Wielka encyklopedia ropy i gazu. Obserwacje stanu korozyjnego rurociągów
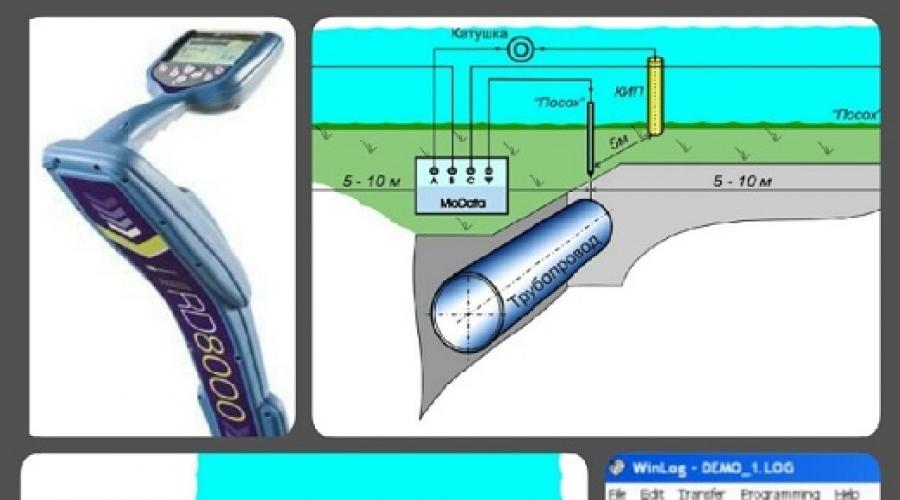
Przeczytaj także
Ocena stanu korozyjnego rurociągu zlokalizowanego w pole elektryczne Linie elektroenergetyczne PT produkowane są w oparciu o różnicę potencjałów pomiędzy rurą a gruntem oraz wielkość prądu w rurociągu.
Lok-schemat kompleksowej oceny stanu technicznego jednostki MG. W przyszłości należy ocenić stan korozji MG LP część integralna kompleksowa ocena stanu technicznego głównego gazociągu.
Schemat pojawiania się i rozmnażania wędrowców. Oceniając stan korozji gazociągu, ważna jest znajomość zarówno średnich, jak i maksymalnych wartości różnicy potencjałów.
Przyrządy do oceny warunków korozyjnych muszą obejmować czujniki, system rejestrujący i odpowiednie źródła zasilania. Przy stosowaniu metod magnetycznych i elektromagnetycznych możliwe jest zastosowanie różnych układów magnesujących. Problem skanowania rozwiązuje się albo poprzez niewielką liczbę czujników poruszających się wewnątrz rury po linii śrubowej, albo przez dużą liczbę czujników poruszających się do przodu wraz z układem magnesującym i rozmieszczonych na obwodzie urządzenia. W takim przypadku najbardziej wskazane jest zastosowanie dwupierścieniowego układu naprzemiennego ułożenia czujników, aby wyeliminować ewentualne pominięcia defektów na rurze. Urządzenia typu Linenalog produkowane w USA składają się z trzech sekcji połączonych zawiasami. Pierwsza sekcja zawiera zasilacze i kołnierze uszczelniające, druga zawiera elektromagnes z systemem kasetowym na czujniki, a trzecia zawiera elementy elektroniczne i urządzenie rejestrujące. Służą one do inspekcji rurociągów.
Wiercenie w celu oceny stanu korozji rurociągu należy przeprowadzić przy całkowitym otwarciu rury i możliwości sprawdzenia jej dolnej tworzącej. Długość odsłoniętej części rury musi wynosić co najmniej trzy średnice.
Skuteczną metodą oceny stanu korozyjnego urządzenia (na etapie jego projektowania, eksploatacji, renowacji) jest monitoring korozji – system obserwacji i przewidywania stanu korozyjnego obiektu w celu uzyskania w porę informacji o ewentualnych jego uszkodzeniach korozyjnych.
W tabeli 6 przedstawiono ocenę rzeczywistego stanu korozji systemów zaopatrzenia w ciepłą wodę z rur czarnych w szeregu miast. Dodatkowo dla porównania podano obliczone wskaźniki nasycenia wodą w temperaturze 60 C, dane dotyczące zawartości rozpuszczonego tlenu i wolnego dwutlenku węgla w wodzie oraz ocenę aktywności korozyjnej.
Rozkład obszarów prędkości ruchu przepływu wody, gazu i oleju dla rurociągów różne średnice. Badania korozyjne strun osłonowych przeprowadza się w celu oceny ich stanu korozyjnego (zarówno w głębi, jak i na obszarze pola), określenia parametrów ochrony elektrochemicznej, identyfikacji przyczyn nieszczelności strun osłonowych w trakcie eksploatacji oraz monitorowania bezpieczeństwa.
Na podstawie analizy powyższych danych dotyczących oceny stanu korozyjnego i niezawodności urządzeń i procesów technologicznych w ONGKM, wyników defektoskopii liniowej i zewnętrznej, polowych i laboratoryjnych badań korozyjno-mechanicznych, badań metalograficznych szablonów i próbek, na podstawie wyników diagnostyki technicznej konstrukcji, a także biorąc pod uwagę aktualne dokumenty normatywne i techniczne (NTD), opracowano metodologię diagnozowania urządzeń i procesów technologicznych złóż ropy i gazu zawierających siarkowodór.
W kraju i za granicą opracowywane są metody i instrumenty umożliwiające ocenę stanu korozyjnego rurociągu bez jego otwierania. Najbardziej obiecujące metody polegają na przepuszczeniu przez rurociąg specjalnie wyposażonego urządzenia, które wykrywa ogniska uszkodzeń korozyjnych ścianki rury od wewnątrz i od zewnątrz. W literaturze można znaleźć dane dotyczące metod monitorowania stanu rurociągów. Główną uwagę zwraca się na metody magnetyczne i elektromagnetyczne, preferując te drugie. W tym miejscu krótko opisano także metody ultradźwiękowe i radiograficzne.
Modele, które nie są opisane żadnymi równaniami matematycznymi i są prezentowane w postaci zestawu tabelarycznych współczynników lub nomogramów zalecanych do oceny stanu korozyjnego metali.
Aby ocenić stan powłoki na rurociągu podczas pracy, zaleca się wykorzystanie rezystancji stykowej izolowany rurociąg, parametry charakteryzujące przepuszczalność materiału powłokowego oraz ilość przeciwutleniacza (dla kompozycji stabilizowanych) pozostającego w powłoce. Do oceny stanu korozyjnego ścianki rury należy wykorzystać dane z pomiarów ubytków korozyjnych metalu pod powłoką lub w miejscach jej uszkodzeń, a także wielkość i względne położenie zmian korozyjnych na ściance rury. Druga obejmuje korozję lokalną (wgłębienia, wżery, plamy), pojedynczą (przy odległości między najbliższymi krawędziami sąsiednich zmian większą niż 15 cm), grupową (przy odległości między najbliższymi krawędziami sąsiednich zmian od 15 do 0,5 cm ) i rozszerzone (z odległością pomiędzy najbliższymi krawędziami sąsiednich zmian mniejszą niż 0,5 cm). Pojedyncze zmiany korozyjne nie powodują uszkodzeń rurociągów.
Aby ocenić stan powłoka izolacyjna na rurociągu w trakcie eksploatacji należy uwzględnić wartości rezystancji przejściowej rurociągu, parametry charakteryzujące przepuszczalność materiału powłokowego oraz ilość przeciwutleniacza (dla kompozycji stabilizowanych) pozostającego w izolacji. Do oceny stanu korozyjnego ścianki rury należy wykorzystać dane z pomiarów ubytków korozyjnych metalu pod powłoką lub w miejscach jej uszkodzeń, a także wielkość i względne położenie zmian korozyjnych na ściance rury.
