Niezawodność w technologii. Hartowanie części maszyn. Wybór trybów aluminizacji dla trwałości. Ogólne wymagania. Stal do aluminiowania
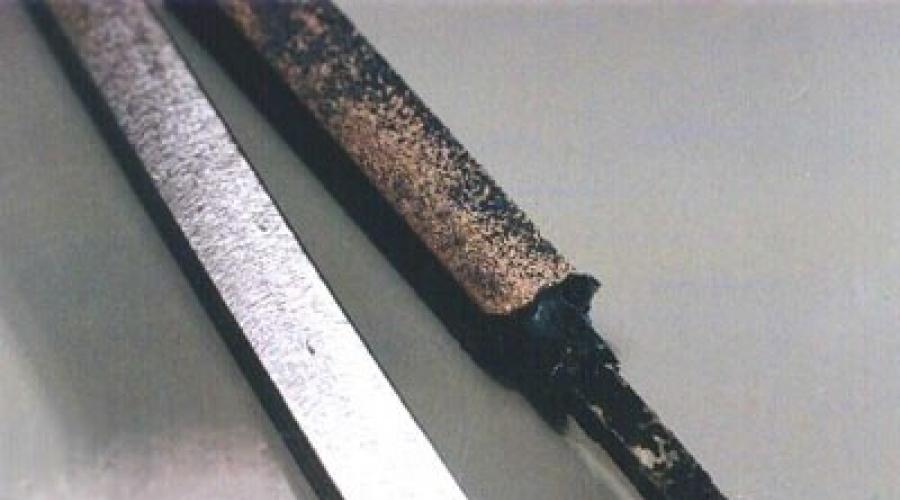
Przeczytaj także
ROZTOPIA
UDC 621.793.6
K. R. Karimova, A. I. Anfinogenov, Ya. B. Chernov, V. V. Chebykin, A. A. Pankratov i B. D. Antonov
DYFUZYJNE WYSYŁANIE W NISKICH TEMPERATURACH STALI I STOPÓW PODCZAS MECHANICZNEJ AKTYWACJI POWIERZCHNI
Streszczenie — Badania wytwarzania aluminidowych powłok dyfuzyjnych na stalach 20, 08Yu, 08Kh18N10T oraz stopach chromowo-niklowych Kh27Yu5T, KhN65VMYuT i Kh15N60-N polegały na mechanicznej aktywacji powierzchni w reaktorze obrotowym w mieszaninach zawierających proszki glinu, chlorku amonu, oraz korund w temperaturach 550–600°C. Określono grubość i skład fazowy powłok aluminidkowych, żaroodporność stali aluminiowanej 08Yu w temperaturze 620 i 912°C oraz stopu KhN65MVTYu w temperaturze 1000°C.
Otrzymane powłoki badano metodą rentgenowskiej analizy fazowej, rentgenowskiej mikroanalizy spektralnej oraz metodą grawimetryczną. Powłoki aluminidkowe na stalach konstrukcyjnych składają się z kolejnych faz, począwszy od warstwy zewnętrznej: ReA13, Re2A15, Re3A1; a także na stalach nierdzewnych z faz: Re2A15, Cr2A1, CrA15, na stopach żaroodpornych z faz: nr A13, nr A1, nr 3A1, Cr2A1, CrA15.
Słowa kluczowe: aluminiowanie termodyfuzyjne, wzrost odporności cieplnej, powłoki aluminidkowe, aktywator chlorkowo-solny.
WPROWADZENIE
Obecnie przemysł stosuje różnorodne powłoki nakładane na powierzchnię produktów w taki czy inny sposób, w zależności od warunków ich eksploatacji. Nasycenie dyfuzyjne pozwala, przy stosunkowo niskich kosztach, tworzyć w warstwy powierzchniowe wytwarza niezbędną strukturę fazową odpowiadającą wymaganym właściwościom i jest jednym z głównych zadań w wspólny systemśrodki chroniące metal przed korozją, zwiększające jego odporność na ciepło i odporność na zużycie. Ponieważ niniejszy artykuł jest pierwszą z serii prac na ten temat, przedstawiamy dalej analizę aktualnego poziomu badań nad powstawaniem powłok dyfuzyjnych, w tym z wpływem aktywacji mechanicznej.
Najbardziej kompletna klasyfikacja dyfuzyjnych procesów nasycenia na podstawie właściwości fizyczne i chemiczne zastosowane podłoże zawierające pierwiastek nasycający zaproponował G.N. Dubinina. Opracowaną i uzupełnioną klasyfikację tych metod przedstawiono w monografii. Zgodnie z tą klasyfikacją, w zależności od rodzaju medium nasycającego, istnieją cztery metody nasycenia dyfuzyjnego: stała, gazowa, cieczowa i gazowo-parowa.
Ta klasyfikacja uwzględnia wszystkie znane sposoby oraz metody technologiczne nasycenie powierzchni metali i stopów różne elementy. Każda z metod powlekania ma swoje zalety i wady. Wszystkie te metody zapewniają albo stworzenie aktywnego ośrodka nasycającego, co jest jednym z niezbędne warunki technologia nasycenia dyfuzyjnego lub dobry kontakt nasycanie składnika powierzchnią części.
Jedną z najskuteczniejszych i najszerzej stosowanych w przemyśle metod zwiększania trwałości wielu krytycznych części jest ich obróbka chemiczno-termiczna (CHT), która wpływa na warstwy powierzchniowe metalu, tj. do tych warstw, w których się koncentrują maksymalne naprężenia, rozwijają się procesy korozji i zużycia. Zaletą powłok dyfuzyjnych uzyskiwanych podczas obróbki chemicznej jest to, że wiązanie pomiędzy nałożonym elementem a chronionym metalem jest najsilniejsze dzięki wzajemnej dyfuzji. stopniowa zmiana Stężenie nałożonego elementu na grubość powłoki zapewnia dobrą przyczepność powłoki do podłoża dzięki płynnej lub skokowej zmianie współczynników rozszerzalności cieplnej faz powłoki, co zapewnia trwałość części przy ostrych wahaniach temperatury.
Najbardziej wszechstronna powłoka metalowa do ochrony przed utlenianiem produktów do różnych celów podczas podwyższonych temperaturach w powietrzu iw niektórych agresywnych środowiskach są powłoki aluminidkowe. Nasycenie powierzchni metali i stopów aluminium nadaje im zwiększoną odporność na zgorzelinę przy wysokie temperatury w wyniku tworzenia się warstewki tlenkowej a-A12O3 na powłoce aluminidkowej i odpowiednio zwiększonej odporności na korozję atmosferyczną.
Istnieje wiele publikacji na temat przygotowania powłok aluminidkowych na temat: różne metale i stopy określonymi metodami. W monografiach przedstawiono wyniki badań nad aluminiowaniem stali, aw książkach wyodrębniono rozdziały dotyczące osadzania powłok aluminidkowych na różnych stalach i stopach. Rozwinięty różne metody aluminiowanie dyfuzyjne: w mediach proszkowych, w kąpielach z roztopionym aluminium, gazie, elektroliza w kąpielach z roztopionym aluminium.
TERMODYFUZJA ZAPEWNIAJĄCA W MIESZANKACH PROSZKOWYCH
Aluminiowanie wyrobów metalowych w mieszankach proszkowych stało się dominujące w przemyśle, zwłaszcza w celu zwiększenia ich odporność na korozję i odporność na ciepło. Do aluminizacji stosuje się różne mieszaniny składające się z proszków aluminium lub żelazoglinu, tlenku glinu, chlorku amonu z dodatkiem pierwiastków stopowych. Aluminiowanie odbywa się w skrzyniach ze stali żaroodpornej w temperaturze 700-1000°C. Jednak aluminiowanie w wysokich temperaturach powoduje szybki wzrost ziarna stali. Aby zmniejszyć zawartość aluminium w powłoce i zmniejszyć jej kruchość, elementy aluminizowane najczęściej poddawane są dodatkowemu wyżarzaniu (normalizacji).
Powikłanie kształt geometryczny a wzrost wielkości szeregu produktów wzbudził zainteresowanie obniżeniem temperatury powierzchniowego utwardzania metali. W temperaturze 500-600°C można znacznie zmniejszyć wypaczenie produktów, zachować właściwości wytrzymałościowe podłoża, zwiększyć żywotność sprzętu, bez obniżania jakości warstwy wierzchniej.
Najbardziej prawdopodobnymi reakcjami aluminizacji są rozkład chlorku amonu na amoniak i chlorowodór, wejście metalicznego glinu w reakcję z chlorowodorem w celu wytworzenia chlorku glinu oraz samoodzyskiwanie glinu do związku glinu o niższej wartościowości. Jednowartościowy chlorek glinu dysproporcjonuje na powierzchni stali, tworząc stop Al-Fe:
MH4a(tv) ^ MH3(g) + HC1(g),
6HC1(ż) + 2A1(s) ^ 2A1C13(ż) + 3H2(ż),
Ryż. 1. Schemat instalacji do nakładania powłok termodyfuzyjnych:
1 - reaktor; 2 - okładka; 3 - rura do pompowania powietrza i zasilania gaz obojętny; 4 - piec; 5 - zawór; 6 - zamek do napełniania proszków stopowych (mieszanina); 7 - mieszanina nasycająca; 8 - szczegóły; 9 - separator; 10 - dodatkowa pojemność; 11 - dodatkowa osłona pojemności; 12 - koło zamachowe zaworu. Węzeł obrotu nie jest pokazany na schemacie.
A1C13(g) + 2A1(telewizja) ^ 3A1C1(g),
3A1C1(g) + 2Fe(ciało stałe) ^ A1C13(g) + 2FeA1(stop).
W literaturze zauważono, że powłoki aluminiowe są bardziej odporne na korozję niż powłoki cynkowe. warunki atmosferyczne, w suchym lub wilgotnym środowisku zawierającym siarkę. Głębokość warstwy aluminiowanej i stężenie w niej aluminium decydują o trwałości części w warunkach pracy. Metoda aluminizacji termodyfuzyjnej, prowadzona w mediach proszkowych, jest najwygodniejsza do nakładania powłok na gwintowane części wyrobów.
