تآكل في المرجل. التآكل والتآكل في غلايات الضغط المتوسط والمنخفض من جانب الفرن. غالبًا ما تظهر ظواهر التآكل في الغلايات على السطح الداخلي المجهد بالحرارة وغالبًا ما تظهر على السطح الخارجي.
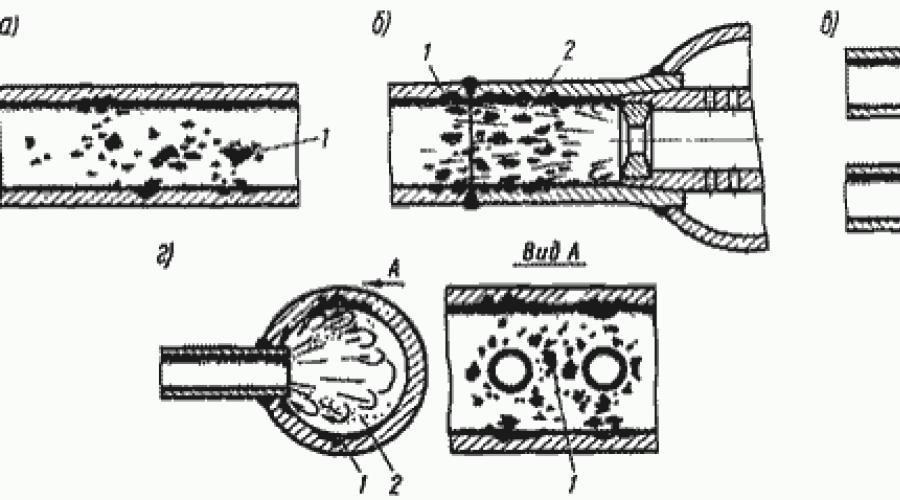
غالبًا ما يكون هذا التآكل في الحجم والشدة أكثر خطورة وخطورة من تآكل الغلايات أثناء تشغيلها.
عند ترك الماء في الأنظمة ، اعتمادًا على درجة حرارته والوصول إلى الهواء ، يمكن أن تحدث مجموعة متنوعة من حالات تآكل وقوف السيارات. بادئ ذي بدء ، تجدر الإشارة إلى عدم الرغبة الشديدة في وجود الماء في أنابيب الوحدات عندما تكون في الاحتياط.
إذا بقي الماء في النظام لسبب أو لآخر ، يمكن أن يحدث تآكل شديد في وقوف السيارات في البخار وخاصة في مساحة الماء في الخزان (بشكل أساسي على طول خط الماء) عند درجة حرارة الماء 60-70 درجة مئوية. لذلك ، من الناحية العملية ، غالبًا ما يتم ملاحظة تآكل وقوف السيارات بكثافة مختلفة ، على الرغم من نفس أوضاع الإغلاق للنظام ونوعية المياه الموجودة فيه ؛ الأجهزة ذات التراكم الحراري الكبير معرضة لتآكل أكثر شدة من الأجهزة التي لها أبعاد الفرن وسطح التسخين ، لأن ماء الغلاية فيها يبرد بشكل أسرع ؛ تنخفض درجة حرارته عن 60-70 درجة مئوية.
عند درجة حرارة الماء أعلى من 85-90 درجة مئوية (على سبيل المثال ، أثناء الإغلاق قصير المدى للجهاز) ، ينخفض التآكل الكلي ، ويقل تآكل معدن حيز البخار ، حيث لوحظ زيادة تكثيف البخار في هذه الحالة ، يمكن أن يتجاوز تآكل معدن الفضاء المائي. يكون تآكل وقوف السيارات في مساحة البخار في جميع الحالات أكثر اتساقًا مما هو عليه في مساحة الماء في الغلاية.
يتم تسهيل تطور تآكل مواقف السيارات بشكل كبير من خلال الحمأة التي تتراكم على أسطح الغلاية ، والتي عادة ما تحتفظ بالرطوبة. في هذا الصدد ، غالبًا ما توجد ثقوب تآكل كبيرة في الركام والأنابيب على طول طبقة المولدات السفلية وفي نهاياتها ، أي في مناطق تراكم الحمأة الأكبر.
طرق حفظ المعدات في الاحتياطي
يمكن استخدام الطرق التالية للحفاظ على المعدات:
أ) التجفيف - إزالة الماء والرطوبة من الركام ؛
ب) ملئها بمحلول الصودا الكاوية والفوسفات والسيليكات ونتريت الصوديوم والهيدرازين ؛
ج) ملء النظام التكنولوجي بالنيتروجين.
يجب اختيار طريقة الحفظ اعتمادًا على طبيعة ومدة التوقف ، بالإضافة إلى نوع الجهاز وميزات تصميمه.
يمكن تقسيم وقت تعطل المعدات إلى مجموعتين حسب المدة: قصيرة الأجل - لا تزيد عن 3 أيام وطويلة الأجل - أكثر من 3 أيام.
هناك نوعان من فترات التوقف قصيرة المدى:
أ) مجدولة ، مرتبطة بالانسحاب إلى الاحتياطي في عطلات نهاية الأسبوع بسبب انخفاض الحمولة أو الانسحاب إلى الاحتياطي ليلاً ؛
ب) قسري - بسبب فشل الأنابيب أو تلف مكونات المعدات الأخرى ، والتي لا يتطلب إزالتها إيقاف تشغيل أطول.
اعتمادًا على الغرض ، يمكن تقسيم فترات التوقف الطويلة الأجل إلى المجموعات التالية: أ) وضع المعدات في الاحتياطي ؛ ب) الإصلاحات الحالية. ج) إصلاحات رأس المال.
في حالة تعطل الجهاز على المدى القصير ، من الضروري استخدام الحفظ عن طريق ملء المياه غير المعزولة مع الحفاظ على الضغط الزائد أو طريقة الغاز (النيتروجين). إذا كان الإغلاق الطارئ مطلوبًا ، فإن الطريقة الوحيدة المقبولة هي الحفظ بالنيتروجين.
عندما يتم وضع النظام في الخدمة الاحتياطية أو تعطله لفترة طويلة دون أعمال إصلاح ، فمن المستحسن إجراء الحفظ عن طريق ملئه بمحلول من النتريت أو سيليكات الصوديوم. في هذه الحالات ، يمكن أيضًا استخدام الحفاظ على النيتروجين ، مع اتخاذ تدابير بالضرورة لإحكام النظام من أجل منع الاستهلاك المفرط للغاز والتشغيل غير المنتج لمصنع النيتروجين ، وكذلك لتهيئة ظروف آمنة لصيانة المعدات.
طرق الحفظ عن طريق خلق ضغط زائد ، يمكن استخدام الملء بالنيتروجين بغض النظر عن ميزات تصميم أسطح تسخين الجهاز.
لمنع تآكل المعدن أثناء وقوف السيارات أثناء الإصلاحات الرئيسية والحالية ، يتم تطبيق طرق الحفظ فقط التي تسمح بإنشاء فيلم واقي على السطح المعدني يحتفظ بخصائصه لمدة لا تقل عن شهر إلى شهرين بعد تصريف محلول المادة الحافظة ، منذ تفريغ وإزالة الضغط من المادة الحافظة. نظام لا مفر منه. يمكن أن تصل مدة الطبقة الواقية على السطح المعدني بعد المعالجة بنتريت الصوديوم إلى 3 أشهر.
طرق الحفظ باستخدام الماء وحلول الكاشف غير مقبولة عمليًا للحماية من تآكل وقوف السيارات في السخانات الفائقة الوسيطة للغلايات بسبب الصعوبات المرتبطة بتعبئتها والتنظيف اللاحق.
تختلف طرق الحفاظ على غلايات الماء الساخن والبخار ذات الضغط المنخفض ، فضلاً عن المعدات الأخرى للدوائر التكنولوجية المغلقة للتدفئة وإمدادات المياه ، في كثير من النواحي عن الطرق المستخدمة حاليًا لمنع تآكل وقوف السيارات في محطات الطاقة الحرارية. فيما يلي وصف للطرق الرئيسية لمنع التآكل في وضع الخمول لمعدات أجهزة أنظمة الدوران هذه ، مع مراعاة خصائص تشغيلها.
طرق الحفظ المبسطة
هذه الطرق مفيدة للغلايات الصغيرة. وهي تتكون من الإزالة الكاملة للمياه من الغلايات ووضع المجففات فيها: كلوريد الكالسيوم المكلس والجير الحي وهلام السيليكا بمعدل 1-2 كجم لكل 1 م 3 من الحجم.
طريقة الحفظ هذه مناسبة لدرجات حرارة الغرفة التي تقل عن الصفر وما فوق. في الغرف التي يتم تسخينها في الشتاء ، يمكن تنفيذ إحدى طرق التلامس للحفظ. يتعلق الأمر بملء الحجم الداخلي الكامل للوحدة بمحلول قلوي (NaOH ، Na 3 P0 4 ، وما إلى ذلك) ، مما يضمن الاستقرار الكامل للفيلم الواقي على السطح المعدني حتى عندما يكون السائل مشبعًا بالأكسجين.
