Nowoczesna, wysoka technologia. Technologie produkcji włókna szklanego Technologia kompozytów – dział technologii materiałów
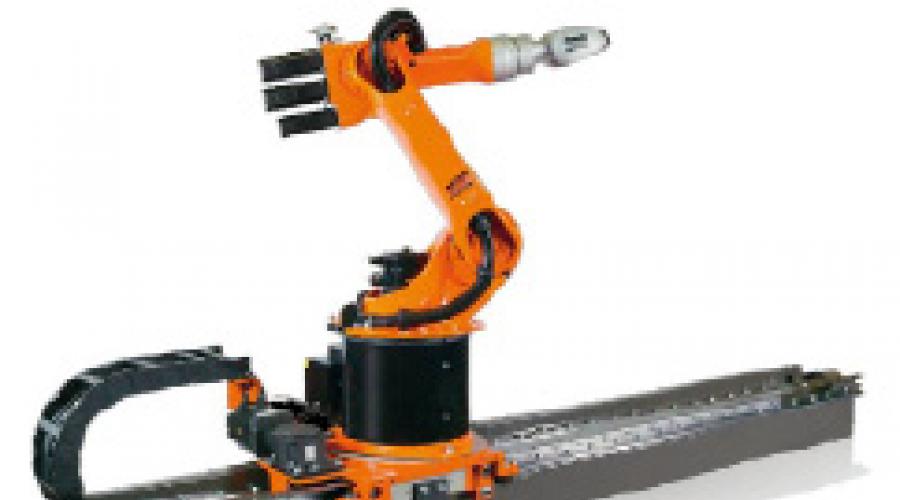
W artykule przedstawiono stan aktulany technologie wytwarzania wyrobów z materiałów kompozytowych, w tym informacje o stosowanych technologiach, oprogramowaniu, sprzęcie do tworzenia matryc, sprzęcie do tworzenia wyrobów kompozytowych, sprzęcie do kontroli geometrii wyrobów i badania nieniszczące.
materiały kompozytowe
sprzęt do tworzenia matrycy
1. Nowoczesne materiały kompozytowe / wyd. P. Krok i L. Browman; uliczka z angielskiego – M., 1978.
2. Budowa i wytrzymałość kadłubów z włókna szklanego i kadłubów statków. Zagraniczny przemysł stoczniowy w latach 1965 – 1973 // Przemysł stoczniowy, 1973.
3. Frolov S.E. Metody tworzenia nowych makroniejednorodnych materiałów kompozytowych i rozwiązania technologiczne do wytwarzania z nich konstrukcji kadłubowych // Przemysł Stoczniowy Nr 3 2003, s. 23. 55-59.
4. CAE – technologie w 2012 roku: przegląd osiągnięć i analiza rynku. – Obserwator CAD/CAM/CAE #4 (80) / 2013.
5. Wywiad z V.A. Seredka i A.Yu. Sofronowa do magazynu CAD/CAM/CAE Observer #2 (78) / 2013.
6. Inteligentne technologie dla przemysłu lotniczego. Zwiększanie konkurencyjności krajowych przedsiębiorstw produkujących statki powietrzne na przykładzie wspólnych projektów firmy Solver i JSC VASO // CAD and Graphics, nr 1. 2011. s. 56-62.
7. Łukjanow N.P. Doświadczenie w zastosowaniu materiałów kompozytowych do budowy statków PMO // Przemysł stoczniowy. Nr 3. 2007. s. 19-26.
Materiał kompozytowy to materiał, którego struktura składa się z kilku składników o różnych właściwościach fizyko-mechanicznych: osnów metalicznych lub niemetalicznych z określonym rozkładem znajdujących się w nich wzmacniaczy, ich połączenie nadaje materiałowi kompozytowemu nowe właściwości. Ze względu na charakter struktury materiały kompozytowe dzielą się na materiały włókniste, wzmacniane włóknami ciągłymi i wąsami, materiały wzmocnione dyspersyjnie, otrzymywane poprzez wprowadzenie do osnowy zdyspergowanych cząstek utwardzaczy, materiały warstwowe powstałe w wyniku prasowania lub walcowania różne materiały.
Obecnie materiały kompozytowe są szczególnie poszukiwane w różnych gałęziach przemysłu. Pierwsze statki z włókna szklanego powstały w drugiej połowie lat 30-tych XX wieku. Od lat 50. przemysł stoczniowy z włókna szklanego stał się powszechny na świecie; zbudowano znaczną liczbę jachtów, łodzi roboczych i ratowniczych oraz statków rybackich, barek desantowych itp. Jednym z pierwszych zastosowań materiałów kompozytowych w lotnictwie było wykonanie w 1967 roku paneli z tworzyw sztucznych wzmocnionych włóknem węglowym na tylną krawędź skrzydła samolotu F-111A. W ostatnie lata W produktach lotniczych coraz częściej można spotkać konstrukcje wykonane z trójwarstwowej „kanapki” z aluminiowym rdzeniem o strukturze plastra miodu i powłokami z włókna węglowego. Obecnie około 50% całkowitej masy samolotu Boeing 787 lub Airbus A350 stanowią materiały kompozytowe. W motoryzacji materiały kompozytowe są stosowane od dawna, opracowano głównie technologię wytwarzania aerodynamicznych zestawów karoseryjnych. Materiały kompozytowe stosowane są w ograniczonym zakresie do produkcji elementów zawieszenia i silnika.
Jednak do niedawna przedsiębiorstwa stosowały głównie ręczne układanie części z kompozytów, a seryjna produkcja wyrobów nie wymagała głębokiej automatyzacji procesów. Dziś, wraz z rozwojem konkurencji na rynku, nie da się bez tego obejść nowoczesne środki projektowania i przedprodukcji, jak i bez wydajny sprzęt do pracy z kompozytami.
Technologie tworzenia wyrobów z materiałów kompozytowych
W większości przypadków jako wypełniacz spoiwa stosuje się żywicę termoutwardzalną utwardzaną chemicznie, proces utwardzania charakteryzuje się egzotermią Reakcja chemiczna. Stosowane są głównie żywice poliestrowe, epoksydowe, fenolowe i wysokotemperaturowe. Najczęściej przy wytwarzaniu części o skomplikowanych konfiguracjach stosuje się technologie, których istotą jest ułożenie „suchego” podłoża, a następnie impregnacja kompozycją wiążącą („mokre” formowanie, nawijanie, wtryskiwanie, formowanie transferowe żywicy / RTM) lub naprzemiennie układanie „suchego” podłoża za pomocą kleju foliowego (impregnacja próżniowa, Resin Film Infusion / RFI). Istnieje kilka podstawowych technologii wytwarzania części z materiałów kompozytowych, obejmujących metody ręczne i zautomatyzowane:
- impregnacja włókien wzmacniających materiałem matrycowym;
- formowanie w formie taśm wzmacniających i osnowy uzyskanej przez nawijanie;
- tłoczenie na zimno elementów, a następnie spiekanie;
- elektrochemiczne powlekanie włókien z późniejszym prasowaniem;
- osadzanie matrycy natryskiwanie plazmowe na wzmacniacz, a następnie ściskanie;
- wsadowe zgrzewanie dyfuzyjne jednowarstwowych taśm komponentów;
- wspólne walcowanie elementów wzmacniających z matrycą itp.
Ponadto rozpowszechniła się technologia wytwarzania części z wykorzystaniem prepregów (półproduktów składających się z materiału bazowego impregnowanego kompozycją wiążącą).
Oprogramowanie
Zadaniem zaprojektowania produktu z materiałów kompozytowych jest prawidłowy wybór kompozycje zapewniające kombinację właściwości wymaganych w konkretnym przypadku operacyjnym. Przy projektowaniu wzmocnionych polimerowych materiałów kompozytowych szeroko stosuje się komputerowe przetwarzanie danych, dla którego zostało opracowane duża liczba różne produkty programowe. Ich zastosowanie pozwala na poprawę jakości wyrobów, skrócenie czasu rozwoju i organizacji produkcji konstrukcji oraz rozwiązanie problemów ich racjonalnego projektowania w sposób kompleksowy, jakościowy i szybki. Uwzględnienie nierównomierności obciążeń pozwala na zaprojektowanie konstrukcji kadłuba ze zbrojonego kompozytu o zróżnicowanej grubości, która może zmieniać się kilkudziesięciokrotnie.
Nowoczesne oprogramowanie można podzielić na dwie grupy: te, które wykonują analizę wsadową laminatów w ujęciu „dwuwymiarowym” lub „belka/płyta” oraz w ujęciu trójwymiarowym. Pierwsza grupa to programy typu Laminator, VerctorLam Cirrus itp. Rozwiązaniem „trójwymiarowym” jest metoda elementów skończonych i tutaj duży wybór wśród dostępnych produktów oprogramowania. Na rynku „technologii modelowania kompozytów” dostępne są różne produkty programowe: FiberSim (Vistagy / Siemens PLM Software), Digimat (e-Xstream / MSC Software Corp.), Helius (Firehole Composites / Autodesk), ANSYS Composite PrepPost, ESAComp (Altair Inżynieria) i itp. .
Prawie każde specjalistyczne oprogramowanie różnych firm posiada możliwość integracji z systemami CAD wysoki poziom- Creo Elements/Pro, Siemens NX, CATIA. Ogólnie praca wygląda tak: wybierany jest materiał warstw, tzw Wspólne parametry pakietu warstw, określa się sposób formowania warstw, przy wytwarzaniu prostych części stosuje się metodę warstwa po warstwie, przy wyrobach złożonych stosuje się metody projektowania strefowego lub konstrukcyjnego. Podczas układania warstw ustalana jest ich kolejność. W zależności od metody produkcji produktu (układanie ręczne, formowanie, układanie taśm, układanie włókien) przeprowadza się analizę materiału warstwa po warstwie pod kątem ewentualnych odkształceń. Skład warstw dostosowany jest do szerokości użytego materiału.
Po zakończeniu formowania warstw użytkownik otrzymuje dane o produkcie, co pozwala na ich wykorzystanie do różnych celów, np.:
- wynik w postaci dokumentacji projektowej;
- użyj jako danych początkowych dla materiału tnącego;
- dane źródłowe dla projektora laserowego w celu wskazania konturów obszarów umieszczenia wzoru.
Iść do nowoczesne technologie projektowanie i przygotowanie produkcji wyrobów pozwala na:
- zmniejszyć zużycie materiały kompozytowe poprzez zastosowanie precyzyjnych rozwiertaków i maszyn do cięcia;
- zwiększyć prędkość i poprawić jakość ręcznego układania materiału poprzez zastosowanie precyzyjnych wykrojów i projekcji laserowych obszarów ich układania;
- osiągnąć wysoki poziom powtarzalności produktu;
- ograniczenie wpływu czynnika ludzkiego na jakość wytwarzanych produktów;
- zmniejszenie wymagań kwalifikacyjnych dla personelu zajmującego się instalacją.
Sprzęt do tworzenia matryc
Wykonanie modelu wzorcowego z drewna jest procesem pracochłonnym i czasochłonnym; w celu skrócenia czasu wykonania matrycy i zwiększenia dokładności stosuje się: trzy/pięcioosiowe frezarki CNC, maszyny kontrolno-pomiarowe czy skanery 3D.
