Vrste termičke obrade metala. Termička obrada legura. Vrste termičke obrade
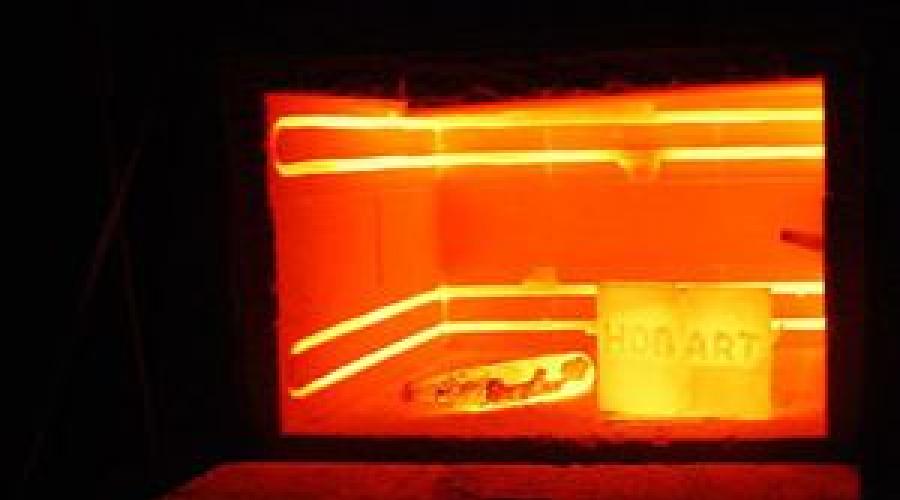
Termička obrada metala
Ali za dalju eksploataciju dijelovi i komponente opreme često zahtijevaju potpuno različite karakteristike - čvrstoću, tvrdoću, krutost itd. U te svrhe je namijenjena termička obrada metala.
Suština procesa termičke obrade
Zadaci razne tehnologije termička obrada je:
- Osiguravanje najpovoljnije mikrostrukture čelika i legura;
- Postizanje željenog nivoa tvrdoće: bilo u tankoj površinskoj (ili podzemnoj) zoni, ili u cijeloj presjek praznine;
- Ispravka hemijski sastav u zrncima makrostruktura razne legure.
U prvom slučaju potrebno je osigurati maksimalan stepen homogenosti svojstava metala, što je važno, na primjer, za naknadnu mehaničku ili – posebno – obradu koja ih deformiše. Kao rezultat, uvjeti za promjenu oblika obratka za sva tri koordinatne ose ispostavi da su identični, a nedostaci u završnom dijelu su otklonjeni.
Osim toga, potrebno je usklađivanje mikro i makrostruktura za procese oblikovanja metala kako bi se povećao stupanj deformacije poluproizvoda, čime se u konačnici oblik obratka približava obliku gotovog proizvoda. Štoviše, u najmanjem broju prijelaza, uz korištenje minimalnog potrebnog napora opreme.
Promjena tvrdoće (kao rezultat toplinske obrade) ima za cilj poboljšanje performansi dijelova. Budući da uslovi rada mogu biti veoma različiti, složeni fizički mehanička svojstva odabire se strogo pojedinačno: ne postoje univerzalni procesi toplinske obrade za legure različitih sastava.
Promjena hemijskog sastava u zrncima mikrostrukture, zbog stvaranja novih spojeva, u većini slučajeva ne samo da povećava pokazatelje tvrdoće, već i povećava otpornost na habanje dijelova koji moraju raditi na povećanom trenju, temperaturi ili povećana specifična opterećenja u odnosu na uobičajena.
Kaljenje-kaljenje
Prva grupa tehnologija toplinske obrade za različite legure, uključujući čelik, uključuje žarenje i kaljenje. Drugi je stvrdnjavanje, normalizacija, poboljšanje, starenje, hladno liječenje. Treće - sve vrste termohemijske obrade.
Žarenje
Suština procesa koji se odvijaju u strukturi većine legura podvrgnutih žarenju je da se obezbedi što uravnoteženija struktura obratka, u kojoj ili nema unutrašnjih naprezanja, ili je njihov nivo dovoljno nizak, pa stoga ne utiče na kasniju obradivost. metala/legura.
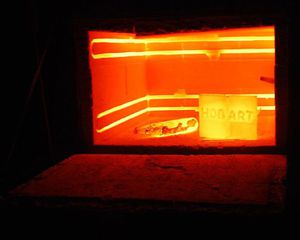
Početna struktura gotovo svih legura i čelika sastoji se od prilično velikih zrna, između kojih se nalaze inkluzije i nečistoće, uglavnom sumpor i fosfor. To povećava krhkost metala, što može biti važno pri oblikovanju proizvoda složenih konfiguracija od ingota (ili žičane šipke). Stoga je potrebno smanjiti veličinu zrna i dati mu optimalan elipsoidni oblik, u kojem će mehanička svojstva biti približno jednaka duž sve tri koordinatne ose.
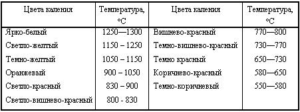
U tu svrhu, početni radni komad mora se zagrijati na temperaturu 50...70 0 C iznad temperature na kojoj počinje austenitna transformacija. Njegov rezultat je formiranje malih i dobro orijentiranih zrna austenita između zrna glavnih strukturnih komponenti čelika - ferita i cementita. Austenit se formira od perlita, strukture koja ima najveća zrna, što doprinosi povećanju krhkosti bilo kojeg ingota. Austenitna transformacija za većinu legura se odvija prilično sporo, tako da je žarenje duga procedura koja bi trebala trajati najmanje sat vremena.
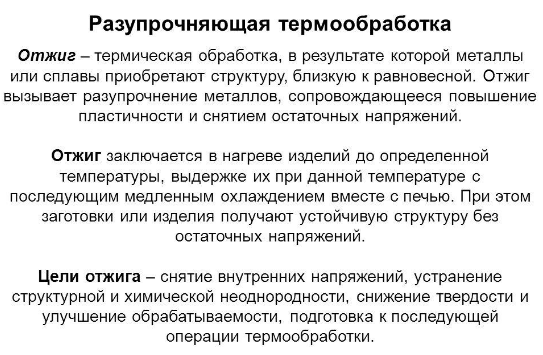
Sekunda važan zadatakžarenje – za uklanjanje unutrašnjih naprezanja koja nastaju u radnom komadu tokom hladne obrade. Činjenica je da je svaka deformacija popraćena fragmentacijom zrna izvorne strukture čelika i legura. Kao rezultat toga, ima više zrna, povećava se otpornost na deformaciju, što ne samo da zahtijeva povećanu silu deformacije, već uzrokuje i uništavanje poluproizvoda, čiji je stupanj deformacije premašio kritičnu vrijednost za dati metal .
U skladu s tim, za realizaciju prvog zadatka koristi se tehnologija visokotemperaturnog žarenja (za čelike, ovisno o sadržaju ugljika, kreće se od 550...750 0 C), au drugom - niskotemperaturno žarenje (180.. .220 0 C).
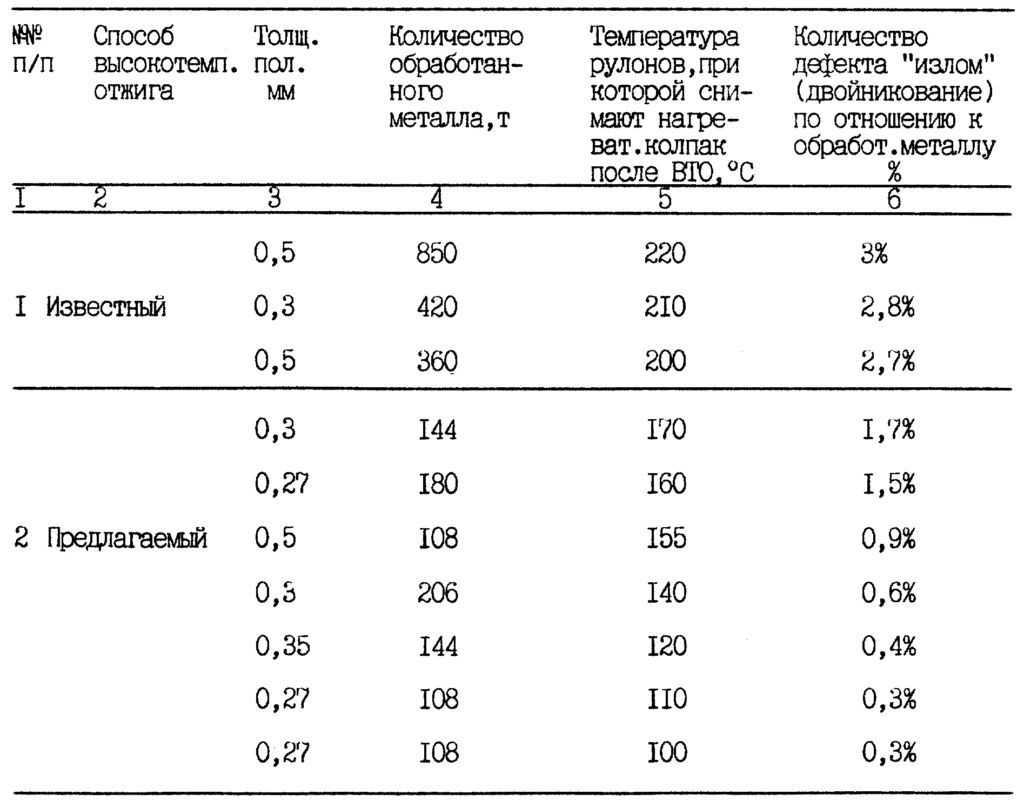
Zagrijavanje se odvija polako, nakon čega slijedi držanje proizvoda na određenoj temperaturi, nakon čega slijedi sporo hlađenje. Kod legiranih čelika i legura takvo hlađenje se vrši posebno malom brzinom, u samoj peći u kojoj se vršilo žarenje.
Odmor
Tehnologija kaljenja nalikuje žarenju, ali se ne izvodi s obratkom, već s gotovim proizvodom, te stoga ima druge ciljeve - ublažavanje unutarnjih naprezanja nakon toplinske obrade, koja je provedena kako bi se povećala tvrdoća dijela.
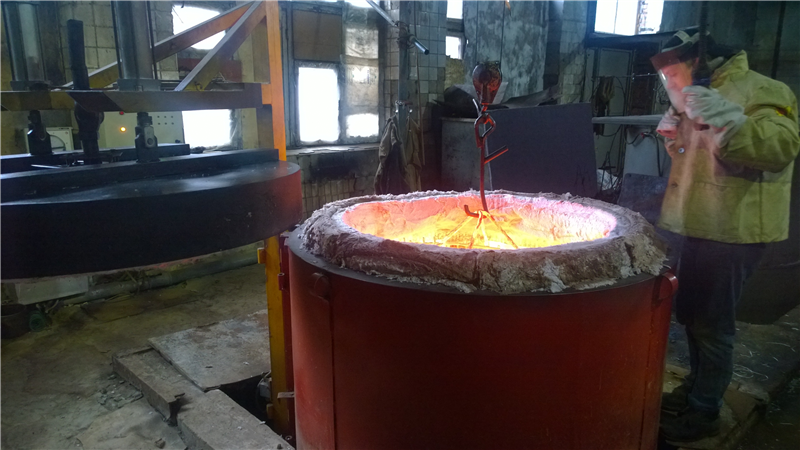
Nezavisan proces termička obrada nije praznik. Za razliku od žarenja, kaljenje se ponekad provodi u nekoliko faza: u većini slučajeva to se odnosi na proizvode za čiju su proizvodnju korišteni. različite vrste visoko legirani čelik.
Stvrdnjavanje
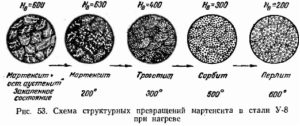
Kaljenje se sastoji od brzog zagrijavanja radnog predmeta do krajnje temperature austenitne transformacije (900...1100 0 C za niskougljične čelike, 750...850 0 C za visokougljične čelike) i naknadnog brzog hlađenja u posebnim medijima za gašenje . Za potonje se koristi voda (za proizvode manjeg značaja) ili ulje.
Načini očvršćavanja karakteriziraju najveću raznolikost. Glavni faktor koji određuje efikasnost kaljenja je intenzitet formiranja martenzita u strukturi - visokotemperaturne komponente koja daje metalu ili leguri povećanu tvrdoću.
Uvjeti za nastanak martenzita određeni su sljedećim okolnostima:
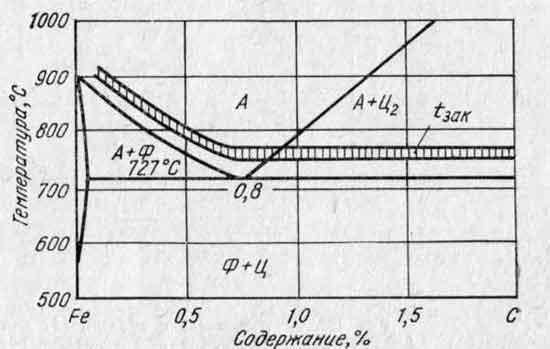
U skladu s tim, za svaki razred čelika ili legure razvijeni su pojedinačni načini kaljenja, koji se razlikuju:
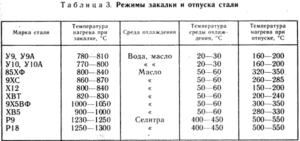
Posebna se pažnja poklanja kaljenju čelika i legura složenog sastava, uključujući nekoliko legirajućih elemenata (posebno kobalt, molibden). U procesu, ovi metali formiraju intermetalne spojeve duž granica zrna glavne strukture, što značajno povećava tvrdoću i čvrstoću čelika (posebno alatnih čelika). Oblik i koncentracija intermetalnih spojeva ovise samo o točnosti tehnologije očvršćavanja.
