Instalacja z czujnikiem zegarowym. Czujniki zegarowe i inne typy głowic pomiarowych. Interpretacja wartości odchyłki poziomej
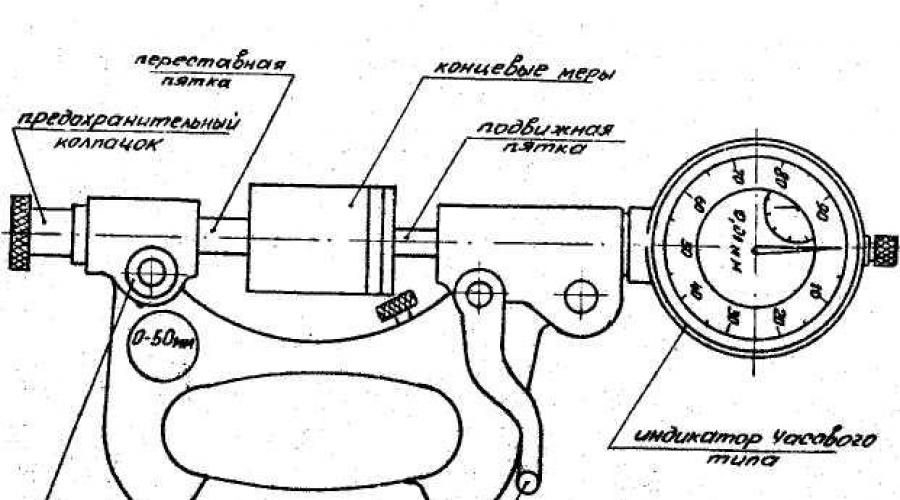
Przeczytaj także
1.1. Czujnik zegarowy o wartości podziału 0,01 mm, modele ICH przeznaczone są do pomiaru wymiarów liniowych metodą bezwzględną i względną, określając wielkość odchyleń od zadanej wartości kształt geometryczny I względne położenie powierzchnie.
1.2. Pogląd wersja klimatyczna UHL4 zgodnie z GOST 15150-69
1.3. Przymocuj wskaźniki albo do tulei łączącej o śr. 8h7 lub za uchem o grubości 5 mm z otworem łączącym śr. 5 mm.
Dane techniczne.
2.1. Dane techniczne Wskaźniki zegarowe ICH podano w tabeli 1.
Tabela 1
Charakterystyka techniczna wskaźników zegarowych ICH
Model | Skala | Błąd, mm, | wymiary | Wartość podziałki, mm | |
klasa dokładny 0 | klasa dokładny 1 | ||||
ICH 02 | 0-2 | ±0,010 | ±0,012 | 75x42x23 | 0,01 |
ICH 05 | 0-5 | ±0,010 | ±0,012 | 86x42x23 | 0,01 |
ICH 10 | 0-10 | ±0,015 | ±0,020 | 108x56x24 | 0,01 |
ICH 25 | 0-25 | ±0,032 | 159x85x51 | 0,01 | |
ICH 50 | 0-50 | ±0,048 | 199x85x51 | 0,01 |
2.2. Zakres odczytów, mikrony, nie więcej niż 3.
2.3. Maksymalna siła pomiarowa podczas skoku do przodu, N - 1,5
2.4. Wahania siły pomiarowej podczas skoku do przodu lub do tyłu, N - nie więcej niż 0,6.
2.5. Wahania siły pomiarowej przy zmianie kierunku ruchu pręta pomiarowego, N - nie więcej niż 0,5.
Warunki korzystania.
3.1. Temperatura przestrzeni roboczej podczas procesu pomiaru powinna wynosić (20±15)˚С.
3.2. Wilgotność względna powietrza nie przekracza 80% przy temperaturze 20˚C.
Kompletność.
Zestaw urządzenia zawiera:
- wskaźnik;
- sprawa;
- paszport.
Urządzenie i zasada działania.
5.1. Pomiar dokonywany jest metodą kontaktową. Ruchomy pręt pomiarowy opiera się na kontrolowanej powierzchni. Ruch pręta pomiarowego odbywa się równolegle do skali wskaźnika i odbywa się za pomocą par kinematycznych przekładni.
5.2. Konstrukcja wskaźnika zapewnia ochronę przed zanieczyszczeniami i uszkodzeniami mechanicznymi.
5.3. Wskaźniki typu ICh dostępne są z oczkiem do mocowania lub bez.
Przygotowanie wskaźnika do pracy.
6.1. Przed rozpoczęciem pracy zapoznaj się z paszportem wskaźnika.
6.2. Usuń tłuszcz ze wskaźnika (szczególnie ostrożnie z powierzchni pomiarowej końcówki szmatką zamoczoną w benzynie i na koniec wytrzyj suchą szmatką.
Procedura obsługi i konserwacja.
7.1. Sprawdź, czy wskaźnik jest ustawiony na zero. Aby to zrobić, nadaj prętowi pomiarowemu napięcie 20-25 działek i obracając obręcz, zrównaj linię zerową skali ze strzałką.
Aby sprawdzić stałość odczytów, należy dwukrotnie lub trzykrotnie podnieść pręt pomiarowy na wysokość 1-2 mm i puścić go. Jeśli strzałka odbiega od pozycji zerowej, konieczne jest ponowne ustawienie z nią linii zerowej skali.
7.2. Wytrzyj mierzony przedmiot czystą, miękką szmatką, np najmniejsza obecność wody, oleju itp. prowadzi do zniekształcenia odczytów.
Upewnij się, że pręt pomiarowy porusza się bez uderzeń na końcu skoku, ponieważ może to prowadzić do zmiażdżenia i wykruszenia zębów mechanizmu oraz zwiększenia błędu wskaźnika. Nie dopuścić do kontaktu emulsji i olejów ze wskaźnikiem.
7.3. Nie obracać wskaźnika, gdy jest on zamocowany w uchwycie za pomocą tulei.
Jeśli ruch stanie się nierówny, dozwolone jest częściowe przepłukanie mechanizmu bez całkowitego demontażu wskaźnika. W tym celu zdejmij pokrywę i zanurz mechanizm wskaźnika w czystej benzynie lotniczej, uważając, aby benzyna nie spadła na skalę wskaźnika. Po umyciu mechanizmu nasmaruj czopy osi olejem zegarkowym.
Zasady przechowywania.
8.1. Po zakończeniu pracy wytrzeć wskaźnik miękką szmatką i nasmarować powierzchnię pomiarową smarem antykorozyjnym.
8.2. Przechowuj wskaźnik w etui, w suchym, ogrzewanym pomieszczeniu o temperaturze powietrza od +5 do +40˚С i wilgotność względna Nie
ponad 80% w temperaturze +20˚С.
8.3. Powietrze w pomieszczeniu nie powinno zawierać domieszek agresywnych par i gazów.
Metody i środki weryfikacji.
