Para śrub. Zasada działania pompy śrubowej. Pary gerotorowe i ich rodzaje Para kul
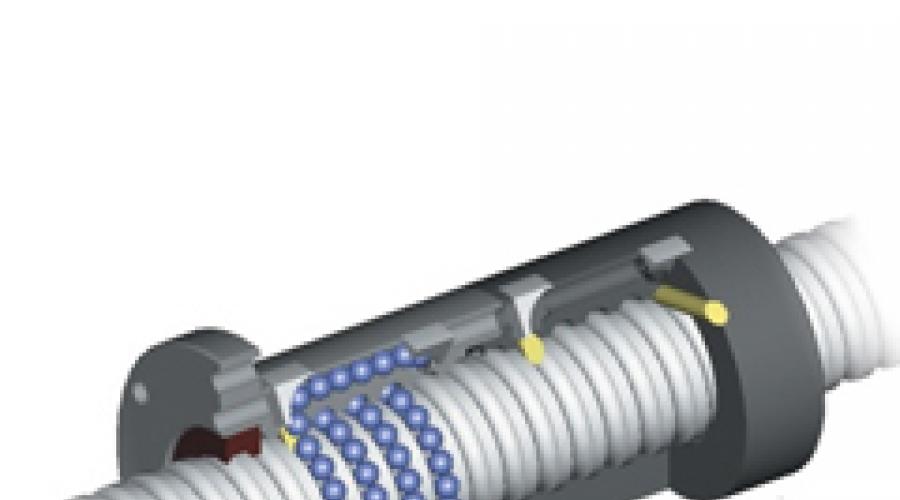
Przeczytaj także
Śruba kulowa- rodzaj napędu liniowego, który przekształca ruch obrotowy na tłumaczący, który ma osobliwość- wyjątkowo niskie tarcie.
Wał (zwykle stalowy - wykonany z gatunków stali wysokowęglowej) o specyficznym kształcie bieżni na powierzchni pełni rolę bardzo precyzyjnej śruby napędowej współpracującej z nakrętką, ale nie bezpośrednio, poprzez tarcie ślizgowe, jak w śrubie konwencjonalnej -przekładnie nakrętkowe, ale poprzez kulki, poprzez tarcie toczne. Determinuje to wysoką charakterystykę przeciążeniową śruby kulowej i bardzo wysoką sprawność. Śruba i nakrętka są produkowane jako dopasowana para z bardzo wąskimi tolerancjami i mogą być stosowane w zastosowaniach wymagających bardzo dużej wytrzymałości wysoka celność. Nakrętka kulkowa jest zwykle nieco większa niż nakrętka ślizgowa ze względu na znajdujące się w niej kanały recyrkulacji kulki. Jest to jednak praktycznie jedyny punkt, w którym śruba kulowa jest gorsza napędy śrubowe tarcie ślizgowe.
Zakres zastosowania śrub kulowych
Śruby kulowe są często używane w samolotach i rakietach do przesuwania powierzchni sterowych, a także w samochodach do kierowania drążek kierowniczy z elektrycznego silnika sterującego. Najszerszy zakres zastosowań śrub kulowych istnieje w inżynierii precyzyjnej, takiej jak maszyny CNC, roboty, linie montażowe, instalatorzy komponentów, a także prasy mechaniczne, wtryskarki itp.
Historia śruby kulowej
Historycznie rzecz biorąc, pierwszą precyzyjną śrubę kulową wykonywano z konwencjonalnej śruby o dość małej precyzji, na którą mocowano konstrukcję z kilku nakrętek, napinanych sprężyną, a następnie docieranych na całej długości śruby. Dzięki ponownemu rozmieszczeniu nakrętek i zmianie kierunku naprężenia można uśrednić błędy skoku śruby i nakrętki. Następnie uzyskany krok pary, określony z dużą powtarzalnością, został zmierzony i zarejestrowany jako krok paszportowy. Podobny proces jest obecnie okresowo stosowany w produkcji.
Zastosowanie śruby kulowej
Aby para piłek służyła w całości okres rozliczeniowy z zachowaniem wszystkiego, m.in. parametrów dokładności, należy zwrócić szczególną uwagę na czystość i zabezpieczenie przestrzeni roboczej, aby uniknąć kontaktu kurzu, wiórów i innych cząstek ściernych z parą. Zwykle rozwiązuje się to poprzez zainstalowanie osłony z tektury falistej, polimerowej, gumowej lub skórzanej, która zapobiega przedostawaniu się obcych cząstek miejsce pracy. Inną metodą jest zastosowanie sprężarki – dostarczającej przefiltrowane powietrze pod ciśnieniem do śmigła zamontowanego na otwartej przestrzeni. Śruby kulowe, dzięki zastosowaniu tarcia tocznego, mogą mieć określone napięcie wstępne, które usuwa luz przekładni - pewną „przerwę” pomiędzy ruchem obrotowym i translacyjnym powstającą przy zmianie kierunku obrotu. Wyeliminowanie luzów jest szczególnie ważne w systemach z sterowany programem Dlatego śruby kulowe z napięciem wstępnym są szczególnie często stosowane w maszynach CNC.
Wady śrub kulowych
W zależności od kąta uniesienia bieżni, śruby kulowe mogą podlegać odwrotnemu przełożeniu – niskie tarcie powoduje, że nakrętka nie blokuje się, lecz przenosi siłę liniową na moment obrotowy. Zwykle nie zaleca się stosowania śrub kulowych ręczne podawanie. Wysoka cenaŚruby kulowe są również czynnikiem, który często skłania konstruktorów maszyn do wyboru bardziej ekonomicznych przekładni.
Zalety śrub kulowych
Niski współczynnik tarcia śruby kulowej powoduje niskie rozproszenie i wysoką wydajność transmisji - znacznie wyższą niż w przypadku jakichkolwiek innych analogów. Sprawność najpopularniejszych śrub kulowych może przekraczać 90%, w porównaniu do maksymalnie 50% w przypadku śrub pociągowych metrycznych i trapezowych. Praktycznie brak poślizgu znacznie zwiększa żywotność śruby kulowej, co skraca przestoje sprzętu podczas napraw, wymiany i smarowania części. Wszystko to w połączeniu z innymi zaletami, takimi jak większa osiągalna prędkość, zmniejszone zapotrzebowanie mocy na elektryczny napęd śmigła, może stanowić istotny argument za śrubą kulową, w przeciwieństwie do jej wysokiego kosztu.
