Confiabilidad en la tecnología. Endurecimiento de piezas de máquinas. La elección de modos de aluminización para mayor durabilidad. Requerimientos generales. Acero aluminizante
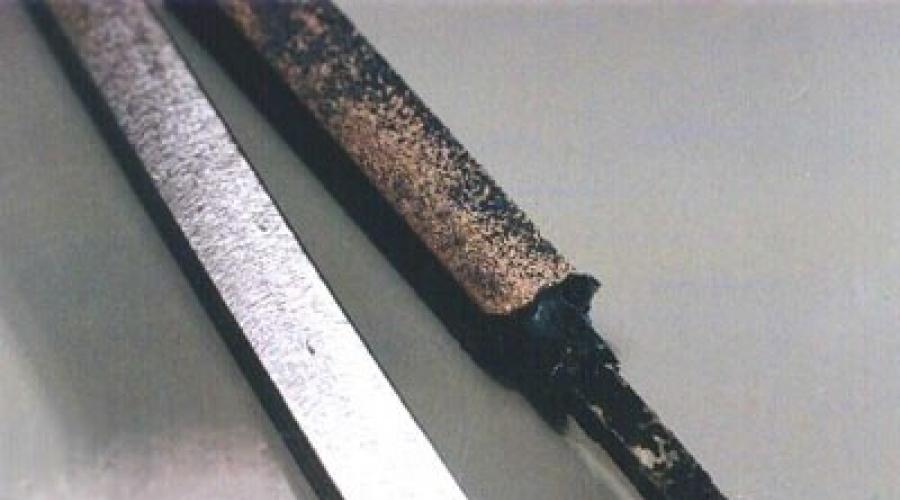
DERRITE
CDU 621.793.6
K. R. Karimova, A. I. Anfinogenov, Ya. B. Chernov, V. V. Chebykin, A. A. Pankratov y B. D. Antonov
ALITIZACIÓN DIFUSIVA A BAJA TEMPERATURA DE ACEROS Y ALEACIONES BAJO ACTIVACIÓN MECÁNICA DE LA SUPERFICIE
Resumen—Se estudió la producción de recubrimientos de difusión de aluminuro sobre aceros 20, 08Yu, 08Kh18N10T y aleaciones de cromo-níquel Kh27Yu5T, KhN65VMYuT y Kh15N60-N mediante activación mecánica de la superficie en un reactor rotatorio en mezclas que contienen polvos de aluminio, cloruro de amonio, y corindón a temperaturas de 550–600°C. Se determinó el espesor y composición de fase de los recubrimientos de aluminuro, la resistencia al calor del acero aluminizado 08Yu a 620 y 912°C y la aleación KhN65MVTYu a 1000°C.
Los recubrimientos obtenidos se estudiaron mediante análisis de fase de rayos X, microanálisis espectral de rayos X y método gravimétrico. Los recubrimientos de aluminuro sobre aceros estructurales constan de fases sucesivas, comenzando desde la capa exterior: ReA13, Re2A15, Re3A1; así como sobre acero inoxidable de las fases: Re2A15, Cr2A1, CrA15, sobre aleaciones resistentes al calor de las fases: No. A13, No. A1, No. 3A1, Cr2A1, CrA15.
Palabras clave: aluminizado por difusión térmica, aumento de la resistencia al calor, recubrimientos de aluminuro, activador de cloruro salino.
INTRODUCCIÓN
Actualmente, la industria utiliza una variedad de recubrimientos aplicados a la superficie de los productos de una forma u otra, dependiendo de las condiciones de operación de los mismos. La saturación por difusión permite, a un costo relativamente bajo, formar en capas superficiales productos la estructura de fase necesaria correspondiente a las propiedades requeridas, y es una de las tareas principales en sistema común medidas para proteger el metal de la corrosión, aumentar su resistencia al calor y al desgaste. Dado que este artículo es el primero de una serie de trabajos sobre este tema, presentamos además un análisis del nivel actual de investigación sobre la formación de recubrimientos por difusión, incluidos aquellos con la influencia de la activación mecánica.
La clasificación más completa de los procesos de saturación por difusión basada en caracteristicas fisicas y quimicas El medio usado que contenía un elemento saturante fue propuesto por G.N. Dubinín. La clasificación desarrollada y complementada de estos métodos se da en la monografía. Según esta clasificación, según el tipo de medio saturante, existen cuatro métodos de saturación por difusión: sólido, gas, líquido y gas-vapor.
Esta clasificación tiene en cuenta todos formas conocidas y metodos tecnologicos saturación superficial de metales y aleaciones varios elementos. Cada uno de los métodos de recubrimiento tiene sus propias ventajas y desventajas. Todos estos métodos proporcionan la creación de un medio de saturación activo, que es uno de los condiciones necesarias tecnología de saturación por difusión, o buen contacto componente saturado con la superficie de la pieza.
Uno de los métodos más eficaces y ampliamente utilizados en la industria para aumentar la durabilidad de muchas piezas críticas es su tratamiento químico-térmico (CHT), que afecta a las capas superficiales del metal, es decir, a aquellas capas en las que se concentran tensiones máximas, se desarrollan procesos de corrosión y desgaste. La ventaja de los recubrimientos de difusión obtenidos durante el tratamiento químico es que la unión entre el elemento aplicado y el metal protegido es más fuerte debido a la difusión mutua. cambio gradual La concentración del elemento aplicado sobre el espesor del recubrimiento asegura una buena adherencia del recubrimiento a la base debido a un cambio suave o escalonado en los coeficientes de expansión térmica de las fases del recubrimiento, lo que asegura la durabilidad de las piezas bajo fuertes fluctuaciones de temperatura.
El recubrimiento metálico más versátil para la protección contra la oxidación de productos para diversos fines durante temperaturas elevadas en el aire y en algunos ambientes agresivos son recubrimientos de aluminuro. La saturación de la superficie de metales y aleaciones con aluminio les da una mayor resistencia a las incrustaciones en altas temperaturas como resultado de la formación de una película de óxido a-A12O3 sobre el recubrimiento de aluminuro y, en consecuencia, una mayor resistencia a la corrosión atmosférica.
Existen numerosas publicaciones sobre la preparación de recubrimientos de aluminuro sobre varios metales y aleaciones por los métodos indicados. Las monografías presentan los resultados de estudios sobre la aluminización de aceros, y los libros contienen secciones separadas sobre la deposición de revestimientos de aluminuro en varios aceros y aleaciones. Desarrollado varios métodos aluminización por difusión: en medios pulverulentos, en baños con aluminio fundido, gas, electrólisis en baños con sales de aluminio fundido.
ALITITACIÓN POR TERMODIFUSIÓN EN MEZCLAS EN POLVO
La aluminización de productos metálicos en mezclas de polvo se ha vuelto predominante en la industria, especialmente para aumentar su resistencia a la corrosión y resistencia al calor. Para la aluminización, se utilizan varias mezclas, que consisten en polvos de aluminio o ferroaluminio, óxido de aluminio, cloruro de amonio con la adición de elementos de aleación. El aluminizado se realiza en cajas de acero resistente al calor a 700-1000°C. Sin embargo, la aluminización a altas temperaturas provoca un rápido crecimiento del grano del acero. Para reducir el contenido de aluminio en el revestimiento y reducir su fragilidad, las piezas aluminizadas suelen someterse a un recocido adicional (normalización).
Complicación forma geometrica y el aumento del tamaño de una serie de productos despertó el interés por reducir la temperatura de endurecimiento superficial de los metales. A 500-600°C, es posible reducir significativamente la deformación de los productos, mantener las propiedades de resistencia de la base, aumentar la vida útil del equipo, sin reducir la calidad de la capa superficial.
Las reacciones de aluminización más probables son la descomposición del cloruro de amonio en amoníaco y cloruro de hidrógeno, la entrada de aluminio metálico en una reacción con cloruro de hidrógeno para formar cloruro de aluminio, y la autorrecuperación del aluminio a un compuesto de aluminio de menor valencia. El cloruro de aluminio monovalente se desproporciona en la superficie del acero para formar una aleación Al-Fe:
MH4a(tv) ^ MH3(g) + HC1(g),
6HC1(g) + 2A1(s) ^ 2A1C13(g) + 3H2(g),
Arroz. 1. Esquema de instalación para la aplicación de recubrimientos de difusión térmica:
1 - reactor; 2 - cubierta; 3 - tubería para bombear aire y suministro gas inerte; 4 - horno; 5 - válvula; 6 - cerradura para llenar polvos de aleación (mezcla); 7 - mezcla saturada; 8 - detalles; 9 - separador; 10 - capacidad adicional; 11 - cubierta de capacidad adicional; 12 - volante para la válvula. El nodo de rotación no se muestra en el diagrama.
A1C13(g) + 2A1(tv) ^ 3A1C1(g),
3A1C1(g) + 2Fe(sólido) ^ A1C13(g) + 2FeA1(aleación).
Se observa en la literatura que los recubrimientos de aluminio resisten mejor la corrosión que los recubrimientos de zinc. condiciones atmosféricas, en un ambiente seco o húmedo que contenga azufre. La profundidad de la capa de aluminuro y la concentración de aluminio en ella determinan la durabilidad de las piezas en condiciones de trabajo. El método de difusión térmica de aluminización, realizado en medios en polvo, es el más conveniente para aplicar recubrimientos a las partes roscadas de los productos.
