Bieżące i docelowe wartości strumienia wartości. Korzyści z filozofii Kaizen. Interpretacja mapy strumienia wartości
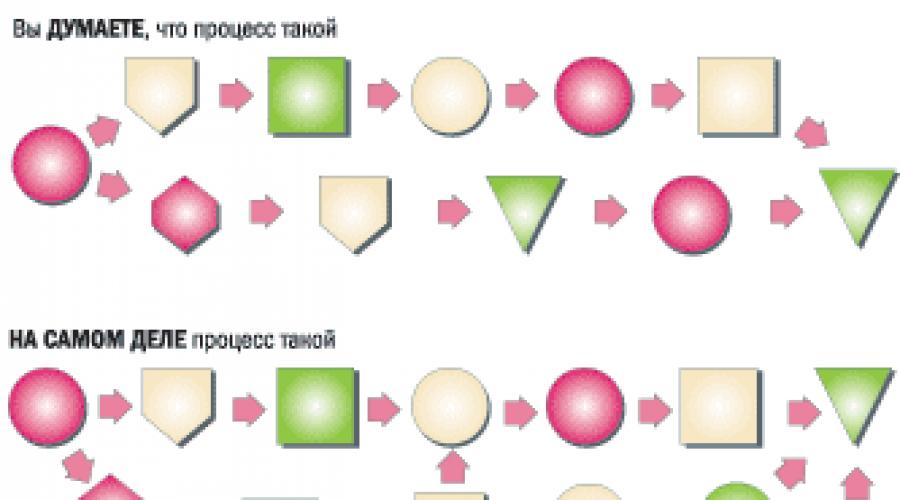
Przeczytaj także
Artykuł z archiwum magazynu „Logistic&System”
Władimir Morskoj
Starszy trener-konsultant w CBSD
Zbuduj dom bez kompilacji projekt architektoniczny i bez sporządzenia rysunków nie jest to możliwe. Nie da się także zmienić procesów produkcyjnych zgodnie z ideologią Lean Production bez mapy obecnego i przyszłego stanu produkcji
W jednym z poprzednich numerów (patrz „Logistyka i System” nr 7/lipiec 2005) pisaliśmy już o produkcji, która opiera się na systemie pull. Zgodnie z ideologią Lean Production („odchudzona produkcja”), rewolucyjne metody są bardziej destrukcyjne niż konstruktywne. Wszelkie zmiany muszą być systematyczne, odbywać się małymi krokami i w kilku etapach. Zanim jednak nastąpi jakikolwiek postęp i zmiany, należy zrozumieć, zrozumieć i namalować pełny obraz tego, co dzieje się w przedsiębiorstwie, gdyż wszelkie wyjaśnienia i przekształcenia powinny dotyczyć całej produkcji, a nie jej poszczególnych procesów. W praktyce z reguły mamy do czynienia z punktowymi usprawnieniami poszczególnych procesów (np. spawanie, montaż, malowanie itp.), co nie pozwala na całkowite przekształcenie i przekształcenie przedsiębiorstwa czy pojedynczego produktu. Co więcej, często innowacyjne pomysły i chęć „tu optymalizacji” prowadzą jedynie do braku równowagi w produkcji, ponieważ jakiś indywidualny proces lub obszar produkcyjny zaczyna działać znacznie lepiej, a sąsiednie obszary lub procesy po prostu nie są w stanie za tym nadążyć.
Wartość
Można go zdefiniować jako produkt lub usługę dostarczoną klientowi we właściwym czasie i za odpowiednią cenę. Łańcuch wartości to sekwencja wszelkiego rodzaju działań wymaganych do wynalezienia, opracowania, wyprodukowania i utrzymania określonego produktu, od koncepcji do wprowadzenia na rynek, od zamówienia do dostawy i od surowców do produktu końcowego w rękach klienta. Każdy klient prawie zawsze jest skłonny zapłacić za te czynności, które dodadzą wartości produktowi (na przykład obróbka skrawaniem, odlewanie, malowanie, montaż, sporządzanie instrukcji obsługi itp.), gdyż ignorowanie ich zmniejsza wartość produktu w oczach klienta, a to już jest obarczone stratami.
Straty pierwszego rzędu
Są to straty, których prawie nie da się pozbyć, ponieważ wydajność całego przedsiębiorstwa zależy od wybranego procesu lub operacji technologicznej (na przykład obliczenia wynagrodzenie). Z punktu widzenia klienta proces ten nie dodaje wartości produktowi, lecz jego wykluczenie z niego cykl ogólny z pewnością doprowadzi do całkowitego zamknięcia przedsiębiorstwa. Takich procesów czy operacji nie da się wyeliminować, można je jedynie zoptymalizować.
Straty drugiego rzędu
Blok ten obejmuje straty, których wykrycie wymaga natychmiastowego podjęcia działań w celu ich wyeliminowania. Musisz znać swoich wrogów z widzenia, więc wymienimy ich.
Nadprodukcja. Z reguły jest to poważna konsekwencja i konsekwencja sposobu myślenia menedżerów, dla których priorytetem jest jak najpełniejsze wykorzystanie sprzętu i dostępnej kadry. W rezultacie wszystko to prowadzi do:
- przedwczesne zużycie surowców i materiałów;
- nieoptymalne wykorzystanie siły roboczej;
- zakup dodatkowego wyposażenia;
- zwiększenie powierzchni użytkowej;
- zwiększenie procentu odliczeń (np. podatku od nieruchomości);
- wzrost rezerw;
- wzrost kosztów transportu i administracji.
Masaki Imai w swojej książce Gemba Kaizen zwraca uwagę, że nadprodukcja jest najgorszy rodzaj strata, która daje złudne poczucie bezpieczeństwa, pomaga ukryć wszelkiego rodzaju problemy i „chmury” informacji, które mogłyby pomóc we wdrażaniu pozytywnych zmian w produkcji.
Nadmiar zapasów. Surowce i materiały, produkty gotowe, części zamienne do naprawy sprzętu oraz pomieszczenia składowane w magazynie nie dodają wartości do produktu. Jednak dla zdecydowanej większości przedsiębiorstw działających na przestrzeni poradzieckiej rezerwy stanowią ochronę przed niepewnością czynniki zewnętrzne(cykl popytu i podaży). Oczywiście istnieje inny, inny rodzaj rezerw, który służy jako ochrona przed czynnikami wewnętrznymi - złym zarządzaniem, niewłaściwą równowagą pracy, niską jakością produktów, nadmiernym czasem wymiany sprzętu, niewystarczającą wymianą informacji między działami itp. A jeśli rezerwa z czynników zewnętrznych jest „wytrenowana” i prawie niemożliwa do regulacji, wówczas po prostu zaleca się optymalizację zapasów bezpieczeństwa (istnieją metody obliczania optymalnego zapasu bezpieczeństwa w warunkach niepewności). A czynniki wpływające na wielkość rezerw należy niestrudzenie zwalczać, aż do ich całkowitego wyeliminowania.
Małżeństwo. Oczywiste straty, drenaż zasobów materialnych i ludzkich. Filozofia Lean mówi, że należy zbudować system, w którym wszelkie odstępstwa od normy będą od razu zauważalne. Już w latach 30. ubiegłego wieku Deming pracujący w AT&T i budujący koncepcję jakości „wbudowanej” pisał: „...występowanie wad w trakcie procesu zależy w 95% od jakości samego procesu i tylko 5% na czynnik ludzki.” Firma Toyota doszła do następującego wniosku: należy tak zbudować proces, aby pracownik wykonując jakąś operację nie mógł jej wykonać błędnie. Nie jest to łatwe zadanie, nad jego rozwiązaniem pracują specjalne wielofunkcyjne grupy specjalistów, składające się nie tylko z inżynierów, ale także z samych pracowników. Robią to, co Japończycy nazywają poka yoke, czyli „ochroną głupców”. Doświadczenie firmy Toyota było klasowo obce Związkowi Radzieckiemu, ale w kwestii nie tylko tarzania się, ale także „ochrony przed głupcami”, nadal odnieśliśmy sukces w dużej mierze dzięki podobnym japońskim grupom zorganizowanym na przełomie lat 70. i 80. w przedsiębiorstwach przemysłu obronnego ZSRR. Obecnie praktyka ta jest stosowana w wielu Rosyjskie przedsiębiorstwa.
Kolejnym osiągnięciem Toyoty, aktywnie wykorzystywanej w produkcji od 50 lat, jest całkowita kontrola jakości produktów i zapobieganie przechodzeniu wadliwych produktów do następnego działu. Eliminację wady przeprowadzamy na miejscu, w którym została ona wykryta, samodzielnie i przy pomocy zespołów specjalnego reagowania (tych samych grup, które opracowują „foolproofing”). Następnie analizowana jest wada, identyfikowane są przyczyny jej wystąpienia i opracowywane są działania zapobiegające jej ponownemu wystąpieniu. Najważniejsza w tym wszystkim jest odpowiedzialność za jakość na wszystkich poziomach, od góry do dołu, a to wymaga całkowitej zmiany świadomości załogi, przyjęcia filozofii jakości. To właśnie nazywa się TQM (Total Quality Management).
Niepotrzebne ruchy w miejscu pracy. Jeśli pracownik szuka wymagany dokument lub idzie po narzędzie kilka metrów od swojego miejsca pracy, to również nie dodaje wartości produktowi. Właściwy sposób unikanie tego jest prawidłowe, to znaczy racjonalna organizacja miejsca pracy.
Nadmierne przetwarzanie. Choć może to zabrzmieć zaskakująco i pompatycznie, podstawą tego typu strat jest „banalny” perfekcjonizm, czyli chęć zrobienia produktu lepszego niż ten, który zamówił klient. Na przykład kierownik produkcji może pominąć specyfikację klienta i ustawić bardziej rygorystyczne tolerancje w zakresie obróbki części. I wszystko byłoby dobrze, ale bardziej precyzyjna obróbka zwiększa ryzyko wystąpienia defektów i wymaga innego, zwykle drogiego narzędzia, w tym takiego do monitorowania operacji i wyższych kwalifikacji wykonawcy. I w końcu po co płacić więcej, jeśli klient prosi o ideał konkretny produkt?! Zapewnienie jakości, jak każda działalność produkcyjna, ma swoją cenę. Przekroczenie danego kosztu jest już stratą, która nieuchronnie wynika z nadmiernego przetwarzania. Ponadto analizując przepływy produkcyjne, odkrywa się operacje, których można całkowicie uniknąć bez uszczerbku dla jakości produktu.
Przestój(czas oczekiwania na przybycie produktów z poprzedniego procesu). Wierni towarzysze braku równowagi pomiędzy obszarami produkcyjnymi, miejscami pracy i warsztatami. Ale mogą również powstać w wyniku awarii sprzętu i przedterminowych dostaw surowców. Wysiłki w tym przypadku powinny być skierowane na utrzymanie zrównoważonej pracy sprzętu i wdrożenie środków zapobiegawczych, aby zapobiec nieplanowanemu wyłączeniu sprzętu. Obecność wysoce produktywnego sprzętu w niektórych obszarach przedsiębiorstwa nie zawsze jest dobrą rzeczą, ponieważ właśnie to najczęściej prowadzi do braku równowagi. Możesz chronić swoją produkcję przed przestojami spowodowanymi przez dostawców, utrzymując zoptymalizowane zapasy bezpieczeństwa lub przechodząc na współpracę z dostawcami na zasadzie just-in-time.
Niepotrzebny transport i przemieszczanie się. Bez słowa „niepotrzebne” operacje te są istotną częścią procesu produkcyjnego, jednak z punktu widzenia klienta ta część nie ma nic wspólnego z wartością produktu – jest mu obojętne, jakie odległości i w jaki sposób produkt został przeniesiony. Jednym z głównych wskaźników mapy strumienia wartości jest długość przepływu od bramy do bramy – im jest ona krótsza, tym bardziej oczywiste jest skrócenie całkowitego czasu produkcji, zapasów, przestrzeni produkcyjnej i strat spowodowanych szkodami spowodowanymi transportem.
Utrata kreatywności wśród pracowników. Bardzo poważny rodzaj straty, który rzutuje na ogólną sytuację firmy. Jeśli ktoś nie przejmuje się tym, co robi, nie można oczekiwać, że będzie odpowiedzialny za wynik, nie mówiąc już o odpowiedzialności za jakość swojej pracy.
Okazuje się więc, że jeśli na wlocie rura zostanie napełniona do pełna, to po przejściu przez szereg strat przepływ na wylocie zmniejsza się o ponad połowę (patrz rysunek 1).
