Biblioteca eletrônica científica. Introdução do conceito de "produção enxuta" na OJSC "Nizhnekamskshina"
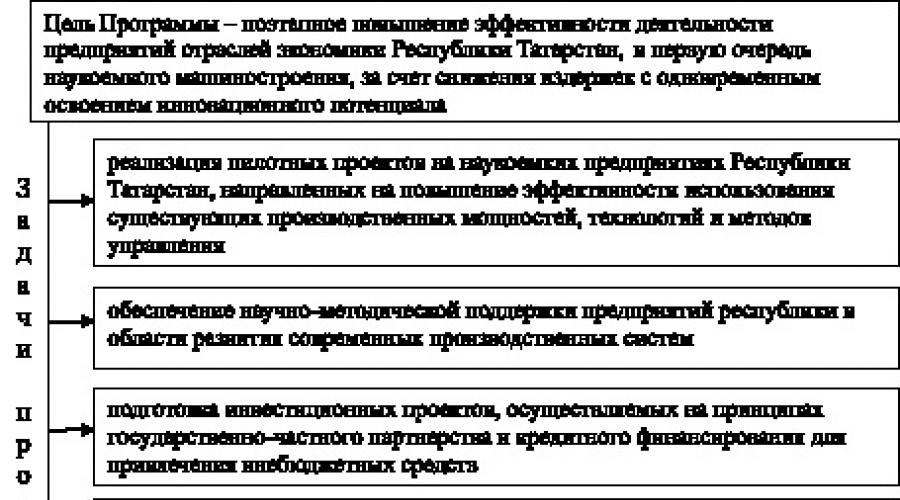
O efeito económico da produção enxuta de apenas uma unidade de negócios da TechnoNIKOL é comparável ao orçamento médio de um programa-alvo regional
/Junho de 2014/ Mais de 200 milhões de rublos por ano - este é o efeito econômico da introdução de princípios de manufatura enxuta nas fábricas Lã de pedra Corporação TechnoNIKOL.
A TechnoNIKOL Corporation é uma das líderes na Rússia em termos de produtividade do trabalho. A produtividade média da empresa é de 12 milhões de rublos em receita por pessoa por ano, enquanto empresas altamente produtivas na Rússia são consideradas empresas nas quais esse número começa em 3 milhões de rublos. Um dos segredos do sucesso na luta para aumentar a produtividade do trabalho é o uso ativo dos princípios da manufatura enxuta nas empresas da empresa.
Segundo o diretor de desenvolvimento sistema de produção Tatyana Bertova, Magro Desde 2010, está implantado, inclusive, em seis unidades produtivas da direção de Isolamento Mineral, localizadas na Ucrânia, no Distrito Federal Central, na região do Volga, na Sibéria, bem como nos Urais e no Extremo Oriente. Em todas as fábricas, é dada grande atenção à formação em sistemas e ferramentas de produção enxuta, que abrange todos - tanto o pessoal de trabalho como a gestão de topo.
Uma parte integrante da produção enxuta na direção de Isolamento Mineral é o trabalho de melhoria, no qual todos os funcionários da SBU estão envolvidos. Mais de duas mil propostas de racionalização recebidas de trabalhadores e especialistas em engenharia são implementadas anualmente. Podem ser tanto pequenas melhorias como projetos inovadores com um grande efeito económico. Por exemplo, melhorar os processos de mudança de uma linha de produção permitiu em três anos reduzir em 60% o tempo de transição de um tipo de produto para outro com um efeito económico de 150 milhões de rublos por ano, e também reduzir o tempo para a substituição planejada de elementos de equipamento em 25% com um efeito econômico de 50 milhões de rublos por ano. Ao construir um sistema TRM (operação e manutenção de equipamentos), as fábricas conseguiram uma redução de 25% nas paradas não programadas de equipamentos.
A eliminação das perdas de superprodução libertou as empresas do uso irracional de recursos energéticos e reduziu os custos de manutenção de armazéns. A logística do armazém, calculada em segundos, permitiu eliminar perdas decorrentes de transportes desnecessários e, no geral, tornou-se 90% mais eficiente. A compra de matérias-primas just in time minimizou as perdas que ocorriam anteriormente quando o excesso de estoque se acumulava. Produtividade do armazém produtos finalizados aumentou 61%.
A redução das perdas na produção de lã mineral também é facilitada pela melhoria dos processos de negócio, incluindo a sua automatização através de sistemas de informação nível mundial. Processos como planejamento de vendas e operações, gerenciamento manutenção técnica e reparos equipamento de produção, planejamento de produção em fábricas, gerenciamento de pedidos de clientes. Devido às inovações, o atendimento ao cliente foi melhorado em 71%.
O uso anual de ferramentas de qualidade integradas permite que a SBU Mineral Insulation aumente a produção de produtos de isolamento térmico de alta qualidade.
O efeito económico total da introdução de princípios de produção enxuta nas fábricas de produção de lã mineral da TechnoNIKOL Corporation ascendeu a mais de 200 milhões de rublos por ano, o que é comparável ao orçamento médio do programa-alvo regional. De acordo com especialistas da TechnoNIKOL Corporation, a disseminação ativa de práticas de manufatura enxuta nas empresas russas nos permitirá aproximar-nos da implementação do decreto do Presidente da Federação Russa “Sobre a Política Econômica do Estado de Longo Prazo” em termos de aumento produtividade do trabalho em 50% até 2018 (em relação ao nível de 2011).
TechnoNIKOL Corporation é um dos maiores fabricantes e fornecedores de coberturas, impermeabilizações e materiais de isolamento térmico. Atuando no mercado de materiais de construção desde 1992, a empresa acumula significativa experiência na produção de materiais de isolamento hídrico, acústico e térmico, e hoje oferece ao mercado materiais mais recentes e tecnologias que combinam experiência global e nossos próprios desenvolvimentos Centro de Ciência. A cooperação com institutos de design e estúdios de arquitetura permite à Corporação responder de forma flexível e rápida às mudanças nas demandas dos consumidores. Hoje, a TechnoNIKOL Corporation possui 38 unidades de produção na Rússia, Ucrânia, Bielorrússia, Lituânia, República Tcheca e Itália, sua própria rede de vendas de 180 filiais e escritórios de representação em 36 países. Os clientes da Corporação incluem mais de 500 parceiros comerciais e mais de 50.000 organizações e indivíduos na Rússia, países da CEI, países bálticos, Europa Central e Oriental.
Enviar seu bom trabalho na base de conhecimento é simples. Utilize o formulário abaixo
Estudantes, estudantes de pós-graduação, jovens cientistas que utilizam a base de conhecimento em seus estudos e trabalhos ficarão muito gratos a você.
Postado em http://www.allbest.ru/
Introdução
A manufatura enxuta é um sistema de organização e gerenciamento do desenvolvimento de produtos, operações, relacionamento com fornecedores e clientes, no qual os produtos são fabricados estritamente de acordo com as solicitações dos clientes e com menos defeitos em comparação aos produtos fabricados com tecnologia de produção em massa. Ao mesmo tempo, os custos de mão-de-obra, espaço, capital e tempo são reduzidos.
Filosofia de Manufatura Enxuta:
Determinar o valor de cada família de produtos do ponto de vista do cliente;
Identificar todas as fases do fluxo de valor para cada família de produtos e eliminar sempre que possível as atividades que não criam valor;
Organizar as operações de criação de valor em uma sequência estrita que garanta a fluidez do produto no fluxo direcionado ao cliente;
Ao finalizar a formação do fluxo, criando oportunidade para o cliente “puxar” valor da etapa anterior;
Uma vez definido o valor, os fluxos de valor foram identificados, as etapas causadoras de desperdício foram eliminadas e um sistema de fluxo e extração foi estabelecido, repetindo todo o processo quantas vezes forem necessárias para atingir um estado de perfeição em que o valor absoluto é criado e não há desperdício.
O ponto de partida do pensamento enxuto é o valor. O valor só pode ser determinado pelo consumidor final, que, por um determinado preço e num determinado momento, consegue satisfazer as necessidades dos clientes. O valor é criado pelo produtor. Do ponto de vista do consumidor, é por isso que existe o fabricante.
Lean Manufacturing é um componente do enorme e integral sistema de gestão japonês Kaizen (melhoria contínua), baseado nas ideias de Deming, Juran, Feigenbaum e seus colegas japoneses Ishikawa, Taguchi e Shingu. Um estudo cuidadoso de outros conceitos apresentados como a última palavra na construção de uma gestão eficaz, expostos em muitos livros que enchiam as prateleiras nacionais, como BSC (balanced scorecard), ABC (contabilidade baseada em uma abordagem de processos), BPR (reengenharia de processos de negócios). ), Agile Manufacturing System (sistema de produção de resposta rápida), Synchronous Manufacturing System (sistema de produção síncrona), revelam-se uma implementação menos eficaz das mesmas ideias. Ou seja, trata-se apenas de sistemas que facilitam a transição de uma gestão empresarial centralizada e rígida para um negócio baseado no envolvimento dos colaboradores e na prevalência de abordagens horizontais de gestão sobre as verticais. Deste ponto de vista, as diversas variantes clássicas de MRP e ERP também fornecem suporte para conceitos de negócios ineficientes que estão se tornando coisa do passado. Estão sendo substituídos por diversas opções de apresentação do Kaizen, um dos componentes mais importantes do qual é a Produção Enxuta.
O tema de estudo deste trabalho é a “Produção Enxuta” na empresa.
O objetivo do projeto de diploma é determinar a eficácia da implementação do conceito Lean Manufacturing na empresa. Para atingir o objetivo, é necessário resolver as seguintes tarefas:
Estudar o conceito de “Lean Manufacturing”, aspectos teóricos e metodológicos do conceito;
História de origem, princípios e ferramentas;
Considerar os tipos de perdas e métodos para avaliar a eficácia da implementação do “Lean Manufacturing”;
Analisar o processo de introdução do “Lean Manufacturing” usando o exemplo da OJSC Nizhnekamskshina;
Avaliar os ganhos de eficiência com a introdução do Lean Manufacturing na indústria nacional.
O objeto do projeto de diploma é OJSC Nizhnekamskshina. A indústria de pneus é um dos ramos da indústria petroquímica em desenvolvimento dinâmico. O fornecimento estável de matérias-primas e as vendas oportunas de produtos acabados permitiram à OJSC Nizhnekamskshina manter sua posição de liderança nas condições de competição acirrada entre fábricas de pneus na Rússia.
OJSC Nizhnekamskshina é a maior empresa da indústria de pneus, ocupando uma posição de liderança entre os fabricantes de pneus em Federação Russa e países da CEI. A empresa produz pneus para automóveis das marcas KAMA e KAMA EURO. A gama inclui mais de 120 tamanhos e modelos de pneus, incluindo aqueles desenvolvidos por especialistas do Centro Científico e Técnico Kama.
Em 22 de julho de 2007, o pneu número 300 milhões saiu da linha de montagem da OAO Nizhnekamskshina. Era o modelo KAMA EURO 228, tamanho 205/75 R15, projetado para carros Chevrolet Niva.
