Metoda ispitivanja bez razaranja u boji. Postoje luminiscentne i kolor metode detekcije kapilarnih nedostataka. Kontrolni uzorci za detekciju kapilarnih nedostataka
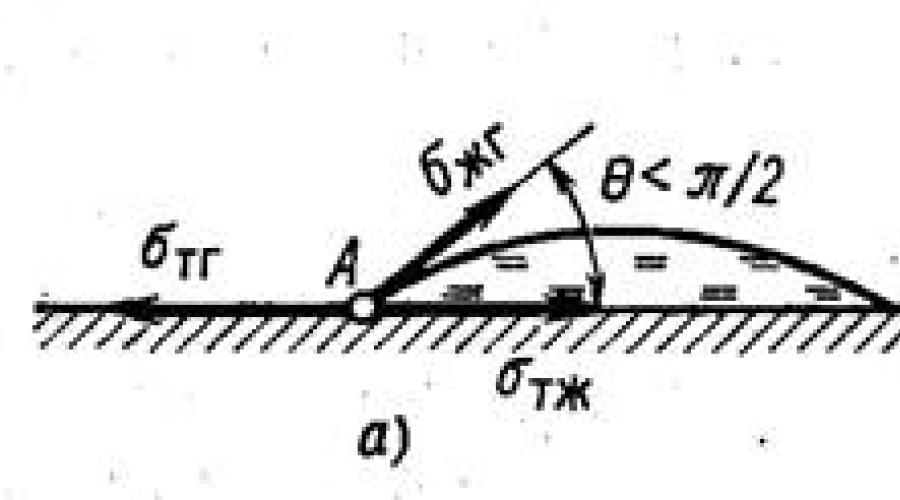
IZVRŠILA: LOPATINA OKSANA
Detekcija kapilarnih nedostataka - metoda otkrivanja nedostataka koja se temelji na prodiranju određenih tekućih tvari u površinske nedostatke proizvoda pod djelovanjem kapilarnog tlaka, uslijed čega se povećava kontrast svjetla i boja neispravnog područja u odnosu na neoštećeno.
Detekcija kapilarnih nedostataka (kapilarna kontrola) dizajniran za otkrivanje nevidljive ili slabo vidljive golim okom površine i niz nedostataka (pukotine, pore, ljuske, nedostatak prodora, intergranularna korozija, fistule, itd.) u ispitnim objektima, određujući njihov položaj, opseg i orijentaciju duž površine.
indikatorska tekućina(penetrant) je obojena tekućina dizajnirana za popunjavanje otvorenih površinskih nedostataka i naknadnog formiranja indikatorskog uzorka. Tekućina je otopina ili suspenzija boje u mješavini organskih otapala, kerozina, ulja s dodacima površinski aktivnih tvari (tenzida), koji smanjuju površinsku napetost vode u šupljinama defekata i poboljšavaju prodiranje penetranata u te šupljine. Penetanti sadrže bojila (metoda boja) ili luminescentne aditive (luminiscentna metoda) ili kombinaciju oboje.
Pročišćivač- služi za prethodno čišćenje površine i uklanjanje viška penetranta
Programer naziva se materijalom za otkrivanje nedostataka dizajniranim za izdvajanje penetranta iz kapilarnog diskontinuiteta kako bi se formirao jasan indikatorski uzorak i stvorila pozadina koja je u suprotnosti s njim. Postoji pet glavnih tipova razvijača koji se koriste s penetrantima:
Suhi prah; - vodena suspenzija; - suspenzija u otapalu; - otopina u vodi; - plastična folija.
Uređaji i oprema za kapilarnu kontrolu:
Materijali za detekciju grešaka u boji, Luminescentni materijali
Setovi za detekciju kapilarnih nedostataka (sredstva za čišćenje, razvijači, penetranti)
Pulverizatori, hidropistoli
Izvori ultraljubičastog osvjetljenja (ultraljubičaste svjetiljke, iluminatori).
Testne ploče (testna ploča)
Kontrolni uzorci za detekciju grešaka u boji.
Proces kapilarne kontrole sastoji se od 5 faza:
1 - prethodno čišćenje površine. Da bi boja prodrla u nedostatke na površini, prvo ju je potrebno očistiti vodom ili organskim sredstvom za čišćenje. Sva onečišćenja (ulja, hrđa, itd.) i bilo koji premazi (lake, premazi) moraju se ukloniti iz kontroliranog područja. Nakon toga se površina suši tako da unutar defekta ne ostane voda ili sredstvo za čišćenje.
2 - primjena penetranta. Penetrant, obično crvene boje, nanosi se na površinu prskanjem, četkom ili uranjanjem predmeta u kadu za dobru impregnaciju i potpunu pokrivenost penetrantom. U pravilu, na temperaturi od 5 ... 50 ° C, tijekom 5 ... 30 minuta.
3 - uklanjanje viška penetranta. Višak penetranta uklanja se brisanjem maramicom, ispiranjem vodom ili istim sredstvom za čišćenje kao u koraku prethodnog čišćenja. U tom slučaju penetrant treba ukloniti samo s kontrolne površine, ali ne i iz šupljine defekta. Zatim se površina osuši krpom koja ne ostavlja dlačice ili zračnim mlazom.
4 - aplikacija programera. Nakon sušenja, razvijač se odmah nanosi na kontrolnu površinu u tankom ravnom sloju (obično bijela boja).
5 - kontrola. Otkrivanje postojećih nedostataka počinje odmah nakon završetka procesa razvoja. Tijekom kontrole otkrivaju se i snimaju tragovi indikatora. Intenzitet boje koji označava dubinu i širinu defekta, što je boja bljeđa, to je defekt manji. Intenzivna obojenost ima duboke pukotine. Nakon kontrole, razvijač se uklanja vodom ili sredstvom za čišćenje.
Na nedostatke kapilarnu kontrolu treba pripisati velikom radnom intenzitetu u odsutnosti mehanizacije, dugom trajanju procesa upravljanja (od 0,5 do 1,5 h), kao i složenosti mehanizacije i automatizacije procesa upravljanja; smanjenje pouzdanosti rezultata pri negativnim temperaturama; subjektivnost kontrole - ovisnost pouzdanosti rezultata o profesionalnosti operatera; ograničeni rok trajanja materijala za detekciju nedostataka, ovisnost njihovih svojstava o uvjetima skladištenja.
Prednosti kapilarne kontrole su: jednostavnost kontrolnih operacija, jednostavnost opreme, primjenjivost na širok raspon materijala, uključujući nemagnetne metale. Glavna prednost kapilarne detekcije kvarova je da ne samo da može otkriti površinske i nizove nedostatke, već i dobiti vrijedne informacije o prirodi kvara, pa čak i o nekim uzrocima njegovog nastanka (koncentracija naprezanja, nepridržavanje tehnologije itd. .).
Materijali za detekciju nedostataka za detekciju grešaka u boji odabiru se ovisno o zahtjevima za kontrolirani objekt, njegovom stanju i uvjetima upravljanja. Kao parametar veličine defekta uzima se poprečna veličina defekta na površini ispitnog objekta – takozvana širina otvora defekta. Minimalna vrijednost otkrivanja otkrivenih nedostataka naziva se nižim pragom osjetljivosti i ograničena je činjenicom da je vrlo mala količina penetranta, zadržana u šupljini malog defekta, nedovoljna za dobivanje kontrastne indikacije za danu debljinu sloj sredstva za razvijanje. Postoji i gornji prag osjetljivosti, koji je određen činjenicom da se iz širokih, ali plitkih defekata, penetrant ispire kada se eliminira višak penetranta na površini. Detekcija indikatorskih tragova koji odgovaraju gore navedenim glavnim značajkama služi kao osnova za analizu prihvatljivosti defekta u smislu njegove veličine, prirode i položaja. GOST 18442-80 utvrđuje 5 razreda osjetljivosti (prema donjem pragu) ovisno o veličini nedostataka
Klasa osjetljivosti |
Širina otvora defekta, µm |
10 do 100 |
|
100 do 500 |
|
tehnološke |
Nije standardizirano |
S osjetljivošću prema klasi 1 kontroliraju se lopatice turbomlaznih motora, brtvene površine ventila i njihovih sjedišta, metalne brtvene brtve prirubnica itd. (otkrivene pukotine i pore do desetinki mikrona). Prema 2. klasi provjeravaju tijela i antikorozivne naplate reaktora, osnovni metal i zavarene spojeve cjevovoda, nosive dijelove (uočljive pukotine i pore veličine do nekoliko mikrona). Za klasu 3 provjeravaju se pričvršćivači brojnih predmeta, s mogućnošću otkrivanja nedostataka s otvorom do 100 mikrona, za klasu 4 - lijevanje debelih stijenki.
Kapilarne metode, ovisno o načinu otkrivanja uzorka indikatora, dijele se na:
· Luminescentna metoda, na temelju registracije luminiscentnog kontrasta u dugovalnoj duljini ultraljubičasto zračenje vidljivi indikatorski uzorak na pozadini površine ispitnog objekta;
· kontrastna (boja) metoda, na temelju registracije kontrasta boja u vidljivo zračenje indikatorski uzorak na pozadini površine ispitnog objekta.
· metoda fluorescentne boje, na temelju registracije kontrasta uzorka boje ili luminiscentnog indikatora na pozadini površine ispitnog objekta u vidljivom ili dugovalnom ultraljubičastom zračenju;
· metoda svjetline, na temelju registracije kontrasta u vidljivom zračenju akromatskog uzorka na pozadini površine predmeta.
NASTUPA: VALUKH ALEKSANDAR
Kapilarna kontrola
Kapilarna metoda ispitivanja bez razaranja
Capilljadetektor manaija - metoda otkrivanja nedostataka koja se temelji na prodiranju određenih tekućih tvari u površinske nedostatke proizvoda pod djelovanjem kapilarnog tlaka, uslijed čega se povećava kontrast svjetla i boja neispravnog područja u odnosu na neoštećeno.
Postoje luminiscentne i kolor metode detekcije kapilarnih nedostataka.
U većini slučajeva, prema tehničkim zahtjevima, potrebno je otkriti nedostatke toliko male da se mogu uočiti kada vizualna kontrola gotovo nemoguće golim okom. Korištenje optičkih mjerni instrumenti, na primjer, povećalo ili mikroskop, ne dopušta otkrivanje površinskih nedostataka zbog nedovoljnog kontrasta slike defekta na pozadini metala i malog vidnog polja pri velikim povećanjima. U takvim slučajevima koristi se metoda kapilarne kontrole.
Tijekom kapilarnog ispitivanja, indikatorske tekućine prodiru u šupljine površine i kroz diskontinuitete u materijalu ispitnih objekata, a dobiveni tragovi indikatora se bilježe vizualno ili pomoću sonde.
Kontrola kapilarnom metodom provodi se u skladu s GOST 18442-80 „Kontrola bez razaranja. kapilarne metode. Opći zahtjevi."
Kapilarne metode dijele se na osnovne, koje koriste kapilarne fenomene, i kombinirane, temeljene na kombinaciji dviju ili više metoda nerazornog ispitivanja koje su različite po fizičkoj biti, od kojih je jedna kapilarno ispitivanje (detekcija kapilarnih nedostataka).
Svrha kapilarnog pregleda (detekcija kapilarnih nedostataka)
Detekcija kapilarnih nedostataka (kapilarna kontrola) dizajniran za otkrivanje nevidljive ili slabo vidljive golim okom površine i niz nedostataka (pukotine, pore, ljuske, nedostatak prodora, intergranularna korozija, fistule, itd.) u ispitnim objektima, određujući njihov položaj, opseg i orijentaciju duž površine.
Kapilarne metode ispitivanja bez razaranja temelje se na kapilarnom prodiranju indikatorskih tekućina (penetranta) u šupljine površine i preko diskontinuiteta u materijalu ispitnog objekta i registraciji vizualno ili pomoću pretvarača formiranih indikatorskih tragova.
Primjena kapilarne metode ispitivanja bez razaranja
Kapilarna metoda upravljanja koristi se u kontroli objekata bilo koje veličine i oblika, izrađenih od željeznih i obojenih metala, legiranih čelika, lijevanog željeza, metalnih premaza, plastike, stakla i keramike u elektroenergetici, zrakoplovstvu, raketiranju, brodogradnji. , kemijskoj industriji, metalurgiji, u izgradnji nuklearnih reaktora, u automobilskoj industriji, elektrotehnici, strojarstvu, ljevaonici, štancanju, instrumentaciji, medicini i drugim industrijama. Za neke materijale i proizvode ova metoda je jedina za utvrđivanje prikladnosti dijelova ili instalacija za rad.
Detekcija kapilarnih nedostataka također se koristi za ispitivanje bez razaranja objekata izrađenih od feromagnetnih materijala, ako njihova magnetska svojstva, oblik, vrsta i mjesto oštećenja ne dopuštaju postizanje osjetljivosti propisane GOST 21105-87 metodom magnetskih čestica i magnetskim Metoda ispitivanja česticama nije dopuštena prema radnim uvjetima objekta.
Neophodan uvjet za otkrivanje nedostataka poput diskontinuiteta materijala kapilarnim metodama je prisutnost šupljina bez onečišćenja i drugih tvari koje imaju pristup površini predmeta i dubina širenja koja je mnogo veća od širine njihova otvaranja.
Kapilarna kontrola se također koristi u detekciji propuštanja te, u kombinaciji s drugim metodama, u praćenju kritičnih objekata i objekata u procesu rada.
Prednosti kapilarnih metoda detekcije nedostataka su: jednostavnost upravljačkih operacija, jednostavnost opreme, primjenjivost na širok raspon materijala, uključujući nemagnetne metale.