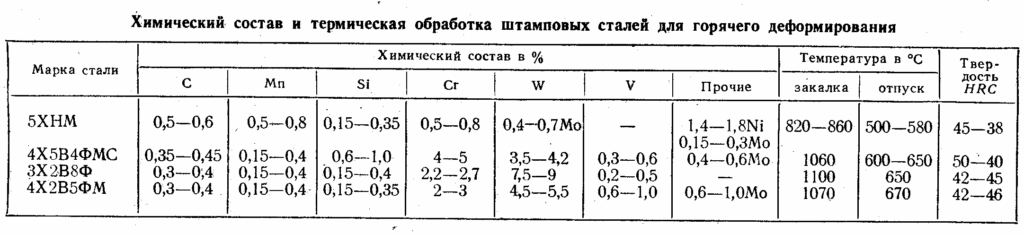
Vrste kaljenja određuju se opremom na kojoj se vrši. Na primjer, za proizvode kao što su zupčanici, osovine, vodilice, gdje je to potrebno optimalna kombinacija visoka površinska tvrdoća i relativno viskozno jezgro, koristi se površinsko očvršćavanje strujama visoke frekvencije.
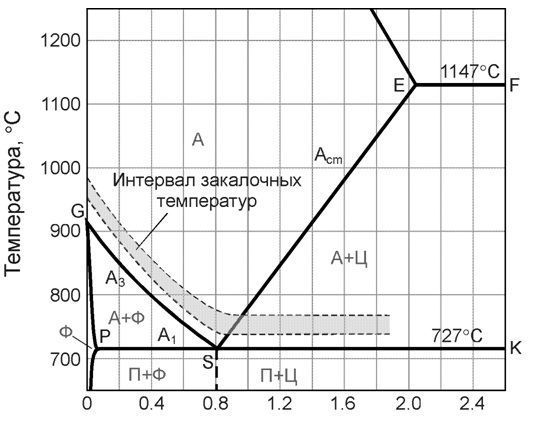
Da bi se to postiglo, proizvod se stavlja u indukcijsku zavojnicu kroz koju prolazi struja visoke frekvencije (do 15.000...25.000 Hz). Prodirući do ograničene dubine, ova struja pomaže u povećanju površinske čvrstoće čelika ili legura. Kao rezultat toga, otpornost na zamor dijelova koji rade pod ciklički promjenjivim naprezanjima zatezanja i kompresije značajno se povećava.
Intenzivnija promjena tvrdoće površine dijela može se postići korištenjem visokoenergetskih izvora topline za otvrdnjavanje - iskre ili lučnog pražnjenja. Pražnjenja moraju biti pobuđena tečni medij, gde se postavlja radni komad ili deo koji se obrađuje.
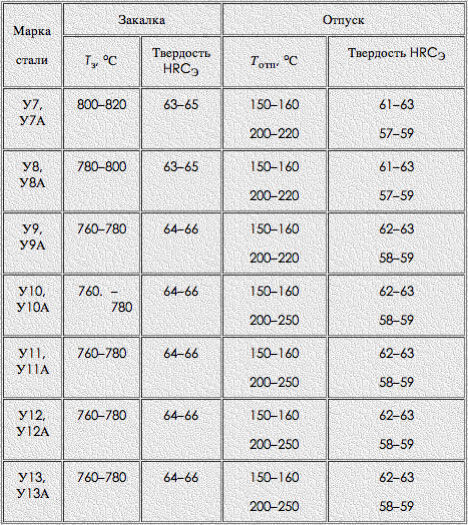
Nakon stvrdnjavanja, u velikoj većini slučajeva, kaljenje je neophodno, inače prekomjerna konačna tvrdoća dijela postaje uzrok povećane lomljivosti pod udarnim opterećenjima.
Poboljšanje i normalizacija
Kao vrste termičke obrade, ovi procesi su slični žarenju, iako su namijenjeni za druge svrhe – povećanje operativne trajnosti kritičnih dijelova strojeva i alata.
Tokom normalizacije, dio se podvrgava laganom zagrijavanju, održava na zadanoj temperaturi, a zatim se nužno hladi zajedno s peći. Kao rezultat toga, struktura dijela postaje uravnoteženija, a nivo unutrašnja naprezanja ide dole.
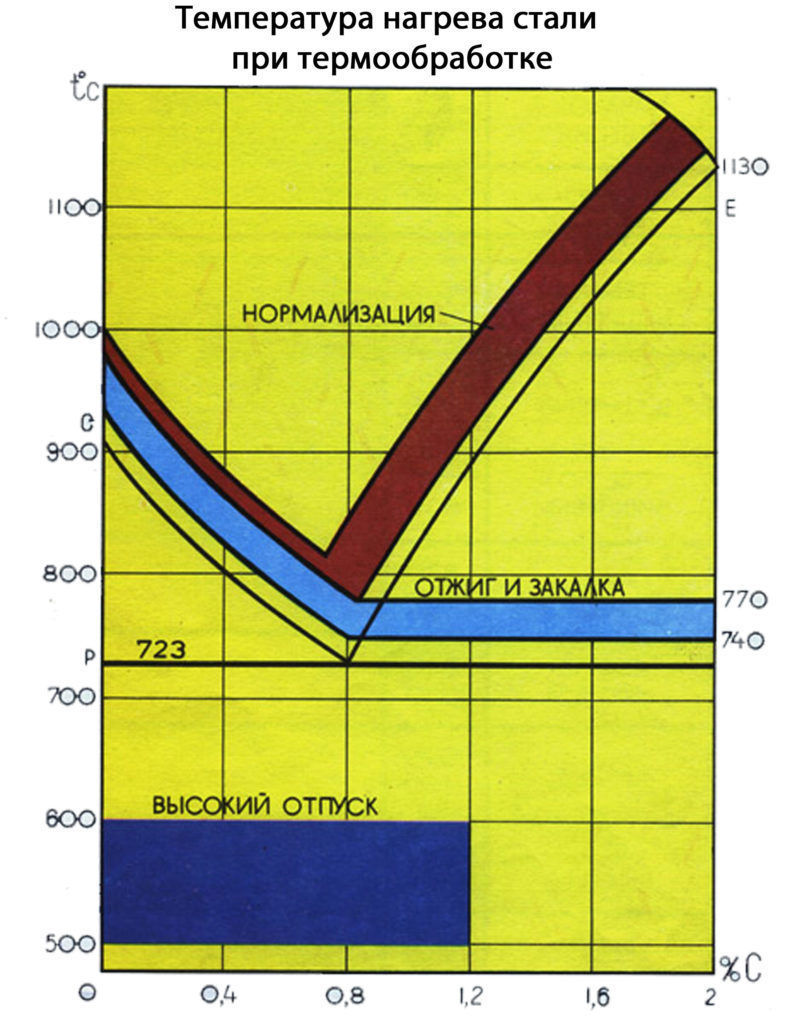
Značajna razlika je u sastavu atmosfere, peći u kojoj se izvode ove operacije termičke obrade. Mora biti neoksidirajući, jer intenzivno formiranje oksida na površini proizvoda ne samo da pogoršava njegov izgled, već i mijenja njegove dimenzije. Izgaranje ugljika, koje također prati toplinsku obradu u konvencionalnoj peći, pogoršava kemijski sastav čelika i smanjuje njegovu čvrstoću.
Smanjenje pristupa kisika površini dijela tijekom normalizacije provodi se na nekoliko načina:
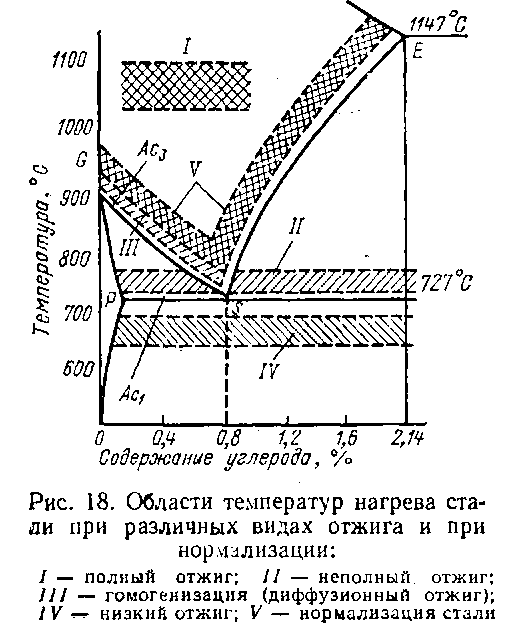
- Zagrevanjem tokom planiranog nedostatka kiseonika. U ovom slučaju, stabilnost plinski gorionici peći za toplinsku obradu kompenziraju se povećanjem brzine dovoda zraka u zonu izgaranja;
- Toplinska obrada u zaštitnom gasnom okruženju. Za kritične dijelove koriste se litijeva para, argon ili drugi plemeniti plinovi, u ostalim slučajevima - ugljični dioksid;
- Nanošenjem zaštitnih premaza na površinu proizvoda koji se normalizira.
Nakon normalizacije, dio se hladi na mirnom zraku, sprječavajući ga da izduva: to može uzrokovati neujednačenu, "pjegavu" mikrostrukturu proizvoda.
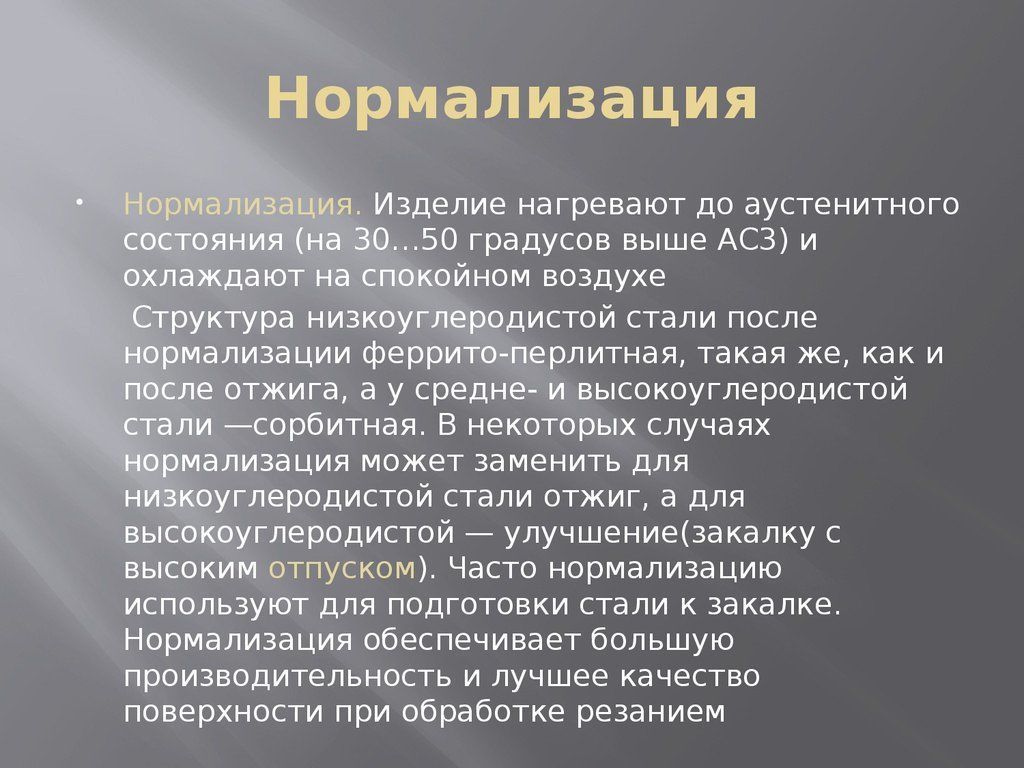
Poboljšanje je operacija toplinske obrade, zbog koje se povećava mehanička obradivost čelika i legura i smanjuje razina zaostalih naprezanja u njima. Ovo je praćeno blagim smanjenjem tvrdoće.
Martenzitna komponenta u strukturi većine čelika i legura može se pojaviti ne samo pri povećanju, već i pri niske temperature. Tehnologija hladnog tretmana ima prednost u odnosu na tradicionalne tehnologije termička obrada kako slijedi:
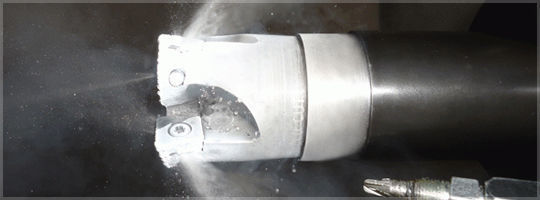
Načini kriogenog tretmana zavise od klase čelika/legure i kreću se od -60...-140 0 C. Tipično, kriogeni tretman se izvodi cikličnom kombinacijom perioda dubokog hlađenja sa periodima starenja - zadržavanje na manjem niske temperature. Kombinacijom ciklusa grijanja i hlađenja, potpuna razgradnja zadržanog austenita postiže se za 4...7 sati (veće vrijednosti za visokolegirane čelike).
Posebnu vrstu termičke obrade predstavljaju procesi hemijsko-termalne obrade. Njihov zadatak je formiranje karbida i nitrida u mikrostrukturi površine - spojeva koji značajno povećavaju mikrotvrdoću dijelova i stvaraju zaostala tlačna naprezanja u njima. Takvi proizvodi pokazuju posebno visoku otpornost pri naizmjeničnim opterećenjima.
