Elementy mocujące i mechanizmy mocujące. Abstrakcyjne typy urządzeń mocujących. Elementy mocujące osprzętu.doc
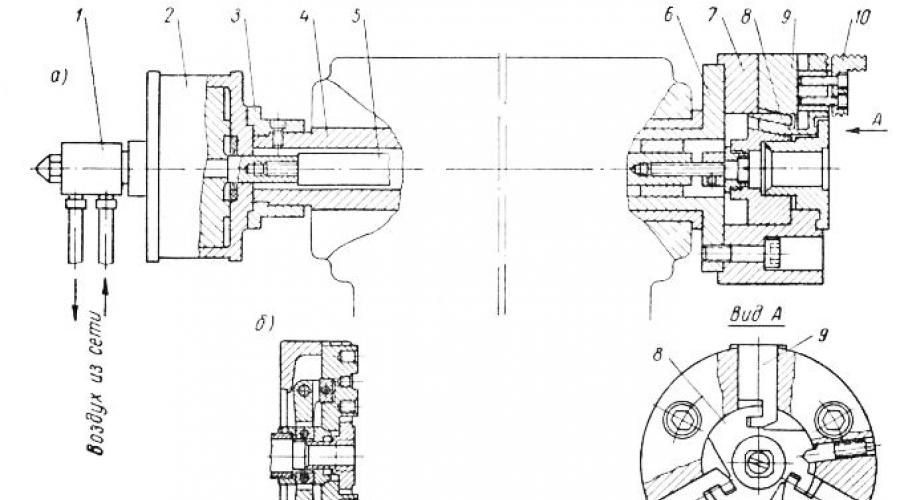
Urządzenia mocujące narzędzia maszynowe
DO Kategoria:
Maszyny do cięcia metalu
Urządzenia mocujące maszyny
Proces podawania automatów przedmiotami obrabianymi odbywa się przy ścisłym współdziałaniu urządzeń załadowczych z automatyką elementy mocujące. W wielu przypadkach automatyczne urządzenia mocujące stanowią część konstrukcji maszyny lub jej integralną część. Dlatego pomimo istnienia specjalistycznej literatury poświęconej urządzeniom mocującym, wydaje się konieczne krótkie zatrzymanie się na niektórych charakterystycznych konstrukcjach,
Elementy ruchome automatycznych urządzeń mocujących odbierają ruch od odpowiednich napędów sterowanych, którymi mogą być napędy sterowane mechanicznie odbierające ruch od napędu głównego korpusu roboczego lub od niezależnego silnika elektrycznego, napędy krzywkowe, napędy hydrauliczne, pneumatyczne i pneumatyczno-hydrauliczne. Poszczególne elementy ruchome urządzeń zaciskowych mogą odbierać ruch zarówno ze wspólnego, jak i kilku niezależnych napędów.
Zadania nie obejmują uwzględniania projektów urządzeń specjalnych, które zależą głównie od konfiguracji i wymiarów konkretnego przedmiotu obrabianego tej pracy, a my ograniczymy się do wprowadzenia kilku urządzeń mocujących ogólnego przeznaczenia.
Uchwyty mocujące. Dostępny duża liczba konstrukcje uchwytów samocentrujących w większości przypadków z tłokowym napędem hydraulicznym i pneumatycznym, które znajdują zastosowanie na tokarkach, rewolwerach i szlifierkach. Uchwyty te, zapewniając jednocześnie niezawodne mocowanie i dobre centrowanie przedmiotu obrabianego, charakteryzują się niewielkim zużyciem szczęk, dlatego przy przechodzeniu od obróbki jednej partii części do drugiej, uchwyt należy przebudować i zapewnić wysoka precyzja proces centrowania powierzchni centrujących krzywek na miejscu; w tym przypadku krzywki hartowane są szlifowane, a krzywki surowe toczone lub wiercone.
Jedną z powszechnych konstrukcji uchwytu z pneumatycznym napędem tłokowym pokazano na ryc. 1. Siłownik pneumatyczny jest zabezpieczony kołnierzem pośrednim na końcu wrzeciona. Dopływ powietrza do cylindra pneumatycznego odbywa się poprzez maźnicę osadzoną na łożyskach tocznych na trzpieniu pokrywy cylindra. Tłok cylindra jest połączony za pomocą pręta z mechanizmem zaciskającym wkładu. Uchwyt pneumatyczny mocowany jest do kołnierza zamontowanego na przednim końcu wrzeciona. Głowica przymocowana do końca pręta ma ukośne rowki, w które mieszczą się występy krzywek w kształcie litery L. Kiedy głowa wraz z prętem przesuwa się do przodu, krzywki zbliżają się do siebie, a podczas ruchu do tyłu rozchodzą się.
Na szczękach głównych, które mają rowki w kształcie litery T, zamocowane są szczęki górne, które są instalowane zgodnie ze średnicą powierzchni mocowanej przedmiotu obrabianego.
Dzięki niewielkiej liczbie ogniw pośrednich przenoszących ruch na krzywki i znaczny rozmiar powierzchnie cierne, wkłady opisywanej konstrukcji charakteryzują się stosunkowo dużą sztywnością i trwałością.
Ryż. 1. Uchwyt pneumatyczny.
W wielu konstrukcjach uchwytów pneumatycznych wykorzystuje się przekładnie dźwigniowe. Takie wkłady mają mniejszą sztywność, a ze względu na obecność wielu połączeń przegubowych zużywają się szybciej.
Zamiast cylindra pneumatycznego można zastosować pneumatyczny napęd membranowy lub cylinder hydrauliczny. Cylindry obracające się wraz z wrzecionem, szczególnie przy dużych prędkościach wrzeciona, wymagają starannego wyważenia, co jest wadą tej opcji konstrukcyjnej.
Napęd tłoka można zamontować stacjonarnie współosiowo z wrzecionem, a tłoczysko cylindra połączone jest z drążkiem dociskowym za pomocą sprzęgła, które zapewnia swobodny obrót tłoczyska wraz z wrzecionem. Stały tłoczysko cylindra można także połączyć z drążkiem zaciskowym za pomocą układu pośrednich przekładni mechanicznych. Takie schematy mają zastosowanie, jeśli w napędzie urządzenia zaciskowego znajdują się mechanizmy samohamujące, ponieważ w przeciwnym razie łożyska wrzeciona zostaną obciążone znacznymi siłami osiowymi.
Oprócz uchwytów samocentrujących stosowane są również uchwyty dwuszczękowe ze specjalnymi szczękami przejmującymi ruch od powyższych napędów oraz uchwyty specjalne.
Podobne napędy stosuje się przy mocowaniu części do różnych trzpieni rozprężnych.
Urządzenia do mocowania tulei zaciskowych. Tuleje zaciskowe są elementem konstrukcyjnym maszyn rewolwerowych i automatów tokarskich przeznaczonych do wytwarzania części z prętów. Jednocześnie znajdują szerokie zastosowanie oraz w specjalnych urządzeniach mocujących.
Ryż. 2. Urządzenia mocujące tuleje zaciskowe.
W praktyce istnieją trzy typy urządzeń do mocowania tulei zaciskowych.
Tuleja zaciskowa, posiadająca kilka nacięć wzdłużnych, jest wyśrodkowana tylnym cylindrycznym ogonem w otworze wrzeciona i przednim stożkowym ogonem w otworze kołpaka. Podczas zaciskania rura przesuwa tuleję do przodu, a jej przednia stożkowa część wchodzi w stożkowy otwór kołpaka wrzeciona. W tym przypadku tuleja zaciskowa jest ściskana i zaciska pręt lub przedmiot obrabiany. Urządzenie zaciskowe tego typu ma wiele istotnych wad.
Dokładność centrowania przedmiotu obrabianego w dużej mierze zależy od współosiowości stożkowej powierzchni kołpaka i osi obrotu wrzeciona. W tym celu należy uzyskać współosiowość stożkowego otworu kołpaka i jego cylindrycznej powierzchni centrującej, współosiowość pierścienia centrującego z osią obrotu wrzeciona oraz minimalną szczelinę pomiędzy powierzchniami centrującymi kołpaka i trzpienia wrzeciono.
Ponieważ spełnienie tych warunków stwarza znaczne trudności, tego typu urządzenia zaciskowe nie zapewniają dobrego centrowania.
Dodatkowo podczas procesu zaciskania tuleja poruszając się do przodu chwyta pręt, który porusza się wraz z tuleją, co może
prowadzić do zmian wymiarów obrabianych części na długości i pojawienia się dużych nacisków na zderzaku. W praktyce zdarzają się przypadki, gdy do zderzaka przyspawany jest obracający się pręt, dociśnięty z dużą siłą do zderzaka.
Zaletą tej konstrukcji jest możliwość zastosowania wrzeciona o małej średnicy. Ponieważ jednak o średnicy wrzeciona w dużej mierze decydują inne względy, a przede wszystkim jego sztywność, okoliczność ta w większości przypadków nie jest znacząca.
Wskutek wspomniane niedociągnięcia Ta wersja urządzenia mocującego tuleję zaciskową ma ograniczone zastosowanie.
Tuleja ma odwrócony stożek i po zaciśnięciu materiału rura wciąga tuleję do wrzeciona. Ten projekt zapewnia dobre centrowanie, gdyż stożek centrujący znajduje się bezpośrednio we wrzecionie. Wadą konstrukcji jest to, że materiał przemieszcza się wraz z tuleją podczas procesu mocowania, co prowadzi do zmiany wymiarów przedmiotu obrabianego, ale nie powoduje żadnych obciążeń osiowych na ograniczniku. Pewną wadą jest także słabość istniejącej sekcji połączenie gwintowane. Średnica wrzeciona nieznacznie wzrasta w porównaniu do poprzedniej wersji.
Ze względu na zauważone zalety i prostotę konstrukcji opcja ta jest szeroko stosowana na maszynach rewolwerowych i automatach tokarskich wielowrzecionowych, których wrzeciona muszą mieć minimalną średnicę.
