القيم الحالية والمستهدفة لتيار القيمة. فوائد فلسفة كايزن. تفسير خريطة تدفق القيمة
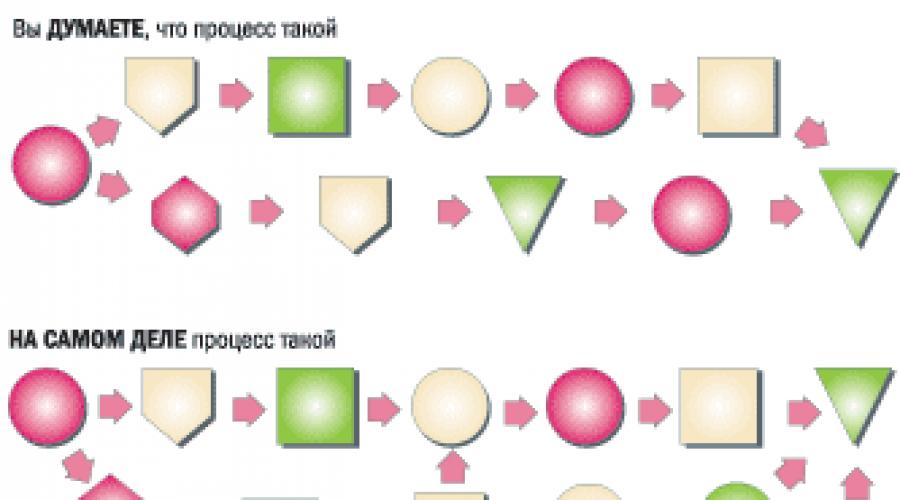
مقال من أرشيف مجلة "Logistic & System"
فلاديمير مورسكوي
مستشار مدرب أول في CBSD
بناء منزل دون تجميع مشروع معماريوبدون رسم الرسومات هذا مستحيل. من المستحيل أيضًا تغيير عمليات الإنتاج وفقًا لإيديولوجية الإنتاج الخالي من الهدر بدون خريطة لحالة الإنتاج الحالية والمستقبلية.
في أحد الإصدارات السابقة (انظر "اللوجيستيات والنظام" رقم 7 / يوليو 2005) أخبرناك بالفعل عن الإنتاج الذي يعتمد على نظام السحب. وفقًا لإيديولوجية الإنتاج الخالي من الهدر ("الإنتاج الخالي من الهدر") ، الأساليب الثوريةأكثر تدميرا من البناء. يجب أن تكون جميع التغييرات منهجية ، وأن تتم بخطوات صغيرة وعلى عدة مراحل. ولكن قبل الشروع في أي تحولات وتغييرات ، من الضروري فهم وفهم وتحديد الخطوط العريضة للصورة الكاملة لما يحدث في المؤسسة ، لأن أي توضيحات وتحولات يجب أن تتعلق بالإنتاج بأكمله ، وليس عملياته الفردية. في الممارسة العملية ، كقاعدة عامة ، يتعين على المرء أن يتعامل مع تحسينات النقطة بدقة في العمليات الفردية (على سبيل المثال ، اللحام ، والتجميع ، والطلاء ، وما إلى ذلك) ، والتي لا تسمح بالتحول الكامل والتحول لمؤسسة أو فرد المنتج. علاوة على ذلك ، غالبًا ما تؤدي الأفكار المبتكرة والرغبة في "التحسين هنا" فقط إلى اختلال التوازن في الإنتاج ، حيث تبدأ عملية أو منطقة إنتاج معينة في العمل بشكل أفضل ، ولا تستطيع المناطق أو العمليات المجاورة مواكبة ذلك.
قيمة
يمكن تعريفها على أنها منتج أو خدمة يتم تقديمها للعميل في الوقت المناسب بالسعر المناسب. سلسلة القيمة هي تسلسل جميع الأنشطة المطلوبة لابتكار منتج معين وتطويره وإنتاجه وصيانته ، من المفهوم إلى الإطلاق ، ومن الطلب إلى التسليم ، ومن المواد الخام إلى المنتج النهائي في يد العميل. يكون أي عميل دائمًا على استعداد دائمًا للدفع مقابل تلك الإجراءات التي ستضيف قيمة إلى المنتج (على سبيل المثال ، التصنيع ، والصب ، والطلاء ، والتجميع ، وصياغة دليل التعليمات ، وما إلى ذلك) ، نظرًا لأن تجاهلها يقلل من قيمة المنتج في في عيون العميل وهذا بالفعل محفوف بالخسائر.
خسارة من الدرجة الأولى
هذه هي الخسائر التي يكاد يكون من المستحيل التخلص منها ، لأن أداء المؤسسة بأكملها يعتمد على العملية المختارة أو العملية التكنولوجية (على سبيل المثال ، الحساب أجور). من وجهة نظر العميل ، لا تضيف هذه العملية قيمة للمنتج ، بل تضيف استبعاده منه الدورة العامةمن المرجح أن يؤدي إلى إغلاق كامل للمؤسسة. لا يمكن القضاء على مثل هذه العمليات أو العمليات ، بل يمكن تحسينها فقط.
خسارة من الدرجة الثانية
تتضمن هذه الكتلة الخسائر ، والتي عند اكتشافها من الضروري اتخاذ تدابير فورية للقضاء عليها. يجب أن يكون الأعداء معروفين بالعين ، وبالتالي سنقوم بإدراجهم في قائمة.
الإفراط في الإنتاج.كقاعدة عامة ، هذه نتيجة خطيرة ونتيجة لطريقة تفكير المديرين ، الذين يضعون التحميل الأكثر اكتمالا للمعدات والموظفين المتاحين في المقدمة. ونتيجة لذلك كل هذا يؤدي إلى:
- الاستهلاك المبكر للمواد الخام والمواد ؛
- الاستخدام دون المستوى الأمثل للقوى العاملة ؛
- شراء معدات إضافية
- زيادة المساحة الصالحة للاستخدام ؛
- زيادة نسبة الخصومات (على سبيل المثال ، ضريبة الأملاك) ؛
- زيادة في المخزونات
- زيادة تكاليف النقل والتكاليف الإدارية.
يشير Masaki Imai ، في كتابه Gemba Kaizen ، إلى أن الإفراط في الإنتاج موجود أسوأ نوعتساعد الخسائر ، التي تعطي إحساسًا زائفًا بالأمان ، على إخفاء جميع أنواع المشاكل والمعلومات "السحابية" التي يمكن أن تساعد في تنفيذ التغييرات الإيجابية في مكان العمل.
جرد فائض.المواد الخام والمنتجات النهائية وقطع الغيار لإصلاح المعدات والمباني المخزنة في المستودع لا تضيف قيمة للمنتج على الإطلاق. لكن بالنسبة للغالبية العظمى من الشركات العاملة في فضاء ما بعد الاتحاد السوفيتي ، فإن الأسهم تشكل حماية ضد عدم اليقين. عوامل خارجية(دورة العرض والطلب). بالطبع ، هناك نوع آخر مختلف من المخزون يعمل كحماية ضد العوامل الداخلية - سوء الإدارة ، وتوازن العمل غير الماهر ، وسوء جودة المنتج ، وأوقات تغيير المعدات المفرطة ، وتبادل المعلومات غير الكافي بين الإدارات ، وما إلى ذلك ، وإذا كان المخزون من العوامل الخارجية هو "مدرب" ويكاد يكون من المستحيل تنظيمه ، ثم يتم وصف التحسين ببساطة لمخزون الأمان (هناك طرق لحساب مخزون الأمان الأمثل في ظل ظروف عدم اليقين). ومع العوامل التي تؤثر على حجم الاحتياطيات ، من الضروري القتال بلا كلل ، حتى يتم القضاء عليها تمامًا.
زواج.خسائر جلية تستنزف الموارد المادية والبشرية. تقول فلسفة اللين أنه يجب بناء نظام بحيث يلفت الانتباه على الفور أي انحراف عن القاعدة. حتى دمينغ في الثلاثينيات من القرن الماضي ، الذي عمل في AT & T وبناء مفهوم الجودة "المضمنة" ، كتب: "... حدوث عيوب في مسار العملية يعتمد على 95٪ من الجودة من العملية نفسها وفقط 5٪ على العامل البشري ". توصلت شركة Toyota إلى الاستنتاج التالي: من الضروري بناء العملية بطريقة لا يمكن للموظف الذي يقوم بالعملية القيام بها بشكل خاطئ. هذه المهمة ليست سهلة ، وتعمل مجموعات خاصة متعددة الوظائف من المتخصصين ، لا تتكون فقط من المهندسين ، ولكن أيضًا من العمال أنفسهم ، على حلها. ما يفعلونه هو ما يسميه اليابانيون نير بوكا ، أو ضمان الخداع. كانت تجربة شركة تويوتا غريبة عن الاتحاد السوفيتي ، ولكن فيما يتعلق ليس فقط بالمرور ، ولكن أيضًا "حماية نفسك من الأحمق" ، فقد نجحنا إلى حد كبير بفضل المجموعات اليابانية المماثلة التي تم تنظيمها في أواخر السبعينيات وأوائل القرن الماضي. الثمانينيات في مؤسسات الدفاع في اتحاد الجمهوريات الاشتراكية السوفياتية. في الوقت الحاضر ، يتم استخدام هذه الممارسة في كثير الشركات الروسية.
من الإنجازات الأخرى لشركة Toyota ، والتي تم استخدامها بنشاط في الإنتاج لمدة 50 عامًا ، التحكم الكامل في جودة البضائع ومنع نقل المنتجات المعيبة إلى القسم التالي. يتم القضاء على الخلل في مكان اكتشافه من تلقاء نفسه وبمساعدة مجموعات الاستجابة الخاصة (نفس المجموعات التي تطور "الحماية الخادعة"). ثم يتم تحليل الخلل وتحديد أسباب حدوثه ووضع تدابير لمنع تكراره. أهم شيء في كل هذا هو المسؤولية عن الجودة على جميع المستويات ، من أعلى إلى أسفل ، وهذا يتطلب تغييراً كاملاً في وعي الموظفين ، واعتماد فلسفة الجودة. هذا هو بالضبط ما يسمى TQM (إدارة الجودة الشاملة - "إدارة الجودة الشاملة").
حركة اضافية في مكان العمل. إذا كان الموظف يبحث عن ملفات مطلوبهأو يذهب لأداة على بعد أمتار قليلة من مكان عمله ، وهذا أيضًا لا يضيف قيمة للمنتج. الطريق الصحيحلتجنب هذا هو الصحيح ، أي. تنظيم عقلانيأماكن العمل.
الإفراط في المعالجة.يبدو الأمر مدهشًا وبطلاقة ، لكن أساس هذا النوع من الخسارة هو الكمال "المبتذل" ، أي الرغبة في جعل المنتج أفضل مما يطلبه العميل. على سبيل المثال ، قد يتجاوز مدير الإنتاج مواصفات العميل ويضع تفاوتات أكثر إحكامًا لتصنيع الأجزاء. وسيكون كل شيء على ما يرام ، ولكن المعالجة الأكثر دقة فقط تزيد من إمكانية الزواج ، وتتطلب ، كقاعدة عامة ، أداة أخرى باهظة الثمن ، بما في ذلك مراقبة العملية ، ومؤهلات أعلى للفنان. وفي النهاية ، لماذا تدفع أكثر إذا طلب العميل تحقيق الكمال منتج معين؟! ضمان الجودة ، مثل أي نشاط صناعي ، له تكلفة. يعد تجاوز تكلفة معينة بالفعل خسارة تنشأ حتمًا مع المعالجة الزائدة. بالإضافة إلى ذلك ، يكشف تحليل تدفقات الإنتاج عن العمليات التي يمكن الاستغناء عنها بالكامل دون المساس بجودة المنتج.
التوقف(وقت انتظار وصول المنتجات من العملية السابقة). الصحابة المخلصون من عدم التوازن بين مواقع الإنتاج وأماكن العمل والورش. ولكن يمكن أن تنشأ أيضًا بسبب تعطل المعدات ، والتسليم في الوقت المناسب للمواد الخام والمواد. يجب توجيه الجهود في هذه الحالة للحفاظ على التشغيل المتوازن للمعدات وتنفيذ التدابير الوقائية لمنع الإغلاق غير المخطط للمعدات. إن وجود معدات فائقة الإنتاجية في مناطق معينة في الشركة ليس دائمًا نعمة ، لأن هذا هو بالضبط ما يؤدي في أغلب الأحيان إلى عدم التوازن. يمكن أن يؤدي الاحتفاظ بمخزون أمان محسّن أو التبديل في الوقت المناسب مع الموردين إلى حماية إنتاجك من الأعطال التي يسببها الموردون.
النقل والسفر غير الضروريين.بدون كلمة "زائدة عن الحاجة" ، تعد هذه العمليات جزءًا أساسيًا من عملية الإنتاج ، ومع ذلك ، من وجهة نظر العميل ، لا علاقة لهذا الجزء بفطيرة قيمة المنتج - لا يهتم العميل بمدى و ما هي الطرق التي يتحرك بها المنتج. أحد المؤشرات الرئيسية لخريطة تدفق القيمة هو طول التدفق من البوابة إلى البوابة - فكلما كان أقصر ، زاد وضوح الانخفاض في إجمالي وقت الإنتاج والمخزون ومساحة الأرضية والخسائر الناجمة عن التلف الناتج عن النقل.
فقدان الإبداع من قبل الموظفين. نوع خطير من الخسارة يؤثر على المركز العام للشركة. إذا كان الشخص لا يهتم بما يفعله ، فلا يجب أن يتوقع منه المسؤولية عن النتيجة ، ناهيك عن المسؤولية عن جودة العمل الذي يقوم به.
لذلك اتضح أنه إذا تم ملء الأنبوب بكامل طاقته عند المدخل ، فبعد مرور سلسلة من الخسائر ، ينخفض التدفق عند المخرج بأكثر من النصف (انظر الشكل 1).