Para mejorar la resistencia a la corrosión de los sistemas de escape fabricados con aceros estructurales para motores Combustión interna en ambientes agresivos con calentamiento cíclico hasta 600°C, además de aumentar la resistencia al calor de los intercambiadores de calor y álabes de turbina hechos de Aceros inoxidables y aleaciones resistentes al calor hasta 1000°C, realizamos estudios sobre la deposición de recubrimientos de aluminuro en aceros 20, 08Yu, 08Kh18N10T y aleaciones Kh27Yu5T, KhN65VMYuT, Kh15N60-N por el método de saturación a baja temperatura en una mezcla (wt. %): aluminio - 2,5, activador MN4S1 - 0,5 y electrocorindón - el resto, a 550-600°C con activación mecánica de la superficie durante 3-5 horas. El cloruro de amonio en este esquema actúa como proveedor de los iones de cloruro necesarios para intensificar la transferencia de aluminio a través de la fase gaseosa. La fuerza motriz del proceso de aluminización es el cambio en la energía de formación de la aleación en la superficie del material que se satura.
TÉCNICA EXPERIMENTAL
Hemos utilizado un método de bajo desperdicio para aplicar revestimientos de aluminuro resistentes al calor y anticorrosión de difusión continua en la superficie de metales ferrosos, no ferrosos y aleaciones (hardware, tuberías, álabes de turbina y otros productos) en la instalación. acción periódica en atmósfera de argón (Fig. 1).
tabla 1
Composición química de aceros y aleaciones (% en peso)
Acero, aleación, GOST Cr N1 Be Mo "Ig A1 T1 Mp 81 C 8 R
Acero 20, Hasta 0,25 Hasta 0,25 Base - - - - 0,35- 0,17- 0,17- Hasta 0,04 Hasta 0,04
1050-88 0.65 0.37 0.24
Acero 08Yu, 0,03 0,06 Base - - 0,02- - 0,20- 0,01 Hasta 0,07 0,025 0,02
9045-80 0.07 0.35
Acero 17.0- 9.0- Base - - - 5.0C-<2.0 <0.8 <0.08 <0.02 <0.3
08X18H10T, 19,0 11,0 0,7
Aleación 26.0-< 0.6 Основа - - 5.0- 0.15- 0.3 0.6 0.05 0.015 0.02
Kh27Yu5T, 28.0 5.8 0.4
Aleación 15.0-Base<3.0 3.5- 8.5- 1.2- 1.2- <0.5 <0.6 0.05 <0.01 <0.02
KhN65VMYUT 17,0 4,5 10,0 1,6 1,6
Aleación 15,0- 55,0- 17,3- - - Hasta 0,2 Hasta 0,3 Hasta 0,2 0,8- Hasta 0,03 Hasta 0,2 Hasta 0,03
Х15Н60-Н, 18.0 61.0 29.2 1.5
La saturación por difusión térmica se llevó a cabo en un reactor rotatorio sellado 1 a una velocidad de 5 rpm a 550–600 °C y un tiempo de 3–5 h, dependiendo del material del sustrato y el espesor del recubrimiento. La mezcla de saturación consistía en polvo de aluminio PA-4 (0,1–0,2 kg m–2 de superficie de la muestra), polvo de electrocorindón (A1203, 50 % del volumen del reactor) y 0,5 % de N^0 en la masa de electrocorindón. A pesar de la naturaleza no isotérmica del reactor, el cloruro de amonio, al condensarse en las partes más frías del reactor, proporcionó el contenido necesario de cloruros de aluminio involucrados en su transferencia. Después de completar el proceso de saturación, la mezcla se separó de las muestras a través de un separador 9 en un recipiente sellado 10 con la válvula 5 abierta. Luego, el reactor se despresurizó y las muestras recubiertas se descargaron al aire para su enfriamiento, la mezcla gastada permaneció en un recipiente adicional sellado, mientras la válvula estaba cerrada. El siguiente lote de muestras se cargó en el reactor a la temperatura del proceso, luego se selló, se evacuó el aire y se llenó con argón. En la mezcla gastada después de enfriar a 300°C negro
El proceso de saturar la superficie del acero inoxidable y el hierro fundido con aluminio se denomina aluminizado o aluminizado. El objetivo principal de este proceso es aumentar la resistencia a la corrosión y la resistencia a las incrustaciones del acero inoxidable.
Los materiales para aluminizar son principalmente acero inoxidable, acero inoxidable bajo en carbono y fundición gris.
Ocasionalmente, la aluminización se usa para acero inoxidable de carbono medio y acero resistente al calor. Dependiendo de la composición química del acero inoxidable, se pueden utilizar varios tipos de aluminizado.
Se conocen los siguientes métodos de aluminizado de acero inoxidable:
- § en mezclas de naturaleza pulverulenta;
- § aluminio fundido en baños especiales;
- § por metalización del acero inoxidable con aluminio seguido de recocido por difusión;
- § sales fundidas en baños especiales;
- § gas aluminizado.
En la industria, los primeros tres métodos de aluminización están en demanda. En producción, hay líneas para aluminizado automático por el método de metalización de piezas de automóviles. En el transportador de avance, las válvulas de los automóviles pasan progresivamente y con rotación por la zona de calentamiento por inducción y se metalizan con aluminio mediante una pistola. En la segunda instalación de inducción, se calientan por difusión hasta 800 grados centígrados. Esto logra una profundidad de capa de difusión de dos centésimas de milímetro.
La aluminización según el primer método permite conseguir una alta concentración de aluminio en la zona superficial de la capa aluminizada. El contenido de aluminio en este caso puede alcanzar el cincuenta por ciento. Cuanto más dura la aluminización del acero inoxidable o del acero inoxidable, menor se vuelve el aumento de la profundidad de la capa de aluminización. El valor óptimo de la duración de la aluminización del acero inoxidable depende del grado del acero y de la presencia de aditivos de elementos químicos. La capa aluminizada se caracteriza por una alta estabilidad a una temperatura significativa en una esfera saturada con sulfuro de hidrógeno.
El aluminio, oxidado, forma una película protectora de óxido de aluminio, que protege al producto de una mayor oxidación. Durante el funcionamiento, la resistencia de los productos aluminizados aumenta entre 6 y 7 (a 1000°) y hasta 20 (a 800°) veces en comparación con los no aluminizados. Hay varias formas.
- 1) Desde 1925, el método A se utiliza en una mezcla en polvo de partes iguales de aluminio (o su aleación con hierro) y óxido de aluminio con 2% de amoníaco. Los productos con una superficie totalmente limpia de óxidos se cargan en una caja de acero o en un tambor giratorio con una mezcla, donde se mantienen a una temperatura de unos 950° durante unas 5 horas. Después de esto, los productos se someten a un recocido a 900--1.000°C, durante el cual el aluminio se difunde desde la superficie hacia las profundidades, como resultado de lo cual se destruye la fragilidad de la capa superficial sobresaturada con aluminio. La última práctica de las fábricas soviéticas ha demostrado que lo más efectivo es el uso de polvo de ferroaluminio, sin la adición de óxido de aluminio.
- 2) Método de inmersión en caliente en un baño de aluminio fundido en el que se disuelve aproximadamente un 8% de hierro. El proceso se lleva a cabo a 800° durante 40--60 minutos. seguido de recocido por difusión. Con este método se obtiene una capa aluminizada relativamente más frágil.
- 3) Método de gases. Se coloca polvo de aluminio y óxido de era con 10% de amoníaco en el extremo de una retorta de acero calentada a 600°; aquí, en una corriente de hidrógeno, como resultado de la reacción del aluminio y el amoníaco con él, se forma cloruro de aluminio volátil. De este producto volátil, que reacciona a 1.000°C con el hierro de las piezas situadas en el otro extremo de la retorta, se libera aluminio en estado atómico, difundiéndose en la capa superficial de las piezas de hierro.
Durante varios siglos, las principales propiedades de rendimiento de los metales han cambiado con la ayuda de efectos químico-térmicos. Las pruebas realizadas indican que el porcentaje de ciertas impurezas en el metal puede afectar su dureza, resistencia, resistencia a la corrosión y muchas otras cualidades. La aluminización del acero al carbono es un proceso de saturación de la capa superficial del producto con aluminio, que tiene lugar a una determinada temperatura. El proceso de aluminizado del acero es bastante complicado, durante el cual se instalan ciertos equipos. Considere las características del trabajo sobre la saturación de la capa superficial de acero y hierro fundido con aluminio.
Aplicación de aluminizado
Las propiedades asociadas al producto determinan en gran medida el alcance de la tecnología considerada de tratamiento químico-térmico. En la producción, la aluminización del acero se utiliza para cambiar las siguientes propiedades del acero tratado:
- Resistencia a gran escala. Esta propiedad está asociada con la formación de una película protectora en la superficie del producto cuando se calienta.
- Alta protección frente a procesos oxidativos.
- Altas propiedades anticorrosivas. Como resultado de la aluminización, el producto se puede utilizar incluso cuando se expone al agua de mar.
- Teniendo en cuenta la dureza de la capa superficial, se debe prestar atención al hecho de que la cifra máxima alcanzable es de aproximadamente 500HV.