Oceniając stan korozji rurociągu, określa się rodzaje korozji, stopień uszkodzeń korozyjnych zewnętrznej ściany rur z ogólną charakterystyką odcinków, ocenia się maksymalną i średnią szybkość korozji oraz stan korozji rurociągu. odcinek przewidywany jest na 3 – 5 lat.
W tabeli 9.12 zapewnia ocenę stanu korozyjnego rurociągu z pełnym zestawem czynników wpływających i odpowiednimi zaleceniami.
W praktyce do ilościowego określenia odporności metali na korozję można wykorzystać dowolną właściwość lub cechę metalu, która zmienia się znacząco i naturalnie podczas korozji. Zatem w instalacjach wodociągowych stan korozji rur można ocenić na podstawie zmian w czasie oporów hydraulicznych instalacji lub jej odcinków.
Aby znaleźć możliwość ograniczenia strat metali w wyniku korozji oraz ograniczenia znacznych bezpośrednich i pośrednich strat z tytułu korozji, należy ocenić stan korozyjny urządzeń i komunikacji chemicznych układów technologicznych. W takim przypadku konieczne jest przeprowadzenie zarówno oceny stanu korozyjnego układu chemiczno-technologicznego, jak i prognozy możliwego rozwoju korozji oraz wpływu tego procesu na pracę urządzeń i komunikację systemów chemiczno-technologicznych .
Technikę pomiaru podano w rozdziale II. Zakres i zestaw pomiarów niezbędnych do oceny stanu korozyjnego konstrukcji określają zatwierdzone w określony sposób instrukcje wydziałowe.
Złożoność i oryginalność procesu korozji podziemnego metalu i konstrukcje żelbetowe doprowadzony do formy specjalne warunkiśrodowisko podziemne, w którym atmosfera, biosfera i hydrosfera oddziałują na siebie. W tym zakresie szczególną uwagę zwraca się na rozwój i tworzenie urządzeń i systemów oceny stanu korozyjnego obiektów znajdujących się pod ziemią. Oceny takiej można dokonać poprzez pomiar uśrednionego w czasie potencjału konstrukcji metalowej względem gruntu. Do określenia średniej wartości potencjału opracowano urządzenia – integratory prądu błądzącego. Są łatwe w produkcji, nie wymagają specjalnych zasilaczy i są niezawodne w działaniu. Zastosowanie tych urządzeń dostarcza informacji o charakterze przestrzennego rozmieszczenia stref anodowych, katodowych i przemiennych, umożliwiających wybór miejsca podłączenia środków ochrony elektrochemicznej i integralne rozliczenie efektywności jego działania. Informacje te można wykorzystać zarówno podczas projektowania, budowy i montażu nowego sprzętu, jak i podczas eksploatacji. Możliwe staje się wdrożenie zaplanowanych środków zapewniających wysoką niezawodność konstrukcji metalowych i żelbetowych w długotrwałych warunkach eksploatacji.
Ocenę ryzyka korozji stalowych rurociągów podziemnych na skutek oddziaływania transportu zelektryfikowanego zasilanego prądem przemiennym należy dokonać w oparciu o wyniki pomiarów różnicy potencjałów pomiędzy rurociągiem a środowisko. Technikę pomiaru podano w rozdziale II. Objętość i kompleks pomiarów niezbędnych do oceny stanu korozyjnego rurociągu określają instrukcje wydziałowe zatwierdzone w określony sposób.
Monitorowanie reżimu odbywa się na podstawie wyników analiz próbek wody i pary, odczytów pH-metrów wody zasilającej i kotłowej, okresowych oznaczeń składu ilościowego i jakościowego osadów, a także oceny stanu metalu kotłowego pod względem korozji. Personel operacyjny monitoruje w szczególności dwa główne wskaźniki reżimu: dawkę kompleksu (w oparciu o spadek poziomu w liczniku roztworu roboczego 7, przeliczoną na zużycie wody zasilającej) i pH wody kotłowej w komorze czystej. Wycinanie reprezentatywnych próbek rur powierzchni grzewczych, analiza jakościowa i ilościowa osadów oraz ocena stanu korozyjnego metalu w porównaniu ze stanem wyjściowym w pierwszych 1 - 2 latach funkcjonowania reżimu przeprowadzane są co 5 - 7 tys. godziny operacji.
Dlatego zdarzają się przypadki, gdy w wyniku niedokładnego określenia lokalizacji uszkodzeń korozyjnych na powierzchni i wewnątrz rurociągu na skutek reasekuracji, dopuszcza się nieuzasadnioną wymianę rurociągu na znacznych obszarach, co prowadzi do dużych przekroczeń środków publicznych. Dlatego wymagana jest rzetelna ocena stanu korozyjnego rurociągów oraz terminowa i prawidłowa naprawa w oparciu o uzyskane dane. W tym celu opracowano, skonstruowano i przetestowano w naszym kraju defektoskopy, umożliwiające ocenę stanu korozyjnego rurociągów bez otwierania ich z wykopu.
Diagnostyka to słowo często używane w nowoczesny świat. Jest tak mocno zintegrowany z naszym codziennym cyklem słownictwa, że nie zwracamy na niego szczególnej uwagi. Złamał pralka- diagnostyka, serwisowanie ulubionego samochodu - diagnostyka, wizyta u lekarza - diagnostyka. Osoba uczona powie: diagnoza z języka greckiego oznacza „umiejętność rozpoznawania”. Co więc tak naprawdę trzeba rozpoznać w stanie technicznym przedmiotu metalowego ulegającego korozji oraz w systemach ochrony elektrochemicznej (głównie katodowej), jeśli takie występują na obiekcie? Porozmawiamy o tym pokrótce w tej recenzji.
Przede wszystkim ustalmy warunki. Termin diagnostyka korozyjna (badanie) używany jest w 90% przypadków mówimy o o zewnętrznej powierzchni danego obiektu. Diagnostykę wykonuje się m.in. na powierzchni zewnętrznej rurociągów podziemnych, zbiornikach i innych konstrukcjach metalowych narażonych na korozję gruntu lub na skutek działania prądów błądzących, powierzchni zewnętrznej konstrukcji nabrzeży skorodowanych pod wpływem soli i świeża woda itp. Jeśli mówimy o analizie procesów korozyjnych na wewnętrznej powierzchni tych samych rurociągów lub zbiorników, to zamiast terminów „diagnostyka” czy „inspekcja” używa się zwykle terminu „monitoring”. Różne terminy sugerują różne zasady zapewnienie bezpieczeństwa korozyjnego - badanie stanu korozyjnego powierzchni zewnętrznej przeprowadza się zazwyczaj dyskretnie, raz na 3-5 lat, a monitorowanie procesów korozyjnych wewnątrz badanego obiektu prowadzi się w sposób ciągły lub w krótkich odstępach czasu (raz na miesiąc) ).