W celu poprawy odporności na korozję układów wydechowych wykonanych ze stali konstrukcyjnych silnika wewnętrzne spalanie w środowiskach agresywnych z cyklicznym nagrzewaniem do 600°C, a także zwiększającym odporność cieplną wymienników ciepła i łopatek turbin wykonanych z stale nierdzewne oraz stopów żaroodpornych do 1000°C, przeprowadziliśmy badania osadzania powłok aluminidkowych na stalach 20, 08Yu, 08Kh18N10T oraz stopach Kh27Yu5T, KhN65VMYuT, Kh15N60-N metodą niskotemperaturowego nasycania w mieszaninie (wt. %): aluminium - 2,5, aktywator MN4S1 - 0,5 i elektrokorund - reszta, w temperaturze 550-600°C z mechaniczną aktywacją powierzchni przez 3-5 godzin. Chlorek amonu w tym schemacie pełni rolę dostawcy jonów chlorkowych niezbędnych do zintensyfikowania przechodzenia glinu przez fazę gazową. Siłą napędową procesu aluminizacji jest zmiana energii tworzenia stopu na powierzchni nasycanego materiału.
TECHNIKA EKSPERYMENTALNA
Zastosowaliśmy niskoodpadową metodę nakładania ciągłych dyfuzyjnych, antykorozyjnych, żaroodpornych powłok aluminidowych na powierzchnie metali żelaznych, nieżelaznych i stopów (sprzęt, rury, łopatki turbin i inne wyroby) na instalacji akcja okresowa w atmosferze argonu (rys. 1).
Tabela 1
Skład chemiczny stali i stopów (% wag.)
Stal, stop, GOST Cr N1 Be Mo "Ig A1 T1 Mp 81 C 8 R
Stal 20, Do 0,25 Do 0,25 Baza - - - - 0,35- 0,17- 0,17- Do 0,04 Do 0,04
1050-88 0.65 0.37 0.24
Stal 08Yu, 0,03 0,06 Baza - - 0,02- - 0,20- 0,01 Do 0,07 0,025 0,02
9045-80 0.07 0.35
Stal 17,0- 9,0- Baza - - - 5,0C-<2.0 <0.8 <0.08 <0.02 <0.3
08X18H10T, 19,0 11,0 0,7
Stop 26,0-< 0.6 Основа - - 5.0- 0.15- 0.3 0.6 0.05 0.015 0.02
X27Yu5T, 28,0 5,8 0,4
Stop 15.0-Podstawa<3.0 3.5- 8.5- 1.2- 1.2- <0.5 <0.6 0.05 <0.01 <0.02
KhN65VMYUT 17,0 4,5 10,0 1,6 1,6
Stop 15,0- 55,0- 17,3- - - Do 0,2 Do 0,3 Do 0,2 0,8- Do 0,03 Do 0,2 Do 0,03
Х15Н60-Н, 18,0 61,0 29,2 1,5
Nasycenie termodyfuzyjne prowadzono w szczelnym reaktorze obrotowym 1 przy prędkości 5 obr/min w temperaturze 550–600°C i czasie 3–5 h, w zależności od materiału podłoża i grubości powłoki. Mieszanina nasycająca składała się z proszku aluminiowego PA-4 (0,1–0,2 kg m–2 powierzchni próbki), proszku elektrokorundowego (A1203, 50% objętości reaktora) oraz 0,5% N^0 w stosunku do masy elektrokorundu. Pomimo nieizotermicznego charakteru reaktora, chlorek amonu kondensujący w chłodniejszych częściach reaktora zapewniał niezbędną zawartość chlorków glinu biorących udział w jego przenoszeniu. Po zakończeniu procesu nasycania mieszaninę oddzielono od próbek przez separator 9 do szczelnego pojemnika 10 z otwartym zaworem 5. Następnie rozhermetyzowano reaktor i powleczone próbki wyładowano na powietrze w celu schłodzenia, zużyta mieszanina pozostała w zamkniętym dodatkowym pojemniku, podczas gdy zawór był zamknięty. Kolejną partię próbek załadowano do reaktora w temperaturze procesu, następnie uszczelniono, odpowietrzono i wypełniono argonem. W zużytej mieszaninie po schłodzeniu do 300°C czarny
Proces nasycania aluminium powierzchni stali nierdzewnej i żeliwa nazywamy aluminizacją lub aluminizacją. Głównym celem tego procesu jest zwiększenie odporności na korozję i zgorzeliny stali nierdzewnej.
Materiały do aluminiowania to głównie stal nierdzewna, stal nierdzewna niskowęglowa i żeliwo szare.
Czasami aluminiowanie stosuje się do stali nierdzewnej o średniej zawartości węgla i stali żaroodpornej. W zależności od składu chemicznego stali nierdzewnej można stosować różne rodzaje aluminiowania.
Znane są następujące metody aluminiowania stali nierdzewnej:
- § w mieszankach o charakterze sypkim;
- § stopione aluminium w specjalnych kąpielach;
- § przez metalizację stali nierdzewnej aluminium, a następnie wyżarzanie dyfuzyjne;
- § sole stopione w specjalnych kąpielach;
- § aluminiowanie gazowe.
W przemyśle potrzebne są trzy pierwsze metody aluminizacji. W produkcji znajdują się linie do automatycznego aluminiowania metodą metalizacji części samochodowych. Na przenośniku przednim zawory samochodowe przechodzą stopniowo i obrotowo przez strefę ogrzewania indukcyjnego i są metalizowane aluminium za pomocą pistoletu. W drugiej instalacji indukcyjnej są one nagrzewane dyfuzyjnie do 800 stopni Celsjusza. Osiąga to głębokość warstwy dyfuzyjnej dwie setne milimetra.
Aluminiowanie według pierwszej metody umożliwia uzyskanie wysokiego stężenia aluminium w strefie powierzchniowej warstwy aluminizowanej. Zawartość aluminium w tym przypadku może osiągnąć pięćdziesiąt procent. Im dłużej trwa aluminiowanie stali nierdzewnej lub stali nierdzewnej, tym mniejszy staje się wzrost głębokości warstwy aluminiowania. Optymalna wartość czasu trwania aluminiowania stali nierdzewnej zależy od gatunku stali oraz obecności dodatków pierwiastków chemicznych. Warstwa aluminiowana charakteryzuje się wysoką stabilnością w znacznej temperaturze w kuli nasyconej siarkowodorem.
Utlenione aluminium tworzy ochronny film z tlenku glinu, który zabezpiecza produkt przed dalszym utlenianiem. Podczas pracy odporność produktów aluminizowanych wzrasta 6-7 (przy 1000 °) i do 20 (przy 800 °) razy w porównaniu do wyrobów niealuminiowanych. Jest kilka sposobów.
- 1) Od 1925 r. metoda A stosowana jest w proszkowej mieszaninie równych części aluminium (lub jego stopu z żelazem) i tlenku glinu z 2% amoniakiem. Produkty o powierzchni dokładnie oczyszczonej z tlenków ładowane są do stalowej skrzyni lub bębna obrotowego z mieszanką, gdzie są utrzymywane w temperaturze ok. 950° przez ok. 5 godzin. Następnie wyroby poddawane są wyżarzaniu w temperaturze 900-1000oC, podczas którego aluminium dyfunduje z powierzchni w głąb, w wyniku czego zniszczona zostaje kruchość przesyconej aluminium warstwy wierzchniej. Najnowsza praktyka sowieckich fabryk pokazała, że najskuteczniejsze jest stosowanie proszku żelazoglinowego, bez dodatku tlenku glinu.
- 2) Metoda zanurzeniowa na gorąco w kąpieli z roztopionego aluminium, w której rozpuszcza się około 8% żelaza. Proces prowadzi się w temperaturze 800° przez 40-60 minut. następnie wyżarzanie dyfuzyjne. Dzięki tej metodzie uzyskuje się stosunkowo bardziej kruchą warstwę aluminiowaną.
- 3) Metoda gazowa. Proszek tlenku glinu i ery z 10% amoniakiem umieszcza się na końcu stalowej retorty ogrzanej do 600°; tutaj w strumieniu wodoru, w wyniku reakcji z nim glinu i amoniaku, powstaje lotny chlorek glinu. Z tego lotnego produktu, który reaguje w temperaturze 1000°C z żelazem elementów znajdujących się na drugim końcu retorty, uwalniane jest aluminium w stanie atomowym, dyfundując do warstwy powierzchniowej elementów żelaznych.
Przez kilka stuleci główne właściwości użytkowe metali zmieniały się za pomocą efektów chemiczno-termicznych. Przeprowadzone testy wskazują, że procent niektórych zanieczyszczeń w metalu może wpływać na jego twardość, wytrzymałość, odporność na korozję i wiele innych cech. Aluminiowanie stali węglowej to proces nasycania aluminium warstwy wierzchniej produktu, który zachodzi w określonej temperaturze. Proces aluminiowania stali jest dość skomplikowany, podczas którego instalowane są określone urządzenia. Rozważ cechy pracy nad nasyceniem warstwy wierzchniej stali i żeliwa aluminium.
Zastosowanie aluminizacji
Właściwości związane z produktem w dużej mierze determinują zakres rozważanej technologii obróbki chemiczno-termicznej. W produkcji aluminiowanie stali stosowane jest do zmiany następujących właściwości stali poddanej obróbce:
- Wysoka odporność na skalę. Ta właściwość jest związana z tworzeniem się filmu ochronnego na powierzchni produktu podczas jego podgrzewania.
- Wysoka ochrona przed procesami oksydacyjnymi.
- Wysokie właściwości antykorozyjne. W wyniku aluminizacji produkt może być stosowany nawet w kontakcie z wodą morską.
- Biorąc pod uwagę twardość warstwy wierzchniej należy zwrócić uwagę, że maksymalna osiągalna wartość to około 500HV.
Biorąc pod uwagę zalety i wady aluminiowania stali, należy zauważyć, że działanie wysokiej temperatury powoduje przegrupowanie sieci atomowej, w wyniku czego warstwa wierzchnia staje się krucha.
Podczas obróbki krytycznych części tą metodą chemiczno-termiczną wypalanie trwa kilka godzin. Dlatego proces wprowadzania aluminium charakteryzuje się długim czasem trwania.

