o zonas con exceso de combustible.
Debido al gran número de PAH diferentes en los gases de combustión y la dificultad de medir sus concentraciones, se acostumbra estimar el nivel de contaminación cancerígena de los productos de combustión y el aire atmosférico por la concentración del carcinógeno más fuerte y estable, el benzo(a). pireno (B(a)P) C 20 H 12 .
Debido a la alta toxicidad, se debe hacer una mención especial a productos de combustión de fuel oil como los óxidos de vanadio. El vanadio está contenido en la parte mineral del fuel oil y, cuando se quema, forma óxidos de vanadio VO, VO 2 . Sin embargo, durante la formación de depósitos sobre superficies convectivas, los óxidos de vanadio están presentes principalmente en forma de V 2 O 5 . El pentóxido de vanadio V 2 O 5 es la forma más tóxica de los óxidos de vanadio, por lo que sus emisiones se contabilizan en términos de V 2 O 5 .
Tabla 7.1.3. Concentración aproximada de sustancias nocivas en los productos de combustión durante la quema de combustibles orgánicos en calderas de potencia
Emisiones = | Concentración, mg / m 3 | ||
Gas natural | gasolina | Carbón | |
Óxidos de nitrógeno NO x (en términos de NO 2) | 200÷ 1200 | 300÷ 1000 | 350 ÷1500 |
Dióxido de azufre SO 2 | - | 2000÷6000 | 1000÷5000 |
Anhídrido sulfúrico SO 3 | - | 4÷250 | 2 ÷ 100 |
Monóxido de carbono CO | 10÷125 | 10÷150 | 15÷150 |
Benz (a) pireno C 20 H 12 | (0.1÷1, 0) 10 -3 | (0.2÷4.0) 10 -3 | (0.3÷14) 10 -3 |
Partículas sólidas | - | <100 | 150÷300 |
Durante la combustión de fueloil y combustibles sólidos, las emisiones también contienen material particulado, consistente en cenizas volantes, partículas de hollín, HAP y combustible no quemado como resultado de la subcombustión mecánica.
Los rangos de concentración de sustancias nocivas en los gases de combustión durante la combustión de varios tipos de combustibles se dan en la Tabla. 7.1.3.
antropotoxinas;
Productos de destrucción de materiales poliméricos;
Sustancias que ingresan a la habitación con aire atmosférico contaminado;
Las sustancias químicas liberadas de los materiales poliméricos, incluso en pequeñas cantidades, pueden causar alteraciones significativas en el estado de un organismo vivo, por ejemplo, en el caso de una exposición alérgica a los materiales poliméricos.
La intensidad de la liberación de sustancias volátiles depende de las condiciones de operación de los materiales poliméricos: temperatura, humedad, tasa de intercambio de aire, tiempo de operación.
Se ha establecido una dependencia directa del nivel de contaminación química del aire ambiente con la saturación total del local con materiales poliméricos.
Un organismo en crecimiento es más sensible a los efectos de los componentes volátiles de los materiales poliméricos. También se ha establecido una mayor sensibilidad de los pacientes a los efectos de las sustancias químicas liberadas por los plásticos, en comparación con los sanos. Los estudios han demostrado que en habitaciones con una alta saturación de polímeros, la susceptibilidad de la población a alergias, resfriados, neurastenia, distonía vegetativa e hipertensión fue mayor que en habitaciones donde los materiales poliméricos se usaron en cantidades más pequeñas.
Para garantizar la seguridad del uso de materiales poliméricos, se acepta que las concentraciones de sustancias volátiles liberadas por los polímeros en edificios residenciales y públicos no deben exceder sus MPC establecidos para el aire atmosférico, y la relación total de las concentraciones detectadas de varias sustancias a su MPC no debe exceder uno. A los efectos de la vigilancia sanitaria preventiva de los materiales poliméricos y productos elaborados con ellos, se propone limitar la liberación de sustancias nocivas al medio ambiente o en la etapa de fabricación, o poco tiempo después de su liberación por parte de los fabricantes. Los niveles permisibles de alrededor de 100 sustancias químicas liberadas de los materiales poliméricos ahora se han comprobado.
En la construcción moderna, la tendencia hacia la quimicalización de los procesos tecnológicos y el uso de diversas sustancias como mezclas, principalmente hormigón y hormigón armado, es cada vez más pronunciada. Desde un punto de vista higiénico, es importante tener en cuenta los efectos adversos de los aditivos químicos en los materiales de construcción debido a la liberación de sustancias tóxicas.
No menos poderosa fuente interna de contaminación del ambiente interior son productos de desecho humano antropotoxinas. Se ha establecido que en el proceso de vida una persona libera aproximadamente 400 compuestos químicos.
Los estudios han demostrado que el ambiente de aire de las habitaciones sin ventilación se deteriora en proporción a la cantidad de personas y el tiempo que pasan en la habitación. El análisis químico del aire interior permitió identificar en ellos una serie de sustancias tóxicas, cuya distribución según las clases de peligro es la siguiente: dimetilamina, sulfuro de hidrógeno, dióxido de nitrógeno, óxido de etileno, benceno (la segunda clase de peligro es altamente peligrosa sustancias); ácido acético, fenol, metilestireno, tolueno, metanol, acetato de vinilo (la tercera clase de peligro son las sustancias de bajo peligro). Una quinta parte de las antropotoxinas identificadas se clasifican como sustancias altamente peligrosas. Al mismo tiempo, se encontró que en una habitación sin ventilación, las concentraciones de dimetilamina y sulfuro de hidrógeno excedían el MPC del aire atmosférico. Las concentraciones de sustancias como dióxido de carbono, monóxido de carbono y amoníaco también excedieron el MPC o estaban en su nivel. El resto de las sustancias, si bien ascendían a décimas y fracciones menores de la MPC, en conjunto daban testimonio del ambiente aéreo desfavorable, ya que incluso una permanencia de dos a cuatro horas en estas condiciones tenía un efecto negativo en el rendimiento mental de los sujetos. .
El estudio del ambiente de aire de locales gasificados mostró que durante la combustión horaria de gas en el aire interior, la concentración de sustancias fue (mg / m 3): monóxido de carbono - un promedio de 15, formaldehído - 0.037, óxido de nitrógeno - 0.62 , dióxido de nitrógeno - 0,44, benceno - 0,07. La temperatura del aire en la habitación durante la combustión del gas aumentó de 3 a 6 ° C, la humedad aumentó de 10 a 15%. Además, se observaron altas concentraciones de compuestos químicos no solo en la cocina, sino también en las viviendas del apartamento. Después de apagar los aparatos de gas, el contenido de monóxido de carbono y otras sustancias químicas en el aire disminuyó, pero a veces no volvió a los valores originales incluso después de 1,5 a 2,5 horas.
El estudio del efecto de los productos de combustión de gas doméstico en la respiración externa humana reveló un aumento en la carga del sistema respiratorio y un cambio en el estado funcional del sistema nervioso central.
Una de las fuentes más comunes de contaminación del aire interior es de fumar. El análisis espectrométrico del aire contaminado con humo de tabaco reveló 186 compuestos químicos. En habitaciones con ventilación insuficiente, la contaminación del aire por productos para fumar puede alcanzar el 60-90%.
Al estudiar los efectos de los componentes del humo del tabaco en los no fumadores (fumadores pasivos), los sujetos experimentaron irritación de las membranas mucosas de los ojos, aumento del contenido de carboxihemoglobina en la sangre, aumento de la frecuencia cardíaca y aumento de la presión arterial. . De este modo, principales fuentes de contaminación El ambiente aéreo de las instalaciones se puede dividir condicionalmente en cuatro grupos:
La importancia de las fuentes internas de contaminación en diferentes tipos de edificios no es la misma. En edificios administrativos, el nivel de contaminación total se correlaciona más estrechamente con la saturación de los locales con materiales poliméricos (R = 0,75), en instalaciones deportivas cubiertas, el nivel de contaminación química se correlaciona más bien con el número de personas en ellos (R = 0,75). Para los edificios residenciales, la estrecha correlación entre el nivel de contaminación química tanto con la saturación del local con materiales poliméricos como con el número de personas en el local es aproximadamente la misma.
