System „uniwersalnej konserwacji sprzętu. Wdrożenie systemu „TPM - Lean Manufacturing Maintenance Utrzymanie urządzeń tpm
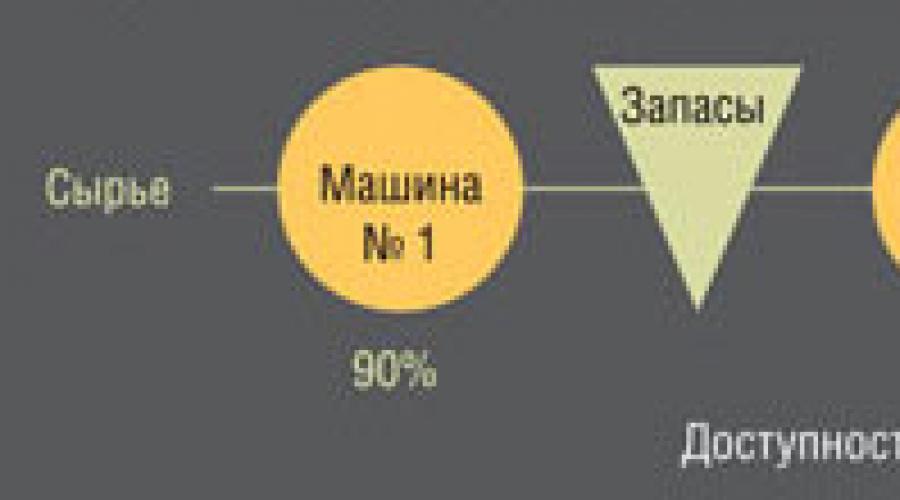
TRM(Total Production Management) to system planowych działań pracowników, nastawników, mechaników jako zespołu, mający na celu maksymalizację wydajności sprzętu poprzez jego konserwację prewencyjną przez cały okres jego eksploatacji.
TRM- to narzędzie zwiększające efektywność pracy, całe wyposażenie przedsiębiorstwa jako jeden system.
TRM- to praca zespołowa, rodzaj kontynuacji systemu 5S.
Bez TPM ani wbudowana jakość, ani just-in-time i jego narzędzie kanban, ani urządzenia Poka-Yoke (ochrona przed błędami) nie mają znaczenia, SMED (szybka zmiana) staje się bez znaczenia.
Co to jest TPM?
Cel TPM- to stworzenie przedsiębiorstwa, które nieustannie dąży do ostatecznego i kompleksowego wzrostu efektywności systemu produkcyjnego.
Środkiem do osiągnięcia celu jest stworzenie mechanizmu obejmującego bezpośrednio miejsca pracy, ukierunkowanego na zapobieganie wszelkiego rodzaju stratom („zero wypadków”, „zero awarii”, „zero odrzutów”) w całym cyklu życia produkcji system.
Aby osiągnąć cel, zaangażowane są wszystkie działy: projektowy, handlowy, zarządczy, ale przede wszystkim produkcyjny.
W osiągnięciu celu uczestniczy cały personel – od najwyższego menedżera do pracownika „pierwszej linii”.
Dążenie do osiągnięcia „zero odpadów” realizowane jest w ramach działań hierarchicznie powiązanych małych grup, które jednoczą wszystkich pracowników.
Co TPM może wnieść do przedsiębiorstwa?
Cel wdrożenia TPM, jak wspomniano powyżej,
Osiągnij najwyższą i wszechstronną wydajność systemu produkcyjnego. Innymi słowy, aby uzyskać maksymalny możliwy wynik w stosunku do wielkości produkcji (Produkcja - P),
jakość produktu (Jakość - Q),
koszt (Koszt - C),
terminy dostaw (Dostawa - D),
bezpieczeństwo pracy (Bezpieczeństwo - S) i inicjatywy pracownicze (Moralność - M) przy minimalnym wykorzystaniu zasobów ludzkich, materialnych i finansowych.
W tabeli 1 przedstawiono uśrednione dane dla kilku japońskich przedsiębiorstw – laureatów nagrody TPM, charakteryzujące zarówno materialne rezultaty, jakie udało im się osiągnąć, jak i niematerialny efekt wdrożenia tego systemu.
Total Productive Maintenance (TPM) to jedno z narzędzi produkcji Lean, które można wykorzystać do zmniejszenia kosztów przestojów sprzętu z powodu awarii i nadmiernej konserwacji. Główną ideą TPM jest zaangażowanie w proces konserwacji sprzętu całego personelu przedsiębiorstwa, a nie tylko odpowiednich usług. Sukces wdrożenia TPM, jak i każdego innego narzędzia lean manufacturing, związany jest z tym, na ile idee metodologii trafiają do umysłów pracowników i są przez nich pozytywnie odbierane.
Etapy TPM
Specyfiką metodyki TPM jest to, że na jej podstawie możliwa jest płynna i planowa transformacja istniejącego systemu obsługi na doskonalszy. W tym celu wygodnie jest przedstawić ścieżkę wdrożenia TPM jako sekwencję etapów, z których każdy realizuje dość konkretne cele i co najważniejsze daje bardzo namacalny efekt.
1. Naprawa usterek operacyjnych – próba usprawnienia istniejącego systemu obsługi i odnalezienia jego słabości.
2. Utrzymanie w oparciu o prognozy – organizowanie zbierania informacji o problemach sprzętowych i ich późniejszej analizy. Planowanie konserwacji zapobiegawczej sprzętu.
3. Konserwacja naprawcza - doskonalenie sprzętu podczas konserwacji w celu wyeliminowania przyczyn systematycznych awarii.
4. Usługa autonomiczna – podział funkcji związanych z utrzymaniem sprzętu pomiędzy personelem obsługującym i konserwującym.
5. Ciągłe doskonalenie jest koniecznością każdego narzędzia lean. W rzeczywistości oznacza to zaangażowanie personelu w ciągłe poszukiwanie źródeł strat eksploatacyjnych i konserwacyjnych, a także propozycję sposobów ich eliminacji.
Tabela 1
Wyniki materialne | Efekt niematerialny | ||
P | Wartość dodana wydajności pracy | 1,5-2 krotny wzrost | Bieżąca konserwacja sprzętu przez operatorów dobiega końca: sami zaczynają dbać o swój sprzęt, nie czekając na instrukcje „z góry” |
Liczba awarii i wypadków wypadkowych | 10-250 razy redukcja | ||
Obciążenie sprzętem | 1,5-2 krotny wzrost | ||
Q | Liczba małżeństw | Zmniejsz o 10 razy | 2. Pracownicy zyskują pewność, że jeśli będą dążyć do doprowadzenia awarii i złomu do zera, to będą w stanie to osiągnąć |
Liczba skarg od konsumentów | 4-krotna redukcja | ||
C | Koszt produkcji | 30% zniżki | |
D | Zapasy wyrobów gotowych i produkcji w toku | 50% zniżki | 3. Dzięki oczyszczeniu miejsca pracy z kurzu, brudu, plam olejowych możliwe staje się przeobrażenie go nie do poznania, czyniąc je jasnym i czystym |
Przypadki naruszenia terminów dostaw | Zero | ||
S | Uraz przy pracy skutkujący absencją | Zero | |
Zanieczyszczenie środowiska | Zero | 4. Odwiedzający tworzą dobre wrażenie przedsiębiorstwa, co ma korzystny wpływ na liczbę zamówień | |
M | Liczba propozycji racjonalizacji | 5-10-krotne powiększenie |
Przed pojawieniem się TPM wierzono, że roślina ze swej natury jest „siedliskiem” trzech „K” (słowa „brud”, „trudne warunki”, „niebezpieczeństwo” zaczynają się od tej litery w języku japońskim). Jakie straty eliminuje: Czas poświęcony na rozwiązywanie problemów ze sprzętem.
Jak wdrożyć system kompleksowej konserwacji sprzętu (TPM)
System Total Equipment Maintenance (TPM), jako narzędzie produkcji Lean, jest wybierany głównie przez firmy, których system produkcyjny obejmuje dużą liczbę głównych urządzeń. Najczęściej produkty w takich przedsiębiorstwach są wytwarzane na zautomatyzowanych liniach.
