Niklowanie w domu - uzyskanie pięknych i niezawodnych powłok. Technologia niklowania w domu Jak niklować metal?
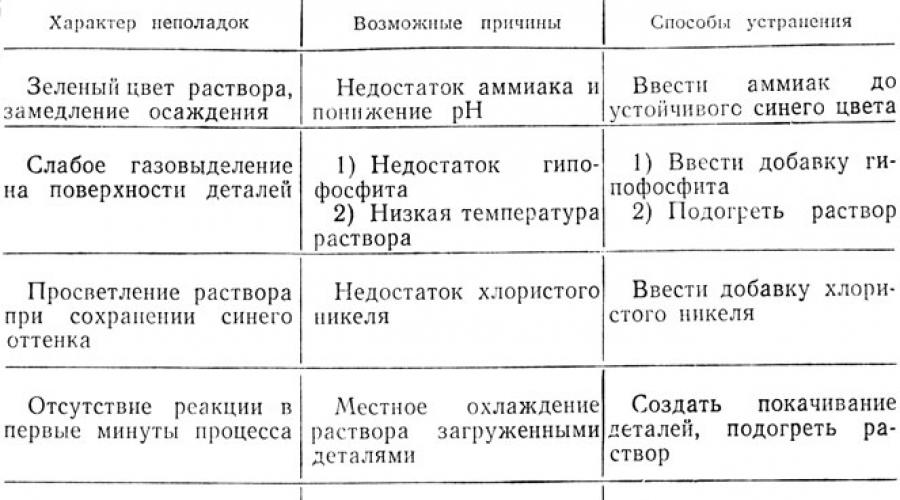
Powłoka chemiczna jednych metali innymi zachwyca prostotą procesu technologicznego. Rzeczywiście, jeśli np. konieczne jest niklowanie chemiczne jakiejkolwiek części stalowej, wystarczy mieć odpowiednie naczynia emaliowane, źródło ogrzewania (kuchenka gazowa, kuchenka itp.) oraz środki chemiczne stosunkowo niewyczerpujące. Godzinę lub dwie - a część pokryta jest błyszczącą warstwą niklu.
Pamiętaj, że tylko z niklowanie chemiczne możliwe jest bezpieczne niklowanie części o złożonym profilu, wewnętrznych wnękach (rury itp.). To prawda, że niklowanie chemiczne (i kilka innych podobnych procesów) nie jest pozbawione wad. Głównym z nich jest niezbyt silna przyczepność folii niklowej do metalu podstawowego. Jednak tę wadę można wyeliminować, w tym celu stosuje się tak zwaną metodę dyfuzji niskotemperaturowej. Pozwala znacznie zwiększyć przyczepność folii niklowej do metalu nieszlachetnego. Ta metoda ma zastosowanie do wszystkich powłoki chemiczne jeden metal z drugim.
Proces niklowania chemicznego opiera się na reakcji redukcji niklu z wodnych roztworów jego soli za pomocą podfosforynu sodu i niektórych innych chemikaliów.
niklowanie
Powłoki niklowe otrzymane metodami chemicznymi mają strukturę amorficzną. Obecność fosforu w niklu sprawia, że powłoka jest zbliżona twardością do powłoki chromowej. Niestety przyczepność folii niklowej do metalu podstawowego jest stosunkowo niska. Obróbka cieplna folii niklowych (dyfuzja niskotemperaturowa) polega na podgrzaniu elementów niklowanych do temperatury 400°C i utrzymywaniu ich w tej temperaturze przez 1 godzinę.
Jeśli części niklowane są utwardzone (sprężyny, noże, haczyki na ryby itp.), to w temperaturze 40 ° C mogą zostać uwolnione, to znaczy mogą stracić swoją główną jakość - twardość. W tym przypadku dyfuzja niskotemperaturowa prowadzona jest w temperaturze 270...300 C z ekspozycją do 3 h. W tym przypadku obróbka cieplna zwiększa również twardość powłoki niklowej.
Wszystko wymienione cnoty niklowanie chemiczne nie umknęło uwadze technologów. Znalazły dla nich praktyczne zastosowanie (poza wykorzystaniem właściwości dekoracyjnych i antykorozyjnych). Tak więc za pomocą niklowania chemicznego naprawia się osie różne mechanizmy, nawlekacze ślimakowe itp.
W domu za pomocą niklowania (oczywiście chemicznego!) można naprawiać części różnych urządzeń gospodarstwa domowego. Technologia tutaj jest niezwykle prosta. Na przykład wyburzono oś urządzenia. Następnie tworzą (z nadmiarem) warstwę niklu na uszkodzonym obszarze. Następnie sekcja robocza osi jest polerowana, doprowadzając ją do pożądanego rozmiaru.
Należy zauważyć, że niklowanie chemiczne nie może obejmować metali takich jak cyna, ołów, kadm, cynk, bizmut i antymon.
Roztwory stosowane do chemicznego niklowania dzielą się na kwaśne (pH - 4...6,5) i zasadowe (pH - powyżej 6,5). Do powlekania metali żelaznych, miedzi i mosiądzu korzystnie stosuje się roztwory kwaśne. Alkaliczne - do stali nierdzewnych.
Roztwory kwaśne (w porównaniu do zasadowych) na polerowanej części dają gładszą (zbliżoną do lustra) powierzchnię, mają mniejszą porowatość, a szybkość procesu jest większa. Inną ważną cechą roztworów kwasowych jest to, że są mniej podatne na samorozładowanie po przekroczeniu temperatura robocza. (Samorozładowanie - natychmiastowe wytrącanie niklu do roztworu z rozpryskiwaniem tego ostatniego.)
W roztworach alkalicznych główną zaletą jest bardziej niezawodna przyczepność folii niklowej do metalu podstawowego.
I ostatni. Woda do niklowania (i przy nakładaniu innych powłok) jest pobierana destylowana (można użyć kondensatu z lodówki domowe). Odczynniki chemiczne są odpowiednie co najmniej czyste (oznaczenie na etykiecie - H).
Przed pokryciem części jakąkolwiek folią metalową konieczne jest specjalne przygotowanie ich powierzchni.
Przygotowanie wszystkich metali i stopów jest następujące. Obrobiona część jest odtłuszczana w jednym z roztworów wodnych, a następnie część jest dekapitowana w jednym z niżej wymienionych roztworów.
Kompozycje roztworów do dekapitacji (g/l)
Do stali
Kwas siarkowy - 30...50. Temperatura roztworu - 20°С, czas przetwarzania - 20...60 s.
Kwas solny - 20...45. Temperatura roztworu - 20°С, czas przetwarzania - 15...40 s.
Kwas siarkowy - 50...80, kwas solny - 20...30. Temperatura roztworu - 20°C, czas przetwarzania - 8...10s.
Do miedzi i jej stopów
Kwas siarkowy - 5% roztwór. Temperatura - 20°C, czas przetwarzania - 20 s.
Do aluminium i jego stopów
Kwas azotowy. (Uwaga, 10 ... 15% rozwiązanie.). Temperatura roztworu wynosi 20°C, czas przetwarzania 5...15 s.
Należy pamiętać, że w przypadku aluminium i jego stopów przed niklowaniem chemicznym przeprowadza się jeszcze jedną obróbkę – tzw. cynkan. Poniżej znajdują się rozwiązania do obróbki cynkiem.
Składy roztworów do obróbki cynkiem (g/l)
Do aluminium
Soda kaustyczna - 250, tlenek cynku - 55. Temperatura roztworu - 20°C, czas obróbki - 3...5 s.
Soda kaustyczna - 120, siarczan cynku - 40. Temperatura roztworu - 20 ° C, czas przetwarzania - 1,5 ... 2 minuty.
Podczas przygotowywania obu roztworów najpierw rozpuszcza się sodę kaustyczną w połowie wody, a składnik cynkowy w drugiej połowie. Następnie oba roztwory wylewa się razem.
Do odlewanych stopów aluminium
Soda kaustyczna - 10, tlenek cynku - 5, sól Rochelle (hydrat kryształu) - 10. Temperatura roztworu - 20 ° C, czas przetwarzania - 2 minuty.
Do stopów aluminium do obróbki plastycznej
Chlorek żelazowy (hydrat kryształu) - 1, wodorotlenek sodu - 525, tlenek cynku 100, sól Rochelle - 10. Temperatura roztworu - 25 ° C, czas przetwarzania - 30 ... 60 s.
Po cynkowaniu części są myte w wodzie i zawieszane w roztworze do niklowania.
Wszystkie rozwiązania do niklowania są uniwersalne, to znaczy nadają się do wszystkich metali (choć są pewne specyfiki). Przygotuj je w określonej kolejności. Tak więc wszystkie chemikalia (oprócz podfosforynu sodu) są rozpuszczane w wodzie (naczynia emaliowane!). Następnie roztwór jest podgrzewany do temperatury roboczej i dopiero po rozpuszczeniu podfosforynu sodu i zawieszaniu części w roztworze.
W 1 litrze roztworu można niklować powierzchnię do 2 dm2 powierzchni.
Składy roztworów do niklowania (g/l)
Siarczan niklu - 25, kwas bursztynowy sodu - 15, podfosforyn sodu - 30. Temperatura roztworu - 90°C, pH - 4,5, szybkość wzrostu filmu - 15...20 µm/h.
Chlorek niklu - 25, kwas bursztynowy sodu - 15, podfosforyn sodu - 30. Temperatura roztworu - 90 ... 92 ° C, pH - 5,5, szybkość wzrostu - 18 ... 25 μm / h.