Video: Kako očvrsnuti bilo koji tip čelika
Obrada metala termički- Ovo je promena unutrašnja struktura(struktura) metala pod uticajem promene temperaturni uslovi i time dobijanje potrebnih mehaničkih i fizička svojstva metal Ogroman dio toplinske obrade odvija se na kritičnim temperaturama pri kojima dolazi do strukturne transformacije u legurama.
Zbog toga se smanjuje toplinska obrada metala do tri sekvencijalne operacije i vrste:
- zagrijavanje metala određenom brzinom do određene temperature;
- držanje metala neko vrijeme na ovoj temperaturi;
- hlađenje brzinom određenom procesom.
Ovisi o tome kako treba promijeniti svojstva određenog čeličnog proizvoda i koristiti različite vrste toplinske obrade, koje se razlikuju po maksimalnoj temperaturi zagrijavanja, vremenu držanja i brzini hlađenja. U mašinstvu, termička obrada je našla najširu primenu.
Termička obrada metala, legura, čelika
Sva svojstva bilo koje legure zavise od njene strukture. Glavna metoda koja vam omogućava promjenu ove strukture je toplinska obrada. Njegove temelje je razvio D.K. Chernov, a kasnije su njegov rad podržali A.A. Bochvara, G.V. Kurdyumova, A.P. Gulyaeva.
Termička obrada metala i legure je niz operacija kao što su: grijanje, držanje i hlađenje, koji se izvode određenim redoslijedom i pod određenim načinom kako bi se promijenila unutrašnja struktura legure i dobila željena svojstva, pri čemu se hemijski sastav metala ne mijenja.
Šta je termička obrada metala i legura?
- U žarenju
- Stvrdnjavanje
- Odmor
- Normalizacija
Žarenje. To je zagrijavanje metala do visoke temperature, a zatim dolazi do sporog hlađenja. Događa se žarenje različite vrste- sve zavisi od toga temperaturni režim stope grijanja i hlađenja.
Stvrdnjavanje. Toplinska obrada čelika, legura, metala, koja se zasniva na rekristalizaciji čelika kada se zagrije iznad kritična temperatura. Nakon držanja čelika na ovoj temperaturi, slijedi vrlo brzo hlađenje. Takav čelik ima neravnotežnu strukturu i stoga nakon stvrdnjavanja slijedi kaljenje.
Odmor. Izvodi se nakon kaljenja kako bi se smanjila ili uklonila zaostala naprezanja u čeliku i legurama, povećala žilavost, smanjila tvrdoća i lomljivost metala.
Normalizacija. Slično je žarenju, jedina razlika je u tome što se normalizacija metala odvija na zraku, a žarenje se događa u peći.
Zagrevanje radnog komada
Ova operacija je veoma odgovorna. Od nje ispravna implementacija zavisi, prvo, od kvaliteta proizvoda, a drugo, od produktivnosti rada. Morate znati da kada se zagrije, metal mijenja strukturu, svojstva i sve karakteristike površinskog sloja. Budući da kada čelik ili legura stupe u interakciju sa zrakom, željezo oksidira i na površini se stvara kamenac. Debljina ljuske zavisi od hemijskog sastava metala, temperature i vremena njegovog zagrevanja.
Čelik počinje intenzivno oksidirati kada se zagreje iznad 900 stepeni, tada se oksidacija povećava dvostruko - kada se zagrije na 1000 stepeni C, a na temperaturi od 1200 stepeni C - 5 puta.
Koja se vrsta oksidacije događa u različitim čelicima?
Krom-nikl čelik- naziva se otpornim na toplinu jer praktički ne podliježe oksidaciji.
Legirani čelik- formira gustu, ali tanki sloj kamenac, koji štiti od dalje oksidacije i sprečava pucanje tokom kovanja.
Ugljični čelik- gubi oko 2-4 mm ugljika sa površine kada se zagrije. Ovo je jako loše za metal, jer gubi snagu, tvrdoću i čelik se kvari kad se stvrdne. A dekarbonizacija je posebno štetna za kovanje malih dijelova s naknadnim otvrdnjavanjem. Kako bi se izbjegle pukotine na visoko legiranom i visokougljičnom čeliku, moraju se polako zagrijavati.
Obavezno pogledajte dijagram željezo-ugljik, koji određuje temperaturu za početak i kraj kovanja. To se mora učiniti tako da kada se metal zagrije, ne dobije grubo zrnastu strukturu i da se njegova duktilnost ne smanji.
Ali pregrijavanje radnog komada može se ispraviti toplinskom obradom, ali to zahtijeva dodatnu energiju i vrijeme. Ako se metal dodatno zagrije viša temperatura, onda će to dovesti do izgaranja, koje će doći do tačke u kojoj je veza između zrna u metalu prekinuta i on će se potpuno srušiti tokom kovanja.
Burnout
Ovo najnepopravljiviji brak. Prilikom zagrijavanja metala ili legure, obavezno pratite temperaturu, vrijeme i kraj zagrijavanja. Kamenac raste ako se vrijeme zagrijavanja poveća, a pri brzom ili intenzivnom zagrijavanju mogu se pojaviti pukotine.
Izgaranje legure nastaje usled difuzije kiseonika na granicama zrna, gde se odmah formiraju oksidi koji razdvajaju zrna na visokoj temperaturi legure i istovremeno čvrstoća odmah naglo opada. A plastičnost u ovom trenutku dolazi na nulu. Ovaj otpad se odmah šalje na topljenje.
Šta je termička obrada metala i legura?
Termičku obradu podijeljen u:
- termalni;
- termomehanički;
- hemijsko-termički
IN termalni obrada obuhvata glavne vrste - žarenje 1. vrste, žarenje 2. vrste, kaljenje i kaljenje. Normalizacija se ne odnosi na sve vrste čelika, sve zavisi od njegovog stepena legiranja.
Sve vrste termičke obrade imaju različite temperature zagrijavanja, trajanje izlaganja na ovoj temperaturi i brzinu hlađenja nakon završetka izlaganja.
Prva vrsta žarenja je difuzijsko žarenje, žarenje koje ublažava stres.
Drugi tip žarenja dijeli se na nepotpuno, potpuno, izotermno žarenje, sferoidizaciju i normalizaciju.
Stvrdnjavanje se koristi kako bi se osiguralo da su proizvodi tvrda, izdržljiva i otporna na habanje.
Hemijsko-termički tretman
To je toplinska obrada čelika koja se kombinira sa zasićenjem površine proizvoda - ugljikom, dušikom, aluminijem, silicijumom, hromom itd., koji formiraju čvrste supstitucijske otopine sa željezom. Oni su dugotrajniji i energetski intenzivni od čelika zasićenog željezom i ugljikom, koji sa željezom stvara međuprostorne čvrste otopine.
Hemijsko-termički tretman pri stvaranju povoljnih zaostalih tlačnih napona na površini proizvoda povećava trajnost i pouzdanost proizvoda. Ona takođe povećava otpornost na koroziju, tvrdoća.
Ovaj tretman je namijenjen za promjenu sastava čelika u određenom sloju. Ove metode uključuju:
- cementiranje - ovom metodom gornji slojčelik je obogaćen ugljikom. Ovo proizvodi proizvode sa kombinovanim svojstvima - mekom i tvrdom jezgrom. površinski sloj;
- nitriranje - uh zatim obogaćivanje površinskog sloja dušikom kako bi se povećala otpornost na koroziju i čvrstoća proizvoda na zamor;
- dosadno - ovo je zasićenje površinskih slojevačelik sa borom, ovom metodom se povećava otpornost proizvoda na habanje, posebno tokom trenja i suhog klizanja. Pored toga, borenje sprečava zaglavljivanje ili zavarivanje delova u hladnom stanju. Nakon borenja, dijelovi postaju vrlo otporni na kiseline i lužine;
- aluminizacija - ovo je zasićenje čelika aluminijumom. To se radi kako bi se čelik učinio otpornim na agresivne plinove - sumporni anhidrid, sumporovodik;
- hromiranje - zasićenje površinskog sloja čelika hromom. Hromiranje niskougljičnih čelika gotovo da nema utjecaja na njihove karakteristike čvrstoće. Hromiranje čelika sa većim sadržajem hroma naziva se tvrdim hromiranjem, jer se na površini delova formira hrom karbid koji ima:
- visoka tvrdoća
- otpor skale
- otpornost na koroziju
- povećana otpornost na habanje
Ovo je ojačavajuća termička obrada metala i legura na kriogenim, vrlo niskim temperaturama - ispod -153 stepena C. Ranije se takva termička obrada nazivala "hladna obrada" ili "toplinska obrada metala na temperaturama ispod nule". Ali ova imena nisu u potpunosti odražavala suštinu kriogene obrade.
Njegova suština je sljedeća: dijelovi koji se obrađuju stavljaju se u kriogeni procesor, gdje se polako hlade, a zatim se dijelovi drže na temperaturi od -196 stepeni C određeno vrijeme. Zatim se postepeno vraćaju na sobnu temperaturu. Kada dođe do ovog procesa, dolazi do strukturnih promjena u metalu. Zbog toga se povećava otpornost na habanje, ciklička čvrstoća, otpornost na koroziju i eroziju.
Osnovna svojstva dobijena tokom obrade, kao što je hladno hlađenje, zadržavaju se tokom celog radnog veka radnog komada i stoga ne zahtevaju ponovnu obradu.
svakako, kriogena tehnologija neće zamijeniti metode termičkog očvršćavanja, ali kada se obradi hladnom daje materijalu nova svojstva.
Alati tretirani ultra niskim temperaturama omogućavaju preduzećima da smanje troškove jer:
- povećava se otpornost na habanje alata, dijelova i mehanizama;
- smanjen je broj nedostataka;
- Smanjuju se troškovi popravke i zamjene tehnološke opreme i alata.
Sovjetski naučnici su omogućili da se u potpunosti procijeni učinak hladnog tretmana na metale i legure i postavili temelje za korištenje ove metode.
IN dato vrijeme Metoda kriogene obrade proizvoda ima široku primjenu u svim industrijama.
Mašinstvo i obrada metala:
- produžava vijek trajanja opreme i alata do 300%;
- povećava otpornost materijala na habanje;
- povećava cikličku snagu;
- povećava otpornost na koroziju i eroziju;
- ublažava rezidualni stres.
Specijalna oprema i transport:
- povećava vijek trajanja kočionih diskova za 250%;
- povećava efikasnost kočionog sistema;
- povećava cikličku čvrstoću opruga ovjesa i drugih elastičnih elemenata za 125%;
- povećava vijek trajanja i snagu motora;
- smanjuje operativne troškove vozila.
Odbrambena industrija:
- povećava preživljavanje cijevi do 200%;
- smanjuje učinak zagrijavanja cijevi na rezultate pucanja;
- povećava resurse komponenti i mehanizama.
Rudarstvo i prerađivačka industrija:
- povećava izdržljivost alata za rezanje kamena do 200%;
- smanjuje abrazivno habanje komponenti i mehanizama;
- povećava otpornost opreme na koroziju i eroziju;
- povećava resurse industrijske i rudarske opreme.
Audio oprema i muzički instrumenti:
- smanjuje izobličenje signala u provodnicima;
- poboljšava muzičke performanse, jasnoću i transparentnost zvuka;
- proširuje opseg zvuka muzičkih instrumenata.
Kriogena obrada se koristi u gotovo svim industrijama gdje je potrebno povećati vijek trajanja, povećati čvrstoću i otpornost na habanje, a također povećati produktivnost.
Pouzdanost i izdržljivost metalne konstrukcije, opreme, cjevovoda ovisi o kvaliteti izrade jedinica, dijelova i elemenata od kojih se sastoje. Tokom rada podložni su statičkim, dinamičkim i cikličnim opterećenjima i uticaju agresivnog okruženja. Moraju raditi na niskim i visoke temperature i nalazi se u uslovima brzog habanja.
Stoga rad bilo kojeg metalnog proizvoda izravno ovisi o otpornosti na habanje, čvrstoći, toplinskoj i korozijskoj otpornosti elemenata od kojih se sastoje.
Kako bi se poboljšale sve ove karakteristike, potrebno je odabrati pravi materijal za dijelove, poboljšati njihov dizajn, eliminirati nepreciznosti montaže i poboljšati metode toplog i hladnog rada.
Materijali u stanju isporuke rijetko ispunjavaju tako visoke zahtjeve. Najveći deo isporučenih strukturni elementi potrebna stabilizacija operativna svojstva tako da se ne menjaju tokom vremena. I za poboljšanje mehaničkih i fizičko-hemijske karakteristike metalni materijali, primeniti toplotnu obradu. Ovo je niz operacija zagrijavanja, držanja i hlađenja metala i legura.
Izvodi se radi promjene strukture i svojstava metala i legura u smjeru koji je specificiran. Toplinska obrada se koristi za promjenu strukture faznog sastava i preraspodjele komponenti, veličine i oblika kristalnih zrna, vrste defekata, njihove količine i distribucije. I sve to čini prilično lakim dobivanje potrebne osobine materijala.
Neophodno je zapamtiti da svojstva metala i legura ne zavise samo od strukture, već i od hemijskog sastava koji se formira tokom metalurškog i livačkog procesa.
Svrha termičke obrade je uklanjanje unutrašnjeg naprezanja u metalu i leguri, poboljšanje mehaničkih i radnih svojstava i drugo.
Podložno termičkoj obradi čelik, liveno gvožđe, legure na bazi obojenih metala.