9.1. Wskaźnik należy zweryfikować metodami i środkami określonymi w GOST 8548-86.
9.2. Częstotliwość kalibracji ustala się w zależności od wymagań eksploatacyjnych, jednak nie rzadziej niż raz na dwa lata.
Informacje o konserwacji.
10.1. Czujnik zegarowy został zakonserwowany zgodnie z wymogami GOST 9014-76. Nazwa i marka środka konserwującego – olej konserwujący K-17.
10.2. Okres trwałości urządzenia bez ponownej konserwacji wynosi 2 lata, pod warunkiem przechowywania w warunkach zgodnych z GOST 15150-69.
Obowiązki gwarancyjne.
Okres gwarancji na produkt wynosi 1 rok, licząc od daty sprzedaży (odbioru przez kupującego) urządzenia, pod warunkiem przestrzegania przez Konsumenta zasad przechowywania i obsługi urządzenia.
Pobierać świadectwo techniczne Z poniższego linku możesz skorzystać bezpłatnie.
W nowoczesna produkcja nie da się tego zrobić bez pewności urządzenia pomiarowe. Ich obecność pozwala na wykonanie wielu rodzajów prac, w tym napraw, zakupu części zamiennych, a także wyprodukowania ich zgodnie z ustalonymi parametrami. Przemysł metalowy szczególnie potrzebuje tych urządzeń, niezależnie od specyfiki wytwarzanych produktów. Aby uzyskać dokładne odczyty wymiarów liniowych, pomiary względne odchylenia od układu powierzchni i wartości nominalnej wymagają czujnika zegarowego.
Co to jest wskaźnik ICH i dlaczego jest potrzebny?
Urządzenie służy do pomiaru wielkości bezwzględnych i względnych, monitorowania odchyłek od zadanego kształtu geometrii produktu oraz względnego położenia powierzchni. Urządzenia typu zegarowego mają szeroki zakres pomiarowy. Są niezastąpione analiza porównawcza, z biciem promieniowym i osiowym części, sprawdzanie boki równoległe na przykład w pryzmatach. Strzałki umożliwiają natychmiastowe wykrycie odchyleń.
Konstrukcja wskaźnika przewiduje obecność łączących kół zębatych i dźwigni, które mają zwiększony wpływ na wibracje pręta (sondy), a przetwarzając ruch, urządzenie generuje odczyty. W zdecydowanej większości mechanizmów przesunięcie pręta o 1 mm jest równoznaczne z jednym obrotem igły. Zatem cena podziału (odpowiednio wartość ruchu sondy), którą urządzenie może wiarygodnie zmierzyć, wynosi 0,01 mm. Progi pomiarowe oznaczone są jako 0-5, 0-10 i 0-25 mm. Wskaźniki typu IP są klasyfikowane według stopnia dokładności:
- zero;
- Pierwszy;
- drugi.
Liczniki klasy zerowej charakteryzują się minimalnym błędem uzyskanych danych, a liczniki klasy drugiej charakteryzują się maksymalnym.
Dokładność, mały błąd i długa żywotność wskaźników umożliwiają ich zastosowanie w produkcji, fabrykach, stacjach Konserwacja. Procedura pomiaru bicia końcowego bębna hamulcowego pojazd wymaga obowiązkowej aktywacji wskaźnika IR.
Istnieją urządzenia działające na przekładniach. W nich drążek i stojak stanowią jedną całość. Zębatka współpracuje z kołem o 16 zębach. Małe urządzenie z przekładnią dźwigniową stosuje się w miejscach o utrudnionym dostępie oraz do produkcji niektórych części instalacji wodno-kanalizacyjnej.
Urządzenie wskaźnikowe
Seria ICH składa się z obudowy, mechanizmu przekładniowego, skali, wskazówki, sondy pomiarowej i sprężyny neutralizującej luz (koła zębate zazębiają się zawsze z jednego profilu zębów). Na obrotowej tarczy można ustawić zero dla pomiarów względnych oraz w dowolnym miejscu znacznik tolerancji. W sprzedaży można znaleźć urządzenia posiadające specjalne oczko umożliwiające montaż na statywie.
Wiele modeli jest wyposażonych w kulkę z węglika na końcu wału w wymiennej ramie. Musi dotykać mierzonej części. Nacisk na sondę odbywa się za pomocą sprężyny umieszczonej pomiędzy korpusem a prętem. Aby dokonać pomiarów, wskaźnik umieszcza się na statywie lub stojaku. U podstawy znajduje się cylindryczny pręt, do którego przymocowane jest ruchome sprzęgło z prętem oraz a urządzenie pomiarowe. Uchwyt często wyposażony jest w podstawę z magnesami, dzięki czemu można go ustawić w pionie lub pod kątem, aby pracować z produktami bez konieczności stosowania dodatkowego mocowania.
Rodzaje wskaźników
Ze względu na charakterystykę obudowy urządzenia IR dzielą się na:
- zwykle chroniące komponenty przed różnego rodzaju zanieczyszczenie i uszkodzenia mechaniczne;
- bryzgoszczelne, ich szczelna obudowa zapobiega przedostawaniu się rozprysków do odpowiedniego środowiska;
- pyłoszczelna, używana otwarte przestrzenie ze zwiększonym tworzeniem się pyłu.
Oprócz, urządzenia uniwersalne, w zależności od ruchu pręta względem skali, dzielą się na:
- równoległy (IC);
- prostopadłe (PCI).
Jak działa mechanizm zliczający i na co zwrócić uwagę przy jego zakupie
- Przed rozpoczęciem pracy wskaźnik mocuje się śrubą na statywie.
- Podnosi się pręt pomiarowy i na podstawie umieszcza obiekt o ustalonych parametrach.
- Urządzenie opuszcza się w dół cylindra statywu, aż końcówka zetknie się z powierzchnią próbki, a strzałka zatrzyma się na 0. Pozycja ta nazywana jest „naprężeniem”. Jego wartość musi być większa niż tolerancja odchylenia od odczytów nominalnych o 1 obrót strzałki.
- Powtarzając czynności „podnoszenia/opuszczania” pręta, monitorowana jest stabilność danych. Jeśli strzałka odbiega od normy, należy ponownie przeprowadzić regulację.
- Pręt jest cofany, a próbkę zastępuje się mierzonym elementem. Sonda jest na nią opuszczana, skala wskaźnika pokazuje różnice w wielkości od podanych (o 0,01 mm).
Przed zakupem wskaźnika ICH należy sprawdzić cenę i zakres podziału. Im mniejszy pierwszy wskaźnik, tym dokładniejszy będzie pomiar. Im większa rozpiętość (zakres), tym maksymalne odchylenie w milimetrach, jakie urządzenie może zmierzyć.