Teniendo en cuenta las ventajas y desventajas de la aluminización del acero, cabe señalar que el efecto de la alta temperatura provoca la reorganización de la red atómica, como resultado de lo cual la capa superficial se vuelve quebradiza.
Cuando se procesan piezas críticas con este método químico-térmico, la cocción se lleva a cabo durante varias horas. Por tanto, el proceso de introducción del aluminio se caracteriza por una larga duración.

Tecnología y métodos de aluminización.
La aluminización por difusión tiene lugar a una temperatura de 700 a 1100 grados Celsius. Los modos de procesamiento óptimos se seleccionan según las características del material que se procesa. Existen varias tecnologías más comunes para la exposición químico-térmica:
- La aluminización en mezclas de polvo se realiza mediante cajas metálicas. El tocho se coloca en un carburador sólido. Al mismo tiempo, la mezcla preparada se puede usar repetidamente, lo que hace que esta tecnología sea rentable. La temperatura del acero aluminizado en este caso se mantiene en el rango de 950 a 1050 grados centígrados, el proceso dura de 6 a 12 horas. La profundidad máxima de penetración del aluminio es de 0,5 milímetros. La composición utilizada está representada por polvo de aluminio, polvo y ciertos aditivos. Los aditivos están representados por óxido de aluminio y arcilla molida, así como variedades de cloruro de amonio y aluminio. En algunos casos, el procedimiento se demora hasta 30 horas, lo que lo hace antieconómico. Este método es aplicable en el caso de una configuración compleja de la pieza, ya que el cambio de etapa superficial se realiza por etapas. Cambiar la composición de la capa superficial con una mezcla de polvo es el método más costoso de todos los utilizados.
- La aluminización por proyección se realiza si es necesario para reducir el tiempo de esta operación. Esta tecnología de aluminización determina el impacto de una temperatura relativamente baja, alrededor de 750 grados centígrados, el aluminio tarda aproximadamente una hora en penetrar a una profundidad de 0,3 milímetros. Las ventajas de este método radican en la rapidez de ejecución, pero no se puede utilizar para obtener piezas críticas resistentes al desgaste, ya que la película superficial es muy fina. Se recomienda la saturación superficial del acero para la producción en masa. La fuerza de adherencia de la capa proyectada en este caso es baja, es de 0,2-2 kg/mm2. Además, las características de esta tecnología determinan la alta porosidad de la estructura.
- La metalización seguida de la cocción se lleva a cabo cuando la pieza se calienta a una temperatura de 900-950 grados centígrados, el tiempo de calentamiento es de 2 a 4 horas. Este método es significativamente inferior al anterior, ya que la capa resultante tiene un grosor de no más de 0,2-0,4 milímetros y los costos aumentan debido a un aumento significativo en el tiempo de calentamiento. Sin embargo, a menudo se utiliza cuando es necesario obtener una pieza con una superficie fuerte y dura, que estará sujeta a cargas importantes. Esto se debe a que el recocido conducido reduce el índice de fragilidad, aumentando la resistencia.
- La aluminización al vacío consiste en la aplicación de un recubrimiento por evaporación del aluminio con su posterior depósito sobre la superficie del producto. El espesor del recubrimiento resultante es insignificante, pero la calidad alcanzada es una de las más altas. Para calentar el medio, se instalan hornos especiales que son capaces de calentar la composición de alimentación a una temperatura de 1400 grados Celsius. Se alcanza una alta cualidad del cubrimiento a expensas de la distribución uniforme del aluminio por toda la superficie. La tecnología en este caso prevé el precalentamiento de la superficie a una temperatura de 175 a 370 grados centígrados. Se debe prestar mucha atención a la preparación preliminar de la pieza, ya que incluso una ligera película de óxido provoca una disminución significativa en la calidad de la adherencia de la superficie y la composición interna. El alto costo del proceso y su complejidad determinan la aplicabilidad solo en la producción de piezas críticas.
- La aluminización por inmersión es muy popular debido al hecho de que el recubrimiento se aplica en 15 minutos. Al mismo tiempo, la temperatura es relativamente baja: de 600 a 800 grados centígrados. Además, este método es uno de los más asequibles en términos de costo. La esencia del procedimiento es sumergir la pieza de trabajo en aluminio líquido calentado a alta temperatura. Esto da como resultado una capa con un espesor de 0,02 a 0,1 mm. Se presta especial atención a la preparación del entorno en el que se llevará a cabo el proceso de cambio de la composición química de la capa superficial.

Existen otros métodos de introducción de aluminio, que le permiten cambiar el rendimiento básico de las piezas de trabajo.
Para controlar la calidad de la superficie mediante un detector de fallas, un dispositivo que se usa para verificar defectos mediante pruebas no destructivas.
Los defectos más comunes son violaciones de la homogeneidad de la estructura, la aparición de una zona de daño por corrosión, la desviación de la composición química requerida, etc.

Materiales permitidos para aluminizar
La metalización es una tecnología que está diseñada para cambiar las propiedades de la capa superficial. Una variación de esta tecnología es la aluminización. La saturación de la capa superficial está sujeta a:
- Aceros al carbono. En este caso, se utilizan predominantemente aceros con bajo contenido de carbono y, con menor frecuencia, aceros con contenido medio de carbono. Con un alto contenido de carbono en la composición, el procedimiento se vuelve ineficaz.
- Los aceros aleados se usan con menos frecuencia, pero con la tecnología adecuada se pueden obtener piezas resistentes al desgaste.
- El hierro fundido también se puede someter a un procedimiento de aluminización para cambiar su rendimiento básico.
Para obtener acero inoxidable, tanto los aceros al carbono como los aleados se someten a aluminización. En algunos casos, se lleva a cabo una preparación preliminar de aceros y aleaciones, representada por procedimientos de endurecimiento u otros tratamientos químico-térmicos.
Si encuentra un error, seleccione un fragmento de texto y presione Ctrl+Enter.
stankiexpert.ru
Tecnología de proceso de aluminización
Tres métodos de aluminizado han encontrado aplicación industrial: en mezclas de polvo sólido, en baños con aluminio fundido, así como el método de metalización superficial con aluminio seguido de recocido por difusión.
También es posible la aluminización al vacío por deposición de la fase vapor-gas, electrolítica en baños constituidos por sales de aluminio, así como la aluminización gaseosa, en la que se hace pasar hidrógeno a través de mezclas sólidas que contienen aluminio.
La aluminización en mezclas sólidas se realiza en recipientes herméticos utilizando polvo de aluminio (49-50%) o ferroaluminio (50-99%) con adiciones de óxido de aluminio (cuando se usa FeAl, la adición de Al2Oz es opcional, ya que el polvo casi no es sujeto a sinterización) y Nh5Cl (1 -2.%).
Las reacciones químicas que tienen lugar en dicho recipiente son similares a las reacciones durante el cromado:
MH4C1=NH3+HC1;
6HC1 + 2A1 = 2A1C1z + ZH2;
A1C1z+2A1=3A1C1;
A1C1z \u003d A1C1 + Cl2.
Se cree que el subcloruro de aluminio A1C1 resultante forma aluminio atómico por autorreparación en la superficie del acero.
ZA1C1 \u003d A1C1z + 2A1.
Sin embargo, una reacción de intercambio del tipo
А1С1з + Fe (producto) = FeС1з + А1.
Se considera que la temperatura óptima del proceso es de 950-1050 ° C. El proceso es bastante largo y, según la profundidad requerida, es de 4-30 horas.
Para reducir la fragilidad de la capa, a veces se lleva a cabo un recocido por difusión a 800-1000° después de dicha aluminización, como resultado de lo cual el contenido de aluminio en la capa superficial disminuye al 20-30% con un aumento en la profundidad total de la capa. capa.
El método de inmersión de productos en un baño de aluminio fundido se distingue por su alta productividad.
El proceso se lleva a cabo a 700-800°, ya se forma una capa con un espesor de 0,02-0,1 mm en 1-15 minutos. Sin embargo, a pesar de su simplicidad y corta duración, este método tiene una serie de desventajas: 1) mayor fragilidad de la capa, que también debe eliminarse mediante el recocido por difusión; 2) corrosión y disolución de productos en aluminio fundido; 3) baja durabilidad de los crisoles; 4) pegado local de películas de aluminio y óxido de aluminio en las piezas; 5) saturación desigual; 6) oxidación del hierro durante el buceo.
Es cierto que hay una serie de medidas para mejorar la calidad de la aluminización en los baños. Agregar 8-12% Fe o 20-22% Ni al baño reduce la intensidad de disolución y corrosión de las piezas.
El método también se ha mejorado mediante el uso de fundentes, lo que reduce la corrosión (el calentamiento se realiza en la capa de fundente), protege la masa fundida de la oxidación, mejora la humectación y, por lo tanto, promueve la formación de una capa más uniforme en profundidad y facilita la superficie. limpieza de la contaminación cuando las piezas se sacuden en la capa de fundente. Como fundentes se utilizan composiciones que contienen NaCl, HC1, LiCl, ZnCl2, A1Fz, NaF, Na3AlF6 en diversas proporciones.
Cuando se aluminizan láminas y alambres de acero por el método considerado, el recocido se lleva a cabo en hornos continuos con una atmósfera reductora de amoníaco disociado antes de cargarlos en el baño. En este caso, se eliminan todas las películas de óxido y el aluminio fundido humedece eficazmente la superficie de acero.
