Pomiary hałasu dla kotłowni blokowej. Jak zmniejszyć hałas w kotłowni: na etapie projektowania i za pomocą specjalnych środków. Wyjście - wibroizolatory i podłogi „pływające”
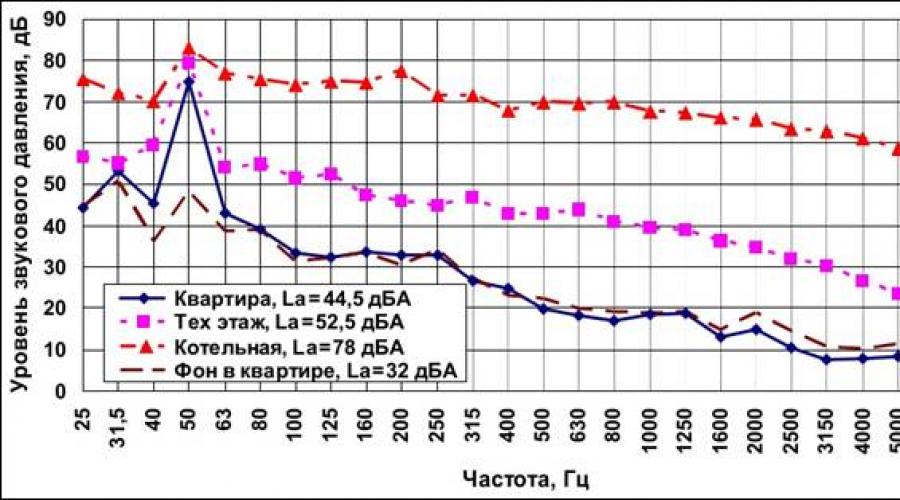
doktorat LV Rodionov, kierownik działu wsparcia badań; doktorat SA Gafurow, starszy pracownik naukowy; doktorat VS. Melentiev, starszy badacz; doktorat JAK. Gvozdev, Samara National Research University nazwany na cześć Academician S.P. Korolewa, Samara
Aby zapewnić ciepłą wodę i ogrzewanie dla nowoczesnych budynków mieszkalnych (MKD), czasami projekty uwzględniają kotły dachowe. To rozwiązanie jest w niektórych przypadkach opłacalne. Jednocześnie często podczas instalowania kotłów na fundamencie nie zapewnia się odpowiedniej izolacji drgań. W efekcie mieszkańcy wyższych pięter narażeni są na stałą ekspozycję na hałas.
Zgodnie z normami sanitarnymi obowiązującymi w Rosji poziom ciśnienia akustycznego w pomieszczeniach mieszkalnych nie powinien przekraczać 40 dBA - w dzień i 30 dBA - w nocy (dBA - decybel akustyczny, jednostka poziomu hałasu, biorąc pod uwagę ludzką percepcję dźwięk - ok. wyd.).
Specjaliści z Instytutu Akustyki Maszyn Samara State Aerospace University (IAM przy SSAU) zmierzyli poziom ciśnienia akustycznego w pomieszczeniach mieszkalnych mieszkania znajdującego się pod dachem kotłowni budynku mieszkalnego. Okazało się, że źródłem hałasu było wyposażenie kotłowni na dachu. Pomimo tego, że mieszkanie to jest oddzielone od kotłowni na dachu kondygnacją techniczną, to zgodnie z wynikami pomiarów odnotowano przekroczenie dobowych norm sanitarnych, zarówno w zakresie poziomu ekwiwalentnego, jak i częstotliwości oktawowej 63 Hz ( Rys. 1).
Pomiary wykonano w ciągu dnia. W nocy tryb pracy kotłowni praktycznie się nie zmienia, a poziom hałasu w tle może być niższy. Ponieważ okazało się, że „problem” występuje już w dzień, postanowiono nie wykonywać pomiarów w nocy.
Obrazek 1 . Poziom ciśnienia akustycznego w mieszkaniu w porównaniu z normami sanitarnymi.
Lokalizacja źródeł hałasu i wibracji
Aby dokładniej określić częstotliwość „problematyczną”, zmierzono poziomy ciśnienia akustycznego w mieszkaniu, kotłowni i na piętrze technicznym w różnych trybach pracy urządzeń.
Najbardziej charakterystycznym trybem pracy urządzenia, w którym częstotliwość tonalna pojawia się w zakresie niskich częstotliwości, jest równoczesna praca trzech kotłów (ryc. 2). Wiadomo, że częstotliwość procesów roboczych kotłów (palenia wewnątrz) jest dość niska i mieści się w przedziale 30-70 Hz.
Rysunek 2. Poziom ciśnienia akustycznego w różnych pomieszczeniach przy jednoczesnej pracy trzech kotłów
Z ryc. 2 pokazuje, że częstotliwość 50 Hz dominuje we wszystkich mierzonych widmach. W ten sposób kotły wnoszą główny wkład w widma poziomów ciśnienia akustycznego w badanych pomieszczeniach.
Poziom hałasu w tle w mieszkaniu nie zmienia się zbytnio po włączeniu urządzeń kotłowych (poza częstotliwością 50 Hz), więc możemy wnioskować, że izolacja akustyczna dwóch pięter oddzielających kotłownię od pomieszczeń mieszkalnych wystarcza do obniżenia poziomu hałasu w powietrzu wytwarzanego przez urządzenia kotłowe do norm sanitarnych. Dlatego należy szukać innych (niebezpośrednich) sposobów propagacji hałasu (wibracji). Prawdopodobnie wysoki poziom ciśnienia akustycznego przy 50 Hz jest spowodowany hałasem materiałowym.
W celu zlokalizowania źródła hałasu strukturalnego w pomieszczeniach mieszkalnych, a także identyfikacji dróg propagacji drgań przeprowadzono dodatkowe pomiary przyspieszeń drgań w kotłowni, na podłodze technicznej, a także w salonie mieszkania na najwyższym piętrze.
Pomiary prowadzono w różnych trybach pracy urządzeń kotłowych. Na ryc. Rysunek 3 przedstawia widma przyspieszeń drgań dla trybu, w którym pracują wszystkie trzy kotły.
Na podstawie wyników pomiarów sformułowano następujące wnioski:
- w mieszkaniu na ostatniej kondygnacji pod kotłownią nie są zachowane normy sanitarne;
- głównym źródłem zwiększonego hałasu w pomieszczeniach mieszkalnych jest pracujący proces spalania w kotłach. Dominującą harmoniczną w widmach hałasu i drgań jest częstotliwość 50 Hz.
- brak odpowiedniej izolacji wibroizolacyjnej kotła od podłoża prowadzi do przenoszenia hałasu konstrukcyjnego na podłogę i ściany kotłowni. Wibracje rozprzestrzeniają się zarówno przez podpory kotła, jak i rury z przeniesieniem z nich na ściany, a także podłogę, tj. w miejscach sztywnego połączenia.
- Należy opracować środki zwalczania hałasu i wibracji na drodze ich rozprzestrzeniania się z kotła.
a) b)
w)
Rysunek 3 . Widma przyspieszeń drgań: a - na podporze i fundamencie kotła, na podłodze kotłowni; b - na podporze rury spalinowej kotła i na podłodze przy rurze spalinowej kotła; c - na ścianie kotłowni, na ścianie podłogi technicznej oraz w salonie mieszkania.
Opracowanie systemu ochrony przed drganiami
Na podstawie wstępnej analizy rozkładu masy konstrukcji kotła gazowego i urządzeń dobierano wibroizolatory linowe VMT-120 i VMT-60 o obciążeniu nominalnym na wibroizolator (VI) odpowiednio 120 i 60 kg dla projekt. Schemat wibroizolatora pokazano na ryc. 4.
Rysunek 4 Model 3D wibroizolatora kablowego z serii modeli TDC.
Rysunek 5 Schematy mocowania wibroizolatorów: a) wsparcie; b) zawieszone; c) boczny.
Opracowano trzy warianty schematu mocowania wibroizolatorów: podporowy, zawieszenia i boczny (rys. 5).
Obliczenia wykazały, że schemat boczny instalacji można zrealizować przy użyciu 33 wibroizolatorów VMT-120 (na każdy kocioł), co nie jest ekonomicznie wykonalne. Ponadto spodziewane są bardzo poważne prace spawalnicze.