الشكل 1. سلسلة القيمة
خريطة القيمة
ساعد في تحديد الخطوات والأنشطة التي لا تضيف قيمة وتصف الحالة بموضوعية عمليات الانتاجيمكن البطاقة الوضع الحاليالإنتاج (انظر الشكل 2). ستتيح لك الصورة الرسومية إجراء تقييم نقدي لنمو القيمة في كل مرحلة وتحديد الأنشطة التي لا تحقق قيمة للمنتج. إنها أداة مهمة من أجل:
- لا ترى فقط إجراءً منفردًا (على سبيل المثال ، اللحام أو التجميع أو الطلاء) ، بل ترى التدفق الكامل لتصنيع المنتج ككل ؛
- لا تكتشف الخسائر فحسب ، بل تكتشف أيضًا مصادرها في تدفق القيمة ؛
- اتخاذ القرارات المتعلقة بالتدفق مفهومة ويمكن الوصول إليها للمناقشة ، وإلا فسيتم تنفيذ القرارات والإجراءات في المتاجر بنفس الطريقة السابقة ، أي بأي حال من الأحوال أو بطريقة ما ؛
- إظهار العلاقة بين المعلومات وتدفق المواد (لا توجد أداة أخرى قادرة على القيام بذلك).
الشكل 2. عملية خلق القيمة
كونها في الواقع مخططًا ، وأساسًا لتنفيذ الإنتاج الخالي من الهدر ، تساعد الخريطة في التخطيط لحركة التدفق بالكامل - غالبًا ما يتم تجاهل هذه الحقيقة ، مما يؤدي إلى فشل محاولات تنفيذ الإنتاج الخالي من الهدر. تعد الخريطة أكثر فائدة بكثير من العديد من الأدوات والمخططات الكمية التي تحسب ببساطة الخطوات غير ذات القيمة المضافة ، والمهل الزمنية ، ومسافات انتقال المنتج ، ومستويات المخزون ، وما إلى ذلك. إنها أداة جودة توضح بالتفصيل كيفية تنظيم العمل. تسوق و قسم منفصل ، بحيث يظهر تدفق مستمر.
يعد إنشاء التدفق المستمر مشروعًا طويل الأجل ومكلفًا في العادة ، لأنه لا يتطلب جهودًا وموارد بشرية فحسب ، بل يتطلب أيضًا استثمارات مالية في معدات جديدة. ومع الأخذ في الاعتبار حقيقة أنه حتى حركة المعدات في ورش العمل تستغرق وقتًا وتكاليف مادية ، يمكنك نسيان التكاليف المنخفضة والبخل. لذلك ، قد يستغرق الأمر أكثر من عام للقضاء على الخسائر في أي منطقة إنتاج واحدة. وقبل إطلاق مشروع بهذا الحجم ، تحتاج إلى تحديد سبب نجاح هذا المشروع وما الذي يمكن تحقيقه نتيجة للتغييرات. يجب أن تكون نقطة البداية خريطة الحالة الحالية.
خريطة تيار القيمة
يعد تخطيط تدفق القيمة أحد أهم الأدوات لبناء مؤسسة Lean. تنقسم هذه العملية إلى مرحلتين.
بناء خريطة للوضع الحالي:
- التحليلات العمليات الحاليةفي تيار القيمة
- تحديد مصادر الخسائر.
بناء خريطة دولة مستقبلية (ما نريد الحصول عليه):
- إنشاء خطة للقضاء على مصادر الخسائر ؛
- تعيين مدير المشروع لتنفيذ التغييرات في هذا المسار ؛
- تحديد مؤشرات الأداء الرئيسية لتنفيذ المشروع ؛
- تحديد توقيت المشروع.
تشبه خريطة تدفق القيمة صورة لما يحدث في المؤسسة في الواقع ، وليس في خيالنا. في كثير من الأحيان ، عند بناء خريطة للوضع الحالي ، يتم الكشف عن انتهاكات جسيمة للتكنولوجيا ، ويختلف وقت تنفيذ عمليات معينة اختلافًا كبيرًا عن ذلك الموضح في المستندات (العملية الفنية). تتيح لك خريطة التدفق رؤية التدفق بالكامل من منظور عين الطائر.
البيانات المسجلة عند بناء خريطة التدفق:
- اسم الجهاز أو العملية ؛
- وقت العملية أو العملية (الوقت الفعلي ، وليس الوقت المشار إليه في الوثائق الموجودة حاليًا) ؛
- موثوقية المعدات (وقت تشغيل المعدات بدون أعطال ،٪) ؛
- عدد المشغلين أو الموظفين الذين يؤدون عملية معينة أو يخدمون العملية ؛
- توافر المخزونات في المستودع من المواد الخام والمواد لتيار معين (بالأيام) ، وكمية المنتجات النهائية (بالأيام) ، وعدد مخزون العمل بين العمليات وبين ورش العمل قيد التنفيذ في هذا التيار ( في الايام)؛
- إجراءات وشروط تقديم الطلبات مع الموردين في هذا التدفق ؛
- ترتيب الشحن وتوقيت تكوين الطلبات من العملاء لـ هذه الأنواعمنتج أو مجموعة منتجات ؛
- takt time - الوقت الذي يجب أن تُصنع فيه وحدة الإنتاج. محسوبة على أساس احتياجات العميل (في اليوم أو في كل وردية). مثال: وقت كامليوم العمل أو المناوبة ، مقسومًا على كمية المنتجات النهائية التي يجب شحنها إلى العميل لنفس الفترة ؛
- وقت الدورة ، أي وقت تنفيذ عملية واحدة (يجب أن يكون أقل من وقت takt أو مساويًا له) ؛
- إجراءات تخطيط الإنتاج في المؤسسة ، وكذلك مستوى تفاصيل هذه الخطط وإجراءات تمرير هذه المستندات.
تتمثل المهمة الرئيسية لهذا العمل في تقييم كفاءة التدفق. يتم حساب كفاءة التدفق على أنها إجمالي وقت العمليات التي تضيف قيمة إلى المنتج من وجهة نظر العميل ، مقسومًا على إجمالي الوقت الذي يمر فيه المنتج عبر التدفق بالكامل ومضروبًا في 100٪. في الشركات الروسية ، هذا الرقم أقل من 2٪ ، لذلك لا يزال هناك الكثير من العمل الذي يتعين القيام به.
ربما تكون خريطة الحالة الحالية هي الأداة الأكثر فاعلية لتحليل أداء أي مؤسسة ، بما في ذلك قطاع الخدمات ، والخدمات المصرفية ، والرعاية الصحية ، وحتى التصنيع. من الواضح أنه يسمح لك بمشاهدة المصادر الرئيسية للخسائر ووضع خطة للقضاء عليها أو تقليلها بشكل كبير.
معلومات عن الشركة
كمثال ، خذ TWI Industries ، التي تصنع مجموعة من مكونات الجرارات. سننظر في مجموعة واحدة فقط من المنتجات - رافعات التوجيه (قضبان) ، المنتجة في تكوينات مختلفة. عملاء هذه المجموعة من المنتجات هم من مصنعي الجرارات ومؤسسات إصلاح مختلفة.
نظرًا لتنوع التكوينات ، تختلف متطلبات العملاء من أمر إلى آخر. تستغرق دورة عملية الإنتاج لتنفيذ الطلب 27 يومًا. طول الإنتاج والعمل الجاري على الطلبات التي تم استلامها بالفعل يجبر الشركة على الإعلان عن مهلة 60 يومًا. لكن عملاء الشركة لا يمكنهم الإشارة بدقة إلى مقدار الطلب قبل أسبوعين من شحن الطلب. تؤدي التعديلات المستمرة إلى حقيقة أن جميع الطلبات التي تدخل المحلات التجارية دائمًا ما تكون عاجلة. يقوم قسم مراقبة الإنتاج بتسليم طلبات العملاء بالترتيب الذي وصلوا به ، ولكن في أرض المتجر يتم تجميعها في مجموعات وفقًا لتكوين الأجزاء من أجل تقليل وقت التغيير قدر الإمكان ، مما يؤدي أيضًا إلى الاندفاع واندفاع العمل.
معلومات المنتج
ذراع التوجيه عبارة عن قضيب معدني بنهايات مختومة ملحومة من كل جانب. تقوم الشركة بتصنيع أذرع التوجيه مقاسات مختلفة، بقطرين ، مع ثلاثة أنواع من النصائح (يمكن أن يكون لكل جانب من جوانب ذراع التوجيه أطراف مختلفة). وهكذا ، تنتج الشركة 240 نوعًا مختلفًا من رافعات التوجيه. يتم توفير قضبان الصلب للإنتاج من قبل شركة Michigan Steel Co (مدة التصنيع 16 أسبوعًا ، ويتم الشحن 23 مرة في الشهر). يتم الحصول على فراغات تلميح من Indiana Castings (مهلة 12 أسبوعًا ، يتم شحنها مرتين في الشهر).
لذلك ، تنخفض متطلبات العملاء إلى ما يلي: يريدون استلام 24 ألف قطعة من البضائع شهريًا ، ولكن في نفس الوقت يجب أن يكون الحد الأدنى لكمية الطلب أقل ما يمكن - من 25 إلى 200 قطعة ، في المتوسط - 50 قطع ، والمنتج النهائي يجب أن يعبأ في صناديق مصنوعة من الكرتون المضلع مع خمسة أذرع توجيه لكل صندوق ويتم تسليمها عدة مرات في اليوم بالشاحنات. في المقابل ، تطلب TWI ، مع الأخذ في الاعتبار التغيير المتكرر في رغبات العملاء ، تقديم الطلبات قبل 560 يومًا من تاريخ شحن المنتج النهائي. ومع ذلك ، لا يمنع هذا العملاء من تعديل كمية الأمر قبل أسبوعين من تاريخ الشحن.
عمليات التصنيع
تشمل عمليات تصنيع ذراع التوجيه في TWI قطع قضيب معدني ، وأغطية نهاية اللحام عليه ، وإزالة الأزيز (تنظيف علامات اللحام على الحائط) ، والطلاء بواسطة مقاول خارجي من الباطن ، وتجميع غطاء النهاية. تصنع البطانات ذات الأطراف المزورة أيضًا بواسطة TWI. يتم تجميع أذرع التوجيه النهائية في مجموعات وشحنها للعملاء يوميًا.
يتطلب تغيير طول الرافعة تغييرًا لمدة 15 دقيقة للمعدات لعمليات القطع واللحام والفصل. يتطلب تغيير قطر القضيب ساعة من تغيير المعدات ، وهو ما يرجع إلى حد كبير إلى معيار مراقبة الجودة. يتطلب التغيير بين الأنواع الثلاثة للرؤوس المطروقة تحولًا لمدة ساعتين إلى عمليات ختم الآلة.
وقت العمل
20 يوم في الشهر. تعمل جميع وحدات الإنتاج في نوبتين لمدة ثماني ساعات مع العمل الإضافي إذا لزم الأمر. تحتوي كل نوبة على فترتين لمدة 15 دقيقة لا يتم خلالها إجراء معالجة يدوية. لا يتم دفع وقت الغداء.
قسم مراقبة الإنتاج
يتلقى قسم التحكم طلبات العملاء في غضون 60 يومًا ، ويقوم بإعداد أمر عمل لكل عميل ونقلها إلى الإنتاج. يضع الطلبات مع الموردين للقضبان والنصائح قبل ستة أسابيع من الاستلام المتوقع للطلب. ينقل قائمة الأولويات يوميًا إلى مديري الإنتاج ، الذين يقومون بتسلسل تنفيذ أوامر التصنيع وفقًا لهذه القائمة. قبل أسبوعين من الشحن ، يتلقى القسم توضيحات من العملاء بشأن أحجام الطلبات ويشير إلى الحاجة إلى الإسراع في تنفيذ هذه الطلبات. يتم إصدار جدول التسليم إلى قسم شحن البضائع الجاهزة على أساس يومي.
معلومات حول العملية والعمليات
يتم تنفيذ عملية "القطع" يدويًا بواسطة عامل واحد بمنشار خاص (لمنتجات TWI المختلفة). وقت الدورة - 15 ثانية. وقت التغيير هو 15 دقيقة لقياس الطول وساعة لقياس القطر. الموثوقية - 100٪. المخزونات المراقبة - 20 يومًا قبل القطع ، وخمسة أيام بعد القطع.
عملية "اللحام أنا".يتم لحام الطرف الأول المعالج بالقضيب. يتم تنفيذ العملية تلقائيًا ، يقوم المشغل بالتحميل والتفريغ الخارجي. مدة الدورة: عامل التشغيل - 10 ثوان ، الآلة - 30 ثانية. وقت التغيير هو 15 دقيقة لتغييرات الطول وساعة لتغيير القطر. الموثوقية - 90٪. جرد مراقب لمدة ثلاثة أيام بعد الصفقة.
عملية "اللحام الثاني".يتم لحام طرف ميكانيكي ثان بالقضيب. يتم تنفيذ العملية تلقائيًا. تتوافق جميع المؤشرات مع مؤشرات عملية "اللحام I" ، باستثناء الموثوقية - فهي أقل قليلاً وتساوي 80٪.
عملية إزالة الأزيز.يتم تنفيذ العملية تلقائيًا. يقوم المشغل بالتحميل والتفريغ الخارجي. مدة الدورة: عامل التشغيل - 10 ثوان ، الآلة - 30 ثانية. وقت التغيير هو 15 دقيقة لتغييرات الطول وساعة لتغيير القطر. الموثوقية - 100٪. جرد مراقب لمدة خمسة أيام بعد إزالة الأزيز.
عملية "الرسم"التي ينتجها مقاول من الباطن خارجي. وقت التلوين - يومين. تقوم الشاحنة كل يوم بتوصيل أذرع غير مصبوغة وتجلب أذرع مطلية. جرد مراقب لمدة يومين لدى المقاول من الباطن وستة أيام بعد الطلاء.
عملية التجميع. يتم تنفيذ العملية يدويًا بواسطة ستة مشغلين. الوقت الكليلكل وحدة إنتاج - 195 ثانية. وقت التغيير - 10 دقائق عند تغيير نوع الإكرامية. الموثوقية - 100٪. جرد مراقب - لمدة أربعة أيام في مستودع البضائع الجاهزة.
