Przygotowanie sprzętu, zapasów i narzędzi. Przygotowanie stanowiska pracy i narzędzi do pracy. Przygotowanie do prac naprawczych Narzędzia i sprzęt
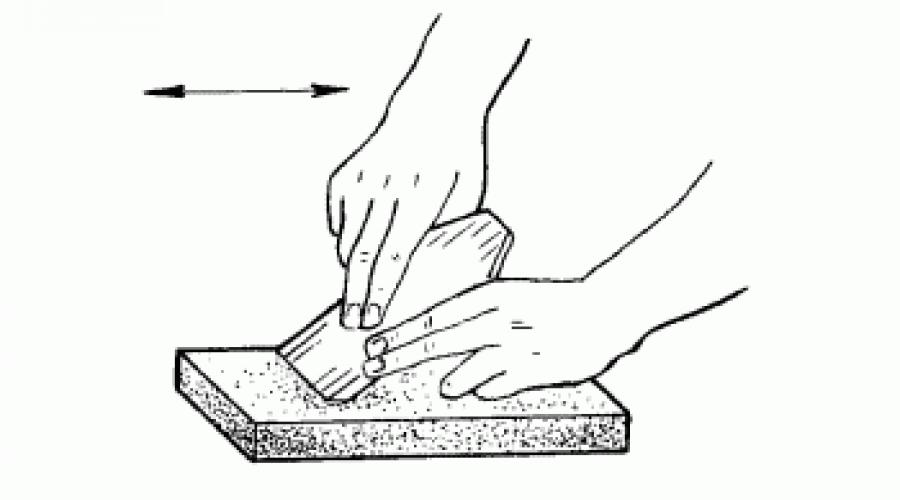
Przeczytaj także
Skrzynki uciosowe i szablony są często używane jako urządzenia. Znacznie ułatwiają pracę i skracają czas wykonywania danej operacji.
Skrzynka uciosowa to rodzaj rynny składającej się z trzech desek. Obie deski należy wbić równolegle do siebie na podstawę, a kąt pomiędzy podstawą a bokami powinien wynosić 45°. Po bokach skrzynki uciosowej wykonuje się kilka specjalnych nacięć pod pewnym kątem, a ich liczba powinna być taka sama po obu stronach. Linia po jednej stronie deski powinna być kontynuowana po drugiej, aby wygodnie było przyciąć deskę pod określonym kątem.
Najczęściej na ścianach wykonuje się 2–3 nacięcia: pod kątem 45, 90 i 60°. To ostatnie jest rzadkie.
Skrzynka uciosowa służy do przyspieszenia procesu cięcia desek pod określonym kątem. W tym celu deskę umieszcza się pomiędzy bokami skrzynki uciosowej i dociska do dalszej strony dopiero po tym rozpoczyna się piłowanie deski.
Szablony służy do szybkiego znakowania części. Do wielokrotnego użytku szablony są wykonane z twardego cienki materiał na przykład ze sklejki, płyty pilśniowej lub cyny.
Przygotowanie narzędzi do pracy
Aby narzędzia były łatwe i wygodne w użyciu, należy je odpowiednio przygotować. Zasady ostrzenia siekiery zostały omówione wcześniej (patrz ryc. 20).
Aby zapobiec utknięciu brzeszczotu w drewnie, zęby piły są rozchylone, czyli zagięte różne strony i ostrzyć. Aby to zrobić, mistrz potrzebuje imadła, szczypiec i trójkątnego pilnika z drobnym nacięciem. Zwykle piły trafiają do sprzedaży z ustawionymi zębami, ale możliwe, że będziesz musiał wykonać tę operację samodzielnie, dlatego omówimy bardziej szczegółowo jej opis. Najpierw z drewniana przekładka zamocuj ostrze w imadle i za pomocą szczypiec zacznij ostrożnie przesuwać wierzchołki zębów naprzemiennie w jednym lub drugim kierunku (ryc. 36, a), ale nie więcej niż o połowę grubości ostrza.
Ryż. 36. Przygotowanie piły do pracy: a – rozwarcie zębów; b – ostrzenie.
Szerszy rozstaw spowoduje jedynie uszkodzenia, ponieważ cięcie będzie zbyt szerokie i nierówne. Należy również zadbać o to, aby rozstaw wszystkich zębów był taki sam, w przeciwnym razie w procesie piłowania nie będą brały udziału wszystkie zęby, a tylko te najbardziej wygięte, a praca taką piłą będzie utrudniona. Rozstawione zęby muszą znajdować się w obrębie elementu dystansowego, dlatego od czasu do czasu należy zmienić położenie ostrza.
Piła ostrzona jest pilnikiem trójkątnym. Ostrze jest zaciśnięte w imadle i przesuwane w miarę ostrzenia zębów. Istnieją dwa rodzaje ostrzenia - ukośne i proste. Jeżeli piła jest przeznaczona do cięcia mieszanego wzdłużno-poprzecznego i ma ukształtowane zęby trójkąt prostokątny, stosuje się prostsze bezpośrednie ostrzenie, podczas którego pilnik trzyma się prostopadle do ostrza (ryc. 36, b). Wkładając je pojedynczo w każdą szczelinę międzyzębową, przy lekkim nacisku przesuwają się wzdłuż ich krawędzi w kierunku od siebie. W takim przypadku krawędzie pliku powinny ściśle przylegać do krawędzi. Ruch wsteczny wykonujemy poprzez podniesienie pilnika tak, aby nie dotykał piły. Nie należy długo prowadzić pilnika po tym samym miejscu, wystarczy trzykrotnie okrążyć każdy ząb, a przy ponownym naostrzeniu wystarczy raz.