Prednost detekcije kapilarnih nedostataka je da je uz njegovu pomoć moguće ne samo otkriti površinske i nizove nedostatke, već i dobiti vrijedne informacije o prirodi kvara, pa čak i o nekim razlozima njegovog nastanka (koncentracija naprezanja, nepridržavanje tehnologije itd. ) ).
Kao indikatorske tekućine koriste se organski fosfori - tvari koje daju vlastiti svijetli sjaj pod djelovanjem ultraljubičastih zraka, kao i razne boje. Površinski nedostaci otkrivaju se sredstvima koja omogućuju izdvajanje indikatorskih tvari iz šupljine defekata i otkrivanje njihove prisutnosti na površini kontroliranog proizvoda.
kapilara (pukotina), koji na površinu objekta upravljanja dolazi samo s jedne strane, naziva se površinski diskontinuitet, a spajanje suprotnih zidova objekta upravljanja - kroz. Ako su površinski i prolazni diskontinuiteti defekti, tada je dopušteno koristiti izraze "površinski defekt" i "prolazni defekt". Slika koju stvara penetrant na mjestu diskontinuiteta i slična obliku presjeka na izlazu na površinu ispitnog objekta naziva se indikatorski uzorak ili indikacija.
S obzirom na diskontinuitet kao što je jedna pukotina, umjesto izraza "indikacija" dopušten je izraz "trag indikatora". Dubina diskontinuiteta - veličina diskontinuiteta u smjeru unutar ispitnog objekta od njegove površine. Duljina diskontinuiteta je uzdužna dimenzija diskontinuiteta na površini predmeta. Otvaranje diskontinuiteta - poprečna veličina diskontinuiteta na njegovom izlazu na površinu ispitnog objekta.
Neophodan uvjet za pouzdano otkrivanje kapilarnom metodom nedostataka koji imaju pristup površini predmeta je njihova relativna nezagađenost stranim tvarima, kao i dubina širenja koja znatno premašuje širinu njihova otvora (najmanje 10/1). ). Za čišćenje površine prije nanošenja penetranta koristi se sredstvo za čišćenje.
Kapilarne metode detekcije mana dijele se na na glavnom, korištenjem kapilarnih fenomena, i kombinirano, na temelju kombinacije dviju ili više metoda ispitivanja bez razaranja, različitih u fizičkoj biti, od kojih je jedna kapilarna.
Detekcija kapilarnih nedostataka
Kapilarna kontrola
Kapilarna metoda ispitivanja bez razaranja
Capillja detektor manai ja - metoda otkrivanja nedostataka koja se temelji na prodiranju određenih tekućih tvari u površinske nedostatke proizvoda pod djelovanjem kapilarnog tlaka, uslijed čega se povećava kontrast svjetla i boja neispravnog područja u odnosu na neoštećeno.
Postoje luminiscentne i kolor metode detekcije kapilarnih nedostataka.
U većini slučajeva, prema tehnički zahtjevi potrebno je otkriti nedostatke tako male da se mogu uočiti kada vizualna kontrola gotovo nemoguće golim okom. Upotreba optičkih mjernih instrumenata, poput povećala ili mikroskopa, ne omogućuje otkrivanje površinskih nedostataka zbog nedovoljnog kontrasta slike defekta na pozadini metala i malog vidnog polja pri visokim povećanja. U takvim slučajevima koristi se metoda kapilarne kontrole.
Tijekom kapilarnog ispitivanja, indikatorske tekućine prodiru u šupljine površine i kroz diskontinuitete u materijalu ispitnih objekata, a dobiveni tragovi indikatora se bilježe vizualno ili pomoću sonde.
Kontrola kapilarnom metodom provodi se u skladu s GOST 18442-80 „Kontrola bez razaranja. kapilarne metode. Opći zahtjevi."
Kapilarne metode dijele se na osnovne, koje koriste kapilarne fenomene, i kombinirane, temeljene na kombinaciji dviju ili više metoda nerazornog ispitivanja koje su različite po fizičkoj biti, od kojih je jedna kapilarno ispitivanje (detekcija kapilarnih nedostataka).
Svrha kapilarnog pregleda (detekcija kapilarnih nedostataka)
Detekcija kapilarnih nedostataka (kapilarna kontrola) dizajniran za otkrivanje nevidljive ili slabo vidljive golim okom površine i niz nedostataka (pukotine, pore, ljuske, nedostatak prodora, intergranularna korozija, fistule, itd.) u ispitnim objektima, određujući njihov položaj, opseg i orijentaciju duž površine.
Kapilarne metode ispitivanja bez razaranja temelje se na kapilarnom prodiranju indikatorskih tekućina (penetranta) u šupljine površine i preko diskontinuiteta u materijalu ispitnog objekta i registraciji vizualno ili pomoću pretvarača formiranih indikatorskih tragova.
Primjena kapilarne metode ispitivanja bez razaranja
Kapilarna metoda upravljanja koristi se u kontroli objekata bilo koje veličine i oblika, izrađenih od željeznih i obojenih metala, legiranih čelika, lijevanog željeza, metalnih premaza, plastike, stakla i keramike u elektroenergetici, zrakoplovstvu, raketiranju, brodogradnji. , kemijskoj industriji, metalurgiji, u izgradnji nuklearnih reaktora, u automobilskoj industriji, elektrotehnici, strojarstvu, ljevaonici, štancanju, instrumentaciji, medicini i drugim industrijama. Za neke materijale i proizvode ova metoda je jedina za utvrđivanje prikladnosti dijelova ili instalacija za rad.
Detekcija kapilarnih nedostataka također se koristi za ispitivanje bez razaranja objekata izrađenih od feromagnetnih materijala, ako njihova magnetska svojstva, oblik, vrsta i mjesto oštećenja ne dopuštaju postizanje osjetljivosti propisane GOST 21105-87 metodom magnetskih čestica i magnetskim Metoda ispitivanja česticama nije dopuštena prema radnim uvjetima objekta.
Neophodan uvjet za otkrivanje nedostataka poput diskontinuiteta materijala kapilarnim metodama je prisutnost šupljina bez onečišćenja i drugih tvari koje imaju pristup površini predmeta i dubina širenja koja je mnogo veća od širine njihova otvaranja.
Kapilarna kontrola se također koristi u detekciji propuštanja te, u kombinaciji s drugim metodama, u praćenju kritičnih objekata i objekata u procesu rada.
Prednosti kapilarnih metoda detekcije nedostataka su: jednostavnost upravljačkih operacija, jednostavnost opreme, primjenjivost na širok raspon materijala, uključujući nemagnetne metale.
Prednost detekcije kapilarnih nedostataka je da je uz njegovu pomoć moguće ne samo otkriti površinske i nizove nedostatke, već i dobiti vrijedne informacije o prirodi kvara, pa čak i o nekim razlozima njegovog nastanka (koncentracija naprezanja, nepridržavanje tehnologije itd. ) ).
Kao indikatorske tekućine koriste se organski fosfor - tvari koje daju vlastiti sjajni sjaj pod djelovanjem ultraljubičaste zrake i razne boje. Površinski nedostaci otkrivaju se sredstvima koja omogućuju izdvajanje indikatorskih tvari iz šupljine defekata i otkrivanje njihove prisutnosti na površini kontroliranog proizvoda.
kapilara (pukotina), koji na površinu objekta upravljanja dolazi samo s jedne strane, naziva se površinski diskontinuitet, a spajanje suprotnih zidova objekta upravljanja - kroz. Ako su površinski i prolazni diskontinuiteti defekti, tada je dopušteno koristiti izraze "površinski defekt" i "prolazni defekt". Slika koju stvara penetrant na mjestu diskontinuiteta i slična obliku presjeka na izlazu na površinu ispitnog objekta naziva se indikatorski uzorak ili indikacija.
S obzirom na diskontinuitet kao što je jedna pukotina, umjesto izraza "indikacija" dopušten je izraz "trag indikatora". Dubina diskontinuiteta - veličina diskontinuiteta u smjeru unutar ispitnog objekta od njegove površine. Duljina diskontinuiteta je uzdužna dimenzija diskontinuiteta na površini predmeta. Otvaranje diskontinuiteta - poprečna veličina diskontinuiteta na njegovom izlazu na površinu ispitnog objekta.
Neophodan uvjet za pouzdano otkrivanje kapilarnom metodom nedostataka koji imaju pristup površini predmeta je njihova relativna nezagađenost stranim tvarima, kao i dubina širenja koja znatno premašuje širinu njihova otvora (najmanje 10/1). ). Za čišćenje površine prije nanošenja penetranta koristi se sredstvo za čišćenje.
Kapilarne metode detekcije mana dijele se na na glavnom, korištenjem kapilarnih fenomena, i kombinirano, na temelju kombinacije dviju ili više metoda ispitivanja bez razaranja, različitih u fizičkoj biti, od kojih je jedna kapilarna.
Uređaji i oprema za kapilarnu kontrolu:
- Kompleti za detekciju kapilarnih kvarova (sredstva za čišćenje, razvijači, penetranti)
- Pištolji za prskanje
- Pneumohidropuške
- Izvori ultraljubičastog osvjetljenja (ultraljubičaste lampe, iluminatori)
- Testne ploče (testna ploča)
Kontrolni uzorci za detekciju grešaka u boji
Osjetljivost metode otkrivanja kapilarnih nedostataka
Osjetljivost kapilarne kontrole- sposobnost otkrivanja diskontinuiteta određene veličine sa zadanom vjerojatnošću pri korištenju određene metode, tehnologije inspekcije i penetrantnog sustava. Prema GOST 18442-80 klasa osjetljivosti kontrole određuje se ovisno o minimalnoj veličini otkrivenih nedostataka s poprečnom veličinom od 0,1 - 500 mikrona.
Metodama kapilarne kontrole ne jamči se identificiranje nedostataka s širinom otvora većom od 0,5 mm.
S osjetljivošću prema klasi 1, pomoću kapilarne detekcije kvarova, kontroliraju se lopatice turbomlaznih motora, brtvene površine ventila i njihovih sjedišta, metalne brtvene brtve prirubnica itd. (otkrivene pukotine i pore do desetinki mikrona). Prema 2. klasi provjeravaju tijela i antikorozivne naplate reaktora, osnovni metal i zavarene spojeve cjevovoda, nosive dijelove (uočljive pukotine i pore veličine do nekoliko mikrona).
Na kontrolnim uzorcima (standardi za detekciju grešaka u boji CD-a) određuju se osjetljivost materijala za detekciju grešaka, kvaliteta međučišćenja i kontrola cjelokupnog kapilarnog procesa, t.j. na metalu određene hrapavosti s normaliziranim umjetnim pukotinama (defektima) nanesenim na njih.
Klasa kontrolne osjetljivosti određuje se ovisno o minimalnoj veličini otkrivenih nedostataka. Obuhvaćena osjetljivost, ako je potrebno, utvrđuje se na predmetima punog mjerila ili umjetnim uzorcima s prirodnim ili simuliranim nedostacima, čije se dimenzije određuju metalografskim ili drugim metodama analize.
Prema GOST 18442-80, klasa osjetljivosti kontrole određuje se ovisno o veličini otkrivenih nedostataka. Kao parametar veličine defekta uzima se poprečna veličina defekta na površini ispitnog objekta - takozvana širina otvora defekta. Budući da dubina i duljina defekta također imaju značajan utjecaj na mogućnost njegovog otkrivanja (posebno, dubina bi trebala biti mnogo veća od otvora), ovi se parametri smatraju stabilnima. Donji prag osjetljivosti, t.j. minimalna vrijednost otkrivanja identificiranih nedostataka ograničena je činjenicom da je vrlo mala količina penetranta; zadržavanje u šupljini malog defekta nije dovoljno za dobivanje kontrastne indikacije za danu debljinu sloja sredstva za razvijanje. Postoji i gornji prag osjetljivosti, koji je određen činjenicom da se iz širokih, ali plitkih defekata, penetrant ispire kada se eliminira višak penetranta na površini.
Postoji 5 razreda osjetljivosti (prema donjem pragu) ovisno o veličini defekata:
Klasa osjetljivosti |
Širina otvora defekta, µm |
Manje od 1 |
|
1 do 10 |
|
10 do 100 |
|
100 do 500 |
|
tehnološke |
Nije standardizirano |
Fizičke osnove i tehnika metode kapilarne kontrole
Kapilarna metoda ispitivanja bez razaranja (GOST 18442-80) temelji se na kapilarnom prodiranju u defekt indikatorske tekućine i dizajniran je za otkrivanje nedostataka koji imaju pristup površini ispitnog objekta. Ova metoda je prikladna za otkrivanje diskontinuiteta poprečne veličine od 0,1 - 500 mikrona, uključujući i prolazne, na površini željeznih i obojenih metala, legura, keramike, stakla itd. Široko se koristi za kontrolu integriteta zavara.
Na površinu ispitnog objekta nanosi se penetrant u boji ili bojila. Zbog posebnih kvaliteta koje se daju odabirom određenih fizikalna svojstva penetrant: površinska napetost, viskoznost, gustoća, pod djelovanjem kapilarnih sila prodire u najmanje nedostatke koji imaju pristup površini ispitnog objekta
Razvijač, koji se nanese na površinu ispitnog objekta neko vrijeme nakon što je penetrant pažljivo uklonjen s površine, otapa boju koja se nalazi unutar defekta i zbog difuzije "povlači" preostali penetrant u defektu na površinu defekta. ispitni objekt.
Postojeći nedostaci su vidljivi dovoljno kontrastno. Tragovi indikatora u obliku linija ukazuju na pukotine ili ogrebotine, pojedinačne točke označavaju pore.
