Desenvolvimentos de design de OAO TKZ "Krasny Kotelshchik" para a introdução de novas tecnologias para a combustão de combustíveis sólidos nos fornos de caldeiras a vapor. Desenvolvimentos de design de OAO TKZ "Krasny Kotelshchik" para a introdução de novas tecnologias para a combustão de combustíveis sólidos nos fornos de caldeiras a vapor
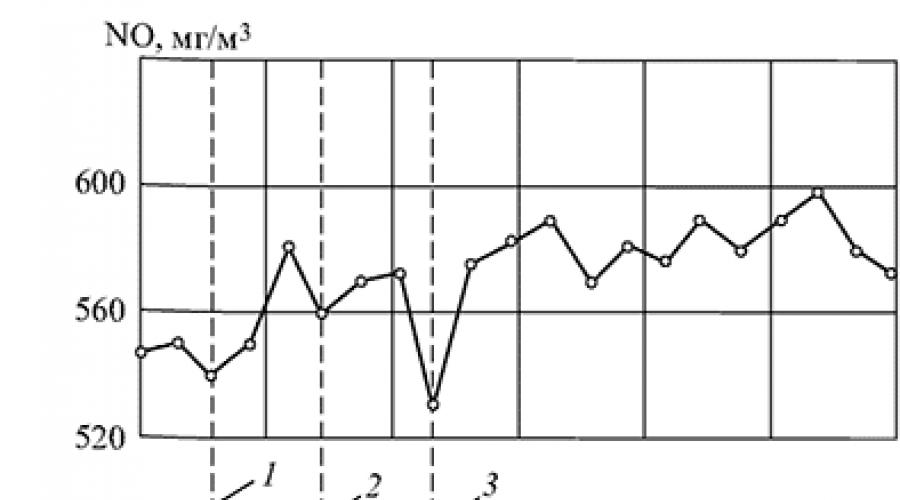
Doutor em Ciências Técnicas G.I. Levchenko, Ph.D. Yu.S. Novikov, Ph.D. P.N. Fedotov, Ph.D. L. M. Khristich, Ph.D. SOU. Kopeliovich, Ph.D. Yu.I. Shapovalov, OAO TKZ Krasny Kotelshchik
Revista "Heat Supply News", nº 12, (28), dezembro de 2002, pp. 25 - 28, www.ntsn.ru
(Com base no relatório do seminário "Novas tecnologias para queima de combustíveis sólidos: seu estado atual e uso futuro", VTI, Moscou)
Nas últimas décadas, o setor energético nacional tem se orientado em grande parte para o gasóleo. Na presença de enormes depósitos de combustível sólido no país, esse estado de coisas dificilmente pode ser justificado por um longo período.
Neste sentido, deve-se reconhecer como natural que a “pausa do gás” esteja terminando e que tenha havido uma reorientação para uma expansão decisiva do uso de hulha, linhite e turfa.
Vários fatores contribuem para isso, entre eles:
Perspectiva socialmente justificada de renascimento da indústria de mineração de carvão;
Diminuição do ritmo de desenvolvimento de campos de gás e volumes de produção de gás natural;
O crescimento de suas necessidades de exportação.
O complexo de problemas financeiros e de transporte nos mercados de energia interno e externo complica a adoção de uma estratégia sustentável e de longo prazo para a política de combustíveis.
Nessas condições, a OJSC TKZ não enfraqueceu sua atenção às questões de combustível sólido por todos os anos, continuou a modernizar suas caldeiras de carvão pulverizado, envolvendo nisso as forças mais autorizadas da ciência (NPO CKTI, VTI, ORGRES, etc.).
Os desenvolvimentos abrangeram todos os tipos de caldeiras produzidas pela fábrica nos últimos 20-30 anos. O principal objetivo desses desenvolvimentos de modernização é aumentar o desempenho ambiental e econômico das caldeiras com sua máxima aproximação ao nível mundial. Isso tornou possível ter um volume suficiente de desenvolvimentos técnicos preparados para implementação.
Nestes trabalhos, destacam-se as seguintes áreas principais, abrangendo uma vasta gama de tecnologias de processamento e combustão de combustíveis:
1. Várias modificações da combustão faseada de combustíveis sólidos;
2. Criação de instalações altamente económicas e amigas do ambiente.
Nessas áreas, toda a variedade de combustíveis na Rússia é coberta: carvão preto e marrom das bacias de Kuznetsk, Kansk-Achinsk e Extremo Oriente, antracito e seus resíduos, turfa, combustível de água-carvão.
Combustão faseada de combustíveis sólidos
Atualmente, as emissões nocivas nos gases de combustão das usinas de energia são regulamentadas por dois padrões estaduais GOST 28269-89 - para caldeiras e GOST 50831-95 - para caldeiras.
Os requisitos mais rigorosos são impostos às emissões das caldeiras que queimam carvão pulverizado. Para atender a esses padrões ao queimar carvão Kuznetsk com remoção de cinzas sólidas, é necessária uma estação de tratamento de gás ou a implementação de todos os meios conhecidos de supressão de NO X.
Além disso, a possibilidade de reduzir as emissões de NO X para esses valores por medidas técnicas para os carvões da bacia de Kuznetsk ainda não foi verificada e requer confirmação em caldeiras com medidas implementadas.
Tal caldeira TKZ, juntamente com a Sibtechenergo, foi desenvolvida com base na caldeira TPE-214 e entregue ao CHPP-5 de Novosibirsk. Esta caldeira para carvão dos graus "G" e "D" utiliza um esquema de combustão multi-etapas: gradação horizontal e vertical na zona do queimador, bem como a criação de uma zona de redução acima dos queimadores utilizando gás natural como agente redutor. A aerodinâmica do forno, testada no modelo, é organizada de forma a evitar a escória das telas em todos os modos de operação da caldeira. O comissionamento da caldeira TPE-214 em Novosibirsk CHPP-5 permitirá ganhar experiência na redução máxima possível das emissões de NOX durante a combustão da câmara de carvões com alto teor de nitrogênio no combustível.
Para a combustão de carvões pouco reativos de Kuzbass (misturas "T" e "SS"), uma caldeira modernizada TP-87M foi desenvolvida e entregue à Usina do Distrito Estadual de Kemerovo com a organização de combustão de carvão em três estágios sob condições de líquido remoção de cinzas. A caldeira utiliza o transporte de pó de alta concentração de PPVC, queimadores com emissão reduzida de NO X e queimadores especiais de pó-gás para criar uma zona de redução acima dos queimadores principais com um uso mínimo de gás natural (3 - 5%). Para queimar o carvão magro de Kuznetsk, a TKZ, em conjunto com a VTI, está reconstruindo as caldeiras TP-80 e TP-87, bem como as caldeiras TPP-210A da TPP-22 da Mosenergo, que também utilizam PPVC e combustão em três estágios com gás natural como redutor.
Para os carvões da região do Extremo Oriente, foi realizado um projeto de reconstrução de baixo custo da caldeira TPE-215 usando combustão em dois estágios na mesma.
Para os carvões da bacia de Kansko-Achinsk, a usina, juntamente com a TsKTI e a SibVTI, desenvolveu e entregou à CHPP-2 de Krasnoyarsk uma caldeira com capacidade de vapor de 670 t/h (TPE-216), que utiliza esquema de combustão usando pó de carvão como agente redutor, bem como medidas especiais para proteger as telas da escória: fornecimento de uma mistura combustível-pobre através dos bicos do queimador (GFCv) do lado das telas do forno, jato de ar ao longo as telas na zona de redução e garantindo que a temperatura do gás na zona de combustão ativa não seja superior a 1250 ° C devido ao fornecimento adicional de 10% de gases de recirculação do ar secundário.
As medidas tecnológicas incorporadas no projeto (organização da combustão a baixa temperatura e aumento do teor de óxido de cálcio nas cinzas) permitem garantir não só as emissões de NO X ao nível de 220-300 mg/m 3 , mas também de S0 2 emissões não superiores a 400 mg/m 3 .
Para turfa de alta umidade, foram desenvolvidos projetos para a modernização das caldeiras TP-208 e TP-170-1 com a organização de combustão em dois estágios nelas.
A combustão escalonada do combustível em suas várias modificações é um meio universal de reduzir significativamente as emissões de NO X, mas para alguns tipos de combustível com alto teor de nitrogênio, o uso desse método, mesmo em combinação com outras medidas no forno, pode ser insuficiente cumprir os requisitos das normas para carvões e fornos com remoção de escória sólida 350 mg/m 3 . Neste caso, é aconselhável utilizar o método de supressão de NO X com a combinação sequencial de combustão em três estágios e redução não catalítica seletiva de NO X (SNCR).
