Шлакоблочный станок своими руками чертежи. Методика изготовления оборудования. Как делают шлакоблок
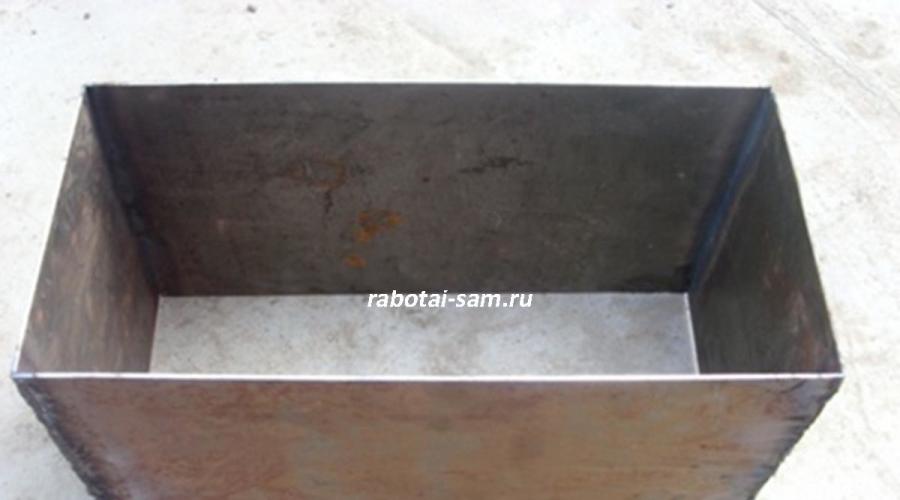
Читайте также
Сначала была идея. Многие загораются купить свой частный дом, гараж или дачу. Потом знакомятся с реальными ценами на недвижимость, и возникает желание построить все самому. Далее потребитель идет на рынок и знакомится с ценами на строительные материалы. И вот теперь, когда вы уже желаете делать кирпичи и шлакоблоки своими руками для будущего строения или собственного бизнеса, вам потребуется найти правильное оборудование.
Далеко не секрет, что такие аппараты стоят тоже дорого (от 60000 рублей), поэтому все дороги приводят к самодельному станку для шлакоблока, сделанному своими руками. В этой статье мы расскажем, как правильно его сделать, чтобы потратить минимум денег, времени и получить в результате хорошее оборудование, служащее долгие годы. Стоимость нашего вибростанка для шлакоблока не будет превышать 10 000 рублей, даже при учете покупке нового электродвигателя.
Выбираем шлакоблочный станок
Для начала определимся, какую установку нам необходимо сделать. Есть несколько типов самодельных станков: на один шлакоблок и несколько штук сразу. Для домашнего строительства (сарай, гараж, летняя кухня) достаточно будет оборудования для изготовления одного блока за один заход. Они делаются достаточно быстро и за 1 день можно без проблем изготовить до 50 шлакоблоков. Если же речь идет о частном бизнесе или строительстве большого дома, есть смысл сделать шлакоблочный станок сразу на 3-4 блока.
Теперь поговорим о конструкции станка. Вы, наверное, уже видели некоторые модели, где форма находится отдельно от виброустановки, а сверху есть еще мощный пресс, который уплотняет всю смесь за несколько подходов. В такой конструкции есть свои преимущества, но она дорогостоящая и делать ее долго. Мы создадим простую машину для изготовления шлакоблока, которая будет оказывать такое же воздействие на смесь, но состоит только из формы с электродвигателем. От пневматических и гидравлических прессов сразу откажемся – они не вписываются в наш бюджет и не соответствуют критерию «дешево и сердито».
Изготовляем простой и недорогой шлакоблочный станок
Как мы уже говорили, существуют более практичные и дорогостоящие установки, где отдельно есть вибростол, форма для засыпки и пресс, который приводится в действие, но наша задача создать эффективный шлакоблочный станок домашнего использования с минимальными затратами. У нас будет форма, которая играет роль и вибростанка, и формы, и пресса одновременно. Рассмотрим, как правильно ее сделать.
ШАГ 1: проектирование и подготовка материалов . Для начала нам надо определить размеры станка шлакоблока. Это сделать проще простого. У нас есть габариты одного шлакоблока: 390х190х190 мм, от них мы и будем отталкиваться. Нам необходимо вырезать из металла 0,2 мм толщиной следующие прямоугольники: 390х190 мм (три штуки), 190х190 мм (два штуки). Можно на 5 мм взять везде с запасом, чтобы кирпичики заливались с запасом.
ШАГ 2:
свариваем все вместе
. Теперь надо собрать наш станок для изготовления шлакоблоков, но сваривать надо все наружным швом
! Это делается для того, чтобы блок получался идеально ровный с нормальными краями, а не заглаженными или деформированными. Поскольку металл толстый, можно использовать любой сварочный аппарат – такой шов положить будет очень просто даже без навыков строителя, причем сильно большая точность нам здесь не надо.
ШАГ 3: де
лаем «начинку»
. Чтобы сделать правильный станок для шлакоблока своими руками, необходимо поместить в него трубы. Берем трубу диаметром 90 мм, нарезам ее тремя кусками по 190 мм (высота шлакоблока), свариваем их параллельно между собой и опускаем в форму. Конечно же, верх трубы необходимо заварить (вырезать круги диаметром 90 мм или купить готовые).