A empresa é o primeiro fornecedor no mercado russo,
recebeu o status de “homologadora” de pneus nas fábricas de automóveis Fiat, Volkswagen, Skoda.
A base teórica do estudo foram os trabalhos de autores que estudam a gestão da qualidade, o conceito de produção enxuta, não apenas como um sistema como um todo, mas também em relação à indústria de pneus, como Boronenkova S.A., Melnik L.A., Loganina V.I. e etc.
A base de informações consiste em materiais regulatórios e legais, literatura especializada e materiais da base prática.
O significado prático do trabalho reside no fato de que os resultados da pesquisa podem ser utilizados tanto na compreensão geral do conceito Lean Manufacturing quanto na sua aplicação prática.
O trabalho utilizou métodos de pesquisa como comparativo, dinâmico, tabular, gráfico, rede, bem como o método de análise e outros métodos estatísticos de gestão da qualidade.
Este trabalho é composto por três capítulos: o primeiro contém aspectos teóricos e metodológicos do conceito de “Produção Enxuta”, o segundo caracteriza as atividades gerais, o sistema de gestão da qualidade, o processo de introdução da “Produção Enxuta” no OJSC “Nizhnekamskshina”, o o terceiro inclui formas de aumentar a eficiência a partir da implementação da “produção enxuta” na indústria nacional.
Assim, o conceito de manufatura enxuta está ganhando cada vez mais popularidade na Rússia. Muitas vezes, a introdução de novos sistemas de produção encontra séria resistência por parte do pessoal da empresa. Muitas empresas industriais estão interessadas em reduzir custos, aumentar a produtividade e melhorar os indicadores de qualidade.
1. Aspectos teóricos e metodológicos do conceito Lean Manufacturing
1.1 A história das origens do “Lean Manufacturing”
O termo “Produção Enxuta”, que mais tarde passou a ser traduzido como “Produção Enxuta”, foi introduzido na circulação científica por John Krafcik no livro “A Máquina que Mudou o Mundo”, publicado em 1990. No entanto, as origens da filosofia de produção enxuta remontam ao início do século XX.
As ideias de “manufatura enxuta” foram formuladas e implementadas pela primeira vez por Henry Ford. Mas estas ideias tiveram a natureza de acontecimentos isolados e não afectaram a própria visão do mundo dos trabalhadores. Em 1913 (algumas fontes dizem que 1908), Henry Ford criou o primeiro modelo de fluxo de produção do mundo, baseado na movimentação de um produto processado entre processos por meio de um transportador. Foi criada uma produção em linha e de baixo custo, e o carro Ford-T não tinha concorrentes no mundo em termos de preço, qualidade e nível de serviço. Mas as ideias de Henry Ford não se difundiram, pois a economia do país se desenvolvia de forma dinâmica, o mercado estava fechado para outros países e havia oportunidades para um amplo desenvolvimento. O Japão não teve tais oportunidades e, por isso, seguiu imediatamente o caminho da utilização racional dos recursos, eliminando todo o tipo de perdas, aumentando a iniciativa e a responsabilidade dos trabalhadores e melhorando constantemente e de forma sistemática a qualidade e os procedimentos.
O centro para o desenvolvimento e implementação dos princípios e métodos da “produção enxuta” foi a empresa automobilística Toyota, que emprestou o que há de melhor nos sistemas de produção de empresas em todo o mundo. Toyota Toyota (Toyota Motor Corporation, Toyota Jidosha KK), uma empresa automobilística japonesa, parte do grupo financeiro e industrial Toyota. Uma das maiores empresas automobilísticas do mundo. Produz seus produtos sob várias marcas, incluindo Daihatsu. A sede está localizada na Toyota (Toyota).
O início da história da empresa Toyota pode ser considerado em 1933, quando a empresa Toyoda Automatic Loom Works, que inicialmente não tinha nada a ver com automóveis e atuava na indústria têxtil, abriu um departamento automobilístico. Foi descoberto pelo filho mais velho do proprietário da empresa, Sakichi Toyoda, Kiichiro Toyoda, que mais tarde trouxe a marca de automóveis Toyota à fama mundial. O capital inicial para o desenvolvimento dos primeiros carros foi o dinheiro arrecadado com a venda dos direitos de patente de máquinas de fiar para a empresa inglesa Platt Brothers.
Em 1935, o primeiro automóvel de passageiros, denominado Modelo A1 (mais tarde AA), e o primeiro caminhão Modelo G1 foram concluídos, e o Modelo AA entrou em produção em 1936. Ao mesmo tempo, foi feita a primeira entrega de exportação - quatro caminhões G1 foram para o norte da China. Um ano depois, em 1937, o departamento automobilístico tornou-se uma empresa separada chamada Toyota Motor Co., Ltd.
O conceito de trabalho sem valor agregado, mais tarde encapsulado no termo MUDA, foi cunhado por Frank Gilbert (1868-1924), que certa vez observou que um pedreiro construindo uma parede produz o efeito colateral de se abaixar para pegar o próximo tijolo. . Depois de estudar as etapas necessárias para um pedreiro concluir um determinado trabalho, Frank Gilbert sugeriu empilhar tijolos em um suporte próximo ao trabalhador. Esta solução aparentemente elementar para o problema levou a um aumento de quase três vezes na velocidade de conclusão do trabalho e a uma redução significativa no esforço despendido nele.
Em 1934, a empresa Toyoda foi reaproveitada no Japão. A partir de então, a empresa passou a se chamar Toyota, e os principais produtos produzidos em suas fábricas não eram têxteis, mas automóveis. Kiichiro Toyoda, o fundador da Toyota Motor Corp., liderou a produção de motores e descobriu constantemente cada vez mais novos problemas associados à sua produção. A principal direção para melhorar a qualidade, reconheceu ele, era o estudo intensivo de cada etapa do processo produtivo. Naqueles tempos do pós-guerra, o Japão estava em ruínas e o país precisava de carros novos. Mas o problema era que a procura não era suficientemente grande para justificar a compra de uma poderosa linha de produção, à la Ford. Eram necessários muitos tipos diferentes de automóveis (automóveis de passageiros, caminhões leves e médios, etc.), mas a demanda por tipo específico O carro era pequeno. Os japoneses tiveram que aprender a trabalhar com eficiência, criando muitos modelos diferentes em condições de baixa demanda por cada modelo. Ninguém tinha resolvido este problema antes, uma vez que a eficiência era entendida exclusivamente em termos de produção em massa.
Em 1936, a Toyota venceu o seu primeiro concurso para a produção de camiões; durante a execução desta encomenda, foram identificados novos problemas no processo tecnológico de produção de veículos; A necessidade de os resolver levou Kiichiro Toyoda a criar grupos “KAIZEN”, cuja principal tarefa era o estudo contínuo de todas as etapas do processo produtivo com o posterior desenvolvimento e implementação de métodos para a sua melhoria.
No Japão do pós-guerra, o nível de procura na economia era baixo, pelo que não era possível reduzir o custo dos produtos produzidos nas fábricas japonesas através de economias de escala.
O pai da manufatura enxuta é considerado Taiichi Ohno (1912-1990), que começou a trabalhar na Toyota Motor Corporation em 1943, integrando as melhores práticas mundiais. Taiichi Ono era funcionário da Toyota Corporation e gradualmente subiu na hierarquia até se tornar o chefe da empresa. Sendo engenheiro, Taiichi Ohno desenvolveu o sistema de gerenciamento de custos Kanban, a manufatura enxuta (método Lean) e o método Just-in-time. A empresa ainda segue esse sistema. Em 1949 foi nomeado chefe da oficina mecânica. No início da década de 1950, quando morreu Kiichiro Toyoda, Taiichi Ono concebeu e depois implementou um sistema de gestão da produção (“kanban”), revolucionário para aquela época, com a ajuda do qual os japoneses conseguiram eliminar qualquer tipo de desperdício do processo produtivo. . Desenvolvimentos científicos, tanto na área de gestão como reequipamento técnico, sempre foram muito valorizados neste empreendimento. Em meados da década de 1950, ele começou a construir um sistema especial de organização da produção denominado Sistema Toyota de Produção ou Sistema Toyota de Produção (TPS). O sistema Toyota ficou conhecido na interpretação ocidental como Produção Enxuta, Manufatura Enxuta, Lean. O termo lean foi proposto por John Krafcik, um dos consultores americanos. A década de 1950 viu a maior atividade da Toyota nesta área. Graças a políticas científicas e industriais avançadas, a empresa conseguiu criar os SUVs Land Cruiser e Crown. Em 1954, Taiichi Ohno assumiu o cargo de diretor da fábrica da Toyota. Tendo passado por vários outros degraus da complexa escada hierárquica japonesa, em 1975 tornou-se vice-presidente executivo de toda a empresa e, desde 1978, presidente do conselho de administração da Toyota Spinning and Weaving.
Nos EUA, Taiichi Ohno escreveu vários livros sobre o sistema, o mais famoso deles é “The Toyota Production System.
Saindo da produção em massa." Taiichi Ono apresenta os pensamentos e ideias de três gestores do século XX - Henry Ford, Sakichi Toyoda e Kiichiro Toyoda.
Uma contribuição significativa para o desenvolvimento da teoria da manufatura enxuta foi feita pelo colega e assistente de Taiichi Ono, Shigeo Shingo, que, entre outras coisas, criou o método SMED. Depois de visitar os EUA e conhecer o sistema operacional dos supermercados, Taiichi Ono chegou à conclusão de que a produção dos produtos não deveria ser baseada nos volumes de vendas planejados (estratégia push), mas na demanda real (estratégia pull).
Foi Taiichi Ono quem reuniu todos os métodos avançados para aumentar a eficiência da produção dentro das paredes da fábrica da Toyota.
Posteriormente, perguntaram a Taiichi Ohno o que o inspirou a criar o Sistema Toyota de Produção, ao que ele respondeu: Aprendi tudo com o livro de Henry Ford. No entanto, foi a escala, a precisão e a melhoria contínua do Sistema Toyota de Produção que lhe permitiu tornar-se um elemento fundamental do Lean Manufacturing, cuja principal vantagem é seguir a sua própria regra de ouro: O efeito máximo só é alcançado através da melhoria contínua.
Os conceitos de manufatura enxuta foram aplicados pela primeira vez às indústrias de manufatura discreta, principalmente à indústria automotiva. Depois o conceito foi adaptado às condições de produção contínua, e depois no comércio, serviços, utilidades públicas, saúde, setor militar e público.
Gradualmente, a manufatura enxuta expandiu-se para além da empresa. Agora, com a ajuda da manufatura enxuta, otimizam o setor de serviços e o processo de comunicação entre consumidor e fornecedor, o processo de entrega e atendimento dos produtos. Conferências internacionais e regionais regulares contribuem para a disseminação de ideias Lean, muitas das quais são realizadas por iniciativa do Lean Enterprise Institute (EUA) e da Lean Enterprise Academy (Inglaterra). Em muitos países, a difusão da produção enxuta é apoio governamental. Num período de intensa concorrência e de crise crescente, as empresas de todo o mundo não têm outra forma senão, utilizando as melhores tecnologias de gestão do mundo, criar produtos e serviços que satisfaçam ao máximo os clientes em termos de qualidade e preço.