Criação de instalações altamente económicas e amigas do ambiente
Com base em muitos anos de experiência na criação e desenvolvimento de caldeiras a vapor de usinas para quase todos os tipos de combustível utilizados no setor de energia, a usina desenvolveu projetos para usinas de nova geração que permitirão um nível fundamentalmente novo de indicadores técnicos do equipamento fabricado.
Modernização da caldeira TPP-210 com a instalação de um forno "ombro"
para queima de carvão de baixa reatividade
Dificuldades conhecidas na queima de cinzas e crescentes exigências ambientais levantam a questão de melhorar ainda mais o processo de queima de cinzas, em particular, usando os chamados fornos “ombro” com remoção de cinzas sólidas, nos quais o combustível de baixa reatividade e alto teor de cinzas é queimados sem iluminação na faixa de cargas utilizadas na prática, com o fornecimento de uma empresa de trabalho a longo prazo da caldeira.
Vantagens de um forno “ombro” com remoção de cinzas sólidas em comparação com a tecnologia de combustão AS em um forno com remoção de cinzas líquidas:
Permite a utilização de queimadores com baixas velocidades da mistura de ar, o que aumenta o tempo de residência das partículas na área do queimador, o que cria condições favoráveis para o aquecimento das partículas e sua ignição;
Obtém-se uma longa permanência das partículas na zona de altas temperaturas (pelo menos 2 vezes maior do que em um forno tradicional), o que garante uma queima de combustível satisfatória;
Permite introduzir de forma mais conveniente o ar necessário para a combustão à medida que a tocha se desenvolve;
Significativamente menos dificuldade com a remoção de escória;
Menos perdas com queima mecânica;
Menores emissões de óxido de nitrogênio.
Para o forno “ombro”, é usado um queimador de ranhura com um intervalo entre os jatos de ar primário e secundário, cuja principal vantagem, em comparação com um vórtice:
A ausência de mistura prematura de ar primário com ar secundário, o que afeta favoravelmente a ignição; .
Fornecimento de ar primário na quantidade necessária apenas para a queima de voláteis;
Uma combinação racional com o forno, que permite criar uma alta taxa de circulação de gases de combustão para a raiz da chama (na zona de ignição).
Um forno “ombro” estanque a gás e um TVP, no corte do qual é instalado um economizador, são instalados na caldeira modernizada para o poço convectivo existente.
Combustão de finos de antracitos degradados em leito fluidizado
A combustão é realizada de acordo com a tecnologia do Instituto Politécnico de Altai, cuja idéia principal é a granulação preliminar de uma mistura de solo, combustível inicial, cinzas e calcário para aproximar a composição do leito fluidizado a um monodisperso mistura. OAO TKZ Krasny Kotelshchik juntamente com o autor da tecnologia concluiu um projeto de modernização de uma das caldeiras existentes TP-230 em Nesvetai GRES para combustão piloto de AS granulado de qualidade degradada em leito fluidizado.
Atualmente, está prevista a instalação de uma caldeira industrial piloto D-220 t/h com leito fluidizado circulante em Nesvetai GRES, cujo desenvolvedor e fornecedor geral é a OJSC Belenergomash. TKZ é co-executor.
Usina para processamento complexo, combustão em escória fundida e uso de resíduos de carvão de baixa reatividade
Breve descrição da unidade de caldeira "Caldeira de fluxo direto tipo TPP-210"
Breve descrição da unidade de caldeira A caldeira de passagem única tipo TPP-210 (p/p 950-235 GOST 3619-59 modelo TKZ TPP-210) com capacidade de vapor de 950 toneladas por hora para parâmetros de vapor supercrítico foi projetada e fabricada pela Planta Taganrog "Krasny Kotelshchik". A unidade de caldeira foi projetada para operar em uma unidade com turbina de condensação K-300-240 com capacidade de 300 MW, fabricada pela KhTGZ. A caldeira é projetada para queima de lodo antracito com remoção de cinzas líquidas e gás natural do depósito Shebelinsky. A unidade da caldeira é de caixa dupla com um layout em forma de U de cada caixa e aquecedores de ar regenerativos removidos sob a caldeira, localizados fora do edifício da caldeira. Caldeiras do mesmo desenho com capacidade de 475 t/h de vapor cada. Os cascos podem funcionar independentemente uns dos outros. Dados gerais da caldeira: Produtividade 475 t/h Temperatura do vapor superaquecido: primário 565 °C Secundário 565 °C Consumo secundário do vapor 400 t/h Pressão do vapor primário após a caldeira 255 kg/cm² Pressão do vapor secundário na entrada da caldeira 39,5 kg/ cm² Pressão do vapor secundário na saída da caldeira 37 kg/cm² Temperatura do vapor secundário na entrada 307 °C Temperatura da água de alimentação 260 °C Temperatura do ar quente 364 °C Peso total do metal da caldeira 3438 t Largura da caldeira ao longo dos eixos da coluna 12 m Caldeira profundidade ao longo dos eixos da coluna 19 m Altura da caldeira 47 m Volume de água da caldeira em estado frio 243 m³ Dimensões do forno em planta (ao longo dos eixos das tubagens): vapor primário e secundário na saída é reduzido a 545 °C) A caldeira é servida por dois exaustores de fumos axiais, dois ventiladores com motores de duas velocidades e dois ventiladores de jacto quente. Esquema de preparação de pó com um bunker e transporte de pó para os queimadores por ar quente. A caldeira está equipada com três moinhos de bolas de tambor ShBM-50 com capacidade de 50 toneladas de pó por hora. Superfícies de aquecimento: Telas do forno 1317 m² Incluindo: NRCh 737 m² THR 747 m² Telas da câmara reversora e teto 1674 m² Superaquecedor SVD: incluindo: Trocador de calor a vapor 800 m² Pacote convectivo intermediário 1994 m² Aquecedor de ar 78730 m² Pacote convectivo de saída 1205 m² Economizador convectivo 199 m²
Em cada corpo de caldeira existem dois fluxos (na descrição da caldeira e nas instruções, o fluxo é chamado de thread). Como o design do casco é semelhante, o esquema e o design de um casco serão descritos no futuro. A água de alimentação com temperatura de 260 °C passa pela unidade de energia e entra nas câmaras de entrada do economizador de água Sh325*50, que também são as vigas de suporte extremas da embalagem. Depois de passar pelas bobinas do economizador de água, a água com temperatura de 302 ° C entra nas câmaras de saída Ø235*50, que são as vigas de suporte intermediárias dessa superfície. Após o economizador de água, a água é direcionada por tubos de derivação Ø159*16 para as vigas de suporte intermediárias desta superfície através de tubos Ø133*15 para a parte inferior (НРЧ). As telas NRC consistem em painéis separados e as superfícies de aquecimento da lareira formam fitas multi-pass de uma peça com a frente e a traseira. O abastecimento de água aos painéis é realizado pela câmara inferior e a drenagem pela superior. Esta disposição das câmaras de entrada e saída melhora o desempenho hidráulico do painel. O fluxograma do meio pelas telas do NRC é o seguinte: Primeiro, o meio entra nos painéis traseiros e nos painéis traseiros da tela lateral, depois é direcionado para a tela frontal e os painéis frontais das telas laterais por bypass tubos Ø 135*15. Arruelas de Ø30 mm são instaladas em tubos de derivação para melhorar a hidrodinâmica. Após o LFC, o meio com uma temperatura de 393 °C é enviado por tubos Ø133*15 para o coletor vertical Ø273*45, e de lá entra nas telas laterais e frontais da parte superior de radiação (RTC) através de tubos de derivação Ø133* 15. A posição relativa das câmaras de entrada e saída dos painéis TRC é semelhante à dos painéis RRC. Tendo passado pelos painéis multi-pass das telas frontal e lateral do TCG, o vapor é direcionado pelos tubos de derivação Ø133*15 para o coletor de mistura vertical Ø325*45, e de lá entra nos painéis em forma de N da tela traseira do TRC através de tubos Ø159*16.