Bramka pięcioosiowa frezarka, (Rysunek 1), jest dostępny tylko dla dużych producentów. Małe firmy wykorzystują zrobotyzowane kompleksy frezarskie na liniowych jednostkach robotów (ryc. 2) lub wykonują modele wzorcowe z sklejonych detali. W tym przypadku podstawą przedmiotu obrabianego jest sztywna pusta rama, która jest przyklejana na zewnątrz, a następnie całkowicie przetwarzana. Firmy, które nie mają możliwości przetworzenia całego produktu, idą inną drogą: Najpierw w systemie CAD z wykorzystaniem płaszczyzn budowany jest uproszczony model 3D produktu, a na podstawie uproszczonego modelu projektowany jest model sztywny. rama mocy ze sklejki. Potem wszystko powierzchnia zewnętrzna jest reprezentowany w systemie CAD jako okładzina ramy wewnętrznej. Wymiary okładziny dobieramy tak, aby można było ją wyfrezować na istniejącej frezarce CNC (rys. 3). Wtedy dokładnie zmontowana rama wklejony okładzina modelu. Przy tej metodzie dokładność modelu wzorcowego jest mniejsza i wymagane jest ręczne wykończenie połączeń okładzin, ale pozwala to na tworzenie produktów, których wymiary znacznie przekraczają możliwości istniejących maszyn CNC.
Ryż. 1. Frezarka pięcioosiowa MR 125 z możliwością obróbki detali o wymiarach 15x5 m i wysokości do 2,5 m
Ryż. 2. Zrobotyzowany kompleks frezujący Kuka
Ryż. 3. „Mała” frezarka pięcioosiowa
Sprzęt do tworzenia kompozytów
Pierwszym krokiem w mechanizacji procesu formowania było zastosowanie maszyn impregnacyjnych, które oprócz impregnacji zbierają tkaniny szklane lub włókno szklane do wielowarstwowych worków o łącznej grubości 4 – 5 mm. Aby zmechanizować procesy, zmniejszyć prawdopodobieństwo błędu personelu i zwiększyć produktywność, stosuje się na przykład metodę natryskiwania, dzięki której można uzyskać okładzina zewnętrzna, panele grodziowe i inne konstrukcje z włókna szklanego. Metoda natryskowa umożliwia uzyskanie kątowników formierskich metodą mechanizacji i zapewnia wyższą wydajność pracy w porównaniu do kątowników formowanych ręcznie z pasków włókna szklanego lub włókna szklanego. Kolejnym etapem rozwoju produkcji wyrobów kompozytowych jest wprowadzenie instalacji do automatycznego nawijania wypełniaczy węglowo-szklanych. Pierwszego „robota” przeznaczonego do układania suchej tkaniny typu roll zademonstrowała amerykańska firma Magnum Venus Plastech. Po raz pierwszy w Rosji taki sprzęt został wprowadzony w JSC VASO. Urządzenie to umożliwia produkcję elementów kompozytowych o długości do 8 m i średnicy do 3 m (rys. 4).
Aby ułatwić ręczne układanie tkaniny i ograniczyć ilość odpadów, stosuje się maszyny tnące, które automatycznie docinają tkaninę/prepreg, projektory laserowe LAP i LPT do projekcji konturowej podczas układania prepregu na urządzeniach produkcyjnych. Wykorzystując moduł projekcji laserowej (rysunek 5) możliwe jest automatyczne generowanie danych projekcyjnych bezpośrednio z modelu 3D produkt złożony. Taki sposób pracy znacznie zmniejsza koszty czasu, zwiększa efektywność procesów, zmniejsza prawdopodobieństwo wystąpienia defektów i błędów oraz ułatwia zarządzanie danymi. Kompleks „oprogramowanie – maszyna do cięcia – laser projekcyjny” w porównaniu do tradycyjnego układania zmniejsza pracochłonność cięcia o około 50%, pracochłonność układania o około 30% oraz zwiększa stopień wykorzystania materiałów, tj. możesz zaoszczędzić od 15 do 30% materiału.
Formowanie tworzyw sztucznych wzmacnianych włóknami węglowymi metodą nawijania pozwala na uzyskanie wyrobów o najwyższych parametrach odkształcalnościowych i wytrzymałościowych. Metody nawijania dzielą się na „suche” i „mokre”. W pierwszym przypadku do nawijania wykorzystuje się prepregi w postaci nici, pasm lub taśm. W drugim materiały wzmacniające są impregnowane spoiwem bezpośrednio podczas procesu nawijania. Ostatnio opracowano sprzęt, który wykorzystuje systemy komputerowe. Dzięki temu możliwe jest wytwarzanie wyrobów rurowych o zagięciach i nieregularnych kształtach, a także wyrobów o złożonej geometrii. Sprzęt do nawijania elastyczna technologia, podczas wzmacniania materiały włókniste można układać na trzpieniu w dowolnym kierunku.
Ryż. 4 Maszyna do automatycznego nawijania i układania wypełniaczy węglowo-szklanych Viper 1200 FPS firmy MAG Cincinnati
Ryż. 5. Laserowy system pozycjonowania (zielony obrys)
Sprzęt do monitorowania geometrii i struktury wewnętrznej produktu
Kontury produktów często posiadają krzywoliniowe generatury, których nie da się sprawdzić tradycyjnymi metodami „plazowymi”. Za pomocą skanowania 3D można określić, jak bardzo próbka fizyczna odpowiada komputerowemu modelowi 3D. Do skanowania 3D można również zastosować wysięgnikową współrzędnościową maszynę pomiarową (CMM) lub bezkontaktowy system skanowania optycznego/laserowego. Jednak w przypadku użycia bezkontaktowych systemów skanujących zazwyczaj nie mogą one działać poprawnie na powierzchniach lustrzanych i o wysokim połysku. W przypadku stosowania „ramion pomiarowych” konieczne będzie kilka kolejnych ponownych instalacji, gdyż przestrzeń robocza, ze względu na konstrukcję ramion pomiarowych, ogranicza się zwykle do kuli o promieniu 1,2-3,6 m.
Również materiały z włókna szklanego Jest wiele problematycznych obszarów. Jednym z głównych jest kontrola jakości. ukończony produkt(brak wnęk powietrznych) i korozją podczas pracy. Do badań nieniszczących kadłubów statków wykonanych z kompozytów szeroko wykorzystuje się promieniowanie rentgenowskie, jednak z wielu powodów dąży się do jego ograniczenia. Ostatnio zaczęły pojawiać się publikacje opisujące wykrywanie rozwarstwień za pomocą termografii w podczerwieni (kamery termowizyjne). Jednocześnie zarówno metody termowizyjne, jak i rentgenowskie NDT wykrywające rozwarstwienia nie pozwalają na pomiar ich rozmiarów i określenie głębokości uszkodzeń w celu oceny ich wpływu na zmiany charakterystyk wytrzymałościowych.
Wniosek
Obecnie w Rosji niemal dopiero rozpoczyna się intensywny rozwój automatyzacji montażu wyrobów kompozytowych, w tym urządzeń do tworzenia matryc. Najczęściej tylko koncertują poszczególne elementy zestaw aerodynamiczny do „tuningu” samochodów. Wdrożenie systemu FiberSIM w Stoczni Srednevsky podczas projektowania i budowy bazowego trałowca Projekt 12700, a także w automatycznej układarce tkanin VASO zakończyło się sukcesem. To jednak pojedyncze przykłady, aby zwiększyć konkurencyjność konieczne jest kompleksowe wprowadzenie nowych technologii.
Link bibliograficzny
Czernyszow E.A., Romanow A.D. NOWOCZESNE TECHNOLOGIE PRODUKCJI WYROBÓW Z MATERIAŁÓW KOMPOZYTOWYCH // Nowoczesne zaawansowana technologia. – 2014. – nr 2. – s. 46-51;Adres URL: http://top-technologies.ru/ru/article/view?id=33649 (data dostępu: 25 listopada 2019 r.). Zwracamy uwagę na czasopisma wydawane przez wydawnictwo „Akademia Nauk Przyrodniczych”
Kompleks robotyczny Dla obróbka produkty wykonane z materiałów kompozytowych przeznaczone są do mechanizacji i automatyzacji niektórych z najbardziej pracochłonnych operacji w cyklu technologicznym:
- Przycinanie i usuwanie wypływki technologicznej
- Frezowanie rowków, wgłębień i pozycjonerów pod elementy osadzone
- Wiercenie i frezowanie otworów przelotowych złożony kształt
- Frezowanie otworów przelotowych duże rozmiary(otwory okienne, włazy itp.)
Kompleks robotyczny pozwala zapewnić następujące korzyści:
- Zwiększona prędkość przetwarzania w porównaniu do metod ręcznych
- Wysoka powtarzalność i jakość obróbki
- Frezowanie z wysoka jakość krawędzie „jednego przejścia”.
- Poprawa warunków pracy
- Tworzenie dodatkowych stanowisk pracy wymagających dużej wiedzy
Na metoda kontaktu Podczas formowania materiał szklany jest ręcznie impregnowany żywicą za pomocą pędzla lub wałka. Impregnację można przeprowadzić jednocześnie z walcowaniem w formie lub osobno. Walcowanie przeprowadza się w celu usunięcia powietrza z laminatu i równomiernego rozprowadzenia spoiwa.
Rakieta, astronautyka, produkcja samolotów, energia jądrowa, inżynieria chemiczna, pojazdy silnikowe, przemysł stoczniowy, elektronika i wiele innych gałęzi przemysłu wymagają materiałów o wysokiej wytrzymałości, odporności na ciepło, odporności na ciepło i odporności na ciepło (dobra odporność na propagację pęknięć), niskiej gęstości, regulowanej w zakresie szeroki zakres wskaźników przewodności cieplnej i elektrycznej, specjalnych właściwości optycznych i magnetycznych itp. Wiele istniejących materiałów przemysłowych już nie! spełnić te prośby.
Można uzyskać jedynie materiał o kompleksie takich cech T podstawa kompozycji. Materiały kompozytowe (CM) to materiały składające się z dwóch lub więcej składników (składników wzmacniających i wiążącej je matrycy) i posiadające określone właściwości, różniące się od sumarycznych właściwości tych składników.
Jeżeli jeden ze składników CM jest ciągły w całej objętości, a drugi jest nieciągły, rozłączony w objętości kompozycji, wówczas pierwszy składnik nazywa się matrycą, a drugi wzmocnieniem lub elementem wzmacniającym. Składnikami wzmacniającymi mogą być różne włókna, proszki, mikrosfery, kryształy i wąsy wykonane z materiałów organicznych, nieorganicznych, metalicznych lub ceramicznych. Jako matrix dajesz herbatę
stosuje się syntetyczne substancje wielkocząsteczkowe o różnym składzie chemicznym.
Pierwszym twórcą materiałów kompozytowych była sama natura. Na przykład drewno to kompozycja składająca się z wiązek rurowych włókien celulozowych o wysokiej wytrzymałości, połączonych ze sobą matrycą materii organicznej (ligniny), która nadaje drewnu sztywność boczną.