Proces otkrivanja nedostataka kapilarnom metodom podijeljen je u 5 faza (provođenje kapilarne kontrole):
1. Prethodno čišćenje površine (koristite sredstvo za čišćenje)
2. Primjena penetranta
3. Uklanjanje viška penetranta
4. Primjena programera
5. Kontrola
Prethodno čišćenje površine. Da bi boja prodrla u nedostatke na površini, prvo ju je potrebno očistiti vodom ili organskim sredstvom za čišćenje. Sva onečišćenja (ulja, hrđa, itd.) i bilo koji premazi (lake, premazi) moraju se ukloniti iz kontroliranog područja. Nakon toga se površina suši tako da unutar defekta ne ostane voda ili sredstvo za čišćenje.
Primjena penetranta. Penetrant, obično crvene boje, nanosi se na površinu prskanjem, četkom ili uranjanjem OK u kadu, za dobru impregnaciju i potpuna pokrivenost penetrant. U pravilu, na temperaturi od 5-50 0 C, u trajanju od 5-30 minuta.
Uklanjanje viška penetranta. Višak penetranta uklanja se brisanjem maramicom, ispiranjem vodom. Ili s istim sredstvom za čišćenje kao u fazi prethodnog čišćenja. U tom slučaju, penetrant se mora ukloniti s površine, ali ne i iz šupljine defekta. Zatim se površina osuši krpom koja ne ostavlja dlačice ili zračnim mlazom. Pri korištenju sredstva za čišćenje postoji opasnost od ispiranja penetranta i njegove netočne indikacije.
Aplikacija programera. Nakon sušenja, na OK se odmah nanosi razvijač, obično bijeli, u tankom ravnom sloju.
Kontrolirati. QA inspekcija počinje odmah nakon završetka procesa razvoja i završava prema različiti standardi ne više od 30 min. Intenzitet boje označava dubinu defekta, što je boja bljeđa, manja je manja. Intenzivna obojenost ima duboke pukotine. Nakon kontrole, razvijač se uklanja vodom ili sredstvom za čišćenje.
Penetrant za bojenje nanosi se na površinu ispitnog objekta (OK). Zbog posebnih kvaliteta koje se osiguravaju odabirom određenih fizikalnih svojstava penetranta: površinske napetosti, viskoznosti, gustoće, on pod djelovanjem kapilarnih sila prodire u najmanje nedostatke koji imaju pristup površini ispitnog objekta. . Razvijač, koji se nanese na površinu ispitnog objekta neko vrijeme nakon što je penetrant pažljivo uklonjen s površine, otapa boju koja se nalazi unutar defekta i zbog difuzije "povlači" preostali penetrant u defektu na površinu defekta. ispitni objekt. Postojeći nedostaci su vidljivi dovoljno kontrastno. Tragovi indikatora u obliku linija ukazuju na pukotine ili ogrebotine, pojedinačne točke označavaju pore.
Najprikladnije prskalice, na primjer aerosolne limenke. Razvijač se također može primijeniti potapanjem. Suhi razvijači se nanose u vrtložnoj komori ili elektrostatski. Nakon nanošenja programera, trebali biste pričekati od 5 minuta za velike nedostatke, do 1 sat za male nedostatke. Nedostaci će se pojaviti kao crvene oznake na bijeloj pozadini.
Nanošenjem razvijača i penetranta mogu se otkriti pukotine na proizvodima tankih stijenki različite stranke proizvodi. Boja koja je prošla bit će jasno vidljiva u sloju razvijača.
Penetrant (penetrant od engleskog penetrate - prodrijeti) naziva kapilarnim materijalom za detekciju grešaka koji ima sposobnost prodiranja u diskontinuitete ispitnog objekta i ukazati na te diskontinuitete. Penetanti sadrže bojila (metoda boja) ili luminescentne aditive (luminiscentna metoda) ili kombinaciju oboje. Aditivi omogućuju razlikovanje područja sloja razvijača impregniranog ovim tvarima iznad pukotine od glavnog (najčešće bijelog) kontinuiranog materijala predmeta bez nedostataka (pozadine).
Programer (programer) naziva se materijalom za otkrivanje nedostataka dizajniranim za izdvajanje penetranta iz kapilarnog diskontinuiteta kako bi se formirao jasan indikatorski uzorak i stvorila pozadina koja je u suprotnosti s njim. Dakle, uloga razvijača u kapilarnom ispitivanju je, s jedne strane, da izvuče penetrant iz defekata zbog kapilarnih sila, s druge strane, programer mora stvoriti kontrastnu pozadinu na površini kontroliranog objekta kako bi pouzdano otkriti obojene ili luminiscentne indikatorske tragove nedostataka. Na prava tehnologijaŠirina traga može premašiti širinu defekta za 10-20 ili više puta, a kontrast svjetline povećava se za 30-50%. Ovaj učinak povećanja omogućuje iskusni profesionalcičak i golim okom za otkrivanje vrlo malih pukotina.
Redoslijed operacija kapilarne kontrole:
Prethodno čišćenje |
Mehanički, brušeni |
Inkjet metoda |
Odmašćivanje vrućom parom |
Čišćenje otapalom |
Prethodno sušenje |
||||
Penetrantna primjena |
uranjanje u kadu |
Nanošenje četkom |
Primjena aerosola/spreja |
Elektrostatička primjena |
Intermedijarno čišćenje |
Krpa ili spužva natopljena vodom, bez dlačica |
Četka natopljena vodom |
isprati vodom |
Krpa ili spužva impregnirana otapalima bez dlačica |
Sušenje |
Suhi zrak |
Obrišite krpom koja ne ostavlja dlačice |
Puhnite čistim, suhim zrakom |
Osušite toplim zrakom |
Aplikacija programera |
Potapanjem (razvijač na bazi vode) |
Primjena aerosola/spreja (razvijač na bazi alkohola) |
Elektrostatička aplikacija (programer na bazi alkohola) |
Nanošenje suhog razvijača (ako je površina vrlo porozna) |
Pregled površine i dokumentacija |
Kontrola tijekom dana odn umjetna rasvjeta min. 500Lux (EN 571-1/ EN3059) Kada koristite fluorescentni penetrant: Rasvjeta:< 20 Lux UV intenzitet: 1000μW/ cm2 |
Dokumentacija o folijama |
Fotooptička dokumentacija |
Dokumentacija foto ili video |
Glavne kapilarne metode ispitivanja bez razaranja dijele se na sljedeće ovisno o vrsti tvari koja prodire:
· Metoda prodornih otopina - tekuća metoda kapilarnog nerazornog ispitivanja, koja se temelji na korištenju tekuće indikatorske otopine kao sredstva za prodiranje.
· Metoda filtracijske suspenzije je tekuća metoda kapilarnog ispitivanja bez razaranja koja se temelji na korištenju indikatorske suspenzije kao sredstva za prodiranje tekućine, koja formira indikatorski uzorak od filtriranih čestica dispergirane faze.
Kapilarne metode, ovisno o načinu otkrivanja uzorka indikatora, dijele se na:
· Luminescentna metoda, na temelju registriranja kontrasta vidljivog indikatorskog uzorka koji svijetli u dugovalnom ultraljubičastom zračenju na pozadini površine ispitnog objekta;
· kontrastna (boja) metoda, na temelju registracije kontrasta boje u vidljivom zračenju indikatorskog uzorka na pozadini površine ispitnog objekta.
· metoda fluorescentne boje, na temelju registracije kontrasta uzorka boje ili luminiscentnog indikatora na pozadini površine ispitnog objekta u vidljivom ili dugovalnom ultraljubičastom zračenju;
· metoda svjetline, na temelju registracije kontrasta u vidljivom zračenju akromatskog uzorka na pozadini površine ispitnog objekta.
Fizičke osnove detekcije kapilarnih nedostataka. Luminescentna detekcija kvarova (LD). Detekcija grešaka u boji (CD).
Postoje dva načina za promjenu omjera kontrasta između defektne slike i pozadine. Prva metoda se sastoji u poliranju površine kontroliranog proizvoda, nakon čega slijedi jetkanje kiselinama. S takvom obradom, kvar je začepljen produktima korozije, crni i postaje vidljiv na svijetloj pozadini poliranog materijala. Ova metoda ima cijela linija ograničenja. Konkretno, u uvjetima proizvodnje potpuno je neisplativo polirati površinu proizvoda, posebno zavare. Osim toga, metoda nije primjenjiva na kontrolu precizno poliranih dijelova ili nemetalnih materijala. Metoda jetkanja češće se koristi za kontrolu nekih lokalnih sumnjivih područja metalnih proizvoda.
Druga metoda se sastoji u promjeni svjetlosnog izlaza defekata punjenjem s površine posebnim tekućinama za indikatore svjetla i kontrasta boja - penetrantima. Ako penetrant sadrži luminiscentne tvari, tj. tvari koje daju blistav sjaj kada su ozračene ultraljubičastim svjetlom, tada se takve tekućine nazivaju luminescentne, a metoda kontrole je luminescentna (luminiscentna detekcija kvarova - LD). Ako su u osnovi penetranta boje vidljive na dnevno svjetlo, tada se metoda kontrole naziva boja (otkrivanje nedostataka u boji - CD). U otkrivanju nedostataka u boji koriste se boje svijetlo crvene boje.
Bit detekcije kapilarnih nedostataka je kako slijedi. Površina proizvoda je očišćena od prljavštine, prašine, masti, ostataka fluksa, premazi itd. Nakon čišćenja na površinu pripremljenog proizvoda nanosi se sloj penetranta i drži neko vrijeme kako bi tekućina mogla prodrijeti u otvorene šupljine defekata. Zatim se površina čisti od tekućine, čiji dio ostaje u šupljinama defekata.
U slučaju luminiscentne detekcije mana proizvod se osvjetljava ultraljubičastim svjetlom (ultraljubičasti iluminator) u zamračenoj prostoriji i podvrgava se pregledu. Nedostaci su jasno vidljivi u obliku jarko svjetlećih pruga, točkica itd.
Kod detekcije nedostataka u boji u ovoj fazi nije moguće otkriti nedostatke, budući da je razlučivost oka premala. Kako bi se povećala uočljivost nedostataka, poseban materijal za razvijanje u obliku suspenzije koja se brzo suši (na primjer, kaolin, kolodij) ili premazi laka nanosi se na površinu proizvoda nakon uklanjanja penetranta iz njega. Materijal za razvijanje (obično bijele boje) izvlači penetrant iz šupljine defekta, što dovodi do stvaranja indikatorskih oznaka na razvijaču. Tragovi indikatora u potpunosti ponavljaju konfiguraciju nedostataka u planu, ali su veće veličine. Takvi indikatorski tragovi lako se razlikuju okom čak i bez upotrebe optičkih sredstava. Povećanje veličine traga indikatora je to veće, što su defekti dublje, t.j. što je veći volumen penetranta koji je ispunio defekt i što je više vremena prošlo od nanošenja sloja za razvijanje.
Fizička osnova metoda otkrivanja kapilarnih nedostataka je fenomen kapilarne aktivnosti, t.j. sposobnost tekućine da se uvuče u najmanje prolazne rupice i na jednom kraju otvoreni kanali.
Kapilarna aktivnost ovisi o sposobnosti vlaženja čvrsto tijelo tekućina. U bilo kojem tijelu molekularne kohezivne sile djeluju na svaku molekulu od drugih molekula. Oni su veći u čvrstom nego u tekućini. Stoga tekućine, za razliku od čvrstih tijela, nemaju elastičnost oblika, ali imaju veliku volumetrijsku elastičnost. Molekule smještene na površini tijela u interakciji su i s istoimenim tjelesnim molekulama, nastojeći ih uvući u volumen, i s molekulama okoline koja okružuje tijelo i imaju najveću potencijalnu energiju. Iz tog razloga, nekompenzirana sila, nazvana sila površinske napetosti, nastaje okomito na granicu prema unutarnjoj strani tijela. Sile površinske napetosti proporcionalne su duljini konture vlaženja i prirodno teže njenom smanjenju. Tekućina na metalu, ovisno o omjeru međumolekulskih sila, proširit će se po metalu ili skupiti u kap. Tekućina vlaži krutinu ako su sile interakcije (privlačenja) tekućine s molekulama krutine veće od sila površinske napetosti. U tom slučaju tekućina će se širiti preko krutine. Ako su sile površinske napetosti veće od sila interakcije s molekulama krutine, tada će se tekućina skupiti u kap.
Kada tekućina uđe u kapilarni kanal, njegova površina se savija, stvarajući takozvani meniskus. Sile površinske napetosti teže smanjenju vrijednosti slobodne granice meniskusa, a u kapilari počinje djelovati dodatna sila, što dovodi do apsorpcije tekućine za vlaženje. Dubina do koje tekućina prodire u kapilaru izravno je proporcionalna površinskoj napetosti tekućine i obrnuto proporcionalna polumjeru kapilare. Drugim riječima, što je manji radijus kapilare (defekt) i što je materijal bolja vlaženost, tekućina brže i dublje prodire u kapilaru.
Ovdje možete kupiti materijale za kapilarnu kontrolu (detekciju grešaka u boji) po niskoj cijeni iz skladišta u Moskvi: penetrant, razvijač, čistač Sherwin, kapilarni sustaviHelling, Magnaflux, ultraljubičasta svjetla, ultraljubičaste lampe, ultraljubičasti iluminatori, ultraljubičaste lampe i kontrolni uzorci (standardi) za defektoskopiju u boji CD-a.
Mi dostavljamo potrošni materijali za detekciju grešaka u boji u Rusiji i CIS-u transportna poduzeća i kurirske usluge.
kapilarna kontrola. kapilarna metoda. Nezakočiva kontrola. Detekcija kapilarnih nedostataka.
Naša baza instrumenata
Organizacijski stručnjaci Neovisno vještačenje Spremni smo pomoći i fizičkim i pravnim osobama u provođenju građevinsko-tehničkih vještačenja, tehničkog pregleda zgrada i građevina, detekcije kapilarnih nedostataka.