Technologia i metody aluminizacji
Aluminiowanie dyfuzyjne odbywa się w temperaturze od 700 do 1100 stopni Celsjusza. Optymalne tryby przetwarzania dobierane są w zależności od właściwości przetwarzanego materiału. Istnieje kilka najpopularniejszych technologii narażenia chemiczno-termicznego:
- Aluminiowanie w mieszankach proszkowych odbywa się za pomocą metalowych skrzynek. Kęs jest umieszczony w solidnym gaźniku. Jednocześnie przygotowaną mieszankę można stosować wielokrotnie, co czyni tę technologię opłacalną. Temperatura stali aluminiowanej w tym przypadku utrzymywana jest w zakresie od 950 do 1050 stopni Celsjusza, proces trwa od 6 do 12 godzin. Maksymalna głębokość penetracji aluminium wynosi 0,5 milimetra. Zastosowana kompozycja jest reprezentowana przez proszek aluminiowy, proszek i niektóre dodatki. Dodatki reprezentowane są przez tlenek glinu i glinę mieloną, a także odmiany chlorkowe amonu i glinu. W niektórych przypadkach zabieg jest opóźniony do 30 godzin, co czyni go nieopłacalnym. Ta metoda ma zastosowanie w przypadku złożonej konfiguracji części, ponieważ etap zmiany powierzchni odbywa się etapami. Zmiana składu warstwy wierzchniej za pomocą mieszanki proszkowej jest najdroższą ze wszystkich stosowanych metod.
- Aluminiowanie metodą natryskiwania odbywa się w przypadku konieczności skrócenia czasu tej operacji. Ta technologia aluminiowania określa wpływ stosunkowo niskiej temperatury, około 750 stopni Celsjusza, penetracja aluminium na głębokość 0,3 milimetra zajmuje około godziny. Zaletą tej metody jest szybkość wykonania, ale nie można jej użyć do uzyskania odpornych na zużycie części krytycznych, ponieważ warstwa powierzchniowa jest bardzo cienka. Przy produkcji masowej zalecane jest nasycenie powierzchni stali. Siła przyczepności natryśniętej warstwy w tym przypadku jest niska, wynosi 0,2-2 kg/mm2. Również cechy tej technologii decydują o wysokiej porowatości struktury.
- Metalizacja, a następnie wypalanie odbywa się po podgrzaniu części do temperatury 900-950 stopni Celsjusza, czas nagrzewania wynosi 2-4 godziny. Ta metoda jest znacznie gorsza od poprzedniej, ponieważ uzyskana warstwa ma grubość nie większą niż 0,2-0,4 milimetra, a koszty wzrastają z powodu znacznego wydłużenia czasu ogrzewania. Jednak często jest stosowany, gdy konieczne jest uzyskanie części o mocnej i twardej powierzchni, która będzie poddawana znacznym obciążeniom. Wynika to z faktu, że przeprowadzone wyżarzanie pozwala na obniżenie wskaźnika kruchości, zwiększając wytrzymałość.
- Aluminiowanie próżniowe polega na nałożeniu powłoki poprzez odparowanie aluminium, a następnie naniesienie go na powierzchnię produktu. Grubość powstałej powłoki jest nieznaczna, ale osiągnięta jakość jest jedną z najwyższych. Do podgrzania medium instalowane są specjalne piece, które są w stanie podgrzać kompozycję wsadu do temperatury 1400 stopni Celsjusza. Wysoką jakość pokrycia uzyskuje się dzięki równomiernemu rozłożeniu aluminium na całej powierzchni. Technologia w tym przypadku przewiduje podgrzanie powierzchni do temperatury od 175 do 370 stopni Celsjusza. Dużo uwagi należy poświęcić wstępnemu przygotowaniu części, ponieważ nawet niewielka warstwa tlenku powoduje znaczne obniżenie jakości przyczepności powierzchni i składu wewnętrznego. Wysoki koszt procesu i jego złożoność decydują o możliwości zastosowania tylko w produkcji części krytycznych.
- Aluminiowanie metodą zanurzania jest bardzo popularne ze względu na fakt, że powłokę nakłada się w ciągu 15 minut. Jednocześnie temperatura jest stosunkowo niska: od 600 do 800 stopni Celsjusza. Ponadto ta metoda jest jedną z najtańszych pod względem kosztów. Istotą zabiegu jest zanurzenie obrabianego przedmiotu w płynnym aluminium rozgrzanym do wysokiej temperatury. Daje to warstwę o grubości od 0,02 do 0,1 mm. Szczególną uwagę przywiązuje się do przygotowania środowiska, w którym będzie prowadzony proces zmiany składu chemicznego warstwy wierzchniej.

Istnieją inne metody wprowadzania aluminium, które pozwalają na zmianę podstawowych parametrów obrabianych przedmiotów.
Do kontroli jakości powierzchni za pomocą defektoskopu - urządzenia, które służy do sprawdzania wad za pomocą badań nieniszczących.
Najczęstsze wady to naruszenia jednorodności struktury, pojawienie się strefy uszkodzenia korozyjnego, odchylenie wymaganego składu chemicznego i tak dalej.

Materiały dopuszczone do aluminizacji
Metalizacja to technologia, która ma na celu zmianę właściwości warstwy wierzchniej. Odmianą tej technologii jest aluminiowanie. Nasycenie warstwy wierzchniej poddaje się:
- Stale węglowe. W tym przypadku stosuje się głównie stale niskowęglowe, rzadziej stale średniowęglowe. Przy wysokiej zawartości węgla w składzie zabieg staje się nieskuteczny.
- Stale stopowe są używane rzadziej, ale dzięki odpowiedniej technologii można uzyskać części odporne na zużycie.
- Żeliwo można również poddać procesowi aluminiowania, aby zmienić jego podstawowe właściwości.
Aby uzyskać stal nierdzewną, aluminiowaniu poddaje się zarówno stale węglowe, jak i stopowe. W niektórych przypadkach przeprowadza się wstępne przygotowanie stali i stopów, reprezentowane przez hartowanie lub inne procedury obróbki chemiczno-termicznej.
Jeśli znajdziesz błąd, zaznacz fragment tekstu i naciśnij Ctrl+Enter.
stankiexpert.ru
Technologia procesu aluminiowania
Zastosowanie przemysłowe znalazły trzy metody aluminizacji: w stałych mieszaninach proszkowych, w kąpielach z roztopionym aluminium oraz metoda metalizacji powierzchniowej aluminium z następowym wyżarzaniem dyfuzyjnym.
Możliwe jest również aluminizowanie w próżni przez osadzanie z fazy gazowo-parowej, elektrolityczne w kąpielach składających się z soli glinu, a także aluminizowanie gazowe, w którym wodór jest przepuszczany przez stałe mieszaniny zawierające glin.
Aluminiowanie w mieszaninach stałych odbywa się w szczelnych pojemnikach przy użyciu proszku aluminiowego (49-50%) lub żelazoglinu (50-99%) z dodatkami tlenku glinu (przy zastosowaniu FeAl dodatek Al2Oz jest opcjonalny, ponieważ proszek prawie nie jest podlegający spiekaniu) i NH5Cl (1 -2%).
Reakcje chemiczne zachodzące w takim pojemniku są zbliżone do reakcji podczas chromowania:
MH4Cl=NH3+HC1;
6HC1 + 2A1 = 2A1C1z + ZH2;
A1C1z+2A1=3A1C1;
A1C1z \u003d A1C1 + Cl2.
Uważa się, że powstały podchlorek glinu A1C1 tworzy atomowy glin przez samoregenerację na powierzchni stali.
ZA1C1 \u003d A1C1z + 2A1.
Jednak reakcja wymiany typu
А1С1з + Fe (produkt) = FeС1з + А1.
Za optymalną temperaturę procesu uważa się 950-1050 ° C. Proces jest dość długi i w zależności od wymaganej głębokości wynosi 4-30 godzin.
W celu zmniejszenia kruchości warstwy po takim aluminizacji przeprowadza się niekiedy wyżarzanie dyfuzyjne w temperaturze 800-1000°, w wyniku czego zawartość aluminium w warstwie wierzchniej spada do 20-30% przy wzroście całkowitej głębokości warstwy warstwa.
Metoda zanurzania produktów w kąpieli stopionego aluminium wyróżnia się wysoką wydajnością.
Proces prowadzi się w temperaturze 700-800°, warstwa o grubości 0,02-0,1 mm powstaje już w ciągu 1-15 minut. Jednak przy całej swojej prostocie i krótkim czasie trwania metoda ta ma szereg wad: 1) zwiększona kruchość warstwy, którą należy również wyeliminować poprzez wyżarzanie dyfuzyjne; 2) korozja i rozpuszczanie produktów w roztopionym aluminium; 3) niska trwałość tygli; 4) miejscowe przyklejanie się folii aluminiowej i tlenku glinu do części; 5) nierównomierne nasycenie; 6) utlenianie żelaza podczas nurkowania.
To prawda, że istnieje szereg środków poprawiających jakość aluminiowania w wannach. Dodanie do kąpieli 8-12% Fe lub 20-22% Ni zmniejsza intensywność rozpuszczania i korozji części.
Udoskonalono również metodę poprzez zastosowanie topników, co ogranicza korozję (nagrzewanie odbywa się w warstwie topnika), chroni stopiony materiał przed utlenianiem, poprawia zwilżanie, a tym samym sprzyja tworzeniu się warstwy bardziej jednolitej na głębokości i ułatwia powierzchnię czyszczenie z zanieczyszczeń, gdy części w warstwie topnika są wstrząśnięte. Jako topniki stosuje się kompozycje zawierające NaCI, HC1, LiCI, ZnCl2, A1Fz, NaF, Na3AlF6 w różnych proporcjach.
Podczas aluminiowania blach i drutów stalowych rozważaną metodą wyżarzanie prowadzi się w piecach ciągłych w atmosferze redukującej zdysocjowanego amoniaku przed załadowaniem do kąpieli. W takim przypadku wszystkie warstwy tlenków są usuwane, a powierzchnia stali jest skutecznie zwilżana przez roztopione aluminium.
