Jak nazywa się odporność materiałów na korozję? Jakie są sposoby na zwiększenie odporności na korozję? Odporność korozyjna materiałów budowlanych
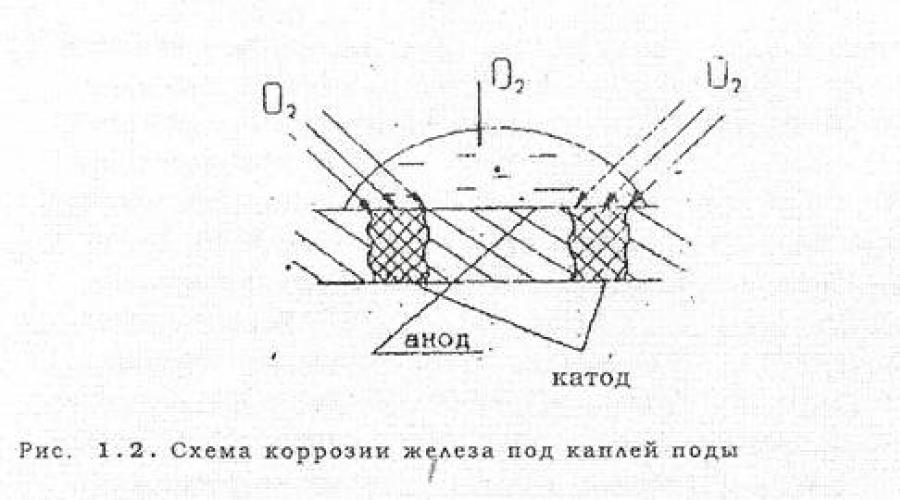
Przeczytaj także
Cel pracy: zapoznanie się z mechanizmami i szybkościami korozyjnego niszczenia metali.
1. Wytyczne
Korozyjne niszczenie metali to spontaniczne przejście metalu do bardziej stabilnego stanu utlenionego pod wpływem środowisko. W zależności od charakteru środowiska wyróżnia się korozję chemiczną, elektrochemiczną i biokorozję.
Korozja elektrochemiczna jest najczęstszym rodzajem korozji. Korozja konstrukcji metalowych w warunkach naturalnych - w morzu, w ziemi, w wody gruntowe, w wyniku kondensacji lub adsorpcji filmów wilgoci (w warunkach atmosferycznych) ma charakter elektrochemiczny. Korozja elektrochemiczna to zniszczenie metalu, któremu towarzyszy wygląd prąd elektryczny w wyniku pracy wielu par makro- i mikrogalwanicznych. Mechanizm korozji elektrycznej dzieli się na dwa niezależny proces:
1) proces anodowy - przejście metalu w roztwór w postaci uwodnionych jonów z pozostawieniem równoważnej ilości elektronów w metalu:
(-)A: Me + mH 2 O → 1+ + ne
2) proces katodowy, asymilacja nadmiaru elektronów w metalu przez niektóre depolaryzatory (cząsteczki lub jony roztworu, które można zredukować na katodzie). W przypadku korozji w środowiskach obojętnych depolaryzatorem jest zwykle korozja tlenu rozpuszczonego w elektrolicie:
(+)K: O 2 + 4e +2H 2O →4OH¯
Do korozji w środowisku kwaśnym - jon wodoru
(+)K: H H 2 O + e → 1/2H 2 + H 2 O
W wyniku kontaktu powstają pary makrogalwaniczne różne metale. W tym przypadku metal o bardziej ujemnym potencjale elektrody jest anodą i ulega utlenianiu (korozji).
Metal o większym potencjale dodatnim służy jako katoda. Działa jako przewodnik elektronów z metalu anody do cząstek otoczenia zdolnych do odbioru tych elektronów. Zgodnie z teorią mikropar przyczyną korozji elektrochemicznej metali jest obecność na ich powierzchni mikroskopijnych zwartych elementów galwanicznych, które powstają na skutek niejednorodności metalu i jego kontaktu z otoczeniem. W odróżnieniu od elementów galwanicznych wyprodukowanych specjalnie w technologii, pojawiają się one samoistnie na powierzchni metalu. W cienka warstwa wilgoć, zawsze istniejąca na powierzchni metalu, rozpuszcza O 2, CO 2, SO 2 i inne gazy z powietrza. Stwarza to warunki, w których metal wchodzi w kontakt z elektrolitem.
Z drugiej strony różne obszary powierzchni danego metalu mają różne potencjały. Powodów tego jest wiele, na przykład potencjalne różnice między różnie obrobionymi częściami powierzchni, różnymi składnikami konstrukcyjnymi stopu, zanieczyszczeniami i metalem nieszlachetnym.
Obszary powierzchni o bardziej ujemnym potencjale stają się anodami i rozpuszczają się (korodują) (rysunek 1.1).
Część uwolnionych elektronów przejdzie z anody na katodę. Polaryzacja elektrod zapobiega jednak korozji, ponieważ elektrony pozostające na anodzie tworzą podwójną warstwę elektryczną z jonami dodatnimi, które przeszły do roztworu i powodują rozpuszczenie metali. W rezultacie może wystąpić korozja elektryczna, jeśli elektrony z miejsc anodowych są w sposób ciągły odciągane na katodzie, a następnie usuwane z miejsc katodowych. Proces usuwania elektronów z miejsc katodowych nazywany jest depolaryzacją, a substancje lub jony powodujące depolaryzację nazywane są depolaryzatorami. Jeśli dojdzie do kontaktu dowolnego metalu ze stopem, stop uzyskuje potencjał odpowiadający potencjałowi najbardziej ujemnego metalu zawartego w jego składzie. Kiedy mosiądz (stop miedzi i cynku) wejdzie w kontakt z żelazem, mosiądz zacznie korodować (z powodu obecności w nim cynku). Kiedy zmienia się środowisko, potencjał elektrody poszczególnych metali może się radykalnie zmienić. Chrom, nikiel, tytan, aluminium i inne metale, których normalny potencjał elektrody jest ostro ujemny, w normalnych warunkach atmosferycznych ulegają silnej pasywacji, pokrywają się warstwą tlenku, w wyniku czego ich potencjał staje się dodatni. W warunkach atmosferycznych i świeża woda Będzie działać następujące ogniwo galwaniczne:
(-)Fe | H2O, O2 | Al2O3(Al)+
(-)A: 2Fe – 4e = 2Fe 2+
(+)K: O 2 + 4e + 2H 2 O = 4OH¯
W rezultacie: 2Fe 2 + 4OH¯ = 2Fe(OH) 2
4Fe(OH) 2 + O 2 + 2H 2 O = 2Fe(OH) 3
Jednak w środowisku kwaśnym, zasadowym lub w środowisku obojętnym, zawierającym jony chloru (na przykład w wodzie morskiej), które niszczą warstwę tlenkową, aluminium w kontakcie z żelazem staje się anodą i ulega procesowi korozji. Następujące ogniwo galwaniczne będzie pracować w roztworze NaCl i wodzie morskiej:
|
(-)A: Al – 3e = Al 3+
(+)K: O 2 +4e + 2H 2 O = 4OH¯
4Al 3 + 12OH¯ = 4Al(OH) 3
Bardzo często do korozji elektrochemicznej dochodzi na skutek zróżnicowanego napowietrzenia, czyli nierównego dostępu tlenu z powietrza do poszczególnych obszarów powierzchni metalu. Na ryc. 1.2. przedstawia przypadek korozji żelaza i kroplę wołów. W pobliżu krawędzi kropli, gdzie tlen łatwiej przenika, pojawiają się odcinki katodowe, a w środku, gdzie grubość warstwy ochronnej wody jest większa i tlen jest trudniej wnikać, pojawia się odcinek anodowy .