Prilikom izvođenja morate znati da su materijali istog hemijskog sastava različiti načini rada toplinskom obradom, možete dobiti nekoliko potpuno različitih struktura koje će imati potpuno različita svojstva. Pri poboljšanju mehaničkih svojstava termičkom obradom moguće je koristiti legure koje su više jednostavna kompozicija. Dozvoljena naprezanja, smanjenje težine dijelova i mehanizama, povećanje njihove pouzdanosti i trajnosti mogu se postići i toplinskom obradom.
Tema 1.2 Termička i hemijsko-termička obrada metala i legura
Toplinska obrada se odnosi na procese čija je suština zagrijavanje i hlađenje proizvoda prema određenim režimima, uslijed čega dolazi do promjene strukture, faznog sastava, mehaničkih i fizičkih svojstava. Koriste se i različite vrste hemijsko-termičke obrade, čija je suština legiranje površinskog sloja proizvoda sa azotom, ugljenikom ili nekim metalima (aluminijum, hrom, berilijum) nakon čega sledi termička obrada.
U zavisnosti od namene termičke obrade, postoje različite vrste termičke obrade, koje se razlikuju po temperaturi grejanja, vremenu držanja i brzini hlađenja.
Glavne vrste termičke obrade čelika su žarenje, normalizacija, kaljenje i kaljenje.
Žarenje primjenjuje za smanjenje tvrdoće, oplemenjivanje zrna, poboljšanje obradivosti, ublažavanje stresa. Za žarenje, čelik se zagrijava do određene temperature, drži i hladi pri maloj brzini u peći s isključenim izvorom topline.
normalizacija - predstavlja zagrijavanje čelika na temperaturu iznad kritične tačke, održavanje na toj temperaturi, hlađenje u mirnom zraku brzinom većom nego tijekom žarenja. Svrha – davanje čeliku fino zrnate strukture. Normalizacija daje uočljivije povećanje čvrstoće, ali manje duktilnosti. Prednost u odnosu na žarenje je niža cijena.
Stvrdnjavanje – sastoji se od zagrijavanja čelika, održavanja na određenoj temperaturi određeno vrijeme i zatim brzog hlađenja. Cilj je povećati tvrdoću i snagu. Tijekom stvrdnjavanja u materijalu nastaju unutarnja naprezanja, a duktilnost i udarna čvrstoća naglo opadaju. To može dovesti do krhkog loma dijela tokom rada.
Za smanjenje unutrašnjih naprezanja i povećanje duktilnosti i žilavosti nakon stvrdnjavanja, koristite odmor, koji se sastoji od zagrijavanja kaljenog čelika na temperaturu koja ne prelazi donju kritičnu tačku, zadržavanja na toj temperaturi i zatim hlađenja.
U zavisnosti od temperature, postoje tri vrste odmora: niske, srednje, visoke.
Nisko kaljenje se izvodi na temperaturi od 150...250°C. Tvrdoća čelika blago se smanjuje. Struktura nastala kao rezultat niskog temperiranja naziva se mar-oslobađanje napetosti ili kaljeni martenzit. Rezanje i merni alat, kalupi za hladno štancanje, kao i dijelovi koji moraju imati visoku otpornost na habanje.
Prosječno kaljenje se izvodi na temperaturi od 350...450°C. Prilikom srednjeg kaljenja cementit se ne formira u obliku ploča, već u obliku sitnih zrna, što pomaže da se poveća žilavost čelika. Proizvodi koji moraju imati visoku elastičnost i dovoljnu rezervu viskoznosti (opruge, opruge itd.) podvrgavaju se srednjem kaljenju.
Visoko kaljenje se izvodi na temperaturi od 500...650°C. Kao rezultat toga, zaostala naprezanja se potpuno eliminiraju, čelik stječe dobru duktilnost i žilavost uz dovoljno visoku čvrstoću. Ovo kaljenje je namijenjeno za kritične dijelove koji doživljavaju udare i naizmjenična opterećenja tijekom rada.
Dvostruka termička obrada, uključujući stvrdnjavanje i naknadno visoko kaljenje se naziva termičko poboljšanje, budući da se čitav kompleks mehaničkih svojstava čelika poboljšava.
Hemijsko-termički tretman. Hemijsko-termički tretman se sastoji od hemijskih i termičkih efekata u cilju promene hemijskog sastava, strukture i svojstava površinskog sloja metala. U procesu hemijsko-termičke obrade dolazi do zasićenja površine metala odgovarajućim elementom u procesu njegove difuzije u atomskom obliku iz tečnog, čvrstog ili gasovitog medija na visokoj temperaturi. Glavne vrste hemijsko-termičke obrade klasificirane su prema nazivima elemenata kojima je površinski sloj zasićen. Na primjer, zasićenje ugljikom naziva se karburizacija, dušik - nitriranje, krom - hromiranje.
Rasprostranjenost hemijsko-termičke obrade u različitim oblastima tehnike objašnjava se činjenicom da se povećanjem tvrdoće, otpornosti na habanje i otpornosti na koroziju površine povećava pouzdanost i izdržljivost mašinskih delova i mehanizama.
Hemijsko-termički tretman se sastoji od:
disocijacija, koji se javlja na kontaktnoj površini „metal - gasovito okruženje"i dovodi do oslobađanja difuznog elementa u atomskom stanju;
apsorpcija - apsorpcija slobodnih atoma površinom;
difuzija - prodiranje zasićenog elementa duboko u površinski sloj.
Glavni fizički proces je difuzija, čija brzina raste s porastom temperature; difuzni element prodire na veću dubinu.
Cementiranje se sastoji u difuzijskom zasićenju površinskog sloja čelika ugljikom kada se zagrije u odgovarajućem okruženju - karburizatoru. Proces karburizacije odvija se na temperaturama (900...950°C), kada je austenit stabilan, otapajući ugljenik u velike količine. Cementiranje se vrši u čvrstim, tečnim i gasnim karburizatorima. Gasna cementacija je najproduktivniji proces. Glavna reakcija koja osigurava karburizaciju je disocijacija metana:
CH → 2H 2 +C at.
Niskougljični i legirani čelici koji sadrže od 0,1 do 0,35% ugljika podvrgavaju se karburizaciji. Površinski sloj čelika nakon karburizacije ima promjenjivu koncentraciju ugljika u cijeloj svojoj debljini, koja se smanjuje od površine do jezgre dijela. S tim u vezi, nakon sporog hlađenja u strukturi cementnog sloja, mogu se razlikovati tri zone (počev od površine): hipereutektoidna, eutektoidna, hipoeutektoidna. Ukupna debljina cementiranog sloja je 0,8...3,0 mm.
Nakon karburizacije, kako bi se dobila potrebna svojstva, provodi se toplinska obrada - kaljenje uz nisko kaljenje. Kao rezultat toplinske obrade, površinski sloj dobiva strukturu otpornu na habanje, a jezgra dijela s niskim udjelom ugljika postaje prilično viskozna. Najčešće se zupčanici različitih mehanizama podvrgavaju karburizaciji kako bi se povećala njihova trajnost.
Nitriranje sastoji se u difuzijskom zasićenju površinskog sloja dušikom u odgovarajućem okruženju. Prije nitriranja čelik se podvrgava toplinskoj obradi - kaljenju i visokom kaljenju.
Nitriranju se podvrgavaju legirani čelici koji sadrže krom, molibden, vanadij i druge elemente koji s dušikom mogu formirati vrlo tvrde i toplinski otporne nitride. Nitriranje se vrši na temperaturi od 500...600°C. Glavna reakcija koja se javlja na površini dijela je reakcija disocijacije amonijaka.
Nakon nitriranja, čelik dobiva visoku tvrdoću, otpornost na habanje i otpornost na koroziju. U pogledu ovih svojstava, nitrirani čelici su bolji od cementiranih čelika. Međutim, nitrirani sloj je manje otporan na udarna opterećenja i ima manju otpornost na kontakt. Zbog dugog trajanja procesa (do 70 sati), upotreba nitriranja je ekonomski isplativa za preradu kritičnih proizvoda, kao što su automobilske radilice, košuljice cilindara motora sa unutrašnjim sagorijevanjem, razni dijelovi ventila itd.
Hromiranje sastoji se u difuzijskom zasićenju površinskog sloja čelika hromom na temperaturi od 900...1300°C u odgovarajućem okruženju. Kromiranje osigurava povećanu otpornost čelika na toplinu do temperature od 800 °C, visoku otpornost na koroziju i eroziju. Dijelovi termoelektrana, spojevi za dovod pare, ventili, ventili i cijevi su podvrgnuti hromiranju. Za povećanje otpornosti na koroziju, transformatorski čelik je hromiran. Istovremeno, čelik dodatno dobiva visoku otpornost na toplinu.
Kontrolna pitanja
Šta karakteriše kristalna struktura metala?
Koje vrste kristalnih rešetki poznajete?
Koji su glavni nedostaci u kristalnoj strukturi?
Šta je alotropija metala?
Koja mehanička svojstva karakteriziraju vlačnu čvrstoću i duktilnost materijala?
Šta je dijagram stanja legura i šta vam omogućava da ustanovite?
Koje su glavne vrste termičke obrade?
Šta je karburizacija čelika?
Odjeljak 2 POLUVODIČKI MATERIJALI
Tema 2.1 Klasifikacija poluvodičkih materijala
Supstance se razlikuju po svojoj sposobnosti provodljivosti struja. Ovu sposobnost karakteriše specifičnost električni otpor– ρ ili specifična električna provodljivost – γ. Vrijednost γ at normalna temperatura je manji od 10 -10 S/m za dielektrike i više od 10 4 S/m za provodnike.
Razmotrimo prirodu promjene specifične provodljivosti čvrstih tijela na temperaturi koja teži apsolutnoj nuli.
Specifična provodljivost provodnika se povećava, a mnogi metali prelaze u supravodljivo stanje, koje karakteriše beskonačno velika vrijednost γ.
Poluprovodnici se ponašaju potpuno drugačije. Kako temperatura pada, njihova provodljivost opada, a pri T → 0 K poluprovodnici uopšte ne provode električnu struju, tj. postaju dielektrici. Ali s povećanjem temperature, γ poluvodiča naglo raste.
Da bi se poluvodiči pojavili kao besplatni nosioci naboja, nije ih potrebno snabdjevati toplotnu energiju. To se kod njih može postići rasvjetom, mehaničkim opterećenjima, električnim poljem itd. Unutrašnja struktura poluprovodnika ima snažan uticaj na električnu provodljivost. Osim toga, uvođenje čak i male količine atoma stranog elementa u poluvodič obično dramatično mijenja njegovu električnu provodljivost. Sve se otvara obilne mogućnosti za kontrolu električnih svojstava poluvodičkih materijala.
dakle, Poluprovodnik je supstanca čije je glavno svojstvo jaka zavisnost njegove električne provodljivosti od uticaja spoljašnjih faktora.
Svi poluvodiči se mogu podijeliti na jednostavne i složene.
Jednostavno je poluprovodnik čiji glavni sastav čine atomi jednog hemijskog elementa (silicijum, germanijum, selen, telur, bor, ugljenik, fosfor, sumpor, arsen, antimon, jod, sivi kalaj).
Struktura kompleks poluprovodnike formiraju atomi različitih hemijski elementi. Ova grupa uključuje čvrste rastvore (silicijum i germanijum) i hemijska jedinjenja označena AB. U ovoj formuli, superskripti (m i n) označavaju broj grupe periodni sistem, koji uključuje odgovarajući element, a niži (x i y) su broj atoma ovog elementa u spoju. Na primjer, poluvodički galijev arsenid GaAr je klasifikovan kao jedinjenje tipa A III B V, a oksid bakra Cu 2 O je klasifikovan kao jedinjenje tipa A 2 I B VI.
Mnoga ternarna i složenija hemijska jedinjenja, na primer ZnSiAs 2, imaju svojstva poluprovodnika. Semiconductor je cela linija organska jedinjenja: antracen, naftalen, ftalocijanin, itd.
Još jedno izvanredno svojstvo poluprovodnika je da dozvoljavaju inverznu transformaciju električna energija na svjetlosnu, termičku ili mehaničku.
Poluprovodnici se koriste za pojačavanje i generisanje električnih signala (tranzistori, diode, integrisana kola), kao primarni pretvarači temperature i izvori toplotne energije (termistori i grijaćih elemenata), kao primarni pretvarači i izvori optičkih signala (fotootpornici, LED diode, laseri), za konverziju mehaničke vibracije(mjerači naprezanja i piezoelektrični senzori) itd.
Energetski nivoi i zone
Atom se sastoji od jezgra i elektrona koji se kreću određenim orbitama.
Ukupna energija elektrona, jednaka zbiru njegove kinetičke (orbitalno kretanje) i potencijalne (privlačenje prema jezgru) energija, naziva se energetsko stanje atoma. Svaka dozvoljena orbita ima svoje energetsko stanje, koje je na dijagramu predstavljeno kao energetski nivo. Pošto se orbite i njihove energije dijele na dozvoljene i zabranjene, onda energijegenetski nivoi takođe mogu biti dozvoljenii zabranjeno.
Energija elektrona E izraženo u elektron voltima. Elektron-volt- to je energija koja se dobijaubrzanje elektrona u električno polje sa različitimbroj potencijala u 1 V.
Interakcija atoma u rešetki dovodi do činjenice da se njihovi energetski nivoi dijele na veliki broj gotovo spojenih podnivoa, formirajući energijegoeticzone.
Energetska zona ispunjena podnivoima je šira, što su atomi bliže i što je energetski nivo viši. Vjerovatnoća da će elektron „ostati“ u pojasu pojasa je nula.