Przygotowanie narzędzia do strugania obejmuje ostrzenie noża i prawidłowa instalacja go w bloku. Do ostrzenia potrzebny będzie drobnoziarnisty kamień ścierny i osełka. Przyjrzyjmy się sekwencji ostrzenia na przykładzie noża płaskiego.
Najpierw nóż ostrzy się na bloku zamocowanym w drewnianej ramie lub wgłębieniu na stole roboczym. W tym przypadku dolna skośna krawędź noża (fazowanie) przechodzi wzdłuż kamienia. Trzymany nóż prawa ręka i lewą ręką odpychają ją od siebie (ryc. 37, a, b).
Ryż. 37. Ostrzenie struga: a – pozycja noża podczas ostrzenia; b – pozycja fazowania; c – gratowanie.
Należy zadbać o to, aby podczas przesuwania noża wzdłuż bloku fazka przylegała całą płaszczyzną do kamienia. Nie można zmienić kąta nachylenia noża, w przeciwnym razie faza stanie się garbata, jej szerokość będzie nierówna, w wyniku czego taki nóż będzie źle strugany. Oczywiście utrzymanie go pod tym samym kątem nie jest łatwe ze względu na ślizganie się po kamieniu. Niezbędną zręczność, jak w każdej innej kwestii, nabywa się poprzez trening.
Aby mieć pewność, że na kamieniu nie pozostaną ślady pyłu metalicznego, podczas ostrzenia blok należy okresowo przecierać wilgotną szmatką.
Skos noża przesuwa się wzdłuż kamienia, aż na całej długości ostrza pojawi się zadzior, który można łatwo wyczuć palcami. Następnie nóż kładzie się płasko przednią krawędzią na bloku (ryc. 37, c) i przesuwa się wzdłuż bloku prostymi lub okrężnymi ruchami z lekkim naciskiem, w wyniku czego zadzior znika z przedniej krawędzi i wystaje na fazowaniu. Nóż odwraca się ponownie, a zadzior usuwa się z fazowania. Jeśli ponownie pojawi się na przedniej krawędzi, powtórz całą pracę. Za każdym razem, gdy wieszak się zmniejsza. Ostatnim krokiem powinno być usunięcie go ze skosu.
Po usunięciu zadziorów zaostrzone ostrze poddaje się obróbce na osełce zwilżonej wodą. Ruchami okrężnymi przesuwają go najpierw wzdłuż fazy, następnie wzdłuż przedniej krawędzi noża i ponownie wzdłuż fazy.
Podczas ostrzenia okresowo sprawdzaj kwadratem, czy krawędź tnąca noża jest przekrzywiona (ryc. 38, a).
Ryż. 38. Korekta krawędzi skrawającej: a – sprawdzenie poprawności; b – eliminacja zniekształceń; c – zaokrąglenie końcówek.
Nawet najmniejsze zniekształcenie jest niedopuszczalne. Jego obecność znacznie komplikuje proces strugania: wióry są miażdżone i zatykają szczelinę między nożem a blokiem, skąd należy je stale czyścić.
Przyczyną zniekształcenia może być wada produkcyjna, a także ostrzenie nożem w niewłaściwej pozycji. W każdym przypadku wadę należy usunąć. Aby to zrobić, najpierw zeszlifuj wyższą część krawędzi, a następnie wypoziomuj resztę (ryc. 38, b). Podczas szlifowania nóż pochyla się w stronę przeciwną do tego, na którym wystąpiła niewspółosiowość, a podczas procesu osiowania przesuwa się go ściśle prostopadle do krawędzi tnącej.
W przypadku znacznej niewspółosiowości nóż należy naostrzyć na kamieniu gruboziarnistym, na którym fazka ściera się szybciej niż na kamieniu drobnoziarnistym. Kamień ten służy do wstępnego ostrzenia noża, przeprowadzanego po zakupie samolotu oraz w przypadku uszkodzenia lub silnego stępienia ostrza. Ostrzenie (szlifowanie) na takim kamieniu okazuje się szorstkie, dlatego po pojawieniu się pierwszych zadziorów przystępują do ostrzenia na bloku.
Początkujący rzemieślnik powinien wziąć pod uwagę jeszcze jedną subtelność: przed włożeniem zaostrzonego noża w blok należy zaokrąglić końce krawędzi tnącej, lekko szlifując rogi (ryc. 38, c). Jeśli nie zostanie to zrobione, ostre rogi pozostawi na struganej powierzchni trudne do usunięcia rowki.
Ostrzenie jest więc zakończone. Teraz nóż można zamontować w bloku. Najważniejszą rzeczą w tym przypadku jest prawidłowe zwolnienie krawędzi tnącej noża. Wkłada się go w szczelinę bloku i lekko dociska klinem w drewnianym bloku lub śrubą w metalowym. Następnie płaszczyznę podnosi się na wysokość oczu z podeszwą do góry i reguluje zwolnienie noża tak, aby krawędź tnąca była ściśle równoległa do podeszwy i wystaje dosłownie na dziesiąte części milimetra (patrząc pod światło, ostrze jest ledwo zauważalne i wygląda jak cienka, równa nić). Następnie lekkimi uderzeniami młotka zabezpieczyć klin lub dokręcić śrubę zaciskową do oporu.
Gdy ostrze zostanie puszczone zbyt daleko, nóż wcina się głęboko w drewno i usuwa grube wióry, które utknęły w szczelinie pomiędzy nożem a blokiem i uniemożliwiają ruch samolotu do przodu.
Podczas montażu noża podwójnego należy zwrócić uwagę, aby podkładka łamacza wiórów nie sięgała do krawędzi skrawającej o około 2 mm. Aby zdemontować samolot należy lekko uderzyć młotkiem w tył drewnianego klocka. Jeśli blok jest metalowy, wystarczy odkręcić śrubę mocującą.