عادة ما تستخدم المحاليل التي تحتوي على 1.5-2 إلى 10 كجم / م 3 هيدروكسيد الصوديوم أو 5-20 كجم / م 3 Na 3 P0 4 اعتمادًا على محتوى الأملاح المحايدة في مصدر المياه. تشير القيم الأصغر إلى المكثفات ، والقيم الأكبر تشير إلى الماء الذي يحتوي على ما يصل إلى 3000 مجم / لتر من الأملاح المحايدة.
يمكن أيضًا منع التآكل من خلال طريقة الضغط الزائد ، حيث يتم الحفاظ على ضغط البخار في الوحدة المتوقفة باستمرار عند مستوى أعلى من الضغط الجوي ، وتظل درجة حرارة الماء أعلى من 100 درجة مئوية ، مما يمنع وصول عامل التآكل الرئيسي ، الأكسجين .
أحد الشروط المهمة لفعالية واقتصاد أي طريقة حماية هو أقصى إحكام ممكن لتركيبات الماء البخاري من أجل تجنب الانخفاض السريع جدًا في الضغط أو فقدان محلول وقائي (أو غاز) أو دخول الرطوبة. بالإضافة إلى ذلك ، في كثير من الحالات ، يكون التنظيف الأولي للأسطح من الرواسب المختلفة (الأملاح ، الحمأة ، الحجم) مفيدًا.
عند تنفيذ طرق مختلفة للحماية من تآكل مواقف السيارات ، يجب مراعاة ما يلي.
1. لجميع أنواع الحفظ ، فإن الإزالة الأولية (الغسل) لرواسب الأملاح القابلة للذوبان بسهولة (انظر أعلاه) ضرورية لتجنب زيادة تآكل وقوف السيارات في مناطق معينة من الوحدة المحمية. من الضروري تنفيذ هذا الإجراء أثناء الحفاظ على التلامس ، وإلا فمن الممكن حدوث تآكل محلي شديد.
2. لأسباب مماثلة ، من المستحسن إزالة جميع أنواع الرواسب غير القابلة للذوبان (الحمأة ، القشور ، أكاسيد الحديد) قبل الحفظ على المدى الطويل.
3. إذا كانت التركيبات غير موثوقة ، فمن الضروري فصل المعدات الاحتياطية من وحدات التشغيل باستخدام المقابس.
يعتبر تسرب البخار والماء أقل خطورة مع الحفاظ على التلامس ، ولكنه غير مقبول مع طرق الحماية من الجفاف والغاز.
يتم تحديد اختيار المجففات من خلال التوافر النسبي للكاشف والرغبة في الحصول على أعلى محتوى رطوبة محدد ممكن. أفضل مادة مجففة هي حبيبات كلوريد الكالسيوم. يعتبر الجير الحي أسوأ بكثير من كلوريد الكالسيوم ، ليس فقط بسبب انخفاض قدرة الرطوبة ، ولكن أيضًا بسبب الفقدان السريع لنشاطه. لا يمتص الجير الرطوبة من الهواء فحسب ، بل يمتص أيضًا ثاني أكسيد الكربون ، ونتيجة لذلك يتم تغطيته بطبقة من كربونات الكالسيوم ، مما يمنع المزيد من امتصاص الرطوبة.
موقع بحري روسيا رقم 05 أكتوبر 2016 تاريخ الإنشاء: 05 أكتوبر 2016 تاريخ التحديث: 05 أكتوبر 2016 المشاهدات: 5363أنواع التآكل. أثناء التشغيل ، تتعرض عناصر الغلاية البخارية لوسائط عدوانية - الماء والبخار وغازات المداخن. يميز بين التآكل الكيميائي والكهروكيميائي.
التآكل الكيميائي، الناجم عن البخار أو الماء ، يدمر المعدن بالتساوي على السطح بالكامل. معدل التآكل في الغلايات البحرية الحديثة منخفض. الأكثر خطورة هو التآكل الكيميائي المحلي الناجم عن المركبات الكيميائية العدوانية الموجودة في رواسب الرماد (الكبريت ، أكاسيد الفاناديوم ، إلخ).
الأكثر شيوعًا وخطورة هو التآكل الكهروكيميائي، تتدفق في المحاليل المائية للكهارل عند حدوث تيار كهربائي ، بسبب اختلاف الجهد بين الأقسام الفردية للمعدن ، والتي تختلف في عدم التجانس الكيميائي أو درجة الحرارة أو جودة المعالجة.
يتم تنفيذ دور المنحل بالكهرباء بواسطة الماء (مع التآكل الداخلي) أو بخار الماء المكثف في الرواسب (مع التآكل الخارجي).
يؤدي حدوث مثل هذه الأزواج الجلفانية الدقيقة على سطح الأنبوب إلى حقيقة أن ذرات أيونات المعادن تمر في الماء على شكل أيونات موجبة الشحنة ، ويكتسب سطح الأنبوب في هذا المكان شحنة سالبة. إذا كان الاختلاف في إمكانات هذه الأزواج الجلفانية الدقيقة غير ذي أهمية ، فسيتم إنشاء طبقة كهربائية مزدوجة تدريجياً في واجهة المعدن والماء ، مما يؤدي إلى إبطاء المسار الإضافي للعملية.
ومع ذلك ، في معظم الحالات ، تختلف إمكانات الأقسام الفردية ، مما يؤدي إلى حدوث EMF موجه من جهد أكبر (أنود) إلى احتمال أصغر (كاثود).
في هذه الحالة ، تمر ذرات أيونات المعادن من القطب الموجب إلى الماء ، وتتراكم الإلكترونات الزائدة على القطب السالب. نتيجة لذلك ، تم تقليل الكهرومغناطيسي وبالتالي شدة عملية تدمير المعادن بشكل حاد.
هذه الظاهرة تسمى الاستقطاب. إذا انخفض جهد الأنود نتيجة لتشكيل طبقة أكسيد واقية أو زيادة في تركيز أيونات المعادن في منطقة الأنود ، وبقي جهد الكاثود دون تغيير عمليًا ، فإن الاستقطاب يسمى أنوديك.
مع الاستقطاب الكاثودي في محلول بالقرب من الكاثود ، ينخفض تركيز الأيونات والجزيئات القادرة على إزالة الإلكترونات الزائدة من سطح المعدن بشكل حاد. ويترتب على ذلك أن النقطة الرئيسية في مكافحة التآكل الكهروكيميائي هي خلق مثل هذه الظروف عندما يتم الحفاظ على كلا النوعين من الاستقطاب.
من المستحيل عمليا تحقيق ذلك ، لأن ماء الغلاية يحتوي دائمًا على مزيلات الاستقطاب - وهي مواد تسبب اضطراب عمليات الاستقطاب.
تشتمل مزيلات الاستقطاب على جزيئات O 2 و CO 2 و H + و Cl - و SO - 4 ، بالإضافة إلى أكاسيد الحديد والنحاس. الذائب في الماء ، يمنع CO 2 و Cl - و SO - 4 تكوين طبقة أكسيد واقية كثيفة على الأنود وبالتالي يساهم في الدورة المكثفة لعمليات الأنوديك. تقلل أيونات الهيدروجين H + الشحنة السالبة للكاثود.
بدأ تأثير الأكسجين على معدل التآكل يظهر في اتجاهين متعاكسين. من ناحية ، يزيد الأكسجين من معدل عملية التآكل ، نظرًا لأنه مزيل استقطاب قوي لأقسام الكاثود ، من ناحية أخرى ، له تأثير خامل على السطح.
عادةً ما تحتوي أجزاء الغلاية المصنوعة من الفولاذ على طبقة أكسيد أولية قوية بدرجة كافية تحمي المادة من التعرض للأكسجين حتى يتم تدميرها بواسطة عوامل كيميائية أو ميكانيكية.
يتم تنظيم معدل التفاعلات غير المتجانسة (بما في ذلك التآكل) من خلال شدة العمليات التالية: توريد الكواشف (بشكل أساسي مزيلات الاستقطاب) إلى سطح المادة ؛ تدمير طبقة الأكسيد الواقية ؛ إزالة نواتج التفاعل من مكان حدوثها.
يتم تحديد شدة هذه العمليات إلى حد كبير من خلال العوامل الهيدروديناميكية والميكانيكية والحرارية. لذلك ، فإن تدابير تقليل تركيز المواد الكيميائية العدوانية بكثافة عالية في العمليتين الأخريين ، كما تظهر تجربة تشغيل الغلايات ، عادة ما تكون غير فعالة.
ويترتب على ذلك أن حل مشكلة منع أضرار التآكل يجب أن يكون معقدًا ، عندما يتم أخذ جميع العوامل التي تؤثر على الأسباب الأولية لتدمير المواد في الاعتبار.
التآكل الكهروكيميائي
اعتمادًا على مكان التدفق والمواد المشاركة في التفاعلات ، يتم تمييز الأنواع التالية من التآكل الكهروكيميائي:
- الأكسجين (وتنوعه - وقوف السيارات) ،
- الحمأة (تسمى أحيانًا "الصدفة") ،
- بين الحبيبات (هشاشة قلوية من فولاذ المرجل) ،
- فتحة و
- كبريتية.