Rysunek 1. Łańcuch wartości
Mapa wartości
Pomóż zidentyfikować kroki i działania, które nie dodają wartości i obiektywnie nakreśl stan procesy produkcji może mapa stan aktulany produkcji (patrz rysunek 2). Graficzne przedstawienie pozwoli krytycznie ocenić wzrost wartości na każdym etapie i zidentyfikować te działania, które nie wnoszą wartości do produktu. To ważne narzędzie, które pozwala na:
- widzieć nie tylko pojedynczą czynność (na przykład spawanie, montaż lub malowanie), ale cały proces wytwarzania produktu jako całości;
- wykryć nie tylko straty, ale także ich źródła w strumieniu wartości;
- podejmuj decyzje związane z przepływem w sposób jasny i dostępny do dyskusji, w przeciwnym razie decyzje i działania na hali produkcyjnej będą realizowane w taki sam sposób jak wcześniej, czyli wcale lub w jakiś sposób;
- pokazać związek pomiędzy przepływami informacji i materiałów (żadne inne narzędzie tego nie potrafi).
Rysunek 2. Proces tworzenia wartości
Będąc w istocie rysunkiem, podstawą wdrożenia Lean Production, mapa pomaga zaplanować ruch całego przepływu – właśnie ten fakt jest bardzo często pomijany, skazując próby wdrożenia Lean Production na niepowodzenie. Mapa jest o wiele bardziej użyteczna niż wiele narzędzi i wykresów ilościowych, które po prostu zliczają kroki niewnoszące wartości dodanej, czasy realizacji, odległości, jakie przebyły produkty, poziomy zapasów itp. - jest to narzędzie jakościowe, które szczegółowo opisuje, w jaki sposób należy zorganizować pracę w warsztacie i oddzielną sekcję, aby zapewnić ciągły przepływ.
Stworzenie ciągłego przepływu jest projektem długotrwałym i z reguły kosztownym, gdyż wymaga nie tylko wysiłku i zasobów ludzkich, ale także inwestycji finansowych w nowy sprzęt. A biorąc pod uwagę fakt, że nawet przenoszenie sprzętu w warsztatach wymaga czasu i kosztów materiałowych, można zapomnieć o niskich kosztach i skąpstwach. Dlatego wyeliminowanie strat w dowolnym obszarze produkcyjnym może zająć więcej niż rok. A przed uruchomieniem projektu tej wielkości trzeba ustalić, dlaczego ten projekt ma się udać i co można osiągnąć w wyniku zmian. Punktem wyjścia powinna być mapa stanu aktualnego.
Map strumienia wartości
Tworzenie mapy strumienia wartości jest jednym z najważniejszych narzędzi budowania organizacji Lean. Proces ten dzieli się na dwa etapy.
Budowa mapy stanu obecnego:
- analiza istniejących procesów w strumieniu wartości
- identyfikowanie źródeł strat.
Budowanie mapy stanu przyszłego (co chcemy uzyskać):
- stworzenie planu eliminacji źródeł strat;
- powołanie kierownika projektu w celu wdrożenia zmian w tym strumieniu;
- określenie kluczowych wskaźników efektywności realizacji projektu;
- określenie terminu realizacji projektu.
Mapa strumienia wartości jest jak fotografia tego, co dzieje się w przedsiębiorstwie w rzeczywistości, a nie w naszej wyobraźni. Często przy konstruowaniu mapy stanu aktualnego ujawniają się bardzo poważne naruszenia technologii, a czas wykonania niektórych operacji znacznie odbiega od opisanego w dokumentach (proces techniczny). Mapa przepływu pozwala zobaczyć cały przepływ jako całość z lotu ptaka.
Dane zapisane podczas konstruowania mapy przepływu:
- nazwa sprzętu lub procesu;
- czas wykonania operacji lub procesu (czas rzeczywisty, a nie czas określony w aktualnie istniejącej dokumentacji);
- niezawodność sprzętu (czas pracy sprzętu bez awarii,%);
- liczba operatorów lub pracowników wykonujących daną operację lub obsługujących proces;
- dostępność zapasów w magazynie surowców i materiałów dla danego przepływu (w dniach), ilość wyrobów gotowych (w dniach), wielkość zapasów międzyoperacyjnych i międzyzakładowych półproduktów w danym przepływie (w dniach) ;
- tryb i termin składania zamówień u dostawców na ten przepływ;
- procedura wysyłki i warunki generowania zamówień od klientów dla ten typ produkty lub grupy produktów;
- Czas taktu to czas, w którym należy wyprodukować jednostkę produktu. Naliczane na podstawie potrzeb klienta (na dzień lub na zmianę). Przykład: pełny etat dzień roboczy lub zmiana, podzielony przez liczbę gotowych produktów, które muszą zostać wysłane do klienta w tym samym okresie;
- czas cyklu, czyli czas potrzebny na wykonanie jednej operacji (musi być mniejszy lub równy czasowi taktu);
- procedurę planowania produkcji w przedsiębiorstwie, a także stopień szczegółowości tych planów i tryb przekazywania tych dokumentów.
Głównym celem tej pracy jest ocena efektywności przepływu. Efektywność przepływu obliczana jest jako łączny czas działań dodających wartość produktowi z punktu widzenia klienta podzielony przez całkowity czas potrzebny produktowi na przejście przez cały przepływ i pomnożony przez 100%. W rosyjskich przedsiębiorstwach odsetek ten wynosi niecałe 2%, zatem pozostaje jeszcze wiele do zrobienia.
Aktualna mapa stanu jest być może najskuteczniejszym narzędziem do analizy pracy każdego przedsiębiorstwa, w tym sektora usług, bankowości, opieki zdrowotnej, a zwłaszcza produkcyjnej. Pozwala w przejrzysty sposób dostrzec główne źródła strat i opracować plan ich eliminacji lub znacznego ograniczenia.
Informacje o firmie
Jako przykład weźmy TWI Industries, firmę produkującą szeroką gamę części do ciągników. Rozważymy tylko jedną grupę produktów - wahacze (drążki), produkowane w różnych konfiguracjach. Klientami tej rodziny produktów są zarówno producenci ciągników, jak i różne organizacje naprawcze.
Ze względu na różnorodność konfiguracji wymagania klientów różnią się w zależności od zamówienia. Cykl produkcyjny realizacji zamówienia trwa 27 dni. Czas produkcji i niedokończona praca nad już otrzymanymi zamówieniami wymuszają na firmie ogłoszenie terminu realizacji wynoszącego 60 dni. Jednak klienci firmy nie są w stanie dokładnie określić wielkości zapotrzebowania wcześniej niż na dwa tygodnie przed wysyłką zamówienia. Ciągłe korekty sprawiają, że każde zamówienie trafiające do warsztatów zawsze okazuje się pilne. Dział kontroli produkcji przekazuje zamówienia klientów w kolejności ich wpływu, jednak w warsztatach grupuje się je w partie zgodnie z konfiguracją części, aby w miarę możliwości skrócić czas przezbrojeń sprzętu, co również prowadzi do pośpiechu i sytuacjach awaryjnych.
Informacje o produkcie
Ramię kierownicze to metalowy pręt z tłoczonymi końcami przyspawanymi z każdej strony. Firma produkuje wahacze różne rozmiary, dwie średnice, z trzema rodzajami końcówek (każda strona wahacza może mieć inną końcówkę). Tym samym firma produkuje 240 wariantów wahaczy. Pręty stalowe do produkcji dostarcza firma Michigan Steel Co. (czas produkcji wynosi 16 tygodni, wysyłka odbywa się 23 razy w miesiącu). Blanki szczytowe pochodzą z firmy Indiana Castings (czas produkcji 12 tygodni, wysyłka dwa razy w miesiącu).
Zatem wymagania klientów sprowadzają się do tego, że chcą otrzymywać 24 tys. sztuk towaru miesięcznie, ale minimalna wielkość zamówienia musi być wyjątkowo niska – od 25 do 200 sztuk, średnio – 50 sztuk, a gotowe produkty muszą być pakowane w pudełka z tektury falistej, po pięć ramion kierowniczych w pudełku i dostarczane kilka razy dziennie ciężarówką. Z kolei TWI, biorąc pod uwagę częstą zmianę życzeń klientów, wymaga od nich składania zamówień na 560 dni przed datą wysyłki gotowych produktów. Nie przeszkadza to jednak Klientom w dostosowaniu wielkości zamówienia na dwa tygodnie przed datą wysyłki.
Procesy produkcji
Procesy TWI w zakresie produkcji wahaczy obejmują cięcie metalowego pręta, przyspawanie do niego końcówek, gratowanie (usuwanie wypukłych śladów spawów ze ściany), zlecanie malowania na zewnątrz i montaż końcówek. TWI produkuje również kute tuleje tulejowe. Gotowe wahacze są składane w zestawy i codziennie wysyłane do klientów.
Zmiana długości dźwigni wymaga 15-minutowej ponownej regulacji sprzętu do operacji cięcia, spawania i usuwania izolacji. Zmiana średnicy pręta wymaga godzinnej ponownej regulacji sprzętu, co w dużej mierze wynika z kryteriów kontroli jakości. Zmiana pomiędzy trzema typami kutych końcówek wymaga dwugodzinnej zmiany w operacji tłoczenia maszynowego.
Czas pracy
20 dni w miesiącu. Wszystkie jednostki produkcyjne pracują na dwie zmiany, których czas trwania wynosi osiem godzin iw razie potrzeby zapewniane są nadgodziny. Każda zmiana ma dwie 15-minutowe przerwy, podczas których nie wykonuje się żadnej ręcznej obróbki. Czas na lunch nie jest płatny.
Dział kontroli produkcji
Dział kontroli przyjmuje zamówienia klientów z 60-dniowym wyprzedzeniem, dla każdego klienta przygotowuje zamówienie zakupu i przekazuje je do produkcji. Składa zamówienia na wędki i szczytówki u dostawców na sześć tygodni przed przewidywaną datą otrzymania zamówienia. Przekazuje codzienną listę priorytetów kierownikom produkcji, którzy sekwencjonują zlecenia produkcyjne zgodnie z tą listą. Na dwa tygodnie przed wysyłką dział otrzymuje wyjaśnienia od klientów dotyczące wielkości zamówień i wskazuje na potrzebę przyspieszenia realizacji tych zamówień. Harmonogram dostaw przekazywany jest codziennie do działu wysyłki wyrobów gotowych.
Informacje o procesie i działaniu
Operację „cięcia” wykonuje ręcznie jeden operator przy pomocy specjalnej piły (do różnych produktów TWI). Czas cyklu – 15 sekund. Czas zmiany wynosi 15 minut przy pomiarze długości i godzinę przy pomiarze średnicy. Niezawodność – 100%. Obserwowane zapasy to 20 dni przed pokrojeniem i pięć dni po pokrojeniu.
Operacja „Spawanie I”. Pierwsza przetworzona końcówka jest przyspawana do pręta. Proces jest automatyczny, a operator wykonuje zewnętrzny załadunek i rozładunek. Czas cyklu: operator – 10 sekund, maszyna – 30 sekund. Czas zmiany wynosi 15 minut przy zmianie długości i godzinę przy zmianie średnicy. Niezawodność – 90%. Obserwowane zapasy obejmują okres trzech dni od daty transakcji.
Operacja „spawanie II”. Druga przetworzona końcówka jest przyspawana do pręta. Proces odbywa się automatycznie. Wszystkie wskaźniki pokrywają się z wynikami operacji „spawanie I”, z wyjątkiem niezawodności – jest ona nieco niższa i wynosi 80%.
Operacja gratowania. Proces odbywa się automatycznie. Operator wykonuje zewnętrzny załadunek i rozładunek. Czas cyklu: operator – 10 sekund, maszyna – 30 sekund. Czas zmiany wynosi 15 minut przy zmianie długości i godzinę przy zmianie średnicy. Niezawodność – 100%. Obserwowany stan zapasów trwa pięć dni po gratowaniu.
Operacja „malowanie” wyprodukowane przez zewnętrznego podwykonawcę. Czas malowania to dwa dni. Codziennie ciężarówka dostarcza dźwignie niemalowane i przywozi pomalowane. Obserwowany stan zapasów wynosi dwa dni u podwykonawcy i sześć dni po malowaniu.
Operacja „montaż”. Proces jest wykonywany ręcznie przez sześciu operatorów. Czas całkowity na jednostkę produkcji – 195 sekund. Czas wymiany wynosi 10 minut przy zmianie rodzaju końcówki. Niezawodność – 100%. Obserwowane zapasy trwają cztery dni w magazynie wyrobów gotowych.
Operacja " renowacja mechaniczna porady." Proces realizowany jest automatycznie przez jednego operatora. Czas cyklu – 30 sekund. Czas zmiany wynosi dwie godziny. Niezawodność – 100%. Zapasy obserwowane – 20 dni przed leczeniem, 4 dni po zabiegu.
