Tipos de tratamento térmico de metais. Tratamento térmico de ligas. Tipos de tratamento térmico
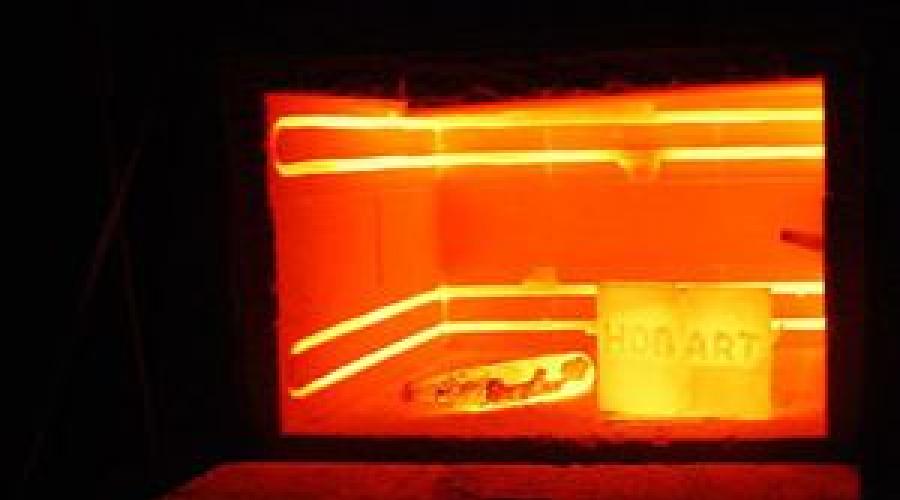
Leia também
Tratamento térmico de metais
Mas pelo exploração adicional peças e componentes de equipamentos geralmente exigem características completamente diferentes - resistência, dureza, rigidez, etc. É para estes fins que se destina o tratamento térmico de metais.
A essência dos processos de tratamento térmico
tarefas várias tecnologias tratamento térmico é:
- Garantir a microestrutura mais favorável dos aços e ligas;
- Obtenção do nível de dureza desejado: seja em uma zona de superfície fina (ou subsuperfície), ou em toda a corte transversal espaços em branco;
- Correção composição química em grãos de macroestruturas várias ligas.
No primeiro caso, é necessário garantir o máximo grau de homogeneidade das propriedades dos metais, o que é importante, por exemplo, para o processamento mecânico subsequente ou, especialmente, de deformação. Como resultado, as condições para a mudança de forma da peça em todos os três eixos de coordenadas são os mesmos, e o casamento da parte final é excluído.
Além disso, o alinhamento da micro e macroestrutura para os processos de conformação de metais é necessário para aumentar o grau de deformação dos produtos semiacabados, aproximando a forma da peça da forma do produto acabado. Além disso, para o menor número de transições, e usando o mínimo esforço de equipamento necessário para isso.
A mudança na dureza (como resultado do tratamento térmico) visa melhorar o desempenho das peças. Como as condições de operação podem ser muito diferentes, o complexo de condições físicas e propriedades mecânicasé selecionado estritamente individualmente: não existem processos universais de tratamento térmico para ligas com diferentes composições.
Uma mudança na composição química dos grãos da microestrutura, devido à formação de novos compostos, na maioria dos casos não só eleva os indicadores de dureza, mas também aumenta a resistência ao desgaste de peças que devem ser operadas com maior atrito, temperatura ou aumentada contra cargas específicas normais.
endurecimento-revenimento
O primeiro grupo de tecnologias de tratamento térmico para várias ligas, incluindo aço, inclui recozimento e revenimento. No segundo - endurecimento, normalização, melhora, envelhecimento, tratamento a frio. No terceiro - todos os tipos de processamento termoquímico.
anelamento
A essência dos processos que ocorrem na estrutura da maioria das ligas submetidas ao recozimento é fornecer a estrutura mais equilibrada da peça, na qual não há tensões internas ou seu nível é suficientemente baixo e, portanto, não afeta a usinabilidade subsequente de metais/ligas.
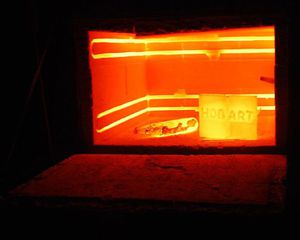
A estrutura inicial de quase todas as ligas e aços é de grãos bastante grandes, entre os quais existem inclusões e impurezas, principalmente enxofre e fósforo. Isso aumenta a fragilidade do metal, o que pode ser importante na formação de produtos de configuração complexa a partir de um lingote (ou fio-máquina). Portanto, é necessário reduzir o tamanho do grão e dar-lhe a forma ideal de um elipsóide, no qual as propriedades mecânicas serão aproximadamente as mesmas ao longo dos três eixos coordenados.
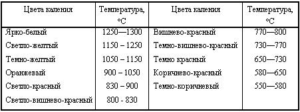
Para isso, a peça inicial deve ser aquecida a uma temperatura de 50 ... 70 0 C acima da temperatura do início da transformação da austenita. Seu resultado é a formação de grãos de austenita pequenos e bem orientados entre os grãos dos principais componentes estruturais do aço - ferrita e cementita. A austenita é formada a partir da perlita, estrutura que possui os grãos maiores, o que contribui para o aumento da fragilidade de qualquer lingote. A transformação austenítica para a maioria das ligas ocorre muito lentamente, então o recozimento é um procedimento demorado que deve durar pelo menos uma hora.
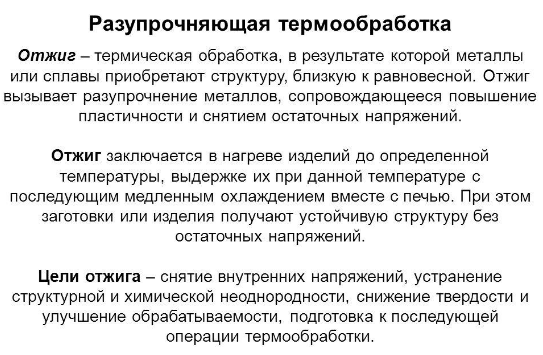
Segundo tarefa importante recozimento - remover as tensões internas que são formadas na peça de trabalho durante seu processamento por pressão no estado frio. O fato é que qualquer deformação é acompanhada pelo esmagamento dos grãos da estrutura original dos aços e ligas. Como resultado, há mais grãos, a resistência à deformação aumenta, o que não apenas requer uma força de deformação aumentada, mas também causa a destruição do produto semi-acabado, cujo grau de deformação excedeu o indicador crítico para este metal.
Assim, para a implementação da primeira tarefa, é utilizada a tecnologia de recozimento de alta temperatura (para aços, dependendo do teor de carbono, varia de 550 ... 750 0 С) e no segundo - recozimento de baixa temperatura (180 ... 220 0 C).
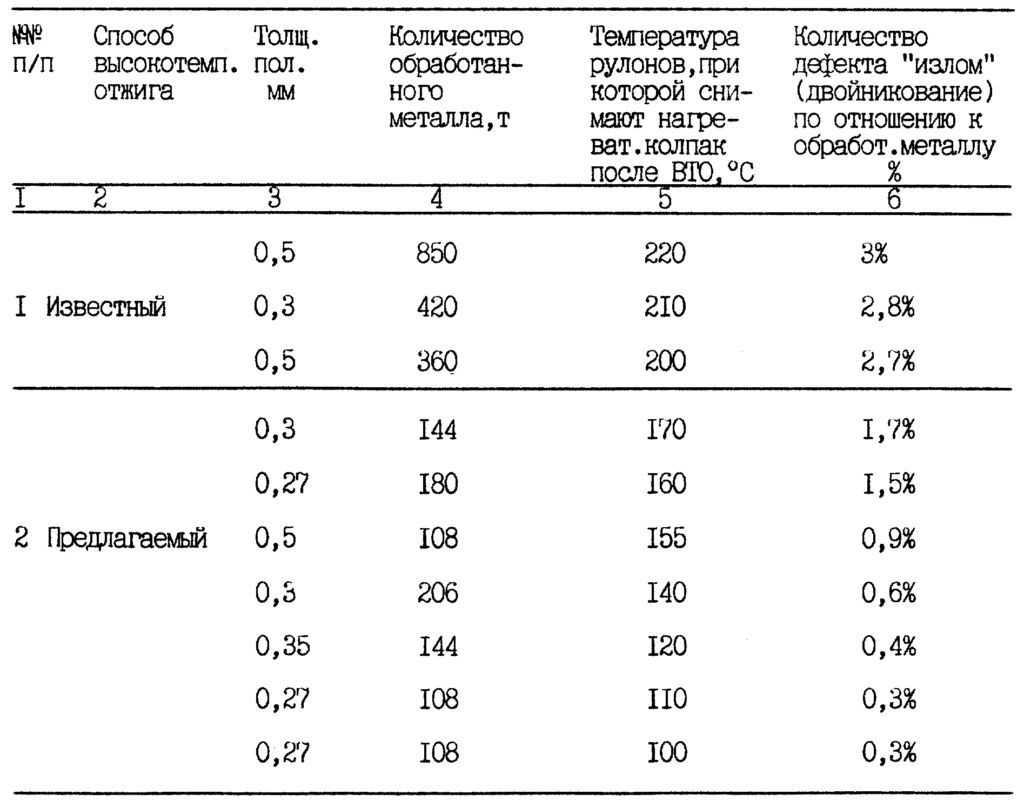
O aquecimento ocorre lentamente, seguido de manutenção do produto a uma determinada temperatura, seguido de resfriamento lento. Para aços-liga e ligas, esse resfriamento é realizado a uma taxa particularmente baixa, no próprio forno, onde ocorreu o recozimento.
Período de férias
O revenimento de acordo com a tecnologia se assemelha ao recozimento, mas é realizado não com uma peça de trabalho, mas com um produto acabado e, portanto, persegue outras tarefas - para aliviar tensões internas após o tratamento térmico, realizado para aumentar a dureza da peça.
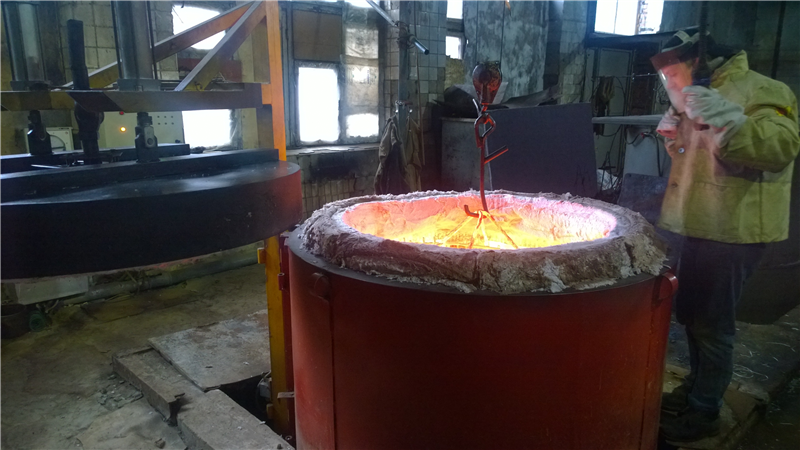
Processo próprio licença de tratamento térmico não é. Ao contrário do recozimento, o revenimento às vezes é realizado em várias etapas: na maioria dos casos, isso se aplica a produtos para a produção dos quais foram usados tipos diferentes aço de alta liga.
endurecimento
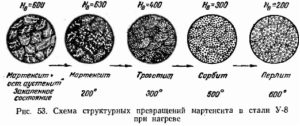
O endurecimento consiste no aquecimento rápido da peça até a temperatura do final da transformação austenítica (900 ... 1100 0 C - para aços de baixo carbono, 750 ... 850 0 C - para aços de alto carbono) e posterior resfriamento rápido em meios de têmpera especiais. Neste último, utiliza-se água (para produtos de baixa responsabilidade) ou óleo.
Os modos de endurecimento são os mais diversos. O principal fator que determina a eficácia do endurecimento é a intensidade da formação de martensita na estrutura - um componente de alta temperatura que confere ao metal ou liga maior dureza.