Produkcja śrub kulowych
Najbardziej precyzyjne śruby kulowe można wyprodukować jedynie poprzez szlifowanie. Śruba może być również wykonana przez radełkowanie - taka śruba będzie miała znacznie niższy koszt, ale jej dokładność będzie ograniczona do błędu rzędu 50 mikronów na 300 mm skoku.
Dokładność śruby kulowej
Śruby o wysokiej precyzji dają zwykle błąd rzędu 1-3 mikronów na 300 mm przesuwu, a nawet dokładniej. Półfabrykaty do takich śrub uzyskuje się poprzez obróbkę zgrubną, następnie półfabrykaty są utwardzane i szlifowane do perfekcji. Wymagane są trzy kroki, ponieważ... obróbka temperaturowa znacznie zmienia powierzchnię śruby kulowej.
Mocne wirowanie jest porównawcze Nowa technologia obróbka metali, która minimalizuje nagrzewanie się przedmiotu obrabianego podczas procesu i umożliwia wytwarzanie precyzyjnych śrub z hartowanego przedmiotu. Oprzyrządowane śruby kulowe zwykle osiągają dokładność 250 nm na centymetr. Produkowane są poprzez frezowanie i szlifowanie na ultraprecyzyjnym sprzęcie pod kontrolą specjalistycznego sprzętu o submikronowej precyzji. W podobne urządzenia wyposażone są linie do produkcji soczewek i luster. Takie śruby są zwykle wykonane z Invaru lub innych stopów Invaru, aby zminimalizować błąd powodowany przez rozszerzalność cieplną śruby.
Systemy recyklingu piłek
Kulki łożyskowe krążą w kanałach gwintowych nakrętki i bieżniach śruby. Gdybyś nie prowadził kulki po zakończeniu jej podróży, kulki po dotarciu do końca toru po prostu wypadłyby z nakrętki na zewnątrz, dlatego w śrubach kulowych stosuje się kilka droższych systemów przywracania kulek na początek - systemy recyrkulacji .
W układzie zewnętrznym zastosowano metalową rurkę łączącą wlot i wylot nakrętki kanałowej. Wylatujące kule wpadają do tuby, a popychane przez kolejne, podążają do wejścia. System wewnętrzny polega na wycięciu podobnego kanału wewnątrz nakrętki, kulki wychodzące z nakrętki kierowane są specjalną wykładziną do wywierconego kanału, a na wyjściu z kanału podobna wykładzina przenosi kulki na wejście bieżni. Bardzo powszechną opcją jest sytuacja, gdy kulki krążą przez kilka zapętlonych kanałów, gdzie powrót zapewnia specjalna wtyczka.
1. Specyfikacje
Śruby kulowe takie jak NBS charakteryzują się ścisłą kontrolą jakości przeprowadzaną podczas każdego procesu produkcyjnego.
Śruby o wysokiej wydajności umożliwiają redukcję momentu obrotowego nawet o 70% w porównaniu z tradycyjnymi śrubami trapezowymi w zastosowaniach ogólny cel(przekształcenie ruchu obrotowego w ruch translacyjny) oraz w specjalne zastosowania(transformacja ruch do przodu w ruch obrotowy).
1.1 Geometria kontaktu
Łuk gotycki zapewnia znaczną wytrzymałość śruby, zapewniając jednocześnie precyzję i niskie wartości momentu obrotowego.
2. Parametry doboru śrub kulowych NBS (z kulkami obiegowymi)
- O wyborze śruby kulowej (z cyrkulacją kulki) decydują następujące parametry:
- -Klasa dokładności
- -Skok gwintu
- -Termin nominalny usługi
- -Sposób mocowania
- -Krytyczna prędkość obrotowa
- -Sztywność
- -Temperatura pracy
- -Smar
2.1 Klasa dokładności
Śruby kulowe NBS (kulki recyrkulacyjne) są dostępne w następujących klasach dokładności:
WSPÓŁ. C1. C2. C3. C5. C7. C10
Każda klasa dokładności jest określona przez następujące parametry:
E. e. e. e2∏
Poniższy wykres przedstawia opis ich znaczenia.
Termin | Połączyć | Definicja |
Kompensacja udaru | T | Kompensacja długości skoku - różnica pomiędzy teoretyczną i nominalną długością skoku; często mała wartość kompensacji (w porównaniu do skoku nominalnego). niezbędne do kompensacji wydłużeń spowodowanych podwyższoną temperaturą lub obciążeniami zewnętrznymi. Jeżeli ta kompensacja nie jest konieczna, skok teoretyczny jest równy skokowi nominalnemu. |
Rzeczywista długość skoku | - | Rzeczywista długość skoku to przemieszczenie osiowe pomiędzy śrubą a nakrętką. |
Średnia długość skoku | - | Średnia długość skoku to linia prosta najbliższa rzeczywistej długości skoku; średnia długość skoku reprezentuje nachylenie rzeczywistej długości skoku. |
Średnie odchylenie długości skoku | mi | Średnie odchylenie długości skoku jest różnicą pomiędzy średnia i teoretyczna długość skoku. |
Zmiana kursu | mi ezo e2п |
Zmiana skoku to pasek z dwiema równoległymi liniami o średniej długości skoku. Maksymalny zakres zmian na długości skoku. Zakres zmian mierzony przy typowej długości skoku 300 mm. Błąd bicia, zakres zmian na obrót (2 radiany). |
Klasa dokładności | C0 | C1 | C2 | C3 | C5 | C7 | C10 | |||||||
Długość postęp [mm] |
z: | zanim: | ±E | mi | ±E | mi | ±E | mi | ±E | mi | ±E | mi | mi | mi |