La aluminización por el método de metalización se lleva a cabo en varios pasos. Se aplica una capa de aluminio de 0,8-1,2 mm de espesor a la superficie previamente limpiada (chorro de arena, procesamiento con virutas de metal para limpiar y crear una mayor rugosidad para aumentar la adherencia del recubrimiento y el metal base). El proceso de recubrimiento consiste en fundir el metal y rociarlo con un chorro de aire comprimido a una presión de 2-4 atm utilizando metalizadores especiales (gas, eléctricos o de alta frecuencia). Esto da como resultado una capa porosa con baja fuerza adhesiva. A continuación, la superficie se recubre con compuestos protectores (grafito de plata, arcilla refractaria, arena de cuarzo, vidrio líquido, etc.) para protegerla contra la oxidación durante el posterior recocido por difusión. El recocido se lleva a cabo a una temperatura de 900-1100 ° con precalentamiento y enfriamiento lento. Este método es bastante económico y puede competir con otros métodos.
§ 17. La estructura de la capa aluminizada y la influencia de varios factores en los resultados del proceso.
La estructura y la composición de fase de la capa aluminizada dependen del método de aluminización. El contenido de aluminio en la superficie puede alcanzar ~ 50% cuando se usan mezclas sólidas, e incluso 75-80% cuando se metaliza con recocido posterior.
De acuerdo con el diagrama Fe-A1 (ver Fig. 32), en este caso, se forman en la superficie compuestos intermetálicos Fe3A1, FeAl, FeAl2, etc.. Estas fases, así como la solución sólida de aluminio en hierro adyacentes al núcleo, en el grabado ordinario se revelan en forma de una zona clara no grabada. Cuando se aluminiza en aluminio fundido, el límite de la capa tiene un carácter sinuoso similar a una aguja.
Esto se debe a las características específicas de la fase Fe2Al5 con una red rómbica formada en la superficie. La velocidad de difusión del aluminio en esta fase es máxima y no se forman otras fases en este método.
Arroz. 33. Cambio en la concentración de aluminio y carbono en la capa aluminizada de acero con 0,4% C (la composición de fase se da para la temperatura de difusión)
Las características de la estructura cristalográfica de esta fase son tales que se observa una difusión predominante en la dirección perpendicular a la superficie, lo que es responsable del carácter direccional acicular de los cristales de esta fase.
En presencia de carbono en el acero, a menudo se observa una zona con un alto contenido de carbono detrás de la zona de fase a (Fig. 33), pero esto no siempre sucede. La ausencia de una zona en aceros con un contenido de más de 0,7% C se explica por la formación de una característica de fase ε del sistema Fe-A1-C. Además, una alta concentración de carbono puede dar lugar a la formación de inclusiones de carburo de Al4C3 en forma de agujas en la capa superficial.
Un aumento en el contenido de carbono reduce la profundidad de la capa aluminizada (Fig. 34a). En la fig. 34.6 muestra a modo de comparación cuánto más intenso es el proceso de aluminización en aluminio fundido en comparación con una mezcla de polvo.
Los datos sobre la influencia de los elementos de aleación en los resultados de la aluminización son bastante contradictorios. Sin embargo, por analogía con la influencia de los elementos sobre el crecimiento de la capa cromada, se puede concluir que en los aceros libres de carbono, la tasa de crecimiento se verá reducida por aquellos elementos que estabilizan la fase γ.
Leer en el mismo libro: Por resta obtenemos | Carburadores para cementación | Aceros para cementación | Capítulo 3. NITRURACIÓN DEL ACERO | Tecnología de nitruración | Aceros sometidos a nitruración | Propiedades del acero nitrurado | Nitrocarburización a alta temperatura | Nitrocarburización a baja temperatura | Cianuración del acero | mybiblioteka.su - 2015-2018. (0.054 seg)
mibiblioteka.su
Aluminizado de acero - Manual del químico 21
Acero al carbono aluminizado. .........................500-600
La metalización también se utiliza para aumentar la resistencia al calor de los aceros mediante aluminización (cajas de carburación, carcasas de termopar, etc.), para aplicar revestimientos decorativos, para proteger los productos de la carburación durante la carburación, etc.
El aluminio puro se utiliza para revestir acero para mejorar su resistencia a la corrosión. La aluminización también se usa para este propósito: saturación de la superficie de acero con aluminio a una profundidad de 0.02-1.2 mm, como resultado de lo cual se crea una película anticorrosión densa y duradera.
aluminizado. El proceso de aluminizado consiste en saturar la superficie de las piezas de acero con aluminio. Al aluminizar, las piezas se empaquetan en cajas con una mezcla de 48% de aluminio, 48% de óxido de aluminio y 2% de amoníaco, luego se incuban de 5 a 15 horas. a temperaturas de 900 a 1050 ° C. La superficie de acero saturada con aluminio tiene una alta resistencia al calor.
B - a 600°C en gases calientes que contienen 8O2 y vapor de agua. La aluminización protege el acero de la corrosión en gases calientes que contienen 80 g.
Dichos revestimientos sobre aceros al carbono y aleados incluyen revestimientos a base de aluminio, cadmio y zinc. C1 se usa ampliamente en varias ramas de la tecnología, ya que protege de manera confiable los productos metálicos contra la corrosión y la destrucción mecánica por corrosión. La aluminización como método de protección contra la corrosión aún no ha encontrado una distribución suficiente, aunque en una serie de ambientes agresivos, especialmente aquellos que contienen compuestos de azufre, es más eficaz que la galvanización.
Hemos estudiado el efecto del galvanizado por difusión y varios métodos de aluminizado sobre la resistencia a la fatiga por corrosión de los aceros al carbono.
El potencial estacionario de los aceros aluminizados es -(915 920) mV (ver Fig. 100), es decir 350-370 mV más negativo que los aceros sin recubrimiento. Sin embargo, después de 4 días de prueba, el potencial del acero 20 cambia en dirección positiva, a aproximadamente -540 mV. El cambio de potencial del acero aluminizado 45 ocurre con menor intensidad y después de 12 días alcanza (-680) -b (-690 mV). La razón del cambio de potencial es la disolución intensiva de la capa de aluminio. Sin embargo, el acero queda protegido del impacto del medio ambiente por una capa de compuesto intermetálico, cuyo potencial es más positivo que el de los aceros, y es de -(530-540) mV. Así, las capas protectoras obtenidas por aluminización líquida funcionan primero como ánodo y luego como revestimiento catódico.
En condiciones de fatiga por corrosión a altos niveles de tensión cíclica, la naturaleza del cambio en el potencial del electrodo y la cinética de destrucción de los aceros aluminizados son similares a las observadas en los aceros galvanizados. Cuando las muestras aluminizadas se cargan con cargas cíclicas más bajas, se produce una intensa destrucción por corrosión y fatiga de la capa de aluminio y, además, la capa intermetálica y el acero se encuentran en protección catódica como resultado de la disolución anódica de la capa de aluminio. Después de cambiar los potenciales de las muestras a (-54) (-550 mV) como resultado de la disolución completa de la capa de aluminio, la destrucción de la capa intermetálica del sistema emergente - acero procede de manera similar a la destrucción de los aceros con recubrimientos catódicos.
El cromado por difusión es más lento que el aluminizado. En la superficie del producto, no solo se forma una capa químicamente resistente, sino también una capa de carburos complejos que es fuerte a altas temperaturas. Para el cromado se utiliza una mezcla compuesta por un 60 % de polvo de cromo metálico, un 36 % de alúmina o caolín y un 4 % de amoníaco, en la que se coloca la parte cromada. El proceso se lleva a cabo a una temperatura de unos 1.000 °C. En 25-30 horas, se forma una capa de cromo con un espesor de 0,05 a 0,1 mm en la superficie de una pieza de acero con bajo contenido de carbono.
Los principales métodos de protección contra la corrosión por gas son la aleación de metales, la creación de revestimientos protectores y la sustitución de un entorno gaseoso agresivo. Para la fabricación de equipos expuestos a gases corrosivos se utilizan aleaciones resistentes al calor. Para impartir resistencia al calor al acero y al hierro fundido, también se utilizan cromo, silicio, aluminio en su composición, también se utilizan aleaciones a base de níquel o cobalto. La protección contra la corrosión por gases se realiza, además, saturando la superficie del producto en estado caliente con ciertos metales que tienen un efecto protector. Estos metales incluyen aluminio y cromo. El efecto protector de estos metales se debe a la formación de una película de óxido muy delgada pero fuerte en su superficie, que evita que el metal interactúe con el medio ambiente. En el caso del aluminio, este método se denomina aluminizado, en el caso del cromo, termocromado. Para la protección, también se utilizan recubrimientos no metálicos hechos de materiales cerámicos y cerámico-metal (cermets).
Para aumentar la resistencia a la oxidación de las chimeneas de carbón, se recomienda aluminizarlas. Según el Pipe Institute, la resistencia de las tuberías aluminizadas contra la oxidación en comparación con las tuberías de acero al carbono sin recubrimiento es de 30 a 50 veces mayor hasta 800°, 10 veces mayor hasta 900°, 5 veces mayor hasta 1000°.