Podczas realizacji schematu podwieszanego cała konstrukcja staje się bardziej skomplikowana, ponieważ konieczne jest przyspawanie szerokich i dość długich narożników do ramy kotła, która będzie również spawana z kilku profili (w celu zapewnienia niezbędnej powierzchni montażowej).
Ponadto technologia montażu ramy kotła na tych płozach z VI jest skomplikowana (niewygodne jest mocowanie VI, niewygodne ustawianie i centrowanie kotła itp.). Kolejną wadą takiego schematu jest swobodny ruch kotła w kierunkach bocznych (kołysanie w płaszczyźnie poprzecznej na VI). Liczba wibroizolatorów VMT-120 dla tego schematu wynosi 14.
Częstotliwość systemu ochrony przed drganiami (VZS) wynosi około 8,2 Hz.
Trzecią, najbardziej obiecującą i prostszą technologicznie opcją jest standardowy obwód odniesienia. Będzie wymagało 18 wibroizolatorów VMT-120.
Obliczona częstotliwość VZS wynosi 4,3 Hz. Ponadto konstrukcja samych VI (część pierścieni kablowych jest umieszczona pod kątem) i ich właściwe rozmieszczenie na obwodzie (ryc. 6), pozwala dostrzec przy takim schemacie obciążenie boczne, wartość co będzie wynosić około 60 kgf na każdy VI, podczas gdy obciążenie pionowe na każdym VI wynosi około 160 kgf.
Rysunek 6 Umieszczenie wibroizolatorów na ramie ze schematem odniesienia.
Projekt systemu ochrony przed drganiami
Na podstawie danych z przeprowadzonych badań statycznych oraz obliczeń dynamicznych parametrów VI opracowano system ochrony przed drganiami dla kotłowni budynku mieszkalnego (rys. 7).
Przedmiotem ochrony przed drganiami są trzy kotły tej samej konstrukcji 1 instalowany na fundamentach betonowych za pomocą metalowych wiązań; system rurociągów 2 do dostarczania zimna i usuwania podgrzanej wody, a także usuwania produktów spalania; system rur 3 do dostarczania gazu do palników kotłów.
Stworzony system antywibracyjny obejmuje zewnętrzne wsporniki antywibracyjne dla kotłów 4 przeznaczony do obsługi rurociągów 2 ; wewnętrzna taśma antywibracyjna kotłów 5 przeznaczony do izolowania wibracji kotłów od podłogi; zewnętrzne podpory antywibracyjne 6 do rur gazowych 3.
Rysunek 7 Widok ogólny kotłowni z zainstalowanym systemem antywibracyjnym.
Główne parametry konstrukcyjne systemu ochrony przed drganiami:
1. Wysokość od podłogi na jaką należy podnieść ramy nośne kotłów wynosi 2 cm (tolerancja montażu minus 5 mm).
2. Ilość wibroizolatorów przypadająca na jeden kocioł: 19 VMT-120 (18 w pasie wewnętrznym dźwigającym ciężar kotła i 1 na podporze zewnętrznej do tłumienia drgań rurociągu wodnego) oraz 2 VMT-60 wibroizolatory na podporach zewnętrznych - do ochrony przed drganiami gazociągu.
3. Schemat obciążenia typu „podpora” działa przy ściskaniu, zapewniając dobrą izolację drgań. Częstotliwość drgań własnych systemu mieści się w zakresie 5,1-7,9 Hz, co zapewnia skuteczną ochronę przed drganiami w obszarze powyżej 10 Hz.
4. Współczynnik tłumienia systemu ochrony przed drganiami wynosi 0,4-0,5, co zapewnia wzmocnienie przy rezonansie nie większym niż 2,6 (amplituda drgań nie większa niż 1 mm przy amplitudzie sygnału wejściowego 0,4 mm).
5. Do regulacji położenia poziomego kotłów po bokach kotła w profilach w kształcie litery U znajduje się dziewięć gniazd na wibroizolatory tego samego typu. Tylko pięć jest nominalnie zainstalowanych.
Podczas montażu możliwe jest rozmieszczenie wibroizolatorów w dowolnej kolejności w dowolnym z dziewięciu miejsc przewidzianych do wyrównania środka masy kotła i środka sztywności systemu antywibracyjnego.
6. Zalety opracowanego systemu antywibracyjnego: prostota konstrukcji i montażu, niewielka ilość unoszenia kotłów nad posadzkę, dobre właściwości tłumienia systemu, możliwość regulacji.
Efekt zastosowania opracowanego systemu ochrony przed drganiami
Wraz z wprowadzeniem opracowanego systemu ochrony przed drganiami poziom ciśnienia akustycznego w pomieszczeniach mieszkalnych mieszkań na wyższych kondygnacjach obniżył się do akceptowalnego poziomu (rys. 8). Pomiary wykonywano również w nocy.
Z wykresu na ryc. 8 widać, że w znormalizowanym zakresie częstotliwości oraz w zakresie równoważnego poziomu dźwięku, normy sanitarne w salonie są spełnione.
Skuteczność opracowanego systemu ochrony przed drganiami mierzona w obszarze mieszkalnym przy częstotliwości 50 Hz wynosi 26,5 dB, a równoważny poziom dźwięku 15 dBA (rys. 9).
Cyfra 8 . Poziom ciśnienia akustycznego w mieszkaniu w porównaniu z normami sanitarnymi z uwzględnieniem opracowany system ochrony przed drganiami.
Rysunek 9 Poziom ciśnienia akustycznego w pasmach częstotliwości 1/3-oktawowych w obszarze mieszkalnym, gdy jednocześnie pracują trzy kotły.
Wniosek
Stworzony system ochrony przed drganiami umożliwia ochronę budynku mieszkalnego wyposażonego w kocioł dachowy przed drganiami generowanymi przez pracę kotłów gazowych, jak również zapewnienie normalnej pracy wibracyjnej samego urządzenia gazowego wraz z instalacją rurową zwiększając żywotność i zmniejszenie prawdopodobieństwa wypadków.
Główne zalety opracowanego systemu antywibracyjnego to prostota konstrukcji i montażu, niski koszt w porównaniu z innymi typami wibroizolatorów, odporność na temperatury i zanieczyszczenia, niewielka wysokość wznoszenia kotłów nad podłogę, dobre właściwości tłumiące system i możliwość dostosowania.
System ochrony przed drganiami zapobiega rozprzestrzenianiu się hałasu konstrukcyjnego z wyposażenia kotła dachowego przez konstrukcję budynku, zmniejszając tym samym poziom ciśnienia akustycznego w pomieszczeniach mieszkalnych do akceptowalnego poziomu.
Literatura
1. Igołkin, AA Redukcja hałasu w obszarze mieszkalnym dzięki zastosowaniu wibroizolatorów [Tekst] / A.A. Igolkina, L.V. Rodionow, E.V. Szachy // Bezpieczeństwo w technosferze. Nr 4. 2008. S. 40-43.
2. SN 2.2.4 / 2.1.8.562-96 „Hałas w miejscach pracy, na terenie budynków mieszkalnych, użyteczności publicznej i na terenie zabudowy mieszkaniowej”, 1996, 8 s.
3. GOST 23337-78 „Hałas. Metody pomiaru hałasu na terenach mieszkalnych oraz w budynkach mieszkalnych i użyteczności publicznej”, 1978, s. 18.
4. Szachmatow, E.V. Kompleksowe rozwiązanie problemów wibroakustyki inżynierii mechanicznej i produktów lotniczych [Tekst] / E.V. Szachy // LAP LAMBERT Academic Publishing GmbH&CO.KG. 2012. 81 s.
Od redaktora. 27 października 2017 r. Rospotrebnadzor opublikował informacje na swojej oficjalnej stronie internetowej „O wpływie czynników fizycznych, w tym hałasu, na zdrowie publiczne”, w którym zauważa, że w strukturze skarg obywateli na różne czynniki fizyczne największy udział (ponad 60%) stanowią skargi na hałas. Głównymi z nich są skargi mieszkańców, w tym dyskomfort akustyczny z systemów wentylacyjnych i urządzeń chłodniczych, hałas i wibracje podczas pracy urządzeń grzewczych.
Przyczynami zwiększonego poziomu hałasu generowanego przez te źródła są niewystarczające środki ochrony przed hałasem na etapie projektowania, montaż urządzeń z odchyleniami od rozwiązań projektowych bez oceny poziomu generowanego hałasu i drgań, niezadowalające wdrożenie środków ochrony przed hałasem na etap uruchomienia, rozmieszczenie sprzętu nieprzewidziane w projekcie, a także niezadowalająca kontrola nad działaniem sprzętu.