تآكل الأكسجينلوحظ في المقتصدات ، والتركيبات ، والأعلاف وأنابيب الصرف ، ومجمعات المياه البخارية ، وأجهزة التجميع الداخلي (الدروع ، والأنابيب ، ومزيلات التسخين ، وما إلى ذلك). ملفات الدائرة الثانوية للغلايات ذات الدائرة المزدوجة ، التي تستخدم الغلايات وسخانات الهواء البخارية ، معرضة بشكل خاص لتآكل الأكسجين. يحدث تآكل الأكسجين أثناء تشغيل الغلايات ويعتمد على تركيز الأكسجين المذاب في ماء الغلاية.
معدل تآكل الأكسجين في الغلايات الرئيسية منخفض ، ويرجع ذلك إلى التشغيل الفعال لأجهزة نزع الهواء ونظام الماء الفوسفاتي-نترات. في غلايات أنابيب المياه المساعدة ، غالبًا ما تصل إلى 0.5 - 1 مم / سنة ، على الرغم من أنها تتراوح في المتوسط بين 0.05 - 0.2 مم / سنة. إن طبيعة الأضرار التي لحقت بفولاذ الغلايات هي حفر صغيرة.
النوع الأكثر خطورة من تآكل الأكسجين هو تآكل وقوف السياراتتتدفق خلال فترة عدم نشاط المرجل. نظرًا لخصائص التشغيل ، فإن جميع غلايات السفن (خاصة الغلايات المساعدة) معرضة لتآكل شديد في مواقف السيارات. كقاعدة عامة ، لا يؤدي تآكل وقوف السيارات إلى تعطل الغلاية ، ومع ذلك ، فإن المعدن المتآكل أثناء الإغلاق ، مع ثبات باقى المتغيرات ، يتم تدميره بشكل مكثف أثناء تشغيل الغلاية.
السبب الرئيسي لتآكل وقوف السيارات هو دخول الأكسجين إلى الماء إذا كان المرجل ممتلئًا ، أو في طبقة رطوبة على السطح المعدني إذا كان المرجل جافًا. تلعب الكلوريدات وهيدروكسيد الصوديوم في الماء ورواسب الملح القابلة للذوبان في الماء دورًا مهمًا.
في حالة وجود الكلوريدات في الماء ، يتم تكثيف التآكل المعدني المنتظم ، وإذا كان يحتوي على كمية صغيرة من القلويات (أقل من 100 مجم / لتر) ، فإن التآكل يكون موضعيًا. لتجنب تآكل الوقوف عند درجة حرارة 20-25 درجة مئوية ، يجب أن يحتوي الماء على 200 مجم / لتر هيدروكسيد الصوديوم.
علامات التآكل الخارجية بمشاركة الأكسجين: قرح محلية صغيرة (الشكل 1 ، أ) ، مليئة بمنتجات التآكل البني ، والتي تشكل درنات فوق القرحات.
تعد إزالة الأكسجين من مياه التغذية أحد الإجراءات المهمة لتقليل تآكل الأكسجين. منذ عام 1986 ، تم تحديد محتوى الأكسجين في مياه التغذية للمراجل البحرية المساعدة والنفايات بـ 0.1 مجم / لتر.
ومع ذلك ، حتى مع وجود مثل هذا المحتوى من الأكسجين لمياه التغذية ، لوحظ تلف التآكل في عناصر الغلاية أثناء التشغيل ، مما يشير إلى التأثير السائد لعمليات تدمير فيلم الأكسيد وترشيح منتجات التفاعل من مراكز التآكل. المثال الأكثر توضيحًا لتأثير هذه العمليات على أضرار التآكل هو تدمير ملفات استخدام الغلايات مع الدوران القسري.
أرز. 1. الضرر الناجم عن تآكل الأكسجين
أضرار التآكلفي حالة تآكل الأكسجين ، عادةً ما يتم تحديد موقعها بدقة: على السطح الداخلي لمقاطع المدخل (انظر الشكل 1 ، أ) ، في منطقة الانحناءات (الشكل 1 ، ب) ، في أقسام المخرج وفي كوع الملف (انظر الشكل 1 ، ج) ، وكذلك في مجمعات بخار الماء لمراجل الاستخدام (انظر الشكل 1 ، د). في هذه المناطق (2 - منطقة التجويف القريب من الجدار) تخلق الخصائص الهيدروديناميكية للتدفق ظروفًا لتدمير فيلم الأكسيد والغسيل المكثف لمنتجات التآكل.
في الواقع ، أي تشوه في تدفق الماء وخليط الماء بالبخار يكون مصحوبًا بالمظهر التجويف في الطبقات القريبة من الجدارتوسيع التدفق 2 ، حيث تتسبب فقاعات البخار المتكونة والمنهارة على الفور في تدمير طبقة الأكسيد بسبب طاقة الصدمات الهيدروليكية الدقيقة.
يتم تسهيل ذلك أيضًا من خلال الضغوط المتناوبة في الفيلم ، الناتجة عن اهتزاز الملفات والتقلبات في درجة الحرارة والضغط. يتسبب اضطراب التدفق المحلي المتزايد في هذه المناطق في الغسل الفعال لمنتجات التآكل.
في أقسام المخرج المباشر للملفات ، يتم تدمير فيلم الأكسيد بسبب التأثيرات على سطح قطرات الماء أثناء النبضات المضطربة لتدفق خليط البخار والماء ، حيث يمر وضع الحركة الحلقي المشتت هنا في واحد مشتت عند سرعة تدفق تصل إلى 20-25 م / ث.
في ظل هذه الظروف ، حتى المحتوى المنخفض من الأكسجين (~ 0.1 مجم / لتر) يسبب تدميرًا شديدًا للمعدن ، مما يؤدي إلى ظهور النواسير في أقسام مدخل ملفات غلايات الحرارة الضائعة من نوع La Mont بعد 2- 4 سنوات من التشغيل وفي مناطق أخرى - بعد 6-12 سنة.
أرز. الشكل 2. أضرار التآكل التي لحقت بملفات الموفر لمراجل الاستخدام KUP1500R للسفينة الآلية "أنديرا غاندي".
كتوضيح لما سبق ، دعونا نفكر في أسباب تلف ملفات المقتصد لاثنين من غلايات الاستخدام من نوع KUP1500R المثبت على حامل ولاعة إنديرا غاندي (نوع أليكسي كوسيجين) ، والذي دخل الخدمة في أكتوبر 1985. بالفعل في فبراير 1987 تم استبدال المقتصدات من كلا الغلايتين بسبب الأضرار. بعد 3 سنوات ، يظهر أيضًا تلف للملفات في هذه المقتصدات ، الموجودة في مناطق تصل إلى 1-1.5 متر من مجمع المدخل. تشير طبيعة الضرر إلى (الشكل 2 ، أ ، ب) تآكل الأكسجين النموذجي متبوعًا بفشل التعب (شقوق عرضية).
ومع ذلك ، تختلف طبيعة الإرهاق في مناطق فردية. ظهور صدع (وتصدع سابق لفيلم الأكسيد) في منطقة اللحام (انظر الشكل 2 ، أ) هو نتيجة للضغوط المتناوبة الناتجة عن اهتزاز حزمة الأنبوب وخاصية تصميم تقاطع الملفات مع الرأس (يتم لحام نهاية الملف بقطر 22 × 3 بتركيب منحني بقطر 22 × 2).
يعود تدمير طبقة الأكسيد وتشكيل شقوق التعب على السطح الداخلي للأقسام المستقيمة للملفات ، بعيدًا عن المدخل بمقدار 700-1000 مم (انظر الشكل 2 ، ب) ، بسبب الضغوط الحرارية المتناوبة التي تحدث أثناء تشغيل الغلاية ، عندما يتم توفير الماء البارد السطحي الساخن. في هذه الحالة ، يتم تعزيز عمل الضغوط الحرارية من خلال حقيقة أن زعانف الملفات يجعل من الصعب على أنبوب المعدن التمدد بحرية ، مما يخلق ضغوطًا إضافية في المعدن.
تآكل التربةعادة ما يتم ملاحظتها في غلايات أنابيب المياه الرئيسية على الأسطح الداخلية للشاشة وأنابيب البخار لحزم التدفق التي تواجه الشعلة. طبيعة تآكل الحمأة السفلية هي حفر بيضاوية بحجم على طول المحور الرئيسي (موازية لمحور الأنبوب) حتى 30-100 مم.
توجد طبقة كثيفة من الأكاسيد على شكل "قذائف" 3 على القرحات (الشكل 3). يستمر التآكل تحت الطين في وجود مزيلات الاستقطاب الصلبة - أكاسيد الحديد والنحاس 2 ، والتي تترسب على أكثر الأنابيب إجهادًا بالحرارة أقسام في أماكن مراكز التآكل النشطة التي تحدث أثناء تدمير أغشية الأكسيد.
يتم تشكيل طبقة فضفاضة من منتجات التآكل والقياس في الأعلى.
بالنسبة للغلايات المساعدة ، فإن هذا النوع من التآكل ليس نموذجيًا ، ولكن في ظل الأحمال الحرارية العالية وأنماط معالجة المياه المناسبة ، لا يتم استبعاد ظهور التآكل تحت الحمأة في هذه الغلايات.