Składniki kompozytów nie powinny się rozpuszczać ani w inny sposób wchłaniać. Muszą mieć dobrą przyczepność i być ze sobą kompatybilne. Właściwości CM nie można określić jedynie na podstawie właściwości komponentów, bez uwzględnienia ich interakcji. Każdy składnik pełni określoną funkcję i wpływa na właściwości kompozytu. Rozważmy wymagania dotyczące wypełniaczy wzmacniających, na przykład włókien.
Nitkowaty kształt elementów wzmacniających ma zarówno dodatni, jak i strony negatywne. Zaletą włókien jest ich duża wytrzymałość oraz możliwość tworzenia zbrojenia tylko w kierunku, w którym jest to konstrukcyjnie wymagane. Wadą tej formy jest to, że włókna są w stanie przenosić obciążenie tylko w kierunku swojej osi, natomiast w kierunku prostopadłym nie następuje wzmocnienie, a w niektórych przypadkach może wystąpić nawet zmiękczenie.
Włókna stosowane jako napełniacze wzmacniające muszą charakteryzować się następującymi właściwościami: wysoką temperaturą topnienia, niską gęstością, dużą wytrzymałością w całym zakresie temperatur pracy, nietoksycznością w procesie produkcji i eksploatacji.
Stosowane są głównie trzy rodzaje wypełniaczy: wąsy, druty metalowe i nieorganiczne włókna polikrystaliczne.
Wąsy („wąsy”) uważane są za obiecujący materiał do wzmacniania matryc wykonanych z metali, polimerów i ceramiki. Ultrawysoka wytrzymałość w szerokim zakresie temperatur przy niskiej gęstości, obojętność chemiczna w stosunku do wielu materiałów osnowy. riale, wysoka żaroodporność i odporność na korozję kryształów wąsów aluminium i tlenków magnezu, węglika krzemu czynią je niezastąpionymi elementami wzmacniającymi. Niestety, na drodze do ich praktycznego zastosowania nadal stoi wiele trudności. Konieczne jest rozwiązanie problemów ich otrzymywania na skalę przemysłową, dobór odpowiednich „wąsów”, ich orientacji w matrycy oraz sposobów tworzenia kompozycji z „wąsami”.
Drut metalowy wykonany ze stali, wolframu, molibdenu i innych metali jest mniej obiecujący niż „wąsy” ze względu na jego dużą gęstość i niższą wytrzymałość. Ma jednak stosunkowo niski koszt i jest szeroko stosowany jako wzmocnienie, zwłaszcza w przypadku materiałów kompozytowych na bazie metali.
Polikrystaliczne włókna nieorganiczne produkowane są w dużych ilościach. Wadą tych włókien jest ich bardzo duża wrażliwość na uszkodzenie mechaniczne. Niska gęstość, wysoka wytrzymałość i odporność chemiczna węgla, boru, szkła, węglika krzemu. kwarc i inne włókna pozwalają na ich szerokie zastosowanie do wzmacniania tworzyw sztucznych,
Włókna węglowe należą do najbardziej obiecujących elementów wzmacniających. Mają niską gęstość (1430 - 1830 kg/m3), wysoką wytrzymałość (3,5 GPa) i moduł sprężystości (250 - 400 GPa).
Zazwyczaj włókna węglowe dzielą się na dwa główne typy: włókna o wysokiej wytrzymałości i włókna o wysokiej elastyczności. W produkcji produkowane są głównie włókna o wysokiej wytrzymałości. Wytrzymałość tych włókien w początkowej fazie rozwoju wynosiła 2,5 GPa. Dzięki udoskonaleniom technologii (obróbka wstępna, włókna ognioodporne, karbonizacja i wykańczanie) zwiększono wytrzymałość m.in. zwykły materiał do 3,5 GPa.
Badania wykazały, że wraz ze wzrostem wytrzymałości włókien wytrzymałość materiału kompozytowego z reguły rośnie liniowo. ,: ;.,
Zazwyczaj włókna węglowe o wysokiej wytrzymałości są produkowane w temperaturze karbonizacji 1000–1500 ° C; mają moduł sprężystości 2250–2350 N/mm2. W temperaturze 2000 - 3000°C w procesie grafityzacji można otrzymać włókna o wyższym module sprężystości.
Do niedawna do produkcji materiałów termoizolacyjnych wykorzystywano włókna węglowe i tkaniny z nich wykonane. Jednak poprawa. Ta technologia wytwarzania cienkich włókien, łączących wysoką wytrzymałość i sztywność z innymi specjalnymi właściwościami (odporność cieplną, przewodność elektryczną itp.), umożliwiła tworzenie metali i tworzyw sztucznych wzmacnianych włóknami węglowymi, charakteryzujących się niską sztywnością i dużą wytrzymałością. Takie kompozycje są coraz częściej stosowane w technologii kosmicznej, rakietowej i lotniczej. Najczęściej stosowanymi włóknami węglowymi są wiskoza i poliakrylonitryl.
W zależności od zawartości węgla włókna węglowe dzielą się na trzy grupy:
karbonizowany (nie więcej niż 95% wag. C); - węgiel (91-98% wag. C);
grafit (ponad 98% wag. C).
Sztywne włókno węglowe uzyskuje się, jeżeli proces technologiczny jest zaprojektowany w taki sposób, aby maksymalna liczba warstw bazowych była równoległa do osi włókna. Aby zwiększyć wytrzymałość włókien węglowych, należy zmniejszyć wielkość krystalitów o bardziej zaawansowanej strukturze. Metody technologiczne nadające włóknom węglowym dodatkową sztywność i wytrzymałość obejmują domieszkowanie ich borem poprzez dyfuzję z fazy gazowej, napromienianie włókien neutronami w reaktorze jądrowym, wprowadzenie do nich boraksu przed pirolizą, a także rozciąganie w procesach utleniania i grafityzacji .
Jeśli w cienkich włóknach występują mikrodefekty, które powodują lokalną koncentrację naprężeń, wówczas wytrzymałość włókien węglowych maleje. Wadliwość włókien powoduje liniową zależność ich wytrzymałości od długości: wraz ze wzrostem długości wytrzymałość znacząco maleje, a moduł sprężystości nieznacznie wzrasta. Ze względu na poziom właściwości mechanicznych włókna węglowe dzieli się na trzy grupy: niski, średni, wysoki (tabela 1.5)
Tabela 1.5 Właściwości mechaniczne włókien węglowych
Grupa Gęstość Wytrzymałość Moduł sprężystości
y, g/cm 3 a, GPa E, GPa
Niski 18 14 42
Średnia 18 14 175
Wysoka 18 25 420
Do wad włókien węglowych należy zaliczyć ich skłonność do utleniania się na powietrzu, aktywność chemiczną podczas interakcji z osnową metalową oraz stosunkowo słabą przyczepność do osnowy polimerowej.
Obróbka powierzchniowa włókien jest ważnym procesem z punktu widzenia zwiększenia ich przyczepności do osnowy. Zazwyczaj powierzchnię włókien węglowych poddaje się obróbce poprzez utlenianie ich w fazie gazowej.
Na właściwości włókien węglowych wpływa obecność metali i innych substancji substancje nieorganiczne. W szczególności zawartość metali alkalicznych, takich jak sód i potas, ma negatywny wpływ na odporność na utlenianie po podgrzaniu, podczas gdy fosfor i bor mają pozytywny wpływ.
Wszystkie materiały kompozytowe dzielą się na izotropowe i anizotropowe. Materiały izotropowe obejmują materiały, które mają te same właściwości we wszystkich kierunkach, natomiast materiały anizotropowe mają różne właściwości.
Elementy wzmacniające mogą mieć w przybliżeniu równy kształt podstawowy lub być krótkimi (oddzielnymi) cząstkami w kształcie igieł, losowo zorientowanymi w przestrzeni. Jako takie cząstki zwykle stosuje się segmenty włókien lub „wąsy”. W tym przypadku CM okazują się być quasi-izotropowe, tj. anizotropowy w mikroobjętościach, ale izotropowy w objętości całego produktu.
Anizotropowe CM obejmują materiały, których włókna są zorientowane w określonych kierunkach - jednokierunkowe, warstwowe i wzmocnione trójwymiarowo. Obrazy anizotropowego CM podano na ryc. 1,24, 1,25.
Ryż. 1,24. Schematyczne przedstawienie struktury CM z poprzecznym ułożeniem włókien
z podłużnym
Ryż. 1,25. Schematyczne przedstawienie struktury jednokierunkowego CM (obszary czarne – włókna; białe – matryca)
Anizotropia technologiczna występuje podczas odkształcenia plastycznego materiałów izotropowych (metali). Anizotropia fizyczna jest charakterystyczna dla kryształów ze względu na cechy strukturalne ich sieci krystalicznej.
W technologii zwykle stosuje się anizotropowe CM o określonej symetrii właściwości.
Równie ważną rolę w kompozycjach zbrojonych pełni matryca, która nadaje produktowi kształt i sprawia, że materiał staje się monolityczny. Łącząc wiele włókien w jedną całość, osnowa powinna pozwalać kompozycji na przyjęcie różnego rodzaju obciążeń zewnętrznych – rozciągania, ściskania, zginania, ścinania itp. Jednocześnie bierze udział w tworzeniu nośności materiału skład, zapewniający przeniesienie sił na włókna. Dzięki plastyczności osnowy siły z uszkodzonych lub dyskretnych (krótkich) włókien przenoszone są na sąsiednie włókna, a koncentracja naprężeń w pobliżu różnego rodzaju defektów maleje. Osnowa pełni także rolę powłoki ochronnej chroniącej włókna przed uszkodzeniami mechanicznymi i utlenianiem. Ponadto osnowa musi zapewniać wytrzymałość i sztywność układu pod obciążeniem rozciągającym lub ściskającym w kierunku prostopadłym do elementów wzmacniających. Jeżeli obciążenie rozciągające jest skierowane wzdłuż osi włókien równoległych do siebie, to aby uzyskać efekt wzmocnienia, maksymalne wydłużenie względne osnowy musi być co najmniej równe wydłużeniu względnemu włókien. Jeśli obciążenie jest prostopadłe do osi włókien, to nie wystarczy. W tym przypadku obciążenie włókien przenoszone jest tylko przez osnowę, a im większe jest stężenie włókien i stosunek modułów sprężystości materiału włóknistego do osnowy, tym większe powinno być maksymalne odkształcenie osnowy. Praca wycenowa, wykonane na modelach sprężystych, pokazują, że aby zapewnić trwałość CM pod obciążeniem poprzecznym, potrzebne są matryce, których wydłużenie względne jest kilkukrotnie większe niż średnie odkształcenie włókien.
Chęć uzyskania maksymalnej wytrzymałości kompozycji powoduje tendencję do zwiększania udziału objętościowego włókien. Jeśli jednak względne wydłużenie osnowy jest małe, to w przypadku dużych wartości tego ułamka, trwałość CM może zostać zakłócona nawet przy małych obciążeniach: pojawią się rozwarstwienia i pęknięcia. Okazało się, że im bardziej plastyczna jest osnowa, tym mniejsza jest dopuszczalna grubość warstwy osnowy pomiędzy włóknami i tym więcej włókien można wprowadzić do CM.