Federalna Służba Nadzoru Ochrony Praw Konsumentów i Opieki Społecznej zwraca uwagę obywateli, że pod niekorzystnym wpływem czynników fizycznych, m.in. hałas, należy skontaktować się z terytorialnym biurem Rospotrebnadzor w sprawie Federacji Rosyjskiej.
Strona 7 z 21
Ze względu na to, że w nowoczesnych elektrowniach hałas z reguły przekracza dopuszczalne poziomy, w ostatnich latach szeroko rozpoczęto prace nad tłumieniem hałasu.
Istnieją trzy główne metody ograniczania hałasu przemysłowego: redukcja hałasu u samego źródła; redukcja hałasu na drogach jego propagacji; rozwiązania architektoniczne, konstrukcyjne i planistyczne.
Metodą redukcji hałasu u źródła jego występowania jest udoskonalenie konstrukcji źródła, zmiana procesu technologicznego. Najskuteczniejsze zastosowanie tej metody w rozwoju nowych urządzeń energetycznych. Zalecenia dotyczące redukcji hałasu u źródła podano w § 2-2.
Do izolacji akustycznej różnych pomieszczeń elektrowni (zwłaszcza maszynowni i kotłowni) jako najbardziej hałaśliwe stosuje się rozwiązania budowlane: pogrubienie ścian zewnętrznych budynków, zastosowanie okien z podwójnymi szybami, pustaków szklanych, drzwi dwuskrzydłowych, wielowarstwowe panele akustyczne, uszczelnienia okien, drzwi, otworów, właściwy dobór miejsc czerpni i wywiewów instalacji wentylacyjnych. Konieczne jest również zapewnienie dobrej izolacji akustycznej między maszynownią a piwnicą, staranne uszczelnienie wszystkich otworów i otworów.
Projektując maszynownię unika się małych pomieszczeń o gładkich, dźwiękochłonnych ścianach, sufitach i podłogach. Okładziny ścienne z materiałów dźwiękochłonnych (SAM) mogą zapewnić redukcję hałasu o około 6-7 dB w pomieszczeniach średniej wielkości (3000-5000 m3). W przypadku dużych pomieszczeń opłacalność tej metody staje się kontrowersyjna.
Niektórzy autorzy, jak G. Koch i H. Schmidt (Niemcy), a także R. French (USA), uważają, że izolacja akustyczna ścian i sufitów pomieszczeń stacji jest mało skuteczna (1-2 dB). Dane opublikowane przez Francuski Urząd ds. Energii (EDF) wskazują na obietnicę tej metody tłumienia hałasu. Obróbka stropów i ścian w kotłowniach w elektrowniach Saint-Depy i Chenevier pozwoliła uzyskać izolację akustyczną na poziomie 7-10 dB A.
Stacje często budują oddzielne dźwiękoszczelne pomieszczenia paneli sterowania, których poziom dźwięku nie przekracza 50-60 dB A, co spełnia wymagania GOST 12.1.003-76. Pracownicy obsługi spędzają w nich 80-90% czasu pracy.
Czasami w maszynowniach instaluje się kabiny akustyczne, aby pomieścić personel serwisowy (dyżurujący elektrycy itp.). Kabiny dźwiękochłonne to niezależna rama na wspornikach, do których mocowana jest podłoga, sufit i ściany. Okna i drzwi kabin muszą mieć podwyższoną izolację akustyczną (drzwi dwuskrzydłowe, podwójne szyby). Do wentylacji zapewniona jest jednostka wentylacyjna z tłumikami na wlocie i wylocie powietrza.
Jeśli konieczne jest szybkie wyjście z kabiny, wykonuje się je półzamknięte, czyli brakuje jednej ze ścian. W tym przypadku wydajność akustyczna kabiny jest zmniejszona, ale nie ma potrzeby stosowania urządzenia wentylacyjnego. Według danych graniczna wartość średniej izolacyjności akustycznej dla kabin półzamkniętych wynosi 12-14 dB.
Stosowanie oddzielnych kabin typu zamkniętego lub półzamkniętego na terenie stacji można przypisać indywidualnym środkom ochrony personelu przed hałasem. Środki ochrony osobistej obejmują również różnego rodzaju wkładki douszne i nauszniki. Efektywność akustyczna wkładek dousznych, a zwłaszcza słuchawek w zakresie wysokich częstotliwości, jest dość wysoka i wynosi co najmniej 20 dB. Wadą tych narzędzi jest to, że wraz z hałasem spada poziom użytecznych sygnałów, poleceń itp., a także możliwe jest podrażnienie skóry, głównie w podwyższonej temperaturze otoczenia. Zaleca się jednak używanie wkładek dousznych i słuchawek podczas pracy w środowiskach o poziomie hałasu przekraczającym dopuszczalne poziomy, zwłaszcza w zakresie wysokich częstotliwości. Oczywiście wskazane jest stosowanie ich do krótkotrwałych wyjść z dźwiękoszczelnych kabin lub paneli sterowniczych do obszarów o podwyższonym poziomie hałasu.
Jednym ze sposobów na ograniczenie hałasu na drogach jego propagacji na terenie stacji są ekrany akustyczne. Przegrody akustyczne są wykonane z cienkiej blachy lub innego gęstego materiału, który może mieć wyściółkę dźwiękochłonną z jednej lub obu stron. Przegrody akustyczne są zazwyczaj niewielkie i zapewniają lokalne redukcje dźwięku bezpośredniego pochodzącego ze źródła hałasu, nie wpływając znacząco na poziom dźwięku odbitego w pomieszczeniu. W tym przypadku sprawność akustyczna nie jest bardzo wysoka i zależy głównie od stosunku dźwięku bezpośredniego i odbitego w obliczonym punkcie. Zwiększenie wydajności akustycznej ekranów można osiągnąć poprzez zwiększenie ich powierzchni, która powinna wynosić co najmniej 25-30% powierzchni przekroju ogrodzenia pomieszczenia w płaszczyźnie ekranu. Jednocześnie zwiększa się efektywność ekranu poprzez zmniejszenie gęstości energii odbitego dźwięku w ekranowanej części pomieszczenia. Zastosowanie ekranów wielkoformatowych pozwala również na znaczne zwiększenie liczby stanowisk pracy, na których zapewniona jest redukcja hałasu.
Najskuteczniejsze zastosowanie ekranów wiąże się z montażem okładzin dźwiękochłonnych na otaczających powierzchniach lokalu. Szczegółową prezentację metod obliczania wydajności akustycznej i zagadnień projektowych ekranów podano w i
Aby zredukować hałas w całej maszynowni, instalacje emitujące intensywny dźwięk są osłonięte obudowami. Obudowy dźwiękochłonne są zwykle wykonane z blachy wyłożonej po wewnętrznej stronie listwy PDU. Istnieje możliwość całkowitego lub częściowego poszycia powierzchni instalacji materiałem dźwiękochłonnym.
Według danych amerykańskich ekspertów w zakresie tłumienia hałasu na Międzynarodowej Konferencji Energetycznej w 1969 roku, kompletne wyposażenie turbozespołów dużej mocy (500-1000 MW) w obudowy dźwiękochłonne pozwala na obniżenie poziomu emitowanego dźwięku o 23-28 dB A. Po umieszczeniu turbozespołów w specjalnych izolowanych skrzynkach wydajność wzrasta do 28-34 dB A.
Asortyment materiałów stosowanych do izolacji akustycznej jest bardzo szeroki i np. dla izolacji 143 jednostek parowych, które zostały wprowadzone do USA po 1971 roku, rozkłada się on następująco: aluminium -30%, blacha stalowa - 27%, żelbest - 18%, cement azbestowy - 11%, cegła - 10%, porcelana z powłoką zewnętrzną - 9%, beton - 4%.
W prefabrykowanych panelach akustycznych stosowane są następujące materiały: izolacja akustyczna – stal, aluminium, ołów; dźwiękochłonne - tworzywa piankowe, wełna mineralna, włókno szklane; tłumienie - masy bitumiczne; uszczelnienie - guma, kit, tworzywa sztuczne.
Szeroko stosowano piankę poliuretanową, włókno szklane, blachę ołowianą, winyl wzmocniony proszkiem ołowianym.
