Domowy warsztat formowania tworzyw sztucznych. Topienie plastiku w domu Topienie plastiku
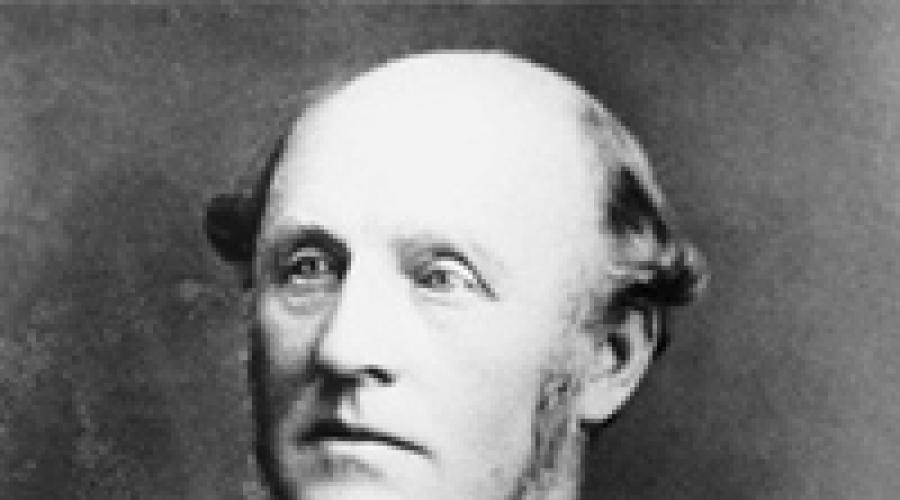
Przeczytaj także
Dziś często wykonując prace domowe czy pracę twórczą, stajemy przed zadaniem przetopienia plastikowego produktu lub jego części. Chcę to zrobić ostrożnie i tak dokładnie, jak to możliwe. Jak to się dzieje topienie plastiku w domu? Nasi redaktorzy zadali to pytanie i oto do czego doszliśmy. Oferujemy Państwu najpopularniejsze metody topienia tworzyw sztucznych.
Technologia topienia gorącego oleju
W gorącym oleju tworzywo sztuczne nagrzewa się bardzo umiarkowanie, co jest bardzo ważne i konieczne przy obróbce tego materiału. Temperaturę ogrzewania kąpieli olejowej można łatwo regulować. Jedyną wadą tej procedury jest to, że po uformowaniu części z tworzywa sztucznego trudno jest je skleić. Zatem całkowite oczyszczenie powierzchni plastiku z oleju jest dość proste.
Inne metody wytapiania
Jest to możliwe także poprzez zastosowanie gorącego piasku. Ta metoda jest najbardziej odpowiednia, jeśli chcesz zgiąć rury wykonane z tworzywa sztucznego. Swoją drogą, jeśli szukasz salonu do depilacji laserowej w Kijowie lub na Krymie, polecamy skontaktować się z firmą Lazerok http://lazerok.ua/action/lazernaya-epilyatsiya-za-49-grn.html.
Ponadto topienie tworzywa sztucznego może nastąpić również pod wpływem strumienia gorącego powietrza. Suszarka do włosów i nawet zwykły odkurzacz. Jedyną rzeczą jest to, że w tym przypadku konieczne jest zainstalowanie specjalnego elektrycznego elementu grzejnego w rurce wkładanej do wylotu odkurzacza.
Można to również osiągnąć za pomocą zwykłej żelaznej linijki. Będzie to jednak istotne, jeśli chcesz stopić się elastycznie cienkie prześcieradła Plastikowy. W takim przypadku użyj jednej lub dwóch żelaznych linijek podgrzanych na kuchence elektrycznej lub nad ogniem.
Do topienia wyjątkowo cienkich arkuszy tworzyw sztucznych lepiej jest użyć drutu elektrodowego podgrzewanego elektrycznie.
Światła podczerwone
Można to również przeprowadzić za pomocą promienników podczerwieni. W takim przypadku najbardziej optymalna temperatura ogrzewania dla różnych materiałów z tworzyw sztucznych będzie inna:
– dla polichlorku winylu 130-140°C;
- Dla szkło organiczne 145-150°C;
– dla celuloidu 100°C.
Podczas podgrzewania materiałów z tworzyw sztucznych bardzo ważne jest przestrzeganie zalecanych temperatur. W końcu zbyt długie podgrzewanie plastiku może wpłynąć na właściwości materiału i jego właściwości wygląd. Z własnego doświadczenia możemy więc powiedzieć, że 1 minuta to wystarczający czas na podgrzanie plastikowego arkusza o szerokości 1 mm. 30 s.
W nowoczesnych samochodach odsetek części z tworzyw sztucznych stale rośnie. Rośnie także liczba napraw powierzchni z tworzyw sztucznych i coraz częściej stajemy przed koniecznością ich pomalowania.
Pod wieloma względami wybarwienie tworzyw sztucznych różni się od wybarwienia powierzchni metalowych, co wynika przede wszystkim z samych właściwości tworzyw sztucznych: są one bardziej elastyczne i mają mniejszą przyczepność do materiałów lakierniczych. A ponieważ asortyment materiałów polimerowych stosowanych w przemyśle motoryzacyjnym jest bardzo zróżnicowany, nie byłoby uniwersalnych materiałów naprawczych, które byłyby w stanie stworzyć wysokiej jakości powłoka dekoracyjna na wielu ich typach malarze prawdopodobnie musieliby otrzymać Specjalna edukacja w chemii.
Na szczęście wszystko faktycznie okaże się dużo prostsze i nie będziemy musieli zagłębiać się w badania chemii molekularnej polimerów. Jednak pewne informacje na temat rodzajów tworzyw sztucznych i ich właściwości, choćby w celu poszerzenia horyzontów, z pewnością się przydadzą.
Dziś się dowiesz
Plastiki dla mas
W XX wieku ludzkość doświadczyła syntetycznej rewolucji; w jej życie wkroczyły nowe materiały - tworzywa sztuczne. Plastik można bezpiecznie uznać za jedno z głównych odkryć ludzkości, bez jego wynalazku wiele innych odkryć uzyskano by znacznie później lub w ogóle by nie istniało.
Pierwszy plastik został wynaleziony w 1855 roku przez brytyjskiego metalurga i wynalazcę Alexandra Parkesa. Kiedy postanowił znaleźć tani zamiennik drogiego kość słoniowa, z którego wykonywano wówczas kule bilardowe, nie mógł sobie wyobrazić, jakie znaczenie nabierze później otrzymany przez niego produkt.
Składniki przyszłego odkrycia to nitroceluloza, kamfora i alkohol. Mieszaninę tych składników ogrzano do stanu płynnego, a następnie wlano do formy i utwardzano normalna temperatura. Tak narodził się parkesin – protoplasta nowoczesnych tworzyw sztucznych.
Od naturalnych i chemicznie modyfikowanych materiałów naturalnych po całkowicie syntetyczne cząsteczki, rozwój tworzyw sztucznych nastąpił nieco później – kiedy niemiecki profesor na Uniwersytecie we Freiburgu, Hermann Staudinger, odkrył makrocząsteczkę – „cegłę”, z której powstają wszystkie tworzywa sztuczne (i naturalne). są zbudowane. materiały organiczne. Odkrycie to przyniosło 72-letniemu profesorowi Nagrodę Nobla w 1953 roku.