La contaminación química del aire ambiental de los edificios residenciales y públicos bajo ciertas condiciones (mala ventilación, saturación excesiva de los locales con materiales poliméricos, grandes multitudes, etc.) puede alcanzar un nivel que tiene un impacto negativo en el estado general del cuerpo humano. .
En los últimos años, según la OMS, el número de informes del llamado síndrome del edificio enfermo ha aumentado significativamente. Los síntomas descritos de deterioro de la salud de las personas que viven o trabajan en dichos edificios son muy diversos, pero también tienen una serie de características comunes, a saber: dolores de cabeza, fatiga mental, aumento de la frecuencia de infecciones y resfriados transmitidos por el aire, irritación de las membranas mucosas de los ojos, nariz, faringe, sensación de sequedad de las membranas mucosas y piel, náuseas, mareos.
La primera categoría - edificios temporalmente "enfermos"- incluye edificios de nueva construcción o reformados recientemente en los que la intensidad de la manifestación de estos síntomas se va debilitando con el tiempo y en la mayoría de los casos desaparecen por completo al cabo de unos seis meses. La disminución en la severidad de la manifestación de los síntomas posiblemente esté asociada a los patrones de emisión de componentes volátiles contenidos en materiales de construcción, pinturas, etc.
En edificios de segunda categoría - constantemente "enfermo" los síntomas descritos se observan durante muchos años, e incluso las actividades recreativas a gran escala pueden no tener efecto. Una explicación para esta situación suele ser difícil de encontrar, a pesar de un estudio cuidadoso de la composición del aire, el funcionamiento del sistema de ventilación y las características estructurales del edificio.
Cabe señalar que no siempre es posible detectar una relación directa entre el estado del ambiente del aire interior y el estado de la salud pública.
Sin embargo, proporcionar un ambiente de aire óptimo para edificios residenciales y públicos es un importante problema de higiene y de ingeniería. El enlace principal para resolver este problema es el intercambio de aire de las instalaciones, que proporciona los parámetros requeridos del ambiente del aire. Al diseñar sistemas de aire acondicionado en edificios residenciales y públicos, la tasa de suministro de aire requerida se calcula en una cantidad suficiente para asimilar las emisiones de calor y humedad humanas, el dióxido de carbono exhalado, y en las habitaciones destinadas a fumar, también se tiene en cuenta la necesidad de eliminar el humo del tabaco. en cuenta.
Además de regular la cantidad de aire de suministro y su composición química, las características eléctricas del ambiente del aire tienen una importancia conocida para garantizar el confort del aire en un espacio cerrado. Este último está determinado por el régimen iónico de las instalaciones, es decir, el nivel de ionización positiva y negativa del aire. Tanto la ionización del aire insuficiente como la excesiva tienen un efecto negativo en el cuerpo.
Vivir en áreas con un contenido de iones de aire negativos del orden de 1000-2000 en 1 ml de aire tiene un efecto positivo en la salud de la población.
La presencia de personas en el local provoca una disminución del contenido de iones ligeros del aire. Al mismo tiempo, la ionización del aire cambia más intensamente, cuanto más personas hay en la habitación y más pequeña es su área.
Una disminución en la cantidad de iones ligeros está asociada con la pérdida de las propiedades refrescantes del aire, con su menor actividad fisiológica y química, lo que afecta negativamente al cuerpo humano y provoca quejas de congestión y "falta de oxígeno". Por ello, son de especial interés los procesos de desionización e ionización artificial del aire interior, que, por supuesto, deben contar con una regulación higiénica.
Debe enfatizarse que la ionización artificial del aire interior sin suficiente suministro de aire en condiciones de alta humedad y polvo del aire conduce a un aumento inevitable en la cantidad de iones pesados. Además, en el caso de la ionización del aire polvoriento, el porcentaje de retención de polvo en las vías respiratorias aumenta considerablemente (el polvo que lleva cargas eléctricas se retiene en las vías respiratorias de una persona en cantidades mucho mayores que el polvo neutro).
En consecuencia, la ionización artificial del aire no es una panacea universal para mejorar el aire interior. Sin mejorar todos los parámetros higiénicos del ambiente del aire, la ionización artificial no solo no mejora las condiciones de vida humana, sino que, por el contrario, puede tener un efecto negativo.
Las concentraciones totales óptimas de iones ligeros son niveles del orden de 3 x 10, y la mínima requerida es de 5 x 10 en 1 cm 3. Estas recomendaciones formaron la base de las normas sanitarias e higiénicas vigentes en la Federación Rusa para los niveles permisibles de ionización del aire en locales industriales y públicos (Tabla 6.1).
Composición y propiedades del gas natural. Gas natural (gas natural combustible; GGP) - Una mezcla gaseosa formada por metano e hidrocarburos más pesados, nitrógeno, dióxido de carbono, vapor de agua, compuestos que contienen azufre, gases inertes . El metano es el principal componente del GGP. HGP generalmente también contiene trazas de otros componentes (Fig. 1).
1. Los componentes combustibles incluyen hidrocarburos:
a) metano (CH 4) - el componente principal del gas natural, hasta el 98% por volumen (otros componentes están presentes en pequeñas cantidades o ausentes). Incoloro, inodoro e insípido, no tóxico, explosivo, más liviano que el aire;
b) hidrocarburos pesados (limitantes) [etano (C 2 H 6), propano (C h H 8), butano (C 4 H 10), etc.] - incoloros, inodoros e insípidos, no tóxicos, explosivos, más pesados que aire.
2. Componentes no combustibles (lastre) :
a) nitrógeno (N 2) - un componente del aire, sin color, olor y sabor; gas inerte, porque no interactúa con el oxígeno;
b) oxígeno (O 2) - una parte integral del aire; incoloro, inodoro e insípido; agente oxidante.
c) dióxido de carbono (dióxido de carbono CO 2) - sin color con un sabor ligeramente agrio. Cuando el contenido en el aire es más del 10% tóxico, más pesado que el aire;
Aire . El aire atmosférico seco es una mezcla de gases de varios componentes que consta de (% en volumen): nitrógeno N 2 - 78%, oxígeno O 2 - 21%, gases inertes (argón, neón, criptón, etc.) - 0,94% y dióxido de carbono - 0,03%.
![]() |
El aire también contiene vapor de agua e impurezas aleatorias: amoníaco, dióxido de azufre, polvo, microorganismos, etc. ( arroz. 2). Los gases que componen el aire se distribuyen uniformemente en él y cada uno de ellos conserva sus propiedades en la mezcla.
3. Componentes nocivos :
a) sulfuro de hidrógeno (H 2 S) - incoloro, con olor a huevos podridos, tóxico, ardiente, más pesado que el aire.
b) ácido cianhídrico (hidrociánico) (HCN) - un líquido ligero incoloro, en un gas tiene un estado gaseoso. Venenoso, provoca la corrosión del metal.
4. Impurezas mecánicas (el contenido depende de las condiciones de transporte del gas):
a) resinas y polvo: cuando se mezclan, pueden formar obstrucciones en los gasoductos;
b) agua: se congela a bajas temperaturas, formando tapones de hielo, lo que conduce a la congelación de los dispositivos reductores.
GGPen caracterización toxicológica pertenecen a sustancias de la clase de peligro ΙV-ésima según GOST 12.1.007. Se trata de productos gaseosos, poco tóxicos, explosivos para el fuego.
Densidad: densidad del aire atmosférico en condiciones normales - 1,29 kg / m 3, y metano - 0,72 kg / m 3 Por lo tanto, el metano es más ligero que el aire.