Imate li neriješenih pitanja ili biste željeli osobno komunicirati s našim stručnjacima ili naručiti neovisna građevinska stručnost, sve informacije potrebne za to možete dobiti u odjeljku "Kontakti".
Veselimo se Vašem pozivu i unaprijed zahvaljujemo na ukazanom povjerenju.
Ispitivanje bez razaranja nabaviti važnost, kada je razvoj premaza već završio i možete nastaviti s njegovim radom industrijska primjena. Prije nego što obloženi proizvod uđe u upotrebu, provjerava se na čvrstoću, pukotine, prekide, pore ili druge nedostatke koji bi mogli uzrokovati kvar. Što je obloženi predmet složeniji, veća je vjerojatnost da će imati nedostatke. U tablici 1. u nastavku su prikazane i opisane postojeće nedestruktivne metode za određivanje kvalitete premaza.
Stol 1. Nedestruktivne metode kontrole kvalitete premaza prije njihovog rada.
# | Metoda kontrole | Svrha i prikladnost testa |
1 | vizualno promatranje | Identifikacija površinskih nedostataka premaza vizualnim pregledom |
2 | Kapilarna kontrola (boja i luminiscentna) | Detekcija površinskih pukotina, pora i sličnih nedostataka premaza |
3 | Radiografska kontrola | Identifikacija nedostataka unutarnjeg premaza |
4 | Elektromagnetsko upravljanje | Detekcija pora i pukotina, metoda nije prikladna za otkrivanje nedostataka u uglovima i rubovima |
5 | Ultrazvučna kontrola | Detekcija površinskih i unutarnjih nedostataka, metoda nije prikladna za tanke slojeve i za otkrivanje nedostataka u uglovima i rubovima |
VIZUALNI PREGLED
Najjednostavnija procjena kvalitete je vanjski pregled premazanog proizvoda. Takva kontrola je relativno jednostavna, a posebno je učinkovita pri dobrom osvjetljenju, kada se koristi povećalo. U pravilu, vanjski pregled treba provoditi kvalificirano osoblje iu kombinaciji s drugim metodama.
PRSKANJE BOJOM
Pukotine i udubljenja na površini premaza otkrivaju se upijanjem boje. Površina koja se ispituje poprska se bojom. Zatim se pažljivo obriše i na nju se poprska indikator. Nakon minute, boja izbija iz pukotina i drugih malih nedostataka i boji indikator, otkrivajući tako konturu pukotine.
FLUORESCENTNA KONTROLA
Ova metoda je slična metodi namakanja boje. Ispitni uzorak se uroni u otopinu koja sadrži fluorescentnu boju, koja se nanosi na sve pukotine. Nakon čišćenja površine, uzorak se prekriva novom otopinom. Ako premaz ima bilo kakve nedostatke, fluorescentna boja na tom području bit će vidljiva pod UV svjetlom.
Obje metode temeljene na apsorpciji koriste se samo za otkrivanje površinskih nedostataka. Unutarnji nedostaci nisu otkriveni. Nedostatke koji leže na samoj površini teško je otkriti, jer se prilikom brisanja površine prije nanošenja indikatora s njih uklanja boja.
RADIOGRAFSKA KONTROLA
Inspekcija prodornim zračenjem koristi se za otkrivanje pora, pukotina i šupljina unutar premaza. X-zrake i gama zrake prolaze kroz materijal koji se ispituje i na fotografski film. Intenzitet rendgenskog i gama zračenja mijenja se kako prolaze kroz materijal. Na filmu će se registrirati sve pore, pukotine ili promjene debljine, a uz odgovarajuću interpretaciju filma može se utvrditi položaj svih unutarnjih nedostataka.
Radiografska kontrola je relativno skupa i spora. Operater mora biti zaštićen od izlaganja. Teško je analizirati proizvode složen oblik. Defekti se definiraju kada su njihove dimenzije veće od 2% ukupne debljine premaza. Stoga radiografska tehnika nije prikladna za otkrivanje malih nedostataka u velikim strukturama složenog oblika, daje dobre rezultate na manje složenim proizvodima.
KONTROLA RUBNE STRUJE
Površinski i unutarnji defekti mogu se odrediti pomoću vrtložnih struja induciranih u proizvodu uvođenjem u elektromagnetsko polje induktora. Prilikom pomicanja dijela u induktoru, ili induktora u odnosu na dio, inducirane vrtložne struje djeluju s induktorom i mijenjaju njegovu impedanciju. Inducirana struja u uzorku ovisi o prisutnosti vodljivih defekata u uzorku, kao io njegovoj tvrdoći i veličini.
Primjenom odgovarajućih induktiviteta i frekvencija, ili kombinacijom oboje, mogu se otkriti defekti. Kontrola vrtložnim strujama je nepraktična ako je konfiguracija proizvoda složena. Ova vrsta pregleda nije prikladna za otkrivanje nedostataka na rubovima i uglovima; u nekim slučajevima od neravnu površinu mogu se primiti isti signali kao i od kvara.
ULTRAZVUČNA KONTROLA
U ultrazvučnom ispitivanju ultrazvuk se prolazi kroz materijal i mjere se promjene zvučnog polja uzrokovane defektima materijala. Energiju reflektiranu od defekata u uzorku percipira pretvarač, koji je pretvara u električni signal i dovodi do osciloskopa.
Ovisno o veličini i obliku uzorka, za ultrazvučno ispitivanje koriste se uzdužni, poprečni ili površinski valovi. Uzdužni valovi šire se u materijalu koji se ispituje pravocrtno sve dok ne naiđu na granicu ili diskontinuitet. Prva granica na koju nailazi dolazni val je granica između pretvarača i proizvoda. Dio energije se reflektira od granice, a primarni impuls se pojavljuje na ekranu osciloskopa. Ostatak energije prolazi kroz materijal sve dok ne naiđe na defekt ili suprotnu površinu, položaj defekta se određuje mjerenjem udaljenosti između signala s defekta te s prednje i stražnje površine.
Diskontinuiteti se mogu rasporediti tako da se mogu identificirati usmjeravanjem zračenja okomito na površinu. U ovom slučaju, zvučna zraka se uvodi pod kutom na površinu materijala kako bi se stvorili posmični valovi. Ako je ulazni kut dovoljno povećan, tada nastaju površinski valovi. Ti valovi putuju duž konture uzorka i mogu otkriti nedostatke blizu njegove površine.
Postoje dvije glavne vrste instalacija za ultrazvučno ispitivanje. Rezonantni test koristi zračenje promjenjive frekvencije. Kada se postigne prirodna frekvencija koja odgovara debljini materijala, amplituda titranja naglo raste, što se odražava na ekranu osciloskopa. Rezonantna metoda se uglavnom koristi za mjerenje debljine.
U metodi pulsnog odjeka u materijal se uvode impulsi konstantne frekvencije u trajanju od djelića sekunde. Val prolazi kroz materijal i energija reflektirana od defekta ili stražnje površine pada na pretvarač. Pretvornik zatim šalje drugi impuls i prima reflektirani.
Transmisiona metoda se također koristi za otkrivanje nedostataka u premazu i za određivanje čvrstoće prianjanja između premaza i podloge. U nekim sustavima premaza mjerenje reflektirane energije ne identificira na odgovarajući način kvar. To je zbog činjenice da je sučelje između premaza i podloge karakterizirano tako visokim koeficijentom refleksije da prisutnost defekata samo neznatno mijenja ukupni koeficijent refleksije.
Korištenje ultrazvučnog ispitivanja je ograničeno. To je vidljivo iz slijedeći primjeri. Ako materijal ima hrapavu površinu, zvučni valovi se raspršuju tako snažno da test postaje besmislen. Za ispitivanje predmeta složenog oblika potrebni su pretvarači koji prate konturu predmeta; površinske nepravilnosti uzrokuju pojavu šiljaka na zaslonu osciloskopa, što otežava prepoznavanje nedostataka. Granice zrna u metalu djeluju slično kao defekti i raspršuju zvučne valove. Defekte koji se nalaze pod kutom u odnosu na snop teško je otkriti, jer se refleksija uglavnom ne događa prema pretvaraču, već pod kutom prema njemu. Često je teško razlikovati diskontinuitete koji se nalaze blizu jedan drugom. Osim toga, otkrivaju se samo oni nedostaci čije su dimenzije usporedive s duljinom zvučni val.
Zaključak
Probirni testovi se provode tijekom početno stanje razvoj premaza. Jer tijekom pretrage optimalni način rada broj različitih uzoraka je vrlo velik, za uklanjanje nezadovoljavajućih uzoraka koristi se kombinacija ispitnih metoda. Ovaj program odabira obično se sastoji od nekoliko vrsta oksidacijskih ispitivanja, metalografskog pregleda, ispitivanja plamena i vlačnih ispitivanja. Premazi koji su uspješno prošli selekcijske testove ispituju se u uvjetima sličnim operativnim.
Nakon što se utvrdi da je određeni sustav premaza izdržao terensko ispitivanje, može se primijeniti kako bi se zaštitio stvarni proizvod. Prije puštanja u rad potrebno je razviti tehniku ispitivanja bez razaranja konačnog proizvoda. Nedestruktivnom tehnikom moguće je detektirati površinske i unutarnje rupe, pukotine i diskontinuitete, kao i slabo prianjanje premaza i podloge.
Kapilarna kontrola zavarenih spojeva služi za identifikaciju vanjskih (površinskih i prolaznih) i. Ova metoda provjere omogućuje vam da identificirate nedostatke kao što su vruće i, nedostatak prodiranja, pore, školjke i neke druge.
Uz pomoć detekcije kapilarnih nedostataka moguće je odrediti mjesto i veličinu defekta, kao i njegovu orijentaciju duž metalne površine. Ova metoda vrijedi i za i za . Također se koristi u zavarivanju plastike, stakla, keramike i drugih materijala.
Bit metode kapilarne kontrole je sposobnost posebnih indikatorskih tekućina da prodru u šupljine defekata zavara. Nedostaci punjenja, indikatorske tekućine formiraju indikatorske tragove, koji se bilježe tijekom vizualnog pregleda, ili uz pomoć sonde. Redoslijed kapilarne kontrole određen je standardima kao što su GOST 18442 i EN 1289.
Klasifikacija metoda otkrivanja kapilarnih nedostataka
Metode kapilarnog ispitivanja dijele se na osnovne i kombinirane. Glavne podrazumijevaju samo kapilarnu kontrolu s prodornim tvarima. Kombinirani se temelje na kombiniranoj uporabi dva ili više, od kojih je jedna kapilarna kontrola.
Osnovne metode kontrole
Glavne metode kontrole dijele se na:
- Ovisno o vrsti prodiranja:
- ispitivanje prodornim otopinama
- ispitivanje s suspenzijama filtera
- Ovisno o načinu čitanja informacija:
- osvjetljenje (akromatsko)
- boja (kromatska)
- luminiscentna
- luminiscentna boja.
Kombinirane metode kapilarne kontrole
Kombinirane metode se dijele ovisno o prirodi i načinu izlaganja površini koja se provjerava. a oni su:
- Kapilarno-elektrostatski
- Kapilarno-elektroindukcija
- Kapilarno magnetno
- Metoda apsorpcije kapilarnog zračenja
- Kapilarno-zračenje metoda zračenja.
Tehnologija detekcije kapilarnih nedostataka
Prije kapilarnog ispitivanja, površina koja se ispituje mora se očistiti i osušiti. Nakon toga na površinu se nanosi indikatorska tekućina - panetrant. Ova tekućina prodire u površinske nedostatke šavova i nakon nekog vremena provodi se međučišćenje, tijekom kojeg se uklanja višak indikatorske tekućine. Zatim se na površinu nanosi razvijač, koji počinje izvlačiti indikatorsku tekućinu iz zavarenih nedostataka. Tako se na kontroliranoj površini pojavljuju defektni uzorci, vidljivi golim okom ili uz pomoć posebnih programera.
Faze kapilarne kontrole
Proces kapilarne kontrole može se podijeliti u sljedeće faze:
- Priprema i prethodno čišćenje
- Intermedijarno čišćenje
- Proces manifestiranja
- Otkrivanje grešaka u zavarivanju
- Izrada protokola u skladu s rezultatima provjere
- Završno čišćenje površine
Materijali za kapilarnu kontrolu
Svitak potrebni materijali za otkrivanje kapilarnih kvarova dat je u tablici:
indikatorska tekućina |
srednji čistač |
Programer |
obojene tekućine Fluorescentne tekućine u boji |
suhi razvijač |
|
Emulgator uključen na bazi ulja |
Tekući razvijač na bazi vode |
|
Topljivo tekuće sredstvo za čišćenje |
Vodeni razvijač u suspenziji |
|
Emulgator osjetljiv na vodu |
||
Voda ili otapalo |
Tekući razvijač na bazi vode ili otapala za posebne primjene |
Priprema i prethodno čišćenje površine koja se provjerava
Ako je potrebno, s kontrolirane površine zavara uklanjaju se onečišćenja poput kamenca, hrđe, mrlja od ulja, boje itd. Ta se onečišćenja uklanjaju mehaničkim ili kemijsko čišćenje ili kombinacija ovih metoda.
Mehaničko čišćenje preporuča se samo u iznimnim slučajevima, ako na kontroliranoj površini postoji labav film oksida ili ima oštrih padova između zrna vara, dubokih podrezivanja. Mehaničko čišćenje je dobilo ograničenu primjenu zbog činjenice da se prilikom provođenja često površinski nedostaci zatvaraju kao rezultat trljanja i ne otkrivaju se tijekom pregleda.