100 | 3 | 3 | 3.5 | 5 | 5 | 7 | 8 | 8 | 18 | 18 | ±50/ 300mm |
±210/ 300mm |
||
100 | 200 | 3.5 | 3 | 4.5 | 5 | 7 | 7 | 10 | 8 | 20 | 18 | |||
200 | 315 | 4 | 3.5 | 6 | 5 | 8 | 7 | 12 | 8 | 23 | 18 | |||
315 | 400 | 5 | 3.5 | 7 | 5 | 9 | 7 | 13 | 10 | 25 | 20 | |||
400 | 500 | 6 | 4 | 8 | 5 | 10 | 7 | 15 | 10 | 27 | 20 | |||
500 | 630 | 6 | 4 | 9 | 6 | 11 | 8 | 16 | 12 | 30 | 23 | |||
630 | 800 | 7 | 5 | 10 | 7 | 13 | 9 | 18 | 13 | 35 | 25 | |||
800 | 1000 | 8 | 6 | 11 | 8 | 15 | 10 | 21 | 15 | 40 | 27 | |||
1000 | 1250 | 9 | 6 | 13 | 9 | 18 | 11 | 24 | 16 | 46 | 30 | |||
1250 | 1600 | 11 | 7 | 15 | 10 | 21 | 13 | 29 | 18 | 54 | 35 | |||
1600 | 2000 | 18 | 11 | 25 | 15 | 35 | 21 | 65 | 40 | |||||
2000 | 2500 | 22 | 13 | 30 | 18 | 41 | 24 | 77 | 46 | |||||
2500 | 3150 | 26 | 15 | 36 | 21 | 50 | 29 | 93 | 54 | |||||
3150 | 4000 | 30 | 18 | 44 | 25 | 60 | 35 | 115 | 65 | |||||
4000 | 5000 | 52 | 30 | 72 | 41 | 140 | 77 | |||||||
5000 | 6300 | 65 | 36 | 90 | 50 | 170 | 93 | |||||||
6300 | 8000 | 110 | 60 | 210 | 115 | |||||||||
8000 | 10000 | 260 | 140 | |||||||||||
10000 | 12500 | 320 | 170 |
Klasa dokładności | C0 | C1 | C2 | północny zachód | C5 | C7 | C10 |
e ogród zoologiczny | 3.5 | 5 | 7 | 8 | 18 | 50 | 210 |
mi 2π | 2.5 | 4 | 5 | 6 | 8 |
2.2 Napięcie wstępne i luz osiowy
Napięcie wstępne i luz osiowy śrub kulowych NBS przedstawiono w poniższej tabeli.
Wstępnie załaduj klasę | P0 | P1 | P2 | RZ | RA |
Luz osiowy | Tak | NIE | NIE | NIE | NIE |
Wstępnie załaduj | NIE | NIE | Łatwy | Przeciętny | Mocny |
Poniższe tabele zawierają podstawowe wytyczne dotyczące wyboru klasy dokładności, napięcia wstępnego i luzu osiowego śrub kulowych NBS.
Klasa dokładności | Napięcie wstępne i luz osiowy | Typ nakrętki | Typ śruby pociągowej |
Od 10 | RO (z luzem osiowym) | Pojedynczy | Radełkowane |
C 7 | P1 lub RO | Na żądanie | Walcowane lub prostowane |
C 5 | Na żądanie; standardowy 0TNBS-P2 |
Na żądanie | błędy kroków |
C 3 | Na żądanie; standardowy 0TNBS-P2 |
Na żądanie | Prostowany, posiada świadectwo kontroli błędy kroków |
Model | Pojedyncza nakrętka | Podwójna nakrętka |
1605 | 1±3N | 3 ± 6 N |
2005 | 1±3N | 3±6N |
2505 | 2 ± 5 N | 3±6N |
3205 | 2 ± 5 N | 5±8N |
4005 | 2 ± 5 N | 5±8N |
2510 | 2 ± 5 N | 5±8N |
3210 | 3 ± 6 N | 5±8N |
4010 | 3 ± 6 N | 5±8N |
5010 | 3 ± 6 N | 8 ± 12 N |
6310 | 6 ± 10 N | 8 ± 12 N |
8010 | 6 ± 10 N | 8 ± 12 N |
2.3 Skok gwintu
Wybór skoku śmigła zależy od następującego wzoru:
Gdzie:
Ph = skok śruby [mm]
Vmax = maksymalna prędkość przesuw systemu [m/min]
n max = tryb maksymalnych obrotów śmigła [min 1]
W przypadku, gdy wynik równania nie jest wynikiem całkowitym, należy wybrać wynik zaokrąglony. duża strona wartość, wybierając jeden z dostępnych kroków.
Uwzględniając możliwą zmienność obciążeń osiowych, spowodowaną np. obecnością sił bezwładności, należy obliczyć wartość obciążenia określaną jako „średnie obciążenie dynamiczne Pm”, które wyznacza te same współczynniki obciążenia zmiennego.
2.4.1 Średnie obciążenie dynamiczne
Do obliczenia śruby kulowej w zmiennych warunkach pracy stosuje się średnie wartości Pm i nm:
P m = średnie dynamiczne obciążenie osiowe [N]
n m = Średnia prędkość[min -1 ]
W warunkach ciągłego obciążenia i zmiennej prędkości można osiągnąć następujące wartości:
W warunkach zmiennego obciążenia i stałej prędkości można osiągnąć następujące wartości:
W warunkach zmiennego obciążenia i zmiennej prędkości można osiągnąć następujące wartości:
O doborze śmigła w zależności od działających i (lub) wymaganych sił trakcyjnych decydują następujące wartości:
- Nośność statyczna Soa
- Nośność dynamiczna Ca
Nośność statyczną Coa (lub współczynnik nośności) definiuje się jako obciążenie o stałym natężeniu działające na oś śruby, które w miejscu maksymalnego uderzenia pomiędzy stykającymi się częściami powoduje trwałe odkształcenie równe 1/10000 średnica elementu tocznego.
Wartości Coa podane są w tabelach rozmiarów.
2.5.1 Statyczny współczynnik bezpieczeństwa a s Statyczny współczynnik bezpieczeństwa a s (lub statyczny współczynnik bezpieczeństwa) określa się za pomocą następującego równania:
2.5.2 Współczynnik twardości f H
Współczynnik twardości uwzględnia twardość powierzchni bieżni:
Gdzie:
twardość bieżni HsV10 = rzeczywista twardość bieżni wyrażona w jednostkach Vickersa przy obciążeniu próbnym 98,07 N
700HV10 = twardość równa 700 Vickersa przy obciążeniu testowym równym 98,07 (700HV10 ≈ 60 HRC)
2.5.3 Współczynnik dokładności fac
Współczynnik dokładności uwzględnia tolerancje obróbki śruby, a co za tym idzie, klasę dokładności odpowiadającą normie.
W tabeli przedstawiono kilka przykładów.