Opcja pokazana na rys. 2, c, różni się od poprzedniego tym, że podczas zaciskania tuleja, która opiera się przednią powierzchnią o kołpaku, pozostaje nieruchoma, a tuleja porusza się pod działaniem rury. Stożkowa powierzchnia tulei jest dociskana do zewnętrznej stożkowej powierzchni tulei, a ta jest ściskana. Ponieważ tuleja zaciskowa pozostaje nieruchoma podczas procesu mocowania, w tej konstrukcji nie występuje przemieszczenie obrabianego pręta. Tuleja posiada dobre centrowanie we wrzecionie, a zapewnienie współosiowości wewnętrznych stożkowych i zewnętrznych powierzchni centrujących tulei nie stwarza trudności technologicznych, dzięki czemu taka konstrukcja zapewnia w miarę dobre centrowanie obrabianego pręta.
Po zwolnieniu tulei rura cofa się w lewo, a tuleja przesuwa się pod działaniem sprężyny.
Aby siły tarcia powstające podczas procesu mocowania powierzchnia końcowa ostrza tulei zaciskowych nie zmniejszyłyby siły docisku, powierzchnia końcowa otrzymuje kształt stożkowy o kącie nieco większym niż kąt tarcia.
Ta konstrukcja jest bardziej złożona niż poprzednia i wymaga zwiększenia średnicy wrzeciona. Jednak ze względu na odnotowane zalety jest szeroko stosowany na maszynach jednowrzecionowych, gdzie wzrost średnicy wrzeciona nie jest znaczący, oraz w wielu modelach maszyn rewolwerowych.
Wymiary najpopularniejszych tulei zaciskowych są znormalizowane przez odpowiedni GOST. Tuleje zaciskowe duże rozmiary wykonane są z wymiennymi szczękami, co pozwala zmniejszyć ilość tulei zaciskowych w zestawie i w przypadku zużycia szczęk wymienić je na nowe.
Powierzchnia szczęk tulei pracujących pod dużym obciążeniem posiada wycięcie, które zapewnia przeniesienie dużych sił na mocowaną część.
Tuleje zaciskowe wykonane są ze stali U8A, U10A, 65G, 9ХС. Część robocza tulei jest hartowana do twardości HRC 58-62. Ogon
część jest odpuszczana do twardości HRC 38-40. Do produkcji tulei zaciskowych stosuje się również stale do nawęglania, w szczególności stal 12ХНЗА.
Rura poruszająca samą tuleję zaciskową otrzymuje ruch z jednego z wymienionych typów napędów za pośrednictwem jednego lub drugiego układu przekładni pośrednich. Niektóre konstrukcje przekładni pośrednich do przesuwania rury dociskowej pokazano na ryc. IV. 3.
Rura zaciskowa odbiera ruch od krakersów, które są częścią tulei z występem pasującym do rowka wrzeciona. Krakersy opierają się na występach końcowych rurki zaciskowej, które utrzymują je w wymaganej pozycji. Krakersy przejmują ruch za pomocą dźwigni, których końce w kształcie litery L pasują do końcowego wgłębienia tulei 6 osadzonej na wrzecionie. Po zaciśnięciu tulei tuleja przesuwa się w lewo i działając swoją wewnętrzną stożkową powierzchnią na końcach dźwigni, obraca je. Obrót następuje względem punktów styku występów dźwigni w kształcie litery L z wgłębieniem tulei. W takim przypadku pięty dźwigni naciskają na krakersy. Na rysunku przedstawiono mechanizmy w położeniu odpowiadającym końcowi obejmy. W tej pozycji mechanizm jest zamknięty, a tuleja jest odciążona od sił osiowych.
Ryż. 3. Mechanizm ruchu rury zaciskowej.
Regulacja siły docisku odbywa się za pomocą nakrętek poruszających tuleję. Aby uniknąć konieczności zwiększania średnicy wrzeciona, montowany jest na nim gwintowany pierścień, który opiera się o półpierścienie pasujące do rowka wrzeciona.
W zależności od średnicy powierzchni zaciskowej, która może zmieniać się w ramach tolerancji, rura zaciskowa będzie zajmować różne położenia w kierunku osiowym. Odchylenia położenia rury są kompensowane przez odkształcenie dźwigni. W innych konstrukcjach wprowadzono specjalne kompensatory sprężynowe.
Opcja ta jest szeroko stosowana na automatach tokarskich jednowrzecionowych. Istnieje wiele modyfikacji konstrukcyjnych, różniących się kształtem dźwigni.
W wielu konstrukcjach dźwignie są zastępowane kulkami lub rolkami podpierającymi. Na końcu rury zaciskowej kołnierz osadzony jest na gwincie. Po zaciśnięciu tulei kołnierz wraz z rurą przesuwa się w lewo. Kołnierz przejmuje ruch od tulei działającej poprzez rolkę na tarczy. Gdy obudowa przesuwa się w lewo, jej wewnętrzna stożkowa powierzchnia powoduje, że rolki baryłkowe przesuwają się w kierunku środka. W tym przypadku rolki poruszając się po stożkowej powierzchni podkładki przesuwają się w lewo, przesuwając tarczę i kołnierz z rurą dociskową w tym samym kierunku. Wszystkie części są osadzone na tulei zamontowanej na końcu wrzeciona. Regulacja siły docisku odbywa się poprzez przykręcenie kołnierza do rury. W wymaganej pozycji kołnierz jest blokowany za pomocą zamka. Mechanizm może być wyposażony w elastyczny kompensator w postaci sprężyn talerzowych, co pozwala na zastosowanie go do mocowania prętów o dużych tolerancjach średnic.
Ruchome tuleje wykonujące zaciskanie odbierają ruch od mechanizmów krzywkowych tokarek automatycznych lub od napędów tłokowych. Rurę zaciskową można także podłączyć bezpośrednio do napędu tłokowego.
Napędy urządzeń mocujących maszyn wielopozycyjnych. Każde z urządzeń mocujących maszyny wielostanowiskowej może posiadać własny napęd, najczęściej tłokowy, lub elementy ruchome urządzenia mocującego mogą być napędzane przez napęd zamontowany na stanowisku załadunku. W tym drugim przypadku mechanizmy zaciskowe wpadające w położenie załadunkowe połączone są z mechanizmami napędowymi. Na końcu zacisku połączenie to zostaje zakończone.
Ostatnia opcja Szeroko stosowany w automatach tokarskich wielowrzecionowych. W pozycji, w której pręt jest podawany i zaciskany, instalowany jest suwak z występem. Podczas obrotu bloku wrzeciona występ wchodzi w pierścieniowy rowek ruchomej tulei mechanizmu zaciskowego i w odpowiednich momentach przesuwa tuleję w kierunku osiowym.
Na podobnej zasadzie można w niektórych przypadkach przesuwać elementy ruchome urządzeń mocujących zainstalowanych na stołach i bębnach wielopozycyjnych. Kolczyk mocowany jest pomiędzy stałymi i ruchomymi pryzmami urządzenia zaciskowego zamontowanego na wielopozycyjnym stole. Pryzmat odbiera ruch z suwaka klinowo-skośnego. Po zaciśnięciu tłok, na którym wycinana jest zębatka, przesuwa się w prawo. Poprzez przekładnię zębatą ruch przekazywany jest na suwak, który przesuwa pryzmat do pryzmatu za pomocą skosu klinowego. Po zwolnieniu zaciśniętej części tłok przesuwa się w prawo, co jest również połączone z suwakiem za pomocą koła zębatego.
Tłoki mogą odbierać ruch od siłowników tłokowych zainstalowanych w pozycji załadunku lub od odpowiednich ogniw w mechanizmach krzywkowych. Zaciskanie i zwalnianie części można również wykonać, gdy stół się obraca. Podczas zaciskania tłok wyposażony w rolkę porusza się po nieruchomej pięści zainstalowanej pomiędzy pozycją załadunku a pierwszą pozycją roboczą. Po zwolnieniu tłok wpada w pięść znajdującą się pomiędzy ostatnią pozycją roboczą i załadunkową. Tłoki znajdują się w różnych płaszczyznach. Aby skompensować odchylenia wymiarów zaciskanej części, wprowadza się kompensatory elastyczne.
Należy zaznaczyć, że tak proste rozwiązania nie są dostatecznie stosowane przy projektowaniu uchwytów mocujących do maszyn wielopozycyjnych przy obróbce małych części.
Ryż. 4. Wielopozycyjne urządzenie do mocowania maszyny, napędzane napędem montowanym na stanowisku załadunku.
Jeżeli dla każdego z urządzeń mocujących maszyny wielopozycyjnej przydzielone są osobne silniki tłokowe, obrotnica lub bęben musi być zasilany sprężonym powietrzem lub olejem pod ciśnieniem. Urządzenie do dostarczania sprężonego powietrza lub oleju jest podobne do opisanego powyżej urządzenia z obrotowym cylindrem. Stosowanie łożysk tocznych w tym przypadku jest niepotrzebne, ponieważ prędkość obrotowa jest niska.
Każde urządzenie może mieć indywidualny zawór sterujący lub suwak, albo też dla wszystkich urządzeń można zastosować wspólne urządzenie dystrybucyjne.
Ryż. 5. Urządzenie rozdzielcze napędów tłokowych urządzeń mocujących stołu wielopozycyjnego.
Indywidualne krany lub urządzenia dystrybucyjne przełączane za pomocą napędów pomocniczych zainstalowanych w pozycji załadunku.
Ogólna rozdzielnica sekwencyjnie łączy napędy tłoków przyrządów, gdy stół lub bęben się obraca. Przybliżony projekt takiego urządzenia dystrybucyjnego pokazano na ryc. 5. Obudowa urządzenia rozprowadzającego, zainstalowana współosiowo z osią obrotu stołu lub bębna, obraca się wraz z nią, a szpule wraz z osią pozostają nieruchome. Suwak steruje dopływem sprężonego powietrza do wnęk, a suwak steruje dopływem sprężonego powietrza do wnęk cylindrów dociskowych.
Sprężone powietrze wchodzi kanałem do przestrzeni pomiędzy szpulami i za jej pomocą kierowane jest do odpowiednich wnęk cylindrów dociskowych. Powietrze wywiewane przedostaje się do atmosfery poprzez otwory.