Klasifikacija materijala prema elektrotehnicisvojstva (teorija bendova)
Klasifikacija električnih materijala prema električnim svojstvima temelji se na konceptima pojasne teorije električne provodljivosti čvrstih tijela, čija je suština sljedeća.
U izolovanom atomu, elektroni kruže oko jezgra u određenim orbitama. Prema Paulijevom principu, na svakom ili-bit ne može sadržavati više od dva elektrona. Svaka orbita odgovara striktno definisanoj energetskoj vrijednosti koju elektron može posjedovati, tj. svaka orbita predstavlja određeni energetski nivo. Pod uticajem privlačenja pozitivno naelektrisanog atomsko jezgro elektroni teže da zauzmu nivoe najbliže jezgru sa minimalnom vrijednošću energije. Stoga se ispostavlja da su donji energetski nivoi ispunjeni elektronima, a gornji nivoi su slobodni. Elektron može skočiti sa nižeg energetskog nivoa W x na drugi besplatni nivo W 2 (Sl. 1). Da bi se to postiglo, elektronu se mora dati dodatna energija ∆ W = W 2 - W 1 . Ako u atomu nema slobodnih nivoa, onda elektron ne može promijeniti svoju energiju, pa stoga ne sudjeluje u stvaranju električne provodljivosti.
W - energija elektrona; W 1 - niži nivo energije; W 2 - nivo slobodne energije; ∆ W C - zona provodljivosti (slobodna zona); ∆ W - zabranjeno područje; ∆ WV, - valentni pojas
Slika 2.1 – Dijagram nivoa energije izolovanog atoma (1) i solidan (2).
U kristalnoj rešetki koja se sastoji od nekoliko atoma, pojedinačni energetski nivoi su podeljeni na podnivoe, koji formiraju energetske zone (vidi sliku 2.1). U ovom slučaju, slobodni i ispunjeni nivoi energije se dijele. Zona ispunjena elektronima naziva se valence Označen je gornji nivo valentnog pojasa W V . Slobodna zona se zove zona provodljivost. Naznačen je donji nivo provodljivog pojasa (slobodni pojas). W a . Razmak između valentnog pojasa i pojasa provodljivosti naziva se zabranjeno zona ∆ W. Vrijednost zapreka značajno utječe na svojstva materijala.
Ako ∆ W je jednaka ili blizu nuli, tada se elektroni mogu kretati na slobodne nivoe zbog sopstvene toplotne energije i povećati provodljivost supstance. Supstance sa takvom strukturom energetskih zona klasifikuju se kao provodnici. Provodni materijali služe za provođenje električne struje. Tipično, provodnici uključuju supstance sa električnom otpornošću p< 10 Ом*м. Типичными проводниками явля-ются металлы.
Ako vrijednost pojasnog razmaka prelazi nekoliko elektron-volti, tada je potrebna značajna energija za prijelaz elektrona iz valentnog pojasa u pojas provodljivosti. Takve supstance se klasifikuju kao dielektrici. Dielektrici imaju visoku električnu otpornost i imaju sposobnost da spriječe prolaz struje. Dielektrični materijali uključuju tvari sa specifičnim električnim otporom p > 10 7 Ohm * m. Zbog visokog specifičnog električnog otpora koriste se kao električni izolacijski materijali.
Ako je vrijednost pojasnog razmaka 0,1...0,3 eV, tada se elektroni lako kreću iz valentnog pojasa u pojas provodljivosti zbog vanjske energije. Supstance sa kontrolisanom provodljivošću se klasifikuju kao poluprovodnici. Električna otpornost poluprovodnika je p 10 9 Ohm * m.
Poluprovodnički materijali imaju provodljivost, koja se može koristiti za kontrolu napona, temperature, svjetlosti itd.
Ovisno o strukturi i vanjskim uvjetima, materijali mogu prelaziti iz jedne klase u drugu. Na primjer, tvrdi i tečni metali- provodnici, a metalni parovi su dielektrici; germanijum i silicijum, tipični poluprovodnici u normalnim uslovima, postaju provodnici kada su izloženi visokim hidrostatičkim pritiscima; ugljenik u dijamantskoj modifikaciji je dielektrik, au grafitnoj modifikaciji je provodnik.
Glavno svojstvo tvari u odnosu na električno polje je električna provodljivost, karakterizirajući sposobnost materijala da provodi električnu struju pod utjecajem konstantnog električnog polja, tj. polje čiji se napon ne menja tokom vremena.
Električnu provodljivost karakterizira specifična električna provodljivost i specifični električni otpor:
Vrijednosti specifične električne provodljivosti i specifičnog električnog otpora različitih materijala značajno razlikuju. U supravodljivom stanju, električna otpornost materijala je nula, a u rijetkim plinovima teži beskonačnosti.
Lako je shvatiti da svojstva provodljivosti kristala zavise od pojasa koji razdvaja valentni pojas i pojas provodljivosti. Što je širi pojas, to je manji (na datoj temperaturi) broj elektrona koji prodiru u pojas provodljivosti, to je niža provodljivost kristala.
Kristali mogu biti dobri provodnicičak i kada je valentni pojas popunjenu potpunosti, ako je direktno uz zonuprovodljivosti ili se s njom ukršta (kao rezultatzamućenje zona tokom formiranja rešetke). Sa povećanimPovećanjem pojasa, kristali dobijajuvraćaju svojstva izolatora. Prosječne vrijednostiširine pojasa odgovarajuPolu profesionalno-na vodi kristali.
Budući da valentni pojas i pojas provodljivosti kristalnih provodnika nisu razdvojeni, elektroni se slobodno kreću s jednog dozvoljenog podnivoa na drugi, postižući uređenu brzinu pod djelovanjem primijenjenog napona. Štoviše, s povećanjem temperature, otpor vodiča raste zbog smanjenja slobodnog puta elektrona u kristalu.
U poluvodičkim kristalima, provodljivost je određena prvenstveno brojem elektrona koji su prešli pojas i ušli u pojas provodljivosti.
Poluprovodnički materijali
Hemijska veza između atoma poluprovodnika odvija se zbog interakcije valentnih elektrona, dok svaki atom prima od svog susjeda u zajednički posjed i daje mu svoje valentne elektrone, koji nedostaju prije formiranja stabilnog pojasa od osam elektrona. . dakle, u idealnom poluprovodniku, svi valentni elektroni Rons učestvuju u obrazovanju hemijska veza i besplatno nema elektrona. Ova vrsta hemijske veze naziva se cova traka.
Na sl. Na slici 2.2 prikazan je dijagram formiranja hemijske veze u kristalnoj rešetki silicijuma, čiji atom u slobodnom izolovanom stanju ima četiri valentna elektrona, a u kristalnoj rešetki spoljašnji elektronski nivo svaki atom je ispunjen sa do osam elektrona, zbog zajedničkog posjedovanja elektrona od strane četiri najbliža susjedna atoma.
Slika 2.2 – Šema formiranja hemijske veze u kristalnoj rešetki silicijuma. Zbog male širine (1 eV) pojasa poluvodiča, termičke vibracije atoma su sposobne da prenesu energiju valentnim elektronima dovoljnu za prijelaz iz ispunjenog valentnog pojasa u pojas slobodnog vodljivosti. Svaki takav prijelaz dovodi do pojave para nosača naboja: slobodni elektron u provodnom pojasu i stanju slobodne energije – rupe– u valentnom pojasu. Pod uticajem napona primenjenog na kristal, provodni elektron se kreće "prema" električno polje, a elektron u valentnom pojasu zauzima slobodni nivo, oslobađajući njegov nivo za drugi elektron. Ovo se može smatrati kretanjem pozitivnog naboja (rupa) u smjeru električnog polja.
Generisanje slobodnih parova, tj. sposobnih za ponovnokreću se pod uticajem primenjenog napona,naelektrisanja čini kristal sposobnim da provodi električnu energijuričnu struju i električnu provodljivost takvog kristalapozvaovlastiti.
Poluprovodnik u kojem se električna provodljivost javlja zbog pobuđivanja elektrona hemijske veze naziva sesopstveni poluprovodnik.
Nosioci struje u takvim poluvodičima su njihovi vlastiti elektroni i rupe.
Na sl. Slika 2.3 prikazuje dijagram kristalne rešetke intrinzičnog poluprovodnika. Kada je vlastiti valentni elektron pobuđen, a n-vrsta nosioca struje - slobodni elektron i R- tip nosilac struje – rupa – nezauzeta hemijska veza.
Istovremeno sa formiranjem parova nosača, neki elektroni iz provodnog pojasa spontano se vraćaju u valentni pojas, emitujući kvante energije. Ovaj proces se zove rekombinacija pare. Pri konstantnoj temperaturi uspostavlja se dinamička ravnoteža koja određuje koncentraciju slobodnih elektrona i rupe (na datoj temperaturi).
Što je temperatura viša, veća je koncentracija slobodnih nosača naboja, veća je intrinzična električna provodljivost kristala.
Na temperaturi od 0K, parovi nosača se ne formiraju, a kristal potpuno gubi sopstvenu električnu provodljivost. U ovom slučaju, elektroni unutar kristala se haotično kreću velikim brzinama (oko 10 6 m/s), ali ne reaguju na primijenjeni vanjski napon.
Slika 2.3 – Dijagram kristalne rešetke intrinzičnog poluprovodnika.
Pravi kristali sadrže brojne defekte kristalne rešetke: točkaste, linearne, volumetrijske i površinske. Na mjestima gdje je periodična struktura kristala poremećena (prodiranje atoma u međuprostore), energija vezivanja elektrona sa jezgrima se mijenja, što rezultira pojavom novih energetskih nivoa koji mogu ići izvan valentnog pojasa i nalaziti se u pojasu. jaz u blizini provodnog pojasa. Ovo olakšava prijelaz elektrona u provodni pojas.
Trening i metodološki kompleks... - daj osnovenauka o materijalima, principi selekcije neophodni materijali usaditi praktične vještine odlučnosti fizički-mehanička... grupa hemijski veze. 6.3.1. Klasifikacija polimera i svojstva polimera prema poreklu polimeri dijeliti ...
Evgeniy Petrovich Prokopiev (rus)(eng) opšta lista publikacija antimaterija i pozitronika pozitronika i nanotehnologija pozitronika anihilacija pozitrona fizika složenih sistema sinergetika nauka o materijalima nanotehnologija drugi srodni problemi
DokumentProkopyev E.P. O površinskim stanjima na granici odjeljak poluprovodnik-metal. M., 1985. 5 str. - Dep. u... procesima. Treća ruska konferencija o nauka o materijalima I fizički-hemijskiosnove tehnologije za proizvodnju dopiranih kristala silicijuma...
Svojstva legure zavise od njene strukture. Glavni način promjene strukture, a time i svojstava, je toplinska obrada.
Osnove termičke obrade razvio je D.K. Chernov. Kasnije su razvijeni u radovima A.A. Bochvara, G.V. Kurdyumova, A.P. Gulyaeva.
Termičku obradu odnosi se na termički učinak na metal kako bi se metalu dala potrebna mehanička i fizička svojstva kao rezultat promjene unutrašnje strukture (strukture) metala.
Većina gotovih proizvoda (poluproizvoda) i proizvoda od čelika i obojenih legura podvrgava se toplinskoj obradi. To je toplinska obrada koja vam omogućava da promijenite strukturu metala u željenom smjeru i omogućuje vam da dobijete potreban nivo tvrdoća, čvrstoća, duktilnost i druga svojstva.
Način toplinske obrade karakteriziraju sljedeći glavni parametri: brzina i način grijanja, Maksimalna temperatura grijanje, vrijeme držanja u pećnici na temperaturi grijanja, te brzina i način hlađenja.
Toplinska obrada je jedna od najčešćih u moderna tehnologija metode za dobijanje određenih svojstava metala. Toplinska obrada se koristi ili kao međuoperacija za poboljšanje obradivosti poluproizvoda pritiskom, rezanjem itd., ili kao završna operacija tehnološki proces, pružajući zadati nivo fizičkih i mehaničkih svojstava dijela.
Termička obrada obuhvata zagrevanje, držanje i hlađenje metala, koje se izvodi u određenom redosledu pod određenim uslovima, kako bi se promenila unutrašnja struktura legure i dobila željena svojstva. Obično se može shematski prikazati kao grafik na osi temperatura – vrijeme (Sl. 21).
Toplinska obrada se deli na samu termičku obradu, hemijsko-termički i termomehanički (ili deformaciono-termički).
Sama termička obrada sastoji se samo od termičkih efekata na metal ili leguru, hemijsko-termička obrada uključuje kombinaciju termičkih i hemijskih efekata, a termomehanička obrada uključuje kombinaciju termičkih efekata i plastične deformacije.
Fig.21. Raspored toplinske obrade
Stvarna toplinska obrada uključuje sljedeće glavne vrste:
Žarenje 1. vrste
Žarenje 2. vrste
Stvrdnjavanje polimorfnom transformacijom
Stvrdnjavanje bez polimorfne transformacije
Starenje
Ove vrste termičke obrade primjenjuju se i na čelike i na obojene metale.
Žarenje
Žarenje– toplinska obrada, koja se sastoji od zagrijavanja metala na određenu temperaturu, držanja i hlađenja uz isključenu peć (tj. moguća brzina, oko 50-100 stepeni/sat).