Operacja „Dział spedycji”. Odbiera gotowe produkty z magazynu i kompletuje zamówienia z dostawą do klienta.
Zatem dane zostały zebrane. Wykorzystując te dane sporządzamy mapę stanu aktualnego (patrz Załącznik 1).
Mapa przyszłego stanu
Celem odchudzonego systemu produkcyjnego jest stworzenie sekwencji operacji jednostkowych: zrobione – przekazanie. Następnie należy przeanalizować przedstawiony graficznie stan produkcji i opracować kroki mające na celu zmianę procesu, zawsze koordynując je ze strategią firmy. Jak ważne jest to widać na przykładzie piór wiecznych Parker. To produkt elitarny, drogi i na prezent. Jeden z menadżerów postanowił poważnie zwiększyć produkcję, tak aby Parker był obecny we wszystkich sklepach z artykułami biurowymi. W rezultacie długopisy w ogóle przestały się sprzedawać, gdyż pozycjonowano je jako produkt elitarny, a nie codzienny, a wizerunek firmy został poważnie nadszarpnięty.
Na mapie stanu obecnego zaznaczamy obszary, w których straty można już ograniczyć. Tam, gdzie nie jest to możliwe, instalujemy supermarkety - magazyny ze ściśle regulowanym stanem magazynowym. Następnie sporządzamy plan działania, przydzielamy odpowiedzialność i ustalamy terminy.
Wszystko musi być konkretne. Przykładowo, jeśli zdecydujemy się na rozpoczęcie budowania przepływu w jakimkolwiek obszarze produkcji, gdzie jest to możliwe, to każde działanie w tym kierunku powinno zostać uregulowane w czasie, zidentyfikowane i przydzielone niezbędne środki oraz osoba odpowiedzialna za należy wyznaczyć tę czynność.
Dlatego warsztaty TWI są zasypywane zamówieniami, które zbyt szybko zostały wprowadzone do produkcji. Byli przestawiani i przestawiani, aby zoptymalizować wymianę sprzętu i zrealizować najpilniejsze zamówienia klientów. Ponieważ pierwsza operacja spawania zajmuje tylko 30 minut na partię, a następnie jest przetwarzana w systemie FIFO aż do wysyłki, czas realizacji zamówienia klienta może zostać skrócony o trzy dni. Konieczne jest skrócenie czasu przezbrojenia w przypadku operacji spawania i gratowania do pięciu minut lub mniej, aby można było wyprodukować różne konfiguracje wahaczy sterujących w ramach czasowych zbliżonych do kolejności zamówień klientów.
Wymagania klientów dotyczące konfiguracji wahaczy sterujących ciągników są różne, a czas uzupełniania zapasów długi, dlatego niepraktyczne jest magazynowanie gotowych ramion jak w supermarkecie na samym końcu łańcucha wartości. Należy zaplanować prace od dołu do góry łańcucha, aż do pierwszej operacji, w której pojawi się różnica w konfiguracji (w tym przypadku pierwsze spawanie), a następnie zastosować zasadę FIFO. W tym momencie planowania, marnując 30 minut na 30-minutowe przyrosty planowania, można uniknąć nadprodukcji i „przepychania” strumienia FIFO.
Rysunek 5. Symbole załączników 1 i 2
Firma może zapewnić ciągły przepływ pomiędzy operacjami spawania i gratowania. Jeden operator będzie obsługiwał te procesy, ładując i przenosząc części z jednego automatu do drugiego. TWI będzie musiało zorganizować czasy cykli spawania/odizolowywania krótsze niż czas taktu wynoszący 45 sekund – do około 39 sekund – aby umożliwić pracę 12 przekaźników na zmianę. Ponieważ przy montażu gotowych produktów nie jest wymagane przezbrajanie, cykl może być zbliżony do czasu taktu, co pozwoli na wykonanie montażu przez pięciu operatorów.
W tym przypadku 30-minutowy czas trwania kroku opiera się na średniej wielkości zamówienia wynoszącej 50 sztuk i pięciu minutach czasu przezbrojenia pomiędzy zamówieniami na spawanie/szlifowanie. Przy wielkości zamówień klientów wynoszącej 600 jednostek na zmianę i czasie cyklu wynoszącym 39 sekund pozostaje godzina na 12 przezbrojeń pomiędzy partiami. Aby zorganizować ten etap, dział zarządzania produkcją skonsoliduje małe zamówienia i podzieli duże zamówienia na partie po 50 sztuk. Dział kontroli produkcji musi również zrównoważyć asortyment produktów, aby zmniejszyć zapasy typu supermarketowego w poprzedzających operacjach cięcia i tłoczenia. Tym samym TWI nie będzie realizować zamówień w kolejności ich otrzymania, ale w bardzo zbliżonej do niej.
Na podstawie zgłoszonych uwag klienci TWI mogą składać zamówienia z dwutygodniowym wyprzedzeniem. Wykonywanie ciętych prętów i końcówek do tłoczenia może obsługiwać system ciągnięcia przypominający supermarket. Podobnie można zamówić nieprzycięte wędki i blanki szczytówek w miarę ich zużycia i magazynowania surowców, jak w supermarkecie. Eliminuje to potrzebę kontroli produkcji, gdzie zamówienia klientów powodowałyby natychmiastowe zamówienia surowców od dostawców. Biorąc pod uwagę przeprowadzoną analizę, zmiany na mapie stanu przyszłego można odzwierciedlić, jak pokazano w Załączniku 2.
Mapa pokazuje o ile zmniejszyły się zapasy międzyoperacyjne, przepływy informacji, miejsca pracy, czas realizacji zamówień, a jednocześnie wzrosła produktywność
Mapowanie wartości strumienia
Mapowanie strumienia wartości to dość prosty i wizualny diagram graficzny przedstawiający przepływy materiałów i informacji niezbędne do dostarczenia produktu lub usługi konsumentowi końcowemu. Mapa strumienia wartości pozwala od razu dostrzec wąskie gardła przepływu i na podstawie jej analizy zidentyfikować wszystkie nieproduktywne koszty i procesy oraz opracować plan usprawnień.
Mapowanie strumienia wartości obejmuje następujące kroki:
1. Dokumentowanie mapy stanu aktualnego
2. Analiza przepływu produkcji
3. Utwórz mapę stanu przyszłego
4. Opracuj plan ulepszeń
Nić Ariadny
Wartość dla klienta to podstawowa zasada Lean Manufacturing, zgodnie z którą celem wdrożenia systemu Lean Manufacturing jest identyfikacja i eliminacja marnotrawstwa, które nie dodaje wartości do produktu i/lub usługi z punktu widzenia klienta. W związku z tym, jeśli zdecydujesz się pójść ścieżką Lean Manufacturing, musisz po prostu nauczyć się widzieć całość powiązanych i oddziałujących na siebie procesów firmy oczami klienta. Ale jak to zrobić? Jak w prosty i przejrzysty sposób przedstawić powiązania pomiędzy przepływami materiałów i informacji w firmie oraz jak można je analizować pod kątem strat?
Jeśli spojrzymy na firmę z punktu widzenia tradycyjnego podejścia, które opisuje ją jako hierarchiczną, funkcjonalną strukturę, zobaczymy prawdziwy labirynt, którego całkowicie nie da się ocenić z punktu widzenia efektywności operacyjnej. Potrzebujemy zatem czegoś w rodzaju nici Ariadny, która pozwoli nam połączyć wszystkie ogniwa łańcucha produkcyjnego, aby stworzyć finalny produkt w jeden obraz. Wątek ten jest podejściem procesowym do opisu działalności firmy. Proces to pewien logiczny związek działań prowadzących do uzyskania końcowego produktu i/lub usługi. Logiczne jest, że nie można zobaczyć wszystkich tych działań w tym samym czasie, ponieważ są one oddzielone w czasie i przestrzeni.
Dlatego do analizy całego strumienia wartości i składających się na niego procesów wymagana jest zastosowana metodologia, która pozwoli na dokładne zbadanie i dokładne opisanie każdego z procesów, przy jednoczesnym wskazaniu ich wzajemnych powiązań. Można opisać słowami procesy i powiązania między nimi (co w rzeczywistości robi się w przepisach fabrycznych, które są niezwykle trudne do jednoznacznego zrozumienia), ale zwiększy to prawdopodobieństwo błędów przy analizie przepływu, ponieważ różni ludzie rozumieć słowa inaczej, ale to samo można opisać schematycznie, korzystając z narzędzi wizualizacyjnych. Dlatego potrzebujemy narzędzia, które pozwoli nam tworzyć opis wizualny procesów z uwzględnieniem ich wzajemnych powiązań. W Lean Manufacturing takim narzędziem jest mapa strumienia wartości (czasami określana jako VSM – skrót od Mapa Strumienia Wartości).
Mapa strumienia wartości (VSM)
Mapa strumienia wartości to dość prosty i wizualny diagram graficzny przedstawiający podstawowe wskaźniki oraz powiązania przepływów materiałów i informacji w celu wytworzenia końcowego produktu i/lub usługi. Korzystanie z narzędzia VSM jest kluczowym punktem podczas wdrażania Lean Manufacturing w firmie. Przede wszystkim mapa strumienia wartości pozwala spojrzeć oczami klienta zarówno na cały strumień wartości od drzwi do drzwi, jak i na poszczególne procesy. Pozwala to zidentyfikować obszary problemowe związane z marnotrawstwem: np. działania, które nie tworzą wartości z punktu widzenia klienta; nadmierne zapasy surowców, produkcji w toku i produktów gotowych; strata czasu pracownika; nierówność i przeciążenie strumienia wartości; nieprawidłowo zorganizowany system planowania i organizacji produkcji itp. Czasami przy konstruowaniu map przepływu przeprowadza się konsultacje z konsumentami w celu poznania ich rzeczywistych wymagań i życzeń, tak aby następnie można było uzgodnić zasady organizacji produkcji zgodnie z tymi wymaganiami. Przecież nie można polegać wyłącznie na własnym mniemaniu o potrzebach klienta: wiadomo, że nierzadko firma produkuje więcej produktów, niż faktycznie potrzebuje klient, nadając tym produktom właściwości niecenne z punktu widzenia klienta. potencjalny konsument. Z reguły okazuje się, że klienta interesuje realny czas dodania wartości, który stanowi zaledwie 2-5% całkowitego czasu wytworzenia produktu i/lub usługi.
Przyszły stan strumienia wartości
Należy pamiętać, że sama mapa aktualnego stanu strumienia wartości nie jest celem samym w sobie metodologii VSM, jest narzędziem analizy przepływów, które zapewnia wspólny język do podejmowania decyzji na wszystkich poziomach przedsiębiorstwa i na dalszych poziomach ich wdrażanie. Dlatego po zbudowaniu mapy obecnego stanu w żadnym wypadku nie należy się na tym zatrzymywać. Kolejnym krokiem w pracach mapujących jest ocena stanu rzeczy w kluczowych obszarach przepływu, identyfikacja głównych obszarów problemowych i opracowanie optymalne rozwiązania aby je ulepszyć. Po analizie tworzona jest mapa stanu przyszłego pokazująca możliwości ulepszeń, aby osiągnąć więcej wysoki poziom efektywność przepływu w pewnym momencie w przyszłości. Jednocześnie opracowywany jest szczegółowy plan wdrożenia zmian usprawniających.
Czasami sensowne jest zbudowanie mapy idealnego stanu strumienia wartości, która definiuje wektor stopniowych ulepszeń strumienia. Ta mapa pokazuje stan przepływu, który można osiągnąć dzięki kompleksowemu wdrożeniu Lean.
Tym samym praca z mapami przepływów pozwala zwiększyć efektywność całej firmy i uniknąć typowych błędów w wyborze narzędzi Lean Manufacturing i obszarów ich wykorzystania, które zazwyczaj prowadzą do tworzenia nieefektywnych izolowanych obszarów doskonalenia.
Kulminacyjnym etapem mapowania strumienia wartości jest kompleksowa praca ze wszystkimi przepływami produkcyjnymi i administracyjnymi w firmie, a także analiza interakcji z dostawcami i klientami, co pozwala na uruchomienie i dalszy rozwój zasady ciągłego doskonalenia w całym łańcuchu wartości, zarówno wewnątrz, jak i na zewnątrz firmy, - a to jest niezwykle ważne, bo w warunkach nowoczesny rynek Konkurują już nie indywidualni producenci, ale łańcuchy dostawców i producentów.