As condições para a formação de martensita são determinadas pelas seguintes circunstâncias:
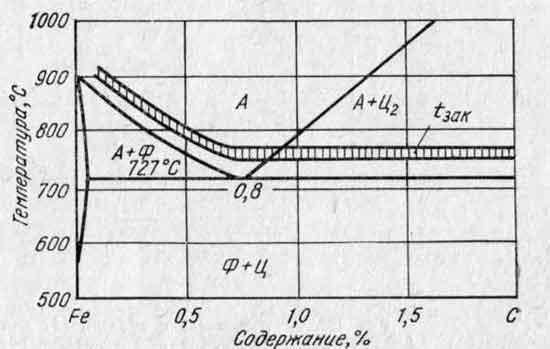
Assim, para cada grau de aço ou liga, foram desenvolvidos modos de endurecimento individuais, que diferem:
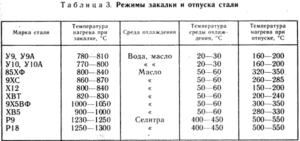
O endurecimento de aços e ligas com composição complexa, incluindo vários elementos de liga (em particular, cobalto, molibdênio), é realizado com cuidado especial. Esses metais no processo formam compostos intermetálicos ao longo dos contornos de grão da estrutura principal, o que aumenta significativamente a dureza e a resistência dos aços (em particular, aços ferramenta). A forma e a concentração dos compostos intermetálicos dependem apenas da precisão da tecnologia de endurecimento.
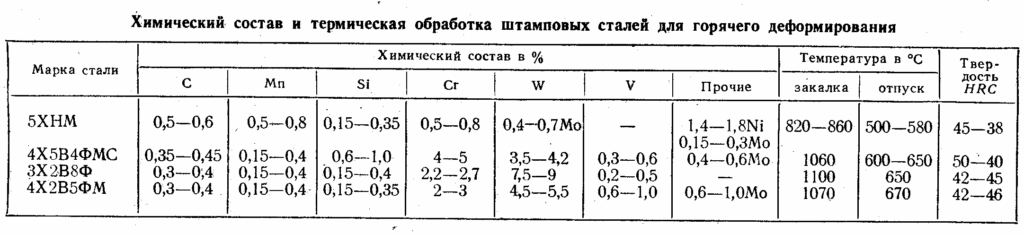
Os tipos de endurecimento são determinados pelo equipamento em que é realizado. Por exemplo, para produtos como engrenagens, eixos, guias de coluna, quando necessário combinação ideal alta dureza de superfície e núcleo relativamente resistente, o endurecimento da superfície por correntes de alta frequência é usado.
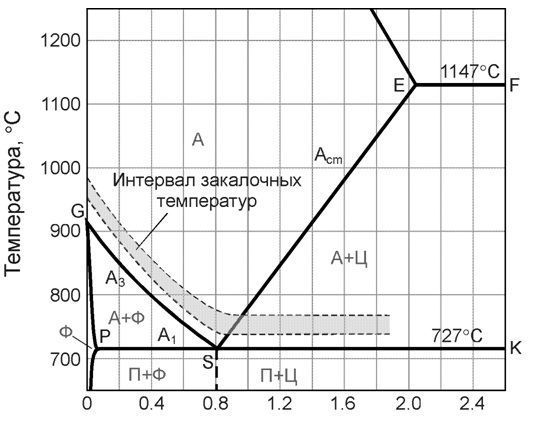
Para isso, o produto é colocado em uma bobina de indução, através da qual passa uma corrente de alta frequência (até 15.000 ... 25.000 Hz). Penetrando a uma profundidade limitada, esta corrente contribui para um aumento na resistência superficial de aços ou ligas. Como resultado, a resistência à fadiga de peças que operam sob tensões de tração e compressão que variam ciclicamente aumenta acentuadamente.
Uma mudança mais intensa na dureza da superfície da peça pode ser obtida usando fontes de calor de alta energia para endurecimento - uma faísca ou descarga de arco. As descargas devem ser excitadas em meio líquido, onde a peça de trabalho ou peça é colocada.
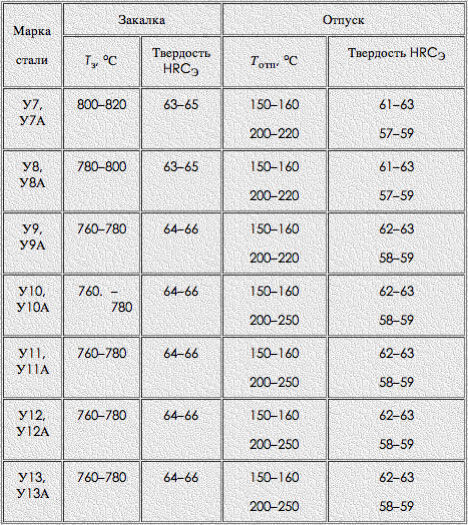
Após a têmpera, na grande maioria dos casos, o revenimento é necessário, caso contrário, a dureza final excessiva da peça torna-se a causa do aumento da fragilidade sob cargas de choque.
Melhoria e normalização
Como tipos de tratamento térmico, esses processos são semelhantes ao recozimento, embora se destinem a outros fins - aumentar a durabilidade operacional de peças e ferramentas críticas de máquinas.
Durante a normalização, a peça é submetida a um aquecimento lento, mantido a uma determinada temperatura, após o que é necessariamente resfriada junto com o forno. Como resultado, a estrutura da peça fica mais equilibrada e o nível tensões internas vai para baixo.
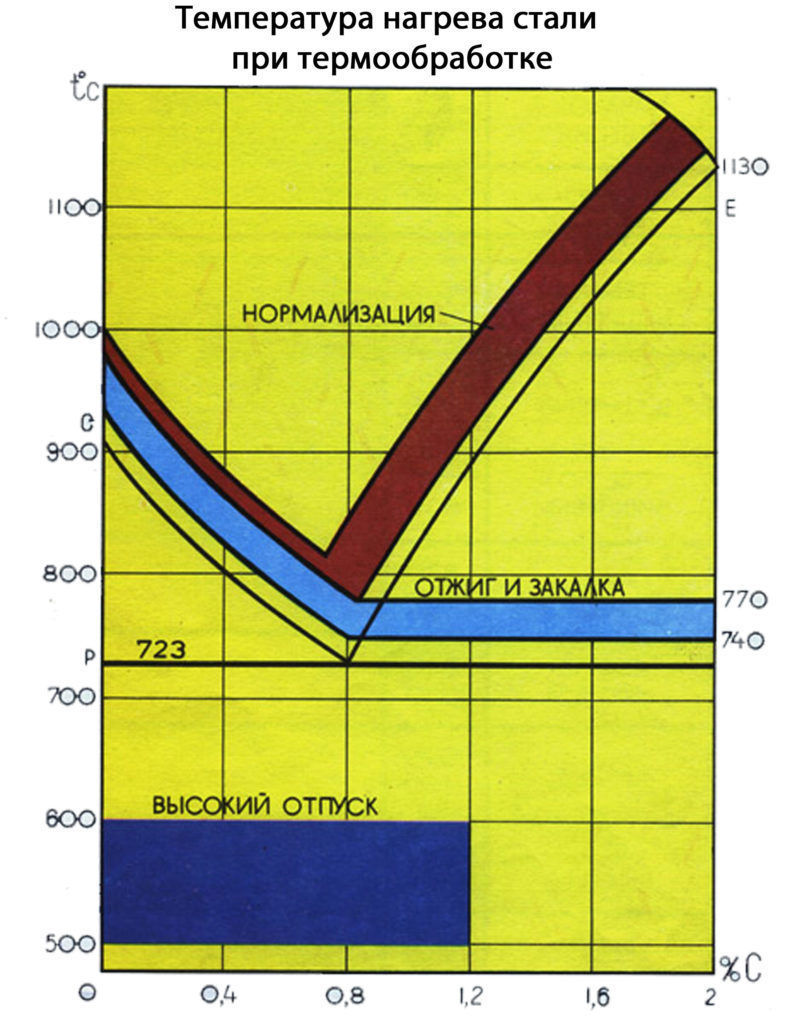
Uma diferença significativa é a composição da atmosfera, o forno em que essas operações de tratamento térmico são realizadas. Deve ser não oxidante, pois a intensa formação de óxidos na superfície do produto não só piora sua apresentação, como também altera suas dimensões. A queima de carbono, que também acompanha o tratamento térmico em um forno convencional, piora a composição química do aço e reduz sua resistência.
A redução do acesso de oxigênio à superfície da peça durante a normalização é realizada de várias maneiras:
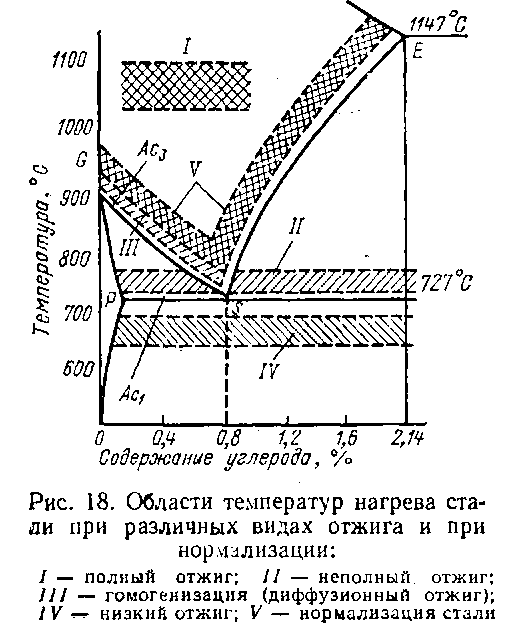
- Aquecimento com falta planejada de oxigênio. Neste caso, a estabilidade queimadores a gás os fornos de tratamento térmico são compensados aumentando a taxa de fornecimento de ar à zona de combustão;
- Tratamento térmico em ambiente de gás protetor. Para peças críticas, são utilizados vapor de lítio, argônio ou outros gases nobres, em outros casos - dióxido de carbono;
- Aplicando revestimentos protetores na superfície do produto a ser normalizado.
Após a normalização, a peça é resfriada ao ar parado, evitando que sopre: isso pode causar uma microestrutura não homogênea e “manchada” do produto.
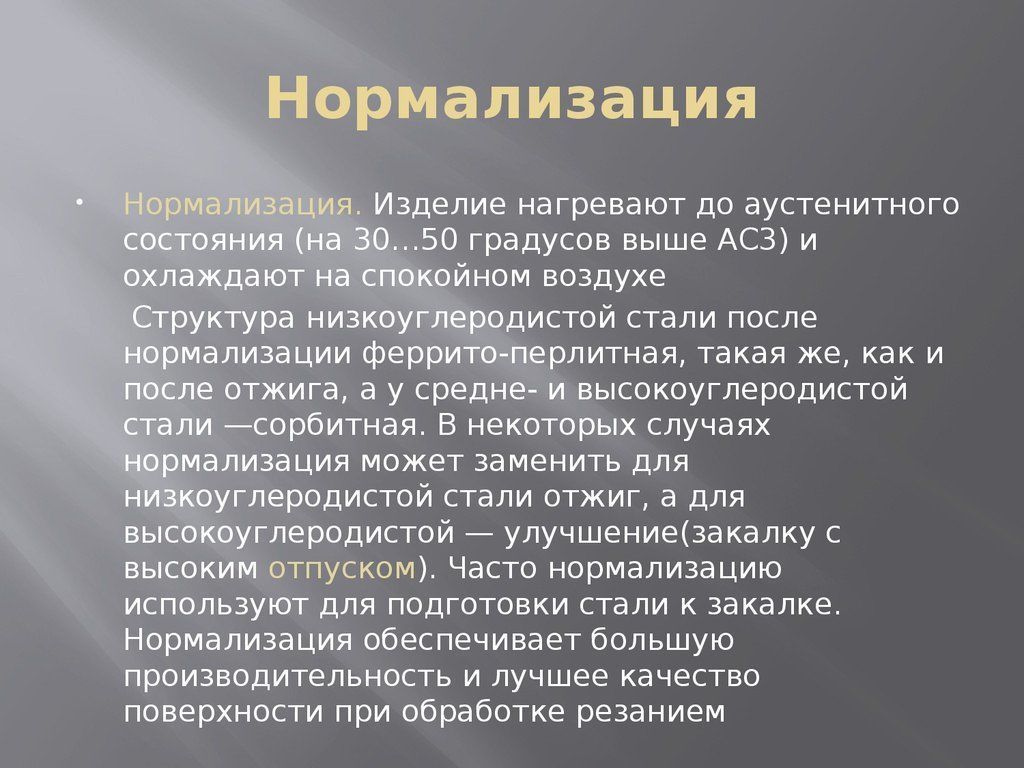
A melhoria é uma operação de tratamento térmico, como resultado do aumento da usinabilidade de aços e ligas e redução do nível de tensões residuais neles. Isto é acompanhado por alguma diminuição na dureza.