Chlorek niklu – 30, kwas glikolowy – 39, podfosforyn sodu – 10. Temperatura roztworu 85…89°C, pH – 4,2, szybkość wzrostu – 15..20 mikronów/h.
Chlorek niklu - 21, octan sodu - 10, podfosforyn sodu - 24. Temperatura roztworu - 97 ° C, pH - 5,2, szybkość wzrostu - do 60 μm / h.
Siarczan niklu - 21, octan sodu - 10, siarczek ołowiu - 20, podfosforyn sodu - 24. Temperatura roztworu - 90 ° C, pH - 5, szybkość wzrostu - do 90 μm / h.
Chlorek niklu - 30, kwas octowy - 15, siarczek ołowiu - 10 ... 15, podfosforyn sodu - 15. Temperatura roztworu - 85 ... 87 ° C, pH - 4,5, szybkość wzrostu - 12 ... 15 mikronów /h
Chlorek niklu - 45, chlorek amonu - 45, cytrynian sodu - 45, podfosforyn sodu - 20. Temperatura roztworu - 90 ° C, pH - 8,5, szybkość wzrostu - 18 ... 20 mikronów / h.
Chlorek niklu - 30, chlorek amonu - 30, kwas bursztynowy sodu - 100, amoniak (roztwór 25% - 35, podfosforyn sodu - 25). Temperatura - 90°C, pH - 8...8,5, tempo wzrostu - 8...12 µm/h.
Chlorek niklu - 45, chlorek amonu - 45, octan sodu - 45, podfosforyn sodu - 20. Temperatura roztworu - 88 .... 90 ° C, pH - 8 ... 9, szybkość wzrostu - 18 ... 20 mikronów / h.
Siarczan niklu - 30, siarczan amonu - 30, podfosforyn sodu - 10. Temperatura roztworu - 85°C, pH - 8,2...8,5, szybkość wzrostu - 15...18 µm/h.
Uwaga! Zgodnie z obowiązującymi normami państwowymi jednowarstwowa powłoka niklowa na 1 cm2 ma kilkadziesiąt porów przelotowych (do metalu podstawowego). Naturalnie na świeżym powietrzu niklowana stalowa część szybko pokryje się „wysypką” rdzy.
Właściwości i zastosowania powłoki. Podstawą procesu chemicznego niklowania jest reakcja redukcji niklu z wodnych roztworów jego soli podfosforynem sodu. Zastosowania przemysłowe otrzymały metody osadzania niklu z roztworów alkalicznych i kwaśnych. Osadzana powłoka ma półbłyszczący metaliczny wygląd, drobnoziarnista struktura i jest stopem niklu z fosforem. Zawartość fosforu w osadzie zależy od składu roztworu i waha się od 4-6% dla roztworów zasadowych do 8-10% dla roztworów kwaśnych.
W zależności od zawartości fosforu zmieniają się również stałe fizyczne osadu niklowo-fosforowego. Środek ciężkości jego równa 7,82-7,88 g / cm 3, temperatura topnienia 890-1200 °, oporność elektryczna 0,60 oma mm 2 /m. Po obróbce cieplnej w temperaturze 300-400° twardość powłoki niklowo-fosforowej wzrasta do 900-1000 kg/mm2. Jednocześnie wielokrotnie wzrasta również siła przyczepności.
Te właściwości powłoki niklowo-fosforowej określają również obszary jej zastosowania.
Wskazane jest stosowanie go do pokrycia części o złożonym profilu, wewnętrzna powierzchnia rury i cewki, do równomiernego powlekania części o bardzo dokładne wymiary, w celu zwiększenia odporności na ścieranie powierzchni trących i części narażonych na działanie temperatury, np. do powlekania form.
Części wykonane z metali żelaznych, miedzi, aluminium i niklu poddawane są powłokom niklowo-fosforowym.
Ta metoda nie nadaje się do osadzania niklu na metalach lub powłokach, takich jak ołów, cynk, kadm i cyna.
Wytrącanie niklu z roztworów alkalicznych. Roztwory alkaliczne charakteryzują się dużą stabilnością, łatwością regulacji, brakiem tendencji do gwałtownego i natychmiastowego wytrącania proszku niklowego (zjawisko samorozładowania) oraz możliwością ich długotrwałej pracy bez wymiany.
Szybkość osadzania niklu wynosi 8-10 mikronów na godzinę. Proces przebiega z intensywnym uwalnianiem wodoru na powierzchni Części.
Przygotowanie roztworu polega na rozpuszczeniu każdego ze składników z osobna, po czym są one razem wlewane do kąpiel robocza, z wyjątkiem podfosforynu sodu. Nalewa się go dopiero po podgrzaniu roztworu do temperatury roboczej i przygotowaniu części do powlekania.
Przygotowanie powierzchni części stalowe do powłoki nie ma szczególnych cech.
Po podgrzaniu roztworu do temperatury roboczej jest on korygowany 25% roztworem amoniaku do stabilnej koloru niebieskiego, wlać roztwór podfosforynu sodu, zawiesić części i przystąpić do powlekania bez wstępnych badań. Roztwór reguluje się głównie amoniakiem i podfosforynem sodu. Przy dużej objętości kąpieli niklowej i wysokim obciążeniu jednostkowym części, roztwór jest regulowany amoniakiem bezpośrednio z butli z gazowym amoniakiem, przy ciągłym dopływie gazu na dno kąpieli przez gumową rurkę.
Dla wygody regulacji przygotowuje się roztwór podfosforynu sodu o stężeniu 400-500 g / l.
Roztwór chlorku niklu jest zwykle przygotowywany do korekty razem z chlorkiem amonu i cytrynianem sodu. W tym celu najbardziej wskazane jest użycie roztworu zawierającego 150 g/l chlorku niklu, 150 g/l chlorku amonu i 50 g/l cytrynianu sodu.
Jednostkowe zużycie podfosforynu sodu na 1 dm2 powierzchni powłoki przy grubości warstwy 10 mikronów wynosi około 4,5 g, a niklu w przeliczeniu na metal około 0,9 g.
Główne problemy związane z chemicznym osadzaniem niklu z roztworów alkalicznych podano w tabeli. osiem.
Osadzanie niklu z roztworów kwasowych. W przeciwieństwie do roztworów alkalicznych, roztwory kwaśne charakteryzują się dużą różnorodnością dodatków do roztworów soli niklu i podfosforynów. Tak więc w tym celu można zastosować octan sodu, kwas bursztynowy, winowy i mlekowy, Trilon B i inne związki organiczne. Wśród wielu kompozycji poniżej znajduje się rozwiązanie o następującym składzie i reżimie opadów:
Wartość pH należy skorygować 2% roztworem wodorotlenku sodu. Szybkość osadzania niklu wynosi 8-10 mikronów na godzinę.
Przegrzanie roztworu powyżej 95° może prowadzić do samorozładowania niklu z natychmiastowym ciemnym gąbczastym osadem i wypryskiwaniem roztworu z kąpieli.
Roztwór reguluje się w zależności od stężenia jego składowych składników tylko do momentu zgromadzenia w nim 55 g/l fosforynu sodu NaH2PO3, po czym fosforyn niklu może wytrącić się z roztworu. Po osiągnięciu określonego stężenia fosforynu roztwór niklu jest spuszczany i zastępowany nowym.
obróbka cieplna. W przypadkach, w których nikiel jest stosowany w celu zwiększenia twardości powierzchni i odporności na zużycie, części są poddawane obróbce cieplnej. W wysokich temperaturach osad niklowo-fosforowy tworzy związek chemiczny, który powoduje gwałtowny wzrost jego twardości.
Zmianę mikrotwardości w zależności od temperatury ogrzewania pokazano na rys. 13. Jak widać z wykresu, największy wzrost twardości występuje w zakresie temperatur 400-500 °. Wybierając reżim temperaturowy, należy pamiętać, że w przypadku wielu stali, które zostały utwardzone lub znormalizowane, wysokie temperatury nie zawsze są dopuszczalne. Ponadto obróbka cieplna przeprowadzana w powietrzu powoduje, że na powierzchni części pojawiają się odcienie od złocistożółtego do fioletowego. Z tych powodów temperatura ogrzewania jest często ograniczana w granicach 350-380°. Konieczne jest również, aby niklowane powierzchnie były czyste przed ułożeniem w piecu, ponieważ wszelkie zanieczyszczenia są wykrywane po obróbce cieplnej bardzo intensywnie, a ich usunięcie jest możliwe tylko przez polerowanie. Czas ogrzewania to 40-60 min. jest wystarczający.
Sprzęt i akcesoria. Głównym zadaniem w produkcji urządzeń do niklowania chemicznego jest dobór wykładzin wanien odpornych na działanie kwasów i zasad oraz przewodzących ciepło. Do prac eksperymentalnych i do powlekania małe części stosować wanny emaliowane porcelaną i stalą.
Przy pokrywaniu dużych przedmiotów w wannach o pojemności 50-100 litrów lub większej stosuje się zbiorniki emaliowane z emaliami odpornymi na działanie silnego kwasu azotowego. Niektóre fabryki stosują stalowe wanny cylindryczne wyłożone powłoką składającą się z kleju nr 88 i sproszkowanego tlenku chromu, pobieranych w równych ilościach. Tlenek chromu można zastąpić mikroproszkami szmerglowymi. Powłoka produkowana jest w 5-6 warstwach z pośrednim suszeniem na powietrzu.