Requisitos GOST 5542-2014 para indicadores GGP:
1) concentración en masa de sulfuro de hidrógeno- no más de 0,02 g/m 3 ;
2) concentración en masa de azufre mercaptano- no más de 0,036 g/m 3 ;
3) fracción molar de oxígeno- no más del 0,050%;
4) contenido permisible de impurezas mecánicas- no más de 0,001 g/m 3;
5) fracción molar de dióxido de carbono en gas natural, no más del 2,5%.
6) Valor calorífico neto GGP en condiciones de combustión estándar según GOST 5542-14 - 7600 kcal / m 3 ;
8) intensidad del olor a gas para fines domésticos con una fracción de volumen del 1% en el aire - al menos 3 puntos, y para gas para uso industrial, este indicador se fija de acuerdo con el consumidor.
Unidad de gastos de ventas GGP - 1 m 3 de gas a una presión de 760 mm Hg. Arte. y temperatura 20 o C;
Temperatura de autoignición- la temperatura más baja de la superficie calentada que, en determinadas condiciones, enciende sustancias combustibles en forma de gas o mezcla de vapor y aire. Para el metano es 537 °C. Temperatura de combustión (temperatura máxima en la zona de combustión): metano - 2043 °C.
Calor específico de combustión del metano: el más bajo - Q H \u003d 8500 kcal / m 3, el más alto - Qv - 9500 kcal / m 3. Con el propósito de comparar tipos de combustible, el concepto combustible equivalente (c.f.) , en RF por unidad el poder calorífico de 1 kg de hulla se tomó igual a 29,3 MJ o 7000 kcal/kg.
Las condiciones para medir el flujo de gas son:
· condiciones normales(norte. a): Condiciones físicas estándar con las que se suelen correlacionar las propiedades de las sustancias. Las condiciones de referencia están definidas por la IUPAC (Unión Internacional de Química Práctica y Aplicada) de la siguiente manera: Presión atmosférica 101325 Pa = 760 mmHg S t..Temperatura del aire 273.15K= 0°C .Densidad del metano en bien.- 0,72 kg/m3,
· condiciones estándar(Con. a) volumen en mutuo ( comercial) acuerdos con los consumidores - GOST 2939-63: temperatura 20°С, presión 760 mm Hg. (101325 N/m), la humedad es cero. (Por GOST 8.615-2013 las condiciones normales se denominan "condiciones estándar"). Densidad del metano en tu- 0,717 kg/m3.
Tasa de propagación de la llama (tasa de combustión)- la velocidad del frente de llama en relación con el chorro fresco de mezcla combustible en una dirección dada. Velocidad estimada de propagación de la llama: propano - 0,83 m/s, butano - 0,82 m/s, metano - 0,67 m/s, hidrógeno - 4,83 m/s, depende depende de la composición, la temperatura, la presión de la mezcla, la proporción de gas y aire en la mezcla, el diámetro del frente de llama, la naturaleza del movimiento de la mezcla (laminar o turbulento) y determina la estabilidad de la combustión.
a desventajas (propiedades peligrosas) GGP incluyen: explosividad (inflamabilidad); ardor intenso; rápida propagación en el espacio; la imposibilidad de determinar la ubicación; efecto sofocante, con falta de oxígeno para respirar .
Explosividad (inflamabilidad) . Distinguir:
a) límite inferior de inflamabilidad ( NSP) - la cantidad más pequeña de gas en el aire en la que el gas se enciende (metano - 4,4%) . Con menor contenido de gas en el aire, no habrá ignición por falta de gas; (Fig. 3)
b) límite superior de inflamabilidad ( REG) - el mayor contenido de gas en el aire en el que se produce el proceso de ignición ( metano - 17%) . Con un mayor contenido de gas en el aire, no se producirá la ignición por falta de aire. (Fig. 3)
A FNP NSP y REG llamó límites de concentración inferior y superior de propagación de la llama ( NKPRP y VKPRP) .
A aumento de la presión del gas el rango entre los límites superior e inferior de la presión del gas disminuye (Fig. 4).
Por explosión de gas (metano) Además su contenido en el aire dentro del rango inflamable necesario fuente externa de energía (chispa, llama, etc.) . Con una explosión de gas en un volumen cerrado (sala, horno, tanque, etc.), más destrucción que una explosión al aire libre (arroz. 5).
Concentraciones máximas permitidas ( MPC) las sustancias nocivas GGP en el aire del área de trabajo se establecen en GOST 12.1.005.
MPC único máximo en el aire del área de trabajo (en términos de carbono) es 300 mg / m 3.
concentración peligrosa GGP (fracción de volumen de gas en el aire) es la concentración igual a 20% límite inferior inflamable de gas.
Toxicidad - la capacidad de envenenar el cuerpo humano. Los gases de hidrocarburos no tienen un fuerte efecto toxicológico en el cuerpo humano, pero su inhalación causa mareos en una persona y su contenido significativo en el aire inhalado. Cuando el oxígeno se reduce a 16% o menos puede llevar a asfixia.
A quema de gas con falta de oxígeno, es decir, con subcombustión, en los productos de combustión se forma monóxido de carbono (CO), o monóxido de carbono, que es un gas altamente tóxico.
odorización de gases - agregar una sustancia de olor fuerte (odorante) al gas para dar un olor GGP antes de la entrega a los consumidores en las redes de la ciudad. A uso para la odorización de etil mercaptano (C 2 H 5 SH - según el grado de impacto en el cuerpo pertenece a la ΙΙ-ésima clase de peligro toxicológico según GOST 12.1.007-76 ), se agrega 16 g por 1000 m 3 . La intensidad del olor de HGP odorizado con una fracción de volumen del 1% en el aire debe ser de al menos 3 puntos según GOST 22387.5.
El gas no odorizado se puede suministrar a empresas industriales, porque La intensidad del olor a gas natural para las empresas industriales que consumen gas de los principales gasoductos se establece de acuerdo con el consumidor.
Gases ardientes. El horno de una caldera (horno) en el que se quema combustible gaseoso (líquido) en una antorcha corresponde al concepto de "horno de cámara de caldera estacionario".
Combustión de gases de hidrocarburos - combinación química de componentes de gas combustible (carbono C e hidrógeno H) con oxígeno atmosférico O 2 (oxidación) con liberación de calor y luz: CH 4 + 2O 2 \u003d CO 2 + 2H 2 O .
En combustión completa el carbono se forma dióxido de carbono (CO 2 ), pero agua tipo - vapor de agua (H 2 O) .
En teoria para quemar 1 m 3 de metano se necesitan 2 m 3 de oxígeno, que están contenidos en 9,52 m 3 de aire (Fig. 6). si un aire de combustión insuficiente , entonces para una parte de las moléculas de componentes combustibles no habrá suficientes moléculas de oxígeno y en los productos de combustión, además de dióxido de carbono (CO 2 ), nitrógeno (N 2) y vapor de agua (H 2 O), productos combustión incompleta del gas :
-monóxido de carbono (CO), que, si se liberan en las instalaciones, pueden causar envenenamiento del personal operativo;
- hollín (C) , que, al depositarse sobre las superficies de calentamiento perjudica la transferencia de calor;
- metano e hidrógeno sin quemar , que puede acumularse en hornos y tiros (chimeneas), formando una mezcla explosiva. Cuando falta el aire, combustión incompleta del combustible o, como se suele decir, el proceso de combustión se produce con subcombustión. El agotamiento también puede ocurrir cuando mala mezcla de gas con aire y baja temperatura en la zona de combustión.
Para una combustión completa del gas, es necesario: la presencia de aire en el lugar de combustión en suficiente y buena mezcla con gas; alta temperatura en la zona de combustión.
Para asegurar la combustión completa del gas, se aporta aire en mayor cantidad de la teóricamente necesaria, es decir, en exceso, mientras que no todo el aire participará en la combustión. Parte del calor se gastará en calentar este exceso de aire y se liberará a la atmósfera junto con los gases de combustión.
La integridad de la combustión se determina visualmente (debe ser una llama azulada - azulada con extremos morados) o analizando la composición de los gases de combustión.