Konieczność stosowania statycznego współczynnika bezpieczeństwa as > 1 wynika z możliwej obecności wstrząsów i (lub) wibracji, momentów rozruchowych i zatrzymujących oraz przypadkowych obciążeń, które mogą prowadzić do nieprawidłowego działania systemu.
Poniższa tabela przedstawia wartości statycznego współczynnika bezpieczeństwa w zależności od rodzaju zastosowania.
Nośność dynamiczna Ca (lub współczynnik obciążenia dynamicznego) to stałe intensywne obciążenie dynamiczne działające na oś śruby, które określa żywotność 10 6 obrotów.
Wartości C a podane są w tabelach rozmiarów.
2.7 Trwałość nominalna L
Trwałość znamionowa L (jest to teoretyczny przebieg przebyty przez co najmniej 90% reprezentatywnej liczby identycznych śrub kulowych (z kulkami obiegowymi) poddanych takim samym obciążeniom i nie wykazujących oznak zmęczenia materiału) jest określana na podstawie następujących warunków:
- Nakrętka bez napięcia wstępnego
- Nakrętka z napięciem wstępnym
2.7.1 Nakrętka bez napięcia wstępnego
W przypadku śrub kulowych (z kulkami obiegowymi) z nakrętką bez napięcia wstępnego obliczenie trwałości znamionowej wyrażonej w liczbie obrotów określa się według następującego wzoru:
Gdzie:
P m = średnie dynamiczne obciążenie osiowe [N]
- Klasa dokładności wkrętów od 1 do 5
- Niezawodność do 90%
Gdzie:
a 1 = współczynnik bezpieczeństwa
2.7.2 Współczynnik a 1
Współczynnik a 1 uwzględnia możliwość braku ugięcia C%.
C% | 80 | 85 | 90 | 92 | 95 | 96 | 97 | 98 | 99 |
1 | 1.96 | 1.48 | 1.00 | 0.81 | 0.62 | 0.53 | 0.44 | 0.33 | 0.21 |
Należy zauważyć, że dla C% = 90 a 1 = 1,00
2.7.3 Nakrętka wstępnie obciążona
Ważność poniższych wzorów zależy od utrzymania stałego napięcia wstępnego; w przeciwnym razie należy uwzględnić przypadek z nakrętką bez napięcia wstępnego.
W przypadku śrub kulowych (śrub kulowych z obiegiem kulowym) ze wstępnie naprężoną nakrętką obliczenie trwałości znamionowej wyrażonej w liczbie obrotów określa się według następującego wzoru:
Gdzie:
L 10 = trwałość znamionowa [obr.]
L 10 b - (C a / Pm 2) x 10 6
L 10a i L1 0b to nominalne zasoby dla dwóch połówek nakrętki.
- Równanie to obowiązuje w następujących przypadkach:
- Twardość bieżni = 60HRC
- Klasa dokładności śruby od 1 do 5;
- Niezawodność do 90%.
Jeżeli warunki pracy nie spełniają powyższych warunków, należy zastosować następujący wzór:
Gdzie:
L 10 = trwałość znamionowa [obr.]
L 10 a = (C a /P m1) 3 X 10 6
L 10 b - (C a / Pm 2) x 10 6
a 1 = współczynnik niezawodności;
f ho = współczynnik twardości (patrz statyczny współczynnik bezpieczeństwa a s)
f ac = współczynnik dokładności (patrz statyczny współczynnik bezpieczeństwa a s)
P m1 i P m2 - średnie osiowe obciążenia dynamiczne dla dwóch połówek nakrętki;
P r = siła napięcia wstępnego [N]
2.7.4 Trwałość znamionowa w godzinach Lh
Mając L 10 (trwałość nominalna wyrażona w liczbie obrotów), można obliczyć trwałość nominalną w godzinach pracy L h;
Gdzie:
L m = czas pracy [godziny]
n m = średnia prędkość obrotowa [min -1 ]
m i = prędkość [MIN -1 ]
qi = rozkład procentowy [%]
2.7.5 Nominalny okres użytkowania w km Lkm
Mając L 10 (zasób nominalny wyrażony w liczbie obrotów), można obliczyć zasób nominalny przebytej drogi w km L km.
Gdzie:
L km = trwałość nominalna [km]
P h = skok śruby [mm]
Poniższa tabela przedstawia typową trwałość śruby kulowej w zastosowaniach ogólnych.
2.8 Sposób montażu
Z reguły są następujące typy montaż śruby kulowej:
Zastosowana metoda mocowania jest funkcją warunków zastosowania, zapewniając sztywność i wymaganą dokładność.
2.9 Krytyczna prędkość obrotowa
Maksymalna prędkość obrotowa śruby kulowej nie powinna przekraczać 80% prędkości krytycznej.
Krytyczna prędkość obrotowa to punkt, w którym śmigło zaczyna wibrować, wytwarzając efekt rezonansowy spowodowany częstotliwością drgań odpowiadającą częstotliwości drgań własnych śmigła.
Wartość prędkości krytycznej zależy od średnicy wewnętrznej śruby pociągowej, sposobu mocowania krawędzi i długości swobodnego ugięcia.
Prędkość krytyczną mierzy się według następującego wzoru:
Gdzie:
n cr = prędkość krytyczna [min -1 ]
f kn = współczynnik metody mocowania
d 2 = średnica wewnętrzna śruby pociągowej [mm]
l n = długość swobodnego ugięcia [mm]
W zależności od rodzaju mocowania podawane są wartości f kn:
Gdzie:
do = średnica nominalna [mm m]
da = średnica kulki [mm]
a = kąt zwilżania (= 45)
Długość swobodnego ugięcia l n określa się w zależności od:
-Nakrętki bez napięcia wstępnego
l n = odległość pomiędzy mocowaniami [mm] (w przypadku mocowania „jednoczęściowego – swobodnego” należy uwzględnić odległość wolnej krawędzi wkrętu od mufy)
-Nakrętka z napięciem wstępnym
l n = maksymalna odległość pomiędzy połówką nakrętki a mocowaniem [mm] (w przypadku mocowania „jednoczęściowego – swobodnego” należy uwzględnić maksymalną odległość połówki nakrętki od wolnej krawędzi śruby)
n max = maksymalna prędkość śmigła [obr/min]
Obciążenie krytyczne to maksymalne obciążenie osiowe, któremu może zostać poddane śmigło bez wpływu na stabilność układu; w przypadku, gdy maksymalne obciążenie osiowe działające na śrubę osiągnie lub przekroczy wartość obciążenia krytycznego, a Nowa forma uderzenie w śrubę, co nazywa się „obciążeniem szczytowym”, powodujące oprócz zwykłego ściskania dodatkowe ugięcie.