ШАГ 4:
делаем сборник
. Это специальный фартук, который наваривается вокруг формы, чтобы удобнее было засыпать строительные материалы, можно сделать его в форме лейки. Сварить металлические пластины под углом. Можно сделать своими руками самодельный станок для шлакоблока вообще без фартука, но будет неудобно работать, к тому же, стоимость такого апгрейда техники невысокая.
ШАГ 5:
делаем пресс
. Собственно, все, что нам необходимо – оказать давление на полусухую смесь. Для этого не надо много денег, изготовление станка для производства шлакоблоков своими руками может быть дешевым. Берем пластину из металла 0,2 – 0,3 мм с размерами 385 х 185 мм (да, чуть меньше нашей формы), потом смазываем верх труб маслом, прикладываем пластину и делаем отпечаток. Теперь вам необходимо вырезать как можно ровнее отверстия в пластике под трубы, можно использовать резак или отдать эту работу специалисту. После этой работы надо просто приварить две ручки сверху пластины, чтобы ее удобно было поднимать.
ШАГ 6:
делаем выброустановку
. Можно было бы рассказать вам о сложной системе подрамника и эксцентриках на осях, которые приводятся в действие ремнем от двигателя, но народные умельцы нашли способ проще. Надо приварить крепления для двигателя мощностью 0,5 кВт прямо к форме, привинтить его туда и повесить на вал гайку с эксцентриком или хомут типа «щечки». Двигатель наберет обороты и создаст большую вибрацию каркаса – то, что нам и надо.
ШАГ 7: ставим форму на ноги . Чтобы сделать передвижной станок для производства шлакоблоков своими руками необходимо поставить эту заготовку на колеса сразу. Варим рамку с размерами 40х30 мм, привариваем колеса со старой тачки. Все готово. Но этого можно и не делать, поскольку шлакоблоки делаются не очень быстро, материал можно просто складировать рядом или относить.
ВАЖНО: двигатель надо купить закрытого типа, чтобы туда не попадала пыль и влага. Идеально подойдут простые китайские аппараты, которые стоят недорого и обеспечивают неплохую защиту от воды и загрязнений. Если же вы хотите поставить туда двигатель со стиральной машины или наждака, тогда надо будет периодически проводить его чистку.
Собственно, теперь вы построили станок для изготовления шлакоблоков своими руками, можно поздравить вас с экономией десятков тысяч рублей и переходить к изготовлению блоков. Такое оборудование прослужит очень долго, оно почти вечное и состоит из ударопрочных деталей, надежно сваренных между собой.
Как изготовить шлакоблок своими руками
Приспособление мы сделали, теперь самое время рассказать, как ним пользоваться. Да, эта штука еще и работать будет! Значит, берем нашу полусухую смесь: крупный песок, гравий диаметром 5-8 мм, цемент и воду в соотношении 6:2:2:1 и доводим до консистенции, когда смесь будет сжиматься в кулаке, но остается сыпучей при падении на землю. Теперь все это засыпаем в станок для шлакоблоков, сделанный своими руками по чертежам нашего мастера (спасибо ему отдельное).
Включаем в розетку двигатель (лучше сделать «горячую кнопку» прямо на форме) на 2 минуты. Ждем, пока все усядется, затем досыпаем сухую смесь при необходимости, снимаем лишнее при помощи мастерка или подручных материалов. Далее ставим пластину-пресс сверху и оказываем на нее давление в пару десятков килограмм. Можно сделать надставку и шарахнуть с небольшой амплитудой тяжелой кувалдой или попрыгать сверху – без разницы. Теперь берем за ручки «пресса», снимаем его и выкладываем из нашего вибростанка для шлакоблока.
У нас есть готовый шлакоблок, который надо оставить на хранение примерно на 48 часов до полного отвердевания, а транспортировать его можно уже через 1 сутки при условии естественной сушки при низкой влажности и температуре +25 С. Мы рассмотрели, как изготовить станок для шлакоблоков своими руками, а теперь предлагаем еще посмотреть интересное видео этого процесса.
В наше время очень популярно строительство одноэтажных помещений, как жилых, так и производственных. В большинстве случаев это гаражи, бани, небольшие постройки возле дома. Каждый из новоявленных строителей, конечно же, ищет всевозможные пути экономии своих средств, не теряя при этом качества, ведь делается в основном все для себя.
Итак, среди огромного выбора строительного материала, мы остановимся на самом выгодном на данный момент — шлакоблоке.
Самодельный строительный материал
Себестоимость шлакоблоков невысока, а по размерам они заменяют собой около 5 обычных кирпичей, есть изделия и равные 8-10 керамическим блокам. Изготавливается они из любого подручного материала, называемого еще заполнителем .
К заполнителям можно отнести:
- Песок.
- Керамзит.
- Зола.
- Шлак.
- Опилки.
- Щебень.
- Битый кирпич.
Примечание!
Выбор следует производить в зависимости от того, насколько вы хотите сделать продукт качественным и долговечным.
Для жилых строений лучше применять керамзит, шлак или песок, а для хозяйственных сооружений подойдут зола и опилки.
В основе укрепляющего элемента выступает цемент. При самостоятельном изготовлении шлакоблоков, вы не только сокращаете стоимость будущей постройки, но имеете полный контроль над качеством производимого материала. Также вы можете самостоятельно выбирать форму будущих блоков.
Что касается оборудования, то стоит взглянуть на чертежи станка для шлакоблоков и лишние вопросы сразу отпадают. Не надо быть строительным гением, чтобы самостоятельно изготовить станков в домашних условиях, именно об это мы поведаем вам в нашей статье.