Sprężone powietrze dostaje się do wnęki przez otwór, rowek łukowy i otwory. Dopóki otwory odpowiednich cylindrów pokrywają się z rowkiem łukowym, sprężone powietrze dostaje się do wnęk cylindrów. Gdy podczas kolejnego obrotu stołu otwór jednego z cylindrów zrówna się z otworem, wnęka tego cylindra zostanie połączona z atmosferą poprzez pierścieniowy rowek, kanał, pierścieniowy rowek i kanał.
Wnęki cylindrów, do których wpływa sprężone powietrze, muszą być połączone z atmosferą. Wnęki są połączone z atmosferą poprzez kanały, rowek łukowy, kanały, rowek pierścieniowy i otwór.
Sprężone powietrze musi dostać się do wnęki cylindra znajdującej się w pozycji załadunku, która jest dostarczana przez otwór i kanały.
Zatem, gdy stół wielopozycyjny jest obracany, automatyczne przełączanie przepływ sprężonego powietrza.
Na podobnej zasadzie steruje się przepływem oleju dostarczanego do urządzeń mocujących maszyn wielopozycyjnych.
Należy zaznaczyć, że podobne urządzenia dystrybucyjne stosowane są także na maszynach do obróbki ciągłej ze stołami obrotowymi lub bębnami.
Zasady wyznaczania sił działających w urządzeniach mocujących. Oprawy mocujące są zwykle projektowane w taki sposób, aby siły powstałe w procesie cięcia były przejmowane przez nieruchome elementy osprzętu. Jeżeli pewne siły powstałe w procesie cięcia są odbierane przez poruszające się elementy, wówczas wielkość tych sił określa się na podstawie równań statyki tarcia.
Metoda wyznaczania sił działających w mechanizmach dźwigniowych urządzeń mocujących tulejki zaciskowe jest podobna do metody stosowanej do wyznaczania sił zadziałania sprzęgieł ciernych z mechanizmami dźwigniowymi.
Głównym celem urządzeń mocujących uchwyty jest zapewnienie niezawodnego kontaktu (ciągłości) przedmiotu obrabianego lub montowanej części z elementami montażowymi, zapobiegając jego przemieszczaniu się podczas obróbki lub montażu.
Zaciski dźwigniowe. Zaciski dźwigniowe (rysunek 2.16) stosuje się w połączeniu z innymi podstawowymi zaciskami, tworząc bardziej złożone systemy mocowania. Umożliwiają zmianę wielkości i kierunku przenoszonej siły.
Mechanizm klinowy. Kliny mają bardzo szerokie zastosowanie w mechanizmach mocujących urządzeń, co zapewnia prostą i zwartą konstrukcję oraz niezawodne działanie. Klin może być albo prostym elementem mocującym działającym bezpośrednio na obrabiany przedmiot, albo można go połączyć z dowolnym innym prostym elementem, tworząc kombinowane mechanizmy. Zastosowanie klina w mechanizmie zaciskowym zapewnia: zwiększenie początkowej siły napędowej, zmianę kierunku działania siły początkowej, samohamowanie mechanizmu (zdolność do utrzymania siły docisku, gdy siła wytwarzana przez napęd przestaje). Jeśli mechanizm klinowy służy do zmiany kierunku siły docisku, wówczas kąt klina wynosi zwykle 45°, a jeśli w celu zwiększenia siły docisku lub zwiększenia niezawodności, przyjmuje się kąt klina równy 6...15 ° (kąty samohamowania).
o mechanizmy z płaskim klinem jednoskośnym (
o mechanizmy wieloklinowe (wielotłokowe);
o mimośrody (mechanizmy z zakrzywionym klinem);
o krzywki końcowe (mechanizmy z klinem cylindrycznym).
11. Działanie sił skrawania, docisków i ich momentów na przedmiot obrabiany
Podczas procesu obróbki narzędzie tnące wykonuje określone ruchy względem przedmiotu obrabianego. Dlatego wymagane rozmieszczenie powierzchni części można osiągnąć tylko w następujące przypadki:
1) jeśli przedmiot obrabiany zajmuje określoną pozycję w miejsce pracy maszyna;
2) jeżeli przed rozpoczęciem obróbki zostanie określone położenie przedmiotu obrabianego w obszarze roboczym, na tej podstawie można korygować ruchy kształtujące.
Dokładne położenie przedmiotu obrabianego w obszarze roboczym maszyny osiąga się podczas jego montażu w uchwycie. Proces montażu obejmuje bazowanie (tj. nadanie obrabianemu przedmiotowi wymaganego położenia względem wybranego układu współrzędnych) oraz zabezpieczenie (tj. przyłożenie sił i par sił do przedmiotu obrabianego w celu zapewnienia stałości i niezmienności jego położenia osiągniętego podczas bazowania).
Rzeczywiste położenie przedmiotu obrabianego zamontowanego w obszarze roboczym maszyny różni się od wymaganego, co jest spowodowane odchyleniem położenia przedmiotu obrabianego (w kierunku utrzymywanego rozmiaru) podczas procesu montażu. To odchylenie nazywa się błędem instalacji i składa się z błędu podstawowego i błędu mocowania.
Powierzchnie należące do przedmiotu obrabianego i użyte do jego podstawy nazywane są bazami technologicznymi, a te, które służą do jego pomiarów, nazywane są bazami pomiarowymi.
Aby zainstalować przedmiot w uchwycie, zwykle stosuje się kilka podstaw. Mówiąc prościej, uważa się, że przedmiot obrabiany styka się z uchwytem w punktach zwanych punktami podparcia. Układ punktów odniesienia nazywany jest schematem bazowym. Każdy punkt odniesienia określa powiązanie przedmiotu z wybranym układem współrzędnych, w którym przedmiot jest obrabiany.
1. Jeżeli wymagania dotyczące dokładności obróbki są wysokie, jako podstawę technologiczną należy przyjąć precyzyjnie obrobioną powierzchnię przedmiotu obrabianego i przyjąć taki schemat podłoża, który zapewni najmniejszy błąd montażowy.
2. Jeden z najbardziej proste sposoby zwiększenie dokładności bazowania polega na przestrzeganiu zasady łączenia baz.
3. Aby zwiększyć dokładność obróbki, należy przestrzegać zasady stałości zasad. Jeśli z jakiegoś powodu nie jest to możliwe, konieczne jest, aby nowe bazy danych były przetwarzane dokładniej niż poprzednie.
4. Jako podstawy należy używać powierzchni o prostych kształtach (płaskich, cylindrycznych i stożkowych), z których w razie potrzeby można utworzyć zestaw podstaw. W przypadkach, gdy powierzchnie przedmiotu obrabianego nie spełniają wymagań stawianych podstawom (tj. ich wielkość, kształt i umiejscowienie nie zapewniają określonej dokładności, stabilności i łatwości obróbki), na przedmiocie obrabianym tworzone są sztuczne podłoża (nakiełka, otwory technologiczne , płyty, podcięcia itp.).
Podstawowe wymagania dotyczące mocowania detali w uchwytach są następujące.
1. Mocowanie powinno zapewniać pewny kontakt przedmiotu obrabianego z podporami urządzeń oraz zapewniać niezmienne położenie przedmiotu obrabianego względem wyposażenia technologicznego podczas obróbki lub po wyłączeniu zasilania.
2. Zaciskanie przedmiotu obrabianego należy stosować tylko w przypadkach, gdy siła obróbcza lub inne siły mogą przesunąć przedmiot obrabiany (np. podczas ciągnięcia wpustu przedmiot nie jest zabezpieczony).
3. Siły mocowania nie powinny powodować dużych odkształceń i zapadnięcia się podstawy.
4. Należy wykonać zabezpieczenie i zwolnienie obrabianego przedmiotu minimalny koszt czasu i wysiłku ze strony pracownika. Najmniejszy błąd mocowania zapewniają urządzenia mocujące, które tworzą
stała siła docisku (np. urządzenia z napędem pneumatycznym lub hydraulicznym).
5. Aby zmniejszyć błąd mocowania, należy stosować podłoża o małej chropowatości; używać urządzeń napędzanych; Umieść elementy obrabiane na płaskich wspornikach z głowicą lub precyzyjnie obrobionych płytach podporowych.
Bilet 13
Mechanizmy mocujące osprzętu Mechanizmy mocujące nazywane są mechanizmami, które eliminują możliwość wibracji lub przemieszczenia przedmiotu obrabianego względem elementów instalacji pod wpływem własnego ciężaru i sił powstających podczas obróbki (montażu). Głównym zadaniem urządzeń mocujących jest zapewnienie niezawodnego kontaktu przedmiotu obrabianego z elementami mocującymi, zapobieganie jego przemieszczaniu się i wibracjom podczas obróbki, a także zapewnienie prawidłowa instalacja i centrowanie przedmiotu obrabianego.
Obliczanie sił docisku
Obliczanie sił docisku można sprowadzić do rozwiązania problemu statycznego dotyczącego równowagi ciała stałego (przedmiotu obrabianego) pod działaniem układu sił zewnętrznych.
Z jednej strony na obrabiany przedmiot przykładana jest grawitacja i siły powstałe podczas obróbki, z drugiej strony pożądane siły docisku – reakcja podpór. Pod wpływem tych sił przedmiot obrabiany musi zachować równowagę.
Przykład 1. Siła mocowania dociska przedmiot do podpór urządzenia, a siła skrawania powstająca podczas obróbki części (rysunek 2.12a) ma tendencję do przesuwania przedmiotu wzdłuż płaszczyzny podparcia.
Siłami działającymi na przedmiot obrabiany są: w górnej płaszczyźnie siła docisku oraz siła tarcia, która zapobiega przesuwaniu się przedmiotu obrabianego; wzdłuż dolnej płaszczyzny siły reakcji podpór (niepokazane na rysunku) są równe sile docisku i sile tarcia pomiędzy przedmiotem obrabianym a podporami. Następnie będzie równanie równowagi przedmiotu obrabianego
,
gdzie jest współczynnik bezpieczeństwa;
– współczynnik tarcia pomiędzy przedmiotem obrabianym a mechanizmem mocującym;
– współczynnik tarcia pomiędzy przedmiotem obrabianym a wspornikami uchwytu.