W zależności od materiału osnowy wszystkie CM można podzielić na trzy grupy: kompozycje z osnową metalową – metalowe materiały kompozytowe (MCM), z osnową polimerową – polimerowe materiały kompozytowe (PCM) oraz z osnową ceramiczną – ceramiczne materiały kompozytowe (CCM) ).. Polimerowe CM są zwykle nazywane w zależności od materiału włókien wzmacniających: wzmocnione włóknami szklanymi nazywane są tworzywami sztucznymi z włókna szklanego (włókno szklane), metalowe - tworzywami metalowymi (włókna metalowe), organicznymi - organoplastami (włókna organiczne), borem - borem tworzywa sztuczne (włókna borowe), tworzywa węglowo-węglowe (włókna węglowe) itp.
Nie ma jeszcze jasno ustalonych zasad nazewnictwa metalowych i ceramicznych CM. Częściej niż inne, najpierw zapisywany jest materiał matrycy, a następnie materiał włóknisty. Na przykład oznaczenie „miedź-wolfram” (Cu-W) odnosi się do CM z osnową miedzianą i włóknami wolframowymi. Jednak w literaturze czasami najpierw wskazuje się materiał włóknisty, a następnie matrycę.
Polimerowe materiały kompozytowe są najbardziej rozpowszechnione w porównaniu z innymi ze względu na łatwość ich wytwarzania, możliwości produkcyjne, niski koszt i niską gęstość. Ich główną wadą jest ograniczony zakres temperatur pracy. Nowoczesne spoiwa polimerowe (matryce) mogą zapewnić trwałość wyrobów do temperatur nie przekraczających 300 - 400°C.
W zależności od ich zachowania podczas ogrzewania i chłodzenia, spoiwa polimerowe dzieli się zwykle na termoplastyczne i termoutwardzalne. Właściwości termoplastycznych spoiw polimerowych umożliwiają wytwarzanie z nich wyrobów metodą wtrysku, wytłaczania, natryskiwania oraz szerokie zastosowanie zautomatyzowanych urządzeń do ich produkcji. Makrocząsteczki polimerów termoplastycznych mają budowę liniową i powstają z monomerów posiadających dwie grupy funkcyjne, które są połączone ze sobą silnymi wiązaniami kowalencyjnymi. Łańcuchy makromolekularne są połączone ze sobą słabymi siłami van der Waalsa.
Termoutwardzalne oligomery pod wpływem ciepła, utwardzaczy i katalizatorów przekształcają się w stan stały (twardnieją). Proces ten jest nieodwracalny. Oligomery są łatwo rozpuszczalne w niektórych rozpuszczalnikach (alkohol, aceton itp.), jednak po utwardzeniu nie są już rozpuszczalne. Żywice termoutwardzalne produkowane są z monomerów mających więcej niż dwa grupy funkcyjne. W procesie utwardzania monomery rosną w trzech kierunkach, tworząc makrocząsteczki o strukturze sieciowej, których wszystkie elementy strukturalne są połączone ze sobą silnymi wiązaniami kowalencyjnymi.
Głównym składnikiem spoiwa polimerowego jest żywica. Temperatura mięknienia, rozpuszczalność, lepkość i końcowe właściwości spoiwa zależą od jego charakteru, reaktywności, masy cząsteczkowej i struktury molekularnej. Oprócz żywicy spoiwo może zawierać: katalizatory lub inicjatory, które dodaje się do żywic w małych ilościach w celu przyspieszenia ich utwardzania; plastyfikatory, które nadają polimerowi rezerwę plastyczności i elastyczności; barwniki barwiące materiał na pożądany kolor; stabilizatory, które zapobiegają rozkładowi polimerów pod wpływem promieniowanie świetlne i podwyższone temperatury.
W zdecydowanej większości przypadków żywice termoutwardzalne stosowane są jako spoiwa konstrukcyjnych PCM pracujących pod obciążeniem. Do najczęściej stosowanych żywic w produkcji strukturalnych PCM należą żywice epoksydowe, poliestrowe, fenolowe, krzemoorganiczne i poliimidowe.
Żywice epoksydowe stanowią 90% żywic stosowanych jako spoiwa* w nowych PCM. W zależności od rodzaju utwardzacza i jego ilości, żywice epoksydowe można utwardzać zarówno w temperaturze pokojowej, jak i podwyższonej. W pierwszym przypadku mowa o żywicach utwardzanych na zimno, w drugim o żywicach utwardzanych na gorąco.
Żywice epoksydowe charakteryzują się uniwersalnymi właściwościami. Mają niski skurcz, dobrą przyczepność do różnych wypełniaczy, wysokie właściwości mechaniczne, niską nasiąkliwość i nadają się do obróbki temperatura pokojowa oraz zmianę czasu utwardzania i temperatury w szerokim zakresie. Można do nich dodawać rozpuszczalniki, modyfikatory i plastyfikatory w celu zmiany lepkości, odporności chemicznej i ciągliwości nieutwardzonego polimeru. Podczas obróbki cieplnej nie wydzielają się lotne produkty reakcji. Są nieco droższe od żywic poliestrowych i fenolowych, ale rekompensują to lepszymi właściwościami technologicznymi i użytkowymi.
Zazwyczaj oparte na KM epoksydowa żywica stosować do 150°C. W ostatnich latach opracowano nowe, bardziej odporne na ciepło żywice epoksydowe, które umożliwiają ich zastosowanie w HLM pracujących w temperaturze 200°C i wyższej.
Bardzo ważną cechą żywic epoksydowych z technologicznego punktu widzenia jest ich zdolność do długotrwałego przebywania w stanie półutwardzonym, co umożliwia produkcję preimpregnowanych i częściowo utwardzonych tkanin, taśm i pasm („prepregów”). ) na ich podstawie, a następnie uzyskać produkty.
Żywice poliestrowe są produktami polikondensacji nienasyconych kwasów dikarboksylowych (głównie maleinowego i metakrylowego) z alkoholami wielowodorotlenowymi lub nienasyconymi (glikol dietylenowy, glikol trietylenowy itp.). W wyniku polimeryzacji powstaje stały, nierozpuszczalny polimer o trójwymiarowej strukturze. Spoiwa poliestrowe powstały znacznie wcześniej niż spoiwa epoksydowe i na ich bazie powstały pierwsze strukturalne CM.
Głównymi zaletami spoiw poliestrowych są ich niski koszt i łatwość stosowania. Są jednak słabsze, mają gorszą przyczepność do większości włókien, są bardziej kruche, wykazują większy skurcz podczas utwardzania i mają krótszą żywotność niż żywice epoksydowe.
Żywice fenolowe otrzymuje się w wyniku polikondensacji fenoli (hydroksybenzenu, krezolu, rezorcyny itp.) z aldehydami (furfuralem, formaldehydem itp.). Żywice te mają ciemną barwę i zwiększoną odporność na wysoką temperaturę w porównaniu do wcześniej omawianych spoiw.
Żywice fenolowe podczas utwardzania przechodzą trzy etapy:
„A” - powstawanie rezolu - produkt wstępnej kondensacji, który nie ma wiązań poprzecznych i jest zdolny do rozpuszczenia się w alkoholu, acetonie i innych rozpuszczalnikach;
„B” - tworzenie resitolu - produkt, w którym rozpoczęło się tworzenie wiązań poprzecznych. Resitol zachowuje się jak żywica termoplastyczna – mięknie pod wpływem ogrzewania, a w temperaturze pokojowej staje się twardy i kruchy;
„C” – otrzymany resit – całkowicie utwardzony produkt termoutwardzalny (nierozpuszczalny i nietopliwy).
Na etapie resitolu, gdy większość substancji lotnych została już usunięta, z żywic fenolowych wytwarza się prepregi. Same żywice fenolowe są bardzo delikatne.
Do ich wad należy toksyczność i konieczność stosowania wysokich ciśnień podczas utwardzania. CM na bazie żywic fenolowych to materiały przeznaczone do pracy w wysokich temperaturach, to jest to! jak są w stanie wytrzymać temperatury stałe 315°C przez długi czas i powyżej 3000°C przez krótki czas.
Żywice krzemoorganiczne, czyli żywice silikonowe, to syntetyczne związki CO6OI zawierające wraz z grupami organicznymi! krzem i tlen, które są zawarte w głównym łańcuchu w postaci ogniw
Powstałe na ich bazie KM zachowują właściwości w temperaturach powyżej 260°C i charakteryzują się odpornością na korozję, odpornością na łuk i iskry oraz zwiększoną przewodnością cieplną. Jednakże w temperaturze pokojowej właściwości CM n; na bazie żywic silikonowych jest niższa niż na bazie żywic epoksydowych, poliestrowych i fenolowych. Poza tym są droższe. Na bazie żywic krzemoorganicznych otrzymuje się CM, które znajdują zastosowanie w konstrukcjach owiewek, silników lotniczych, rakiet i innych wyrobów pracujących w wysokich temperaturach.
Żywice poliimidowe charakteryzują się dużą odpornością na ciepło i promieniowanie. Oparte na nich CM są w stanie pracować przez długi czas w temperaturach powyżej 300°C. W końcowej fazie powstawania żywice poliimidowe tracą swoją plastyczność i rozpuszczalność] i przekształcają się w policykliczne polimery sieciowe. Wiążą się z nimi perspektywy tworzenia wysokotemperaturowych CM. Istnieją wady: żywice poliimidowe – konieczność stosowania wysokich temperatur i ciśnienia podczas ich utwardzania.
Technologia wytwarzania produktów z PCM obejmuje następujące główne etapy:
1. Wstępna obróbka powierzchni włókna węglowego w celu poprawy jego zwilżalności roztworami lub stopionymi spoiwami.
Włókna węglowe dostarczane są do konsumenta pokryte środkiem smarnym, który jest wymagany jako dodatek technologiczny. Usunięcie klejonu z powierzchni włókien (odklejenie) jest operacją konieczną. vrx Kochamy Cię. Pojemniki z tym węglowodorem przepuszcza się przez benzynę, roztwory boru kwasu oleinowego (2% wag.), trietanoloaminę (1% wag.) lub inne rozpuszczalniki. Smar można również usunąć poprzez kalcynację włókna węglowego w temperaturze 200 - 450°C. Dobry efekt daje mycie w wodzie za pomocą ultradźwięków. Po odklejeniu niektóre rodzaje włókien silnie adsorbują wilgoć, co pogarsza przyczepność do nich spoiwa i pogarsza właściwości użytkowe PCM jako całości. Etapem wykańczania nazywa się nałożenie na powierzchnię powłok hydrofobowych (wodoodpornych), które zwiększają siłę wiązania włókien ze spoiwem i zmniejszają nasiąkliwość PCM. Środki zaklejające utrwala się poprzez ogrzewanie włókien do temperatury 80–150°C przez 20–60 minut. W przypadku gdy włókna docierają na szpulach nienadających się do nawinięcia lub impregnacji, układa się je na jednokierunkowym pasie, tzw. niedoprzędzie, zapewniając jednocześnie równomierne napięcie. Ta operacja nazywa się wypaczaniem.