Zjawisko to, związane z właściwościami sprężystymi elementu, staje się bardziej wrażliwe, gdy długość swobodnego ugięcia śruby ma dużą godny uwagi wartości w stosunku do jego cięcia. Wartość obciążenia krytycznego określa się według następującego wzoru:
Gdzie:
P cr = Obciążenie krytyczne [N]
f kp = współczynnik metody mocowania
d 2 = średnica wewnętrzna śruby pociągowej [mm] (patrz prędkość krytyczna)
l cr = długość swobodnego ugięcia [mm]
W zależności od rodzaju mocowania podawane są wartości fkp:
Jednoczęściowy - Jednoczęściowy | f kр = 40,6 | |
Jednoczęściowe - wsparcie | f kp = 20,4 | |
Odniesienie - Odniesienie | f kp = 10,2 | |
Jednoczęściowe - gratis | fkp = 2,6 |
Aby obliczyć obciążenie krytyczne, wartość la określa się na podstawie maksymalnej odległości połówki nakrętki od łącznika.
Dla większego bezpieczeństwa maksymalne dopuszczalne obciążenie osiowe należy uznać za równe połowie obciążenia krytycznego:
P max = maksymalne dopuszczalne obciążenie osiowe [N]
2.11 Twardość
Sztywność osiową układu ruchomego wyposażonego w śrubę kulową określa się ze wzoru:
Gdzie:
K = sztywność osiowa układu
P = obciążenie osiowe [N]
e = odkształcenie osiowe układu [µm]
Sztywność osiowa układu K jest funkcją sztywności osiowej poszczególnych elementów, które go tworzą: śruby pociągowej, nakrętki, wsporników, wsporników łączących i nakrętki.
Gdzie:
K s = sztywność osiowa śruby pociągowej
K N = sztywność osiowa nakrętki
K in = sztywność osiowa podpór
Kn = sztywność osiowa połączenia elementy wspierające i orzechy
2.11.1 Ks - Sztywność osiowa śruby pociągowej
Wartość sztywności Ks jest funkcją systemu mocowania.
Sposób montażu: Jednoczęściowy - Jednoczęściowy
Gdzie:
d 2 = średnica wewnętrzna (patrz krytyczna prędkość obrotowa)
l s = odległość pomiędzy osią środkową dwóch mocowań
Sposób montażu: Jednoczęściowy - Wsparcie
Gdzie:
d 2 = średnica wewnętrzna [mm] (patrz prędkość krytyczna)
l s = maksymalna odległość pomiędzy osiami środkowymi mocowania a nakrętką [mm].
2.11.2 K N - Sztywność osiowa nakrętki
Podwójna nakrętka z napięciem wstępnym
Gdzie:
K = sztywność stołu
F pr = siła napięcia wstępnego [N]
Prosta nakrętka bez napięcia wstępnego
Wartość K N określa się za pomocą następującego wzoru:
Gdzie:
P = obciążenie osiowe [N]
C a = nośność dynamiczna [N]
2.11.3 Kv - Sztywność osiowa podpór
Sztywność osiowa wsporników śrubowych zależy od sztywności łożysk.
W przypadku sztywnych łożysk kulkowych skośnych promieniowych obowiązują następujące wzory:
Gdzie:
bv = odkształcenie osiowe łożyska
Q = obciążenie każdej kuli [N]
β = kąt zwilżania (45°)
d = średnica kulek [mm]
N = liczba piłek
Sztywność łączących elementów nośnych i nakrętek jest cechą charakterystyczną maszyny, co oznacza, że nie zależy ona od układu śrub, nakrętek i podpór.
2.12 Temperatura robocza
W przypadku mocowania na stałe w jednym kawałku należy uwzględnić możliwość wydłużenia cieplnego spowodowanego wzrostem temperatury wkrętu podczas pracy; takie wydłużenie, jeśli zostało odpowiednio uwzględnione, powoduje dodatkowe obciążenie osiowe układu , co może prowadzić do nieprawidłowego działania systemu. Aby rozwiązać problemy, konieczne jest wystarczające wstępne naprężenie śruby.
Gdzie:
AL = zmiana długości [mm] a = współczynnik rozszerzalności cieplnej
(11,7 x 10 -6 [°С -1 ])
L = długość śruby [mm]
AT = zmiana temperatury [°C]
2.13 Smarowanie
Aby nasmarować śruby kulowe NBS, należy przestrzegać poniższych instrukcji.
2.13.1 Smarowanie płynnym smarem
Powinno być preferowane ten typ smarowanie w przypadku pracy na duże prędkości obroty. Smary substancje płynne jakie można zastosować mają takie same właściwości jak substancje stosowane do smarowania łożysk tocznych (od VG 68 do VG 460). Wybór lepkości jest funkcją charakterystyki roboczej i środowiska pracy: temperatury, prędkości obrotowej, obciążeń eksploatacyjnych; Zaleca się stosować wyłącznie do śrub o małej prędkości obrotowej wysokie klasy lepkość (około VG 400).
W tym przypadku nie ma potrzeby płacenia specjalna uwaga konserwacji, z wyjątkiem stałego dostarczania oleju smarowego do układu (okresy dosmarowywania są krótsze niż w instalacjach smarowanych smarem plastycznym).
W każdym przypadku należy postępować zgodnie z instrukcjami producenta oleju płynnego.
2.13.2 Smar
Smarowanie smarem przeznaczonym jest do niskich prędkości obrotowych.
Przy wyborze środka smarnego należy wziąć pod uwagę przepisy dotyczące smarowania łożysk tocznych; Dlatego zaleca się stosowanie smarów na bazie mydła litowego zamiast smarów z dodatkami stałymi (takich jak smary MoS2 lub grafitowe), z wyjątkiem bardzo niskich prędkości obrotowych; zaleca się jednak przestrzeganie instrukcji producenta smaru.