Para obtener 1 kg de NH por el método de R. Albert e I. Mahe, se utiliza un recipiente fabricado en acero bajo en carbono, protegido exteriormente de la acción directa de la llama por un manguito de acero aluminizado. La parte superior del recipiente y su tapa plana, reforzada con un anillo de goma, se enfrían con agua. El recipiente está equipado con tubos laterales para pasar hidrógeno, conectarse a un sistema de vacío e introducir un termopar. Dentro del recipiente hay dos crisoles cilíndricos, de los cuales uno encaja firmemente en el otro,
Al igual que la aluminización, cuando los productos de acero se calientan en mezclas de polvo apropiadas, se lleva a cabo el cromado y la siliconización del acero. Durante el cromado (a 1050-1150 ° C), la capa superficial del acero se satura con cromo, como resultado de lo cual aumentan las propiedades anticorrosivas de los aceros con bajo contenido de carbono y la dureza y la resistencia a la abrasión de los aceros con alto contenido de carbono. Los aceros también aumentan. La siliconación (a 1100-1200 °C) satura la capa superficial con silicio, lo que aumenta la resistencia a los ácidos del acero.
Sobre la base del aluminio, las aleaciones de aluminio sinterizado, que se distinguen por su alta resistencia al calor, se crean mediante pulvimetalurgia. A. se utiliza para la desoxidación del acero, la producción de ciertos metales por el método de aluminotermia, explosivos y también en materiales compuestos sobre diversas bases. Véase también Bronce al aluminio. Latón aluminio. Fundición de aluminio, Aluminizante, Aluminizante.
Aluminizado por difusión (aluminizante). Los aceros sin alear aluminizados se utilizan ampliamente en lugar de los aceros de alta aleación resistentes al calor.
Las pruebas a largo plazo de tuberías con varios revestimientos de difusión (boruración, aluminización y aluminización de cromo) han demostrado que no aumentan la resistencia a la corrosión de las tuberías de acero 12Kh1MF durante la operación en la parte de radiación inferior y en el sobrecalentador de los generadores de vapor. El resultado especificado se obtuvo en generadores de vapor con varios tipos de combustible: fuelóleo sulfuroso, finos de antracita y esquisto estonio.
La aluminización líquida o, como se le llama, aluminización, no tuvo un efecto notable en el límite de resistencia de las muestras hechas de acero 45 en aire y aumentó el límite condicional de resistencia a la corrosión de las muestras en una solución de Na I al 3% de 50 a 160 MPa. Un superior similar
En la práctica 3. de a. aplican ampliamente la aleación superficial de las aleaciones baratas que tienen la piel buena. características. La capa superficial de acero común se puede convertir en una aleación con alta resistencia a la corrosión calentándola en una carga en polvo que contiene Zn (recubrimiento de zinc por difusión). A1 (aluminizado) o Cr (cromado), a veces con especial. aditivos activadores. También es posible recubrir un material barato y de baja resistencia con una capa delgada de un material más resistente a la corrosión, por ejemplo, mediante laminación conjunta en caliente de dos láminas hasta el espesor deseado del bimetal resultante.
Por la naturaleza del cambio en chem. composición de la pieza de trabajo l.-t. o, se puede dividir en saturación por difusión con no metales o metales y eliminación por difusión de elementos (más a menudo carbono en un medio débilmente oxidante o hidrógeno en el vacío). Variedades H.-t. acerca de. cementación-saturación cap. arreglo productos de acero nitruración de carbono - saturación de nitrógeno del acero, aleaciones a base de Ti y metales refractarios oxidación-oxidación de las capas superficiales de aleaciones de aluminio y magnesio cianuración y nitrocarburación - saturación simultánea de carbono y nitrógeno de productos de acero (maravilloso) acc. a partir de sales fundidas y boruración en fase gaseosa - saturación con boro de productos siderúrgicos, aleaciones a base de Ni, Co y metasiliconización refractaria - saturación con aluminización de silicio - saturación con aluminio Cap. arreglo aceros, con menos frecuencia hierros fundidos y aleaciones a base de Ni y Co, cromado y saturación de zinc del acero acc. Recubrimiento de cobre con cromo y zinc: saturación de cobre de productos de acero. De todos los tipos de H.-t. acerca de. Naib, la saturación del acero con carbono y nitrógeno es ampliamente utilizada. El carbono y el nitrógeno se difunden rápidamente en el hierro, formando soluciones sólidas, fases de carburo y nitruro, que difieren mucho en términos físicos y químicos. San usted de hierro.
La saturación por difusión del acero con aluminio es uno de los métodos más fiables de protección contra el oxígeno a altas temperaturas. Se pueden utilizar productos aluminizados en lugar de aceros resistentes al calor.
Para proteger los aceros de la oxidación, se utilizan métodos de difusión térmica para endurecer la superficie de los metales (cromado, aluminizado, siliconado).
quimica21.info
Proceso - aluminizado - The Big Encyclopedia of Oil and Gas, artículo, página 2
Proceso - aluminizado
Página 2
El proceso de aluminizado no presenta dificultades tanto en términos de equipamiento como en términos de dominio de la tecnología del proceso.
El proceso de aluminizado en aluminio fundido se desarrolla a una temperatura de 660 - 750 C.
El proceso de aluminizado también se utiliza para mejorar la resistencia a la oxidación de los aceros inoxidables.
El proceso de aluminizado consiste en saturar la superficie de las piezas de acero con aluminio, lo que aumenta significativamente su resistencia al calor.
En [20, p. La saturación se lleva a cabo en recipientes sellados a 950 C; se produce como consecuencia de la desproporción de los cloruros de aluminio y de las reacciones de intercambio entre ellos y el aluminio. Mientras esta fase exista en la superficie y no se disuelva como resultado de la difusión mutua de los componentes de la aleación, la película de alúmina continúa formándose y protege el sustrato de la oxidación. Con la disolución de la fase Ni3Al comienza una intensa oxidación de las aleaciones. La aluminización según esta tecnología protege las aleaciones de níquel de la oxidación a temperaturas de 950 - 1000 C durante varios miles de horas.
Aunque el proceso de aluminizado, como uno de los métodos de tratamiento químico-térmico de metales, es bastante conocido y se utiliza para metales ferrosos, no ha sido suficientemente estudiado en su aplicación al cobre y sus aleaciones.
La química del proceso de aluminización puede ser.
En el proceso de aluminización, los productos se calientan a alta temperatura en un ambiente que contiene aluminio. En este caso, la capa superficial se satura con aluminio como resultado del proceso de difusión térmica.
Para llevar a cabo los procesos de aluminizado se ha desarrollado el diseño de un aluminizador fabricado en UKM. Los elementos principales del aluminizador son las cubetas, en las que se vierte la carga, y las rejillas, sobre las que se colocan las piezas de trabajo. Se imponen requisitos bastante altos de rigidez y resistencia a los elementos del aluminizador. Se consideran las características tecnológicas del proceso de fabricación de elementos aluminizadores.
Al final del proceso de aluminización, se lleva a cabo un recocido por difusión durante 3 a 5 horas, que es necesario para eliminar la fragilidad de la capa exterior.
Con respecto al proceso de aluminización, la tecnología, las condiciones y los modos de aplicación del recubrimiento tienen una serie de características.
El artículo analiza el proceso de aluminización del níquel y presenta los resultados de un estudio de la composición de fases de capas aluminizadas sobre níquel y aleaciones de níquel. Cuando se expone al aire en una atmósfera oxidante a 950, se forma óxido de aluminio a - A12O3 en la superficie aluminizada, que protege la muestra de la oxidación hasta que las capas intermetálicas se disuelven debajo de la capa de óxido, debido a la contradifusión de aluminio y níquel, intermetálica capas: Sh2A13 , NiAl, NisAl. En las aleaciones termorresistentes aluminizadas, a diferencia del níquel aluminizado, bajo las capas de compuestos intermetálicos del sistema Ni - Al no existe una solución sólida monofásica, sino una capa heterofásica de alta dureza, constituida por un compuesto Ni3Al y un fase dispersa, que se forma cuando la subcapa se empobrece en níquel. El níquel de la subcapa se destina a la formación de compuestos intermetálicos de Ni - Al que cubren la muestra. La presencia de una solución sólida saturada de aluminio y una fase dispersa de Ni3AI fortalecedora en aleaciones de níquel de alta temperatura es la razón del equilibrio termodinámico relativo entre la composición de fase de la capa aluminizada y la composición de fase de las aleaciones. Las propiedades protectoras de la capa y su durabilidad están determinadas por la presencia de una fina película de óxido de aluminio en la superficie. Una capa de Ni3Al y NiAl, recubierta con óxido de aluminio a - A1203, con una subcapa de Ni3Al, en la que se distribuye una segunda fase dispersa, se almacena en aleaciones de níquel resistentes al calor a 950 durante varios miles de horas.
www.ngpedia.ru
Alitización - Manual del químico 21
Se logra una buena resistencia a la corrosión por sulfuro de hidrógeno al aluminizar el acero al carbono y al cromo (con 7% Cr) del fundido.La saturación por difusión de la superficie del acero con aluminio se utiliza principalmente para aumentar la resistencia al calor del acero, en la oxidación y especialmente en entornos que contienen sulfuro de hidrógeno. El acero aluminizado a temperaturas de 500-600 °C compite con éxito con el acero inoxidable al cromo-níquel tipo 18-8 en ambientes que contienen sulfuro de hidrógeno. La aluminización afecta la resistencia del acero de manera diferente según el espesor de la capa. Por lo tanto, la aluminización en polvo a una profundidad de 0,1-0,2 mm reduce drásticamente el límite de resistencia del acero y prácticamente no tiene efecto sobre la fatiga por corrosión. La aluminización a una profundidad de 0,04-0,05 mm afecta ligeramente el límite de fatiga del acero y duplica con creces el límite de fatiga por corrosión condicional. La capa aluminizada también reduce la influencia de los concentradores de tensión, especialmente en un ambiente corrosivo.