O componente martensítico na estrutura da maioria dos aços e ligas pode aparecer não apenas em aumento, mas também em temperatura baixa. A tecnologia de tratamento a frio compara-se favoravelmente com tecnologias tradicionais tratamento térmico da seguinte forma:
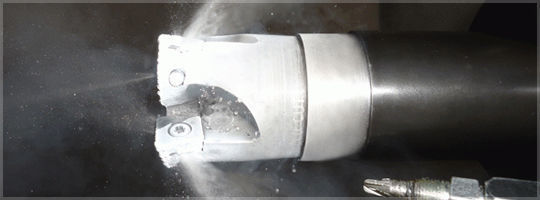
Os modos de tratamento criogênico dependem do grau de aços/ligas e flutuam na faixa de -60…-140 0 С. Baixas temperaturas. Com uma combinação de ciclos de aquecimento e resfriamento, a decomposição completa da austenita residual é alcançada em 4 ... 7 horas (valores mais altos para aços de alta liga).
Um tipo especial de tratamento térmico são os processos de tratamento químico-térmico. Sua tarefa é formar carbonetos e nitretos na microestrutura da superfície - compostos que aumentam significativamente a microdureza das peças e criam tensões de compressão residuais nelas. Tais produtos apresentam uma resistência particularmente alta a cargas alternadas.
Vídeo: Como endurecer qualquer tipo de aço
Processamento de metal termicamenteé uma mudança estrutura interna(estrutura) de metal sob a influência da mudança condições de temperatura e obtendo, como resultado, as necessárias mecânicas e propriedades físicas metal. Uma grande parte do tratamento térmico ocorre em temperaturas críticas nas quais a transformação estrutural ocorre em ligas.
Portanto, o tratamento térmico do metal é reduzido por três operações consecutivas e tipos:
- aquecer o metal a uma determinada taxa a uma determinada temperatura;
- exposição do metal por algum tempo a essa temperatura;
- resfriamento na taxa especificada pelo processo.
Depende de como alterar as propriedades de um determinado produto de aço e vários tipos de tratamento térmico são usados, que diferem na temperatura máxima de aquecimento, tempo de retenção e taxa de resfriamento. Na engenharia mecânica, o tratamento térmico encontrou a aplicação mais ampla.
Tratamento térmico de metal, liga, aço
Todas as propriedades de qualquer liga dependem de sua estrutura. A principal maneira que permite alterar essa estrutura é o tratamento térmico. Seus fundamentos foram desenvolvidos por D.K. Chernov, e mais tarde seu trabalho foi apoiado por A.A. Bochvar, G.V. Kurdyumov, A.P.
O tratamento térmico de metal e liga é uma sequência de operações como: aquecimento, retenção e resfriamento, que são realizados em uma determinada sequência e sob um determinado modo, a fim de alterar a estrutura interna da liga e obter as propriedades desejadas, enquanto a composição química do metal não muda.
Qual é o tratamento térmico de metal e liga?
- em recozimento
- endurecimento
- Período de férias
- Normalização
anelamento. Este é o aquecimento do metal a uma alta temperatura e, em seguida, ocorre um resfriamento lento. O recozimento acontece tipo diferente- tudo depende regime de temperatura taxa de aquecimento e resfriamento.
endurecimento. Tratamento térmico de aço, ligas, metal, que se baseia na recristalização do aço quando aquecido acima temperatura critica. Após manter o aço nesta temperatura, segue-se um resfriamento muito rápido. Tal aço possui uma estrutura fora de equilíbrio e, portanto, após o endurecimento, segue-se o revenimento.
Período de férias. É realizado após o endurecimento para reduzir ou remover tensões residuais em aços e ligas, aumentar a tenacidade, reduzir a dureza e a fragilidade do metal.
Normalização. É semelhante ao recozimento, a única diferença é que a normalização do metal ocorre no ar e o recozimento ocorre em um forno.
Aquecimento da peça
Esta operação é muito responsável. Dela conduta adequada depende, em primeiro lugar, da qualidade do produto e, em segundo lugar, da produtividade do trabalho. É necessário saber que quando aquecido, o metal altera a estrutura, propriedades e todas as características da camada superficial. Uma vez que quando o aço ou liga interage com o ar, o ferro é oxidado e a incrustação é formada na superfície. A espessura da escala depende da composição química do metal, da temperatura e do tempo de seu aquecimento.
O aço começa a oxidar rapidamente quando aquecido acima de 900 graus, então a oxidabilidade dobra - quando aquecido a 1000 graus C e a uma temperatura de 1200 graus C - 5 vezes.
Qual é a oxidação de diferentes aços?
Aço cromo-níquel- é chamado de resistente ao calor porque praticamente não é suscetível à oxidação.
Liga de aço- forma um denso, mas camada fina escama, que protege contra oxidação adicional e evita rachaduras durante o forjamento.
Aço carbono- perde cerca de 2–4 mm de carbono da superfície quando aquecido. Isso é muito ruim para o metal, pois perde sua resistência, dureza e o aço se deteriora no endurecimento. E especialmente muito prejudicial é a descarbonetação para forjamento de peças pequenas, seguida de endurecimento. Para evitar rachaduras em aços de alta liga e alto carbono, eles devem ser aquecidos lentamente.
Certifique-se de consultar o diagrama "ferro-carbono", onde a temperatura para o início e o fim do forjamento é determinada. Isso deve ser feito para que o metal, quando aquecido, não adquira uma estrutura de granulação grossa e sua plasticidade não diminua.
Mas o superaquecimento da peça de trabalho pode ser corrigido por tratamento térmico, mas isso requer energia e tempo adicionais. Se o metal for aquecido a temperatura mais alta, isso levará à queima excessiva, que chegará ao ponto em que a ligação entre os grãos será quebrada no metal e entrará em colapso completamente durante o forjamento.
Esgotamento
Isso é o casamento mais incorrigível. Ao aquecer um metal ou liga, é imperativo monitorar a temperatura, o tempo e o final do aquecimento. A escória cresce se o tempo de aquecimento for prolongado e rachaduras podem aparecer com aquecimento rápido ou intenso.
O superaquecimento da liga ocorre devido à difusão de oxigênio nos contornos de grão, onde são imediatamente formados óxidos, que separam os grãos em alta temperatura da liga e, ao mesmo tempo, a resistência imediatamente cai drasticamente. E a plasticidade neste momento chega a zero. Este casamento é imediatamente enviado para derreter.
Qual é o tratamento térmico de metais e ligas
Tratamento térmico subdividido em:
- térmico;
- termomecânico;
- quimiotérmico
NO térmico o processamento inclui os principais tipos - recozimento do 1º tipo, recozimento do 2º tipo, endurecimento e revenimento. A normalização não é aplicada a todos os tipos de aço, tudo depende do seu grau de liga.
Todos os tipos de tratamento térmico têm diferentes temperaturas de aquecimento, a duração da retenção a esta temperatura e a taxa de resfriamento após o término da retenção.
O primeiro tipo de recozimento é o recozimento por difusão, recozimento de alívio de tensão.
O segundo tipo de recozimento é subdividido em recozimento incompleto, completo, isotérmico, esferoidização e normalização.
O endurecimento é usado para garantir que os produtos sejam duro, forte e resistente ao desgaste.
Tratamento térmico químico
Este é um tratamento térmico do aço, que é acoplado à saturação da superfície do produto - carbono, nitrogênio, alumínio, silício, cromo etc., que formam soluções sólidas substitutivas com ferro. Eles são mais longos e mais intensivos em energia do que o aço saturado com ferro e carbono, que forma soluções sólidas intersticiais com ferro.
O tratamento químico-térmico, ao criar tensões compressivas residuais favoráveis na superfície dos produtos, aumenta a durabilidade e a confiabilidade do produto. Ela também levanta resistência à corrosão, dureza.
Tal processamento visa alterar a composição do aço em uma determinada camada. Esses métodos incluem:
- cimentação - com este método camada superior o aço é enriquecido com carbono. Neste caso, são obtidos produtos com propriedades combinadas - um núcleo mole e um núcleo duro. camada superficial;
- nitretação - e enriquecimento da camada superficial com nitrogênio para aumentar a resistência à corrosão e a resistência à fadiga do produto;
- bordear -é saturação camadas superficiais aço com boro, com esse método, a resistência ao desgaste do produto aumenta, principalmente durante o atrito e o deslizamento a seco. Além disso, quando a perfuração, a gripagem a frio ou a soldagem de peças são excluídas. Os detalhes após a perfuração são muito resistentes a ácidos e álcalis;
- aluminizante - esta é a saturação do aço com alumínio. Isso é feito para dar resistência ao aço a gases agressivos - anidrido sulfúrico, sulfeto de hidrogênio;
- cromagem - saturação da camada superficial de aço com cromo. A cromagem de aços macios quase não tem efeito sobre suas características de resistência. A cromagem de aço com maior teor de cromo é chamada de cromagem dura, pois o carboneto de cromo é formado na superfície das peças, que possui:
- alta dureza
- resistência de escala
- resistência à corrosão
- maior resistência ao desgaste
Trata-se de um tratamento térmico de endurecimento de metais e ligas a temperaturas criogênicas muito baixas - abaixo de -153 graus C. Anteriormente, esse tratamento térmico era chamado de "tratamento a frio" ou "tratamento térmico de metal a uma temperatura abaixo de zero". Mas esses nomes não refletiam toda a essência do processamento criogênico.
Sua essência é a seguinte: as peças são colocadas em um processador criogênico, onde são resfriadas lentamente e, em seguida, as peças são mantidas a uma temperatura de -196 graus C por um determinado tempo. Em seguida, eles retornam gradualmente à temperatura ambiente. Quando este processo ocorre, ocorrem mudanças estruturais no metal. Devido a isso, a resistência ao desgaste, a resistência cíclica, a resistência à corrosão e à erosão são aumentadas.
As principais propriedades obtidas durante o processamento, como o resfriamento a frio, são mantidas por toda a vida útil da peça e, portanto, não requerem retratamento.
Certamente, tecnologia criogênica não substituirá os métodos de endurecimento térmico, mas quando processado a frio, dará ao material novas propriedades.
As ferramentas tratadas com temperatura ultrabaixa permitem que as empresas reduzam custos porque:
- aumenta a resistência ao desgaste de ferramentas, peças e mecanismos;
- o número de casamentos diminui;
- o custo de reparo e substituição de equipamentos e ferramentas tecnológicas é reduzido.
Foram os cientistas soviéticos que tornaram possível avaliar completamente o efeito do tratamento a frio em metais e ligas e lançaram as bases para o uso desse método.
NO Tempo dado o método de processamento criogênico de produtos é amplamente utilizado em todas as indústrias.
Engenharia mecânica e metalurgia:
- aumenta o recurso de equipamentos e ferramentas em até 300%;
- aumenta a resistência ao desgaste do material;
- aumenta a força cíclica;
- aumenta a resistência à corrosão e à erosão;
- alivia o estresse residual.
Equipamentos especiais e transporte:
- aumenta o recurso de discos de freio em 250%;
- melhora a eficiência do sistema de freio;
- aumenta a resistência cíclica das molas de suspensão e outros elementos elásticos em 125%;
- aumenta o recurso e a potência do motor;
- reduz os custos operacionais do veículo.
Indústria de defesa:
- aumenta a capacidade de sobrevivência do barril em até 200%;
- reduz o efeito do aquecimento do barril nos resultados de disparo;
- aumenta o recurso de nós e mecanismos.
Indústria de mineração e manufatura:
- aumenta a durabilidade da ferramenta de corte de rocha em até 200%;
- reduz o desgaste abrasivo de componentes e mecanismos;
- aumenta a resistência à corrosão e erosão dos equipamentos;
- aumenta o recurso de equipamentos industriais e de mineração.
Equipamentos de áudio e instrumentos musicais:
- reduz a distorção do sinal nos condutores;
- melhora a atividade musical, clareza e transparência do som;
- expande a gama de sons dos instrumentos musicais.
O processamento criogênico é usado em quase todas as indústrias onde é necessário aumentar o recurso, aumentar a resistência e a resistência ao desgaste, além de aumentar a produtividade.
Confiabilidade e durabilidade estruturas metálicas, equipamentos, tubulações depende da qualidade das unidades de fabricação, peças, elementos dos quais consistem. Durante a operação, estão sujeitos a cargas estáticas, dinâmicas e cíclicas e à influência de ambientes agressivos. Eles têm que trabalhar em baixa e temperaturas altas e é em condições de desgaste rápido.
E, portanto, o funcionamento de qualquer produto metálico depende diretamente da resistência ao desgaste, resistência, resistência térmica e à corrosão dos elementos que os compõem.
Para melhorar todas essas características, é necessário escolher o material certo para as peças, melhorar seu design, eliminar imprecisões de montagem e melhorar os métodos de trabalho a quente e a frio.