2. Przygotowanie spoiwa.
Oprócz głównego składnika (żywicy) do spoiwa dodaje się różne ilości utwardzaczy, katalizatorów, plastyfikatorów i pigmentów, w zależności od jego charakteru. Stosuje się następujące rozpuszczalniki: aceton, benzen, toluen, dichloroetan, czterochlorek węgla. Oczywiście pracując z nimi należy przestrzegać odpowiednich wymogów bezpieczeństwa.
Rozcieńczalniki pomagają uzyskać wymaganą lepkość technologiczną spoiwa i pozostają w nim po utwardzeniu. Rozcieńczalniki pełnią jednocześnie funkcję plastyfikatora, zwiększając plastyczność utwardzonych spoiw. Na przykład żywice epoksydowe o niskiej lepkości, składające się z glikolu dietylenowego i glikolu trietylenowego, stosuje się jako rozcieńczalnik do żywic epoksydowych o dużej lepkości. Mieszankę wszystkich składników tworzących spoiwo nazywa się związkiem.
Ważną cechą technologiczną spoiwa jest jego żywotność (żywotność) - zdolność do utrzymania lepkości technologicznej w określonych granicach przez określony czas (od kilku minut do kilku dni). Z biegiem czasu ze spoiwa odparowują rozpuszczalniki, co zwiększa lepkość masy i pogarsza jej właściwości impregnacyjne. Jeśli rozpuszczalnik odparowuje powoli, związek ma wysoką żywotność, ale czas suszenia produktów znacznie się wydłuża. Może się nawet okazać, że tym razem całkowite usunięcie rozpuszczalnik przekroczy czas utwardzania spoiwa. W tym przypadku utwardzony polimer będzie miał wiele porów i pęcherzyków gazu. Stosowanie wysoce lotnych rozpuszczalników znacznie zmniejsza żywotność spoiwa, co jest również niepożądane. Na przykład w przypadku żywic epoksydowych zaleca się średniolotny rozpuszczalnik toluen lub jego roztwór w alkoholu etylowym.
Podczas transportu i przechowywania spoiwa czasami dostaje się do niego wilgoć. Dlatego przed użyciem żywicę podgrzewa się w specjalnych metalowych pojemnikach do temperatury 100 - 140°C i po usunięciu wody rozcieńcza rozpuszczalnikami lub rozcieńczalnikami.
3. Impregnacja.
Jest to operacja połączenia wypełniacza ze spoiwem poprzez nałożenie związku na powierzchnię włókna węglowego i wypełnienie nim przestrzeni pomiędzy włóknami.
Obecnie wyroby PCM produkowane są głównie dwiema metodami: „na mokro” i „na sucho”. Metodą mokrą włókna impregnuje się płynnym spoiwem bezpośrednio przed nawinięciem, tj. impregnacja jest technologicznie połączona z formowaniem produktu. Metodą suchą impregnacja; wydzielony na niezależną operację, w wyniku której z węglowodorów i spoiwa. kup prepregi. Impregnacja i suszenie przeprowadzane są w wyspecjalizowanych zakładach niezależnie od nawijania, co pozwala na poszerzenie gamy stosowanych spoiw polimerowych poprzez zastosowanie innych; rozpuszczalniki. Spoiwa z rozpuszczalnikami charakteryzują się niską lepkością technologiczną, co pozwala na osiągnięcie wysokiej jakości przy jednolitej impregnacji. Prepregi mogą być w stanie częściowo utwardzonym. od kilku dni do kilku miesięcy w zależności od temperatury otoczenia.
Nawijanie na sucho jest metodą bardziej postępową niż nawijanie na mokro. Wady uzwojenia na mokro sprowadzają się do:
Wybór spoiw do nawojów na mokro ogranicza się do żywic, w których można je zastosować postać płynna na przykład żywica epoksydowa lub poliester.
Ogólnie rzecz biorąc, niepożądane jest stosowanie rozpuszczalników, ponieważ substancje lotne usunięte podczas utwardzania rany prowadzą do powstawania porów i pęcherzyków oraz pogarszają trwałość i wytrzymałość.
Stosowanie płynnych spoiw pogarsza warunki sanitarne w miejscu pracy.
Wydajność nawijania na mokro jest ograniczona prędkością spoiwa.
Zastosowanie ogrzewania w celu zmniejszenia lepkości technologicznej żywicy zmniejsza żywotność spoiwa i przyspiesza proces polimacji< гризации и ухудшает пропиточные свойства смолы.
6. Przy nawijaniu na mokro trudno jest dostosować stężenie składników w produkcie. Część żywicy znika przy metodzie mokrej.
Nawijanie prepregów na sucho nie ma wszystkich wymienionych wad. Prędkość nawijania nie jest ograniczona szybkością impregnacji i jest całkowicie zależna* od możliwości sprzętu nawojowego. Nawijanie prepregami umożliwia zastosowanie szerokiej gamy żywic, zapewnia równomierne rozprowadzenie spoiwa w całej objętości produktu, ogranicza możliwość pojawienia się lepkiego wyglądu, co pozwala na uzyskanie wyrobów o skomplikowanych kształtach, zwiększonej szczelności i niskich porowatość. Przy ich formowaniu pozostaje jedynie zapewnić wysokiej jakości połączenie warstw spoiwa ze sobą (autohezja) i z włóknami wzmacniającymi (adhezja).
Do głównych wad suchego uzwojenia należy konieczność użycia specjalne maszyny i inne urządzenia technologiczne.
Wyróżnia się następujące metody impregnacji: przeciąganie zbrojenia (nici) przez płynne spoiwo; wałek do kąpieli; natryskiwanie z wymuszoną impregnacją.
Przy produkcji HLM ze wzmocnieniem w postaci pasm, nici i tkanin najczęstszą metodą jest impregnacja polegająca na przeciąganiu ich przez ciekłe spoiwo (ryc. 1.26).
Ryż. 1,26. Schemat pionowej maszyny do impregnacji; 1 - bęben, 2 - armatura, 3 - wanna z płynnym spoiwem, 4 - walce kąpielowe, 5 - szyb suszący, 6 - grzejniki, 7 - urządzenie wydechowe, 8 - napinacz, 9 - bęben odbiorczy
Zbrojenie (2) jest odwijane z bębna (narzuta) (1) i przechodząc przez układ rolek (4) wchodzi do kąpieli (3) z ciekłym spoiwem. Zaimpregnowana armatura wchodzi do szybu suszącego (5), gdzie znajdują się grzejniki (6) i urządzenie wyciągowe (7). W tym przypadku zbrojenie kilkakrotnie zmienia kierunek ruchu, aby wydłużyć czas przebywania w strefie podwyższonej temperatury. W efekcie z mieszanki usuwane są substancje lotne, a przestrzeń pomiędzy włóknami wypełniana jest spoiwem. Wysuszony prepreg nawija się za pomocą wału napędowego przez urządzenie napinające (8) n; odbierający bęben.
W przypadku GLM o bardzo sztywnym wzmocnieniu (grafit borowy o wysokim module sprężystości lub inne włókna), które nie dopuszcza małych promieni zgięcia, wygodnie jest zastosować metodę impregnacji wałkiem nasączającym (rys. 1.27).
Ryż. 1,27. Schemat impregnacji wałkiem kąpielowym: 1 - zbrojenie, 2 - pojemnik z płynnym spoiwem, 3 - pojemnik, 4 - wałek kąpielowy
Wałek obracając się, wychwytuje spoiwo na swojej powierzchni i przenosi je na zbrojenie.
Metoda natryskowa z wymuszoną impregnacją pozwala radykalnie skrócić czas wypełniania spoiwem przestrzeni międzywłóknowych; Stosuje się impregnację wymuszoną hydrauliczną, próżniową i mechaniczną. .
W procesie impregnacji hydraulicznej wymuszonej płynny ev; Płyn jest pompowany przez armaturę.
Impregnacja wymuszona próżnią odbywa się poprzez zasysanie cieczy do próżniowej komory, w której znajduje się armatura.
Impregnacja mechaniczna wymuszona jest prostsza. To może być użyte; wykonywać w specjalnej komorze (klinowej) lub przy użyciu twarzy ugniatającej. W komorze klinowej (rys. 1.28) masa jest przenoszona przez ruchome ramię; zaokrąglić do wnęki klina. Tutaj poprzez zmniejszenie przekroju kanału komory: ciśnienie płynu wzrasta prostopadle do ruchomych złączek. Pod wpływem tego ciśnienia przestrzeń pomiędzy włóknami zostaje wypełniona.
Podczas impregnacji wałkiem prasującym (ryc. 1.286) ciśnienie potrzebne do impregnacji i usunięcia pęcherzyków parnych z przestrzeni międzywłóknowej powstaje w wyniku reakcji walca na napiętą taśmę.
Ryż. 1,28. Schematy mechanicznej impregnacji wymuszonej w komorze klinowej (a) i przy użyciu walca prasującego (b): 1 - zbrojenie, 2 - spoiwo, 3 - walce
4. Odlewanie.
Jest to operacja nadawania produktowi określonego kształtu i rozmiaru. Formowanie można przeprowadzić za pomocą pras, kontaktowych, próżniowych, autoklawowych i nawijania.
Przed formowaniem na prasach wstępnie zaimpregnowany niedoprzęd lub tkaninę tnie się ręcznie lub przy użyciu specjalnych maszyn na kawałki o wymaganej długości. W zależności od określonej struktury PCM elementy układane są w jednym lub kilku naprzemiennych kierunkach. Pakiet umieszcza się pomiędzy płytami prasy hydraulicznej i zagęszcza pod ciśnieniem od kilku do kilkudziesięciu atmosfer, w zależności od charakteru i budowy elementów. Jeżeli zbrojenie jest impregnowane spoiwem utwardzanym na gorąco, wówczas płyty dociskowe są podgrzewane. Ta metoda jest zwykle stosowana do produkcji materiałów arkuszowych, takich jak PCB.
Formowanie kontaktowe polega na zwijaniu impregnowanej taśmy lub tkaniny za pomocą wałka. Zazwyczaj zagęszczanie przeprowadza się w temperaturze pokojowej przy użyciu żywic utwardzanych na zimno. Metodę tę stosuje się przy produkcji na małą skalę wyrobów wielkogabarytowych i lekkich.
Formowanie próżniowe wyrobów PCM odbywa się dzięki różnicy ciśnienia atmosferycznego i wewnętrznego (w objętości, w której znajduje się wyrób). Formowanie próżniowe stosuje się do wytwarzania małych partii produktów, ponieważ jest to metoda mało wydajna i stosunkowo droga.
Stosując metodę formowania w autoklawie, produkt jest formowany pod niskim ciśnieniem wytwarzanym przez wodę lub gaz. Metodę tę można zastosować do produkcji dużych serii dużych części o skomplikowanych kształtach.
Jedną z najczęstszych metod wytwarzania PCM i wyrobów z nich wykonanych jest metoda nawijania. W tym przypadku zbrojenie zaimpregnowane spoiwem nawija się na bęben (trzpień) z napięciem. Nawijanie pozwala zautomatyzować proces formowania i zaprogramować anizotropię właściwości produktu końcowego. Uzwojenie jest najczęściej stosowane do wytwarzania wyrobów w kształcie ciał obrotowych (cylindry, kule, stożki, toroidy itp.).