Kemijsko čišćenje se provodi pomoću raznih kemijskih sredstava za čišćenje koja s provjeravane površine uklanjaju onečišćenja kao što su boja, uljne mrlje itd. Kemijski ostaci mogu reagirati s indikatorskim tekućinama i utjecati na točnost kontrole. Zato kemijske tvari nakon prethodnog čišćenja, moraju se isprati s površine vodom ili drugim sredstvima.
Nakon prethodnog čišćenja površine, mora se osušiti. Sušenje je potrebno kako na vanjskoj površini fuge koja se provjerava ne ostane ni voda, ni otapalo, niti bilo koje druge tvari.
Primjena indikatorske tekućine
Nanošenje indikatorskih tekućina na kontroliranu površinu može se izvesti na sljedeće načine:
- kapilarni način. U ovom slučaju, punjenje zavarenih nedostataka događa se spontano. Tekućina se nanosi vlaženjem, uranjanjem, strujanjem ili prskanjem. potisnut zrak ili inertni plin.
- Vakuumski način. Ovom metodom u šupljinama defekata stvara se razrijeđena atmosfera i tlak u njima postaje manji od atmosferskog, t.j. u šupljinama se dobiva svojevrsni vakuum koji u sebe usisava indikatorsku tekućinu.
- Metoda kompresije. Ova metoda je suprotna od vakuumske metode. Ispunjavanje nedostataka nastaje pod utjecajem tlaka koji prelazi atmosferski tlak na indikatorsku tekućinu. Pod visokim tlakom, tekućina ispunjava nedostatke, istiskujući zrak iz njih.
- ultrazvučna metoda. Defektne šupljine se popunjavaju u ultrazvučnom polju pomoću ultrazvučnog kapilarnog efekta.
- metoda deformacije. Defektne šupljine se pune pod utjecajem elastičnih oscilacija zvučnog vala na indikatorsku tekućinu ili pod statičkim opterećenjem koje povećava minimalna veličina nedostatke.
Za bolje prodiranje indikatorske tekućine u šupljine defekata, temperatura površine treba biti u rasponu od 10-50°C.
Srednje čišćenje površine
Međusrednja za čišćenje površina treba nanositi na način da se indikatorska tekućina ne ukloni s površinskih nedostataka.
Čišćenje vode
Višak indikatorske tekućine može se ukloniti prskanjem ili brisanjem vlažnom krpom. Istodobno treba izbjegavati mehanički utjecaj na kontroliranu površinu. Temperatura vode ne smije prelaziti 50°C.
Čišćenje otapalom
Najprije se višak tekućine uklanja čistom krpom koja ne ostavlja dlačice. Nakon toga, površina se čisti krpom navlaženom otapalom.
Pročišćavanje emulgatorima
Za uklanjanje indikatorskih tekućina koriste se emulgatori osjetljivi na vodu ili emulgatori na bazi ulja. Prije nanošenja emulgatora, višak indikatorske tekućine isperite vodom i odmah nanesite emulgator. Nakon emulgiranja potrebno je metalnu površinu isprati vodom.
Kombinirano čišćenje vodom i otapalom
Ovom metodom čišćenja prvo se višak indikatorske tekućine ispire s kontrolirane površine vodom, a zatim se površina čisti krpom koja ne ostavlja dlačice navlaženom otapalom.
Sušenje nakon međučišćenja
Za sušenje površine nakon međučišćenja može se koristiti nekoliko metoda:
- brisanje čistom, suhom krpom koja ne ostavlja dlačice
- isparavanje na temperaturi okoline
- sušenje na povišena temperatura
- sušenje na zraku
- kombinacija gore navedenih metoda sušenja.
Postupak sušenja mora se provesti na način da se indikatorska tekućina ne osuši u šupljinama s nedostacima. Da biste to učinili, sušenje se provodi na temperaturi koja ne prelazi 50°C.
Proces ispoljavanja površinskih nedostataka u zavaru
Razvijač se nanosi na kontroliranu površinu u ravnomjernom tankom sloju. Proces razvoja treba započeti što je prije moguće nakon međučišćenja.
suhi razvijač
Suhi razvijač može se koristiti samo s fluorescentnim indikatorskim tekućinama. Suhi razvijač nanosi se prskanjem ili elektrostatičkim prskanjem. Kontrolirana područja trebaju biti pokrivena jednoliko, ravnomjerno. Lokalna nakupljanja programera nisu dopuštena.
Tekući razvijač na bazi vodene suspenzije
Razvijač se nanosi jednoliko umakanjem kontroliranog spoja u njega ili prskanjem uz pomoć aparata. Kada koristite metodu uranjanja, za najbolje rezultate, trajanje uranjanja treba biti što kraće. Nakon toga, kontrolirani spoj se mora osušiti isparavanjem ili puhanjem u pećnici.
Tekući razvijač na bazi otapala
Razvijač se nanosi raspršivanjem na podlogu koja se pregledava na način da se površina ravnomjerno navlaži i da se na njoj formira tanak i ujednačen film.
Tekući razvijač u obliku vodene otopine
Ujednačena primjena takvog razvijača postiže se uranjanjem kontroliranih površina u njega, ili prskanjem posebnim uređajima. Uranjanje treba biti kratko, u tom slučaju se postiže najbolji rezultat ispitivanja. Nakon toga se kontrolirane površine suše isparavanjem ili puhanjem u pećnici.
Trajanje procesa razvoja
Trajanje procesa razvoja nastavlja se, u pravilu, 10-30 minuta. U nekim slučajevima dopušteno je povećanje trajanja manifestacije. Odbrojavanje vremena razvoja počinje: za suhi razvijač odmah nakon nanošenja, a za tekući razvijač - odmah nakon što se površina osuši.
Identifikacija grešaka u zavarivanju kao posljedica detekcije kapilarnih nedostataka
Ako je moguće, pregled površine koju treba pregledati počinje odmah nakon nanošenja razvijača ili nakon što se osuši. Ali konačna kontrola se događa nakon završetka procesa manifestacije. Kao pomoćni uređaji za optičko upravljanje koriste se povećala ili naočale s povećalom.
Kada koristite fluorescentne indikatorske tekućine
Fotokromne naočale nisu dopuštene. Potrebno je da se oči inspektora barem 5 minuta prilagode mraku u ispitnoj kabini.
Ultraljubičasto zračenje ne smije dospjeti u oči inspektora. Sve kontrolirane površine ne smiju fluorescirati (reflektirati svjetlost). Također, predmeti koji reflektiraju svjetlost pod utjecajem ultraljubičastih zraka ne bi trebali pasti u vidno polje kontrolera. Opće UV osvjetljenje može se koristiti kako bi se inspektoru omogućilo slobodno kretanje po ispitnoj komori.
Kada koristite indikatorske tekućine u boji
Sve kontrolirane površine pregledavaju se na dnevnoj ili umjetnoj rasvjeti. Osvjetljenje na ispitivanoj površini mora biti najmanje 500 lx. Istodobno, na površini ne smije biti odsjaja zbog refleksije svjetlosti.
Ponovljena kapilarna kontrola
Ako postoji potreba za ponovnim pregledom, tada se cijeli proces otkrivanja kapilarnih nedostataka ponavlja, počevši od postupka prethodnog čišćenja. Da biste to učinili, potrebno je, ako je moguće, osigurati više povoljni uvjeti kontrolirati.
Za ponovni pregled dopušteno je koristiti samo iste indikatorske tekućine, istog proizvođača, kao i tijekom prve kontrole. Korištenje drugih tekućina, ili istih tekućina, ali različitih proizvođača, nije dozvoljeno. U tom slučaju potrebno je izvršiti temeljito čišćenje površine kako na njoj ne bi ostali tragovi prethodne provjere.
Prema EN571-1, glavne faze kapilarne kontrole prikazane su na dijagramu:
Video na temu: "Kapilarna detekcija nedostataka zavarenih spojeva"
§ 9.1. Opće informacije o metodi
Metoda kapilarne kontrole (CMC) temelji se na kapilarnom prodiranju indikatorskih tekućina u šupljinu diskontinuiteta u materijalu ispitnog objekta i registraciji rezultirajućih indikatorskih tragova vizualno ili pomoću sonde. Metoda omogućuje otkrivanje površinskih (tj. izbijanja na površinu) i preko (tj. spajanja suprotnih površina OC zidova.) nedostataka koji se također mogu otkriti vizualnim pregledom. Takva kontrola, međutim, zahtijeva visoki troškovi vrijeme, osobito kod otkrivanja slabo uočenih nedostataka, kada se vrši temeljit pregled površine pomoću alata za povećanje. Prednost KMC-a je u višestrukom ubrzanju procesa upravljanja.
Detekcija prolaznih nedostataka uključena je u zadatak metoda detekcije curenja, o kojima se govori u pogl. 10. U metodama detekcije curenja, uz ostale metode, koristi se CMC, a tekućina indikatora se nanosi na jednu stranu zida OK, a snima na drugu. Ovo poglavlje govori o varijanti CMC-a, u kojoj se indikacija izvodi s iste površine OK, s koje se nanosi indikatorska tekućina. Glavni dokumenti koji reguliraju korištenje CMC-a su GOST 18442 - 80, 28369 - 89 i 24522 - 80.
Proces kapilarne kontrole sastoji se od sljedećih glavnih operacija (slika 9.1):
a) čišćenje površine 1 OK i šupljine defekta 2 od prljavštine, masnoće i sl. njihovim mehaničko uklanjanje i otapanje. Time se osigurava dobro vlaženje cijele površine epruvete indikatorskom tekućinom i mogućnost njenog prodiranja u šupljinu defekta;
b) impregnacija nedostataka indikatorskom tekućinom. 3. Da biste to učinili, mora dobro navlažiti materijal proizvoda i prodrijeti u nedostatke kao rezultat djelovanja kapilarnih sila. Na temelju toga metoda se naziva kapilarna, a indikatorska tekućina naziva se indikatorski penetrant ili jednostavno penetrant (od latinskog penetro - prodiram, dobijem);
c) uklanjanje viška penetranta s površine proizvoda, dok penetrant ostaje u šupljini defekta. Za uklanjanje se koriste učinci disperzije i emulgiranja, koriste se posebne tekućine - sredstva za čišćenje;
Riža. 9.1 - Osnovne operacije za otkrivanje kapilarnih nedostataka
d) otkrivanje penetranta u šupljini defekta. Kao što je gore navedeno, to se radi češće vizualno, rjeđe - uz pomoć posebnih uređaja - pretvarača. U prvom slučaju na površinu se nanose posebne tvari - razvijači 4, koji izvlače penetrant iz šupljine defekta zbog fenomena sorpcije ili difuzije. Sorpcijski razvijač je u obliku praha ili suspenzije. Sve spomenute fizičke pojave razmatraju se u § 9.2.
Penetrant impregnira cijeli sloj razvijača (obično prilično tanak) i formira tragove (indikacije) 5 na njegovoj vanjskoj površini. Ove se indikacije otkrivaju vizualno. Razlikuju se metoda svjetline ili akromatske metode, u kojoj indikacije imaju tamniji ton u usporedbi s bijelim razvijačem; metoda boja, kada penetrant ima svijetlu narančastu ili crvenu boju, i luminescentna metoda, kada penetrant svijetli pod ultraljubičastim zračenjem. Završna operacija za KMK je čišćenje OK od programera.
U literaturi o kapilarna kontrola Materijali za otkrivanje nedostataka označeni su indeksima: indikatorski penetrant - "I", čistač - "M", razvijač - "P". Ponekad poslije slovna oznaka iza kojih slijede brojevi u zagradama ili u obliku indeksa, što ukazuje na osobitost primjene ovog materijala.
§ 9.2. Osnovne fizikalne pojave koje se koriste u detekciji kapilarnih nedostataka
Površinska napetost i vlaženje. Najviše važna karakteristika indikatorska tekućina je njihova sposobnost vlaženja materijala proizvoda. Vlaženje je uzrokovano međusobnim privlačenjem atoma i molekula (u daljnjem tekstu molekule) tekućine i krutine.
Kao što je poznato, između molekula medija djeluju sile međusobnog privlačenja. Molekule unutar tvari doživljavaju, u prosjeku, isto djelovanje drugih molekula u svim smjerovima. Molekule smještene na površini podliježu nejednakom privlačenju sa strane unutarnjih slojeva tvari i sa strane uz površinu medija.
Ponašanje sustava molekula određeno je uvjetom minimuma slobodne energije, t.j. taj dio potencijalna energija, koji se može pretvoriti u rad izotermno. Slobodna energija molekula na površini tekućine i krutine veća je od unutarnje energije kada je tekućina ili krutina u plinu ili vakuumu. U tom smislu, oni imaju tendenciju da stječu oblik s minimalnom vanjskom površinom. U čvrstom tijelu to je spriječeno fenomenom elastičnosti forme, dok tekućina u bestežinskom stanju pod utjecajem te pojave dobiva oblik lopte. Dakle, površine tekućine i čvrste tvari imaju tendenciju skupljanja i nastaje pritisak površinske napetosti.
Vrijednost površinske napetosti određena je radom (pri konstantnoj temperaturi) koji je potreban za formiranje jedinice, područje međufaza između dviju faza u ravnoteži. Često se naziva sila površinske napetosti, snižavajući sljedeće pod tim. Na sučelju mediji dodjeljuju proizvoljno područje. Napetost se smatra rezultatom djelovanja raspoređene sile primijenjene na perimetar ovog područja. Smjer sila je tangencijalan na sučelje i okomit na perimetar. Sila po jedinici duljine perimetra naziva se sila površinske napetosti. Dvije jednake definicije površinske napetosti odgovaraju dvjema jedinicama koje se koriste za mjerenje: J/m2 = N/m.