Tendo passado pelos painéis multi-pass das telas frontal e lateral do TRC, o vapor é direcionado pelos tubos de desvio Sh133 * 15 para o coletor de mistura vertical Sh325 * 45 e após o aquecimento a 440 ° C nas superfícies radiantes do forno, o vapor é direcionado para os painéis de blindagem das paredes laterais e traseiras das câmeras rotativas. Tendo passado pelas telas da câmara de reversão, o vapor entra através de tubos em 1 dessuperaquecedor de injeção Ø279*36. Em 1 dessuperaquecedor de injeção, os fluxos são transferidos ao longo da largura da chaminé. Após o dessuperaquecedor, o vapor é fornecido ao superaquecedor de teto por tubos Ø159*16. No superaquecedor de teto, o vapor se move da parede traseira da chaminé para a frente da caldeira e entra nas câmaras de saída do teto Ø273*45 com uma temperatura de 463 °C. Nas tubulações de vapor Ш273*39, que são uma continuação das câmaras de saída do superaquecedor de teto, são instaladas válvulas (VZ) DU-225 embutidas no trato. Após o superaquecedor de teto, os fluxos são transferidos ao longo da largura do duto de gás e o vapor é direcionado através dos tubos Ø159*18 para as telas de entrada do primeiro estágio do superaquecedor de tela, localizado na parte central do duto de gás. Depois de passar pelas telas de entrada, o vapor com temperatura de 502 °C entra no segundo dessuperaquecedor de injeção Ø325*50, após o qual é direcionado para as telas de saída do primeiro estágio, localizadas ao longo das bordas da chaminé. A câmara de recepção de vapor das telas de entrada e a linha de vapor do segundo dessuperaquecedor realizam a transferência de fluxos ao longo da largura da chaminé. Antes da segunda injeção, há uma tubulação de vapor Ø194*30 para retirar parte do vapor HPS para o trocador de calor gás-vapor e, após a injeção, uma tubulação de vapor para retorno desse vapor. O segundo dessuperaquecedor de injeção possui uma arruela de retenção. Atrás das telas de saída do primeiro estágio, há um terceiro dessuperaquecedor de injeção Ø325*50, cuja tubulação de vapor transfere fluxos ao longo da largura do duto de gás. O vapor é então direcionado para as partes intermediárias do duto de gás e, após passar por elas, é transferido pela tubulação de vapor Ø325*60 com uma temperatura de 514 °C ao longo da largura do duto de gás para as telas de saída do segundo estágio, localizado ao longo das bordas do duto de gás. Após as telas de saída do segundo estágio, o vapor com temperatura de 523 °C entra no quarto dessuperaquecedor de injeção Ø325*60. Ambas as telas de entrada e saída de ambos os estágios do superaquecedor de tela têm um esquema de co-corrente de movimento mútuo do vapor e gases. Após o dessuperaquecedor, o vapor com uma temperatura de 537 °C através da tubulação de vapor Ø237 * 50 entra no pacote convectivo, que é feito de acordo com o esquema de co-corrente, passa com uma temperatura de 545 °C e é alimentado à turbina . A partir das câmaras de entrada do economizador de água, todos os tubos e câmaras de derivação do trato SVD são feitos de aço 12Kh1MF. Após o HPC da turbina, vapor com pressão de 39,5 atm. A temperatura de 307 °C é enviada ao superaquecedor intermediário em duas correntes. Uma linha “fria” de vapor de baixa pressão se aproxima do corpo; eles se dividem em dois antes do reaquecedor. No reaquecedor de cada carcaça existem dois fluxos de vapor de baixa pressão com controle de temperatura independente ao longo das roscas. Projeto da caldeira As paredes da câmara de combustão são completamente blindadas por tubos de superfícies radiantes de aquecimento. A câmara de combustão de cada corpo é dividida por beliscões formados por saliências das telas dianteiras e traseiras na câmara de combustão (pré-forno) e na câmara de pós-combustão. Telas na área do pré-forno até el. 15,00 totalmente cravejado e coberto com massa de cromita. O isolamento da câmara de combustão e o pinçamento no forno reduzem a transferência de calor da radiação do núcleo da tocha, o que aumenta o nível de temperatura no pré-forno e, portanto, melhora as condições de ignição e combustão do combustível, e também contribui para uma melhor formação de escória líquida. O processo de combustão do AS ocorre principalmente no pré-forno, porém, a combustão continua no pós-combustor, onde a subcombustão mecânica diminui de 7,5-10% para 2,5%. No mesmo local, a temperatura dos gases diminui para 1210 °C, o que garante o funcionamento das superfícies de aquecimento, o superaquecedor SVD sem escória. A tensão térmica de todo o volume do forno é Vт=142*103 kcal m3/hora, e o pré-forno Vтп=491*103 kcal m³/hora.
O forno de cada um dos dois edifícios está equipado com 12 queimadores turbulentos de poeira-gás dispostos em duas camadas (três queimadores em cada camada das paredes frontal e traseira do forno). O fornecimento de gás aos queimadores é periférico, o desempenho do queimador em pó é de 0,5 t/h. Cada queimador turbulento possui um bico de óleo de atomização mecânico integrado com refrigeração e um suprimento de ar organizado. Para a remoção da escória líquida, o pré-forno possui dois orifícios resfriados; o pré-forno é feito com inclinação de 80 em relação aos orifícios e é fechado com tijolos refratários. Cada forno é equipado com duas unidades mecanizadas de remoção de escória (de acordo com o número de entalhes). A escória líquida é granulada em banho-maria e removida em canais de lavagem de escória. O agente secante é descarregado através de queimadores retangulares, localizados nas paredes laterais do pré-forno em duas camadas: há 4 queimadores na camada inferior e 2 na camada superior. . A fornalha é blindada na parte inferior até 23,00 m por tubos da parte inferior de radiação (LRC) e na parte superior - por tubos da parte superior de radiação (RTC) do teto. Os tubos das telas traseira e frontal do NRCH possuem curvas, que formam a pinça do forno. A tela traseira do TRC na parte superior possui uma saliência, que melhora a aerodinâmica do fluxo de gás na saída do forno e protege parcialmente as superfícies da tela da radiação direta do forno. As telas frontal e traseira do NRCH são estruturalmente idênticas, cada tela consiste em seis fitas idênticas, com tubos conectados em paralelo Sh42 * 6 material 12X1MF. Os tubos de fita são primeiramente peneirados sob e na parte inferior do pré-forno, e depois passam para o painel vertical do NRCH, onde fazem cinco passagens de elevação e abaixamento e saem para a câmara superior. Os tubos NRCH são ligados para as brechas dos queimadores, bueiros, espiões. As telas laterais do NRC consistem em quatro painéis, que são feitos da seguinte forma.
Saindo da câmara inferior, a fita, composta por 17 bobinas conectadas em paralelo Ш42*5, material 12Х1МФ, primeiro protege a parte inferior da parede lateral, depois se move para a parte vertical, onde também faz cinco movimentos de elevação e abaixamento e então sai para a câmara superior. As telas frontal e traseira do NFC possuem dois níveis de montagens fixas no nível de 22,00 e 14,5 m. A compensação da expansão da temperatura ocorre devido à curvatura dos tubos no aperto. As telas laterais são suspensas por suportes fixos a 21,9 m e podem ser abaixadas livremente. Para evitar a saída de tubos individuais para dentro do forno, as telas possuem cinco correias de fixadores móveis. As telas frontal e traseira do TCG também consistem em painéis multi-pass com movimentos de elevação e abaixamento do vapor. O vapor é fornecido à câmara inferior dos painéis, retirado dos superiores. Os painéis do meio da tela frontal e todos os painéis das telas laterais consistem em oito, e os painéis extremos da tela frontal de nove tubos conectados em paralelo, formando uma fita. O painel em forma de N da tela traseira do TCG consiste em vinte tubos conectados em paralelo. Todas as superfícies de aquecimento do VRC são feitas de tubos Ш42*5, material 12Х1МФ. As telas frontais e laterais do TCG são suspensas fixamente no nível de 39,975 m e se expandem livremente para baixo. A tela traseira do TCG tem duas montagens fixas em 8,2 e 32,6. A compensação da expansão térmica dos tubos ocorre devido à curvatura dos tubos na parte superior da tela traseira do TCG. As telas frontal e lateral têm sete fileiras de suportes móveis, a traseira - três. Todas as telas NRC e TRC têm um passo entre os tubos de 45 mm. O teto do forno e o topo da chaminé horizontal são protegidos por tubos do superaquecedor de teto. No total, existem 304 tubos conectados em paralelo (154 por rosca) Ш32*4, material 12Х1МФ. Ao longo do comprimento dos tubos do superaquecedor de teto, existem 8 fileiras de fixadores, que são presos à estrutura com hastes.