Jako przykład możemy wymienić takie firmy jak Baltika (zautomatyzowane linie do produkcji i rozlewu piwa), Nestle (zautomatyzowane linie do produkcji wyrobów cukierniczych), KATKO (zautomatyzowana produkcja do wydobycia i wzbogacania uranu), Bella (zautomatyzowane linie do produkcji artykułów higienicznych) i inne.
Wydajność takich systemów produkcyjnych zależy głównie od 2 czynników:
- Od procentu załadunku sprzętu, który bezpośrednio zależy od wielkości popytu na gotowe produkty przedsiębiorstwa,
- Całkowity przestój sprzętu z różnych przyczyn, takich jak awarie, konserwacja, przezbrojenie, regulacje, oczekiwanie itp.
W firmach, które wybrały „Total Equipment Maintenance (TPM)” jako główną metodologię poprawy efektywności operacyjnej systemu produkcyjnego, pojawia się pytanie o strategię i taktykę jego wdrażania.
Poniżej przedstawiono jedną z możliwych opcji wdrożenia systemu Total Productivity Maintenance (TPM), w oparciu o metodologię Japan Institute of Manufacturing Maintenance ( JIPM).
FAZA 1 - PRZYGOTOWANIE (12 - 18 miesięcy)
KROK 1 - Powiadomienie o decyzji kierownictwa o wdrożeniu systemu TPM w firmie (1 miesiąc)
Na tym etapie ważne jest zapewnienie odpowiedniego zrozumienia, zaangażowania i aktywnego udziału najwyższego kierownictwa. Następnie na dużą skalę ogłaszane jest wszystkim pracownikom firmy ogłoszenie o rozpoczęciu fazy przygotowań do wdrożenia systemu TPM. Publikacje powstają w mediach korporacyjnych. W razie potrzeby wysyłane są e-maile.
KROK 2 - Wstępne szkolenie i promocja TPM (6-8 miesięcy)
Szkolenia powinny być organizowane w oparciu o rzeczywiste potrzeby. Niektórym pracownikom zapewniane jest intensywne szkolenie, dla niektórych tylko ogólne, aby osiągnąć zrozumienie i zaangażowanie. Na tym etapie ważne jest zorganizowanie szkolenia praktycznego opartego na projektach pilotażowych, podczas których rozwijane są również (adaptowane) metody nauczania TRM. Najczęściej na tym etapie w szkolenia zaangażowani są zewnętrzni trenerzy-konsultanci.
Na tym etapie tworzona jest niezbędna struktura organizacyjna TPM oraz system rad TPM. Zdefiniowane są obszary odpowiedzialności, uprawnienia, zasoby i schematy interakcji.
System rad składa się z Wysokiej Rady TRM i Małych Rad.
Rada Najwyższa składa się z przedstawicieli najwyższego kierownictwa firmy. Na czele rady najwyższej stoi zwykle dyrektor generalny lub wykonawczy, ich zastępcy lub inny przedstawiciel najwyższego kierownictwa.
Małe rady TRM powstają w 8 głównych obszarach TRM:
- skoncentrowane ulepszenia
- usługa offline,
- zaplanowana konserwacja,
- edukacja i rozwój,
- zarządzanie nowym sprzętem i nowymi produktami,
- usługi zorientowane na jakość
- ochrona pracy i środowiska,
- poprawa efektywności działów zarządzania i obsługi.
Częściej na początku tworzone są małe rady tylko w pierwszych 4 kierunkach. W przypadku pozostałych kierunków, w miarę wdrażania systemu, tworzone są małe rady. Małe rady TRM aktywnie rekrutują personel przeszkolony w kroku 2 podczas projektów pilotażowych.
Powstaje również biuro TPM w stawce 1 osoba / 300-400 pracowników firmy. Kierownik biura TRM jest członkiem rady naczelnej TRM. Głównym zadaniem biura TRM jest udzielanie wsparcia metodycznego oraz koordynacja pracy rad TRM. Zazwyczaj pracownicy biura TRM są zwolnieni z innych obowiązków.
KROK 4 – Opracowanie polityki TRM i wyznaczanie celów (2-4 miesiące)
Opracowywana jest polityka TPM. Opracowywany jest system wskaźników do oceny skuteczności i efektywności wdrożenia systemu TPM. Przeprowadzany jest benchmarking i ustalane są aktualne cele osiągalne dla firmy i dla każdego oddziału. Tworzony jest system monitorowania wskaźników oraz niezbędne narzędzia analityczne.
KROK 5 - Opracowanie mapy drogowej i planu generalnego wdrożenia systemu TPM. (2-4 miesiące)
Określane są główne etapy i ich wyniki. Opracowuje się i uzgadnia główne plany wdrożenia TPM dla każdej jednostki.
FAZA 2 – URUCHOMIENIE (1 miesiąc)
Na tym etapie analizowane są wyniki I fazy przygotowawczej wdrożenia TPM i podejmowana jest decyzja o pełnym wdrożeniu systemu w całej firmie. Do wszystkich uczestników dociera szerokie oficjalne ogłoszenie o rozpoczęciu aktywnej fazy wdrażania systemu TRM w firmie. Akcjonariusze, wszyscy pracownicy firmy, klienci, dostawcy i prasa są powiadamiani. W mediach korporacyjnych prowadzona jest szeroka kampania informacyjna.
FAZA 3 - WDROŻENIE (12 - 18 miesięcy)
Na tym etapie następuje uszczegółowienie i realizacja planów wdrożenia TPM we wszystkich działach. W celu realizacji działań planu tworzone są małe grupy TMR-ów, które realizują cały zakres prac praktycznych we wszystkich obszarach.
FAZA 4 – INSTYTUCJONALIZACJA (6-12 miesięcy)
Na tym etapie przeprowadzana jest standaryzacja wszystkich procesów TPM.
Pomimo obecności dużej liczby zastrzeżonych narzędzi i podejść (mających zastosowanie tylko do sprzętu), TPM jest częścią lean, jednym z obszarów wymagających poprawy. Ogólne zasady lean obowiązują w każdym procesie, łącznie z konserwacją i obsługą sprzętu. Filozofia niczemu nie zaprzecza, a wręcz przeciwnie, harmonijnie uzupełnia filozofię lean.
- Całkowite zaangażowanie personelu.
Już od słowa „uniwersalny” widać, że w pracę zaangażowany jest każdy pracownik firmy, który w taki czy inny sposób może wpływać na działanie sprzętu. Praca wymaga zaangażowania całego personelu. Przede wszystkim są to pracownicy remontowo-produkcyjni (operacyjni) oraz odpowiedni kierownicy. Ich praca jest bezpośrednio związana ze sprzętem.
Ale oprócz tego w TPM zaangażowane są również inne usługi: technologiczne, jakościowe, projektowe itp. Wszystko, w taki czy inny sposób, może wpłynąć na wydajność sprzętu i przyczynić się do poprawy jego wydajności. Aby wyeliminować przestoje sprzętu, TPM wymaga udziału menedżerów na wszystkich poziomach zarządzania. Główny nacisk w pracy kładziony jest na profilaktykę, która jest realizowana przez personel produkcyjny i konserwacyjny.
- TPMoznacza podział odpowiedzialności.
Po pierwsze, między personelem naprawczym a produkcyjnym. Jednym z zadań jest nawiązanie relacji jak w nowoczesnych dobrych serwisach samochodowych: kierowca sam dba o swój samochód, a personel naprawczy szybko i sprawnie wykonuje przeglądy. Nie interesuje go często odwiedzany przez niego kierowca. Taki sam podział odpowiedzialności zakłada się między innymi usługami firmy.
- Pracuj dla profilaktyki, a nie korekty.
Pomimo rozbudowanego zestawu narzędzi i podejść mających na celu poprawę wydajności sprzętu, TPM opiera się na zasadzie prewencji. Nie jest tajemnicą, że lepiej przewidzieć awarię lub awarię i zapobiec jej, niż heroicznie sobie z tym poradzić później. Większość podejść i narzędzi TPM opiera się na tej zasadzie.
- Organizacja miejsc pracy (S) - podstawa usprawnień.