Gdzie
Rysunek 2.12 – Schematy obliczania sił zaciskających
Przykład 2. Siła skrawania skierowana jest pod kątem do siły mocowania (rysunek 2.12b).
Następnie będzie równanie równowagi przedmiotu obrabianego
Z rysunku 2.12b znajdujemy składowe siły skrawania
Podstawiając, otrzymujemy
Przykład 3. Przedmiot jest obrabiany tokarka i jest zamocowany w uchwycie trójszczękowym. Siły skrawania wytwarzają moment obrotowy, który powoduje obrót przedmiotu obrabianego w szczękach. Siły tarcia powstające w punktach styku szczęk z przedmiotem obrabianym wytwarzają moment tarcia, który uniemożliwia obrót przedmiotu obrabianego. Wtedy będzie stan równowagi przedmiotu obrabianego
.
Moment skrawania zostanie określony na podstawie wielkości składowej pionowej siły skrawania
.
Moment tarcia
.
Elementarne mechanizmy mocujące
Do elementarnych urządzeń mocujących zalicza się najprostsze mechanizmy służące do mocowania detali lub pełniące funkcję ogniw pośrednich w skomplikowanych układach mocujących:
śruba;
klin;
ekscentryczny;
dźwignia;
krążyna;
zębatka i dźwignia.
Zaciski śrubowe. Mechanizmy śrubowe (rysunek 2.13) są szeroko stosowane w urządzeniach z ręcznym mocowaniem detali, z napędem zmechanizowanym, a także na liniach automatycznych podczas korzystania z urządzeń satelitarnych. Ich zaletą jest prostota konstrukcji, a nie wysoka cena i wysoką niezawodność działania.
Mechanizmy śrubowe stosowane są zarówno do mocowania bezpośredniego, jak i w połączeniu z innymi mechanizmami. Siłę działającą na rękojeść niezbędną do wytworzenia siły docisku można obliczyć ze wzoru:
,
gdzie jest średni promień gwintu, mm;
– przesunięcie wpustu, mm;
– kąt skoku gwintu;
Kąt tarcia w parze gwintowanej.
Mechanizm klinowy. Kliny mają bardzo szerokie zastosowanie w mechanizmach mocujących urządzeń, co zapewnia prostą i zwartą konstrukcję oraz niezawodne działanie. Klin może być albo prostym elementem mocującym działającym bezpośrednio na obrabiany przedmiot, albo można go połączyć z dowolnym innym prostym elementem, tworząc kombinowane mechanizmy. Zastosowanie klina w mechanizmie zaciskowym zapewnia: zwiększenie początkowej siły napędowej, zmianę kierunku działania siły początkowej, samohamowanie mechanizmu (zdolność do utrzymania siły docisku, gdy siła wytwarzana przez napęd przestaje). Jeśli mechanizm klinowy służy do zmiany kierunku siły docisku, wówczas kąt klina wynosi zwykle 45°, a jeśli w celu zwiększenia siły docisku lub zwiększenia niezawodności, przyjmuje się kąt klina równy 6...15 ° (kąty samohamowania).
Klin jest używany w następujący sposób opcje projektowania zaciski:
mechanizmy z płaskim klinem jednoskośnym (rysunek 2.14b);
mechanizmy wieloklinowe (wielotłokowe);
mimośrody (mechanizmy z zakrzywionym klinem);
krzywki końcowe (cylindryczne mechanizmy klinowe).
Rysunek 2.14a przedstawia schemat klina dwukątowego.
Podczas mocowania przedmiotu klin porusza się w lewo pod wpływem siły. Podczas ruchu klina na jego płaszczyznach powstają siły normalne i siły tarcia (rysunek 2.14, b).
Znacząca wada rozważanym mechanizmem jest niski współczynnik przydatna akcja(wydajność) z powodu strat tarcia.
Przykład użycia klina w uchwycie pokazano w
Rysunek 2.14, d.
Dla zwiększenie wydajności mechanizmu klinowego tarcie ślizgowe na powierzchniach klina zastępuje się tarciem tocznym za pomocą rolek podporowych (rysunek 2.14, c).
Mechanizmy wieloklinowe są wyposażone w jeden, dwa lub więcej tłoków. Jako zaciskowe stosuje się jedno- i dwutłokowe; wielotłokowe służą jako mechanizmy samocentrujące.
Zaciski krzywkowe. Mimośród to połączenie w jednej części dwóch elementów - okrągłego dysku (rysunek 2.15e) i płaskiego klina o pojedynczym skosie. Kiedy mimośród obraca się wokół osi obrotu tarczy, klin wchodzi w szczelinę między tarczą a przedmiotem obrabianym i wytwarza siłę docisku.
Powierzchnia robocza mimośrodów może mieć kształt koła (okrągłego) lub spirali (krzywoliniowa).
Zaciski krzywkowe to najszybciej działające ze wszystkich ręcznych mechanizmów zaciskających. Pod względem prędkości dorównują dociskom pneumatycznym.
Wadami zacisków mimośrodowych są:
mały udar;
ograniczone wielkością mimośrodu;
zwiększone zmęczenie pracownika, ponieważ podczas odpinania przedmiotu obrabianego pracownik musi przyłożyć siłę ze względu na właściwość samohamowania mimośrodu;
zawodność zacisku, gdy narzędzie pracuje pod wpływem wstrząsów lub wibracji, ponieważ może to prowadzić do samoodłączenia przedmiotu obrabianego.
Pomimo tych wad dociski mimośrodowe są szeroko stosowane w osprzętach (rysunek 2.15b), zwłaszcza w produkcji na małą i średnią skalę.
Za osiągnięcia niezbędną siłę mocowania, określimy największy moment na uchwycie mimośrodowym
gdzie jest siła działająca na uchwyt,
- Długość rękojeści;
– mimośrodowy kąt obrotu;
– kąty tarcia.
Zaciski dźwigniowe. Zaciski dźwigniowe (rysunek 2.16) stosowane są w połączeniu z innymi podstawowymi zaciskami, tworząc bardziej złożone układy mocowania. Umożliwiają zmianę wielkości i kierunku przenoszonej siły.
Odmiany projektowe Zacisków dźwigniowych jest wiele, jednak wszystkie sprowadzają się do trzech obwodów mocy pokazanych na rysunku 2.16, który zawiera także wzory na obliczenie wymaganej siły do wytworzenia siły docisku przedmiotu obrabianego dla idealnych mechanizmów (bez uwzględnienia sił tarcia ). Siłę tę wyznacza się z warunku, że momenty wszystkich sił względem punktu obrotu dźwigni są równe zeru. Rysunek 2.17 przedstawia schematy konstrukcyjne zacisków dźwigniowych.
Podczas wykonywania wielu operacji obróbka sztywność narzędzia skrawającego i całego układu technologicznego jako całości jest niewystarczająca. Aby wyeliminować ugięcia i odkształcenia narzędzia, stosuje się różne elementy prowadzące. Podstawowe wymagania dla takich elementów: dokładność, odporność na zużycie, wymienność. Takie urządzenia nazywane są przewodniki lub tulejki przewodzące i służą do wiercenia i wytaczania .
Konstrukcje i wymiary przepustów przewodzących do wiercenia są ujednolicone (ryc. 11.10). Tuleje są trwałe (rys. 11.10 a) i wymienne
Ryż. 11.10. Konstrukcje przepustów przewodzących: a) trwałe;
b) wymienny; c) szybka wymiana z zamkiem
(Rys. 11.10 b). Tuleje trwałe stosowane są w produkcji jednostkowej przy obróbce jednym narzędziem. Tuleje zamienne stosowane są w produkcji seryjnej i masowej. Tuleje szybkowymienne z blokadą (ryc. 11.10 c) stosuje się przy obróbce otworów kilkoma kolejno wymienianymi narzędziami.
Tuleje o średnicy otworu do 25 mm wykonane są ze stali U10A, hartowanej do 60...65. Przy średnicy otworu większej niż 25 mm tuleje są wykonane ze stali 20 (20X), a następnie utwardzane dyfuzyjnie i utwardzane do tej samej twardości.
Jeżeli narzędzia prowadzone są w tulei nie przez część roboczą, ale przez cylindryczne sekcje centrujące, wówczas stosuje się specjalne tuleje (ryc. 11.11). Na ryc. 11.11a przedstawia tuleję do wiercenia otworów na pochyłości
15. Elementy regulacyjne urządzeń.
-Ustawianie elementów (ustawienia wysokości i kąta) służą do kontrolowania położenia narzędzia podczas ustawiania maszyny.)