Szwajcarska firma Air Force, w celu zmniejszenia hałasu aparatu szczotkowego i wzbudników turbozespołów dużej mocy, pokrywa je ciągłą obudową ochronną z grubą warstwą materiału dźwiękochłonnego, w ścianki którego wbudowane są tłumiki wlot i wylot powietrza chłodzącego.
Konstrukcja obudowy zapewnia swobodny dostęp do tych jednostek w celu bieżących napraw. Jak wykazały badania tej firmy, dźwiękoszczelność obudowy przedniej części turbiny jest najbardziej widoczna przy wysokich częstotliwościach (6-10 kHz), gdzie wynosi 13-20 dB, przy niskich częstotliwościach (50-100 Hz ) jest nieznaczny - do 2-3 dB.
Ryż. 2-10. Poziomy ciśnienia akustycznego w odległości 1 m od korpusu turbiny gazowej GTK-10-Z
1 - z ozdobną obudową; 2- z usuniętą obudową
Szczególną uwagę należy zwrócić na izolację akustyczną w elektrowniach z napędami turbin gazowych. Z obliczeń wynika, że w elektrowniach z turbiną gazową rozmieszczenie silników turbogazowych (GTE) i sprężarek jest najbardziej ekonomiczne w pojedynczych boksach (jeśli liczba GTE jest mniejsza niż pięć). Umieszczając cztery silniki turbogazowe we wspólnym budynku, koszt budowy budynku jest o 5% wyższy niż przy zastosowaniu pojedynczych skrzynek, a przy dwóch silnikach turbogazowych różnica w kosztach wynosi 28% Dlatego też, gdy jest więcej niż pięć jednostek , bardziej ekonomiczne jest umieszczenie ich we wspólnym budynku. Na przykład Westinghouse instaluje pięć turbin gazowych typu 501-AA w jednym izolowanym akustycznie budynku.
Zazwyczaj do pojedynczych skrzynek stosuje się panele blaszane, wewnątrz których znajduje się wyściółka dźwiękochłonna. Okładzina dźwiękochłonna może być wykonana z wełny mineralnej lub półsztywnych płyt z wełny mineralnej w osłonie z włókna szklanego i osłoniętych od strony źródła hałasu blachą perforowaną lub siatką metalową. Panele są połączone śrubami, na połączeniach - elastycznymi uszczelkami.
Bardzo efektowne są stosowane za granicą wielowarstwowe panele, wykonane z wewnętrznej perforowanej stali i zewnętrznej blachy ołowianej, pomiędzy którymi umieszczony jest porowaty materiał dźwiękochłonny. Stosowane są również panele z wielowarstwową okładziną wewnętrzną wykonaną z warstwy winylu wzmocnionego proszkiem ołowianym i umieszczonej pomiędzy dwiema warstwami włókna szklanego – wewnętrzną o grubości 50 mm i zewnętrzną o grubości 25 mm.
Jednak nawet najprostsze skórki dekoracyjne i dźwiękochłonne zapewniają znaczną redukcję hałasu otoczenia w maszynowniach. Na ryc. Na rysunkach 2-10 przedstawiono poziomy ciśnienia akustycznego w pasmach oktawowych mierzone w odległości 1 m od powierzchni obudowy ozdobnej sprężarki gazu typu GTK-10-3. Dla porównania mamy też widmo szumów mierzone przy zdjętej osłonie w tych samych punktach. Widać, że efekt obudowy wykonanej z blachy stalowej o grubości 1 mm, wyłożonej wewnątrz włóknem szklanym o grubości 10 mm, wynosi 10–15 dB w zakresie wysokich częstotliwości. Pomiary wykonano w warsztacie wybudowanym według standardowego projektu, w którym zainstalowano 6 jednostek GTK-10-3 pokrytych okładziną dekoracyjną.
Powszechnym i bardzo ważnym problemem dla wszelkiego rodzaju przedsiębiorstw energetycznych jest izolacja akustyczna rurociągów. Rurociągi nowoczesnych instalacji tworzą złożony rozbudowany system o ogromnej powierzchni promieniowania ciepła i dźwięku.
Ryż. 2-11. Izolacja akustyczna gazociągu w TPP Kirchleigeri: a - schemat izolacji; b - elementy panelu wielowarstwowego
1- poszycie metalowe z blachy stalowej; 2 - maty z wełny mineralnej o grubości 20 mm; 3-folia aluminiowa; 4 - płyta wielowarstwowa o grubości 20 mm (waga I m2 to 10,5 kg); 5 - filc bitumiczny; 6 warstw izolacji termicznej; 7-warstwowa pianka
Dotyczy to zwłaszcza elektrowni gazowo-parowych, które czasami posiadają złożoną, rozgałęzioną sieć rurociągów i system bramek.
Aby zmniejszyć hałas rurociągów transportujących silnie zakłócone przepływy (na przykład w obszarach za zaworami redukującymi ciśnienie), wzmocniona izolacja akustyczna, pokazana na ryc. 2-11.
Izolacyjność akustyczna takiej powłoki wynosi około 30 dB A (redukcja poziomu dźwięku w porównaniu z „gołym” rurociągiem).
Do okładzin rurociągów o dużych średnicach stosuje się wielowarstwową izolację termiczną i akustyczną, która jest wzmocniona żebrami i hakami przyspawanymi do izolowanej powierzchni.
Izolacja składa się z warstwy izolacji z mastyksu z kowalitu o grubości 40-60 mm, na której ułożona jest zbrojona siatka druciana o grubości 15-25 mm. Siatka służy do wzmocnienia warstwy kowelitu i stworzenia szczeliny powietrznej. Warstwę zewnętrzną tworzą maty z wełny mineralnej o grubości 40-50 mm, na które nakładana jest warstwa tynku azbestowo-cementowego o grubości 15-20 mm (80% azbest gat. 6-7 i 20% cement gat. 300). Warstwa ta jest zamykana (wklejana) za pomocą tkaniny technicznej. W razie potrzeby powierzchnia jest malowana. Podobna metoda izolacji akustycznej przy użyciu istniejących wcześniej elementów izolacji termicznej może znacznie zmniejszyć hałas. Dodatkowe koszty związane z wprowadzeniem nowych elementów izolacji akustycznej są znikome w porównaniu z konwencjonalną izolacją termiczną.
Jak już zauważono, najintensywniejszy hałas aerodynamiczny występuje podczas pracy wentylatorów, oddymiaczy, turbin gazowych i elektrociepłowni, urządzeń odpadowych (linie nadmuchowe, linie bezpieczeństwa, linie zaworów przeciwprzepięciowych sprężarek turbin gazowych). Tutaj można również uwzględnić ROU.
Tłumiki służą do ograniczenia rozprzestrzeniania się takiego hałasu wzdłuż przepływu transportowanego medium i jego uwalniania do otaczającej atmosfery. Tłumiki zajmują ważne miejsce w całym systemie środków do redukcji hałasu w elektrowniach, ponieważ dźwięk z wnęk roboczych może być bezpośrednio przenoszony przez urządzenia wlotowe lub wylotowe do otaczającej atmosfery, tworząc najwyższe poziomy ciśnienia akustycznego (w porównaniu z innymi źródłami promieniowanie dźwiękowe). Przydatne jest również ograniczenie rozprzestrzeniania się hałasu przez transportowane medium w celu zapobieżenia jego nadmiernemu przenikaniu przez ściany rurociągu na zewnątrz poprzez zainstalowanie tłumików hałasu (np. odcinek rurociągu za zaworem redukcyjnym).
W nowoczesnych potężnych zespołach turbin parowych tłumiki są umieszczane na wlocie wentylatorów dmuchaw. W takim przypadku spadek ciśnienia jest ściśle ograniczony przez górną granicę rzędu 50-f-100 Pa. Wymagana skuteczność tych tłumików wynosi zwykle od 15 do 25 dB w zakresie 200-1000 Hz pod względem efektu instalacyjnego.
I tak w Robinson TPP (USA) o mocy 900 MW (dwa bloki po 450 MW każdy), w celu zmniejszenia hałasu wentylatorów nadmuchowych o wydajności 832 000 m3/h zainstalowano tłumiki ssania. Tłumik składa się z obudowy (blacha stalowa o grubości 4,76 mm), w której znajduje się siatka z płyt dźwiękochłonnych. Korpus każdej płyty wykonany jest z perforowanej blachy stalowej ocynkowanej. Materiał dźwiękochłonny - wełna mineralna, zabezpieczona włóknem szklanym.