3. Moment obrotowy i moc znamionowa
Aby w przybliżeniu obliczyć wartości momentu obrotowego i mocy silnika w celu przekształcenia ruchu obrotowego w ruch liniowy, należy skorzystać z następujących wzorów:
Gdzie:
Pmax = maksimum efektywne obciążenie[H]
Ph = skok gwintu [mm]
ɳ v = sprawność mechaniczna śmigła (ok. 0,9)
ɳ t = sprawność mechaniczna przekładni silnik-śmigła
(przekładnia z biegami ɳ t = 0,95+0,98);
z = przełożenie silnika - śmigło
W przypadku bezpośredniego połączenia silnika ze śmigłem z=1 i ɳ 2 =1.
Gdzie:
Nm = moc znamionowa silnika [kW]
Mm = moment znamionowy [Nm]
Pmax = maksymalne obroty śmigła [min]
z = przełożenie silnika - śmigło (silnik Ptah X Z = P)
W przypadku konwersji ruch prostoliniowy w ruchu obrotowym występuje:
M r = moment obciążenia [Nm]
P max = maksymalne obciążenie efektywne [N]
P h = skok gwintu [mm]
ɳ r = sprawność mechaniczna (ok. 0,8
4. Przykłady instalacji
Kod typu nakrętki | Kierunek śruba |
Nominalny średnica śruba [mm] |
Podziałka [mm] | Typ kołnierza | Kod przetwarzania | Klasa dokładność |
Ogólny długość śruba [mm] |
Kod wstępne załadowanie |
||
Pojedynczy lub podwójnie |
Kołnierzowe lub nie kołnierzowy |
Typ | ||||||||
V = pojedynczy W = podwójne |
F = kołnierzowy C = kołnierzowe |
U I mi DO M |
R = prawda L = w lewo |
_ | - | N = brak cięcia S = pojedynczy plasterek D = podwójne cięcie |
C = wyprostowany F = radełkowane |
Od 0 C 1 C 2 C 3 C 5 C 7 Od 10 |
- | P0 P1 P2 RZ P4 |
6. Program obliczeniowy NBS dla śrub kulowych (z cyrkulacją kulek)
W naszym sklepie internetowym możesz go kupić samodzielnie
Lub kontaktując się z naszymi specjalistami, dzwoniąc na nasz bezpłatny numer 8 800 700 72 07
A także wysyłając wniosek na adres E-mail sprzedaż@strona
Pary Gerotorowe
W tym artykule chciałbym omówić zasadę działania pomp śrubowych (lub gerotorowych). Pompy tego typu znajdują szerokie zastosowanie w przemyśle, a opisy ich działania nie wszędzie można spotkać.
Z tym samym wygląd pompy te mogą mieć zupełnie inne parametry pracy.
Spróbujmy dowiedzieć się, jaka jest różnica.
Rysunek przedstawia typową pompę śrubową w przekroju:
Gdzie: 1. Zespół łożyskowy, 2. Uszczelnienie wału, 3. Zawiasy, 4. Pręt, 5. Śruba (wirnik), 6. Klatka (stojan).
Para gerotorów (ciało robocze pompa śrubowa), zwaną parą wirnik-stojan (lub uchwytem śruby). Kiedy wirnik obraca się w stojanie, ciecz przepływa przez spiralny kanał stojana. W ten sposób pompowana jest ciecz.
Stojan to wewnętrzna spirala n+1, zwykle wykonana z elastomeru (gumy), nierozłącznie (lub osobno) połączona z metalowym uchwytem (tuleją).
Wirnik jest zewnętrzną spiralą n-ołowiową, która jest zwykle wykonana ze stali z lub bez późniejszej powłoki.
Warto zauważyć, że obecnie najpopularniejsze są jednostki ze stojanem 2-startowym i wirnikiem 1-startowym, ta konstrukcja jest klasyczna dla prawie wszystkich producentów sprzętu śrubowego;
Ważnym punktem jest to, że środki obrotu spiral stojana i wirnika są przesunięte o wielkość mimośrodu, co umożliwia utworzenie pary ciernej, w której podczas obracania się wirnika powstają wewnątrz zamknięte, uszczelnione wnęki stojan wzdłuż całej osi obrotu. W tym przypadku liczba takich zamkniętych wnęk na jednostkę długości pary śrub określa końcowe ciśnienie jednostki, a objętość każdej wnęki określa jej produktywność.
Różnica pomiędzy pompami polega właśnie na zastosowaniu par gerotorów o różnej geometrii.
Istnieją cztery główne typy par gerotorów, które są zwykle oznaczone literami alfabetu łacińskiego: S, L, D, P.
W naszym kraju i krajach sąsiednich produkowane są dotychczas tylko pompy z parami S i L. Trudniejsze w produkcji pary D i P produkowane są wyłącznie za granicą, np. w Niemczech.
Rodzaje par gerotorowych:
1. Geometria „S”:
Witkow: 1/2
Produktywność: 100%
Różny. ciśnienie: 12 barów
Zalety geometrii S:
bardzo płynna dostawa
mimo kompaktowych wymiarów duża liczba kroki
duży przekrój wlotu
niska prędkość przepływ/wysoka wydajność ssania
możliwe jest pompowanie sprężonych cząstek
pompowanie dużych cząstek
Należy zaznaczyć, że klips o geometrii „S” jest „blokujący”, czyli tzw. po zatrzymaniu pompy nie będzie przez nią przepływać żadna ciecz.
2. Geometria „L”:
Witkow: 1/2
Produktywność:200%
Różny. ciśnienie: 6 barów
Zalety geometrii L:
dobre właściwości objętościowe przy długim czasie realizacji dzięki długiej linii styku pomiędzy wirnikiem a stojanem
kompaktowe wymiary i wysoka wydajność
mniejsza prędkość tarcia
Ten typ klipsa nie jest blokowany. Gdy pompa jest zatrzymana, ciecz może przepływać przez parę gerotorów.
3. Geometria „D”:
Witkow: 2/3
Produktywność:150%
Różny. ciśnienie: 12 barów
Zalety geometrii D:
bardzo małe wymiary z wysokie ciśnienie krwi i produktywność
pompowanie prawie bez pulsacji
wysoka dokładność dozowania
4. Geometria „P”:
Witkow: 2/3
Produktywność:300%
Różny. ciśnienie: 6 barów
Zalety geometrii P:
kompaktowe wymiary i bardzo wysoka wydajność
prawie brak pulsacji
wysoka dokładność dozowania
dobre wskaźniki objętościowe, długi okres remontu ze względu na długi linia kontaktowa pomiędzy rotorem a stojanem
Podaliśmy przykłady geometrii par gerotorów o tej samej długości. Z rysunków widać, że liczba zwojów dla par „S” jest dwukrotnie większa niż dla pary „L” o tej samej długości. Ma to wpływ na maksymalne ciśnienie pary gerotorowej. Im więcej zakrętów, tym wyżej maksymalne ciśnienie.