Na występowanie korozyjnych ogniw galwanicznych wpływają różnice w stężeniu rozpuszczonego elektrolitu, różnice w temperaturze i oświetleniu oraz inne warunki fizyczne.
Ochrona przed korozją
Przyczyny niszczenia korozyjnego metali są liczne. Istnieją również różne metody zabezpieczenia przed korozją:
leczenie otoczenie zewnętrzne;
powłoki ochronne;
ochrona elektrochemiczna;
produkcja stopów o specjalnej odporności na korozję.
Oczyszczanie środowiska zewnętrznego polega na usunięciu lub ograniczeniu działania znajdujących się w nim substancji powodujących korozję. Na przykład usuwanie tlenu rozpuszczonego w jodzie (odpowietrzanie). Czasami do roztworu dodaje się specjalne substancje hamujące korozję, zwane opóźniaczami lub INHIBITORAMI (urotropina, tiomocznik, anilina i inne).
Części przeznaczone do ochrony w warunkach atmosferycznych umieszcza się wraz z inhibitorami w pojemniku lub zawija w papier, warstwę wewnętrzną impregnuje się inhibitorem, a warstwę zewnętrzną impregnuje się parafiną. Inhibitor odparowując, adsorbuje się na powierzchni części, powodując zahamowanie procesów elektrodowych.
Rola powłoki ochronne sprowadza się do odizolowania metalu od wpływu ochronnego środowiska zewnętrznego. Osiąga się to poprzez nakładanie lakierów, farb i powłok metalowych na powierzchnię metalu.
Powłoki metalowe dzielą się na anodowe i katodowe. W przypadku powłoki ANODOWEJ potencjał elektrody metalu powłoki jest bardziej ujemny niż potencjał zabezpieczanego metalu. W przypadku powłoki KATODOWEJ potencjał elektrody metalu powłoki jest bardziej dodatni niż potencjał metalu nieszlachetnego.
Do widzenia warstwa ochronna całkowicie izoluje metal nieszlachetny od otoczenia, nie ma zasadniczej różnicy pomiędzy powłoką anodową i katodową. W przypadku naruszenia integralności powłoki pojawiają się nowe warunki. Powłoka katodowa, np. cyna na żelazie, nie tylko przestaje chronić metal nieszlachetny, ale także swoją obecnością wzmaga korozję żelaza (w powstałym ogniwie galwanicznym żelazo jest anodą).
W przypadku ochrony elektrochemicznej redukcję lub całkowite zaprzestanie korozji osiąga się poprzez wytworzenie wysokiego potencjału elektroujemnego na chronionym produkcie metalowym. W tym celu chroniony produkt podłącza się albo do metalu o większym potencjale elektrody ujemnej, zdolnego do łatwiejszego oddawania elektronów (ochrona protektorowa), albo do bieguna ujemnego zewnętrznego źródła prądu (katodowa ochrona elektryczna).
Powłoka anodowa, na przykład cynk na żelazie, wręcz przeciwnie, jeśli integralność warstwy powłoki zostanie uszkodzona, sama ulegnie zniszczeniu, chroniąc w ten sposób metal nieszlachetny przed korozją (w powstałym ogniwie galwanicznym cynk jest anodą) .
Produkcja specjalnych stopów odpornych na korozję, stali nierdzewnych itp. sprowadza się do wprowadzenia do nich dodatków różnych metali.
Dodatki te wpływają na mikrostrukturę stopu i przyczyniają się do powstawania w nim pierwiastków mikrogalwanicznych, w których całkowity emf, na skutek wzajemnej kompensacji, zbliża się do zera. Takimi przydatnymi dodatkami, zwłaszcza do stali, są chrom, nikiel i inne metale.
1. Wykonanie zadania
Ćwiczenie 1
Przeprowadzanie wysokiej jakości reakcji chemicznych, które umożliwiają wykrycie jonów metali, które przeszły do roztworu podczas procesu korozji anodowej.
Instrumenty i odczynniki: roztwory ZnSO 4, FeSO 4 i K 3, komplet probówek.
Procedura: Do probówek wlać 1-2 ml roztworu soli:
a) ZnSO4 i kilka kropli K3;
b) FeSO i kilka kropli K3.
Uwaga na opady. Zapisz odpowiednie reakcje w postaci molekularnej i jonowej.
Zadanie 2
Badanie mechanizmu korozji metali pod wpływem bezpośredniego kontaktu w środowisku obojętnym.
Doświadczenie przeprowadzono na instalacji pokazanej na rys. 1.7
Do probówki w kształcie litery U wlej 5-10 ml wodnego roztworu NaCl. Opuszczane są do niego metalowe płyty, połączone ze sobą za pomocą zacisków.
Metalowe płytki należy dokładnie oczyścić papierem ściernym, a punkt styku płytki z zaciskiem znajduje się poza roztworem. Podczas wykonywania doświadczenia należy zwrócić uwagę na zmianę barwy roztworu na katodzie i anodzie.
Pisać:
1) procesy korozji anodowej i katodowej
2) odpowiednie reakcje, w wyniku których wykryto jon metalu w roztworze
3) obwód ogniwa galwanicznego.
1. Opuszcza się płyty Zn i Fe.
Do roztworu, w którym znajduje się elektroda cynkowa, w którym znajduje się elektroda żelazna, dodaj kilka kropli K3 i kilka kropli fenoloftaleiny.
2. Opuszcza się płyty Fe i Cu,
Do roztworu, w którym znajduje się elektroda żelazna, dodać kilka kropli K3; do roztworu, w którym znajduje się elektroda miedziana, dodać kilka kropli fenoloftaleiny.
Porównaj zachowanie żelaza w obu przypadkach i wyciągnij odpowiednie wnioski.
Zadanie 3
Badanie mechanizmu korozji metali podczas ich bezpośredniego kontaktu w środowisku kwaśnym.