Tais requisitos elevados raramente são atendidos por materiais na condição de entrega. A parte principal do entregue elementos estruturais precisa de estabilização propriedades operacionais para que não mudem com o tempo. E para melhorar a mecânica e características físico-químicas materiais metálicos, aplicar tratamento térmico. Esta é uma sequência de operações de aquecimento, retenção e resfriamento de metais e ligas.
É realizado para alterar a estrutura e as propriedades dos metais e ligas na direção que foi definida. O tratamento térmico é usado para alterar a estrutura da composição da fase e a redistribuição dos componentes, o tamanho e a forma dos grãos cristalinos, os tipos de defeitos, seu número e distribuição. E tudo isso torna bastante fácil obter a propriedade necessária do material.
Deve-se lembrar que as propriedades do metal e das ligas dependem não apenas da estrutura, mas também da composição química formada durante o processo metalúrgico e de fundição.
A tarefa do tratamento térmico é a eliminação do estresse interno no metal e na liga, a melhoria das propriedades mecânicas e operacionais e muito mais.
submetido a tratamento térmico aço, ferro fundido, ligas não ferrosas.
Você precisa saber que materiais com a mesma composição química durante modos diferentes tratamento térmico, você pode obter várias estruturas completamente diferentes que terão propriedades completamente diferentes. Ao melhorar as propriedades mecânicas por meio de tratamento térmico, ligas com maior composição simples. As tensões admissíveis, reduzindo a massa de peças e mecanismos, aumentando sua confiabilidade e durabilidade, também podem ser alcançadas usando tratamento térmico.
Tópico 1.2 Tratamento térmico e químico-térmico de metais e ligas
O tratamento térmico é um processo cuja essência é o aquecimento e resfriamento de produtos de acordo com certos modos, como resultado do qual há uma mudança na estrutura, composição de fases, propriedades mecânicas e físicas. Vários tipos de tratamento químico-térmico também são usados, cuja essência é ligar a camada superficial dos produtos com nitrogênio, carbono ou alguns metais (alumínio, cromo, berílio) com tratamento térmico subsequente.
Dependendo da finalidade do tratamento térmico, existem vários tipos, diferindo na temperatura de aquecimento, tempo de retenção e taxa de resfriamento.
Os principais tipos de tratamento térmico do aço são recozimento, normalização, têmpera e revenimento.
anelamento aplicado para reduzir a dureza, refinamento de grãos, melhorar a usinabilidade, alívio de tensões. Para o recozimento, o aço é aquecido a uma certa temperatura, mantido e resfriado em baixa velocidade em um forno com a fonte de calor desligada.
Normalização - representa o aquecimento do aço a uma temperatura acima do ponto crítico, mantendo-se nessa temperatura, resfriando em ar parado a uma taxa maior do que durante o recozimento. Objetivo - dar ao aço uma estrutura de grão fino. A normalização dá um aumento mais perceptível na força, mas menos ductilidade. A vantagem sobre o recozimento é o menor custo.
Endurecimento - Consiste em aquecer o aço, mantê-lo a uma determinada temperatura por um determinado tempo e depois resfriá-lo abruptamente. O objetivo é aumentar a dureza e a resistência. Durante o endurecimento, surgem tensões internas no material, a ductilidade e a resistência ao impacto diminuem drasticamente. Isso pode levar à fratura frágil da peça durante a operação.
Para reduzir as tensões internas e aumentar a ductilidade e resistência ao impacto após o endurecimento, período de férias, que consiste em aquecer o aço endurecido a uma temperatura que não ultrapasse o ponto crítico inferior, mantendo-se nesta temperatura e subsequente resfriamento.
Dependendo da temperatura, existem três tipos de férias: baixa, média, alta.
O baixo revenimento é realizado a uma temperatura de 150...250°C. A dureza do aço diminui ligeiramente. A estrutura formada como resultado do baixo revenimento é chamada de mar-liberação tensa ou martensita temperada. O corte e ferramenta de medida, matrizes para conformação a frio, bem como peças que devem ter alta resistência ao desgaste.
As férias médias fazem-se em uma temperatura de 350...450 °C. Durante o revenimento médio, a cementita é formada não na forma de placas, mas na forma de pequenos grãos, o que contribui para o aumento da tenacidade do aço. Os produtos que devem ter alta elasticidade e margem de viscosidade suficiente (molas, molas, etc.) são submetidos a revenimento médio.
O alto revenimento é realizado a uma temperatura de 500...650°C. Como resultado, as tensões residuais são completamente eliminadas, o aço adquire boa ductilidade e tenacidade com uma resistência suficientemente alta. Essa folga destina-se a peças críticas que sofrem choque e cargas alternadas durante a operação.
O tratamento térmico duplo, que inclui endurecimento e revenimento subsequente, é chamado de melhoria térmica, já que todo o complexo de propriedades mecânicas do aço é melhorado.
Tratamento químico-térmico. O tratamento químico-térmico consiste na exposição química e térmica a fim de alterar a composição química, estrutura e propriedades da camada superficial do metal. No processo de tratamento químico-térmico, a saturação da superfície do metal com o elemento correspondente ocorre no processo de sua difusão na forma atômica de um meio líquido, sólido ou gasoso a alta temperatura. Os principais tipos de tratamento químico-térmico são classificados de acordo com os nomes dos elementos com os quais a camada superficial está saturada. Por exemplo, a saturação com carbono é chamada de cimentação, nitrogênio - nitretação, cromo - cromagem.
O uso generalizado do tratamento químico-térmico em vários campos da tecnologia é explicado pelo fato de que, ao aumentar a dureza, a resistência ao desgaste e a resistência à corrosão da superfície, aumenta a confiabilidade e a durabilidade da operação de peças e mecanismos de máquinas.
O tratamento químico-térmico consiste em:
dissociação, que ocorre na superfície de contato "metal - ambiente gasoso"e leva à liberação de um elemento difusor no estado atômico;
absorção - absorção superficial de átomos livres;
difusão - penetração do elemento saturante profundamente na camada superficial.
O principal processo físico é a difusão, cuja taxa aumenta com o aumento da temperatura, o elemento difusor penetra a uma profundidade maior.
A cementação consiste na saturação por difusão da camada superficial do aço com carbono quando aquecida em um meio apropriado - um carburador. O processo de cementação ocorre em temperaturas (900 ... 950 ° C), quando a austenita é estável, dissolvendo carbono em grandes quantidades. A cementação é realizada em carburadores sólidos, líquidos e gasosos. A cementação a gás é o processo mais produtivo. A principal reação que fornece carburação é a dissociação do metano:
CH → 2H 2 + C at.
A cementação é realizada em aços de baixo carbono e ligas contendo de 0,1 a 0,35% de carbono. A camada superficial do aço após cementação possui uma concentração variável de carbono em espessura, diminuindo da superfície para o núcleo da peça. A este respeito, após o resfriamento lento na estrutura da camada de banho de cimento, podem ser distinguidas três zonas (a partir da superfície): hipereutetóide, eutetóide, hipoeutetóide. A espessura total da camada cimentada é de 0,8...3,0 mm.
Após a cimentação, para obter as propriedades necessárias, é realizado o tratamento térmico - endurecimento com baixo revenimento. Como resultado do tratamento térmico, a camada superficial adquire uma estrutura resistente ao desgaste e o núcleo de baixo carbono da peça acaba sendo bastante viscoso. Na maioria das vezes, as engrenagens de vários mecanismos são submetidas à cementação para aumentar sua durabilidade.
Nitretação consiste na saturação por difusão da camada superficial com nitrogênio no meio apropriado. Antes da nitretação, os aços são submetidos a tratamento térmico - endurecimento e alto revenimento.
Nitretados são aços ligados contendo cromo, molibdênio, vanádio e outros elementos capazes de formar nitretos muito duros e resistentes ao calor com nitrogênio. A nitretação é realizada a uma temperatura de 500...600°C. A principal reação que ocorre na superfície da peça é a reação de dissociação da amônia.
Após a nitretação, o aço adquire alta dureza, resistência ao desgaste e resistência à corrosão. Nestas propriedades, os aços nitretados são superiores aos cementados. No entanto, a camada nitretada resiste pior às cargas de choque e tem uma resistência de contato menor. Devido à longa duração do processo (até 70 horas), o uso da nitretação é economicamente viável para o processamento de produtos críticos, como virabrequins de automóveis, camisas de cilindros para motores de combustão interna, acessórios diversos, etc.
Cromagem consiste na saturação por difusão da camada superficial de aço com cromo a uma temperatura de 900 ... 1300 ° C em um meio apropriado. A cromagem proporciona maior resistência ao calor do aço até uma temperatura de 800 ° C, alta resistência à corrosão e à erosão. Partes de usinas de energia a vapor, acessórios de tubulação de vapor, válvulas, válvulas, tubos de ramal são submetidos a cromagem. Para aumentar a resistência à corrosão, o aço do transformador é submetido a cromagem. Neste caso, o aço adquire adicionalmente alta resistência ao calor.
perguntas do teste
O que caracteriza a estrutura cristalina dos metais?
Que tipos de redes cristalinas você conhece?
Quais são os principais defeitos na estrutura cristalina?
O que é alotropia de metais?
Que propriedades mecânicas caracterizam a resistência e a ductilidade dos materiais sob tensão?
O que é um diagrama de estado de liga e o que ele permite que você estabeleça?
Quais são os principais tipos de tratamento térmico?
O que é cementação de aço?
Seção 2 MATERIAIS DE SEMICONDUTORES
Tópico 2.1 Classificação de materiais semicondutores
As substâncias distinguem-se pela sua capacidade de conduzir eletricidade. Essa habilidade é caracterizada pelo valor de resistência elétrica– ρ ou condutividade elétrica – γ. O valor de γ em temperatura normalé inferior a 10-10 S/m para dielétricos e mais de 10 4 S/m para condutores.
Consideremos a natureza da mudança na condutividade específica dos sólidos a uma temperatura tendendo ao zero absoluto.
Nesse caso, a condutividade específica dos condutores aumenta e muitos metais passam para um estado supercondutor, caracterizado por um infinito grande valor γ.
Os semicondutores se comportam de maneira bastante diferente. À medida que a temperatura diminui, sua condutividade específica diminui e, em T → 0 K, os semicondutores não conduzem corrente elétrica, ou seja, tornar dielétrico. Por outro lado, com o aumento da temperatura, γ dos semicondutores aumenta acentuadamente.
Para o aparecimento de portadores de carga livre em semicondutores, não é necessário trazê-los para energia térmica. Isso pode ser alcançado neles por iluminação, cargas mecânicas, campo elétrico, etc. A estrutura interna dos semicondutores tem uma forte influência na condutividade elétrica. Além disso, a introdução de até mesmo uma pequena quantidade de átomos de um elemento estranho em um semicondutor geralmente altera drasticamente sua condutividade elétrica. Tudo isso abre amplas oportunidades para controlar as propriedades eletrofísicas de materiais semicondutores.
Então, Um semicondutor é uma substância cuja principal propriedade é a forte dependência de sua condutividade elétrica da influência de fatores externos.
Todos os semicondutores podem ser divididos em simples e complexos.
Simples esse semicondutor é chamado, cuja composição principal é formada por átomos de um elemento químico (silício, germânio, selênio, telúrio, boro, carbono, fósforo, enxofre, arsênico, antimônio, iodo, estanho cinza).
Estrutura complexo semicondutores é formado por átomos de vários elementos químicos. Este grupo inclui soluções sólidas (silício e germânio) e compostos químicos, designados AB. Nesta fórmula, os sobrescritos (m e n) indicam o número do grupo sistema periódico, que inclui o elemento correspondente, e os inferiores (x e y) são o número de átomos desse elemento no composto. Por exemplo, o semicondutor arseneto de gálio GaAr é classificado como um composto do tipo A III B V, e o óxido de cobre Cu 2 O é classificado como um composto do tipo A 2 I B VI.
Muitos compostos químicos ternários e mais complexos possuem propriedades semicondutoras, como o ZnSiAs 2 . Semicondutor é linha inteira compostos orgânicos: antraceno, naftaleno, ftalocianina, etc.
Uma propriedade notável dos semicondutores é também que eles permitem a transformação inversa energia elétrica em luz, térmica ou mecânica.
Os semicondutores são usados para amplificar e gerar sinais elétricos (transistores, diodos, circuitos integrados), como conversores primários de temperatura e fontes de energia térmica (termistores e elementos de aquecimento), como conversores primários e fontes de sinais ópticos (fotoresistores, LEDs, lasers), para conversão vibrações mecânicas(resistores de deformação e sensores piezoelétricos), etc.