Nie bez powodu wszystkie przemiany, zgodnie z klasycznymi teoriami rozwoju Lean Production, zaczynają się od organizacji miejsc pracy. Jest to główny warunek rozpoczęcia wdrażania modułu TPM. Sposób organizowania zadań został szczegółowo opisany w książce „”. Znajdziesz tam metody krok po kroku, konkretne rozwiązania i wiele przykładów. Racjonalna organizacja stanowisk pracy pozwala na wyeliminowanie głównych strat na stanowiskach pracy, w tym na sprzęcie. Pozwala ustabilizować procesy. Jakość i wydajność stają się bardziej stabilne i przewidywalne, co pozwala na wprowadzanie dalszych ulepszeń. Co najważniejsze, organizacja miejsc pracy angażuje i interesuje pracowników. Dlatego 5S nazywa się fundamentem doskonalenia.
- TPMjest filozofia.
System zakłada kształtowanie się w organizacji: kultury lean. Podczas wdrażania TPM kształtuje się oszczędny stosunek do sprzętu, zmienia się podejście do jego konserwacji i naprawy. Sprzęt jest umieszczony w centrum, ponieważ to właśnie tworzy
ROSS KENNEDY
Prezes Centrum TPM w Australazji
Wszystkie elementy systemu zarządzania firmą produkcyjną lub, jak to często się nazywa, systemu produkcyjnego, z których główne to 5S („Zamawianie”), produkcja Just In Time (JIT), Total Quality Based Management Management (TQM) , totalna produktywna konserwacja sprzętu - Total Productive Maintenance (TPM) oraz system ciągłych ulepszeń - kaizen, po pierwsze są ze sobą bardzo ściśle powiązane, a po drugie stale się rozwijają, wzajemnie na siebie wpływając. Jak uzyskać synergiczny efekt ze wspólnego wykorzystania systemów 5S i TPM, na łamach magazynu w przeglądzie materiałów opisali specjaliści z australijskiego Centrum TPM R. Kennedy i L. Mazza. Niniejsza publikacja analizuje interakcję systemu TPM z produkcją szczupłą (Lean Production) oraz systemem TQM.
Dzisiaj stało się jasne, że system TPM, dzięki wbudowanym możliwościom obsługi TQM (zmniejszenie zmienności) i JIT (zmniejszenie opóźnień), jest nie tylko krytycznym ogniwem w osiąganiu światowej klasy wydajności sprzętu, ale także stać się potężnym narzędziem do poprawy ogólnej efektywności firmy.
Jego pomyślne wdrożenie poprawia wydajność sprzętu, znacznie obniża koszty konserwacji, zmniejsza ogólne koszty operacyjne oraz tworzy bezpieczne i zdrowe miejsca pracy. Dzięki czemu uzyskuje się taki efekt?
WYDAJNOŚĆ PROCESÓW I WYMAGANIA DOTYCZĄCE NOWEGO SPRZĘTU
Tradycyjnie dopuszczono znaczne zapasy bezpieczeństwa pomiędzy elementami wyposażenia, które stanowią integralny łańcuch technologiczny, tak aby wystąpienie problemu z jednym elementem wyposażenia nie prowadziło do awarii w kolejnych ogniwach tego łańcucha. Tak więc rolą konserwacji było opłacalne zagwarantowanie dostępności kluczowych urządzeń procesowych przez określony ułamek czasu produkcji, na przykład 90% 1 .
Ze względu na przyjętą praktykę utrzymywania wysokiego poziomu zapasów bezpieczeństwa, wiele rodzajów sprzętu można rozpatrywać oddzielnie. W tym przypadku osiągnięcie 90% dostępności każdego urządzenia spowodowało, że dostępność całego procesu wyniosła również 90% (schemat 1). Niezgodności i wady, które pojawiły się w wyniku nieprawidłowego działania sprzętu, zostały wykryte podczas kontroli jakości odbioru, a przyczynę można było prześledzić i zidentyfikować w sprzęcie, w którym wystąpiła awaria.
Schemat 1. Oddzielne elementy wyposażenia uważane są za „niezależne” o wysokim poziomie zapasów bezpieczeństwa
W celu maksymalizacji wartości klienta poprzez osiągnięcie najwyższego poziomu jakości przy najniższych kosztach, przy dobrej responsywności serwisu i obsłudze klienta na najwyższym poziomie, konieczne było znaczne ograniczenie zapasów bezpieczeństwa i poprawa jakości poprzez wprowadzenie kontroli u źródła niezgodności . Umożliwiło to skrócenie czasu cyklu produkcyjnego poprzez skrócenie czasu oczekiwania i szybką identyfikację problemów pogarszających jakość lub ich całkowite uniknięcie. Wdrożenie takiego podejścia doprowadziło do tego, że problemy z poszczególnymi elementami wyposażenia zaczęły wpływać na cały proces (Schemat 2).
Schemat 2. Jednostki wyposażenia uznawane są za „zależne” ze względu na zmniejszenie zapasów bezpieczeństwa
Jeśli zatrzyma się jeden element wyposażenia, cały proces zatrzymuje się bardzo szybko. To sprawiło, że poszczególne maszyny były współzależne. W tych okolicznościach dostępność procesu jako całości uzależniona była od indywidualnych wartości dostępności poszczególnych elementów wyposażenia. W ten sposób proces obejmujący cztery elementy wyposażenia, każdy z obsługą o 90% dostępności, miał teraz ogólną dostępność nie 90%, ale 90% × 90% × 90% × 90%, czyli 66%!
Ponieważ koncentracja zapewniania jakości przesunęła się z kontroli akceptacji na kontrolę źródła i kontrolę parametrów procesu, wzrosła potrzeba jak najwcześniejszego identyfikowania problemów z wydajnością. Dużo większego znaczenia nabrały kwestie zgodności sprzętu z postawionymi wymaganiami oraz problemy niezawodności.
W zakresie, w jakim zmniejszyły się zapasy bezpieczeństwa, wzrosła presja na usługi konserwacji i naprawy sprzętu, aby usprawnić procesy konserwacji. Wydajność tych usług nie spadła, ale wzrosło zapotrzebowanie na ciągłe doskonalenie dostępności sprzętu. Wywołało to tarcia między działami produkcyjnymi i technicznymi. Producenci żądali jednakowych poziomów dostępności procesu produkcyjnego i szybkiego reagowania na prośby o konserwację urządzeń, czego nie można było zrealizować ze względu na starą strukturę organizacyjną, która nie była nastawiona na spełnianie tak rygorystycznych wymagań. Rzeczywiście, przy obniżonych stanach magazynowych dla linii czterech urządzeń, aby kontynuować powyższy przykład, aby utrzymać początkowy poziom dostępności 90%, konieczne było zwiększenie dostępności każdego urządzenia z 90 do 97,5%.
Tradycyjne podejście do utrzymania ruchu z jednej strony wymagało zachowania równowagi pomiędzy kosztami utrzymania a niezbędnym poziomem dostępności i niezawodności, z drugiej zaś koszty te często zależały od poziomu zapasów ubezpieczeniowych, które maskują bezpośrednie konsekwencje problemów ze sprzętem. W tradycyjnych firmach usługa jest postrzegana jako pozycja kosztowa, którą można łatwo zmniejszyć jako udział w całkowitych kosztach działalności, zwłaszcza w krótkim okresie. Jednocześnie kierownicy serwisu technicznego zawsze sprzeciwiali się, że w celu zwiększenia poziomu dostępności i niezawodności sprzętu konieczne jest zwiększenie budżetu na jego naprawę. Skupiając się na rozwiązaniu problemu zwiększonej dostępności, który wynikał z nowego sposobu zarządzania przedsiębiorstwem, kierownictwo szybko zorientowało się, że samo zapewnienie większej ilości zasobów usługom technicznym nie prowadzi do opłacalnego rozwiązania.