Koppers produkuje standardowe bloki dźwiękochłonne stosowane w tłumikach wentylatorów służących do suszenia miału węglowego, doprowadzenia powietrza do palników kotłów, wentylacji pomieszczeń.
Hałas wyciągów dymu często stanowi duże niebezpieczeństwo, ponieważ może wydostawać się do atmosfery przez komin i rozprzestrzeniać się na znaczne odległości.
Na przykład w TPP „Kirchlengern” (Niemcy) poziom dźwięku w pobliżu komina wynosił 107 dB przy częstotliwości 500-1000 Hz. W związku z tym postanowiono zainstalować aktywny tłumik w kominie budynku kotłowni (rys. 2-12). Tłumik składa się z dwudziestu skrzydeł 1 o średnicy 0,32 mi długości 7,5 m. Biorąc pod uwagę złożoność transportu i montażu, skrzydła podzielone są na części na długości, które są ze sobą połączone i przykręcone śrubami. struktura wspierająca. Rocker składa się z korpusu wykonanego z blachy stalowej oraz absorbera (wełny mineralnej) zabezpieczonego włóknem szklanym. Po zamontowaniu tłumika poziom dźwięku przy kominie wyniósł 89 dB A.
Złożone zadanie redukcji hałasu turbin gazowych wymaga zintegrowanego podejścia. Poniżej przykład zestawu środków do zwalczania hałasu turbin gazowych, których istotną częścią są tłumiki na drogach gaz-powietrze.
W celu obniżenia poziomu hałasu zespołu turbiny gazowej z silnikiem turboodrzutowym Olympus 201 o mocy 17,5 MW przeprowadzono analizę wymaganego stopnia tłumienia hałasu instalacji. Wymagano, aby oktawowe widmo hałasu mierzone w odległości 90 m od podstawy stalowego komina nie przekraczało PS-50. Układ przedstawiony na ryc. 2-13 zapewnia tłumienie hałasu ssania GTU przez różne elementy (dB):
Średnia geometryczna częstotliwości pasma oktawowego, Hz ............................................. ..... | 1000 2000 4000 8000 |
|||||||
Poziomy ciśnienia akustycznego w odległości 90 m od ssania turbozespołu gazowego do tłumienia dźwięku ............................................. .............................. ............. | ||||||||
Tłumienie w skręcie o 90° bez podszewki (kolanko) ............................................. ...... | ||||||||
Tłumienie w wyłożonym obrocie 90° (kolanko) ............................................. ...... | ||||||||
Osłabienie z powodu filtra powietrza. . . .................................................. ....................... | ||||||||
Osłabienie z powodu okiennic .............. | ||||||||
Tłumienie w części tłumika o wysokiej częstotliwości ................................................ ...... ... | ||||||||
Tłumienie w części tłumika o niskiej częstotliwości ............................................. ...... ................ | ||||||||
Poziomy ciśnienia akustycznego w odległości 90 m po wyciszeniu hałasu.... |
Na wlocie powietrza do turbiny gazowej montowany jest dwustopniowy tłumik płytowy ze stopniami wysokiej i niskiej częstotliwości. Stopnie tłumika są instalowane za cyklem filtra oczyszczania powietrza.
Na wydechu GTU jest zainstalowany pierścieniowy tłumik niskiej częstotliwości. Wyniki analizy pola hałasu GTU z silnikiem turboodrzutowym na wydechu przed i po montażu tłumika (dB):
Średnia geometryczna częstotliwości pasma oktawowego, Hz........ | ||||||||
Poziom ciśnienia akustycznego, dB: przed montażem tłumika. . . | ||||||||
po zamontowaniu tłumika. . |
W celu zmniejszenia hałasu i wibracji generator gazu GTU został zamknięty w obudowie, a na wlocie powietrza do instalacji wentylacyjnej zamontowano tłumiki. W efekcie hałas mierzony w odległości 90 m wyniósł:
Podobne systemy tłumienia hałasu są stosowane w swoich turbinach gazowych przez amerykańskie firmy Solar, General Electric i japońską firmę Hitachi.
W przypadku turbin gazowych o dużej wydajności tłumiki na wlocie powietrza są często bardzo nieporęcznymi i złożonymi konstrukcjami inżynierskimi. Przykładem jest system tłumienia hałasu w elektrociepłowni gazowej Var (Niemcy), w której znajdują się dwie jednostki Brown-Boveri GTU o mocy 25 MW każda.
Ryż. 2-12. Montaż tłumika w kominie Kirchlengerä TPP
Ryż. 2-13. System tłumienia hałasu dla przemysłowej turbiny gazowej z samolotowym silnikiem turbogazowym jako generatorem gazu
1- zewnętrzny pierścień dźwiękochłonny; 2- wewnętrzny pierścień dźwiękochłonny; 3- osłona obejściowa; 4 - filtr powietrza; 5-turbinowy wydech; 6 - płytki tłumika wysokiej częstotliwości na ssaniu; 7- płytki tłumika niskiej częstotliwości na ssaniu
Stacja znajduje się w centralnej części zaludnionego obszaru. Na wlocie GTU montowany jest tłumik składający się z trzech stopni ustawionych szeregowo. Materiałem dźwiękochłonnym pierwszego stopnia, przeznaczonym do tłumienia dźwięków o niskiej częstotliwości, jest wełna mineralna pokryta tkaniną syntetyczną i zabezpieczona blachą perforowaną. Drugi etap jest podobny do pierwszego, ale różni się mniejszymi odstępami między płytami. Trzeci krok
składa się z blach pokrytych materiałem dźwiękochłonnym i służy do pochłaniania dźwięków o wysokiej częstotliwości. Po zamontowaniu tłumika hałas elektrowni nawet w nocy nie przekraczał przyjętej dla tego obszaru normy (45 dB L).
Podobne złożone tłumiki dwustopniowe są instalowane w wielu potężnych instalacjach domowych, na przykład w Elektrociepłowni Krasnodar (GT-100-750), Elektrowni Okręgu Nevinnomysskaya (PGU-200). Opis ich budowy znajduje się w § 6-2.
Koszt środków tłumienia hałasu na tych stacjach wyniósł 1,0-2,0% całkowitego kosztu stacji, czyli ok. 6% kosztów samej turbiny gazowej. Ponadto stosowanie tłumików wiąże się z pewną utratą mocy i wydajności.Budowa tłumików wymaga użycia dużej ilości drogich materiałów i jest dość pracochłonna. Dlatego szczególne znaczenie mają kwestie optymalizacji konstrukcji tłumików, co jest niemożliwe bez znajomości najbardziej zaawansowanych metod obliczeniowych i podstaw teoretycznych tych metod.
Izolacja akustyczna kotłowni W niniejszej publikacji rozważymy przyczyny wzrostu poziomu hałasu i wibracji z kotłów gazowych i kotłowni, a także sposoby ich eliminacji w celu osiągnięcia standardowych wskaźników i poziomu komfortu mieszkańców.
Coraz większą popularnością wśród deweloperów cieszy się montaż autonomicznych modułowych kotłów gazowych na dachach budynków mieszkalnych. Zalety takiej kotłowni są oczywiste. Pomiędzy nimi
Brak konieczności wznoszenia osobnego budynku na wyposażenie kotłowni
Zmniejszenie strat ciepła o 20% ze względu na małą ilość sieci ciepłowniczych w porównaniu z ogrzewaniem z sieci centralnego ogrzewania
Oszczędności na instalacji komunikacji od chłodziwa do konsumenta
Brak konieczności wymuszonej wentylacji
Możliwość pełnej automatyzacji systemu przy minimum personelu
Jedną z wad kotła na dachu są wibracje z kotła i pomp. Z reguły są one wynikiem niedociągnięć w projektowaniu, budowie i montażu wyposażenia kotłowni. Dlatego odpowiedzialność za wyeliminowanie podwyższonego poziomu hałasu i wygłuszenie kotłowni spoczywa na deweloperze lub firmie zarządzającej mieszkaniem.
Hałas z kotłowni ma niską częstotliwość i jest przenoszony przez elementy konstrukcyjne budynku bezpośrednio ze źródła i przez komunikację. Jej natężenie w pomieszczeniu przystosowanym do kotłowni wynosi 85-90dB. Izolacja akustyczna kotłowni na dachu jest uzasadniona, jeśli jest produkowana od strony źródłowej, a nie w mieszkaniu. Wygłuszanie sufitu i ścian w mieszkaniu z takim hałasem jest drogie i nieefektywne.