Žarenje 1. vrste - koristi se za sve metale i legure. Njegova implementacija nije posljedica faznih transformacija u čvrstom stanju. Zagrijavanjem, prilikom žarenja prve vrste, povećava se pokretljivost atoma, djelimično ili potpuno eliminiše hemijska heterogenost i smanjuje se unutrašnja naprezanja. Temperatura grijanja i vrijeme zadržavanja su od primarne važnosti. Karakteristika je sporo hlađenje
Vrste žarenja prvog reda su:
homogenizacija (difuzija)
· rekristalizacija;
· žarenje za ublažavanje unutrašnjeg naprezanja nakon kovanja, zavarivanja, livenja.
Homogenizacijsko (difuzijsko) žarenje je toplinska obrada u kojoj je glavni proces eliminacija efekata dendritske segregacije (hemijske heterogenosti) u odljevcima i ingotima. Uključuje dugo izlaganje na visokim temperaturama, pri čemu se javljaju procesi difuzije koji nemaju vremena da se završe tokom kristalizacije. Približna temperatura za čelik je -1100-1300 o C tokom 20-50 sati, za legure aluminijuma 420-450 o C.
Rekristalizaciono žarenje je termička obrada deformisanog metala, u kojoj je glavni proces rekristalizacija metala. Ova vrsta žarenja eliminiše odstupanja u strukturi od ravnotežnog stanja do kojih dolazi prilikom plastične deformacije. Prilikom obrade pod pritiskom, posebno hladnog, metal se stvrdnjava, povećava mu se čvrstoća, a smanjuje duktilnost zbog povećanja gustine dislokacija u kristalitima. Kada se hladno obrađeni metal zagrije iznad određene temperature, razvija se primarna, a zatim i kolektivna rekristalizacija, pri čemu se gustina dislokacija naglo smanjuje. Kao rezultat, metal omekšava i postaje duktilniji. Ovo žarenje se koristi za poboljšanje obradivosti i davanje metala potrebne kombinacije tvrdoće, čvrstoće i duktilnosti. U pravilu se pri rekristalizacijskom žarenju nastoji dobiti materijal bez teksture u kojem nema anizotropije svojstava. U proizvodnji transformatorskih čeličnih limova koristi se rekristalizacijsko žarenje kako bi se dobila željena tekstura metala koja nastaje prilikom rekristalizacije.
Žarenje radi ublažavanja unutrašnjeg naprezanja je termička obrada u kojoj je glavni proces potpuna ili djelomična relaksacija zaostalih naprezanja tijekom zagrijavanja i hlađenja. Žarenje za smanjenje naprezanja koristi se za proizvode kod kojih su nastala neprihvatljivo velika zaostala naprezanja tokom obrade pod pritiskom, livenja, zavarivanja, termičke obrade i drugih tehnoloških procesa, koji su međusobno uravnoteženi unutar tela bez učešća spoljašnjih opterećenja. Zaostala naprezanja mogu uzrokovati izobličenje oblika i dimenzija proizvoda tokom njegove obrade, rada ili skladištenja u skladištu. Kada se proizvod zagrije, granica popuštanja se smanjuje i, kada postane manja od zaostalih napona, dolazi do njihovog brzog pražnjenja kroz plastično strujanje u različitim slojevima metala.
Žarenje drugog tipa je žarenje metala i legura koji prolaze kroz fazne transformacije u čvrstom stanju. Ova vrsta žarenja se izvodi za legure u kojima postoje polimorfne ili eutektoidne transformacije, kao i promjenjiva topljivost komponenti u čvrstom stanju.
22. Promjena strukture tokom žarenja tipa II
Žarenje drugog tipa vrši se kako bi se dobila ravnotežna struktura i pripremila za dalju obradu. Kao rezultat žarenja, zrno se rafinira, povećava se plastičnost i viskoznost, smanjuje čvrstoća i tvrdoća, a obradivost se poboljšava. Karakterizira ga zagrijavanje na temperature iznad kritične i vrlo sporo hlađenje, obično zajedno sa peći ili na zraku. U drugom slučaju, proces se naziva normalizacija. Žarenje 2. tipa najčešće se koristi za generalno usavršavanje strukture, omekšavanje i poboljšanje obradivosti.
Termička obrada metala i legura
Rad na kursu
na temu: “Termička obrada metala i legura”
Uvod
Toplinska obrada se koristi u različitim fazama proizvodnje mašinskih delova i metalnih proizvoda. U nekim slučajevima, to može biti međuoperacija koja služi za poboljšanje obradivosti legura pritiskom i rezanjem; u drugim, to je završna operacija koja obezbjeđuje neophodan skup pokazatelja mehaničkih, fizičkih i operativnih svojstava proizvoda ili poluproizvoda. -gotovi proizvodi. Poluproizvodi se podvrgavaju termičkoj obradi kako bi se poboljšala struktura, smanjila tvrdoća (poboljšana obradivost), a dijelovi - da bi im se dala određena, potrebna svojstva (tvrdoća, otpornost na habanje, čvrstoća i dr.).
Kao rezultat termičke obrade, svojstva legura mogu se mijenjati u širokim granicama. Mogućnost značajnog povećanja mehaničkih svojstava nakon termičke obrade u odnosu na početno stanje omogućava povećanje dopuštenih naprezanja, smanjenje veličine i težine strojeva i mehanizama, te povećanje pouzdanosti i vijeka trajanja proizvoda. Poboljšanje svojstava kao rezultat toplinske obrade omogućava korištenje legura jednostavnijih sastava, a samim tim i jeftinijih. Legure također dobijaju neka nova svojstva, pa se stoga širi njihov opseg primjene.
Namjena i vrste termičke obrade
Termička (termička) obrada se odnosi na procese čija je suština zagrijavanje i hlađenje proizvoda prema određenim režimima, što rezultira promjenom strukture, faznog sastava, mehaničkih i fizičkih svojstava materijala, bez promjene hemijskog sastava.
Svrha termičke obrade metala je postizanje potrebne tvrdoće i poboljšanje karakteristika čvrstoće metala i legura. Toplinska obrada se deli na termičku, termomehaničku i hemijsko-termičku. Toplinska obrada je samo termičko izlaganje, termomehanička je kombinacija termičkog izlaganja i plastične deformacije, hemijsko-termalna je kombinacija termičkog i hemijskog izlaganja. Toplinska obrada, ovisno o strukturnom stanju dobivenom njegovom primjenom, dijeli se na žarenje (prva i druga vrsta), kaljenje i kaljenje.
Žarenje
Žarenje je toplinska obrada koja se sastoji od zagrijavanja metala na određene temperature, zadržavanja i zatim vrlo sporog hlađenja zajedno sa peći. Koristi se za poboljšanje rezanja metala, smanjenje tvrdoće, dobijanje zrnaste strukture, a takođe i za ublažavanje naprezanja, eliminiše delimično (ili potpuno) sve vrste nehomogenosti koje su unete u metal tokom prethodnih operacija (mašinska obrada, obrada pritiskom, livenje, zavarivanje), poboljšava strukturu čelika.
Žarenje prve vrste. To je žarenje u kojem se ne dešavaju fazne transformacije, a ako do njih dođe, ne utječu na konačne rezultate predviđene za njegovu svrhu. Razlikuju se sljedeće vrste žarenja prve vrste: homogenizacija i rekristalizacija.
Homogenizacija je žarenje uz dugu ekspoziciju na temperaturi iznad 950°C (obično 1100–1200°C) u cilju izjednačavanja hemijskog sastava.
Rekristalizacija je žarenje kaljenog čelika na temperaturi koja prelazi temperaturu na kojoj počinje rekristalizacija, kako bi se eliminisalo stvrdnjavanje i dobila određena veličina zrna.
Žarenje druge vrste. To je žarenje, u kojem fazne transformacije određuju njegovu namjenu. Razlikuju se sljedeće vrste: potpuna, nepotpuna, difuzijska, izotermna, lagana, normalizirana (normalizacija), sferoidizirajuća (za granulirani perlit).
Potpuno žarenje se izvodi zagrijavanjem čelika 30–50 °C iznad kritične tačke, zadržavanjem na ovoj temperaturi i polaganim hlađenjem na 400–500 °C brzinom od 200 °C na sat za ugljične čelike, 100 °C na sat za niskolegirane čelike i 50 °C na sat za visokolegirane čelike. Struktura čelika nakon žarenja je ravnotežna i stabilna.
Djelomično žarenje se provodi zagrijavanjem čelika na jednu od temperatura koje se nalaze u području transformacije, zadržavanjem i polaganim hlađenjem. Djelomično žarenje se koristi za smanjenje unutrašnjih naprezanja, smanjenje tvrdoće i poboljšanje obradivosti.
Difuzijsko žarenje. Metal se zagreva na temperature od 1100-1200°C, jer se u tom slučaju potpunije odvijaju procesi difuzije neophodni za izjednačavanje hemijskog sastava.
Izotermno žarenje se sastoji od sljedećeg: čelik se zagrijava i zatim brzo hladi (obično prebacivanjem u drugu peć) na temperaturu ispod kritične temperature za 50-100°C. Uglavnom se koristi za legirane čelike. Ekonomski isplativo, jer je trajanje konvencionalnog žarenja (13 – 15) sati, a izotermnog žarenja (4 – 6) sati
Sferoidizirajuće žarenje (za granulirani perlit) uključuje zagrijavanje čelika iznad kritične temperature za 20-30 °C, održavanje na toj temperaturi i polagano hlađenje.
Svijetlo žarenje se izvodi prema potpunom ili nepotpunom načinu žarenja uz korištenje zaštitnih atmosfera ili u pećima s djelomičnim vakuumom. Koristi se za zaštitu metalne površine od oksidacije i dekarbonizacije.
Normalizacija – sastoji se od zagrevanja metala na temperaturu (30–50) °C iznad kritične tačke i naknadnog hlađenja na vazduhu. Svrha normalizacije varira u zavisnosti od sastava čelika. Umjesto žarenja, niskougljični čelici se normaliziraju. Za srednje ugljične čelike koristi se normalizacija umjesto kaljenja i visokog kaljenja. Visokougljični čelici se podvrgavaju normalizaciji kako bi se eliminirala cementitna mreža. Za korekciju strukture legiranih čelika umjesto žarenja koristi se normalizacija praćena visokim temperiranjem. Normalizacija je, u poređenju sa žarenjem, ekonomičnija operacija, jer ne zahtijeva hlađenje peći.
Stvrdnjavanje
Stvrdnjavanje je zagrijavanje na optimalnu temperaturu, držanje i naknadno brzo hlađenje kako bi se dobila neravnotežna struktura.
Kao rezultat kaljenja, povećava se čvrstoća i tvrdoća čelika i smanjuje duktilnost čelika. Glavni parametri tokom stvrdnjavanja su temperatura zagrijavanja i brzina hlađenja. Kritična brzina gašenja je brzina hlađenja koja osigurava formiranje strukture - martenzita ili martenzita i zadržanog austenita.
Ovisno o obliku dijela, vrsti čelika i potrebnom skupu svojstava, koriste se različite metode kaljenja.
Gašenje u jednom hladnjaku. Dio se zagreva na temperaturu očvršćavanja i hladi u jednom hladnjaku (voda, ulje).
Kašenje u dva okruženja (intermitentno kaljenje) je kaljenje u kojem se dio hladi uzastopno u dvije sredine: prvi medij je rashladno sredstvo (voda), drugi je zrak ili ulje.
Stepen otvrdnjavanje. Dio zagrijan na temperaturu gašenja hladi se u rastopljenim solima, a nakon držanja potrebnog vremena da se temperatura izjednači na cijelom poprečnom presjeku, dio se hladi na zraku, što pomaže u smanjenju napona gašenja.
Izotermno kaljenje, kao i stepenasto otvrdnjavanje, izvodi se u dva rashladna okruženja. Temperatura vrućeg medija (solne, nitratne ili alkalne kupke) je različita: ovisi o kemijskom sastavu čelika, ali je uvijek 20-100 °C iznad točke martenzitne transformacije za dati čelik. Završno hlađenje na sobnu temperaturu vrši se na zraku. Izotermno kaljenje se široko koristi za dijelove izrađene od visokolegiranih čelika. Nakon izotermnog kaljenja, čelik dobiva svojstva visoke čvrstoće, odnosno kombinaciju visoke žilavosti i čvrstoće.
Samokaljenje se široko koristi u proizvodnji alata. Proces se sastoji u tome da se dijelovi drže u rashladnom mediju ne dok se potpuno ne ohlade, već se u određenom trenutku iz njega uklone kako bi zadržali određenu količinu topline u jezgri dijela, zbog koje se vrši naknadno kaljenje.
Odmor
Kaljenje čelika je konačna operacija toplinske obrade koja oblikuje strukturu i, posljedično, svojstva čelika. Kaljenje se sastoji od zagrijavanja čelika na različite temperature (ovisno o vrsti kaljenja, ali uvijek ispod kritične tačke), održavanja na toj temperaturi i hlađenja različitim brzinama. Svrha kaljenja je ublažavanje unutrašnjih naprezanja koja nastaju tokom procesa kaljenja i dobijanje potrebne strukture.
U zavisnosti od temperature zagrijavanja kaljenog dijela razlikuju se tri vrste kaljenja: visoko, srednje i nisko.
Visoko kaljenje se izvodi na temperaturama zagrevanja iznad 350–600 °C, ali ispod kritične tačke; takvo se kaljenje koristi za konstrukcijske čelike.
Prosječno kaljenje se izvodi na temperaturama grijanja od 350 – 500 °C; Takvo kaljenje se široko koristi za opružne i opružne čelike.