Nos últimos anos, na Rússia, bem como nos países da antiga União Soviética, o interesse pelas questões de gestão, gestão empresarial e transformações das estruturas organizacionais das empresas aumentou significativamente. Infelizmente, esse interesse só surgiu recentemente. Na prática mundial, muitos novos conceitos e métodos de gestão foram criados recentemente: reengenharia de processos de negócios (BPR), Gestão da Qualidade Total (TQM), Balanced Scorecard (BSC), controle estatístico de processos (SPC), coaching, modelos de padrões internacionais ISO 9000 , ISO 14000, HACCP, Five S, Six Sigma e muito mais. Infelizmente, os países do espaço pós-soviético não têm desenvolvimentos próprios nesta indústria. Não existem tradições, escolas, experiências de antecessores, nem sistemas de gestão estabelecidos. Portanto, os gestores russos terão de aprender muito com as técnicas estrangeiras para sobreviver e permanecer competitivos.
O conceito de “Lean Thinking and Manufacturing” ocupa um dos lugares de maior destaque entre ofertas modernas na gestão. Porém, a cultura do nosso país como um todo está muito longe do conceito de “poupança”. Isso pode ser evidenciado pelo fato de que em nosso país os chips são armazenados em oficinas e as peças metálicas são armazenadas ao ar livre; as cercas são construídas com madeira natural e os móveis são feitos de serragem; uma oficina está localizada a vários quilômetros da outra. Para ser honesto, é impossível encontrar uma explicação razoável para isso. Vantagem competitiva Empresas russas só pode ser assegurada por alta qualidade e baixos custos.
Assim, hoje é necessário reconsiderar toda a organização da produção para eliminar todo tipo de perdas. Ao mesmo tempo, há necessidade de uma abordagem integrada, incluindo a qualidade e o conceito, métodos e ferramentas de produção enxuta. Com base nos problemas de funcionamento das empresas russas, especialistas na área de gestão da qualidade acreditam que dominar o conceito de “Manufatura Enxuta” e aplicar seus métodos é um fator extremamente importante para melhorar o desempenho de todas as partes do sistema de produção.
1.2 Princípios e ferramentas do Lean Manufacturing
perda de produção enxuta
A manufatura enxuta é um conceito moderno de organização da produção que visa reduzir Vários tipos perdas através da introdução de novas tecnologias de produção e gestão, acelerando a produção de produtos e garantindo a competitividade a longo prazo da organização sem investimentos de capital significativos.
Princípios da manufatura enxuta.
O princípio da compreensão do valor – implica a necessidade de compreender o que é valor para o consumidor final. O valor é considerado um conceito fora da produção. O valor é o ponto de partida do pensamento enxuto. O valor (de um produto, serviço) só pode ser determinado pelo consumidor final. Faz sentido falar sobre isso apenas se você quiser dizer produto específico(produto ou serviço ou todos juntos), que a um determinado preço e em um determinado momento é capaz de satisfazer as necessidades dos clientes. O valor é criado pelo produtor. Do ponto de vista do consumidor, é justamente por isso que o fabricante existe. No entanto, por uma série de razões, é muito difícil para um fabricante determinar exatamente qual é o valor de um produto ou serviço. Via de regra, os gestores prestavam maior atenção aos sistemas de gestão: processos, departamentos, empresas inteiras que incluíam muitos produtos ao mesmo tempo. Na realidade, você precisa gerenciar todos os fluxos de valor de cada produto ou serviço.
O princípio do combate às perdas - prevê uma redução significativa ou eliminação completa de sete tipos principais de perdas:
1 – perda de superprodução;
2 - perdas por defeitos e necessidade de retrabalho;
3 - perdas durante o movimento;
4 - perdas durante o transporte;
5 - perdas por excesso de estoques;
6 - perdas por processamento excessivo;
7 - perda de tempo de espera.
Princípio do fluxo do produto - em vez de movimentar o produto de um centro de trabalho para outro em lotes, é necessário criar um fluxo no qual haja um movimento contínuo das matérias-primas aos produtos acabados através de células de produção especializadas.
O princípio pull, que significa que em vez de trabalhar para um armazém, o consumidor deve ter a oportunidade de “puxar” os produtos acabados do sistema de produção. Nenhum trabalho é executado a menos que seus resultados possam ser imediatamente utilizados em operações subsequentes.
O princípio da melhoria contínua - quando todos os desperdícios dos processos tecnológicos forem eliminados e os produtos se moverem de forma suave e contínua à medida que são entregues ao consumidor, ficará claro que não haverá fim para o processo de melhoria contínua, como a redução da operação tempo, custo, espaço, defeitos e carga de trabalho.
Ferramentas de manufatura enxuta
Para a implementação prática da manufatura enxuta, são utilizadas as seguintes ferramentas:
5S – cinco passos para manter a ordem. 5S é formado por cinco palavras japonesas que constituem a base para manter a limpeza e a ordem. A ausência de 5S numa célula de trabalho indica:
Para baixa eficiência;
Presença de perdas;
Autodisciplina e moralidade fracas;
Má qualidade;
Altos custos;
Falta de disciplina na entrega, tanto para consumidores internos quanto externos.
Os clientes potenciais não levarão os fornecedores a sério se não praticarem o 5S. Estes cinco pontos de pureza são o ponto de partida para qualquer empresa que se esforce para se tornar um fabricante responsável cujos produtos sejam de classe mundial.
Existem cinco maneiras de avaliar o nível 5S em cada estágio:
Auto estima;
Avaliação por consultor especializado;
Avaliação gerencial;
Uma combinação dos três primeiros métodos;
Competições entre células de trabalho.
Kaizen: A ideia central do kaizen é que não se deve passar um dia sem melhorias na empresa. Kaizen não é apenas uma técnica, é o guarda-chuva sob o qual vive a maioria das práticas “exclusivas do Japão”.
A compreensão japonesa de gestão resume-se ao seguinte: manter padrões e melhorá-los. O trabalho da administração na manutenção é garantir que todos na empresa possam seguir o procedimento operacional padrão. Se os funcionários não conseguirem seguir um procedimento padrão, a administração deverá treiná-los ou revisar e corrigir o padrão para que possam agir de acordo com ele. Quanto maior o nível de gestão, mais tempo ela dedica à melhoria. O ponto de partida para a melhoria é reconhecer que existe um problema. Complacência e complacência são os inimigos jurados do kaizen. É por isso que uma reclamação de um cliente deve ser tratada como um presente. Reconhecendo que a reclamação
relacionado ao problema, você tem a chance de melhorar a qualidade do produto ou
Serviços. Ao ignorar a reclamação, você perde essa chance.
Kanban: método just-in-time. A correta especificação das peças e do produto acabado - com a quantidade correta - em tempo certo- sem casamento. O sistema just-in-time é um sistema pull - é uma organização do processo em que cada etapa subsequente da produção consome tudo o que é necessário da etapa anterior no momento certo. A saída da fase final de produção, neste caso, é baseada nas solicitações do cliente ou corresponde ao cronograma de produção. O sistema just-in-time oferece ao fabricante as seguintes vantagens:
Redução do nível de estoques, materiais adquiridos e produtos acabados no almoxarifado;
Reduzindo o espaço ocupado;
Aumento da qualidade do produto, redução de defeitos e processamento;
Maior flexibilidade na produção;
Aumento da produtividade e taxa de ocupação dos equipamentos;
Participação dos trabalhadores na resolução de problemas;
Bom relacionamento com o consumidor.
Troca rápida (SMED): produção flexível em minutos. Graças a esta ferramenta, a empresa economiza recursos materiais e trabalhistas, aumenta a produtividade e agiliza o atendimento de pedidos.
Poka-yoke: “infalível”: envolve construir o processo de forma a eliminar a própria possibilidade de erro. Foi formulado de forma mais ampla por programadores: se um usuário puder cometer um erro, com certeza cometerá um. Na verdade, qualquer elemento importante não funcionará de forma suficientemente eficaz se o fator humano não for levado em consideração antecipadamente.
Existem 10 tipos de erros humanos que levam a defeitos:
Esquecimento;
Incompreensão dos motivos (ocorrência de algo);
Subestimação de qualquer situação (ou incapacidade de identificar algum objeto);
Inexperiência;
Relutância (em seguir procedimentos e regras);
Desatenção;
Lentidão (na tomada de decisões);
Falta de padrões;
Surpresa;
Cometer intencionalmente um erro (ou sabotagem).
As fontes dos defeitos são os seguintes fatos:
Operação perdida;
Erros de processamento;
Erros de posicionamento de peças;
Detalhe faltando;
Parte incorreta;
Processando a peça errada;
Operação incorreta na peça correta;
Erros de configuração;
Instalação incorreta de equipamentos e utilização de ferramentas ou acessórios incorretos.
É necessário distinguir três fases principais na implementação dos princípios da manufatura enxuta: estudar a demanda, garantir a continuidade dos fluxos de valor e suavizá-los. Só um estudo aprofundado da procura, dos fluxos de valor e das formas de os suavizar, juntamente com a utilização de recomendações para a gestão dos fluxos de valor, pode dar fiabilidade não só ao próprio processo de transformação, mas também garantir a sua sustentabilidade.
Fase de pesquisa de demanda do consumidor. É necessário, antes de tudo,
identificar quem são os consumidores dos resultados de algum trabalho, quais são
suas necessidades, só então você será capaz de satisfazer o consumidor
há uma grande demanda por seus resultados. Várias ferramentas e métodos podem ser usados para identificar e satisfazer a demanda do consumidor, por exemplo:
Cálculos de tempo takt;
Cálculos de pitch;
Cálculos de estoques reguladores e de segurança;
Aplicação do sistema 5S;
Usando técnicas de resolução de problemas.
Fase de continuidade do fluxo de valor. Nesta fase é aceito medidas necessárias garantir que os resultados dos trabalhos em questão são entregues a todos os clientes internos e externos em tempo útil e em quantidades adequadas. Por exemplo:
Criação de supermercados dentro de processos;
Sistema Kanban;
Aplicação do princípio FIFO (“primeiro a entrar, primeiro a sair”);
Garantir o equilíbrio no carregamento das linhas de produção;
Padronização do trabalho;
Layout adequado das áreas de produção.
Fase de suavização. Finalmente, uma vez identificada a procura dos resultados do trabalho pelos consumidores e estabelecido um processo contínuo para a sua implementação, eles passam a suavizá-la, a fim de garantir uma distribuição uniforme e eficiente dos volumes de trabalho ao longo de dias, semanas e meses. Para fazer isso, são utilizadas as seguintes ferramentas de suavização de fluxo:
Utilização de quadro para sugestões e discussão de ideias (pitch board visível);
Caixas niveladoras de carga (heijunka);
Uso de logísticos.
Assim, a promoção de um determinado sistema é impossível sem compreendê-lo. Portanto, os funcionários responsáveis pela eficácia das principais atividades da empresa devem ser fornecidos
oportunidade de aprender conceitos de manufatura enxuta.