Od tego momentu wszystko się zaczęło... Niemal co roku z laboratoriów chemicznych napływały raporty o kolejnym materiał syntetyczny o nowych, niespotykanych dotąd właściwościach, a dziś świat produkuje rocznie miliony ton wszelkiego rodzaju tworzyw sztucznych, bez których życie współczesnego człowieka jest absolutnie nie do pomyślenia.
Tworzywa sztuczne wykorzystuje się wszędzie tam, gdzie to możliwe: w zapewnieniu komfortowego życia ludziom, w rolnictwie, we wszystkich gałęziach przemysłu. Branża motoryzacyjna nie jest wyjątkiem, gdzie tworzywa sztuczne znajdują coraz szersze zastosowanie, w niekontrolowany sposób wypierając swojego głównego konkurenta – metal.
W porównaniu z metalami tworzywa sztuczne są materiałami bardzo młodymi. Ich historia nie sięga nawet 200 lat wstecz, podczas gdy cyna, ołów i żelazo były znane ludzkości już w starożytności – 3000-4000 lat p.n.e. mi. Ale mimo to materiały polimerowe znacznie przewyższają swojego głównego konkurenta technologicznego pod wieloma wskaźnikami.
Zalety tworzyw sztucznych
Przewaga tworzyw sztucznych nad metalami jest oczywista.
Po pierwsze, plastik jest znacznie lżejszy. Dzięki temu możesz zmniejszyć waga całkowita pojazdu i opór powietrza podczas jazdy, a tym samym zmniejszenie zużycia paliwa i w konsekwencji emisji spalin.
Całkowita redukcja masy pojazdu o 100 kg dzięki zastosowaniu części z tworzyw sztucznych pozwala zaoszczędzić aż do jednego litra paliwa na 100 km.
Po drugie, zastosowanie tworzyw sztucznych daje niemal nieograniczone możliwości kształtowania, pozwalając na przełożenie dowolnych pomysłów projektowych na rzeczywistość i uzyskanie części o najbardziej skomplikowanych i pomysłowych kształtach.
Do zalet tworzyw sztucznych zalicza się także ich wysokość odporność na korozję, odporność na wpływy atmosferyczne, kwasy, zasady i inne agresywne produkty chemiczne, doskonałe właściwości elektroizolacyjne i termoizolacyjne, wysoki współczynnik redukcji hałasu... Jednym słowem, nic dziwnego, dlaczego materiały polimerowe są tak popularne szerokie zastosowanie w branży motoryzacyjnej.
Czy ktoś próbował stworzyć samochód w całości wykonany z plastiku? Ale oczywiście! Wystarczy przypomnieć sobie znanego Trabanta, wyprodukowanego w Niemczech ponad 40 lat temu w fabryce w Zwickkau – jego nadwozie zostało w całości wykonane z laminowanego tworzywa sztucznego.
Aby otrzymać to tworzywo, sprasowano 65 warstw bardzo cienkiej tkaniny bawełnianej (z fabryk tekstylnych) na przemian z warstwami zmielonej żywicy krezolowo-formaldehydowej w bardzo trwały materiał Grubość 4 mm przy ciśnieniu 40 atm. i temperaturze 160°C przez 10 minut.
Do tej pory ciała NRD „Trabantów”, o których śpiewano pieśni, opowiadano legendy (ale częściej pisano dowcipy), leżą na wielu wysypiskach śmieci w całym kraju. Kłamią... ale nie rdzewieją!
Trabanta. Najpopularniejszy plastikowy samochód na świecie
Pomijając żarty, już obecnie istnieją obiecujące opracowania nadwozi samochodów seryjnych wykonanych w całości z tworzyw sztucznych; Tradycyjnie w wielu samochodach części metalowe (maski, błotniki) są obecnie zastępowane także plastikowymi, np. w Citroënie, Renault, Peugeocie i innych.
Jednak w przeciwieństwie do paneli nadwozia popularnych „Trabi”, części plastikowe nowoczesne samochody nie wywołują już ironicznego uśmiechu. Wręcz przeciwnie – ich odporność na obciążenia udarowe, zdolność miejsc odkształconych do samonaprawy, najwyższa odporność antykorozyjna i niska środek ciężkości sprawi, że poczujesz głęboki szacunek dla tego materiału.
Kończąc rozmowę o zaletach tworzyw sztucznych, nie można nie zauważyć faktu, że choć z pewnymi zastrzeżeniami, większość z nich nadal doskonale nadaje się do malowania. Gdyby szara masa polimerowa nie miała takiej możliwości, jest mało prawdopodobne, aby zyskała taką popularność.
Po co malować plastik?
Konieczność malowania tworzyw sztucznych wynika z jednej strony ze względów estetycznych, z drugiej zaś z konieczności ich zabezpieczenia. W końcu nic nie jest wieczne. Chociaż tworzywa sztuczne nie gniją, podczas użytkowania i narażenia gniją wpływy atmosferyczne nadal podlegają procesom starzenia i niszczenia. Nałożona warstwa farby chroni powierzchnię tworzywa sztucznego przed różnymi agresywnymi wpływami, a tym samym wydłuża jego żywotność.
Jeśli w warunkach produkcyjnych malowanie powierzchni plastikowych jest bardzo proste - w tym przypadku mówimy o o dużej liczbie nowych identycznych części wykonanych z tego samego plastiku (i mają własne technologie), wówczas malarz w warsztacie samochodowym staje przed problemami niejednorodności materiałów różnych części.
W tym miejscu należy odpowiedzieć na pytanie: „Co to w ogóle jest plastik? Z czego jest wykonany, jakie ma właściwości i główne rodzaje?
Co to jest plastik?
Zgodnie z krajowym standardem państwowym:
Tworzywa sztuczne to materiały, których głównym część integralna które są wielkocząsteczkowymi związkami organicznymi, które powstają w wyniku syntezy lub transformacji produktów naturalnych. Podczas przetwarzania w określonych warunkach wykazują tendencję do wykazywania plastyczności i zdolności do formowania
odkształcenie.
Jeśli z tak trudnego opisu usuniemy pierwsze słowo „plastiki”, nawet do przeczytania, a nie tylko do zrozumienia, być może mało kto zgadnie, o czym mówimy. Cóż, spróbujmy to trochę rozgryźć.
„Tworzywa sztuczne” lub „masy plastyczne” zostały tak nazwane, ponieważ materiały te mają zdolność mięknięcia pod wpływem ogrzewania, stając się plastycznymi, a następnie pod ciśnieniem można im nadać określony kształt, który zostaje zachowany po dalszym ochłodzeniu i utwardzeniu.
Podstawą każdego plastiku jest (ta sama „wysoka masa cząsteczkowa związek organiczny„z definicji powyżej).
Słowo polimer pochodzi od greckich słów poli (wiele) i meros (części lub jednostki). Jest to substancja, której cząsteczki składają się z dużej liczby identycznych jednostek połączonych ze sobą. Te linki to tzw monomery(„mono” - jeden).
Przykładowo tak wygląda monomer polipropylenu, rodzaju tworzywa sztucznego najczęściej stosowanego w przemyśle motoryzacyjnym:
Łańcuchy molekularne polimeru składają się z niemal niezliczonej liczby takich elementów połączonych w jedną całość.