Superaquecedores de tela Na saída do forno há um superaquecedor de tela, que consiste em duas fileiras de telas. Em uma fileira de 16 telas com um passo de 630 mm, suspensas verticalmente. No curso do vapor, as telas de cada estágio são divididas em entrada e saída, localizadas mais próximas das paredes laterais do duto de gás. Estruturalmente, as telas de entrada e saída do primeiro estágio são idênticas (exceto pela localização de conexões e tubos de derivação nas câmaras). A tela do primeiro estágio da caldeira 20 consiste em 42 bobinas Ш32*6, o material do tubo é principalmente 12Х1МФ, mas para 11 bobinas extremas a seção de saída é feita por tubos Ш32*6, material 1Х18Н12Т. Na caldeira, 19 telas do primeiro estágio consistem em 37 bobinas, material 1X18H12T. Para dar rigidez à estrutura, a tela é conectada por suas 5 bobinas, que possuem tiras de fixação feitas de aço X20H14S2. As telas do segundo estágio consistem em 45 bobinas Ø32*6. O material das telas de entrada é 12Kh1MF, e o restante das bobinas são feitas de aço 1Kh18N12T. A tela é conectada por suas seis bobinas. As câmaras de entrada e saída, exceto as câmaras das telas de saída do segundo estágio, são unidas em coletores únicos separados por uma divisória. As câmaras em hastes são suspensas nas vigas da estrutura. As paredes da câmara de giro são protegidas por quatro blocos. Os blocos são feitos na forma de fitas de dois loops. Em cada bloco existem 38 bobinas conectadas em paralelo Ш32*6 material 12Х1МФ, localizadas horizontalmente. Os blocos têm cintos de reforço. A suspensão dos blocos é realizada por meio de três fileiras (por bloco) de fixadores. As seguintes superfícies de aquecimento estão localizadas no duto de gás descendente: uma pilha SVD convectiva, um superaquecedor LP com um trocador de calor gás-vapor e um economizador de água. Para todas as superfícies convectivas, é adotado um arranjo escalonado de bobinas. Todas as superfícies são feitas de bobinas paralelas à frente da caldeira.
Superaquecedor convectivo SVD
O pacote do superaquecedor convectivo SVD de cada linha consiste em 129 bobinas Ш32*6, material 1Х18Н12Т, que são apoiadas em racks feitos de material Х23Н13, e aquelas em vigas de suporte resfriadas por água de alimentação. São três fileiras de tiras espaçadoras em aço 1X18H12T para suportar degraus e tornar a estrutura mais rígida; o pacote tem uma altura de 557 mm. Superaquecedor de baixa pressão O superaquecedor LP está localizado atrás do pacote convectivo do SVD. Os pacotes de cada fluxo estão localizados nas metades correspondentes do downcomer, a transferência de fluxos ao longo da largura da chaminé não é realizada. O superaquecedor LP consiste em um pacote de saída, um pacote intermediário e um estágio de controle. A parte de saída do superaquecedor LP consiste em 108 bobinas suspensas Sh42*3.5, o material de aço combinado: Kh2MFSR e 12Kh1MF. As bobinas são montadas em embalagens com racks, material X17H2, que são suspensas nos coletores de suporte da embalagem de alta pressão. Altura do pacote 880 mm. O pacote intermediário também consiste em 108 bobinas duplas Ш42*3.5 bobinas duplas Ш42*3.5 material 12Х1МФ. Altura do pacote 1560 mm. As bobinas são baseadas em racks, material Kh17N2, e aquelas nas câmaras de entrada do pacote intermediário Sh325 * 50, material 12Kh1MF. Assim, as câmaras de entrada da embalagem industrial também são vigas de suporte para esta superfície de aquecimento. As câmaras, além do isolamento, possuem resfriamento de ar adicional necessário durante os modos de partida e quando a turbina é desligada. Atrás do pacote industrial ao longo do fluxo de gás, em ambos os corpos das caldeiras TPP-210, em vez do GPP TO, é instalado um estágio de controle, que é o primeiro estágio do reaquecedor ao longo do fluxo de vapor, é feito de aço perlite e , de acordo com as condições de operação confiável das tubulações com desvaporização significativa, está localizado na zona onde a temperatura dos gases está na entrada não deve exceder 600°C. Seu trabalho é totalmente baseado em alterar a absorção de calor do vapor secundário alterando sua distribuição pelas tubulações de vapor de desvio. De acordo com os cálculos, na carga nominal da unidade, 20% do fluxo total de vapor passa pelo estágio de controle. Quando a carga da unidade é reduzida para 70%, o consumo de vapor é de 88%. O aumento da eficiência da unidade de energia é alcançado expandindo a faixa de cargas nas quais a temperatura de projeto do superaquecimento secundário é garantida com excesso ideal ar. A superfície de controle é instalada nas dimensões do GPP TO desmontado, os coletores de entrada são abaixados 300 mm mais baixos. A superfície de controle consiste em partes esquerda e direita com uma superfície de aquecimento total de 2020 m² por corpo. Ambas as partes são montadas a partir de pacotes de bobinas duplas e possuem 4 loops ao longo do fluxo de gás com um padrão de fluxo de vapor em contracorrente. As bobinas são feitas de tubos Ш32*4, aço 12Х1МФ e são dispostas em padrão quadriculado com degraus de 110 e 30 mm. As bobinas são montadas em embalagens utilizando racks estampados em aço 12X13. 5 racks são instalados ao longo do comprimento de cada pacote. Dois deles são instalados em coletores resfriados a água localizados no duto de gás, que são abaixados 290 mm durante o reparo. O vapor do HPC entra nas câmaras de entrada da superfície de controle Sh425*20 aço 20. Tendo passado pelas bobinas, o vapor entra nas câmaras de saída com diâmetro de aço 426*20 12Kh1MF, onde se mistura com o vapor proveniente do bypass tubulação de vapor. As antigas válvulas RKT foram cortadas ao longo das linhas "B" e "C" da antiga RKT, as partes internas foram retiradas e os corpos RKT foram escaldados e usados como tees. Na linha de desvio entre os coletores de entrada e saída, novas válvulas de gaveta RKT são instaladas. Quando a válvula é aberta a 100%, vapor na quantidade de 80% passa pela superfície de controle e o p/p diminui. Quando a válvula é fechada, o vapor passa pela superfície de controle e a temperatura de reaquecimento aumenta. O KDU e as chaves de controle do novo RKT permaneceram os mesmos. As bobinas economizadoras de água em ambos os cascos foram substituídas (100%). As arruelas de retenção foram desmontadas nos manifolds da segunda injeção e as saídas para o GPP TO foram desligadas. O economizador convectivo é a última superfície de aquecimento no fluxo de gás, localizado no downcomer. Consiste em tubos Ø32*6, material st20. As câmaras de saída e entrada do economizador também são vigas de suporte - o peso dessa superfície de aquecimento é transferido para elas através dos racks. A armação da caldeira é feita na forma de armações idênticas de ambos os edifícios, interligadas por ligações entre cascos e andaimes de transição. O peso da superfície de aquecimento, revestimento e isolamento é transferido com a ajuda de vigas e treliças horizontais para três fileiras de colunas verticais, uma fileira ao longo da frente da caldeira, a outra entre o forno e os tubos de queda e a terceira na traseira da caldeira. Para endurecer a estrutura, existem várias vigas inclinadas. Revestimento do forno, os dutos de gás da caldeira são feitos na forma de escudos separados. O forno e as chaminés são revestidos com chapas de 3 mm de espessura, o que garante uma alta densidade do forno e das chaminés.
A caldeira a vapor de passagem única TPP-210A é considerada como objeto de regulação, os sistemas de controle existentes são analisados, suas vantagens e desvantagens são observadas, é proposto um diagrama de blocos do regulador de carga térmica da caldeira TPP-210A a combustível gasoso usando o controlador microprocessado regulador Remikont R-130
O cálculo dos parâmetros de configuração e modelagem do processo de regulação da carga térmica da caldeira TPP-210A em combustível gasoso, incluindo, a aproximação de dados experimentais e modelagem do objeto de controle para um sistema de controle de duas malhas, o cálculo da configurações de sistemas de controle de duas malhas, bem como a simulação do processo transitório na regulação de sistemas de duas malhas. É realizada uma análise comparativa das características transitórias obtidas.
Extraia do texto
Em termos de nível de automação, a engenharia de energia térmica ocupa um dos lugares de liderança entre outras indústrias. As usinas termelétricas caracterizam-se pela continuidade dos processos que nelas ocorrem. Quase todas as operações em usinas termelétricas são mecanizadas e automatizadas.