Od czego więc zacząć diagnozowanie stanu korozji danego obiektu? Z oceny potencjalnego zagrożenia i obecna sytuacja od rzeczy. Jeżeli obiekt znajduje się np. pod wodą, to w pierwszym etapie potencjalnie istnieje możliwość przeprowadzenia oględzin pod kątem występowania uszkodzeń korozyjnych i śladów korozji, a w przypadku ich wystąpienia, oceny aktualnego i przewidywanego zagrożenia. W miejscach, w których nie jest możliwa kontrola wzrokowa, potencjalne zagrożenie ocenia się na podstawie sygnałów pośrednich. Rozważmy poniżej główne diagnozowalne parametry potencjalnego zagrożenia korozyjnego i ich wpływ na proces niszczenia korozyjnego:

Oprócz głównych czynników wskazanych powyżej, diagnozując stan korozji, w zależności od charakterystyki obiektu, bada się dużą liczbę dodatkowych parametrów, takich jak: wartość pH gleby lub wody (szczególnie przy potencjalnym zagrożeniu stresem pękanie korozyjne), obecność substancji żrących, mikroorganizmy, zawartość soli w glebie lub wodzie, możliwość napowietrzenia i zawilgocenia obiektu itp. Wszystkie te czynniki mogą w pewnych warunkach gwałtownie zwiększyć tempo niszczenia korozyjnego badanego obiektu.
Po zbadaniu parametrów potencjalnego zagrożenia korozyjnego często przeprowadza się bezpośrednie pomiary głębokości uszkodzeń korozyjnych na miejscu. Do tych celów wykorzystuje się całą gamę metod badań nieniszczących – badania wizualne i pomiarowe, metody ultradźwiękowe, badania magnetometryczne itp. Miejsca kontroli wybierane są pod kątem potencjalnego zagrożenia, jakie stwarzają, na podstawie wyników oceny przeprowadzonej w pierwszym etapie. W przypadku obiektów podziemnych wykopy wykonuje się w celu zapewnienia bezpośredniego dostępu do obiektu.
NA Ostatni etap może zostać spełniony badania laboratoryjne np. ocena szybkości korozji w warunkach laboratoryjnych czy badania metalograficzne składu i struktury metalu w miejscach uszkodzeń korozyjnych.
Jeżeli diagnostykę przeprowadza się na obiekcie, który jest już wyposażony w elektrochemiczne systemy antykorozyjne, to oprócz badania stanu korozyjnego samego obiektu przeprowadza się diagnostykę przydatności i jakości pracy istniejącego systemu ECP, tj. ogólnie jego wydajność, a w szczególności wartości parametrów wyjściowych i kontrolowanych. Opiszemy najwięcej ważne parametry Systemy ECP, które należy monitorować podczas przeprowadzania kompleksowego przeglądu systemów ECP.
- Potencjał katodowy. Główny parametr funkcjonalność katody i ochrona bieżnika. Określa stopień ochrony obiektu przed korozją za pomocą środków ECP. Standardowe wartości są ustalane przez fundamentalne dokumenty regulacyjne dla ochrony antykorozyjnej: GOST 9.602-2005 i GOST R 51164-98. Pomiar odbywa się zarówno w punktach stacjonarnych (oprzyrządowanie i centra kontroli), jak i wzdłuż trasy metodą zdalnej elektrody.
- Stan obiektów ECP: stacje ochrony katodowej, protektorowej i drenażowej, uziemienia anodowe, oprzyrządowanie, kołnierze izolacyjne, linie kablowe itp. Wszystkie cechy badanego sprzętu muszą mieścić się w wartościach określonych w projekcie. Dodatkowo należy sporządzić prognozę pracy sprzętu na okres do kolejnego przeglądu. Przykładowo stacje ochrony katodowej muszą posiadać rezerwę prądu, aby móc regulować potencjał ochronny obiektu podczas nieuniknionego starzenia się powłoki izolacyjnej. W przypadku braku rezerwy prądowej należy zaplanować wymianę stacji ochrony katodowej na mocniejszą i/lub naprawę uziemienia anodowego.
- Wpływ systemu ECP na obiekty obce. W przypadku błędów w projektowaniu systemów ECP, mogą one mieć szkodliwy wpływ na konstrukcje metalowe innych firm. Dzieje się tak szczególnie często w przypadku rurociągów na polach naftowych i gazowych, w obiektach przemysłowych i obiektach znajdujących się w gęstych obszarach miejskich. Mechanizm tego wpływu został szczegółowo opisany. Ocenę takiego wpływu należy koniecznie przeprowadzić w ramach diagnostyki systemów ECP.
Na podstawie wyników oględzin należy sporządzić protokół techniczny, który musi zawierać wszystkie dane liczbowe wykonanych pomiarów, wykresy potencjałów ochronnych i tzw. ślady, opis stwierdzonych braków i usterek, szczegółowe zdjęcia itp. . W raporcie należy również wyciągnąć wnioski na temat zagrożenia korozyjnego obiektu wraz z lokalizacją obszarów wysokiego ryzyka i zagospodarowaniem rozwiązania techniczne w sprawie zabezpieczenia antykorozyjnego.
Zatem po zakończeniu wszystkich etapów diagnostycznych Klient otrzymuje raport zawierający dokładna informacja w zależności od stanu korozyjnego obiektu i stanu układu ECP. Jednak informacje uzyskane przez zespoły diagnostyczne (czasami z dużym trudem, biorąc pod uwagę specyfikę terenu i klimatu) po prostu znikną i staną się nieistotne, jeśli nie zostaną przetworzone w określonym czasie, tj. nieterminowe usunięcie usterek stwierdzonych podczas oględzin lub brak wyposażenia obiektu kontroli w dodatkowe zabezpieczenia antykorozyjne. Sytuacja korozyjna w obiekcie stale się zmienia i jeśli otrzymane informacje diagnostyczne nie zostaną natychmiast przetworzone, mogą stać się bardzo nieaktualne. Dlatego też, jeśli właścicielowi zależy na bezpieczeństwie antykorozyjnym swoich obiektów, to system zabezpieczenia antykorozyjnego swoich obiektów jest regularnie modernizowany w oparciu o wyniki regularnie przeprowadzanych badań diagnostycznych, a ryzyko wystąpienia uszkodzeń korozyjnych na takich obiektach jest minimalne.
Tagi: prądy błądzące, diagnostyka korozji, diagnostyka stanu korozji, powłoka izolacyjna, wpływ indukcyjny, źródła prąd przemienny, zagrożenie korozyjne, mikroorganizmy niebezpieczne dla korozji, kontrola korozji, pękanie korozyjne naprężeniowe, stan korozji, odporność elektrolitu, stan powłoki izolacyjnej, ochrona elektrochemiczna, potencjał elektrochemiczny, ECP
Strona 2
Kontrola stanu korozji istniejących rurociągów i kabli znajdujących się w strefie oddziaływania prądów błądzących odbywa się poprzez pomiar różnicy potencjałów pomiędzy rurą a gruntem za pomocą woltomierza wysokooporowego. Strefy anodowe konstrukcji podziemnej są bardzo niebezpieczne i wymagają pilnych działań ochronnych. Stopień zagrożenia korozją w strefach naprzemiennych ocenia się na podstawie wartości współczynnika asymetrii (tabela I.
Analiza stanu korozyjnego prefabrykowanych rurociągów wodociągowych wykazała, że ich żywotność na polach Zachodni Surgut i Sołkinskoje nie przekracza 3–6 lat. W trakcie eksploatacji całkowicie wymieniono 14 km rurociągów w układzie utrzymania ciśnienia złożowego samego złoża West Surgut. W 1978 r. zarejestrowano 30 pęknięć i przetok na rurociągach na polu Sołkinskoje i 60 pęknięć na polu Zachodnie Surgutskoje.
Analiza stanu korozyjnego konstrukcji metalowych OOGKM wskazuje, że niedopuszczalne są stopniowe rozwarstwienia, które wnikają w materiał ścianek urządzeń typu skorupowego o więcej niż 50%.
Wykazała to analiza stanu korozji urządzeń instalacji oczyszczania gazu na złożu Orenburg powierzchnia wewnętrzna sprzęt pokryty jest jednolitą warstwą o grubości około 0,1 mm, stanowiącą osady piroforyczne.