Za vodu u zraku (točnije, u zraku zasićenom isparavanjem s površine vode) na temperaturi od 26 ° C normalno atmosferski pritisak sila površinske napetosti σ = 7,275 ± 0,025) 10-2 N/m. Ova vrijednost opada s porastom temperature. U različitim plinovita okruženja Površinska napetost tekućina ostaje gotovo nepromijenjena.
Razmotrimo kap tekućine koja leži na površini: čvrsto tijelo (slika 9.2). Zanemarujemo silu gravitacije. Izdvojimo elementarni cilindar u točki A, gdje čvrsto tijelo, tekućina i okolni plin dolaze u dodir. Na jedinicu duljine ovog cilindra djeluju tri sile površinske napetosti: čvrsto tijelo - plin σtg, čvrsto tijelo - tekućina σtzh i tekućina - plin σlg = σ. Kada kap miruje, rezultanta projekcija ovih sila na površinu tijela je nula:
(9.1)
Kut 9 naziva se kut vlaženja. Ako je σtg>σtzh, onda je oštar. To znači da tekućina vlaži krutinu (slika 9.2, a). Što je manje 9, to je vlaženje jače. U granici σtg>σtzh + σ, omjer (σtg - σtzh)/st u (9.1) je veći od jedinice, što ne može biti, budući da je kosinus kuta uvijek manji od jedinice u apsolutnoj vrijednosti. Granični slučaj θ = 0 odgovarat će potpunom vlaženju, t.j. širenje tekućine po površini krute tvari do debljine molekularnog sloja. Ako je σtzh>σtg, tada je cos θ negativan, dakle, kut θ je tup (slika 9.2, b). To znači da tekućina ne vlaži krutinu.
Riža. 9.2. Vlaženje (a) i nekvašenje (b) površine tekućinom
Površinska napetost σ karakterizira svojstvo same tekućine, a σ cos θ je kvašenje površine danog čvrstog tijela ovom tekućinom. Komponenta sile površinske napetosti σ cos θ, koja "razvlači" kap duž površine, ponekad se naziva i sila vlaženja. Za većinu dobro vlažećih tvari, cos θ je blizu jedinice, na primjer, za granicu stakla s vodom je 0,685, s kerozinom - 0,90, s etilnim alkoholom - 0,955.
Čistoća površine ima snažan utjecaj na vlaženje. Na primjer, sloj ulja na površini čelika ili stakla naglo smanjuje njegovu sposobnost vlaženja vodom, cos θ postaje negativan. Najtanji sloj ulje, ponekad ostaje na površini OK i puca, uvelike ometa korištenje penetranta na bazi vode.
Mikroreljef OC površine uzrokuje povećanje površine navlažene površine. Za procjenu kontaktnog kuta θsh on gruba površina upotrijebi jednadžbu
gdje je θ kontaktni kut za glatka površina; α je prava površina hrapave površine, uzimajući u obzir neravnine njenog reljefa, a α0 je njena projekcija na ravninu.
Otapanje se sastoji u raspodjeli molekula otopljene tvari među molekulama otapala. U kapilarnoj metodi kontrole, otapanje se koristi prilikom pripreme predmeta za kontrolu (za čišćenje šupljine od nedostataka). Otapanje plina (obično zraka) prikupljenog na kraju slijepe kapilare (defekta) u penetrantu značajno povećava maksimalnu dubinu prodiranja penetranta u defekt.
Za procjenu međusobne topljivosti dviju tekućina koristi se pravilo prema kojem "slično otapa slično". Na primjer, ugljikovodici se dobro otapaju u ugljikovodicima, alkoholi u alkoholima itd. Međusobna topljivost tekućina i krutih tvari u tekućini ima tendenciju povećanja s povećanjem temperature. Topljivost plinova općenito opada s povećanjem temperature i poboljšava se s povećanjem tlaka.
Sorpcija (od lat. sorbeo - apsorbiram) je fizikalno-kemijski proces, uslijed kojeg neka tvar iz okoliša apsorbira plin, paru ili otopljenu tvar. Razlikovati adsorpciju – apsorpciju tvari na međufaznoj granici i apsorpciju – apsorpciju tvari cijelim volumenom apsorbera. Ako se sorpcija događa uglavnom kao rezultat fizičke interakcije tvari, tada se naziva fizikalna.
U metodi kapilarne kontrole razvoj uglavnom koristi fenomen fizičke adsorpcije tekućine (penetranta) na površini čvrstog tijela (čestica razvijača). Isti fenomen uzrokuje taloženje na defektu kontrastnih sredstava otopljenih u tekućoj bazi penetranta.
Difuzija (od latinskog diffusio - širenje, širenje) - kretanje čestica (molekula, atoma) medija, što dovodi do prijenosa tvari i izjednačavanja koncentracije čestica različitih vrsta. U metodi kapilarne kontrole, fenomen difuzije se opaža kada penetrant stupi u interakciju sa zrakom komprimiranim na slijepom kraju kapilare. Ovdje se ovaj proces ne razlikuje od otapanja zraka u penetrantu.
Važna primjena difuzija u otkrivanju kapilarnih nedostataka - razvoj pomoću programera kao npr brzosušeće boje i lakovi. Čestice penetranta zatvorene u kapilari dolaze u dodir s takvim razvijačem (u prvom trenutku - tekućim, a nakon stvrdnjavanja - čvrstim) nanesenim na površinu OK, i difundiraju kroz tanki film razvijača do njegove suprotnosti površinski. Dakle, ovdje se koristi difuzija tekućih molekula, prvo kroz tekućinu, a zatim kroz čvrsto tijelo.
Proces difuzije uzrokovan je toplinskim gibanjem molekula (atoma) ili njihovim asocijacijama (molekularna difuzija). Brzina prijenosa preko granice određena je koeficijentom difuzije, koji je konstantan za dani par tvari. Difuzija se povećava s temperaturom.
Disperzija (od latinskog dispergo - raspršujem) - fino mljevenje tijela u okoliš. Disperzija krutih tvari u tekućini igra bitnu ulogu prilikom čišćenja površine od onečišćenja.
Emulzifikacija (od lat. emulsios - pomuzena) - stvaranje dispergiranog sustava s tekućom disperznom fazom, t.j. tekuća disperzija. Primjer emulzije je mlijeko, koje se sastoji od sitnih kapi masti suspendiranih u vodi. Emulzifikacija ima bitnu ulogu u čišćenju, uklanjanju, višku penetranta, pripremi penetranta, razvijačima. Emulgatori se koriste za aktiviranje emulgiranja i održavanje emulzije u stabilnom stanju.
Surfaktanti (tenzidi) - tvari koje se mogu akumulirati na dodirnoj površini dvaju tijela (mediji, faze), snižavajući je slobodna energija. Sredstvima za čišćenje površine OK dodaju se surfaktanti, ubrizgavaju se u penetrante, čistače, budući da su emulgatori.
Najvažniji tenzidi otapaju se u vodi. Njihove molekule imaju hidrofobne i hidrofilne dijelove, t.j. nakvašene i nenakvašene vodom. Ilustrirajmo djelovanje tenzida pri ispiranju uljnog filma. Obično ga voda ne vlaži i ne uklanja. Molekule surfaktanta adsorbiraju se na površini filma, njihovi hidrofobni krajevi su orijentirani prema njoj, a hidrofilni krajevi orijentirani prema vodenom mediju. Kao rezultat toga, dolazi do naglog povećanja vlaženja, a masni film se ispere.
Suspenzija (od latinskog supspensio - visim) je grubo dispergirani sustav s tekućim disperzijskim medijem i čvrstom disperznom fazom, čije su čestice dovoljno velike i prilično brzo talože ili plutaju. Suspenzije se obično pripremaju mehaničkim mljevenjem i miješanjem.
Luminescencija (od lat. lumen - svjetlost) - sjaj određenih tvari (fosfora), višak nad toplinskim zračenjem, u trajanju od 10-10 s ili više. Oznaka konačnog trajanja je neophodna kako bi se luminiscencija razlikovala od drugih optičkih pojava, na primjer, od raspršenja svjetlosti.
U metodi kapilarne kontrole, luminiscencija se koristi kao jedna od metoda kontrasta za vizualnu detekciju indikatorskih penetranata nakon razvoja. Da bi se to postiglo, fosfor se ili otopi u glavnoj tvari penetranta, ili je tvar samog penetranta fosfor.
Svjetlina i kontrasti boja u KMC-u razmatraju se sa stajališta sposobnosti ljudskog oka da fiksira luminiscentni sjaj, boju i tamnu indikaciju na svijetloj pozadini. Svi podaci odnose se na oko prosječne osobe, sposobnost razlikovanja stupnja svjetline objekta naziva se kontrastna osjetljivost. Određuje se promjenom koeficijenta refleksije koja je vidljiva oku. U metodi kontrole boje uvodi se koncept kontrasta svjetlina-boja, koji istovremeno uzima u obzir svjetlinu i zasićenost traga od defekta koji se otkriva.
Sposobnost oka da razlikuje male predmete s dovoljnim kontrastom određena je minimalni kut vizija. Utvrđeno je da se predmet u obliku trake (tamne, obojene ili luminiscentne) može vidjeti okom s udaljenosti od 200 mm s minimalnom širinom većom od 5 mikrona. U radnim uvjetima, objekti se razlikuju po redu veličine - širine 0,05 ... 0,1 mm.
§ 9.3. Procesi otkrivanja kapilarnih nedostataka
Riža. 9.3. Na pojam kapilarnog tlaka
Punjenje prolaznog makrokapilara. Analizirajmo poznati pokus iz kolegija fizike: kapilarna cijev promjera 2r okomito je na jednom kraju uronjena u tekućinu za vlaženje (slika 9.3). Pod djelovanjem sila vlaženja tekućina u cijevi se diže do visine l iznad površine. Ovo je fenomen kapilarne apsorpcije. Sile vlaženja djeluju na jedinicu duljine opsega meniskusa. Njihova ukupna vrijednost Fk=σcosθ2πr. Ovoj sili suprotstavlja težina stupa ρgπr2 l, gdje je ρ gustoća, a g ubrzanje zbog gravitacije. U stanju ravnoteže σcosθ2πr = ρgπr2 l. Otuda visina porasta tekućine u kapilari l= 2σ cos θ/(ρgr).
U ovom primjeru smatralo se da se sile vlaženja primjenjuju na liniju kontakta između tekućine i krutine (kapilara). Također se mogu smatrati silom napetosti na površini meniskusa koju formira tekućina u kapilari. Ova površina je, takoreći, rastegnuti film koji ima tendenciju skupljanja. Stoga se uvodi pojam kapilarnog tlaka, koji je jednak omjeru sile FK koja djeluje na meniskus i površine presjek cijevi: (9.2)
Kapilarni tlak raste s povećanjem vlaženja i smanjenjem radijusa kapilare.
Općenitija Laplaceova formula za tlak od napetosti površine meniskusa ima oblik pk=σ(1/R1+1/R2), gdje su R1 i R2 polumjeri zakrivljenosti površine meniskusa. Formula 9.2 koristi se za okruglu kapilaru R1=R2=r/cos θ. Za širinu utora b s ravnoparalelnim zidovima R1®¥, R2= b/(2cosθ). Kao rezultat (9.3)
Impregnacija defekata penetrantom temelji se na fenomenu kapilarne apsorpcije. Procijenite vrijeme potrebno za impregnaciju. Razmotrimo horizontalnu kapilarnu cijev, čiji je jedan kraj otvoren, a drugi je stavljen u tekućinu za vlaženje. Pod djelovanjem kapilarnog pritiska meniskus tekućine pomiče se prema otvorenom kraju. Prijeđena udaljenost l povezan je s vremenom približnom ovisnošću. (9.4)
gdje je μ koeficijent dinamičke posmične viskoznosti. Iz formule se može vidjeti da je vrijeme potrebno da penetrant prođe kroz prolaznu pukotinu povezano s debljinom stijenke l, u kojem se pojavila pukotina, s kvadratnom ovisnošću: ona je manja što je niža viskoznost i veća je kvašenje. Ovisnost orijentacijske krivulje 1 l iz t prikazano na sl. 9.4. Trebao je; imajući na umu da prilikom punjenja pravim penetrantom; pukotine, uočene pravilnosti su sačuvane samo ako penetrant istovremeno dodiruje cijeli perimetar pukotine i njezinu jednoličnu širinu. Nepoštivanje ovih uvjeta dovodi do narušavanja relacije (9.4), međutim, utjecaj navedenih fizikalnih svojstava penetranta na vrijeme impregnacije je očuvan.
Riža. 9.4. Kinetika punjenja kapilara penetrantom:
kroz (1), slijepa ulica s (2) i bez (3) fenomenom difuzijske impregnacije
Punjenje slijepe kapilare razlikuje se po tome što plin (zrak) komprimiran u blizini slijepe ulice ograničava dubinu prodiranja penetranta (krivulja 3 na slici 9.4). Izračunajte maksimalnu dubinu punjenja l 1 na temelju jednakosti pritisaka na penetrant izvan i unutar kapilare. Vanjski tlak je zbroj atmosferskog R i kapilarni R do. Unutarnji pritisak u kapilari R c je određen iz Boyle-Mariotteovog zakona. Za kapilaru stalnog presjeka: str a l 0S= str u( l 0-l 1)S; R u = R a l 0/(l 0-l 1), gdje l 0 je ukupna dubina kapilare. Iz jednakosti pritisaka nalazimo
Vrijednost R do<<R a, dakle, dubina punjenja izračunata ovom formulom nije veća od 10% ukupne dubine kapilare (zadatak 9.1).