Po opanowaniu sekwencji przygotowania samolotu do pracy można przystąpić do ustawiania sherhebela, którego nóż podczas ostrzenia musi być stale obracany w jedną lub drugą stronę, aby w każdej chwili można go było przesunąć w kierunek promienia krzywizny krawędzi tnącej, dzięki czemu następuje ostrzenie całego ostrza. Nóż Scherhebel powinien wystawać z bloku w postaci wąskiego pióra, tak aby jego krawędź tnąca była wysunięta o 1–1,5 mm.
Dłuta i dłuta ostrzy się w taki sam sposób, jak nóż płaski.
Dla udana praca Elektronarzędzia wymagają pewnych umiejętności. Ich przygotowanie należy przeprowadzić ze szczególną starannością. Na przykład użycie strugarki elektrycznej, której ostrza są nieprawidłowo ustawione lub naostrzone, prowadzi do nieodwracalnego uszkodzenia przedmiotu obrabianego, a wysoka prędkość a zasilanie wiertarki elektrycznej może spowodować zapalenie się drewna. Dlatego zaleca się najpierw sprawdzić prawidłowe ustawienie elektronarzędzia na niepotrzebnym kawałku drewna, a następnie przejść do wykonywania głównej pracy.
1417 Razem 1 Dzisiaj
1) Przed uruchomieniem maszyny należy przeprowadzić kontrolę tolerancji sprzętu; obejmuje to poinformowanie zmiany nadawczej o problemach w sprzęcie (jeśli występują), sprawdzenie osłon, drzwi, włazów - wszystko musi być zamknięte.
2) Uchwyty wrzeciona i nakrętki muszą znajdować się w położeniu neutralnym.
3) Należy upewnić się, że dopływ chłodziwa jest wyłączony, a dysze doprowadzające chłodziwo są skierowane w dół. Tokarz musi także upewnić się, że na podłodze w pobliżu urządzenia nie ma rozlanych olejów ani że nie znajdują się tam żadne przedmioty może spowodować potknięcie się podczas pracy.
4) Odzież tokarza nie powinna mieć żadnych wiszących klap.
5) Klucz należy wyjąć z uchwytu. Po zakończeniu kontroli tolerancji włączany jest wyłącznik główny i wyłączniki dodatkowe oraz następuje smarowanie maszyny.
6) Przed uruchomieniem wrzeciona tokarz musi upewnić się, że obrotowe elementy uchwytu nie są blokowane przez nieruchome części urządzenia.
7) Ustawienia włączone wymagane częstotliwości obroty wrzeciona realizowane są za pomocą przełączników dźwigniowych na jego węzłach do żądanego położenia.
8) Nie można przełączyć ani zakończyć przełączania, jeśli takie przełączenie powoduje charakterystyczny dźwięk zębów przekładni, które nie znajdują się w sprzęgle. W tym przypadku przełączenie następuje po zatrzymaniu się wrzeciona.
Na wszystkich tokarkach obroty do przodu aktywuje się poprzez popchnięcie rączki poprzez przełączenie w swoją stronę, natomiast obroty do tyłu włącza się samodzielnie. Obroty do przodu odpowiadają obrotom wrzeciona w kierunku zgodnym z ruchem wskazówek zegara, patrząc od tyłu wrzeciona. Wrzeciono należy hamować za pomocą hamulca.
Przy obróbce frezem nie można wyłączyć obrotów wrzeciona przy włączonym posuwie i frezie nie odsuniętym od detalu. W większości przypadków prowadzi to do złamania ostrza.
Podczas montażu przedmiotu obrabianego w trójszczękowym uchwycie samocentrującym lewą ręką rozsuń szczęki uchwytu za pomocą klucza, tak aby przedmiot przeszedł pomiędzy szczękami; Prawą ręką włóż przedmiot pomiędzy szczęki i najpierw zaciśnij go lewą ręką, a następnie obracając klucz obiema rękami, mocno zabezpiecz obrabiany przedmiot w uchwycie.
Jeżeli obróbka odbywa się w kłach, to po zdjęciu uchwytu należy dokładnie przetrzeć stożkowy otwór wrzeciona i stożkowy trzpień środka. Następnie prawą ręką włóż środek (trzon) w otwór wrzeciona i ostrym ruchem wsuń go do końca. Włącz obrót wrzeciona i sprawdź środek pod kątem bicia promieniowego. Jeśli środek obraca się z biciem, należy go wybić mosiężnym prętem i ponownie włożyć do otworu wrzeciona, obróconego o 30-45 stopni wokół osi. Następnie lewą ręką włóż środek w pióro konika.
Po regulacji tokarka skonfiguruj to. Przed ustawieniem maszyny na daną prędkość obrotową wrzeciona i posuw należy ustawić uchwyt obrotu wrzeciona w położeniu neutralnym (środkowym), uchwyty obrotu posuwu wzdłużnego i poprzecznego w położeniu spoczynkowym, a zacisk przesuwa się na konik tak, aby odległość między nimi wynosiła 100-150 mm. W pierwszej kolejności reguluje się poszczególne łańcuchy kinematyczne maszyny (ruch główny i posuwy), a następnie montuje się elementy sterujące (rączki przekładni i podajnika) w określonym położeniu, aby uzyskać wymaganą prędkość skrawania i posuw. Konkretną wartość prędkości obrotowej wrzeciona i wałka ustala się na podstawie racjonalnych warunków obróbki przedmiotu obrabianego.