Najczęściej spotykanymi głowicami pomiarowymi są czujniki zegarowe z podziałką 0,01 mm. Przeznaczone są do stosowania w warunkach warsztatowych przy wykonywaniu procesów technologicznych wytwarzania, montażu, testowania i kontroli wyrobów. Są również szeroko stosowane w warsztatach naprawczych przy naprawie sprzętu i regeneracji zużytych części.
Czujniki zegarowe dostępne są w dwóch wersjach, typu ICH– ze strzałką poruszającą się równolegle do skali i czcionki, TO– przesuwając pręt pomiarowy prostopadle do skali.
Zgodnie z projektem nadwozia Wskaźniki zegarowe dzielą się na:
1) zwykły; 2) bryzgoszczelny; 3) pyłoszczelny.
W normalnym wykonaniu Mechanizm wskaźnika jest chroniony przed zanieczyszczeniami i uszkodzeniami mechanicznymi.
Konstrukcja odporna na zachlapania zapewnia ochronę wskaźnika przed przedostawaniem się rozprysków do mechanizmu, gdy wskaźnik znajduje się w środowisku narażonym na rozpryski.
Konstrukcja pyłoszczelna zabezpiecza mechanizm wskaźnika przed wnikaniem kurzu w środowisku o dużym stężeniu pyłu.
Na przedniej stronie czujnika zegarowego znajdują się dwie skale:
1) duża skala z 100 podziały z ceną podziału 0,01 mm (ryc. 28);
2) mała skala z podziałką milimetrową.
Przesunięcie pręta pomiarowego o wielkość równą 1 mm, powoduje obrót dużej strzałki w kierunku 360°(jeden pełny obrót), a małą wskazówkę o jedną działkę, czyli o 1 mm.
Podczas konfigurowania wskaźnika do zadanej wielkości, dużą skalę można obrócić ręcznie o 360° i zabezpieczyć w żądanej pozycji za pomocą zatyczki lub na skutek siły tarcia powstającej pomiędzy obrzeżem dużej skali a korpusem wskaźnika.
Pomiary wskaźnikiem polegają na przeliczeniu ruchów liniowych pręta pomiarowego na ruchy kątowe strzałek względem ich podziałek poprzez przekładnię dźwigniowo-zębatą.
Na pręcie pomiarowym nacinane są zęby zębatki zazębiające się z kołem zębatym, z liczbą zębów z= 16. Na tej samej osi z tym kołem zębatym znajduje się drugie koło zębate z liczbą zębów z= 100 większa średnica. Z tego koła obrót jest przenoszony na przekładnię centralną za pomocą z= 10. Duża strzałka jest przymocowana do osi centralnego koła zębatego, umieszczonego nad dużą skalą. Drugie duże koło zębate jest zazębione z kołem centralnym. z= 100. Do osi tego koła na jednym końcu przymocowana jest sprężyna spiralna, której drugi koniec jest przymocowany do korpusu wskaźnika. Sprężyna zapewnia pracę kół zębatych po jednej stronie profilu, zmniejszając w ten sposób wpływ luzu w parach kół zębatych na błąd pomiaru. Strzałka skali milimetrowej wskaźnika jest ustalona na osi drugiego biegu.
Specyficzne zastosowania czujników zegarowych:
Do pomiaru rozmiarów;
Aby kontrolować odchylenia kształtu;
Do kontroli położenia powierzchni w stojaku, statywie lub specjalnym urządzeniu.
Pomiary przeprowadza się metodami bezwzględnymi (ocena bezpośrednia) i względnymi (porównanie z miarą).
Bezwzględne pomiary wymiarów, takie jak pomiary odchyłek kształtu i położenia powierzchni, można wykonywać w zakresie pomiarowym wskaźnika, czyli w granicach 0 – 2 mm (ze wskaźnikiem ICh2), 0 – 5 mm ( ze wskaźnikiem ICh5), 0 – 10 mm (ze wskaźnikiem ICh5), ICH10), 0 – 25 mm (wskaźnik ICH25). Poniżej przedstawiono charakterystykę metrologiczną czujnika zegarowego o podziałce skali 0,01 mm modelu ICH MN.
Podstawowe charakterystyki metrologiczne czujnika zegarowego z podziałką 0,01 mm, model ICH 10 MN:
Wartość podziału skali głównej w mm. . . . . . . . . . . . . . . 0,01
Zakres pomiarowy w mm. . . . . . . . . . . . . . . . . . . . . . 0 – 10
Klasa dokładności. . . . . . . . . . . . . . . . . . . . . . . . . . . . . . . . . .0; 1
Największa różnica w błędach wskaźników mieści się w granicach:
0,1 mm w dowolnej części zakresu pomiarowego:
0 klasa . . . . . . . . . . . . . . . . . . . . . . . . . . . . . . . . . . . . . . . . . . 4
1 klasa... . . . . . . . . . . . . . . . . . . . . . . . . . . . . . . . . . . . . . . . . .6
1 mm w dowolnej części zakresu pomiarowego:
0 klasa... . . . . . . . . . . . . . . . . . . . . . . . . . . . . . . . . . . . . . . . . 8
1 klasa . . . . . . . . . . . . . . . . . . . . . . . . . . . . . . . . . . . . . . . . 10
Całkowity zakres pomiarowy:
0 klasa . . . . . . . . . . . . . . . . . . . . . . . . . . . . . . . . . . . . . . . . .15
1 klasa . . . . . . . . . . . . . . . . . . . . . . . . . . . . . . . . . . . . . . . . .20
Zmienność wskazań nie większa niż:
0 klasa... . . . . . . . . . . . . . . . . . . . . . . . . . . . . . . . . . . . . . . . . 2
1 klasa . . . . . . . . . . . . . . . . . . . . . . . . . . . . . . . . . . . . . . . . . .3
Maksymalna siła pomiarowa, N. . . . . . . . . . . . . 1,5
Wahania siły pomiarowej podczas skoku do przodu i do tyłu, N, nie więcej. . . . . . . . . . . . . . . . . . . . . . . ……………0,6
Wahania siły pomiarowej przy zmianie kierunku ruchu pręta pomiarowego, N, nie więcej. . . .0.5
Zmiana wskazań wskaźnika przy naciśnięciu pręta pomiarowego w kierunku prostopadłym do jego osi z siłą 2 - 2,5 N wynosi nie więcej niż 0,5 podziałki skali.
We wszystkich urządzeniach grupy wskaźników urządzeniem pomiarowym jest czujnik zegarowy (ryc. 5 a).
Mechanizm przekładni kierunkowskazów (rys. 5 b) składa się z par kół zębatych. Trzon pomiarowy 1 posiada w środkowej części zębatkę, która zazębia się z kołem zębatym 2. Ruch posuwisto-zwrotny pręta pomiarowego zamieniany jest na ruch obrotowy (okrężny) strzałki 3 poprzez koła zębate 4 i 5. Błędy z zakresu boczne luzy w zębatkach eliminowane są za pomocą włosa sprężystego 7, którego jeden koniec jest przymocowany do osi dodatkowego koła zębatego 6, a drugi do korpusu wskaźnika. Urządzenie posiada dwie skale: dużą do odczytu ułamków milimetra i małą do odczytu całych milimetrów (duża strzałka wskazuje pełne obroty).
