Aditivne tehnologije: SLS - Selektivno lasersko sinterovanje
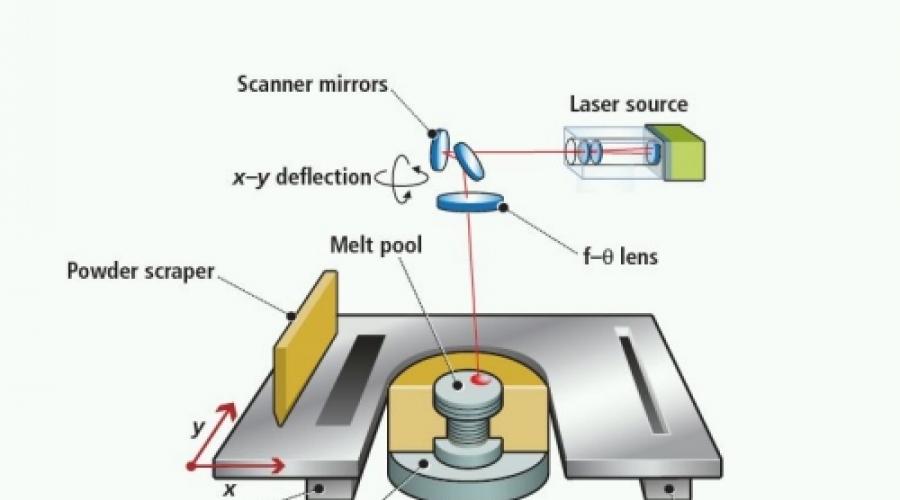
Pročitajte također
Krivilev M.D., Kharanzhevsky E.V., Ankudinov V.E., Gordeev G.A. // Upravljanje dnevnikom veliki sistemi: zbornik radova, broj 31 / 2010, UDK 62.1 + 53.043, LBC 34.5
Sažetak—Razmatran je problem optimizacije načina laserskog sinterovanja ultrafinih metalnih prahova, koji karakteriše nestacionarni prenos toplote u poroznom mediju uz istovremenu pojavu faznih transformacija. Na osnovu analize mehanizama prenosa i geometrijske karakteristike poroznog medija, izračunate su brzine zagrijavanja/hlađenja i dubina sinteriranja praha na različiti načini rada obrada. Numeričkom simulacijom utvrđeno je da su glavni kontrolni parametri sistema brzina skeniranja zraka i koeficijent penetracije laserskog zračenja, koji zavisi od poroznosti i strukture sloja praha. Mehanizam prijenosa topline pri vrijednostima poroznosti iznad 70
OPIS NA ENGLESKOM:
Kontrola laserskog sinterovanja u metalnim prahovima
Krivilev M.D., Haranzhevskiy Evgeniy, Gordeev Georgiy, Ankudinov Vladimir, Udmurtski državni univerzitet
Optimizacija laserskog sinterovanja submikronskih metalnih prahova proučavana je u vezi sa nestalnim prenosom toplote u poroznom sloju pri istovremenim faznim transformacijama. Brzine raspadanja/hlađenja i dubina sinterovanog sloja se procjenjuju nakon analize geometrijskih karakteristika metalnog praha. Računarsko modeliranje je pokazalo da su kontrolni parametri procesa brzina skeniranja i koeficijent propusnosti koji ovisi o poroznosti i strukturi sloja praha. Kod visoke poroznosti >70
Uvod
Lasersko sinterovanje praškastih materijala bazira se na aktivno razvijenoj metodi selektivnog laserskog sinterovanja.
(selektivno lasersko sinterovanje - SLS) kada se mešavina materijala sa različite temperature topljenje se podvrgava termičkoj obradi. Kao rezultat, sintetizira se materijal složene strukture, gdje se keramičke i metalne čestice povezuju kroz matricu na bazi organske tvari, što postaje moguće brzo kreiranje prototipovi dijelova od gotovo bilo kojeg materijala. Fleksibilnost tehnologije postiže se direktnom kompjuterskom kontrolom procesa, a za razliku od tradicionalnih metoda izrade dijelova, koji zahtijevaju mehaničku obradu, trodimenzionalni dijelovi se izrađuju direktno sloj-po-slojnim pečenjem u prahu. Metalni proizvodi izrađeni metodom SLS koriste se u maloj proizvodnji, na primjer, za proizvodnju kalupa za ljevanje, uključujući brizganje. Unatoč činjenici da SLS tehnologija osigurava dobru dimenzionalnu točnost dijelova i ponovljivost proizvodnje, njena upotreba je ograničena naglim smanjenjem mehaničkih i tribotehničkih svojstava dijelova. Štaviše, kao rezultat topljenja čestica praha (obično se koriste praškovi prosječne veličine čestica od 5 µm) i djelovanja termokapilarnih sila, u materijalu nastaju pore i šupljine veličine do 100 µm, što je kvar koji ograničava upotrebu dijelova.
zajednička karakteristika SLS tehnologija je mala brzina uvođenje toplotne energije. Najčešće se u ovim procesima koristi kontinuirani način generiranja laserskog zračenja.
Razumijevanje mehanizama koji upravljaju procesima formiranja strukture tokom laserske obrade prirodno dovodi do ideje o nadogradnji porodice SLS tehnologija promjenom energetskih režima laserske obrade materijala u pravcu značajnog povećanja stope kristalizacije. Visoka lokacija brze laserske obrade ultrafinih materijala omogućava da se izbjegnu nedostaci koji su svojstveni tradicionalnim SLS tehnologijama (toplinska naprezanja, velike pore, hrapavost površine i veliki dopušteni obrada), da se formira i popravi metastabilno strukturno stanje s jedinstvenim mehanička svojstva.