Aluminiowanie metodą metalizacji odbywa się w kilku etapach. Na wstępnie oczyszczoną powierzchnię nakłada się warstwę aluminium o grubości 0,8-1,2 mm (piaskowanie, obróbka wiórami metalowymi w celu oczyszczenia i wytworzenie zwiększonej chropowatości w celu zwiększenia przyczepności powłoki i metalu podstawowego). Proces powlekania polega na topieniu metalu i natryskiwaniu go strumieniem sprężonego powietrza pod ciśnieniem 2-4 atm za pomocą specjalnych metalizatorów (gazowych, elektrycznych lub wysokiej częstotliwości). Daje to porowatą warstwę o niskiej przyczepności. Następnie powierzchnia jest pokrywana związkami ochronnymi (srebrny grafit, glina ogniotrwała, piasek kwarcowy, płynne szkło itp.) w celu ochrony przed utlenianiem podczas późniejszego wyżarzania dyfuzyjnego. Wyżarzanie odbywa się w temperaturze 900-1100 ° z podgrzewaniem i powolnym chłodzeniem. Ta metoda jest dość ekonomiczna i może konkurować z innymi metodami.
§ 17. Struktura warstwy aluminiowanej i wpływ różnych czynników na wyniki procesu
Struktura i skład fazowy warstwy aluminizowanej zależą od metody aluminizacji. Zawartość aluminium na powierzchni może sięgać ~50% w przypadku stosowania stałych mieszanin, a nawet 75-80% w przypadku metalizacji z późniejszym wyżarzaniem.
Zgodnie z diagramem Fe-A1 (patrz ryc. 32) w tym przypadku na powierzchni tworzą się związki międzymetaliczne Fe3A1, FeAl, FeAl2 itp. Te fazy, a także stały roztwór glinu w żelazie przylegające do rdzenia, przy zwykłym trawieniu ujawniają się w postaci lekkiej nietrawionej strefy. Podczas aluminiowania w roztopionym aluminium granica warstwy ma kręty charakter przypominający igłę.
Wynika to ze specyfiki fazy Fe2Al5 z rombową siatką utworzoną na powierzchni. Szybkość dyfuzji aluminium w tej fazie jest maksymalna i inne fazy nie powstają w tej metodzie.
Ryż. 33. Zmiana stężenia aluminium i węgla w aluminiowanej warstwie stali o 0,4% C (skład fazowy podano dla temperatury dyfuzji)
Cechy struktury krystalograficznej tej fazy są takie, że dominuje dyfuzja w kierunku prostopadłym do powierzchni, co odpowiada za iglastokierunkowość kryształów tej fazy.
W przypadku obecności węgla w stali, za strefą fazy a często obserwuje się strefę o wysokiej zawartości węgla (rys. 33), ale nie zawsze tak się dzieje. Brak strefy w stalach o zawartości powyżej 0,7% C tłumaczy się tworzeniem charakterystycznej dla układu Fe-A1-C fazy ε. Ponadto wysokie stężenie węgla może prowadzić do tworzenia igiełkowatych wtrąceń węglika Al4C3 w warstwie powierzchniowej.
Wzrost zawartości węgla zmniejsza głębokość warstwy aluminizowanej (rys. 34a). Na ryc. 34,6 pokazuje dla porównania, o ile bardziej intensywny jest proces aluminizacji w stopionym aluminium w porównaniu z mieszaniną proszków.
Dane dotyczące wpływu pierwiastków stopowych na wyniki aluminizacji są dość sprzeczne. Jednak przez analogię do wpływu pierwiastków na wzrost warstwy chromowanej można stwierdzić, że w stalach bezwęglowych tempo wzrostu będą redukowane przez te pierwiastki, które stabilizują fazę γ.
Przeczytaj w tej samej książce: Przez odejmowanie otrzymujemy | Nawęglacze do nawęglania | Stale do nawęglania | Rozdział 3. AZOTOWANIE STALI | Technologia azotowania | Stale poddane azotowaniu | Właściwości stali azotowanej | Azotonawęglanie w wysokiej temperaturze | Niskotemperaturowe azotonawęglanie | Cyjanizacja stali mybiblioteka.su - 2015-2018. (0,054 s)
mojabiblioteka.su
Aluminiowanie stali - Podręcznik chemika 21
Aluminiowa stal węglowa. ...................500-600
Metalizacja stosowana jest również w celu zwiększenia odporności cieplnej stali poprzez aluminiowanie (puszki do nawęglania, osłony termopar itp.), do nakładania powłok dekoracyjnych, do zabezpieczania wyrobów przed nawęglaniem podczas nawęglania itp.
Czyste aluminium jest używane do pokrywania stali, aby poprawić jej odporność na korozję. W tym celu stosuje się również aluminiowanie - nasycenie powierzchni stali aluminium do głębokości 0,02-1,2 mm, w wyniku czego powstaje gęsty i trwały film antykorozyjny.
Aluminiowanie. Proces aluminizacji polega na nasycaniu aluminium powierzchni elementów stalowych. Podczas aluminiowania części są pakowane w pudełka z mieszaniną 48% aluminium, 48% tlenku glinu i 2% amoniaku, a następnie inkubowane od 5 do 15 godzin. w temperaturach od 900 do 1050°C. Stalowa powierzchnia nasycona aluminium ma wysoką odporność termiczną.
B - w 600°C w gorących gazach zawierających 8O2 i parę wodną. Aluminiowanie chroni stal przed korozją w gorących gazach zawierających 80 g.
Takie powłoki na stalach węglowych i stopowych obejmują powłoki na bazie aluminium, kadmu i cynku. C1 ma szerokie zastosowanie w różnych gałęziach techniki, ponieważ niezawodnie zabezpiecza wyroby metalowe przed korozją i zniszczeniem korozyjno-mechanicznym. Aluminiowanie jako metoda ochrony antykorozyjnej nie znalazło jeszcze dostatecznej dystrybucji, chociaż w wielu agresywnych środowiskach, zwłaszcza zawierających związki siarki, jest skuteczniejsze niż cynkowanie.
Zbadaliśmy wpływ cynkowania dyfuzyjnego i różnych metod aluminizacji na wytrzymałość zmęczeniową stali węglowych.
Potencjał stacjonarny stali aluminizowanych wynosi -(915 920) mV (patrz rys. 100), tj. 350-370 mV bardziej ujemny niż stale niepowlekane. Jednak po 4 dniach testów potencjał stali 20 przesuwa się w kierunku dodatnim do około -540 mV. Potencjalne przesunięcie stali aluminiowanej 45 występuje z mniejszą intensywnością i po 12 dniach osiąga (-680) -b (-690 mV). Powodem potencjalnego przesunięcia jest intensywne rozpuszczanie się warstwy aluminium. Stal pozostaje jednak chroniona przed wpływem środowiska warstwą związku międzymetalicznego, którego potencjał jest bardziej dodatni niż stali i wynosi -(530-540) mV. Tak więc warstwy ochronne otrzymane przez aluminiowanie w płynie działają najpierw jako anoda, a następnie jako powłoka katody.
W warunkach zmęczenia korozyjnego przy wysokich poziomach naprężeń cyklicznych charakter zmiany potencjału elektrody i kinetyka niszczenia stali aluminiowanych są podobne do obserwowanych w stalach ocynkowanych. Przy obciążeniu próbek aluminizowanych mniejszymi obciążeniami cyklicznymi dochodzi do intensywnego korozyjno-zmęczeniowego zniszczenia warstwy aluminiowej, a ponadto warstwa międzymetaliczna i stal znajdują się w ochronie katodowej w wyniku anodowego rozpuszczania się warstwy aluminiowej. Po przesunięciu potencjałów próbek do (-54) (-550 mV) w wyniku całkowitego rozpuszczenia warstwy aluminium, niszczenie powstającej układowej warstwy międzymetalicznej – stal przebiega podobnie jak niszczenie stali z powłokami katodowymi.
Chromowanie dyfuzyjne przebiega wolniej niż aluminiowanie. Na powierzchni produktu tworzy się nie tylko odporna chemicznie, ale również warstwa złożonych węglików, wytrzymała w wysokich temperaturach. Do chromowania stosuje się mieszankę składającą się z 60% proszku metalicznego chromu, 36% tlenku glinu lub kaolinu i 4% amoniaku, w której umieszcza się chromowaną część. Proces przeprowadza się w temperaturze około 1000 °C. W ciągu 25-30 godzin na powierzchni części ze stali niskowęglowej tworzy się warstwa chromu o grubości od 0,05 do 0,1 mm.
Głównymi metodami ochrony przed korozją gazową są stopowanie metali, tworzenie powłok ochronnych oraz zastępowanie agresywnego środowiska gazowego. Do produkcji urządzeń narażonych na działanie gazów korozyjnych stosuje się stopy żaroodporne. Aby nadać odporność cieplną stali i żeliwa, w ich składzie stosuje się również chrom, krzem, aluminium, stosuje się również stopy na bazie niklu lub kobaltu. Ochrona przed korozją gazową odbywa się dodatkowo poprzez nasycenie powierzchni produktu w stanie gorącym niektórymi metalami, które mają działanie ochronne. Metale te obejmują aluminium i chrom. Ochronne działanie tych metali wynika z tworzenia na ich powierzchni bardzo cienkiej, ale mocnej warstwy tlenku, która zapobiega oddziaływaniu metalu z otoczeniem. W przypadku aluminium metoda ta nazywana jest aluminiowaniem, w przypadku chromu termochromowaniem. Do ochrony stosuje się również powłoki niemetaliczne wykonane z materiałów ceramicznych i ceramiczno-metalowych (cermetali).
W celu zwiększenia odporności kominów węglowych na utlenianie zaleca się ich aluminiowanie. Według Instytutu Rur odporność rur aluminiowanych na utlenianie w porównaniu z niepowlekanymi rurami ze stali węglowej jest 30-50 razy wyższa do 800°, 10 razy wyższa do 900°, 5 razy wyższa do 1000°.