Razmatranje popunjavanja slijepog proreza s neparalelnim stijenkama (dobro simuliraju stvarne pukotine) ili konusne kapilare (simuliraju pore) teže je od kapilara stalnog presjeka. Smanjenje poprečnog presjeka pri punjenju uzrokuje porast kapilarnog tlaka, ali se volumen ispunjen komprimiranim zrakom još brže smanjuje, pa je dubina punjenja takve kapilare (s istom veličinom otvora) manja od one kapilare od stalni presjek (zadatak 9.1).
U stvarnosti, granična dubina punjenja slijepe kapilare je u pravilu veća od izračunate vrijednosti. To je zbog činjenice da se zrak komprimiran blizu kraja kapilare djelomično otapa u penetrantu i difundira u njega (difuzijsko punjenje). Za duge nedostatke u slijepoj ulici ponekad dolazi do povoljne situacije za punjenje kada punjenje počinje na jednom kraju duž duljine defekta, a istisnuti zrak izlazi s drugog kraja.
Kinetika gibanja tekućine za vlaženje u slijepoj kapilari određena je formulom (9.4) samo na početku procesa punjenja. Kasnije, pri približavanju l do l 1, brzina procesa punjenja se usporava, asimptotski se približava nuli (krivulja 2 na slici 9.4).
Prema procjenama, vrijeme punjenja cilindrične kapilare polumjera oko 10-3 mm i dubine l 0 = 20 mm do razine l = 0,9l 1 ne više od 1 s. To je znatno manje od vremena izlaganja penetrantu preporučenog u kontrolnoj praksi (§ 9.4), koje iznosi nekoliko desetaka minuta. Razlika se objašnjava činjenicom da nakon procesa prilično brzog punjenja kapilara počinje puno sporiji proces difuzijskog punjenja. Za kapilaru stalnog poprečnog presjeka, kinetika difuzijskog punjenja podliježe zakonima tipa (9.4): l p= KÖt, gdje l p je dubina difuzijskog punjenja, ali koeficijent Do tisuće puta manje nego za punjenje kapilara (vidi krivulju 2 na slici 9.4). Raste proporcionalno porastu tlaka na kraju kapilare pk/(pk + pa). Stoga je potrebno dugo vrijeme impregnacije.
Uklanjanje viška penetranta s površine OK obično se izvodi pomoću tekućine za čišćenje. Važno je odabrati sredstvo za čišćenje koje će dobro ukloniti penetrant s površine, minimalno ga isprati iz šupljine defekta.
proces manifestacije. U otkrivanju kapilarnih nedostataka koriste se difuzijski ili adsorpcijski razvijači. Prvi su brzosušeće bijele boje ili lakovi, drugi su puderi ili suspenzije.
Proces razvoja difuzije sastoji se u tome da tekući razvijač kontaktira penetrant na ušću defekta i upija ga. Penetrant prvo difundira u razvijač - kao u tekućem sloju, a nakon što se boja osuši - kao u čvrstom kapilarno-poroznom tijelu. Istodobno se odvija proces otapanja penetranta u razvijaču, koji se u ovom slučaju ne razlikuje od difuzije. U procesu impregnacije penetrantom mijenjaju se svojstva razvijača: postaje gušći. Ako se razvijač koristi u obliku suspenzije, tada u prvoj fazi razvoja dolazi do difuzije i otapanja penetranta u tekućoj fazi suspenzije. Nakon što se suspenzija osuši, djeluje ranije opisan razvojni mehanizam.
§ 9.4. Tehnologija i kontrole
Shema opće tehnologije kapilarne kontrole prikazana je na sl. 9.5. Pogledajmo njegove glavne korake.
Riža. 9.5. Tehnološka shema kapilarne kontrole
Pripremne radnje imaju za cilj iznijeti otvore nedostataka na površinu proizvoda, eliminirati mogućnost pozadinskih i lažnih indikacija, te očistiti šupljinu od nedostataka. Način pripreme ovisi o stanju površine i potrebnoj klasi osjetljivosti.
Mehaničko čišćenje se provodi kada je površina proizvoda prekrivena kamencem ili silikatom. Na primjer, površina nekih zavarenih spojeva obložena je slojem tvrdog silikatnog toka "breza kora". Takvi premazi pokrivaju usta nedostataka. Galvanski premazi, filmovi, lakovi se ne uklanjaju ako puknu zajedno s osnovnim metalom proizvoda. Ako se takvi premazi nanose na dijelove koji već mogu imati nedostatke, tada se kontrola provodi prije nanošenja premaza. Čišćenje se vrši rezanjem, abrazivnim brušenjem, obradom metalnim četkama. Ove metode uklanjaju dio materijala s površine OK. Ne mogu očistiti slijepe rupe, niti. Prilikom mljevenja mekih materijala, nedostatke je moguće prekriti tankim slojem deformiranog materijala.
Mehaničko čišćenje naziva se puhanje sačmom, pijeskom, kamenim komadićima. Nakon mehaničkog čišćenja, njegovi proizvodi se uklanjaju s površine. Čišćenju deterdžentima i otopinama podliježu svi predmeti koji ulaze u kontrolu, uključujući i one koji su prošli mehaničko čišćenje i čišćenje.
Činjenica je da mehaničko čišćenje ne čisti šupljine nedostataka, a ponekad njegovi proizvodi (pasta za mljevenje, abrazivna prašina) mogu pridonijeti njihovom zatvaranju. Čišćenje se provodi vodom s aditivima tenzida i otapalima, a to su alkoholi, aceton, benzin, benzol itd. Koriste se za uklanjanje masnoća od konzervansa, nekih boja: Po potrebi se vrši višekratna obrada otapalom.
Za potpunije čišćenje površine OC i šupljine nedostataka koriste se metode intenziviranja čišćenja: izlaganje parama organskog otapala, kemijsko jetkanje (pomaže u uklanjanju produkata korozije s površine), elektroliza, zagrijavanje OC, izlaganje niskofrekventnim ultrazvučnim vibracijama.
Nakon čišćenja površina se osuši OK. Time se uklanjaju ostaci tekućina za pranje i otapala iz šupljina s nedostacima. Sušenje se pojačava povećanjem temperature, puhanjem, na primjer, pomoću mlaza toplinskog zraka iz sušila za kosu.
Penetrantna impregnacija. Postoji niz zahtjeva za penetrante. Dobra kvasljivost OK površine je glavna. Da bi se to postiglo, penetrant mora imati dovoljno visoku površinsku napetost i kontaktni kut blizu nule kada se širi preko OC površine. Kao što je navedeno u § 9.3, najčešće se kao osnova za penetrante koriste tvari kao što su kerozin, tečna ulja, alkoholi, benzol, terpentin, koji imaju površinsku napetost od (2,5 ... 3,5) 10-2 N / m . Rjeđe se koriste penetranti na bazi vode s aditivima površinski aktivnih tvari. Za sve te tvari cos θ nije manji od 0,9.
Drugi zahtjev za penetrante je niska viskoznost. Potrebno je smanjiti vrijeme impregnacije. Treći važan zahtjev je mogućnost i praktičnost otkrivanja indikacija. Nasuprot tome, KMC penetrant se dijeli na akromatski (svjetlina), u boji, luminescentan i luminescentan u boji. Osim toga, postoje kombinirani CMC, u kojima se indikacije ne otkrivaju vizualno, već uz pomoć različitih fizičkih učinaka. Prema vrstama penetranata, točnije, prema metodama njihove indikacije, KMC se klasificira. Postoji i gornji prag osjetljivosti, koji je određen činjenicom da se iz širokih, ali plitkih nedostataka, penetrant ispire kada se višak penetranta ukloni s površine.
Prag osjetljivosti određene odabrane CMC metode ovisi o kontrolnim uvjetima i materijalima za detekciju grešaka. Utvrđeno je pet razreda osjetljivosti (prema donjem pragu) ovisno o veličini defekata (tablica 9.1).
Za postizanje visoke osjetljivosti (nizak prag osjetljivosti) potrebno je koristiti penetrante visokog kontrasta koji dobro vlažu, razvijače boja (umjesto suspenzija ili prahova), pojačati UV zračenje ili osvjetljenje predmeta. Optimalna kombinacija ovih čimbenika omogućuje otkrivanje nedostataka s otvorom od desetinki mikrona.
U tablici. 9.2 daje preporuke za izbor metode i kontrolnih uvjeta koji osiguravaju potrebnu klasu osjetljivosti. Osvjetljenje se daje kombinirano: prvi broj odgovara žaruljama sa žarnom niti, a drugi - fluorescentnim. Pozicije 2,3,4,6 temelje se na korištenju komercijalno dostupnih setova materijala za detekciju grešaka.
Tablica 9.1 - Razredi osjetljivosti
Ne treba nepotrebno težiti postizanju viših razreda osjetljivosti: to zahtijeva skuplje materijale, bolju pripremu površine proizvoda i povećava vrijeme pregleda. Primjerice, za primjenu luminiscentne metode potrebna je zamračena prostorija, ultraljubičasto zračenje, što štetno djeluje na osoblje. U tom smislu, korištenje ove metode preporučljivo je samo kada je potrebna visoka osjetljivost i produktivnost. U drugim slučajevima treba koristiti boju ili jednostavniju i jeftiniju metodu osvjetljenja. Metoda filtrirane suspenzije je najproduktivnija. U njemu nestaje radnja manifestacije. Međutim, ova metoda je inferiorna u odnosu na druge u osjetljivosti.
Zbog složenosti njihove implementacije, kombinirane metode se koriste vrlo rijetko, samo ako je potrebno riješiti bilo koji specifični problem, na primjer, postizanje vrlo visoke osjetljivosti, automatiziranje traženja nedostataka i ispitivanje nemetalnih materijala.
Provjera praga osjetljivosti KMK metode prema GOST 23349 - 78 provodi se pomoću posebno odabranog ili pripremljenog stvarnog uzorka OK s nedostacima. Također se koriste uzorci s započetim pukotinama. Tehnologija izrade takvih uzoraka svodi se na pojavu površinskih pukotina određene dubine.
Prema jednoj od metoda, uzorci se izrađuju od legiranog čelika u obliku ploča debljine 3...4 mm. Ploče se ispravljaju, bruse, nitriraju s jedne strane do dubine od 0,3 ... 0,4 mm, a ova površina se ponovno melje do dubine od oko 0,05 ... 0,1 mm. Parametar hrapavosti površine Ra £ 0,4 µm. Zbog nitriranja površinski sloj postaje krhak.
Uzorci se deformiraju ili zatezanjem ili savijanjem (pritiskom kuglice ili cilindra sa strane suprotne od nitrirane). Sila deformacije se postupno povećava sve dok se ne pojavi karakteristično krckanje. Kao rezultat toga, u uzorku se pojavljuje nekoliko pukotina koje prodiru do cijele dubine nitriranog sloja.
Tablica: 9.2
Uvjeti za postizanje potrebne osjetljivosti
br. p / str |
Klasa osjetljivosti |
Materijali za defektoskopiju |
Kontrolni uvjeti |
|||||
Penetrant |
Programer |
Pročišćivač |
Hrapavost površine, µm |
Izlaganje UV zrakama, rel. jedinice |
Osvjetljenje, lx |
|||
Fluorescentna boja |
Boja Pr1 |
|||||||
Luminescentno |
Boja Pr1 |
|||||||
Smjesa ulja i kerozina |
||||||||
Luminescentno |
Magnezijev oksid u prahu |
|||||||
Benzin, norinol A, terpentin, boja |
Kaolin suspenzija |
Tekuća voda |
||||||
Luminescentno |
MgO2 prah |
Voda s surfaktantom |
||||||
Suspenzija luminiscentnog filtera |
Voda, emulgator, lumoten |
Ne manje od 50 |
Ovako proizvedeni uzorci su certificirani. Odredite mjernim mikroskopom širinu i duljinu pojedinih pukotina i unesite ih u obrazac uzorka. Uz obrazac je priložena fotografija uzorka s naznakama nedostataka. Uzorci se pohranjuju u kutije kako bi se zaštitili od kontaminacije. Uzorak je prikladan za korištenje ne više od 15...20 puta, nakon čega su pukotine djelomično začepljene suhim ostacima penetranta. Stoga laboratorij obično ima radne uzorke za svakodnevnu upotrebu i kontrolne uzorke za arbitražna pitanja. Uzorci se koriste za ispitivanje materijala za detekciju nedostataka na učinkovitost zajedničkog korištenja, za određivanje ispravne tehnologije (vrijeme impregnacije, razvoj), certificiranje detektora mana i određivanje donjeg praga osjetljivosti CMC.
§ 9.6. Objekti kontrole
Kapilarna metoda kontrolira proizvode izrađene od metala (uglavnom ne-feromagnetnih), nemetalnih materijala i kompozitnih proizvoda bilo koje konfiguracije. Proizvodi izrađeni od feromagnetnih materijala obično se kontroliraju metodom magnetskih čestica, koja je osjetljivija, iako se kapilarna metoda također ponekad koristi za kontrolu feromagnetnih materijala ako postoje poteškoće s magnetizacijom materijala ili složena površinska konfiguracija proizvoda stvara veliki gradijenti magnetskog polja koji otežavaju otkrivanje nedostataka. Kontrola kapilarnom metodom provodi se prije ultrazvučne ili magnetske kontrole čestica, u suprotnom (u potonjem slučaju) potrebno je demagnetizirati OK.
Kapilarna metoda otkriva samo nedostatke koji izlaze na površinu, čija šupljina nije ispunjena oksidima ili drugim tvarima. Da se penetrant ne bi isprao iz defekta, njegova dubina mora biti znatno veća od širine otvora. Takvi nedostaci uključuju pukotine, nedostatak prodiranja zavara, duboke pore.