Lasersko sinterovanje prahova je proces koji se ponavlja i uključuje nekoliko faza: (a)
nanošenje sloja praha i izravnavanje valjkom; (b) laserska obrada (skeniranje) sloja praha uz potpunu penetraciju topljive komponente praha; (c) čišćenje rezultirajućeg sloja; (d) pomeranje stola sa uzorkom prema dole za debljinu jednog sloja; (e) ponavljanje cijelog procesa, odnosno nanošenje sljedećeg sloja praha, lasersko skeniranje itd. Obrada se vrši u komori za pročišćavanje inertni gas i kontrolisano od strane kompjutera za dobijanje zadate 3D geometrije dela.
Površina nastalih premaza je složeno nanostrukturno stanje koje karakteriše prisustvo metastabilnih faza. Karakteristika strukture je sistem povezanih pora različitih razmjera: od pora nano veličine do pora veličine nekoliko mikrometara. Ovi zaključci se donose na osnovu rezultata poređenja nekoliko istraživačkih metoda: Auger spektroskopija, difrakcija rendgenskih zraka, skeniranje elektronska mikroskopija. U radu su prikazani rezultati strukturnih studija i pokazuju složenu zavisnost strukturnih parametara sinterovanih slojeva od režima laserskog zračenja.
U ovoj recenziji pokušao sam u popularnoj formi predstaviti osnovne podatke o proizvodnji metalnih proizvoda laserskom aditivnom proizvodnjom, relativno novoj i zanimljivoj tehnološkoj metodi koja se pojavila kasnih 80-ih godina, a danas je postala obećavajuća tehnologija za male ili proizvodnja u jednom komadu u oblasti medicine, aviona i raketne nauke.
Ukratko opisati princip rada instalacije za aditivnu proizvodnju pomoću laserskog zračenja može biti kako slijedi. Uređaj za nanošenje i izravnavanje sloja praha uklanja sloj praha sa hranilice i ravnomjerno ga raspoređuje po površini podloge. Nakon toga, laserska zraka skenira površinu ovog sloja praha i formira proizvod topljenjem ili sinteriranjem. Na kraju skeniranja sloja praha, platforma sa proizvedenim proizvodom se spušta za debljinu nanesenog sloja, a platforma sa prahom se podiže, a proces nanošenja sloja praha i skeniranja se ponavlja. Nakon što je proces završen, platforma sa proizvodom se podiže i čisti od neiskorištenog praha.
Jedan od glavnih dijelova u instalacijama za aditivnu proizvodnju je laserski sistem koji koristi CO 2 , Nd:YAG, iterbijumska vlakna ili disk lasere. Utvrđeno je da je za zagrevanje metala i karbida poželjna upotreba lasera talasne dužine od 1-1,1 μm, jer apsorbuju zračenje koje generiše laser za 25-65%. Istovremeno, upotreba CO 2 lasera s talasnom dužinom od 10,64 µm je najprikladnija za materijale kao što su polimeri i oksidna keramika. Veći kapacitet apsorpcije omogućava povećanje dubine prodiranja i variranje parametara procesa u širem rasponu. Obično laseri koji se koriste u aditivnoj proizvodnji rade kontinuirano. U poređenju s njima, upotreba lasera koji rade u pulsnom i Q-switched modu zbog velike energije impulsa i kratkog trajanja impulsa (nanosekunde) omogućava poboljšanje čvrstoće veze između slojeva i smanjenje zona zahvaćena toplotom. U zaključku, može se primijetiti da karakteristike laserski sistemi leže u sledećim granicama: snaga lasera - 50-500 W, brzina skeniranja do 2 m/s, brzina pozicioniranja do 7 m/s, prečnik fokusirane tačke - 35-400 mikrona.
Pored lasera, kao izvor zagrevanja praha može se koristiti i grejanje elektronskim snopom. Ovu opciju je predložio Arcam i implementirao u svoje instalacije 1997. Instalaciju sa elektronskim snopom topom karakteriše odsustvo pokretnih delova, budući da se elektronski snop fokusira i usmerava pomoću magnetnog polja i deflektora, te stvaranje vakuum u komori pozitivno utiče na kvalitet proizvoda.
Jedan od važnih uslova u proizvodnji aditiva je stvaranje zaštitnog okruženja koje sprečava oksidaciju praha. Za ispunjavanje ovog uslova koristi se argon ili dušik. Međutim, upotreba dušika kao zaštitnog plina je ograničena, zbog mogućnosti stvaranja nitrida (na primjer, AlN, TiN u proizvodnji proizvoda od aluminijskih i titanovih legura), koji dovode do smanjenja plastičnosti materijal.
Metode proizvodnje laserskih aditiva prema karakteristikama procesa zbijanja materijala mogu se podijeliti na selektivno lasersko sinteriranje (Selective Laser Sintering (SLS)), indirektno lasersko sinteriranje metala (Indirect Laser Metal Sintering (ILMS)), direktno lasersko sinteriranje metala (Direct Laser Metal Sintering (DLMS)) i selektivno lasersko topljenje (Selective Laser Melting (SLM)). U prvoj varijanti dolazi do zbijanja sloja praha zbog sinterovanja u čvrstoj fazi. U drugom slučaju, zbog impregnacije prethodno formiranog poroznog okvira vezivom lasersko zračenje. Direktno lasersko sinterovanje metala zasniva se na zbijanju mehanizmom tečnofaznog sinterovanja usled topljenja topljive komponente u praškastoj mešavini. U potonjoj verziji, do zbijanja dolazi zbog potpunog topljenja i širenja taline. Vrijedi napomenuti da ova klasifikacija nije univerzalna, budući da jedna vrsta procesa aditivne proizvodnje može pokazati mehanizme zbijanja koji su karakteristični za druge procese. Na primjer, DLMS i SLM mogu doživjeti sinterovanje u čvrstom stanju, što se dešava sa SLS, dok SLM može doživjeti sinterovanje u tečnoj fazi, što je više karakteristično za DLMS.