Badanie stanu korozji urządzeń do produkcji HDPE pokazuje, że główną przyczyną korozji urządzeń jest narażenie na agresywne środowisko zawierające chlorowodór powstający podczas rozkładu katalizatora. Proces korozji sprzętu prowadzi do skrócenia jego żywotności, częste naprawy sprzętu i zanieczyszczenia polietylenu produktami korozji. Związki żelaza dostające się do polimeru negatywnie wpływają na jego właściwości fizykochemiczne i właściwości mechaniczne. Powodują przedwczesne starzenie się (zniszczenie) polimeru, niepożądane zabarwienie wyrobów na ciemnoszary kolor, zwiększają kruchość i zmniejszają właściwości dielektryczne polimeru. Dodatkowo, gdy sprzęt pokryty lakierami ulega korozji, zdarza się, że cząsteczki lakieru przedostają się do polietylenu, co prowadzi do jego pęcznienia lub powstania porów wewnątrz polimeru.
Przez stan korozyjny MG LC rozumie się wyrażenie ilościowe wskaźniki operacyjne odcinka głównego gazociągu zawierające defekty korozji i (lub) pochodzenia korozyjnego naprężeniowego.
W celu określenia stanu korozji (diagnostyka) i szybkiego wykrycia ewentualnych uszkodzeń korozyjnych, maszyny w eksploatacji poddawane są okresowym przeglądom.
W przyszłości zdalne określenie stanu korozji umożliwi prowadzenie przyspieszonych badań z kontrolowanym eksperymentem i modelowaniem poszczególnych etapów procesu korozji.
Określenie stanu korozji i dobór sposobu zabezpieczenia nowo budowanych gazociągów przed oddaniem ich do eksploatacji (przed przyłączeniem do istniejącej sieci), pomiary elektryczne. Wstępnie nowo ułożone rurociągi są manewrowane przez eksploatowanych w celu uzyskania prawdziwego obrazu stanu elektrycznego gazociągów, jaki występuje po ich podłączeniu do istniejącej sieci. Jeśli w trakcie pomiarów okaże się, że potencjały nie przekraczają 0,1 V, to zazwyczaj połączenie wykonuje się bez żadnych warunków. Przy potencjałach powyżej OD V (do 0,6 V) można podłączyć nowy gazociąg do gazu pod warunkiem zapewnienia zabezpieczenia w ciągu 3 – 5 miesięcy. Przy wysokich potencjałach nowo budowane gazociągi nie mogą być podłączone do gazu przed urządzeniem ochronnym, ponieważ po krótkim czasie gazociąg może zostać zniszczony przez prąd, co z kolei może prowadzić do poważnych konsekwencji. Z praktyki znane są liczne przypadki zniszczenia niezabezpieczonych gazociągów przez prądy błądzące 1 - 2 miesiące po ich oddaniu do eksploatacji, a także przed oddaniem do eksploatacji, zwłaszcza w rejonie podstacji trakcji kolejowej.
Długoterminowa prognoza stanu korozyjnego odcinków gazociągów wymaga wybrania punktów charakterystycznych do monitorowania dynamiki korozji w stacjonarnych i mobilnych systemach monitorowania korozji oraz dostosowania przepisów dotyczących monitorowania parametrów korozyjnych i zabezpieczania gazociągów przed czynnikami korozyjnymi. różne rodzaje korozja.
Do kontroli stanu korozji stosuje się metody kontroli perdestrukcyjnej, które można stosować zarówno stale, jak i okresowo (ewentualnie dodatkowo) oraz na każdym etapie eksploatacji obiektów, niezależnie od ich stanu. Do takich metod zaliczają się ultradźwiękowe, radiograficzne i akustyczne metody wykrywania wad barwnych.
Do określenia stanu korozyjnego układu wykorzystuje się parametry termodynamiczne i eksperymentalne tego układu oraz zależności empiryczne. Program obejmuje prognozowanie potencjału metalu układu, siły prądu korozyjnego, przebiegu krzywych polaryzacji, obszaru odporności (aktywnej i pasywnej), pozwala znaleźć najbardziej niekorzystne kombinacje warunków, które zapewnić rozwój korozji. Autorzy zarysowali sposoby udoskonalenia programu prognozowania korozji, co powinno zwiększyć dokładność i wiarygodność prognozy wielkości charakteryzujących układ korodujący.
Stan korozji rurociągów jest jednym z głównych czynników charakteryzujących pracę MG LC, niezawodność i bezpieczeństwo jego eksploatacji. O ochronie rurociągów decyduje stan powłoki izolacyjnej i systemów ECP.
Do instalacji ochrony elektrochemicznej (ECP) kontrola stanu technicznego poszczególnych urządzeń odbywa się poprzez przeglądy okresowe. Jednocześnie sprawdzane są wskazania elektrycznych przyrządów pomiarowych urządzenia sterujące, pomiar potencjałów w punktach drenażowych, pomiar opór elektryczny więzy prąd stały, ocena ciągłości pracy instalacji ochrony katodowej za pomocą specjalnego miernika lub miernika energia elektryczna, kontrola połączenia kontaktowe, uziemienia anodowe, zespoły i zespoły instalacji.
Przeglądy przeprowadza się co najmniej: 4 razy w miesiącu dla instalacji ochrony drenażowej, 2 razy w miesiącu dla instalacji ochrony katodowej.
Stały monitoring pracy instalacji ochrony katodowej zapewniają urządzenia telemetryczne. Pozwala to na redukcję kosztów i czasu objazdów instalacji, skrócenie czasu przerw w ich pracy od momentu wykrycia awarii do chwili wymiany lub naprawy instalacji oraz zwiększa dokładność regulacji i stabilność parametrów urządzeń ECP.
Podczas sprawdzania stanu ochrony elektrochemicznej głównego odcinka gazociągu określa się:
Poziom ochrony katodowej rurociągu;
Wielkość potencjałów polaryzacyjnych metodą wyłączania źródła polaryzacji (MSS) lub metodami ekstrapolacji wykorzystującymi tę samą metodę systemy pomiarowe;
Prądy polaryzacyjne przepływające przez rurociąg zgodnie z metodą zalecaną przez GOST;
Wielkość oporności elektrycznej gleby;
Skład próbek elektrolitu międzywarstwowego zawartego w miejscach wybrzuszeń, worków i innych uszkodzeń powłoki izolacyjnej.
Monitorowanie bezpieczeństwa rurociągów polega na okresowym pomiarze potencjałów „konstrukcja-uziemienie” na całej długości rurociągu i porównaniu uzyskanych wartości z wartością wzorcową, a także określeniu całkowitego czasu, przez który rurociąg posiada wartość potencjału ochronnego na całej swojej długości .
Pomiar potencjałów na całej długości rurociągu odbywa się za pomocą zewnętrznej elektrody odniesienia z krokiem pomiarowym 10-20 m nie rzadziej niż raz na pięć lat. W takim przypadku pierwszy pomiar należy wykonać co najmniej 10 miesięcy po zasypaniu rurociągu.
Pomiary potencjału w kolumnach kontrolno-pomiarowych (CMC) i zdalnych elektrodach w punktach trasy, które posiadają wartości minimalne potencjał, produkowany co najmniej dwa razy w roku. Dodatkowo pomiary wykonywane są podczas prac związanych z rozwojem układów ECP, zmianami trybu pracy instalacji ochrony katodowej oraz podczas prac związanych z eliminowaniem źródeł prądów błądzących.
Na podstawie wyników pomiarów potencjałów należy skonstruować wykresy i określić zabezpieczenie na całej długości, a na podstawie danych z telemonitoringu dotyczących pracy instalacji ochrony katodowej lub ich przeglądów technicznych, zabezpieczenia rurociągów w czasie.