W Zakładzie Kirowa z powodzeniem stosuje się w tym celu wyłożenie wanien cylindrycznych ze zdejmowanymi plastikowymi pokrywami. Jeśli konieczne jest czyszczenie wanien, roztwory są wypompowywane za pomocą pompy, a pokrywy są zdejmowane i traktowane kwasem azotowym. Jako materiał na wieszaki i kosze należy użyć stali węglowej. Oddzielne sekcje części i zawiesin są izolowane emaliami perchlorowinylowymi lub związkami tworzyw sztucznych.
Użyj do podgrzania roztworu grzejniki elektryczne z przenoszeniem ciepła przez płaszcz wodny. Obróbka cieplna małych części odbywa się w termostatach. Do dużych produktów piece szybowe z automatyczna regulacja temperatura.
Niklowanie stali nierdzewnych i kwasoodpornych. Niklowanie przeprowadza się w celu zwiększenia twardości powierzchni i odporności na zużycie, a także w celu ochrony przed korozją w tych agresywnych środowiskach, w których stale te są niestabilne.
Dla adhezji warstwy niklowo-fosforowej do powierzchni stali wysokostopowych decydujące znaczenie ma sposób przygotowania do powlekania. Tak więc dla stali nierdzewnej gatunku 1×13 i podobnych przygotowanie powierzchni polega na jej anodowaniu w roztworach alkalicznych. Części montuje się na zawiesinach ze stali węglowej, w razie potrzeby za pomocą katod wewnętrznych, zawieszonych w kąpieli z 10-15% roztworem sody kaustycznej i anodą obrabianą w temperaturze elektrolitu 60-70 ° i gęstości prądu anodowego 5 10 A/dm2 przez 5-10 minut. aż powstanie jednolita brązowa powłoka bez metalowych szczelin. Następnie części są myte w zimnej bieżącej wodzie, dekapitowane w kwasie solnym (waga sp. 1,19), dwukrotnie rozcieńczane w temperaturze 15-25° przez 5-10 sekund. Po umyciu pod bieżącą zimną wodą części zawiesza się w kąpieli niklowania chemicznego w roztworze alkalicznym i przykrywa Tryb normalny do określonej grubości warstwy.
Dla części wykonanych ze stali kwasoodpornej typu IX18H9T obróbkę anodową należy prowadzić w elektrolicie kwasu chromowego o następującym składzie i trybie procesu:
Po obróbce anodowej części są myte pod bieżącą zimną wodą, dekapitowane w kwasie solnym, jak wskazano dla ze stali nierdzewnej, i zawieszony w wannie do niklowania.
Niklowanie metali nieżelaznych. Aby osadzić nikiel na wcześniej osadzonej warstwie niklu, części są odtłuszczane, a następnie trawione w 20-30% roztworze kwasu solnego na 1 min., po czym zawiesza się je w wannie do chemicznego niklowania. Części wykonane z miedzi i jej stopów są niklowane w kontakcie z bardziej elektroujemnym metalem, takim jak żelazo lub aluminium, przy użyciu w tym celu drutu lub zawieszek wykonanych z tych metali. W niektórych przypadkach, aby zaszła reakcja osadzania, wystarczy stworzyć krótkotrwały kontakt pręta żelaznego z powierzchnią części miedzianej.
W przypadku niklowania aluminium i jego stopów części są wytrawiane w alkaliach, rozjaśniane kwasem azotowym, tak jak to robiono wcześniej, we wszystkich rodzajach powłok i poddawane podwójnej obróbce cynkowej w roztworze zawierającym 500 g/l wodorotlenku sodu i 100 g/l tlenku cynku w temperaturze 15-25°. Pierwsze zanurzenie trwa 30 sekund, po czym osad kontaktowego cynku jest wytrawiany w rozcieńczonym kwasie azotowym, drugie zanurzenie trwa 10 sekund, po czym części są myte w zimnej bieżącej wodzie i niklowane w kąpieli z alkalicznym fosforo niklem rozwiązanie. Powstała powłoka jest bardzo luźno związana z aluminium, a w celu zwiększenia przyczepności części podgrzewa się przez zanurzenie ich w oleju smarnym o temperaturze 220-250 ° na 1-2 godziny.
Po obróbce cieplnej części są odtłuszczane rozpuszczalnikami i w razie potrzeby przecierane, polerowane lub poddawane innym rodzajom obróbki.
Niklowanie cermetali i ceramiki. Proces technologiczny Niklowanie ferrytów polega na następujących operacjach: części odtłuszcza się w 20% roztworze sody kalcynowanej, przemywa gorącą wodą destylowaną i marynuje przez 10-15 minut. w alkoholowym roztworze kwasu solnego o stosunku składników 1:1. Następnie części są ponownie myte gorącą wodą destylowaną podczas czyszczenia osadu za pomocą szczotek do włosów. Na powlekane powierzchnie części nanosi się pędzlem roztwór chlorku palladu o stężeniu 0,5-1,0 g/l i pH 3,54:0,1. Po wysuszeniu na powietrzu ponownie nanosi się chlorek palladu, suszy i zanurza do wstępnego niklowania w kąpieli z kwaśnym roztworem zawierającym 30 g/l chlorku niklu, 25 g/l podfosforynu sodu i 15 g/l kwas bursztynowy sodu. Do tej operacji konieczne jest utrzymanie temperatury roztworu w granicach 96-98° i pH 4,5-4,8. Następnie części są myte w gorącej wodzie destylowanej i niklowane w tym samym roztworze, ale w temperaturze 90 °, aż do uzyskania warstwy o grubości 20-25 mikronów. Następnie części gotuje się w wodzie destylowanej, miedziuje w elektrolicie pirofosforanowym do uzyskania warstwy 1-2 mikronów, po czym poddaje lutowaniu bezkwasowemu. Siła adhezji powłoki niklowo-fosforowej na podłożu ferrytowym wynosi 60-70 kg/cm2.
Ponadto chemicznemu niklowaniu poddawane są różne rodzaje ceramiki, np. ultraporcelana, kwarc, steatyt, piezoceramika, tikond, termokond itp.
Technologia niklowania składa się z następujących operacji: części są odtłuszczane alkoholem, myte w gorącej wodzie i suszone.
Następnie w przypadku części wykonanych z tikondu, termoprzewodu i kwarcu uczula się ich powierzchnię roztworem zawierającym 10 g/l chlorku cyny SnCl 2 i 40 ml/l kwasu solnego. Czynność tę wykonuje się za pomocą pędzla lub pocierając drewnianą podkładką zwilżoną roztworem lub zanurzając części w roztworze na 1-2 minuty. Następnie powierzchnia części jest aktywowana w roztworze chlorku palladu PdCl 2 2H 2 O.
W przypadku ultraporcelany stosuje się podgrzany roztwór o stężeniu PdCl2·2H2O 3-6 g/lz czasem zanurzenia 1 sek. W przypadku tikondu, termokondu i kwarcu stężenie spada do 2-3 g / l ze wzrostem ekspozycji od 1 do 3 minut, po czym części zanurza się w roztworze zawierającym podfosforyn wapnia Ca (H 2 PO 2) 2 w ilość 30 g/l, bez podgrzewania, przez 2-3 minuty.
Części wykonane z ultraporcelany z aktywowaną powierzchnią zawiesza się na 10-30 sekund. do kąpieli do niklowania wstępnego z roztworem alkalicznym, po czym części są myte i zawieszane ponownie w tej samej kąpieli w celu uzyskania warstwy o określonej grubości.
Części wykonane z tikondu, termoprzewodnika i kwarcu po obróbce podfosforynem wapnia są niklowane w roztworach kwaśnych.
Chemiczne osadzanie niklu ze związków karbonylowych. Podczas ogrzewania par czterokarbonylku niklu Ni(CO) 4 w temperaturze 280°±5 następuje reakcja rozkładu termicznego związków karbonylowych z osadzaniem metalicznego niklu. Proces osadzania odbywa się w hermetycznie zamkniętym pojemniku w ciśnienie atmosferyczne. Medium gazowe składa się z 20-25% (objętościowo) tetrakarbonylu niklu i 80-75% tlenku węgla CO. Dopuszczalna jest domieszka tlenu w gazie nie większa niż 0,4%. W celu równomiernego osadzania należy zapewnić cyrkulację gazu z szybkością posuwu 0,01-0,02 m/s i odwrócenie kierunku posuwu co 30-40 sekund. . Przygotowanie części do malowania polega na usunięciu tlenków i tłuszczu. Szybkość osadzania niklu wynosi 5-10 mikronów/min. Wytrącony nikiel ma matowa powierzchnia, ciemnoszary odcień, drobnokrystaliczna struktura, twardość 240-270 Vickersów i stosunkowo niska porowatość.
Siła adhezji powłoki do metalu wyrobów jest bardzo niska i aby zwiększyć ją do zadowalających wartości konieczna jest obróbka cieplna w temperaturze 600-700°C przez 30-40 minut.
PŁYTA NIKLOWANA, proces techniczny nakładania na powierzchnię metali b. lub m. cienka warstwa metalicznego niklu lub stopów niklu; celem tego zastosowania jest zmniejszenie korozji metalu, zwiększenie twardości warstwy zewnętrznej, zwiększenie lub zmiana współczynnika odbicia powierzchni, nadanie jej piękniejszego wyglądu. Po raz pierwszy uzyskany przez Bettgera w 1842 r. i stosowany komercyjnie w USA od 1860 r., niklowanie stało się obecnie jedną z najpowszechniej stosowanych metod powlekania metalem w przemyśle.