Do uzyskania 1 kg NH metodą R. Alberta i I. Mahe stosuje się naczynie wykonane ze stali niskowęglowej, zabezpieczone od zewnątrz przed bezpośrednim działaniem płomienia mankietem ze stali aluminiowanej. Górna część naczynia i jego płaska pokrywa, wzmocniona gumowym pierścieniem, są chłodzone wodą. Naczynie wyposażone jest w boczne rurki do przepuszczania wodoru, podłączenie do układu próżniowego i wprowadzenie termopary. Wewnątrz naczynia znajdują się dwa cylindryczne tygle, z których jeden ściśle przylega do drugiego,
Podobnie jak w przypadku aluminizacji, podczas podgrzewania wyrobów stalowych w odpowiednich mieszankach proszków, przeprowadza się chromowanie i silikonowanie stali. Podczas chromowania (w temperaturze 1050-1150 °C) warstwa wierzchnia stali jest nasycana chromem, w wyniku czego wzrastają właściwości antykorozyjne stali niskowęglowych, a twardość i odporność na ścieranie wysokowęglowych stale wzrastają. Silikonizacja (w temperaturze 1100-1200°C) nasyca warstwę wierzchnią krzemem, co zwiększa kwasoodporność stali.
Na bazie aluminium metodą metalurgii proszków powstają spiekane stopy aluminium, które wyróżniają się wysoką odpornością cieplną. A. służy do odtleniania stali, produkcji niektórych metali metodą aluminotermii, materiałów wybuchowych, a także w materiałach kompozytowych na różnych podłożach. Zobacz także brąz aluminiowy. Mosiądz aluminiowy. Żeliwo aluminiowe, aluminiowanie, aluminiowanie.
Aluminiowanie dyfuzyjne (aluminiowanie). Aluminiowane stale niestopowe są szeroko stosowane zamiast żaroodpornych stali wysokostopowych.
Wieloletnie badania rur z różnymi powłokami dyfuzyjnymi – borowaniem, aluminiowaniem i aluminiowaniem chromowym – wykazały, że nie zwiększają one odporności korozyjnej rur wykonanych ze stali 12Kh1MF podczas pracy w dolnej części radiacyjnej oraz w przegrzewaczu wytwornic pary. Podany wynik uzyskano w wytwornicach pary z różnymi rodzajami paliwa – siarkowym olejem opałowym, miałem antracytowym i estońskim łupkiem.
Aluminiowanie płynne lub, jak to się nazywa, aluminiowanie nie miało zauważalnego wpływu na granicę wytrzymałości próbek ze stali 45 w powietrzu i zwiększyło warunkową granicę wytrzymałości korozyjnej próbek w 3% roztworze Na I z 50 do 160 MPa. Podobna wyższa
W praktyce 3. od do szeroko stosuje się powierzchowne stopowanie niedrogich stopów o dobrej sierści. cechy. Warstwę wierzchnią ze zwykłej stali można przerobić na stop o wysokiej odporności na korozję przez ogrzewanie w proszku zawierającym Zn (cynkowanie dyfuzyjne). A1 (aluminiowanie) lub Cr (chromowanie), czasem ze specjalnym. dodatki aktywujące. Możliwe jest również pokrycie taniego materiału o małej wytrzymałości cienką warstwą materiału bardziej odpornego na korozję, na przykład poprzez wspólne walcowanie na gorąco dwóch blach do pożądanej grubości powstałego bimetalu.
Z natury zmiany w chemii. skład detalu l.-t. o, można podzielić na nasycanie dyfuzyjne niemetalami lub metalami oraz usuwanie dyfuzyjne pierwiastków (najczęściej węgiel w środowisku słabo utleniającym lub wodór w próżni). Odmiany H.-t. o. cementacja-saturacja Ch. przyb. wyroby hutnicze azotowanie węgla - nasycanie azotem stali, stopów na bazie tytanu i metali ogniotrwałych utlenianie-utlenianie warstw wierzchnich stopów aluminium i magnezu cyjanowanie i węgloazotowanie - jednoczesne nasycanie węglem i azotem wyrobów stalowych (cudowne) wg. z soli stopionych i borowania w fazie gazowej - nasycanie borem wyrobów stalowych, stopów na bazie Ni, Co i ogniotrwałej metasilikonizacji - nasycanie aluminiowaniem krzemowym - nasycanie aluminium Ch. przyb. stale, rzadziej żeliwa i stopy na bazie Ni i Co, chromowanie i nasycanie cynkiem stali wg. miedziowanie chromem i cynkiem - nasycanie miedzią wyrobów stalowych. Ze wszystkich typów H.-t. o. Naib, nasycanie stali węglem i azotem jest szeroko stosowane. Węgiel i azot szybko dyfundują do żelaza, tworząc roztwory stałe, fazy węglika i azotku, które różnią się znacznie pod względem fizycznym i chemicznym. St. ty z żelaza.
Nasycenie dyfuzyjne stali aluminium to jedna z najbardziej niezawodnych metod ochrony przed tlenem w wysokich temperaturach. Produkty aluminiowane mogą być stosowane zamiast stali żaroodpornych.
W celu ochrony stali przed utlenianiem stosuje się metody termodyfuzyjne do utwardzania powierzchni metali (chromowanie, aluminiowanie, silikonowanie).
chem21.info
Proces - aluminiowanie - The Big Encyclopedia of Oil and Gas, artykuł, strona 2
Proces - aluminizacja
Strona 2
Proces aluminizacji nie nastręcza trudności zarówno sprzętowych, jak i opanowania technologii procesu.
Proces aluminizacji w stopionym aluminium przebiega w temperaturze 660 - 750 C.
Proces aluminizacji jest również stosowany do poprawy odporności na utlenianie stali nierdzewnych.
Proces aluminizacji polega na nasycaniu powierzchni części stalowych aluminium, co znacznie zwiększa ich odporność cieplną.
Proces aluminiowania stopów niklu w mieszaninie proszkowej składającej się z 98% żelazoglinu [50% (wagowo) A1] i 2% MH4C1 badano w [20, s. Nasycanie przeprowadza się w szczelnie zamkniętych pojemnikach w temperaturze 950 C; powstaje w wyniku dysproporcjonowania chlorków glinu i reakcji wymiany między nimi a glinem. Dopóki faza ta znajduje się na powierzchni i nie rozpuszcza się w wyniku wzajemnej dyfuzji składników stopu, tworzy się warstwa tlenku glinu, która chroni podłoże przed utlenianiem. Wraz z rozpuszczeniem się fazy Ni3Al rozpoczyna się intensywne utlenianie stopów. Aluminiowanie według tej technologii chroni stopy niklu przed utlenianiem w temperaturach 950 - 1000 C przez kilka tysięcy godzin.
Chociaż proces aluminizacji, jako jedna z metod obróbki chemiczno-termicznej metali, jest dosyć dobrze znany i stosowany do metali żelaznych, to jednak nie został wystarczająco zbadany w stosunku do miedzi i jej stopów.
Chemia procesu aluminizacji może być.
W procesie aluminizacji produkty są podgrzewane do wysokiej temperatury w środowisku zawierającym aluminium. W tym przypadku warstwa wierzchnia jest nasycana aluminium w wyniku procesu dyfuzji termicznej.
Do realizacji procesów aluminiowania opracowano projekt aluminiizatora wykonanego z UKM. Głównymi elementami aluminizatora są kuwety, do których wsypuje się wsad oraz kraty, na których umieszczane są detale. Na elementy aluminiatora stawiane są dość wysokie wymagania dotyczące sztywności i wytrzymałości. Uwzględniono technologiczne cechy procesu wytwarzania elementów aluminiatora.
Pod koniec procesu aluminiowania przeprowadza się wyżarzanie dyfuzyjne przez 3-5 godzin, co jest konieczne do wyeliminowania kruchości warstwy zewnętrznej.
W odniesieniu do procesu aluminizacji technologia, warunki i tryby nakładania powłok mają szereg cech.
W artykule omówiono proces aluminizacji niklu oraz przedstawiono wyniki badań składu fazowego warstw aluminizowanych na niklu i stopach niklu. Po wystawieniu na działanie powietrza w atmosferze utleniającej o temperaturze 950, na aluminiowanej powierzchni tworzy się tlenek glinu a - A12O3, który chroni próbkę przed utlenianiem do momentu rozpuszczenia warstw międzymetalicznych pod warstwą tlenku, dzięki przeciwdyfuzji aluminium i niklu, międzymetaliczne warstwy: Sh2A13, NiAl, NisAl. Na aluminiowanych stopach żaroodpornych, w przeciwieństwie do aluminiowanego niklu, pod warstwami związków międzymetalicznych układu Ni - Al nie występuje jednofazowy roztwór stały, lecz warstwa heterofazowa o wysokiej twardości, składająca się ze związku Ni3Al i faza rozproszona, która powstaje, gdy podwarstwa jest zubożona w nikiel. Nikiel z podwarstwy przechodzi do powstania związków międzymetalicznych Ni - Al pokrywających próbkę. Obecność w wysokotemperaturowych stopach niklu stałego roztworu nasyconego glinem oraz wzmacniającej fazy rozproszonej Ni3AI jest przyczyną względnej równowagi termodynamicznej między składem fazowym warstwy aluminizowanej a składem fazowym stopów. O właściwościach ochronnych warstwy i jej trwałości decyduje obecność na powierzchni cienkiej warstwy tlenku glinu. Warstwa Ni3Al i NiAl, pokryta tlenkiem glinu a - A1203, z podwarstwą Ni3Al, w której rozproszona jest druga faza, jest przechowywana na żaroodpornych stopach niklu w temperaturze 950 przez kilka tysięcy godzin.
www.ngpedia.ru
Alitizing - Podręcznik chemika 21
Dobrą odporność na korozję siarkowodorową uzyskuje się poprzez aluminiowanie stali węglowej i chromowej (z zawartością 7% Cr) ze stopu.Nasycenie dyfuzyjne powierzchni stali aluminium służy głównie do zwiększenia odporności cieplnej stali, w środowiskach utleniających, a zwłaszcza zawierających siarkowodór. Stal aluminiowana w temperaturach 500-600 ° C z powodzeniem konkuruje ze stalą nierdzewną chromowo-niklową typu 18-8 w środowiskach zawierających siarkowodór. Aluminiowanie wpływa na wytrzymałość stali w różny sposób w zależności od grubości warstwy. W ten sposób aluminiowanie proszkowe na głębokość 0,1-0,2 mm znacznie zmniejsza wytrzymałość stali i praktycznie nie ma wpływu na zmęczenie korozyjne. Aluminiowanie na głębokość 0,04-0,05 mm nieznacznie wpływa na granicę zmęczenia stali i ponad dwukrotnie zwiększa warunkową granicę zmęczenia korozyjnego. Warstwa aluminiowana zmniejsza również wpływ koncentratorów naprężeń, szczególnie w środowisku korozyjnym.