Nisko kaljenje se izvodi na temperaturama od 150–250 °C. Tvrdoća dijela nakon stvrdnjavanja ostaje gotovo nepromijenjena; nisko kaljenje se koristi za ugljične i legirane alatne čelike, koji zahtijevaju visoku tvrdoću i otpornost na habanje.
Kontrola kaljenja se vrši tako što se na površini dijela pojavljuju tamne boje.
Starenje
Starenje je proces promjene svojstava legura bez primjetnih promjena u mikrostrukturi. Poznata su dva tipa starenja: termičko i deformaciono.
Termičko starenje nastaje kao rezultat promjena u topljivosti ugljika u željezu ovisno o temperaturi.
Ako se promjene tvrdoće, duktilnosti i čvrstoće javljaju na sobnoj temperaturi, tada se takvo starenje naziva prirodnim.
Ako se proces odvija na povišenim temperaturama, starenje se naziva umjetnim.
Deformacijsko (mehaničko) starenje nastaje nakon hladne plastične deformacije.
Hladni tretman
Nova vrsta termičke obrade za povećanje tvrdoće čelika pretvaranjem zadržanog austenita kaljenog čelika u martenzit. To se postiže hlađenjem čelika na temperaturu donje martenzitne tačke.
Metode površinskog očvršćavanja
Površinsko kaljenje je proces toplinske obrade koji uključuje zagrijavanje površinskog sloja čelika na temperaturu iznad kritične i naknadno hlađenje kako bi se dobila martenzitna struktura u površinskom sloju.
Razlikuju se sljedeće vrste: indukcijsko kaljenje; stvrdnjavanje u elektrolitu, stvrdnjavanje pri zagrijavanju visokofrekventnim strujama (HF), otvrdnjavanje zagrijavanjem plinskim plamenom.
Indukcijsko stvrdnjavanje temelji se na fizičkom fenomenu čija je suština da električna struja visoke frekvencije koja prolazi kroz vodič stvara elektromagnetno polje oko njega. Vrtložne struje induciraju se na površini dijela postavljenog u ovo polje, uzrokujući zagrijavanje metala do visokih temperatura. Ovo omogućava da dođe do faznih transformacija.
Ovisno o načinu grijanja, indukcijsko kaljenje se dijeli na tri tipa:
istovremeno zagrijavanje i stvrdnjavanje cijele površine (koristi se za male dijelove);
sekvencijalno zagrevanje i očvršćavanje pojedinih delova (koristi se za radilice i slične delove);
kontinuirano-sekvencionalno zagrijavanje i gašenje kretanjem (koristi se za dugačke dijelove).
Stvrdnjavanje gasnim plamenom. Proces gasno-plamenskog stvrdnjavanja sastoji se od brzog zagrevanja površine dela acetilen-kiseonikom, gasno-kiseoničkim ili kiseonik-kerozinskim plamenom do temperature stvrdnjavanja, nakon čega sledi hlađenje vodom ili emulzijom.
Gašenje u elektrolitu. Proces stvrdnjavanja u elektrolitu je sljedeći: dio koji se stvrdnjava spušta u kadu s elektrolitom (5-10% otopina kalcinirane soli) i kroz nju se propušta struja od 220-250 V. Kao rezultat, dio se zagrijava na visoke temperature. Dio se hladi ili u istom elektrolitu (nakon isključivanja struje) ili u posebnom spremniku za gašenje.
Termomehanička obrada
Termomehanička obrada (T.M.O.) je nova metoda ojačavanja metala i legura uz održavanje dovoljne duktilnosti, kombinirajući plastičnu deformaciju i ojačavanje toplinskom obradom (očvršćavanje i kaljenje). Postoje tri glavne metode termomehaničke obrade.
Niskotemperaturna termomehanička obrada (L.T.M.T.) zasniva se na stepenastom kaljenju, odnosno plastično deformisanje čelika se vrši na temperaturama relativne stabilnosti austenita, nakon čega sledi kaljenje i kaljenje.
Visokotemperaturna termomehanička obrada (H.T.M.T.), u kojoj se plastična deformacija izvodi na temperaturama stabilnosti austenita, nakon čega slijedi kaljenje i kaljenje.
Preliminarna termomehanička obrada (P.T.M.O) deformacija se može izvesti na temperaturama N.T.M.O i V.T.M.O ili na temperaturi od 20°C. Zatim se provodi uobičajena toplinska obrada: kaljenje i kaljenje.
Svrha i vrste hemijsko-termičke obrade
Hemijsko-termička obrada je proces koji predstavlja kombinaciju termičkog i hemijskog dejstva u cilju promene sastava, strukture i svojstava površinskog sloja čelika.
Svrha hemijsko-termičke obrade: povećanje površinske tvrdoće, otpornosti na habanje, granice izdržljivosti, otpornosti na koroziju, otpornosti na toplotu (otpornost na kamenac), otpornost na kiseline.
U industriji se najčešće koriste sljedeći tipovi kemijsko-termičke obrade: cementiranje; nitrocarburizacija; nitriranje; cijanidacija; difuziona metalizacija.
Cementiranje je proces površinskog zasićenja ugljikom, koji se provodi u svrhu površinskog očvršćavanja dijelova.
U zavisnosti od korišćenog karburizatora, karburizacija se deli na tri tipa: karburizacija sa čvrstim karburizatorom; gasna cementacija (metan, propan, prirodni gas).
Gasna cementacija. Dijelovi se zagrijavaju na 900-950ºC u posebnim hermetički zatvorenim pećima, u koje se u kontinuiranom toku dovodi cementirajući plin koji sadrži ugljik (prirodni (prirodni) ili umjetni).
Proces karburizacije u čvrstom karburizatoru je sljedeći. Dijelovi, upakovani u kutiju zajedno sa karburizatorom (mješavina drvenog uglja s aktivatorom), zagrijavaju se na određenu temperaturu i drže na toj temperaturi dugo vremena, a zatim se hlade i podvrgavaju toplinskoj obradi.
Dijelovi izrađeni od ugljičnog i legiranog čelika s udjelom ugljika ne većim od 0,2% podvrgavaju se cementiranju bilo kojom od gore navedenih metoda. Karburizacija legiranih čelika koji sadrže elemente za stvaranje karbida Cr, W, V daje posebno dobre rezultate: osim povećanja površinske tvrdoće i otpornosti na habanje, povećava se i njihova granica zamora.
Nitriranje je proces zasićenja površinskog sloja različitih metala i legura, čeličnih proizvoda ili dijelova dušikom kada se zagrijavaju u odgovarajućem okruženju. Povećava se površinska tvrdoća proizvoda, izdržljivost, otpornost na habanje i otpornost na koroziju.
Cijanidacija– zasićenje površinskog sloja proizvoda i ugljikom i dušikom.
Ovisno o korištenom mediju, cijanidacija se razlikuje: u čvrstim medijima; u tečnim medijima; u gasnim sredinama.
Ovisno o temperaturi grijanja, cijanidacija se dijeli na niskotemperaturnu i visokotemperaturnu.
Cijanizacija u tečnim medijima se vrši u kupkama rastopljenih soli.
Cijanidacija u gasovitim medijima (nitrokarburizacija). Proces istovremenog zasićenja površine dijela ugljikom i dušikom. Da bi se to postiglo, dijelovi se zagrijavaju u okruženju koje se sastoji od cementnog plina i amonijaka, odnosno nitrocarburizacija kombinira procese naugljičenja i nitriranja plina.
Difuzijsko zasićenje metalima i metaloidima
Postoje i koriste se u industriji metode za zasićenje površine delova raznim metalima (aluminijum, hrom i dr.) i metaloidima (silicijum, bor itd.) Svrha takvog zasićenja je povećanje otpornosti kamenca, otpornosti na koroziju. , otpornost na kiseline, tvrdoću i otpornost na habanje dijelova. Kao rezultat, površinski sloj poprima posebna svojstva, što omogućava uštedu legirajućih elemenata.
Aluminiziranje– proces zasićenja površinskog sloja čelika aluminijem kako bi se povećala otpornost na toplinu (otpornost na kamenac) i otpornost na atmosfersku koroziju.
Aluminizacija se vrši u prahu, u kupkama sa rastopljenim aluminijumom, u gasnom okruženju i prskanjem tečnog aluminijuma.
Hromiranje– proces zasićenja površinskog sloja čelika hromom za povećanje otpornosti na koroziju i otpornost na toplinu, a kod kromiranja visokougljičnih čelika – za povećanje tvrdoće i otpornosti na habanje.
Silikonizacija– proces zasićenja površinskog sloja dijela silicijumom radi povećanja otpornosti na koroziju i otpornosti na kiseline. Silikonizaciji su podvrgnuti dijelovi od nisko i srednje ugljičnih čelika, kao i od duktilnog i lijevanog željeza visoke čvrstoće.
Dosadno– proces zasićenja površinskog sloja dijela borom. Svrha bordiranja je povećanje tvrdoće, otpornosti na abrazivno habanje i koroziju u agresivnim sredinama, otpornost na toplinu i toplinsku otpornost čeličnih dijelova. Postoje dvije metode borenja: tečna elektroliza i gasno borenje.
Sulfidacija– proces zasićenja površinskog sloja čeličnih dijelova sumporom kako bi se poboljšala svojstva ekstremnog pritiska i povećala otpornost dijelova na habanje.
Sulfocijanizacija– proces površinskog zasićenja čeličnih dijelova sumporom, ugljikom i dušikom. Kombinovani uticaj sumpora i azota u površinskom sloju metala obezbeđuje veća svojstva ekstremnog pritiska i otpornost na habanje u poređenju sa zasićenjem samim sumporom.
Termička obrada livenog gvožđa
Toplinska obrada livenog gvožđa vrši se kako bi se ublažila unutrašnja naprezanja koja nastaju tokom livenja i uzrokuju promene u veličini i obliku odlivaka tokom vremena, smanjila tvrdoću i poboljšala obradivost, te povećala mehanička svojstva. Liveno gvožđe se podvrgava žarenju, normalizaciji, kaljenju i kaljenju, kao i nekim vrstama hemijske i termičke obrade (nitriranje, aluminijum, hromiranje).
Žarenje za ublažavanje unutrašnjeg stresa. Liveno gvožđe se podvrgava ovom žarenju na sledećim temperaturama: sivi liveni gvožđe sa grafitom u pahuljici 500 – 570ºC; liveno gvožđe visoke čvrstoće sa nodularnim grafitom 550 – 650ºC; niskolegirano liveno gvožđe 570 – 600°C; visokolegirani liveni gvožđe 620 – 650êS. Tokom ovog žarenja ne dolazi do faznih transformacija, ali se unutarnja naprezanja oslobađaju, viskoznost se povećava, a savijanje i pucanje tokom rada se eliminišu.
Omekšavajući žarenje (niskotemperaturno grafitizirajuće žarenje). Izvedite kako biste poboljšali obradivost i povećali duktilnost. Izvodi se produženim izlaganjem na 680 – 700°C ili sporim hlađenjem odlivaka na 760 – 700°C. Za dijelove složene konfiguracije, hlađenje je sporo, a za dijelove jednostavnih oblika, hlađenje je ubrzano.
Grafitiziranje žarenjem, zbog čega se od bijelog lijeva dobiva kovno lijevano željezo.
Normalizacija koristi se za povećanje fiksnog ugljika, povećanje tvrdoće, čvrstoće i otpornosti na habanje sivog, kovnog i lijevanog željeza visoke čvrstoće. Prilikom normalizacije liveno gvožđe (odlivci) se zagreva iznad temperature transformacionog opsega od 850 – 950°C i nakon držanja hladi na vazduhu.
Stvrdnjavanje sivo, duktilno i nodularno gvožđe se tretiraju radi poboljšanja tvrdoće, čvrstoće i otpornosti na habanje. Prema načinu izvođenja, kaljenje livenog gvožđa može biti kontinuirano volumetrijsko, izotermno i površinsko.
Tokom volumetrijskog kontinuiranog kaljenja, liveno gvožđe se zagreva na temperaturu od 850 – 950°C. Zatim se drži da se zagrije i potpuno otopi ugljik. Hlađenje se vrši u vodi ili ulju. Nakon stvrdnjavanja vrši se kaljenje na temperaturi od 200 – 600°C. Kao rezultat, povećava se tvrdoća, čvrstoća i otpornost na habanje lijevanog željeza.
Prilikom izotermnog očvršćavanja liveno gvožđe se zagreva na isti način kao i pri volumetrijskom neprekidnom očvršćavanju, drži 10 do 90 minuta i hladi u rastopljenoj soli na 200 - 400 °C, a nakon držanja se hladi na vazduhu.
Površinsko stvrdnjavanje zagrijavanjem površinskog sloja kisik-acetilenskim plamenom, visokofrekventnim strujama ili u elektrolitu. Temperatura grijanja 900 – 1000°C. Hlađenje u vodi, ulju ili uljnoj emulziji.
Starenje koristi se za stabilizaciju dimenzija dijelova od livenog gvožđa, sprečavanje savijanja i ublažavanje unutrašnjih naprezanja. Obično se starenje vrši nakon grube mehaničke obrade. Postoje dvije vrste starenja: prirodno i umjetno.
Prirodno starenje se događa na otvorenom ili u zatvorenom prostoru. Proizvodi nakon livenja odležavaju 6 – 15 meseci.
Veštačko starenje se vrši na povišenim temperaturama; trajanje - nekoliko sati. Prilikom veštačkog starenja liveno gvožđe se ubacuje u peć zagrejanu na 100 - 200°C, zagreva na temperaturu od 550 - 570°C brzinom od 30 - 60°C na sat, drži 3 - 5 sati i hladi. sa peći brzinom od 20 - 40°C na sat do temperature od 150 – 200°C, a zatim se hladi na vazduhu.