Istniejące liczne metody niklowania można podzielić na dwie główne grupy: metody kontaktowe i metody galwanotechnika; obecnie szczególnie często sięga się po te ostatnie. Aplikacja folii niklowej na powierzchnie różne metale, a zgodnie z naturą niklowania można je podzielić na grupy: 1) miedź, mosiądz, brąz, cynk, 2) żelazo, 3) cyna, ołów oraz ze stopów takich jak Britain-metal, 4) aluminium i ze stopów aluminium. Folie niklowe zapewniają dość zadowalającą ochronę żelaza przed rdzą w pomieszczeniach.
Są jednak niewystarczające otwarte niebo; dodatkowo gorące tłuszcze, ocet, herbata, musztarda działają na polerowane powierzchnie niklowane, w wyniku czego niklowane zastawy stołowe i przybory kuchenne ulegają zabrudzeniu. W przypadkach, w których wymagana jest dość niezawodna ochrona przed skutkami złej pogody, a jednocześnie elegancki wygląd niklowanej powierzchni, należy zastosować żelazo. nakładana jest podwójna folia - cynk, a następnie nikiel. Ta metoda podwójnego powlekania (cynkiem a następnie niklem) stosowana jest również do tzw. gorset ze stali. W przypadku konieczności uzyskania szczególnie odpornych folii, takich jak np. na drutach, osadza się jednocześnie nikiel i platynę, stopniowo zwiększając zawartość tych ostatnich od 25% do 100% i na koniec wypala się przedmiot w strumień wodoru w temperaturze 900-1000 ° C Duże produkty, np. kotły warzelne, bębny wirówek lub wentylatory, jeśli ze względu na warunki ekonomiczne nie mogą być wykonane z czystego niklu, ale nie są wystarczająco odporne folią niklową na żelazie lub miedzi, są wyłożone kilkumilimetrową warstwą ołowiu, a nad nim warstwą niklu 1-2 mm. Rdzewienie niklowanych wyrobów żelaznych i stalowych jest spowodowane obecnością elektrolitu pozostającego w cienkich porach filmu niklowego. Zjawisko to jest eliminowane, jeśli produkty są przechowywane w oleju w temperaturze 200°C przed niklowaniem, odtłuszczone po schłodzeniu, lekko miedziowane, następnie niklowane w niskoprądowej kąpieli niklowo-cytrynianowej, a na koniec suszone w szafie w temperaturze 200° C; następnie wilgoć jest usuwana z porów, które są zatkane przez zawarty w nich olej.
Istnieje szereg propozycji narzucenia podwójnego folie ochronne na żeliwie, żelazie lub blachy stalowe, druty i taśmy w odwrotnej kolejności niż powyżej, tj. najpierw pokrywa się produkty cienką warstwą niklu w sposób kontaktowy lub elektrolityczny, a następnie zanurza je w kąpieli ze stopionego cynku lub cyny (Vivien i Lefebvre, 1860) . Proponuje się również dodanie pewnej ilości niklu do stopu 25-28 kg cynku, 47-49 kg ołowiu i 15 kg cyny, który służy do powlekania blach żelaznych na gorąco. Odporność powierzchni aluminium i jego stopów na działanie soli i woda morska m. b. uzyskuje się na nich galwanicznie, po oczyszczeniu piaskiem, kolejne warstwy niklu o grubości 6 µm, miedzi 20 µm i ponownie niklu 50 µm, po czym powierzchnia jest polerowana. Odporność aluminium na 15% wodorotlenek sodu uzyskuje się dzięki powłoce niklowej o grubości 40 mikronów. W niektórych przypadkach powłokę nakłada się nie czystym niklem, ale stopem, na przykład nikiel-miedź; w tym celu elektrolizę przeprowadza się w kąpieli zawierającej kationy w stosunku do wymaganego stopu; osadzony film jest następnie przenoszony do stopu przez podgrzanie produktu do rozgrzanego do czerwoności ciepła.
Kontakt niklowanie. Przedmioty stalowe, zgodnie z instrukcją F. Stolby (1876), po wypolerowaniu i odpowiednim odtłuszczeniu gotuje się w kąpieli z 10-15% wodnego roztworu czystego chlorku cynku, do którego dodaje się siarczan niklu aż do powstania zielonego zmętnienia zasadowa sól niklu. Niklowanie trwa około 1 godziny. Następnie przedmiot spłukuje się w wodzie z kredą, a kąpiel, po przefiltrowaniu i dodaniu soli niklowej, można ponownie wykorzystać. Powstała warstwa niklu jest cienka, ale mocno trzyma. W celu podwyższenia temperatury kąpieli zaproponowano przeprowadzenie procesu pod ciśnieniem (F. Stolba, 1880) lub zastosowanie kąpieli ze stężonym roztworem chlorku cynku. W celu uniknięcia rdzewienia przedmiotów trzyma się je przez 12 godzin w mleku wapiennym. Bardziej złożona kąpiel do przedmiotów żelaznych, uprzednio miedziowana w kąpieli 250 g siarczanu miedzi w 23 litrach wody z kilkoma kroplami kwasu siarkowego, zawiera 20 g kremu winowego, 10 g amoniaku, 5 g chlorek sodu, 20 g chlorku cyny, 30 g siarczanu niklu i 50 g podwójnego siarczanu soli niklowo-amonowej.
niklowanie galwaniczne. Wyczerpanie kąpieli niklowej m. b. zapobiega to dość łatwemu rozpuszczaniu anod niklowych. Walcowane, a zwłaszcza z czystego niklu, anody są trudne do rozpuszczenia, dlatego w technicznym niklowaniu jako anody stosuje się pręty niklowe zawierające do 10% żelaza. Jednak takie anody prowadzą do osadzania żelaza na przedmiocie, a obecność żelaza w warstwie niklowej pociąga za sobą szereg wad w niklowaniu. Jak wskazali Kalgane i Gammage (1908), nie można uzyskać przy anodach zawierających żelazo osadu całkowicie pozbawionego tego ostatniego. Ale złoże niklu będzie już zawierało tylko 0,10-0,14% żelaza, jeśli zawartość żelaza w anodach zostanie zmniejszona do 7,5%; zawartość żelaza w osadzie można dodatkowo zmniejszyć przez zamknięcie anod w workach z tkaniny, podczas gdy obrót elektrod prowadzi do zwiększenia zawartości żelaza w osadzie i zmniejszenia jego wydajności. Obecność żelaza w warstwie niklu prowadzi do osadzania się osadów o stopniowo zmniejszającej się zawartości żelaza, a zatem niejednorodnych pod względem właściwości mechanicznych na różnych głębokościach; K. Engemann (1911) uważa tę niejednorodność za jedyny powód łatwego odrywania się folii niklowych. Obecność żelaza m. in. przyczyna szeregu innych wad w niklowaniu (patrz tabela), na przykład łatwość rdzewienia folii.