Ściągawka do budowania mapy wartości klienta
1. Wybór produktu do budowy mapy (produkt musi być wyprodukowany w momencie mapowania)
2. Przedstawienie obserwatora kierownictwu warsztatu i pracownikom w celu wyjaśnienia celów pracy i nawiązania kontaktów
3. Przygotowanie do mapowania: wydrukuj niezbędne formularze, papier do mapowania, ołówki, stoper itp.
4. Przejdź wzdłuż przepływu od konsumenta produktu (może magazyn wyrobów gotowych lub miejsce montażu), produkcji, warsztatu zaopatrzeniowego do magazynu metali lub magazynu półproduktów
5. Zbuduj „Standaryzowaną Mapę Pracy”, Załącznik nr 1, odzwierciedlającą rzeczywisty ruch części pomiędzy miejscami pracy, zakładem, warsztatem, zakładem (Diagram Spaghetti)
6. Do każdej operacji dokonaj pomiarów i wypełnij formularz „Karta drogowa”, Załącznik nr 2
7. Na podstawie pomiarów wypełnić formularz „Karta czasu pracy”, Załącznik nr 2 (wykaz operacji, średni czas produkcji operacji, używany sprzęt)
8. Wypełnij formularz „Karta czasu pracy”, Załącznik nr 2 dla wszystkich procesów (czas cyklu, czas przetwarzania, czas przerwy itp.)
9. Na kartce papieru ułóż operacje zgodnie z procesem.
10. Określ liczbę półfabrykatów i gotowych części znajdujących się w miejscu pracy i zaznacz je na arkuszu w formie trójkąta i wskaż ilość
11. Umieść ruchy na mapie w formie strzałki i wskaż: odległość, czas i sposób przemieszczania się (dźwig z belką, na wózku itp.)
Czas utrzymywania zapasów określa się poprzez pomnożenie ilości zapasów przez czas cyklu kolejnej operacji.
12. Na dole mapy narysuj oś czasu i zaznacz momenty, w których wartość dodana jest i nie.
- niegenerujące wartości dodanej: ruchy, zapasy, oczekiwania itp.
- dodanie: czasu przetwarzania części
13. W górnej części mapy wskaż przepływ informacji.
14. Wypełnij tabelę na arkuszu „Wskaźniki stanu bieżącego”.
15. Przeanalizuj mapę stanu obecnego, aby określić „wąskie gardło” (miejsce eliminacji strat) i oznacz je gwiazdką
16. Na podstawie analizy zbuduj mapę przyszłego stanu, uwzględniającą cele (zmniejszenie zapasów, zwiększenie wykorzystania sprzętu, zmniejszenie powierzchni, czasu taktu itp.) i uzupełnij „wskaźniki stanu przyszłego”.
17. Zbuduj „diagram spaghetti” przyszłego okresu
18. Koordynuj wersję wstępną z kierownictwem warsztatu i opiekunem projektu
19. Opracuj środki umożliwiające stopniowe przejście od stanu obecnego do przyszłości, określ kamienie milowe wraz z terminami.
20. Oblicz efekt ekonomiczny dla każdego elementu działania
21. Zatwierdź gotowy projekt od kuratora projektu
PRZYKŁAD
Mapa strumienia wartości: czym jest produkt strumieniowy?
Vrungel: Przepraszam, Lom powiedział, że wiesz, jak rozumieć karty?
Fuchs: Och, tyle, ile chcesz. Karty to mój chleb. Tylko nie karty morskie, ale karty do gry.
„Przygody kapitana Vrungla”
Kiedy po raz pierwszy otrzymałem zadanie „zbudowania mapy przepływu”, pomyślałem: łatwiej nie może być. Wiem, jak oznaczać różne szczegóły proces produkcyjny, wiem od czego zacząć i jak kontynuować... Przecież w swoim „poprzednim życiu” rysowałem procesy biznesowe dla standardów korporacyjnych, a tu są różne ikony i pewne warunki. To wszystko.
Zabawne szczegóły zaczęły się, gdy klienci pytali: „Jak szczegółowa powinna być narysowana mapa?” Od tego się zaczęło... Przez ostatnie kilka lat takie proste i złożone problemy Pojawiło się sporo problemów związanych z mapami przepływu...
Ale żeby nie było niespójności, chciałbym zacząć od innego pytania.
Tak naprawdę pierwsza pułapka czeka na Ciebie w momencie, gdy próbujesz określić, który produkt chcesz odzwierciedlić w strumieniu.
Co to jest „produkt”? Zacznijmy od definicji.
Mapowanie strumienia wartości (VSM)
Prosty schemat przedstawiający każdy etap przepływu materiałów i informacji potrzebnych do realizacji zamówienia konsumenckiego. („Ilustrowany słownik Lean Manufacturing” pod red. C. Marchwinskiego i D. Shooka, Alpina Business Books, 2005, s. 51)
Niezbyt jasne. Ale logicznie rzecz biorąc, mapa strumienia wartości przedstawia strumień wartości. Oto definicja przepływu:
Strumień wartości
Wszystkie działania, zarówno tworzące wartość, jak i nietworzące wartości, które przeprowadzają produkt przez wszystkie procesy od opracowania koncepcji do uruchomienia produkcji i od przyjęcia zamówienia do dostawy. Czynności te obejmują przetwarzanie informacji otrzymanych od klienta, a także operacje mające na celu transformację produktu w trakcie jego przekazywania do klienta. („Ilustrowany słownik Lean Manufacturing” pod red. C. Marchwinskiego i D. Shooka, Alpina Business Books, 2005, s. 78)
Tutaj znajduje się już link do produktu. Jednak w glosariuszu nie ma definicji produktu – jest to pojęcie zbyt proste, aby je wstawić do słownika. Jasne jest jednak, że jeśli przepływ obejmuje wszystkie działania od koncepcji do uruchomienia produkcji i od przyjęcia zamówienia do dostawy, to produkt musi być odpowiedni dla użytkownika końcowego – tj. musi mieć rzeczywistą wartość dla tych, którym ją sprzedajemy.
Pomijam definicję wartości, bo inaczej posuniemy się za daleko na bok.
Zatem w przypadku produktów znajdujących się w zwykłej produkcji pierwsze pytania zaczynają się przy konstruowaniu mapy strumienia wartości. Co należy uznać za produkt przepływowy – jeden produkt, grupę produktów, na jakiej zasadzie grupować produkty itd. Właściwie wszystko zaczyna się jeszcze wcześniej – w końcu każdy produkt ma swojego konsumenta, co oznacza możesz grupować tylko produkty, które mają tych samych konsumentów. Ale to znowu dygresja.
Niewiele jest firm, które produkują tylko jeden, dwa lub trzy podobne produkty. Jeśli pracujesz w takiej produkcji, jesteś szczęściarzem. Ale co, jeśli modeli jest kilka tysięcy, a ich produkcja jest częściowo powiązana - jeśli chcesz zrobić jeden „Produkt A”, to musisz jednocześnie wyprodukować trzy „Produkt B”?
Załóżmy, że rysujemy mapę produkcji nagrobków z naturalnego granitu. Bierze się duży blok granitu, piłuje go na kawałki, z niektórych robi się nagrobki, z innych - tylko kamienie krawężnikowe. A te bardzo małe to przyciski do papieru. Przycisk do papieru to nie tylko kawałek granitu, ale także niewielka żeliwna figurka-uchwyt, która jest wykonywana przy użyciu osobnego sprzętu. A szlifowanie przycisków do papieru, nagrobków i płyt chodnikowych odbywa się przy użyciu tego samego sprzętu. Jak w tym przypadku narysować przebieg produkcji nagrobków?
To jeszcze nie jest mapa, to dopiero szkic, ale już pojawiło się wiele pytań.
Idealnym rozwiązaniem jest rozwikłanie plątaniny szlaków, oddzielenie od siebie grup produktów i wypuszczenie poszczególnych produktów osobno – najpierw „Produkt A”, potem w razie potrzeby „Produkt B”. I tyle, ile potrzebujesz, i nie tyle, ile dostaniesz.
Czasami jednak tak idealne rozwiązanie wymaga rewizji koncepcji produkcji, a nawet całkowitej wymiany parku maszynowego. Co robić?
Pamiętajmy, dlaczego potrzebujemy mapy strumienia wartości = Mapy strumienia wartości. Oto dwa główne cele:
1. Spójrz na cały przepływ jako całość (i pozwól menedżerom mówić tym samym językiem o problemach różnych „etapów” przepływu).
2. Zobacz wszystkie straty występujące w przepływie.
Wiemy już, że mamy „plątaninę problemów” związaną z trudnym routingiem i że tę plątaninę należy rozwikłać. Przyda się do tego szczegółowa mapa, ale pierwsze kroki można podjąć i bez niej.
W jaki więc sposób można zrezygnować z „ideału”, aby karta nadal miała wartość?
Precyzyjna definicja „produktu”, a dokładniej „produktu bazowego mapy przepływów”.
Załóżmy, że za „produkt bazowy” przyjmujemy coś nietypowego, czy nawet nie produkt kompletny, ale jakąś jego część, nie przejmując się tym, jak przebiega produkcja reszty tego produktu, aż do momentu ich połączenia.
Czy uda nam się zobaczyć cały przepływ, po którym porusza się ten „nietypowy produkt” lub ta część jakiegoś produktu?
Weźmy na przykład „przycisk do papieru” jako produkt podstawowy. I narysujmy jego trasę. Co się stanie? Czynności związane z obróbką „płyt chodnikowych” wypadną z naszej uwagi. Ale jednocześnie zobaczymy wszystkie opóźnienia związane z etapami oddzielania kawałków przycisków od całkowitej masy granitu, zobaczymy, że przed zmieleniem półprodukty czekają na swoją kolej, a przed połączeniem z figurką-uchwytem partie przycisków do papieru rozdrabnia się na części odpowiadające partiom, z których odlewane są figurki.
Czy będziemy w stanie zobaczyć cały przebieg od początku do końca? Część związana z produkcją przycisków do papieru - tak. Reszta nie. Czy będziemy w stanie odnotować straty – tak, te związane z produkcją przycisków do papieru. Reszta nie. Czy jest jakaś korzyść z tej karty? Jeść. Dlaczego taka karta jest niebezpieczna? Optymalizując część przepływu, ryzykujemy powstanie jeszcze większych strat w skali całego przepływu. Jak zmniejszyć to zagrożenie? Zmierz siedmiokrotnie te zmiany w tym przepływie, które mogą wpłynąć na wszystko, co pozostaje „poza granicami”.
Decydując się na zawsze w pierwszej kolejności mielenie półfabrykatów, wstrzymujemy produkcję „nagrobków” i „płyt chodnikowych”. Takie decyzje należy dokładnie przeanalizować.
Trzeba jednak szukać kompromisu. Czasami, aby być bliżej rzeczywistości, trzeba dość daleko odejść od „akademickich” definicji przepływu czy produktu. Przykładowo, opisując produkcję mebli skrzyniowych, nie udało nam się wyodrębnić przepływu „szafa” czy „szafa”, ponieważ cały tygodniowy wolumen produkcji wycinany jest jednocześnie z tych samych płyt wiórowych laminowanych, a części z różnych kawałków meble są mieszane w celu zredukowania niewykorzystanych resztek płyty wiórowej laminowanej (w zasadzie zgodnie z zadaniem cięcie płyty wiórowej laminowanej jest problemem kombinatorycznym - jak ułożyć części na arkuszach tak, aby zmarnować jak najmniej płyt wiórowych laminowanych i aby jak najmniej resztek płyt poszło na marne). W rezultacie zbudowano mapę przepływu tylko dla jednej z grup części. Nie było ogólnego obrazu przepływu, ale pomiary wskaźników dla wybranej grupy części pozwoliły udokumentować główne problemy przepływowe i ponownie skoncentrować prace na ich rozwiązaniu.
Zdefiniowanie produktu przepływu może być zagadnieniem bardzo trudnym, a zmiana procesu tworzenia produktu może prowadzić do rewizji rozumienia przepływów i co za tym idzie do rewizji grupowania produktów, a co za tym idzie zmiany odpowiedź na pytanie „co jest produktem tego przepływu?”
Głównym zadaniem systemu produkcyjnego jest ciągłe doskonalenie tzw. „strumienia wartości” dla docelowej grupy odbiorców. Opiera się na racjonalnym połączeniu wszystkich procesów. Dzięki temu produkty mogą być wytwarzane przy minimalnych kosztach pracy. Ponadto wpływa to na wskaźniki ekonomiczne, a także wyniki działalności produkcyjnej i ekonomicznej organizacji, w tym koszt produktu, rentowność produkcji, zysk, wysokość kapitału obrotowego i wielkość produkcji w toku.
Jednocześnie dla wielu organizacji najważniejszą kwestią pozostaje efektywność procesów produkcyjnych pod względem złożoności i czasu trwania cyklu produkcyjnego. Im dłuższy, tym więcej jest w to zaangażowanej dodatkowej produkcji i ogólnie mniej wydajna jest produkcja. Ponadto należy włożyć wiele wysiłku w koordynację procesu i zapewnienie jego płynnego działania.