Łańcuchy cząsteczek polipropylenu
W zależności od pochodzenia wszystkie polimery dzielą się na syntetyczny I naturalny. Naturalne polimery stanowią podstawę wszystkich organizmów zwierzęcych i roślinnych. Należą do nich polisacharydy (celuloza, skrobia), białka, kwasy nukleinowe, kauczuku naturalnego i innych substancji.
Chociaż znaleziono modyfikowane polimery naturalne Aplikacja na skalę przemysłową, większość tworzyw sztucznych jest syntetyczna.
Polimery syntetyczne otrzymuje się w procesie syntezy chemicznej z odpowiednich monomerów.
Ropa naftowa jest zwykle wykorzystywana jako surowiec, gazu ziemnego lub węgiel. W wyniku reakcji chemicznej polimeryzacji (lub polikondensacji) powstaje wiele „małych” monomerów materiał wyjściowyłączą się ze sobą niczym koraliki na sznurku w „ogromne” cząsteczki polimeru, które następnie są formowane, odlewane, prasowane lub przędzone w gotowy produkt.
I tak na przykład tworzywo polipropylenowe otrzymuje się z palnego gazowego propylenu, z którego wykonane są zderzaki:
Teraz już zapewne domyślacie się, skąd wzięły się nazwy tworzyw sztucznych. Do nazwy monomeru dodaje się przedrostek „poly-” („wiele”): etylen → polietylen, propylen → polipropylen, chlorek winylu → polichlorek winylu itp.
Międzynarodowe skróty tworzyw sztucznych są skrótami ich nazw chemicznych. Na przykład polichlorek winylu jest oznaczony jako PCV(Polichlorek winylu), polietylen - PE(Polietylen), polipropylen - PP(Polipropylen).
Oprócz polimeru (zwanego także spoiwem) tworzywa sztuczne mogą zawierać różne wypełniacze, plastyfikatory, stabilizatory, barwniki i inne substancje, które nadają tworzywu określone właściwości technologiczne i konsumenckie, np. płynność, plastyczność, gęstość, wytrzymałość, trwałość, itp.
Rodzaje tworzyw sztucznych
Tworzywa sztuczne klasyfikuje się według różne kryteria: skład chemiczny, zawartość tłuszczu, twardość. Jednak głównym kryterium wyjaśniającym naturę polimeru jest zachowanie tworzywa sztucznego po podgrzaniu. Na tej podstawie wszystkie tworzywa sztuczne dzieli się na trzy główne grupy:
- tworzywa termoplastyczne;
- termoutwardzalne;
- elastomery.
O przynależności do określonej grupy decyduje kształt, wielkość i położenie makrocząsteczek, a także skład chemiczny.
Tworzywa termoplastyczne (polimery termoplastyczne, plastomery)
Tworzywa termoplastyczne to tworzywa sztuczne, które topią się pod wpływem ogrzewania i powracają do pierwotnego stanu po ochłodzeniu.
Tworzywa te składają się z liniowych lub lekko rozgałęzionych łańcuchów molekularnych. W niskich temperaturach cząsteczki przylegają ściśle do siebie i prawie się nie poruszają, dlatego w tych warunkach tworzywo sztuczne jest twarde i kruche. Przy niewielkim wzroście temperatury cząsteczki zaczynają się poruszać, wiązanie między nimi słabnie, a plastik staje się plastyczny. Jeśli plastik podgrzeje się jeszcze bardziej, wiązania międzycząsteczkowe staną się jeszcze słabsze, a cząsteczki zaczną się ślizgać względem siebie - materiał przechodzi w stan elastyczny i lepki. Gdy temperatura spada i ochładza się, cały proces przebiega w odwrotnej kolejności.
Jeśli uniknie się przegrzania, w którym to momencie łańcuchy molekularne pękną, a materiał ulegnie rozkładowi, proces ogrzewania i chłodzenia można powtarzać dowolną liczbę razy.
Ta cecha tworzyw termoplastycznych polegająca na wielokrotnym mięknięciu pozwala na wielokrotne przetwarzanie tych tworzyw na różne produkty. Oznacza to, że teoretycznie jedno skrzydełko można zrobić z kilku tysięcy kubków jogurtowych. Z punktu widzenia ochrony środowisko jest to bardzo ważne, ponieważ późniejsze przetwarzanie lub utylizacja stanowi duży problem dla polimerów. Produkty z tworzyw sztucznych, które dostaną się do gleby, rozkładają się w ciągu 100–400 lat!
Ponadto dzięki tym właściwościom tworzywa termoplastyczne dobrze nadają się do spawania i lutowania. Pęknięcia, załamania i odkształcenia można łatwo wyeliminować za pomocą ciepła.
Większość polimerów stosowanych w przemyśle motoryzacyjnym to tworzywa termoplastyczne. Wykorzystuje się je do produkcji różnych elementów wnętrza i nadwozia samochodu: paneli, ram, zderzaków, osłon chłodnicy, obudów lamp i lusterek zewnętrznych, kołpaków kół itp.
Do tworzyw termoplastycznych zalicza się polipropylen (PP), polichlorek winylu (PVC), kopolimery akrylonitryl-butadien-styren (ABS), polistyren (PS), polioctan winylu (PVA), polietylen (PE), polimetakrylan metylu (pleksi) (PMMA), poliamid ( PA), poliwęglan (PC), polioksymetylen (POM) i inne.
Tworzywa termoutwardzalne (tworzywa termoutwardzalne, duroplasty)
Jeżeli w przypadku tworzyw termoplastycznych proces mięknienia i utwardzania można powtarzać wielokrotnie, to termoutwardzalne tworzywa sztuczne po jednorazowym podgrzaniu (podczas formowania produktu) przechodzą w nierozpuszczalny stan stały, a po wielokrotnym ogrzewaniu nie miękną już. Następuje nieodwracalne stwardnienie.
W stanie początkowym termoutwardzalne mają struktura liniowa makrocząsteczek, ale po podgrzaniu podczas produkcji produkt formowany makrocząsteczki ulegają „usieciowaniu”, tworząc przestrzenną strukturę siatkową. To właśnie dzięki tej strukturze ściśle powiązanych, „usieciowanych” cząsteczek materiał okazuje się twardy i nieelastyczny oraz traci zdolność do ponownego przejścia w stan lepkiego płynięcia.
Ze względu na tę cechę tworzywa termoutwardzalne nie mogą być poddawane recyklingowi. Nie można ich również spawać i formować w stanie nagrzanym - po przegrzaniu łańcuchy molekularne rozpadają się, a materiał ulega zniszczeniu.
Materiały te są dość żaroodporne, dlatego wykorzystuje się je na przykład do produkcji części skrzyni korbowej w komorze silnika. Wielkogabarytowe zewnętrzne części nadwozia (maski, błotniki, pokrywy bagażnika) produkowane są z tworzyw termoutwardzalnych wzmacnianych (np. włóknem szklanym).
Do grupy termoutwardzalnych zaliczają się materiały na bazie żywic fenolowo-formaldehydowych (PF), mocznikowo-formaldehydowych (UF), epoksydowych (EP) i poliestrowych.
Elastomery to tworzywa sztuczne charakteryzujące się dużą elastycznością. Poddane działaniu siły wykazują elastyczność, a po usunięciu naprężeń wracają do pierwotnego kształtu. Elastomery różnią się od innych elastycznych tworzyw sztucznych zdolnością do utrzymania elastyczności w szerokim zakresie temperatur. Przykładowo kauczuk silikonowy pozostaje elastyczny w zakresie temperatur od -60 do +250°C.