Hemijsko-termički tretman livenog gvožđa
Da bi se povećala površinska tvrdoća i otpornost na habanje, sivi ljevak se podvrgava nitriranju. Sivi perlitni liveni gvožđe legirani hromom, molibdenom i aluminijumom najčešće se nitriraju. Temperatura nitriranja 550 – 580°C, vrijeme držanja 30 – 70 sati. Pored nitriranja, povećanje površinske tvrdoće i otpornosti na habanje legiranog sivog perlitnog liva može se postići gasnom i tečnom cijanidacijom na temperaturi od 570°C. Da bi se povećala otpornost na toplinu, odljevci od lijevanog željeza mogu se podvrgnuti aluminizaciji, a za postizanje visoke otpornosti na koroziju u kiselinama - silikonizaciji.
Termička obrada legura obojenih metala
Aluminijske legure
Aluminijske legure se podvrgavaju tri vrste termičke obrade: žarenju, otvrdnjavanju i starenju. Glavni tipovi žarenje su: difuzione, rekristalizacione i termički ojačane legure.
Homogenizacija se koristi za izravnavanje hemijske mikroheterogenosti zrna čvrstog rastvora. Da bi se izvršila homogenizacija, legure aluminijuma se zagrevaju na 450–520°C i drže na tim temperaturama 4 do 40 sati; nakon držanja - hlađenje u peći ili na vazduhu. Kao rezultat, struktura postaje homogenija i povećava se plastičnost.
Rekristalizacijsko žarenje se mnogo više koristi za aluminij i legure na bazi aluminija nego za čelik. To se objašnjava činjenicom da metali poput aluminija i bakra, kao i mnoge legure na njihovoj bazi, ne ojačavaju kaljenjem i povećanje mehaničkih svojstava može se postići samo hladnom obradom, a međuoperacija pri takvoj preradi je rekristalizacijsko žarenje. Temperatura rekristalizacijskog žarenja aluminijskih legura je 300 – 500 °C, vrijeme držanja 0,5 – 2 sata.
Za potpuno uklanjanje stvrdnjavanja koristi se žarenje termički ojačanih legura, provodi se na temperaturama od 350-450°C uz zadržavanje 1-2 sata i naknadno prilično sporo hlađenje.
Poslije otvrdnjavanječvrstoća legure se neznatno povećava, ali duktilnost se ne mijenja. Nakon stvrdnjavanja, legure aluminijuma se podvrgavaju starenje, u kojem dolazi do raspada prezasićene čvrste otopine.
Kovane legure aluminijuma
U očvrslom stanju, duralumin je plastičan i lako se deformiše. Nakon stvrdnjavanja i prirodnog ili umjetnog starenja, čvrstoća duraluminija se naglo povećava.
Legure livenog aluminijuma
Za legure livenog aluminijuma koriste se različite vrste termičke obrade u zavisnosti od hemijskog sastava. Za ojačanje, legure livenog aluminijuma se podvrgavaju kaljenju da bi se dobila prezasićena čvrsta otopina i veštačkom starenju, kao i samo gašenju bez starenja da bi se dobila stabilna čvrsta otopina u kaljenom stanju.
Legure magnezijuma
Legure magnezija, kao i legure aluminija, podliježu žarenju, stvrdnjavanju i starenju. Da bi se izravnala hemijska mikroheterogenost zrna čvrstog rastvora difuzijom, ingoti legure magnezijuma se podvrgavaju homogenizaciji na temperaturama od 350-400°C uz izlaganje od 18-24 sata. Poluproizvedene kovane legure magnezijuma podvrgavaju se rekristalizacionom žarenju na temperaturi od ≈ 350°C, kao i žarenju na nižim temperaturama od 150 – 250°C radi otklanjanja zaostalih naprezanja.
Legure magnezija su podvrgnute kaljenju, odnosno kaljenju i vještačkom starenju. Na temperaturi od 20C ne dolazi do promjena u očvrslim legurama magnezijuma, odnosno nisu podložne prirodnom starenju.
Bakar i legure bakra
Termička obrada bakra. Deformacija bakra je praćena povećanjem njegove čvrstoće i smanjenjem duktilnosti. Da bi se povećala duktilnost, bakar se podvrgava rekristalizacijskom žarenju na 500-600 ° C, zbog čega se duktilnost naglo povećava, a čvrstoća smanjuje.
Termička obrada mesinga. Oni se podvrgavaju samo rekristalizacionom žarenju na 600 – 700°C (da bi se uklonilo stvrdnjavanje). Mesing se hladi tokom žarenja na vazduhu ili radi ubrzanja hlađenja i boljeg odvajanja kamenca u vodi. Dijelovi od mesinga koji nakon deformacije imaju zaostala naprezanja karakteriziraju spontano pucanje u vlažnoj atmosferi. Da bi se to izbjeglo, mjedeni dijelovi se podvrgavaju niskotemperaturnom žarenju na 200 - 300 C, zbog čega se zaostala naprezanja uklanjaju, ali stvrdnjavanje ostaje. Niskotemperaturno žarenje je posebno neophodno za aluminijumske mesinge koji su skloni spontanom pucanju.
Toplinska obrada bronze. Da bi se izjednačio hemijski sastav bronce, ona se podvrgava homogenizaciji na 700 – 750°C, nakon čega sledi brzo hlađenje. Da bi se smanjila unutrašnja naprezanja, odlivci se žare na 550°C. Kako bi se povratila plastičnost između hladnih operacija, oni se podvrgavaju rekristalizacijskom žarenju na 600 – 700°C.
Aluminijumske bronce sa sadržajem aluminijuma od 8 do 11%, koje prolaze faznu rekristalizaciju kada se zagrevaju i ohlade, mogu se podvrgnuti kaljenju. Kao rezultat stvrdnjavanja povećavaju se čvrstoća i tvrdoća, ali se duktilnost smanjuje. Nakon stvrdnjavanja slijedi kaljenje na 400 – 650°C, ovisno o traženim svojstvima. Takođe se podvrgavaju homogenizaciji, a deformabilni poluproizvodi se podvrgavaju rekristalizacionom žarenju na 650 – 800°C.
Berilijum bronza se gasi u vodi od temperature od 760 – 780°C; u ovom slučaju, višak faze nema vremena da se odvoji, a nakon gašenja legura se sastoji od prezasićene čvrste otopine i ima nisku tvrdoću i čvrstoću i visoku duktilnost. Nakon stvrdnjavanja vrši se kaljenje (starenje) na 300 - 350°C u trajanju od 2 sata. Da bi se povećala stabilnost prezasićene čvrste otopine i olakšalo gašenje, berilijum bronze se dodatno legiraju niklom.
Legure titanijuma
Titanijumske legure se podvrgavaju rekristalizacionom žarenju i žarenju sa faznom rekristalizacijom, kao i očvršćavanju termičkom obradom – kaljenjem i starenjem. Da bi se povećala otpornost na habanje i habanje, legure titana se podvrgavaju nitriranju, karburizaciji ili oksidaciji.
Rekristalizaciono žarenje se koristi za titanijum i legure za uklanjanje stvrdnjavanja nakon hladnog rada. Temperatura rekristalizacionog žarenja je 520 – 850°C, u zavisnosti od hemijskog sastava legure i vrste poluproizvoda.
Žarenje sa faznom rekristalizacijom se koristi za smanjenje tvrdoće, povećanje plastičnosti, pročišćavanje zrna i eliminaciju strukturne heterogenosti. Koriste se jednostavno, izotermno i dvostruko žarenje; temperatura zagrevanja tokom žarenja 750 – 950°C u zavisnosti od legure.
Prilikom izotermnog žarenja, nakon držanja na temperaturi žarenja, dijelovi se hlade na 500 - 650 °C (u zavisnosti od legure) u istoj peći ili se prenose u drugu peć i drže određeno vrijeme, a hlade na zraku. Izotermnim žarenjem vrijeme žarenja se smanjuje, a duktilnost je veća.
Kod dvostrukog žarenja, dijelovi se zagrijavaju do temperature žarenja, drže i hlade na zraku. Zatim ga ponovo zagrejem na 500 – 650°C, držim i ohladim na vazduhu. Dvostruko žarenje, u poređenju sa izotermnim žarenjem, povećava vlačnu čvrstoću uz blago smanjenje duktilnosti i skraćuje vrijeme obrade.
Od svih vrsta hemijsko-termičke obrade titanijumskih legura, najrasprostranjenije je nitriranje, koje se izvodi u azotnoj sredini ili u mešavini azota i argona na temperaturama od 850 - 950 C u trajanju od 10 - 50 sati. Dijelovi napravljeni od titanijumskih legura nakon nitriranja imaju dobra svojstva protiv trenja.
Zaključak
Toplotna obrada je jedna od glavnih, najvažnijih operacija općeg tehnološkog ciklusa obrade, od čijeg pravilnog izvođenja zavisi kvalitet (mehanička i fizičko-hemijska svojstva) proizvedenih mašinskih dijelova i mehanizama, alata i drugih proizvoda. Razvijeni su i racionalizovani tehnološki procesi za termičku obradu sivog i belog liva i legura obojenih metala.
Obećavajući smjer za poboljšanje tehnologije toplinske obrade je ugradnja jedinica za toplinsku obradu u mehaničkim radionicama, stvaranje automatskih linija koje uključuju procese toplinske obrade, kao i razvoj metoda koje osiguravaju povećanje svojstava čvrstoće dijelova, njihove pouzdanost i izdržljivost.
Književnost
B.V. Zakharov. V.N. Berseneva “Progresivni tehnološki procesi i oprema za termičku obradu metala” M. “ postdiplomske škole» 1988
V.M. Zuev “Termička obrada metala” M. Viša škola 1986
B.A. Kuzmin “Tehnologija metala i konstrukcijskih materijala” M. “Mašinstvo” 1981.
V.M. Nikiforov “Tehnologija metala i konstrukcijskih materijala” M. “Viša škola” 1968.
A.I. Samokhotsky N.G. Parfenovskaya “Tehnologija termičke obrade metala” M. Mašinstvo 1976.
Izbor materijala i razvoj tehnološkog procesa za termičku obradu matrice
Radni uslovi matrice, alat za narezivanje navoja za rezanje spoljni navoj ručno ili na mašini za rezanje metala. Karakteristike čelika, njegova hemijska, mehanička i druga svojstva. Metode praćenja načina termičke obrade i kvaliteta proizvoda.
Kvalitet čelika 18HGT: hrom-mangan čelik sadrži 0,18% ugljika, do 1% hroma, mangana. Redoslijed preliminarne i završne termičke obrade dijelova. Način rada za preliminarnu i završnu termičku obradu dijelova.
Teorijska osnova termička obrada čelika. Difuzijsko i rekristalizacijsko žarenje. Kaljenje je termička obrada u kojoj čelik poprima neravnotežnu strukturu i povećava se tvrdoća čelika. Primena termičke obrade u praksi.
Suština namjene rezača i njegova primjena. Analiza tehnoloških svojstava i hemijskog sastava brzoreznih čelika. Faze tehnološkog procesa preliminarne i termičke obrade otvrdnjavanja, izbor uređaja, nedostataka i njihovo otklanjanje.
Osnove tehnologije termičke obrade metala i legura. Toplinska obrada je faza u tehnološkom procesu izrade dijelova. Poboljšanje obradivosti materijala pritiskom ili rezanjem. Formiranje tehničkih i električnih svojstava.
Opis postupka primjene kaljenja ugljičnih čelika i određivanja temperature kaljenja prema specifikaciji. Proračun potrebnog trajanja stvrdnjavanja. Zadavanje žarenja i određivanje njegovog vremena prema zadatku. Pravila za sastavljanje protokola.
Formiranje svojstava materijala dijela. Uticaj mašinska obrada na svojstva materijala radnog predmeta. Učinak tekućine za rezanje (rashladnog sredstva).
Dekodiranje klase čelika. Priroda utjecaja ugljika i legirajućih elemenata datog čelika na položaj kritičnih tačaka. Izbor i opravdanje redoslijeda operacija za preliminarnu i završnu toplinsku obradu dijelova. Način toplinske obrade dijelova.
Teorija termičke obrade. Transformacije u čelik pri zagrijavanju i hlađenju. Žarenje i normalizacija. Defekti termičke obrade. Defekti tokom žarenja i normalizacije. Defekti tokom stvrdnjavanja. Hemijsko-termička obrada i površinsko kaljenje čelika.
Teorija i tehnologija termičke obrade. Vrste termičke obrade. Žarenje, normalizacija, stvrdnjavanje, starenje, poboljšanje. Hemijsko-toplinska obrada. Njegove vrste. Kompozitni materijali.
Pravila za obradu dijelova rezanjem - uklanjanjem iz obratka upotrebom alat za rezanje dodatak, dosljedno približavajući svoj oblik i dimenzije potrebnim, pretvarajući ga u gotov proizvod. Kontrola kvaliteta površine hemijsko-termičkom obradom.
Upoznavanje sa metodologijom za izradu tehnološkog procesa za termičku obradu delova: automobila, traktora i poljoprivrednih mašina. Dešifrovanje kvaliteta datog čelika, opisivanje njegove mikrostrukture, mehanička svojstva pre termičke obrade.
Čelik 20HNR - hrom-nikl čelik sa sadržajem ugljenika od 0,20%, do 1% hroma, nikla i bora. Način rada za preliminarnu i završnu termičku obradu dijelova - temperatura zagrijavanja i mikrostruktura u zagrijanom stanju, rashladni medij.