Selektivno lasersko sinterovanje (SLS)
Čvrstofazno selektivno lasersko sinterovanje nije postalo široko rasprostranjeno, jer je za potpuniji tok volumetrijske i površinske difuzije, viskoznog toka i drugih procesa koji se javljaju tokom sinterovanja praha potrebno relativno dugo izlaganje laserskom zračenju. To dovodi do dugotrajnog rada lasera i niske produktivnosti procesa, što ovaj proces čini ekonomski neizvodljivim. Osim toga, postoje poteškoće u održavanju temperature procesa u rasponu između tačke topljenja i temperature sinterovanja čvrstog stanja. Prednost selektivnog laserskog sinterovanja u čvrstoj fazi je mogućnost upotrebe šireg spektra materijala za izradu proizvoda.
Indirektno lasersko sinterovanje metala (ILMS)
Proces nazvan "indirektno lasersko sinterovanje metala" razvio je DTMcorp iz Austina 1995. godine, koji je u vlasništvu 3D Systems-a od 2001. godine. ILMS proces koristi mješavinu praha i polimera ili prah obložen polimerom, gdje polimer djeluje kao vezivo i daje potrebnu čvrstoću za dalju obradu. termičku obradu. U fazi termičke obrade polimer se destilira, okvir se sinterira, a porozni okvir impregnira vezivnim metalom, čime se dobiva gotov proizvod.
Za ILMS se mogu koristiti prahovi metala i keramike ili njihove mješavine. Priprema mješavine praha sa polimerom vrši se mehaničkim miješanjem, pri čemu je sadržaj polimera oko 2-3% (težinski), a u slučaju korištenja praha obloženog polimerom debljina sloja na površini čestice je oko 5 μm. Koristi se kao veza epoksidne smole, tečno staklo, poliamidi i drugi polimeri. Temperatura destilacije polimera određena je temperaturom njegovog topljenja i raspadanja i iznosi u prosjeku 400-650 o C. Nakon destilacije polimera, poroznost proizvoda prije impregnacije je oko 40%. Tokom impregnacije, peć se zagrijava za 100-200 0 C iznad tačke topljenja materijala za impregnaciju, jer se s povećanjem temperature smanjuje ugao vlaženja i smanjuje viskozitet taline, što povoljno utiče na proces impregnacije. Obično se impregnacija budućih proizvoda vrši u zatrpavanju od aluminijevog oksida, koji igra ulogu nosećeg okvira, jer u periodu od destilacije polimera do stvaranja jakih međučestičnih kontakata postoji opasnost od uništenja. ili deformacije proizvoda. Zaštita od oksidacije organizirana je stvaranjem inertne ili redukcijske sredine u peći. Za impregnaciju možete koristiti dosta različitih metala i legura koje zadovoljavaju sljedeće uvjete. Materijal za impregnaciju treba da se odlikuje potpunim odsustvom ili beznačajnom međufaznom interakcijom, malim uglom vlaženja i tačkom taljenja nižom od baze. Na primjer, ako komponente međusobno djeluju jedna na drugu, tada se tijekom procesa impregnacije mogu javiti neželjeni procesi, kao što je stvaranje više vatrostalnih spojeva ili čvrstih otopina, što može dovesti do zaustavljanja procesa impregnacije ili negativno utjecati na svojstva i dimenzije. proizvoda. Obično za impregnaciju metalni okvir koristi se bronza, dok je skupljanje proizvoda 2-5%.
Jedan od nedostataka ILMS-a je nemogućnost kontrole sadržaja vatrostalne faze (baznog materijala) u širokom rasponu. Jer ona postotak u gotovom proizvodu određuje se nasipna gustina praha, koja u zavisnosti od karakteristika praha može biti tri ili više puta manja od teorijske gustine praškastog materijala.
Materijali i njihova svojstva korišteni za ILMS
Direktno lasersko sinteriranje metala (DLMS)
Proces direktnog laserskog sinterovanja metala sličan je ILMS-u, ali se razlikuje po tome što se umjesto polimera koriste legure ili spojevi s niskom tačkom taljenja, a također ne postoji takva tehnološka operacija kao što je impregnacija. U središtu stvaranja DMLS koncepta je bio Njemačka kompanija EOS GmbH, koji je 1995. godine izgradio komercijalnu mašinu za direktno lasersko sinterovanje sistema praha čelik-nikl bronza. Proizvodnja različitih proizvoda DLMS metodom zasniva se na strujanju formirane taline veziva u šupljine između čestica pod dejstvom kapilarnih sila. Istovremeno, za uspješan završetak procesa, mješavini praha se dodaju spojevi sa fosforom koji smanjuju površinski napon, viskozitet i stepen oksidacije taline, čime se poboljšava kvašenje. Prašak koji se koristi kao vezivo obično je manji od osnovnog praha, jer to povećava gustinu praškaste mješavine i ubrzava proces formiranja taline.
Materijali i njihova svojstva koje EOS GmbH koristi za DLMS
Selektivno lasersko topljenje (SLM)
Dalje unapređenje pogona aditivne proizvodnje povezano je s pojavom mogućnosti upotrebe snažnijeg lasera, manjeg prečnika fokusne tačke i nanošenja tanjeg sloja praha, što je omogućilo upotrebu SLM-a za izradu proizvoda od razni metali i legure. Tipično, proizvodi dobijeni ovom metodom imaju poroznost od 0-3%.
Kao iu gore navedenim metodama (ILMS, DMLS), kvašenje, površinski napon i viskozitet taline igraju važnu ulogu u procesu proizvodnje proizvoda. Jedan od faktora koji ograničavaju upotrebu različitih metala i legura za SLM je efekat "formiranja kugle" ili sferoidizacije, koji se manifestuje u obliku formiranja kapljica koje leže odvojeno jedna od druge, a ne kontinuiranog puta taljenja. Razlog tome je površinska napetost pod čijim uticajem talina teži da smanji slobodnu površinsku energiju formirajući oblik sa minimalna površina površine, tj. lopta. U ovom slučaju se u traci taline uočava Marangonijev efekat, koji se manifestuje u obliku konvektivnih strujanja zbog gradijenta površinski napon u funkciji temperature, i ako su konvekcijske struje dovoljno jake, tada se traka taline dijeli na zasebne kapi. Takođe, kap taline, pod dejstvom površinskog napona, uvlači u sebe obližnje čestice praha, što dovodi do formiranja rupice oko kapi i, na kraju, do povećanja poroznosti.