Níveis de energia e zonas
Um átomo consiste em um núcleo e elétrons que se movem em certas órbitas.
A energia total dos elétrons, igual à soma de suas energias cinética (movimento orbital) e potencial (atração ao núcleo), é chamada de estado de energia do átomo. Cada órbita permitida tem seu próprio estado de energia, que é representado no diagrama como um nível de energia. Como as órbitas e suas energias são divididas em permitidas e proibidas, então energizarníveis géticos também podem ser permitidose proibido.
Energia eletrônica E expressa em elétron-volts. Elétron-volt- é a energia queelétron acelerando em campo elétrico com diferentespotenciais em 1 V.
A interação dos átomos na rede leva ao fato de que seus níveis de energia são divididos em um grande número de subníveis quase fundidos, formando energizargóticozonas.
A banda de energia preenchida com subníveis é mais larga, quanto mais próximos os átomos estiverem localizados e maior o nível de energia. A probabilidade de um elétron "permanecer" no band gap é zero.
Classificação de materiais por elétricapropriedades (teoria da banda)
A classificação de materiais elétricos de acordo com suas propriedades elétricas é baseada nas idéias da teoria de bandas da condutividade elétrica dos sólidos, cuja essência é a seguinte.
Em um átomo isolado, os elétrons giram em torno do núcleo em certas órbitas. De acordo com o princípio de Pauli, em cada or-Um bit pode ter no máximo dois elétrons. Cada órbita corresponde a um valor de energia estritamente definido que um elétron pode ter, ou seja, cada órbita representa um nível de energia específico. Sob a influência da atração de uma carga positiva núcleo atômico os elétrons tendem a ocupar os níveis mais próximos do núcleo com um valor mínimo de energia. Portanto, os níveis de energia mais baixos são preenchidos com elétrons e os níveis superiores são livres. Um elétron pode saltar de um nível de energia mais baixo C x para outro nível gratuito C 2 (Figura 1). Para fazer isso, o elétron deve receber energia adicional ∆ C = C 2 - C 1 . Se não houver níveis livres no átomo, o elétron não pode alterar sua energia, portanto, não participa da criação da condutividade elétrica.
C - energia do elétron; C 1 - nível de energia mais baixo; C 2 - nível de energia livre; ∆ C C - banda de condução (zona livre); ∆ C - zona proibida; ∆ Cdentro, - banda de valência
Figura 2.1 - Diagrama de níveis de energia de um átomo isolado (1) e corpo sólido (2).
Em uma rede cristalina que consiste em vários átomos, os níveis de energia individuais são divididos em subníveis que formam zonas de energia (veja a Fig. 2.1). Neste caso, os níveis de energia livre e preenchido são divididos. A área preenchida com elétrons é chamada de valência. O nível superior da banda de valência é indicado C dentro . A zona livre é chamada de zona condutividade. O nível mais baixo da banda de condução (banda livre) é indicado C uma . O intervalo entre a banda de valência e a banda de condução é chamado de Entrada zona ∆ C. O valor do intervalo da banda afeta significativamente as propriedades dos materiais.
Se um ∆ C for igual ou próximo de zero, então os elétrons podem ir para níveis livres devido à sua própria energia térmica e aumentar a condutividade da substância. Substâncias com tal estrutura de bandas de energia são chamadas de condutores. Materiais condutores são usados para conduzir corrente elétrica. Normalmente, os condutores incluem substâncias com resistividade elétrica p< 10 Ом*м. Типичными проводниками явля-ются металлы.
Se o band gap exceder alguns elétron-volts, então é necessária uma energia significativa para transferir elétrons da banda de valência para a banda de condução. Essas substâncias são chamadas de dielétricos. Os dielétricos têm uma alta resistividade elétrica e têm a capacidade de impedir a passagem de corrente. Materiais dielétricos incluem substâncias com resistividade elétrica p > 10 7 Ohm * m. Devido à sua alta resistividade elétrica, eles são usados como materiais isolantes elétricos.
Se o band gap for de 0,1 ... 0,3 eV, os elétrons passam facilmente da banda de valência para a banda de condução devido à energia externa. Substâncias com condutividade controlada são semicondutores. A resistência elétrica específica dos semicondutores é p 10 9 ohm * m.
Os materiais semicondutores têm condutividade, que pode ser usada para controlar tensão, temperatura, iluminação, etc.
Dependendo da estrutura e das condições externas, os materiais podem passar de uma classe para outra. Por exemplo, duro e metais líquidos- condutores e pares metálicos - dielétricos; os semicondutores germânio e silício, típicos em condições normais, tornam-se condutores quando expostos a altas pressões hidrostáticas; o carbono na modificação de diamante é um dielétrico e na modificação de grafite é um condutor.
A principal propriedade da matéria em relação ao campo elétrico é condutividade elétrica, caracterizando a capacidade de um material para conduzir uma corrente elétrica sob a influência de um campo elétrico constante, ou seja, campo, cuja tensão não muda com o tempo.
A condutividade elétrica é caracterizada por condutividade elétrica específica e resistência elétrica específica:
Os valores de condutividade elétrica e resistividade elétrica y materiais diferentes diferem significativamente. No estado supercondutor, a resistência elétrica específica dos materiais é zero, enquanto para gases rarefeitos tende ao infinito.
É fácil entender que as propriedades condutoras de um cristal dependem do gap que separa as bandas de valência e condução. Quanto maior o band gap, menor (a uma determinada temperatura) o número de elétrons que penetram na banda de condução, menor a condutividade do cristal.
Cristais podem ser bons condutoresmesmo que a banda de valência esteja preenchidainteiramente, se for diretamente adjacente à zonacondutividade ou cruza com ela (como resultadodesfocagem de zonas durante a formação de uma grade). Com ampliaçãoaumentando o band gap, os cristais adquiriramrestaurar as propriedades dos isolantes. Valores médiosintervalos de banda correspondem asemi-profissional-agua cristais.
Como as bandas de valência e condução dos condutores cristalinos não são separadas, os elétrons se movem livremente de um subnível permitido para outro, adquirindo uma velocidade ordenada sob a ação de uma tensão aplicada. Ao mesmo tempo, com o aumento da temperatura, a resistência do condutor aumenta devido à diminuição do caminho livre dos elétrons no cristal.
Em cristais semicondutores, a condutividade é determinada principalmente pelo número de elétrons que ultrapassaram o gap e penetraram na banda de condução.
materiais semicondutores
A ligação química entre os átomos de um semicondutor é realizada devido à interação de elétrons de valência, enquanto cada átomo recebe de um vizinho em posse conjunta e lhe dá seus elétrons de valência, que estão faltando antes da formação de uma banda estável de oito elétrons . Por isso, em um semicondutor ideal, todos os elétrons de valência rons participam da educação ligação química e livre não há elétrons. Este tipo de ligação química é chamado de cova. fita.
Na fig. 2.2 mostra um diagrama da formação de uma ligação química na rede cristalina de silício, um átomo do qual tem quatro elétrons de valência em um estado isolado livre, e um externo nível eletrônico cada átomo é preenchido com até oito elétrons, devido à propriedade conjunta dos elétrons dos quatro átomos vizinhos mais próximos.
Figura 2.2 - Esquema da formação de uma ligação química na rede cristalina do silício. Devido à pequena largura (1 eV) do gap do semicondutor, as vibrações térmicas dos átomos são capazes de transmitir energia aos elétrons de valência suficiente para a transição da banda de valência preenchida para a banda de condução livre. Cada uma dessas transições leva ao aparecimento de um par de portadores de carga: elétron livre na banda de condução e no estado de energia livre - furos- na banda de valência. Sob a ação da tensão aplicada ao cristal, o elétron de condução se move "em direção" campo elétrico, e um elétron na banda de valência ocupa um nível livre, liberando seu nível para outro elétron. Isso pode ser considerado como o movimento de uma carga positiva (buraco) na direção do campo elétrico.
Geração de pares de livre, ou seja, capaz de transferirmover sob a influência de uma tensão aplicada,cargas torna o cristal capaz de conduzir eletricidadecorrente rica e a condutividade elétrica de tal cristalchamadoter.
Um semicondutor no qual a condutividade elétrica é realizada devido à excitação de elétrons de ligação química é chamado depróprio semicondutor.
Os portadores de corrente em tais semicondutores são seus próprios elétrons e buracos.
Na fig. 2.3 mostra um diagrama da rede cristalina de seu próprio semicondutor. Após a excitação de seu próprio elétron de valência, n-tipo de portador de corrente - elétron livre e R- tipo portador atual - buraco - ligação química desocupada.
Simultaneamente à formação de pares de portadores, uma parte dos elétrons da banda de condução volta espontaneamente para a banda de valência, emitindo quanta de energia. Esse processo é chamado recombinação vapor. A uma temperatura constante, um equilíbrio dinâmico é estabelecido, o que determina a concentração elétrons livres e furos (a uma determinada temperatura).
Quanto maior a temperatura, maior a concentração de portadores de carga livre, maior a condutividade elétrica intrínseca do cristal.
A uma temperatura de 0K, nenhum par de portadores é formado e o cristal perde completamente sua própria condutividade elétrica. Nesse caso, os elétrons dentro do cristal se movem aleatoriamente em altas velocidades (da ordem de 10 6 m/s), mas não reagem à tensão externa aplicada.
Figura 2.3 - Esquema da rede cristalina do seu próprio semicondutor.
Cristais reais contêm numerosos defeitos na rede cristalina: ponto, linear, massa e superfície. Em locais de violação da estrutura periódica do cristal (implantação de átomos em interstícios), a energia de ligação dos elétrons com os núcleos muda, como resultado do surgimento de novos níveis de energia, que podem ir além da banda de valência e localizar-se na band gap próximo à banda de condução. Isso facilita a transição de elétrons para a banda de condução.
Complexo de treinamento e metodologia... - dar FundamentosCiência de materiais, princípios de seleção materiais necessários, incutir as habilidades de definição prática físico-mecânico... grupo químico conexões. 6.3.1. Classificação de polímeros e propriedades de polímeros Por polímeros de origem compartilhar ...
Evgeny Petrovich Prokopyev (rus)(eng) lista geral de publicações antimatéria e positrônica positrônica e nanotecnologia positrônica aniquilação de pósitrons física de sistemas complexos sinergética materiais ciência nanotecnologia outros problemas relacionados
DocumentoProkopiev E.P. Em estados de superfície na fronteira seção semicondutor-metal. M., 1985. 5 p. - Dep. em... processos. Terceira Conferência Russa sobre Ciência de materiais e físico-químicoFundamentos tecnologias para obtenção de cristais de silício dopado...
As propriedades de uma liga dependem de sua estrutura. A principal forma de alterar a estrutura e, consequentemente, as propriedades é o tratamento térmico.
Os fundamentos do tratamento térmico foram desenvolvidos por D.K. Chernov. Mais tarde, eles foram desenvolvidos nos trabalhos de A.A. Bochvar, G.V. Kurdyumov, A.P. Gulyaev.
tratamento térmico chamado de efeito térmico sobre o metal para dar ao metal as propriedades mecânicas e físicas necessárias como resultado de uma mudança na estrutura interna (estrutura) do metal.
A maioria dos blanks (produtos semi-acabados) e produtos feitos de aço e ligas não ferrosas são submetidos a tratamento térmico. É o tratamento térmico que permite alterar a estrutura do metal na direção certa e permite obter nível requerido dureza, resistência, plasticidade e outras propriedades.
Modo de tratamento térmico caracterizar os seguintes parâmetros principais: velocidade e modo de aquecimento, Temperatura máxima aquecimento, tempo de permanência no forno na temperatura de aquecimento e taxa e modo de resfriamento.
O tratamento térmico é um dos mais comuns tecnologia moderna maneiras de obter as propriedades especificadas do metal. O tratamento térmico é usado como operação intermediária para melhorar a usinabilidade de um produto semi-acabado por pressão, corte, etc., ou como operação final. processo tecnológico, proporcionando um determinado nível de propriedades físicas e mecânicas da peça.
O tratamento térmico inclui o aquecimento, retenção e resfriamento do metal, realizado em uma determinada sequência sob determinados modos, a fim de alterar a estrutura interna da liga e obter as propriedades desejadas. Normalmente, pode ser representado esquematicamente como um gráfico nos eixos temperatura-tempo (Fig. 21).
O tratamento térmico é subdividido em térmico propriamente dito, químico-térmico e termomecânico (ou deformação-térmico).
O tratamento térmico real consiste apenas no efeito térmico sobre o metal ou liga, tratamento químico-térmico - em uma combinação de efeitos térmicos e químicos, termomecânico - em uma combinação de efeito térmico e deformação plástica.