Racjonalny wybór trybu skrawania polega na przypisaniu takich wartości posuwu, głębokości i prędkości skrawania, które pozwalają na maksymalne wykorzystanie możliwości narzędzie tnące i możliwości eksploatacyjne maszyny. Tryb skrawania wybiera się zwykle w następującej kolejności: głębokość skrawania ustala się na podstawie naddatku na obróbkę i wykonania obróbki najmniejsza liczba intymny stosunek dwojga ludzi; posuw ustalany jest z uwzględnieniem wytrzymałości mechanizmu posuwu i sztywności przedmiotu obrabianego (w przypadku obróbki zgrubnej) oraz w oparciu o wymaganą chropowatość powierzchni, geometrię narzędzia i materiał obrabianego przedmiotu (w przypadku obróbki wykańczającej); ustawić dopuszczalną prędkość skrawania w oparciu o wybraną głębokość skrawania i posuw, moc maszyny, materiał przedmiotu obrabianego, materiał, geometrię i trwałość narzędzia.
Przygotowanie narzędzi kontrolno-pomiarowych, skrawających, szlifierskich, urządzenia uniwersalne, technologiczny
Narzędzia i sprzęt
1) Przygotowanie narzędzi kontrolno-pomiarowych:
Przed pracą powierzchnie pomiarowe przyrządu, a także powierzchnie badane są wycierane do sucha i oczyszczane z kurzu i innych cząstek mogących mieć wpływ na wynik pomiaru.
2) Przygotowanie narzędzie ścierne do szlifowania metalu.
Do szlifowania taśmowego z rolki papieru ściernego wycina się pas o wymaganej długości i szerokości. Przyklej końce taśmy koniec do końca pod kątem 45° do krawędzi lub na zakładkę pod kątem prostym do krawędzi. W pierwszym przypadku końce skóry przyklejamy na lnianą taśmę o szerokości 100...200 mm. W drugim przypadku na jednym ze sklejonych końcówek gorąca woda Ziarna ścierne usuwa się na obszarze o długości 50...80 mm, na uwolnione podłoże nanosi się klej, przykleja drugi koniec taśmy, zaciska i suszy szew. Taśmę nałóż na koła pasowe tak, aby zewnętrzny koniec w szwie znajdował się w kierunku ruchu paska.
3) Przygotowanie do pracy przecinarek wszystkich typów polega na wyważeniu, ostrzeniu i zamontowaniu w maszynie.
Wyważanie frezu. Istnieją dwa rodzaje równoważenia – statyczne i dynamiczne. Frezy łupinowe wyważane są najczęściej statycznie, czyli bez obracania frezu z prędkością roboczą. Wykrywanie niewyważenia noża zamontowanego na trzpieniu na pryzmatycznych równoległościach urządzenia PB (maksymalna średnica frezu 400 mm); cięższa część noża znajduje się na dole. Kontrola odbywa się 3... 4 razy. Stopień niewyważenia (niewyważenia) ustala się poprzez przymocowanie ciężarków (na przykład kawałków plasteliny) do lekkiej części noża. Po osiągnięciu równowagi następuje ważenie odważników. Iloczyn dodatkowej masy i promienia jej zamocowania daje wartość niewyważenia (g.cm). Dla frezów o średnicy 120...180 mm dopuszczalne jest niewyważenie do 3...5 g-cm. Wyważanie frezu odbywa się poprzez usunięcie (szlifowanie, wiercenie) metalu z jego ciężkiej części w strefie nieobrobionej. Równoważenie dynamiczne przeprowadzane jest na specjalne maszyny. Ona ci na to pozwala wysoka celność(nierównowaga resztkowa nie większa niż 1 g cm) równoważy nie tylko siły, ale także momenty. Jest to szczególnie ważne w przypadku dłuższych instrumentów. Wyważanie odbywa się na maszynie DB-10. Ostrzenie noża. Podczas ostrzenia należy zapewnić zgodność profilu obróbki, kątów cięcia i równości promieni zębów o tej samej nazwie. Zamontowane frezy z podkładem pełnym i kompozytowym ostrzone są wzdłuż przedniej krawędzi przy zachowaniu wartości kąta czołowego γ. W tym celu należy przesunąć oś frezu względem płaszczyzny roboczej ściernicy o odległość Н1 = Rsinγ, gdzie R jest promieniem frezu.
4) Przygotowanie narzędzi do wiercenia i dłutowania.
Wiertła z środkiem prowadzącym i nacinakami ostrzy się na tylnej stronie ostrzy głównych, po wewnętrznej stronie nacinaków i wzdłuż krawędzi środkowej piramidy. Prawidłowo naostrzone wiertło powinno mieć środek prowadzący z symetrycznie rozmieszczonymi krawędziami i osią piramidy pokrywającą się z osią wiertła, ostrza główne umieszczone na tym samym poziomie oraz nacięcia o tym samym kształcie. Przy stożkowym ostrzeniu części tnącej obie krawędzie tnące muszą mieć tę samą długość, ten sam kąt nachylenia do osi wiertła i ten sam kąt przyłożenia (15...25°). Środkowa część krawędzi poprzecznej (mostka) wiertła musi pokrywać się z osią jego obrotu, długość mostka nie powinna przekraczać 1,5...2 mm. Odchylenia kątów wiercenia od wartości nominalnych muszą mieścić się w granicach 1°.
Sprzęt i akcesoria do ostrzenie wierteł: ostrzarka ZB633, ostrzarka uniwersalna ZA64, urządzenia do ostrzenia wierteł, szablony kontrolne do sprawdzania prawidłowego ostrzenia wierteł.
Zęby łańcuchów frezujących ostrzone są wzdłuż przedniej krawędzi przy zachowaniu kąta czołowego y = 15...20°. Dopuszczalne odchylenie parametrów kątowych ±1°. Ubytki zębów powinny być zaokrąglone (g=1,5 mm), zęby powinny być ostro zaostrzone i wykończone. Zadziory i zasinienie wierzchołków zębów są niedopuszczalne. Krawędzie tnące zębów tego samego typu muszą znajdować się w tej samej odległości od siebie i leżeć na tym samym poziomie (przy prostym układzie łańcucha). Dopuszczalne odchyłki podziałki ogniw i wysokości zębów wynoszą ±0,1 mm. Ręczne ostrzenie łańcuchów bez prowadnic jest niedozwolone. Łańcuchy ostrzone są na maszynie TchFK.