Wskaźniki zwykłe mają zakresy pomiarowe 0...5 i 0...I0 mm, małogabarytowe - 0...2, 0...3 mm z podziałką skali 0,01 mm.
4.2.2. Ustawianie wspornika wskaźnika i wykonywanie pomiarów
Wspornik wskaźnikowy służy do pomiarów zewnętrznych metodą względną. Standardowe rozmiary zszywek ustalane są z limitami wymiarowymi: 0...50, 50...100, 100...200 mm itp. po 100 mm do 1000 mm. Główne części urządzenia pokazano na rys. 6.
Ryc.5. Wskaźnik zegarowy
1. Zgodnie z wymiarem nominalnym dobrać płytkę wzorcową.
2. Za pomocą płytki wzorcowej wyregulować urządzenie do zera. W tym celu należy zdjąć nasadkę zabezpieczającą, poluzować śrubę blokującą i zamontować blok pomiędzy ruchomą i regulowaną piętą. Poruszając regulowaną piętką, doprowadź powierzchnie pomiarowe pięt do płytki wzorcowej, a duża strzałka wskaźnika powinna wykonać około jednego obrotu. Zablokuj tę pozycję regulowanego pięty za pomocą śruby zabezpieczającej i zamknij ją zatyczką zabezpieczającą. Obracaj ramkę wskaźnika, aż podział zerowy tarczy zrówna się ze strzałką. Uruchom 2...3 razy na ograniczniku, aby upewnić się, że ustawienie zera jest prawidłowe, i wyjmij płytkę manometru.
3. Zmierz zewnętrzną średnicę części. W tym celu za pomocą blokady należy umieścić część pomiędzy piętami, lekko dociskając ją do regulowanej pięty. Podczas pomiaru trzymaj cęgę pionowo. Wyrównaj płaszczyznę środkową części z linią pomiarową urządzenia, ustalając ogranicznik w tej pozycji. Zrób odliczanie. Rzeczywista wielkość Sudette jest równa sumie wielkości płytek wzorcowych i wskazań na skali wskaźnika. Odchylenia w kierunku zgodnym z ruchem wskazówek zegara są dodatnie, w kierunku przeciwnym do ruchu wskazówek zegara są ujemne.
Ryc.6. Wspornik wskaźnika
4.3. Wskaźnik średnicy otworu
4.3.1. Struktura urządzenia
Średnicówka wskaźnikowa służy do pomiaru wymiarów wewnętrznych metoda względna. Do każdego średnicówki dołączony jest zestaw wymiennych prętów pomiarowych stosowanych w
Rys.7 Średnica wskaźnika
zgodnie z zmierzoną średnicą. Zestaw dziesięciu średnicówek wskaźnikowych umożliwia pomiar średnic od 6 do I000 mm: 6....10, 10...18, 18...35, 35...50 mm itp.
Średnicówka składa się ze wskaźnika 1 (rys. 7 a), rurowego; obudowa 3, komora pomiarowa 6, w której umieszczone są ruchomy pręt pomiarowy 9, wymienny stały pręt pomiarowy 7 oraz układ dźwigni. Sprężynowy mostek centrujący 11 zapewnia montaż średniceomierza wzdłuż osi mierzonego otworu.
Ruch pręta 9 (rys. 7 b), odpowiadający odchyłce średnicy mierzonego otworu, przekazywany jest na wskaźnik 1 poprzez dźwignię 8, obracającą się wokół osi 10, oraz ruchomy pręt 5, który porusza się w tulejach prowadzących wewnątrz rurki. Sprężyna 4 wytwarza siłę pomiarową.
Ryż. 5.40 Metoda wskaźnika odwrotnego
Do pomiaru położenia wału ruchomego względem nieruchomego w dwóch płaszczyznach wzdłuż ich długości służą dwa wskaźniki promieniowe.
Ryż. 5.41 Wskaźnik stacjonarny (SI) mierzy przemieszczenie w płaszczyźnie nieruchomego wału lub połówki sprzęgła
Ryż. 5.42 Wskaźnik ruchomy (PI) mierzy przemieszczenie w płaszczyźnie ruchomego wału lub połówki sprzęgła
Na podstawie obu wartości przemieszczeń, a także wymiarów osprzętu i samej maszyny, w drodze obliczeń lub wykresu określa się względne położenie ruchomego wału.
5.6.2 Porównanie z metodą promieniowo-osiową
Przy centrowaniu maszyn metodą promieniowo-osiową, których wały mają rozbieg osiowy i drgania te są większe niż 0,025 mm, szczególnie w przypadku maszyn z łożyskami ślizgowymi, przy pomiarze wskaźnikiem osiowym pojawiają się błędy. Ponieważ metoda odwrotnego wskaźnika nie wymaga pomiarów osiowych, błędy tego rodzaju są wykluczone.B. >
Ryż. 5.43 Porównanie z metodą promieniowo-osiową
5.6.3 Przegląd elementów złącznych metodą odwróconego wskaźnika
Do pracy z metodą wskaźnika odwrotnego dostępna jest szeroka gama konstrukcji mocowania wału. Zaleca się wybór i stosowanie specjalnie zaprojektowanych konstrukcji, aby zapewnić ich przydatność do montażu na wałach różne średnice. Łączniki te muszą zawierać zestaw prętów wypełniających szczelinę pomiędzy połówkami złącza. Za pomocą tych elementów złącznych można szybko i sprawnie przeprowadzić wyrównanie. Ale najpierw musisz określić ugięcie prętów zawartych w standardowych zestawach.
Niektóre elementy złączne są zaprojektowane tak, aby umożliwić rozłączenie połówek sprzęgła podczas ustawiania wskaźnika kierunku wstecznego, podczas gdy inne wymagają montażu połówek sprzęgła podczas tego procesu.
Ryż. 5.44 Mocowania na otwartych wałach
Ryż. 5.45 Mocowania na zmontowanych wałach
Wiele mocowań przystosowanych jest do wykonywania zestrojenia ze kierunkowskazami zamontowanymi w tym samym położeniu na obwodzie wałów (jak pokazano powyżej) lub obróconymi o 180° względem siebie, czyli w przeciwnych punktach tarczy zegarka.
Ryż. 5.46 Łączniki montowane naprzeciw siebie
5.6.3.1 Montaż łączników metodą odwrotnego wskaźnika
Procedura instalacji będzie oczywiście zależeć od konkretnego rodzaju zastosowanych opraw. Rozważmy ustawienie połączonych wałów, gdy wskaźniki znajdują się w tym samym położeniu na obwodzie.Aby zainstalować elementy złączne, wykonaj następujące kroki:

5.6.3.2 Uwagi dotyczące elementów złącznych
W zależności od rodzaju zastosowanego mocowania należy przestrzegać poniższych środków ostrożności.