Wice | Przyczyna | miara walki |
Nie występuje wytrącanie niklu, nie ma tworzenia się gazu | Źródło zasilania nie działa | Weryfikacja i odnowienie źródła energii |
Przewody podłączone nieprawidłowo | Przełączanie przewodów | |
Kąpiel jest za zimna | Podgrzanie kąpieli do temperatury powyżej 15°C | |
Kąpiel jest zbyt kwaśna | Dodawanie roztworu wodnego amoniak lub wodna zawiesina węglanu niklu z ciągłym mieszaniem i częstym testowaniem papieru z Kongo | |
Kąpiel zawiera cynk | Kąpiel jest alkalizowana węglanem niklu, mieszana przez kilka godzin, filtrowana i zakwaszana 10% kwasem siarkowym. | |
Niepełne pokrycie obiektu folią niklową | Niewystarczający prąd | Przedmioty zawieszone są w równych odległościach od anod, kąpiel jest podgrzewana do co najmniej 20°C |
Bardzo głębokie wklęsłości na powierzchni obiektu | Zainstalowane są małe anody pomocnicze, wsuwane we wnęki obiektu | |
Zasadowość kąpieli | Ostrożne zakwaszanie kąpieli 10% kwasem siarkowym z jednoczesnym mieszaniem i ciągłym testowaniem papierkiem lakmusowym | |
Niewielkie odpryski białego lub żółto-niklowegofolie polerskie | Zanieczyszczenie powierzchni przedmiotów tlenkami i tłuszczem | Dodatkowe czyszczenie powierzchni |
Za duże napięcie (powyżej 4 v) | Zwiększ liczbę przedmiotów niklowanych lub zmniejsz napięcie do 2,5-3 V | |
Zbyt kwaśna kąpiel | Neutralizacja amoniakiem lub wodną zawiesiną węglanu niklu | |
Ubóstwo kąpieli niklowej | Usunięcie części elektrolitu i dodanie soli niklu, aż kąpiel będzie miała normalny zielony kolor | |
Nieprawidłowa lepkość i napięcie powierzchniowe kąpieli | Dodatek gliceryny lub alkoholu amylowego lub wywarów ziołowych lub innych koloidów | |
Izolacja jonów wodorowych | Dodawanie utleniaczy lub absorberów wodoru; zastosowanie niezrównoważonego prądu przemiennego | |
Niewłaściwe przygotowanie powierzchni obiektów | Szorstkowanie powierzchni mechanicznie lub chemicznie, pokrywanie ich cienką warstwą niklu z gorącego roztworu chlorku niklu lub zimnego stężonego roztworu etylosiarczanu niklu | |
Opóźnienie lub rozdarcie folii niklowej, gdy przedmioty są zginane i rozciągane | Obecność kapilarnych warstw elektrolitu | Suszenie i podgrzewanie obiektów do 250-270 °С |
Niewystarczająca skrawalność blach pokrytych grubą warstwą niklu | Prawdopodobnie to samo | Płukanie, suszenie bez dostępu powietrza i na koniec podgrzewanie do niskiego, rozgrzanego do czerwoności ciepła |
Wgłębiona powierzchnia i film podziurawiony niezliczonymi porami | Cząsteczki kurzu i włókien unoszące się w wannie | Kąpiel jest gotowana, filtrowana i ustalana jest w niej prawidłowa reakcja. |
Powstawanie pęcherzyków gazu | Dotykanie pręta przewodzącego prąd. Bąbelki są usuwane; ustalić lekko kwaśną reakcję | |
Chropowatość i nierówności powierzchni | Ewolucja wodoru | Wprowadzenie od czasu do czasu wolnego chloru wiążącego wodór w postaci gazowej przez strumień lub roztwór wodny; z nieco mniejszym powodzeniem, chlor może. zastąpiony przez brom; wysoce zalecane jest dodanie roztworu chlorku kobaltu |
Niewystarczająca elastyczność folii | Wysoka odporność na kąpiel | Dodatek soli sodowej |
Zażółcenie filmu; powierzchnia staje się matowa, a następnie żółknie i ciemnożółty | Obecność w kąpieli zanieczyszczeń żelazowych, których zawartość wzrasta w starych kąpielach | Unikaj starych wanien, nie przesuwaj zbytnio wanien, pracuj ze słabymi prądami |
Czerń filmu, ciemne smugi w miejscach opóźnień przy prawidłowej gęstości prądu | Zawartość metali obcych w kąpieli (do 1%) | Usuwanie metali obcych |
Brak soli przewodzących |
Dodatek soli przewodzących w ilości 2-3 kg na 100 litrów kąpieli: amoniaku, chlorku potasu i chlorku sodu daje wzrost przewodności odpowiednio o 84,31 i 18% | |
Ubóstwo w kąpieli z solą niklową | Dodatek do soli niklowej | |
Opalenizna powierzchniowa | Zbyt wysoka przewodność wanny ze względu na jej nadmierną wytrzymałość | Kontrola stężenia kąpieli (np. stałej gęstości przy 5° Vẻ) i gęstości prądu |
Banding | Brud wytwarzany przez tarczę polerską w małych zagłębieniach | Eliminacja jest trudna; osiągnął do do pewnego stopnia natychmiastowe zanurzenie w kotle z ługiem lub mechanicznym nacieraniem przedmiotów |
Zmiany stężeń i występowanie przepływów cieczy | Zmniejszenie gęstości prądu i zwiększenie temperatury kąpieli | |
Plamienie | Niewystarczające czyszczenie gotowych produktów niklowanych | Dokładne mycie pod bieżącą wodą produktów po niklowaniu, a następnie zanurzenie we wrzącej wodzie czystej wody, strząsanie produktów i suszenie w rozgrzanych trocinach |
Słaba przyczepność folii niklowej do żelaza | Obecność rdzy | Dokładne usuwanie rdzy. Galwaniczne osadzanie warstwy pośredniej z kąpieli cyjankowej, po czym następuje zagęszczenie filmu w kąpieli kwasowej |
Kąpiel elektrolityczna do niklowania została opracowana przez Ch. z podwójnej soli niklowo-amonowej i słabych kwasów dodaje się w celu wyeliminowania soli zasadowych. Wyższa kwasowość kąpieli prowadzi do twardszych filmów. Należy pamiętać, że techniczny witriol niklu nie nadaje się do kąpieli, ponieważ często zawiera miedź; należy go usunąć przepuszczając siarkowodór przez wodny roztwór witriolu. Stosowane są również sole chlorowe, ale w kąpielach siarczanowych osady są twardsze, bielsze i bardziej odporne niż w przypadku kąpieli chlorkowych. Korzystne jest obniżenie wysokiej rezystancji kąpieli niklowej poprzez dodanie różnych soli przewodzących – zwłaszcza amoniaku i chlorku sodu – oraz przez ogrzewanie. Neutralizację nadmiaru kwasu siarkowego w starych roztworach z powodzeniem prowadzi się za pomocą węglanu niklu, który otrzymuje się z ciepłego wodnego roztworu siarczanu niklu wytrąconego sodą. W celu uzyskania bieli i gładkości folii pojawiło się wiele propozycji, aby do kąpieli niklowej dodawać różne kwasy organiczne (winowy, cytrynowy itp.) i ich sole, na przykład sole octowe, cytrynowe i winowe zasad i metale ziem alkalicznych (Keith, 1878), nikiel propionowy, sole boranowo-winianowe metali alkalicznych. W przypadku konieczności uzyskania gęstych osadów niklu proponuje się dodanie kwasu borowego, benzoesowego, salicylowego, galusowego lub pirogalowego, a dodatkowo 10 kropli kwasu siarkowego, mrówkowego, mlekowego na 1 litr kąpieli, aby zapobiec polaryzacji produktu. Jak zauważył Powell (1881), dodatek kwasu benzoesowego (31 g na kąpiel 124 g siarczanu niklu i 93 g cytrynianu niklu w 4,5 litra wody) eliminuje potrzebę stosowania chemicznie czystych soli i kwasów. Osad niklu ma dobre właściwości również z prostą kąpielą siarczanu niklowo-amonowego, ale pod warunkiem zasadowości roztworu, którą uzyskuje się przez dodanie amoniaku. Bardzo dobre osady uzyskuje się z obojętnego roztworu fluorku niklu-boranu w temperaturze pokojowej (w temperaturze powyżej 35°C roztwór rozkłada się na nierozpuszczalną sól zasadową) i gęstości prądu 1,1-1,65 A/dm 2 . Oto kilka przepisów na kąpiel. 1) 50 godzin wodorosiarczynu sodu, 4 godziny azotanu tlenku niklu i 4 godziny stężonego amoniaku rozpuszcza się w 150 godzinach wody. 2) 10-12 godzin siarczanu niklu, 4 godziny podwójnej soli niklowo-amonowej, 1-3 godziny kwasu borowego, 2 godziny chlorku magnezu, 0,2-0,3 godziny cytrynianu amonu, uzupełniane do 100 godzin. ) woda. Gęstość prądu 1,6 A/dm 2 nakłada błonę z szybkością 2 µm/h; Podnosząc temperaturę do 70°C można dwukrotnie lub trzykrotnie zmniejszyć opór kąpieli, a tym samym przyspieszyć niklowanie. 3) Elektrolit złożony z 72 g podwójnego siarczanu niklowo-amonowego, 8 g siarczanu niklu, 48 g kwasu borowego i 1 litr wody jest szczególnie korzystny dla miękkości i nieporowatości osadu, ponieważ zmniejsza uwalnianie wodór.
Uzyskiwanie specjalnych folii niklowych. 1) Białą warstwę na metalicznym cynku, cynie, ołowiu i brytanie otrzymuje się w kąpieli 20 g podwójnego siarczanu niklowo-amonowego i 20 g węglanu niklu rozpuszczonego w 1 litrze wrzącej wody i zobojętnionego w temperaturze 40 ° C kwasem octowym ; kąpiel musi być neutralna. 2) Matowy biały film otrzymuje się w kąpieli 60 g podwójnego siarczanu niklowo-amonowego, 15 g rekrystalizowanego siarczanu niklu, 7,4 g amoniaku, 23 g chlorku sodu i 15 g kwasu borowego na 1 litr wody; kąpiel e. b stężona do 10 ° Vẻ; napięcie od 2 do 2,5 V. 3) Czarną powłokę uzyskuje się na powierzchniach dokładnie odtłuszczonych lub pokrytych cienką warstwą białego niklu metodą elektrolizy w kąpieli 60 g podwójnego siarczanu niklowo-amonowego, 1,5 g rodanku amonu i około 1 g siarczanu cynku na 1 litr wody 4) Czarną powłokę otrzymuje się również w elektrolicie z 9 g podwójnej soli siarczanu niklowo-amonowego w 1 litrze wody, a następnie dodaje się 22 g tiocyjanianu potasu, 15 g węglan miedzi i 15 g białego arsenu, uprzednio rozpuszczonego w węglanie amonu; głębia odcienia czerni wzrasta wraz z zawartością arsenu w roztworze. 5) Ciemnoniebieski film otrzymuje się w kąpieli równych części podwójnych i prostych siarczanów niklu, doprowadzonych do 12 ° Bẻ, i dodaje się 2 godziny wywaru amoniaku z korzenia lukrecji na litr; elektroliza trwa 1 godzinę przy 3,5 V, a następnie kolejne 1/2 godziny przy 1,4 V. sól i 60 g siarczanu niklu, rozpuszczone w jak najmniejszej ilości wrzącej wody, dodawane do 50 cm3, a następnie mieszane z roztworami po 30 g siarczanu niklu i 60 g tiocyjanianu sodu, każdy w 0,5 l wody, po czym roztwór dodaje się do 4, 5 l. Powstały czarny film uzyskuje brązowy odcień poprzez zanurzenie produktu na kilka sekund w kąpieli 100,6 g nadchloranu żelaza i 7,4 g kwasu solnego w 1 litrze wody: po umyciu i wysuszeniu powierzchnia produktu jest lakierowana do naprawić ton.