5. Odnalezienie.
W procesie utwardzania spoiwa powstaje ostateczna struktura; PCM, kształtują się jego właściwości i ustalany jest kształt produktu. Głównymi parametrami technologicznymi utwardzania są temperatura i czas. Należy ściśle przestrzegać parametrów opracowanych dla każdej kombinacji spoiwa i zbrojenia.
Utwardzanie można przeprowadzić w temperaturze pokojowej (utwardzanie na zimno*). podwyższonych temperaturach(utwardzanie na gorąco), elektryczne lub piece indukcyjne z automatyczną regulacją temperatury, metoda radiacyjna.
Podczas utwardzania obserwuje się dwa charakterystyczne etapy, przez które kolejno przechodzi spoiwo termoutwardzalne: początkowy – dzień wystąpienia siatka polimerowa i ostatni - w procesie tworzenia sieci polimerowej. Te dwa etapy oddziela od siebie tzw. punkt żelowania. Punkt żelowania odpowiada momentowi, w którym spoiwo traci zdolność do przejścia w stan ciekły i rozpuszczania się w rozpuszczalnikach.
W pewnym zakresie temperatur płynne spoiwo przechodzi w stan szklisty. Wszystkie właściwości spoiwa zmieniają się radykalnie: zmniejsza się objętość właściwa, wzrasta twardość i pojawia się odporność na odkształcenia. Temperatura, w której zachodzi to zjawisko, nazywana jest temperaturą zeszklenia. Temperatura zeszklenia nie jest punktem, ale średnią temperaturą przedziału. Zeszklenie nie jest przejściem fazowym; szkliste spoiwo ma strukturę amorficzną i z termodynamicznego punktu widzenia można je uważać za przechłodzoną ciecz.
Kolejnym charakterystycznym punktem materiałów polimerowych jest temperatura zniszczenia – temperatura, w której rozpoczyna się zauważalny rozkład polimeru, któremu towarzyszy zerwanie wiązań molekularnych. Zniszczenie, podobnie jak zeszklenie, zachodzi w pewnym zakresie temperatur. Zrównoważony rozwój! spoiwo na zniszczenie charakteryzuje się odpornością cieplną (stabilność termiczna, odporność cieplna). Pojęcie to należy odróżnić od odporności cieplnej, która odzwierciedla zdolność polimeru do mięknięcia.
Do czasu całkowitego wyczerpania grup reaktywnych reakcja utwardzania może zachodzić tylko wtedy, gdy temperatura utwardzania jest wyższa od temperatury zeszklenia. W przeciwnym razie nie będzie możliwe całkowite utwardzenie. W polimerze nadal występują grupy reaktywne, ale stopień ich oddziaływania z innymi grupami jest bardzo niski ze względu na bardzo dużą lepkość układu. Jeżeli ShSM z niecałkowicie utwardzonym spoiwem będzie eksploatowany w podwyższonych temperaturach, wówczas utwardzanie będzie kontynuowane. Prowadzi to do zmiany kształtu i wielkości produktu oraz pojawienia się dodatkowych naprężeń wewnętrznych.
Często reakcji utwardzania towarzyszy wydzielanie ciepła, materiał nagrzewa się samoczynnie i spoiwo może całkowicie stwardnieć. Na tej zasadzie opiera się utwardzanie na zimno spoiw termoutwardzalnych. Jednakże w przypadku produktów krytycznych w większości przypadków stosuje się utwardzanie na gorąco.
Zbrojenie i spoiwo w kompozycji znajdują się pod wpływem naprężeń wewnętrznych, które można podzielić na trzy rodzaje: strukturalne, skurczowe i termiczne.
Naprężenia konstrukcyjne powstają w wyniku naprężeń procesowych działających na zbrojenie podczas procesu nawijania. Przed usunięciem z trzpienia naprężenia strukturalne działają tylko we włóknach, nie występują one w spoiwie.
Naprężenia skurczowe występują we włóknach i spoiwie w wyniku zmniejszenia objętości (skurczu) spoiwa podczas utwardzania. Stopień skurczu może wahać się od 2 do 30% obj., w zależności od charakteru związku.
Naprężenia termiczne powstają na skutek różnicy współczynników rozszerzalności liniowej zbrojenia i spoiwa oraz nierównomiernego rozkładu temperatur w objętości wyrobu. Z reguły współczynnik rozszerzalności liniowej polimerów jest znacznie wyższy niż włókien.
W prawdziwym PCM wszystkie uwzględnione naprężenia są sumowane, a materiał poddawany jest działaniu powstałych naprężeń, które z czasem ulegają relaksacji. Aby zapewnić pełniejszą relaksację naprężeń i uniknąć wypaczeń i pęknięć, zaleca się powolne podgrzewanie i schładzanie produktów PCM.
Tworzywa sztuczne wzmocnione włóknem węglowym i włóknami o niskim module nie są stosowane jako materiały konstrukcyjne. Służą do wytwarzania materiałów przewodzących, chroniących przed ciepłem i przeciwciernych.
Konstrukcyjne tworzywa sztuczne wzmocnione włóknem węglowym zawierają jako wypełniacz włókna węglowe o wysokim module (E = 342 - 540 GPa) i wysokiej wytrzymałości (cm - 2,5 GPa). Konstrukcyjne tworzywa sztuczne wzmocnione włóknem węglowym charakteryzują się niską gęstością i współczynnikiem rozszerzalności liniowej oraz wysokim modułem sprężystości, wytrzymałością, odpornością cieplną, przewodnością cieplną i elektryczną.
Właściwości tworzyw sztucznych wzmocnionych włóknem węglowym zależą od materiału spoiwa, właściwości, stężenia i orientacji włókien. Tworzywa sztuczne wzmacniane włóknem węglowym na bazie żywic epoksydowych charakteryzują się wysokimi właściwościami wytrzymałościowymi w temperaturach poniżej 200°C (tabela 1.6). PCM-y te produkowane są najczęściej z prepregów, produkowanych w formie pasków o różnej szerokości. Wytrzymałość na rozciąganie i zginanie jednokierunkowych tworzyw sztucznych z włókna węglowego może wynosić 1000 - 1600 MPa lub więcej, a moduł sprężystości (1 - 2,5) - 10 MPa lub więcej. Pod względem wytrzymałości właściwej i sztywności tworzywa sztuczne z włókna węglowego są daleko w tyle za tworzywami szklanymi, stalą, aluminium i stopami tytanu.
Tabela 1.(
Właściwości wysokomodułowych i wytrzymałych tworzyw epoksydowych wzmocnionych włóknem węglowym
Wskaźniki |
Epoksydowe włókno węglowe! |
|
wysoce modułowy |
wysoka wytrzymałość |
|
Gęstość, kg/m 3 | ||
Wytrzymałość, MPa, przy ściskaniu, rozciąganiu i zginaniu na ścinanie międzywarstwowe | ||
Moduł sprężystości przy rozciąganiu i zginaniu, GPa | ||
Wytrzymałość zmęczeniowa na zginanie w oparciu o 10 7 cykli, GPa |
W tworzywach z włókna węglowego przeznaczonych do długotrwałej pracy w temperaturach do 250°C stosuje się tworzywa fenolowe i krzemoorganiczne do 300°C. I do 330°C - spoiwa poliimidowe. Opracowywane są spoiwa o temperaturach pracy do 420°C. Jeszcze bardziej wyraźną wadą tworzyw sztucznych wzmocnionych włóknem węglowym niż włókna szklanego jest niska wytrzymałość podczas ścinania międzywarstwowego. Wynika to ze słabej adhezji polimerów do włókien węglowych. Aby: zwiększyć przyczepność, stosuje się kilka metod: trawienie powierzchni włókien środkami utleniającymi (na przykład kwasem azotowym), wypalanie smaru; wykańczanie - wstępne powlekanie włókien cienką warstwą zwilżającego je monomeru; wnętrzności - rosnące „wąsy” (kłaczki) we włóknach węglowych. Tworzywa sztuczne wzmocnione włóknem węglowym, w których oprócz zorientowanych włókien ciągłych jako wypełniacz stosuje się wąsy, nazywam je! wąsaty lub worseryzowany.
Anizotropia właściwości tworzyw sztucznych wzmocnionych włóknem węglowym jest jeszcze bardziej wyraźna niż tworzyw sztucznych wzmocnionych włóknem szklanym. To jest z tym powiązane. że stosunek modułów sprężystości wypełniacza i spoiwa dla tworzyw sztucznych z włókna węglowego (100 lub więcej) jest znacznie wyższy niż dla tworzyw sztucznych z włókna szklanego (20 - 30). Ponadto tworzywa z włókna węglowego charakteryzują się różnicą właściwości sprężystych samych włókien w kierunku wzdłuż osi i prostopadle do niej, co prowadzi do dodatkowej anizotropii. Zazwyczaj projekty wymagają mniejszej anizotropii właściwości mechanicznych*. W tym przypadku stosuje się materiały wzmocnione krzyżowo. Zmieniając zawartość objętościową włókien i teksturę PCM, można zmieniać właściwości kompozycji w bardzo szerokim zakresie.
Tworzywa sztuczne wzmocnione włóknem węglowym charakteryzują się dużą odpornością na obciążenia zmęczeniowe. Pod względem wytrzymałości na jednostkę masy tworzywa sztuczne wzmocnione włóknem węglowym są znacznie lepsze od tworzyw sztucznych i metali wzmocnionych włóknem szklanym. Jedną z przyczyn jest mniejsze (niż np. włókno szklane) odkształcenie przy tym samym poziomie naprężeń, co ogranicza pękanie osnowy polimerowej. Ponadto wysoka przewodność cieplna włókien węglowych pomaga rozproszyć energię drgań, co zmniejsza samonagrzewanie się materiału na skutek wewnętrznych sił tarcia.
Cenną właściwością tworzyw sztucznych wzmocnionych włóknem węglowym jest ich wysoka zdolność tłumienia i odporność na wibracje. Pod względem tych wskaźników tworzywa sztuczne wzmocnione włóknem węglowym są lepsze od metali i niektórych innych materiałów konstrukcyjnych. Zdolność tłumienia można regulować poprzez zmianę kąta pomiędzy kierunkami zbrojenia i przyłożenia obciążenia.
Z tworzyw sztucznych wzmacnianych włóknem węglowym wykonuje się konstrukcje zachowujące stabilność pod wpływem zewnętrznego momentu zginającego, ciśnienia lub ściskania osiowego: łopatki wirników helikopterów, obudowy sprężarek i wentylatorów, łopatki wentylatorów, tarcze wirników stojanów i sprężarek niskociśnieniowych silników lotniczych. Zastosowanie w tych elementach tworzyw sztucznych wzmocnionych włóknem węglowym zamiast metali umożliwia zmniejszenie masy silnika o 15 - 20%. W technologii kosmicznej tworzywa sztuczne z włókna węglowego są wykorzystywane do paneli słonecznych, cylindrów wysokociśnieniowych i powłok chroniących przed ciepłem.