Teórico (estequiométrico) volumen de aire de combustión es la cantidad de aire necesaria para la combustión completa de una unidad de volumen ( 1 m 3 de gas seco o masa de combustible, calculado a partir de la composición química del combustible ).
Válido (real, requerido) El volumen de aire de combustión es la cantidad de aire que realmente se utiliza para quemar una unidad de volumen o masa de combustible.
Relación de aire de combustión α es la relación entre el volumen real de aire para la combustión y el teórico: α = V f / V t >1,
dónde: V f - volumen real de aire suministrado, m 3 ;
vt - volumen teórico de aire, m 3.
Coeficiente espectáculos en exceso cuantas veces el consumo real de aire para la combustión de gas supera el teórico depende del diseño del quemador de gas y del horno: cuanto más perfectos sean, el coeficiente α menos. Cuando el coeficiente de exceso de aire para calderas es inferior a 1, se produce una combustión incompleta del gas. Un aumento en la proporción de exceso de aire reduce la eficiencia. planta de gas. Para varios hornos donde se funde metal, para evitar la corrosión por oxígeno: α < 1 y después del horno, se instala una cámara de postcombustión para componentes combustibles no quemados.
Para controlar el tiro se utilizan paletas guía, válvulas de compuerta, válvulas de mariposa y acoplamientos electromecánicos.
Ventajas de los combustibles gaseosos frente a los sólidos y líquidos– bajo costo, facilitando el trabajo del personal, baja cantidad de impurezas nocivas en los productos de combustión, mejores condiciones ambientales, sin necesidad de transporte por carretera y ferrocarril, buena mezcla con el aire (menos de α), automatización completa, alta eficiencia.
Métodos de combustión de gases. El aire de combustión puede ser:
1) primario, se introduce en el quemador, donde se mezcla con gas (se utiliza una mezcla de gas y aire para la combustión).
2) secundario, entra directamente en la zona de combustión.
Existen los siguientes métodos de combustión de gas:
1. método de difusión- el gas y el aire para la combustión se suministran por separado y se mezclan en la zona de combustión, es decir todo el aire es secundario. La llama es larga, se requiere un gran espacio de horno. (Figura 7a).
2. método cinético - todo el aire se mezcla con gas dentro del quemador, es decir todo el aire es primario. La llama es corta, se requiere un espacio de combustión pequeño (Figura 7c).
3. metodo mixto - una parte del aire se suministra al interior del quemador, donde se mezcla con el gas (este es el aire primario), y una parte del aire se suministra a la zona de combustión (secundario). La llama es más corta que con el método de difusión (Fig. 7b).
Eliminación de productos de la combustión. La rarefacción en el horno y la eliminación de los productos de la combustión se producen por la fuerza de tracción que vence la resistencia del recorrido de los humos y surge por la diferencia de presión entre las columnas de aire frío exterior de igual altura y los humos calientes más ligeros. En este caso, los gases de combustión se mueven del horno a la tubería y el aire frío ingresa al horno en su lugar (Fig. 8).
La fuerza de tracción depende de: temperatura del aire y de los gases de combustión, altura, diámetro y espesor de pared de la chimenea, presión barométrica (atmosférica), estado de los conductos de gas (chimeneas), aspiración de aire, rarefacción en el horno .
Natural fuerza de tiro - creada por la altura de la chimenea, y artificial, que es un aspirador de humos con tiro natural insuficiente. La fuerza de tracción está regulada por compuertas, paletas guía de extractores de humo y otros dispositivos.
Proporción de exceso de aire (α ) depende del diseño del quemador de gas y del horno: cuanto más perfectos son, menor es el coeficiente y muestra: cuántas veces el consumo real de aire para la combustión de gas supera al teórico.
Sobrealimentación: eliminación de productos de la combustión del combustible debido al funcionamiento de los sopladores .Cuando se trabaja "bajo sobrealimentación", se requiere una cámara de combustión (horno) fuerte y densa que pueda soportar el exceso de presión creado por el ventilador.
Quemadores de gas.Quemadores de gas- proporcionar el suministro de la cantidad requerida de gas y aire, su mezcla y regulación del proceso de combustión, y equipado con un túnel, dispositivo de distribución de aire, etc., se denomina dispositivo quemador de gas.
requisitos del quemador:
1) los quemadores deben cumplir con los requisitos de los reglamentos técnicos pertinentes (tener un certificado o declaración de conformidad) o pasar un examen de seguridad industrial;
2) garantizar la integridad de la combustión del gas en todos los modos de funcionamiento con un exceso mínimo de aire (excepto algunos quemadores de hornos de gas) y una emisión mínima de sustancias nocivas;
3) poder utilizar control automático y seguridad, así como medir los parámetros de gas y aire frente al quemador;
4) debe tener un diseño simple, ser accesible para reparación y revisión;
5) trabajar de manera constante dentro del reglamento de trabajo, si es necesario, tener estabilizadores para evitar la separación y el retroceso de la llama;
Parámetros de los quemadores de gas.(Figura 9). Según GOST 17356-89 (Quemadores a gas, combustible líquido y combinados. Términos y definiciones. Rev. N 1) :Límite de estabilidad del quemador , en el cual aun no surge extinción, ruptura, desprendimiento, estallido de llama y vibraciones inaceptables.
Nota. Existir Superior e inferior límites de la sostenibilidad.
1) Potencia calorífica del quemador N g. - la cantidad de calor generado como resultado de la combustión del combustible suministrado al quemador por unidad de tiempo, N g \u003d V. Q kcal/h, donde V es el consumo horario de gas, m 3 /h; Q n. - calor de combustión del gas, kcal / m 3.
2) Límites de estabilidad del quemador , en el cual aun no surge extinción, estancamiento, desprendimiento, retorno de llama y vibraciones inaceptables . Nota. Existir superior - N vp . y menor -N n.p. límites de la sostenibilidad.
3) potencia mínima N mín. - potencia térmica del quemador, que es de 1,1 potencia, correspondiente al límite inferior de su funcionamiento estable, es decir potencia de límite bajo aumentada en un 10%, N mín. =1.1N np
4) límite superior de funcionamiento estable del quemador N v.p. – la potencia estable más alta, trabajo sin separación y flashover de la llama.
5) potencia máxima del quemador N max - potencia térmica del quemador, que es 0,9 de potencia, correspondiente al límite superior de su funcionamiento estable, es decir, potencia límite superior reducida en un 10%, N máx. = 0,9 N v.p.
6) potencia nominal N nom - la potencia térmica más alta del quemador, cuando los indicadores de rendimiento cumplen con los estándares establecidos, es decir la potencia más alta con la que el quemador funciona durante mucho tiempo con alta eficiencia.
7) rango de control de funcionamiento (salida de calor del quemador): un rango regulado en el que la salida de calor del quemador puede cambiar durante el funcionamiento, es decir, valores de potencia de N min a N nom. .