Sferoidizacija čelika M3/2 pod suboptimalnim SLM uslovima
Efekat sferoidizacije je takođe olakšan prisustvom kiseonika, koji, otapanjem u metalu, povećava viskoznost taline, što dovodi do pogoršanja rasprostiranja i vlaženja taline ispod sloja ispod. Iz gore navedenih razloga nije moguće dobiti proizvode od metala kao što su kalaj, bakar, cink i olovo.
Treba napomenuti da je formiranje visokokvalitetne trake taline povezano s potragom za optimalnim rasponom parametara procesa (snaga laserskog zračenja i brzina skeniranja), koji je obično prilično uzak.
Utjecaj parametara SLM zlata na kvalitetu formiranih slojeva
Drugi faktor koji utiče na kvalitet proizvoda je pojava unutrašnjih naprezanja, čija prisutnost i veličina zavise od geometrije proizvoda, brzine zagrijavanja i hlađenja, koeficijenta toplinskog širenja, te faznih i strukturnih promjena u metalu. Značajna unutrašnja naprezanja mogu dovesti do deformacije proizvoda, stvaranja mikro- i makropukotina.
Djelomično smanjiti Negativan uticaj Gore navedeni faktori mogu se postići korištenjem grijaćih elemenata, koji se obično nalaze unutar postrojenja oko supstrata ili hranilice praha. Zagrijavanjem praha također je moguće ukloniti adsorbiranu vlagu sa površine čestica i na taj način smanjiti stupanj oksidacije.
Kod selektivnog laserskog topljenja metala kao što su aluminijum, bakar, zlato nije nevažna njihova visoka reflektivnost, što zahteva upotrebu moćnog laserskog sistema. Ali povećanje snage laserskog snopa može negativno utjecati na točnost dimenzija proizvoda, jer ako se prašak pretjerano zagrije, on će se otopiti i sinterovati izvan laserske točke zbog prijenosa topline. Velika snaga lasera se također može promijeniti hemijski sastav kao rezultat isparavanja metala, što je posebno karakteristično za legure koje sadrže komponente niskog taljenja i imaju visok pritisak pare.
Mehanička svojstva materijala dobijenih SLM metodom (EOS GmbH)
Ako proizvod dobijen jednom od gore navedenih metoda ima zaostalu poroznost, onda, ako je potrebno, primijeniti dodatnu tehnološke operacije da se poveća njegova gustina. U tu svrhu koriste se metode metalurgije praha - sinterovanje ili vruće izostatičko prešanje (HIP). Sinterovanjem je moguće eliminisati zaostalu poroznost i poboljšati fizička i mehanička svojstva materijala. Istovremeno, treba naglasiti da su formirana svojstva materijala tokom sinterovanja određena sastavom i prirodom materijala, veličinom i brojem pora, prisustvom defekata i brojnim drugim faktorima. HIP je proces u kojem se radni komad smješten u plinsku presu sabija pod djelovanjem visoke temperature i sveobuhvatne kompresije inertnim plinom. Radni pritisak i maksimalna temperatura koju postiže gasostat zavisi od njegovog dizajna i zapremine. Na primjer, plinski stat s radnom komorom veličine 900x1800 mm može razviti temperaturu od 1500 o C i pritisak od 200 MPa. Upotreba HIP-a za eliminaciju poroznosti bez upotrebe zatvorenog omotača moguća je ako poroznost nije veća od 8%, jer će pri višoj vrijednosti plin ulaziti u proizvod kroz pore, čime se sprječava zbijanje. Prodiranje plina u proizvod moguće je isključiti izradom čelične hermetičke ljuske koja ponavlja oblik površine proizvoda. Međutim, proizvodi dobiveni aditivnom proizvodnjom uglavnom imaju složen oblik, što onemogućuje proizvodnju takve školjke. U ovom slučaju za zaptivanje se može koristiti evakuisana zatvorena posuda u kojoj se proizvod stavlja u rastresiti medij (Al 2 O 3 , BN hex, grafit) koji prenosi pritisak na zidove proizvoda.
Nakon aditivne proizvodnje SLM metodom, materijale karakterizira anizotropija svojstava, povećana čvrstoća i smanjena duktilnost zbog prisutnosti zaostalih naprezanja. Za uklanjanje zaostalih naprezanja, postizanje uravnoteženije strukture, povećanje viskoznosti i plastičnosti materijala, provodi se žarenje.
Prema niže navedenim podacima može se primijetiti da su proizvodi dobiveni selektivnim laserskim topljenjem u nekim slučajevima jači od livenih proizvoda za 2-12%. To se može objasniti malom veličinom zrna i mikrostrukturnim komponentama, koje nastaju kao rezultat brzog hlađenja taline. Brzo prehlađenje taline značajno povećava broj jezgara čvrste faze i smanjuje njihovu kritičnu veličinu. U tom slučaju, kristali koji brzo rastu na embrionima, u kontaktu jedni s drugima, počinju sprječavati njihov daljnji rast, formirajući tako fino zrnatu strukturu. Jezgra kristalizacije su obično nemetalne inkluzije, mjehurići plina ili čestice koje se oslobađaju iz taline sa svojom ograničenom topljivošću u tečnoj fazi. A u opštem slučaju, prema Hall-Petch relaciji, sa smanjenjem veličine zrna, čvrstoća metala raste zbog razvijene mreže granica zrna, što je efikasna prepreka kretanju dislokacija. Treba napomenuti da se, zbog različitog hemijskog sastava legura i njihovih svojstava, kao i uslova SLM, gore navedene pojave koje se javljaju tokom hlađenja rastopa ispoljavaju različitim intenzitetom.