عملية " الترميم الميكانيكينصائح."يتم تنفيذ العملية تلقائيًا بواسطة مشغل واحد. وقت الدورة - 30 ثانية. وقت التغيير ساعتان. الموثوقية - 100٪. قوائم الجرد المرصودة - 20 يومًا قبل المعالجة ، وأربعة أيام بعد المعالجة.
تشغيل قسم الشحن.يلتقط المنتجات النهائية من المستودع ويكمل الطلبات لتسليمها إلى العميل.
لذلك يتم جمع البيانات. بناءً على هذه البيانات ، نرسم خريطة للحالة الحالية (انظر الملحق 1).
خريطة الدولة المستقبلية
الغرض من نظام lean manufacturing هو إنشاء سلسلة من عمليات الوحدة: تم - تمرر. يجب بعد ذلك تحليل حالة الإنتاج المعروضة بيانياً ويجب تطوير خطوات لتغيير العملية ، مع التأكد من تنسيقها مع إستراتيجية الشركة. ما مدى أهمية هذا يمكن رؤيته من مثال أقلام نافورة باركر. هذا منتج النخبة ، باهظ الثمن ، هدية. قرر أحد المديرين زيادة الإنتاج بجدية بحيث كان Parker موجودًا في جميع متاجر القرطاسية. نتيجة لذلك ، توقف بيع الأقلام على الإطلاق ، حيث تم وضعها على أنها منتجات النخبة ، وليس منتجًا يوميًا ، وتعرضت صورة الشركة لأضرار جسيمة.
على خريطة الحالة الحالية ، نسلط الضوء على المناطق التي يمكن بالفعل تقليل الخسائر فيها. عندما يكون من المستحيل القيام بذلك ، نقوم بتركيب محلات السوبر ماركت - المستودعات بمخزون منظم بشكل صارم. بعد ذلك ، نضع خطة عمل ، ونعين أشخاصًا مسؤولين ، ونضع مواعيد نهائية.
يجب أن يكون كل شيء محددًا. على سبيل المثال ، إذا قررنا البدء في بناء تدفق في أي موقع إنتاج ، حيثما أمكن ذلك ، فيجب تنظيم كل إجراء في هذا الاتجاه في الوقت المناسب ، ويجب تحديد الأموال اللازمة وتخصيصها ، ويجب تعيين شخص مسؤول عن هذا الإجراء .
لذلك ، تغرق متاجر TWI بالطلبات التي تم وضعها في الإنتاج بسرعة كبيرة. تم تبديلها وتعديلها لتحسين عمليات تغيير المعدات وتلبية طلبات العملاء الأكثر إلحاحًا. نظرًا لأن عملية اللحام الأولى تستغرق 30 دقيقة فقط لكل دفعة ، ومن ثم تتم معالجتها أولاً يصرف أولاً حتى الشحن ، يمكن تقليل مهلة طلب العميل بمقدار ثلاثة أيام. يجب تقليل أوقات التغيير لعمليات اللحام وإزالة الحواف إلى خمس دقائق أو أقل بحيث يمكن إنتاج تكوينات مختلفة لذراع التوجيه أقرب إلى تسلسل طلب العميل.
تتنوع متطلبات العملاء لتكوينات ذراع توجيه الجرارات وتكون أوقات إعادة الطلب طويلة ، لذلك من غير العملي للغاية تخزين أذرع جاهزة مثل السوبر ماركت في نهاية سلسلة القيمة. من الضروري جدولة العمل من الأسفل إلى الأعلى على طول السلسلة حتى العملية الأولى حيث يظهر الاختلاف في التكوين (في هذه الحالة ، اللحام الأول) ، ثم استخدام مبدأ FIFO. في نقطة الجدولة هذه ، من خلال إضاعة 30 دقيقة بخطوة جدولة مدتها 30 دقيقة ، يمكن تجنب الإفراط في الإنتاج و "الدفع" عبر تيار FIFO.
الشكل 5. رموز الملحق 1 و 2
يمكن للشركة تطوير تدفق مستمر بين عمليات اللحام وإزالة الحواف. سيخدم أحد المشغلين هذه العمليات ، ويقوم بتحميل ونقل الأجزاء من آلة أوتوماتيكية إلى أخرى. سوف تحتاج TWI إلى توقيت دورة اللحام / المسح بشكل أسرع من وقت takt البالغ 45 ثانية إلى 39 ثانية تقريبًا للسماح بـ 12 عملية إعادة تموضع لكل نوبة. نظرًا لعدم وجود تغيير مطلوب عند تجميع المنتجات النهائية ، يمكن أن تكون الدورة قريبة من وقت takt ، مما يسمح لخمسة مشغلين بالتجميع.
في هذه الحالة ، يعتمد طول الخطوة البالغ 30 دقيقة على متوسط كمية الطلب البالغة 50 وحدة وخمس دقائق من التغيير بين أوامر اللحام / التنظيف. مع حجم طلب العميل 600 وحدة لكل وردية ووقت دورة يبلغ 39 ثانية ، هناك ساعة متبقية لـ 12 عملية تبديل بين الدُفعات. لتنظيم خطوة ، سيقوم قسم التحكم في الإنتاج بدمج الطلبات الصغيرة وتقسيم الطلبات الكبيرة إلى مجموعات من 50 وحدة. يجب أن يجد قسم مراقبة الإنتاج أيضًا توازنًا في مزيج المنتجات لتقليل مخزون السوبر ماركت في عمليات القطع والختم الأولية. وبالتالي ، لن تفي TWI بالأوامر في التسلسل الذي تأتي به ، ولكنها قريبة جدًا منه.
مع مراعاة التعليقات المقدمة ، يمكن لعملاء TWI تقديم طلباتهم قبل أسبوعين. يمكن أن يؤدي إنتاج قضبان القطع وختم الأطراف إلى دفع نظام السحب بطريقة السوبر ماركت. وبالمثل ، يمكن طلب قضبان وفراغات غير مقطوعة للنصائح عند استخدامها وعند تخزين المواد الخام ، مثل السوبر ماركت. هذا يلغي الحاجة إلى التحكم في الإنتاج ، حيث تؤدي طلبات العملاء إلى طلب المواد الخام من الموردين على الفور. بالنظر إلى التحليل الذي تم إجراؤه ، يمكن عكس التغييرات في خريطة الحالة المستقبلية كما هو موضح في الملحق 2.
توضح الخريطة كيف انخفضت المخزونات بين العمليات وتدفقات المعلومات والوظائف ووقت تنفيذ الطلبات ، وفي نفس الوقت زادت الإنتاجية.
رسم الخرائط تيار القيمة
مخطط تدفق القيمة هو رسم تخطيطي بسيط ومرئي إلى حد ما يصور المواد وتدفق المعلومات اللازمة لتوفير منتج أو خدمة للمستهلك النهائي. تتيح خريطة تدفق القيمة رؤية الاختناقات في التدفق على الفور ، وبناءً على تحليلها ، تحدد جميع التكاليف والعمليات غير المنتجة ، وتضع خطة تحسين.
يتضمن تخطيط تدفق القيمة الخطوات التالية:
1. توثيق خريطة الدولة الحالية
2. تحليل تدفق الإنتاج
3. إنشاء خريطة الدولة المستقبلية
4. تطوير خطة التحسين
خيط أريادن
قيمة العميل هي مبدأ أساسي من مبادئ اللين ، والذي بموجبه يتمثل الهدف من نشر نظام ليّن في تحديد الهدر الذي لا يضيف قيمة للمنتج و / أو الخدمة من وجهة نظر العميل والقضاء عليه. وفقًا لذلك ، إذا قررت أن تسلك طريق الإنتاج الخالي من الهدر ، فأنت تحتاج فقط إلى تعلم رؤية مجمل العمليات المترابطة والمتفاعلة للشركة من خلال عيون عميلك. ولكن كيف يمكن القيام بذلك؟ ما مدى سهولة ووضوح تصور العلاقة بين تدفقات المواد والمعلومات الخاصة بالشركة ، وكيفية تحليلها بحثًا عن الخسائر؟
إذا نظرنا إلى الشركة من وجهة نظر النهج التقليدي ، الذي يصفها بأنها هيكل وظيفي هرمي ، فسنرى متاهة حقيقية ، والتي من المستحيل تمامًا تقييمها من حيث الكفاءة التشغيلية. لذلك ، نحتاج إلى نوع من خيط Ariadne ، والذي من شأنه أن يسمح لنا بربط صورة واحدة بجميع الروابط في سلسلة الإنتاج لإنشاء المنتج النهائي. مثل هذا الخيط هو نهج العملية لوصف أنشطة الشركة. العملية عبارة عن علاقة منطقية معينة من الإجراءات للحصول على المنتج النهائي و / أو الخدمة. من المنطقي أنه من المستحيل رؤية كل هذه الإجراءات في نفس الوقت ، حيث يتم فصلها في الزمان والمكان.
لذلك ، من أجل تحليل تيار القيمة بأكمله والعمليات المكونة له ، هناك حاجة إلى منهجية تطبيقية تسمح للفرد بدراسة ووصف كل عملية بدقة ، مع الإشارة إلى علاقتها. من الممكن وصف العمليات وعلاقاتها المتبادلة بالكلمات (وهو ما يحدث في الواقع في لوائح المصنع التي يصعب للغاية فهمها بشكل لا لبس فيه) ، ولكن هذا سيزيد من احتمال حدوث أخطاء في تحليل التدفق ، حيث أناس مختلفونفهم الكلمات بشكل مختلف ، ولكن يمكنك وصف الشيء نفسه بشكل تخطيطي باستخدام أدوات التخيل. لهذا السبب نحتاج إلى أداة تسمح لنا بالإنشاء وصف مرئيالعمليات ، مع مراعاة علاقتها. في Lean manufacturing ، تُعد هذه الأداة خريطة تدفق القيمة (يُشار إليها أحيانًا باسم VSM - وهذا اختصار لخريطة تدفق القيمة الإنجليزية).
خريطة تدفق القيمة (VSM)
خريطة تدفق القيمة هي رسم تخطيطي بسيط ومرئي إلى حد ما يصور المؤشرات الأساسية والعلاقة بين تدفقات المواد والمعلومات لإنشاء المنتج النهائي و / أو الخدمة. يعد استخدام أداة VSM عاملاً أساسيًا لنشر Lean في الشركة. بادئ ذي بدء ، تسمح خريطة تدفق القيمة للعميل برؤية تدفق القيمة بالكامل "من الباب إلى الباب" والعمليات الفردية. يتيح لك هذا تحديد مجالات المشاكل المرتبطة بالخسائر: على سبيل المثال ، الأنشطة التي لا تخلق قيمة من وجهة نظر العميل ؛ فائض مخزون المواد الخام والعمل الجاري والمنتجات النهائية ؛ ضياع وقت الموظف ؛ تيار القيمة غير المتكافئ والمضغوط ؛ نظام منظم بشكل غير صحيح لتخطيط وتنظيم الإنتاج ، إلخ. في بعض الأحيان عند إنشاء خرائط التدفق ، يتم إجراء مشاورات مع المستهلكين من أجل تحديد متطلباتهم الفعلية ورغباتهم ، بحيث يمكن بعد ذلك الاتفاق على مبادئ تنظيم الإنتاج وفقًا لهذه المتطلبات. بعد كل شيء ، لا يمكن للمرء التركيز فقط على رأي الفرد حول احتياجات العميل: من المعروف أنه في كثير من الأحيان تنتج الشركة منتجات أكثر مما يتطلبه العميل بالفعل ، مع منح هذه المنتجات بخصائص ليست ذات قيمة من وجهة نظر وجهة نظر المستهلك المحتمل. كقاعدة عامة ، اتضح أن العميل مهتم بإضافة القيمة في الوقت الفعلي ، والتي لا تمثل سوى 2-5٪ من إجمالي وقت الإنتاج للمنتج و / أو الخدمة.
الحالة المستقبلية لتيار القيمة
يجب أن نتذكر أن خريطة تدفق القيمة الحالية في حد ذاتها ليست غاية في حد ذاتها لمنهجية VSM ، إنها أداة تحليل التدفق التي توفر لغة مشتركة لصنع القرار على جميع مستويات الشركة ولتنفيذها الإضافي. لذلك ، بعد أن قمنا ببناء خريطة للوضع الحالي ، يجب ألا نتوقف عند هذا الحد بأي حال من الأحوال. تتمثل الخطوة التالية في عمل الخرائط في تقييم الوضع في المجالات الرئيسية للتدفق ، وتحديد مجالات المشكلة الرئيسية وتطويرها. الحلول المثلىلتحسينها. بعد التحليل ، يتم إنشاء خريطة حالة مستقبلية توضح خيارات التحسين لتحقيق المزيد مستوى عالكفاءة التدفق في وقت ما في المستقبل. وبالتوازي مع ذلك ، يتم وضع خطة تنفيذ مفصلة لتغييرات التحسين.
في بعض الأحيان يكون من المنطقي بناء خريطة حالة مثالية لتيار القيمة تحدد متجهًا لتحسينات التدفق المتزايد. تُظهر هذه الخريطة حالة التدفق التي يمكن تحقيقها من خلال النشر الشامل لـ Lean.
وبالتالي ، يتيح لك العمل باستخدام خرائط التدفق زيادة كفاءة الشركة بأكملها وتجنب الأخطاء النموذجية في اختيار أدوات Lean ومجالات استخدامها ، والتي تؤدي عادةً إلى إنشاء مجالات تحسين معزولة غير فعالة.
تتويج تخطيط تدفق القيمة هو العمل المتكامل مع جميع التدفقات الإنتاجية والإدارية في الشركة ، فضلاً عن تحليل التفاعلات مع الموردين والعملاء ، مما يسمح لك بإطلاق مبدأ التحسين المستمر وتطويره في جميع أنحاء سلسلة القيمة بأكملها ، داخل الشركة وخارجها - وهذا مهم للغاية ، لأنه في ظل الظروف السوق الحديثلم يعد المنتجون الأفراد هم من يتنافسون ، ولكن سلاسل الموردين والمنتجين.