- Ustawianie elementów , dostarczanie prawidłowa pozycja narzędzie tnące podczas ustawiania (regulowania) maszyny w celu uzyskania określonych wymiarów. Takie elementy są instalacje wysokościowe i kątowe urządzeń frezujących, służące do kontroli położenia frezu podczas ustawiania i dostrajania maszyny. Ich zastosowanie ułatwia i przyspiesza ustawianie maszyny podczas obróbki detali poprzez automatyczne uzyskanie zadanych wymiarów
Elementy nastawcze pełnią następujące funkcje : 1) Zapobiegaj dryftowi narzędzia podczas pracy. 2) Podają instrumentowi dokładną pozycję względem urządzenia, obejmują one ustawienia (wymiary), kopiarki. 3) Wykonuj obie funkcje określone powyżej, obejmują one przepusty przewodzące i tulejki prowadzące. Tulejki przewodzące stosuje się podczas wiercenia otworów za pomocą wierteł, pogłębiaczy i rozwiertaków. Istnieją różne typy przepustów przewodzących: trwałe, szybkowymienne i wymienne. Stałe z kołnierzem i bez uszczelki przy obróbce otworu jednym narzędziem. Wciskane są w część korpusu - płytkę przewodzącą H7/n6. Wymienne tuleje stosuje się przy obróbce jednym narzędziem, ale z uwzględnieniem wymiany ze względu na zużycie. Szybkie notatki, gdy otwór w operacji jest przetwarzany sekwencyjnie za pomocą kilku narzędzi. Różnią się od wymiennych przelotowym rowkiem w kołnierzu. Stosowane są również specjalne przepusty przewodzące, posiadające konstrukcję odpowiadającą charakterystyce przedmiotu obrabianego i operacji. Tuleja wydłużona Tuleja z nachylonym końcem Tuleje prowadzące, które pełnią jedynie funkcję zapobiegania cofaniu się narzędzia, są wykonane na stałe. Na przykład w maszynach rewolwerowych jest on montowany w otworze wrzeciona i obraca się wraz z nim. Otwór w tulejach prowadzących wykonany jest zgodnie z H7. Kopiarki służą do precyzyjnego pozycjonowania narzędzia względem uchwytu podczas obróbki powierzchni zakrzywionych. Kopiarki są dostępne w wersji napowietrznej i wbudowanej. Faktury umieszczane są na obrabianym przedmiocie i razem z nim zabezpieczane. Część prowadząca narzędzia ma ciągły kontakt z kopiarką, a część tnąca wykonuje wymagany profil. Wbudowane kopiarki są instalowane na korpusie urządzenia. Wzdłuż kopiarki prowadzony jest palec śledzący, który poprzez specjalnie wbudowane w maszynę urządzenie przekazuje odpowiedni ruch na wrzeciono z narzędziem do obróbki zakrzywionego profilu. Instalacje są standardowe i specjalne, wieżowe i narożne. Instalacje na wysokościach ustawiają narzędzie w jednym kierunku, pod kątem w 2 kierunkach. Koordynacja narzędzia zgodnie z ustawieniami odbywa się za pomocą standardowych sond płaskich o grubości 1,3,5 mm lub sond cylindrycznych o średnicy 3 lub 5 mm. Instalacje umieszczone są na korpusie urządzenia z dala od przedmiotu obrabianego, z uwzględnieniem penetracji narzędzia, i są zabezpieczone śrubami oraz mocowane za pomocą kołków. Sonda służąca do dostosowania narzędzia do montażu na rysunku montażowym urządzenia jest wskazana w wymaganiach technicznych, a także jest dozwolona graficznie.
Do ustawienia (dostosowania) położenia stołu maszyny wraz z urządzeniem względem narzędzia tnącego stosuje się specjalne szablony montażowe, wykonane w postaci płytek, pryzm i kwadratów o różnych kształtach. Jednostki są przymocowane do korpusu urządzenia; ich powierzchnie odniesienia powinny znajdować się poniżej powierzchni przedmiotu obrabianego, aby nie zakłócać przejścia narzędzia skrawającego. Najczęściej instalacje są używane podczas przetwarzania frezarki, skonfigurowany tak, aby automatycznie uzyskiwał wymiary z zadaną dokładnością.
Istnieją instalacje wieżowe i narożne. Pierwsze służą do prawidłowego ustawienia części względem noża na wysokości, drugie - zarówno na wysokości, jak i w kierunku bocznym. Wykonane ze stali 20X, nawęglanej na głębokość 0,8 - 1,2 mm, a następnie hartowanej do twardości 55...60 jednostek HRC.
Elementy nastawcze narzędzi skrawających (przykład)
Kompleksowe badania produkcyjne dotyczące dokładności działania istniejących linii automatycznych, badania eksperymentalne i analizy teoretyczne powinny dostarczyć odpowiedzi na następujące podstawowe pytania w projektowaniu procesów technologicznych produkcji części karoserii na liniach automatycznych: a) uzasadnienie wyboru metody technologiczne oraz liczbę kolejno wykonywanych przejść do obróbki najbardziej krytycznych powierzchni części, z uwzględnieniem określonych wymagań dokładności b) ustalenie optymalnego stopnia koncentracji przejść w jednym położeniu, na podstawie warunków obciążenia i wymaganej dokładności obróbki c) dobór metod i schematy instalacji przy projektowaniu elementów instalacyjnych automatycznych urządzeń liniowych w celu zapewnienia dokładności obróbki d) zalecenia dotyczące stosowania i projektowania automatycznych zespołów liniowych zapewniających kierunek i mocowanie narzędzi skrawających w powiązaniu z wymaganiami dotyczącymi dokładności obróbki e) dobór metod ustawiania dostosowujemy maszyny do wymaganych wymiarów i doboru środki kontrolne dla niezawodnego utrzymania wielkości nastawczej f) uzasadnienie wymagań dotyczących dokładności obrabiarek i dokładności montażu linii automatycznej według parametrów mających bezpośredni wpływ na dokładność obróbki g) uzasadnienie wymagań dotyczących dokładności czerni detale w związku z dokładnością ich montażu i klarowaniem podczas obróbki, a także ustaleniem standardowych wartości do obliczania naddatków na obróbkę h) identyfikacja i formowanie postanowienia metodyczne do precyzyjnych obliczeń przy projektowaniu linii automatycznych.
16. Napędy pneumatyczne. Cel i wymagania wobec nich.
Napęd pneumatyczny (napęd pneumatyczny)- zespół urządzeń przeznaczonych do napędzania części maszyn i mechanizmów wykorzystujących energię sprężonego powietrza.
Napęd pneumatyczny, podobnie jak napęd hydrauliczny, jest rodzajem „wkładki pneumatycznej” pomiędzy silnikiem napędowym a obciążeniem (maszyną lub mechanizmem) i spełnia te same funkcje, co przekładnia mechaniczna (przekładnia, napęd pasowy, mechanizm korbowy itp.). . Głównym celem napędu pneumatycznego , a także przekładnia mechaniczna, - transformacja właściwości mechaniczne silnik napędowy zgodnie z wymaganiami obciążenia (przeliczenie rodzaju ruchu łącza wyjściowego silnika, jego parametrów, a także regulacja, zabezpieczenie przed przeciążeniem itp.). Obowiązkowymi elementami napędu pneumatycznego są sprężarka (pneumatyczny generator energii) i silnik pneumatyczny
W zależności od charakteru ruchu członu wyjściowego silnika pneumatycznego (wał silnika pneumatycznego lub cylinder pneumatyczny prętowy) i odpowiednio od charakteru ruchu elementu roboczego, napęd pneumatyczny może być obrotowy lub translacyjne. Siłowniki pneumatyczne z ruch do przodu są najczęściej stosowane w technologii.
Zasada działania maszyn pneumatycznych
W Ogólny zarys, przekazywanie energii w napędzie pneumatycznym przebiega następująco:
1. Silnik napędowy przenosi moment obrotowy na wał sprężarki, który przekazuje energię gazowi roboczemu.
2. Gaz roboczy po specjalnym przygotowaniu przepływa przewodami pneumatycznymi przez urządzenia sterujące do silnika pneumatycznego, gdzie energia pneumatyczna zamieniana jest na energię mechaniczną.
3. Następnie gaz roboczy jest uwalniany do otoczenia, w przeciwieństwie do napędu hydraulicznego, w którym płyn roboczy jest zawracany przewodami hydraulicznymi albo do zbiornika hydraulicznego, albo bezpośrednio do pompy.
Wiele maszyn pneumatycznych ma swoje odpowiedniki konstrukcyjne wśród wolumetrycznych maszyn hydraulicznych. W szczególności szeroko stosowane są silniki pneumatyczne i sprężarki z tłokami osiowymi, silniki pneumatyczne z przekładnią i łopatkami, cylindry pneumatyczne...
Typowy schemat napędu pneumatycznego
Typowy schemat napędu pneumatycznego: 1 - wlot powietrza; 2 - filtr; 3 - sprężarka; 4 - wymiennik ciepła (lodówka); 5 - separator wilgoci; 6 - kolektor powietrza (odbiornik); 7 -Zawór bezpieczeństwa; 8- Przepustnica; 9 - rozpylacz oleju; 10 - zawór redukcyjny ciśnienia; 11 - przepustnica; 12 - dystrybutor; 13 silnik pneumatyczny; M - manometr.
Powietrze dostaje się do układu pneumatycznego przez wlot powietrza.
Filtr oczyszcza powietrze, aby zapobiec uszkodzeniu elementów napędowych i zmniejszyć ich zużycie.
Sprężarka spręża powietrze.
Ponieważ zgodnie z prawem Charlesa powietrze sprężone w sprężarce ma wysoką temperaturę, przed dostarczeniem powietrza do odbiorców (zwykle silników pneumatycznych) powietrze jest schładzane w wymienniku ciepła (w lodówce).
Aby zapobiec oblodzeniu silników pneumatycznych na skutek rozszerzania się w nich powietrza, a także zmniejszyć korozję części, w układzie pneumatycznym montowany jest separator wilgoci.
Odbiornik służy do wytworzenia dopływu sprężonego powietrza, a także do wygładzenia pulsacji ciśnienia w układzie pneumatycznym. Pulsacje te wynikają z zasady działania sprężarek objętościowych (na przykład sprężarek tłokowych), które porcjami dostarczają powietrze do układu.
W opryskiwaczu oleju do sprężonego powietrza dodawany jest smar, zmniejszając w ten sposób tarcie pomiędzy ruchomymi częściami napędu pneumatycznego i zapobiegając ich zakleszczaniu.
W napędzie pneumatycznym należy zamontować reduktor ciśnienia, zapewniający dopływ sprężonego powietrza do silników pneumatycznych pod stałym ciśnieniem.
Dystrybutor steruje ruchem ogniw wyjściowych silnika pneumatycznego.
W silniku pneumatycznym (silniku pneumatycznym lub cylindrze pneumatycznym) energia sprężonego powietrza zamieniana jest na energię mechaniczną.
Siłowniki pneumatyczne wyposażone są w:
1. urządzenia stacjonarne montowane na stołach frezarek, wiertarek i innych maszyn;
2. urządzenia obrotowe - uchwyty, trzpienie itp.
3) urządzenia instalowane na stołach obrotowych i dzielących do obróbki ciągłej i pozycyjnej.