Wykonaj doświadczenie na instalacji pokazanej na rys. 1.8.
Do porcelanowego kubka wlej 10% roztwór HCl. Zanurz dwa metale Al i Cu w roztworze i obserwuj zachowanie metali. Który metal wytwarza pęcherzyki wodoru? Napisz odpowiednie reakcje. Doprowadź do kontaktu prawie metali ze sobą. Który metal wytwarza pęcherzyki wodoru, gdy metale się zetkną? Narysuj schemat ogniwa galwanicznego oraz procesów zachodzących na jego elektrodach. Zapisz ogólne równanie reakcji.
3. Przykłady rozwiązywania problemów
Przykład 1
Rozważmy proces korozji, gdy żelazo wchodzi w kontakt z ołowiem w roztworze HCl
W roztworze elektrolitu (HCl) układem tym jest ogniwo galwaniczne, w obwodzie wewnętrznym którego anodą jest Fe (E° = 0,1260). Atomy żelaza, przenosząc dwa elektrony na ołów, przechodzą do roztworu w postaci jonów. Elektrony na ołowiu redukują jony wodoru w roztworze, ponieważ
HCl = H + + Cl¯
Proces anodowy Fe 0 – 2e = Fe 2+
Proces katodowy 2H + + 2e = 2H 0
Przykład 2
Proces korozji pod wpływem kontaktu Fe z Ph w roztworze NaCl. Ponieważ roztwór NaCl ma odczyn obojętny (sól utworzona przez mocną zasadę i mocny kwas), to
Proces anodowy Fe – 2e = Fe 2+,
Proces katodowy O 2 + 4e + 2H 2 O = 4OH¯
Chlorek sodu (NaCl) nie bierze udziału w procesach korozji; na schemacie jest on pokazany jedynie jako substancja mogąca zwiększyć przewodność elektryczną roztworu elektrolitu.
Przykład 3
Dlaczego chemicznie czyste żelazo jest bardziej odporne na korozję niż żelazo przemysłowe? Ułóż równania elektroniczne dla procesów anodowych i katodowych zachodzących podczas korozji żelaza przemysłowego.
Rozwiązanie
Proces korozji żelaza przemysłowego ulega przyspieszeniu w wyniku tworzenia się w nim pierwiastków mikro i submikrogalwanicznych. W parach mikrogalwanicznych metal nieszlachetny z reguły służy jako anoda, tj. żelazo. Katody to wtrącenia w metalu, na przykład ziarna grafitu i cementu. W miejscach anodowych jony metali przechodzą do roztworu (utlenianie).
Odp.: Fe – 2e = Fe 2+
Na odcinkach katodowych elektrony przenoszone tutaj z odcinków anodowych wiązane są albo przez tlen z powietrza rozpuszczony w wodzie, albo przez jony wodoru. W środowiskach neutralnych zachodzi depolaryzacja tlenu:
K: O 2 + 4e + 2H 2 O = 4OH¯
W środowiskach kwaśnych (wysokie stężenie jonów H) dochodzi do depolaryzacji wodoru
K: 2H + + 2e = 2H 0
Przykład 4
Wymień, czy powłoka cynkowa na wyrobie żelaznym jest katodowa czy anodowa? Jakie procesy będą miały miejsce, jeśli integralność powłoki zostanie naruszona, a produkt znajdzie się w wilgotnym powietrzu?
Rozwiązanie
Potencjał elektrody cynku ma niższą wartość algebraiczną niż potencjał elektrody żelaza, dlatego powłoka jest anodowa. Jeżeli integralność warstwy cynku zostanie naruszona, powstaje korozyjna para galwaniczna, w której cynk będzie anodą, a żelazo katodą. Proces anodowy polega na utlenianiu cynku:
Zn 2+ + 2OH = Zn(OH) 2
Proces katodowy zachodzi na żelazie. W wilgotnym powietrzu występuje głównie depolaryzacja tlenu.
K(Fe): O 2 + 4e + 2H 2 O = 4OH¯
Przykład 5
Płyty kadmowe i niklowe zanurzone w rozcieńczonym kwasie siarkowym rozpuszczają się w nim, uwalniając wodór. Co się zmieni, jeśli oba jednocześnie opuścimy do naczynia z kwasem, łącząc końce drutem?
Rozwiązanie
Jeśli połączymy końce płytek kadmowych i niklowych drutem, powstanie kadm, niklowe ogniwo galwaniczne, w którym kadm, jako bardziej aktywny metal, jest anodą. Kadm utlenia się:
O:Cd – 2e = Cd 2+ ,
Nadmiar elektronów trafi na płytkę niklową, gdzie nastąpi proces redukcji jonów wodorowych:
K(Ni): 2H + 2e =2H 0.
W ten sposób rozpuszcza się tylko kadm; nikiel stanie się jedynie przewodnikiem elektronów i sam się nie rozpuści. Wodór będzie uwalniany tylko na płycie niklowej.
Przykład 6
Jak pH środowiska wpływa na szybkość korozji aluminium?
Rozwiązanie
Obniżenie pH środowiska, tj. wzrost stężenia jonów H gwałtownie zwiększa szybkość korozji niklu - ponieważ kwaśne środowisko zapobiega tworzeniu się warstw ochronnych wodorotlenku niklu, aktywne utlenianie niklu zachodzi w środowisku kwaśnym
Odp.: Ni – 2e = Ni 2+
Spadek stężenia jonów H, tj. Wzrost stężenia OH sprzyja tworzeniu się warstwy wodorotlenku niklu:
Ni 2+ - 2OH¯ = NI(OH) 2
Wodorotlenek glinu ma właściwości amfoteryczne, tj. rozpuszcza się w kwasach i zasadach:
Al(OH) 3 + 3HCl = AlCl 3 + 3H 2 O
Al(OH) 3 + NaOH = Na AlO 2 + 2H 2 O
Dokładniej, reakcja ta przebiega w następujący sposób:
Al(OH)3 + NaOH = Na
Zatem szybkość korozji niklu jest najniższa w środowisku zasadowym, aluminium - w środowisku neutralnym.
4. Zadania
1. Zanurzona płyta żelazna kwas chlorowodorowy, bardzo powoli uwalnia wodór, ale jeśli dotkniesz go drutem cynkowym, natychmiast pokrywa się on pęcherzykami wodoru. Wyjaśnij to zjawisko. Jaki metal przechodzi do roztworu w tym przypadku?
2. Produkt żelazny zawiera części wykonane z niklu. Jak wpłynie to na korozję żelaza? Zapisz odpowiednie procesy anodowe i katodowe, jeśli produkt znajduje się w wilgotnej atmosferze.