Monitorowanie stanu technicznego powłok izolacyjnych w trakcie budowy realizowanych na ukończonych budowach. Kontrola ciągłości odbywa się za pomocą polaryzacji katodowej. Dane o wynikach wprowadzane są do dokumentacji wykonawczej.
Kontrola powłok izolacyjnych w trakcie eksploatacji przeprowadzone w ramach kompleksowego badania MG. Porównanie danych uzyskanych podczas badania MG z danymi dokumentacja wykonawcza pozwala ocenić zmiany właściwości ochronnych powłok w czasie i długości.
Określenie stanu powłoki na badanym obszarze ocenia się dwuetapowo, stosując zarówno metodę bezpośrednią, jak i pośrednią.
Pośrednio na podstawie analizy danych dotyczących zmian gęstości prądu ochronnego w funkcji czasu i długości, wyników pomiarów potencjału rurociąg-ziemia oraz elektrometrycznych badań korozji;
Metoda bezpośrednia z selektywnym wżerowaniem.
Metody pośrednie Określenie stanu izolacji i systemu ECP obejmuje pomiary integralne i lokalne.
Metodami integralnymi określić charakterystykę badanego odcinka gazociągu jako całości. Metody te pozwalają ocenić stan powłoki na całej długości odcinka oraz określić miejsca złuszczenia i uszkodzeń izolacji. Jednocześnie identyfikowane są poszczególne specyficzne strefy, w których konieczne jest zastosowanie lokalnych metod monitorowania powłok i środków ECP.
Głównymi kryteriami określania częstotliwości kontroli izolacji bez otwierania wykopu są gęstość prądu ochronnego na rurociągu oraz rezystancja przejścia rurociąg-ziemia, które pozwalają na integralną ocenę jakości powłoki izolacyjnej. Na podstawie tych danych przy pomocy poszukiwaczy wyszukują miejsca uszkodzeń powłoki izolacyjnej i przeprowadzają selektywne kopanie.
Metoda bezpośrednia lub selektywne wżery polega na otwarciu gazociągu, oczyszczeniu jego powierzchni z ziemi, oględzinach powłoki izolacyjnej i pomiarze rezystancji styków np. metodą „ręczną”. W takim przypadku należy przeprowadzić pomiary ciągłości, przyczepności, grubości i przejściowej rezystancji elektrycznej powłoki. Pobieranie próbek izolacji i badania laboratoryjne powłok przeprowadza się co 3 lata eksploatacji. Jednocześnie pobierane są próbki gleby i elektrolitu w celu monitorowania systemu ECP.
Po kontroli izolacja jest otwierana, głównie w obszarach uszkodzenie mechaniczne i inne wady. Jeśli w oczyszczonych obszarach wykryta zostanie korozja i inne uszkodzenia, strefa inspekcji rozszerza się, aby określić granice uszkodzonego odcinka rury. Obowiązkowa kontrola obejmuje odcinek obwodowego złącza spawanego.
Stan powłok izolacyjnych monitoruje się metodą wżerów selektywnych po 3 latach od rozpoczęcia eksploatacji powłok oraz raz w roku po osiągnięciu krytycznych wartości ECP i obniżeniu miejscowej rezystancji styków do 10 om.
Zarówno metody całkowe, jak i lokalne są metodami elektrometrycznymi. Wykorzystują urządzenia prądu stałego i przemiennego i dzielą się na kontaktowe i bezdotykowe.
Stan korozji ocenia się na podstawie oględzin i pomiarów instrumentalnych w studzienkach kontrolnych. Najpierw dokonuje się ustaleń:
Na obszarach o niezadowalającym stanie powłoki ochronne;
W obszarach nie wyposażonych w ciągłą polaryzację katodową o wartości ochronnej;
Na odcinkach trasy zagrożonych korozją, do których zaliczają się odcinki gorące, na których temperatura przewożonych produktów przekracza 40°C, odcinki rurociągów eksploatowane na południe od 50. równoleżnika północna szerokość geograficzna, na glebach zasolonych (słone bagna, solonetzy, solody, takyry, sors itp.), na glebach nawadnianych;
W obszarach prądów błądzących;
Na obszarach, gdzie rurociągi wychodzą z ziemi;
Na skrzyżowaniach rurociągów;
Na zboczach wąwozów, wąwozów i rzek;
Na obszarach ścieków przemysłowych i bytowych;
Na obszarach z okresowym podlewaniem gleby.
Na oględziny oraz indywidualny pomiar stanu korozyjnego rurociągu w wykopie określa się:
Obecność i charakter produktów korozji;
Maksymalna głębokość jaskini;
Powierzchnia uszkodzona przez korozję.
Przeprowadzono kompleksowe badania stanu korozyjnego istniejących głównych rurociągów gazowych i naftowych oraz ich systemów ochrony elektrochemicznej w celu określenia zależności występowania uszkodzeń korozyjnych i naprężeniowo-korozyjnych na zewnętrznym CPZ od trybów pracy urządzeń ECP, identyfikacja i eliminacja przyczyn powstawania i rozwoju uszkodzeń korozyjnych i naprężeniowo-korozyjnych. Rzeczywiście, główne rurociągi gazowe i naftowe praktycznie nie ulegają starzeniu się w trakcie swojej eksploatacji. O niezawodności ich działania decyduje przede wszystkim stopień korozji i zużycia naprężeniowo-korozyjnego. Jeśli weźmiemy pod uwagę dynamikę wypadkowości gazociągów w latach 1995-2003, to staje się oczywiste, że ma miejsce proces zwiększania wypadkowości w czasie na skutek powstawania na KZP uszkodzeń korozyjnych i naprężeniowo-korozyjnych.
Ryż. 5.1.
Rozważając dynamikę usuwania szczególnie niebezpiecznych usterek na istniejących głównych gazociągach, staje się oczywiste, że w trakcie eksploatacji wzrasta liczba szczególnie niebezpiecznych usterek wymagających priorytetowej naprawy, spowodowanych korozją zewnętrzną i pęknięciami korozyjnymi naprężeniowymi (ryc. 5.1). Z pokazanego na ryc. Wykres 5.1 pokazuje, że prawie wszystkie wyeliminowane szczególnie niebezpieczne defekty mają charakter korozyjny lub naprężeniowo-korozyjny. Wszystkie te defekty wykryto na zewnętrznej powierzchni chronionej katodą.
Wyniki kompleksowych badań zabezpieczeń antykorozyjnych rurociągów gazowych i naftowych (obecność wżerów korozyjnych i pęknięć naprężeniowo-korozyjnych, przyczepność i ciągłość powłoki izolacyjnej, stopień ochrony elektrochemicznej) wskazują, że rozwiązaniem problemu ochrona antykorozyjna głównych rurociągów gazowych i naftowych za pomocą powłok izolacyjnych i polaryzacji katodowej pozostaje aktualna do dziś. Bezpośrednim potwierdzeniem tego są wyniki diagnostyki in-line. Według danych diagnostyki in-line, na niektórych odcinkach głównych rurociągów naftowych i gazowych o żywotności przekraczającej 30 lat, odsetek usterek korozja zewnętrzna(w tym korozja naprężeniowa) osiąga 80%. Łączna zidentyfikowane wady.
