Step-by-step instructions for building a house from foam blocks
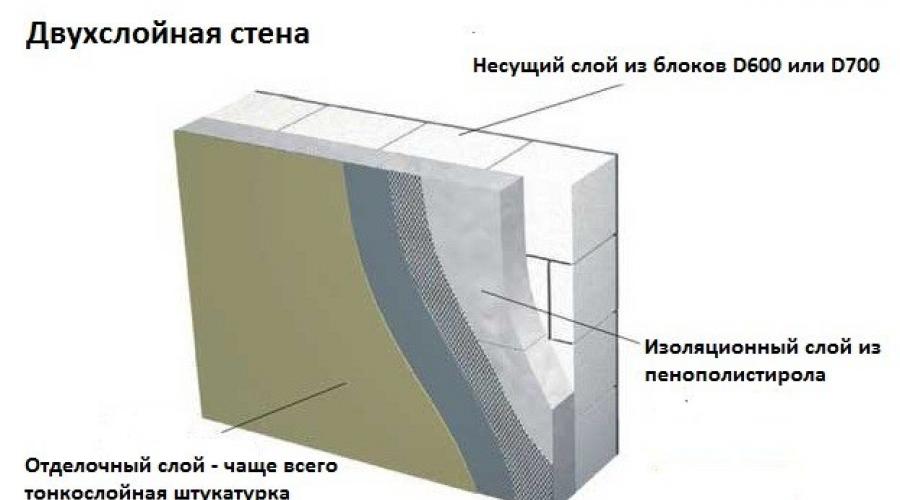
Read also
Currently, the construction of structures from foam blocks is widely used. The use of this material is due to a number of its positive properties. Such a question as the step-by-step construction of a house from foam blocks clarifies many of the nuances of the process.
Foam block technology has made it possible to create a wide range of new building materials. Some of their properties are unique. This allows the material to be used both in the construction of residential buildings and in the construction of various economic and industrial structures. The step-by-step construction of a house from foam blocks takes into account all the features of the material both during the construction of walls and during finishing work.
Material Features
In general, the foam block is a building material based on foam concrete. Foam concrete is obtained by curing an aqueous solution of cement with sand, into which a foam-forming substance (air bubbles) is introduced.
Unlike aerated concrete, air bubbles in the mass of the material are obtained due to mechanical mixing, and not as a result of chemical gas evolution. Air bubbles are evenly distributed throughout the volume of the block. Blocks of the desired size are produced by cutting a solid mass or by molding in molds.
Foam concrete has a number of undeniable advantages over other building materials.
It has high compressive strength, frost resistance, low thermal conductivity, good sound insulation properties, and very high fire resistance.
The material tolerates sudden temperature changes well. It is practically not subject to shrinkage. Its ability to "breathe" is important.
The properties of foam blocks significantly depend on the density of the material, i.e. on the content of air pores. According to the density value, it is customary to distinguish the following types of foam concrete: heat-insulating (density up to 500 kg / m³), structural and heat-insulating (500-900 kg / m³) and structural (1000-1200 kg / m³).
An increase in density leads to an increase in strength, but to a decrease in thermal insulation properties. Foam blocks are also characterized by high manufacturability, which is expressed in the ease of processing and fixing fasteners in them.
During construction, one should take into account the differences in the properties of different brands of foam blocks, as well as choose the optimal block sizes.
So, it is recommended to use foam blocks of grades from D600 to D1000 with a size of 20x30x60 cm for load-bearing walls, and from D100 to D400 up to 10x30x60 cm in size for internal partitions. Foam blocks can be cut with a hacksaw, nails are driven into them and screws are screwed in.
Back to index
Features of building a house from foam blocks
A number of advantages and creates some specific features of building a house from foam blocks. The first feature is associated with an alternative choice of foam block brand. You have to choose between increased heat resistance and strength. In temperate climates, the issue is resolved in the direction of increased strength, which allows the use of a single-layer wall of high-density blocks. In cold areas, a two-layer design should be used, where the inner layer is made of a more porous material and serves as a heater.
In general, the walls of a house made of foam blocks have a smaller mass than walls made of other materials. Consequently, the load on the foundation is reduced, it can be done in a lightweight version.
The disadvantages of porous concrete include low resistance to vertical loads. This property makes it necessary to install reinforcing belts or jumpers in the area of such loads.
Building a house from foam blocks is carried out quickly due to the fact that the blocks are much larger than the size of a brick. However, this requires special care and precision when laying the first 2-3 layers of blocks. It is they who ensure the quality of further construction. The laying itself can be done using special glue, which reduces the gaps between the blocks.
The properties of foam blocks deteriorate significantly when moisture penetrates into the air pores. To avoid deterioration of heat resistance, it is necessary to apply external waterproofing. Unprotected foam concrete on the facade can darken under the influence of external factors, which requires the application of plaster with the addition of special compositions for foam blocks. Good breathability in cold winds can noticeably cool the house. To eliminate this effect, it is necessary to use external insulation (mineral wool, expanded polystyrene, etc.). This property limits the use if you need to build a bath.