A aplicação dos princípios e o uso habilidoso das ferramentas de manufatura enxuta garantirão competitividade em qualquer área de negócio. A viabilidade de introdução do Lean Manufacturing em uma organização:
Altos custos de produção;
Produtos de baixa qualidade;
Tecnologias desatualizadas;
Equipamentos desatualizados;
Alta intensidade energética;
Altos custos de produção;
Violação de prazos de entrega;
Falta de pessoal qualificado;
Alta concorrência no mercado.
São as ferramentas de manufatura enxuta que nos permitem resolver esses e outros problemas.
A organização estabelece para si uma meta global - melhorar a cada dia, progredir dia a dia. Avançar depende dos próprios gestores, porque não basta introduzir ferramentas, é preciso mudar a cultura de gestão e o comportamento dos gestores.
1.3 Tipos de perdas e métodos de avaliação da eficácia da implementação do conceito Lean Manufacturing
O Lean Manufacturing é um conceito de gestão que aposta na otimização dos processos de negócio com a máxima orientação para o mercado e tendo em conta a motivação de cada colaborador. A manufatura enxuta constitui a base de uma nova filosofia de gestão. O objetivo é: minimizar custos trabalhistas e prazos para criação de novos produtos; garantia de entrega do produto ao cliente; máxima qualidade em
custo mínimo. A ideia principal é eliminar desperdícios
qualquer atividade que consome recursos, mas não cria valor.
Taiichi Ohno, o fundador deste sistema, identificou sete tipos de desperdício: devido à superprodução; tempo devido à espera; durante transporte desnecessário; devido a etapas de processamento desnecessárias; devido ao excesso de estoques; devido a movimentos desnecessários; devido ao lançamento de produtos defeituosos. Existem também mais duas fontes de perdas - “carga excedente da capacidade” e “carga irregular”, o que acaba levando ao lançamento de produtos defeituosos.
Superprodução. A superprodução é geralmente chamada de produção de quantidades excessivas de produtos ou sua produção prematura antes que surja a demanda real. Nas oficinas, a superprodução leva à produção de produtos em excesso, e nos escritórios leva à criação de documentos desnecessários ou de informações redundantes. A produção de quantidades excessivas de produtos ou a sua produção prematura não contribui para o aumento da eficiência, uma vez que estão associadas ao consumo de material adicional e recursos trabalhistas, a necessidade de armazenar produtos excedentes. Isso obriga os funcionários a trabalhar mais rápido do que o necessário, o que vem acompanhado de outras perdas.
Para eliminar as perdas causadas pela superprodução, é necessário:
Desenvolver processos tecnológicos de forma que as operações anteriores forneçam de forma confiável as subsequentes;
Estabelecer normas e padrões de produção para cada posto de trabalho do processo;
Fornece sinais para evitar o início prematuro da produção.
Expectativa. Qualquer expectativa – de pessoas, documentos, equipamentos ou informações – é sempre uma perda. Esperar significa ficar ocioso e isso faz com que todo o processo seja interrompido. Nenhum valor agregado é criado durante a espera e o consumidor fica naturalmente relutante em pagar pelo tempo de inatividade. Esse tipo de perda é o mais fácil de detectar. Eles são especialmente irritantes para os trabalhadores. Em qualquer escritório, não é incomum que os funcionários esperem muito tempo pelas assinaturas dos chefes, pela oportunidade de utilizar equipamentos ocupados, telefonemas, recebimento de materiais de fornecedores, etc.
Analisar quais assinaturas nos documentos são realmente necessárias, eliminar todas as desnecessárias e padronizar o novo procedimento;
Treinar funcionários em profissões afins para que possam substituir uns aos outros;
Distribuir as cargas de trabalho uniformemente ao longo do dia, a fim de otimizar o uso dos recursos de trabalho disponíveis;
Garanta a produção para todos equipamento necessário e entrega pontual de produtos e materiais adquiridos.
Superprocessamento. Consideram-se operações supérfluas aquelas operações desnecessárias aos consumidores que não desejam pagar a mais pela sua implementação. Muitas vezes, tais operações envolvem ações desnecessárias (por exemplo, verificações mútuas do trabalho realizado por diferentes funcionários), obtenção de um número excessivo de assinaturas, consideração desnecessária de documentos e resultados de trabalho.
Para eliminar esse tipo de perda você precisa:
Analisar todos os trabalhos que criem valor acrescentado, otimizar ou eliminar todas as operações desnecessárias;
Determine quais assinaturas de aprovação nos documentos são realmente necessárias e elimine todas as desnecessárias.
Inventário em excesso. Qualquer excesso de estoque disponível na empresa é uma perda. O armazenamento desses suprimentos requer espaço adicional e pode impactar negativamente a segurança ao sobrecarregar corredores e áreas de produção. Esses estoques podem se tornar desnecessários e obsoletos à medida que a demanda por produtos muda. A manufatura enxuta requer uma mudança radical na forma como pensamos sobre o estoque. O excesso de estoque significa que é necessário um esforço adicional para gerenciá-lo e pode retardar outros processos de produção, revirando pilhas de papéis e materiais para encontrar o que você precisa.
Para eliminar esse tipo de perda você precisa:
Produzir em cada local ou local de trabalho apenas a quantidade de produtos exigida pelos consumidores localizados a jusante do fluxo de produção;
Padronizar o layout das áreas de produção e seu carregamento;
Garanta que tudo o que é necessário chegue às áreas subsequentes do processo de produção exatamente na hora marcada e evite atrasos na movimentação adicional de materiais ao longo do processo de produção.
Movimentos extras. Qualquer movimento não necessário para concluir com êxito a operação em questão é um desperdício. Tais movimentações são consideradas uma forma de desperdício, pois cada movimentação realizada deverá aumentar o valor agregado do produto ou serviço. Muitas vezes, a organização ineficaz do processo de trabalho e o layout inadequado dos locais de trabalho causam movimentos desnecessários dos artistas - caminhar, alcançar, curvar-se, etc.
Para eliminar esse tipo de perda você precisa:
Padronize pastas de documentos, gavetas e armários em todo o escritório, use códigos de cores tão amplamente quanto possível;
Organizar arquivos (com documentos em tabelas ou eletrônicos em computadores) de forma a facilitar seu acesso;
Localize equipamentos de escritório comuns em
parte central do escritório, adquira equipamentos adicionais para reduzir o número de funcionários circulando pelo escritório.
Perdas por defeitos ou retrabalho. O custo de retrabalhar ou repetir
A nova conclusão de obra já realizada, na qual são constatados defeitos, certamente se enquadra na categoria de perdas, pois qualquer obra além do necessário é desnecessária, aumentando os prejuízos do empreendimento. As perdas por defeitos também incluem perda de produtividade devido à interrupção do fluxo normal de trabalho para corrigir defeitos ou retrabalhar produtos. Este tipo de resíduo é muito mais fácil de identificar do que outros tipos de resíduos.
Para eliminar perdas por defeitos, você precisa:
Introduzir métodos de trabalho padronizados e formulários de documentos de escritório;
Desenvolver e implementar ajudas para facilitar o trabalho.
Transporte. O transporte em distâncias superiores ao necessário, ou a criação de locais temporários, armazenamento e armazenagem, movimentos desnecessários de um local para outro de materiais, pessoas, informações ou documentos - tudo isto conduz à perda de tempo e energia. Os materiais e itens adquiridos são frequentemente movidos de um lugar para outro dentro de uma fábrica várias vezes até chegarem ao seu destino final. Naturalmente, todos esses movimentos levam a perdas. Além disso, a colocação de produtos em áreas de armazenamento temporário aumenta a probabilidade de danos, perdas e roubos e interfere na movimentação normal dentro do empreendimento.
Para eliminar perdas causadas por excesso de transporte,
obrigatório:
Minimizar as distâncias de qualquer transporte;
Elimine todos os armazenamentos temporários ou áreas de armazenamento
materiais.
O problema de determinar a eficiência econômica predetermina
a necessidade de levar em conta e analisar corretamente o nível e a escala
implementação de atividades de manufatura enxuta. Isso significa que determinar a eficiência requer o uso de métodos quantitativos de análise e medição, o que envolve estabelecer uma relação entre o aumento da escala de implementação do conceito de manufatura enxuta e o aumento do lucro da empresa.
A análise da eficiência económica da implementação do conceito de produção enxuta começa com o cálculo do volume total de produção anual das unidades estruturais onde foi introduzida a produção enxuta V?
j é o índice da unidade estrutural;
J é o número de unidades estruturais onde a manufatura enxuta foi implementada;
Vj - volume de produção unidade estrutural, onde a manufatura enxuta foi introduzida.
Assim, a parcela é determinada pela fórmula:
Para determinar melhor a relação custo-benefício, as seguintes etapas são executadas:
O volume de investimentos para implementação de atividades de produção enxuta está previsto para cada atividade implementada em
unidade estrutural;
Dependendo do volume de investimento projetado e da cobertura das unidades estruturais por medidas de produção enxuta, é determinada a parcela do volume de produção (g);
O valor limite g* é determinado por meios especializados, no qual o efeito económico da implementação de medidas de produção enxuta começará a aparecer na forma de um aumento no lucro da empresa (?P).
O valor limite r* também pode depender da eficácia com que a atividade é implementada. Quanto maior for a eficácia da implementação da atividade, menor será o valor limite r*.
A relação entre o aumento da percentagem de g acima do limiar do valor de g* (?g = g - g*) e o aumento do lucro da empresa pode ser expressa como:
K é um indicador que caracteriza o aumento do lucro da empresa por unidade de aumento na escala de implementação de medidas de produção enxuta. Na passagem ao limite, este indicador é expresso como uma derivada:
O efeito económico de qualquer evento, incluindo as atividades de produção enxuta, reside no lucro adicional recebido. O lucro adicional recebido, por sua vez, é determinado por quanto as receitas e os custos de produção da empresa mudarão em conexão com a implementação dessas medidas de produção enxuta. Assim, a principal abordagem para calcular o efeito de qualquer atividade (incluindo atividades de manufatura enxuta) é determinar quanto mais a empresa receberá e quanto mais pagará em conexão com a implementação do conceito.
manufatura enxuta.
Como critérios de eficiência económica da implementação de medidas de organização da produção enxuta, propõe-se a utilização de indicadores tradicionais de eficácia do Programa, tais como: valor presente líquido (VPL), taxa interna de retorno (TIR) e período de retorno descontado.
Valor presente líquido (VPL).
Na prática internacional, um indicador amplamente utilizado para avaliar a eficácia dos projetos é o valor presente líquido ou valor presente líquido (VPL), que é determinado pela fórmula:
É o valor do investimento (custo) em t-ésimo período para atividades de manufatura enxuta;
T é o número total de anos, onde t = 0, 1, 2,…, n;
r - taxa de desconto;
Pt é o aumento no lucro da empresa com a implementação do conceito de manufatura enxuta.
Se o valor do VPL calculado for positivo, isso indica que a soma de todas as perdas que deveriam ser eliminadas é maior que o investimento no evento de LP, o que significa que o evento em questão deve ser aceito para implementação. Se o VPL for inferior a zero, esta atividade deverá ser abandonada.