To napięcie między zmianami w kosztach utrzymania sprzętu a jego dostępnością jest podobne do starego podejścia do jakości sprzed TQM: wyższy poziom jakości wymagał więcej zasobów, a tym samym środków do kontroli jakości i naprawy. TQM ma na celu „zapobieganie problemom tam, gdzie one występują”, a nie identyfikowanie ich na końcu procesu. Dlatego zamiast zwiększania kadry nadzorców, pracownicy i operatorzy zostali przeszkoleni w zakresie jak najwcześniejszego identyfikowania i zapobiegania problemom w procesie produkcyjnym w celu minimalizacji kosztów ich korygowania. Jednocześnie utrzymano służby kontroli jakości, ale nacisk w ich działaniach położono na zmniejszenie zmienności właściwości wyrobów poprzez lepszą organizację kontroli procesów. Stosując nowe podejście do zapewniania jakości, wykazano, że uzyskanie wysokiej jakości produktów „za pierwszym razem” nie jest drogie, ale znacznie obniża ogólne koszty operacyjne firmy.
Podejście opracowane dla zapewnienia jakości - "zapobieganie problemom w miejscu pochodzenia" - zostało przeniesione na obszar utrzymania sprzętu poprzez koncepcję TPM - Total Productive Equipment Maintenance. Słowo „całkowite” odnosi się do zaangażowania wszystkich pracowników, „produktywnych” – co pozwala uzyskać większy zwrot z inwestycji oraz „usługowych” – dbałości o wyposażenie zakładu w celu osiągnięcia maksymalnej produktywności i zwrotu. System TPM opiera się na idei „zapobiegania awariom u źródła” i skupia się na identyfikacji i wyeliminowaniu przyczyn zużycia sprzętu, w przeciwieństwie do bardziej tradycyjnego podejścia, w którym sprzęt „dopuszczono” do zepsucia się przed naprawą lub stosuje strategie prewencyjne i predykcyjne w celu identyfikacji awarii i naprawy sprzętu po tym, jak zacznie się zużywać i potrzebna jest kosztowna konserwacja.
Aby lepiej odzwierciedlić trend w kierunku integracji z produkcją i nacisk na „zapobieganie awariom u źródła i ich występowaniu”, skrót TPM jest obecnie często ujawniany w inny sposób, na przykład Total Productive Manufacturing (ogólna produkcja produkcyjna), Total Productive Management (ogólna produkcja produkcyjna). zarządzania), Total Productive Mining (ogólne produkcyjne wydobycie), Total Process Management (ogólne zarządzanie procesami), a nawet Praca zespołowa między produkcją a utrzymaniem ruchu (relacja między produkcją a usługą).
Od momentu wprowadzenia w 1970 roku system TPM stale ewoluuje, pogłębia się i integruje z innymi obszarami zarządzania (ewolucja systemu do 2004 roku została opisana w).
System TPM pierwszej generacji (lata 70-te XX wieku) dotyczył wyłącznie jednostek produkcyjnych.
W drugiej generacji (lata 90. XX w.) utrzymanie urządzeń zaczęto rozpatrywać w kontekście poprawy efektywności całego procesu produkcyjnego i skoncentrowano na stworzeniu systemu produkcyjnego typu „pull”, usprawnieniu planowania, zwiększeniu poziomu wyważenia linii oraz nadawanie stabilności i stabilności procesom. Stąd czasami używana inna nazwa dla tej wersji systemu TPM to Total Process Management (ogólne zarządzanie procesami).
Australijska wersja systemu TPM trzeciej generacji została opracowana w Australasian TPM Center w oparciu o japońską wersję systemu TPM trzeciej generacji, która pojawiła się na początku XXI wieku. Cechą tej opcji, którą można nazwać „koncentracją na firmie”, jest to, że:
- zintegrowany z systemem TQM i lean manufacturing;
- skoncentrowany na zapobieganiu wszelkiego rodzaju problemom u źródła ich powstawania;
- obejmuje całą firmę.
System TPM trzeciej generacji jest obecnie w trakcie opracowywania nowej wersji – „supply chain focus”, która polega na wdrożeniu systemu TPM w przedsiębiorstwach w całym łańcuchu dostaw. W tabeli przedstawiono analizę porównawczą kluczowych kierunków rozwoju systemu TPM w tych dwóch wersjach.
Porównanie kierunków rozwoju dwóch wersji systemu TPM 3 (trzeciej generacji)
Skup się na firmie |
Skoncentruj się na łańcuchu dostaw |
8. Bezpieczeństwo i zarządzanie środowiskowe |
1. Zarządzanie bezpieczeństwem i środowiskiem |
1. Wybrane ulepszenia |
2. Indywidualne ulepszenia sprzętu i procesów |
|
3. Zarządzanie obszarem roboczym |
2. Niezależna konserwacja sprzętu przez Operatorów |
4. Niezależna konserwacja sprzętu przez operatorów |
3. Zaplanowana konserwacja |
5. Zarządzanie dla doskonałej konserwacji sprzętu |
5. Zarządzanie sprzętem na wczesnych etapach jego cyklu życia |
6. Zarządzanie nowym sprzętem, obszarami produkcyjnymi, produktami |
6. TPM w jednostkach administracyjnych i wsparcia |
7. Ulepszenia w jednostkach wsparcia |
|
8. Zarządzanie strumieniem wartości |
4. Szkolenie i edukacja |
9. Rozwój potencjału ludzkiego i doskonalenie cech przywódczych pracowników |
7. Utrzymanie jakości |
10. Zapewnienie jakości procesu |
Ważną konsekwencją tego nowego podejścia do zarządzania sprzętem, popartego wieloma historiami sukcesu z całego świata w wielu branżach, było zrozumienie przez najwyższe kierownictwo nie tylko, że system TPM jest ważny ze strategicznego punktu widzenia do stworzenia konkurencyjnego przedsiębiorstwa, ale także, że jego wdrożenie nie może ograniczać się do działu zajmującego się konserwacją i naprawą sprzętu. System TPM obejmuje całą firmę, cały łańcuch dostaw, jest nastawiony na inicjatywy usprawniające, które angażują wszystkich pracowników.
Chociaż każde przedsiębiorstwo może wdrożyć system TPM na swój własny sposób, w większości przypadków uznaje się znaczenie pomiaru i poprawy ogólnego współczynnika wydajności (CFR) urządzeń procesowych (więcej informacji na temat obliczania CFR, patrz ), który wspiera proces ciągłego doskonalenia, przy jednoczesnym obniżeniu kosztów operacyjnych i wydatków na serwis.
Kiedy wiele organizacji mierzy CEF po raz pierwszy, często okazuje się, że jest on na poziomie 40-60% w produkcji jednostkowej lub 50-75% w produkcji ciągłej, podczas gdy na świecie najlepszy wynik to zwykle 85% lub więcej w produkcji pojedyncze sztuki i 95% lub więcej w ciągłej produkcji. W rzeczywistości CEF w przykładowych przedsiębiorstwach w dużej mierze zależy od tego, jak zorganizowana jest praca przedsiębiorstwa: czy planowana konserwacja lub przezbrojenie może być przeprowadzane poza godzinami pracy, czy liczba przezbrojeń jest niezbędna do produkcji wyrobów spełniających wymagania rynku popyt jest duży itp. Dlatego też wartości docelowe CEF sformułowane dla konkretnego miejsca produkcji.
UKRYTE PRZYCZYNY AWARII
Wdrożenie systemu TPM prowadzi do znacznego obniżenia kosztów eksploatacji i utrzymania poprzez skupienie się na pierwotnych przyczynach awarii (Root Cause of Failure), poprzez wytworzenie „poczucia własności” wśród operatorów i personelu wsparcia technicznego, w celu zachęcać do działań „zapobiegających problemom w ich źródle”. Aby pomóc zrozumieć logikę myślenia w systemie TPM, musimy ustalić, co dokładnie powoduje awarie.
Wady lub niedoskonałości sprzętu są subtelne i nie zawsze oczywiste. „Przenikają” do urządzeń różnymi „kanałami”: zły projekt wstępny, zmiany w wyposażeniu ze względu na zmieniające się wymagania dotyczące wyrobów gotowych, zmiany w systemie konserwacji i napraw, zmianę środowiska produkcyjnego, w którym funkcjonuje zakład przemysłowy, niedoskonałości materiałowe , które są serwisowane oraz, co ważne, konsekwencje występujących awarii.