Łańcuch frezujący zamontowany w głowicy dłutarki łańcuchowej musi być odpowiednio napięty. Średnia siła naciągu (wzdłuż osi linijki prowadzącej) wynosi 100 N. Siła ta odpowiada ugięciu łańcucha o 6 mm, gdy jest on wyciągany z linijki prowadzącej w połowie długości z siłą 20 N.
5) Przygotowanie narzędzi tokarskich.
Narzędzia tokarskie ręczne z jedną fazką ostrzy się wzdłuż powierzchni tylnej, przy pomocy dwóch fazek - wzdłuż powierzchni przedniej i tylnej. Frezy tokarskie maszynowe (przelotowe, tnące itp.) ostrzone są od powierzchni tylnej i przedniej. Do ostrzenia narzędzi tokarskich stosuje się ściernice o uziarnieniu 20...40 i twardości CM1. Po naostrzeniu frezy są wykańczane na maszynie wykańczającej lub ręcznie za pomocą osełki. Noże z okrągłą główką ostrzone są wzdłuż przedniej fazy. Zazwyczaj stosuje się uniwersalne ostrzarki. Prawidłowe naostrzenie ocenia się na podstawie kształtu ostrza (kontrolowanego za pomocą szablonu) oraz ostrości krawędzi tnącej.
6) Przygotowanie urządzeń technologicznych.
Przygotowanie oprzyrządowania technologicznego do pilotażowej i małoseryjnej produkcji nowych maszyn często zajmuje tyle samo czasu, co produkcja prototyp lub pierwsza seria produktu. Spowalnia to rozwój i wypuszczanie nowych produktów.
Na wybór metody wykonania przedmiotu wpływa czas przygotowania oprzyrządowania technologicznego (produkcja matryc, modeli, form itp. Wraz ze wzrostem dokładności przedmiotu obrabianego i zbliżaniem jego kształtu do konfiguracji ukończona część środek ciężkości obróbka zauważalnie maleje. Jednak kiedy mały program produkcji, nie wszystkie metody mogą być opłacalne ze względu na fakt, że koszty wyposażenia procesów zakupowych nie zwracają się ekonomicznie.
System USP pozwala na sekwencyjne przygotowanie urządzeń technologicznych w najkrótszy i najbardziej ekonomiczny sposób. Ścieżka ta przebiega przez cztery etapy: złożenie zamówienia na montaż USP; utworzenie i instalacja układu; ustawienie i obsługa USP w miejscu pracy, zwrócenie go na miejsce montażu; demontaż na części składowe i składowanie elementów do wykorzystania w kolejnych montażach.
Na wybór metody wykonania przedmiotu duży wpływ ma czas przygotowania oprzyrządowania technologicznego (produkcja matryc, modeli, form itp. Wraz ze wzrostem dokładności wykonania przedmiotu obrabianego, wielkość obróbki ulega zauważalnemu zmniejszeniu. Jednak przy małej produkcji programu nie wszystkie metody mogą być opłacalne ze względu na fakt, że koszty wyposażenia procesów zakupowych nie zwracają się ekonomicznie.
Normalizacja radykalnie zmniejsza głośność Praca projektowa, zmniejsza pracochłonność, koszt i czas przygotowania urządzeń technologicznych. Przechodząc od tłoczenia jednej części do tłoczenia drugiej, wiele znormalizowanych zespołów i części stempla może być wielokrotnie używanych poprzez montaż małych matryc z wcześniej używanych części ze względu na wymienność wielu części stempla. Normy i normy mają charakter ogólnounijny, międzybranżowy, sektorowy, zakładowy i warsztatowy. Przestrzeganie standardów i norm jest obowiązkowe.
Główną rolę w rytmicznej pracy produkcji uzwojeń transformatorów mocy odgrywa organizacja procesów pomocniczych, a mianowicie: przygotowanie urządzeń technologicznych, przygotowanie przewodów zgodnie z danymi projektowymi elektrycznymi, dostarczanie materiałów składowych i podzespołów na stanowiska pracy i transport gotowych uzwojeń do hal montażowych zakładu.
Wszystkie funkcje gospodarki narzędziowej zakładu, mające na celu zapewnienie terminowego zaopatrzenia w narzędzia i urządzenia do bieżącej produkcji, a także przygotowanie oprzyrządowania technologicznego do wykonania prototypów nowych maszyn i rozwój ich produkcji masowej, są ściśle powiązane z obsługą technologiczną zakładu. Takie problemy zarządzania narzędziami, jak zastosowanie narzędzi postępowych, osprzętu, matryc, form, nie mogą zostać rozwiązane bez wstępnego opracowania odpowiednich procesy technologiczne oraz wyposażenie warsztatów zakładowych w niezbędny sprzęt.
Do kompleksu Praca przygotowawcza dowolny sposób prowadzenia ciągów obudowy obejmuje: przegląd prewencyjny i przygotowanie elementów oraz komunikację wiertnicy, opracowanie (szablon, kalibrację) wierconego szybu, dodatkowe przetwarzanie płuczka wiertnicza, próba ciśnieniowa, znakowanie i rozmieszczenie rury osłonowe, przygotowanie oprzyrządowania technologicznego do ciągów osłonowych, dobór receptur rozwiązania fugujące, przygotowanie materiałów cementujących, odczynników, płynu buforowego, sprzętu cementującego i inne operacje.