Taxa interna de retorno (TIR).
A TIR de um projeto é a taxa de retorno (taxa barreira, taxa de desconto) à qual o valor presente líquido do investimento é zero, ou é a taxa de desconto à qual o rendimento descontado do projeto é igual aos custos de investimento. Taxa interna de retorno
determina a taxa de desconto máxima aceitável na qual é possível
investir fundos sem quaisquer perdas para o proprietário.
TIR = r, em que VPL = f(r) = 0.
O valor da TIR é encontrado usando a seguinte fórmula:
O significado económico deste indicador é que ele mostra a taxa de retorno esperada (retorno do investimento) ou o máximo nível permitido custos de investimento no projeto que está sendo avaliado.
Período de retorno com desconto.
O período de retorno é o tempo que leva para um investimento gerar fluxo de caixa suficiente para reembolsar os custos de investimento.
Fórmula geral para cálculo do período de retorno:
Atual - período de retorno do investimento;
Io é o valor do investimento inicial no período zero.
Assim, torna-se possível não só obter uma visão rápida do estado dos processos de negócio na organização, mas também melhorar o estado de coisas existente.
A eficácia resultante da implementação de medidas de produção enxuta pode ser usada tanto para analisar os resultados da implementação das medidas como para determinar os departamentos nos quais é mais lucrativo implementar a produção enxuta. Portanto, esta abordagem permitirá (especialmente em condições de recursos limitados) distribuir racionalmente os investimentos de capital entre os departamentos que visam implementar o conceito de produção enxuta.
2. Análise e avaliação de atividadesJSC« Nizhnekamskshina" na área de "Produção Enxuta"
2.1 Características gerais das atividades,indicadores técnicos e econômicos do empreendimento
Hoje OJSC Nizhnekamskshina é a maior empresa de produção de pneus na Rússia e nos países da CEI. Quase um em cada três pneus produzidos na Rússia é fabricado na cidade de Nizhnekamsk.
OJSC Nizhnekamskshina foi criada de acordo com o Decreto do Presidente da República do Tartaristão “Sobre medidas para transformar empresas estatais, organizações e associações em sociedades por ações" datado de 26 de setembro de 1992 No. UP-466, Lei da República do Tartaristão "Sobre a transformação da propriedade estadual e municipal na República do Tartaristão (sobre desnacionalização e privatização)."
OJSC Nizhnekamskshina foi criada em 2 de março de 1994 através da transformação da associação de produção Nizhnekamskshina. A transformação foi realizada com base no plano de privatização aprovado pela Resolução do Comitê de Propriedade do Estado da República do Tartaristão nº 64, de 15 de fevereiro de 1994, e foi inscrita no registro de sociedades por ações sob o número 700. O empresa foi criada por tempo indeterminado.
A empresa existe como entidade legal independente desde 1971. A empresa consiste em duas fábricas - uma fábrica de pneus produzidos em massa e uma fábrica de pneus para caminhões. Em 1994 Associação de Produção"Nizhnekamskshina" foi transformado em Sociedade por Ações Tipo aberto; em 1997 - na OJSC Nizhnekamskshina.
A fábrica de pneus produzidos em massa foi projetada levando em consideração o fornecimento de pneus para a Fábrica de Automóveis Volzhsky, a Fábrica de Automóveis Ulyanovsk e a frota de veículos nas regiões adjacentes à fábrica. A linha principal são pneus para automóveis e caminhões.
A fábrica de pneus para caminhões foi projetada levando em consideração o fornecimento de pneus para a KamAZ e a frota de veículos nas regiões adjacentes à fábrica. A linha principal são pneus para caminhões.
A estrutura da Fábrica de Pneus Massificados e da Fábrica de Pneus para Caminhões inclui o diretor da fábrica, a quem está diretamente subordinado Engenheiro chefe, Diretor Adjunto de Produção, Tecnólogo Chefe, Diretor Adjunto de Análise Econômica, bem como a produção principal da planta e oficinas auxiliares das plantas.
A principal produção da planta inclui:
Preparação de matérias-primas e expedição de produtos acabados;
Produção preparatória, que trata da preparação;
matérias-primas para a futura produção de pneus;
Produção de calendários, que coleta molduras para oficinas de montagem;
Produção de montagem nº 1;
Produção de montagem nº 2;
Produção de vulcanização de pneus de passageiros;
Produção de pneus para caminhões;
Produção automática de câmaras.
As oficinas auxiliares da planta incluem oficina elétrica, oficina de aquecimento, oficina mecânica, transporte elétrico interno, sistemas de fluxo tecnológico, sistemas de controle automatizados e oficina de utilidades.
Os órgãos de administração da OJSC Nizhnekamskshina, de acordo com o Estatuto da Empresa, são:
- Assembleia Geral de Acionistas;
- Conselho Administrativo;
- Órgão executivo único;
- O órgão executivo colegial é o Conselho de Administração.
JSC"Nizhnekamskshina" é o maior pneu russo
empresa de fábricas por capacidade de produção, volume e gama de produtos. Na produção total de pneus pelas fábricas russas, a participação da Nizhnekamskshina OJSC foi de 30%. Quase um terço dos produtos é fornecido às fábricas de automóveis russas.
Em 2009, os líderes de produção são - em primeiro lugar está Nizhnekamskshina OJSC, produzindo 27% da produção de pneus toda russa, seguida pela Yaroslavl Tire Plant OJSC - 16% e Omskshina OJSC - 14%. A capacidade total das empresas nacionais de pneus é de 38,7 milhões de pneus por ano.
A versatilidade de produção do empreendimento é garantida pela produção de uma grande variedade de pneus. A empresa produz pneus para várias condições: estrada, universal (todas as estações), inverno, todo-o-terreno, pedreira. Os pneus produzidos são projetados para diversos tipos de veículos automotores e, dependendo disso, são divididos em tipos. Os pneus da empresa são fornecidos para muitas fábricas de automóveis, não apenas na Rússia, mas também na Ucrânia.
Os principais consumidores dos produtos OAO Nizhnekamskshina são apresentados na Tabela 2.1.1.
Tabela 2.1.1. Principais consumidores de produtos OAO Nizhnekamskshina
A partir dos dados da tabela verifica-se que a maior parte do consumo do produto recai sobre JSC AVTOVAZ - 61%; 11% dos produtos de pneus são distribuídos entre as fábricas do Grupo Volkswagen Rus LLC, Kaluga, SHKODA, UAZ OJSC, Ulyanovsk; 6,0% na LLC "OAG", Izhevsk, o consumo insignificante de produtos recai sobre JSC "AK" Bogdan Motros, Ucrânia.
Mais visual percentagem você pode ver a fig. 2.1.3.
Arroz. 2.1.3. Principais consumidores de produtos da OJSC Nizhnekamskshina
OJSC Nizhnekamskshina acumulou vasta experiência no desenvolvimento e melhoria de pneus fabricados e no teste de produtos acabados. O desenvolvimento de designs de pneus de nova geração e a mais recente tecnologia tornaram possível garantir alta qualidade e o nível de desempenho dos produtos acabados no mercado mundial. Hoje, a empresa produz mais de 120 tamanhos padrão para todos os tipos de pneus e máquinas agrícolas. Levando em consideração as crescentes exigências das montadoras quanto à qualidade dos pneus, o fluxo de passageiros da Mass Tire Plant foi reconstruído e a tecnologia de fabricação de pneus radiais de passageiros utilizando equipamentos e sob licença da Pirelli (Itália) foi dominada.
Em 2001, a reconstrução do fluxo de passageiros da Mass Tire Plant continuou. De acordo com o plano de desenvolvimento de longo prazo da OJSC Nizhnekamskshina, foi adquirida uma licença para novas tecnologias e a produção de pneus radiais de passageiros foi organizada e colocada em operação em 2004. O projeto foi financiado com fundos da OAO Tatneft.
Em 1º de julho de 2004, foi introduzida a capacidade de pneus radiais de passageiros de alto desempenho “KAMA-EURO” - 500 mil unidades.
A capacidade projetada para produção de pneus do empreendimento em 1º de janeiro de 2006 era de 11.900 mil pneus por ano, incluindo para a Fábrica de Pneus Massificados - 8.940 mil pneus, para a Fábrica de Pneus de Caminhões - 2.960 mil pneus, para a produção de pneus de passageiros pneus radiais - 500 mil pneus.
Os fatores internos da OAO Nizhnekamskshina incluem uma parceria estratégica com a OAO Tatneft, porque a empresa opera como parte dela. A função de fornecimento de matéria-prima na quantidade demandada é desempenhada pela LLC Tatneft-Neftekhimsnab, a função de venda de produtos acabados é desempenhada pela LLC Trading House "Kama". Por decisão extraordinária reunião geral acionistas da OAO Nizhnekamskshina, ata de 27 de junho de 2002, os poderes do órgão executivo único foram transferidos para a sociedade gestora Tatneft-Neftekhim LLC.
A fábrica implementou e opera efetivamente o sistema de qualidade ISO -
9001:2000, certificado pelo organismo de certificação internacional TUV CERT, que prevê o controle cuidadoso das matérias-primas, materiais e componentes que entram na planta, estrito cumprimento das normas de processo tecnológico ao longo de todo o ciclo de produção e testes dos produtos acabados.
Dominar a produção de pneus radiais de passageiros de alto desempenho “KAMA-EURO” utilizando novas tecnologias em equipamentos importados utilizando matérias-primas importadas e homologadas. Por decisão do Conselho de Administração, foi tomado um conjunto de medidas para retirar serviços, estruturas não essenciais e atividades de serviços do OJSC
"Nizhnekamskshina".
A empresa OAO Nizhnekamskshina, numa economia de mercado, presta considerável atenção aos problemas de otimização do processo de promoção de bens do fabricante ao consumidor.
A dinâmica de produção dos produtos da OJSC Nizhnekamskshina é apresentada na Tabela 2.1.2.
Tabela 2.1.2. Dinâmica de produção de produtos da OJSC Nizhnekamskshina
Volume de produção, |
Taxa de crescimento, % |
|||
Básico |
||||
A tabela mostra que o volume de produção em 2011 diminuiu 1.096,3 mil unidades. (10%) em relação a 2010; Em comparação com 2009, a produção de pneus em 2011 foi inferior em 4.939,2 mil unidades. (33,4%). A diminuição significativa do volume de produção deve-se à cessação da produção da principal gama de pneus para camiões no 2º semestre de 2011. Uma representação visual desta dinâmica é apresentada na Fig. 2.1.4.