Tego typu defekty sprzętowe są często trudne do zidentyfikowania i naprawienia, ponieważ tradycyjnie uważa się je za normę, mimo że są główną przyczyną utraty produktywności.
Istnieje wyraźny związek między awariami a usterkami sprzętu. Jednym z celów systemu TPM jest skupienie się na usterkach sprzętu, naprawach awarii i zapobieganiu przedwczesnemu zużyciu (rysunek 3).
Schemat 3. Przyczyny przyspieszonego (sztucznego) zużycia sprzętu
W miejscu pracy rzadko szukamy pierwotnej przyczyny, ponieważ musimy reagować na objawy zaistniałych problemów. Jednak dopóki nie zidentyfikujemy pierwotnej przyczyny, problemy będą pojawiać się raz po raz. Jaka jest główna przyczyna awarii? Często przed awarią odnotowuje się niską wydajność sprzętu, dodatkowo mogą pojawić się wczesne sygnały ostrzegawcze: wibracje, hałas, przegrzanie, dym z maszyn. Może to być spowodowane naturalnym zużyciem (gdy sprzętowi wyczerpią się jego zasoby), a także przyspieszonym (sztucznym) zużyciem (patrz rysunek 3).
Co rozumiemy przez przyspieszone (sztuczne) zużycie? Jest to zużycie całej jednostki lub części wyposażenia w krótszym czasie niż oczekiwano. W ten sposób żywotność jest skrócona, ponieważ naturalne zużycie jest przyspieszone.
Jeśli weźmiemy pod uwagę części robocze sprzętu, które stanowią większość całkowitych kosztów utrzymania, to ich przyspieszone zużycie obserwuje się, gdy:
- brak smarowania;
- wybrane niewłaściwe smarowanie zespołu;
- smarowanie między powierzchniami jest przemieszczane przez przeciążenie;
- smar zużywa się;
- smar jest zanieczyszczony.
Czy widziałeś, jak operator „przedmuchuje” sprzęt sprężonym powietrzem lub spłukuje go strumieniem wody? Jak ten proces wpływa na sprzęt? Najprawdopodobniej w tym przypadku operator zwiększa zanieczyszczenie sprzętu, nawet nie zdając sobie z tego sprawy. To zanieczyszczenie jest głównym źródłem przyspieszonego zużycia.
Przeprowadzono wiele badań w celu oceny skutków przyspieszonego zużycia. Rozważ sytuację z działającymi częściami twojego sprzętu. Gdybyś miał wykreślić, powiedzmy, 30-letnią historię części maszyny, która zwykle psuje się po 12 miesiącach, czy uzyskasz prostą linię? W większości badań wynik opisuje rozkład normalny, w którym dana część pęka w większości przypadków po 12 miesiącach, ale w innych przypadkach może pęknąć prędzej czy później, w przedziale 6 miesięcy przed lub po 12 miesiącach. maksymalny. Tę okoliczność należy wziąć pod uwagę przy opracowywaniu planu konserwacji okresowej lub prewencyjnej, który stanowiłby podstawę Twojej strategii. Oczywiście, gdybyś wymienił część po 12 miesiącach, nadal miałbyś znaczną liczbę awarii. Gdyby można było wymieniać części co sześć miesięcy, znacznie zmniejszyłoby to liczbę awarii, ale jednocześnie znacznie zwiększyłoby koszty konserwacji. Więc gdzie jest rozwiązanie?
Właśnie w tym miejscu do gry wkracza system TPM. Opiera się na następujących wymaganiach:
- zrozumieć, co powoduje zmienność;
- zmniejszyć lub zminimalizować zmienność;
- wprowadzać ulepszenia.
Zgodnie z tym podejściem pierwszym zadaniem jest identyfikacja przyczyn zmienności.
Badania przeprowadzone przez Japan Institute of Plan Maintenance (JIPM) oraz DuPont i Tennessee Eastman Chemical Company wykazały, że aż 80% wszystkich zmienności jest powodowane trzema podstawowymi warunkami fizycznymi: luźnymi elementami złącznymi, zanieczyszczeniami i niewłaściwym smarowaniem.
Wyeliminowanie tych trzech czynników jest znane jako ustanawianie podstawowe warunki dla sprzętu. Gdy to zrobimy, zobaczymy, że nasz rozkład normalny straci 80% skumulowanego prawdopodobieństwa i przesunie się w prawo, odzwierciedlając w ten sposób wzrost żywotności części sprzętu.
Zrozumienie tej logiki prowadzi, jak zauważył japoński specjalista T. Suzuki, do ważnego praktycznego wniosku, że wprowadzenie systemu napraw okresowych/prewencyjnych przed ustaleniem warunków wyjściowych – tj. gdy sprzęt jest zabrudzony, brakuje śrub i nakrętek , smarownice nie działają normalnie - często prowadzi do awarii aż do następnej zaplanowanej sesji konserwacyjnej. Aby temu zapobiec, należałoby niepotrzebnie skrócić okresy międzyobsługowe, tracąc w ten sposób korzyści z programu konserwacji zapobiegawczej. Szybkie przejście na usługę predykcyjną „na warunkach” jest również ryzykowne. Wiele firm kupuje drogi sprzęt monitorujący i diagnostyczny oraz oprogramowanie, jednocześnie odmawiając wykonywania podstawowych czynności konserwacyjnych.
Niemożliwe jest jednak przewidzenie optymalnych interwałów konserwacji w środowisku produkcyjnym, w którym występuje przyspieszone zużycie i błędy.
PIELĘGNACJA SPRZĘTU W ORYGINALNYM ŹRÓDLE
Chociaż generaliści często odnoszą sukcesy w zwiększaniu elastyczności siły roboczej, dzisiejsze doświadczenie pokazuje, że dopóki pracownicy przechodzą z jednego sprzętu lub obszaru produkcji do drugiego, mają niewielką motywację do identyfikowania podstawowych problemów ze sprzętem lub wad, które, jeśli nie zostaną naprawione w odpowiednim czasie powodować awarie w przyszłości. Operatorzy często nie dbają wystarczająco o sprzęt, ponieważ wiedzą, że wkrótce zostaną przeniesieni do innego obszaru produkcji lub innego elementu wyposażenia.
Zapewnienie elastyczności zasobów pracy i jednocześnie kształtowanie „poczucia właściciela” w miejscu pracy przejawia się w tworzeniu zespołów pracowników i operatorów przypisanych do określonego obszaru produkcyjnego. Te zespoły składające się z czterech do ośmiu operatorów, w tym kierownika zespołu, tworzą środowisko, w którym sami pracownicy uświadamiają sobie korzyści płynące z najlepszych praktyk dotyczących sprzętu i utrzymania podstawowych warunków pracy.
Dzięki takiej organizacji pracy członkowie zespołu mogą skoncentrować się na różnych podstawowych umiejętnościach, aby zachować elastyczność zespołu jako całości i rozwijać swoje umiejętności, aby stać się ekspertami w zakresie optymalnego wykorzystania sprzętu i terminowego wykrywania usterek. Nasze doświadczenie pokazuje, że bez pracy małych zespołów przydzielonych do urządzeń koszty eksploatacji i konserwacji zawsze będą wygórowane.
Samoobsługa operatora to „opieka nad oryginalnym sprzętem” mająca na celu zapewnienie, że „warunki wyjściowe sprzętu” są osiągnięte i utrzymane, oraz aby umożliwić pomyślne wdrożenie konserwacji predykcyjnej zgodnie z planem. To operatorzy stają się odpowiedzialni za ogólną sprawność urządzeń w przedsiębiorstwie, opierając się na metodach zapobiegania awariom w miejscu ich powstania.
Tworzenie zespołów przydzielonych do zakładów produkcyjnych to nietrywialne zadanie, którego rozwiązanie wiąże się z rozwojem „poczucia właściciela” i elastyczności umiejętności, a także doskonaleniem kunsztu. To wymaga czasu. Należy przyjąć systematyczne podejście, poparte zdrowym rozsądkiem, aby dostosować zmiany do kultury organizacyjnej przedsiębiorstwa.