8) coeficiente de regulación de trabajo K rr. es la relación entre la potencia calorífica nominal del quemador y su potencia calorífica mínima de funcionamiento, es decir muestra cuántas veces la potencia nominal supera la mínima: K rr. = N nominal / N min
carnet de régimen.De acuerdo con las "Reglas para el uso de gas ...", aprobadas por el Gobierno de la Federación Rusa el 17 de mayo de 2002 No. 317(modificado el 19/06/2017) , una vez finalizados los trabajos de construcción e instalación de los equipos que utilizan gas construidos, reconstruidos o modernizados y los equipos convertidos a gas a partir de otros tipos de combustible, se llevan a cabo los trabajos de puesta en marcha y mantenimiento. Lanzamiento de gas a los equipos que utilicen gas construidos, reconstruidos o modernizados y a los equipos convertidos a gas a partir de otros tipos de combustible para la realización de puesta en marcha (pruebas integradas) y la aceptación del equipo en operación se lleva a cabo sobre la base de un acto sobre la preparación de las redes de consumo de gas y el equipo que usa gas del objeto de construcción de capital para la conexión (conexión tecnológica). Las reglas establecen que:
· equipo que usa gas - calderas, hornos de producción, líneas de proceso, plantas de recuperación de calor residual y otras instalaciones que utilizan gas como combustible con el fin de generar energía térmica para calefacción centralizada, abastecimiento de agua caliente, en procesos tecnológicos de diversas industrias, así como otros dispositivos, aparatos, unidades, equipos de proceso e instalaciones que utilicen gas como materia prima;
· trabajos de puesta en marcha- complejo de obras, incluida la preparación para la puesta en marcha y puesta en marcha de equipos que utilizan gas con comunicaciones y equipamientos, llevando la carga de equipos que utilizan gas hasta el nivel acordado con la organización - el propietario del equipo, a también el ajuste del modo de combustión de los equipos que utilizan gas sin optimización de la eficiencia;
· régimen y obras de ajuste- un conjunto de obras, incluido el ajuste de los equipos que utilizan gas para lograr la eficiencia de diseño (pasaporte) en el rango de cargas operativas, el ajuste del control automático de los procesos de combustión de combustible, plantas de recuperación de calor y equipos auxiliares, incluidos los equipos de tratamiento de agua para salas de calderas.
Según GOST R 54961-2012 (Sistemas de distribución de gas. Redes de consumo de gas) se recomienda:Modos de funcionamiento equipos que utilizan gas en empresas y salas de calderas debe coincidir con los mapas de régimen aprobado por el gerente técnico de la empresa y PAGS producido al menos una vez cada tres años con ajuste (si es necesario) de tarjetas de régimen .
El ajuste de régimen no programado de los equipos que utilizan gas debe realizarse en los siguientes casos: después de una revisión general de los equipos que utilizan gas o de realizar cambios estructurales que afecten la eficiencia del uso del gas, así como en caso de desviaciones sistemáticas de los parámetros controlados de los equipos que utilizan gas a partir de mapas de régimen.
Clasificación de los quemadores de gas. Según GOST Los quemadores de gas se clasifican según: método de suministro del componente; el grado de preparación de la mezcla combustible; la tasa de caducidad de los productos de combustión; la naturaleza del flujo de la mezcla; presión de gas nominal; grado de automatización; la capacidad de controlar el coeficiente de exceso de aire y las características de la antorcha; localización de la zona de combustión; posibilidad de aprovechar el calor de los productos de combustión.
A horno de cámara de una planta que utiliza gas gaseoso el combustible se quema en una bengala.
De acuerdo con el método de suministro de aire, los quemadores pueden ser:
1) Quemadores atmosféricos -El aire entra en la zona de combustión directamente desde la atmósfera:
una. Difusión – este es el quemador más simple en diseño, que, por regla general, es un tubo con agujeros perforados en una o dos filas. El gas ingresa a la zona de combustión desde la tubería a través de los orificios, y aire - debido a difusión y energía de chorro de gas (arroz. 10 ), todo el aire es secundario .
Ventajas del quemador : simplicidad de diseño, fiabilidad de trabajo ( no es posible el flashover ), funcionamiento silencioso, buena regulación.
Defectos: bajo consumo, antieconómico, llama alta (larga), se necesitan retardantes de llama para evitar que se apague la llama del quemador en la separación .
b. inyección - aire se inyecta, es decir aspirado en el interior del quemador debido a la energía del chorro de gas que sale de la boquilla . El chorro de gas crea un vacío en el área de la boquilla, donde se aspira aire a través del espacio entre el limpiador de aire y el cuerpo del quemador. En el interior del quemador se mezclan gas y aire, entrando la mezcla gas-aire en la zona de combustión, y el resto del aire necesario para la combustión del gas (secundario) entra en la zona de combustión por difusión (Fig. 11, 12, 13 ).
Dependiendo de la cantidad de aire inyectado, hay quemadores de inyección: con mezcla previa incompleta y completa de gas y aire.
El quemador gas de media y alta presion se aspira todo el aire necesario, es decir, todo el aire es primario, hay una premezcla completa de gas con aire. Una mezcla de gas y aire completamente preparada ingresa a la zona de combustión y no hay necesidad de aire secundario.
El quemador baja presión parte del aire necesario para la combustión es aspirado (se produce una inyección de aire incompleta, este aire es primario), y el resto del aire (secundario) entra directamente en la zona de combustión.
La relación "gas - aire" en estos quemadores está regulada por la posición del lavador de aire con respecto al cuerpo del quemador. Los quemadores son de llama única y llama múltiple con suministro de gas central y periférico (BIG y BIGm) que consisten en un conjunto de tubos - mezcladores 1 con un diámetro de 48x3, unidos por un colector de gas común 2 (Fig. 13 ).
Ventajas de los quemadores: simplicidad de diseño y regulación de potencia.
Desventajas de los quemadores: alto nivel de ruido, posibilidad de retroceso de llama, pequeño rango de regulación de funcionamiento.
2) Quemadores de aire forzado - Son quemadores en los que el aire comburente se alimenta de un ventilador. El gas del gasoducto ingresa a la cámara interna del quemador (Fig. 14 ).
El aire forzado por el ventilador se suministra a la cámara de aire. 2 , pasa por el remolino de aire 4 , torcido y mezclado en la batidora 5 con gas que entra en la zona de combustión desde el canal de gas 1 a través de salidas de gas 3 .La combustión tiene lugar en un túnel cerámico 7 .
![]() | ![]() |
Ventajas de los quemadores: alta potencia térmica, amplio rango de regulación de funcionamiento, posibilidad de regulación de la relación de exceso de aire, posibilidad de precalentamiento de gas y aire.
Desventajas de los quemadores.: suficiente complejidad de diseño; es posible la separación y el avance de la llama, en relación con lo cual se hace necesario utilizar estabilizadores de combustión (túnel cerámico).
Los quemadores diseñados para quemar varios tipos de combustible (gaseoso, líquido, sólido) se denominan conjunto (arroz. 15 ). Pueden ser de un solo hilo y de doble hilo, es decir. con uno o más suministros de gas al quemador.
3) quemador de bloque – es un quemador automático con suministro de aire forzado (arroz. 16 ), arreglado con un ventilador en una sola unidad. El quemador está equipado con un sistema de control automático.
El proceso de combustión del combustible en los quemadores de bloque está controlado por un dispositivo electrónico llamado administrador de combustión.
Para quemadores de aceite, esta unidad incluye la bomba de combustible o la bomba de combustible y el precalentador de combustible.
La unidad de control (gestor de combustión) controla y controla el funcionamiento del quemador, recibiendo órdenes del termostato (controlador de temperatura), del electrodo de control de llama y de los sensores de presión de gas y aire.
El flujo de gas está controlado por una válvula de mariposa ubicada fuera del cuerpo del quemador.
La arandela de retención es responsable de mezclar el gas con el aire en la parte cónica del tubo de llama y se utiliza para controlar el aire de entrada (regulación en el lado de presión). Otra posibilidad para cambiar la cantidad de aire suministrado es cambiar la posición de la válvula de mariposa de aire en la caja del regulador de aire (ajuste en el lado de succión).
La regulación de las relaciones gas-aire (control de válvulas de mariposa de gas y aire) puede ser:
conectado, desde un actuador:
· regulación de frecuencia del caudal de aire, mediante la variación de la velocidad del motor del ventilador mediante un inverter, que consta de un convertidor de frecuencia y un sensor de pulso.
El encendido del quemador se realiza automáticamente por el dispositivo de encendido utilizando el electrodo de encendido. La presencia de una llama es monitoreada por un electrodo de control de llama.
La secuencia de operación para encender el quemador:
Solicitud de producción de calor (desde el termostato);
· la inclusión del electromotor del ventilador y la ventilación preliminar del fogón;
Habilitación encendido electrónico
apertura de la electroválvula, alimentación de gas y encendido del quemador;
señal del sensor de control de llama sobre la presencia de una llama.