Jakość izolacji głównych rurociągów gazowych i naftowych charakteryzuje się wartością rezystancji przejścia, określoną na podstawie parametrów ochrony elektrochemicznej. Jednym z głównych parametrów ochrony elektrochemicznej rurociągów, charakteryzującym jakość powłoki izolacyjnej, jest wielkość prądu ochrony katodowej. Dane dotyczące eksploatacji urządzeń ECP wskazują, że wartość prądu ochronnego RMS na odcinku liniowym D 1220 mm w ciągu 30 lat eksploatacji na skutek starzenia się izolacji wzrosła prawie 5-krotnie. Pobór prądu na zabezpieczenie elektrochemiczne 1 km rurociągu naftowego w obszarze potencjałów ochronnych 1,2...2,1 V m.s. mi. wzrósł z 1,2 do 5,2 A/km, co wskazuje na proporcjonalny spadek oporu przejścia rurociągu naftowego. Przejściowa rezystancja izolacji po 30 latach eksploatacji rurociągów gazowych i naftowych jest tego samego rzędu (2,6-10 3 Ohm - m 2) na całej długości, z wyjątkiem obszarów, w których przeprowadzono remonty główne rurociągów gazowych i naftowych z wymianą izolacji, natomiast wielkość korozji i naprężeń – uszkodzeń korozyjnych na zewnętrznej powierzchni chronionej katodą waha się w znaczących granicach – od 0 do 80% całkowitej liczby defektów identyfikowanych za pomocą defektoskopii in-line, które są zlokalizowane zarówno na na skrzyżowaniach stref ochronnych oraz w pobliżu punktów odwadniających SCP na terenach nizinnych i podmokłych trasy. Wody gruntowe podmokłe części środkowej Zachodnia Syberia Charakteryzują się słabą mineralizacją (0,04% mas.) i co za tym idzie dużą rezystancją omową (60… 100 Ohm·m). Ponadto gleby bagienne są kwaśne. Wartość pH wód bagiennych osiąga wartość 4. Wysoka rezystancja omowa i kwasowość elektrolitu bagiennego to najważniejsze czynniki wpływające na szybkość korozji rurociągów gazowych i naftowych oraz skuteczność ich ochrony elektrochemicznej. Na uwagę zasługuje fakt, że w roztworach porowych gleb bagiennych zawartość siarkowodoru sięga 0,16 mg/l, czyli jest o rząd wielkości wyższa niż w glebach zwykłych i zbiornikach płynących. Siarkowodór, jak pokazują dane z badań, wpływa również na stan korozyjny rurociągów gazowych i naftowych. Na wystąpienie korozji siarkowodorowej na skutek działania bakterii redukujących siarczany (SRB) wskazuje np. fakt, że w innych identycznych warunkach maksymalna głębokość wnikania korozji zewnętrznej przez wady izolacji gazowej i rurociągów naftowych na stojących bagnach jest większa niż w zbiornikach płynących średnio o 70%, z jednej strony i prawie wszędzie, pęknięcia naprężeniowo-korozyjne na zewnętrznym KZP występują również na bagnach stojących o dużej zawartości H 2 S , na inne. Według współczesnych koncepcji molekularny siarkowodór stymuluje uwodornienie stali. Elektroredukcja H 2 S w rurociągu CCP przebiega poprzez reakcje H,S + 2-»2Н alc + S a ~ c i H,S + V-^Hads + HS”ac, który zwiększa stopień wypełnienia warstwy chemisorbowanej wodorem atomowym w ok, dyfundując w strukturę stali rurowej. Dwutlenek węgla jest również skutecznym stymulatorem uwodornienia: HC0 3 +e-> 2H adc +C0 3”. Problem korozyjności i
Zniszczenie spowodowane korozją naprężeniową rurociągów naftowych i gazowych na podmokłych obszarach trasy nie zostało jeszcze w pełni wyjaśnione i pozostaje aktualne. Wyniki badań korozyjnych głównych gazociągów i ropociągów na terenach podmokłych wykazały, że niemal cała zewnętrzna powierzchnia rurociągów ropy i gazu, zarówno w ubytkach izolacji, jak i pod złuszczoną izolacją, pokryta jest brunatnymi osadami (przypominającymi proszek aluminiowy). Wżery korozyjne o maksymalnej głębokości zlokalizowane są w otworowych uszkodzeniach izolacji. Parametry geometryczne uszkodzenia korozyjne niemal dokładnie odpowiadają geometrii uszkodzeń izolacji. Pod zerwaną izolacją, w miejscu kontaktu ścianki rury z wilgocią gruntową, stwierdza się ślady korozji bez widocznych wżerów korozyjnych ze śladami pęknięć korozyjnych naprężeniowych.
Doświadczalnie, wykorzystując próbki stali rurowej zamontowane przy ścianie głównego rurociągu naftowego o średnicy 1220 mm (w tworzących górnym, bocznym i dolnym), stwierdzono, że w glebach rejonu bagienno-tajgi środkowej części Rosji W zachodniej Syberii szybkość korozji próbek bez ochrony katodowej w przypadku uszkodzeń izolacji sięga 0,084 mm/rok. Poniżej potencjału ochronnego (ze składową omową) minus 1,2 V m.s. np. gdy gęstość prądu ochrony katodowej przekracza graniczną gęstość prądu tlenu 8...12 razy, szybkość korozji szczątkowej nie przekracza 0,007 mm/rok. Ta szczątkowa szybkość korozji, zgodnie z dziesięciopunktową skalą odporności na korozję, odpowiada stanowi korozji bardzo wytrwały oraz dla głównych rurociągów gazowych i naftowych jest dopuszczalne. Stopień ochrony elektrochemicznej w tym przypadku wynosi:
Podczas kompleksowych badań stanu korozyjnego zewnętrznej katodowej powierzchni rurociągów gazowych i naftowych w dołach, w ubytkach izolacji przelotowej stwierdza się wżery korozyjne o głębokości 0,5...1,5 mm. Nietrudno obliczyć czas, w którym ochrona elektrochemiczna nie hamowała szybkości korozji gleby, aż do r dopuszczalne wartości, odpowiedni bardzo wytrwały stan korozji rurociągów gazowych i naftowych:
przy głębokości wnikania korozji 0,5 mm przy głębokości wnikania korozji 1,5 mm
To za 36 lat działalności. Przyczyną spadku skuteczności elektrochemicznej ochrony rurociągów gazowych i naftowych przed korozją jest zmniejszenie przejściowej rezystancji izolacji, pojawienie się uszkodzeń przelotowych izolacji i w efekcie zmniejszenie gęstości prądu ochrona katodowa na skrzyżowaniach stref ochronnych SCZ do wartości, które nie osiągają wartości granicznej gęstości prądu dla tlenu, które nie zapewniają tłumienia korozji gleby do dopuszczalnych wartości, chociaż wartości ochronne potencjały mierzone ze składową omową są zgodne z normą. Ważną rezerwą, która pozwala zmniejszyć szybkość niszczenia korozyjnego rurociągów gazowych i naftowych, jest terminowa identyfikacja obszarów niedostatecznej ochrony, gdy 1 1 Lr
Korelacja uszkodzeń korozji zewnętrznej rurociągu naftowego z czasem trwania przerw w trasowych liniach napowietrznych wskazuje, że to właśnie w czasie przerw w trasowych liniach napowietrznych i przestojach VL występuje korozja wżerowa poprzez defekty izolacji, którego szybkość osiąga 0,084 mm/rok.

Ryż. 5.2.