Chociaż wdrożenie Zarządzania Sprzętem Operatora powinno być specyficzne dla konkretnej sytuacji i środowiska zakładu, ostatecznym celem jest kształcenie dojrzałych operatorów, którzy są kompetentni w obsłudze sprzętu, aby rekrutować z liczby zespołów przypisanych do określonej produkcji obszary. Zespoły te będą odpowiedzialne za osiągnięcie pożądanych wartości CEF dla sprzętu i zakładu jako całości.
Nie oznacza to, że operatorzy zlecają wszystkie prace konserwacyjne sprzętu na zewnątrz, ale muszą wiedzieć, kiedy muszą samodzielnie wykonać proste procedury zapobiegania usterkom, a kiedy muszą wezwać specjalistów ds. naprawy, aby rozwiązać problemy, które do tego czasu już wyraźnie zrozumieć. zidentyfikowane.
Z powyższego wynika, że wdrożenie systemu TPM to długi proces polegający na zmianie środowiska pracy i wyposażenia w celu stworzenia czystych, komfortowych, bezpiecznych miejsc pracy poprzez kulturę produkcji „pull” w przeciwieństwie do tradycyjnego „push”. kultura. Znaczące usprawnienia powinny być widoczne w ciągu sześciu miesięcy, ale pełne wdrożenie może potrwać kilka lat. Długość tego przedziału czasowego zależy od tego, w jaki sposób firma prowadzi prace związane z zapewnieniem jakości i konserwacją sprzętu oraz od tego, w jaki sposób zasoby są wykorzystywane do realizacji nowych pomysłów na konserwację sprzętu.
Materiał został przygotowany na podstawie artykułu R. Kennedy'ego zamieszczonego w 2013 roku na stronie internetowej Centrum TPM w Australazji (http://www.ctpm.org.au)
RA Iskandaryan
Uwaga 1 do wpisu: Dostępność odnosi się do ułamka czasu, w którym sprzęt może wytworzyć dane wyjściowe.
WYKAZ UŻYWANEJ LITERATURY
1. Ratimeshin V.E., Kupriyanova T.M. Od szczupłej produkcji po szczupłe biura, logistykę, serwis! // Metody zarządzania jakością. - 2012r. - nr 11.
2. Kennedy R., Mazza L. Współdziałanie 5S i TPM w systemie TRM3 // Metody zarządzania jakością. - 2004. - nr 3.
3. Pshennikov V.V. Na początku była to... kluczowa koncepcja // Metody zarządzania jakością. - 2014r. - nr 1.
4. Pshennikov V.V. Technologia zerowej kontroli jakości // Metody zarządzania jakością. - 2014r. - nr 3.
5. Pshennikov V.V. Jakość dzięki TPM, czyli O najwyższej wydajności urządzeń przemysłowych // Metody zarządzania jakością. - 2001 r. - nr 10 (opublikowany na stronie http://www.tpm-centre.ru).
6. Ichikawa A., Takagaki I., Takebe Y. i in. TPM w prostej i przystępnej prezentacji / Per. z japońskiego JAKIŚ. Sterliażnikow; W ramach naukowych wyd. W.E. Rastimeshina, T.M. Kupriyanova. - M.: RIA "Standardy i jakość", 2008. - 128 s.
Total Productive Maintenance (TPM) to jedno z narzędzi produkcji Lean, które można wykorzystać do zmniejszenia kosztów przestojów sprzętu z powodu awarii i nadmiernej konserwacji. Główną ideą TPM jest zaangażowanie w proces konserwacji sprzętu całego personelu przedsiębiorstwa, a nie tylko odpowiednich usług. Sukces wdrożenia TPM, jak i każdego innego narzędzia lean manufacturing, związany jest z tym, na ile idee metodologii trafiają do umysłów pracowników i są przez nich pozytywnie odbierane. Aby ułatwić proces szkolenia personelu, można z niego korzystać z magazynu plików portalu. Ten artykuł zawiera bardziej szczegółowy opis materiałów prezentacyjnych, które można wykorzystać zarówno samodzielnie, jak i do prowadzenia szkoleń z wykorzystaniem prezentacji. Dla wygody pracy z prezentacją tytuły rozdziałów artykułu całkowicie pokrywają się z tytułami slajdów prezentacji.
Jak to zwykle bywa
Nieprzerwana praca sprzętu jest kluczem do stabilnego funkcjonowania produkcji, a zatem podstawą gwarantowanej realizacji zamówień i osiągnięcia planowanych wskaźników wydajności przedsiębiorstwa jako całości.
Cykl życia sprzętu składa się z sekwencyjnej przemiany dwóch faz: eksploatacji i konserwacji. Odpowiedzialność za realizację tych etapów jest zwykle przypisywana różnym usługom. W eksploatację urządzeń zaangażowany jest personel technologiczny, a służby konserwacyjne (mechanicy, elektrycy, programiści itp.) zajmują się konserwacją prewencyjną i naprawą. Ten podział obowiązków jest całkiem naturalny, ponieważ obsługa i konserwacja wymagają określonych umiejętności. Personel operacyjny kontroluje technologię produkcji, monitoruje jakość oraz zapewnia realizację zaplanowanych wskaźników. Personel zajmujący się konserwacją przeprowadza czynności w celu monitorowania stanu sprzętu, konserwacji zapobiegawczej i rozwiązywania problemów. Niestety takie rozdzielenie funkcji powoduje często wzajemne nieporozumienia pomiędzy służbami eksploatacyjnymi i konserwacyjnymi, a w efekcie prowadzi do nieefektywnego utrzymania urządzeń jako całości.
Dlaczego to się dzieje?
Dla wielu przedsiębiorstw dość powszechne jest, że usługi naprawcze i konserwacyjne mają różne, niezwiązane ze sobą cele, a co za tym idzie różne wskaźniki charakteryzujące efektywność ich działań. Dla operatorów najważniejsze jest spełnienie zaplanowanych wskaźników. Często jest to rozumiane jako realizacja planu za wszelką cenę i prowadzi do bezlitosnej eksploatacji sprzętu wymagającego konserwacji profilaktycznej lub, co gorsza, wymagającego natychmiastowej naprawy. W przypadku usług naprawczych najważniejsze jest wykonywanie zadań mających na celu doprowadzenie wadliwego sprzętu do stanu roboczego. Jednak, gdy sprzęt raz po raz ulega awarii z powodu niewłaściwego użytkowania, w środowisku service desk pojawia się naturalne poczucie, że praca mechanika nie jest doceniana, a osiągnięcie zaplanowanych wskaźników wydajności nie zależy od włożonych wysiłków.
Co się dzieje?
Konflikt interesów personelu technologicznego i konserwacyjnego nie może nie wpływać na ogólną wydajność produkcji. „Przeciąganie liny” wymaga dużego wysiłku i w żaden sposób nie przyczynia się do czystej, nieprzerwanej pracy sprzętu. Z kolei niestabilność funkcjonowania produkcji prowadzi do trudności w planowaniu, przesuwania terminów realizacji zamówień i wzrostu kosztów. Atmosfera moralna i psychologiczna w zespole, który okazuje się być podzielony na wojujące plemiona, w żaden sposób nie ulega poprawie.
Co byś chciał?
Idealnym przypadkiem jest sytuacja, w której stan sprzętu (eksploatacja-konserwacja) można przewidzieć w dowolnym przewidywalnym momencie. Taką przewidywalność można osiągnąć tylko wtedy, gdy możliwe jest całkowite pozbycie się przestojów sprzętu spowodowanych siłą wyższą z powodu jego awarii. To całkiem naturalne, że każdy sprzęt ulega zużyciu i prędzej czy później nadchodzi moment, w którym zużyte części ulegają zniszczeniu, co prowadzi do awarii całego sprzętu. Ważne jest, aby zapobiegać takiemu rozwojowi wydarzeń, przewidywać na czas początek sytuacji krytycznej i podejmować działania, aby temu zapobiec. Tym samym czas potrzebny na naprawy nadzwyczajne powinien być całkowicie wyeliminowany z fazy konserwacji. W takim przypadku sprzęt może być w fazie eksploatacji lub w fazie planowej konserwacji.
Jak to zrobić?