Czyste aluminium jest używane do pokrywania stali, aby poprawić jej odporność na korozję. W tym celu stosuje się również aluminiowanie - nasycenie powierzchni stali aluminium do głębokości 0,02-1,2 mm, w wyniku czego powstaje gęsty i trwały film antykorozyjny.
I,) istnieją również metody aluminiowania na gorąco, które polegają na tym, że części są zanurzane w kąpieli topnikowej, a następnie w roztopionym aluminium w temperaturze 770-800 ° C.
Bardzo obiecujące jest również aluminiowanie - nasycenie powierzchni metalu aluminium do głębokości 0,02-1,2 mm, w wyniku czego powstaje gęsty i trwały film antykorozyjny.
Ważnym obszarem zastosowania A1 jest jego zastosowanie do nasycania (aluminowania) powierzchni wyrobów żelaznych i stalowych, w celu nadania im odporności cieplnej i ochrony przed korozją. Najwyższą wartością pod tym względem jest A1 o wysokiej czystości.
Bardzo ważne jest stosowanie aluminium do aluminiowania - nasycanie powierzchni wyrobów stalowych lub żeliwnych aluminium w celu ochrony ich przed utlenianiem po podgrzaniu do 900 ° C. Aluminiowanie odbywa się poprzez zanurzenie produktu w roztopionym aluminium lub częściej przez ogrzewanie produktu mieszaniną sproszkowanego aluminium i tlenku glinu (1P). W tym przypadku aluminium wnika w warstwę powierzchniową produktu, tworząc z żelazem stały roztwór.
Na ryc. 79 przedstawia wpływ czasu trwania i temperatury aluminizacji na grubość warstwy aluminizowanej stali gatunku 10, a na ryc. 80 - rozkład stężenia glinu w żelazie na głębokości warstwy po aluminizacji w mieszaninie proszkowej.
Metoda termodyfuzji jest szeroko stosowana do otrzymywania żaroodpornych powłok z aluminium (aluminiowanie), krzemu (krzem
Metoda termodyfuzji jest szeroko stosowana do otrzymywania żaroodpornych powłok z aluminium (aluminiowanie), krzemem (krzemowanie), chromem (chromowanie), tytanem (tytanizowanie). Powłoki żaroodporne umożliwiają połączenie wysokiej odporności cieplnej materiału bazowego z wysoką odpornością cieplną warstwy wierzchniej.
Wśród innych metod obróbki zwracamy uwagę na aluminiowanie - nasycenie powierzchni wyrobów stalowych i żelaznych metalem aluminiowym, co nadaje im odporność cieplną.
Żelazo > 99,9 Pa Żelazo aluminiowane
Aluminiowanie na gorąco stosowane jest w produkcji taśm stalowych w sposób ciągły. Stal aluminiowana ma odporność na korozję aluminium i wytrzymałość blachy stalowej. Powierzchnia blach aluminiowanych to srebro matowe. Tol-
Blachy aluminiowane charakteryzują się odpornością na korozję w atmosferze, wodzie oraz produktach spalania paliw w wysokich temperaturach. Zaleca się łączenie tych blach metodą zgrzewania punktowego,
Głównymi metodami ochrony przed korozją gazową są stopowanie metali, tworzenie powłok ochronnych oraz zastępowanie agresywnego środowiska gazowego. Do produkcji urządzeń narażonych na działanie gazów korozyjnych stosuje się stopy żaroodporne. Aby nadać odporność cieplną stali i żeliwa, w ich składzie stosuje się również chrom, krzem, aluminium, stosuje się również stopy na bazie niklu lub kobaltu. Ochrona przed korozją gazową odbywa się dodatkowo poprzez nasycenie powierzchni produktu w stanie gorącym niektórymi metalami, które mają działanie ochronne. Metale te obejmują aluminium i chrom. Ochronne działanie tych metali wynika z tworzenia na ich powierzchni bardzo cienkiej, ale mocnej warstwy tlenku, która zapobiega oddziaływaniu metalu z otoczeniem. W przypadku aluminium metoda ta nazywana jest aluminiowaniem, w przypadku chromu termochromowaniem. Do ochrony stosuje się również powłoki niemetaliczne wykonane z materiałów ceramicznych i ceramiczno-metalowych (cermetali).Aluminiowanie dyfuzyjne małych przedmiotów odbywa się w podobny sposób, ale w temperaturze ok. 1000°C. Powłoki oprócz tego, co zostało powiedziane, są odporne na produkty spalania w wysokich temperaturach. Aluminiowanie dyfuzyjne rur lub dużych przedmiotów odbywa się w następujący sposób. W pierwszej kolejności czyszczona jest powierzchnia produktu (najlepiej przez śrutowanie), natryskiwana jest warstwa aluminium i kilka warstw płynnego szkła, a następnie utrzymywane w temperaturze 900-1050°C przez 2-4 godziny. tworzy warstwę ochronną, pod którą aluminium dyfunduje do stali. Rury z takimi powłokami stosowane są w wymiennikach przeznaczonych do pracy w środowisku dwutlenku siarki, siarkowodoru, produktów spalania itp.
Głównymi środkami do zwalczania korozji w nieelektrolitach jest stosowanie materiałów odpornych na korozję, takich jak stale nierdzewne i aluminiowane itp. W większości przypadków proces korozji elektrochemicznej zachodzi również w oleju, co umożliwia stosowanie inhibitorów i ochrona ochraniacza.
Ważne jest, aby do aluminiowania stosować aluminium, które polega na nasycaniu powierzchni wyrobów stalowych lub żeliwnych aluminium w celu ochrony materiału bazowego przed utlenianiem podczas silnego nagrzewania. W metalurgii tlenek glinu jest używany do produkcji wapnia, baru, litu i niektórych innych metali metodą aluminotermii (patrz 192).
Stale chromowe aluminiowane mogą znacznie rozszerzyć zakres ich zastosowania w podwyższonych temperaturach w środowiskach agresywnych zawierających siarkowodór. Odporność na korozję stali aluminizowanych z 3% chromem w czystym siarkowodorze w temperaturze 500-550 °C jest wyższa niż odporność na korozję stali 12Kh18N10T. Do produkcji wężownic pieców rurowych, a także rurociągów komunikacyjnych i wiązek rurowych wymienników ciepła w Stanach Zjednoczonych i niektórych innych krajach, zamiast rur wykonanych z drogiego typu stosuje się rury aluminiowe wykonane ze stali 15X5M na skalę przemysłową lub eksperymentalną Stal 18-8. Doświadczenie potwierdza wykonalność takiej materialnej substytucji.
W celu poprawy niezawodności pieców rurowych w warunkach zwiększonej korozji wanadowo-siarkowej zaleca się mocowanie rur promieniujących i rusztu konwekcyjnego ze stali 25Kh23N7SL ze wstępnym aluminiowaniem. Ponadto znaczne ograniczenie korozji wanadowo-siarczkowej można osiągnąć wprowadzając do strumienia gazu pył dolomitowy lub wprowadzając do oleju opałowego dodatek VTI-4st (39).Według danych Ogólnounijnego Instytutu Techniki Cieplnej nazwany na cześć FE pozwala
Powłoki dyfuzyjne (aluminiowanie) uzyskuje się przez obróbkę bębnową w atmosferze wodoru w temperaturze około 1000 ° C w mieszaninie proszku aluminiowego, AljOa i niewielkiej ilości Nh5 1. Otrzymuje się powierzchniowy stop aluminium z żelazem, który zapewnia odporność zarówno na utlenianie w wysokiej temperaturze w powietrzu (do 850-950 °C), jak i na korozję w atmosferze zawierającej siarkę (np. podczas rafinacji ropy naftowej). Dyfuzyjne powłoki aluminiowe na stali zwykle nie zapewniają
Badania przepuszczalności wodoru w podwyższonych temperaturach stali gatunku 12Kh18N9T z warstwami aluminizowanymi, borowanymi, chromowanymi wykazały, że powłoki te stanowią skuteczną barierę dla przepływu wodoru. Dla stali z powłoką aluminiowaną o grubości 90 µm zależność temperaturowa przepuszczalności wodoru w zakresie 800-550 °C jest liniowa, energia aktywacji w tym obszarze wynosi Ер = 158 kJ/mol, czyli jest nieco wyższa niż w przypadku stali niepowlekanej stali (p = 122 kJ/mol), przepuszczalność wody zmniejsza się prawie 5-krotnie. Dla próbek borowanych o grubości warstwy 80 μm obserwuje się 13-krotny spadek przepuszczalności wodoru w temperaturze 800°C i 70-krotny w temperaturze 400°C, energia aktywacji n = 168 kJ/mol.
Proces aluminizacji dyfuzyjnej otrzymał specjalną nazwę - aluminizacja (rzadziej kaloryzacja).
W metodzie powlekania termodyfuzyjnego produkt umieszcza się w mieszaninie zawierającej proszek metalu powłoki. W podwyższonej temperaturze osadzony metal dyfunduje do metalu podstawowego. W ten sposób uzyskuje się powłoki z aluminium (aluminiowanie) i cynku. Czasami powłoki są nakładane w reakcjach w fazie gazowej. Na przykład podczas przechodzenia parowego CrCl przez powierzchnię stali w temperaturze 1000°C powstaje stop powierzchniowy Cr-Fe zawierający do
Aluminium chroni metale przed korozją np. poprzez nasycanie ich powierzchni aluminium (aluminiowanie) lub poprzez galwanizację-
Powłokę nakłada się w hermetycznie zamkniętym pojemniku. Oczyszczone wyroby metalowe są zanurzane w proszku zawierającym metal powłoki. W ciągu kilku godzin pojemnik jest podgrzewany do temperatury bliskiej (ale niższej) temperaturze topnienia metalu. Powłoki cynkowe nakładane na stal nazywane są szeradyzacją. Warstwa dyfuzyjna to stop zawierający 8-9% żelaza w cynku. Powłoki aluminiowe na stali lub miedzi nazywane są aluminizowanymi. Tlenek glinu powstaje na nich we wszystkich warstwach powierzchniowych o zawartości aluminium powyżej 8%. Ten film tlenkowy zapewnia wysoką odporność na korozję, ale silnie kruszy warstwy powierzchniowe, dlatego po aluminiowaniu konieczne jest poddanie produktu wyżarzaniu.