Elastomery, podobnie jak termoutwardzalne, składają się z przestrzennie połączonych makrocząsteczek. Tylko, w przeciwieństwie do termoutwardzalnych, makrocząsteczki elastomerów są rozmieszczone szerzej. To właśnie to umiejscowienie decyduje o ich właściwościach sprężystych.
Elastomery ze względu na swoją sieciową strukturę są nietopliwe i nierozpuszczalne, podobnie jak termoutwardzalne, ale pęcznieją (termosety nie pęcznieją).
Do grupy elastomerów zaliczają się różnego rodzaju kauczuki, poliuretany i silikony. W przemyśle motoryzacyjnym wykorzystywane są przede wszystkim do produkcji opon, uszczelek, spojlerów itp.
Wszystkie trzy rodzaje tworzyw sztucznych stosowane są w przemyśle motoryzacyjnym. Produkowane są także mieszaniny wszystkich trzech rodzajów polimerów – tzw. „mieszanki”, których właściwości zależą od proporcji mieszaniny i rodzaju składników.
Określanie rodzaju tworzywa sztucznego. Cechowanie
Jakakolwiek naprawa części z tworzywa sztucznego musi rozpocząć się od określenia rodzaju tworzywa sztucznego, z którego jest wykonana. Jeśli w przeszłości nie zawsze było to łatwe, teraz łatwo jest „zidentyfikować” plastik - z reguły wszystkie części są oznaczone.
Producenci zazwyczaj stemplują oznaczenie typu tworzywa sztucznego wewnątrz części, czy to zderzaka, czy osłony telefon komórkowy. Rodzaj tworzywa jest zwykle ujęty w charakterystyczne nawiasy i może wyglądać następująco: >PP/EPDM<, >PUR<,
Zadanie testowe: Zdejmij obudowę telefonu komórkowego i zobacz, z jakiego rodzaju plastiku jest wykonany. Najczęściej jest to >PC<.
Może istnieć wiele odmian takich skrótów. Nie będziemy w stanie uwzględnić wszystkiego (i nie ma takiej potrzeby), więc skupimy się na kilku najpopularniejszych rodzajach tworzyw sztucznych w motoryzacji.
Przykłady najpopularniejszych rodzajów tworzyw sztucznych w przemyśle motoryzacyjnym
Polipropylen – PP, polipropylen modyfikowany – PP/EPDM
Najpopularniejszy rodzaj tworzywa sztucznego w przemyśle motoryzacyjnym. W większości przypadków podczas naprawy uszkodzonych części lub malowania nowych części będziemy mieli do czynienia z różnymi modyfikacjami polipropylenu.
Polipropylen ma być może kombinację wszystkich zalet, jakie mogą mieć tworzywa sztuczne: niska gęstość (0,90 g/cm3 - najniższa wartość dla wszystkich tworzyw sztucznych), wysoka wytrzymałość mechaniczna, odporność chemiczna (odporny na rozcieńczone kwasy i większość zasad, detergentów, olejów , rozpuszczalniki), odporność na ciepło (zaczyna mięknąć w temperaturze 140°C, temperatura topnienia 175°C). Prawie nie podlega pękaniu korozyjnemu i ma dobrą zdolność odzyskiwania. Ponadto polipropylen jest materiałem przyjaznym dla środowiska.
Właściwości polipropylenu dają podstawy do uznania go za idealny materiał dla przemysłu motoryzacyjnego. Ze względu na swoje cenne właściwości otrzymał nawet tytuł „króla tworzyw sztucznych”.
Prawie wszystkie zderzaki wykonane są z polipropylenu; materiał ten jest również wykorzystywany do produkcji spojlerów, części wewnętrznych, tablic przyrządów, zbiorników wyrównawczych, osłon chłodnicy, kanałów powietrza, obudów i pokryw akumulatorów itp. W życiu codziennym nawet walizki są wykonane z polipropylenu.
Podczas odlewania większości powyższych części nie stosuje się czystego polipropylenu, ale jego różne modyfikacje.
„Czysty” niemodyfikowany polipropylen jest bardzo wrażliwy na promieniowanie ultrafioletowe i tlen, w trakcie użytkowania szybko traci swoje właściwości i staje się kruchy. Z tego samego powodu nałożone na niego powłoki malarskie nie mogą mieć trwałej przyczepności.
Dodatki wprowadzone do polipropylenu – często w postaci gumy i talku – znacząco poprawiają jego właściwości i umożliwiają jego zabarwienie.
Barwić można wyłącznie modyfikowany polipropylen. Na „czystym” polipropylenie przyczepność będzie bardzo słaba! Wykonane z czystego polipropylenu >PP< изготавливают бачки омывателей, расширительные емкости, одноразовую посуду, стаканчики и т.д.
Wszelkie modyfikacje polipropylenu, niezależnie od tego jak długi jest skrót jego oznaczenia, są oznaczone dwoma pierwszymi literami jako >PP...<. Наиболее распространенный продукт этих модификаций — >PP/EPDM< (сополимер полипропилена и этиленпропиленового каучука).
ABS (kopolimer akrylonitryl-butadien-styren)
ABS to elastyczne, ale jednocześnie odporne na uderzenia tworzywo sztuczne. Za elastyczność odpowiada składnik gumowy (butadien), a akrylonitryl za wytrzymałość. Tworzywo to jest wrażliwe na promieniowanie ultrafioletowe – pod jego wpływem tworzywo szybko się starzeje. Dlatego produkty ABS nie mogą być długo wystawione na działanie światła i muszą zostać pomalowane.
Najczęściej stosowany do produkcji obudów lamp i lusterek zewnętrznych, osłon chłodnicy, tapicerki deski rozdzielczej, tapicerki drzwi, kołpaków, tylnych spojlerów itp.
Poliwęglan - PC
Jeden z najbardziej odpornych na uderzenia tworzyw termoplastycznych. Aby zrozumieć, jak trwały jest poliwęglan, wystarczy wiedzieć, że materiał ten jest wykorzystywany do produkcji kuloodpornych lad bankowych.
Oprócz wytrzymałości poliwęglany charakteryzują się lekkością, odpornością na starzenie pod wpływem światła i zmianami temperatury oraz bezpieczeństwem pożarowym (jest to materiał trudnopalny, samogasnący).
Niestety poliwęglany są dość wrażliwe na rozpuszczalniki i podatne na pękanie pod wpływem naprężeń wewnętrznych.
Nieodpowiednie agresywne rozpuszczalniki mogą poważnie pogorszyć właściwości wytrzymałościowe tworzyw sztucznych, dlatego podczas malowania części, w których wytrzymałość ma ogromne znaczenie (na przykład poliwęglanowy kask motocyklowy), należy zachować szczególną ostrożność i ściśle przestrzegać zaleceń producenta, a czasem nawet odmówić z zasady malować. Ale spojlery, osłony chłodnicy i panele zderzaków wykonane z poliwęglanu można malować bez problemów.
Poliamidy - PA
Poliamidy to materiały sztywne, trwałe i jednocześnie elastyczne. Części wykonane z poliamidu wytrzymują obciążenia zbliżone do dopuszczalnych dla metali nieżelaznych i stopów. Poliamid charakteryzuje się dużą odpornością na zużycie i chemikalia. Jest prawie nieprzepuszczalny dla większości rozpuszczalników organicznych.