Aby rozwiązać ten problem, wiele firm wprowadza do swojej działalności system odchudzonej produkcji, który pozwala na optymalizację procesu produkcyjnego, poprawę jakości wytwarzanego produktu i redukcję kosztów. Ten artykuł jest mu poświęcony.
Czym jest odchudzona produkcja?
Lean Manufacturing (w języku angielskim ma dwie nazwy: „lean Manufacturing” i „lean Production”) to specjalne podejście do zarządzania przedsiębiorstwem, które pozwala na poprawę jakości pracy poprzez redukcję strat. Straty oznaczają wszystko, co zmniejsza efektywność pracy. Do głównych rodzajów strat zalicza się:
- Przemieszczenia (niepotrzebne przemieszczenia sprzętu i operatorów prowadzące do wydłużenia czasu i kosztów)
- Transport (niepotrzebne przemieszczanie prowadzące do opóźnień, uszkodzeń itp.)
- Technologia (wady technologiczne, które nie pozwalają na realizację wszystkich wymagań konsumentów w produkcie)
- Nadprodukcja (niesprzedane produkty wymagające dodatkowych kosztów księgowości, przechowywania itp.)
- Oczekiwanie (niedokończone produkty czekające w kolejce do przetworzenia i rosnące koszty)
- Wady (wszelkie wady powodujące dodatkowe koszty)
- Zapasy (nadwyżka wyrobów gotowych zwiększająca koszty)
System Lean Manufacturing można wdrożyć na etapie projektowania, w samej produkcji, a nawet w procesie sprzedaży produktu.
System ten powstał na przełomie lat 80. i 90. XX wieku Inżynierowie japońscy Taiichi Ono i Shigeo Shingo (ogólnie jego początki pojawiły się w połowie XX wieku, ale adaptacja nastąpiła dopiero pod jego koniec). Celem inżynierów było ograniczenie czynności nie dodających wartości w całym cyklu życia produktu. Zatem system to nie tylko technologia, ale cała koncepcja zarządzania z maksymalnym zorientowaniem rynkowym produkcji i zainteresowanych udziałem całego personelu firmy.
Doświadczenie zdobyte przy wdrażaniu systemu (czasami jego poszczególnych elementów) do pracy różnych organizacji pokazało jego skuteczność i perspektywę, i jest obecnie wykorzystywane w różnych branżach. Jeśli początkowo system był używany tylko w fabrykach samochodów „Toyota”, „Honda” itp. (i nosił nazwę Toyota Production System), dziś można go znaleźć w wielu innych obszarach:
- Medycyna
- Handel
- Logistyka
- Usługi bankowe
- Edukacja
- Produkcja oleju
- Budowa
- Technologia informacyjna
Niezależnie od obszaru, w którym stosuje się system odchudzonej produkcji, może on znacząco poprawić efektywność pracy i znacznie ograniczyć straty, choć wymaga pewnego dostosowania do konkretnego przedsiębiorstwa. W tym filmie opisujemy jak może zmienić się praca organizacji dzięki zastosowaniu technologii Lean.
Nawiasem mówiąc, przedsiębiorstwa, które wdrażają w swojej działalności system odchudzonej produkcji, często nazywane są „szczupłymi”. Różnią się od innych przedsiębiorstw kilkoma ważnymi cechami.
Po pierwsze, podstawą produkcji tych przedsiębiorstw są ludzie. Pełnią rolę siły twórczej w procesie produkcyjnym. Sprzęt i technologia z kolei są jedynie środkiem do osiągnięcia celu. Głównym przesłaniem jest to, że żadna technologia, strategia ani teoria nie mogą sprawić, że firma odniesie sukces, do której nie doprowadzi wysokie wyniki Tylko ludzie z ich potencjałem twórczym i intelektualnym mogą to zrobić.
Po drugie, systemy produkcyjne tych przedsiębiorstw skupiają się na jak największej eliminacji odpadów i ciągłym doskonaleniu procesów produkcyjnych. Ciekawostką jest to, że w codziennych działaniach dbających o to biorą udział wszyscy pracownicy organizacji, od zwykłych pracowników po kadrę kierowniczą wyższego szczebla.
I po trzecie, wszystkie decyzje podejmowane przez kierownictwo tych przedsiębiorstw koniecznie uwzględniają perspektywy dalszego rozwoju, a bieżące interesy materialne nie mają decydującego znaczenia. Menedżerowie organizacji wyłączają ze swoich działań administracyjno-dowódczych, nieuzasadnioną ścisłą kontrolę i ocenę pracowników najbardziej złożone systemy różne wskaźniki. Funkcje zarządzania umożliwiające odpowiednią organizację procesu produkcyjnego, szybkie wykrywanie, rozwiązywanie i zapobieganie problemom. Umiejętność rozpoznawania i rozwiązywania problemów w miejscu pracy jest wysoko ceniona u każdego pracownika.
Jednak wdrożenie Lean Manufacturing wymaga obowiązkowego zrozumienia podstawowych zasad tego systemu i umiejętności pracy z jego narzędziami. Najpierw porozmawiajmy krótko o zasadach.
Zasady odchudzonej produkcji
Pomimo tego, że praktyczne wdrożenie zasad Lean Manufacturing wymaga od przedsiębiorstwa dość poważnych wysiłków, same w sobie są dość proste. W sumie jest ich pięć i można je sformułować w następujący sposób:
- Określ, co tworzy wartość produktu z punktu widzenia konsumenta. W przedsiębiorstwie można prowadzić różnorodne działania i nie wszystkie z nich są istotne dla konsumenta. Tylko wtedy, gdy firma dokładnie wie, czego potrzebuje klient końcowy, jest w stanie określić, które procesy mogą zapewnić mu wartość, a które nie.
- Określ, które działania są absolutnie niezbędne w łańcuchu produkcyjnym, a następnie wyeliminuj marnotrawstwo. Aby zoptymalizować działania i zidentyfikować marnotrawstwo, konieczne jest szczegółowe opisanie każdego działania od momentu złożenia zamówienia do momentu dostarczenia produktu konsumentowi. Dzięki temu możliwe jest określenie, w jaki sposób można usprawnić procesy produkcyjne.
- Zreorganizuj działania w łańcuchu produkcyjnym tak, aby stały się całościowym przepływem pracy. Proces produkcyjny musi być tak skonstruowany, aby wyeliminować wszelkie straty (przestoje, oczekiwanie itp.) pomiędzy operacjami. Może to wymagać nowych technologii lub przeprojektowania procesów. Należy pamiętać, że każdy proces powinien obejmować jedynie te czynności, które dodają wartość do produktu końcowego, ale nie zwiększają jego kosztu.
- Działaj w oparciu o interes konsumenta. Pożądane jest, aby przedsiębiorstwo wytwarzało tylko taki produkt i w takiej ilości, jakiej potrzebuje konsument końcowy. Pozwala to uniknąć niepotrzebnych działań, niepotrzebnych strat i kosztów.
- Staraj się doskonalić, stale ograniczając niepotrzebne czynności. Konieczne jest zastosowanie i wdrożenie systemu Lean Production więcej niż raz. Maksymalny efekt będzie można osiągnąć jedynie wtedy, gdy poszukiwanie strat i ich eliminowanie będą prowadzone regularnie i systematycznie.
Na tych pięciu zasadach należy polegać przy wdrażaniu systemu Lean Manufacturing i dotyczy to każdego obszaru działalności, od projektowania i zarządzania projektami po samą produkcję i zarządzanie. Zwiększ produktywność pracy, znajdź i zmniejsz straty, zoptymalizuj produkcję itp. Narzędzia systemu Lean pomagają.
Narzędzia odchudzonej produkcji
Poniżej przyjrzymy się głównym narzędziom Lean Manufacturing:
- Standaryzacja pracy. Stanowią przejrzysty i maksymalnie zwizualizowany algorytm wykonywania dowolnej konkretnej pracy. Algorytm ten obejmuje różne standardy, na przykład standardy dotyczące czasu trwania cyklu produkcyjnego, standardy dotyczące sekwencji działań w jednym cyklu, standardy dotyczące ilości materiałów do pracy itp.
- SMED (jednominutowa wymiana matrycy). Jest to specjalna technologia umożliwiająca szybką wymianę sprzętu. Do przezbrojenia stosuje się z reguły dwie kategorie operacji. Pierwszą z nich są operacje zewnętrzne, które można przeprowadzić bez zatrzymywania sprzętu (obejmuje to przygotowanie materiałów i narzędzi itp.). Drugi to operacje wewnętrzne i do ich wykonania należy zatrzymać sprzęt. Istotą SMED jest to maksymalna ilość operacje wewnętrzne przekładają się na zewnętrzne. Osiąga się to poprzez innowacje organizacyjne i technologiczne.
- Produkcja ciągniona. Podejście do organizacji przepływu produkcji eliminujące straty związane z oczekiwaniem (do zakończenia poprzedniego etapu pracy) i nadprodukcją. Tutaj każda operacja proces technologiczny jakby „wyciągał” potrzebną ilość produktu z poprzedniej operacji i przenosił ją do kolejnej. Pozwala to uniknąć zarówno nadwyżek, jak i niedoborów produktów.
- System składania i opiniowania wniosków. Zgodnie z nią każdy pracownik może zgłaszać swoje pomysły na usprawnienie procesu pracy. Wszystkim pracownikom zapewniamy przejrzysty mechanizm realizacji swoich propozycji. W systemie znajdują się także metody zachęcania pracowników do zgłaszania swoich pomysłów.
- Metoda Przełomu w Przepływie. Służy do wygładzenia i poprawy wydajności przepływu produkcji. W tym celu tworzone są stałe cykle produkcyjne, w każdym z których wprowadzane są zasady pracy standaryzowanej.
- TPM (Całkowite Utrzymanie Produktywności). System usługa powszechna sprzęt. Podczas jego użytkowania eksploatacja sprzętu łączy się z jego stałą konserwacją. O taki stały monitoring i utrzymanie sprzętu w dobrym stanie dbają wykwalifikowani pracownicy. TPM pomaga ograniczyć straty związane z naprawami, przestojami i awariami oraz zapewnia maksymalną wydajność przez cały cykl życia sprzętu. Kolejną korzyścią jest to, że personel konserwacyjny może skupić się na innych zadaniach.
- System 5S– technika zarządzania, pozwalając na efektywną organizację przestrzeni pracy. Pod skrótem kryją się następujące pojęcia:
- o Usystematyzowanie (wszystkie pozycje znajdują się w konkretnym miejscu, do którego jest łatwy dostęp)
- o Utrzymanie porządku i czystości
- o Sortowanie (dokumentacja i/lub przedmioty umieszczane są w miejscu pracy w oparciu o częstotliwość ich używania; obejmuje to również eliminację wszystkiego, co nie jest już potrzebne)
- o Standaryzacja (miejsca pracy zorganizowane są według tej samej zasady)
- o Doskonalenie (ustalone standardy i zasady są stale udoskonalane)
Inne narzędzia Lean Manufacturing obejmują:
- (podejście do zarządzania przedsiębiorstwem oparte na ciągłym doskonaleniu jakości)
- „” (podejście do zarządzania produkcją w oparciu o zapotrzebowanie konsumentów)
- Kanban (system zarządzania projektami oraz system zarządzania towarami i materiałami wewnątrz i na zewnątrz firmy)
- Andon (system wizualnego sprzężenia zwrotnego w produkcji)
- Narzędzia zarządzania jakością (diagram PDPC, macierz priorytetów, diagram sieci, diagram macierzowy, diagram drzewa, diagram połączeń, diagram powinowactwa itp.)
- Narzędzia kontroli jakości (karty kontrolne, arkusz kontrolny, wykres punktowy, wykres Pareto, stratyfikacja, histogram itp.)
- Narzędzia do analizy i projektowania jakości (metoda „5 Why”, metoda „Quality House”, analiza FMEA itp.)
W tej części należy osobno omówić metodę stosowaną do modelowania i zapobiegania błędom w procesach produkcyjnych oraz ograniczania strat związanych z defektami. To jest metoda Poka-yoke.
Metoda Poka-yoke polega na znajdowaniu przyczyn błędów oraz opracowywaniu technologii i metod eliminujących możliwość ich wystąpienia. Opiera się na założeniu, że jeśli nie da się wykonać pracy w inny sposób niż właściwy, ale sama praca została wykonana, to jest ona wykonana prawidłowo, tj. bez błędów.
Błędy mogą pojawiać się z różnych powodów: nieostrożności, nieuwagi, nieporozumień, ludzkiego zapomnienia itp. Biorąc pod uwagę czynnik ludzki, wszystkie te błędy są naturalne i nieuniknione i aby znaleźć sposób na ich uniknięcie, należy na nie spojrzeć pod tym kątem.