Mehanička svojstva materijala dobijenih SLM i livenjem
Naravno, to ne znači da su proizvodi dobiveni selektivnim laserskim topljenjem bolji proizvodi primljeno tradicionalnim načinima. Zbog velike fleksibilnosti tradicionalnih metoda za proizvodnju proizvoda, moguće je varirati svojstva proizvoda u širokom rasponu. Na primjer, korištenjem metoda kao što je promjena temperaturni uslovi kristalizacijom, legiranjem i uvođenjem modifikatora u rastop, termičkim ciklusom, metalurgijom praha, termomehaničkom obradom itd., moguće je postići značajno povećanje svojstava čvrstoće metala i legura.
Posebno je zanimljiva upotreba ugljičnog čelika za aditivnu proizvodnju, jer je jeftin i vrlo složen. mehanička svojstva materijal. Poznato je da se povećanjem sadržaja ugljika u čeliku poboljšava njegova fluidnost i kvašenje. Zahvaljujući tome moguće je dobiti jednostavne proizvode koji sadrže 0,6-1% C sa gustinom od 94-99%, dok je u slučaju korišćenja čistog gvožđa gustina oko 83%. U procesu selektivnog laserskog topljenja ugljičnog čelika, staza taline tokom brzog hlađenja se kaljuje i temperira na troostitnu ili sorbitnu strukturu. Istovremeno, zbog toplinskih naprezanja i strukturnih transformacija, u metalu mogu nastati značajna naprezanja koja dovode do povodca proizvoda ili do stvaranja pukotina. Također važnost geometrija proizvoda ima, budući da oštri prijelazi duž presjeka, mali polumjeri zakrivljenosti i oštri rubovi uzrokuju pukotine. Ako nakon “štampanja” čelik nema zadati nivo mehaničkih svojstava i treba ga podvrgnuti dodatnoj toplinskoj obradi, tada će biti potrebno uzeti u obzir prethodno navedena ograničenja u obliku proizvoda kako bi se kako bi se izbjegla pojava defekata stvrdnjavanja. Ovo donekle smanjuje izglede za korištenje SLM-a za ugljične čelike.
Prilikom proizvodnje proizvoda tradicionalnim metodama, jedan od načina da se izbjegnu pukotine i uzice prilikom kaljenja proizvoda složenog oblika je upotreba legiranih čelika, u kojima prisutni legirajući elementi, osim povećanja mehaničkih i fizičko-hemijskih svojstava, odlažu transformaciju austenita pri hlađenju, što rezultira smanjenjem kritične brzine stvrdnjavanja i povećava sposobnost kaljenja legiranog čelika. Zbog niske kritične brzine gašenja, čelik se može kaliti u ulju ili na zraku, čime se smanjuje razina unutrašnjih naprezanja. Međutim, zbog brzog odvođenja topline, nemogućnosti kontrole brzine hlađenja i prisustva ugljika u legiranom čeliku, ova tehnika ne dozvoljava da se izbjegne pojava značajnih unutrašnjih naprezanja tokom selektivnog laserskog topljenja.
U vezi sa navedenim karakteristikama, za SLM se koriste martenzitni čelici (MS 1, GP 1, PH 1), kod kojih se očvršćavanje i povećanje tvrdoće postiže taloženjem dispergovanih intermetalnih faza tokom termičke obrade. Ovi čelici sadrže malu količinu ugljika (stotine postotka), zbog čega se martenzitna rešetka formirana tijekom brzog hlađenja odlikuje niskim stupnjem izobličenja i, posljedično, ima nisku tvrdoću. Niska tvrdoća i visoka duktilnost martenzita osiguravaju relaksaciju unutrašnjih naprezanja tokom kaljenja, a visok sadržaj legirajućih elemenata omogućava žarenje čelika do velike dubine pri skoro svakoj brzini hlađenja. Kao rezultat toga, složeni proizvodi se mogu proizvoditi i termički obrađivati SLM-om bez straha od pucanja ili savijanja. Pored maraging čelika, nešto austenitnog nerđajući čelici, na primjer 316L.
U zaključku, može se primijetiti da su sada napori naučnika i inženjera usmjereni na više detaljna studija uticaj parametara procesa na strukturu, mehanizam i karakteristike zbijanja razni materijali pod dejstvom laserskog zračenja u cilju poboljšanja mehaničkih svojstava i povećanja spektra materijala pogodnih za proizvodnju laserskih aditiva.
Selektivno lasersko sinterovanje (SLS) je metoda aditivne proizvodnje koju je krajem 80-ih razvio Carl Deckard sa Univerziteta Teksas u Austinu uz podršku DARPA-e. Tehnologija koristi laser velike snage za sinterovanje malih čestica plastike, keramike, staklenog brašna ili metala u trodimenzionalnu strukturu.
Laserski snop selektivno spaja čestice praha radni prostor, dobivanje podataka o obliku dijela provjerom sa virtuelnim modelom koji generiše računar. Nakon što je sloj završen, dio se umače u prah i postupak se ponavlja. Približno ista metoda se koristi u laserskoj stereolitografiji, gdje je radni materijal tečni fotopolimer koji se stvrdnjava pod laserskim snopom.
Budući da gustoća dijela ovisi o snazi lasera, a ne o trajanju zagrijavanja, SLS štampači koriste pulsne lasere (na primjer lasere na ugljični dioksid). U ovom slučaju, izvorni materijal se prethodno zagreva do stanja blizu tačke topljenja kako bi laseru bilo lakše da dostigne vršnu tačku. Izlaz je dio sa poroznom i hrapavom površinom.