Jako korpus roboczy zastosowano komory pneumatyczne jednostronnego i dwustronnego działania.
Przy podwójnym działaniu tłok porusza się w obu kierunkach skompresowane powietrze.
Przy jednostronnym działaniu tłok poruszany jest sprężonym powietrzem podczas mocowania przedmiotu obrabianego i sprężyną podczas jego odpinania.
Aby zwiększyć siłę mocowania, stosuje się cylindry dwu- i trzytłokowe lub dwu- i trzykomorowe komory powietrzne. W tym przypadku siła mocowania wzrasta 2... 3 razy
Zwiększenie siły mocowania można uzyskać poprzez zintegrowanie dźwigni wzmacniających z napędem pneumatycznym.
Należy zwrócić uwagę na pewne zalety napędów pneumatycznych urządzeń.
W porównaniu do napędu hydraulicznego jest czysty, nie ma konieczności posiadania stacji hydraulicznej dla każdego urządzenia, jeśli maszyna, na której urządzenie jest zamontowane, nie jest wyposażona w stację hydrauliczną.
Napęd pneumatyczny charakteryzuje się szybkością działania, przewyższa nie tylko napędy ręczne, ale wiele napędów zmechanizowanych. Jeżeli np. natężenie przepływu oleju pod ciśnieniem w rurociągu urządzenia hydraulicznego wynosi 2,5...4,5 m/s, to maksymalnie możliwe jest 9 m/s, to powietrze pod ciśnieniem 4... 5 MPa, rozprzestrzenia się rurociągami z prędkością do 180 m/s lub większą. Dzięki temu w ciągu 1 godziny można wykonać aż 2500 operacji siłownika pneumatycznego.
Zaletami napędu pneumatycznego jest to, że jego działanie nie jest uzależnione od wahań temperatury otoczenia. Dużą zaletą jest to, że zapewnia napęd pneumatyczny ciągłe działanie siłę docisku, dzięki czemu siła ta może być znacznie mniejsza niż przy napędzie ręcznym. Ta okoliczność jest bardzo ważna przy obróbce cienkościennych przedmiotów, które są podatne na odkształcenia podczas mocowania.
Zalety
· w odróżnieniu od napędu hydraulicznego nie ma konieczności zawracania czynnika roboczego (powietrza) z powrotem do sprężarki;
· mniejsza masa płynu roboczego w porównaniu z napędem hydraulicznym (istotne dla nauki rakietowej);
· mniejsza waga siłowników w porównaniu do siłowników elektrycznych;
· możliwość uproszczenia układu poprzez wykorzystanie butli ze sprężonym gazem jako źródła energii; czasami zamiast żarówek stosuje się takie układy, w których ciśnienie w butli sięga 500 MPa;
· prostota i wydajność dzięki niskiemu kosztowi gazu roboczego;
· szybkość reakcji i duże prędkości obrotowe silników pneumatycznych (do kilkudziesięciu tysięcy obrotów na minutę);
· bezpieczeństwo przeciwpożarowe i neutralność środowiska pracy, zapewniające możliwość zastosowania napędu pneumatycznego w kopalniach i zakładach chemicznych;
· w porównaniu z napędem hydraulicznym – możliwość przesyłania energii pneumatycznej na duże odległości (do kilku kilometrów), co pozwala na zastosowanie napędu pneumatycznego jako napędu głównego w kopalniach i kopalniach;
· w odróżnieniu od napędu hydraulicznego, napęd pneumatyczny jest mniej wrażliwy na zmiany temperatury otoczenia ze względu na mniejszą zależność sprawności od wycieków czynnika roboczego (gazu roboczego), a co za tym idzie, zmiany szczelin pomiędzy elementami urządzeń pneumatycznych oraz lepkości czynnika czynnik roboczy nie ma istotnego wpływu na parametry pracy napędu pneumatycznego; dzięki temu napęd pneumatyczny jest wygodny w użyciu w gorących sklepach przedsiębiorstw metalurgicznych.
Wady
· ogrzewanie i chłodzenie gazu roboczego podczas sprężania w sprężarkach i rozprężania w silnikach pneumatycznych; ten niedobór wynika z praw termodynamiki i prowadzi do następujących problemów:
· możliwość zamrożenia układów pneumatycznych;
· kondensacja pary wodnej z gazu roboczego i w związku z tym konieczność jego osuszenia;
· wysoki koszt energii pneumatycznej w porównaniu do energii elektrycznej (ok. 3-4 razy większy), co ma znaczenie np. przy zastosowaniu napędu pneumatycznego w kopalniach;
· jeszcze niższa wydajność niż w przypadku napędu hydraulicznego;
· niska dokładność działania i płynność działania;
· możliwość wybuchowego pęknięcia rurociągów lub obrażeń przemysłowych, dlatego stosuje się przemysłowe napędy pneumatyczne małe ciśnienia gazu roboczego (zwykle ciśnienie w układach pneumatycznych nie przekracza 1 MPa, choć znane są układy pneumatyczne o ciśnieniu roboczym do 7 MPa – np. w elektrowniach jądrowych), a w efekcie siły działające na części jest znacznie mniej w porównaniu do napędu hydraulicznego). Tam, gdzie nie ma takiego problemu (w rakietach i samolotach) lub rozmiary systemów są małe, ciśnienia mogą sięgać 20 MPa i nawet więcej.
· do regulacji wielkości obrotu drążka siłownika konieczne jest zastosowanie drogich urządzeń – pozycjonerów.
Elementy mocujące muszą zapewniać niezawodny kontakt przedmiotu obrabianego z elementami montażowymi i zapobiegać jego przerwaniu pod wpływem sił powstających podczas obróbki, szybkie i równomierne zaciśnięcie wszystkich części oraz nie powodować odkształceń i uszkodzeń powierzchni mocowanych części.
Elementy mocujące dzielą się na:
Przez projekt - do śruby, klina, mimośrodu, dźwigni, zawiasu dźwigniowego (stosuje się również kombinowane elementy mocujące - dźwignia śrubowa, dźwignia mimośrodowa itp.).
Według stopnia mechanizacji - ręczne i zmechanizowane z napędem hydraulicznym, pneumatycznym, elektrycznym lub podciśnieniowym.
Mieszki mocujące można zautomatyzować.
Zaciski śrubowe używane do mocowania bezpośredniego lub za pomocą prętów zaciskowych lub przytrzymywania jednej lub więcej części. Ich wadą jest toże mocowanie i odpinanie części wymaga dużo czasu.
Dociskacze mimośrodowe i klinowe, podobnie jak śrubowe, umożliwiają mocowanie części bezpośrednio lub poprzez listwy zaciskowe i dźwignie.
Najbardziej rozpowszechnione otrzymał okrągłe zaciski mimośrodowe. Docisk mimośrodowy jest szczególnym przypadkiem docisku klinowego i aby zapewnić samohamowanie, kąt klina nie powinien przekraczać 6-8 stopni. Zaciski krzywkowe wykonane są ze stali wysokowęglowej lub stali utwardzanej powierzchniowo i poddane obróbce cieplnej do twardości HRC55-60. Dociskacze mimośrodowe to zaciski szybko działające, ponieważ... wymagane do zaciśnięcia obróć mimośród pod kątem 60-120 stopni.
Elementy z zawiasami dźwigniowymi stosowane jako ogniwa napędowe i wzmacniające mechanizmów zaciskowych. Z założenia dzielą się na jednodźwigniowe, dwudźwigniowe (jedno- i dwustronnego działania - samocentrujące i wielowahaczowe). Mechanizmy dźwigniowe nie mają właściwości samohamownych. Najprostszym przykładem mechanizmów przegubowych są listwy zaciskowe urządzeń, dźwignie wkładów pneumatycznych itp.
Zaciski sprężynowe służy do mocowania produktów przy niewielkim wysiłku występującym podczas ściskania sprężyny.
Aby wytworzyć stałe i duże siły mocowania, skróć czas mocowania, zastosuj pilot stosowane są zaciski napędy pneumatyczne, hydrauliczne i inne.
Najpopularniejszymi napędami pneumatycznymi są tłokowe cylindry pneumatyczne i komory pneumatyczne z elastyczną membraną, stacjonarne, obrotowe i wahadłowe.
Napędzane są siłowniki pneumatyczne sprężone powietrze pod ciśnieniem 4-6 kg/cm² W przypadku konieczności zastosowania napędów o małych gabarytach i wytworzenia dużych sił docisku stosuje się napędy hydrauliczne, ciśnienie operacyjne oleje, w których osiąga 80 kg/cm².
Siła działająca na tłoczysko cylindra pneumatycznego lub hydraulicznego jest równa iloczynowi powierzchni roboczej tłoka w cm2 i ciśnieniu powietrza lub płynu roboczego. Należy w tym przypadku uwzględnić straty tarcia pomiędzy tłokiem a ściankami cylindra, pomiędzy tłoczyskiem a tulejami prowadzącymi i uszczelkami.
Elektromagnetyczne urządzenia mocujące Wykonywane są w formie płyt i płyt czołowych. Przeznaczone są do mocowania detali ze stali i żeliwa o płaskiej powierzchni podstawy do szlifowania lub toczenia wykańczającego.
Magnetyczne urządzenia mocujące mogą być wykonane w formie pryzm, które służą do mocowania cylindrycznych detali. Istnieją płyty, które wykorzystują ferryty jako magnesy trwałe. Płyty te charakteryzują się dużą siłą trzymania oraz mniejszą odległością pomiędzy biegunami.
Celem urządzeń mocujących jest zapewnienie niezawodnego kontaktu przedmiotu obrabianego z elementami montażowymi oraz zapobieganie jego przemieszczaniu się i drganiom podczas obróbki. Rysunek 7.6 przedstawia niektóre typy urządzeń zaciskowych.
Wymagania dotyczące elementów mocujących:
Niezawodność w działaniu;
Prostota konstrukcji;
Łatwość konserwacji;
Nie powinien powodować deformacji obrabianych przedmiotów i uszkodzeń ich powierzchni;
Podczas mocowania przedmiotu obrabianego nie należy go przesuwać z elementów montażowych;
Mocowanie i odłączanie przedmiotów obrabianych powinno odbywać się przy minimalnym nakładzie pracy i czasu;
Elementy zaciskowe muszą być odporne na zużycie i, jeśli to możliwe, wymienne.