Przyczyny zwiększonego poziomu hałasu w kotłowni na dachu.
Niewystarczająca grubość i masywność podstawy, na której stoi wyposażenie kotłowni. Prowadzi to do przenikania dźwięków powietrznych do mieszkań przez płytę stropową i podłogę techniczną.
Brak odpowiedniej wibroizolacji kotła. Jednocześnie na sufity i ściany przenoszone są drgania, które emitują dźwięk do mieszkań.
Sztywne mocowanie rurociągów, komunikacji i ich podpór jest również źródłem hałasu strukturalnego. Zwykle rury powinny przechodzić przez przegrody budowlane w elastycznym rękawie, otoczonym warstwą materiału dźwiękochłonnego.
Niewystarczająca grubość rurociągu, jako błąd projektowy, prowadzący do dużej prędkości wody i powstania zwiększonego poziomu hałasu hydrodynamicznego.
Izolacja akustyczna kotłowni na dachu. Lista wydarzeń.
Montaż podpór wibroizolacyjnych pod wyposażeniem kotłowni. Obliczenia materiałów do izolacji drgań dokonuje się z uwzględnieniem powierzchni podparcia i ciężaru sprzętu;
Eliminacja „twardych połączeń” w miejscach mocowania podpór rurociągów za pomocą silomera materiałowego, izolacji termodźwiękowej lub montażu łączników wibracyjnych na kołkach mocujących komunikację;
W przypadku braku elastycznych tulei rozszerzenie przejścia rurociągu przez konstrukcje wsporcze, owinięcie elastycznym materiałem (k-flex, vibrostack itp.) I warstwą żaroodporną (tektura bazaltowa);
Owinięcie rurociągu materiałem redukującym straty ciepła i posiadającym właściwości dźwiękochłonne: , Texound 2ft AL;
Dodatkowa izolacja akustyczna konstrukcji otaczających kotłownię dachową;
Montaż gumowych kompensatorów w celu zmniejszenia przenoszenia drgań przez rurociąg;
Montaż tłumików w kanale spalin;
Montaż materiałów dźwiękochłonnych na bazie bazaltu (Stopsound BP) lub włókna szklanego (włókno Acustiline) pozwala zredukować hałas tła w kotłowni o 3-5dB.
IZOLACJA AKUSTYCZNA KOTŁA W DOMU DREWNIANYM.
Przepisy budowlane i przepisy przeciwpożarowe nakazują instalację kotła w specjalnym pomieszczeniu wyposażonym w osobne wejście. Z reguły znajduje się w piwnicy lub piwnicy. Przy takim układzie skargi na zwiększony poziom hałasu z kotła są rzadkie.
Kocioł zainstalowany na tym samym piętrze z salonami, który ma wysoki poziom hałasu przy całkowitej ciszy w wiejskim domu, może powodować niedogodności dla mieszkańców. Dlatego istotna może być izolacja akustyczna kotła.
Przyczyny zwiększonego poziomu hałasu mogą być podobne jak w przypadku kotła dachowego, ale na mniejszą skalę. Obejmują one również
Cechy konstrukcji zewnętrznej skrzynki kotła. W większości modeli kotłów palnik i wentylator są zamykane osobną przepustnicą, co zmniejsza hałas wytwarzany przez palnik. Jeśli jedynym zabezpieczeniem dźwiękochłonnym jest plastikowa obudowa kotła, hałas palnika może być wyczuwalny.
Głośny wentylator od producenta.
Niewyważenie wentylatora, przywieranie brudu z powodu kurzu z zewnątrz oraz zaniedbanie czynności konserwacyjnych.
Powietrze wchodzące do systemu grzewczego.
Nieprawidłowe ustawienie palnika gazowego.
Sztywny system mocowania rur kotłowych i wylotowych.
Izolacja akustyczna kotła rozpoczyna się od zidentyfikowania przyczyn zwiększonego poziomu hałasu i wiąże się z pracą obsługujących go pracowników serwisu gazowego lub firmy zajmującej się wygłuszaniem pomieszczeń.
Jeżeli praca kotła i instalacji jest wyregulowana, to
Kocioł montujemy na platformie wibroizolacyjnej na wspornikach z siłomierzem
W miejscach wyjścia rur z korpusu kotła montujemy kompensatory gumowe
Kupujemy obudowę dźwiękoszczelną do kotła
Wykonujemy dodatkowe wygłuszenie ścian kotłowni
Aby zredukować hałas w tle w kotłowni
Witamy w Strefie Komfortu!
Nasza strona internetowa to nasza wizytówka. Podobnie jak na wizytówce umieściliśmy tylko najpotrzebniejsze naszym zdaniem informacje.
Nasza strona internetowa została stworzona po to, aby odwiedzając tutaj mogli Państwo do nas zadzwonić:
- kotłownie, wyposażenie kotłowni, kotły grzewcze, palniki
- limity gazu
I uzyskaj kwalifikowane odpowiedzi na swoje pytania w rozsądnym czasie.
Wykonane prace:
- Uzyskanie specyfikacji technicznych (TU) do następujących rodzajów prac: zgazowanie obiektu, zaopatrzenie w wodę, zaopatrzenie w energię elektryczną, kanalizacja. A także - wszystkie pozwolenia dla kotłowni w SES, Straży Pożarnej i innych organizacjach. Limity gazowe - przygotowanie dokumentacji, odbiór.
- Projektowanie kotłowni. Realizowana jest jako odrębna usługa oraz w kompleksie prac przy budowie kotłowni pod klucz. Do kotłów gazowych, kotłów na olej napędowy i kotłów opalanych drewnem. Prowadzone są prace projektowe dla następujących obiektów - kotłów gazowych, kotłów na olej napędowy oraz kotłów na odpady drzewne.
- Wyposażenie kotła . Dostawa sprzętu importowanego i rosyjskiego - bezpośrednio przez producentów. Udzielamy rabatów organizacjom projektowym i instalacyjnym, które dokonują zakupów za pośrednictwem naszych przedstawicielstw. Główny wyposażenie kotła: moduły blokowe, kotły, palniki, wymienniki ciepła, kominy.
Można również osobno zamówić następujące wyposażenie kotła:
- kotły gazowe (mała i średnia moc),
- kotły grzewcze,
- palniki (gazowe, wysokoprężne i kombinowane),
- budynki modułowe (z płyt warstwowych).
- Montaż kotłowni produkowana jest zarówno u Klienta, jak iz możliwością częściowego wykonania na bazie firmy, z dalszą dostawą na plac budowy i montażem blokowym. Główne rodzaje: blokowe, modułowe kotłownie, dachowe, do zabudowy, doczepiane, przenośne.
- Dostawa wykonanych prac. Wykonywanie wszelkich prac związanych z dokumentacją i kontaktami z przedstawicielami organów nadzorczych. Współpraca ze wszystkimi konstrukcjami związanymi zarówno z kotłami parowymi, jak i kotłami na gorącą wodę.
Zalety:
- Warunki, jakość, cena- zadeklaruj wszystko. Nie wszyscy się zgadzają. Spełniamy.
- Dział zarządzania dostarczy do Ciebie maksymalna wygoda podczas współpracy z nami.
Kotłownie są projektowane i instalowane zgodnie z szeregiem zasad, na przykład:
- GOST 21.606-95 SPDS „Zasady wykonania dokumentacji roboczej dla rozwiązań termomechanicznych dla kotłowni”
- GOST 21563-93 Kotły na gorącą wodę. Główne parametry i wymagania techniczne
- PU i BE „Zasady projektowania i bezpiecznej eksploatacji kotłów parowych”
- PB 12-529-03 „Zasady bezpieczeństwa dla systemów dystrybucji i zużycia gazu”.
Jeśli masz zadanie, aby uzyskać prawidłowy obiekt do początku sezonu grzewczego oferujemy Ci opcję „Kotłownia blokowo-modułowa” w oparciu o standardowe rozwiązania. Kotłownie modułowe dostarczane w ramach tego programu mają następujące zalety: a) zastosowanie standardowego projektu skraca czas projektowania i koordynacji projektu, b) możliwy staje się zakup głównego wyposażenia równolegle z zabudową poszczególnych części projekt.