تذكير عند بناء خريطة قيمة العميل
1. اختيار منتج لرسم الخرائط (يجب إنتاج المنتج في وقت التعيين)
2. عرض المراقب على إدارة الورشة على العاملين لتوضيح أهداف العمل وإقامة الاتصالات
3. التحضير لرسم الخرائط: اطبع النماذج الضرورية وورق الخرائط وأقلام الرصاص وساعة التوقيت وما إلى ذلك.
4. انتقل إلى أسفل من مستهلك المنتج (قد يكون مستودعًا للمنتجات النهائية أو موقع تجميع) ، أو الإنتاج ، أو متجر فارغ ، أو إلى مستودع معدني أو مستودع فارغ
5. إنشاء تطبيق "خريطة العمل الموحد" رقم 1 الذي يعكس الحركة الفعلية للجزء عبر مكان العمل ، والموقع ، وورشة العمل ، والمصنع (مخطط سباغيتي)
6. أخذ القياسات لكل عملية وملء استمارة "بطاقة تسجيل الوقت" رقم 2
7. بناءً على القياسات ، املأ نموذج "بطاقة تسجيل الوقت" التذييل رقم 2 (قائمة العمليات ، متوسط وقت الإنتاج للعمليات ، المعدات المستخدمة)
8. املأ نموذج "بطاقة تسجيل الوقت" الملحق رقم 2 لجميع العمليات (وقت الدورة ، ووقت المعالجة ، وأوقات الراحة ، وما إلى ذلك)
9. على ورقة ، رتب العمليات وفقًا لتنفيذ العملية
10. تحديد عدد الفراغات والأجزاء النهائية الموجودة في مكان العمل ووضع علامة على الورقة في شكل مثلث وتحديد الكمية
11. رتب الحركات على الخريطة في شكل سهم ووضح: المسافة والوقت وطريقة الحركة (رافعة بشعاع ، على عربة ، إلخ)
يتم تحديد وقت الاحتفاظ بالمخزون بضرب كمية المخزون في وقت دورة العملية التالية.
12. في الجزء السفلي من الخريطة ، قم بتمييز الجدول الزمني ووقت القيمة المضافة والمؤامرة غير ذي القيمة المضافة
- عدم إضافة القيمة: الحركات ، الأسهم ، التوقعات ، إلخ.
- الإضافة: وقت المعالجة الجزئي
13. في الجزء العلوي من الخريطة ، حدد تدفق المعلومات.
14. املأ الجدول الموجود في ورقة "مؤشرات الوضع الحالي".
15. تحليل خريطة الحالة الحالية لتحديد الاختناقات (أماكن للقضاء على الخسائر) وتعيينها كنجمة
16. بناءً على التحليل ، قم بإنشاء خريطة حالة مستقبلية مع مراعاة الأهداف (تقليل المخزون ، وزيادة استخدام المعدات ، وتقليل المساحة ، ووقت takt ، وما إلى ذلك) وقم بملء "مؤشرات الحالة المستقبلية".
17. بناء "مخطط سباغيتي" للفترة المقبلة
18. تنسيق النسخة الأولية مع إدارة ورشة العمل وأمين المشروع
19. تجميع الأنشطة من أجل الانتقال خطوة بخطوة من الحالة الحالية إلى المستقبل ، وتحديد المعالم مع الإشارة إلى الموعد النهائي
20. احسب التأثير الاقتصادي لكل بند من بنود الأنشطة
21. الموافقة على المشروع النهائي مع أمين المشروع
مثال
خريطة تدفق القيمة: ما هو منتج التدفق؟
Vrungel: معذرةً ، قال لوم إنك تعرف كيف تفهم البطاقات؟
فوكس: أوه ، هذا كل ما تريده. البطاقات هي خبزي. ليس فقط البحرية ، ولكن أوراق اللعب.
"مغامرات الكابتن فرونجيل"
لأول مرة عندما تلقيت مهمة "إنشاء خريطة تدفق" ، فكرت: الأمر بسيط مثل تقشير الكمثرى. أنا أعرف كيفية التسمية تفاصيل متنوعةفي عملية الإنتاج ، أعرف من أين أبدأ وكيف أستمر ... بعد كل شيء ، قمت برسم العمليات التجارية لمعايير المؤسسة في "حياتي الماضية" ، وإليكم رموز أخرى وشروط معينة. و هذا كل شيء.
بدأت تفاصيل المرح عندما سأل العملاء ، "ما مدى التفاصيل التي ينبغي رسم الخريطة؟" هذا هو المكان الذي بدأت فيه ... على مدى السنوات القليلة الماضية ، بهذه البساطة و أسئلة صعبةالمتعلقة بخرائط التدفق ، تراكمت الكثير ...
ولكن لكي لا أكون غير متسق ، أود أن أبدأ بسؤال آخر.
في الواقع ، ينتظر "الخطأ" الأول في الوقت الذي تحاول فيه تحديد المنتج الذي تريد عكسه في الدفق.
ما هو "المنتج"؟لنبدأ بالتعريفات.
مخطط تدفق القيمة (VSM)
رسم تخطيطي بسيط يصور كل خطوة في تدفق المواد والمعلومات اللازمة لتلبية طلب العميل. (مسرد مصور لـ Lean Manufacturing ، محرر سي مارشوينسكي ودي شوك ، ألبينا بيزنس بوكس ، 2005 ، ص 51)
ليس واضحا جدا. ولكن ، منطقيًا ، تصور خريطة تدفق القيمة تدفق القيمة. دعنا نحصل على تعريف التدفق:
قيمة التيار
جميع الأنشطة ، سواء خلق القيمة أو عدم إنشاء القيمة ، والتي تسمح للمنتج بالمرور بجميع العمليات: من تطوير المفهوم إلى إطلاق الإنتاج ومن قبول الطلب إلى التسليم. تشمل هذه الأنشطة معالجة المعلومات الواردة من العميل ، وكذلك عمليات تحويل المنتج أثناء انتقاله إلى العميل. (مسرد مصور لتصنيع العجاف ، طبعة سي مارشوينسكي ود. شوك ، ألبينا بيزنس بوكس ، 2005 ، ص 78)
يوجد بالفعل رابط للمنتج هنا. لكن لا يوجد تعريف للمنتج في المسرد - مفهوم بسيط للغاية بحيث لا يمكن وضعه في القاموس. ومع ذلك ، من الواضح أنه إذا كان التدفق يشمل جميع الأنشطة من المفهوم إلى الإطلاق ومن قبول الطلب إلى التسليم ، فيجب أن يكون المنتج مناسبًا للمستهلك النهائي - أي يجب أن يكون لها قيمة خاصة بها لأولئك الذين نبيعها لهم.
لقد حذفت تعريف القيمة ، وإلا فإننا سنذهب بعيدًا إلى الجانب.
لذلك مع المنتجات في الإنتاج التقليدي ، تبدأ الأسئلة الأولى عند إنشاء خريطة تدفق القيمة. ما يعتبر منتجًا للتدفق - منتج واحد ، مجموعة منتجات ، على أي أساس لتجميع المنتجات ، وما إلى ذلك ... في الواقع ، كل شيء يبدأ حتى قبل ذلك - بعد كل شيء ، كل منتج له مستهلكه الخاص ، مما يعني أنه يمكنك فقط تجميع المنتجات التي لها نفس المستهلكين. لكن هذا مرة أخرى خروج.
لا تصنع العديد من الصناعات منتجًا واحدًا أو اثنين أو ثلاثة منتجات متشابهة. إذا كنت تعمل في مثل هذا الإنتاج ، فأنت محظوظ. ولكن ماذا لو كان هناك عدة آلاف من النماذج وكان إنتاجها مترابطًا جزئيًا - إذا كنت تريد إنشاء "منتج أ" واحد ، فأنت بحاجة إلى عمل ثلاثة "منتج ب" في نفس الوقت؟
لنفترض أننا رسمنا خريطة لإنتاج شواهد القبور الجرانيتية الطبيعية. يتم أخذ كتلة كبيرة من الجرانيت ، ونشرها إلى قطع ، ويتم الحصول على بعض شواهد القبور ، والبعض الآخر - فقط حجارة الرصيف. ومن الصغار جدا - ثقالة الورق. ثقالة الورق ليست فقط قطعة من الجرانيت ، ولكنها أيضًا مقبض تمثال صغير من الحديد الزهر ، مصنوع على جهاز منفصل. ويتم طحن الأوزان الورقية وشواهد القبور وألواح الرصف على نفس الجهاز. كيفية رسم تدفق إنتاج شواهد القبور في هذه الحالة؟
إنها ليست خريطة بعد ، إنها مجرد رسم تخطيطي ، وقد أثيرت بالفعل الكثير من الأسئلة.
الحل المثالي هو حل تشابك المسارات ، وفصل مجموعات المنتجات عن بعضها البعض ، وإطلاق المنتجات الفردية بشكل منفصل - أولاً "المنتج أ" ، ثم "المنتج ب" إذا لزم الأمر. وبقدر الضرورة ، وليس بقدر ما اتضح.
لكن في بعض الأحيان ، يتطلب مثل هذا الحل المثالي مراجعة مفهوم الإنتاج ، أو حتى الاستبدال الكامل لمجمع الماكينات. ما يجب القيام به؟
لنتذكر لماذا نحتاج إلى خريطة تدفق القيمة = خريطة تدفق القيمة. فيما يلي الهدفان الرئيسيان:
1. انظر إلى التدفق بأكمله ككل (ومكّن المديرين من التحدث باللغة نفسها حول مشاكل "مراحل" التدفق المختلفة).
2. انظر جميع الخسائر الموجودة في الدفق.
نحن نعلم بالفعل أن لدينا "مجموعة متشابكة من المشاكل" المرتبطة بالتوجيه الماكرة وأن هذا التشابك يحتاج إلى حل. ستكون الخريطة التفصيلية مفيدة لذلك ، ولكن يمكن اتخاذ الخطوات الأولى بدونها.
إذن ما الذي يمكن أن يضحّي به "المثالي" حتى تظل البطاقة ذات قيمة؟
بالضبط تعريف "المنتج" أو ، على وجه التحديد ، "المنتج الأساسي لخريطة التدفق".
لنفترض أننا نأخذ شيئًا غير نمطي على أنه "المنتج الأساسي" ، أو حتى أنه ليس منتجًا كاملاً ، ولكن جزءًا منه ، لا نهتم بكيفية استمرار إنتاج بقية هذا المنتج حتى لحظة دمجها.
هل سنتمكن من رؤية التدفق الكامل لهذا "المنتج غير العادي" أو هذا الجزء من بعض المنتجات؟
خذ على سبيل المثال المنتج الأساسي لثقل الورق. ورسم طريقه. ماذا سيحدث؟ العمليات المتعلقة بمعالجة "بلاطات الرصيف" سوف تقع خارج اهتمامنا. لكن في الوقت نفسه ، سنرى كل التأخيرات المرتبطة بمراحل فصل قطع وزن الورق عن كتلة الجرانيت الكلية ، سنرى أنه قبل طحن المنتجات شبه المصنعة تنتظر في طابور ، وقبل الانضمام إلى مقبض التمثال ، يتم سحق دفعات الأوزان الورقية إلى قطع لتتناسب مع الدُفعات التي يتم من خلالها صب التماثيل.
هل سنتمكن من رؤية التدفق بالكامل من البداية إلى النهاية؟ الجزء المرتبط بإنتاج أوزان الورق - نعم. الباقي - لا. هل سنتمكن من رؤية الخسائر - نعم ، تلك المرتبطة بإنتاج الأوزان الورقية. الباقي - لا. هل هذه البطاقة مفيدة؟ هنالك. ما مدى خطورة هذه البطاقة؟ من خلال تحسين جزء من التدفق ، فإننا نجازف بإنشاء المزيد من الخسائر على مقياس التدفق بأكمله. كيف تقلل من هذا الخطر؟ سبع مرات لقياس تلك التغييرات في هذا التيار والتي يمكن أن تؤثر على كل ما تبقى "بعد".
من خلال اتخاذ قرار باستخدام الأوزان الورقية نصف المصنعة دائمًا أولاً ، فإننا نعمل على إبطاء إنتاج "شواهد القبور" و "ألواح الرصف". مثل هذه القرارات تحتاج إلى تحليل دقيق.
ومع ذلك ، يجب إيجاد بعض الحلول الوسط. في بعض الأحيان ، لكي تكون أقرب إلى الواقع ، عليك أن تنحرف كثيرًا عن التعريفات "الأكاديمية" للتدفق أو المنتج. على سبيل المثال ، عند وصف إنتاج أثاث الخزائن ، لم نتمكن من عزل "الخزانة" أو "الخزانة" المتدفقة ، لأن الحجم الأسبوعي للإنتاج بالكامل يتم قطعه في وقت واحد من نفس اللوح الرقائقي ، وتفاصيل قطع الأثاث المختلفة مختلطة من أجل تقليل المخلفات غير المستخدمة من اللوح الرقائقي (حسب الجوهر ، المهمة قطع اللوحهي مهمة اندماجية - كيفية ترتيب الأجزاء على الأوراق بحيث يتم إنفاق أقل عدد ممكن من ألواح الألواح الخشبية ، بحيث تضيع بقايا اللوحات قدر الإمكان). نتيجة لذلك ، تم إنشاء خريطة التدفق لمجموعة واحدة فقط من مجموعات التفاصيل. لم تظهر الصورة العامة للتدفق ، لكن قياسات المؤشرات الخاصة بمجموعة الأجزاء المختارة جعلت من الممكن توثيق مشاكل التدفق الرئيسية وإعادة تركيز العمل على حلها.