A automação de parâmetros oferece benefícios significativos
Lista de literatura usada
Bibliografia
1. Grigoriev V.A., Zorin V.M. "Usinas termelétricas e nucleares". Diretório. — M.: Energoatomizdat, 1989.
2. Pletnev G. P. Sistemas de controle automatizado para usinas termelétricas: Textbook for university / G. P. Pletnev. - 3ª ed., revisada. e adicional — M.: Ed. MPEI, 2005, - 355 s
3. Pletnev T.P. Automação de processos e produções tecnológicas na indústria termelétrica. /MPEI. M, 2007. 320 p.
4. Controlador microprocessado regulador multifuncional de pequeno canal Remikont R-130″ Conjunto de documentação YALBI.421 457.001TO 1−4
5. Pletnev G.P. Zaichenko Yu.P. "Projeto, instalação e operação de sistemas de controle automatizados para processos de calor e energia" MPEI 1995 316 s.- ill.
6. Rotach V.Ya. Teoria do controle automático de processos de calor e energia, - M.: MPEI, 2007. - 400s.
7. Kozlov O.S. e outros Complexo de software "Modelagem em dispositivos técnicos" (PK "MVTU", versão 3.7).
Manual do usuário. - M.: MSTU im. Bauman, 2008.
Fil S. A., Golyshev L. V., engenheiros, Mysak I. S., Doutor em Engenharia. Sci., Dovgoteles G. A., Kotelnikov I. I., Sidenko A. P., engenheiros da JSC LvovORGRES - Universidade Nacional "Lviv Polytechnic" - Trypilska TPP
Combustão de carvões duros de baixa reatividade (Vdaf< 10%) в камерных топках котельных установок сопровождается повышенным механическим недожогом, который характеризуется двумя показателями: содержанием горючих в уносе Гун и потерей тепла от механического недожога q4.
Goon é geralmente determinado por um método de laboratório usando amostras de cinzas individuais retiradas dos dutos de gás da última superfície convectiva da caldeira usando instalações de purga regulares. A principal desvantagem do método laboratorial é a demora muito grande na obtenção do resultado Gong (mais de 4 - 6 horas), que inclui o tempo de acúmulo lento da amostra de cinzas na planta de sopro e a duração do laboratório análise. Assim, em uma única amostra de cinzas, todas as possíveis mudanças no gong são resumidas por um longo tempo, o que dificulta o ajuste e a otimização do regime de combustão de forma rápida e eficiente.
De acordo com os dados nos modos variável e não estacionário da caldeira, o coeficiente de coleta de cinzas (grau de purificação) do ciclone da configuração de transporte muda na faixa de 70 - 95%, o que leva a erros adicionais na determinando o gongo.
As desvantagens das instalações de cinzas volantes são superadas pela introdução de sistemas de medição contínua de gongos, como analisadores de teor de carbono em cinzas volantes.
Em 2000, oito conjuntos (dois para cada recipiente) de analisadores estacionários de operação contínua RCA-2000 fabricados por Mark e Wedell (Dinamarca).
O princípio de funcionamento do analisador RCA-2000 é baseado no método de análise de fotoabsorção na região do infravermelho do espectro.
Faixa de medição 0 - 20% dos valores absolutos de Gong, erro de medição relativo na faixa de 2 - 7% - não mais que ± 5%.
A amostragem de cinzas para o sistema de medição do analisador é realizada a partir dos dutos de gás na frente dos precipitadores eletrostáticos.
A gravação contínua dos gongos foi realizada em um aparelho de autogravação da sala de controle com frequência de um ciclo completo de medição em 3 minutos.
Ao queimar cinzas de composição e qualidade variadas, os valores absolutos reais de Gong, como regra, excederam 20%. Portanto, atualmente, analisadores são usados como indicadores de mudanças nos valores relativos do conteúdo de combustíveis no arrastamento de Gv ° dentro da escala do registrador 0 - 100%.
Para uma estimativa aproximada do nível real de Gong, foi compilada uma característica de calibração do analisador, que é a relação entre os valores absolutos de Gong determinados pelo método de laboratório e os valores relativos do analisador G°Gong. Na faixa de variação de gong de 20 a 45%, a característica na forma analítica é expressa pela equação
Durante os estudos experimentais e operação normal da caldeira, os analisadores podem ser usados para realizar os seguintes trabalhos:
otimização do modo de combustão;
avaliar a mudança de gong durante a mudança tecnológica planejada de sistemas e unidades da caldeira;
determinação da dinâmica e nível de diminuição da eficiência nos modos não estacionário e pós-arranque da caldeira, bem como no caso de combustão alternada de ASh e gás natural.
Durante o período de teste térmico da caldeira, foram utilizados analisadores para otimizar o regime de combustão e avaliar o efeito da comutação planejada dos equipamentos na estabilidade do processo de combustão do carvão pulverizado.
Os experimentos foram realizados com cargas estacionárias da caldeira na faixa de 0,8-1,0 nominal e combustão de AS com as seguintes características: menor poder calorífico específico Qi = 23,06 - 24,05 MJ/kg (5508 - 5745 kcal/kg), cinzas teor por peso de trabalho Ad = 17,2 - 21,8%, umidade no peso de trabalho W = 8,4 - 11,1%; a participação do gás natural para a iluminação da chama de carvão pulverizado foi de 5-10% da liberação total de calor.
Os resultados e análises de experimentos para otimizar o modo de combustão usando analisadores são fornecidos. Ao configurar a caldeira, foram otimizados:
velocidades de saída do ar secundário variando a abertura das comportas periféricas nos queimadores;
velocidades de saída do ar primário alterando a carga do ventilador de jato quente;
proporção de iluminação da chama com gás natural selecionando (de acordo com as condições para garantir a estabilidade da combustão) o número mínimo possível de queimadores a gás em funcionamento.
As principais características do processo de otimização do modo de combustão são apresentadas na Tabela. 1.
Dado na tabela. 1, os dados indicam o importante papel dos analisadores no processo de otimização, que consiste na medição e registro contínuos das informações atuais sobre a mudança de H°h, o que possibilita a medição oportuna e
fixar claramente o modo ideal, a conclusão do processo de estabilização e o início da caldeira no modo ideal.
Ao otimizar o modo de combustão, a atenção principal foi dada para encontrar o menor nível possível de valores relativos de H°un. Nesse caso, os valores absolutos de gong foram determinados pela característica de calibração do analisador.
Assim, a eficácia do uso de analisadores para otimizar o modo de combustão da caldeira pode ser aproximadamente estimada reduzindo o teor de combustíveis no arrastamento em uma média de 4% e a perda de calor por subqueima mecânica em 2%.
Nos modos estacionários da caldeira, a comutação tecnológica regular, por exemplo, em sistemas de poeira ou queimadores, interrompe o processo de combustão estável do carvão pulverizado.
tabela 1
Características do processo de otimização do modo de combustão
A caldeira TPP-210A está equipada com três sistemas de pó com moinhos de tambor de esferas do tipo ShBM 370/850 (Sh-50A) e um caixote do pó comum.
A partir do sistema de pó, o agente secante gasto é descarregado na câmara de combustão (pré-forno) usando um ventilador do moinho do tipo MB 100/1200 através de bicos de descarga especiais localizados acima dos queimadores principais de pó e gás.
O pré-forno de cada corpo de caldeira recebe uma descarga total do sistema de pó externo correspondente e metade da descarga do sistema de pó intermediário.
O agente de secagem usado é um ar umidificado e empoeirado de baixa temperatura, cujos principais parâmetros estão dentro dos seguintes limites:
a parcela de ar residual é de 20 a 30% do consumo total de ar do corpo (caldeira); temperatura 120 - 130°C; a participação do pó fino de carvão, que não foi capturado pelo ciclone do sistema de pó, 10 - 15% da produtividade do moinho;
A umidade corresponde à quantidade de umidade liberada durante o processo de secagem do combustível de trabalho moído.
O agente de secagem gasto é descarregado na zona de temperaturas máximas de chama e, portanto, afeta significativamente a integridade da queima do pó de carvão.
Durante a operação da caldeira, o sistema de poeira intermediária é mais frequentemente interrompido e reiniciado, com a ajuda de que o nível de poeira necessário é mantido no bunker industrial.
A dinâmica das mudanças nos principais indicadores do regime de combustão do corpo da caldeira - o conteúdo de combustíveis no arrastamento e a concentração em massa de óxidos de nitrogênio nos gases de combustão (NO) - durante um desligamento planejado do sistema de poeira média é mostrada na fig. 1.
Nas figuras acima e em todas as figuras subsequentes, as seguintes condições são aceitas ao construir dependências gráficas:
o conteúdo de combustíveis no arrastamento corresponde aos valores das escalas de dois eixos verticais de coordenadas: as medições médias de Gong e os dados de recálculo de acordo com a característica de calibração Gong;
a concentração de massa de NO com excesso de ar nos gases de combustão (sem redução a NO2) foi obtida a partir de medições continuamente registradas do analisador de gás estacionário Mars-5 MP "Ekomak" (Kyiv);
a dinâmica das mudanças de H°un e NO é fixada em
durante todo o período da operação tecnológica e do modo de estabilização; o início da operação tecnológica é tomado próximo à referência de tempo zero.