Fig.21. Cronograma de Tratamento Térmico
Na verdade, o tratamento térmico inclui os seguintes tipos principais:
Recozimento do 1º tipo
Recozimento do 2º tipo
Endurecimento com transformação polimórfica
Endurecimento sem transformação polimórfica
Envelhecimento
Esses tipos de tratamento térmico se aplicam a aços e metais não ferrosos.
anelamento
anelamento- tratamento térmico, que consiste em aquecer o metal a uma determinada temperatura, mantendo e resfriando com o forno desligado (ou seja, com um mínimo de velocidade possível, cerca de 50-100 graus/hora).
Recozimento do 1º tipo - é usado para quaisquer metais e ligas. Sua implementação não se deve a transformações de fase no estado sólido. O aquecimento durante o recozimento do primeiro tipo, aumentando a mobilidade dos átomos, elimina parcial ou completamente a falta de homogeneidade química, reduz as tensões internas. A temperatura de aquecimento e o tempo de espera são de importância primordial. Caracterizado por resfriamento lento
As variedades de recozimento do primeiro tipo são:
homogeneização (difusão)
· recristalização;
· recozimento para aliviar o estresse interno após forjamento, soldagem, fundição.
O recozimento por homogeneização (difusão) é um tratamento térmico em que o principal processo é a eliminação das consequências da segregação dendrítica (heterogeneidade química) em fundidos e lingotes. É uma longa exposição a altas temperaturas, na qual ocorrem processos de difusão que não tiveram tempo de se completar durante a cristalização. A temperatura aproximada para aços é -1100-1300°C por 20-50 horas, para ligas de alumínio 420-450°C.
O recozimento de recristalização é um tratamento térmico de um metal deformado, no qual o principal processo é a recristalização do metal. Este tipo de recozimento elimina desvios na estrutura do estado de equilíbrio que ocorrem durante a deformação plástica. Durante o tratamento por pressão, especialmente a frio, o metal é rebitado, sua resistência aumenta e a plasticidade diminui devido ao aumento da densidade das discordâncias nos cristalitos. Quando o metal trabalhado a frio é aquecido acima de uma certa temperatura, desenvolve-se a recristalização primária e coletiva, na qual a densidade de discordância diminui drasticamente. Como resultado, o metal amolece e se torna mais dúctil. Esse recozimento é usado para melhorar a trabalhabilidade por pressão e para dar ao metal a combinação necessária de dureza, resistência e ductilidade. Como regra, durante o recozimento de recristalização, procura-se obter um material sem textura no qual não haja anisotropia de propriedades. Na produção de chapas de aço para transformadores, o recozimento de recristalização é utilizado para obter a textura metálica desejada resultante da recristalização.
O recozimento de alívio de tensão é um tratamento térmico em que o processo principal é o relaxamento total ou parcial das tensões residuais durante o aquecimento e resfriamento. O recozimento redutor de tensão é aplicado a produtos nos quais, durante o tratamento sob pressão, fundição, soldagem, tratamento térmico e outros processos tecnológicos, surgiram tensões residuais inaceitavelmente grandes que são mutuamente equilibradas dentro do corpo sem a participação de cargas externas. As tensões residuais podem causar distorção da forma e dimensões do produto durante o seu processamento, operação ou armazenamento em armazém. Quando o produto é aquecido, a tensão de escoamento diminui e, quando se torna menor que as tensões residuais, elas são rapidamente descarregadas pelo fluxo plástico em diferentes camadas do metal.
O recozimento do segundo tipo é o recozimento de metais e ligas que sofrem transformações de fase no estado sólido. Este tipo de recozimento é realizado para ligas nas quais há transformações polimórficas ou eutetóides, bem como solubilidade variável dos componentes no estado sólido.
Fig. 22. Mudança de estrutura durante o recozimento do segundo tipo
O recozimento do segundo tipo é realizado para obter uma estrutura de equilíbrio e prepará-la para processamento posterior. Como resultado do recozimento, o grão é triturado, a ductilidade e a tenacidade aumentam, a resistência e a dureza diminuem e a usinabilidade melhora. Caracteriza-se pelo aquecimento a temperaturas acima do crítico e resfriamento muito lento, via de regra, junto com um forno ou ao ar. Neste último caso, o processo é chamado de normalização. O recozimento do 2º tipo é mais frequentemente usado para refinamento geral da estrutura, amolecimento e melhoria da usinabilidade.
Tratamento térmico de metais e ligas
Trabalho do curso
sobre o tema: "Tratamento térmico de metais e ligas"
Introdução
O tratamento térmico é usado em vários estágios da produção de peças de máquinas e produtos metálicos. Em alguns casos, pode ser uma operação intermediária que serve para melhorar a usinabilidade de ligas por pressão, corte, em outros, é a operação final que fornece o conjunto necessário de indicadores de propriedades mecânicas, físicas e operacionais de produtos ou semi- produtos finalizados. Os produtos semi-acabados são submetidos a tratamento térmico para melhorar a estrutura, reduzir a dureza (melhorar a usinabilidade) e as peças - para lhes dar certas propriedades necessárias (dureza, resistência ao desgaste, resistência e outras).
Como resultado do tratamento térmico, as propriedades das ligas podem ser alteradas em uma ampla faixa. A possibilidade de um aumento significativo das propriedades mecânicas após o tratamento térmico em comparação com o estado inicial permite aumentar as tensões permitidas, reduzir o tamanho e o peso das máquinas e mecanismos e aumentar a confiabilidade e a vida útil dos produtos. A melhoria das propriedades como resultado do tratamento térmico permite o uso de ligas de composições mais simples e, portanto, mais baratas. As ligas também adquirem algumas novas propriedades, em conexão com as quais o escopo de sua aplicação está se expandindo.
Finalidade e tipos de tratamento térmico
O tratamento térmico (calor) é um processo cuja essência é o aquecimento e resfriamento de produtos em determinados modos, resultando em mudanças na estrutura, composição de fases, propriedades mecânicas e físicas do material, sem alterar a composição química.
O objetivo do tratamento térmico de metais é obter a dureza necessária, melhorar as características de resistência dos metais e ligas. O tratamento térmico é dividido em térmico, termomecânico e químico-térmico. Tratamento térmico - apenas ação térmica, termomecânico - uma combinação de ação térmica e deformação plástica, químico-térmico - uma combinação de efeitos térmicos e químicos. O tratamento térmico, dependendo do estado estrutural obtido como resultado de sua aplicação, é dividido em recozimento (primeiro e segundo tipo), endurecimento e revenimento.
anelamento
O recozimento é um tratamento térmico que consiste em aquecer o metal a determinadas temperaturas, mantendo e depois resfriando muito lentamente junto com o forno. Eles são usados para melhorar o processamento de metais por corte, para reduzir a dureza, para obter uma estrutura granular, bem como para aliviar tensões, eliminando parcialmente (ou completamente) todos os tipos de heterogeneidades que foram introduzidas no metal durante as operações anteriores (usinagem , tratamento de pressão, fundição, soldagem), melhora a estrutura de aço.
Recozimento do primeiro tipo. Trata-se de um recozimento durante o qual não ocorrem transformações de fase e, caso ocorram, não afetam os resultados finais previstos para o fim a que se destinam. Existem os seguintes tipos de recozimento do primeiro tipo: homogeneização e recristalização.
A homogeneização é um recozimento com uma longa exposição a uma temperatura acima de 950ºC (geralmente 1100–1200ºC) para equalizar a composição química.
A recristalização é o recozimento do aço endurecido por trabalho a uma temperatura superior à temperatura do início da recristalização para eliminar o endurecimento por trabalho e obter um determinado tamanho de grão.
Recozimento do segundo tipo. Isso é recozimento, no qual as transformações de fase determinam sua finalidade. Os seguintes tipos são distinguidos: completo, incompleto, difusão, isotérmico, leve, normalizado (normalização), esferoidização (para perlita granular).
O recozimento completo é realizado aquecendo o aço 30-50°C acima do ponto crítico, mantendo a esta temperatura e resfriando lentamente até 400-500°C a uma taxa de 200°C por hora para aços carbono, 100°C por hora para aços de baixa liga e 50°C por hora para aços de alta liga. A estrutura de aço após o recozimento é equilibrada e estável.
O recozimento incompleto é realizado aquecendo o aço a uma das temperaturas na faixa de transformação, mantendo e resfriamento lento. O recozimento incompleto é usado para reduzir as tensões internas, diminuir a dureza e melhorar a usinabilidade.
Recozimento por difusão. O metal é aquecido a temperaturas de 1100–1200ºC, pois neste caso os processos de difusão necessários para equalizar a composição química prosseguem de forma mais completa.
O recozimento isotérmico é o seguinte: o aço é aquecido e depois resfriado rapidamente (muitas vezes por transferência para outro forno) a uma temperatura de 50 a 100 °C abaixo da temperatura crítica. Usado principalmente para ligas de aço. Econômico, desde a duração do recozimento convencional (13 - 15) h, e do recozimento isotérmico (4 - 6) h
O recozimento por esferoidização (para perlita granular) consiste em aquecer o aço acima da temperatura crítica de 20 a 30 °C, mantendo-o nessa temperatura e resfriando lentamente.
O recozimento brilhante é realizado de acordo com os modos de recozimento completo ou incompleto usando atmosferas protetoras ou em fornos com vácuo parcial. É usado para proteger a superfície metálica da oxidação e descarbonetação.
Normalização - consiste em aquecer o metal a uma temperatura de (30–50) ºС acima do ponto crítico e posterior resfriamento ao ar. O objetivo da normalização é diferente dependendo da composição do aço. Em vez de recozimento, os aços de baixo carbono são normalizados. Para aços de médio carbono, a normalização é usada em vez de têmpera e revenimento alto. Os aços de alto carbono são submetidos à normalização para eliminar a rede de cementita. A normalização seguida de alto revenimento é usada em vez de recozimento para corrigir a estrutura dos aços ligados. A normalização é uma operação mais econômica que o recozimento, pois não requer resfriamento junto com o forno.
endurecimento
O endurecimento é o aquecimento até a temperatura ideal, a retenção e o resfriamento rápido subsequente para obter uma estrutura fora do equilíbrio.
Como resultado do endurecimento, a resistência e a dureza aumentam e a ductilidade do aço diminui. Os principais parâmetros durante o endurecimento são a temperatura de aquecimento e a taxa de resfriamento. A taxa de têmpera crítica é a taxa de resfriamento que proporciona a formação de uma estrutura - martensita ou martensita e austenita residual.
Dependendo da forma da peça, do tipo de aço e do conjunto de propriedades necessário, vários métodos de endurecimento são usados.
Endurecimento em um refrigerador. A peça é aquecida até a temperatura de endurecimento e resfriada em um refrigerante (água, óleo).
Endurecimento em dois ambientes (endurecimento intermitente) é um endurecimento em que a peça é resfriada sucessivamente em dois ambientes: o primeiro meio é um refrigerante (água), o segundo é ar ou óleo.
Endurecimento passo. A peça aquecida à temperatura de endurecimento é resfriada em sais fundidos, após manter o tempo necessário para equalizar a temperatura em toda a seção, a peça é resfriada ao ar, o que ajuda a reduzir as tensões de endurecimento.
O endurecimento isotérmico, como o endurecimento escalonado, é realizado em dois meios de resfriamento. A temperatura do meio quente (banhos de sal, nitrato ou alcalino) é diferente: depende da composição química do aço, mas é sempre 20–100 °C superior ao ponto de transformação martensítico para um determinado aço. O resfriamento final até a temperatura ambiente é realizado ao ar. O endurecimento isotérmico é amplamente utilizado para peças feitas de aços de alta liga. Após o endurecimento isotérmico, o aço adquire propriedades de alta resistência, ou seja, uma combinação de alta tenacidade com resistência.
O endurecimento com auto-revenimento é amplamente utilizado na fabricação de ferramentas. O processo consiste no fato de que as peças são mantidas em um meio de resfriamento não até que estejam completamente resfriadas, mas em um determinado momento são retiradas dele para economizar uma certa quantidade de calor no núcleo da peça, devido ao qual o posterior revenimento é realizado.
Período de férias
A têmpera do aço é a operação final do tratamento térmico, que forma a estrutura e, consequentemente, as propriedades do aço. A têmpera consiste em aquecer o aço a diferentes temperaturas (dependendo do tipo de têmpera, mas sempre abaixo do ponto crítico), mantendo-se nessa temperatura e resfriando em diferentes taxas. O objetivo do revenimento é aliviar as tensões internas que surgem durante o processo de endurecimento e obter a estrutura necessária.
Dependendo da temperatura de aquecimento da peça endurecida, existem três tipos de revenimento: alto, médio e baixo.