Trzecią metodą zmniejszenia szybkości korozji gazowej jest zabezpieczenie powierzchni metalu specjalnymi powłokami żaroodpornymi, termodyfuzyjnymi powłokami żelazowo-aluminiowymi lub żelazowo-chromowymi (procesy nakładania tych powłok określane są jako aluminiowanie i termochromowanie), metalowo-ceramiczny powłoki lub cermetale, powłoki z tlenków metali, dla których materiały ogniotrwałe są stosowane jako składniki niemetaliczne, tlenki, na przykład A12O3, M0 oraz związki takie jak azotki i węgliki. Składnikami metalowymi są metale z grupy żelaza, chrom, wolfram i molibden.
Chemia nieorganiczna (1981) — [ok.438]
Fizyka i chemia w rafinacji ropy naftowej (1955) -- [ c.8 ]
Chemia ogólna (tom 3) (1979) - [c.387]
Kurs Chemii Ogólnej (1964) -- [ ok. 245 ]
Chemia nieorganiczna, tom 2 (1976) - [c.397]
Chemia ogólna 1982 (1982) - [ ok. 555 , ok. 637 ]
Chemia ogólna 1986 (1986) -- [ ok. 537 , ok. 617 ]
Chemia nieorganiczna (1981) — [ok.438]
sprzęt do produkcji podstawowej syntezy organicznej i kauczuków syntetycznych (1965) -- [ ok. 31 ]
Chemia nieorganiczna (1978) — [ok.293]
Corrosion and Electroplating Fundamentals Vol. 2 (1987) - [c.91]
Chemia ogólna, tom 4 (1965) - [c.238]
Naprawa i montaż wyposażenia rafinerii chemicznych i naftowych Wydanie 2 (1980) -- [ ok.71 ]
Korozja sprzętu chemicznego i materiałów odpornych na korozję (1950) -- [c.162]
Chemia ogólna Vol. 18 (1976) - [c.629]
General Chemistry Vol. 22 (1982) - [c.555, c.637]
Podstawy ogólnej technologii chemicznej (1963) -- [ ok.194 ]
Wydanie sprzętu produkcyjnego 2 (1974) -- [ ok. 24 ]
Ogólna technologia chemiczna Tom 2 (1959) -- [ ok. 153 , ok. 154 ]
Krótka Encyklopedia Chemiczna Tom 2 (1963) -- [ ok. 97 ]
Podstawy chemii ogólnej, tom 2 (1967) — [c.194]
Fundamentals of General Chemistry Tom 2 Wydanie 3 (1973) -- [ c.37 ]
Pasywność korozyjna i ochrona metali (1941) - [ c.7 ]
Korozja metali Księga 1,2 (1952) -- [ c.667 , c.668 ]
Kurs chemii ogólnej (0) -- [ c.236 ]
Chemia (0) -- [ c.236 ]
Korozja metali Księga 2 (1952) -- [ c.0 ]
chem21.info
Metalizacja dyfuzyjna
Metalizacja dyfuzyjna to proces dyfuzyjnego nasycania warstw wierzchnich stali różnymi metalami. Może być wykonywany w mediach stałych, ciekłych i gazowych.
W metalizacji dyfuzyjnej w ośrodkach stałych stosuje się mieszaniny proszkowe, składające się zwykle z żelazostopów z dodatkiem chlorku amonu.
Metalizacja dyfuzyjna cieczy odbywa się poprzez zanurzenie części w stopionym metalu (na przykład cynku, aluminium).
W metodzie nasycenia gazem stosuje się lotne związki chlorków metali, które powstają podczas oddziaływania chloru z metalami w wysokich temperaturach. Chlorki dysocjują na powierzchni żelaza, a metal uwolniony w stanie atomowym dyfunduje do żelaza.
Dyfuzja metali w żelazie jest znacznie wolniejsza niż w przypadku węgla i azotu, ponieważ węgiel i azot tworzą z żelazem śródmiąższowe roztwory stałe, podczas gdy metale tworzą zastępcze roztwory stałe. Prowadzi to do tego, że warstwy dyfuzyjne podczas metalizacji są dziesięciokrotnie cieńsze. Nasycanie powierzchni stali metalami odbywa się w temperaturach 900-1200 ° C.
Aluminiowanie (Al)
Aluminiowanie to proces nasycania powierzchni stali aluminium. W wyniku aluminiowania stal uzyskuje wysoką odporność na zgorzelinę (do 850-900 °C) oraz odporność na korozję w atmosferze i wielu środowiskach.
Podczas aluminiowania w mieszankach proszkowych czyste części są pakowane razem z mieszaniną w żelazne pudełko. Mieszanina robocza zawiera: sproszkowane aluminium (25-50%) lub żelazoglin (50-75%), tlenek glinu (25-50%) i chlorek glinu (~1,0%). Proces prowadzony jest w temperaturze 900-1000°C przez 3-12 godzin.
Rzadko stosowane wanny aluminizujące z roztopionym aluminium. Części aluminiowane są zanurzane w stopionym aluminium (92-94% A1 i 6-8% Fe). Żelazo jest dodawane, aby zapobiec rozpuszczaniu się obrabianych przedmiotów w aluminium. Proces prowadzony jest w temperaturze 700-800°C przez 45-90 minut.
Aluminiowanie w stopionym aluminium różni się od aluminizacji w mieszankach proszkowych prostotą metody, szybkością i niższymi temperaturami. Główną wadą procesu jest przyklejanie się aluminium do powierzchni części.
Czasami stosuje się metalizację powierzchni stali aluminium (napylanie warstwy aluminium na obrabianej powierzchni), a następnie wyżarzanie dyfuzyjne w temperaturze 900-1000°C przez 1-3 godziny.
Aby chronić aluminium przed utlenianiem podczas wyżarzania dyfuzyjnego, produkt pokryty jest powłoką składającą się z grafitu srebrnego (48%), piasku kwarcowego (30%), gliny (20%), chlorku glinu (2%) i 20-25% waga pierwszych czterech składników - płynne szkło.
Stal aluminiowana z metalizacją, a następnie wyżarzaniem dyfuzyjnym jest kilkakrotnie tańsza niż w przypadku proszków. Mieszana warstwa jest stałym roztworem aluminium w żelazie, stężenie aluminium w warstwie powierzchniowej sięga 30-40%. Aluminiowanie stosuje się do rur, narzędzi do odlewania stopów metali nieżelaznych, obudów termopar, części maszyn wytwarzających gaz itp.
studfiles.net
Proces - aluminiowanie - The Big Encyclopedia of Oil and Gas, artykuł, strona 1
Proces - aluminizacja
Strona 1
Proces aluminizacji składa się z następujących operacji: przygotowanie powierzchni, nałożenie warstwy aluminium (najczęściej metodą napylania), powlekanie i wyżarzanie.
Proces aluminizacji przeprowadza się na przykład przez ogrzewanie rury w proszku aluminiowym zmieszanym z tlenkiem glinu w obecności chlorku amonu w temperaturze około 1000°C.
Proces aluminizacji trwa 3-5 minut, temperatura topnienia utrzymywana jest na poziomie około 700°C. W takich warunkach grubość warstwy dyfuzyjnej dla stali wynosi 0,02-0,04 mm. Grubość sklejanego aluminium nie przekracza 0,3 - 0,4 mm.
Proces aluminizacji polega na nasycaniu aluminium powierzchni elementów stalowych. Podczas aluminiowania części są pakowane w pudełka z mieszaniną 48% aluminium, 48% tlenku glinu i 2% amoniaku, a następnie przechowywane przez 5 do 15 godzin. Stalowa powierzchnia nasycona aluminium ma wysoką odporność termiczną.
Proces aluminizacji trwa od 5 do 15 godzin. Stal z aluminiowaną powierzchnią jest bardzo odporna na ciepło i jest stosowana w częściach mających kontakt z płomieniem.
Proces aluminizacji trwa od 5 do 15 godzin. Stal o aluminiowanej powierzchni jest bardzo żaroodporna i jest stosowana w częściach mających kontakt ze stalą.
Proces aluminizacji trwa od 5 do 15 godzin. Stal z aluminiowaną powierzchnią jest bardzo odporna na ciepło i jest stosowana w częściach mających kontakt z płomieniem.
Proces aluminiowania z proszków według opracowanej technologii przebiega w kilku etapach, z których głównym jest przeniesienie atomów glinu z powierzchni ziaren żelazoglinu na powierzchnię detalu oraz chemisorpcja aluminium przez nikiel.
Proces aluminizacji polega na nasycaniu aluminium warstwy wierzchniej żelaza, stali i żeliwa w wyniku dyfuzji sproszkowanego metalu w wysokiej temperaturze. Głębokość warstwy dyfuzyjnej zależy od temperatury ogrzewania i czasu trwania procesu aluminizacji; w praktyce waha się od 0,3 do 0,8 mm. Części przeznaczone do aluminizacji są ładowane do hermetycznie zamkniętej żelaznej skrzyni i starannie pokrywane określoną mieszanką. Ogrzewanie prowadzi się w temperaturze 1000 przez 3-4 godziny.
Proces aluminizacji przeprowadza się w następujący sposób. Części stalowe przeznaczone do aluminiowania umieszcza się w pudłach i posypuje mieszaniną aluminiującą składającą się z następujących części (w % wagowych): 1) proszek aluminiowy 40 – 60, 2) proszek tlenku glinu 60 – 40 lub drobno zmielony szamot, lub wypalana glina ogniotrwała, 3) 1 5 - 3 chlorek amonu. Substancje te są dokładnie wymieszane. Ekspozycję w tej temperaturze prowadzi się przez 5-14 godzin. Oprócz aluminizacji w stanie stałym stosuje się również aluminizację gazową, podobną do nawęglania gazowego.