Metalna štampa
Tehnologija je od posebnog interesa u smislu mogućnosti stvaranja metalnih proizvoda. Zapravo, koristeći ovu metodu, možete stvoriti ne prototipove, već punopravne radne dijelove. Istina, kada se radi s metalima, tehnologija ima nekoliko ograničenja. Kako bi se spriječila oksidacija metalnih čestica, proces sinteriranja se mora odvijati u vakuumu ili inertnom okruženju, što je nemoguće učiniti kod kuće. Profesionalni SLS štampači opremljeni su specijalnim vakuum komorama, veliki su i skupi.
Materijal za štampu je specijalni prah koji se sastoji od metalnih čestica presvučenih polimerom. Nakon završenog procesa sinterovanja, dio se stavlja u visokotemperaturnu peć, gdje plastika sagorijeva, a na njeno mjesto dolazi nisko topljiva bronca.
Prednosti i nedostaci
SLS tehnologija ima nekoliko značajnih prednosti:
- Nema potrebe za pomoćnim materijalima. Dio je uronjen u prah, koji obavlja funkciju potpore nadvijenih dijelova;
- Veliki izbor materijala, uključujući metale;
- Velika brzina štampe (do 35 mm/sat).
minusi:
- Gruba struktura modela koji zahtijevaju daljnju obradu;
- Dugo vremena za pripremu štampača za rad (grejanje i stabilizacija temperature);
- Nemogućnost štampanja metala kod kuće.
U ovoj recenziji pokušao sam u popularnoj formi predstaviti osnovne podatke o proizvodnji metalnih proizvoda laserskom aditivnom proizvodnjom, relativno novoj i zanimljivoj tehnološkoj metodi koja se pojavila kasnih 80-ih godina, a danas je postala obećavajuća tehnologija za male ili proizvodnja u jednom komadu u oblasti medicine, aviona i raketne nauke.
Ukratko opisati princip rada instalacije za aditivnu proizvodnju pomoću laserskog zračenja može biti kako slijedi. Uređaj za nanošenje i izravnavanje sloja praha uklanja sloj praha sa hranilice i ravnomjerno ga raspoređuje po površini podloge. Nakon toga, laserska zraka skenira površinu ovog sloja praha i formira proizvod topljenjem ili sinteriranjem. Na kraju skeniranja sloja praha, platforma sa proizvedenim proizvodom se spušta za debljinu nanesenog sloja, a platforma sa prahom se podiže, a proces nanošenja sloja praha i skeniranja se ponavlja. Nakon što je proces završen, platforma sa proizvodom se podiže i čisti od neiskorištenog praha.
Jedan od glavnih dijelova u instalacijama za aditivnu proizvodnju je laserski sistem koji koristi CO 2 , Nd:YAG, iterbijumska vlakna ili disk lasere. Utvrđeno je da je za zagrevanje metala i karbida poželjna upotreba lasera talasne dužine od 1-1,1 μm, jer apsorbuju zračenje koje generiše laser za 25-65%. Istovremeno, upotreba CO 2 lasera s talasnom dužinom od 10,64 µm je najprikladnija za materijale kao što su polimeri i oksidna keramika. Veći kapacitet apsorpcije omogućava povećanje dubine prodiranja i variranje parametara procesa u širem rasponu. Obično laseri koji se koriste u aditivnoj proizvodnji rade kontinuirano. U poređenju s njima, upotreba lasera koji rade u pulsnom i Q-switched modu zbog velike energije impulsa i kratkog trajanja impulsa (nanosekunde) omogućava poboljšanje čvrstoće veze između slojeva i smanjenje zona zahvaćena toplotom. U zaključku, može se napomenuti da karakteristike laserskih sistema koji se koriste leže u sledećim granicama: snaga lasera - 50-500 W, brzina skeniranja do 2 m/s, brzina pozicioniranja do 7 m/s, prečnik fokusirane tačke - 35-400 μm.
Pored lasera, kao izvor zagrevanja praha može se koristiti i grejanje elektronskim snopom. Ovu opciju je predložio Arcam i implementirao u svoje instalacije 1997. Instalaciju sa elektronskim snopom topom karakteriše odsustvo pokretnih delova, budući da se elektronski snop fokusira i usmerava pomoću magnetnog polja i deflektora, te stvaranje vakuum u komori pozitivno utiče na kvalitet proizvoda.
Jedan od važnih uslova u proizvodnji aditiva je stvaranje zaštitnog okruženja koje sprečava oksidaciju praha. Za ispunjavanje ovog uslova koristi se argon ili dušik. Međutim, upotreba dušika kao zaštitnog plina je ograničena, zbog mogućnosti stvaranja nitrida (na primjer, AlN, TiN u proizvodnji proizvoda od aluminijskih i titanovih legura), koji dovode do smanjenja plastičnosti materijal.
Metode proizvodnje laserskih aditiva prema karakteristikama procesa zbijanja materijala mogu se podijeliti na selektivno lasersko sinteriranje (Selective Laser Sintering (SLS)), indirektno lasersko sinteriranje metala (Indirect Laser Metal Sintering (ILMS)), direktno lasersko sinteriranje metala (Direct Laser Metal Sintering (DLMS)) i selektivno lasersko topljenje (Selective Laser Melting (SLM)). U prvoj varijanti dolazi do zbijanja sloja praha zbog sinterovanja u čvrstoj fazi. U drugom slučaju, zbog impregnacije poroznog okvira prethodno formiranog laserskim zračenjem vezivom. Direktno lasersko sinterovanje metala zasniva se na zbijanju mehanizmom tečnofaznog sinterovanja usled topljenja topljive komponente u praškastoj mešavini. U potonjoj verziji, do zbijanja dolazi zbog potpunog topljenja i širenja taline. Vrijedi napomenuti da ova klasifikacija nije univerzalna, budući da jedna vrsta procesa aditivne proizvodnje može pokazati mehanizme zbijanja koji su karakteristični za druge procese. Na primjer, DLMS i SLM mogu doživjeti sinterovanje u čvrstom stanju, što se dešava sa SLS, dok SLM može doživjeti sinterovanje u tečnoj fazi, što je više karakteristično za DLMS.