W trakcie kompleksowych badań systemów ochrony elektrochemicznej głównych rurociągów gazowych i naftowych stwierdzono, że w obszarze potencjałów ochrony katodowej o wartości 1,5...3,5 V m.s. mi. (ze składnikiem omowym) gęstość prądu ochrony katodowej ja przekracza gęstość prądu ograniczającą tlen J 20... 100 razy lub więcej. Co więcej, przy tych samych potencjałach ochrony katodowej, gęstość prądu, w zależności od rodzaju gleby (piasek, torf, glina), zmienia się znacznie, prawie 3...7 razy. W warunkach terenowych, w zależności od rodzaju gruntu i głębokości ułożenia rurociągu (głębokość zanurzenia sondy wskaźnika korozji), graniczna gęstość prądu dla tlenu, mierzona na elektrodzie roboczej wykonanej ze stali 17GS o średnicy 3,0 mm, zmieniała się w granicach 0,08...0,43 A/m”, a gęstość prądu ochrony katodowej przy potencjałach ze składową omową od
1,5...3,5 V ms e., mierzone na tej samej elektrodzie, osiągnęły wartości 8...12 A/m 2, co powoduje intensywne wydzielanie się wodoru na powierzchnia zewnętrzna rurociąg. Część adatomów wodoru w tych trybach ochrony katodowej trafia do przypowierzchniowych warstw ścianki rurociągu, powodując jego uwodornienie. NA zwiększona zawartość wodór w próbkach wyciętych z rurociągów poddanych zniszczeniu naprężeniowo-korozyjnemu wskazywany jest w pracach autorów krajowych i zagranicznych. Wodór rozpuszczony w stali działa zmiękczająco, co ostatecznie prowadzi do zmęczenia wodorowego i pojawienia się pęknięć naprężeniowo-korozyjnych w strefach ochronnych podziemnych rurociągów stalowych. Problem zmęczenia wodorowego stali rurowych (klasy wytrzymałości X42-X70) przyciąga w ostatnich latach szczególną uwagę badaczy ze względu na rosnącą częstotliwość wypadków na głównych gazociągach. Zmęczenie wodorowe pod wpływem cyklicznie zmieniającego się ciśnienia roboczego w rurociągu obserwuje się niemal w całości czysta forma podczas nadprotekcji katodowej, kiedy j KZ /j >10.
Gdy gęstość prądu ochrony katodowej osiąga graniczną gęstość prądu dla tlenu (lub nieznacznie, nie więcej niż 3...5 razy przekracza ce), szybkość korozji szczątkowej nie przekracza 0,003...0,007 mm/rok. Znaczący nadmiar (ponad 10-krotny) j K t powyżej J praktycznie nie prowadzi do dalszego zahamowania procesu korozji, lecz prowadzi do uwodornienia ścianki rurociągu, co powoduje pojawienie się na KZP pęknięć naprężeniowo-korozyjnych. Pojawienie się kruchości wodorowej podczas cyklicznych zmian ciśnienia roboczego w rurociągu jest zmęczeniem wodorowym. Zmęczenie wodorowe rurociągów występuje, gdy stężenie wodoru katodowego w ściance rurociągu nie spada poniżej pewnego poziomu minimalnego. Jeżeli desorpcja wodoru ze ścianki rury następuje szybciej niż rozwój procesu zmęczeniowego, gdy zwarcie przekracza /pr nie więcej niż 3...5 razy, zmęczenie wodorowe
niewidoczny. Na ryc. Rysunek 5.3 przedstawia wyniki pomiarów gęstości prądu czujników wodoru przy włączonym (1) i wyłączonym (2) SCP na rurociągu Gryazowiec.

Ryż. 5.3.
i odłączony (2) SPS w punkcie kontrolnym I; 3 - potencjał ochrony katodowej przy włączonym SCZ - (a) oraz zależność prądów czujnika wodoru od potencjału rury przy włączonym i wyłączonym SCZ na CP 1 - (b)
Potencjał ochrony katodowej w okresie pomiaru mieścił się w zakresie minus 1,6...1,9 V m.s. mi. Postęp wyników pomiarów elektrycznych trasy przedstawiony na rys. 5.3a wskazuje, że maksymalna gęstość strumienia wodoru w ściankę rury przy włączonym RMS wynosiła 6...10 μA/cm2. Na ryc. 5.3, B Przedstawiono obszary zmian prądów czujników wodoru i potencjałów ochrony katodowej przy włączonym i wyłączonym SCZ.
Autorzy pracy zauważają, że potencjał rurociągu przy wyłączonym RMS nie spadł poniżej minus 0,9...1,0 V m.s. e., co wynika z wpływu sąsiedniego SCZ. Jednocześnie gęstości prądu czujników wodoru przy włączonym i wyłączonym SCZ różnią się
2...3 razy. Na ryc. Rysunek 5.4 pokazuje krzywe zmian prądów czujników wodoru i potencjałów ochrony katodowej na KP 08 węzła Krasnoturinsky.
Postęp badań eksperymentalnych pokazany na ryc. 5.4 wskazuje, że maksymalna gęstość strumienia wodoru w ściance rury nie przekraczała 12...13 μA/cm2. Zmierzone potencjały ochrony katodowej mieściły się w zakresie od minus 2,5...3,5 V m.s. mi. Powyżej wykazano, że objętość wodoru uwolnionego w CPC zależy od wartości kryterium bezwymiarowego jK z/u pr. W tym zakresie interesujące jest porównanie wyników diagnostyki liniowej istniejących głównych rurociągów naftowych i gazowych z trybami ochrony katodowej.

Ryż. 5.4.
W tabeli 5.1 przedstawia porównanie wyników diagnostyki in-line z wynikami kompleksowych badań systemów ECP istniejących rurociągów naftowych i gazowych w środkowej części zachodniej Syberii. Wyniki pomiarów elektrochemicznych na części liniowej istniejących rurociągów naftowych i gazowych wskazują, że w różnych gruntach przy tych samych wartościach mierzonego potencjału gęstości prądu ochrony katodowej wahają się w szerokich granicach, co powoduje konieczność dodatkowej kontroli katodowej gęstość prądu ochronnego przy doborze i regulacji potencjałów ochronnych rurociągów podziemnych w porównaniu z gęstością prądu ograniczającego tlen. Dodatkowe pomiary elektrochemiczne na trasie istniejących głównych rurociągów gazowych i naftowych zapobiegną lub zminimalizują powstawanie dużych naprężeń lokalnych w ściankach rurociągów, spowodowanych molizacją wodoru (o dużej energii figuratywnej). Wzrost poziomu naprężeń lokalnych w ścianie rurociągu wiąże się ze zmianą trójosiowości stanu naprężeń w lokalnych obszarach wzbogaconych w wodór katodowy, gdzie tworzą się mikropęknięcia, prekursory pęknięć naprężeniowo-korozyjnych na zewnętrznym CCP.