يتجلى التآكل الأكثر نشاطًا لأنابيب الغربال في الأماكن التي تتركز فيها شوائب سائل التبريد. يتضمن ذلك أقسامًا من أنابيب الجدار ذات الأحمال الحرارية العالية ، حيث يحدث تبخر عميق لمياه الغلايات (خاصة إذا كانت هناك رواسب مسامية منخفضة التوصيل للحرارة على سطح التبخر). لذلك ، فيما يتعلق بمنع الأضرار التي لحقت بأنابيب الغربال المرتبطة بتآكل المعدن الداخلي ، من الضروري مراعاة الحاجة إلى نهج متكامل ، أي التأثير على كل من أنظمة المياه والكيميائية والأفران.
يتسم تلف أنبوب الجدار بشكل أساسي بطبيعة مختلطة ، ويمكن تقسيمها بشكل مشروط إلى مجموعتين:
1) تلف مع علامات ارتفاع درجة حرارة الفولاذ (تشوه وترقق جدران الأنابيب عند نقطة التدمير ؛ وجود حبيبات الجرافيت ، إلخ).
2) كسور هشة بدون علامات مميزة لارتفاع درجة حرارة المعدن.
لوحظ وجود رواسب كبيرة ذات طابع من طبقتين على السطح الداخلي للعديد من الأنابيب: الجزء العلوي مرتبط بشكل ضعيف ، والسفلي متقشر ، ومرتبط بإحكام بالمعدن. سمك الطبقة السفلية من 0.4-0.75 مم. في منطقة الضرر ، يتم تدمير المقياس الموجود على السطح الداخلي. بالقرب من مواقع التدمير وعلى مسافة ما منها ، يتأثر السطح الداخلي للأنابيب بحفر التآكل والأضرار الدقيقة الهشة.
يشير المظهر العام للضرر إلى الطبيعة الحرارية للتدمير. التغييرات الهيكلية على الجانب الأمامي من الأنابيب - الكريات العميقة وتحلل البيرلايت ، وتشكيل الجرافيت (انتقال الكربون إلى الجرافيت 45-85٪) - تشير ليس فقط إلى درجة حرارة التشغيل للشاشات ، ولكن أيضًا المسموح به للصلب 20500 درجة مئوية. يؤكد وجود الحديد O أيضًا على المستوى العالي لدرجات حرارة المعدن أثناء التشغيل (أعلى من 845 درجة مئوية - أي 572 درجة مئوية).
يحدث التلف الهش الناجم عن الهيدروجين عادةً في المناطق ذات التدفقات الحرارية العالية ، وتحت طبقات سميكة من الترسبات ، والأنابيب المائلة أو الأفقية ، وكذلك في مناطق نقل الحرارة بالقرب من حلقات دعم اللحام أو الأجهزة الأخرى التي تمنع الحركة الحرة للتدفقات. أظهر أن تلف الهيدروجين يحدث في الغلايات التي تعمل تحت ضغط أقل من 1000 رطل / بوصة مربعة. بوصة (6.9 ميجا باسكال).
عادة ما ينتج عن تلف الهيدروجين تمزق بحواف سميكة. الآليات الأخرى التي تساهم في تكوين تشققات ذات حواف سميكة هي التشقق الناتج عن التآكل الإجهادي ، والتعب الناتج عن التآكل ، وكسور الإجهاد ، و (في بعض الحالات النادرة) ارتفاع درجة الحرارة الشديدة. قد يكون من الصعب التمييز بصريًا بين الضرر الناجم عن تلف الهيدروجين وأنواع الضرر الأخرى ، ولكن بعض ميزاتها يمكن أن تساعد هنا.
على سبيل المثال ، يرتبط تلف الهيدروجين دائمًا بتكوين ثقوب في المعدن (انظر الاحتياطات الواردة في الفصلين 4 و 6). أنواع الضرر الأخرى (باستثناء إجهاد التآكل ، الذي يبدأ غالبًا في قذائف فردية) لا يرتبط عادةً بالتآكل الشديد.
غالبًا ما تظهر أعطال الأنابيب نتيجة تلف الهيدروجين للمعدن على أنها تشكل "نافذة" مستطيلة في جدار الأنبوب ، وهو أمر غير معتاد بالنسبة لأنواع التدمير الأخرى.
لتقييم قابلية تلف أنابيب الغربال ، يجب أن يؤخذ في الاعتبار أن المحتوى المعدني (الأولي) للهيدروجين الغازي في الفولاذ البرليتيك (بما في ذلك st. 20) لا يتجاوز 0.5-1 سم 3/100 جم. عندما يكون محتوى الهيدروجين أعلى من 4-5 سم 3/100 جم ، تتدهور الخواص الميكانيكية للفولاذ بشكل كبير. في هذه الحالة ، من الضروري التركيز بشكل أساسي على المحتوى المحلي للهيدروجين المتبقي ، لأنه في حالة الكسور الهشة لأنابيب الغربال ، يلاحظ تدهور حاد في خصائص المعدن فقط في منطقة ضيقة على طول المقطع العرضي للأنبوب مع هيكل مرضٍ دائمًا وخصائص ميكانيكية للمعدن المجاور على مسافة 0.2-2 مم فقط.
القيم التي تم الحصول عليها لمتوسط تركيزات الهيدروجين عند حافة الكسر هي 5-10 مرات أعلى من محتواها الأولي للمحطة 20 ، والتي لا يمكن أن يكون لها تأثير كبير على تلف الأنابيب.
تشير النتائج المقدمة إلى أن تقصف الهيدروجين كان العامل الحاسم في تلف الأنابيب الجدارية لمراجل KrCHPP.
مطلوب دراسة إضافية لأي من العوامل التي لها تأثير حاسم على هذه العملية: أ) الدوران الحراري بسبب زعزعة استقرار نظام الغليان العادي في مناطق زيادة تدفق الحرارة في وجود رواسب على سطح التبخر ، ونتيجة لذلك ، الأضرار التي لحقت بأغشية الأكسيد الواقية التي تغطيها ؛ ب) وجود الشوائب المسببة للتآكل في وسط العمل ، مع التركيز في الرواسب بالقرب من سطح التبخر ؛ ج) العمل المشترك للعوامل "أ" و "ب".
مسألة دور نظام الفرن ذات أهمية خاصة. تشير طبيعة المنحنيات إلى تراكم الهيدروجين في عدد من الحالات بالقرب من السطح الخارجي لأنابيب الغربال. هذا ممكن ، أولاً وقبل كل شيء ، إذا كانت هناك طبقة كثيفة من الكبريتيد على السطح المشار إليه ، والتي تكون غير منفذة إلى حد كبير لانتشار الهيدروجين من السطح الداخلي إلى السطح الخارجي. يرجع تكوين الكبريتيدات إلى: نسبة عالية من الكبريت في الوقود المحترق ؛ إلقاء شعلة على لوحات الشاشة. سبب آخر لهدرجة المعدن على السطح الخارجي هو حدوث عمليات التآكل عندما يتلامس المعدن مع غازات المداخن. كما أظهر تحليل الرواسب الخارجية لأنابيب الغلايات ، عادة ما يحدث كلا السببين.
يتجلى دور وضع الاحتراق أيضًا في تآكل أنابيب الغربال تحت تأثير الماء النقي ، والذي غالبًا ما يتم ملاحظته في مولدات البخار عالية الضغط. عادة ما توجد مراكز التآكل في منطقة الأحمال الحرارية المحلية القصوى وفقط على السطح الساخن للأنبوب. تؤدي هذه الظاهرة إلى تكوين المنخفضات المستديرة أو الإهليلجية بقطر أكبر من 1 سم.
يحدث ارتفاع درجة حرارة المعدن غالبًا في وجود رواسب نظرًا لحقيقة أن كمية الحرارة المتصورة ستكون متماثلة تقريبًا لكل من الأنبوب النظيف والأنبوب الذي يحتوي على مقياس ، وستكون درجة حرارة الأنبوب مختلفة.
غالبًا ما تظهر ظواهر التآكل في الغلايات على السطح الداخلي المجهد بالحرارة وغالبًا ما تظهر على السطح الخارجي.
في الحالة الأخيرة ، يعود تدمير المعدن - في معظم الحالات - إلى العمل المشترك للتآكل والتآكل ، والذي يكون له أحيانًا أهمية سائدة.
علامة خارجية على تدمير التآكل هو سطح معدني نظيف. تحت تأثير التآكل ، عادة ما تبقى منتجات التآكل على سطحه.
يمكن أن تؤدي عمليات التآكل والقشور الداخلية (في البيئة المائية) إلى تفاقم التآكل الخارجي (في بيئة الغاز) بسبب المقاومة الحرارية لطبقة المقياس ورواسب التآكل ، وبالتالي زيادة درجة الحرارة على سطح المعدن.
يعتمد تآكل المعدن الخارجي (من جانب فرن الغلاية) على عوامل مختلفة ، ولكن قبل كل شيء ، يعتمد على نوع وتكوين الوقود الذي يتم حرقه.