Selektivno lasersko sinterovanje (SLS)
Čvrstofazno selektivno lasersko sinterovanje nije postalo široko rasprostranjeno, jer je za potpuniji tok volumetrijske i površinske difuzije, viskoznog toka i drugih procesa koji se javljaju tokom sinterovanja praha potrebno relativno dugo izlaganje laserskom zračenju. To dovodi do dugotrajnog rada lasera i niske produktivnosti procesa, što ovaj proces čini ekonomski neizvodljivim. Osim toga, postoje poteškoće u održavanju temperature procesa u rasponu između tačke topljenja i temperature sinterovanja čvrstog stanja. Prednost selektivnog laserskog sinterovanja u čvrstoj fazi je mogućnost upotrebe šireg spektra materijala za izradu proizvoda.
Indirektno lasersko sinterovanje metala (ILMS)
Proces nazvan "indirektno lasersko sinterovanje metala" razvio je DTMcorp iz Austina 1995. godine, koji je u vlasništvu 3D Systems-a od 2001. godine. ILMS proces koristi mješavinu praha i polimera ili prah obložen polimerom, gdje polimer djeluje kao vezivo i pruža potrebnu čvrstoću za daljnju toplinsku obradu. U fazi termičke obrade polimer se destilira, okvir se sinterira, a porozni okvir impregnira vezivnim metalom, čime se dobiva gotov proizvod.
Za ILMS se mogu koristiti prahovi metala i keramike ili njihove mješavine. Priprema mješavine praha sa polimerom vrši se mehaničkim miješanjem, pri čemu je sadržaj polimera oko 2-3% (težinski), a u slučaju korištenja praha obloženog polimerom debljina sloja na površini čestice je oko 5 μm. Kao vezivo koriste se epoksidne smole, tečno staklo, poliamidi i drugi polimeri. Temperatura destilacije polimera određena je temperaturom njegovog topljenja i raspadanja i iznosi u prosjeku 400-650 o C. Nakon destilacije polimera, poroznost proizvoda prije impregnacije je oko 40%. Tokom impregnacije, peć se zagrijava za 100-200 0 C iznad tačke topljenja materijala za impregnaciju, jer se s povećanjem temperature smanjuje ugao vlaženja i smanjuje viskozitet taline, što povoljno utiče na proces impregnacije. Obično se impregnacija budućih proizvoda vrši u zatrpavanju od aluminijevog oksida, koji igra ulogu nosećeg okvira, jer u periodu od destilacije polimera do stvaranja jakih međučestičnih kontakata postoji opasnost od uništenja. ili deformacije proizvoda. Zaštita od oksidacije organizirana je stvaranjem inertne ili redukcijske sredine u peći. Za impregnaciju možete koristiti dosta različitih metala i legura koje zadovoljavaju sljedeće uvjete. Materijal za impregnaciju treba da se odlikuje potpunim odsustvom ili beznačajnom međufaznom interakcijom, malim uglom vlaženja i tačkom taljenja nižom od baze. Na primjer, ako komponente međusobno djeluju jedna na drugu, tada se tijekom procesa impregnacije mogu javiti neželjeni procesi, kao što je stvaranje više vatrostalnih spojeva ili čvrstih otopina, što može dovesti do zaustavljanja procesa impregnacije ili negativno utjecati na svojstva i dimenzije. proizvoda. Obično se bronza koristi za impregniranje metalnog okvira, dok je skupljanje proizvoda 2-5%.
Selektivno lasersko sinterovanje (SLS) je tehnika aditivne proizvodnje koja se koristi za stvaranje funkcionalnih prototipova i malih serija gotovih proizvoda(pogledajte video). Tehnologija se zasniva na sukcesivnom sinterovanju slojeva praškastog materijala pomoću lasera velike snage. SLS se često zamjenjuje sa sličnim procesom koji se naziva selektivno lasersko topljenje (SLM). Razlika je u tome što SLS obezbeđuje samo delimičnu talinu koja je potrebna za sinterovanje materijala, dok selektivna laserska talina obezbeđuje potpunu taljenje neophodnu za izgradnju monolitnih modela.
Tehnologija
Tehnologija (SLS) uključuje upotrebu jednog ili više lasera (obično ugljičnog dioksida) za sinterovanje čestica praškastog materijala kako bi se formirao trodimenzionalni fizički objekt. Kao potrošni materijal koriste se plastika, metali, keramika ili staklo. Sinterovanje se izvodi crtanjem kontura ugrađenih u digitalni model (tzv. "skeniranje") pomoću jednog ili više lasera. Kada je skeniranje završeno, radna platforma se spušta i nanosi se novi sloj materijala. Proces se ponavlja dok se ne formira kompletan model.
Budući da gustoća proizvoda ne ovisi o trajanju ozračivanja, već o maksimalnoj energiji lasera, uglavnom se koriste pulsni emiteri. Prije početka štampe, potrošni materijal se zagrije na tik ispod tačke topljenja kako bi se olakšao proces sinteriranja.
Za razliku od aditivnih metoda proizvodnje kao npr stereolitografija(SLA) ili simulacija metoda depozicije(FDM), SLS ne zahtijeva izgradnju potpornih konstrukcija. Šarnirski dijelovi modela poduprti su nepotrošenim materijalom. Ovaj pristup omogućava postizanje praktično neograničene geometrijske složenosti proizvedenih modela.
Materijali i primjena
Neki SLS uređaji koriste jednolični prah proizveden u mlinovima sa bubnjem i kuglicama, ali u većini slučajeva, kompozitne granule sa vatrostalnim jezgrom i omotačem od materijala sa niske temperature topljenje.