Вы с легкостью найдете в интернете самодельные станки для шлакоблоков, выполненные такими же «мастерами», как вы, поэтому не стоит сомневаться в своих способностях.
Важно!
Перед началом работ ознакомьтесь с возможными вариациями габаритов строительного материала.
Если вы хотите изготовить блок стандартной формы, то она имеет следующие параметры -400 × 200 × 200 мм.
Что касается пустот, то их не более 30 % от общего объема.
Изготовление станка
Станки для шлакоблока продаются в широком ассортименте, их цена варьируется от 3-4 тысяч рублей до нескольких десятков.
Но, так как сегодня мы рассказываем о самостоятельном изготовлении, то начнем с определения того, для каких именно масштабов, вам нужен такой станок:
- Если вам нужно сделать небольшую постройку, то вам отлично подойдет станок на одновременное изготовление одного или двух блоков.
- Если же вы хотите поставить это дела «на конвейер», то тут уже необходимо делать матрицу на четыре, а то и больше блоков.
Из чего состоит оборудование
Определившись с тем, какое количество шлакоблоков вы желаете изготавливать в сутки, давайте рассмотрим строение данного станка:
- Самая главная деталь в станке, это матрица, поэтому нужно уделить особое внимание данному этапу изготовления. Ведь от нее, в дальнейшем будет зависеть форма, точность и размеры будущих шлакоблоков.
Примечание!
Все остальные узлы агрегата, предназначены лишь для упрощения пользования таким станком, это наполнение, уплотнение, извлечение, передвижение.
Хотя каждый процесс по-своему важен для положительного конечного результата.
- Для уплотнения раствора существует несколько способов, наиболее подходящий и простой в изготовлении – это электродвигатель со смещенным центром тяжести для создания вибрации.Двигатель прикрепляется непосредственно к форме (матрице) и обязательно закрывается кожухами. Смещения центра тяжести можно добиться путем перпендикулярного приваривания к валу двигателя болта с гайкой.
К сведению!
Чтобы понять, как это все происходит, посмотрите на фото ниже. На них представлены чертежи вибростанка для шлакоблоков.
Как сделать самому
Зная размеры желаемого блока, приступаем к изготовлению матрицы:
- Из листового метала с толщиной 3 – 5 мм, вырезаются заготовки.
- Для изготовления пустот в блоке понадобится пустотообразователь, который можно изготовить из труб нужного диаметра. Желательно использовать конусные трубы, для облегчения изъятия из готового блока. На ваше усмотрение можно использовать не только трубы, но и прямоугольные пустотообразователи, главное — не забывать делать их конусообразными.
- Соединяем заготовки при помощи прихваток, так как от непрерывного шва, может повести металл.
Примечание!
Швы делаются только снаружи формы, иначе блок не будет иметь правильную геометрическую форму.
- Форма по высоте должна быть на 5 см выше размеров готового блока. Это связано с тем, что при вибрации смесь имеет свойство утрамбовываться, а также для установки сверху прижимного листа.
- Следующий этап – это рама. Для более простого перемещения станка, основа ставится на колесики, что позволяет перемещать станок, не нарушая при этом готовый блок. Стойки, по которым будет ходить форма, рекомендуется делать чуть длиннее, так сказать с запасом, ведь отрезать вы всегда успеете – для удобства.Все механизмы и детали делаются из индивидуального предпочтения, и исходя из вашего роста.
Шлакоблок - искусственный стеновой камень из смеси шлака и цемента, предназначенный для возведения стен одноэтажных строений. Его применяют также в качестве дополнительного утеплителя при строительстве каркасных домов. Производство этого материала возможно и в домашних условиях своими силами. Не рекомендуется делать самому лишь фундаментные панели. Требования к надежности основания здания очень высокие, поэтому лучше не экономить и купить готовые элементы.
Различают такие разновидности:
- полнотелые - обладают наибольшей прочностью, предназначены для возведения несущих стен и перегородок, облицовки;
- пустотелые со степенью пустотности 40 % - отличаются более высокими тепло- и звукоизолирующими свойствами за счет наличия полостей внутри, стоят дешевле, но уступают по прочности из-за тонкости стенок;
- пустотелые со степенью пустотности от 25 до 30 % - обладают оптимальными пропорциями по теплопроводности и прочности, самые популярные.
В зависимости от толщины блоки бывают:
- стеновые - стандартный размер 390 х 190 х 188 мм;
- перегородочные - 390 х 90 х 188 мм.
При самостоятельном изготовлении размеры могут быть произвольными, обязательное условие - стабильность габаритов.
Технические характеристики
- Шлакоблоки обладают сравнительно низким коэффициентом теплопроводности - от 0,20 до 0,65 Вт/м3 (лучше чем у кирпича). За счет этого их применяют часто не только как конструкционный материал, но и как утеплитель.
- Плотность - от 750 до 1450 кг/м3. От всех прочих видов отличается высокой прочностью - марка от М35 до М125. Параметр нужно учитывать при проектировании коммуникаций, так как он с трудом режется.
- Морозостойкость составляет до 50 циклов замораживания-размораживаниия без появления видимых повреждений.
Достоинства:
- невысокая цена;
- доступность и разнообразие материалов для изготовления, возможность получения изделий с нужным набором параметров, подходящих для конкретных целей;
- польза для экологии - за счет использования отходов металлургической промышленности (шлака), а так же боя кирпича и бетона, остающегося при сносе старых зданий, уменьшается количество свалок строительного мусора;
- огнестойкость;
- не является благоприятной средой для развития грибков, плесени, не подвержен порче грызунами;
- простота монтажа стен.