Rodzaje elementów mocujących:
Śruby mocujące, które obraca się za pomocą kluczy, uchwytów lub pokręteł (patrz ryc. 7.6)
Rys.7.6 Rodzaje zacisków:
a – śruba mocująca; b – zacisk śrubowy
Szybkie działanie zaciski pokazane na rys. 7.7.
Ryc.7.7. Rodzaje zacisków szybkozamykających:
a – z podkładką dzieloną; b – z urządzeniem tłokowym; c – z ogranicznikiem składania; g – z urządzeniem dźwigniowym
Ekscentryczny zaciski, które są okrągłe, ewolwentowe i spiralne (wzdłuż spirali Archimedesa) (ryc. 7.8).
Ryc.7.8. Rodzaje zacisków mimośrodowych:
a – dysk; b – cylindryczny z dociskiem w kształcie litery L; g – pływający stożkowy.
Zaciski klinowe– wykorzystuje się efekt klinowania i stosuje się go jako ogniwo pośrednie w skomplikowanych układach mocowania. Pod pewnymi kątami mechanizm klinowy ma właściwość samohamowania. Na ryc. Rysunek 7.9 pokazuje obliczony schemat działania sił w mechanizmie klinowym.
Ryż. 7.9. Schemat obliczeniowy sił w mechanizmie klinowym:
a- jednostronny; b – podwójnie skośny
Zaciski dźwigniowe stosowane w połączeniu z innymi zaciskami w celu utworzenia bardziej złożonych systemów mocowania. Za pomocą dźwigni można zmienić zarówno wielkość, jak i kierunek siły docisku, a także jednocześnie i równomiernie zabezpieczyć obrabiany przedmiot w dwóch miejscach. Na ryc. Rysunek 7.10 przedstawia schemat działania sił w zaciskach dźwigniowych.
Ryż. 7.10. Schemat działania sił w zaciskach dźwigniowych.
Tuleje zaciskowe Są to dzielone tuleje sprężynowe, których odmiany pokazano na ryc. 7.11.
Ryż. 7. 11. Rodzaje opasek zaciskowych:
a – z rurką napinającą; b – z rurką dystansową; c – typ pionowy
Tulejki zapewniają koncentryczność mocowania przedmiotu obrabianego w zakresie 0,02...0,05 mm. Powierzchnię bazową przedmiotu obrabianego pod zaciski zaciskowe należy poddać obróbce zgodnie z klasami dokładności 2…3. Tuleje zaciskowe wykonywane są ze stali wysokowęglowych typu U10A poddawanych późniejszej obróbce cieplnej do twardości HRC 58...62. Kąt stożka tulei zaciskowej d = 30…40 0 . Przy mniejszych kątach tuleja może się zaciąć.
Trzpienie rozszerzające, których rodzaje pokazano na ryc. 7.4.
Blokada rolkowa(ryc. 7.12)
Ryż. 7.12. Rodzaje zamków rolkowych
Zaciski kombinowane– połączenie elementarnych zacisków różnych typów. Na ryc. 7.13 pokazuje niektóre typy takich urządzeń mocujących.
Ryż. 7.13. Rodzaje kombinowanych urządzeń mocujących.
Kombinowane urządzenia mocujące obsługiwane są ręcznie lub za pomocą urządzeń mechanicznych.
Elementy prowadzące urządzeń
Przy wykonywaniu niektórych operacji obróbczych (wiercenie, wytaczanie) sztywność narzędzia skrawającego i całego układu technologicznego jest niewystarczająca. Aby wyeliminować elastyczne dociskanie narzędzia do przedmiotu obrabianego, stosuje się elementy prowadzące (tuleje prowadzące podczas wytaczania i wiercenia, kopiarki podczas obróbki powierzchni kształtowych itp. (patrz ryc. 7.14).
Ryc.7.14. Rodzaje przepustów przewodzących:
stała; b – wymienny; c – szybka zmiana
Tuleje prowadzące wykonane są ze stali w gatunku U10A lub 20X, hartowanej do twardości HRC 60...65.
Elementy prowadzące urządzeń - kopiarki - służą do obróbki powierzchni kształtowych złożony profil, których zadaniem jest prowadzenie narzędzia skrawającego po obrobionej powierzchni przedmiotu obrabianego w celu uzyskania określonej dokładności trajektorii ich ruchu.
Wszystkie projekty narzędzia maszynowe opierają się na wykorzystaniu standardowych elementów, które można podzielić na następujące grupy:
elementy instalacyjne określające położenie części w oprawie;
elementy zaciskowe – urządzenia i mechanizmy do mocowania części lub ruchomych części urządzeń;
elementy do prowadzenia narzędzia tnącego i kontrolowania jego położenia;
urządzenia zasilające do uruchamiania elementów zaciskowych (mechaniczne, elektryczne, pneumatyczne, hydrauliczne);
obudowy urządzeń, na których mocowane są wszystkie pozostałe elementy;
elementy pomocnicze, które służą do zmiany położenia części w uchwycie względem narzędzia, do łączenia ze sobą elementów mocowania i regulacji ich wzajemnego położenia.
1.3.1 Typowe elementy bazowe urządzeń. Podstawowymi elementami oprzyrządowania są części i mechanizmy zapewniające prawidłowe i równomierne ułożenie przedmiotów obrabianych względem narzędzia.
Długotrwałe zachowanie dokładności wymiarów tych elementów i ich wzajemnego położenia jest najważniejszym wymaganiem przy projektowaniu i wytwarzaniu urządzeń. Spełnienie tych wymagań chroni przed defektami w trakcie obróbki oraz skraca czas i pieniądze wydane na naprawę urządzenia. Dlatego bezpośrednie użycie korpusu osprzętu nie jest dozwolone do mocowania przedmiotów obrabianych.
Podstawa lub elementy instalacyjne urządzenia muszą charakteryzować się dużą odpornością na zużycie powierzchni roboczych, dlatego są wykonane ze stali i poddane obróbce obróbka cieplna w celu uzyskania wymaganej twardości powierzchni.
Podczas montażu przedmiot opiera się na elementach montażowych osprzętu, dlatego elementy te nazywane są podporami. Podpory można podzielić na dwie grupy: grupę podpór głównych i grupę podpór pomocniczych.
Głównymi podporami są elementy montażowe lub bazowe, które pozbawiają przedmiot obrabiany podczas obróbki wszystkich lub kilku stopni swobody, zgodnie z wymaganiami obróbki. Kołki i płytki są często używane jako główne podpory do mocowania przedmiotów obrabianych na płaskich powierzchniach w osprzętach.
Ryż. 12.
Kołki (rys. 12.) stosowane są z łbami płaskimi, kulistymi i karbowanymi. Kołki z łbem płaskim (ryc. 12, a) przeznaczone są do montażu detali z płaszczyznami obrobionymi, drugie i trzecie (ryc. 12, b i c) do montażu z powierzchniami nieobrobionymi, a kołki z łbem kulistym, ponieważ zużywają się bardziej, stosowane są w przypadkach szczególnych, np. podczas montażu półfabrykatów wąskich części o nieobrobionej powierzchni w celu uzyskania maksymalna odległość pomiędzy punktami odniesienia. Kołki karbowane służą do mocowania części na nieobrobionych powierzchniach bocznych, ponieważ zapewniają stabilniejsze położenie przedmiotu obrabianego, a zatem w niektórych przypadkach pozwalają na użycie mniejszej siły do jego zamocowania.
W uchwycie kołki są zwykle instalowane w otworach z pasowaniem wciskowym o klasie dokładności 7. Czasami w otwór w korpusie urządzenia wciskane są hartowane tuleje przejściowe (ryc. 12, a), w które wchodzą kołki z pasowaniem o małej szczelinie o jakości 7.
Najpopularniejsze konstrukcje płyt pokazano na ryc. 13. Konstrukcja to wąska płyta zabezpieczona dwoma lub trzema. Aby ułatwić ruch przedmiotu obrabianego, a także bezpiecznie oczyścić urządzenie z wiórów ręcznie, powierzchnia robocza płyty jest obszyta fazą pod kątem 45° (rysunek 13, a). Głównymi zaletami takich płyt jest prostota i zwartość. Łby śrub mocujących płytę są zwykle zagłębione o 1-2 mm w stosunku do powierzchni roboczej płyty.


Ryż. 13 Płyty nośne: a - płaskie, b - z nachylonymi rowkami.
W przypadku opierania przedmiotów na powierzchni cylindrycznej, przedmiot obrabiany jest mocowany na pryzmie. Pryzmat to element montażowy z powierzchnią roboczą w postaci rowka utworzonego przez dwie płaszczyzny nachylone do siebie pod kątem (ryc. 14). Pryzmy do mocowania krótkich detali są znormalizowane.
W urządzeniach zastosowano pryzmaty o kątach 60°, 90° i 120°. Najczęściej spotykane są pryzmaty o b = 90

Ryż. 14
Podczas montażu detali z czysto obrobionymi podstawami stosuje się pryzmy o szerokich powierzchniach nośnych, a przy chropowatych podstawach - z wąskimi powierzchniami nośnymi. Ponadto używają szorstkich podstaw podpory punktowe, wciśnięty w powierzchnie robocze pryzmatu (ryc. 15, b). W tym przypadku detale z krzywizną osi, beczkowatym kształtem i innymi błędami kształtu podstawy technologicznej zajmują w pryzmacie stabilną i określoną pozycję.


Ryc.15
Podpory pomocnicze. Podczas obróbki niesztywnych detali, oprócz elementów montażowych, często stosuje się dodatkowe lub dostarczane w komplecie podpory, które są mocowane do przedmiotu obrabianego po jego osadzeniu w 6 punktach i zabezpieczeniu. Liczba dodatkowych podpór i ich umiejscowienie zależą od kształtu przedmiotu obrabianego, miejsca przyłożenia sił i momentów skrawania.