El aluminio puro se utiliza para revestir acero para mejorar su resistencia a la corrosión. La aluminización también se usa para este propósito: saturación de la superficie de acero con aluminio a una profundidad de 0.02-1.2 mm, como resultado de lo cual se crea una película anticorrosión densa y duradera.
Y,) también existen métodos de aluminizado en caliente, que consisten en que las piezas se sumergen en un baño de fundente, y luego en aluminio fundido a 770-800 °C.
La aluminización también es muy prometedora: la saturación de la superficie metálica con aluminio a una profundidad de 0,02-1,2 mm, como resultado de lo cual se crea una película anticorrosión densa y duradera.
Un importante campo de aplicación de A1 es su uso para la saturación (aluminización) de la superficie de productos de hierro y acero, para darles resistencia al calor y protección contra la corrosión. El valor más alto a este respecto es A1 de alta pureza.
Es muy importante usar aluminio para aluminizar: saturación de la superficie de acero o productos de hierro fundido con aluminio para protegerlos de la oxidación cuando se calientan a 900 ° C. La aluminización se realiza sumergiendo el producto en aluminio fundido o, más a menudo, calentando el producto con una mezcla de aluminio en polvo y óxido de aluminio (1P). En este caso, el aluminio penetra en la capa superficial del producto, formando una solución sólida con hierro.
En la fig. 79 muestra el efecto de la duración y la temperatura de aluminizado sobre el espesor de la capa aluminizada de acero grado 10, y en la fig. 80 - distribución de la concentración de aluminio en hierro sobre la profundidad de la capa después de aluminizar en una mezcla de polvo.
El método de difusión térmica es muy utilizado para obtener recubrimientos resistentes al calor con aluminio (aluminizante), silicio (silicio
El método de difusión térmica es ampliamente utilizado para obtener recubrimientos resistentes al calor con aluminio (aluminizado), silicio (silicado), cromo (cromado), titanio (titanizado). Los revestimientos resistentes al calor permiten combinar la alta resistencia al calor del material base con la alta resistencia al calor de la capa superficial.
Entre otros métodos de procesamiento, observamos la aluminización: la saturación de la superficie de los productos de acero y hierro con aluminio metálico, que les da resistencia al calor.
Hierro > 99,9 Pa Hierro aluminizado
La aluminización en caliente se utiliza en la producción de tiras de acero de forma continua. El acero aluminizado tiene la resistencia a la corrosión del aluminio y la fuerza de la lámina de acero. La superficie de las láminas aluminizadas es plata mate. Tol-
Las láminas aluminizadas tienen resistencia a la corrosión en la atmósfera, el agua y los productos de combustión de los combustibles a altas temperaturas. Se recomienda unir estas láminas mediante soldadura por puntos,
Los principales métodos de protección contra la corrosión por gas son la aleación de metales, la creación de revestimientos protectores y la sustitución de un entorno gaseoso agresivo. Para la fabricación de equipos expuestos a gases corrosivos se utilizan aleaciones resistentes al calor. Para impartir resistencia al calor al acero y al hierro fundido, también se utilizan cromo, silicio, aluminio en su composición, también se utilizan aleaciones a base de níquel o cobalto. La protección contra la corrosión por gases se realiza, además, saturando la superficie del producto en estado caliente con ciertos metales que tienen un efecto protector. Estos metales incluyen aluminio y cromo. El efecto protector de estos metales se debe a la formación de una película de óxido muy delgada pero fuerte en su superficie, que evita que el metal interactúe con el medio ambiente. En el caso del aluminio, este método se denomina aluminizado, en el caso del cromo, termocromado. Para la protección, también se utilizan recubrimientos no metálicos hechos de materiales cerámicos y cerámico-metal (cermets).La aluminización por difusión de objetos pequeños se realiza de manera similar, pero a una temperatura de unos 1000 °C. Los recubrimientos, además de lo dicho, son resistentes a los productos de combustión a altas temperaturas. La aluminización por difusión de tuberías u objetos grandes se lleva a cabo de la siguiente manera. En primer lugar, se limpia la superficie del producto (preferiblemente con granallado), se rocía una capa de aluminio y varias capas de vidrio líquido, y luego se mantiene a una temperatura de 900-1050 ° C durante 2-4 horas. forma una capa protectora, bajo la cual el aluminio se difunde en el acero. Las tuberías con dichos revestimientos se utilizan en intercambiadores diseñados para operar en un ambiente de dióxido de azufre, sulfuro de hidrógeno, productos de combustión, etc.
La principal medida para combatir la corrosión en no electrolitos es el uso de materiales resistentes a la corrosión, como aceros inoxidables, aluminizados, etc. En la mayoría de los casos, también se produce un proceso de corrosión electroquímica en el aceite, lo que permite utilizar inhibidores y protección protectora.
Es importante usar aluminio para la aluminización, que consiste en saturar la superficie de los productos de acero o hierro fundido con aluminio para proteger el material base de la oxidación durante un fuerte calentamiento. En metalurgia, la alúmina se utiliza para producir calcio, bario, litio y algunos otros metales mediante aluminotermia (véase 192).
La aluminización de los aceros al cromo le permite ampliar significativamente el alcance de su aplicación a temperaturas elevadas en entornos agresivos que contienen sulfuro de hidrógeno. La resistencia a la corrosión de los aceros aluminizados al 3% de cromo en sulfuro de hidrógeno puro a 500-550 °C es superior a la resistencia a la corrosión del acero 12Kh18N10T. Para la fabricación de serpentines de hornos tubulares, así como para tuberías de comunicación y paquetes de intercambiadores de calor tubulares en los Estados Unidos y algunos otros países, se utilizan tubos aluminizados de acero 15X5M a escala industrial o experimental en lugar de tubos de tipo costoso. Acero 18-8. La experiencia confirma la viabilidad de tal sustitución material.
Para mejorar la confiabilidad de los hornos tubulares en condiciones de mayor corrosión por azufre y vanadio, se recomienda que los tubos radiantes y la rejilla de convección se sujeten con aceros 25Kh23N7SL con aluminización preliminar. Además, se puede lograr una reducción significativa de la corrosión por sulfuro de vanadio introduciendo polvo de dolomita en el flujo de gas o introduciendo el aditivo VTI-4st en el fuel oil [39].
Los recubrimientos de difusión (aluminizantes) se obtienen por tratamiento en tambor en atmósfera de hidrógeno a una temperatura de unos 1000 °C en una mezcla de polvo de aluminio, AljOa y una pequeña cantidad de Nh5 1. Se obtiene una aleación superficial de aluminio con hierro, que proporciona resistencia tanto a la oxidación a alta temperatura en el aire (hasta 850-950 °C) como a la corrosión en una atmósfera que contiene azufre (por ejemplo, durante la refinación del petróleo). Los revestimientos de aluminio por difusión sobre acero no suelen proporcionar
Los estudios de la permeabilidad al hidrógeno a temperaturas elevadas del acero de grado 12Kh18N9T con capas aluminizadas, boradas y cromadas demostraron que estos recubrimientos son una barrera eficaz para el flujo de hidrógeno. Para el acero con un revestimiento aluminizado de 90 µm de espesor, la dependencia de la temperatura de la permeabilidad al hidrógeno en el rango de 800-550 °C es lineal, la energía de activación en esta área es Ер = 158 kJ/mol, que es ligeramente superior a la del acero sin revestimiento. acero (p = 122 kJ/mol), la permeabilidad al agua se reduce casi 5 veces. Para muestras boradas con un espesor de capa de 80 μm, se observa una disminución de la permeabilidad al hidrógeno por un factor de 13 a una temperatura de 800 °C y por un factor de 70 a una temperatura de 400 °C, la energía de activación n = 168 kJ/mol.
El proceso de aluminización por difusión ha recibido un nombre especial: aluminización (con menos frecuencia calorización).
En el método de recubrimiento por difusión térmica, el producto se coloca en una mezcla que contiene polvo del metal de recubrimiento. A una temperatura elevada, el metal depositado se difunde en el metal base. De esta forma se obtienen recubrimientos con aluminio (aluminizante) y zinc. A veces se aplican recubrimientos en reacciones en fase gaseosa. Por ejemplo, al pasar CrCl vaporoso sobre la superficie del acero a 1000 °C, se forma una aleación superficial de Cr-Fe que contiene hasta
El aluminio protege los metales de la corrosión, por ejemplo, al saturar su superficie con aluminio (aluminización) o al enchapar-
El recubrimiento se aplica en un recipiente herméticamente cerrado. Los productos metálicos limpios se sumergen en un polvo que contiene el metal de recubrimiento. En unas pocas horas, el recipiente se calienta a una temperatura cercana (pero inferior) al punto de fusión del metal. Los recubrimientos de zinc aplicados al acero se denominan sheradización. La capa de difusión es una aleación que contiene 8-9% de hierro en zinc. Los revestimientos de aluminio sobre acero o cobre se denominan aluminizados. Sobre ellos se forma óxido de aluminio en todas las capas superficiales con un contenido de aluminio superior al 8%. Esta película de óxido proporciona una alta resistencia a la corrosión, pero fragiliza fuertemente las capas superficiales, por lo que después de la aluminización es necesario someter el producto a recocido.