Najczęściej poliamidy wykorzystuje się do produkcji zdejmowanych kołpaków samochodowych, różnego rodzaju tulei i wkładek, obejm do rur, języczków i zatrzasków zamków drzwiowych.
Poliuretan - PU, PUR
Przed powszechnym wprowadzeniem polipropylenu do produkcji, poliuretan był najpopularniejszym materiałem do produkcji różnych elastycznych części samochodowych: kierownic, błotników, nakładek na pedały, miękkich klamek, spojlerów itp.
Wielu osobom ten rodzaj plastiku kojarzy się z marką Mercedes. Do niedawna zderzaki, listwy drzwi bocznych i progi w prawie wszystkich modelach były wykonane z poliuretanu.
Produkcja części z tego typu tworzyw sztucznych wymaga mniej skomplikowanego sprzętu niż w przypadku polipropylenu. Obecnie wiele prywatnych firm, zarówno za granicą, jak i w krajach byłego Związku Radzieckiego, preferuje obróbkę tego rodzaju tworzyw sztucznych przy produkcji wszelkiego rodzaju części do tuningu samochodów.
Włókno szklane - SMC, BMC, UP-GF
Włókno szklane jest jednym z najważniejszych przedstawicieli tzw. „tworzyw sztucznych wzmocnionych”. Wykonywane są na bazie żywic epoksydowych lub poliestrowych (są to termoutwardzalne) z dodatkiem włókna szklanego jako wypełniacza.
Wysokie właściwości fizyczne i mechaniczne, a także odporność na różne agresywne środowiska, zdecydowały o powszechnym zastosowaniu tych materiałów w wielu dziedzinach przemysłu. Znany produkt stosowany przy produkcji nadwozi do amerykańskich minivanów.
Przy produkcji wyrobów z włókna szklanego możliwe jest zastosowanie technologii warstwowej, gdy części składają się z kilku warstw różnych materiałów, z których każdy spełnia określone wymagania (wytrzymałość, odporność chemiczna, odporność na ścieranie).
Legenda nieznanego plastiku
Tutaj trzymamy w rękach plastikową część, która nie ma na sobie żadnych znaków identyfikacyjnych ani oznaczeń. Musimy jednak koniecznie poznać jego skład chemiczny lub przynajmniej rodzaj – czy jest on termoplastyczny czy termoutwardzalny.
Bo jeśli mówimy np. o spawaniu, to jest to możliwe tylko w przypadku tworzyw termoplastycznych (do naprawy tworzyw termoutwardzalnych stosuje się kompozycje klejowe). Ponadto można spawać tylko materiały o tej samej nazwie; różne po prostu nie wchodzą w interakcje. W związku z tym konieczne staje się zidentyfikowanie tworzywa sztucznego „no name”, aby prawidłowo wybrać ten sam dodatek spawalniczy.
Określenie rodzaju plastiku nie jest łatwym zadaniem. Tworzywa sztuczne są analizowane w laboratoriach pod kątem różnych wskaźników: spektrogramu spalania, reakcji na różne odczynniki, zapachu, temperatury topnienia i tak dalej.
Istnieje jednak kilka prostych testów, które pozwalają określić przybliżony skład chemiczny tworzywa sztucznego i zaklasyfikować go do tej lub innej grupy polimerów. Jednym z nich jest analiza zachowania próbki tworzywa sztucznego w otwartym źródle ognia.
Do testu będziemy potrzebować wentylowanego pomieszczenia oraz zapalniczki (lub zapałek), za pomocą której musimy ostrożnie podpalić kawałek badanego materiału. Jeśli materiał się topi, to mamy do czynienia z tworzywem termoplastycznym, jeśli się nie topi, mamy do czynienia z tworzywem termoutwardzalnym.
Teraz usuwamy płomień. Jeśli tworzywo sztuczne nadal się pali, może to być tworzywo ABS, polietylen, polipropylen, polistyren, pleksi lub poliuretan. Jeśli zgaśnie, najprawdopodobniej jest to polichlorek winylu, poliwęglan lub poliamid.
Następnie analizujemy barwę płomienia oraz zapach powstający podczas spalania. Na przykład polipropylen pali się jasnym, niebieskawym płomieniem, a jego dym ma ostry i słodkawy zapach, podobny do zapachu laku lub spalonej gumy. Polietylen pali się słabym, niebieskawym płomieniem, a gdy płomień zgaśnie, można poczuć zapach płonącej świecy. Styropian pali się jasno, a przy tym mocno dymi i pachnie całkiem przyjemnie – ma słodkawo-kwiatowy zapach. Przeciwnie, polichlorek winylu pachnie nieprzyjemnie - jak chlor lub kwas solny, a poliamid - jak spalona wełna.
Jego wygląd może powiedzieć coś o rodzaju plastiku. Na przykład, jeśli na części widoczne są wyraźne ślady spawania, to prawdopodobnie jest ona wykonana z tworzywa termoplastycznego, a jeśli są ślady zadziorów usuniętych przez piaskowanie, to jest to tworzywo termoutwardzalne.
Możesz także wykonać test twardości: spróbuj odciąć nożem lub ostrzem mały kawałek plastiku. Z tworzywa termoplastycznego (jest bardziej miękki) wióry zostaną usunięte, ale tworzywo termoutwardzalne będzie się kruszyć.
Lub inny sposób: zanurzenie plastiku w wodzie. Dzięki tej metodzie dość łatwo można zidentyfikować tworzywa sztuczne należące do grupy poliolefin (polietylen, polipropylen itp.). Te tworzywa sztuczne będą unosić się na powierzchni wody, ponieważ ich gęstość jest prawie zawsze mniejsza niż jeden. Inne polimery mają gęstość większą niż jeden, więc będą tonąć.
Te i inne znaki, za pomocą których można określić rodzaj tworzywa sztucznego, przedstawiono poniżej w formie tabeli.
P.S. Zwrócimy uwagę na przygotowanie i malowanie części plastikowych.
Bonusy
Pełnowymiarowe wersje obrazów otwierają się w nowym oknie po kliknięciu obrazu!
Odszyfrowanie oznaczenia tworzyw sztucznych
Oznaczenia najpopularniejszych tworzyw sztucznych
Klasyfikacja tworzyw sztucznych ze względu na twardość
Główne modyfikacje polipropylenu i obszary ich zastosowania w samochodach
Metody określania rodzaju tworzywa sztucznego
Wyroby z tworzyw sztucznych stały się integralną częścią naszego życia, dlatego dziś temat recyklingu plastiku w domu nabrał szczególnego znaczenia. Recykling tworzyw sztucznych, nawet w domu, przyczynia się do ochrony środowiska przed ogromnymi stosami prawie nie ulegających rozkładowi odpadów z tworzyw sztucznych.
Podstawą wszystkich tworzyw sztucznych są polimery (związki o dużej masie cząsteczkowej i składające się z monomerów). Możliwość recyklingu tworzyw sztucznych zależy od rodzaju surowca, z którego wykonany jest wyrób z tworzywa sztucznego. Obecnie istnieje wiele rodzajów tworzyw sztucznych, które jednak można połączyć w dwie duże grupy:
- Termoplastyczny. Około 80% wyrobów z tworzyw sztucznych jest wykonanych z tego materiału. Obejmuje typy: HDPE, LDPE, PET, PP, PS, PVC itp.