A completude da combustão do combustível de carvão pulverizado foi estimada pela qualidade do modo de combustão (KTR), que foi analisada por dois indicadores Gong e NO, que, via de regra, mudaram em direções opostas.
Arroz. 1. Mudanças nos indicadores do modo de combustão quando o sistema de poeira intermediária está parado
A influência do desligamento planejado do sistema de poeira média nos indicadores KTP (Fig. 1) foi analisada dependendo da sequência das seguintes operações tecnológicas:
operação 1 - desligar o alimentador de carvão bruto (CFC) e interromper o fornecimento de carvão para a usina reduziu o carregamento do tambor SBM, reduziu a finura do pó de carvão e aumentou a temperatura do ar de exaustão, o que causou um curto-circuito melhora a prazo no CTE: diminuição do Hn° e aumento do NO; o processo de maior emasculação da fábrica contribuiu para a retirada de poeira do ar residual e o aumento do excesso de ar no pré-forno, o que afetou negativamente o CTE;
operação 2 - desligar o SHM e reduzir a ventilação do sistema de poeira primeiro melhorou ligeiramente o CTE, e depois, com um atraso no desligamento do ventilador do moinho (MF), o CTE piorou;
operação 3 - parar o MW e parar a descarga do agente de secagem gasto na câmara de combustão melhorou significativamente o CTE.
Assim, todas as outras coisas sendo iguais, parar o sistema de poeira melhorou o processo de combustão do combustível, reduzindo a subqueima mecânica e aumentando a concentração de massa de NO.
Uma violação típica da estabilidade do sistema de pó é sobrecarregar o tambor do moinho com combustível ou “manchar” as bolas de moagem com material de argila úmida.
A influência da emasculação a longo prazo do tambor da fresa de topo no CTE do corpo da caldeira é mostrada na fig. 2.
Desligamento da PSU (operação 1) por motivos semelhantes aos considerados durante o desligamento do sistema de pulverização, na primeira etapa de emasculação do moinho melhorou o CTE por um curto período de tempo. Na emasculação posterior do moinho até a inclusão da PSU (operação 2), houve tendência à deterioração do CTE e ao crescimento do G°un.
Arroz. Fig. 2. Mudanças nos indicadores do regime de combustão durante a emasculação do tambor do último moinho
Arroz. 3. Alterações nos indicadores do modo de combustão ao iniciar o último sistema de poeira e desligar os queimadores a gás
Em menor grau, a operação automática da PSU desestabiliza periodicamente o modo do forno, que regula o carregamento necessário do moinho com carvão desligando e ligando o acionamento da PSU.
A influência do modo de partida do sistema de poeira extrema no KTP é mostrada na fig. 3.
A seguinte influência das operações de partida do sistema de poeira no modo de combustão foi observada:
funcionamento 1 - o arranque do MW e a ventilação (aquecimento) do percurso do sistema de poeiras com a descarga de ar relativamente frio no pré-forno aumentou o excesso de ar na zona de combustão e reduziu a temperatura do maçarico, o que levou a uma deterioração no CTE;
operação 2 - o lançamento do SHBM e a continuidade da ventilação do trato impactaram negativamente no CTE;
operação 3 - a partida da PSU e o carregamento do moinho com combustível com aumento do consumo nominal do agente secante piorou significativamente o CTE.
Pode-se concluir que a inclusão do sistema de poeira em operação afeta negativamente o CTE, aumentando a subqueima mecânica e reduzindo a concentração mássica de NO.
O pré-forno do corpo da caldeira TPP-210A está equipado com seis queimadores de pó e gás tipo caracol com potência térmica de 70 MW, instalados em uma camada nas paredes frontal e traseira, e dois queimadores a gás-óleo acima da lareira para garantir a remoção estável de cinzas líquidas em toda a faixa de cargas operacionais da caldeira.
Durante a combustão do pó de carvão ASh, o gás natural foi fornecido a uma taxa de fluxo constante (cerca de 5% da liberação total de calor) para os queimadores sobre lareira e uma taxa de fluxo variável através dos principais queimadores de pó-gás para estabilizar o processo de combustão de carvão pulverizado. O fornecimento de gás para cada queimador principal foi realizado com a menor vazão possível, correspondendo a 1,0 - 1,5% da liberação total de calor. Portanto, a mudança na participação do gás natural para a iluminação da tocha foi realizada ligando ou desligando um certo número de queimadores principais a gás.
O efeito de desligar os queimadores a gás (reduzindo a participação do gás natural) no CTE do corpo da caldeira é mostrado na fig. 3.
O desligamento sequencial de primeiro um queimador a gás (operação 4) e depois três queimadores a gás (operação 5) teve um efeito positivo no CTE e levou a uma redução significativa na subqueima mecânica.
O efeito de ligar os queimadores a gás (aumentando a participação do gás natural) no CTE é mostrado na fig. 4. O acendimento sequencial de um queimador a gás (operação 1), dois queimadores (operação 2) e um queimador (operação 3) afetou negativamente o CTE e aumentou significativamente a subqueima mecânica.
Arroz. 4. Mudança nos indicadores do modo de combustão quando os queimadores a gás são ligados
mesa 2
Mudanças no conteúdo de combustíveis no transporte durante a troca tecnológica de equipamentos
Equipamento | Modo | ||
diminuir | aumentar |
||
Sistema de Poeira Extrema/Média | |||
emasculação | Emergência | ||
alimentador cru | |||
Queimador de gás principal | Desligar | ||
Inclusão |
Uma avaliação aproximada do impacto da mudança tecnológica comprovada do equipamento da caldeira na mudança no CTE (Kun) está resumida na Tabela. 2.
A análise dos dados apresentados mostra que o maior decréscimo na eficiência da caldeira em modo estacionário ocorre como resultado das operações de partida do sistema de poeira e com um consumo superestimado de gás natural para iluminação da chama.
Deve-se notar que a necessidade de realizar operações de partida do sistema de poeira é determinada apenas por razões tecnológicas, e o consumo superestimado de gás natural para iluminação de chamas, em regra, é definido pelo pessoal operacional para evitar possíveis violações da estabilidade do processo de combustão no caso de uma deterioração repentina na qualidade do AS.
O uso de analisadores RCA-2000 permite mudanças contínuas,
avaliar quaisquer alterações na qualidade do combustível e manter constantemente o valor da iluminação da chama no nível ideal adequado com o consumo mínimo necessário de gás natural, o que ajuda a reduzir o consumo de combustível gasoso escasso e aumentar a eficiência da caldeira.
descobertas
- O sistema de medição contínua do conteúdo de combustíveis em transporte permite avaliar de forma rápida e eficiente o fluxo dos processos de combustão durante a combustão do AS na caldeira TPP-210A, recomendado para uso em comissionamento e trabalhos de pesquisa, pois bem como para o monitoramento sistemático da eficiência dos equipamentos da caldeira.
- A eficiência do uso dos analisadores RCA-2000 para otimizar o modo de combustão é estimada provisoriamente pela redução dos indicadores de subcombustão mecânica - o conteúdo de combustíveis no arraste em média de 4% e, consequentemente, a perda de calor por subcombustão mecânica em 2% .
- Nos modos estacionários da caldeira, a troca tecnológica regular de equipamentos afeta a qualidade do processo de combustão. As operações de partida do sistema de pó e o consumo superestimado de gás natural para acender o maçarico de carvão pulverizado reduzem significativamente a eficiência da caldeira.
Bibliografia
- Madoyan A. A., Baltyan V. N., Grechany A. N. Combustão eficiente de carvões de baixa qualidade em caldeiras de força. Moscou: Energoatomizdat, 1991.
- Uso do analisador de conteúdo combustível RCA-2000 no transporte e do analisador de gás Mars-5 para otimizar o modo de combustão da caldeira de carvão pulverizado TPP-210A de Tripolskaya TPP / Golyshev L. V., Kotelnikov N. I., Sidenko A. P. et al. - Tr. Instituto Politécnico de Kiev. Energia: economia, tecnologia, ecologia, 2001, nº 1.
- Zusin S. I. Mudança na perda de calor com subqueima mecânica dependendo do modo de operação da unidade da caldeira. - Engenharia de energia térmica, 1958, nº 10.