O alto revenimento é realizado em temperaturas de aquecimento acima de 350–600 °C, mas abaixo do ponto crítico; tal revenimento é usado para aços estruturais.
O revenimento médio é realizado em temperaturas de aquecimento de 350 - 500 °C; tal revenimento é amplamente utilizado para molas e aços de mola.
O baixo revenimento é realizado em temperaturas de 150–250 °С. A dureza da peça após o endurecimento quase não muda; O baixo revenimento é usado para aços-ferramentas de carbono e ligas onde são necessárias alta dureza e resistência ao desgaste.
O controle de têmpera é realizado pelas cores de têmpera que aparecem na superfície da peça.
Envelhecimento
O envelhecimento é um processo de alteração das propriedades das ligas sem uma alteração perceptível na microestrutura. Existem dois tipos de envelhecimento: térmico e deformação.
O envelhecimento térmico ocorre como resultado de mudanças na solubilidade do carbono no ferro, dependendo da temperatura.
Se a mudança na dureza, ductilidade e resistência ocorrer à temperatura ambiente, esse envelhecimento é chamado de natural.
Se o processo ocorre a uma temperatura elevada, o envelhecimento é chamado de artificial.
O envelhecimento por deformação (mecânico) prossegue após a deformação plástica a frio.
Tratamento a frio
Um novo tipo de tratamento térmico para aumentar a dureza do aço convertendo a austenita retida do aço endurecido em martensita. Isso é feito resfriando o aço até a temperatura do ponto martensítico inferior.
Métodos de endurecimento de superfície
O endurecimento superficial é um processo de tratamento térmico, que consiste no aquecimento da camada superficial de aço a uma temperatura acima da temperatura crítica e posterior resfriamento a fim de obter uma estrutura de martensita na camada superficial.
Existem os seguintes tipos: têmpera por indução; têmpera em um eletrólito, têmpera por aquecimento com correntes de alta frequência (HFC), têmpera com aquecimento por chama.
O endurecimento por indução é baseado em um fenômeno físico, cuja essência é que uma corrente elétrica de alta frequência, passando por um condutor, cria um campo eletromagnético ao seu redor. Correntes parasitas são induzidas na superfície de uma peça colocada neste campo, fazendo com que o metal aqueça a altas temperaturas. Isso possibilita a ocorrência de transformações de fase.
Dependendo do método de aquecimento, o endurecimento por indução é dividido em três tipos:
aquecimento e endurecimento simultâneos de toda a superfície (usado para peças pequenas);
aquecimento sequencial e endurecimento de seções individuais (usado para virabrequins e peças similares);
aquecimento sequencial contínuo e endurecimento por movimento (usado para peças longas).
Endurecimento por chama de gás. O processo de endurecimento por chama consiste no aquecimento rápido da superfície da peça com uma chama de oxi-acetileno, oxi-combustível ou oxigênio-querosene até a temperatura de endurecimento, seguido de resfriamento com água ou uma emulsão.
Endurecimento em eletrólito. O processo de endurecimento em um eletrólito é o seguinte: a parte a ser endurecida é mergulhada em um banho com um eletrólito (solução de 5 a 10% de sal calcinado) e uma corrente de 220 a 250 V é passada. a peça é aquecida a altas temperaturas. A peça é resfriada no mesmo eletrólito (após desligar a corrente) ou em um tanque de endurecimento especial.
Processamento termomecânico
O tratamento termomecânico (T.M.O.) é um novo método de fortalecimento de metais e ligas, mantendo plasticidade suficiente, combinando deformação plástica e tratamento térmico de endurecimento (têmpera e revenimento). Existem três métodos principais de processamento termomecânico.
O processamento termomecânico de baixa temperatura (L.T.M.O.) é baseado no endurecimento gradual, ou seja, a deformação plástica do aço é realizada em temperaturas de relativa estabilidade da austenita, seguida de endurecimento e revenimento.
Processamento termomecânico de alta temperatura (H.T.M.O.), neste caso, a deformação plástica é realizada em temperaturas de estabilidade da austenita, seguida de têmpera e revenimento.
A deformação do processamento termomecânico preliminar (P.T.M.O) neste caso pode ser realizada nas temperaturas N.T.M.O e V.T.M.O ou a uma temperatura de 20ºC. Além disso, o tratamento térmico usual é realizado: endurecimento e revenimento.
Finalidade e tipos de tratamento químico-térmico
O tratamento químico-térmico é um processo que é uma combinação de efeitos térmicos e químicos com o objetivo de alterar a composição, estrutura e propriedades da camada superficial do aço.
O objetivo do tratamento químico-térmico é aumentar a dureza da superfície, resistência ao desgaste, limite de resistência, resistência à corrosão, resistência ao calor (resistência à incrustação), resistência ao ácido.
Os seguintes tipos de tratamento químico-térmico têm recebido maior aplicação na indústria: cementação; nitrocarbonetação; nitretação; cianetação; metalização por difusão.
Cimentaçãoé um processo de carbonização superficial produzido com a finalidade de endurecimento superficial de peças.
Dependendo do carburador utilizado, a cementação é dividida em três tipos: cementação com carburador sólido; cementação a gás (metano, propano, gás natural).
Carburação a gás. As peças são aquecidas a 900-950ºC em fornos especiais hermeticamente fechados, nos quais o gás de cimento contendo carbono [natural (natural) ou artificial) é fornecido em fluxo contínuo.
O processo de cementação em um carburador sólido é o seguinte. As peças embaladas em uma caixa juntamente com um carburador (uma mistura de carvão com um ativador) são aquecidas a uma determinada temperatura e mantidas nessa temperatura por um longo tempo, depois resfriadas e submetidas a tratamento térmico.
Peças feitas de aço carbono e ligas com teor de carbono não superior a 0,2% são cementadas por qualquer um dos métodos discutidos acima. A cementação de aços ligados contendo elementos formadores de metal duro Cr, W, V, dá resultados particularmente bons: além de aumentar a dureza superficial e a resistência ao desgaste, eles também aumentam o limite de fadiga.
Nitretação- este é o processo de saturação da camada superficial de vários metais e ligas, produtos de aço ou peças com nitrogênio quando aquecidos em ambiente adequado. Aumenta a dureza da superfície do produto, resistência, resistência ao desgaste, aumenta a resistência à corrosão.
Cianetação– .saturação da camada superficial de produtos simultaneamente com carbono e nitrogênio.
Dependendo do meio utilizado, distingue-se a cianetação: em meio sólido; em meios líquidos; em ambientes gasosos.
Dependendo da temperatura de aquecimento, a cianetação é dividida em cianetação de baixa temperatura e cianetação de alta temperatura.
A cianetação em meio líquido é realizada em banhos de sal fundido.
Cianificação em meio gasoso (nitrocarbonetação). O processo de saturar simultaneamente a superfície de uma peça com carbono e nitrogênio. Para isso, as peças são aquecidas em um ambiente composto por gás carburante e amônia, ou seja, a nitrocarbonetação combina os processos de cementação gasosa e nitretação.
Saturação de difusão com metais e metalóides
Existem e são usados na indústria métodos para saturar a superfície de peças com diversos metais (alumínio, cromo, etc.) e metalóides (silício, boro, etc.). resistência a ácidos, dureza e resistência ao desgaste das peças. Como resultado, a camada superficial adquire propriedades especiais, o que permite economizar elementos de liga.
Aluminização– o processo de saturação da camada superficial do aço com alumínio para aumentar a resistência ao calor (resistência à incrustação) e a resistência à corrosão atmosférica.
A aluminização é realizada em misturas em pó, em banhos com alumínio fundido, em meio gasoso e por pulverização de alumínio líquido.
Cromagem- o processo de saturação da camada superficial do aço com cromo para aumentar a resistência à corrosão e resistência ao calor, e no caso de cromagem de aços de alto carbono - para aumentar a dureza e a resistência ao desgaste.
Siliconização– o processo de saturação da camada superficial da peça com silício para aumentar a resistência à corrosão e resistência a ácidos. A silicificação é aplicada em peças feitas de aços de baixo e médio carbono, além de ferros fundidos maleáveis e de alta resistência.
Bording- o processo de saturação da camada superficial da peça com boro. O objetivo da boretação é aumentar a dureza, resistência ao desgaste abrasivo e à corrosão em ambientes agressivos, resistência ao calor e resistência ao calor das peças de aço. Existem dois métodos de boretação: eletrólise líquida e boretação gasosa.
Sulfetação– o processo de saturação da camada superficial das peças de aço com enxofre para melhorar as propriedades de extrema pressão e aumentar a resistência ao desgaste das peças.
Sulfocianação– o processo de saturação superficial de peças de aço com enxofre, carbono e nitrogênio. O efeito combinado de enxofre e nitrogênio na camada superficial do metal fornece propriedades de extrema pressão e resistência ao desgaste mais altas em comparação com a saturação apenas com enxofre.
Tratamento térmico de ferro fundido
O tratamento térmico do ferro fundido é realizado com o objetivo de aliviar as tensões internas que surgem durante a fundição e causar alterações no tamanho e forma da peça fundida ao longo do tempo, reduzir a dureza e melhorar a usinabilidade e melhorar as propriedades mecânicas. O ferro fundido é submetido a recozimento, normalização, endurecimento e revenimento, bem como alguns tipos de tratamento químico-térmico (nitretação, aluminização, cromagem).
Recozimento de alívio de estresse. Os ferros fundidos são submetidos a este recozimento nas seguintes temperaturas: ferro fundido cinzento com grafite lamelar 500 - 570ºС; ferro dúctil com grafite nodular 550 - 650ºС; ferro fundido de baixa liga 570 - 600ºС; ferro fundido de alta liga 620 - 650ºС. Durante este recozimento, as transformações de fase não ocorrem, mas as tensões internas são removidas, os aumentos de viscosidade, deformações e rachaduras durante a operação são excluídos.
Recozimento de amolecimento (recozimento de grafitização de baixa temperatura). Realizado para melhorar a usinabilidade e aumentar a ductilidade. É realizado por exposição prolongada a 680 - 700ºC ou resfriamento lento das peças fundidas a 760 - 700ºC. Para detalhes de uma configuração complexa, o resfriamento é lento e, para peças de formato simples, é acelerado.
Grafitização de recozimento, como resultado do qual o ferro maleável é obtido a partir do ferro fundido branco.
Normalização usado para aumentar o carbono ligado, aumentar a dureza, força e resistência ao desgaste de ferros fundidos cinzentos, dúcteis e de alta resistência. Durante a normalização, o ferro fundido (fundição) é aquecido acima das temperaturas da faixa de transformação de 850 - 950ºС e, após a exposição, é resfriado ao ar.
endurecimento submetidos ao ferro cinzento, maleável e dúctil para aumentar a dureza, resistência e resistência ao desgaste. De acordo com o método de execução, o endurecimento do ferro fundido pode ser volumétrico contínuo, isotérmico e superficial.
Durante o endurecimento contínuo volumétrico, o ferro fundido é aquecido a uma temperatura de 850 - 950ºC. Em seguida, aguarde o aquecimento e a dissolução completa do carbono. O resfriamento é realizado em água ou óleo. Após a têmpera, o revenimento é realizado a uma temperatura de 200 - 600ºС. Como resultado, a dureza, resistência e resistência ao desgaste do ferro fundido aumentam.
Durante a têmpera isotérmica, os ferros fundidos são aquecidos da mesma forma que durante a têmpera volumétrica contínua, mantidos por 10 a 90 minutos e resfriados em sal fundido a 200-400ºC, e após a espera, resfriados ao ar.
Endurecimento da superfície com aquecimento da camada superficial com uma chama de oxigênio-acetileno, correntes de alta frequência ou em um eletrólito. Temperatura de aquecimento 900 - 1000ºС. Resfriamento em água, óleo ou emulsão de óleo.
Envelhecimento usado para estabilizar as dimensões de peças de ferro fundido, evitar empenamento e aliviar tensões internas. Normalmente, o envelhecimento é realizado após a usinagem de desbaste. Existem dois tipos de envelhecimento: natural e artificial.
O envelhecimento natural é realizado ao ar livre ou dentro de casa. Os produtos após a fundição são envelhecidos por 6 a 15 meses.
O envelhecimento artificial é realizado em temperaturas elevadas; duração - várias horas. Com envelhecimento artificial, os fundidos de ferro fundido são carregados em um forno aquecido a 100 - 200º C, aquecido a uma temperatura de 550 - 570º C a uma taxa de 30 - 60º C por hora, mantidos por 3 - 5 horas e resfriados junto com o forno a uma velocidade de 20 - 40º C por hora a uma temperatura de 150 - 200ºC, e depois resfriado ao ar.