Składniki metody Poka-yoke:
- Stworzono warunki do bezbłędnej pracy
- Wprowadzane są bezbłędne metody działania
- Występujące błędy są na bieżąco eliminowane
- Podjęto środki ostrożności
- Wprowadzane są proste systemy techniczne, które pozwalają pracownikom uniknąć błędów
Metoda ta stosowana w połączeniu z innymi narzędziami systemu Lean Manufacturing zapewnia, że gotowy produkt nie będzie miał wad, a proces produkcyjny będzie przebiegał sprawnie.
Wszystkie te narzędzia stosowane łącznie wpływają na efektywność pracy, eliminują różnego rodzaju straty, minimalizują prawdopodobieństwo wystąpienia sytuacji awaryjnych i przyczyniają się do tworzenia sprzyjającej atmosfery w miejscu pracy. Dodatkowo wspólne wykorzystanie tych narzędzi pozwala na ich wzajemne wzmacnianie i uelastycznienie samego podejścia Lean.
Wszystko to jest głównym powodem, dla którego wiele organizacji za granicą i w Rosji wprowadza do swojej działalności system odchudzonej produkcji. A teraz czas porozmawiać o prawdziwych przykładach.
Niska wydajność
Zdaniem twórców systemu Lean Production, jego wdrożenie może mieć istotny wpływ na wiele procesów biznesowych. Dokładniej:
- Czas cyklu produkcyjnego można skrócić 10-100 razy
- Liczba usterek może zostać zmniejszona od 5 do 50 razy
- Przestoje można skrócić 5-20 razy
- Wydajność może wzrosnąć 3-10 razy
- Zapasy magazynowe mogą zostać zmniejszone 2-5 razy
- Dostawy mogą zostać przyspieszone 2-5 razy Nowe Produkty Na rynek
Według holdingu medialnego Expert, odchudzoną produkcję zaczęto wprowadzać w Rosji dopiero w 2004 roku. A do roku 2007 (w ciągu zaledwie trzech lat praktyki) system wykazał imponujące wyniki. Jest na to więcej niż jeden przykład:
- Koszty zostały obniżone o 30% w obszarach produkcji oleju, produkcji instrumentów i montażu komponentów samochodowych
- Przestrzeń produkcyjna w zakresie budowy instrumentów została zwolniona o 30%
- Produkcja w toku przy wydobyciu ropy naftowej spadła o 50%
- Cykl produkcyjny w obszarach produkcji przyrządów i przemysłu lotniczego został skrócony o 60%
- Wydajność urządzeń w dziedzinie metalurgii metali nieżelaznych wzrosła o 45%
- Zasoby pracy w obszarze wydobycia ropy naftowej zostały zwolnione o 25%
- W przemyśle żelaza i stali czasy przezbrajania skrócono o 70%.
Według tego samego holdingu medialnego „Ekspert” do 2017 roku praktyka stosowania odchudzonej produkcji w Rosji i za granicą przyniosła następujące rezultaty:
- Powierzchnia produkcyjna w branży elektronicznej została zwolniona o 25%
- Produkcja w przemyśle lotniczym przyspieszyła 4-krotnie
- W obszarze metalurgii metali nieżelaznych produktywność wzrosła o 35%.
- Odpady w przemyśle farmaceutycznym zostały zmniejszone 5-krotnie
- Produkcja wzrosła o 55%, cykl produkcyjny został skrócony o 25%, a zapasy w produkcji dóbr konsumpcyjnych zmniejszyły się o 35%.
- Powierzchnia produkcyjna w branży motoryzacyjnej została zwolniona o 20%
Jeśli chodzi szczególnie o firmy rosyjskie, technologie Lean są obecnie wykorzystywane w ich pracy przez UC Rusal, LLC Expert Volga, EPO Signal, OJSC Khlebprom VSMPO-AVISMA, PJSC KamAZ, LLC Oriflame Cosmetics, LLC „TechnoNIKOL”, PG „Group Gas”, LLC „EuroChem” i dziesiątki innych największych organizacji.
Jednak na rynku rosyjskim eksperci zauważają obecnie niedobór specjalistów zdolnych do optymalizacji procesów produkcyjnych poprzez wdrożenie odchudzonego systemu produkcyjnego. (Nawiasem mówiąc, ci, którzy dziś opanują podejście Lean, prawdopodobnie będą mieli stabilną pracę, kariera, perspektywy i bezpieczną przyszłość.)
wnioski
Lean Manufacturing pomaga firmom, bez uciekania się do dużych inwestycji i wykorzystując głównie wewnętrzne rezerwy, osiągnąć wymierny wzrost wydajności pracy. Ale system Lean to specjalne podejście do produkcji i wszystkich jej elementów, oferujące nie tylko zwiększenie wydajności pracy i usprawnienie produkcji, ale także stworzenie korzystne warunki stworzyć kulturę korporacyjną, w której każdy pracownik uczestniczy w osiąganiu sukcesu firmy.
Myśląc szerzej, system Lean Manufacturing jest paradygmatem produkcyjnym służącym wdrażaniu innowacyjnych metod zarządzania przedsiębiorstwem, zwiększaniu efektywności produkcji, rozwoju personelu i eliminacji wszelkiego rodzaju marnotrawstwa. A dziś prawie każda firma może wdrożyć na swojej bazie system Lean.
Autonomia— wprowadzenie ludzkiej inteligencji do maszyn, które potrafią samodzielnie wykryć pierwszą usterkę, a następnie natychmiast zatrzymać się i zasygnalizować potrzebę pomocy. To podejście nazywane jest także jidoką.
Analiza strumienie (CPSC) to narzędzie systemu produkcyjnego (lean Manufacturing), którego zadaniem jest opisanie strumieni wartości poprzez mapowanie PSC, w celu oceny strat i opracowania planów działań mających na celu ich eliminację.
Analiza zwrotów— analiza realizacji operacji produkcyjnych w celu ustalenia liczby powrotów do poprzedniego etapu w celu korekty lub unieszkodliwienia.
Andona— narzędzie do wizualnego monitorowania procesu produkcyjnego.
Rewizja(z łac. „słuchanie, słuchanie”) - proces oceny aktualnej sytuacji pod kątem zgodności ze standardami, światowego poziomu organizacji produkcji. Audyt określa także: docelowe wyniki, potencjalne możliwości, aktualne możliwości i pomoc w opracowaniu planu zmian.
Zapas buforowy- zobacz akcje.
Kontrola wizualna- takie rozmieszczenie narzędzi, części, pojemników i innych wskaźników stanu produkcji, w którym każdy na pierwszy rzut oka może zrozumieć stan systemu - normalny lub odchylenie (anomalia).
Kontrola wizualna(kontrola wizualna) - ocena jakości wykonania wyrobów metodą kontrolną lub dotykową.
Czas kolejki(czas kolejki) - czas, w którym produkt stoi w kolejce w oczekiwaniu na kolejny etap produkcji lub projektowania, przetworzenie dokumentu (zamówienie) lub rozmowę telefoniczną.
Czas realizacji(czas realizacji) – czas od momentu złożenia zamówienia do momentu jego skompletowania i przekazania konsumentowi.
Inne wskaźniki czasu wpływające Czas realizacji:
Poświęć czas(takt time) – odstęp czasu lub częstotliwość, z jaką konsument otrzymuje od konsumenta zamówione produkty. Czas taktu określa prędkość produkcji, która musi dokładnie odpowiadać istniejącemu zapotrzebowaniu.
Czas cyklu(czas cyklu) - czas potrzebny operatorowi na wykonanie wszystkich czynności przed ich ponownym powtórzeniem. Kiedy czas cyklu każdej operacji w procesie staje się dokładnie równy czasowi taktu, następuje przepływ jednoczęściowy.
Czas stworzyć wartość- czas operacji lub działań, w wyniku których produkt lub usługa otrzymuje właściwości, za które klient jest skłonny zapłacić.
Czas cyklu produkcyjnego— czas, jakiego potrzebuje produkt, materiał lub przedmiot obrabiany, aby przejść przez proces lub strumień wartości od początku do końca.
Całkowita usługa produkcyjna(Total Productive Maintenance, TRM) to zbiór ideologii, metod i narzędzi mających na celu utrzymanie stałej wydajności urządzeń w celu zapewnienia ciągłości procesów produkcyjnych.
Ciągnąć(pull) – system produkcyjny, w którym dostawca wyższego szczebla (lub dostawca wewnętrzny) nie robi nic, dopóki dalszy konsument (lub klient wewnętrzny) nie powie mu, aby to zrobił. Odwrotna sytuacja nazywa się pchaniem. Zobacz także kanban.
Wyrównanie produkcji(Poziomowanie) patrz Heijunka to narzędzie mające na celu wygładzenie szczytów i spadków załadunku oraz uniknięcie nadprodukcji. Ściśle powiązany z sekwencją startów i równoważeniem linii.
Popychanie(Push) - system wydawania produktów i „przepychania” ich do kolejnej operacji, bez uwzględnienia potrzeb konsumenta. Przeciwieństwo ciągnięcia.
Gemba- przetłumaczone z japońskiego - „moja twarz”. W terminologii Lean – przedsiębiorstwo, warsztat, zakład, miejsce, w którym wytwarzany jest produkt materialny (gdzie bezpośrednio tworzona jest wartość dla konsumenta) itp. oraz biuro, w którym świadczone są usługi lub prowadzone są inwestycje.
Jidoka(jidoka) - patrz autonomizacja.
Schemat spaghetti(wykres spaghetti) – trajektoria, którą opisuje produkt (operator) poruszając się wzdłuż strumienia wartości. Nazwa powstała, ponieważ ta trajektoria jest całkowicie chaotyczna i wygląda jak talerz spaghetti.
Mapa drogowa(mapa drogowa) - planu krok po kroku działania zmierzające do osiągnięcia określonego celu lub rozwiązania bieżącego problemu.
Proces nadawania tempa(racemakerprocess) – dowolny proces w strumieniu tworzenia wartości, który wyznacza rytm całego przepływu. Zazwyczaj umiejscowiony bliżej „końca klienta” strumienia wartości. Przykład: linia montażu produktu końcowego.
Rezerwy— nagromadzenie materiałów oczekujących na obróbkę lub przemieszczanie się pomiędzy procesami (etapami) przepływu. Zapasy z natury klasyfikuje się ze względu na ich lokalizację w strumieniu wartości oraz według cel funkcjonalny. Zapasy według lokalizacji: surowce, dostawy, produkcja w toku, wyroby gotowe. Surowce, materiały - wartości materialne, zlokalizowane w przedsiębiorstwie (w procesach) i niepoddawane przetwarzaniu.
Niedokończona produkcja(WIP) - aktywa materialne zlokalizowane pomiędzy etapami i w procesach przetwarzania (wartość dodana).
Zapasy według przeznaczenia: buforowe, ubezpieczeniowe, do wysyłki.
Zapas buforowy- zaprojektowane tak, aby w sposób ciągły zabezpieczać proces produkcyjny na wypadek nieplanowanego wzrostu zapotrzebowania na te części. Wielkość zapasów wyliczana jest na podstawie analizy statystyk odchyleń (maksymalnych przestojów obszarów produkcyjnych) na skutek nieplanowanego wzrostu zapotrzebowania na części.
Akcje ubezpieczeniowe— mające na celu ciągłe zapewnienie postępu procesu produkcyjnego w przypadku nieprzewidzianych okoliczności: awaria sprzętu, dostawa wadliwych produktów, opóźnienia dostaw na trasie itp. Wolumen wyliczany jest na podstawie analizy maksymalnego czasu przestoju Klienta (zwykle 3 miesiące) spowodowanego niedostarczeniem części przez dostawcę lub wadliwą wysłaną partią.
Zapasy wysyłkowe- produkty znajdujące się na końcu linii produkcyjnej i przygotowane do wysyłki do konsumenta.
Koszty oparte na działaniach; koszt oparty na działaniu Rachunek kosztów działań (ABC) to system rachunkowości zarządczej, który wiąże koszty produktu w oparciu o ilość wykorzystanych zasobów (w tym powierzchni produkcyjnej, surowców, maszyn, mechanizmów, robocizny) wydanych na projektowanie, zamawianie i wytwarzanie tego produktu. W odróżnieniu od standardowego systemu kalkulacji kosztów.
Kaizen(kaizen) - ciągłe doskonalenie działań w celu zwiększenia wartości dla konsumenta i ograniczenia marnotrawstwa (muda).
Kaikaku(kaikaku) - radykalne (kardynalne) usprawnienie procesu mającego na celu osiągnięcie celu lub wyeliminowanie strat (muda).