A tecnologia de partida das caldeiras de passagem única difere, por não possuírem um sistema de circulação fechado, não haver um tambor no qual o vapor seria continuamente separado da água e no qual um determinado suprimento de água seria mantido por um determinado Tempo. Nestes, é realizada uma única circulação forçada do meio. Portanto, durante a ignição (e ao trabalhar sob carga), é necessário garantir o movimento forçado contínuo do meio pelas superfícies aquecidas e, ao mesmo tempo, remover o meio aquecido da caldeira, e o movimento da água nas tubulações deve começar mesmo antes da ignição dos queimadores.
Nestas condições, o modo de ignição é inteiramente determinado pela confiabilidade, condições adequadas de temperatura do metal dos tubos de telas, telas, superaquecedores e ausência de ajustes termo-hidráulicos inaceitáveis.
A experiência e os cálculos mostraram que o resfriamento das superfícies de aquecimento durante a partida de uma caldeira de passagem única é confiável se o fluxo de água de ignição for pelo menos 30% do nominal. Nesta vazão, a velocidade de massa mínima do meio nas telas é de 450-500 kg/(m2*s) de acordo com as condições de confiabilidade. Neste caso, a pressão mínima do meio nas telas deve ser mantida próxima à nominal, ou seja, para caldeiras de 14 MPa - no nível de 12-13 MPa, e para caldeiras de pressão supercrítica - 24-25 MPa.
Existem dois modos básicos de queima para caldeiras de passagem única: passagem única e separador.
No modo de queima única, o meio de trabalho se move por todas as superfícies de aquecimento da caldeira, exatamente como quando está sob carga. No primeiro período de acendimento, este meio é retirado da caldeira através da ROU e, após a formação do vapor com os parâmetros necessários, é enviado para a tubulação principal de vapor ou diretamente para a turbina (em instalações em bloco).
As figuras abaixo mostram um esquema simplificado para iniciar a caldeira a partir de um estado “frio” em modo de fluxo direto:
Outra figura abaixo mostra a mudança no fluxo de água de alimentação (1), pressão do vapor atrás da caldeira (2), temperatura do meio (3), vapor fresco (4) e secundário (5), bem como a temperatura do metal das telas dos superaquecedores primário (7) e secundário (5). Como pode ser visto, no início da ignição, quando a pressão do vapor atinge 4 MPa, a temperatura do meio e do metal nas telas do superaquecedor intermediário cai drasticamente de 400 para 300-250 °C, o que é explicado pela abertura da ROU para descarregar o meio no sistema de drenagem, e Em todo o caminho primário 23-24 MPa, as condições de operação das telas dos superaquecedores primários e secundários, cuja temperatura excede 600 ° C, também se deterioram acentuadamente.
É possível evitar elevações excessivas da temperatura da tela metálica apenas aumentando o fluxo de água de ignição e, consequentemente, aumentando a perda de condensado e calor em relação ao modo de partida do separador. Dado isso, bem como o fato de que o esquema de partida única para iniciar a caldeira a partir do estado “frio” não tem nenhuma vantagem sobre o separador, atualmente não é usado para partida.
O modo de partida de fluxo direto da caldeira do estado "quente" e "não resfriado" cria o perigo de um resfriamento acentuado das partes mais aquecidas da caldeira e das tubulações de vapor, bem como um aumento inaceitável de a temperatura do metal do superaquecedor no modo de não consumo quando os gravetos BROU e ROU são fechados no primeiro período. Tudo isso dificulta a partida de um estado "quente", razão pela qual esse modo foi substituído por um circuito de partida separador.
A única área de aplicação para o modo de partida única foi o acendimento de uma caldeira de duplo efeito do estado "frio" e a partida da caldeira de passagem da reserva quente após um tempo de inatividade de até 1 hora.
Ao iniciar uma caldeira de concha dupla, ambas as conchas são acionadas sucessivamente: caldeiras assimétricas (por exemplo, TPP-110) são acionadas a partir da concha, na qual não há superaquecedor secundário. Casos de caldeiras simétricas são derretidos em uma sequência arbitrária. O primeiro corpo de ambos os tipos de caldeiras de casco duplo é acionado de acordo com o modo do separador. A ignição do segundo corpo é iniciada com uma pequena carga elétrica do bloco e é realizada de acordo com qualquer modo.
A ignição da caldeira após uma paragem curta (até 1 hora) pode ser realizada em modo de fluxo directo, uma vez que os parâmetros do vapor ainda mantêm os seus valores de funcionamento e os elementos e componentes individuais da unidade da caldeira não tiveram tempo de esfriar significativamente. O modo de fluxo direto neste caso deve ser preferido, pois não requer treinamento especial, o que seria necessário ao mudar para um circuito separador, o que permite economizar tempo e acelerar a partida da caldeira. A ignição neste caso é realizada em modo de fluxo direto com a descarga de todo o meio de trabalho através da ROU ou BRDS através da válvula principal de vapor (MGS) até que a temperatura do vapor primário e secundário exceda a temperatura do vapor da turbina entrada em cerca de 50 °C. Se a temperatura do vapor durante o desligamento do bloco tiver diminuído menos de 50 °C, a temperatura do vapor atrás da caldeira é imediatamente aumentada para o valor nominal, após o que o fornecimento de vapor da ROU para a turbina é comutado.
Com tal partida da caldeira a partir da reserva quente, deve-se levar em consideração que durante a parada de curto prazo da caldeira, a temperatura do meio na entrada e saída em muitos tubos das telas é equalizada e a circulação natural do meio ocorre dentro de painéis individuais e entre painéis. Essa circulação pode ser tão estável que persiste por algum tempo depois que as bombas de alimentação são reiniciadas. Como resultado, leva algum tempo até que o ambiente de trabalho comece a se mover firmemente na direção certa. Até que o movimento instável do meio pare, não é recomendado começar a acender a unidade da caldeira para evitar danos aos tubos aquecidos.
Comparado com o modo de partida de caldeira de passagem única, é caracterizado por alta estabilidade, temperaturas relativamente baixas do meio de trabalho e metal em todo o caminho da caldeira e permite que a turbina seja iniciada em parâmetros de vapor deslizante. As telas do superaquecedor intermediário da caldeira começam a esfriar em um estágio inicial de partida e seu metal não superaquece a valores inaceitáveis. O modo de partida do separador é realizado usando um dispositivo de ignição especial, a chamada unidade de ignição, consistindo de uma válvula embutida (2), um separador embutido (7), um expansor de ignição (9) e válvulas de estrangulamento 5, 6, 8. O separador embutido é projetado para separar a umidade do vapor e é um tubo com uma grande seção transversal (425 × 50 mm), no qual um desumidificador de parafuso está instalado e ligado durante o período de acionar a caldeira entre as superfícies geradoras de vapor (1) e superaquecimento (3) da caldeira através dos dispositivos de estrangulamento 5 e 6. A válvula embutida 2 serve para desconectar as telas e o superaquecedor convectivo das superfícies de aquecimento geradoras de vapor e é colocados entre os dispositivos de saída da última seção das superfícies da tela e os coletores de entrada dos superaquecedores da tela. Durante o acionamento da caldeira, a válvula de vapor principal (4) permanece aberta em uma planta de bloco e fechada em uma planta de cogeração reticulada.
O expansor de graveto é um estágio intermediário entre o separador embutido e os dispositivos para receber o meio descarregado do separador. Uma vez que a pressão no expansor é mantida mais baixa do que no separador (geralmente cerca de 2 MPa), o meio de trabalho é descarregado para ele através da válvula de estrangulamento 8 e, após estrangulamento repetido, evapora parcialmente. O vapor do expansor de gravetos é enviado para o coletor de necessidades da própria planta, de onde pode entrar nos desaeradores e demais consumidores, e a água é descarregada no canal de saída da água circulante, ou no tanque de condensado de reserva, ou (em instalações de bloco) diretamente no condensador.
A ideia de uma partida do separador de uma unidade de caldeira de passagem única é dividir o processo de partida em três fases, de modo que em cada uma dessas fases conduzidas sequencialmente, a confiabilidade de todas as superfícies de aquecimento seja totalmente garantida e na última fase, é possível iniciar o equipamento de potência do bloco em parâmetros de vapor deslizante, mantendo nas superfícies geradoras de vapor pressão nominal constante.