- Nigdy nie mocuj elementów dodatkowych do elastycznych części sprzęgła.
- Jeśli to możliwe, zwiększ odległość między wskaźnikami na całej długości maszyny, którą zamierzasz wycentrować. Z reguły odległość między prętami wskaźnikowymi powinna być większa niż 100 mm.
- Upewnij się, że elementy mocujące są zamontowane w pozycji, która nie utrudnia obrotu wałów. Wskazane jest, aby móc wykonać pełny obrót.
- Przed dokonaniem pomiarów należy określić ugięcie prętów wskaźnika i upewnić się, że wskazania wskaźnika są prawidłowe i powtarzalne.
5.6.4 Wprowadzanie wymiarów liniowych metodą odwrotnego wskaźnika
Dla precyzyjna definicja położenie wału ruchomego, na podstawie obliczeń metodą wskaźnika odwrotnego lub konstrukcji graficznej, należy określić położenie wskaźników względem przednich i tylnych nóg poruszającej się maszyny.
Wymiary te określa się za pomocą standardowej miarki krawieckiej. Każdy wymiar musi być mierzony z dokładnością do 1/8 cala (1-2 mm).
Ryż. 5.48 Wymiary wejściowe metodą odwrotnego wskaźnika
Rozmiar „A”
Wymiar „A” to odległość pomiędzy prętami wskaźnikowymi. Mierzy się go równolegle do osi wałów. Jest to najbardziej krytyczny wymiar i należy go zmierzyć bardzo dokładnie. Jak wspomniano wcześniej, podczas instalowania urządzeń do wyrównywania wskaźników odwrotnych należy pamiętać o pozostawieniu jak największej przestrzeni pomiędzy prętami wskaźnikowymi, w zależności od wielkości maszyny i dostępnej przestrzeni.
Rozmiar „B”
Wymiar „B” to odległość od wskaźnika na boku poruszającej się maszyny do środka śruby mocującej przednią łapę. Odległość tę mierzy się równolegle do osi wału. Szczególnie w przypadku dużych maszyn czasami przydatne jest użycie sznurka lub prostej krawędzi w celu przeniesienia położenia ruchomego pręta wskaźnikowego na podstawę maszyny przed pomiarem tego wymiaru.
Rozmiar „C”
Wymiar „C” to odległość pomiędzy środkami śrub mocujących przednie i tylne nogi. Odległość tę mierzy się równolegle do wału.
5.6.5 Znaki w metodzie wskaźnika odwrotnego
Podczas wykonywania pomiarów ważne jest, aby wiedzieć, że różne ustawienia wskaźników wpływają na znak odczytów w różny sposób. Efekt ten wynika z tego, że oba wskaźniki mają ten sam kierunek pomiaru – plus/minus i są zamontowane, jak wynika z nazwy metody, naprzeciwko siebie.
Wpływ różne instalacje pokazane poniżej.

Ryż. 5.50 Reset o godzinie 12 lub 3. Zmiana znaku PI
Resetuj o godzinie 6 lub 9. Zmiana znaku SI
Poniższa procedura pomiarowa opisuje obie sytuacje dla instalacji pokazanej na rysunku 5.50.
5.6.6 Procedura osiowania metodą odwrotnego wskaźnika
5.6.6.1 Opis procesu pomiarowego
Proces pomiaru metodą odwrotnego wskaźnika składa się z następujących operacji:
- Pomiar i rejestracja ustalonego stanu niewspółosiowości.
- Pomiar niewspółosiowości pionowej i poziomej.
Uzyskanie serii zmierzonych wartości jest w niektórych przypadkach uważane za opcjonalne, ale nadal jest wysoce zalecane. W przypadku większości zadań związanych z osiowaniem pożądane jest posiadanie zapisu pełny zasięg dane, w tym rozmiary „A”, „B” i „C”. Zmierzone wartości są wykorzystywane do wielu celów:
- Wstępne nagranie stanu osiowania przed demontażem sprzętu i wysłaniem go do naprawy.
- Ustalenie, czy istnieje podejrzenie niewspółosiowości.
- Wspieraj i oceniaj działania wykonywane przez personel serwisowy, dealera i producenta sprzętu.
- Prowadzenie historii konserwacji mechanizmu.
- Lepsza interakcja pomiędzy różnymi specjalistami zajmującymi się osiowaniem sprzętu.
5.6.6.2 Wykonywanie pomiarów
Aby uzyskać pełną serię pomiarów, wykonaj następujące czynności:
- Ustaw kierunkowskazy na pozycję 12:00.
- Ustaw oba wskaźniki na wartości dodatnie.
- Zanotuj odczyty obu wskaźników na pozycji 12:00.
- Ustaw wskaźniki w pozycji 3:00.
- Ustaw wskaźniki na pozycję 6:00.
- Określ i zapisz odczyty obu wskaźników.
- Ustaw wskaźniki na pozycję 9:00.
- Określ i zapisz odczyty obu wskaźników.
- Obróć wskaźniki do pozycji 12:00 i sprawdź, czy oba wskaźniki powróciły do swoich pierwotnych odczytów.
Aby zapisać wyniki, użyj typu nagrywania pokazanego poniżej.
Ryż. 5.51 Dokumentacja wartości początkowych
5.6.6.3 Pomiar odchyłki pionowej
Aby zmierzyć przesunięcie pionowe, wykonaj następujące kroki:

5.6.6.4 Interpretacja wartości odchyłki pionowej
Aby określić przesunięcie w płaszczyzna pionowa W zależności od zakresu wskazań wskaźników na pozycji 6:00 obowiązują następujące zasady:
- Przesunięcie strony stacjonarnej = rozpiętość SI / 2
- Przesunięcie strony ruchomej = rozpiętość PI s przeciwny znak(+ do -) lub (- do +)
- Przesunięcie w środku sprzęgła = (Przesunięcie strony stacjonarnej + Przesunięcie strony ruchomej) / 2
Aby wyznaczyć pęknięcie kątowe na podstawie dwóch odczytów przemieszczenia w płaszczyźnie pionowej, należy postępować zgodnie z zasadą:
- Kąt linii wału = (Przesunięcie strony ruchomej - Przesunięcie strony stacjonarnej) / Wymiar A
Rozważmy następny przykład zakres wskazań wskaźnika na pozycji 6:00.
Ryż. 5.55 Przykład zakresu wskaźników
- Rozpiętość SI = +24 milicali (0,610 mm). Nieruchome przesunięcie boczne = +12 milicali lub 12 milicali w górę (0,305 mm).