- Termoutwardzalne tworzywo sztuczne. Reprezentowany przez żywice poliuretanowe, epoksydowe, fenolowe itp.
Tworzyw sztucznych typu 2 nie da się poddać recyklingowi w domu, bo... Tworzywa termoutwardzalnego nie można ponownie stopić (w niektórych przypadkach jest ono kruszony w fabrykach i wykorzystywane jako wypełniacz). Tworzywa termoplastyczne topią się po podgrzaniu, nie tracąc swoich pierwotnych właściwości, a po ochłodzeniu odzyskują swój pierwotny kształt. Dlatego „w domu” można przetwarzać wyłącznie tworzywa termoplastyczne przy użyciu specjalnego, ale „prostego” sprzętu i pozyskiwać z takich odpadów nowych, użytecznych produktów i materiałów.
Najpopularniejszymi materiałami pochodzącymi z recyklingu są butelki PET i inne plastikowe pojemniki.
Pomocna informacja! Aby zrozumieć, z jakiego tworzywa sztucznego wykonany jest dany produkt, należy zwrócić uwagę na oznaczenia znajdujące się na jego powierzchni (często na spodzie). Ma kształt trójkąta, wewnątrz którego znajduje się liczba odpowiadająca rodzajowi polimeru. Również pod trójkątem znajduje się literowe oznaczenie rodzaju tworzywa sztucznego.
Czego potrzebujesz do recyklingu w domu
Maszyny przemysłowe przetwarzające tworzywa sztuczne są drogie i wymagają dużych powierzchni. Oczywiście takie jednostki nie nadają się do realizacji idei recyklingu odpadów plastikowych w domu. Aby wyprodukować nowe produkty z odpadów tworzyw sztucznych metodą rękodzielniczą, będziesz musiał samodzielnie zaprojektować kilka specjalnych maszyn.
Podążając za projektem Precious Plastic
Aby poddać recyklingowi plastik „własnymi rękami”, będziesz potrzebować następujących urządzeń (lub jednego z nich, w zależności od celu):
- Niszczarka. Mieli odpady tworzyw sztucznych na okruszki o zadanej wielkości, które następnie poddawane są dalszej obróbce. Urządzenie składa się z kilku głównych elementów: części rozdrabniającej, leja zasypowego, ramy i źródła prądu. Najbardziej pracochłonnym etapem produkcji urządzenia jest wykonanie elementu mielącego, składającego się z wału z „nawleczonymi” na niego ostrzami. Lej załadowczy wykonany jest z blachy (można tu wykorzystać również odpady, np. stare części samochodowe). Wymagany rozmiar powstałej frakcji plastycznej ustala się za pomocą siatki zainstalowanej pod częścią mielącą.
- Urządzenie kompresyjne (naciśnij). Załadowane do maszyny wióry tworzywa poddawane są działaniu wysokiego ciśnienia i wysokiej temperatury, w wyniku procesu powstają nowe wyroby ze sprasowanych tworzyw sztucznych o różnorodnych kształtach. Główne elementy urządzenia: piekarnik, łoże, prasa i elektronika.
- Wtryskiwacz („wtryskiwacz”). Zasada działania tego urządzenia polega na tym, że pod wpływem wysokiej temperatury okruchy plastiku stapiają się w płynną masę, którą następnie wtryskiwano w dowolną postać. Po ostygnięciu plastycznej masy otrzymuje się nowe stałe obiekty o niewielkich rozmiarach.
- Wytłaczarka. Podgrzana masa plastyczna przetłaczana jest przez kanał urządzenia, w wyniku procesu tworzywo wychodzi z urządzenia w postaci nitek. Za pomocą wytłaczarki można wyprodukować granulat tworzywa sztucznego.
Rysunki montażu wszystkich tych urządzeń można pobrać bezpłatnie ze strony cenneplastiku.com. Można tam również obejrzeć instrukcje wideo, które w jasny i przejrzysty sposób wyjaśniają technologie tworzenia urządzeń, niezbędne materiały i kolejność czynności.
Projekt Precious Plastic ma charakter międzynarodowy. Jej twórca, Dave Hakkens, poprawił znalezione w Internecie rysunki urządzeń do przetwórstwa polimerów i korzystając ze swojej wiedzy zaprojektował skuteczne urządzenia, które ułatwiają wytwarzanie nowych produktów z odpadów tworzyw sztucznych. Projekt pomaga zwykłym ludziom stworzyć maszyny, które poddają recyklingowi plastik, a przy ich pomocy skorzystają nie tylko oni sami, ale także środowisko.
Prosty mechanizm do cięcia plastikowych butelek
Istotą tego noża jest to, że wycina on nitki o określonej grubości z krawędzi plastikowej butelki (wzdłuż jej obwodu). Wynik osiąga się dzięki stałemu ostrzu przesuwającemu się wzdłuż plastikowego produktu. Proces nie wymaga energii elektrycznej, urządzenie składa się jedynie z uchwytu i samego noża. Z plastikowych nici uzyskanych własnymi rękami możesz stworzyć różne elementy wyposażenia wnętrz, kosze i inne przedmioty, dla których dana osoba ma wystarczającą wyobraźnię.
Kilka słów o środkach ostrożności
Recykling plastiku w domu nie wymaga zaawansowanej wiedzy na temat bezpieczeństwa. Podczas topienia plastiku warto uzbroić się w rękawice ognioodporne (można używać rękawic spawalniczych), aby uniknąć poparzeń. Ponadto podczas pracy z produktami z tworzyw sztucznych należy wiedzieć, że nie można ich spalić, ponieważ... Niektóre rodzaje tworzyw sztucznych podczas spalania uwalniają toksyczne związki do środowiska. Oczywiście lepiej jest, jeśli odpady z tworzyw sztucznych zostaną rozdrobnione, stopione itp. odbędzie się w specjalnie wyznaczonym miejscu, np. w garażu.
Nie zapomnij o bezpieczeństwie podczas produkcji urządzeń do przetwarzania surowców tworzyw sztucznych. Tutaj również konieczne jest stosowanie środków ochrony osobistej: specjalnych okularów, maski (spawalniczej), rękawiczek płóciennych lub skórzanych itp.
Jak stopić odpady plastikowe w domu
Odpady z tworzyw sztucznych możesz przetapiać w domu za pomocą jednego z opisanych wcześniej urządzeń (prasa, inżektor, wytłaczarka). Ich stworzenie wymaga jednak pewnych umiejętności i czasu. Możesz skorzystać z topienia plastiku, stosując bardziej prymitywne metody. Na przykład, aby uzyskać plastikową zakrętkę, możesz zbudować metalową strzykawkę i solidną formę.
Opis procesu
Jako surowiec można zastosować polipropylen (oznaczony „PP”). Rozdrobniony materiał umieszcza się w wyprodukowanej strzykawce i ugniata metalowym tłokiem. Strzykawkę wypełnioną tworzywem sztucznym umieszcza się w tradycyjnym piekarniku na około 30 minut w temperaturze 220-240°C. Następnie stopioną masę plastyczną wyciska się ze strzykawki do przygotowanej formy i materiał należy przez pewien czas utrzymywać pod ciśnieniem. Po ostygnięciu gotowy produkt można wyjąć z formy.