Недостатки:
- очень высокая степень гигроскопичности - сильно впитывает влагу из воздуха, обязательно требуется надежная облицовка с обеих сторон;
- наличие опасных для здоровья веществ (серы) - для полного их выветривания блоки выдерживают на открытом воздухе не менее года, при покупке необходимо проверять сертификат экологической безопасности;
- из-за необходимости качественной гидроизоляции, облицовки общая стоимость строения незначительно ниже, чем при использовании более дорогих стройматериалов, существенная экономия получается лишь при изготовлении своим руками.
Из шлакобетона чаще строят подсобные, хозяйственные, производственные помещения, гаражи.
О шлаке для производства блоков
Это силикатный отход обработки металлов, его просеивают через сито. Шлак, полученный при сжигании различных видов твердого топлива (уголь, дрова), содержит радиоактивные компоненты, поэтому для строительства жилых помещений его не применяют.
Разновидности шлаков:
- гранулированные (граншлак);
- негранулированные.
Для изготовления строительных блоков отбирают самую крупную фракцию гранулированных отходов, более мелкие (негранулированные) идут на производство асфальта, тротуарной плитки. Цена за 1 тонну материала - от 100 рублей. Различают отходы цветной и черной металлургии (доменные), предпочтительнее второй вариант, так как полученные при обработке цветных металлов стоят дороже.
Состав смеси для получения блоков
В качестве вяжущего выбирается цемент марки не ниже М400. Наполнитель либо полностью состоит из шлака, либо смешанный - добавляют в небольшом соотношении щебень (допустимо вторичный), песок обычный или керамзитовый, мелкий керамзит, дробленый кирпич. Пропорции для шлакоблоков: на 8-9 частей наполнителя 1,5-2 части вяжущего. Если цемент марки М500, то его можно брать примерно на 15 % меньше, чем М400.
Шлак обычно составляет не менее 65 % всего объема заполнителя. Например, из 9 частей не менее 6 приходится на него, остальное дополняют песком, щебнем. Но теоретически возможно использовать для производства своими руками кирпичный или бетонный бой, отсев. Вне зависимости от типа материала принято условно называть и такие изделия шлакобетоном. Классические пропорции: 2 части песка, 2 части щебня, 7 частей шлака, 2 части портландцемента М400.
Воду добавляют в соотношении примерно 0,5 части. Готовая смесь получается полусухой. Чтобы проверить качество, горсть бросают на твердую поверхность. Если ком рассыпался, но при сжатии вновь легко обретает прежнюю форму, то состав пригоден для использования.
Для получения цветного блока вносят окрашенный мел или измельченную кирпичную крошку. Для повышения прочности вводят профессиональные пластификаторы. Иногда добавляют гипс, опилки, золу как частичную замену шлака.
Смешивать компоненты лучше в бетономешалке или смесителе, но такое оборудование стоит дорого. Небольшое количество замешивают вручную, процесс трудоемкий.
Технология производства шлакоблоков
Их делают двумя способами:
- вручную - качество готовых изделий невысокое, неравномерное, но в целом соответствует требованиям стандартов;
- вибролитьем, с использованием вибростола или вибростанка - получаются более прочными.
В больших объемах изготавливают методом вибропрессования. Оборудование для этого способа стоит дорого, поэтому для домашнего производства не подходит. Помещение должно быть хорошо проветриваемым, с ровным твердым полом. Это необходимое условие для просушивания и хранения.
Вне зависимости от выбранного способа подготовленную смесь предварительно помещают в специальные прямоугольные каркасы. Их делают из пластика, деревянных досок или металлических листов, обязательно разборными и без дна - для легкого извлечения. С этой же целью перед заливкой стенки смазывают солидолом или мыльной водой. Удобнее использовать опалубку из нескольких ячеек (обычно от 4 до 6). При изготовлении из дерева выбирают доски с абсолютно гладкой поверхностью, иначе при распалубке сучки и неровности будут цепляться.
Ко дну формы для пустотелых блоков дополнительно крепят пустотообразователи - цилиндрические или прямоугольные из металла или дерева. Вместо них можно ставить стеклянные бутылки, после застывания смеси их вынимают.
2. Станок своими руками.
Простой готовый станок для шлакоблоков стоит от 6500 рублей. Но при желании и наличии набора необходимых инструментов и деталей его нетрудно изготовить дома самостоятельно.
Порядок действий:
- Из четырех стальных листов толщиной 3-4 мм сварить прямоугольную форму без дна со внутренним размером 390х190х190 мм.
- По периметру верха короба приварить стальную полосу-бортик.
- К нижним частям коротких сторон приварить направляющие для удобного снятия и перемещения станка.
- Нарезать из металлической трубы круглого сечения диаметром около 6 см три детали равной длины.
- Установить отрезки в вертикальном положении в ряд по одной линии на расстоянии примерно 4 см друг от друга и соединить их, приварив или приклеив между ними перемычки. К внешним сторонам крайних труб тоже прикрепить перемычки для соединения со стенками. Точные размеры всех деталей зависят от диаметра пустотообразователей и длины короба.
- Закрыть трубы сверху заглушками. Вставить конструкцию из труб внутрь формы и прикрепить.
- Установить на внутренних стенках короба ограничители высоты.
- К коротким сторонам прикрепить ручки.