3. W jakim środowisku tempo niszczenia żelaza jest większe? Jakie środowisko sprzyja anodowemu utlenianiu cynku? Napisz odpowiednie reakcje.
4. Jak zachodzi korozja atmosferyczna cynowanego żelaza i cynowanej miedzi, gdy uszkodzona jest integralność powłoki? Napisz równania elektroniczne procesów anodowych i katodowych.
5. Miedź nie wypiera wodoru z rozcieńczonych kwasów. Dlaczego? Jeśli jednak zetkniesz płytkę miedzianą z płytką cynkową, na miedzi rozpocznie się gwałtowna wydzielanie wodoru. Wyjaśnij to, sporządzając równania elektroniczne dla procesów katodowych i anodowych.
6. Płytkę cynkową i płytkę cynkową częściowo pokrytą miedzią zanurzono w roztworze elektrolitu zawierającym rozpuszczony tlen. W którym przypadku proces korozji cynku zachodzi intensywniej? Napisz równania elektroniczne procesów katodowych i anodowych.
7. Co może się stać, jeśli produkt, w którym żelazo techniczne styka się z miedzią, pozostawi się w powietrzu wysoka wilgotność? Zapisz równania odpowiednich procesów.
8. Aluminium nitowane żelazem. Który metal będzie korodował? Jakie procesy zajdą, jeśli produkt dostanie się do wody morskiej?
9. Dlaczego podczas kontaktu produkty żelazne z aluminium - produkty żelazne ulegają intensywniejszej korozji, chociaż aluminium ma bardziej ujemny potencjał elektrody standardowej?
10. Opuszczone płyty żelazne:
a) w wodzie destylowanej
b) do wody morskiej
W którym przypadku proces korozji jest bardziej intensywny? Umotywuj swoją odpowiedź.
11. Ułóż równania procesów zachodzących podczas korozji aluminium zanurzonego w roztworze:
a) kwasy
b) zasady
12. Dlaczego cynk techniczny oddziałuje z kwasem intensywniej niż cynk czysty chemicznie?
13. Płytkę zanurza się w roztworze elektrolitu:
b) miedź częściowo pokryta cyną
W którym przypadku proces korozji jest bardziej intensywny?
Umotywuj swoją odpowiedź
14. Dlaczego niklując wyroby żelazne, najpierw pokrywa się je miedzią, a następnie niklem?
Ułóż równania elektroniczne dla reakcji zachodzących w procesach korozji, gdy powłoka niklowa ulegnie uszkodzeniu.
15. Wyrób żelazny pokryto kadmem. Jaki to rodzaj powłoki - anodowa czy katodowa?
Umotywuj swoją odpowiedź. Który metal ulegnie korozji, jeśli warstwa ochronna zostanie uszkodzona? Ułóż równania elektroniczne dla odpowiednich procesów (ośrodek neutralny).
16. Który metal:
b) kobalt
c) magnez
może być ochraniaczem stopu na bazie żelaza. Ułóż równania elektroniczne dla odpowiednich procesów (ośrodek kwaśny).
17. Jakie procesy zajdą na płytkach cynkowych i żelaznych, jeśli każdą z nich zanurzymy oddzielnie w roztworze siarczan miedzi? Jakie procesy zajdą, jeśli zewnętrzne końce znajdujące się w roztworze płytek zostaną połączone z przewodnikiem? Napisz równania elektroniczne
18. Opuszczona płyta aluminiowa
a) w wodzie destylowanej
b) w roztworze chlorku sodu
W którym przypadku proces korozji jest bardziej intensywny? Sporządzić równania procesów korozji anodowej i katodowej aluminium handlowego w środowisku obojętnym.
19. Jeśli wbijesz gwóźdź w mokre drewno, część znajdująca się wewnątrz drewna zardzewieje. Jak możemy to wyjaśnić? Czy ta część gwoździa jest anodą czy katodą?
20. Ostatnio inne metale powlekano kobaltem w celu ochrony przed korozją. Czy powłoka kobaltu na stali jest anodowa czy katodowa? Jakie procesy zachodzą w wilgotnym powietrzu, gdy integralność powłoki zostaje naruszona?
©2015-2019 strona
Wszelkie prawa należą do ich autorów. Ta witryna nie rości sobie praw do autorstwa, ale zapewnia bezpłatne korzystanie.
Data utworzenia strony: 2016-04-11
Jak oni nazywają odporność na korozję materiały? Jakie są sposoby na zwiększenie odporności na korozję?
Zniszczenie produktów z różne materiały pod wpływem czynników fizykochemicznych i biologicznych nazywa się to korozją (od łacińskiego słowa oznaczającego korodować).
Zdolność materiałów do przeciwstawienia się korozyjnemu działaniu środowiska zewnętrznego nazywa się odpornością na korozję.
W wyniku korozyjnego niszczenia maszyn i aparatów, konstrukcji budowlanych i różnych wyrobów metalowych, w różnych gałęziach przemysłu około 12% wytopu metali ulega bezpowrotnej zniszczeniu Gospodarka narodowa. Wydłużenie żywotności produktów i urządzeń pozwoli zaoszczędzić miliony ton metalu i jednocześnie obniżyć koszty jego produkcji.
Sposoby zwiększenia odporności na korozję:
* Zastosowanie metali odpornych na korozję. Najczęściej spotykane w tej grupie są stale chromowe (13-30%), chromowo-niklowe (do 10-12%, tzw. „stal nierdzewna”), chromowo-niklowo-molibdenowe i inne stale. Stale te zachowują odporność na korozję w temperaturach do 300-400°C. Materiały takie stosowane są w wilgotnej atmosferze, w wodzie wodociągowej i rzecznej, kwasach azotowych i organicznych. Dodatek molibdenu Mo, cyrkonu 2g, berylu Be i manganu Mn również zwiększa odporność na korozję.
* Zastosowanie materiałów pasywujących tworzących się na powierzchni folia ochronna. Do materiałów tych zalicza się: tytan i jego stopy.
* Brąz i mosiądz są odporne na korozję kawitacyjną (zniszczenie na skutek współdziałanie obciążenia udarowe i wpływ elektrochemiczny).
Zastosowanie niemetalowych materiałów odpornych na korozję:
ѕ Materiały silikatowe-- związki krzemu otrzymywane przez topienie lub spiekanie skały. Topi się skała (bazalt), kwarc i szkło silikatowe, kwasoodpornych materiałów ceramicznych, cementów i betonów.
* Tworzywa sztuczne (polipropylen, pcv, tekstolit, żywica epoksydowa).
* Guma (guma).
Zastosowanie powłok metalowych:
* Powłoki galwaniczne (cynkowanie, cynowanie, kadmowanie, niklowanie, srebrzenie, złocenie).
* Napawanie to proces zabezpieczania metalu nieszlachetnego lub stopu przed korozją za pomocą innego metalu odpornego na agresywne środowisko.