El tercer método para reducir la tasa de corrosión por gas es proteger la superficie del metal con recubrimientos especiales resistentes al calor, recubrimientos de termodifusión de hierro-aluminio o hierro-cromo (los procesos de aplicación de estos recubrimientos se conocen como aluminizado y termocromado), metal-cerámica recubrimientos, o cermets, recubrimientos de óxidos metálicos, para los cuales se utilizan materiales refractarios como componentes no metálicos, óxidos, por ejemplo A12O3, M 0, y compuestos tales como nitruros y carburos. Los componentes metálicos son metales del grupo del hierro, cromo, tungsteno y molibdeno.
Química inorgánica (1981) -- [c.438]
Física y Química en la Refinación de Petróleo (1955) -- [ c.8 ]
Química general (vol. 3) (1979) -- [ c.387 ]
Curso de Química General (1964) -- [ c.245 ]
Química inorgánica Vol. 2 (1976) -- [ c.397 ]
Química General 1982 (1982) -- [ c.555 , c.637 ]
Química General 1986 (1986) -- [ c.537 , c.617 ]
Química inorgánica (1981) -- [c.438]
equipo para la producción de cauchos sintéticos y orgánicos básicos de síntesis (1965) -- [ c.31 ]
Química inorgánica (1978) -- [c.293]
Fundamentos de Corrosión y Galvanoplastia Vol. 2 (1987) -- [ c.91 ]
Química General Vol. 4 (1965) -- [ c.238 ]
Reparación e instalación de equipos de refinerías químicas y petroleras Edición 2 (1980) -- [ c.71 ]
Corrosión de equipos químicos y materiales resistentes a la corrosión (1950) -- [c.162]
Química General Vol. 18 (1976) -- [ c.629 ]
Química General Vol. 22 (1982) -- [ c.555 , c.637 ]
Fundamentos de la tecnología química general (1963) -- [ c.194 ]
Equipo de producción Edición 2 (1974) -- [ c.24 ]
Tecnología química general Volumen 2 (1959) -- [ c.153 , c.154 ]
Breve Enciclopedia Química Volumen 2 (1963) -- [ c.97 ]
Fundamentos de Química General Volumen 2 (1967) -- [ c.194 ]
Fundamentos de Química General Volumen 2 Edición 3 (1973) -- [ c.37 ]
Pasividad frente a la corrosión y protección de los metales (1941) - [ c.7 ]
Corrosión de Metales Libro 1,2 (1952) -- [ c.667 , c.668 ]
Curso de química general (0) -- [ c.236 ]
Química (0) -- [ c.236 ]
Corrosión de Metales Libro 2 (1952) -- [ c.0 ]
quimica21.info
metalización por difusión
La metalización por difusión es un proceso de saturación por difusión de las capas superficiales de acero con varios metales. Se puede realizar en medios sólidos, líquidos y gaseosos.
En la metalización por difusión en medios sólidos, se utilizan mezclas de polvos, que generalmente consisten en ferroaleaciones con la adición de cloruro de amonio.
La metalización por difusión líquida se lleva a cabo sumergiendo la pieza en metal fundido (por ejemplo, zinc, aluminio).
En el método de saturación de gas, se utilizan compuestos volátiles de cloruro metálico, que se forman durante la interacción del cloro con los metales a altas temperaturas. Los cloruros se disocian en la superficie del hierro y el metal liberado en estado atómico se difunde en el hierro.
La difusión de los metales en el hierro es mucho más lenta que la del carbono y el nitrógeno, porque el carbono y el nitrógeno forman soluciones sólidas intersticiales con el hierro, mientras que los metales forman soluciones sólidas de sustitución. Esto conduce al hecho de que las capas de difusión durante la metalización son diez veces más delgadas. La saturación de la superficie del acero con metales se lleva a cabo a temperaturas de 900-1200 ° C.
Aluminizante (Al)
La aluminización es el proceso de saturar la superficie del acero con aluminio. Como resultado de la aluminización, el acero adquiere una gran resistencia a las incrustaciones (hasta 850-900 °C) y resistencia a la corrosión en la atmósfera y en una serie de entornos.
Cuando se aluminiza en mezclas de polvo, las piezas limpias se empaquetan junto con la mezcla en una caja de hierro. La mezcla de trabajo incluye: aluminio en polvo (25-50%) o ferroaluminio (50-75%), óxido de aluminio (25-50%) y cloruro de aluminio (~1,0%). El proceso se lleva a cabo a una temperatura de 900-1000°C durante 3-12 horas.
Baños de aluminización con aluminio fundido poco utilizados. Las piezas aluminizadas se sumergen en aluminio fundido (92-94 % A1 y 6-8 % Fe). Se agrega hierro para evitar que las piezas de trabajo se disuelvan en el aluminio. El proceso se lleva a cabo a temperaturas de 700-800°C durante 45-90 minutos.
La aluminización en aluminio fundido difiere de la aluminización en mezclas de polvo por la simplicidad del método, la velocidad y las temperaturas más bajas. La principal desventaja del proceso es la adherencia del aluminio a la superficie de las piezas.
A veces se utiliza la metalización de la superficie de acero con aluminio (pulverización de una capa de aluminio sobre la superficie tratada) seguida de recocido por difusión a una temperatura de 900-1000°C durante 1-3 horas.
Para proteger el aluminio de la oxidación durante el recocido por difusión, el producto se recubre con una capa que consiste en grafito de plata (48 %), arena de cuarzo (30 %), arcilla (20 %), cloruro de aluminio (2 %) y 20-25 % de peso de los primeros cuatro componentes - vidrio líquido.
La aluminización del acero con metalización seguida de recocido por difusión es varias veces más económica que en polvo. La capa agitada es una solución sólida de aluminio en hierro, la concentración de aluminio en la capa superficial alcanza el 30-40%. La aluminización se aplica a tuberías, herramientas para fundir aleaciones no ferrosas, cajas de termopares, partes de máquinas generadoras de gas, etc.
studfiles.net
Proceso - aluminizado - The Big Encyclopedia of Oil and Gas, artículo, página 1
Proceso - aluminizado
Página 1
El proceso de aluminizado consta de las siguientes operaciones: preparación de la superficie, aplicación de una capa de aluminio (generalmente por pulverización catódica), recubrimiento y recocido.
El proceso de aluminización se lleva a cabo, por ejemplo, calentando un tubo en polvo de aluminio mezclado con óxido de aluminio en presencia de cloruro de amonio a una temperatura de unos 1000 C.
El proceso de aluminización dura de 3 a 5 minutos, la temperatura de fusión se mantiene a unos 700 C. En tales condiciones, el espesor de la capa de difusión del acero es de 0,02 a 0,04 mm. El espesor del aluminio adherido no supera los 0 3 - 0 4 mm.
El proceso de aluminizado consiste en saturar la superficie de las piezas de acero con aluminio. Al aluminizar, las piezas se empaquetan en cajas con una mezcla de 48% de aluminio, 48% de óxido de aluminio y 2% de amoníaco, luego se mantienen de 5 a 15 horas. La superficie de acero saturada con aluminio tiene una alta resistencia al calor.
El proceso de aluminizado dura de 5 a 15 horas. El acero con superficie aluminizada es muy resistente al calor y se utiliza en piezas que entran en contacto con una llama.
El proceso de aluminizado dura de 5 a 15 horas. El acero con superficie aluminizada es muy resistente al calor y se utiliza en piezas que entran en contacto con el acero.
El proceso de aluminizado dura de 5 a 15 horas. El acero con superficie aluminizada es muy resistente al calor y se utiliza en piezas que entran en contacto con una llama.
El proceso de aluminización a partir de polvos según la tecnología desarrollada se desarrolla en varias etapas, la principal de las cuales es la transferencia de átomos de aluminio desde la superficie de los granos de ferroaluminio a la superficie de la pieza y la quimisorción del aluminio por el níquel.
El proceso de aluminizado consiste en saturar la capa superficial de hierro, acero y hierro fundido con aluminio debido a la difusión del metal en polvo a alta temperatura. La profundidad de la capa de difusión depende de la temperatura de calentamiento y la duración del proceso de aluminización; en la práctica, varía de 0 3 a 0 8 mm. Las piezas a aluminizar se cargan en una caja de hierro herméticamente cerrada y se cubren cuidadosamente con la mezcla especificada. El calentamiento se lleva a cabo a una temperatura de 1000 durante 3 a 4 horas.
El proceso de aluminización se lleva a cabo de la siguiente manera. Las piezas de acero a aluminizar se colocan en cajas y se rocían con una mezcla aluminizante compuesta por las siguientes partes (en % en peso): 1) 40 - 60 polvo de aluminio, 2) 60 - 40 polvo de óxido de aluminio, o arcilla refractaria finamente molida, o arcilla refractaria cocida, 3) 1 5 - 3 cloruro de amonio. Estas sustancias se mezclan completamente. La exposición a esta temperatura se lleva a cabo durante 5 a 14 horas. Además de la aluminización sólida, también se utiliza la aluminización con gas, similar a la cementación con gas.