يمكن أن يكون تحديد منتج التدفق مشكلة صعبة للغاية ، ويمكن أن يؤدي تغيير عملية إنشاء منتج إلى مراجعة فهم التدفقات ، وبالتالي إلى مراجعة تجميع المنتجات ، وبالتالي تغيير في الإجابة على السؤال "ما هو نتاج هذا التيار؟"
تتمثل المهمة الرئيسية لنظام الإنتاج في التحسين المستمر لما يسمى "تدفق القيمة" للجمهور المستهدف. أساسه هو مزيج عقلاني من جميع العمليات. بفضل هذا ، يمكن إنتاج المنتجات بأقل تكلفة للعمالة. بالإضافة إلى ذلك ، يؤثر ذلك على المؤشرات الاقتصادية ، وكذلك نتائج الأنشطة الإنتاجية والاقتصادية للمؤسسة ، بما في ذلك تكلفة المنتج ، وربحية الإنتاج ، والربح ، ومقدار رأس المال العامل ، وحجم العمل الجاري. .
في الوقت نفسه ، بالنسبة للعديد من المنظمات ، فإن القضية الأكثر أهمية هي كفاءة عمليات الإنتاج من حيث التعقيد ومدة دورة الإنتاج. فكلما طالت المدة ، كلما زاد عدد المنتجات الإضافية التي تدخل فيها ، قل الإنتاج بشكل عام. بالإضافة إلى ذلك ، عليك بذل الكثير من الجهود لتنسيق العملية وضمان التشغيل السلس.
لحل هذه المشكلة ، تقوم العديد من الشركات بتطبيق نظام إنتاج بسيط في أنشطتها ، مما يسمح لها بتحسين عملية الإنتاج وتحسين جودة المنتج وخفض التكاليف. هذا المقال مخصص له.
ما هو التصنيع الخالي من الهدر؟
Lean manufacturing (في اللغة الإنجليزية له اسمان: "lean manufacturing" و "lean production") هو نهج خاص لإدارة المؤسسات يسمح لك بتحسين جودة العمل عن طريق تقليل الخسائر. الخسائر هي أي شيء يقلل من كفاءة العمل. الأنواع الرئيسية للخسائر هي:
- الحركات (التحركات غير الضرورية للمعدات والمشغلين تؤدي إلى زيادة الوقت والتكلفة)
- النقل (الحركات المفرطة التي تؤدي إلى التأخير والتلف وما إلى ذلك)
- التكنولوجيا (عيوب تكنولوجية لا تسمح بتنفيذ جميع متطلبات المستهلك في المنتج)
- الإفراط في الإنتاج (المنتجات غير المباعة التي تتطلب تكاليف إضافية للمحاسبة والتخزين وما إلى ذلك)
- قيد الانتظار (تنتظر المنتجات غير المكتملة في طابور المعالجة وزيادة التكلفة)
- العيوب (أي عيوب ينتج عنها تكاليف إضافية)
- المخزون (البضائع الجاهزة الزائدة التي تضيف قيمة)
يمكن تطبيق نظام lean manufacturing في التصميم والإنتاج نفسه وحتى في عملية تسويق المنتجات.
تم تطوير هذا النظام في مطلع الثمانينيات والتسعينيات مهندسين يابانيين Taiichi Ono و Shigeo Shingo (بشكل عام ، ظهرت بداياتها في منتصف القرن العشرين ، ولكن تم تكييفها فقط في نهاية ذلك). كان هدف المهندسين هو تقليل الأنشطة غير ذات القيمة المضافة طوال دورة حياة المنتج. وبالتالي ، فإن النظام ليس مجرد تقنية ، ولكنه مفهوم إدارة كامل مع توجيه الإنتاج الأقصى إلى السوق والمشاركة المهتمة لجميع موظفي الشركة.
أظهرت الخبرة المكتسبة في تنفيذ النظام (أحيانًا عناصره الفردية) في عمل المنظمات المختلفة فعاليته وآفاقه ، ويستخدم حاليًا في مجموعة متنوعة من الصناعات. إذا تم استخدام النظام في البداية فقط في مصانع سيارات Toyota و Honda وغيرها. (وكان يسمى نظام إنتاج تويوتا) ، يوجد اليوم في العديد من المجالات الأخرى:
- الدواء
- تجارة
- الخدمات اللوجستية
- خدمات بنكية
- تعليم
- انتاج البترول
- بناء
- تكنولوجيا المعلومات
بغض النظر عن المنطقة التي يتم فيها استخدام نظام التصنيع الخالي من الهدر ، يمكن أن يزيد بشكل كبير من كفاءة العمل ويقلل الخسائر عدة مرات ، حتى لو كان يتطلب بعض التكيف مع شركة معينة. يوضح هذا الفيديو كيف يمكن أن يتغير عمل المنظمة باستخدام تقنيات Lean.
بالمناسبة ، غالبًا ما يطلق على المؤسسات التي تطبق نظام الإنتاج الخالي من الهدر في أنشطتها اسم "العجاف". وهي تختلف عن أي مؤسسات أخرى في العديد من الخصائص الهامة.
أولاً ، أساس إنتاج هذه المؤسسات هم الناس. يلعبون دور القوة الإبداعية في عملية الإنتاج. المعدات والتكنولوجيا ، بدورها ، ليست سوى وسيلة لتحقيق غاية. الرسالة الرئيسية هنا هي أنه لا توجد تقنية أو استراتيجية أو نظرية يمكن أن تجعل الشركة ناجحة أو تقودها إليها نتائج عاليةيمكن فقط للأشخاص الذين لديهم إمكانات إبداعية وفكرية.
ثانيًا ، تركز أنظمة الإنتاج في هذه الشركات على الحد الأقصى من التخلص من النفايات والتحسين المستمر لعمليات الإنتاج. من المثير للاهتمام أن يشارك جميع موظفي المنظمة ، بدءًا من العمال العاديين وانتهاءً بالإدارة العليا ، في الأنشطة اليومية لضمان ذلك.
وثالثاً ، تأخذ جميع القرارات التي تتخذها إدارة هذه الشركات بالضرورة في الحسبان آفاق المزيد من التطوير ، ولا تعتبر المصالح المادية الحالية ذات أهمية حاسمة. مديرو المنظمات يستبعدون من أنشطتهم القيادة الإدارية غير المربحة ، والرقابة المشددة بشكل غير معقول ، وتقييم الموظفين من خلال أكثر الأنظمة تعقيدًامؤشرات مختلفة. وظائف الإدارة لتنظيم عملية الإنتاج بشكل مناسب ، واكتشاف المشكلات وحلها ومنعها في الوقت المناسب. إن القدرة على التعرف على المشكلات وحلها في مكان عملك تحظى بتقدير كبير لدى أي موظف.
ومع ذلك ، فإن إدخال الإنتاج الخالي من الهدر يتطلب فهمًا إلزاميًا للمبادئ الأساسية لهذا النظام والقدرة على العمل بأدواته. أولاً ، لنتحدث بإيجاز عن المبادئ.
مبادئ التصنيع الهزيل
على الرغم من حقيقة أن التنفيذ العملي لمبادئ التصنيع الخالي من الهدر يتطلب جهودًا جادة من المؤسسة ، إلا أنها في حد ذاتها بسيطة للغاية. هناك خمسة منهم ، ويمكن صياغتها على النحو التالي:
- تحديد ما يشكل قيمة المنتج من وجهة نظر المستهلك. يمكن تنفيذ مجموعة متنوعة من الإجراءات في مؤسسة ، وليست جميعها مهمة للمستهلك. فقط عندما تعرف الشركة بالضبط ما يحتاجه العميل النهائي ، تكون قادرة على تحديد العمليات التي تقدم قيمة وأيها ليست كذلك.
- حدد الإجراءات المطلوبة في سلسلة الإنتاج ، ثم تخلص من الهدر. من أجل تحسين الأداء وتحديد الهدر ، من الضروري وصف كل إجراء بالتفصيل من لحظة استلام الطلب إلى اللحظة التي يتم فيها تسليم المنتج إلى المستهلك. بفضل هذا ، من الممكن إنشاء بمساعدة تحسين عمليات الإنتاج.
- إعادة تصميم الأنشطة في سلسلة الإنتاج بحيث تتحول إلى سير عمل شامل. يجب أن يتم بناء عملية الإنتاج بحيث يتم استبعاد أي خسائر (توقف ، انتظار ، إلخ) بين العمليات. قد يتطلب هذا تقنيات جديدة أو عملية إعادة تصميم. من المهم أن تتذكر أن أي عملية يجب أن تتضمن فقط تلك الأنشطة التي تضيف قيمة إلى المنتج النهائي ، ولكن لا تزيد من تكلفته.
- التصرف لصالح المستهلك. من المرغوب فيه أن تنتج المؤسسة المنتج فقط وبهذا الحجم الضروري للمستهلك النهائي. هذا يتجنب الإجراءات غير الضرورية والخسائر والتكاليف غير الضرورية.
- احرص على التحسين من خلال تقليل الأنشطة غير الضرورية باستمرار. من الضروري تطبيق وتنفيذ نظام التصنيع الخالي من الهدر أكثر من مرة. سيكون التأثير الأقصى فقط إذا تم البحث عن الخسائر والقضاء عليها بشكل منتظم ومنهجي.
يجب أن تستند هذه المبادئ الخمسة إلى تنفيذ نظام التصنيع الخالي من الهدر ، وهذا ينطبق على أي مجال من مجالات النشاط ، من التصميم وإدارة المشروع إلى الإنتاج المباشر والإدارة. لزيادة إنتاجية العمل ، والعثور على الخسائر وتقليلها ، وتحسين الإنتاج ، وما إلى ذلك. تساعد أدوات النظام الخالي من الهدر.
أدوات العجاف
فيما يلي سنلقي نظرة على الأدوات الرئيسية للتصنيع الخالي من الهدر:
- عمل موحد. إنها خوارزمية واضحة ومرئية لأقصى حد لأداء أي عمل محدد. تتضمن هذه الخوارزمية معايير مختلفة ، على سبيل المثال ، معايير لمدة دورة الإنتاج ، ومعايير لتسلسل الإجراءات خلال دورة واحدة ، ومعايير كمية المواد للعمل ، وما إلى ذلك.
- SMED (تبادل دقيقة واحدة للقالب). هذه تقنية خاصة للتبديل السريع للمعدات. للتحويل ، كقاعدة عامة ، يتم استخدام فئتين من العمليات. الأول هو العمليات الخارجية ، ويمكن إجراؤها دون إيقاف المعدات (وهذا يشمل تجهيز المواد والأدوات ، إلخ). والثاني هو العمليات الداخلية ، ولتنفيذها يجب إيقاف المعدات. معنى SMED هو أن الحد الأقصى للمبلغيتم ترجمة العمليات الداخلية إلى عمليات خارجية. يتم تحقيق ذلك من خلال الابتكارات التنظيمية والتكنولوجية.
- سحب الإنتاج. نهج لتنظيم تدفق الإنتاج ، والذي يقضي على الخسائر المرتبطة بالانتظار (حتى اكتمال المرحلة السابقة من العمل) والإفراط في الإنتاج. هنا كل عملية العملية التكنولوجيةوكأنه "يسحب" الحجم المطلوب للمنتج من العملية السابقة ثم ينقله إلى العملية التالية. وهذا يجنب ظهور كل من فوائض المنتج ونقصه.
- نظام تقديم المقترحات والنظر فيها. وفقًا لذلك ، يمكن لأي موظف تقديم أفكاره لتحسين سير العمل. يتم تزويد جميع الموظفين بآلية واضحة لتنفيذ مقترحاتهم. يتضمن النظام أيضًا طرقًا لتشجيع الموظفين على طرح أفكارهم.
- طريقة "اختراق التدفق". يتم استخدامه لتسوية وتحسين كفاءة تدفق الإنتاج. لهذا ، يتم إنشاء دورات إنتاج ثابتة ، يتم فيها تقديم مبادئ العمل القياسي في كل منها.
- TPM (الصيانة الإنتاجية الإجمالية). نظام الخدمة الشاملةمعدات. عند استخدامه ، يتم الجمع بين تشغيل الجهاز وصيانته المستمرة. يتم توفير هذه المراقبة المستمرة وصيانة المعدات في حالة جيدة من قبل موظفين مؤهلين. تساعد TPM على تقليل الخسائر المرتبطة بالإصلاحات ووقت التوقف عن العمل والأعطال ، وتضمن أقصى قدر من الكفاءة طوال دورة الحياة الكاملة للمعدات. ميزة أخرى هي أن موظفي الصيانة يحصلون على وقت لمهام أخرى.
- نظام 5S- منهجية الإدارةمما يسمح لك بتنظيم مساحة العمل الخاصة بك بكفاءة. تحت الاختصار المفاهيم التالية:
- o التنظيم (توجد جميع العناصر في مكان محدد يسهل الوصول إليه)
- o الحفاظ على النظام والنظافة
- o الفرز (يتم ترتيب الوثائق و / أو العناصر في مكان العمل بناءً على تكرار استخدامها ؛ وهذا يشمل التخلص من أي شيء لم تعد هناك حاجة إليه)
- o التوحيد (يتم تنظيم الوظائف وفقًا لنفس المبدأ)
- o التحسين (يتم تحسين المعايير والمبادئ المعمول بها باستمرار)
تشمل أدوات التصنيع الأخرى الخالية من الهدر ما يلي:
- (نهج لإدارة المشاريع على أساس التحسين المستمر للجودة)
- "" (نهج لإدارة الإنتاج على أساس طلب المستهلك)
- كانبان (نظام إدارة المشاريع ونظام إدارة السلع والمواد داخل وخارج الشركة)
- Andon (نظام التغذية المرتدة للإنتاج المرئي)
- أدوات إدارة الجودة (مخطط PDPC ، مصفوفة الأولوية ، مخطط الشبكة ، مخطط المصفوفة ، مخطط الشجرة ، مخطط الارتباط ، مخطط التقارب ، إلخ.)
- أدوات مراقبة الجودة (مخططات التحكم ، ورقة التحكم ، مخطط التبعثر ، مخطط باريتو ، التقسيم الطبقي ، الرسم البياني ، إلخ.)
- أدوات تحليل وتصميم الجودة (طريقة 5 Whys ، طريقة House of Quality ، تحليل FMEA ، إلخ.)
في نفس القسم ، من الضروري التحدث بشكل منفصل عن الطريقة المستخدمة لنمذجة ومنع الأخطاء في عمليات الإنتاج وتقليل الخسائر المرتبطة بالعيوب. هذه هي طريقة بوكا نير.