*Najpowszechniej stosowaną metodą jest walcowanie łączone dwóch metali. Jako materiały okładzinowe stosuje się stale nierdzewne, aluminium, nikiel, tytan, tantal itp.
* Metalizacja metodą natryskową. Służy do zabezpieczania dużych pojemników przed korozją: mosty kolejowe, stosy, rury okrętowe. Natryskiwać cynk, aluminium, ołów, wolfram.
Zastosowanie powłok niemetalicznych:
Powłoki malarskie i lakiernicze (oleje schnące, lakiery, farby, emalie, podkłady, szpachlówki, żywice syntetyczne). Farby i lakiery nanosi się na powierzchnię wyrobów metodą wałkowania, natryskiwania, zanurzania, polewania, za pomocą pędzla lub metodą elektrostatyczną.
Przykład: Na kadłuby statków morskich nakłada się specjalną farbę przeciwporostową, aby zabezpieczyć je przed zanieczyszczeniem przez muszle organizmów morskich. W ciągu jednego roku warstwa zanieczyszczeń w morzach południowych sięga 0,5 m, tj. 100-150kg/m. Zwiększa to opory ruchu jednostki, co pochłania aż do 8% mocy silnika i zwiększa zużycie paliwa. Usunięcie takiej warstwy z powierzchni jest bardzo trudne. Dlatego podwodna część statku pokryta jest farbą przeciwporostową zawierającą tlenek rtęci, żywice i związki arsenu.
Powłoki polimerowe (polietylen, polipropylen, fluoroplast, polistyren, epoksydowa żywica itd.). Żywicę nanosi się w postaci stopu lub zawiesiny poprzez szczotkowanie, zanurzanie lub natryskiwanie. Fluoroplasty są odporne na uderzenia woda morska kwasy nieorganiczne, z wyjątkiem oleum i kwasu azotowego, mają wysokie właściwości elektroizolacyjne.
Gumowanie to powlekanie aparatury chemicznej, rurociągów, zbiorników, pojemników do transportu i przechowywania produktów chemicznych itp. gumą i ebonitem. Miękka guma urządzenia narażone na wstrząsy, wahania temperatury lub zawierające zawiesiny są gumowane, a do urządzeń pracujących w stałej temperaturze i nienarażonych na naprężenia mechaniczne stosuje się gumy twarde (twarda guma).
Powłoki z emaliami silikatowymi (substancja szklista). Sprzęt pracujący w podwyższonych temperaturach, ciśnieniach i w środowiskach silnie agresywnych poddawany jest emaliowaniu.
Powłoki ze smarami i pastami. Smary antykorozyjne są przygotowywane na bazie oleje mineralne(maszyna, wazelina) i substancji woskowych (parafina, mydło, kwasy tłuszczowe).
Stosowanie ochrona elektrochemiczna(katoda i anoda). DO konstrukcje metalowe z zewnątrz przymocowana jest zewnętrzna mocna anoda (źródło prąd stały), co powoduje katodową polaryzację elektrod na powierzchni chronionego metalu, w wyniku czego obszary anodowe metalu zamieniają się w katodowe. A Nie. oznacza, że to nie metal konstrukcji zostanie zniszczony, ale dołączona do niej anoda.
Odporność na korozję
Odporność na korozję- odporność materiałów na korozję, określona przez szybkość korozji w danych warunkach. Aby ocenić szybkość korozji, stosuje się zarówno cechy jakościowe, jak i ilościowe. Zmiana wygląd powierzchni metalu, zmiany w jego mikrostrukturze są przykładami jakościowej oceny szybkości korozji. Do oceny ilościowej możesz użyć:
- czas, jaki upłynął do pojawienia się pierwszego źródła korozji;
- liczba ognisk korozji powstałych w określonym czasie;
- zmniejszenie grubości materiału w jednostce czasu;
- zmiana masy metalu na jednostkę powierzchni w jednostce czasu;
- objętość gazu uwolnionego (lub wchłoniętego) podczas korozji jednostkowej powierzchni na jednostkę czasu;
- gęstość prądu odpowiadająca szybkości danego procesu korozji;
- zmiana dowolnej właściwości w określonym czasie korozji (na przykład oporność elektryczna, współczynnik odbicia materiału, właściwości mechaniczne).
Różne materiały mają różną odporność na korozję, a w celu jej poprawy stosuje się specjalne metody. Zatem zwiększenie odporności na korozję możliwe jest poprzez dodawanie stopów (np. stali nierdzewnych), nakładanie powłok ochronnych (chromowanie, niklowanie, aluminiowanie, cynkowanie, malowanie wyrobów), pasywację itp. Odporność materiałów na korozję typowa dla warunków morskich bada się w komorach mgły solnej.
Źródła
Fundacja Wikimedia. 2010.
Zobacz, co oznacza „odporność na korozję” w innych słownikach:
Odporność na korozję- zdolność metalu do przeciwstawiania się korozyjnemu działaniu środowiska. Źródło: snip id 5429: Wytyczne dotyczące projektowania i zabezpieczania antykorozyjnego podziemnych metalowych konstrukcji komunikacyjnych Co... Słownik-podręcznik terminów dokumentacji normatywnej i technicznej
Odporność materiałów na korozję. W przypadku metali i stopów określa się ją na podstawie szybkości korozji, tj. masy materiału przetworzonego w produkty korozji na jednostkę powierzchni w jednostce czasu lub grubości zniszczonej warstwy w mm na rok.... ... Duży słownik encyklopedyczny
odporność na korozję- Zdolność materiału do wytrzymywania działania środowiska korozyjnego bez zmiany jego właściwości. W przypadku metalu może to być lokalne uszkodzenie powierzchni - wżery lub rdza; Dla materiały organiczne- to jest powstawanie włosów... Przewodnik tłumacza technicznego
Odporność materiałów na korozję. W przypadku metali i stopów określa się ją na podstawie szybkości korozji, to znaczy masy materiału przekształconego w produkty korozji na jednostkę powierzchni w jednostce czasu lub grubości zniszczonej warstwy w... ... słownik encyklopedyczny
Odporność na korozję Odporność na korozję. Zdolność materiału do wytrzymywania działania środowiska korozyjnego bez zmiany jego właściwości. W przypadku metalu może to być miejscowe uszkodzenie powierzchni, wżery lub rdza; dla organicznych... ... Słownik terminów hutniczych
ODPORNOŚĆ NA KOROZJĘ- właściwość materiałów odpornych na korozję. Odporność na korozję określa się na podstawie masy materiału przetworzonego w produkty korozji w jednostce czasu na jednostkę powierzchni produktu oddziałującego z agresywnym środowiskiem, a także wielkości... ... Słownik metalurgiczny
odporność na korozję- atsparumas korozijai statusas T sritis Standartizacija ir metrologija apibrėžtis Metalo gebėjimas priešintis korozinės aplinkos poveikiui. atitikmenys: pol. odporność na korozję vok. Korozjaszerszystand, m; Rostbeständigkeit, f; Rostsicherheit… Penkiakalbis aiškinamasis metrologijos terminų žodynas
odporność na korozję- korozinis atsparumas statusas T sritis chemija apibrėžtis Metalo atsparumas aplinkos medžiagų poveikiui. atitikmenys: pol. odporność na korozję rus. odporność na korozję... Chemijos terminų aiškinamasis žodynas
odporność na korozję- odporność materiału, na przykład metali i stopów, na korozję w środowisku korozyjnym; oceniane na podstawie szybkości korozji; Zobacz także: Odporność, odporność chemiczna, odporność na relaksację... Encyklopedyczny słownik metalurgii
Metale, zdolność metalu lub stopu do przeciwstawienia się korozyjnemu działaniu środowiska. K. s. określana na podstawie szybkości korozji w danych warunkach. Szybkość korozji charakteryzuje się jakością i wskaźniki ilościowe. Do pierwszego... ... Wielka encyklopedia radziecka
Książki
- Odporność na korozję materiałów w agresywnych środowiskach produkcji chemicznej, G. Ya. Vorobyova. W książce podsumowano dane dotyczące właściwości i odporności na korozję materiałów metalicznych i niemetalowych. Zawiera tabele i wykresy odporności korozyjnej metali i stopów...