Páginas: 1 2 3 4
La metalización por difusión es un proceso de saturación por difusión de las capas superficiales de acero con varios metales. Se puede realizar en medios sólidos, líquidos y gaseosos.
En la metalización por difusión en medios sólidos, se utilizan mezclas de polvos, que generalmente consisten en ferroaleaciones con la adición de cloruro de amonio.
La metalización por difusión líquida se lleva a cabo sumergiendo la pieza en metal fundido (por ejemplo, zinc, aluminio).
En el método de saturación de gas, se utilizan compuestos volátiles de cloruro metálico, que se forman durante la interacción del cloro con los metales a altas temperaturas. Los cloruros se disocian en la superficie del hierro y el metal liberado en estado atómico se difunde en el hierro.
La difusión de los metales en el hierro es mucho más lenta que la del carbono y el nitrógeno, porque el carbono y el nitrógeno forman soluciones sólidas intersticiales con el hierro, mientras que los metales forman soluciones sólidas de sustitución. Esto conduce al hecho de que las capas de difusión durante la metalización son diez veces más delgadas. La saturación de la superficie del acero con metales se lleva a cabo a temperaturas de 900-1200 ° C.
Aluminizante (Al)
La aluminización es el proceso de saturar la superficie del acero con aluminio. Como resultado de la aluminización, el acero adquiere una gran resistencia a las incrustaciones (hasta 850-900 °C) y resistencia a la corrosión en la atmósfera y en una serie de entornos.
Cuando se aluminiza en mezclas de polvo, las piezas limpias se empaquetan junto con la mezcla en una caja de hierro. La mezcla de trabajo incluye: aluminio en polvo (25-50%) o ferroaluminio (50-75%), óxido de aluminio (25-50%) y cloruro de aluminio (~1,0%). El proceso se lleva a cabo a una temperatura de 900-1000°C durante 3-12 horas.
Baños de aluminización con aluminio fundido poco utilizados. Las piezas aluminizadas se sumergen en aluminio fundido (92-94 % A1 y 6-8 % Fe). Se agrega hierro para evitar que las piezas de trabajo se disuelvan en el aluminio. El proceso se lleva a cabo a temperaturas de 700-800°C durante 45-90 minutos.
La aluminización en aluminio fundido difiere de la aluminización en mezclas de polvo por la simplicidad del método, la velocidad y las temperaturas más bajas. La principal desventaja del proceso es la adherencia del aluminio a la superficie de las piezas.
A veces se utiliza la metalización de la superficie de acero con aluminio (pulverización de una capa de aluminio sobre la superficie tratada) seguida de recocido por difusión a una temperatura de 900-1000°C durante 1-3 horas.
Para proteger el aluminio de la oxidación durante el recocido por difusión, el producto se recubre con una capa que consiste en grafito de plata (48 %), arena de cuarzo (30 %), arcilla (20 %), cloruro de aluminio (2 %) y 20-25 % de peso de los primeros cuatro componentes - vidrio líquido.
La aluminización del acero con metalización seguida de recocido por difusión es varias veces más económica que en polvo. La capa agitada es una solución sólida de aluminio en hierro, la concentración de aluminio en la capa superficial alcanza el 30-40%. La aluminización se aplica a tuberías, herramientas para fundir aleaciones no ferrosas, cajas de termopares, partes de máquinas generadoras de gas, etc.
métodos de aluminización
La aluminización se aplica a menudo a los aceros con bajo contenido de carbono, con menos frecuencia a los hierros fundidos y de medio carbono. Las tecnologías de aluminización se desarrollaron a principios del siglo XX. Por ejemplo, la tecnología de aluminizado en mezclas de polvo se desarrolló en 1927-1930. UN. Minkevich, Nevada Ageev y O.I. versión En 1934 V. A. Plotnikov, N. G. Gritsiansky y K.L. Makovets propuso un método de aluminización por electrólisis. La aluminización en baños con aluminio fundido fue estudiada en detalle ya en 1932 por F.G. Nikonov.
Para obtener una unión metálica entre el hierro y el aluminio y sus aleaciones, se utilizan varios métodos de aluminizado, siendo los principales:
Aluminización en mezclas de polvo;
Aluminización por fusión y pulverización;
Aluminización al vacío;
aluminizado de gas;
revestimiento;
revestimiento electrolítico;
Aluminizado por inmersión en aluminio fundido o su aleación;
Aluminizado en mezclas de polvo
Las piezas preparadas se envasan en autoclaves herméticos, tambores y se llenan con una mezcla aluminosa. La mezcla consiste en polvo de aluminio o polvo y aditivos. Los aditivos incluyen óxido de aluminio o arcilla molida (para evitar la sinterización) y cloruro de amonio o cloruro de aluminio (para proteger los productos y el aluminio de la oxidación).
La temperatura a la que se lleva a cabo el proceso es de 900-1080 °C, la duración del proceso, dependiendo de la composición de la mezcla y la temperatura del proceso, es de 4 a 30 horas.
Aluminizado por pulverización
Una superficie prelimpiada se rocía con una cierta capa de aluminio. El proceso de recubrimiento consiste en fundir el metal depositado y rociarlo con un chorro de aire comprimido a una presión de 2-4 atm. utilizando metalizadores especiales.
La fuerza de adhesión de dicha aplicación es baja y asciende a 0,2-2 kg/mm2. Con este método de aluminización, la adhesión no solo ocurre entre el metal base y el revestimiento, sino también entre capas individuales y partículas de aluminio, como resultado de lo cual la capa rociada tiene una mayor porosidad.
Para aumentar la fuerza de adhesión del recubrimiento al metal base, así como para aumentar la densidad, se recomienda realizar un recocido a largo plazo a 950-1080 °C después de la aluminización.
Aluminizado al vacío
Este proceso es similar al anterior. El recubrimiento se aplica evaporando el aluminio y depositándolo sobre el producto. El grosor del recubrimiento es de décimas de micras, y la calidad del recubrimiento en este caso es mayor.
Para la aluminización, se requieren cámaras de alto vacío con una presión de 10-3-10-5 mm Hg. Las instalaciones de haz de electrones se utilizan para calentar aluminio hasta 1400. El grosor del recubrimiento resultante es proporcional a la duración de la evaporación del aluminio y es de 0,08 a 2,5 micras. Con este método de aplicación de aluminio, el recubrimiento es uniforme, sin poros y no contiene una capa intermedia de hierro-aluminio.
Para obtener una fuerte adherencia del recubrimiento a la base, la tira o pieza se precalienta a 175 - 370 °C. La preparación preliminar de la superficie debe ser minuciosa, ya que la presencia de películas de óxido afecta significativamente la calidad de la adherencia.
Debido a la complejidad y alto costo del proceso, este tipo de recubrimiento es principalmente para las partes más críticas.
revestimiento
Este método consiste en la laminación conjunta de láminas de acero y aluminio. Durante la compresión, se proporciona una unión metálica entre el aluminio y el acero, lo que da como resultado una tira bimetálica o estaño.
La fuerza de unión del acero y el aluminio aumenta con el recocido posterior. Este método se utiliza principalmente para la obtención de chapas, flejes y tubos.
galvanoplastia
Tal recubrimiento se aplica en electrolitos anhidros que consisten en mezclas de sales fundidas de cloruro de aluminio y cloruros de metales alcalinos, o en electrolitos inorgánicos que contienen compuestos de aluminio en bromoetilo y benceno.
El electrolito puede consistir en 80% AlCl3 y 20% NaCl, luego el proceso se realiza a una temperatura de 175 °C y una densidad de corriente de 1.6 A/dm2.
Antes del recubrimiento, el producto debe limpiarse bien, desengrasarse y decaparse en una solución de ácido clorhídrico. La tasa de depósito de aluminio es insignificante y es de aproximadamente 0,01 mm en 30 minutos.
Este método tiene una serie de desventajas: en primer lugar, la composición del electrolito incluye cloruro de aluminio, que es muy volátil, higroscópico y puede descomponerse incluso en condiciones normales, y cuando se funde, se evapora del baño, lo que provoca un cambio en el composición del electrolito, y el segundo método es extremadamente lento y no muy económico.
Aluminizado por inmersión
Este método está desprovisto de las desventajas mencionadas anteriormente. Su principal ventaja es la rapidez de aluminizado (de 1 a 15 minutos), temperaturas relativamente bajas (600-800°C) y sencillez. Además, la aluminización por inmersión es el método más económico en comparación con otros métodos.
La esencia del método consiste en sumergir un producto de acero con una superficie metálica limpia en aluminio líquido o su aleación y mantenerlo durante un tiempo determinado. En este caso, la capa superficial del metal se disuelve en aluminio e interactúa con él. La reacción de interacción y difusión es muy rápida, por lo que se forma una capa con un espesor de 0,02-0,10 mm en 1-15 minutos. El proceso de aluminizado se lleva a cabo a una temperatura de 700-800°C.
Del material anterior, podemos concluir que la opción más prometedora es la aluminización por inmersión seguida de recocido por difusión.