Jak widać, każda para gerotorów wytwarza określone maksymalne ciśnienie (jeśli weźmiemy pod uwagę pary o tej samej długości).
Powstaje pytanie: co zrobić, jeśli potrzebujesz większego (lub mniejszego) ciśnienia wyjściowego niż wytwarza ta czy inna para.
W tym przypadku długość pary gerotorów zwiększa się (zmniejsza). Na przykład podwojenie długości pary „S” prowadzi do dwukrotnego wzrostu maksymalnego ciśnienia pompy, tj. ciśnienie wzrośnie do 12 atmosfer.
Pompy śrubowe mogą być również produkowane w różne projekty do pracy w określonych warunkach.
Opcje konfiguracji pompy:
1. Klasyczny układ poziomy z ramą nośną
2. Układ poziomy bez ramy nośnej
3. Dodatkowy ślimak podporowy
4. Zasobnik i podajnik ślimakowy
5. Dodatkowy mecerator (rozdrabniacz)
Film przedstawiający działanie pompy śrubowej do beczek
Para śrub składa się z dwóch części (śruby i nakrętki) połączonych wzdłuż powierzchni śruby. Para śrub służy do przekształcania ruchu obrotowego w ruch translacyjny i odwrotnie.
Pary śrub są dostępne z trójkątnymi, prostokątnymi i okrągłymi profilami powierzchni śrub.
W inżynierii powierzchnia śruby jest często nazywana gwintem. Gwinty o profilu trójkątnym dzielą się na metryczne, calowe, trapezowe i oporowe.
Podstawowe parametry geometryczne gwintów metrycznych według GOST 9150–81 (ryc. 5.3):
N– wysokość profilu pierwotnego (trójkąt równoboczny);
D, D 2 , D 1 – średnica zewnętrzna, środkowa i wewnętrzna;
Ryż. 5.5. Pary śrub z gwintem prostokątnym i trójkątnym:
c – śruba, d – nakrętka, R I D 2 – podziałka i średnia średnica gwintu
krok R– odległość pomiędzy najbliższymi podobnymi punktami konturu wzdłuż linii równoległej do osi gwintu;
kąt profilu = 60;
kąt pochylenia gwintu (ryc. 5.4).
P
Ryż. 5.6. Para śrub: w T I w A– prędkości obwodowe i osiowe nakrętki; D G - średnica zewnętrzna nakrętki; – kąt pochylenia linii śrubowej
Lub
Tutaj T– okres ruchu obrotowego.
Okres obrotu nakrętki
gdzie i N– prędkość kątowa i częstotliwość obrotu nakrętki.
Nakrętka prędkości translacji
Tarcie w parze śrub
Rozważmy parę śrub z prostokątnym profilem gwintu (ryc. 5.7). Zakładamy, że obciążenie osiowe F A na śrubie koncentruje się na jednym zwoju i aby reakcja nakrętki przebiegała wzdłuż linii środkowej gwintu, tj. D 2 .
Ryż. 5.7. Wyznaczanie sił tarcia w parze śrub o prostokątnym profilu gwintu
Ruch nakrętki wzdłuż śruby można uznać za ruch suwaka po nachylonej płaszczyźnie o kącie nachylenia (ryc. 5.8).
Gdy suwak porusza się równomiernie, obowiązuje następujące równanie równowagi:
Gdzie F T = M/R 2 – siła pozioma działająca na suwak (nakrętkę), M– moment obrotowy pary sił przyłożonych na odległość do nakrętki R 2 od osi śruby w płaszczyźnie prostopadłej do osi (w płaszczyźnie poziomej).
Z planu siły (ryc. 5.9) jasno wynika, że siła napędowa F T, wymagane do równomiernego ruchu suwaka w górę po pochyłej płaszczyźnie, jest powiązane z wielkością siły osiowej F A stosunek
F T = F A tg ( + ),
i moment obrotowy M pary dołączone do nakrętki będą
M = F T R 2 = F A tg ( + ) R 2 .
Z prawa Coulomba-Amontona wynika
F t = F N = N tg .
Z planu sił wyznaczamy siłę tarcia działającą w parze śrub:
Dzielenie licznika i mianownika tego wyrażenia przez cos i biorąc to pod uwagę F= tan , otrzymujemy
W parze śrub z gwintem trójkątnym siła normalna N > F A(Rys. 5.10), a zatem siła tarcia F t więcej niż w omówionej powyżej parze wkrętów z prostokątnym profilem gwintu. Odpowiednio
Ryż. 5.10. Zależności sił normalnych i osiowych w parach śrub z gwintem trójkątnym i prostokątnym
kąt tarcia i współczynnik tarcia F Na para śrub z gwintem trójkątnym będzie większa niż para śrub z prostokątnym profilem gwintu.
W parze śrub z gwintem trójkątnym współczynnik tarcia i kąt będą wynosić
I
.
Współczynniki uzyskane dla pary śrub z trójkątnym profilem gwintu F a kąt nazywane są zredukowanym współczynnikiem i kątem tarcia.
Większość producentów sprężarek oferuje gwarancję na pracę bez wyremontować sprężarka do 40 000 godzin. Na idealne warunki które nie występują w rzeczywistej eksploatacji.
Żywotność nowoczesnych łożysk podporowych pary śrub nie osiągnęła jeszcze poziomu, przy którym interwencja i wymiana nie są w tym czasie wymagane. Łożyska pracują średnio i uczciwie od 10 000 do 20 000 godzin, w zależności od jakości łożysk zamontowanych fabrycznie w bloku śrubowym i regularności Konserwacja od właściciela sprężarki. Po upływie tego czasu pod obciążeniem pary śrub pojawia się hałas, narastający wraz ze wzrostem zużycia przez kolejne 5 000-15 000 tysięcy godzin. W rezultacie sprężarka zaczyna się przegrzewać, a blok śrubowy zacina się z powodu zmienionych szczelin w parze śrub. W przypadku poważnego przegrzania końce pary śrub są „przyspawane” do korpusu, co gwałtownie zwiększa koszty pracy związanej z naprawą zespołu śrubowego. Lub łożyska rozpadają się, pozostawiając nieprzewidywalne uszkodzenia - od lokalnego przegrzania pary śrub po zarysowania i wyszczerbione trzpienie śrub.