- Odporność na korozję i ochrona antykorozyjna metali, proszków i materiałów kompozytowych, Władimir Wasiliew. Niniejsza instrukcja poświęcona jest opisowi odporności na korozję najczęściej stosowanych nowoczesna technologia i technologia materiały budowlane: żelazo, stal, żeliwo, aluminium,…
Ocena odporności na korozję
Aby scharakteryzować właściwości korozyjne materiałów, zwykle bada się je pod kątem odporności przed korozją ogólną, korozją międzykrystaliczną i pękaniem korozyjnym.
Ogólne badania korozyjne. Ogólne badania korozyjne przeprowadza się na próbkach o wysokim stosunku powierzchni do objętości. Środowisko korozyjne dobiera się biorąc pod uwagę warunki pracy materiału. Badania przeprowadza się w cieczy przy stałym lub wielokrotnie powtarzanym, naprzemiennym zanurzeniu próbek, we wrzącym roztworze soli, w parze lub w otaczającej atmosferze.
Szybkość korozji metali i stopów charakteryzuje się wskaźnikiem korozji wgłębnej hK, mm/rok – tabela. 2 lub ubytek masy g K, g/(m 2 ∙h) – tabela. 3.
Obydwa wskaźniki przelicza się według wzoru:
hK = 8,76 gK/ρ,(1)
Gdzie h K – szybkość korozji, mm/rok;
ρ – gęstość, g/cm 3 ;
g K – ubytek masy próbki, g/(m 2 h).
Charakterystyka h K I g K zakładają równomierną korozję i zwykle reprezentują szybkość korozji uśrednioną na powierzchni. Wiadomo jednak, że najbardziej niebezpieczne są lokalne rodzaje korozji. Przy stosunkowo niewielkiej całkowitej utracie masy metalu następuje poważne lokalne zniszczenie konstrukcji, co prowadzi do przedwczesnej awarii sprzętu.
Tabela 2
Dziesięciopunktowa skala odporności korozyjnej metali w oparciu o głębokość korozji
Wynik odporności na korozję | Szybkość korozji h K, mm/rok | Grupa trwałości |
≤ 0,001 | Absolutnie odporny | |
(> 0,001) – 0,005 | Bardzo odporny | |
(> 0,005) – 0,01 | Bardzo odporny | |
(> 0,01) – 0,05 | Uporczywy | |
(> 0,05) – 0,1 | Uporczywy | |
(> 0,1) – 0,5 | Zmniejszone trwałe | |
(> 0,5) – 1,0 | Zmniejszone trwałe | |
(> 1,0) – 5,0 | Niska odporność | |
(> 5,0) – 10,0 | Niska odporność | |
> 10,0 | Nietrwały |
Tabela 3.
Dziesięciopunktowa skala odporności na korozję oparta na szybkości korozji próbki
Ocena kor. hart | Grupa trwałości | Ubytek masy, g K, g/(m 2 ∙h) | |||||
Czarne metale | Miedź i stopy | Nikiel i stopy | Ołów i stopy | Aluminium i stopy | Magnez i stopy | ||
Absolutnie odporny | <0,0009 | <0,001 | <0,001 | <0,0012 | <0,0003 | <0,0002 | |
Bardzo odporny | 0,0009-0,0045 | 0,001-0,0051 | 0,001-0,005 | 0,0012-0,0065 | 0,0003-0,0015 | 0,0002-0,001 | |
Bardzo odporny | (>0,0045)-0,009 | (>0,0051)-0,01 | (>0,005)-0,01 | (>0,0065)-0,012 | (>0,0015)-0,003 | (>0,001)-0,002 | |
Uporczywy | 0,009-0,045 | 0,01-0,051 | 0,01-0,05 | 0,012-0,065 | 0,003-0,015 | 0,002-0,01 | |
Uporczywy | (>0,045)-0,09 | (>0,051)-0,1 | (>0,05)-0,1 | (>0,065)-0,12 | (>0,015)-0,03 | (>0,01)-0,02 | |
Zmniejszone trwałe | (>0,09)-0,45 | (>0,1)-0,5 | (>0,1)-0,5 | (>0,12)-0,65 | (>0,03)-0,15 | (>0,02)-0,1 | |
Zmniejszone trwałe | (>0,45)-0,9 | (>0,5)-1,02 | (>0,5)-1,0 | (>0,65)-1,2 | (>0,15)-0,31 | (>0,1)-0,2 | |
Niska odporność | (>0,9)-4,5 | (>1,02)-5,1 | (>1,0)-5,0 | (>1,2)-6,5 | (>0,31)-1,54 | (>0,2)-1,0 | |
Niska odporność | (>4,5)-9,1 | (>5,1)-10,2 | (>5,0)-10,0 | (>6,5)-12,0 | (>1,54)-3,1 | (>1,0)-2,0 | |
Nietrwały | >9,1 | >10,2 | >10,0 | >12,0 | >3,1 | >2,0 |
Dlatego też konieczne jest sprawdzenie odporności korozyjnej materiałów w określonych warunkach eksploatacyjnych, szczególnie w przypadkach, gdy istnieje niebezpieczeństwo wystąpienia korozji miejscowej.