...A essência do conceito de “produção enxuta”, a história da sua origem, aspectos teóricos e metodológicos. Avaliar a eficácia da sua implementação na empresa. Análise da competitividade da Energoshinservice LLC no âmbito do conceito de produção enxuta.
tese, adicionada em 24/06/2014
História do desenvolvimento do pensamento gerencial. Desvantagens e vantagens da teoria de gestão para a implementação de atividades de gestão competentes. Disposições básicas, princípios e ideias das tendências modernas de gestão. O conceito de “Manufatura Enxuta”.
resumo, adicionado em 01/04/2016
Tecnologia de manufatura enxuta na teoria e prática de gestão. Revisão de ferramentas de manufatura enxuta. Análise das possibilidades de introdução e operação da produção enxuta na Rússia e no exterior. Características do modelo de gestão japonês.
trabalho do curso, adicionado em 28/01/2014
O foco da Toyota na produção baseada em pedidos, minimizando os estoques de produtos acabados. A manufatura enxuta como uma abordagem progressiva de gestão e gestão da qualidade. A necessidade de usar apenas tecnologia confiável e comprovada.
teste, adicionado em 22/03/2014
As principais atividades da OJSC "EVRAZ Kachkanar Mining and Processing Plant". Processo tecnológico de obtenção de produtos. Estrutura organizacional da gestão do trabalho. Política e objetivos de qualidade. Princípios da manufatura enxuta.
relatório prático, adicionado em 12/03/2015
A manufatura enxuta como conceito de gestão logística, suas metas e objetivos, vantagens e desvantagens. Características das ferramentas Lean: Método Kaizen, sistema 5S, sistema geral de manutenção de equipamentos produtivos, sistema Kanban.
teste, adicionado em 03/12/2013
A essência e o conteúdo principal da abordagem processual, etapas e princípios de sua implementação em uma empresa moderna. A Trilogia Juran. Informações gerais sobre OJSC "Tatar Meat Processing Plant", implementação da abordagem de processo e avaliação da eficácia deste conceito.
trabalho do curso, adicionado em 09/09/2012
O conceito de gestão da qualidade total, seus objetivos, elementos e características. O problema da introdução do conceito de “Gestão da Qualidade Total” nas atividades de uma organização. Propriedades do produto que determinam suas principais funções. Avaliação da qualidade dos produtos acabados.
Ao implementar métodos e ferramentas de manufatura enxuta, surge frequentemente a questão: como avaliar o efeito das mudanças feitas? Acima de tudo, é claro, os gestores estão interessados no efeito económico, isto é, no efeito expresso em rublos ou dólares de lucro adicional (que é melhor) ou redução de custos (que é pior, mas, em princípio, também é aceite). .
Muitas vezes, nos primeiros meses de implementação da produção enxuta, temos que falar sobre a impossibilidade de calcular o efeito económico e aqui está o porquê...
Existem fundamentalmente duas abordagens para avaliar o efeito económico.
A primeira envolve avaliação especializada baseada em uma quantidade limitada de dados digitais, quando é calculado um certo “efeito potencial”. Por exemplo, estamos falando sobre que uma das propostas para melhorar o trabalho do operador da máquina permite-lhe reduzir o tempo self made ao carregar e descarregar peças da máquina por 15 minutos por turno. Conhecendo o custo de uma hora de trabalho deste operador, por exemplo, 100 rublos, você pode calcular que a economia potencial por turno é de 25 rublos, por mês - 500 rublos, por ano - 6.000 rublos.
Este método tem muitas desvantagens. A desvantagem óbvia é a imprecisão avaliação especializada economizando tempo - não é fato que esse operador economize 15 minutos por turno. Como se costuma dizer, se você evitar que uma pessoa tenha que fazer um trabalho inútil, ela imediatamente encontrará mais dez coisas para fazer nas quais poderá gastar todo o tempo economizado. Portanto, esses 15 minutos não se transformarão automaticamente em trabalho que realmente gere dinheiro.
A segunda abordagem envolve uma avaliação com base nos resultados do trabalho durante um período de tempo, por exemplo, um mês ou um trimestre. O departamento de contabilidade resume todos os números e relatórios: o lucro passou a ser tal e tal. (por exemplo, no nosso caso, o lucro da empresa no mesmo mês aumentou 2 milhões 127 mil rublos, mas não é verdade que tudo isso se deveu apenas à economia de 15 minutos de trabalho do operador da máquina). Neste caso, os números de poupança ou lucro adicional são muito mais credíveis, mas se você espera que os contadores sejam capazes de lhe dar a resposta à pergunta “quanto dinheiro recebemos (poupamos) após implementar esta proposta”, então você estão enganados. Eles não vão dar:
- a oferta implementada é apenas um dos fatores que afetam o lucro entre todos os tipos de flutuações no nível de demanda dos clientes, atrasos nos fornecedores, atrasos no pagamento dos clientes, quebras de equipamentos em outras áreas de produção, etc. e assim por diante. Na grande maioria dos casos, é quase impossível isolar a influência deste fator específico - avaliar o resultado obtido SOMENTE graças à proposta implementada.
- Muitos custos indiretos levados em consideração no cálculo da rentabilidade de produtos ou obras individuais são distribuídos de acordo com proporções convencionalmente especificadas (por exemplo, acontece que o custo de manutenção de edifícios e estruturas é transferido para o custo de produção dependendo da área de instalações ocupadas pelos correspondentes recursos de produção) e quando essa proporção deixa de corresponder ao nosso entendimento de uma avaliação justa dos custos, a exactidão do efeito económico começa a levantar questões óbvias.
Em termos simples, um economista que olha para os números do efeito económico acreditará neles apenas num caso:
- quando a estrutura do efeito econômico corresponde integralmente à estrutura de custo dos produtos/serviços adotada em sua empresa
- quando os dados são confirmados por documentos contábeis
- quando houver dados históricos sobre quais resultados econômicos existiam ANTES da implementação desta proposta
Agora vamos ver o que os iniciantes em manufatura enxuta encontram com mais frequência:
- muitas empresas não possuem métodos aprovados para calcular os custos dos produtos (cálculo do custo de produção de um determinado tipo de produto ou o custo de prestação de um determinado tipo de serviço) com uma estrutura de custos estabelecida
- nem todas as transações internas são acompanhadas de documentos contábeis e, portanto, é improvável que todos os dados sobre despesas estejam disponíveis no departamento de contabilidade
- Muitas vezes não é possível restaurar dados históricos, inclusive devido ao fato de que alterações e ajustes são frequentemente feitos pelo Estado no sistema contábil das empresas russas, razão pela qual os dados de produção de anos diferentes nem sempre permanecem comparáveis.
Se você não estiver convencido por esses argumentos, contarei outro fato notável.
Normas internacionais de relatórios financeiros IFRS e Padrões russos A contabilidade RAS possui uma característica que impede seu uso direto para contabilidade em uma empresa enxuta: ambos os padrões foram desenvolvidos na era da produção em massa e postulam o alto valor da disponibilidade de recursos de produção e grandes estoques de matérias-primas, produtos semiacabados e produtos finalizados.
Do ponto de vista da contabilidade clássica, o excesso de estoque nos armazéns é “bom” e “bom” em muitos aspectos. Do ponto de vista da produção enxuta, qualquer excesso de estoque é “mau”. Parece que se trata apenas de palavras gerais, mas no final, na elaboração do balanço, da demonstração de lucros e perdas, isso leva ao facto de que os factos que do ponto de vista da produção enxuta devem ser avaliados como conquistas e resultados positivos efeitos, do ponto de vista da contabilidade clássica, são percebidos como um resultado negativo.
Não quero convencer ninguém de que, ao implementar a produção enxuta, o efeito económico não pode ser calculado. Precisa ser calculado. Mas ao avaliar a poupança, deve-se ter em mente que os números obtidos serão justamente percebidos com um grande grau de ceticismo. E esse ceticismo tem razões completamente objetivas.
A quem possa interessar
No contexto da implementação prática da “produção enxuta”, as questões de avaliação do estado real e outras perspectivas de utilização de ferramentas de “produção enxuta” adquirem particular importância. Porque, em primeiro lugar, pode haver a ilusão de que muito já foi feito na empresa, e a atividade de introdução de ferramentas e métodos de produção enxuta pode ser reduzida e, em segundo lugar, cada próximo passo para reduzir perdas e aumentar a eficiência da empresa exigirá esforços mais significativos.
Maioria métodos eficazes organização "Produção enxuta" na empresa é a determinação de indicadores-alvo, implementação projetos piloto e cálculo do efeito econômico.
As metas de manufatura enxuta são necessárias para orientar o desenvolvimento de estratégias e políticas pela alta administração, por meio das quais os recursos são direcionados para as metas que são críticas para o negócio. É necessário unificar os recursos e desenvolver indicadores mensuráveis específicos que monitorizem regularmente a concretização dos objetivos principais. Característica chave O modelo é um bloco de avaliação de eficiência e desenvolvimento de novas metas, totalmente consistente com a filosofia de “produção enxuta” e visando a melhoria contínua. O modelo inclui uma avaliação especializada da eficácia da implementação do sistema Lean Manufacturing, apresentada na Tabela. 9.
Os resultados de uma avaliação especializada sobre a eficácia da implementação da produção enxuta na KAMAZ OJSC demonstram o seguinte:
1. O subsistema “pessoal” recebeu maior desenvolvimento na KAMAZ OJSC em comparação com outros subsistemas (5,5 pontos em 10 no máximo); o subsistema “processos” tem o menor desenvolvimento na empresa (4,6 pontos).
2. Todos os subsistemas “processos”, “pessoal”, “gestão estratégica” foram avaliados pelos especialistas do KAMAZ OJSC em um nível médio (pontuação máxima - 10 pontos), o que indica que ainda existem reservas significativas para a implementação de ferramentas enxutas e produção de métodos.
3. Indicadores como (4,0 pontos), (3,2 pontos), (3,7 pontos), trabalho com fornecedores em produção enxuta (3,7 pontos), (3,8 pontos), trabalho com revendedores em produção enxuta (3,9 pontos), recebidos na KAMAZ OJSC, possuem a pontuação mais baixa e são diretrizes para intensificar o trabalho.
Tabela 9
Avaliando a eficácia da organização da “Produção Enxuta” na KAMAZ OJSC
Indicadores avaliados |
Parcela de avaliações de especialistas,% |
|||||||||||
Subsistema "gestão estratégica" |
||||||||||||
Disponibilidade da filosofia BP |
||||||||||||
Declaração e princípios da BP |
||||||||||||
KPI - principais indicadores de desempenho |
||||||||||||
Estudando os requisitos do consumidor |
||||||||||||
Avaliação de satisfação do cliente |
||||||||||||
subsistema "pessoal" |
Treinamento de funcionário |
|||||||||||
Coesão dos funcionários |
||||||||||||
Subsistema de processos |
Disponibilidade de 5C |
|||||||||||
Usando um sistema pull |
||||||||||||
Reduzindo perdas |
||||||||||||
Melhorando a qualidade do produto |
||||||||||||
Trabalhando com fornecedores na BP |
||||||||||||
Trabalhando com revendedores BP |
Apesar do fato de KAMAZ OJSC ser líder entre as empresas de engenharia mecânica da Federação Russa na implementação de ferramentas e métodos de produção enxuta, as avaliações dos especialistas sobre a situação na KAMAZ OJSC não diferem radicalmente da avaliação nas empresas de engenharia mecânica da Rússia Federação. Tudo isso indica que os especialistas internos são propensos à autocrítica, veem as deficiências existentes e as perspectivas de desenvolvimento da empresa na introdução de ferramentas e métodos de produção enxuta.