- Из пятого стального листа вырезать прижимную крышку. Она в процессе производства блоков надевается на пустотообразователи, таким образом, чтобы они выступали. Поэтому в крышке должны быть прорези под трубы и перемычки между ними, по размеру большие на 1-2 мм.
- Сверху к полученной детали приварить две П-образные ручки. Их устанавливают вдоль коротких сторон крышки вертикально.
- Прикрепить к одной из длинных сторон формы болтами или приваренными шпильками площадочный двигатель-вибратор. Так как стоимость его сравнительно высока и приобрести его трудно, возможно использовать вместо него двухвальный мотор от стиральной машины. К самодельному двигателю крепят балансиры.
3. Изготовление блоков из шлакобетона вручную.
- На ровном основании или полу расстелить полиэтиленовую пленку. Поставить на нее смазанные формы.
- Приготовить смесь, соблюдая рекомендуемые пропорции.
- Распределить ее по формам. Для пустотелых блоков вставить бутылки (если нет пустотообразователей).
- Разровнять поверхность, удалить излишки раствора.
- Через 5 часов вынуть бутылки.
- Через 24 часа достать блоки.
- Разложить на ровной горизонтальной плоскости.
- Через неделю сложить в несколько рядов и оставить сушиться еще на 21 день. В процессе сушки их накрывают пленкой. Оптимальные условия - температура воздуха от +20 до +25°C, отсутствие прямого солнечного света.
При наличии вибростола формы устанавливают на его поверхность. Вибрацию включают примерно на минуту. Точное время лучше определить опытным путем, сделав пробные кирпичи. Превышение времени воздействия вибрации приводит к ухудшению качества. Затем конструкции с утрамбованной смесью снимают со стола и поступают с ними так же, как при ручном изготовлении (см. п. 5-8 инструкции).
4. Производство шлакоблоков своими руками в домашних условиях на вибростанке.
Схема изготовления с помощью простого станка:
- Разложить на полу куски фанеры или ОСП размером 500х300 мм. Они будут служить подложками под блоки.
- Установить станок на первый лист фанеры.
- Приготовить состав, соблюдая рекомендуемые пропорции.
- Заполнить форму.
- Включить двигатель на 20-30 с (для более точного определения оптимального времени воздействия вибратора на шлакобетон рекомендуется сделать пробные кирпичи и оценить их прочность, равномерность готового материала).
- Отключить вибрацию - смесь оседает на несколько сантиметров, снова заполнить короб доверху. Включить мотор и прижать крышку. Она должна упереться в ограничители высоты на внутренних стенках.
- Отключив вибрацию, снять станок с блока и переместить на следующую подложку.
- Повторить все действия на каждом подготовленном листе фанеры.
Сроки готовности и условия сушки такие же, как и при ручном изготовлении.
Шлакоблоки недороги, обеспечивают хорошую тепло- и звукоизоляцию. Технология их производства проста, а готовую продукцию не нужно сертифицировать. Поэтому наладить изготовление своими руками может любой желающий.
Технология изготовления шлакоблоков
Производство шлакоблочных кирпичей осуществляется в несколько стадий.
Составление смеси из шлака, цемента и воды. В качестве сырья подходит щебенка, битый кирпич, керамзит, зола, песок. В зависимости от доступного сырья состав смеси можно сделать разным. Важно соблюсти правильную пропорцию сухих и жидких компонентов:
- 1 вариант: цемент, шлак и воду смешать в объемном соотношении 1:9:0,5;
- 2 вариант: цемент, граншлак, мелкий отсев и воду смешать в соотношении: 1:4:4:0,5.
В любом случае объем воды должен быть в 2 раза меньше объема цемента!
Месить можно вручную, бетономешалкой или смесителем. Смесь должна быть полусухой, в нее желательно добавить пластифицирующий агент, который:
- ускоряет затвердевание (полезное свойство при небольших производственных площадях);
- повышает плотность, снижает вероятность появления трещин;
- повышает производительность труда.
На малых производствах с небольшими станками можно замешивать смесь и вручную, но это достаточно трудоемкий процесс.
Загрузка бетонной смеси в формы. Стандартные размеры форм для вибропрессования 39 х 19 х18,8 см. Формы могут быть с пустотообразователями или цельными. В формах смесь прессуется пуансоном при постоянной вибрации. Длительность прессования варьирует в пределах 10 — 90 секунд и зависит от возможностей станка. Усиленное оборудование прессует шлакоблоки быстрее.
Формы снимают и блоки оставляют до полного высыхания. После съема форм блоки должны сохранять форму, не распадаться в процессе испарения влаги. Поэтому очень важно выдерживать соотношение компонентов во время замеса жесткой бетонной смеси. Если сделать смесь чересчур жидкой, блоки растекутся. При недостатке влаги — рассыпятся.
Этап затвердевания протекает от 48 до 96 часов. Сушка происходит при положительной температуре. Но окончательно изделия затвердеют только спустя 30 дней в условиях повышенной влажности. Пониженная влажность при высыхании провоцирует растрескивание блоков. При более высоких температурах высушивание происходит быстрее. На процесс созревания положительно влияют специальные компоненты (релаксол, фулерон). При наличии производственных мощностей, блоки подъемниками складывают в стеллажи, где их пропаривают.
Оборудование для изготовления шлакоблоков
Своими руками можно изготавливать шлакоблоки, используя следующие станки и оборудование:
- вибростанок универсальный;
- бетономешалка;
- лопата;
- строительная тележка
- вибросито.