تتمثل طريقة Poka-yoke في العثور على أسباب الأخطاء وتطوير تقنيات وطرق للقضاء على احتمال حدوثها. وهو يقوم على فكرة أنه إذا كان من المستحيل القيام بالعمل بأي وسيلة غير الطريقة الصحيحة ، ولكن تم إنجاز العمل نفسه ، فعندئذ يتم القيام به بشكل صحيح ، أي. لا أخطاء.
يمكن أن تظهر الأخطاء لأسباب مختلفة: الإهمال ، وعدم الانتباه ، وسوء الفهم ، ونسيان الشخص ، وما إلى ذلك. بالنظر إلى العامل البشري ، كل هذه الأخطاء طبيعية وحتمية ، ولكي تجد طريقة لمنعها ، يجب أن تفكر فيها من هذه الزاوية.
مكونات طريقة Poka-yoke:
- تم إنشاء المتطلبات الأساسية للعمل الخالي من الأخطاء
- تم تقديم طرق عمل خالية من الأخطاء
- يتم التخلص من الأخطاء التي تحدث بشكل منهجي
- يتم اتخاذ الاحتياطات
- تم تقديم أنظمة فنية بسيطة تسمح للعمال بتجنب الأخطاء
تُستخدم هذه الطريقة جنبًا إلى جنب مع الأدوات الأخرى لنظام التصنيع الخالي من الهدر وتضمن عدم وجود عيوب في المنتج النهائي ، وسير عملية الإنتاج بسلاسة.
كل هذه الأدوات ، عند استخدامها معًا ، تؤثر على كفاءة العمل ، وتقضي على أنواع مختلفة من الخسائر ، وتقلل من احتمالية حدوث حالات الطوارئ ، وتساهم في خلق جو ملائم في مكان العمل. بالإضافة إلى ذلك ، يتيح الاستخدام المشترك لهذه الأدوات تعزيز بعضها البعض ، وجعل نهج اللين أكثر مرونة.
كل هذا هو السبب الرئيسي وراء قيام العديد من المنظمات في الخارج وفي روسيا بتطبيق نظام إنتاج بسيط في أنشطتها. والآن حان الوقت للحديث عن أمثلة حقيقية.
كفاءة التصنيع الهزيل
وفقًا لمطوري نظام lean manufacturing ، يمكن أن يكون لتطبيقه تأثير كبير على العديد من العمليات التجارية. وبشكل أكثر تحديدًا ، إذن:
- يمكن تقليل مدة دورة التصنيع بمقدار 10-100 مرة
- يمكن تقليل حالات الزواج بمقدار 5-50 مرة
- يمكن تقليل وقت التوقف عن العمل بمقدار 5-20 مرة
- يمكن زيادة الأداء بنسبة 3-10 مرات
- يمكن تقليل مخزون المستودعات بمقدار 2-5 مرات
- يمكن تسريع عمليات التسليم بمقدار 2-5 مرات منتجات جديدةإلى السوق
وفقًا لـ Expert media Holding ، بدأ إدخال الإنتاج الخالي من الهدر في روسيا فقط في عام 2004. وبحلول عام 2007 (في ثلاث سنوات فقط من الممارسة) ، أظهر النظام نتائج مبهرة. وهناك أكثر من مثال على ذلك:
- انخفضت التكاليف بنسبة 30٪ في مجالات إنتاج النفط والأجهزة وتجميع مكونات السيارات
- تم تحرير 30٪ من مناطق الإنتاج في مجال الأجهزة
- انخفض العمل في مجال إنتاج النفط بنسبة 50٪
- 60٪ تخفيض في دورة الإنتاج في مجالات الأجهزة وصناعة الطيران
- زادت كفاءة معدات التعدين غير الحديدية بنسبة 45٪.
- 25٪ حرروا موارد عاملة في مجال إنتاج النفط
- تقليل وقت التغيير بنسبة 70٪ في صناعة الحديد والصلب
وفقًا لـ Expert media Holding ، بحلول عام 2017 ، أدت ممارسة استخدام التصنيع الخالي من الهدر في روسيا والخارج إلى النتائج التالية:
- 25٪ حرروا مساحة إنتاج في صناعة الإلكترونيات
- تسارع الإنتاج في صناعة الطيران 4 مرات
- 35٪ زيادة في إنتاجية المعادن غير الحديدية
- تم تقليل النفايات في صناعة الأدوية بمقدار 5 مرات
- 55٪ زيادة في الإنتاج ، 25٪ انخفاض في دورة الإنتاج ، 35٪ انخفاض في المخزون في مجال إنتاج السلع الاستهلاكية
- تحرير مناطق الإنتاج في صناعة السيارات بنسبة 20٪
بالنسبة للشركات الروسية على وجه التحديد ، تُستخدم تقنيات Lean حاليًا في عملها بواسطة UC Rusal و LLC Expert Volga و EPO Signal و OJSC Khlebprom و VSMPO-AVISMA و PJSC KamAZ و LLC Oriflame Cosmetics و TechnoNIKOL LLC و Gas Group PG و EuroChem LLC وعشرات المنظمات الكبرى الأخرى.
ومع ذلك ، في السوق الروسية في الوقت الحاضر ، يلاحظ الخبراء نقصًا في المهنيين القادرين على تحسين عمليات الإنتاج من خلال إدخال نظام التصنيع الخالي من الهدر. (بالمناسبة ، من المؤكد أن أولئك الذين يتقنون نهج اللين اليوم سيحصلون على وظيفة مستقرة ، حياة مهنيةوآفاق ومستقبل آمن.)
الموجودات
يساعد التصنيع الخالي من الهدر الشركات ، دون اللجوء إلى الاستثمارات الكبرى واستخدام احتياطياتها الداخلية بشكل أساسي ، على تحقيق زيادات ملموسة في إنتاجية العمالة. لكن نظام Lean هو نهج خاص للإنتاج وجميع مكوناته ، ولا يعرض فقط زيادة إنتاجية العمل وجعل الإنتاج أكثر كفاءة ، ولكن أيضًا لخلق الظروف المواتيةلتكوين ثقافة مؤسسية يشارك فيها كل موظف في تحقيق نجاح الشركة.
بمعنى أوسع ، يعد نظام التصنيع الخالي من الهدر نموذجًا صناعيًا لتنفيذ الأساليب المبتكرة لإدارة المؤسسات ، وزيادة كفاءة الإنتاج ، وتطوير الأفراد والقضاء على أي نوع من النفايات. واليوم ، يمكن لأي شركة تقريبًا نشر نظام Lean في قاعدتها.
استقلال- إدخال الذكاء البشري إلى آلات يمكنها الكشف بشكل مستقل عن العيب الأول ، وبعد ذلك تتوقف على الفور وتدل على الحاجة إلى المساعدة. يُعرف هذا النهج أيضًا باسم Jidoka.
التحليلاتالتدفقات (CVSC) هي أداة من أدوات نظام الإنتاج (التصنيع الخالي من الهدر) ، تهدف إلى وصف تدفقات القيمة من خلال تعيين رأس المال الاستثماري ، من أجل تقييم الخسائر ووضع خطة عمل للقضاء عليها.
تحليل تدفق العائد (تحليل العودة)- تحليل أداء عمليات التصنيع لتحديد عدد المرتجعات للمرحلة السابقة للتصحيح أو التخلص.
و على- أداة للتحكم البصري في عملية الإنتاج.
مراجعة(من اللاتينية "الاستماع ، الاستماع") هي عملية تقييم الوضع الحالي ، من حيث الامتثال للمعايير ، وتنظيم الإنتاج على مستوى عالمي ، كما تحدد المراجعة: النتائج المستهدفة ، والفرص المحتملة ، والقدرات الحالية وتساعد في تطوير التغيير خطة.
مخزون احتياطي- انظر الأسهم.
تحكم بصري- مثل هذا الترتيب للأدوات والأجزاء والحاويات وغيرها من مؤشرات حالة الإنتاج ، حيث يمكن للجميع في لمحة فهم حالة النظام - القاعدة أو الانحراف (الشذوذ).
تحكم بصري(التحكم البصري) - تقييم جودة تصنيع المنتجات عن طريق الفحص أو طريقة اللمس.
الوقت في الخط(وقت الانتظار) - الوقت الذي يكون فيه المنتج خاملاً في قائمة الانتظار في انتظار المرحلة التالية من الإنتاج أو التصميم أو تنفيذ مستند (طلب) أو محادثة هاتفية.
المهلة(مهلة) - الوقت من لحظة تقديم الطلب إلى إتمامه وتحويله إلى المستهلك.
مؤشرات زمنية أخرى تؤثر المهلة:
تاكت الوقت(takt time) - الفاصل الزمني أو التكرار الذي يتلقى به المستهلك المنتجات المطلوبة من المستهلك. يحدد وقت Takt سرعة الإنتاج ، والتي يجب أن تتطابق تمامًا مع الطلب الحالي.
دورة الزمن(وقت الدورة) - الوقت المطلوب للمشغل لإكمال جميع الإجراءات قبل تكراره مرة أخرى. عندما يصبح وقت دورة كل عملية في العملية مساويًا تمامًا لوقت takt ، يتم إنشاء تدفق من قطعة واحدة.
حان الوقت لخلق القيمة- وقت العمليات أو الإجراءات ، ونتيجة لذلك يتم إعطاء المنتج أو الخدمة خصائص يكون العميل على استعداد لدفع ثمنها.
وقت دورة الإنتاج- الوقت الذي يستغرقه عنصر أو مادة أو قطعة عمل للتنقل خلال عملية أو تدفق قيمة من البداية إلى النهاية.
خدمة التصنيع العالمية(Total Productive Maintenance، TPM) هي مجموعة من الأيديولوجيا والأساليب والأدوات التي تهدف إلى الحفاظ على الأداء المستمر للمعدات لضمان استمرارية عمليات الإنتاج.
سحب(سحب) نظام إنتاج لا يقوم فيه مورد المنبع (أو المورد المحلي) بأي شيء حتى يبلغه المستهلك النهائي (أو المستهلك المحلي). الوضع العكسي يسمى البثق. انظر أيضا كانبان.
تسوية الإنتاج(التسوية) انظر هي أداة مصممة لتخفيف فترات الذروة والانخفاضات في التنزيلات وتجنب الإنتاج الزائد. ترتبط ارتباطًا وثيقًا ببدء التسلسل وموازنة الخط.
قذف(Push) - نظام لإطلاق المنتجات و "دفعها" إلى العملية التالية ، دون مراعاة احتياجات المستهلك. عكس التمدد.
جيمبا- مترجم من اليابانية - "وجهي". في المصطلحات اللينة - مشروع ، ورشة عمل ، موقع ، مكان يتم فيه إنتاج منتج مادي (حيث يتم إنشاء القيمة مباشرة للمستهلك) ، ربما. والمكتب حيث يتم تقديم الخدمات أو تنفيذ التطوير.
جيدوكا(جيدوكا) - انظر الحكم الذاتي.
مخطط السباغيتي(مخطط السباغيتي) - المسار الذي يصفه المنتج (المشغل) ، يتحرك على طول تدفق القيمة. نشأ الاسم لأن هذا المسار فوضوي تمامًا ويبدو مثل طبق من السباغيتي.
خريطة الطريق(خريطة الطريق) - خطة مرحليةإجراءات لتحقيق هدف معين أو حل مشكلة حالية.
عملية منظم ضربات القلب(racemakerprocess) - أي عملية في تدفق القيمة تحدد وتيرة التدفق بأكمله. يقع عادةً بالقرب من "نهاية العميل" لتدفق القيمة. Nr: خط تجميع المنتج النهائي.
مخازن- تراكم المواد في انتظار المعالجة أو الحركة بين عمليات (مراحل) التدفق. يتم تصنيف المخزون المادي حسب موقعه في تدفق القيمة وحسب الغرض الوظيفي. المخزونات حسب الموقع: المواد الخام ، المواد ، العمل الجاري ، المنتجات النهائية. المواد الخام والمواد - القيم المادية، الموجودة في المؤسسة (في العمليات) ولا تخضع للمعالجة.
إنتاج غير مكتمل(WIP) - قيم المواد الموجودة بين المراحل وفي عمليات المعالجة (إضافة القيمة).
الاحتياطيات حسب الوجهة: مخزن مؤقت ، تأمين ، عند الشحن.
مخزون احتياطي- مصممة لضمان استمرار عملية الإنتاج في حالة حدوث زيادة غير مخطط لها في الطلب على هذه الأجزاء. يتم حساب كمية المخزون بناءً على تحليل إحصائيات الانحرافات (الحد الأقصى لوقت تعطل مواقع الإنتاج) بسبب الزيادة غير المخطط لها في الطلب على الأجزاء.
تأمين الأسهم- مصممة لضمان استمرار تقدم عملية الإنتاج في حالات الظروف غير المتوقعة: تعطل المعدات ، تسليم المنتجات المعيبة ، التأخير في التسليم أثناء النقل ، إلخ. يتم حساب الحجم بناءً على تحليل الحد الأقصى لوقت تعطل العميل (عادةً 3 أشهر) بسبب عدم تسليم قطع الغيار من قبل المورد أو شحنة معيبة.
مخزون الشحن- المنتجات الموجودة في نهاية خط الإنتاج والمعدة للشحن إلى المستهلك.
التكاليف على أساس النشاط ؛ التكلفة على أساس النشاط(التكلفة على أساس النشاط ، ABC) هو نظام محاسبة إداري يربط تكاليف المنتجات بناءً على كمية الموارد المستخدمة (بما في ذلك مرافق الإنتاج والمواد الخام والآلات والآليات والعمالة) التي يتم إنفاقها على تصميم هذا المنتج وطلبه وتصنيعه. على عكس نظام التكلفة القياسي.
كايزن(كايزن) - التحسين المستمر للأنشطة من أجل زيادة قيمة العملاء وتقليل الهدر (مدى).
كايكاكو(kaikaku) - تحسين جذري (أساسي) للعملية يهدف إلى تحقيق هدف أو القضاء على الهدر (muda).