1.3.2 Elementy i urządzenia mocujące. Urządzenia lub mechanizmy mocujące to mechanizmy eliminujące możliwość drgań lub przemieszczeń przedmiotu obrabianego względem elementów montażowych urządzenia pod wpływem własnego ciężaru i sił powstających podczas obróbki (montażu).
Konieczność stosowania urządzeń zaciskowych znika w dwóch przypadkach:
1. Gdy poddawany jest obróbce (montażowi) ciężki, stabilny przedmiot (zespół montażowy), w porównaniu do ciężaru, którego siły obróbcze (montażowe) są niewielkie;
2. Gdy siły powstające podczas obróbki (montażu) przykładane są w taki sposób, że nie mogą zakłócić położenia przedmiotu obrabianego uzyskanego poprzez bazowanie.
Do urządzeń mocujących mają zastosowanie następujące wymagania:
1. Podczas mocowania nie należy zakłócać pozycji przedmiotu obrabianego uzyskanej poprzez bazowanie. Osiąga się to poprzez racjonalny * wybór kierunku i punktu przyłożenia siły docisku.
2. Zacisk nie powinien powodować odkształcenia mocowanych w uchwycie przedmiotów obrabianych ani uszkodzenia (zgniecenia) ich powierzchni.
3. Siła docisku powinna być minimalna niezbędna, ale wystarczająca, aby zapewnić niezawodne położenie przedmiotu obrabianego względem elementów montażowych osprzętu podczas obróbki.
4. Mocowanie i zdejmowanie przedmiotu obrabianego musi odbywać się przy minimalnym wysiłku i czasie pracownika. W przypadku stosowania zacisków ręcznych siła ręczna nie powinna przekraczać 147 N (15 kgf).
5. Siły tnące, jeśli to możliwe, nie powinny być przejmowane przez urządzenia mocujące.
6. Mechanizm zaciskowy powinny być proste w konstrukcji, możliwie wygodne i bezpieczne w użyciu.
Spełnienie większości tych wymagań wiąże się z poprawna definicja wielkość, kierunek i położenie sił zaciskających.
Szeroką dystrybucję urządzeń śrubowych tłumaczy się ich względną prostotą, wszechstronnością i bezproblemową pracą. Nie zaleca się jednak najprostszego zacisku w postaci pojedynczej śruby działającej bezpośrednio na część, ponieważ w miejscu jej działania część ulega odkształceniu, a dodatkowo pod wpływem momentu tarcia powstającego na końcu śruby, położenie przedmiotu obrabianego w uchwycie względem narzędzia może zostać zakłócone.
Prawidłowo zaprojektowany prosty zacisk śrubowy, oprócz śruby 3 (rys. 16, a), powinien składać się z tulei prowadzącej gwintowanej 2 z korkiem 5 uniemożliwiającym jej samowolne odkręcenie, końcówki 1 oraz nakrętki z uchwytem lub łbem 4.
Konstrukcje końcówek (ryc. 16, b - e) różnią się od konstrukcji pokazanej na ryc. 18, a tym, że koniec śruby jest trwalszy, ponieważ średnica szyjki śruby dla końcówek (ryc. 16, b i d) można przyjąć jako równą średnicy wewnętrznej gwintowanej części śruby, a w przypadku końcówek (ryc. 16, c i d) średnica ta może być równa zewnętrznej średnicy śruby. Końcówki (ryc. 16, b-d) nakręca się na gwintowany koniec śruby i w taki sam sposób, jak końcówka pokazana na ryc. 16, a, można dowolnie instalować na przedmiocie obrabianym. Końcówka (ryc. 16, d) jest luźno umieszczona na kulistym końcu śruby i przytrzymywana na niej specjalną nakrętką.

Ryż. 16.
Końcówki (ryc. 16, e-h) różnią się od poprzednich tym, że są precyzyjnie prowadzone przez otwory w korpusie urządzenia (lub w tulei wciśniętej w korpus) i przykręcane bezpośrednio do śruby dociskowej 15, która. w tym przypadku jest on blokowany, aby zapobiec jego ruchom osiowym. Sztywne, precyzyjnie skierowane końcówki (rys. 16, f, g i h) zalecane są do stosowania w przypadkach, gdy w trakcie obróbki powstają siły przesuwające przedmiot w kierunku prostopadłym do osi śruby. Wahliwe końcówki (ryc. 16, a-e) należy stosować w przypadkach, gdy takie siły nie występują.
Uchwyty do sterowania śrubą wykonane są w postaci zdejmowanych łbów o różnej konstrukcji (ryc. 17) i są umieszczane na gwintowanym, fasetowanym lub cylindrycznym końcu śruby za pomocą klucza, na którym zwykle są blokowane za pomocą kołka. Łeb walcowy I (rys. 17, a) z radełkowaną łbem „baranek” gwiazda II i łbem czteroostrzowym III stosuje się przy obsłudze śruby jedną ręką i sile docisku w zakresie 50–100 N (5– 10kg).
Nakrętka główkowa VI z sztywno osadzonym w niej krótkim, skośnym uchwytem; głowica VII ze składaną rączką, Stanowisko pracy który jest zamocowany za pomocą sprężynowej kuli; głowica V z cylindrycznym otworem na klucz, również sztywno zamocowana za pomocą poziomego uchwytu; głowica kierownicza IV z czterema przykręcanymi lub wciskanymi uchwytami (ryc. 17). Head IV jest najbardziej niezawodny i łatwy w użyciu.

Ryż. 17.
1.3.3 Obudowy. Korpusy opraw stanowią główną część opraw, na których mocowane są wszystkie pozostałe elementy. Dostrzega wszystkie siły działające na część podczas jej mocowania i obróbki oraz zapewnia dane względne rozmieszczenie wszystkich elementów i urządzeń urządzeń, łącząc je w jedną całość. Korpusy osprzętu wyposażone są w elementy montażowe, które zapewniają osadzenie osprzętu, czyli jego wymagane położenie na maszynie, bez wyrównania.
Obudowy urządzeń wykonane są z żeliwa, spawane ze stali lub prefabrykowane poszczególne elementy, mocowane za pomocą śrub.
Ponieważ korpus pochłania siły powstające podczas mocowania i obróbki przedmiotu obrabianego, musi być mocny, sztywny, odporny na zużycie, wygodny do spuszczania chłodziwa i czyszczenia wiórów. Dzięki temu, że osprzęt jest zamontowany na maszynie bez wyrównania, korpus musi pozostać stabilny w różnych pozycjach. Obudowy mogą być odlewane, spawane, kute, montowane za pomocą śrub lub z gwarantowanym wciskiem.
Odlany korpus (ryc. 18, a) ma wystarczającą sztywność, ale jest trudny w produkcji.
Obudowy wykonane z żeliwa SCh 12 i SCh 18 stosowane są w urządzeniach do obróbki małych i średnich detali. Korpusy żeliwne mają przewagę nad stalowymi: są tańsze, łatwiej jest dać z nich więcej złożony kształt, są łatwiejsze do wykonania. Wadą korpusów żeliwnych jest możliwość wypaczenia, dlatego po wstępnej obróbce mechanicznej poddawane są obróbce cieplnej (starzeniu naturalnemu lub sztucznemu).
Spawany korpus stalowy (ryc. 18, b) jest łatwiejszy w produkcji, ale także mniej sztywny niż żeliwo. Części do takich skrzynek są wycinane ze stali o grubości 8... 10 mm. Spawane obudowy stalowe są lżejsze niż obudowy żeliwne.


Ryż. 18. Obudowy urządzeń: a - odlewane; b - spawany; c - prefabrykowane; g - kute
Wadą korpusów spawanych jest odkształcenie podczas spawania. Naprężenia szczątkowe powstające w częściach obudowy wpływają na dokładność spawać. Aby złagodzić te naprężenia, obudowy są wyżarzane. Aby uzyskać większą sztywność, do spawanych obudów przyspawane są narożniki, które służą jako usztywnienia.
Na ryc. 18b przedstawia obudowę złożoną z różnych elementów. Jest mniej skomplikowany, mniej sztywny niż odlewany czy spawany i charakteryzuje się niską pracochłonnością produkcji. Obudowę można zdemontować i wykorzystać w całości lub poszczególne części w innych projektach.
Na ryc. 18, d pokazuje korpus urządzenia wykonany metodą kucia. Jego produkcja jest mniej pracochłonna niż odlewanie, przy jednoczesnym zachowaniu właściwości sztywności. Do obróbki detali wykorzystywane są kute korpusy stalowe małe rozmiary prosta forma.
Jakość wykonania ich powierzchni roboczych ma znaczenie dla działania urządzenia. Muszą być przetwarzane z chropowatością powierzchni Ra 2,5 ... 1,25 mikrona; tolerancja z równoległości i prostopadłości powierzchni roboczych obudów - 0,03. ..0,02 mm na długości 100 mm.
1.3.4 Mechanizmy orientujące i samocentrujące. W niektórych przypadkach instalowane części muszą być zorientowane wzdłuż ich płaszczyzn symetrii. Mechanizmy stosowane w tym celu zwykle nie tylko orientują, ale także zaciskają części, dlatego nazywane są zaciskaniem montażowym.

Ryż. 19.
Mechanizmy montażowe i mocujące dzielą się na orientujące i samocentrujące. Te pierwsze orientują części tylko w jednej płaszczyźnie symetrii, drugie - w dwóch wzajemnie prostopadłych płaszczyznach.
Grupa mechanizmów samocentrujących obejmuje wszelkiego rodzaju konstrukcje wkładów i trzpieni.
Aby orientować i centrować części nieokrągłe, często stosuje się mechanizmy ze stałymi (GOST 12196--66), instalacyjnymi (GOST 12194--66) i ruchomymi (GOST 12193--66) pryzmatami. W mechanizmach orientujących jeden z pryzmatów jest sztywno zamocowany - nieruchomy lub pozycjonujący, a drugi jest ruchomy. W mechanizmach samocentrujących oba pryzmaty poruszają się jednocześnie.