تآكل غلايات الغاز والنفط
يحتوي زيت الوقود على مركبات عضوية من الفاناديوم والصوديوم. إذا تراكمت الرواسب المنصهرة من الخبث المحتوي على مركبات الفاناديوم (V) على جدار الأنبوب المواجه للفرن ، فعندئذ مع وجود فائض كبير من الهواء و / أو درجة حرارة سطح معدني تتراوح من 520 إلى 880 درجة مئوية ، تحدث التفاعلات التالية:
4Fe + 3V2O5 = 2Fe2O3 + 3V2O3 (1)
V2O3 + O2 = V2O5 (2)
Fe2O3 + V2O5 = 2FeVO4 (3)
7Fe + 8FeVO4 = 5Fe3O4 + 4V2O3 (4)
(مركبات الصوديوم) + O2 = Na2O (5)
آلية تآكل أخرى تشمل الفاناديوم (خليط سائل سهل الانصهار) ممكنة أيضًا:
2Na2O. V2O4. 5V2O5 + O2 = 2Na2O. 6V2O5 (6)
Na2O. 6V2O5 + M = Na2O. V2O4. 5V2O5 + MO (7)
(م - معدن)
تتأكسد مركبات الفاناديوم والصوديوم أثناء احتراق الوقود إلى V2O5 و Na2O. في الرواسب الملتصقة بالسطح المعدني ، Na2O عبارة عن مادة رابطة. السائل المتكون نتيجة تفاعلات (1) - (7) يذوب الطبقة الواقية من المغنتيت (Fe3O4) ، مما يؤدي إلى أكسدة المعدن تحت الرواسب (درجة حرارة انصهار الرواسب (الخبث) هي 590-880 درجة ج).
نتيجة لهذه العمليات ، يتم ترقق جدران أنابيب الغربلة التي تواجه الفرن بشكل موحد.
يتم تسهيل زيادة درجة حرارة المعدن ، حيث تصبح مركبات الفاناديوم سائلة ، من خلال ترسبات المقياس الداخلية في الأنابيب. وبالتالي ، عندما يتم الوصول إلى درجة حرارة نقطة العائد للمعدن ، يحدث انقطاع في الأنابيب - نتيجة للعمل المشترك للرواسب الخارجية والداخلية.
تتآكل أيضًا أجزاء التثبيت لشبكات الأنابيب ، وكذلك نتوءات اللحامات الأنبوبية - يتسارع ارتفاع درجة الحرارة على سطحها: لا يتم تبريدها بواسطة خليط البخار والماء ، مثل الأنابيب.
قد يحتوي زيت الوقود على كبريت (2.0-3.5٪) على شكل مركبات عضوية ، كبريت عنصري ، كبريتات الصوديوم (Na2SO4) ، والذي يدخل الزيت من مياه التكوين. على سطح المعدن في ظل هذه الظروف ، يكون تآكل الفاناديوم مصحوبًا بتآكل أكسيد الكبريتيد. يكون تأثيرها المشترك أكثر وضوحًا عندما تحتوي الترسبات على 87٪ V2O5 و 13٪ Na2SO4 ، وهو ما يتوافق مع محتوى الفاناديوم والصوديوم في زيت الوقود بنسبة 13/1.
في فصل الشتاء ، عند تسخين زيت الوقود بالبخار في الخزانات (لتسهيل التصريف) ، يدخله الماء الإضافي بنسبة 0.5-5.0٪. النتيجة: تزداد كمية الرواسب على الأسطح ذات درجة الحرارة المنخفضة للغلاية ، ومن الواضح أن تآكل أنابيب زيت الوقود وخزانات زيت الوقود يزيد.
بالإضافة إلى المخطط الموصوف أعلاه لتدمير أنابيب غربال الغلاية ، فإن تآكل السخانات الفائقة ، وأنابيب الإكليل ، وحزم الغلايات ، والمقتصدات لها بعض الميزات بسبب زيادة - في بعض الأقسام - سرعات الغاز ، خاصة تلك التي تحتوي على جزيئات زيت الوقود غير المحترقة والمُقشرة جزيئات الخبث.
تحديد التآكل
السطح الخارجي للأنابيب مغطى بطبقة كثيفة تشبه المينا من الرواسب الرمادية والرمادية الداكنة. على الجانب المواجه لصندوق الاحتراق ، يوجد ترقق للأنبوب: تظهر المقاطع المسطحة والشقوق الضحلة على شكل "علامات" بوضوح إذا تم تنظيف السطح من الرواسب وأغشية الأكسيد.
إذا تم تدمير الأنبوب في حالة الطوارئ ، فسيظهر صدع ضيق طولي.
تآكل غلايات الفحم المسحوق
في التآكل الناتج عن عمل منتجات احتراق الفحم ، يكون للكبريت ومركباته أهمية حاسمة. بالإضافة إلى ذلك ، تؤثر الكلوريدات (بشكل رئيسي كلوريد الصوديوم) والمركبات الفلزية القلوية على مسار عمليات التآكل. يكون التآكل على الأرجح عندما يحتوي الفحم على أكثر من 3.5٪ كبريت و 0.25٪ كلور.
يترسب الرماد المتطاير المحتوي على مركبات قلوية وأكاسيد الكبريت على سطح المعدن عند درجة حرارة 560-730 درجة مئوية. في هذه الحالة ، نتيجة للتفاعلات المستمرة ، تتشكل كبريتات قلوية ، على سبيل المثال ، K3Fe (SO4) 3 و Na3Fe (SO4) 3. هذا الخبث المنصهر ، بدوره ، يدمر (يذوب) طبقة الأكسيد الواقية على المعدن - أكسيد الحديد الأسود (Fe3O4).
يبلغ معدل التآكل الحد الأقصى عند درجة حرارة المعدن من 680-730 درجة مئوية ، مع زيادته ، ينخفض المعدل بسبب التحلل الحراري للمواد المسببة للتآكل.
يحدث التآكل الأكبر في أنابيب مخرج السخان الفائق ، حيث تكون درجة حرارة البخار أعلى.
تحديد التآكل
على أنابيب الغربال ، يمكن ملاحظة المساحات المسطحة على جانبي الأنبوب ، والتي تتعرض للتآكل. تقع هذه المناطق بزاوية 30-45 درجة مئوية مع بعضها البعض ومغطاة بطبقة من الرواسب. يوجد بينهما منطقة "نظيفة" نسبيًا ، تخضع للتأثير "الأمامي" لتدفق الغاز.
تتكون الرواسب من ثلاث طبقات: الطبقة الخارجية عبارة عن رماد متطاير مسامي ، والطبقة الوسطى عبارة عن كبريتات قلوية بيضاء قابلة للذوبان في الماء ، والطبقة الداخلية عبارة عن أكاسيد الحديد الأسود اللامع (Fe3O4) والكبريتيدات (FeS).
في الأجزاء ذات درجة الحرارة المنخفضة من الغلايات - الموفر ، سخان الهواء ، مروحة العادم - تنخفض درجة حرارة المعدن إلى ما دون "نقطة الندى" لحمض الكبريتيك.
عند حرق الوقود الصلب ، تنخفض درجة حرارة الغاز من 1650 درجة مئوية في الشعلة إلى 120 درجة مئوية أو أقل في المدخنة.
بسبب تبريد الغازات ، يتشكل حامض الكبريتيك في مرحلة البخار ، وعند ملامسته لسطح معدني أكثر برودة ، تتكثف الأبخرة لتكوين حمض الكبريتيك السائل. تبلغ "نقطة الندى" لحمض الكبريتيك 115-170 درجة مئوية (ربما أكثر - تعتمد على محتوى بخار الماء وأكسيد الكبريت (SO3) في تيار الغاز).
يتم وصف العملية من خلال ردود الفعل:
S + O2 = SO2 (8)
SO3 + H2O = H2SO4 (9)
H2SO4 + Fe = FeSO4 + H2 (10)
في وجود أكاسيد الحديد والفاناديوم ، من الممكن حدوث أكسدة تحفيزية لـ SO3:
2SO2 + O2 = 2SO3 (11)
في بعض الحالات ، يكون تآكل حامض الكبريتيك عند احتراق الفحم أقل أهمية منه عند حرق الغاز البني والصخري والجفت وحتى الغاز الطبيعي - بسبب إطلاق بخار الماء بشكل أكبر نسبيًا منها.
تحديد التآكل
هذا النوع من التآكل يسبب تدميرًا موحدًا للمعدن. عادة ما يكون السطح خشنًا ، مع طلاء طفيف من الصدأ ، ويشبه السطح بدون ظواهر تآكل. مع التعرض المطول ، يمكن تغطية المعدن برواسب من منتجات التآكل ، والتي يجب إزالتها بعناية أثناء الفحص.
التآكل أثناء انقطاع الخدمة
يظهر هذا النوع من التآكل على المقتصد وفي أماكن المرجل حيث يتم تغطية الأسطح الخارجية بمركبات الكبريت. عندما يبرد المرجل ، تنخفض درجة حرارة المعدن إلى ما دون "نقطة الندى" ، وكما هو موصوف أعلاه ، إذا كان هناك رواسب كبريتية ، يتشكل حمض الكبريتيك. ربما يكون المركب الوسيط هو حمض الكبريتيك (H2SO3) ، لكنه غير مستقر للغاية ويتحول على الفور إلى حمض الكبريتيك.