Velika većina nedostataka otkrivenih kapilarnim ispitivanjem može se otkriti običnim vizualnim pregledom, osobito ako je proizvod prethodno urezan (defekti postaju crni) i ako se koriste alati za povećanje. Međutim, prednost kapilarnih metoda je u tome što se kada se koriste, kut gledanja na defekt se povećava za 10-20 puta (zbog činjenice da je širina indikacija veća od širine defekata), a kontrast svjetline se povećava. za 30-50%. Zbog toga nema potrebe za temeljitim pregledom površine, a vrijeme inspekcije se uvelike smanjuje.
Kapilarne metode se široko koriste u elektroenergetici, zrakoplovstvu, raketnoj tehnologiji, brodogradnji i kemijskoj industriji. Oni kontroliraju osnovni metal i zavarene spojeve od austenitnih čelika (nehrđajući), titana, aluminija, magnezija i drugih obojenih metala. Osjetljivost klase 1 koristi se za kontrolu lopatica turbomlaznih motora, brtvenih površina ventila i njihovih sjedišta, metalnih brtvi prirubnica itd. Klasa 2 koristi se za provjeru tijela reaktora i antikorozivnih površina, običnih metala i zavarenih spojeva cjevovoda, ležajeva. dijelovi. Prema klasi 3, provjeravaju se pričvršćivači brojnih predmeta, prema klasi 4 - odljevci debelih stijenki. Primjeri feromagnetskih proizvoda kontroliranih kapilarnim metodama: kavezi ležaja, navojni spojevi.
Riža. 9.10. Defekti na lopaticama:
a - zamorna pukotina, otkrivena luminiscentnom metodom,
b - zakov, identificiran metodom boja
Na sl. 9.10 prikazuje otkrivanje pukotina i okova na lopaticama zrakoplovne turbine korištenjem luminiscentnih metoda i metoda boja. Vizualno se takve pukotine promatraju pri povećanju od 10 puta.
Vrlo je poželjno da ispitni objekt ima glatku, na primjer obrađenu površinu. Površine nakon hladnog štancanja, valjanja, argon-lučnog zavarivanja prikladne su za ispitivanje u klasama 1 i 2. Ponekad se provodi mehanička obrada kako bi se površina izravnala, na primjer, površine nekih zavarenih ili zavarenih spojeva obrađuju se abrazivnim kotačem kako bi se uklonilo smrznuto zavarivanje: fluks, troska između zrna vara.
Ukupno vrijeme potrebno za pregled relativno malog predmeta kao što je lopatica turbine je 0,5...1,4 h, ovisno o korištenim materijalima za detekciju grešaka i zahtjevima osjetljivosti. Vrijeme provedeno u minutama raspoređuje se na sljedeći način: priprema za pregled 5...20, impregnacija 10...30, uklanjanje viška penetranta 3...5, razvoj 5...25, pregled 2...5, završno čišćenje 0...5. Obično se izlaganje tijekom impregnacije ili razvoja jednog proizvoda kombinira s kontrolom drugog proizvoda, zbog čega se prosječno vrijeme kontrole proizvoda smanjuje za 5-10 puta. U zadatku 9.2 dat je primjer izračunavanja vremena praćenja objekta s velikom površinom kontrolirane površine.
Automatsko upravljanje se koristi za provjeru malih dijelova kao što su lopatice turbine, pričvrsni elementi, kuglični i valjkasti ležajevi. Instalacije su kompleks kupki i komora za sekvencijsku obradu OK (sl. 9.11). U takvim instalacijama široko se koriste sredstva za intenziviranje kontrolnih operacija: ultrazvuk, povećanje temperature, vakuum itd. .
Riža. 9.11. Shema automatske instalacije za kontrolu dijelova kapilarnim metodama:
1 - transporter, 2 - pneumatski lift, 3 - automatska hvataljka, 4 - kontejner s dijelovima, 5 - kolica, 6 ... 14 - kupke, komore i peći za obradu dijelova, 15 - valjkasti stol, 16 - mjesto za pregled dijelovi tijekom UV zračenja, 17 - mjesto za pregled u vidljivom svjetlu
Transporter dovodi dijelove u ultrazvučnu kupku za čišćenje, zatim u kadu za ispiranje tekućom vodom. Vlaga se uklanja s površine dijelova na temperaturi od 250...300°C. Vrući dijelovi se hlade komprimiranim zrakom. Penetrantna impregnacija se provodi pod djelovanjem ultrazvuka ili u vakuumu. Uklanjanje viška penetranta provodi se uzastopno u kadi s tekućinom za čišćenje, zatim u komori s jedinicom za tuširanje. Vlaga se uklanja komprimiranim zrakom. Razvijač se nanosi prskanjem boje u zraku (u obliku magle). Pregled detalja se vrši na radnim mjestima gdje je osigurano UV zračenje i umjetna rasvjeta. Operaciju odgovorne inspekcije teško je automatizirati (vidi §9.7).
§ 9.7. Izgledi razvoja
Važan smjer u razvoju KMK-a je njegova automatizacija. Alati o kojima smo ranije govorili automatiziraju kontrolu iste vrste malih proizvoda. Automatizacija; upravljanje proizvodima raznih vrsta, uključujući i one velikih, moguće je korištenjem adaptivnih robotskih manipulatora, t.j. ima sposobnost prilagođavanja promjenjivim uvjetima. Takvi roboti uspješno se koriste u operacijama lakiranja, koje su po mnogo čemu slične CMC operacijama.
Najteže je automatizirati pregled površine proizvoda i donošenje odluke o prisutnosti nedostataka. Trenutno se za poboljšanje uvjeta za izvođenje ove operacije koriste iluminatori velike snage i UV ozračivači. Kako bi se smanjio učinak na regulator UV zračenja, koriste se svjetlosni vodiči i televizijski sustavi. Međutim, time se ne rješava problem potpune automatizacije s eliminacijom utjecaja subjektivnih kvaliteta kontrolora na rezultate kontrole.
Stvaranje automatskih sustava za ocjenjivanje rezultata upravljanja zahtijeva razvoj odgovarajućih algoritama za računala. Rad se odvija u nekoliko smjerova: određivanje konfiguracije indikacija (dužina, širina, površina) koje odgovaraju neprihvatljivim nedostacima, te korelacijsko usporedba slika kontroliranog područja objekata prije i nakon obrade materijalima za detekciju mana. Osim označenog područja, računala u KMC-u služe za prikupljanje i analizu statističkih podataka uz izdavanje preporuka za prilagodbu tehnološkog procesa, za optimalan odabir materijala za detekciju grešaka i tehnologije upravljanja.
Važno područje istraživanja je potraga za novim materijalima za detekciju nedostataka i tehnologijama za njihovu primjenu, s ciljem povećanja osjetljivosti i produktivnosti ispitivanja. Predložena je uporaba feromagnetskih tekućina kao penetranta. U njima se u tekućoj bazi (na primjer, kerozin) suspendiraju feromagnetske čestice vrlo male veličine (2 ... 10 mikrona), stabilizirane površinski aktivnim tvarima, zbog čega se tekućina ponaša kao jednofazni sustav . Prodiranje takve tekućine u nedostatke pojačano je magnetskim poljem, a detekcija indikacija je moguća magnetskim senzorima, što olakšava automatizaciju upravljanja.
Vrlo obećavajući smjer za poboljšanje kapilarne kontrole je korištenje elektronske paramagnetske rezonancije. Relativno nedavno su dobivene tvari tipa stabilnih nitroksi radikala. Sadrže slabo vezane elektrone koji mogu rezonirati u elektromagnetskom polju frekvencije od desetaka gigaherca do megaherca, a spektralne linije se određuju s visokim stupnjem točnosti. Nitroksilni radikali su stabilni, nisko toksični i mogu se otopiti u većini tekućih tvari. To omogućuje njihovo uvođenje u tekuće penetrante. Indikacija se temelji na registraciji apsorpcijskog spektra u uzbudljivom elektromagnetskom polju radio spektroskopa. Osjetljivost ovih instrumenata je vrlo visoka, omogućuju otkrivanje nakupina od 1012 paramagnetskih čestica i više. Time je riješeno pitanje objektivnih i visokoosjetljivih indikacijskih sredstava za detekciju kapilarnih nedostataka.
Zadaci
9.1. Izračunajte i usporedite maksimalnu dubinu penetrantnog punjenja kapilare u obliku proreza s paralelnim i neparalelnim stijenkama. Dubina kapilara l 0=10 mm, širina otvora b=10 µm, penetrant na bazi kerozina s σ=3×10-2N/m, cosθ=0,9. Atmosferski tlak prihvatiti R a-1,013×105 Pa. Difuzijsko punjenje se zanemaruje.
Riješenje. Dubina punjenja kapilare s paralelnim stijenkama izračunavamo pomoću formula (9.3) i (9.5):
Rješenje je dizajnirano da pokaže da je kapilarni tlak oko 5% atmosferskog i da je dubina punjenja oko 5% ukupne kapilarne dubine.
Izvedimo formulu za popunjavanje utora s neparalelnim površinama, koji u presjeku ima oblik trokuta. Iz Boyle-Mariotteovog zakona nalazimo tlak zraka komprimiranog na kraju kapilare R u:
gdje je b1 razmak između zidova na dubini od 9,2. Izračunajte potreban broj materijala za detekciju nedostataka iz seta u skladu s položajem 5 tablice. 9.2 i vrijeme za izvođenje CMC antikorozivne površine na unutarnjoj površini reaktora. Reaktor se sastoji od cilindričnog dijela promjera D=4 m, visine H=12 m s polukuglastim dnom (zavaren na cilindrični dio i čini tijelo) i poklopca, kao i četiri mlaznice promjera od d=400 mm, dužine h=500 mm. Vrijeme nanošenja bilo kojeg materijala za detekciju nedostataka na površinu uzima se τ=2 min/m2.
Riješenje. Izračunajte površinu kontroliranog objekta po elementima:
cilindrični S1=πD2N=π42×12=603,2 m2;
dio
dno i poklopac S2=S3=0,5πD2=0,5π42=25,1 m2;
mlaznice (svaka) S4=πd2h=π×0,42×0,5=0,25 m2;
ukupne površine S=S1+S2+S3+4S4=603,2+25,1+25,1+4×0,25=654,4 m2.
Uzimajući u obzir da je kontrolirana površina navlake neravna, smještena uglavnom okomito, prihvaćamo potrošnju penetranta q=0,5 l/m2.
Stoga potrebna količina penetranta:
Qp = S q\u003d 654,4 × 0,5 \u003d 327,2 litara.
Uzimajući u obzir moguće gubitke, ponovni pregled i sl., pretpostavljamo da je potrebna količina penetranta 350 litara.
Potrebna količina razvijača u obliku suspenzije je 300 g na 1 litru penetranta, dakle Qpr=0,3×350=105 kg. Sredstvo za čišćenje je potrebno 2...3 puta više od penetranta. Uzimamo prosječnu vrijednost - 2,5 puta. Dakle, Qoch \u003d 2,5 × 350 \u003d 875 litara. Tekućina (npr. aceton) za prethodno čišćenje zahtijeva približno 2 puta više od Qoch-a.
Kontrolno vrijeme se izračunava uzimajući u obzir činjenicu da se svaki element reaktora (tijelo, poklopac, grane cijevi) kontrolira zasebno. Ekspozicija, t.j. vrijeme kada je objekt u kontaktu sa svakim materijalom za detekciju nedostataka uzima se kao prosjek standarda danih u § 9.6. Najznačajnija izloženost penetrantu - u prosjeku t n=20 min. Izloženost ili vrijeme provedeno u kontaktu s drugim materijalima za detekciju nedostataka je manje nego s penetrantom i može se povećati bez ugrožavanja učinkovitosti kontrole.
Na temelju toga prihvaćamo sljedeću organizaciju procesa kontrole (nije jedina moguća). Tijelo i poklopac, gdje se kontroliraju velike površine, podijeljeni su u sekcije, za svaki od kojih je vrijeme nanošenja bilo kojeg materijala za detekciju nedostataka jednako t uh = t n = 20 min. Tada vrijeme primjene bilo kojeg materijala za otkrivanje nedostataka neće biti manje od izloženosti za njega. Isto vrijedi i za vrijeme izvođenja tehnoloških operacija koje se ne odnose na materijale za detekciju nedostataka (sušenje, pregled i sl.).
Površina takve parcele Sch = tch/τ = 20/2 = 10 m2. Vrijeme inspekcije elementa s velikom površinom jednako je broju takvih površina, zaokruženo, pomnoženo s t uch = 20 min.
Područje tijela dijelimo na (S1 + S2) / Takvi = (603,2 + 25,1) / 10 = 62,8 = 63 dijela. Vrijeme potrebno za njihovu kontrolu je 20×63 = 1260 min = 21 h.
Područje pokrivača dijelimo na S3 / Takvi = 25, l / 10 = 2,51 = 3 odjeljka. Vrijeme kontrole 3×20=60 min = 1 sat.
Upravljamo mlaznicama u isto vrijeme, tj. nakon što smo izvršili bilo koju tehnološku operaciju na jednoj, prelazimo na drugu, nakon toga također izvodimo sljedeću operaciju itd. Njihova ukupna površina 4S4=1 m2 je mnogo manja od površine jedne kontrolirane površine. Vrijeme inspekcije je uglavnom određeno zbrojem prosječnih vremena izlaganja za pojedinačne operacije, kao za mali proizvod u § 9.6, plus relativno kratko vrijeme za primjenu materijala za otkrivanje nedostataka i inspekciju. Ukupno će to biti približno jednako 1 satu.
Ukupno vrijeme kontrole je 21+1+1=23 sata Pretpostavljamo da će kontrola zahtijevati tri smjene od 8 sati.
NEKOČIVO UPRAVLJANJE. Knjiga. I. Opća pitanja. Kontrola penetracije. Gurvič, Ermolov, Sažin.
Dokument možete preuzeti