- Odchylenie PI = -35 mils (-0,889 mm). Przesunięcie strony ruchomej = +17,5 milicala lub 17,5 milicala w górę (0,444 mm). (Pamiętaj, że aby określić przesunięcie, musisz odwrócić znak PI).>
- Przesunięcie pionowe na środku sprzęgła = (+12+17,5)/2 = 14,75 milicala lub 14,75 milicala wyższe (0,375 mm).
- Niech wymiar A = 8 cali (203,2 mm), wówczas przerwa pionowa będzie wynosić (17,5-12)/8 = +0,69 mil na cal ((0,444-0,305)/203,2=0,069 mm / 100 mm).
5.5.6.5 Pomiar odchyłki poziomej
Podczas pomiaru i interpretacji wartości przesunięcia poziomego należy ustalić właściwy kierunek patrzenia. Wszystkie pozycje związane ze wskazówką godzinową tarczy odpowiadają pozycji widza pokazanej na poniższym rysunku, czyli stojącego za maszyną poruszającą się twarzą do maszyny nieruchomej.
Ryż. 5.56 Pomiar przesunięcia poziomego
Aby zmierzyć przesunięcie poziome, wykonaj następujące czynności:

5.6.6.6 Interpretacja wartości odchyłki poziomej
Aby określić przesunięcie poziome na podstawie odczytów zakresu w pozycji 3:00, postępuj zgodnie z poniższymi zasadami:
- Stacjonarne przesunięcie boczne = zakres SI/2 z przeciwnym znakiem (+ do -) lub (- do +)
- Odsunięcie strony ruchomej – rozpiętość PI / 2
- Przesunięcie w środku sprzęgła = (Przesunięcie strony stacjonarnej + Przesunięcie strony ruchomej)/2.
Aby określić pęknięcie kątowe w płaszczyźnie poziomej na podstawie dwóch odczytów przesunięcia, należy zastosować następującą regułę:
- Złamanie narożnika = (Przesunięcie strony ruchomej - Przesunięcie strony ruchomej)/(Wymiar A), (?100 = mm/100 mm)
Rozważmy następujący przykład zakresu odczytów wskaźników na pozycji 3:00.
Ryż. 5.59 Odczyty na pozycji 3:00.
- Rozpiętość SI = +34 mils (0,864 mm). Nieruchome przesunięcie boczne = -17 mils, czyli 17 mils w lewo (-0,432 mm). (Pamiętaj, że aby określić przesunięcie, należy odwrócić znak SI (patrz rozdział 5.6.5).
- Odchylenie PI = +8 mil (0,203 mm). Przesunięcie strony ruchomej = +4 mils, czyli 4 mils w prawo (0,101 mm).
- Przesunięcie poziome na środku sprzęgła = (-17+-4)/2 = -6,5 milicala ((-0,432+0,101)/2=-0,165 mm) lub 6,5 milicala w lewo (0,165 mm).
- Niech wymiar A = 8 cali (203,2 mm), wówczas przerwa pozioma będzie wynosić (4-(-17)/8 = 2,63 milicala na cal ((0,101-(-0,432)/203,2)=0,263 mm / 100 mm).
5.6.7 Obliczenia metodą odwrotnego wskaźnika
Do wykonywania obliczeń można używać wielu różnych równań różne opcje metoda wskaźników odwrotnych. Informacje przedstawione tutaj dotyczą konfiguracji kierunkowskazu pokazanej na poniższym rysunku. Rozważane równania służą do obliczenia położenia przednich i tylnych nóg poruszającej się maszyny według odczytów SI i PI.
Obliczenia niewspółosiowości dotyczą zarówno płaszczyzn poziomych, jak i pionowych. Chociaż są one zwykle używane głównie w płaszczyźnie pionowej. Jak przedstawiono wcześniej, niewspółosiowość w płaszczyźnie poziomej można znaleźć bez obliczania lub wykreślania dokładnego położenia przednich i tylnych łap.
5.6.7.1 Obliczenia pozycji przednich i tylnych nóg
Jak pokazano wcześniej i przedstawiono na poniższym rysunku, jest on używany kolejna instalacja, wymiary i znak przemieszczenia.
Ryż. 5.60 Instalacja do obliczania pozycji łapy
Położenie przednich nóg poruszającej się maszyny określa się za pomocą następującego równania:
Ryż. 5.61 Obliczenia dla przednich łap
Położenie tylnych nóg poruszającej się maszyny określa się za pomocą następującego równania:
Ryż. 5.62 Obliczenia dla tylnych nóg
- M = przemieszczenie w płaszczyźnie ruchomego wskaźnika.
- S = przemieszczenie w płaszczyźnie wskaźnika stacjonarnego.
- A = odległość pomiędzy prętami wskaźnika stacjonarnego i ruchomego.
- B = odległość od ruchomego pręta wskaźnikowego do środka śruby mocującej ruchome przednie ramię maszyny.
- C = odległość między środkami śrub przednich i tylnych nóg poruszającej się maszyny.
- Wartości dodatnie oznaczają, że łapa jest wyżej (w pionie) lub w prawo (w poziomie).
- Wartości ujemne oznaczają, że łapy są niżej (w pionie) lub w lewo (w poziomie).
5.6.7.2 Przykłady obliczeń metodą odwrotnego wskaźnika
Wstępne dane
Określono następujące wartości przesunięcia pionowego:
- Przesunięcie strony stacjonarnej (S) wynosi +12 milicali (0,305 mm) lub 12 milicali więcej.
- Przesunięcie strony ruchomej (M) wynosi +17,5 milicala (0,444 mm) lub 17,5 milicala więcej.
- A=5 cali (127 mm), B=7 cali (177,8 mm), C=24 cale (609,6 mm)
Obliczanie położenia przednich łap
Ryż. 5,63 Przednie łapy 25,2 milicala (0,64 mm) wyższe; podkładki trzeba zdjąć
Ryż. 5,64 Tylne nogi 51,6 milicala (1,31 mm) wyższe; podkładki trzeba zdjąć
5.6.7.3 Uwagi dotyczące obliczeń metodą wskaźnika odwrotnego
- Przed przystąpieniem do obliczeń należy upewnić się, że w wykonanych pomiarach prawidłowo określono rozpiętość wskaźnika stacjonarnego i ruchomego.
- NIE popełniaj błędów matematycznych podczas podstawiania podpisanych danych we wzorach.
- Uważaj na nawiasy w równaniach. Najpierw wykonaj obliczenia w nawiasach.
- NIE popełniaj subiektywnych błędów podczas podstawiania rzeczywistych wartości do równań.
5.6.8 Konstrukcje graficzne w metodzie wskaźników odwrotnych
Jak wspomniano powyżej, jednym ze sposobów określenia położenia przednich i tylnych nóg poruszającej się maszyny na podstawie odczytów SI i PI jest wykonanie obliczeń metodą wskaźnika odwrotnego.