Accidentes (incidentes) en quemadores. rotura de llama - mover la zona de la raíz de la antorcha desde las salidas de los quemadores en la dirección del flujo de combustible o mezcla combustible. Ocurre cuando la velocidad de la mezcla gas-aire o gas se hace mayor que la velocidad de propagación de la llama. La llama se aleja del quemador, se vuelve inestable y puede apagarse. El gas continúa fluyendo a través del quemador apagado y se puede formar una mezcla explosiva en el horno.
La separación ocurre cuando: un aumento en la presión del gas por encima de lo permitido, un fuerte aumento en el suministro de aire primario, un aumento en la rarefacción en el horno. Para protección contra rasgaduras aplicar estabilizadores de combustión (arroz. 17): toboganes y postes de ladrillo; túneles de cerámica de varios tipos y ranuras de ladrillo; cuerpos poco aerodinámicos que se calientan durante el funcionamiento del quemador (cuando se apaga la llama, se encenderá un chorro fresco del estabilizador), así como quemadores piloto especiales.
Linterna - mover la zona de la antorcha hacia la mezcla combustible, en la que la llama penetra en el quemador . Este fenómeno ocurre solo en quemadores con una mezcla preliminar de gas y aire y ocurre cuando la velocidad de la mezcla gas-aire se vuelve menor que la velocidad de propagación de la llama. La llama salta al interior del quemador, donde continúa ardiendo, provocando que el quemador se deforme por sobrecalentamiento.
El avance ocurre cuando: la presión del gas frente al quemador cae por debajo del valor permitido; encendido del quemador cuando se suministra aire primario; gran suministro de gas a baja presión de aire. Durante el deslizamiento, puede ocurrir un pequeño estallido, como resultado de lo cual la llama se apagará, mientras que el gas puede continuar fluyendo a través del quemador inactivo y puede formarse una mezcla explosiva en el horno y los conductos de gas de la instalación que usa gas. Para proteger contra el deslizamiento, se utilizan estabilizadores de placa o malla., ya que a través de ranuras estrechas y pequeños agujeros no hay paso de la llama.
Actuaciones del personal en caso de accidente en los quemadores
En caso de accidente en el quemador (separación, flameo o extinción de la llama) durante el encendido o en proceso de regulación, es necesario: detener inmediatamente el suministro de gas a este quemador (quemadores) y al dispositivo de encendido; ventile el horno y los conductos de gas durante al menos 10 minutos; averiguar la causa del problema; informar a la persona responsable; después de eliminar las causas de las fallas y verificar la estanqueidad de la válvula de cierre frente al quemador, bajo la dirección de la persona responsable, de acuerdo con las instrucciones, vuelva a encender.
Cambio de carga del quemador.
Hay quemadores con varias formas de cambiar la salida de calor:
Quemador con control de salida de calor de varias etapas- se trata de un quemador, durante el cual se puede instalar el regulador de flujo de combustible en varias posiciones entre las posiciones máxima y mínima de funcionamiento.
Quemador con regulación de potencia calorífica en tres etapas- se trata de un quemador, durante cuyo funcionamiento el regulador de caudal de combustible se puede regular en las posiciones "caudal máximo" - "caudal mínimo" - "cerrado".
Quemador con control de salida de calor de dos etapas- un quemador funcionando en las posiciones "abierto - cerrado".
Quemador modulante- este es un quemador, durante el cual el regulador de flujo de combustible puede instalarse en cualquier posición entre las posiciones máxima y mínima de funcionamiento.
Es posible regular la potencia térmica de la instalación por el número de quemadores en funcionamiento, si lo proporciona el fabricante y tarjeta de régimen.
Cambiar la salida de calor manualmente, para evitar la separación de la llama, se realiza:
Al aumentar: primero aumente el suministro de gas y luego el de aire.
Al disminuir: primero reduzca el suministro de aire y luego el gas;
Para evitar accidentes en los quemadores, el cambio de potencia debe realizarse de manera suave (en varias etapas) de acuerdo con el mapa de régimen.
La combustión del gas natural es un proceso físico y químico complejo de interacción de sus componentes combustibles con un comburente, mientras que la energía química del combustible se convierte en calor. La quema puede ser completa o incompleta. Cuando el gas se mezcla con aire, la temperatura en el horno es lo suficientemente alta para la combustión, el combustible y el aire se suministran continuamente y se lleva a cabo la combustión completa del combustible. La combustión incompleta del combustible ocurre cuando no se observan estas reglas, lo que conduce a una menor liberación de calor (CO), hidrógeno (H2), metano (CH4) y, como resultado, a la deposición de hollín en las superficies de calefacción, empeorando la transferencia de calor y aumentando pérdida de calor, lo que a su vez conduce a un consumo excesivo de combustible y una disminución de la eficiencia de la caldera y, en consecuencia, a la contaminación del aire.
La proporción de exceso de aire depende del diseño del quemador de gas y del horno. El coeficiente de exceso de aire debe ser al menos 1, de lo contrario puede provocar una combustión incompleta del gas. Y también un aumento en el coeficiente de exceso de aire reduce la eficiencia de la instalación que usa calor debido a las grandes pérdidas de calor con los gases de escape.
La integridad de la combustión se determina utilizando un analizador de gases y por color y olor.
Combustión completa de gas. metano + oxígeno \u003d dióxido de carbono + agua CH4 + 2O2 \u003d CO2 + 2H2O Además de estos gases, el nitrógeno y el oxígeno restante ingresan a la atmósfera con gases combustibles. N2 + O2 Si la combustión del gas es incompleta, se emiten sustancias combustibles a la atmósfera: monóxido de carbono, hidrógeno, hollín.CO + H + C
La combustión incompleta del gas ocurre debido a la falta de aire. Al mismo tiempo, lenguas de hollín aparecen visualmente en la llama El peligro de una combustión incompleta del gas es que el monóxido de carbono puede provocar el envenenamiento del personal de la sala de calderas. El contenido de CO en el aire 0,01-0,02% puede causar una intoxicación leve. Una concentración más alta puede provocar intoxicaciones graves y la muerte. El hollín resultante se deposita en las paredes de las calderas, lo que dificulta la transferencia de calor al refrigerante y reduce la eficiencia de la sala de calderas. El hollín conduce el calor 200 veces peor que el metano Teóricamente, se necesitan 9 m3 de aire para quemar 1 m3 de gas. En condiciones reales, se necesita más aire. Es decir, se necesita una cantidad excesiva de aire. Este valor, denominado alfa, muestra cuántas veces se consume más aire del teóricamente necesario. El coeficiente alfa depende del tipo de quemador en particular y generalmente se prescribe en el pasaporte del quemador o de acuerdo con las recomendaciones de la organización encargada. Con un aumento en la cantidad de exceso de aire por encima del recomendado, aumentan las pérdidas de calor. Con un aumento significativo en la cantidad de aire, puede ocurrir una separación de llamas, creando una emergencia. Si la cantidad de aire es inferior a la recomendada, la combustión será incompleta, lo que creará un riesgo de intoxicación para el personal de la sala de calderas. La combustión incompleta se determina por:
Propiedades físicas y químicas del gas natural.
El gas natural es incoloro, inodoro e insípido, no tóxico.
Densidad de los gases a t = 0°C, Р = 760 mm Hg. Art.: metano - 0,72 kg / m 3, aire -1,29 kg / m 3.
La temperatura de autoignición del metano es de 545 a 650 °C. Esto significa que cualquier mezcla de gas natural y aire calentado a esta temperatura se encenderá sin una fuente de ignición y se quemará.
La temperatura de combustión del metano es de 2100°C en hornos de 1800°C.
Valor calorífico del metano: Q n \u003d 8500 kcal / m 3, Q en \u003d 9500 kcal / m 3.
Explosividad. Distinguir:
- el límite explosivo inferior es el contenido de gas más bajo en el aire en el que se produce una explosión, es del 5% para el metano.
Con un menor contenido de gas en el aire, no habrá explosión por falta de gas. Al introducir una fuente de energía de terceros, pops.