Mistrz, rozwiązując problemy zapewnienia wymaganej jakości produktów, może wiele zaoferować oryginalne projekty sprzęt i narzędzia, za pomocą których możliwe jest osiągnięcie wymaganej dokładności i wydajności obróbki. Dlatego jego udział w procesie przygotowania urządzeń technologicznych jest niezbędny do uzyskania wysokiej wydajności w procesie produkcyjnym.
Stanowisko przygotowania narzędzi dla CMM wyposażone jest w: przyrządy do ustawiania narzędzi, regały do przechowywania narzędzi, dokumentację techniczną i oprogramowanie; płytki kontrolne; szafki narzędziowe; stoły warsztatowe, stoły recepcyjne; wózki do transportu narzędzi na budowie i w miejscu pracy.
Podczas wymiarowania narzędzia poza maszyną, krawędź skrawająca jest ustawiana na wymagana odległość w kierunku promieniowym i osiowym od wybranych podstaw. Regulowane wymiary są ustawiane zgodnie z zadaniami dostrajania określonymi na kartach ustawień i współrzędnymi wierzchołków narzędzia tnącego.
Aby ustawić narzędzia skrawające dla tokarek, mod. BV-2010, który składa się z ramy i dwóch ruchomych, wzajemnie prostopadłych wózków, na których wyraźnie zapewnia aktywny dialog pomiędzy urządzeniami a innymi jednostkami konstrukcyjnymi tej produkcji, z uwzględnieniem obszaru planowania i przygotowania oraz procesów technologicznych.
W tym przypadku ze strefy magazynowej (strefy magazynowej) narzędzie (zgodnie z konkretną kartą konfiguracyjną dla konkretnej maszyny) trafia do strefy instalacji i konfiguracji. Sekcja strefy wyposażona jest w maszynę pomiarową, która dokonuje pełnej kontroli przychodzące bloki narzędzi. Za pomocą uchwytów operator wyrównuje końcówkę noża z krzyżem nitkowym na ekranie cieni , obraz instrumentu, na którym wykonywane jest badanie poprzez układ optyczny. Dane pomiarowe, w szczególności położenie wierzchołka krawędzi tnącej frezu względem powierzchnie bazowe, są wyświetlane na ekranie pilota . Maszyna posiada również systemy odczytu wskaźników do kontroli narzędzia oraz urządzenie do odczytu i zapisu , wykonany w formie specjalnego adaptera z główką szpilkową.
Operator mierzy położenie elementów tnących bloku względem powierzchni bazowych oraz inne niezbędne parametry bloku i wprowadza te dane do komputera maszyny pomiarowej za pomocą klawiatury pilota . Dla nowego bloku, zgodnie z dostępną dla operatora kartą konfiguracyjną, do komputera wprowadzane są także inne dane o bloku, np. kod podstawowy(identyfikacja), kod płytki skrawającej, numer maszyny i numer pozycji narzędzia w magazynie, określona trwałość narzędzia, itp.
Następnie operator sprawdza wszystkie dane na ekranie maszyny pomiarowej, a następnie wprowadza je do elektronicznego czujnika kodu narzędzia za pomocą specjalnego systemu rejestrującego połączonego jednym interfejsem z maszyną pomiarową. Głównym elementem układu rejestrującego jest głowica odczytowo-zapisująca. Układ rejestrujący posiada specjalny adapter , który jest umieszczony na bloku narzędziowym. W tym przypadku sonda głowicy współpracuje z elektronicznym czujnikiem kodu bloku. Dokładny kierunek adaptera jest względem blok instrumentu gdy adapter jest skierowany na blok, odbywa się to za pomocą prowadnic adaptera, które wchodzą w odpowiednie rowki w korpusie bloku narzędziowego. Naturalnie rowki wszystkich bloków narzędziowych i ich położenie są takie same. W zależności od konstrukcji maszyny pomiarowej montaż adaptera na bloku może odbywać się ręcznie lub automatycznie za pomocą urządzenia pneumatycznego lub hydraulicznego. W tym drugim przypadku adapter z głowicą montowany jest na tłoczysku cylindra pneumatycznego (lub cylindra hydraulicznego), a pneumatyka (hydraulika) jest włączana zgodnie z sygnałami z urządzenia sterującego.
W praktyce stosuje się kilka różnych konstrukcji adapterów i głowic czytających (rys. 4.22); ich zastosowanie zależy od rodzaju i konstrukcji igieł narzędziowych.
W automatycznej maszynie pomiarowej proces kontroli i pomiaru narzędzia oraz jego kodowania jest w pełni zautomatyzowany. Podstawą maszyny jest optyka urządzenie pomiarowe z czujnikami fotooptycznymi , który otrzymuje obraz instrumentu , oświetlane ze źródła poprzez układ optyczny. Ruchoma głowica optyczna, poruszająca się w trzech osiach, pozwala na inspekcję instrumentu i wyświetlanie jego obrazu na fotokomórkach. Lustro odchylające zapewnia pewną wielowymiarowość obrazu. Sygnały z fotokomórek trafiają do specjalnego analizatora, który wytwarza te sygnały, tworząc matematyczny model obrazu instrumentu.