Film przedstawiający recykling tworzyw sztucznych w domu
Rzemieślnicy wytwarzają różnorodne produkty z odpadów plastikowych. Aby dowiedzieć się, jak w domu można wykonać formowanie tworzyw sztucznych w celu wyprodukowania skrzydełka śrubowego, obejrzyj ten film:
Możesz stopić kilka plastikowych kapsli za pomocą suszarki do włosów. Proces formowania przydatnych małych wyrobów z tworzyw sztucznych przedstawiono na poniższym filmie:
Korzyść
Główną zaletą samodzielnego recyklingu plastiku jest to, że niepotrzebne i tanie materiały wykorzystywane są do tworzenia nowych produktów, które mają szerokie zastosowanie w życiu codziennym i innych obszarach naszego życia. Po zbudowaniu specjalnego sprzętu możesz zorganizować małą firmę opartą na produkcji i sprzedaży materiałów do późniejszej obróbki (na przykład flex) lub przedmiotów gotowych do użycia (naczynia z tworzywa sztucznego, meble z wikliny itp.).
Przemysłowy recykling tworzyw sztucznych wiąże się z rozwiązaniem wielu problemów. O wiele łatwiej jest poddać recyklingowi plastikowe odpady w domu. Ważne jest tylko, aby wyznaczyć sobie cel i zdecydować o kierunku przetwarzania. A za pomocą „wszechwiedzącego” Internetu można projektować urządzenia do przetwórstwa tworzyw sztucznych o dowolnej złożoności.
Tworzywo sztuczne jest materiałem uniwersalnym, znalazło szerokie zastosowanie przy produkcji różnorodnych komponentów i części zarówno w sprzęcie przemysłowym, jak i gospodarstwa domowego. Produkty z niego wykonane znajdują zastosowanie w aranżacji wnętrz lokali mieszkalnych i biur.
Rodzaj materiału zwany płynnym plastikiem umożliwia tworzenie rękodzieła o szerokiej gamie kształtów i rozmiarów. Dzięki temu możliwe jest wdrożenie oryginalnych rozwiązań konstrukcyjnych. Jak zrobić płynny plastik w domu?
Materiały do produkcji
Aby zrobić płynny plastik własnymi rękami, musisz przygotować:
- pojemnik wykonany ze szkła lub metalu;
- aceton;
- Styropian.
W tym przypadku ilość użytego acetonu zależy od pożądanej objętości gotowego produktu.
Jeśli chcesz zrobić płynny plastik własnymi rękami, przepis na jego przygotowanie będzie oparty na rozpuszczeniu styropianu w acetonie. W tym celu wykorzystuje się Jest to pojemnik do pakowania różnego sprzętu AGD i RTV.
Jak zrobić płynny plastik własnymi rękami
Przepis krok po kroku Przygotowanie wymienionego materiału wygląda następująco:
- Otwórz pojemnik z acetonem i wlej płyn do szklanego pojemnika tak, aby jego poziom od dna wynosił około 1 cm.
- Styropian należy rozbić na wiele małych kawałków, z których każdy będzie można łatwo umieścić pod grubością rozpuszczalnika.
- Możesz zrobić płynny plastik własnymi rękami, wrzucając każdy kawałek do pojemnika i czekając, aż całkowicie się rozpuści.
- Do pojemnika należy dodawać styropian, aż przestanie się topić. Następnie należy poczekać 5-10 minut, aż niewykorzystany aceton odparuje.
- Następnie na dnie pojemnika tworzy się lepka masa, którą można wykorzystać do wytworzenia różnorodnych produktów.
Wiedząc, jak zrobić płynny plastik, pamiętaj, że całkowite utwardzenie masy trwa 20-30 godzin. W rezultacie wytwarzana część nie może zostać usunięta z formy w tym czasie.
Substancję należy nakładać za pomocą małej gumowej szpatułki. Ruchy powinny być płynne. Płynny plastik należy rozciągnąć na obrabianej powierzchni. Jeśli używasz go do wypełniania pęknięć, lepiej użyć pędzli z twardym włosiem. Muszą „wcisnąć” mieszaninę w szczeliny. Po stwardnieniu tworzywa zaleca się nałożenie kolejnej warstwy substancji.
Opisywany produkt od dawna sprzedawany jest w postaci gotowej. Należy go jedynie podgrzać w łaźni wodnej lub w specjalnym sprzęcie. Często używa się do tego również suszarki do włosów.
Z reguły płynny plastik produkowany jest w gęstych opakowaniach. Jego warunki i warunki przechowywania są rygorystyczne. Temperatura w pomieszczeniu, w którym się znajduje, nie powinna spaść poniżej 15 stopni. W przeciwnym razie produkt straci swoje właściwości użytkowe:
- lepkość;
- elastyczność;
- twardość po hartowaniu;
- praktyczność;
- trwałość.
Koszt płynnego plastiku jest dość wysoki. Dlatego lepiej zrobić to samemu.
Środki ostrożności
Aceton jest bardzo niebezpieczną cieczą, która ma niezwykle negatywny wpływ na organizm ludzki. Dlatego dozwolone jest wytwarzanie płynnego plastiku własnymi rękami tylko wtedy, gdy ściśle przestrzegane są następujące środki ostrożności:
- Przed pracą z acetonem należy dokładnie zapoznać się z instrukcją jego użycia. Jest to wskazane na etykiecie pojemnika.
- Należy używać specjalnych szczelnych okularów ochronnych. Ochronią Twoje oczy w przypadku kropel cieczy i oparów. Praca bez nich może spowodować poważne obrażenia oczu.
- Aceton jest toksyczny, dlatego należy go stosować wyłącznie w dobrze wentylowanym pomieszczeniu. W takim przypadku konieczne jest stosowanie ochrony dróg oddechowych.
- Jest to produkt wysoce łatwopalny. Dlatego płynny plastik wytwarza się własnymi rękami z dala od źródeł otwartego ognia. Podczas wykonywania pracy obowiązuje całkowity zakaz palenia.
- Resztek acetonu nie wolno wylewać do kanalizacji.
- Pod koniec procesu, a także po wlaniu gotowego plastiku do foremek, należy dokładnie umyć ręce.
Zastosowania ciekłych tworzyw sztucznych w wykończeniach
Produkt używany do wykończenia przez długi czas. Po nałożeniu na obrabianą powierzchnię pojawia się elastyczny film. Jest wysoce wodoodporny i odporny na promieniowanie UV. Materiał chroniony taką folią nie boi się narażenia na działanie agresywnych detergentów. Gładka powierzchnia ma przyjemny połysk i zachowuje swoje właściwości przez wiele lat.
Płynny plastik do prac okiennych
Większość nowo zainstalowanych okien plastikowych ma szczeliny w obszarze łączenia. Aby wyeliminować to zjawisko, wszystkie połączone ze sobą części konstrukcji okna są traktowane opisaną substancją. Po wyschnięciu tworzy na powierzchni elastyczną, szczelną powłokę. Nakładanie płynnego plastiku na okna własnymi rękami jest możliwe po wykonaniu materiału zgodnie z powyższą metodą.
Środek antykorozyjny
Płynne tworzywo sztuczne charakteryzuje się także wysokim stopniem przyczepności do obrabianej powierzchni metalu. Tę właściwość substancji zaczęto wykorzystywać w antykorozyjnej obróbce stali. Płynny plastik nakłada się na powierzchnię bez wcześniejszego gruntowania. Wysycha w ciągu kilku godzin. Następnie na powierzchni tworzy się film, który chroni materiał przed rdzą.