Tłumaczymy również kotły parowe w trybie ciepłej wody. Dzięki tej operacji kotły parowe stracić z mocy znamionowej, rozwiązując jednocześnie pewne problemy z ogrzewaniem. Są to rozwiązania głównie dla kotłów rosyjskich. Zaletą tej operacji jest to, że istniejące kotły parowe nie muszą być wymieniane na nowe, co w krótkim okresie może być korzystne z ekonomicznego punktu widzenia.
Wszystkie dostarczone urządzenia kotłowe są certyfikowane i posiadają dopuszczenia do użytkowania na terenie Federacji Rosyjskiej - kotły gazowe, kotły grzewcze, palniki, wymienniki ciepła, zawory itp. Podana dokumentacja wchodzi w zakres dostawy.
Z roku na rok rośnie liczba apeli obywateli, które wpłynęły do urzędu Rospotrebnadzor w regionie Tiumeń, w sprawie pogorszenia warunków życia z powodu narażenia na nadmierny poziom hałasu.
W 2013 r. wpłynęły 362 odwołania (łącznie za naruszenia ciszy i spokoju, noclegów i hałasu), w 2014 r. 416 odwołań, w 2015 r. wpłynęło już 80 odwołań.
Zgodnie z przyjętą praktyką, po apelu mieszkańców, Zakład wyznacza pomiary poziomu hałasu i drgań w budynku mieszkalnym. W razie potrzeby pomiary są przeprowadzane w organizacjach zlokalizowanych w pobliżu mieszkań, w których używany jest na przykład „hałaśliwy” sprzęt - źródło hałasu (restauracja, kawiarnia, sklep itp.). W przypadku stwierdzenia, że poziom hałasu i wibracji przekracza wartości dopuszczalne, zgodnie z SN 2.2.4/2.1.8.562-96 „Hałas w miejscach pracy, w budynkach mieszkalnych, użyteczności publicznej i na terenie zabudowy mieszkaniowej”, właścicielom hałasu źródła – osoby prawne, indywidualni przedsiębiorcy – Urząd wydaje nakaz usunięcia stwierdzonych naruszeń przepisów sanitarnych.
Jak można zmniejszyć hałas z wyżej wymienionych urządzeń, aby nie było skarg ze strony mieszkańców domu podczas jego eksploatacji? Oczywiście idealnym rozwiązaniem jest zapewnienie niezbędnych środków na etapie projektowania budynku mieszkalnego, wówczas opracowanie środków redukcji hałasu jest zawsze możliwe, a ich realizacja podczas budowy jest dziesięciokrotnie tańsza niż w tych domach, które już były wybudowany.
Sytuacja wygląda zupełnie inaczej, jeśli budynek został już wybudowany i znajdują się w nim źródła hałasu przekraczające obowiązujące normy. Wówczas najczęściej hałaśliwe jednostki są zastępowane mniej hałaśliwymi i podejmowane są działania mające na celu odizolowanie jednostek i prowadzącej do nich komunikacji. Następnie przyjrzymy się konkretnym źródłom izolacji akustycznej i wibracji sprzętu.
HAŁAS Z KLIMATYZATORA
Zastosowanie trójelementowej wibroizolacji, gdy klimatyzator jest montowany na ramie za pomocą wibroizolatora, a rama - na płycie żelbetowej przez gumowe uszczelki (w tym przypadku płyta żelbetowa jest montowana na wibroizolatorach sprężynowych na dachu budynku), prowadzi do zmniejszenia przenikającego hałasu konstrukcyjnego do poziomów dopuszczalnych w pomieszczeniach mieszkalnych.
W celu zmniejszenia hałasu, oprócz wzmocnienia izolacji akustycznej i wibracyjnej ścian kanałów powietrznych oraz zamontowania tłumika na kanale powietrznym centrali wentylacyjnej (od strony lokalu) konieczne jest zamocowanie komory rozprężnej i kanałów powietrznych do sufitu za pomocą wieszaków lub uszczelek wibroizolacyjnych.
HAŁAS Z KOTŁOWNI NA DACHU
W celu ochrony przed hałasem kotłowni znajdującej się na dachu domu, płyta fundamentowa kotłowni dachowej montowana jest na wibroizolatorach sprężynowych lub macie wibroizolacyjnej wykonanej ze specjalnego materiału. Pompy i agregaty kotłowe wyposażone w kotłownię montuje się na wibroizolatorach z zastosowaniem wkładów miękkich.
Pomp w kotłowni nie wolno ustawiać silnikiem do dołu! Muszą być zamontowane w taki sposób, aby obciążenie z rurociągów nie było przenoszone na obudowę pompy. Ponadto poziom hałasu jest wyższy w przypadku pompy o większej mocy lub w przypadku zainstalowania kilku pomp. W celu zmniejszenia hałasu płytę fundamentową kotłowni można również postawić na amortyzatorach sprężynowych lub wysokowytrzymałych wielowarstwowych wibroizolatorach gumowo-gumowo-metalowych.
Obecne przepisy nie pozwalają na umieszczenie kotła dachowego bezpośrednio na stropie lokalu mieszkalnego (strop lokalu mieszkalnego nie może stanowić podstawy posadzki kotłowni), jak również w sąsiedztwie lokalu mieszkalnego. Nie wolno projektować kotłowni dachowych na budynkach placówek przedszkolnych i szkolnych, budynkach medycznych przychodni i szpitali z całodobowym pobytem pacjentów, na budynkach sypialnych sanatoriów i obiektów rekreacyjnych. Przy montażu sprzętu na dachach i stropach wskazane jest umieszczanie go w miejscach najbardziej oddalonych od chronionych obiektów.
HAŁAS SPRZĘTU INTERNETOWEGO
Zgodnie z zaleceniami dotyczącymi projektowania systemów łączności, informatyzacji i ekspedycji obiektów budownictwa mieszkaniowego, na kondygnacjach technicznych, strychach lub klatkach schodowych wyższych kondygnacji zaleca się montaż wzmacniaczy antenowych w szafie metalowej z blokadą. W przypadku konieczności montażu wzmacniaczy domowych na różnych kondygnacjach budynków wielopiętrowych, należy je zamontować w metalowych szafkach w bezpośrednim sąsiedztwie pionu pod sufitem, zwykle na wysokości co najmniej 2 m od dołu szafy na podłogę.
Podczas instalowania wzmacniaczy na podłogach technicznych i strychach, aby wyeliminować przenoszenie wibracji metalowej szafki z urządzeniem blokującym, należy je zainstalować na wibroizolatorach.
WYDAJNOŚĆ - IZOLATORY WIBRACJI I PODŁOGI PŁYWAJĄCE
W przypadku wentylacji, urządzeń chłodniczych na górnych, dolnych i pośrednich kondygnacjach technicznych budynków mieszkalnych, hoteli, kompleksów wielofunkcyjnych lub w pobliżu pomieszczeń dźwiękochłonnych, w których stale przebywają ludzie, można zainstalować urządzenia na fabrycznych wibroizolatorach na płycie żelbetowej . Płyta ta montowana jest na warstwie wibroizolacyjnej lub sprężynach na „pływającej” podłodze (dodatkowa płyta żelbetowa na warstwie wibroizolacyjnej) w pomieszczeniu technicznym. Należy zauważyć, że wentylatory, agregaty skraplające zewnętrzne, które są obecnie produkowane, są wyposażone w wibroizolatory tylko na życzenie klienta.
Podłogi „pływające” bez specjalnych wibroizolatorów mogą być używane tylko z urządzeniami o częstotliwości roboczej powyżej 45-50 Hz. Są to z reguły małe maszyny, których wibroizolację można zapewnić w inny sposób. Wydajność podłóg na elastycznym podłożu przy tak niskich częstotliwościach jest niska, dlatego stosuje się je wyłącznie w połączeniu z innymi typami wibroizolatorów, co zapewnia wysoką izolację drgań przy niskich częstotliwościach (dzięki wibroizolatorom), a także przy średnich i wysokie częstotliwości (dzięki wibroizolatorom i „pływającej” podłodze).
Podłoga pływająca musi być starannie odizolowana od ścian i nośnej płyty stropowej, ponieważ powstanie nawet niewielkich sztywnych mostków między nimi może znacznie pogorszyć jego właściwości w zakresie wibroizolacji. W miejscach, w których podłoga „pływająca” przylega do ścian, musi być wykonany szew z materiałów nietwardniejących, który nie przepuszcza wody.