Współczynnik rozszerzalności liniowej wysokomodułowych jednokierunkowych tworzyw sztucznych wzmocnionych włóknem węglowym w kierunku wzdłużnym jest bliski zeru, a w zakresie 120 - 200°C jest nawet ujemny (-0,5-10"6 1/°C). Dlatego wymiary wyrobów z tworzyw sztucznych z włókna węglowego zmieniają się bardzo niewiele podczas ogrzewania i chłodzenia.
Tworzywa sztuczne wzmocnione włóknem węglowym mają dość wysoką przewodność elektryczną, co pozwala na ich zastosowanie jako antystatyczne i elektryczne materiały grzewcze. Wraz ze wzrostem zawartości CF w PCM do określonego ułamka objętościowego (40 - 70%), w zależności od rodzaju polimerów i CF, tekstylnej postaci CF, obserwuje się wzrost wytrzymałości i modułu sprężystości. Następnie wskaźniki te zaczynają się pogarszać na skutek niewystarczającej ilości polimeru wymaganej do uzyskania monolitycznego kompozytu oraz niszczenia kruchych włókien węglowych na etapie formowania przy dużym stopniu zagęszczenia. Maksymalna zawartość węglowodorów w PCM jest również ograniczona przez słabą zwilżalność spoiwa węglowodorowego.
W niektórych przypadkach zastosowanie samych włókien węglowych jako wypełniacza nie zapewnia niezbędnej lepkości, odporności na erozję, wytrzymałości na ściskanie, rozciąganie i ścinanie. Następnie spoiwa wzmacnia się wspólnie włóknami węglowymi i szklanymi lub węglowymi i borowymi. Łączone zbrojenie pozwala na poszerzenie asortymentu! wartości wytrzymałości, sztywności i gęstości PCM.
Odporność chemiczna tworzyw z włókna węglowego pozwala na ich zastosowanie do produkcji pomp i uszczelnień kwasoodpornych. Włókna węglowe charakteryzują się niskim współczynnikiem tarcia, dzięki czemu można je stosować jako wypełniacz do różnych spoiw, z których wykonane są łożyska, uszczelki, tuleje i przekładnie.
Rozwój technologii wymaga materiałów mocnych mechanicznie i żaroodpornych. Spowodowało to szczególne zainteresowanie materiałami kompozytowymi węgiel-węgiel (CCM), zawierającymi węgiel zarówno jako wypełniacz wzmacniający, jak i materiał matrycy.
W CCCM odporność na wysoką temperaturę łączy się z niską gęstością, wysoką wytrzymałością i modułem sprężystości oraz odpornością na ciepło; uderzyć. Materiały te zachowują długi czas pracy w temperaturach do 500°C (w środowisku utleniającym i do 3000°C w środowisku obojętnym i w próżni.
Wypełniacz i osnowa CCCM, w zależności od składu i warunków karbonizacji, mogą posiadać różne modyfikacje. W przyjętej klasyfikacji najpierw wskazuje się strukturę wypełniacza węglowego, a następnie osnowę, na przykład materiał węgiel-węgiel, grafit-węgiel, grafit-grafit.
W CCCM wypełniacz węglowy występuje w postaci dyskretnych włókien, ciągłych nici lub kabli, filców, taśm, tkanin o splocie płaskim i wolumetrycznym oraz struktur wolumetrycznych. Włókna ułożone są losowo w kierunkach jedno-, dwu- i trójkierunkowych. Wykorzystują włókna węglowe niskomodułowe, wysokomodułowe i wysokowytrzymałe otrzymywane z wiskozy, włókien poliakrylonitrylowych i paku węglowego.
Jako osnowę można stosować węgiel pirolityczny, a także pak węglowy i polimery koksujące, które w procesie termicznego niszczenia wytwarzają ponad 50% wag. koksu. Najczęściej stosuje się żywice fenolowe (wydajność koksu 54 - 60% mas.). Znane jest stosowanie poliamidu (63-74% mas.), żywic krzemoorganicznych (84-87% mas.), produktów kondensacji fenolu i naftenów z formaldehydem (70% mas.), popiołów oligobenzimidowych (74% mas.), żywice furfurylowe i inne polimery. Im wyższa wydajność i wytrzymałość koksu, a także siła jego przyczepności do wypełniacza, tci, tym wyższa jakość CCCM.
, .„.„ Aby otrzymać kompozyt o określonych właściwościach, należy określić najkorzystniejszą kombinację napełniacza i osnowy oraz: v 6paTb, najkorzystniejszy reżim technologiczny otrzymania osnowy yraepoj.
W zależności od stanu fazowego substancji zawierających węgiel wyróżnia się następujące metody zagęszczania wypełniaczy z włókna węglowego (CFF) węglem:
stosowanie węglowodorów w fazie gazowej lub parowej (gaz ziemny, propan-butan, benzen itp.);
stosowanie węglowodorów ciekłych charakteryzujących się dużą zawartością węgla i wysokim udziałem uzysku koksu (smoły, żywice);
kombinowane, obejmujące impregnację porowatych ram ciekłymi węglowodorami i karbonizację, a następnie zagęszczanie węglem pirolitycznym uzyskanym w wyniku pirolizy węglowodorów w fazie gazowej.
Proces zagęszczania ramy można przeprowadzić na kilka sposobów.
Metoda izotermiczna polega na przepuszczeniu gazu zawierającego węgiel po powierzchni nagrzanej ramy pod stosunkowo umiarkowanym ciśnieniem. Wadą jest czas trwania procesu, tworzenie się skorupy powierzchniowej, która zapobiega przedostawaniu się gazu do ramy. Ta metoda jest najskuteczniejsza w przypadku produktów o małej grubości.
Inną metodą ustala się różnicę ciśnień na całej grubości ramy i na siłę filtruje się przez nią gaz zawierający węgiel. Wymuszona filtracja przyspiesza proces zagęszczania i znacznie zwiększa grubość impregnacji. Jednak ze względu na zmniejszenie stężenia gazu zawierającego węgiel wzdłuż grubości warstwy struktura materiału jest nierównomiernie gęsta.
Najbardziej rozpowszechnioną metodą jest metoda termogradientowa, gdy na całej grubości porowatej ramy ustala się pewną różnicę temperatur, a gaz zawierający węgiel przepływa od strony powierzchni o niskiej temperaturze. W tym przypadku eliminuje się tworzenie się skorupy powierzchniowej, co przyczynia się do produkcji materiału wysokiej jakości. Metoda ta jest najskuteczniejsza przy zagęszczaniu ram o średniej i dużej grubości.
Podczas termicznego rozkładu węglowodorów w fazie gazowej zachodzą jednocześnie różne procesy chemiczne, w wyniku których powstają zarówno lżejsze, jak i cięższe węglowodory, wodór i różne stałe produkty węglowe. Struktura i właściwości produktów węglowych są zróżnicowane i zależą od warunków procesu. Przykładowo produkty rozkładu termicznego, w zależności od zewnętrznego kształtu geometrycznego, zawierają:
węgiel warstwowy lub błyszczący, zwany pirowęglanem (PU);
Węgiel włóknisty lub nitkowaty; rozproszony węgiel lub sadza.
Tworzenie się PU odbywa się w szerokim zakresie temperatur od 700 do 3000°C. Skład gazów źródłowych określa wydajność PU i szybkość jego osadzania. Największą wydajność PU uzyskuje się z metanu, który ma najniższą masę cząsteczkową. Węglowodory o dużej masie cząsteczkowej charakteryzują się zwiększoną wydajnością sadzy. Istotne znaczenie ma ciśnienie gazu w reaktorze.
Wyróżnia się dwa główne rodzaje PU, których strukturę i właściwości określa temperatura powstawania: niska temperatura (1000 - 1100°C) i wysoka temperatura (1400 - 2200°C), zwane pirografitem.
Proces osadzania PU w fazie gazowej prowadzony jest w instalacji (rys. 1.29), składającej się z reaktora chłodzonego wodą, stacji sterującej układami zasilania gazem ziemnym, urządzeń do wytwarzania próżni, urządzeń chłodniczych i energetycznych. Obrabiany przedmiot - rama karbonowa (4) jest zainstalowana na grzejnikach grafitowych (3), umieszczonych pomiędzy przewodami prądowymi (2). Po opróżnieniu komora jest wprowadzana do reaktora. gazu ziemnego. Ogrzewanie odbywa się poprzez bezpośredni przepływ prądu przez grzejnik (3), kontrola temperatury odbywa się za pomocą ruchomych termopar chromowo-alumelowych (5) umieszczonych w kwarcowych obudowach. Na początku procesu termopara jest instalowana jako złącze w pobliżu powierzchni grzejnika Przy przyjętym schemacie zagęszczania PU strefa pirolizy przesuwa się dookoła - od środka przedmiotu obrabianego do obwodu.
W przypadku osadzania PU w fazie gazowej jednym z kryteriów jakości powstałego materiału jest jego gęstość. Jest to funkcja wielu parametrów i zależy od gęstości ramy, prędkości frontu pirolizy, stężenia odczynnika i ciśnienia gazu w reaktorze.
Rozpad węgla pirolitycznego z fazy gazowej w węglanie ultrafioletowym przeprowadza się głównie w temperaturach 1100 - 1500°C i obniżonym ciśnieniu w atmosferze zawierającej 91 - 93% metanu i 7 - 9% argonu. Grafizacja odbywa się w obojętnej atmosferze.
Proces technologiczny wytwarzania CCCM metodą fazy ciekłej!* obejmuje wytworzenie porowatej ramy, jej impregnację ciekłymi węglowodorami, karbonizację pod ciśnieniem oraz grafityzację. Wybierając materiał impregnacyjny do impregnacji, należy wziąć pod uwagę jego następujące cechy:
lepkość;
odpady koksowe;
mikrostruktura koksu;
Struktura krystaliczna koksu.
Wszystkie te właściwości zależą od ciśnienia i temperatury podczas procesu utwardzania kompozytów węgiel-węgiel. Najczęściej stosowanymi żywicami są fenolowe, poliamidowe, poliwinylosiloksanowe, polifenylosiloksanowe, furfurylowe i epoksynowolakowe. Postępowym i obiecującym kierunkiem jest wykorzystanie paków naftowych i węglowych jako materiałów impregnacyjnych. Spoiwa te charakteryzują się następującymi zaletami: niski koszt, wysoka zawartość węgla przy zachowaniu termoplastyczności oraz zdolność do grafityzacji przygotowanych paków mezofazowych. Wady obejmują: toksyczność, niespójną jakość.
Cii
Ryż. 1,29. Schemat instalacji termogradientowej metody osadzania węgla pirolitycznego w fazie gazowej: 1 - reaktor chłodzony wodą, 2 - przewody prądowe, 3 - grzejnik, 4 - rama węglowa, 5 - termopara w rurce kwarcowej, 6 - mechanizm poruszający termoparę, 7 - płaszcz wodny; przepływy: I – gaz, II – gazowe produkty pirolizy, Ř – woda.
Skład chemiczny i właściwości paków różnią się znacznie w zależności od rodzaju surowca i warunków technologicznych. W pewnych warunkach faza ciekłokrystaliczna (mezofaza) może zarodkować i rosnąć w pakach, co zapewnia powstawanie anizotropowego koksu grafityzującego. Pod tym względem obecnie dzieli się wysokości na izotropowe (regularne, niemezofazowe) i anizotropowe (mezofazowe).