Na primeira fase da partida, a circulação forçada do meio de trabalho é organizada em circuito fechado: bomba de alimentação - caldeira - unidade de ignição - receptores para o meio residual (em um condensador de turbina de instalação em bloco) - bomba de alimentação. Isso elimina a possibilidade de ajustes termo-hidráulicos perigosos nas superfícies geradoras de vapor e a perda de condensado e calor é minimizada. Nesta fase de arranque, o meio de trabalho não tem saída para as superfícies de sobreaquecimento, uma vez que são cortadas das superfícies geradoras de vapor pelo registo incorporado e válvula de estrangulamento 17, que estão fechadas durante este período de arranque, e estão no chamado modo gratuito. Apesar de os tubos dessas superfícies não serem resfriados por dentro com vapor em modo sem fluxo, a temperatura de seu metal permanece dentro de limites aceitáveis, pois o consumo de combustível inicial durante esse período permanece constante e relativamente baixo , não superior a 20% da vazão nominal.
A segurança do modo sem fluxo para superaquecedores durante o período de inicialização da caldeira foi confirmada por testes especiais das caldeiras TPP-110 e TPP-210. Como pode ser visto, com consumos de combustível (gás natural) de até 20% da temperatura nominal, as paredes dos tubos terminais mais aquecidos das telas não ultrapassam a temperatura permitida de 600 °C no estado estacionário. Tendo em conta que o consumo de combustível no período inicial de arranque da caldeira é significativamente inferior a 20% (por exemplo, quando a caldeira está a funcionar com óleo combustível, o seu consumo não é superior a 14-15% do valor nominal ), o modo de não consumo para superaquecedores pode ser considerado bastante aceitável neste período de ignição.
Em conexão com os experimentos realizados, nota-se que em nenhuma das partidas das caldeiras testadas a temperatura das paredes do tubo ultrapassou 550 °C ao longo de toda a duração do regime de não escoamento. Esta temperatura está abaixo do máximo permitido para o aço baixa liga 12Kh1MF, normalmente utilizado para a fabricação de tubos de telas estágio I, e ainda mais para o aço austenítico 1Kh18N12T, utilizado para telas estágio II em superaquecedores convectivos.
O desligamento dos superaquecedores na primeira fase de partida simplifica a manobra e o controle da unidade da caldeira, permitindo, após a conexão das superfícies de superaquecimento, aumentar suavemente os parâmetros de vapor e sua quantidade, mantendo a estabilidade do fornecimento de água de alimentação. O início da segunda fase da partida é considerado o momento em que o vapor começa a ser liberado no separador embutido, que é direcionado para as superfícies de superaquecimento, abrindo gradativamente a válvula borboleta e aumentando gradativamente a temperatura e a pressão do vapor. Nesta fase de arranque, a caldeira funciona a duas pressões: nominal - até à válvula incorporada, que continua fechada, e "deslizante" - atrás da válvula borboleta nas superfícies de sobreaquecimento. Este modo é possível devido ao fato de que as superfícies de superaquecimento são separadas das superfícies geradoras de vapor pelo espaço de vapor do separador, assim como nas caldeiras de tambor. Na terceira fase do arranque, a unidade da caldeira é transferida para o modo de fluxo direto. Esta transferência deve começar após os parâmetros do vapor atingirem 80-85% dos valores nominais. Abra gradualmente a válvula embutida, leve os parâmetros ao valor nominal e desligue a unidade de ignição.
No final do acendimento da unidade de caldeira em uma UTE sem bloco, ela é conectada à tubulação principal de vapor, e as regras de conexão permanecem as mesmas das caldeiras de tambor. A principal é a igualdade aproximada de pressões atrás da caldeira e na tubulação principal de vapor no momento da conexão.
Nas instalações em bloco, a partida da caldeira é combinada com a partida da turbina e a transferência da caldeira para o modo one-through geralmente é realizada após a carga elétrica do bloco atingir 60-70% do o valor nominal.
As figuras abaixo mostram as características de partida de uma caldeira de passagem única de uma UTE sem bloco em modo separador: 1 - pressão de vapor atrás da caldeira; 2 - consumo de água de alimentação; 3 - temperatura máxima do meio na saída do NRC; 4 - temperatura da água de alimentação; 5 - temperatura de superaquecimento intermediário; 6 - temperatura do vapor fresco; 8, 7 - temperatura máxima do metal das telas II e do superaquecedor intermediário; 9 - temperatura dos gases de combustão na câmara rotativa.
As características do acendimento durante uma partida "quente" são as seguintes. Antes da ignição dos queimadores, a temperatura do metal dos separadores embutidos é reduzida de 490 para 350-320 ° C pela ventilação do vapor dos separadores, e a taxa de diminuição neste caso não deve exceder 4 ° C / min . Ao mesmo tempo, a pressão na caldeira ~~ é reduzida da nominal (25 MPa) para 10-15 MPa. 30-40 minutos após o resfriamento dos separadores de acordo com o mesmo cronograma do estado "não resfriado", ou seja, após estabelecer a vazão mínima de ignição da água de alimentação, a pressão na frente da válvula embutida fechada aumenta para 24 -25 MPa, os queimadores de óleo são ligados com um óleo de vazão inicial e, ao mesmo tempo, as válvulas de alívio de 8 separadores embutidos abrem. Em seguida, abrem-se gradualmente as válvulas de estrangulamento 5. As outras operações são as mesmas que quando se inicia a partir de um estado "frio". Ao reduzir a pressão na caldeira antes da ignição, exclui-se a condensação de vapor nas telas, que são, portanto, resfriadas menos do que na partida no modo de fluxo direto.
A unidade de energia com a caldeira TPP-210A foi desligada de emergência por dispositivos de proteção devido a falhas na operação da bomba de alimentação. Quando a válvula da linha de óleo combustível foi fechada automaticamente, o fornecimento de combustível líquido não foi completamente desligado e em um corpo de caldeira uma pequena quantidade de óleo combustível continuou a queimar na fornalha, o que contribuiu não apenas para o aumento das distorções térmicas e um aumento da circulação nos painéis LFC, mas também ao aparecimento de tubos fixos individuais nas curvas superiores, bolhas de vapor ligeiramente sobreaquecido, que ocupavam toda a secção dos tubos e impediam a circulação do meio de trabalho nos mesmos. Embora o vapor de pressão supercrítica tenha a mesma densidade que a água no momento de sua formação, um aumento em sua temperatura em apenas alguns graus leva a uma diminuição em sua densidade em dezenas de por cento. Com o aumento da velocidade da água, as bolhas de vapor devem ser levadas pelo seu fluxo, no entanto, grandes bolhas podem permanecer temporariamente, devido às quais a temperatura do metal dos tubos correspondentes deve ter aumentado acentuadamente.
Após uma pausa de cinco minutos, a caldeira foi alternada para o modo de fluxo direto e, contrariamente às regras, a água de alimentação foi fornecida não anteriormente, mas simultaneamente com um aumento acentuado no fornecimento de óleo combustível ao forno. Logo, na seção de saída não aquecida de um dos tubos NRCH, foi registrado um aumento de temperatura de até 570 °C. O intervalo entre os registos automáticos desta temperatura foi de 4 minutos, mas antes de esta temperatura ser novamente registada, ocorreu uma ruptura de emergência da tubagem, na qual existia um troço na zona da cantoneira do queimador que não estava protegido por cintas incendiárias. A caldeira foi novamente desligada de emergência.
Outro exemplo refere-se à deterioração da separação, que ocorreu quando as válvulas de alívio não foram totalmente abertas, o que removeu a umidade separada do separador embutido. Quando a caldeira de passagem única foi acionada, essas válvulas foram fechadas para reduzir a temperatura do vapor vivo em caso de mau funcionamento dos dessuperaquecedores de injeção. Este método de controle está associado a mudanças abruptas e significativas na temperatura do vapor e leva ao aparecimento de trincas de fadiga nos coletores do superaquecedor próximos ao separador embutido ao longo do caminho do vapor.
O fechamento das válvulas 8 e a abertura 5 devem ser feitos lentamente para evitar a liberação de água nos coletores próximos do superaquecedor devido a uma violação do movimento estável do meio de trabalho no separador. Além disso, é necessário abrir os drenos antes e depois da válvula borboleta 5 com antecedência para evitar que o condensado acumulado nas tubulações escape da unidade de ignição.
A abertura lenta das válvulas de estrangulamento 5 leva a um aumento do tempo de aquecimento das condutas principais de vapor e da duração do acendimento da caldeira. É claro que flutuações significativas na temperatura do vapor são inaceitáveis, no entanto, se a caldeira for acionada apenas algumas vezes por ano, não há motivo para atrasar adicionalmente as operações de partida para evitar uma ligeira diminuição na temperatura do vapor. Mas se a caldeira for acionada e parada com frequência, mesmo pequenas gotas de água nas telas podem ter consequências perigosas. Portanto, ao acender caldeiras de passagem única, é necessário observar rigorosamente o cronograma de partida, que regula a abertura lenta e gradual das válvulas 5.