Niklowanie aluminium i jego stopów. Zaproponowano kilka procesów. 1) Przygotowanie powierzchni wyrobów aluminiowych polega na odtłuszczeniu, następnie oczyszczeniu pumeksem i na końcu zanurzeniu w 3% wodnym roztworze cyjanku potasu; po elektrolizie w kąpieli niklowej produkty myje się zimną wodą. 2) Po przemyciu 2% roztworem cyjanku potasu produkty zanurza się w roztworze 1 g chlorku żelazowego (żelazochlorku) na 0,5 l wody i technicznego kwasu solnego, aż powierzchnia stanie się srebrnobiała, a następnie niklu- platerowane przez 5 minut. przy napięciu 3 V. 3) Produkty polerujące, usunięcie kompozycji polerującej benzyną, ekspozycja na kilka minut w ciepłym wodnym roztworze fosforanu sodu, sody i żywicy, mycie, zanurzenie na krótki czas w mieszaninie równych części 66% kwas siarkowy (zawierający trochę chlorku żelazowego) i 38% kwas azotowy, świeże mycie i elektroliza w kąpieli zawierającej sól niklu, sól gorzką i kwas borowy; napięcie 3-3,25 V. 4) Wg J.Kanaka i E.Tassilly'ego: wytrawianie produktu wrzącą zasadą potasową, szczotkowanie w mleku wapiennym, kąpiel 0,2% cyjano-potasowa, kąpiel 1 g żelaza w 500 g chlorowodoru kwas i 500 g wody, mycie, niklowanie w 1 litrze wody, 500 g chlorku niklu i 20 g kwasu borowego przy napięciu 2,5 V i gęstości prądu 1 A/dm 2 , na koniec polerowanie matowy szary osad. żelazna kąpiel służy do szorstkowania powierzchni aluminium, a tym samym przyczynia się do wytrzymałości, z jaką folia jest utrzymywana na metalu. 5) Według Fischera kąpiel do niklowania składa się z 50 g siarczanu niklu i 30 g amoniaku w 1 litrze wody przy gęstości prądu 0,1-0,15 A/dm2, w ciągu 2-3 godzin gęsty osad uzyskuje się wysoki połysk po wypolerowaniu olejem stearynowym i wapnem wiedeńskim. 6) wanna z hydromasażem(60°C) składa się z 3400 g podwójnego siarczanu niklowo-amonowego, 1100 g siarczanu amonu i 135 g cukru mlecznego w 27 litrach wody. 7) Zimna kąpiel zawiera azotan niklu, cyjanek potasu i fosforan amonu.
Kontrola folii niklowej. Rozpoznanie składu metalowej folii na przedmiocie, według L. Lovitona (1886), można przeprowadzić przez podgrzanie przedmiotu w zewnętrznym płomieniu palnika Bunsena: folia niklowa zmienia kolor na niebieski, otrzymuje czarne odbicie i pozostaje nienaruszony; srebro nie zmienia się w płomieniu, ale czernieje po potraktowaniu rozcieńczonym roztworem siarczku amonu; wreszcie powłoka cyny szybko zmienia kolor na szaro-żółty do szarego i znika po potraktowaniu wskazanym odczynnikiem. Sprawdzenie jakości filmu niklowego na żelazie i miedzi w odniesieniu do porów i wad można wykonać za pomocą tzw. test ferroksylowy i ze szczególną wygodą przy użyciu bibuły ferroksylowej pokrytej żelem agarowo-agarowym z błękitnym siarczkiem potasu i chlorkiem sodu. Nanieść zwilżoną powierzchnię na badaną powierzchnię i po 3-5 minutach. utrwalony w wodzie, papier ten daje dokumentalny obraz najmniejszych porów, które mogą być. zapisane.
Odzyskiwanie niklu ze starych produktów. Usuwanie powłoki niklowej z produktów wykonanych z żelaza i innych metali niepołączonych odbywa się w następujący sposób: a) za pomocą par rtęci w próżni lub pod zwykłym ciśnieniem; b) podgrzewanie skrawków siarką, po czym warstwę metalu można łatwo usunąć młotkami; c) podgrzewanie złomu z substancjami uwalniającymi siarkę, gdy wysoka temperatura) po nagłym ochłodzeniu film niklowy odskakuje; d) traktowanie kwasem siarkowym lub azotowym ogrzanym do 50-60°C; żelazo przechodzi do roztworu, a nikiel pozostaje prawie nierozpuszczony; jednak mimo swojej prostoty metoda ta ma niewielkie zastosowanie, gdyż otrzymany nikiel nadal zachowuje znaczną zawartość żelaza, którego nie usuwa się nawet podczas powtórnej obróbki kwasem (T. Fleitman); e) długotrwałe ogrzewanie z dostępem do powietrza lub pary wodnej, po którym lamówki poddawane są wstrząsom mechanicznym i odbijaniu niklu; e) rozpuszczanie elektrolityczne: żelazo platerowane niklem tworzy anodę w kąpieli zawierającej węglan amonu; jeśli powłoka składa się ze stopu niklu, konieczne jest wyregulowanie napięcia, a przy 0,5 V osadza się miedź, a przy napięciu większym niż 2 V - nikiel; w tym procesie żelazo nie ulega korozji; g) złom żelaza lub stali wykonuje się jako anodę w kąpieli wodnego roztworu azotanu sodu, podczas gdy katoda składa się z pałeczki węglowej; napięcie nie powinno przekraczać 20 V; h) Nikiel usuwa się z kubków cynkowych metodą elektrolizy przedmiotów wykonanych z anodą w kwasie siarkowym 50°; kwas o tym stężeniu ma właściwość rozpuszczania tylko niklu, srebra i złota, ale nie innych metali, jeśli jest prąd; przyłożone napięcie 2-5V; blachy żelazne służą jako katody, na których osadza się nikiel w postaci pyłu; cynk nie rozpuszcza się, mimo że krążki pozostają w elektrolicie przez długi czas.
Podczas pracy materiały podlegają fizycznemu zużyciu. W celu przywrócenia właściwości metalu stosuje się liczne metody ochrony. Jedną z najskuteczniejszych metod ochrony jest niklowanie materiałów.
Do nakładania niklu w domu stosuje się metody niklowania chemicznego i elektrolitycznego.
Co to jest niklowanie?
Niklowanie to proces nakładania cienkiej powłoki niklowej na powierzchnię materiału. Przyjmuje się, że warstwa niklu wynosi 1–50 µm.
Warstwa niklu służy do poprawy właściwości antykorozyjnych i odporności na zużycie materiałów. Dość często taka powłoka ma wartość ochronną i dekoracyjną.
Niklowanie służy do obróbki stali i stopów metali nieżelaznych. Cienka warstwa niklu służy do ochrony produktów wykonanych z manganu, tytanu, wolframu, molibdenu i stopów na ich bazie.
Opracowano i pomyślnie wdrożono metody nakładania niklowej powłoki ochronnej na ceramikę, plastik, porcelanę, szkło i inne powierzchnie niemetaliczne.
Rodzaje niklowania
Niklowanie w prostych warunkach domowych odbywa się na dwa sposoby:
- elektrolityczny;
- chemiczny.
Wybór metody zależy od struktury i kształtu materiału.
W metodzie elektrolitycznej stosuje się substancje, które częściowo lub całkowicie składają się z jonów i mają przewodnictwo jonowe. Powłoka niklowa jest nakładana ze względu na właściwości elektrochemiczne tych substancji. Najbardziej rozpowszechniony otrzymał elektrolity siarczanu sodu i chromu.
W zależności od stopnia odbicia powłoki rozróżnia się niklowanie:
Funkcje niklowania elektrolitycznego
- matowy;
- znakomity.
Do powlekania matowego stosuje się elektrolity bez dodatków. Produkty o matowym wykończeniu nie mają metalicznego połysku.
Brylantowe niklowanie uzyskuje się przez dodanie do elektrolitu specjalnych wybielaczy na bazie chloraminy, alkoholu propargilowego, bepzosulfamidu i innych środków utleniających.
Najlepszą ochronę powłoki niklowej uzyskuje się przy minimalnej porowatości warstwy ochronnej. W tym celu jest pokryty miedzią lub stosuje się wielowarstwową strukturę materiału.
Notatka. Przy tej samej grubości powłoki wielowarstwowe są kilkakrotnie bardziej niezawodne niż materiały jednowarstwowe.
Najczęstszymi przykładami materiałów wielowarstwowych są powłoki miedziowo-niklowo-chromowe.
Główne wady niklowania elektrolitycznego to:
- wysoki stopień porowatości;
- nierównomierne osadzanie się niklu;
- złożoność obróbki powierzchni o skomplikowanych kształtach.
Metoda opiera się na właściwości redukcji jonów niklu w środowisku płynnym. W tym celu stosuje się podfosforyn sodu lub inne odczynniki chemiczne. Metoda chemiczna pozwala na przetwarzanie produktów o złożonym kształcie powierzchni.
Wadą tej metody jest stosunkowo wysoki koszt suchych odczynników stosowanych do przygotowania wodnych roztworów chemicznych.
Przeprowadzanie niklowania elektrolitycznego w domu
Niklowanie elektrolityczne (galwaniczne) części odbywa się na dwa sposoby:
- zanurzenie części w elektrolicie;
- bez zanurzania części w elektrolicie.