Kanban(kanban) - przetłumaczone z japońskiego - karta lub ikona. Narzędzie systemu pull, które instruuje produkcję lub usuwanie (przenoszenie) elementów z jednego procesu do drugiego. Można używać - tagów, kart, pojemników, e-maili. Używany w Systemie Produkcyjnym Toyoty do organizowania ściągania poprzez informowanie poprzedniego etapu produkcji o rozpoczęciu pracy.
Mapowanie wartości strumienia(KPSTS) (mapowanie strumienia wartości) to proces badania i wizualnego przedstawiania przepływów materiałów i towarzyszących im informacji w trakcie tworzenia wartości, gdy materiały przechodzą przez procesy od dostawcy do konsumenta. Składa się z etapów: 1. Wybór strumienia. 2. Opis aktualnego stanu przepływu. 3. Opis przyszłego stanu przepływu. 4. Opracowanie planu (mapy drogowej) osiągnięcia przyszłego stanu przepływu.
Trasa pierścieniowa(mleko run) – system dostarczania części (np. do naprawy), w którym ciężarówka jadąc stale tą samą trasą może zatrzymać się w określonych miejscach i dostarczyć potrzebną część.
Czerwone etykiety— narzędzie do wizualizacji problemów i anomalii w gembie (biurze), stosowane w formie kart, na których można wskazać: numer problemu w kolejności (z listy problemów); data instalacji etykiety; PEŁNE IMIĘ I NAZWISKO. kto zidentyfikował problem lub inne informacje.
Obsługa wielu maszyn(praca wielomaszynowa) – praca, w której jeden operator steruje jednocześnie kilkoma maszynami różnego typu, a także prowadzi szkolenia i konserwację sprzętu.
Pomnik(pomnik) – dowolny obiekt (maszyna) lub proces, którego skala (wielkość) jest taka, że napływające części, projekty lub zamówienia zmuszone są czekać w kolejce do realizacji.M. zazwyczaj obsługuje więcej niż jeden strumień wartości i działa w dużych partiach, z długimi czasami realizacji i powolnymi zmianami.
Muda(muda) lub marnotrawstwo to każda działalność, która zużywa zasoby, ale nie tworzy wartości. Istnieje siedem głównych rodzajów strat: nadprodukcja materiałów lub informacji (kiedy nie pojawił się jeszcze na nie popyt); oczekiwanie na kolejny etap produkcji; niepotrzebnego transportu materiałów lub informacji; niepotrzebne etapy przetwarzania (wymagane ze względu na braki sprzętowe lub niedoskonałości procesu); dostępność wszelkich rezerw, z wyjątkiem wymaganego minimum; niepotrzebne przemieszczanie się osób podczas pracy (na przykład w poszukiwaniu części, narzędzi, dokumentów, pomocy itp.); powstawanie defektów Utrata potencjału twórczego personelu to ósmy rodzaj straty, który jest najtrudniejszy do oszacowania, ale ma kluczowe znaczenie w budowaniu systemu ciągłego doskonalenia wydajności.
Moore'a(mura) "nierówność" - zmienność metod pracy lub wyników procesu.
Muri(muri) „nadmiar” - stres, przepracowanie (nadgodziny) osoby lub sprzętu, nierozsądność.
Ciągły przepływ - organizowanie pracy przepływu materiałów według zasady - „jeden po drugim” lub „z ręki do ręki” bez przystanków i przerw.
Posłuchaj(z japońskiego pokoju lub lokalu) to narzędzie do zarządzania projektami, które promuje skuteczną i szybką komunikację i jest aktywnie wykorzystywane na etapie rozwoju. Działa na zasadzie „dowództwa wojskowego”.
Operacja(operacja) - czynność (lub czynności) wykonywana przez jedną maszynę na jednym produkcie, a nie proces.
Praca wsadowo-kolejkowa (wsadowo-kolejkowa)- praktyka produkcji masowej. Polega na wyprodukowaniu dużych partii części, które następnie ustawiane są w kolejce do kolejnej operacji w procesie produkcyjnym. W przeciwieństwie do przepływu pojedynczych produktów.
Zmiana(przezbrojenie) - montaż nowego typu narzędzia na maszynie do obróbki metalu, wymiana farby w farbiarce, napełnienie nowej porcji tworzywa i wymiana formy na wtryskarce, montaż nowej na komputerze oprogramowanie i tak dalej. Termin ten stosuje się zawsze, gdy konieczne jest przygotowanie sprzętu do produkcji innego rodzaju produktu (wykonywania innej pracy).
SMED(SMED - Single Minute Exchange of Dies) to szybka (w czasie krótszym niż dziesięć minut) procedura wymiany form lub innego sprzętu lub narzędzi w celu rekonfiguracji urządzeń produkcyjnych.
System planowania zapotrzebowania materiałowego (Planowanie zapotrzebowania materiałowego, MRP)- Skomputeryzowany system służący do określenia ilości materiałów i tego, kiedy będą one potrzebne w produkcji. System MRP wykorzystuje: główny harmonogram produkcji, zamówienie materiałowe zawierające listę wszystkiego, co jest potrzebne do wytworzenia każdego produktu, informacje o aktualnym stanie zapasów tych materiałów w celu zaplanowania produkcji i dostawy każdego z nich. System planowania zasobów produkcyjnych (MRP II) uzupełnia MRP, umożliwiając planowanie zdolności produkcyjnych sprzętu, optymalizację przepływów finansowych oraz modelowanie i ocenę różne opcje plany produkcyjne. System MRP jest systemem typu push-out.
Poka Yoke- „ochrona przed niezamierzonym użyciem” - specjalne urządzenie lub metoda, dzięki której defekt po prostu nie może powstać. Inną nazwą poka-yoke jest baka-yoke – „odporny na głupców” lub „odporny na głupców”.
Przepływ(przepływ) - przepływ materiałów i informacji w procesie ich przekształcania w produkt lub usługę dla konsumenta. Tam, gdzie jest produkt (usługa) dla konsumenta, tam jest przepływ. Każde działanie można przekształcić w przepływ.
Przepływ jednostkowy jednolity przepływ — metoda działania, w której maszyna lub proces (taki jak projektowanie, przyjmowanie zamówień lub produkcja) przetwarza nie więcej niż jeden produkt na raz. W przeciwieństwie do metody wsadowej i kolejkowej.
Strumień wartości(strumień wartości) - Wszystkie działania, które są obecnie niezbędne do przekształcenia surowców i informacji w gotowy produkt lub usługę. „Właściwa” maszyna(narzędzie o odpowiedniej wielkości) - obiekt (narzędzie do projektowania, planowania lub produkcji), który łatwo wpasowuje się w przepływ produkcji w ramach jednej rodziny produktów, eliminując w ten sposób odpady powstałe w wyniku niepotrzebnego transportu lub oczekiwania. Inaczej niż pomnik.
Linia produkcyjna- to jest kolekcja (produktów lub produktów) kot. w obrębie wybranych granic przepływu przebiega ta sama ścieżka i sekwencja procesów. Zestaw ten składa się z produktów, które mają podobne cechy, a także parametry (czas cyklu), aby mogły zostać poddane podobnym procesom.
Proces(proces) - ciąg pojedynczych operacji (działań), w wyniku których powstaje projekt, składane jest zamówienie lub wytwarzany jest produkt.
Wioski procesowe(wioski procesowe) – miejsca, w których grupuje się urządzenia tego samego typu lub przeprowadzane są podobne procesy, np. gdzie Szlifierki lub zamówienie jest przetwarzane. W przeciwieństwie do komórek.
Pięć „dlaczego”.(pięć „dlaczego”) – sposób podejścia Taiichi Ohno do poszukiwania przyczyny każdego problemu, który polegał na tym, że aby znaleźć pierwotną przyczynę problemu (pierwotną przyczynę), należy zadać pytanie „dlaczego” co najmniej pięć razy. Dopiero potem możemy zacząć opracowywać i wdrażać działania naprawcze.
Pięć S(Pięć Ss) - system efektywna organizacja miejsce pracy (przestrzeń pracy), oparte na kontroli wzrokowej. Zawiera pięć zasad, z których każda zaczyna się na literę „S” w języku japońskim. Seiri: osobno niezbędne narzędzia, części i dokumenty od niepotrzebnych, aby te ostatnie odłożyć (usunąć). Seyton: rozmieszczaj (i oznaczaj) części i narzędzia w miejscu pracy tak, aby łatwo było z nimi pracować. Seiso: Utrzymuj czyste środowisko pracy, przede wszystkim w celu jak najwcześniejszego identyfikowania i rozwiązywania problemów. Seiketsu: Regularnie (np. codziennie) wykonuj seiri, seiton i seiso, aby utrzymać Miejsce pracy w świetnym stanie. Shitsuke: Niech robienie pierwszych czterech C stanie się nawykiem, standardem pracy.
wdrożenie polityki- patrz hoshin kanri.
Produkcja wygładzająca(wygładzanie produkcji) - patrz heijunka.
Wygładzanie sprzedaży(sprzedaż pozioma) to system długotrwałych relacji z konsumentem, mający na celu uzyskanie od niego informacji o przyszłych zakupach, co pozwala na lepsze planowanie produkcji i tym samym pozbycie się nieoczekiwanych „skoków” sprzedaży.
Produkt rodzinny(rodzina produktów) - zbiór produktów, które mogą być wydawane jeden po drugim w komórce produkcyjnej. Mówi się, że produkty z tej samej rodziny powstają na „tej samej platformie”.
Sensei(sensei) - nauczyciel, mistrz w określonej dziedzinie (w tym przypadku w dziedzinie Lean Manufacturing).
Doskonałość(doskonałość) - całkowity brak marnotrawstwa (muda), dzięki czemu wszelkiego rodzaju działania w strumieniu wartości faktycznie tworzą wartość.
Kosztorys standardowy(koszt standardowy) - system rachunku kosztów, w którym koszty są odpisywane na produkt na podstawie liczby godzin pracy maszyny i roboczogodzin przepracowanych przez całą produkcję w określonym przedziale czasu. Standard kosztowy zachęca menedżerów do wytwarzania niepotrzebnych produktów lub niewłaściwego zestawu produktów, dzięki czemu dzięki temu pełne wykorzystanie maszyny i pracownicy, aby zminimalizować koszty jednostkowe produktu.
Standard(Standard). W przeciwieństwie do tradycyjnych podejść w koncepcji Lins. - Ten Najlepszym sposobem wykonywanie jakiejkolwiek czynności przy użyciu technik najskuteczniejszych pod względem ograniczenia strat, łatwości wykonania i szybkości pracy. Techniki te zostały wcześniej przetestowane w praktyce, jasno zaprezentowane w prostej i zrozumiałej formie za pomocą narzędzi wizualizacyjnych oraz przekazane poprzez szkolenia wszystkim pracownikom wykonującym tę czynność. W potocznym znaczeniu standard (z angielskiego standardu - norma, próbka) to próbka, standard, model (niekoniecznie najbardziej optymalny), traktowany jako wyjściowy do porównania z innymi podobnymi obiektami i nie zawsze najlepszy.
Normalizacja to system zarządzania produkcją, w którym uczestniczy cały personel i wykorzystuje zbiór zasad, działań i procedur mających na celu identyfikację i eliminację strat oraz stworzenie systemu ciągłego doskonalenia działalności operacyjnej przedsiębiorstwa. W zwykłym znaczeniu, s. to proces opisywania i formalizowania procedur i procesów w działalności przedsiębiorstwa.
Standaryzacja pracy(praca standardowa) to narzędzie służące do analizy i zrozumienia strat podczas operacji (procesu). To dokładny opis każdej akcji, uwzględniający czas cyklu, czas taktu, kolejność wykonywania poszczególnych elementów, minimalna ilość materiały potrzebne do dokończenia pracy.
Standardowe Karty Transakcyjne, SOC(SOP, Standardowe Procedury Operacyjne) – dokumenty opisujące kroki procedury, których należy przestrzegać. Zwykle składa się z tekstu, grafiki/rysunków i fotografii ułatwiających zrozumienie procedury.
Statystyczna kontrola procesu(SPC, Statistical Process Control) - wykorzystanie narzędzi statystycznych pomagających zarządzać jakością operacji.
Dokładnie na czas(Just-in time, JIT) to system, w którym produkty są produkowane i dostarczane we właściwe miejsce, dokładnie we właściwym czasie i we właściwej ilości. Kluczowe elementy systemy just-in-time: flow, pull, standardowa praca(oraz standardowy poziom pracy w toku) i czas taktu. Systemy JIT eliminują przestoje i zaległości materiałowe pomiędzy operacjami.
Procesy transakcyjne(procesy transakcyjne) - procesy, w których transfer materiałów, wiedzy, informacji lub usług następuje pomiędzy dwiema osobami lub pomiędzy osobą a sprzętem. Ogólnie rzecz biorąc, większość procesów, które nie obejmują wytwarzania produktów, należy do tej kategorii.