Strony: 1 2 3 4
Metalizacja dyfuzyjna to proces dyfuzyjnego nasycania warstw wierzchnich stali różnymi metalami. Może być wykonywany w mediach stałych, ciekłych i gazowych.
W metalizacji dyfuzyjnej w ośrodkach stałych stosuje się mieszaniny proszkowe, składające się zwykle z żelazostopów z dodatkiem chlorku amonu.
Metalizacja dyfuzyjna cieczy odbywa się poprzez zanurzenie części w stopionym metalu (na przykład cynku, aluminium).
W metodzie nasycenia gazem stosuje się lotne związki chlorków metali, które powstają podczas oddziaływania chloru z metalami w wysokich temperaturach. Chlorki dysocjują na powierzchni żelaza, a metal uwolniony w stanie atomowym dyfunduje do żelaza.
Dyfuzja metali w żelazie jest znacznie wolniejsza niż w przypadku węgla i azotu, ponieważ węgiel i azot tworzą z żelazem śródmiąższowe roztwory stałe, podczas gdy metale tworzą zastępcze roztwory stałe. Prowadzi to do tego, że warstwy dyfuzyjne podczas metalizacji są dziesięciokrotnie cieńsze. Nasycanie powierzchni stali metalami odbywa się w temperaturach 900-1200 ° C.
Aluminiowanie (Al)
Aluminiowanie to proces nasycania powierzchni stali aluminium. W wyniku aluminiowania stal uzyskuje wysoką odporność na zgorzelinę (do 850-900 °C) oraz odporność na korozję w atmosferze i wielu środowiskach.
Podczas aluminiowania w mieszankach proszkowych czyste części są pakowane razem z mieszaniną w żelazne pudełko. Mieszanina robocza zawiera: sproszkowane aluminium (25-50%) lub żelazoglin (50-75%), tlenek glinu (25-50%) i chlorek glinu (~1,0%). Proces prowadzony jest w temperaturze 900-1000°C przez 3-12 godzin.
Rzadko stosowane wanny aluminizujące z roztopionym aluminium. Części aluminiowane są zanurzane w stopionym aluminium (92-94% A1 i 6-8% Fe). Żelazo jest dodawane, aby zapobiec rozpuszczaniu się obrabianych przedmiotów w aluminium. Proces prowadzony jest w temperaturze 700-800°C przez 45-90 minut.
Aluminiowanie w stopionym aluminium różni się od aluminizacji w mieszankach proszkowych prostotą metody, szybkością i niższymi temperaturami. Główną wadą procesu jest przyklejanie się aluminium do powierzchni części.
Czasami stosuje się metalizację powierzchni stali aluminium (napylanie warstwy aluminium na obrabianej powierzchni), a następnie wyżarzanie dyfuzyjne w temperaturze 900-1000°C przez 1-3 godziny.
Aby chronić aluminium przed utlenianiem podczas wyżarzania dyfuzyjnego, produkt pokryty jest powłoką składającą się z grafitu srebrnego (48%), piasku kwarcowego (30%), gliny (20%), chlorku glinu (2%) i 20-25% waga pierwszych czterech składników - płynne szkło.
Stal aluminiowana z metalizacją, a następnie wyżarzaniem dyfuzyjnym jest kilkakrotnie tańsza niż w przypadku proszków. Mieszana warstwa jest stałym roztworem aluminium w żelazie, stężenie aluminium w warstwie powierzchniowej sięga 30-40%. Aluminiowanie stosuje się do rur, narzędzi do odlewania stopów metali nieżelaznych, obudów termopar, części maszyn wytwarzających gaz itp.
Metody aluminiowania
Aluminiowanie jest często stosowane do stali niskowęglowych, rzadziej do żeliw średniowęglowych i żeliwnych. Technologie aluminiowania zostały opracowane na początku XX wieku. Na przykład technologia aluminiowania w mieszankach proszkowych została opracowana w latach 1927-1930. JAKIŚ. Minkiewicz, N.V. Ageev i O.I. Wer. W 1934 V.A. Płotnikow, N.G. Gritsiansky i K.L. Makovets zaproponował metodę elektrolitycznego aluminiowania. Aluminiowanie w kąpielach z roztopionym aluminium zostało szczegółowo zbadane już w 1932 roku przez F.G. Nikonow.
Aby uzyskać metaliczne wiązanie między żelazem a aluminium i jego stopami, stosuje się różne metody aluminizacji, z których główne to:
Aluminiowanie w mieszankach proszkowych;
Aluminiowanie przez topienie i natryskiwanie;
Aluminiowanie w próżni;
Aluminiowanie gazowe;
okładzina;
powłoka elektrolityczna;
Aluminiowanie przez zanurzenie w roztopionym aluminium lub jego stopie;
Aluminiowanie w mieszankach proszkowych
Przygotowane części pakowane są w hermetyczne retorty, bębny i wypełniane mieszanką aluminującą. Mieszanina składa się z proszku lub proszku aluminiowego oraz dodatków. Dodatki obejmują tlenek glinu lub zmieloną glinkę (w celu zapobiegania spiekaniu) oraz chlorek amonu lub chlorek glinu (w celu ochrony produktów i glinu przed utlenianiem).
Temperatura w jakiej przebiega proces to 900-1080 °C, czas trwania procesu w zależności od składu mieszanki i temperatury procesu wynosi od 4 do 30 godzin.
Aluminiowanie przez natryskiwanie
Wstępnie oczyszczoną powierzchnię spryskuje się pewną warstwą aluminium. Proces powlekania polega na stopieniu osadzonego metalu i rozpyleniu go strumieniem sprężonego powietrza o ciśnieniu 2-4 atm. przy użyciu specjalnych metalizatorów.
Siła przyczepności takiej aplikacji jest niska i wynosi 0,2-2 kg/mm2. Przy tej metodzie aluminiowania adhezja nie występuje tylko pomiędzy metalem bazowym a powłoką, ale również pomiędzy poszczególnymi warstwami i cząsteczkami aluminium, dzięki czemu natryskiwana warstwa ma zwiększoną porowatość.
Aby zwiększyć przyczepność powłoki do metalu podstawowego, a także zwiększyć gęstość, zaleca się po aluminiowaniu przeprowadzenie długotrwałego wyżarzania w temperaturze 950-1080 °C.
Aluminiowanie w próżni
Ten proces jest podobny do poprzedniego. Powłoka nakładana jest poprzez odparowanie aluminium i nałożenie go na produkt. Grubość powłoki to dziesiąte części mikrona, a jakość powłoki w tym przypadku jest wyższa.
Do aluminiowania wymagane są komory wysokopróżniowe o ciśnieniu 10-3-10-5 mm Hg.Instalacje wiązek elektronów służą do podgrzewania aluminium do 1400. Grubość powstałej powłoki jest proporcjonalna do czasu trwania parowania aluminium i wynosi 0,08-2,5 mikrona. Dzięki tej metodzie nakładania aluminium powłoka jest jednolita, bez porów i nie zawiera pośredniej warstwy żelazowo-aluminiowej.
Aby uzyskać silną przyczepność powłoki do podłoża, pasek lub część podgrzewa się do temperatury 175 - 370 °C. Wstępne przygotowanie powierzchni musi być dokładne, ponieważ obecność warstw tlenków znacząco wpływa na jakość przyczepności.
Ze względu na złożoność i wysoki koszt procesu, ten rodzaj powlekania jest przeznaczony głównie do najbardziej krytycznych części.
Okładzina
Metoda ta polega na wspólnym walcowaniu blach stalowych i aluminiowych. Podczas ściskania powstaje metaliczne wiązanie pomiędzy aluminium i stalą, w wyniku czego powstaje bimetaliczny pasek lub cyna.
Dzięki późniejszemu wyżarzaniu zwiększa się siłę wiązania stali i aluminium. Metoda ta stosowana jest głównie do pozyskiwania blach, taśm i rur.
Galwanotechnika
Taką powłokę nakłada się albo w bezwodnych elektrolitach składających się z mieszanin stopionych soli chlorku glinu i chlorków metali alkalicznych, albo w elektrolitach nieorganicznych zawierających związki glinu w bromoetylu i benzenie.
Elektrolit może składać się z 80% AlCl3 i 20% NaCl, wówczas proces prowadzi się w temperaturze 175°C i gęstości prądu 1,6 A/dm2.
Przed powlekaniem produkt musi być dobrze oczyszczony, odtłuszczony i wytrawiony w roztworze kwasu solnego. Szybkość osadzania aluminium jest znikoma i wynosi około 0,01 mm w ciągu 30 minut.
Metoda ta ma szereg wad: po pierwsze, w skład elektrolitu wchodzi chlorek glinu, który jest bardzo lotny, higroskopijny i może rozkładać się nawet w normalnych warunkach, a po stopieniu odparowuje z kąpieli, co prowadzi do zmiany skład elektrolitu, a druga metoda jest niezwykle powolna i mało ekonomiczna.
Aluminiowanie przez zanurzanie
Ta metoda jest pozbawiona wad wymienionych powyżej. Jego główną zaletą jest szybkość aluminizacji (od 1 do 15 minut), stosunkowo niskie temperatury (600-800°C) oraz prostota. Ponadto aluminiowanie zanurzeniowe jest najtańszą metodą w porównaniu z innymi metodami.
Istota metody polega na zanurzeniu produktu stalowego o czystej metalowej powierzchni w ciekłym aluminium lub jego stopie i przytrzymaniu go przez pewien czas. W tym przypadku warstwa powierzchniowa metalu rozpuszcza się w aluminium i wchodzi z nim w interakcje. Reakcja interakcji i dyfuzji przebiega bardzo szybko, dzięki czemu w ciągu 1-15 minut tworzy się warstwa o grubości 0,02-0,10 mm. Proces aluminizacji odbywa się w temperaturze 700-800°C.
Z powyższego materiału możemy wywnioskować, że najbardziej obiecującą opcją jest aluminiowanie przez zanurzenie, a następnie wyżarzanie dyfuzyjne.