Pierwsza metoda jest stosowana podczas obróbki małych części. Druga metoda stosowana jest przy obróbce dużych i ciężkich przedmiotów.
Przed niklowaniem metal jest pokryty miedzią.
Metoda zanurzenia w elektrolicie
Zgodnie z pierwszą metodą powierzchnia produktu jest szlifowana papierem ściernym w celu usunięcia warstwy tlenku. Próbka jest następnie myta w ciepła woda. Następnie jest traktowany roztworem sody i ponownie myty w ciepłej, czystej wodzie.
Następnie dwie cienkie miedziane płytki umieszcza się w szklanym lub porcelanowym naczyniu. Płyty pełnią rolę anod. Są umieszczone w pozycja pionowa, równolegle do siebie.
Produkt jest umieszczany między tymi dwoma płytami. Aby to zrobić, próbkę zawiesza się za pomocą drutu. Drut jest przymocowany do płytek z obu końców.
Do naczyń dodaje się wodny roztwór elektrolitu o następującym składzie:
- woda destylowana;
- 20% niebieski witriol;
- 2% kwas siarkowy.
Do zasilania podłączone są miedziane płytki. Wartość napięcia określa się na poziomie 15–20 mA na 1 cm2 powierzchni materiału.
Notatka. Elektrolit niklu jest wrażliwy na zmiany kwasowości. Aby utrzymać poziom kwasowości stosuje się związki buforowe na bazie kwasu borowego.
W roztworze elektrolitu chlorek miedzi dysocjuje (rozkłada się) na swoje składniki składowe. Jony przemieszczają się w kierunku katody i stają się neutralnymi atomami. Jony chloru są utleniane na anodzie.
Kiedy prąd przepływa przez elektrolit, jony miedzi przechodzą do roztworu. Z roztworu miedź osadza się na katodzie w postaci obojętnych atomów. Zanieczyszczenia pozostają na dnie naczynia. Czystość uzyskanej miedzi wynosi prawie 100%.
Po 30 minutach na części uformowanej cienka warstwa miedź. Oddziaływanie prądu elektrycznego powoduje wzrost grubości warstwy miedzi. Im większa grubość warstwy, tym mniej porów pozostaje na obrabianej powierzchni.
Metoda bez zanurzania części w elektrolicie
Niklowanie galwaniczne dużych części odbywa się bez zanurzania ich w elektrolicie. Aby to zrobić, użyj pędzla od luzu druty miedziane. Jako szczotkę często stosuje się linkę miedzianą, pozbawioną izolacji.
Poprzez zwiększenie osadzonej warstwy miedzi eliminuje się porowatość powierzchni próbki.
Proces osadzania niklu przebiega podobnie jak proces miedziowania powierzchniowego. W tym celu do pojemnika dodaje się elektrolit. Skład elektrolitu obejmuje następujące odczynniki chemiczne, g/l:
- roztwór siarczanu sodu - 310;
- roztwór chlorku niklu - 65;
- kwas ortoborowy - 45;
- 1,4-butanodiol - 0,15;
- orto-sulfobenzimid (sacharyna) - 2,0;
- kaolin (limonka) - 1,0.
Cienkie płytki niklowe są zanurzane w elektrolicie. Pełnią rolę anod. Produkt umieszcza się między nimi. Końce płytek są połączone z zaciskiem zasilającym z ładunkiem dodatnim. Korpus części jest połączony z biegunem ujemnym.
Reostat służy do kontrolowania prądu. Kontrola wielkości dostarczanego prądu elektrycznego odbywa się za pomocą miliamperomierza. Przyłożony prąd nie powinien przekraczać 6 V. Osadzanie niklu odbywa się w temperaturze około 50°C i gęstości prądu elektrycznego 4–5 A/dm2. Czas trwania procesu to 3 minuty.
Notatka. Niklowanie bez podkładu ma raczej słabą przyczepność do powierzchni. Aby poprawić przyczepność, użyj obróbka cieplna produkty w temperaturze 450 stopni.
Ostatni etap obróbki części
Obrobiona część jest myta pod strumieniem czystej ciepłej wody i suszona.
Niklowane wykończenie ma matowe wykończenie. Aby nadać połysk, część jest polerowana.
Wadliwe powłoki niklowe są usuwane przez rozpuszczenie anodowe w elektrolicie. W tym celu w skład elektrolitu wchodzi kwas siarkowy. Przyjmuje się, że gęstość chemiczna kwasu wynosi 1,2-2,8 kg/m3. Proces usuwania warstwy niklu odbywa się w temperaturze 20-25°C i gęstości prądu anodowego 5 A/dm2.
Przeprowadzanie niklowania chemicznego w domu
Chemiczna metoda niklowania w domu odbywa się za pomocą roztworów roboczych. W zależności od ilości suchych odczynników szybkość narastania warstwy niklu wynosi 80 µm/h lub więcej.
Skład roztworu roboczego obejmuje następujące odczynniki, g/l:
- witriol niklu (proszek siarczanu niklu) - 20;
- galena (proszek siarczku ołowiu) - 20;
- octan sodu - 15;
- roztwór podfosforynu sodu - 25.
Temperatura robocza roztworu chemicznego wynosi 90°C. Po usunięciu odczynnika wiodącego szybkość reakcji spada do 50 µm/h lub mniej.
Po osiągnięciu temperatury roboczej obrabiany przedmiot jest opuszczany do pojemnika z roztworem. Przed niklowaniem powłoka jest czyszczona i odtłuszczana.
Produkt utrzymuje się w roztworze roboczym przez 1 godzinę. Gdy odparowuje, dodaje się wodę destylowaną.
Pod koniec procesu część jest wyjmowana i myta w ciepłej wodzie. Po spłukaniu produkt poddawany jest dokładnemu suszeniu. Jeśli to konieczne, dokładnie wypoleruj.
Wydłużona żywotność niklowania
Niklowanie może podlegać ciągłej korozji powierzchni. Proces korozji zachodzi tylko w okres początkowy. Wraz ze wzrostem temperatury roztworu roboczego korozja powierzchniowa wnika głęboko w materiał. Wtedy proces ten zwalnia i zatrzymuje się całkowicie.
Aby wydłużyć żywotność powłoki niklowej, stosuje się technologię miedziowania. Miedziowanie eliminuje również drobne defekty powierzchni. Zastosowanie miedzi jako podłoża zapewnia niezawodność i trwałość ochrony niklowej.
Porowatość miedziowanie powoduje zniszczenie warstwy ochronnej i skraca żywotność ukończony produkt. Metal podłoża ulega korozji, po której następuje złuszczanie warstwy ochronnej.
Najczęściej produkty z jednowarstwową powłoką ochronną narażone są na procesy korozyjne. Części wielowarstwowe są odsłonięte szkodliwe czynniki mniej.
Aby chronić produkty przed uszkodzeniem, podejmuje się szereg dodatkowych środków. Do zamykania porów stosuje się specjalne dodatki.
Notatka. Aby zapobiec utracie twardości, niklowanie stali odbywa się w temperaturze 250-300ºС.
Dodatkowa obróbka części w celu przedłużenia żywotności
Niklowanie w domu odbywa się następującymi metodami:
- Suchy odczynnik tlenku magnezu miesza się z wodą do stanu papkowatego. Z powstałą masą część jest starannie przetwarzana i zanurzana na kilka minut w 50% kwasie solnym lub siarkowym.
- Powierzchnię roboczą przeciera się penetrującym smarem. Następnie produkt zanurza się w oczyszczonym oleju rybim. Nadmiar tłuszczu jest usuwany po dniu za pomocą benzyny lub innych rozpuszczalników.
- Duże części są traktowane olejem rybnym w dwóch przejściach. Odstęp między zabiegami powinien wynosić co najmniej 12 godzin. Po dwóch dniach nadmiar tłuszczu niewolnika zostaje usunięty.
Zastosowanie stopów niklu z innymi metalami może poprawić właściwości fizykochemiczne niklu.
Aluminium przyczynia się do wzrostu oporu elektrycznego i odporność na korozję nikiel.
Wolfram, molibden i tytan zwiększają jego odporność na ciepło.
Dodatek chromu prowadzi do wzrostu odporności powłoki niklowej w roztworach utleniających i redukujących.
Miedź zwiększa odporność niklu na działanie różnych kwasów.
Niklowanie to proces nakładania bardzo cienkiej warstwy niklu na metalową powierzchnię.
Grubość warstwy niklu w zależności od zadania, gabarytów detalu i jego dalszego wykorzystania zawiera się w przedziale od 0,8 do 55 mikronów.
Niklowanie na czarno chroni metalowy przedmiot przed destrukcyjnym wpływem otoczenie zewnętrzne– utlenianie, korozja i reakcje z solą, alkaliami i kwasami.
Przedmioty, które mogą wymagać takiej ochrony to:
- produkty metalowe, które będą na świeżym powietrzu;
- części karoserii pojazdów mechanicznych i motocykli, w tym wykonane z aluminium;
- sprzęt medyczny i stomatologiczny;
- produkty, które mają przedłużony kontakt z wodą;
- ozdobne ogrodzenia metalowe, w tym aluminiowe;
- przedmioty, które wchodzą w kontakt z silnym środki chemiczne I tak dalej.
Jak widać, technologia różnego niklowania jest stosowana nie tylko w przemyśle, ale czerń może być potrzebna w domu, własnymi rękami.