Оборудование по изготовлению шлакоблоков на небольшое производство легко подобрать в специализированных магазинах. Есть недорогие модели MARS с подъемом матриц вручную, с помощью рычага или 1ИКС. Небольшой станок для шлакоблоков М310 с механизированными операциями хорош для более крупных производств, он изготавливает до 400 блоков за рабочую смену. Еще большую производительность обеспечивают станки для шлакоблоков Дракон и Команч — около 600 штук за смену. Любой из мини-вибростанков для изготовления блоков своими руками работает от электросети 220 В.
Модель | Производительность за 8 часов работы, бл\смену | Мощность, Вт | Вес, кг | Тип |
МЗ-10 универсал | До 700 | 150 | От 19 | ручной |
1 ИКС | До 500 | 150 | От 28 | Механико-ручной |
MARS-2 | До 650 | 200 | От 55 | Механико-ручной |
Команч Усиленный | До 1500 | 500 | От 190 кг | Механико-ручной |
Дракон-4 | До 2000 | До 1000 | От 250 | полуавтоматический |
Таблица 1. Характеристики вибростанков
При желании своими руками изготавливать блоки наиболее приемлемыми будут модели Дракон-4 или Команч Усиленный. Хотя это достаточно серьезные денежные вложения, они окупятся. Ведь изделия пользуются устойчивым спросом в частном строительстве. Кроме блоков, такое оборудование предназначено для производства тротуарной плитки.
Для собственного строительства своими руками больше других подойдет станок 1 ИКС. Он занимает мало места, недорог, поэтому называется мини-станком. В отличие от более совершенных моделей, на нем изготавливают только шлакоблоки.
Конструкция самодельного вибростанка
устройство стола-вибратора: 1 — электромотор; 2 — груз для разбалансировки; 3 — шкив
Устройство вибростанка состоит из вибратора и матрицы-шаблона. Шаблонов может быть от одного до десятка, в зависимости от размеров самодельного станка. Матрица может быть любого удобного размера, если объединить несколько форм и установить их на электрический вибратор получается самодельный небольшой станок для изготовления шлакоблоков.
Вариантов чертежей в сети множество.
чертеж форм для шлакоблоков: 1 — матрица в развертке; 2, 3, 4 — поддоны; 5, 6, 7 — нижняя рамка матрицы делается из уголка 25х25; 8 — рейка для крепежа пустотников; 9 — пустотник; 10 — верхняя пробка пустотника; 11 — нижняя пробка пустотника
Матрицу своими руками делается по чертежу из металлического листа толщиной 3 мм. Форма представляет собой короб без дна, чтобы его поднимать предусмотрены ручки. Чтобы нижняя поверхность получилась ровнее и аккуратнее, сушат их на резиновых матах, обработанных любым моющим средством.
Еще один чертеж матрицы, которую несложно изготовить своими руками.
Простая схема, позволяющая своими руками получать шлакоблоки без вибростола. В качестве пустотелов используются обычные стеклянные бутылки. Такую форму заполняют раствором с повышенным количеством влаги. Особенность этого метода в более продолжительном выстаивании раствора в формах — до нескольких часов. После чего форма разбирается и шлакоблоки досушиваются на воздухе.
Больше всего в качестве пустотелов подходят бутылки от шампанского. У них толстые стенки, которые не лопаются при засыхании раствора.
Самодельные формы собирают из фанеры или листового металла, перед заливкой бетонной смеси изнутри форму обрабатывают техническим маслом.
Существует два варианта самодельных мини-станков:
- с вибростолом;
- в виде формы, к которой прикреплен двигатель со смещенным центром тяжести.
Второй вариант дает возможность изготавливать блоки без переворачивания, за один подход, поэтому он предпочтительнее при больших объемах производства.
схема станка типа «несушка»
Сделанный своими руками мини-станок, работает за счет электромотора, установленного снаружи. Вибрация обеспечивается разновеликими грузами, которые разбалансируют корпус. Чтобы форма снималась легче, пустотники выполнены в форме конусов с разницей диаметров до 3 мм.
Необходимые материалы и инструменты:
- углошлифовальная машина (болгарка);
- сварочный аппарат;
- лист металла толщиной 2,5 — 3 мм;
- уголки 25х25;
- труба для пустотников;
- 2 жесткие пружины;
- асинхронный электродвигатель мощностью 120 — 180 Вт.
Использование шлакоблоков в строительстве позволяет снизить расходы на сооружение стен в несколько раз. Для изготовления данного материала требуется специальное оборудования, покупка которого является довольно затратным процессом. Предлагаем изучить рекомендации о том как сделать станок для шлакоблоков своими руками.
Шлакоблок - особенности материала и его назначение
Шлакоблоком называют строительный материал, по внешнему виду схож с камнем, который изготавливают с применением метода вибро пресса. Для его производства используется наполнитель в виде шлака, а связующим веществом выступает цементный раствор.
Существует два варианта производства шлакоблоков:
- промышленный;
- самостоятельный или домашний.
Чтобы изготовить шлакоблок своими руками применяют вибростанки малогабаритного типа, которые способны изготовить небольшие партии данного материала.
В соотношении с основными составляющими шлакоблока, а именно шлаком, в его состав входит один из материалов в виде:
- шлака;
- вулканического пепла;
- гранитного отсева;
- гранитного щебня;
- речной щебенки;
- песка;
- кирпичного камня;
- цемента;
- керамзита и т.д.
Материал, об изготовлении которого поговорим далее, имеет более низкие качественные характеристики и долговечность. Он отлично подойдет для сооружения построек хозяйственного назначения, сараев, складских сооружений.