W każdym z tych przypadków wykonamy następujące prace:
Wymiana łożysk oporowych pary śrub.
- wymiana uszczelnień wału śrubowego.
- regulacja luzów roboczych bloku śrubowego.
- przywrócenie roboczych końcówek śrub.
- przywrócenie profilu śruby.
- regeneracja trzpienia wału śruby napędowej.
- renowacja obudowy bloku śrubowego.
Prace przebiegają równie pomyślnie, niezależnie od producenta agregatu śrubowego, czy to: Ceccato, Aerzener, GHH-Rand, Rotorcomp, Fini, Enduro, Tamrotor, Termomeccanica, VMC, domowy Arsenal czy jakikolwiek inny producent.
Przykładowa praca, kliknij tytuł aby zobaczyć:
Naprawa bloku śrubowego 250 kW
Podwójny blok śrubowy z bezpośrednią przekładnią poprzez skrzynię biegów. Agregat pracował prawidłowo przez 5 lat, po czym podczas pracy agregatu śrubowego zaczęły pojawiać się coraz większe hałasy i drgania. Waga 1100 kg i wymiary urządzenia budzą szacunek u każdego, kto stoi obok tego dzieła inżynierii.
Po ustaleniu zakresu prac z klientem przeprowadziliśmy diagnostykę usterek zespołu śrubowego wraz z całkowitym demontażem:
Sekcja zwłok wykazała całkowite zużycie łożysk oporowych obu par śrub, jednej części nieco więcej, drugiej nieco mniej oraz niewielkie, miejscowe przetarcia na jednym z bloków śrub. Najwyraźniej niekontrolowana moc tego urządzenia wessała i pożarła bardzo solidne śmieci:
Zużycie łożysk zbliżało się do krytycznego, co oprócz zanieczyszczeń wpłynęło również na końcówki wirników śrubowych:
W skrzyni korbowej i zamkniętych wnękach znajdowały się opiłki metalu, które wskazywały na ekstremalne zużycie łożysk i grożące przegrzanie i zakleszczenie. Gdyby nie dokładność i uważność personelu zajmującego się konserwacją sprężarek, trochę więcej, a ilość napraw znacznie wzrosłaby:
Po wynikach wykrycia wady zamówiliśmy nowe łożyska par śrubowych, wymieniliśmy je, a także wymieniliśmy łożyska skrzyni biegów. Zebraliśmy wszystkie wióry metalowe, umyliśmy skrzynię korbową i usunęliśmy wszystkie zadziory z wirników i pokryw. Starannie zmontowaliśmy i wyregulowaliśmy oba zespoły śrubowe tak dokładnie i ostrożnie, jak to możliwe, aby uniknąć zniekształceń ładunku podczas pracy.
Teraz przez kolejne 4-5 lat Klient nie ma się czym martwić poza terminową wymianą oleju i filtrów w tym aucie.
Naprawa bloku śrubowego 75 kW
Blok śrubowy z przekładnią zębatą. Problem wynikał z silnika elektrycznego Siemens, który zepsuł jego łożyska i odpowiednio reduktor, co doprowadziło do zakleszczenia. Wpusty na zębatkach nie zostały odcięte i stało się to, co miało się stać - rozerwała się mała zębatka i trzpień wirnika napędowego.
Analiza materiału pary śrub wykazała, że było to zwykłe żeliwo. Skuteczny pod względem tarcia, ale trudny do naprawy. To wyjaśnia również, dlaczego stalowy klucz nie został przecięty, co tylko czyni naprawę bardziej interesującą.
Zepsuty sprzęt:
Uszkodzenia trzonka wału napędowego:
Biorąc pod uwagę fakt, że koszt nowego bloku śrubowego jest 4-5 razy większy droższe niż naprawy, klient podjął decyzję od razu.
Odtworzono chwyt i wpust. Należy jeszcze raz pamiętać, że materiałem śrub jest żeliwo:
Zamówiliśmy i zamontowaliśmy nowy sprzęt:
Oczywiście zmieniliśmy łożyska podporowe, jednocześnie udoskonalając konstrukcję - zamiast jednego łożyska wzdłużno-promieniowego zamontowano dwa, co naprawiło szczelinę roboczą w parze śrub i uczyniło je jeszcze bardziej niezawodnym niż fabrycznie:
Naprawa agregatu śrubowego Rotorcomp NK100 22kW
Dotarł do nas blok śrubowy Rotorcomp ze sprężarki Renner-Kompressoren baza naprawcza w stanie zakleszczenia, szczerze przepracowując 5 lat od 2007 r.:
Pomimo regularnej konserwacji sprężarki czas zrobił swoje, zużycie łożysk oporowych osiągnęło krytyczne tolerancje, olej nie pomagał już w chłodzeniu pary śrubowej, a wirniki śrubowe opierały się o powierzchnia robocza, przyspawany do niego. Tego typu naprawa jest zawsze nieprzewidywalna pod względem zakresu prac i po otrzymaniu od Klienta carte blanche przystąpiliśmy do demontażu zespołu śrubowego. Podjęto decyzję o demontażu powoli i delikatnie, aby zminimalizować uszkodzenia podczas usuwania spawanych części. Po zaciętej walce o bezpieczeństwo para śrub poddała się przy minimalnych stratach dla portfela Klienta:
Zminimalizowano również uszkodzenia pokrywy bloku śrubowego:
Odtworzyliśmy powierzchnie robocze końcówek śrub oraz płaszczyznę pokrywy przy pomocy spawarek, tokarek i frezarek oraz bezcennej wiedzy i doświadczenia naszych mechaników. Wymieniono łożyska oporowe pary śrub. Zmontowaliśmy i skonfigurowaliśmy jednostkę śrubową. Wróciłem do Klienta z uwagami z kim się skontaktować i co zrobić gdy po 4-5 latach ciężkiej pracy kompresora, temperatura pracy poziom oleju zacznie ponownie rosnąć.