Back to index
Detailed step by step instructions
Back to index
Preparation for construction
Tools and equipment needed to build a house from foam blocks:
- welding machine;
- Bulgarian;
- electric drill;
- sawmill;
- concrete mixer;
- hammer (sledgehammer);
- screwdriver;
- hacksaw;
- vise;
- Sander;
- chisel;
- bit;
- chisel;
- file;
- pliers;
- ticks;
- shovel;
- roulette;
- plumb;
- level;
- putty knife;
- scissors;
- roulette;
- ruler meter;
- mallet;
- Master OK.
Any construction should begin with the development of a house project and the approval of all necessary documents for the construction. During the construction of a residential building, a project for water supply, sewerage and heating systems must be developed and agreed with the relevant organizations. If necessary, a plan for electricity and gas supply is developed. For yourself, you need to draw up a plan that includes the phased construction of a house, as well as an estimate of costs.
Step number 1 - obtaining the necessary permits for the development of the site. Such a major event as the construction of a house cannot be started without resolving the issue of providing the construction site with water. It is necessary to have a place to store materials and tools. In the absence of a water source, it is possible to drill a well.
Step number 2 - solving the issue of water supply and storage. An important preparatory stage for the construction of a house is the purchase of building materials for the first stages of construction - the construction of a foundation and the beginning of laying a wall of foam blocks. It is not advisable to purchase all building materials, a phased purchase is better.
Step number 3 - the purchase of the first batch of building materials.
Back to index
Digging a foundation pit
The construction of the house itself begins with marking and digging a foundation pit. Thus, step number 4 is digging a pit.
The most common type of foundation for a private house, including a house made of foam blocks, is a strip foundation. Under it, the marking of the pit is made.
For a standard foam block house, a foundation pit is dug 80-170 cm deep, depending on the depth of soil freezing in winter. The dimensions of the pit correspond to the dimensions of the house with a margin of 60-100 cm on each side.
The pit is dug manually or with the involvement of an excavator, if possible. The fertile soil extracted from the pit should not be taken far away: it can be useful in the future when arranging the site, garden.
Back to index
Building the foundation of a house
The phased construction of a foam concrete house includes step number 5 - the construction of the foundation. The foundation is the basis of any house, which determines the stability and strength of the structure. First, at the bottom of the pit, a pillow is created for the foundation by filling in sand and crushed stone up to 30 cm thick. The pillow is well compacted.
Then the reinforcing frame of the foundation (reinforcement) is assembled. For the manufacture of the frame, steel reinforcement with a diameter of up to 15 mm is used. Vertical rods are installed every 1-1.5 m to the height of the foundation, which are connected by horizontal rods. The connection is made by welding.
Next, a formwork for pouring concrete is installed. It is made of boards or plywood, interconnected in the form of a shield. The distance between the sides of the formwork depends on the thickness of the wall and is usually 30-50 cm, the height is at least 70 cm. The panels are installed so that the reinforcement is inside the foundation pour, and are placed parallel to each other. From above, the side panels of the formwork are connected by wooden lintels.
The foundation is poured with concrete based on M500 cement (one part of cement, three parts of sand, fine gravel). The solution should have a thick consistency. First, a small layer of cement mortar with sand, without crushed stone, is laid on top of the sand cushion. The formwork is then filled with concrete. During the pouring process, it is necessary to compact the concrete with a shovel. Within 7-10 days the foundation dries. After that, the formwork is dismantled. During the drying of the foundation, care should be taken to purchase building material for the construction of walls.
Back to index
Features of masonry walls
Step number 6 is very important when building a house - laying walls from foam blocks. This step includes several stages. First of all, the foundation surface is leveled with a layer of cement mortar, and the horizontalness should be checked with a level. A waterproofing layer is laid on top, which is 1-2 layers of roofing material. The sheets are overlapped with an overlap of at least 10 cm.
The next stage is the laying of the first row of foam blocks. is made on a special glue, which is applied with a notched trowel. The laying of the first rows begins with the laying of corner blocks. The corners of the house are formed to a height of 4-5 blocks. Linking blocks in the corner is as follows. The first row of the facade wall begins with laying the block along the foundation, and the second row - from the end of the block of the perpendicular wall. Layering alternates.
Thus, the displacement of blocks relative to each other in adjacent rows is ensured. A twine is stretched between the first corner blocks, and the entire first row is laid out along it. When laying, glue is applied to the surface of the masonry and the bottom of the block. The horizontality of the row is checked by a level, and if necessary, a mallet is used. All irregularities in the blocks should be eliminated immediately.
To strengthen the walls of foam blocks, it is necessary to carry out reinforcement during the masonry process.
After laying the first row, two parallel channels (strobes) about 40x40 mm in size are cut out on its surface in the middle of the block. Reinforcing rods with a diameter of 8 mm are laid in the channel around the entire perimeter of the house. This operation is repeated every 4-5 layers of masonry.
The laying of the walls is carried out taking into account the door and window openings. If necessary, reduce the length of the block, use a grinder or a regular hacksaw. A reinforcing element must be laid above the window and door openings. It is usually made from a steel corner of at least 80x80 mm. The length of the corner must exceed the width of the opening by at least 60 cm. Instead of the corner, you can use a reinforced concrete floor.