Innym sposobem jest narysowanie rysunku na papierze milimetrowym. Główną zaletą konstrukcji graficznej jest wyraźne przedstawienie linii środkowych i stanu niewspółosiowości.
Informacje przedstawione tutaj są stosowane w urządzeniu wykorzystującym metodę odwrotnego wskaźnika, w którym oba wskaźniki są przymocowane w tym samym miejscu na obwodzie.
Konstrukcję graficzną można zastosować zarówno do obliczeń niewspółosiowości poziomych, jak i pionowych płaszczyzn. Chociaż zwykle jest używany głównie w płaszczyźnie pionowej. Jak stwierdzono powyżej, korektę przesunięcia poziomego można przeprowadzić bez obliczania lub wykreślania dokładnego położenia przednich i tylnych łap.
5.6.8.1 Układ mapy
Aby narysować wykres w odpowiedniej skali, wykonaj następujące kroki:
- Weź papier wielkoformatowy - „papier milimetrowy”.
- Obróć papier dłuższą stroną do siebie.
- Narysuj poziomą linię na środku arkusza.
Linia ta reprezentuje oś obrotu nieruchomego wału maszyny i przebiega przez środek arkusza, dzieląc go na pół. Lepiej jest narysować tę linię wzdłuż grubej linii siatki papieru milimetrowego. - Wybierz poziomą skalę obrazu.
Zawsze staraj się wybierać największą skalę waga. Zmierz odległość od nieruchomego pręta wskaźnikowego do środka śruby mocującej tylną nogę poruszającej się maszyny. Na standardowy arkusz papier milimetrowy o szerokości około 260mm, największa skala pozioma będzie wynikiem podzielenia rozmiaru maszyny przez tę szerokość. Zaznacz skalę osi poziomej na wykresie. - Narysuj pionową linię wzdłuż lewej krawędzi rysunku.
Reprezentuje punkt, w którym ramię nieruchomego wskaźnika dotyka wału lub połówki sprzęgła i jest oznaczony jako SI. - Używając odpowiedniej skali, narysuj drugą pionową linię na prawo od pierwszej.
Reprezentuje punkt, w którym ruchoma nóżka wskaźnika dotyka wału lub połówki sprzęgła i jest oznaczony jako PI. - Narysuj trzecią pionową linię przedstawiającą rzut na oś wału przednich nóg poruszającej się maszyny (ML).
- Narysuj czwartą pionową linię przedstawiającą rzut na oś wału tylnych nóg poruszającej się maszyny (ML).
Po wykonaniu wszystkich powyższych kroków otrzymasz rysunek podobny do poniższego. W tym przykładzie wymiary A, B i C wynoszą 100 mm.
Ryż. 5.65 Układ rysunku
5.6.8.2 Graficzne wykreślenie przemieszczenia
Po zaznaczeniu rysunku należy przystąpić do konstruowania przemieszczeń w płaszczyznach wskaźnika stacjonarnego (SI) i wskaźnika ruchomego (PI). Aby utworzyć rysunek, wykonaj następujące czynności:
- Wybierz skalę pionową. Zazwyczaj wybierana jest skala pionowa wynosząca 0,01 mm na działkę. Czasami w przypadku dużych przesunięć, gdy przesunięcia nie mieszczą się na rysunku, wymagana jest większa skala - 0,02-0,03 mm na działkę.
- Narysuj przemieszczenie od strony stacjonarnej wzdłuż linii SI.
Jako punkt odniesienia należy zastosować linię poziomą przedstawiającą oś wału maszyny stacjonarnej. Wszystkie punkty powyżej tej linii mają wartości dodatnie (+), a wszystkie punkty poniżej mają wartości ujemne (-). - Narysuj przesunięcie po stronie ruchomej wzdłuż linii PI.
W poniższym przykładzie przesunięcie SI wynosi -0,2 mm, a przesunięcie PI wynosi -0,1 mm.
Ryż. 5.66 Obraz na rysunku
5.6.8.3 Określanie położenia wału ruchomego
Po naniesieniu na rysunek przesunięć SI i PI w celu określenia położenia ruchomego wału wykonaj następujące czynności:
- Za pomocą linijki narysuj linię przechodzącą przez dwa punkty przesunięcia prowadzące do tylnych nóg poruszającej się maszyny.
- Policz liczbę kwadratów w płaszczyźnie przednich i tylnych łap, aby określić położenie i niezbędne korekty.
W poniższym przykładzie przednie nogi maszyny są ustawione prawidłowo; nie ma potrzeby ich dostosowywania. Tylne nogi znajdują się 0,1 mm wyżej; Konieczne jest usunięcie opuszek spod obu tylnych nóg.
Ryż. 5.67 Określanie położenia wału ruchomego
5.6.8.4 Uwagi dotyczące konstrukcji graficznej w metodzie wskaźnika odwrotnego
- Upewnij się, że wybrana skala jest prawidłowa w obu osiach.
- Zawsze dokładnie sprawdź położenie pionowych linii reprezentujących SI, PI, PL i ZL.
- Upewnij się, że dwa wykreślone punkty są prawidłowo zidentyfikowane na podstawie odczytów zakresu wskaźników.
- Upewnij się, że dodatnie wartości przesunięcia znajdują się powyżej poziomej linii odniesienia, a ujemne wartości przesunięcia znajdują się poniżej.
- Interpretując wykres określający położenie przednich i tylnych nóg poruszającej się maszyny w płaszczyźnie pionowej, należy zwrócić uwagę na następujące zasady:
- Jeżeli ruchomy wał na rysunku znajduje się wyżej niż pozioma linia odniesienia położenia stacjonarnego wału, oznacza to, że wał jest za wysoki.
- Jeżeli wał ruchomy na rysunku znajduje się poniżej poziomej linii odniesienia położenia wału nieruchomego, oznacza to, że wał jest za niski.
- Interpretując wykres służący do określenia położenia przednich i tylnych nóg poruszającej się maszyny w płaszczyźnie poziomej, wygląd wykresu odzwierciedla sposób, w jaki widzisz maszynę, czyli stojąc za poruszającą się maszyną, twarzą do maszyny nieruchomej. Tutaj również zwróć uwagę na następujące zasady:
- Jeżeli wał ruchomy na rysunku znajduje się powyżej poziomej linii odniesienia położenia wału nieruchomego, wówczas wał jest przesunięty w prawo.
- Jeżeli wał ruchomy na rysunku znajduje się poniżej poziomej linii odniesienia położenia wału nieruchomego, wówczas wał jest przesunięty w lewo.
5.6.9 Korekty metodą odwrotnego wskaźnika
5.6.9.1 Przegląd procesu regulacji
Aby skorygować niewspółosiowość, stosuje się wiele różnych operacji. Kolejność kroków w procesie regulacji różni się nieznacznie w zależności od konkretnych warunków ustawienia maszyny.