Badania korozji międzykrystalicznej(GOST 6032-84). Główną przyczyną korozji międzykrystalicznej materiałów odpornych na korozję jest nagrzewanie podczas obróbki ciśnieniowej lub spawania, co prowadzi do niejednorodności elektrochemicznej pomiędzy obszarami granicznymi a objętością ziaren.
Strefę temperaturowo-czasową wytrącania węglików chromu wzdłuż granic ziaren stali odpornych na korozję przedstawiono na rys. 4. Wewnątrz znajduje się obszar uczulenia - zwiększona wrażliwość na korozję międzykrystaliczną. Skłonność do korozji międzykrystalicznej objawia się w zakresie temperatur T max – T min przez minimalny czas τ min podczas którego następuje uczulenie.
Ryż. 4. Dziedzina skłonności temperatura-czas
odporna na korozję stal austenityczna na korozję międzykrystaliczną (ICC), związaną z wyczerpaniem granic ziaren w chromie:
Тр – temperatura rozpuszczania węglików; γ – austenit;
K – węgliki
Podczas badania MCC stale chromowe poddaje się prowokacyjnemu ogrzewaniu w temperaturze 1100°C przez 30 godzin, a chromowo-niklowe stale austenityczne poddaje się prowokacyjnemu ogrzewaniu w temperaturze około 700°C przez 60 godzin próbki przechowuje się przez długi czas we wrzącym wodnym roztworze kwasu siarkowego lub azotowego. Wybór czasu ekspozycji i rodzaju środowiska korozyjnego zależy od konkretnego gatunku stali i jej przeznaczenia. Aby kontrolować skłonność do MCC, próbki są albo wyginane na trzpieniu pod kątem 90°, albo poddawane trawieniu specjalnymi odczynnikami i badaniom metalograficznym. Brak pęknięć na powierzchni próbki wskazuje na jej odporność na MCC.
Na ryc. Na rys. 5 przedstawiono mikrostrukturę stali 08Х18Н10 po badaniach korozji międzykrystalicznej w różnych środowiskach.
Ryc.5. Mikrostruktura stali 08Х18Н10
po hartowaniu w wodzie w temperaturze 1050°C i odpuszczaniu w temperaturze 700°C:
a – korozja międzykrystaliczna w czasie badań
w roztworze 25% HNO 3 + 40 g/l Cr 6+, czas trwania 200 godzin;
b – to samo w roztworze wrzącego 65% HNO 3 + Cr 6+, × 500
Badania pękania korozyjnego. Ten rodzaj testu przeprowadza się poprzez umieszczenie próbki w środowisku korozyjnym odpowiadającym warunkom eksploatacji części. Środowisko nie powinno powodować ogólnej korozji i nie powinno wpływać na nieobciążone próbki metali. W przypadku austenitycznych stali chromowo-niklowych przykładem takiego ośrodka jest wrzący roztwór mieszaniny soli MgCl2, NaCl i NaNO. Agresywność środowiska nie może być mniejsza niż ta, w której mają służyć badane materiały.
Badania pękania pod wpływem korozji naprężeniowej można przeprowadzić w warunkach powodujących zniszczenie materiałów (próby rozciągania, odporności na pękanie i zmęczenie) lub poprzez określenie czasu, w którym pojawia się pierwsze pęknięcie. Ostatni rodzaj badania polega na unieruchomieniu obciążonych próbek specjalne urządzenia lub poprzez wytworzenie naprężenia klinem w wyciętych pierścieniach. Czas do pojawienia się pęknięć charakteryzuje odporność materiałów na pękanie korozyjne.
1. Wymienić metody ochrony metali i stopów przed korozją.
2. Od czego zależy wybór metody zabezpieczenia antykorozyjnego?
3. Co to jest stal stopowa?
4. Czym są bimetale?
5. Jaką metodą wytwarza się bimetale?
6. Czym są inhibitory korozji?
7. Jaki jest mechanizm ochrony metali i stopów przed korozją za pomocą inhibitorów anodowych?
8. Jaki jest mechanizm ochrony metali i stopów przed korozją za pomocą inhibitorów katodowych?
9. Jakie są korzyści ze stosowania lotnych inhibitorów?
10. W jakiej formie produkty najlepiej spowalniają procesy korozyjne?
11. Jak czystość obróbki części wpływa na szybkość korozji?
12. Co wyjaśnia wysoką odporność na korozję aluminium i jego stopów?
13. Wymień najbardziej odporne na korozję stopy żelaza.
14. Wymień najbardziej odporne na korozję stopy metali nieżelaznych.
15. Od czego zależy wybór rodzaju zabezpieczenia antykorozyjnego?
16. Jakie rodzaje korozji bada się podczas badań odporności na korozję?
17. W jakim środowisku korozyjnym przeprowadza się ogólne badania korozyjne?
18. Jakie wskaźniki charakteryzują szybkość korozji metali i stopów?
19. Jaki jest wymiar wskaźnika korozji wgłębnej?
20. Jaki jest wymiar ubytku masy próbki podczas korozji?
21. Jaką szybkością korozji charakteryzują się materiały zaliczane do kategorii całkowicie odpornych?
22. Jaka jest szybkość korozji materiałów o wysokiej odporności?
23. Jaka jest szybkość korozji materiałów odpornych?
24. Jaką szybkością korozji charakteryzują się materiały zaliczane do kategorii niskoodpornych?
25. Jaką szybkością korozji charakteryzują się materiały zaliczane do niestabilnych?
26. Jaki jest ubytek masy próbki stopu żelaza o klasie odporności na korozję wynoszącej 3?
27. Jaki jest ubytek masy próbki stopu miedzi o klasie odporności na korozję wynoszącej 7?
28. Jaka jest utrata masy próbki stopu niklu o klasie odporności na korozję wynoszącej 4?
29. Jaki jest ubytek masy próbki stopu ołowiu o klasie odporności na korozję wynoszącej 5?
30. Jaki jest ubytek masy próbki stopu aluminium o klasie odporności na korozję wynoszącej 9?
31. Jaki jest ubytek masy próbki stopu magnezu o klasie odporności na korozję wynoszącej 10?
32. Jaka jest główna przyczyna korozji międzykrystalicznej?
33. Odszyfruj gatunek stopu 08Х18Н10.
34. W jakim środowisku korozyjnym przeprowadza się badania pękania korozyjnego naprężeniowego?
35. W jaki sposób przeprowadza się badania pękania korozyjnego naprężeniowego?
1. Podstawowe pojęcia, terminy i definicje
Odporność na korozję- zdolność materiału do wytrzymywania działania agresywnych środowisk (korozja).
Korozja (dt lat, corrosio - korozja) - zniszczenie materiałów na skutek chemicznego lub elektrochemicznego oddziaływania z otoczeniem.