تحديد التآكل
عادة ما تكون الأسطح المعدنية مطلية بالطلاء. إذا تمت إزالتها ، فسيتم العثور على مناطق تدمير المعادن ، حيث توجد رواسب الكبريت ومناطق من المعدن غير المتآكل. يميز هذا المظهر التآكل على غلاية متوقفة عن التآكل الموصوف أعلاه للمعدن المقتصد والأجزاء "الباردة" الأخرى من غلاية التشغيل.
عند غسل الغلاية ، تتوزع ظاهرة التآكل بشكل متساوٍ على سطح المعدن بسبب تآكل رواسب الكبريت وعدم كفاية تجفيف الأسطح. مع الغسل غير الكافي ، يكون التآكل موضعيًا حيث توجد مركبات الكبريت.
تآكل المعادن
في ظل ظروف معينة ، تتعرض أنظمة الغلايات المختلفة لتآكل المعدن ، سواء من الداخل أو الخارج للمعدن المسخن ، وحيث تحدث التدفقات المضطربة بسرعة عالية.
تم تناول تآكل التوربينات فقط أدناه.
التوربينات عرضة للتآكل من تأثير الجزيئات الصلبة وقطرات البخار المتكثف. تقشر الجسيمات الصلبة (الأكاسيد) من السطح الداخلي للمسخنات الفائقة وخطوط أنابيب البخار ، خاصة في ظل ظروف العمليات الحرارية العابرة.
تعمل قطرات مكثفات البخار بشكل أساسي على تدمير أسطح ريش المرحلة الأخيرة من التوربين وأنابيب الصرف. من الممكن حدوث تأثيرات أكالة ومسببة للتآكل لمكثف البخار إذا كان المكثف "حامضًا" - يكون الرقم الهيدروجيني أقل من خمس وحدات. يعد التآكل أيضًا خطيرًا في وجود بخار الكلوريد (حتى 12٪ من وزن الرواسب) والصودا الكاوية في قطرات الماء.
تحديد التآكل
يكون تدمير المعدن من تأثيرات قطرات المكثفات أكثر وضوحًا على الحواف الأمامية لشفرات التوربينات. الحواف مغطاة بأسنان مستعرضة رقيقة وأخاديد (أخاديد) ، وقد تكون هناك نتوءات مخروطية مائلة موجهة نحو الصدمات. توجد نتوءات على الحواف الأمامية للشفرات وتكاد تكون غائبة في طائراتها الخلفية.
يكون التلف الناتج عن الجسيمات الصلبة على شكل فجوات ، ومكونات دقيقة وشقوق على الحواف الأمامية للشفرات. الأخاديد والمخاريط المائلة غائبة.
يعد تحديد أنواع التآكل أمرًا صعبًا ، وبالتالي ، فإن الأخطاء ليست غير شائعة في تحديد التدابير المثلى من الناحية التكنولوجية والاقتصادية لمواجهة التآكل. يتم اتخاذ التدابير الضرورية الرئيسية وفقًا للوائح التي تحدد حدود المبادرين الرئيسيين للتآكل.
GOST 20995-75 "غلايات بخارية ثابتة بضغط يصل إلى 3.9 ميجا باسكال. مؤشرات الجودة لمياه التغذية والبخار "توحد المؤشرات في مياه التغذية: الشفافية ، أي كمية الشوائب المعلقة ؛ الصلابة العامة ومحتوى الحديد ومركبات النحاس - منع تكون القشور ورواسب أكسيد الحديد والنحاس ؛ قيمة الرقم الهيدروجيني - منع التآكل القلوي والحمضي وكذلك تكوين رغوة في أسطوانة الغلاية ؛ محتوى الأكسجين - منع تآكل الأكسجين ؛ محتوى النتريت - منع تآكل النتريت ؛ محتوى الزيت - منع الرغوة في أسطوانة المرجل.
يتم تحديد قيم المعايير بواسطة GOST اعتمادًا على الضغط في المرجل (وبالتالي ، على درجة حرارة الماء) ، وعلى قوة تدفق الحرارة المحلي وعلى تقنية معالجة المياه.
عند التحقيق في أسباب التآكل ، أولاً وقبل كل شيء ، من الضروري فحص أماكن تدمير المعادن (إن وجدت) ، وتحليل ظروف تشغيل الغلاية في فترة ما قبل الحادث ، وتحليل جودة مياه التغذية والبخار والرواسب ، وتحليل ميزات تصميم المرجل.
في الفحص الخارجي ، يمكن الاشتباه في الأنواع التالية من التآكل.
تآكل الأكسجين
: أقسام أنابيب مدخل المقتصدات الفولاذية ؛ خطوط الإمداد عند الالتقاء بالمياه غير المؤكسدة (فوق العادية) غير الكافية - "اختراقات" للأكسجين في حالة ضعف نزع الهواء ؛ سخانات مياه التغذية جميع المناطق الرطبة في الغلاية أثناء غلقها وعدم اتخاذ الإجراءات لمنع دخول الهواء إلى الغلاية ، خاصة في المناطق الراكدة ، عند تصريف المياه ، حيث يصعب إزالة البخار المتكثف أو ملئه بالماء تمامًا ، على سبيل المثال ، أنابيب عمودية من سخانات. أثناء فترة التعطل ، يتم تعزيز التآكل (المترجمة) في وجود القلويات (أقل من 100 مجم / لتر).
نادرًا ما يظهر تآكل الأكسجين (عندما يكون محتوى الأكسجين في الماء أعلى بكثير من القاعدة - 0.3 مجم / لتر) في أجهزة فصل البخار في براميل الغلايات وعلى جدار البراميل عند حدود مستوى الماء ؛ في downpipes. في الأنابيب الصاعدة ، لا يحدث التآكل بسبب تأثير نزع الهواء لفقاعات البخار.
نوع الضرر وطبيعته. قرحات بأعماق وأقطار مختلفة ، غالبًا ما تكون مغطاة بدرنات ، ويكون قشرتها العلوية عبارة عن أكاسيد حديدية ضاربة إلى الحمرة (ربما الهيماتيت Fe 2 O 3). دليل على التآكل النشط: تحت قشرة الدرنات - سائل أسود مترسب ، من المحتمل أن يكون مغنتيت (Fe 3 O 4) ممزوجًا بالكبريتات والكلوريدات. مع التآكل الرطب ، يوجد فراغ تحت القشرة ، وقاع القرحة مغطى برواسب من القشور والحمأة.
عند درجة الحموضة> 8.5 - تكون القرحات نادرة ولكنها أكبر وأعمق عند درجة الحموضة< 8,5 - встречаются чаще, но меньших размеров. Только вскрытие бугорков помогает интерпретировать бугорки не как поверхностные отложения, а как следствие коррозии.
عندما تزيد سرعة الماء عن 2 م / ث ، قد تأخذ الدرنات شكلًا مستطيلًا في اتجاه التدفق.
. قشور المغنتيت كثيفة بدرجة كافية ويمكن أن تكون بمثابة حاجز موثوق لاختراق الأكسجين إلى الدرنات. ولكن غالبًا ما يتم تدميرها نتيجة الإجهاد الناتج عن التآكل ، عندما تتغير درجة حرارة الماء والمعدن دوريًا: الإغلاق المتكرر وبدء تشغيل الغلاية ، والحركة النبضية لخليط الماء والبخار ، وتقسيم خليط البخار والماء إلى بخار منفصل و سدادات المياه تتبع واحدًا تلو الآخر.
يشتد التآكل مع زيادة درجة الحرارة (حتى 350 درجة مئوية) وزيادة محتوى الكلوريد في ماء الغلاية. في بعض الأحيان يتم تعزيز التآكل من خلال منتجات التحلل الحراري لبعض المواد العضوية في مياه التغذية.
أرز. 1. ظهور تآكل الأكسجين
القلوية (بمعنى أضيق - بين الحبيبات) التآكل
أماكن تآكل المعدن. الأنابيب في مناطق التدفق الحراري عالية الطاقة (منطقة الموقد ومقابل الشعلة الممدودة) - 300-400 كيلو واط / م 2 وحيث تكون درجة حرارة المعدن 5-10 درجة مئوية أعلى من نقطة غليان الماء عند ضغط معين ؛ الأنابيب المائلة والأفقية ، حيث يوجد ضعف في دوران المياه ؛ أماكن تحت الرواسب السميكة ؛ مناطق بالقرب من حلقات الدعم وفي اللحامات نفسها ، على سبيل المثال ، في أماكن لحام أجهزة فصل البخار داخل الأسطوانة ؛ أماكن بالقرب من المسامير.
نوع الضرر وطبيعته. تمتلئ المنخفضات نصف الكروية أو الإهليلجية بمنتجات التآكل ، وغالبًا ما تشتمل على بلورات لامعة من أكسيد الحديد الأسود (Fe 3 O 4). معظم التجاويف مغطاة بقشرة صلبة. على جانب الأنابيب المواجهة للفرن ، يمكن توصيل التجاويف لتشكيل ما يسمى بمسار التآكل بعرض 20-40 مم ويصل طوله إلى 2-3 أمتار.