Ze względu na swoją wszechstronność, niski koszt i trwałość tworzywo sztuczne znalazło zastosowanie we wszystkich sferach życia. Obecnie plastik jest najpopularniejszym sztucznym materiałem na naszej planecie. Jest także pierwszy na liście śmieci. Ilość odpadów z tworzyw sztucznych na planecie osiąga rozmiary epidemii. Wielu naukowców, wynalazców i przedsiębiorców zaczęło zwracać uwagę na ten problem.
Maszyny przemysłowe do recyklingu tworzyw sztucznych są zazwyczaj bardzo drogie i dość skomplikowane w konstrukcji. I nie oszukujmy się, recykling plastiku na skalę przemysłową się nie opłaca. Ponieważ cykl produkcyjny jest „ surowiec - produkt z tworzywa sztucznego„znacznie krócej i taniej niż -” śmieci - sortowanie - wyroby z tworzyw sztucznych - recykling - sprzątanie - surowce - wyroby z tworzyw sztucznych" Dlatego nie wszystkie miasta na świecie posiadają fabryki przetwarzające odpady z tworzyw sztucznych. A ich masowy wygląd nie jest spodziewany w najbliższej przyszłości.
Okazuje się, że nisza recykling plastiku w domu otwarty. I czeka na tych, którzy z dowolnej strony na nim zarobią. Ale przeciętny człowiek nie potrzebuje wiele. W końcu piękno tej niszy polega na tym, że odpady plastikowe, w zasadzie śmieci, leżą pod nogami wszystkich i nikomu nie są przydatne. Czyli doskonały i trwały materiał - gratis! Pozostaje tylko je zebrać, przetworzyć w tej czy innej formie i ponownie wykorzystać. A jeśli nie podoba ci się wynik, przerób go jeszcze raz!
Projekt " Cenny plastik» pomaga wszystkim konsumentom dać odpadom z tworzyw sztucznych nowe życie. Zachęca wszystkich do samodzielnego recyklingu plastiku przy użyciu domowych maszyn, których rysunki są swobodnie rozpowszechniane w Internecie.
Projekt ten, opracowany przez holenderskiego projektanta Dave'a Hakkensa, pokazuje, co można zrobić, aby powstrzymać „plastyczną plagę” w środowisku.
Dave zaniepokojony problemem odpadów z tworzyw sztucznych znalazł w Internecie rysunki kilku urządzeń, które pozwalają mu w jakiś sposób poddać recyklingowi plastik w domu. Po zebraniu pierwszych próbek, udoskonaleniu ich i opracowaniu koncepcji modułowej przyszłych urządzeń, Hakkens stworzył międzynarodowy projekt „ Cenny plastik" W którym zaprasza wszystkich do złożenia i wykorzystania czterech prostych, ale skutecznych maszyn do recyklingu tworzyw sztucznych.
Korzystanie z urządzeń pozwala przedłużyć żywotność różnych plastikowych artykułów gospodarstwa domowego poprzez proste przetworzenie ich na inne. Niepotrzebne lub konieczne. Naczynia, sztuczny rattan, różne elementy wyposażenia wnętrz – oto mała lista przedmiotów, które można wyprodukować z domowych odpadów plastikowych za pomocą tych maszyn.
Cztery urządzenia, w zależności od rodzaju i jakości tworzywa, pozwalają na jego obróbkę na różne sposoby:
- Niszczarka lub rozdrabniacz - urządzenie do mielenia odpadów z tworzyw sztucznych na okruchy w celu późniejszego przetworzenia - ogrzewanie;
- Wytłaczarka lub wytłaczarka – urządzenie, które wytłacza podgrzaną masę plastyczną w postaci liny lub taśmy. Oznacza to, że efektem jest sztuczny rattan lub materiały eksploatacyjne do drukarki 3D.
- Wtryskiwacz lub wtryskiwacz - podgrzewa okruchy polimeru do plastycznej masy i wtryskuje je do pożądanego kształtu;
- Naciskać— okruchy plastiku pod ciśnieniem i w wysokiej temperaturze wciskane są w różne nowe przedmioty.
Najbardziej niesamowitą rzeczą w tym projekcie” Cenny plastik» fakt, że tak wyjątkowe samochody rozdawane są za darmo. Dokładniej, rysunki urządzenia i instrukcje ich montażu są dostępne dla wszystkich (instrukcje wideo będą poniżej). Pozostaje tylko złożyć samochody i zacząć na nich zarabiać.
Jak zarabiać na recyklingu plastiku w domu? Recykling tworzyw sztucznych i polimerów w domu!
Po pierwsze. Poprzez recykling niepotrzebnego plastiku w przydatne produkty z tworzyw sztucznych i sprzedaż ich jako unikalnych, ręcznie robionych przedmiotów. To najprostsze i najtańsze rozwiązanie.
Po drugie. Otwierają się całe laboratoria kreatywne i przestrzenie coworkingowe oparte na maszynach Hakkens. Gdzie każdy może przyjść ze swoimi plastikowymi odpadami, zapłacić i popracować przy maszynach.
Trzeci. Pomoc w montażu i sprzedaży urządzeń. Nie każdy może opanować rysunki urządzeń. A co więcej, zbieraj je. Ale są gotowi kupić zmontowane podobne maszyny. Dlaczego by z tego nie skorzystać? Ponadto gotowe urządzenia są dość drogie. Montaż, jeśli masz wszystko, czego potrzebujesz, zajmie każdemu poręcznikowi w garażu nie więcej niż miesiąc.
Czwarty. Zdecydowanie masz własne pomysły!
Film nr 1: jak złożyć niszczarkę do rozdrabniania plastiku
Film nr 2: jak złożyć wytłaczarkę do przetwórstwa tworzyw sztucznych
Film nr 3: jak zamontować wtryskiwacz do recyklingu tworzyw sztucznych
Film nr 4: jak złożyć prasę do recyklingu tworzyw sztucznych
Po przestudiowaniu wideo możesz rozpocząć montaż urządzeń. Aby zapewnić wygodniejszą pracę, zalecamy przestudiowanie rysunków na oficjalnej stronie projektu. Po angielsku.
Jeśli urządzenia są zbyt skomplikowane, możesz przyjrzeć się prostemu sposobowi na recykling plastikowych butelek w domu.
Bonus: najprostsze urządzenie do cięcia plastikowych butelek
Pojawił się na Kickstarterze nowy projekt « Obcinak do plastikowych butelek”, co daje konsumentom możliwość korzystania plastikowe butelki Ponownie.
Najprostsze urządzenie (a zobaczysz to na zdjęciu poniżej) pozwala zamienić zwykłą plastikową butelkę w plastikową nić o różnych grubościach, którą możesz wykorzystać według własnego uznania.
Z tego wątku możesz tkać różne przedmioty- od małych koszyczków po eleganckie meble.
Ogólnie rzecz biorąc, jednorazowe butelki plastikowe są cennym zasobem ze względu na fakt, że są wykonane z tworzywa sztucznego. najwyższa jakość. Jednak większość ludzi nie bierze tej zalety pod uwagę i butelki są po prostu wyrzucane. Liczba rzucanych butelek rośnie z każdym dniem. Zatem problem skuteczności ponowne użycie a recykling tych materiałów jest po prostu konieczny i obowiązkowy. Zmniejszy to zanieczyszczenie środowiska.