Na prática, isso significa a necessidade de intensificar o trabalho na implantação das ferramentas do sistema de produção KAMAZ - são soluções que permitem enxergar oportunidades de melhoria e reduzir significativamente as perdas.
É necessário melhorar constantemente toda a gama de processos de negócio, aumentar a transparência e controlabilidade da organização, aproveitar o potencial de cada colaborador da empresa, aumentar a competitividade e obter um efeito económico significativo sem incorrer em grandes custos financeiros (Fig. 22 ).
Tabela 10
Avaliação da eficácia da implementação do sistema Lean Production na KAMAZ OJSC e em empresas de engenharia mecânica da Federação Russa
Indicadores avaliados |
Qua. pontuação para KAMAZ OJSC |
Qua. pontuação em engenharia mecânica da Federação Russa |
|
Subsistema "gestão estratégica" |
Disponibilidade de gestão estratégica |
||
Disponibilidade da filosofia BP |
|||
Declaração e princípios da BP |
|||
Envolvimento da alta administração, implementação projetos pessoais |
|||
KPI - principais indicadores de desempenho |
|||
Estudando os requisitos do consumidor |
|||
Avaliação de satisfação do cliente |
|||
Subsistema "pessoal" |
Treinamento de funcionário |
||
Coesão dos funcionários |
|||
Disponibilidade e qualidade das propostas kaizen |
|||
Desenvolvendo líderes que professam a filosofia da BP |
|||
Criando uma organização de autoaprendizagem |
|||
Subsistema de processos |
Disponibilidade de 5C |
||
Usando um sistema pull |
|||
Distribuição uniforme do trabalho |
|||
Usando inspeção visual |
|||
Reduzindo perdas |
|||
Melhorando a qualidade do produto |
|||
Melhorando a qualidade do serviço |
|||
Trabalhando com fornecedores na BP |
|||
Trabalhando com revendedores BP |
Cada uma das ferramentas do Sistema de Produção KAMAZ resolve uma parte específica do problema, e somente o seu uso combinado resolverá o problema completamente, ou minimizá-lo-á para valores aceitáveis.
Arroz. 22. Aplicação de ferramentas do Sistema de Produção KAMAZ
Convencionalmente, as ferramentas do Sistema de Produção KAMAZ podem ser divididas em três grupos principais: ferramentas de análise e identificação de perdas, ferramentas de melhoria, ferramentas de gestão e envolvimento (Tabela 11).
Tabela 11
Ferramentas do sistema de produção KAMAZ
Como os especialistas avaliaram a eficácia da implementação de ferramentas e métodos de manufatura enxuta em um nível médio, a empresa terá que intensificar o trabalho em áreas como KPIs - indicadores-chave de desempenho, uso de um sistema pull, estudo dos requisitos do cliente, avaliação da satisfação do cliente, distribuição uniforme de trabalho, melhorando a qualidade dos serviços, trabalhando com fornecedores na manufatura enxuta, trabalhando com revendedores na manufatura enxuta.
Arroz. 23. Metas e objetivos do Programa da República do Tartaristão “Implementação do projeto de Produção Enxuta na República do Tartaristão para 2011-2013”
A intensificação deste trabalho é facilitada pela implementação do Programa da República do Tartaristão “Implementação do projeto “Produção Enxuta” na República do Tartaristão para 2011-2013”, que prevê o financiamento de projetos para a implementação de ferramentas e métodos da produção enxuta, incluindo projetos de treinamento de pessoal em produção enxuta.
Como resultado da implementação das atividades do Programa da República do Tartaristão “Implementação do Projeto de Manufatura Enxuta na República do Tartaristão para 2011-2013”, está previsto garantir o cumprimento dos indicadores apresentados na Tabela. 12.
Tabela 12
Indicadores do Programa da República do Tartaristão “Implementação do Projeto de Produção Enxuta para 2011-2013”
Nome do indicador |
||
Índice de produção industrial das empresas participantes do programa, % |
||
Taxa de crescimento da produtividade do trabalho (em comparação com o período correspondente do ano passado) das empresas participantes do programa, em % |
||
Participação de empresas industriais que implementam programas de desenvolvimento de manufatura enxuta no número total de empresas industriais com mais de 500 funcionários, em % |
||
Nível de rentabilidade da produção das empresas participantes do programa, em % |
||
Número de empresas cujo pessoal passou por desenvolvimento profissional no âmbito do Programa |
Esta abordagem para aumentar gradualmente a eficiência das empresas na economia da República do Tartaristão, incluindo OJSC KAMAZ, através da redução de perdas e da formação de pessoal, contribui para o crescimento do potencial de produção da economia regional e para o aumento da competitividade.
Até o momento, um extenso arsenal de métodos foi acumulado e testado pelos quais uma empresa pode implementar ferramentas de produção enxuta. Os métodos mais eficazes para implementar o sistema Lean Manufacturing em uma empresa são definir indicadores-alvo, implementar projetos piloto e calcular o efeito econômico. As metas de produção enxuta e o cumprimento das metas do Sistema de Produção KAMAZ são apresentados na Tabela. 13.
Tabela 13
Dinâmica de indicadores para cumprimento dos objetivos do sistema de produção KAMAZ
Indicadores |
|||||||
Treinado em princípios e métodos de BP |
|||||||
projetos abertos |
|||||||
projetos implementados |
|||||||
propostas de kaizen enviadas |
|||||||
implementou propostas kaizen |
|||||||
estandardização |
|||||||
visualização |
|||||||
área liberada m². |
|||||||
unidades de equipamentos liberadas |
|||||||
efeito econômico alcançado (milhões de rublos) |
|||||||
incluindo. Kaizens |
|||||||
os custos para o desenvolvimento do PSK totalizaram |
|||||||
% do efeito econômico |
Metas do sistema de produção KAMAZ para 2012:
1. Aumentar a eficiência operacional do KAMAZ OJSC, reduzindo o tempo de inatividade do equipamento de emergência em 50% e aumentando a produtividade do trabalho em 16%. reduzindo os custos específicos de energia em 5% por veículo, reduzindo os custos nas atividades de compra em 1.500 milhões de rublos, trazendo o número de configurações atuais de veículos de acordo com o plano de negócios para 2012, dotando a produção de uma reserva de pessoal para operação estável no verão.
2. Aumentar a eficiência do sistema de gestão da KAMAZ OJSC através da introdução da norma “SFM - gestão de processos desde o ponto de criação de valor”, introduzindo o princípio “logística entrega, montagem monta” através do desenvolvimento e implementação de normas no processo principal: montagem, logística, implantação da quinta e sexta fase do projeto “Calendário”, desenvolvimento e implantação de mapa de desenvolvimento de pessoas do processo principal, implantação de sistema de reporte para gestores baseado em KPIs do processo principal.
3. Aumentar a qualidade e a confiabilidade dos produtos KAMAZ OJSC introduzindo um sistema de qualidade integrado nos principais processos em 100%, reduzindo as perdas por defeitos em 10%, reduzindo o PPM em 25%.
4. Envolver 100% do pessoal na melhoria do sistema de produção KAMAZ, treinando todo o pessoal recém-contratado nos princípios, métodos e ferramentas do PSK, apresentando 4 propostas kaizen por 1 funcionário por ano, abrindo 4.200 projetos kaizen, implementando pelo menos 3.800, implementando 80% das propostas e projetos kaizen apresentados, abertura de um projeto pessoal por cada gestor do KAMAZ OJSC.
5. Garantir o desenvolvimento sustentável de fornecedores, subsidiárias, joint ventures nos princípios do sistema de produção KAMAZ por meio de treinamento curso básico PSK para gerentes de todos os centros automotivos e principais fornecedores, realizando um seminário de 3 dias sobre o curso básico de PSK para gerentes de concessionárias KAMAZ OJSC, apresentando o PSK em todos subsidiárias com 100% de capital da KAMAZ OJSC, criando sites de referência nos princípios PSK em 3 fornecedores principais e em uma das fábricas -
representante do cliente, abertura pelos gestores da joint venture de projetos pessoais para integração dos sistemas de produção da joint venture e PSK.
6. Garantir a lealdade do pessoal da empresa, clientes, residentes da cidade e da República do Tartaristão ao KAMAZ OJSC através da transmissão sistemática de experiência bem sucedida no desenvolvimento do sistema de produção KAMAZ.
7. Obter um efeito econômico ao reduzir perdas no valor de 1.418 milhões de rublos.
Um elemento importante que aumenta a eficiência da implementação da “fabricação enxuta” é a implementação de projetos piloto. Por exemplo, o projeto Mayak na Fábrica de Automóveis KAMAZ foi inaugurado em 8 de setembro de 2010 com o objetivo de introduzir intensivamente padrões, métodos e tecnologias de gerenciamento modernos do sistema operacional TOS (Daimler AG) para otimizar os processos da Fábrica de Automóveis KAMAZ. Durante o projeto Mayak, a carga de trabalho dos operadores foi nivelada em um ciclo de clock de 240 s, e um novo foi desenvolvido estrutura organizacional. Os objetivos, resultados e ferramentas utilizadas no projeto Mayak são apresentados na Tabela. 14.
Além disso, durante o projeto Mayak, a taxa de controlabilidade do mestre foi alterada: era 1:35, passou a ser 1:10 (o capataz é o líder da equipe e seu ideólogo, para apoiar a nova estrutura do transportador). Organizou o trabalho operacional dos gestores e Opinião através de centros de informação de 3 níveis: brigada, oficina, fábrica. Mais de 60% das reuniões foram transferidas para centros de informação para garantir o fluxo de informações e os procedimentos de escalonamento. Os locais de trabalho são organizados de acordo com 15 princípios de montagem da Daimler (de 19% a 69% de conformidade). Desde o início do projeto, os funcionários apresentaram cerca de 1.300 propostas de kaizen com um efeito económico no valor de mais de 17 milhões de rublos. O trabalho do serviço logístico é organizado com base nos 14 princípios logísticos da Daimler. Durante o projeto, ocorreu o treinamento contínuo de pessoal nos princípios, ferramentas e métodos do Lean (foram treinados cerca de 1.400 trabalhadores e 350 engenheiros). Um elemento integrante da implementação de um sistema de produção enxuta em uma empresa é calcular o efeito econômico da introdução de ferramentas e métodos de produção enxuta.
Tabela 14
Metas, resultados e ferramentas utilizadas no projeto Mayak
Metas do projeto |
Resultados do projeto |
Princípios, ferramentas e métodos do Lean Manufacturing utilizados no projeto |
Reduzir em 50% o número de modificações (montagem) dos carros montados |
Objetivo alcançado |
Mapeamento detalhado de todos os processos da área do projeto. Planejamento de trabalho em cascata no formato de planos táticos padrão. Eliminação |
Implementando Qualidade Integrada |
Implementados ciclos de qualidade 1, 2, portões de qualidade, postos de qualidade |
|
Implementação do sistema Andon |
Objetivo alcançado |
|
Implementação de padrões TOS em montagem e logística |
Objetivo alcançado |
|
Aumentar a produtividade do trabalho |
A produtividade do trabalho aumentou 49%. |
|
Garantir a capacidade de montar 48.100 carros na GSK 1 em 2012 (24.000 carros foram montados na GSK 1 em 2010) |
A capacidade de montar 48.100 carros na GSK 1 foi garantida em 2011 |
|
Implementar o padrão de gerenciamento empresarial Gerenciamento de chão de fábrica |
O padrão de gerenciamento empresarial Shop Floor Management foi implementado na área do projeto |
|
Os custos do projeto devem ser recuperados ao longo de sua implementação. |
O efeito econômico do projeto foi de 629 milhões de rublos. e excedeu os custos |
O cálculo do efeito econômico é realizado com base em indicadores-chave de desempenho (redução de estoques, redução de rotas de transporte, redução de paradas não planejadas de equipamentos, etc.) e expresso na resultante economia de recursos ou produção adicional de produtos em o local, a oficina, a organização são considerados como um efeito condicional.