Домашнее изготовление шлакоблока не позволяет провести весь технологический процесс в соотношении со всеми требованиями, которые к нему предъявляются.
Для того, чтобы шлакоблок приобрел необходимую жесткость требуется выдержать пропаривание, с помощью которого происходит насыщение его влагой и нагревание до определенной температуры, которая повышает прочность цемента. Хотя с помощью блоков, изготовленных на домашнем вибростанке получится отличное одноэтажное здание, срок службы которого составит минимум 25 лет.
Станок для шлакоблоков: особенности изготовления
Чтобы соорудить такого рода станок, следует иметь навыки работы со сварочным аппаратом и слесарским инструментом.
В качестве главной детали самодельного станка для шлакоблока выступает матрица, которая имеет форму для установки раствора. Матрица имеет вид металлического короба, в котором имеются определенные элементы, обеспечивающие пустоты в уже изготовленном изделии.
Именно матрица и является своего рода станком, для изготовления которого потребуется наличие:
- сварочного аппарата;
- болгарки;
- тисков;
- слесарного инструмента.
В качестве материалов потребуется приобрести:
- лист металла, толщиной в 3 мм, размером в 1 м²;
- один метр стальной трубы, диаметром от 7,5 до 9 см;
- стальной полосы толщиной 3 мм, а длиной в 30 см;
- электрического мотора, мощностью до 0,75 кВт;
- крепежи в виде болтов и гаек.
Инструкция по изготовлению станка для шлакоблока своими руками:
1. Сначала определитесь с размерами изделия, которое необходимо для строительства. Возможен вариант измерения уже готового шлакоблока, промышленного производства.
2. Из металлического листа вырежьте боковые участки станка, их должно быть две штуки, а между ними присутствует перегородка. Получится короб, имеющий две равные части.
3. В пустотах остается донная стенка, толщина которой минимум 3 см. Таким образом, удастся определить высоту цилиндра, который будет ограничивать пустоты.
4. Разрежьте трубу на шесть частей, длина которых будет равняться высоте пустоты.
5. Чтобы сделать каждый из цилиндров конусообразным, необходимо произвести надрезы каждого из них до центра, а затем сжать с помощью тисков и приварить друг к другу сваркой. При этом размер диаметра станет на два миллиметра меньше.
6. Приварите цилиндры с двух сторон и соедините их между собой с длинной стороны блока. Они должны быть расположены таким образом, чтобы пустоты, которые будут образовываться в точности копировали пустоты промышленного производства.
7. К крайним участкам добавляется по пластине, размером в 3 см. Она должна иметь отверстие, которое обеспечит ее фиксацию на поверхности проушин.
8. На центральной части каждого из матричных отсеков пропилите поверхность и к ней приварите проушины. Они помогу обеспечить возможность в временном креплении ограничителей для образования пустоты. Получится механизм, с помощью которого будут производиться шлакоблоки как монолитного или и не монолитного типа.
9. Выберите одну поперечную стенку, на которую приварите болты, в количестве четырех штук. Они выступают в качестве крепежей, для фиксации мотора.
10. В стороне загрузки смеси следует приварить детали в виде фартука и лопастей.
11. Произведите зачистку и полировку всех компонентов под дальнейшее их окрашивание.
12. Сделайте пресс, форма которого будет точно такой как и сам механизм, Для его сооружения понадобится пластина, отверстия которой будут больше диаметра цилиндра на четыре миллиметра. Она должна с легкостью помещаться в короб на высоту минимум 5 см.
13. Для обеспечения удобства работы с прессом, приварите к нему детали в виде ручек.
14. Покройте все составляющие механизма с помощью антикоррозийной грунтовки, а после ее высыхания установите мотор.
Для того, чтобы из стандартного электрического двигателя сделать мотор вибрационного характера следует установить на его валовые участки приваренные болты в виде эксцентриков. Они должны совпадать в осевом пространстве. На болтах устанавливаются гайки, от величины накрута которых зависит скорость и тип вибрации.
Чертежи станка для шлакоблока:
С помощью такой матрицы изготавливают как шагающий, так и дистанционный тип станка. Чтобы ее усовершенствовать требуется иметь хороший слесарский инструмент и опыт работы с ним.
Для изготовления такого рода блоков подойдет любой материал в виде глины, опилкобетона, керамзитбетона и т.д. Стандартная смесь должна состоять из одной части песчаного наполнителя, одной части цемента и трех частей шлаковых отходов.
Очень важную роль играет коэффициент влаги, которая содержится в готовой смеси. Для ее оптимального определения достаточно осмотреть состав, он не должен разваливаться, но в то же время должен быть эластичным и хорошо держащим форму.
Именно такую заготовку укладывают в матрицу для получения готового шлакоблока. Для образования пустот рекомендуется использование стеклянных бутылок, битого кирпича или остроугольного камня.
Учтите, что перед началом работы на станке для производства шлакоблоков, следует все детали смазать с помощью масла, таким образом удастся предотвратить прилипание готовой смеси к металлу. Включение вибратора возможно на любой из стадий производства, но лучше всего это делать перед прессовкой готового блока. Кроме того, электромотор следует надежно изолировать, с помощью фартука предотвращается попадание раствора на поверхность мотора.
Уже готовые шлакоблоки должны выдерживаться на улице, летом, при температуре от +12 до +30 градусов. Для того, чтобы блоки не пересушились, их накрывают полиэтиленовой пленкой.