HAŁAS Z KANAŁU ODPADOWEGO
Aby zmniejszyć hałas, należy przestrzegać wymagań norm i nie projektować bagażnika zsypu śmieci sąsiadującego z lokalami mieszkalnymi. Pień zsypu nie powinien przylegać ani znajdować się w ścianach otaczających lokale mieszkalne lub usługowe o znormalizowanym poziomie hałasu.
Najczęstsze środki mające na celu zmniejszenie hałasu z zsypów śmieci są następujące:
- w pomieszczeniach do zbierania śmieci przewidziana jest „pływająca” podłoga;
- za zgodą mieszkańców wszystkich mieszkań przy wejściu spawana jest (lub likwidowana) śmietnik z umieszczeniem w pomieszczeniu komór śmieci dla wózków inwalidzkich, pomieszczeń concierge itp. (pozytywne jest to, że oprócz hałasu znikają zapachy, eliminuje się możliwość szczurów i owadów, prawdopodobieństwo pożaru, brudu itp.);
- wiadro zaworu załadowczego jest zamontowane za pomocą gumowych lub magnetycznych uszczelek w ramie;
- dekoracyjna okładzina cieplno-akustyczna szybu zsypowego wykonana z materiałów budowlanych oddzielona jest od konstrukcji budynku uszczelkami dźwiękochłonnymi.
Dziś wiele firm budowlanych oferuje swoje usługi, różne projekty zwiększające izolacyjność akustyczną ścian i obiecujące całkowitą ciszę. Należy zauważyć, że w rzeczywistości żadna konstrukcja nie jest w stanie usunąć hałasu strukturalnego przenoszonego przez podłogi, sufity i ściany podczas zrzucania stałych odpadów komunalnych do zsypu na śmieci.
HAŁAS Z WIND
W SP 51.13330.2011 „Ochrona przed hałasem. Zaktualizowane wydanie SNiP 23-03-2003 mówi, że wskazane jest umieszczenie szybów windowych w klatce schodowej między biegami schodów (punkt 11.8). W rozwiązaniu architektoniczno-planistycznym budynku mieszkalnego należy przewidzieć, że do zabudowy szybu windy przylegają pomieszczenia niewymagające zwiększonej ochrony przed hałasem i drganiami (hale, korytarze, kuchnie, pomieszczenia sanitarne). Wszystkie szyby wind, niezależnie od rozwiązania planistycznego, muszą być samonośne i posiadać niezależne fundamenty.
Szyby należy oddzielić od innych konstrukcji budowlanych spoiną akustyczną o grubości 40-50 mm lub podkładkami wibroizolacyjnymi. Jako materiał warstwy elastycznej zalecane są płyty z akustycznej wełny mineralnej na bazie bazaltowej lub z włókna szklanego oraz różne spienione materiały w rolkach polimerowych.
W celu ochrony przed hałasem strukturalnym instalacji windy, jej silnik napędowy wraz z przekładnią i wciągarką, zwykle montowany na jednej wspólnej ramie, jest wibroizolowany od powierzchni nośnej. Nowoczesne jednostki napędowe wind wyposażone są w odpowiednie wibroizolatory montowane pod metalowymi ramami, na których na sztywno osadzone są silniki, przekładnie i wciągarki, w związku z czym zazwyczaj nie jest wymagana dodatkowa izolacja drgań jednostki napędowej. Jednocześnie dodatkowo zaleca się wykonanie dwustopniowego (dwułącznikowego) systemu wibroizolacji poprzez montaż ramy nośnej poprzez wibroizolatory na płycie żelbetowej, która również jest odseparowana od posadzki wibroizolatorami.
Eksploatacja wciągarek zainstalowanych na dwustopniowych systemach wibroizolacyjnych wykazała, że poziomy hałasu z nich nie przekraczają wartości normatywnych w najbliższym lokalu mieszkalnym (przez 1-2 ściany). Ze względów praktycznych należy zadbać o to, aby izolacja drgań nie została zakłócona przez przypadkowe sztywne mostki między metalową ramą a powierzchnią nośną. Kable zasilające muszą mieć wystarczająco długie elastyczne pętle. Jednak pracy innych elementów instalacji dźwigowych (panele sterownicze, transformatory, buty samochodowe i przeciwwagi itp.) może towarzyszyć hałas powyżej wartości normatywnych.
Zabrania się projektowania podłogi maszynowni windy jako kontynuacji stropu stropu salonu na piętrze.
HAŁAS Z TRANSFORMATORAPODSTACJENA PARTERZE
Aby chronić przed hałasem podstacje transformatorowe w pomieszczeniach mieszkalnych i innych o znormalizowanych poziomach hałasu, należy przestrzegać następujących warunków:
- pomieszczenia wbudowanych podstacji transformatorowych;
- nie powinny sąsiadować z pomieszczeniami chronionymi przed hałasem;
- wbudowane podstacje transformatorowe powinny:
- zlokalizowane w piwnicach lub na pierwszych piętrach budynków;
- transformatory muszą być instalowane na odpowiednio zaprojektowanych wibroizolatorach;
- panele elektryczne zawierające urządzenia komunikacji elektromagnetycznej oraz oddzielnie instalowane wyłączniki olejowe z napędem elektrycznym muszą być montowane na gumowych wibroizolatorach (odłączniki powietrzne nie wymagają wibroizolacji);
- urządzenia wentylacyjne pomieszczeń wbudowanych podstacji transformatorowych muszą być wyposażone w tłumiki hałasu.
Aby jeszcze bardziej zredukować hałas z wbudowanej podstacji transformatorowej, zaleca się pokrycie jej sufitów i ścian wewnętrznych wykładziną dźwiękochłonną.
We wbudowanych podstacjach transformatorowych należy wykonać ochronę przed promieniowaniem elektromagnetycznym (siatka ze specjalnego materiału z uziemieniem w celu obniżenia poziomu promieniowania elementu elektrycznego oraz blacha stalowa na magnes).
HAŁAS Z ZAMONTOWANYCH KOTŁÓW,POMPY I RURY PIWNICZNE
Wyposażenie kotłowni (pompy i rurociągi, centrale wentylacyjne, kanały powietrzne, kotły gazowe itp.) muszą być wibroizolowane za pomocą podkładów wibracyjnych i miękkich wkładów. Centrale wentylacyjne wyposażone są w tłumiki.
W celu odizolowania pomp znajdujących się w piwnicach, agregatów windowych w indywidualnych punktach grzewczych (ITP), central wentylacyjnych, komór chłodniczych, określony sprzęt montowany jest na fundamentach wibracyjnych. Rurociągi i kanały powietrzne są wibroizolowane od konstrukcji domu, ponieważ dominującym hałasem w mieszkaniach położonych powyżej może nie być hałas podstawowy z urządzeń w piwnicy, ale ten, który jest przenoszony na przegrodę budynku poprzez wibracje rurociągów fundamentów i sprzętu. Zabrania się urządzania kotłowni w zabudowie w budynkach mieszkalnych.
W układach rurowych podłączonych do pompy konieczne jest zastosowanie wkładek elastycznych - rękawów gumowo-tkaninowych lub rękawów gumowo-tkaninowych zbrojonych spiralami metalowymi, w zależności od ciśnienia hydraulicznego w sieci o długości 700-900 mm. Jeżeli pomiędzy pompą a łącznikiem elastycznym znajdują się odcinki rur, należy je przymocować do ścian i sufitów pomieszczenia na podporach wibroizolacyjnych, wieszakach lub podkładkach amortyzujących. Łączniki elastyczne powinny znajdować się jak najbliżej zespołu pompującego, zarówno na przewodzie tłocznym, jak i na przewodzie ssawnym.
W celu zmniejszenia poziomu hałasu i wibracji w budynkach mieszkalnych z pracy sieci ciepłowniczych i wodociągowych konieczne jest odizolowanie rurociągów dystrybucyjnych wszystkich systemów od konstrukcji budowlanych budynku w miejscach ich przejścia przez konstrukcje wsporcze (wejście do i poza budynkami mieszkalnymi). Odstęp między rurociągiem a fundamentem na wlocie i wylocie musi wynosić co najmniej 30 mm.
Opracowano na podstawie materiałów czasopisma Rozmówca sanitarno-epidemiologiczny (nr 1 (149), 2015 r.)