Podczas karbonizacji w niskiej temperaturze (550–650°C) mezofaza przechodzi w postać stałą. Procesowi temu towarzyszy pęcznienie pod wpływem uwalniających się gazów, co prowadzi do powstania drobno porowatej struktury koksu. Podczas pęcznienia następuje głębokie odkształcenie koksu i zwiększa się liczba wadliwych struktur, co w trakcie późniejszej obróbki cieplnej prowadzi do pojawienia się pęknięć skurczowych.
Kształtowanie się struktury i właściwości osnowy węglowo-koksowej uzależnione jest od warunków obróbki cieplnej, które można podzielić na kilka etapów:
Karbonatyzacja (900 - 1423°C) - rozkład związków organicznych
tworzenie i tworzenie molekularnej uporządkowanej struktury koksu węglowego
prekrystalizacja (1400 - 2000°C) - uporządkowanie atomów yi
leroda w doskonalszą strukturę z utworzeniem tzw. pasów<
obecne formy węgla;
grafityzacja jednorodna (2000 - 3000°C) - transformacja przejściowa; wszelkich form węgla w krystaliczny grafit.
Na ryc. Rysunek 1.30 przedstawia schemat instalacji do impregnacji tkaniny węglowej.
Ryż. 1.30. Schemat instalacji impregnacji tkaniny węglowej: 1 - szpula podająca, 2 - tkanina węglowa, 3 - rolki dociskowe, 4 - piekarnik elektryczny, 5 - urządzenie regulujące prędkość podawania tkaniny, 6 - szpula odbiorcza; 7 - napęd elektryczny, 8 - wanna
Tkanina jest rozwijana ze szpuli podającej (1) i przechodzi przez twój (8), w którym trzy szybkoobrotowe mieszadła intensywnie mieszają proszek pakowy z wodą, tworząc stabilną zawiesinę wodno-smolarną. Podczas dalszego przejścia tkaniny przez rolki dociskowe (3) i elektron 1 (4) woda odparowuje, a pak, topiąc się, impregnuje powstały prepreg, wykorzystując napęd elektryczny (7) i sterowanie prędkością podawania tkaniny urządzenie (5), nawijana jest na szpulę odbiorczą (6). Na wylocie z pieca taśma jest dociskana przez wał nagrzany do temperatury 100 - 120°C i wyciskana! zapieczone w objętości tkaniny.
Wstępną impregnację porowatej ramy węglowej pakem można przeprowadzić pod ciśnieniem od 0,5 do 3 MPa, karbonizację - pod ciśnieniem 100 - 200 MPa i temperaturą 900 - 1100 ° C.
Cechą CCCM jest stosunkowo duża porowatość osnowy węglowej, a także jej przecięcie z pęknięciami w kierunku prostopadłym do wypełniacza. Pęknięcia w osnowie powstają podczas schładzania produktu od temperatury produkcyjnej (3000°C) do temperatury pokojowej na skutek dużych naprężeń termicznych. Aby wyeliminować porowatość, kilkakrotnie powtarza się operację impregnacji-karbonizacji, a następnie grafityzacji i operację impregnacji węglem pirolitycznym (ryc. 1.31).
Po wielokrotnym powtórzeniu cyklu impregnacji-karbonizacji gęstość materiału może osiągnąć 2000 - 2100 kg/m3. Jeżeli temperatura obróbki nie przekracza 800 - 1500°C, następuje karbonizacja spoiwa, a w temperaturach 2300 - 3000°C otrzymuje się materiał grafitowany. Karbonizację tworzyw sztucznych z włókna węglowego przeprowadza się w przepływie gazu obojętnego lub atmosferze redukującej pod podwyższonym ciśnieniem z ogrzewaniem izotermicznym, dynamicznym lub „stopniowym” – w atmosferze obojętnej;
Włókna węglowe
Warstwa uzwojenia 3 \ ^Produkcja
obszerne wyroby dziewiarskie\tkaniny
Struktury\
Oprogramowanie sprzętowe
Impregnacja smoły
* Karbonizacja
Ponowna impregnacja Ponowna karbonatyzacja
Grafityzacja Rys. 1.31. Schemat otrzymywania CCCM metodą impregnacji
Połączoną lub złożoną metodę uzyskiwania CCCM można wdrożyć zgodnie z następującymi schematami:
Impregnacja porowatej ramy pakem, karbonizacja pod ciśnieniem, dodatkowe zagęszczenie PU z fazy gazowej;
Zagęszczanie ramy PU z fazy gazowej do zadanej gęstości, impregnacja pakem, a następnie karbonizacja, obróbka mechaniczna i zagęszczanie PU.
Metoda ta zapewnia maksymalną gęstość, wysokie właściwości fizyczne i mechaniczne oraz nie wymaga dodatkowego wyposażenia.
W przypadkach, gdy karbonizacja CCCM odbywa się bez ciśnienia
Proces można prowadzić w trybie prażenia konwencjonalnego (komora gazowa) str
chakhs, którego projekt został omówiony wcześniej. Technologia produkcji]
CCCM wykorzystujący metodę fazy ciekłej pod kątem karbonizacji pod ciśnieniem Może<
być realizowane za pomocą pras.
Grafityzacja (grafityzacja) prowadzona jest w piecach Acheson, których budowę omówiono w poprzednich rozdziałach.
Właściwości CCCM różnią się w szerokim zakresie. Wytrzymałość zwęglonego CCCM jest proporcjonalna do gęstości. Grafityzacja węglanu węglowego zawierającego węgiel zwiększa jego wytrzymałość. Siła CCCM oparta na wysokim: mocny CF jest wyższa niż siła CM oparta na wysokim module CF, bądź lepszy! nykh w różnych temperaturach przetwarzania. Unikalne właściwości CCCM obejmują odporność na wysoką temperaturę w środowiskach obojętnych i redukujących. Pod względem zdolności do zachowania kształtu oraz właściwości fizycznych i mechanicznych w tych środowiskach CCCM przewyższa znane materiały konstrukcyjne. Niektóre CCCM, szczególnie te otrzymywane poprzez karbonizację włókna węglowego na bazie polimerów organicznych, charakteryzują się wzrostem wytrzymałości wraz ze wzrostem temperatury pracy od 20 do 2700°C. W temperaturach powyżej 3000°C CCCM działają przez krótki czas, gdyż rozpoczyna się intensywna sublimacja grafitu. Im doskonalsza jest struktura krystaliczna grafitu, tym w wyższej temperaturze i mniejszej prędkości zachodzą procesy termodestrukcyjne. Właściwości] CCCM zmieniają się w powietrzu pod wpływem długotrwałej ekspozycji na stosunkowo niskie temperatury. Tak więc w temperaturze powietrza 400 - 650°C to się dzieje! utlenianie CCCM i w efekcie szybki spadek wytrzymałości. ten wzrost porowatości. Utlenianie matrycy wyprzedza utlenianie węglowodorów, np< ли последние имеют более совершенную структуру углерода. Скорость оки>Wraz ze wzrostem temperatury maleje wzrost temperatury ich wytwarzania i spadek liczby wad. Skutecznie zapobiega utlenianiu CCCM< питка их кремнийорганическими соединениями из-за образования карбида оксида кремния.
Na ryc. 1.32 przedstawia obszary zastosowań CCCM.
odporny na działanie
Ryż. 3.32. Obszary zastosowań CCCM w warunkach dużych obciążeń termicznych
Dlatego CCCM znajdują zastosowanie w różnych gałęziach techniki tam, gdzie tradycyjne materiały są nieskuteczne, tj. w warunkach dużych obciążeń termicznych i w jednostkach tarcia.
Materiały kompozytowe to materiały utworzone z kilku komponentów. Wykonane są głównie z podstawy z tworzywa sztucznego, wypełniacza wzmacniającego i niektórych innych substancji. Dzięki temu kompozyt charakteryzuje się dużą wytrzymałością, sztywnością i wieloma innymi przydatnymi właściwościami.
Technologie kompozytów polimerowych to metody tworzenia materiałów, których matrycą jest polimer. Mają ogromną liczbę typów i gatunków, co zapewniło ich rozpowszechnienie i popularność. Istnieją następujące typy polimerów ceramicznych:
Włókno szklane;
tworzywa sztuczne wzmocnione włóknem węglowym;
boroplastyka;
tworzywa organiczne;
polimery wypełnione proszkami;
tablice tekstowe.
Kompozytowe materiały ceramiczne są stosowane w wielu różnych dziedzinach, w tym w następujących:
Budowa;
Inżynieria elektryczna;
przemysł chemiczny;
budowa dróg;
telekomunikacja;
przemysł lotniczy itp.
Powszechność i popularność technologii kompozytowych wiąże się z wieloma zaletami tej metody wytwarzania materiałów. Warto zwrócić uwagę na następujące pozytywne cechy:
Polepszone właściwości fizyczne i chemiczne;
dość niski ciężar właściwy;
odporność na korozję, gnicie lub wypaczenie;
niska toksyczność podczas spalania;
niepalność lub trudnopalność;
wyjątkowa odporność chemiczna;
niski współczynnik rozszerzalności liniowej pod wpływem ciepła;
dość szeroki zakres temperatur funkcjonalności;
wysokie właściwości elektroizolacyjne;
zwiększona czystość środowiska.
W XXI wieku materiały kompozytowe na bazie polimerów ceramicznych stały się jedną z dość popularnych substancji, za pomocą których rozwiązują różne problemy technologiczne w najróżniejszych dziedzinach, takich jak budownictwo, inżynieria czy inne gałęzie przemysłu. Osiągnięto to dzięki wielu zaletom, które wyróżniają kompozyty spośród innych, popularnych do tej pory rodzajów materiałów.
Przywracanie diagonalnego koła pompy
Do renowacji diagonalnego koła pompy można również zastosować materiały kompozytowe. Poseł Angarsky Vodokanal zwrócił się do Ceramet z podobną prośbą o naprawę urządzenia pompującego ścieki o nazwie KSB Sewatec.
W ciągu trzech lat eksploatacji wydajność pompy spadła do 70% począwszy od pierwszego dnia jej pracy. Naprawa obejmowała odbudowę metalu, zastosowanie materiału kompozytowego i wyważenie dynamiczne. Tym samym, dzięki zastosowaniu technologii kompozytowych, możliwe było wydłużenie żywotności pompy i osiągnięcie 4,5-krotnych oszczędności.
Cechy materiału Ceramet
Kompozytowe materiały ceramiczne Ceramet mają za zadanie chronić sprzęt, przedłużając jego żywotność i zwiększając jego żywotność. Znacząco ogranicza to przestoje i konieczność zakupu dodatkowych części zamiennych.
Osobliwością materiału Ceramet jest jego dość szeroki zakres zastosowań, który obejmuje:
Naprawa sprzętu pompującego;
odnowienie ślimaków;
poprawa funkcjonalności wymienników ciepła;
naprawa rurociągów, rynien itp.
Dzięki temu materiał kompozytowy Ceramet można wykorzystać do wielu różnych celów, co jest korzystniejsze niż inne metody odnawiania sprzętu.