Economia. effect = [Custos antes - Custos depois] - - Custos de implementação do evento. (1)
O efeito económico é um efeito no cálculo do qual todos os tipos de resultados e custos associados à implementação do evento são tidos em conta em termos monetários.
Custos = Consumo físico de recursos? (2)
Custos de pré-implementação - calculados com base nos resultados do mapeamento Estado atual processo ou dados de contabilidade, contabilidade gerencial.
W para = P r para? (3)
Custos após - são calculados conforme planejado (na fase de avaliação preliminar) ou consumo real de recursos após a implementação do evento
Z depois = P r depois?
onde R r antes, R r depois - consumo de recursos antes e depois da implementação do evento, C res - custo dos recursos
Os custos de implementação de um evento são custos únicos de implementação do evento (custos de energia, materiais, custos de mão de obra, etc.)
A utilização da metodologia proposta para avaliar a eficiência permitirá à empresa avaliar com mais precisão o efeito da introdução de ferramentas e métodos de produção enxuta, com base nos quais é possível tomar uma decisão de gestão sobre a eficácia do trabalho da empresa em enxuta produção e a necessidade de intensificar esse trabalho.
Correlação conduzida e análise de regressão série temporal permitiu avaliar o grau de influência dos fatores sobre a variável dependente e entre si. Os resultados da análise indicam a presença de uma ligação particularmente estreita entre a capacidade de produção da empresa e o volume de produtos expedidos, receitas de vendas de produtos, salários médios mensais, custo total de produção, produtividade do capital e produtividade do trabalho. Com o aumento desses indicadores, o indicador de capacidade de produção aumenta (relação direta).
A análise de regressão de séries temporais mostra o seguinte. Em primeiro lugar, o indicador de produtividade de capital tem uma relação direta e estreita com a capacidade de produção, a produção de produtos em termos físicos, a taxa de utilização da capacidade de produção, o volume de produtos expedidos, a receita de vendas de produtos, o salário médio mensal e o custo total dos produtos vendidos. Ao mesmo tempo, existe uma relação inversa com o custo dos ativos fixos de produção. Em segundo lugar, a rentabilidade do produto alto nível estreita ligação com o lucro das vendas de produtos e o número de funcionários. Neste caso, existe uma ligação direta entre os indicadores. O valor negativo do coeficiente de correlação (-0,716) com o indicador de custos por 1 rublo de produtos vendidos indica um feedback próximo.
Contudo, deve-se ressaltar que os coeficientes de correlação pareados foram obtidos sujeitos à influência de outros fatores no resultado. Para abstrair sua influência e obter uma descrição quantitativa da relação entre os indicadores resultantes e os indicadores fatoriais em sua forma pura, são calculados coeficientes de correlação parciais.
Como resultado da construção de uma matriz de coeficientes de correlação parcial para os dados de desenvolvimento do KAMAZ OJSC, foi possível identificar uma relação positiva bastante próxima entre os custos de desenvolvimento do PSK e indicadores como o número de propostas kaizen apresentadas e implementadas e a quantidade de espaço liberado (os coeficientes de correlação foram 0,888, 0,894 e 0,891, respectivamente). O número de projetos abertos está positivamente correlacionado com o número de projetos implementados, bem como com o número de propostas de kaizen apresentadas e implementadas. A quantidade de espaço liberado está intimamente relacionada ao número de projetos abertos e implementados, bem como de propostas de kaizen apresentadas e implementadas. Altos coeficientes de correlação indicam um nível significativo de dependência dos indicadores.
Parece apropriado determinar o impacto do desenvolvimento do PSK nos principais indicadores económicos da empresa. O melhor efeito positivo é observado quando as variáveis são defasadas por 3 anos (Tabela 15). Em particular, existe uma estreita relação positiva entre a capacidade produtiva do empreendimento e os custos de desenvolvimento do complexo industrial, bem como os indicadores de projetos abertos e implementados e propostas de kaizen. Além disso, esses indicadores têm efeito positivo no volume de produtos expedidos, na receita de vendas e na produtividade de capital.
Uma nova mudança de indicadores devido à fonte limitada de dados para a empresa parece inadequada.
A próxima etapa da análise de correlação é o cálculo da equação de relacionamento (regressão). Os coeficientes da equação mostram o impacto quantitativo de cada fator no indicador de desempenho, mantendo os demais constantes. Parece apropriado construir um modelo de regressão linear múltipla com os melhores coeficientes de correlação para o modelo, ou seja, quando as variáveis estão defasadas por três anos.
No nosso caso, as equações de regressão terão a seguinte forma:
y = 0,582x16 + 0,04x19 + 86,04x27 + 63692,33, (5)
Neste caso, podemos dar a seguinte interpretação à equação resultante: a lucratividade aumenta em 0,582 unidades. com o aumento do número de projetos abertos; por 0,04 unidades. - com o aumento do número de propostas de kaizen implementadas; para 86,04 unidades. - com um aumento nos custos de implementação do PSK em 1 milhão de rublos.
Tabela 15
Matriz de coeficiente de correlação de pares (deslocamento - 3 anos)
Treinado nos princípios e métodos de segurança pessoal |
Projetos abertos |
Projetos implementados |
Propostas Kaizen enviadas |
Propostas Kaizen implementadas |
Espaço liberado m². |
Unidades de equipamentos liberadas. |
Efeito econômico recebido (milhões de rublos) |
Incluindo Kaizens |
Percentagem de impacto económico |
Os custos para o desenvolvimento do PSK totalizaram (milhões de rublos) |
|
Capacidade de produção, unid. |
|||||||||||
Produção de produtos em termos físicos, unid. |
|||||||||||
Fator de utilização da capacidade |
|||||||||||
Volume de produtos expedidos, |
|||||||||||
Receita de vendas de produtos, milhões de rublos. |
|||||||||||
Salário médio mensal, esfregue. |
|||||||||||
Custo total dos produtos vendidos, milhões de rublos. |
|||||||||||
Custo dos ativos fixos de produção, milhões de rublos. |
|||||||||||
Lucro (perda) de produtos vendidos, milhões de rublos. |
|||||||||||
Número de pessoal de produção industrial, pessoas. |
|||||||||||
Produtividade de capital, esfregue. |
|||||||||||
Produtividade do trabalho, milhões de rublos. |
Além disso, o valor de R2 = 0,995 indica que 99,5% da variação da produtividade do trabalho se deve à influência linear dos fatores acima.
A aplicação dos métodos propostos para organizar a produção enxuta em uma empresa envolve a criação de um ambiente adaptativo e sistema flexível gestão e produção, capazes de melhoria contínua, e ajudarão a reduzir perdas na empresa, aumentar a competitividade e aumentar a produtividade do trabalho.
Chamamos a sua atenção revistas publicadas pela editora "Academia de Ciências Naturais"
Efeito econômico: a essência do conceito, a necessidade de cálculo e análise
Definição 1
No contexto do conceito de “manufatura enxuta”, efeito económico representa a diferença entre os resultados das atividades de uma entidade empresarial e os custos incorridos para obtê-los; em outras palavras, trata-se de receitas adicionais recebidas pelo fato de que, utilizando certas abordagens e métodos, a empresa opera de forma mais eficiente.
Você precisa entender a diferença entre redução de custos (minimização de custos) e eliminação/redução de desperdícios. Na verdade, são coisas um pouco diferentes (embora, por outro lado, a redução de perdas leve a custos mais baixos).
O efeito económico da implementação de uma determinada melhoria é a diferença entre os estados “antes” e “depois” (menos os custos associados à implementação do evento). Às vezes, a diferença entre os custos unitários por unidade de produção, “antes” e “depois” e outros indicadores é tomada como o efeito económico.
Na maioria das vezes, o efeito económico é calculado numa escala de 1 ano. Assim, por exemplo, se os movimentos diários de turno do operador forem reduzidos em 5 minutos, então a economia em 1 semana será de 50 minutos (com turno de cinco dias e dois turnos). semana de trabalho); por ano já é de aproximadamente 2.400 minutos (ou 5 dias úteis). Assim, o cálculo do efeito económico à escala anual permite ver com mais clareza todo o potencial da melhoria implementada.
Os cálculos preliminares do potencial efeito económico permitem definir corretamente as prioridades, bem como concentrar a atenção e os esforços nas obras e projetos que podem trazer mais benefícios e devem render mais rapidamente. A princípio, deve-se dar preferência àqueles que são de fácil implementação, baratos e projetos de curto prazo. Se tiver de escolher entre dois projetos de custo e complexidade semelhantes, deverá escolher aquele com maior efeito económico potencial.
Indicadores de desempenho de eventos
É necessário analisar a implementação de medidas do conceito de manufatura enxuta apenas com base em dados confiáveis de pesquisas sobre a dinâmica dos indicadores de produção. Definitivamente, você também deve se concentrar no custo unitário de produção.
Em geral, a implementação de um projeto de manufatura enxuta é considerada bem-sucedida se as seguintes condições forem atendidas:
- A produtividade do trabalho aumentou e os volumes de produção aumentaram
- A taxa de casamento diminuiu
- o indicador de entrega pontual de produtos manufaturados melhorou
- o custo unitário diminuiu.
Nota 1
Se pelo menos um indicador apresentasse dinâmica positiva e os demais permanecessem no mesmo nível, o projeto deveria ser aceito. Se a maioria dos indicadores calculados mostram uma dinâmica adequada, mas um dos indicadores mostra o contrário, é necessária uma análise adicional e mais aprofundada das razões para tal.
Entre outras coisas, podem ser alcançadas poupanças significativas nos custos de produção numa fábrica através da implementação das seguintes medidas:
- introdução de tecnologias de poupança de energia
- otimização de custos de manutenção e reparos atuais de ativos fixos liberados
- mudança na depreciação devido à liberação de equipamentos e espaço (principalmente armazém)
- otimização de impostos, leasing, aluguel, pagamentos de seguros, custos de segurança, etc.
- redução na taxa de defeitos
- eliminação do excesso de estoque
- perda de tempo de trabalho associada à espera de fornecimento de recursos materiais e técnicos
- aceleração do giro, minimizando ou eliminando estoque, tempo de inatividade, etc.
- eliminando desperdício de materiais, etc.
Portanto, o resultado final é que tudo o que não agrega valor ao cliente precisa ser eliminado ou minimizado.