إذا لم تكن القشرة كثيفة ومستقرة بدرجة كافية ، فقد يؤدي التآكل - في ظل ظروف الضغط الميكانيكي - إلى ظهور تشققات في المعدن ، خاصة بالقرب من الشقوق: المسامير ، وصلات الدرفلة ، نقاط اللحام لأجهزة فصل البخار.
أسباب أضرار التآكل. في درجات حرارة عالية - أكثر من 200 درجة مئوية - وتركيز عالٍ من الصودا الكاوية (هيدروكسيد الصوديوم) - 10٪ أو أكثر - يتم تدمير الطبقة الواقية (القشرة) الموجودة على المعدن:
4NaOH + Fe 3 O 4 \ u003d 2NaFeO 2 + Na 2 FeO 2 + 2H 2 O (1)
يخضع المنتج الوسيط NaFeO 2 للتحلل المائي:
4NаFeО 2 + 2Н 2 О = 4NаОН + 2Fe 2 О 3 + 2Н 2 (2)
أي ، في هذا التفاعل (2) ، يتم تقليل هيدروكسيد الصوديوم ، في التفاعلات (1) ، (2) لا يتم استهلاكه ، ولكنه يعمل كمحفز.
عند إزالة أكسيد الحديد الأسود ، يمكن أن يتفاعل هيدروكسيد الصوديوم والماء مع الحديد مباشرةً لإطلاق الهيدروجين الذري:
2NaOH + Fe \ u003d Na 2 FeO 2 + 2H (3)
4H 2 O + 3Fe \ u003d Fe 3 O 4 + 8H (4)
الهيدروجين المنطلق قادر على الانتشار في المعدن وتشكيل الميثان (CH 4) مع كربيد الحديد:
4H + Fe 3 C \ u003d CH 4 + 3Fe (5)
من الممكن أيضًا دمج الهيدروجين الذري في الهيدروجين الجزيئي (H + H = H 2).
لا يمكن للميثان والهيدروجين الجزيئي اختراق المعدن ؛ بل يتراكمان عند حدود الحبوب ، وفي حالة وجود الشقوق ، يتم توسيعهما وتعميقهما. بالإضافة إلى ذلك ، تمنع هذه الغازات تكوين وضغط الأغشية الواقية.
يتكون محلول مركَّز من الصودا الكاوية في أماكن التبخر العميق لمياه الغلايات: رواسب كثيفة من الأملاح (نوع من التآكل الناجم عن الحمأة السفلية) ؛ أزمة غليان الفقاعات ، عندما يتشكل فيلم بخار مستقر فوق المعدن - هناك المعدن غير متضرر تقريبًا ، لكن الصودا الكاوية تتركز على طول حواف الفيلم ، حيث يحدث التبخر النشط ؛ وجود تشققات حيث يحدث التبخر ، والتي تختلف عن التبخر في الحجم الكامل للماء: تتبخر الصودا الكاوية بشكل أسوأ من الماء ، ولا يغسلها الماء وتتراكم. تعمل الصودا الكاوية على المعدن ، وتشكل شقوقًا عند حدود الحبوب الموجهة داخل المعدن (نوع من التآكل بين الخلايا الحبيبية هو تآكل شق).
غالبًا ما يتركز التآكل بين الحبيبات تحت تأثير مياه الغلايات القلوية في أسطوانة الغلاية.
أرز. الشكل 3. التآكل بين الخلايا الحبيبية: أ - البنية المجهرية المعدنية قبل التآكل ، ب - البنية المجهرية في مرحلة التآكل ، وتشكيل الشقوق على طول حدود الحبيبات المعدنية
مثل هذا التأثير المسبب للتآكل على المعدن ممكن فقط مع التواجد المتزامن لثلاثة عوامل:
- ضغوط الشد الميكانيكية الموضعية قريبة من مقاومة الخضوع أو تتجاوزها قليلاً ، أي 2.5 مليون نيوتن / مم 2 ؛
- مفاصل مفكوكة لأجزاء الأسطوانة (مذكورة أعلاه) ، حيث يمكن أن يحدث تبخر عميق لمياه الغلايات وحيث تعمل الصودا الكاوية المتراكمة على إذابة الطبقة الواقية من أكاسيد الحديد (تركيز هيدروكسيد الصوديوم أكثر من 10٪ ، ودرجة حرارة الماء أعلى من 200 درجة مئوية و- على وجه الخصوص - أقرب إلى 300 درجة مئوية). إذا تم تشغيل المرجل بضغط أقل من جواز السفر (على سبيل المثال ، 0.6-0.7 ميجا باسكال بدلاً من 1.4 ميجا باسكال) ، فإن احتمال حدوث هذا النوع من التآكل ينخفض ؛
- تركيبة غير مواتية من المواد في ماء الغلايات ، حيث لا توجد تركيزات وقائية ضرورية لمثبطات هذا النوع من التآكل. يمكن أن تعمل أملاح الصوديوم كمثبطات: كبريتات ، كربونات ، فوسفات ، نترات ، سائل كبريتيت السليلوز.
أرز. 4. ظهور التآكل الحبيبي
لا تتطور شقوق التآكل إذا لوحظت النسبة:
(Na 2 SO 4 + Na 2 CO 3 + Na 3 PO 4 + NaNO 3) / (NaOH) ≥ 5، 3 (6)
حيث Na 2 SO 4 ، Na 2 CO 3 ، Na 3 PO 4 ، NaNO 3 ، NaOH - محتوى كبريتات الصوديوم ، كربونات الصوديوم ، فوسفات الصوديوم ، نترات الصوديوم وهيدروكسيد الصوديوم ، على التوالي ، مجم / كجم.
لا تحتوي الغلايات المصنعة حاليًا على حالة تآكل واحدة على الأقل.
يمكن أن يؤدي وجود مركبات السيليكون في مياه الغلايات أيضًا إلى تعزيز التآكل الحبيبي.
كلوريد الصوديوم في ظل هذه الظروف ليس مانعًا للتآكل. تم توضيحه أعلاه: أيونات الكلور (Сl -) هي مسرعات تآكل ، نظرًا لقابليتها العالية للحركة وصغر حجمها ، فهي تخترق بسهولة أغشية الأكسيد الواقية وتشكل أملاحًا عالية الذوبان مع الحديد (FeCl 2 ، FeCl 3) بدلاً من أكاسيد الحديد ضعيفة الذوبان .
في مياه بيوت الغلايات ، يتم التحكم تقليديًا في قيم التمعدن الكلي ، وليس محتوى الأملاح الفردية. لهذا السبب على الأرجح ، تم إدخال التقنين ليس وفقًا للنسبة المشار إليها (6) ، ولكن وفقًا لقيمة القلوية النسبية لمياه الغلايات:
SH kv rel = SH ov rel = SH ov 40100 / S ov ≤ 20، (7)
حيث U q rel - القلوية النسبية لمياه الغلايات،٪؛ Shch ov rel - القلوية النسبية للمياه المعالجة (الإضافية) ،٪ ؛ Shch ov - القلوية الكلية للمياه المعالجة (الإضافية) ، مليمول / لتر ؛ S ov - تمعدن المياه المعالجة (الإضافية) (بما في ذلك محتوى الكلوريدات) ، مجم / لتر.
يمكن أخذ القلوية الكلية للمياه المعالجة (الإضافية) بالتساوي ، مليمول / لتر:
- بعد كاتيون الصوديوم - القلوية الكلية لمياه المصدر ؛
- بعد موازاة كاتيون الهيدروجين - الصوديوم - (0.3-0.4) ، أو بالتتابع مع التجديد "الجائع" لمرشح كاتيونيت الهيدروجين - (0.5-0.7) ؛
- بعد كاتيون الصوديوم مع التحميض وتأين كلور الصوديوم - (0.5-1.0) ؛
- بعد كاتيون الأمونيوم - الصوديوم - (0.5-0.7) ؛
- بعد التجيير عند 30-40 درجة مئوية - (0.35-1.0) ؛
- بعد التخثر - (W حول المرجع - D إلى) ، حيث W حول المرجع - القلوية الكلية لمياه المصدر ، مليمول / لتر ؛ D إلى - جرعة التخثر ، مليمول / لتر ؛
- بعد الجير الصودا عند 30-40 درجة مئوية - (1.0-1.5) ، وعند 60-70 درجة مئوية - (1.0-1.2).
تُقبل قيم القلوية النسبية لمياه الغلايات وفقًا لمعايير Rostekhnadzor ،٪ ، لا تزيد عن:
- للغلايات مع براميل برشام - 20 ؛
- للمراجل ذات الأسطوانات الملحومة والأنابيب الملفوفة فيها - 50 ؛
- للغلايات ذات الأسطوانات الملحومة والأنابيب الملحومة بها - بأي قيمة ، غير موحدة.
أرز. 4. نتيجة التآكل الحبيبي
وفقًا لمعايير Rostekhnadzor ، يعد U kv rel أحد معايير التشغيل الآمن للغلايات. من الأصح التحقق من معيار العدوانية القلوية المحتملة لمياه الغلايات ، والتي لا تأخذ في الاعتبار محتوى أيون الكلور:
K u = (S ov - [Сl -]) / 40 u ov ، (8)
حيث K u - معيار العدوانية القلوية المحتملة لمياه الغلايات ؛ S s - ملوحة المياه المعالجة (الإضافية) (بما في ذلك محتوى الكلوريدات) ، مجم / لتر ؛ Cl - محتوى الكلوريدات في المياه المعالجة (الإضافية) ، ملغم / لتر ؛ Shch ov - القلوية الكلية للمياه المعالجة (الإضافية) ، مليمول / لتر.