Оборудование для производства шлакоблоков и технология их изготовления
Изготовления шлакоблока начинают с подготовки бетонного раствора, который состоит из цемента, воды и шлака. Все компоненты смешиваются между собой бетономешалкой или смесителем. Ручной замес раствора осуществляется дольше и требует огромных физических усилий, для его осуществления.
Все работы проводят исключительно при плюсовой температуре воздуха, так как при морозе происходит застывание воды. Когда раствор готов, его засыпают в форму, которая бывает пустотной или монолитной. Стандартный размер каждого блока 39х19х18.
Когда блок имеет уже уплотненную структуру, с него снимают форму, а сам блок устанавливается на пол или на поддон. Процедура высыхания шлакоблока длится при естественной температуре воздуха, которая не должна быть менее двадцати градусов. Таким образом, удастся получить материал, пригодный для дальнейшего строительства. Во избежание пересыхания материала следует обеспечить максимальную влажность воздуха.
После высыхания шлакоблоков они приобретают дополнительную прочность и отправляются на хранение в сухое место в виде складского помещения.
В качестве сырья используются разнообразные по составу материалы. На выбор того или иного сырья влияют возможности оборудования, на котором изготавливается шлакоблок и тип сооружения, которое будет из него возводиться.
Самыми распространенными вариантами наполнителей для изготовления шлакоблоков своими руками выступают материалы в виде:
- кирпичных отходов;
- песка;
- щебня;
- золы;
- керамзита и т.д.
Количество того или иного ингредиента зависит от требований к конечной продукции.
Довольно частым составляющим для изготовления шлакоблока выступает пластификатор, который улучшает технические характеристики готового материала. Кроме того, использование пластификаторов увеличивает прочность готового здания его устойчивость перед морозом и влагой.
После изготовления шлакоблоков предстоит процесс строительства и непосредственного возведения стен из шлакоблоков. Еще один важный фактор, влияющий на качество конструкции из шлакоблока - финишная отделка и утепление готового здания.
Стандартный состав приготовления смеси для шлакоблоков состоит из:
- одной части цемента;
- девяти частей шлака;
- 50% от количества цемента воды.
Еще один вариант изготовления шлакоблоков предполагает использование:
- четырех частей мелкого отсева;
- четырех частей гранитного шлака;
- одной части цемента на 50% воды.
Производство шлакоблоков - общие требования к выполнению работ
Для изготовления качественного шлакоблока следует придерживаться таких правил:
- знать четкую рецептуру и состав смеси;
- следовать технологии изготовления шлакоблоков;
- иметь достаточно профессиональное оборудование.
Кроме того, залогом качественного шлакоблока, изготовленного в домашних условиях является использование крупного песка, доменного шлака, качественного цемента с минимальной маркой в 400. Кроме этого, требуется наличие специального оборудования, имеющего вибропресс.
Для изготовления шлака отлично подходит перегоревший уголь, который используется в качестве наполнителя. Одним из важных требований к производству шлакоблоков выступает соблюдение симметричной и ровной геометрической формы готового изделия. Так как от количества неровностей и изъянов шлакоблока зависит количество раствора, который требуется для возведения готового здания. Во избежание появления данного дефекта, следует наполнять форму до верха и даже больше, так как при проведении вибрации готовая смесь уплотняется и уменьшается в размере.
Включение виброформы происходит каждый раз с интервалом в 6-15 секунд. Далее происходит прекращение вибрации и оценка готового изделия. Если раствор находится ниже, чем крайняя черта матрицы, то на него устанавливается прижимная крышка и снова включается вибрация. Далее происходит упирание прижима в ограничитель, вибрация выключается, а форма вытаскивается с устройства.
Шлакоблоки своими руками: инструкция по изготовлению
При самостоятельном изготовлении шлакоблоков следует подбирать состав смеси исходя из типа шлакоблочного станка. Так как качество вибрации напрямую определяет свойства конечного продукта.
Предлагаем вариант стандартного рецепта для изготовления шлакоблоков:
- семь ведер шлакового наполнителя;
- два ведра песка;
- два ведра гравия;
- полтора ведра цемента;
- от полтора до трех ведер воды.
Учтите, что количество воды влияет на структуру и качество блоков. Раствор после прессования не должен растекаться. Если готовую смесь кинуть на землю и при этом она растечется, а в кулаке - снова соединится, то именно такой тип раствора подойдет для изготовления шлакоблоков.
Если для изготовления шлакоблоков используется помещение, то в нем должен присутствовать ровный пол и хорошая вентиляция, но все же, рекомендуется производить шлакоблоки на открытом воздухе.
Самодельные станки для шлакоблоков предполагают изготовление данного материала по нижеприведенной инструкции:
1. Налейте раствор в форму для шлакоблоков. Включите вибратор на пять секунд. При недостаточном количестве раствора добавляется еще немного смеси. Установите прижим, и включите вибратор еще раз. Когда прижимное устройство находится на ограничителях, то процесс изготовления считается завершенным.
2. Происходит включение виброформы еще на 8 секунд и далее форму вынимают без выключения вибратора.
3. Сушка блоков занимает период времени от четырех до девяти дней. Полная прочность достигается по истечению месяца. Главными условиями их хранения выступает высокая влажность и температура.
4. Транспортировка блоков в помещение происходит по истечению минимум дня, после их изготовления. При наличии пластификатора в составе для приготовления шлакоблоков, их транспортировка происходит через шесть часов, после изготовления.
5. Хранение шлакоблоков происходит в виде пирамиды. По истечению нескольких месяцев, они становятся пригодными к строительству.