Aby uzyskać pełną kontrolę nad wydajnością urządzeń produkcyjnych, konieczne jest radykalne przemyślenie stosunku do niej. Przede wszystkim dbałość o sprzęt powinna dotyczyć nie tylko serwisu naprawczego, ale także personelu produkcyjnego. Oznacza to, że wskaźnik efektywności wykorzystania sprzętu powinien stać się decydujący dla obu jednostek strukturalnych. Prostą konserwację prewencyjną, monitorowanie stanu, rejestrację problemów ze sprzętem można przypisać pracownikom operacyjnym. W końcu, kimkolwiek są, przez większość czasu używają sprzętu zgodnie z jego przeznaczeniem. To oni mają możliwość ciągłego monitorowania jego stanu i podejmowania na czas działań zapobiegających krytycznym sytuacjom. Jednocześnie zadaniem służb remontowych jest prowadzenie konserwacji w taki sposób, aby do nieskończenie małej wartości zredukować prawdopodobieństwo jej awarii podczas eksploatacji. W tym celu należy na bieżąco analizować pojawiające się problemy techniczne i wykorzystywać wyniki analizy do planowania konserwacji zapobiegawczej zgodnie z potrzebami konserwacji, a także tworzenia instrukcji utrzymania sprzętu w eksploatacji.
Baza metodologiczna
Total Productive Maintenance (TPM) pozwala znacznie zwiększyć efektywność użytkowania sprzętu. Tutaj i poniżej zrozumiemy efektywność użytkowania sprzętu jako kombinację dwóch wskaźników, które charakteryzują względny czas pracy sprzętu i względny czas nieplanowanych przestojów spowodowanych awariami sprzętu (oba wskaźniki odnoszą się do całkowitego czasu pracy produkcyjnej). Zadaniem TPM jest maksymalizacja pierwszego wskaźnika i zmniejszenie (najlepiej do zera) drugiego.
Aby rozwiązać ten problem, TPM opiera się na kilku fundamentalnych zasadach.
1. Stan sprzętu jest nierozerwalnie związany z ogólną kulturą pracowników (zarówno operatorów, jak i warsztatów). Ważne jest, aby personel znał swój sprzęt, potrafił identyfikować usterki, a co najważniejsze, nie był obojętny na problemy części technicznej.
2. Ponieważ eksploatacja sprzętu zajmuje najwięcej czasu, nadzór, rejestrację faktów odchyleń i podstawową konserwację należy powierzyć personelowi obsługującemu. Rzeczywiście, kto, jeśli nie osoba, która stale pracuje ze sprzętem, może określić podstawowe oznaki problemu? Kto inny oprócz niego jest w stanie dokręcić śrubę na czas lub nasmarować, nie tracąc czasu na czekanie na wiecznie zajętych mechaników.
3. Jak każda metodologia, TPM wymaga ścisłej konsekwencji w jej implementacji. Czynności konserwacyjne należy dokumentować w języku zrozumiałym dla wszystkich pracowników. Czynności konserwacyjne muszą być stale monitorowane. Nieefektywne działania powinny zostać poddane przeglądowi. Problemy powinny być rejestrowane i systematycznie analizowane. Wyniki analizy powinny służyć jako punkt wyjścia do rewizji metodologii.
4. Pełne zaangażowanie personelu firmy, od pracowników po najwyższe kierownictwo. Generalnie, jeśli chodzi o zaangażowanie personelu w konkretny proces, nie można oddzielić zaangażowania pracowników od zaangażowania menedżerów. Dopiero w przypadku, gdy idee TPM są wspierane na dowolnym poziomie hierarchii zarządzania, dopiero wtedy możemy mówić o skutecznym zastosowaniu metodologii. Oczywiście formy zaangażowania są znacząco różne dla kierowników i podwładnych. Dla jednych jest to obserwacja, rejestracja i bezpośrednie utrzymanie, dla innych analiza przestojów, opracowanie dokumentacji, kontrola, a dla innych podejmowanie decyzji organizacyjnych i zarządczych, analiza skuteczności metodyki itp. Pojawienie się „słabego ogniwa” w dowolnym miejscu może prowadzić do spadku skuteczności techniki i jej dalszego całkowitego upadku.
Utrata działania sprzętu
Metodologia TPM ma na celu eliminację systemowych strat pracy urządzeń. Co to znaczy? Oznacza to, że ewentualne straty, które są związane z istniejącym systemem eksploatacji i konserwacji urządzeń, mogą zostać potencjalnie wyeliminowane. Przede wszystkim dotyczy to strat związanych z awariami sprzętu i związanym z tym spadkiem wydajności oraz zwiększonymi kosztami napraw. TPM pozwala wyeliminować straty związane z nadmiernym czasem i zasobami materiałowymi podczas ustawiania i rekonfiguracji sprzętu. Praca na biegu jałowym, zwalnianie i zatrzymywanie sprzętu prowadzą do zwiększonego zużycia, a zatem również podlegają metodologii TPM. Wadliwy sprzęt prowadzi do wzrostu wydajności wadliwych produktów, więc zastosowanie TPM pozwala obniżyć koszty odrzutów. Obejmuje to również straty podczas rozruchu sprzętu.
Właściwe wykorzystanie TPM może znacznie zmniejszyć, a nawet całkowicie wyeliminować wszystkie te straty.
Oczekiwany efekt
Niezbędnym warunkiem skutecznego wdrożenia TPM jest wymóg doskonalenia ogólnej kultury obsługi sprzętu przez personel. Utrwalenie podstaw takiej kultury w zespole roboczym prowadzi do tego, że sprzęt zaczyna być traktowany nie jako środek produkcji, ale jako podstawa prosperity przedsiębiorstwa i gwarancja dobrobytu finansowego swoich pracowników. Naturalnie eliminacja strat związanych z utrzymaniem sprzętu powoduje reakcję łańcuchową zwiększania wydajności produkcji jako całości. W skrócie efekt wdrożenia TPM można opisać jako: zwiększyć produktywność i jakość przy jednoczesnym zmniejszeniu kosztów konserwacji i złomu.
Etapy TPM
Specyfiką metodyki TPM jest to, że na jej podstawie możliwa jest płynna i planowa transformacja istniejącego systemu obsługi na doskonalszy. W tym celu wygodnie jest przedstawić ścieżkę wdrożenia TPM jako sekwencję etapów, z których każdy realizuje dość konkretne cele i co najważniejsze daje bardzo namacalny efekt.
1. Naprawa usterek operacyjnych – próba usprawnienia istniejącego systemu obsługi i odnalezienia jego słabości.
2. Utrzymanie w oparciu o prognozy – organizowanie zbierania informacji o problemach sprzętowych i ich późniejszej analizy. Planowanie konserwacji zapobiegawczej sprzętu.
3. Konserwacja naprawcza - doskonalenie sprzętu podczas konserwacji w celu wyeliminowania przyczyn systematycznych awarii.
4. Usługa autonomiczna – podział funkcji związanych z utrzymaniem sprzętu pomiędzy personelem obsługującym i konserwującym.
5. Ciągłe doskonalenie jest koniecznością każdego narzędzia lean. W rzeczywistości oznacza to zaangażowanie personelu w ciągłe poszukiwanie źródeł strat eksploatacyjnych i konserwacyjnych, a także propozycję sposobów ich eliminacji.
Etap 1: Naprawa operacyjna
Pierwszym krokiem we wdrażaniu TPM jest wyciśnięcie wszystkiego, co możliwe z istniejącego systemu usług. Prowadzi to do tego, że ujawniają się jego wady i potrzeba zmiany staje się oczywista.
Oczywiście należy zacząć od całkowitej rewizji dokumentów regulujących czynności eksploatacyjne i naprawcze. Po drodze należy zwrócić uwagę na to, jakie rodzaje pracy wykonuje się spontanicznie lub nierozsądnie, a które powstały pod wpływem obiektywnej konieczności. Wszystkie rodzaje prac powinny być uregulowane, wskazując osoby odpowiedzialne, ramy czasowe i podstawy realizacji odpowiednich działań.
Ponadto konieczne jest przeanalizowanie schematu ruchu przepływów materiałowych części zamiennych i materiałów eksploatacyjnych. Na tym etapie należy zwrócić uwagę na wygodę i szybkość pozyskiwania niezbędnych materiałów z magazynu, a także mechanizm ich dostarczania do serwisu.