- el límite explosivo superior es el contenido de gas más alto en el aire en el que se produce una explosión, es del 15% para el metano.
Con un mayor contenido de gas en el aire, no habrá explosión por falta de aire. Cuando se introduce una fuente de energía de terceros: fuego, fuego.
Para una explosión de gas, además de mantenerlo en el aire dentro de los límites de su explosividad, se necesita una fuente de energía externa (chispa, llama, etc.).
Durante una explosión de gas en un volumen cerrado (una habitación, una cámara de combustión, un tanque, etc.), hay más destrucción que al aire libre.
Cuando se quema gas con subcombustión, es decir, con falta de oxígeno, se forma monóxido de carbono (CO) o monóxido de carbono en los productos de combustión, que es un gas altamente tóxico.
La velocidad de propagación de la llama es la velocidad a la que se mueve el frente de la llama en relación con el chorro de mezcla fresca.
Velocidad estimada de propagación de llama metano - 0,67 m / s. Depende de la composición, la temperatura, la presión de la mezcla, la proporción de gas y aire en la mezcla, el diámetro del frente de llama, la naturaleza del movimiento de la mezcla (laminar o turbulento) y determina la estabilidad de la combustión.
odorización de gases- esta es la adición de una sustancia de olor fuerte (odorante) al gas para darle un olor antes de entregarlo a los consumidores.
Requisitos para los odorantes:
- un fuerte olor específico;
- no debe impedir la combustión;
- no debe disolverse en agua;
– debe ser inofensivo para las personas y los equipos.
El etil mercaptano (C 2 H 5 SH) se usa como odorante, se agrega al metano: 16 g por 1000 m 3, en invierno la tasa se duplica.
Una persona debe oler el olor en el aire cuando el contenido de gas en el aire es del 20 % del límite explosivo inferior para el metano: 1 % por volumen.
Este es un proceso químico de combinación de componentes combustibles (hidrógeno y carbono) con el oxígeno contenido en el aire. Ocurre con la liberación de calor y luz.
Cuando el carbono se quema, se forma dióxido de carbono (CO 2 ) y el hidrógeno se convierte en vapor de agua (H 2 0).
Etapas de combustión: suministro de gas y aire, formación de una mezcla gas-aire, encendido de la mezcla, su combustión, eliminación de los productos de la combustión.
Teóricamente, cuando todo el gas se quema y toda la cantidad de aire necesaria participa en la combustión, la reacción de combustión de 1 m 3 de gas:
CH 4 + 20 2 \u003d CO 2 + 2H 2 O + 8500 kcal / m 3.
Para quemar 1 m 3 de metano se necesitan 9,52 m 3 de aire.
Prácticamente no todo el aire aportado a la combustión participará en la combustión.
Por tanto, además del dióxido de carbono (CO 2 ) y el vapor de agua (H 2 0), en los productos de la combustión aparecerán:
- el monóxido de carbono, o monóxido de carbono (CO), si entra en la habitación, puede provocar la intoxicación de los asistentes;
- el carbono atómico u hollín (C), al depositarse en conductos de gas y hornos, empeora la tracción y la transferencia de calor en las superficies de calefacción.
- gas sin quemar e hidrógeno - acumulados en hornos y conductos de gas, forman una mezcla explosiva.
Con falta de aire, se produce una combustión incompleta del combustible: el proceso de combustión se produce con subcombustión. La subcombustión también ocurre con una mala mezcla de gas con aire y baja temperatura en la zona de combustión.
Para una combustión completa del gas, el aire de combustión se suministra en cantidad suficiente, el aire y el gas deben estar bien mezclados y se requiere una temperatura alta en la zona de combustión.
Para la combustión completa del gas, se aporta aire en mayor cantidad que la teóricamente necesaria, es decir, con exceso, no todo el aire participará en la combustión. Parte del calor se gastará en calentar este exceso de aire y se liberará a la atmósfera.
El coeficiente de exceso de aire α es un número que indica cuántas veces el consumo real para la combustión es mayor que el requerido teóricamente:
α = V re / V t
donde V d - consumo real de aire, m 3;
V t - aire teóricamente necesario, m 3.
α = 1,05 - 1,2.
Métodos de quema de gas
El aire de combustión puede ser:
- primario: se alimenta al quemador, se mezcla con gas y la mezcla de gas y aire se usa para la combustión;
- secundario - entra en la zona de combustión.
Métodos de combustión de gas:
1. Método de difusión: el gas y el aire de combustión se suministran por separado y se mezclan en la zona de combustión, todo el aire es secundario. La llama es larga, se requiere un gran espacio de horno.
2. Método mixto: parte del aire se suministra al quemador, mezclado con gas (aire primario), parte del aire se suministra a la zona de combustión (secundario). La llama es más corta que con el método de difusión.
3. Método cinético: todo el aire se mezcla con gas dentro del quemador, es decir, todo el aire es primario. La llama es corta, se requiere un pequeño espacio en el horno.
Dispositivos quemadores de gas
Los quemadores de gas son dispositivos que suministran gas y aire al frente de combustión, forman una mezcla gas-aire, estabilizan el frente de combustión y aseguran la intensidad requerida del proceso de combustión.
Un quemador equipado con un dispositivo adicional (túnel, dispositivo de distribución de aire, etc.) se denomina dispositivo quemador de gas.
Requisitos del quemador:
1) debe estar hecho en fábrica y pasar las pruebas estatales;
2) debe garantizar la integridad de la combustión del gas en todos los modos de funcionamiento con un mínimo exceso de aire y una mínima emisión de sustancias nocivas a la atmósfera;
3) poder utilizar control automático y seguridad, así como medir los parámetros de gas y aire frente al quemador;
4) debe tener un diseño simple, ser accesible para reparación y revisión;
5) debe trabajar de manera estable dentro del reglamento de funcionamiento, si es necesario, tener estabilizadores para evitar la separación y el retroceso de la llama;
6) para quemadores en funcionamiento, el nivel de ruido no debe exceder los 85 dB y la temperatura de la superficie no debe exceder los 45 ° C.
Parámetros de los quemadores de gas.
1) potencia térmica del quemador N g - la cantidad de calor liberado durante la combustión de gas en 1 hora;
2) el límite inferior de funcionamiento estable del quemador N n. .PAGS. . - la potencia más baja a la que el quemador funciona de manera estable sin separación ni descarga disruptiva de la llama;
3) potencia mínima N min - la potencia del límite inferior, aumentada en un 10%;
4) el límite superior de funcionamiento estable del quemador N in. .PAGS. . - la potencia más alta a la que el quemador funciona de manera estable sin separación ni descarga disruptiva de la llama;
5) potencia máxima N max - potencia del límite superior, reducida en un 10%;
6) potencia nominal N nom: la potencia más alta con la que funciona el quemador durante mucho tiempo con la mayor eficiencia;
7) rango de control operativo: valores de potencia de N min a N nom;
8) coeficiente de regulación de trabajo: la relación entre la potencia nominal y el mínimo.
Clasificación de los quemadores de gas:
1) según el método de suministro de aire para la combustión:
- sin explosión: el aire ingresa al horno debido a la rarefacción en él;
- inyección: el aire es aspirado en el quemador debido a la energía del chorro de gas;
- explosión: se suministra aire al quemador o al horno mediante un ventilador;
2) según el grado de preparación de la mezcla combustible:
– sin mezcla preliminar de gas con aire;
- con mezcla previa completa;
- con mezcla previa incompleta o parcial;
3) por la velocidad de salida de los productos de combustión (baja - hasta 20 m / s, media - 20-70 m / s, alta - más de 70 m / s);
4) según la presión del gas frente a los quemadores:
- bajo hasta 0,005 MPa (hasta 500 mm de columna de agua);
- promedio de 0,005 MPa a 0,3 MPa (de 500 mm de columna de agua a 3 kgf / cm 2);
- alto más de 0,3 MPa (más de 3 kgf / cm 2);
5) según el grado de automatización del control del quemador: con control manual, semiautomático, automático.