Model ten jest odbierany przez mikrokomputer sterujący , będący głównym urządzeniem sterującym całej maszyny pomiarowej Mikrokomputer porównuje dane pomiarowe z podstawowymi danymi narzędzia określonymi przez bibliotekę narzędzi i generuje wartości oraz charakter korekcji narzędzia. Dane korekcyjne zapisywane są w koderze narzędzia, przesyłane (w razie potrzeby) do komputera centralnego, a następnie do maszyn CNC lub wyprowadzane na dowolne urządzenia peryferyjne w celu odbioru dokumentu
Narzędzie dostarczane jest do maszyny pomiarowej za pomocą zautomatyzowanego transportu montowanego w magazynie. Z za pomocą robota , który jest również kontrolowany przez mikrokomputer , narzędzie jest ładowane na stojak pomiarowy . Na pozycji wejściowej, za pomocą adaptera z głowicą odczytująco-zapisującą, narzędzie jest identyfikowane na podstawie danych jego enkodera. Informacje identyfikacyjne trafiają do mikrokomputera, który ustala schemat sterowania narzędziem, a następnie, gdy narzędzie znajduje się na stanowisku pomiarowym, steruje procesem tego sterowania. przesunięcie optyczne głowica pomiarowa wzdłuż osi x i y, ogniskowanie obrazu (przemieszczenie do osi z), obracając narzędzie w gnieździe stojaka. Narzędzie dociera (poprzez obrócenie stojaka ) do pozycji wyjściowej, którą w zasadzie można połączyć z pozycją wejściową. W tej pozycji głowica odczytowo-zapisująca jest ponownie podłączona do enkodera narzędzia , a wszystkie niezbędne dane powstałe w trakcie procesu kontrolno-pomiarowego zapisywane są do czujnika z mikrokomputera tego instrumentu. Następnie narzędzie jest albo zwracane przez robota do magazynu, albo do innego magazynu (np. magazynu dyskowego, który jest przystosowany do pracy na konkretnej maszynie, lub do przechowywania w magazynie magazynowym). Z i do maszyn, z magazynu narzędzi lub do magazynu, zapasy wysyłane są środkami zautomatyzowanymi (np. specjalnymi wózkami).
Aby narzędzia były łatwe i wygodne w obsłudze, należy je odpowiednio przygotować: narzędzie posiadające optymalną część tnącą powinno być odpowiednio naostrzone.
Dla ręczne ostrzenie używane narzędzia to ostrzałka, osełka, osełka i pilnik. Kolejność ostrzenia siekiery wyraźnie pokazano na rycinie 49.
Ryż. 49. Kolejność ostrzenia siekiery: a – fazowanie kamieniem gruboziarnistym; b – ostrzenie drobnoziarnistym kamieniem; c – finalizacja na kamieniu probierczym.
Podczas używania osełki ostrze narzędzia należy trzymać obiema rękami i przesuwać tam i z powrotem po powierzchni osełki. Nacisk wywierany jest na narzędzie podczas ruchu do przodu; podczas ruchu do tyłu nacisk można pominąć. Powierzchnia cięcia jest nachylona w taki sposób, że faza dotyka całej płaszczyzny bloku.
Nacisk na ostrze nie powinien być zbyt silny. Co jakiś czas blok należy zwilżyć wodą. Ostrzenie prowadzi się do momentu pojawienia się zadziorów po stronie przeciwnej do szlifowanej fazki.
Stosując ostrzałkę z tarczą szlifierską należy zachować szczególną ostrożność, aby uniknąć nadmiernego nagrzania metalu. Końcówkę roboczą należy częściej zanurzać w wodzie. Podczas procesu ostrzenia ostrze jest równomiernie i równomiernie dociskane do koła, zapewniając zachowanie kąta ostrzenia ostrza i prostoliniowości jego krawędzi tnących (ryc. 50).
Ryż. 50. Ściernica.
Po naostrzeniu krawędzie ostrza są uszlachetniane osełką, usuwając wyszczerbienia, zadziory i inne wady. Chwyć narzędzie obiema rękami i płynnie przesuwaj je po powierzchni osełki, utrzymując prawidłowy kąt nachylenie Powierzchnię osełki należy okresowo zwilżać wodą lub olejem.
Po serii ruchów ostrze należy obrócić w drugą stronę, następnie położyć płasko na osełce i odciągnąć w celu usunięcia zadziorów.
Ostrzenie pozwala sprawdzić jakość samego narzędzia. Podczas ostrzenia instrument jakości powstałe zadziory można łatwo usunąć podczas edycji na osełce. Jeśli w ogóle nie ma zadziorów lub szybko odpadają, oznacza to, że narzędzie jest zbyt hartowane i szybko się zużyje. Tworzenie się długich zadziorów świadczy o tym, że narzędzie jest wykonane ze zbyt miękkiego materiału.
Dłuta i strugi ostrzy się na ściernicy, której powierzchnię należy zwilżyć.
Prawie wszystko rodzaje ćwiczeń można ostrzyć na osełce lub osełce. Można do tego celu użyć drobno przyciętego pilnika, a do usunięcia zadziorów użyć osełki.
Wskazane jest naostrzenie frezu i końcówek drogowych do wierteł. Strona zewnętrzna Lepiej nie dotykać robotników drogowych, aby nie zmniejszyć średnicy wiertła.
Lepiej ostrzyć wewnętrzna strona. Jeśli to możliwe, należy zachować ten sam kształt części roboczych, ponieważ nadmierne piłowanie prowadzi do szybkiej awarii wiertła. Nóż poziomy ostrzy się od góry, a powstałe zadziory należy usunąć osełką. Nie zaleca się ostrzenia noża poziomego od dołu, ponieważ spowoduje to usunięcie krawędzi tnącej.
Podczas ostrzenia poziomego wiertła tnącego należy oprzeć końcówkę o kawałek drewna, pomagając sobie lewą ręką; część przylegająca do środka nad końcówką śruby musi być zaokrąglona. Wiertło do drewna powinno mieć również ostrą gwintowaną końcówkę centrującą. Żądło ostrzy się trójkątnym pilnikiem z drobnym nacięciem lub pilnikiem igłowym.