Należy zwrócić szczególną uwagę na wynik prac naprawczych i konserwacyjnych. Czy świadczona usługa jest wystarczająca? Czy jego funkcjonalność została w pełni przywrócona? Jak często używane są tymczasowe środki odzyskiwania węzłów? Co jest potrzebne do poprawy jakości prac naprawczych?
Głównym celem tego etapu jest usystematyzowanie istniejącej procedury konserwacji i naprawy sprzętu, a także całkowite przywrócenie jego funkcjonalności.
Etap 2: Konserwacja oparta na prognozach
Większość firm stosuje jakąś formę konserwacji zapobiegawczej swojego sprzętu. Zasadniczo w formie planowych napraw prewencyjnych (PPR). Główną ideą PPR jest dokonywanie niezbędnych napraw lub wymiany części zanim awaria sprzętu doprowadzi do zatrzymania produkcji. W zdecydowanej większości przypadków zakres prac wykonywanych w PPR jest determinowany charakterystyką paszportową sprzętu (na podstawie danych producenta) oraz listą wad, którą tworzą serwisanci, kierując się obecną sytuacją. Aby jednak odpowiednio przewidzieć zapotrzebowanie na konkretny rodzaj usługi, nie wystarczy tylko znać obecną sytuację, trzeba też znać historię konserwacji i eksploatacji każdego elementu wyposażenia. Dopiero z analizy historii można poznać schematy występowania pewnych usterek. A do tego zalecenia producenta bynajmniej nie wystarczą - wymieniać to łożysko co sześć miesięcy. W końcu sprzęt nie działa w warunkach laboratoryjnych. Jest prawdopodobne, że producent nie mógł wziąć pod uwagę warunków Twojego przedsiębiorstwa. Dlatego ważne jest nie tylko uwzględnienie danych producenta, ale także samodzielne zbieranie informacji statystycznych o problemach, ich analiza i wykorzystanie do planowania prac konserwacyjnych sprzętu.
Etap 3: Konserwacja naprawcza
Dostawca jakiegokolwiek sprzętu oczekuje, że będzie on działał w bardzo specyficznych warunkach iw bardzo określonym celu. W prawdziwym przedsiębiorstwie nie zawsze jest możliwe dokładne przestrzeganie zaleceń producenta. Powodów tego jest wiele: od warunków klimatycznych po warunki rynkowe, które powodują konieczność modernizacji sprzętu w celu poszerzenia asortymentu. Tak czy inaczej, sprzęt może nie zawsze spełniać wymagania określonych warunków, co oczywiście powinno prowadzić do odpowiedniej zmiany w konserwacji sprzętu. W takim przypadku konserwacja powinna obejmować zestaw środków, które pozwolą, aby sprzęt jak najlepiej spełniał warunki jego eksploatacji. Tak naprawdę mówimy o ulepszaniu sprzętu, zwiększaniu jego niezawodności, łatwości obsługi i konserwacji. Na tym etapie, oprócz osób zajmujących się naprawami, personel operacyjny powinien być bezpośrednio zaangażowany w działania mające na celu zidentyfikowanie sposobów ulepszenia sprzętu.
Etap 4: Usługa offline
Ten etap jest najtrudniejszy w procesie wdrażania TPM, ponieważ wiąże się z bezpośrednim zaangażowaniem personelu operacyjnego w czynności związane z utrzymaniem urządzeń. Do tego kroku należy podejść bardzo ostrożnie, aby dodatkowe cechy były postrzegane, jeśli nie z entuzjazmem, to przynajmniej ze świadomością ich przydatności. Zaangażowanie personelu w samodzielną konserwację sprzętu musi być poprzedzone badaniem zasad działania sprzętu, jego głównych cech, możliwych usterek i metod ich diagnozowania. W związku z tym należy zrewidować instrukcje dotyczące pracy i pracy dla personelu. Aby ułatwić konserwację w trybie offline, musisz korzystać z narzędzi wizualizacyjnych, które przypominają o zwracaniu uwagi na krytyczne obszary i pamiętaniu o ich konserwacji. Pod koniec czwartego etapu pracownicy muszą jasno zrozumieć, jaką pracę muszą wykonać, a która wymaga obecności wykwalifikowanych specjalistów serwisowych. Równie ważny jest udział personelu w zbieraniu informacji o stanie sprzętu. Jednocześnie nie powinno być drobiazgów, z których można zrezygnować. Każdą zmianę parametrów sprzętu, pojawienie się zabrudzeń, smug, zapachów należy odnotować, a na informację zwrócić uwagę osobom odpowiedzialnym za analizę stanu sprzętu.
Etap 5: Ciągłe doskonalenie
Działania w zakresie ciągłego doskonalenia nie wymagają specjalnego komentarza. To jedna z podstawowych zasad lean manufacturing. W odniesieniu do TPM oznacza to motywowanie pracowników do ciągłego podnoszenia swoich umiejętności, poszukiwanie możliwości unowocześniania sprzętu oraz zwiększania jego łatwości konserwacji i niezawodności. Ponadto należy systematycznie poddawać przeglądowi istniejący system TPM. W takim przypadku należy zwrócić szczególną uwagę na metody interakcji między usługami, skuteczność zbierania informacji o awariach oraz aktualność dokumentacji regulacyjnej. System TPM nie może być sprzeczny z przepisami BHP i ochrony środowiska. W oparciu o te rozważania należy nakreślić ogólne kierunki doskonalenia systemu TPM i postępować zgodnie z nimi przy definiowaniu zadań dla poszczególnych sekcji i działów.
Grupy robocze
Skuteczne wprowadzenie metodyki ogólnego utrzymania produkcyjnego urządzeń jest możliwe tylko w przypadku systematycznie skoordynowanych działań wszystkich działów produkcyjnych i remontowych. Aby połączyć wysiłki i skoordynować ich stosowanie, należy zorganizować grupę roboczą, która będzie odpowiedzialna za planowanie działań i monitorowanie rezultatów realizacji zaplanowanych działań. Podstawowe zasady tworzenia grup roboczych zostały omówione w artykule „Organizacja działań grup roboczych”. Proponowane tam podejścia mają pełne zastosowanie w przypadku wprowadzenia TPM.
Gdzie zacząć?
Wdrażanie TPM możesz rozpocząć już teraz, nie czekając na pierwsze efekty działań grupy roboczej. Jedną z podstawowych zasad TPM jest to, że brudny sprzęt nie może być serwisowany! Brud przyczynia się do zwiększonego zużycia i pogorszenia warunków pracy. Ponadto brud ukrywa wady, które można natychmiast wykryć na czystym sprzęcie. Zacznij od małych rzeczy - uporządkuj w miejscu pracy i cały czas je utrzymuj! To mały, ale bardzo ważny krok na drodze do sprawnego sprzętu.
Cóż, wyznaczmy sobie cel, dobrze? (zamiast konkluzji)
Skuteczność metodologii TPM została udowodniona na przestrzeni czasu i przez dużą liczbę firm, które wybrały tę ścieżkę. W dziedzinie TPM przyznawana jest nawet nagroda dla przedsiębiorstw odnoszących największe sukcesy, które wdrożyły tę metodologię. Trzeba przyznać, że nie jest to łatwe. Główną trudnością jest skoordynowane ujednolicenie wysiłków wszystko pracownicy przedsiębiorstwa (o czym już wspomniano powyżej). Nie należy jednak zapominać, że efektywność całego przedsiębiorstwa zależy od skoordynowanego działania działów. A im trudniejsze warunki zaoferuje gospodarka rynkowa, tym pilniejsze stanie się zadanie budowania zespołu. Zacznij już teraz, zwłaszcza że nić przewodnia jest już w Twoich rękach.
Literatura
1. A. Ichikawa, I. Takagi, Y. Takebe, K. Yamasaki, T. Izumi, S. Shinotsuka TPM w prostej i przystępnej prezentacji / Per. z japońskiego A.N. Sterlyazhnikova; W ramach naukowych Wyd. V.E. Rastimeshina, T.M. Kupriyanova. - M .: RIA "Standardy i jakość", 2008. - 128 s., chory - (seria "Business Excellence").