كانبان(كانبان) - مترجم من اليابانية - بطاقة أو شارة. أداة نظام سحب تشير إلى إنتاج أو سحب (نقل) الأصناف من عملية إلى أخرى. يمكن استخدامها - العلامات والبطاقات والحاويات والبريد الإلكتروني. تُستخدم في نظام إنتاج Toyota لتنظيم السحب من خلال الإبلاغ عن خطوة إنتاج سابقة لبدء العمل.
رسم الخرائط تيار القيمة(KPSTS) (تخطيط تدفق القيمة) هي عملية دراسة وتصور المواد وتدفق المعلومات المصاحبة في سياق إنشاء القيمة ، عندما تنتقل المواد عبر العمليات من المورد إلى المستهلك. يتكون من مراحل: 1. اختيار تيار. 2. وصف الحالة الحالية للموضوع. 3. وصف الحالة المستقبلية للتدفق. 4. رسم خطة (خارطة طريق) لتحقيق حالة التدفق المستقبلية.
الطريق الدائري(تشغيل الحليب) - نظام توصيل الأجزاء (على سبيل المثال ، للإصلاحات) ، حيث يمكن للشاحنة التي تؤدي باستمرار نفس المسار أن تتوقف في أماكن معينة وتوصيل الجزء المطلوب.
تسميات حمراء- أداة لتصور المشاكل والشذوذ على gemba (المكتب) ، تستخدم في شكل بطاقات يمكن الإشارة إليها: رقم المشكلة بالترتيب (من قائمة المشاكل) ؛ تاريخ تثبيت الملصق ؛ الاسم الكامل. حددت المشكلة أو غيرها من المعلومات.
خدمة متعددة المحطات(عمل متعدد الماكينات) - العمل الذي يتحكم فيه مشغل واحد في عدة آلات من أنواع مختلفة في وقت واحد ، كما يوفر التدريب وصيانة المعدات.
نصب(نصب تذكاري) - أي كائن (آلة) أو عملية ، يكون مقياسها (حجمها) بحيث تضطر الأجزاء أو المشاريع أو الطلبات الواردة إلى انتظار المعالجة في قائمة الانتظار. M. يخدم عادةً أكثر من تدفق قيم واحد ويتم تشغيله على دفعات كبيرة ، مع فترات زمنية طويلة وعمليات تبديل بطيئة.
مودا(muda) أو الهدر - أي نشاط يستهلك الموارد ولكن لا ينتج عنه قيمة. هناك سبعة أنواع رئيسية من النفايات ، وهي الإفراط في إنتاج المواد أو المعلومات (عندما لا يكون الطلب عليها قد ظهر بعد) ؛ انتظار مرحلة الإنتاج التالية ؛ النقل غير الضروري للمواد أو المعلومات ؛ خطوات المعالجة الزائدة عن الحاجة (مطلوبة بسبب نقص المعدات أو عيوب العملية) ؛ توافر أي مخزون ، باستثناء الحد الأدنى المطلوب ، حركة الأشخاص غير الضرورية أثناء العمل (على سبيل المثال ، البحث عن الأجزاء والأدوات والمستندات والمساعدة وما إلى ذلك) ؛ إنتاج العيوب: يعتبر فقدان القدرة الإبداعية للأفراد هو النوع الثامن من الخسارة ، وهو الأصعب في التقييم ، ولكنه المفتاح لبناء نظام للتحسين المستمر للأنشطة.
مورا(mura) "التفاوت" - التباين في أساليب العمل أو في نتائج العملية.
موري(موري) "فائض" - التوتر ، الحمل الزائد (العمل الإضافي) لشخص أو معدات ، عدم المعقولية.
تدفق مستمر -تنظيم عمل تدفق المواد وفقًا لمبدأ - "واحدًا تلو الآخر" أو "من يد إلى يد" بدون توقف وانقطاعات.
أوبيا(من Jap. room or room) هي أداة لإدارة المشاريع تعزز التواصل الفعال والسريع ، وتُستخدم بنشاط في مرحلة التطوير. يعمل على مبدأ "القيادة العسكرية".
عملية(عملية) - إجراء (أو إجراءات) يقوم به جهاز واحد على منتج واحد ، بدلاً من عملية.
"في مجموعات وقوائم الانتظار" ، العمل (الدُفعة وقائمة الانتظار)- ممارسة الإنتاج الضخم. وهو يتألف من تصنيع مجموعات كبيرة من الأجزاء ، والتي يتم وضعها بعد ذلك في قائمة الانتظار للعملية التالية في عملية الإنتاج. على عكس تدفق المنتجات الفردية.
التغيير(التحويل) - تثبيت نوع جديد من الأدوات على آلة الأشغال المعدنية ، وتغيير الطلاء في آلة الصباغة ، وملء جزء جديد من البلاستيك وتغيير القالب في آلة التشكيل بالحقن ، وتركيب واحد جديد على الكمبيوتر البرمجياتإلخ. يستخدم المصطلح دائمًا عندما تحتاج المعدات إلى التحضير لإنتاج نوع مختلف من المنتجات (أداء وظيفة أخرى).
كميد(SMED - تبادل القوالب في دقيقة واحدة) - إجراء سريع (أقل من عشر دقائق) لاستبدال القوالب أو أي أدوات أخرى ، وهي أداة لتغيير معدات الإنتاج.
تخطيط متطلبات المواد ، النظام (تخطيط متطلبات المواد ، MRP)- نظام محوسب يستخدم لتحديد كمية المواد وتوقيت الحاجة إليها في الإنتاج. يستخدم نظام MRP: جدول إنتاج رئيسي ، أمر مادة يسرد كل ما هو مطلوب لإنتاج كل منتج ، معلومات حول مستوى المخزون الحالي لهذه المواد ، لجدولة الإنتاج والتسليم لكل منها. يكمل نظام تخطيط موارد التصنيع (MRP II) تخطيط موارد التصنيع (MRP) من خلال السماح لك بتخطيط القدرة الإنتاجية للمعدات ، وتحسين التدفقات المالية ، ووضع النماذج والتقييم خيارات مختلفةخطط الإنتاج. نظام MRP - نوع الدفع.
بوكا نير- "الحماية من الاستخدام غير المتعمد" - جهاز أو طريقة خاصة لا يمكن أن يتشكل بسببها العيب ببساطة. اسم آخر لـ poka-yoke هو baka-yoke (baka-yoke) - "fool-proof" أو "fool-proof".
تدفق(flow) - حركة المواد والمعلومات في عملية تحويلها إلى منتج أو خدمة للمستهلك. عندما يكون هناك منتج (خدمة) للمستهلك ، يكون هناك تدفق. يمكن تحويل أي نشاط إلى تدفق.
تدفق قطعة واحدة(تدفق أحادي السلام) - طريقة عمل لا تعالج فيها آلة أو عملية (على سبيل المثال ، التصميم أو قبول الطلب أو الإنتاج) أكثر من منتج واحد في المرة الواحدة. على عكس طريقة "الدُفعات والصف".
قيمة التيار(تيار القيمة) - جميع الأنشطة المطلوبة حاليًا لتحويل المواد الخام والمعلومات إلى منتج أو خدمة منتهية. الجهاز "الصحيح"(أداة الحجم المناسب) - كائن (وسيلة تصميم أو تخطيط أو إنتاج) يتناسب بسهولة مع تدفق الإنتاج ضمن نفس عائلة المنتج ، بحيث لا يكون هناك المزيد من النفايات من النقل أو الانتظار غير الضروري. على عكس النصب
خط الانتاج- هذه مجموعة (من المنتجات أو المنتجات) قطة. داخل حدود التدفق المحددة ، يمر نفس مسار وتسلسل العمليات. تتكون هذه المجموعة من منتجات لها خصائص متشابهة ، بالإضافة إلى معلمات (وقت الدورة) لمرورها لعمليات مماثلة.
معالجة(عملية) - سلسلة من العمليات (الإجراءات) المنفصلة التي يتم من خلالها إنشاء مشروع أو تقديم طلب أو إنتاج منتج.
القرى العملية(قرى المعالجة) - الأماكن التي يتم فيها تجميع المعدات من نفس النوع أو إجراء عمليات مماثلة ، على سبيل المثال ، أين آلات طحنأو تتم معالجة الطلب. على عكس الخلايا.
خمسة أسباب(الأسباب الخمسة) - الطريقة التي تعامل بها Taiichi Ohno مع البحث عن سبب أي مشكلة ، وتمثلت في حقيقة أنه من أجل العثور على السبب الجذري (السبب العميق) للمشكلة (السبب الجذري) ، يجب على المرء أن يسأل " لماذا "خمس مرات على الأقل خمس مرات. عندها فقط يمكن تطوير وتنفيذ الإجراءات التصحيحية.
خمسة اس(خمس قواطع) - النظام منظمة فعالةمكان العمل (مساحة العمل) ، بناءً على التحكم البصري. يتضمن خمسة مبادئ ، كل منها يبدأ باليابانية بالحرف "C". صعيري: منفصل الأدوات الصحيحةوالتفاصيل والمستندات من غير الضرورية من أجل إزالة الأخير بعيدًا (حذفها). Seiton: قم بترتيب (وتسمية) الأجزاء والأدوات في منطقة العمل بحيث يسهل التعامل معها. Seiso: الحفاظ على نظافة مكان العمل ، وذلك في المقام الأول لتحديد المشكلات وحلها في أقرب وقت ممكن. Seiketsu: قم بإجراء seiri و seiton و seiso بانتظام (على سبيل المثال ، كل يوم) للمحافظة عليه مكان العملفي حالة ممتازة. شيتسوكي: اجعل أول أربع قواعد سلوكية عادة ، معيارًا للعمل.
نشر سياسة- انظر هوشين كانري.
تجانس الإنتاج(تجانس الإنتاج) - انظر heijunka.
تجانس المبيعات(مستوى البيع) - نظام علاقات طويلة الأمد مع المستهلك ، يهدف إلى الحصول على معلومات منه حول عمليات الشراء المستقبلية ، مما يسمح لك بتخطيط الإنتاج بشكل أفضل وبالتالي التخلص من "الاندفاعات" غير المتوقعة في المبيعات.
عائلة المنتج(عائلة المنتج) - مجموعة من المنتجات التي يمكن إنتاجها واحدة تلو الأخرى في خلية إنتاج. يقال إن منتجات نفس العائلة مصنوعة على "نفس المنصة".
سنسي(سنسي) - مدرس ، ماجستير في منطقة معينة (في هذه الحالة ، في مجال التصنيع الهزيل).
حد الكمال(الكمال) - الغياب التام للهدر (muda) ، حيث تخلق جميع أنواع الإجراءات في تدفق القيمة قيمة فعلية.
التكلفة القياسية(التكلفة القياسية) - نظام محاسبة التكاليف حيث يتم تحميل التكاليف على المنتج بناءً على عدد ساعات الماكينة وساعات العمل التي يقضيها الإنتاج بأكمله خلال فترة زمنية معينة. يشجع معيار التكلفة المديرين على إنتاج منتجات غير ضرورية أو مجموعة خاطئة من المنتجات من أجل ذلك استخدام كاملالآلات والعاملين لتقليل تكاليف الوحدة لكل منتج.
اساسي(اساسي). على عكس الأساليب التقليدية في مفهوم Lins. - هذه أفضل طريقةأداء أي نشاط باستخدام التقنيات الأكثر فعالية من حيث تقليل الخسائر وسهولة التنفيذ وسرعة العمل. تم اختبار هذه التقنيات سابقًا في الممارسة العملية ، وتم تقديمها بوضوح في شكل بسيط ومفهوم باستخدام أدوات التصور ، وتم إيصالها من خلال التدريب لجميع الموظفين الذين يؤدون هذا النشاط. بالمعنى المعتاد - معيار (من المعيار الإنجليزي - معيار ، عينة) - عينة ، معيار ، نموذج (ليس بالضرورة الأكثر مثالية) ، مأخوذ كنقطة انطلاق لمقارنة أشياء أخرى مماثلة معهم وليس الأفضل دائمًا.
التوحيدهو نظام إدارة إنتاج يشمل جميع الموظفين ويستخدم مجموعة من القواعد والإجراءات والإجراءات التي تهدف إلى تحديد الخسائر والقضاء عليها وإنشاء نظام للتحسينات المستمرة في عمليات المؤسسة. بالمعنى المعتاد ، - هذه هي عملية وصف وإضفاء الطابع الرسمي على الإجراءات والعمليات في أنشطة المؤسسة.
عمل موحد(العمل القياسي) هو أداة لتحليل وفهم الخسائر أثناء عملية (عملية). إنه وصف دقيق لكل إجراء ، بما في ذلك وقت الدورة ، ووقت takt ، وتسلسل تنفيذ عناصر معينة ، الحد الأدنى من المبلغجرد لإنجاز المهمة.
بطاقات التشغيل القياسية ، SOC(SOP ، إجراءات التشغيل القياسية) - المستندات التي تصف الخطوات في الإجراء التي يجب اتباعها. تتكون عادةً من نصوص ورسومات / رسومات وصور فوتوغرافية لتسهيل فهم الإجراء.
التحكم في العمليات الإحصائية(SPC ، التحكم في العمليات الإحصائية) - استخدام الأدوات الإحصائية للمساعدة في إدارة جودة العملية.
في الوقت المحدد(Just-in time، JIT) - نظام يتم من خلاله إنتاج المنتجات وتسليمها إلى المكان المناسب في الوقت المناسب تمامًا وبالكمية المناسبة. العناصر الأساسيةأنظمة في الوقت المناسب: التدفق ، والسحب ، عمل قياسي(و WIP القياسي) و takt time. تقضي أنظمة JIT على التوقف وتراكم المواد بين العمليات.
عمليات المعاملات(عمليات المعاملات) - العمليات التي يتم فيها نقل المواد أو المعرفة أو المعلومات أو الخدمات بين شخصين أو بين فرد ومعدات. بشكل عام ، تندرج معظم العمليات التي لا تنطوي على تصنيع المنتجات ضمن هذه الفئة.