Materiały budowlane, a przede wszystkim ich powierzchnie, ulegają zniszczeniu w trakcie długotrwałej eksploatacji głównie na skutek dwóch rodzajów oddziaływań: korozyjnego, związanego z wpływem na materiał zewnętrznego, agresywnego środowiska oraz erozyjnego, wywołanego naprężeniami mechanicznymi.
Zniszczenie erozyjne postępuje intensywnie i stosunkowo szybko
rum przenoszący medium lub materiał. Erozja osiąga szczególnie duże rozmiary, gdy materiał wchodzi w kontakt ze stopionymi metalami i żużlami, a także z gazowymi utleniaczami itp.
Zjawiska korozji i erozji często towarzyszą sobie, dlatego nie zawsze można je rozdzielić. W materiałoznawstwie budowlanym zjawiska te rozpatrywane są oddzielnie. Podczas studiów uwzględnia się procesy erozji właściwości operacyjne wykładziny podłogowe, nawierzchnie drogowe itp.
2. Rodzaje korozji materiały budowlane
Korozja materiałów budowlanych różni się w zależności od rodzaju środowiska korozyjnego, charakteru zniszczeń i procesów w nich zachodzących:
Środowisko korozyjne:
Gaz
Gaz reaktywny;
Płyn:
Kwaśny;
Solankowy;
Alkaliczny;
Morski;
w stopieniu:
metale;
krzemiany;
2) charakter zniszczenia:
Mundur;
Nierówny:
Selektywny;
Powierzchowny;
Pękanie;
Lokalny;
międzykrystaliczny;
3) rodzaje oddziaływań (procesów);
Chemiczny;
Elektrochemiczny;
Biologiczny;
Organogenne.
Rodzaje środowiska korozyjnego:
Korozja gazowa reprezentuje korozję w środowisko gazowe przy całkowitym braku kondensacji wilgoci na powierzchni materiału. Ten rodzaj korozji wpływa na materiały pracujące w warunkach wysokie temperatury w środowisku suchego gazu (ceramika).
Korozja gazowa odnosi się do procesów niszczenia chemicznego. Jego prędkość zależy; na charakter materiału, jego strukturę i właściwości nowych formacji na jego powierzchni.
Korozja płynna Materiały z kamienia naturalnego i sztucznego, które powstają pod wpływem roztworów elektrolitów i nieelektrolitów, a także różnych stopów, mają głównie charakter chemiczny, chociaż w zależności od rodzaju i właściwości cieczy różnią się szeregiem cech.
Najważniejsza cecha cieczami jest obecność w nich sił oddziaływania międzycząsteczkowego. Dzieje się tak za sprawą dwóch właściwości stan ciekły: ciśnienie molekularne i związane z nim napięcie powierzchniowe.
Napięcie powierzchniowe cieczy ma duży wpływ na intensywność niszczenia materiału, o której decydują także właściwości zwilżające cieczy.
Charakter zniszczenia:
Korozja jednolita powstaje w wyniku działania agresywnego środowiska o wystarczającej grubości wyrobu i równomiernym rozłożeniu naprężeń ściskających, zginających lub rozciągających. Korozja tego typu w odróżnieniu od innych w znacznie mniejszym stopniu wpływa na właściwości wytrzymałościowe materiału.
Nierówna lub miejscowa korozja(plamy, wrzody, plamy) występuje przy różnym stężeniu agresywnego środowiska w poszczególnych obszarach lub niejednorodności samego materiału (jego składu i struktury). Zatem w wyniku nierównomiernego rozkładu faz krystalicznych i szklistych w materiał ceramiczny następuje zniszczenie korozyjne w poszczególnych obszarach przy różnych prędkościach. Ponadto w fazie szklistej proces przebiega znacznie szybciej niż w fazie krystalicznej. Obecność niejednorodnej porowatości w materiale również przyczynia się do powstawania nierównomiernej korozji w materiale.
Korozja selektywna charakterystyka materiałów, w których jeden ze składników tworząc strukturę tworzy związki łatwo rozpuszczalne. Podczas pracy związki te mogą rozpuścić się, tworząc na powierzchni materiału tzw. „wykwity”.
Korozja międzykrystaliczna powstaje w wyniku zniszczenia materiału wzdłuż granic ziaren i szybko rozprzestrzenia się w głąb materiału, gwałtownie pogarszając jego właściwości. Ten rodzaj korozji jest nieodłącznym elementem niektórych materiałów wypalanych, podczas spiekania których powstają nowe fazy, roztwory stałe itp., A w konsekwencji powierzchnie międzyfazowe.
Ogólnie rzecz biorąc, działanie korozyjne może mieć dwa podstawowe skutki: różne mechanizmy: interakcja chemiczna i rozpuszczanie.
Interakcja chemiczna sprowadza się do reakcji pomiędzy ośrodkiem a materiałem, w wyniku której powstają nowe związki. Jeśli w agresywnym środowisku znajdują się zanieczyszczenia lub dodatki w materiale, mogą wystąpić reakcje chemiczne pomiędzy wszystkimi elementami interakcji.
Ponieważ materiały kamienne są dielektrykami i ich oddziaływaniu z agresywnym środowiskiem nie towarzyszy występowanie prądów elektrycznych, proces niszczenia materiałów nazywa się korozja chemiczna.
Kiedy metale są wystawione na działanie agresywnego środowiska, zachodzi proces elektrochemiczny, podczas którego elektrony są przenoszone z warstwy metalu o niższym potencjale elektrycznym do warstwy o wyższym potencjale i przywracają jony elektrododatnie, a następnie niszczą warstwę powierzchniową. Ten proces niszczenia jest powszechnie nazywany korozją elektrochemiczną.
Korozja biologiczna- niszczenie materiału pod bezpośrednim wpływem organizmów roślinnych i zwierzęcych oraz mikroorganizmów.
1. Wyższe organizmy roślinne ( system korzeniowy, łodygi, liście, nasiona itp.) w procesie życia produktu Różne rodzaje substancje, z których większość jest agresywna w stosunku do materiałów budowlanych.
2. Organizmy żywe powodują biologiczne uszkodzenia materiałów zarówno bezpośrednio poprzez działanie mechaniczne (gryzonie, ptaki itp.), jak i poprzez produkty swojej życiowej działalności.
3. Organizmy roślin niższych i mikroorganizmy (glony, porosty, mchy, grzyby, bakterie itp.) niszczą powierzchniowe warstwy betonu i stwarzają warunki do gnicia konstrukcji drewnianych.
Korozja wynikająca z narażenia materiałów budowlanych na działanie produktów przetworzonych materia organiczna jako biogenne (owoce, warzywa, oleje roślinne, krew, soki, tłuszcze itp.) i pochodzenia niebiogennego (ropa naftowa, węgiel, łupki, skały wapienne, gazy spalinowe, sadza itp.), akceptowane przez korozję organogeniczną.