(frontloading) - dostawa i wysyłka materiałów na linię produkcyjną lub usługową przez operatora. Zapobiega konieczności obracania się operatora w celu podniesienia i przeniesienia części.Heijunka(heijunka) - organizacja „wygładzania” planu produkcji, w którym zamówienia realizowane są cyklicznie, a dzienne wahania poziomu zamówień sprowadzane są do ich wartości w długoterminowy. Niektóre rodzaje wygładzania są nieuniknione w każdym rodzaju produkcji: zarówno masowej, jak i chudej. Lean Manufacturing koncentruje się na tworzeniu nadwyżek mocy produkcyjnych w miarę upływu czasu poprzez uwalnianie zasobów i skracanie czasu przezbrajania. Jednocześnie minimalizowane są powstające rozbieżności pomiędzy heijunką a rzeczywistym popytem, co znacznie ułatwia proces „wygładzania sprzedaży” (sprzedaży na poziomie).
Hoshin Kanri(hosing kanri) to sposób opracowywania strategii zarządzania przedsiębiorstwem przez najwyższe kierownictwo, w którym zasoby są kierowane na cele krytyczne dla przedsiębiorstwa. Stosując diagram macierzowy podobny do tego stosowanego przy konstruowaniu funkcji jakości, wybiera się od trzech do pięciu kluczowych celów, a pozostałe cele ignoruje się. Do pracy nad wybranymi celami tworzone są projekty, których sposoby realizacji omawiane są na niższym szczeblu zarządzania. Hoshin Kanri pozwala na ujednolicenie zasobów i opracowanie jasnych, mierzalnych wskaźników, dzięki którym na bieżąco monitorowana jest realizacja kluczowych celów. Inna nazwa Hoshin Kanri to wdrażanie polityki.
Wartość (wartość użytkowa)(wartość) – określona przez Klienta jako prawidłowa i oczekiwana jakość, ilość, cena i termin dostawy. Wartość to zespół cech produktu lub usługi, za które konsument jest skłonny zapłacić dostawcy, gdyż te cechy produktu lub usługi powodują subiektywne odczucie konsumentowi, że rzecz (usługa), której potrzebuje, zostanie dostarczona (dostarczona) w odpowiedniej ilości wymaganą jakość, we właściwym czasie i w we właściwym miejscu(powoduje uczucie satysfakcji) .
Chaku-chaku(chaku-chaku) – metoda realizacji ciągłego przepływu pojedynczych produktów, w której operator przemieszczając się w komórce od maszyny do maszyny, pobiera gotową część z jednej maszyny i ładuje ją do drugiej, i tak dalej. W języku japońskim dosłownie oznacza „ładunek-ładunek”.
Czystsza produkcja(greenfield) to nowy system organizacji produkcji, w którym metody Lean Manufacturing są od samego początku integrowane z systemem zarządzania (w przeciwieństwie do reorganizacji istniejącej produkcji).
Komórki(ogniwa) – Układ sprzętu i/lub operatorów połączonych ze sobą na ograniczonym obszarze. To jest sposób na układ różne rodzaje sprzęt, który pozwala na wykonywanie operacji produkcyjnych w przejrzystej kolejności, bez przerw. Typowa konfiguracja ogniw ma kształt litery U. Taki układ umożliwia organizację ciągłego przepływu pojedynczych produktów i elastyczne rozmieszczenie osób (jeden operator może obsługiwać kilka jednostek jednocześnie).
Rozmawialiśmy o wartości i stracie. Porozmawiajmy teraz o konieczności budowania procesu tworzenia wartości w formie ciągłego przepływu.
W miarę rozwoju metod produkcji z rzemieślniczych na przemysłowe logistyka procesu przenoszenia i przetwarzania obiektów pracy zmieniała się kilkakrotnie. Dawno, dawno temu rzemieślnik zaczynał pracę nad kolejnym produktem dopiero po całkowitym zakończeniu pracy nad poprzednim. Później precyzja obróbki umożliwiła bezosobowe wykorzystanie części, bez indywidualnego dopasowywania; pracę podzielono na operacje i zaczęto produkować detale partiami. Utworzono osobne stanowiska pracy, sekcje i warsztaty, które ustawiono w określonej kolejności. Po raz pierwszy pojawiło się takie pojęcie jak przepływ produkcji.
Uderzającym przełomem było wprowadzenie przez Henry'ego Forda na początku XX wieku montażu liniowego, najpierw silników, a później w ogóle samochodów. To radykalnie zwiększyło produktywność i obniżyło koszty o 90%. Wcześniej pracownicy montowali samochód od początku do końca na jednym stanowisku pracy. Wraz z pojawieniem się przenośnika przepływ produkcji uporządkował się i osiągnął idealną formę.
Innowacje dotyczyły jedynie montażu produktu, natomiast obróbka części odbywała się metodą „partii i kolejki”, ale w tamtym czasie nadawało się to do produkcji masowej. Metody Forda szybko rozprzestrzeniły się na inne gałęzie przemysłu. Następnie I i II wojna światowa pobudziły dalszy rozwój masowej produkcji towarów.
Przejście do spokojnego życia ożywiło potrzebę indywidualizacji dóbr. A metody Forda, które pozwalały przez lata produkować ten sam produkt w ogromnych ilościach, popadły w konflikt z wymaganiami rynku. Przypomnijmy, że w latach 1908-1027 produkowany był jeden model „T”, i to wyłącznie w kolorze czarnym. W ciągu 20 lat z linii montażowej zjechało 15 milionów absolutnie identycznych egzemplarzy.
Rynek coraz bardziej domagał się różnorodności, jednak przez kilka kolejnych dekad wiele gałęzi przemysłu przez inercję w dalszym ciągu skupiało się na masowej i wielkoseryjnej produkcji produktów. Nie był wyjątkiem przemysł meblowy. W ZSRR w dużych zakładach do końca lat 80. nadal produkowano w trybie in-line standardowe „ściany”.
Poszerzenie asortymentu, zakres kolorów, różnorodność projektów, szczególnie w przypadku towarów użytku domowego, czyli meble, zrodziło szereg pytań. Jak efektywnie produkować w nowych warunkach? Jak możemy zachować szczupłą sylwetkę, jednocześnie zapewniając różnorodność?
Odpowiedzi na te pytania dał rozwój organizacji procesów produkcyjnych w Toyocie w latach 50. i 60. XX wieku, który znalazł odzwierciedlenie w sformułowanej później ideologii odchudzonej produkcji.
Koncepcja Lean Manufacturing proponuje wykorzystanie najlepszych pomysłów Forda – metody przepływowej, ale dostosowanie jej do nowoczesne warunki– zamiast masowej produkcji metodą „wsadowo-kolejkową” zastosuj ciągły przepływ małych partii aż do pojedynczych produktów.
Jeśli widzimy, że wszystkie maszyny na produkcji są obciążone do pełna i żaden z pracowników nie stoi bezczynnie, daje to nam podświadomą satysfakcję. Nie jest brany pod uwagę fakt, że detale leżące pomiędzy maszynami czekają godzinami na obróbkę. Lean Manufacturing sugeruje przeniesienie uwagi z obciążenia ludzi i maszyn na ciągły ruch przedmiotów i produktów, ponieważ to właśnie determinuje wydajność. Zadanie to podzielone jest na dwa etapy: budowanie samego przepływu i kontrolowanie ruchu materiału wzdłuż przepływu.
Proponuje się uwzględnić nie tylko przepływ produkcji, ale ogólny przepływ tworzenia wartości dla konsumenta końcowego. W tym celu obejmuje procesy realizacji zamówień, projektowania, dostaw i przygotowania produkcji, a także logistykę i dystrybucję gotowych produktów. Idealnie byłoby, gdyby cały strumień wartości budowany był poza granicami jednego przedsiębiorstwa, wspólnie z dostawcami, firmami transportowymi i handlowymi. Strumień wartości klienta obejmuje przepływy materiałów i informacji.
Do wstępnej analizy przepływu wygodnie jest użyć narzędzia Lean Manufacturing, takiego jak „”. Aby to sporządzić, na planie przedsiębiorstwa lub warsztatu rysuje się trasy ruchomych części (lub pracowników) z wyznaczonymi miejscami pracy i wyposażeniem. Wynik zwykle przypomina talerz spaghetti, dlatego diagram ma swoją nazwę.
Takie proste, ale wizualne narzędzie stanowi uzasadnienie dla następujących kroków w celu optymalizacji przepływu:
— skrócenie całkowitej długości ruchów części i pracowników,
- eliminacja pętli, skrzyżowań, powrotów w ruchach,
— maksymalna bliskość wszystkich tras do wspólna linia połączenie magazynu surowców z magazynem wyrobów gotowych.
Na podstawie analizy diagramu spaghetti reorganizacji ulegają urządzenia i miejsca pracy, a czasem całe obszary produkcyjne. W rezultacie przepływ staje się bardziej równomierny i ciągły, a co za tym idzie, szybszy.
Do analizy strat czasowych wykorzystuje się bardziej złożone narzędzie – mapy strumieni wartości (VSM – mapa strumienia wartości). Ten dokument to warunkowe (bez skali i bez odniesienia do rzeczywistego planu) graficzne przedstawienie całego procesu produkcyjnego, wskazujące przepływy materiałów i informacji. Mapowanie przepływu (mapowanie) rozpoczyna się zwykle od zakończenia operacji produkcji i jest prowadzone w przeciwnym kierunku aż do początku cyklu i dalej, włączając procedury poprzedzające produkcję (przyjmowanie i przetwarzanie zamówień, przygotowanie produkcji, zamawianie materiałów itp.).
W każdym miejscu odnotowywany jest czas trwania operacji, czas oczekiwania i transportu, ilość produktów w toku, ilość odpadów, liczba personelu i inne parametry. Format mapy zapewnia możliwość przypisania przypisów do każdej operacji i obliczenia wynikających z tego proporcji całkowitego czasu produkcji produktu do czasu straconego.
Kiedy mapa przepływu jest tworzona po raz pierwszy i w pełni uwzględnia się wszystkie straty, wyniki są zwykle szokujące. Okazuje się, że obróbka bezpośrednia zajmuje mniej niż 1% czasu cyklu. Na przykład dla cyklu produkcyjnego meble tapicerowane w ciągu dwóch tygodni dodanie wartości może nastąpić w zaledwie 100 minut, a w przypadku mebli skrzyniowych wyprodukowanych w ciągu 5 dni części są przetwarzane w ciągu pół godziny. Należy jednak mieć na uwadze, że lider Lean Manufacturing, Toyota, osiągnęła współczynnik wartości dodanej na poziomie zaledwie 20%, więc dla producentów mebli wynik nawet 5% można uznać za całkiem akceptowalny.
Analiza mapy strumienia wartości pozwala szczegółowo zidentyfikować i wyeliminować główne źródła strat, zobaczyć, które obszary charakteryzują się niską przepustowością i podjąć działania mające na celu wyrównanie przepływu. Zaleca się utworzenie dwóch map przepływu – dla stanu istniejącego i stanu przyszłego – oraz opracowanie planu osiągnięcia tego nowego stanu. Po ukończeniu planu sporządzana jest nowa mapa przyszłego stanu itp.
Oprócz analizy przepływu i doskonalenia jego parametrów konieczne jest podporządkowanie mu struktury przedsiębiorstwa. Zamiast pionowej hierarchicznej organizacji funkcjonalnej z działami i usługami wprowadzono płaską strukturę produktów. Warsztaty produkcyjne a obszary zostają reorganizowane w komórki produkcyjne pod kontrolą zespołów roboczych (produktowych). Zmiana struktury i utworzenie komórek stwarza warunki do redukcji personelu.
Ideologia Lean Manufacturing opiera się na tym, że najlepsze rezultaty można osiągnąć, jeśli po optymalizacji procesów w swoim przedsiębiorstwie zacznie się współpracować z dostawcami i sprzedawcami. Badając pełny strumień wartości wraz z kontrahentami w górę i w dół łańcucha, możesz znaleźć ukryte rezerwy i zgodzić się na podzielenie się korzyściami wspólne działania dla jego poprawy.
Po zbudowaniu i optymalizacji przepływu zaczynają wdrażać zasadę „pull”, czyli wytwarzać produkty wyłącznie na zamówienie klienta (wewnętrznego lub zewnętrznego). Oznacza to, że należy zadbać o to, aby operacja (proces, pracownik) nie rozpoczęła wytwarzania produktu bez sygnału z następnej operacji, procesu, pracownika w łańcuchu technologicznym. I tak dalej, aż do klienta końcowego. Ale o tym więcej w następnym artykule.