Tratamento químico-térmico de ferro fundido
Para aumentar a dureza da superfície e a resistência ao desgaste, os ferros fundidos cinzentos são submetidos à nitretação. Mais frequentemente, ferros fundidos perlíticos cinzentos ligados com cromo, molibdênio e alumínio são nitretados. Temperatura de nitretação 550 - 580ºС, tempo de exposição 30 - 70 horas. Além da nitretação, o aumento da dureza superficial e resistência ao desgaste do ferro fundido perlítico cinzento ligado pode ser obtido por cianetação gasosa e líquida a uma temperatura de 570ºC. Para aumentar a resistência ao calor, os fundidos de ferro fundido podem ser submetidos à aluminização, e para obter alta resistência à corrosão em ácidos, siliconizados.
Tratamento térmico de ligas de metais não ferrosos
Ligas de alumínio
As ligas de alumínio são submetidas a três tipos de tratamento térmico: recozimento, endurecimento e envelhecimento. Tipos principais anelamento são: difusão, recristalização e ligas endurecidas termicamente.
A homogeneização é usada para equalizar a microheterogeneidade química dos grãos da solução sólida. Para realizar a homogeneização, as ligas de alumínio são aquecidas a 450 - 520ºС e mantidas nessas temperaturas de 4 a 40 horas; após a exposição - resfriamento junto com o forno ou no ar. Como resultado, a estrutura torna-se mais homogênea e a plasticidade aumenta.
O recozimento de recristalização para alumínio e ligas com base nele é usado muito mais amplamente do que para o aço. Isso se explica pelo fato de que metais como alumínio e cobre, bem como muitas ligas à base deles, não são endurecidos por têmpera e um aumento nas propriedades mecânicas só pode ser obtido por trabalho a frio, e uma operação intermediária nesse processamento é recozimento de recristalização. Temperatura de recozimento de recristalização de ligas de alumínio 300 - 500ºC exposição 0,5 - 2 horas.
O recozimento de ligas endurecidas termicamente é usado para remover completamente o endurecimento; é realizado a temperaturas de 350 - 450 ° C com um tempo de espera de 1 - 2 horas e resfriamento subsequente bastante lento.
Depois endurecimento a resistência da liga aumenta ligeiramente, mas a ductilidade não muda. Após a têmpera, as ligas de alumínio são submetidas a envelhecimento, no qual ocorre a decomposição de uma solução sólida supersaturada.
Ligas de alumínio forjado
No estado endurecido, os duralumínios são dúcteis e facilmente deformados. Após o endurecimento e envelhecimento natural ou artificial, a resistência do duralumínio aumenta drasticamente.
Ligas de alumínio fundido
Para ligas de alumínio fundido, vários tipos de tratamento térmico são usados, dependendo da composição química. Para o endurecimento, as ligas de alumínio fundido são submetidas a têmpera para obter uma solução sólida supersaturada e envelhecimento artificial, além de apenas têmpera sem envelhecimento para obter uma solução sólida estável no estado temperado.
ligas de magnésio
As ligas de magnésio, como o alumínio, são submetidas a recozimento, endurecimento e envelhecimento. Para equalizar a microheterogeneidade química dos grãos da solução sólida por difusão, os lingotes de liga de magnésio são submetidos à homogeneização a temperaturas de 350 a 400°C com exposição de 18 a 24 horas. Produtos semi-acabados de ligas de magnésio forjado são submetidos ao recozimento de recristalização a uma temperatura de ≈ 350ºC, e também a temperaturas mais baixas de 150 - 250ºC para aliviar as tensões residuais.
As ligas de magnésio são endurecidas ou endurecidas e envelhecidas artificialmente. A uma temperatura de 20 ° C, não ocorrem alterações nas ligas de magnésio endurecidas, ou seja, não estão sujeitas ao envelhecimento natural.
Cobre e ligas de cobre
Tratamento térmico do cobre. A deformação do cobre é acompanhada por um aumento em sua resistência e uma diminuição na ductilidade. Para aumentar a plasticidade, o cobre é submetido ao recozimento de recristalização a 500 - 600ºC, como resultado do qual a plasticidade aumenta acentuadamente e a resistência diminui.
Tratamento térmico do latão. Eles são submetidos apenas ao recozimento de recristalização a 600 - 700ºC (para remover o endurecimento). O latão é resfriado durante o recozimento ao ar ou para acelerar o resfriamento e melhor separação da incrustação na água. Para peças de latão que apresentam tensões residuais após a deformação, em ambiente úmido, o fenômeno de fissuração espontânea é característico. Para evitar isso, as peças de latão são submetidas a um recozimento de baixa temperatura a 200 - 300 C, como resultado das tensões residuais são removidas e o endurecimento permanece. O recozimento a baixa temperatura é especialmente necessário para latões de alumínio, que são propensos a rachaduras espontâneas.
Tratamento térmico de bronzes. Para equalizar a composição química do bronze é submetido à homogeneização a 700 - 750ºC, seguida de resfriamento rápido. Para aliviar as tensões internas, as peças fundidas são recozidas a 550°C. Para restaurar a plasticidade entre as operações de trabalho a frio por pressão, eles são submetidos ao recozimento de recristalização a 600 - 700ºС.
Bronzes de alumínio com um teor de alumínio de 8 a 11%, que sofrem recristalização de fase durante o aquecimento e resfriamento, podem ser endurecidos. Como resultado do endurecimento, a resistência e a dureza aumentam, mas a ductilidade diminui. A têmpera é seguida de revenimento a 400 - 650º C, dependendo das propriedades requeridas. Também sujeito a homogeneização, e produtos semi-acabados deformáveis - recozimento de recristalização a 650 - 800ºC.
O bronze de berílio é endurecido em água a uma temperatura de 760 - 780ºС; neste caso, a fase em excesso não tem tempo para precipitar, e após a têmpera, a liga consiste em uma solução sólida supersaturada e possui baixa dureza e resistência e alta ductilidade. Após a têmpera, o revenimento (envelhecimento) é realizado a 300 - 350ºС por 2 horas. Para aumentar a estabilidade da solução sólida supersaturada e facilitar o endurecimento, os bronzes de berílio são adicionalmente ligados com níquel.
ligas de titânio
As ligas de titânio são submetidas a recozimento por recristalização e recozimento com recristalização de fase, bem como endurecimento por tratamento térmico - têmpera e envelhecimento. Para melhorar a resistência ao desgaste e ao desgaste, as ligas de titânio são submetidas a nitretação, cementação ou oxidação.
O recozimento de recristalização é usado para titânio e ligas para remover o encruamento após o trabalho a frio. A temperatura de recozimento de recristalização é de 520 - 850ºC, dependendo da composição química da liga e do tipo de produto semi-acabado.
O recozimento com recristalização de fase é usado para reduzir a dureza, aumentar a ductilidade, refinamento de grão e eliminar a heterogeneidade estrutural. Aplicar recozimento simples, isotérmico e duplo; temperatura de aquecimento durante o recozimento 750 - 950ºС dependendo da liga.
Durante o recozimento isotérmico, após manter a temperatura de recozimento, as peças são resfriadas a 500 - 650ºС (dependendo da liga) no mesmo forno ou transferidas para outro forno e mantidas por um certo tempo e resfriadas ao ar. Com o recozimento isotérmico, o tempo de recozimento é reduzido e a ductilidade é maior.
No recozimento duplo, as peças são aquecidas até a temperatura de recozimento, mantidas e resfriadas ao ar. Então eu aqueço até 500 - 650ºС novamente, seguro e esfrio no ar. O recozimento duplo, em comparação com o recozimento isotérmico, aumenta a resistência à tração com uma ligeira diminuição da ductilidade e reduz o tempo de processamento.
De todos os tipos de tratamento químico-térmico de ligas de titânio, a nitretação é a mais utilizada, realizada em ambiente de nitrogênio ou em uma mistura de nitrogênio e argônio a temperaturas de 850-950 C por 10-50 horas. Peças feitas de ligas de titânio após nitretação apresentam boas propriedades antifricção.
Conclusão
O tratamento térmico é uma das principais e mais importantes operações do ciclo tecnológico geral de processamento, a qualidade (propriedades mecânicas e físico-químicas) das peças fabricadas de máquinas e mecanismos, ferramentas e outros produtos depende da correta implementação do mesmo. Processos tecnológicos de tratamento térmico de ferros fundidos cinzentos e brancos, ligas de metais não ferrosos foram desenvolvidos e racionalizados.
Uma direção promissora para melhorar a tecnologia de tratamento térmico é a instalação de unidades de tratamento térmico em oficinas mecânicas, a criação de linhas automáticas com a inclusão de processos de tratamento térmico nelas, bem como o desenvolvimento de métodos que melhoram as propriedades de resistência das peças, sua confiabilidade e durabilidade.
Literatura
B.V. Zakharov. V.N. Berseneva "Processos tecnológicos progressivos e equipamentos para tratamento térmico de metais" M. " pós-graduação» 1988
V.M. Zuev "Tratamento térmico de metais" M. Escola superior 1986
BA. Kuzmin "Tecnologia de metais e materiais estruturais" M. "Engenharia" 1981
V.M. Nikiforov "Tecnologia de metais e materiais estruturais" M. "Higher School" 1968
IA Samohotsky N. G. Parfenovskaya "Tecnologia de tratamento térmico de metais" M. Engenharia 1976
A escolha do material e o desenvolvimento do processo tecnológico de tratamento térmico da matriz
Condição de trabalho da matriz, ferramenta de rosqueamento para corte fio externo manualmente ou em uma máquina-ferramenta. Características do aço, suas propriedades químicas, mecânicas e outras. Métodos para monitorar os modos de tratamento térmico e a qualidade do produto.
Grau de aço 18KhGT: aço cromo-manganês contém 0,18% de carbono, até 1% de cromo, manganês. A sequência de operações de tratamento térmico preliminar e final de peças. Modo de operação de tratamento térmico preliminar e final de peças.
Base teórica tratamento térmico do aço. Recozimento por difusão e recristalização. A têmpera é um tratamento térmico no qual o aço adquire uma estrutura fora de equilíbrio e a dureza do aço aumenta. Aplicação do tratamento térmico na prática.
A essência da finalidade do cortador e sua aplicação. Análise de propriedades tecnológicas e composição química de aços rápidos. Etapas do processo tecnológico de tratamento térmico preliminar e de endurecimento, seleção de acessórios, defeitos e sua eliminação.
Fundamentos da tecnologia de tratamento térmico de metais e ligas. O tratamento térmico é uma etapa do processo tecnológico de fabricação de peças. Melhorar a usinabilidade de materiais por pressão ou corte. Formação de propriedades técnicas e elétricas.
Descrição do procedimento de aplicação do endurecimento de aços carbono e determinação da temperatura de endurecimento de acordo com a tarefa. Cálculo do tempo de endurecimento necessário. Nomeação de recozimento e determinação do seu tempo de acordo com a tarefa. Regras de protocolo.
Formação das propriedades do material da peça. Impacto usinagem nas propriedades do material das peças. Influência do fluido de corte (refrigerante).
Decifrando o grau de aço. A natureza da influência do carbono e dos elementos de liga de um determinado aço na posição dos pontos críticos. Seleção e justificação da sequência de operações de tratamento térmico preliminar e final de peças. O modo de tratamento térmico das peças.
Teoria do tratamento térmico. Transformações em aço durante o aquecimento e resfriamento. Recozimento e normalização. Defeitos de tratamento térmico. Defeitos durante o recozimento e normalização. Defeitos de endurecimento. Tratamento químico-térmico e endurecimento superficial do aço.
Teoria e tecnologia do tratamento térmico. Tipos de tratamento térmico. Recozimento, normalização, endurecimento, envelhecimento, melhoria. Tratamento químico-térmico. Os tipos dela. Materiais compostos.
Regras para usinagem de peças por corte - remoção da peça de trabalho usando ferramenta de corte subsídio, trazendo consistentemente sua forma e dimensões para as necessárias, transformando-o em produto pronto. Controle de qualidade de superfície por tratamento químico-térmico.
Familiarização com a metodologia de desenvolvimento do processo tecnológico de tratamento térmico de peças: automóveis, tratores e máquinas agrícolas. Decifrar o grau de um determinado aço, uma descrição de sua microestrutura, propriedades mecânicas antes do tratamento térmico.
Aço grau 20HNR - aço cromo-níquel com teor de carbono de 0,20%, até 1% cromo, níquel e boro. O modo de operação do tratamento térmico preliminar e final das peças é a temperatura de aquecimento e a microestrutura no estado aquecido, o meio de resfriamento.