يمكن أخذ قيمة K u:
- للغلايات ذات البراميل المثبتة بضغط يزيد عن 0.8 ميجا باسكال 5 ؛
- للغلايات ذات الأسطوانات الملحومة والأنابيب الملفوفة فيها بضغط يزيد عن 1.4 ميجا باسكال ≥ 2 ؛
- بالنسبة للغلايات ذات الأسطوانات الملحومة والأنابيب الملحومة بها ، وكذلك للغلايات ذات الأسطوانات الملحومة والأنابيب الملفوفة بضغط يصل إلى 1.4 ميجا باسكال والمراجل ذات الأسطوانات المثبتة بضغط يصل إلى 0.8 ميجا باسكال - لا يتم توحيدها.
تآكل التربة
يجمع هذا الاسم بين عدة أنواع مختلفة من التآكل (قلوي ، أكسجين ، إلخ). يتسبب تراكم الرواسب السائبة والمسامية والحمأة في مناطق مختلفة من المرجل في تآكل المعدن الموجود تحت الحمأة. السبب الرئيسي: تلوث مياه التغذية بأكاسيد الحديد.
تآكل النتريت
. أنابيب الغربال والغلاية الموجودة على الجانب المواجه للفرن.
نوع الضرر وطبيعته. قرح كبيرة نادرة ومحدودة بشكل حاد.
. في حالة وجود أيونات النتريت (NO - 2) في مياه التغذية بأكثر من 20 ميكروغرام / لتر ، تكون درجة حرارة الماء أكثر من 200 درجة مئوية ، تعمل النتريت كمزيلات استقطاب كاثودية للتآكل الكهروكيميائي ، وتعود إلى HNO 2 ، NO ، N 2 (انظر أعلاه).
تآكل بخار الماء
أماكن تآكل المعدن. جزء المخرج من لفائف التسخين الفائق ، وأنابيب البخار شديدة التسخين ، وأنابيب توليد البخار الأفقية والمائلة قليلاً في المناطق ذات الدورة الدموية الضعيفة للمياه ، وأحيانًا على طول المولد العلوي لملفات مخرج موفرة المياه المغلية.
نوع الضرر وطبيعته. لويحات من أكاسيد الحديد السوداء الكثيفة (Fe 3 O 4) ، ملتصقة بشدة بالمعدن. مع التقلبات في درجة الحرارة ، يتم كسر استمرارية اللويحة (القشرة) ، وتسقط المقاييس. ترقق موحد للمعادن مع انتفاخات وشقوق طولية وكسور.
يمكن تعريفه على أنه تآكل تحت الملاط: في شكل حفر عميقة ذات حواف محددة بشكل غير واضح ، وغالبًا ما تكون بالقرب من اللحامات البارزة داخل الأنبوب ، حيث يتراكم الطين.
أسباب أضرار التآكل:
- غسيل متوسط - بخار في سخانات عالية ، وأنابيب بخار ، و "وسائد" بخارية تحت طبقة من الحمأة ؛
- درجة حرارة المعدن (الصلب 20) أكثر من 450 درجة مئوية ، وتدفق الحرارة إلى القسم المعدني 450 كيلو واط / م 2 ؛
- انتهاك وضع الاحتراق: خبث الشعلات ، وزيادة تلوث الأنابيب من الداخل والخارج ، والاحتراق غير المستقر (الاهتزازي) ، واستطالة الشعلة نحو أنابيب الشاشات.
نتيجة لذلك: تفاعل كيميائي مباشر بين الحديد وبخار الماء (انظر أعلاه).
التآكل الميكروبيولوجي
تسببها البكتيريا الهوائية واللاهوائية ، وتظهر في درجات حرارة 20-80 درجة مئوية.
أماكن تلف المعادن. مواسير وحاويات المرجل بالماء بدرجة الحرارة المحددة.
نوع الضرر وطبيعته. درنات بأحجام مختلفة: قطرها من عدة مليمترات إلى عدة سنتيمترات ، نادرًا - عدة عشرات من السنتيمترات. الدرنات مغطاة بأكاسيد الحديد الكثيفة - وهي نفايات من البكتيريا الهوائية. الداخل - مسحوق أسود ومعلق (كبريتيد الحديد FeS) - منتج من البكتيريا اللاهوائية التي تقلل الكبريتات ، تحت التكوين الأسود - القرحات المستديرة.
أسباب الضرر. توجد دائمًا كبريتات الحديد والأكسجين والبكتيريا المختلفة في المياه الطبيعية.
تشكل بكتيريا الحديد في وجود الأكسجين طبقة من أكاسيد الحديد ، والتي تحتها البكتيريا اللاهوائية تختزل الكبريتات إلى كبريتيد الحديد (FeS) وكبريتيد الهيدروجين (H 2S). بدوره ، يؤدي كبريتيد الهيدروجين إلى تكوين أحماض كبريتية (غير مستقرة جدًا) وأحماض الكبريتيك ، ويتآكل المعدن.
هذا النوع من التآكل له تأثير غير مباشر على تآكل المرجل: تدفق الماء بسرعة 2-3 م / ث من الدرنات ، يحمل محتوياتها إلى المرجل ، مما يزيد من تراكم الحمأة.
في حالات نادرة ، يمكن أن يحدث هذا التآكل في الغلاية نفسها ، إذا تم ملؤها بالماء بدرجة حرارة 50-60 درجة مئوية أثناء الإغلاق الطويل للغلاية في الاحتياطي ، ويتم الحفاظ على درجة الحرارة بسبب اختراق البخار العرضي من الغلايات المجاورة.
تآكل "مخلب"
مواقع أضرار التآكل. المعدات التي يتم فيها فصل البخار عن الماء: أسطوانة الغلاية ، وفواصل البخار داخل وخارج الأسطوانة ، أيضًا - نادرًا - في أنابيب تغذية المياه وموفر.
نوع الضرر وطبيعته. سطح المعدن أملس ، ولكن إذا تحرك الوسيط بسرعة عالية ، فإن السطح المتآكل ليس أملسًا ، وله انخفاضات على شكل حدوة حصان و "ذيول" موجهة في اتجاه الحركة. السطح مغطى بفيلم رقيق غير لامع أو أسود لامع. لا توجد رواسب واضحة ، ولا توجد نواتج تآكل ، لأن "المخلَّب" (مركبات عضوية من مادة البولي أمينات تم إدخالها خصيصًا في الغلاية) قد تفاعلت بالفعل.
في ظل وجود الأكسجين ، والذي نادرًا ما يحدث في غلاية تعمل بشكل طبيعي ، فإن السطح المتآكلة يكون "بهيجًا": خشونة ، جزر معدنية.
أسباب أضرار التآكل. تم وصف آلية عمل "المخلّب" سابقًا ("المراجل الصناعية والتدفئة و mini-CHP" ، 1 (6) ΄ 2011 ، ص 40).
يحدث التآكل "المخلبي" عندما يكون من الممكن تناول جرعة زائدة من "مخلّب" ، ولكن حتى مع جرعة عادية ، حيث يتركز "مخلّب" في المناطق التي يوجد فيها تبخر مكثف للماء: يتم استبدال غليان النواة بالرشاش. في أجهزة فصل البخار ، هناك حالات من التأثير المدمر بشكل خاص للتآكل "المخلّب" بسبب السرعات المضطربة العالية لخليط الماء والبخار والماء.
يمكن أن يكون لجميع أضرار التآكل الموصوفة تأثير تآزري ، بحيث يمكن أن يتجاوز الضرر الكلي الناتج عن العمل المشترك لعوامل التآكل المختلفة مقدار الضرر الناجم عن أنواع التآكل الفردية.
كقاعدة عامة ، يعمل عمل العوامل المسببة للتآكل على تعزيز النظام الحراري غير المستقر للغلاية ، مما يتسبب في إجهاد التآكل ويثير تآكل التعب الحراري: عدد مرات البدء من الحالة الباردة أكثر من 100 ، ويبلغ إجمالي عدد مرات البدء أكثر من 200 بما أن هذه الأنواع من تدمير المعادن نادرة ، فإن الشقوق وأنابيب التمزق لها مظهر مماثل للآفات المعدنية من أنواع مختلفة من التآكل.
عادة ، لتحديد سبب تدمير المعادن ، يلزم إجراء دراسات معدنية إضافية: التصوير الشعاعي والموجات فوق الصوتية واللون والكشف عن عيوب الجسيمات المغناطيسية.
اقترح العديد من الباحثين برامج لتشخيص أنواع أضرار التآكل في فولاذ الغلايات. يُعرف برنامج VTI (A.F. Bogachev وزملاء العمل) - بشكل أساسي لمراجل الطاقة عالية الضغط ، وتطوير جمعية Energochermet - بشكل أساسي لمراجل الطاقة منخفضة ومتوسطة الضغط وغلايات تسخين النفايات.