Skuteczna praca z elektronarzędziami wymaga pewnych umiejętności. Ich przygotowanie należy przeprowadzić ze szczególną starannością. Na przykład użycie strugarki elektrycznej, której ostrza są nieprawidłowo ustawione lub naostrzone, prowadzi do nieodwracalnego uszkodzenia obrabianego przedmiotu, a duża prędkość i posuw wiertarki elektrycznej może spowodować zapalenie się drewna. Dlatego zaleca się najpierw sprawdzić prawidłowe ustawienie elektronarzędzia na niepotrzebnym kawałku drewna, a następnie przejść do wykonywania głównej pracy.
Narzędzia skrawające można ostrzyć przy użyciu ostrzarek uniwersalnych i specjalnych. Ostrzarka służy do ostrzenia noży płaskich, piły tarczowe, dłutowanie i piłowanie łańcuchowe. Posiada napęd elektryczny oraz zestaw wymiennych mechanizmów przeznaczonych do różnych prac związanych z ostrzeniem.
Z książki: Korshever N. G. Pracuje na drewnie i szkle
Jeden z niezbędne warunki efektywne działanie narzędzi skrawających jest terminowe i staranne przygotowanie go do pracy.
Ostrzenie noże tnące maszyny do rozdrabniania. W praktyka domowa Istnieją dwa rodzaje pracy zrębarek: opcje technologiczne ostrzenie noży tnących. Pierwsza z nich przeznaczona jest do stosowania standardowego sprzętu ostrzącego i polega na wyjęciu noży tnących z części roboczej (tarcza, bęben) maszyny w celu ostrzenia. Druga opcja polega na zastosowaniu specjalnych mechanizmów i urządzeń ostrzących instalowanych bezpośrednio na rozdrabniarce lub instalowanych podczas ostrzenia noża. Opcja ta nie wymaga wyjmowania zestawu noży z maszyny.
Pierwsza opcja ostrzenia noży stała się bardziej powszechna, co pozwala wysoka jakość i dokładność ostrzenia noży. Zaletą drugiej opcji jest to, że ostrzenie jest mniej pracochłonne. Oczywiście jakość ostrzenia w tym przypadku będzie nieco niższa. Ponadto noże ostrzone w pozycji roboczej wymagają regulacji, szczególnie jeśli podczas ostrzenia zostanie usunięta duża warstwa. W tym celu należy poluzować śruby mocujące, ustawić noże według szablonu i ponownie je skręcić, co wiąże się ze znanymi kosztami robocizny. Druga opcja ostrzenia stosowana jest na rębaku DU-2.
Noże tnące rębaków MRNP-30, MRG-20N i MRG-40 ostrzy się według pierwszego wariantu, przy użyciu standardowych maszyn nożowych produkowanych na rynku.
W zależności od sposobu podawania, maszyny nożowe są automatyczne, z ręcznym posuwem wzdłużnym i poprzecznym, lub półautomatyczne, w których posuw wzdłużny noża (lub okręgu) następuje automatycznie, a posuw poprzeczny ręcznie za pomocą koła zamachowego. Najbardziej rozpowszechnione Do ostrzenia noży skrawających zrębarek otrzymaliśmy automatyczne ostrzarki typu TchN.
Aby nadać skośnemu skosowi noża spiralny kształt ze zmiennym kątem ostrzenia, zainstaluj specjalne urządzenie(imadło), które zapewnia wstępne zgięcie noża przed ostrzeniem pod określonym kątem. Nóż naostrzony w pozycji zakrzywionej, po zwolnieniu z imadła, bierze Płaski, a zaostrzona faza jest spiralna.
W urządzeniu montowane są jednocześnie dwa noże, które zabezpieczane są zaciskami za pomocą nakrętek. W adaptacji do maszyny MRG-40 noże montuje się w taki sposób, aby po naostrzeniu krawędź tnąca znajdowała się w odległości 2,5 ± 0,5 mm od końcówek płytek, na których oparty jest nóż.
Po dokręceniu nakrętek zacisków mocujących noże przyjmują kształt spiralny. Stół obrotowy maszyna do ostrzenia ustawiony na tarczy pod kątem ostrzenia 0,56 rad.
Po naostrzeniu sprawdź prostoliniowość krawędzi tnących noży za pomocą linijki. Tolerancja wynosi 0,3 mm. Krawędź tnąca jest wypełniona (wykończona) ręcznie drobnoziarnistym kamieniem.
Szerokość montażową noży tnących po naostrzeniu reguluje się za pomocą podkładek umieszczonych pod blokami podporowymi noży i sprawdza się kalibrem. Odchylenie szerokości zabudowy nie powinno przekraczać 0,1 mm.
Wybierając rodzaj ostrza maszyny, należy wziąć pod uwagę wielkość noży, które mają być ostrzone oraz nakład pracy.
Przygotowanie pił tarczowych polega na naostrzeniu, usunięciu wad i kuciu ostrza. Ostrzenie pił odbywa się na maszynach z ręcznym lub półautomatycznym przesuwaniem tarczy ostrzącej. Najkorzystniejszy jest półautomatyczny model maszyny TchPA-3.
Podczas prostowania pił eliminowane są różne defekty zakłócające płaskość krawędzi piły (zagięcia, fałdy i wybrzuszenia). Aby zwiększyć sztywność i stabilność krawędzi tnącej podczas pracy, piła jest kuta wzdłuż strefy pierścieniowej. Zwykle krawędzie piły i część środkowa nie są kute. Prawidłowo kuta piła, zawieszona na środkowym otworze, przy lekkim uderzeniu ręką od dołu w powierzchnię boczną powinna dać wynik czysty dźwięk i lekko wibrują w części peryferyjnej. Grzechotający dźwięk i silne wibracje wskazują na obecność wad lub nieprawidłowe kucie. Do prostowania i kucia pił wykorzystuje się zestaw narzędzi piłowych, w skład którego wchodzą młotki do prostowania i kucia, linijki i kowadła.