U poređenju sa drugim metodama aditivne proizvodnje, SLS je veoma svestran u pogledu potrošnog materijala. To uključuje različite polimere (kao što su najlon ili polistiren), metale i legure (čelik, titan, plemeniti metali, legure kobalt-hrom, itd.), kao i kompozite i mješavine pijeska.
SLS tehnologija je postala široko rasprostranjena u cijelom svijetu zbog svoje sposobnosti da proizvodi funkcionalne dijelove složenih geometrijskih oblika. Iako je tehnologija prvobitno stvorena za brzu izradu prototipa, u novije vrijeme SLS se koristi za proizvodnju gotovih proizvoda u maloj mjeri. Prilično neočekivana, ali zanimljiva primjena SLS-a bila je upotreba tehnologije u stvaranju umjetničkih predmeta.
Direktno lasersko sinteriranje metala (DMLS)
Direktno lasersko sinterovanje metala(DMLS) je tehnologija proizvodnje metalnih aditiva koju je razvio EOS iz Minhena. DMLS se često miješa sa sličnim tehnologijama selektivno lasersko sinterovanje("Selektivno lasersko sinterovanje" ili SLS) i selektivno lasersko topljenje("Selektivno lasersko topljenje" ili SLM).
Proces uključuje korištenje 3D STL modela kao nacrta za izgradnju fizičkih modela. 3D model predmet digitalna obrada za virtuelno razdvajanje na tanke slojeve debljine koja odgovara debljini slojeva nanesenih štamparskim uređajem. Gotova "konstrukcijska" datoteka se koristi kao set crteža tokom štampanja. Kao grijaći element za sinteriranje metalnog praha koriste se optički laseri relativno velike snage, oko 200 W. Neki uređaji koriste više moćni laseri sa povećana brzina skeniranje (tj. pomicanje laserskog snopa) za veću produktivnost. Alternativno, moguće je povećati produktivnost korištenjem više lasera.
Praškasti materijal se unosi u radnu komoru u količinama potrebnim za nanošenje jednog sloja. Specijalni valjak poravnava uneti materijal u ravnomeran sloj i uklanja višak materijala iz komore, nakon čega laserska glava sinteruje čestice svežeg praha između sebe i sa prethodnim slojem prema konturama definisanim digitalnim modelom. Nakon završetka izvlačenja sloja, proces se ponavlja: valjak ubacuje svježi materijal i laser počinje sinterirati sljedeći sloj. Atraktivna karakteristika ove tehnologije je veoma visoka rezolucija štampe – u proseku oko 20 mikrona. Poređenja radi, tipična debljina sloja u hobi i potrošačkim štampačima koji koriste FDM/FFF tehnologiju je reda veličine 100 mikrona.
Drugi zanimljiva karakteristika proces je odsustvo potrebe za izgradnjom potpora za nadvišene konstrukcijske elemente. Zeleni prah se ne uklanja tokom štampe, već ostaje u radnoj komori. Dakle, svaki sljedeći sloj ima potpornu površinu. Osim toga, neiskorišteni materijal se može prikupiti iz komore za izgradnju nakon što je štampanje završeno i ponovo upotrijebiti. Proizvodnja DMLS-a se može smatrati gotovo bez otpada, što je važno prilikom upotrebe skupi materijali kao što su plemeniti metali.
Tehnologija praktički nema ograničenja na geometrijsku složenost konstrukcije, i visoka tačnost izvođenje minimizira potrebu za mehaničkom obradom štampanih proizvoda.
Prednosti i nedostaci
DMLS tehnologija ima nekoliko prednosti u odnosu na tradicionalne metode proizvodnje. Najočitija je mogućnost brze izrade geometrijski složenih dijelova bez potrebe za strojnom obradom (tzv. „subtractive“ metode – glodanje, bušenje i sl.). Proizvodnja je praktički bez otpada, što razlikuje DMLS od subtraktivnih tehnologija. Tehnologija vam omogućava da kreirate nekoliko modela istovremeno s ograničenjem samo na veličinu radne komore. Izrada modela traje oko nekoliko sati, što je neuporedivo isplativije od procesa livenja, koji može potrajati i do nekoliko mjeseci, uzimajući u obzir cijeli proizvodni ciklus. S druge strane, dijelovi proizvedeni laserskim sinteriranjem nemaju čvrstoću, pa stoga ne postižu iste vrijednosti čvrstoće kao liveni uzorci ili dijelovi proizvedeni subtraktivnim metodama.
DMLS se aktivno koristi u industriji zbog mogućnosti izgradnje unutrašnjih konstrukcija od čvrstih dijelova koji su po složenosti nepristupačni. tradicionalne metode proizvodnja. Detalji složene geometrije mogu se izrađivati kao cjelina, a ne od sastavnih dijelova, što povoljno utječe na kvalitetu i cijenu proizvoda. Pošto DMLS ne zahtijeva specijalni alati(na primjer, livnički kalupi) i ne proizvodi veliki broj otpada (kao što je slučaj sa subtraktivnim metodama), proizvodnja malih serija ovom tehnologijom je mnogo isplativija nego tradicionalnim metodama.
Aplikacija
DMLS tehnologija se primjenjuje na proizvodnju malih i srednjih gotovih proizvoda u različitim industrijama, uključujući avio, stomatologiju, medicinu, itd. Tipična veličina građevinskog područja postojeće instalacije je 250x250x250mm, iako ne postoje nikakva tehnološka ograničenja u veličini - stvar je samo u cijeni uređaja. DMLS se koristi za brzu izradu prototipa, smanjenje vremena razvoja novih proizvoda, kao i u proizvodnji, smanjenje troškova malih serija i pojednostavljivanje sklapanja složenih geometrijskih oblika.
Sjeverozapadni politehnički univerzitet Kine koristi DMLS sisteme za proizvodnju strukturnih komponenti aviona. Istraživanje koje je proveo EADS takođe ukazuje na smanjenje troškova i otpada kada se koristi DMLS tehnologija za proizvodnju složene strukture u pojedinačnim primjercima ili u malim serijama.