Przed skorygowaniem niewspółosiowości
Przed skorygowaniem niewspółosiowości wykonywane są następujące operacje:
- Przeprowadzić wstępne kontrole i regulacje.
- Montaż mocowań metodą odwrotnego wskaźnika.
- Korekta „miękkiej łapy”
- Pomiar niewspółosiowości.
- Określanie tolerancji wyrównania.
Po korekcie niewspółosiowości
Po skorygowaniu niewspółosiowości wykonywane są następujące operacje:
- Powtarzany pomiar stanu wyrównania.
- Porównanie stanu niewspółosiowości z przypisanymi tolerancjami.
- Zapisz wyniki końcowe.
Ogólne problemy z regulacją
Jeśli chodzi o faktyczne przeniesienie maszyny, czyli ROZWIĄZANIE PROBLEMU, często pojawia się kilka pytań:
- Czy powinienem zacząć w pionie czy w poziomie?
- A co z gotowymi uszczelkami?
- Czy muszę dokonać ponownego pomiaru po przesunięciu maszyny w pionie lub w poziomie?
- Czy konieczne jest użycie czujnika zegarowego do kontroli ruchów poziomych?
- Czy konieczne jest przestrzeganie kolejności dokręcania śrub?
- Czy powinieneś najpierw poruszać przednimi czy tylnymi nogami?
Każde z tych pytań jest warte rozważenia i znajdziesz na nie odpowiedź.
Ustalanie kolejności regulacji
Korekcja niewspółosiowości obejmuje początkowy i końcowy etap regulacji. Pierwsze mają na celu zminimalizowanie wielkości niewspółosiowości i zwiększenie dokładności pomiarów współosiowości.
Przed przeprowadzką spójrz poziomy i pionowy położenie poruszającej się maszyny. Zasadniczo proces regulacji rozpoczniesz od płaszczyzny, w której niewspółosiowość jest większa, a następnie przejdziesz do regulacji końcowej.
Dokonywanie korekt | Jeśli | To |
Niewspółosiowość równa lub mniejsza niż 0,5 mm |
||
Zarówno w pionie, jak i w poziomie dla przednich i tylnych nóg |
Niewspółosiowość większa niż 0,5 mm |
|
Pionowe lub poziome dla przednich i tylnych nóg |
Niewspółosiowość większa niż 0,5 mm |
|
Weź pod uwagę następujące dane:
W tym przykładzie przesunięcie poziome jest dwukrotnie większe od przesunięcia pionowego. W związku z tym zostanie dokonana wstępna regulacja pozioma; następnie przejdą do regulacji poziomej.
5.6.9.2 Wykonywanie regulacji pionowej
Definiować pozycja pionowa maszynę mobilną wykorzystującą obliczenia i/lub konstrukcję graficzną.
Ryż. 5.68 Wykonywanie regulacji w pionie. Wartości dodatnie na łapach oznaczają, że poruszająca się maszyna jest wysoka, więc zdemontujesz podkładki. Wartości ujemne oznaczają, że maszyna ruchoma jest niska i dodasz podkładki.
Wskazówki dotyczące regulacji pionowej
- Dokonaj tej samej zmiany grubości podkładek dla przednich i tylnych nóg.
- Zawsze sprawdzaj grubość uszczelek za pomocą mikrometru. Prefabrykowane uszczelki nie zawsze odpowiadają ich oznaczeniom; Wielu producentów uszczelek podaje ich „nominalną” grubość.
- Zastosuj odpowiednią i prawidłową procedurę dokręcania śrub.
- Po założeniu podkładek sprawdź i staraj się unikać miękkiej stopy.
5.6.9.3 Proces regulacji poziomej
Z reguły podczas pracy metodą wskaźnika odwrotnego stosuje się dwie różne procedury regulacji poziomej:
- Określanie regulacji za pomocą obliczeń lub konstrukcji graficznej oraz kontrola ruchów za pomocą wskaźników zegarowych na stopach maszyny.
- Sterowanie ruchem za pomocą wskaźników zegarowych przymocowanych do sprzęgła.
Aby skorygować niewspółosiowość poziomą poprzez monitorowanie ruchów stóp poruszającej się maszyny, wykonuje się następujące kroki:
- Zmierzyć niewspółosiowość poziomą zgodnie z procedurą opisaną w 5.6.6.5.
- Wyznaczanie poziomego położenia poruszającej się maszyny za pomocą obliczeń lub wykresów określonych w 5.67 i 5.68.
- Upewnij się, że stoisz przodem do maszyn, ruchoma po prawej i nieruchoma po lewej.
- Dodatnie wartości na stopach oznaczają, że poruszająca się maszyna oddala się od Ciebie, więc musi ruszyć w Twoją stronę.
- Ujemne wartości na stopach oznaczają, że poruszająca się maszyna jest blisko Ciebie, dlatego należy ją odsunąć od Ciebie.
- Przymocuj wskaźniki godzin do przednich i tylnych nóg.
- Poruszaj przednią i tylną łapą o wymaganą ilość, obserwując odczyty wskaźnika.
Ryż. 5.69 Korekty poziome. Wskaźniki na łapach
Aby skorygować niewspółosiowość poziomą poprzez monitorowanie odczytów wskaźników przymocowanych do sprzęgła, wykonuje się następujące czynności:
- Obróć wskaźniki do pozycji 9:00 i zresetuj ich odczyty do zera.
- Obróć wały na 3:00.
- Ustaw wskaźniki na połowę ich odczytów.
- Poruszaj przednimi nogami ruchomej maszyny, aż ruchomy wskaźnik wskaże zero.
- Poruszaj tylnymi nogami poruszającej się maszyny, aż nieruchomy wskaźnik wskaże zero.
- Powtarzaj kroki 4 i 5, aż oba wskaźniki pokażą wartości zerowe.
Ryż. 5.70 Korekty poziome. Sterowanie za pomocą wskaźników zamontowanych na sprzęgle.
Wskazówki dotyczące regulacji poziomej
- Zacznij od przesunięcia łap w miejscu, w którym niewspółosiowość jest większa.
- Jeśli nie ma śrub zwalniających, spróbuj je zainstalować, jeśli to możliwe.
- Ustaw przednie i tylne nogi w jednej linii, są one ze sobą połączone.
- Jeśli łapy są odchylone od upragniona pozycja nie więcej niż 0,05 mm, zacznij dokręcać śruby i monitoruj odczyty wskaźników. Zastosuj odpowiednią sekwencję dokręcania krzyżowego.
5.6.9.4 Działania po regulacji pionowej i poziomej
Po dokonaniu ostatecznych regulacji w pionie i poziomie należy:
- Wykonaj powtarzające się pomiary.
- Porównaj wyniki z przypisanymi tolerancjami.
- Powtarzaj regulacje, aż znajdziesz się w granicach tolerancji.
- Wykonaj i udokumentuj końcową serię pomiarów.
- Przywróć sprzęt do prawidłowego stanu.