Rozważ główne metody nakładania warstwy ochronnej własnymi rękami w domu, metale, które pozwalają nakładać nikiel, subtelności i cechy każdego procesu.
W praktyce stosowane są dwie metody nakładania warstwy niklu - elektrolityczna i chemiczna.
Nie będziemy studiować zawiłości procesu przemysłowego, ale opiszemy wdrożenie w domu.
Na filmie przedstawiono technologię nakładania warstwy niklu.
niklowanie elektrolityczne
Przed niklowaniem elektrolitycznym (inaczej nazywanym również galwanicznym) konieczne jest wykonanie elektrochemicznego miedziowania części lub przedmiotu obrabianego.
Istnieją dwie metody, w tym galwaniczna - z zanurzeniem w roztworze elektrolitu i bez zanurzenia.
W pierwszym przypadku metalowy przedmiot jest starannie obrabiany papierem ściernym, usuwany jest z niego film tlenkowy, najpierw myje się go ciepłą wodą w celu usunięcia rozpuszczalnika, a następnie w roztworze sody i ponownie w wodzie.
Umieść dwie anody miedziane i część w szklanym pojemniku, mocując je drutem między płytami anodowymi.
Wyprodukujemy w domu miedziowanie elektrochemiczne przy użyciu elektrolitu składającego się z wody z dodatkiem 20% siarczanu miedzi i 2% kwasu siarkowego.
Po półgodzinnej obróbce prądem na części pojawi się cienka warstwa miedzi, a im dłużej trwa miedziowanie elektrochemiczne, tym warstwa będzie grubsza.
Jeśli część jest duża lub nie ma odpowiednich pojemników szklanych, można zastosować miedziowanie elektrochemiczne bez zanurzania w elektrolicie.
W tym celu wykonujemy miedziany pędzel (można użyć skręcanego kabel miedziany, oczywiście zdejmując izolację tylko na końcach), którą dołączamy do plusa źródła prądu i mocujemy drewnianym patyczkiem.
Oczyszczoną, odtłuszczoną płytkę metalową wkładamy do dość szerokiego szklanego pojemnika, napełniamy roztworem elektrolitu (można wziąć nasycony siarczan miedzi) i podłączamy do minusa źródła prądu.
Teraz zanurzamy pędzel w elektrolicie i zbliżamy się do powierzchni części. Ważna jest stała obecność roztworu na miedzianej szczotce.
Po chwili zauważysz, że na powierzchni obrabianego przedmiotu pojawiła się warstwa miedzi. Im grubsza warstwa miedzi zostanie nałożona, tym mniej porów pozostanie.
Na przykład na 1 cm2 przy jednowarstwowym osadzeniu miedzi będzie kilkadziesiąt porów przelotowych, a przy zastosowaniu trójwarstwowym praktycznie nie będzie ich.
Zabiegać pożądana grubość miedź i możesz przejść do następnego kroku.
Nakładanie warstwy niklowej (galwanicznej) odbywa się podobnie jak proces miedziowania z zanurzeniem w elektrolicie.
Tak więc część zawieszona na drucie i anody niklowe są opuszczane do elektrolitu, druty z anod są połączone z plusem, a drut z części jest podłączony do minusa.
- Siarczan niklu, sód i magnez w proporcjach 14:5:3, 0,5% chlorek sodu i 2% kwas borowy;
- 30% siarczan niklu, 4% chlorek niklu i 3% kwas borowy.
Wlej suchą mieszankę z jednym litrem neutralna woda, dokładnie wymieszać iw razie potrzeby pozbyć się wytrąconego osadu i użyć go jako elektrolitu w niklowaniu elektrolitycznym.
Galwanizacja wystarcza do przeprowadzenia w ciągu pół godziny od ekspozycji prąd stały o mocy 5,8-6 V.
W wyniku przetwarzania prądu przez elektrolit otrzymujemy matową nierówną warstwę szary kolor. Aby go wyrównać, metalowy przedmiot musi być dokładnie oczyszczony i wypolerowany.
Ta technologia nie może być stosowana do części z szorstką powłoką lub z wąskimi i głębokimi otworami.
W takim przypadku musisz użyć metoda chemiczna niklowanie lub czernienie części.
Technologia czernienia polega na tym, że na metal nakładana jest pośrednia powłoka cynkowa lub niklowa, a od góry część pokryta jest cienką, nie większą niż 2 mikrony, powłoką z czarnego niklu.
Dekoracyjna metalowa balustrada wykonana z elementów niklowanych w kolorze czarnym będzie dobrze trzymała się i pięknie wyglądała.
W niektórych przypadkach wymagane jest niklowanie i chromowanie.
Metoda niklowania chemicznego
Technologia chemicznego niklowania części polega na tym, że metalowy półfabrykat zanurza się na pewien czas we wrzącym roztworze, podczas którego na jego powierzchni osadzają się cząsteczki niklu.
Nie ma efektu elektrochemicznego, nie jest potrzebny prąd.
Technologia ma na celu uzyskanie silnej adhezji warstwy niklu do metalu (szczególną jakość przyczepności powierzchni i osadzonej warstwy obserwuje się podczas niklowania stali i żelaza).
Wykonanie niklowania chemicznego różnych części w garażu lub małym warsztacie jest realistyczne.
Rozważ krok po kroku:
- Suche odczynniki miesza się w emaliowanych naczyniach i napełnia wodą;
- Doprowadzić powstałą ciekłą mieszaninę do wrzenia i dopiero wtedy dodać podfosforyn sodu;
- Zanurz obrabiany przedmiot w pojemniku z płynem, aby nie dotykał krawędzi i dna. W rzeczywistości wymagana będzie instalacja do chemicznego niklowania, którą można wykonać niezależnie od emaliowanej miski o odpowiednim rozmiarze i wspornika dielektrycznego, na którym będzie zawieszony przedmiot;
- W zależności od użytego roztworu gotowanie powinno trwać od jednej do trzech godzin;
- Obrabiany przedmiot jest wyjmowany i myty wodą zawierającą wapno gaszone, po czym można wykonać polerowanie.
Wszystkie kompozycje do chemicznego niklowania części będą koniecznie zawierać chlorek lub siarczan niklu, podfosforyn sodu o różnej kwasowości i niektóre kwasy.
Technologia przewiduje obróbkę 20 cm2 powierzchni w jednym litrze roztworu.
Kompozycje kwasowe tworzą warstwę niklu na metalach żelaznych, podczas gdy kompozycje alkaliczne lepiej nadają się do stali nierdzewnej.
Kilka subtelności:
- Folia niklowa osadzona na metalu bez miedziowania ma słabą przyczepność do powierzchni. Aby to poprawić, można zastosować obróbkę cieplną, utrzymując przedmiot w temperaturze powyżej 450 stopni;
- Do tej temperatury nie można podgrzać utwardzonych produktów, po podgrzaniu do 350-400 stopni stracą swoją twardość. Ten problem rozwiązuje dłuższa ekspozycja, ale w temperaturze w zakresie 250-300ºС;
- Podczas nakładania warstwy niklu na duże części konieczne staje się wymieszanie roztworu, co prowadzi do konieczności ciągłej filtracji. Jest to główna trudność w prowadzeniu procesu w warunkach nieprzemysłowych.
Podobnie, ale używając innej kompozycji, możesz pokryć części warstwą srebra. W sprzęcie wędkarskim często stosuje się srebrzenie, aby zapobiec matowieniu haczyków i przynęt.
Technologia nakładania srebra jest prosta i różni się od niklowania składem elektrolitu, czasem i temperaturą roztworu roboczego (aby uzyskać równomierną warstwę srebra, wymagana jest kompozycja podgrzana do 90 stopni).
Roztwory srebra można przygotować z wody, lapisu leczniczego i 10% roztworu soli fizjologicznej.
Wytrącone srebro wypłukać i wymieszać z 2% podsiarczynem, przefiltrować, dodać pył kredowy i wymieszać do uzyskania kremowego stanu.
Ta mieszanina może pocierać metal, aż utworzy się na nim warstwa srebra.
Przechowywanie tego roztworu jest dozwolone przez kilka dni, roztwór srebra, który pozwala na długotrwałe przechowywanie - do sześciu miesięcy, można przygotować w następujący sposób: 15 g lapisu, 55 g kwasu cytrynowego (odpowiedni jest kulinarny) i 30 g chlorek amonu.
Wszystkie składniki są mielone na pył i mieszane. Proszek do nakładania srebra jest przechowywany na sucho.
Aby pracować wilgotną ściereczką, dotknij mieszaniny i przetrzyj nią powierzchnię, która ma być leczona.
Na oczyszczoną część nakładane jest napylanie srebrem, ale nie jest konieczne specjalne przygotowanie.
Powyższe metody nakładania niklu i srebra na części metalowe można łatwo powtórzyć samodzielnie w domu.
Czasami możesz napotkać potrzebę niklowania aluminium. Niklowanie aluminium jest procesem dość kosztownym i zawodnym. Elektrolit do niklowania aluminium jest dość drogi, ale często bąbelkuje.
Problem z niklowaniem aluminium w domu to słaba przyczepność - błyszcząca niklowa powłoka "łzy".
Do chemicznego niklowania aluminium odpowiedni jest następujący skład:
- Siarczan niklu - 20g/l;
- Octan sodu - 10g/l;
- Podfosforyn sodu - 25g/l;
- Timocznik, roztwór o stężeniu 1 g/l – 3 ml;
- Fluorek sodu - 0,4 g/l;
- Kwas octowy - 9 ml