Porównanie wyników diagnostyki wewnątrzrurowej z wynikami kompleksowego badania instalacji
ochrona elektrochemiczna istniejących rurociągów gazowych i naftowych w środkowej części zachodniej Syberii
Dystans, |
Rozkład potencjału ochronnego (0WB) (Osoba A/m 2) |
Oznaczający kryteria J k.z Referencje |
operacja, mm |
Gęstość wady strata metan, |
Gęstość wady rozwarstwienie, | |||
Lilia część głównego rurociągu naftowego D 1220 mm |
||||||||
Dystans, |
Graniczna gęstość prądu dla tlenu (LrHA/m 2 |
Rozkład potencjału ochronnego i gęstość prądu ochrony katodowej (Rzęsy>A/m 2) |
Oznaczający kryteria Ук.з ^ Ур |
Maksymalna głębokość penetracji korozji przez cały okres operacja, mm |
Gęstość wady strata metal, |
Gęstość defektów rozwarstwienie, szt./km |
Całkowity czas przestoju VCS w całym okresie eksploatacji (wg organizacji obsługującej), dni |
|
Analiza wyników przedstawionych w tabeli. 5.1, biorąc pod uwagę czas przestoju, RMS wskazuje odwrotnie proporcjonalną zależność pomiędzy gęstością defektów korozyjnych a wartością kryterium bezwymiarowego jK S/ J, także wtedy, gdy stosunek ten był równy
zero. Rzeczywiście, maksymalna gęstość defektów korozja zewnętrzna obserwowane w obszarach, gdzie czas przestoju urządzeń ochrony elektrochemicznej (wg organizacji eksploatujących) przekraczał wartości standardowe. Z drugiej strony maksymalna gęstość wad typu rozwarstwienie zaobserwowano na podmokłych odcinkach trasy zalewowych, gdzie czas przestoju urządzeń ECP nie przekraczał wartości normatywnych. Analiza trybów pracy SCP w obszarach o minimalnym czasie ich przestoju na tle dużego rozrzutu danych wskazuje na niemal proporcjonalną zależność pomiędzy gęstością defektów tego typu rozwarstwienie i kryterium jK 3 / / gdy gęstość prądu ochrony katodowej przekroczyła graniczną gęstość prądu dla tlenu dziesięciokrotnie lub więcej razy w ciągu długi okres pracy (przy minimalnym czasie przestoju VCS). Analiza trybów ochrony katodowej w porównaniu z defektami korozyjnymi i naprężeniowo-korozyjnymi na CSC potwierdza wyciągnięte wcześniej wnioski, że stosunek jK 3 / jnp może służyć jako bezwymiarowe kryterium monitorowania szybkości korozji szczątkowej rurociągu przy różnych potencjałach ochrony katodowej, z jednej strony w celu zapobiegania tworzeniu się defektów na PSC korozja zewnętrzna oraz określenie intensywności uwodornienia elektrolitycznego ścianki rurociągu - z drugiej w celu wyeliminowania powstawania i wzrostu defektów takich jak rozwarstwienie w pobliżu powierzchni chronionej katodowo.
Dane tabeli 5.1 wskazują, że maksymalny czas przestoju prawie wszystkich SCP w całym okresie eksploatacji głównych rurociągów ropy i gazu, czyli ponad 36 lat, wyniósł średnio 536 dni (prawie 1,5 roku). Według organizacji operacyjnych, za rok przestój VCS wynosił średnio 16,7 dnia, za kwartał - 4,18 dnia. Ten czas przestoju SCP na liniowej części badanych rurociągów naftowych i gazowych praktycznie jest zgodny z wymaganiami dokumentów regulacyjnych i technicznych (GOST R 51164-98, klauzula 5.2).
W tabeli 6.2 przedstawia wyniki pomiarów stosunku gęstości prądu ochrony katodowej do gęstości prądu granicznego dla tlenu górna tworząca główny rurociąg naftowy D 1220 mm. Obliczenie szybkości korozji szczątkowej rurociągu przy danych potencjałach ochrony katodowej określa wzór 4.2. Podane w tabeli. Dane 5.1 i 5.2 wskazują, że przez cały okres eksploatacji głównego rurociągu naftowego, biorąc pod uwagę przestój urządzeń ochrony elektrycznej
(wg organizacji użytkującej) maksymalna głębokość wnikania korozji na zewnętrznym KZP nie powinna przekraczać 0,12...0,945 mm. Rzeczywiście, graniczna gęstość prądu dla tlenu na poziomie ułożenia badanych odcinków rurociągów naftowych i gazowych wahała się od 0,08 A/m 2 do 0,315 A/m 2 . Nawet przy maksymalnej wartości granicznej gęstości prądu dla tlenu wynoszącej 0,315 A/m 2 maksymalna głębokość wnikania korozji w ciągu 36 lat eksploatacji przy planowanym przestoju RMS wynoszącym 1,15 roku nie przekroczy 0,3623 mm. Stanowi to 3,022% nominalnej grubości ścianki rurociągu. Jednak w praktyce widzimy inny obraz. W tabeli 5.1 przedstawiono wyniki diagnostyki wewnątrzrurowej odcinka głównego rurociągu naftowego D u 1220 mm po 36 latach jego eksploatacji. Wyniki diagnostyki in-line wskazują, że maksymalne zużycie korozyjne ścianki rurociągu przekroczyło 15% nominalnej grubości ścianki rury. Maksymalna głębokość wnikania korozji osiągnęła 2,0 mm. Oznacza to, że przestój urządzeń ECP nie spełnia wymagań GOST R 51164-98, pkt 5.2.
Wykonane pomiary elektrometryczne przedstawiono w tabeli. 5.2 wskazują, że przy danym trybie ochrony katodowej szybkość korozji szczątkowej nie przekraczała 0,006...0,008 mm/rok. Ta szczątkowa szybkość korozji, zgodnie z dziesięciopunktową skalą odporności na korozję, odpowiada stanowi korozji odporny na korozję oraz dla głównych rurociągów ropy i gazu jest dopuszczalne. Oznacza to, że w ciągu 36 lat eksploatacji rurociągu, biorąc pod uwagę informacje o przestojach urządzeń ECP według organizacji eksploatującej, głębokość wnikania korozji nie przekroczyłaby 0,6411 mm. Rzeczywiście, w okresie planowanego postoju urządzeń ECP (1,15 roku) głębokość wnikania korozji wyniosła 0,3623 mm. W okresie eksploatacji urządzeń ECP (34,85 lat) głębokość wnikania korozji wyniosła 0,2788 mm. Całkowita głębokość wnikania korozji na KZP wyniesie 0,3623 + 0,2788 = 0,6411 (mm). Wyniki diagnostyki wewnątrzrurowej wskazują, że rzeczywista maksymalna głębokość wnikania korozji w ciągu 36 lat eksploatacji na badanym odcinku głównego rurociągu naftowego D u 1220 mm wyniosła 1,97 mm. Na podstawie dostępnych danych łatwo obliczyć czas, w którym ochrona elektrochemiczna nie zahamowała tempa korozji gleby do akceptowalnych wartości: T = (1,97 - 0,6411) mm/0,08 mm/rok = 16,61 lat. Czas przestoju urządzeń ECP na głównym gazociągu o średnicy 1020 mm biegnącym w jednym korytarzu technicznym, po którym znajduje się teren zalewowy rzeki. Ob., odkryto pęknięcia naprężeniowe i korozyjne, co zbiega się z czasem przestoju SCP na głównym rurociągu naftowym, gdyż SCP gazociągu i ropociągu zasilane są z jednej wzdłużnej linii napowietrznej.
W tabeli 5.3 przedstawiono wyniki wyznaczania rzeczywistego czasu przestoju SCP w całym okresie eksploatacji (36 lat) głównych rurociągów ropy i gazu na podstawie pomiarów elektrometrycznych.
Tabela 5.2
Rozkład szybkości korozji szczątkowej na odcinkach eksploatowanych rurociągów gazowych i naftowych w środkowej części zachodniej Syberii
Tabela 5.3
Wyniki określenia rzeczywistego czasu przestoju SCP w całym okresie eksploatacji (36 lat) głównych rurociągów gazowych i naftowych na podstawie pomiarów elektrometrycznych
Dystans, |
Maksymalny możliwa prędkość korozja rurociągu bez zwarcia, mm/rok |
Resztkowa szybkość korozji rurociągu w danym trybie zwarcia, mm/rok |
Maksymalna głębokość wnikania korozji na powierzchnię chronioną katodowo, mm |
Prawdziwy |
Część liniowa głównego rurociągu naftowego D 1220 mm |
||||
Część liniowa główny gazociąg Dł. 1020 mm |
||||
Analiza wyników przedstawionych w tabeli. 5.3 na to wskazuje czas rzeczywisty czas przestoju urządzeń ochrony elektrochemicznej znacznie przekracza znaczenie normatywne, co jest przyczyną intensywnego zużycia korozyjnego ścianki rurociągu od strony zewnętrznej, chronionej katodowo.