Según el método de suministro de aire, los quemadores pueden ser:
1) Difusión. Todo el aire entra en la antorcha desde el espacio circundante. El gas se alimenta al quemador sin aire primario y, al salir del colector, se mezcla con el aire del exterior.
El quemador de diseño más simple, por lo general un tubo con orificios perforados en una o dos filas.
Variedad - quemador de hogar. Consiste en un colector de gas hecho de un tubo de acero, tapado en un extremo. Los agujeros se perforan en dos filas en la tubería. El colector está instalado en una ranura, hecha de ladrillos refractarios, a base de una rejilla. El gas a través de los orificios del colector sale al espacio. El aire entra por la misma ranura a través de la rejilla debido a la rarefacción en el horno o con la ayuda de un ventilador. Durante el funcionamiento, el revestimiento refractario de la ranura se calienta, lo que garantiza la estabilización de la llama en todos los modos de funcionamiento.
Ventajas del quemador: diseño simple, operación confiable (el retroceso de la llama es imposible), silencio, buena regulación.
Desventajas: bajo consumo, antieconómico, llama alta.
2) Quemadores de inyección:
a) baja presión o atmosférica (aplica a quemadores con premezclado parcial). El chorro de gas sale por la boquilla a gran velocidad y, debido a su energía, capta aire en el confusor, arrastrándolo al interior del quemador. La mezcla de gas con aire se lleva a cabo en un mezclador que consta de un cuello, un difusor y una boquilla contra incendios. El vacío creado por el inyector aumenta con el aumento de la presión del gas, mientras cambia la cantidad de aire primario aspirado. La cantidad de aire primario se puede cambiar usando una arandela de ajuste. Al cambiar la distancia entre la arandela y el confusor, se regula el suministro de aire.
Para asegurar la combustión completa del combustible, parte del aire entra por rarefacción en el horno (aire secundario). La regulación de su consumo se realiza cambiando el vacío.
Tienen la propiedad de autorregulación: al aumentar la carga, aumenta la presión del gas, lo que inyecta una mayor cantidad de aire en el quemador. A medida que disminuye la carga, disminuye la cantidad de aire.
Los quemadores se utilizan de forma limitada en equipos de alta capacidad (más de 100 kW). Esto se debe al hecho de que el colector del quemador está ubicado directamente en el horno. Durante el funcionamiento, se calienta a altas temperaturas y falla rápidamente. Tienen una alta relación de exceso de aire, lo que conduce a una combustión de gas antieconómica.
b) Media presión. Cuando se aumenta la presión del gas, se inyecta todo el aire necesario para la combustión completa del gas. Todo el aire es primario. Operan a una presión de gas de 0,005 MPa a 0,3 MPa. Se refieren a quemadores de premezcla completa de gas con aire. Como resultado de una buena mezcla de gas y aire, funcionan con una pequeña proporción de exceso de aire (1,05-1,1). Quemador Kazantsev. Consta de regulador de aire primario, tobera, mezclador, tobera y placa estabilizadora. Al salir de la tobera, el gas tiene energía suficiente para inyectar todo el aire necesario para la combustión. En el mezclador, el gas se mezcla completamente con el aire. El regulador de aire primario al mismo tiempo amortigua el ruido que se produce debido a la alta velocidad de la mezcla gas-aire. ventajas:
- simplicidad de diseño;
- funcionamiento estable cuando cambia la carga;
- falta de suministro de aire a presión (sin ventilador, motor eléctrico, conductos de aire);
– la posibilidad de autorregulación (manteniendo una relación gas-aire constante).
Defectos:
- grandes dimensiones de los quemadores a lo largo, especialmente quemadores con mayor productividad;
– alto nivel de ruido.
3) Quemadores con suministro de aire forzado. La formación de la mezcla gas-aire comienza en el quemador y termina en el horno. El aire es suministrado por un ventilador. El suministro de gas y aire se realiza a través de tuberías separadas. Funcionan con gas de baja y media presión. Para una mejor mezcla, el flujo de gas se dirige a través de los orificios en ángulo con respecto al flujo de aire.
Para mejorar la mezcla, se le da al flujo de aire un movimiento de rotación utilizando remolinos con un ángulo de pala constante o ajustable.
Quemador de gas de remolino (GGV): el gas del colector de distribución sale a través de orificios perforados en una fila y, en un ángulo de 90 0, ingresa al flujo de aire girando con un remolino de palas. Las paletas están soldadas en un ángulo de 45° a la superficie exterior del colector de gas. Dentro del colector de gas hay una tubería para monitorear el proceso de combustión. Cuando se trabaja con fuel oil, se instala una boquilla mecánica de vapor.
Los quemadores diseñados para quemar varios tipos de combustible se denominan combinados.
Ventajas de los quemadores: alta potencia térmica, amplio rango de regulación de funcionamiento, capacidad de controlar la relación de exceso de aire, posibilidad de precalentamiento de gas y aire.
Desventajas de los quemadores: suficiente complejidad de diseño; es posible el desprendimiento y la ruptura de la llama, en relación con lo cual se hace necesario el uso de estabilizadores de combustión (túnel de cerámica, antorcha piloto, etc.).
Accidentes de quemadores
La cantidad de aire en la mezcla gas-aire es el factor más importante que afecta la velocidad de propagación de la llama. En mezclas en las que el contenido de gas supera el límite superior de su ignición, la llama no se propaga en absoluto. A medida que aumenta la cantidad de aire en la mezcla, aumenta la velocidad de propagación de la llama, alcanzando el valor más alto cuando el contenido de aire es aproximadamente el 90% de su cantidad teórica necesaria para la combustión completa del gas. Aumentar el flujo de aire al quemador crea una mezcla que es más pobre en gas, capaz de quemarse más rápido y provocar un destello de llama en el quemador. Por lo tanto, si se requiere aumentar la carga, primero aumente el suministro de gas y luego el de aire. Si es necesario reducir la carga, hacen lo contrario: primero reducen el suministro de aire y luego el gas. Al momento de encender los quemadores, no debe entrar aire en ellos y el gas se enciende en un modo de difusión debido al aire que ingresa al horno, seguido de una transición al suministro de aire al quemador.
1. Separación de llamas: movimiento de la zona de la antorcha desde las salidas de los quemadores en la dirección de combustión del combustible. Ocurre cuando la velocidad de la mezcla gas-aire se hace mayor que la velocidad de propagación de la llama. La llama se vuelve inestable y puede apagarse. El gas continúa fluyendo a través del quemador extinguido, lo que conduce a la formación de una mezcla explosiva en el horno.
La separación ocurre cuando: un aumento en la presión del gas por encima de lo permitido, un fuerte aumento en el suministro de aire primario, un aumento en el vacío en el horno, el funcionamiento del quemador en modos trascendentes en relación con los indicados en el pasaporte.
2. Flashback: mover la zona de la llama hacia la mezcla combustible. Ocurre solo en quemadores con una mezcla preliminar de gas y aire. Ocurre cuando la velocidad de la mezcla gas-aire se vuelve menor que la velocidad de propagación de la llama. La llama salta dentro del quemador, donde continúa ardiendo, provocando que el quemador se deforme por sobrecalentamiento. Cuando es posible un resbalón, es posible un pequeño estallido, la llama se apagará, se producirá gas en el horno y los conductos de gas a través del quemador inactivo.
El avance ocurre cuando: la presión del gas frente al quemador cae por debajo del valor permitido; encendido del quemador cuando se suministra aire primario; Gran suministro de gas a baja presión de aire, lo que reduce el rendimiento de los quemadores al premezclar gas y aire por debajo de los valores especificados en el pasaporte. No es posible con el método de difusión de combustión de gas.
Actuaciones del personal en caso de accidente en el quemador:
- apagar el quemador,
- ventilar el horno,
- averiguar la causa del accidente,
- hacer una entrada en el diario