(التحميل) - توريد المواد وشحنها في خطوط الإنتاج أو الخدمة من جانب المشغل. يمنع المشغل من الاضطرار إلى الالتفاف لالتقاط ونقل الأجزاء.هيجونكا(heijunka) - تنظيم "تجانس" خطة الإنتاج ، حيث يتم تنفيذ الأوامر في دورات ، ويتم تقليل التقلبات اليومية في مستوى الأوامر إلى قيمتها في طويل الأمد. بعض أنواع التنعيم أمر لا مفر منه في أي نوع من الإنتاج ، سواء على نطاق واسع أو هزيل. يركز Lean manufacturing على إنشاء طاقة إنتاجية زائدة بمرور الوقت بسبب تحرير الموارد وتقليل وقت التغيير. في الوقت نفسه ، يتم تقليل التناقضات الناتجة بين heijunka والطلب الحقيقي ، والذي يتم تسهيله بشكل كبير من خلال عملية "تجانس المبيعات" (مستوى البيع).
هوشين كانري(hosing kanri) - طريقة لتطوير إستراتيجية لإدارة مؤسسة من قبل الإدارة العليا ، حيث يتم توجيه الموارد لتلك الأهداف الحاسمة للأعمال. يتم تحديد ثلاثة إلى خمسة أهداف رئيسية باستخدام مخطط مصفوفة مماثل لتلك المستخدمة في هيكلة وظيفة الجودة ، بينما يتم تجاهل الأهداف الأخرى. للعمل على الأهداف المحددة ، يتم إنشاء المشاريع ، وتناقش طرق تنفيذها على مستوى إداري أدنى. يسمح لك Hoshin Kanri بتوحيد الموارد وتطوير مؤشرات واضحة قابلة للقياس تراقب بانتظام تحقيق الأهداف الرئيسية. اسم آخر لهوشين كانري هو نشر السياسة (الهيكلة).
القيمة (قيمة الاستخدام)(القيمة) - يعرفها العميل على أنها الجودة الصحيحة والمتوقعة والكمية والسعر ووقت التسليم. القيمة هي مجموعة من خصائص المنتج أو الخدمة التي يكون المستهلك على استعداد لدفعها للمورد ، لأن هذه الخصائص للمنتج أو الخدمة تسبب شعور شخصيالمستهلك أن الشيء (الخدمة) الذي يحتاجه يتم تسليمه (توفيره) بالكمية المناسبة ، معه الجودة المناسبةفي الوقت المناسب و المكان الصحيح(تسبب شعوراً بالرضا) .
شاكو شاكو(chaku-chaku) - طريقة لتنفيذ التدفق المستمر للمنتجات المنفردة ، حيث ينتقل المشغل في خلية من آلة إلى أخرى ، ويأخذ الجزء النهائي من آلة ويحمّله في الجهاز التالي ، وهكذا. في اليابانية ، تعني حرفيا "تحميل".
صافي الإنتاج(Greenfield) - نظام تنظيم إنتاج جديد يتم فيه دمج أساليب الإنتاج الخالي من الهدر في نظام الإدارة من البداية (على عكس إعادة تنظيم الإنتاج الحالي).
الخلايا(الخلايا) - موقع المعدات و / أو المشغلين في ربط بيني ضمن منطقة محدودة. هذه هي طريقة التخطيط أنواع مختلفةالمعدات التي تسمح لك بتنفيذ عمليات الإنتاج بتسلسل واضح دون انقطاع. يكون تكوين الخلية المعتاد في شكل الحرف U. هذا الترتيب يسهل تنظيم التدفق المستمر للمنتجات الفردية والتوزيع المرن للأشخاص (يمكن لمشغل واحد أن يخدم عدة وحدات في نفس الوقت).
تحدثنا عن القيمة والخسارة. الآن دعنا نتحدث عن الحاجة إلى بناء عملية خلق القيمة في شكل تدفق مستمر.
نظرًا لتطور طريقة الإنتاج من الحرف اليدوية إلى الصناعة ، تغيرت الخدمات اللوجستية لعملية نقل ومعالجة كائنات العمل عدة مرات. ذات مرة ، بدأ الحرفي المنتج التالي فقط بعد أن أنهى العمل بالكامل على المنتج السابق. في وقت لاحق ، مكنت دقة المعالجة من استخدام الأجزاء بشكل غير شخصي ، دون تعديل فردي ، تم تقسيم العمل إلى عمليات وبدأ عمل الفراغات على دفعات. تم تشكيل أماكن عمل وأقسام ومتاجر منفصلة ، تصطف في تسلسل معين. لأول مرة ، ظهر شيء مثل تدفق الإنتاج.
كان الإنجاز اللامع هو تقديم هنري فورد في بداية القرن العشرين لخط التجميع ، أولاً المحركات ، ثم السيارات بشكل عام. وقد أدى ذلك إلى زيادة كبيرة في الإنتاجية وتخفيض التكلفة بنسبة 90٪. قبل ذلك ، قام العمال بتجميع سيارة في مكان عمل واحد من البداية إلى النهاية. مع ظهور الناقل ، تم تقويم تدفق الإنتاج ووصل إلى شكله المثالي.
كانت الابتكارات تتعلق فقط بتجميع المنتج ، بينما تمت معالجة الأجزاء باستخدام طريقة "الدُفعة والصف" ، ولكن في ذلك الوقت كان هذا مناسبًا للإنتاج الضخم. انتشرت أساليب فورد بسرعة إلى صناعات أخرى. ثم حفزت الحربان العالميتان الأولى والثانية على زيادة تطوير الإنتاج الضخم للسلع في الخط.
أعاد الانتقال إلى حياة سلمية إحياء الحاجة إلى إضفاء الطابع الفردي على السلع. وتعارضت أساليب فورد ، التي أتاحت إنتاج نفس المنتج بكميات ضخمة لسنوات ، مع متطلبات السوق. تذكر أنه من عام 1908 إلى عام 1027 ، تم إنتاج نموذج واحد "T" باللون الأسود فقط. لمدة 20 عامًا ، تم إخراج 15 مليون نسخة متطابقة تمامًا من خط التجميع.
طالب السوق أكثر فأكثر بإصرار على التنوع ، ولكن لعدة عقود استمرت العديد من الصناعات في التركيز على الإنتاج الضخم والواسع النطاق للمنتجات عن طريق القصور الذاتي. لم يكن استثناء و صناعة الأثاث. في اتحاد الجمهوريات الاشتراكية السوفياتية ، في المصانع الكبيرة ، استمر إنتاج "الجدران" القياسية في خط الإنتاج حتى نهاية الثمانينيات.
توسيع النطاق ، الألوان، مجموعة متنوعة من التصميمات خاصة للبضائع الغرض المنزلي، وهو أثاث ، أثار عددًا من الأسئلة. كيف ننتج بكفاءة في ظل الظروف الجديدة؟ كيف تحافظ على الاقتصاد ، ولكن تقدم التنوع؟
تم تقديم الإجابات على هذه الأسئلة من خلال التطورات في مجال تنظيم عمليات الإنتاج من قبل تويوتا في الخمسينيات والستينيات من القرن الماضي ، والتي انعكست في أيديولوجية الإنتاج الهزيل التي تمت صياغتها لاحقًا.
يقترح مفهوم التصنيع الخالي من الهدر الاستفادة من أفضل أفكار فورد - طريقة التدفق ، ولكن التكيف معها الظروف الحديثة- بدلاً من الإنتاج الضخم بطريقة "الدُفعة والصف" ، استخدم التدفق المستمر للدفعات الصغيرة حتى المنتجات الفردية.
إذا رأينا أنه في الإنتاج يتم تحميل جميع الآلات بالكامل ولم يكن أي من العمال في وضع الخمول ، فهذا يمنحنا الرضا اللاواعي. لا تؤخذ في الاعتبار حقيقة أن قطع العمل الموجودة بين الآلات لساعات في انتظار المعالجة. يقترح Lean manufacturing تحويل الانتباه من عبء العمل على الأشخاص والآلات إلى الحركة المستمرة لقطع العمل والمنتجات ، لأنه يحدد الكفاءة. تنقسم هذه المهمة إلى مرحلتين: بناء التدفق نفسه والتحكم في حركة المواد على طول التدفق.
يُقترح ألا يقتصر الأمر على تدفق الإنتاج فحسب ، بل أيضًا في تدفق القيمة الإجمالية للمستخدم النهائي. للقيام بذلك ، يشمل عمليات معالجة الطلبات والتصميم والتوريد وما قبل الإنتاج ، بالإضافة إلى الخدمات اللوجستية وتوزيع المنتجات النهائية. من الناحية المثالية ، يتم بناء تدفق القيمة المشتركة عبر حدود مؤسسة واحدة ، جنبًا إلى جنب مع الموردين وشركات النقل والتجارة. يتضمن تيار قيمة العميل تدفقات المواد والمعلومات.
لإجراء تحليل أولي للتدفق ، من الملائم استخدام أداة تصنيع بسيطة مثل "". لتجميعها ، يتم تطبيق مسارات الأجزاء المتحركة (أو العمال) على خطة مؤسسة أو ورشة عمل مع وظائف ومعدات محددة. وعادة ما تشبه النتيجة طبق معكرونة ، ولهذا حصل الرسم البياني على اسمه.
توفر هذه الأداة البسيطة والمرئية الأساس المنطقي لخطوات تحسين التدفق التالية:
- تقليل الطول الإجمالي لتحركات الأجزاء والعمال ،
- استبعاد الحلقات والتقاطعات والعودة في الحركات ،
- أقصى تقدير تقريبي لجميع المسارات الخط المشتركربط مخزن المواد الخام ومخزن المنتجات النهائية.
بناءً على تحليل مخطط السباغيتي ، يعيدون ترتيب المعدات والوظائف ، وأحيانًا مواقع الإنتاج بأكملها. نتيجة لذلك ، يصبح التدفق أكثر اتساقًا واستمرارية ، وبالتالي أسرع.
لتحليل الخسائر المرتبطة بالوقت ، يتم استخدام أداة أكثر تعقيدًا - خرائط تدفق القيمة (VSM - خريطة تدفق القيمة). هذا المستندهو تمثيل رسومي مشروط (ليس للقياس وبدون الرجوع إلى خطة حقيقية) لعملية الإنتاج بأكملها ، مع تحديد المواد وتدفق المعلومات. يبدأ رسم الخرائط (رسم الخرائط) عادةً بإتمام عملية الإنتاج ويتم تنفيذه في الاتجاه المعاكس حتى بداية الدورة وما بعدها ، بما في ذلك الإجراءات التي تسبق الإنتاج (قبول الطلبات ومعالجتها ، وإعداد الإنتاج ، وطلب المواد ، إلخ.).
في كل موقع ، يتم تسجيل مدة العملية ، ووقت الانتظار والنقل ، وعدد المنتجات قيد التنفيذ ، وكمية النفايات ، وعدد الموظفين والمعايير الأخرى. يوفر تنسيق الخريطة القدرة على عمل الحواشي لكل عملية وحساب النسب الناتجة من إجمالي وقت إنتاج المنتج ووقت الهدر.
إذا تم رسم خريطة التدفق لأول مرة وتم أخذ جميع الخسائر في الاعتبار بالكامل ، فإن النتائج عادة ما تكون مروعة. اتضح أن المعالجة المباشرة تستغرق أقل من 1٪ من وقت الدورة. على سبيل المثال ، لدورة الإنتاج الأثاث المنجدفي غضون أسبوعين ، يمكن أن تستغرق القيمة المضافة 100 دقيقة فقط ، وبالنسبة لأثاث الخزائن المصنوع في غضون 5 أيام ، يمكن معالجة الأجزاء في غضون نصف ساعة. ومع ذلك ، يجب ألا يغيب عن الأذهان أن الشركة الرائدة في مجال التصنيع الخالي من الهدر ، تويوتا ، قد حققت نسبة قيمة مضافة قدرها 20٪ فقط ، لذلك بالنسبة لصانعي الأثاث ، يمكن اعتبار النتيجة حتى 5٪ مقبولة تمامًا.
يتيح تحليل خريطة تدفق القيمة إمكانية التحديد بالتفصيل والقضاء على المصادر الرئيسية للخسائر ، ومعرفة المناطق ذات الإنتاجية المنخفضة واتخاذ التدابير لمعادلة التدفق. يوصى برسم خريطتي تدفق ، واحدة للحالة الحالية والأخرى للمستقبل ، ووضع خطة للوصول إلى هذه الحالة الجديدة. بعد اكتمال الخطة ، يتم رسم خريطة جديدة للوضع المستقبلي ، إلخ.
بالإضافة إلى تحليل التدفق وتحسين معاييره ، من الضروري إخضاع هيكل المؤسسة له. بدلاً من التنظيم الوظيفي الهرمي العمودي مع الإدارات والخدمات ، يتم تقديم هيكل منتج مسطح. محلات الإنتاجويتم إعادة تنظيم المواقع في خلايا إنتاج تحت سيطرة فرق العمل (المنتج). يؤدي تغيير الهيكل وإنشاء الخلايا إلى تهيئة الظروف لتقليل عدد الموظفين.
تأتي فكرة التصنيع الخالي من الهدر من حقيقة أنه يمكن تحقيق أفضل النتائج إذا بدأت ، من خلال تحسين العمليات في مؤسستك ، في التعاون مع الموردين والبائعين. من خلال فحص تدفق القيمة الكاملة مع نظرائك في أعلى وأسفل السلسلة ، يمكنك العثور على احتياطيات مخفية والموافقة على مشاركة الفوائد من العمل المشتركلتحسينه.
بعد بناء التدفق وتحسينه ، يبدأون في تنفيذ مبدأ "السحب" ، أي إنتاج المنتجات فقط بناءً على طلب العميل (داخليًا أو خارجيًا). بمعنى ، من الضروري التأكد من أن العملية (العملية ، العامل) لا تبدأ في إنتاج المنتج دون إشارة من العملية أو العملية التالية أو العامل في السلسلة التكنولوجية. وهكذا ، حتى العميل النهائي. لكن المزيد عن ذلك في المقالة التالية.